This is a modern-English version of Handwork in Wood, originally written by Noyes, William.
It has been thoroughly updated, including changes to sentence structure, words, spelling,
and grammar—to ensure clarity for contemporary readers, while preserving the original spirit and nuance. If
you click on a paragraph, you will see the original text that we modified, and you can toggle between the two versions.
Scroll to the bottom of this page and you will find a free ePUB download link for this book.
HANDWORK IN
WOOD
By WILLIAM NOYES, M.A.
Assistant Professor, Department of Industrial Arts.
Teachers College, Columbia University
NEW YORK CITY

The Manual Arts Press
Peoria, IL
COPYRIGHT
WILLIAM NOYES
1910

FOREWORD
This book is intended primarily for teachers of woodwork, but the author hopes that there will also be other workers in wood, professional and amateur, who will find in it matter of interest and profit.
This book is mainly for woodwork teachers, but the author also hopes that other woodworkers, both professional and amateur, will find it interesting and useful.
The successful completion of the book is due chiefly to the untiring assistance of my wife, Anna Gausmann Noyes, who has made almost all of the drawings, corrected the text, read the proof, and attended to numberless details.
The successful completion of the book is mainly thanks to the tireless help of my wife, Anna Gausmann Noyes, who created almost all of the drawings, edited the text, proofread the pages, and managed countless details.
Acknowledgments are hereby thankfully given for corrections and suggestions in the text made by the following persons:
Acknowledgments are sincerely given for the corrections and suggestions in the text made by the following people:
Mr. Chas. W. Weick of Teachers College, and Mr. W. F. Vroom of Public School No. 5, of New York City, for revision of Chapters IV and V on tools and fastenings.
Mr. Chas. W. Weick from Teachers College and Mr. W. F. Vroom from Public School No. 5 in New York City, for revising Chapters IV and V on tools and fastenings.
Mr. Clinton S. VanDeusen of Bradley Polytechnic Institute, for revision of Chapter X on wood finishing.
Mr. Clinton S. VanDeusen from Bradley Polytechnic Institute, for updating Chapter X on wood finishing.
The Forest Service, Washington, D. C. for the originals of Figs. 1, 2, 3, 5, 7, 8, 9, 10, 11, 13, 17, 18, 21, 22, 23, 24, 26, 27, 28, 29, 31, 33, and 54.
The Forest Service, Washington, D.C. for the originals of Figs. 1, 2, 3, 5, 7, 8, 9, 10, 11, 13, 17, 18, 21, 22, 23, 24, 26, 27, 28, 29, 31, 33, and 54.
The New York State Forest Fish and Game Commission for the originals of Figs. 12, 14, 15, and 47.
The New York State Forest Fish and Game Commission for the originals of Figs. 12, 14, 15, and 47.
T. H. McAllister of New York for the originals of Figs. 16 and 20.
T. H. McAllister from New York for the originals of Figs. 16 and 20.
The Detroit Publishing Company for the original of Fig. 6.
The Detroit Publishing Company for the original of Fig. 6.
The B. F. Sturtevant Company, Hyde Park, Mass., for the original of Fig. 57.
The B. F. Sturtevant Company, Hyde Park, Mass., for the original of Fig. 57.
Doubleday, Page & Co. for the original of Fig. 30.
Doubleday, Page & Co. for the original of Fig. 30.
Mr. Louis A. Bacon, Indianapolis. Ind., for the clamping device shown in Fig. 255.
Mr. Louis A. Bacon, Indianapolis, Indiana, for the clamping device shown in Fig. 255.
Sargent & Company, New Haven, Conn., W. C. Toles & Company, Chicago, Ill., The Berlin Machine Works, Beloit, Wis., A. A. Loetscher, Dubuque, Iowa, and the Stanley Rule and Level Co., New Britain, Conn., for electrotypes.
Sargent & Company, New Haven, CT, W. C. Toles & Company, Chicago, IL, The Berlin Machine Works, Beloit, WI, A. A. Loetscher, Dubuque, IA, and the Stanley Rule and Level Co., New Britain, CT, for electrotypes.
And most of all, I wish to acknowledge my obligation to the numerous writers of whose books and articles I have made free use, to which references are made in the appropriate places.
And most importantly, I want to express my gratitude to the many writers whose books and articles I've freely used, with references included in the right spots.
CONTENTS.
CHAPTER |
PAGE | ||
General Bibliography | 4 | ||
I. | Logging | 7 | |
II. | Sawmilling | 30 | |
III. | The Seasoning and Measuring of Wood | 45 | |
IV. | Wood Hand Tools | 51 | |
V. | Wood Fastenings | 123 | |
VI. | Equipment and Care of the Shop | 136 | |
VII. | The Common Joints | 151 | |
VIII. | Types of Wooden Structures | 183 | |
IX. | Principles of Joinery | 203 | |
X. | Wood Finishing | 209 | |
Index | 224 |
GENERAL BIBLIOGRAPHY
Adams, Henry, Joints in Wood-Work. London: 60 Queen Victoria St. 1894.
Adams, Henry, Joints in Wood-Work. London: 60 Queen Victoria St. 1894.
Alexander, Jerome, The Grading and Use of Glue. Wood Craft, 5: 168, Sep. '06.
Alexander, Jerome, The Grading and Use of Glue. Wood Craft, 5: 168, Sep. '06.
Bailey, Charles H., A Study of Manual Training Equipments. Manual Training Magazine, 6: 82. Jan. '05.
Bailey, Charles H., A Study of Manual Training Equipment. Manual Training Magazine, 6: 82. Jan. '05.
Barnard, Charles, Tools and Machines. N. Y.: Silver, Burdett and Co. 1903.
Barnard, Charles, Tools and Machines. New York: Silver, Burdett and Co. 1903.
Barter, S. M., Woodwork. London: Whittaker and Co. 1892.
Barter, S. M., Woodwork. London: Whittaker and Co. 1892.
Benson, W. A. S., Elements of Handicraft and Design. London: Macmillan and Co. 1893.
Benson, W. A. S., Elements of Handicraft and Design. London: Macmillan and Co. 1893.
Brannt, W. T., Painter, Gilder and Varnisher. Philadelphia: H. C. Baird & Co. 1893.
Brannt, W. T., Painter, Gilder and Varnisher. Philadelphia: H. C. Baird & Co. 1893.
Bruncken, Ernest, North American Forests and Forestry. N. Y.: G. P. Putnam's Sons. 1899.
Bruncken, Ernest, North American Forests and Forestry. N.Y.: G.P. Putnam's Sons. 1899.
Clark, R. I., Varnish and Fossil Remains. London: Chas. Letts & Co. No date.
Clark, R. I., Varnish and Fossil Remains. London: Chas. Letts & Co. No date.
Compton, A. G., First Lessons in Woodworking. N. Y.: Ivison, Blakeman, Taylor and Co. 1888.
Compton, A. G., First Lessons in Woodworking. New York: Ivison, Blakeman, Taylor and Co. 1888.
Crawshaw, Fred D., Problems in Furniture Making. Peoria. Ill.: The Manual Arts Press. 1906.
Crawshaw, Fred D., Problems in Furniture Making. Peoria, IL: The Manual Arts Press. 1906.
Disston, Henry, and Sons, Handbook for Lumbermen. Philadelphia, Pa.
Disston, Henry, and Sons, Handbook for Lumbermen. Philadelphia, PA.
Dunlap, Frederick. Kiln-drying Hardwood Lumber. Wood Craft, 6: 133, Feb. '07.
Dunlap, Frederick. Kiln-drying Hardwood Lumber. Wood Craft, 6: 133, Feb. '07.
Ellis, George, Modern Practical Joinery. London: B. T. Batsford, 486 pp., 1902, '03, '04 and '07.
Ellis, George, Modern Practical Joinery. London: B. T. Batsford, 486 pages, 1902, '03, '04, and '07.
Encyclopedia Britannica, Lac, Varnish. N. Y.: Scribner's. 1878.
Encyclopedia Britannica, Lac, Varnish. New York: Scribner's. 1878.
Foster, Edwin W., Elementary Woodworking. Boston: Ginn and Co.
Foster, Edwin W., Elementary Woodworking. Boston: Ginn and Co.
Goss, W. F. M., Bench Work in Wood. Boston: Ginn and Co. 1887 and 1905.
Goss, W. F. M., Bench Work in Wood. Boston: Ginn and Co. 1887 and 1905.
Griffith, Ira S., Essentials of Woodworking. Peoria Ill.: Manual Arts Press. 1908.
Griffith, Ira S., Essentials of Woodworking. Peoria, IL: Manual Arts Press. 1908.
Hammacher, Schlemmer & Co., Tools. Catalog No. 355. N. Y. 1908.
Hammacher, Schlemmer & Co., Tools. Catalog No. 355. New York, 1908.
Hammacher, Schlemmer & Co., Cabinet Hardware. Catalog No. 151. N. Y. 1904.
Hammacher, Schlemmer & Co., Cabinet Hardware. Catalog No. 151. New York, 1904.
Hodgson, Fred T., The Up-to-date Hardwood Finisher. Chicago: Fred J. Drake and Co. 1904.
Hodgson, Fred T., The Up-to-date Hardwood Finisher. Chicago: Fred J. Drake and Co. 1904.
Hodgson, Fred T., The Carpenter's Steel Square and Its Uses. N. Y.: Industrial Publishing Co. 1880.
Hodgson, Fred T., The Carpenter's Steel Square and Its Uses. New York: Industrial Publishing Co. 1880.
Hovey-King, Alvin, The Lumber Industry of the Pacific Coast. Review of Reviews, 27: 317, Mr., '03.
Hovey-King, Alvin, The Lumber Industry of the Pacific Coast. Review of Reviews, 27: 317, March, '03.
Hulbert, W. H., The Lumber Jack and His Job. Outlook, 76: 801, Ap. 2, '04.
Hulbert, W. H., The Lumber Jack and His Job. Outlook, 76: 801, Apr. 2, '04.
International Correspondence School, The Building Trades Pocketbook. Scranton, Pa. International Textbook Co. 2nd edition. 1905.
International Correspondence School, The Building Trades Pocketbook. Scranton, PA. International Textbook Co. 2nd edition. 1905.
International Encyclopedia, Lac-Insect Varnish. N. Y.: Dodd, Mead and Co. 1902-1904.
International Encyclopedia, Lac-Insect Varnish. New York: Dodd, Mead and Company. 1902-1904.
Jones, J. E., Lumbering in the Northwest. Cosmopolitan, 15: 63, May 1893.
Jones, J. E., Lumbering in the Northwest. Cosmopolitan, 15: 63, May 1893.
Larsson, Gustaf, Elementary Sloyd and Whittling. N. Y.: Silver, Burdett & Co. 1906.
Larsson, Gustaf, Elementary Sloyd and Whittling. N. Y.: Silver, Burdett & Co. 1906.
Maire, F., The Modern Wood Finisher. Chicago: Press of the Western Painter.
Maire, F., The Modern Wood Finisher. Chicago: Press of the Western Painter.
Munn, M. J., Great Industries of the U. S.—Lumber. Cosmopolitan, 37: 441, Aug. '04.
Munn, M. J., Great Industries of the U. S.—Lumber. Cosmopolitan, 37: 441, Aug. '04.
Murray, M. W., Problems in Wood-working. Peoria, Ill.: Manual Arts Press. 1905.
Murray, M. W., Problems in Wood-working. Peoria, IL: Manual Arts Press. 1905.
Murray, M. W., The Manual Training Room and Its Equipment. Year Book of the Council of Supervisors for 1906, pp. 69-86.
Murray, M. W., The Manual Training Room and Its Equipment. Year Book of the Council of Supervisors for 1906, pp. 69-86.
Park, Joseph C. Educational Woodworking for School and Home. The Macmillan Co., 1908.
Park, Joseph C. Educational Woodworking for School and Home. The Macmillan Co., 1908.
Pichot, Gifford, A Primer of Forestry. Parts I and II, U. S. Dept. of Agric. For. Serv. Bull. No. 24. 1899 and 1905.
Pichot, Gifford, A Primer of Forestry. Parts I and II, U.S. Dept. of Agric. For. Serv. Bull. No. 24. 1899 and 1905.
Purfield, H. T., The Length of Nails. Wood Craft, 5: 181, Sp. '06.
Purfield, H. T., The Length of Nails. Wood Craft, 5: 181, Sp. '06.
Rivingston, see South Kensington Council on Education.
Rivingston, see South Kensington Council on Education.
Rouillion, Louis, Economies of Manual Training. N. Y.: The Derry Collard Company. 1905.
Rouillion, Louis, Economies of Manual Training. New York: The Derry Collard Company. 1905.
Roth, Filibert, A First Book of Forestry. Boston: Ginn & Co. 1902.
Roth, Filibert, A First Book of Forestry. Boston: Ginn & Co. 1902.
Sargent & Co., Standard Steel Squares. New Haven, Conn.
Sargent & Co., Standard Steel Squares. New Haven, CT.
Seaton, Geo. A., A Clamp for Use at the Grindstone. Woodcraft, 6: 96. Jan., '07.
Seaton, Geo. A., A Clamp for Use at the Grindstone. Woodcraft, 6: 96. Jan., '07.
Selden, F. H., Elementary Woodwork. N. Y.: Rand, McNally & Co. 1906.
Selden, F. H., Elementary Woodwork. New York: Rand, McNally & Co. 1906.
Sickels, Ivin, Exercises in Woodworking. N. Y.: D. Appleton & Co. 1889.
Sickels, Ivin, Exercises in Woodworking. New York: D. Appleton & Co. 1889.
Smith, K., Lumbering by Machinery. World's Work, 7: 4435. Feb. '04.
Smith, K., Lumbering by Machinery. World's Work, 7: 4435. Feb. '04.
Smith, R. H., Cutting Tools. London: Cassell & Co. 1884.
Smith, R. H., Cutting Tools. London: Cassell & Co. 1884.
South Kensington Council on Education, Notes on Building Construction. 3 vols. London: Rivington. 1883-1889.
South Kensington Council on Education, Notes on Building Construction. 3 vols. London: Rivington. 1883-1889.
Standage, H. C., Glues and Cements for the Use of Woodworkers. Wood Craft, 7: 48, May, '07.
Standage, H. C., Glues and Cements for the Use of Woodworkers. Wood Craft, 7: 48, May 1907.
Tate, James M., Training in Wood Work. Minneapolis: North Western School Supply Co. About 1905.
Tate, James M., Training in Wood Work. Minneapolis: North Western School Supply Co. Around 1905.
Trout, W. H., The Modern Saw Mill. Cassier's Magazine, 11: 83-95. 184-195, Dec. '96 and Jan. '97.
Trout, W. H., The Modern Saw Mill. Cassier's Magazine, 11: 83-95. 184-195, Dec. '96 and Jan. '97.
U. S. Department of Agriculture Forest Service Classified List of Publications. Forest Service Bulletins:
U.S. Department of Agriculture Forest Service Classified List of Publications. Forest Service Bulletins:
[page 6]No. 10. Filibert, Roth. Timber. 1895.
No. 10. Filibert, Roth. Timber. 1895.
No. 34. Wm. F. Fox, A History of the Lumber Industry in the State of New York, 1902.
No. 34. Wm. F. Fox, A History of the Lumber Industry in the State of New York, 1902.
No. 41. Hermann von Schrenk, Seasoning of Timber. 1903.
No. 41. Hermann von Schrenk, Seasoning of Timber. 1903.
Van Deusen, Clinton S., Methods of Wood Finishing. Manual Training Magazine, 6: 93. Jan. '05.
Van Deusen, Clinton S., Methods of Wood Finishing. Manual Training Magazine, 6: 93. Jan. '05.
Van Deusen, Clinton S., Logging in the South. Manual Training Magazine, 1: 93. Jan. '00.
Van Deusen, Clinton S., Logging in the South. Manual Training Magazine, 1: 93. Jan. '00.
Wheeler, C. G., Woodworking for Beginners. N. Y.: G. P. Putnam's Sons. 1899.
Wheeler, C. G., Woodworking for Beginners. New York: G. P. Putnam's Sons. 1899.
White, Stewart Edward, The Blazed Trail. N. Y.: McClure, Phillips & Co. 1904.
White, Stewart Edward, The Blazed Trail. N. Y.: McClure, Phillips & Co. 1904.
White, Stewart Edward, From Forest to Saw Mill. Junior Munsey, 10: 362, Je. '01.
White, Stewart Edward, From Forest to Saw Mill. Junior Munsey, 10: 362, Je. '01.
Anonymous.
Anon.
Nails. Wood Craft. 5: 103, Jl. '06.
Nails. Wood Craft. 5: 103, July '06.
A Dry-Kiln of Progressive Style. Wood Craft, 6: 31. Nov. '06.
A Dry-Kiln of Progressive Style. Wood Craft, 6: 31. Nov. '06.
Lumbering in Louisiana. Wood Craft, 4: 55, Nov. '05.
Lumbering in Louisiana. Wood Craft, 4: 55, Nov. '05.
The Lac Industry of Assam. Journal of the Society of Arts. 49: 192. Feb 8 '01.
The Lac Industry of Assam. Journal of the Society of Arts. 49: 192. Feb 8, 2001.
Chapter 1.
LOGGING.
The rough and ready methods common in American logging operations are the result partly of a tradition of inexhaustible supply, partly of the fear of fire and the avoidance of taxes, partly of an eagerness to get rich quick. Most of the logging has been done on privately owned land or on shamelessly stolen public land, and the lumberman had no further interest in the forest than to lumber it expeditiously.
The tough and straightforward methods typical in American logging are partly due to a belief in endless resources, partly because of the fear of fires and the desire to dodge taxes, and partly because of a desire to get rich quickly. Most logging has occurred on privately owned land or on blatantly stolen public land, and the logger had little concern for the forest beyond cutting it down as quickly as possible.

Fig. 1. Making a Valuation Survey.

Fig. 2. "Blazes" on Trees.
Preliminary to the actual logging are certain necessary steps. First of all is landlooking. This includes the survey of the forest land for the purpose of locating good timber. Fig. 1. Most of the woodland has previously been roughly surveyed by the government and maps made indicating which parts are private land and which are still held by the government. The boundaries of townships, sections, quarter sections, eighties, forties, etc., are indicated by "blazes" [page 8] on trees, Fig. 2, so that the "cruiser" or "looker" as he goes thru the woods can identify them with those on his oil paper map. The cruiser also studies the kinds and character of the trees, the contour of the ground, the proximity to streams,—all with the view to marketing the product. Acting on the information thus gained by the cruiser, the lumberman purchases his sections at the proper land office, or if he is less scrupulous, buys only enough to serve as a basis for operations. Enormous fortunes have been made by timber thieves, now respectable members of the community. As a further preliminary step to lumbering itself, the tote road and camp are built. The tote road is a rough road on which supplies for crew and cattle can be taken to camp from civilization.
Before the actual logging begins, there are some necessary steps to take. First up is landlooking. This involves surveying the forest land to find quality timber. Fig. 1. Most of the woodland has been roughly surveyed by the government, and maps show which areas are private land and which are still government-owned. The boundaries of townships, sections, quarter sections, eighties, forties, etc., are marked by "blazes" [page 8] on trees, Fig. 2, so that the "cruiser" or "looker" can identify them with their oil paper map as they navigate through the woods. The cruiser also examines the types and quality of the trees, the terrain, and the distance to streams—all with the goal of marketing the timber product. Based on the information gathered by the cruiser, the lumberman purchases his sections at the appropriate land office, or if he's less ethical, buys just enough to form a basis for operations. Huge fortunes have been made by timber thieves, who are now considered respectable members of the community. As a further preliminary step to actual lumbering, the tote road and camp are constructed. The tote road is a rough path for bringing supplies for the crew and cattle from civilization to the camp.
It is barely passable for a team and a wagon, but it serves its purpose, and over it come more men and horses. Lumber for the floors and roofs of the shanties and for the rude pieces of furniture that will be needed, tarred paper to make the roofs tight, a few glazed window sashes, a huge range and a number of box stoves, dishes and kitchen utensils, a little stock of goods for the van, blankets by the dozen and score, and countless boxes and barrels and bags of provisions.1
It's just wide enough for a team and a wagon, but it works, and more men and horses are coming across it. Lumber for the floors and roofs of the shanties and the essential furniture, tar paper to waterproof the roofs, a few glazed window frames, a large cooking range and several box stoves, dishes and kitchen tools, a small supply of goods for the van, dozens of blankets, and countless boxes, barrels, and bags of food supplies.1
Footnote 1: Hulbert: The Lumber Jack; Outlook, 76: 801, April 2, '04.
Footnote 1: Hulbert: The Lumber Jack; Outlook, 76: 801, April 2, 2004.
The camp itself, Fig. 3, is built of logs, roofed with plank, covered with heavy tar paper, and dimly lighted. There are usually five buildings,—the men's camp, the cook camp, the office, the barn, and the blacksmith's shop. Many camps accommodate from eighty to one hundred men. The men's camp is filled with bunks and is heated by a stove and in general roughly furnished. Cooking and eating are done in the cook camp, where the cook and his assistant, the "cookee," sleep. The office is occupied by the foreman, log-sealers [page 9] and clerks. Here the books and accounts are kept, and here is the "van," stocked with such goods as will supply the immediate needs of the lumber jacks.
The camp itself, Fig. 3, is made of logs, has a plank roof, covered with heavy tar paper, and is dimly lit. There are usually five buildings: the men's camp, the cook camp, the office, the barn, and the blacksmith's shop. Many camps house between eighty to one hundred men. The men's camp is filled with bunk beds and heated by a stove, and it is generally simply furnished. Cooking and dining take place in the cook camp, where the cook and his assistant, known as the "cookee," sleep. The office is occupied by the foreman, log-sealers, and clerks. This is where the books and accounts are maintained, and it also contains the "van," stocked with supplies to meet the immediate needs of the lumberjacks. [page 9]

Fig. 3. Winter Logging Camp. Itasco County, Minnesota.
Before winter sets in the main road is built, Fig. 15, p. 17, very carefully graded from the camp down to the nearest mill or railway siding, or oftener to the stream down which the logs are to be floated. This road has to be as wide as a city street, 25 feet. The route is carefully chosen, and the grade is made as easy as possible. Much labor is spent upon it, clearing away stumps and rocks, leveling up with corduroy, building bridges strong enough to carry enormous loads, and otherwise making it as passable as can be; for when needed later, its good condition is of first importance. This main road is quite distinct from and much superior to the tote road.
Before winter arrives, the main road is built, Fig. 15, p. 17, carefully graded from the camp down to the nearest mill or railway siding, or more often to the stream where the logs will be floated. This road needs to be as wide as a city street—25 feet. The route is chosen with care, and the incline is made as gentle as possible. A lot of work goes into it, clearing away stumps and rocks, leveling with corduroy, building bridges strong enough to support heavy loads, and making it as passable as possible; because when it’s needed later, its good condition is crucial. This main road is clearly different from and much better than the tote road.
At intervals alongside the main road, small squares called skidways are cleared of brush and in each of them two tree trunks, "skids," are laid at right angles to the road. On these the logs, when cut later, are to be piled. Back from the skidways, into the woods the swampers cut rough, narrow roads called dray roads or travoy roads,—mere trails sufficiently cleared of brush to allow a team of horses to pull a log thru.
At intervals along the main road, small clearings called skidways are kept free of brush, and in each of them, two tree trunks, known as "skids," are placed at right angles to the road. The logs that will be cut later are to be stacked on these. Further back from the skidways, into the woods, the swampers carve out rough, narrow paths called dray roads or travoy roads—just trails cleared enough of brush for a team of horses to pull a log through.

Fig. 4. Tools used in Logging.
All these are operations preliminary to the felling of trees. The tools commonly used in logging are shown in Fig. 4. When everything is ready for felling, the "fitter" goes ahead marking each tree to be felled and the direction in which it is to fall by cutting a notch on that side. Then come the sawyers in pairs, Fig. 5. First they chop a deep gash on the side of the tree toward which it is to fall, and then from the opposite side begin cutting with a long, Tuttle-tooth, crosscut-saw. The saw is a long, flexible ribbon of steel, with handles so affixed to each end that they can be removed easily. The cut is made on the pulling stroke, and hence the kerf can be very narrow. As soon as the saw is well within the trunk, the sawyers drive iron wedges into the kerf behind it, partly to keep the weight of the trunk from binding the saw, and partly to direct its fall. Then the saw is pulled back and forth, and the wedges [page 11] driven in farther and farther, until every stroke of the maul that drives them sends a shiver thru the whole tree. Just as the tree is ready to go over, the saw handle at one end is unhooked and the saw pulled out at the other side. "Timber!," the men cry out as a warning to any working near by, for the tree has begun to lean slightly. Then with a hastening rush the top whistles thru the air, and tears thru the branches of other trees, and the trunk with a tremendous crash strikes the ground. Even hardened loggers can hardly keep from shouting, so impressive is the sight of a falling giant tree.
All these are steps taken before cutting down trees. The tools typically used in logging are shown in Fig. 4. Once everything is set for cutting, the "fitter" proceeds to mark each tree to be cut down and the direction it should fall by making a notch on that side. Then the sawyers come in pairs, as shown in Fig. 5. They start by chopping a deep gash on the side of the tree where it will fall, and then from the opposite side, they begin cutting with a long, Tuttle-tooth, crosscut saw. The saw is a long, flexible strip of steel, with removable handles on each end. The cut is made on the pulling stroke, which allows for a very narrow kerf. Once the saw is deep enough into the trunk, the sawyers drive iron wedges into the kerf behind the saw, partly to prevent the weight of the trunk from binding the saw and partly to control its fall. Then, the saw is pulled back and forth, with the wedges driven in further and further until every stroke of the maul that drives them sends vibrations through the tree. Just as the tree is about to fall, one saw handle is unhooked and the saw is pulled out from the other side. "Timber!" the men shout to warn anyone nearby, as the tree starts to lean slightly. Then, with a swift rush, the top flies through the air, crashing into the branches of other trees, and the trunk hits the ground with a loud crash. Even seasoned loggers can hardly refrain from shouting; the sight of a giant tree falling is truly impressive.

Fig. 5. Felling Red Spruce with a Saw.
Adirondack Mountains, New York.

Fig. 6. Sawing Logs into Lengths.
All this seems simple enough in outline, but the actual execution requires considerable skill. Trees seldom stand quite vertical, there is danger of lodging in some other tree in thick woods, and it is therefore necessary to throw trees quite exactly. Some men become so expert at this that they can plant a stake and drive it into the [page 12] ground by the falling trunk as truly as if they hit it with a maul. On the other hand, serious accidents often happen in falling trees. Most of them come from "side winders," i. e., the falling of smaller trees struck by the felled trees.
All this seems straightforward in theory, but actually doing it takes a lot of skill. Trees rarely fall perfectly upright; there's a risk of getting stuck in another tree in dense woods, so it’s crucial to drop trees very precisely. Some people get so good at this that they can plant a stake and drive it into the ground with the falling trunk as accurately as if they hit it with a mallet. On the flip side, serious accidents can often occur when trees fall. Most of these incidents are caused by "side winders," meaning the smaller trees that get struck by the trees being cut down.
After "falling" a tree, the sawyers mark off and saw the trunk into log lengths, Fig. 6, paying due attention to the necessity of avoiding knots, forks, and rotten places, so that some of the logs are eighteen feet, some sixteen feet, some fourteen feet, and some only twelve feet in length. Meanwhile the swampers trim off the branches, Fig. 7, a job requiring no little skill, in order that the trunk may be shaved close but not gashed.
After cutting down a tree, the sawyers measure and saw the trunk into logs, Fig. 6, making sure to avoid knots, forks, and rotting areas. As a result, some logs are eighteen feet long, some are sixteen feet, some are fourteen feet, and some are only twelve feet. Meanwhile, the swampers trim the branches, Fig. 7, a task that requires quite a bit of skill to ensure the trunk is smoothly shaved but not damaged.
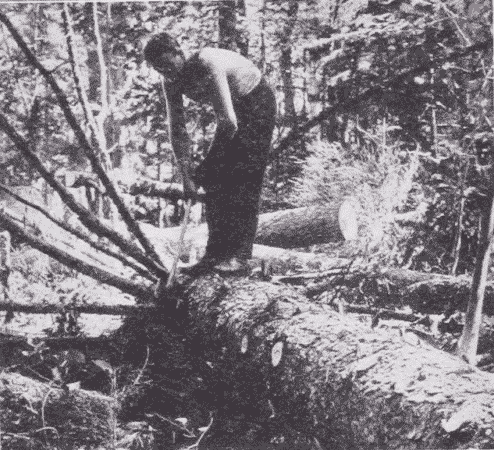
Fig. 7. Trimming off Branches of Spruce.
Adirondack Mountains, New York.

Fig. 8. Hauling Spruce Logs to the Skidway.
Adirondack Mountains, New York.
This finishes the second group of operations, the felling. Next the logs are dragged out to the dray roads, Fig. 8. A heavy pair of tongs, like ice-tongs, is attached to one end, and the log is snaked out by horses to the skidway. If the log is very heavy, one end is put on a dray. By one way or another the log is dragged out and across the two parallel skids, on which it is rolled by cant-hooks to the end of skids toward the road way. If other logs already occupy the skids, each new log as it arrives is piled on the first tier. As the pile grows higher, each log is "decked," that is, rolled up parallel poles laid slanting up the face of the pile, by means of a chain passed under and over the log and back over the pile, Fig. 11. A horse hitched to the end of the chain hauls up the log, which is guided by the "send-up men" with their cant-hooks.
This wraps up the second group of operations, which is the felling. Next, the logs are pulled out to the dray roads, Fig. 8. A heavy pair of tongs, similar to ice tongs, is attached to one end, and the log is pulled out by horses to the skidway. If the log is really heavy, one end is placed on a dray. One way or another, the log is dragged out and across the two parallel skids, where it is rolled by cant-hooks to the end of the skids toward the roadway. If other logs are already on the skids, each new log is stacked on the first tier as it arrives. As the pile gets taller, each log is "decked," meaning it's rolled up parallel to poles that are positioned at an angle up the face of the pile, using a chain that goes under and over the log and then back over the pile, Fig. 11. A horse tied to the end of the chain pulls up the log, which is directed by the "send-up men" using their cant-hooks.
Once piled the logs are "scaled," that is measured in order to compute the number of board feet in them, Fig. 9. The scaler generally has an assistant, for logs in large piles must be measured at both ends in order to determine which is the top, the body of the log being out of sight. When measured each end of the log is stamped with a hammer with the owner's mark, by which it can afterward be identified. Here the logs rest and the felling and skidding continue until deep snow falls and then the sleigh haul begins.
Once the logs are piled up, they are "scaled," which means they're measured to calculate the number of board feet in them, Fig. 9. The scaler usually has an assistant because logs in large piles need to be measured at both ends to figure out which is the top, since the body of the log is out of sight. During the measurement, each end of the log is stamped with a hammer that has the owner's mark, allowing it to be identified later. Here, the logs sit while the felling and skidding continue until deep snow falls, at which point the sleigh haul begins.

Fig. 9. "Scaling" Logs on the Skids.

Fig. 10. Making an Ice Road by Flooding.

Fig. 11. Decking Logs on Skidway.
For this the main road is especially prepared. First the road is carefully plowed with an immense V plow, weighted down by logs. To the plow are attached fans. Only an inch or two of snow is left on the ground by this plow, which is followed by another special plow to gouge the ruts, and by a gang of "road monkeys" who clear the road thoroly. Then follows an immense tank set on runners and holding perhaps seventy-five barrels of water, and so arranged as to flood the road from holes in the bottom of the tank, a sort of rough road sprinkler, Fig. 10. The sprinkler goes over the road again and again until the road is covered by a clear, solid sheet of ice often [page 15] two feet thick, extending from the skidways to the banking grounds. This ice road is one of the modern improvements in logging. Once finished, these roads are beautiful pieces of construction with deep, clear ruts. They have to be constantly watched and repaired, and this is the work of the "road monkeys." If possible the road has been made entirely with down grades but some of these are so steep that a man must be prepared with sand or hay to check too headlong a descent.
For this, the main road is specially prepared. First, the road is carefully plowed with a huge V plow, weighed down by logs. Fans are attached to the plow, leaving only an inch or two of snow on the ground. This plow is followed by another special plow that digs out the ruts, and a team of "road monkeys" who thoroughly clear the road. Next comes a massive tank on runners, holding about seventy-five barrels of water, designed to flood the road through holes in the bottom, acting like a rough road sprinkler, Fig. 10. The sprinkler goes over the road repeatedly until it’s covered by a clear, solid sheet of ice often [page 15] two feet thick, extending from the pickup points to the storage areas. This ice road is one of the modern innovations in logging. Once completed, these roads are beautiful constructions with deep, clear ruts. They need constant monitoring and maintenance, which is the job of the "road monkeys." If possible, the road is designed to have all downhill sections, but some of these are so steep that a person must be ready with sand or hay to slow down a too rapid descent.

Fig. 12. Loading a Sled from a Skidway.

Fig. 13. A Load of Logs. Flathead County, Montana.
When all is ready the sleigh haul begins. Piling on the sleighs or bobs, Fig. 12, is similar to piling on the skidways, but more difficult, for the load has to be carefully balanced, Fig. 13. Chains bind the loads but the piling is only too apt to be defective, and the whole load "squash out" with a rush. It is a time of feverish activity. The sprinklers are at work till after midnight, the loaders are out long before daylight. The blacksmith is busy with repairs, the road monkeys work [page 16] overtime, and the cook works all the time. "Everybody works." The haul itself is full of excitement. The ponderous load of logs, weighing anywhere from eight to thirty-five tons has to be conducted largely by its own momentum down this glassy road. If a horse fall nothing can save its life. If the runners get out of the ruts, the whole load, driver and all, is likely to be upset. It is an extremely hazardous job, Fig. 15.
When everything is ready, the sleigh haul starts. Loading the sleighs or bobs, Fig. 12, is similar to loading the skidways, but it's more challenging because the load has to be carefully balanced, Fig. 13. Chains secure the loads, but the piling often ends up being unstable, causing the entire load to "squash out" rapidly. It's a time filled with intense activity. The sprinklers are running until after midnight, and the loaders are out long before dawn. The blacksmith is busy with repairs, the road crew is working overtime, and the cook is always busy. "Everyone is working." The haul itself is packed with excitement. The heavy load of logs, weighing between eight and thirty-five tons, has to be mostly driven by its own momentum down this smooth road. If a horse falls, there's no saving its life. If the runners get out of the grooves, the entire load, along with the driver, is likely to tip over. It’s a very dangerous job, Fig. 15.
As each load comes down to the banking grounds, Fig. 14, or log dump, it is stopped opposite long parallel skids. The wrapping chains are unhooked and the lower log on the skid side is worked out with cant-hooks till the whole load flattens out. The logs are then "decked" on immense piles, sometimes a mile long and filling the whole river from bank to bank. A decking chain 300 feet long is sometimes required to roll the logs to their proper places. Here the logs rest till the spring freshets come. This completes the transportation by land.
As each load arrives at the banking grounds, Fig. 14, or log dump, it stops in front of long parallel skids. The wrapping chains are unhooked, and the lower log on the skid side is worked out using cant-hooks until the whole load flattens out. The logs are then "decked" into huge piles, sometimes a mile long and filling the entire river from bank to bank. A decking chain that’s 300 feet long is sometimes needed to roll the logs into their proper positions. The logs stay here until the spring floods arrive. This wraps up the transportation by land.

Fig. 14. Banking Grounds.
With the coming of the spring thaw, the river bed is filled with a freshet of water which seizes and carries the logs down stream. Many on the banks, however, have to be started on their way, and this is called "breaking out the roll ways." They often start on their water journey with a great crash.
With the arrival of spring thaw, the riverbed is filled with a rush of water that grabs and carries the logs downstream. However, many logs on the banks need to be nudged into motion, and this is known as "breaking out the roll ways." They often begin their journey on the water with a loud crash.

Fig. 15. The Sleigh Haul.

Fig. 16. Sacking the Rear.
Now comes the drive, an arduous and often perilous task. Some of the men are stationed along the shores to prevent the logs from lodging or floating into bays or setbacks. Some stand at the heads of bars or islands, where with pike poles they shove off the logs that might stop there and form a jam; others follow "sacking the rear" to clean out such logs as may have become stranded. This "sacking the rear" takes most of the time, Fig. 16. While "on the drive" men often work fourteen hours a day, a good part of the time up to their waists in ice water. Their boots are shod with "caulks," or [page 18] spikes, to keep them from slipping on the logs, and they carry either pike poles or peaveys, Fig. 17. The latter are similar to cant-hooks, except that they have sharp pikes at their ends. So armed, they have to "ride any kind of a log in any water, to propel a log by jumping on it, by rolling it squirrel fashion with the feet, by punting it as one would a canoe; to be skilful in pushing, prying, and poling other logs from the quarter deck of the same cranky craft." Altho the logs are carried by the river, they have to be "driven" with amazing skill and bravery.
Now comes the drive, a tough and often dangerous job. Some of the guys are stationed along the banks to stop the logs from getting stuck or floating into bays or obstacles. Some are positioned at the heads of bars or islands, where they use pike poles to push off any logs that might settle there and create a jam; others follow "sacking the rear" to clear out any logs that may have gotten stranded. This "sacking the rear" takes most of the time, Fig. 16. While "on the drive," the men often work fourteen hours a day, spending much of that time up to their waists in icy water. Their boots are equipped with "caulks" or spikes to prevent slipping on the logs, and they carry either pike poles or peaveys, Fig. 17. The latter are similar to cant-hooks but have sharp pikes at their ends. Armed this way, they have to "ride any type of log in any water, push a log by jumping on it, roll it like a squirrel with their feet, and punt it as you would a canoe; they need to be skilled at pushing, prying, and poling other logs from the quarter deck of the same unstable craft." Although the logs are carried by the river, they have to be maneuvered with incredible skill and courage.

Fig. 17. Log Driving on the Ausable River.
The climax of hardship and courage is reached when a "jam" is formed, Fig. 18. Sometimes one or two logs are caught in such a way as to be locked or jammed and then soon other logs begin to accumulate behind them, till the whole river is full of a seemingly inextricable mass. Sometimes these jams can be loosened by being pulled apart, one log at a time. A hundred men can pull out an amazing number of logs in a day. The problem always is to set free or cut out certain "key" logs, which lock the whole mass. Following is a description by Stewart Edward White of the breaking of such a jam:
The peak of struggle and bravery occurs when a "jam" forms, Fig. 18. Sometimes one or two logs get caught in such a way that they’re locked together, and then soon other logs start stacking up behind them until the entire river fills with what looks like an impossible tangle. Sometimes these jams can be broken apart by pulling them apart, one log at a time. A hundred people can remove an impressive number of logs in a single day. The challenge is always to free or cut out certain "key" logs that hold the entire mass together. Here’s a description by Stewart Edward White of how such a jam is broken:
The crew were working desperately. Down on the heap somewhere, two logs were crossed in such a manner as to lock the whole. They sought those logs.
The crew was working frantically. Somewhere in the pile, two logs were crossed in a way that locked everything in place. They searched for those logs.
Thirty feet above the bed of the river six men clamped their peaveys into the soft pine; jerking, pulling, lifting, sliding the great logs from their places. Thirty feet below, under the threatening face, six other men coolly picked out and set adrift one by one, the timbers not inextricably imbedded. From time to time the mass creaked, settled, perhaps even [page 19] moved a foot or two; but always the practised rivermen, after a glance, bent more eagerly to their work. * * * Suddenly the six men below the jam scattered. * * * holding their peaveys across their bodies, they jumped lightly from one floating log to another in the zig-zag to shore. * * *
Thirty feet above the riverbed, six men secured their peaveys into the soft pine, pulling, lifting, and sliding the massive logs from their spots. Thirty feet below, under the looming mass, six other men calmly selected and released, one by one, the timbers that weren’t stuck. Occasionally, the pile creaked, shifted, or even moved a foot or two; but the experienced rivermen, after a quick glance, eagerly returned to their work. * * * Suddenly, the six men below the jam scattered. * * * With their peaveys held across their bodies, they jumped lightly from one floating log to another, zig-zagging toward the shore. * * *

Fig. 18. Log Jam. Adirondack Mountains, New York.
In the meantime a barely perceptible motion was communicating itself from one particle to another thru the center of the jam. * * * The crew redoubled its exertion, clamping its peaveys here and there, apparently at random, but in reality with the most definite of purposes. A sharp crack exploded immediately underneath. There could no longer exist any doubt as to the motion, altho it was as yet sluggish, glacial. Then in silence a log shifted—in silence and slowly—but with irresistible force * * * other logs in all directions up-ended. * * *
In the meantime, a barely noticeable movement was transferring from one particle to another through the center of the log jam. * * * The crew ramped up their efforts, clamping their peaveys here and there, seemingly at random, but actually with a clear intention. A loud crack suddenly echoed right underneath. There was no longer any doubt about the movement, even though it was still slow, like ice. Then, in silence, a log shifted—slowly and quietly—but with unstoppable force * * * other logs flipped up in all directions. * * *
Then all at once down by the face something crashed, the entire stream became alive. It hissed and roared, it shrieked, groaned, and grumbled. At first slowly, then more rapidly, the very fore-front of the center melted inward and forward and downward, until it caught the fierce rush of the freshet and shot out from under the jam. Far up-stream, bristling and formidable, the tons of logs, grinding savagely together, swept forward. * * *
Then suddenly, something crashed down at the front, and the entire stream came to life. It hissed and roared, screamed, groaned, and grumbled. At first slowly, then more quickly, the very edge of the center melted inward, forward, and downward, until it caught the strong rush of the flood and shot out from under the blockage. Far upstream, stacked high and menacing, the tons of logs ground against each other fiercely and surged forward. * * *
Then in a manner wonderful to behold, thru the smother of foam and spray, thru the crash and yell of timbers, protesting the flood's hurrying, thru the leap of destruction, the drivers zigzagged calmly and surely to the shore.
Then, in an amazing sight, through the thick foam and spray, through the noise and shouts of wood protesting against the rushing flood, through the leap of destruction, the drivers zigzagged confidently and steadily toward the shore.
Sometimes cables have to be stretched across the chasm, and special rigging devised to let the men down to their dangerous task and more especially to save them from danger when the crash comes.
Sometimes cables need to be stretched across the chasm, and special rigging is created to lower the workers into their risky job and, more importantly, to protect them from danger when the crash happens.
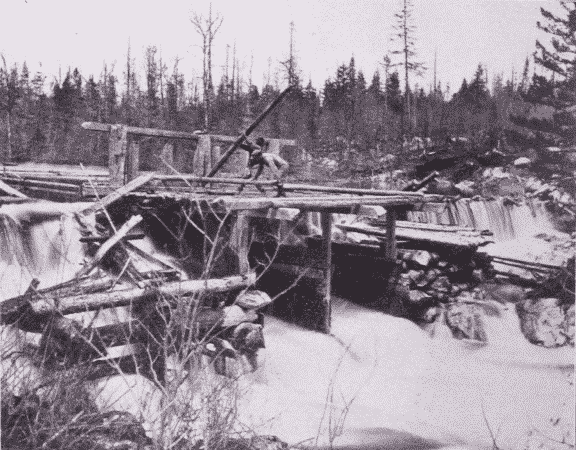
Fig. 20. Splash-Dam.

Fig. 21. Logs in Boom. Glens Falls, New York.
In case such efforts are unavailing, it is necessary to "shoot" the jam with dynamite. Another device resorted to where the supply of water is insufficient is the splash-dam, Fig. 20. The object is to make the operator independent of freshets, by accumulating a head of water and then, by lifting the gates, creating an artificial freshet, sufficient to float the timber down stream.
If these efforts don't work, it's necessary to "blast" the jam with dynamite. Another tool used when there's not enough water is the splash-dam, Fig. 20. The goal is to make the operator independent of sudden floods by gathering a reservoir of water and then, by opening the gates, creating an artificial flood strong enough to float the timber downstream.

Fig. 22. A Sorting Jack.
Thus by one means and another, the logs are driven along until caught by a boom, Fig. 21, which consists of a chain of logs stretched across the river, usually at a mill. Since the river is a common carrier, the drives of a number of logging companies may float into the mill pond together. But each log is stamped on both ends, so that it can be sorted out, Fig. 22, and sent into the boom of its owner.
Thus, through various methods, the logs are moved along until they’re caught by a boom, Fig. 21, which is a series of logs stretched across the river, typically at a mill. Because the river is a shared transport route, logs from several logging companies may arrive at the mill pond simultaneously. However, each log is marked on both ends, ensuring it can be identified, Fig. 22, and directed into the boom of its owner.
MECHANICAL METHODS IN LUMBERING.
The operations described above are those common in the lumber regions of the northeast and the Lake States. But special conditions produce special methods. A very effective device where streams are small is the flume, Fig. 23. This is a long wooden trough thru which water is led, and the logs floated end on. It is sometimes many miles long; in one case in California twenty-five miles.
The processes mentioned above are typical in the lumber areas of the northeast and the Lake States. However, unique conditions create unique methods. A highly effective solution for smaller streams is the flume, Fig. 23. This is a long wooden trough through which water flows, carrying the logs floating upright. It can be several miles long; in one instance in California, it measured twenty-five miles.
In the South where there is no snow, logs are largely brought out to the railway or river by being hung under immense two-wheeled trucks, called slip-tongue carts, drawn by mules, Fig. 24. The wheels are nearly eight feet in diameter.
In the South where there's no snow, logs are mostly transported to the railway or river by being hung under huge two-wheeled trucks known as slip-tongue carts, pulled by mules, Fig. 24. The wheels are almost eight feet in diameter.

Fig. 23. Six Mile Flume. Adirondack Mountains, New York.
Some kinds of wood are so heavy that they will not float at all, and some sink so readily that it does not pay to transport them by river. In such cases temporary railways are usually resorted to.
Some types of wood are so heavy that they won't float at all, and some sink so easily that it's not worth transporting them by river. In these situations, temporary railways are typically used.

Fig. 24. Hauling Logs by Mules. Oscilla, Georgia.
On the Pacific coast, where the forests are dense, the trees of enormous size, and no ice road is possible, still other special methods have been devised. On so great a scale are the operations conducted that they may properly be called engineering feats. Consider for a moment the size of the trees: red fir ranges from five to fifteen feet in diameter, is commonly two hundred fifty feet high, and sometimes three hundred twenty-five feet high. The logs are commonly cut twenty-five feet long, and such logs often weigh thirty to forty tons [page 23] each, and the logs of a single tree may weigh together one hundred fifty tons. The logging of such trees requires special appliances. Until recently all the improved methods were in forms of transportation, the felling still being done by hand with very long saws, Fig. 25, but now even the felling and sawing of logs in the forest is partly done by machinery.
On the Pacific coast, where the forests are thick, the trees are massive, and there's no possibility for ice roads, other unique methods have been developed. The operations are so extensive that they can truly be called engineering marvels. Just think about the size of the trees: red fir can have diameters from five to fifteen feet, typically reaches heights of two hundred fifty feet, and can even grow up to three hundred twenty-five feet tall. The logs are usually cut to twenty-five feet long, and these logs can often weigh thirty to forty tons each, with the logs from a single tree totaling around one hundred fifty tons. Logging such trees requires specialized equipment. Until recently, all advancements were focused on transportation, while the cutting was still done manually with very long saws, Fig. 25, but now the cutting and sawing of logs in the forest is also partially done by machinery. [page 23]

Fig. 25. A Twenty-Five Foot Saw used for Crosscutting Big Logs.

Fig. 26. Hauling Big Logs by Donkey Engine.
To work the saw, power is supplied by a steam or gasoline engine mounted upon a truck which can be taken readily from place to place. As the maximum power required is not over ten-horse-power, the apparatus is so light that it can be moved about easily. The saw can be adjusted to cut horizontally, vertically, or obliquely, and hence is used for sawing into lengths as well as for felling.
To operate the saw, a steam or gasoline engine is mounted on a truck that can be easily transported. Since the maximum power needed is no more than ten horsepower, the equipment is lightweight and can be moved around effortlessly. The saw can be adjusted to cut horizontally, vertically, or at an angle, making it suitable for cutting lumber to length as well as for felling trees.
Falling beds. Since the weight of a two hundred fifty foot fir is such that if the impact of its fall be not gradually checked the force with which it strikes the ground may split the trunk, a bed for its fall is prepared by the swampers. Usually piles of brush are placed as buffers along the "falling line" so that the trunk will strike these. If the tree stands on the hill side, it is thrown up hill, in order to shorten the fall.
Falling trees. Since the weight of a two hundred fifty-foot fir is so great that if its fall isn't gradually slowed down, the force of the impact could split the trunk, a landing area is prepared by the swampers. Typically, piles of brush are placed as buffers along the "fall line" so that the trunk will hit these. If the tree is on a hillside, it is pushed uphill to shorten the fall.
After the felling comes the trimming of branches and knots and "rossing" of bark, to lessen the friction in sliding along the skidway.
After cutting down the tree, the next step is to trim the branches and knots and "ross" the bark to reduce friction while sliding along the skidway.
The skidway. By the skidway in the Puget Sound region is meant a corduroy road. This is constructed of trunks of trees ranging from a foot to two feet in diameter. These are "rossed," that is, stripped of their bark and laid across the road, where they are held in place by pegs driven into the ground, and by strips spiked upon the tops of the logs. If possible they are laid in swampy places to keep the surface damp and slippery. At turns in the road, pulleys are hung, thru which the hauling cables pass. The skidway runs to the railway siding or water's edge. Over these skidways the logs are hauled out by various means. Formerly "strings" of oxen or Percheron horses were used, but they are now largely superseded by some form of donkey engine, Fig. 26. These are placed at the center of a "yard."
The skidway. The skidway in the Puget Sound area refers to a corduroy road. This is made from tree trunks that are about one to two feet in diameter. These trunks are "rossed," meaning they are stripped of their bark and laid across the road, anchored in place by pegs driven into the ground and by strips nailed onto the tops of the logs. If possible, they are placed in wet areas to keep the surface moist and slippery. At the bends in the road, pulleys are installed, through which hauling cables run. The skidway leads to the railway siding or the edge of the water. Logs are pulled out over these skidways by various means. In the past, teams of oxen or Percheron horses were commonly used, but they have mostly been replaced by some type of donkey engine, Fig. 26. These engines are positioned at the center of a "yard."
Yarding is the skidding of logs to the railway or water way by means of these donkey engines. Attached to the donkey engine are two drums, one for the direct cable, three-fourths to one inch in diameter and often half a mile long, to haul in the logs, the other for the smaller return cable, twice as long as the direct cable and used to haul back the direct cable. At the upper end of the skidway, when the logs are ready to be taken to the railway or boomed, they are fastened together, end to end, in "turns" of four or more. The direct cable is attached to the front of the "turn", and the return cable to the rear end. By winding the direct cable on its drum, the "turn" is hauled in. The return cable is used to haul back the end [page 25] of the direct cable, and also, in case of a jam, to pull back and straighten out the turn. Instead of a return cable a horse is often used to haul out the direct cable. Signaling from the upper end of the skidway to the engineer is done by a wire connected to the donkey's whistle, by an electric bell, or by telephone.
Yarding is the process of dragging logs to the railway or waterway using donkey engines. Each donkey engine has two drums: one for the main cable, which is about three-fourths to one inch in diameter and can be up to half a mile long, used for pulling in the logs; and another for the smaller return cable, which is twice the length of the main cable and is used to pull back the main cable. At the top of the skidway, once the logs are ready to be transported to the railway or boom, they are tied together end to end in "turns" of four or more. The main cable is attached to the front of the "turn," and the return cable is connected to the back. By winding the main cable on its drum, the "turn" is pulled in. The return cable is used to pull back the end of the main cable and, in case of a jam, to pull back and straighten the turn. Sometimes a horse is used instead of a return cable to pull out the main cable. Communication from the top of the skidway to the engineer is done using a wire connected to the donkey's whistle, an electric bell, or a telephone. [page 25]
Sometimes these donkey engines are in relays, one engine hauling a turn of logs to within reach of the next one, which passes it on to the next until the siding is reached.
Sometimes these donkey engines work in relays, with one engine pulling a load of logs close to the next one, which then passes it on to the following engine until they reach the siding.
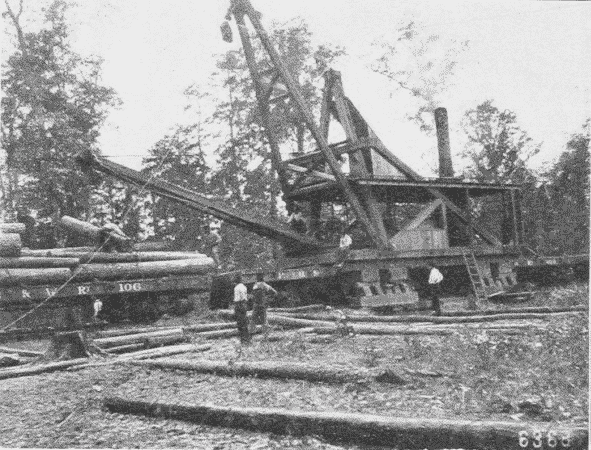
Fig. 27. Steam Skidder at Work. Grant County, Arkansas.
Where there are steep canons to be crossed, a wire trolley may be stretched and the great logs carried over suspended from it.
Where there are steep canyons to cross, a wire trolley can be set up to carry the big logs suspended from it.
In the South a complicated machine called a steam skidder, Fig. 27, equipped with drums, booms, etc., is much used both for skidding in the logs and then for loading them on the cars. It is itself mounted on a flat car.
In the South, a complex machine known as a steam skidder, Fig. 27, fitted with drums, booms, and other features, is widely used for both dragging logs and loading them onto cars. It is mounted on a flat car.
An improvement on this is the locomotive boom derrick which is widely used both on the Pacific coast and of late in the Lake Superior region. It is a combined locomotive, skidder and loader. Its most unique feature is that it can be lifted off the track so as to allow flat cars to run underneath it. This feat is accomplished thus: A device, which is something like that used in elevating the bodies of coal wagons, lifts the engine several feet above the rails. Then steel legs, which are curved outwardly, are lowered until the shoes which [page 26] are attached to them rest on the outward end of the railroad ties. The truck of the locomotive is then folded up under it out of the way and cars can run under it, the curved legs giving plenty of clearance. The derrick attached is of the breast type, the two legs being firmly fastened. When anchored the engine can be used either for skidding or loading. For skidding, there are two cables, one being run out while the other is being wound on its drum.
A newer version of this is the locomotive boom derrick, which is commonly used along the Pacific coast and recently in the Lake Superior area. It's a combination of a locomotive, skidder, and loader. Its most notable feature is that it can be lifted off the tracks, allowing flat cars to move underneath it. This is done by a device similar to what is used to raise the bodies of coal wagons, which lifts the engine several feet above the rails. Then, curved steel legs are lowered until the shoes attached to them rest on the outer ends of the railroad ties. The truck of the locomotive is then folded up underneath it, clearing the way for cars to pass under it, thanks to the ample clearance provided by the curved legs. The attached derrick is of the breast type, with the two legs securely fastened. When anchored, the engine can be used for either skidding or loading. For skidding, there are two cables: one is released while the other is wound onto its drum.
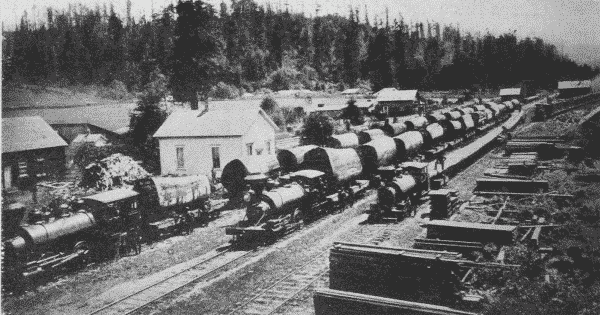
Fig. 28. Log Train, Humboldt County, California.
In loading, the machine is located so that the empty car will be directly in front of it, and then the logs are lifted up and placed on the car by the derrick. When the car is loaded the machine can either move on to the next car, or pull it under itself into place. With the help of four men it can load from 125,000 to 150,000 feet of timber in a day. By means of the cable it can make up a train, and then by lowering the truck and raising the legs out of the way, it is converted into a locomotive and hauls the train away to the mill or railway station at the rate of three or four miles at hour.
In loading, the machine is positioned so that the empty car is directly in front of it, and then the derrick lifts the logs and places them on the car. Once the car is loaded, the machine can either move on to the next car or pull it into position underneath itself. With the help of four workers, it can load between 125,000 and 150,000 feet of timber in a day. Using the cable, it can create a train, and then by lowering the truck and raising the legs out of the way, it transforms into a locomotive and pulls the train away to the mill or railway station at a speed of three to four miles per hour.
As forests are cut away along the water courses, railways have to be resorted to more and more, Fig. 28. This has had a stimulative effect on the logging business, for now the logger is independent of the snow. On account of the steep grades and sharp curves often necessary in logging railways, a geared locomotive is sometimes used, Fig. 29. It can haul a train of twenty loaded cars up a twelve per cent grade. The geared engine has also been used as a substitute for cable power, in "yarding" operations. The "turns" of logs are drawn over the ground between the rails, being fastened to the rear of the engine by hook and cable. This has proved to be a very economical use of power and plant.
As forests are cleared along the waterways, railways are being used more and more, Fig. 28. This has boosted the logging industry, as loggers no longer rely on snow conditions. Due to the steep inclines and sharp curves often required for logging railways, a geared locomotive is sometimes implemented, Fig. 29. It can pull a train of twenty loaded cars up a twelve percent grade. The geared engine has also been used instead of cable power in "yarding" operations. The "turns" of logs are pulled over the ground between the rails, connected to the back of the engine with a hook and cable. This has proven to be a very cost-effective use of power and equipment.

Fig. 29. Donkey Engine Yarding.

Fig. 30. Giant Raft. In the background is a completed raft;
in the foreground a cradle in which a raft is being built.
Another method of traction where the woodland is open enough is with a traction engine. The ones employed have sixty to one hundred horse power. The great logs may be placed on wood rollers, as a house is when moved, or the logs may be hauled in on a low truck with broad wheels. The "tractor" hauls the log direct to the railway if the distance is not too great.
Another way to move heavy logs in an open forest is by using a traction engine. These engines have between sixty and one hundred horsepower. The large logs can be placed on wooden rollers, similar to how a house is moved, or they can be loaded onto a low truck with wide wheels. The "tractor" pulls the log directly to the railway if it's not too far away.

Fig. 31. Snow Locomotive. Takes the place of 12 teamsters and 12 horses. Minnesota.
In Northern Michigan a "snow locomotive," Fig. 31, is coming into use, which has tremendous tractive power, hauling one hundred to one hundred fifty tons of lumber over snow or ice. It moves on runners, but there is between them a large cylinder armed with teeth. This cylinder can be raised or lowered by the operator as it moves over the surface of the ground. The teeth catch in the snow or ice, and since the cylinder is heated by the exhaust steam, it melts and packs the snow for the trucks following it. The drum is six feet in diameter, with walls an inch and a half thick, and it weighs seven tons. It is used in all sorts of places where horses cannot go, as in swamps, and by substituting wheels for runners it has even been used on sand.
In Northern Michigan, a "snow locomotive," Fig. 31, is being put to use, with impressive tractive power, pulling one hundred to one hundred fifty tons of lumber over snow or ice. It moves on runners, but there’s a large cylindrical component with teeth between them. The operator can raise or lower this cylinder as it travels over the ground. The teeth grip the snow or ice, and because the cylinder is heated by exhaust steam, it melts and compacts the snow for the trucks that follow. The drum measures six feet in diameter, has walls that are an inch and a half thick, and weighs seven tons. It's useful in all kinds of areas where horses can’t go, like swamps, and by swapping wheels for runners, it has even been used on sand.
In the Canadian lakes there has been devised a queer creature called an "alligator," a small and heavily equipped vessel for hauling the logs thru the lakes. When its operations in one lake are finished, a wire cable is taken ashore and made fast to some tree or other safe anchorage, the capstan on its forward deck is revolved by steam and the "alligator" hauls itself out of the water across lots to the next lake and begins work there.
In the Canadian lakes, there’s a strange machine called an "alligator," a small, heavily equipped boat used for transporting logs through the lakes. After it finishes its work in one lake, a wire cable is attached to a tree or another secure spot on land. The steam-powered capstan on its front deck is turned, and the "alligator" pulls itself out of the water across land to the next lake to start working there.
The greatest improvement in water transportation is the giant raft, Fig. 30. When such a raft is made up, logs of uniform length are placed together, the width of the raft being from sixty to one hundred feet and its length, one thousand feet or more. It may contain a million board feet of timber. The different sections are placed end to end, and long boom sticks, i. e., logs sixty to seventy feet long, are placed around them to bind the different sections together, and finally the whole mass is heavily chained. Such a raft has been towed across the Pacific.
The biggest advancement in water transportation is the massive raft, Fig. 30. To create such a raft, logs of equal length are lined up, with the raft's width ranging from sixty to one hundred feet and its length over one thousand feet. It can hold up to a million board feet of timber. The various sections are aligned end to end, and long boom sticks—logs about sixty to seventy feet long—are used to secure the sections together, with the entire structure then heavily chained. Such a raft has even been towed across the Pacific.
LOGGING.
References*
References*
River Lumbering.
River Logging.
Pinchot, Primer, II, pp. 40-53.
Pinchot, Primer, II, pp. 40-53.
White, Blazed Trail, pp. 5-15, 25, 38-39, 52-53, 63-65, 72-85, 91-99, 113-125, 134, 181-196, 216-229, 257, 268, 320-343, 355, 365 ff.
White, Blazed Trail, pp. 5-15, 25, 38-39, 52-53, 63-65, 72-85, 91-99, 113-125, 134, 181-196, 216-229, 257, 268, 320-343, 355, 365 ff.
For. Bull., No. 34, pp. 33-41, Fox.
For. Bull., No. 34, pp. 33-41, Fox.
White, Jun. Mun., 10: 362.
White, *June Mun.*, 10: 362.
Hulbert, Outl., 76; 801.
Hulbert, Outl., 76; 801.
Wood Craft, 4: 55.
Woodworking, 4:55.
Smith, K., World's Work, 7: 4435.
Smith, K., World's Work, 7: 4435.
Mechanical Methods.
Mechanical Techniques.
World's Work, 7: 4435.
World's Work, 7: 4435.
Outl., 76: 812.
Outl., 76: 812.
Bruncken, p. 86.
Bruncken, p. 86.
Bruncken, pp. 76-87.
Bruncken, pp. 76-87.
Munn, Cosmop., 37: 441.
Munn, Cosmop., 37: 441.
Roth, First Book, pp. 133-174.
Roth, *First Book*, pp. 133-174.
Hovey-King, Rev. of Rev., 27: 317.
Hovey-King, *Rev. of Rev.*, 27: 317.
Jones, Cosmop., 15: 63.
Jones, Cosmop., 15: 63.
Price, World's Work, 5: 3207.
Price, World's Work, 5: 3207.
For. Bull., No. 61.
For. Bull., No. 61.
Cassier, 29: 443, April, '06.
Cassier, 29: 443, April 2006.
Cosmop., 37: 445.
Cosmop., 37: 445.
Rev. of Rev., 28: 319.
Rev. of Rev., 28: 319.
* For general bibliography see p. 4.
* For general bibliography see __A_TAG_PLACEHOLDER_0__
Chapter II.
SAWMILLING.
The principal saws in a mill are of three kinds, the circular, Fig. 32, the gang, Fig. 33, and the band, Fig. 34. The circular-saw, tho very rapid, is the most wasteful because of the wide kerf, and of course the larger the saw the thicker it is and the wider the kerf. The waste in sawdust is about one-fifth of the log. In order to lessen this amount two smaller saws, one hung directly above the other, have been used. One saws the lower half of the log and the other the upper half. In this way, it is possible to cut very large logs with the circular-saw and with less waste. The circular-saw is not a perfectly flat disc, but when at rest is slightly convex on one side and concave on the other. This fullness can be pushed back and forth as can the bottom of an oil-can. When moving at a high rate of speed, however, the saw flattens itself by centrifugal force. This enables it to cut straight with great accuracy.
The main types of saws used in a mill are the circular saw, Fig. 32, the gang saw, Fig. 33, and the band saw, Fig. 34. While the circular saw is very fast, it is also the most wasteful due to its wide kerf, and naturally, the larger the saw, the thicker it is and the wider the kerf becomes. The sawdust waste is about one-fifth of the log. To reduce this waste, two smaller saws, one positioned directly above the other, have been used. One saw cuts the lower half of the log while the other cuts the upper half. This method allows for the cutting of very large logs with the circular saw while minimizing waste. The circular saw is not perfectly flat; when stationary, it has a slight convex shape on one side and a concave shape on the other. This curvature can be adjusted back and forth, similar to the bottom of an oil can. However, when the saw is spinning at a high speed, centrifugal force causes it to flatten, allowing for straight and precise cuts.

Fig. 32. Double Circular-Saw and Carriage.
A gang-saw is simply a series of straight saw-blades set in a vertical frame. This has a reciprocating motion, enabling it to cut a log into a number of boards at one time. It has this drawback, that it must cut the size of lumber for which it is set; that is, the sawyer has no choice in cutting the thickness, but it is very economical, wasting only one-eighth of the log in sawdust. A special form is the flooring gang. It consists of a number of saws placed one inch apart. Thick planks are run thru it to saw up flooring.
A gang-saw is basically a series of straight saw blades arranged in a vertical frame. It moves back and forth, allowing it to slice a log into multiple boards at once. However, it has a limitation: it can only cut the lumber to the size it is set for, meaning the sawyer has no options when it comes to thickness. On the plus side, it is very efficient, wasting just one-eighth of the log as sawdust. A specialized version is the flooring gang, which has several saws positioned one inch apart. Thick planks are fed through this to be cut into flooring.

Fig. 33. Gang-Saw.

Fig. 34. Band-Saw.
The band-saw is fast displacing the other two, wherever it can be used. It cuts with great rapidity and the kerf is narrow. When first used it could not be depended upon to cut straight, but by utilizing the same principle that is used in the circular-saw, of putting the cutting edge under great tension by making it slightly shorter than the middle of the saw, it now cuts with great accuracy. Band-saws are now made up to 12 inches wide, 50 feet long, and run at the rate of 10,000 feet a minute. They are even made with the cutting teeth on both edges, so that the log can be sawed both going and coming. This idea was unsuccessful until the invention of the telescopic band-mill, Fig. 35. In this the entire mechanism carrying [page 32] the wheels on which the band-saw revolves can be moved up and down, so as to bring the point where the saw leaves the upper wheel as close to the top of the different sized logs as possible.
The band saw is quickly replacing the other two wherever it's applicable. It cuts very quickly and the kerf is narrow. Initially, it couldn't reliably cut straight, but by applying the same technique used in the circular saw—putting the cutting edge under high tension by making it slightly shorter than the middle of the saw—it now cuts with high precision. Band saws are now made up to 12 inches wide, 50 feet long, and operate at speeds of 10,000 feet per minute. They are even designed with cutting teeth on both edges, allowing the log to be cut from both directions. This concept was unsuccessful until the invention of the telescopic band mill, Fig. 35. In this design, the entire mechanism carrying the wheels on which the band saw moves can be adjusted up and down, bringing the point where the saw leaves the upper wheel as close to the top of various sized logs as possible.

Fig. 35. Double-Carrying Telescopic Band-Mill.
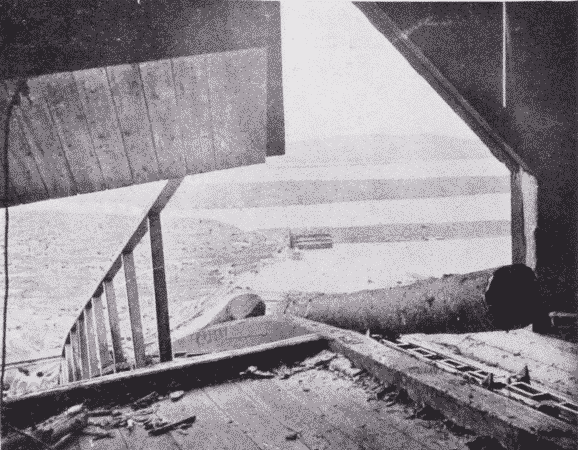
Fig. 36. Jack-Ladder, with Endless Chain. Mill in raised position for large log.
The usual modern mill is a two story building, Fig. 37, built at a convenient locality both for receiving the logs and for shipping the lumber. Whether the logs arrive by water or by rail, they are, if possible, stored in a mill-pond until used in order to prevent checking, discoloration, decay, and worm attack. From the pond they are hauled up out of the water on to a "jack-ladder," by means of an endless chain, provided with saddles or spurs which engage the logs and [page 33] draw them up into the second story on to the log slip, Fig. 36.
The typical modern mill is a two-story building, Fig. 37, located conveniently for both receiving the logs and shipping the lumber. Whether the logs come by water or rail, they are, if possible, stored in a mill pond until used to prevent cracking, discoloration, decay, and insect damage. From the pond, they are pulled out of the water onto a "jack-ladder" using an endless chain with saddles or spurs that grip the logs and [page 33] lift them up to the second story onto the log slip, Fig. 36.

Fig. 37. Two-Story Mill at Virginia, Minnesota, Showing Jack-Ladders and Consumer.

Fig. 38. Log-Flipper.

Fig. 39. Log-Stop and Loader. By letting steam into the cylinder, the projecting arm revolves, rolling one log over onto the carriage and holding the next one till wanted.
After the logs have entered the mill, they are inspected for stones lodged in the bark, and for spikes left by the river men, and then measured. Under the log-slip is the steam "flipper" or "kicker," Fig. 38, by means of which the scaler or his assistant, throwing a lever, causes the log to be kicked over to one side or the other, on to the log-deck, an inclined floor sloping toward the saw-carriage. Down this the log rolls until stopped by a log-stop, or log-loader, Fig. 39, a double-aimed projection, which prevents it from rolling on the carriage till wanted. This stop is also worked by steam. By letting the steam into the cylinder which controls it, one log is rolled over on the carriage and the next one held. The log on the carriage is at once "dogged," that is, clamped tight by iron dogs, the carriage is set for the proper cut, and moves forward to the saw which cuts off the first slab. The carriage is then "gigged" or reversed. This operation offsets the carriage one-eighth of an inch so that the log returns entirely clear of the saw. In the same way two or three 1" boards are taken off, the dogs are then knocked out, and the log canted over half a revolution. This is done by means of the "steam nigger," Fig. 40, a long, perpendicular toothed bar which comes up thru the floor, engages the log, and turns it over till the sawn side comes up against the knees of the carriage. [page 35] The log is dogged again and a second slab and several boards are taken off. The log or "stock" as it is now called, is 10", 12", 14", or 16" thick; the "nigger" then gives it a quarter-turn, leaving it lying on a sawn side. It is dogged again, and all sawn up except enough to make a few boards. This last piece is given a half-turn, bringing the sawn side against the knees, and it is sawn up. Each board as it is sawn off is thrown by the board-flipper or cant-flipper,2 Fig. 41, on to the "live rollers," which take it to the next process. Another log comes on the carriage and the process is repeated.
After the logs arrive at the mill, they are checked for stones stuck in the bark and for spikes left by the river workers, and then they are measured. Below the log slide is the steam "flipper" or "kicker," Fig. 38, which allows the scaler or their assistant to pull a lever that flips the log to one side or the other, onto the log deck, an inclined floor sloping toward the saw carriage. The log rolls down this slope until it's stopped by a log stop or log loader, Fig. 39, a double-ended projection that prevents it from rolling onto the carriage until it's needed. This stop is also controlled by steam. By releasing steam into the cylinder that operates it, one log is rolled onto the carriage while the next one is held back. The log on the carriage is immediately "dogged," meaning it's clamped tightly by iron dogs, the carriage is set for the correct cut, and moves forward to the saw, which cuts off the first slab. The carriage is then "gigged" or reversed. This action shifts the carriage a fraction, about one-eighth of an inch, so that the log moves completely clear of the saw. Similarly, two or three 1" boards are removed, the dogs are knocked out, and the log is tilted over halfway. This is done with the "steam nigger," Fig. 40, a long, vertical toothed bar that comes up through the floor, engages the log, and flips it over until the sawn side faces the knees of the carriage. The log is dogged again, and a second slab and several boards are removed. The log, or "stock" as it's now called, is 10", 12", 14", or 16" thick; the "nigger" then gives it a quarter turn, leaving it lying on a sawn side. It's dogged again and sawn up except for enough to make a few boards. This last piece is given a half turn, bringing the sawn side against the knees, and it is sawn up. Each board, as it is cut off, is thrown by the board flipper or cant flipper,2 Fig. 41, onto the "live rollers," which carry it to the next process. Another log comes onto the carriage, and the process is repeated.
Footnote 2: A "cant" is a squared or partly squared log.
Footnote 2: A "cant" is a log that is squared on one or more sides.

Fig. 40. The Steam Nigger.
The toothed bar turns the log over into the desired position.
![]() ![]() ![]() ![]() ![]() ![]() ![]() ![]() ![]() ![]() Fig. 41. Steam Cant-Flipper. This machine is used to move cants, timber, or lumber from live rollers to gangs, band resaw mills, or elsewhere. The timber is discharged upon skid rollers, as shown, or upon transfer chains. Fig. 41. Steam Cant-Flipper. This machine is used to move cants, timber, or lumber from live rollers to gangs, band resaw mills, or elsewhere. The timber is discharged onto skid rollers, as shown, or onto transfer chains. |
The saw-carriage, Fig. 42, is propelled forward and back by a piston running in a long cylinder, into either end of which steam can be turned by the operator.
The saw carriage, Fig. 42, is pushed forward and backward by a piston moving within a long cylinder, into either end of which steam can be directed by the operator.
As the sawn boards fall off the log, they land on "live," that is, revolving rollers, which carry them along at the rate of 200 to 250 feet a minute. Stops are provided farther along to stop the boards wherever wanted, as at the edger, Fig. 43, or the slasher. From the live rollers the [page 36] boards are transferred automatically, Fig. 44, by chains running at right angles to the rollers and brought within reach of the edger man. About one-third of the boards of a log have rough edges, and are called "waney." These must go thru the edger to make their edges parallel. The edger man works with great speed. He sees at once what can be made out of a board, places it in position and runs it thru. From the edger the boards are carried to the trimmer, which cuts the length. The lumberman's rule is to "cut so that you can cut again." The so-called 16' logs are really 16' 6". The trimmer, Fig. 45, now trims these boards to 16' 1", so that if desired they can still be cut again. The trimmer may be set to cut at any desired length according to the specifications.
As the cut boards drop off the log, they land on “live” rollers that rotate, moving them along at a speed of 200 to 250 feet per minute. Stops are placed further down the line to halt the boards whenever needed, such as at the edger, Fig. 43, or the slasher. From the live rollers, the boards are automatically transferred, Fig. 44, by chains that run perpendicular to the rollers and are brought within reach of the edger worker. About one-third of the boards from a log have rough edges, known as "waney." These need to go through the edger to make their edges straight. The edger worker operates quickly, instantly recognizing what can be made from each board, placing it correctly, and running it through. After passing through the edger, the boards are sent to the trimmer, which cuts them to the desired length. The lumberman's rule is to "cut so that you can cut again.” The so-called 16' logs are actually 16' 6". The trimmer, Fig. 45, now cuts these boards to 16' 1", so they can still be trimmed further if needed. The trimmer can be adjusted to cut to any specified length.

Fig. 42. Log-Carriage, holding quartered log in position to saw.

Fig. 43. Double Gang Edger. This machine trims off the rough edges of the "waney" boards by means of the four saws in the main frame of the machine.

Fig. 44. Automatic Steam Transfer for Timber, Lumber and Slabs. The boards are carried along by the cylinders, CCC, until they hit the bumper, B. This movement admits steam to the cylinder, CY, which raises the revolving chains or skids, which transfers the stock sidewise to other live rollers as required.

Fig. 45. Automatic Gang Lumber-Trimmer. It may be set to cut automatically to any desired length.

Fig. 46. Lumber Sorting Shed. Virginia, Minnesota.

Fig. 47. Wood is carefully and regularly piled in the seasoning-yard.
The boards are now graded as to quality into No. 1, No. 2, etc., Fig. 46, and run out of the mill, to be stacked up in piles, Fig. 47. Big timbers go directly from the saw on the rolls to the back end of the mill, where the first end is trimmed by a butting-saw or cut-off-saw which swings, Fig. 48. The timber is then shoved along on dead rolls and the last end [page 39] trimmed by the butting-saw to a definite length as specified, and shoved out.
The boards are now categorized by quality into No. 1, No. 2, etc., Fig. 46, and come out of the mill to be stacked in piles, Fig. 47. Large timbers go straight from the saw onto the rolls at the back end of the mill, where the first end is trimmed by a butting saw or cut-off saw that swings, Fig. 48. The timber is then pushed along on dead rolls, and the final end is trimmed by the butting saw to a specific length as specified, and then pushed out. [page 39]
One of the most remarkable features of the modern mill is its speed. From the time the log appears till the last piece of it goes racing out of the mill, hardly more than a minute may have elapsed.
One of the most impressive things about the modern mill is its speed. From the moment the log arrives until the last piece races out of the mill, no more than a minute might pass.

Fig. 48. Cut-off-Saw. This saw trims the ends of timbers.
A large part of the problem of sawmilling is the disposal of the waste. The first of these is the sawdust. In all first class mills, this together with shavings (if a planing-mill is combined) is burned for fuel. It is sucked up from the machines and carried in large tubes to the boiler-room and there is mechanically supplied to the fires. The slabs, once considered as waste, contain much material that is now utilized. From the live rolls, on which all the material falls from the main band-saw, the slabs are carried off by transfer chains, and by another set of five rollers to the "slasher," Fig. 50, which consists of a line of circular-saws placed 4' 1" apart. This slasher cuts up the slabs into lengths suitable for lath or fence-pickets, Fig. 49. Or they can be resawn into 16" lengths for shingles or fire-wood.
A big part of the issue with sawmilling is getting rid of the waste. The first type of waste is sawdust. In all top-tier mills, this, along with shavings (if there's a planing mill included), is burned for fuel. It's collected from the machines and transported in large tubes to the boiler room where it's automatically fed to the fires. The slabs, which were once seen as waste, now contain a lot of material that’s put to use. From the live rolls, where all the material falls from the main band saw, the slabs are moved away by transfer chains and then pushed by another set of five rollers to the "slasher," Fig. 50, which is made up of a line of circular saws spaced 4' 1" apart. This slasher cuts the slabs into lengths that are suitable for lath or fence pickets, Fig. 49. Alternatively, they can be resawn into 16" lengths for shingles or firewood.

Fig. 49. Ten Saw Gang Lath Bolter. This machine cuts up material lengthwise into laths.

Fig. 50. Slab-Slasher. This machine cuts up the slabs into lengths suitable for lath or fence-pickets.
From the "slasher" the 4' 1" lengths are carried on by traveling platforms, chains, etc., to the lath-machines, Fig. 51, where they are sawn up, counted as sawn, bound in bundles of 100, trimmed to exactly 4' in length and sent off to be stored. The shingle bolts are picked off the moving platforms by men or boys, and sent to the shingle-machine, Fig. 52, where they are sawn into shingles and dropped down-stairs to [page 41] be packed. Shingle-bolts are also made from crooked or otherwise imperfect logs.
From the "slasher," the 4' 1" lengths are transported on moving platforms, chains, etc., to the lath machines, Fig. 51, where they are cut, counted as sawn, bundled in stacks of 100, trimmed to exactly 4' in length, and sent off to storage. The shingle bolts are picked up from the moving platforms by men or boys and taken to the shingle machine, Fig. 52, where they are cut into shingles and dropped downstairs to be packed. Shingle bolts are also made from crooked or otherwise flawed logs.
Of what is left, a good part goes into the grinder or "hog," Fig. 53, which chews up all sorts of refuse into small chips suitable for fuel to supplement the sawdust if necessary. Band-saws make so little dust and such fine dust that this is often necessary.
Of what’s left, a good portion goes into the grinder or "hog," Fig. 53, which crushes all kinds of waste into small chips that can be used as fuel to supplement the sawdust if needed. Band saws produce very little dust and such fine dust that this is often required.

Fig. 51. Combination Lath-Binder and Trimmer. With this machine the operator can trim the bundles of lath simply by tilting the packing frame over from him causing the bundles to pass between the saws, thereby trimming both ends at one movement.

Fig. 52. Hand Shingle-Machine. This machine is used in Sawmills in which it is desired to utilize slabs and trimmings by sawing shingles therefrom, or to saw shingles from prepared bolts.
If there is any refuse that cannot be used at all it goes to the scrap-pile, Fig. 54, or to the "consumer," the tall stack shown in Fig. 37, see p. 33.
If there's any waste that can't be used at all, it goes to the scrap pile, Fig. 54, or to the "consumer," the tall stack shown in Fig. 37, see p. 33.
Boards ordinarily sawn from logs are "slash-sawn," i. e., they are tangential or bastard, each cut parallel to the previous one. By this process, only the central boards would be radial or "rift" boards.
Boards typically cut from logs are "slash-sawn," meaning they are tangential or bastard, with each cut running parallel to the one before it. Because of this method, only the central boards would be radial or "rift" boards.

Fig. 53. Edging grinder or Hog. It cuts any kind of wood into coarse or fine chips suitable to be handled by chain conveyor or blower.
But, for a number of reasons, radial boards are better. They warp less because the annual rings cross the board more evenly. Yellow pine flooring that is rift-sawn is more valuable than slash-sawn, because the edge of the annual rings makes a more even grain, Fig. 55. Where slash-grained flooring is used, the boards should be laid so that the outside of each board will be up in order that the inner rings may not "shell out."
But for several reasons, radial boards are superior. They warp less because the annual rings intersect the board more evenly. Rift-sawn yellow pine flooring is more valuable than slash-sawn, as the edge of the annual rings creates a more uniform grain, Fig. 55. When using slash-grained flooring, the boards should be installed with the outer side facing up to prevent the inner rings from "shelling out."
In sawing oak for valuable furniture or trim, the log is first "quartered" and then the quarters sawn up as nearly radially as is desired. There are various methods of cutting quartered logs, as illustrated in Fig. 56.
In cutting oak for valuable furniture or trim, the log is first "quartered" and then the quarters are sawed as close to radially as desired. There are different methods for cutting quartered logs, as shown in Fig. 56.
In making staves for water-tight barrels, it is essential that they be cut radially in the log, in order that the staves be as non-permeable to water as possible.
In making staves for water-tight barrels, it is essential that they be cut radially in the log, in order that the staves be as non-permeable to water as possible.

Fig. 54. Scrap-Pile. Oscilla. Georgia.

Fig. 55. Slash-Grain and Comb-Grain Flooring.

Fig. 56. Methods of Sawing Quartered Logs.
SAWMILLING.
References*
References*
Trout, Cassier 11: 83, 184.
Trout, Cassier 11: 83, 184.
Woodcraft 5: 56, May '06.
Woodcraft May '06, 5:56.
* For general bibliography see p. 4.
* For general bibliography see __A_TAG_PLACEHOLDER_0__

Fig. 57. Lumber-Kiln.
Chapter 3.
SEASONING.
The seasoning of wood is important for several reasons. It reduces weight, it increases strength, it prevents changes in volume after it is worked into shape, and it prevents checking and decay. Decay can also be prevented by submergence and burying, if by so doing logs are kept from fungal attacks. The piles of the Swiss Lake dwellings, which are in a state of good preservation, are of prehistoric age. Wood under water lasts longer than steel or iron under water. But for almost all purposes wood has to be dried in order to be preserved. The wood is cut up, when green, to as thin pieces as will be convenient for its use later, for the rate of drying depends largely upon the shape and size of the piece, an inch board drying more than four times as fast as a four inch plank, and more than twenty times as fast as a ten inch timber.
The seasoning of wood is important for several reasons. It reduces weight, increases strength, prevents changes in volume after it's shaped, and stops checking and decay. Decay can also be avoided by submerging or burying the logs, keeping them safe from fungal attacks. The piles from the Swiss Lake dwellings, which are well-preserved, date back to prehistoric times. Wood submerged in water lasts longer than steel or iron. However, for most purposes, wood needs to be dried to be preserved. When the wood is fresh, it's cut into thin pieces that are convenient for future use, as the drying rate depends heavily on the shape and size of the piece; a one-inch board dries more than four times faster than a four-inch plank and over twenty times faster than a ten-inch timber.
There are various methods of seasoning:
There are different ways to season:
(1) Natural or air-seasoning is the most common, and in some respects the best. In this method, the wood is carefully and regularly piled in the seasoning-yard, so as to be protected as far as possible from sun and rain, but with air circulating freely on all sides of the boards, Fig. 47, see p. 38. To accomplish this, "sticking" is employed, i. e., strips of wood are placed crosswise close to the ends and at intervals between the boards. In this way the weight of the superposed boards tends to keep those under them from warping. The pile is skidded a foot or two off the ground and is protected above by a roof made of boards so laid that the rain will drain off.
(1) Natural or air seasoning is the most common and, in some ways, the best method. In this approach, the wood is carefully and regularly stacked in the seasoning yard to protect it as much as possible from sun and rain while allowing air to circulate freely around all sides of the boards, Fig. 47, see p. 38. To achieve this, "sticking" is used, which means placing strips of wood crosswise near the ends and at intervals between the boards. This way, the weight of the stacked boards helps prevent the ones underneath from warping. The pile is elevated a foot or two off the ground and is shielded on top by a roof made of boards arranged so that rain drains off.
Fire-wood is best dried rapidly so that it will check, making air spaces which facilitate ignition, but lumber needs to be slowly dried in cool air so that the fibers may accommodate themselves to the change of form and the wood check as little as possible. Good air-drying consumes from two to six years, the longer the better.
Firewood should be dried quickly to create air pockets that help it catch fire, but lumber needs to be dried slowly in cool air so the fibers can adjust to the change in shape and minimize cracking. Good air-drying takes anywhere from two to six years, with a longer period being preferable.
(2) Kiln-drying or hot-air-seasoning is a much more rapid process than air-seasoning and is now in common use, Fig. 57. The drying is also more complete, for while air-dried wood retains from 10% to 20% of moisture, kiln-dried wood may have no more than 5% as it comes from the kiln. It will, however, reabsorb some moisture from the air, when exposed to it.
(2) Kiln-drying or hot-air seasoning is a much faster process than air seasoning and is now commonly used, Fig. 57. The drying is also more thorough, as air-dried wood holds on to about 10% to 20% moisture, while kiln-dried wood may have only 5% moisture when it comes out of the kiln. However, it will reabsorb some moisture from the air when exposed to it.
The wood of conifers, with its very regular structure, dries and shrinks more evenly and much more rapidly than the wood of broad-leaved trees, and hence is often put into the kiln without previous air-drying, and dried in a week or even less time.
The wood from conifers has a uniform structure, so it dries and shrinks more evenly and much faster than the wood from broad-leaved trees. As a result, it's often placed in the kiln without being air-dried first and can be dried in a week or even less.
Oak is the most difficult wood to dry properly. When it and other hardwoods are rapidly dried without sufficient surrounding moisture, the wood "case-hardens," that is, the outer part dries and shrinks before the interior has had a chance to do the same, and this forms a shell or case of shrunken, and often checked wood around the interior which also checks later. This interior checking is called honeycombing. Hardwood lumber is commonly air-dried from two to six months, before being kiln-dried. For the sake of economy in time, the tendency is to eliminate yard-drying, and substitute kiln-drying. Kiln-drying of one inch oak, takes one or two weeks, quarter-sawn boards taking one and a half times as long as plain-sawn.
Oak is the hardest wood to dry correctly. When it and other hardwoods are dried too quickly without enough surrounding moisture, the wood “case-hardens.” This means that the outer part dries and shrinks before the inside gets a chance to do the same, creating a shell of shriveled, often cracked wood around an interior that also develops cracks later. This internal cracking is called honeycombing. Hardwood lumber is usually air-dried for two to six months before being kiln-dried. To save time, there's a tendency to skip yard-drying and go straight to kiln-drying. Drying one-inch oak in a kiln takes one to two weeks, with quarter-sawn boards taking about one and a half times longer than plain-sawn boards.
The best method of drying is that which gradually raises the temperature of both the wood and of the water which it contains to the point at which the drying is to take place. Care is therefore taken not to let the surface become entirely dry before the internal moisture is heated. This is done by retaining the moisture first vaporized about the wood, by means of wet steam. When the surface is made permeable to moisture, drying may take place rapidly. Curtains of canvas are hung all around the lumber on the same principle that windows in newly plastered buildings are hung with muslin. The moisture is absorbed on the inner surface of the curtain and evaporates from the outer surface. Improvements in kiln-drying are along the line of moist air operation. In common practice, however, the moist air principle is often neglected.
The best way to dry wood is to gradually raise the temperature of both the wood and the water it contains to the drying point. It's important not to let the surface dry out completely before heating the internal moisture. This is achieved by trapping the vaporized moisture around the wood using wet steam. Once the surface can take in moisture, drying can happen quickly. Canvas curtains are hung around the lumber, similar to how muslin is used to cover windows in newly plastered buildings. The moisture collects on the inner surface of the curtain and evaporates from the outer surface. Improvements in kiln-drying focus on using moist air. However, in everyday practice, the moist air method is often overlooked.
There are two methods in operation, the progressive method and the charge method. In the progressive, the process is continuous, the loads going in at one end of the kiln, and out at the other, the temperature and the moisture being so distributed in the kiln, that in passing from the green to the dry end, a load of lumber is first [page 47] moistened, then heated, and finally dried out. In the charge system, the process is intermittent, one charge being removed before a new one is admitted. This gives the best results with high grade lumber for special uses.
There are two methods in use: the progressive method and the charge method. In the progressive method, the process is continuous, with loads entering one end of the kiln and exiting from the other. The temperature and moisture are distributed in such a way that, as a load of lumber moves from the wet end to the dry end, it is first moistened, then heated, and finally dried out. In the charge system, the process is intermittent; one batch is removed before another is added. This method yields the best results for high-quality lumber used for specific purposes. [page 47]
A modification of hot-air-seasoning is that which subjects the wood to a moderate heat in a moist atmosphere charged with the products of the combustion of fuel.
A version of hot-air seasoning involves exposing the wood to moderate heat in a humid environment filled with the byproducts of burning fuel.
(3) Small pieces of wood may be effectively seasoned by being boiled in water and then dried. The process seems to consist of dissolving out albuminous substances and thus allowing freer evaporation. Its effect is probably weakening.
(3) Small pieces of wood can be effectively dried by boiling them in water and then letting them dry. The process seems to work by dissolving proteins and allowing for easier evaporation. Its impact is likely to be weakening.
(4) Soaking in water is sometimes used as a good preparation for air-seasoning. Previous soaking hastens seasoning. River men insist that timber is improved by rafting. It is a common practice to let cypress logs soak in the swamps where they grow for several months before they are "mined out." They are eagerly sought after by joiners and carpenters, because their tendency to warp is lessened. Ebony is water-soaked in the island of Mauritius as soon as cut. Salt water renders wood harder, heavier, and more durable and is sometimes applied to ship timbers, but cannot be used with timbers intended for ordinary purposes, as the presence of salt tends to absorb atmospheric moisture.
(4) Soaking in water is sometimes a good way to prepare for air-drying. Soaking beforehand speeds up the drying process. People who work on rivers believe that timber gets better when it's rafted. It's common to let cypress logs soak in the swamps where they grow for several months before they're "mined out." These logs are in high demand by joiners and carpenters because soaking reduces their tendency to warp. Ebony is soaked in water in Mauritius as soon as it's cut. Saltwater makes wood harder, heavier, and more durable, and is sometimes used on ship timbers, but it can't be used on wood meant for regular purposes, as the salt tends to draw in moisture from the air.
(5) Boiling in oil is resorted to for special purposes, both for preservation and to give strength. For example, the best handscrews are so treated. The oil also prevents glue from sticking, the most frequent cause of injury to handscrews.
(5) Boiling in oil is used for specific purposes, both for preservation and to provide strength. For instance, the best handscrews undergo this process. The oil also stops glue from sticking, which is the most common cause of damage to handscrews.
(6) There are a number of "impregnation" methods of preserving timber, and their practice is spreading rapidly. Of the various preservative processes, those using coal tar creosote and zinc chloride have proved most efficient. The purpose is to force the preservative into the pores of the wood, either by painting, soaking, or putting under pressure. Such impregnation methods double or treble the life of railway ties. It is now being used with great success to preserve electric wire poles, mine-props, piling, fence-posts, etc.
(6) There are several "impregnation" methods for preserving wood, and their use is growing quickly. Among the different preservative processes, those using coal tar creosote and zinc chloride have been the most effective. The goal is to push the preservative into the wood’s pores, either by painting, soaking, or applying pressure. These impregnation methods can double or triple the lifespan of railway ties. They are now being used successfully to preserve electric poles, mine props, pilings, fence posts, and more.
Wood preservation has three great advantages, it prolongs the life of timbers in use, reduces their cost, and makes possible the use of species that once were considered worthless. For example, the cheap and abundant loblolly pine can be made, by preservative methods, to take the place of high priced long-leaf pine for many purposes.
Wood preservation has three major benefits: it extends the lifespan of timber in use, lowers costs, and allows for the utilization of species that were previously seen as useless. For instance, the inexpensive and plentiful loblolly pine can be treated with preservatives to replace the more expensive longleaf pine for various applications.
PRACTICAL SUGGESTIONS FOR STORING LUMBER.
Under the hasty methods prevalent in the mill, very little wood comes to the shop well seasoned, and it should therefore be carefully stored before using, so as to have the fullest possible air circulation around it. Where the boards are large enough, "sticking" is the best method of storage, i. e., narrow strips of wood are placed at short intervals between the pieces which are piled flat. The weight of the boards themselves helps to prevent warping. Boards set upright or on edge are likely to be distorted soon. It is often wise to press together with weights or to clamp together with handscrews boards that show a tendency to warp, putting the two concave sides together. Then the convex side is exposed and the board may straighten thus: Fig. 58. By wrapping up small boards in paper or cloth in the intervals between work on them, they may be kept straight until they are assembled.
Due to the fast methods used in the mill, very little wood arrives at the shop properly dried, so it should be stored carefully before use to ensure the best air circulation around it. For larger boards, the best storage method is "sticking," meaning narrow strips of wood are placed at short intervals between the pieces stacked flat. The weight of the boards helps prevent warping. Boards stored upright or on their edges are likely to warp quickly. It’s often a good idea to press together with weights or clamp together with handscrews any boards that are prone to warping, putting the two concave sides together. This way, the convex side is exposed, and the board may straighten out. By wrapping small boards in paper or cloth during breaks between work, they can be kept straight until they are used.

Fig. 58. Clamping up Boards to Prevent Warping.
Another precaution to take is to be sure to plane both sides of a board if either is planed, especially if the board has been exposed to air-drying for some time.
Another precaution to take is to make sure to plane both sides of a board if one side is planed, especially if the board has been exposed to air-drying for a while.
WOOD MEASUREMENTS.
Lumber is a general term for all kinds of sawn wood. Logs may be sawn into timber, that is, beams and joists, into planks, which are 2" to 4" thick, or into boards which are from ¼" to 1¾" thick. These may be resawn into special sizes.
Lumber is a general term for all types of cut wood. Logs can be cut into timber, which includes beams and joists, into planks that are 2" to 4" thick, or into boards that are ¼" to 1¾" thick. These can also be cut again into specific sizes.
Lumber is measured by the superficial foot, which is a board 1" thick, 12" wide, and 12" long, so that a board 1" thick, (or ⅞" dressed) 6" wide and 12' 0" long, measures 6' B. M. (board measure). Boards 1" or more thick are sold by the "board foot" which is equivalent to 12" square and 1" thick. Boards less than 1" thick are sold by the square foot, face measure. Dressed lumber comes in sizes ⅛" less than sawn lumber. Regular sizes are:
Lumber is measured in board feet, which is a board that's 1" thick, 12" wide, and 12" long. For example, a board that's 1" thick (or ⅞" after dressing), 6" wide, and 12' long measures 6 board feet. Boards that are 1" thick or thicker are sold by the board foot, which equals a piece that's 12" square and 1" thick. Boards thinner than 1" are sold by the square foot based on their face area. Dressed lumber is sized ⅛" less than sawn lumber. The standard sizes are:
⅝ | " | dressed to | ½" | |
¾ | " | dressed to | ⅝" | |
1 | " | dressed to | ⅞" | |
1 | ¼ | " | dressed to | 1⅛" |
1 | ½ | " | dressed to | 1⅜" |
2 | " | dressed to | 1⅞" |
Any of these may be dressed down to thinner boards, or resawn on a special band-saw.
Any of these can be cut down to thinner boards or re-sawn using a special band saw.
In ordering it is common to give the dimensions wanted, in the order of thickness, width, and length, because that is the order in which dimensions are gotten out. E. g.:
In placing an order, it's typical to specify the desired dimensions in the order of thickness, width, and length, as that's how dimensions are usually listed. For example:
6 pcs. quar. oak, ⅞" × 6" × 3'0"
6 pcs. quartered oak, ⅞" × 6" × 3'0"
2 pcs. quar. oak, ¾" × 7½" × 15"
2 pieces quartered oak, ¾" × 7½" × 15"
If a piece wanted is short the way the grain goes, the order would be the same, thus: ¾" × 11" (wide) × 6" (long). That is, "long" means the way the grain runs. It is always safe to specify in such a case. It is common when small pieces are ordered to add one-quarter to the cost for waste.
If a requested piece is short in the direction of the grain, the order would be the same: ¾" × 11" (wide) × 6" (long). Here, "long" refers to the direction of the grain. It's always best to clarify in this situation. When ordering small pieces, it's typical to add a quarter to the cost for waste.
In large lots lumber is ordered thus: 800' (B. M.) whitewood, dressed 2 sides to ⅞", 10" and up. This means that the width of any piece must not be less than 10". Prices are usually given per "M," i. e., per 1000 ft.: e. g.: basswood may be quoted at $40.00 per M.
In large quantities, lumber is ordered like this: 800' (B. M.) whitewood, planed on 2 sides to ⅞", 10" and up. This means that the width of any piece must be at least 10". Prices are typically listed per "M," which means per 1000 ft.; for example, basswood might be priced at $40.00 per M.
When thin boards are desired it is often economical to buy inch stuff and have it resawn.
When thin boards are needed, it’s often more cost-effective to buy inch stock and have it resawn.
Some lumber is also ordered by the "running" or lineal foot, especially moldings, etc., or by the piece, if there is a standard size as in fence-posts, studs, etc. Laths and shingles are ordered by the bundle to cover a certain area. 1000 4" shingles (= 4 bundles) cover 110 sq. ft. with 4" weather exposure. 100 laths (1 bundle) each ¼" × 1½" × 4'0" cover about 150 sq. ft.
Some lumber is also ordered by the "running" or linear foot, especially moldings, etc., or by the piece if there is a standard size, like with fence posts, studs, etc. Lath and shingles are ordered by the bundle to cover a specific area. 1000 4" shingles (which is 4 bundles) cover 110 sq. ft. with 4" weather exposure. 100 laths (1 bundle) each measuring ¼" × 1½" × 4'0" cover about 150 sq. ft.
There are several methods of measuring lumber. The general rule is to multiply the length in feet by the width and thickness in inches and divide by 12, thus: 1" × 6" × 15' ÷ 12 = 7½ feet. The use of the Essex board-measure and the Lumberman's board-measure are described in Chapter 4, pp. 109 and 111.
THE SEASONING AND MEASURING OF WOOD.
References*
References*
seasoning.
seasoning.
For. Bull., No, 41, pp. 5-12, von Schrenk.
For. Bull., No. 41, pp. 5-12, von Schrenk.
Dunlap, Wood Craft, 6: 133, Feb. '07.
Dunlap, Wood Craft, 6: 133, Feb. '07.
For. Circ. No. 40, pp. 10-16, Herty.
For. Circ. No. 40, pp. 10-16, Herty.
Barter, pp. 39-53.
Barter, pp. 39-53.
Boulger, pp. 66-70, 80-88.
Boulger, pp. 66-70, 80-88.
Wood Craft, 6: 31, Nov. '06.
Wood Craft, 6: 31, Nov. '06.
For. Circ. No. 139.
For. Circ. No. 139.
Agric. Yr. Bk., 1905, pp. 455-464.
Agric. Yr. Bk., 1905, pp. 455-464.
measuring.
measuring.
Sickels, pp. 22, 29.
Sickels, pp. 22, 29.
Goss, p. 12.
Goss, p. 12.
Building Trades Pocketbook, pp. 335, 349, 357.
Building Trades Pocketbook, pp. 335, 349, 357.
Tate, p. 21.
Tate, p. 21.
* For general bibliography see p. 4.
For general bibliography see __A_TAG_PLACEHOLDER_0__
Chapter 4.
WOOD HAND TOOLS.
The hand tools in common use in woodworking shops may, for convenience, be divided into the following classes: 1, Cutting; 2, Boring; 3, Chopping; 4, Scraping; 5, Pounding; 6, Holding; 7, Measuring and Marking; 8, Sharpening; 9, Cleaning.
The hand tools commonly used in woodworking shops can be conveniently categorized into the following classes: 1. Cutting; 2. Boring; 3. Chopping; 4. Scraping; 5. Pounding; 6. Holding; 7. Measuring and Marking; 8. Sharpening; 9. Cleaning.
1. CUTTING TOOLS.
The most primitive as well as the simplest of all tools for the dividing of wood into parts, is the wedge. The wedge does not even cut the wood, but only crushes enough of it with its edge to allow its main body to split the wood apart. As soon as the split has begun, the edge of the wedge serves no further purpose, but the sides bear against the split surfaces of the wood. The split runs ahead of the wedge as it is driven along until the piece is divided.
The most basic and straightforward tool for splitting wood into pieces is the wedge. The wedge doesn’t actually cut the wood; it just crushes enough of it with its edge to let its main body split the wood apart. Once the splitting starts, the edge of the wedge isn’t needed anymore, and the sides push against the split surfaces of the wood. The split keeps moving ahead of the wedge as it's driven in until the piece is completely divided.
It was by means of the wedge that primitive people obtained slabs of wood, and the great change from primitive to civilized methods in manipulating wood consists in the substitution of cutting for splitting, of edge tools for the wedge. The wedge follows the grain of the wood, but the edge tool can follow a line determined by the worker. The edge is a refinement and improvement upon the wedge and enables the worker to be somewhat independent of the natural grain of the wood.
It was through the use of the wedge that early humans managed to get slabs of wood, and the major shift from primitive to modern techniques in handling wood involves replacing splitting with cutting, and using edge tools instead of wedges. The wedge follows the grain of the wood, but an edge tool can follow a line set by the craftsman. The edge represents a refinement and improvement over the wedge, allowing the craftsman to be somewhat independent of the wood's natural grain.
In general, it may be said that the function of all cutting tools is to separate one portion of material from another along a definite path. All such tools act, first, by the keen edge dividing the material into two parts; second, by the wedge or the blade forcing these two portions apart. If a true continuous cut is to be made, both of these actions must occur together. The edge must be sharp enough to enter between the small particles of material, cutting without bruising them, and the blade of the tool must constantly force apart the two portions in order that the cutting action of the edge may continue.
In general, the role of all cutting tools is to separate one part of a material from another along a specific path. These tools work by first, the sharp edge slicing through the material into two parts; and second, by the wedge or blade pushing these two pieces apart. For a smooth, continuous cut to happen, both of these actions need to happen at the same time. The edge must be sharp enough to slip between the tiny particles of material, cutting them without crushing, and the tool's blade must continuously push the two parts apart to keep the cutting action of the edge going.

Fig. 59. Wedge Action.

Fig. 60. Edge Action.
When a knife or chisel is pressed into a piece of wood at right angles to the grain, and at some distance from the end of the wood, as in Fig. 60, a continuous cutting action is prevented, because soon the blade cannot force apart the sides of the cut made by the advancing edge, and the knife is brought to rest. In this case, it is practically only the first action which has taken place.
When a knife or chisel is pressed into a piece of wood at a right angle to the grain, and slightly away from the end of the wood, as shown in Fig. 60, a continuous cutting action stops because soon the blade can’t push apart the sides of the cut made by the advancing edge, and the knife comes to a halt. In this case, only the initial action has really occurred.
Both the actions, the cutting and the splitting, must take place together to produce a true continuous cut. The edge must always be in contact with the solid material, and the blade must always be pushing aside the portions which have been cut. This can happen only when the material on one side of the blade is thin enough and weak enough to be readily bent out of the way without opening a split in front of the cutting edge. This cutting action may take place either along the grain, Fig. 61, or across it, Fig. 62.
Both actions, cutting and splitting, need to happen simultaneously to make a true continuous cut. The edge must always touch the solid material, and the blade must always push aside the pieces that have been cut. This can only occur when the material on one side of the blade is thin and weak enough to be easily bent out of the way without creating a split in front of the cutting edge. This cutting can happen either along the grain, Fig. 61, or across it, Fig. 62.
The bending aside of the shaving will require less force the smaller the taper of the wedge. On the other hand, the wedge must be strong enough to sustain the bending resistance and also to support the cutting edge. In other words, the more acute the cutting edge, the easier the work, and hence the wedge is made as thin as is consistent with strength. This varies all the way from hollow ground razors to cold-chisels. For soft wood, the cutting angle (or bevel, or bezel) of chisels, gouges and plane-irons, is small, even as low as 20°; for hard wood, it must be greater. For metals, it varies from 54° for wrought iron to 66° for gun metal.
The way the shaving is pushed aside will need less force the smaller the wedge's taper. However, the wedge also needs to be strong enough to handle the bending resistance and to support the cutting edge. In simpler terms, the sharper the cutting edge, the easier the work, so the wedge is made as thin as possible while still being strong. This can range from hollow ground razors to cold chisels. For soft wood, the cutting angle (or bevel) of chisels, gouges, and plane irons is small, sometimes as low as 20°; for hard wood, it needs to be larger. For metals, the angle varies from 54° for wrought iron to 66° for gun metal.

Fig. 61. Edge and Wedge Action With the Grain.

Fig. 62. Edge and Wedge Action Across the Grain.
Ordinarily a cutting tool should be so applied that the face nearest the material lies as nearly as possible in the direction of the cut desired, sufficient clearance being necessary to insure contact of the actual edge.
Ordinarily, a cutting tool should be positioned so that the side closest to the material is aligned as closely as possible with the direction of the desired cut, while allowing enough clearance to ensure that the actual edge makes contact.
There are two methods of using edge tools: one, the chisel or straight cut, by direct pressure; the other, the knife or sliding cut.
There are two ways to use edge tools: one is the chisel or straight cut, using direct pressure; the other is the knife or sliding cut.
The straight cut, Fig. 63, takes place when the tool is moved into the material at right angles to the cutting edge. Examples are: the action of metalworking tools and planing machines, rip-sawing, turning, planing (when the plane is held parallel to the edge of the board being planed), and chiseling, when the chisel is pushed directly in line with its length.
The straight cut, Fig. 63, occurs when the tool is moved into the material at a right angle to the cutting edge. Examples include: the actions of metalworking tools and planing machines, rip-sawing, turning, planing (when the plane is held parallel to the edge of the board being planed), and chiseling, when the chisel is pushed straight along its length.
The knife or sliding cut, Fig. 64, takes place when the tool is moved forward obliquely to its cutting edge, either along or across the grain. It is well illustrated in cutting soft materials, such as bread, meat, rubber, cork, etc. It is an advantage in delicate chiseling and gouging. That this sliding action is easier than the straight pressure can easily be proved with a penknife on thin wood, or by planing with the plane held at an angle to, rather than in line with, the direction of the planing motion. The edge of the cutter then slides into the material. The reason why the sliding cut is easier, is partly because the angle of the bevel with the wood is reduced by holding the tool obliquely, and partly because even the sharpest cutting edge is notched with very fine teeth all along its edge so that in the sliding cut it acts like a saw. In an auger-bit, both methods of cutting take place at once. The scoring nib cuts with a sliding cut, while the cutting lip is thrust directly into the wood.
The knife or sliding cut, Fig. 64, happens when the tool is moved forward diagonally to its cutting edge, either with or against the grain. This is clearly shown when cutting soft materials like bread, meat, rubber, cork, etc. It’s beneficial for delicate chiseling and gouging. It’s easy to demonstrate that this sliding action is simpler than applying straight pressure using a penknife on thin wood or by planing while holding the plane at an angle instead of in line with the direction of the planing motion. The cutter's edge then glides into the material. The reason the sliding cut is easier is partly because the angle of the bevel with the wood is reduced when holding the tool at an angle and partly because even the sharpest edge has very fine teeth along its edge, making it act like a saw during the sliding cut. In an auger bit, both cutting methods occur simultaneously. The scoring nib uses a sliding cut while the cutting lip is pushed directly into the wood.

Fig. 63. Straight Cut.

Fig. 64. Sliding Cut.
The chisel and the knife, one with the edge on the end, and the other with the edge on the side, are the original forms of all modern cutting tools.
The chisel and the knife, one with the blade on the end and the other with the blade on the side, are the basic designs of all modern cutting tools.
The chisel was at first only a chipped stone, then it came to be a ground stone, later it was made of bronze, and still later of iron, and [page 54] now it is made of steel. In its early form it is known by paleontologists as a celt, and at first had no handle, but later developed into the ax and adze for chopping and hewing, and the chisel for cuts made by driving and paring. It is quite likely that the celt itself was simply a development of the wedge.
The chisel started out as just a chipped stone, then it became a ground stone, later made from bronze, and eventually iron, and now it's made of steel. In its original form, paleontologists refer to it as a celt, which initially had no handle but later evolved into the axe and adze for chopping and shaping, and the chisel for making cuts through driving and paring. It's quite possible that the celt itself was simply an evolution of the wedge. [page 54]
In the modern chisel, all the grinding is done on one side. This constitutes the essential feature of the chisel, namely, that the back of the blade is kept perfectly flat and the face is ground to a bevel. Blades vary in width from 1⁄16 inch to 2 inches. Next to the blade on the end of which is the cutting edge, is the shank, Fig. 65. Next, as in socketed chisels, there is the socket to receive the handle, or, in tanged chisels, a shoulder and four-sided tang which is driven into the handle, which is bound at its lower end by a ferrule. The handle is usually made of apple wood.
In the modern chisel, all the grinding is done on one side. This is a key feature of the chisel, meaning the back of the blade is kept perfectly flat while the face is ground to a bevel. The blades range in width from 1⁄16 inch to 2 inches. Next to the blade, where the cutting edge is located, is the shank, Fig. 65. Then, as with socketed chisels, there is a socket to hold the handle, or in tanged chisels, a shoulder and a four-sided tang that is driven into the handle, which is secured at its lower end by a ferrule. The handle is typically made of apple wood.

Fig. 65. Firmer-Chisel.
The most familiar form is the firmer-chisel, Fig. 65, which is said to get its name from the fact that it is firmer or stiffer than the paring-chisel. (See below.) The firmer-chisel is a general utility tool, being suited for hand pressure or mallet pounding, for paring or for light mortising.
The most common type is the firmer-chisel, Fig. 65, which gets its name because it's firmer or stiffer than the paring-chisel. (See below.) The firmer-chisel is a versatile tool, suitable for hand pressure or mallet pounding, for paring, or for light mortising.
Different varieties of chisels are named; (1) according to their uses; as paring-chisels, framing-chisels, mortise-chisels, carving-chisels, turning-chisels, etc.
Different types of chisels are named; (1) based on their uses; such as paring chisels, framing chisels, mortise chisels, carving chisels, turning chisels, etc.

Fig. 66. Paring-Chisel. Fig. 67. Framing-Chisel. Fig. 68. Mortise-Chisel.
The framing-chisel, Fig. 67, is thick and heavy and was formerly much used in house framing. It is usually made with the handle fitting into a socket on the shank, in order to withstand the shock of heavy blows from the mallet.
The framing-chisel, Fig. 67, is thick and heavy and was commonly used in house framing in the past. It typically has a handle that fits into a socket on the shank, designed to withstand the impact of heavy blows from a mallet.
The mortise-chisel, Fig. 68, is made abnormally thick to give the stiffness necessary for levering the waste out of mortises.
The mortise-chisel, Fig. 68, is made unusually thick to provide the stiffness needed for prying the waste out of mortises.
(2) Chisels are also named according to their shapes: as, skew-chisels, corner-chisels, round-nosed chisels, etc.
(2) Chisels are also referred to based on their shapes: like skew chisels, corner chisels, round-nosed chisels, etc.
The angle of the bevel of a chisel is determined by the kind of wood for which it is most used, hard wood requiring a wider angle than soft wood, in. For order to support the edge ordinary work, the bevel is correctly ground to an angle of about 20°. The chisel is a necessary tool in making almost every kind of joint. It may almost be said that one mark of a good workman is his preference for the chisel. Indeed an excellent motto for the woodworker is: "When in doubt, use a chisel".
The angle of a chisel's bevel depends on the type of wood it's primarily used on, with hard wood requiring a wider angle than soft wood. To support the edge during regular use, the bevel is typically ground to an angle of about 20°. A chisel is an essential tool for creating nearly every type of joint. One way to recognize a skilled craftsman is by their preference for the chisel. In fact, a great motto for woodworkers is: "When in doubt, use a chisel."
In general, there are two uses for the chisel (1), when it is driven by a push with the hand, as in paring, and (2), when it is driven by blows of a mallet, as in digging mortises.
In general, there are two uses for the chisel (1), when it's pushed by hand, as in paring, and (2), when it's struck with a mallet, as in digging mortises.
In relation to the grain of the wood, it is used in three directions: (1) longitudinally, that is with the grain, called paring; (2) laterally, across the surface, called cutting sidewise; (3) transversely, that is across the end, called cutting end-wood.
In relation to the grain of the wood, it is used in three directions: (1) longitudinally, which means with the grain, called paring; (2) laterally, across the surface, called cutting sidewise; (3) transversely, that is across the end, called cutting end-wood.
1. Paring. To remove shavings rapidly, the chisel is held flat side up, the handle grasped by the right hand, with the thumb pointing toward the shank, and the blade held in the left hand, as in Fig. 69. Held in this way great control can be exerted and much force applied. For paring the surface as flat and smooth as possible, the chisel should be reversed, that is, held so that the flat side will [page 56] act as a guide. Held in this way the chisel has no equal for paring except the plane. Paring with the chisel is the method used in cutting stop chamfers. (See p. 185, Chapter VIII.) By holding the cutting edge obliquely to the direction of the grain and of the cut, the effective "sliding cut" is obtained, Fig. 64.
1. Paring. To quickly remove shavings, hold the chisel flat side up, gripping the handle with your right hand, your thumb pointing toward the shank, and the blade in your left hand, as shown in Fig. 69. This grip allows for great control and significant force application. To pare the surface as flat and smooth as possible, the chisel should be reversed, meaning the flat side acts as a guide. When held this way, the chisel is unmatched for paring, except for the plane. Paring with the chisel is the method used for cutting stop chamfers. (See p. 185, Chapter VIII.) By positioning the cutting edge at an angle to the grain and the cut, you achieve an effective "sliding cut," as illustrated in Fig. 64.
2. In sidewise chiseling the chisel is held in the same manner as in paring. A typical form of sidewise chiseling is the cutting out of a dado, Fig. 70. The work may be placed on the bench-hook or held in the vise with the side up from which the groove is to be cut. The chisel is pushed directly across the grain, the blade being somewhat inclined to the upper surface so as to cut off a corner next the saw kerf. After a few cuts thus made with the chisel inclined alternately both ways, the ridge thus formed is taken off, Fig. 71. In this way the surface is lowered to the required depth. If more force be required, the palm of the hand may be used as a mallet.
2. In sidewise chiseling, hold the chisel the same way as when paring. A common example of sidewise chiseling is cutting out a dado, as shown in Fig. 70. You can place the work on a bench-hook or hold it in a vise with the side that needs the groove facing up. Push the chisel directly across the grain, angling the blade slightly towards the upper surface to cut off a corner next to the saw kerf. After making a few cuts with the chisel angled alternately in both directions, remove the ridge that forms, as illustrated in Fig. 71. This method will lower the surface to the desired depth. If you need more force, you can use your palm as a mallet.
3. In chiseling end-wood, it is well, if possible, to rest the piece to be trimmed flat on the cutting board or on a piece of waste wood. Work done in this way is often called perpendicular chiseling, Fig.72. The handle is grasped in the right hand, [page 57] thumb up, while the blade of the chisel passes between the thumb and first finger of the left hand, the back of which rests on the work and holds it in place. As the right hand pushes the chisel downwards the thumb and first finger of the left hand control its motion. When chiseling it is well to stand so as to look along the line being cut. Incline the chisel toward you, and use the near part of the cutting edge for a guide and the farther corner for cutting, pushing the handle both down and forward at the same time, Fig. 73. Or, by pushing the chisel sidewise with the thumb of the left hand at the same time that the right hand pushes it downward, the effective sliding cut is obtained.
3. When chiseling end-wood, it's best, if possible, to lay the piece you want to trim flat on the cutting board or on a scrap piece of wood. This method is often referred to as perpendicular chiseling, Fig.72. Hold the handle in your right hand, thumb up, while the blade of the chisel goes between the thumb and index finger of your left hand, with the back of your left hand resting on the work to keep it steady. As you push the chisel down with your right hand, your left hand's thumb and index finger guide its movement. When chiseling, it's advisable to stand so you can see along the line you're cutting. Angle the chisel toward you, using the near part of the cutting edge as a guide and the farther corner for cutting, pushing the handle down and forward simultaneously, Fig. 73. Alternatively, you can achieve an effective sliding cut by pushing the chisel sideways with your left hand's thumb while your right hand pushes it downward.

Fig. 73. Chiseling End Wood.

Fig. 75. Right and Wrong Ways of Perpendicular Chiseling.
End chiseling requires considerable force and therefore only thin shavings should be cut off at a time. Or the mallet may be used with caution. In order to leave a smooth surface the chisel must be very sharp. Even then the lower arris (corner) is likely to be splintered off. This can be prevented by clamping the work down tight with a handscrew to a perfectly smooth cutting board. It is often advisable however, to set the piece upright in the vise and pare off thin shavings horizontally, Fig. 74. In rounding a corner, both this and perpendicular chiseling are common methods. In both cases care should be taken to cut from the side toward the end and not into the grain, lest the piece split, Fig. 75. In horizontal end paring, [page 58] Fig. 74, in order to prevent splintering, it is well to trim down the arrises diagonally to the line and then to reduce the rest of the end surface.
End chiseling requires a lot of force, so only thin layers should be removed at a time, or the mallet can be used carefully. To achieve a smooth surface, the chisel must be very sharp. Even then, the lower edge (corner) is likely to splinter. This can be avoided by securely clamping the work with a handscrew to a perfectly smooth cutting board. However, it's often better to set the piece upright in the vise and shave off thin layers horizontally, as shown in Fig. 74. When rounding a corner, both this method and perpendicular chiseling are commonly used. In both cases, care should be taken to cut from the side toward the end and not against the grain to prevent the piece from splitting, as illustrated in Fig. 75. In horizontal end paring, [page 58] Fig. 74, to avoid splintering, it's helpful to trim the edges diagonally to the line and then reduce the rest of the end surface.
In all hand chiseling, it is a wise precaution not to try to cut out much material at each stroke but to work back gradually to the line.
In all hand chiseling, it's a good idea not to try to remove too much material with each stroke but to gradually work back to the line.
A typical form of mallet chiseling is the digging of a mortise, Fig. 76. (See also p. 56.) The chisel is held perpendicular in the left hand, while the right hand drives blows with the mallet. The hammer should never be used. (See mallet, p. 96.) By rocking the chisel and at the same time giving it a twisting motion while the edge is kept on the wood, the edge can be stepped to the exact place desired. Care should be taken to work back to the lines gradually, to cut only part way thru from each side (in the case of a thru mortise-and-tenon), and to keep the cut faces perpendicular to the surfaces.
A common technique for mallet chiseling is digging a mortise, Fig. 76. (See also p. 56.) Hold the chisel perpendicularly in your left hand while your right hand strikes it with the mallet. Never use a hammer. (See mallet, p. 96.) By rocking the chisel and twisting it while keeping the edge on the wood, you can position the edge exactly where you want it. Be careful to gradually work back to the lines, only cut partway through from each side (for a through mortise-and-tenon), and ensure the cut faces are perpendicular to the surfaces.
In sharpening a chisel it is of first importance that the back be kept perfectly flat. The bevel is first ground on the grindstone to an angle of about 20° and great care should be taken to keep the edge straight and at right angles to the sides of the blade.
In sharpening a chisel, it’s crucial to keep the back completely flat. First, grind the bevel on the grindstone at an angle of about 20°, and be very careful to maintain a straight edge that’s at a right angle to the sides of the blade.

Fig. 77 Whetting a Plane-Bit.
After grinding it is necessary to whet the chisel and other edged tools. (See also under oilstones, p. 121.) First see that there is plenty of oil on the stone. If an iron box be used, Fig. 77, the oil is obtained simply by turning the stone [page 59] over, for it rests on a pad of felt which is kept wet with kerosene.
After grinding, it's essential to sharpen the chisel and other cutting tools. (See also under oilstones, p. 121.) First, make sure there's plenty of oil on the stone. If you’re using an iron box, Fig. 77, you can get the oil by simply flipping the stone over since it sits on a pad of felt that's kept damp with kerosene. [page 59]
Place the beveled edge flat on the stone, feeling to see if it does lie flat, then tip up the chisel and rub it at an angle slightly more obtuse than that which it was ground, Fig. 78. The more nearly the chisel can be whetted at the angle at which it was ground the better. In rubbing, use as much of the stone as possible, so as to wear it down evenly. The motion may be back and forth or spiral, but in either case it should be steady and not rocking. This whetting turns a light wire edge over on the flat side. In order to remove this wire edge, the back of the chisel, that is, the straight, unbeveled side, is held perfectly flat on the whetstone and rubbed, then it is turned over and the bevel rubbed again on the stone. It is necessary to reverse the chisel in this way a number of times, in order to remove the wire edge, but the chisel should never be tipped so as to put any bevel at all on its flat side. Finally, the edge is touched up (stropped) by being drawn over a piece of leather a few times, first on one side, then on the other, still continuing to hold the chisel so as to keep the bevel perfect.
Place the beveled edge flat on the stone and check if it lies flat. Then, tilt the chisel up and rub it at an angle that's slightly wider than the angle it was originally ground to, as shown in Fig. 78. The closer the chisel can be sharpened to the original angle, the better. When rubbing, use as much of the stone's surface as possible to wear it down evenly. You can move it back and forth or in a spiral, but whichever way you choose, make sure the motion is steady and doesn't rock. This sharpening creates a small wire edge on the flat side. To remove this wire edge, hold the back of the chisel, which is the flat, unbeveled side, perfectly flat on the whetstone and rub it. Then, flip it over and rub the bevel side again on the stone. You need to alternate the chisel this way several times to eliminate the wire edge, but do not tilt it at all to put any bevel on the flat side. Finally, touch up the edge by drawing it over a piece of leather a few times, starting with one side and then the other, while still keeping the bevel perfect.

Fig. 78. Grinding Angle, 20°. Whetting Angle, 25°.
To test the sharpness of a whetted edge, draw the tip of the finger or thumb lightly along it, Fig. 79. If the edge be dull, it will feel smooth: if it be sharp, and if care be taken, it will score the skin a little, not enough to cut thru, but just enough to be felt.
To check how sharp a sharpened edge is, lightly run the tip of your finger or thumb along it, as shown in Fig. 79. If the edge is dull, it will feel smooth; if it's sharp and you’re careful, it will slightly mark the skin—not enough to cut through, but just enough to be noticeable.

Fig. 79. Testing the Sharpness of a Chisel.
The gouge is a form of chisel, the blade of which is concave, and hence the edge curved. When the bevel is on the outside, the common form, it is called an outside bevel gouge or simply a "gouge," Fig. 80; if the bevel is on the inside, it is called an inside bevel, or inside ground, or scribing-gouge, or paring-gouge, Fig. 81.3
The gouge is a type of chisel with a curved blade, making the edge rounded. When the bevel is on the outside, which is the usual type, it's referred to as an outside bevel gouge or just a "gouge," Fig. 80; if the bevel is on the inside, it's known as an inside bevel, inside ground, scribing-gouge, or paring-gouge, Fig. 81.3
Footnote 3: Another confusing nomenclature (Goss) gives the name "inside gouges" to those with the cutting edge on the inside, and "outside gouges" to those with the cutting edge on the outside.
Footnote 3: Another confusing term (Goss) refers to those with the cutting edge on the inside as "inside gouges," while those with the cutting edge on the outside are called "outside gouges."

Fig. 80. Firmer-Gouge Outside Bevel. |
Fig. 81. Inside bevel Gouge. |
Carving tools are, properly speaking, all chisels, and are of different shapes for facility in carving.
Carving tools, in essence, are all chisels and come in various shapes to make carving easier.
For ordinary gouging, Fig. 82, the blade is gripped firmly by the left hand with the knuckles up, so that a strong control can be exerted over it. The gouge is manipulated in much the same way as the chisel, and like the chisel it is used longitudinally, laterally, and transversely.
For regular gouging, Fig. 82, hold the blade firmly in your left hand with your knuckles facing up to maintain strong control over it. The gouge is used similarly to the chisel, and like the chisel, it can be used lengthwise, sideways, and across.

Fig. 82. Gouging.
In working with the grain, by twisting the blade on its axis as it moves forward, delicate paring cuts may be made. This is particularly necessary in working cross-grained wood, and is a good illustration of the advantage of the sliding cut.
In working with the grain, by turning the blade on its axis as it moves forward, fine paring cuts can be made. This is especially important when working with cross-grained wood and is a great example of the benefit of the sliding cut.
In gouging out broad surfaces like trays or saddle seats it will be found of great advantage to work laterally, that is across the surface, especially in even grained woods as sweet gum. The tool is not so likely to slip off and run in as when working with the grain.
In carving out wide areas like trays or saddle seats, it's very helpful to work side-to-side, meaning across the surface, especially in woods with a consistent grain like sweet gum. This way, the tool is less likely to slip and go off course compared to working with the grain.
The gouge that is commonly used for cutting concave outlines on end grain, is the inside bevel gouge. Like the chisel in cutting convex outlines, it is pushed or driven perpendicularly thru the wood laid flat on a cutting board on the bench, as in perpendicular chiseling, Fig. 72. p. 56.
The gouge typically used for cutting curved shapes on end grain is the inside bevel gouge. Similar to how a chisel is used for cutting outward curves, it is pushed or driven straight down through the wood that is laid flat on a cutting board on the bench, as shown in perpendicular chiseling, Fig. 72. p. 56.
In sharpening an outside bevel gouge, the main bevel is obtained on the grindstone, care being taken to keep the gouge rocking on its axis, so as to get an even curve. It is then whetted on the flat side of a slipstone, Fig. 83, the bevel already obtained on the grindstone being made slightly more obtuse at the edge. A good method is to rock the gouge on its axis with the left hand, while the slipstone held in the right hand is rubbed back and forth on the edge. Then the concave side is rubbed on the round edge of [page 61] the slipstone, care being taken to avoid putting a bevel on it. Inside bevel gouges need to be ground on a carborundum or other revolving stone having a round edge. The outfit of the agacite grinder, (Fig. 224, p. 120), contains one of these stones. The whetting, of course, is the reverse of that on the outside bevel gouge.
In sharpening an outside bevel gouge, you get the main bevel on the grindstone, making sure to keep the gouge rocking on its axis to achieve an even curve. After that, it's sharpened on the flat side of a slipstone, as shown in Fig. 83, making the bevel slightly more obtuse at the edge. A good technique is to rock the gouge on its axis with your left hand while rubbing the slipstone back and forth on the edge with your right hand. Next, the concave side is rubbed on the round edge of [page 61] the slipstone, taking care not to create a bevel on it. Inside bevel gouges should be ground on a carborundum or other revolving stone with a round edge. The setup for the agacite grinder (Fig. 224, p. 120) includes one of these stones. The sharpening process, of course, is the opposite of that used for the outside bevel gouge.

Fig. 83. Whetting a Gouge.

Fig. 84. Sloyd Knife.
The knife differs from the chisel in two respects, (1) the edge is along the side instead of the end, and (2) it has a two-beveled edge. Knives are sometimes made with one side flat for certain kinds of paring work, but these are uncommon. The two-beveled edge is an advantage to the worker in enabling him to cut into the wood at any angle, but it is a disadvantage in that it is incapable of making flat surfaces. The knife is particularly valuable in woodwork for scoring and for certain emergencies. The sloyd knife, Fig. 84, is a tool likely to be misused in the hands of small children, but when sharp and in strong hands, has many valuable uses. A convenient size has a 2½ inch blade. When grinding and whetting a knife, the fact that both sides are beveled alike should be kept in mind.
The knife is different from the chisel in two ways: (1) the edge runs along the side instead of the end, and (2) it has a two-beveled edge. Knives are sometimes made with one flat side for specific paring tasks, but these are rare. The two-beveled edge helps the user cut into the wood at any angle, but it makes it difficult to create flat surfaces. The knife is especially useful in woodworking for scoring and in certain situations. The sloyd knife, Fig. 84, is a tool that can easily be misused by small children, but when it’s sharp and in capable hands, it has many valuable applications. A convenient size features a 2½ inch blade. When grinding and sharpening a knife, it’s important to remember that both sides are beveled the same way.

Fig. 85. Draw-Knife.
The draw-knife, Fig. 85, is ground like a chisel, with the bevel only on one side, but the edge is along the side like a knife. Instead [page 62] of being pushed into the wood, like a chisel, it is drawn into it by the handles which project in advance of the cutting edge. The handles are sometimes made to fold over the edge, and thus protect it when not in use. The size is indicated by the length of the cutting edge. It is particularly useful in reducing narrow surfaces and in slicing off large pieces, but it is liable to split rather than cut the wood.
The draw-knife, Fig. 85, is shaped like a chisel, with the bevel on just one side, but the edge is along the side like a knife. Instead of being pushed into the wood like a chisel, it's drawn into it by the handles that stick out in front of the cutting edge. The handles can sometimes fold over the edge to protect it when not in use. The size is determined by the length of the cutting edge. It's especially helpful for smoothing narrow surfaces and slicing off large pieces, but it tends to split the wood instead of cutting it.
SAWS.

Fig. 86. Hand Saw.
The object of the saw is to cut thru a piece of material along a determined line. Its efficiency depends upon (1) the narrowness of the saw cut or "kerf," and (2) upon the force required to drive it thru the material. The thinner the blade, the less material will be cut out and wasted, and the less force will have to be applied. In order to have the saw as thin as possible, almost all the people of the world, except the Anglo Saxons, have saws that cut when they are pulled toward the worker. The blade is in tension while cutting and in compression only when being returned for a new cut. German carpenters use a saw like our turning-saw. English and Americans have developed the saw on the opposite principle, namely, that it should cut on the pushing stroke. As a matter of fact, the crosscut-saw cuts somewhat on the back stroke. The pushing stroke necessitates a thickening of the blade sufficient to prevent buckling,—a not uncommon occurrence in the bands of a novice, in spite of this thickening. But tho this requires more force, and involves more waste, there are the compensations that the arm can exert more pressure in pushing than in pulling, especially when the worker stands upright or stoops over his work, and the stiffer wide blade acts as a guide to the sawyer. Each method has its advantages. Whatever may be true of hand-saws, in machine-saws the tension method, as illustrated by the gang-saw and the band-saw, is steadily displacing the compression method utilized in the circular-saw. Many kinds of work, however, can be done only on the circular-saw.
The purpose of a saw is to cut through a piece of material along a specific line. Its effectiveness relies on (1) the narrowness of the saw cut or "kerf," and (2) the force needed to push it through the material. The thinner the blade, the less material gets cut away and wasted, meaning less force is needed. To make the saw as thin as possible, almost everyone in the world, except for Anglo Saxons, has saws that cut when pulled toward the worker. The blade is under tension while cutting and in compression only when being pulled back for a new cut. German carpenters use a saw similar to our turning saw. The English and Americans have developed their saws based on the opposite approach, where the saw cuts on the pushing stroke. In fact, the crosscut saw cuts somewhat on the return stroke. The pushing stroke requires a thicker blade to prevent buckling, which is a common issue for beginners, despite this thickness. Although this method requires more force and leads to more waste, it has the benefit that the arm can apply more pressure when pushing than when pulling, especially when the worker is standing upright or bending over the work, and the stiffer, wider blade acts as a guide for the sawyer. Each method has its benefits. While hand saws have their nuances, in machine saws, the tension method, as shown by gang saws and band saws, is increasingly replacing the compression method used in circular saws. Nevertheless, there are many types of work that can only be performed with circular saws.
In order to diminish the disadvantages of the thrusting stroke, the modern hand-saw, Fig. 86, has been gradually improved as the result of much experience and thought. The outline of the blade is tapered in width from handle to point; it is thicker also at the [page 63] heel (the handle end) than at the point; its thickness also tapers from the teeth to the back. All these tapers gives stiffness where it is most needed. It is made wide for the sake of giving steadiness in sawing. The fact that it is thinner at the back than along the teeth gives it clearance in passing back and forth in the kerf, but the friction is still great, especially in sawing soft or damp wood. To avoid this binding still further, the teeth are "set" alternately one to one side and the next to the other, and so on.
To reduce the drawbacks of the thrusting stroke, the modern hand saw, Fig. 86, has been gradually improved through a lot of experience and thought. The blade's outline tapers in width from the handle to the tip; it’s also thicker at the heel (the handle end) than at the tip, and its thickness tapers from the teeth to the back. These tapers provide stiffness where it's most needed. It's made wide for better stability during sawing. The fact that it's thinner at the back than along the teeth helps it move easily back and forth in the kerf, but friction is still significant, especially when cutting soft or damp wood. To further reduce this binding, the teeth are "set" alternately to one side and then the other, and so on.

Fig. 87. Rip Saw Teeth: A-edge view, B-side view, C cross-section.
Crosscut-Saw Teeth: A'-edge view, B'-side view, C'-cross-section.
The size of saws is indicated by the length of the blade in inches. The coarseness of the tooth is indicated by the number of "points" to the inch. "Points" should not be confused with teeth as there is always one more point per inch than there are teeth. For example, a five point rip-saw has five points to the inch but only four full teeth, Fig. 87. Rip-saws run from 4 to 7 points per inch; crosscut-saws from 6 to 12 points per inch.
The size of saws is measured by the length of the blade in inches. The coarseness of the teeth is measured by the number of "points" per inch. "Points" shouldn't be confused with teeth since there is always one more point per inch than there are teeth. For example, a five-point rip saw has five points per inch but only four full teeth. Rip saws have between 4 to 7 points per inch, while crosscut saws have between 6 to 12 points per inch.
In general, saws are of two kinds, rip-saws and crosscut-saws.
In general, there are two types of saws: rip saws and crosscut saws.
The rip-saw, Fig. 87, may be thought of as a series of chisels set in two parallel rows which overlap each other, for each tooth is filed to a sharp edge which, at each stroke, chisels off a small particle from the end of the wood fibers.
The rip-saw, Fig. 87, can be seen as a set of chisels arranged in two overlapping parallel rows, with each tooth sharpened to a fine edge that carves off small pieces from the ends of the wood fibers with every stroke.
The shape of the teeth is the result of experience in uniting a number of factors: as, strength of the individual tooth, the acuteness of the cutting angle, and the ease of sharpening. The steel of a saw is softer than that of a chisel, in order that it may be filed and set. Hence it is weaker and the edge cannot be so acute. A typical form of tooth is shown in Fig. 87, in which A is an edge view, B the side view, and C a cross section. The angle of each tooth covers 60°, one side, the "face", being at right angles to the line of the teeth. The cutting edge runs at right angles to the sides of the blade.
The shape of the teeth comes from a combination of several factors: the strength of each tooth, the sharpness of the cutting angle, and how easy it is to sharpen them. The steel used for a saw is softer than that used for a chisel so that it can be filed and adjusted. Because of this, it is weaker and can't have an edge that's as sharp. A typical tooth shape is shown in Fig. 87, where A is an edge view, B is the side view, and C is a cross section. The angle of each tooth covers 60°, with one side, the "face," being at a right angle to the line of the teeth. The cutting edge is at a right angle to the sides of the blade.
In the crosscut-saw, therefore, the teeth are filed to points, and the cutting edge is on the forward side of each alternate tooth. In Fig. 87. A' is the edge view, B' is the side view and C' is a cross-section. In a properly filed crosscut-saw a needle will slide between these two rows of teeth from one end of the saw to the other.
In the crosscut-saw, the teeth are sharpened to a point, and the cutting edge is on the front side of every other tooth. In Fig. 87, A' shows the edge view, B' shows the side view, and C' is a cross-section. In a properly sharpened crosscut-saw, a needle will fit between these two rows of teeth from one end of the saw to the other.
In action the points, especially their forward edges, cut or score the fibres of wood, and then the triangular elevation of wood left between the two rows of points is crumbled off by friction as the saw passes through. Thus it drops farther and farther into the cut. A crosscut-saw may be thought of as a series of knife points, arranged in two parallel rows. Ordinarily the angle of the "face" of each tooth with the line of the teeth is about 65°, and slightly steeper than the back of the tooth. The angle of the cutting edge of each tooth may be filed more acute when the saw is to be used for soft wood only.
In action, the points, especially their forward edges, slice or score the fibers of wood, and then the triangular piece of wood left between the two rows of points gets crumbled away by friction as the saw passes through. As a result, it sinks deeper into the cut. A crosscut saw can be seen as a series of knife points, arranged in two parallel rows. Normally, the angle of the "face" of each tooth with the line of the teeth is about 65°, which is slightly steeper than the back of the tooth. The angle of the cutting edge of each tooth can be sharpened to a more acute point if the saw is intended solely for softwood.
A crosscut-saw when used to rip a board, works slowly, for there is no chisel action to cut out the fibres between the points, but the cut, tho slow, is smooth. In cutting diagonally across a piece of wood, especially soft wood, a rip-saw cuts faster, but a crosscut, smoother. In ripping a board, allowance should always be made for planing to the line afterward. In starting a cut with the rip-saw, the weight of the saw should be borne by the right hand so that the teeth may [page 65] pass over the edge of the wood as lightly as possible. The left thumb acts as a guide. If the saw be handled thus, and the angle with the board be quite acute, it is not necessary to start with a back stroke. When the kerf is well started, the whole weight of the saw may be applied. An easy light stroke is better than a furious one. The line should be followed carefully, but if the saw runs from the line it may be brought back by taking short strokes near the point of the saw and twisting the blade slightly in the desired direction. If the saw binds and buckles because of the springing together of the wood, the kerf may be wedged open with a screwdriver or a bit of waste wood. A drop of oil rubbed across each side of the saw will make it work more easily.
A crosscut saw works slowly when ripping a board, since it doesn't have a chisel action to cut the fibers between the teeth, but the cut is smooth even if it's slow. When cutting diagonally across a piece of wood, especially soft wood, a rip saw is faster, but a crosscut is smoother. When ripping a board, always plan for some allowance to plane to the line afterward. When starting a cut with the rip saw, support the weight of the saw with your right hand so the teeth can pass over the edge of the wood as lightly as possible. The left thumb serves as a guide. If the saw is handled this way and the angle with the board is quite acute, you won’t need to start with a backstroke. Once the kerf is well established, you can apply the full weight of the saw. A gentle light stroke is better than a heavy one. Follow the line closely, but if the saw strays from it, you can correct it by making short strokes near the tip and slightly twisting the blade in the direction you want. If the saw gets stuck because the wood springs back together, you can wedge the kerf open with a screwdriver or a piece of scrap wood. A drop of oil rubbed on each side of the saw will help it work more smoothly.
Care should be taken in finishing a cut to hold up firmly the part of the wood which is being sawn off so that it will not split off or splinter.
Care should be taken when finishing a cut to firmly hold the part of the wood that is being sawed off so that it doesn’t split or splinter.

Fig. 88. Rip-Sawing on a Horse.
Sawing may be done either on a saw-horse, Fig. 88, or at a bench. For big, rough work, the former is the common way, the worker holding the material in place with one knee, because this method enables him to exert his greatest strength. A convenient way for rip-sawing a small piece of wood is to insert it in the vise, Fig. 89, with the broad side of the board parallel to the vise screw, and the board inclined away from the worker who stands upright. The start is easy, the sawdust does not cover the line, and the board is not in danger of splitting. The board, however, has to be reversed after it is sawn part way thru, in order to finish the saw cut.
Sawing can be done either on a saw horse, Fig. 88, or at a workbench. For larger, rougher tasks, the former is the usual method, with the worker holding the material in place with one knee, as this technique allows him to use his full strength. A handy way to rip-saw a small piece of wood is to clamp it in the vise, Fig. 89, with the broad side of the board parallel to the vise screw and the board tilted away from the worker who is standing upright. Starting is easy, sawdust doesn’t obscure the line, and the board is less likely to split. However, the board needs to be flipped after cutting part of the way through to complete the saw cut.

Fig. 89. Rip-sawing with Wood Held in Bench-Vise.
The back-saw or tenon-saw, Fig. 90. is a fine crosscut-saw, with a rib of steel along the back, which gives to it its name. Since it is intended for small accurate work, the teeth have little or no set.
The back-saw or tenon-saw, Fig. 90, is a great crosscut saw with a steel rib along the back, which is how it gets its name. Because it's designed for small, precise work, the teeth have little to no set.

Fig. 90. Using the Back-Saw with Bench-Hook.
In sawing, the wood may be held either in the vise or on the bench-hook. To help start the saw and at the same time to keep the edges of the cut sharp, it is well to make a little groove [page 66] with the knife, on the waste side of the line to be followed, cutting the side of the groove next to the line at right angles to the surface. The saw drops directly into this groove, Fig. 91. In starting the saw cut, the saw should be guided by holding the thumb of the left hand against the side of the saw just above the teeth. Until the kerf is well started, the saw should be held so that the teeth just touch the wood. It is better not to attempt to start the saw level, i. e., with the teeth resting clear across the wood, but the handle should be raised so that the start is made only at the farther edge of the wood. Then as the saw is gradually lowered, the kerf will extend quite across the wood, Fig. 92. When the back-saw is used for ripping, the wood is held in the vise, end up. Begin sawing as in crosscutting, that is, at the farther corner with the handle end of the saw up, and gradually drop the handle. Watch the lines on both the front and back sides, and if necessary, reverse the piece to follow them.
In sawing, you can hold the wood either in a vise or on a bench hook. To help start the saw while keeping the edges of the cut sharp, it's a good idea to make a small groove with a knife on the waste side of the line you want to follow, cutting the side of the groove next to the line at a right angle to the surface. The saw drops right into this groove, as shown in Fig. 91. When starting the saw cut, guide the saw by pressing the thumb of your left hand against the side of the saw just above the teeth. Until the kerf is well established, hold the saw so that the teeth just touch the wood. It's better not to try to start the saw level, meaning having the teeth resting flat across the wood; instead, raise the handle so that the cut starts only at the far edge of the wood. Then, as you gradually lower the saw, the kerf will extend across the wood, as shown in Fig. 92. When using a back saw for ripping, hold the wood in the vise with the end up. Start sawing like you would for crosscutting, beginning at the far corner with the handle end of the saw raised, and then gradually lower the handle. Keep an eye on the lines on both the front and back sides, and if needed, flip the piece to follow them.

Fig. 91. Starting a Saw Cut in a Trough Cut With Knife.

Fig. 92. Direction of the Back-Saw.
The dovetail-saw, Fig. 93, is a small back-saw for delicate work.
The dovetail-saw, Fig. 93, is a small back-saw designed for fine, detailed work.

Fig. 93. Dovetail-saw.

Fig. 94. Compass-Saw.
The turning-saw, Fig. 95, is a narrow saw, set in a frame, which stretches the saw tight, so that it works as a tension saw (cf. p. 62). The best frames are made so that the handles which hold the blade can revolve in the frame. The turning-saw is used chiefly for cutting curves. A 14 inch blade, 3⁄16 of an inch wide is a good size for ordinary use. The teeth are like those of a rip-saw, so that they are quite likely to tear the wood in cutting across the grain. Allowance should be made for this and the surplus removed with a spokeshave. The turning-saw may be used to cut on either the pulling or the pushing stroke, with the teeth pointed either toward or away from the worker. The pulling cut is generally better, as it puts less strain on the frame than the pushing cut. Both hands should grasp the frame as near the end of the blade as possible, Fig. 95. Turns are made by revolving the frame on the blade as an axis, which should always be kept at right angles to the surface of the board. Care should be taken not to twist the blade.
The turning saw, Fig. 95, is a narrow saw set in a frame that keeps the saw taut, allowing it to function as a tension saw (cf. p. 62). The best frames are designed so the handles that hold the blade can rotate within the frame. The turning saw is mainly used for cutting curves. A 14-inch blade, 3⁄16 of an inch wide is a good size for regular use. The teeth are similar to those of a rip saw, so they can easily tear the wood when cutting across the grain. You should account for this and smooth out the excess with a spokeshave. The turning saw can cut on either the pulling or pushing stroke, with the teeth facing either towards or away from the worker. The pulling cut is generally preferred because it puts less stress on the frame than the pushing cut. Both hands should hold the frame as close to the end of the blade as possible, Fig. 95. Turns are made by rotating the frame around the blade as an axis, which should always be kept at right angles to the surface of the board. Care should be taken not to twist the blade.

Fig. 95. Using a Turning Saw.

Fig. 96. Saw-Vise.
To file and set a saw, the saw is first fastened in [page 68] the saw-vise, Fig. 96, with the teeth up. It is then top-jointed by running a flat file or a saw-jointer, Fig. 97, back and forth lengthwise along the tops of the teeth to bring them to a level. After jointing the saw should be set. For this purpose a saw-set. Fig. 98, is necessary. Every alternate tooth is bent in the direction of its set by the plunger in the instrument pushing against the anvil, which is an adjustable eccentric disc. After the saw is set, it is filed. This is done with a triangular file, Fig. 144, p. 90, which is held in the right hand and its point in the thumb and fingers of the left. Pressure is applied only on the forward stroke, which should be long and even, the file being raised above the tooth on the return stroke. The file should cut in the direction of the set, that is, the teeth having the set away from the worker are filed first. Every alternate tooth, 1st. 3d, 5th, etc., is filed, and then the saw is reversed and the other set, the 2nd, 4th, 6th, etc., is filed.
To file and set a saw, the saw is first secured in the [page 68] saw-vise, Fig. 96, with the teeth facing up. It is then top-jointed by using a flat file or a saw-jointer, Fig. 97, moving it back and forth along the tops of the teeth to level them out. After jointing, the saw needs to be set. For this, a saw-set, Fig. 98, is required. Every alternate tooth is bent in the direction of its set by the plunger in the tool pressing against the anvil, which is an adjustable eccentric disc. Once the saw is set, it is filed. This is done with a triangular file, Fig. 144, p. 90, held in the right hand with its point resting in the thumb and fingers of the left hand. Pressure is applied only on the forward stroke, which should be long and even, raising the file above the tooth on the return stroke. The file should cut in the direction of the set, meaning the teeth angled away from the worker are filed first. Every alternate tooth, 1st, 3rd, 5th, etc., is filed, then the saw is flipped, and the others, the 2nd, 4th, 6th, etc., are filed.

Fig. 97. A Saw-Jointer.

Fig. 98. Saw-Set.
In filing a rip-saw the file should move exactly perpendicularly to the plane of the saw blade, that is, directly across the teeth. The filing is done on the back of the teeth, the file just touching the face of the next one. The filing is continued, with one, two, or three strokes, for each tooth, as the case may require, or just until each tooth is sharp.
In filing a rip saw, the file should be positioned straight up and down relative to the plane of the saw blade, meaning it should move directly across the teeth. The filing is done on the back of the teeth, with the file just touching the face of the next tooth. Continue filing, making one, two, or three strokes for each tooth, depending on what is needed, or just until each tooth is sharp.
In filing a crosscut-saw, the file is held pointing upward and toward the point of the saw. The file should cut in the direction of the set. The angle of the cutting edge is determined by the horizontal inclination of the file to the blade; the angle of the point is determined by the perpendicular inclination of the file to the blade. Finally the sides of the teeth are rubbed lightly with a slipstone to remove the wire edge. It should always be remembered that a saw is an edge tool, and its edges are as liable to injury as any edges.
In filing a crosscut saw, hold the file pointing upwards and towards the tip of the saw. The file should cut in the direction of the teeth. The angle of the cutting edge is determined by how horizontally you tilt the file in relation to the blade; the point's angle is determined by how vertically you hold the file to the blade. Finally, lightly rub the sides of the teeth with a slipstone to remove any burrs. It's important to remember that a saw is an edge tool, and its edges can be just as prone to damage as any other edges.
PLANES.
The plane is a modified chisel. The chief difference in action between a chisel and a plane in paring is this: the back of the chisel lies close down on the surface of the wood that is cut, and acts as a guide; whereas, in the plane, the cutter is elevated at an angle away from the surface of the wood, and only its cutting edge touches the wood, and it is held and guided mechanically by the plane mechanism. In other words, a plane is a chisel firmly held in a device which raises the cutter at an angle from the work, regulates the depth of the cut, and favors the cutting rather than the splitting action. An illustration of a chisel converted into a plane is the adjustable chisel-gage, Fig. 99.
The plane is a modified chisel. The main difference in how a chisel and a plane work for shaping wood is this: the back of the chisel rests flat against the wood surface being cut, acting as a guide; on the other hand, in a plane, the cutter is positioned at an angle away from the wood surface, with only its cutting edge making contact. It is held and guided mechanically by the plane's mechanism. In other words, a plane is essentially a chisel that is securely held in a device that angles the cutter away from the workpiece, controls the cut's depth, and promotes a cutting action rather than a splitting one. An example of a chisel turned into a plane is the adjustable chisel-gage, Fig. 99.

Fig. 99. Adjustable Chisel-Gage. Fig. 100. Wooden Bench-Plane.
The plane has developed as follows: it was first a chisel held in a block of wood. This is all that oriental planes are now, simply a sharpened wedge driven into a block of wood. When the hole works too loose, the Japanese carpenter inserts a piece of paper to tighten it, or he makes a new block. The first improvement was the addition of a wooden wedge to hold in place the "plane-iron", as the cutter was formerly called. In this form, the cutter or plane-iron, tho still [page 70] wedge-shaped, was reversed, being made heavier at the cutting edge in order to facilitate fastening it in the wooden plane-stock by means of the wooden wedge. Then a handle was added for convenience. Then came the cap, the object of which is to break back the shaving and thus weaken it as soon as possible after it is cut. Until a few years ago, this was all that there was in a plane, and such planes are still common, Fig. 100. Finally there appeared the iron plane, Fig. 101, with it various mechanical adjustments. The following are the parts of the Bailey iron plane:4
The plane has evolved as follows: it started as a chisel held in a block of wood. This is what oriental planes still are, just a sharpened wedge driven into a block of wood. When the hole is too loose, the Japanese carpenter puts in a piece of paper to tighten it, or he makes a new block. The first improvement was adding a wooden wedge to hold the "plane-iron," as the cutter used to be called, in place. In this form, the cutter or plane-iron, although still wedge-shaped, was flipped, becoming heavier at the cutting edge to make it easier to secure in the wooden plane-stock with the wooden wedge. Then a handle was added for convenience. Next came the cap, which is designed to break the shaving and weaken it as soon as it is cut. Until a few years ago, this was all there was to a plane, and such planes are still common, Fig. 100. Finally, the iron plane appeared, Fig. 101, along with various mechanical adjustments. The following are the parts of the Bailey iron plane:4
Footnote 4: The numbers and names in italics are those given in Stanley's Catalog, No. 34. Some of these names, as "plane-iron," are survivals from the days of the wooden plane and are obviously unsuitable now.
Footnote 4: The numbers and names in italics are those listed in Stanley's Catalog, No. 34. Some of these names, like "plane-iron," are leftovers from the time of the wooden plane and are clearly not appropriate now.

Fig. 101 Section of Jack Plane.
1. Cutter, or bit, or blade, or plane-iron.
1. Cutter, or bit, or blade, or plane iron.
2. Cap, or plane-iron cap, or curling iron.
2. Cap, or plane-iron cap, or curling iron.
3. Cutter screw, or plane-iron Screw.
Cutter screw, or plane-iron screw.
4. Clamp, or lever cap, or wedge.
4. Clamp, or lever cap, or wedge.
5. Clamp screw, or cap screw.
Clamp screw, or cap screw.
6. Frog.
6. Frog.
7. Y Adjustment.
7. Y Adjustment.
8. Brass set screw, or brass adjusting nut.
8. Brass set screw, or brass adjusting nut.
9. Lever (for lateral adjustment).
9. Lever (for lateral adjustment).
10. Frog screw.
10. Frog screw.
11. Handle.
11. Grip.
12. Knob.
12. Button.
13. Handle bolt and nut.
13. Use bolt and nut.
14. Knob screw, or Knob bolt and nut.
14. Knob screw, or Knob bolt and nut.
15. Handle screw.
15. Adjustable screw.
16. Bottom, or sole.
16. Bottom or sole.
17. Toe.
Toe.
18. Heel.
18. Heel.
19. Throat.
Throat.
20. Thumb piece, or clamp lever, or cam.
20. Thumb piece, clamp lever, or cam.
There are various principles involved in the action of the plane. The effect of the flat sole is to regulate the cut of the cutter. If the surface be uneven, the cutter will not cut at all, or but little, in passing over low places, since the toe and heel of the sole will then be resting on higher places; but when the cutter reaches a high place a shaving will be taken off. Hence it follows that the longer the plane, the straighter will be the surface produced. The length of the plane used is determined by the length of the wood to be planed, and the degree of straightness desired.
There are several principles involved in how the plane works. The flat sole helps control how the cutter does its job. If the surface is uneven, the cutter won’t cut much, if at all, over low spots, because the front and back of the sole will be resting on the higher areas; however, when the cutter hits a high spot, it will take off a shaving. Therefore, the longer the plane, the straighter the surface it will create. The length of the plane used depends on the length of the wood being planed and how straight you want it to be.
The part of the sole directly in front of the cutter presses firmly down on the wood and so prevents the shaving from splitting far in advance of the edge. It follows that the narrowness of the mouth in a plane is an important factor in the production of smooth surfaces. This can be regulated by adjusting the toe in the block-plane, and by moving the frog in the jack- and smooth-planes.
The part of the sole right in front of the cutter presses down firmly on the wood, which stops the shaving from splitting too far ahead of the edge. This means that the narrowness of the mouth in a plane is a key factor in creating smooth surfaces. You can adjust this by changing the toe in the block-plane and moving the frog in the jack- and smooth-planes.
A recent improvement in jack-, smooth-, and fore-planes consists of an adjustable frog, by means of which the throat can be narrowed or widened at will by means of a set-screw in the rear of the frog without removing the clamp and cutter. It is made by Sargent and Company. The Stanley "Bed Rock" plane has a similar but less convenient device.
A recent improvement in jack, smooth, and fore planes features an adjustable frog, allowing you to easily narrow or widen the throat using a set screw at the back of the frog without having to remove the clamp and cutter. This innovation is made by Sargent and Company. The Stanley "Bed Rock" plane has a similar but less convenient mechanism.
The splitting of the wood in advance of the edge is also prevented by the breaking of the shaving as it hits against the cutter or its cap. Hence the advantage of bending up and breaking or partly breaking the shaving as soon as possible after it is cut. This shows why the cap is set close to the edge of the cutter. Another reason is that it thereby stiffens the cutter and prevents "chattering." If a thick shaving be desired the cap has to be set farther back. In a smooth-plane 1⁄32 inch is enough, in a jack-plane ⅛ inch is often desirable. The following are the planes in common use:
The wood splitting before it reaches the edge is also stopped by the shaving breaking when it hits the cutter or its cap. This is why it's beneficial to bend up and break or partially break the shaving as soon as it's cut. This explains why the cap is positioned close to the edge of the cutter. Another reason is that this arrangement stiffens the cutter and prevents "chattering." If a thicker shaving is needed, the cap must be set back further. In a smooth plane, 1/32 inch is sufficient, while in a jack plane, 1/8 inch is often preferable. The following are the planes commonly used:
The jack-plane, Fig. 102, 14" to 15" long, is the one used where a considerable amount of material is to be taken off to bring a piece of wood to size, and therefore the outline of the cutting edge instead of being straight is slightly curved or "crowned" so that in planing the surface of a board it makes a series of shallow grooves, the ridges of which must afterward be smoothed off by another plane. Also for beginners whose hands are not strong it is sometimes wise to grind the cutter with some "crown", in order to take off narrow shavings, which require less strength. For school use, where the jack-plane is used for all purposes, the cutter [page 72] is usually ground almost straight and only the corners rounded as in the smooth-plane and the fore-plane.5
The jack-plane, Fig. 102, 14" to 15" long, is the tool used when you need to remove a lot of material to get a piece of wood to the right size. Its cutting edge is slightly curved or "crowned" instead of straight, so when you plane the surface of a board, it creates a series of shallow grooves that need to be smoothed out with another plane afterward. For beginners with less hand strength, it can be beneficial to grind the cutter with some "crown" to produce narrower shavings, which are easier to handle. For school use, where the jack-plane is employed for various tasks, the cutter [page 72] is typically ground almost straight, with only the corners rounded like in the smooth-plane and the fore-plane.5
Footnote 5: In whetting a plane-bit, a slight crown may be given it by rubbing a bit harder at the ends of the edge than in the middle. Strop in the same way as a chisel (p. 59).
Footnote 5: When sharpening a plane bit, you can create a slight crown by applying a little more pressure at the edges than in the center. Strop it in the same way you would a chisel (p. 59).

Fig. 102. Sighting Along the Sole of Jack-Plane.
The fore-plane, 22" to 26" long, and the jointer, 28" to 30" long, are large planes, similar to the jack-plane, except that the cutting edge is straight. They are used for straightening and smoothing long pieces.
The fore-plane, 22" to 26" long, and the jointer, 28" to 30" long, are big planes, similar to the jack-plane, except the cutting edge is straight. They are used for straightening and smoothing long pieces.
The smooth-plane, 5½" to 10" long, is a short plane, similar to the jack-plane, except that the cutting edge is straight. It is used for smoothing.
The smooth-plane, 5½" to 10" long, is a short plane, like the jack-plane, but it has a straight cutting edge. It's used for smoothing.
These four planes, the jack-plane, the fore-plane, the jointer, and the smooth-plane, are essentially alike, and directions for the use of one apply to all.
These four types of planes—the jack plane, fore plane, jointer, and smooth plane—are fundamentally similar, and the instructions for using one apply to all.
There are two chief adjustments in the Bailey iron plane: the brass set-screw, see 8 in Fig. 101, which regulates the depth of the cut, and the lever, 9, which moves the cutter sidewise so that it may be made to cut evenly. The skilful worker keeps constant watch of these adjustments. It is well to form the habit of always sighting along the sole before beginning to plane, in order to see that the cutter projects properly, Fig. 102. It is a common mistake among beginners to let the cutter project too far.
There are two main adjustments on the Bailey iron plane: the brass set-screw, see 8 in Fig. 101, which controls the depth of the cut, and the lever, 9, which shifts the cutter sideways to ensure an even cut. A skilled worker keeps a close eye on these adjustments. It's a good idea to make it a habit to always look along the sole before starting to plane, to check that the cutter is properly extended, Fig. 102. Many beginners often make the mistake of letting the cutter extend too far.
It is important to know what is the best order of procedure in planing up a board. There are often reasons for omitting the planing up of one or more surfaces, but it is wise to form the habit of following a regular order, and the following is suggested as a good one:
It’s essential to understand the best order of operations for planning a board. There are often reasons to skip planing one or more surfaces, but it’s smart to get into the habit of following a consistent order. The following is suggested as a good approach:
1. Working face. Plane one broad side flat and smooth. Finish with the plane set to cut line shavings. Test with try-square. Mark this face with a distinct pencil mark, A, Fig. 103.
1. Working face. Plane one broad side flat and smooth. Finish with the plane set to take thin shavings. Test with a try-square. Mark this face with a clear pencil mark, A, Fig. 103.
2. Working edge. Plane one narrow side straight and square with the working face. Test with try-square, pressing the block of the try-square against the working face. Mark the working edge with two distinct pencil marks, B, Fig. 103.
2. Working edge. Plane one narrow side straight and square with the working face. Test with a try-square by pressing the block of the try-square against the working face. Mark the working edge with two clear pencil marks, B, Fig. 103.
3. End. First mark the width on the working face with the marking-gage, C, 1-2, Fig. 103. Chisel off the corner, a, of the piece outside this gaged line. True and smooth this end with the plane, making it square with both working face and working edge, D, 2, 3, 4, Fig. 103.
3. End. First, mark the width on the working face with the marking gauge, C, 1-2, Fig. 103. Chisel off the corner, a, of the piece outside this marked line. Use the plane to make this end flat and smooth, ensuring it’s square with both the working face and the working edge, D, 2, 3, 4, Fig. 103.
4. Length. Measure the length from the finished end, D, 2-3-4, score across the working face, D, 5-6, and working edge, D, 6-7, [page 73] using a sharp knife point and the try-square. Saw just outside this line, D, 5-6-7, with the back-saw, cut off the narrow corner, D, b, beyond the gaged line and plane true, E, Fig. 103.
4. Length. Measure the length from the finished end, D, 2-3-4, mark across the working face, D, 5-6, and working edge, D, 6-7, [page 73] using a sharp knife point and a try-square. Saw just outside this line, D, 5-6-7, with a back-saw, cut off the narrow corner, D, b, beyond the marked line and plane it true, E, Fig. 103.
5. Width. Plane to the center of the gaged line, E, 1-2. Test this edge from the working face, F, Fig. 103.
5. Width. Plan to the center of the gaged line, E, 1-2. Test this edge from the working face, F, Fig. 103.
6. Thickness. Mark the thickness with the marking-gage all around the piece, F, 8-9-10. Plane to the center of the gaged line, G, Fig. 103. Test this face for flatness.
6. Thickness. Use a marking gauge to mark the thickness all around the piece, F, 8-9-10. Plane to the center of the marked line, G, Fig. 103. Check this face for flatness.
In a word, the order to be followed is graphically represented in H, Fig. 103. The surfaces are numbered consecutively in the order in which they are to be planed.
In short, the order to be followed is clearly shown in H, Fig. 103. The surfaces are numbered sequentially in the order they should be planed.
The advantages of this order are these: by planing the working face first, a broad surface is secured to which the others may be made true. By planing the ends before the width is planed, the danger of splitting off fragments can be avoided by chiseling the corner of the unfinished edges, C, a, and D, b, Fig. 103, into a buttress. By planing the ends and the width before the thickness is planed, a dressed face is secured all around for gaging the thickness. In following this order all measurements and markings are made on a dressed face.
The benefits of this process are as follows: by planing the working face first, you create a wide surface that the other sides can be aligned with. By planing the ends before adjusting the width, you avoid the risk of breaking off pieces by chiseling the corners of the unfinished edges, C, a, and D, b, Fig. 103, into a support structure. By planing the ends and the width before adjusting the thickness, you ensure that there’s a smooth surface all around for measuring the thickness. By following this sequence, all measurements and markings are done on a smooth surface.
If there be any "wind" or twist in the board, this should be discovered first of all. This may be done roughly by sighting across the broad side of the board, Fig. 104, and more accurately by the use of "winding sticks," see Fig. 205, p. 113. Or the surface may be tested with the plane itself by tilting the plane on its long corner edge, and resting it on the board, while the worker looks between the board and the plane toward the light. It is evident that the plane must be turned in various directions to test for wind, and that a board only as long or as wide as the plane is long can be tested in this way. The try-square or any straight edge may be used for the same purpose, Fig. 105. If there be any wind in the board, this should at once be taken out of one face by planing down the high corners.
If there’s any “warp” or twist in the board, this should be found out first. You can do this roughly by looking across the wide side of the board, Fig. 104, and more accurately by using "winding sticks," see Fig. 205, p. 113. Another method is to test the surface with the plane itself by tilting it on its long corner edge and resting it on the board while you look between the board and the plane toward the light. It’s clear that the plane needs to be turned in different directions to check for warp, and that you can only test a board that’s as long or as wide as the plane. You can also use a try-square or any straight edge for the same purpose, Fig. 105. If there’s any warp in the board, you should immediately remove it from one side by planing down the high corners.
![]() Fig. 104. Sighting for Wind. |
![]() Fig. 105. Testing from Edge to Edge. |
In starting to plane, the worker should bear down on the knob at the front end of the plane. When the plane is well on the board, he should bear down equally on both [page 75] knob and handle, and as the plane begins to pass off the board he should put all the pressure on the handle end, Fig. 106. By taking pains thus, a convex surface will be avoided, the making of which is a common error of beginners. On the return stroke, the plane should be lifted or tilted so that the cutting edge will not be dulled by rubbing on the wood. This is especially important on rough and dirty boards, as it saves the cutting edge, and in fine work, as it saves the work. If the plane tear the wood instead of cutting it smooth, as it should, it is because the planing is "against the grain". This can often be avoided by noticing the direction of the grain before beginning to plane. But even if it be not noted beforehand, a stroke or two will show the roughness. In such a case, it is necessary simply to turn the wood around.
When starting to plane, the worker should press down on the knob at the front of the plane. Once the plane is securely on the board, he should apply equal pressure on both the knob and the handle. As the plane starts to come off the board, he should shift all the pressure to the handle end, as shown in Fig. 106. By doing this carefully, a convex surface can be avoided, which is a common mistake among beginners. On the return stroke, the plane should be lifted or tilted so that the cutting edge doesn’t get dulled by rubbing against the wood. This is particularly important on rough or dirty boards, as it preserves the cutting edge, and in fine work, as it protects the overall result. If the plane tears the wood instead of cutting it smoothly as it should, it's likely because the planing is "against the grain." This can usually be avoided by checking the direction of the grain before starting to plane. However, if the direction isn’t noted beforehand, a stroke or two will reveal any roughness. In such cases, it’s simply necessary to turn the wood around.

Fig. 106. Planing an Edge.
The accuracy of the work as it progresses should frequently be tested, and the eye should constantly be trained so that it can more and more be depended upon to detect inaccuracy, Fig. 107. As each surface is trued, it should be carefully smoothed with the cutter set to cut fine shavings.
The accuracy of the work as it progresses should be frequently tested, and the eye should constantly be trained so that it can increasingly be relied upon to detect inaccuracies, Fig. 107. As each surface is smoothed out, it should be carefully finished with the cutter adjusted to take fine shavings.

Fig. 107. Sighting an Edge.
In planing a very cross-grained piece of wood, there are several methods to use for securing a smooth surface. The frog of the plane should be moved forward so that the throat in the front of the cutter is a mere slit. In the ordinary plane it is necessary to remove the cutter in order to reset the frog, but in the Sargent plane and the Stanley "bed rock" plane, it can be set by a set-screw at the rear of the frog. Next, the cap should be set so that the cutter projects but very little beyond it, or, in technical language, the cutter should be set "fine." A sliding cut, see p. 53, should be taken with the plane, and sometimes it may be necessary to move the plane nearly at right angles to the general direction [page 76] of the grain. By these means even refractory pieces of wood can be well smoothed. See also scrapers, p. 91.
In planing a piece of wood with a tough grain, there are several methods to achieve a smooth surface. The frog of the plane should be adjusted forward so that the throat in front of the cutter is just a small slit. With a standard plane, you need to remove the cutter to reset the frog, but in the Sargent plane and the Stanley "bed rock" plane, it can be adjusted using a set-screw at the back of the frog. Next, the cap should be adjusted so that the cutter barely extends beyond it, or, in technical terms, the cutter should be set "fine." A sliding cut, see p. 53, should be made with the plane, and sometimes you may need to move the plane almost at a right angle to the general direction of the grain. By following these methods, even difficult pieces of wood can be smoothed effectively. Also, see scrapers, p. 91.
The choking of a plane is the stoppage of the throat by shavings. It may be due simply to the fact that the cutter is dull or that it projects too far below the sole of the plane. In a wooden plane choking is sometimes due to the crowding of shavings under some part of the wedge. When the adjustable frog in a modern plane is improperly placed choking may result. The frog should be far enough forward so that the cutter rests squarely upon it.
The choking of a plane happens when shavings block the throat. This can be caused by a dull cutter or one that sticks out too much below the sole of the plane. In a wooden plane, choking can sometimes happen because shavings get packed under part of the wedge. If the adjustable frog in a modern plane is not set correctly, it can also lead to choking. The frog should be positioned far enough forward so that the cutter rests evenly on it.
Choking may, and most commonly does, take place because the cap does not fit down tight on the cutter. This happens if the cap be nicked or uneven. In consequence, minute shavings are driven between these two irons and choking soon results. The remedy is to sharpen the cap, so that its edge makes a close fit with the cutter. The fit may be made still tighter by rubbing with a screwdriver the edge of the cap down on the cutter after it is screwed in place.
Choking usually happens because the cap doesn’t fit tightly on the cutter. This can occur if the cap is chipped or uneven. As a result, tiny shavings get stuck between the two pieces, leading to choking. The solution is to sharpen the cap so that its edge fits snugly against the cutter. You can make the fit even tighter by rubbing the edge of the cap down on the cutter with a screwdriver after it’s been screwed in place.
In no tool is it more important to keep the cutter sharp than in the plane. To remove the cutter, in order to sharpen it, first loosen the clamp lever and remove the clamp. Carefully remove the cap and cutter taking pains not to let the edge hit any part of the plane, then using the clamp as a screwdriver, loosen the cap-screw and slide the cap back along the slot in the cutter, where it can be held fast by a turn of the cap-screw. The edge is now free and can readily be whetted. When the cap needs to be entirely removed, for instance, for grinding, after it has been slid along the cutter slot, as before, it is turned at right angles to the cutter, and then slid down the slot until the cap-screw unbuttons from the cutter. The object in sliding the cap up the slot before turning it, is to prevent the danger of injuring the edge. Some caps are now made with the buttonhole at the upper end of the slot.
In no tool is it more important to keep the blade sharp than in the plane. To remove the blade for sharpening, first loosen the clamp lever and take off the clamp. Carefully remove the cap and blade, making sure not to let the edge touch any part of the plane. Then, using the clamp as a screwdriver, loosen the cap screw and slide the cap back along the slot in the blade, where it can be secured by turning the cap screw. The edge is now free and can be easily sharpened. When the cap needs to be completely removed, for example, for grinding, after sliding it along the blade slot as before, turn it at a right angle to the blade and slide it down the slot until the cap screw detaches from the blade. The reason for sliding the cap up the slot before turning it is to avoid damaging the edge. Some caps are now designed with the buttonhole at the top end of the slot.
After sharpening, (see under sharpening, p. 117.) the order is reversed for replacing the cutter. The cap is set at right angles to the cutter, the cap-screw dropped into the slot, the cap is slid up the slot, and turned into line with the cutter, and then slid down the slot till the edge of the cap comes quite near the edge of the cutter. Then the two are held firmly together with the left hand until the cap screw is turned tight.
After sharpening (see under sharpening, p. 117), the order for replacing the cutter is reversed. The cap is positioned at a right angle to the cutter, the cap screw is dropped into the slot, the cap is slid up the slot, and then aligned with the cutter. Next, it is slid down the slot until the edge of the cap is close to the edge of the cutter. Then, hold the two firmly together with your left hand while tightening the cap screw.
In replacing the cutter and cap in the plane, care should be taken not to injure the edge and to see that the Y adjustment lever fits [page 77] into the little slot in the cap; then finally the lever is thrown down tight. Then, by turning the plane sole upward and glancing down it, the proper adjustments with the brass set-screw and lateral adjustment lever are made. When the plane is not being used, it should rest either on a pillow (a little strip of wood in the bench trough), or on its side. In no case should it be dropped sole down flat on the bench.
When replacing the cutter and cap in the plane, be careful not to damage the edge and make sure the Y adjustment lever fits into the small slot in the cap; then finally, push the lever down tight. Next, by turning the plane upside down and looking at it, you can make the necessary adjustments with the brass set-screw and lateral adjustment lever. When not in use, the plane should rest either on a cushion (a small strip of wood in the bench trough) or on its side. It should never be dropped sole down flat on the bench.
The block-plane, Fig. 108, gets its name from the fact that it was first made for planing off the ends of clap-boards, a process called "blocking in".
The block-plane, Fig. 108, gets its name from the fact that it was first made for planing off the ends of clapboards, a process called "blocking in".

Fig. 108. Section of Block-Plane.
The names of the parts of the Bailey block-plane are6:
The names of the parts of the Bailey block-plane are6:
1. Cutter or bit or plane-iron.
Cutter, bit, or plane iron.
2. Clamp or lever cup.
2. Clamp or lever cup.
3. Cap-screw.
Cap screw.
4. Adjusting lever.
4. Adjustable lever.
5. Adjusting nut.
5. Adjustment nut.
6. Lateral adjustment.
6. Side adjustment.
7. Bottom.
7. Footer.
8. Mouth piece.
8. Speaker.
9. Eccentric plate.
9. Unique plate.
10. Knob.
10. Button.
Footnote 6: See footnote 4, p. 70
Footnote 6: See footnote 4, __A_TAG_PLACEHOLDER_0__
The block-plane was devised for use with one hand, as when it is used by carpenters in planing pieces not readily taken to a vise or in planing with a bench-hook. Hence it is made small, 3½" to 8" long, the clamp is rounded so as to act as a handle, and the cutter is lowered to an angle of about 20° to make the plane easy to grasp. The lower angle of the cutter makes it necessary that the bevel be on the upper side. Otherwise, to give clearance, the bevel would have to be made so long and so thin as to be weak. By putting the bevel up, the angle between the wood and the cutter is maintained practically [page 78] as in the smooth-plane. Since the block-plane is intended chiefly for use on end grain, no cap is needed to break the shavings. The adjustable throat makes it possible to cut a very fine shaving. To facilitate the cutting action, several forms of block-planes with a very low angle are now made.
The block plane was designed to be used with one hand, just like how carpenters use it for planing pieces that can't easily be held in a vise or for planing with a bench hook. Because of this, it's kept small, ranging from 3½" to 8" long. The clamp is rounded to function as a handle, and the cutter is set at an angle of about 20° to make the plane comfortable to hold. The lower angle of the cutter requires that the bevel be on the upper side. If the bevel were on the other side, it would have to be very long and thin to provide clearance, which would make it weak. By placing the bevel up, the angle between the wood and the cutter is maintained almost the same as in a smooth plane. Since the block plane is mainly used on end grain, no cap is needed to break the shavings. The adjustable throat allows for very fine shavings to be cut. To enhance the cutting action, several versions of block planes with a much lower angle are now available.
Where both hands are free to hold the plane, the block-plane has no advantage over a smooth-plane, even on end grain. Moreover, the cutter cannot be held so firmly in place as that of a smooth-plane, so that it requires constant adjustment. Hence it is not an easy tool for amateurs to handle. There is considerable lost motion in the adjusting nut, and the set-screw, which acts as a knob, is likely to work loose and be lost. It is hardly to be recommended as a part of the equipment of the individual bench in school shops.
Where both hands are free to hold the plane, the block plane doesn’t have any advantages over a smooth plane, even on end grain. Also, the cutter can't be held as securely as in a smooth plane, so it needs constant adjustments. This makes it a challenging tool for beginners to use. There’s quite a bit of play in the adjusting nut, and the set screw, which acts as a knob, can easily come loose and be lost. It's not really recommended as part of the equipment for an individual bench in school shops.
The piece to be planed with the block-plane may be held either in the vise, end up, or on a bench-hook, Fig. 109. In end planing in the vise, in order to avoid splintering the precaution should be taken to trim off a corner on the undressed edge, as directed on page 73, or else the planing must be done from both edges toward the center. The sliding cut is much easier than the straight cut, and hence there is a constant temptation to turn the plane at an angle perhaps at an expense of the flat surface desired.
The piece to be planed with the block plane can be held either in the vise, end up, or on a bench hook, Fig. 109. When planing the end in the vise, to prevent splintering, you should trim off a corner on the rough edge, as mentioned on page 73, or you should plane from both edges toward the center. The sliding cut is much easier than the straight cut, so there’s a constant temptation to angle the plane, which might compromise the flat surface you want.

Fig. 109, Using the Block-Plane and Bench-Hook.
In using the bench-hook the piece to be block-planed is placed with the working edge against the block, with the end to be planed to the right and flush with the edge of the bench-hook, in which position it is held with the left hand. The block-plane, held in the right hand, is placed on its side on the bench facing toward the work. In planing, the left hand holds the work firmly against the block of the bench-hook, pressing it somewhat to the right against the plane. The right hand holds the side of the plane flat on the bench and presses it to the left against the bench-hook and work. Held in this position the plane is pushed forward and back until the end is smoothed. Considerable practice is necessary to handle the block-plane well.
When using the bench-hook, place the piece you want to block-plane with the working edge against the block, with the end to be planed on the right and flush against the edge of the bench-hook. Hold it in this position with your left hand. The block-plane, which you hold in your right hand, should be placed on its side on the bench facing the work. While planing, your left hand should hold the work firmly against the block of the bench-hook, pressing it slightly to the right against the plane. Your right hand should keep the side of the plane flat on the bench and press it to the left against the bench-hook and work. With the plane in this position, push it forward and back until the end is smoothed out. It takes quite a bit of practice to use the block-plane effectively.
The scrub-plane is a short plane in which the crown of the cutter, Fig. 110, is quite curved. It is used to reduce surfaces rapidly.
The scrub-plane is a short plane with a highly curved cutter, as shown in Fig. 110. It's used for quickly flattening surfaces.
The scratch-plane, Fig. 111, has a toothed cutter which scratches fine lines along its course. It is used to roughen surfaces of hard wood which are to be glued together, for otherwise the glue would not adhere well. Some tropical woods are so hard that their surfaces can be reduced only by a scratch-plane. It is also useful in preparing the surface of a very cross-grained piece of wood which cannot be planed without chipping. By first scratching it carefully in all directions, it can then be scraped smooth. It is also called a scraper-plane, because accompanying the plane is a scraper which can be inserted in the same stock and inclined at any required angle. This plane-stock prevents the scraper from unduly lowering some portions of the surface. See also veneer-scraper, p. 92.
The scratch-plane, Fig. 111, has a serrated cutter that makes fine lines as it moves along. It’s used to roughen the surfaces of hard wood that need to be glued together, otherwise the glue won’t stick well. Some tropical woods are so tough that they can only be processed with a scratch-plane. It’s also helpful for preparing the surface of very irregularly grained wood that can't be planed without chipping. By carefully scratching it in all directions first, the surface can then be smoothed with a scraper. It's also called a scraper-plane, because it comes with a scraper that can be inserted into the same stock and tilted at the angle needed. This plane stock keeps the scraper from overly lowering some areas of the surface. See also veneer-scraper, p. 92.

Fig. 110. Cutter of Scrub-Plane. Fig. 111. Scratch-Plane and Scraper-Plane.

Fig. 112. Rabbet-Plane. Fig. 113. Molding-Plane.
The rabbeting- or rebating-plane, Fig. 112, is designed for use in cutting out a rectangular recess, such as the rabbet on the back of the picture-frames. In line with the right hand corner of the cutter is a removable spur to score the wood so that the shaving which follows [page 80] may be cut out clean and not torn out. With the addition of a guiding fence it is called a filletster. This may be used on either the right or left side. In the form shown in Fig. 112, there is also a depth gage.
The rabbeting- or rebating-plane, Fig. 112, is made for cutting out a rectangular recess, like the rabbet on the back of picture frames. Next to the right corner of the cutter, there’s a removable spur to score the wood so that the shaving that follows [page 80] can be cut out smoothly without tearing. When you add a guiding fence, it’s called a filletster. This can be used on either the right or left side. In the version shown in Fig. 112, there’s also a depth gauge.
In using this plane see that the corner of the cutter is in line with the sole, and that both it and the spur are sharp. Set the fence and the stop at the desired width and depth of the rabbet. At the first stroke the spur will score the width. This and every stroke should be taken as evenly and carefully as if it were the only one. In the effort to keep the fence pressed close to the side of the wood, the tendency is to tilt the plane over. This causes the very opposite effect from that desired, for the spur runs off diagonally, as in Fig. 114.
In using this plane, make sure the cutter's corner is aligned with the sole, and that both it and the spur are sharp. Set the fence and the stop to the desired width and depth of the rabbet. On the first stroke, the spur will mark the width. Every stroke should be taken as evenly and carefully as if it were the only one. In trying to keep the fence pressed firmly against the side of the wood, there's a tendency to tilt the plane. This creates the opposite effect, causing the spur to run off diagonally, as shown in Fig. 114.

Fig. 114. Result of Careless use of Rabbet-Plane.
If this happens stop planing at once, clean out the recess properly with a chisel and then proceed.
If this happens, stop planning immediately, clean out the recess thoroughly with a chisel, and then continue.
The dado-plane is much like the rabbeting-plane, except that it is provided with two spurs, one at each side of the cutting edge, to score the wood before cutting.
The dado-plane is pretty similar to the rabbeting-plane, but it has two spurs, one on each side of the cutting edge, to score the wood before making the cut.
The molding-plane, Fig. 113, as it name indicates, is for making moldings of various forms; as, quarter-round, half-round, ogee, etc.
The molding-plane, Fig. 113, as its name suggests, is used for creating moldings in different shapes, such as quarter-round, half-round, ogee, etc.

Fig. 115. Tonguing-and-Grooving Plane.
The circular-plane, Fig. 116. has a flexible steel face which can be adjusted to any required arc, convex or concave, so that curved surfaces may be planed.
The circular-plane, Fig. 116, has a flexible steel face that can be adjusted to any required arc, whether convex or concave, allowing curved surfaces to be planed.

Fig. 116. Circular-Plane.
The universal plane, Fig. 117, is a combination of various molding-, rabbeting-, matching- and other planes. It is capable of many adjustments and applications. The principal parts of this plane are: a main stock, A, with two sets of transverse sliding arms, a depth-gage, F, adjusted by a screw, and a slitting cutter with stop, a sliding section, B, with a vertically adjustable bottom, the auxiliary center bottom, C, to be placed when needed in front of the cutter as an extra support or stop. This bottom is adjustable both vertically and laterally. Fences, D and E. For fine work, fence D has a lateral adjustment by means of a thumb-screw. The fences can be used on either side of the plane, and the rosewood guides can be tilted to any desired angle up to 45°, by loosening the screws on the face. Fence E can be reversed for center-beading wide boards. For work thinner than the depth of the fence, the work may overhang the edge of the bench and fence E be removed. An adjustable stop, to be used in beading the edges of matched boards, is inserted on the left side of the sliding section B. A great variety of cutters are supplied, such as: molding, matching, sash, beading, reeding, fluting, hollow, round, plow, rabbet, and filletster. Special shapes can be obtained by order.
The universal plane, Fig. 117, is a combination of various molding, rabbeting, matching, and other planes. It can be adjusted and used in many ways. The main parts of this plane include: a main stock, A, with two sets of sliding arms that move sideways, a depth-gage, F, which is adjusted with a screw, and a slitting cutter with a stop. There’s also a sliding section, B, that has a bottom which can be adjusted vertically, plus an auxiliary center bottom, C, that can be placed in front of the cutter when needed for extra support or a stop. This bottom can be adjusted both up and down as well as sideways. Fences, D and E. For precision work, fence D has a lateral adjustment using a thumb screw. The fences can be attached to either side of the plane, and the rosewood guides can be tilted to any angle up to 45° by loosening the screws on the face. Fence E can be turned around for center-beading wide boards. If working with materials thinner than the fence’s depth, the work can hang over the edge of the bench, and fence E can be removed. An adjustable stop, used for beading the edges of matched boards, is placed on the left side of the sliding section B. A wide variety of cutters are supplied, including: molding, matching, sash, beading, reeding, fluting, hollow, round, plow, rabbet, and filletster. Special shapes can be ordered.

Fig. 117. Universal Plane.
The Use of the Universal Plane. Insert the proper cutter, adjusting it so that the portion of it in line with the main stock, A, will project below the sole the proper distance for cutting.
The Use of the Universal Plane. Insert the right cutter, adjusting it so that the part aligned with the main stock, A, extends below the sole the correct distance for cutting.
Adjust the bottom of the sliding section, B, so that the lowest portion of the cutter will project the proper distance below it for cutting. Tighten the check nuts on the transverse arms and then tighten the thumb-screws which secure the sliding section to the arms. The sliding section is not always necessary, as in a narrow rabbet or bead.
Adjust the bottom of the sliding section, B, so the lowest part of the cutter extends the correct distance below it for cutting. Tighten the check nuts on the transverse arms, and then tighten the thumb-screws that secure the sliding section to the arms. The sliding section isn't always needed, such as in a narrow rabbet or bead.
When an additional support is needed for the cutter, the auxiliary center bottom, C, may be adjusted in front of it. This may also be used as a stop.
When extra support is needed for the cutter, the auxiliary center bottom, C, can be adjusted in front of it. This can also be used as a stop.
Adjust one or both of the fences, D and E, and fasten with the thumb-screws. Adjust the depth-gage, F, at the proper depth.
Adjust one or both of the fences, D and E, and secure them with the thumb screws. Set the depth gauge, F, at the correct depth.
For a dado remove the fences and set the spurs parallel with the edges of the cutter. Insert the long adjustable stop on the left hand of the sliding section. For slitting, insert the cutter and stop on the right side of the main stock and use either fence for a guide.
For a dado, take off the fences and align the spurs parallel to the edges of the cutter. Place the long adjustable stop on the left side of the sliding section. For slitting, position the cutter and stop on the right side of the main stock and use either fence as a guide.
For a chamfer, insert the desired cutter, and tilt the rosewood guides on the fences to the required angle. For chamfer beading use in the same manner, and gradually feed the cutter down by means of the adjusting thumb-nut.
For a chamfer, insert the desired cutter and tilt the rosewood guides on the fences to the needed angle. For chamfer beading, do the same and gradually lower the cutter using the adjusting thumb-nut.
There are also a number of planelike tools such as the following:
There are also several plane-like tools such as the following:
The spoke-shave, Fig. 118. works on the same principle as a plane, except that the guiding surface is very short. This adapts it to work with curved outlines. It is a sort of regulated draw-shave. It is sometimes made of iron with an adjustable mouth, which is a convenient form for beginners to use, and is easy to sharpen. The pattern-makers spokeshave, Fig. 119, which has a wooden frame, is better suited to more careful work. The method of using the spokeshave is shown in Fig. 120.
The spoke-shave, Fig. 118, operates on the same principle as a plane, but the guiding surface is much shorter. This makes it suitable for working with curved shapes. It's like a controlled draw-shave. Sometimes, it's made of iron with an adjustable mouth, which is a handy option for beginners and easy to sharpen. The pattern-makers spokeshave, Fig. 119, which has a wooden frame, is more appropriate for detailed work. The technique for using the spokeshave is illustrated in Fig. 120.

Fig. 118. Iron Spokeshave. Fig. 119. Pattern-maker's Spokeshave.

Fig. 120. Using a Spokeshave.
The router-plane, Figs. 121 and 122, is used to lower a certain part of a surface and yet keep it parallel with the surrounding part, and it is particularly useful in cutting panels, dadoes, and grooves. The cutter has to be adjusted for each successive cut. Where there are a number of dadoes to be cut of the same depth, it is wise not to finish them one at a time, but to carry on the cutting of all together, lowering the cutter after each round. In this way all the dadoes will be finished at exactly the same depth.
The router-plane, Figs. 121 and 122, is used to lower a specific part of a surface while keeping it parallel to the surrounding area. It's especially helpful for cutting panels, dadoes, and grooves. The cutter needs to be adjusted for each cut. When you have several dadoes to cut to the same depth, it's better to avoid finishing them one by one; instead, work on them all at once, lowering the cutter after each pass. This way, all the dadoes will be finished at exactly the same depth.

Fig. 121. Router-Plane.

Fig. 122. Using a Router-Plane.
The dowel-pointer, Fig. 123, is a convenient tool for removing the sharp edges from the ends of dowel pins. It is held in a brace. The cutter is adjustable and is removable for sharpening.
The dowel-pointer, Fig. 123, is a handy tool for smoothing out the sharp edges on the ends of dowel pins. It’s held in a brace. The cutter is adjustable and can be removed for sharpening.
The cornering tool, Fig. 124, is a simple device for rounding sharp corners. A cutter at each end cuts both ways so that it can be used with the grain without changing the position of the work. The depth of the cut is fixed.
The cornering tool, Fig. 124, is a straightforward device for rounding sharp corners. A cutter on each end cuts in both directions so that it can be used with the grain without needing to change the position of the work. The depth of the cut is set.

Fig. 123. Dowel-Pointer. Fig. 124. Cornering Tool.
2. BORING TOOLS.
Some boring tools, like awls, force the material apart, and some, like augers, remove material.
Some basic tools, like awls, push the material apart, while others, like augers, take material away.
The brad-awl, Fig. 125, is wedge-shaped, and hence care needs to be taken in using it to keep the edge across the grain so as to avoid splitting the wood, especially thin wood. The size is indicated by the length of the blade when new,—a stupid method. The awl is useful for making small holes in soft wood, and it can readily be sharpened by grinding.
The brad-awl, Fig. 125, has a wedge shape, so you need to be careful when using it to ensure the edge is across the grain to avoid splitting the wood, especially when working with thin pieces. The size is measured by the length of the blade when it's new—a rather inefficient method. The awl is helpful for creating small holes in soft wood, and you can easily sharpen it by grinding.

125 | 126 | 127 | 128 | 129 | 130 |
Fig. 125. Brad-Awl. Fig. 126. Twist-Drill. Fig. 127. Twist-Bit. Fig. 128. German Gimlet-Bit. Fig. 129. Bit-Point Drill. Fig. 130. Auger-Bit. |

131 | 132 | 133 | 134 | 135 | 136 |
Fig. 131. Plug-Cutter. Fig. 132. Center-Bit. Fig. 133. Foerstner Auger-Bit. Fig. 134. Expansive-Bit. Fig. 135. Reamer. Fig. 136. Rose Countersink. |
Gimlets and drills are alike in that they cut away material, but unlike in that the cutting edge of the gimlet is on the side, while the cutting edge of the drill is on the end.
Gimlets and drills are similar because they remove material, but they differ in that the cutting edge of the gimlet is on the side, while the cutting edge of the drill is at the tip.
Twist-drills, Fig. 126, are very hard and may be used in drilling metal. They are therefore useful where there is danger of meeting nails, as in repair work. Their sizes are indicated by a special drill gage, Fig. 220, p. 116.
Twist drills, Fig. 126, are very tough and can be used for drilling metal. They are particularly helpful when there's a chance of hitting nails, like in repair jobs. Their sizes are shown on a specific drill gauge, Fig. 220, p. 116.
Twist-bits, Fig. 127, are like twist-drills except that they are not hard enough to use for metal. Their sizes are indicated on the tang in 32nds of an inch. Both twist-bits and drill-bits have the advantage over gimlet-bits in that they are less likely to split the wood.
Twist-bits, Fig. 127, are similar to twist-drills but aren't hard enough for metal use. Their sizes are marked on the tang in 32nds of an inch. Both twist-bits and drill-bits are better than gimlet-bits because they're less likely to split the wood.
Twist-bits and twist-drills are sharpened on a grindstone, care being taken to preserve the original angle of the cutting edge so that the edge will meet the wood and there will be clearance.
Twist bits and twist drills are sharpened on a grindstone, ensuring that the original angle of the cutting edge is maintained so that the edge will contact the wood properly and allow for clearance.
German gimlet-bits, Fig. 128, have the advantage of centering well. The size is indicated on the tang in 32nds of an inch. They are useful in boring holes for short blunt screws as well as deep holes. They cannot be sharpened readily but are cheap and easily replaced.
German gimlet-bits, Fig. 128, are great for centering accurately. The size is marked on the tang in 32nds of an inch. They work well for boring holes for both short blunt screws and deep holes. They can’t be sharpened easily, but they are inexpensive and can be replaced without much hassle.
Bit-point drills, Fig. 129, are useful for accurate work, but are expensive.
Bit-point drills, Fig. 129, are great for precise work, but they come at a high cost.
Auger-bits, Fig. 130, have several important features. The spur centers the bit in its motion, and since it is in the form of a pointed screw draws the auger into the wood. Two sharp nibs on either side score the circle, out of which the lips cut the shavings, which are then carried out of the hole by the main screw of the tool. The size of auger-bits is indicated by a figure on the tang in 16ths of an inch. Thus 9 means a diameter of 9⁄16".
Auger bits, Fig. 130, have several important features. The spur centers the bit while it’s in motion, and since it’s shaped like a pointed screw, it pulls the auger into the wood. Two sharp edges on either side score the circle, and then the lips cut the shavings, which are carried out of the hole by the main screw of the tool. The size of auger bits is marked by a number on the tang in 16ths of an inch. So, a 9 means a diameter of 9⁄16".
There are three chief precautions to be taken in using auger-bits. (1) One is to bore perpendicularly to the surface. A good way to do this is to lay the work flat, either on the bench or in the vise, and sight first from the front and then from the side of the work, to see that the bit is perpendicular both ways. The test may also be made with the try-square, Fig. 137, or with a plumb-line, either by the worker, or in difficult pieces, by a fellow worker. The sense of perpendicularity, however, should constantly be cultivated. (2) Another precaution is that, in thru boring, the holes should not be bored quite thru from one side, lest the wood be splintered off on the back. When the spur pricks thru, the bit should be removed, the piece turned over, and the boring finished, putting the spur in the hole which is pricked [page 86] thru in boring from the first side. It is seldom necessary to press against the knob of the brace in boring, as the thread on the spur will pull the bit thru, especially in soft wood. Indeed, as the bit reaches nearly thru the board, if the knob is gently pulled back, then when the spur pricks thru the bit will be pulled out of its hole. This avoids the necessity of constantly watching the back of the board to see if the spur is thru. (3) In stop boring, as in boring for dowels or in making a blind mortise, care should be taken not to bore thru the piece. For this purpose an auger-bit-gage, Fig. 219, p. 116, may be used, or a block of wood of the proper length thru which a hole has been bored, may be slipped over the bit, or the length of bit may be noted before boring, and then the length of the projecting portion deducted, or the number of turns needed to reach the required depth may be counted on a trial piece. Tying a string around a bit, or making a chalk mark on it is folly.
There are three main precautions to take when using auger bits. (1) First, you should drill straight into the surface. A good way to ensure this is to lay the work flat, either on the bench or in a vise, and sight from both the front and the side to make sure the bit is vertical in both directions. You can also check with a try-square, Fig. 137, or with a plumb line, either by yourself or with a coworker for more challenging pieces. However, you should always develop a sense of what’s perpendicular. (2) Another precaution is to avoid drilling all the way through from one side, as this can splinter the wood on the back. When the spur breaks through, remove the bit, flip the piece over, and finish drilling by placing the spur in the hole made when boring from the first side. Generally, you don’t need to push against the knob of the brace while drilling, as the thread on the spur will pull the bit through, especially in soft wood. In fact, as the bit approaches the other side, if you gently pull back on the knob, the spur will pull the bit out once it breaks through. This way, you don’t have to constantly check the back of the board to see if the spur has come through. (3) When stop boring, as in drilling for dowels or making a blind mortise, be careful not to drill all the way through the piece. For this, you can use an auger-bit gauge, Fig. 219, p. 116, or a block of wood of the correct length with a hole bored through it can be placed over the bit. Alternatively, note the length of the bit before drilling, then subtract the length of the part that sticks out, or count the number of turns needed to reach the desired depth on a test piece. Tying a string around a bit or making a chalk mark on it is pointless. [page 86]

Fig. 137. Using a Try-Square as a Guide in Boring.
Auger-bits are sharpened with an auger-bit file, Fig. 142, p. 90, a small flat file with two narrow safe edges at one end and two wide safe edges at the other. The "nibs" should be filed on the inside so that the diameter of the cut may remain as large as that of the body of the bit. The cutting lip should be sharpened from the side toward the spur, care being taken to preserve the original angle so as to give clearance. If sharpened from the upper side, that is, the side toward the shank, the nibs will tend to become shorter.
Auger bits are sharpened using an auger bit file, Fig. 142, p. 90, which is a small flat file with two narrow safe edges on one end and two wide safe edges on the other. The "nibs" should be filed on the inside to ensure that the diameter of the cut remains as large as that of the body of the bit. The cutting lip should be sharpened from the side toward the spur, making sure to maintain the original angle for proper clearance. If sharpened from the upper side, meaning the side facing the shank, the nibs will tend to become shorter.
The plug-cutter, Fig. 131, is useful for cutting plugs with which to cover the heads of screws that are deeply countersunk.
The plug-cutter, Fig. 131, is handy for cutting plugs to cover the heads of screws that are set deep into the surface.
Center-bits, Fig. 132, work on the same principle as auger-bits, except that the spurs have no screw, and hence have to be pushed forcibly into the wood. Sizes are given in 16ths of an inch. They are useful for soft wood, and in boring large holes in thin material which is likely to split. They are sharpened in the same way as auger-bits.
Center-bits, Fig. 132, operate on the same principle as auger-bits, except that the spurs don’t have a screw, so they need to be pushed hard into the wood. Sizes are specified in 16ths of an inch. They are great for soft wood and for drilling large holes in thin materials that might split. They are sharpened in the same way as auger-bits.
Foerstner bits, Fig. 133, are peculiar in having no spur, but are centered by a sharp edge around the circumference. The size is indicated on the tang, in 16ths of an inch. They are useful in boring into end grain, and in boring part way into wood so thin that a spur would pierce thru. They can be sharpened only with special appliances.
Foerstner bits, Fig. 133, are unique because they don’t have a spur, but they are centered by a sharp edge along the outer edge. The size is marked on the tang, in 16ths of an inch. They are great for drilling into end grain and for partially drilling into wood that’s so thin that a spur would go through. They can only be sharpened with specific tools.
Expansive-bits, Fig. 134, are so made as to bore holes of different sizes by adjusting the movable nib and cutter. There are two sizes, the small one with two cutters, boring from ½" to 1½" and the large one with three cutters boring from ⅞" to 4". They are very useful on particular occasions, but have to be used with care.
Expansive-bits, Fig. 134, are designed to drill holes of various sizes by adjusting the movable nib and cutter. There are two sizes: the small one with two cutters, which drills from ½" to 1½", and the large one with three cutters, which drills from ⅞" to 4". They are very useful on certain occasions, but need to be used carefully.
Reamers, Fig. 135, are used for enlarging holes already made. They are made square, half-round and six cornered in shape.
Reamers, Fig. 135, are used for enlarging holes that have already been made. They come in square, half-round, and six-sided shapes.
Countersinks, Fig. 136, are reamers in the shape of a flat cone, and are used to make holes for the heads of screws. The rose countersink is the most satisfactory form.
Countersinks, Fig. 136, are reamers shaped like a flat cone and are used to create holes for screw heads. The rose countersink is the most effective type.

Fig 138. Washer-Cutter.
The washer-cutter, Fig. 138, is useful not only for cutting out washers but also for cutting holes in thin wood. The size is adjustable.
The washer-cutter, Fig. 138, is handy for not just cutting out washers but also for making holes in thin wood. The size can be adjusted.
3. CHOPPING TOOLS.
The primitive celt, which was hardly more than a wedge, has been differentiated into three modern hand tools, the chisel, see above, p. 53, the ax, Fig. 139, and the adze, Fig. 141.
The basic celt, which was basically just a wedge, has evolved into three modern hand tools: the chisel, see above, p. 53, the ax, Fig. 139, and the adze, Fig. 141.
The ax has also been differentiated into the hatchet, with a short handle, for use with one hand, while the ax-handle is long, for use with two hands. Its shape is an adaption to its manner of use. It is oval in order to be strongest in the direction of the blow and also in order that the axman may feel and guide the direction of the blade. The curve at the end is to avoid the awkward raising of the left hand at the moment of striking the blow, and the knob keeps it from slipping thru the hand. In both ax and hatchet there is a two-beveled edge. This is for the sake of facility in cutting into the wood at any angle.
The ax has also been adapted into the hatchet, which has a short handle for one-handed use, while the ax-handle is longer for two-handed use. Its shape is designed for how it’s used. It’s oval to provide strength in the direction of the blow and to help the axman feel and control the angle of the blade. The curve at the end prevents the awkward lifting of the left hand at the moment of impact, and the knob stops it from slipping out of the hand. Both the ax and the hatchet have a two-beveled edge. This design makes it easier to cut into the wood at any angle.
There are two principal forms, the common ax and the two bitted ax, the latter used chiefly in lumbering. There is also a wedge-shaped ax for splitting wood. As among all tools, there is among axes a great variety for special uses.
There are two main types: the common axe and the double-bit axe, with the latter primarily used in logging. There's also a wedge-shaped axe for splitting wood. Like all tools, there is a wide variety of axes designed for specific purposes.

Fig. 139. Ax. | Fig. 140. Shingling Hatchet. | Fig. 141. Carpenter's Adze. |
The hatchet has, beside the cutting edge, a head for driving nails, and a notch for drawing them, thus combining three tools in one. The shingling hatchet, Fig. 140, is a type of this.
The hatchet has, along with the cutting edge, a head for driving nails and a notch for pulling them out, effectively combining three tools into one. The shingling hatchet, Fig. 140, is a type of this.
The adze, the carpenter's house adze, Fig. 141, is flat on the lower side, since its use is for straightening surfaces.
The adze, the carpenter's house adze, Fig. 141, is flat on the bottom side because it’s used for smoothing out surfaces.
WOOD HAND TOOLS.
References:*
References:*
(1) Cutting.
Cutting.
Goss, p. 22.
Goss, p. 22.
Smith, R. H., pp. 1-8.
Smith, R. H., pp. 1-8.
Chisel.
Chisel tool.
Barnard, pp. 59-73.
Barnard, pp. 59-73.
Selden, pp. 44-50, 145-147.
Selden, pp. 44-50, 145-147.
Barter, pp. 93-96.
Barter, pp. 93-96.
Griffith, pp. 53-64.
Griffith, pp. 53-64.
Goss, pp. 20-26.
Goss, pp. 20-26.
Sickels, pp. 64-67.
Sickels, pp. 64-67.
Wheeler, 357, 421, 442.
Wheeler, 357, 421, 442.
Knife.
Knife.
Barnard, pp. 48-58.
Barnard, pp. 48-58.
Selden, pp. 26-28, 158.
Selden, pp. 26-28, 158.
Saw.
Saw.
Griffith, pp. 20-27.
Griffith, pp. 20-27.
Barnard, pp. 114-124.
Barnard, pp. 114-124.
Selden, pp. 41-43, 179-182.
Selden, pp. 41-43, 179-182.
Wheeler, pp. 466-473.
Wheeler, pp. 466-473.
Hammacher, pp. 309-366.
Hammacher, pp. 309-366.
Goss, pp. 26-41.
Goss, pp. 26-41.
Sickels, pp. 76-79, 84.
Sickels, pp. 76-79, 84.
Smith, R. H., 43-55.
Smith, R. H., 43-55.
Diston, pp. 129-138.
Diston, pp. 129-138.
Plane.
Flight.
Barnard, pp. 74-80.
Barnard, pp. 74-80.
Selden, pp. 11-26, 165-175.
Selden, pp. 11-26, 165-175.
Sickels pp. 72-75, 116.
Sickels pp. 72-75, 116.
Wheeler, pp. 445-458.
Wheeler, pp. 445-458.
Hammacher, pp. 377-400.
Hammacher, pp. 377-400.
Smith, R. H., pp. 16-31.
Smith, R. H., pp. 16-31.
Larsson, p. 19.
Larsson, p. 19.
Goss, pp. 41-52.
Goss, pp. 41-52.
Barter, pp. 96-109.
Barter, pp. 96-109.
Griffith, pp. 28-45.
Griffith, pp. 28–45.
(2) Boring Tools.
Dull Tools.
Barnard, pp. 125-135.
Barnard, pp. 125-135.
Goss, pp. 53-59.
Goss, pp. 53-59.
Griffith, pp. 47-52.
Griffith, pp. 47-52.
Seldon, pp. 38-40, 141-144.
Seldon, pp. 38-40, 141-144.
Wheeler, pp. 353-356.
Wheeler, pp. 353-356.
(3) Chopping Tools.
Cutting Tools.
Barnard, pp. 80-88.
Barnard, pp. 80-88.
Chapter 4, Continued.
WOOD HAND TOOLS.
4. SCRAPING TOOLS.
Scraping tools are of such nature that they can only abrade or smooth surfaces.
Scraping tools are designed to either roughen or smooth surfaces.
142 | 143 | 144 | 145 | 146 | 147 | 148 |
Fig. 142. Auger-Bit-File. Fig. 143. Single-Cut Blunt, Flat, Bastard File. Fig. 144. Three-Square Single-Cut File. Fig. 145. Open Cut, Taper, Half-Round File. Fig. 146. Double-Cut File. Fig. 147. Cabinet Wood-Rasp. Fig. 148. File-Card. |
Files. Figs. 142-146, are formed with a series of cutting edges or teeth. These teeth are cut when the metal is soft and cold and then the tool is hardened. There are in use at least three thousand varieties of files, each of which is adapted to its particular purpose. Lengths are measured from point to heel exclusive of the tang. They are classified: (1) according to their outlines into blunt, (i. e., having a uniform cross section thruout), and taper; (2) according to the shape of their [page 91] cross-section, into flat, square, three-square or triangular, knife, round or rat-tail, half-round, etc.; (3) according to the manner of their serrations, into single cut or "float" (having single, unbroken, parallel, chisel cuts across the surface), double-cut, (having two sets of chisel cuts crossing each other obliquely,) open cut, (having series of parallel cuts, slightly staggered,) and safe edge, (or side,) having one or more uncut surfaces; and (4) according to the fineness of the cut, as rough, bastard, second cut, smooth, and dead smooth. The "mill file," a very common form, is a flat, tapered, single-cut file.
Files. Figs. 142-146 are made with a set of cutting edges or teeth. These teeth are shaped when the metal is soft and cold, and then the tool is hardened. There are at least three thousand types of files in use, each designed for a specific purpose. Lengths are measured from the tip to the heel, not including the tang. They are classified: (1) by their shape into blunt (i.e., having a consistent cross-section throughout) and taper; (2) by the shape of their [page 91] cross-section into flat, square, triangular, knife, round or rat-tail, half-round, etc.; (3) by how their serrations are arranged, into single cut or "float" (with single, unbroken, parallel, chisel cuts across the surface), double-cut (with two sets of chisel cuts crossing each other diagonally), open cut (with a series of parallel cuts, slightly staggered), and safe edge (or side), which has one or more uncut surfaces; and (4) by the fineness of the cut, as rough, bastard, second cut, smooth, and dead smooth. The "mill file," a very common type, is a flat, tapered, single-cut file.
Rasps, Fig. 147, differ from files in that instead of having cutting teeth made by lines, coarse projections are made by making indentations with a triangular point when the iron is soft. The difference between files and rasps is clearly shown in Fig. 149.
Rasps, Fig. 147, are different from files because instead of having cutting teeth created by lines, they have rough protrusions made by pressing indentations with a triangular point when the metal is soft. The distinction between files and rasps is clearly illustrated in Fig. 149.

Fig. 149. a. Diagram of a Rasp Tooth.
b. Cross-Section of a Single-Cut File.
It is a good rule that files and rasps are to be used on wood only as a last resort, when no cutting tool will serve. Great care must be taken to file flat, not letting the tool rock. It is better to file only on the forward stroke, for that is the way the teeth are made to cut, and a flatter surface is more likely to be obtained.
It’s a good rule that files and rasps should only be used on wood as a last resort, when no cutting tool will do. You need to be very careful to file flat, making sure the tool doesn’t rock. It’s best to file only on the forward stroke, since that’s how the teeth are designed to cut, and you’re more likely to get a flatter surface that way.
Both files and rasps can be cleaned with a file-card, Fig. 148. They are sometimes sharpened with a sandblast, but ordinarily when dull are discarded.
Both files and rasps can be cleaned with a file-card, Fig. 148. They are sometimes sharpened with a sandblast, but usually when they become dull, they are thrown away.
Scrapers are thin, flat pieces of steel. They may be rectangular, or some of the edges may be curved. For scraping hollow surfaces curved scrapers of various shapes are necessary. Convenient shapes are shown in Fig. 150. The cutting power of scrapers depends upon the delicate burr or feather along their edges. When properly sharpened they take off not dust but fine shavings. Scrapers are particularly useful in smoothing cross-grained pieces of wood, and in cleaning off glue, old varnish, etc.
Scrapers are flat, thin pieces of steel. They can be rectangular, or some edges might be curved. For scraping curved hollow surfaces, different shapes of curved scrapers are needed. Convenient shapes are shown in Fig. 150. The cutting effectiveness of scrapers relies on the fine burr or feather along their edges. When sharpened correctly, they remove not dust but fine shavings. Scrapers are especially helpful for smoothing wood with cross-grain and for cleaning off glue, old varnish, and so on.

Fig. 150. Molding-Scrapers.
There are various devices for holding scrapers in frames or handles, such as the scraper-plane, Fig. 111, p. 79, the veneer-scraper, and box-scrapers. The veneer-scraper, Fig. 151, has the advantage that the blade may be sprung to a slight curve by a thumb-screw in [page 92] the middle of the back, just as an ordinary scraper is when held in the hands.
There are different tools for attaching scrapers to frames or handles, like the scraper-plane, Fig. 111, p. 79, the veneer-scraper, and box-scrapers. The veneer-scraper, Fig. 151, has the benefit that the blade can be adjusted to a slight curve using a thumb-screw located in the middle of the back, much like a regular scraper when held in your hands. [page 92]

Fig. 151. Using a Veneer-Scraper.
In use, Fig. 152, the scraper may be either pushed or pulled. When pushed, the scraper is held firmly in both hands, the fingers on the forward and the thumbs on the back side. It is tilted forward, away from the operator, far enough so that it will not chatter and is bowed back slightly, by pressure of the thumbs, so that there is no risk of the corners digging in. When pulled the position is reversed.
In use, Fig. 152, the scraper can either be pushed or pulled. When pushing, hold the scraper firmly with both hands, fingers on the front and thumbs on the back. Tilt it forward, away from you, enough to prevent chattering, and slightly bow it back with your thumbs to avoid the corners digging in. When pulling, just reverse the position.

Fig. 152. Using a Cabinet-Scraper.
One method of sharpening the scraper is as follows: the scraper is first brought to the desired shape, straight or curved. This may be done either by grinding on the grindstone or by filing with a smooth, flat file, the scraper, while held in a vise. The edge is then carefully draw-filed, i. e., the file, a smooth one, is held (one hand at each end) directly at right angles to the edge of the scraper, Fig. 153, and moved sidewise from end to end of the scraper, until the edge is quite square with the sides. Then the scraper is laid flat on the oilstone and rubbed, first on one side and then on the other till the sides are bright and smooth along the edge, Fig. 154. Then it is set on edge on the stone and rubbed till there are two sharp square corners all along the edge, Fig. 155. Then it is put in the vise again and by means of a burnisher, or scraper steel, both of these corners are carefully turned or bent over so as to form a fine burr. This is done by tipping the scraper steel at a slight angle with the edge and rubbing it firmly along the sharp corner, Fig. 156.
One way to sharpen the scraper is as follows: first, shape the scraper into the desired form, whether straight or curved. You can do this by grinding it on a grindstone or by filing it with a smooth, flat file while it's held in a vise. Next, carefully draw-file the edge, meaning that you hold the file (one hand at each end) directly at right angles to the edge of the scraper, as shown in Fig. 153, and move it side to side from one end of the scraper to the other until the edge is perfectly square with the sides. Then, lay the scraper flat on an oilstone and rub it, first on one side and then on the other, until the sides are bright and smooth along the edge, as shown in Fig. 154. After that, place it on edge on the stone and rub it until both corners along the edge are sharp and square, as shown in Fig. 155. Then, put it back in the vise and, using a burnisher or scraper steel, carefully turn or bend both corners over to create a fine burr. Do this by angling the scraper steel slightly with the edge and rubbing it firmly along the sharp corner, as shown in Fig. 156.

Fig. 153. Sharpening a Cabinet-Scraper: 1st Step, Drawfiling.
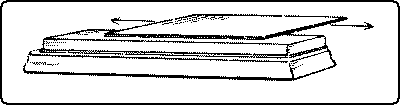
Fig. 154. Sharpening a Cabinet-Scraper: 2nd Step, Whetting.

Fig. 155. Sharpening a Cabinet-Scraper: 3rd Step, Removing the Wire-Edge.

Fig. 156. Sharpening a Cabinet-Scraper: 4th Step, Turning the Edge.
To resharpen the scraper it is not necessary to file it afresh every time, but only to flatten out the edges and turn them again with [page 93] slightly more bevel. Instead of using the oilstone an easier, tho less perfect, way to flatten out the burr on the edges is to lay the scraper flat on the bench near the edge. The scraper steel is then passed rapidly to and fro on the flat side of the scraper, Fig. 157. After that the edge should be turned as before.
To resharpen the scraper, you don't need to file it down completely every time; just flatten out the edges and bevel them again slightly. Instead of using an oilstone, a simpler, although less effective, method to smooth out the burrs on the edges is to lay the scraper flat on the bench near the edge. Then, quickly move the scraper steel back and forth on the flat side of the scraper, as shown in Fig. 157. After that, you should turn the edge as before.

Fig. 157. Resharpening a Cabinet-Scraper: Flattening the Edge.
Sandpaper. The "sand" is crushed quartz and is very hard and sharp. Other materials on paper or cloth are also used, as carborundum, emery, and so on. Sandpaper comes in various grades of coarseness from No. 00 (the finest) to No. 3, indicated on the back of each sheet. For ordinary purposes No. 00 and No. 1 are sufficient. Sandpaper sheets may readily be torn by placing the sanded side down, one-half of the sheet projecting over the square edge of the bench. With a quick downward motion the projecting portion easily parts. Or it may be torn straight by laying the sandpaper on a bench, sand side down, holding the teeth of a back-saw along the line to be torn. In this case, the smooth surface of the sandpaper would be against the saw.
Sandpaper. The "sand" is crushed quartz, which is very hard and sharp. Other materials used on paper or cloth include carborundum, emery, and more. Sandpaper comes in different grades of coarseness, from No. 00 (the finest) to No. 3, which is indicated on the back of each sheet. For everyday use, No. 00 and No. 1 are enough. Sandpaper sheets can easily be torn by placing the sanded side down, with half of the sheet hanging over the edge of the bench. With a quick downward motion, the hanging portion comes off easily. Alternatively, it can be torn straight by laying the sandpaper on the bench, sand side down, and using the teeth of a back-saw along the line to be torn. In this case, the smooth side of the sandpaper will be against the saw.
Sandpaper should never be used to scrape and scrub work into shape, but only to obtain an extra smoothness. Nor ordinarily should it be used on a piece of wood until all the work with cutting tools is done, for the fine particles of sand remaining in the wood dull the edge of the tool. Sometimes in a piece of cross-grained wood rough places will be discovered by sandpapering. The surface should then be wiped free of sand and scraped before using a cutting tool [page 94] again. In order to avoid cross scratches, work should be "sanded" with the grain, even if this takes much trouble. For flat surfaces, and to touch off edges, it is best to wrap the sandpaper over a rectangular block of wood, of which the corners are slightly rounded, or it may be fitted over special shapes of wood for specially shaped surfaces. The objection to using the thumb or fingers instead of a block, is that the soft portions of the wood are cut down faster than the hard portions, whereas the use of a block tends to keep the surface even.
Sandpaper should never be used to scrape and scrub a workpiece into shape; it's meant only for achieving a smoother finish. It shouldn’t be applied to wood until all cutting tool work is done since fine particles of sand left in the wood can dull the tool's edge. Occasionally, when sanding cross-grained wood, rough spots may be uncovered. The surface should then be cleared of sand and scraped before using a cutting tool [page 94] again. To prevent cross scratches, always sand with the grain, even if it takes more effort. For flat surfaces and to refine edges, it's best to wrap sandpaper around a rectangular block of wood with slightly rounded corners, or it can be fitted to specially shaped pieces of wood for uniquely shaped surfaces. The downside of using your thumb or fingers instead of a block is that the softer parts of the wood get cut down faster than the harder areas, while a block helps keep the surface even.
Steel wool is made by turning off fine shavings from the edges of a number of thin discs of steel, held together in a lathe. There are various grades of coarseness, from No. 00 to No. 3. Its uses are manifold: as a substitute for sandpaper, especially on curved surfaces, to clean up paint, and to rub down shellac to an "egg-shell" finish. Like sandpaper it should not be used till all the work with cutting tools is done. It can be manipulated until utterly worn out.
Steel wool is created by removing fine shavings from the edges of several thin discs of steel that are held together in a lathe. There are different grades of coarseness, ranging from No. 00 to No. 3. Its applications are numerous: it can be used as a substitute for sandpaper, especially on curved surfaces, to clean up paint, and to achieve an "egg-shell" finish on shellac. Similar to sandpaper, it should not be used until all cutting tool work is finished. It can be manipulated until it is completely worn out.
5. POUNDING TOOLS.
The hammer consists of two distinct parts, the head and the handle. The head is made of steel, so hard that it will not be indented by hitting against nails or the butt of nailsets, punches, etc., which are comparatively soft. It can easily be injured tho, by being driven against steel harder than itself. The handle is of hickory and of an oval shape to prevent its twisting in the hand.
The hammer has two main parts: the head and the handle. The head is made of steel, which is so tough that it won't get dented when it strikes nails or the back of nail sets, punches, etc., which are relatively softer. However, it can get damaged if hit against something made of steel that’s harder than it. The handle is made of hickory and has an oval shape to stop it from twisting in your hand.
Hammers may be classified as follows: (1) hammers for striking blows only; as, the blacksmith's hammer and the stone-mason's hammer, and (2) [page 95] compound hammers, which consist of two tools combined, the face for striking, and the "peen" which may be a claw, pick, wedge, shovel, chisel, awl or round head for other uses. There are altogether about fifty styles of hammers varying in size from a jeweler's hammer to a blacksmith's great straight-handled sledge-hammer, weighing twenty pounds or more. They are named mostly according to their uses; as, the riveting-hammer, Fig. 159, the upholsterer's hammer, Fig. 160, the veneering-hammer, Fig. 162, etc. Magnetized hammers, Fig. 161, are used in many trades for driving brads and tacks, where it is hard to hold them in place with the fingers.
Hammers can be categorized as follows: (1) hammers designed for striking only, such as the blacksmith's hammer and the stone mason's hammer, and (2) [page 95] compound hammers, which combine two tools: a striking face and a "peen" that can be a claw, pick, wedge, shovel, chisel, awl, or round head for various other uses. There are about fifty different styles of hammers, ranging in size from a jeweler's hammer to a blacksmith's heavy straight-handled sledgehammer, which can weigh twenty pounds or more. They are mostly named based on their functions, such as the riveting hammer, Fig. 159, the upholsterer's hammer, Fig. 160, the veneering hammer, Fig. 162, and so on. Magnetized hammers, Fig. 161, are used in many trades for driving brads and tacks, especially where it's difficult to hold them in place with your fingers.

158 | 159 | 160 | 161 | 162 |
Fig. 158. Claw-Hammer. Fig. 159. Riveting-Hammer. Fig. 160. Upholster's Hammer. Fig. 161. Magnetized Hammer. Fig. 162. Veneering-Hammer. |
In the "bell-faced" hammer, the face is slightly convex, in order that the last blow in driving nails may set the nail-head below the surface. It is more difficult to strike a square blow with it than with a plain-faced hammer. For ordinary woodwork the plain-faced, that is, flat-faced claw-hammer, Fig. 158, is best. It is commonly used in carpenter work.
In the "bell-faced" hammer, the face is slightly curved so that the final hit when driving nails can set the nail head below the surface. It’s harder to hit straight with it compared to a flat-faced hammer. For typical woodworking, the flat-faced claw hammer, Fig. 158, is the best choice. It’s commonly used in carpentry.
It is essential that the face of the hammer be kept free from glue in order to avoid its sticking on the nail-head and so bending the [page 96] nail. Hammers should be used to hit iron only; for hitting wood, mallets are used. In striking with the hammer, the wrist, the elbow and the shoulder are one or all brought into play, according to the hardness of the blow. The essential precautions are that the handle be grasped at the end, that the blow be square and quick, and that the wood be not injured. At the last blow the hammer should not follow the nail, but should be brought back with a quick rebound. To send the nail below the surface, a nailset is used. (See below.)
It’s important to keep the hammer's face clean of glue to prevent it from sticking to the nail head and bending the nail. Hammers should only be used for hitting iron; for wood, use mallets. When you strike with the hammer, you can involve your wrist, elbow, and shoulder depending on how hard you need to hit. Key precautions include holding the handle at the end, delivering a straight and quick blow, and making sure not to damage the wood. On the final blow, the hammer shouldn’t follow the nail but should be pulled back quickly. To drive the nail below the surface, use a nail set. (See below.)
The claw is used for extracting nails. To protect the wood in withdrawing a nail a block may be put under the hammer-head. When a nail is partly drawn, the leverage can be greatly increased by continuing to block up in this way, Fig. 163.
The claw is used for pulling out nails. To protect the wood when removing a nail, you can place a block under the hammerhead. When a nail is partially pulled out, the leverage can be significantly increased by continuing to add blocks in this way, Fig. 163.

Fig. 163. Drawing a Nail with Claw-Hammer.

Fig. 164. Mallets.
The mallet, Fig. 164, differs from the hammer in having a wooden instead of a steel head. A maul or beetle is a heavy wooden mallet. The effect of the blow of a mallet is quite different from that of a hammer, in that the force is exerted more gradually; whereas the effect of the hammer blow is direct, immediate, and local, and is taken up at once. But a mallet continues to act after the first impulse, pushing, as it were. This is because of the elasticity of the head. A chisel, therefore, should always be driven with a mallet, for the chisel handle would soon go to pieces under the blows of a hammer, because of their suddenness; whereas the mallet blow which is slower will not only drive the blade deeper with the same [page 97] force, but will not injure the handle so rapidly. Mallet-heads are made square, cylindrical, and barrel-shaped. Carver's mallets are often turned from one piece, hammer and head on one axis.
The mallet, Fig. 164, is different from a hammer because it has a wooden head instead of a steel one. A maul or beetle is a heavy wooden mallet. The way a mallet strikes is quite different from a hammer, as the force is applied more gradually. In contrast, a hammer delivers a direct, immediate, and localized impact that is taken in right away. A mallet, however, keeps acting after the initial hit, pushing, so to speak. This is due to the elasticity of its head. A chisel should always be struck with a mallet because the chisel handle would quickly break under the sudden blows of a hammer; meanwhile, the slower blow of a mallet will drive the blade deeper with the same force without damaging the handle as quickly. Mallet heads come in square, cylindrical, and barrel shapes. Carver’s mallets are often made from a single piece, with the hammer and head aligned on one axis. [page 97]
Nailsets, Fig. 165, are made with hardened points, but softer butts, so that the hammer will not be injured. They were formerly made square when nail heads were square, but now round ones are common. To obviate slipping, some have "cup points," that is, with a concave tip, and some spur points.
Nailsets, Fig. 165, are designed with hardened tips but softer ends, so the hammer won't get damaged. They used to be made square when nail heads were square, but now round ones are more common. To prevent slipping, some have "cup points," which have a concave tip, and others have spur points.

Fig. 165. Using a Nailset.
To keep the nailset in its place on the nail-head it may be held closely against the third finger of the left hand, which rests on the wood close to the nail. When a nailset is lacking, the head of a brad, held nearly flat, may be used. But care is necessary to avoid bruising the wood.
To keep the nail set in position on the nail head, hold it tightly against the third finger of your left hand, which should rest on the wood close to the nail. If you don't have a nail set, you can use the flat head of a brad instead. Just be careful not to damage the wood.
6. HOLDING TOOLS.
A. Tools for Holding Work.
The advance in ease of handworking may largely be measured by the facilities for holding materials or other tools. The primitive man used no devices for holding except his hands and feet. The Japanese, who perhaps are the most skilful of joiners, still largely use their fingers and toes. On the other hand, Anglo-Saxons have developed an enormous variety of methods for holding work and tools.
The progress in the ease of craftsmanship can largely be gauged by the tools available for holding materials or other tools. Primitive people only used their hands and feet for holding things. The Japanese, known for being some of the most skilled craftsmen, still rely heavily on their fingers and toes. In contrast, Anglo-Saxons have created a wide range of methods for securing their work and tools.

Fig. 166. Bench made with Pinned Mortise-and-Tenon Joints, Low Back.

Fig. 167. Woodworking Bench used at Pratt Institute, Showing Self-Adjusting Upright Vise.
Benches. The essential features of a work-bench are a firm, steady table with a vise and places for tools. The joints are either pinned or wedged mortise-and-tenon, or draw-bolt joints. The best benches are made of maple, the tops being strips joined or tongued-and-grooved together. It is common also to have a trough at the back of the top of the bench, i. e., a space 6" or 8" wide, set lower than the upper surface, in which tools may be placed so as not to roll off. A low pillow, fastened at the left hand end of the trough, on which to set planes in order that the edge of the cutter may not be injured, is an advantage. The tool-rack is of capital importance. It has [page 99] been common in school benches to affix it to a board, which rises considerably above the top of the bench, Fig. 169, but a better plan is to have the top of it no higher than the bench-top, Fig. 166. Then the light on the bench is not obscured, and when a flat top is needed for large work it can readily be had by removing the tools. Elaborate benches with lock drawers are also much used in the shops of large city schools.
Benches. The main features of a workbench include a stable, solid table with a vise and space for tools. The joints can be pinned or use wedged mortise-and-tenon, or draw-bolt joints. The best benches are made of maple, with the tops being made of strips that are joined or tongued-and-grooved together. It’s also common to have a trough at the back of the bench top, which is a space 6" or 8" wide, set lower than the surface, for keeping tools from rolling off. A low pillow attached to the left end of the trough for resting planes is useful to protect the edge of the cutter. The tool rack is very important. It often attaches to a board that extends significantly above the bench top, Fig. 169, but a better approach is to keep it level with the bench top, Fig. 166. This way, the light on the bench is unobstructed, and if a flat surface is needed for larger projects, it can easily be cleared by removing the tools. More complex benches with lockable drawers are also commonly found in the shops of large city schools. [page 99]

Fig. 168. A Rapid-Acting Vise.
Vises for holding wood are of three general styles, (1) those with an upright wooden jaw, Fig. 167, which holds wide pieces of work well. They are now made with an automatic adjusting device by which the jaw and the face of the bench are kept parallel; (2) wooden vises with a horizontal jaw, guided by parallel runners, Fig. 166, and, (3) metal rapid-acting vises, Fig. 168. The latter are the most durable and in most respects more convenient. Special vises are also made for wood-carvers, for saw-filing, etc.
Vises for holding wood come in three main types: (1) those with a vertical wooden jaw, Fig. 167, which hold wide pieces of work securely. These now feature an automatic adjustment mechanism that keeps the jaw and the face of the bench aligned; (2) wooden vises with a horizontal jaw, guided by parallel runners, Fig. 166, and (3) metal quick-action vises, Fig. 168. The last type is the most durable and generally more convenient. There are also specialized vises designed for wood-carving, saw-filing, and other tasks.

Fig. 169. Holding a Large Board in Vise for Planing.
The best woodworking benches are equipped with both side- and tail-vises. The tail-vise is supplemented by movable bench-stops for [page 100] holding pieces of different lengths. In planing the side of a board it is held in place between the tail-vise and one of the bench-stops. A board should not be squeezed sidewise between the jaws of a vise when it is to be planed, lest it be bent out of shape. In planing the edge of a board it is ordinarily held in the side-vise. A long board, one end of which is in the vise, may also need to be supported at the other end. This may be done by clamping to it a handscrew, the jaw of which rests on the top of the bench, Fig. 169. When the vise is likely to be twisted out of square by the insertion of a piece of wood at one end of it, it is well to insert another piece of equal thickness at the other end of the vise to keep it square, as in Fig. 120, p. 82. In this case, (Fig. 120,) the extra piece also supports the piece being worked upon.
The best woodworking benches come with both side vises and tail vises. The tail vise is complemented by movable bench stops for holding pieces of various lengths. When planing the side of a board, it is positioned between the tail vise and one of the bench stops. A board shouldn’t be squeezed sideways between the jaws of a vise during planing, as this can cause it to bend. For planing the edge of a board, it’s usually secured in the side vise. A long board, with one end in the vise, may need additional support at the other end. This can be done by clamping a handscrew to it, with the jaw resting on top of the bench, Fig. 169. If the vise tends to twist out of square when inserting a piece of wood at one end, it’s a good idea to insert another piece of equal thickness at the opposite end of the vise to keep it square, as shown in Fig. 120, p. 82. In this case (Fig. 120), the extra piece also supports the piece being worked on.
The vise is also of great use in carrying on many other processes, but a good workman does not use it to the exclusion of the saw-horse and bench-hook.
The vise is also really helpful for many other tasks, but a skilled worker doesn’t rely on it alone; they also use the saw-horse and bench-hook.
Horses are of great use both for the rough sawing of material and in supporting large pieces during the process of construction. The common form is shown in Fig. 170, but a more convenient form for sawing has an open top, as in Fig. 171.
Horses are very useful for both rough sawing of materials and supporting large pieces during construction. The typical design is shown in Fig. 170, but a more convenient design for sawing has an open top, as shown in Fig. 171.

Fig. 170. Saw-Horse.

Fig. 171. Saw-Horse.
The picture-frame-vise, Fig. 172, is a very convenient tool for making mitered joints, as in picture-frames. The vise holds two sides firmly so that after gluing they may be either nailed together or a spline inserted in a saw cut previously made. See Fig. 268, [page 101] No. 55, p. 181. If the last joint in a picture-frame does not quite match, a kerf may be sawn at the junction of the two pieces, which can then be drawn close together.
The picture-frame-vise, Fig. 172, is a very handy tool for making mitered joints, like in picture frames. The vise securely holds two sides so that after gluing, they can either be nailed together or have a spline inserted in a previously made saw cut. See Fig. 268, [page 101] No. 55, p. 181. If the last joint in a picture frame doesn’t quite line up, you can saw a kerf at the junction of the two pieces, which can then be pulled close together.

Fig. 172. Picture-Frame-Vise.
Handscrews, Fig. 173, consist of four parts, the shoulder jaw and the screw jaw, made of maple, and the end spindle and the middle spindle, made of hickory. The parts when broken can be bought separately. Handscrews vary in size from those with jaws four inches long to those with jaws twenty-two inches long. The best kind are oiled so that glue will not adhere to them. In adjusting the jaws, if the handle of the middle spindle is held in one hand, and the handle of the end spindle in the other hand, and both are revolved together, the jaws may be closed or opened evenly, Fig. 174. In use care must be taken to keep the jaws parallel, in order to obtain the greatest pressure and to prevent the spindles from being broken. It is always important to have the jaws press on the work evenly. To secure this, the middle spindle should be tightened first, and then the end spindle. Handscrews are convenient for a great variety of uses, as clamping up glued pieces, holding pieces together temporarily for boring, Fig. 247, p. 152, holding work at any desired angle in the vise, as for chamfering or beveling, Fig. 175, etc.
Handscrews, Fig. 173, are made up of four parts: the shoulder jaw and the screw jaw, which are made of maple, and the end spindle and the middle spindle, which are made of hickory. When broken, the parts can be purchased separately. Handscrews come in sizes ranging from jaws that are four inches long to those that are twenty-two inches long. The best ones are oiled to prevent glue from sticking to them. To adjust the jaws, hold the handle of the middle spindle in one hand and the handle of the end spindle in the other, and turn both together to open or close the jaws evenly, Fig. 174. When in use, it's crucial to keep the jaws parallel to ensure maximum pressure and avoid breaking the spindles. It's always important for the jaws to press evenly on the work. To achieve this, tighten the middle spindle first, then the end spindle. Handscrews are versatile for many tasks, like clamping glued pieces, temporarily holding pieces together for drilling, Fig. 247, p. 152, and holding work at any angle in the vise, such as for chamfering or beveling, Fig. 175, etc.

Fig. 173. Handscrew.

Fig. 174. Adjusting Handscrew.

Fig. 175. Using a Handscrew to hold a Board at an Angle.
Clamps are made of both wood and iron, the most satisfactory for speed, strength, and durability are steel-bar carpenter clamps, Fig. 176. They vary in length from 1½ ft. to 8 ft. The separate parts are the steel bar A, the cast-iron frame B, the tip C [page 102] into which fits the screw D, on the other end of which is the crank E, and the slide F with its dog G, which engages in the notches on the bar. Any part, if broken, can be replaced separately.
Clamps are made from both wood and iron, but the best ones for speed, strength, and durability are steel-bar carpenter clamps, Fig. 176. They come in lengths ranging from 1½ ft. to 8 ft. The individual parts include the steel bar A, the cast-iron frame B, the tip C [page 102] that holds the screw D, which has the crank E on the other end, and the slide F with its dog G that fits into the notches on the bar. If any part breaks, you can replace it individually.

Fig. 176. Steel-Bar Carpenter's Clamp. a. Steel Bar. b. Frame. c. Tip. d. Screw. e. Crank. f. Slide. g. Dog.
Iron Handscrews, also called C clamps and carriage-makers' clamps. Fig. 177, are useful in certain kinds of work, as in gluing in special places and in wood-carving. All iron clamps need blocks of soft wood to be placed between them and the finished work.
Iron Handscrews, also known as C clamps and carriage-makers' clamps. Fig. 177, are useful for certain types of work, like gluing in specific areas and in wood-carving. All iron clamps require blocks of soft wood to be placed between them and the finished work.

Fig. 177. Iron Handscrew, (Carriage-Maker's Clamp).
Pinch-dogs, Fig. 178, are a convenient device for drawing together two pieces of wood, when injury to the surfaces in which they are driven does not matter. They vary in size from ¾" to 2¾". For ordinary purposes the smallest size is sufficient. For especially fine work, double-pointed tacks, properly filed, are convenient.
Pinch-dogs, Fig. 178, are a handy tool for holding two pieces of wood together when damage to the surfaces where they're driven in isn't a concern. They come in sizes ranging from ¾" to 2¾". For general use, the smallest size works well. For particularly delicate work, double-pointed tacks, properly sharpened, are useful.

Fig. 178. Pinch-Dog.
The bench-hook, Fig. 179, is a simple device for holding firmly small pieces of work when they are being sawn, chisled, etc. It also saves the bench from being marred. The angles should be kept exactly square.
The bench-hook, Fig. 179, is a straightforward tool for securely holding small workpieces while they're being sawed, chiseled, and so on. It also protects the bench from damage. The angles should be kept perfectly square.

Fig. 179. Bench-Hook.

Fig. 180. Miter-Box.

Fig. 181. Iron Miter-Box.
Such tools as pliers, Fig. 182, pincers, Fig. 183, and nippers, Fig. 184, made for gripping iron, are often useful in the woodworking shop. So are various sorts of wrenches; as fixed, socketed, adjustable, monkey- and pipe-wrenches.
Such tools like pliers, Fig. 182, pincers, Fig. 183, and nippers, Fig. 184, designed for gripping metal, are often handy in the woodworking shop. Different kinds of wrenches are also useful, including fixed, socketed, adjustable, monkey, and pipe wrenches.

Fig. 182. Pliers. | Fig. 183. Pincers. | Fig. 184. Nippers. |
B. Tools for holding other tools.
The brace or bit-stock, Fig. 185, holds all sorts of boring tools as well as screwdrivers, dowel-pointers, etc. The simple brace or bit-stock consists of a chuck, a handle, and a knob, and is sufficient for ordinary use; but the ratchet-brace enables the user to bore near to surfaces or corners where a complete sweep cannot be made. It is also useful where sufficient power can be applied only at one part of the sweep. By means of pawls which engage in the ratchet-wheel, the bit can be turned in either direction at the will of the user. The size of the brace is indicated by the "sweep," that is, the diameter of the circle thru which the swinging handle turns. To insert a bit or other tool, Fig. 186, grasp firmly with one hand the sleeve of the chuck pointing it upward, and revolve the handle with the other hand, unscrewing the [page 104] sleeve until the jaws open enough to admit the whole tang of the bit. Then reverse the motion and the bit will be held tightly in place. Various hand-, breast-, bench-, bow-drills and automatic drills are of use in doing quick work and for boring small holes, Fig. 187.
The brace or bit-stock, Fig. 185, holds various boring tools as well as screwdrivers, dowel-pointers, and more. The basic brace or bit-stock consists of a chuck, a handle, and a knob, which is enough for regular use; however, the ratchet-brace allows the user to bore close to surfaces or corners where a full sweep isn't possible. It's also handy when enough force can only be applied at one part of the sweep. Using pawls that engage with the ratchet-wheel, the bit can be turned in either direction according to the user’s preference. The size of the brace is indicated by the "sweep," which is the diameter of the circle through which the swinging handle moves. To insert a bit or other tool, Fig. 186, hold the sleeve of the chuck firmly with one hand, pointing it upward, and turn the handle with the other hand, unscrewing the sleeve until the jaws open wide enough to let the whole tang of the bit in. Then, reverse the motion, and the bit will be secured tightly in place. Various hand drills, breast drills, bench drills, bow drills, and automatic drills are useful for quick work and for boring small holes, Fig. 187.

Fig. 185. Ratchet-Brace.

Fig. 186. Inserting a Bit in Stock.

Fig. 187. Hand-Drill.
The screwdriver, Fig. 188, is a sort of holding tool for turning, and so driving screws. Various devices have been tried to prevent the twisting in the handle. This is now practically assured in various makes. The other important matter in a screwdriver is that the point be of the right temper, so as neither to bend nor to break. If the corners break they can be reground, but care should be taken not to make the angle too obtuse or the driver will slip out of the slot in the screw-head. The bevel should have a long taper. A shop should be equipped with different sizes of screwdrivers to fit the different sizes of screws. Screwdrivers vary in size, the shank ranging in length from 2½" to 18". A long screwdriver is more powerful than a short one, for the [page 105] screwdriver is rarely exactly in line with the axis of the screw, but the handle revolves in a circle. This means an increased leverage, so that the longer the screwdriver, the greater the leverage.
The screwdriver, Fig. 188, is a tool used for turning and driving screws. Different designs have been attempted to stop the handle from twisting. This issue is now generally resolved in various brands. Another key factor in a screwdriver is that the tip must be properly tempered to avoid bending or breaking. If the corners break, they can be reground, but it's important not to make the angle too obtuse, or the driver will slip out of the screw head slot. The bevel should have a long taper. A workshop should have screwdrivers in different sizes to match the various screw sizes. Screwdrivers come in sizes, with the shank length ranging from 2½" to 18". A long screwdriver is more effective than a short one, as it's rare for the screwdriver to be perfectly aligned with the screw's axis; instead, the handle turns in a circle. This results in increased leverage, so the longer the screwdriver, the greater the leverage.

188 | 189 | 190 |
Fig. 188. Screwdriver. Fig. 189. Screwdriver-Bit. Fig. 190. Spiral Screwdriver. |
For heavy work, screwdriver-bits, Fig. 189, in a bit-stock are useful, and for quick work, the spiral screwdriver, Fig. 190, and for small work, the ratchet-screwdriver.
For heavy-duty tasks, screwdriver bits, Fig. 189, in a bit stock are helpful, and for fast jobs, the spiral screwdriver, Fig. 190, is great, and for smaller tasks, the ratchet screwdriver works well.
7. MEASURING AND MARKING TOOLS.
It is a long step from the time when one inch meant the width of the thumb, and one foot meant the length of the foot, to the measuring of distances and of angles which vary almost infinitesimally. No such accuracy is necessary in measuring wood as in measuring metal, but still there is a considerable variety of tools for this purpose.
It’s a big jump from when an inch was defined as the width of a thumb and a foot was the length of a foot, to measuring distances and angles that can be incredibly precise. While you don’t need that level of accuracy when measuring wood as you do with metal, there’s still a wide range of tools available for these measurements.
For measuring distances, the rule, Fig. 191, is the one in most common use. It is usually made of boxwood. For convenience it is hinged so as to fold. A rule is called "two-fold" when it is made of two pieces, "four-fold" when made of four pieces, etc. When measuring or marking from it, it can be used more accurately by turning it on edge, so that the lines of the graduations may come directly against the [page 107] work. The one in most common use in school shops, is a two-foot, two-fold rule. Some instructors prefer to have pupils use a four-fold rule, because that is the form commonly used in the woodworking trades. Steel bench-rules, Fig. 192, are satisfactory in school work because unbreakable and because they do not disappear so rapidly as pocket rules. They need to be burnished occasionally.
For measuring distances, the ruler, Fig. 191, is the most commonly used tool. It’s typically made of boxwood and is hinged for easy folding. A ruler is referred to as "two-fold" when it consists of two pieces, "four-fold" when it has four pieces, and so on. To measure or mark more accurately, it can be turned on edge so that the graduation lines align directly against the [page 107] work surface. The most commonly used ruler in school shops is a two-foot, two-fold ruler. Some instructors prefer students to use a four-fold ruler, as that’s the standard in the woodworking trades. Steel bench rulers, Fig. 192, are effective for schoolwork because they are unbreakable and don’t go missing as quickly as pocket rulers. They do need to be polished occasionally.

Fig. 191. Two-Foot Rule. Two Fold.
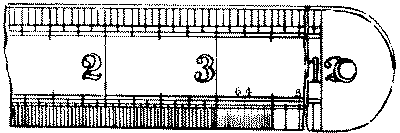
Fig. 192. Steel Bench-Rule.
The steel square, Figs. 193, 194, 196, 197, is useful, not only as a straight-edge and try-square, but also for a number of graduations and tables which are stamped on it. There are various forms, but the one in most common use consists of a blade or "body" 24" × 2" and a "tongue," 16" × 1½", at right angles to each other. Sargent's trade number for this form is 100. It includes graduations in hundredths, thirty-seconds, sixteenths, twelfths, tenths, and eighths of an inch, also a brace-measure, an eight-square measure, and the Essex board-measure. Another style, instead of an Essex board-measure, and the hundredths graduation has a rafter-table. The side upon which the name of the maker is stamped, is called the "face," and the reverse side the "back."
The steel square, Figs. 193, 194, 196, 197, is helpful not just as a straightedge and try-square, but also for various measurements and tables that are printed on it. There are different types, but the most commonly used one has a blade or "body" that measures 24" × 2" and a "tongue" that measures 16" × 1½", forming a right angle. Sargent's trade number for this type is 100. It features measurements in hundredths, thirty-seconds, sixteenths, twelfths, tenths, and eighths of an inch, as well as a brace measure, an eight-square measure, and the Essex board measure. Another version has a rafter table instead of the Essex board measure and the hundredths measurement. The side where the manufacturer's name is stamped is known as the "face," and the opposite side is called the "back."
The brace-measure is to be found along the center of the back of the tongue, Fig. 193. It is used thus: the two equal numbers set one above the other represent the sides of a square, and the single number to their right, represents in inches and decimals, the diagonal of that square.
The brace-measure is located along the center of the back of the tongue, Fig. 193. It is used like this: the two equal numbers stacked on top of each other represent the sides of a square, and the single number to their right represents, in inches and decimals, the diagonal of that square.
E. g., | 54 | 76.37 means that a square the sides of which are 54" would have a diagonal of 76.37". |
54 |
For determining the length of the long side (hypothenuse) of a right angle triangle, when the other two given sides are not equal, the foot rule, or another steel square may be laid diagonally across the [page 108] blade and arm, and applied directly to the proper graduations thereon, and the distance between them measured on the rule. If the distance to be measured is in feet, use the 1⁄12" graduations on the back of the square.
To find the length of the long side (hypotenuse) of a right triangle when the other two sides are different, you can use a measuring tape or a steel square placed diagonally across the [page 108] blade and arm. Align it with the correct markings and measure the distance between them on the tape. If you need to measure in feet, use the 1⁄12" measurements on the back of the square.
To use the octagonal (or 8-square) scale, Fig. 194, which is along the center of the face of the tongue, with the dividers, take the number of spaces in the scale to correspond with the number of inches the piece of wood is square, and lay this distance off from the center point, on each edge of the board. Connect the points thus obtained, diagonally across the corners, and a nearly exact octagon will be had. E.g., on a board 12" square, Fig. 195, find A.B.C.D., the centers of each edge. Now with the dividers take 12 spaces from the 8-square scale. Lay off this distance on each side as A' A" from A, B' B" from B, etc. Now connect A" with B', B" with C', C" with D', D" with A', and the octagon is obtained.
To use the octagonal (or 8-square) scale, Fig. 194, which is in the center of the tongue, take the number of spaces on the scale that matches the number of inches the piece of wood is square, and measure this distance from the center point on each edge of the board. Then, connect the points you’ve marked diagonally across the corners to create a nearly perfect octagon. For example, on a 12" square board, Fig. 195, find A.B.C.D., which are the centers of each edge. Now, using the dividers, take 12 spaces from the 8-square scale. Mark this distance on each side as A' A" from A, B' B" from B, and so on. Finally, connect A" to B', B" to C', C" to D', and D" to A', and you've created the octagon.

Fig. 195. Method of Using the Eight-Square Scale on the Steel-Square.
In making a square piece of timber octagonal, the same method is used on the butt, sawed true. When the distance from one center is laid off, the marking-gage may be set to the [page 109] distance from the point thus obtained to the corner of the timber, and the piece gaged from all four corners both ways. Cutting off the outside arrises to the gaged lines leaves an octagonal stick.
In transforming a square piece of timber into an octagon, the same technique is applied to the end, ensuring it's cut straight. Once you've measured the distance from the center, you can set the marking gauge to the distance from that point to the corner of the timber, then gauge from all four corners in both directions. Cutting off the outer edges along the gauged lines results in an octagonal piece.
The board-measure is stamped on the back of the blade of the square, Fig. 196. The figure 12 on the outer edge of the blade is the starting point for all calculations. It represents a 1" board, 12" wide, and the smaller figures under it indicate the length of boards in feet. Thus a board 12" wide, and 8' long measures 8 square feet and so on down the column. To use it, for boards other than 12" wide:—find the length of the board in feet, under the 12" marked on the outer edge of the blade, then run right or left along that line to the width of the board in inches. The number under the width in inches on the line showing the length in feet, gives the board feet for lumber 1" thick.
The board-measure is marked on the back of the blade of the square, Fig. 196. The number 12 on the outer edge of the blade is the starting point for all calculations. It represents a 1" board that is 12" wide, and the smaller numbers below it indicate the length of boards in feet. So, a board that is 12" wide and 8' long measures 8 square feet, and this continues down the column. To use it for boards that are not 12" wide: find the length of the board in feet below the 12" mark on the outer edge of the blade, then move right or left along that line to the width of the board in inches. The number below the width in inches on the line that shows the length in feet gives the board feet for lumber that is 1" thick.
For example, to measure a board 14' long, and 11" wide,—under the figure 12, find 14 (length of the board); to the left of this, under 11 is the number 12.10; 12' 10" is the board-measure of the board in question. Since a board 12' long would have as many board feet in it as it is inches wide, the B. M. is omitted for 12' boards. Likewise a board 6' long would have ½ the number of board feet that it is inches wide. If the board is shorter than the lowest figure given (8) it can be found by dividing its double by 2.; e. g., to measure a board 5' long and 9" wide, take 10 under the 12, run to the left of the number under 9, which is 7' 6"; ½ of this would be 3' 9", the number of board feet in the board.
For example, to measure a board that is 14' long and 11" wide, look under the figure 12 to find 14 (length of the board); to the left of this, under 11, is the number 12.10. So, 12' 10" is the board measure for the board in question. Since a board that is 12' long has the same number of board feet as it is inches wide, the B. M. is not listed for 12' boards. Similarly, a board that is 6' long will have half the number of board feet as it is inches wide. If the board is shorter than the lowest figure given (8), you can find it by doubling the measurement and then dividing by 2. For example, to measure a board that is 5' long and 9" wide, take 10 under 12, go to the left under the number for 9, which is 7' 6"; half of this would be 3' 9", the number of board feet in the board.
If the board to be measured is longer than any figure given, divide the length into two parts and add the result of the two parts obtained separately. For example, for a board 23' long and 13" wide,—take 12' × 13" =13'; add to it, 11' × 13"=11' 11"; total, 24'11".
If the board you need to measure is longer than any of the provided lengths, split the length into two sections and then sum the results of those two sections. For example, if you have a board that is 23' long and 13" wide—first calculate 12' × 13"=13'; then calculate 11' × 13"=11' 11"; finally, total it up to get 24'11".
A good general rule is to think first whether or not the problem can be done in one's head without the assistance of the square.
A good general rule is to first consider whether the problem can be solved in your head without using graph paper.
The table is made, as its name, Board-Measure (B. M.) implies, for measuring boards, which are commonly 1" thick. For materials more than 1" thick, multiply the B. M. of one surface by the number of inches thick the piece measures.
The table is designed, as its name, Board-Measure (B. M.) suggests, for measuring boards, which are usually 1" thick. For materials thicker than 1", multiply the B. M. of one surface by the number of inches thick the piece is.
The rafter-table is found on the back of the body of the square, Fig. 197. Auxiliary to it are the twelfth inch graduations, on the outside edges, which may represent either feet or inches.
The rafter table is located on the back of the body of the square, Fig. 197. Supporting it are the twelfth-inch graduations on the outer edges, which can represent either feet or inches.

Fig. 198. The "Run" and "Rise" of a Rafter.
By the "run" of the rafter is meant the horizontal distance when it is set in place from the end of its foot to a plumb line from the ridge end, i. e., one half the length of the building, Fig. 198. By the "rise" of the rafter is meant the perpendicular distance from the ridge end [page 111] to the level of the foot of the rafter. By the pitch is meant the ratio of the rise to twice the run, i. e., to the total width of the building. In a ½ pitch, the rise equals the run, or ½ the width of the building; in a ⅓ pitch the rise is ⅓ the width of the building; in a ¾ pitch the rise is ¾ the width of the building.
By the "run" of the rafter, we mean the horizontal distance when it is installed, from the end of its foot to a vertical line from the ridge end, which is half the length of the building, Fig. 198. By the "rise" of the rafter, we mean the vertical distance from the ridge end to the level of the foot of the rafter. The pitch refers to the ratio of the rise to double the run, which is the total width of the building. In a ½ pitch, the rise equals the run, or ½ the width of the building; in a ⅓ pitch, the rise is ⅓ the width of the building; and in a ¾ pitch, the rise is ¾ the width of the building. [page 111]
To find the length of a rafter by the use of the table, first find the required pitch, at the left end of the table. Opposite this and under the graduation on the edge representing the run in feet, will be found the length of the rafter; e.g., a rafter having a run of 12' with a ¼ pitch, is 13' 5" long, one with a run of 11' and a ⅓ pitch, is 13' 28⁄12", one with a run of 7' and a ⅝ pitch, is 11' 26⁄12" long, etc.
To determine the length of a rafter using the table, first locate the desired pitch at the left side of the table. Directly across from this and below the measurement on the edge that shows the run in feet, you’ll find the length of the rafter; for example, a rafter with a run of 12' and a ¼ pitch is 13' 5" long, one with a run of 11' and a ⅓ pitch is 13' 28⁄12", and one with a run of 7' and a ⅝ pitch is 11' 26⁄12" long, etc.
When the run is in inches, the readings are for 1⁄12 of the run in feet: e.g., a rafter with a run of 12" and a ¼ pitch is 135⁄12", one with a run of 11" and a ⅓ pitch, is 133⁄12". Where the run is in both feet and inches, find the feet and the inches separately; and add together; e.g., a rafter with a run of 11' 6", and a ½ pitch, is 15' 68⁄12" + 86⁄12" = 16' 32⁄12".
When the run is measured in inches, the readings correspond to 1⁄12 of the run in feet: for example, a rafter with a run of 12" and a ¼ pitch is 135⁄12", and one with a run of 11" and a ⅓ pitch is 133⁄12". When the run is in both feet and inches, calculate the feet and inches separately and then combine them; for instance, a rafter with a run of 11' 6" and a ½ pitch amounts to 15' 68⁄12" + 86⁄12" = 16' 32⁄12".
The try-square, Fig. 200, which is most commonly used for measuring the accuracy of right angles, is also convenient for testing the width of a board at various places along its length, for making short measurements, and as a guide in laying out lines with a pencil or knife at right angles to a surface or edge. The sizes are various and are indicated by the length of the blade. A convenient size for the individual bench and for ordinary use has a blade 6" long. It is also well to have in the shop one large one with a 12" blade.
The try-square, Fig. 200, is mainly used to check the accuracy of right angles, but it’s also handy for measuring the width of a board at different points along its length, for making short measurements, and for guiding lines with a pencil or knife at right angles to a surface or edge. They come in various sizes, which are indicated by the length of the blade. A convenient size for individual workbenches and everyday use has a blade that is 6" long. It's also a good idea to have a larger one in the shop with a 12" blade.
Fig. 200. Try-Square. | Fig. 201. Miter-Square. | Fig. 202. Sliding-T Bevel. |
In testing the squareness of work with the try-square, care must be taken to see that the head rests firmly against the surface from which the test is made, and then slipped down till the blade touches the edge being tested, Fig. 203. The edge should be tested at a number of places in the same way: that is, it should not be slid along the piece. The try-square is also of great use in scribing lines across boards, Fig. 204. A good method is to put the point of the knife at the beginning of the desired line, slide the square, along until it touches the knife-edge; then, resting the head of the square firmly against the edge, draw the knife along, pressing it lightly against [page 113] the blade, holding it perpendicularly. To prevent the knife from running away from the blade of the try-square, turn its edge slightly towards the blade.
When checking if a workpiece is square with a try-square, make sure the head is pressed firmly against the surface you're testing. Then slide it down until the blade touches the edge you’re checking. The edge should be checked at several points in the same way; don't slide it along the piece. The try-square is also really helpful for marking lines across boards. A good technique is to place the knife point at the start of the line you want, slide the square until it meets the knife edge, then hold the head of the square firmly against the edge and draw the knife along while lightly pressing against the blade and keeping it vertical. To stop the knife from drifting away from the try-square's blade, slightly tilt its edge towards the blade. [page 113]

Fig. 203. Using the Try-Square.

Fig. 204. Scribing with Knife by Try-Square.
The miter-square, Fig. 201, is a try-square fixed at an angle of 45°.
The miter-square, Fig. 201, is a try-square set at a 45° angle.
The sliding T bevel, Fig. 202, has a blade adjustable to any angle. It may be set either from a sample line, drawn on the wood, from a given line on a protractor, from drawing triangles, from the graduations on a framing square, or in other ways. It is used similarly to the T-square.
The sliding T bevel, Fig. 202, has an adjustable blade that can be set to any angle. You can align it with a sample line drawn on the wood, a specific line on a protractor, drawing triangles, the measurements on a framing square, or in other ways. It's used in a similar way to a T-square.
Fig. 200. Try-Square. | Fig. 201. Miter-Square. | Fig. 202. Sliding-T Bevel. |
Winding-sticks, Fig. 205, consist of a pair of straight strips of exactly the same width thruout. They are used to find out whether there is any twist or "wind" in a board. This is done by placing them parallel to each other, one at one end of the board, and the other at the other end. By sighting across them, one can readily see whether the board be twisted or not, Fig. 206. The blades of two framing-squares may be used in the same manner.
Winding sticks, Fig. 205, are a pair of straight strips that are the same width all the way through. They're used to check if a board has any twist or "wind." To do this, place them parallel to each other, one at each end of the board. By looking across them, you can easily tell if the board is twisted or not, Fig. 206. You can also use the blades of two framing squares in the same way.

Fig. 205. Winding-Sticks, 12 inches Long.

Fig. 206. Method of Using the Winding-Sticks.
Compasses or dividers, Fig. 207, consist of two legs turning on a joint, and having sharpened points. A convenient form is the wing divider which can be accurately adjusted by set-screws. A pencil can be substituted for the removable point. They are used for describing circles and arcs, for spacing, for measuring, for subdividing distances, and for scribing. In scribing a line parallel with a given outline, one leg follows the given edge, or outline, and the point of the other, marks the desired line. Used in this way they are very convenient for marking out chamfers, especially on curved edges, a sharp pencil being substituted for the steel point.
Compasses or dividers, Fig. 207, have two legs that pivot on a joint and have pointed tips. A useful version is the wing divider, which can be precisely adjusted with set-screws. You can also use a pencil in place of the removable point. They're used for drawing circles and arcs, for spacing, for measuring, for breaking down distances, and for marking. When marking a line parallel to a certain edge, one leg follows the edge, while the point of the other leg marks the line you want. This method is particularly handy for marking chamfers, especially on curved edges, where a sharp pencil can replace the steel point.
The beam-compass, Fig. 208, consists of two trammel-points running on a beam which may be made of any convenient length. It is used for describing large circles. A pencil may be attached to one point.
The beam-compass, Fig. 208, has two trammel-points that move along a beam, which can be any length you need. It's used for drawing large circles. You can attach a pencil to one point.
Calipers, outside and inside, Figs. 209, 210, are necessary for the accurate gaging of diameters, as in wood-turning.
Calipers, both outside and inside, Figs. 209, 210, are essential for accurately measuring diameters, like in wood-turning.

207 | 208 | 209 | 210 |
Fig. 207. Winged Dividers. Fig. 208. Beam-Compass or Trammel Points. Fig. 209. Outside Calipers. Fig. 210. Inside Calipers. |
The marking-gage, Fig. 211, consists of a head or block sliding on a beam or bar, to which it is fixed by means of a set-screw. On the face of the head is a brass shoe to keep the face from wearing. Projecting thru the beam is a steel spur or point, which should be filed to a flat, sharp edge, a little rounded and sharpened on the edge toward which the gage is to be moved, Fig. 212. It should project about ⅛" from the beam. If the spur be at all out of place, as it is likely to be, the graduations on a beam will be unreliable. Hence it is best to neglect them entirely when setting the gage and always to measure with the rule from the head to the spur, Fig. 213.
The marking-gage, Fig. 211, features a head or block that slides along a beam or bar, secured by a set screw. The front of the head has a brass shoe to prevent wear. A steel spur or point extends through the beam, which should be filed to a flat, sharp edge, slightly rounded, and sharpened on the side toward which the gage will move, Fig. 212. It should stick out about ⅛" from the beam. If the spur is misaligned, which can easily happen, the markings on the beam won't be reliable. Therefore, it's best to ignore the markings altogether when setting the gage and always measure with a ruler from the head to the spur, Fig. 213.

Fig. 211. Marking-Gage.

Fig. 212. Spur of Marking-Gage.
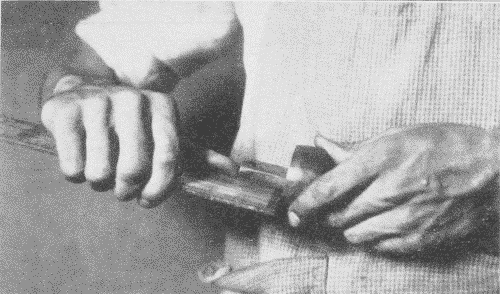
Fig. 213. Setting a Marking-Gage.
In use the beam should be tilted forward, so as to slide on its corner, Fig. 214. In this way [page 115] the depth of the gage line can be regulated. Ordinarily, the finer the line the better. The head must always be kept firmly pressed against the edge of the wood so that the spur will not run or jump away from its desired course. Care should also be taken, except in rough pieces, to run gage lines no farther than is necessary for the sake of the appearance of the finished work. To secure accuracy, all gaging on the surface of wood, should be done from the "working face" or "working edge."
When using the beam, it should be tilted forward to glide on its corner, as shown in Fig. 214. This way, the depth of the gage line can be adjusted. Generally, the finer the line, the better. The head must always be pressed firmly against the edge of the wood to prevent the spur from veering off course. Additionally, except for rough pieces, gage lines should not be extended further than necessary for the finished appearance. To ensure accuracy, all gaging on the wood surface should be done from the "working face" or "working edge."

Fig. 214. Using the Marking-Gage.
It is sometimes advisable, as in laying out chamfers, not to mark their edges with a marking-gage, because the marks will show after the chamfer is planed off. A pencil mark should be made instead. For this purpose a pencil-gage may be made by removing the spur of a marking-gage, and boring in its place a hole to receive a pencil stub with a blunt point, or a small notch may be cut in the back end of the beam, in which a pencil point is held while the gage is worked as usual except that its position is reversed. For work requiring less care, the pencil may [page 116] be held in the manner usual in writing, the middle finger serving as a guide, or a pair of pencil compasses may be used, one leg serving as a guide. A special gage is made for gaging curved lines, Fig. 215.
It’s sometimes better, like when laying out chamfers, not to mark their edges with a marking gauge, because those marks will still be visible after the chamfer is planed off. Instead, a pencil mark should be used. You can create a pencil gauge by taking off the spur of a marking gauge and drilling a hole to fit a blunt pencil stub in its place, or you can cut a small notch in the back end of the beam to hold a pencil point while you use the gauge as normal, but in reverse. For less precise work, the pencil can be held like you would when writing, with your middle finger as a guide, or you could use a pair of pencil compasses, with one leg acting as the guide. A special gauge is made for measuring curved lines, Fig. 215.

Fig. 215. Marking-Gage for Curves.
The cutting-gage, Fig. 216, is similar to a marking-gage, except that it has a knife-point inserted instead of a spur. It is very useful in cutting up soft, thin wood even as thick as ¼".
The cutting-gage, Fig. 216, is like a marking-gage, but it has a knife-point instead of a spur. It's great for cutting soft, thin wood, even up to ¼" thick.

Fig. 216. Cutting-Gage.
The slitting-gage is used in a similar way, but is larger and has a handle.
The slitting-gage is used in a similar way, but it's larger and has a handle.
The mortise-gage, Fig. 217, is a marking-gage with two spurs, with which two parallel lines can be drawn at once, as in laying out mortises. One form is made entirely of steel having, instead of spurs, discs with sharpened edges.
The mortise-gage, Fig. 217, is a marking gage with two spurs that allows you to draw two parallel lines at the same time, useful for laying out mortises. One version is made entirely of steel and features discs with sharpened edges instead of spurs.

Fig. 217. Roller Mortise-Gage.
The scratch-awl, Fig. 218, has a long, slender point which is useful not only for marking lines, but for centering.
The scratch-awl, Fig. 218, has a long, thin point that is helpful not just for marking lines, but also for centering.

Fig. 218. Scratch-Awl.
The auger-bit-gage, Fig. 219, is a convenient tool for measuring the depth of holes bored, but for ordinary purposes a block of wood sawn to the proper length thru which a hole is bored, is a satisfactory substitute.
The auger-bit-gage, Fig. 219, is a handy tool for measuring the depth of drilled holes, but for everyday use, a block of wood cut to the right length with a hole drilled through it serves as a good alternative.

Fig. 219. Auger-Bit-Gage.
Screw- and wire-gages, Fig. 220, are useful in measuring the lengths and sizes of screws and wire when fitting or ordering.
Screw and wire gauges, Fig. 220, are helpful for measuring the lengths and sizes of screws and wire when fitting or ordering.

Fig. 220. Screw- and Wire-Gages. a. Screw-Gage. b. Wire-Gage. c. Twist-Drill-Gage.
The spirit-level, and the plumb-line which it has largely replaced, are in constant use in carpentering, but are rarely needed in shopwork.
The spirit-level and the plumb-line that it has mostly taken over from are frequently used in carpentry, but are seldom required in workshop tasks.
Blackboard compasses, triangles, etc., are convenient accessories in a woodworking classroom.
Blackboard compasses, triangles, etc., are handy tools in a woodworking classroom.
8. SHARPENING TOOLS.
The grindstone for woodworking tools is best when rather fine and soft. The grinding surface should be straight and never concave. The stone should run as true as possible. It can be made true by using a piece of 1" gas pipe as a truing tool held against the stone when run dry. Power grindstones usually have truing devices attached to them, Fig. 221. A common form is a hardened steel screw, the thread of which, in working across the face of the grindstone, as they both revolve, shears off the face of the stone. The surface should always be wet when in use both to carry off the particles of stone and steel, and thus preserve the cutting quality of the stone, and to keep the tool cool, as otherwise, its temper would be drawn, which would show by its turning blue. But a grindstone should never stand in water or it would rot.
The grindstone for woodworking tools works best when it's fairly fine and soft. The grinding surface should be flat and never curved. The stone should spin as evenly as possible. You can make it true by using a piece of 1" gas pipe as a truing tool pressed against the stone while it runs dry. Power grindstones usually have truing devices attached to them, as shown in Fig. 221. A common type is a hardened steel screw, which, as it rotates across the face of the grindstone, shaves off the surface of the stone. The surface should always be wet during use to remove particles of stone and steel, which helps maintain the stone's cutting quality and keeps the tool cool; otherwise, the tool's temper could be ruined, indicated by it turning blue. However, a grindstone should never sit in water, or it will rot.
It is well to have the waste from the grindstone empty into a cisternlike box under it, Fig. 221. In this box the sediment will settle while the water overflows from it into the drain. Without such a box, the sediment will be carried into and may clog the drain. The box is to be emptied occasionally, before the sediment overflows.
It’s a good idea to have the waste from the grindstone flow into a cistern-like box underneath it, Fig. 221. In this box, the sediment will settle while the water overflows into the drain. Without this box, the sediment could get carried into the drain and potentially clog it. The box should be emptied regularly, before the sediment starts to overflow.
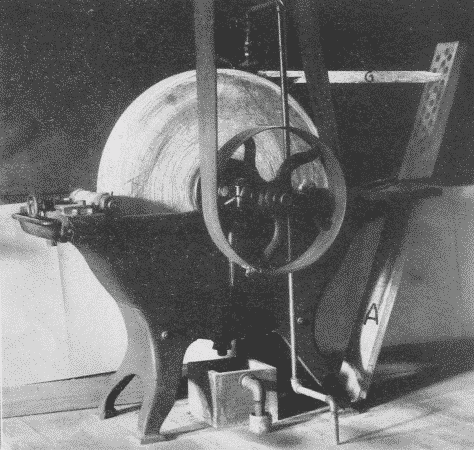
Fig. 221. Power Grindstone.
In order that the tool may be ground accurately, there are various devices for holding it firmly and steadily against the stone. A good one is shown in Figs. 221 and 222. This device is constructed as follows: A board A is made 2" thick, 6" wide, and long enough when in position to reach from the floor to a point above the level of the top of the stone. It is beveled at the lower end so as to rest snugly against a cleat nailed down at the proper place on the floor. The board is held in place by a loop of iron, B, which hooks into the holes in the trough of the grindstone. In the board a series of holes (say 1" in diameter) are bored. These run parallel to the floor when the board is in place, and receive the end of the tool-holder. [page 119] The tool-holder consists of four parts: (1) a strip C, 1½" thick, and as wide as the widest plane-bit to be ground. The forward end is beveled on one side; the back end is rounded to fit the holes in the main board A. Its length is determined by the distance from the edge of the tool being ground to the most convenient hole in A, into which the rear end is to be inserted. It is better to use as high a hole as convenient, so that as the grindstone wears down, the stick will still be serviceable; (2) a strip, D, of the same width as A and ⅞" thick, and 15" to 18" long; (3) a cleat, E, ⅝" × ¾", nailed across D; (4) a rectangular loop of wrought iron or brass, F, [page 120] which passes around the farther end of the two strips, C and D, and is fastened loosely to D by staples or screws.
To ensure the tool is ground accurately, there are various devices to hold it firmly and steadily against the stone. A good example is shown in Figs. 221 and 222. This device is constructed as follows: A board A is made 2" thick, 6" wide, and long enough to reach from the floor to a point above the top of the stone when positioned. It is beveled at the lower end to rest snugly against a cleat nailed down at the right spot on the floor. The board is held in place by an iron loop, B, that hooks into the holes in the grindstone's trough. A series of holes (about 1" in diameter) are bored into the board. These run parallel to the floor when the board is in place and hold the end of the tool-holder. [page 119] The tool-holder consists of four parts: (1) a strip C, 1½" thick and as wide as the widest plane-bit to be ground. The front end is beveled on one side; the back end is rounded to fit the holes in the main board A. Its length is based on the distance from the edge of the tool being ground to the most convenient hole in A where the rear end will be inserted. It's better to use the highest hole that's convenient so that as the grindstone wears down, the stick will still work; (2) a strip D, the same width as A, measuring ⅞" thick and 15" to 18" long; (3) a cleat E, ⅝" × ¾", nailed across D; (4) a rectangular loop of wrought iron or brass, F, [page 120] that goes around the far end of the two strips, C and D, and is loosely fastened to D with staples or screws.

Fig. 222. Grinding Device.

Fig. 223. Holder for Grinding Chisels or Plane-Bits.
The tool to be ground slips between this loop and the strip C, and is held firmly in place by the pressure applied to the back end of D, which thus acts as a lever on the fulcrum E.
The tool to be ground fits between this loop and the strip C and is held securely in place by the pressure applied to the back end of D, which acts as a lever on the fulcrum E.
Any desired bevel may be obtained on the tool to be sharpened, by choosing the proper hole in A for the back end of C or by adjusting the tool forward or backward in the clamp. As much pressure may be put on the tool as the driving belt will stand without slipping off.
Any bevel you want can be achieved on the tool you're sharpening by selecting the right hole in A for the back end of C or by moving the tool forward or backward in the clamp. You can apply as much pressure to the tool as the driving belt can handle without slipping off.
A still simpler holder for the plane-bit only, is a strip of wood 1½" thick and 2" wide, cut in the shape G shown in Fig. 223. The plane-bit fits into the saw-kerf K, and in grinding is easily held firmly in place by the hand. By inserting the rear end of the stick G into a higher or lower hole in the board A, any desired angle may be obtained. G is shown in position in Fig. 221.
A simpler holder for just the plane-bit is a piece of wood that is 1½" thick and 2" wide, shaped like G shown in Fig. 223. The plane-bit fits into the saw-kerf K, and you can hold it securely in place by hand while grinding. By inserting the back end of the stick G into a higher or lower hole in the board A, you can achieve any angle you want. G is shown in position in Fig. 221.
All such devices necessitate a perfectly true stone. The essential features are, to have a rigid support against which the tool may be pushed by the revolving stone, to hold the tool at a fixed angle which may be adjusted, and to press the tool against the stone with considerable pressure. The wheel should revolve toward the edge which is being ground, for two reasons. It is easier to hold the tool steadily thus, and the danger of producing a wire edge is lessened. The edge as it becomes thin, tends to spring away from the stone and this tendency is aggravated if the stone revolves away from the edge. If the stone does not run true and there is a consequent danger of digging into the stone with the tool which is being sharpened, the stone would better revolve away from the edge. The grinding should continue until the ground surface reaches the cutting edge and there is no bright line left along the edge. If the grinding is continued beyond this point, nothing is gained, and a heavy wire edge will be formed.
All such devices require a perfectly flat stone. The key features are to have a sturdy support against which the tool can be pushed by the spinning stone, to hold the tool at a fixed adjustable angle, and to press the tool against the stone with significant pressure. The wheel should spin towards the edge being ground for two reasons: it's easier to hold the tool steady this way, and it reduces the risk of creating a wire edge. As the edge becomes thinner, it tends to bend away from the stone, and this tendency is worsened if the stone rotates away from the edge. If the stone isn’t running true, which increases the risk of digging into the stone with the tool being sharpened, then it would be better for the stone to spin away from the edge. Grinding should continue until the ground surface reaches the cutting edge and there’s no bright line left along the edge. If grinding continues beyond this point, nothing is gained, and a heavy wire edge will form.

Fig. 224. Agacite Grinder.
A very convenient and inexpensive grinding tool, Fig. 224, sold as the "Agacite grinder,"7 has a number of different shaped grinding stones made chiefly of carborundum.
A very convenient and affordable grinding tool, Fig. 224, sold as the "Agacite grinder,"7 has several differently shaped grinding stones made mainly of carborundum.
Footnote 7: Made by the Empire Implement Co., Albany, N. Y.
Footnote 7: Made by the Empire Implement Company, Albany, NY.
The oilstone. After grinding, edge tools need whetting. This is done on the whetstone, or oilstone. The best natural stones are found near Hot Springs, Arkansas. The fine white ones are called Arkansas stones, and the coarser ones Washita stones. The latter are better for ordinary woodworking tools. The India oilstone, an artificial stone, Fig. 77, p. 58, cuts even more quickly than the natural stones. It is made in several grades of coarseness. The medium grade is recommended for ordinary shop use. Oil is used on oilstones for the same purpose as water on a grindstone. When an oilstone becomes hollow or uneven by use, it may be trued by rubbing it on a flat board covered with sharp sand, or on sandpaper tacked over a block of wood.
The oilstone. After sharpening, edge tools need to be honed. This is done on a whetstone, or oilstone. The best natural stones come from near Hot Springs, Arkansas. The fine white ones are called Arkansas stones, and the coarser ones are Washita stones. The latter are better for regular woodworking tools. The India oilstone, an artificial stone, Fig. 77, p. 58, cuts even faster than the natural stones. It comes in several grades of coarseness. The medium grade is recommended for general shop use. Oil is applied on oilstones just like water is on a grindstone. When an oilstone becomes hollow or uneven from use, it can be restored by rubbing it on a flat board covered with sharp sand, or on sandpaper attached to a block of wood.
Slipstones, Fig. 225, are small oilstones, made into various shapes in order to fit different tools, as gouges, the bits of molding-planes, etc.
Slipstones, Fig. 225, are small oilstones shaped to fit different tools, like gouges, the bits of molding planes, and so on.

Fig. 225. Slipstone.
Files are used for sharpening saws, augers, scrapers, etc. See above, p. 90.
Files are used for sharpening saws, augers, scrapers, etc. See above, p. 90.
9. CLEANING TOOLS.
The bench duster. One may be noted hanging on the bench shown in Fig. 166, p. 98. Bristle brushes for cleaning the benches are essential if the shop is to be kept tidy.
The bench duster. You might see one hanging on the bench shown in Fig. 166, p. 98. Bristle brushes for cleaning the benches are crucial if the shop is going to stay tidy.
Buffer. Wherever a lathe or other convenient revolving shaft is available, a buffer made of many thicknesses of cotton cloth is very valuable for polishing tools. The addition of a little tripoli greatly facilitates the cleaning.
Buffer. Whenever there's a lathe or another suitable rotating shaft available, a buffer made from multiple layers of cotton fabric is really useful for polishing tools. Adding a bit of tripoli makes the cleaning process much easier.
WOOD HAND TOOLS.—Continued.
References:*
References:
(4) Scraping Tools.
Scraping Tools.
Barnard, pp. 136-142.
Barnard, pp. 136-142.
Wheeler, pp. 465, 473.
Wheeler, pp. 465, 473.
Griffith, pp. 71-75.
Griffith, pp. 71-75.
Selden, pp. 149, 177, 182.
Selden, pp. 149, 177, 182.
Hodgson, I, pp. 61-74.
Hodgson, I, pp. 61-74.
(5) Pounding Tools.
Hammering Tools.
Barnard, pp. 24-47.
Barnard, pp. 24-47.
Sickels, p. 70.
Sickels, p. 70.
Wheeler, pp. 414, 428-432.
Wheeler, pp. 414, 428-432.
Selden, pp. 31, 111, 156.
Selden, pp. 31, 111, 156.
Goss, p. 60.
Goss, p. 60.
Barter, p. 128.
Barter, p. 128.
(6) Punching Tools.
(6) Punch Tools.
Barnard, p. 29.
Barnard, p. 29.
Wheeler, p. 433.
Wheeler, p. 433.
Selden, p. 161.
Selden, p. 161.
(7) Gripping Tools.
(7) Hand Tools.
For holding work:
For pending work:
Goss, p. 63.
Goss, p. 63.
Wheeler, pp. 65-75, 475.
Wheeler, pp. 65-75, 475.
Selden, pp. 140, 147, 186, 194.
Selden, pp. 140, 147, 186, 194.
Hammacher, pp. 286-291.
Hammacher, pp. 286-291.
For holding other tools:
For storing other tools:
Goss, pp. 56-59.
Goss, pp. 56-59.
Selden, p. 143.
Selden, p. 143.
(8) Measuring and Marking Tools.
(8) Measuring and marking tools.
Goss, pp. 9-20.
Goss, pp. 9-20.
Griffith, pp. 9-19.
Griffith, pp. 9-19.
Hodgson, The Steel Square.
Hodgson, *The Steel Square*.
Wheeler, p. 465.
Wheeler, p. 465.
Tate, pp. 21-25.
Tate, pp. 21-25.
Building Trades Pocketbook, pp. 234-237.
Building Trades Pocketbook, pp. 234-237.
Selden, pp. 149, 150-152, 175.
Selden, pp. 149, 150-152, 175.
Sargent's Steel Squares.
Sargent's Steel Squares.
(9) Sharpening Tools.
(9) Tool Sharpening.
Barnard, pp. 136-142.
Barnard, pp. 136-142.
Sickels, pp. 80-85.
Sickels, pp. 80-85.
Wheeler, pp. 480-488.
Wheeler, pp. 480-488.
Selden, pp. 153, 162, 172, 180.
Selden, pp. 153, 162, 172, 180.
Goss, pp. 39, 64-69.
Goss, pp. 39, 64-69.
Chapter 5.
WOOD FASTENINGS.
The following are the chief means by which pieces of wood are fastened together: nails, screws, bolts, plates, dowels, glue, hinges, and locks.
The main ways to join pieces of wood together are: nails, screws, bolts, plates, dowels, glue, hinges, and locks.
NAILS
Nails, Fig. 226, may be classified according to the material of which they are made; as, steel, iron, copper, and brass. Iron nails may be galvanized to protect them from rust. Copper and brass nails are used where they are subject to much danger of corrosion, as in boats.
Nails, Fig. 226, can be categorized based on the materials they’re made from: steel, iron, copper, and brass. Iron nails can be galvanized to prevent rust. Copper and brass nails are used in areas prone to corrosion, like on boats.

Fig. 226. |
a. Cut nail, common. |
b. Flat-head wire nail, No. 1, common. |
c. Finishing nail, or brad. |
Nails may also be classified according to the process of manufacture; as, cut nails, wrought nails, and wire nails. Cut nails are cut from a plate of metal in such a way that the width of the nail is equal to the thickness of the plate, and the length of the nail to the width of the plate. In the third dimension, the nail is wedge-shaped, thin at the point and thick at the head. Unless properly driven, such nails are likely to split the wood, but if properly driven they are very firm. In driving, the wedge should spread with and not across the grain.
Nails can also be categorized based on how they're made: cut nails, wrought nails, and wire nails. Cut nails are shaped from a metal plate so that the nail's width matches the thickness of the plate, and its length matches the width of the plate. In terms of shape, the nail is wedge-shaped, being thin at the tip and thicker at the head. If not driven correctly, these nails can split the wood, but when driven properly, they hold very securely. When driving, the wedge should spread with the grain rather than across it.
Wrought nails are worked into shape from hot steel, and have little or no temper, so that they can be bent over without breaking, as when clinched. Horseshoe- and trunk-nails are of this sort. They are of the same shape as cut nails.
Wrought nails are shaped from hot steel and have little to no temper, which means they can be bent without breaking, like when they're clinched. Horseshoe nails and trunk nails are this type. They are the same shape as cut nails.
Wire nails are made from drawn steel wire, and are pointed, headed, and roughened by machinery. They are comparatively cheap, hold nearly if not quite as well as cut nails, which they have largely displaced, can be bent without breaking, and can be clinched.
Wire nails are made from drawn steel wire and are pointed, headed, and roughened by machines. They are relatively inexpensive, hold almost as well as cut nails (which they have mostly replaced), can be bent without snapping, and can be clinched.
Nails are also classified according to the shape of their heads; as, common or flat-heads, and brads or finishing nails. Flat-heads are used in ordinary work, where the heads are not to be sunk in the wood or "set."
Nails are also categorized based on the shape of their heads: common or flat-heads and brads or finishing nails. Flat-heads are used for general tasks where the heads don’t need to be sunk into the wood or "set."
Some nails get their names from their special uses; as, shingle-nails, trunk-nails, boat-nails, lath-nails, picture-nails, barrel-nails, etc.
Some nails are named after their specific uses, like shingle nails, trunk nails, boat nails, lath nails, picture nails, barrel nails, and so on.
The size of nails is indicated by the length in inches, and by the size of the wire for wire nails. The old nomenclature for cut nails also survives, in which certain numbers are prefixed to "penny." For example, a threepenny nail is 1¼" long, a fourpenny nail is 1½" long, a fivepenny nail is 1¾" long, a sixpenny nail is 2" long. In other words, from threepenny to tenpenny ¼" is added for each penny, but a twelvepenny nail is 3¼" long, a sixteenpenny nail is 3½" long, a twentypenny nail is 4" long. This is explained as meaning that "tenpenny" nails, for example, cost tenpence a hundred. Another explanation is that originally 1000 of such nails weighed a pound. The size of cut nails is usually still so indicated. Nails are sold by the pound.
The size of nails is marked by their length in inches and by the wire gauge for wire nails. The old naming system for cut nails is still around, where certain numbers are placed before "penny." For example, a threepenny nail is 1¼" long, a fourpenny nail is 1½" long, a fivepenny nail is 1¾" long, and a sixpenny nail is 2" long. This means that from threepenny to tenpenny, you add ¼" for each penny, but a twelvepenny nail is 3¼" long, a sixteenpenny nail is 3½" long, and a twentypenny nail is 4" long. This is understood to mean that "tenpenny" nails, for instance, cost ten pence per hundred. Another explanation is that originally, 1000 of these nails weighed a pound. The size of cut nails is usually still indicated this way. Nails are sold by the pound.
The advantages of nails are that they are quickly and easily applied, they are strong and cheap, and the work can be separated, tho with difficulty. The disadvantages are the appearance and, in some cases, the insecurity.
The advantages of nails are that they are quick and easy to use, they are strong and inexpensive, and the work can be taken apart, though with some difficulty. The downsides are the appearance and, in some cases, the lack of security.
The holding power of nails may be increased by driving them into the wood at other than a right angle, especially where several nails unite two pieces of wood. By driving some at one inclination and some at another, they bind the pieces of wood together with much greater force than when driven in straight.
The holding power of nails can be improved by driving them into the wood at an angle rather than straight in, especially when multiple nails connect two pieces of wood. By angling some nails one way and others a different way, they connect the wood pieces much more securely than if they were driven in straight.
The term brads was once confined to small finishing nails, but is now used for all finishing nails, in distinction from common or flat-headed nails. The heads are made round instead of flat so that they may be set easily with a nailset and the hole filled with a plug, or, where the wood is to be painted, with putty. They are used for interior finishing and other nice work.
The term "brads" used to refer specifically to small finishing nails, but now it applies to all finishing nails, distinguishing them from common or flat-headed nails. The heads are round instead of flat, making them easy to set with a nail set, and the hole can be filled with a plug or, if the wood will be painted, with putty. They’re used for interior finishing and other fine work.
Tacks, Fig. 227, vary in size and shape according to their use; as, flat-headed, gimp, round-headed, and double-pointed or matting tacks, a sort of small staple. Their size is indicated by the word "ounce." For example, a two-ounce tack is ¼" long, a three-ounce [page 125] tack is ⅜" long, a four-ounce tack is 7⁄16" long, a six-ounce tack is ½" long, etc. This term once meant the number of ounces of iron required to make 1000 tacks.
Tacks, Fig. 227, come in different sizes and shapes based on their purpose; like flat-headed, gimp, round-headed, and double-pointed or matting tacks, which are a type of small staple. Their size is shown by the word "ounce." For instance, a two-ounce tack is ¼" long, a three-ounce tack is ⅜" long, a four-ounce tack is 7⁄16" long, a six-ounce tack is ½" long, and so on. This term used to refer to the number of ounces of iron needed to make 1000 tacks.

Fig. 227. Tack.
Tacks are useful only in fastening to wood thin material, such as veneers, textiles, leather, matting, tin, etc. Tinner's tacks, which are used for clinching, are commonly called clinch-nails. Wire tacks, altho made, are not so successful as cut tacks because they lack a sharp point, which is essential.
Tacks are only useful for attaching thin materials to wood, like veneers, fabrics, leather, matting, tin, and so on. Tinner's tacks, used for clinching, are usually referred to as clinch nails. Wire tacks, while produced, are not as effective as cut tacks because they don’t have a sharp point, which is necessary.
Corrugated fasteners, Fig. 228, or fluted nails, are used to fasten together two pieces of wood by driving the fastener so that one-half of it will be on each side of the joint. Their size is indicated by the length and the number of corrugations, as ½", four. They are often useful where nails are impracticable.
Corrugated fasteners, Fig. 228, or fluted nails, are used to join two pieces of wood by driving the fastener so that half of it is on each side of the joint. Their size is indicated by the length and the number of corrugations, such as ½", four. They are often helpful in situations where nails aren't practical.

Fig. 228. Corrugated Fastener.
Glaziers' points are small, triangular pieces of zinc, used to fasten glass into sashes.
Glaziers' points are small, triangular pieces of zinc used to secure glass into frames.
SCREWS
(a) Wood-screws, Fig. 229, may be classified by the material of which they are made; as, steel or brass. Steel screws may be either bright,—the common finish,—blued by heat or acid to hinder rusting, tinned, or bronzed. Brass screws are essential wherever rust would be detrimental, as in boats.
(a) Wood screws, Fig. 229, can be categorized by the material they're made from, such as steel or brass. Steel screws can be bright—the standard finish—blued through heat or acid to prevent rust, tinned, or bronzed. Brass screws are crucial where rust would be harmful, like in boats.
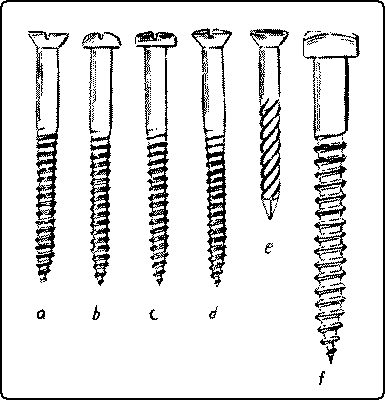
Fig. 229. |
a. Flat-head Wood-screw. |
b. Round-head Wood-screw. |
c. Fillister-head Wood-screw. |
d. Oval-countersunk-head Wood-screw. |
e. Drive-screw. |
f. Square-head (lag- or coach-) Screw. |
(b) Screws are also classified by shape; as, flat-headed, round-headed, fillister-headed, oval-countersunk-headed, and square-headed screws. Flat-heads are most commonly used. There are also special shapes for particular purposes. Round-heads may be used either for decoration or where great drawing power is desirable. In the latter case, washers are commonly inserted under the heads to prevent them from sinking into the wood. Oval-heads are used decoratively, the head filling the countersunk hole, as with flat-heads, and projecting a trifle besides. They are much used in the interior finish of railway cars. They are suitable for the strap hinges of a chest.
(b) Screws are also categorized by shape: flat-headed, round-headed, fillister-headed, oval-countersunk-headed, and square-headed screws. Flat-headed screws are the most commonly used. There are also special shapes for specific purposes. Round-headed screws can be used for decoration or where strong holding power is needed. In the latter case, washers are usually placed under the heads to stop them from sinking into the wood. Oval-headed screws are used for decorative purposes, with the head filling the countersunk hole like flat-headed screws but sticking out slightly. They are frequently used in the interior finish of train cars. They are also suitable for the strap hinges of a chest.
The thread of the screw begins in a fine point so that it may penetrate the wood easily where no hole has been bored as is often the case in soft wood. The thread extends about two-thirds the length of the screw. Any longer thread would only weaken the [page 126] screw where it most needs strength, near the head, and it does not need friction with the piece thru which it passes.
The screw has a sharp tip that helps it go into the wood easily, especially when there's no pre-drilled hole, which is common in soft wood. The threading goes about two-thirds of the way up the screw. Longer threading would just make the screw weaker where it needs to be strongest, near the head, and it doesn’t require friction with the piece it goes through. [page 126]
The size of screws is indicated by their length in inches, and by the diameter of the wire from which they are made, using the standard screw-gage, Fig. 220, p. 116. They vary in size from No. 0 (less than 1⁄16") to No. 30 (more than 7⁄16") in diameter, and in length from ¼" to 6".
The size of screws is shown by their length in inches and by the diameter of the wire they're made from, using the standard screw gauge, Fig. 220, p. 116. They range in size from No. 0 (less than 1⁄16") to No. 30 (more than 7⁄16") in diameter, and in length from ¼" to 6".
The following is a good general rule for the use of screws: make the hole in the piece thru which the screw passes, large enough for the screw to slip thru easily. Countersink this hole enough to allow the head to sink flush with the surface. Make the hole in the piece into which the screw goes small enough for the thread of the screw to catch tight. Then all the strength exerted in driving, goes toward drawing the pieces together, not in overcoming friction. The hole must be deep enough, especially in hard wood and for brass screws, to prevent the possibility of twisting off and breaking the screw. Soap is often useful as a lubricant to facilitate the driving of screws. Where it is desirable that the heads do not show, a hole may first be bored with an auger-bit large enough to receive the head and deep enough to insert a plug of wood, which is cut out with a plug-cutter, Fig. 131, p. 84, and glued in place. If pains are taken to match the grain, the scar thus formed is inconspicuous.
The following is a good general rule for using screws: make the hole in the piece where the screw passes large enough for the screw to slide through easily. Countersink this hole enough to allow the head to sit flush with the surface. Make the hole in the piece where the screw goes small enough for the screw's threads to grip tightly. Then, all the force used to drive the screw helps pull the pieces together instead of just overcoming friction. The hole should be deep enough, especially in hardwood and for brass screws, to avoid the risk of twisting off and breaking the screw. Soap is often helpful as a lubricant to make driving screws easier. If you want the heads to be hidden, start by boring a hole with an auger bit that’s big enough to hold the head and deep enough to insert a wood plug, which can be cut out with a plug cutter, Fig. 131, p. 84, and glued in place. If care is taken to match the grain, the resulting scar will be less noticeable.
In rough work, the screw may be driven into place with a hammer thru most of its length, and then a few final turns be given with a screwdriver, but this breaks the fibers of the wood and weakens their hold. In "drive-screws," Fig. 229, e, the slot is not cut all the way across the head, in order that the blows of the hammer may not close the slot.
In rough work, you can drive the screw into place with a hammer for most of its length, and then give it a few final turns with a screwdriver, but this breaks the wood fibers and weakens their grip. In "drive-screws," Fig. 229, e, the slot isn't cut all the way across the head to prevent the hammer blows from closing the slot.
The advantages of screws are, that they are very strong and that the work can easily be taken apart. If they loosen they can be [page 127] retightened. The disadvantages are, that they are expensive, that they take time to insert, that they show very plainly, and that they do not hold well in end grain.
BOLTS
Bolts with nuts are useful where great strength is desired. There are three chief varieties, Fig. 230.
Bolts with nuts are useful when strong connections are needed. There are three main types, Fig. 230.

Fig. 230. |
a. Stove-bolt. |
b. Carriage-bolt. |
c. Machine-bolt. |
Stove-bolts are cheaply made (cast) bolts having either flat or round heads with a slot for the screwdriver, like ordinary screws.
Stove-bolts are inexpensive (cast) bolts that have either flat or round heads with a slot for a screwdriver, similar to regular screws.
Carriage-bolts are distinguished by having the part of the shank which is near the head, square.
Carriage bolts are characterized by the square section of the shank that is close to the head.
Machine-bolts have square, hexagonal, or button heads.
Machine bolts have square, hex, or button heads.
Machine-screws, Fig. 231, are similar to stove-bolts, but are accurately cut and are measured with a screw-gage. The varieties are, a, flat-head, b, round-head, c, fillister-head, d, oval-countersunk-head, all with slots for screwdriver.
Machine screws, Fig. 231, are similar to stove bolts, but they are precisely manufactured and are measured with a screw gauge. The types include, a, flat head, b, round head, c, fillister head, d, oval countersunk head, all with slots for a screwdriver.

Fig. 231. Machine-screws. |
a. Flat-head. |
b. Round-head. |
c. Fillister-head. |
d. Oval-countersunk-head. |
Plates, Fig. 232, include corner-irons, straight plates and panel-irons. These are made of either iron or brass and are used in fastening legs to the floor, in stiffening joints, affixing tops, etc.
Plates, Fig. 232, include corner brackets, flat plates, and panel brackets. These are made of either iron or brass and are used to secure legs to the floor, reinforce joints, attach tops, and more.

Fig. 232. |
a. Corner-iron. |
b. Straight plate. |
c. Panel-iron. |
Dowel-rods. Dowel-rods are cylindrical rods, from 3⁄16" to 1" in diameter, and 36", 42", and 48" long. They are commonly made of birch or maple, but maple is more satisfactory as it shrinks less and is stronger than birch.
Dowel rods. Dowel rods are cylindrical rods, ranging from 3⁄16" to 1" in diameter, and 36", 42", and 48" long. They are usually made of birch or maple, but maple is preferred because it shrinks less and is stronger than birch.
Dowels are used as pins for joining boards edge to edge, and as a substitute for mortise-and-tenon joints.
Dowels are used as pins to join boards edge to edge and as an alternative to mortise-and-tenon joints.
There is, to be sure, a prejudice against dowels on the part of cabinet-makers due, possibly, to the willingness to have it appear that doweling is a device of inferior mechanics. But doweling is cheaper and quicker than tenoning, [page 128] and there are many places in wood construction where it is just as satisfactory and, if properly done, just as strong. Certain parts of even the best furniture are so put together.
There’s definitely a bias against dowels among cabinet-makers, likely because they want to make it seem like doweling is a less skilled technique. However, doweling is cheaper and faster than tenoning, [page 128] and there are plenty of areas in wood construction where it works just as well and can be just as strong if done correctly. Some parts of even the finest furniture are assembled this way.
Shoe pegs serve well as small dowels. They are dipped in glue and driven into brad-awl holes.
Shoe pegs work great as small dowels. They're dipped in glue and pushed into brad-awl holes.
Wedges are commonly used in door construction between the edges of tenons and the insides of mortises which are slightly beveled, No. 34, Fig. 266, p. 179. Or the end of a tenon may be split to receive the wedges, No. 35, Fig. 266. The blind wedge is used in the fox-tail joint, No. 36, Fig. 266.
Wedges are commonly used in door construction between the edges of tenons and the insides of mortises, which are slightly beveled. No. 34, Fig. 266, p. 179. Alternatively, the end of a tenon may be split to receive the wedges. No. 35, Fig. 266. The blind wedge is used in the fox-tail joint. No. 36, Fig. 266.
GLUE
Glue is an inferior kind of gelatin, and is of two kinds,—animal glue and fish glue. Animal glue is made of bones and trimmings, cuttings and fleshings from hides and skins of animals. Sinews, feet, tails, snouts, ears, and horn pith are also largely used. Cattle, calves, goats, pigs, horses, and rabbits, all yield characteristic glues.
Glue is a lower-quality type of gelatin, and there are two main types—animal glue and fish glue. Animal glue is made from bones and scraps, as well as trimmings and remnants from the hides and skins of animals. Parts like tendons, feet, tails, snouts, ears, and horn pith are also commonly used. Cattle, calves, goats, pigs, horses, and rabbits all produce distinct types of glue.
The best glue is made from hides of oxen, which are soaked in lime water until fatty or partly decayed matter is eaten out and only the glue is left. The product is cleaned, boiled down and dried.
The best glue is made from ox hides, which are soaked in lime water until the fatty or partially decayed material is removed, leaving only the glue. The product is then cleaned, boiled down, and dried.
The best and clearest bone glues are obtained by leaching the bones with dilute acid which dissolves out the lime salts and leaves the gelatinous matters. Such leached bone is sold as a glue stock, under the name of "osseine." This material together with hides, sinews, etc., has the gelatin or glue extracted by boiling again and again, just as soup stock might be boiled several times. Each extraction is called a "run." Sometimes as many as ten or fifteen runs are taken from the same kettle of stock, and each may be finished alone or mixed with other runs from other stock, resulting in a great variety of commercial glues.
The best and clearest bone glues come from treating bones with a diluted acid that removes the lime salts and leaves behind the gelatinous material. This treated bone is sold as glue stock, referred to as "osseine." This material, along with hides, sinews, and others, has the gelatin or glue extracted by boiling multiple times, similar to making soup stock. Each extraction is known as a "run." Sometimes, up to ten or fifteen runs are taken from the same kettle of stock, and each may be finished on its own or blended with runs from other stock, resulting in a wide variety of commercial glues.
Manufacturers use many tests for glue, such as the viscosity or running test, the odor, the presence of grease or of foam, rate of set, the melting-point, keeping properties, jelly strength (tested between the finger tips), water absorption (some glues absorb only once their weight, others ten or twelve times), and binding or adhesive tests. This latter varies so much with different materials that what may be good glue for one material is poor for another.
Manufacturers perform a variety of tests for glue, including the viscosity or flow test, smell, presence of grease or foam, setting time, melting point, shelf life, jelly strength (tested between the fingertips), water absorption (some glues only absorb their weight once, while others can absorb ten to twelve times their weight), and adhesive tests. The effectiveness of the glue varies so much with different materials that what works well for one material might not work at all for another.
Putting all these things together, glues are classified from grade 10 to 160, 10 being the poorest. The higher standards from 60 and upwards are neutral hide glues, clear, clean, free from odor, foam, and grease. The lower standards are chiefly bone glues, used for sizing straw hats, etc. They are rigid as compared with the flexibility of hide glues. For wood joints the grade should be 70 or over. For leather, nothing less than 100 should be used, and special cements are better still.
Putting all these things together, glues are rated from 10 to 160, with 10 being the lowest quality. The higher grades, starting at 60 and above, are neutral hide glues that are clear, clean, odorless, and free from foam and grease. The lower grades are mainly bone glues, which are used for sizing straw hats, among other things. They are stiff compared to the flexibility of hide glues. For wood joints, you should use a grade of 70 or higher. For leather, you shouldn’t use anything less than 100, and special adhesives are even better.
The best glue is transparent, hard in the cake, free from spots, of an amber color, and has little or no smell. A good practical test for glue is to soak it in water till it swells and becomes jelly-like. The more it swells without dissolving the better the quality. Poor glue dissolves. Glue is sometimes bleached, becoming brownish white in color, but it is somewhat weakened thereby.
The best glue is clear, hard when dry, free from blemishes, has an amber color, and barely smells. A good way to test glue is to soak it in water until it swells and turns jelly-like. The more it swells without falling apart, the better the quality. Cheap glue dissolves. Glue can sometimes be bleached to a brownish white color, but this weakens it a bit.
Fish glue is made from the scales and muscular tissue of fish. Isinglass is a sort of glue made from the viscera and air bladder of certain fish, as cod and sturgeon.
Fish glue is made from the scales and muscle tissue of fish. Isinglass is a type of glue made from the innards and swim bladder of certain fish, like cod and sturgeon.
Liquid glue may be made either from animal or fish glue. The LePage liquid glue is made in Gloucester, Mass., one of the greatest fish markets in the country. Liquid glue is very convenient because always ready, but is not so strong as hot glue, and has an offensive odor. Liquid glues are also made by rendering ordinary glue non-gelatinizing, which can be done by several means; as, for instance, by the addition of oxalic, nitric, or hydrochloric acid to the glue solution.
Liquid glue can be made from either animal or fish glue. LePage liquid glue is produced in Gloucester, Massachusetts, which is one of the largest fish markets in the country. Liquid glue is super convenient because it’s always ready to use, but it’s not as strong as hot glue and has a bad smell. Liquid glues can also be made by making regular glue non-gelatinizing, which can be achieved through various methods, such as adding oxalic, nitric, or hydrochloric acid to the glue solution.
To prepare hot glue, break it into small pieces, soak it in enough cold water to cover it well, until it is soft, say twelve hours, and heat in a glue-pot or double boiler, Fig. 243, p. 149. The fresher the glue is, the better, as too many heatings weaken it. When used it should be thin enough to drip from the brush in a thin stream, so that it will fill the pores of the wood and so get a grip. Two surfaces to be glued together should be as close as possible, not separated [page 130] by a mass of glue. It is essential that the glue be hot and the wood warm, so that the glue may remain as liquid as possible until the surfaces are forced together. Glue holds best on side grain. End grain can be made to stick only by sizing with thin glue to stop the pores. Pieces thus sized and dried can be glued in the ordinary way, but such joints are seldom good. Surfaces of hard wood that are to be glued should first be scratched with a scratch-plane, Fig. 111, p. 79.
To prepare hot glue, break it into small pieces and soak it in enough cold water to completely cover it until it softens, which takes about twelve hours. Then, heat it in a glue pot or double boiler, Fig. 243, p. 149. The fresher the glue, the better it works, as repeated heating weakens it. When you use it, it should be thin enough to drip from the brush in a steady stream, allowing it to fill the pores of the wood and create a bond. The two surfaces being glued together should be as close as possible, without a lot of glue separating them. It's crucial that the glue is hot and the wood is warm so the glue stays as liquid as possible until the surfaces are pressed together. Glue bonds best on side grain. End grain only sticks well if you first size it with thin glue to seal the pores. Pieces that have been sized and dried can then be glued together as normal, but those joints are rarely strong. Surfaces of hardwood that need to be glued should be scratched with a scratch plane first, Fig. 111, p. 79.
To make waterproof glue, add one part of potassium bichromate to fifty parts of glue. It will harden when exposed to the air and light and be an insoluble liquid.8
To create waterproof glue, mix one part potassium bichromate with fifty parts glue. It will harden when it comes into contact with air and light, becoming an insoluble liquid.8
Footnote 8: For recipes for this and other glues, see Woodcraft, May '07, p. 49.
Footnote 8: For recipes for this and other glues, check out Woodcraft, May '07, p. 49.
General directions for gluing.9 Before applying glue to the parts to be fastened together, it is a good plan to assemble them temporarily without glue, to see that all the parts fit. When it is desirable that a certain part, as the panel, in panel construction, should not be glued in place, it is a wise precaution to apply wax, soap, or oil to its edges before insertion. Since hot glue sets quickly, it is necessary after the glue is applied to get the parts together as soon as possible. One must learn to work fast but to keep cool. To expedite matters, everything should be quite ready before the process is begun, clamps, protecting blocks of wood, paper to protect the blocks from sticking to the wood, braces to straighten angles, mallet, try-square, and all other appliances likely to be required.
General directions for gluing.9 Before applying glue to the pieces that need to be joined, it's a good idea to temporarily assemble them without glue to ensure everything fits correctly. If there's a part, like the panel in panel construction, that shouldn't be glued in place, it's smart to apply wax, soap, or oil to its edges before putting it in. Since hot glue sets quickly, it’s important to put the pieces together as soon as the glue is applied. You need to learn to work quickly while staying calm. To speed things up, everything should be organized and ready before starting the process, including clamps, protective blocks of wood, paper to prevent the blocks from sticking to the wood, braces to help align angles, a mallet, a try-square, and any other tools you might need.
Footnote 9: For special directions, for particular joints, see under the various joints, (Chap. VII.)
Footnote 9: For specific instructions regarding particular joints, see the section on the various joints (Chap. VII.)
Whenever it is possible to break up the process into steps, each step can be taken with more deliberation. For example, in assembling framed pieces that are doweled, it is well to glue the dowels into one set of holes beforehand, making tenons of them, as it were. Time is thus saved for the final assembling when haste is imperative. The superfluous glue around the dowels should be carefully wiped off.
Whenever you can break the process into steps, each step can be done more thoughtfully. For instance, when assembling framed pieces that are doweled, it’s a good idea to glue the dowels into one set of holes ahead of time, essentially turning them into tenons. This saves time for the final assembly when you need to hurry. Make sure to carefully wipe off any excess glue around the dowels.
Likewise in gluing up framed pieces, sections may be put together separately: as, the ends of a table, and when they are dry then the whole may be assembled. When the pieces are together the joints should be tested to see that they are true, and that there are no twists.
Similarly, when gluing framed pieces, sections can be assembled separately; for example, the ends of a table, and once they're dry, the whole thing can be put together. When the pieces are joined, the joints should be checked to ensure they are straight and that there are no twists.
A good way to insure squareness, is to insert a diagonal brace on the inside, corner to corner, as in Fig. 294, p. 196. Such a brace [page 131] should be provided when the trial assembly is made. Another good way to insure squareness is to pass a rope around two diagonally opposite posts, and then by twisting the rope, to draw these corners toward each other until the frame is square.
A great way to make sure everything is square is to put a diagonal brace inside, from corner to corner, like in Fig. 294, p. 196. You should add this brace when you're doing the trial assembly. Another effective method for ensuring squareness is to wrap a rope around two opposite posts and then twist the rope to pull those corners together until the frame is square. [page 131]
The superfluous glue may be wiped off at once with a warm damp cloth, but not with enough water to wet the wood. Or by waiting a few minutes until the glue thickens, much of it can readily be peeled off with an edge tool. Either of these ways makes the cleaning easier than to let the superfluous glue harden.
The extra glue can be wiped off immediately with a warm, damp cloth, but don't use so much water that it soaks the wood. Alternatively, if you wait a few minutes for the glue to thicken, you can easily peel off most of it using a sharp tool. Both methods make cleaning easier than if you let the extra glue harden.
The work when glued should remain at least six hours in the clamps to harden.
The glued work should stay in the clamps for at least six hours to set.
HINGES
Hinges, Fig. 233, are made in several forms. The most common are the butt-hinge or butt, the two leaves of which are rectangular, as in a door-hinge; the strap-hinge, the leaves of which are long and strap-shaped; the Tee-hinge, one leaf of which is a butt, and the other strap-shaped; the chest-hinge, one leaf of which is bent at a right angle, used for chest covers; the table-hinge used for folding table tops with a rule joint; the piano-hinge, as long as the joint; the blank hinge or screen-hinge which opens both ways; the stop-hinge, which opens only 90°; and the "hook-and-eye" or "gate" hinge.
Hinges, Fig. 233, come in various types. The most common are the butt hinge, which has two rectangular leaves like a door hinge; the strap hinge, with long, strap-shaped leaves; the Tee hinge, featuring one butt leaf and one strap-shaped leaf; the chest hinge, which has one leaf bent at a right angle for use on chest covers; the table hinge, designed for folding table tops with a rule joint; the piano hinge, which runs the entire length of the joint; the blank hinge or screen hinge, which opens in both directions; the stop hinge, which only opens 90°; and the "hook-and-eye" or "gate" hinge.
Fig. 233. |
a. Butt-hinge. |
b. Tee-hinge. |
c. Chest-hinge. |
d. Table-hinge. |
e. Blank or Screen-hinge. |
The knuckle of the hinge is the cylindrical part that connects the two leaves, Fig. 234. The "acorn" is the head of the "pintle" or pin that passes thru the knuckle. Sizes of butts are indicated in inches for length, and as "narrow," "middle," "broad" and "desk" for width. The pin may be either riveted into the knuckle as in box-hinges or removable as in door-butts. Sometimes, as in blind-hinges, [page 132] the pintle is fastened into one knuckle, but turns freely in the other.
The knuckle of the hinge is the cylindrical part that connects the two leaves, Fig. 234. The "acorn" is the head of the "pintle" or pin that goes through the knuckle. Sizes of butts are listed in inches for length and categorized as "narrow," "middle," "broad," and "desk" for width. The pin can either be riveted into the knuckle like in box-hinges or be removable like in door-butts. Sometimes, as in blind-hinges, [page 132] the pintle is attached to one knuckle but rotates freely in the other.
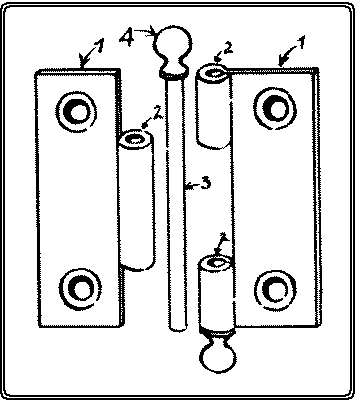
Fig. 234. Parts of a butt-hinge. |
1.1. Leaves. |
2.2.2. Knuckle. |
3. Pintle. |
4. Acorn. |
A butt-hinge may be set in one of three positions, Fig. 235: (1) Where it is desired to have the hinge open as wide as possible, as in a door. Here the knuckle is set well out from the wood. (2) Where it is desired to have the hinged portion open flat and no more. Here the center of the pin is in line with the outside surface of the wood. This is less likely to rack the hinge than the other two positions. (3) Where it is desired to have the knuckle project as little as possible.
A butt hinge can be positioned in one of three ways, as shown in Fig. 235: (1) When you want the hinge to open as wide as possible, like on a door. In this case, the knuckle sticks out far from the wood. (2) When you want the hinged part to open flat and not further. Here, the center of the pin is aligned with the outer surface of the wood. This position minimizes the chance of the hinge getting out of alignment compared to the other two positions. (3) When you want the knuckle to stick out as little as possible.

Fig. 235. Three Positions of Hinges.
HINGING
In setting the hinges of a box cover, first see that the cover fits the box exactly all the way around.
In setting the hinges for a box cover, first make sure that the cover fits the box perfectly all the way around.
In the case of a door, see that it fits its frame, evenly all the way around, but with a little play. To insure a tighter fit at the swinging edge this edge should be slightly beveled inwards.
In the case of a door, make sure it fits its frame evenly all around, but with a little play. To ensure a tighter fit at the swinging edge, this edge should be slightly beveled inward.
In attaching a butt-hinge, the essential thing is to sink the hinge into the wood, exactly the thickness of the knuckle. The gains may be cut in one or both of the pieces to be hinged together.
In attaching a butt hinge, the key thing is to embed the hinge into the wood, matching the thickness of the knuckle. The recesses can be cut into either or both of the pieces that need to be hinged together.
With these matters determined proceed as follows: In the case of a box cover, the hinges should be set about as far from the ends of the box as the hinge is long.
With these issues settled, proceed as follows: For a box cover, the hinges should be positioned roughly the same distance from the ends of the box as the length of the hinge itself.
In the case of an upright door, locate the hinges respectively above and below the lower and upper rails of the door. Mark with the knife on the edge of the door the length of the hinge, and square across approximately the width of the gain to receive it. Do this for both hinges. Between these lines gage the proper width of the gains. Set another gage to one half the thickness of the knuckle and gage on the door face the depth of the gains. Chisel out the gains, set the hinges in place, bore the holes, and drive the screws. Place the door in position again to test the fit. If all is well, mark the position of the hinges on the frame, gage and cut the gains, and fasten in the hinges. Where the hinge is gained its full thickness into the door, [page 133] no gain, of course, is cut in the frame. If the hinges are set too shallow, it is an easy matter to unscrew one leaf of each and cut a little deeper. If they are set too deep the screws may be loosened and a piece of paper or a shaving inserted underneath along the outer arris of the gain.
For an upright door, find the hinges above and below the lower and upper rails of the door. Use a knife to mark the hinge length on the edge of the door, then square across about the width of the recess to fit it. Do this for both hinges. Between these lines, measure the correct width of the recesses. Set another gauge to half the thickness of the knuckle and measure on the door face the depth of the recesses. Chisel out the recesses, position the hinges, drill the holes, and drive in the screws. Put the door back in place to check the fit. If everything looks good, mark the hinge positions on the frame, measure and cut the recesses, and secure the hinges. When the hinge is fully recessed into the door, there’s no recess needed in the frame. If the hinges are too shallow, it’s easy to unscrew one leaf of each and carve a little deeper. If they're too deep, you can loosen the screws and slip a piece of paper or a shaving under the outer edge of the recess.
LOCKS
The chief parts of a lock are: the bolt, its essential feature, the selvage, the plate which appears at the edge of the door or drawer, the box, which contains the mechanism including the tumbler, ward, spring, etc., the key-pin, into or around which the key is inserted, the strike, the plate attached opposite the selvage, (often left out as in drawer-locks, but essential in hook-bolt locks, and self-locking locks,) and the escutcheon, the plate around the keyhole.
The main parts of a lock are: the bolt, which is the key feature, the selvage, the plate seen at the edge of the door or drawer, the box, which houses the mechanism including the tumbler, ward, spring, etc., the key-pin, where the key is inserted, the strike, the plate mounted opposite the selvage (often omitted in drawer locks, but crucial in hook-bolt locks and self-locking locks), and the escutcheon, the plate surrounding the keyhole.
Locks may be classified: (1) According to their uses, of which there are two types. (a), Fig. 236, For drawers, cupboards, tills, wardrobes, and doors. In these the bolt simply projects at right angles to the selvage into the strike, and resists pressure sidewise of the lock. (b), Fig. 237, For desks, roll-top desks, chests, boxes and sliding doors. In these, the bolt includes a hook device of some kind to resist pressure perpendicular to the selvage. In some locks, the hook or hooks project sidewise from the bolt, in others the bolt engages in hooks or eyes attached to the strike.
Locks can be categorized: (1) Based on their uses, which fall into two types. (a) Fig. 236, For drawers, cabinets, cash registers, wardrobes, and doors. In these, the bolt simply extends at a right angle to the edge into the strike, resisting sideways pressure on the lock. (b) Fig. 237, For desks, roll-top desks, chests, boxes, and sliding doors. In these, the bolt contains some kind of hook mechanism to withstand pressure perpendicular to the edge. In some locks, the hook or hooks extend sideways from the bolt, while in others, the bolt fits into hooks or eyes attached to the strike.

Fig. 236. Rim-lock, for Drawer.
1. Bolt. 2. Selvage.
3. Box. 4. Key-pin.

Fig. 237. Mortise-lock, for Box.
(2) According to the method of application, as rim locks, which are fastened on [page 134] the surface, and mortise locks which are mortised into the edge of a door or drawer or box.
(2) Based on the method of application, there are rim locks, which are mounted on the surface, and mortise locks, which are fitted into the edge of a door, drawer, or box.
INSERTING LOCKS
To insert a rim-lock, measure the distance from the selvage to the key-pin, locate this as the center of the keyhole, and bore the hole. If the lock has a selvage, gain out the edge of the door or drawer to receive it. If the lock box has to be gained in, do that next, taking care that the bolt has room to slide. Cut the keyhole to the proper shape with a keyhole-saw or small chisel. Fasten the lock in place, and if there is a strike or face-plate, mark its place and mortise it in.
To install a rim-lock, measure the distance from the edge to the key-pin to find the center of the keyhole, then drill the hole. If the lock includes an edge, hollow out the edge of the door or drawer to accommodate it. If the lock box needs to be recessed, do that next, ensuring that the bolt has enough space to slide. Shape the keyhole correctly with a keyhole saw or a small chisel. Secure the lock in place, and if there's a strike or faceplate, mark its position and mortise it in.
To insert a mortise-lock, locate and bore the keyhole, mortise in the box and the selvage, finish the keyhole, fasten in the lock, add the escutcheon, locate and mortise in the strike, and screw it in place.
To install a mortise-lock, find and drill the keyhole, cut the mortise in the box and the edge, finish the keyhole, secure the lock, attach the escutcheon, find and cut the mortise for the strike, and screw it in place.
WOOD FASTENINGS
References*:
Sources*:
Hammacher & Schlemmer.
Hammacher & Schlemmer.
Catalog No. 151.
Catalog No. 151.
Nails.
Nail products.
Goss, p. 153.
Goss, p. 153.
Purfield, Wood Craft, 5: 181.
Purfield, Wood Craft, 5: 181.
Park, pp. 129-135.
Park, pp. 129-135.
Griffith, pp. 75-78.
Griffith, pp. 75-78.
Wood Craft, 5: 103.
Woodworking, 5: 103.
Wheeler, pp. 428-433.
Wheeler, pp. 428-433.
Tacks.
Thumbtacks.
Wheeler, pp. 429-433.
Wheeler, pp. 429-433.
Sickels, p. 70.
Sickels, p. 70.
Goss, p. 155.
Goss, p. 155.
Barter, pp. 84-86.
Barter, pp. 84-86.
Screws.
Screws.
Goss, p. 155.
Goss, p. 155.
Wheeler, p. 476.
Wheeler, p. 476.
Barter, p. 86.
Barter, p. 86.
Griffith, pp. 78-80.
Griffith, pp. 78-80.
Park, pp. 136-140.
Park, pp. 136-140.
Dowels.
Dowels.
Goss, p. 153.
Goss, p. 153.
Wheeler, p. 374.
Wheeler, p. 374.
Sickels, p. 104.
Sickels, p. 104.
Griffith, p. 92.
Griffith, p. 92.
Wedges.
Wedge shoes.
Goss, p. 151.
Goss, p. 151.
Glue.
Adhesive.
Goss, p. 156.
Goss, p. 156.
Rivington, III, p. 432.
Rivington, III, p. 432.
Barter, p. 82.
Barter, p. 82.
Standage, Wood Craft, 7: 48.
Standage, Wood Craft, 7:48.
Park, pp. 141-146.
Park, pp. 141-146.
Sickels, p. 106.
Sickels, p. 106.
Wheeler, pp. 391-396.
Wheeler, pp. 391-396.
Alexander, Wood Craft, 5: 168.
Alexander, *Wood Craft*, 5: 168.
Griffith, pp. 80-83.
Griffith, pp. 80-83.
Hinges.
Hinges.
Sickels, p. 118.
Sickels, p. 118.
Wheeler, p. 402.
Wheeler, p. 402.
* For general bibliography see p. 4.
* For general bibliography see __A_TAG_PLACEHOLDER_0__
Chapter VI.
EQUIPMENT AND CARE OF THE SHOP.
Tool equipment. The choice of tools in any particular shop best comes out of long experience. Some teachers prefer to emphasize certain processes or methods, others lay stress on different ones. The following tentative list is suggested for a full equipment for twenty-four students. One bench and its tools may be added for the teacher.
Tool equipment. Choosing the right tools for any shop really comes from years of experience. Some instructors prioritize certain processes or methods, while others focus on different ones. The following suggested list is for a complete setup for twenty-four students. One additional bench and its tools can be added for the instructor.
The prices given are quoted from Discount Sheet No. 1 for Catalogue of Tools, No. 355 issued by Hammacher, Schlemmer & Co., Fourth Avenue and 13th Street, New York City, dated 1908, and are correct at the present date (1910). Aggregate orders, however, are always subject to special concessions, and it is suggested that before ordering the purchaser submit a list of specifications for which special figures will be quoted.
The prices listed are taken from Discount Sheet No. 1 for Catalogue of Tools, No. 355 published by Hammacher, Schlemmer & Co., Fourth Avenue and 13th Street, New York City, dated 1908, and are accurate as of now (1910). However, bulk orders are always eligible for special discounts, and it’s recommended that before placing an order, the buyer submits a list of specifications for which special pricing will be provided.
There are good benches, vises, and tools of other makes on the market, but those specified below are typical good ones.
There are great benches, vises, and tools from various brands available, but the ones listed below are typical high-quality options.
Following are two equipments for classes of twenty-four pupils, one severely economical to cost approximately $400, and the other more elaborate to cost approximately $750.
Following are two pieces of equipment for classes of twenty-four students, one very budget-friendly costing about $400, and the other more advanced costing about $750.
$400 TOOL EQUIPMENT.
INDIVIDUAL TOOLS.
THE CARE OF THE WOODWORKING SHOP
The general arrangement of the room. The important factors are the source or sources of light, and the lines of travel. The common arrangement of benches where two sides of the room are lighted, is shown in a, Fig. 238. By this arrangement, as each worker faces his bench, he also faces one set of windows and has another set of windows at his left. The advantage of this arrangement is that it is easy to test one's work with the try-square by lifting it up to the light. Another arrangement, shown in b, Fig. 238, has this advantage, that there are no shadows on the work when it is lying on the bench and the worker is holding his rule or try-square on it with his left hand. When all the windows are on one side of the room the latter is the more advantageous arrangement.
The general layout of the room. Key factors include the source or sources of light and the pathways for movement. The typical setup of benches where two sides of the room receive light is illustrated in a, Fig. 238. In this setup, as each worker faces their bench, they also face one set of windows and have another set of windows to their left. The benefit of this arrangement is that it's easy to check one's work with the try-square by holding it up to the light. Another setup, shown in b, Fig. 238, offers the advantage of having no shadows on the work when it's on the bench and the worker is using their left hand to hold the rule or try-square on it. When all the windows are on one side of the room, this latter setup is more beneficial.
In determining the position of the benches, especially with reference to their distance from each other, thought should be given to the general lines of travel, from the individual benches to the general tool-rack, to the finishing-table, to the lockers, etc. Even if all the aisles cannot be wide enough both for passage and for work, one wider one thru the center of the room may solve the difficulty. Where [page 143] rooms are crowded, space may be economized by placing the benches in pairs, back to back, c and d, Fig. 238. In any case, room should always be reserved for a tier of demonstration seats, facing the teacher's bench, for the sake of making it easy for the pupils to listen and to think.
In deciding where to place the benches, especially how far apart they should be, consideration should be given to the main paths of movement from each bench to the general tool rack, to the finishing table, to the lockers, and so on. Even if not all aisles can be wide enough for both walking and working, having one wider aisle through the center of the room may help resolve the issue. In crowded areas, space can be saved by arranging the benches in pairs, back to back, c and d, Fig. 238. In any case, space should always be reserved for a row of demonstration seats facing the teacher's bench, to make it easier for students to listen and think.

Fig. 238. Four Different Arrangements of Benches in a Shop.
The Tools. Every shop soon has its own traditions as to the arrangement of tools, but there are two principles always worth observing. (1) It is an old saying that there should be "a place for everything and everything in its place." This is eminently true of a well-ordered woodworking shop, and there is another principle just as important. (2) Things of the same sort should be arranged together, and arranged by sizes, whether they be general tools or individual tools. In arranging the rack for general tools, a few suggestions are offered. In the first place, arrange them so that there will be no danger of cutting one's fingers on one tool when attempting to take down another. [page 144] Where the rack must needs be high, all the tools can be brought within reach, by placing long tools, like files, screwdrivers, etc., at the top. Such an arrangement is shown in Fig. 239.
The Tools. Every workshop eventually develops its own way of organizing tools, but there are two principles that are always worth keeping in mind. (1) There's an old saying that goes, "a place for everything and everything in its place." This is especially true for a well-organized woodworking shop, and there's another principle that's just as important. (2) Similar items should be grouped together and sorted by size, whether we're talking about general tools or specific ones. When setting up the rack for general tools, here are a few tips. First, arrange the tools so there's no risk of cutting your fingers on one tool while trying to grab another. [page 144] If the rack has to be high, you can still keep all the tools accessible by placing longer tools, like files and screwdrivers, at the top. This arrangement is illustrated in Fig. 239.
As to the individual benches, those without high backs are to be preferred, not only because of their convenience when it is desired to work on large pieces, like table tops, and because the backs do not interfere with the light, but because it is easier for the teacher to look over the room to see that everything is in order. If the equipment is kept complete, it is an easy matter to glance over all the benches and the general rack to see that everything is in place.
When it comes to the individual benches, those without high backs are preferred, not just for their convenience when working on large pieces like tabletops, but also because the backs don’t block the light. Plus, it’s easier for the teacher to scan the room and make sure everything is in order. If the equipment is kept complete, it’s simple to glance over all the benches and the general rack to ensure everything is in its place.
In general, there are two methods of keeping guard over tools, the open and the closed. In the open method, everything is kept in sight so that empty places can be discovered readily. This method is a convenient one, and, besides, the tools are always easily accessible. In the closed method, the tools are kept in drawers and cases where they can be locked up. This method is suitable where pupils are [page 145] equipped with individual sets of cutting tools. In such a case, the common tools for each bench are kept in a common drawer and individual pupils' tools in separate drawers. This method has the disadvantage that things are out of sight, and if they disappear their loss may not be discovered immediately. On the other hand, where the drawers and cases are kept carefully locked, the danger of loss is reduced almost to a minimum. Sometimes a combination of both methods is tried, the tools being kept in unlocked drawers. This method furnishes the greatest difficulty in keeping tools from disappearing.
In general, there are two ways to keep track of tools: the open method and the closed method. With the open method, everything is visible, making it easy to spot any empty spots. This approach is convenient, and the tools are always easy to access. With the closed method, tools are stored in drawers and cases that can be locked. This method works well when students have their own sets of cutting tools. In this situation, shared tools for each workspace are kept in a common drawer, while each student’s tools are stored in separate drawers. The downside of this method is that items are out of sight, and if something goes missing, it might not be noticed right away. However, when the drawers and cases are kept securely locked, the risk of losing tools is greatly minimized. Sometimes a combination of both methods is used, with tools kept in unlocked drawers. This approach makes it much harder to prevent tools from disappearing.
Even when tools are well arranged, one of the most serious difficulties in the way of shop order, is to keep tools in their places. Pupils who are in a hurry, slip in the tools wherever they will fit, not where they belong. Labels at the places of the different sets may [page 146] help somewhat; a more efficient method is to paste or paint the form of each tool on the wall or board against which it hangs. Pupils will see that, when they will not stop to read a label.
Even when tools are organized, one of the biggest challenges to keeping a tidy workshop is making sure tools stay in their designated spots. Students who are in a rush tend to shove tools wherever they can fit, not where they actually belong. Labels at the locations for different sets can help a bit; a more effective approach is to stick or paint the outline of each tool on the wall or board where it hangs. Students will notice this even when they don't take the time to read a label. [page 146]
In spite of all precautions, some tools will disappear. A plan to cover the cost of these, which works well in some schools, is to require a deposit at the beginning of the year to cover these losses. Then at the end of the year, after deducting the cost of losses, the balance is returned pro rata.
In spite of all precautions, some tools will go missing. A plan to cover the cost of these, which works well in some schools, is to ask for a deposit at the start of the year to cover these losses. Then at the end of the year, after subtracting the cost of the losses, the remaining amount is returned proportionally.
There is diversity of practice in the distribution of tools on the general case and on the individual benches. Some tools, like the [page 147] plane and chisel, and try-square, are so frequently in use that each worker must have one at hand. As to others, the demand must determine the supply. One other consideration may be expressed by the principle that those tools, the use of which is to be encouraged, should be kept as accessible as possible, and those whose use is to be discouraged, should be kept remote. Some tools, like files, it may be well to keep in a separate locker to be had only when asked for.
There are different practices in how tools are distributed in general and on individual workspaces. Some tools, like the [page 147] plane, chisel, and try-square, are used so often that each worker needs to have one readily available. For other tools, the demand will dictate how many are supplied. Another point to consider is that tools that should be used more often should be kept as accessible as possible, while those that should be used less often should be stored away. Some tools, like files, might be best kept in a separate locker and only given out when requested.
A cabinet of drawers, such as that shown in Fig. 240, for holding nails, screws, and other fastenings, is both a convenience and a material aid in preserving the order of the shop.
A cabinet of drawers, like the one in Fig. 240, for storing nails, screws, and other fasteners, is both useful and helps keep the shop organized.

Fig. 240. Nail and Screw Cabinet.
As for the care of tools during vacation, they should be smeared with vaseline, which is cheap, and put away out of the dampness. The planes should be taken apart and each part smeared. To clean them again for use, then becomes an easy matter. The best method of removing rust and tarnish is to polish the tools on a power buffing wheel on which has been rubbed some tripoli. They may then be polished on a clean buffer without tripoli.
As for taking care of tools during vacation, they should be coated with Vaseline, which is inexpensive, and stored away from moisture. The planes should be disassembled and each part coated. Cleaning them up for use later becomes a simple task. The best way to remove rust and tarnish is to polish the tools on a power buffing wheel that has some tripoli on it. After that, they can be polished on a clean buffer without tripoli.
The Lockers. In order to maintain good order in the shop, an almost indispensable part of the equipment is a set of lockers for holding [page 148] the unfinished work of pupils. An inexpensive outfit may consist simply of sets of shelves, say 5" apart, 12" deep, and 18" long, Fig. 241. Ordinary spring-roller curtains may be hung in front of each set of shelves to conceal and protect the contents. Such a case should cost at the rate of about 40c. for each compartment. A more substantial and more convenient case, shown in Fig. 242, consists of compartments each 9½" high, 6" wide, and 18" deep. These proportions may be changed to suit varying conditions. In front of each tier of 12 compartments is a flap door opening downward. Such a case built of yellow pine (paneled) may cost at the rate of $1.00 per compartment.
The Lockers. To keep the shop organized, a set of lockers is an essential piece of equipment for storing students' unfinished work. A budget-friendly option could be simple shelves, around 5" apart, 12" deep, and 18" long, as shown in Fig. 241. Regular spring-roller curtains can be hung in front of each shelf unit to hide and protect the items inside. This type of unit should cost about 40 cents for each compartment. A more durable and user-friendly version, illustrated in Fig. 242, has compartments that are 9½" high, 6" wide, and 18" deep. These dimensions can be adjusted based on specific needs. Each row of 12 compartments features a flap door that opens downward. A case made from yellow pine (paneled) may cost approximately $1.00 per compartment.
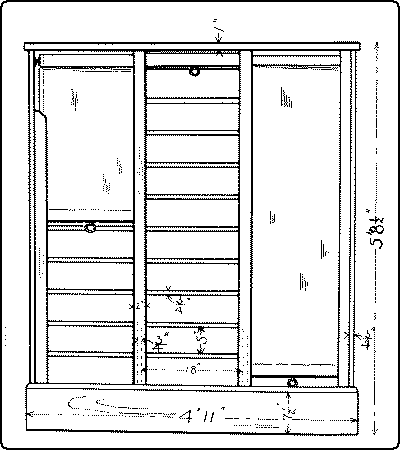
Fig. 241. An Inexpensive Locker for Unfinished Work.

Fig. 242. A More Expensive Locker for Unfinished Work.
There should, of course, be a separate compartment for each pupil using the shop. Where possible, there should be a special table [page 149] for staining and gluing. Where strict economy must be practiced, a good sized kitchen table covered with oilcloth answers every purpose. A better equipment would include a well-built bench, such as that shown in Fig. 243, the top and back of which are covered with zinc.
There should definitely be a separate space for each student using the shop. Whenever possible, there should be a dedicated table for staining and gluing. If strict budgeting is necessary, a good-sized kitchen table covered with oilcloth will work just fine. An improved setup would include a sturdy bench, like the one shown in Fig. 243, with the top and back covered in zinc. [page 149]
Where no staining-table is possible, temporary coverings of oilcloth may be provided to lay over any bench which is convenient for the purpose.
Where a staining table isn't available, temporary oilcloth covers can be placed over any bench that's suitable for the job.
Care of brushes and materials used in finishing wood. Shellac should be kept in glass or pottery or aluminum receptacles but not in any metal like tin, which darkens it. A good plan is to have a bottle for fresh, untouched shellac, a wide-mouthed jar for that which has been diluted and used, and an enameled cup for use. There should also be a special brush, Fig. 244. At the time of using, first see that the brush is soft and pliable. If it is stiff, it can be soaked quickly and softened in a little alcohol in the cup. This alcohol may then be poured into the jar and mixed in by shaking. Then pour out a little from the jar into the cup, and if it is too thin, thicken with some fresh shellac. After using, pour back the residue into the jar, carefully wiping the brush on the edge of the jar; and if it is not to be used again for some time, rinse it in a little alcohol, which may also be poured into the jar, which should then be covered. What little shellac remains in the brush and cup will do no harm and the brush may be left standing in the cup until required. The important things are to keep the shellac cup and brush for shellac only, (indeed, it is a good plan to label them "SHELLAC ONLY,") and to keep the shellac covered so that the alcohol in it will not evaporate. In a pattern-making shop, where the shellac cup is to be frequently used, it is well to have cups with covers thru which the brushes hang, like the brush in a mucilage jar.
Care of brushes and materials used in finishing wood. Shellac should be stored in glass, pottery, or aluminum containers, but not in any metal like tin, which can darken it. A good approach is to have one bottle for fresh, unused shellac, a wide-mouthed jar for diluted and used shellac, and an enameled cup for application. There should also be a special brush, Fig. 244. Before using, make sure the brush is soft and flexible. If it feels stiff, you can quickly soak it in a little alcohol in the cup to soften it. This alcohol can then be poured into the jar and mixed by shaking. Next, pour a little from the jar into the cup, and if it’s too thin, thicken it with some fresh shellac. After using, pour any leftover mixture back into the jar, carefully wiping the brush on the edge; if the brush isn’t going to be used for a while, rinse it in a little alcohol, which can also go into the jar that should then be covered. Any shellac left in the brush and cup won’t cause harm, and the brush can stay in the cup until needed. It’s important to keep the shellac cup and brush for shellac only (in fact, labeling them "SHELLAC ONLY" is a good idea) and to keep the shellac covered so the alcohol doesn't evaporate. In a pattern-making shop, where the shellac cup is used often, it’s useful to have cups with covers that allow the brushes to hang, similar to how brushes are stored in a mucilage jar.

Fig. 244. Shellac Utensils.
Varnish brushes need to be cleaned thoroly after each using. If they get dry they become too hard to be cleaned without great difficulty.
Varnish brushes need to be cleaned thoroughly after each use. If they dry out, they become too hard to clean without a lot of trouble.
Brushes for water stains are easily taken care of by washing with water and then laying them flat in a box. Cups in which the water stains have been used can also be easily rinsed with water.
Brushes for water stains are easy to clean by washing them with water and then laying them flat in a box. Cups that have been used for water stains can also be easily rinsed with water.
Brushes for oil stains are most easily kept in good condition, by being hung in a brush-keeper, Fig. 245, (sold by Devoe & Reynolds, 101 Fulton St., N. Y. C.) partly filled with turpentine. The same brushes may also be used for fillers.
Brushes for oil stains are easiest to keep in good condition by hanging them in a brush holder, Fig. 245, (sold by Devoe & Reynolds, 101 Fulton St., N. Y. C.) that's partially filled with turpentine. You can also use the same brushes for fillers.

Fig. 245. Brush-keeper.
Oil stains should be poured back into their respective bottles, and the cups wiped out with cotton waste. When they get in bad condition, they can be cleaned readily after a preliminary soaking in a strong solution of potash. The same treatment may be given to brushes, but if they are left soaking too long in the solution, the bristles will be eaten off.
Oil stains should be poured back into their bottles, and the cups cleaned out with cotton waste. When they’re in bad shape, they can be easily cleaned after soaking in a strong potash solution. The same method can be used for brushes, but if they’re left soaking in the solution too long, the bristles will get damaged.
EQUIPMENT AND CARE OF THE SHOP
References*
Sources*
Murray, Year Book 1906, p. 69.
Murray, *Yearbook* 1906, p. 69.
Bailey, M. T. Mag., 9: 138. Dec. '07.
Bailey, M. T. Mag., 9: 138. Dec. '07.
Robillion, pp. 48-90.
Robillion, pp. 48-90.
Hammacher and Schlemmer, passim.
Hammacher and Schlemmer, various mentions.
* For general bibliography, see p. 4.
* For general bibliography, see __A_TAG_PLACEHOLDER_0__
CHAPTER 7.
THE COMMON JOINTS.
Wherever two or more pieces of wood are fastened together we have what is properly called joinery. In common usage the term indicates the framing of the interior wood finish of buildings and ships, but it is also used to include cabinet-making, which is the art of constructing furniture, and even the trades of the wheelwright, carriage-maker, and cooper. Since joinery involves the constant use of joints, a reference list of them, with illustrations, definitions, uses, and directions for making typical ones may be of convenience to workers in wood.
Wherever two or more pieces of wood are joined together, it's called joinery. In everyday language, this term usually refers to the framework of the interior wood finish in buildings and ships, but it also includes cabinet-making, which is the craft of making furniture, as well as the trades of the wheelwright, carriage-maker, and cooper. Since joinery relies heavily on joints, having a list of them, complete with illustrations, definitions, uses, and instructions for making common types, can be helpful for those working with wood.
HEADING JOINTS
No. 1. A lapped and strapped joint is made by laying the end of one timber over another and fastening them both together with bent straps on the ends of which are screws by which they may be tightened. It is a very strong joint and is used where the beams need lengthening as in false work or in long ladders and flag poles.
No. 1. A lapped and strapped joint is created by placing the end of one timber over another and securing them together with bent straps that have screws on the ends for tightening. It's a very strong joint and is used when beams need to be extended, such as in false work, long ladders, and flagpoles.

Fig. 264-1 Lapped and Strapped
No. 2. A fished joint is made by butting the squared ends of two timbers together and placing short pieces of wood or iron, called fish-plates, over the faces of the timbers and bolting or spiking the whole firmly together. It is used for joining timbers in the direction of their length, as in boat construction.
No. 2. A fished joint is created by connecting the squared ends of two pieces of timber and placing short wood or iron strips, known as fish-plates, over the faces of the timbers, then bolting or spiking everything securely together. It is used to join timbers along their length, such as in boat building.

Fig. 264-2 Fished
No 3. In a fished joint keys are often inserted between the fish-plate and beam at right angles to the bolts in order to lessen the strain that comes upon the bolts when the joint is subjected to tension. In wide pieces and for extra strength, as in bridge work, the bolts may be staggered.
No 3. In a fished joint, keys are often placed between the fish-plate and beam at right angles to the bolts to reduce the strain on the bolts when the joint is under tension. In wider components and for added strength, such as in bridge construction, the bolts may be staggered.

Fig. 264-3 Fished and keyed
Nos. 4, 5, 6 and 7. A scarf or spliced joint is made by joining together with flush surfaces the ends of two timbers in such a way as to enable them to resist compression, as in No. 4; tension, as in No. 5; both, as in No. 6, where the scarf is tabled; or cross [page 152] strain as in No. 7. No. 4 is used in house sills and in splicing out short posts, Nos. 5 and 6 in open frame work. No. 7 with or without the fish-plate, is used in boats and canoes, and is sometimes called a boat-builder's joint, to distinguish it from No. 4, a carpenter's joint. A joint to resist cross strain is stronger when scarfed in the direction of the strain than across it. No. 7 is the plan, not elevation, of a joint to receive vertical cross strain.
Nos. 4, 5, 6 and 7. A scarf or spliced joint is created by connecting the ends of two pieces of wood with smooth surfaces in a way that allows them to withstand compression, as shown in No. 4; tension, as in No. 5; both forces, as in No. 6, where the scarf is tabled; or cross strain, as in No. 7. No. 4 is used in house sills and for extending short posts, while Nos. 5 and 6 are used in open framework. No. 7, with or without the fish-plate, is utilized in boats and canoes, and is sometimes referred to as a boat-builder's joint to differentiate it from No. 4, which is a carpenter's joint. A joint designed to resist cross strain is stronger when scarfed in the direction of the strain rather than across it. No. 7 is the plan, not elevation, of a joint meant to handle vertical cross strain.

Fig. 264-4 Spliced for compression

Fig. 264-5 Spliced for tension

Fig. 264-6 Spliced and Tabled

Fig. 264-7 Spliced for cross strain
BUTT JOINTS
No. 8. A doweled butt-joint is made by inserting, with glue, dowel-pins into holes bored into the two members. The end of one member is butted against the face or edge of the other. It is used in cabinet-making where the presence of nails would be unseemly.
No. 8. A doweled butt-joint is created by inserting dowel pins into holes drilled into both pieces, along with glue. The end of one piece is pressed against the face or edge of the other. This method is used in cabinet-making where showing nails would look unattractive.

Fig. 264-8 Dowelled butt

Fig. 246. Lay-out by Thru Dowling.
In a doweled butt-joint the dowels may go clear thru the outside member, and be finished as buttons on the outside, where they show. To lay out this joint mark near the ends of the edges of the abutting member, X, Fig. 246, center-lines A B. Draw on the other member Y, a sharp pencil-line to which when the lines AB on X are fitted, X will be in its proper place. Carry the line around to the other side of Y and locate on it the proper centers for the dowel-holes E and F. Then fasten on the end of X a handscrew in such a way that the jaws will be flush with the end. With another handscrew, clamp this handscrew to Y in such a way that the marks on the two pieces match, A to C and B to D, Fig. 247. Bore at the proper places, E and F, holes directly thru Y into X.
In a doweled butt joint, the dowels can go all the way through the outer piece and be finished as buttons on the outside, where they are visible. To lay out this joint, mark near the ends of the edges of the adjoining piece, X, as shown in Fig. 246, with center lines A B. Draw a sharp pencil line on the other piece Y. When the lines AB on X align with this line, X will be in the correct position. Extend the line around to the other side of Y and mark the correct centers for the dowel holes E and F. Next, attach a handscrew to the end of X so that the jaws are flush with the end. Use another handscrew to clamp this handscrew to Y in such a way that the marks on the two pieces align, A to C and B to D, as shown in Fig. 247. Drill holes at the designated locations, E and F, directly through Y into X.

Fig. 247. Thru Boring for a Butt Joint.
Fig. 248 illustrates the gluing together of a four-legged stand in which the joints are made in this way. The cross-lap joints of the stretchers are first glued together, then the other joints are assembled without glue, to see that all the parts fit and finally two opposite [page 153] sides are glued at a time. Pieces of paper are laid inside the gluing blocks to prevent them from sticking to the legs.
Fig. 248 shows how to glue together a four-legged stand with these joint techniques. First, glue the cross-lap joints of the stretchers, then assemble the other joints without glue to ensure all parts fit together. Finally, glue two opposite sides at a time. Place pieces of paper inside the gluing blocks to keep them from sticking to the legs. [page 153]

Fig. 248. Gluing-Up a Four-Legged Stand.
In case the dowels are to be hidden the chief difficulty is to locate the holes properly. One method of procedure is as follows: To dowel the end of one member against the face of the other as a stringer into a rail or a rail into a table leg, first lay out the position of the dowels in the end of the first member, X, Fig. 249. Gage a center-line, A B, across this end lengthwise, locate the centers of the dowel-holes, and square across with a knife point, as CD and EF. Gage a line on the other member to correspond with the line AB. On the face so gaged, lay the first member on its side so that one arris lies along this gaged line and prick off the points D and F, to get the centers of the dowel-holes.
If the dowels are meant to be hidden, the main challenge is to locate the holes accurately. One approach is as follows: To dowel the end of one piece against the face of another, like a stringer into a rail or a rail into a table leg, first mark where the dowels will go on the end of the first piece, X, Fig. 249. Draw a center line, A B, across this end lengthwise, find the centers of the dowel holes, and square across with a knife point, like CD and EF. Mark a corresponding line on the other piece that matches line AB. Then, place the first piece on its side so that one edge aligns with this marked line and mark the points D and F to determine the centers of the dowel holes.

Fig. 249. Laying out a Dowel Joint.
If, as is usual, there are a number of similar joints to be made, a device like that shown in Fig. 249 will expedite matters. 1 and 2 are points of brads driven thru a piece of soft wood, which has been notched out, and are as far apart as the dowels. A-1 is the distance from the working edge of the rail to the first dowel. The same measure can be used from the end of the leg.
If there are several similar joints to be made, a tool like the one shown in Fig. 249 will make the process faster. Points 1 and 2 are locations of brads driven through a piece of soft wood that's been notched out, and they are spaced the same distance as the dowels. A-1 is the distance from the working edge of the rail to the first dowel. You can use the same measurement from the end of the leg.
When the centers are all marked, bore the holes. Insert the dowels into the holes and make a trial assembly. If any rail is twisted from its proper plane, note carefully where the error is, take apart, glue a dowel into the hole, that is wrong, pare it off flush with the surface, and re-bore in such a place that the parts, when assembled will come up true. When everything fits, glue and clamp together.
When all the centers are marked, drill the holes. Insert the dowels into the holes and do a test assembly. If any rail is twisted out of alignment, carefully note where the mistake is, take it apart, glue a dowel into the incorrect hole, trim it flush with the surface, and re-drill in a spot where, when assembled, the parts will align properly. Once everything fits, glue and clamp them together.
No. 9. A toe-nailed joint is made by driving nails diagonally thru the corners of one member into the other. It is used in fastening the studding to the sill in balloon framing.
No. 9. A toe-nailed joint is created by driving nails diagonally through the corners of one piece into the other. It's used to attach the studs to the sill in balloon framing.

Fig. 264-9 Toe-nailed

Fig. 264-10 Draw-bolt
No. 11. A plain butt-joint is one in which the members join endwise or edgewise without overlapping. It is used on returns as in ordinary boxes and cases.
No. 11. A plain butt-joint is one where the pieces connect end to end or edge to edge without overlapping. It's used on returns like in regular boxes and cases.

Fig. 264-11 Plain butt
No. 12. A glued and blocked joint is made by gluing and rubbing a block in the inside corner of two pieces which are butted and glued together. It is used in stair-work and cabinet-work, as in the corners of bureaus.
No. 12. A glued and blocked joint is created by gluing and positioning a block in the inside corner of two pieces that are joined and glued together. It's used in stair construction and cabinet making, like in the corners of dressers.

Fig. 264-12 Glued and blocked
No. 13. A hopper-joint is a butt-joint, but is peculiar in that the edges of the boards are not square with their faces on account of the pitch of the sides. It is used in hoppers, bins, chutes, etc. The difficulty in laying out this joint is to obtain the proper angle for the edges of the pieces. This may be done as follows: After the pieces are planed to the correct thickness, plane the upper and lower edges of the end pieces to the correct bevel as shown by the pitch of the sides. Lay out the pitch of the sides of the hopper on the outside of the end pieces. From the ends of these lines, on the upper and lower beveled edges score lines at right angles with the knife and try-square. Connect these lines on what will be the inside of the hopper. Saw off the surplus wood and plane to the lines thus scored. The side pieces may be finished in the same way, and the parts are then ready to be assembled.
No. 13. A hopper-joint is a butt-joint, but it's unique because the edges of the boards aren't square with their faces due to the angle of the sides. It's used in hoppers, bins, chutes, etc. The challenge in creating this joint is finding the right angle for the edges of the pieces. Here's how to do it: After the pieces are planed to the right thickness, plane the upper and lower edges of the end pieces to the correct bevel according to the angle of the sides. Mark the angle of the sides of the hopper on the outside of the end pieces. From the ends of these lines, on the upper and lower beveled edges, score lines at right angles using a knife and try-square. Connect these lines on what will be the inside of the hopper. Cut off the excess wood and plane to the scored lines. The side pieces can be finished the same way, and then the parts are ready to be assembled.

Fig. 264-13 Hopper
HALVING-JOINTS
A halved joint is one in which half the thickness of each member is notched out and the remaining portion of one just fits into the notch in the other, so that the upper and under surfaces of the members are flush.
A halved joint is one where half the thickness of each part is cut out, and the remaining part of one fits perfectly into the notch of the other, making the top and bottom surfaces of the parts even.
No. 14. A cross-lap joint is a halved joint in which both members project both ways from the joint. This is a very common joint used in both carpentry and joinery, as where stringers cross each other in the same plane.
No. 14. A cross-lap joint is a halved joint where both pieces extend outwards from the joint. This is a very common joint used in both carpentry and joinery, like when stringers overlap each other in the same plane.

Fig. 264-14 Cross lap
The two pieces are first dressed exactly to the required size, either separately or by the method of making duplicate parts, see Chap. IX, p. 204. Lay one member, called X, across the other in the position which they are to occupy when finished and mark plainly their upper faces, which will be flush when the piece is finished. Locate the middle of the length of the lower piece, called Y, on one [page 156] arris, and from this point lay off on this arris half the width of the upper piece, X. From this point square across Y with the knife and try-square. Lay X again in its place, exactly along the line just scored. Then mark with the knife on Y the width of X, which may then be removed and the second line squared across Y. From these two lines square across both edges of Y to approximately one-half the thickness. Now turn X face down, lay Y on it, and mark it in the same way as Y. Set the gage at one-half the thickness of the pieces, and gage between the lines on the edges, taking care to hold the head of the gage against the marked faces. Then even if one piece is gaged so as to be cut a little too deep, the other will be gaged so as to be cut proportionately less, and the joint will fit.
The two pieces are first cut to the exact size needed, either individually or by creating duplicate parts; see Chap. IX, p. 204. Place one piece, called X, across the other at the position they will occupy when finished, and clearly mark their upper surfaces, which will be flush in the final piece. Find the midpoint of the length of the lower piece, called Y, on one edge, and from that point measure half the width of the upper piece, X, on that edge. From this point, draw a line across Y using a knife and try-square. Place X back in position, aligned with the line just marked. Then use the knife to mark the width of X on Y, which you can then remove, and square a second line across Y. From these two lines, draw lines across both edges of Y to about half its thickness. Now turn X face down, place Y on it, and mark it the same way you did with Y. Set the gauge to half the thickness of the pieces and score between the lines on the edges, making sure to press the head of the gauge against the marked faces. Even if one piece is gauged slightly too deep, the other will be gauged to be cut proportionately less, ensuring the joint fits well.
The bottom of the dado thus cut should be flat so as to afford surface for gluing. When well made, a cross-lap joint does not need to be pounded together but will fit tight under pressure of the hands.
The bottom of the dado that’s cut should be flat to provide a surface for gluing. When made correctly, a cross-lap joint doesn’t need to be hammered together but will fit snugly under hand pressure.
No. 15. A middle-lap joint or halved tee is made in the same way as a cross-lap joint, but one member projects from the joint in only one direction, it is used to join stretchers to rails as in floor timbers.
No. 15. A middle-lap joint or halved tee is created in the same way as a cross-lap joint, but one part extends from the joint in just one direction. It's used to connect stretchers to rails, like in floor beams.

Fig. 265-15 Middle lap
No. 16. An end-lap joint is made in the same way as a cross-lap joint except that the joint is at the end of both members. It is used at the corners of sills and plates, also sometimes in chair-seats.
No. 16. An end-lap joint is made in the same way as a cross-lap joint, except that the joint is at the ends of both pieces. It's used at the corners of sills and plates, and sometimes in chair seats.

Fig. 265-16 End lap
To make an end-lap joint, place the members in their relative positions, faces up, and mark plainly. Mark carefully on each member the inside corner, allowing the end of each member slightly (1⁄16") to overlap the other. Square across at these points with a sharp knife point, on the under side of the upper member, and on the upper side of the lower member. Now proceed as in the cross-lap joint, except that the gaged line runs around the end and the cutting must be done exactly to this line.
To create an end-lap joint, position the pieces in their correct places, with the faces facing up, and mark clearly. Carefully indicate on each piece the inside corner, making sure the end of each piece overlaps slightly (1⁄16"). Draw a square line at these points using a sharp knife on the underside of the upper piece and the top side of the lower piece. Next, follow the same steps as in the cross-lap joint, but remember that the marked line will go around the end, and the cutting must be done precisely along this line.
No. 17. In an end-lap joint on rabbeted pieces the joint must be adapted to the rabbet. The rabbet should therefore be plowed before the joint is made. The rabbet at the end of the piece X is cut not the entire width of the piece Y, but only the width of the lap,—c-f = a-e. This joint is used occasionally in picture-frames.
No. 17. In an end-lap joint on rabbeted pieces, the joint needs to fit the rabbet. So, the rabbet should be prepared before making the joint. The rabbet at the end of piece X is cut not to the full width of piece Y, but just to the width of the lap,—c-f = a-e. This joint is sometimes used in picture frames.

Fig. 265-17 End lap with rabbet
No. 18. A dovetail halving or lap-dovetail is a middle-lap joint with the pin made dovetail in shape, and is thus better able to resist tension. It is used for strong tee joints.
No. 18. A dovetail halving or lap-dovetail is a middle-lap joint with the pin shaped like a dovetail, making it more effective at resisting tension. It's used for sturdy tee joints.

Fig. 265-18 Dovetail halving
No. 19. A beveled halving is made like a middle-lap joint except that the inner end of the upper member is thinner so that the adjoining cheeks are beveled. It is very strong when loaded above. It was formerly used in house framing.
No. 19. A beveled halving is made like a middle-lap joint, except that the inner end of the upper piece is thinner, which causes the adjoining sides to be beveled. It is very strong when weight is placed on top. It was previously used in house framing.

Fig. 265-19 Beveled halving
MODIFIED HALVING JOINTS
No. 20. A notched joint is made by cutting out a portion of one timber. It is used where it is desired to reduce the height occupied by the upper timber. Joists are notched on to wall plates.
No. 20. A notched joint is created by cutting out a section of one piece of wood. It's used when you want to lower the height taken up by the upper piece of wood. Joists are notched onto wall plates.

Fig. 265-20 Notched
No. 21. A checked joint or double notch is made by cutting out notches from both the timbers so as to engage each other. It is used where a single notch would weaken one member too much.
No. 21. A checked joint or double notch is created by cutting notches in both pieces of wood so they fit together. It's used when a single notch would weaken one part too much.

Fig. 265-21 Checked
No. 22. A cogged or corked or caulked joint is made by cutting out only parts of the notch on the lower piece, leaving a "cog" uncut. From the upper piece a notch is cut only wide enough to receive the cog. A cogged joint is stronger than a notched because the upper beam is not weakened at its point of support. It is used in heavy framing.
No. 22. A cogged or corked or caulked joint is created by cutting out only parts of the notch on the lower piece, leaving a "cog" uncut. From the upper piece, a notch is cut just wide enough to fit the cog. A cogged joint is stronger than a notched joint because the upper beam isn’t weakened at its support point. It’s used in heavy framing.

Fig. 265-22 Cogged
No. 23. A forked tenon joint is made by cutting a fork in the end of one member, and notching the other member to fit into the fork, so that neither piece can slip. It is used in knock-down furniture and in connecting a muntin to a rail, where it is desired that the muntin should run thru and also that the rail be continuous.
No. 23. A forked tenon joint is created by making a fork in the end of one piece and notching the other piece to fit into the fork, ensuring that neither piece can move out of place. This joint is commonly used in collapsible furniture and in connecting a muntin to a rail, where it's necessary for the muntin to extend through while keeping the rail continuous.

Fig. 265-23 Forked
No. 24. A rabbet or rebate or ledge joint is made by cutting out a portion of the side or end of a board or timber X to receive the end or side of another, Y. It may then be nailed from either the side or end or from both. The neatest way in small boxes is from the end, or better still it may be only glued.
No. 24. A rabbet or rebate or ledge joint is created by cutting out a section of the side or end of a board or timber X to fit the end or side of another piece, Y. It can then be nailed from either the side or end, or both. The cleanest method for small boxes is to nail it from the end, or even better, it can just be glued.

Fig. 266-24 Rabbet
No. 25. A dado or grooved joint is made by cutting in one member a groove into which the end or edge of the other member fits. Properly speaking a groove runs with the grain, a dado across it, so that the bottom of a drawer is inserted in a groove while the back of the drawer is inserted in a dado. Where the whole [page 158] of the end of one member is let into the other, such a dado is also called a housed dado. Treads of stairs are housed into string boards.
No. 25. A dado or grooved joint is created by cutting a groove in one piece that fits the end or edge of another piece. Technically, a groove goes with the grain, while a dado goes across it, so the bottom of a drawer fits into a groove, whereas the back of the drawer fits into a dado. When the entire end of one piece fits into the other, this type of dado is also referred to as a housed dado. The treads of stairs are housed into string boards.
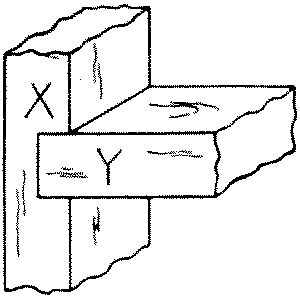
Fig. 266-25 Dado
To lay out a dado joint: After carefully dressing up both pieces to be joined, locate accurately with a knife point, on the member to be dadoed, called X, one side of the dado, and square across the piece with a try-square and knife. Then locate the other side of the dado by placing, if possible, the proper part of the other member, called Y, close to the line drawn. If this method of superposition is not possible, locate by measurement. Mark, with a knife point, on X, the thickness thus obtained. Square both these lines as far across the edges of X as Y is to be inserted. Gage to the required depth on both edges with the marking-gage.
To create a dado joint: After preparing both pieces that need to be joined, use a knife point to accurately mark one side of the dado on the piece being dadoed, called X. Then, use a try-square and knife to square the line across the piece. Next, mark the other side of the dado by positioning the corresponding part of the other piece, called Y, close to the line you just drew. If you can’t place them together like this, measure instead. Use a knife point to mark the thickness you've measured on X. Square these lines across the edges of X to the depth that Y will be inserted. Use a marking gauge to mark the required depth on both edges.
To cut the joint: First make with the knife a triangular groove on the waste side of each line, as indicated in Fig. 91, p. 66, and starting in the grooves thus made, saw with the back-saw to the gaged lines on both edges. The waste may now be taken out either with a chisel or with a router, Fig. 122, p. 83. The second member, Y, should just fit into a dado thus made, but if the joint is too tight, the cheeks of the dado may be pared with a chisel. In delicate work it is often wise not to saw at all, but to use only the knife and chisel.
To cut the joint: First, create a triangular groove on the waste side of each line with the knife, as shown in Fig. 91, p. 66, and starting in the grooves you just made, saw with the back-saw to the marked lines on both edges. You can now remove the waste using either a chisel or a router, Fig. 122, p. 83. The second piece, Y, should fit snugly into the dado you've created, but if the joint is too tight, you can shave the sides of the dado with a chisel. For more delicate work, it’s often better to avoid sawing and just use the knife and chisel.
No. 26. A dado and rabbet is made by cutting a dado in one member, X, and a rabbet on the other, Y, in such a way that the projecting parts of both members will fit tight in the returns of the other member. It is used in boxes and gives plenty of surface for gluing.
No. 26. A dado and rabbet is created by cutting a dado in one piece, X, and a rabbet on the other piece, Y, so that the protruding parts of both pieces fit snugly into the recesses of the other piece. It's used in boxes and provides a lot of surface area for gluing.

Fig. 266-26 Dado and rabbet
No. 27. A dado, tongue and rabbet is a compound joint, made by cutting a rabbet on one member, Y, and then a dado in this rabbet, into which fits a tongue of the other member, X. It is used in machine-made drawers.
No. 27. A dado, tongue and rabbet is a combined joint, created by cutting a rabbet on one piece, Y, and then a dado within this rabbet, into which a tongue from the other piece, X, fits. It's commonly used in factory-made drawers.

Fig. 266-27 Dado tongue and rabbet
No. 28. A dovetail dado or gain is made by cutting one or both of the sides of the infitting member, Y, on an angle so that it has to be slid into place and cannot be pulled out sidewise. It is used in book-cases and similar work, in which the shelves are fixed.
No. 28. A dovetail dado or gain is created by cutting one or both sides of the fitting piece, Y, at an angle so that it must be slid into position and cannot be pulled out sideways. It is used in bookcases and similar projects where the shelves are固定.

Fig. 266-28 Dovetail dado
To make this joint, first lay out the dovetail on the member to be inserted, called Y, thus: Across one end square a line (A B, No. 28), at the depth to which this member is to be dadoed in. Set the bevel-square at the proper angle for a dovetail, Fig. 250. Score this angle on the edges of the member, as at C D. Cut a groove with [page 159] a knife on the waste side of A B. Saw to the depth A C, and chisel out the interior angle A C D.
To create this joint, first mark out the dovetail on the piece being inserted, called Y, like this: At one end, draw a straight line (A B, No. 28) at the depth where this piece will fit in. Set the bevel-square to the correct angle for a dovetail, Fig. 250. Mark this angle on the edges of the piece, as shown at C D. Use a knife to cut a groove on the waste side of A B. Saw down to the depth A C, and then chisel out the interior angle A C D.
Then lay out the other member, X, thus: mark with the knife the proper place for the flat side of Y, square this line across the face and on the edges as for a simple dado. Lay out the thickness of Y on the face of X by superposition or otherwise and square the face and edges, not with a knife but with a sharp pencil point. Gage the required depth on the edges. Now with the bevel-square as already set, lay out the angle A C D on the edges of X, and across the face at C score a line with knife and try-square. Cut out grooves in the waste for the saw as in a simple dado, and saw to the proper depth and at the proper angle. Chisel or rout out the waste and when complete, fit the pieces together.
Then lay out the other piece, X, like this: mark with the knife where the flat side of Y should go, and draw this line across the face and edges as you would for a simple dado. Measure the thickness of Y on the face of X by overlapping them or using another method and square the face and edges, not with a knife but with a sharp pencil. Mark the required depth on the edges. Now, using the bevel-square as already set, lay out the angle A C D on the edges of X, and across the face at C, score a line with the knife and try-square. Cut out notches in the waste for the saw as you would in a simple dado, and saw to the correct depth and angle. Chisel or rout out the waste, and once finished, fit the pieces together.
No. 29. A gain joint is a dado which runs only partly across one member, X. In order to make the edges of both members flush and to conceal the blind end of the gain, the corner of the other member, Y, is correspondingly notched out. In book shelves a gain gives a better appearance than a dado.
No. 29. A gain joint is a dado that only goes partway across one piece, X. To make the edges of both pieces flush and hide the blind end of the gain, the corner of the other piece, Y, is notched out accordingly. In bookshelves, a gain looks better than a dado.

Fig. 266-29 Gain
A gain joint is laid out in the same way as the dado, except that the lines are not carried clear across the face of X, and only one edge is squared and gaged to the required depth. Knife grooves are made in the waste for starting the saw as in the dado. Before sawing, the blind end of the gain is to be chiseled out for a little space so as to give play for the back-saw in cutting down to the required depth. To avoid sawing too deep at the blind end, the sawing and chiseling out of waste may be carried on alternately, a little at a [page 160] time, till the required depth is reached. It is easy to measure the depth of the cut by means of a small nail projecting the proper amount from a trial stick, Fig. 251. The use of the router, Fig. 122, p. 83, facilitates the cutting, and insures an even depth.
A gain joint is set up similarly to a dado, but the lines don't extend all the way across the face of X, and only one edge is squared and marked to the required depth. Knife grooves are made in the waste area to help start the saw, just like with the dado. Before sawing, the blind end of the gain should be chiseled out a bit to allow space for the back-saw to cut down to the desired depth. To prevent sawing too deep at the blind end, you can alternate between sawing and chiseling out the waste a little at a time until you reach the required depth. It's easy to measure the depth of the cut using a small nail set to the right length from a trial stick, Fig. 251. Using a router, Fig. 122, p. 83, makes the cutting easier and ensures an even depth.

Fig. 251. Depth-gage for Dado.
MORTISE-AND-TENON JOINTS
The tenon in its simplest form is made by dividing the end of a piece of wood into three parts and cutting out rectangular pieces on both sides of the part left in the middle. The mortise is the rectangular hole cut to receive the tenon and is made slightly deeper than the tenon is long. The sides of the tenon and of the mortise are called "cheeks" and the "shoulders" of the tenon are the parts abutting against the mortised piece.
The tenon, in its basic form, is created by splitting the end of a piece of wood into three sections and removing rectangular sections on both sides of the middle part. The mortise is the rectangular hole made to fit the tenon and is slightly deeper than the length of the tenon. The sides of the tenon and the mortise are referred to as "cheeks," while the "shoulders" of the tenon are the parts that press against the mortised piece.
No. 30. A stub mortise-and-tenon is made by cutting only two sides of the tenon beam. It was formerly used for lower ends of studding or other upright pieces to prevent lateral motion.
No. 30. A stub mortise-and-tenon is created by cutting just two sides of the tenon beam. It used to be used for the bottom ends of studs or other vertical pieces to stop side-to-side movement.

Fig. 266-30 Stub mortise and tenon
No. 31. A thru mortise-and-tenon is made by cutting the mortise clear thru one member and by cutting the depth of the tenon equal to or more than the thickness of the mortised member. The cheeks of the tenon may be cut on two or four sides. It is used in window sashes.
No. 31. A through mortise-and-tenon is created by cutting the mortise completely through one piece and by cutting the depth of the tenon to be equal to or greater than the thickness of the piece with the mortise. The cheeks of the tenon can be cut on two or four sides. It's used in window sashes.

Fig. 266-31 Thru mortise and tenon
A thru mortise-and-tenon joint is made in the same way as a blind mortise-and-tenon (see below), except that the mortise is laid out on the two opposite surfaces, and the boring and cutting are done from both, cutting first from one side and then from the other.
A through mortise-and-tenon joint is made the same way as a blind mortise-and-tenon (see below), except that the mortise is marked on the two opposite surfaces, and the boring and cutting are done from both sides, starting on one side and then moving to the other.
No. 32. A blind mortise-and-tenon is similar to the simple mortise-and-tenon described in 30. The tenon does not extend thru the mortised member and the cheeks of the tenon may be cut on two or four sides.
No. 32. A blind mortise-and-tenon is like the simple mortise-and-tenon detailed in 30. The tenon doesn't go all the way through the mortised piece, and the cheeks of the tenon can be cut on two or four sides.

Fig. 266-32 Blind mortise and tenon
To make a blind mortise-and-tenon, first make the tenon thus: Locate accurately with a knife point the shoulders of the tenon and square entirely around the piece. On the working edge near the end mark the thickness of the tenon. Set the marking-gage at the proper distance from the working face to one cheek of the tenon and gage the end and the two edges between the end and the knife-lines. Reset the gage to mark the thickness of the tenon and gage that in the same way from the working face. Then mark and gage the width of the [page 161] tenon in the same way. Whenever there are several tenons of the same size to be cut, they should all be laid out together, that is the marking-gage set once to mark all face cheeks and once to mark all back cheeks. If a mortise-gage is available, use that. Always mark from the working face or working edge. Cut out a triangular groove on the waste side of the knife lines (at the shoulders) as in cutting a dado, Fig. 91, p. 66.
To create a blind mortise-and-tenon, start by making the tenon like this: Carefully mark the shoulders of the tenon with a knife point and square it completely around the piece. On the working edge near the end, indicate the thickness of the tenon. Adjust the marking gauge to the correct distance from the working face to one side of the tenon and mark the end and the two edges between the end and the knife lines. Change the gauge to mark the thickness of the tenon and do the same from the working face. Then mark and gauge the width of the [page 161] tenon in a similar manner. When you have several tenons of the same size to cut, lay them all out together, meaning the marking gauge should be set once to mark all face cheeks and once to mark all back cheeks. If you have a mortise gauge, use that. Always mark from the working face or edge. Cut a triangular groove on the waste side of the knife lines (at the shoulders) as you would when cutting a dado, Fig. 91, p. 66.
In cutting the tenon, first rip-saw just outside the gaged lines, then crosscut at the shoulder lines. Do all the rip-sawing before the crosscutting. If the pieces are small the back-saw may be used for all cuts. It is well to chamfer the arrises at the end of the tenon to insure its starting easily into the mortise.
In making the tenon, first, use a rip saw just outside the marked lines, and then use a crosscut saw at the shoulder lines. Complete all the rip sawing before you start crosscutting. If the pieces are small, you can use a back saw for all the cuts. It's a good idea to bevel the edges at the end of the tenon to help it fit easily into the mortise.
Locate the ends of the mortise and square lines across with a sharp pencil in order to avoid leaving knife marks on the finished piece. Then locate the sides of the mortise from the thickness of the tenon, already determined, and gage between the cross lines. As in the case of like tenons, if there are a number of mortises all alike, set the gage only twice for them all.
Locate the ends of the mortise and draw straight lines across with a sharp pencil to prevent leaving knife marks on the finished piece. Then mark the sides of the mortise based on the thickness of the tenon, which you've already measured, and gauge between the cross lines. Similar to other tenons, if you have multiple identical mortises, only set the gauge twice for all of them.
In cutting the mortice, first fasten the piece so that it will rest solid on the bench. This may be done either in a tail vise or by a handscrew, or by clamping the bench-hook firmly in the vise in such a way that the cleat of the bench-hook overhangs the piece. Then tap the bench-hook with a mallet and the piece will be found to be held tightly down on the bench. See Fig. 76, p. 58.
In cutting the mortice, first secure the piece so it sits firmly on the bench. You can do this using a tail vise, a handscrew, or by clamping the bench-hook tightly in the vise so that the cleat of the bench-hook overhangs the piece. Then, tap the bench-hook with a mallet, and the piece will be held snugly against the bench. See Fig. 76, p. 58.
It is common to loosen up the wood by first boring a series of adjoining holes whose centers follow the center-line of the mortise and whose diameter is slightly less than the width of the mortise. Take care to bore perpendicularly to the surface, see Fig. 137, p. 86, and no deeper than necessary. Dig out the portions of wood between the auger holes and chisel off thin slices, back to the gage-lines and to the knife-lines, taking care all the time to keep the sides of the mortise perpendicular to the face. This may be tested by placing the chisel against the side of the mortise and standing alongside it a try-square with its head resting on the surface.
It’s common to prepare the wood by first drilling a series of connected holes along the center line of the mortise, making sure the holes are slightly smaller in diameter than the width of the mortise. Be careful to drill straight down into the surface, see Fig. 137, p. 86, and only as deep as needed. Remove the wood between the drilled holes and chisel off thin slices, following the gage-lines and knife-lines, always making sure the sides of the mortise remain vertical to the face. You can check this by placing the chisel against the side of the mortise and holding a try-square next to it with its head resting on the surface.
Finally test the tenon in the mortise noting carefully where it pinches, if anywhere, and trim carefully. The tighter it fits without danger of splitting the mortised member, the stronger will be the joint.
Finally, check the tenon in the mortise, paying close attention to where it might pinch, if at all, and trim it carefully. The tighter it fits without risking splitting the mortised piece, the stronger the joint will be.
Many prefer to dig mortises without first boring holes. For this purpose a mortise-chisel, Fig. 68, p. 54, is desirable. The method is [page 162] to begin at the middle of the mortise, placing the chisel—which should be as wide as the mortise—at right angles to the grain of the wood. Chisel out a V shaped opening about as deep as the mortise, and then from this hole work back to each end, occasionally prying out the chips. Work with the flat side of the chisel toward the middle except the last cut or two at the ends of the mortise.
Many people prefer to create mortises without first drilling holes. For this, a mortise chisel, Fig. 68, p. 54, is recommended. The method is to start in the center of the mortise, positioning the chisel— which should be as wide as the mortise—perpendicularly to the grain of the wood. Cut out a V-shaped opening approximately as deep as the mortise, and then from this hole, work your way back to each end, occasionally prying out the chips. Keep the flat side of the chisel facing the center, except for the last couple of cuts at the ends of the mortise.
No. 33. In a mortise-and-tenon joint on rabbeted pieces, Fig. 266, the tenon is as much shorter on one side than the other as the rabbet is wide. In Fig. 33, ab = cd.
No. 33. In a mortise-and-tenon joint on rabbeted pieces, Fig. 266, the tenon is shorter on one side than the other by the width of the rabbet. In Fig. 33, ab = cd.

Fig. 266-33 Mortise and tenon with rabbet
No. 34. A wedged mortise-and-tenon joint is a thru joint in which after the tenon is driven home, wedges are driven in between the tenon and the sides of the mortise. The wedges are dipped in glue or white lead before being inserted. The sides of the mortise may be slightly dovetailed. It is used to keep a tenon tightly fixed as in wheel spokes.
No. 34. A wedged mortise-and-tenon joint is a through joint where, after the tenon is fully inserted, wedges are hammered in between the tenon and the sides of the mortise. The wedges are coated with glue or white lead before being added. The sides of the mortise can be slightly angled. This joint is used to secure a tenon tightly in place, like in wheel spokes.

Fig. 266-34 Wedged mortise and tenon
No. 35. A wedged mortise-and-tenon joint may also be made by driving the wedges into saw kerfs in the tenon instead of along its sides as in No. 34. It is used in ornamental joints as well as in carpentry.
No. 35. A wedged mortise-and-tenon joint can also be created by driving wedges into saw cuts in the tenon instead of along its sides like in No. 34. It's used in decorative joints as well as in woodworking.

Fig. 266-35 Wedged mortise and tenon
No. 36. A fox-tail tenon is a blind mortise-and-tenon in which the mortise is made slightly wider at the bottom than the width of the tenon. Wedges are driven into saw kerfs in the tenon before inserting into the mortise; then when it is driven home the wedges spread out the tenon and make it fill out the mortise. It is used in strong doors and also where the mortised member is already in place so that a wedged mortise-and-tenon is impossible.
No. 36. A fox-tail tenon is a hidden mortise-and-tenon joint where the mortise is slightly wider at the bottom than the tenon. Wedges are driven into saw cuts in the tenon before it’s inserted into the mortise; when it’s pushed in all the way, the wedges expand the tenon to fill the mortise. This joint is used in sturdy doors and also when the mortised piece is already installed, making a traditional wedged mortise-and-tenon joint unfeasible.

Fig. 266-36 Fox tail tenon
No. 37. A dovetail mortise-and-tenon is a thru mortise-and-tenon beveled on one side so as to form half a dovetail. The corresponding side of the mortise is also beveled and made wide enough so that when the tenon is pressed well up against its beveled side a wedge may be driven into the space left on the straight side. It is used to tenon a beam into a post especially where the post is fixed against a wall. It is also used in machinery frames which are made of wood.
No. 37. A dovetail mortise-and-tenon is a through mortise-and-tenon that is angled on one side to create half a dovetail. The matching side of the mortise is also beveled and widened enough so that when the tenon is pushed firmly against its beveled side, a wedge can be inserted into the gap left on the flat side. It’s used to connect a beam to a post, especially when the post is secured against a wall. It’s also used in wooden machinery frames.

Fig. 266-37 Dovetail mortise and tenon
No. 38. A pinned mortise-and-tenon is one in which a pin is driven thru holes bored thru the mortised beam and thru the tenon to keep them from drawing apart. It is used in heavy framing as in bridges, in wagon-making, in window-sash, etc.
No. 38. A pinned mortise-and-tenon is one where a pin is inserted through holes drilled in the mortised beam and the tenon to prevent them from coming apart. It's commonly used in heavy framing like bridges, wagon-making, window sashes, etc.

Fig. 267-38 Pinned mortise and tenon
No. 39. A keyed mortise-and-tenon is one in which the tenon protrudes thru the mortise far enough to receive a removable key and thus be drawn up tight to the mortised member. It is used in work-benches and in ornamental joints like knock-down bookcases and in other mission furniture.
No. 39. A keyed mortise-and-tenon is one where the tenon sticks out through the mortise far enough to hold a removable key, allowing it to be tightened against the mortised piece. It’s commonly used in workbenches and decorative joints like knock-down bookcases and other mission-style furniture.

Fig. 267-39 Keyed mortise and tenon
The keyed mortise-and-tenon is made as in a thru mortise-and-tenon, except that before cutting the tenons the holes for wedges should be laid out thus: measuring from the shoulder of the tenon, locate by superposition or measurement the outside of the mortised member. Deduct from this 1⁄16" and square a fine pencil-line across the face and opposite side. This line will be the inside of the hole for the wedge, and the 1⁄16" is deducted to make sure that the key wedges against the mortised member. On the upper surface of the tenon, lay off toward the end the width of the wedge at this point, A B, Fig. 252, and square across. On the under surface, lay off the width of the wedge at this point, C D, and square across.
The keyed mortise-and-tenon is created similarly to a through mortise-and-tenon, except that before cutting the tenons, you should mark the holes for the wedges as follows: starting from the shoulder of the tenon, determine the outside of the mortised piece either by overlaying or by measuring. Subtract 1⁄16" from this measurement and draw a fine pencil line across the face and the opposite side. This line will indicate the inside of the hole for the wedge, with the 1⁄16" subtracted to ensure that the key fits tightly against the mortised piece. On the top surface of the tenon, measure toward the end the width of the wedge at this point, A B, Fig. 252, and draw a square line across. On the bottom surface, measure the width of the wedge at this point, C D, and draw a square line across.

Fig. 252. Keyed Mortise-and-Tenon Joint.
Gage the sides of the wedge hole on both upper and lower surfaces of the tenon. After cutting the mortise and tenon, bore and chisel out the hole for the wedge, taking care to cut the side toward the end on a bevel to fit the wedge.
Gage the sides of the wedge hole on both the top and bottom surfaces of the tenon. After cutting the mortise and tenon, drill and chisel out the hole for the wedge, making sure to cut the side toward the end at an angle to fit the wedge.
No. 40. A tusk tenon or shoulder tenon is one in which the tenon proper is quite thin but is reinforced by a thicker shoulder called a "tusk." The upper shoulder is beveled. The object of this form is to weaken the mortised member as little as possible but at the same time to increase the strength of the tenon. It is used in joining tail beams to headers in floor framing.
No. 40. A tusk tenon or shoulder tenon is one where the tenon itself is quite thin but is supported by a thicker shoulder known as a "tusk." The upper shoulder is angled. The purpose of this design is to minimize the weakening of the mortised piece while simultaneously enhancing the strength of the tenon. It's used to connect tail beams to headers in floor framing.

Fig. 267-40 Tusk tenon
No. 41. A double mortise-and-tenon consists of two tenons side by side in one piece fitting into two corresponding mortises. It is used in joinery, as in door-frames, but not in carpentry.
No. 41. A double mortise-and-tenon consists of two tenons side by side in one piece fitting into two corresponding mortises. It's used in joinery, like in door frames, but not in carpentry.

Fig. 267-41 Double mortise and tenon
No. 42. A haunched mortise-and-tenon is made by cutting away part of the tenon so that that part of it will be much shorter than the rest. The haunch gives the tenon great lateral [page 164] strength and saves cutting so large a mortise hole. It is used in panel construction, as where the rails are joined to the stiles of doors.
No. 42. A haunched mortise-and-tenon is created by trimming part of the tenon so that this section is significantly shorter than the rest. The haunch provides the tenon with excellent lateral strength and eliminates the need for a larger mortise hole. It's commonly used in panel construction, such as when the rails connect to the stiles of doors. [page 164]

Fig. 267-42 Haunched mortise and tenon
First plow the groove in all the members. This should be of the same width as the thickness of the tenons, which is ordinarily one-third of the thickness of the frame. The groove is approximately as deep as it is wide. Lay out and cut the tenon the width of the entire piece, minus, of course, the depth of the groove. The mortise should not come too near the end, or the portion of wood outside it will shear out. Hence the tenon is narrowed on the outside enough to insure strength in the mortised piece. The rule is that the tenon should be one-half the width of the rail, minus the groove. But enough of the tenon is left full width to fill up the groove at the outer end of the mortised piece. This is called the haunch. The width of the mortise is equal to the width of the groove, its length to the width of the tenon. Before assembling the panel frame, put soap or tallow on the corners of the panel to prevent its being glued to the frame.
First, plow the groove in all the pieces. This should be the same width as the thickness of the tenons, which is usually one-third of the thickness of the frame. The groove is about as deep as it is wide. Lay out and cut the tenon to the width of the entire piece, minus the depth of the groove. The mortise shouldn't be too close to the end, or the wood outside it will break off. So, the tenon is tapered on the outside enough to ensure strength in the mortised piece. The guideline is that the tenon should be half the width of the rail minus the groove. But enough of the tenon is left full width to fill the groove at the outer end of the mortised piece. This is called the haunch. The width of the mortise is equal to the width of the groove, and its length is the same as the width of the tenon. Before putting the panel frame together, apply soap or tallow on the corners of the panel to prevent it from sticking to the frame.
No. 43. Table or taper haunching. Sometimes, as in table construction, for the sake of stiffening the rail, or in places where it is desirable that the haunch does not show, the haunch is beveled from the tenon to the edge of the rail.
No. 43. Table or taper haunching. Sometimes, like in table building, to reinforce the rail, or in areas where it's important that the haunch isn't visible, the haunch is angled from the tenon to the edge of the rail.

Fig. 267-43 Table haunching
No. 44. A bare-faced tenon is one in which a cheek is cut from only one side. It is used where the rail is thinner than the stile and it is desirable to keep the mortise near the middle of the stile.
No. 44. A bare-faced tenon is one where a cheek is cut from just one side. It's used when the rail is thinner than the stile and it's important to keep the mortise close to the center of the stile.

Fig. 267-44 Bare faced tenon
No. 45. A housed mortise-and-tenon is one in which the whole of the end of one member is let in for a short distance or "housed" into the other. It is common in grill work and in railings.
No. 45. A housed mortise-and-tenon is one where the entire end of one piece is inserted for a short distance or "housed" into the other. It's often used in grill work and railings.

Fig. 267-45 Housed mortise and tenon
No. 46. A slip-joint or end or open mortise-and-tenon is what would remain if a mortised member were sawn off along one side of the tenoned member. Window screens and other light frames such as those for slates and for printing photographs have this joint. This joint multiplied is used for small machine-made boxes, and is then called corner locking.
No. 46. A slip-joint or end or open mortise-and-tenon is what you get if a mortised piece is cut off along one side of the tenoned piece. Window screens and other lightweight frames, like those for slates and printing photographs, use this joint. When this joint is repeated, it is used for small machine-made boxes and is referred to as corner locking.

Fig. 267-46 Slip
DOVETAIL JOINTS
"Dovetail" refers to the shape of the projections of one member, when looked at broadside. These projections are called dovetails, or merely tails.
"Dovetail" refers to the shape of the projections of one part when viewed from the side. These projections are called dovetails, or simply tails.
The projections on the other member are called tenons or pins, and the spaces between both tails and tenons are called mortises or sockets.
The projections on the other member are called tenons or pins, and the spaces between both tails and tenons are called mortises or sockets.
No. 47. A thru single dovetail is similar to a slip-joint except that instead of a tenon there is a dovetail. It is used in window-sashes.
No. 47. A thru single dovetail is like a slip-joint, but instead of a tenon, it has a dovetail. It's used in window sashes.

Fig. 267-47 Thru single dovetail
No. 48. A thru-multiple dovetail consists of a series of alternate tails and tenons which fit one another closely. It is used in tool-chests and in other strong as well as fine boxes.
No. 48. A thru-multiple dovetail consists of a series of alternating tails and tenons that fit together closely. It's used in tool chests and in other strong as well as fine boxes.

Fig. 267-48 Thru multiple dovetail
To make a thru multiple dovetail joint, first square lines with a sharp pencil around the ends of both members to locate the inner ends of the dovetails and the pins, d e on X, Fig. 250, and l m on Y. The distance of this line from the ends of each member may, if desired, be slightly (1⁄32") greater than the thickness of the other member. Divide this line, d e, on the member to be dovetailed, X, into as many equal spaces as there are to be tails (dovetails). From the division points of these spaces, a b c, to the right and left lay off one-half of the greatest width of the mortises to be cut out, and also the same distance from d and from e, as at f f f f and g g g g.
To create a through multiple dovetail joint, start by marking sharp lines with a pencil around the ends of both pieces to identify where the inner ends of the dovetails and the pins will be, labeled d e on X and l m on Y. If you want, the distance from this line to the ends of each piece can be slightly (1⁄32") greater than the thickness of the other piece. Divide this line, d e, on the piece that will be dovetailed, X, into as many equal sections as there are tails (dovetails). From the division points of these sections, a b c, measure to the right and left to mark off half of the widest area of the mortises that need to be cut out, and do the same from points d and e, as shown at f f f f and g g g g.
Set the bevel-square so that it will fit the angle A B C, Fig. 250, p. 159, in a right angle triangle, the long side of which is 3" and the short side ⅝". This is approximately an angle of 80° or a little more than one to five. From the points f f f f and g g g g lay off this angle to the end of the piece. Carry these lines across the end at right angles to the surface, h i, Fig. 250, and repeat the dovetail angles on the other surface. Mark plainly the parts to be cut out (the mortises), as on X in Fig. 250. Score with a knife point the inner ends of the mortises, d to f, g to f, etc., and across the edge at d and at e. With a dovetail-saw, Fig. 93, p. 67, cut on the mortise side of each line down to the cross line, d-e, and also along the cross line from d to f and e to g. Chisel out the mortises taking care to keep the line d-e straight and square. The ends (not the sides) of the mortises may be slightly undercut to insure a tight fit.
Set the bevel square so it fits the angle A B C, Fig. 250, in a right triangle where the long side is 3" and the short side is ⅝". This is about an angle of 80° or just over one to five. From the points f f f f and g g g g, mark off this angle to the end of the piece. Extend these lines across the end at right angles to the surface, h i, Fig. 250, and repeat the dovetail angles on the other side. Clearly mark the areas to be cut out (the mortises), as shown with X in Fig. 250. Score the inner ends of the mortises, d to f, g to f, etc., and across the edge at d and e with a knife point. Using a dovetail saw, Fig. 93, cut on the mortise side of each line down to the cross line, d-e, and also along the cross line from d to f and e to g. Chisel out the mortises, making sure to keep the line d-e straight and square. The ends (not the sides) of the mortises may be slightly undercut to ensure a tight fit.
Fasten the other member, Y, upright in the vise so that the end to be tenoned will be flush with the top of the bench, and with the working [page 166] face toward the bench. Place on it the working face of X, (the member already dovetailed,) taking care that the inner ends of the mortises are in line with the working face of Y, and that the edges of the two members are in the same plane, as X on Y in Fig. 250. Scribe with a knife point along the sides of the tails on the end of Y (f'-j' and g'-h'). Remove Y from the vise and square down these lines to the cross line l-m (j'-n and h'-o). Score with the knife point the inner ends of the mortises of Y (n-o). Saw with a dovetail-saw on the mortise sides of these lines, chisel out the mortises and fit the parts together. When glued together, the joints should be dressed off.
Secure the other piece, Y, upright in the vise so that the end to be tenoned is flush with the top of the bench, and with the working face facing the bench. Place the working face of X (the member that’s already dovetailed) on it, making sure that the inner ends of the mortises align with the working face of Y and that the edges of both pieces are in the same plane, like X on Y in Fig. 250. Use a knife to scribe along the sides of the tails on the end of Y (f'-j' and g'-h'). Take Y out of the vise and square down these lines to the cross line l-m (j'-n and h'-o). Score the inner ends of the mortises on Y (n-o) with the knife. Use a dovetail saw to cut along the mortise sides of these lines, chisel out the mortises, and fit the pieces together. Once glued, the joints should be dressed down.
Where there are several parts to be made alike, it is necessary to lay out the dovetails on only one X member. This may be used as a templet for laying out the others and they can then be sawn separately. Or all the X members may be clamped carefully together, with one X already laid out, rights and lefts in pairs, and edges and ends flush, the depth mark gaged all around, and then all sawn at once.
Where there are multiple parts to be made the same, you only need to lay out the dovetails on one X member. This can serve as a template for laying out the others, which can then be sawed separately. Alternatively, all the X members can be clamped together carefully, with one X member already laid out, matched in pairs for right and left, and with edges and ends flush. The depth mark can then be measured all around, allowing them all to be sawed at once.
The dovetail joint is also made by first laying out and cutting the members having the pins, and then superposing this on the piece to be dovetailed, and scribing around the pins.
The dovetail joint is also created by first laying out and cutting the parts that have the pins, and then placing this on top of the piece to be dovetailed, and marking around the pins.
No. 49. A lap or half blind dovetail is a dovetail joint in which the tails on one member do not extend entirely thru the thickness of the other member. It is used in joining the sides to the fronts of drawers and other fittings where only one side is seen.
No. 49. A lap or half blind dovetail is a dovetail joint where the tails on one piece don't go all the way through the thickness of the other piece. It's used to connect the sides to the fronts of drawers and other fixtures where only one side is visible.

Fig. 267-49 Lap dovetail
If the joint is to be used for a drawer front, the groove for the drawer bottom should be cut or at least laid out before laying out the joint. See also drawers, p. 190, and Fig. 287, p. 191. On the end of the drawer front, gage the depth of the joint. Gage the same distance on both broad surfaces of the drawer sides, marking from the front ends. Lay out and cut the dovetails as in a thru dovetail joint, taking especial care to have the groove for the bottom completely within the lower tail. Take care also to make the sides, one right and one left, not both alike, so that the groove will come inside. Lay out the drawer front by superposing the dovetailed side, X, on the end of the front, Y, as in a thru dovetail. Saw and chisel out the mortises and fit together.
If the joint is going to be used for a drawer front, you should cut or at least outline the groove for the drawer bottom before laying out the joint. See also drawers, p. 190, and Fig. 287, p. 191. On the end of the drawer front, measure the depth of the joint. Measure the same distance on both broad surfaces of the drawer sides, marking from the front ends. Lay out and cut the dovetails like you would in a through dovetail joint, making sure that the groove for the bottom is completely within the lower tail. Also, be careful to make one side right and one left, so that the groove fits inside. Lay out the drawer front by placing the dovetailed side, X, on the end of the front, Y, as in a through dovetail. Saw and chisel out the mortises and fit them together.
No. 50. A stopped lap dovetail is one in which neither the tails nor the pins extend thru the other members. Hence the joint is concealed. The lap may be rounded. It is used in fine boxes, trays, etc.
No. 50. A stopped lap dovetail is one where neither the tails nor the pins go through the other pieces. This makes the joint hidden. The lap can be rounded. It's typically used in fine boxes, trays, and similar items.

Fig. 267-50 Stopped lap dovetail
No. 51. The blind miter or secret dovetail is a joint in which only part, say one-half, of both boards is dovetailed, the outer portion being mitered. The edges of the boards are also mitered right thru for a short distance so that when finished the dovetails are invisible. It is used in highly finished boxes.
No. 51. The blind miter or secret dovetail is a joint where only part, about half, of both boards is dovetailed, while the outer part is mitered. The edges of the boards are also mitered for a short distance so that, when completed, the dovetails are hidden. This joint is used in finely crafted boxes.

Fig. 267-51 Blind dovetail
BEVELED JOINTS
A beveled joint is made by beveling the members so that the plane of the joint bisects the angle at which the members meet. This is called the "miter" and may be 45 degrees or any other angle. It is a neat but weak joint unless reinforced by a spline, nails, or in some other way.
A beveled joint is created by beveling the pieces so that the plane of the joint cuts the angle where the pieces meet in half. This is known as the "miter" and can be 45 degrees or any other angle. It looks clean but is a weak joint unless it's reinforced with a spline, nails, or some other method.
No. 52. A plain miter is a joint where the beveled edges or ends abut and are simply glued or nailed together. It is commonly used in picture-frames, inside trim, columns, boxes, and taborets, four or more sided.
No. 52. A plain miter is a joint where the beveled edges or ends meet and are just glued or nailed together. It's commonly used in picture frames, interior trim, columns, boxes, and tables with four or more sides.

Fig. 268-52 Miter
For gluing mitered frames, the most convenient way is with the aid of the picture-frame-vise, Fig. 172, p. 101. Nails are driven or splines inserted as soon as each joint is glued. Where this vise is not available, an ordinary metalworking vise may be used, as follows: Fasten one member, X, face side up, firmly in the vise. Bore holes [page 168] in the other member, Y, at the proper places for the nails. Insert nails in the holes, apply the glue to both mitered surfaces, place the glued surfaces together, letting Y project about ⅛" beyond X. A convenient way to hold Y in place is in the left hand, palm up, while the left forearm rests upon X. Drive one of the nails home, and continue driving until the parts exactly fit. Then drive home the other nail. Now fasten together in the same way the other two members of the picture-frame, and then, one at a time, the third and fourth joint. This is the method used in picture-frame factories, and when once learned is very simple.
For gluing mitered frames, the easiest method is using a picture-frame vise, Fig. 172, p. 101. Drive in nails or insert splines as soon as each joint is glued. If this vise isn't available, you can use an ordinary metalworking vise like this: Secure one piece, X, face up in the vise. Drill holes in the other piece, Y, at the correct spots for the nails. Insert the nails into the holes, apply glue to both mitered surfaces, then press the glued surfaces together, letting Y stick out about ⅛" beyond X. A helpful way to hold Y in place is to use your left hand with the palm up while resting your left forearm on X. Hammer one of the nails in, then keep driving until the parts fit perfectly. After that, drive in the other nail. Next, attach the other two pieces of the picture frame in the same way, then do the third and fourth joints one at a time. This is the method used in picture-frame factories, and once you learn it, it’s very straightforward.
For gluing together at once all the members of a mitered frame, the device shown in Fig. 253 is convenient and is easily made. Out of two pieces of wood somewhat longer than the two end [page 169] pieces of the frame, gains are cut of the exact length of the ends, as shown in the illustration. By applying two clamps lengthwise on the frame, all four joints may be glued together at once. If the frame does not come up square, it may be squared by means of a temporary brace, A, in Fig. 253.
To glue all parts of a mitered frame together at once, the device shown in Fig. 253 is practical and easy to make. Cut two pieces of wood slightly longer than the two end pieces of the frame, with notches the exact length of the ends, as illustrated. By applying two clamps along the frame, you can glue all four joints simultaneously. If the frame isn't square, you can adjust it using a temporary brace, A, in Fig. 253. [page 169]

Fig. 253. Gluing Together a Picture-Frame (See also Fig. 254.)
The device shown in Figs. 254 and 255, is also an easily made and efficient tool. At least the small pieces, which receive the corners of the frame, should be made of hard wood such as maple. It is self-adjusting but care must be taken not to buckle the parts of a narrow frame by over pressure. It is well to soap or oil the corner pieces to prevent their being glued to the frame.
The device illustrated in Figs. 254 and 255 is also a simple and effective tool. At a minimum, the small pieces that hold the corners of the frame should be made from a sturdy wood like maple. It's designed to self-adjust, but you need to be careful not to bend the parts of a narrow frame by applying too much pressure. It’s a good idea to apply soap or oil to the corner pieces to stop them from getting glued to the frame.

Fig. 254. Picture-Frame-Clamp.

Fig. 255. Picture-Frame-Clamp. (See also Fig. 254.)
In gluing together long mitered joints, in six or eight sided taborets or columns, in which the members meet edgewise, one method is to wrap a few turns of bale wire around the parts and drive in wedges under the wire to obtain pressure, Fig. 256. Another method is to wrap a stout rope, such as is used for window weights, around all the pieces, properly set up, then to tighten it by twisting it with a stick thru a loop, Fig. 257. A still more effective way is by means of the Noxall Column Clamp, a powerful device, used chiefly for gluing up such pieces as the pillar of a centrally supported table, Fig. 259. Care must be taken with all these devices to protect the corners, unless they are to be rounded off afterward. A good way to protect them is with pieces fastened together in the shape shown in Fig. 258, b, and Fig. 257, the interior angle being equal to the exterior angle of the piece to be glued. In the case of a taboret with slender legs, care must be taken to insert blocks between the separate legs as well, to brace them apart and to keep them from bending under [page 170] the pressure. These methods have the advantage that they are speedy, since all the pieces go together at once; but unless the pieces fit exactly the joints will not close.
In joining long mitered joints in six or eight-sided tables or columns where the pieces meet edge-to-edge, one way is to wrap a few turns of baling wire around the parts and drive in wedges under the wire to create pressure, Fig. 256. Another option is to wrap a strong rope, like the kind used for window weights, around all the pieces in place, and then tighten it by twisting it with a stick through a loop, Fig. 257. An even more effective method is with the Noxall Column Clamp, a powerful tool mainly used for gluing together pieces like the pillar of a centrally supported table, Fig. 259. It's important to protect the corners with all these methods unless they will be rounded off later. A good way to protect them is using pieces fastened together as shown in Fig. 258, b, and Fig. 257, where the interior angle matches the exterior angle of the piece being glued. For a taboret with slender legs, make sure to insert blocks between the separate legs to brace them apart and prevent bending under pressure. These methods are quick since all the pieces go together at the same time; however, if the pieces don’t fit perfectly, the joints won’t close. [page 170]

Fig. 256. Gluing up a Column Joint.
(Pinch-Dogs at Top of Joints.)

Fig. 257. One Method of Gluing up a Six-Sided Taboret.

Fig. 258. Devices for Gluing Beveled Edges.

Fig. 259. Column-Clamp.
Another method is to glue and clamp the pieces of the taboret together two by two, using blocks as shown in Fig. 258, a. Care should be taken to put the pressure of the handscrews as far out as possible so as to be sure that the outside of the joint closes. This method has the advantage that, as only one joint is glued at a time, the work can be done more deliberately. Moreover, if when three pairs of a six-sided taboret are together, the other three joints do not fit exactly, they can then be refitted.
Another way is to glue and clamp the taboret pieces together in pairs, using blocks as shown in Fig. 258, a. Make sure to place the pressure of the handscrews as far out as possible to ensure that the outside of the joint closes properly. This method is beneficial because, since only one joint is glued at a time, the work can be done more carefully. Additionally, if three pairs of a six-sided taboret are assembled and the other three joints don't fit perfectly, they can be adjusted.
Another method is to glue pieces of soft wood on the exterior of each pieces as shown in Fig. 258, c. These blocks should be of such shape that the opposite sides of each pair are parallel. When the glue is dry, they are used as corners on which to clamp the handscrews. This method has the disadvantage that the blocks may break loose at a critical moment.
Another method is to glue soft wood pieces on the outside of each part as shown in Fig. 258, c. These blocks should be shaped so that the opposite sides of each pair are parallel. Once the glue dries, they can be used as corners to clamp the handscrews. However, this method has the downside that the blocks might come loose at a crucial moment.
No. 53. A doweled miter is one in which one or more dowels are inserted and glued into holes bored into the beveled edges. It may be used instead of nails, as in large picture frames.
No. 53. A doweled miter is one where one or more dowels are inserted and glued into holes drilled into the beveled edges. It can be used instead of nails, like in large picture frames.

Fig. 268-53 Doweled miter
No. 54. A spline or tongue miter is one which has a spline or tongue inserted at right angles to the joint. Since it furnishes more gluing surface, it is stronger than a plain miter.
No. 54. A spline or tongue miter is one that has a spline or tongue inserted at a right angle to the joint. Because it provides more surface area for gluing, it is stronger than a regular miter.

Fig. 268-54 Spline miter
No. 55. A slip-feather or slip-key miter is one which is strengthened by a slip of hardwood glued into a saw kerf cut across the mitered angle. It is used in picture-frames and in boxes.
No. 55. A slip-feather or slip-key miter is one that is reinforced with a piece of hardwood glued into a saw cut across the mitered angle. It's used in picture frames and boxes.

Fig. 268-55 Slip feather miter
No. 56. A slip-dovetail miter is one in which a trapezoidal shaped key is inserted in a dovetail socket cut straight across the miter. When dressed off, it gives the appearance of a dovetail on each face. It is used for the same purpose as a spline miter.
No. 56. A slip-dovetail miter is one where a trapezoidal-shaped key fits into a dovetail socket that's cut straight across the miter. When finished, it looks like a dovetail on each side. It's used for the same purpose as a spline miter.

Fig. 268-56 Slip dovetail miter
No. 57. A double dovetail keyed miter is one in which a double dovetail key made of hard wood is inlaid across the joint. This is a favorite joint with Oriental joiners.
No. 57. A double dovetail keyed miter is one where a double dovetail key made of hardwood is set into the joint. This is a favorite joint with Oriental carpenters.

Fig. 268-57 Double dovetail keyed
No. 58. A ledge and miter or lipped miter joint is made by rabbeting and mitering the boards to be joined so that the outer portion of the two boards meet in a miter. It is strong and good looking and may be glued or nailed. It is used for fine boxes.
No. 58. A ledge and miter or lipped miter joint is made by cutting a rabbet and miter on the boards to be joined so that the outer edges of both boards come together in a miter. It's strong and visually appealing, and you can glue or nail it. It's used for high-quality boxes.

Fig. 268-58 Ledge and miter
No. 59. A stopped miter is useful for joining pieces of different widths, when both sides can be seen.
No. 59. A stopped miter is great for connecting pieces of different widths when both sides are visible.

Fig. 268-59 Stopped miter
No. 60. A double-tongue miter is made by cutting on the adjoining edges tongues which engage in each other. It is used in high class joinery, on members that join lengthwise of the grain.
No. 60. A double-tongue miter is created by cutting tongues on the adjacent edges that interlock with each other. It's used in high-quality woodworking, specifically on pieces that align along the grain.

Fig. 268-60 Double tongue miter
No. 61. A stretcher joint is a slip joint in which one or both sides is mitered. It is used in frames for stretching canvass for paintings by driving wedges from the inside. Two forms are shown in 61a and 61b.
No. 61. A stretcher joint is a slip joint where one or both sides are cut at an angle. It's used in frames for stretching canvas for paintings by driving wedges from the inside. Two designs are shown in 61a and 61b.


Fig. 268-61 Stretcher
No. 62. A strut joint is a form of miter joint used in making trusses.
No. 62. A strut joint is a type of miter joint used in building trusses.

Fig. 268-62 Strut
No. 63 and 64. A thrust joint or tie joint or toe joint is one in which two beams meet at an oblique angle, one receiving the thrust of the other. The toe may be either square as in 63, or oblique as in 64. The pieces are bolted or strapped together with iron. It is used for the batter braces of bridges.
No. 63 and 64. A thrust joint or tie joint or toe joint is one where two beams connect at an angle, with one beam taking the force from the other. The toe can be either square, like in 63, or angled, as shown in 64. The pieces are fastened together with bolts or straps made of iron. This type of joint is used for the support braces of bridges.

Fig. 268-63 Square thrust

Fig. 268-64 Oblique thrust
No. 65. A plain brace joint is one in which the brace is simply mitered and nailed into place. It is used for bracket supports.
No. 65. A plain brace joint is one where the brace is just mitered and nailed in position. It's used for bracket supports.

Fig. 269-65 Brace
No. 66. A housed brace joint is a joint in which the brace is housed into the rectangular members except that the outer end of the mortise is cut at right angles and the inner end diagonally to receive the brace which is cut to correspond. It is much stronger than 65.
No. 66. A housed brace joint is a joint where the brace fits into the rectangular members, except that the outer end of the mortise is cut straight across and the inner end is angled to match the brace, which is also cut to fit. It is significantly stronger than 65.

Fig. 269-66 Housed brace
No. 67. An oblique mortise-and-tenon or bevel-shoulder joint is one in which the shoulders of the tenoned beam are cut obliquely and its end is cut off at right angles. The cheeks of the mortise are correspondingly sunk. By these means the tenon prevents lateral motion while the whole width of the beam presses against the abutment. Thus a much larger bearing surface is obtained. The whole is bolted or strapped together. It is used in heavy truss work.
No. 67. An oblique mortise-and-tenon or bevel-shoulder joint is one where the shoulders of the tenoned beam are cut at an angle and its end is cut off straight. The sides of the mortise are also cut to match. This design helps the tenon to stop any sideways movement, while the entire width of the beam presses against the support. This results in a much larger bearing surface. Everything is bolted or strapped together. It's commonly used in heavy truss work.

Fig. 269-67 Oblique mortise and tenon
No. 68. A bridle joint is an oblique joint in which a bridle or "tongue" is left in an oblique notch cut out of one beam. Over this tongue is fitted a grooved socket cut obliquely in the other beam. It is used in truss construction.
No. 68. A bridle joint is an angled joint where a bridle or "tongue" extends from an angled notch carved in one beam. A grooved socket, also cut at an angle, fits over this tongue in the other beam. It is used in truss construction.

Fig. 269-68 Bridle
No. 69. A bird's mouth joint is an angular notch cut in a timber to allow it to fit snugly over the member on which it rests. It is used in rafters where they fit over the plate.
No. 69. A bird's mouth joint is an angled notch cut into a beam to let it fit tightly over the piece it rests on. It's used in rafters where they connect to the plate.

Fig. 269-69 Bird's mouth
No. 70. A plain or rubbed or squeezed or glue joint is one in which the edges of two boards are glued and rubbed together tight. It is used in table-tops, drawing-boards, etc.
No. 70. A plain or rubbed or squeezed or glue joint is one where the edges of two boards are glued and pressed tightly together. It's used in table tops, drawing boards, and similar applications.

Fig. 269-70 Glue
To make this joint, first the boards are all laid down flat, side by side, and arranged in the proper order. Three considerations determine what this order is to be: (1), if the grain is of prime importance, as in quartered oak, then the boards are arranged so as to give the best appearance of the grain. (2), if possible, the boards should be so arranged that the warping of each board shall counteract that of the adjacent ones. For this purpose the boards are so laid that the annual rings of one shall alternate in direction with the annual rings of the next, Fig. 280, a, p. 186. (3), if possible, the boards should be so arranged that after being glued together they can all be planed smooth in the same direction. When the above requirements have been met so far as possible, this order should be marked on adjoining edges for later identification. The edges of the boards to be joined should be finished with a jointer.
To create this joint, first lay all the boards flat, side by side, and arrange them in the correct order. Three factors determine what this order should be: (1) if the grain is the main focus, like with quartered oak, arrange the boards to showcase the best appearance of the grain. (2) If possible, arrange the boards so that the warping of each board counteracts that of the ones next to them. For this, place the boards so the annual rings of one alternate direction with the rings of the next, Fig. 280, a, p. 186. (3) If possible, arrange the boards so that after being glued together, they can all be planed smooth in the same direction. Once you have addressed these requirements as much as possible, mark this order on the adjoining edges for future reference. The edges of the boards to be joined should be finished with a jointer.
There are two principal methods of gluing edge-to-edge joints, rubbing and squeezing. In a rubbed joint, the surfaces to be joined should be planed so as to meet thruout exactly. After properly planing [page 173] one edge of each board, keep one board in the vise, jointed edge up, and place its to-be neighbor in position upon it. Then use these four tests for an exact fit. (1) Sight down the end to see that the faces lie in the same plane. (2) Examine the crack from both sides. Be sure that both ends touch. Test this by pulling down hard on one end of the upper board and noticing if the other end is still in contact. If the other end opens, swing the upper board horizontally on the lower board to see where the high place is and then correct it. (3) See if the upper board stands firmly on the lower board by feeling gently to see if it rocks, or by rapping lightly the lower board. (4) Slide the top board slowly on the lower one to see if it adheres or "sucks."
There are two main ways to glue edge-to-edge joints: rubbing and squeezing. In a rubbed joint, the surfaces that are being joined should be planed so they fit together perfectly. After properly planing one edge of each board, secure one board in the vise with the jointed edge facing up, and place the other board on top of it. Then use these four tests to ensure a perfect fit. (1) Look down the end to check that the faces are in the same plane. (2) Check the gap from both sides. Make sure both ends meet. You can test this by pulling down hard on one end of the upper board and seeing if the other end stays in contact. If it opens up, move the upper board horizontally on the lower one to find the high spot and fix it. (3) Check if the upper board sits firmly on the lower board by gently feeling for any rocking or by tapping the lower board lightly. (4) Slowly slide the top board on the lower one to see if it sticks or "sucks."

Fig. 260. Applying Glue for an Edge-to-Edge Joint.
After the pieces have been warmed, which should be done if possible, the glue is spread on them, Fig. 260, and they are then rubbed slowly back and forth in the direction of the grain, pressure being applied by the hand and care being taken not to open the joint in the least. As the glue sets, the rubbing becomes more difficult. It should be stopped when the boards are in their proper relative positions. In rubbing together the edges of two boards, handscrews may be fastened to one in such a way that their jaws serve as guides for the other board to slide between, Fig. 261. Care must be taken to make the jaws of the handscrew diverge enough not to pinch the upper board.
After the pieces have been warmed up, which should be done if possible, the glue is applied to them, Fig. 260, and they are then rubbed slowly back and forth in the direction of the grain, applying pressure with your hand and being careful not to open the joint at all. As the glue sets, the rubbing gets tougher. It should be stopped when the boards are aligned correctly. When rubbing the edges of two boards together, handscrews can be attached to one in such a way that their jaws act as guides for the other board to slide against, Fig. 261. Be careful to make sure the jaws of the handscrew are spread wide enough so they don’t pinch the upper board.

Fig. 261. Rubbing a Glued Joint.
Another method is to clamp a spare board alongside and projecting above the lower board. This spare board acts as a guide against [page 174] which the upper board can be pushed as it is rubbed back and forth. The rubbed joint is especially suitable for short boards.
Another method is to attach a spare board next to and extending above the lower board. This spare board serves as a guide for the upper board to slide against as it is moved back and forth. The rubbed joint is particularly effective for short boards.
In joining long boards, a squeezed joint is common. In this case, the edges are planed so as to be very slightly concave from end to end. The object of this is to counteract the subsequent shrinkage which is likely to take place at the ends of the boards before it does at the middle. The pressure of the clamps may be depended upon to close up the middle, and, especially if dowels are inserted, as in No. 75, the joint will be strong enough to resist the elasticity of the boards.
In joining long boards, a squeezed joint is common. In this case, the edges are planed to be slightly concave from end to end. The goal is to counteract the shrinkage that is likely to happen at the ends of the boards before it occurs in the middle. The pressure from the clamps will close up the middle, and especially if dowels are inserted, as in No. 75, the joint will be strong enough to resist the elasticity of the boards.
When the fit is good, warm the wood if possible, prepare the clamps, put a thin film of glue over both edges which are to be together, apply the clamps rapidly, keeping the faces flush, and set away to dry for at least six hours. Then another piece may be added in the same manner. If the boards are thin and wide, and therefore likely to buckle, they may first be handscrewed to cross-strips to prevent their buckling. The cross-strips are, of course, slightly shorter than the combined width of the boards so that the full pressure of the clamps may come on the glued joint.
When the fit is right, warm the wood if you can, prepare the clamps, put a thin layer of glue on both edges that will be joined, quickly apply the clamps while ensuring the faces are flush, and leave it to dry for at least six hours. Then you can add another piece in the same way. If the boards are thin and wide and might warp, you can first screw them to cross-strips to avoid buckling. The cross-strips should be a bit shorter than the total width of the boards so that the clamps can fully pressure the glued joint.
No. 71. A rebated, rabbeted or fillistered joint. Rebating is the cutting of a rectangular slip out of the side of a piece of wood. The re-entering angle left upon the wood is called the rebate or rabbet. A rebated joint, then, is one in which corresponding rebates are taken off edges so that the joined boards may overlap. It is used in flooring and siding.
No. 71. A rebated, rabbeted or fillistered joint. Rebating is the process of cutting a rectangular groove out of the side of a piece of wood. The inward angle that's left on the wood is known as the rebate or rabbet. A rebated joint, then, is where matching rebates are removed from the edges so that the joined boards can overlap. It’s commonly used in flooring and siding.

Fig. 269-71 Rabbeted
A board is rebated and filleted when two adjoining rebates are filled with a fillet.
A board is shaped and trimmed when two connected grooves are filled with a trim piece.

Fig. 262. Edge-to-Edge Joint, Doweled.
No. 72. A matched or tongue-and-groove joint is made by making a projection or "tongue" in the center of the edge of one board, and a corresponding groove in the center of the other so that they will match together. When used for flooring, the lower side of the grooved board is slightly rebated so that the upper edges will surely touch. This sort of flooring can be blind-nailed.
No. 72. A matched or tongue-and-groove joint is created by cutting a projection, or "tongue," in the center of one board's edge, and a corresponding groove in the center of the other board so that they fit together perfectly. When used for flooring, the underside of the grooved board is slightly recessed to ensure that the upper edges come into contact. This type of flooring can be blind-nailed.

Fig. 269-72 Matched
No. 73. A beaded joint is similar to a matched joint except that a bead is worked on one edge to disguise the joint for decorative purposes.
No. 73. A beaded joint is similar to a matched joint except that a bead is carved on one edge to hide the joint for decorative reasons.

Fig. 269-73 Beaded
No. 74. A spline-joint is made by plowing corresponding grooves in the edges to be joined and inserting a spline or slip-feather. It is used in plank flooring.
No. 74. A spline joint is created by cutting matching grooves in the edges that need to be joined and placing a spline or slip feather in between. It is commonly used in plank flooring.

Fig. 269-74 Spline
No. 75. A doweled joint is made by jointing the two edges carefully, boring holes opposite each other and inserting dowel pins when the two edges are glued together. It is used in table tops, etc.
No. 75. A doweled joint is created by carefully aligning the two edges, drilling holes directly across from each other, and inserting dowel pins when the edges are glued together. It's commonly used in table tops and similar projects.

Fig. 269-75 Doweled
Where the boards are thick enough to allow it, a squeezed joint is greatly strengthened by the insertion of dowels.
Where the boards are thick enough, a tight joint is greatly strengthened by adding dowels.
The essential point in inserting dowels is to have the holes for them directly opposite one another and at right angles to the surface. The following is a convenient method where boards are to be joined edge to edge, Fig. 262. Place the two boards back to back in the vise with the edges and ends flush. Determine approximately where the dowels are to be inserted. With the gage, mark short lines at the points of insertion in the center of each edge, gaging from the outside faces. Across these lines score accurately with a try-square and knife. Then bore the holes with a dowel-bit at the intersection of the lines, Fig. 263. If this is carefully done, the holes will be directly opposite one another, and equidistant from the faces of both boards. All the holes should be of equal depth, say 1", in order that the dowel-pins, which should also be cut of equal lengths, may be interchangeable. After boring, the holes may be slightly countersunk in order to insure a tight joint and the easy slipping of the pins into place. The latter result may also be obtained by slightly pointing the pins with a dowel-pointer, Fig. 123, p. 83. It is also a wise precaution to cut a small groove along the [page 176] length of the pin to allow superfluous glue to escape from the hole. The dowel should be dipped in glue and inserted when the glue is applied to the joint.
The key point in inserting dowels is to make sure the holes for them are directly opposite each other and at right angles to the surface. Here's an easy method for joining boards edge to edge, as shown in Fig. 262. Place the two boards back to back in the vise with the edges and ends flush. Figure out approximately where the dowels will go. Use a gauge to mark short lines at the insertion points in the center of each edge, gauging from the outside faces. Use a try-square and knife to accurately score across these lines. Then, drill the holes with a dowel bit at the intersection of the lines, as shown in Fig. 263. If done carefully, the holes will be directly opposite each other and equidistant from the faces of both boards. All the holes should be the same depth, about 1", so that the dowel pins, which should also be cut to the same lengths, can be interchangeable. After drilling, you can slightly countersink the holes to ensure a tight joint and make it easier to slip the pins into place. You can also achieve this by slightly pointing the pins with a dowel pointer, as shown in Fig. 123. It’s also a good idea to cut a small groove along the length of the pin to let excess glue escape from the hole. The dowel should be dipped in glue and inserted when applying glue to the joint.

Fig. 263. Boring for Dowels in an Edge-to-Edge Joint.
THE COMMON JOINTS
References*
References
Rivington, Vol. I, pp. 57-77, 135-137, 238-242; Vol.II, pp. 291-295.
Rivington, Vol. I, pp. 57-77, 135-137, 238-242; Vol. II, pp. 291-295.
Adams, pp. 1-30.
Adams, pp. 1-30.
Sickels, pp. 86-124.
Sickels, pp. 86-124.
Goss, pp. 128-152.
Goss, pp. 128-152.
Ellis, pp. 135-151.
Ellis, pp. 135-151.
Barter, pp. 211-275.
Barter, pp. 211-275.
Selden, pp. 56-130.
Selden, pp. 56-130.
Building Trades Pocketbook, pp. 217-221, 237.
Building Trades Pocketbook, pp. 217-221, 237.
Griffith, pp. 86-104, 164-170.
Griffith, pp. 86-104, 164-170.
* For general bibliography see p. 4.
* For general bibliography see __A_TAG_PLACEHOLDER_0__
Transcriber's Note: The following six pages of diagrams are as they appeared in the original book. They are of poor quality, and the page enlargements are not much improved. These pages have been kept to preserve the original layout, and because they have been linked to from various places in the book. For the convenience of readers, the 75 diagrams have been individually enlarged, repaired where necessary, and inserted after their relevant, numbered, descriptions in the text (above), with links to them from the added lists at the tops of the original pages. |
Fig. 264.
Fig. 265.
Fig. 266.
30 Stub mortise and tenon
31 Thru mortise and tenon
32 Blind mortise and tenon
33 Mortise and tenon with rabbet
Fig. 267.
39 Keyed mortise and tenon
40 Tusk tenon
41 Double mortise and tenon
42 Haunched mortise and tenon
Fig. 268.
Fig. 269.
Chapter 8.
TYPES OF WOODEN STRUCTURES.
The articles suitable to be made in wood with hand tools may for convenience be divided into four general classes: (1) Unjoined pieces; (2) board structures; (3) panel structures; (4) framed structures. A few illustrations of each class are given below.
The items that can be made from wood using hand tools can conveniently be divided into four main categories: (1) Unjoined pieces; (2) board structures; (3) panel structures; (4) framed structures. A few examples of each category are provided below.
(1) SIMPLE OR UNJOINED PIECES
Of these there are a number that are advantageous for the learning of tool processes; at the same time they give opportunity for expression in design, and when finished are of use.
Of these, several are helpful for learning tool processes; they also provide a chance for creative expression in design, and when completed, they are useful.
Examples are: key-boards, chiseling-boards, bread-boards, sleeve-boards, ironing-boards, coat- and skirt-hangers, and gouged trays. Some of these are so simple as to include hardly any process but planing, directions for which are given above, p. 72.
Examples include: keyboards, carving boards, cutting boards, sleeve boards, ironing boards, coat and skirt hangers, and carved trays. Some of these are so simple that they hardly involve any process other than planing, instructions for which are provided above, p. 72.

Fig. 270. Pen-Tray.
Where there is more than one process involved, the order of procedure is of importance. In general, a safe rule to follow in each case is to plane up the piece true and square, or, in technical language, to "true" it up. At least as many of its surfaces should be trued as are necessary for the "lay out." Where the piece is to be rectangular all the surfaces should be true; where some of the surfaces are to be curved it is unnecessary and a waste of time to square them first. For example, in making a gouged tray with curved outline, Fig. 270, the working face, the working edge, and the thickness should all be true before the plan is laid out. Then, after the outline is drawn, the trough may be gouged, the outline cut with turning-saw, chisel, and spokeshave, and the edges molded with the gouge or chisel. If there is incised decoration it should be cut [page 184] before the molding is cut, so that while being incised, the piece will lie flat without tipping.
Where more than one process is involved, the order of operations matters. Generally, a good rule to follow in each case is to make the piece straight and square, or, in technical terms, to "true" it up. At the very least, as many surfaces should be trued as are needed for the layout. If the piece is supposed to be rectangular, all the surfaces should be true; however, if some surfaces will be curved, it's unnecessary and a waste of time to square them first. For instance, when making a gouged tray with a curved outline, Fig. 270, the working face, the working edge, and the thickness should all be true before the plan is drawn up. Then, after the outline is sketched, the trough can be gouged, the outline cut with a turning saw, chisel, and spokeshave, and the edges shaped with the gouge or chisel. If there is any incised decoration, it should be cut [page 184] before the molding is done, so that while being incised, the piece can lie flat without tipping.
These simple pieces, as well as others, are often embellished by chamfering. A chamfer is a surface produced by cutting away an arris. It differs from a bevel in that a bevel inclines all the way to the next arris, while a chamfer makes a new arris, Fig. 271. A thru chamfer extends the whole length or width of a piece, while a stop chamfer extends only part way. For the laying out of a chamfer see p. 115.
These simple shapes, along with others, are often enhanced by chamfering. A chamfer is a surface created by cutting away a sharp edge. It’s different from a bevel in that a bevel tapers all the way to the next edge, while a chamfer creates a new edge, Fig. 271. A thru chamfer runs the entire length or width of a piece, while a stop chamfer only goes part of the way. For instructions on laying out a chamfer, see p. 115.

Fig. 271. Difference Between Chamfer and Bevel.
Thru chamfering is best done with a plane, Fig. 272. For this purpose the piece may be held in the bench-vise and the plane tipped to the proper angle, or the piece may be held in a handscrew which in turn is held in the vise as in Fig. 175, p. 101. The chamfers with the grain should be planed before those across the grain.
Thru chamfering is best done with a plane, Fig. 272. For this purpose, the piece can be held in the bench vise with the plane tilted to the right angle, or the piece can be secured in a handscrew, which is then held in the vise as shown in Fig. 175, p. 101. The chamfers along the grain should be planed before those against the grain.
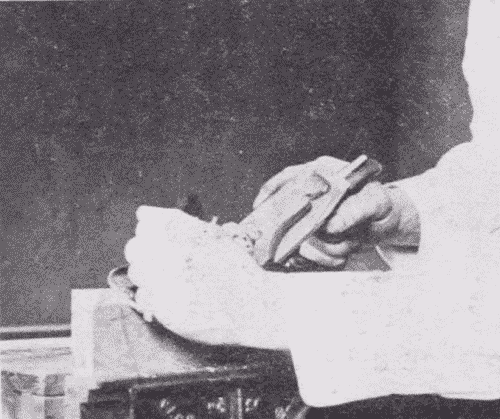
Fig. 272. Thru Chamfering.
In chamfering a four-square stick into an eight-square, the piece may be gripped in the vise diagonally, Fig. 273, or it may be held in a trough made of two strips of wood from each of which an arris has been chamfered and then the two nailed together, Fig. 274. A dowel or nail may be inserted in the trough for a stop. Stop chamfers are pared best with a chisel, Fig. 275, held according to convenience either flat side or bevel side up. See under chisel, p. 53.
In chamfering a square stick into an octagonal shape, you can grip the piece diagonally in the vise, as shown in Fig. 273, or hold it in a trough made of two wooden strips that have both had one edge chiseled off and then nailed together, as illustrated in Fig. 274. A dowel or nail can be inserted in the trough as a stop. It’s best to pare stop chamfers with a chisel, as shown in Fig. 275, which can be held either flat side up or bevel side up, depending on what’s more comfortable. See under chisel, p. 53.

Fig. 273. Piece Held in Vise to Chamfer.

Fig. 274. Trough for Planing Chamfers.

Fig. 275. Stop Chamfering.
(2) BOARD STRUCTURES.
These include such pieces as wall brackets, sets of shelves, book-racks, plate-racks, drawing-boards, foot-stools, taborets, and boxes.
These include items like wall brackets, shelving units, book racks, plate racks, drawing boards, footstools, small tables, and boxes.
The advantage of this form of construction is that it is comparatively easy to make; the disadvantage is that if the boards are wide, they are sure to shrink and swell. It is wise in all such work to true and smooth up all the pieces at once, and if the wood is not thoroly [page 185] seasoned, to keep the boards under pressure till they are assembled. In the case of several boards to be jointed into one piece, they should be glued together before the surfaces are smoothed. Suggestions regarding a few typical pieces follow:
The benefit of this type of construction is that it's relatively easy to do; however, the downside is that if the boards are wide, they will definitely shrink and swell. It's advisable in all such projects to make all the pieces level and smooth at the same time, and if the wood isn't fully dried, to keep the boards under pressure until they are put together. When joining several boards into one piece, they should be glued together before the surfaces are smoothed out. Here are some suggestions for a few typical pieces:
Wall Brackets. (1) There are three essential parts, the shelf, the support or supports, and the back: the shelf to hold the articles, the support to hold up the shelf, and the back to hold all together, Fig. 276, a. The grain of the wood in the shelf should run left and right, not forward and back, because thus it rests on the support in such a way as not to break easily, and it also acts as a stiffener for the back. In case the back extends above the shelf, as in Fig. 276, a, the shelf can be secured firmly to the back, since there is side grain in which to drive nails or screws. As to the direction of the grain of the support and the back, this should run in the direction of the largest dimension of each. Where the back is long horizontally, for security in hanging, it is better to have two supports.10
Wall Brackets. (1) There are three key components: the shelf, the support or supports, and the back. The shelf holds the items, the support keeps the shelf up, and the back holds everything together, as shown in Fig. 276, a. The grain of the wood in the shelf should run horizontally, not vertically, because that way it rests on the support in a way that prevents it from breaking easily, and it also provides extra stability for the back. If the back extends above the shelf, as illustrated in Fig. 276, a, the shelf can be securely attached to the back, since there’s side grain available for driving in nails or screws. The grain of the support and the back should follow the longest dimension of each piece. When the back is long horizontally, it's better to use two supports for added stability when hanging.10
Footnote 10: See the School Arts Book for Nov., 1906, "Design in the Woodworking Class," by Anna and William Noyes.
Footnote 10: See the School Arts Book for Nov. 1906, "Design in the Woodworking Class," by Anna and William Noyes.

Fig. 276. Wall Brackets, Double-Hung: a. Single Support. b. Double Support.
Wall book-shelves, Fig. 277, plate-racks, etc., are simply compound brackets. The shelf is the essential piece, the sides take the place of the supports, and the back is often reduced to strips merely wide enough to give rigidity.
Wall book-shelves, Fig. 277, plate-racks, etc., are just combined brackets. The shelf is the main component; the sides serve as the supports, and the back is often reduced to strips that are just wide enough to provide stability.
The shelves may be either gained into the supports, Fig. 266, No. 28 or No. 29, p. 179, or a keyed mortise-and-tenon may be used, Fig. 277. In the latter case the back strip may have a short barefaced blind tenon which is mortised into [page 186] the upright, Fig. 278. It also fits into a rabbet on the upper back side of the shelf. Made in this way the shelves can be knocked down easily.
The shelves can either be fitted into the supports, Fig. 266, No. 28 or No. 29, p. 179, or a keyed mortise-and-tenon joint can be used, Fig. 277. In the latter case, the back strip can have a short, faceless blind tenon that is mortised into the upright, Fig. 278. It also fits into a rabbet on the upper back side of the shelf. This design allows the shelves to be easily taken apart.

Fig. 277. Wall Book-Case.

Fig. 278. Construction of a Knock-Down Book-Shelf Seen From the Back.
Foot Stool or Cricket, Fig. 279. The grain of the supports should run up and down, because pieces with the grain horizontal would be likely to break under pressure. Braces or a rail give additional support. The top should not be larger than the base of the legs; otherwise a person standing carelessly on the stool is in danger of being upset.
Foot Stool or Cricket, Fig. 279. The grain of the supports should run vertically, because pieces with the grain horizontal are more likely to break under pressure. Braces or a rail provide extra support. The top shouldn't be larger than the base of the legs; otherwise, a person standing carelessly on the stool risks tipping over.

Fig. 279. Cricket.
A Drawing-Board is made up of narrow boards, with glued joints, with the boards so laid that the annual rings will alternate in direction, Fig. 280, a. It must be made so that it can shrink and swell and yet remain flat. For the purpose of giving lateral stiffness cleats are added. They may simply be screwed on the underside, the screw holes being large enough to allow for shrinkage, or they may be dadoed in with a dovetail dado, Fig. 280, b, or they may be grooved to admit a tongue on the end of a board, Fig. 280, c. In this case screws passing thru large holes in the cleats hold them in place.
A Drawing-Board is made from narrow boards that are glued together, arranged so that the growth rings alternate in direction, as shown in Fig. 280, a. It needs to be designed in a way that allows it to shrink and swell while still staying flat. To provide lateral stiffness, cleats are added. They can be simply screwed onto the underside, with the screw holes large enough to accommodate shrinkage, or they can be fitted in place using a dovetail joint, as shown in Fig. 280, b, or they can be grooved to accept a tongue on the end of a board, as shown in Fig. 280, c. In this case, screws pass through large holes in the cleats to hold them securely.

Fig. 280. Drawing-Board Construction:
a. With Cleats Screwed on Beneath;
b. With Cleats Dovetail-Dadoed in;
c. With Cleats Matched on Ends.
Taborets. The term taboret originally meant a little tabor or drum, and was therefore used to designate a small stool, the seat of which consisted of a piece of stretched leather. The term now includes small, tablelike structures for holding flowerpots, vases, etc. It might more properly be called a "table-ette."
Taborets. The word taboret originally referred to a small tabor or drum, which is why it was used to describe a small stool with a seat made of stretched leather. Now, the term includes small, table-like structures for holding flowerpots, vases, and similar items. It could be more accurately called a "table-ette."
When made up with boards having their long edges mitered, it has from four to eight sides. A six-sided one is shown in Fig. 281. In making, it is best to fit the joints exactly first, while the board is stiff, and then to cut out the pattern of the legs. Directions for gluing are given on p. 169.
When assembled with boards that have their long edges cut at an angle, it can have anywhere from four to eight sides. A six-sided version is shown in Fig. 281. When making it, it’s best to fit the joints perfectly first while the board is rigid, and then cut out the pattern for the legs. Instructions for gluing are provided on p. 169.

Fig. 281. Taboret.
Scrap-boxes, Fig. 282, and flower-pot boxes may be made with the same construction.
Scrap-boxes, Fig. 282, and flower-pot boxes can be made with the same design.

Fig. 282. Scrap-Box.

Fig. 283. Reinforced Butt Joint in Box.
The rabbet and dado joint, Fig. 266, No. 26, can be glued without nails and is good for small boxes.
The rabbet and dado joint, Fig. 266, No. 26, can be glued without nails and is great for small boxes.
The housed dado, Fig. 266, No. 25, is good for water-tight boxes.
The housed dado, Fig. 266, No. 25, is ideal for water-tight boxes.
The mitered ledge, Fig. 268, No. 58, makes a very neat, strong joint which can be nailed or glued, but is more difficult to fit than a simpler joint.
The mitered ledge, Fig. 268, No. 58, creates a clean, sturdy joint that can be nailed or glued, but it's trickier to fit than a simpler joint.
The dovetail joint, Fig. 267, No. 48, is very strong and honest, but the joint is prominent from the outside and it takes much time and labor to make. It is glued.
The dovetail joint, Fig. 267, No. 48, is very strong and reliable, but the joint is visible from the outside and takes a lot of time and effort to create. It is glued.
The blind dovetail, Fig. 267, No. 51, is very neat and strong, and the [page 188] joint is entirely concealed when done, but is very difficult to make.
The blind dovetail, Fig. 267, No. 51, is very neat and strong, and the [page 188] joint is completely hidden when finished, but it's quite challenging to create.
The Bottoms of Boxes. The plain or full bottom, Fig. 284, A, is likely to shrink (see dotted line), and it is held in place only by the friction of the nails. The extended bottom, Fig. 284, B, overcomes the objection to shrinkage and adds a decorative feature. The bottom may be set in, Fig. 284, C. This is stronger than the plain bottom, but the nail holes show. The bottom may be rabbeted in, Fig. 284, D. This is better than the set-in bottom so far as the showing of the nail holes goes, for the nails may be driven in from below, and a little shrinkage is not conspicuous. It is practicable, if a rabbet or mitered joint is used in the sides, but if the side pieces are butted or dadoed, the rabbet for the bottom shows. This may be cleverly concealed by an insert, but that is patchwork, and not first-rate construction.
The Bottoms of Boxes. The plain or full bottom, Fig. 284, A, is likely to shrink (see dotted line), and it’s only held in place by the friction of the nails. The extended bottom, Fig. 284, B, addresses the shrinkage issue and adds a decorative touch. The bottom may be set in, Fig. 284, C. This offers more strength than the plain bottom, but the nail holes are visible. The bottom may be rabbeted in, Fig. 284, D. This is an improvement over the set-in bottom in terms of the visibility of nail holes since the nails can be driven in from underneath, and a little shrinkage isn’t very noticeable. This method works well if a rabbet or mitered joint is used on the sides, but if the side pieces are butted or dadoed, the rabbet for the bottom will be visible. This can be cleverly hidden with an insert, but that’s considered patchwork and not top-notch construction.
Reinforced bottom, Fig. 284, E. A plain or full bottom is sometimes covered by a base or cover strip to hide the joint and secure the bottom, as in tool chests. This strip may be mitered at the corners.
Reinforced bottom, Fig. 284, E. A plain or full bottom is sometimes covered by a base or cover strip to conceal the joint and secure the bottom, like in tool chests. This strip may be mitered at the corners.

Fig. 284. Methods of Attaching Box Bottoms.
The Lids of Boxes. The simplest form is a full flat cover, Fig. 285, A, which may be nailed or screwed to the box, as in packing cases. The cover may slide into a groove, Fig. 285, B, along the sides and into one end, the other end being lowered to admit it. The cover may have cleats on its underside, Fig. 285, C, which fit just inside the box and keep the top in place. The cleats also prevent the [page 189] top from warping. This is a common Japanese construction, even in fine boxes. The Japanese tie the top on with a tape or ribbon.
The Lids of Boxes. The simplest design is a completely flat cover, Fig. 285, A, which can be nailed or screwed onto the box, like in packing cases. The cover can slide into a groove, Fig. 285, B, along the sides and into one end, with the other end lowered to let it in. The cover can have cleats on its underside, Fig. 285, C, that fit just inside the box to keep the top stable. The cleats also stop the top from warping. This is a typical Japanese design, even in high-quality boxes. The Japanese secure the top with a tape or ribbon.
The lid may be boxed, Fig. 285, D, that is, portions of the sides may be affixed to the top. These extra pieces are a help to stiffen the top and to keep it from warping. A boxed top may have the top board flush with the sides, Fig. 285, E. The disadvantage of this is that the top may shrink and part from the sides and give a bad appearance. The overlapping top, Fig. 285, F, obviates this trouble of shrinkage and adds a decorative element. In this case the top may be glued on or screwed from below thru the side strips.
The lid can be boxed, as shown in Fig. 285, D, meaning that parts of the sides can be attached to the top. These extra pieces help to strengthen the top and prevent it from warping. A boxed top can have the top board level with the sides, as seen in Fig. 285, E. The downside of this design is that the top might shrink and separate from the sides, which can look unattractive. The overlapping top, shown in Fig. 285, F, solves this issue of shrinkage and adds a decorative touch. In this case, the top can either be glued on or screwed in from below through the side strips.
The top may be mitered into the sides, Fig. 285, G. The shrinkage trouble still obtains here. Otherwise the appearance is excellent. The top may be paneled into the sides, Fig. 285, H. This has a good appearance if the sides are mitered and ledged but not if the sides are butted or dadoed, because then the groove for the top shows.
The top can be mitered into the sides, Fig. 285, G. The issue of shrinkage still exists here. Other than that, it looks great. The top can also be paneled into the sides, Fig. 285, H. This looks good if the sides are mitered and ledged, but not if the sides are butted or dadoed, because then the groove for the top is visible.
Any of these lids may be made removable or hinged, except the sliding top. For methods of hinging see p. 132.
Any of these lids can be either removable or hinged, except for the sliding top. For details on how to hinge them, see p. 132.
In gluing boxes together, it is a good plan to glue the ends and sides together first and to let these joints dry before gluing on the bottom and, in the case of a boxed top, Fig. 285, D, the top. Care must be taken to see that the sides do not bow under the pressure. To prevent this, one or more false, temporary partitions as A, B, in Fig. 286, of exactly the length to keep the sides straight, may be inserted. In gluing together boxes with rabbeted joints, Fig. 285, H, pressure should be applied in both directions. [page 190] In gluing on the bottom of a box that is also to be nailed, the nails should be driven into the bottom first, so that the points just come thru. These points sticking into the sides will prevent the bottom from slipping when pressure is applied. It is often undesirable to have nail heads show, as in a top. In such a case, and also to prevent the top from slipping under pressure, a couple of small brads may be driven part way into the upper edges of the sides, the heads bitten off with the nippers, and points filed on the projecting portion.
When gluing boxes together, it’s best to glue the ends and sides first and let those joints dry before attaching the bottom and, if there’s a lid, the top as shown in Fig. 285, D. Make sure the sides don’t bend under pressure. To avoid this, insert one or more temporary supports like A, B in Fig. 286 that are just the right length to keep the sides straight. When gluing boxes with rabbeted joints, as seen in Fig. 285, H, apply pressure in both directions. [page 190] When gluing the bottom of a box that will also be nailed, first drive the nails into the bottom so that the tips barely stick through. These tips will help keep the bottom in place when pressure is applied. Nail heads can be unsightly, especially on a lid. In that case, and to stop the lid from slipping under pressure, you can partially drive in a couple of small brads into the upper edges of the sides, clip off the heads with nippers, and file points on the ends that stick out.

Fig. 286. Glueing Together a Box.
Drawers. In the best form, the sides are dovetailed to the front for strength, Fig. 287, for whenever the drawer is opened the front tends to pull away from the sides. This dovetail is half blind, so that the joint will not appear when the drawer is shut. In order that the drawer may always run freely and yet the front fit the opening as close as possible, it is common practice to cut a shallow rabbet on the ends of the front, so that the body of the drawer is a little narrower than the front is long, Fig. 287. Or the front may be attached [page 191] to the sides with a dado tongue and rabbet joint, Fig. 266, No. 27, p. 179.
Drawers. Ideally, the sides are dovetailed to the front for strength, Fig. 287, because whenever the drawer is opened, the front tends to pull away from the sides. This dovetail is half-blind, so the joint isn't visible when the drawer is closed. To ensure that the drawer slides smoothly while still fitting the opening as snugly as possible, it's common to cut a shallow rabbet on the ends of the front, making the body of the drawer slightly narrower than the length of the front, Fig. 287. Alternatively, the front may be attached to the sides using a dado tongue and rabbet joint, Fig. 266, No. 27, p. 179.

Fig. 287. Dovetailed Drawer Construction.
The bottom is grooved into the sides with its grain parallel to the front and fastened only to the front so that it has plenty of play for shrinkage. The back is dadoed into the sides, with either a straight dado, Fig. 266, No. 25, p. 179, or dovetail dado, Fig. 266, No. 28, and rests on the bottom. The extension of the bottom beyond the back allows ample room for shrinkage.
The bottom is grooved into the sides with the grain lined up with the front and secured only to the front, giving it plenty of flexibility for shrinkage. The back is fitted into the sides using either a straight groove, Fig. 266, No. 25, p. 179, or a dovetail groove, Fig. 266, No. 28, and it rests on the bottom. The extension of the bottom beyond the back provides enough space for shrinkage.
The best machine-made drawers are now made with the bottom paneled or dadoed in all around so that papers cannot slip out. The back, as well as the front, is dovetailed.
The best machine-made drawers today are designed with the bottom panel secured all around, so papers can't slide out. Both the back and the front are dovetailed.
Directions for Making a Table Drawer. Dress the front and sides to size. Fit the front of the drawer to its place in the table or cabinet, leaving a little play all around it. Plow the groove in the front and sides for the drawer bottom. For ordinary drawers, a groove ¼" wide is proper. If the ends of the front are to be rabbeted (see above), do this next. The sides are best joined to the front with the half-blind dovetail joint. (For directions see p. 166). After fitting these, lay out and cut the dadoes for the back of the drawer. Prepare the bottom of the drawer thus: the [page 192] grain should run right and left, never front and back. If the drawer is so long as to require it, glue-joint the bottom, and fit it snugly to place. There need be no play right and left, and the bottom should extend as far back as the sides. If necessary, bevel the under side to fit the grooves. Assemble all the parts to see that they fit, take them apart, glue the sides to the front and back, slip the bottom into place, apply the clamps, and see to it that all joints are square, using a diagonal brace if necessary, Fig. 294. Fasten the bottom to the front by means of a thin block glued into the interior angle between the under side of the bottom and the back side of the front. When dry, clean up the drawer and fit it to its place.
Instructions for Making a Table Drawer. Cut the front and sides to size. Fit the front of the drawer in its spot in the table or cabinet, leaving a little space all around it. Create a groove in the front and sides for the drawer bottom. For standard drawers, a groove ¼" wide works well. If the ends of the front need to be rabbeted (see above), do this next. The sides are best attached to the front using a half-blind dovetail joint. (For instructions, see p. 166). After fitting these pieces, mark and cut the dadoes for the back of the drawer. Prepare the bottom of the drawer like this: the grain should run side to side, not front to back. If the drawer is long enough to need it, glue-joint the bottom and fit it snugly in place. There shouldn't be any movement side to side, and the bottom should extend as far back as the sides. If needed, bevel the underside to fit into the grooves. Assemble all the parts to check that they fit, disassemble them, glue the sides to the front and back, slip the bottom into place, apply clamps, and ensure all joints are square, using a diagonal brace if needed, Fig. 294. Attach the bottom to the front using a thin block glued into the corner between the underside of the bottom and the back side of the front. Once dry, clean up the drawer and fit it into its spot.
(3) PANEL STRUCTURES
These include doors and cabinets of all sorts. The principle of panel or cabinet construction is that there shall be a frame composed of narrow members whose grain follows the principal dimensions. In the best construction this frame is mortised and tenoned together and within this frame there is set a thin board or panel which is free to shrink or swell but is prevented from warping by the stiffer frame. The object is to cover an extended surface in such a way that the general dimensions and good appearance will not be affected by whatever shrinkage there is. Since the frame itself is made up of narrow pieces, there is but little shrinkage in them. That shrinkage is all that affects the size of the whole structure, because wood does not shrink longitudinally to any appreciable extent. The shrinking or swelling of the panel does not affect the general size. The cross construction of the frame also prevents [page 193] warping, since, in the best construction every joint is mortised and tenoned. The panel may simply be fastened on the back of the frame, but a better construction is to insert it in a groove made in the inside of the frame in which the panel is to lie and have free play. The panel may be made of one board or of matched boards, may be plain or have raised or carved surfaces, or be of glass; and the joints between frame and panel may be embellished with moldings mitered in, but the principle is the same in all cases.
These include all kinds of doors and cabinets. The basic idea behind panel or cabinet construction is that there’s a frame made of narrow pieces whose grain runs along the main lengths. In high-quality construction, this frame is joined together with mortises and tenons, and within this frame, there’s a thin board or panel that can expand or contract but is kept from warping by the sturdier frame. The goal is to cover a large surface in such a way that overall size and appearance are not impacted by any shrinkage that may occur. Because the frame itself is built from narrow pieces, there’s very little shrinkage in them. That shrinkage is what affects the size of the entire structure, as wood doesn’t shrink significantly along its length. The expansion or contraction of the panel doesn’t change the overall size. The cross construction of the frame also helps prevent warping, as, in top-notch construction, every joint is mortised and tenoned. The panel can simply be attached to the back of the frame, but a better method is to fit it into a groove on the inside of the frame where the panel can move freely. The panel can be a single board or multiple matched boards, can be flat or have raised or carved designs, or even be made of glass; and the joints between the frame and panel can be enhanced with mitered moldings, but the core principle remains the same in all situations. [page 193]
The frame of a door, Fig. 288, illustrates the panel construction. The upright, outside pieces are called the "stiles," the horizontal pieces the "rails." There are also the "top-rail," the "bottom-rail," the "lock-rail" (where the door-knob and lock are inserted), and sometimes the "frieze-rail" between the lock rail and the top rail. The "muntin" is the upright between the two stiles.
The frame of a door, Fig. 288, shows the panel construction. The vertical outer pieces are called the "stiles," and the horizontal pieces are the "rails." There are also the "top rail," the "bottom rail," the "lock rail" (where the door knob and lock are placed), and sometimes the "frieze rail" between the lock rail and the top rail. The "muntin" is the vertical piece between the two stiles.

Fig. 288. Door, Illustrating Panel Construction: S. Stile; T. R. Top Rail; L. R. Lock Rail; B. R. Bottom Rail; M. Muntin; P. Panel; A. Double Mortise-and-Tenon; F. Fillet; A. B. C. Forms of Panels.
The joint commonly used is the haunched or relished mortise-and-tenon, Fig. 267, No. 42, p. 180; (See p. 163 for directions for making). The tenon is sometimes doubled, Fig. 288, and a fillet (f) may be inserted to cover the ends of the tenons, or the joint may be a blind mortise-and-tenon, Fig. 266, No. 32, or in cheap construction, dowels may be used. The best doors are now made with cores of pine covered on the visible sides with heavy veneer. Large surfaces are covered by increasing the [page 194] number of parts rather than their size, as in wainscoting.
The joint that's commonly used is the haunched or relished mortise-and-tenon, Fig. 267, No. 42, p. 180; (See p. 163 for making instructions). The tenon is sometimes doubled, Fig. 288, and a fillet (f) can be added to cover the ends of the tenons, or the joint can be a blind mortise-and-tenon, Fig. 266, No. 32, or in budget-friendly construction, dowels may be used. The best doors today are made with pine cores covered on the visible sides with heavy veneer. Large surfaces are covered by increasing the number of parts instead of their size, as seen in wainscoting.
Picture-frames also belong in this class of structures, the glass taking the place of the panel. They are made with mortise-and-tenon joints, Fig. 266, No. 33, slip joints, Fig. 267, No. 46, dowelled butt joints, Fig. 264, No. 8, end lap joints, Fig. 265, No. 17, and, far more commonly, mitered joints, Fig. 268, No. 52. Mitered joints are the easiest to make, for the joints can be cut in a miter-box, Fig. 181, p. 103, and glued in a picture-frame-vise, Fig. 172, p. 101. This joint needs reinforcement by nails, Fig. 268, No. 52, by dowels, No. 53, or by splines, No. 55. If the sides are of different widths, the fitting of the joint is more difficult. Mitered joints are the only kind suitable for molded frames. The rabbets are cut out with a rabbeting-plane before mitering and assembling.
Picture frames also fall into this category of structures, with the glass replacing the panel. They're constructed using mortise-and-tenon joints, Fig. 266, No. 33, slip joints, Fig. 267, No. 46, dowelled butt joints, Fig. 264, No. 8, end lap joints, Fig. 265, No. 17, and, much more commonly, mitered joints, Fig. 268, No. 52. Mitered joints are the easiest to create since the cuts can be made in a miter box, Fig. 181, p. 103, and glued in a picture frame vise, Fig. 172, p. 101. This joint requires reinforcement with nails, Fig. 268, No. 52, dowels, No. 53, or splines, No. 55. If the sides have different widths, fitting the joint becomes more challenging. Mitered joints are the only type suitable for molded frames. The rabbets are cut out with a rabbeting plane before mitering and assembling.
The principle disadvantage of a mitered joint is that, if the wood shrinks at all, it opens at the inside corners, as in Fig. 289, because wood shrinks sidewise but not lengthwise.
The main disadvantage of a mitered joint is that if the wood shrinks, it will open at the inside corners, as shown in Fig. 289, because wood shrinks sideways but not lengthwise.

Fig. 289. The Way a Mitered Joint Opens on Account of Shrinkage.
In window sashes, the dovetail joint, Fig. 267, No. 47, is the common one at the upper end of the lower sash and the lower end of the upper sash, and the mortise-and-tenon joint modified is used at the lower end of the lower and upper end of the upper sash. The glass takes the place of the panel. In blind sashes, the pinned mortise-and-tenon joint, Fig. 267, No. 38, is commonly used.
In window sashes, the dovetail joint, Fig. 267, No. 47, is typically found at the top of the lower sash and the bottom of the upper sash, while a modified mortise-and-tenon joint is used at the bottom of the lower sash and the top of the upper sash. The glass replaces the panel. In blind sashes, the pinned mortise-and-tenon joint, Fig. 267, No. 38, is commonly used.
When panels are joined together to enclose a space, then we have what is properly called cabinet construction. Illustrations are cabinets, bureaus, desks, lockers, chests, etc.
When panels are connected to create an enclosed space, this is what we refer to as cabinet construction. Examples include cabinets, dressers, desks, lockers, chests, and so on.
In all these cases, the constructed panels may be treated as separate boards and joined together with dowel pins or splines or dadoed together without any other framework, tho the corners are often reinforced by cleats or blocks glued into them. Sometimes, however, as in chests, Fig. 290, posts are used instead of stiles, and rails are mortised or doweled into them and the panels set into grooves in both posts and rails. In this case the bottom is raised from the floor, and may be dadoed into the bottom rails, or dowelled into them or even supported by strips attached along their lower inside edges. The chest really is a union of both paneled and framed structures.
In all these cases, the constructed panels can be treated as separate boards and connected using dowel pins or splines, or they can be joined together with dado joints without any additional framing, although the corners are often reinforced with cleats or blocks that are glued in place. However, in some cases, like with chests, as shown in Fig. 290, posts are used instead of stiles, and the rails are either mortised or doweled into them, with the panels set into grooves in both the posts and rails. In this design, the bottom is elevated from the floor and may be dadoed into the bottom rails, doweled into them, or even supported by strips attached along their lower inside edges. The chest is essentially a combination of both paneled and framed structures.

Fig. 290. Chest Construction.
(4) FRAMED STRUCTURES
The principle of the framed structure is similar to that of the panel construction in that the object is to allow for shrinkage without harm to construction and also to economize materials. Common examples are tables, chairs, work-benches, and frame houses.
The principle of the framed structure is similar to that of panel construction in that the goal is to allow for shrinkage without damaging the construction and to save materials. Common examples include tables, chairs, workbenches, and frame houses.
The Making of a Table. The standard height of a table is 30". There should be 25" clearance under the rails. This leaves approximately 4" for the width of the rails. Assuming that the table is to be of a simple straight line type with one drawer, the following method of procedure is suggested:
The Making of a Table. The standard height of a table is 30". There should be 25" of clearance under the rails. This leaves about 4" for the width of the rails. Assuming the table is designed as a simple straight-line style with one drawer, the following method is recommended:
Cut the boards for the top to the approximate length and stick, (see p. 48) and clamp them, so as to season them as well as possible before jointing.
Cut the boards for the top to the right length and stick, (see p. 48) and clamp them to let them season as well as possible before joining.
Dress to size the legs and rails. Stand the legs in their proper positions relative to each other, and mark them F R (front right), F L (front left), B R (back right), and B L (back left). Plow out the grooves on the inside of the rails for the fastenings of the top, Fig. 297, D, if they are to be used. Lay out and cut the tenons and mortises for the end rails and back rail.
Dress to fit the legs and rails. Position the legs correctly relative to each other, and mark them F R (front right), F L (front left), B R (back right), and B L (back left). Carve out the grooves on the inside of the rails for the fastenings of the top, Fig. 297, D, if they are to be used. Plan and cut the tenons and mortises for the end rails and back rail.
The proper form of the tenon is one with a wide shoulder above it so that the top of the leg above the mortise will not shear out. The [page 196] rails should be set near the outside of the leg so that the tenon may be as long as possible and the portion of the leg inside it as strong as possible. A haunched mortise-and-tenon joint, Fig. 267, No. 43 is sometimes used, giving additional lateral stiffness to the rail. The proper proportions are shown in Fig. 291. When cut, these parts should be temporarily assembled to see if they fit.
The ideal shape of the tenon has a wide shoulder at the top so that the upper part of the leg above the mortise won't break off. The[page 196]rails should be positioned close to the outside of the leg, allowing the tenon to be as long as possible and making the part of the leg inside it as sturdy as possible. A haunched mortise-and-tenon joint, Fig. 267, No. 43 is sometimes used to provide extra lateral stability to the rail. The right proportions are shown in Fig. 291. Once cut, these pieces should be temporarily put together to check if they fit.

Fig. 291. A. Cross-Section Thru Back Left Leg and Adjoining Rails of Table. (Plan).
B. Elevation, Showing Wide Shoulder on Tenon of Rail.
Inasmuch as a drawer takes the place of a front rail, the front legs must be tied together in some other way. For this purpose two stringers or drawer rails may be used, their front edges being as far from the face of the legs as are the rails from the side and back. The upper drawer rail may be dovetailed at both ends into the tops of the legs, as shown in Fig. 292. If this takes more room than can well be spared from the depth of the drawer, it may be omitted, but it adds greatly to the stiffness of the table and is an excellent means of fastening on the top by the use of screws passing thru it.
Since a drawer replaces the front rail, the front legs need to be connected in another manner. For this, you can use two stringers or drawer rails, ensuring their front edges are the same distance from the legs as the rails are from the sides and back. The upper drawer rail can be dovetailed at both ends into the tops of the legs, as shown in Fig. 292. If this takes up more space than you can afford to lose from the drawer's depth, it can be left out, but it significantly increases the table's sturdiness and provides a great way to attach the top using screws that go through it.

Fig. 292. Table Construction: Upper Drawer Rail of Table Dovetailed into Left Front Leg.
The drawer rail, also called the fore edge, is long enough to partly overlap the side rails, into the lower edges of which it is gained so as to be flush with them, and may be fastened to them with screws, Fig. 293. The construction may be further strengthened by also doweling the end of this stretcher into the legs. If there are two drawers, the partition between them may be doweled or gained into these upper and lower stretchers.
The drawer rail, also known as the fore edge, is long enough to partially overlap the side rails, into the lower edges of which it is fitted so that it is flush with them, and can be secured to them with screws, Fig. 293. The structure can be further reinforced by also doweling the end of this stretcher into the legs. If there are two drawers, the divider between them can be doweled or fitted into these upper and lower stretchers.

Fig. 293. The Fixing of a Drawer Rail, Seen From Below.
If the legs are to be tapered or otherwise shaped, that should be done next. Then glue and assemble the end rails with their proper legs, taking care to see not only that the joints come up square, but that the legs are in the same plane. Finally assemble the whole, inserting, if necessary, a temporary diagonal brace to insure squareness, Fig. 294. When dry, clean up the joints. For the making of a table drawer, see above, p. 191.
If you're going to taper the legs or shape them in any way, do that next. Then glue and assemble the end rails with the correct legs, making sure that the joints are square and the legs are all aligned properly. Finally, put the whole thing together, adding a temporary diagonal brace if needed to ensure everything is square, Fig. 294. Once it's dry, clean up the joints. For making a table drawer, see above, p. 191.

Fig. 294. Brace to Insure Right Angles in Assembling a Framed structure.
To fit the drawer to its place, runners and guides, Fig. 295, must first be fastened in. The runners are in line with the drawer rail, and are glued and nailed or screwed to the side rails between the back of the lower stringer and the back posts. On top of them and [page 197] in line with the inner face of the legs are the guides running between the front and back posts. Or the runner and guide may be made of one piece properly rabbeted out.
To install the drawer, you first need to secure the runners and guides, as shown in Fig. 295. The runners should align with the drawer rail and are either glued, nailed, or screwed to the side rails between the back of the lower stringer and the back posts. On top of the runners, aligned with the inner side of the legs, are the guides that run between the front and back posts. Alternatively, the runner and guide can be made from a single piece that's been properly rabbeted out. [page 197]

Fig. 295. Drawer Mechanism.
If there are two drawers, a double runner lies between, and is gained into the middles of the back rail and the stringer, and on it is a guide for both drawers, equal in width to the partition between the drawers. The drawers should run easily in their proper places. In order to insure this, the drawer should be slightly narrower than the opening which receives it. A little French chalk, rubbed on the sides and runners, makes the running smoother. Sometimes the opening for a drawer is cut out of the front rail, as in Fig. 296. In this case the drawer runners are supported between the front and back rails, into which they may be gained.
If there are two drawers, a double runner sits between them and is fitted into the middle of the back rail and the stringer. There's a guide for both drawers that is the same width as the space between the drawers. The drawers should slide smoothly in their designated spots. To ensure this, the drawer should be a little narrower than the opening that holds it. A bit of French chalk, rubbed on the sides and runners, helps the drawers move more smoothly. Sometimes, the opening for a drawer is cut out of the front rail, as shown in Fig. 296. In this case, the drawer runners are supported between the front and back rails, where they can be fitted in.
For the making of the table top see edge-to-edge joint, p. 172. Dress up the top to size, taking special pains with the upper surface. If the grain is crossed, use the veneer-scraper, Fig. 151, p. 92, then sand, first with No. 1, then with No. 00 sandpaper, finish the edges carefully, and attach to the frame.
For how to make the table top, see edge-to-edge joint, p. 172. Size the top carefully, paying extra attention to the upper surface. If the grain is uneven, use the veneer scraper, Fig. 151, p. 92, then sand it, starting with No. 1 sandpaper and then using No. 00 sandpaper. Finish the edges carefully and attach it to the frame.
For fastening the top to the table rails, several methods are used. The top may be screwed to the rails by the screws passing thru the rails themselves either straight up, Fig. 297, A, or diagonally from the inside, B, or thru blocks or angle irons, C, which are screwed to the inside of the rails, or thru buttons, or panel irons, D, which are free to move in a groove cut near the top of the rail. The last [page 198] method is the best because it allows for the inevitable shrinkage and swelling of the top.
To attach the tabletop to the table rails, several methods can be used. The top can be screwed to the rails with screws going straight up through the rails themselves, as shown in Fig. 297, A, or at an angle from the inside, B, or through blocks or angle irons, C, which are screwed to the inside of the rails, or through buttons or panel irons, D, which can move freely in a groove cut near the top of the rail. The last method is the best because it accommodates the natural shrinkage and swelling of the top. [page 198]
Chairs may be so simplified in form as to be possible for the amateur to construct. The two front legs and the rail and stretcher between them offer little difficulty because the angles are square.
Chairs can be designed simply enough for anyone to build. The two front legs and the rail and stretcher between them are easy to work with since the angles are square.
The two back legs, may, for the purpose of simplification, be kept parallel to each other and at right angles to the seat rails between them, as in Fig. 298, A, and not at an angle as in B. The joining of the back will then offer little difficulty. The principal difficulties lie in the facts that for comfort and appearance the back of the chair should incline backward both above and below the seat, and that the back of the seat should be narrower than the front. By keeping at right angles to the floor the part of the back legs which receives the seat rail, the side seat rails will meet the back legs at a right angle in a side view, Fig. 298. The back legs should be slightly shorter than the front legs, as shown in D.
The two back legs can be kept parallel to each other and at right angles to the seat rails between them for simplicity, as shown in Fig. 298, A, instead of at an angle like in B. This makes it easier to connect the back. The main challenges are that, for comfort and looks, the back of the chair should tilt backward both above and below the seat, and the back of the seat should be narrower than the front. By keeping the part of the back legs that connects to the seat rail at right angles to the floor, the side seat rails will connect to the back legs at a right angle in a side view, as in Fig. 298. The back legs should be slightly shorter than the front legs, as illustrated in D.

Fig. 298. Chair Construction.
The second difficulty involves the making of inclined mortise-and-tenon joints, A, where the side rails fit into the legs. The making [page 199] of these can be facilitated by laying out a plan of the full size and taking the desired angles directly from that. It is common to reinforce these joints with corner blocks glued and screwed in place as shown in A. If there are additional rails below the seat rails, the easiest way to fit them in place is first to fit and clamp together the chair with the seat rails only, taking pains to have all angles perfectly true, and then to take the exact measurements for the lower rails directly from the chair. The same method may be used for laying out a stringer between the lower rails.
The second difficulty involves making inclined mortise-and-tenon joints, A, where the side rails connect to the legs. Creating these can be made easier by laying out a full-size plan and taking the desired angles directly from it. It’s common to reinforce these joints with corner blocks that are glued and screwed in place as shown in A. If there are extra rails below the seat rails, the simplest way to fit them is to first assemble and clamp the chair using only the seat rails, making sure all angles are perfectly square, and then take the exact measurements for the lower rails directly from the chair. The same method can be used to lay out a stringer between the lower rails.
If it is desired to bow the rails of the back, which are above the seat rail, this can be done by boiling them in water for 30 minutes and then clamping them over a form of the proper shape, with a piece of stiff sheet iron on the outside, as in Fig. 299. They should be thoroly dried in a warm place. Then the tenons may be laid out on the ends parallel to a straight-edge laid along the concave side. The chair bottom may be made of solid wood, either flat or modeled into a "saddle seat;" it may be covered with cane or rush, or it may be upholstered.
If you want to bend the back rails that are above the seat rail, you can do this by boiling them in water for 30 minutes and then clamping them around a properly shaped mold, using a piece of stiff sheet metal on the outside, as shown in Fig. 299. They should be thoroughly dried in a warm place. After that, you can lay out the tenons at the ends parallel to a straight edge placed along the concave side. The chair bottom can be made of solid wood, either flat or shaped into a "saddle seat"; it can be covered with cane or rush, or it can be upholstered.

Fig. 299. Bending Boards into Shape after Boiling Them.
To upholster a chair seat, a frame should first be made of the shape shown in Fig. 298, C. The strips are about 2" wide and ½" thick with their ends half-lapped. The seat rails are rabbeted ½" deep and ½" wide to receive this frame, which should be ⅛" smaller all around than the place to receive it. The returns at the corners fit around the legs at ⅛" distance from them. This ⅛" provides space for the coverings. After the frame is fitted, it is covered [page 200] with 3" webbing tacked firmly to the upper side. The webbing which goes back and forth is interwoven with that which goes from right to left. Over this is stretched and tacked (also to the upper side) a piece of unbleached muslin. A second piece of muslin is tacked to the back edge and part way along the side edges, leaving for the time the corners unfinished. In the pocket thus formed horsehair or other stuffing is pushed, care being taken to distribute it evenly and not too thick. When the pocket is filled, the muslin is tacked farther along the sides and more hair put in, until the front is reached, when the muslin is tacked to the front edge. The corners are now drawn in tight, a careful snip with the scissors parting them diagonally so as to lie in well. The partings may be turned down and tacked on the under side of the frame.
To upholster a chair seat, you should first create a frame shaped like the one shown in Fig. 298, C. The strips should be about 2 inches wide and ½ inch thick, with their ends overlapping. The seat rails should be notched ½ inch deep and ½ inch wide to hold this frame, which needs to be ⅛ inch smaller all around than the space it will fit into. The returns at the corners should fit around the legs with a ⅛ inch gap for the coverings. Once the frame is in place, cover it with 3-inch webbing securely tacked to the top side. The webbing that goes back and forth is woven together with the webbing that goes from side to side. On top of this, stretch and tack a piece of unbleached muslin to the upper side as well. Then, attach a second piece of muslin to the back edge and partially along the side edges, leaving the corners unfinished for now. In the pocket that’s created, push in horsehair or other stuffing, making sure it’s evenly distributed and not too thick. Once the pocket is filled, tack the muslin further along the sides and add more stuffing until reaching the front, where the muslin is tacked to the front edge. Now, pull the corners in tight, making a careful snip with scissors to separate them diagonally so they lay flat. The cut edges can be turned down and tacked to the underside of the frame.
Finally the leather or other covering is stretched over the whole as evenly as possible. The corners should be left to the last, then [page 201] clipped diagonally to the exact inside corner and the partings drawn down and tacked, as was the muslin. The superfluous leather may then be trimmed off, and the seat should fit in its place. Or the seat frame may be omitted, and the coverings tacked directly to the chair rails.
Finally, stretch the leather or other covering over the entire surface as evenly as you can. Leave the corners for last, then clip them diagonally to match the exact inside corner and pull the edges down to tack them in place, just like you did with the muslin. You can then trim off any excess leather, and the seat should fit properly. Alternatively, you could skip the seat frame and tack the coverings directly to the chair rails.
The balloon-frame house is a typical form of framed construction, Fig. 300. The essential parts of a balloon-frame are:
The balloon-frame house is a common type of framed construction, Fig. 300. The key components of a balloon-frame are:
- 1. SILL, 4" × 8", which rests on the foundation.
- 2. BEAMS, 4" × 8", which rest on the cellar posts, 6"×6". (Not shown in illustration.)
- 3. FLOOR JOISTS, 2" × 8", which rest on the sill and beams.
- 4. CORNER POSTS, 4" × 6", with 2"×4" studs nailed to them.
- 5. STUDDING, 2" × 4", which stand 16" between centers.
- 6. WALL RIBBON, or girt, 1" × 8", which supports the upper story joists.
- 7. PLATES, two 2" × 4" nailed together, resting on studs.
- 8. RAFTERS, 2" × 6", which support the roof.
- 9. TIE-BEAMS, 2" × 6", which prevent the roof from spreading the walls. (Not shown in illustration.)
- 10. RIDGE-POLE, 2" × 8", against which the rafters butt.
- 11. BRIDGING, 2" × 2", which stiffens the floor joists.
- 12. SHEATHING, (1" thick), put on diagonally to brace the building. The rest is covering.
- 13. FLOORING, (See also Fig. 301.)
- In flooring, Fig. 301, the boards are made narrow so as to reduce the size of openings at the joints when they shrink, and also to reduce the tendency to warp. They may be laid side by side as in the cheapest floors, or matched to close the joint. For difference between slash- and comb-grain flooring, see Fig. 55, p. 42.
- 14. BUILDING PAPER.
- 15. SIDING OR CLAPBOARDS, (See Fig. 301.) may either overlap without a joint or be rabbeted to fit. The best siding is rabbeted.
- 16. WATER-TABLE.
- 17. CORNER-BOARD.
- 18. FURRING.
- 19. SHINGLES.
- 20. LATHING.
- 21. CEILING, Fig. 301, consists of matched boards having a "bead" to disguise the joint and give a decorative effect.

Fig. 301. Siding, Ceiling, Flooring.
TYPES OF WOODEN STRUCTURES
References*
References*
Simple Joined Structures.
Simple Combined Structures.
Benson, pp. 32-37.
Benson, pp. 32-37.
Goss, pp. 91-96.
Goss, pp. 91-96.
Noyes, School Arts Book, 6: 89, 179.
Noyes, School Arts Book, 6: 89, 179.
Wheeler, pp. 86, 219-227, 376.
Wheeler, pp. 86, 219-227, 376.
Sickels, p. 120.
Sickels, p. 120.
Griffith, pp. 84-104.
Griffith, pp. 84-104.
Panel and Cabinet Construction.
Panel and Cabinet Building.
Goss, pp. 117-118, 148-151.
Goss, pp. 117-118, 148-151.
Compton, pp. 146-151.
Compton, pp. 146-151.
Sickels, p. 134.
Sickels, p. 134.
Wheeler, pp. 366-372.
Wheeler, pp. 366-372.
Framed Structures.
Framed Designs.
Crawshaw.
Crawshaw.
Wheeler, pp. 203-206, 238-297.
Wheeler, pp. 203-206, 238-297.
Sickels, p. 124.
Sickels, p. 124.
Building Trades Pocketbook, pp. 221, 230.
Building Trades Pocketbook, pp. 221, 230.
Coverings.
Coverings.
Sickels, pp. 128-131.
Sickels, pp. 128-131.
Goss, pp. 141-144.
Goss, pp. 141-144.
* For general bibliography see p. 4.
* For general bibliography see __A_TAG_PLACEHOLDER_0__
Chapter 9.
PRINCIPLES OF JOINERY.11
Footnote 11: Professor Rankine's Five Principles:
Footnote 11: Professor Rankine's Five Principles:
1. To cut the joints and arrange the fastenings so as to weaken the pieces of timber they connect as little as possible.
1. To cut the joints and arrange the fastenings in a way that minimizes the weakening of the timber pieces they connect.
2. To place each abutting surface in a joint as nearly as possible perpendicular to the pressure which it has to transmit.
2. To position each adjacent surface in a joint as close to perpendicular as possible to the pressure it needs to carry.
3. To proportion the area of each surface to the pressure which it has to bear so that the timber may be safe against injury under the heaviest load which occurs in practice, and to form and fit every pair of such surfaces accurately in order to distribute the stress uniformly.
3. To adjust the area of each surface to the pressure it has to handle, ensuring that the timber remains safe from damage under the heaviest load it might experience in real life, and to shape and fit every pair of these surfaces precisely to distribute the stress evenly.
4. To proportion the fastenings so that they may be of equal strength with the pieces which they connect.
4. To size the fastenings so that they're just as strong as the pieces they connect.
5. To place the fastenings in each piece of timber so that there shall be sufficient resistance to the giving way of the joint by the fastenings shearing or crushing their way thru the timber.
5. To position the fasteners in each piece of wood so that there is enough resistance to prevent the joint from failing due to the fasteners shearing or crushing through the wood.
1. Avoid multiplication of errors by making all measurements (as far as possible) from a common starting point, and laying off all angles from the same line or surface. Illustrations of this principle are as follows: Before proceeding with other processes, a working face and working edge and as many other surfaces as will finally appear in the finished piece, should be trued up. At least the working face and working edge are essential to the proper "lay-out" of the piece, whenever measurements are made from an edge.
1. Avoid multiplying errors by making all measurements (as much as you can) from a common starting point, and setting all angles from the same line or surface. Examples of this principle are as follows: Before moving on to other steps, a working face, working edge, and as many other surfaces as will be seen in the final piece should be squared up. At minimum, the working face and working edge are crucial for the correct "layout" of the piece whenever measurements are taken from an edge.
In laying out a series of measurements, it is important, when possible, that the rule be laid down once for all, and the additions be made on that, rather than that the rule should be moved along for each new member of the series.
In setting up a series of measurements, it’s important, whenever possible, to establish a rule once and for all, and then make additions based on that, instead of moving the rule for each new item in the series.
In scoring around a board with knife and try-square, the head of the try-square should be held against the working face in scoring both edges, and against the working edge in scoring both faces, and not passed from one surface to another in succession.
In marking on a board with a knife and try-square, you should hold the head of the try-square against the working face when marking both edges, and against the working edge when marking both faces, rather than moving it from one surface to another in turn.
In the laying out of a halved joint, Fig. 265, Nos. 15-19, p. 178, the gaging is all done from what will be one of the flush surfaces of [page 204] the joined pieces. Then, if the gaged line should be slightly more or less than half the thickness of the pieces the closeness of the joint would not be affected.
In setting up a halved joint, Fig. 265, Nos. 15-19, p. 178, the measuring is all done from what will become one of the flush surfaces of the joined pieces. Then, if the measured line ends up being a bit more or less than half the thickness of the pieces, the tightness of the joint won't be impacted.
2. When possible, in laying out a joint, use the method of superposition. Fig. 302. By this is meant the method by which the lay-out of one member is obtained directly from the other by laying (superposing) the latter on the former and marking or scribing the needed dimensions directly, instead of by measurement. It has the advantages of simplicity, speed, and greater probability of fit.
2. Whenever you can, use the method of superposition when laying out a joint. Fig. 302. This means that you get the layout of one piece directly from the other by placing (superposing) the second piece on top of the first and marking or scribing the needed dimensions directly, rather than measuring. This method is simple, quick, and more likely to result in a proper fit.

Fig. 302. Marking by Superposition.
3. Work systematically. In case the same process is to be repeated on a number of parts, complete this process in all before taking up another process. This is the principle of the division of labor applied to the individual workman.
3. Work systematically. If you need to repeat the same process on multiple parts, finish that process on all of them before moving on to another task. This is the principle of dividing labor applied to individual workers.
In laying out duplicate or multiple parts, the proper cross measurements should be carefully laid out on one piece and then transferred with a try-square to the other parts laid accurately beside it. So when a number of like pieces are to be gaged, all the parts requiring the same setting should be gaged before the gage is reset for another gaging. This is a great saving of time and insures accuracy.
In laying out duplicate or multiple parts, the correct cross measurements should be carefully marked on one piece and then transferred with a try-square to the other parts placed accurately next to it. So when several identical pieces need to be measured, all the parts that need the same settings should be measured before the gauge is reset for another measurement. This saves a lot of time and ensures accuracy.
In making a number of like parts, if they are not too large much of the work can often be done in one piece before it is cut up. For example, to make a number of slats from a given piece of wood, the piece may first be brought to such dimensions that the length will be correct for the finished pieces and the thickness of the piece be equal to the width of the slats, Fig. 303. The face may then be gaged with a series of lines so that every other space will be equal to the required thickness of each slat, and the alternate spaces be just sufficient for [page 205] the saw kerf and dressing. The slats may then be ripped apart and dressed to size.
When creating multiple similar parts, if they're not too large, a lot of the work can often be done in one piece before cutting them apart. For instance, to make several slats from a piece of wood, you can first adjust the wood to the right dimensions so that the length matches the final pieces and the thickness is equal to the width of the slats, Fig. 303. You can then mark the surface with a series of lines so that every other space corresponds to the required thickness of each slat, while the alternate spaces are just enough for the saw blade width and finishing. After that, the slats can be separated and sized properly.

Fig. 303. Making a Number of Like Pieces from a Given Piece.
Or a long strip may be planed to thickness and width and then be sawn up and finished to the proper lengths. For example, in a mitered picture-frame it may be convenient to plane up two pieces, each one long enough to make one long side and one short side.
Or a long strip can be planed to the right thickness and width and then sawed and finished to the correct lengths. For example, in a mitered picture frame, it might be convenient to plane two pieces, each long enough to create one long side and one short side.
In fitting up framed structures each part when fitted should be distinctly marked, so that there may be no confusion in assembling.
In setting up framed structures, each part should be clearly labeled when assembled to avoid any confusion during assembly.
4. Where practicable secure the same conditions of grain in different elements of joined structures.
4. Where possible, ensure the same quality of grain in different parts of joined structures.
Illustrations of this are as follows: The grain of the sides of a box should run continuously around the box, or, in the case of a tall, slim box, the grain of all the sides should run up and down. In either case, the grain in the different sides is parallel. In a rubbed joint, Fig. 269, No. 70, p. 182, to be planed down afterward, in case the grain is not straight, much trouble in planing may be saved if the different pieces are laid so that they can all be planed smooth in the same direction. This may not be possible where the boards are joined so as to match the grain, as in quartered oak, or where the annual rings of slash boards are made to alternate in direction so as to lessen warping, Fig. 280, p. 186.
Illustrations of this are as follows: The grain on the sides of a box should run continuously around the box, or, in the case of a tall, slim box, all the sides should have the grain running up and down. In both cases, the grain on the different sides is parallel. In a rubbed joint, Fig. 269, No. 70, p. 182, to be planed down later, if the grain isn’t straight, you can save a lot of trouble during planing if the different pieces are arranged so they can all be planed smooth in the same direction. This might not be possible when boards are joined to match the grain, like with quartered oak, or when the annual rings of slash boards alternate in direction to reduce warping, Fig. 280, p. 186.
5. Where possible, allow for shrinkage without prejudice to construction.
5. Where possible, permit shrinkage without compromising construction.
The most obvious illustration of this principle is panel construction. In a panel, the frame, which is comparatively narrow, follows the principal dimensions, and hence does not seriously shrink or swell itself. But the panel, which is grooved into the frame can shrink or swell without harm to the general structure.
The most obvious example of this principle is panel construction. In a panel, the frame, which is relatively narrow, follows the main dimensions, so it doesn't shrink or swell significantly. However, the panel, which is fitted into the frame, can expand or contract without damaging the overall structure.
In a gained joint, as in a case of shelves, Fig. 266, No. 29, p. 179, the gain in the uprights does not extend quite to the front of the shelves, and there is a corresponding slight shoulder at the front end of the shelf, so that if the shelf and support shrink unevenly, no gap will be apparent.
In a joint with a gain, like in the case of shelves, Fig. 266, No. 29, p. 179, the gain in the vertical pieces doesn't reach all the way to the front of the shelves, leaving a small shoulder at the front edge of the shelf. This way, if the shelf and support shrink unevenly, there won't be any visible gap.
A drawing-board, Fig. 280, p. 186, is so made that it can shrink or swell without losing its flatness. Shingles when properly laid, can shrink or swell without the roof leaking.
A drawing board, Fig. 280, p. 186, is designed to expand or contract while still remaining flat. Shingles, when installed correctly, can also expand or contract without causing the roof to leak.
6. Where feasible, undercut joined surfaces so as to give clearance on the inside and insure a tight appearance. But glued surfaces should be made to meet flat.
6. Where possible, create an undercut on joined surfaces to allow for clearance on the inside and ensure a smooth look. However, glued surfaces should be aligned flat.
The shoulder of any tenon may be undercut so as to allow the edges of the tenoned piece to close up tight against the mortised piece.
The shoulder of any tenon can be undercut to let the edges of the tenoned piece fit snugly against the mortised piece.
In matched flooring, the underside of the boards is slightly narrower than the upper side so that the joint may close on the upper side without fail, Fig. 301, p. 201. The ends of flooring boards are also slightly beveled so as to make a tight fit on the upper side.
In matched flooring, the bottom of the boards is a bit narrower than the top so that the joint can close properly on the top side without issue, Fig. 301, p. 201. The ends of the flooring boards are also slightly angled to create a tight fit on the top side.
7. Select the simplest form of joint and use the smallest number of abutments (bearing surfaces) possible, because the more complicated the joint or the greater the number of bearing surfaces, the less likelihood there is of a sound and inexpensive construction.
7. Choose the simplest type of joint and use the fewest number of bearing surfaces possible, because the more complicated the joint or the more bearing surfaces there are, the less likely it is to have a strong and cost-effective construction.
Illustrations of this principle are as follows: Usually a single mortise-and-tenon joint is better than a double one because of simplicity, strength and ease of making. Where much surface is required for gluing, a double one may be better.
Illustrations of this principle are as follows: Typically, a single mortise-and-tenon joint is better than a double one due to its simplicity, strength, and ease of construction. When a large surface area is needed for gluing, a double joint might be more effective.
8. Keep a due proportion of strength between the fastenings (joints) and the pieces fastened: i. e., the construction should neither be frail on the one hand, because the pieces of wood are weakened by too much cutting, nor clumsy, on the other hand, because then the fastenings would be inordinately strong. In other words, the different parts should be equally strong.
8. Maintain a proper balance of strength between the joints and the pieces being joined. In other words, the construction shouldn’t be fragile due to excessive cutting of the wood, nor should it be overly heavy, as that would result in the fastenings being excessively strong. Essentially, all the different parts should have similar strength.
Illustrations of this principle are as follows: In a fished joint, Fig. 264, No. 2, the plate should be attached so as to reinforce the splice at the weakest point.
Illustrations of this principle are as follows: In a fished joint, Fig. 264, No. 2, the plate should be attached to reinforce the splice at the weakest point.
In a tusk tenon, Fig. 267, No. 40, the tenon is made but one-sixth the thickness of the timber, whereas the tusk is made much larger.
In a tusk tenon, Fig. 267, No. 40, the tenon is only one-sixth the thickness of the timber, while the tusk is made significantly larger.
Where a mortise is to be cut in a timber bearing weight, it should be cut in the neutral axis, where the cutting of fibres will weaken it least.
Where a mortise needs to be cut in a load-bearing timber, it should be done along the neutral axis, where cutting the fibers will weaken it the least.
In the mortise-and-tenon of a table-rail, Fig. 267, No. 43, there should be a wide shoulder above the tenon of the rail so that the top of the leg above the mortise will not shear out. The mortise should be as near the outside of the leg as possible so that the inner corner of the leg may remain strong. The tenon should be strong enough to share the strain with the shoulders.
In the mortise-and-tenon joint of a table rail, Fig. 267, No. 43, there should be a wide shoulder above the tenon of the rail to prevent the top of the leg above the mortise from breaking off. The mortise should be positioned as close to the outer edge of the leg as possible to keep the inner corner of the leg sturdy. The tenon needs to be robust enough to share the load with the shoulders.
A dado joint, Fig. 266, No. 25, should not be so deep as to weaken the supporting board.
A dado joint, Fig. 266, No. 25, shouldn't be too deep to compromise the strength of the supporting board.
A tenon should not be so large as to weaken the mortised piece.
A tenon shouldn't be so big that it weakens the mortised piece.
9. Place each abutting surface in a joint as nearly as possible perpendicular to the pressure which it has to transmit.
9. Make sure each adjoining surface in a joint is as close to perpendicular as possible to the pressure it needs to handle.
Illustrations of this principle are as follows: the angle in a strut joint, Fig. 266, No. 62, should be equally divided between the two beams.
Illustrations of this principle are as follows: the angle in a strut joint, Fig. 266, No. 62, should be split evenly between the two beams.
The thrust joint, Fig. 268, No. 63, in a bridge truss, is exactly at right angles to the pressure.
The thrust joint, Fig. 268, No. 63, in a bridge truss, is positioned precisely at right angles to the pressure.
A joint to resist vertical cross strain is stronger when scarfed vertically than horizontally.
A joint that resists vertical cross strain is stronger when scarfed vertically instead of horizontally.
THE PRINCIPLES OF JOINERY
References*
References*
Goss, p. 132.
Goss, p. 132.
Adams, p. 12.
Adams, p. 12.
Rivington, Vol. I, p. 57.
Rivington, Vol. 1, p. 57.
* For general bibliography see p. 4.
* For general bibliography see __A_TAG_PLACEHOLDER_0__
Chapter X.
WOOD FINISHING.
STAINS.
The function of stains is to change the color, and to enchance the grain and texture of the wood. Stains may be divided into four general classes, which are not, however, entirely distinct. (1) Oil stains, (2) Water stains, (a) made from anilines, (b) made from dyes other than anilines, (3) Spirit stains, (4) Stains due to chemical changes.
The purpose of stains is to alter the color and enhance the grain and texture of the wood. Stains can be categorized into four general types, which are not completely separate. (1) Oil stains, (2) Water stains, (a) made from anilines, (b) made from dyes other than anilines, (3) Spirit stains, (4) Stains resulting from chemical changes.
(1) Oil stains. Advantages: they are easily prepared, are easy to apply evenly, and they do not raise the grain. Disadvantages: they cover the grain somewhat, are apt to give a muddy effect, they do not penetrate very deeply into the wood, and it is impossible to stain hard wood dark with them and at the same time keep the grain and texture of the wood clear. A convenient form in which to handle these pigments is Devoe's "coach colors," ground in japan. To prevent evaporation from cans once opened, it is well to keep them partly filled with water and the water covered with a little oil. For use, the pigments are thinned with turpentine or benzine, in the proportion of one pound of color to one-half gallon of turpentine or benzine. Benzine is much cheaper than turpentine, but evaporates more quickly. The addition of a little boiled oil gives a body to the stain, so that when the wood is well rubbed down a soft lustre can be had without any further finish. The stain should be applied with a brush to the wood, which may then be rubbed clean with cotton waste. Oil stains penetrate hard woods better when the wood has first been fumed in ammonia. (See below, p. 211). Or, the addition of a little ammonia to the stain just before applying aids it in penetrating the wood.
(1) Oil stains. Advantages: they are easy to prepare, easy to apply evenly, and they don’t raise the grain. Disadvantages: they somewhat obscure the grain, tend to produce a muddy appearance, don't penetrate deeply into the wood, and you can't darken hard wood while keeping the grain and texture clear. A convenient way to handle these pigments is with Devoe's "coach colors," which are ground in Japan. To prevent evaporation from opened cans, it's a good idea to keep them partially filled with water and cover the water with a bit of oil. For use, thin the pigments with turpentine or benzene at a ratio of one pound of color to half a gallon of turpentine or benzene. Benzene is cheaper than turpentine but evaporates faster. Adding a little boiled oil gives the stain more body, allowing for a soft luster after rubbing the wood down, without needing any further finish. Apply the stain with a brush, then clean the wood with cotton waste. Oil stains penetrate hard woods better if the wood has been previously fumed with ammonia. (See below, p. 211). Alternatively, adding a little ammonia to the stain just before applying it helps it penetrate the wood.
The pigments most used for oil stains are: burnt and raw umber, burnt and raw sienna, Vandyke brown, drop black, and medium chrome yellow. These colors may be varied by mixing. For example, for a green stain, take two parts of drop black and one part of medium chrome yellow, and dissolve in turpentine or benzine. [page 210] The addition of a little vermilion gives a grayer green. The green may be made bluer by the addition of Prussian blue, but the blue already contained in the black gives a soft, pleasant green.
The most commonly used pigments for oil stains are burnt and raw umber, burnt and raw sienna, Vandyke brown, drop black, and medium chrome yellow. These colors can be mixed to create variations. For instance, to make a green stain, combine two parts of drop black with one part of medium chrome yellow, and dissolve in turpentine or benzine. [page 210] Adding a bit of vermilion results in a grayer green. You can make the green bluer by adding Prussian blue, but the blue already present in the black gives a soft, pleasing green.
For antique oak, add a trifle of burnt umber and black to raw sienna thinned to the right consistency.
For antique oak, mix a bit of burnt umber and black with raw sienna thinned to the right consistency.
For a reddish brown, thin burnt umber to the right consistency. This may be grayed by the addition of a little green.
For a reddish-brown, use a thin burnt umber until you reach the right consistency. You can mute it by adding a bit of green.
A walnut stain may be had by adding a little Venetian red to asphaltum, thinned with turpentine or benzine.
A walnut stain can be made by mixing a bit of Venetian red with asphaltum, thinned out with turpentine or benzene.
Aniline oil stains. Advantages: the colors are clear and easily obtainable. Disadvantages: the colors are likely to be crude and too bright, and unless great care is taken the tones are metallic and not soft enough to suit wood. It is necessary to purchase colors soluble in oil. These can be had of William Zinnser and Company, 197 William Street, New York. Four colors are necessary to get the desired shades, Bismarck brown, dark yellow, dark blue, and black. Bismarck brown comes in powdered form at $2.40 per lb., dark yellow comes in powdered form at $2.40 per lb., dark blue comes in lumps at $3.20 per lb., black comes in lumps at $2.40 per lb. These may be dissolved in three ounces of turpentine to one ounce of boiled oil, to one teaspoonful of color, a process that will take place much faster if the mixture is heated. Great care must be taken, however, not to set fire to the turpentine. When cool, thin with turpentine to the proper consistency, apply to the wood with a brush and rub clean with cotton waste.
Aniline oil stains. Advantages: the colors are bright and easy to find. Disadvantages: the colors can be harsh and too vivid, and if you're not careful, the tones can appear metallic and not soft enough for wood. You need to buy colors that dissolve in oil. You can get these from William Zinnser and Company, 197 William Street, New York. You need four colors to achieve the desired shades: Bismarck brown, dark yellow, dark blue, and black. Bismarck brown is available in powdered form for $2.40 per lb., dark yellow also comes in powdered form for $2.40 per lb., dark blue is sold in lumps for $3.20 per lb., and black is in lumps for $2.40 per lb. These can be mixed with three ounces of turpentine, one ounce of boiled oil, and one teaspoon of color; this process works much quicker if the mixture is heated. However, be very careful not to ignite the turpentine. Once it cools, thin it with turpentine until you reach the right consistency, apply it to the wood with a brush, and wipe clean with cotton waste.
(2) Water Stains. Advantages: they are cheap and clear and do not obscure the grain as oil stains are likely to do, and they penetrate deeply into the wood, especially when applied hot. They may be made of any coloring matter that is soluble in water, and are particularly good for hard woods and for use in large quantities. It is possible to stain wood much darker with them than with oil stains. Moreover, the brushes used with them are easily taken care of. Disadvantages: they are difficult to prepare and they raise the grain of the wood. The former disadvantage may be overcome by buying them all prepared.
(2) Water Stains. Advantages: they are inexpensive and transparent, and they don’t hide the wood grain like oil stains often do. They soak deeply into the wood, especially if applied hot. They can be made from any coloring agent that dissolves in water, and they work particularly well on hardwoods and can be used in large amounts. You can achieve a much darker stain with these compared to oil stains. Plus, the brushes used with them are easy to clean. Disadvantages: they can be tricky to prepare, and they can raise the wood grain. The first disadvantage can be addressed by buying them already prepared.
The difficulty of the raising of the grain is to be obviated either by washing the wood in water and, when dry, rubbing down with sandpaper before applying the stain, or rubbing down after staining and re-staining when necessary.
The challenge of growing the grain can be avoided by either soaking the wood in water and, once it's dry, sanding it with sandpaper before applying the stain, or sanding it after staining and re-staining as needed.
a. Water stains made from anilines. Aniline stains are likely to fade, but the addition of a little vinegar is said to hinder fading. For Mahogany, dissolve 1 oz. Bismarck brown in 3 quarts of boiling water. Use when cool.
a. Water stains made with anilines. Aniline stains might fade, but adding a bit of vinegar is said to help prevent fading. For Mahogany, dissolve 1 oz. of Bismarck brown in 3 quarts of boiling water. Use it when it's cool.
b. Water stains made from dyes other than anilines. The number of these is legion; some of the simpler are given.
b. Water stains made from dyes other than anilines. There are countless types; some of the simpler ones are listed.
Reddish Brown. Dissolve extract of logwood of the size of a walnut in ½ cup (4 oz.) of hot water. Apply hot to wood repeatedly until desired color is obtained.
Reddish Brown. Dissolve a walnut-sized piece of logwood extract in ½ cup (4 oz.) of hot water. Apply it hot to the wood repeatedly until you achieve the desired color.
Black. Dissolve extract of logwood of the size of a walnut in ½ cup (4 oz.) of boiling water. Add a teaspoonful of alum. Apply repeatedly until the wood is dark brown. Prepare acetate of iron according to directions for making dark brown, on next page. Apply this to wood already browned with logwood. If the grain is raised, sandpaper lightly, or rub with steel wool and then with boiled oil.
Black. Dissolve a walnut-sized piece of logwood extract in ½ cup (4 oz.) of boiling water. Add a teaspoon of alum. Apply repeatedly until the wood turns dark brown. Prepare iron acetate following the instructions for making dark brown on the next page. Apply this to the wood that has already been darkened with logwood. If the grain is raised, lightly sand it or rub it with steel wool, then finish with boiled oil.
(3) Spirit Stains. These are expensive and hence little used. A few illustrations are given.12
(3) Spirit Stains. These are pricey and therefore not used much. A few examples are provided.12
Footnote 12: For detailed directions for treatment of different woods, see Hodgson, pp. 112-153.
Footnote 12: For detailed instructions on how to treat various types of wood, see Hodgson, pp. 112-153.
Black. Aniline black, cut in alcohol, gives a bluish effect but if the wood thus stained is rubbed with raw linseed oil, it becomes black.
Black. Aniline black, dissolved in alcohol, creates a bluish effect, but if the wood stained this way is rubbed with raw linseed oil, it turns black.
Another Black. Dissolve extract of logwood in wood alcohol. Develop the color by going over the work with tincture of muriate of iron.
Another Black. Dissolve logwood extract in wood alcohol. Enhance the color by applying tincture of muriate of iron over the work.
Golden Oak. Dissolve asphaltum in naphtha until it is as thin as water and makes a yellowish stain; or to equal parts of asphaltum, varnish, and gold size japan, add enough turpentine to thin to proper consistency.
Golden Oak. Dissolve asphaltum in naphtha until it’s as thin as water and creates a yellowish stain; or mix equal parts of asphaltum, varnish, and gold size japan, adding enough turpentine to achieve the right consistency.
Mahogany. Dissolve Bismarck Brown in alcohol.
Mahogany. Dissolve Bismarck Brown in alcohol.
Aniline stains may be cut in alcohol and mixed with equal parts of white shellac and banana oil (amyl acetate) and all applied in one coat.
Aniline stains can be diluted in alcohol and combined with equal amounts of white shellac and banana oil (amyl acetate), all applied in a single coat.
(4) Stains due to chemical changes. Certain substances like ammonia, potassium bichromate, and acetate of iron, give chemical reactions on certain woods and make very effective and inexpensive stains. Moreover the artistic effect of some of them is unexcelled. When applied in solution they are likely to raise the grain.
(4) Stains from chemical changes. Some substances like ammonia, potassium bichromate, and iron acetate create chemical reactions on specific types of wood, resulting in very effective and affordable stains. Additionally, the artistic effect of some of these stains is unmatched. When applied in solution, they can raise the grain.
The effect of ammonia, either the liquid or fumes, is much the same as the effect produced by aging or weathering. Ammonia also cuts the pith rays of oak and makes it possible for other stains to [page 212] take hold. For this reason it is much used as a preliminary treatment for oak finishes. The color effect is to lessen the yellow and increase the gray.
The impact of ammonia, whether in liquid form or as fumes, is very similar to the effects of aging or weathering. Ammonia also cuts through the pith rays of oak, allowing other stains to [page 212] adhere better. Because of this, it’s commonly used as a first step in treating oak finishes. The color effect is to reduce the yellow and enhance the gray.
The method of application is simply to expose the wood for a day or more to the fumes of strong ammonia (28%) in a tightly closed box. If the surface of the wood is moistened with water just before exposure, it turns darker than if exposed dry. The stain penetrates so deeply that it may be sandpapered after the exposure without harm. After fuming and sandpapering the surface should be oiled to prevent finger marks.
The application method is straightforward: place the wood in a tightly sealed box and expose it to strong ammonia fumes (28%) for a day or more. If the wood surface is dampened with water just before exposure, it will darken more than if it's dry. The stain soaks in deeply enough that you can sand it afterward without damaging it. After fuming and sanding, you should oil the surface to avoid fingerprint marks.
Dark brown for chestnut, or oak, or mahogany. This is obtained with a solution of acetate of iron, made as follows: digest one part by measure of iron dust in 8 parts of glacial acetic acid. After the chemical action is well started, add several times as much water to keep the mixture liquid. When the chemical action has ceased, the stain is ready for use. If a lighter shade is desired it may be still further diluted.
Dark brown for chestnut, oak, or mahogany can be achieved with a solution of iron acetate. To make this, mix one part of iron dust with eight parts of glacial acetic acid. Once the chemical reaction is underway, add several times more water to keep the mixture fluid. When the reaction is complete, the stain is ready to be used. If you want a lighter shade, you can dilute it even more.
To darken mahogany. Make a saturate solution of bichromate of potash. Dilute a portion of it with water 1⁄2, or 1⁄3, or 1⁄4, or in any proportion according to the darkness required. One part of the solution to two or three parts of water gives a good color. Apply the solution to mahogany with a brush. This solution alone is likely to be too brown. The reddish tinge of the wood may be saved by mixing as follows:
To darken mahogany, create a saturated solution of potassium bichromate. Dilute some of it with water in a ratio of 1⁄2, 1⁄3, or 1⁄4, or in any proportion based on the desired darkness. A mix of one part solution to two or three parts water provides a good color. Use a brush to apply the solution to the mahogany. This solution by itself might be too brown. To preserve the reddish tint of the wood, mix it as follows:
100% solution of bichromate of potash | 1 part |
Breinig's mahogany water stain | 1 part |
Water | 2 parts |
Apply with a brush and wipe off the surplus. |
Bichromate of potash on oak gives a rich brown.
Bichromate of potash on oak produces a deep brown color.
Bichromate of potash on ash gives a rich red.
Bichromate of potash on ash produces a deep red color.
Bichromate of potash on black walnut gives a dark brown.
Bichromate of potash on black walnut creates a dark brown color.
A decoction of logwood treated with tannin gives yellow red, with sugar of lead gives gray brown, with ferric nitrate gives black. A decoction of fustic extract treated with dilute nitric acid gives brown, etc.13
A decoction of logwood treated with tannin produces yellow-red, with lead acetate creates gray-brown, and with ferric nitrate results in black. A decoction of fustic extract treated with dilute nitric acid yields brown, etc.13
Footnote 13: For other effects obtained by chemical changes, see table on pp. 185-189 in Brannt's Painter, Gilder and Varnisher, and also Woodcraft 9: 71, June, '08.
Footnote 13: For additional effects achieved through chemical changes, see the table on pp. 185-189 in Brannt's Painter, Gilder and Varnisher, and also Woodcraft 9: 71, June '08.
Commercial Stains. Some of the more noteworthy commercial stains, suitable for school use, are those of:
Commercial Stains. Some of the more notable commercial stains, suitable for school use, are those of:
The Bridgeport Wood Finishing Company, 55 Fulton St., New York. Among their water stains some of the best are: Flemish oak, weathered oak, walnut, silver gray, forest green, and mahogany, especially if the latter is modified with bichromate of potash. Other effects may be obtained by mixing these, as forest green, which is too bright alone, mixed with walnut or some other reddish color gives a grayish green. Of the penetrating oil stains the golden oak and mahogany are very good.
The Bridgeport Wood Finishing Company, 55 Fulton St., New York. Among their water stains, some of the best are Flemish oak, weathered oak, walnut, silver gray, forest green, and mahogany, especially when the latter is enhanced with bichromate of potash. You can create other effects by mixing these; for instance, forest green, which is too bright on its own, mixed with walnut or another reddish color gives a grayish green. Of the penetrating oil stains, golden oak and mahogany are quite good.
The Sherwin Williams Company, of Cleveland, Newark, Chicago, etc., produce a fine line of spirit stains.
The Sherwin-Williams Company, based in Cleveland, Newark, Chicago, and other locations, produces a great range of spirit stains.
The Adams and Elting Company, Chicago, have a stain called adelite, in which banana oil appears to be the solvent. It is very easy of application, only one coat being needed. It is applied with the brush.
The Adams and Elting Company in Chicago has a stain called adelite, which seems to use banana oil as the solvent. It's very easy to apply, requiring just one coat. You apply it with a brush.
Berry Brothers, of Detroit, Mich., the famous varnish makers, furnish a great variety of colors in their water stains and also a combined stain and finish under the trade name of Lacklustre.
Berry Brothers, based in Detroit, Michigan, the well-known varnish manufacturers, offer a wide range of colors in their water stains and also a combo stain and finish called Lacklustre.
Devoe and Reynolds, 101 Fulton Street, New York, make a variety of oil stains which can be applied either in one coat with a brush or rubbed in with cotton waste.
Devoe and Reynolds, 101 Fulton Street, New York, offer a range of oil stains that can be applied either in one coat with a brush or rubbed in with cotton waste.
The Chicago Varnish Company, make a specialty of artistic, chemical stains, but unfortunately they are not yet (1910) available in small quantities.
The Chicago Varnish Company specializes in artistic, chemical stains, but unfortunately, they are not yet (1910) available in small quantities.
S. C. Johnson and Son, Racine, Wis., furnish a variety of spirit stains called "wood dyes."
S. C. Johnson and Son, Racine, Wis., provides a range of spirit stains known as "wood dyes."
The Craftsman Workshops, Eastwood, N. Y., furnish oil stains to be applied with a brush or waste. These are deservedly famous for they give especially soft, agreeable effects on fumed oak.
The Craftsman Workshops, Eastwood, N. Y., provide oil stains to be applied with a brush or rags. These are well-known because they produce particularly soft, pleasant effects on fumed oak.
In general, it should be remembered that oil stains are better for soft woods, water stains for hard woods, and the spirit stains are good for both. But without a sense of color, no number of recipes will avail.
In general, it should be remembered that oil stains work better on soft woods, water stains on hard woods, and spirit stains are good for both. But without an understanding of color, no amount of recipes will help.
FILLING
The object of filling is to give a perfectly level and non-absorbent basis for varnish covering or other finish. This can be done with shellac carefully rubbed down with fine oiled sandpaper, but this method requires much toil and patience, and has therefore been given [page 214] up by furniture finishers. The best fillers, (such as "Wheeler's Wood filler"),14 are made of silex in needle-shaped particles mixed with raw linseed oil, japan and turpentine. When applied to wood it should be thinned with turpentine or benzine, and applied with a brush along the grain. As it dries, the color becomes grayish and it should then be rubbed off across the grain with fine shavings or cotton waste. It is best to have fillers of several colors on hand, such as light, black, mahogany, and "golden oak" to be used according to the stain applied. The filler should be applied after staining the wood and should be allowed to dry thoroly, say forty-eight hours, before it is covered with shellac or varnish. Its use is more necessary on open grained woods, like oak, chestnut, and mahogany, than on close grained woods, like whitewood, maple, and pine, but it is best to use it on all woods that are to be highly polished.
The purpose of filling is to create a perfectly level and non-absorbent surface for varnish or other finishes. This can be achieved with shellac, carefully sanded down with fine oiled sandpaper, but this method is labor-intensive and time-consuming, so furniture finishers have largely abandoned it. The best fillers, such as "Wheeler's Wood filler," are made of needle-shaped particles of silex mixed with raw linseed oil, japan, and turpentine. When applying to wood, it should be thinned with turpentine or benzine and brushed on along the grain. As it dries, it turns a grayish color, and then it should be wiped off across the grain with fine shavings or cotton waste. It's helpful to have fillers in various colors, such as light, black, mahogany, and "golden oak," to match the stain used. The filler should be applied after staining the wood and left to dry thoroughly, about forty-eight hours, before being covered with shellac or varnish. Its use is more important on open-grained woods like oak, chestnut, and mahogany than on close-grained woods like whitewood, maple, and pine, but it's best to use it on all woods intended for a high polish.
Footnote 14: Made by the Bridgeport Wood Finishing Co., 155 Fulton St., N. Y.
Footnote 14: Created by the Bridgeport Wood Finishing Company, 155 Fulton St., New York.
Cans should be kept tightly covered when not in use. Since oil darkens wood, if wood is to be kept light, a filler without oil, as whiting and turpentine, should be used.
Cans should be kept tightly closed when not in use. Since oil darkens wood, if you want to keep the wood light, you should use a filler that doesn't contain oil, like whiting and turpentine.
POLISHES
There are three principal forms of wood polishes, each of which has its virtues and defects. They are: (a) oil, (b) wax, (c) the varnishes.
There are three main types of wood polish, each with its own advantages and disadvantages. They are: (a) oil, (b) wax, (c) varnishes.
(a) Oil. The great advantage of oil polishing is its permanence. It will stand both wetting and warmth and gives a dull, glossy finish. In some woods, as sweet gum and mahogany, it brings up the figure.
(a) Oil. The main benefit of oil polishing is that it lasts a long time. It can handle moisture and heat, giving a soft, shiny finish. On certain types of wood, like sweet gum and mahogany, it enhances the grain.
Process. Apply either raw or boiled linseed oil diluted with five parts of benzine or turpentine. The advantages of dilution are that the mixture penetrates the wood better, leaves a thinner film on the surface and is more economical. Then rub, rub, rub, day after day. Little and often with unlimited friction, is the best rule. This makes a nice finish for well-fumed chestnut, turning the color to a rich brown.
Process. Use either raw or boiled linseed oil mixed with five parts of benzene or turpentine. The benefits of dilution are that the mixture absorbs into the wood more effectively, leaves a thinner layer on the surface, and is more cost-effective. Then rub, rub, rub, day after day. A little bit frequently with plenty of friction is the best approach. This gives a nice finish for well-fumed chestnut, transforming the color to a deep brown.
(b) Wax. Wax is an old English polish, commonly used before French polish and varnish were introduced, especially for hard woods like oak. Its advantages are that it is cheap, easily prepared, easily applied, and easily repaired. Its disadvantages are that it will not stand wetting, is easily marred, requires constant care, is not so hard [page 215] and dry as varnish, turns slightly sticky with warmth, and is likely to turn white in crevices.
(b) Wax. Wax is an old English polish that was commonly used before French polish and varnish became popular, especially for hard woods like oak. Its benefits are that it's affordable, easy to make, simple to apply, and can be easily repaired. However, its drawbacks are that it doesn't hold up well to water, can be easily damaged, requires regular maintenance, isn't as hard and dry as varnish, becomes slightly sticky in warm temperatures, and can turn white in tight spaces. [page 215]
To prepare it. To one part of melted beeswax add one part of turpentine. Mix and cool. It can be bought prepared, as, Bridgeport Wood Finishing Company's "Old Dutch Finish," Butcher's Wax, Johnson's Wax, and others.
To make it, mix one part melted beeswax with one part turpentine. Stir and let it cool. You can also buy it ready-made, like Bridgeport Wood Finishing Company's "Old Dutch Finish," Butcher's Wax, Johnson's Wax, and others.
Process. Rub the wax evenly over the surface with a stiff brush or the fingers. Let it dry for some hours, and then rub with a cloth: flannel or a piece of felt is best. Put on several coats, leaving the work over night between coats. Rub often with a warm cloth.
Process. Apply the wax evenly across the surface using a stiff brush or your fingers. Allow it to dry for a few hours, then buff it with a cloth: flannel or a piece of felt works best. Apply multiple coats, letting the work rest overnight between coats. Frequently rub with a warm cloth.
(c) Varnishes. The function of varnishes is to cover wood with a hard, transparent coating that is non-porous and impervious to moisture. There is a great range among them, from thin, easily worn, dull finishes to durable, strong, and highly polished coatings called "rubbing varnishes." The polished surface can be secured only by much labor thru the application of successive thin coats of good varnish, carefully rubbed down.
(c) Varnishes. The purpose of varnishes is to coat wood with a hard, transparent layer that is non-porous and resistant to moisture. They vary widely, ranging from thin, easily damaged, dull finishes to tough, strong, and highly polished coatings known as "rubbing varnishes." Achieving a polished surface requires a lot of effort through the application of several thin layers of quality varnish, which must be carefully smoothed down.
Varnish may be applied to wood, stained, painted, or in its natural condition as well as to metal, leather, paper, and various other substances. A good varnish should be adhesive, that is, it should cling firmly to the surface to which it is applied; it should be elastic, so as not to crack on account of the expansion and contraction of the material to which it is applied; it should dry in a reasonable time; it should be limpid so as to flow easily in application; it should be transparent and brilliant when polished; and it should be durable. The necessary conditions for all good varnishing are a perfectly smooth, even, filled surface of dry wood, a temperature of about 70° and no dust in the air.
Varnish can be applied to wood, whether it's stained, painted, or in its natural state, as well as to metal, leather, paper, and various other materials. A good varnish should adhere well, meaning it should stick firmly to the surface it’s applied to; it should be flexible to avoid cracking due to the expansion and contraction of the material; it should dry within a reasonable time; it should be clear for easy application; it should be transparent and shiny once polished; and it should last long. The requirements for effective varnishing are a perfectly smooth, even, filled surface of dry wood, a temperature of about 70°F, and no dust in the air.
In general, there are two classes of varnish, based on the character of the solvent, (1) Spirit varnishes and (2) Oil varnishes.
In general, there are two types of varnish, based on the type of solvent: (1) Spirit varnishes and (2) Oil varnishes.
(1) Spirit varnishes are sometimes made with copal resins dissolved in some spirit, as one of the alcohols, benzine, acetone, etc. They dry with great rapidity owing to the volatilization of the solvent spirit, leaving a coat of pure resin of great hardness and brilliance, but one which is likely to crack and scale when exposed. They are not much used. Shellac is the most common and the most useful of the spirit varnishes. Its basis is resin lac, a compound resinous substance exuded from an East India scale insect (Carteria lacca) found mostly in the province of Assam. The term "lac" is the same [page 216] as "lakh" which means 100,000 and is indicative of the countless hosts of insects which are the source from which this gum is obtained. The larval insects insert their proboscides into the bark of young shoots of certain lac-bearing trees, varieties of Ficus, draw out the sap for nutriment, and at once exude a resinous secretion which entirely covers their bodies and the twigs, often to the thickness of one-half inch. The females never escape and after impregnation their ovaries become filled with a red fluid which forms a valuable dye known as lac dye. The encrusted twigs are gathered by the natives in the spring and again in the autumn, before the young are hatched, and in this condition the product is known as "stick lac." After being crushed and separated from the twigs and washed free from the coloring matter the product is known as "seed lac." It is then melted and strained and spread out in thin layers in a form called "shell lac." This is what is known as orange shellac in the market. It may be bleached by boiling in caustic potash, and passing chlorine thru it until the resin is precipitated. It is further whitened by being pulled. This is what is known in the market as "white shellac." It comes in lumps. Orange shellac is the stronger and is less likely to deteriorate, but white is easier to apply because it sets less rapidly. Another advantage of the white is its colorlessness. Shellac is soluble in both grain alcohol (ethyl alcohol) and wood alcohol (methyl alcohol), but grain alcohol is preferable. Great care must be taken not to mix even a drop of water in it or it will curdle. To make perfect the process of ordinary filling, shellac may be used as a filler either by itself or preparatory to other processes. Since it dries quickly it can be rubbed down in six or eight hours either with No. 00 sandpaper oiled, or better, with No. 00 steel wool. This process when repeated several times gives a good "egg-shell" finish. It may be applied alone over stained wood or the shellac itself may be colored with aniline dyes cut in alcohol. This, for example, is an easy way to get a black finish.
(1) Spirit varnishes are sometimes made with copal resins dissolved in various solvents like alcohol, benzene, or acetone. They dry very quickly because the solvent evaporates, leaving behind a layer of pure resin that is hard and shiny but can crack and peel when exposed. Because of this, they aren't widely used. Shellac is the most common and practical type of spirit varnish. Its main ingredient is resin lac, a resinous substance produced by a scale insect from East India (Carteria lacca), mainly found in Assam. The term "lac" is related to "lakh," meaning 100,000, which reflects the vast number of insects that produce this gum. The larval insects insert their feeding tubes into the bark of young shoots of certain lac trees, like varieties of Ficus, taking in the sap for nourishment while exuding a resinous secretion that covers their bodies and the twigs, sometimes up to half an inch thick. The females do not escape, and after mating, their ovaries fill with a red fluid that becomes a valuable dye known as lac dye. Natives gather the encrusted twigs in spring and autumn, before the larvae hatch, and refer to this as "stick lac." After crushing and washing out the coloring matter, the product is called "seed lac." This is then melted, strained, and spread in thin layers known as "shell lac." In the market, this is called orange shellac. It can be bleached by boiling in caustic potash and bubbling chlorine through it until the resin precipitates. It is further whitened by being pulled, resulting in what is sold as "white shellac." This comes in chunks. Orange shellac is stronger and less likely to deteriorate, while white shellac is easier to apply since it sets more slowly. An advantage of white shellac is that it is colorless. Shellac dissolves in both grain alcohol (ethyl alcohol) and wood alcohol (methyl alcohol), though grain alcohol is preferred. Care must be taken not to let even a drop of water get in, or it will curdle. Shellac can be used as a filler either alone or to prep for other finishing processes. Since it dries quickly, it can be sanded down in six to eight hours using No. 00 sandpaper with oil or, preferably, No. 00 steel wool. Repeating this process several times results in a nice "egg-shell" finish. It can be applied directly over stained wood, or the shellac can be tinted with aniline dyes mixed in alcohol, which is an easy way to achieve a black finish.
A good waterproof wood polish is made thus: 1 pint alcohol, 2 oz. gum benzoin, ¼ oz. gum sandarac, ¼ oz. gum anime. Put in a bottle, and put the bottle in a hot water bath until all solids are dissolved. Strain and add ¼ gill clear poppy oil. Shake well and apply with cotton cloth.
A good waterproof wood polish is made this way: 1 pint of alcohol, 2 ounces of gum benzoin, ¼ ounce of gum sandarac, and ¼ ounce of gum anime. Put it in a bottle, and place the bottle in a hot water bath until all the solids are dissolved. Strain and add ¼ gill of clear poppy oil. Shake well and apply with a cotton cloth.
A soft, dull, glossy finish may be obtained by applying two coats of a mixture of one part each of white shellac and banana oil (amyl acetate). When dry, sandpaper lightly and wax.
A smooth, dull, shiny finish can be achieved by applying two coats of a mixture of one part white shellac and one part banana oil (amyl acetate). Once it's dry, lightly sand it and then apply wax.
French polishing. The finest of shellac finishes is French polish. It is a thin, clear, permanent finish, but the process takes time and patience. It is not much used in practical work, because of the time expense, but is often employed in school shops, because only a few materials are necessary, it dries quickly, and gives a beautiful finish. The polished surface is obtained by adding successive thin coats according to the following process:
French polishing. The best shellac finish is French polish. It's a thin, clear, and long-lasting finish, but the process requires time and patience. It's not used much in practical applications due to the time it takes, but it's commonly used in school workshops since it needs only a few materials, dries quickly, and provides a gorgeous finish. The polished surface is achieved by applying several thin layers using the following method:
(1) Preparation. The surface of the wood must be perfectly smooth and even, sandpapered in the direction of the grain, stained, if desired, filled, rubbed smooth and quite dry. (2) Apply two or three thin coats of shellac. After each coat when dry, rub with No. 00 oiled sandpaper or No. 00 steel wool. Wipe thoroly. (3) Make three pads, about the size of a walnut, of clean, white, cotton waste, enclosed in some fine old or washed cloth with no sizing or lint,—one pad for shellac, one for oil, and one for alcohol. Fill one pad with shellac of the consistency of milk, enough in the pad so that when squeezed hard it will ooze out. The common mistake is to put too much shellac into the pad. Rub with circular motion, as indicated in Fig. 304, never letting the pad stop on the surface. (4) Sprinkle a very little finely powdered pumicestone and put a little oil on the surface of the wood here and there with the tip of a finger. Rub with second pad until surface is dull. Wipe clean. Repeat (3) and (4) several times. Some use raw linseed oil to prevent sticking. Others use three or four cloth coverings on the shellac pad, removing the outer one as it dries. A simpler way is to keep the shellac in pad, 1, thin by moistening with a little alcohol. (5) Spiriting off (Follows process 4.) Dampen pad, 3, with very little alcohol and wipe quickly in the direction of the grain. This should remove the circular marks. Too much alcohol in this third pad will "burn" a dull spot. The rubbers are said to improve with use, and may be preserved in closely stoppered jars to prevent evaporation. The different kinds of pads [page 218] should be kept separate. Or the cotton waste may be thrown away, and the cloths washed in strong borax water. In the process just described, shellac alone, dissolved in alcohol, is used. The shellac may be used with other ingredients: for example, 1 pint grain alcohol, ¼ oz. gum copal, ¼ oz. gum arabic, 1 oz. shellac. Strain through muslin.
(1) Preparation. The wood must be completely smooth and even, sanded with the grain, stained if you want, filled, rubbed smooth, and completely dry. (2) Apply two or three thin coats of shellac. After each coat dries, rub it with No. 00 oiled sandpaper or No. 00 steel wool. Wipe thoroughly. (3) Make three pads roughly the size of a walnut out of clean, white cotton waste, wrapped in fine old or washed cloth that has no sizing or lint—one pad for shellac, one for oil, and one for alcohol. Fill one pad with shellac that’s the consistency of milk, enough so that when you squeeze it hard, it will ooze out. A common mistake is to put too much shellac in the pad. Rub in a circular motion, as shown in Fig. 304, and never let the pad stop on the surface. (4) Sprinkle a little finely powdered pumice stone, and apply a bit of oil to the surface of the wood here and there with your fingertip. Rub with the second pad until the surface looks dull. Wipe clean. Repeat steps (3) and (4) several times. Some people use raw linseed oil to prevent sticking. Others apply three or four cloth coverings on the shellac pad, removing the outer one as it dries. A simpler method is to keep the shellac in pad 1 thin by moistening it with a little alcohol. (5) Spiriting off (follows process 4). Dampen pad 3 with very little alcohol and wipe quickly in the direction of the grain. This should take away the circular marks. Too much alcohol in this third pad will “burn” a dull spot. The pads are said to get better with use and can be stored in tightly closed jars to prevent evaporation. The different types of pads should be kept separate. Or you can throw away the cotton waste and wash the cloths in strong borax water. In the method described, shellac alone, dissolved in alcohol, is used. The shellac can also be combined with other ingredients: for instance, 1 pint of grain alcohol, ¼ oz. of gum copal, ¼ oz. of gum arabic, and 1 oz. of shellac. Strain through muslin. [page 218]

Fig. 304. Direction of the Pad in French Polishing.
Another recipe for finishing. Use 4 drams grain alcohol, 2 drams orange shellac, 5 drams tincture of benzoin, 1 teaspoonful of olive oil. Dissolve and strain. Apply with pad in direction of grain.
Another recipe for finishing. Use 4 drams of grain alcohol, 2 drams of orange shellac, 5 drams of tincture of benzoin, and 1 teaspoon of olive oil. Dissolve and strain. Apply with a pad in the direction of the grain.
Oil or Copal Varnishes. The old Cremona varnish once used for violins is supposed to have had amber (Greek, electron) as its base. It was a fossilized coniferous resin found on the shore of the Baltic Sea. The art of making it is said to be lost, probably because of the difficulty and danger of melting it, for this can be done only in oil on account of the danger of ignition. Hence its use has been abandoned.
Oil or Copal Varnishes. The old Cremona varnish that was once used for violins is believed to have been based on amber (Greek, electron). This amber was a fossilized resin from conifer trees found along the shores of the Baltic Sea. The technique for making it is thought to be lost, likely due to the challenges and risks involved in melting it, which can only be done using oil because of the fire hazard. As a result, its use has been discontinued.
Perhaps the most beautiful of all varnishes is lacquer, much used in China and Japan. It is made from the juice of the lacquer tree, (Rhus vernicifera) which is tapped during the summer months. The juice is strained and evaporated and then mixed with various substances, such as oil, fine clay, body pigment, and metallic dust, according to the ware for which it is intended. The manufacturing secrets are carefully guarded. The application of it is very difficult, the sap of young trees being used for first coats, and of old trees for the finishing coats. It must be dried in a damp, close atmosphere. For the best work ten or twelve coats are elaborately rubbed down and polished. Even the presence of it is very poisonous to some people and all workers in it are more or less affected.
Perhaps the most beautiful of all finishes is lacquer, which is widely used in China and Japan. It's made from the sap of the lacquer tree, (Rhus vernicifera), which is tapped during the summer months. The sap is strained and evaporated, then mixed with different substances like oil, fine clay, body pigment, and metallic dust, depending on what it's intended for. The manufacturing secrets are kept very private. Applying it is quite challenging; the sap from young trees is used for the first layers, while the sap from older trees is used for the final layers. It needs to dry in a humid, enclosed environment. For the best results, ten to twelve layers are meticulously sanded and polished. Even being around it can be very toxic to some people, and all workers handling it experience some level of effect.
The solvent or vehicle of the modern copal varnishes consists principally of linseed oil with some turpentine. Their base is Copal, a fossil, resinous substance of vegetable origin. The gums of which they are made have been chemically altered by long exposure in the earth. Other gums, as mastic, dammar, sandarac, and even resin are sometimes mixed with copal to cheapen the product or to cause more rapid drying. Copal is a generic name given originally to all fossil resins. Copals, as they are called, come from New Zealand, Mozambique, Zanzibar, West Africa, Brazil, and the Philippines. The best of the Copals is said to be the Kauri gum, originally exuded from the Kauri pine tree of New Zealand. The tree is still existent and [page 219] produces a soft, spongy sap, but the resin used in varnish is dug up from a few feet under ground in regions where there are now no trees. A commercially important copal and one noted for its hardness is the Zanzibar or East African Copal. It is found imbedded in the earth at a depth not greater than four feet over a wide belt of the mainland coast of Zanzibar, on tracts where not a single tree now grows. It occurs in lumps from the size of small pebbles to pieces weighing four or five pounds. The supply is said to be practically inexhaustible.
The solvent or vehicle for modern copal varnishes mainly consists of linseed oil mixed with some turpentine. Their base is copal, which is a fossilized, resinous substance that comes from plants. The gums used to make these varnishes have been chemically changed by long periods underground. Sometimes, other gums like mastic, dammar, sandarac, and even resin are added to copal to lower costs or speed up drying. "Copal" is a general term that was originally used for all fossil resins. These copals, as they are often called, are sourced from New Zealand, Mozambique, Zanzibar, West Africa, Brazil, and the Philippines. The finest copal is said to be Kauri gum, which comes from the Kauri pine tree in New Zealand. This tree still exists and produces a soft, spongy sap, but the resin used in varnish is excavated from several feet below the surface in areas where there are no longer any trees. A commercially significant type of copal known for its hardness is the Zanzibar or East African copal. It can be found embedded in the ground at depths of no more than four feet along a wide coastal belt of Zanzibar, in places where no trees currently grow. It appears in lumps ranging from the size of small pebbles to pieces weighing four or five pounds. The supply is said to be practically limitless. [page 219]
As to the manufacture of the Copal varnishes: first of all, a high grade oil is boiled at a high temperature, with different materials to oxidize it; for instance, red lead or oxide of manganese. The heat throws off the oxygen from the red lead or manganese. The oxygen is absorbed by the linseed oil, which is then put away to settle and age. When a batch of varnish is made, the gums are melted in a large kettle and then the requisite amount of oil is added and these carefully boiled together. This is removed from the fire and cooled down to a point, where turpentine can be added without volatilizing. These are thoroly mixed and then filtered under pressure and tanked and aged. The different grades of varnish depend upon the treatment of the oil, the proportion of oil and turpentine, the qualities of the gums, the aging, etc. Some by rubbing give a very high polish, some give a dull waxy finish, some are for out-of-door use, as Spar varnish and carriage varnish, some are for floors, some for furniture, some are high priced, some are cheap.
As for making Copal varnishes: first, a high-quality oil is heated to a high temperature with various materials to oxidize it; for example, red lead or manganese oxide. The heat releases oxygen from the red lead or manganese. The linseed oil absorbs this oxygen, and then it’s set aside to settle and age. When it’s time to make varnish, the gums are melted in a large kettle, and then the necessary amount of oil is added, and they are carefully boiled together. This mixture is taken off the heat and cooled to a point where turpentine can be added without evaporating. The two are thoroughly mixed and then filtered under pressure, stored in tanks, and aged. The different varnish grades depend on how the oil is treated, the ratio of oil to turpentine, the quality of the gums, the aging process, etc. Some varnishes create a very high polish when rubbed, some have a dull waxy finish, some are for outdoor use, like Spar varnish and carriage varnish, some are for floors, some for furniture, some are expensive, and some are affordable.
Process of Varnishing. The preliminary processes are the same as those for applying shellac, i. e., the surface of the wood must be perfectly even and smooth, and the staining, filling, and drying complete. Quick drying varnishes, like shellac, are applied, with but little on the brush. The heavy, high lustre varnishes, on the other hand, are applied with the brush full so that the varnish may even drip off the work. Then proceed as follows: Wipe off from the work the extra varnish with the brush and clean the brush on the edge of the cup. Repeat till the varnish is flowed over the work evenly. Be particularly careful, in that respect, of edges and corners. Set to dry in a dustless place. When dry and hard repeat the process from three to six times. Each coat must dry thoroly before the next coat is applied.
Process of Varnishing. The initial steps are the same as those for applying shellac, meaning the wood surface must be perfectly even and smooth, and the staining, filling, and drying must be complete. Quick-drying varnishes, like shellac, are applied with just a little on the brush. In contrast, the heavier, high-gloss varnishes are applied with a full brush, so that the varnish may even drip off the surface. Then proceed as follows: Wipe off the excess varnish from the surface with the brush, and clean the brush on the edge of the cup. Repeat this until the varnish is spread evenly over the surface. Pay special attention to the edges and corners. Set aside to dry in a dust-free area. Once dry and hard, repeat the process three to six times. Each coat must dry thoroughly before applying the next one.
Varnish polishing consists in rubbing off the varnish, not in rubbing it on, as in French polishing. To polish varnish, rub with a felt pad, powdered pumice-stone and water. Rub till the surface is smooth, unpitted and even, being careful not to rub thru the edges. Wipe clean with a wet sponge and chamois skin. This gives a dull or "egg-shell" finish. For polishing varnish, a simple method is to rub with a rotary motion, using a mixture of 1⁄2 sweet oil or cottonseed oil, and 1⁄2 alcohol.
Varnish polishing involves rubbing off the varnish instead of applying it, like in French polishing. To polish varnish, use a felt pad along with powdered pumice stone and water. Rub until the surface is smooth, free of pits, and even, being careful not to rub through the edges. Wipe clean with a wet sponge and chamois leather. This will give a dull or "egg-shell" finish. A simple technique for polishing varnish is to rub in a circular motion, using a mixture of 1Please provide a short piece of text for me to modernize.2 sweet oil or cottonseed oil and 1⁄2 alcohol.
A more laborious process is as follows: After rubbing to a dull finish, rub ground rotten stone and water with chamois skin in a circular motion. Let the rotten stone dry on the surface. Then wipe off with the naked hand, rubbing in a circular direction and wiping the hand every time after passing over the work. This looks simple, but is really a fine art. These processes have practically replaced French polishing in the trade.
A more detailed process is as follows: After sanding to a smooth finish, use ground rotten stone and water with chamois leather in a circular motion. Allow the rotten stone to dry on the surface. Then wipe it off with your bare hand, rubbing in a circular motion and wiping your hand each time after going over the work. It seems simple, but it's actually a skilled technique. These methods have mostly taken the place of French polishing in the industry.
PAINTING
Paints are used for the same purpose as other finishes, with the additional one of giving an opaque colored covering. The materials used are:
Paints are used for the same purpose as other finishes, plus they provide an opaque colored covering. The materials used are:
1. A body whose function is to give covering power. This is usually white lead, but it is often adulterated with zinc oxide; 2. Pigments; 3. Linseed oils, raw and boiled, which are used to give consistency, adhesiveness and also elasticity to the coat when dry. For outdoor work boiled oil is used and for indoor work, raw oil; 4. Turpentine, which is used to thin out the paint and to make it dry more quickly.
1. A substance meant to provide coverage. This is typically white lead, but it’s often mixed with zinc oxide; 2. Pigments; 3. Raw and boiled linseed oils, which are used to add thickness, stickiness, and elasticity to the dried coat. Boiled oil is used for outdoor projects, while raw oil is used indoors; 4. Turpentine, which is used to thin the paint and help it dry faster.
The common method of painting is: 1. Set any nails with nailset; 2. Sandpaper; 3. Shellac the knots; 4. Prime with a thin coat of paint, mostly white lead, (that is, little color,) boiled oil, and turpentine (the proportion of drying oil is greater than in ordinary paint); 5. Putty up cracks, nail holes, etc.; 6. Sandpaper if a small nice job; 7. Then paint two or three coats with paint thick enough so it will not run, with long, even strokes with the grain. The order of painting a door is, panels, muntins, rails, and last, stiles.
The usual process for painting is: 1. Set any nails with a nail set; 2. Sand it down; 3. Seal the knots with shellac; 4. Prime with a thin coat of paint, mainly white lead (which means little color), boiled oil, and turpentine (the amount of drying oil is more than in regular paint); 5. Fill in cracks, nail holes, etc., with putty; 6. Sand it down again if you want a smooth finish; 7. Then apply two or three coats of paint that's thick enough not to drip, using long, even strokes in the direction of the wood grain. The order for painting a door is: panels, muntins, rails, and finally, stiles.
For inside work use half as much turpentine as oil. This gives a dull finish. For outside work, where lustre is wanted, little or no turpentine is used.
For indoor projects, use half as much turpentine as oil. This results in a matte finish. For outdoor projects, where a shiny look is desired, use little or no turpentine.
This is the old way, and is still used for all common work. But for fine painting, as carriage work, a filler is now used first, because a priming to be durable should unite with the wood, grasping the fibers and filling the pores, so that after coats cannot sink in. The object is to cement the surface. Priming is often called "rough stuff." The old way did not do this, with the result that the oil separated from the lead and kept soaking into the wood. The principal makers of paints now recommend a filler before any white lead is added.
This is the traditional method, and it’s still used for all basic tasks. However, for detailed painting, like with vehicle work, a filler is now applied first because a durable primer needs to bond with the wood, penetrating the fibers and filling the pores so that subsequent coats won’t sink in. The goal is to create a solid surface. Priming is often referred to as "rough stuff." The old method didn’t achieve this, resulting in the oil separating from the lead and continuously soaking into the wood. Nowadays, leading paint manufacturers suggest using a filler before adding any white lead.
TOOLS AND MATERIALS FOR WOOD FINISHING
Brushes. It is well to have several varieties to help keep them distinct. For varnish and shellac, the best are those with the bristles set in hard rubber. For ordinary purposes, brushes one inch wide are satisfactory. For stains, cheap, tin-bound brushes are good enough, and are easily replaced.
Brushes. It's a good idea to have different types to keep them separate. For varnish and shellac, the best brushes have bristles set in hard rubber. For general use, one-inch wide brushes work well. For stains, inexpensive, tin-bound brushes are sufficient and can be easily replaced.
Cups. Half-pint enameled steel cups are cheap, satisfactory, and easily kept clean. For the care of cups and brushes, see Chapter VI, The Equipment and Care of the Shop.
Cups. Half-pint enameled steel cups are affordable, reliable, and easy to clean. For information on maintaining cups and brushes, see Chapter VI, The Equipment and Care of the Shop.
Steel wool. This consists of shavings, turned from thin steel discs set together in a lathe. It comes in various grades, No. 00 to No. 3. The finest, No. 00, is coarse enough for ordinary purposes.
Steel wool. This consists of shavings, made from thin steel discs connected together in a lathe. It comes in various grades, No. 00 to No. 3. The finest, No. 00, is coarse enough for regular use.
Sandpaper. Use No. 00 smeared with boiled oil. Pulverized pumice stone and pulverized rotten stone, both very fine, are used to rub down inequalities and to give a dull finish to shellac or varnish. Use with oil on shellac and with oil or water on copal varnish. Horsehair and soft wood shavings are often used to rub down varnish. French felt, medium hard, is used for rubbing down copal varnish with pumice stone.
Sandpaper. Use No. 00 coated with boiled oil. Finely ground pumice stone and finely ground rotten stone are used to smooth out imperfections and create a matte finish on shellac or varnish. Use with oil on shellac and with oil or water on copal varnish. Horsehair and soft wood shavings are often used to buff out varnish. Medium hard French felt is used for smoothing copal varnish with pumice stone.
Cotton waste is the cheapest available material for wiping.
Cotton waste is the most affordable material for wiping.
Cheese cloth is better for some purposes, but more expensive.
Cheesecloth is better for some uses, but it's pricier.
Soft cloth without lint is necessary for French polishing. "Berkeley muslin," "Old Glory," and "Lilly White" are trade names. A fine quality is necessary. The starch should be washed out and the cloth dried before using, and then torn into little pieces, say 4" square.
Soft, lint-free cloth is essential for French polishing. "Berkeley muslin," "Old Glory," and "Lilly White" are brand names. A high-quality fabric is required. The starch should be removed, and the cloth needs to be dried before using it, then cut into small pieces, about 4 inches square.
Fillers consist of silex or of ground earths mixed with oil, japan, and turpentine. Their object is to give a perfectly level and non-absorbent basis for varnish covering.
Fillers are made from silex or ground earth mixed with oil, Japan, and turpentine. Their purpose is to create a completely smooth and non-absorbent surface for varnish application.
Oils. Raw linseed oil is very fat and dries slowly. It is used for interior work.
Oils. Raw linseed oil is quite thick and takes a long time to dry. It's used for indoor projects.
Boiled oil is linseed oil boiled with litharge (PbO) and white vitriol, which removes much of the fatty ingredient and gives it drying quality.
Boiled oil is linseed oil that has been heated with litharge (PbO) and white vitriol, which removes a lot of the fatty content and gives it drying properties.
Turpentine is a volatile oil from the sap of long-leaf pine. It is mixed with oil in painting to give further drying qualities.
Turpentine is a quick-evaporating oil derived from the sap of longleaf pine. It's blended with oil in painting to enhance its drying properties.
Benzine is a cheap substitute for turpentine. It is a highly inflammable product of coal tar and evaporates quickly.
Benzine is an affordable alternative to turpentine. It's a highly flammable product of coal tar and evaporates rapidly.
Drier is an oil in which resin has been dissolved. It is mixed with varnishes and paint to make them dry quickly. It is also sometimes used as a varnish itself.
Drier is an oil that has resin dissolved in it. It's mixed with varnishes and paint to help them dry quickly. It's also sometimes used as a varnish on its own.
Japan is a varnish-like liquid made of shellac or other resin, linseed oil, metallic oxides, and turpentine. It is used as a medium in which to grind colors and as a drier.
Japan is a glossy liquid made from shellac or other resins, linseed oil, metallic oxides, and turpentine. It's used as a medium for grinding colors and as a drying agent.
WOOD FINISHING
References:*
References:*
(1) Stains.
Stains.
Hodgson, II, pp. 25-59, 155-164.
Hodgson, II, pp. 25-59, 155-164.
Van Deusen, Man. Tr. Mag., 6: 93.
Van Deusen, Man. Tr. Mag., 6: 93.
Maire, pp. 46-64.
Maire, pp. 46-64.
(2) Fillers.
(2) Fillers.
Hodgson, II, pp. 7-25.
Hodgson, II, pp. 7-25.
Maire, 65-72.
Maire, 65-72 years old.
(3) Oil Finish.
Oil Finish.
Hodgson, II, pp. 99-103.
Hodgson, II, pp. 99-103.
Maire, p. 117.
Maire, p. 117.
(4) Wax.
(4) Wax.
Hodgson, II, pp. 93-99.
Hodgson, II, pp. 93-99.
Maire, pp. 112-116.
Maire, pp. 112-116.
(5) Varnish.
(5) Finish.
Shellac.
Shellac.
Maire, pp. 73-80, 101-111.
Maire, pp. 73-80, 101-111.
Journal, Soc. Arts, 49: 192.
Journal of Social Arts, 49: 192.
Ency. Brit., Vol. XIV, "Lac."
Ency. Brit., Vol. 14, "Lac."
Hodgson, II, pp. 66-93.
Hodgson, II, pp. 66-93.
Inter. Encyc., Vol. X, "Lac."
Inter. Encyc., Vol. 10, "Lac."
Oil Varnish.
Oil Finish.
Hodgson, II, pp. 59-66.
Hodgson, II, pp. 59-66.
Clark, pp. 1-69.
Clark, pp. 1-69.
Maire, pp. 81-100.
Maire, pp. 81-100.
Encyc. Brit., Vol. XXIV, "Varnish."
Encyc. Brit., Vol. 24, "Varnish."
(6) Paints.
(6) Paints.
Brannt, p. 134-152.
Brannt, pp. 134-152.
Building Trades Pocketbook, pp. 357-360.
Building Trades Pocketbook, pp. 357-360.
For detailed directions for the treatment of different woods, see Hodgson,
For detailed instructions on treating different types of wood, see Hodgson,
II, pp. 112-153, Maire, pp. 124-141.
II, pp. 112-153, Maire, pp. 124-141.
* For general bibliography see p. 4.
* For general bibliography see __A_TAG_PLACEHOLDER_0__
INDEX.
__A_TAG_PLACEHOLDER_0__ | __A_TAG_PLACEHOLDER_1__ | __A_TAG_PLACEHOLDER_2__ | __A_TAG_PLACEHOLDER_3__ |
__A_TAG_PLACEHOLDER_4__ | __A_TAG_PLACEHOLDER_5__ | __A_TAG_PLACEHOLDER_6__ | __A_TAG_PLACEHOLDER_7__ |
__A_TAG_PLACEHOLDER_8__ | __A_TAG_PLACEHOLDER_9__ | __A_TAG_PLACEHOLDER_10__ | __A_TAG_PLACEHOLDER_11__ |
__A_TAG_PLACEHOLDER_12__ | __A_TAG_PLACEHOLDER_13__ | __A_TAG_PLACEHOLDER_14__ |
__A_TAG_PLACEHOLDER_15__ | __A_TAG_PLACEHOLDER_16__ | __A_TAG_PLACEHOLDER_17__ |
__A_TAG_PLACEHOLDER_18__ | __A_TAG_PLACEHOLDER_19__ | __A_TAG_PLACEHOLDER_20__ |
- Acorn of hinge, 131.
- Adjustment of plane, 70, 72.
- Adze, 88.
- Agacite grinder, 61, 120, 121, 137.
- Alcohol:
- Alligator, 28.
- Ammonia, 209, 211.
- Angle of bevel, 58, 59.
- Aniline stains:
- Antique oak, 210.
- Anvil, 141.
- Arrangement of shop, 142-144.
- Arris, 57, 184.
- Asphaltum, 210.
- Auger-bit, 53, 84, 85, 137, 140.
- Auger-bit-gage, 116.
- Ax, 10, 51, 87.
- Back-saw, 65, 136, 138.
- Balloon frame, 201.
- Banana oil, 213, 216.
- Band-saw, 31.
- Banking grounds, 16.
- Beam-compass, 114.
- Beams, 201.
- Bench, 97-99, 136, 138, 141, 143.
- Bench-hook, 78, 100, 102, 137, 139, 161.
- Bending wood, 199.
- Benzine, 209, 210, 214, 222.
- Bevel of cutting tools, 52, 55, 120.
- Bevel, Sliding T, 113, 137, 140.
- Bezel, See Bevel.
- Bill-hook, 10.
- Binding of saw, 63, 65.
- Bit, Plane, 70, 77.
- Bits, 84-87, 137, 140.
- Bit, Twist, 84, 85.
- Bit-point drill, 84, 85.
- Bit-stock, See Brace.
- Black, 209, 211.
- Blank-hinge, 131.
- Blazes on trees, 7, 8.
- Blinds, 194.
- Block, Corner, 155 No. 12, 177, 199.
- Block-plane, See Plane, Block.
- Blue, Prussian, 210.
- Board, 48.
- Board construction, 184-192.
- Board-dipper, 35, 36.
- Board foot, 48, 109.
- Board measure, 48, 109, 110.
- Board structures, 184-192.
- Bolt of lock, 133.
- Bolts, 127.
- Book shelves, 185.
- Boom, Log, 20, 21.
- Boring, Directions for, 85.
- Boring tools, 83-87.
- Box, 187-191.
- Brace, 103, 105, 137, 140.
- Brace, Ratchet, 103, 105, 137.
- Brace-measure, 107.
- Bracket, 185.
- Brad-awl, 83, 84, 138, 140.
- Brads, 124.
- Breaking out the roll-ways, 16.
- Bridging, 201.
- Brown, Bismarck, 210, 211.
- Brush, 138, 141, 149, 209, 210, 221.
- Brush, See also Duster.
- Brush-Keeper, 150.
- Buckling of saw, 62, 65, 67.
- Buffer, 121, 147.
- Burn of shellac, 217.
- Butt-hinge, 131.
- Cabinet construction, 192-195.
- Cabinet for nails and screws, 142, 145, 147.
- Calipers, 114.
- Camp, logging, 8, 9.
- Cant, 35, foot-note.
- Cant-flipper, 35, 36.
- Cant-hook, 10, 13.
- Cape-chisel, 141.
- Care of the shop, 142-150.
- Carriage-bolts, 127.[page 225]
- Carteria lacca, 215.
- Carving tools, 60, 140.
- Case-hardening, 46.
- C-Clamps.
- See carriage-makers' clamps.
- Ceiling, 201.
- Center-bit, 84, 86.
- Chain, 10, 13, 15, 16.
- Chair, 198-201.
- Chalk, French, 197.
- Chamfer, 82, 115, 161, 184.
- Chatter, 71, 92.
- Cheek of joint, 160.
- Cheese-cloth, 221.
- Chest, 193, 195.
- Chest-hinge, 131.
- Chisel, 52-59, 136, 137,
139, 140, 183.
- See also Chiseling end-wood,
Paring, Sidewise chiseling.
- See also Chiseling end-wood,
- Chisel, Cape, 141.
- Chisel-gage, 69.
- Chiseling, end-wood, 56, 57, 183.
- Choking of Plane, 76.
- Chopping tools, 87, 88.
- Clamp, 101, 138, 141, 169.
- Clapboards, 201.
- Claw hammer, 96.
- Cleaning tools, 121.
- Cleats, 186, 188.
- Comb-grain, 41, 42.
- Compass, 113, 114, 137, 139.
- Compass-saw, 67, 139.
- Consumer, 33, 41.
- Copal, 218.
- Coping-saw, 139.
- Copper, Soldering, 141.
- Corner-blocks, 155, No. 12, 177, 199.
- Corner-board, 201.
- Cornering tool, 83.
- Corner-iron, 127.
- Corner locking, 164.
- Corrugated fasteners, 125, 170.
- Cost of Equipment, 136-142.
- Countersink, 84, 87, 126, 138, 140, 141.
- Cricket, 186.
- Crosscut-saw, 10, 64-66, 137, 139.
- Cross-grained wood, Planing, 75.
- Crowbar, 10.
- Crown of Plane-cutter, 71.
- Cruising, 8.
- Cup, 138, 141, 221.
- Curling-iron, 70.
- Cutter, Plane, 70, 76, 77, 138.
- Cutting-gage, 116, 140.
- Cutting tools, 51.
- Dado, 56, 80.
- See also Joint, Dado.
- Dado-plane, 80.
- Dam, Splash, 20, 21.
- Decay, 32, 45.
- Decking logs, 13.
- Demonstration seats, 143.
- Derrick, Locomotive boom, 25.
- Destructive lumbering, causes of, 7.
- Die, 141.
- Die-holder, 141.
- Dividers, 113, 114, 137, 140.
- Dogs, log, 34.
- Donkey engine, 24.
- Door, 192, 193.
- Dovetail-saw, 66, 137, 139.
- Doweling, 127, 130, 152, 154, 175.
- Dowel-plate, 139, 140.
- Dowel-pointer, 83, 139, 175.
- Dowel-rods, 127, 175.
- Draw-bolt, 155.
- Draw-knife, 61, 139.
- Drawer, 166, 190-192.
- Drawing-board, 186, 205.
- Dray-road, 9, 13.
- Drier, 222.
- Drill. See Hand Drill.
- Drive, The log, 16-18.
- Duplicate parts, 155, 204.
- Duster, Bench, 121, 137, 139.
- Dynamite, 21.
- Edge action, 52.
- Edged Tools, 51 ff.
- Edger, 35, 36, 37.
- Eight-square scale, 108.
- Egg-shell finish, 94, 216.
- Equipment, Chap. VI, 136-150.
- Escutcheon of lock, 133.[page 226]
- Expansive-bit, 84, 87, 137, 140.
- Falling beds, 24.
- Fastenings, Chap. V, 123-135.
- Felling trees, 10, 11, 23.
- Ferrule, 54.
- File, 90, 91, 137, 140, 142, 147.
- File-card, 91, 137, 140.
- Filing a saw, 67.
- Filletster, 80, 137, 139.
- Filler, 213, 221.
- Finishing, Wood, Chap. X, 209-223.
- Firmer-chisel,
- See under Chisel.
- Firmer-gouge,
- See under Gouge.
- Fish glue, 129.
- Fitter, 10.
- Flooring, 30, 42, 174, 201, 206.
- Flume, 21, 22.
- Foerstner Auger-bit, 84, 87.
- Foot-stool, 186.
- Fore-edge, 196.
- Fore-plane,
- See under Plane.
- Framed structures, 195-201.
- Framing-chisel,
- See under Chisel.
- Frog, Plane, 70, 75.
- Fuming with ammonia, 212, 214.
- Furring, 201.
- Gages, 114-116.
- Gelatin, 128.
- Gimlet-bit, 84, 85, 137, 140.
- Glass-cutter, 138, 141.
- Glaziers points, 125.
- Glue, 128-131.
- Glue-pot, 129, 138, 141, 149.
- Gluing, Directions for, 130, 153, 167-170, 173, 189, 190.
- Golden Oak, 211.
- Gouge, 59, 60, 137, 140, 183.
- Grading of lumber, 38.
- Grain of wood, 60, 75, 172, 185, 186, 192, 205, 209, 210.
- Green, 209.
- Grinder or Hog, 41.
- Grinder, Empire Tool, 61, 120, 121, 137, 140.
- Grinding of tools. See sharpening.
- Grindstone, 117-120, 137, 140.
- Groove for drawer, 191.
- Groove for panel, 164.
- Groove, Triangular, 66, 156, 158, 159, 161.
- Hack-saw, 137, 141.
- Hammer, 58, 94, 95, 96, 136, 139.
- Hand-drill, 104, 138, 141.
- Handscrew, 101, 102, 138, 141, 170, 173.
- Handscrew, Iron, 102.
- See also Clamp, carriage-makers.
- Hatchet, 88.
- Hauling logs, 13, 15, 22, 23.
- Hinges, 131-133.
- Hinges,sizes of, 131.
- Hinging, Directions for, 132.
- Hog, 41.
- Holding tools, 97-105.
- Honeycombing, 46.
- Horse, 65, 100.
- Horsehair, 200.
- House construction, 200, 201.
- Jack-ladder, 32.
- Jack-plane. See Plane.
- Jam, log, 18, 19, 21.
- Japan, 209, 222.
- Japanese, 69, 97, 189.
- Joinery, 151.
- Joint, Beaded, 175, No. 73, 182.
- Bevel-shoulder, 172, No. 67, 182.
- Bird's mouth, 172, No. 69, 182.
- Boat-builders, 152, No. 7, 177.
- Brace, 171, No. 65, 182.
- Brace, Housed, 172, No. 66, 182, 207.
- Bridle, 172, No. 68, 182.
- Butt, 155, No. 11, 177, 187, 206.
- Butt, Doweled, 152, No. 8, 153, 177, 194.
- Caulked, 157, No. 22, 178.
- Checked, 157, No. 21, 178.
- Cogged, 157, No. 22, 178.[page 227]
- Corked, 157, No. 22, 178.
- Column, 169, No. 52, 181.
- Cross-lap, 155, No. 14, 177.
- Dado, 158, No. 25, 179, 191.
- Dado and rabbet, 158, No. 26, 179, 187.
- Dado, Dovetail, 158, No. 28, 179, 191, 206.
- Dado, housed, 158, No. 25, 179, 187, 207.
- Dado, tongue, and rabbet, 158, No. 27, 179, 191.
- Dovetail, Blind miter, 167, No. 51, 180, 188.
- Draw-bolt, 155, No. 10, 177.
- Edge-to-edge, 172 (70)-174.
- End-lap, 156, No. 16, No. 17, 178, 194, 206.
- Fillistered, 174, No. 71, 182.
- Fished, 151, No. 2, 177, 207.
- Forked tenon, 157, No. 23, 178.
- Gain, 159, No. 29, 179, 205.
- Glue, 172, No. 70, 182.
- Glued-and-blocked, 155, No. 12, 177.
- Grooved, 157, No. 25, 179.
- Halved Tee, 156, No. 15, 178.
- Halving, Dovetail, 157, No. 18, 178.
- Halving, Beveled, 157, No. 19, 178.
- Halving, 155-157.
- See also Joint, Cross-lap, End-lap, Middle lap.
- Haunching, Table, 164, No. 43, 180.
- Hopper, 155, No. 13, 177.
- Lap-dovetail, 157, No. 18, 178.
- Lapped and strapped, 151, No. 1, 177.
- Ledge, 157, No. 24, 179, 187.
- Ledge and miter, 171, No. 58, 181, 187, 206.
- Matched, 174, No. 72, 182.
- Middle-lap, 156, No. 15, 178.
- Miter, 167, No. 52, 181,
187, 194, 206.
- Double dovetail keyed, 171, No. 57, 181.
- Double tongue, 171, No. 60, 181.
- Doweled, 170, No. 53, 181.
- Lipped, 171, No. 58, 181.
- Slip dovetail, 171, No. 56, 181.
- Slip-feather, 170, No. 55, 181.
- Slip-key, 170, No. 55, 181.
- Spline, 170, No. 54, 181, 187.
- Stopped, 171, No. 59, 181.
- Tongue, 170, No. 54, 181.
- Mortise-and-tenon, 58, 127, 160-164,
172, 194.
- Bare-faced, 164, No. 44, 180, 185.
- Blind, 160, No. 32, 179, 193.
- Double, 163, No. 41, 180.
- Dovetail, 162, No. 37, 179.
- End, 164, No. 46, 180.
- Foxtail, 162, No. 36, 179.
- Haunched, 163, No. 42, 180, 193, 196, 207.
- Housed, 164, No. 45, 180.
- Keyed, 163, No. 39, 180, 185.
- Oblique, 172, No. 67, 182.
- Open, 164, No. 46, 180.
- Pinned, 162, No. 38, 180, 194, 207.
- Shoulder, 163, No. 40, 180.
- Stub, 160, No. 30, 179.
- Thru, 160, No. 31, 179.
- Tusk, 163, No. 40, 180, 207.
- Wedged, 128, 162, Nos. 34 and 35, 179.
- Notched, 157, No. 20, 178.
- Notch, Double, 157, No. 21, 178.
- Rabbet, 157, No. 24, 179, 174; No. 71, 182, 187.
- Rebated, See Joint, Rabbet.
- Rubbed, 172, No. 70, 173, 182, 205.
- Scarf, 151, Nos. 4, 5, 6 and 7, 177, 204, 207.
- Slip, 164, No. 46, 180, 194.
- Spliced, 151, Nos. 4, 5, 6, 7, 177, 204, 206, 207.
- Spline, 175, No. 74, 182.
- Squeezed, 172, No. 70, 174, 182.
- Stretcher, 171, No. 61, 181.
- Strut, 171, No. 62, 181, 207.
- Thrust, 171, Nos. 63 and 64, 181, 207.
- Tie, 171, Nos. 63 and 64, 181.
- Toe, 171, Nos. 63 and 64[page 228], 181.
- Toe-nailed, 154, No. 9, 177.
- Tongue-and-groove, 174, No. 72, 182.
- Jointer-plane, 72.
- Jointing a saw, 68.
- Joints, Chap. VII, 151-182.
- Joists, 201.
- Kerf, 10, 30, 62, 65.
- Key-pin of lock, 133.
- Kiln, lumber, 44, 46.
- Knife, 61, 136, 139.
- Knife, Sloyd, 61.
- Knob, Plane, 70.
- Knock-down furniture, 163.
- Knuckle of hinge, 131.
- Lac, insect, 215.
- Lacquer, 218.
- Ladle, 141.
- Landlooking, 7.
- Lath-machines, 39, 41.
- Laths, 39, 49, 201.
- Lay-out, 152, 154, 155, 156, 158, 159, 160, 163, 165, 183, 191, 195, 203, 204.
- Leather, 59, 201.
- Leaves of hinge, 132.
- Level, Spirit, 116.
- Lever-cap, 70, 77.
- Lid of box, 188.
- Lighting of shop, 142.
- Live rollers, 35.
- Loading logs, 15.
- Lock, mortise, 134.
- Lockers, 138, 142, 147, 148.
- Locks, 133, 134.
- Locomotive, Geared, 26.
- Log-boom, 20, 21.
- Log-carriage, 34, 35, 36.
- Log-flipper, 34.
- Logging, Chap. I, 7-29.
- Log-kicker, 34.
- Log-slip, 34.
- Log-stop, 34.
- Logwood, 211, 212.
- Loss of tools, 144-146.
- Lumber, 48.
- Lumber yard, 38.
- Lumberman's board rule, 111.
- Lumber mill, 32, 33.
- M (1000 feet), 49.
- Machine-screws, 127.
- Mahogany, 211.
- Mallet, 58, 96, 139.
- Marking-gage, 114-116, 136, 139, 203.
- Marking tools, 113-117.
- Matching-plane, 80, 139.
- Maul, 10.
- Measurements, 203.
- Measuring-tools, 105-117.
- Measuring wood, 13, 48, 49, 105-116.
- Mill-pond, 21, 32.
- Miter-box, 103, 137, 139, 194.
- Miter-clamp, 138, 141.
- Miter-square, 113, 137, 140.
- Molding-plane, 80.
- Monkey-wrench, 103, 138, 141.
- Mortise, 58, 160.
- Mortise-and-tenon.
- See Joint, Mortise-and-tenon.
- Mortise-chisel, 54, 55, 161.
- Mortise-gage, 116, 140, 161.
- Multiple parts, 204.
- Muntin, 193.
- Muslin, 200, 221.
- Octagonal scale, 108.
- Oil, 65, 130, 221.
- Oiler, 137, 140.
- Oilstone, 58, 121, 137, 140.
- Ordering of lumber, 49.
- Paint, 220-221.
- Panel construction, 164, 192-195, 205.
- Panel-iron, 127.
- Paper, Building, 201.
- Paring, 55, 57.
- Paring-chisel, 54.
- Peavey, 18.
- Peen of hammer, 95.
- Picture-frame, 167-169, 194, 205.[page 229]
- Pigments, 209.
- Pillow, 77.
- Pincers, 103.
- Pinch-dog, 102, 141, 170.
- Pintle of hinge, 132.
- Plane, parts of, 70.
- Bed rock, 71, 75, 137, 139.
- Block, 77, 137, 139.
- Circular, 80.
- Fore, 72, 137, 139.
- Jack, 71, 136, 138.
- Jointer, 72.
- Matching, 81, 139.
- Molding, 80.
- Oriental, 69.
- Rabbet, 79, 137, 139, 194.
- Router, 83, 139, 160.
- Scraper, 79, 139.
- Scratch, 79, 130.
- Scrub, 78.
- Smooth, 72, 75, 137, 139.
- Tongue-and-groove, 80.
- Universal, 81, 82.
- Plane-iron, 70, 77.
- Planes, 69-82.
- Planing, Directions for, 74-76, 78.
- Order of, 72.
- Plate-rack, 184.
- Plates, metal, 127.
- Plate, wall, 201.
- Pliers, 103, 138, 141.
- Plow, Snow, 14.
- Plug-cutter, 84, 86, 126, 140.
- Points in saw-teeth, 63.
- Polish, French, 217-218.
- Polishes, 214-220.
- Position of benches, 142.
- Posts, corner, 201.
- Potash, 150.
- Potassium bichromate, 130, 211, 212.
- Pounding tools, 94-97.
- Preservation of lumber, 47.
- See also seasoning.
- Principles of joinery, Chap. IX, 203-208.
- Pumice stone, 217.
- Rabbet-plane, 79, 137, 139, 194.
- Raft, Giant, 27, 29.
- Rafter-table, 110.
- Rafters, 201.
- Rail, 186, 193.
- Rail, Drawer, 196.
- Railways, logging, 22, 26.
- Rasp, 91.
- Ratchet-brace, 103, 105, 137.
- Reamer, 84, 87.
- Rebate. See Rabbet.
- Red, Venetian, 210.
- Ribbon, Wall, 201.
- Ridge-pole, 201.
- Rift-sawing, 41.
- Rip-saw, 63, 137, 139.
- Rivet-set, 141.
- Road, Ice, 14, 15.
- Rollers, Dead, 39.
- Rollers, Live, 35.
- Roll-ways, 16.
- Rossing of bark, 24.
- Router-plane, 83, 139, 160.
- Rule, 105, 107, 137, 139, 203.
- Running foot, 49.
- Rust, 125.
- On tools, 147.
- Sacking the rear, 17.
- Saddle seat, 60, 199.
- Sandpaper, 93, 221.
- Saw, 62-68.
- Selvage of lock, 133.
- Saw, Back, 65, 136, 138.
- Saw-carriage, 34, 35, 36.
- Sawdust, 39.
- Saw-filing and setting, 67, 68.
- Saw-horse, 65, 100.
- Sawing, Directions for, 64, 65.
- Saw-jointer, 68.
- Sawmill, 32, 33.
- Sawmilling, Chap. II, 30-44.
- Saw-set, 68.[page 230]
- Saw-vise, 67, 68.
- Sawing into lengths, 11, 12, 24.
- Scaling logs, 13.
- Scrap-box, 187.
- Scraper, 76, 91, 137, 139.
- Scraper, Veneer, 91, 92, 137, 139.
- Scraper-plane, 79, 139.
- Scraper steel, 92, 137, 139.
- Scraping tools, 90-94.
- Scrap pile, 41, 42.
- Scratch-awl, 116, 140.
- Scratch-plane, 79, 130.
- Screen-hinge, 131.
- Screw-box, 139.
- Screwdriver, 104, 105, 138, 140.
- Screw-gage, 116, 126.
- Screws, 125-127.
- Scribing, 112.
- Scrub-plane, 78.
- Seasoning, Chap. III, 45-48.
- Set of saw, 63, 68.
- Shank, 54.
- Sharpening of tools, The, 54, 58, 59, 60, 67, 76, 85, 86, 92-93, 117-121.
- Sharpening-tools, 117-121.
- Sheathing, 201.
- Shellac, 149, 215-218.
- Shelves, 185, 205.
- Shingles, 49, 201, 205.
- Shingle-machine, 39, 41.
- Shoe-pegs, 128.
- Shoulder of joint, 160.
- Shrinkage, 186, 188, 189, 191, 192, 194, 205.
- Siding, 201.
- Sienna, 209.
- Sighting, 72, 75.
- Silex, 214.
- Sill, 201.
- Sizing, 130.
- Skidder, steam, 25.
- Skidway, 9, 13, 24.
- Slab, 34, 35, 39.
- Slab-slasher, 39, 40.
- Slash-grain, 41, 42.
- Slash-sawing, 41.
- Sleigh haul, 13, 15.
- Sliding cut, 53, 56, 75, 78.
- Sliding T bevel, 113.
- Slipstone, 60, 121, 137, 140.
- Slip-tongue carts, 22.
- Smooth-plane, 72, 137, 139.
- Snips, 141.
- Snow-locomotive, 28.
- Soap, as a lubricant, 126.
- To prevent gluing, 130.
- Sole of Plane, 70.
- Sorting-jack, 21.
- Sorting-shed, 38.
- Spiriting off, 217.
- Splash-dam, 20, 21.
- Splitting tools, 51.
- Spokeshave, 82, 137, 139, 183.
- Stains, 209-213.
- Steel square, 107-111, 137, 140.
- Steel wool, 94, 211, 217, 221.
- Sticking, 45, 48.
- Stile, 193.
- Storing of lumber, 48.
- Stove, Gas, 138, 141.
- Stove-bolts, 127.
- Straight cut, 53.
- Strength of joints, 206.
- Strike of lock, 133.
- Stringer, 196.
- Stropping, 59.
- Studding, 201.
- Superposition, Method of, 156, 158, 159, 163, 166, 204.
- Survey of forest land, 7.
- Swamper, 12.
- Sweep of brace, 103.
- Table-hinge, 131.
- Table construction, 130, 164, 195.
- See also Table Top.
- Table top, 172, 175, 197.
- Taboret, 169, 170, 186.
- Tacks, 124.
- Tacks, double-pointed, 102, 124.
- Tang, 54.
- Tank, 14.
- Taper of cutting tools, 52.
- Tee-hinge, 131.
- Teeth of saw, 63.
- Tenon, 160, 206.
- See also Mortise and tenon.
Joint, Mortise and tenon.
- See also Mortise and tenon.
- Tenon-saw, 65.
- Toe of Plane, 70, 71.
- Throat of Plane, 70.[page 231]
- Tie-beams, 201.
- Timber, 48.
- Tonguing-and-grooving-plane, 80.
- Tool-grinder, 61, 120, 121, 137, 140.
- Tool-holder for grinding, 118-120.
- Tool-rack, 143, 144.
- Tools, Chap. IV, pp. 51-122.
- Tools, logging, 10.
- Traction engine, 28.
- Tools, Loss of, 144-146.
- Tractor, 28.
- Trammel-points, 114, 140.
- Transfer, Lumber, 36, 37.
- Transportation of logs, 13, 15, 16 ff, 23.
- Travoy, 9.
- Tray, 60, 183.
- Triangle, Blackboard, 141.
- Trimmer, 36, 38.
- Trimming logs, 12.
- Tripoli, 121, 147.
- Trolley for logs, 25.
- Try-square, 112, 136, 139, 140, 203.
- Tumbler of lock, 133.
- Turning-saw, 67, 137, 139, 183.
- Turpentine, 209, 210, 214, 222.
- Tusk.
- See Joint, mortise-and-tenon, tusk.
- Twist-bit, 84, 85.
- Twist-drill, 84, 85, 138.
- Twist-drill-gage, 116.
- Valuation survey, 7.
- Van, Logging camp, 9.
- Varnish, 149, 215-220.
- Varnishing, Process of, 219.
- Vaseline, 147.
- Veining tools, 140.
- Veneer-scraper, 91, 92, 137, 139.
- Vermilion, 210.
- Vise, 99, 138.
- Walnut, 210.
- Waney boards, 36.
- Warping, 48.
- Washer-cutter, 87, 140.
- Waste,cotton, 209, 221.
- Waste, sawmill, 39.
- Waterproof glue, 130.
- Water-stains, 210.
- Water-table, 201.
- Wax, 214.
- Webbing, 200.
- Wedge, Plane, 69, 70.
- Wedge, 10, 51, 52, 128, 162.
- Whetting tools, 58.
- Wind in board, 74.
- Winding sticks, 74, 113.
- Window-sash, 194.
- Wire edge, 59.
- Wire-gage, 116.
- Wooden structures, types of, Chap. VIII, 183-202.
- Working edge, 72, 115.
- Working face, 72, 115.
- Wrench, 103.
- See also Monkey-wrench.
Transcriber's Note:There is no Fig. 19; and Fig. 47 had no caption—caption added from text.Some of the illustrations were on numbered pages which contained no text. Illustrations have been moved to more relevant places, and extraneous page numbers removed. Page number references from the Index, and from within the text, have been corrected where necessary. (sundry commas added to Bibliograpy, as needed for consistency.) ERRATA, and [sic]Page 13: 'thoroly' [sic] period spelling for 'thoroughly'.Page 16: 'If a horse fall ...' [sic] 'If a horse (should) fall ...' Page 47: 'eargerly' corrected to 'eagerly'. (They are eagerly sought after...). Page 47: 'chlorid' corrected to 'chloride'. (zinc chloride). Page 58: 'splinttering' corrected to 'splintering'. Page 63: 'especally' corrected to 'especially'. Page 90: 'varities' corrected to 'varieties'. Page 160: 'shouders' corrected to 'shoulders'. (Locate accurately with a knife point the shoulders...). Page 162: Replaced two gaps in text with 'wedges' and 'No. 34'. (No. 35. A wedged ... by driving the wedges into saw kerfs in the tenon instead of along its sides as in No. 34.) Page 189: 'Fig. 285, E' corrected to 'Fig. 285, C' (The cover may have cleats on its underside, Fig. 285, C, which fit just inside the box and keep the top in place.) Page 219: 'funiture' corrected to 'furniture'. (...some are for floors, some for furniture,...) |
Download ePUB
If you like this ebook, consider a donation!