This is a modern-English version of The Traveling Engineers' Association to Improve the Locomotive Engine Service of American Railroads: Examination Questions and Answers for Firemen for Promotion and New Men for Employment, originally written by Traveling Engineers' Association.
It has been thoroughly updated, including changes to sentence structure, words, spelling,
and grammar—to ensure clarity for contemporary readers, while preserving the original spirit and nuance. If
you click on a paragraph, you will see the original text that we modified, and you can toggle between the two versions.
Scroll to the bottom of this page and you will find a free ePUB download link for this book.
The
Traveling Engineers’
Association
To Improve The Locomotive
Engine Service
of American Railroads
To Enhance the Locomotive Engine Service of American Railroads
Examination Questions and Answers
For Firemen for Promotion and New Men for Employment
:-:
Copyrighted by W. O. Thompson, March, 1911
Revised January, 1919
For Firefighters Seeking Promotion and New Hires for Employment
:-:
Copyrighted by W. O. Thompson, March, 1911
Revised January, 1919
Contents
PREFACE | 3 |
EXAMINATION QUESTIONS: FIRST SERIES | 7 |
AIR BRAKE QUESTIONS | 22 |
EXAMINATION QUESTIONS: SECOND SERIES | 25 |
AIR BRAKE QUESTIONS | 44 |
OIL BURNING LOCOMOTIVES | 47 |
MECHANICAL EXAMINATION: THIRD SERIES | 62 |
COMPOUND LOCOMOTIVES | 98 |
WALSCHAERT AND BAKER-PILLIOD VALVE GEARS | 113 |
SOUTHERN VALVE GEAR | 119 |
LUBRICATION | 120 |
FEDERAL REGULATIONS | 126 |
PYLE-NATIONAL ELECTRIC HEADLIGHT | 127 |
SCHROEDER HEADLIGHT | 141 |
"BUDA-ROSS" ELECTRIC HEADLIGHT | 143 |
DUPLEX LOCOMOTIVE STOKER | 154 |
AIR BRAKE QUESTIONS | 164 |
INDEX | 245 |
It is the policy of railroads to employ firemen who will in time become competent locomotive engineers. This requires that a man should have at least a common school education, good habits and be in good physical condition. He should be alert, with good reasoning faculties and a man of sound judgment. Having these qualifications, advancement will come to those who are conscientious in discharging their duties and who devote some of their leisure hours to study.
It’s the policy of railroads to hire firemen who will eventually become skilled locomotive engineers. This means a person should have at least a basic education, good habits, and be in good physical shape. They should be attentive, have strong reasoning skills, and possess sound judgment. With these qualifications, those who are diligent in their responsibilities and spend some of their free time studying will see advancement.
As an aid to this end, and that the railroad companies may derive the highest efficiency from the man employed as a locomotive engineman, a code of questions is given him, and it is expected that the preparation necessary to correctly answer the questions will indicate how well he has progressed.
To help with this goal and ensure that railroad companies get the best performance from the workers as locomotive engineers, a set of questions is provided for them. It's expected that the preparation needed to answer these questions correctly will show how much progress they've made.
The list of questions is also intended as a guide to the matters on which he should be correctly informed, both during his term of service as a fireman and for future promotion to engineer.
The list of questions is also meant to guide him on the topics he should be well-informed about, both during his time as a fireman and for any future promotion to engineer.
When a man is first employed as a fireman he will be given a list of questions on which he will be examined at the end of the first year; having passed this examination successfully he will then be given the examination questions for the following year; [Pg 4]having passed this examination satisfactorily, he will be given a third and final set of examination questions on which he will be examined before being promoted to engineer. All these examinations will be both written and oral. The third year examination for promotion will be before the General Board of Examiners. At any of these examinations, if he fails to pass 80 per cent. of the questions asked, another trial, not less than two months and not more than six months later, will be given him to pass the same examination; if he fails to pass by a percentage of 80 per cent. he shall be dropped from the service.
When a man first gets hired as a fireman, he’ll receive a list of questions that he gets tested on at the end of his first year. If he passes this exam successfully, he’ll then get the questions for the next year. [Pg 4] After passing this exam satisfactorily, he will be given a third and final set of exam questions before he can be promoted to engineer. All these exams will include both written and oral components. The promotion exam in the third year will be in front of the General Board of Examiners. If he fails to score at least 80 percent on any of these exams, he will be given another chance, scheduled no less than two months and no more than six months later, to pass the same exam. If he fails to achieve 80 percent again, he will be let go from the service.
Where the examinations consist of both air brake and machinery, the candidate must pass 80 per cent. in each to be successful.
Where the exams include both air brake and machinery, the candidate must score 80 percent in each to pass.
Firemen passing the third and final series of questions will be promoted in the order of their seniority as firemen, except that those who pass on the first trials shall rank, when promoted, above those who passed on the second trials.
Firefighters who pass the third and final set of questions will be promoted based on their seniority as firefighters. However, those who pass on the first try will be ranked higher when promoted than those who pass on the second try.
Engineers employed who have had service on other roads, will be required to pass the third series of questions before entering the service.
Engineers who have worked on other railroads will need to pass the third set of questions before starting their job here.
It is not expected that the man will pass these examinations without assistance, and in order that he will understand the use of locomotive and air brake appliances properly, he is expected to go to the Master Mechanic, General Foreman, Road Foreman or Traveling Engineer, also Air Brake Inspector or Instructor, or any other official, and ask them for [Pg 5]such information as may be required on any of the questions or on any points in connection with the work. He is not only invited, but also urged to do this, as the more knowledge of his business a man possesses, the better will be the results obtained. He will have ample time to study each set of questions; there is no doubt that with a reasonable amount of study each week, supplemented with close observation of the working of the locomotive, the information necessary to answer satisfactorily the entire list of questions can be easily mastered in the time given. In regard to breakdowns, it is advised that he carefully inspect each breakdown or disabled engine that comes to his notice, see where the parts have given way and in what manner the work of blocking up it done. It is not expected that all the breakdowns which may happen to a locomotive will occur on the engine that he is with; therefore it is good practice to observe how other men care for these breakdowns. In connection with these examinations the work done by the fireman during the year and how the work compares with that of other firemen in the same class of service will be carefully noted; his record as to the use of coal, supplies and attention to duty will be taken into consideration.
It’s not expected that the man will pass these exams without help, and to ensure he understands how to properly use locomotive and air brake tools, he should go to the Master Mechanic, General Foreman, Road Foreman, Traveling Engineer, or Air Brake Inspector or Instructor, or any other official, and ask for [Pg 5] any information he may need about the questions or any related points. He is not only encouraged but also urged to do this, because the more knowledge he has about his job, the better the results will be. He will have plenty of time to study each set of questions; there’s no doubt that with a reasonable amount of studying each week, along with closely observing how the locomotive works, he can easily master all the necessary information to answer the full list of questions in the time provided. Regarding breakdowns, he is advised to carefully inspect each breakdown or disabled engine he comes across, to see where parts have failed and how blocking is done. It’s not expected that all the breakdowns a locomotive experiences will happen to the engine he is with; therefore, it’s good practice to observe how others handle these breakdowns. In relation to these exams, the work done by the fireman over the year and how it compares to other firemen in the same type of service will be closely monitored; his record regarding coal usage, supplies, and attention to duty will be factored in.
It is hoped that he will give everything in detail the consideration it merits and realize fully that it is by looking after the little things that a man succeeds. It should be borne in mind that by filling well the position he holds he becomes entitled to the confidence that makes better positions possible. It is[Pg 6] understood that those who conduct the examination may ask any question or questions bearing on any subject of this examination, in order to determine how well the persons being examined understands the subject. A mere memorized answer will not be sufficient. The full meaning of each answer must be understood.
It’s expected that he will give everything the attention it deserves and fully realize that taking care of the small details is how a person succeeds. It's important to remember that by doing well in his current role, he earns the trust that can lead to better opportunities. It is[Pg 6] understood that those conducting the exam may ask any questions related to any part of this examination to see how well the individuals being tested understand the material. Simply memorizing answers won’t be enough. The full meaning of each answer must be grasped.
1. Q. What do you consider essential for your success in regard to the use of fuel?
1. Q. What do you think is essential for your success when it comes to using fuel?
A. I deem it essential to my success to be as economical in the use of fuel and supplies as is consistent with the work to be performed, exercising good judgment in my work, harmonious co-operation with my engineer, and showing a willingness to learn and practice the best methods in my work.
A. I believe it's crucial for my success to use fuel and supplies as efficiently as possible while still getting the job done, using good judgment in my work, cooperating well with my engineer, and being open to learning and applying the best practices in my work.
2. Q. What are the fireman's duties on arrival at enginehouse previous to going out on a locomotive?
2. Q. What are the fireman's responsibilities upon arriving at the engine house before heading out on a locomotive?
A. He is required to examine the bulletin board, guards on water and lubricator glasses; try gauge cocks to find true water level; then examine grates, ash-pan, flues and fire-box. Put fire in proper shape; see that a proper supply of firing tools, water, coal, oil and waste are provided, that all lamps and markers are filled, cleaned and in proper condition; and to perform such other duties as may be required by the engineer to assist him in getting the engine in readiness.
A. He needs to check the bulletin board, guards on the water and lubricator glasses; try the gauge cocks to find the actual water level; then look over the grates, ash-pan, flues, and firebox. Get the fire in the right condition; ensure that there's a sufficient supply of firing tools, water, coal, oil, and waste available, that all lamps and markers are filled, cleaned, and in proper shape; and to carry out any other tasks the engineer might need to help get the engine ready.
3. Q. What pressure is indicated by the steam gauge? What is meant by atmospheric pressure?
3. Q. What pressure does the steam gauge show? What does atmospheric pressure mean?
A. The pressure per square inch inside of the boiler. Atmospheric pressure is the pressure represented by the density of the atmosphere in pounds per square inch, which is at sea level 14.7 pounds.
A. The pressure per square inch inside the boiler. Atmospheric pressure is the pressure indicated by the density of the atmosphere in pounds per square inch, which is 14.7 pounds at sea level.
4. Q. On what principle does a steam gauge work?
4. Q. How does a steam gauge work?
A. The steam gauge pointer is actuated by a flattened or bent round tube to straighten itself under[Pg 8] the pressure of steam against the water inside of tube. The gauge pointer receives movement from suitable mechanism connected with the tube.
A. The steam gauge pointer is activated by a flattened or curved tube that straightens under the pressure of steam against the water inside the tube. The gauge pointer moves thanks to a mechanism connected to the tube.
5. Q. What is the source of power in a steam locomotive?
5. Q. Where does a steam locomotive get its power?
A. Heat is the source of power in all steam engines. It is necessary to have fuel and water. When fuel is burned, the water coming in contact with the hot sheets evaporates and becomes steam, which is then used in the cylinders to force the pistons back and forth.
A. Heat is the source of power in all steam engines. You need fuel and water. When fuel is burned, the water touches the hot surfaces, evaporates, and turns into steam, which is then used in the cylinders to push the pistons back and forth.
6. Q. About what quantity of water should be evaporated in a locomotive boiler to the pound of coal?
6. Q. How much water should be evaporated in a locomotive boiler for each pound of coal?
A. From five to seven pounds of water. For example, one gallon of water weighs eight and one-third pounds, therefore 100 pounds of coal should evaporate from sixty to eighty-four gallons of water.
A. From five to seven pounds of water. For example, one gallon of water weighs eight and one-third pounds, so 100 pounds of coal should evaporate between sixty and eighty-four gallons of water.
7. Q. What is steam, and how is it generated?
7. Q. What is steam, and how is it produced?
A. Steam is water in the condition of a vapor and is generated by heating the water above the boiling point.
A. Steam is water in vapor form and is created by heating the water past its boiling point.
8. Q. What is the purpose of the water gauge glass and gauge cocks?
8. Q. What’s the purpose of the water gauge glass and gauge cocks?
A. To indicate the level of water in the boiler.
A. To show the water level in the boiler.
9. Q. What would indicate to you that the boiler connections of water gauge glasses were becoming clogged?
9. Q. What signs would suggest to you that the boiler connections of the water gauge glasses were getting clogged?
A. The up and down movement of the water in the glass would become slow and inactive, or it would not register correctly with the gauge cocks.[Pg 9]
A. The movement of the water in the glass would become slow and unresponsive, or it wouldn't register accurately with the gauge cocks.[Pg 9]
10. Q. At what temperature does water boil?
10. Q. At what temperature does water boil?
A. At atmospheric pressure, which is 14.7 pounds at sea level, water boils at 212 degrees Fahrenheit; the temperature, however, increases as the pressure under which the water is boiled increases. At 200 pounds boiler pressure the temperature would be 388 degrees Fahrenheit.
A. At atmospheric pressure, which is 14.7 pounds at sea level, water boils at 212 degrees Fahrenheit; however, the temperature increases as the pressure under which the water is boiled increases. At 200 pounds of boiler pressure, the temperature would be 388 degrees Fahrenheit.
11. Q. What is carbon?
11. Q. What’s carbon?
A. Carbon forms the greatest part of all kinds of coal; the higher the per cent. of carbon, the higher the grade of coal.
A. Carbon makes up the largest portion of all types of coal; the more carbon it contains, the higher the quality of the coal.
12. Q. What is the composition of bituminous coal?
12. Q. What is bituminous coal made of?
A. It is composed of carbon about 75 per cent. and many gaseous substances, as is shown by its burning with a large flame and much smoke. Anthracite, on the contrary, is nearly pure carbon and burns with a small flame.
A. It is made up of about 75 percent carbon and many gaseous substances, which is evident from its burning with a large flame and a lot of smoke. Anthracite, on the other hand, is almost pure carbon and burns with a small flame.
13. Q. What is combustion?
13. Q. What is burning?
A. Combustion or burning is a chemical process, it is the action of fire on inflammable substances and is the union of the oxygen in the air with the carbon in the fuel; this is called rapid combustion. Slow combustion is the decaying of wood or iron by the elements.
A. Combustion or burning is a chemical process; it's the action of fire on flammable substances and involves the combination of oxygen in the air with carbon in the fuel; this is known as rapid combustion. Slow combustion, on the other hand, refers to the decay of wood or iron due to environmental factors.
14. Q. Is air necessary for combustion?
14. Q. Is air needed for burning?
A. Yes.
A. Yes.
15. Q. About how many cubic feet of air is necessary for the combustion of a pound of coal in a locomotive fire-box?
15. Q. Approximately how many cubic feet of air do you need for burning a pound of coal in a locomotive firebox?
A. About 300 cubic feet of air must pass through[Pg 10] the grates and fire for complete combustion of one pound of coal.
A. About 300 cubic feet of air needs to flow through[Pg 10] the grates and fire for one pound of coal to burn completely.
16. Q. Why must air be heated before combining with coal?
16. Q. Why does air need to be heated before mixing with coal?
A. Air, like coal and its gases, must be heated before they will unite to form what is known as combustion and so as not to reduce the temperature of the fire-box below the igniting point of the gases.
A. Air, just like coal and its gases, needs to be heated up before it can come together to create what we call combustion, and to avoid lowering the temperature of the firebox below the ignition point of the gases.
17. Q. Why is it necessary to provide for combustion a supply of air through the fuel in the furnace?
17. Q. Why is it necessary to ensure that the fuel in the furnace has a supply of air for combustion?
A. In order to supply the oxygen necessary for combustion.
A. To provide the oxygen needed for combustion.
18. Q. What is the effect upon combustion if too little air is supplied? If too much air is supplied?
18. Q. What happens to combustion if there isn't enough air? What if there's too much air?
A. If too little air is supplied, combustion is not complete, and only one-third as much heat is obtained. If too much air is supplied, combustion is complete; but the excess air must be heated, resulting in a lower temperature. If twice the amount of air required for complete combustion be supplied, the temperature of the fire-box will be about one-half as high.
A. If insufficient air is provided, combustion doesn't fully occur, yielding only one-third of the possible heat. If too much air is supplied, combustion is complete; however, the extra air needs to be heated, which leads to a lower temperature. If twice the necessary amount of air for complete combustion is provided, the temperature in the fire-box will be around half of what it should be.
19. Q. Give a practical definition of the igniting temperature.
19. Q. Provide a practical definition of the ignition temperature.
A. In all ordinary combustion there is a definite temperature, called the ignition or kindling temperature, to which combustible substance must be heated in order that it may unite with the gas in supporting the combustion. The burning substance must not only be heated up to the kindling temperature, but it must be kept as high as this temperature, or combustion will cease.[Pg 11]
A. In any typical combustion process, there is a specific temperature, known as the ignition or kindling temperature, that a combustible material must reach to combine with the gas and sustain the combustion. The burning material not only needs to be heated to this kindling temperature, but it also has to be maintained at this temperature; otherwise, the combustion will stop.[Pg 11]
20. Q. State why such temperature is necessary and at what place in the fire-box it is most required.
20. Q. Explain why this temperature is necessary and where in the firebox it is most needed.
A. The center is the hottest part of the fire-box. There is a much lower temperature in the fire-box at the sides and end sheets, due to the water on the opposite sides of the sheets being of a lower temperature than the fire-box; therefore if we get as high a temperature as possible at the side and end sheets, we will increase the steam-making efficiency of the boiler. The gases which are liberated from the coal as soon as it becomes heated must attain a temperature of about 1,800 degrees Fahrenheit, known as the "temperature of ignition," before they will unite with air which must also be heated up to that point.
A. The center is the hottest part of the firebox. The temperature is much lower in the firebox at the sides and end sheets because the water on the opposite sides of the sheets is cooler than the firebox. Therefore, if we can raise the temperature at the side and end sheets as high as possible, we will boost the steam-making efficiency of the boiler. The gases released from the coal as soon as it heats up must reach around 1,800 degrees Fahrenheit, known as the "ignition temperature," before they can combine with air, which also needs to be heated to that point.
21. Q. How is draft created through the fire?
21. Q. How is draft created through the fire?
A. Exhaust steam escaping through the stack reduces the pressure in the smoke-box below the pressure of the atmosphere outside, therefore the air tends to force itself into the smoke-box through all openings; with everything in good condition, the easiest and largest passage for it is through the grates and other openings into the fire-box and from it through the tubes into the smoke-box and up the stack.
A. Exhaust steam escaping through the stack lowers the pressure in the smoke-box below the outside atmospheric pressure, so air naturally tries to rush into the smoke-box through any openings. When everything is functioning properly, the easiest and most significant path for the air is through the grates and other openings into the fire-box, and then from there through the tubes into the smoke-box and up the stack.
22. Q. Is smokeless firing practicable?
22. Q. Is using smokeless powder practical?
A. Yes, but it is necessary in order to obtain good results that boiler and fire-box be in good condition, coal broken to the proper firing size; then, with the hearty and intelligent co-operation of both engineer and fireman, smokeless firing is both economical and practicable.
A. Yes, but to achieve good results, the boiler and firebox need to be in good condition, and the coal must be broken down to the right size for firing. Then, with the enthusiastic and smart cooperation of both the engineer and the fireman, smokeless firing can be both cost-effective and feasible.
23. Q. In what condition should the fire be in order that the best results may be obtained from the combustion of the coal?[Pg 12]
23. Q. What should the fire be like to get the best results from burning the coal?[Pg 12]
A. The fire should be as light as the work being done by the engine will permit, evenly distributed over the grates and free from clinkers.
A. The fire should be as light as the work that the engine can handle, evenly spread across the grates and clear of clinkers.
24. Q. How should the blower be used?
24. Q. How do you use the blower?
A. A blower should be used very lightly, being careful not to draw too much air into the fire-box and through the flues, especially when fire is being cleaned or thin on grates.
A. A blower should be used very gently, making sure not to pull too much air into the firebox and through the flues, especially when the fire is being cleaned or is low on the grates.
25. Q. What is the result of opening the fire-door when the engine is working steam?
25. Q. What happens if you open the fire-door while the engine is running on steam?
A. It will cause a cooling effect in the fire-box and is liable to start the flues leaking.
A. It will create a cooling effect in the firebox and may cause the flues to start leaking.
26. Q. What is the effect of putting too many scoops of coal on a bright fire? Is this a waste of fuel?
26. Q. What happens if you add too many scoops of coal to a bright fire? Is this a waste of fuel?
A. It has the effect of temporarily deadening and cooling the fire, causes emission of quantities of black smoke, as only a limited amount of gas can be burned in a fire-box at a time; all in excess of that amount escapes from the stack and is a waste of fuel.
A. It temporarily reduces and cools the fire, leading to the release of large amounts of black smoke, since only a limited amount of gas can be burned in a firebox at a time; any excess escapes from the stack and is wasted fuel.
27. Q. What effect has the fire upon a scoopful of coal when it is placed in the fire-box?
27. Q. What happens to a scoop of coal when it’s put in the firebox?
A. The heat from the fire drives the gases from the coal and they are ignited by the hot flame as they pass over the bright fire; the coke which is left burns where it is.
A. The heat from the fire pushes the gases out of the coal, and they catch fire from the hot flame as they go over the bright fire; the coke that remains burns in place.
28. Q. In what condition should the fire be to consume these gases?
28. Q. What should the fire be like to burn these gases?
A. A bright white coke fire, almost incandescent.
A. A bright white coke fire, nearly glowing.
29. Q. What is the temperature of the fire when in this condition?
29. Q. What’s the temperature of the fire when it’s in this state?
A. It must not be less than 1,800 degrees Fahrenheit to consume the gases liberated from the coal,[Pg 13] and it only requires from 750 to 900 degrees Fahrenheit to burn the coke that remains on the grate; as coke burns from the outside, less heat is required to consume it.
A. It must be at least 1,800 degrees Fahrenheit to burn off the gases released from the coal,[Pg 13] and it only takes between 750 to 900 degrees Fahrenheit to burn the coke that stays on the grate; since coke burns from the outside, it needs less heat to be consumed.
30. Q. How can the fire be maintained in this condition?
30. Q. How can the fire be kept going in this condition?
A. By adding coal to the fire in small quantities, spreading it over the grate surface and no faster than it is burned.
A. By adding coal to the fire in small amounts, spreading it evenly over the grate surface and no quicker than it burns.
31. Q. What is black smoke? Is it combustible?
31. Q. What is black smoke? Is it flammable?
A. Black smoke consists of small particles of carbon suspended in the gases of combustion and indicates incomplete combustion. Black smoke is not combustible, it is like lampblack and cannot be burned after having been produced. The production of it can be prevented by suitable arrangements and manipulation.
A. Black smoke is made up of tiny carbon particles floating in the gases produced by burning and shows that combustion is incomplete. Black smoke itself isn't flammable; it's similar to lampblack and can't be burned once it's created. You can avoid its production with the right setups and techniques.
32. Q. Should the gas not burn in the fire-box, will it burn after it enters the flues? Why?
32. Q. If the gas doesn’t burn in the fire-box, will it burn after it enters the flues? Why?
A. Gas will not burn only a short distance in the flues of a boiler, as the water absorbs the heat so quickly that the temperature of gas is lowered below the igniting point.
A. Gas won't burn very far in the flues of a boiler because the water absorbs the heat so quickly that the gas temperature drops below its ignition point.
33. Q. What is the effect on the flow of air through the fire from opening the door? What on the burning of the gases? What on the flues and sheets of the fire-box?
33. Q. How does opening the door affect the flow of air through the fire? What happens to the burning of the gases? What impact does it have on the flues and walls of the firebox?
A. When the furnace door is opened, the flow of air through the grate is stopped in proportion to the amount that passes through the door. The vacuum will be filled from the quickest source and the door is closer than some parts of the grate. The gases mix with the air from the door and pass out through[Pg 14] the flues; no combustion takes place, as the air is not hot enough to unite with the gas. The flues and sheets of the box will be caused to leak on account of the rapid contraction.
A. When the furnace door is opened, the airflow through the grate slows down based on how much air comes in through the door. The vacuum will draw air from the nearest source, and the door is closer than some areas of the grate. The gases mix with the air coming from the door and exit through[Pg 14] the flues; no combustion occurs because the air isn't hot enough to mix with the gas. The flues and panels of the box will start to leak due to the rapid contraction.
34. Q. Can the firing be done more effectively if the water level is observed closely?
34. Q. Can the firing be done more effectively if the water level is monitored closely?
A. Yes, in order to know how much water there is in the boiler and whether it is necessary to hurry the fire; if the boiler is full, it is possible to prevent the pops opening by delaying the fire.
A. Yes, to find out how much water is in the boiler and whether we need to speed up the fire; if the boiler is full, we can avoid the pops opening by slowing down the fire.
35. Q. How should the fire and water be handled in starting from a terminal or other station?
35. Q. How should the fire and water be managed when starting from a terminal or another station?
A. The steam pressure should be near the maximum and there should be sufficient water in the boiler to last until such time as the fire is burning well so that the pressure will not be reduced when water is put into the boiler. There should be a moderately heavy bed of fire well burned and distributed evenly over the grates. After the fire is burning well, the injector should be started lightly; the feed being gradually increased so as not to cause any decrease of steam pressure.
A. The steam pressure should be close to the maximum, and there should be enough water in the boiler to last until the fire is fully established, ensuring that the pressure doesn’t drop when adding water to the boiler. There should be a decent, even layer of well-burned fuel spread evenly across the grates. Once the fire is burning well, the injector should be started gently, and the feed should be gradually increased to avoid any drop in steam pressure.
36. Q. What is the purpose of a safety valve on a locomotive boiler? Why are more than one used?
36. Q. What’s the purpose of a safety valve on a locomotive boiler? Why are multiple ones used?
A. A safety valve is used to limit the maximum pressure in the boiler by opening and allowing steam to escape. More than one safety valve are used as additional protection against excessive pressure; one is set at the maximum pressure and the others are set at two or three pounds above the maximum pressure.
A. A safety valve is used to limit the maximum pressure in the boiler by opening and letting steam escape. More than one safety valve is used as extra protection against excessive pressure; one is set at the maximum pressure, and the others are set two or three pounds above that maximum pressure.
37. Q. What is usually the reason for steam being wasted from the safety valve? What can be done to prevent this waste?[Pg 15]
37. Q. What usually causes steam to escape from the safety valve? What can be done to stop this waste?[Pg 15]
A. Careless firing, careless running. Both engineer and fireman work in harmony to obtain the best results.
A. Careless shooting, careless running. Both the engineer and the firefighter work together to achieve the best outcomes.
38. Q. What is the estimated waste of coal for each minute the safety valve is open?
38. Q. What is the estimated amount of coal wasted for each minute the safety valve is open?
A. About fifteen pounds. The estimated waste of steam when an engine pops equals every second all the heat obtained from a quarter pound of coal. Safety valves usually remain open about half a minute, resulting in the loss of about eight pounds of coal.
A. About fifteen pounds. The estimated steam waste when an engine releases pressure equals the heat produced from a quarter pound of coal every second. Safety valves typically stay open for about half a minute, leading to a loss of around eight pounds of coal.
39. Q. What should be the condition of the fire on arriving at a station where a stop is to be made?
39. Q. What should the state of the fire be when arriving at a station where a stop will be made?
A. On approaching the station where a stop is to be made, firing should be stopped far enough back to allow the carbon gases to be consumed before the throttle is closed, so there will be little or no black smoke from the stack and yet have sufficient fire that it will not be necessary to feed the fire again if a short stop is to be made until the train is started and the engine cut back or nearly to the running cut-off.
A. When getting close to the station where a stop is planned, firing should be halted far enough back to let the carbon gases burn off before the throttle is closed. This way, there will be minimal or no black smoke from the stack, while still maintaining enough fire so that there's no need to add more fuel for a short stop until the train is underway and the engine is cut back or almost to the running cut-off.
40. Q. How should you build up the fire when at stations in order to avoid black smoke?
40. Q. How should you start a fire at stations to prevent black smoke?
A. Put in small quantities of coal at a time, have the door slightly open and have the blower on lightly; good judgment must be exercised by the fireman.
A. Add small amounts of coal at a time, keep the door slightly open, and set the blower to a low setting; the fireman must use good judgment.
41. Q. Why is it that if there is a thin fire with a hole in it the steam pressure will fall at once?
41. Q. Why does the steam pressure drop immediately if there’s a thin fire with a hole in it?
A. Because too much cold air is drawn into the fire-box and through the tubes, retarding combustion and cooling the fire-box and tubes.
A. Because too much cold air is pulled into the firebox and through the tubes, slowing down combustion and cooling the firebox and tubes.
42. Q. If the injector is to be used after throttle is shut off, how should the fire be maintained?
42. Q. If the injector is going to be used after the throttle is turned off, how should the fire be kept going?
A. A sufficient quantity of coal should be placed[Pg 16] on the grates to maintain the maximum steam pressure and the blower used to keep the fire burning brightly.
A. A good amount of coal should be placed[Pg 16] on the grates to keep the steam pressure at its highest and the blower used to keep the fire burning brightly.
43. Q. What would be the result of starting a heavy train or allowing drivers to slip with the fire too thin on the grates?
43. Q. What would happen if you started a heavy train or let drivers run with the fire too low on the grates?
A. The fire would be pulled off the grates and into the tubes, leaving the fire bed full of holes and some of the fire remaining on the grates turned over. Large quantities of cold air would be drawn in, resulting in a rapid decrease of temperature and pressure. The tubes would possibly start leaking and the fire would be in such condition that it could not be built up properly in a long distance. Possibly the grates would become clogged up with green coal—an excellent opportunity for forming clinkers. In this condition, the engine would fail to make steam for the entire trip.
A. The fire would be pulled off the grates and into the tubes, leaving the fire bed full of holes and some of the fire remaining on the turned-over grates. Large amounts of cold air would be sucked in, causing a quick drop in temperature and pressure. The tubes might start leaking, and the fire would be in such a state that it couldn't be properly built up over a long distance. The grates could get clogged with wet coal—creating a perfect situation for clinkers to form. In this condition, the engine wouldn’t be able to make steam for the entire trip.
44. Q. Where should the coal, as a rule, be placed in the fire-box?
44. Q. Where should the coal generally be placed in the firebox?
A. As a rule, more coal is burned along the sides and in the corners than in the middle of the grates; the fire should consequently be kept somewhat heavier along the sides and corners than in the middle.
A. Generally, more coal is used along the sides and in the corners than in the middle of the grates; therefore, the fire should be maintained a bit stronger along the sides and corners than in the middle.
45. Q. How is the fire affected by and what causes clinkers?
45. Q. How does the fire get affected by clinkers, and what causes them?
A. A clinker shuts off area of grate surface according to its size, and thereby shutting off that much of the air supply and interfering with proper combustion. Clinkers are caused by firing too heavy in spots, which prevents sufficient air passing up through these spots and allows the coal to run together, melting the ash, and sand; running a hoe or slash bar through[Pg 17] the fire will bring the points of melted sand together, thereby causing a clinker.
A. A clinker blocks part of the grate surface based on its size, which reduces the airflow and disrupts proper combustion. Clinkers form when the firing is too heavy in certain areas, preventing enough air from flowing through and causing the coal to clump together, melting the ash and sand. Running a hoe or slash bar through[Pg 17] the fire will gather the melted sand, thereby creating a clinker.
46. Q. How can you best avoid their formation and dispose of them?
46. Q. What's the best way to prevent their formation and get rid of them?
A. Light firing and occasionally moving the grates lightly is the best preventive. When once formed, they should be removed if possible by firing around and burning them out.
A. Gently using the fire and occasionally shifting the grates a bit is the best way to prevent issues. Once they’ve formed, you should try to get rid of them by firing around and burning them out if you can.
47. Q. How can you explain the slower burning of the coke and how understand the proper manner of supplying fresh coal?
47. Q. How do you explain the slower burning of the coke and what's the right way to add fresh coal?
A. The gases of coal are lighter than air and will pass away whether consumed or not. The slow burning of the coke is due to the fact that it burns from the outside only. When a fire reaches a white or incandescent heat it indicates that the gases are burned and a fresh supply of coal should be added; this is to be done as light as the service performed by the engine will permit.
A. The gases from coal are lighter than air and will escape whether they are used or not. The slow burning of coke happens because it only burns on the outside. When a fire gets to a white or glowing heat, it means the gases are burned and a new supply of coal should be added; this should be done as lightly as the engine's workload allows.
48. Q. When and for what purpose is the use of a rake on the fire bed allowable?
48. Q. When and why is it okay to use a rake on the fire bed?
A. The rake should be used on the fire very seldom, because raking the fire bed tends to form clinkers, especially when the rake is plunged down through the fire to the grate. It may be used when necessary to rake the fire lightly when on the road for the purpose of breaking the crust, which may be found as a consequence of too heavy firing.
A. The rake should be used on the fire very rarely because raking the fire bed often creates clinkers, especially when the rake is pushed down through the fire to the grate. It can be used when needed to lightly rake the fire while on the road to break up the crust, which may form due to overly heavy firing.
49. Q. Within what limits may steam pressure be allowed to vary, and why?
49. Q. What are the acceptable limits for steam pressure variations, and why?
A. Pressure should not be allowed to vary more than five pounds from the maximum for the reason[Pg 18] that too much expansion and contraction will take place, which many times is the cause of flues leaking, cracked or broken side sheets and stay bolts.
A. Pressure should not be allowed to vary more than five pounds from the maximum because too much expansion and contraction can occur, which often leads to flues leaking, cracked or broken side sheets, and stay bolts.
50. Q. Has improper firing any tendency to cause the tubes to leak? How?
50. Q. Can improper firing cause the tubes to leak? If so, how?
A. Yes; if the pressure is not regularly maintained, the fluctuations of temperature cause constant contraction and expansion to take place. If the fire is not carried level, but is carried heavy in some parts of the fire-box and light in others, holes will be worked in, cold air drawn through, lowering the temperature, chilling the tubes and causing leaks. Carrying the fire too heavy in some places, causes clinkers to form. If the door is open too long, too much cold air is drawn over the fire, causing the tubes to leak.
A. Yes; if the pressure isn't kept consistent, the temperature changes lead to constant expansion and contraction. If the fire isn't uniform, burning heavily in some areas of the firebox and lightly in others, it will create holes, allowing cold air in, which lowers the temperature, cools the tubes, and causes leaks. Having the fire too heavy in certain spots can lead to clinkers forming. If the door is left open for too long, it lets in too much cold air over the fire, which makes the tubes leak.
51. Q. What do you consider abuse of a boiler?
51. Q. What do you think constitutes abuse of a boiler?
A. Careless or improperly supplying water to the boiler, improper firing or allowing steam to vary from high to low pressure, causing unnecessary expansion and contraction.
A. Carelessly or incorrectly supplying water to the boiler, firing it improperly, or allowing steam pressure to fluctuate between high and low, which leads to unnecessary expansion and contraction.
52. Q. Does the stopping up of flues affect the steaming capacity of the engine?
52. Q. Does blocking off the flues impact the engine's steaming capacity?
A. Yes; obstructed flues reduce the heating surface, reduce the steaming capacity of the engine, and, as a rule, result in causing the flues to leak. They also cause an increase of speed of the gases through the remaining flues and a poor steaming engine.
A. Yes; blocked flues decrease the heating surface, lower the engine's steaming capacity, and typically lead to flue leaks. They also cause the gases to move faster through the remaining flues, resulting in a poorly performing engine.
53. Q. What causes honeycomb over the flues?
53. Q. What causes honeycomb to form over the flues?
A. Honeycomb on flues is usually caused by the draft through the fire picking up the sulphur and molten clay which is in a molten and sticky condition[Pg 19] in the fire; as it passes on its way to the stack, some of it strikes the flue-sheet and sticks or passes through the flues, clogging up the netting in the front end.
A. Honeycomb in flues is typically caused by the draft from the fire picking up sulfur and molten clay that are in a molten and sticky state[Pg 19] in the fire; as it moves toward the stack, some of it hits the flue-sheet and sticks or moves through the flues, clogging up the netting at the front end.
54. Q. How would you take care of a boiler with leaky tubes or fire-box, and why?
54. Q. How would you handle a boiler with leaking tubes or a firebox, and why?
A. Keep a bright, clean fire, especially up next to the flue-sheet, and as even a pressure of steam as possible and not use the blower any stronger than is absolutely necessary.
A. Maintain a bright, clean fire, especially next to the flue sheet, and keep the steam pressure as consistent as possible without using the blower any stronger than absolutely necessary.
55. Q. Why is it very important that coal should be broken so that it will not be larger than an ordinary sized apple before being put into the fire-box?
55. Q. Why is it crucial for coal to be broken down to no larger than a regular-sized apple before being placed in the firebox?
A. In order to get rapid and complete combustion, coal should be broken into small pieces; this aids combustion by exposing a larger surface to the flame and can be fired more economically and better results are obtained.
A. To achieve fast and complete combustion, coal should be broken into small pieces; this helps combustion by exposing a larger surface to the flame, allowing for more economical firing and better results.
56. Q. Should rapid firing be practiced?
56. Q. Should we practice rapid firing?
A. No; it should not be practiced for the same reason that heavy firing is wrong. A few moments should intervene between each shovelful to allow the fresh coal to get to burning and to maintain the high temperature in the fire-box.
A. No; it shouldn't be done for the same reason that heavy firing is incorrect. There should be a brief pause between each shovelful to give the fresh coal time to ignite and to keep the high temperature in the firebox.
57. Q. When and why should you wet the coal on the tender?
57. Q. When and why should you wet the coal on the tender?
A. Coal should be wet for the purpose of cleanliness to keep dust from flying and because moderately wet coal gives out more heat for the reason that there is not so much fine coal drawn through the tubes. It should be wet as often as necessary to accomplish these purposes.[Pg 20]
A. Coal should be damp to maintain cleanliness, preventing dust from being airborne, and because moderately wet coal produces more heat since there's less fine coal passing through the tubes. It should be kept damp as often as needed to achieve these goals.[Pg 20]
58. Q. What are the advantages of a large grate surface?
58. Q. What are the benefits of a large grate surface?
A. Greater heating surface, lighter fire and more complete combustion are possible with the larger grate surface, because a larger amount is burning at one time at a slower rate of combustion.
A. A larger grate surface allows for greater heating area, a lighter fire, and more complete combustion, as more fuel can burn simultaneously at a slower combustion rate.
59. Q. Why are grates made to shake, and how, when and where should they be shaken?
59. Q. Why are grates designed to shake, and how, when, and where should they be shaken?
A. For the purpose of breaking any clinkers that might form and to shake out all refuse from the grates. The best time to shake grates is when throttle is closed, as there is no exhaust to carry the unconsumed gases and sulphur through the flues into the front end, which is liable to choke or clog up netting and cause a steam failure. Grates should not be shaken while passing over bridges, near lumber or hay yards or through prohibited territory.
A. To break up any clinkers that might form and to remove all debris from the grates. The best time to shake the grates is when the throttle is closed, as there is no exhaust to carry the unburned gases and sulfur through the flues into the front end, which could choke or clog the netting and cause a steam failure. Grates should not be shaken while crossing bridges, near lumber or hay yards, or in restricted areas.
60. Q. Do you understand that coal furnished represents money invested, and should be fired economically and not allowed to fall out of the gangway?
60. Q. Do you understand that the coal provided represents money invested and should be used efficiently instead of being wasted?
A. The fuel of locomotives is property and represents money invested the same as do buildings, rolling stock, etc.; careless or inefficient firemen who waste fuel destroy property as certainly as though cars or engines were smashed up. The coal should be carefully raked off the deck and in from the gangways; it should not be allowed to fall, as it is wasted and dangerous to people near the track. The deck should be kept clean for greater comfort and convenience.
A. The fuel for locomotives is an asset and represents money invested just like buildings, rolling stock, etc.; careless or inefficient firemen who waste fuel damage property just as surely as if cars or engines were destroyed. The coal should be carefully raked off the deck and brought in from the gangways; it shouldn't be allowed to fall, as it is wasted and poses a danger to people near the track. The deck should be kept clean for better comfort and convenience.
61. Q. Is is objectionable to fill the tanks too full of coal or overflow tank at standpipes or water tanks?[Pg 21]
61. Q. Is it a problem to fill the tanks too full of coal or to overflow the tank at standpipes or water tanks?[Pg 21]
A. It is. Tanks filled too full of coal are dangerous and a great waste of coal, as the jar when running will cause a part of it to fall off; water overflowing from tanks results in washing away the ballast and in cold weather freezes over the tracks.
A. It is. Tanks that are overfilled with coal are hazardous and a significant waste of coal, as the jarring while in motion will cause some of it to spill out; water spilling over from tanks leads to the ballast being washed away and, in cold weather, can freeze over the tracks.
62. Q. What are the duties of a fireman on arrival at the terminal?
62. Q. What are the responsibilities of a firefighter upon arriving at the station?
A. Different roads have different assigned duties for the firemen to perform. They should leave the cab, boiler head, oil cans and deck in a clean condition, boiler full of water, enough fire and steam, so that the hostler will not be required to put in fuel while the engine is in his charge; should know that throttle valve is securely closed, reverse lever in center of quadrant, cylinder cocks open, and if equipped with independent brake, it to be applied; in fact, it is an excellent opportunity for a mechanical officer to judge the ability of the fireman and future engineer.
A. Different routes have different responsibilities for the firemen. They should leave the cab, boiler head, oil cans, and deck clean, the boiler full of water, and ensure there’s enough fire and steam so that the hostler won’t have to add fuel while the engine is under his care. They need to make sure the throttle valve is securely closed, the reverse lever is in the center position, the cylinder cocks are open, and if equipped with an independent brake, it should be applied. In fact, this is a great chance for a mechanical officer to assess the skills of the fireman and future engineer.
63. Q. Is the engineer responsible for the fireman's conduct while on duty and for the manner in which the fireman's duties are performed?
63. Q. Is the engineer responsible for the fireman's behavior while on duty and for how the fireman performs his duties?
A. He is. The fireman is under the direction of the engineer, and the fireman's duties are to be performed in accordance with the engineer's instructions.
A. He is. The firefighter works under the engineer's guidance, and the firefighter's responsibilities are to be carried out according to the engineer's directions.
64. Q. What is the duty of the superheater damper, and how does it operate?
64. Q. What is the purpose of the superheater damper, and how does it work?
A. The duty of the damper is to control the flow of gases through the large flues, thereby protecting the units which are contained therein from being overheated after throttle is closed. The position of damper when the engine is not working steam, is closed.[Pg 22]
A. The damper's job is to manage the gas flow through the large flues, which helps keep the units inside from overheating once the throttle is closed. When the engine isn't using steam, the damper is in a closed position.[Pg 22]
65. Q. What will be the effect on the steaming of the engine if the damper does not open properly?
65. Q. What will happen to the engine's steaming if the damper doesn't open correctly?
A. Engine will steam poorly for the reason that there will be no draft through the large flues. The steam will not be superheated because heated gases cannot come in contact with superheated units contained in the large flues.
A. The engine will produce steam inefficiently because there won't be enough airflow through the large flues. The steam won't be superheated since heated gases can't reach the superheated components inside the large flues.
66. Q. How may steam failure be avoided in case the damper fails to operate?
66. Q. How can steam failure be prevented if the damper doesn't work?
A. The counterweight may be tied up, thereby opening the damper.
A. The counterweight can be secured, which will open the damper.
1. Q. What is an air brake?
1. Q. What’s an air brake?
A. A brake operated by compressed air.
A. A brake that works using compressed air.
2. Q. How is this air compressed?
2. Q. How is this air compressed?
A. By an air compressor on the locomotive.
A. By an air compressor on the train.
3. Q. Name the different parts of the air brake as applied to the locomotive.
3. Q. Name the different parts of the air brake used in the locomotive.
A. The air compressor, compressor governor, automatic and independent brake valves, distributing valve, triple valve, auxiliary reservoir, brake cylinders, main reservoir, air gauges, angle cocks, cut-out cocks and the necessary piping.
A. The air compressor, compressor governor, automatic and independent brake valves, distributing valve, triple valve, auxiliary reservoir, brake cylinders, main reservoir, air gauges, angle cocks, cut-out cocks, and the required piping.
4. Q. What is the purpose of the main reservoir?
4. Q. What's the purpose of the main reservoir?
A. It is used for storing a large volume of air for the purpose of promptly charging and recharging the brakes. Where the engine is equipped with either the[Pg 23] E. T. or L. T. type of brakes, main reservoir air is used to supply the air to the brake cylinders on the locomotive.
A. It's used to store a large amount of air to quickly charge and recharge the brakes. When the engine has either the[Pg 23] E. T. or L. T. type of brakes, the main reservoir air is used to supply air to the brake cylinders on the locomotive.
5. Q. What other appliances use main reservoir air?
5. Q. What other devices use air from the main reservoir?
A. It is used in the operation of the power reverse gear, sand blower, bell ringer, water scoop, air signal, fire door, water sprinkler and other devices.
A. It is used in the operation of the power reverse gear, sand blower, bell ringer, water scoop, air signal, fire door, water sprinkler, and other devices.
6. Q. What does the red hand on each of the air gauges indicate?
6. Q. What does the red hand on each of the air gauges mean?
A. The red hand on the large gauge indicates main reservoir pressure; on the small gauge, brake cylinder pressure.
A. The red hand on the big gauge shows the main reservoir pressure; on the small gauge, it shows the brake cylinder pressure.
7. Q. What does the black hand on each of the air gauges indicate?
7. Q. What does the black hand on each of the air gauges mean?
A. The black hand on the large gauge indicates the equalizing reservoir pressure; on the small gauge, brake pipe pressure.
A. The black hand on the large gauge shows the pressure in the equalizing reservoir; on the small gauge, it shows the brake pipe pressure.
8. Q. What pressure is usually carried in the main reservoir?
8. Q. What pressure is typically maintained in the main reservoir?
A. Ninety pounds in freight and 130 pounds in passenger service. But where freight engines are equipped with duplex compressor governor, the low pressure top is adjusted to ninety pounds and the high pressure top to 130 pounds.
A. Ninety pounds for freight and 130 pounds for passenger service. However, when freight engines have a duplex compressor governor, the low pressure setting is adjusted to ninety pounds and the high pressure setting to 130 pounds.
9. Q. What pressure is usually carried in the brake pipe?
9. Q. What pressure is typically maintained in the brake pipe?
A. Seventy pounds in freight and 110 pounds in passenger service.
A. Seventy pounds for freight and 110 pounds for passenger service.
10. Q. What must the air pass through in flowing from the main reservoir to the brake pipe?
10. Q. What does the air need to go through when flowing from the main reservoir to the brake pipe?
11. Q. Name the different positions of the automatic brake valve.
11. Q. What are the different positions of the automatic brake valve?
A. Release, running, lap, service and emergency positions. The brake valve used with the E. T. and L. T. equipment has still another position known as holding position, which is located between running and lap positions.
A. Release, running, lap, service, and emergency positions. The brake valve used with the E. T. and L. T. equipment also has another position called holding position, which is located between the running and lap positions.
12. Q. Name the different positions of the independent brake valve.
12. Q. What are the different positions of the independent brake valve?
A. Release, running, lap, slow application and quick application positions.
A. Release, running, lap, slow application, and fast application positions.
13. Q. How many kinds of triple valves are there in use?
13. Q. How many types of triple valves are currently in use?
A. Two; plain and quick action.
A. Two; straightforward and fast action.
14. Q. How is the automatic brake applied? How released?
14. Q. How is the automatic brake applied? How is it released?
A. The automatic brake is applied by a reduction of brake pipe pressure, and is released by restoring the brake pipe pressure.
A. The automatic brake engages when there’s a drop in brake pipe pressure, and it releases when the brake pipe pressure is restored.
15. Q. When the independent brake valve handle is placed in application position, are the train brakes affected?
15. Q. When the independent brake valve handle is put in the application position, do the train brakes get affected?
A. No; only the brakes on the locomotive are applied.
A. No; only the brakes on the train are applied.
16. Q. What controls the pressure in the main reservoir?
16. Q. What regulates the pressure in the main reservoir?
A. The compressor governor.
The compressor governor.
1. Q. What, in your opinion, is the best way to fire a locomotive?
1. Q. What do you think is the best way to fire a locomotive?
A. To carry a nice, level fire on the grate, or it may be just a little heavier at the sides and front, so the air cannot come through it near the sheets as rapidly as in the center of the fire-box; always fire as light as consistent with the work required, endeavor to maintain a uniform steam pressure at all times, and avoid unnecessary black smoke and a waste of steam through the safety valves by the engine popping.
A. To maintain a good, even fire in the grate, it can be a bit heavier around the sides and front so that air doesn't flow through it as quickly near the sheets compared to the center of the firebox; always keep the fire as light as possible while still meeting the work demands, try to keep a consistent steam pressure at all times, and prevent unnecessary black smoke and steam waste by avoiding the engine from blowing off steam through the safety valves.
2. Q. What are the advantages of superheated steam over saturated steam in locomotive service?
2. Q. What are the benefits of superheated steam compared to saturated steam in locomotive operation?
A. Saving in water; saving in fuel; increased boiler capacity and a more powerful locomotive. Superheated steam does away entirely with all condensation in the cylinders, while saturated steam coming in contact with passages in cylinder saddle and walls of cylinders, is immediately cooled and in cooling, a part of it is changed back into water which affects the pressure and therefore its capacity to do work.
A. Saving water; saving fuel; larger boiler capacity and a more powerful locomotive. Superheated steam eliminates all condensation in the cylinders, while saturated steam that contacts the passages in the cylinder saddle and walls of the cylinders is immediately cooled. As it cools, part of it turns back into water, which affects the pressure and, consequently, its ability to do work.
3. Q. How is the saving in water produced?
3. Q. How is water conservation achieved?
A. By the elimination of all cylinder condensation present in saturated steam locomotives and the increase in volume of a given weight of steam.
A. By removing all cylinder condensation found in saturated steam locomotives and increasing the volume of a specific weight of steam.
4. Q. How is the saving in coal accomplished?
4. Q. How is the coal savings achieved?
A. Because there is less steam used to do the same amount of work, there is less water evaporated[Pg 26] and consequently less coal required to evaporate the water.
A. Because there is less steam used to do the same amount of work, less water is evaporated[Pg 26] and therefore less coal is needed to evaporate the water.
5. Q. How is the increased boiler capacity obtained?
5. Q. How is the higher boiler capacity achieved?
A. A boiler will evaporate a certain amount of water into steam and if part of the steam is lost by condensation, only that remaining is available for running the engine. Superheating eliminates the losses, thereby increasing the available useful steam. Further, superheating increases the volume of a given weight of steam, thereby reducing the consumption of steam required to develop a certain power and consequently increases the capacity.
A. A boiler will turn a certain amount of water into steam, and if some of that steam is lost due to condensation, only the remaining steam can be used to power the engine. Superheating prevents these losses, which increases the amount of useful steam available. Additionally, superheating increases the volume of a specific weight of steam, reducing the amount of steam needed to generate a certain amount of power and, as a result, increasing capacity.
6. Q. How is a more powerful engine obtained?
6. Q. How do you get a more powerful engine?
A. By reason of the increased boiler capacity an engine may be worked farther down before a steam failure occurs.
A. Because of the increased boiler capacity, an engine can operate longer before a steam failure happens.
7. Q. What type of fire tube superheater is in most general use in locomotive service?
7. Q. What kind of fire tube superheater is most commonly used in locomotive service?
A. The top header fire tube type, known as the "Schmidt Superheater." A system of units located in large flues through which the steam passes on its way from the dry pipe to the steam pipes, and a damper mechanism which controls the flow of gases through the large flues.
A. The top header fire tube type, known as the "Schmidt Superheater." It’s a system of units located in large ducts that the steam flows through on its way from the dry pipe to the steam pipes, along with a damper mechanism that regulates the gas flow through the large ducts.
8. Q. Describe the construction and location of the header.
8. Q. Describe how the header is built and where it is located.
A. The header is a simple casting, divided by partition walls into saturated and superheated steam passages. It is located between the dry pipe and the steam pipes, the same as the nigger head in a saturated locomotive. The dry pipe is in communication with the saturated steam passages and the[Pg 27] steam pipes with the superheated steam passages and these are in communication with each other through the superheated units.
A. The header is a basic casting, separated by partition walls into channels for saturated and superheated steam. It's positioned between the dry pipe and the steam pipes, similar to the device found in a saturated locomotive. The dry pipe connects with the saturated steam channels, and the[Pg 27] steam pipes connect with the superheated steam channels, and these are interconnected through the superheated units.
9. Q. Describe the construction of superheater units and their connection to the header.
9. Q. Describe how superheater units are built and how they connect to the header.
A. The units are composed of four seamless steel pipes, connected by three return bends. Of the four pipes, two are straight and two are bent upward and connected to the header by means of a clamp and bolt; one end of the unit is in communication with the saturated steam passage and the other with the superheated steam passage in the header casting.
A. The units consist of four seamless steel pipes, linked by three return bends. Out of the four pipes, two are straight while the other two bend upwards and connect to the header using a clamp and bolt; one end of the unit connects to the saturated steam passage and the other connects to the superheated steam passage in the header casting.
10. Q. Trace the flow of steam through the top header fire tube superheater.
10. Q. Follow the path of steam through the top header fire tube superheater.
A. When the engine throttle is open, saturated steam passes through the dry pipe into the saturated steam passage of the header casting. From this passage it enters one end of the unit, passing backward toward the fire-box, forward through one of the straight pipes and the front return bend, backward through the other straight pipe to the back return bend, and forward through the bent pipe and upward into the superheater steam passage of the header, from which it enters the steam pipes and is carried to the steam chest.
A. When the engine throttle is open, saturated steam flows through the dry pipe into the saturated steam passage of the header casting. From there, it enters one end of the unit, moving backward toward the firebox, forward through one of the straight pipes and the front return bend, backward through the other straight pipe to the back return bend, and forward through the bent pipe and upward into the superheater steam passage of the header, from which it enters the steam pipes and is directed to the steam chest.
11. Q. What should be the position of throttle valve when running a superheater locomotive?
11. Q. What should the position of the throttle valve be when operating a superheater locomotive?
A. The engine should always be run with as wide open throttle as the conditions will permit, regulating the steam admission to the cylinders according to work to be performed.
A. The engine should always be operated with as wide open throttle as the conditions allow, adjusting the steam flow to the cylinders based on the work that needs to be done.
12. Q. What should be the position of throttle while drifting?[Pg 28]
12. Q. Where should the throttle be positioned while drifting?[Pg 28]
A. The throttle valve should be kept slightly open while drifting, so as to admit a small quantity of steam in valve chamber and cylinder above atmospheric pressure, to prevent the inrush of hot air and gases which destroy lubrication, also to prevent excessive wear to valve, cylinder and piston rod packing.
A. The throttle valve should be kept slightly open while drifting to let in a small amount of steam into the valve chamber and cylinder above atmospheric pressure. This helps prevent hot air and gases from coming in that can ruin lubrication, as well as to avoid excessive wear on the valve, cylinder, and piston rod packing.
13. Q. How should the water be carried in boiler of superheater locomotives?
13. Q. How should the water be carried in the boilers of superheater locomotives?
A. As low as the conditions will permit, because this practice reduces the tendency to work water over into the dry pipe and units, as the superheater locomotive will use one-third less water than the saturated locomotive.
A. As low as conditions allow, because this practice decreases the likelihood of water flowing into the dry pipe and units, since the superheated locomotive will use one-third less water than the saturated locomotive.
14. Q. What care should be exercised in lubricating a superheater locomotive?
14. Q. What precautions should be taken when lubricating a superheater locomotive?
A. The supply of oil to steam chest should be watched very closely by the engineer, he to know that lubricator is feeding constantly and evenly over entire division, and according to work performed.
A. The engineer should closely monitor the supply of oil to the steam chest, ensuring that the lubricator is feeding consistently and evenly across the entire section, based on the workload.
15. Q. Describe the general form of a locomotive boiler.
15. Q. Describe the basic design of a locomotive boiler.
A. A locomotive boiler is cylindrical in form, it usually has a rectangular shaped fire-box at one end and a smoke-box at the other, and flues extend through the cylindrical part, and, like the fire-box, are surrounded by water.
A. A locomotive boiler is shaped like a cylinder; it typically has a rectangular firebox at one end and a smoke box at the other, with flues running through the cylindrical section, which are, like the firebox, surrounded by water.
16. Q. How does the wide fire-box type of boiler differ from the ordinary boiler, and what are its advantages?
16. Q. How does the wide fire-box boiler differ from the regular boiler, and what are its benefits?
A. The wide fire-box type of boiler is built so the fire-box is above the frame and extends out over the driving wheels. The advantages of this are to obtain[Pg 29] a larger grate area in the same length of fire-box and to give a slower rate of combustion per square foot of grate surface. The deep fire-box is limited in width to the distance between the frames, while the shallow fire-box sets on top of the frames and between the driving wheels.
A. The wide fire-box type of boiler is designed with the fire-box positioned above the frame, extending over the driving wheels. This setup has the advantages of providing a larger grate area within the same length of fire-box and allowing for a slower rate of combustion per square foot of grate surface. The deep fire-box is restricted in width to the distance between the frames, while the shallow fire-box sits on top of the frames and between the driving wheels.
17. Q. Why have two fire-box doors been placed in the large type of locomotive boilers?
17. Q. Why are there two fire-box doors in large locomotive boilers?
A. For convenience of the fireman on account of the greater width of the fire-box, so that coal can easily be distributed to all parts of the fire-box.
A. For the convenience of the firefighter due to the wider firebox, allowing coal to be easily spread throughout all areas of the firebox.
18. Q. Describe a locomotive fire-box.
18. Q. Describe a locomotive firebox.
A. The modern form is a rectangular shaped structure located at the back end of the boiler. It has a door and is composed of two side sheets, a crown sheet, a back sheet and a flue sheet from which the flues extend to the smoke-box at the other end of the boiler.
A. The modern design is a rectangular-shaped structure positioned at the rear of the boiler. It features a door and consists of two side panels, a top panel, a back panel, and a flue panel, from which the flues extend to the smoke box at the opposite end of the boiler.
19. Q. To what strains is a fire-box subjected?
19. Q. What stresses does a fire-box experience?
A. To crushing strains and to those of unequal contraction and expansion.
A. To intense pressures and to those of uneven contraction and expansion.
20. Q. How are the sheets of a fire-box supported?
20. Q. How are the sheets of a firebox supported?
A. They are supported by staybolts screwed through the inside and outside sheets with their ends riveted over.
A. They are held in place by staybolts that are screwed through the inner and outer sheets, with their ends riveted over.
21. Q. In what manner is a crown sheet supported?
21. Q. How is a crown sheet supported?
A. By crown bars or radial staybolts.
A. By crown bars or radial staybolts.
22. Q. What are the bad features about crown bars?[Pg 30]
22. Q. What are the drawbacks of crown bars?[Pg 30]
A. They are hard to keep clean and frequently cause crown sheets to become mud burned.
A. They’re difficult to keep clean and often make the crown sheets get mud burned.
23. Q. What are the advantages of radial stayed crown sheets?
23. Q. What are the benefits of radial stayed crown sheets?
A. They are easier to keep clean and cheaper to repair.
A. They're easier to clean and cheaper to fix.
24. Q. How are the inside and outside sheets of a fire-box secured at the bottom?
24. Q. How are the inner and outer sheets of a fire-box fastened at the bottom?
A. They are riveted to a wrought iron ring called a mud-ring.
A. They are fastened to a wrought iron ring called a mud-ring.
25. Q. Describe the ash-pan and its use.
25. Q. Explain what the ash-pan is and how it’s used.
A. It is a receptacle secured to the fire-box and usually provided with dampers to regulate the flow of air to the fire. It collects the ashes that drop from the fire-box and prevents them from setting fire to bridges or other property along the track. Engine-men must know that ash-pan slide and hopper bottoms are closed before leaving enginehouse.
A. It’s a container attached to the firebox and typically equipped with dampers to control the airflow to the fire. It gathers the ashes that fall from the firebox and stops them from igniting bridges or other property along the track. Engine crew must ensure that the ash-pan slide and hopper bottoms are closed before leaving the engine house.
26. Q. What is a "wagon-top" boiler?
26. Q. What is a "wagon-top" boiler?
A. It is a boiler that has the fire-box end made larger than the cylindrical part to provide more steam space.
A. It’s a boiler with the fire-box end that’s wider than the cylindrical part to create more steam space.
27. Q. Why are boilers provided with steam domes?
27. Q. Why are boilers equipped with steam domes?
A. To furnish more steam space and to obtain dryer steam and to provide a place for the safety valves, steam pipes, throttle valve and whistle.
A. To provide more steam space, obtain drier steam, and create a location for the safety valves, steam pipes, throttle valve, and whistle.
28. Q. What must be the condition of a boiler to give the best results?[Pg 31]
28. Q. What must be the condition of a boiler to give the best results?[Pg 31]
A. It must have good circulation and be clean and free from mud or scale.
A. It should have good circulation and be clean and free from dirt or buildup.
29. Q. What is meant by "circulation" in a boiler?
29. Q. What does "circulation" mean in a boiler?
A. Free movement of the water, so that it may come in contact with the heating surface and after being converted into steam be immediately replaced by a fresh supply of water.
A. Free movement of the water, so it can contact the heating surface and, after being turned into steam, be quickly replaced by a new supply of water.
30. Q. What would be the effect if a "leg" of the fire-box became filled with mud?
30. Q. What would happen if one of the legs of the firebox got filled with mud?
A. There would be no water in contact with the fire-box sheets and they would quickly become overheated and mud-burned.
A. There wouldn’t be any water touching the fire-box sheets, and they would rapidly get too hot and sustain damage from the heat.
31. Q. What would be the result if the fire-box sheets became overheated?
31. Q. What would happen if the fire-box sheets got too hot?
A. They would be weakened and forced off the staybolts and an explosion would occur.
A. They would be weakened and forced off the staybolts, leading to an explosion.
32. Q. Would it be advisable to put water into a boiler after the sheets had become bare and red hot?
32. Q. Would it be wise to add water to a boiler after the metal sheets have become completely exposed and red hot?
A. No. The fire should be killed at once.
A. No. The fire should be put out immediately.
33. Q. What effect has the stoppage of a large number of flues?
33. Q. What is the impact of shutting down a large number of flues?
A. The heating surface and draft are decreased by just that much area.
A. The heating surface and draft are reduced by exactly that much area.
34. Q. Why are boiler checks placed so far away from the fire-box?
34. Q. Why are boiler checks located so far from the firebox?
A. To introduce the water into the boiler at as great a distance from the fire-box as possible. This permits the water to become heated to a high tem[Pg 32]perature before it comes in contact with the fire-box and also improves circulation.
A. To bring the water into the boiler as far away from the firebox as possible. This allows the water to heat to a high temperature before it reaches the firebox and also enhances circulation.
35. Q. What part of the boiler has the greatest pressure? Why?
35. Q. Which part of the boiler has the highest pressure? Why?
A. The bottom, because it is subject to the weight of the water in addition to the steam pressure in the boiler.
A. The bottom, since it bears the weight of the water along with the steam pressure in the boiler.
36. Q. What are the advantages of the extension front end?
36. Q. What are the benefits of the extension front end?
A. To provide room for suitable draft and spark appliances.
A. To create space for proper draft and ignition devices.
37. Q. What is the purpose of a netting in a smoke-box or front end?
37. Q. What's the purpose of a netting in a smoke-box or front end?
A. To act as a crusher of all cinders and prevent large cinders from passing out of the front end to the atmosphere.
A. To function as a filter for all ashes and stop large ashes from escaping out of the front end into the air.
38. Q. What is the object of hollow staybolts?
38. Q. What are hollow staybolts used for?
A. To indicate when the staybolt is broken by the escape of steam through the small hole in the bolt.
A. To show when the staybolt is broken by the escape of steam through the small hole in the bolt.
39. Q. What will cause the engine to tear holes in the fire?
39. Q. What will make the engine create holes in the fire?
A. Working hard or slipping when the dampers are open and the door closed, or too thin a fire.
A. Working hard or slipping when the dampers are open and the door is closed, or a fire that is too weak.
40. Q. Name the various adjustable appliances in the front end by which the draft may be regulated.
40. Q. Name the different adjustable devices at the front end that can be used to control the draft.
A. The exhaust nozzle, the diaphragm and the draft pipes or petticoat pipe.
A. The exhaust nozzle, the diaphragm, and the draft pipes or petticoat pipe.
41. Q. What object is there in having the exhaust steam go through the stack?[Pg 33]
41. Q. What’s the point of having the exhaust steam go through the stack?[Pg 33]
A. To create a draft through the tubes and fire-box.
A. To create a draft through the tubes and firebox.
42. Q. How does this affect the fire?
42. Q. How does this impact the fire?
A. The exhaust steam escaping through the stack tends to empty the smoke-box of gases and produces a partial vacuum there, atmospheric pressure then forces air through the grates and tubes to refill the smoke-box, and in this way the draft through the fire is established and maintained.
A. The exhaust steam coming out of the stack tends to clear out the smoke-box of gases and creates a partial vacuum there. This change in pressure causes atmospheric air to flow through the grates and tubes to fill up the smoke-box again, which in turn establishes and maintains the draft through the fire.
43. Q. Explain what adjustments can be made and the effect of each adjustment on the fire.
43. Q. Describe what changes can be made and how each change affects the fire.
A. Larger or smaller nozzle tips cause less or greater draft on the fire; raising or lowering the draft pipes and diaphragm causes the engine to burn the fire more at the rear or front end of the fire-box; the size and position of the draft pipes increase the draft through the top or bottom flues; the latter adjustments should always be attempted before reducing the nozzle.
A. Larger or smaller nozzle tips create less or more draft on the fire; adjusting the draft pipes and diaphragm raises or lowers the engine's ability to burn the fire more at the rear or front end of the firebox; the size and placement of the draft pipes enhance the draft through the top or bottom flues; these adjustments should always be made before reducing the nozzle.
44. Q. What does it indicate when the exhaust issues strongest from one side of the stack?
44. Q. What does it mean when the exhaust is coming out more strongly from one side of the stack?
A. The stack, exhaust pipe or petticoat pipe are out of plumb.
A. The stack, exhaust pipe, or petticoat pipe are not aligned correctly.
45. Q. What is the effect of leaky steam pipe joints inside the smoke-box?
45. Q. What happens when steam pipe joints inside the smoke-box are leaking?
A. The engine will not steam freely.
A. The engine won't steam properly.
46. Q. What causes "pull" on the fire-box door?
46. Q. What causes the "pull" on the fire-box door?
A. The partial vacuum in the front end; when excessive it indicates dampers closed, fire clinkered or insufficient opening for the admission of air under the fire.[Pg 34]
A. The partial vacuum in the front end; when it’s too high, it suggests that the dampers are closed, the fire is clinkered, or there's not enough opening for air to flow in under the fire.[Pg 34]
47. Q. If upon opening the fire-box door you discover there what is commonly called a red fire, what might be the cause?
47. Q. If you open the firebox door and find what's often called a red fire, what could be the reason?
A. The grates may have become clogged with ashes or clinkers so that sufficient air could not pass through them to the fire.
A. The grates might have gotten blocked with ashes or clinkers, preventing enough air from flowing through to the fire.
48. Q. Is it not a waste of fuel to open the fire-box door to prevent pops from opening? How can this be prevented more economically?
48. Q. Isn’t it a waste of fuel to open the fire-box door to stop the pops from opening? How can this be done more efficiently?
A. Yes. This can usually be prevented by putting the heater into the tank, or putting on the injector, or by more careful firing.
A. Yes. This can usually be avoided by placing the heater in the tank, installing the injector, or by being more careful with the firing.
49. Q. Describe the principle upon which the injector works.
49. Q. Explain how the injector works.
A. The action of the injector is due first to the difference between "kinetic" or moving energy and "static" or standing energy; second, to the fact that steam at a pressure travels at a very high velocity and when placed in contact with a stream of water it is condensed into water, and at the same time it imparts enough velocity to the water to give it sufficient momentum to overcome a pressure even greater than the original pressure of the steam. By imparting this velocity to the water it gives it sufficient energy to throw open the check valves and enter the boiler against high pressure.
A. The injector works primarily because of the difference between "kinetic" (moving) energy and "static" (standing) energy. Secondly, steam at high pressure moves very quickly, and when it comes into contact with a stream of water, it condenses into water while also giving the water enough speed to build up enough momentum to surpass an even greater pressure than that of the steam. By giving the water this speed, it provides enough energy to open the check valves and enter the boiler against high pressure.
50. Q. What is the difference between a lifting and a non-lifting injector?
50. Q. What’s the difference between a lifting injector and a non-lifting injector?
A. A lifting injector will create sufficient vacuum to raise the water from the level of the tank. The steam tubes in a non-lifting injector are different and it will not raise the water, but merely force it into[Pg 35] the boiler. A non-lifting injector must be placed below the level of the water in the tank so the water will flow to it by gravity.
A lifting injector will create enough vacuum to pull the water up from the tank level. The steam tubes in a non-lifting injector are different, and it won't lift the water; it just pushes it into[Pg 35] the boiler. A non-lifting injector needs to be positioned below the water level in the tank so that gravity can bring the water to it.
51. Q. Will an injector work with a leak between the injector and tank? Why? Will it prime?
51. Q. Will an injector function if there's a leak between the injector and the tank? Why? Will it be able to prime?
A. A lifting injector will not work if the leak is bad. It will not prime because the air admitted through the leak destroys the vacuum necessary to raise the water to the injector level. A non-lifting injector will work, as the water will escape from the pipe instead of air being drawn into it as with the lifting injector.
A. A lifting injector won't work if there's a significant leak. It can't prime because the air coming in through the leak ruins the vacuum needed to pull the water up to the injector level. A non-lifting injector will function, since the water will flow out of the pipe instead of allowing air to be drawn in like with the lifting injector.
52. Q. If it primes well, but breaks when the steam is turned on wide, where would you look for the trouble?
52. Q. If it primes well but breaks when the steam is fully on, where would you look for the problem?
A. Insufficient water supply due to tank valve partly closed, strainer stopped up or tank hose kinked, injector tubes out of line, limed up, or delivery tube cut, or wet steam from the throttle.
A. Insufficient water supply due to the tank valve being partly closed, a clogged strainer, a kinked tank hose, misaligned injector tubes, scaled up, a cut delivery tube, or wet steam from the throttle.
53. Q. If it would not prime, where would you expect to find the trouble?
53. Q. If it won't start, where would you expect to find the problem?
A. Insufficient water supply, priming valve out of order, or with the lifting injector the trouble might be caused by a leak between the injector and tank.
A. Lack of water supply, malfunctioning priming valve, or with the lifting injector, the issue could be due to a leak between the injector and the tank.
54. Q. Will an injector prime if the boiler check leaks badly or if it is stuck up? If the injector throttle leaks badly?
54. Q. Will an injector prime if the boiler check is leaking badly or if it is jammed? What if the injector throttle is leaking badly?
A. No.
A. No.
55. Q. If steam or water shows at the overflow pipe when the injector is not working, how can you[Pg 36] tell whether it comes from the boiler check or the injector throttle?
55. Q. If steam or water comes out of the overflow pipe when the injector isn't working, how can you[Pg 36] figure out if it's coming from the boiler check or the injector throttle?
A. Close the main steam valve at the boiler, that will stop the leak if it comes from the injector throttle.
A. Close the main steam valve at the boiler; that will stop the leak if it's coming from the injector throttle.
56. Q. Will an injector prime if primer valve leaks? Will that prevent its working?
56. Q. Will an injector prime if the primer valve is leaking? Will that stop it from working?
A. It will prime, but not as readily as with priming valve in good condition. This will not prevent its working, but it may waste some water from the overflow.
A. It will prime, but not as easily as with the priming valve in good condition. This won’t stop it from working, but it might waste some water from the overflow.
57. Q. Will an injector work if air cannot get into the tank as fast as the water is taken out?
57. Q. Will an injector work if air can't get into the tank as quickly as the water is being removed?
A. No.
No.
58. Q. If you had to take down a tank hose, how would you stop the water from flowing out of the tank that has the syphon connections instead of the old-style tank valves?
58. Q. If you needed to remove a tank hose, how would you prevent the water from flowing out of the tank that has the siphon connections instead of the old-fashioned tank valves?
A. Open the pet cock at the top of the syphon before taking the hose down.
A. Open the petcock at the top of the siphon before removing the hose.
59. Q. Is any more water used when the engine foams than when the water is solid?
59. Q. Is more water used when the engine is foaming compared to when the water is solid?
A. Yes, very much more.
A. Yes, a lot more.
60. Q. How would you prevent injector feed pipes or tank hose from freezing in winter when not in use?
60. Q. How can you stop injector feed pipes or tank hoses from freezing during winter when they're not being used?
A. The steam valve should be slightly open to permit a slight circulation of steam through the feed and branch pipes. The heater cock should be closed[Pg 37] and the drip cock under the boiler check or on the branch pipe should be opened to insure a circulation of steam through the branch pipe.
A. The steam valve should be slightly open to allow a small flow of steam through the feed and branch pipes. The heater cock should be closed[Pg 37] and the drain cock under the boiler check or on the branch pipe should be opened to ensure steam circulates through the branch pipe.
61. Q. How would you prevent the overflow pipe from freezing with a lifting injector?
61. Q. How would you keep the overflow pipe from freezing when using a lifting injector?
A. The overflow valve should be opened just enough to permit a little steam to escape through the overflow pipe to prevent it from freezing.
A. The overflow valve should be opened just enough to let a little steam escape through the overflow pipe to keep it from freezing.
62. Q. Name the various parts of the injector.
62. Q. What are the different parts of the injector?
A. The injector consists of a body supplied with a steam valve, a steam nozzle, a primer, a combining tube, a delivery tube, a line check valve, an overflow valve, a water valve, and a lifting injector has a lifting tube.
A. The injector has a body equipped with a steam valve, a steam nozzle, a primer, a combining tube, a delivery tube, a check valve, an overflow valve, a water valve, and a lifting injector that includes a lifting tube.
63. Q. What may be done if a combining tube is obstructed?
63. Q. What can be done if a combining tube is blocked?
A. The steam valve bonnet may be removed and the obstruction forced out with a piece of stiff wire, or uncouple the delivery pipe from the injector and unscrew and remove the tubes; the obstruction can then be removed and the tubes replaced.
A. You can take off the steam valve bonnet and push out the blockage with a stiff wire, or disconnect the delivery pipe from the injector and unscrew and remove the tubes; then you can clear the blockage and put the tubes back in.
64. Q. How is the greatest injury done to a boiler when cleaning or knocking the fire?
64. Q. What’s the biggest damage that can happen to a boiler when cleaning or tampering with the fire?
A. By excessive use of the blower drawing cold air through the fire-box and flues.
A. By overusing the blower to pull cold air through the firebox and flues.
65. Q. Why does putting a large quantity of cold water into a boiler when the throttle is closed cause the flues to leak? When is this most serious?
65. Q. Why does adding a large amount of cold water to a boiler when the throttle is closed cause the flues to leak? When is this the most serious?
A. When steam is not being used there is not much circulation of water in the boiler, and the water[Pg 38] entering the boiler at about 150 degrees temperature is heavier than the water in the boiler. The cooler water will go to the bottom and reduce the temperature in that part of the boiler and causing the flues to contract in length as well as in diameter and this has a tendency to pull them out of the sheet. This will loosen them and cause them to leak. After the fire has been knocked this tendency is much greater, and for that reason cold water should not be put into a boiler after the fire has been knocked out. Always fill the boiler before the fire is knocked out.
A. When steam isn't being used, there isn't much water circulation in the boiler, and the water[Pg 38] entering the boiler at about 150 degrees is heavier than the water already in the boiler. The cooler water sinks to the bottom, lowering the temperature in that part of the boiler, which causes the flues to contract in both length and diameter. This can pull them away from the sheet, loosening them and causing leaks. After the fire has been extinguished, this tendency is much greater, so cold water shouldn't be added to a boiler once the fire is out. Always fill the boiler before the fire is extinguished.
66. Q. Is warm water in the tank of any advantage in making steam rapidly?
66. Q. Does having warm water in the tank help in making steam quickly?
A. Yes; careful experiments have shown that a locomotive will generate one per cent. more steam for every eleven degrees that the tank water is heated; thus by heating the feed water in the tank from 39 degrees to 94 would effect a saving of five per cent.
A. Yes; careful experiments have shown that a locomotive will generate one percent more steam for every eleven degrees that the tank water is heated; therefore, heating the feed water in the tank from 39 degrees to 94 would result in a saving of five percent.
67. Q. Then why not heat the feed water to the boiling point (212 degrees)?
67. Q. So why not heat the feed water to the boiling point (212 degrees)?
A. If the feed water is heated much above 100 degrees it will not condense enough steam in the injector to cause it to work properly. Some injectors will work hotter water than others. It would also spoil the paint on the tank if heated to a much higher temperature.
A. If the feed water is heated well above 100 degrees, it won't condense enough steam in the injector to function properly. Some injectors can handle hotter water than others. Additionally, it would damage the paint on the tank if heated to a significantly higher temperature.
68. Q. At 200 pounds pressure per square inch, what is the pressure per square foot on the sheets of a boiler?
68. Q. At 200 pounds of pressure per square inch, what is the pressure per square foot on the sheets of a boiler?
A. About fifteen tons.
About 15 tons.
69. Q. What is the total pressure on the fire-box of a large locomotive?[Pg 39]
69. Q. What is the total pressure on the firebox of a large locomotive?[Pg 39]
A. Over 3,000 tons.
Over 3,000 tons.
70. Q. Give a practical definition of heating surface.
70. Q. Provide a practical definition of heating surface.
A. The heating surface of a boiler includes all parts of the boiler and tubes that are directly exposed to fire or heat from the fire and are surrounded by water.
A. The heating surface of a boiler includes all the parts of the boiler and tubes that are directly exposed to fire or heat from the fire and are surrounded by water.
71. Q. Should an engine be slipped to get water out of the cylinders or steam passages?
71. Q. Should an engine be slipped to get water out of the cylinders or steam passages?
A. No; the water should be worked out by opening the cylinder cocks and starting the engine slowly.
A. No; the water should be drained by opening the cylinder cocks and starting the engine slowly.
72. Q. What does it indicate when the smoke trails back over the train and into the coaches after shutting off?
72. Q. What does it mean when the smoke trails back over the train and into the cars after it's turned off?
A. It indicates poor firing or a lack of understanding between the engineer and fireman in regard to where the engine was to be shut off.
A. It shows bad communication or a lack of understanding between the engineer and the fireman about where the engine was supposed to be turned off.
73. Q. Before shaking grates or dumping the ash-pan, what should be observed?
73. Q. Before shaking the grates or emptying the ash pan, what should be checked?
A. That the engine is not passing over bridges or cattle guards, crossings, switches, interlocking fixtures, or in yards. Fire on the track should be extinguished promptly at places where ash-pans are cleaned.
A. That the engine is not crossing bridges or cattle guards, crossings, switches, interlocking devices, or in yards. Fires on the track should be put out quickly at locations where ash pans are cleaned.
74. Q. Which is easier and more satisfactory on a long run, to stop and clean the fire if necessary or to continue to the end of a long, hard trip with a dirty fire?
74. Q. Which is easier and more satisfying in the long run: stopping to clean the fire if needed, or pushing through a long, tough journey with a dirty fire?
A. Stop and clean the fire if necessary. It will save fuel and labor during the remainder of the trip and may also save an engine failure.[Pg 40]
A. Stop and clean the fire if needed. It will save fuel and effort for the rest of the journey and might also prevent an engine failure.[Pg 40]
75. Q. Should you examine the flues to see if they are stopped up and leaking, and inspect the grate and grate rigging carefully before leaving the engine at a terminal?
75. Q. Should you check the flues to see if they are blocked or leaking, and thoroughly inspect the grate and grate rigging before leaving the engine at a terminal?
A. Yes, so they can be reported if necessary. Clean flues and grates working well make a vast difference in the success of a fireman, and a great many engine failures could be avoided by keeping the flues and grates in proper condition.
A. Yes, so they can be reported if needed. Clean flues and grates that function properly make a huge difference in a fireman's success, and many engine failures could be prevented by maintaining the flues and grates in good condition.
76. Q. How should cab lamps, signal lamps, oil cans and lanterns be cared for?
76. Q. How should you take care of cab lamps, signal lamps, oil cans, and lanterns?
A. They should be kept clean, free from leaks and always filled and ready for service before leaving terminals.
A. They should be kept clean, free from leaks, and always filled and ready for use before leaving terminals.
77. Q. About how many drops in a pint of valve oil when fed through a lubricator?
77. Q. Approximately how many drops are in a pint of valve oil when it's fed through a lubricator?
A. About 4,500 drops.
About 4,500 drops.
78. Q. Assuming that five drops per minute are fed to each of two valves and one drop per minute to the air pump, how many hours would be required to feed one pint of valve oil?
78. Q. If five drops per minute are supplied to each of two valves and one drop per minute to the air pump, how many hours would it take to provide one pint of valve oil?
A. About eight hours.
Around eight hours.
79. Q. Assuming that the engine is running twenty-miles per hour, how many miles per pint would be run?
79. Q. If the engine is running at twenty miles per hour, how many miles can be covered per pint?
A. About 160 miles per pint.
A. About 160 miles per gallon.
80. Q. How many drops per minute should ordinarily be fed?
80. Q. How many drops per minute should usually be given?
A. This will vary with the size of the locomotive and the work to be performed. On small yard engines[Pg 41] one drop per minute for each cylinder is usually sufficient and one drop for the air pump every two or three minutes. This depends on the condition of the pump and the service being performed. For large engines in slow freight service four to five drops per minute, and for large engines in heavy fast passenger service from five to seven drops per minute should be fed. Air pumps in freight service where the brake pipe is in moderately good condition can usually be run with one or two drops per minute when handling long trains of cars equipped with air brakes.
A. This will change depending on the size of the locomotive and the tasks required. For small yard engines[Pg 41], one drop per minute for each cylinder is typically enough, and one drop for the air pump every two or three minutes. This varies based on the condition of the pump and the type of service being performed. For large engines in slow freight service, four to five drops per minute should be used, and for large engines in heavy fast passenger service, five to seven drops per minute is recommended. Air pumps in freight service, where the brake pipe is in decent condition, can usually operate with one or two drops per minute when managing long trains of cars with air brakes.
81. Q. Will any bad results ensue from filling the lubricator full of cold oil?
81. Q. Will there be any negative consequences from filling the lubricator with cold oil?
A. Yes; when the oil gets hot it will expand and may break the glass or bulge or burst the lubricator.
A. Yes; when the oil heats up, it will expand and might break the glass or cause the lubricator to bulge or burst.
82. Q. If a sight feed gets stopped up, how could you clean it out?
82. Q. If a sight feed gets clogged, how can you clear it out?
A. Close the water valve and the regulating valves to the other feeds. Open drain cock and draw out a small quantity of water so as to bring the oil in top part of lubricator below the top end of oil pipe leading to feed arm, then open wide the regulating valve to feed that is stopped up and the pressure from the equalizing tube will force the obstruction out of the feed nozzle and up into the body of the lubricator. Next, close this regulating valve until the feed glass fills with water, then open water valve and start feeds.
A. Shut off the water valve and the regulating valves for the other feeds. Open the drain cock and let out a small amount of water to bring the oil in the top part of the lubricator below the top end of the oil pipe that leads to the feed arm. Then, open the regulating valve wide for the feed that’s blocked, and the pressure from the equalizing tube will push the blockage out of the feed nozzle and into the body of the lubricator. Next, close this regulating valve until the feed glass fills with water, then open the water valve and start the feeds.
83. Q. How would you clean out chokes?
83. Q. How do you clean out chokes?
A. First, shut off boiler pressure and condenser valve; next, remove feed valve bonnet, then open main throttle valve, when the steam from steam chest will blow back through the choke plug, clearing it of any obstruction.[Pg 42]
A. First, turn off the boiler pressure and the condenser valve; next, take off the feed valve bonnet, then open the main throttle valve, and steam from the steam chest will blow back through the choke plug, clearing it of any blockage.[Pg 42]
84. Q. What is superheated steam?
84. Q. What is superheated steam?
A. It is the saturated steam separated from the water from which it is generated with more heat added, increasing its temperature from 100 degrees to 250 degrees Fahrenheit above the saturated steam temperature.
A. It is the saturated steam that has been separated from the water it was generated from, with additional heat added, raising its temperature from 100 degrees to 250 degrees Fahrenheit above the saturated steam temperature.
85. Q. What is the advantage of superheating or increasing the temperature of the steam?
85. Q. What’s the benefit of superheating or raising the temperature of the steam?
A. By increasing the temperature of the steam the volume of a given weight of steam is increased and all losses due to cylinder condensation are eliminated, which result in a reduced steam consumption, a saving in coal and water and increased boiler capacity.
A. By raising the temperature of the steam, the volume of a specific weight of steam increases, and all losses from cylinder condensation are eliminated, leading to reduced steam consumption, savings in coal and water, and greater boiler capacity.
86. Q. How is the increased temperature obtained by the use of the superheater?
86. Q. How is the higher temperature achieved using the superheater?
A. By admitting the saturated steam into a partitioned receiver which has a number of 1½-inch pipes attached to it. These are located in and extend nearly the full length of the large flues, the steam having to pass through these 1½-inch pipes on its way back to the receiver, absorbs the heat from the gases passing through the large tubes, causing its temperature to rise, or in other words, become superheated.
A. By introducing the saturated steam into a divided receiver that has several 1½-inch pipes connected to it. These pipes are positioned in and nearly span the entire length of the large flues. As the steam travels back to the receiver through these 1½-inch pipes, it absorbs heat from the gases moving through the large tubes, which causes its temperature to increase, or in simpler terms, become superheated.
87. Q. How much is the volume of steam increased by superheating?
87. Q. How much does the volume of steam increase when it's superheated?
A. For each 100 degrees of superheat added to saturated steam, at temperatures ordinarily used in locomotive practice, the volume of a given weight is increased roughly from sixteen to seventeen per cent.
A. For every 100 degrees of superheat added to saturated steam, at temperatures typically used in locomotive practice, the volume of a specific weight increases by about sixteen to seventeen percent.
88. Q. Why is the superheated steam so much[Pg 43] more economical on coal and water than the saturated steam?
88. Q. Why is superheated steam so much[Pg 43] more efficient with coal and water compared to saturated steam?
A. Because for a given amount of water evaporated you can increase the volume of steam 33 per cent. by superheating. It is readily seen that the coal does not have to be burned if the steam used has 33 per cent. more volume for filling space, or in other words, only so much steam can be admitted to the cylinders for every movement of the valve, and what can not be used must remain in the boiler, so if the engine can not use all of the steam that the boiler is capable of generating, the saving must show in coal and water. If you can not use all of the steam you do not have to burn coal to make it.
A. Because with a specific amount of water evaporated, you can increase the volume of steam by 33 percent through superheating. It's clear that the coal doesn't need to be burned if the steam produced has 33 percent more volume to occupy space. In other words, only a limited amount of steam can enter the cylinders with each valve movement, and any steam that can't be used has to stay in the boiler. So, if the engine can't utilize all the steam that the boiler can create, the savings will reflect in reduced coal and water usage. If you can't use all of the steam, you don't need to burn coal to produce it.
89. Q. Which is the better practice, to close the feed valves or water valve while waiting on sidings, etc.?
89. Q. What’s the better practice: closing the feed valves or the water valve while waiting on sidings, etc.?
A. Close the feed valves; the water valve may leak.
A. Close the feed valves; the water valve might leak.
90. Q. How can you tell if equalizer tubes become stopped up or broken?
90. Q. How can you tell if the equalizer tubes are clogged or damaged?
A. If they were stopped up the equalization would be destroyed, and when the steam-chest pressure was less than the boiler pressure the feed would work too fast, the oil would enter the feed glass in a stream instead of forming into drops. If they were broken, the lubricator could not be used. The auxiliary oilers would have to be used to lubricate the cylinders.
A. If they were clogged, the balance would be ruined, and when the steam-chest pressure fell below the boiler pressure, the feed would operate too quickly, causing the oil to flow into the feed glass in a stream rather than forming drops. If they were damaged, the lubricator couldn’t be used. The auxiliary oilers would need to be used to lubricate the cylinders.
1. Q. Explain how an air compressor should be started.
1. Q. Describe how to start an air compressor.
A. A compressor should be started slowly, with the drain cocks open to allow the water of condensation to escape; and as no provision is made in the steam end to cushion the pistons at the end of their stroke, it should be allowed to work slowly until a pressure of thirty or forty pounds has accumulated in the main reservoir; the piston, having to work against this pressure, will be cushioned at the end of each stroke. After the compressor is warm, the drain cocks should be closed and the throttle opened sufficiently to run the compressor at the proper speed. The lubricator should then be started and allowed to feed freely until eight or ten drops have passed, when the feed should be reduced to an amount sufficient for proper lubrication.
A. A compressor should be started slowly, with the drain cocks open to let out any condensation. Since there’s no system in place to cushion the pistons at the end of their stroke, it should be allowed to operate slowly until a pressure of thirty to forty pounds builds up in the main reservoir. The piston, having to work against this pressure, will have cushioning at the end of each stroke. Once the compressor is warm, the drain cocks should be closed, and the throttle opened enough to run the compressor at the right speed. The lubricator should then be turned on and allowed to feed freely until eight to ten drops have come through, after which the feed should be adjusted to provide just enough for proper lubrication.
2. Q. What kind of oil should be used to lubricate both the steam and air cylinders of the compressor?
2. Q. What type of oil should be used to lubricate both the steam and air cylinders of the compressor?
A. Valve oil.
Valve oil.
3. Q. Where does the main reservoir pressure begin and end?
3. Q. Where does the main reservoir pressure start and stop?
A. Begins at the discharge valves in the compressor and ends at the engineer's brake valve.
A. Begins at the discharge valves in the compressor and ends at the engineer's brake valve.
4. Q. Where does the brake pipe pressure begin and end?
4. Q. Where does the brake pipe pressure start and finish?
A. The brake pipe pressure begins at the feed valve and ends at the brake pipe side of the triple piston, conductor's valve and at the rear angle cock.[Pg 45]
A. The brake pipe pressure starts at the feed valve and ends at the brake pipe side of the triple piston, conductor's valve, and at the rear angle cock.[Pg 45]
5. Q. What is meant by excess pressure, and where is this pressure carried?
5. Q. What does excess pressure mean, and where is this pressure located?
A. Excess pressure is carried in the main reservoir and is the pressure above that in the brake pipe.
A. Excess pressure is held in the main reservoir and is the pressure above what is in the brake pipe.
6. Q. Why is excess pressure necessary?
6. Q. Why is extra pressure needed?
A. To insure the prompt release of all brakes and quick recharge of the brake pipe and auxiliary reservoirs.
A. To ensure the quick release of all brakes and fast recharge of the brake pipe and auxiliary reservoirs.
7. Q. How is the amount of excess pressure regulated?
7. Q. How is the excess pressure amount regulated?
A. By the compressor governor.
A. By the compressor controller.
8. Q. Name the different parts of the air brake as applied to a car.
8. Q. What are the different components of the air brake system used in a car?
A. The triple valve, auxiliary reservoir, brake cylinder, brake pipe, angle cocks, cut-out cock, retaining valve, centrifugal dirt collector and strainer tee.
A. The triple valve, auxiliary reservoir, brake cylinder, brake pipe, angle cocks, cut-out cock, retaining valve, centrifugal dirt collector, and strainer tee.
9. Q. What is the duty of the triple valve?
9. Q. What does the triple valve do?
A. The triple valve has three duties to perform: Charge the auxiliary reservoir; apply the brake; and release the brake.
A. The triple valve has three tasks to handle: Fill the auxiliary reservoir; engage the brake; and release the brake.
10. Q. What is the purpose of the auxiliary reservoir?
10. Q. What is the purpose of the auxiliary reservoir?
A. It is here that the air is stored that is admitted to the brake cylinder when the brake is applied; thus, each car carries its own brake power.
A. This is where the air is stored that gets sent to the brake cylinder when the brake is applied; therefore, each car has its own braking power.
11. Q. What is the purpose of the brake cylinder?[Pg 46]
11. Q. What does the brake cylinder do?[Pg 46]
A. It is here where the power of the compressed air is converted into work by forcing the brake piston out, moving the brake levers, rods and brake beams, forcing the brake shoes against the wheels, applying the brake.
A. This is where the power of compressed air is turned into work by pushing the brake piston out, moving the brake levers, rods, and brake beams, which press the brake shoes against the wheels, applying the brake.
12. Q. What is the purpose of the brake pipe and angle cocks?
12. Q. What are the brake pipe and angle cocks used for?
A. It is through the brake pipe that all brakes in the train are placed into communication with the brake valve on the locomotive; and through the brake pipe, air from the main reservoir flows to the triple valves and auxiliary reservoirs on the different cars. The angle cocks are for the purpose of opening and closing the ends of the brake pipe.
A. The brake pipe connects all the brakes in the train to the brake valve on the locomotive; and through the brake pipe, air from the main reservoir flows to the triple valves and auxiliary reservoirs on the various cars. The angle cocks are used to open and close the ends of the brake pipe.
13. Q. What is the purpose of the cut-out cock?
13. Q. What is the purpose of the cut-out cock?
A. To cut out any brake that is not in operating condition.
A. To remove any brake that is not working properly.
14. Q. How is a brake cut out?
14. Q. How do you cut out a brake?
A. By closing the cut-out cock in the cross-over pipe and bleeding the auxiliary reservoir.
A. By shutting off the cut-out valve in the cross-over pipe and draining the auxiliary reservoir.
15. Q. How would you bleed an auxiliary reservoir?
15. Q. How do you bleed an auxiliary reservoir?
A. By holding open the release valve on the reservoir until all air has escaped.
A. By keeping the release valve on the reservoir open until all the air has escaped.
16. Q. How would you bleed off a stuck brake?
16. Q. How would you release pressure from a stuck brake?
A. By holding open the auxiliary release valve until the brake piston starts to move toward release position.
A. By holding open the auxiliary release valve until the brake piston begins to move into the release position.
1. Q. What are the fireman's duties on arrival at the enginehouse previous to going out on an oil burning locomotive?
1. Q. What are the fireman's duties when they arrive at the engine house before heading out on an oil-burning locomotive?
A. In addition to the duties usually performed on any engine, the fireman should observe the condition of draft pans and arch, observe the condition of burner and dampers; try the oil regulating valve; see that the burner is properly delivering fuel oil to the fire; see that the oil heaters are in working order; that the fuel oil is heated to proper temperature; and see that proper supplies of fuel oil, sand and water have been provided as well as the necessary tools for handling an oil fire.
A. In addition to the usual tasks performed on any engine, the fireman should check the condition of the draft pans and arch, inspect the burner and dampers, test the oil regulating valve, ensure that the burner is supplying fuel oil to the fire correctly, verify that the oil heaters are functioning properly, confirm that the fuel oil is heated to the right temperature, and make sure that there are adequate supplies of fuel oil, sand, and water, as well as the necessary tools for handling an oil fire.
2. Q. How warm should the oil be at all times in the tank.
2. Q. What temperature should the oil always be in the tank?
A. Warm enough to flow freely at all times, usually about 112 degrees. This temperature is about that which the hand can bear on the outside of the tank.
A. Warm enough to flow freely at all times, usually around 112 degrees. This temperature is about what the hand can comfortably stand on the outside of the tank.
3. Q. If the oil is too warm, what happens?
3. Q. What happens if the oil is too hot?
A. Many of the good qualities of the oil may be lost by keeping it too warm, and the burner is more difficult to operate and does not work as well when the oil is kept at too high a temperature. Should the oil be too warm, it will give off too much gas which would be liable to cause an explosion in the oil tank.
A. Many of the beneficial properties of the oil can be lost if it’s kept too warm, and the burner becomes harder to operate and doesn’t function as effectively when the oil is at a high temperature. If the oil gets too warm, it will emit too much gas, which could potentially lead to an explosion in the oil tank.
4. Q. What tools are necessary for firing purposes on an oil burning locomotive?
4. Q. What tools are needed for firing an oil-burning locomotive?
A. The tools necessary for firing an oil burning engine include sand horn, brick hook, and a small iron bar to be used in cleaning carbon from the mouth of the burner.[Pg 48]
A. The tools needed for operating an oil-burning engine include a sand horn, a brick hook, and a small iron bar for cleaning carbon from the burner.[Pg 48]
5. Q. What is liable to happen if the heater valve is open too much?
5. Q. What could happen if the heater valve is opened too much?
A. If the heater valve is opened too much it would be liable to burst the heater hose as well as to heat the oil to a too high temperature and place an unnecessary strain on all the heater connections, causing them to leak.
A. If the heater valve is opened too much, it could burst the heater hose and heat the oil to a temperature that’s too high, putting unnecessary strain on all the heater connections and causing them to leak.
6. Q. What should be done on approaching stations where additional supply of fuel oil is to be taken?
6. Q. What should be done when approaching stations where an extra supply of fuel oil is needed?
A. Shut off the fire, close safety and main oil valves, remove any lamps that are so close as to be unsafe when manhole cover is open.
A. Turn off the fire, close the safety and main oil valves, and take away any lamps that are too close to be safe when the manhole cover is open.
7. Q. What care must be exercised in the use of lamps, torches or lanterns about oil tanks whether hot or cold?
7. Q. What precautions should be taken when using lamps, flashlights, or lanterns around oil tanks, whether they are hot or cold?
A. Never permit oil lamps or oil torches to be carried within ten feet of the tank opening. Only incandescent lamps or pocket flash lights should be used around oil tank manhole when taking oil.
A. Never allow oil lamps or oil torches to be carried within ten feet of the tank opening. Only incandescent lamps or pocket flashlights should be used around the oil tank manhole when taking oil.
8. Q. How can oil in the tank be measured without taking a light to the manhole?
8. Q. How can you measure the oil in the tank without using a light to look into the manhole?
A. By inserting a measuring stick into oil in tank and taking stick to the light for reading.
A. By inserting a measuring stick into the oil tank and holding the stick up to the light for a reading.
9. Q. What precautions must be taken before entering tanks that have been used for oil to clean or make repairs?
9. Q. What safety measures should be followed before entering tanks that have been used for oil to clean or make repairs?
A. Oil tanks, before being entered by workmen, should be thoroughly steamed and cooled before being entered. For safety they should be steamed from six to eight hours.
A. Oil tanks, before being entered by workers, should be thoroughly steamed and cooled. For safety, they should be steamed for six to eight hours.
10. Q. How should the fire be lighted in an oil burning locomotive?[Pg 49]
10. Q. How should the fire be started in an oil-burning locomotive?[Pg 49]
A. First see that no one is working under the engine, that there is the proper amount of water in the boiler and that it will flow through the gauge cocks, that there is no accumulation of oil in the ash-pan or fire-box or existing leaks throughout. If there is no steam in the boiler, the steam connections can be made to the three-way cock at the smoke-arch that will answer for blower and atomizer. If there are twenty pounds of steam in the boiler, it can be operated with its own blower. If oil in the tank is too cold to flow into the burner readily, it must be heated. Open the front damper and put on the blower strong enough to create the necessary draft, open the atomizer valve long enough to blow out any water that might be in the steam pipe to the burner, then close the valve and throw a piece of burning waste in front of the burner and open the atomizer valve enough to carry oil to the burning waste and open the regulating valve slowly until the oil is known to be ignited. Watch the ignition through the hole in the fire-box door, then regulate the steam and oil supply to suit. Be sure that no oil is wasting below the burner or an explosion may result that will prove disastrous.
A. First, make sure no one is working under the engine, that there’s enough water in the boiler and that it flows through the gauge cocks, and that there’s no buildup of oil in the ash-pan or fire-box, or any leaks anywhere. If there’s no steam in the boiler, you can connect the steam lines to the three-way cock at the smoke-arch that serves for the blower and atomizer. If there are twenty pounds of steam in the boiler, you can use its own blower. If the oil in the tank is too cold to flow easily into the burner, it needs to be warmed up. Open the front damper and set the blower on high enough to create the required draft, then open the atomizer valve briefly to clear out any water that might be in the steam pipe to the burner. After that, close the valve and put a piece of burning waste in front of the burner. Open the atomizer valve enough to get oil to the burning waste and slowly open the regulating valve until you see that the oil is ignited. Watch the ignition through the hole in the fire-box door and then adjust the steam and oil supply as needed. Make sure that no oil is leaking below the burner, or it could cause an explosion that might be disastrous.
11. Q. Should the fire go out and it is desired to rekindle it while bricks are hot, is it safe to depend on the hot bricks to ignite the oil without the use of lighted waste?
11. Q. If the fire goes out and you want to relight it while the bricks are still hot, can you rely on the hot bricks to ignite the oil without using lit waste?
A. No; depending upon the heat from the firebricks to re-light the fire is dangerous and forbidden.
A. No; relying on the heat from the firebricks to re-light the fire is risky and not allowed.
12. Q. What is termed an atomizer, and what does it perform?
12. Q. What is an atomizer, and what does it do?
A. The atomizer is a casting containing two long ports with an extension lip; the upper port is for oil and the lower one for steam. The lip aids the steam in atomizing and spreading the oil, which, when prop[Pg 50]erly mingled with the air and ignited, will produce combustion. The atomizer is located just under the mud-ring and pointed a little upward, so the stream of oil and spray of steam would strike the opposite wall a few inches above the bottom if it would pass clear across the fire-box.
A. The atomizer is a device with two long openings and an extension lip; the upper opening is for oil and the lower one is for steam. The lip helps the steam atomize and spread the oil, which, when mixed with air and ignited, will create combustion. The atomizer is positioned just below the mud-ring and angled slightly upward, so that the stream of oil and spray of steam would hit the opposite wall a few inches above the bottom if it were to travel entirely across the fire-box.
13. Q. In starting or closing the throttle of the locomotive, how should the fireman regulate the fire, in advance or after the action of the engineer?
13. Q. When starting or stopping the throttle of the locomotive, how should the fireman adjust the fire, before or after the engineer's actions?
A. In starting an oil burning engine the oil should gradually be brought up as the throttle is opened and the movement and amount of oil should be kept slightly in advance of the action of the engineer in order to prevent an inrush of cold air as the engine is working, which would result in injury to the fire-box and flues. When the throttle is to be closed, the fire should be reduced very slightly in advance of the closing of the throttle. This is to prevent the engine from popping off and black smoke drifting back over the train.
A. When starting an oil-burning engine, the oil should be gradually increased as the throttle is opened, and the oil flow should be maintained just ahead of the engineer's actions to avoid a rush of cold air while the engine is running, which could damage the firebox and flues. When it's time to close the throttle, the fire should be reduced slightly before closing the throttle to prevent the engine from popping off and black smoke from drifting back over the train.
14. Q. Is it necessary that the engineer and fireman on an oil burning locomotive work in perfect harmony and advise each other of intended action at every change of conditions?
14. Q. Is it necessary for the engineer and the fireman on an oil-burning locomotive to work in perfect harmony and communicate their intended actions during every change of conditions?
A. Yes; they should work in harmony with each other on any locomotive. The fireman should watch every move the engineer makes, and the engineer should advise the fireman of every intended change of the throttle, so he can operate his valves accordingly and save fuel and avoid black smoke.
A. Yes; they should work together smoothly on any train. The fireman should pay attention to everything the engineer does, and the engineer should inform the fireman of any planned changes to the throttle, so he can adjust his valves accordingly to save fuel and prevent black smoke.
15. Q. What is the effect of forcing the fire on an oil burning locomotive?
15. Q. What happens when you push the fire on an oil-burning locomotive?
A. Forcing the fire is very hard on fire-box sheets and flues, and will cause them to leak. An even[Pg 51] temperature should be maintained in the fire-box of any locomotive.
A. Forcing the fire puts a lot of stress on fire-box sheets and flues, which can lead to leaks. It's important to keep a consistent[Pg 51] temperature in the fire-box of any locomotive.
16. Q. Is a careful regulation of steam and oil valves and dampers necessary to obtain the most economical results?
16. Q. Is it important to carefully regulate the steam and oil valves and dampers to achieve the most cost-effective results?
A. Yes; the fireman's oil valve should be opened just wide enough to permit a sufficient amount of oil to be fed to produce a good fire, but not wide enough to waste oil or produce a volume of black smoke.
A. Yes; the fireman's oil valve should be opened just wide enough to allow enough oil to create a good fire, but not so wide that it wastes oil or produces a lot of black smoke.
17. Q. How can you judge whether the combustion is good or bad, so the valve may be regulated accordingly?
17. Q. How can you tell if the combustion is good or bad, so the valve can be adjusted as needed?
A. By the color of the fire in the fire-box. When it is a dull red color, the temperature is below 1,000 degrees and combustion is incomplete, dense black smoke will issue from the stack. If it is a bright red, the temperature will be about 1,800 degrees and combustion very good, and no black smoke will appear from the stack.
A. By the color of the fire in the firebox. When it’s a dull red color, the temperature is below 1,000 degrees and combustion is incomplete, causing dense black smoke to come from the stack. If it’s a bright red, the temperature will be around 1,800 degrees and combustion is very good, with no black smoke coming from the stack.
18. Q. How should the flues be cleaned from soot when running, and about how often is this necessary?
18. Q. How should the flues be cleaned of soot while in use, and how often is this needed?
A. By placing a small quantity of sand in an elbow shaped funnel or horn, and by inserting same in an opening provided in fire door while engine is working hard, allowing the exhaust to draw the sand through the flues, thus cutting soot and gum from them in its passage and discharging it from the stack. It is necessary that the flues be cleaned of soot on leaving terminals or sidings where the engine has been at rest for any length of time, and also as often as found necessary to aid the engine in steaming. This depends to a great extent upon the degree of perfection with[Pg 52] which combustion is obtained. Attention should also be given flues just prior to entering points where engine is to be put in roundhouse or otherwise detained in order to leave the flues clean, as this will aid in putting engine under steam with little delay where the blower alone is to be relied on for draft.
A. By putting a small amount of sand into an elbow-shaped funnel or horn and inserting it into an opening in the fire door while the engine is working hard, the exhaust will pull the sand through the flues, cleaning out soot and gum as it passes and then releasing it from the stack. It's essential to clean the flues of soot when leaving terminals or sidings where the engine has been idle for a while, and also as often as needed to help the engine generate steam. This largely depends on how effectively combustion is achieved. Attention should also be paid to the flues just before entering places where the engine will be stored in a roundhouse or otherwise held up, to ensure the flues are clean. This will help in getting the engine up to steam quickly when relying solely on the blower for draft.
19. Q. Is the injudicious use of the blower particularly injurious on an oil burning locomotive?
19. Q. Is the careless use of the blower especially harmful on an oil-burning locomotive?
A. Yes; the injudicious use of a blower is injurious to any boiler. The cold air drawn through the fire-box is hard on the sheets and flues and will cause them to leak.
A. Yes; using a blower incorrectly can damage any boiler. The cold air pulled through the fire-box is tough on the sheets and flues and can cause them to leak.
20. Q. Is the blower more injurious when a light smoke is emitting from the stack or when a dense black smoke is emitting?
20. Q. Is the blower more harmful when there's light smoke coming from the stack or when there's thick black smoke coming out?
A. It is most injurious when a light smoke is emitting.
A. It is most harmful when a light smoke is coming out.
21. Q. In drifting down long grades should the fire be shut off or burned lightly? Why?
21. Q. Should the fire be turned off or kept low when going down long slopes? Why?
A. The fire should be burned lightly and not permitted to get low enough to allow the fire-box to lose its temperature, as this will contract the flues and cause them to leak.
A. The fire should be kept burning gently and should not be allowed to drop low enough for the fire-box to lose its heat, as this will cause the flues to contract and leak.
22. Q. How should the fire be handled when switching?
22. Q. How should the fire be managed during switching?
A. The fire must be regulated to meet the requirements of the work the engine is performing on each move and to protect against any possibility of the fire being drawn out by the exhaust.
A. The fire needs to be controlled to match the demands of the work the engine is doing on each movement and to prevent any chance of the fire being pulled out by the exhaust.
23. Q. Would not some fuel be wasted in this way?[Pg 53]
23. Q. Wouldn't some fuel be wasted this way?[Pg 53]
A. Not necessarily. A waste of fuel can be avoided by close attention on the part of the fireman when switching as well as when running.
A. Not necessarily. A waste of fuel can be avoided with the fireman’s close attention during both switching and running.
24. Q. How should the fire be handled when leaving stations?
24. Q. How should the fire be managed when leaving stations?
A. It should be burning brightly and strong enough to prevent the draft from putting it out when the throttle is opened. And a little smoke should show up at the stack, which would indicate that the fire was being forced just a little ahead of the working of the engine.
A. It should be burning brightly and strong enough to keep the draft from blowing it out when the throttle is opened. And a little smoke should appear at the stack, which would indicate that the fire is being pushed just a bit ahead of the engine's operation.
25. Q. Which is desirable, to use as much or as little steam jet atomizer as possible?
25. Q. Is it better to use as much steam jet atomizer as possible, or just a little?
A. It is desirable to use as little atomizer as will make engine show perfect combustion and economy.
A. It's best to use the least amount of atomizer needed to ensure the engine demonstrates perfect combustion and efficiency.
26. Q. What is the result of too little steam jet atomizer when standing at stations or when the engine is working light?
26. Q. What happens if there's not enough steam in the jet atomizer when the train is stopped or when the engine is running light?
A. The result of too little atomizer when standing at station or when engine is working lightly, will result in the oil not being carried far enough into the fire-box or arch and not properly atomized and the fire is liable to go out. The oil will drop from the mouth of the burner into the draft pan to the ground where it is very liable to start a fire under the engine.
A. If there’s not enough atomizer when the engine is idling or running lightly, the oil won’t get carried far enough into the firebox or arch and won’t be properly atomized, causing the fire to possibly go out. The oil will drip from the burner into the draft pan and then to the ground, which could easily start a fire underneath the engine.
27. Q. If too much steam jet atomizer is used with a light fire?
27. Q. What happens if too much steam jet atomizer is used with a light fire?
A. It will create a disagreeable gas, which will cause the fire to burn with a succession of light explosions and kicks, also a waste of steam, and which would reduce the fire-box temperature.
A. It will produce an unpleasant gas, which will make the fire burn with a series of light explosions and jolts, as well as wasting steam, and which would lower the temperature of the firebox.
28. Q. When the fire kicks and smokes, what should be done?[Pg 54]
28. Q. When the fire starts to flare up and produce smoke, what should you do?[Pg 54]
A. The atomizer should be adjusted. If this does not overcome the trouble, the heater should be put in service, for, possibly, the oil is too cold to flow freely. Another cause of the fire kicking and smoking results from water being mixed with the oil. If this is the case, it should be drained out of the oil tank immediately.
A. The atomizer needs to be adjusted. If that doesn't fix the issue, the heater should be turned on because the oil might be too cold to flow properly. Another reason for the fire sputtering and smoking is if there's water mixed with the oil. If that's the case, it should be drained from the oil tank right away.
29. Q. How should the dampers be used on an oil burning locomotive?
29. Q. How should the dampers be used on an oil-burning locomotive?
A. They should be opened just enough to admit sufficient air to produce perfect combustion, but not enough to cool the fire-box. The dampers should be closed when the engine is drifting or when at rest and the fire is cut very low or is out entirely.
A. They should be opened just enough to let in enough air for perfect combustion, but not so much that it cools the firebox. The dampers should be closed when the engine is coasting or when it's not in use and the fire is very low or completely out.
30. Q. About how much smoke do you consider an oil burning locomotive should make under adverse conditions, when the engine is steaming well, but is being crowded by the engineer?
30. Q. How much smoke do you think an oil-burning locomotive should produce in bad conditions, when the engine is running well but is being pushed by the engineer?
A. Only a light smoke should show at the stack.
A. Only a thin wisp of smoke should be visible at the stack.
31. Q. What color is most desirable at peep holes in the fire-box?
31. Q. What color is best for peepholes in the firebox?
A. A white color is most desirable.
A. White is the most desirable color.
32. Q. What will produce the bright red color?
32. Q. What causes the bright red color?
A. Leaky steam pipes, side seams, flues and improper combustion will produce a ruddy color in the fire-box.
A. Leaky steam pipes, side seams, flues, and poor combustion will create a reddish color in the fire box.
33. Q. How does water in the oil affect the fire?
33. Q. How does water in the oil impact the fire?
A. Water in the oil will produce popping or kicking with the fire in the fire-box and at times the fire[Pg 55] will die down entirely and then flash up as the water disappears and the oil reaches the burner. The most noticeable result of water in the oil is the fact that the fire will get very low. It will almost go out entirely and then will suddenly flash up again as the oil appears. Water in the oil produces a very dangerous condition and should be prevented immediately by draining the water from the fuel oil tank.
A. Water in the oil will cause popping or kicking in the firebox, and at times the fire[Pg 55] will completely die down, only to flare up again as the water evaporates and the oil reaches the burner. The most obvious effect of water in the oil is that the fire will burn very low. It will almost go out completely, then suddenly flare up again as the oil comes through. Water in the oil creates a very dangerous situation and should be addressed immediately by draining the water from the fuel oil tank.
34. Q. Do you consider it advisable to keep the burners clean, and how often?
34. Q. Do you think it's a good idea to keep the burners clean, and how often should that be done?
A. When equipped with steam blow-out pipes, they should be blown out before commencing trip so that burners will distribute oil evenly to each side of fire-box.
A. When using steam blow-out pipes, they should be blown out before starting the trip so that burners will distribute oil evenly to each side of the firebox.
35. Q. What position should burner be with reference to level and in line with center of fire-box?
35. Q. What position should the burner be in relation to the level and aligned with the center of the firebox?
A. It is very essential that burners be level and throw flames just to clear floor of arch in order to derive full benefit of heating surface, as the draft has a great tendency to elevate flames, at opposite end of the fire-box.
A. It is crucial that burners are level and direct flames just enough to clear the floor of the arch to fully benefit from the heating surface, as the draft tends to lift flames at the opposite end of the firebox.
36. Q. Are you aware that in course of time the atomizer port will become worn too large and will discharge too large a volume of steam to properly atomize, and the remedy?
36. Q. Are you aware that over time the atomizer port will wear out and become too large, causing it to release too much steam to properly atomize? What is the solution?
A. Yes; the lip or bushing should be closed to proper opening so that steam will be restricted at the nozzle and escape with a bursting effect to properly atomize the oil instead of flowing out in quantities against flash walls before it has time to ignite.
A. Yes; the lip or bushing should be closed to the proper opening so that steam is restricted at the nozzle and escapes with a bursting effect to properly atomize the oil instead of flowing out in large amounts against flash walls before it has time to ignite.
37. Q. What is the real object of having the fire-box lined with bricks, and will engine steam without them?[Pg 56]
37. Q. What’s the actual purpose of lining the fire-box with bricks, and can the engine operate without them?[Pg 56]
A. Not so well as with the brick, the sheets being in contact with water are too cool to flash the oil readily and hence the use of what is called a "flash wall" built of fire brick and heated to a very high temperature aids combustion very materially.
A. Not as effectively as with the brick, since the sheets in contact with water are too cool to ignite the oil easily. Therefore, using what's known as a "flash wall," made of firebrick and heated to a very high temperature, significantly helps with combustion.
38. Q. Do you consider it your duty to keep close inspection of brick work as to need of repairs, such as air entering between brick and side sheets?
38. Q. Do you think it's your responsibility to closely check the brickwork for repairs, like air coming in between the bricks and the side sheets?
A. Yes. To see that plaster is kept between the walls and sheets to keep cold air from being drawn in.
A. Yes. To ensure that plaster is kept between the walls and sheets to prevent cold air from coming in.
39. Q. Will engine steam if brick falls in front of burners or in path of flame and what may be done?
39. Q. Will the engine steam if a brick falls in front of the burners or in the path of the flame, and what can be done about it?
A. No. Remove them with the brick hook or rod by pulling them out through damper of draft pan.
A. No. Take them out with the brick hook or rod by pulling them through the damper of the draft pan.
40. Q. Where engine is equipped with an oil-reheater or oil line, do you consider it a help to engine's steaming qualities when used?
40. Q. When an engine has an oil-reheater or oil line, do you think it improves the engine's steaming performance when it's used?
A. Yes; at all times this heater should be used.
A. Yes, this heater should be used at all times.
41. Q. Why use second heater? Why not heat it to a high temperature in oil tank with oil heater?
41. Q. Why use a second heater? Why not just heat it to a high temperature in the oil tank with the oil heater?
A. Too much gas generating and boiling the oil continually destroys the higher qualities besides being hard to control the flow through regulation valve.
A. Too much gas being produced and boiling the oil constantly ruins the higher qualities and makes it difficult to control the flow with the regulation valve.
42. Q. Do you consider a vent hole in oil tank advisable, and why?
42. Q. Do you think it's a good idea to have a vent hole in an oil tank, and why?
A. Yes; to allow any accumulation of gas to escape and to admit the air so that oil will flow freely.
A. Yes; to let any buildup of gas escape and to let in air so that oil can flow smoothly.
43. Q. Do you inspect your oil pipes and report[Pg 57] all leaks? What other bad effect has a pipe leak aside from waste of oil?
43. Q. Do you check your oil pipes and report[Pg 57] all leaks? What other negative impact does a pipe leak have besides wasting oil?
A. Yes. It will cause oil to feed irregularly.
A. Yes. It will cause the oil to flow irregularly.
44. Q. Are you aware that keeping the flues clean is the greatest one thing that you can do in regard to fuel economy, and how often should they be cleaned?
44. Q. Do you know that keeping the flues clean is the most important thing you can do for fuel efficiency, and how often should they be cleaned?
A. Yes. At least every ten miles.
A. Yes. At least every ten miles.
45. Q. Do you know that the engine should be working hard and at a speed not less than twenty miles per hour when sanding flues to avoid the sand falling to floor of the fire-box and accumulating in front of them?
45. Q. Do you know that the engine should be working hard and at a speed of at least twenty miles per hour when sanding flues to prevent the sand from falling to the floor of the firebox and piling up in front of them?
A. Yes.
A. Yep.
46. Q. Do you realize that on first closing throttle you should not adjust fire too low? Explain best method.
46. Q. Are you aware that when you first close the throttle, you shouldn't set the fire too low? Please explain the best method.
A. Yes. I would allow steam pressure to fall back some fifteen pounds before throttle is closed and on having closed same leave a good fire in box, allowing it to cool gradually to avoid leaky flues, broken staybolts, cracked sheets caused by sudden fall of temperature.
A. Yes. I would let the steam pressure drop by about fifteen pounds before shutting the throttle, and after closing it, I would keep a strong fire in the box, letting it cool down slowly to prevent leaky flues, broken staybolts, and cracked sheets from a sudden temperature drop.
47. Q. How is the flow of oil controlled?
47. Q. How is oil flow managed?
A. By the valves in tank and pipe connections.
A. By the valves in tank and pipe connections.
48. Q. Name these valves, their location and purpose.
48. Q. Name these valves, where they are located, and what they do.
A. The safety valve controls the flow of oil from the fuel oil tank through an opening in bottom sheet of tank to the pipes leading to burner. This valve is[Pg 58] forced to its seat by a heavy spring and is held off its seat by a key in the upright rod extending above the top of tank. To this key a rope or chain is attached and also attached to the cab to cause the pin in rod to be pulled in case of a separation between engine and tank and allow the valve to be seated by its spring and avoid a waste of oil. The second or main oil valve is located in oil pipe under deck leading to burner. It is usually of the plug-cock pattern connected by bell crank and this connected to some part of the engine by chain, in which case it also acts as a safety valve in case of separation between engine and tender. In other cases it is connected by an operating rod extending above deck of tender where it can be operated by hand in case of safety valves failure to shut off the flow of oil. The third or firing valve is usually located between heater box and burner, and is provided with an upright rod extending into cab where it is provided with a handle or lever in position to be conveniently handled by fireman while seated in cab. This valve regulates the flow of oil desired to reach the fire.
A. The safety valve controls the flow of oil from the fuel oil tank through an opening in the bottom of the tank to the pipes leading to the burner. This valve is [Pg 58] held in place by a heavy spring and is kept open by a key on an upright rod that extends above the top of the tank. A rope or chain is attached to this key and also connected to the cab, so if there is a separation between the engine and tank, the pin in the rod gets pulled, allowing the valve to close with the spring and preventing any oil waste. The second or main oil valve is located in the oil pipe under the deck leading to the burner. It's usually a plug-cock type connected by a bell crank to some part of the engine by a chain, so it also acts as a safety valve if there’s a separation between the engine and tender. In other cases, it connects to an operating rod that extends above the tender deck, allowing for manual operation if the safety valve fails to stop the oil flow. The third or firing valve is typically found between the heater box and burner and has an upright rod that extends into the cab, where it's fitted with a handle or lever for easy access by the fireman while seated. This valve regulates the desired oil flow to the fire.
49. Q. When shutting out fire which valve should be closed first? Why?
49. Q. When putting out a fire, which valve should be closed first? Why?
A. The safety valve. To allow the oil in pipes to be consumed and to see that this valve is in working order.
A. The safety valve. To ensure that the oil in the pipes can be used and to check that this valve is functioning properly.
50. Q. Should safety valve fail to shut off the flow of oil in such cases would it be safe to rely on the firing valve to shut off the fire?
50. Q. If the safety valve doesn't stop the flow of oil in these situations, can we trust the firing valve to put out the fire?
A. No. The main valve should then be closed.
A. No. The main valve should be closed.
51. Q. Should the firing valve be depended upon to shut off the fire at any time? Why?
51. Q. Can we rely on the firing valve to turn off the fire at any time? Why?
A. No. From constant use they are frequently[Pg 59] leaking and the trouble is not detected while in use, and again there is always danger of the handle being moved by workmen or others about the cab.
A. No. Due to constant use, they often[Pg 59] leak, and the problem goes unnoticed while they're being used. Plus, there's always a risk of someone moving the handle, whether it's workers or others in the cab.
52. Q. What is a heater box?
52. Q. What is a heater box?
A. It is an apparatus having two passages, one for steam passing from boiler to heater pipes in tank and another passage for oil from tank before it is delivered to burner. In this manner the oil before reaching the burner is heated much higher than the temperature of that contained in tank.
A. It is a device with two pathways, one for steam flowing from the boiler to the heater pipes in the tank and another for oil from the tank before it is sent to the burner. This way, the oil is heated to a much higher temperature than what is in the tank before it reaches the burner.
53. Q. In the event of the heater pipes or connections becoming defective, how could the oil be heated in tank?
53. Q. If the heater pipes or connections break, how can the oil in the tank be heated?
A. By closing the firing valve, closing the valve on heater pipe, and opening valve on heater box, the steam from heater throttle can be passed directly through the oil feed pipe to the fuel supply.
A. By closing the firing valve, shutting the valve on the heater pipe, and opening the valve on the heater box, the steam from the heater throttle can be directed straight through the oil feed pipe to the fuel supply.
54. Q. In the event of an objectionable quantity of water in oil, how can it be removed?
54. Q. If there's an unacceptable amount of water in the oil, how can it be removed?
A. In some instances the tanks are provided with drain pipes for this purpose, but in the absence of same, the feed hose or pipe between engine and tank can be disconnected and used as a drain to fuel oil tank.
A. In some cases, the tanks come with drain pipes for this purpose, but if they aren't available, the feed hose or pipe between the engine and the tank can be disconnected and used to drain the fuel oil tank.
55. Q. What effect has leaks between fuel tank and firing valve?
55. Q. What happens if there are leaks between the fuel tank and the firing valve?
A. A waste of oil only.
A. Just a waste of oil.
56. Q. What effect has leaks between firing valve and burner?
56. Q. What happens if there's a leak between the firing valve and the burner?
A. In addition to a loss of oil while fire is burning low, and but little steam atomizer being used, it[Pg 60] interferes very materially with the engine's steaming by admitting air when using considerable steam atomizer. This causes a very irregular oil feed.
A. Along with losing oil while the fire is burning low, and with minimal use of the steam atomizer, it[Pg 60] significantly disrupts the engine's steaming by letting in air when using a substantial amount of steam atomizer. This results in a very inconsistent oil feed.
57. Q. What action of the fire would indicate leaks in pipes between firing valve and burner?
57. Q. What signs of the fire would suggest leaks in the pipes between the firing valve and the burner?
A. The fire-box will give off sounds similar to slight explosions, and the smoke at stack will indicate irregular fuel feeding.
A. The firebox will make sounds like small explosions, and the smoke from the stack will indicate uneven fuel feeding.
58. Q. What would you consider the proper adjustment of burner?
58. Q. How would you describe the correct way to adjust the burner?
A. That which will provide for the delivery of the oil from burner to flash wall without striking arch, side walls, or floor brick while doing so.
A. This will ensure that the oil is delivered from the burner to the flash wall without hitting the arch, side walls, or floor bricks in the process.
59. Q. In case it becomes necessary to fire up an oil burning engine with wood, what parts should be given particular attention?
59. Q. If you need to start an oil-burning engine using wood, what parts should you focus on?
A. The brick work. To see that same is not damaged or displaced while placing the wood in fire-box, also to protect by placing brick over that portion of burner extending into fire-box ahead of mud ring, or by so arranging the wood in fire-box as to prevent any great amount of heat from reaching the burner and melting nozzle of same.
A. The brick work. Make sure it isn't damaged or moved while putting the wood in the firebox. Also, protect it by placing bricks over the part of the burner that sticks into the firebox in front of the mud ring, or by organizing the wood in the firebox in a way that stops too much heat from hitting the burner and melting its nozzle.
60. Q. In case of sudden drop in steam pressure, what might be the cause?
60. Q. What could cause a sudden drop in steam pressure?
A. Loose brick perhaps fallen in front of burner and obstructed the flow of oil. The petticoat pipe may be loose and out of line or the dampers may have fallen shut.
A. A loose brick might have fallen in front of the burner and blocked the flow of oil. The petticoat pipe could be loose and misaligned, or the dampers might have closed unexpectedly.
61. Q. In case brick have fallen in front of burner, how can they be removed?[Pg 61]
61. Q. If bricks have fallen in front of the burner, how can they be removed?[Pg 61]
A. By a hook provided for that purpose. They can usually be forced out through the vent openings, but if this cannot be done, they should be thrown against the blast wall in order to get them as far as possible out of the course of the fuel feed.
A. By a hook designed for that purpose. They can typically be pushed out through the vent openings, but if that’s not possible, they should be thrown against the blast wall to get them as far as possible away from the fuel feed.
62. Q. In case a petticoat pipe becomes deranged, what can be done?
62. Q. If a petticoat pipe gets messed up, what can be done?
A. In case it cannot be put back in proper position, it should be removed altogether. (Trips have been successfully completed in this manner.)
A. If it can't be put back in the right position, it should be removed entirely. (Trips have been successfully completed this way.)
63. Q. Will a corroded burner mouth prevent the proper delivery of fuel to fire?
63. Q. Will a rusty burner opening stop the fuel from flowing properly to the fire?
A. Yes.
A. Yup.
64. Q. What causes the mouth of burner to corrode?
64. Q. What causes the burner’s mouth to corrode?
A. The asphaltum and sand contained in the oil.
A. The asphalt and sand found in the oil.
65. Q. How can this be removed on the road?
65. Q. How can this be taken off while on the road?
A. By having a hook or rod provided with a point that can be inserted into mouth of burner.
A. By using a hook or rod with a pointed end that can be inserted into the mouth of the burner.
66. Q. Why should a fuel oil tank not be filled to its holding capacity?
66. Q. Why shouldn't a fuel oil tank be filled to its maximum capacity?
A. Because when heater is applied the oil would expand and overflow.
A. Because when the heater is turned on, the oil would expand and spill over.
67. Q. In case of derailment or other accident that might cause the fireman to desert his position in cab, what should he do?
67. Q. If there's a derailment or another accident that might make the fireman leave his position in the cab, what should he do?
A. Pull key out of safety valve rod, thereby allowing oil feed from tank to be shut off.
A. Remove the key from the safety valve rod to stop the oil flow from the tank.
1. Q. What are the duties of an engineman before attaching a locomotive to the train?
1. Q. What are the responsibilities of an engineer before connecting a locomotive to the train?
A. He should make a complete inspection of the locomotive, observing all important nuts and bolts, look for any signs of hot bearings on previous trip, see that the engine is equipped with necessary tools and supplies, test both of the injectors and the air brake equipment to be sure they are in good working order, see that headlight and signal lamps are in place and ready for service, observe water conditions in boiler, inspect the interior of the fire-box and see that the locomotive is properly lubricated.
A. He should thoroughly check the locomotive, making sure to look at all the important nuts and bolts, check for any signs of overheated bearings from the last trip, ensure the engine has all the necessary tools and supplies, test both injectors and the air brake system to confirm they’re functioning properly, verify that the headlight and signal lamps are installed and ready to go, check the water levels in the boiler, inspect the inside of the firebox, and ensure the locomotive is well-lubricated.
2. Q. What tools should there be on the locomotive?
2. Q. What tools should be on the train?
A. Such as are necessary to properly operate the locomotive, care for the machinery, disconnect and block up in case of breakdown and the necessary firing tools.
A. Such as are necessary to properly operate the locomotive, care for the machinery, disconnect and block in case of a breakdown, and the essential firing tools.
3. Q. What examination should be made after any repair work has been done on valve, brasses, etc.?
3. Q. What check should be done after any repair work has been completed on the valve, brasses, etc.?
A. See that brasses are properly fitted, keys fastened and nuts made tight. If any repairs have been made on valves or valve gear, would see that the reverse lever could be moved freely and that all movable parts had been properly replaced; would also give especial attention with reference to lubrication of these parts.[Pg 63]
A. Make sure the brasses are fitted correctly, the keys are secured, and the nuts are tightened. If any repairs have been done on the valves or valve gear, check that the reverse lever can move freely and that all movable parts have been properly reinstalled; also pay special attention to the lubrication of these parts.[Pg 63]
4. Q. What attention should be given to boiler attachments, such as gauge cocks, water glasses, etc.?
4. Q. What care should be taken with boiler attachments, like gauge cocks, water glasses, and so on?
A. Would see that the gauge cocks can be opened to try the water and closed, so steam and water would not come out into cab. Observe the water glass and note if water is moving up and down in the glass, see that the steam valve at the top and water valve at bottom of glass could be opened and closed, and allow water and steam to circulate freely through the glass.
A. Would see that the gauge cocks can be opened to check the water and closed, so steam and water wouldn't come out into the cab. Observe the water glass and note if the water is moving up and down in the glass. Make sure that the steam valve at the top and the water valve at the bottom of the glass can be opened and closed, allowing water and steam to circulate freely through the glass.
5. Q. What do you consider necessary to report on locomotive boilers?
5. Q. What do you think is important to report about locomotive boilers?
A. Should report all defects on boiler and its attachments while engine is in engineer's charge.
A. Should report all defects on the boiler and its attachments while the engine is under the engineer's supervision.
6. Q. Trace the steam from the boiler through the cylinders to the atmosphere and explain how it transmits power.
6. Q. Follow the steam from the boiler through the cylinders to the atmosphere and explain how it transfers power.
A. Steam enters the throttle valve located in the highest part of the dome in order to get the driest steam, then passes through the standpipe and dry pipe out of the boiler to the steam pipe tee or nigger-head located in the front end, then through steam pipes to the steam chest. A steam valve in each steam chest distributes the steam so that it enters the cylinders at or just before the beginning of the stroke; pushing the piston to the end of its stroke; just before the piston reaches the end of the cylinder, the steam valve opens communication to the exhaust port through a cavity in its exhaust side, then through the exhaust pipes and tips up through the draft or petticoat pipe and stack to the atmosphere. When steam pushes the piston through the cylinder, its power is transmitted by the main rod to the main crank pin[Pg 64] which causes the wheels to revolve, thus moving the engine and its train.
A. Steam enters the throttle valve located at the highest part of the dome to ensure the driest steam. It then flows through the standpipe and dry pipe, exiting the boiler into the steam pipe tee at the front end, and from there, it moves through the steam pipes to the steam chest. A steam valve in each steam chest distributes the steam so that it enters the cylinders at or just before the beginning of the stroke, pushing the piston to the end of its stroke. Just before the piston reaches the end of the cylinder, the steam valve opens a passage to the exhaust port through a cavity on its exhaust side, allowing the steam to exit through the exhaust pipes and up through the draft or petticoat pipe and stack into the atmosphere. When steam pushes the piston through the cylinder, its power is transmitted by the main rod to the main crank pin[Pg 64], causing the wheels to turn and thereby moving the engine and its train.
7. Q. Why is it important that there be no holes through the smoke-box door or front end and none in smoke-box seams or joints?
7. Q. Why is it important that there are no holes in the smoke-box door or at the front end, and none in the seams or joints of the smoke-box?
A. So as to maintain as good a vacuum as possible in the smoke-box and prevent small amounts of air coming in through leaks which tend to heat and warp the smoke-box and its door.
A. To maintain the best vacuum possible in the smoke-box and prevent small amounts of air from leaking in, which can heat and warp the smoke-box and its door.
8. Q. How should the locomotive be started to avoid jerks, and what train and other signals should be looked out for at the time of starting?
8. Q. How should the locomotive be started to avoid jolting, and what train and other signals should be watched for when starting?
A. Place the reverse lever in full gear, open the throttle valve gradually so as to start the train one car at a time and easily. Look for signals ahead to show that the track is clear and switch is in correct position, then look for signals from the rear end that the train is all coming.
A. Set the reverse lever to full gear, gradually open the throttle valve to start the train one car at a time and smoothly. Check for signals ahead to ensure that the track is clear and the switch is in the correct position, then check for signals from the rear to confirm that the entire train is coming.
9. Q. Will an engine equipped with superheat units move as quickly as a saturated steam locomotive when throttle valve is first opened?
9. Q. Will an engine with superheat units move as quickly as a saturated steam locomotive when the throttle valve is first opened?
A. No.
A. No.
10. Q. Why?
10. Q. Why?
A. Because steam must first pass through superheat units before it enters the steam pipes leading to steam chest.
A. Because steam has to go through superheat units first before it enters the steam pipes that lead to the steam chest.
11. Q. In placing engine on the turntable, at water or stand pipes, or at other similar places, what must be done?
11. Q. When putting the engine on the turntable, at water or standpipes, or at similar locations, what needs to be done?
A. Close throttle valve sooner so that the steam confined in superheat units, pipes and steam chests, will have passed out to the atmosphere.[Pg 65]
A. Close the throttle valve sooner so that the steam trapped in superheat units, pipes, and steam chests will have escaped into the atmosphere.[Pg 65]
12. Q. After a locomotive has been started, how can it be run most economically?
12. Q. After a locomotive has been started, how can it be run most efficiently?
A. By regulating the supply of steam to the steam chest with the throttle and the point of cut-off with the reverse lever; so that no more steam be used than necessary to maintain the proper speed, whenever possible working the engine at short cut-off so as to use steam expansively.
A. By controlling the amount of steam supplied to the steam chest with the throttle and the cut-off point with the reverse lever; ensuring that no more steam is used than needed to keep the right speed, and whenever possible, operating the engine at a short cut-off to use steam more efficiently.
13. Q. What is meant by working steam expansively?
13. Q. What does it mean to work steam expansively?
A. Hooking the reverse lever up toward the center gives the valve a shorter travel and closes the live steam port when the piston has made only a part of its stroke. This cuts off the supply of live steam coming from the steam chest. The expansion of the steam already in the cylinder pushes the piston to the end of its stroke without the use of a full cylinder of live steam.
A. Pulling the reverse lever up toward the center shortens the valve's travel and closes the live steam port when the piston has only moved partway. This stops the flow of live steam from the steam chest. The steam that’s already in the cylinder expands and pushes the piston to the end of its stroke without needing a full cylinder of live steam.
14. Q. How rapidly should water be supplied to the boiler?
14. Q. How quickly should water be fed into the boiler?
A. No faster than it is evaporated into steam, unless just before a hard pull; or when shutting off with a heavy bright fire in the fire-box to prevent waste of steam at the pops.
A. No faster than it evaporates into steam, unless just before a tough pull; or when shutting off with a strong, bright fire in the firebox to prevent steam waste at the pops.
15. Q. What is the difference between priming and foaming of a locomotive boiler?
15. Q. What’s the difference between priming and foaming in a locomotive boiler?
A. Priming is caused by carrying the water too high in the boiler so that when the throttle valve is opened some of it passes over with the steam in the form of a spray. Foaming is caused by the water becoming dirty from animal or alkaline matter, so that heat makes it foam like soap suds. Muddy water or certain vegetable matters will also make a boiler foam.[Pg 66]
A. Priming happens when the water level in the boiler is too high, causing some of it to escape with the steam as a spray when the throttle valve is opened. Foaming occurs when the water gets contaminated with animal or alkaline substances, making it foam up like soap bubbles when heated. Muddy water or certain plant materials can also lead to foaming in a boiler.[Pg 66]
16. Q. What should you do in a case of foaming? What in a case of priming?
16. Q. What should you do if there's foaming? What should you do if there's priming?
A. In a case of foaming, if possible, allow the boiler to cool off a little, increase the supply of feed water to prevent water getting too low, and whenever possible blow some of the dirty water out of the boiler, replacing it with clean water. In case of priming, shut off the supply of feed water until the water level drops to the proper height in the boiler.
A. If the boiler is foaming, try to let it cool down a bit, increase the supply of feed water to avoid the water level getting too low, and whenever you can, remove some of the dirty water from the boiler and replace it with clean water. If priming occurs, turn off the feed water supply until the water level drops to the correct height in the boiler.
17. Q. What danger is there when the water foams badly? When it primes badly?
17. Q. What risks are there when the water foams excessively? When it primes poorly?
A. There is danger of knocking out cylinder heads, cutting the valves, stalling on some grade or getting on some train's time because the engine cannot be worked to its proper power. When shutting off steam, the water is liable to drop below the crown sheet and thus risk burning the fire-box. When water primes badly, it is liable to break cylinder packing rings, knock out cylinder heads, break bolts in the steam chest and cut the valves. In such a case additional oil should be fed to the steam chest until the valves are properly lubricated.
A. There is a risk of damaging cylinder heads, cutting valves, stalling on inclines, or missing a train schedule because the engine can’t operate at its full power. When shutting off steam, the water may drop below the crown sheet, which can lead to burning the firebox. If the water doesn’t prime properly, it could break cylinder packing rings, damage cylinder heads, break bolts in the steam chest, and cut valves. In this situation, more oil should be added to the steam chest until the valves are adequately lubricated.
18. Q. Suppose that with the water glass in good working order, immediately after closing the throttle the water disappeared from the water glass, what should be done?
18. Q. If the water glass is functioning properly and the water disappears immediately after closing the throttle, what should be done?
A. Would open the throttle and endeavor to raise water until both injectors would put enough water into the boiler to make it entirely safe to close the throttle. If unable to raise the water level to the lower gauge cock would smother the fire or put it out entirely, if necessary, keeping both injectors working.[Pg 67]
A. Would open the throttle and try to raise the water level until both injectors put enough water into the boiler to safely close the throttle. If he couldn't raise the water level to the lower gauge cock, he would either smother the fire or put it out completely, if needed, while keeping both injectors running.[Pg 67]
19. Q. What work about a locomotive should be done by the engineman?
19. Q. What tasks should the engineer handle concerning a locomotive?
A. Inspection of the engine both before and after the trip. The engineer should do any necessary work on the engine after starting out on the trip to avoid breakdowns and insure getting over the road promptly. This means tightening up any important bolts that work loose on the trip and keeping parts from working out of position, adjusting wedges and rod keys.
A. Check the engine before and after the trip. The engineer should take care of any necessary maintenance on the engine after starting the trip to prevent breakdowns and ensure timely travel. This includes tightening any important bolts that may loosen during the trip and keeping parts from shifting out of position, as well as adjusting wedges and rod keys.
20. Q. How should the work of setting up the wedges be done?
20. Q. How should the process of setting up the wedges be carried out?
A. Place the engine on the upper quarter on the side with the loose wedge. Do not set the brake if brake shoe will push the driving box against the defective wedge, but block engine truck wheels so the engine cannot move, push the boxes against the shoe or dead wedge with a little steam, set the wedge up until it is a snug fit, then pull it down about one-sixteenth of an inch and fasten. Provision should be made for expansion of the box when it gets warm.
A. Put the engine on the upper quarter on the side with the loose wedge. Don’t engage the brake if the brake shoe will push the driving box against the faulty wedge, but secure the engine truck wheels so the engine can’t move. Gently push the boxes against the shoe or dead wedge with a little steam, set the wedge until it fits snugly, then pull it down about one-sixteenth of an inch and secure it. Make sure to allow for the box to expand when it heats up.
21. Q. How should rod brasses be keyed?
21. Q. How should rod brasses be secured?
A. If properly fitted they should be keyed brass to brass; if not so fitted, they should be keyed on the large part of the pin so they will be free enough to run without heating and snug enough to run without pounding. Do not key them so tight at either end as to prevent the lateral motion of the brass on the pins.
A. If fitted correctly, they should be secured brass to brass; if not properly fitted, they should be secured on the larger part of the pin so they can move smoothly without overheating and tightly enough to avoid excessive movement. Do not secure them so tightly at either end that it restricts the side-to-side motion of the brass on the pins.
22. Q. How should an engine be placed for the purpose of keying the rod brasses?
22. Q. How should you position an engine to key the rod brasses?
A. For the main rod, place the engine on the quarter or the top forward eighth, whichever place gives the largest diameter of the pin to key the brass[Pg 68] against. After keying up, test by moving the wheel to another position and see if brasses are free on the pin. For the side or parallel rods, always place the engine on the center for the side that is to be keyed.
A. For the main rod, position the engine on the quarter or the top forward eighth, whichever spot gives the largest diameter of the pin to secure the brass[Pg 68] against. After securing, check by moving the wheel to a different position and see if the brass is free on the pin. For the side or parallel rods, always position the engine in the center for the side that needs to be secured.
23. Q. How should the side rods on a mogul or consolidation locomotive be keyed?
23. Q. How should the side rods on a mogul or consolidation locomotive be fastened?
A. Place the engine on the center on that side, key up the brass on the main pin first, work each way toward the ends of the rods, being careful to keep them the proper length so they do not bind when passing either center. Be sure that wedges are properly set up before keying the side rods.
A. Position the engine in the center on that side, secure the brass on the main pin first, and work outwards towards the ends of the rods, making sure to maintain the correct length so they don't get stuck when passing either center. Ensure that the wedges are correctly set up before securing the side rods.
24. Q. What is the necessity for keeping the brasses keyed up properly?
24. Q. Why is it important to keep the brasses properly adjusted?
A. If too tight, they will surely run hot; if too loose, they will pound and injure the brasses as well as endanger the safety of the straps and rod bolts. Very loose brasses can pound enough to get hot.
A. If they're too tight, they'll definitely overheat; if they're too loose, they'll bounce around and harm the components while also risking the safety of the straps and rod bolts. Really loose components can bounce hard enough to become hot.
25. Q. What is meant by an engine out of tram? Out of quarter?
25. Q. What does it mean when an engine is out of tram? Out of alignment?
A. When corresponding wheels on opposite sides of the engine on different axes are not spaced equally apart; where the axle of any wheel is not at a right angle to the center line from front to rear of engine, so they do not run square on the rails, or where the space between the axle centers on opposite sides is not equal. This is sometimes indicated by unequal flange wear and should be reported at once. Wheels are out of quarter when the crank pin in one wheel is not exactly 90 degrees or one quarter of a turn from the pin in the wheels on the other end of the same axle. This is usually caused by slipping the engine with sand on one rail only and the condition of engine should be reported at once.[Pg 69]
A. When the corresponding wheels on opposite sides of the engine on different axes aren't spaced evenly apart; where the axle of any wheel isn't at a right angle to the center line from front to back of the engine, so they don't run square on the tracks, or where the distance between the axle centers on opposite sides isn't equal. This is sometimes shown by uneven flange wear and should be reported immediately. Wheels are out of quarter when the crank pin in one wheel isn't exactly 90 degrees or one-quarter of a turn from the pin in the wheels on the other end of the same axle. This is usually caused by slipping the engine with sand on just one rail, and the condition of the engine should be reported immediately.[Pg 69]
26. Q. Describe a piston valve.
26. Q. What is a piston valve?
A. A piston valve is a cylindrical spool-shaped valve constructed with packing rings much the same as the steam piston that moves through the cylinder, except that a piston valve is double or composed of two pistons connected by center rod or spool working in a bushing of equal diameter. Steam and exhaust ports are cut through this bushing; steam ports to the cylinder and exhaust port to the exhaust pipe. There is also a steam port for live steam from the boiler. As the pressure on this valve is equal in both directions it is practically balanced.
A. A piston valve is a cylindrical spool-shaped valve made with packing rings, similar to the steam piston that moves through the cylinder. However, a piston valve is double or made of two pistons linked by a center rod or spool that operates in a bushing of the same diameter. Steam and exhaust ports are cut through this bushing; steam ports lead to the cylinder and the exhaust port connects to the exhaust pipe. There’s also a steam port for live steam from the boiler. Since the pressure on this valve is equal in both directions, it is essentially balanced.
27. Q. What is a balanced slide valve? How is it balanced, and why? For what purpose is the hole drilled through the top of the valve?
27. Q. What is a balanced slide valve? How is it balanced, and why? What is the purpose of the hole drilled through the top of the valve?
A. One in which the steam pressure on the top and bottom of the valve is nearly equalized. This is done by protecting a portion of the top of the valve from the steam pressure. It is usually balanced by strips held against the pressure or balance plate by one or more springs. This is done to prevent live steam from getting on top of valve and thus relieve the valve from the top pressure which would cause excessive friction between the bottom of the valve and its seat. The hole through the top is to allow any steam which might leak by the strips to pass into the exhaust, so pressure could not accumulate on the top of the valve, also to equalize the exhaust pressure between the top of the valve and exhaust cavity as well as to assist in lubricating the balance plate.
A. One in which the steam pressure on the top and bottom of the valve is almost balanced. This is achieved by shielding a part of the top of the valve from the steam pressure. It’s typically balanced by strips pressed against the pressure or balance plate by one or more springs. This is meant to stop live steam from getting on top of the valve, which would relieve the valve from the top pressure and prevent excessive friction between the bottom of the valve and its seat. The hole in the top allows any steam that might leak past the strips to flow into the exhaust, so pressure cannot build up on top of the valve, as well as equalizing the exhaust pressure between the top of the valve and the exhaust cavity, and it also helps lubricate the balance plate.
28. Q. What is meant by inside and outside admission valves?[Pg 70]
28. Q. What do inside and outside admission valves mean?[Pg 70]
A. With an inside admission valve (usually a piston valve), the live steam comes between the piston valve heads, the outside end of the heads being connected with and exposed to exhaust pressure, it admits steam past the inside edges of the valves. An outside admission valve has the space between the ends connected to the exhaust and a space at the ends connected with the live steam. It admits steam past its outside edges. A piston valve can be either inside or outside admission, while a slide valve is always outside admission.
A. With an inside admission valve (usually a piston valve), live steam enters between the piston valve heads, with the outer ends of the heads connected to and exposed to exhaust pressure, allowing steam to flow past the inner edges of the valves. An outside admission valve has the space between the ends linked to the exhaust and a space at the ends connected to the live steam. It allows steam to flow past its outer edges. A piston valve can be inside or outside admission, while a slide valve is always outside admission.
29. Q. What is the relative motion of the main piston and the steam valves for inside admission, and, on the other hand, for outside admission?
29. Q. What is the relationship between the main piston and the steam valves for inside admission, and how does it differ for outside admission?
A. If the piston is in the front end of the cylinder, an inside admission valve must move forward in order to connect the inside of the valve with the front live steam port to admit steam against the piston. The outside end of the valve opens the exhaust port for the back end of the cylinder. In the same position of the piston an outside admission valve must move backwards to open the steam port or in the same direction as the steam piston when commencing its stroke.
A. If the piston is at the front end of the cylinder, an inside admission valve needs to move forward to connect the inside of the valve with the front live steam port to let steam in against the piston. The outside end of the valve opens the exhaust port for the back end of the cylinder. In the same position of the piston, an outside admission valve must move backward to open the steam port or in the same direction as the steam piston when starting its stroke.
30. Q. What is an Allen ported valve, and what is its object?
30. Q. What is an Allen ported valve, and what is its purpose?
A. An Allen ported valve is an outside admission slide valve having an extra port from one end of the valve to the other, above the exhaust cavity and through the body of the valve. This extra port is calculated to admit steam through the valve at the same time that steam passes by the end of the valve into the same steam port, thus doubling the area of opening for live steam when the port is first opened.[Pg 71]
A. An Allen ported valve is an outside admission slide valve with an extra port extending from one end of the valve to the other, above the exhaust cavity and through the valve body. This extra port is designed to allow steam to enter the valve at the same time that steam flows past the end of the valve into the same steam port, effectively doubling the opening area for live steam when the port is initially opened.[Pg 71]
31. Q. What is the difference in the valve motion for outside admission valves and for inside admission valves?
31. Q. What’s the difference in valve motion between outside admission valves and inside admission valves?
A. An outside admission valve must be moved in the opposite direction to an inside admission valve in relation to the movement of the steam piston when beginning its stroke; therefore either the position of the eccentric or the position of the rocker arms in relation to the rocker shaft must be opposite for a change in these valves.
A. An external admission valve needs to be moved in the opposite direction to an internal admission valve regarding the movement of the steam piston when starting its stroke; therefore, either the position of the eccentric or the position of the rocker arms in relation to the rocker shaft must be opposite for a change in these valves.
32. Q. What is a direct motion valve gear? What is an indirect motion valve gear?
32. Q. What is a direct motion valve gear? What is an indirect motion valve gear?
A. A direct motion valve gear is one in which the valve moves in the same direction as the eccentric rod, that is doing the work, in many cases no rocker arm is used. In case a rocker arm is used, both arms point in the same direction like the letter U. An indirect motion valve gear is one in which the valve moves in an opposite direction to the eccentric rod doing the work. A rocker is used in which the arms point in opposite directions from the shaft connecting them. Owing to the design and construction of the Walschaert valve gear, it is a direct motion gear when the engine is running in one direction with the link block in the bottom of the link, an indirect motion when the engine is running in an opposite direction with the link block in the top of the link; usually direct motion when running forward.
A. A direct motion valve gear is one where the valve moves in the same direction as the eccentric rod that is doing the work; often, no rocker arm is used. If a rocker arm is used, both arms point in the same direction, like the letter U. An indirect motion valve gear is one where the valve moves in the opposite direction to the eccentric rod doing the work. A rocker is used where the arms point in opposite directions from the shaft connecting them. Due to the design and construction of the Walschaert valve gear, it operates as a direct motion gear when the engine runs in one direction with the link block at the bottom of the link, and as an indirect motion when the engine runs in the opposite direction with the link block at the top of the link; it is usually direct motion when running forward.
33. Q. How can you detect the difference between a blow in valve or piston packing?
33. Q. How can you tell the difference between a blow in valve or piston packing?
A. A blow from the valve is more constant and has a somewhat different sound, while a blow from cylinder or piston packing will blow stronger at the[Pg 72] beginning of the stroke and gradually decrease as the stroke is completed.
A. A blow from the valve is more consistent and has a slightly different sound, while a blow from the cylinder or piston packing will be stronger at the[Pg 72] beginning of the stroke and gradually decrease as the stroke finishes.
34. Q. How would you place engine to locate broken admission steam ring in piston valve?
34. Q. How would you position the engine to find the broken intake steam ring in the piston valve?
A. Would place engine on quarter, reverse lever in center so as to cover ports, then open throttle; and the steam will blow out of cylinder cock at the end of cylinder where broken valve ring is located.
A. Would position the engine at a quarter, set the reverse lever to the center to cover the ports, then open the throttle; and the steam will escape from the cylinder cock at the end of the cylinder where the broken valve ring is found.
35. Q. How would you locate broken exhaust ring in piston valve?
35. Q. How do you find a broken exhaust ring in a piston valve?
A. Watch the cross-head when engine is working steam. As there will be three normal and one light exhausts, you can determine on which side of the engine the light exhaust takes place.
A. Watch the cross-head when the engine is running steam. Since there will be three normal exhausts and one light exhaust, you can figure out which side of the engine the light exhaust occurs on.
36. Q. What is meant by lead? What by line and line?
36. Q. What does lead mean? What do line and line refer to?
A. Lead is the amount of port opening for live steam to cylinder ahead or back of piston when the piston is on the dead center. If the steam edge of the valve is in line with the edge of the steam port when the piston is on the center, it is said to be line and line.
A. Lead is the gap in the port that allows live steam to enter the cylinder in front of or behind the piston when the piston is at dead center. If the steam edge of the valve lines up with the edge of the steam port when the piston is at center, it is referred to as lining up.
37. Q. What is meant by steam lap?
37. Q. What does steam lap mean?
A. The distance that the valve overlaps the live steam edges of the steam ports when it is in the center of its travel over the seat. This distance is measured at one end only, although the valve laps equally at both ends.
A. The distance that the valve overlaps the live steam edges of the steam ports when it's in the center of its movement over the seat. This distance is measured at one end only, even though the valve overlaps equally at both ends.
38. Q. What is meant by exhaust lap? What by exhaust clearance?
38. Q. What does exhaust lap mean? What does exhaust clearance refer to?
A. Exhaust lap is the distance that the exhaust edge of the valve overlaps the exhaust edge of the[Pg 73] steam port when the valve is in central position. Exhaust clearance is the opening between the exhaust edge of the valve and the exhaust edge of the steam port with valve in central position. If the valve has neither exhaust lap or clearance it is said to be line and line.
A. Exhaust lap is the distance that the exhaust edge of the valve overlaps the exhaust edge of the[Pg 73] steam port when the valve is in the middle position. Exhaust clearance is the gap between the exhaust edge of the valve and the exhaust edge of the steam port with the valve in the middle position. If the valve has neither exhaust lap nor clearance, it is referred to as line and line.
39. Q. What is meant by release? What by compression?
39. Q. What does release mean? What does compression mean?
A. Release is the point in the travel of the piston when the port is opened. Compression is the distance the piston travels after exhaust port closes before the live steam port opens. During this travel of the piston the exhaust port is closed so the moving piston compresses the steam left in the cylinder.
A. Release is the moment in the piston’s movement when the port opens. Compression is the distance the piston moves after the exhaust port closes and before the live steam port opens. During this movement of the piston, the exhaust port is closed, allowing the moving piston to compress the steam that remains in the cylinder.
40. Q. With an indirect valve motion and outside admission valve, what would be the position of the eccentric relative to the crank pin on that side? What with a direct valve gear? What difference between outside admission valve and inside admission valve as to this position?
40. Q. With an indirect valve motion and outside admission valve, where would the eccentric be positioned in relation to the crank pin on that side? What about with direct valve gear? What is the difference in position between an outside admission valve and an inside admission valve?
A. With an indirect valve motion and an outside admission valve, the go-ahead eccentric follows the crank pin with engine running ahead. Without any lap or lead it would be a quarter of a turn or 90 degrees behind the pin, but as all valves have lap and lead, the eccentric is advanced or placed toward the pin enough to move the valve the amount of the lap and lead. With a direct valve gear and an outside admission valve, the eccentric will be a quarter of a turn or 90 degrees ahead of the crank pin and advanced enough to move the valve the amount of the lap and lead. With an inside admission valve and an indirect valve motion, the eccentric will come the[Pg 74] same as for an outside admission valve and direct motion, or more than a quarter of a turn ahead of the pin. With an inside admission valve and direct motion, as piston valves are usually put up, the eccentric will follow the pin less than a quarter of a turn.
A. With an indirect valve motion and an outside admission valve, the go-ahead eccentric follows the crank pin with the engine running forward. Without any lap or lead, it would be a quarter of a turn or 90 degrees behind the pin, but since all valves have lap and lead, the eccentric is advanced or positioned toward the pin enough to move the valve the amount of the lap and lead. With a direct valve gear and an outside admission valve, the eccentric will be a quarter of a turn or 90 degrees ahead of the crank pin and advanced enough to move the valve the amount of the lap and lead. With an inside admission valve and an indirect valve motion, the eccentric will come the same as for an outside admission valve and direct motion, or more than a quarter of a turn ahead of the pin. With an inside admission valve and direct motion, as piston valves are usually set up, the eccentric will follow the pin less than a quarter of a turn.
41. Q. What effect would be produced upon the lap and lead by changing the length of the eccentric rod?
41. Q. How would changing the length of the eccentric rod affect the lap and lead?
A. Lap depends on the construction of the valve. A change of the eccentric rod would not effect it, but would widen the port opening at one end of the travel and reduce it at the other. It should be equal at both ends. Lead is controlled by the position of the eccentric on the axle and it must be equal at both ends. Changing the length of the eccentric rod from the proper one does not really affect the lead, because no proper measurement can be made until lead is equal at both ends. Therefore improper length of eccentric rods varies the port opening at the beginning of the stroke of the piston at both ends.
A. Lap depends on how the valve is built. Changing the eccentric rod won’t affect it, but it will make the port opening wider at one end of the movement and smaller at the other. It should be the same at both ends. Lead is determined by where the eccentric is positioned on the axle, and it must also be the same at both ends. Adjusting the length of the eccentric rod from the correct length doesn't really change the lead because you can't get an accurate measurement until the lead is equal at both ends. So, using the wrong length of eccentric rods changes the port opening at the start of the piston’s stroke at both ends.
42. Q. Why are eccentric rods made adjustable?
42. Q. Why are eccentric rods designed to be adjustable?
A. In order to change their length to make adjustment of the valve gear not as easily made in other ways.
A. To adjust their length for the valve gear, which isn’t as easy to modify in other ways.
43. Q. Why is it necessary to keep the cylinders free from water?
43. Q. Why is it important to keep the cylinders dry?
A. In order to avoid damaging valves and cylinders, to insure perfect lubrication and obtain the most efficient service from the locomotive.
A. To prevent damage to the valves and cylinders, ensure proper lubrication, and achieve the best performance from the locomotive.
44. Q. Where is the piston rod packing located? Where cylinder packing?[Pg 75]
44. Q. Where is the piston rod packing located? Where is the cylinder packing? [Pg 75]
A. Piston rod packing is usually soft metallic rings located inside of a gland at the back end of cylinder and around the rod. Cylinder packing rings are usually cast iron, placed around the piston head and bearing against the walls of the cylinder.
A. Piston rod packing typically consists of soft metal rings that are found inside a gland at the rear of the cylinder and around the rod. Cylinder packing rings are generally made of cast iron and are positioned around the piston head, pressing against the cylinder walls.
45. Q. How are metallic packing rings on piston rods and valve stems held in place? What provisions are made for the uneven movements of the rod?
45. Q. How are metallic packing rings on piston rods and valve stems secured? What arrangements are in place to accommodate the uneven movements of the rod?
A. The packing rings fit into a vibrating cup or cone located inside the gland, being held therein by means of a spring as well as by the steam pressure. Provision is made for uneven movement of the rod by making the inside of the gland larger than the vibrating cup and using a ball-joint ring between the vibrating cup and gland.
A. The packing rings fit into a vibrating cup or cone inside the gland, held in place by a spring and the steam pressure. To accommodate the uneven movement of the rod, the inside of the gland is made larger than the vibrating cup, and a ball-joint ring is used between the vibrating cup and the gland.
46. Q. While running under steam and there is a failure of part of the locomotive which does not seem to prevent running at full speed, how would you proceed?
46. Q. While operating under steam and experiencing a failure of a part of the locomotive that doesn't appear to affect running at full speed, how would you handle the situation?
A. Keep the locomotive running if in your judgment it is safe. Try to ascertain what the injury is and be prepared at the next stop to do such work as the case demands, being careful to make the stop at such a place that the work can be done without interfering with the movements of main line trains.
A. Keep the train running if you think it's safe. Try to figure out what the injury is and be ready at the next stop to do whatever work is needed, making sure to stop in a spot where you can work without disrupting the main line trains.
47. Q. If one side of a locomotive is disabled, what would you do in a general way to make it possible to use steam on the other side?
47. Q. If one side of a locomotive is out of order, what would you generally do to enable the use of steam on the other side?
A. Disconnect enough parts to allow for the turning of the wheels and for reversing of the opposite side without moving the valve on the disabled side.
A. Disconnect enough parts to enable the wheels to turn and to let the opposite side reverse without shifting the valve on the inactive side.
48. Q. In case a locomotive in your care became disabled on the road, what would you do?[Pg 76]
48. Q. If a locomotive you're responsible for broke down on the track, what would you do?[Pg 76]
A. First see that the train is protected. Next examine the locomotive and see what is necessary to do to move it and if possible the train. If unable to make repairs at once to bring the engine and train forward, would advise exact condition of engine and ask for help. In the meantime endeavor to move the train so as to give other trains the use of the main line.
A. First, make sure the train is secure. Next, check the locomotive to determine what needs to be done to get it moving and, if possible, the train as well. If you're not able to make immediate repairs to bring the engine and train forward, I recommend reporting the exact condition of the engine and requesting assistance. In the meantime, try to move the train to allow other trains to use the main line.
49. Q. Suppose a wash-out plug blew out or a blow-off cock broke off or would not close, what should be done?
49. Q. What should you do if a wash-out plug blows out or a blow-off cock breaks off or won’t close?
A. Kill the fire, get the train on a side track, if possible, and if unable to make repairs get the engine in condition to be towed in. In all cases with a disabled engine allow the train to drift to a siding, when possible, and stop between the switches so as to allow other trains to pass through siding.
A. Extinguish the fire, move the train to a side track if you can, and if repairs aren't possible, make sure the engine is ready to be towed in. In any situation with a broken engine, let the train roll to a siding if possible, and stop it between the switches to let other trains pass through the siding.
50. Q. Can a locomotive boiler without steam pressure be filled by being towed by another engine? If towed, how filled?
50. Q. Can a locomotive boiler without steam pressure be filled by being towed by another engine? If it can be towed, how is it filled?
A. Yes. Close all openings where air could enter the boiler. All relief valves, cylinder cocks, gauge cocks, the whistle valve and air pump steam valve should be closed. Place the reverse lever in full gear in the direction the engine is to be towed with water supply valve and injector throttle open. Use engine oil through auxiliary oil cups to oil valves and pistons. The movement of the pistons in the cylinders will pump the air out of the boiler and atmospheric pressure on water in the tank will force water into boiler when the engine is towed.
A. Yes. Close all openings where air could enter the boiler. Make sure all relief valves, cylinder cocks, gauge cocks, the whistle valve, and the air pump steam valve are closed. Set the reverse lever to full gear in the direction the engine will be towed, with the water supply valve and injector throttle open. Use engine oil through the auxiliary oil cups to lubricate the valves and pistons. The movement of the pistons in the cylinders will pump air out of the boiler, and atmospheric pressure on the water in the tank will push water into the boiler when the engine is towed.
51. Q. What should be done if grates should be burned out or broken while on the road?
51. Q. What should you do if the grates get burned out or break while you're on the road?
A. Pull the fire off the broken or burned grates, cover that section with any pieces of iron at hand[Pg 77] (fish-plates or angle-bars are very good), then level up the fire, clean ash-pan and proceed with full train.
A. Remove the fire from the damaged or burnt grates, cover that area with any available pieces of iron[Pg 77] (fish plates or angle bars work well), then even out the fire, clean the ash pan, and continue with a full load.
52. Q. What precaution should be taken to prevent locomotive throwing fire?
52. Q. What steps should be taken to prevent locomotives from throwing sparks?
A. The netting and smoke-arch should be kept in good condition; cinder slide and hand hole plates securely fastened, ash-pan clean and slide dampers for dumping ashes closed. Care should be exercised in working the engine, especially in the vicinity of stations or places where fire is liable to catch. Avoid working the engine hard so as to prevent throwing cinders.
A. The netting and smoke-arch should be maintained in good shape; make sure the cinder slide and hand hole plates are securely fastened, the ash-pan is clean, and the slide dampers for dumping ashes are closed. Be careful when operating the engine, especially near stations or areas where fire could easily start. Avoid overworking the engine to prevent throwing cinders.
53. Q. What shall be done with a badly leaking or bursted flue?
53. Q. What should be done about a badly leaking or burst flue?
A. Plug it if possible with an iron or wooden plug. If in the fire-box end, a piece of scantling or post can be sharpened and driven into the flue from the fire-box door; it will then burn off up to where the water from the bursted flue keeps it wet. If a bottom flue, would cover it with ashes or green coal so that the leakage would not put out the balance of the fire. If able to maintain steam pressure, would then proceed with a full train.
A. If you can, plug it with an iron or wooden plug. If it's at the fire-box end, you can sharpen a piece of wood or a post and drive it into the flue from the fire-box door; it will burn off until it reaches the spot where the water from the broken flue keeps it wet. If it's a bottom flue, cover it with ashes or green coal so the leakage won't extinguish the rest of the fire. If you can maintain steam pressure, then proceed with a full train.
54. Q. What should be done in case the throttle valve stem became disconnected while the valve is closed? If it became disconnected leaving valve open?
54. Q. What should you do if the throttle valve stem disconnects while the valve is closed? What if it disconnects while the valve is open?
A. Would notify the train crew and Dispatcher and arrange to be towed in. With lubricator working, unless in very cold weather so there is danger of the water freezing in the cylinders or steam chest passages, would not disconnect. By taking out lubricator chokes and steam chest valves from the oil pipe, a[Pg 78] larger supply of steam could be got into the cylinders. If in to clear of other trains and practicable, would take up the dome cap and connect the throttle again. If disconnected and valve stuck open, would notify the train crew and Dispatcher, reduce steam pressure until the engine could be handled with reverse lever and brake, and proceed with such a train as the engine can handle.
A. Would inform the train crew and Dispatcher and arrange for a tow. With the lubricator working, unless it's very cold and there's a risk of the water freezing in the cylinders or steam chest passages, would not disconnect. By removing the lubricator chokes and steam chest valves from the oil pipe, a[Pg 78] larger supply of steam could be directed into the cylinders. If clear of other trains and it's feasible, would remove the dome cap and reconnect the throttle. If disconnected and the valve is stuck open, would notify the train crew and Dispatcher, reduce steam pressure until the engine can be controlled with the reverse lever and brake, and continue with whatever train the engine can manage.
55. Q. In case a valve yoke or stem became broken inside of steam chest, how can the breakage be located?
55. Q. If a valve yoke or stem breaks inside the steam chest, how can the damage be found?
A. In this case the disabled valve is always pushed to the front end of the steam chest so that with a slide valve or outside admission piston valve the back port is open to live steam. When given steam, the engine will stop on the eighth, and when reversed will move over to the other eighth, being stopped there by the live steam in the back end of the cylinder having the disabled valve. Steam will blow from the back cylinder cock on the disabled side and cannot be changed by reversing the engine. If the valve is pushed far enough ahead to open the exhaust port, steam will blow through the exhaust so the engine cannot be moved. With an inside admission valve the forward steam port will be opened and steam will come out of the forward cylinder cock on the disabled side.
A. In this case, the disabled valve is always pushed to the front end of the steam chest so that with a slide valve or outside admission piston valve, the back port is open to live steam. When steam is supplied, the engine will stop at the eighth position, and when reversed, it will move to the other eighth position, being stopped there by the live steam in the back end of the cylinder with the disabled valve. Steam will blow from the back cylinder cock on the disabled side and cannot be changed by reversing the engine. If the valve is pushed far enough ahead to open the exhaust port, steam will blow through the exhaust, preventing the engine from moving. With an inside admission valve, the forward steam port will open, and steam will come out of the forward cylinder cock on the disabled side.
56. Q. After locating a breakage of this kind, how would you proceed to put the engine in safe running order?
56. Q. After finding a break like this, how would you go about making the engine safe to run again?
A. Would move the valve to central position so as to cover both steam ports, if possible. This may be done by taking out the relief valve if on front side of[Pg 79] the steam chest and pushing valve back, or taking up the cover for a slide valve; or taking off front head for a piston valve. Disconnect the valve rod from rocker arm and block valve stem so it cannot blow out of the gland or let valve work back. Loosen cylinder head in order to provide for lubricating cylinder so as to leave the main rod up on the disabled side and proceed on one side. If unable to cover the open steam port it would be necessary to disconnect the main rod on the disabled side, blocking the piston at the proper end of the guides so live steam coming into the cylinder would not move it.
A. Move the valve to the center position to cover both steam ports, if possible. You can do this by removing the relief valve if it's on the front side of[Pg 79] the steam chest and pushing the valve back, or by taking off the cover for a slide valve; or by removing the front head for a piston valve. Disconnect the valve rod from the rocker arm and block the valve stem so it cannot blow out of the gland or allow the valve to move back. Loosen the cylinder head to allow for lubricating the cylinder, keeping the main rod up on the disabled side and proceeding on one side. If you can't cover the open steam port, you'll need to disconnect the main rod on the disabled side, blocking the piston at the correct end of the guides so that live steam entering the cylinder won't move it.
57. Q. If a slide valve is broken, what can be done to run the engine on one side?
57. Q. If a slide valve is broken, what can be done to operate the engine on one side?
A. Remove the steam chest cover, place a thin board between the valve and the steam passages in the seat, replace steam chest cover, disconnect valve rod, and if able to lubricate the cylinders leave up the main rod and proceed on one side.
A. Remove the steam chest cover, put a thin board between the valve and the steam passages in the seat, replace the steam chest cover, disconnect the valve rod, and if you can lubricate the cylinders, lift up the main rod and proceed on one side.
58. Q. If one of the bolts connecting the two parts of a built-up link on Stephenson gear breaks or is lost, how would you proceed?
58. Q. If one of the bolts connecting the two parts of a built-up link on Stephenson gear breaks or is lost, how would you handle it?
A. If temporary bolt cannot be supplied, take down the forward part of the link, disconnect and remove link block, fasten valve to cover ports, and proceed. If moving link will clear rocker arm or other parts of the machinery after link block is taken out, it will not be necessary to disconnect eccentrics.
A. If a temporary bolt isn't available, take down the front section of the link, disconnect and remove the link block, secure the valve to cover the ports, and continue. If the moving link can clear the rocker arm or other parts of the machinery after the link block is removed, you won't need to disconnect the eccentrics.
59. Q. What should be done in case of link saddle pin breaking?
59. Q. What should you do if the link saddle pin breaks?
A. Remove the broken parts and block the disabled link in such a position that the entire train could be started, using a very short block above the link block in the link slot and a longer one below it.[Pg 80]
A. Take out the damaged parts and secure the disabled link in a way that allows the whole train to get moving, using a short block above the link block in the link slot and a longer one below it.[Pg 80]
60. Q. With one link blocked up, what should be guarded against?
60. Q. If one link is blocked, what should be protected against?
A. Reversing the engine or moving the tumbling shaft arm down so the link on the disabled side can strike it.
A. Reversing the engine or lowering the tumbling shaft arm so that the link on the disabled side can hit it.
61. Q. How can it be known if an eccentric has slipped on the axle?
61. Q. How can you tell if an eccentric has slipped on the axle?
A. By the uneven exhaust of the engine and a thorough inspection to determine the cause.
A. By the uneven exhaust from the engine and a thorough inspection to figure out the cause.
62. Q. Having determined which eccentric has slipped, how should it be reset?
62. Q. Now that we know which eccentric has slipped, how do we reset it?
A. Place the engine on the center on disabled side and if a back-up eccentric has slipped, would place the reverse lever in full forward gear and mark the valve stem flush with the gland; then place the reverse lever in full back gear and move the slipped eccentric until the mark on the stem returns to its original position, taking notice that the throw of the eccentric is on the other side of the axle from the go-ahead eccentric used as a marker, and tighten up set-screws. To set a go-ahead eccentric, use the back-up one on that side for the marker. If the eccentric had been keyed on, would move the cam until the key-way in the axle came in line with the slot in the cam. Knowing the position of the eccentric in relation to the crank pin, an inspection would show where it belongs. The eccentrics are usually opposite the third spoke in the driving wheel from the pin, sometimes ahead of the pin, in other cases back of the pin, depending on whether it is an inside or outside admission valve, a go-ahead or back-up eccentric.
A. Position the engine at the center on the disabled side, and if a backup eccentric has slipped, place the reverse lever in full forward gear and mark the valve stem level with the gland; then switch the reverse lever to full back gear and adjust the slipped eccentric until the mark on the stem returns to its original spot, noting that the throw of the eccentric is on the opposite side of the axle from the go-ahead eccentric used as a marker, and tighten the set screws. To set a go-ahead eccentric, use the backup one on that side as the marker. If the eccentric was keyed on, adjust the cam until the keyway in the axle aligns with the slot in the cam. Understanding the position of the eccentric in relation to the crank pin, an inspection will reveal its proper placement. The eccentrics are typically opposite the third spoke in the driving wheel from the pin, sometimes ahead of the pin, and in other cases behind the pin, depending on whether it is an inside or outside admission valve, a go-ahead or backup eccentric.
63. Q. What should be done in case of a broken eccentric strap or rod?[Pg 81]
63. Q. What should you do if an eccentric strap or rod breaks?[Pg 81]
A. For a go-ahead strap or rod take down all broken parts, disconnect valve rod, cover ports, and come in on one side. It is safer to take down also the back-up strap and rod on that side. If the back-up strap and rod is broken, it is possible to secure the bottom end of the link so it will not turn over, work the engine full stroke ahead, proceeding with full train until the main line is clear.
A. To replace a go-ahead strap or rod, remove all broken parts, disconnect the valve rod, cover the ports, and approach from one side. It's safer to also remove the back-up strap and rod on that side. If the back-up strap and rod are broken, you can secure the bottom end of the link to prevent it from turning over, operate the engine at full stroke ahead, and continue with the full train until the main line is clear.
64. Q. How should the engine be disconnected if the lower rocker arm became broken? If link block pin?
64. Q. How do you disconnect the engine if the lower rocker arm breaks? What about if the link block pin breaks?
A. Would remove broken parts; if moving link would strike anything connected with the rocker box or broken arm it would be necessary to take down both eccentric straps and rods. Block valve central over ports and come ahead on one side. If a link block pin was broken, it might be possible to put a bolt in there to do the work, otherwise block the valve on the center of its seat and if the link will not clear the lower end of the rocker arm take down the eccentric straps and rod. In any case where necessary to take off the eccentric rod always take off the strap also.
A. Remove any broken parts; if the moving link strikes anything connected to the rocker box or broken arm, you’ll need to take down both the eccentric straps and rods. Position the block valve directly over the ports and advance on one side. If a link block pin is broken, you might be able to use a bolt to fix it; otherwise, block the valve in the center of its seat. If the link doesn’t clear the lower end of the rocker arm, take down the eccentric straps and rod. Whenever it’s necessary to remove the eccentric rod, always remove the strap as well.
65. Q. For what breakdown is it necessary to take down the main rod? The side rod?
65. Q. When is it necessary to take down the main rod? What about the side rod?
A. A broken main crank pin, broken main rod or strap, broken piston rod when near the middle of the rod, broken cross-head or guide, broken valve or seat when steam cannot be kept out of the cylinder. Side rods must come down for broken side rod, broken main pin, or broken side rod pin affecting that rod.
A. A broken main crank pin, a broken main rod or strap, a broken piston rod near the middle, a broken cross-head or guide, a broken valve or seat when steam can't be kept out of the cylinder. Side rods must be removed for a broken side rod, a broken main pin, or a broken side rod pin affecting that rod.
66. Q. If it is not necessary to take down the main rod of disabled side of the engine, how would you arrange to lubricate the cylinders?[Pg 82]
66. Q. If it’s not necessary to remove the main rod on the disabled side of the engine, how would you go about lubricating the cylinders?[Pg 82]
A. If cylinder and piston are in good shape and it is possible to block the valve to admit a small quantity of steam into the back end of the cylinder, oil from the lubricator will go through this opening and oil the piston rod and cylinder packing. If not possible to block the valve properly, cover the ports and oil the cylinder through the indicator plug openings or relief plug holes. If not possible to do this, slack off the bolts on the front cylinder head, wedge the head open so oil can be introduced. In some cases it may be necessary to take the head off; that however, allows dust and grit to enter the cylinder.
A. If the cylinder and piston are in good condition and you can block the valve to let a small amount of steam into the back end of the cylinder, oil from the lubricator will pass through this opening and lubricate the piston rod and cylinder packing. If you can't block the valve properly, cover the ports and oil the cylinder through the indicator plug openings or relief plug holes. If that's not doable, loosen the bolts on the front cylinder head, prop the head open so you can add oil. In some cases, you might need to remove the head; however, that can allow dust and grit to get into the cylinder.
67. Q. What is the by-pass valve, and what is its duty?
67. Q. What is the by-pass valve, and what does it do?
A. By-pass valves are connected to the steam port leading to the cylinder. Its duty is to open when the engine is drifting with steam shut off, and close when working steam, to allow air to pass back and forth from opposite sides of the moving piston.
A. By-pass valves are linked to the steam port that leads to the cylinder. Their job is to open when the engine is coasting with the steam turned off and close when steam is active, allowing air to flow back and forth from both sides of the moving piston.
68. Q. What is a vacuum relief valve? What a cylinder relief valve?
68. Q. What is a vacuum relief valve? What is a cylinder relief valve?
A. A vacuum relief valve is usually located on the steam chest or the live steam passage to the chest and opens when steam is shut off and engine drifting, allowing atmospheric pressure to pass into the steam chest, closing when working steam. A cylinder relief valve is a pop valve screwed into the cylinder head and set at high enough pressure so it does not open in ordinary service, but will open to allow water to pass out when the exhaust port is closed by valves; or on compound engines when the pressure in the low-pressure cylinder gets too high.
A. A vacuum relief valve is typically found on the steam chest or the live steam pipe leading to the chest. It opens when steam is turned off and the engine is coasting, allowing atmospheric pressure to flow into the steam chest, and closes when there is working steam. A cylinder relief valve is a pop valve screwed into the cylinder head, set at a high enough pressure so that it doesn’t open during normal operation, but will open to let water out when the exhaust port is closed by valves; or in compound engines when the pressure in the low-pressure cylinder becomes too high.
69. Q. What would be considered a bad engine or tender truck wheel?[Pg 83]
69. Q. What would be considered a faulty engine or tender truck wheel?[Pg 83]
A. One loose on axle; having bad flat spots; very sharp flanges; bad sand spots; cracks shelled out; or other defect that would make the wheel unsafe.
A. One that is loose on the axle; has bad flat spots; very sharp flanges; bad sand spots; cracks or chips; or any other defect that would make the wheel unsafe.
70. Q. What should be done if a tender truck wheel or axle should break?
70. Q. What should you do if a tender truck wheel or axle breaks?
A. Would place a piece of timber or rail across the tender, jack up the corner of the truck that is disabled chain it to the timber and fasten the timber at the other end to hold it so it would carry the disabled truck. If it is possible to slide the wheel or truck, place a tie across the rail and keep the wheel from turning, then slide it to a siding.
A. Would put a piece of wood or rail across the tender, lift up the corner of the disabled truck, chain it to the wood, and secure the wood at the other end to support the disabled truck. If it’s possible to move the wheel or truck, place a tie across the rail to stop the wheel from turning, then slide it to a siding.
71. Q. What should be done if an engine truck wheel or axle should break?
71. Q. What should you do if a wheel or axle on the engine truck breaks?
A. Would block between the engine frame and truck frame over the good wheel on disabled side, swing the disabled corner of the truck to the engine frame with a chain. Look out when crossing frogs that disabled truck does not leave the track. With a broken flange, would block the wheel to prevent its turning and skid it to a siding.
A. Would place a block between the engine frame and the truck frame over the good wheel on the disabled side, swinging the disabled corner of the truck to the engine frame with a chain. Be careful when crossing frogs to ensure that the disabled truck doesn't derail. If there's a broken flange, block the wheel to stop it from turning and skid it to a siding.
72. Q. What should be done for a broken tender truck spring?
72. Q. What should you do for a broken tender truck spring?
A. Jack the tender up to where it belongs and put a block in place of the broken spring.
A. Jack the lift up to where it needs to be and put a block in for the broken spring.
73. Q. What should be done with a broken engine truck spring or equalizer?
73. Q. What should you do with a broken engine truck spring or equalizer?
A. For a broken spring, raise the front end of the engine and place blocks across the equalizers under the truck spring near the spring band. For a broken equalizer, block on top of engine truck boxes and under truck frame.[Pg 84]
A. If you have a broken spring, lift the front end of the engine and put blocks across the equalizers under the truck spring close to the spring band. If the equalizer is broken, place blocks on top of the engine truck boxes and under the truck frame.[Pg 84]
74. Q. What should be done if a driving spring hanger or equalizer should break?
74. Q. What should be done if a driving spring hanger or equalizer breaks?
A. Would block between the driving box affected and under the frame over it, using hardwood block or piece of iron. Would also block the equalizer up to its proper position between the disabled end and the frame, or over the other end, as the type of spring rigging requires, to hold the equalizer level. For a broken equalizer, would block on top of all boxes affected, would raise the engine by running the proper driving wheels upon an incline or wedge to lift the engine while other boxes were blocked; a re-railing frog comes handy for this work.
A. You would place blocks between the affected driving box and the frame above it, using either a hardwood block or a piece of iron. You would also block the equalizer up to its correct position between the disabled end and the frame, or over the other end, depending on the type of spring rigging, to keep the equalizer level. For a broken equalizer, you would block on top of all affected boxes and lift the engine by running the appropriate driving wheels up an incline or wedge to raise the engine while the other boxes were blocked; a re-railing frog is useful for this task.
75. Q. How can an engine be moved if the reverse lever or reach rod were caught at short cut-off by a broken spring or hanger?
75. Q. How can you move an engine if the reverse lever or reach rod gets stuck at a short cut-off due to a broken spring or hanger?
A. By removing the pin at the forward end of reach rod, to free the tumbling shaft and allow it to be moved either forward or back to move the engine. A block should be placed over the link block to avoid damaging it when uncoupled, as well as to hold link in proper position to move the engine. This would allow the engine to be moved and clear the main line.
A. By removing the pin at the front of the reach rod, you can detach the tumbling shaft and move it either forward or backward to adjust the engine. A block should be placed over the link block to prevent damage when uncoupled, and to keep the link in the correct position for moving the engine. This will enable the engine to be moved and clear the main line.
76. Q. How can the blowing of steam past cylinder packing, a valve or valve strip be distinguished or located?
76. Q. How can we identify or locate steam blowing past cylinder packing, a valve, or a valve strip?
A. Test for a leaky slide valve, place the engine on the quarter on the suspected side with the reverse lever in center notch; the valve should be in the middle of its travel and cover both ports. If steam blows through the open cylinder cocks on that side, the valve or seat are defective. A leaky balanced valve strip will allow steam to blow through the hole on top of the valve into the exhaust port in the seat[Pg 85] and very little steam will come out of the cylinder cock; in some cases with the valve barely opening a steam port to the exhaust, air will draw in at the cylinder cock. If there is a drip cock in the exhaust pipe under the saddle, the steam will blow out there. After testing for leaky valve, place the engine on about the forward bottom or top back eighth, block the wheels or set the brakes solid, put reverse lever in corner, open cylinder cocks and give the engine steam. If steam comes out of both cylinder cocks, and testing valve shows it is tight, then the packing is blowing. Cylinder packing should be tested with steam first on one side of the piston and then on the other.
A. To test for a leaking slide valve, position the engine on the quarter of the suspected side with the reverse lever in the center notch; this should place the valve in the middle of its travel, covering both ports. If steam escapes through the open cylinder cocks on that side, the valve or seat is faulty. A leaking balanced valve strip will permit steam to escape through the hole on top of the valve into the exhaust port in the seat[Pg 85] and very little steam will exit from the cylinder cock; in some cases, with the valve barely opening a steam port to the exhaust, air will be drawn in at the cylinder cock. If there's a drip cock in the exhaust pipe under the saddle, steam will escape from there. After testing for a leaky valve, position the engine around the forward bottom or top back eighth, block the wheels or set the brakes securely, move the reverse lever to the corner, open the cylinder cocks, and supply steam to the engine. If steam comes out of both cylinder cocks, and the testing valve indicates it’s tight, then the packing is leaking. Cylinder packing should be tested with steam first on one side of the piston and then on the other.
77. Q. If engine should blow badly and be unable to start the train when on the right dead center, on which side would be the blow generally?
77. Q. If the engine were to explode and couldn't start the train when it's in the correct position, which side would the explosion usually be on?
A. On the left side. If the side standing on the quarter cannot start the train, the trouble is usually there.
A. On the left side. If the side on the quarter can't start the train, the issue is typically there.
78. Q. If throttle were closed and steam came out of cylinder cocks, what might be the cause?
78. Q. If the throttle was closed and steam was escaping from the cylinder cocks, what could be the reason?
A. To test for this, first shut off steam connection to the lubricator; steam leaking into the cylinders can come from a leaky throttle or leaky dry pipe.
A. To test for this, first turn off the steam connection to the lubricator; steam leaking into the cylinders can come from a faulty throttle or a leaking dry pipe.
79. Q. Is it possible to distinguish between a leaky throttle and a leaky dry pipe?
79. Q. Can you tell the difference between a leaking throttle and a leaking dry pipe?
A. Yes; a leaky throttle usually leaks steam at all times. A leaky dry pipe will leak both steam and water. It will show a stream of water at the cylinder cocks when the water level in the boiler is raised above the leak in the dry pipe.
A. Yes; a leaking throttle typically leaks steam constantly. A leaking dry pipe will leak both steam and water. It will show a stream of water at the cylinder cocks when the water level in the boiler rises above the leak in the dry pipe.
80. Q. What effect have leaky steam pipes in the smoke-arch, and how should they be tested?[Pg 86]
80. Q. What impact do leaking steam pipes in the smoke-arch have, and how should they be tested?[Pg 86]
A. Leaky steam pipes waste steam and very seriously affect the draft in the front end. A bad leak in the back part of the joint at the bottom will blow into the tubes and make the engine smoke at the door with throttle wide open while standing still. To test them, open the front door and cover the joint with fine cinders. When the engine is given steam, the cinders will blow away from the leak; to properly test them in the shop, water under heavy pressure should be used.
A. Leaky steam pipes waste steam and really affect the draft in the front end. A bad leak at the back of the joint at the bottom will blow into the tubes and cause the engine to smoke at the door with the throttle wide open while standing still. To test them, open the front door and cover the joint with fine cinders. When steam is applied to the engine, the cinders will blow away from the leak; to properly test them in the shop, use water under heavy pressure.
81. Q. How should the test for a leaky exhaust pipe joint, or a leaky nozzle joint be made?
81. Q. How should you test for a leaking exhaust pipe joint or a leaking nozzle joint?
A. About the only test that can be made on the road is to open the front end and reverse the engine with throttle partly opened, watching the suspected joint at the same time. For the bottom one with cinders around the joint, for the top one it can sometimes be detected by holding a torch near the joint.
A. The only real test you can do on the road is to open the front end and reverse the engine with the throttle partially open while keeping an eye on the suspected joint at the same time. For the bottom one, look for cinders around the joint; for the top one, you can sometimes spot it by holding a flashlight near the joint.
82. Q. What should be done if a steam chest cracks?
82. Q. What should you do if a steam chest cracks?
A. Would loosen up the steam chest cover to free the sides, and wedge between the studs and walls of chest, crowding the broken parts together. A brake shoe key does this nicely. Would then tighten down on steam chest cover and proceed.
A. Would loosen the steam chest cover to free the sides and wedge between the studs and walls of the chest, pushing the broken parts together. A brake shoe key does this nicely. Then, would tighten down the steam chest cover and proceed.
83. Q. What should be done if a steam chest breaks?
83. Q. What should you do if a steam chest breaks?
A. Would take off steam chest cover, place strips of boards over the steam inlets and block on top of them so that the steam chest cover would hold them in place and prevent live steam coming out of inlet. Would then make the necessary disconnection and proceed on one side.[Pg 87]
A. Would remove the steam chest cover, put strips of wood over the steam inlets, and place a block on top of them so that the steam chest cover would secure them and stop live steam from escaping the inlet. Then, would make the necessary disconnection and proceed on one side.[Pg 87]
84. Q. If a link lifter or arm were broken, what should be done?
84. Q. If a link lifter or arm is broken, what should be done?
A. Take off the disabled parts, block between the top of the link and link block, having the disabled link blocked down very nearly in full strokes. For safety, both the top and bottom of the disabled link should have blocks in its slot; the good link would be held in place by the reverse lever and should under no consideration be dropped down any farther than the disabled link was.
A. Remove the disabled parts, and block the space between the top of the link and the link block, ensuring the disabled link is blocked down almost completely. For safety, both the top and bottom of the disabled link should have blocks in their slot; the working link will be secured by the reverse lever and should not be lowered any farther than the disabled link was.
85. Q. If the reverse lever or reach rod should break, what should be done?
85. Q. If the reverse lever or reach rod breaks, what should you do?
A. If either breaks, place an iron bar or suitable piece of material across the top of both frames, securely fastening it in position, then fasten the arm of the tumbling shaft to the bar. This will require the engine to be worked at about half cut-off; handle such part of the train as the road conditions would permit.
A. If either breaks, place a metal bar or appropriate piece of material across the top of both frames, securing it in place, then attach the arm of the tumbling shaft to the bar. This will need the engine to be operated at about half cut-off; manage such part of the train as the road conditions allow.
86. Q. What should be done if the piston, piston rod, cross-head, main rod or crank pin are broken or bent?
86. Q. What should you do if the piston, piston rod, cross-head, main rod, or crank pin is broken or bent?
A. If a piston should break, would remove broken parts, disconnect valve stem, clamp valve in central position, and if moving piston would not damage cylinder, leave main rod up and proceed. If a piston rod, cross-head, main rod or crank pin are broken or bent, would take down the main rod, block the valve and cross-head; if piston rod is broken off at the cross-head, leave main rod up.
A. If a piston breaks, remove the
87. Q. What should be done when there is a loose or lost cylinder key?
87. Q. What should you do if there’s a loose or missing cylinder key?
A. If the cylinder key is loose, it should be tightened up; if lost, something should be substituted. In[Pg 88] case nothing solid can be found to take the place of the key, the engine should be run in light to avoid further damage.
A. If the cylinder key is loose, it should be tightened; if it's lost, something should be used as a substitute. In[Pg 88] case nothing solid can be found to replace the key, the engine should be run in light to prevent further damage.
88. Q. What should be done if a safety valve spring or stud breaks?
88. Q. What should you do if a safety valve spring or stud breaks?
A. The steam pressure should be reduced. With broken spring, screw the parts down solid or clamp the stem down. This can be done by laying a piece of scantling across the top of the valve, fastening each end to the hand rail on opposite sides of the engine in case of broken stud. Would then raise steam pressure and proceed. Care should be taken to see that the other safety valves relieve the steam pressure properly.
A. The steam pressure should be lowered. If there's a broken spring, tighten the parts securely or clamp the stem down. You can do this by placing a piece of lumber across the top of the valve and securing each end to the handrail on opposite sides of the engine, in case there's a broken stud. Then, raise the steam pressure and continue. Make sure that the other safety valves are functioning correctly to relieve the steam pressure.
89. Q. How can an engine be brought in with a broken front end or stack?
89. Q. How can you bring in an engine with a broken front end or stack?
A. By boarding up the front end to make it as near air tight as possible and using a barrel or a petticoat pipe in place of the stack, wiring it fast to the smoke-arch. Where a portion of the stack is inside the smoke-box the engine might steam without the barrel or petticoat pipe.
A. By sealing up the front end to make it as close to airtight as possible and using a barrel or a petticoat pipe instead of the stack, securely attaching it to the smoke-arch. When part of the stack is inside the smoke-box, the engine can operate without the barrel or petticoat pipe.
90. Q. What should be done if the frame is broken between the main driver and cylinder?
90. Q. What should you do if the frame is broken between the main driver and the cylinder?
A. Either give up the train and come in light, or disconnect the engine on that side and come in with reduced tonnage, depending on how badly the engine pounds when working steam.
A. Either abandon the train and come in light, or detach the engine on that side and come in with reduced weight, depending on how hard the engine vibrates when using steam.
91. Q. If the frame is broken back of the main driver?
91. Q. What if the frame is broken behind the main driver?
A. Do not disconnect and do not try to pull a heavy train; it is safer to come in with light tonnage.
A. Do not disconnect and do not try to pull a heavy train; it's safer to come in with a lighter load.
92. Q. In case of broken side rods, what should be done?[Pg 89]
92. Q. What should you do if the side rods are broken?[Pg 89]
A. Take down the broken rod and corresponding rod on the other side of the engine.
A. Remove the broken rod and the matching rod on the opposite side of the engine.
93. Q. What can be done if the intermediate side rods were broken on a consolidation engine having the eccentric on the axle ahead of the main wheel?
93. Q. What can be done if the middle side rods are broken on a consolidation engine that has the eccentric on the axle in front of the main wheel?
A. In this case the engine must be towed in. It is possible when the main pin is broken, so that all rods on one side are taken off, to leave the rods up on the other side and move the engine with her own steam, but very few roads will allow this, because engineers will be inclined to leave the main rod up on the disabled side to prevent engine catching on the center. If main rod is left up on the disabled side, the wheels will surely slip and wreck the rods on the other side.
A. In this situation, the engine needs to be towed in. It's possible to leave the rods on one side while removing all the rods on the other side when the main pin is broken, allowing the engine to move under its own steam. However, very few railroads will permit this because engineers are likely to keep the main rod up on the side that’s not working to avoid the engine catching on the center. If the main rod is left up on the disabled side, the wheels will definitely slip and damage the rods on the other side.
94. Q. Should one of the forward tire, main tire, intermediate tire, back tire, or a trailer tire break, what must be done to bring the engine up?
94. Q. If one of the front tires, main tires, intermediate tires, back tires, or a trailer tire gets a flat, what needs to be done to get the engine running again?
A. Would run the wheel of the broken tire on a block in order to raise the wheel clear of the rail and the box up in the driving box jaws. Remove the oil cellar and place a block between the driving journal and pedestal brace to carry the disabled wheel center clear of the rail. Would also block up on top of the box of the wheel ahead or back as the case might be, in order to take the weight from the disabled wheel. It might not be necessary to take off any of the rods, but would run the engine light to the shop, giving special attention to lubrication of the disabled wheel and using extra precaution in entering side tracks and passing over frogs and switches. With the tire of a back driver or trailer wheel broken, it is usually necessary to swing the rear end of the engine from the tender to keep the rear end on the track. With an[Pg 90] inside radial journal, box on the trailer axle; for a broken trailer tire, both trailer wheels must be blocked and swung clear of the rail.
A. Would run the wheel of the broken tire on a block to lift the wheel off the rail and the box up in the driving box jaws. Remove the oil cellar and place a block between the driving journal and pedestal brace to keep the disabled wheel center off the rail. Would also block up on top of the box of the wheel ahead or behind, depending on the situation, to take the weight off the disabled wheel. It might not be necessary to remove any of the rods, but would run the engine light to the shop, paying special attention to the lubrication of the disabled wheel and taking extra care when entering side tracks and crossing frogs and switches. If the tire of a back driver or trailer wheel is broken, it's usually necessary to swing the rear end of the engine from the tender to keep the rear end on the track. With an[Pg 90] inside radial journal box on the trailer axle; for a broken trailer tire, both trailer wheels must be blocked and swung clear of the rail.
95. Q. What is a good method of raising a wheel when jacks are not available?
95. Q. What’s a good way to lift a wheel when you don’t have any jacks?
A. By raising the wheel on a hardwood block or iron wedge; a re-railing frog comes very handy for this purpose.
A. By lifting the wheel onto a hardwood block or an iron wedge, a re-railing frog is very useful for this purpose.
96. Q. How can it be known when the wedges are set up too tight and the driving box sticks, and in what manner can they be pulled down?
96. Q. How can you tell when the wedges are too tight and the driving box gets stuck, and how can they be loosened?
A. If wedges are set up too tight, it causes the boxes to stick and the engine to ride rough. Inspection of the engine when moving will locate the disabled box; usually this gets hot at once and the wedges should be immediately pulled down. Loosen the jam nuts on the wedge bolts and back them down; if the wedge is stuck very tight it may be necessary to run one or more of the wheels over a block; or to loosen the pedestal, brace bolt and allow the jaws to spread to release the box.
A. If the wedges are too tight, it makes the boxes stick and the engine runs roughly. Inspecting the engine while it’s moving will help find the disabled box; it usually heats up quickly, and the wedges should be loosened immediately. Loosen the jam nuts on the wedge bolts and back them off; if the wedge is stuck really tight, you might need to roll one or more of the wheels over a block, or loosen the pedestal and brace bolt to let the jaws spread and release the box.
97. Q. What are some of the various causes for pounds?
97. Q. What are some of the different reasons for pounds?
A. Wedges not properly adjusted, loose or worn driving box brasses, rod brasses not keyed or in need of reducing, loose side rod bushings or side rod connections, worn cross-heads, wrist pins, broken frame, loose cylinder key, loose piston on rod, or rod loose in cross-head, loose follower bolts or obstruction in the cylinder.
A. Wedges that aren’t properly adjusted, loose or worn driving box brasses, rod brasses that aren’t keyed or need to be reduced, loose side rod bushings or connections, worn cross-heads, wrist pins, broken frames, loose cylinder keys, loose pistons on rods, rods loose in cross-heads, loose follower bolts, or blockages in the cylinder.
98. Q. How may a pound in driving boxes, wedges or rod brasses be located, and after locating what should be done?[Pg 91]
98. Q. How can a pound in driving boxes, wedges, or rod brasses be found, and what should be done after locating it?[Pg 91]
A. Place the engine at half stroke on side to be tested. Do not set brake when testing for loose wedges or defective boxes; set brake when testing for other pounds. Reverse engine from forward to back gear under steam, noting the movement of the axle in the boxes, the driving boxes between the wedges, rod brasses on the pins and movement of cross-head between the guides. If possible would adjust wedges or rod brasses at once and report repairs needed at the terminal.
A. Position the engine at half stroke on the side to be tested. Do not apply the brake when checking for loose wedges or faulty boxes; apply the brake when testing for other weights. Reverse the engine from forward to reverse gear while under steam, observing the movement of the axle in the boxes, the driving boxes between the wedges, rod bushings on the pins, and the cross-head movement between the guides. If possible, adjust the wedges or rod bushings immediately and report any repairs needed at the terminal.
99. Q. How locate loose follower bolts?
99. Q. How can I find loose follower bolts?
A. Shut off steam and allow engine to drift; there will be a pound in the cylinder when the loose follower bolt strikes a forward cylinder-head as the engine passes the forward center on that side; give engine steam while still moving and if the pound stops it is likely to be a loose or broken follower bolt. When working steam, the compression or pre-admission takes up the lost motion in the rod and connections, so the loose bolt does not strike the head; when shut off the piston travels the extra amount of this lost motion and the bolt strikes the head.
A. Turn off the steam and let the engine coast; there will be a thump in the cylinder when the loose follower bolt hits the front cylinder head as the engine moves past the forward center on that side. Give the engine steam while it's still moving, and if the thump stops, it’s probably due to a loose or broken follower bolt. When using steam, the compression or pre-admission takes up the lost motion in the rod and connections, so the loose bolt doesn’t hit the head; but when the steam is turned off, the piston moves the extra distance caused by this lost motion and the bolt hits the head.
100. Q. When should cross-heads or guides be reported to be lined?
100. Q. When should crossheads or guides be reported as lined?
A. When there is excessive lost motion between the cross-head and the top and bottom guides, or between the cross-head and the guide at the sides, or when the piston rod is not central between the guides.
A. When there is too much lost motion between the cross-head and the top and bottom guides, or between the cross-head and the side guides, or when the piston rod is not centered between the guides.
101. Q. When should driving box wedges be reported to be lined?
101. Q. When should driving box wedges be reported to be aligned?
A. When they have been set up as far as possible and the boxes are still loose between the wedge and shoe. At this time would also report any excessive flange wear on any one particular tire.[Pg 92]
A. When they have been assembled as much as possible and the boxes remain loose between the wedge and shoe. At this point, it’s also important to report any significant flange wear on any specific tire.[Pg 92]
102. Q. When should rod brasses be reported to be reduced? When to be lined?
102. Q. When should rod brasses be reported as worn down? When should they be relined?
A. Rod brasses should be reported reduced when they are larger than the pins and are pounding and cannot be keyed up properly. They should be reported to be lined when the key has been drawn or driven to its full length and the brasses do not close together or are too loose in the strap lengthwise of the rod.
A. Rod brasses should be reported as reduced when they are larger than the pins, cause pounding, and cannot be properly secured. They should be reported as needing to be lined when the key has been fully drawn or driven in, and the brasses do not close together or are too loose in the strap along the length of the rod.
103. Q. When should lost motion between engine and tender be taken up?
103. Q. When should the play between the engine and tender be adjusted?
A. When the lost motion becomes so great as to endanger the breaking of connections.
A. When the lost motion becomes so significant that it risks breaking connections.
104. Q. How do you proceed to pack a driving box equipped with a grease cellar?
104. Q. How do you go about packing a driving box that's got a grease cellar?
A. Remove the filling plate on the inside of the cellar. Pull down the indicators and follower plates, insert the grease between the follower plate and perforated plate; when full, replace the filling plate on the inside of the cellar and allow the spring and follower plate to force the grease through the perforated plate to the journal.
A. Take off the filling plate from the inside of the cellar. Pull down the indicators and follower plates, and add grease between the follower plate and the perforated plate; once it's full, put the filling plate back on the inside of the cellar and let the spring and follower plate push the grease through the perforated plate to the journal.
105. Q. Please explain the principle on which an injector works.
105. Q. Can you explain how an injector works?
A. With a lifting injector the steam valve is opened a small amount to furnish steam for the priming or starting jet. This forces the air in the body of the injector and top end of suction pipe out through the overflow valve, producing a partial vacuum in the body of the injector. Atmospheric pressure in the tank then forces the water into the injector body. When it begins to come out through the overflow, a further movement of the steam valve opens the forcing valve wide, so a full supply of steam strikes the water[Pg 93] at a high velocity and at the same time condensing. This action of the steam gives the water sufficient velocity to overcome the boiler pressure and pass into the boiler.
A. With a lifting injector, the steam valve is opened slightly to provide steam for the priming or starting jet. This pushes the air out of the injector body and the top end of the suction pipe through the overflow valve, creating a partial vacuum in the injector body. The atmospheric pressure in the tank then pushes the water into the injector body. When water starts to flow out through the overflow, moving the steam valve further opens the forcing valve wide, allowing a full supply of steam to hit the water at a high speed while also condensing. This steam action gives the water enough velocity to overcome the boiler pressure and flow into the boiler.[Pg 93]
106. Q. Explain the passage of steam from the boiler to the steam heat pipe.
106. Q. Describe how steam travels from the boiler to the steam heat pipe.
A. Steam is admitted to the steam heat pipe, in which there is placed a reducing valve through which it passes at reduced pressure, into the steam heat pipe under the entire length of the train. The reducing valve is located in the cab close to the steam heat throttle.
A. Steam is let into the steam heat pipe, where there’s a reducing valve that lowers the pressure before it flows into the steam heat pipe along the entire length of the train. The reducing valve is situated in the cab, near the steam heat throttle.
107. Q. If the steam heat gauge shows proper pressure, but the steam heat pipe pressure appears to be low, what should be done?
107. Q. If the steam heat gauge shows the correct pressure, but the steam heat pipe pressure seems to be low, what should be done?
A. If the steam heat gauge is showing the correct pressure, there is an obstruction in the pipe somewhere, most likely in the steam heat hose, and this should be looked for and remedied; if the gauge is correct, then it is the reducing valve that is at fault and this should be readjusted, as well as the gauge.
A. If the steam heat gauge shows the correct pressure, there’s a blockage in the pipe somewhere, probably in the steam heat hose, and this should be found and fixed; if the gauge is accurate, then the issue lies with the reducing valve, which should be readjusted, along with the gauge.
108. Q. What is the cause of failure with the second injector, and what should be done to obviate this failure?
108. Q. What causes the second injector to fail, and what can be done to prevent this failure?
A. Lack of attention and failure to use every day will allow joints to work loose and boiler check to fill up with mud and scale. It should be tested every day and worked regularly so as to keep it in good working order.
A. Not paying attention and not using it every day will cause joints to loosen and the boiler check to clog up with mud and scale. It should be tested daily and used regularly to keep it in good working condition.
109. Q. If an injector stops working while on the road, what should you do?
109. Q. If an injector fails while you’re driving, what should you do?
A. Would first ascertain if sufficient water was in[Pg 94] the tender and tender valve open, and that water was cool enough in the tender so the injector would handle it. Would next see that no obstruction was in the feed pipe or strainer and that the feed pipe was free from leaks, and that the injector was getting a sufficient supply of steam. If the injector would not prime, would see whether overflow or heater valve could open wide, or if overflow pipe was obstructed. If suction pipe was very hot would blow water back into tank and let suction fill with cold water. If possible, examine for obstruction in the steam priming tube and water tubes. If it would prime and fail to deliver water to the boiler, would see that the delivery tube was not obstructed and then look for trouble at the boiler check. An obstruction in the tubes would stop the injector working at once, while wear of the tubes or filling up with scale would affect the injector gradually.
A. Would first check if there was enough water in[Pg 94] the tender and that the tender valve was open, ensuring the water was cool enough for the injector to work properly. Next, would make sure there were no blockages in the feed pipe or strainer, that the feed pipe was leak-free, and that the injector was receiving enough steam. If the injector wouldn’t prime, would check if the overflow or heater valve could open completely, or if the overflow pipe was blocked. If the suction pipe was very hot, would blow water back into the tank to let the suction fill with cold water. If possible, check for blockages in the steam priming tube and water tubes. If it primed but failed to deliver water to the boiler, would ensure the delivery tube wasn’t blocked and then look for issues at the boiler check. A blockage in the tubes would cause the injector to stop working immediately, while wear on the tubes or a build-up of scale would gradually impair the injector's function.
110. Q. What are the advantages of the combination boiler check and stop valve?
110. Q. What are the benefits of having a combination boiler check and stop valve?
A. A combination boiler check is fitted with a valve similar to a globe valve and can be closed at will. Its advantage is that the boiler pressure can be shut off from the check and the valve repaired without cooling the boiler. This hand-operated valve can be closed to prevent the boiler water passing back in case the check valve sticks up and allows the boiler water to pass back to the injector when not working.
A. A combination boiler check is equipped with a valve similar to a globe valve that can be closed whenever needed. The benefit of this is that the boiler pressure can be turned off from the check, allowing for the valve to be repaired without cooling down the boiler. This manually operated valve can be closed to stop the boiler water from flowing back in case the check valve gets stuck open and lets the boiler water flow back to the injector when it’s not in use.
111. Q. How can a disconnected tank valve be opened without stopping?
111. Q. How can you open a disconnected tank valve without stopping?
A. Close the overflow or heater valve and turn steam back toward the tank; this will usually lift the valve from its seat or turn it around so it opens.[Pg 95]
A. Shut the overflow or heater valve and redirect the steam back to the tank; this will typically lift the valve off its seat or rotate it so that it opens.[Pg 95]
112. Q. What comprises the steam heat equipment on a locomotive?
112. Q. What makes up the steam heat equipment on a locomotive?
A. A globe valve throttle at the boiler, a reducing valve, a steam gauge connected to the steam heat pipe and the proper piping and hose connections.
A. A globe valve throttle at the boiler, a pressure-reducing valve, a steam gauge linked to the steam heat pipe, and the appropriate piping and hose connections.
113. Q. What pressure is carried in the steam heat pipe, and how is it controlled?
113. Q. What pressure is present in the steam heat pipe, and how is it managed?
A. From twenty to sixty pounds in the train pipe, depending on the length of the train, and is controlled by the regulating valve.
A. From twenty to sixty pounds in the train pipe, depending on the length of the train, and is controlled by the regulating valve.
114. Q. What would you do in case the regulating valve failed to operate?
114. Q. What would you do if the regulating valve stopped working?
A. In case the regulating valve would not admit sufficient steam to the train pipe, would take it apart and block the steam valve open. If the pressure ran up too high in the steam heat train pipe, would control it with the steam throttle at the boiler head.
A. If the regulating valve doesn’t let enough steam into the train pipe, take it apart and keep the steam valve open. If the pressure gets too high in the steam heat train pipe, control it with the steam throttle at the boiler head.
115. Q. How does the steam heat reducing valve control the pressure?
115. Q. How does the steam heat reducing valve manage the pressure?
A. The inlet valve for live steam is opened and closed by the movement of a metallic diaphragm in the valve which is opened by spring pressure on one side and closed by steam pressure on the other side. To regulate this pressure, stiffen the spring to carry more, weaken it to carry less by turning the handle connected to this spring either up or down.
A. The inlet valve for live steam is opened and closed by the movement of a metal diaphragm in the valve, which is opened by spring pressure on one side and closed by steam pressure on the other side. To adjust this pressure, tighten the spring to handle more or loosen it to handle less by turning the handle connected to this spring either up or down.
116. Q. If steam heat gauge showed the required pressure and cars were not being heated properly, how would you proceed to locate the trouble?
116. Q. If the steam heat gauge showed the right pressure and the cars weren't heating properly, how would you go about finding the problem?
A. First note where the hand on the steam heat gauge stands when steam is shut off; if it does not[Pg 96] drop back to zero see how much it lacks of this and note the rise of pressure shown by the gauge when steam is turned on. This is to test the gauge. If gauge is not correct, pay no attention to it, but send back steam enough to heat the train. Over sixty pounds will usually make the hose couplings on the cars rise up and leak at the joints.
A. First, check where the needle on the steam heat gauge is when the steam is turned off; if it doesn't drop back to zero, see how much it’s lacking and note the pressure increase shown by the gauge when the steam is turned on. This is to test the gauge. If the gauge isn't accurate, disregard it, but ensure there’s enough steam to heat the train. Over sixty pounds will typically cause the hose couplings on the cars to rise and leak at the joints.
117. Q. When engine is detached from the train, what precaution should you take to prevent freezing of the steam heat train pipe? What to prevent damage of steam heat hose?
117. Q. When the engine is separated from the train, what precautions should you take to prevent the steam heat train pipe from freezing? What should you do to prevent damage to the steam heat hose?
A. Open steam throttle to allow a very little steam to pass into steam heat train pipe to prevent its freezing. If end of hose is liable to strike frogs or crossings, hang it up where it will be safe.
A. Open the steam throttle just enough to let a small amount of steam flow into the steam heat train pipe to keep it from freezing. If the end of the hose might hit frogs or crossings, hang it up in a safe place.
118. Q. What constitutes abuse of an engine?
118. Q. What is considered abuse of an engine?
A. Improper use of injector by filling boiler at a rapid rate when drifting or standing in a siding, unless you have a heavy bright fire to heat the injected water to the boiler temperature as fast as it comes into the boiler. Excessive use of the blower, especially with a light fire or when cleaning the fire. Improper attention to machinery, such as keeping parts not properly lubricated, rods not properly keyed, wedges not adjusted, carrying too much or too little water in the boiler, working water through the cylinders, allowing engine to slip unnecessarily, use of sand on one rail only or otherwise improperly; being careless in any way where care is required and not properly reporting the necessary work so it can be done promptly.
A. Misusing the injector by filling the boiler too quickly when drifting or parked on a siding, unless you have a strong, bright fire to heat the injected water to the boiler temperature as it enters. Overusing the blower, especially with a light fire or while cleaning the fire. Neglecting machinery maintenance, such as failing to lubricate parts properly, not securing rods correctly, not adjusting wedges, carrying either too much or too little water in the boiler, letting water flow through the cylinders, allowing the engine to slip unnecessarily, using sand on only one rail or using it incorrectly; being careless in any situation that requires attention and not reporting necessary maintenance promptly so that it can be addressed.
119. Q. How are accidents and breakdown best prevented?[Pg 97]
119. Q. What are the best ways to prevent accidents and breakdowns?[Pg 97]
A. By inspection both at and after leaving terminals, frequently while on the road, keeping all parts properly adjusted, water in the boiler at the proper level and using good judgment in the handling of the engine and train. It is much better to use care and prevent accidents than to make repairs after they occur.
A. By checking both when arriving at and leaving terminals, often while on the road, ensuring all parts are properly adjusted, keeping the water in the boiler at the correct level, and using good judgment in operating the engine and train. It’s much better to be careful and prevent accidents than to make repairs after they happen.
120. Q. What are the duties of an engineman when leaving his engine at the terminal?
120. Q. What are the responsibilities of an engineman when he leaves his engine at the terminal?
A. Place her on the proper track to be turned over to the hostler, leave throttle closed securely, reverse lever in center notch, cylinder cocks open, and lubricator feeds to steam chest and cylinders closed. The boiler should be full of water and sufficient fire to maintain steam pressure until fire is knocked out. Call fireman's attention to anything of special importance. Inspect the engine very thoroughly, ascertain whether any tools or signals have been lost on the trip and make a full report of the condition of the entire locomotive.
A. Put her on the right track to be handed over to the hostler, keep the throttle securely closed, the reverse lever in the center notch, the cylinder cocks open, and the lubricator feeds to the steam chest and cylinders closed. The boiler should be full of water with enough fire to maintain steam pressure until the fire is put out. Alert the fireman to anything particularly important. Check the engine thoroughly, see if any tools or signals were lost on the trip, and make a complete report on the condition of the entire locomotive.
121. Q. What is the most important bolt or nut on the locomotive?
121. Q. What’s the most important bolt or nut on the locomotive?
A. The loose one. It should be cared for immediately.
A. The loose one. It needs to be taken care of right away.
122. Q. In reporting work on an engine, is it sufficient to do it in a general way, such as saying: "Injector won't work," "lubricator won't work," "engine won't steam," "engine blows," etc.? Or would you report each special defect so it could be located after the engine was put in roundhouse or on designated track whether it had steam pressure in boiler or not?
122. Q. When reporting on engine issues, is it enough to be general, like saying: "Injector won't work," "lubricator isn't working," "engine isn't steaming," "engine is blowing steam," etc.? Or should you detail each specific problem so it can be identified once the engine is in the roundhouse or on the designated track, regardless of whether it has steam pressure in the boiler?
A. No. Report all defects noticed so plainly that they can be located by the repair man without un[Pg 98]necessary work and whether there is steam in the boiler or not at the time repairs are to be made. If the engine blows, make a test to locate the blow and report it correctly. Also report any unusual feature in the operation of the engine during the trip.
A. No. Report all defects you notice clearly so that the repair person can find them without unnecessary work, regardless of whether there's steam in the boiler when the repairs are to be made. If the engine blows, perform a test to locate the issue and report it accurately. Also, report any unusual behavior of the engine during the trip.
1. Q. Wherein do compound locomotives differ from ordinary or simple ones?
1. Q. How do compound locomotives differ from regular or simple ones?
A. Simple engines take live steam from the boiler and after one expansion in a single cylinder it is exhausted to the atmosphere. A compound engine has two cylinders, sometimes one on each side of the locomotive; other types have four cylinders or two on each side of the locomotive. The live steam first passes into one cylinder, expanding down for a portion of its pressure, and then being allowed to pass into the second cylinder where it expands a second time, thus getting two expansions from each volume of live steam. Both simple and compound locomotives consist of two engines coupled to the same set of driving wheels. Balanced compounds have four sets of main rods and crank pins. Mallet compounds have two complete sets of engines under one boiler.
A. Simple engines take live steam from the boiler and after one expansion in a single cylinder, it’s released into the atmosphere. A compound engine has two cylinders, sometimes one on each side of the locomotive; other types can have four cylinders or two on each side of the locomotive. The live steam first goes into one cylinder, expanding for a portion of its pressure, and then it passes into the second cylinder where it expands a second time, getting two expansions from each volume of live steam. Both simple and compound locomotives consist of two engines coupled to the same set of driving wheels. Balanced compounds have four sets of main rods and crank pins. Mallet compounds have two complete sets of engines under one boiler.
2. Q. Why is one cylinder on a compound locomotive called the high-pressure cylinder and the other one a low-pressure cylinder?
2. Q. Why is one cylinder on a compound locomotive referred to as the high-pressure cylinder and the other as the low-pressure cylinder?
A. The high-pressure cylinder takes that name because it works live steam direct from the boiler at high pressure. The low-pressure cylinder receives the steam after the first expansion and works with a low[Pg 99] pressure. It is always larger than its companion high-pressure cylinder in order to get the same power from the low-pressure steam.
A. The high-pressure cylinder is named for its function of using live steam directly from the boiler at high pressure. The low-pressure cylinder gets the steam after it's expanded the first time and operates at a low[Pg 99] pressure. It is always larger than the high-pressure cylinder to generate the same power from the low-pressure steam.
3. Q. In the Schenectady two-cylinder compound, what is the duty of the oil dash-pot?
3. Q. In the Schenectady two-cylinder compound, what does the oil dash-pot do?
A. It is intended to prevent the too rapid movement of the intercepting valve which might damage the valve or seat, and it is necessary that the dash-pot should be full of oil to make it work properly.
A. It's meant to stop the intercepting valve from moving too quickly, which could harm the valve or the seat, and it's essential that the dash-pot is filled with oil for it to function correctly.
4. Q. Explain how a Schenectady two-cylinder compound may be operated as a simple engine.
4. Q. Explain how a Schenectady two-cylinder compound engine can be operated as a simple engine.
A. To operate the compound as a simple engine, the separate exhaust valve is opened which will cause the intercepting valve to move and stay in position to allow the high-pressure cylinder to exhaust direct to the atmosphere and admits live steam at a reduced pressure to the low-pressure cylinder. This should be done when starting a train or when moving very slowly and about to stall on a grade. The engine should not be operated simple while running except when at low speed.
A. To run the compound as a simple engine, the separate exhaust valve is opened, which causes the intercepting valve to move and remain in position, allowing the high-pressure cylinder to exhaust directly into the atmosphere and letting in live steam at a lower pressure to the low-pressure cylinder. This should be done when starting a train or when moving very slowly and about to stall on an incline. The engine should not be operated simply while running except at low speed.
5. Q. Explain how a two-cylinder compound is changed from simple to compound.
5. Q. Describe how a two-cylinder compound engine is transformed from a simple to a compound design.
A. Place the handle of the three-way cock or simpling valve in the cab so as to release the air from the cylinder of the separate exhaust valve. A coiled spring will then close this valve. This permits the exhaust steam of the high-pressure cylinder to accumulate in the receiver until sufficient pressure is obtained to force the intercepting valve into compounding position. This shuts off live steam from the low-pressure cylinder and allows exhaust steam[Pg 100] from the high-pressure cylinder to feed through the receiver into the low-pressure steam chest.
A. Position the handle of the three-way valve or simplifying valve in the cab to release the air from the cylinder of the separate exhaust valve. A coiled spring will then close this valve. This allows the exhaust steam from the high-pressure cylinder to build up in the receiver until there's enough pressure to push the intercepting valve into a compounding position. This stops live steam from entering the low-pressure cylinder and lets the exhaust steam from the high-pressure cylinder flow through the receiver into the low-pressure steam chest.
6. Q. How should a compound engine be lubricated?
6. Q. How do you lubricate a compound engine?
A. One-third more oil should be fed to the high than the low-pressure cylinder, using more oil at high speed than at slow.
A. One-third more oil should be supplied to the high-pressure cylinder than to the low-pressure cylinder, using more oil at high speeds than at slow speeds.
7. Q. Why feed more oil to high than to a low-pressure cylinder?
7. Q. Why provide more oil to a high-pressure cylinder than to a low-pressure cylinder?
A. Because some of the oil from the high-pressure cylinder follows the steam into the low-pressure cylinder.
A. Because some of the oil from the high-pressure cylinder follows the steam into the low-pressure cylinder.
8. Q. How would you lubricate the valve of low-pressure cylinder if the oil feed became inoperative on that side?
8. Q. How would you lubricate the valve of a low-pressure cylinder if the oil supply stopped working on that side?
A. Feed an increased quantity through the oil pipe to the intercepting valve. Shut the engine off occasionally and cut into simple position. Oil will then go direct from the intercepting valve into the low-pressure steam chest and cylinders. This would avoid going out on steam chest to oil by hand.
A. Feed a larger amount of oil through the oil pipe to the intercepting valve. Occasionally turn off the engine and switch to a simple position. Oil will then flow directly from the intercepting valve into the low-pressure steam chest and cylinders. This will eliminate the need to manually transfer oil to the steam chest.
9. Q. How much water should be carried in the boiler of a compound locomotive?
9. Q. How much water should be in the boiler of a compound locomotive?
A. A very moderate level, never allowing it to get so high that moist steam will pass through the cylinders, because for satisfactory service a compound engine should always have dry steam.
A. A very moderate level, never letting it get so high that wet steam will pass through the cylinders, because for good performance, a compound engine should always have dry steam.
10. Q. How should a compound locomotive be started with a long train?
10. Q. How should you start a compound locomotive when pulling a long train?
A. In simple position with cylinder cocks open.[Pg 101]
A. In a straightforward position with cylinder cocks open.[Pg 101]
11. Q. When drifting what should be the position of the separate exhaust valve, the cylinder and port cocks?
11. Q. When drifting, what should the positions of the separate exhaust valve, the cylinder, and the port cocks be?
A. Open position.
A. Job opening.
12. Q. What will cause two exhausts of air to blow from the three-way cock or simpling valve in the cab when the engine is being changed to compound?
12. Q. What will make two bursts of air come out from the three-way cock or simpling valve in the cab when the engine is being switched to compound?
A. A sticky exhaust valve. It does not move when air is first discharged. The second exhaust comes when it does move.
A. A stuck exhaust valve. It doesn’t move when air is first released. The second exhaust happens when it finally moves.
13. Q. What does steam blowing at the three-way cock indicate?
13. Q. What does steam blowing at the three-way valve mean?
A. The separate exhaust valve not seating properly caused by stuck valves, a weak or broken spring, or the packing rings of separate exhaust valve leaking.
A. The separate exhaust valve not seating properly is caused by stuck valves, a weak or broken spring, or leaking packing rings of the separate exhaust valve.
14. Q. What can be done if the engine will not operate compound when the air pressure on the separate exhaust valve is released by the three-way cock?
14. Q. What should you do if the engine won’t run properly when the air pressure on the separate exhaust valve is released by the three-way cock?
A. The separate exhaust valve has failed to close. Try jarring it with a hammer on the front side, near the exhaust valve. With a bad case, take the valve out, clean it and replace, if not broken.
A. The separate exhaust valve hasn't closed properly. Try tapping it with a hammer on the front side, close to the exhaust valve. If it's seriously jammed, remove the valve, clean it, and replace it if it's not broken.
15. Q. If the engine stands with high-pressure side on the dead center and will not move when given steam, where is the trouble, and what may be done to start the engine? Why?
15. Q. If the engine is positioned with the high-pressure side at dead center and doesn’t move when steam is applied, what’s the issue, and what can be done to get the engine started? Why?
A. The intercepting valve is stuck in compound position, so live steam cannot get to the low-pressure cylinder. In a case of this kind, close the throttle, open cylinder and port cocks; when all pressure is[Pg 102] relieved, use a bar to move forward the rod that works through the oil dash-pot, thus moving the valve to simple position and steam will pass to the low-pressure cylinder as soon as throttle is open. The engine will not start, because with the low-pressure piston on the quarter, steam must be admitted to its cylinder to start the engine.
A. The intercepting valve is stuck in the combined position, so live steam can't reach the low-pressure cylinder. In this situation, close the throttle and open the cylinder and port cocks; once all pressure is[Pg 102] relieved, use a bar to push the rod that works through the oil dash-pot, moving the valve to the simple position. This will allow steam to flow to the low-pressure cylinder as soon as the throttle is opened. The engine won't start because, with the low-pressure piston in the quarter position, steam must be allowed into its cylinder to start the engine.
16. Q. In the event of a breakdown, how should one disconnect?
16. Q. If something goes wrong, how should you disconnect?
A. The same as a simple engine with separate exhaust valve open, so engine will work simple instead of compound.
A. The same as a simple engine with a separate exhaust valve open, so the engine will operate simply instead of in a compound manner.
17. Q. What may be done to shut off steam pressure from the steam chest and low-pressure cylinder?
17. Q. What can be done to stop steam pressure from the steam chest and low-pressure cylinder?
A. To shut off steam from the low-pressure chest, pull out the rod that runs through the dash-pot as far as possible and fasten it in this position. Then open the separate exhaust valve.
A. To stop steam from the low-pressure chest, pull out the rod that goes through the dash-pot as far as you can and secure it in that position. Then, open the separate exhaust valve.
18. Q. Is it important that air be pumped up on a two-cylinder compound before the engine is moved? Why?
18. Q. Is it important to pump air into a two-cylinder compound before moving the engine? Why?
A. Yes. Because the separate exhaust valve is opened by air pressure and the engine cannot be simpled without sufficient pressure.
A. Yes. The separate exhaust valve opens due to air pressure, and the engine cannot function properly without enough pressure.
19. Q. How are the blows in a compound located?
19. Q. How are the impacts in a compound identified?
A. The same as in a simple engine with the exception that any blow on the high-pressure side will not be heard when the separate exhaust valve is closed. A blow on the high-pressure side will increase the pressure in the low-pressure side, so relief valves will pop on low-pressure side when working compound with full throttle.[Pg 103]
A. It's the same as in a simple engine, except that any pressure surge on the high-pressure side won't be heard when the separate exhaust valve is closed. A surge on the high-pressure side will raise the pressure on the low-pressure side, causing the relief valves to activate on the low-pressure side when operating the compound engine at full throttle.[Pg 103]
20. Q. What should be done if high-pressure piston of a cross compound is broken off the rod, or if the high-pressure or low-pressure cylinder head is broken?
20. Q. What should you do if the high-pressure piston of a cross compound breaks off the rod, or if the high-pressure or low-pressure cylinder head is damaged?
A. Cover the ports on that side, open separate exhaust valve and run in; use live steam in low-pressure cylinder only, for the broken piston. With broken cylinder head, would cover ports on that side. Open separate exhaust and run in with low-pressure side. Would not take down main rod, but would take out pop valves in both cylinder heads and see that the cylinder is properly oiled. For low-pressure head broken, would cover ports on that side, open separate exhaust valve and use high-pressure side; need not take down main rod, but would see that the cylinder is well oiled.
A. Cover the ports on that side, open a separate exhaust valve, and run it in; use live steam only in the low-pressure cylinder due to the broken piston. For a broken cylinder head, cover the ports on that side. Open the separate exhaust and run it in with the low-pressure side. There's no need to take down the main rod, but make sure to remove the pop valves in both cylinder heads and ensure the cylinder is properly oiled. If the low-pressure head is broken, cover the ports on that side, open a separate exhaust valve, and use the high-pressure side; you don’t need to take down the main rod, but make sure the cylinder is well oiled.
21. Q. In the event of separate exhaust valves failing to work when throttle is wide open, what can be done to assist in opening?
21. Q. If the separate exhaust valves fail to open when the throttle is wide open, what can be done to help them open?
A. Ease throttle off very fine to reduce the receiver pressure; in a moment or two the separate exhaust valve should then move. If this did not work, would shut off entirely, even at the risk of stalling, as in that event the train could be started again with engine cut in simple.
A. Slowly reduce the throttle to lower the receiver pressure; after a moment or two, the separate exhaust valve should move. If that doesn't work, turn it off completely, even if it risks stalling, because the train can easily be restarted with the engine turned back on.
22. Q. If a transmission bar on a cross compound is broken, what would you do for the right side? For the left side?
22. Q. If a transmission bar on a cross compound is broken, what would you do for the right side? For the left side?
A. For right side would cover ports on that side, take out pop from cylinder head, open separate exhaust and run in with other cylinder. For left side, cover ports and fasten valve stem same as for right side. Would leave main rods up, keep separate exhaust open in both cases and see that cylinder is well oiled.[Pg 104]
A. For the right side, cover the ports on that side, remove the plug from the cylinder head, open the separate exhaust, and run it in with the other cylinder. For the left side, cover the ports and secure the valve stem just like on the right side. Keep the main rods up, keep the separate exhaust open in both cases, and make sure the cylinder is well-oiled.[Pg 104]
23. Q. In the event of a cross compound beginning to jerk badly and cylinder head pops in low-pressure cylinder popping, where would you look for the trouble?
23. Q. If a cross compound starts to shake badly and the cylinder head in the low-pressure cylinder pops, where would you check for the problem?
A. That either the high-pressure valve or piston packing was blowing live steam into the receiver and then into low-pressure steam chest. If possible would locate trouble and report accordingly.
A. That either the high-pressure valve or piston packing was leaking live steam into the receiver and then into the low-pressure steam chest. If possible, I would find the issue and report back accordingly.
24. Q. If during a trip you found the piston valve rings of a cross compound were broken, what would you do?
24. Q. If you found that the piston valve rings of a cross compound were broken while on a trip, what would you do?
A. If nothing but rings were broken, would reduce boiler pressure about 25 per cent. and go on with my train if possible.
A. If only the rings were broken, it would reduce the boiler pressure by about 25 percent, and I would continue with my train if I could.
25. Q. If piston valve on cross compound was broken so it became necessary to remove it, what should you do?
25. Q. If the piston valve on the cross compound is broken and needs to be removed, what should you do?
A. Remove the broken piston valve, reduce boiler pressure to 100 pounds and proceed.
A. Take out the broken piston valve, lower the boiler pressure to 100 pounds, and continue.
26. Q. What is the difference between a Vauclain four-cylinder compound, a four-cylinder tandem, a balanced and a Mallet compound in their arrangement of cylinders?
26. Q. What’s the difference between a Vauclain four-cylinder compound, a four-cylinder tandem, a balanced compound, and a Mallet compound in how their cylinders are arranged?
A. A Vauclain compound has two cylinders on each side, one above the other, and both piston rods connected to one cross-head. A four-cylinder tandem has four cylinders, the high pressure being ahead of the low pressure on each side, and both pistons connected to one piston rod and one cross-head. A balanced compound has four cylinders, the two high-pressure cylinders being between the frames, each having a main rod connected to a crank axle. The two low-pressure cylinders are located outside the[Pg 105] frame, each having a main rod and crank pin connected to the driving wheel center. A Mallet compound consists of two separate and independent engines, one fixed to the boiler, the other swinging from a center and sliding back and forth under the front end of the boiler. The rear engine works steam at high pressure; steam from this engine exhausts through a receiver pipe having flexible joints to the forward engine which works the steam at low pressure, then exhausts it to the front end and stack.
A Vauclain compound has two cylinders on each side, one above the other, with both piston rods connected to one cross-head. A four-cylinder tandem has four cylinders, with the high-pressure ones in front of the low-pressure ones on each side, and both pistons linked to one piston rod and one cross-head. A balanced compound has four cylinders, with the two high-pressure cylinders between the frames, each having a main rod connected to a crank axle. The two low-pressure cylinders are situated outside the[Pg 105] frame, each with a main rod and crank pin connected to the center of the driving wheel. A Mallet compound consists of two separate and independent engines, one attached to the boiler and the other swinging from a center and sliding back and forth under the front end of the boiler. The rear engine operates on high-pressure steam; the steam from this engine exhausts through a receiver pipe with flexible joints to the forward engine, which operates on low-pressure steam and then exhausts it to the front end and stack.
27. Q. How many main steam valves has each type?
27. Q. How many main steam valves does each type have?
A. The Vauclain has one valve on each side, distributing steam to the high and low-pressure cylinder on that side. The four-cylinder tandem has two valves on each side, one for each of the two cylinders. A Baldwin balanced compound has two valves the same as the Vauclain. The American balanced compound has four valves, one for each cylinder, the two valves for one side of the engine being connected to one valve rod. A Mallet compound has a separate valve for each cylinder the same as a simple locomotive.
A. The Vauclain has one valve on each side, distributing steam to the high and low-pressure cylinder on that side. The four-cylinder tandem has two valves on each side, one for each of the two cylinders. A Baldwin balanced compound has two valves just like the Vauclain. The American balanced compound has four valves, one for each cylinder, with the two valves on one side of the engine connected to a single valve rod. A Mallet compound has a separate valve for each cylinder, just like a simple locomotive.
28. Q. How do you test for blow in high and low-pressure cylinder packing for each type of compound engine?
28. Q. How do you check for blow in high and low-pressure cylinder packing for each type of compound engine?
A. Simple the engine if a cross compound, then make test the same as for a simple engine. For Vauclain four-cylinder compounds, test low pressure first. A blow past the low-pressure piston will show the same as on a simple engine; a blow past the high-pressure piston will make the engine stronger on that side when working a full throttle and the exhaust from the low-pressure cylinder will be heavier. To[Pg 106] test the valve on either side, cover the ports. Broken packing rings in the steam valve will show a blow in one position and be tight in another. For tandem compound, to test high-pressure piston packing, stand engine on the top quarter, lever in back gear, drivers blocked and starting valve closed; remove back indicator plug or open back cylinder cock of high-pressure cylinder. Steam coming from the back cylinder cock must get by the piston packing or by-pass or starting valve. Now put reverse lever ahead and try the other indicator plug or cylinder cock. If a leaky by-pass valve in the front end is the trouble, no steam will come through. To test the low-pressure piston packing, place the engine in the same position, lever in position to admit steam into the front end of high-pressure cylinder. Open starting valve, remove back indicator plug of low-pressure cylinder and give engine steam; if steam comes from the indicator plug opening or open back cylinder cock, either packing or by-pass is leaking. To determine which one, put reverse lever in another position, close back indicator plug and open forward one; if blow still continues, the packing rings are leaking or else both by-pass valves. Would then inspect the by-pass valves.
A. If it's a cross-compound engine, test it like you would a simple engine. For Vauclain four-cylinder compounds, start by testing the low pressure first. A blow past the low-pressure piston will indicate the same results as on a simple engine; a blow past the high-pressure piston will make the engine run stronger on that side when it’s at full throttle, and the exhaust from the low-pressure cylinder will be heavier. To[Pg 106] test the valve on either side, cover the ports. Broken packing rings in the steam valve will show a blow in one position and be sealed in another. For tandem compound engines, to test the high-pressure piston packing, place the engine in the top quarter position, with the lever in reverse gear, wheels blocked, and the starting valve closed; then, remove the back indicator plug or open the back cylinder cock of the high-pressure cylinder. Steam coming from the back cylinder cock must pass through the piston packing or by-pass or starting valve. Now, move the reverse lever forward and try the other indicator plug or cylinder cock. If there's a leaky by-pass valve in the front end, no steam will come through. To test the low-pressure piston packing, keep the engine in the same position, with the lever set to allow steam into the front end of the high-pressure cylinder. Open the starting valve, remove the back indicator plug of the low-pressure cylinder, and give the engine steam; if steam escapes from the indicator plug opening or the back cylinder cock, either the packing or the by-pass is leaking. To find out which one is leaking, change the reverse lever position, close the back indicator plug, and open the forward one; if the blow continues, either the packing rings are leaking or both by-pass valves are faulty. Then inspect the by-pass valves.
29. Q. How can the blow through sleeve packing between high and low-pressure cylinder of the tandem compound be located?
29. Q. How can you find the blow-through sleeve packing between the high-pressure and low-pressure cylinders of the tandem compound?
A. Place the engine as before on the top quarter, put reverse lever in forward gear, see that starting valve is closed, block the drivers or set the brakes solid and open the throttle. Until the engine moves, unless there is a leak, no steam can get into the front side of the low-pressure cylinder. Remove the indicator plug in front end of the low-pressure cylinder for this test.[Pg 107]
A. Position the engine as before at the top quarter, set the reverse lever to forward gear, ensure the starting valve is closed, secure the drivers or firmly set the brakes, and open the throttle. The engine won't move, and as long as there's no leak, no steam can enter the front side of the low-pressure cylinder. Take out the indicator plug at the front end of the low-pressure cylinder for this test.[Pg 107]
30. Q. How test for piston packing blow with balanced compound?
30. Q. How do you test for piston packing blow with a balanced compound?
A. For a Baldwin balanced compound to test the high-pressure piston packing, place the engine with the outside main pin on that side of the engine on the bottom quarter, the reverse lever in the forward notch, starting valve closed, set the brakes solid or block the drivers, remove the indicator plug in the front end of either the high or low-pressure cylinder. With throttle open this will admit steam to the back end of high-pressure cylinder. Steam coming out of this plug opening, will indicate a leak past the piston or the high-pressure valve. If uncertain, next test the high-pressure valve by moving the reverse lever to the center notch. This should cover the ports and if the valve is tight the blow will stop. To test the low-pressure piston, place the engine in the same position with wheels blocked, starting valve open, back indicator plug out; when throttle is opened, the leaky packing will be shown by steam issuing from the plug opening. If uncertain, the valve can be tested by bringing reverse lever to the center of quadrant, which will spot valve over port and if it is tight the blow will stop. In any compound engine a blow past the high-pressure packing tends to increase the pressure in the low-pressure cylinder. A blow past the low-pressure packing can always be heard at the exhaust, and is usually on both forward and back strokes, while a blow past the by-pass valves or valve bushings occurs at a certain part of a complete revolution only.
A. To test the high-pressure piston packing on a Baldwin balanced compound, position the engine with the outside main pin at the bottom quarter on that side, set the reverse lever in the forward notch, close the starting valve, secure the brakes solidly or block the drivers, and remove the indicator plug from the front end of either the high or low-pressure cylinder. Opening the throttle will allow steam to enter the back end of the high-pressure cylinder. If steam comes out of this plug opening, it indicates a leak past the piston or the high-pressure valve. If you're not sure, next test the high-pressure valve by moving the reverse lever to the center notch. This should cover the ports, and if the valve is tight, the exhaust will stop. To test the low-pressure piston, position the engine the same way with the wheels blocked, keep the starting valve open, and remove the back indicator plug; when you open the throttle, leaky packing will be indicated by steam coming from the plug opening. If uncertain, you can test the valve by moving the reverse lever to the center of the quadrant, which will cover the valve over the port, and if it is tight, the exhaust will stop. In any compound engine, a blow past the high-pressure packing typically increases pressure in the low-pressure cylinder. A blow past the low-pressure packing can always be heard at the exhaust, and it usually occurs on both the forward and backward strokes, while a blow past the by-pass valves or valve bushings happens at certain points in a complete revolution only.
31. Q. In case it was necessary to disconnect on one side of a compound engine, how would you cover ports and hold valves in position?
31. Q. If it becomes necessary to disconnect one side of a compound engine, how would you cover the ports and keep the valves in place?
A. The easiest way is to clamp the valve stem to hold valve in mid position; this should cover all ports.[Pg 108] It may be necessary to take off head of piston valve chest and block in there.
A. The simplest method is to clamp the valve stem to keep the valve in the middle position; this should block all the ports.[Pg 108] You might need to remove the head of the piston valve chest and secure it inside.
32. Q. Is it a disadvantage to work a compound engine in short cut-off? Why?
32. Q. Is it a disadvantage to operate a compound engine with a short cut-off? Why?
A. Yes. If cut-off is too short the proper proportion of steam passing the throttle will not get to the low-pressure cylinder. The work should be divided between the two cylinders on same side.
A. Yes. If the cut-off is too short, the right amount of steam passing through the throttle won't reach the low-pressure cylinder. The workload should be shared between the two cylinders on the same side.
33. Q. In what way do the Mallet or articulated compounds differ from other steam locomotives in the distribution of the steam?
33. Q. How do Mallet or articulated compounds differ from other steam locomotives in how steam is distributed?
A. Mallet compounds have two separate and complete engines under one boiler. The rear engine has a rigid connection to the back end of the boiler; this engine works boiler steam direct the same as a simple locomotive. Under the front end of the boiler is another engine so constructed that the entire front engine can move from side to side under the boiler, having a hinged connection at the front end of the rear engine to allow the locomotive to pass curves more easily. The front engine takes the exhaust steam from the rear engine through a flexible pipe or receiver and works it through a larger set of cylinders and thus compounds the steam. From the low-pressure cylinders the steam is exhausted to the atmosphere through the stack.
A. Mallet locomotives have two fully functional engines beneath one boiler. The rear engine is firmly connected to the back of the boiler, and it uses steam from the boiler in the same way a standard locomotive does. At the front of the boiler is another engine designed so that the whole front engine can shift side to side under the boiler, with a hinged connection at the front of the rear engine to help the locomotive navigate curves more smoothly. The front engine uses the exhaust steam from the rear engine through a flexible pipe or receiver and processes it through a larger set of cylinders, effectively compounding the steam. The low-pressure cylinders then release the steam into the atmosphere through the stack.
34. Q. How do you get the use of both engines when starting a train?
34. Q. How do you use both engines when starting a train?
A. To get steam into the low-pressure cylinders before the high-pressure engine has exhausted, some types of the Mallet compound have a live steam pipe with a valve in the cab to admit boiler steam to the receiver pipe and thus get the use of the front engine[Pg 109] in starting a train. The American Locomotive Company articulated compounds have an intercepting valve similar to the one used in the Richmond cross compound, located between the exhaust passage of the rear engine and the flexible receiving pipe of the front one. This intercepting valve when in SIMPLE position, allows the high-pressure cylinders of the rear engine to exhaust directly to the stack instead of into the receiver, and feeds boiler steam at a reduced pressure into the receiver pipe for the low-pressure cylinders without giving any back pressure on the high-pressure pistons. This increases the power of the complete locomotive about 20 per cent. When in compound position, the intercepting valve cuts off the supply of live steam to the receiver pipe and forces the exhaust steam to go to the low-pressure engine ahead.
A. To get steam into the low-pressure cylinders before the high-pressure engine has finished exhausting, some types of the Mallet compound have a live steam pipe with a valve in the cab to let boiler steam into the receiver pipe, which allows the front engine[Pg 109] to help start a train. The American Locomotive Company articulated compounds have an intercepting valve similar to the one used in the Richmond cross compound, placed between the exhaust passage of the rear engine and the flexible receiving pipe of the front one. When the intercepting valve is in SIMPLE position, it lets the high-pressure cylinders of the rear engine exhaust directly to the stack instead of into the receiver, and it supplies boiler steam at a lower pressure into the receiver pipe for the low-pressure cylinders without creating any back pressure on the high-pressure pistons. This boosts the overall power of the locomotive by about 20 percent. When in compound position, the intercepting valve stops the supply of live steam to the receiver pipe and directs the exhaust steam to the low-pressure engine in front.
35. Q. How is the American articulated compound changed from compound to simple, and back to compound again?
35. Q. How is the American articulated compound transformed from compound to simple, and then reverted back to compound again?
A. To work the locomotive simple, place the handle of operating valve in the cab to point toward the rear. This admits steam against the piston that operates the emergency exhaust valve and opens it. Exhaust steam from the high-pressure engine can pass to the exhaust nozzle instead of to the low-pressure engine. The intercepting valve then moves over so that live steam reduced to 40 per cent. of boiler pressure goes through the receiver pipe to the low-pressure engine. To work compound, place the handle of the operating valve to point forward. This will exhaust the steam, holding the emergency exhaust valve open; a spring and the pressure of the steam exhausted from the rear engine will close the emergency exhaust valve and build up a pressure against[Pg 110] the intercepting valve that will open it so exhaust steam from the rear engine will go to the forward one and at the same movement close the reducing valve so no more live steam goes to the receiver.
A. To operate the locomotive in simple mode, position the handle of the operating valve in the cab so that it faces the rear. This allows steam to drive the piston that operates the emergency exhaust valve, which opens it. Exhaust steam from the high-pressure engine can then flow to the exhaust nozzle instead of the low-pressure engine. The intercepting valve then shifts to allow live steam reduced to 40% of boiler pressure to flow through the receiver pipe to the low-pressure engine. To switch to compound mode, turn the handle of the operating valve to point forward. This will release the steam while keeping the emergency exhaust valve open; a spring and the pressure of the steam released from the rear engine will close the emergency exhaust valve and create pressure against[Pg 110] the intercepting valve, causing it to open so that exhaust steam from the rear engine can go to the front engine, while simultaneously closing the reducing valve to prevent any more live steam from entering the receiver.
36. Q. When is it necessary to use the operating valve to change the locomotive from compound to simple, or from simple to compound?
36. Q. When do you need to use the operating valve to switch the locomotive from compound to simple, or from simple to compound?
A. When giving the engines steam to start, the intercepting valve should automatically go to simple position until exhaust steam from the rear engine builds up a receiver pressure that shifts the valve to compound; if it does not, use the operating valve. When moving less than four miles an hour or when about to stall on a grade, set the engines working simple; changing to compound when the danger of stalling is over or the speed is more than four miles an hour. If there is no intercepting valve to furnish live steam to the forward engine, open the starting valve to admit live steam to the receiver pipe and low-pressure engine.
A. When starting the engines, the intercepting valve should automatically switch to simple mode until exhaust steam from the rear engine builds up enough pressure to shift the valve to compound; if it doesn't, use the operating valve. When moving at less than four miles an hour or if you're about to stall on an incline, set the engines to work in simple mode; switch to compound once the risk of stalling has passed or the speed exceeds four miles an hour. If there's no intercepting valve to provide live steam to the front engine, open the starting valve to let live steam into the receiver pipe and low-pressure engine.
37. Q. If in starting the locomotive the forward engine does not take steam, what is the trouble?
37. Q. If the front engine doesn't start getting steam when you try to start the locomotive, what could be the problem?
A. The reducing valve may be stuck shut on account of being dirty or stuck on the stem of the intercepting valve. In case the reducing valve is stuck shut, the head of the dash-pot can be taken off and the valve worked back and forth to loosen it. The intercepting valve should be liberally oiled just before starting and occasionally during long runs to keep it free from sticking.
A. The reducing valve might be stuck shut because it's dirty or jammed on the stem of the intercepting valve. If the reducing valve is stuck, you can remove the head of the dash-pot and move the valve back and forth to loosen it. The intercepting valve should be oiled generously right before starting and occasionally during long runs to prevent it from sticking.
38. Q. Why does the Mallet compound have more power when working simple than compound?
38. Q. Why does the Mallet compound have more power when working simply than when working with a compound?
A. If a starting valve is used to admit live steam[Pg 111] to the receiver pipe and thence to the low-pressure engine, this gives a higher pressure to the low-pressure cylinders. If an intercepting valve is used, the open emergency exhaust valve allows exhaust steam from the rear engine to go direct to the stack; this takes away the back pressure of the receiver steam from the high-pressure pistons, about 30 per cent. of the boiler pressure, and thus adds to the power of the rear engine. The reducing valve when feeding live steam gives about 40 per cent. of boiler pressure to the low-pressure engine instead of the 30 per cent. it gets from the receiver; the added power of both engines working simple is about 20 per cent. over the compound operation.
A. If a starting valve is used to allow live steam[Pg 111] into the receiver pipe and then to the low-pressure engine, it increases the pressure in the low-pressure cylinders. If an intercepting valve is used, the open emergency exhaust valve lets exhaust steam from the rear engine go straight to the stack; this reduces the back pressure of the receiver steam from the high-pressure pistons, which is about 30 percent of the boiler pressure, thereby increasing the power of the rear engine. The reducing valve, when supplying live steam, provides about 40 percent of boiler pressure to the low-pressure engine instead of the 30 percent it receives from the receiver; the extra power from both engines operating simply is about 20 percent more than the compound operation.
39. Q. What is the duty of the by-pass valves on the sides of the low-pressure cylinders? Should they be kept clean of gum and grit?
39. Q. What is the purpose of the by-pass valves on the sides of the low-pressure cylinders? Should they be kept free from gum and grit?
A. These valves are connected to the steam ports at each end of the cylinders and open to allow air and steam to pass from one end of the cylinder to the other; away from the moving piston when the engine is drifting. If not kept clean they may stick open; when working steam the engine will blow badly; if they stick shut the engine will pound when drifting.
A. These valves are connected to the steam ports at each end of the cylinders and open to let air and steam flow from one end of the cylinder to the other; away from the moving piston when the engine is coasting. If they aren’t kept clean, they may get stuck open; when using steam, the engine will run poorly; if they get stuck shut, the engine will vibrate while coasting.
40. Q. In what position should the reverse lever be when the steam is shut off and the engine drifting?
40. Q. In what position should the reverse lever be when the steam is off and the engine is coasting?
A. Below three-quarters of full gear, so the valves will have nearly full travel.
A. Below 75% of full gear, so the valves will have almost full range of motion.
41. Q. Why should the power reversing gear of the Mallet compound always have its dash-pot cylinder full of oil?
41. Q. Why should the power reversing gear of the Mallet compound always have its dash-pot cylinder filled with oil?
A. To prevent the too rapid movement of the reverse gear piston and its damage.[Pg 112]
A. To stop the reverse gear piston from moving too quickly and getting damaged.[Pg 112]
42. Q. In what position should the engines stand to test for blows in valves and piston packing?
42. Q. In what position should the engines be to check for issues with the valves and piston seals?
A. Put the operating valve, or starting valve, in simple position. Spot the engine in the proper position and test each engine for blows the same as for a simple engine.
A. Set the operating valve, or starting valve, to the simple position. Position the engine correctly and test each engine for vibrations just like you would for a simple engine.
43. Q. What power is used with Ragonnet or Baldwin power reverse gear?
43. Q. What power is used with Ragonnet or Baldwin power reverse gear?
A. Air pressure.
A. Air pressure.
44. Q. Can and should steam pressure be used?
44. Q. Can steam pressure be used, and should it be?
A. Yes. However, steam should never be used except in an emergency when air is not available.
A. Yes. However, steam should only be used in an emergency when air isn't available.
45. Q. What precaution should be taken regarding steam check and throttle?
45. Q. What precautions should be taken with the steam check and throttle?
A. That they are tight and check working properly, to insure that steam is kept from entering main reservoir, for if it should do so it would burn out the gaskets in the air brake equipment, allow moisture to accumulate, which would result in freezing and bursting of equipment as well as being dangerous.
A. That they are secure and functioning correctly, to ensure that steam is prevented from entering the main reservoir, because if it does, it would damage the gaskets in the air brake equipment, allow moisture to build up, which could lead to freezing and breaking of equipment as well as being hazardous.
46. Q. What would cause the gear to fail to hold links in intended cut-off, and allow them to raise and lower without operating valve in the cab being changed?
46. Q. What would cause the gear to fail to hold links in the intended cut-off, allowing them to raise and lower without the valve in the cab being adjusted?
A. Leaks in main valve and piston packing.
A. Leaks in the main valve and piston packing.
1. Q. Give a brief explanation of the Walschaert valve gear.
1. Q. Provide a short explanation of the Walschaert valve gear.
A. The Walschaert gear has an eccentric crank attached to the end of the main pin on each side of the locomotive, with an eccentric rod from this pin to the connection at the bottom end of the link. This eccentric is located so it serves for both forward and back motion. The link swings on a center trunnion and cannot be moved up and down as the Stephenson link, but the link block can be moved from one end of the link to the other to reverse the engine; or part way toward the center of the link to change the cut-off. A radius rod connects the link block to the valve stem. There are two motions given to the valve stem, one from the link block which regulates the travel of the valve for the cut-off and reversing; the other motion is from a connection with the cross-head which gives the valve a positive motion to take care of the lap and lead. To give this motion there is used a combination lever or a lap and lead lever connected to a cross-head arm by the union link.
A. The Walschaert gear has an eccentric crank attached to the end of the main pin on each side of the locomotive, with an eccentric rod connecting this pin to the joint at the bottom end of the link. This eccentric is positioned to work for both forward and reverse motion. The link pivots on a central trunnion and can't be moved up and down like the Stephenson link, but the link block can shift from one end of the link to the other to reverse the engine or partially toward the center of the link to change the cut-off. A radius rod connects the link block to the valve stem. The valve stem has two motions: one from the link block that controls the valve's travel for cutting off and reversing, and the other motion comes from a connection with the cross-head, which gives the valve a positive motion to manage the lap and lead. To create this motion, a combination lever or lap and lead lever is connected to a cross-head arm by the union link.
2. Q. Is the Walschaert gear direct or indirect?
2. Q. Is the Walschaert gear direct or indirect?
A. It is direct when the link block is below the center of the link; it is indirect when the link block is above the center of the link.
A. It is direct when the link block is below the center of the link; it is indirect when the link block is above the center of the link.
3. Q. What are the principal differences in the location of the Stephenson and Walschaert gears, and what advantages does this give the Walschaert?
3. Q. What are the main differences in the location of the Stephenson and Walschaert gears, and what advantages does this provide the Walschaert?
A. The Stephenson gear is placed between the main frames and employs two eccentrics, with straps and rods on each side of the locomotive; one for[Pg 114] forward and one for backward motion. The Walschaert gear is placed outside the driving wheels and frame, has but one eccentric, which is a simple arm connected to the outside end of the crank pin for both forward and back motion. The links are set above the wheels on a level with the steam chest, the combination lever next to the cross-head. This gives it an advantage of a better chance to inspect all parts, the eccentric connections are much lighter and direct, which makes them less liable to wear or breakdown, and the valve has a constant lead.
A. The Stephenson gear is positioned between the main frames and uses two eccentrics, with straps and rods on each side of the locomotive; one for forward and one for backward motion. The Walschaert gear is located outside the driving wheels and frame, has only one eccentric, which is a simple arm connected to the outside end of the crank pin for both forward and reverse motion. The links are positioned above the wheels at the same level as the steam chest, with the combination lever next to the cross-head. This design offers a better opportunity to inspect all parts, as the eccentric connections are lighter and more direct, making them less likely to wear out or fail, and the valve maintains a consistent lead.
4. Q. How is the lead affected by movement of the reverse lever with the two gears?
4. Q. How does moving the reverse lever with the two gears affect the lead?
A. With the Stephenson gear the lead increases as the reverse lever is hooked toward the center in both forward and back motion. With the Walschaert gear the lead is the same in all positions of the lever, so that the lever is used to reverse the engine or adjust the cut-off.
A. With the Stephenson gear, the lead increases as the reverse lever is pulled toward the center in both forward and backward movements. With the Walschaert gear, the lead remains the same in all positions of the lever, allowing the lever to be used to reverse the engine or adjust the cut-off.
5. Q. In reversing, how do the two gears differ as to the movement of the link and link block?
5. Q. When going in reverse, how do the two gears differ in terms of the movement of the link and link block?
A. With the Stephenson gear, when reversing, the link is raised and lowered, bringing the block which is not moved by the reverse lever under control of either the forward or back-up eccentric as is desired to move the engine the proper way. With the Walschaert gear the link is not moved by the reverse lever, but the link block is raised and lowered in the link; the position of the block above or below the center of the link controlling the direction of motion.
A. With the Stephenson gear, when reversing, the link is raised and lowered, allowing the block that isn’t moved by the reverse lever to be controlled by either the forward or backward eccentric, as needed, to move the engine in the correct direction. With the Walschaert gear, the link isn’t moved by the reverse lever; instead, the link block is raised and lowered within the link, with the block's position above or below the center of the link determining the direction of motion.
6. Q. What would you disconnect if the eccentric crank, eccentric rod, or the arm at the bottom of the link should break?[Pg 115]
6. Q. What would you disconnect if the eccentric crank, eccentric rod, or the arm at the bottom of the link were to break?[Pg 115]
A. Would remove the broken parts, disconnect the link lifter from the radius rod and block the link block in the center of the link; the combination lever would then move the valve twice the amount of its lap and lead, which would be sufficient to provide for lubricating the cylinder.
A. Would take out the broken parts, disconnect the link lifter from the radius rod, and secure the link block in the center of the link; the combination lever would then move the valve twice the distance of its lap and lead, which would be enough to ensure lubrication of the cylinder.
7. Q. If the main crank pin was broken?
7. Q. What if the main crank pin was broken?
A. Take down eccentric rod, eccentric crank, main rod and all connecting rods, block cross-head, disconnect from end of radius rod, chain it to running board and block steam valve to cover ports.
A. Remove the eccentric rod, eccentric crank, main rod, and all connecting rods. Block the cross-head, disconnect it from the end of the radius rod, secure it to the running board, and block the steam valve to cover the ports.
8. Q. Broken cross-head pin, main rod, strap or brasses?
8. Q. Is the cross-head pin, main rod, strap, or brasses broken?
A. Take down main rod, block cross-head, disconnect front end of radius rod and chain to running board and block the valve to cover ports.
A. Remove the main rod, block the cross-head, disconnect the front end of the radius rod and chain from the running board, and block the valve to cover the ports.
9. Q. With a broken combination lever, union link or cross-head arms, what would you do?
9. Q. If you have a broken combination lever, union link, or cross-head arms, what would you do?
A. Would disconnect the forward end of the radius rod and secure it to the running board with a small chain, wire or rope, remove all broken parts, take off the combination lever, even if not broken, secure the valve in its central position, loosen cylinder head to provide for lubrication, leave up main rod and proceed on one side. If valve was blocked to open rear port slightly, this would provide for lubrication and the cylinder head need not be loosened.
A. Disconnect the front end of the radius rod and attach it to the running board with a small chain, wire, or rope. Remove all broken parts, take off the combination lever even if it's not broken, secure the valve in the central position, loosen the cylinder head to allow for lubrication, raise the main rod, and work on one side. If the valve was blocked, slightly open the rear port; this will allow for lubrication and you won't need to loosen the cylinder head.
10. Q. If the radius rod on Walschaert gear is disabled, what should be done?
10. Q. If the radius rod on Walschaert gear is broken, what should be done?
A. If broken in front of the link block, take off the broken part by disconnecting from combination lever, take down eccentric rod, fasten valve to cover[Pg 116] ports and proceed on one side. If broken back of the link block, block the link block in the desired position and proceed with both sides.
A. If it's broken in front of the link block, remove the broken part by disconnecting it from the combination lever, take down the eccentric rod, secure the valve to cover[Pg 116] ports, and continue on one side. If it's broken at the back of the link block, secure the link block in the desired position and continue with both sides.
11. Q. What would you disconnect with a Walschaert gear if a valve yoke should break?
11. Q. What would you disconnect with a Walschaert gear if the valve arm breaks?
A. Disconnect the forward end of the radius rod, suspend it from running board, block the valve, provide for lubricating the piston and proceed.
A. Disconnect the front end of the radius rod, hang it from the running board, block the valve, make provisions for lubricating the piston, and proceed.
12. Q. How proceed with a broken reach rod?
12. Q. How do you deal with a broken reach rod?
A. Remove the reach rod, block links on lower side to hold them in running position for proper direction. Unless radius rod lifters can be uncoupled, leave a little slack in the blocking.
A. Remove the reach rod, block the links on the lower side to keep them in the running position for the correct direction. If you can't uncouple the radius rod lifters, leave a little slack in the blocking.
13. Q. How can you tell without opening the steam chest if the valve covers the port with Stephenson gear? With Walschaert gear?
13. Q. How can you tell without opening the steam chest if the valve covers the port with Stephenson gear? With Walschaert gear?
A. Place the rocker shaft vertical with Stephenson gear. Place the combination lever vertical with reverse lever in mid gear so the link block is in the center of Walschaert link.
A. Position the rocker shaft vertically with the Stephenson gear. Set the combination lever vertically with the reverse lever in the middle position so that the link block is centered in the Walschaert link.
14. Q. What is the Baker-Pilliod valve gear?
14. Q. What is the Baker-Pilliod valve gear?
A. It is an outside gear with an eccentric crank, similar to the Walschaert gear, but without a reversing link. The motion is reversed by means of a reversing yoke instead of a link; the cut-off is changed in the same manner. It uses a combination lever connected with a union link to its cross-head arm. In case of breakdown remove the broken parts the same as described for Walschaert gear, blocking the reversing yoke, if necessary, in the proper position.[Pg 117]
A. It’s an external gear with an eccentric crank, similar to the Walschaert gear, but it doesn’t have a reversing link. The motion is reversed using a reversing yoke instead of a link; the cut-off is adjusted in the same way. It has a combination lever connected to its cross-head arm by a union link. If there’s a breakdown, remove the broken parts just like you would for Walschaert gear, blocking the reversing yoke in the correct position if needed.[Pg 117]
15. Q. Is the Baker gear a direct or an indirect motion?
15. Q. Is the Baker gear a direct or indirect motion?
A. It is direct, going ahead for an inside admission and indirect backing up, and just the opposite for the outside admission type.
A. It is straightforward, moving forward for an internal admission and indirectly supporting it, and the reverse for the external admission type.
16. Q. What parts of the Baker gear take the place of the link which is used by the Stephenson or Walschaert motion?
16. Q. Which parts of the Baker gear replace the link used in the Stephenson or Walschaert motion?
A. The radius bars and reverse yoke.
A. The radius bars and reverse yoke.
17. Q. What relation to the main pin is the eccentric crank set to?
17. Q. How is the eccentric crank positioned in relation to the main pin?
A. The eccentric crank always follows the main pin.
A. The unusual crank always trails the main pin.
18. Q. Should the eccentric rod or eccentric crank break how is the engine put in condition to proceed?
18. Q. If the eccentric rod or eccentric crank breaks, how is the engine fixed up to continue?
A. The disabled side can have lap and lead travel and a port opening equal to the lead for all cut-offs. First block the bell crank by using a "U" bolt (which should be provided) in the holes placed in the gear frame for this purpose. Throwing reverse lever in mid-gear will help to get bell crank in position to block. Second, take down broken parts. Third, knock out back pin of short reach rod and throw reverse yoke in forward motion against gear frame.
A. The disabled side can have lap and lead travel and a port opening equal to the lead for all cut-offs. First, block the bell crank using a "U" bolt (which should be provided) in the holes in the gear frame designed for this purpose. Setting the reverse lever in mid-gear will help position the bell crank to block. Second, remove the broken parts. Third, knock out the back pin of the short reach rod and push the reverse yoke forward against the gear frame.
19. Q. What is to be done should a gear connection rod break?
19. Q. What should you do if a gear connection rod breaks?
A. Do the same as for a broken eccentric or crank.
A. Do the same thing as you would for a broken eccentric or crank.
20. Q. What is to be done should the upper part of gear connection rod break?
20. Q. What should be done if the upper part of the gear connection rod breaks?
A. If break is close to the middle pin, do the same as for a broken eccentric rod and also tie lower end[Pg 118] of gear connection rod to keep it from swinging. If break is near the top and below the jaw, first block the bell crank and wire the connection rod fast to radius bars. If break is through top jaw, do the same as for broken eccentric rod.
A. If the break is near the middle pin, treat it the same way you would for a broken eccentric rod, and also tie the lower end[Pg 118] of the gear connection rod to prevent it from swinging. If the break is near the top and below the jaw, first block the bell crank and secure the connection rod tightly to the radius bars. If the break is through the top jaw, follow the same procedure as for a broken eccentric rod.
21. Q. What is to be done should a radius bar break?
21. Q. What should be done if a radius bar breaks?
A. Do the same as for broken eccentric rod.
A. Do the same as for the broken eccentric rod.
22. Q. If the horizontal arm of bell crank should break?
22. Q. What happens if the horizontal arm of the bell crank breaks?
A. Same as broken eccentric rod.
A. Same as a broken eccentric rod.
23. Q. What is to be done should the vertical arm or bell crank break?
23. Q. What should be done if the vertical arm or bell crank breaks?
A. Take down union link combination lever and valve rod, then block valve over ports by using set-screw in valve stem cross-head provided for that purpose.
A. Remove the union link combination lever and valve rod, then block the valve over the ports using the set-screw in the valve stem cross-head designed for that purpose.
24. Q. Should you break cross-head arm or union link, what would you do?
24. Q. If you break a cross-head arm or a union link, what would you do?
A. If rod be provided to secure lower end of the combination lever to guide yoke, remove broken parts and proceed with full train, working engine at long cut-off. Otherwise would remove broken parts, combination lever and valve rod, cover ports, and proceed on one side.
A. If a rod is available to secure the lower end of the combination lever to the guide yoke, remove the broken parts and continue with the full train, operating the engine at a long cut-off. Otherwise, remove the broken parts, combination lever, and valve rod, cover the ports, and proceed on one side.
25. Q. What do you do if a union link should break?
25. Q. What do you do if a union link breaks?
A. Same as for a broken cross-head arm.
A. Same as for a broken cross-head arm.
26. Q. What is to be done if a combination lever should break?[Pg 119]
26. Q. What should you do if a combination lever breaks?[Pg 119]
A. Tie combination lever plumb, same as for a broken cross-head arm, if it is possible. If not possible, take down the combination lever and valve rod and cover the ports.
A. Adjust the tie combination lever to be vertical, just like you would for a broken cross-head arm, if you can. If that's not possible, remove the combination lever and valve rod and cover the ports.
27. Q. What is to be done if a valve rod breaks?
27. Q. What should you do if a valve rod breaks?
A. Take down the broken parts and cover ports, leaving the rest of the gear intact.
A. Remove the broken parts and cover the ports, while keeping the rest of the equipment intact.
28. Q. What is to be done if a reverse yoke breaks?
28. Q. What should you do if a reverse yoke breaks?
A. If lugs for holding reach rod breaks, block yoke securely at whatever cut-off you wish to work the engine and take down the short reach rod. If break is below the lugs, do the same as for broken eccentric rod.
A. If the lugs that hold the reach rod break, securely block the yoke at the cut-off where you want to work the engine and remove the short reach rod. If the break is below the lugs, do the same as you would for a broken eccentric rod.
29. Q. What do you do if reach rod should break?
29. Q. What should you do if the measuring rod breaks?
A. If short reach rod breaks, block the yoke at cut-off desired and wire fast so it cannot move. If main reach rod breaks, block between tumbling shaft arm and cross-tie brace, wiring same securely.
A. If the short reach rod breaks, secure the yoke at the cut-off you want and wire it tightly so it can't move. If the main reach rod breaks, block it between the tumbling shaft arm and the cross-tie brace, wiring it securely as well.
30. Q. What is to be done if the engine breaks down other than valve gear?
30. Q. What should be done if the engine breaks down, excluding the valve gear?
A. In this case do the same as for any other valve.
A. In this case, do the same as you would for any other valve.
1. Q. If the eccentric crank or eccentric rods fail?
1. Q. What happens if the eccentric crank or eccentric rods fail?
A. Disconnect the eccentric rod from crank, radius hanger and transmission yoke, tie up the hanger and yoke, clamp valve central position and proceed.[Pg 120]
A. Disconnect the eccentric rod from the crank, radius hanger, and transmission yoke. Tie up the hanger and yoke, clamp the valve in the central position, and proceed.[Pg 120]
2. Q. If radius hanger fails?
2. Q. What happens if the radius hanger fails?
A. Disconnect the hanger from rod and take down eccentric rod, clamp valve in central position and proceed.
A. Disconnect the hanger from the rod and remove the eccentric rod, clamp the valve in the center position, and continue.
3. Q. If transmission yoke fails?
3. Q. What happens if the transmission yoke fails?
A. Disconnect from the eccentric rod and clamp valve in central position and proceed.
A. Disconnect from the odd rod and clamp valve in the center position and continue.
4. Q. If horizontal arm of bell crank fails?
4. Q. What happens if the horizontal arm of the bell crank fails?
A. Disconnect the yoke from the eccentric rod, tie up to clear, clamp valve in central position and proceed.
A. Disconnect the yoke from the eccentric rod, tie it up to clear, clamp the valve in the central position, and proceed.
5. Q. If vertical arm to bell crank breaks?
5. Q. What happens if the vertical arm of the bell crank breaks?
A. Clamp valve in central position and proceed. Take the broken arm down if necessary.
A. Secure the valve in the center position and continue. Remove the broken arm if needed.
6. Q. If one auxiliary reach rod or reverse shaft arm fail?
6. Q. What happens if one auxiliary reach rod or reverse shaft arm fails?
A. Block both link blocks in same position of links, and in such a position as to give port opening enough to start train and control speed by throttle.
A. Block both link blocks in the same position of links, and in a way that allows for enough port opening to start the train and control speed with the throttle.
7. Q. If main reach rod, or middle arm to reverse shaft fail? If both auxiliary reach rods fail?
7. Q. What happens if the main reach rod or the middle arm connected to the reverse shaft fails? What if both auxiliary reach rods fail?
A. Block link blocks in full valve travel, controlling power and speed with the throttle.
A. Block link blocks during full valve travel, controlling power and speed with the throttle.
1. Q. What produces friction, and what is the result of excessive friction?
1. Q. What causes friction, and what happens when there's too much friction?
A. Friction as considered in locomotive service is produced by one body being rubbed across the sur[Pg 121]face of another when they are held in contact by pressure, and the result of excessive friction is heat more or less intense and the destruction of the journal and its bearing or the roughening of the sliding surfaces.
A. Friction in locomotive service happens when one object rubs against the surface of another while being pressed together, and too much friction leads to heat, which can range from mild to severe, and it can damage the journal and its bearing or roughen the sliding surfaces.
2. Q. What is lubrication and its object?
2. Q. What is lubrication and what is its purpose?
A. The object of lubrication is to interpose a film of oil, grease or some lubricant between the two surfaces that will prevent these rubbing surfaces from coming into too intimate contact.
A. The purpose of lubrication is to place a layer of oil, grease, or another lubricant between the two surfaces to keep them from making direct contact.
3. Q. What examinations should be made by the engineer to insure successful lubrication?
3. Q. What checks should the engineer perform to ensure effective lubrication?
A. See that all oil holes are open, cups filled and in good working order, the packing in cellars evenly put in and in contact with the journal. That waste on top of driving or truck boxes is in proper shape, also that grease cups are filled, and the plugs and jam nuts in good shape, and that the grease cellars contain sufficient grease for the next trip.
A. Make sure all oil holes are clear, cups are filled, and everything is working properly. The packing in the cellars should be evenly installed and in contact with the journal. Check that the waste on top of the driving or truck boxes is in good condition, the grease cups are filled, the plugs and jam nuts are in good shape, and that the grease cellars have enough grease for the next trip.
4. Q. How should feeders of all oil cups be adjusted?
4. Q. How should the feeders for all oil cups be adjusted?
A. To feed as small a quantity of oil as possible and regularly to give perfect lubrication.
A. To provide just a small amount of oil and consistently ensure perfect lubrication.
5. Q. Why is it bad practice to keep engine oil close to boiler in warm weather?
5. Q. Why is it a bad idea to keep engine oil near the boiler in warm weather?
A. The oil is thinned to such a degree by the heat of the boiler that it runs off as soon as applied, and very often a hot bearing is the result.
A. The oil is heated to the point where it becomes so thin that it runs off as soon as it's applied, and very often this leads to a hot bearing.
6. Q. In what manner would you care for a hot bearing if discovered on the road?
6. Q. How would you handle a hot bearing if you found one while on the road?
A. Use as much time as available in cooling the[Pg 122] same, making sure that all moving parts are free and carefully lubricated before proceeding.
A. Use as much time as you have to cool the[Pg 122] same, making sure that all moving parts are free and properly lubricated before moving on.
7. Q. What kind of oil should be used on hot bearings?
7. Q. What type of oil should be used on hot bearings?
A. Use engine oil unless the temperature of bearing consumes it, when a small quantity of valve oil may be used while the bearing is warm enough to make this oil flow. The valve oil must be removed as soon as the bearing cools to prevent reheating.
A. Use engine oil unless the temperature of the bearing burns it up; then a small amount of valve oil can be used while the bearing is warm enough for the oil to flow. The valve oil must be removed as soon as the bearing cools to avoid reheating.
8. Q. At completion of trip what is necessary?
8. Q. What is required at the end of the trip?
A. Close all adjustable feeds and examine all lubricated parts by contact with the hand to determine that they are not above running temperature.
A. Close all adjustable feeds and check all lubricated parts by touch to ensure they are not hotter than normal operating temperature.
9. Q. How would you determine what boxes to report examined? Why not report all boxes examined?
9. Q. How would you figure out which boxes to report as examined? Why not report every box that was examined?
A. By placing the hand on driving box, on hub of engine truck wheel and on top of tender truck boxes nearest the brass, and would not report them examined unless the temperature of same was above running heat. It is not necessary to report all boxes examined, because they do not all give trouble at the same time. If this report was made, it would appear that a proper inspection had not been made and would result in unnecessary work and waste of material.
A. By placing your hand on the driving box, on the hub of the engine truck wheel, and on the top of the tender truck boxes closest to the brass, you should only report them checked if their temperature is above running heat. It's not necessary to report every box checked, as they don’t all malfunction simultaneously. If this report was made, it would suggest that a proper inspection hadn't been done, leading to unnecessary work and waste of materials.
10. Q. Why is it bad practice to disturb the packing on top of driving and engine truck boxes with spout of oil can when oiling engine?
10. Q. Why is it a bad idea to mess with the packing on top of the driving and engine truck boxes when using the spout of an oil can to oil the engine?
A. This packing is put on top of boxes to assist in keeping dirt and dust out of oil holes, also to aid in gradual lubrication from the top. If this packing is disturbed it will permit dirt and grit to work into[Pg 123] oil holes and on the bearings as well as feed the oil away too rapidly.
A. This packing is placed on top of boxes to help keep dirt and dust out of oil holes and to support gradual lubrication from above. If this packing is disturbed, it will allow dirt and grit to get into[Pg 123] the oil holes and on the bearings, as well as cause the oil to drain away too quickly.
11. Q. How do you adjust grease cups as applied to rods?
11. Q. How do you adjust grease cups for rods?
A. Screw down plug until you feel a slight resistance from the grease, stop when grease shows between brass and pin; this should be sufficient over the division.
A. Screw down the plug until you feel a little resistance from the grease, and stop when grease starts to appear between the brass and the pin; this should be enough over the division.
12. Q. Is it usual for pins to run warm when using grease?
12. Q. Is it normal for pins to get warm when using grease?
A. Yes; grease does not work properly until it gets warm enough to flow readily over the bearing.
A. Yes; grease doesn’t work properly until it warms up enough to flow easily over the bearing.
13. Q. What effect does too much pressure produce?
13. Q. What happens when there's too much pressure?
A. Wastes grease and increases the friction until the surplus amount is worked out so the bearing runs free on its journal.
A. Wastes grease and increases friction until the excess amount is worked out so the bearing runs smoothly on its journal.
14. Q. Is it necessary to use oil with grease on crank pins?
14. Q. Do I need to use oil with grease on crank pins?
A. No.
A. Nope.
15. Q. When an engine is equipped with Elvin driving box lubricator, how can you tell whether a sufficient amount of lubricant is in the grease receptacle?
15. Q. When an engine has an Elvin driving box lubricator, how can you check if there's enough lubricant in the grease receptacle?
A. The indicator wire fastened to the bottom of the grease cellar indicates the amount of grease left in the cellar.
A. The indicator wire attached to the bottom of the grease cellar shows how much grease is left in the cellar.
16. Q. Why should engine oil not be used on valves and cylinders?
16. Q. Why shouldn't engine oil be used on valves and cylinders?
A. Engine oil loses its lubricating qualities before it gets up to the temperature of the valves and cylinders when they are working steam.[Pg 124]
A. Engine oil loses its ability to lubricate before it reaches the temperature of the valves and cylinders when they are running hot.[Pg 124]
17. Q. At what temperature does engine oil lose its lubricating qualities? At what temperature for valve oil?
17. Q. At what temperature does engine oil lose its ability to lubricate? At what temperature does valve oil lose its effectiveness?
A. Engine oil begins to separate and give off gas at 345 degrees F. The temperature of steam at 120 pounds is 350 degrees F., while valve oil has a flash test of 520 degrees F. The temperature of steam at 235 pounds is 431 degrees F., much lower than the flash test of valve oil.
A. Engine oil starts to separate and release gas at 345 degrees F. The steam temperature at 120 pounds is 350 degrees F, while valve oil has a flash test of 520 degrees F. The steam temperature at 235 pounds is 431 degrees F, which is much lower than the flash test of valve oil.
18. Q. How and by what means are valves, cylinders and the steam end of air pumps lubricated?
18. Q. How and with what methods are valves, cylinders, and the steam part of air pumps lubricated?
A. By a sight-feed hydrostatic lubricator.
A. By a sight-feed hydrostatic lubricator.
19. Q. What is the principle on which a lubricator operates. How does the oil get from the cup to the steam chest?
19. Q. What is the principle behind how a lubricator functions? How does the oil travel from the cup to the steam chest?
A. The lubricator is located in the cab so there is a gradual descent in the oil pipe from the lubricator to the steam chest. Above the oil reservoir is a condenser that is kept filled with water condensed from steam fed from the boiler. The pressure of this water comes on the oil in the oil tank below it, forcing oil through the sight-feed valves; it then passes up by the sight-feed glasses to the oil pipe and steam chest. The use of the glasses is to make the drop of oil visible as it leaves the sight-feed nipple so the amount of oil fed can be regulated. Steam from the boiler fed to the lubricator at boiler pressure through the equalizing tubes balances the pressure which comes from the steam chest when the engine is working steam.
A. The lubricator is in the cab, which allows for a smooth downward flow of oil from the lubricator to the steam chest. Above the oil reservoir, there's a condenser that stays filled with water created from steam coming from the boiler. The pressure from this water acts on the oil in the tank below, pushing oil through the sight-feed valves; it then moves up through the sight-feed glasses to the oil pipe and steam chest. The purpose of the glasses is to make the oil drop visible as it exits the sight-feed nipple, so the oil output can be adjusted. Steam from the boiler is supplied to the lubricator at boiler pressure through the equalizing tubes, balancing the pressure from the steam chest when the engine is in operation.
20. Q. How should the lubricator be filled?
20. Q. How do you fill the lubricator?
A. First close all valves connected with the lubricator, open drain plug and remove filling plug, allow[Pg 125]ing water to escape until oil appears with it. Drain plug should then be closed. Fill the oil tank in the usual way, being careful not to overflow it; then replace filling plug. If the supply of oil is insufficient to fill the lubricator, water can be used to finish it, as the lubricator will begin feeding sooner when filled full.
A. First, close all the valves connected to the lubricator, open the drain plug, and remove the filling plug. Allow[Pg 125] for water to escape until oil starts to come out with it. Then close the drain plug. Fill the oil tank as usual, making sure not to overflow it; then replace the filling plug. If there isn't enough oil to fill the lubricator, you can use water to top it off, as the lubricator will start feeding sooner when it’s completely full.
21. Q. After filling lubricator, what should be done?
21. Q. After filling the lubricator, what should you do?
A. Open the steam throttle to the lubricator wide, then carefully open the water valve, but do not open the feeds until sure the chamber in the glass is filled with water.
A. Open the steam throttle to the lubricator fully, then carefully open the water valve, but do not open the feeds until you are sure the chamber in the glass is filled with water.
22. Q. How long before leaving terminal should the feed valves be opened? Why?
22. Q. How long before leaving the terminal should the feed valves be opened? Why?
A. About fifteen minutes; this time is necessary to allow oil to feed through the oil pipe and reach the steam chests.
A. About fifteen minutes; this time is needed to let oil flow through the oil pipe and reach the steam chests.
23. Q. How many drops should be fed per minute?
23. Q. How many drops should you administer each minute?
A. From one to seven, timed by the watch, depending on conditions. Cylinders of large size require more oil than smaller ones.
A. From one to seven, timed by the clock, depending on the conditions. Larger cylinders need more oil than smaller ones.
24. Q. If lubricator feeds regularly when working steam and too rapidly after shutting off, what is the trouble?
24. Q. If the lubricator feeds regularly while using steam and too quickly after shutting it off, what's the problem?
A. The opening in the choke plug at the lubricator or through the steam valves at the steam chest is too large and should be reduced to the proper size by applying new chokes or valves.
A. The opening in the choke plug at the lubricator or through the steam valves at the steam chest is too large and should be resized by installing new chokes or valves.
25. Q. When valves appear dry while using steam and the lubricator is working all right, what would you do to relieve these conditions?[Pg 126]
25. Q. When the valves look dry while using steam and the lubricator is functioning properly, what would you do to fix this situation?[Pg 126]
A. Ease off throttle for a few seconds to reduce the steam chest pressure and drop the reverse lever a few notches to give the valve a longer travel; oil held in the pipes will then flow down.
A. Ease off the throttle for a few seconds to lower the steam chest pressure and drop the reverse lever a few notches to allow the valve to travel further; oil held in the pipes will then flow down.
For Inspection of Locomotive Boilers and Safety Appliances
For Checking Locomotive Boilers and Safety Equipment
1. Q. What is the purpose of the federal rules and regulations for inspection of locomotive boilers?
1. Q. What is the purpose of the federal rules and regulations for inspecting locomotive boilers?
A. So that all railroads operating under the laws of the United States government, would be obliged to maintain their boilers in a safe working condition.
A. So that all railroads operating under the laws of the United States government would be required to keep their boilers in a safe working condition.
2. Q. What is the purpose of the quarterly and monthly interstate inspection cards placed in the cab of the locomotive?
2. Q. What is the purpose of the quarterly and monthly interstate inspection cards kept in the cab of the locomotive?
A. So that the federal inspector or engineer may see that the locomotive boiler has received its monthly or quarterly inspection.
A. So that the federal inspector or engineer can see that the locomotive boiler has had its monthly or quarterly inspection.
3. Q. What constitutes a safety appliance, as applied to a locomotive?
3. Q. What is considered a safety device when it comes to a locomotive?
A. Any appliance that is placed on a locomotive for the purpose of protecting the employees from personal injury.
A. Any device installed on a train to protect employees from getting hurt.
4. Q. Name some of the safety appliances found on a locomotive?
4. Q. What are some of the safety features found on a train engine?
A. Shield for tubular glass lubricators, also shields for water glass, automatic couplers, with lever attachments, air brakes, etc.
A. Shield for tubular glass lubricators, also shields for water glass, automatic couplers with lever attachments, air brakes, etc.
5. Q. In what condition should safety appliances be maintained?[Pg 127]
5. Q. How should safety equipment be kept in good condition?[Pg 127]
A. They should be maintained in first class condition.
A. They should be kept in top-notch condition.
6. Q. What should be done in event of any of the safety appliances being damaged while engine is in service so as to render it unsafe?
6. Q. What should be done if any of the safety devices are damaged while the engine is in service, making it unsafe?
A. Warn all employees whose duties require them to work around the locomotive of its unsafe condition, then make report to those in authority so that it may be taken out of service until repairs are made.
A. Inform all employees whose jobs involve working near the locomotive about its unsafe condition, then report it to those in charge so it can be taken out of service until repairs are completed.
7. Q. What effort should be made on the part of the engineer to prevent persons using a safety appliance which he knows is damaged and unsafe?
7. Q. What actions should the engineer take to prevent people from using a safety device that he knows is broken and unsafe?
A. He should use such precaution as in his judgment would protect from injury all persons who are on or around the locomotive.
A. He should take precautions that, in his opinion, would protect all individuals who are on or near the locomotive from harm.
8. Q. What is the duty of the engineer in event of his discovering a safety appliance which is in an unsafe condition when taking an engine from roundhouse territory?
8. Q. What should the engineer do if he finds a safety device in an unsafe condition while taking an engine out of the roundhouse?
A. He should report at once to the person in authority so that necessary repairs may be made before engine goes into service.
A. He should report immediately to the person in charge so that necessary repairs can be made before the engine goes into service.
1. Q. Why are electric headlights applied to locomotives?
1. Q. Why are electric headlights used on trains?
A. Electric headlights are applied to locomotives so that the engineer may have a clear view of the track for enough ahead of the train to enable him to protect the company's property in his charge.
A. Electric headlights are used on locomotives so the engineer can clearly see the track far enough ahead of the train to protect the company's property under his care.
2. Q. How far ahead of the engine should the arc headlight illuminate the track?[Pg 128]
2. Q. How far in front of the engine should the arc headlight light up the track?[Pg 128]
A. Not less than from fifteen to twenty telegraph poles.
A. No fewer than fifteen to twenty telegraph poles.
3. Q. State how you would focus the lamp.
3. Q. Explain how you would adjust the lamp's focus.
A. First, would adjust back of the reflector so front edge of reflector will be parallel with front edge of case. Second, adjust the lamp to have point of copper electrode as near the center of reflector as possible with carbons as near the center of the chimney holes as you can set them. Third, have the locomotive on straight track. Now move the base of the lamp around until you get a parallel beam of white light straight down the center of the track, then tighten the lamp down.
A. First, adjust the back of the reflector so the front edge of the reflector is parallel with the front edge of the case. Second, position the lamp so that the tip of the copper electrode is as close to the center of the reflector as possible, with the carbon rods as close to the center of the chimney holes as you can manage. Third, place the locomotive on straight track. Now move the base of the lamp around until you achieve a parallel beam of white light straight down the center of the track, then tighten the lamp in place.
4. Q. If the light throws shadows upon the track, is it properly focused?
4. Q. If the light casts shadows on the track, is it properly focused?
A. No.
A. No.
5. Q. If the light is properly focused, that is, if the rays are leaving the reflector in parallel lines, but the light does not strike the center of the track, what should be done?
5. Q. If the light is properly focused, meaning the rays are leaving the reflector in parallel lines, but the light doesn't hit the center of the track, what should be done?
A. When the light rays are thrown out in parallel lines and they do not strike the center of the track, it denotes that the headlight case is not set straight with the engine, and the entire case on base board must be shifted until the shaft of light strikes the track as desired.
A. When the light rays are projected in parallel lines and they don't hit the center of the track, it indicates that the headlight case isn't aligned properly with the engine, and the entire case on the baseboard needs to be adjusted until the beam of light hits the track as intended.
6. Q. What can you do to insure a good and unfailing light for the entire trip?
6. Q. What can you do to ensure a reliable and consistent light for the whole journey?
A. By carefully inspecting the entire equipment before departing on each trip, and know that there are no wires with insulation charred or worn off, that all screws and connections are tight, commutator clean and brushes set in brush holder in proper man[Pg 129]ner. Carbon in lamp of sufficient length to complete trip, and that the carbon will feed through the clutch freely and rests central over the copper electrode. Copper electrode cleaned off, oil in both bearings and see that steam does not blow at stuffing box gland.
A. By carefully checking all the equipment before leaving on each trip, make sure that there are no wires with damaged or worn insulation, that all screws and connections are tight, the commutator is clean, and the brushes are properly placed in the brush holder. Ensure the carbon in the lamp is long enough to complete the trip, and that it feeds through the clutch smoothly and is centered over the copper electrode. The copper electrode should be cleaned, oil should be in both bearings, and check that steam isn’t leaking from the stuffing box gland.
7. Q. What kind of oil and how much would you use in the bearings of the electric headlight equipment?
7. Q. What type of oil and how much should you use in the bearings of the electric headlight system?
A. Would use the best grade of black or engine oil furnished for both bearings and only enough oil in oil cellar that the revolving loose oil ring may trail through the oil. When bearings are supplied with oil cups, use a heavy oil such as good engine or valve oil.
A. Use the highest quality black or engine oil provided for both bearings, with just enough oil in the oil chamber so that the spinning loose oil ring can dip into it. When the bearings have oil cups, use a thick oil, like quality engine or valve oil.
8. Q. Why should you not use valve oil in these bearings?
8. Q. Why shouldn't you use valve oil in these bearings?
A. Valve oil cannot be used successfully in the main bearing because of its heavy body. Valve oil could not be carried up to shaft by the oil ring in cold weather, as the ring will not revolve.
A. Valve oil can't be used successfully in the main bearing because it's too thick. In cold weather, the oil ring won't rotate, so valve oil can't be brought up to the shaft.
9. Q. What is the most vital part of the dynamo?
9. Q. What is the most important part of the dynamo?
A. The commutator.
A. The commutator.
10. Q. What care or attention should be given the commutator?
10. Q. What care or attention should be given to the commutator?
A. The commutator must be kept clean, free from dirt, and the mica must be kept filed a trifle below the surface of the copper bars.
A. The commutator needs to be kept clean and free of dirt, and the mica should be filed slightly below the surface of the copper bars.
11. Q. What kind of a bearing should the brush have on the commutator?
11. Q. What type of contact should the brush have with the commutator?
A. Brushes should be fitted to have a bearing with the same contour as the commutator.
A. Brushes should be designed to match the shape of the commutator.
12. Q. How are the brushes fitted?
12. Q. How are the brushes attached?
A. Brushes are fitted by cutting a strip of No. 0 sandpaper about the width of the commutator surface[Pg 130] (have the dynamo idle), place the strips of sandpaper under the brush, then pull the sandpaper from left to right; continue this process until the brush has been fitted to a true smooth bearing. Then trim about one-eighth inch off of the front edge of the brush.
A. Brushes are installed by cutting a strip of No. 0 sandpaper about the same width as the commutator surface[Pg 130] (with the dynamo running idle), place the sandpaper strips under the brush, then pull the sandpaper from left to right; keep doing this until the brush is fitted to a perfectly smooth surface. Then trim about one-eighth inch off the front edge of the brush.
13. Q. Is it advisable to ever try to fit a brush with a file or knife?
13. Q. Is it ever a good idea to try to attach a brush to a file or knife?
A. Most emphatically no. You could not get a bearing across the brush no matter how hard you might try with either a file or a knife.
A. Absolutely not. You couldn't get a sense of direction through the underbrush no matter how hard you tried with either a file or a knife.
14. Q. Why is it important to clean the scale off of the point of the copper electrode each trip?
14. Q. Why is it important to clean the scale off the tip of the copper electrode every time?
A. The scale on the copper electrode after it has cooled off is a non-conductor of current, and acts as a blind gasket between the carbon and the copper electrode. Unless this scale is removed, the current cannot pass between the points of carbon and electrode and you cannot, therefore, have a light. When the dynamo fields are compound wound, it is unnecessary to clean scale from copper electrode oftener than once a week, at which time copper electrode should be removed from holder and all scale cleaned off. (With compound wound dynamo fields the cab lamps will continue to burn when head-lamp is extinguished by lifting carbon by hand.)
A. The scale on the copper electrode after it cools down is an insulator and acts as a barrier between the carbon and the copper electrode. If this scale isn’t removed, the current can't flow between the carbon and the electrode, which means you won’t have any light. When the dynamo fields are compound wound, you don’t need to clean the scale off the copper electrode more often than once a week. During that time, the copper electrode should be taken out of the holder and all the scale should be cleaned off. (With compound wound dynamo fields, the cab lamps will keep burning when the headlamp is turned off by lifting the carbon by hand.)
15. Q. How should the copper electrode be trimmed at the point?
15. Q. How should the copper electrode be trimmed at the tip?
A. The copper electrode should have about one-eighth inch surface on the contact point.
A. The copper electrode should have about one-eighth inch of surface at the contact point.
16. Q. How far should the copper electrode project over the holder?
16. Q. How far should the copper electrode stick out from the holder?
A. About one inch.
About one inch.
17. Q. Should the electrode be raised up to one and one-half inches, what might happen?
17. Q. If the electrode is raised up to one and a half inches, what could happen?
A. If the copper electrode was run at a point so[Pg 131] near the clutch, the intense heat of the arc might do damage to the top carbon holder and clutch.
A. If the copper electrode was operated too[Pg 131] close to the clutch, the extreme heat from the arc could cause damage to the top carbon holder and clutch.
18. Q. What regulation should be given to the tension spring No. 93 of the lamp, and why?
18. Q. What adjustments should be made to the tension spring No. 93 of the lamp, and why?
A. This tension spring, No. 93, should be regulated when the current is off the lamp and should be adjusted only tight enough to pull the magnet yoke up against the top stop lug on the side of lamp column.
A. This tension spring, No. 93, should be adjusted when the lamp is off, and it should only be tightened enough to pull the magnet yoke up against the top stop lug on the side of the lamp column.
19. Q. If this tension spring was tightened too tightly, what might happen?
19. Q. If this tension spring is tightened too much, what could happen?
A. At usual speed between stations, the movement of the engine would impart an added resistance against the pull of the solenoid by the tension spring, which would shorten up the arc and dim down the light.
A. At regular speed between stations, the engine's movement would create extra resistance against the solenoid's pull from the tension spring, which would reduce the arc and dim the light.
20. Q. Is there anything else that could cause the light to dim down when the engine is running fast?
20. Q. Is there anything else that might make the light dim while the engine is running fast?
A. Yes; if the spring No. 92-A that hold the heel of the clutch should be too weak, the heel of the clutch would be forced up by the motion of the locomotive; this would release the carbon which would fall to the point of the copper electrode, causing the light to dim down, or, if the clutch should be used until the sharp edge that grips the carbon should have become worn smooth or round, the same would occur.
A. Yes; if the spring No. 92-A that holds the heel of the clutch is too weak, the heel of the clutch would be pushed up by the movement of the locomotive; this would release the carbon, which would drop to the point of the copper electrode, causing the light to dim, or, if the clutch is used until the sharp edge that grips the carbon has worn smooth or rounded, the same thing would happen.
21. Q. If the light burns satisfactorily while the engine is in motion, but goes out when engine is stopped, where would you find the trouble?
21. Q. If the light works well while the engine is running but goes out when the engine stops, where do you think the problem might be?
A. This trouble is most always found to be caused by the tension spring No. 93 being too weak, though if the dash-pot plunger has become corroded until it sticks in the dash-pot, the light will act the same as if the tension spring were too weak.[Pg 132]
A. This issue is usually caused by the tension spring No. 93 being too weak, but if the dash-pot plunger has corroded and is sticking in the dash-pot, the light will behave as if the tension spring is too weak.[Pg 132]
22. Q. If the dash-pot should be found stuck, would you put oil in it?
22. Q. If the dash pot is stuck, would you add oil to it?
A. Coal oil could be used to clean and cut the dirt out of the pot and from off the plunger, but after the dash-pot and plunger have been cleaned, all oil must be wiped off, for oil would cause the plunger to stick as well as collect dirt.
A. Coal oil can be used to clean and remove dirt from the pot and the plunger, but after the dash-pot and plunger are cleaned, all oil must be wiped off, as oil would cause the plunger to stick and also attract dirt.
23. Q. If the carbon of lamp should "jig or pound", what can be done to stop it?
23. Q. If the carbon in the lamp is "jigging or pounding," what can be done to stop it?
A. If the carbons pound the electrode, it is evidence that the iron armature No. 64 may be too far out of the solenoid, or the speed of the turbine engine may be too slow. This trouble can be remedied by adding another link to the suspension link, which has one end connected to the magnet yoke, the other end being connected to the iron armature No. 64. If, however, when the arc is formed, it is found that the bottom end of iron armature No. 64 measures one-half inch from bottom of solenoid, the pounding is caused by the speed of turbine engine being too slow.
A. If the carbon hits the electrode, it means that iron armature No. 64 might be too far out of the solenoid, or the turbine engine could be running too slowly. You can fix this by adding another link to the suspension link, which connects one end to the magnet yoke and the other end to iron armature No. 64. However, if when the arc is formed, the bottom end of iron armature No. 64 is found to be half an inch from the bottom of the solenoid, then the hitting is due to the turbine engine running too slowly.
24. Q. If the copper electrode was fusing, how would you know it?
24. Q. If the copper electrode was melting, how would you know?
A. When the copper electrode is fused, a green light is always given off.
A. When the copper electrode is melted, a green light is always emitted.
25. Q. What should be done when a green light is seen?
25. Q. What should you do when you see a green light?
A. Immediately close off on the steam throttle until a white light re-appears.
A. Immediately shut off the steam throttle until a white light comes back on.
26. Q. What is the cause of the fusing of the copper electrode?
26. Q. What causes the copper electrode to fuse?
A. Usually too high speed of the armature, although should you connect the wires up wrong that the current flowing from the dynamo to the lamp[Pg 133] should enter the lamp at the electrode instead of passing through the carbon first, you would get a green light and fuse the electrode.
A. Usually, the armature runs at too high a speed. However, if you connect the wires incorrectly, causing the current from the dynamo to flow into the lamp at the electrode instead of passing through the carbon first, you would see a green light and damage the electrode.
27. Q. What arrangements have been made so that you cannot connect the wires wrong?
27. Q. What measures have been put in place to ensure you can't connect the wires incorrectly?
A. The positive binding posts, both at the dynamo and the lamp, have been provided with a much larger hole to receive the wire than has been made in the negative binding posts, and the ends of the positive wire should always be bent or doubled back, so that they will just enter the receptacle in the positive binding posts, but cannot be connected at the negative binding posts.
A. The positive binding posts, both on the dynamo and the lamp, have larger holes to accommodate the wire compared to the negative binding posts. The ends of the positive wire should always be bent or doubled back so that they can fit into the receptacle of the positive binding posts but can't be connected to the negative binding posts.
28. Q. Should the copper electrode and holder become fused until no longer serviceable while on the road, what would you do?
28. Q. If the copper electrode and holder get stuck together and become unusable while you're on the road, what would you do?
A. Would remove the damaged holder from the lamp and substitute either an iron bolt of sufficient length or a carbon, securing the improvised electrode in the bracket of lamp same as the electrode holder is held, only being sure that the end of the bolt or carbon comes up into the center of the reflector and did not rest on the base of reflector or lamp.
A. Would take out the damaged holder from the lamp and replace it with either a long iron bolt or a piece of carbon, securing the makeshift electrode in the lamp's bracket just like the electrode holder is secured, making sure that the end of the bolt or carbon reaches the center of the reflector and doesn't rest on the base of the reflector or lamp.
29. Q. What is the difference between a series wound equipment and a compound wound equipment, and what advantages are obtained from the use of the compound equipment.
29. Q. What’s the difference between series wound equipment and compound wound equipment, and what benefits come from using compound equipment?
A. With the series wound equipment, the incandescent cab lights burn only with the arc lamp, while with the compound machine the incandescent lamps are independent of the arc and can be used as desired.
A. With the series-wound equipment, the incandescent cab lights operate only with the arc lamp, whereas with the compound machine, the incandescent lamps are independent of the arc and can be used whenever needed.
30. Q. If you were running along with your light burning steadily and nicely, then suddenly the light[Pg 134] began to flash badly and kept it up, where would you look for the trouble?
30. Q. If you were running along with your light shining bright and steady, and then suddenly it started to flicker badly and wouldn’t stop, where would you look for the problem?
A. Trouble would usually be found at one of the binding posts, where one of the binding post screws would be found loose.
A. Trouble would usually be at one of the binding posts, where a screw would be loose.
31. Q. If you were running along with light burning satisfactorily and suddenly it went out, where would you be likely to find the trouble?
31. Q. If you were running along with the light working well and it suddenly went out, where would you most likely find the problem?
A. You would find that either the carbon had burned out, one of the lead wires had broken between the dynamo and the lamp, or one of the wires had gotten loose at the binding post and fallen out.
A. You would find that either the carbon had burned out, one of the lead wires had broken between the dynamo and the lamp, or one of the wires had come loose at the binding post and fallen out.
32. Q. If the light goes out while you are between stations, what course should an engineer pursue?
32. Q. If the power goes out while you are between stations, what should an engineer do?
A. If the light goes out while you are between stations and an investigation cannot be made within a few minutes thereafter to determine the cause, the steam should be shut off from the turbine and the dynamo stopped until such time when the cause of failure can be determined.
A. If the light goes out while you are between stations and an investigation cannot be done within a few minutes to find out why, the steam should be turned off from the turbine and the dynamo should be stopped until the cause of the failure can be identified.
33. Q. Why is it essential to shut off steam and stop the equipment?
33. Q. Why is it important to turn off the steam and stop the equipment?
A. For the reason that if the failure was due to a short circuit, damage might be done to the coils or armature by overheating.
A. Because if the failure was caused by a short circuit, it could damage the coils or armature due to overheating.
34. Q. How does the equipment act when short-circuited?
34. Q. What happens to the equipment when there’s a short circuit?
A. When there is short circuit, the engine will labor heavily, run slow with a large volume of steam blowing at the exhaust, there will be no light shown either at the arc or cab lamps, and the carbon point and cab lights will only show a dull red or go entirely out.[Pg 135]
A. When there’s a short circuit, the engine will struggle, run slowly, and a lot of steam will blow out the exhaust. There won’t be any light from the arc or cab lamps, and the carbon point and cab lights will only glow a dull red or go completely dark.[Pg 135]
35. Q. How will the equipment act when the circuit is broken, either by a broken disconnected wire or a burned-out carbon?
35. Q. What will happen to the equipment if the circuit is broken, either by a disconnected wire or a burnt-out carbon?
A. With a broken circuit the engine will run noiselessly and fast with very little steam blowing at exhaust and no light will be seen at the arc or on cab lights.
A. With a broken circuit, the engine will run quietly and quickly, with very little steam escaping at the exhaust, and no light will be seen at the arc or on the cab lights.
36. Q. If the insulation on the cab wires is worn off until your two wires can come together either directly or through the medium of some metallic substance, what would occur?
36. Q. If the insulation on the cab wires is worn off so that your two wires can touch each other directly or through some metal object, what would happen?
A. A short circuit would result that would put out all of your lights.
A. A short circuit would happen that would turn off all your lights.
37. Q. What should be done?
37. Q. What needs to be done?
A. Wrap the exposed wire, if you can locate it, with a piece of waste, or if you cannot locate the short circuit, disconnect one of your cab wires from the dynamo. This would give you the benefit of the arc lamp and you can look for the trouble at your leisure.
A. If you can find the exposed wire, wrap it with a piece of waste. If you can’t find the short circuit, disconnect one of your cab wires from the dynamo. This will allow you to use the arc lamp while you take your time to look for the issue.
38. Q. If the light goes out when steam drops back fifteen to twenty pounds, what is the trouble?
38. Q. If the light goes off when the steam pressure drops by fifteen to twenty pounds, what’s the problem?
A. Either one of the governor valves is stuck shut, short bushing No. 18 in engine cab is worn badly, allowing wheel to drop away from the governor stand so steam passes around wheel to exhaust, or governor springs are too weak.
A. Either one of the governor valves is stuck closed, short bushing No. 18 in the engine cab is badly worn, causing the wheel to drop away from the governor stand so steam escapes around the wheel to exhaust, or the governor springs are too weak.
39. Q. In this case what should be done?
39. Q. What should be done in this situation?
A. Report of the action of the dynamo should be made upon the work book at the terminal.[Pg 136]
A. A report on the dynamo's performance should be recorded in the work book at the terminal.[Pg 136]
40. Q. If clutch rod No. 78-B should break while on the road, what could be done to get use of the lamp?
40. Q. If the clutch rod No. 78-B breaks while you're on the road, what can you do to use the lamp?
A. A piece of wire could be used by fastening one end around the end of top lever No. 59, the other end being attached to clutch through eye.
A. You can use a piece of wire by fastening one end around the top lever No. 59 and attaching the other end to the clutch through the eye.
41. Q. If you should lose the clothespin holder or top carbon clutch, what could be done to get the light?
41. Q. If you lose the clothespin holder or top carbon clutch, what can you do to get the light?
A. Would fasten a wire around the carbon and top holder to keep carbon in line, being careful not to get the wire either too tight or too loose.
A. Would wrap a wire around the carbon and top holder to keep the carbon aligned, making sure not to have the wire too tight or too loose.
42. Q. If you should lose the iron armature No. 64 in solenoid, what could be done to get use of light?
42. Q. If you lose the iron armature No. 64 in the solenoid, what can be done to get light?
A. Would use a common iron bolt and suspend same by wire in magnet.
A. Would use a standard iron bolt and hang it by wire in a magnet.
43. Q. What would be the result if any of the levers of the lamp should bind?
43. Q. What would happen if any of the lamp's levers got stuck?
A. All levers of the lamp must work absolutely free and must not drag, for if they are not perfectly free the carbon cannot feed properly.
A. All levers of the lamp must move completely freely and should not stick, because if they aren't perfectly free, the carbon won't feed properly.
Pyle-National Electric Incandescent Headlight
Pyle-National Electric LED Headlight
44. Q. What is meant by an incandescent headlight equipment?
44. Q. What does incandescent headlight equipment mean?
A. A headlight having an electric incandescent lamp in the reflector in place of the usual oil or acetylene gas flame, and electric instead of oil cab lamps, the electricity being generated by a small combina[Pg 137]tion steam-turbine and electric generator. Suitable wiring distributes the electric current.
A. A headlight that uses an electric incandescent lamp in the reflector instead of the usual oil or acetylene gas flame, along with electric cab lamps instead of oil ones, with electricity being generated by a small combination steam turbine and electric generator. Proper wiring distributes the electric current.
45. Q. In what manner does the incandescent headlight differ from the arc headlight?
45. Q. How does the incandescent headlight differ from the arc headlight?
A. It is not so powerful. An incandescent or bulb type of lamp takes the place of the arc lamp in the headlight reflector. The current being less than is required for an arc, is supplied by a smaller turbine.
A. It is not as powerful. An incandescent or bulb-type lamp replaces the arc lamp in the headlight reflector. Since the current is less than what's needed for an arc, it's provided by a smaller turbine.
46. Q. What type of incandescent lamp is used in the reflector?
46. Q. What kind of incandescent bulb is used in the reflector?
A. A low voltage, gas filled bulb, containing a very compact or concentrated fillament.
A. A low voltage, gas-filled bulb with a very compact or concentrated filament.
47. Q. Why cannot a standard or house type of lamp be successfully used in the reflector?
47. Q. Why can’t a standard or house-type lamp work well in the reflector?
A. Because the fillament or light-giving wire inside the bulb is not sufficiently compact or concentrated to reflect the light in the form of a beam. The voltage of the house lamp is also too high to be used on a locomotive installation.
A. Because the filament or light-producing wire inside the bulb isn't compact enough to reflect the light as a beam. The voltage of the house lamp is also too high to be used in a locomotive setup.
48. Q. How is the lamp held in place in the reflector?
48. Q. How is the lamp secured in the reflector?
A. By the usual socket, into which the lamp screws. The socket is a part of the focusing device, one type of which holds the lamp in a horizontal position, while in the other the lamp is held vertically or upright.
A. By the standard socket, into which the lamp screws. The socket is part of the focusing mechanism, one type of which keeps the lamp horizontal, while the other holds it vertically or upright.
49. Q. Before turning the steam into the turbine, what precautions should be observed?
49. Q. Before sending the steam to the turbine, what precautions should be taken?
A. The turbo-generator should be lubricated by a small amount of black or engine oil, placed in the cup on the turbine or steam end. On the generator end, the oil should be maintained within one-half inch of the top of the hinge-cover cup; using black oil.[Pg 138] The drainage of the steam end is cared for automatically by a three-eighth inch drain pipe without a valve. The pipe should be kept open.
A. The turbo-generator should be lubricated with a small amount of black or engine oil, placed in the cup on the turbine or steam end. On the generator end, the oil level should be kept within half an inch from the top of the hinge-cover cup, using black oil.[Pg 138] The steam end drainage is managed automatically by a three-eighth inch drain pipe without a valve. The pipe should remain open.
50. Q. How do you proceed when you wish to use the light?
50. Q. How do you go about using the light?
A. Open the globe valve in the steam pipe to the turbo-generator, at least two turns. The water-glass, steam and air gauge lamps in the cab, and the number indicator lamp in the headlight case should light up as soon as the turbo-generator reaches full speed. A double-throw knife switch in the cab controls the headlight. In one position the switch gives the full brilliancy of the headlight. The opposite or "dimmer" position reduces the brilliancy about one-half. When the switch bar is in neither position the headlight is entirely out, and only the number lamp is burning. The classification lamp, lubricator and order or reading lamp, are controlled by a small switch on the socket of each lamp.
A. Open the globe valve in the steam pipe to the turbo-generator at least two turns. The water gauge, steam and air gauge indicator lights in the cab, as well as the number indicator light in the headlight case, should turn on as soon as the turbo-generator reaches full speed. A double-throw knife switch in the cab controls the headlight. In one position, the switch provides full brightness for the headlight. The other position, or "dimmer" setting, reduces the brightness by about half. When the switch is in neither position, the headlight is completely off, and only the number light is on. The classification lamp, lubricator, and order or reading lamp are controlled by a small switch on the socket of each lamp.
51. Q. For what purpose is the dimmer, and how does it operate?
51. Q. What is the purpose of the dimmer, and how does it work?
A. It is to reduce the intensity of the headlight when locomotive is in yards or around stations. It consists of a small resistance tube in the wiring circuit, and with the cab switch in dimmer position, a portion of the current is converted into heat instead of light.
A. It is to lower the brightness of the headlight when the train is in yards or near stations. It includes a small resistance tube in the wiring circuit, and with the cab switch in the dimmer position, some of the current converts into heat instead of light.
52. Q. How is an incandescent headlight focussed?
52. Q. How is an incandescent headlight focused?
A. By moving the lamp in its position in the reflector until the most brilliant and compact beam of light is obtained. If the beam does not strike the track centrally, or as high or low, the headlight case must be moved on its platform until the beam is properly directed. It is often necessary to raise the front[Pg 139] or back of the case by shimming between the case and its platform in order to direct the beam of light the proper distance ahead of the locomotive.
A. By adjusting the lamp in its reflector until you achieve the brightest and most focused beam of light. If the beam isn’t hitting the track straight on, or is too high or low, the headlight case needs to be repositioned on its platform until the beam is correctly aimed. It’s often necessary to elevate the front[Pg 139] or back of the case by placing shims between the case and its platform to direct the beam of light the right distance in front of the locomotive.
53. Q. What provision is made for moving or focussing the lamp in the reflector?
53. Q. What arrangements are there for adjusting or positioning the lamp in the reflector?
A. When the lamp is mounted horizontally there are thumb screws by which the lamp may be moved sidewise, up and down, and forward and backward. This mounting is called the "micrometer" device, because of the accuracy of adjustment. With the vertical mounting, a flat head thumb screw at the base of the lamp support releases the ball joint so that the lamp may be easily moved sidewise or forward and backward. To raise or lower the lamp, the thumb screw higher on the lamp stand must be loosened.
A. When the lamp is mounted horizontally, there are thumb screws that allow the lamp to be moved side to side, up and down, and forward and backward. This setup is called the "micrometer" device due to its precise adjustment capabilities. With the vertical mounting, a flat head thumb screw at the base of the lamp support releases the ball joint, making it easy to move the lamp side to side or forward and backward. To raise or lower the lamp, you need to loosen the thumb screw higher up on the lamp stand.
54. Q. What causes a "black spot" in the illumination ahead of the locomotive?
54. Q. What causes a "black spot" in the light in front of the train?
A. The lamp is out of focus, being too far ahead or back of the proper position in the reflector.
A. The lamp is out of focus, positioned too far forward or back from the correct spot in the reflector.
55. Q. How would you remedy the following possible defects?
55. Q. How would you fix the following possible issues?
A. (a) All lamps fail to burn. If turbine is not running the wrong steam valve in the cab may have been opened, or there may be a second valve, closed, in the steam pipe. The screen on the governor valve in the turbine may be clogged. Remove brass cap at top of turbine and unscrew screen or strainer-cap.
A. (a) All lamps won’t turn on. If the turbine isn’t running, the wrong steam valve in the cab might have been opened, or there could be a second valve that’s closed in the steam pipe. The screen on the governor valve in the turbine might be blocked. Take off the brass cap at the top of the turbine and unscrew the screen or strainer cap.
(b) Turbo-generator runs, but no lights. Wires may be "short-circuited" (crossed) which will cause brushes to spark badly, and turbo-generator to pull hard. The "short" can usually be found by an occa[Pg 140]sional sparking or smoke at the point of trouble. Separate and protect wires when short is found. The brushes may be "cocked up" as left by some repair man. Open the dynamo door and see that the brushes bear on the copper commutator. A wire may be loose at the dynamo binding posts (which may be seen when the dynamo door is open), or at the main switch in the cab. A main wire may have broken. (All locomotives are not equipped with fuse plugs.) A fuse plug may have become loose or burnt out. Replace with new fuse plugs or break an incandescent lamp and twist the leads in the base together, when the base may be screwed into the fuse plug socket, answering the purpose of a fuse plug, temporarily.
(b) Turbo-generator is running, but there are no lights. The wires might be "short-circuited" (crossed), which can cause sparking at the brushes and make the turbo-generator work harder. You can usually find the "short" by watching for occasional sparking or smoke at the trouble spot. Separate and protect the wires when you find the short. The brushes might be "tilted up" as left by some technician. Open the dynamo door and check that the brushes make contact with the copper commutator. A wire could be loose at the dynamo binding posts (which you can see when the dynamo door is open) or at the main switch in the cab. A major wire might have broken. (Not all locomotives are equipped with fuse plugs.) A fuse plug may have come loose or burned out. Replace it with new fuse plugs or break an incandescent lamp and twist the leads in the base together; then, the base can be screwed into the fuse plug socket, temporarily serving as a fuse plug.
(c) Headlight fails to burn. Examine the wires between cab switch and head lamp for breaks or disconnections. Examine fuse plugs (which are sometimes in head lamp circuit only) and proceed as in (b) if trouble is found there. Headlight bulb may not be screwed in far enough to make contact in the socket, as the lock-sockets provided to prevent lamps loosening cause lamp to screw in hard. Lamp may have broken fillament. Replace with proper type of lamp or use a cab lamp.
(c) Headlight won't light up. Check the wires between the cab switch and the headlamp for any breaks or disconnections. Inspect the fuse plugs (which are sometimes only in the headlamp circuit) and follow the same steps as in (b) if you find any issues there. The headlight bulb might not be screwed in tight enough to connect in the socket, since the lock-sockets designed to keep the lamps secure can make them difficult to screw in. The bulb might also have a broken filament. Replace it with the correct type of bulb or use a cab lamp.
(d) Lamps burn dim. Steam valve not open wide enough. Boiler pressure too low. Brushes sparking badly on commutator of dynamo—due to poor contact. Governor or steam-valve of turbine improperly adjusted.
(d) Lamps are dim. The steam valve isn't opened wide enough. The boiler pressure is too low. The brushes are sparking badly on the commutator of the dynamo—this is due to poor contact. The governor or steam valve of the turbine is not adjusted properly.
(e) Lamps burn too brightly. Improper turbine regulation. Throttle the steam valve in cab until lamps are reduced to proper brilliancy. Report all irregularities on arriving at terminal.
(e) Lamps are too bright. There's an issue with turbine regulation. Adjust the steam valve in the cab until the lamps are at the right brightness. Report any irregularities upon arrival at the terminal.
1. Q. What is the speed of a Schroeder headlight dynamo?
1. Q. What’s the speed of a Schroeder headlight dynamo?
A. About 2,800 revolutions per minute.
About 2,800 RPM.
2. Q. How is the speed altered?
2. Q. How is the speed changed?
A. By a governor in the turbine.
A. By a governor in the turbine.
3. Q. How would you proceed to change the speed of the governor?
3. Q. How would you go about changing the speed of the governor?
A. Remove cover No. 3 and loosen lock nut No. 14 and turn nut No. 13 to the right to increase the speed and to the left to decrease it.
A. Remove cover No. 3 and loosen lock nut No. 14, then turn nut No. 13 to the right to speed it up and to the left to slow it down.
4. Q. What is a short circuit?
4. Q. What’s a short circuit?
A. A connection between the positive and negative wires of the dynamo without any resistance between.
A. A direct link between the positive and negative wires of the dynamo with no resistance in between.
5. Q. How does the dynamo act when short-circuited?
5. Q. What happens to the dynamo when it’s short-circuited?
A. It will run very slowly as it is under a heavy strain.
A. It will run very slowly because it's under a heavy strain.
6. Q. What would be the result if left to run under that strain?
6. Q. What would happen if it were allowed to continue under that pressure?
A. The armature or fields would burn out.
A. The armature or fields would fail.
7. Q. What would you do if a short circuit developed while on the road?
7. Q. What would you do if a short circuit happened while driving?
A. Shut the steam off and remove the positive or right-hand wire of the cab circuit from the dynamo, start up and see if the headlight went to work properly; if not, replace the cab wire and remove the positive or left-hand wire and see if the cab lights burned properly. If such was the case, let it run, using the small incandescent light in the case for a headlight and report it at the roundhouse.[Pg 142]
A. Turn off the steam and disconnect the positive or right-hand wire of the cab circuit from the dynamo, then start it up and check if the headlight works properly; if it doesn’t, reconnect the cab wire and disconnect the positive or left-hand wire to see if the cab lights are working. If they are, let it run, using the small incandescent light in the case for a headlight, and report it at the roundhouse.[Pg 142]
8. Q. What is a volt?
8. Q. What is a volt?
A. The unit of pressure of electricity.
A. The unit of electrical pressure.
9. Q. What is an ampere?
9. Q. What's an amp?
A. The unit of quantity of electricity.
A. The measurement of electrical quantity.
10. Q. What is the proper voltage of a Schroeder headlight?
10. Q. What is the correct voltage for a Schroeder headlight?
A. About 28 volts.
About 28 volts.
11. Q. Can a person be injured by that voltage?
11. Q. Can someone get hurt by that voltage?
A. No.
A. Nope.
12. Q. What is the proper amperage of a Schroeder headlight?
12. Q. What is the correct amperage for a Schroeder headlight?
A. About 30.
A. Around 30.
13. Q. How often should the ball bearings be oiled?
13. Q. How often should the ball bearings be oiled?
A. About three times a week.
A. About three times a week.
14. Q. How often should the governor be oiled?
14. Q. How often should the governor be lubricated?
A. Before leaving every trip.
A. Before leaving for every trip.
15. Q. What kind of oil should be used?
15. Q. What type of oil should be used?
A. Valve oil.
Valve oil.
16. Q. Is it necessary to clean the electrode every trip?
16. Q. Is it necessary to clean the electrode every time?
A. No.
A. No.
17. Q. Why?
17. Q. Why?
A. The dynamo is provided with shunt fields which build up the current regardless of the arc light.
A. The dynamo is equipped with shunt fields that generate the current independently of the arc light.
18. Q. What are the two causes of lamp burning green?
18. Q. What are the two reasons the lamp burns green?
A. Speed too high, or wires to the lamp being reversed.[Pg 143]
A. Speed is too high, or the wires to the lamp are reversed.[Pg 143]
19. Q. If the carbons burned away too fast, but otherwise the lamp appeared to be burning properly, where would you look for the trouble?
19. Q. If the carbons are burning out too quickly, but the lamp seems to be functioning properly otherwise, where would you check for the issue?
A. It would indicate that tripping spring No. 209 was too tight.
A. It would suggest that tripping spring No. 209 was too tight.
20. Q. If tripping spring No. 209 was being annealed from heat and sparks were noticed at the clutch, where would you look for the trouble?
20. Q. If tripping spring No. 209 was being heated and sparks were seen at the clutch, where would you check for the issue?
A. Flexible wire No. 251 would be broken.
A. Flexible wire No. 251 would break.
1. Q. What are the three essential elements in the "Buda-Ross" electric headlight equipment?
1. Q. What are the three key components in the "Buda-Ross" electric headlight setup?
A. Steam turbine engine, dynamo directly connected on the same shaft, and self-focusing arc lamp.
A. Steam turbine engine, dynamo directly connected on the same shaft, and self-focusing arc lamp.
2. Q. At what speed should the turbine run?
2. Q. At what speed should the turbine operate?
A. 2,800 revolutions per minute.
2,800 RPM.
3. Q. How is the speed controlled?
3. Q. How is the speed regulated?
A. By a centrifugal governing device.
A. By a centrifugal control mechanism.
4. Q. How does the steam enter the turbine?
4. Q. How does the steam get into the turbine?
A. Through a main valve which is perfectly balanced in all steam pressures directly and impinged on the buckets directly from a nozzle.
A. Through a main valve that is perfectly balanced in all steam pressures, which directly impacts the buckets from a nozzle.
5. Q. About how much opening should this valve have?
5. Q. How much should this valve be opened?
6. Q. Can the lift of this valve be changed?
6. Q. Can the lift of this valve be adjusted?
A. Yes.
A. Yeah.
7. Q. How?
7. Q. How?
A. By adjusting the inner sleeve of the valve with a common monkey wrench after removing cap nut on top of turbine.
A. By adjusting the inner sleeve of the valve with a regular monkey wrench after taking off the cap nut on top of the turbine.
8. Q. Can this be done while the light is burning?
8. Q. Can this be done while the light is on?
A. Yes.
Yes.
9. Q. What is necessary to do this?
9. Q. What do you need to do this?
A. Take a monkey wrench and screw the inner sleeve down to the right to reduce the lift, and to the left to increase the lift. In reducing the lift you reduce the speed, and by increasing the lift you increase the speed.
A. Use a monkey wrench to turn the inner sleeve down to the right to lower the lift, and to the left to raise the lift. Lowering the lift decreases the speed, while raising the lift increases the speed.
10. Q. Is there any other method of setting speed?
10. Q. Is there any other way to set the speed?
A. Yes.
A. Yes.
11. Q. How?
11. Q. How?
A. By removing oil box on the turbine cap and adjusting the nuts on the governor studs on the face of wheel.
A. By taking off the oil box on the turbine cap and adjusting the nuts on the governor studs on the front of the wheel.
12. Q. Is any provision made for operating the light with low pressure steam?
12. Q. Is there any setup for running the light using low-pressure steam?
A. Yes.
Yes.
13. Q. What?
What?
A. An auxiliary valve is used which operates automatically at any predetermined pressure, which is adjusted by an adjusting stem at the bottom of the engine and which can also be adjusted while the light is burning.[Pg 145]
A. An auxiliary valve is used that automatically operates at a specific pressure, which can be adjusted using a stem at the bottom of the engine and can also be modified while the light is on.[Pg 145]
14. Q. What kind of oil should be used in the "Buda-Ross" bearings?
14. Q. What type of oil should be used in the "Buda-Ross" bearings?
A. Cylinder or valve oil.
A. Cylinder or valve oil.
15. Q. What style of generator is used.
15. Q. What type of generator is used?
A. An iron-clad type with no outside magnetism.
A. A solid type with no external magnetism.
16. Q. How many fields in this generator?
16. Q. How many fields does this generator have?
A. Two.
Two.
17. Q. What style field is used?
17. Q. What style field is used?
A. Compound wound.
A. Compound fracture.
18. Q. What kind of wire is used on these fields?
18. Q. What type of wire is used in these fields?
A. Deltabeston wire.
Deltabeston wire.
19. Q. Why is Deltabeston wire used in preference to cotton-covered wire?
19. Q. Why is Deltabeston wire preferred over cotton-covered wire?
A. So that it cannot be injured by short circuits, for if a short circuit occurs and afterwards is removed there is no danger done to the insulation on this make of wire.
A. So that it can't be damaged by short circuits, because if a short circuit happens and is then fixed, there’s no harm done to the insulation on this type of wire.
20. Q. Where are the fields located?
20. Q. Where are the fields situated?
A. One on each side of the dynamo.
A. One on each side of the generator.
21. Q. Why?
21. Q. Why?
A. So that they cannot be injured by waste oil from the ball bearing, or by water or snow.
A. So that they can’t be harmed by waste oil from the ball bearing, or by water or snow.
22. Q. How should ball bearing on dynamo end be lubricated?
22. Q. How should the ball bearing at the end of the dynamo be lubricated?
A. By removing oil plug in frame just back of dynamo and introducing cylinder oil.[Pg 146]
A. By taking out the oil plug in the frame just behind the dynamo and adding cylinder oil.[Pg 146]
23. Q. Is it necessary to remove the top carbon holder from the lamp to remove reflector from case?
23. Q. Do you need to take off the top carbon holder from the lamp to take the reflector out of the case?
A. No.
A. No.
24. Q. Why not?
24. Q. Why not?
A. Because there is no top guide to the carbon, as the carbon is guided by the clutches.
A. Because there isn't a top guide for the carbon, it is guided by the clutches.
25. Q. How many levers are there in the lamp?
25. Q. How many switches are there in the lamp?
A. Only one.
Just one.
26. Q. What regulation should be given to top lever spring No. 308 on lamp?
26. Q. What adjustment should be made to the top lever spring No. 308 on the lamp?
A. Top lever spring No. 308 should be adjusted as loose as possible and not have light go out standing still.
A. Top lever spring No. 308 should be adjusted as loosely as possible and should not cause the light to go out when it’s standing still.
27. Q. If this spring was tightened until the light burned steady when the locomotive was at rest, what might occur when engine was running high speed?
27. Q. If this spring was tightened so that the light burned steadily when the locomotive was stopped, what might happen when the engine was running at high speed?
A. It might cause the light to dim down.
A. It might make the light dim.
28. Q. Is there anything else that would cause the light to dim down when the engine is running fast?
28. Q. Is there anything else that could cause the light to dim while the engine is running fast?
A. If the clutches should be used until the sharp edge that grips the carbon have become worn smooth or round they would allow the carbon to feed too fast and the light would burn dim.
A. If the clutches are used until the sharp edge that grips the carbon becomes worn smooth or round, they would let the carbon feed too quickly, causing the light to burn dim.
29. Q. If the light burns satisfactory while engine is in motion, but goes out when engine is stopped, where would you find the trouble?
29. Q. If the light works fine while the engine is running, but turns off when the engine stops, where would you look for the problem?
A. This trouble is most always found to be caused by the top lever springs No. 308 being too weak; or, an imperfect carbon, though if the dash pot plunger[Pg 147] has become corroded until it sticks in the dash pot, the light will act the same as if the tension spring was too weak.
A. This issue is usually due to the top lever springs No. 308 being too weak, or a faulty carbon. However, if the dash pot plunger[Pg 147] has corroded and is sticking in the dash pot, the light will behave just like it would if the tension spring were weak.
30. Q. Is it possible to apply the bottom electrode holder wrong?
30. Q. Can the bottom electrode holder be installed incorrectly?
A. No
A. No
31. Q. Why not?
31. Q. Why not?
A. For the reason that its support is on a center line with the electrode and the holder can be turned in any direction and the electrode is held central with the top carbon.
A. Because its support is aligned with the center line of the electrode, the holder can be rotated in any direction, and the electrode is kept centered with the top carbon.
32. Q. What would you do if you had no bottom electrode holder?
32. Q. What would you do if you didn’t have a bottom electrode holder?
A. Place a piece of 5/8-inch carbon in the hole through the bottom bracket having top end in focal point of reflector and tighten with set-screw; as this carbon would burn away the light would be raised and it would therefore be necessary to raise the carbon about every hour, as the carbon would burn away about one-half inch per hour.
A. Put a 5/8-inch carbon rod into the hole at the bottom bracket, making sure the top end is at the focal point of the reflector, and tighten it with a set screw. Since this carbon will burn away, you'll need to raise it about every hour, as it will burn down about half an inch each hour.
GENERAL QUESTIONS AND ANSWERS ON ELECTRIC HEADLIGHTS
GENERAL QUESTIONS AND ANSWERS ABOUT ELECTRIC HEADLIGHTS
33. Q. Describe the passage of the current through the lamp and tell how arc light is formed?
33. Q. Explain how electricity flows through the lamp and how arc light is created?
A. It enters the lamp at the binding posts with the large hole, then to the top carbon holder, carbon, then into the electrode and holder; from there to the solenoid and back to the dynamo, leaving the lamp at the binding post with the small hole in it. The[Pg 148] magnetism from the current while passing through the solenoid attracts magnet in a downward motion, and it in turn, by the levers on the lamp, separate the carbon from the copper, thereby forming the arc.
A. It enters the lamp at the binding posts with the large hole, then goes to the top carbon holder, carbon, and then into the electrode and holder; from there, it moves to the solenoid and back to the dynamo, exiting the lamp at the binding post with the small hole. The[Pg 148] magnetism from the current, while passing through the solenoid, attracts the magnet downward, and this action, through the levers on the lamp, separates the carbon from the copper, thus creating the arc.
34. Q. Why should sandpaper be used to smooth commutator instead of emery cloth?
34. Q. Why should sandpaper be used to smooth the commutator instead of emery cloth?
A. In using emery paper a piece of emery might lodge in the grooves between the commutator segments, and being a conductor of electricity, causes short. Will also get embedded in the copper and cut the brushes. Sand will not do this.
A. When using emery paper, a piece of emery can get stuck in the grooves between the commutator segments, and since it conducts electricity, it can cause a short circuit. It can also embed itself in the copper and damage the brushes. Sand won't cause this issue.
35. Q. State how you would go about to focus a lamp?
35. Q. Describe how you would focus a lamp.
A. (1) Would adjust back of reflector so front edge of reflector would be parallel with front edge of case. (2) Adjust lamp to have point of copper electrode as near the center of reflector as possible with carbons as near the center of chimney hole as you can set them. (3) Have the locomotive on straight track. Now move the base of the lamp around until you get a parallel beam of white light straight down the center of the track, then tighten lamp down.
A. (1) Adjust the back of the reflector so that the front edge of the reflector is parallel with the front edge of the case. (2) Position the lamp so that the tip of the copper electrode is as close to the center of the reflector as possible, with the carbon rods as centered in the chimney hole as you can manage. (3) Place the locomotive on straight track. Then, move the base of the lamp until you get a parallel beam of white light shining straight down the center of the track, and then secure the lamp in place.
36. Q. If the light throws shadows upon the track, is it properly focused?
36. Q. If the light casts shadows on the track, is it properly focused?
A. No.
A. No.
37. Q. If the light is properly focused, that is, if the rays are leaving the reflector in parallel lines, but the light does not strike the center of the track, what should be done?
37. Q. If the light is focused correctly, meaning the rays are coming from the reflector in parallel lines, but the light isn't hitting the center of the track, what should be done?
A. When the light rays are thrown out in parallel lines and they do not strike the center of the track,[Pg 149] it denotes that the headlight case is not set straight with the engine, and the entire case on baseboard must be shifted until the shaft of light strikes the track as desired.
A. When the light rays are emitted in parallel lines and they do not hit the center of the track,[Pg 149] it indicates that the headlight casing is not aligned with the engine. The entire casing on the baseboard needs to be adjusted until the beam of light hits the track as intended.
38. Q. What can you do to insure a good and unfailing light for the entire trip?
38. Q. What can you do to ensure a good and reliable light for the whole trip?
A. By carefully inspecting the entire equipment before departing on each trip and know that there are no wires with insulation chafed or worn off; that all screws and connections are tight; commutator clean; brushes set in brush holder in the proper manner; carbon in lamp of sufficient length to complete trip; copper electrode cleaned off and oil in both bearings.
A. By thoroughly checking all the equipment before leaving on each trip, make sure there are no wires with frayed or worn insulation; that all screws and connections are secure; the commutator is clean; brushes are correctly positioned in the brush holder; the carbon in the lamp is long enough to last the trip; and the copper electrode is clean and there’s oil in both bearings.
39. Q. Why would you not fill the main oil cellar full of oil?
39. Q. Why wouldn’t you fill the main oil cellar all the way up with oil?
A. If you should fill the main oil cellar full of oil, the oil would run out of the overflow holes on the side and all over the equipment and locomotive and could do the dynamo no good but possibly harm.
A. If you fill the main oil cellar to the top with oil, the oil will spill out of the overflow holes on the side and all over the equipment and locomotive, which could damage the dynamo instead of helping it.
40. Q. What is the most vital part of the dynamo?
40. Q. What is the most essential part of the dynamo?
A. The commutator.
A. The commutator.
41. Q. What care and attention should be given the commutator?
41. Q. What care and attention should be given to the commutator?
A. The commutator must be kept clean, free from dirt and grease; the mica must be kept filed down about one-sixty-fourth of an inch below the surface of the bars.
A. The commutator needs to be kept clean, free from dirt and grease; the mica should be filed down about one-sixty-fourth of an inch below the surface of the bars.
42. Q. How should you clean the commutator, and when?
42. Q. How do you clean the commutator, and when should you do it?
A. The commutator should be cleaned before[Pg 150] starting out on each trip by using a piece of damp waste, rubbing the bars lengthwise, then wipe dry with clean dry piece of waste.
A. The commutator should be cleaned before[Pg 150] starting each trip by using a damp cloth, rubbing the bars along their length, and then wiping them dry with a clean, dry cloth.
43. Q. What kind of a bearing should the brush have on the commutator?
43. Q. What kind of contact should the brush have with the commutator?
A. Brushes should be fitted to have a bearing with the same contour as the commutator, with bearing covering no less than two of the commutator bars, nor more than three of the bars.
A. Brushes should be designed to have a bearing that matches the shape of the commutator, covering at least two of the commutator bars and no more than three of the bars.
44. Q. How are the brushes fitted?
44. Q. How are the brushes attached?
A. Brushes are fitted by cutting a strip of No. O sandpaper about the width of the commutator surface. (Have the dynamo idle.) Place the strip of sandpaper under the brush on the commutator with the rough side towards the brush, then pull the sandpaper from right to left; continue this process until the brush has been fitted to a true smooth bearing. Then trim about one-eighth of an inch off the front edge of the brush.
A. Brushes are adjusted by cutting a strip of No. O sandpaper about the same width as the commutator surface. (Keep the dynamo running idle.) Place the strip of sandpaper under the brush on the commutator with the rough side facing the brush, then pull the sandpaper from right to left; keep doing this until the brush fits a completely smooth surface. Then trim about one-eighth of an inch off the front edge of the brush.
45. Q. Is it advisable to ever try to fit a brush up with a file or knife?
45. Q. Is it ever a good idea to try to use a brush with a file or knife?
A. No.
A. No.
46. Q. Why is it important to clean the scale off the point of the copper electrode each trip?
46. Q. Why is it important to remove the scale from the tip of the copper electrode every time?
A. To allow the point of the carbon and the electrode to touch to form a circuit; this scale being a non-conductor of electricity and with it on, the current would not pass from the carbon to the electrode and holder.
A. To let the carbon point and the electrode touch to create a circuit; since this scale doesn't conduct electricity, with it in place, the current won't flow from the carbon to the electrode and holder.
47. Q. How should the copper electrode be trimmed at the point?[Pg 151]
47. Q. How should you trim the copper electrode at the tip?[Pg 151]
A. Copper electrode should have about ¼-inch surface at contact point.
A. The copper electrode should have about a ¼-inch surface at the contact point.
48. Q. How far should the copper electrode project above the holder?
48. Q. How far should the copper electrode stick out above the holder?
A. One inch.
One inch.
49. Q. Should the electrode be raised up to 1½ inches, what might happen?
49. Q. If the electrode is raised to 1½ inches, what could happen?
A. If the copper electrode was run at a point so near the clutch, the intense heat of the arc might do damage to the top carbon holder and clutch.
A. If the copper electrode was operated very close to the clutch, the intense heat from the arc could potentially damage the top carbon holder and the clutch.
50. Q. If the dash pot should be found stuck, would you put oil in it?
50. Q. If the dash pot is stuck, would you add oil to it?
A. Coal oil should be used to clean and cut the dirt out of the pot and from off the plunger, but after the dash pot and plunger have been cleaned all oil should be wiped off of same, as the oil would cause the plunger to collect dirt and stick.
A. Coal oil should be used to clean the dirt out of the pot and off the plunger, but after cleaning the dash pot and plunger, all oil should be wiped off, as the oil would cause the plunger to attract dirt and become stuck.
51. Q. If one carbon of lamp should "jig or pound", what can be done to stop it?
51. Q. If one carbon of the lamp starts to "jig or pound", what can be done to fix it?
A. If the carbon jumps or pounds the electrode, it is evident that the iron armature is too far out of the solenoid, or the speed is too low.
A. If the carbon hits or strikes the electrode, it is clear that the iron armature is too far out of the solenoid, or the speed is too low.
52. Q. Does the pounding of the lamp occur with the old series wound machines or with the new compound wound machines?
52. Q. Does the flickering of the lamp happen with the old series-wound machines or with the new compound-wound machines?
A. The pounding of the lamp occurs with the new compound wound machines.
A. The banging of the lamp happens with the new compound wound machines.
53. Q. If the copper electrode was fusing, how would you know it?
53. Q. How would you know if the copper electrode was melting?
A. By the fact, when copper is fused a shaft of[Pg 152] green light will be thrown off instead of a shaft of white light.
A. In fact, when copper is melted, it emits a beam of[Pg 152] green light instead of a beam of white light.
54. Q. What should be done when a green light is seen?
54. Q. What should you do when you see a green light?
A. Close the throttle to turbine engine, then open slowly until a white light re-appears.
A. Close the throttle on the turbine engine, then open it slowly until a white light reappears.
55. Q. What is the cause of the copper electrode fusing?
55. Q. What causes the copper electrode to fuse?
A. The cause of the copper electrode fusing is due to too high speed of the generator, or having lead wires connected up wrong, allowing positive current to get into copper electrode first.
A. The reason the copper electrode is fusing is because the generator is running too fast, or the lead wires are connected incorrectly, causing the positive current to flow into the copper electrode first.
56. Q. What arrangements have been made so that you cannot connect your wires wrong?
56. Q. What arrangements have been made to ensure you can't connect your wires incorrectly?
A. The positive binding post both at the dynamo and lamp have been provided with a much larger hole to receive the wire than has been made in the negative binding post, and the ends of the positive wire should always be bent or doubled back so they will just enter the receptacle in the positive binding posts, but cannot be connected to the negative binding post.
A. The positive binding post at both the dynamo and the lamp has a much larger hole for the wire than the negative binding post. The ends of the positive wire should always be bent or doubled back so they fit into the positive binding posts but can't connect to the negative binding post.
57. Q. Should the copper electrode and holder become fused until no longer serviceable out on the road, what would you do?
57. Q. If the copper electrode and holder get stuck together and are no longer usable while you're out on the road, what would you do?
A. Would remove the damaged holder from the lamp and substitute a carbon, securing the substituted electrode in the bracket of lamp same as the electrode holder is held. Be sure that the end of the carbon comes up to center of reflector and does not rest on base of reflector or lamp.[Pg 153]
A. Remove the damaged holder from the lamp and replace it with a carbon element, securing the new electrode in the lamp's bracket just like the original holder was held. Ensure that the end of the carbon aligns with the center of the reflector and doesn't touch the base of the reflector or lamp.[Pg 153]
58. Q. If you were running along with your light burning steady and nice, then suddenly the light began to flash badly and kept it up, where would you look for the trouble?
58. Q. If you were running with your light shining steadily and brightly, and then suddenly the light started to flicker badly and continued to do so, where would you look for the problem?
A. You would no doubt find one of the lead wires loose in binding post.
A. You would probably find one of the lead wires loose in the binding post.
59. Q. If you were running along with light burning satisfactorily and suddenly your light went out, where would you be likely to find the trouble?
59. Q. If you were running with your light working well and suddenly it went out, where would you probably look for the problem?
A. You would undoubtedly find carbon burned out, or a lead wire was broken off or out of the binding posts.
A. You would probably find that the carbon was burned out, or a lead wire was broken off or removed from the binding posts.
60. Q. If the light goes out while between stations, what course would an engineer pursue?
60. Q. If the light goes out while between stations, what steps should an engineer take?
A. If investigation cannot be made within a few minutes thereafter to determine the cause, the steam should be shut off from the turbine engine until such time when cause of failure can be determined.
A. If an investigation cannot be conducted within a few minutes to determine the cause, the steam should be turned off from the turbine engine until the cause of the failure can be identified.
61. Q. Why is it essential to shut off steam and stop the equipment?
61. Q. Why is it important to turn off the steam and stop the equipment?
A. If failure was due to a short circuit, damage might be done to the armature or field coils by overheating.
A. If the failure was caused by a short circuit, it could lead to damage to the armature or field coils due to overheating.
62. Q. How does the equipment act when short circuited?
62. Q. What happens to the equipment when it's short-circuited?
A. The engine will labor heavily and run slowly with a large volume of steam blowing at the exhaust, the carbon points and cab lights will only show a dull red light.
A. The engine will struggle and run slowly, with a lot of steam coming out of the exhaust, and the carbon points and cab lights will emit only a dim red light.
63. Q. How would you test for a broken circuit?
63. Q. How would you check for a broken circuit?
A. Would test for a broken circuit or open circuit: First, by placing a carbon across the binding posts at[Pg 154] dynamo. If the trouble was in the dynamo, no flash would be seen, but if dynamo was all right you would get a flash; this would indicate that the trouble was on towards the lamp. Second: Go to the lamp, place your carbon across binding posts. If wire was broken between dynamo and lamp you would not get a flash. If your wires were all right you would get a flash and you would find your trouble in the lamp. No doubt, it would be a burned-out carbon.
A. Would test for a broken circuit or open circuit: First, place a carbon across the binding posts at[Pg 154] the dynamo. If there’s an issue with the dynamo, you won't see a flash, but if the dynamo is working fine, you’ll see a flash; this indicates the problem is further along toward the lamp. Second: Go to the lamp and place your carbon across the binding posts. If there’s a broken wire between the dynamo and the lamp, you won’t see a flash. If your wires are intact, you’ll see a flash, and the issue will be with the lamp. Most likely, it will be a burned-out carbon.
64. Q. How would you proceed to locate the point of trouble with a short circuit?
64. Q. How would you go about finding the problem with a short circuit?
A. Would remove (1) one of the lead wires from the binding post at dynamo; if trouble was in dynamo you would not note any difference in action of speed. (2) Would disconnect one of the cab wires; if the trouble is in cab circuit, speed would increase and lamp would burn. (3) If trouble is not in cab circuit, would go to lamp, disconnect one of the main wires from binding post; if short circuit is in the wires between dynamo and lamp, there would be no change in speed of dynamo, but if the wires are O. K. the speed of engine would increase and your trouble would be in the lamp.
A. (1) Remove one of the lead wires from the binding post at the dynamo; if there's an issue with the dynamo, you won't see any change in speed. (2) Disconnect one of the cab wires; if the problem is in the cab circuit, the speed will increase and the lamp will light up. (3) If the problem isn't in the cab circuit, go to the lamp and disconnect one of the main wires from the binding post; if there's a short circuit in the wires between the dynamo and the lamp, the speed of the dynamo won't change, but if the wires are fine, the engine speed will increase and the issue will be with the lamp.
1. Q. Of what does the driving mechanism of a Duplex Locomotive Stoker consist?
1. Q. What is the driving mechanism of a Duplex Locomotive Stoker made up of?
A. It consists of a steam cylinder with reverse head and valve arrangement similar to the steam end of an eleven inch Westinghouse air pump.
A. It includes a steam cylinder with a reverse head and valve setup similar to the steam section of an eleven-inch Westinghouse air pump.
2. Q. How is the power controlled?
2. Q. How is the power managed?
A. The speed is variable, and by turning the valve controlling the engine steam inlet, can be made greater or less according to the amount of coal needed.[Pg 155]
A. The speed can change, and by adjusting the valve that controls the steam intake for the engine, it can be increased or decreased based on the amount of coal required.[Pg 155]
3. Q. For ordinary operation, how much steam pressure is required?
3. Q. For regular operation, what steam pressure is needed?
A. About fifteen pounds, with piston strokes varying from 10 to 15 per minute.
A. About fifteen pounds, with piston strokes varying from 10 to 15 per minute.
4. Q. How can the duplex stoker driving engine be started, stopped, or reversed?
4. Q. How can you start, stop, or reverse the duplex stoker driving engine?
A. By means of operating and reversing rod, fastened to the back head and connected with the valve on reverse head of engine cylinder.
A. Using an operating and reversing rod, attached to the back head and connected to the valve on the reverse head of the engine cylinder.
5. Q. How can the conveying screws be started, stopped, or reversed separately or together?
5. Q. How can the conveying screws be turned on, off, or reversed individually or at the same time?
A. By ratchet and pawl arrangement controlling each.
A. By a ratchet and pawl system controlling each.
6. Q. What practice should be followed in building up the fire before leaving a terminal?
6. Q. What steps should be taken to properly build up the fire before leaving a terminal?
A. Build up a light even fire by hand and do not bring stoker into use until the locomotive is working steam.
A. Build a steady, even fire by hand, and only use the stoker once the locomotive is producing steam.
7. Q. How should the stoker be oiled and operated?
7. Q. How should the stoker be lubricated and used?
A. It should be thoroughly oiled before leaving the terminal, then see that operating rod on back head is in center or running position, open main jet line so they register about fifteen pounds on the jet steam gauge if coal is coarse, or ten pounds if coal is small. Next, the driving engine steam valve should be opened wide and the throttle valve opened just enough to supply the proper amount of coal to the fire-box.
A. It should be well oiled before leaving the terminal, then make sure the operating rod on the back head is in the center or running position, open the main jet line so they register about fifteen pounds on the jet steam gauge if the coal is coarse, or ten pounds if the coal is small. Next, the driving engine steam valve should be fully opened and the throttle valve opened just enough to provide the right amount of coal to the firebox.
8. Q. How is the distribution of coal over the grate area accomplished?
8. Q. How is coal distributed across the grate area?
[Pg 156] A. By means of a low-pressure constant steam jet located in the back and bottom portion of each distributor elbow, as indicated by its individual pointer on steam gauge.
[Pg 156] A. Using a low-pressure constant steam jet located at the back and bottom of each distributor elbow, as shown by its individual pointer on the steam gauge.
9. Q. By increasing the jet pressure, will more coal be carried to forward end of fire-box and against the flue-sheet?
9. Q. If we increase the jet pressure, will more coal be pushed to the front of the firebox and against the flue sheet?
A. Yes, it will, and by decreasing the jet pressure more coal will be fed at middle and back end of fire-box.
A. Yes, it will, and by reducing the jet pressure, more coal will be supplied at the middle and back end of the firebox.
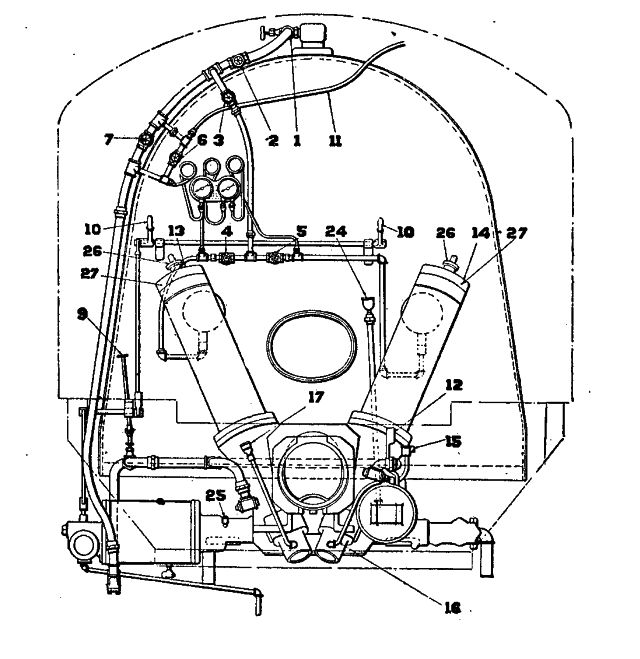
[Pg 157]10. Q. Can the fireman direct the even distribution of coal in the fire-box?
[Pg 157]10. Q. Can the firefighter ensure the coal is evenly spread in the firebox?
A. Yes; by changing position of the dividing rib located in the transfer hopper, and by moving the regulating lever to either side.
A. Yes; by adjusting the position of the dividing rib in the transfer hopper and by shifting the regulating lever to either side.
11. Q. Should the sliding plates at the bottom of the tank be closed before coal is put on tank?
11. Q. Should the sliding plates at the bottom of the tank be closed before adding coal to the tank?
A. Yes, so that screw conveyor will not become clogged and inoperative. Only one slide should be opened at a time and coal fed from tank as required.
A. Yes, this way the screw conveyor won't get clogged and stop working. Only one slide should be opened at a time, and coal should be fed from the tank as needed.
12. Q. In case the stoker becomes clogged or it is desired to reverse it for any reason, what must be done?
12. Q. If the stoker gets clogged or needs to be reversed for any reason, what should be done?
A. The operating rod located on the back-head of the locomotive boiler—if the piston is making a power stroke—should be moved to its lower position, and if the piston is making a return stroke, it should be moved to its upper position. This moves a small valve in the auxiliary head, bolted to reverse head, and steam is admitted to opposite head of cylinder, causing the piston to change its direction. The return of the operating rod handle to a central position causes the driving engine to resume its normal operation.
A. The operating rod at the back of the locomotive boiler—when the piston is pushing power—should be moved to its lower position, and when the piston is pulling back, it should be moved to its upper position. This action adjusts a small valve in the auxiliary head, attached to the reverse head, allowing steam to enter the opposite side of the cylinder, which changes the direction of the piston. Returning the operating rod handle to a central position lets the driving engine go back to its normal operation.
13. Q. How can the fireman observe the condition of fire in fire-box?
13. Q. How can the firefighter check the condition of the fire in the firebox?
A. The elbows are provided with peep valves with swinging covers through which the coal supply and condition of fire may be seen.
A. The elbows have peep valves with swinging covers that allow you to see the coal supply and the condition of the fire.
14. Q. Why are two gauges necessary?
14. Q. Why do we need two gauges?
[Pg 159]>A. The driving engine gauge on the left indicates the pressure of steam used by the driving engine. The one on the right has two indicators, the red indicator showing the steam pressure on the jet in left elbow, and the black indicator showing the pressure on the jet in the right elbow.
[Pg 159]>A. The engine gauge on the left shows the steam pressure used by the engine. The one on the right has two indicators: the red one shows the steam pressure on the left elbow's jet, and the black one shows the pressure on the right elbow's jet.
15. Q. When train is standing on siding for a short period, what should be done?
15. Q. When a train is stopped on a siding for a short time, what should be done?
A. Shut stoker off by throwing operating rod on back head of locomotive boiler out of running position.
A. Turn off the stoker by moving the operating rod on the back head of the locomotive boiler out of the running position.
16. Q. When train is to stand for a long time or engine is left at terminal, what should be done?
16. Q. When a train needs to stop for a long time or the engine is left at the terminal, what should be done?
A. The driving engine should be cut out entirely by closing main steam line inlet and main lubricator connection, and in winter time all drain cocks should be opened.
A. The driving engine should be completely shut down by closing the main steam line inlet and the main lubricator connection, and during winter, all drain cocks should be opened.
17. Q. If sufficient coal can not be supplied over front grates, what may be the cause?
17. Q. If enough coal can't be provided over front grates, what could be the reason?
A. Distributors may be warped and point too low, or steam jets may be plugged with pipe scale and not blowing freely.
A. Distributors may be misaligned and set too low, or steam jets might be blocked by pipe scale and not functioning properly.
18. Q. How would you start and operate stoker?
18. Q. How would you start and run a stoker?
A. First open main valve No. 1 at steam turret. Valve 2 is then opened; this is the main valve in stoker steam line. Next open valve 3, which allows the steam to flow to the distributor jet line; open valves 4 and 5, which govern the pressure on the jets until ten pound pressure shows on the right-hand gauge. See valve 8 to the exhaust line is open, and valve 9 to the transfer hopper is closed.[Pg 160]
A. First, open main valve No. 1 at the steam turret. Then, open valve 2; this is the main valve in the stoker steam line. Next, open valve 3, which allows the steam to flow to the distributor jet line; open valves 4 and 5, which control the pressure on the jets until ten pounds of pressure is displayed on the right-hand gauge. Ensure that valve 8 to the exhaust line is open, and valve 9 to the transfer hopper is closed.[Pg 160]
19. Q. How would you start the stoker engine?
19. Q. How do you start the stoker engine?
A. Place operating lever 10 in horizontal or running position. Place conveyor reversing lever 12 in forward position. Open valve 6, which allows the steam to pass to the operating valve and starts stoker running. Valve 7 is to be used as an emergency valve only in case of clogging. Stoker should be run slowly at first. Do not feed too much coal and carry a light fire.
A. Put the operating lever 10 in the horizontal or running position. Set the conveyor reversing lever 12 to forward. Open valve 6 to let the steam flow to the operating valve and start the stoker. Use valve 7 only in case of an emergency or if there's a clog. Start the stoker slowly at first. Don’t add too much coal and maintain a light fire.
20. Q. How would you reverse conveyor screw in tank?
20. Q. How would you reverse the conveyor screw in the tank?
A. Lower handle 10 on operation rod on boiler head to bottom position. Move screw conveyor, reverse lever 12 back to rear or reverse position, raise handle 10 on operating rod to center position.
A. Lower handle 10 on the operation rod of the boiler head to the lowest position. Move the screw conveyor by shifting the reverse lever 12 to the rear or reverse position, then raise handle 10 on the operating rod to the center position.
21. Q. How would you stop conveyor screw in tank?
21. Q. How would you stop the conveyor screw in the tank?
A. Place conveyor reversing lever 12 in center position.
A. Move conveyor reversing lever 12 to the center position.
22. Q. How would you reverse right or left elevator screw?
22. Q. How do you reverse the right or left elevator screw?
A. Raise elevator pawl shifter 26 on top of the vertical shaft to upper position.
A. Raise elevator pawl shifter 26 on top of the vertical shaft to the upper position.
23. Q. How would you stop right or left elevator screw?
23. Q. How would you stop the right or left elevator screw?
A. Raise elevator pawl shifter 26 on top of the elevator to middle position.
A. Raise elevator pawl shifter 26 on top of the elevator to the middle position.
24. Q. How would you locate clogs in case the stoker stalls?[Pg 161]
24. Q. How would you find clogs if the stoker stops working?[Pg 161]
A. First, shut off pressure to stoker engine cylinder by closing valve 6. Second, move operating valve lever 10 to its lowest position. Third, place tender conveyor reverse lever 12 in center. Fourth, place right elevator pawl shifter 26 in neutral position. Fifth, raise operating valve lever 10 to center position. Sixth, open valve 6 sufficiently to run left elevator to ascertain if it operates freely. Cut in right elevator by lowering pawl shifter 26, and if stoker stops, the obstruction is in the right elevator. If it continues to operate, then the obstruction is in the tank conveyor.
A. First, turn off the pressure to the stoker engine cylinder by closing valve 6. Second, move the operating valve lever 10 to its lowest position. Third, set the tender conveyor reverse lever 12 to the center position. Fourth, put the right elevator pawl shifter 26 in the neutral position. Fifth, raise the operating valve lever 10 to the center position. Sixth, open valve 6 enough to run the left elevator to check if it operates smoothly. Engage the right elevator by lowering the pawl shifter 26, and if the stoker stops, the obstruction is in the right elevator. If it keeps running, then the blockage is in the tank conveyor.
25. Q. How would you remove clogs?
25. Q. How do you unclog something?
A. Clogs in upright elevators usually occur at the bottom. Raise the door in the engine deck and remove the obstruction if in the elevator, reverse the elevator screw forcing the obstruction back down in transfer hopper. It may be a small mine spike lodged above this point, and by removing the nut at top of elevator casing and removing the door the obstruction can be easily removed.
A. Clogs in upright elevators typically happen at the bottom. Open the door on the engine deck and clear the blockage if it's in the elevator. Reverse the elevator screw to push the blockage back down into the transfer hopper. It could be a small mine spike stuck above this spot, and by taking off the nut at the top of the elevator casing and removing the door, you can easily take out the blockage.
26. Q. If the clog is in the tank conveyor, how would it be removed?
26. Q. If there's a blockage in the tank conveyor, how would it be removed?
A. The clog will usually be found in the crushing zone. Reverse the tank conveyor screw, forcing the obstruction back, when it can be removed from the trough.
A. The clog will usually be found in the crushing zone. Reverse the tank conveyor screw to push the obstruction back, allowing it to be removed from the trough.
27. Q. How far should the conveyor screw be run backwards?
27. Q. How far should the conveyor screw be run in reverse?
A. Not more than three revolutions.
A. No more than three revolutions.
[Pg 163]PARTS OF DUPLEX LOCOMOTIVE STOKER
PARTS OF DUPLEX LOCOMOTIVE STOKER
1. Conveyor Trough.
2. Conveyor Screw.
3. Angle Ring.
4. Crusher.
5. Operating Head.
6. Driving Engine Cylinder.
7. Reverse Valve.
8. Piston Rod.
9. Transfer Hopper.
10. Left Elevator Casing.
11. Left Elevator Screw.
12. End of Elevator Screw Shaft.
13. Elevator Pawl Shifter.
14. Elevator Pawl Casing.
15. Distributors.
16. Left Distributor Elbow.
17. Right Distributor Elbow.
18. Dividing Rib.
19. Right Elevator Casing.
20. Oil Box.
21. Conveyor Reverse Lever.
22. Conveyor Oil Cups.
23. Rack Housing.
24. Rack.
25. Conveyor Pawl Casing.
26. Conveyor Screw Flexible Connection Sleeve.
27. Conveyor Screw Flexible Connection.
28. Conveyor Slide Support Roller.
29. Conveyor Slide Support.
30. Conveyor End Bearing and Gear Case.
31. Conveyor Screw Gear.
32. Conveyor Screw Driving Gear.
1. Conveyor Trough.
2. Conveyor Screw.
3. Angle Ring.
4. Crusher.
5. Operating Head.
6. Driving Engine Cylinder.
7. Reverse Valve.
8. Piston Rod.
9. Transfer Hopper.
10. Left Elevator Casing.
11. Left Elevator Screw.
12. End of Elevator Screw Shaft.
13. Elevator Pawl Shifter.
14. Elevator Pawl Casing.
15. Distributors.
16. Left Distributor Elbow.
17. Right Distributor Elbow.
18. Dividing Rib.
19. Right Elevator Casing.
20. Oil Box.
21. Conveyor Reverse Lever.
22. Conveyor Oil Cups.
23. Rack Housing.
24. Rack.
25. Conveyor Pawl Casing.
26. Conveyor Screw Flexible Connection Sleeve.
27. Conveyor Screw Flexible Connection.
28. Conveyor Slide Support Roller.
29. Conveyor Slide Support.
30. Conveyor End Bearing and Gear Case.
31. Conveyor Screw Gear.
32. Conveyor Screw Driving Gear.
COMPRESSOR GOVERNOR
Compressor governor
1. Q. When steam is first turned on, what must it pass through before entering the compressor?
1. Q. When steam is first turned on, what does it need to go through before entering the compressor?
A. The compressor governor.
The compressor governor.
2. Q. What does Fig. 1 represent?
2. Q. What does Fig. 1 show?
A. This shows a sectional view of the SF compressor governor in open position.
A. This shows a sectional view of the SF compressor governor in the open position.
3. Q. What is the duty of the compressor governor?
3. Q. What does the compressor governor do?
A. To automatically regulate the main reservoir pressure by controlling the steam to the compressor.
A. To automatically control the pressure of the main reservoir by managing the steam supply to the compressor.
4. Q. How are the regulating portions of the governor designated?
4. Q. How are the regulating parts of the governor labeled?
A. The one having two pipe connections and a light regulating spring is known as the excess pressure head; the other, with a single pipe connection and heavy regulating spring, as the maximum pressure head.
A. The one with two pipe connections and a light regulating spring is called the excess pressure head; the other, with a single pipe connection and a heavy regulating spring, is referred to as the maximum pressure head.
5. Q. When does the excess pressure head control the flow of steam to the compressor?
5. Q. When does the excess pressure head manage the flow of steam to the compressor?
A. When the automatic brake valve is in any one of its first three positions; namely, release, running and holding positions.
A. When the automatic brake valve is in any of its first three positions: release, running, and holding positions.
6. Q. With the automatic brake valve in release, running or holding position, what pressure is in chamber "f" above the diaphragm? In chamber "d" below the diaphragm?
6. Q. With the automatic brake valve in release, running, or holding position, what pressure is in chamber "f" above the diaphragm? In chamber "d" below the diaphragm?
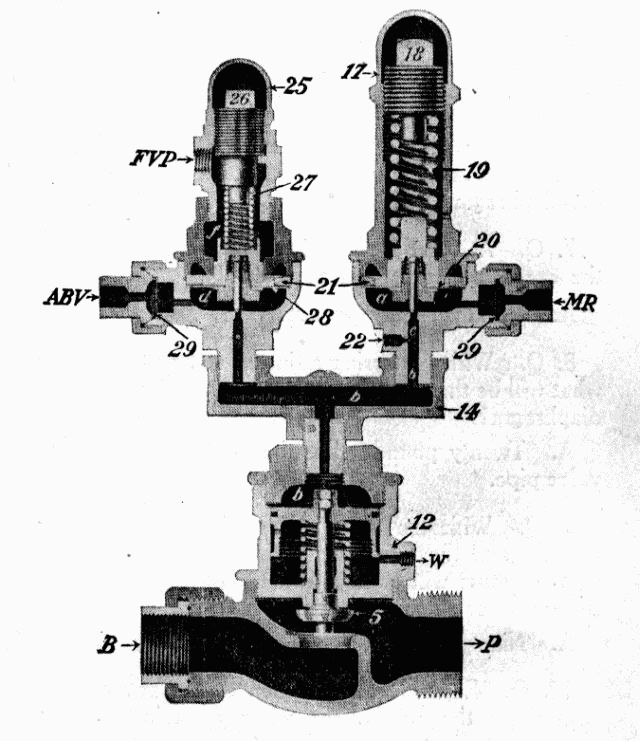
Fig. 1: The SF-4 Compressor Governor.
Connections: FVP, Feed Valve Pipe. ABV, Automatic Brake
Valve. MR, Main Reservoir. B, From Boiler. P, To Air Pump.
Fig. 1: The SF-4 Compressor Governor.
Connections: FVP, Feed Valve Pipe. ABV, Automatic Brake
Valve. MR, Main Reservoir. B, From Boiler. P, To Air Pump.
[Pg 166] A. Air, at feed valve pipe pressure, enters at the connection marked "FVP" and flows to chamber "f" above the diaphragm; this pressure acts in conjunction with the regulating spring 27 in creating the total pressure on the diaphragm. Air at main reservoir pressure flows through the automatic brake valve to the connection marked "ABV" to chamber "d" under the diaphragm.
[Pg 166] A. Air, at the pressure of the feed valve pipe, enters through the connection labeled "FVP" and moves into chamber "f" above the diaphragm; this pressure works together with the regulating spring 27 to create the total pressure on the diaphragm. Air at the main reservoir pressure flows through the automatic brake valve to the connection labeled "ABV" to chamber "d" underneath the diaphragm.
7. Q. At what pressure is the regulating spring in the excess pressure head adjusted?
7. Q. At what pressure is the regulating spring in the excess pressure head set?
A. Usually twenty pounds.
A. Usually £20.
8. Q. With the spring adjusted at twenty pounds, what will be the total pressure on the upper side of the diaphragm?
8. Q. With the spring set at twenty pounds, what will the total pressure be on the upper side of the diaphragm?
A. Twenty pounds, plus the pressure in the feed valve pipe.
A. Twenty pounds, plus the pressure in the feed valve pipe.
9. Q. With the feed valve adjusted at seventy pounds, and the regulating spring at twenty pounds, what pressure will be had in the main reservoir when the governor stops the compressor?
9. Q. With the feed valve set at seventy pounds and the regulating spring at twenty pounds, what pressure will be in the main reservoir when the governor shuts off the compressor?
A. Ninety pounds.
Ninety bucks.
10. Q. Explain the operation of the governor in controlling the compressor when a main reservoir pressure of ninety pounds is reached.
10. Q. Describe how the governor operates to control the compressor when the main reservoir pressure hits ninety pounds.
A. When the main reservoir pressure in chamber "d" slightly exceeds the pressure on top of the diaphragm it will move upward, carrying the pin valve with it. The air in chamber "d" passes by the unseated pin valve through port "b" into chamber "b" above the governor piston, forcing it downward, seating the steam valve 5, thus shutting off the steam to the compressor.[Pg 167]
A. When the main reservoir pressure in chamber "d" slightly goes above the pressure on top of the diaphragm, it will move up, taking the pin valve with it. The air in chamber "d" flows past the unseated pin valve through port "b" into chamber "b" above the governor piston, pushing it down and seating the steam valve 5, which then shuts off the steam to the compressor.[Pg 167]
11. Q. How long will the governor remain in this position?
11. Q. How long will the governor stay in this position?
A. Until the main reservoir pressure falls below ninety pounds, when the combined spring and air pressure in chamber "f" will force the diaphragm 28 down, seating the pin valve. This shuts off the supply of air from chamber "d", and the air confined in chamber "b" will escape to the atmosphere through the vent port "c". The pressure now being removed from above the governor piston, the spring 9 aided by the steam pressure under the valve 5, will force the piston upward, unseating the steam valve 5, allowing steam to pass through the governor to the compressor.
A. Until the main reservoir pressure drops below ninety pounds, the combination of spring and air pressure in chamber "f" will push the diaphragm 28 down, closing the pin valve. This stops the air supply from chamber "d," and the air trapped in chamber "b" will release into the atmosphere through the vent port "c." With the pressure now removed from above the governor piston, spring 9, combined with the steam pressure under valve 5, will push the piston upward, reopening the steam valve 5, allowing steam to flow through the governor to the compressor.
12. Q. When the steam valve is seated, is steam entirely shut off from the compressor?
12. Q. When the steam valve is closed, is steam completely cut off from the compressor?
A. No; there is a small port drilled through the valve; its purpose is to maintain a circulation in the steam pipe and keep the compressor working slowly; thereby preventing condensation when the steam valve is closed.
A. No; there's a small hole drilled through the valve; its purpose is to keep circulation in the steam pipe and allow the compressor to run slowly, which prevents condensation when the steam valve is closed.
13. Q. With the automatic brake valve in release, running, or holding position, does the maximum pressure head operate?
13. Q. When the automatic brake valve is in release, running, or holding position, does the maximum pressure head work?
A. No; as during this time the main reservoir pressure is not sufficiently high to actuate its diaphragm.
A. No; because during this time the main reservoir pressure isn't high enough to activate its diaphragm.
14. Q. Where does the air come from that operates the maximum pressure head?
14. Q. Where does the air come from that powers the maximum pressure head?
A. From the main reservoir direct. (See Fig. 1.)
A. From the main reservoir directly. (See Fig. 1.)
15. Q. When does the maximum pressure head control the compressor?[Pg 168]
15. Q. When does the highest pressure head take control of the compressor?[Pg 168]
A. When the automatic brake valve is in either lap, service or emergency position, also when the main reservoir cut-out cock is closed.
A. When the automatic brake valve is in either the lap, service, or emergency position, and also when the main reservoir cut-out cock is closed.
16. Q. How is the pressure created on top of the diaphragm in the maximum pressure head?
16. Q. How is the pressure generated above the diaphragm at the maximum pressure head?
A. By the regulating spring 19.
A. By the regulating spring 19.
17. Q. What is the adjustment of this spring?
17. Q. How do you adjust this spring?
A. Spring 19 is adjusted to the maximum pressure desired in the main reservoir usually 130 pounds.
A. Spring 19 is set to the maximum pressure desired in the main reservoir, which is typically 130 pounds.
18. Q. Explain the operation of the governor when the main reservoir pressure exceeds the tension of the regulating spring 19.
18. Q. Describe how the governor works when the main reservoir pressure is greater than the tension of the regulating spring 19.
A. When the pressure in chamber "a" exceeds the tension of the regulating spring 19, the diaphragm 20 is forced upward, unseating the pin valve, allowing air to flow from chamber "a" to chamber "b" above the governor piston, forcing it down, shutting off steam and stopping the compressor.
A. When the pressure in chamber "a" is greater than the tension of the regulating spring 19, the diaphragm 20 pushes up, dislodging the pin valve, which lets air flow from chamber "a" to chamber "b" above the governor piston, pushing it down, shutting off the steam and stopping the compressor.
19. Q. How long will the governor remain in this position?
19. Q. How long will the governor stay in this position?
A. Until the main reservoir pressure in chamber "a" under the diaphragm becomes slightly less than the adjustment of the regulating spring 19, when the diaphragm 20 will move down, seating the pin valve, shutting off the flow of air from chamber "a" to chamber "b". The air entrapped above the governor piston will escape to the atmosphere through the relief port "c"; this will allow the governor piston to raise, unseating the steam valve 5, again allowing steam to pass through the governor to the compressor.
A. Until the main reservoir pressure in chamber "a" under the diaphragm is slightly less than the setting of the regulating spring 19, the diaphragm 20 will move down, closing the pin valve and stopping the flow of air from chamber "a" to chamber "b." The air trapped above the governor piston will escape to the atmosphere through the relief port "c," which will allow the governor piston to rise, opening the steam valve 5 and letting steam flow through the governor to the compressor.
20. Q. Is the maximum pressure head cut out in any position of the automatic brake valve?[Pg 169]
20. Q. Is the maximum pressure head disabled in any position of the automatic brake valve?[Pg 169]
A. No; as the air that operates this head comes direct from the main reservoir, therefore is not controlled by the brake valve.
A. No; the air that powers this head comes directly from the main reservoir, so it isn't controlled by the brake valve.
21. Q. Is the excess pressure head cut out in any position of the brake valve?
21. Q. Is the extra pressure head removed in any position of the brake valve?
A. Yes; as the air that operates this head comes through the automatic brake valve, and when the handle is moved beyond holding position, the port in the rotary valve seat, through which the air flows to chamber "d" is closed, thereby cutting out this head, leaving the compressor under the control of the maximum pressure head.
A. Yes; the air that powers this head comes through the automatic brake valve, and when the handle is moved beyond the holding position, the port in the rotary valve seat, which allows air to flow to chamber "d," is closed, effectively taking this head out of operation and leaving the compressor under the control of the maximum pressure head.
22. Q. What is the object of the duplex or double head governor?
22. Q. What is the purpose of the double head governor?
A. By use of the duplex governor the main reservoir pressure may be controlled at two different predetermined pressures; as when running along the excess or low pressure head controls the compressor, at the low pressure—usually ninety pounds—this being sufficient to keep the brakes released and fully charged; whereas, in lap position, as following a brake application, the maximum or high pressure head controls the compressor at the maximum pressure used—generally 130 pounds—this for a prompt release and quick recharge of the brakes. From this it will be seen that the compressor has to work against the high pressure only during the time the brake is applied.
A. By using the dual governor, the main reservoir pressure can be managed at two different preset levels; for example, when operating under excess or low pressure, the compressor is controlled at low pressure—usually ninety pounds— which is enough to keep the brakes released and fully charged. In lap position, after a brake application, the maximum or high pressure controls the compressor at the highest pressure used—typically 130 pounds—allowing for a quick release and fast recharge of the brakes. This shows that the compressor only has to work against high pressure while the brake is applied.
23. Q. In what position should the automatic brake valve handle be placed when adjusting the excess pressure head? The maximum pressure head?
23. Q. In what position should the automatic brake valve handle be when adjusting the excess pressure head? The maximum pressure head?
A. Running position for the excess pressure head; lap position for the maximum pressure head.
A. Running position for the excess pressure head; lap position for the maximum pressure head.
24. Q. If, with the automatic brake valve handle in running position, the brake pipe and main reservoir[Pg 170] do not stand twenty pounds apart, where would you look for the trouble?
24. Q. If the automatic brake valve handle is in the running position and the brake pipe and main reservoir[Pg 170] aren't twenty pounds apart, where would you check for the issue?
A. Would first learn if the maximum pressure head was properly adjusted, and if it were, would then look for the trouble in the adjustment of the regulating spring in the excess pressure head.
A. Would first check if the maximum pressure head was set correctly, and if it was, would then search for issues in the adjustment of the regulating spring in the excess pressure head.
25. Q. What should be done?
25. Q. What needs to be done?
A. The regulating spring should be properly adjusted.
A. The regulating spring needs to be adjusted correctly.
26. Q. How should the adjustment of the regulating spring in either pressure head be made?
26. Q. How should the adjustment of the regulating spring in either pressure head be made?
A. By removing the cap nut 25 or 17 and screwing the regulating nut 26 or 18 up or down as may be required.
A. By taking off the cap nut 25 or 17 and adjusting the regulating nut 26 or 18 up or down as necessary.
DEFECTS OF THE GOVERNOR
Governor's flaws
27. Q. What would be the effect if one or both of the pin valves leaked?
27. Q. What would happen if one or both of the pin valves leaked?
A. Would cause a delay in opening of the steam valve after the pin valve had seated; and if air leaks by faster than it can escape through the relief port "c", pressure will accumulate in chamber "b" and force the governor piston downward, so as to partially or wholly close the steam valve 5.
A. Would delay the opening of the steam valve after the pin valve had seated; and if air leaks in faster than it can exit through the relief port "c", pressure will build up in chamber "b" and push the governor piston downward, which could partially or completely close the steam valve 5.
28. Q. How can you tell if the pin valves leak?
28. Q. How can you tell if the pin valves are leaking?
A. Leakage past the pin valve in the maximum pressure head will cause a constant blow at the relief port in all positions of the brake valve; leakage past the pin valve in the excess pressure head will cause a blow in the first three positions of the brake valve only.
A. Leakage around the pin valve at maximum pressure will result in a continuous blow at the relief port in all positions of the brake valve; leakage around the pin valve at excess pressure will cause a blow only in the first three positions of the brake valve.
29. Q. What would be the effect if the relief port "c" stopped up?[Pg 171]
29. Q. What would happen if the relief port "c" got blocked?[Pg 171]
A. The compressor will not start promptly after the pin valve seats.
A. The compressor won't start right away after the pin valve seats.
30. Q. What would be the effect if the drain port "W" were stopped up?
30. Q. What would happen if the drain port "W" got clogged?
A. Steam leaking into the chamber under the governor piston will form a pressure and prevent the piston being forced downward to close the steam valve; the compressor will therefore continue to work until the main reservoir pressure is about equal to boiler pressure.
A. Steam leaking into the chamber under the governor piston will create pressure and stop the piston from being pushed down to close the steam valve; the compressor will continue to operate until the main reservoir pressure is about equal to the boiler pressure.
31. Q. If the pipe leading from the feed valve pipe to the excess pressure head of the governor breaks, what effect will it have on the compressor?
31. Q. If the pipe from the feed valve to the excess pressure head of the governor breaks, what impact will it have on the compressor?
A. The compressor will stop when the main reservoir pressure reaches about forty-five pounds.
A. The compressor will stop when the main reservoir pressure hits around forty-five pounds.
32. Q. If the pipe breaks, what should be done?
32. Q. If the pipe bursts, what should we do?
A. Plug the end toward the feed valve and put a blind gasket in the pipe leading from the automatic brake valve to the governor, at the connection marked ABV.
A. Plug the end directed at the feed valve and insert a blind gasket in the pipe connecting the automatic brake valve to the governor, at the point labeled ABV.
33. Q. If the pipe leading from the automatic brake valve to the governor breaks, what should be done?
33. Q. If the pipe from the automatic brake valve to the governor breaks, what should be done?
A. Plug the pipe toward the brake valve; the compressor will now be controlled by the maximum pressure head.
A. Connect the pipe to the brake valve; the compressor will now be controlled by the highest pressure level.
34. Q. If the pipe leading from the main reservoir to the maximum head of the governor breaks, what should be done?
34. Q. If the pipe connecting the main reservoir to the highest point of the governor breaks, what should be done?
A. Plug the main reservoir end of the pipe. The excess pressure head will now control the compressor in the first three positions of the automatic brake valve handle, but will have no control after the handle is moved as far as lap position.[Pg 172]
A. Plug the main reservoir end of the pipe. The excess pressure will now control the compressor in the first three settings of the automatic brake valve handle, but will have no effect after the handle is moved to the lap position.[Pg 172]
PARASITE GOVERNOR
PARASITE GOVERNOR
35. Q. What is the purpose of the parasite governor, and where is this governor located?
35. Q. What is the role of the parasite governor, and where is it situated?
A. This governor is located in the pipe connection between the main reservoir and parasite reservoir, and its purpose is to control the flow of air from the main to the parasite reservoir.
A. This governor is positioned in the pipe connection between the main reservoir and the auxiliary reservoir, and its purpose is to manage the flow of air from the main to the auxiliary reservoir.
36. Q. What is the purpose of the parasite reservoir?
36. Q. What is the role of the parasite reservoir?
A. It is here that air is stored for use in all air operated devices on the locomotive, except the brake.
A. This is where air is stored for use in all air-operated devices on the locomotive, except for the brake.
37. Q. Explain the operation of the parasite governor.
37. Q. Describe how the parasite governor works.
A. The operation of this governor is much the same as the compressor governor, and differs only in that the supply valve is open when it is in its lower position.
A. This governor works similarly to the compressor governor, with the only difference being that the supply valve is open when it’s in its lower position.
38. Q. At what pressure is the regulating spring adjusted?
38. Q. What pressure is the regulating spring set to?
A. About fifteen pounds.
About fifteen bucks.
39. Q. What pressure is required in the main reservoir before air is admitted to the parasite reservoir?
39. Q. What pressure does the main reservoir need to be at before air can be allowed into the parasite reservoir?
A. At least fifteen pounds above that in the brake pipe.
A. At least fifteen pounds higher than that in the brake pipe.
40. Q. What pressure is obtained in the parasite reservoir?
40. Q. What pressure is found in the parasite reservoir?
A. The same as that in the main reservoir, when the main reservoir pressure is fifteen pounds greater than that in the brake pipe.
A. The same as in the main reservoir, when the pressure in the main reservoir is fifteen pounds higher than that in the brake pipe.
41. Q. What will prevent the charging of the parasite reservoir, and what should be done?[Pg 173]
41. Q. What will stop the charging of the parasite reservoir, and what should be done?[Pg 173]
A. This may be caused by the feed valve being improperly adjusted, sticking in open position or leakage of main reservoir air past the valve to the feed valve pipe and governor top.
A. This might be due to the feed valve being adjusted incorrectly, getting stuck in the open position, or air leaking from the main reservoir past the valve to the feed valve pipe and governor top.
WESTINGHOUSE 9½ OR 11-INCH COMPRESSOR
WESTINGHOUSE 9½ OR 11-INCH COMPRESSOR
42. Q. What is the duty of the air compressor?
42. Q. What does the air compressor do?
A. To furnish the compressed air used in the operation of the brakes, and all other air operated appliances on both locomotive and cars.
A. To provide the compressed air used in the operation of the brakes and all other air-operated devices on both the locomotive and cars.
43. Q. Explain the operation of the steam end of the compressor.
43. Q. Explain how the steam part of the compressor works.
A. When steam is turned on at the boiler it flows through the steam pipe and governor, entering the compressor at the steam enlet, then through the steam passage "a" to the reversing valve chamber "C" also to the main valve chamber "A" between the differential pistons 77 and 79. The area of the piston at the right being greater than the one at the left, the main valve is moved to the right, (See Fig. 2) admitting steam to port "b" which leads to the lower end of the steam cylinder; steam is now free to flow under the main piston, forcing it upward. When the piston has almost completed its upward stroke, the reversing plate 69 on top of the piston 65 engages a shoulder on the reversing rod 71, moving the rod and reversing valve 72 upward (See Fig. 3). The upward movement of the reversing valve closes the ports "f" and "h" and opens port "g"; thus permitting steam to enter the chamber at the right of the large piston 77, balancing the pressure on this piston, and the pressure acting on the right side of the small piston 79—the chamber at the left being open to the [Pg 174] exhaust—will force the main valve to the left.
A. When steam is turned on at the boiler, it flows through the steam pipe and governor, entering the compressor at the steam inlet, then through the steam passage "a" to the reversing valve chamber "C" and also to the main valve chamber "A" between the differential pistons 77 and 79. Since the area of the piston on the right is larger than the one on the left, the main valve moves to the right, (See Fig. 2) allowing steam to enter port "b," which leads to the lower end of the steam cylinder; steam can now flow under the main piston, pushing it upward. When the piston is almost at the end of its upward stroke, the reversing plate 69 on top of the piston 65 engages a shoulder on the reversing rod 71, moving the rod and reversing valve 72 upward (See Fig. 3). The upward movement of the reversing valve closes ports "f" and "h" and opens port "g," allowing steam to enter the chamber to the right of the large piston 77, balancing the pressure on this piston. The pressure acting on the right side of the small piston 79—the chamber on the left being open to the [Pg 174] exhaust—will force the main valve to the left.
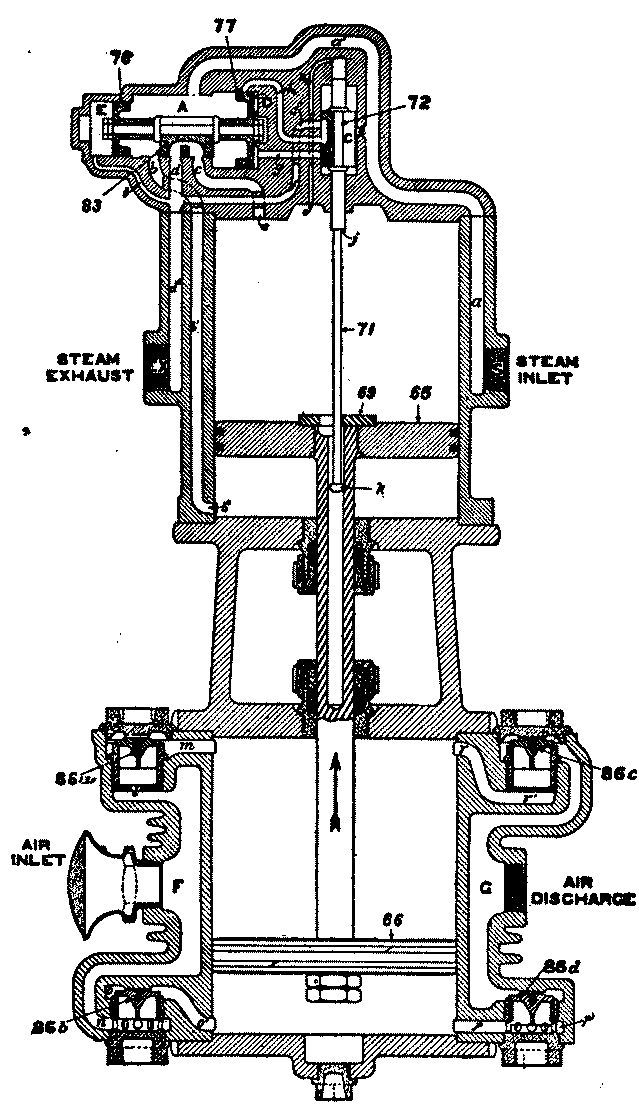
Fig. 2: Diagrammatic View, Up Stroke.
Fig. 2: Diagrammatic View, Up Stroke.
[Pg 175] When the main valve moves to the left, steam is admitted through port "c" to the upper end of the cylinder on top of the piston 65, forcing it downward. At the same time the lower end of the cylinder is connected through exhaust cavity "b" of the main valve to the exhaust port "d", allowing the steam below the piston to escape to the atmosphere.
[Pg 175] When the main valve shifts to the left, steam flows in through port "c" to the top of the cylinder above piston 65, pushing it downwards. At the same time, the bottom end of the cylinder connects through exhaust cavity "b" of the main valve to exhaust port "d", letting the steam below the piston escape into the atmosphere.
44. Q. When the piston has about completed its downward stroke, what takes place?
44. Q. What happens when the piston is almost done with its downward stroke?
A. The reversing plate 69 engages the button "k" on the end of the reversing rod 71 pulling the rod and the reversing valve down. This movement of the reversing valve closes port "g" and the cavity in the face of the valve connects ports "f" and "h", which allows the steam in chamber "D" at the right of the large differential piston to escape to the exhaust, thus allowing the main valve to move to the right, exhausting the steam from the top end of the cylinder, and at the same time admitting steam to the lower end, causing an upward stroke of the piston.
A. The reversing plate 69 engages the button "k" at the end of the reversing rod 71, pulling the rod and the reversing valve down. This action of the reversing valve shuts off port "g" and connects the cavity in the valve face to ports "f" and "h," allowing steam in chamber "D" on the right side of the large differential piston to escape to the exhaust. As a result, the main valve shifts to the right, releasing steam from the top end of the cylinder while simultaneously letting steam into the lower end, which initiates an upward stroke of the piston.
45. Q. Explain the operation of the air end of the compressor.
45. Q. Describe how the air part of the compressor works.
A. The movement of the steam piston 65 is imparted to the air piston 66 by means of the piston rod. When the air piston moves up, a partial vacuum is formed below it, and air from the atmosphere will enter through passage "F" thence through passage "n" to the under side of receiving valve 86b (see Fig. 2), lifting this valve from its seat, and will fill the cylinder with air at about atmosphere pressure.
A. The movement of the steam piston 65 is transferred to the air piston 66 via the piston rod. When the air piston moves up, it creates a partial vacuum underneath, and air from the atmosphere will flow in through passage "F" and then through passage "n" to the underside of receiving valve 86b (see Fig. 2), lifting this valve off its seat and filling the cylinder with air at approximately atmospheric pressure.
[Pg 177] In the meantime the air above the piston, being compressed, will hold the upper receiving valve 86a to its seat, and when the pressure is slightly greater than that in the main reservoir, this pressure acting under the upper discharge valve 86c, will lift this valve from its seat and now the air will be free to flow through passage "G" to the main reservoir connection. On the down stroke the action is similar, air is taken in through the upper receiving valve 86a, while the air below the piston is being compressed and forced past the lower discharge valve 86d, to the main reservoir. (See Fig. 3.)
[Pg 177] Meanwhile, the air above the piston gets compressed, which keeps the upper receiving valve 86a seated. When the pressure slightly exceeds that of the main reservoir, this pressure acting on the upper discharge valve 86c will lift the valve off its seat, allowing the air to flow through passage "G" to the main reservoir connection. During the downstroke, the process is similar; air is drawn in through the upper receiving valve 86a while the air below the piston gets compressed and pushed past the lower discharge valve 86d to the main reservoir. (See Fig. 3.)
46. Q. What lift should the air valves have?
46. Q. How high should the air valves be?
A. All valves should have a lift of three thirty-second of an inch.
A. All valves should have a lift of three thirty-seconds of an inch.
47. Q. At what speed should the compressor be run to obtain the best results?
47. Q. What speed should the compressor be run at to get the best results?
A. At 100 to 120 single strokes per minute.
A. At 100 to 120 single strokes per minute.
48. Q. What kind of oil should be used in the air end of the compressor and on the swab?
48. Q. What type of oil should be used in the air end of the compressor and on the swab?
A. Valve oil.
Valve oil.
49. Q. How often should the air end of the compressor be oiled?
49. Q. How often should the air end of the compressor be oiled?
A. No fixed rule can be given as so much depends on the condition of the compressor, as well as the amount of work required; but in any case it should be used sparingly.
A. There isn't a set rule since it depends a lot on the state of the compressor and how much work needs to be done; however, it should always be used carefully.
CROSS-COMPOUND COMPRESSOR
Cross-Compound Compressor
50. Q. What do Figures 4 and 5 represent?
50. Q. What do Figures 4 and 5 show?
A. These are diagramatic views of a cross-compound compressor.
A. These are diagrammatic views of a cross-compound compressor.
51. Q. Why is this called a cross-compound compressor?
51. Q. Why is this called a cross-compound compressor?
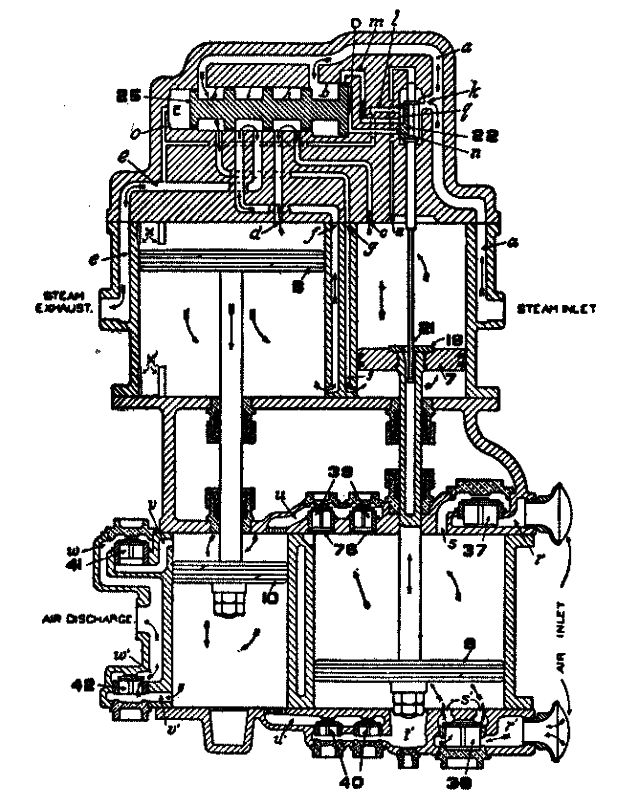
Fig. 4: Diagram of 8½" Cross-Compound Compressor.
High Pressure Steam (Low Pressure Air) Piston on Its Upward Stroke
Fig. 4: Diagram of 8½" Cross-Compound Compressor.
High Pressure Steam (Low Pressure Air) Piston on Its Upward Stroke
A. Because both steam and air are compounded, that is, the steam is used the second time before it is exhausted to the atmosphere, while the air is com[Pg 179]pressed the second time before it is delivered to the main reservoir.
A. Because both steam and air are combined, meaning the steam is used a second time before it's released into the atmosphere, while the air is compressed a second time before it's sent to the main reservoir.
52. Q. How many cylinders have the cross-compound compressor?
52. Q. How many cylinders does the cross-compound compressor have?
A. Four; two steam cylinders and two air cylinders.
A. Four; two steam cylinders and two air cylinders.
53. Q. What is the diameter of the different cylinders?
53. Q. What are the diameters of the various cylinders?
A. The high pressure steam cylinder is 8½ inches; the low pressure steam cylinder 14½ inches; the low pressure air cylinder 14½ inches; high pressure air cylinder 9 inches.
A. The high pressure steam cylinder is 8.5 inches; the low pressure steam cylinder is 14.5 inches; the low pressure air cylinder is 14.5 inches; the high pressure air cylinder is 9 inches.
54. Q. Explain the valve gear of this compressor.
54. Q. Describe the valve system of this compressor.
A. The valve gear is the same as that of the 9½ or 11 inch compressor, only that a piston valve is used to distribute the steam instead of a slide valve.
A. The valve gear is the same as that of the 9½ or 11-inch compressor, except that a piston valve is used to distribute the steam instead of a slide valve.
55. Q. Where does the steam come from that is used in the high pressure steam cylinder?
55. Q. Where does the steam used in the high pressure steam cylinder come from?
A. Direct from the boiler.
A. Straight from the boiler.
56. Q. Where does the steam come from that is used in the low pressure steam cylinder?
56. Q. Where does the steam come from that is used in the low pressure steam cylinder?
A. The steam after doing work in the high pressure steam cylinder is exhausted into the low pressure steam cylinder, where it becomes the working pressure of this cylinder.
A. The steam that has done work in the high-pressure steam cylinder is released into the low-pressure steam cylinder, where it becomes the working pressure for this cylinder.
57. Q. Explain the operation of this compressor.
57. Q. Describe how this compressor works.
A. When steam is first turned on, it enters the compressor at the steam inlet (see Fig. 4) and flows through passage "a" into the reversing valve chamber[Pg 180] "C" and on to chambers "b" and "y" against the inner faces of the differential pistons, causing the main valve to move to the right. In this position of the main valve, port "g" is open to chamber "b", thus admitting live steam to the lower end of the high pressure steam cylinder, causing an upward movement of the piston 7. When the piston 7 has nearly completed its up stroke, the reversing plate 18, which is attached to the top of this piston, comes in contact with a shoulder on the reversing rod 21, forcing it upward, carrying with it the reversing valve 22, the movement of which closes port "m", at the same time opens port "n", filling chamber "D" with live steam from chamber "C" and passage "a". This balances the pressure on the two sides of the large piston of the differential pistons, and the pressure acting against the inner side of the small piston causes the main valve to move to the left (see Fig. 5). The main valve moving to the left closes port "g" to the live steam and at the same time connects this port with port "f" leading to the lower end of the low pressure steam cylinder, causing an up stroke of the low pressure steam piston 8. In the meantime port "c", which leads to the upper end of the high pressure steam cylinder, is open to chamber "y", allowing live steam to flow down on top of the high pressure steam piston 7, forcing it downward. As the high pressure steam piston about completes its downward stroke, the reversing plate 18 engages the button on the lower end of the reversing rod 21, pulling the rod and reversing valve 22 down, closing port "n" and at the same time connecting port "m" and "l" through the exhaust cavity "q", thus allowing the steam in chamber "D" to escape to the exhaust. The pressure being removed from the outer face of the large differential piston, the main valve will again move to the right,[Pg 181] opening port "g", admitting live steam beneath the piston 7, and at the same time connecting the upper end of the high pressure steam cylinder through port "c", chamber "h" and port "d" to the upper end of the low pressure steam cylinder, causing a downward movement of the low pressure steam piston; the steam below this piston will now be free to escape to the exhaust through port "f", chamber "i" and port "e". Thus it will be seen that the steam used in the high pressure steam cylinder is live steam from the boiler, while the steam used in the low pressure steam cylinder is the exhaust steam from the high pressure steam cylinder.
A. When the steam is first activated, it enters the compressor at the steam inlet (see Fig. 4) and flows through passage "a" into the reversing valve chamber "C," and then to chambers "b" and "y" against the inner sides of the differential pistons, causing the main valve to shift to the right. In this position, the main valve opens port "g" to chamber "b," allowing live steam into the lower end of the high-pressure steam cylinder, which pushes the piston 7 upward. When piston 7 is almost at the end of its upward stroke, the reversing plate 18, attached to the top of this piston, hits a ledge on the reversing rod 21, pushing it up and moving the reversing valve 22. This action closes port "m" while opening port "n," filling chamber "D" with live steam from chamber "C" and passage "a." This balances the pressure on both sides of the large piston of the differential pistons, and the pressure pressing against the inner side of the small piston makes the main valve slide to the left (see Fig. 5). As the main valve goes left, it closes port "g" to the live steam and connects it to port "f," which leads to the lower end of the low-pressure steam cylinder, causing the low-pressure steam piston 8 to move upward. Meanwhile, port "c," which goes to the upper end of the high-pressure steam cylinder, is open to chamber "y," allowing live steam to flow onto the high-pressure steam piston 7, pushing it downward. As the high-pressure steam piston finishes its downward stroke, the reversing plate 18 hits the button at the bottom of the reversing rod 21, pulling it down along with the reversing valve 22, which closes port "n" and opens ports "m" and "l" via the exhaust cavity "q," letting steam in chamber "D" escape to the exhaust. With the pressure removed from the outer face of the large differential piston, the main valve shifts back to the right,[Pg 181] opening port "g" to let live steam in under the piston 7, while also connecting the upper end of the high-pressure steam cylinder through port "c," chamber "h," and port "d" to the upper end of the low-pressure steam cylinder, causing the low-pressure steam piston to move downward; the steam below this piston can now escape through the exhaust via port "f," chamber "i," and port "e." Thus, it can be seen that the steam used in the high-pressure steam cylinder is live steam from the boiler, while the steam used in the low-pressure steam cylinder is the exhaust steam from the high-pressure steam cylinder.
58. Q. Explain the operation of the air end of the compressor.
58. Q. Describe how the air end of the compressor works.
A. As the low pressure air piston 9 moves up, a partial vacuum is created beneath it and air from the atmosphere enters the air inlet and passage "r" past the lower receiving valve 38 and fills the lower end of the cylinder with air at about atmospheric pressure (see Fig. 4). In the meantime the air above the piston being compressed will hold the upper receiving valve 37 to its seat, thus preventing a back-flow of air to the atmosphere; at the same time the upper intermediate discharge valves 39 are forced from their seats, allowing the air from the low pressure air cylinder to flow through passage "u" to the high pressure air cylinder, the piston of which is now moving downward. The air beneath the high pressure air piston 10 being compressed will hold the lower intermediate discharge valves 40 to their seats, thus preventing the air in the high pressure air cylinder flowing back to the low pressure air cylinder. When the pressure in the high pressure air cylinder becomes slightly greater than the main reservoir pressure, the[Pg 182] final discharge valve 42 will be forced from its seat and the air beneath the piston allowed to flow to the main reservoir through passage "w". On the opposite strokes of these pistons air is compressed in a similar manner, but the opposite air valves are used.
A. As the low pressure air piston 9 moves up, it creates a partial vacuum below it, causing air from the atmosphere to flow into the air inlet and passage "r" past the lower receiving valve 38, filling the lower end of the cylinder with air at about atmospheric pressure (see Fig. 4). Meanwhile, the air above the piston gets compressed, which keeps the upper receiving valve 37 sealed, preventing air from flowing back to the atmosphere; at the same time, the upper intermediate discharge valves 39 are pushed off their seats, allowing air from the low pressure air cylinder to flow through passage "u" into the high pressure air cylinder, whose piston is now moving down. The compressed air beneath the high pressure air piston 10 holds the lower intermediate discharge valves 40 in place, thus stopping the air in the high pressure air cylinder from flowing back to the low pressure air cylinder. When the pressure in the high pressure air cylinder slightly exceeds the main reservoir pressure, the[Pg 182] final discharge valve 42 will be forced from its seat, allowing the air beneath the piston to flow into the main reservoir through passage "w". On the opposite strokes of these pistons, air is compressed in a similar way, but the opposite air valves are used.
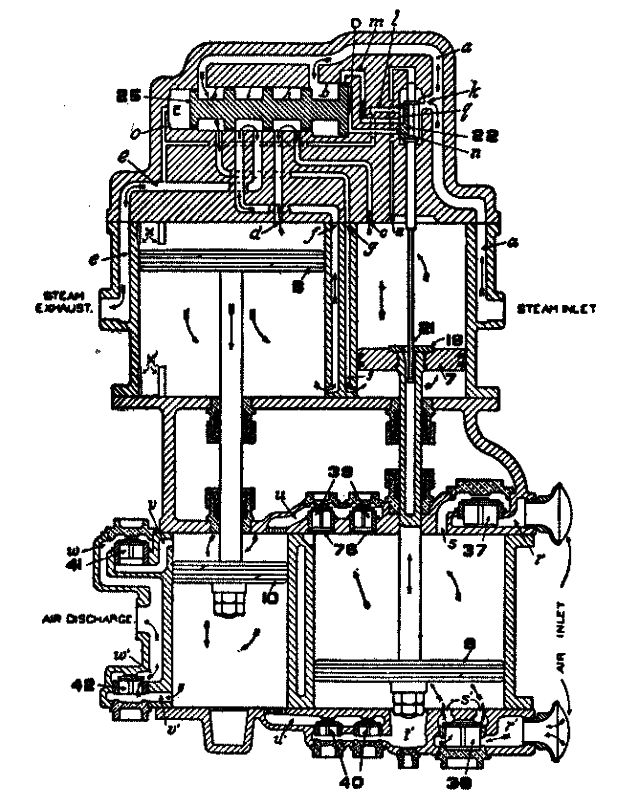
Fig. 5: Diagram of 8½" Cross-Compound Compressor.
The High Pressure Steam (Low Pressure Air) Piston on Its Downward Stroke
Fig. 5: Diagram of 8½" Cross-Compound Compressor.
The High Pressure Steam (Low Pressure Air) Piston on Its Down Stroke
[Pg 183] 59. Q. How many valves are there in the air end of the compressor?
[Pg 183] 59. Q. How many valves are in the air end of the compressor?
A. Ten; two upper and two lower receiving valves; two upper and two lower intermediate discharge valves; one upper and one lower final discharge valves.
A. Ten; two upper and two lower receiving valves; two upper and two lower intermediate discharge valves; one upper and one lower final discharge valves.
60. Q. Are the air valves all the same size?
60. Q. Are all the air valves the same size?
A. No; the receiving and final discharge valves are the same size and of the size used in the 11-inch compressor, while the intermediate valves are the same as used in the 9½-inch compressor. The receiving and final discharge valves are two inches in diameter, while the intermediate valves are one and one-half inches.
A. No; the receiving and final discharge valves are the same size as those used in the 11-inch compressor, while the intermediate valves are the same as those used in the 9½-inch compressor. The receiving and final discharge valves are two inches in diameter, while the intermediate valves are one and a half inches.
61. Q. What lift is given the different air valves?
61. Q. How much lift is provided to the different air valves?
A. All valves have 3/32-inch lift.
A. All valves have a 3/32-inch lift.
DEFECTS OF THE COMPRESSOR
COMPRESSOR DEFECTS
62. Q. What are some of the common causes for the compressor stopping?
62. Q. What are some common reasons the compressor stops?
A. Lack of lubrication; bent, worn or broken reversing rod; loose or worn reversing plate; nuts on air end of piston rod coming off; defective compressor governor; and, in addition with the cross-compound compressor, final discharge valve broken or stuck open, or packing rings in main valve pistons breaking and catching in the steam ports.
A. Insufficient lubrication; bent, worn, or broken reversing rod; loose or worn reversing plate; nuts on the air end of the piston rod coming off; faulty compressor governor; and, in the case of the cross-compound compressor, a broken or stuck open final discharge valve, or packing rings in the main valve pistons breaking and getting caught in the steam ports.
63. Q. What will cause the piston to make an uneven stroke?[Pg 184]
63. Q. What can cause the piston to move unevenly?[Pg 184]
A. This may be caused by a broken or stuck open air valve, or air valves not having proper lift. Where the piston short strokes, it is generally caused by over-lubrication of the steam end.
A. This might happen because of a broken or stuck-open air valve, or if the air valves aren't lifting properly. When the piston has short strokes, it’s usually due to too much lubrication in the steam end.
64. Q. What are some of the common causes for the compressor running hot?
64. Q. What are some common reasons for the compressor running hot?
A. The overheating of the compressor may be due to any one of the following causes: Running at high speed; working against high pressure; packing rings in air piston badly worn; air cylinder worn; defective air valves; air passages or air discharge pipe partially stopped up; leaky piston rod packing; lack of lubrication.
A. The compressor may be overheating for several reasons: running at high speeds, working against high pressure, worn packing rings in the air piston, a worn air cylinder, defective air valves, partially clogged air passages or air discharge pipes, leaky piston rod packing, or lack of lubrication.
65. Q. What will cause the compressor to run slow?
65. Q. What can make the compressor run slowly?
A. This may be caused by leaky air piston packing rings; final discharge valves leaking, or air passages partially stopped up. A defective governor may also cause the compressor to run slow.
A. This might be due to leaking air piston packing rings, leaking final discharge valves, or partially blocked air passages. A faulty governor could also make the compressor run slowly.
66. Q. What will cause the compressor to run very fast and heat, and not compress any air?
66. Q. What can make the compressor run really fast and heat up without compressing any air?
A. This may be caused by the strainer becoming clogged with ice or dirt, preventing air entering the cylinder.
A. This may be caused by the strainer getting clogged with ice or dirt, blocking air from entering the cylinder.
67. Q. If, when steam is first turned on, the piston makes a stroke up and stops, where would you look for the trouble?
67. Q. If the steam is turned on and the piston moves up but then stops, where would you check for the problem?
A. The shoulder on the reversing rod may be worn; the opening in the reversing plate too large to engage the shoulder on the reversing rod; loose reversing plate studs preventing the piston traveling far enough to reverse the compressor, or the main valve stuck in its position at the right.[Pg 185]
A. The shoulder on the reversing rod might be worn down; the hole in the reversing plate could be too big to catch the shoulder on the reversing rod; loose studs on the reversing plate might stop the piston from moving far enough to reverse the compressor, or the main valve could be stuck in place on the right.[Pg 185]
68. Q. If the piston makes a stroke up and a stroke down and stops, where is the trouble?
68. Q. If the piston moves up and down and then stops, what's the problem?
A. This may be caused by a loose reversing plate, or the button on the lower end of the reversing rod worn or broken off, or the nuts off the piston rod in the air end, or the main valve stuck in its position at the left.
A. This could be due to a loose reversing plate, a worn or broken button on the lower end of the reversing rod, nuts missing from the piston rod in the air end, or the main valve stuck in place on the left.
69. Q. What will cause the piston to make a quick up stroke?
69. Q. What will make the piston move quickly upwards?
A. This may be caused by a broken or stuck open upper receiving or lower discharge valve.
A. This could be due to a broken or stuck open upper receiving valve or lower discharge valve.
70. Q. What will cause the piston to make a quick down stroke?
70. Q. What will make the piston move down quickly?
A. Lower receiving or upper discharge valve broken or stuck open.
A. Lower receiving or upper discharge valve is broken or stuck open.
71. Q. If a receiving valve breaks or sticks open, how may it be located?
71. Q. If a receiving valve breaks or gets stuck open, how can it be found?
A. The air will flow back to the atmosphere as the piston moves toward the defective valve and may be detected by holding the hand over the strainer.
A. The air will flow back into the atmosphere as the piston moves toward the faulty valve and can be felt by placing your hand over the strainer.
72. Q. If a receiving valve in a cross-compound compressor breaks, what may be done?
72. Q. If a receiving valve in a cross-compound compressor fails, what can be done?
A. Remove the broken valve, blocking the opening made by its removal, and as there are two upper and two lower receiving valves the compressor will now take air through the other valve.
A. Remove the broken valve, blocking the opening made by its removal, and since there are two upper and two lower receiving valves, the compressor will now take in air through the other valve.
73. Q. If an intermediate discharge valve breaks or sticks open, how may it be located?
73. Q. If an intermediate discharge valve is broken or stuck open, how can you find it?
A. No air will be taken in to that end of the compressor as the piston moves from the defective valve, and may be located by holding the hand over the strainer.[Pg 186]
A. No air will enter that part of the compressor due to the faulty valve, which can be identified by placing your hand over the strainer.[Pg 186]
74. Q. If an intermediate discharge valve breaks, what may be done?
74. Q. If a middle discharge valve breaks, what should be done?
A. Remove the broken valve, blocking the opening made by its removal, and as there are two upper and two lower intermediate discharge valves the air will now pass from the low pressure cylinder to the high pressure cylinder through the other valve.
A. Take out the broken valve, sealing the opening left behind, and since there are two upper and two lower intermediate discharge valves, the air will now flow from the low pressure cylinder to the high pressure cylinder through the other valve.
75. Q. If a final discharge valve breaks, what effect will it have on the compressor?
75. Q. If a final discharge valve breaks, what impact will it have on the compressor?
A. Will cause the compressor to stop when the main reservoir pressure is in excess of forty pounds.
A. Will cause the compressor to stop when the main reservoir pressure exceeds forty pounds.
76. Q. How would you test for a defective final discharge valve?
76. Q. How would you check for a faulty final discharge valve?
A. To test for this defect, bleed the main reservoir pressure below forty pounds, and if the compressor starts it indicates a defective discharge valve.
A. To check for this issue, reduce the main reservoir pressure to below forty pounds, and if the compressor starts, it means there’s a faulty discharge valve.
77. Q. If a final discharge valve breaks, what may be done?
77. Q. If a discharge valve fails, what can be done?
A. As the receiving valves and final discharge valves are the same size, the defective valve may be replaced by one of the receiving valves, blocking the opening made by the removal of the receiving valve.
A. Since the receiving valves and final discharge valves are the same size, the faulty valve can be swapped with one of the receiving valves, closing off the opening created by the removal of the receiving valve.
78. Q. Where piston rod packing is blowing bad, what may be done to stop it?
78. Q. If the piston rod packing is leaking badly, what can be done to fix it?
A. This generally indicates lack of lubrication, and by cleaning and oiling the swab the trouble may be overcome. However, there are times when leakage by the packing is so great that the oil is blown off the swab as fast as it is applied, therefore is of no value in lubricating the parts. Where this condition exists, a little hard grease wrapped up in an old flag and tied around the piston rod will ensure its being lubricated.[Pg 187]
A. This usually means there's not enough lubrication, and cleaning and oiling the swab might fix the issue. However, sometimes the leakage from the packing is so severe that the oil gets blown off the swab as quickly as it's applied, making it useless for lubricating the parts. When this happens, wrapping a bit of hard grease in an old rag and tying it around the piston rod will ensure it's properly lubricated.[Pg 187]
79. Q. If the compressor stops, how can you tell if the governor is responsible for the trouble?
79. Q. If the compressor stops, how can you tell if the governor is the reason for the problem?
A. By opening the drain cock in the steam passage between the governor and the compressor; if steam flows freely, the trouble is in the compressor; if not, it is in the governor.
A. By opening the drain valve in the steam pathway between the governor and the compressor; if steam flows freely, the issue is with the compressor; if it doesn't, the problem lies with the governor.
80. Q. How may a compressor often be started when it stops?
80. Q. How can you usually restart a compressor when it stops?
A. By closing the steam throttle for a few seconds, then opening it quickly; if this does not start it, try tapping the main valve chamber. This will usually overcome the trouble where the compressor stops on account of lack of lubrication.
A. By shutting the steam throttle for a few seconds, then quickly opening it; if this doesn't get it going, try tapping the main valve chamber. This usually fixes the problem when the compressor shuts down due to lack of lubrication.
81. Q. What will cause a compressor to short-stroke or dance?
81. Q. What makes a compressor short-stroke or shake?
A. Too much oil in the steam end; bent reversing rod; or low steam pressure, as when the governor has almost shut off the steam.
A. Excess oil in the steam section; a bent reversing rod; or low steam pressure, like when the governor has nearly cut off the steam.
ENGINEER'S BRAKE VALVE
Engineer’s Brake Valve
82. Q. Name the different positions of the G-6 and H-6 brake valves.
82. Q. What are the various positions of the G-6 and H-6 brake valves?
A. Release, running, lap, service, and emergency position, with the G-6; release, running, holding, lap, service, and emergency positions, with the H-6.
A. Release, running, lap, service, and emergency position with the G-6; release, running, holding, lap, service, and emergency positions with the H-6.
83. Q. What is the purpose of release position?
83. Q. What is the purpose of the release position?
A. To provide a large and direct opening from the main reservoir to the brake pipe, for the free flow of air, when charging and recharging the brakes.
A. To create a large and direct connection from the main reservoir to the brake pipe, allowing air to flow freely when charging and recharging the brakes.
84. Q. What pressure will be had in the brake pipe if the brake valve be left in release position?
84. Q. What pressure will be in the brake pipe if the brake valve is left in the release position?
A. Main reservoir pressure.[Pg 188]
A. Main reservoir pressure.
85. Q. Can the locomotive brake be released by the automatic brake valve in release position, when using the H-6 valve?
85. Q. Can the locomotive brake be released using the automatic brake valve in the release position when using the H-6 valve?
A. No; as the port in the automatic brake valve to which the distributing valve release pipe is attached is blanked in this position of the valve.
A. No; because the port in the automatic brake valve that the distributing valve release pipe is connected to is sealed in this position of the valve.
86. Q. What is the purpose of running position, and when should it be used?
86. Q. What is the purpose of the running position, and when should it be used?
A. This is the proper position for the brake valve when the brakes are charged and not in use, also when it is desired to release the locomotive brake with this valve. In this position the brake pipe pressure is maintained at a predetermined amount by the feed valve, as all air that now enters the brake pipe must pass through the feed valve.
A. This is the correct position for the brake valve when the brakes are charged and not in use, as well as when you want to release the locomotive brake using this valve. In this position, the brake pipe pressure is kept at a specific level by the feed valve, since all air that enters the brake pipe must go through the feed valve.
87. Q. What is the purpose of holding position?
87. Q. What’s the point of holding a position?
A. To hold the locomotive brake applied while recharging the brakes. The charging of the brake pipe and equalizing reservoir is the same in holding as in running position.
A. To keep the locomotive brake engaged while recharging the brakes. The process of charging the brake pipe and equalizing reservoir is the same in both the holding and running positions.
88. Q. What is the purpose of lap position?
88. Q. What is the purpose of lap position?
A. To hold both the locomotive and train brakes applied after an automatic application.
A. To keep both the locomotive and train brakes engaged after an automatic application.
89. Q. What is the purpose of service position?
89. Q. What is the purpose of the service position?
A. This position of the brake valve enables the engineer to make a gradual reduction of brake pipe pressure, thus causing a service application of the brakes.
A. This position of the brake valve allows the engineer to slowly decrease the brake pipe pressure, resulting in a service application of the brakes.
90. Q. What is the purpose of emergency position?
90. Q. What is the purpose of the emergency position?
A. In this position of the brake valve, the brake pipe is connected directly with the atmosphere through[Pg 189] the large ports in the valve, causing a sudden reduction of brake pipe pressure, this in turn causing the distributing valve on the engine and all operating triple valves on cars in the train to move to emergency position, thus insuring a quick and full application of the brake.
A. In this position of the brake valve, the brake pipe is connected directly to the atmosphere through[Pg 189] the large ports in the valve, which leads to a sudden drop in brake pipe pressure. This, in turn, causes the distributing valve on the engine and all operating triple valves on cars in the train to shift to emergency position, ensuring a quick and complete application of the brake.
91. Q. How should the brake valve be handled when making an emergency application of the brake?
91. Q. How should the brake valve be operated when making an emergency brake application?
A. The valve should be placed in full emergency position and left there until the train stops, even though the danger may have disappeared.
A. The valve should be set to the full emergency position and kept there until the train comes to a complete stop, even if the danger has passed.
DEFECTS OF THE BRAKE VALVE
BRAKE VALVE DEFECTS
92. Q. What will cause a constant blow at the brake pipe exhaust port, and what may be done to overcome it?
92. Q. What will cause a steady leak at the brake pipe exhaust port, and what can be done to fix it?
A. This indicates that the brake pipe exhaust valve is being held off its seat, due no doubt to dirt; tapping the side of the valve will sometimes stop the blow; if not, close the brake pipe cut-out cock and make a heavy service reduction; next, place the brake valve handle in release position. This will cause a strong blow at the exhaust port, which will invariably remove the trouble.
A. This indicates that the brake pipe exhaust valve is stuck off its seat, likely because of dirt; tapping the side of the valve will sometimes stop the blowing sound; if it doesn’t, close the brake pipe cut-out valve and make a heavy service reduction; then, put the brake valve handle in the release position. This will create a strong blow at the exhaust port, which will usually fix the issue.
93. Q. If the pipe connecting the brake valve with the equalizing reservoir breaks, can both locomotive and train brakes be operated with the automatic brake valve?
93. Q. If the pipe linking the brake valve to the equalizing reservoir breaks, can both the locomotive and train brakes be operated using the automatic brake valve?
A. Yes; by placing a blind gasket in the pipe connection at the brake valve and plugging the brake pipe exhaust port. To apply the brake, move the handle carefully toward emergency position, making a gradual reduction of brake pipe pressure through[Pg 190] the direct exhaust ports of the brake valve; when the desired reduction is made, the handle should be moved gradually back to lap position.
A. Yes; by putting a blind gasket in the pipe connection at the brake valve and sealing the brake pipe exhaust port. To engage the brake, gently pull the handle toward the emergency position, gradually reducing the brake pipe pressure through [Pg 190] the direct exhaust ports of the brake valve; once the desired reduction is achieved, the handle should be slowly returned to the lap position.
94. Q. What would be the effect if the handle were moved to lap quickly?
94. Q. What would happen if the handle was moved to your lap quickly?
A. Would cause the release of the brakes on the head end of the train.
A. Would cause the brakes on the front of the train to be released.
95. Q. What will cause air to blow at the brake pipe exhaust port when the handle is moved to lap position?
95. Q. What will make air blow out of the brake pipe exhaust port when the handle is moved to the lap position?
A. This is caused by a leak from the equalizing reservoir or its connections, which reduces the pressure in chamber "D" above the equalizing piston, allowing brake pipe pressure under the piston to force it up, unseating the brake pipe exhaust valve, permitting brake pipe air to flow to the atmosphere.
A. This happens because of a leak from the equalizing reservoir or its connections, which lowers the pressure in chamber "D" above the equalizing piston. This allows the brake pipe pressure beneath the piston to push it up, disengaging the brake pipe exhaust valve and letting brake pipe air escape into the atmosphere.
96. Q. What is the purpose of the equalizing reservoir?
96. Q. What is the purpose of the equalizing reservoir?
A. The purpose of the equalizing reservoir is to furnish a larger volume of air above the equalizing piston than is found in chamber "D", thus to enable the engineer to make a graduated reduction of the pressure above the equalizing piston.
A. The purpose of the equalizing reservoir is to provide a larger volume of air above the equalizing piston than what is in chamber "D," allowing the engineer to gradually decrease the pressure above the equalizing piston.
97. Q. What defect will cause the brake pipe and main reservoir pressure to equalize when the handle is in running position?
97. Q. What issue will cause the brake pipe and main reservoir pressure to balance out when the handle is in the running position?
A. This may be caused by leakage past the rotary valve, defective body gasket, or leakage by the feed valve or its case gasket. To determine which part is at fault, close the cut-out cock under the brake valve[Pg 191] and move the handle to service position, exhausting all air from chamber "D" and the brake pipe; return the handle to lap position. Leakage of air past the rotary valve is generally into the brake pipe port which allows the air to come in under the equalizing piston, thus forcing it upward, unseating the brake pipe exhaust valve, allowing this air to escape to the atmosphere at the brake pipe exhaust port. Leakage past the body gasket allows air to enter chamber "D", above the equalizing piston, holding it in its lower position, keeping the brake pipe exhaust port closed, thereby preventing the escape of this air to the atmosphere. Since the capacity of the equalizing reservoir and chamber "D" is small, such a leak will cause the black hand to quickly move up to the position of the red hand. To determine if the leakage be in the feed valve or its gasket, recharge the brake pipe to some pressure below the adjustment of the feed valve, then place the handle in lap position. If the black hand on the air gauge remains stationary, it is fair to assume that the trouble is in the feed valve or its gasket, as in this position of the brake valve the feed valve is cut out.
A. This might be due to a leak past the rotary valve, a faulty body gasket, or a leak by the feed valve or its case gasket. To figure out which part is causing the issue, close the cut-out cock under the brake valve[Pg 191] and switch the handle to service position, releasing all the air from chamber "D" and the brake pipe; then return the handle to the lap position. Air usually leaks past the rotary valve into the brake pipe port, allowing air to flow under the equalizing piston, which pushes it upward, unseating the brake pipe exhaust valve and letting this air escape into the atmosphere at the brake pipe exhaust port. If there is a leak past the body gasket, air enters chamber "D," above the equalizing piston, holding it down and keeping the brake pipe exhaust port closed, which stops the air from escaping to the atmosphere. Since the equalizing reservoir and chamber "D" have a small capacity, such a leak will quickly cause the black hand to rise to the position of the red hand. To check if the leak is in the feed valve or its gasket, recharge the brake pipe to a pressure below the setting of the feed valve, then place the handle in the lap position. If the black hand on the air gauge stays still, it's safe to assume that the problem is with the feed valve or its gasket, since in this position of the brake valve, the feed valve is cut out.
98. Q. With the engine alone, the brake pipe pressure will equalize with that in the main reservoir, while when coupled to a train the pressure will remain at that for which the feed valve is adjusted; where is the trouble?
98. Q. When operating the engine by itself, the brake pipe pressure will balance out with the pressure in the main reservoir. However, when it's connected to a train, the pressure will stay at the level set by the feed valve; what’s causing the problem?
A. This is caused by light leakage of main reservoir air into the brake pipe, and may come past the rotary valve, body gasket, or feed valve, and with the lone engine is sufficient to raise the brake pipe pressure to that in the main reservoir; while, when coupled to a train, the brake pipe leakage of which is greater than this amount, this leakage will not be noticed.[Pg 192]
A. This happens when air from the main reservoir leaks into the brake pipe. It can come through the rotary valve, body gasket, or feed valve. With just one engine, this leak is enough to increase the brake pipe pressure to match that of the main reservoir. However, when connected to a train, if the brake pipe's leakage exceeds this amount, the leak won't be noticeable.[Pg 192]
THE FEED VALVE AND ITS DEFECTS
99. Q. What do Figures 6 and 7 represent?
99. Q. What do Figures 6 and 7 show?
A. These are diagrams of the B-6 feed valve in both open and closed positions.
A. These are diagrams of the B-6 feed valve in both open and closed positions.
100. Q. Name the different parts of the feed valve.
100. Q. What are the different parts of the feed valve?
A. The valve consists of the following parts: 2, valve body; 3, pipe bracket; 5, cap nut; 6, piston spring; 7, piston spring tip; 8, supply valve piston; 9, supply valve; 10, supply valve spring; 11, regulating valve cap nut; 12, regulating valve; 13, regulating valve spring; 14, diaphragm; 15, diaphragm ring; 16, diaphragm spindle; 17, regulating spring; 18, spring box; 19 and 20, stop rings; 21, clamping screw; 22, hand wheel.
A. The valve is made up of the following parts: 2, valve body; 3, pipe bracket; 5, cap nut; 6, piston spring; 7, piston spring tip; 8, supply valve piston; 9, supply valve; 10, supply valve spring; 11, regulating valve cap nut; 12, regulating valve; 13, regulating valve spring; 14, diaphragm; 15, diaphragm ring; 16, diaphragm spindle; 17, regulating spring; 18, spring box; 19 and 20, stop rings; 21, clamping screw; 22, hand wheel.
101. Q. Explain the operation of the feed valve.
101. Q. Describe how the feed valve works.
A. The feed valve consists of two portions, the supply and regulating portions. The supply portion consists of a slide valve 9 and a piston 8 (see Fig. 6). The supply valve 9 opens and closes communication between the main reservoir and the feed valve pipe and is moved by the piston 8 which is operated by main reservoir air entering through passage "a" on one side or by the pressure of the spring 6 on the other side. The regulating portion consists of a brass diaphragm 14, on one side of which is the diaphragm spindle 16, held against the diaphragm by the regulating spring 17, and on the other side a regulating valve 12, held against the diaphragm or its seat, as the case may be, by the spring 13. Chamber "L" at the left of the diaphragm is open to the feed valve pipe through the passage "e" and "d". The feed valve is adjusted by turning the hand wheel 22 in or out, thus increasing or decreasing the pressure exerted by the spring on the diaphragm. The same results[Pg 193] are obtained in turning the hand wheel 22 as when turning the adjusting screw in the older types of feed valves.
A. The feed valve has two parts: the supply and regulating parts. The supply part includes a slide valve 9 and a piston 8 (see Fig. 6). The supply valve 9 opens and closes the connection between the main reservoir and the feed valve pipe, and it is operated by the piston 8, which is moved by air from the main reservoir entering through passage "a" on one side or by the pressure from spring 6 on the other side. The regulating part consists of a brass diaphragm 14, with the diaphragm spindle 16 on one side, pressed against the diaphragm by the regulating spring 17, and on the other side a regulating valve 12, pushed against the diaphragm or its seat by spring 13. Chamber "L" to the left of the diaphragm is connected to the feed valve pipe through passages "e" and "d". The feed valve is adjusted by turning hand wheel 22 in or out, which increases or decreases the pressure applied by the spring on the diaphragm. The same effect[Pg 193] is achieved by turning hand wheel 22 as when adjusting the screw in older types of feed valves.
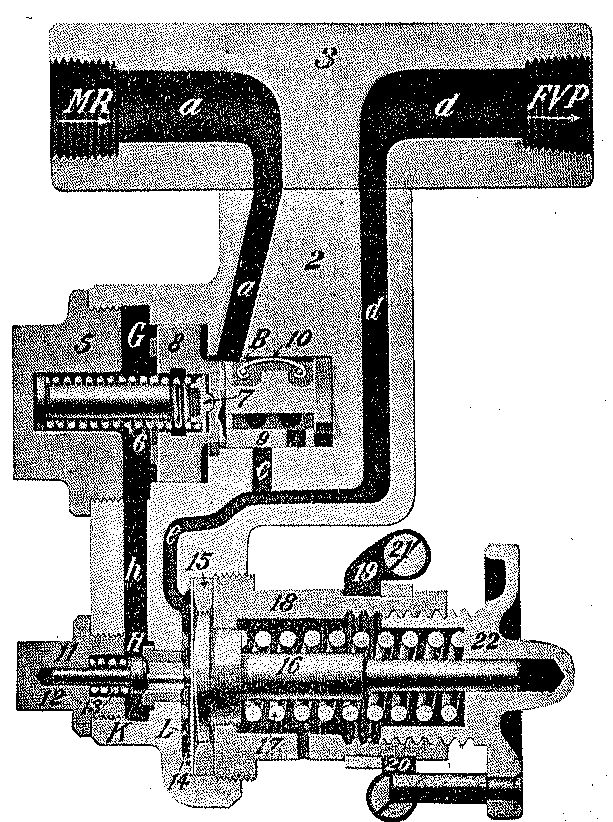
Fig 6: Diagram of B-6 Feed Valve, Closed.
Connections: MR, Main Reservoir Pipe; FVP, Feed Valve Pipe.
Fig 6: Diagram of B-6 Feed Valve, Closed.
Connections: MR, Main Reservoir Pipe; FVP, Feed Valve Pipe.
[Pg 194] Air from the main reservoir flowing through passage "a" into chamber "B" will force the piston 8 to the left against the tension of the spring 6; the piston in moving will take with it the supply valve 9, opening the supply port in the valve to port "c" in its seat as shown in Fig. 7. Main reservoir air will now be free to flow through passage "a", chamber "B", port "c" and passage "d" to the feed valve pipe. Air coming through port "c" also flows through passage "e" to chamber "L" at the left of the diaphragm 14, and this pressure tends toward forcing the diaphragm to the right; but the diaphragm being supported by the regulating spring 17, will remain in its position at the left, holding the regulating valve 12 off its seat, until the pressure in chamber "L" exceeds the tension of the regulating spring 17. Air, therefore, continues to flow from the main reservoir through a, B, c, d and e to the feed valve pipe and chamber "L", increasing the pressure, until the pressure on the diaphragm 14 overcomes the tension of the regulating spring 17, when the diaphragm will move to the right, allowing the spring 13 to force the regulating valve 12 to its seat, closing port "K". Chambers "G" and "H" are then no longer open to chamber "L" and the feed valve pipe, and these chambers being small, the pressure raises quickly to main reservoir pressure due to the leakage of air past the supply piston 8, which forms but a loose fit in its bushing. When the pressure in chamber "G" becomes nearly equal to that in chamber "B", the piston spring "6" forces the piston 8 and its slide valve 9 to closed position, which prevents further flow of air from the main reservoir to the feed valve pipe (see Fig. 6). The feed valve will remain in closed position until the pressure in chamber "L" is slightly reduced so that the pressure on the diaphragm 14 is no longer able to withstand the pressure of the regulating spring 17, which then forces the[Pg 195] diaphragm to the left, lifting the regulating valve 12 from its seat and again opening port "K" to chamber "L", thus dropping the pressure at the left of piston 8 below that of the main reservoir acting on the opposite side of the piston.
[Pg 194] Air from the main reservoir moves through passage "a" into chamber "B," pushing piston 8 to the left against the tension of spring 6. As the piston moves, it also moves supply valve 9, opening the supply port in the valve to port "c" in its seat, as shown in Fig. 7. Air from the main reservoir can now flow freely through passage "a," chamber "B," port "c," and passage "d" to the feed valve pipe. Air entering through port "c" also flows through passage "e" to chamber "L" on the left side of diaphragm 14, creating pressure that pushes the diaphragm to the right; however, since the diaphragm is supported by regulating spring 17, it stays in its position on the left, keeping regulating valve 12 off its seat, until the pressure in chamber "L" exceeds the tension of spring 17. Therefore, air continues to flow from the main reservoir through a, B, c, d, and e to the feed valve pipe and chamber "L," increasing the pressure until the pressure on diaphragm 14 surpasses the tension of spring 17. When that happens, the diaphragm moves to the right, allowing spring 13 to push regulating valve 12 back onto its seat, closing port "K." Chambers "G" and "H" are then no longer connected to chamber "L" and the feed valve pipe. Because these chambers are small, the pressure quickly rises to match the main reservoir pressure due to air leaking past supply piston 8, which has a loose fit in its bushing. When the pressure in chamber "G" becomes almost equal to that in chamber "B," piston spring "6" forces piston 8 and slide valve 9 to close, stopping any further air flow from the main reservoir to the feed valve pipe (see Fig. 6). The feed valve remains closed until the pressure in chamber "L" drops slightly, allowing the pressure on diaphragm 14 to weaken against the force of regulating spring 17, which then pushes the diaphragm to the left, lifting regulating valve 12 off its seat and reopening port "K" to chamber "L," thereby lowering the pressure on the left side of piston 8 below that of the main reservoir on the opposite side of the piston. [Pg 195]
Main reservoir pressure then forces the supply piston and valve over into open position, as shown in Fig. 7, and allows a further flow of air through port "c" to the feed valve pipe to again raise its pressure to the adjustment of the feed valve, when the valve will again close.
Main reservoir pressure then pushes the supply piston and valve into an open position, as shown in Fig. 7, and lets more air flow through port "c" to the feed valve pipe, which raises its pressure to the setting of the feed valve, at which point the valve will close again.
102. Q. What is the duty of the feed valve?
102. Q. What does the feed valve do?
A. To control and maintain a constant pressure in the brake pipe when the brake valve is in running or holding position.
A. To control and keep a consistent pressure in the brake pipe when the brake valve is in running or holding position.
103. Q. What defect in the feed valve will cause the brake pipe pressure to equalize with that in the main reservoir?
103. Q. What issue with the feed valve will cause the brake pipe pressure to match the pressure in the main reservoir?
A. This may be caused by a defective feed valve case gasket, permitting main reservoir air to leak into the feed valve pipe, or leakage past the supply valve, or the regulating valve held from its seat, or the supply valve piston too tight a fit in its cylinder.
A. This could be due to a faulty feed valve case gasket, which allows air from the main reservoir to leak into the feed valve pipe, or a leak past the supply valve, or the regulating valve not sitting correctly in its seat, or the supply valve piston being too tightly fitted in its cylinder.
104. Q. If the brake pipe charges too slowly when nearing the maximum pressure, where is the trouble?
104. Q. If the brake pipe is filling up too slowly as it approaches the maximum pressure, what’s the issue?
A. This may be caused by a loose-fitting supply valve piston 8, or the port past the regulating valve 12 partly stopped up.
A. This may be caused by a loose-fitting supply valve piston 8, or the port past the regulating valve 12 being partially blocked.
105. Q. How should the feed valve be tested?
105. Q. How should the feed valve be tested?
A. With the brakes released, and charged to the adjustment of the feed valve, create a brake pipe leak of from seven to ten pounds and note the black hand on the brake pipe gauge. The fluctuation of this hand will indicate the opening and closing of the feed valve, which should not permit a variation of over two pounds in brake pipe pressure; if it does, it indicates a dirty condition of the valve, and should be cleaned.[Pg 197]
A. With the brakes released and the feed valve adjusted, create a brake pipe leak of seven to ten pounds and observe the black hand on the brake pipe gauge. The movement of this hand will show the opening and closing of the feed valve, which should not allow a variation of more than two pounds in brake pipe pressure; if it does, it suggests the valve is dirty and needs to be cleaned.[Pg 197]
106. Q. If the main reservoir pipe connection to the feed valve breaks, what should be done?
106. Q. If the main reservoir pipe connection to the feed valve breaks, what should you do?
A. This will cause a loss of main reservoir air, and both ends of the pipe must be plugged. As no air now comes to the feed valve to charge the brake pipe in running or holding position of the brake valve, the handle must be carried in release position.
A. This will lead to a loss of air from the main reservoir, and both ends of the pipe must be sealed off. Since no air is now reaching the feed valve to charge the brake pipe while in either the running or holding position of the brake valve, the handle must be kept in the release position.
107. Q. What must be done if the pipe between the feed valve and automatic brake valve breaks?
107. Q. What should you do if the pipe between the feed valve and the automatic brake valve breaks?
A. Slack off on the regulating nut of the feed valve until all tension is removed from the regulating spring and plug the pipe toward the brake valve. To charge the brake pipe, the brake valve handle must be carried in release position.
A. Loosen the regulating nut on the feed valve until all tension is released from the regulating spring and block the pipe leading to the brake valve. To fill the brake pipe, the brake valve handle must be in the release position.
108. Q. If the feed valve becomes defective so that it will not control brake pipe pressure, what may be done?
108. Q. If the feed valve is faulty and can't control the brake pipe pressure, what can be done?
A. As the reducing valve used for the independent brake, and the feed valve are practically the same, they may be changed one for the other, the reducing valve taking the place of the feed valve.
A. Since the reducing valve used for the independent brake and the feed valve are basically the same, they can be swapped for each other, with the reducing valve replacing the feed valve.
INDEPENDENT BRAKE VALVE
Independent Brake Valve
109. Q. Name the different positions of the independent brake valve used with the E-T equipment.
109. Q. Name the various positions of the independent brake valve used with the E-T equipment.
A. Release, running, lap, slow-application position, quick-application position.
A. Release, running, lap, slow-application position, quick-application position.
110. Q. What is the purpose of release position?
110. Q. What is the purpose of the release position?
A. To release the locomotive brake when the automatic brake valve is in other than running position.
A. To release the train brake when the automatic brake valve is not in the running position.
111. Q. What is the purpose of running position?[Pg 198]
111. Q. What is the purpose of the running position?[Pg 198]
A. This is the proper position for the brake valve when not in use, and to release the locomotive brake when the automatic brake valve is in running position.
A. This is the correct position for the brake valve when it’s not in use and to release the locomotive brake when the automatic brake valve is in the running position.
112. Q. What is the purpose of lap position?
112. Q. What’s the purpose of lap position?
A. To hold the locomotive brake applied after an independent application.
A. To keep the train brake engaged after an independent application.
113. Q. What is the purpose of slow-application position?
113. Q. What is the purpose of the slow-application position?
A. This position may be used when it is desired to make a light or gradual application of the brake, as in stretching or bunching the slack of a train.
A. This position can be used when there's a need to apply the brake lightly or gradually, like when stretching or gathering the slack of a train.
114. Q. What is the purpose of quick-application position?
114. Q. What is the purpose of the quick-application position?
A. To apply the locomotive brake quickly, as in short switching.
A. To quickly use the train brake, like in short switching.
115. Q. What brake cylinder pressure is usually developed with this brake?
115. Q. What brake cylinder pressure is typically created with this brake?
A. About forty-five pounds.
About forty-five lbs.
DEAD ENGINE FEATURE
Dead Engine Feature
116. Q. What is the dead engine device?
116. Q. What is the dead engine device?
A. The dead engine device is a pipe connection between the main reservoir and the brake pipe. In this pipe is found a combined strainer and check valve with a choke fitting and cut-out cock, which when open forms a connection between the brake pipe and the main reservoir.
A. The dead engine device is a pipe link between the main reservoir and the brake pipe. In this pipe, there is a combined strainer and check valve with a choke fitting and cut-out cock, which, when opened, connects the brake pipe to the main reservoir.
117. Q. What is the purpose of this device?
117. Q. What is the purpose of this device?
A. To provide a means of charging the main reservoir of an engine whose compressor is inoperative.[Pg 199]
A. To offer a way to charge the main reservoir of an engine when the compressor is not working.[Pg 199]
118. Q. What is the object of charging a main reservoir of an engine with a disabled compressor?
118. Q. What’s the purpose of charging the main reservoir of an engine when the compressor is not working?
A. As the air used in the locomotive brake cylinders comes from the main reservoir, for the brakes to be operated on this engine it is necessary that its main reservoir be charged.
A. Since the air used in the locomotive brake cylinders comes from the main reservoir, the main reservoir needs to be charged for the brakes to work on this engine.
119. Q. With a 70-pound brake pipe pressure, what pressure should be had in the main reservoir when using this device?
119. Q. With a 70-pound brake pipe pressure, what pressure should be in the main reservoir when using this device?
A. About fifty pounds.
Around fifty pounds.
120. Q. When the dead engine feature is being used, in what position should the automatic and independent brake valves be carried?
120. Q. When using the dead engine feature, where should the automatic and independent brake valves be positioned?
A. Running position.
A. Running stance.
121. Q. What should be the position of the brake pipe cut-out cock below the brake valve?
121. Q. Where should the brake pipe cut-out cock be positioned in relation to the brake valve?
A. It should be closed.
It should be shut down.
DISTRIBUTING VALVE
Distribution Valve
122. Q. What is the duty of the distributing valve?
122. Q. What is the purpose of the distributing valve?
A. To admit air from the main reservoir to the locomotive brake cylinders when applying the brake, to automatically maintain the brake cylinder pressure against leakage, to develop the proper brake cylinder pressure regardless of piston travel and to exhaust the air from the brake cylinders when releasing the brake.
A. To let air from the main reservoir into the locomotive brake cylinders when the brake is applied, to automatically keep the brake cylinder pressure steady against any leaks, to create the right brake cylinder pressure no matter how far the piston moves, and to release the air from the brake cylinders when the brake is released.
123. Q. To what is the distributing valve attached?
123. Q. What is the distributing valve connected to?
A. To the distributing valve reservoir.
A. To the distribution valve reservoir.
124. Q. How many chambers has the distributing valve reservoir?[Pg 200]
124. Q. How many chambers does the distributing valve reservoir have?[Pg 200]
A. Two; pressure chamber and application chamber.
A. Two: pressure chamber and application chamber.
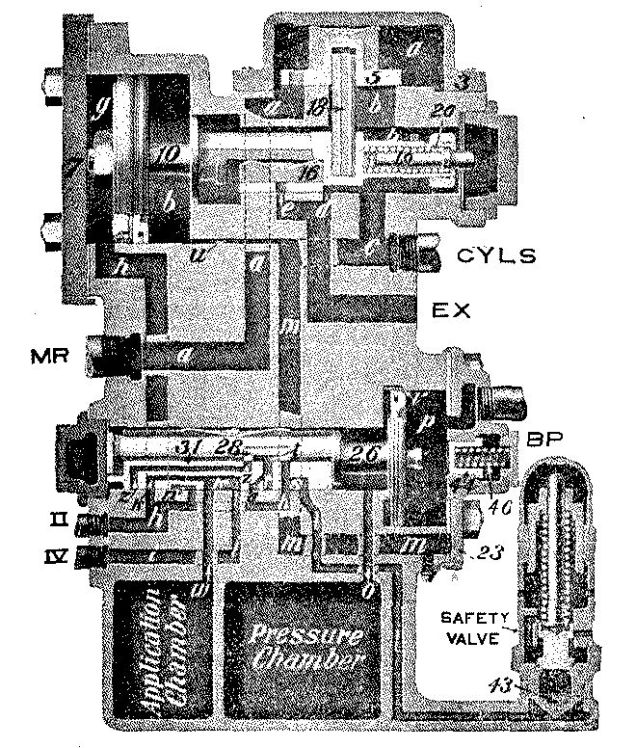
Fig. 8: Release, Automatic or Independent.
Connections: MR, Main Reservoir Pipe; IV, Distributing Valve Release Pipe;
II, Application Cylinder Pipe; CYLS, Brake Cylinder Pipe; BP, Brake Pipe.
Fig. 8: Release, Automatic or Independent.
Connections: MR, Main Reservoir Pipe; IV, Distributing Valve Release Pipe; II, Application Cylinder Pipe; CYLS, Brake Cylinder Pipe; BP, Brake Pipe.
125. Q. Name the different pipe connections to the distributing valve reservoir.
125. Q. What are the different pipe connections to the distributing valve reservoir?
A. Referring to Fig. 8, the connection marked "MR" is the main reservoir supply pipe; "II", application cylinder pipe; "IV", distributing valve release pipe; "BP", brake pipe; "CYLS", brake cylinder pipe.
A. Referring to Fig. 8, the connection labeled "MR" is the main reservoir supply pipe; "II" is the application cylinder pipe; "IV" is the distributing valve release pipe; "BP" is the brake pipe; and "CYLS" is the brake cylinder pipe.
126. Q. To what do these different pipes connect?
126. Q. What do these different pipes connect to?
A. The main reservoir supply pipe connects the distributing valve with the main reservoir pipe. The application cylinder pipe connects the application cylinder of the distributing valve with the independent and automatic brake valves. The distributing valve release pipe connects the application cylinder exhaust port in the distributing valve with the independent brake valve, and through it, when in running position, to the automatic brake valve. The brake cylinder pipe connects the distributing valve with the different brake cylinders on the locomotive. The brake pipe branch pipe connects the distributing valve with the brake pipe.
A. The main reservoir supply pipe links the distributing valve to the main reservoir pipe. The application cylinder pipe connects the application cylinder of the distributing valve to the independent and automatic brake valves. The distributing valve release pipe connects the exhaust port of the application cylinder in the distributing valve to the independent brake valve, and when in running position, to the automatic brake valve. The brake cylinder pipe connects the distributing valve to the various brake cylinders on the locomotive. The brake pipe branch pipe connects the distributing valve to the brake pipe.
127. Q. Explain the operation of the distributing valve when making an automatic service application of the brake.
127. Q. Describe how the distributing valve works when you use the brakes automatically.
A. When the brakes are fully charged, the brake pipe and pressure chamber pressures are equal, and when a gradual reduction of brake pipe pressure is made it will be felt in chamber "p" at the right of the equalizing piston 26, creating a difference in pressure on the two sides of the piston, causing it to move to the right. The first movement of the piston closes the feed groove "v", also moves the graduating valve 28, uncovering the service port "z" in the equalizing slide valve 31; this movement of the piston also causes the shoulder on the end of its stem to engage[Pg 202] the equalizing slide valve, and the continued movement of the piston moves the valve to service position, in which port "z" connects with port "h" in the seat of the valve, as shown in Fig. 9. As the equalizing slide valve chamber is at all times connected to the pressure chamber, air can now flow from this chamber to both the application cylinder and chamber through ports "z" and "h", cavity "n" and port "w" until the pressure on the left or pressure chamber side of the equalizing piston 26 becomes slightly less than that in the brake pipe, when the piston and graduating valve will move to the left until the shoulder on the piston stem strikes the slide valve; this movement of the graduating valve closes the service port "z", thus closing the communication between the pressure chamber and application chamber and cylinder, also closing port "l" which leads to the safety valve. The distributing valve is now said to be in service lap position. (See Fig. 10.)
A. When the brakes are fully charged, the pressures in the brake pipe and pressure chamber are equal. If the pressure in the brake pipe is gradually reduced, this change will be felt in chamber "p" on the right side of the equalizing piston 26, creating a pressure difference on both sides of the piston, which causes it to move to the right. The initial movement of the piston closes the feed groove "v" and also shifts the graduating valve 28, exposing the service port "z" in the equalizing slide valve 31. This movement also causes the shoulder at the end of the piston stem to engage the equalizing slide valve, and the continued motion of the piston pushes the valve into the service position, where port "z" connects with port "h" in the valve seat, as shown in Fig. 9. Since the equalizing slide valve chamber is always connected to the pressure chamber, air can now flow from this chamber to both the application cylinder and chamber through ports "z" and "h", cavity "n", and port "w" until the pressure on the left side or pressure chamber side of the equalizing piston 26 becomes just a little lower than that in the brake pipe. This will cause the piston and graduating valve to shift to the left until the shoulder on the piston stem hits the slide valve; this movement of the graduating valve closes the service port "z", thereby stopping the communication between the pressure chamber and the application chamber and cylinder, and also closing port "l", which goes to the safety valve. The distributing valve is now in the service lap position. (See Fig. 10.)
128. Q. Upon what does the pressure in the application chamber and cylinder depend when making a service application of the brake?
128. Q. What factors affect the pressure in the application chamber and cylinder when using the brake for service?
A. On the amount of brake pipe reduction; and as the relative volume of the pressure chamber and application cylinder and chamber is practically the same as that of an auxiliary reservoir and brake cylinder, it will be understood that one pound from the pressure chamber will make two and one-half pounds in the application chamber and cylinder; in other words, with the pressure chamber charged to seventy pounds and no pressure in the application chamber and cylinder, if they were connected and the pressure allowed to equalize it would do so at about fifty pounds; that is, twenty pounds from the pressure chamber will make fifty pounds in the application chamber and cylinder.
A. Regarding the amount of brake pipe reduction; since the relative volume of the pressure chamber and the application cylinder and chamber is basically the same as that of an auxiliary reservoir and brake cylinder, it's clear that one pound from the pressure chamber will result in two and a half pounds in the application chamber and cylinder. In other words, if the pressure chamber is charged to seventy pounds and there is no pressure in the application chamber and cylinder, connecting them and allowing the pressure to equalize would settle around fifty pounds. That means twenty pounds from the pressure chamber will equal fifty pounds in the application chamber and cylinder.
129. Q. How is the application piston 10 affected by the air pressure in the application cylinder "g"?
129. Q. How does the air pressure in the application cylinder "g" impact the application piston 10?
A. Pressure forming in this cylinder will force the piston to the right; the piston in moving will carry with it the exhaust valve 16, closing the exhaust ports "e" and "d", at the same time moving the application[Pg 204] valve 5, opening the supply port "b", allowing main reservoir air from chamber "a" to flow through ports "b" and "C" to the connection marked "CYLS", and on to the different brake cylinders of the locomotive until the pressure in the brake cylinders and at the right of the application piston becomes slightly greater than that in chamber "g" when the application piston and valve will move back to lap position as shown in Figures 9 and 10.
A. Pressure building up in this cylinder will push the piston to the right; as the piston moves, it will also move the exhaust valve 16, closing the exhaust ports "e" and "d". At the same time, it will move the application valve 5, opening the supply port "b", which allows main reservoir air from chamber "a" to flow through ports "b" and "C" to the connection labeled "CYLS", and into the various brake cylinders of the locomotive. This will continue until the pressure in the brake cylinders and to the right of the application piston becomes slightly higher than that in chamber "g", at which point the application piston and valve will return to the lap position, as shown in Figures 9 and 10.
130. Q. With the application valve in lap position, if there be brake cylinder leakage, will the locomotive brake leak off?
130. Q. When the application valve is in the lap position, if there's a leak in the brake cylinder, will the locomotive brake lose pressure?
A. No; any drop in brake cylinder pressure will be felt in chamber "b" at the right of the application piston 10, causing a difference in pressure on the two sides of the piston, thus allowing the pressure in the application cylinder to move the application piston and valve to the right, again opening the supply port "b" allowing a further flow of main reservoir air from chamber "a" to the brake cylinders until the pressure is again slightly greater than that in the application cylinder "g", when the application piston and valve will move back to lap position. Thus in this way air will be supplied to the brake cylinders of the locomotive, holding the brake applied regardless of leakage.
A. No; any drop in brake cylinder pressure will be felt in chamber "b" on the right side of application piston 10, creating a pressure difference on both sides of the piston. This allows the pressure in the application cylinder to move the application piston and valve to the right, reopening supply port "b" and enabling further airflow from main reservoir air in chamber "a" to the brake cylinders until the pressure is once again slightly higher than that in the application cylinder "g," at which point the application piston and valve will shift back to the lap position. This ensures that air is supplied to the locomotive's brake cylinders, keeping the brakes applied regardless of any leakage.
131. Q. What effect will piston travel have on the pressure developed in the brake cylinders?
131. Q. How will the movement of the piston affect the pressure created in the brake cylinders?
A. None; as the pressure in the brake cylinders is entirely dependent on the pressure in the application cylinder, which is not affected by piston travel.
A. None; the pressure in the brake cylinders completely relies on the pressure in the application cylinder, which isn’t influenced by piston travel.
132. Q. Explain the movement of the parts in the distributing valve when the automatic brake valve is moved to release position, after an automatic application of the brake.[Pg 205]
132. Q. Describe how the parts in the distributing valve move when the automatic brake valve is set to release after the brakes are automatically applied.[Pg 205]
A. In release position of the brake valve, air from the main reservoir flows direct to the brake pipe, causing a rise of pressure which is felt in chamber "p" on the right or brake pipe side of the equalizing piston 26; this increase of pressure will cause the piston to move toward the left, carrying the graduating valve 28 and slide valve 31 to release position.
A. In the release position of the brake valve, air from the main reservoir flows directly to the brake pipe, which increases the pressure felt in chamber "p" on the right or brake pipe side of the equalizing piston 26; this rise in pressure causes the piston to move left, pushing the graduating valve 28 and slide valve 31 to the release position.
This allows the air from the application chamber and cylinder to flow to the distributing valve release pipe "IV" and on through the independent brake valve to the automatic brake valve, where the port to which this pipe leads is blanked by the automatic rotary valve, thus preventing the air from leaving the application chamber and cylinder, holding the locomotive brake applied while the train brakes are being released. The movement of the parts, and the results obtained are the same where the release is made in holding position.
This lets the air from the application chamber and cylinder flow to the distributing valve release pipe "IV" and through the independent brake valve to the automatic brake valve, where the port that this pipe connects to is blocked by the automatic rotary valve, preventing the air from escaping the application chamber and cylinder, which keeps the locomotive brake engaged while the train brakes are being released. The movement of the parts and the results achieved remain the same when the release is made in the holding position.
133. Q. Explain the movement of the parts in the distributing valve when the brake valve is moved to running position after having first been moved to release or holding position, following a brake application.
133. Q. Describe how the parts in the distributing valve move when the brake valve is switched to the running position after it was previously moved to the release or holding position following a brake application.
A. In this position of the brake valve the port to which the distributing valve release pipe is connected is open to the exhaust, thus allowing the air to escape from the application chamber and cylinder. The reduction of pressure in chamber "g", will allow the brake cylinder pressure in chamber "b" to force the application piston and its valves to release position, thus allowing the brake cylinder air to escape to the atmosphere, through the exhaust ports "e" and "d". (See Fig. 8.)
A. In this setting of the brake valve, the port connected to the distributing valve release pipe is open to the exhaust, allowing the air to flow out from the application chamber and cylinder. The drop in pressure in chamber "g" will enable the brake cylinder pressure in chamber "b" to push the application piston and its valves into the release position, which lets the brake cylinder air escape into the atmosphere through the exhaust ports "e" and "d". (See Fig. 8.)
134. Q. Explain how an independent release of the locomotive brake is obtained after an automatic application has been made.
134. Q. Explain how to manually release the locomotive brake after it has been automatically applied.
A. If the brakes have been applied throughout the train, by means of the automatic brake valve, and it is desired to release the locomotive brakes without releasing the train brakes, the handle of the independent brake valve is placed in release position. In this position of the independent brake valve, the application cylinder in the distributing valve is con[Pg 207]nected through the application cylinder pipe to the direct exhaust port of the independent brake valve; thus exhausting the air from the application cylinder, causing a release of the locomotive brake. This independent release of the locomotive brake does not cause the equalizing piston and its slide valve in the distributing valve to change their position.
A. If the brakes have been applied across the train using the automatic brake valve, and you want to release the locomotive brakes without releasing the train brakes, you position the handle of the independent brake valve to the release setting. In this position of the independent brake valve, the application cylinder in the distributing valve is connected through the application cylinder pipe to the direct exhaust port of the independent brake valve; this expels the air from the application cylinder, resulting in a release of the locomotive brake. This independent release of the locomotive brake does not cause the equalizing piston and its slide valve in the distributing valve to change their position.
135. Q. Explain what takes place when an automatic emergency application is made.
135. Q. Describe what happens when an automatic emergency application is initiated.
A. Any sudden reduction of brake pipe pressure is felt on the brake pipe side of the equalizing piston 26 and will cause it and the slide valve 31 to move to the extreme right, compressing the graduating spring 60. (See Fig. 11.) In this position pressure chamber air can flow to the application cylinder only as the application chamber is now cut off. This will cause a quick rise of pressure in the application cylinder, forcing the application piston and its valves to full application position, admitting main reservoir air to the brake cylinders and applying the brake. In emergency position of the automatic brake valve there is a small port in the rotary valve, called the blow-down timing port, through which main reservoir air is free to flow to the application cylinder "g" through the application cylinder pipe "II", causing a rise of pressure equal to the adjustment of the safety valve.
A. Any sudden drop in brake pipe pressure is felt on the brake pipe side of the equalizing piston 26 and will cause it and the slide valve 31 to move all the way to the right, compressing the graduating spring 60. (See Fig. 11.) In this position, air in the pressure chamber can only flow to the application cylinder since the application chamber is now blocked. This will lead to a rapid increase in pressure in the application cylinder, pushing the application piston and its valves to the fully applied position, allowing main reservoir air to enter the brake cylinders and apply the brakes. In the emergency position of the automatic brake valve, there is a small port in the rotary valve, known as the blow-down timing port, through which main reservoir air can freely flow to the application cylinder "g" through the application cylinder pipe "II," causing a pressure rise equal to the setting of the safety valve.
136. Q. At what pressure is the safety valve adjusted?
136. Q. What pressure is the safety valve set to?
A. At sixty-eight pounds.
At 68 pounds.
137. Q. What is the purpose of the quick action cap, and where is it located?
137. Q. What’s the purpose of the quick action cap, and where is it located?
A. Its purpose is to assist the brake valve in venting brake pipe air when an emergency application[Pg 208] of the brake is made, and is located on the brake pipe side of the distributing valve in place of the plain cap. (See Figs. 8 and 11.)
A. Its purpose is to help the brake valve release air from the brake pipe when an emergency brake is applied, and it is found on the brake pipe side of the distributing valve instead of the plain cap. (See Figs. 8 and 11.)
138. Q. Explain the operation of the quick action cap.
138. Q. Describe how the quick action cap works.
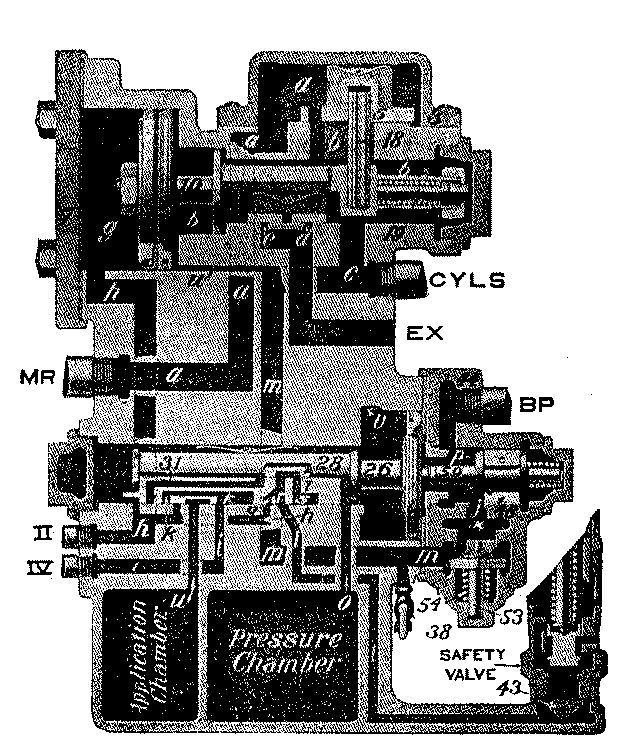
Fig. 11: Emergency Position of No. 6 Distributing Valve with Quick-Action Cap.
Fig. 11: Emergency Position of No. 6 Distributing Valve with Quick-Action Cap.
A. In an emergency application, the equalizing piston 26 moves to the extreme right, the knob on the piston strikes the graduating stem 59, causing it to compress the graduating spring 46, and move the slide valve 48 to the right, opening port "j".
A. In an emergency application, the equalizing piston 26 moves all the way to the right, the knob on the piston hits the graduating stem 59, which compresses the graduating spring 46 and shifts the slide valve 48 to the right, opening port "j".
Brake pipe pressure in chamber "p" flows to chamber "X", pushes down check valve 53, and passes to the brake cylinders through port "m" in the cap and distributing valve body. When the brake cylinders and brake pipe pressures equalize, check valve 53 is forced to its seat by spring 54, thus preventing air in the brake cylinders from flowing back into the brake pipe. When a release of the brake occurs and piston 26 is moved back to its normal position, spring 46 forces graduating stem 59 and slide valve 48 back to release position.
Brake pipe pressure in chamber "p" flows to chamber "X," pushes down check valve 53, and moves into the brake cylinders through port "m" in the cap and distributing valve body. When the pressures in the brake cylinders and brake pipe equalize, check valve 53 is pushed to its seat by spring 54, preventing air in the brake cylinders from flowing back into the brake pipe. When the brake is released and piston 26 moves back to its normal position, spring 46 pushes graduating stem 59 and slide valve 48 back to the release position.
139. Q. Explain the operation of the distributing valve when making an independent application of the brake.
139. Q. Describe how the distributing valve works when applying the brake independently.
A. When the independent brake valve handle is moved to application position, air is admitted from the reducing valve pipe through the application cylinder pipe to the application chamber and cylinder. Pressure forming in the application cylinder will move the application piston 10 to the right, carrying with it the exhaust valve 16 and the application valve 5, closing the exhaust port and opening the supply port, admitting main reservoir air from chamber "a" to the brake cylinders (see Fig. 12) until the pressure in the brake cylinders and chamber "b" slightly exceeds that in chamber "g", when the application piston 10 and valve 5 will move back to lap position. By moving the brake valve handle to either release or running position, the air is exhausted from the application cylinder and chamber, thus reducing the pressure in chamber "g", allowing the pressure in chamber "b" to force the piston to the left, carrying with it the exhaust valve 16, opening the exhaust ports "e" and "d", allowing the air from the brake cylinders to escape to the atmosphere, thus releasing the brake.[Pg 211]
A. When the independent brake valve handle is moved to the application position, air enters from the reducing valve pipe through the application cylinder pipe to the application chamber and cylinder. The pressure building up in the application cylinder will push the application piston 10 to the right, which also moves the exhaust valve 16 and the application valve 5, closing the exhaust port and opening the supply port, allowing main reservoir air from chamber "a" to flow into the brake cylinders (see Fig. 12) until the pressure in the brake cylinders and chamber "b" is slightly higher than that in chamber "g". At this point, the application piston 10 and valve 5 will return to the lap position. By moving the brake valve handle to either the release or running position, air is released from the application cylinder and chamber, which decreases the pressure in chamber "g", allowing the pressure in chamber "b" to push the piston to the left, bringing with it the exhaust valve 16, which opens the exhaust ports "e" and "d", letting the air from the brake cylinders escape into the atmosphere, thus releasing the brake.[Pg 211]
DISTRIBUTING VALVE DEFECTS
VALVE DEFECTS DISTRIBUTION
140. Q. If the locomotive brake released with the automatic brake valve in lap position, where would you look for the trouble?
140. Q. If the train's brake released while the automatic brake valve was in the lap position, where would you check for the issue?
A. Would look for a leak in the application cylinder pipe or in the application cylinder cap gasket.
A. Would check for a leak in the application cylinder pipe or in the application cylinder cap gasket.
141. Q. If the brake remained applied in lap position, but released in release or holding position, where would you look for the trouble?
141. Q. If the brake stayed applied in the lap position but released in the release or holding position, where would you check for the problem?
A. Would look for a leak in the distributing valve release pipe.
A. would check for a leak in the distribution valve release pipe.
142. Q. If the distributing valve release pipe and application cylinder pipe were crossed, what would be the effect?
142. Q. If the outlet pipe of the distributing valve and the pipe to the application cylinder were swapped, what would happen?
A. A brake application made by the automatic brake valve cannot be released by the independent brake valve.
A. A brake application made by the automatic brake valve can’t be released by the independent brake valve.
143. Q. If the safety valve leaks, what will be the effect?
143. Q. If the safety valve leaks, what will happen?
A. This may prevent the brake applying, and in an independent application if the brake does apply, it will release when the brake valve is returned to lap position.
A. This might stop the brake from engaging, and if the brake does engage during an independent application, it will release when the brake valve is returned to the neutral position.
BROKEN PIPES
LEAKING PIPES
144. Q. If the main reservoir supply pipe to the distributing valve breaks, what should be done?
144. Q. If the main supply pipe from the reservoir to the distributing valve breaks, what should be done?
A. Plug the pipe toward the main reservoir. The locomotive brake is lost, but if the distributing valve is equipped with a quick action cap, when an emergency application is made, the air coming from the brake pipe, through the quick action cap, will apply the locomotive brake.[Pg 212]
A. Connect the pipe to the main reservoir. The locomotive brake is disengaged, but if the distributing valve has a quick action cap, when an emergency application occurs, the air from the brake pipe, via the quick action cap, will activate the locomotive brake.[Pg 212]
145. Q. If the application cylinder pipe breaks, what effect will it have on the locomotive brake?
145. Q. If the application cylinder pipe breaks, what will happen to the locomotive brake?
A. The locomotive brake cannot be applied with either automatic or independent brake valve. By plugging the pipe toward the distributing valve the automatic brake will be restored.
A. The locomotive brake can't be applied using either the automatic or independent brake valve. By blocking the pipe leading to the distributing valve, the automatic brake will be reset.
146. Q. If the distributing valve release pipe breaks, what will be the effect?
146. Q. If the distributing valve release pipe breaks, what will happen?
A. The holding feature of the brake will be lost; that is, the locomotive brake will release when the automatic brake valve is moved to either release or holding position, the same as with the old G-6 equipment.
A. The holding feature of the brake will be lost; that is, the locomotive brake will release when the automatic brake valve is moved to either the release or holding position, just like with the old G-6 equipment.
147. Q. If the release pipe is broken and not plugged, can the independent brake be applied?
147. Q. If the release pipe is broken and not blocked, can the independent brake be used?
A. Yes, by placing the brake valve handle in quick-application position the brake will apply, but there will be a waste of air through the broken pipe, and the brake will release when the brake valve is returned to lap position.
A. Yes, by putting the brake valve handle in quick-application position, the brake will engage, but air will escape through the broken pipe, and the brake will release when the brake valve is moved back to lap position.
148. Q. If the brake cylinder pipe breaks, can the locomotive brake be applied?
148. Q. If the brake cylinder pipe breaks, can the locomotive brake be used?
A. This depends on where the pipe breaks; if between the cut-out cock and any one of the brake cylinders, close the cut-out cock to that cylinder, and the other cylinders may be used. But if the pipe breaks at the distributing valve, the locomotive brake will be lost.
A. This depends on where the pipe breaks; if it's between the cut-out valve and any of the brake cylinders, close the cut-out valve to that cylinder, and the other cylinders can still be used. But if the pipe breaks at the distributing valve, you'll lose the locomotive brake.
149. Q. If the brake pipe connection to the distributing valve breaks, what should be done?
149. Q. If the brake pipe connection to the distributing valve fails, what should be done?
A. Plug the end from the brake pipe; the locomotive brake must now be released by placing the independent valve in release position.[Pg 213]
A. Plug the end of the brake pipe; the locomotive brake must now be released by switching the independent valve to the release position.[Pg 213]
150. Q. If the brake pipe connection to the distributing valve breaks and is plugged, can the locomotive brake be operated?
150. Q. If the connection between the brake pipe and the distributing valve breaks and is blocked, can the locomotive brake still be operated?
A. The independent brake may be applied and released in the usual manner, but the automatic brake will be lost for service braking.
A. The independent brake can be applied and released as usual, but the automatic brake will not be available for service braking.
TYPE K TRIPLE VALVE
Type K Triple Valve
151. Q. On what is this type of triple valve designed to operate?
151. Q. What is this type of triple valve designed to operate on?
A. On freight equipment cars only.
A. On freight equipment cars only.
152. Q. Explain the operation of the "K" triple valve.
152. Q. Describe how the "K" triple valve works.
A. When air is admitted to the brake pipe it is free to enter the triple at "a" (see Fig. 13) and flow through the passage "e" to chamber "f", thence through port "g" to chamber "h" in front of the triple valve piston 4. Pressure forming in chamber "h" will force the piston to the left until its packing ring uncovers the feed groove "i" in the bushing, thus creating a communication between chamber "h" and the slide valve chamber. Brake pipe air will now be free to flow past the piston to the slide valve chamber and out at "R" to the auxiliary reservoir. Air will continue to feed through the groove "i" until the auxiliary reservoir and brake pipe pressures are equal, and it is then we say that the brake is fully charged. Brake pipe air entering chamber "a" will lift the check valve 15, and charge chamber "Y" to brake pipe pressure. When a gradual reduction of brake pipe pressure is made, as in a service application of the brakes, the pressure being reduced in chamber "h", auxiliary reservoir pressure will move the piston 4 toward service position. (See Fig. 14.) The first movement of the piston closes the feed groove "i", thus closing communication between the auxiliary reservoir and the brake pipe, preventing a back-flow of air from the auxiliary to the brake pipe, and at the same time moving the graduating valve 7, opening the service port "Z" in the slide valve. The continued movement of the piston will move the slide valve until the service port "Z" registers with the brake cylinder port "r" in the valve seat, thus creating a communication between the auxiliary reservoir and the brake cylinder. Air will now flow from the auxiliary to the brake cylinder until the pressure on the auxiliary side of the piston 4 becomes slightly less than in the brake pipe, when the piston and the graduating valve 7 will move back just far enough to close the service port "Z", thus closing communication[Pg 215] between the auxiliary reservoir and the brake cylinder. At the same time, the first movement of the graduating valve connects the two ports "o" and "q" in the slide valve through the cavity "v" in the graduating valve, and the movement of the slide valve brings port "o" to register with port "y" in the slide valve seat, and port "q" with port "t". This permits the air in chamber "Y" to flow through port "y", "o", "v", "q", and "t", thence around the emergency piston 8, which fits loosely in its cylinder, to chamber "X" and the brake cylinder. When the pressure in chamber "Y" has reduced below the brake pipe pressure remaining in chamber "a", the check valve 15 is raised and allows brake pipe air to flow past the check valve and through the ports above mentioned to the brake cylinder.
A. When air enters the brake pipe, it can flow into the triple at "a" (see Fig. 13) and then move through passage "e" to chamber "f", and from there through port "g" to chamber "h" in front of the triple valve piston 4. Pressure building up in chamber "h" pushes the piston to the left until its packing ring uncovers the feed groove "i" in the bushing, creating a connection between chamber "h" and the slide valve chamber. Air from the brake pipe can now flow past the piston to the slide valve chamber and out at "R" to the auxiliary reservoir. Air will continue to flow through groove "i" until pressures in the auxiliary reservoir and brake pipe equalize, at which point we say the brake is fully charged. Air from the brake pipe entering chamber "a" will lift check valve 15 and charge chamber "Y" to brake pipe pressure. When there is a gradual reduction in brake pipe pressure, as in a standard brake application, the pressure in chamber "h" decreases, and the pressure in the auxiliary reservoir moves piston 4 toward the service position. (See Fig. 14.) The piston’s initial movement closes the feed groove "i", cutting off the connection between the auxiliary reservoir and the brake pipe to prevent air from flowing back, while also moving the graduating valve 7 to open service port "Z" in the slide valve. The piston’s continued movement shifts the slide valve until service port "Z" aligns with the brake cylinder port "r" in the valve seat, establishing a link between the auxiliary reservoir and the brake cylinder. Air will now flow from the auxiliary reservoir to the brake cylinder until the pressure on the auxiliary side of piston 4 drops slightly below that in the brake pipe, causing the piston and graduating valve 7 to move back just enough to close service port "Z", thereby stopping communication between the auxiliary reservoir and the brake cylinder. At the same time, the first movement of the graduating valve connects ports "o" and "q" in the slide valve through cavity "v" in the graduating valve, and the slide valve movement aligns port "o" with port "y" in the slide valve seat, and port "q" with port "t". This allows air in chamber "Y" to flow through ports "y", "o", "v", "q", and "t", around the emergency piston 8, which fits loosely in its cylinder, to chamber "X" and the brake cylinder. When the pressure in chamber "Y" drops below the remaining brake pipe pressure in chamber "a", check valve 15 lifts, allowing brake pipe air to flow past the check valve and through the aforementioned ports to the brake cylinder.
The size of these ports are so proportioned that the flow of air from the brake pipe to the top of the emergency piston 8, is not sufficient to force the latter downward and thus cause an emergency application, but at the same time takes enough air from the brake pipe to cause a local reduction of brake pipe pressure at that point, thus assisting the brake valve in increasing the rapidity with which the brake pipe reduction travels through the train. The triple valve is now said to be in "Quick Service" position. (See Fig. 14.)
The size of these ports is designed so that the airflow from the brake pipe to the top of the emergency piston 8 isn’t strong enough to push it downward and trigger an emergency application. However, it does remove enough air from the brake pipe to create a local drop in brake pipe pressure at that point, which helps the brake valve speed up the reduction of brake pipe pressure throughout the train. The triple valve is now in "Quick Service" position. (See Fig. 14.)
153. Q. Will the triple valve move to quick service position whenever a gradual reduction brake pipe reduction is made?
153. Q. Will the triple valve switch to quick service position whenever there's a gradual decrease in the brake pipe pressure?
A. No; with short trains, the brake pipe volume being comparatively small, will reduce more rapidly for a certain reduction at the brake valve than with a long train. Therefore, with a short train, the brake pipe pressure reducing more quickly, the triple piston and its valves will move to "full service" position, as shown in Fig. 15. In this position the quick service port "y" is closed, so that no air flows from the brake pipe to the brake cylinder. Thus, when the brake pipe reduction is sufficiently rapid, there is no need for this quick service reduction, and the triple valve automatically cuts out this feature of the valve when not required.
A. No; with short trains, the brake pipe volume is relatively small, so it will decrease more quickly for a certain reduction at the brake valve than with a long train. Therefore, with a short train, as the brake pipe pressure drops faster, the triple piston and its valves will shift to the "full service" position, as shown in Fig. 15. In this position, the quick service port "y" is closed, preventing any air from flowing from the brake pipe to the brake cylinder. So, when the brake pipe reduction happens quickly enough, there's no need for this quick service reduction, and the triple valve automatically disables this feature when it's not needed.
154. Q. How long will the auxiliary reservoir air continue to flow to the brake cylinder?
154. Q. How long will the auxiliary reservoir air keep flowing to the brake cylinder?
A. Air will continue to flow to the brake cylinder until the pressure on the auxiliary side of the triple piston becomes slightly less than that on the brake pipe side, when the piston 4 and the graduating valve [Pg 217] 7 will move to the left until the shoulder on the piston stem strikes the slide valve. (See Fig. 16.) This movement has caused the graduating valve to close the service port "Z", thus cutting off any further flow of air from the auxiliary to the brake cylinder and also port "o", thus preventing any further flow of air from the brake pipe to the brake cylinder. The triple valve is now said to be in lap position.
A. Air will keep flowing to the brake cylinder until the pressure on the auxiliary side of the triple piston becomes slightly lower than that on the brake pipe side, at which point piston 4 and the graduating valve [Pg 217] 7 will move to the left until the shoulder on the piston stem hits the slide valve. (See Fig. 16.) This movement causes the graduating valve to close the service port "Z", stopping any further air flow from the auxiliary to the brake cylinder and also port "o", which prevents any more air flow from the brake pipe to the brake cylinder. The triple valve is now in lap position.
155. Q. How is the triple valve affected by a further reduction of brake pipe pressure?
155. Q. How does a further decrease in brake pipe pressure affect the triple valve?
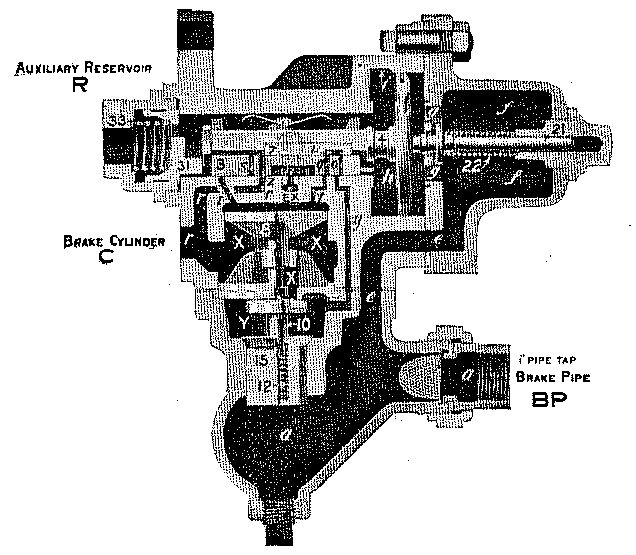
Fig. 15: Full Service Position.
Fig. 15: Full Service Mode.
A. A further reduction of brake pipe pressure will cause the triple piston 4 and the graduating valve [Pg 218]7 to again move to the right, opening ports "Z" and "o", allowing a further flow of brake pipe and auxiliary air to the brake cylinder. This may be continued until the auxiliary reservoir and brake cylinder pressures become equal, after which any further reduction of brake pipe pressure is only a waste of air. With seventy pounds brake pipe pressure, and eight-inch piston travel, a twenty-pound reduction will cause equalization at about fifty pounds.
A. If the brake pipe pressure is reduced further, the triple piston 4 and the graduating valve [Pg 218]7 will move to the right again, opening ports "Z" and "o", which will allow more brake pipe and auxiliary air to flow into the brake cylinder. This can continue until the pressures in the auxiliary reservoir and brake cylinder equalize, after which any additional reduction in brake pipe pressure just wastes air. With a brake pipe pressure of seventy pounds and an eight-inch piston travel, a twenty-pound reduction will lead to equalization at about fifty pounds.
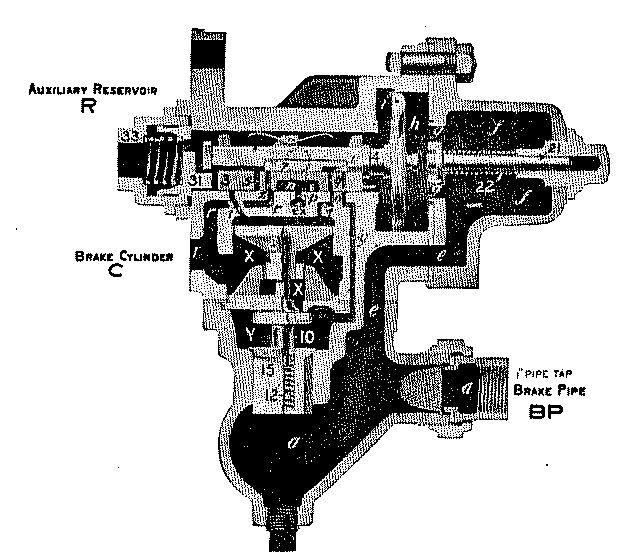
Fig. 16: Lap Position.
Fig. 16: Lap Position.
156. Q. Explain the operation of the triple valve in the release of the brake.
156. Q. Describe how the triple valve works when releasing the brake.
A. To release the brakes and recharge the auxiliary reservoirs, air is admitted through the brake valve[Pg 219] to the brake pipe. This increase of pressure on the brake pipe side of the triple valve piston 4 above that on the other side causes the piston and slide valve to move back to release position, which permits the air in the brake cylinder to flow to the atmosphere, through the exhaust port of the triple, thus releasing the brake. At the same time, air from the brake pipe flows through the feed groove "i" around the triple piston to the auxiliary reservoir, which is thus recharged. Now the "K" triple valve has two release positions: Full Release and Retarded Release. To which of these two positions the parts will move when the brakes are released, depends upon how the brake pipe pressure is increased. It is generally understood that those cars toward the head end of the train, receiving the air first, will have their brake pipe pressure raised more rapidly than those in the rear; thus the friction of the brake pipe causes the pressure to build up more rapidly in the chamber "h" of the triple valve toward the front end of the train than in those in the rear. As soon as the pressure is enough greater than the auxiliary reservoir pressure to overcome the friction of the piston, graduating valve and slide valve, all three are moved toward the left until the piston stem strikes the retarding stem 31, which is held in position by the retarding spring 33. Where the rate of increase of brake pipe pressure is slow, it will be impossible to raise the pressure in chamber "h" sufficiently to overcome the tension of the retarding spring 33, and the triple valve will remain in full release position, as shown in Fig. 13. Brake cylinder air will now be free to exhaust through port "r", large cavity "n" in the slide valve and port "p" leading to the atmosphere. If, however, the triple valve is near the head end of the train, and the brake pipe pressure builds up more rapidly than the auxiliary can recharge, an excess of pressure will be obtained in[Pg 220] chamber "h" over that in the auxiliary reservoir, and will cause the piston 4 to compress the retarding spring 33, and move the triple valve parts to retarded release position as shown in Fig. 17.
A. To release the brakes and recharge the auxiliary reservoirs, air is let in through the brake valve[Pg 219] to the brake pipe. This increase in pressure on the brake pipe side of the triple valve piston 4, compared to the other side, causes the piston and slide valve to move back to the release position, allowing the air in the brake cylinder to flow out into the atmosphere through the exhaust port of the triple, thus releasing the brake. At the same time, air from the brake pipe flows through the feed groove "i" around the triple piston to recharge the auxiliary reservoir. Now the "K" triple valve has two release positions: Full Release and Retarded Release. Whether the parts move to one of these two positions when the brakes are released depends on how the brake pipe pressure increases. It’s generally understood that the cars toward the front of the train, which receive the air first, will have their brake pipe pressure rise faster than those in the back; thus, the friction in the brake pipe causes the pressure to build up more quickly in chamber "h" of the triple valve at the front than in those at the rear. Once the pressure is significantly higher than the auxiliary reservoir pressure to overcome the friction of the piston, graduating valve, and slide valve, all three are pushed to the left until the piston stem hits the retarding stem 31, which is kept in place by the retarding spring 33. If the brake pipe pressure increases slowly, it will be difficult to raise the pressure in chamber "h" enough to overcome the tension of the retarding spring 33, and the triple valve will stay in the full release position, as shown in Fig. 13. The air from the brake cylinder will now be able to flow out through port "r", the large cavity "n" in the slide valve, and port "p" leading to the atmosphere. However, if the triple valve is near the front end of the train and the brake pipe pressure increases faster than the auxiliary can recharge, an excess pressure will build up in[Pg 220] chamber "h" compared to that in the auxiliary reservoir, causing piston 4 to compress the retarding spring 33 and move the triple valve components to the retarded release position, as shown in Fig. 17.
157. Q. What effect has retarded release position of the triple valve on the release of the brakes?
157. Q. How does the delayed release position of the triple valve affect the braking system?
A. In this position of the triple valve, cavity "n" in the slide valve connects port "r" leading to the brake cylinder, with port "p" to the atmosphere, and the brake will release; but as the small "tail port" extension of cavity "n" is over exhaust port "p", the discharge of air from the brake cylinder is quite slow.
A. In this position of the triple valve, cavity "n" in the slide valve connects port "r" leading to the brake cylinder with port "p" to the atmosphere, and the brake will release; however, since the small "tail port" extension of cavity "n" is over exhaust port "p," the release of air from the brake cylinder is quite slow.
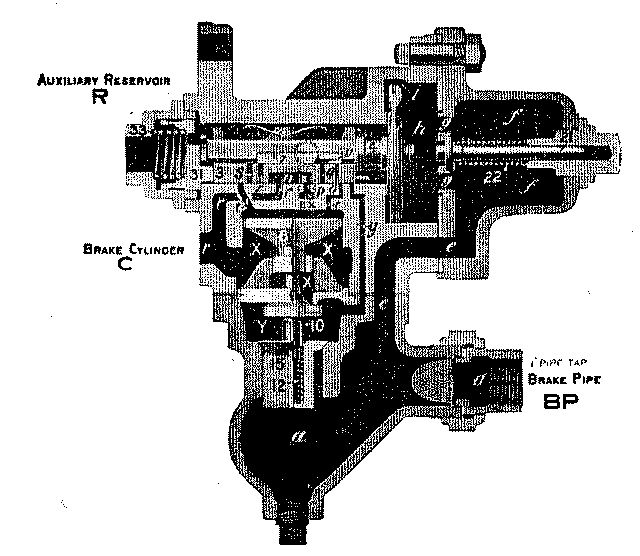
Fig. 17: Retarded Release and Charging Position.
Fig. 17: Delayed Release and Charging Position.
158. Q. What is the object of delaying the exhaust of the brake cylinder air?
158. Q. What’s the purpose of holding back the release of air from the brake cylinder?
A. In this way, the brakes on the front end of the train require a longer time to release than those on the rear. This feature is called retarded release, and although the triple valves near the locomotive commence to release before those in the rear, yet the exhaust of air from the brake cylinder is sufficiently slow to hold back the release of the brakes at the front end of the train long enough to insure a uniform release of the brakes on the train as a whole. This permits of releasing the brakes on very long trains at low speeds without danger of damaging train.
A. In this way, the brakes on the front of the train take longer to release than those on the back. This feature is called retarded release, and although the triple valves near the locomotive start to release before those in the back, the exhaust of air from the brake cylinder is slow enough to delay the release of the brakes at the front long enough to ensure a smooth release of the brakes on the entire train. This allows for braking on very long trains at low speeds without risking damage to the train.
159. Q. What other desirable feature is found in this position of the triple valve?
159. Q. What other useful feature is present in this position of the triple valve?
A. In this position, the back of the piston is in contact with the end of the slide valve bush, and, as these two surfaces are ground to an accurate fit, the piston makes a tight "seal" on the end of the bush except at one point, where a feed groove is cut in the piston to allow air to pass around the end of the slide valve bush into chamber "R" and the auxiliary reservoir. This feed groove is much smaller than the feed groove "i" in the piston bush, so that when the triple valve piston is in Retarded Release position the recharge of the auxiliary reservoir takes place much more slowly than when it is in Full Release position, thus permitting a greater volume and pressure of air to flow toward the rear of the train.
A. In this position, the back of the piston is touching the end of the slide valve bush, and because these two surfaces are accurately ground to fit together, the piston creates a tight "seal" on the end of the bush except at one spot, where a feed groove is cut into the piston to let air pass around the end of the slide valve bush into chamber "R" and the auxiliary reservoir. This feed groove is much smaller than the feed groove "i" in the piston bush, so when the triple valve piston is in Retarded Release position, the recharge of the auxiliary reservoir happens much more slowly compared to when it is in Full Release position, allowing a greater volume and pressure of air to flow toward the back of the train.
160. Q. Explain the operation of the triple valve in emergency position.
160. Q. Describe how the triple valve works in an emergency situation.
A. When any sudden reduction of brake pipe pressure is made below that in the auxiliary reservoir, it will be felt in chamber "h" in front of piston 4 and cause this piston to move to the extreme right, as shown in Fig. 18. This movement of the parts will open port "t" in the slide valve seat and allow air from the auxiliary reservoir to flow to the top of the emergency piston 8, forcing the latter downward and opening emergency valve 10. The unseating of the emergency valve allows the air in chamber "Y" to escape to the brake cylinder, thus permitting brake pipe pressure in chamber "a" to lift the check valve 15 and flow to the brake cylinder through chambers "Y" and "X", until brake cylinder and brake pipe pressure nearly equalize, when the check valve is forced to its seat by the check valve spring 12, preventing the air in the cylinder from escaping back[Pg 223] into the brake pipe again. The emergency valve and piston will now return to their normal position. At the same time port "s" in the slide valve registers with port "r" in the slide valve seat, and allows air from the auxiliary reservoir to flow to the brake cylinder. This sudden discharge of brake pipe air into the brake cylinder has the effect on the next triple valve, which in turn vents brake pipe air that affects the following triple valve and so on throughout the train.
A. When there’s a sudden drop in brake pipe pressure below that of the auxiliary reservoir, it will be felt in chamber "h" in front of piston 4, causing this piston to move all the way to the right, as shown in Fig. 18. This movement will open port "t" in the slide valve seat, allowing air from the auxiliary reservoir to flow to the top of the emergency piston 8, pushing it downwards and opening emergency valve 10. When the emergency valve opens, the air in chamber "Y" can escape to the brake cylinder, allowing brake pipe pressure in chamber "a" to lift check valve 15 and flow to the brake cylinder through chambers "Y" and "X", until the pressures in the brake cylinder and brake pipe are nearly equalized, at which point the check valve is pushed back into place by check valve spring 12, preventing the air in the cylinder from escaping back into the brake pipe. The emergency valve and piston will then return to their normal position. At the same time, port "s" in the slide valve aligns with port "r" in the slide valve seat, enabling air from the auxiliary reservoir to flow to the brake cylinder. This sudden release of brake pipe air into the brake cylinder affects the next triple valve, which in turn vents brake pipe air that influences the following triple valve, and so on throughout the train.
NEW YORK AIR BRAKE
AIR COMPRESSOR
New York Air Brake Air Compressor
161. Q. What do Figures 19 and 20 represent?
161. Q. What do Figures 19 and 20 show?
A. These are cross-sectional views of the New York compressor.
A. These are side views of the New York compressor.
162. Q. Of what does the valve gear of this compressor consist?
162. Q. What is the valve gear of this compressor made up of?
A. Of two main valves, actuated by tappet rods which enter into the hollow piston rods, and are moved by tappet plates, which are fastened to the steam piston heads.
A. Of two main valves, operated by tappet rods that go into the hollow piston rods and are moved by tappet plates attached to the steam piston heads.
163. Q. How is the admission and exhaust of steam controlled?
163. Q. How is the intake and exhaust of steam controlled?
A. The valve under the cylinder at the right controls the flow of steam to and from the cylinder at the left; while the valve under the cylinder at the left controls the flow of steam to and from the cylinder at the right.
A. The valve under the cylinder on the right controls the flow of steam to and from the cylinder on the left, while the valve under the cylinder on the left controls the flow of steam to and from the cylinder on the right.
164. Q. Explain the operation of the steam end of the compressor.
164. Q. Describe how the steam side of the compressor works.
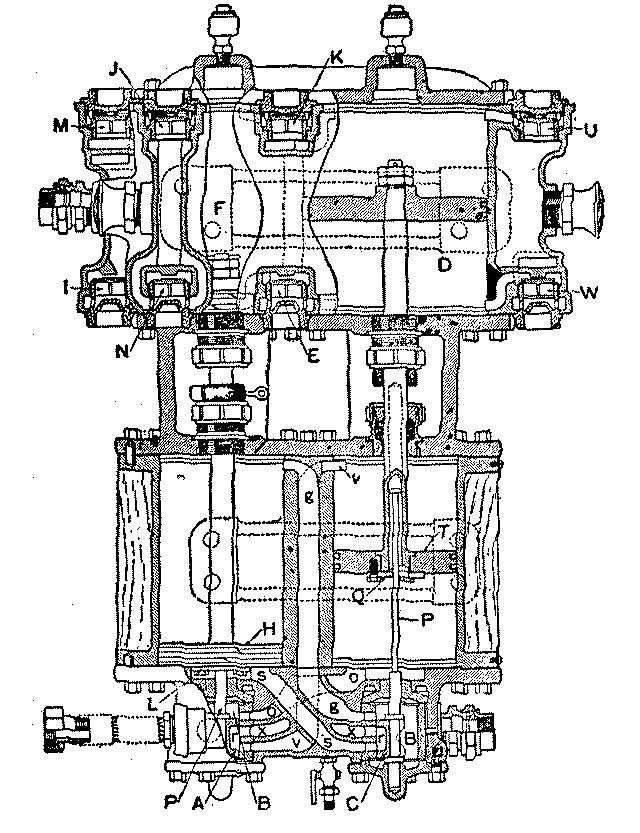
Fig. 19: Low Pressure Piston Moving Upward. High Pressure Piston at Rest.
Fig. 19: Low Pressure Piston Moving Up. High Pressure Piston Stationary.
[Pg 225]A. Assuming both pistons are at the bottom of their cylinders, when the compressor throttle is opened, live steam will flow to both steam chests "B" (see Fig. 19), and through port "o" to the under side of the piston "T" and through port "g" to the upper side of piston "H". The steam under piston "T" will force it upward, and when it very nearly completes its stroke, the tappet plate "Q" will engage the button on the end of the tappet rod "P", moving the main valve "C" to its upper position. In this position the exhaust cavity "r" in the main valve connects port "g" with the exhaust port "X", thus allowing steam above the piston "H" to escape to the exhaust, at the same time steam is admitted through port "s" to the under side of piston "H", forcing it upward. As this piston very nearly completes its stroke, the tappet plate "L" (see Fig. 20) engages the button on the tappet rod "P", moving the main valve "A" to its upper position. Exhaust cavity "r" now connects port "o", which leads to the lower end of the cylinder at the right, with the exhaust port "X", thus allowing the steam under piston "T" to escape to the exhaust, at the same time steam is admitted through port "V" to the upper end of the cylinder at the right, on top of piston "T", forcing it downward; as it very nearly completes its stroke, the tappet plate "Q" engages the shoulder on the tappet rod "P", moving the main valve "C" to its lower position. The exhaust cavity "r" in the valve now connects port "s" with the exhaust port "X", allowing steam below piston "H" to escape to the exhaust, and at the same time steam is admitted to the top of this piston, forcing it down, thus completing a cycle of the compressor.
[Pg 225]A. Assuming both pistons are at the bottom of their cylinders, when the compressor throttle is opened, live steam will flow to both steam chests "B" (see Fig. 19), and through port "o" to the underside of piston "T" and through port "g" to the upper side of piston "H". The steam under piston "T" will push it upward, and when it nearly completes its stroke, the tappet plate "Q" will engage the button on the end of the tappet rod "P", moving the main valve "C" to its upper position. In this position, the exhaust cavity "r" in the main valve connects port "g" with the exhaust port "X", allowing steam above piston "H" to escape to the exhaust, while steam is admitted through port "s" to the underside of piston "H", pushing it upward. As this piston nears the end of its stroke, the tappet plate "L" (see Fig. 20) engages the button on the tappet rod "P", moving the main valve "A" to its upper position. The exhaust cavity "r" now connects port "o", which leads to the lower end of the cylinder on the right, with the exhaust port "X", allowing steam under piston "T" to escape to the exhaust, while steam is admitted through port "V" to the upper end of the cylinder on the right, above piston "T", pushing it downward; as it nears the end of its stroke, the tappet plate "Q" engages the shoulder on the tappet rod "P", moving the main valve "C" to its lower position. The exhaust cavity "r" in the valve now connects port "s" with the exhaust port "X", allowing steam below piston "H" to escape to the exhaust, while steam is admitted to the top of this piston, pushing it down, thus completing a cycle of the compressor.
165. Q. Explain the operation of the air end of the compressor.
165. Q. Describe how the air end of the compressor works.
A. As the piston in the low pressure cylinder "D"[Pg 226] moves up (see Fig. 19), a partial vacuum is formed below it, and air flowing through the strainer passes downward through the air passage, then past the lower receiving valve "W" into the lower end of the cylinder, filling it with air at about atmospheric pressure. In the meantime the air that is being compressed above the piston holds the receiving valve "U" to its seat, and lifts the upper intermediate discharge valve "K" from its seat, allowing the air to pass from the low to the high pressure cylinder "F". The high pressure piston now moving up causes a partial vacuum to be formed below it, and air from the atmosphere flows past the lower receiving valve "N", filling this end of the cylinder with air at about atmospheric pressure. The air above the piston being compressed, holds the upper intermediate valve "K" and receiving valve "J" to their seats and lifts the upper final discharge valve "M", allowing the air to pass to the main reservoir. The action is the same on the down stroke, only air is compressed in the opposite end of the cylinders and the opposite air valves are used.
A. As the piston in the low-pressure cylinder "D"[Pg 226] moves up (see Fig. 19), a partial vacuum forms below it, and air flows through the strainer down through the air passage, then past the lower receiving valve "W" into the lower end of the cylinder, filling it with air at about atmospheric pressure. Meanwhile, the air being compressed above the piston keeps the receiving valve "U" in place and lifts the upper intermediate discharge valve "K" off its seat, allowing the air to pass from the low-pressure cylinder to the high-pressure cylinder "F". As the high-pressure piston moves up, it creates a partial vacuum below it, causing air from the atmosphere to flow past the lower receiving valve "N", filling this end of the cylinder with air at about atmospheric pressure. The compressed air above the piston keeps the upper intermediate valve "K" and receiving valve "J" in place and lifts the upper final discharge valve "M", allowing the air to pass to the main reservoir. The process is the same during the downstroke; only the air is compressed at the opposite end of the cylinders, and the opposite air valves are used.
166. Q. What should be the lift of the different air valves?
166. Q. What should the lift of the various air valves be?
A. In the No. 1 and No. 2 compressors all valves should have 1/16-inch lift; in the No. 5 and No. 6 all valves should have 3/16-inch lift.
A. In the No. 1 and No. 2 compressors, all valves should have a 1/16-inch lift; in the No. 5 and No. 6, all valves should have a 3/16-inch lift.
167. Q. If a receiving valve to the low pressure air cylinder breaks or sticks open, what effect will it have on the compressor, and how may it be located?
167. Q. If a receiving valve for the low-pressure air cylinder breaks or gets stuck open, what impact will it have on the compressor, and how can it be identified?
A. No air will be compressed in the low pressure cylinder, as the piston moves toward the defective valve, and may be located by noting the movement of the low pressure piston, as it will be much quicker toward the defective valve than the opposite stroke. Air will blow back to the atmosphere as the piston[Pg 227] moves toward the defective valve, and may be detected by holding the hand over the strainer.
A. No air will be compressed in the low-pressure cylinder as the piston moves toward the faulty valve, and you can identify this by observing the movement of the low-pressure piston, as it will move much faster toward the faulty valve than in the opposite direction. Air will blow back into the atmosphere as the piston[Pg 227] moves toward the faulty valve, and this can be detected by placing your hand over the strainer.
168. Q. If an intermediate discharge valve breaks or sticks open, what effect will it have on the compressor, and how may it be located?
168. Q. If an intermediate discharge valve fails or gets stuck open, what impact will it have on the compressor, and how can it be identified?
A. If an intermediate discharge valve breaks or sticks open, no air will be compressed by that end of the compressor where is located the defective valve, as the air will simply flow back and forth from the high to the low pressure cylinders; no air will be taken in from the atmosphere through the strainer as the pistons move from the defective valve.
A. If an intermediate discharge valve fails or gets stuck open, no air will be compressed at that end of the compressor where the faulty valve is located. The air will just flow back and forth between the high- and low-pressure cylinders; no air will be taken in from the atmosphere through the strainer as the pistons move away from the defective valve.
169. Q. If a final discharge valve breaks, what effect will it have on the compressor?
169. Q. If a final discharge valve fails, what impact will it have on the compressor?
A. Main reservoir air will be free to return to the high pressure cylinder as the high pressure piston moves from the defective valve; therefore, no air will be taken in through the receiving valve of the high pressure air cylinder at the end where is located the defective valve. The low pressure piston will make a slow stroke toward the defective valve and a normal stroke from it; while the high pressure piston will make a slow stroke toward the defective valve and a quick stroke from it. Defective air valves may generally be located by noting the temperature of the valve chamber in which they are located.
A. The main reservoir air will be allowed to flow back into the high-pressure cylinder as the high-pressure piston moves away from the faulty valve; therefore, no air will be drawn in through the receiving valve of the high-pressure air cylinder at the end where the faulty valve is located. The low-pressure piston will make a slow stroke toward the faulty valve and a normal stroke away from it, while the high-pressure piston will make a slow stroke toward the faulty valve and a fast stroke away from it. Faulty air valves can usually be identified by checking the temperature of the valve chamber where they are located.
170. Q. What will cause the compressor to run hot?
170. Q. What can make the compressor overheat?
A. Running the compressor too fast; working against high pressure; air piston packing rings leaking; air cylinder worn; air passages or discharge pipe partially stopped up; air valves leaking; air valves stuck shut; or lack of lubrication.
A. Running the compressor too quickly; working against high pressure; air piston packing rings leaking; air cylinder worn down; air passages or discharge pipe partially blocked; air valves leaking; air valves stuck closed; or insufficient lubrication.
171. Q. How should the air end of the compressor be oiled, and what grade of oil used?[Pg 228]
171. Q. How should you oil the air end of the compressor, and what type of oil should be used?[Pg 228]
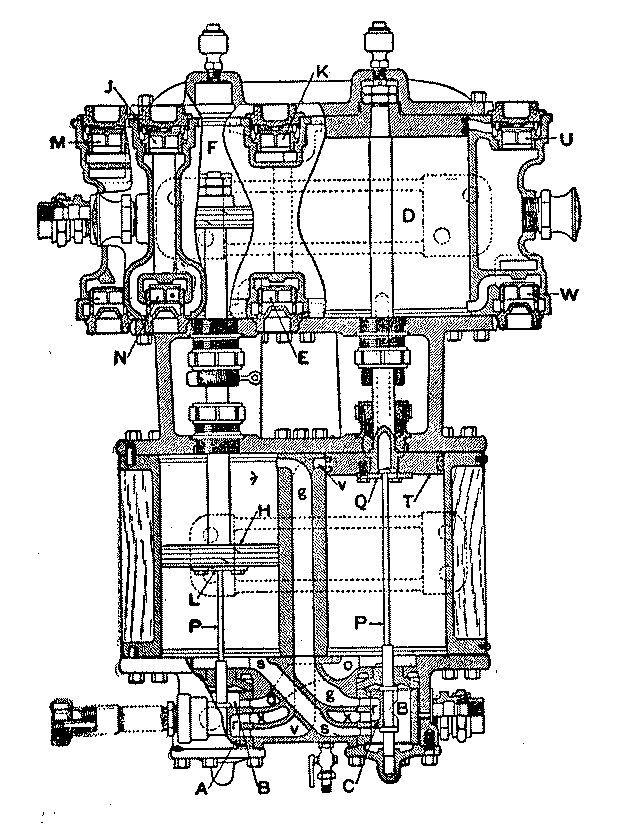
Fig. 20: High Pressure Piston Moving Upward. Low Pressure Piston at Rest.
Fig. 20: High Pressure Piston Moving Up. Low Pressure Piston Stationary.
A. Oil should be used sparingly in the low pressure cylinder, but more is required in the high pressure cylinder, owing to higher temperature. A good quality of valve oil should be used.
A. Oil should be used sparingly in the low pressure cylinder, but more is needed in the high pressure cylinder because of the higher temperature. A high-quality valve oil should be used.
172. Q. How is the steam end of the compressor affected by the use of too much oil?
172. Q. How does using too much oil affect the steam end of the compressor?
A. This may cause the compressor to short stroke, and where the piston type of valve is used, may cause the compressor to stop.
A. This may cause the compressor to short stroke, and if a piston-type valve is used, it may cause the compressor to stop.
L-T EQUIPMENT
AUTOMATIC CONTROL VALVE
L-T Equipment
Auto Control Valve
173. Q. What is the duty of the control valve?
173. Q. What does the control valve do?
A. To admit air from the main reservoir to the locomotive brake cylinders when applying the brakes; to automatically maintain the brake cylinder pressure against leakage; to develop the proper brake cylinder pressure regardless of piston travel; and to exhaust the air from the brake cylinders when releasing the brake, in all automatic applications of the brake.
A. To allow air from the main reservoir into the locomotive brake cylinders when the brakes are applied; to automatically keep the brake cylinder pressure steady against leaks; to generate the right brake cylinder pressure no matter how far the piston travels; and to release the air from the brake cylinders when the brakes are disengaged, in all automatic brake applications.
174. Q. Explain the operation of the control valve when making an automatic service application of the brake.
174. Q. Describe how the control valve works during an automatic brake service application.
A. Air enters the control valve at the connection marked "BP" (Fig. 21), which leads to chamber "F" above the piston 3, forcing it down, uncovering the feed groove "G" in the bushing, allowing air to feed past the piston into the slide valve chamber, and then through port "H" to the auxiliary reservoir. The air will feed through in this manner until the auxiliary reservoir and brake pipe pressure equalize. When a gradual reduction of brake pipe pressure is made, it[Pg 230] will be felt in chamber "F", above piston 3, creating a difference in pressure on the two sides of the piston, which will cause it to move upward.
A. Air enters the control valve at the connection marked "BP" (Fig. 21), which leads to chamber "F" above the piston 3, forcing it down and uncovering the feed groove "G" in the bushing. This allows air to pass past the piston into the slide valve chamber, and then through port "H" to the auxiliary reservoir. The air will continue to flow this way until the auxiliary reservoir and brake pipe pressure equalize. When there is a gradual reduction in brake pipe pressure, it[Pg 230] will be felt in chamber "F", above piston 3, creating a difference in pressure on both sides of the piston, which will cause it to move upward.
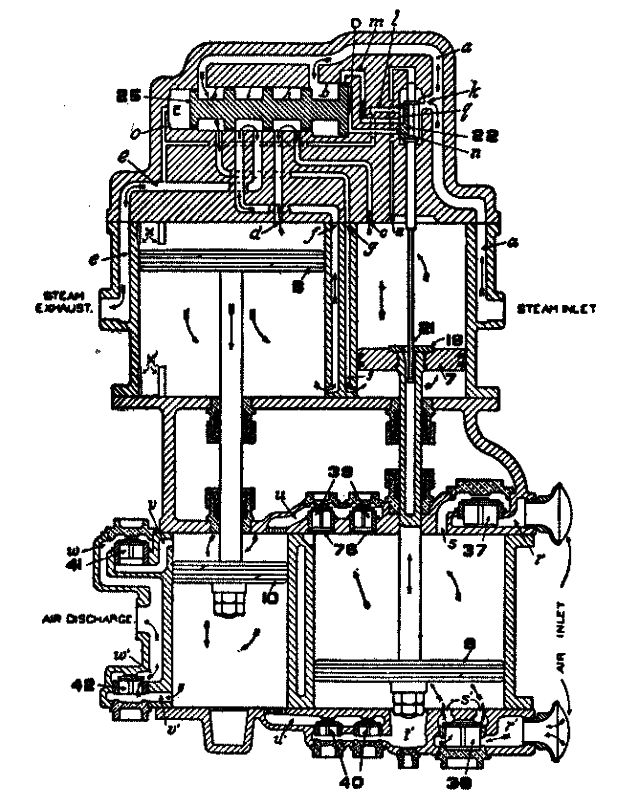
Fig. 21: Automatic Control Valve. Full Release.
Fig. 21: Automatic Control Valve. Full Release.
The first movement of the piston closes the feed groove "G", also moves the graduating valve 10, uncovering the service port "J" in the slide valve 4, and the continued movement of the piston moves the slide valve to service position, in which the service port "J" connects with port "E" in the valve seat. (See Fig. 22.) As the slide valve chamber and auxiliary reservoir are connected at all times, air can now flow from the auxiliary to the control cylinder "D" and control reservoir, through ports "H", "J" and "E", until the pressure on the lower or auxiliary side of piston 3 becomes slightly less than that in chamber "F" or brake pipe side, when the piston and graduating valve will move down until the shoulder on the piston strikes the slide valve; this movement of the graduating valve closes the service port "J", thus closing the communication between the auxiliary and control cylinder and reservoir, also closing port "W", which leads to the safety valve. (See Fig. 23.)
The first movement of the piston closes the feed groove "G," also shifts the graduating valve 10, exposing the service port "J" in the slide valve 4. The piston continues to move, positioning the slide valve so that service port "J" connects with port "E" in the valve seat. (See Fig. 22.) Since the slide valve chamber and auxiliary reservoir are always connected, air can now flow from the auxiliary to the control cylinder "D" and control reservoir through ports "H," "J," and "E" until the pressure on the lower or auxiliary side of piston 3 is slightly lower than that in chamber "F" or the brake pipe side. When this happens, the piston and graduating valve will move down until the shoulder on the piston hits the slide valve. This movement of the graduating valve closes the service port "J," cutting off communication between the auxiliary and control cylinder and reservoir, and also closes port "W," which leads to the safety valve. (See Fig. 23.)
[Pg 232] 175. Q. How is piston 2 affected by the air pressure in the control cylinder "D"?
[Pg 232] 175. Q. How does the air pressure in control cylinder "D" affect piston 2?
A. Pressure forming in this cylinder will force the piston downward. The piston in moving down will carry the exhaust valve 7 with it, closing the exhaust port "N" and moves the preliminary admission valve "1A" from its seat against the tension of spring 8, allowing the pressure in chamber "O" to pass to the brake cylinders, thus creating a balancing effect on valve 1, which allows it to be opened against main reservoir pressure, thus allowing main reservoir air to flow from chamber "A" to chamber "B" and the brake cylinders on the locomotive (see Fig. 22) until the pressure in the brake cylinders and chamber "B", below piston 2, becomes slightly greater than that in the control cylinder "D" when the piston will move up just far enough to allow the valves "1" and "1A" to be seated, or to lap position. (See Fig. 23.)
A. Pressure building up in this cylinder will push the piston down. As the piston moves down, it will carry the exhaust valve 7 with it, closing the exhaust port "N" and moving the preliminary admission valve "1A" from its seat against the tension of spring 8, allowing the pressure in chamber "O" to flow to the brake cylinders, creating a balancing effect on valve 1, which lets it open against the main reservoir pressure. This allows air from the main reservoir to flow from chamber "A" to chamber "B" and into the brake cylinders on the locomotive (see Fig. 22) until the pressure in the brake cylinders and chamber "B," beneath piston 2, becomes slightly higher than that in the control cylinder "D," at which point the piston will move up just enough to let the valves "1" and "1A" close, or reach the lap position. (See Fig. 23.)
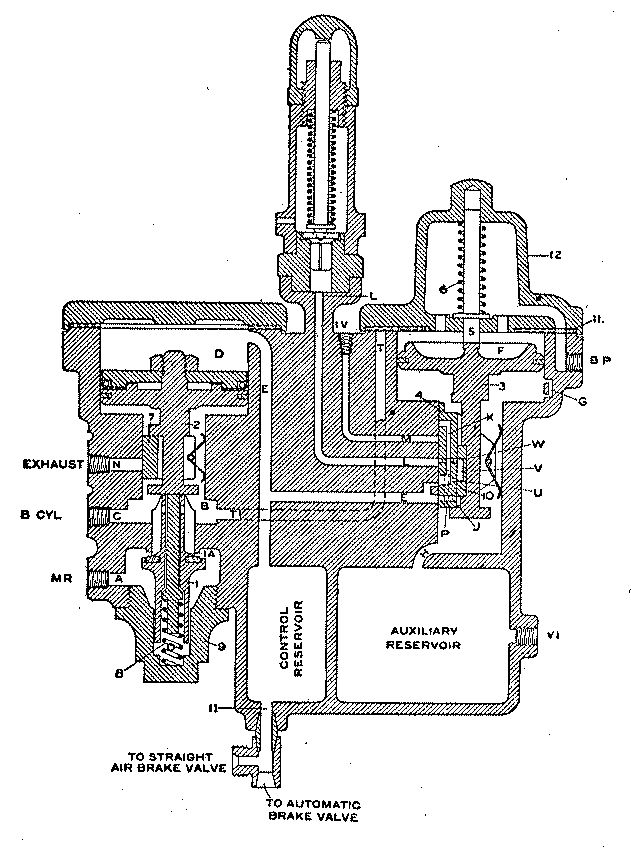
Fig. 22: Automatic Control Valve. Service Position.
Fig. 22: Automatic Control Valve. Service Position.
176. Q. With the control valve now in lap position, will the brake release on account of brake cylinder leakage?
176. Q. With the control valve now in lap position, will the brake release due to leakage in the brake cylinder?
A. Any drop in brake cylinder pressure will be felt in chamber "B" below the piston 2, causing a difference in pressure on the two sides of the piston, allowing the pressure in the control cylinder "D" to move the piston 2 down, unseating the admission valves, allowing a further flow of main reservoir air from chamber "A" to chamber "B" and the brake cylinders until the pressure is again slightly greater than that in the control cylinder "D", when the piston 2 will again move up, allowing the admission valves to close. Thus in this way air will be supplied to the brake cylinders of the locomotive, holding the brakes applied regardless of leakage.
A. Any decrease in brake cylinder pressure will be felt in chamber "B" below piston 2, causing a pressure difference on either side of the piston. This allows the pressure in control cylinder "D" to push piston 2 down, opening the admission valves and enabling more air from main reservoir chamber "A" to flow into chamber "B" and the brake cylinders until the pressure is slightly greater than that in control cylinder "D." At that point, piston 2 will move back up, closing the admission valves. In this way, air will be supplied to the locomotive's brake cylinders, keeping the brakes engaged despite any leakage.
177. Q. Explain the movement of the parts in the control valve, when the automatic brake valve is moved to release position, following an automatic application of the brake.
177. Q. Describe how the components in the control valve move when the automatic brake valve is switched to the release position after an automatic brake application.
A. In release position of the brake valve, air from the main reservoir flows direct to the brake pipe, causing an increase of pressure, which is felt in chamber "F" on the upper side of piston 3; this increase of pressure will cause the piston to move down, carrying with it the graduating valve 10 and slide valve 4 to release position. This allows air from the control cylinder "D" and control reservoir to flow through the release pipe "IV" and on to the automatic brake valve, where the port to which this pipe leads is blanked by the automatic rotary valve, which prevents the air leaving the control cylinder and reservoir, thus holding the locomotive brake applied while the train brakes are being released. The movement of the parts are the same where the releaserelease is made in holding position.
A. In the release position of the brake valve, air from the main reservoir flows directly to the brake pipe, causing an increase in pressure, which is felt in chamber "F" on the upper side of piston 3; this pressure increase will cause the piston to move down, carrying with it the graduating valve 10 and slide valve 4 to the release position. This allows air from the control cylinder "D" and control reservoir to flow through the release pipe "IV" and on to the automatic brake valve, where the port connected to this pipe is blocked by the automatic rotary valve, which prevents air from escaping the control cylinder and reservoir, thereby keeping the locomotive brake applied while the train brakes are being released. The movement of the parts is the same whether the releaserelease is made in the holding position.
[Pg 234] 178. Q. Explain the movements of the parts in the control valve when the automatic brake valve is moved to running position, after having first been moved to release or holding position.
[Pg 234] 178. Q. Describe what happens to the parts of the control valve when the automatic brake valve is switched to the running position after it was first set to the release or holding position.
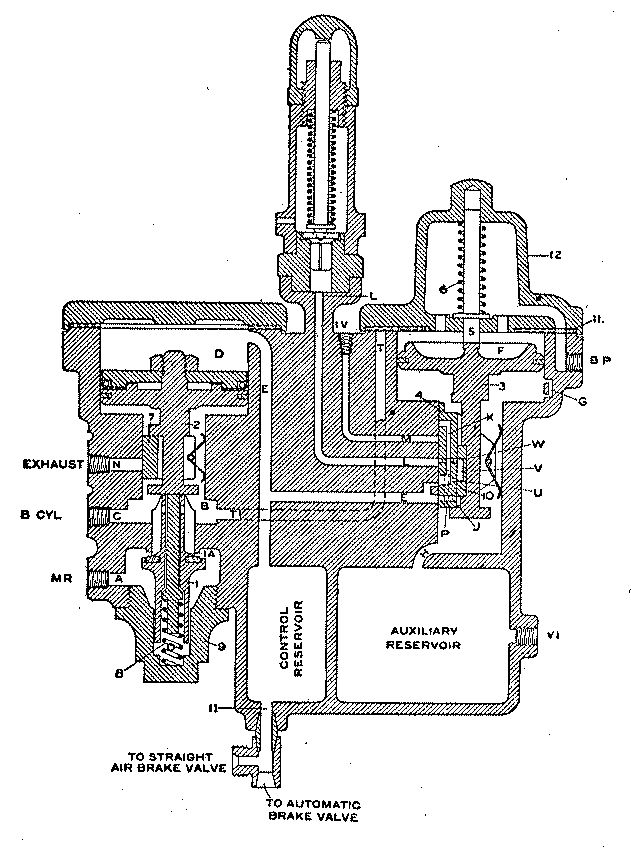
Fig. 23: Automatic Control Valve. Service Lap Position.
Fig. 23: Automatic Control Valve. Service Lap Position.
A. In this position of the brake valve the port to which the release pipe "IV" is connected is open to the exhaust, thus allowing the air in the control cylinder and reservoir to escape to the atmosphere. The reduction of pressure in the control cylinder "D" below that in chamber "B" causes the control piston 2 to move up, carrying with it the exhaust valve 7 to release position, opening the exhaust port "N", thus allowing the air to return from the brake cylinders through ports "C" and "N" to the atmosphere, releasing the brake. (See Fig. 21.)
A. In this position of the brake valve, the port connected to the release pipe "IV" is open to the exhaust, allowing the air in the control cylinder and reservoir to escape to the atmosphere. The drop in pressure in the control cylinder "D" below that in chamber "B" makes the control piston 2 move up, which lifts the exhaust valve 7 to the release position, opening the exhaust port "N". This lets the air flow back from the brake cylinders through ports "C" and "N" to the atmosphere, releasing the brake. (See Fig. 21.)
179. Q. Explain what takes place in the control valve when an automatic emergency application of the brake is made.
179. Q. Describe what happens in the control valve when an automatic emergency brake is applied.
A. Any sudden reduction of brake pipe pressure will be felt on the brake pipe side of piston 3, and will cause it and the valve 4 to move to their extreme upper position, the knob on the piston striking the graduating stem 13, causing it to compress the spring 14, moving the emergency valve 15 upward, opening port "Q"; this allows brake pipe air to flow against valve 16, unseating it, then through port "T" to the brake cylinder. (See Fig. 24.) In the meantime auxiliary reservoir air can flow past the end of the slide valve through port "E" to the control cylinder "D" and control reservoir, forcing piston 2 downward unseating valves "I" and "IA", thus allowing main reservoir air to flow to the brake cylinders, applying the brake.
A. Any sudden drop in brake pipe pressure will be felt on the brake pipe side of piston 3 and will cause it and valve 4 to move to their highest position, with the knob on the piston hitting the graduated stem 13. This compresses spring 14, pushing the emergency valve 15 upward and opening port "Q." This allows brake pipe air to flow against valve 16, pulling it off its seat, then through port "T" to the brake cylinder. (See Fig. 24.) Meanwhile, air from the auxiliary reservoir can flow past the end of the slide valve through port "E" to the control cylinder "D" and control reservoir, pushing piston 2 downward and unseating valves "I" and "IA," allowing main reservoir air to flow to the brake cylinders, applying the brake.
180. Q. At what pressure will the auxiliary reservoir and control reservoir equalize when using seventy pounds brake pipe pressure?
180. Q. What pressure will the auxiliary reservoir and control reservoir equalize at when using seventy pounds of brake pipe pressure?
A. At about fifty pounds; however, with the automatic brake valve in emergency position, there is a small port in the rotary valve (called the blow-down[Pg 236] timing port) opened to the control reservoir pipe and control reservoir which allows main reservoir air to flow to the control reservoir and cylinder, raising the pressure to the adjustment of the safety valve.
A. At around fifty pounds; however, when the automatic brake valve is in the emergency position, a small port in the rotary valve (referred to as the blow-down[Pg 236] timing port) opens to the control reservoir pipe and control reservoir, allowing main reservoir air to flow into the control reservoir and cylinder, increasing the pressure to the setting of the safety valve.
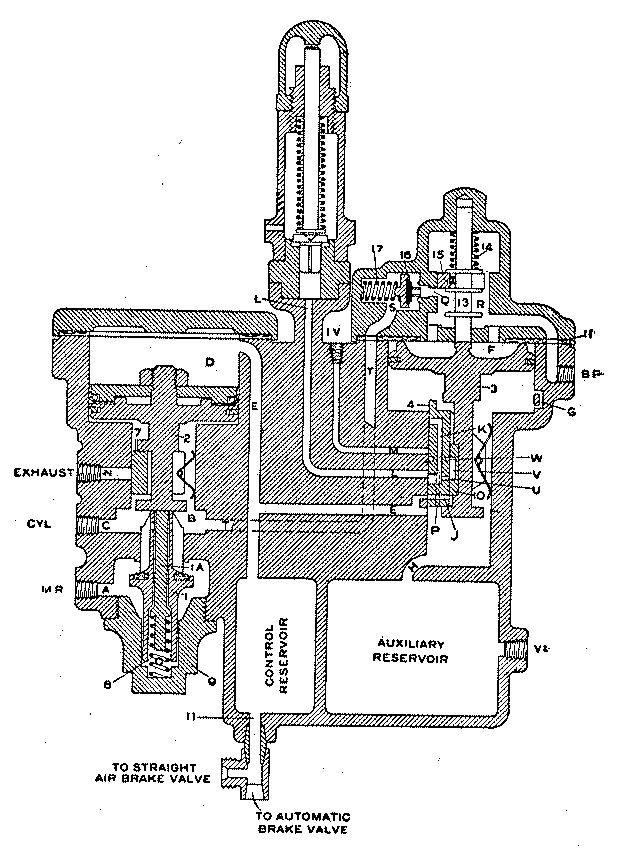
Fig. 24: Automatic Control Valve.
Emergency Position. (With Quick Action Cylinder Cap.)
Fig. 24: Automatic Control Valve.
Emergency Position. (With Quick Action Cylinder Cap.)
181. Q. At what pressure is the safety valve adjusted?
181. Q. What pressure is the safety valve set to?
A. At fifty pounds.
At $50.
182. Q. What types of brake valve are used with this equipment?
182. Q. What kinds of brake valves are used with this equipment?
A. The automatic brake valve is of the rotary valve type and is the same valve as used with the E-T equipment. The straight air brake valve is of the slide valve type. The control valve takes no part in the application or release of the straight air brake. What has been said of the H-6 brake valve used with the E-T equipment, applies to the automatic brake valve used with the L-T equipment.
A. The automatic brake valve is a rotary valve and is the same type used with the E-T equipment. The straight air brake valve is a slide valve. The control valve does not play a role in applying or releasing the straight air brake. What has been mentioned about the H-6 brake valve used with the E-T equipment also applies to the automatic brake valve used with the L-T equipment.
BROKEN PIPES
Leaky pipes
183. Q. If the main reservoir supply pipe to the automatic control valve breaks, what should be done?
183. Q. If the main supply pipe to the automatic control valve breaks, what should be done?
A. Plug the pipe toward the main reservoir. The locomotive brake cannot be applied in an automatic service application; but if the control valve be equipped with a quick action cap and an emergency application is made, the air vented from the brake pipe to the brake cylinder will apply the brake. The independent brake will not be affected.
A. Plug the pipe leading to the main reservoir. The locomotive brake can't be used in an automatic service application; however, if the control valve has a quick action cap and an emergency application is made, the air released from the brake pipe to the brake cylinder will engage the brake. The independent brake will not be impacted.
184. Q. What will be the effect if the release pipe breaks?
184. Q. What will happen if the release pipe breaks?
A. The holding feature of the brake will be lost; that is, the brake will release when the automatic brake valve is returned to release or holding position.[Pg 238]
A. The braking feature will no longer hold; that is, the brake will let go when the automatic brake valve is returned to the release or holding position.[Pg 238]
185. Q. If the brake cylinder pipe breaks, can the locomotive brake be applied with the automatic brake valve? With the independent brake valve?
185. Q. If the brake cylinder pipe breaks, can the locomotive brake be applied using the automatic brake valve? What about the independent brake valve?
A. This depends on where the pipe breaks; if between the cut-out cock and any one of the brake cylinders, close the cut-out cock to that cylinder, and the other cylinders may be used. But if the pipe breaks between the control valve and the double-throw check valve, the automatic brake is lost; if the break be between the independent brake valve and double-throw check valve, the independent brake is lost.
A. This depends on where the pipe breaks; if it’s between the shut-off valve and any one of the brake cylinders, close the shut-off valve to that cylinder, and the other cylinders can still be used. But if the pipe breaks between the control valve and the double-throw check valve, the automatic brakes are lost; if the break is between the independent brake valve and the double-throw check valve, the independent brake is lost.
186. Q. If the brake cylinder pipe breaks and is not plugged, what must be done?
186. Q. If the brake cylinder pipe breaks and isn't sealed, what needs to be done?
A. Close the cut-out cock in the main reservoir supply pipe, this to avoid the waste of air when a brake application is made on the train.
A. Close the cut-out cock in the main reservoir supply pipe to prevent wasting air when the train applies the brakes.
187. Q. If the brake pipe connection to the control valve breaks, what should be done?
187. Q. If the brake pipe connection to the control valve breaks, what should you do?
A. Plug the end leading from the brake pipe; the automatic brake cannot be applied on the locomotive, but the independent brake will not be affected.
A. Plug the end coming from the brake pipe; the automatic brake can't be applied on the locomotive, but the independent brake will still work.
188. Q. If the control cylinder pipe breaks, what effect will it have and what must be done?
188. Q. If the control cylinder pipe breaks, what will happen and what needs to be done?
A. The locomotive brake cannot be applied with the automatic brake valve; by plugging the pipe, this feature of the brake will be restored, but the independent release feature will be lost.
A. The locomotive brake can't be activated with the automatic brake valve; by blocking the pipe, this brake function will be restored, but the independent release feature will be lost.
189. Q. If any of the pipes here enumerated breaks, will it in any way affect an application of the independent brake?[Pg 239]
189. Q. If any of the pipes listed here breaks, will it affect the use of the independent brake in any way?[Pg 239]
A. No; as the independent and automatic features are entirely separate from each other; that is, the automatic control valve is not brought into use when an independent application of the brake is made.
A. No; the independent and automatic features are completely separate from each other; that is, the automatic control valve does not activate when there is an independent application of the brake.
CONTROL VALVE DEFECTS
Control valve issues
190. Q. If there is a blow at the control valve exhaust port when the brake is released, where would you look for the trouble?
190. Q. If there's a noise coming from the control valve exhaust port when the brake is released, where would you check for the issue?
A. This would indicate a leaky application valve, or a leak past the emergency valve.
A. This would suggest a leaking application valve, or a leak around the emergency valve.
191. Q. If there be a continuous blow at the control valve exhaust port when the brake is applied, where would you look for the trouble?
191. Q. If there’s a constant leak at the control valve exhaust port when the brake is applied, where would you check for the problem?
A. This would indicate leakage past the exhaust valve 7.
A. This would suggest leakage through the exhaust valve 7.
192. Q. If the locomotive brake released with the automatic brake valve in lap position, where is the trouble?
192. Q. If the locomotive brake releases while the automatic brake valve is in the lap position, what's the issue?
A. Would look for a leak in the control reservoir pipe or special release valve.
A. Would check for a leak in the control reservoir pipe or the special release valve.
193. Q. If the brake remained applied in lap position, but released in release or holding position, where would you look for the trouble?
193. Q. If the brake stays engaged in lap position, but releases in the release or holding position, where would you look for the problem?
A. This would indicate a leak in the control valve release pipe.
A. This would suggest a leak in the control valve release pipe.
MISCELLANEOUS
Miscellaneous
194. Q. What is meant by an application of the brake?
194. Q. What does it mean to apply the brake?
A. The first and all following reductions, until the brake is released.[Pg 240]
A. The first reduction and all subsequent reductions, until the brake is released.[Pg 240]
195. Q. How many applications of the brake should be made when making a stop with a passenger train, and why?
195. Q. How many times should the brakes be applied when stopping a passenger train, and why?
A. Two; the first a heavy one to reduce the speed quickly, and the second a light one to complete the stop; thereby preventing wheel sliding and shock to the train.
A. Two; the first a heavy one to slow down quickly, and the second a light one to finish the stop; thus preventing wheel sliding and jarring the train.
196. Q. How many applications of the brake should be made when making a stop with a long freight train?
196. Q. How many times should the brakes be applied when stopping a long freight train?
A. One; this to prevent the possibility of causing damage to the train.
A. One; this is to prevent the possibility of causing damage to the train.
197. Q. Explain how a stop should be made with a freight train.
197. Q. Explain how to make a stop with a freight train.
A. Probably no more difficult question to answer could be asked, as the service braking of a train must be governed by the condition surrounding it; meaning, relation of brake power to weight of train; rail condition; speed and grade. To prevent breaking in two and other damage, freight trains should be stopped with one brake application, which may consist of one or more reductions, up to full service. Generally speaking, the slack should be bunched before the brakes are applied, and this may best be done by gradually closing the throttle and allow the train to drift some little distance. The first reduction should not be less than five or more than eight pounds. The brakes should be applied as soon as possible after the slack has had time to run in, the object of this being to have the train slack adjusted while the brakes are least effective, due to the high speed and light brake cylinder pressure. It is at this time that damage may be done to the train; therefore, if the slack be kept bunched or stretched, as the case may be, the[Pg 241] possibility of train damage will be greatly reduced. To obtain this condition, complete the stop with as light a brake application as permissible. When the brake is first applied, the engineer should note if the tendency be for the train slack to bunch or stretch, and having learned that the train is inclined to stretch badly, he can keep the slack stretched by making the initial brake pipe reduction before shutting off steam, then shut off steam gradually as soon as the brake valve exhaust port closes, the object in working steam being to prevent the slack running in as the application is made, which in turn will prevent severe jerks due to the slack running out as the rear brakes become effective. Where the locomotive is equipped with an independent release feature, its brakes should be kept released while the train brakes are being applied.
A. Probably no more difficult question to answer could be asked, as the service braking of a train must be influenced by its surroundings; that is, the relationship of brake power to the train's weight, rail conditions, speed, and grade. To prevent the train from breaking in two and other damage, freight trains should be stopped with a single brake application, which may involve one or more reductions, up to full service. Generally speaking, the slack should be bunched before the brakes are applied, and the best way to do this is by gradually closing the throttle and allowing the train to drift a short distance. The first reduction should be no less than five pounds and no more than eight pounds. The brakes should be applied as soon as possible after the slack has had time to settle, as the goal is to have the train's slack adjusted while the brakes are least effective due to high speed and low brake cylinder pressure. This is when damage to the train can occur; therefore, if the slack is kept bunched or stretched, depending on the situation, the possibility of train damage will be greatly reduced. To achieve this, finish the stop with the lightest brake application allowed. When the brake is first applied, the engineer should notice whether the train slack tends to bunch or stretch. If the train tends to stretch significantly, he can keep the slack stretched by making the initial brake pipe reduction before shutting off the steam, then gradually shutting off the steam as soon as the brake valve exhaust port closes. The purpose of using steam is to prevent the slack from running in as the brake application is made, which will, in turn, prevent sharp jerks due to the slack running out as the rear brakes become effective. If the locomotive is equipped with an independent release feature, its brakes should remain released while the train brakes are being applied.
198. Q. Is it considered good practice to attempt making an accurate stop with a freight train?
198. Q. Is it considered good practice to try to make an accurate stop with a freight train?
A. It may be said to be very poor judgment to attempt making an accurate stop with a freight train, such as a spot stop for coal or water or a close-up stop for a switch. Some engineers seem to think that it is a reflection on their judgment if an accurate stop is not made, but this is not so, due to the fact that no two trains brake alike, and the same train may not brake twice alike. Therefore, aim for a smooth stop, which means a safe stop, leaving accuracy out of the question until the time comes when you are handling a passenger train.
A. It can be considered very poor judgment to try to make an exact stop with a freight train, like a specific stop for coal or water or a close-up stop for a switch. Some engineers believe that not making an accurate stop reflects on their judgment, but that’s not true because no two trains brake the same way, and the same train might not brake the same way twice. So, focus on a smooth stop, which ensures a safe stop, and leave accuracy aside until you’re dealing with a passenger train.
199. Q. What precaution should be taken after a stop is made on a heavy grade?
199. Q. What should you do after stopping on a steep incline?
A. The air brakes should be released and a sufficient number of hand brakes applied to hold the[Pg 242] train. Never rely on the air brake to hold the train for any length of time.
A. The air brakes should be released and enough hand brakes applied to secure the[Pg 242] train. Never count on the air brake to hold the train for an extended period.
200. Q. Why is it dangerous to repeatedly apply and release the brakes without giving time for the auxiliaries to fully recharge?
200. Q. Why is it risky to keep applying and releasing the brakes without letting the auxiliary systems fully recharge?
A. As time is required to charge the auxiliaries, the feed groove in the triple valve being small, if the brakes are repeatedly applied and released without giving time to recharge, the braking power will be lost.
A. Since it takes time to recharge the auxiliaries, and the feed groove in the triple valve is small, if the brakes are applied and released repeatedly without allowing time to recharge, the braking power will be diminished.
201. Q. What benefits are derived from the use of the retaining valve?
201. Q. What are the benefits of using the retaining valve?
A. By use of the retaining valve the brake is held applied while the triple valve is in release position and the auxiliary is being recharged; thereby assisting in retarding the movement of the train down grade, also keeps the train bunched and gives a higher brake power on the second application with the same reduction of brake pipe pressure.
A. Using the retaining valve, the brake stays engaged while the triple valve is in the release position and the auxiliary is being recharged; this helps slow down the train when going downhill, keeps the train tightly grouped, and provides more braking power on the second application with the same reduction in brake pipe pressure.
202. Q. With a seventy-pound brake pipe pressure how much of a reduction is necessary to set the brakes in full, and why?
202. Q. With a seventy-pound brake pipe pressure, how much do we need to reduce it to fully set the brakes, and why?
A. About twenty pounds. This will cause the auxiliary reservoir and brake cylinder pressures to equalize.
A. About twenty pounds. This will make the auxiliary reservoir and brake cylinder pressures balance out.
203. Q. What effect has piston travel on the pressure developed in the brake cylinder?
203. Q. How does piston travel affect the pressure created in the brake cylinder?
A. The longer the piston travel the greater the volume or space to be filled with air; therefore the lower the pressure.
A. The longer the piston moves, the bigger the volume or space that needs to be filled with air; therefore, the lower the pressure.
204. Q. When should brakes be tested?
204. Q. When should brakes be tested?
A. Brakes should be tested before leaving a terminal and after any change in the make-up of the[Pg 243] train, at all designated points, also, whenever the engineer is in doubt as to his having the control of all brakes.
A. Brakes should be tested before leaving a terminal and after any changes in the make-up of the[Pg 243] train, at all designated points, and whenever the engineer is unsure if he has control of all the brakes.
205. Q. How should a terminal test of the brakes be made?
205. Q. How should a final test of the brakes be conducted?
A. After the pressure is pumped up, a reduction of about ten pounds should be made and the length and force of the brake pipe exhaust should be noted, also the manner in which the exhaust closes; then a further reduction of ten pounds should be made and the brake held applied until signaled to release.
A. After the pressure is pumped up, reduce it by about ten pounds and note the length and force of the brake pipe exhaust, as well as how the exhaust closes; then make another reduction of ten pounds and keep the brake applied until you get the signal to release.
206. Q. If, when making a service application of the brake, the brake pipe exhaust closes suddenly and then begins to blow again, what does it indicate?
206. Q. If, when applying the brake during service, the brake pipe exhaust suddenly shuts off and then starts blowing again, what does that indicate?
A. That the brakes, or at least part of them, have applied in quick action.
A. That the brakes, or at least some of them, have engaged suddenly.
207. Q. What is meant by a running test, and when should this test be made?
207. Q. What does a running test mean, and when should this test be conducted?
A. A running test is made while the train is in motion, and steam is being used, when a sufficient reduction should be made to apply all brakes. After noting the efficiency of the brakes they should be released. Running tests should be made following all standing tests and at all other points on the road as required by the rules.
A. A running test is conducted while the train is moving and using steam, during which a significant reduction should be made to engage all brakes. After assessing how well the brakes work, they should be released. Running tests should be performed after all stationary tests and at any other necessary locations along the route as specified by the rules.
208. Q. When double-heading, which engineman should have full control of the brakes?
208. Q. When double-heading, which engineer should have full control of the brakes?
A. The head engineer; the cut-out cock under the brake valve on the second engine should be closed and the compressor allowed to run.
A. The head engineer; the cut-out cock under the brake valve on the second engine should be closed and the compressor should be allowed to run.
209. Q. How may the engineman assist the trainman in finding a bursted hose?[Pg 244]
209. Q. How can the engineer help the conductor find a burst hose?[Pg 244]
A. After the train has come to a stop, the brake valve should be placed in running position; by so doing, air will be admitted to the brake pipe and cause a blow at the point where the hose is burst.
A. After the train has stopped, the brake valve should be set to the running position; this will allow air to flow into the brake pipe and create a blowout at the point where the hose is broken.
210. Q. If the locomotive brake creeps on with the automatic and independent brake valves in running position, where would you look for the trouble?
210. Q. If the train brake gradually engages while the automatic and independent brake valves are in the running position, where would you check for the issue?
A. This is caused by the pressure chamber being overcharged or a non-sensitive feed valve allowing brake pipe pressure to vary, which in turn causes an automatic application of the brake.
A. This happens when the pressure chamber is overfilled or a non-sensitive feed valve lets the brake pipe pressure change, which then leads to an automatic application of the brake.
211. Q. How often should the main reservoir be drained?
211. Q. How often should the main reservoir be drained?
A. The main reservoir should be drained at the beginning of each trip.[Pg 245]
A. The main reservoir should be emptied at the start of each trip.[Pg 245]
INDEX
Air Brake Questions, First Series, 22
Air Brake Questions, Second Series, 44
Air Brake Questions, Third Series, 164
Compound Locomotives, 98
Examination Questions, First Series, 7
Examination Questions, Second Series, 25
Examination Questions, Third Series, Mechanical, 62
Federal Regulations, 126
Headlight, Pyle National, 127
Headlight, Schroeder, 141
Headlight, "Buda-Ross" Electric, 143
Lubrication, 120
Oil Burning Locomotives, 47
Preface, 3
Southern Valve Gear, 119
Stoker, Duplex, 154
Walschaert and Baker-Pilliod Valve Gears, 113
Air Brake Questions, First Series, 22
Air Brake Questions, Second Series, 44
Air Brake Questions, Third Series, 164
Compound Locomotives, 98
Examination Questions, First Series, 7
Examination Questions, Second Series, 25
Examination Questions, Third Series, Mechanical, 62
Federal Regulations, 126
Headlight, Pyle National, 127
Headlight, Schroeder, 141
Headlight, "Buda-Ross" Electric, 143
Lubrication, 120
Oil Burning Locomotives, 47
Preface, 3
Southern Valve Gear, 119
Stoker, Duplex, 154
Walschaert and Baker-Pilliod Valve Gears, 113
Transcriber's notes:
Punctuation normalized.
Punctuation normalized.
Section headings normalized.
Section headings standardized.
Table of Contents added.
Table of Contents added.
The remaining corrections made are indicated by dotted lines under the corrections. Scroll the mouse over the word and the original text will appear.
The remaining corrections are shown with dotted lines underneath. Hover the mouse over the word, and the original text will appear.
Download ePUB
If you like this ebook, consider a donation!