This is a modern-English version of How it Works: Dealing in simple language with steam, electricity, light, heat, sound, hydraulics, optics, etc., and with their applications to apparatus in common use, originally written by Williams, Archibald.
It has been thoroughly updated, including changes to sentence structure, words, spelling,
and grammar—to ensure clarity for contemporary readers, while preserving the original spirit and nuance. If
you click on a paragraph, you will see the original text that we modified, and you can toggle between the two versions.
Scroll to the bottom of this page and you will find a free ePUB download link for this book.
Transcriber’s Note
Note from the Transcriber
The punctuation and spelling from the original text have been faithfully preserved. Only obvious typographical errors have been corrected.
The punctuation and spelling from the original text have been faithfully preserved. Only obvious typographical errors have been corrected.
HOW IT WORKS
AUTHOR'S NOTE.
I beg to thank the following gentlemen and firms for the help they have given me in connection with the letterpress and illustrations of "How It Works"—
I want to thank the following gentlemen and companies for the support they provided regarding the text and illustrations of "How It Works"—
Messrs. F.J.C. Pole and M.G. Tweedie (for revision of MS.); W. Lineham; J.F. Kendall; E. Edser; A.D. Helps; J. Limb; The Edison Bell Phonograph Co.; Messrs. Holmes and Co.; The Pelton Wheel Co.; Messrs. Babcock and Wilcox; Messrs. Siebe, Gorman, and Co.; Messrs. Negretti and Zambra; Messrs. Chubb; The Yale Lock Co.; The Micrometer Engineering Co.; Messrs. Marshall and Sons; The Maignen Filter Co.; Messrs. Broadwood and Co.
Messrs. F.J.C. Pole and M.G. Tweedie (for reviewing the manuscript); W. Lineham; J.F. Kendall; E. Edser; A.D. Helps; J. Limb; The Edison Bell Phonograph Co.; Messrs. Holmes and Co.; The Pelton Wheel Co.; Messrs. Babcock and Wilcox; Messrs. Siebe, Gorman, and Co.; Messrs. Negretti and Zambra; Messrs. Chubb; The Yale Lock Co.; The Micrometer Engineering Co.; Messrs. Marshall and Sons; The Maignen Filter Co.; Messrs. Broadwood and Co.
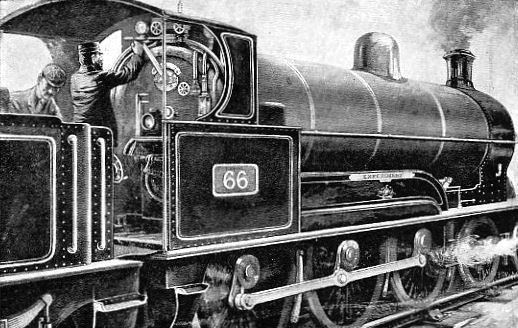
How It Works
How It Works
Dealing in Simple Language with Steam, Electricity,
Light, Heat, Sound, Hydraulics, Optics, etc.
and with their applications to Apparatus
in Common Use
By
ARCHIBALD WILLIAMS
Author of "The Romance of Modern Invention,"
"The Romance of Mining," etc., etc.
THOMAS NELSON AND SONS
London, Edinburgh, Dublin, and New York
Explaining steam, electricity,
light, heat, sound, hydraulics, optics, and more,
and how they relate to everyday devices.
By
ARCHIE WILLIAMS
Author of "The Romance of Modern Invention,"
"The Romance of Mining," and others.
THOMAS NELSON & SONS
London, Edinburgh, Dublin, and New York
PREFACE.
How does it work? This question has been put to me so often by persons young and old that I have at last decided to answer it in such a manner that a much larger public than that with which I have personal acquaintance may be able to satisfy themselves as to the principles underlying many of the mechanisms met with in everyday life.
How to does it work? I've been asked this question so many times by people of all ages that I've finally decided to answer it in a way that a much larger audience, beyond just those I personally know, can understand the principles behind many of the mechanisms we encounter in everyday life.
In order to include steam, electricity, optics, hydraulics, thermics, light, and a variety of detached mechanisms which cannot be classified under any one of these heads, within the compass of about 450 pages, I have to be content with a comparatively brief treatment of each subject. This brevity has in turn compelled me to deal with principles rather than with detailed descriptions of individual devices—though in several cases recognized types are examined. The reader will look in vain for accounts of the Yerkes telescope, of the latest thing in motor cars, and of the largest locomotive. But he will be put in the way of understanding the essential nature of all telescopes, motors, and steam-engines so far as they are at present developed, which I think may be of greater ultimate profit to the uninitiated.
To cover steam, electricity, optics, hydraulics, thermodynamics, light, and various other mechanisms that don’t fit neatly into these categories within about 450 pages, I have to keep each topic relatively brief. This brevity means I focus on principles instead of detailed descriptions of specific devices—though I do examine some well-known types. Readers looking for explanations of the Yerkes telescope, the latest motor vehicles, or the biggest locomotives will be disappointed. However, they will gain insight into the fundamental nature of all telescopes, motors, and steam engines as they exist today, which I believe will be more beneficial for those new to the subject.
While careful to avoid puzzling the reader by the use of mysterious phraseology I consider that the parts of a machine should be given their technical names wherever possible. To prevent misconception, many of the diagrams accompanying the letterpress have words as well as letters written on them. This course also obviates the wearisome reference from text to diagram necessitated by the use of solitary letters or figures.
While being careful not to confuse the reader with complicated language, I believe that the parts of a machine should be labeled with their technical names whenever possible. To avoid misunderstandings, many of the diagrams that go along with the text include both words and letters. This approach also eliminates the tedious back-and-forth referencing between the text and the diagrams that would be required if only letters or numbers were used.
I may add, with regard to the diagrams of this book, that they are purposely somewhat unconventional, not being drawn to scale nor conforming to the canons of professional draughtsmanship. Where advisable, a part of a machine has been exaggerated to show its details. As a rule solid black has been preferred to fine shading in sectional drawings, and all unnecessary lines are omitted. I would here acknowledge my indebtedness to my draughtsman, Mr. Frank Hodgson, for his care and industry in preparing the two hundred or more diagrams for which he was responsible.
I should mention that the diagrams in this book are intentionally a bit unconventional; they aren't drawn to scale and don't follow the strict rules of professional drawing. In some cases, I've exaggerated parts of a machine to highlight specific details. Generally, I've preferred solid black over fine shading in sectional drawings, and I've left out any unnecessary lines. I want to acknowledge my thanks to my draftsman, Mr. Frank Hodgson, for his dedication and hard work in creating the more than two hundred diagrams he was responsible for.
Four organs of the body—the eye, the ear, the larynx, and the heart—are noticed in appropriate places. The eye is compared with the camera, the larynx with a reed pipe, the heart with a pump, while the ear fitly opens the chapter on acoustics. The reader who is unacquainted with physiology will thus be enabled to appreciate the better these marvellous devices, far more marvellous, by reason of their absolutely automatic action, than any creation of human hands.
Four organs of the body—the eye, the ear, the larynx, and the heart—are highlighted in relevant sections. The eye is likened to a camera, the larynx to a reed pipe, the heart to a pump, while the ear appropriately begins the chapter on sound. This allows readers who aren't familiar with physiology to better appreciate these amazing mechanisms, which are even more incredible due to their fully automatic function, than anything made by human hands.
A.W.
A.W.
Uplands, Stoke Poges, Bucks.
Uplands, Stoke Poges, Bucks.
CONTENTS.
Chapter I.—THE STEAM-ENGINE. | |
What is steam?—The mechanical energy of steam—The boiler—The
circulation of water in a boiler—The enclosed furnace—The
multitubular boiler—Fire-tube boilers—Other types of boilers—Aids
to combustion—Boiler fittings—The safety-valve—The
water-gauge—The steam-gauge—The water supply to a
boiler |
13 |
Chapter II.—THE CONVERSION OF HEAT ENERGY INTO MECHANICAL MOTION. | |
Reciprocating engines—Double-cylinder engines—The function of
the fly-wheel—The cylinder—The slide-valve—The eccentric—"Lap"
of the valve: expansion of steam—How the cut-off is
managed—Limit of expansive working—Compound engines—Arrangement
of expansion engines—Compound locomotives—Reversing
gears—"Linking-up"—Piston-valves—Speed governors—Marine-speed
governors—The condenser |
44 |
Chapter III.—THE STEAM TURBINE. | |
How a turbine works—The De Laval turbine—The Parsons turbine—Description
of the Parsons turbine—The expansive action of
steam in a Parsons turbine—Balancing the thrust—Advantages
of the marine turbine |
74 |
Chapter IV.—THE INTERNAL-COMBUSTION ENGINE. | |
The meaning of the term—Action of the internal-combustion engine—The
motor car—The starting-handle—The engine—The carburetter—Ignition
of the charge—Advancing the spark—Governing
the engine—The clutch—The gear-box—The compensating
gear—The silencer—The brakes—Speed of cars |
87 |
Chapter V.—ELECTRICAL APPARATUS. | |
What is electricity?—Forms of electricity—Magnetism—The permanent
magnet—Lines of force—Electro-magnets—The electric
bell—The induction coil—The condenser—Transformation of
current—Uses of the induction coil |
112 |
Chapter VI.—THE ELECTRIC TELEGRAPH. | |
Needle instruments—Influence of current on the magnetic needle—Method
of reversing the current—Sounding instruments—Telegraphic
relays—Recording telegraphs—High-speed telegraphy |
127 |
Chapter VII.—WIRELESS TELEGRAPHY. | |
The transmitting apparatus—The receiving apparatus—Syntonic transmission—The advance of wireless telegraphy |
137 |
Chapter VIII.—THE TELEPHONE. | |
The Bell telephone—The Edison transmitter—The granular carbon
transmitter—General arrangement of a telephone circuit—Double-line
circuits—Telephone exchanges—Submarine telephony |
147 |
Chapter IX.—DYNAMOS AND ELECTRIC MOTORS. | |
A simple dynamo--Continuous-current dynamos--Multipolar dynamos--Exciting
the field magnets--Alternating current dynamos--The
transmission of power--The electric motor--Electric
lighting--The incandescent lamp--Arc lamps--"Series" and
"parallel" arrangement of lamps--Current for electric lamps--Electroplating |
159 |
Chapter X.—RAILWAY BRAKES. | |
The Vacuum Automatic brake—The Westinghouse air-brake |
187 |
Chapter XI.—RAILWAY SIGNALLING. | |
The block system—Position of signals—Interlocking the signals—Locking
gear—Points—Points and signals in combination—Working
the block system—Series of signalling operations—Single
line signals—The train staff—Train staff and ticket—Electric
train staff system—Interlocking—Signalling operations—Power
signalling—Pneumatic signalling—Automatic
signalling |
200 |
Chapter XII.—OPTICS. | |
Lenses—The image cast by a convex lens—Focus—Relative position
of object and lens—Correction of lenses for colour—Spherical
aberration—Distortion of image—The human eye—The use of
spectacles—The blind spot |
230 |
Chapter XIII.—THE MICROSCOPE, THE TELESCOPE, AND THE MAGIC-LANTERN. | |
The simple microscope—Use of the simple microscope in the telescope—The
terrestrial telescope—The Galilean telescope—The
prismatic telescope—The reflecting telescope—The parabolic
mirror—The compound microscope—The magic-lantern—The
bioscope—The plane mirror |
253 |
Chapter XIV.—SOUND AND MUSICAL INSTRUMENTS. | |
Nature of sound—The ear—Musical instruments—The vibration of
strings—The sounding-board and the frame of a piano—The
strings—The striking mechanism—The quality of a note |
270 |
Chapter XV.—WIND INSTRUMENTS. | |
Longitudinal vibration—Columns of air—Resonance of columns of
air—Length and tone—The open pipe—The overtones of an
open pipe—Where overtones are used—The arrangement of the
pipes and pedals—Separate sound-boards—Varieties of stops—Tuning
pipes and reeds—The bellows—Electric and pneumatic
actions—The largest organ in the world—Human reeds |
287 |
Chapter XVI.—TALKING-MACHINES. | |
The phonograph—The recorder—The reproducer—The gramophone—The
making of records—Cylinder records—Gramophone
records |
310 |
Chapter XVII.—WHY THE WIND BLOWS. | |
Why the wind blows—Land and sea breezes—Light air and moisture—The
barometer—The column barometer—The wheel barometer—A
very simple barometer—The aneroid barometer—Barometers
and weather—The diving-bell—The diving-dress—Air-pumps—Pneumatic
tyres—The air-gun—The self-closing door-stop—The
action of wind on oblique surfaces—The balloon—The
flying-machine |
322 |
Chapter XVIII.—HYDRAULIC MACHINERY. | |
The siphon—The bucket pump—The force-pump—The most marvellous
pump—The blood channels—The course of the blood—The
hydraulic press—Household water-supply fittings—The
ball-cock—The water-meter—Water-supply systems—The household
filter—Gas traps—Water engines—The cream separator—The
"hydro" |
350 |
Chapter XIX.—HEATING AND LIGHTING. | |
The hot-water supply—The tank system—The cylinder system—How
a lamp works—Gas and gasworks—Automatic stoking—A
gas governor—The gas meter—Incandescent gas lighting |
386 |
Chapter XX.—VARIOUS MECHANISMS. | |
Clocks & Watches:—A short history of timepieces—The construction
of timepieces—The driving power—The escapement—Compensating
pendulums—The spring balance—The cylinder
escapement—The lever escapement—Compensated balance-wheels—Keyless
winding mechanism for watches—The hour hand
train. Padlocks:—The Chubb lock—The Yale lock. The Cycle:—The
gearing of a cycle—The free wheel—The change-speed gear.
Farming Equipment:—The threshing-machine—Mowing-machines.
Natural Phenomena:—Why sun-heat varies
in intensity—The tides—Why high tide varies daily |
410 |
HOW IT WORKS.
Chapter I.
THE STEAM-ENGINE.
What is steam?—The mechanical energy of steam—The boiler—The circulation of water in a boiler—The enclosed furnace—The multitubular boiler—Fire-tube boilers—Other types of boilers—Aids to combustion—Boiler fittings—The safety-valve—The water-gauge—The steam-gauge—The water supply to a boiler.
What is steam?—The mechanical energy of steam—The boiler—The circulation of water in a boiler—The enclosed furnace—The multitubular boiler—Fire-tube boilers—Other types of boilers—Aids to combustion—Boiler fittings—The safety valve—The water gauge—The steam gauge—The water supply to a boiler.
WHAT IS STEAM?
WHAT IS STEAM?
If ice be heated above 32° Fahrenheit, its molecules lose their cohesion, and move freely round one another—the ice is turned into water. Heat water above 212° Fahrenheit, and the molecules exhibit a violent mutual repulsion, and, like dormant bees revived by spring sunshine, separate and dart to and fro. If confined in an air-tight vessel, the molecules have their flights curtailed, and beat more and more violently against their prison walls, so that every square inch of the[Pg 14] vessel is subjected to a rising pressure. We may compare the action of the steam molecules to that of bullets fired from a machine-gun at a plate mounted on a spring. The faster the bullets came, the greater would be the continuous compression of the spring.
If ice is heated above 32° Fahrenheit, its molecules lose their cohesion and move freely around each other—the ice turns into water. Heat the water above 212° Fahrenheit, and the molecules start to violently push away from each other, moving about like bees waking up in the spring sunshine. If they're trapped in an airtight container, their movement is restricted, and they bang harder and harder against the walls, causing the pressure inside the[Pg 14] vessel to rise. We can compare the behavior of the steam molecules to bullets being shot from a machine gun at a plate on a spring. The faster the bullets hit, the more the spring gets compressed continuously.
THE MECHANICAL ENERGY OF STEAM.
STEAM'S MECHANICAL ENERGY.
If steam is let into one end of a cylinder behind an air-tight but freely-moving piston, it will bombard the walls of the cylinder and the piston; and if the united push of the molecules on the one side of the latter is greater than the resistance on the other side opposing its motion, the piston must move. Having thus partly got their liberty, the molecules become less active, and do not rush about so vigorously. The pressure on the piston decreases as it moves. But if the piston were driven back to its original position against the force of the steam, the molecular activity—that is, pressure—would be restored. We are here assuming that no heat has passed through the cylinder or piston and been radiated into the air; for any loss of heat means loss of energy, since heat is energy.
If steam is released into one end of a cylinder with an airtight but freely-moving piston, it will hit the walls of the cylinder and the piston. If the combined force of the molecules on one side of the piston is stronger than the resistance on the other side that is opposing its motion, the piston will move. As the molecules gain some freedom, they become less active and don’t move around as energetically. The pressure on the piston decreases as it moves. However, if the piston were pushed back to its original position against the steam's force, the molecular activity—that is, the pressure—would return. We’re assuming no heat has escaped through the cylinder or piston and dissipated into the air; because any loss of heat means a loss of energy, since heat is energy.
THE BOILER.
THE BOILER.
The combustion of fuel in a furnace causes the[Pg 15] walls of the furnace to become hot, which means that the molecules of the substance forming the walls are thrown into violent agitation. If the walls are what are called "good conductors" of heat, they will transmit the agitation through them to any surrounding substance. In the case of the ordinary house stove this is the air, which itself is agitated, or grows warm. A steam-boiler has the furnace walls surrounded by water, and its function is to transmit molecular movement (heat, or energy) through the furnace plates to the water until the point is reached when steam generates. At atmospheric pressure—that is, if not confined in any way—steam would fill 1,610 times the space which its molecules occupied in their watery formation. If we seal up the boiler so that no escape is possible for the steam molecules, their motion becomes more and more rapid, and pressure is developed by their beating on the walls of the boiler. There is theoretically no limit to which the pressure may be raised, provided that sufficient fuel-combustion energy is transmitted to the vaporizing water.
The burning of fuel in a furnace makes the[Pg 15] walls heat up, which causes the molecules in the walls to move around wildly. If the walls are what we call "good conductors" of heat, they will pass that movement through to anything around them. In a typical household stove, that's the air, which gets agitated or warms up. A steam boiler has its walls surrounded by water, and its job is to transfer that molecular movement (heat or energy) through the furnace walls to the water until it reaches the point where steam is produced. At atmospheric pressure—meaning it's not confined—steam would take up 1,610 times the space that its molecules occupied as water. If we seal the boiler so that the steam molecules can’t escape, their movement speeds up, creating pressure as they bang against the walls of the boiler. In theory, there's no limit to how much pressure can build up, as long as enough energy from the burning fuel is supplied to the water turning into steam.
To raise steam in large quantities we must employ a fuel which develops great heat in proportion to its weight, is readily procured, and cheap. Coal[Pg 16] fulfils all these conditions. Of the 800 million tons mined annually throughout the world, 400 million tons are burnt in the furnaces of steam-boilers.
To generate steam in large amounts, we need to use a fuel that produces a lot of heat relative to its weight, is easy to obtain, and is inexpensive. Coal[Pg 16] meets all these criteria. Out of the 800 million tons mined each year worldwide, 400 million tons are burned in steam-boiler furnaces.
A good boiler must be—(1) Strong enough to withstand much higher pressures than that at which it is worked; (2) so designed as to burn its fuel to the greatest advantage.
A good boiler must be—(1) strong enough to handle much higher pressures than what it operates at; (2) designed to burn its fuel as efficiently as possible.
Even in the best-designed boilers a large part of the combustion heat passes through the chimney, while a further proportion is radiated from the boiler. Professor John Perry[1] considers that this waste amounts, under the best conditions at present obtainable, to eleven-twelfths of the whole. We have to burn a shillingsworth of coal to capture the energy stored in a pennyworth. Yet the steam-engine of to-day is three or four times as efficient as the engine of fifty years ago. This is due to radical improvements in the design of boilers and of the machinery which converts the heat energy of steam into mechanical motion.
Even in the best-designed boilers, a significant amount of combustion heat escapes through the chimney, and even more is lost through radiation from the boiler. Professor John Perry[1] estimates that this waste, under the best current conditions, amounts to eleven-twelfths of the total. We need to burn a shilling's worth of coal to obtain the energy stored in a penny's worth. However, today's steam engines are three or four times more efficient than those from fifty years ago. This improvement is due to major advancements in the design of boilers and the machinery that converts the heat energy of steam into mechanical motion.
CIRCULATION OF WATER IN A BOILER.
CIRCULATION OF WATER IN A BOILER.
If you place a pot filled with water on an open fire, and watch it when it boils, you will notice[Pg 17] that the water heaves up at the sides and plunges down at the centre. This is due to the water being heated most at the sides, and therefore being lightest there. The rising steam-bubbles also carry it up. On reaching the surface, the bubbles burst, the steam escapes, and the water loses some of its heat, and rushes down again to take the place of steam-laden water rising.
If you put a pot of water on an open fire and watch it boil, you'll see[Pg 17] that the water rises at the edges and sinks in the middle. This happens because the water heats up more at the sides, making it lighter there. The rising steam bubbles also lift it up. When these bubbles reach the surface, they burst, releasing steam, and the water loses some of its heat, rushing back down to replace the steam-filled water that's rising.
![]() |
![]() |
If the fire is very fierce, steam-bubbles may rise from all points at the bottom, and impede downward currents (Fig. 1). The pot then "boils over."
If the fire is really intense, steam bubbles might rise from all areas at the bottom, blocking the downward currents (Fig. 1). The pot then "boils over."
Fig. 2 shows a method of preventing this trouble. We lower into our pot a vessel of somewhat smaller diameter, with a hole in the bottom, arranged in such a[Pg 18] manner as to leave a space between it and the pot all round. The upward currents are then separated entirely from the downward, and the fire can be forced to a very much greater extent than before without the water boiling over. This very simple arrangement is the basis of many devices for producing free circulation of the water in steam-boilers.
Fig. 2 shows a way to prevent this issue. We lower a smaller vessel into our pot, which has a hole in the bottom, set up so that there’s space all around it. This way, the upward currents are completely separated from the downward ones, allowing us to increase the fire much more than before without the water boiling over. This straightforward setup is the foundation of many devices designed to ensure free circulation of water in steam boilers.
We can easily follow out the process of development. In Fig. 3 we see a simple U-tube depending from a vessel of water. Heat is applied to the left leg, and a steady circulation at once commences. In order to increase the heating surface we can extend the heated leg into a long incline (Fig. 4), beneath which three lamps instead of only one are placed. The direction of the circulation is the same, but its rate is increased.
We can easily trace the process of development. In Fig. 3, we see a simple U-tube connected to a water container. Heat is applied to the left leg, and a steady circulation immediately begins. To increase the heating surface, we can extend the heated leg into a long slope (Fig. 4), with three lamps set up underneath instead of just one. The direction of the circulation remains the same, but its speed increases.
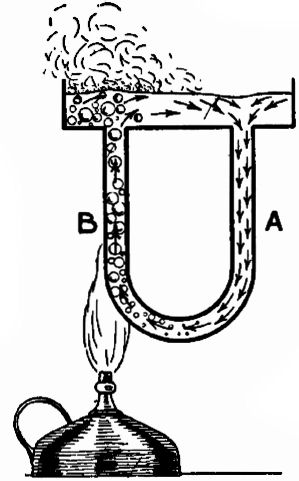
A further improvement results from increasing the number of tubes (Fig. 5), keeping them all on the slant, so that the heated water and steam may rise freely.
A further improvement comes from adding more tubes (Fig. 5), keeping them all at an angle so that the heated water and steam can rise freely.
THE ENCLOSED FURNACE.
THE ENCLOSED HEATER.
![]() |
![]() |
Still, a lot of the heat gets away. In a steam-boiler the burning fuel is enclosed either by fire-brick or a "water-jacket," forming part of the boiler. A water-jacket signifies a double coating of metal plates with a space between, which is filled with water (see Fig. 6). The fire is now enclosed much as it is in a kitchen range. But our boiler must not be so wasteful of the heat as is that useful household fixture. On their way to the funnel the flames and hot gases should act on a very large metal or other surface in contact with the water of the boiler, in order to give up a due proportion of their heat.
Still, a lot of the heat escapes. In a steam boiler, the burning fuel is surrounded either by firebrick or a "water jacket," which is part of the boiler. A water jacket means there are double layers of metal plates with a space in between, filled with water (see Fig. 6). The fire is now enclosed much like it is in a kitchen stove. However, our boiler shouldn't waste heat like that handy household appliance. As the flames and hot gases travel to the funnel, they should interact with a large metal or other surface in contact with the boiler's water to release a proper amount of their heat.
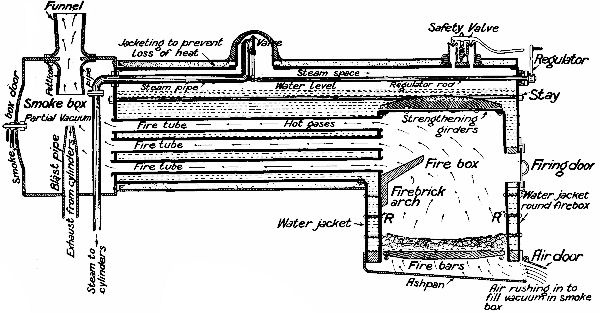
THE MULTITUBULAR BOILER.
The multi-tube boiler.
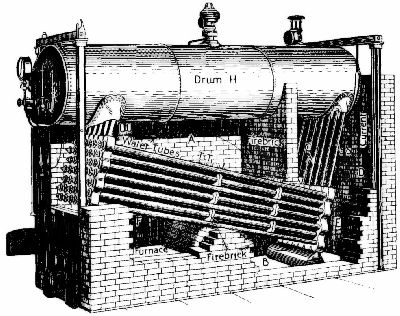
To save room, boilers which have to make steam very quickly and at high pressures are largely composed of pipes. Such boilers we call multitubular. They are of two kinds—(1) Water-tube boilers; in which the water circulates through tubes exposed to the furnace heat. The Babcock and Wilcox boiler (Fig. 7) is typical of this variety.[Pg 22] (2) Fire-tube boilers; in which the hot gases pass through tubes surrounded by water. The ordinary locomotive boiler (Fig. 6) illustrates this form.
To save space, boilers that need to produce steam quickly and at high pressures are mostly made up of pipes. We refer to these boilers as multitubular. There are two types: (1) Water-tube boilers, where water flows through tubes that are exposed to the heat of the furnace. The Babcock and Wilcox boiler (Fig. 7) is a common example of this type.[Pg 22] (2) Fire-tube boilers, where hot gases move through tubes that are surrounded by water. The typical locomotive boiler (Fig. 6) illustrates this design.
The Babcock and Wilcox boiler is widely used in mines, power stations, and, in a modified form, on shipboard. It consists of two main parts—(1) A drum, H, in the upper part of which the steam collects; (2) a group of pipes arranged on the principle illustrated by Fig. 5. The boiler is seated on a rectangular frame of fire-bricks. At one end is the furnace door; at the other the exit to the chimney. From the furnace F the flames and hot gases rise round the upper end of the sloping tubes TT into the space A, where they play upon the under surface of H before plunging downward again among the tubes into the space B. Here the temperature is lower. The arrows indicate further journeys upwards into the space C on the right of a fire-brick division, and past the down tubes SS into D, whence the hot gases find an escape into the chimney through the opening E. It will be noticed that the greatest heat is brought to bear on TT near their junction with UU, the "uptake" tubes; and that every succeeding passage of the pipes brings the gradually cooling gases nearer to the "downtake" tubes SS.
The Babcock and Wilcox boiler is commonly used in mines, power plants, and, in a modified version, on ships. It has two main components—(1) A drum, H, where steam collects at the top; (2) a set of pipes arranged based on the principle shown in Fig. 5. The boiler is placed on a rectangular frame made of fire bricks. One end has the furnace door, while the other leads to the chimney. Flames and hot gases rise from the furnace F around the upper end of the inclined tubes TT into the space A, where they heat the underside of H before moving back down among the tubes into the space B. Here, the temperature is lower. The arrows indicate additional paths upward into the space C on the right of a fire-brick wall and past the down tubes SS into D, where the hot gases exit into the chimney through the opening E. It's notable that the highest heat is focused on TT near the junction with UU, the "uptake" tubes; and that each subsequent passage of the gases brings them closer to the "downtake" tubes SS.
The pipes TT are easily brushed and scraped after the removal of plugs from the "headers" into which the tube ends are expanded.
The pipes TT are easy to clean after the plugs are taken out from the "headers" where the tube ends are expanded.
Other well-known water-tube boilers are the Yarrow, Belleville, Stirling, and Thorneycroft, all used for driving marine engines.
Other well-known water-tube boilers include the Yarrow, Belleville, Stirling, and Thorneycroft, all used for powering marine engines.
FIRE-TUBE BOILERS.
Fire-tube boilers.
Fig. 6 shows a locomotive boiler in section. To the right is the fire-box, surrounded on all sides by a water-jacket in direct communication with the barrel of the boiler. The inner shell of the fire-box is often made of copper, which withstands the fierce heat better than steel; the outer, like the rest of the boiler, is of steel plates from ½ to ¾ inch thick. The shells of the jacket are braced together by a large number of rivets, RR; and the top, or crown, is strengthened by heavy longitudinal girders riveted to it, or is braced to the top of the boiler by long bolts. A large number of fire-tubes (only three are shown in the diagram for the sake of simplicity) extend from the fire-box to the smoke-box. The most powerful "mammoth" American locomotives have 350 or more tubes, which, with the fire-box, give 4,000 square feet of surface[Pg 24] for the furnace heat to act upon. These tubes are expanded at their ends by a special tool into the tube-plates of the fire-box and boiler front. George Stephenson and his predecessors experienced great difficulty in rendering the tube-end joints quite water-tight, but the invention of the "expander" has removed this trouble.
Fig. 6 shows a section view of a locomotive boiler. On the right is the fire-box, completely surrounded by a water-jacket that connects directly with the barrel of the boiler. The inner shell of the fire-box is usually made of copper, which handles intense heat better than steel; the outer shell, like the rest of the boiler, uses steel plates that are ½ to ¾ inch thick. The shells of the jacket are held together with many rivets, RR; and the top, or crown, is reinforced with heavy longitudinal girders riveted to it, or is connected to the top of the boiler by long bolts. A large number of fire-tubes (only three are shown in the diagram for simplicity) run from the fire-box to the smoke-box. The most powerful "mammoth" American locomotives have 350 or more tubes, which, along with the fire-box, provide 4,000 square feet of surface[Pg 24] for the furnace heat to act upon. These tubes are expanded at their ends using a special tool to fit into the tube-plates of the fire-box and boiler front. George Stephenson and his predecessors faced significant challenges in making the tube-end joints completely water-tight, but the invention of the "expander" has solved this issue.
The fire-brick arch shown (Fig. 6) in the fire-box is used to deflect the flames towards the back of the fire-box, so that the hot gases may be retarded somewhat, and their combustion rendered more perfect. It also helps to distribute the heat more evenly over the whole of the inside of the box, and prevents cold air from flying directly from the firing door to the tubes. In some American and Continental locomotives the fire-brick arch is replaced by a "water bridge," which serves the same purpose, while giving additional heating surface.
The fire-brick arch shown (Fig. 6) in the firebox is designed to redirect the flames towards the back of the firebox, which slows down the hot gases a bit and improves their combustion. It also helps to spread the heat more evenly throughout the entire interior of the box and stops cold air from rushing directly from the firing door to the tubes. In some American and European locomotives, the fire-brick arch is replaced by a "water bridge," which fulfills the same role while providing extra heating surface.
The water circulation in a locomotive boiler is—upwards at the fire-box end, where the heat is most intense; forward along the surface; downwards at the smoke-box end; backwards along the bottom of the barrel.
The water circulation in a locomotive boiler is—upwards at the fire-box end, where the heat is strongest; forward along the surface; downwards at the smoke-box end; and backwards along the bottom of the barrel.
OTHER TYPES OF BOILERS.
OTHER TYPES OF BOILERS.
For small stationary land engines the vertical[Pg 25] boiler is much used. In Fig. 8 we have three forms of this type—A and B with cross water-tubes; C with vertical fire-tubes. The furnace in every case is surrounded by water, and fed through a door at one side.
For small stationary land engines, the vertical[Pg 25] boiler is commonly used. In Fig. 8, we see three variations of this type—A and B with cross water tubes, and C with vertical fire tubes. The furnace in each case is surrounded by water and is supplied through a door on one side.
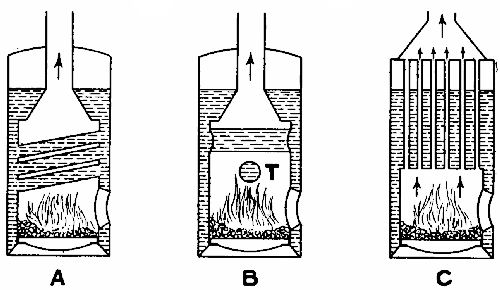
The Lancashire boiler is of large size. It has a cylindrical shell, measuring up to 30 feet in length and 7 feet in diameter, traversed from end to end by two large flues, in the rear part of which are situated the furnaces. The boiler is fixed on a seating of fire-bricks, so built up as to form three flues, A and BB, shown in cross section in Fig. 9. The furnace gases, after leaving the two furnace flues, are deflected downwards into the channel A, by which they pass underneath the boiler to a point[Pg 26] almost under the furnace, where they divide right and left and travel through cross passages into the side channels BB, to be led along the boiler's flanks to the chimney exit C. By this arrangement the effective heating surface is greatly increased; and the passages being large, natural draught generally suffices to maintain proper combustion. The Lancashire boiler is much used in factories and (in a modified form) on ships, since it is a steady steamer and is easily kept in order.
The Lancashire boiler is quite large. It has a cylindrical shell that's up to 30 feet long and 7 feet in diameter, featuring two large flues running from one end to the other, with the furnaces located in the rear section. The boiler is mounted on a base made of fire-bricks, arranged to create three flues, A and BB, illustrated in cross section in Fig. 9. After the furnace gases exit the two furnace flues, they are directed downwards into channel A, where they pass underneath the boiler to a point[Pg 26] almost directly beneath the furnace. Here, the gases split to the right and left and move through side passages into channel BB, traveling along the sides of the boiler to the chimney exit C. This design significantly increases the effective heating surface, and the large passages generally allow for sufficient natural draught to maintain proper combustion. The Lancashire boiler is widely used in factories and, in a modified version, on ships, as it provides steady steam and is easy to maintain.

In marine boilers of cylindrical shape cross water-tubes and fire-tubes are often employed to increase the heating surface. Return tubes are also led through the water to the funnels, situated at the same end as the furnace.
In cylindrical marine boilers, cross water-tubes and fire-tubes are often used to enhance the heating surface. Return tubes are also passed through the water to the funnels, which are located at the same end as the furnace.
AIDS TO COMBUSTION.
COMBUSTION AIDS.
We may now turn our attention more particularly to the chemical process called combustion, upon[Pg 27] which a boiler depends for its heat. Ordinary steam coal contains about 85 per cent. of carbon, 7 per cent. of oxygen, and 4 per cent. of hydrogen, besides traces of nitrogen and sulphur and a small incombustible residue. When the coal burns, the nitrogen is released and passes away without combining with any of the other elements. The sulphur unites with hydrogen and forms sulphuretted hydrogen (also named sulphurous acid), which is injurious to steel plates, and is largely responsible for the decay of tubes and funnels. More of the hydrogen unites with the oxygen as steam.
We can now focus more closely on the chemical process known as combustion, which is essential for the heat produced by a boiler. Regular steam coal is made up of about 85% carbon, 7% oxygen, and 4% hydrogen, along with small amounts of nitrogen and sulfur, and a little bit of incombustible residue. When the coal burns, the nitrogen is released and escapes without reacting with any of the other elements. The sulfur combines with hydrogen to create hydrogen sulfide (also known as sulfurous acid), which is harmful to steel plates and contributes significantly to the deterioration of tubes and funnels. More of the hydrogen combines with oxygen to form steam.
The most important element in coal is the carbon (known chemically by the symbol C). Its combination with oxygen, called combustion, is the act which heats the boiler. Only when the carbon present has combined with the greatest possible amount of oxygen that it will take into partnership is the combustion complete and the full heat-value (fixed by scientific experiment at 14,500 thermal units per pound of carbon) developed.
The key component in coal is carbon (chemically represented by the symbol C). Its reaction with oxygen, known as combustion, is what heats the boiler. Combustion is only complete when the carbon has bonded with as much oxygen as it can, producing the maximum heat value (determined through scientific testing to be 14,500 thermal units per pound of carbon).
Now, carbon may unite with oxygen, atom for atom, and form carbon monoxide (CO); or in the proportion of one atom of carbon to two of [Pg 28]oxygen, and form carbon dioxide (CO2). The former gas is combustible—that is, will admit another atom of carbon to the molecule—but the latter is saturated with oxygen, and will not burn, or, to put it otherwise, is the product of perfect combustion. A properly designed furnace, supplied with a due amount of air, will cause nearly all the carbon in the coal burnt to combine with the full amount of oxygen. On the other hand, if the oxygen supply is inefficient, CO as well as CO2 will form, and there will be a heat loss, equal in extreme cases to two-thirds of the whole. It is therefore necessary that a furnace which has to eat up fuel at a great pace should be artificially fed with air in the proportion of from 12 to 20 pounds of air for every pound of fuel. There are two methods of creating a violent draught through the furnace. The first is—
Now, carbon can combine with oxygen, atom for atom, to create carbon monoxide (CO); or in a ratio of one atom of carbon to two of [Pg 28]oxygen, producing carbon dioxide (CO2). The first gas is flammable, meaning it can incorporate another carbon atom into the molecule, while the latter is saturated with oxygen and won't ignite, or in other words, is the result of perfect combustion. A well-designed furnace, with the right amount of air, will ensure that nearly all the carbon in the coal burned combines with the full amount of oxygen. However, if the oxygen supply is insufficient, both CO and CO2 will form, leading to a heat loss that could be as high as two-thirds of the total in extreme cases. Therefore, it’s crucial for a furnace that needs to consume fuel quickly to be provided artificially with air in the amount of 12 to 20 pounds of air for every pound of fuel. There are two ways to create a strong draft through the furnace. The first is—
The forced draught; very simply exemplified by the ordinary bellows used in every house. On a ship (Fig. 10) the principle is developed as follows:—The boilers are situated in a compartment or compartments having no communication with the outer air, except for the passages down which air is forced by powerful fans at a pressure considerably greater than that of the atmosphere. There is only one "way out"—namely, through the furnace[Pg 29] and tubes (or gas-ways) of the boiler, and the funnel. So through these it rushes, raising the fuel to white heat. As may easily be imagined, the temperature of a stokehold, especially in the tropics, is far from pleasant. In the Red Sea the thermometer sometimes rises to 170° Fahrenheit or more, and the poor stokers have a very bad time of it.
The forced draught is simply illustrated by the common bellows found in every home. On a ship (Fig. 10), the concept works like this: The boilers are located in a section or sections that have no connection to the outside air, except for the ducts where air is pushed in by powerful fans at a pressure much higher than atmospheric pressure. There’s only one way out—through the furnace[Pg 29] and the tubes (or gas passages) of the boiler, and then out the funnel. The air rushes through, heating the fuel to an intense level. As you can imagine, the temperature in the stokehold, especially in tropical regions, is quite uncomfortable. In the Red Sea, temperatures can sometimes reach 170° Fahrenheit or more, making life very tough for the stokers.


The second system is that of the induced draught. Here air is sucked through the furnace by creating a vacuum in the funnel and in a chamber opening into it. Turning to Fig. 6, we see a pipe through which the exhaust steam from the locomotive's cylinders is shot upwards into the funnel, in which, and in the smoke-box beneath it, a strong vacuum is formed while the engine is running. Now, "nature abhors a vacuum," so air will get into the smoke-box if there be a way open. There is—through the air-doors at the bottom of the furnace, the furnace itself, and the fire-tubes; and on the way oxygen combines with the carbon of the fuel, to form carbon dioxide. The power of the draught is so great that, as one often notices when a train passes during the night, red-hot cinders, plucked from the fire-box, and dragged through the tubes, are hurled far into the air. It might be mentioned in parenthesis that the so-called "smoke" which pours from the funnel of a moving engine is mainly condensing steam. A steamship, on the other hand, belches smoke only from its funnels, as fresh water is far too precious to waste as steam. We shall refer to this later on (p. 72).
The second system is the induced draught. Here, air is sucked into the furnace by creating a vacuum in the chimney and in a chamber connected to it. Looking at Fig. 6, we can see a pipe that directs exhaust steam from the locomotive's cylinders up into the chimney, where a strong vacuum is generated while the engine is running. Now, "nature abhors a vacuum," so air will enter the smoke-box if there's an opening. There is—through the air doors at the bottom of the furnace, the furnace itself, and the fire-tubes; and along the way, oxygen combines with the carbon in the fuel to create carbon dioxide. The power of the draught is so strong that, as you often see when a train passes at night, red-hot cinders, pulled from the fire-box and dragged through the tubes, are thrown high into the air. It's worth noting that the so-called "smoke" seen coming from the chimney of a moving engine is mostly condensing steam. A steamship, on the other hand, only releases smoke from its funnels, as fresh water is much too valuable to waste as steam. We will discuss this later on (p. 72).
BOILER FITTINGS.
Boiler Components.
The most important fittings on a boiler are:—(1) the safety-valve; (2) the water-gauge; (3) the steam-gauge; (4) the mechanisms for feeding it with water.
The most important parts of a boiler are:—(1) the safety valve; (2) the water gauge; (3) the steam gauge; (4) the systems for supplying it with water.
THE SAFETY-VALVE.
The pressure release valve.
Professor Thurston, an eminent authority on the steam-engine, has estimated that a plain cylindrical[Pg 32] boiler carrying 100 lbs. pressure to the square inch contains sufficient stored energy to project it into the air a vertical distance of 3½ miles. In the case of a Lancashire boiler at equal pressure the distance would be 2½ miles; of a locomotive boiler, at 125 lbs., 1½ miles; of a steam tubular boiler, at 75 lbs., 1 mile. According to the same writer, a cubic foot of heated water under a pressure of from 60 to 70 lbs. per square inch has about the same energy as one pound of gunpowder.
Professor Thurston, a leading expert on steam engines, has calculated that a plain cylindrical[Pg 32] boiler with a pressure of 100 lbs. per square inch has enough stored energy to launch it into the air vertically for a distance of 3½ miles. For a Lancashire boiler at the same pressure, the distance would be 2½ miles; for a locomotive boiler at 125 lbs., it would be 1½ miles; and for a steam tubular boiler at 75 lbs., it would be 1 mile. According to the same author, a cubic foot of heated water under a pressure of 60 to 70 lbs. per square inch has about the same energy as one pound of gunpowder.
Steam is a good servant, but a terrible master. It must be kept under strict control. However strong a boiler may be, it will burst if the steam pressure in it be raised to a certain point; and some device must therefore be fitted on it which will give the steam free egress before that point is reached. A device of this kind is called a safety-valve. It usually blows off at less than half the greatest pressure that the boiler has been proved by experiment to be capable of withstanding.
Steam is a useful tool, but a dangerous boss. It needs to be managed carefully. No matter how sturdy a boiler is, it will explode if the steam pressure inside gets too high; so, some mechanism must be installed to allow the steam to escape before that happens. This mechanism is known as a safety-valve. Typically, it releases steam at less than half the maximum pressure that the boiler has been tested to handle.
In principle the safety-valve denotes an orifice closed by an accurately-fitting plug, which is pressed against its seat on the boiler top by a weighted lever, or by a spring. As soon as the steam pressure on the face of the plug exceeds the counteracting force[Pg 33] of the weight or spring, the plug rises, and steam escapes until equilibrium of the opposing forces is restored.
In simple terms, the safety valve is an opening that's sealed by a plug that fits perfectly. This plug is pushed against its seat on the top of the boiler by a weighted lever or a spring. When the steam pressure on the plug’s surface is higher than the opposing force[Pg 33] from the weight or spring, the plug moves up, allowing steam to escape until the forces balance out again.
On stationary engines a lever safety-valve is commonly employed (Fig. 11). The blowing-off point can be varied by shifting the weight along the arm so as to give it a greater or less leverage. On locomotive and marine boilers, where shocks and movements have to be reckoned with, weights are replaced by springs, set to a certain tension, and locked up so that they cannot be tampered with.
On stationary engines, a lever safety valve is commonly used (Fig. 11). The release point can be adjusted by moving the weight along the arm to give it more or less leverage. On locomotives and marine boilers, where vibrations and movements need to be considered, weights are replaced with springs that are set to a specific tension and locked in place to prevent tampering.

Boilers are tested by filling the boilers quite full and (1) by heating the water, which expands slightly, but with great pressure; (2) by forcing in additional water with a powerful pump. In either case a rupture[Pg 34] would not be attended by an explosion, as water is very inelastic.
Boilers are tested by filling them to the top and (1) heating the water, which expands slightly but creates a lot of pressure; (2) by pushing in more water with a strong pump. In either situation, a rupture[Pg 34] wouldn’t result in an explosion since water is very inelastic.
The days when an engineer could "sit on the valves"—that is, screw them down—to obtain greater pressure, are now past, and with them a considerable proportion of the dangers of high-pressure steam. The Factory Act of 1895, in force throughout the British Isles, provides that every boiler for generating steam in a factory or workshop where the Act applies must have a proper safety-valve, steam-gauge, and water-gauge; and that boilers and fittings must be examined by a competent person at least once in every fourteen months. Neglect of these provisions renders the owner of a boiler liable to heavy penalties if an explosion occurs.
The days when an engineer could simply "sit on the valves"—meaning tighten them down—to increase pressure are gone, along with many of the dangers associated with high-pressure steam. The Factory Act of 1895, which is in effect across the British Isles, states that every boiler used for generating steam in a factory or workshop covered by the Act must be equipped with a proper safety valve, steam gauge, and water gauge. Additionally, boilers and their fittings must be inspected by a qualified person at least once every fourteen months. Failing to comply with these requirements makes the boiler owner subject to significant penalties in the event of an explosion.
One of the most disastrous explosions on record took place at the Redcar Iron Works, Yorkshire, in June 1895. In this case, twelve out of fifteen boilers ranged side by side burst, through one proving too weak for its work. The flying fragments of this boiler, striking the sides of other boilers, exploded them, and so the damage was transmitted down the line. Twenty men were killed and injured; while masses of metal, weighing several tons each, were hurled 250 yards, and caused widespread damage.
One of the worst explosions on record happened at the Redcar Iron Works in Yorkshire in June 1895. In this incident, twelve out of fifteen boilers installed side by side exploded because one was too weak for its job. The flying pieces of this boiler hit the sides of the other boilers, causing them to explode as well, and the damage spread along the line. Twenty men were killed and injured, while massive pieces of metal, weighing several tons each, were thrown 250 yards and caused extensive damage.
The following is taken from a journal, dated December 22, 1895: "Providence (Rhode Island).—A recent prophecy that a boiler would explode between December 16 and 24 in a store has seriously affected the Christmas trade. Shoppers are incredibly nervous. One store advertises, 'No boilers are being used; lifts running electrically.' All stores have had their boilers inspected."
The following is taken from a journal, dated December 22, 1895: "Providence (Rhode Island).—A recent prediction that a boiler will explode between December 16 and 24 at a store has significantly impacted the Christmas shopping season. Customers are extremely anxious. One store is advertising, 'No boilers in use; elevators operating on electricity.' All stores have had their boilers checked."
THE WATER-GAUGE.
THE WATER METER.
No fitting of a boiler is more important than the water-gauge, which shows the level at which the water stands. The engineer must continually consult his gauge, for if the water gets too low, pipes and other surfaces exposed to the furnace flames may burn through, with disastrous results; while, on the other hand, too much water will cause bad steaming. A section of an ordinary gauge is seen in Fig. 12. It consists of two parts, each furnished with a gland, G, to make a steam-tight joint round the glass tube, which is inserted through the hole covered by the plug P1. The cocks T1 T2 are normally open, allowing the ingress of steam and water respectively to the tube. Cock T3 is kept closed unless for any reason it is necessary to blow steam or water [Pg 36]through the gauge. The holes C C can be cleaned out if the plugs P2 P3 are removed.
No fitting of a boiler is more important than the water-gauge, which shows the level of the water. The engineer must constantly check the gauge, because if the water gets too low, the pipes and other surfaces exposed to the furnace flames can burn through, leading to disastrous consequences. On the other hand, too much water will cause poor steaming. A section of a standard gauge is shown in Fig. 12. It consists of two parts, each equipped with a gland, G, to create a steam-tight seal around the glass tube, which is inserted through the hole covered by the plug P1. The cocks T1 T2 are usually open, allowing steam and water to flow into the tube. Cock T3 is kept closed unless it's necessary to blow steam or water [Pg 36] through the gauge. The holes C C can be cleaned out by removing the plugs P² P³.

Most gauges on high-pressure boilers have a thick glass screen in front, so that in the event of the tube breaking, the steam and water may not blow directly on to the attendants. A further precaution is to include two ball-valves near the ends of the gauge-glass. Under ordinary conditions the balls lie in depressions clear of the ways; but when a rush of steam or water occurs they are sucked into their seatings and block all egress.
Most gauges on high-pressure boilers have a thick glass cover in front, so that if the tube breaks, the steam and water won't spray directly onto the workers. Another safety measure is to have two ball valves near the ends of the gauge glass. Normally, the balls sit in depressions away from the openings, but when there’s a sudden rush of steam or water, they get pulled into their seats and block any escape.
On many boilers two water-gauges are fitted, since any gauge may work badly at times. The glasses are tested to a pressure of 3,000 lbs. or more to the square inch before use.
On many boilers, two water gauges are installed in case one of them malfunctions. The gauges are tested to withstand a pressure of 3,000 pounds or more per square inch before being put into use.
THE STEAM-GAUGE.
The steam gauge.
It is of the utmost importance that a person in charge of a boiler should know what pressure the[Pg 37] steam has reached. Every boiler is therefore fitted with one steam-gauge; many with two, lest one might be unreliable. There are two principal types of steam-gauge:—(1) The Bourdon; (2) the Schäffer-Budenberg. The principle of the Bourdon is illustrated by Fig. 13, in which A is a piece of rubber tubing closed at one end, and at the other drawn over the nozzle of a cycle tyre inflator. If bent in a curve, as shown, the section of the tube is an oval. When air is pumped in, the rubber walls endeavour to assume a circular section, because this shape encloses a larger area than an oval of equal circumference, and therefore makes room for a larger volume of air. In doing so the tube straightens itself, and assumes the position indicated by the dotted lines. Hang an empty "inner tube" of a pneumatic tyre over a nail and inflate it, and you will get a good illustration of the principle.
It's really important for anyone in charge of a boiler to know the pressure the [Pg 37] steam has reached. That's why every boiler is equipped with one steam gauge; many have two in case one isn't accurate. There are two main types of steam gauges: (1) The Bourdon; (2) the Schäffer-Budenberg. The Bourdon principle is shown in Fig. 13, where A is a piece of rubber tubing sealed at one end, and the other end is connected to a cycle tire inflator nozzle. When bent into a curve, as illustrated, the tube's cross-section becomes oval. When air is pumped in, the rubber walls try to change back to a circular cross-section because that shape holds more area than an oval with the same perimeter, making more room for a larger amount of air. As it does this, the tube straightens out, reaching the position shown by the dotted lines. If you hang an empty "inner tube" from a pneumatic tire over a nail and inflate it, you'll see a clear example of this principle.


Fig. 14.—Bourdon steam gauge. A section of the dial has been removed to show the mechanism.
In Fig. 14 we have a Bourdon gauge, with part of the dial face broken away to show the internal mechanism. T is a flattened metal tube soldered at one end into a hollow casting, into which screws a tap connected with the boiler. The other end (closed) is attached to a link, L, which works an arm of a quadrant rack, R, engaging with a small pinion, P, actuating the pointer. As the steam pressure rises,[Pg 39] the tube T moves its free end outwards towards the position shown by the dotted lines, and traverses the arm of the rack, so shifting the pointer round the scale. As the pressure falls, the tube gradually returns to its zero position.
In Fig. 14, we see a Bourdon gauge, with part of the dial face removed to reveal the internal mechanism. T is a flattened metal tube that is soldered at one end to a hollow casting, which has a tap connected to the boiler screwed into it. The other end (closed) is connected to a link, L, that operates an arm of a quadrant rack, R, which engages with a small pinion, P, to move the pointer. As the steam pressure increases,[Pg 39] the tube T pushes its free end outward to the position indicated by the dotted lines, moving along the arm of the rack and adjusting the pointer around the scale. When the pressure decreases, the tube gradually returns to its zero position.
The Schäffer-Budenberg gauge depends for its action on the elasticity of a thin corrugated metal plate, on one side of which steam presses. As the plate bulges upwards it pushes up a small rod resting on it, which operates a quadrant and rack similar to that of the Bourdon gauge. The principle is employed in another form for the aneroid barometer (p. 329).
The Schäffer-Budenberg gauge works based on the elasticity of a thin, corrugated metal plate, with steam pressing against one side. As the plate bulges upward, it lifts a small rod resting on it, which operates a quadrant and rack similar to that used in the Bourdon gauge. This principle is used in a different way for the aneroid barometer (p. 329).
THE WATER SUPPLY TO A BOILER.
THE WATER SUPPLY TO A BOILER.
The water inside a boiler is kept at a proper level by (1) pumps or (2) injectors. The former are most commonly used on stationary and marine boilers. As their mechanism is much the same as that of ordinary force pumps, which will be described in a later chapter, we may pass at once to the injector, now almost universally used on locomotive, and sometimes on stationary boilers. At first sight the injector is a mechanical paradox, since it employs the steam from a boiler to blow water into the boiler. In Fig. 15 we have an illustration of the principle of[Pg 40] an injector. Steam is led from the boiler through pipe A, which terminates in a nozzle surrounded by a cone, E, connected by the pipe B with the water tank. When steam is turned on it rushes with immense velocity from the nozzle, and creates a partial vacuum in cone E, which soon fills with water. On meeting the water the steam condenses, but not before it has imparted some of its velocity to the water, which thus gains sufficient momentum to force down the valve and find its way to the boiler. The overflow space O O between E and C allows steam and water to escape until the water has gathered the requisite momentum.
The water in a boiler is maintained at the right level by (1) pumps or (2) injectors. Pumps are mostly used in stationary and marine boilers. Since their operation is similar to regular force pumps, which will be discussed in a later chapter, we can move on to the injector, which is now almost universally used in locomotives and sometimes in stationary boilers. At first glance, the injector seems like a mechanical puzzle because it uses steam from the boiler to push water back into the boiler. In Fig. 15, we see an illustration of how an injector works. Steam is directed from the boiler through pipe A, which ends in a nozzle surrounded by a cone, E, connected by pipe B to the water tank. When steam is turned on, it rushes out of the nozzle at a high speed, creating a partial vacuum in cone E, which quickly fills with water. When the steam meets the water, it condenses, but not before transferring some of its velocity to the water, giving it enough momentum to push down the valve and flow into the boiler. The overflow space O O between E and C allows steam and water to escape until the water has gained the necessary momentum.

Fig. 15.—Diagram showing how a steam-injector works.

A form of injector very commonly used is Giffard's (Fig. 16). Steam is allowed to enter by screwing up the valve V. As it rushes through the nozzle of the cone A it takes up water and projects it into the "mixing cone" B, which can be raised or lowered by the pinion D (worked by the hand-wheel wheel shown) so as to regulate the amount of water admitted to B.[Pg 42] At the centre of B is an aperture, O, communicating with the overflow. The water passes to the boiler through the valve on the left. It will be noticed that the cone A and the part of B above the orifice O contract downward. This is to convert the pressure of the steam into velocity. Below O is a cone, the diameter of which increases downwards. Here the velocity of the water is converted back into pressure in obedience to a well-known hydromechanic law.
A commonly used type of injector is Giffard's (Fig. 16). Steam enters by tightening valve V. As it rushes through the nozzle of cone A, it draws in water and sprays it into the "mixing cone" B, which can be raised or lowered using the pinion D (operated by the hand-wheel shown) to control the amount of water entering B.[Pg 42] At the center of B is an opening, O, that connects to the overflow. The water then flows to the boiler through the valve on the left. You'll notice that the cone A and the section of B above the opening O narrow as they go down. This design is meant to convert the pressure of the steam into velocity. Below O is a cone that widens downwards. Here, the velocity of the water is turned back into pressure, following a well-known hydromechanical principle.
An injector does not work well if the feed-water be too hot to condense the steam quickly; and it may be taken as a rule that the warmer the water, the smaller is the amount of it injected by a given weight of steam.[2] Some injectors have flap-valves covering the overflow orifice, to prevent air being sucked in and carried to the boiler.
An injector doesn't function effectively if the feed water is too hot to condense the steam quickly; as a general rule, the warmer the water, the less of it is injected by a given weight of steam.[2] Some injectors have flap valves over the overflow opening to stop air from being drawn in and sent to the boiler.
When an injector receives a sudden shock, such as that produced by the passing of a locomotive over points, it is liable to "fly off"—that is, stop momentarily—and then send the steam and water through the overflow. If this happens, both steam and water must be turned off, and the injector be restarted; unless it be of the self-starting variety, which automatically[Pg 43] controls the admission of water to the "mixing-cone," and allows the injector to "pick up" of itself.
When an injector experiences a sudden shock, like when a locomotive goes over the points, it can "fly off"—meaning it stops for a moment—and then release steam and water through the overflow. If this occurs, both steam and water need to be turned off, and the injector must be restarted; unless it's a self-starting type, which automatically[Pg 43] manages the water intake to the "mixing cone," allowing the injector to restart itself.
For economy's sake part of the steam expelled from the cylinders of a locomotive is sometimes used to work an injector, which passes the water on, at a pressure of 70 lbs. to the square inch, to a second injector operated by high-pressure steam coming direct from the boiler, which increases its velocity sufficiently to overcome the boiler pressure. In this case only a fraction of the weight of high-pressure steam is required to inject a given weight of water, as compared with that used in a single-stage injector.
For the sake of efficiency, some of the steam released from a locomotive's cylinders is sometimes used to power an injector that delivers water at a pressure of 70 lbs. per square inch to a second injector, which is driven by high-pressure steam directly from the boiler. This increases the speed enough to exceed the boiler pressure. In this situation, only a small amount of high-pressure steam is needed to inject a specific weight of water, compared to what is used in a single-stage injector.
[1] "The Steam-Engine," p. 3.
__A_TAG_PLACEHOLDER_0__ "The Steam Engine," p. 3.
[2] By "weight of steam" is meant the steam produced by boiling a certain weight of water. A pound of steam, if condensed, would form a pound of water.
[2] By "weight of steam," we mean the steam generated by boiling a specific weight of water. A pound of steam, when condensed, would turn into a pound of water.
Chapter II.
THE CONVERSION OF HEAT ENERGY INTO MECHANICAL MOTION.
Reciprocating engines—Double-cylinder engines—The function of the fly-wheel—The cylinder—The slide-valve—The eccentric—"Lap" of the valve: expansion of steam—How the cut-off is managed—Limit of expansive working—Compound engines—Arrangement of expansion engines—Compound locomotives—Reversing gears—"Linking-up"—Piston-valves—Speed governors—Marine-speed governors—The condenser.
Reciprocating engines—Double-cylinder engines—The role of the flywheel—The cylinder—The slide valve—The eccentric—"Lap" of the valve: steam expansion—How the cut-off is controlled—Limit of expansive operation—Compound engines—Design of expansion engines—Compound locomotives—Reversing gears—"Linking up"—Piston valves—Speed governors—Marine speed governors—The condenser.
Having treated at some length the apparatus used for converting water into high-pressure steam, we may pass at once to a consideration of the mechanisms which convert the energy of steam into mechanical motion, or work.
Hsaving discussed in detail the equipment used to turn water into high-pressure steam, we can now move directly to examining the mechanisms that transform the energy of steam into mechanical motion, or work.
Steam-engines are of two kinds:—(1) reciprocating, employing cylinders and cranks; (2) rotary, called turbines.
Steam engines come in two types: (1) reciprocating, which use cylinders and cranks; (2) rotary, known as turbines.
RECIPROCATING ENGINES.
Reciprocating engines.

Fig. 17 is a skeleton diagram of the simplest form of reciprocating engine. C is a cylinder to which steam is admitted through the steam-ways[3] W W, first on one side of the piston P, then on the other. The pressure on the piston pushes it along the cylinder, and the force is transmitted through the piston rod P R to the connecting rod C R, which causes the crank K to revolve. At the point where the two rods meet there is a "crosshead," H, running to and fro in a guide to prevent the piston rod being broken or bent by the oblique thrusts and pulls which it imparts through C R to the crank K. The latter is keyed to a shaft S carrying the fly-wheel, or, in the case of a locomotive, the driving-wheels. The crank shaft revolves in bearings. The internal diameter of a cylinder is called its bore. The travel of the piston is called its stroke. The distance from the centre of the shaft to the centre of the crank pin is called the crank's throw, which is half of the piston's stroke. An engine of this type is called double-acting, as the piston is pushed alternately backwards and forwards by the steam. When piston rod, connecting rod, and crank lie in a straight line—that is, when the piston is fully out, or fully in—the crank is said to be at a "dead point;" for, were the crank turned to such a position, the admission of steam would not produce motion, since the thrust or pull would be entirely absorbed by the bearings.
Fig. 17 is a skeleton diagram of the simplest form of reciprocating engine. C is a cylinder where steam enters through the steam-ways[3] W W, first filling one side of the piston P, then the other side. The pressure on the piston pushes it along the cylinder, transmitting the force through the piston rod P R to the connecting rod C R, which makes the crank K spin. Where the two rods meet, there's a "crosshead," H, moving back and forth in a guide to keep the piston rod from breaking or bending due to the angled thrusts and pulls from C R to the crank K. The crank is attached to a shaft S that carries the flywheel, or in the case of a locomotive, the driving wheels. The crankshaft rotates in bearings. The internal diameter of a cylinder is called its bore. The movement of the piston is called its stroke. The distance from the center of the shaft to the center of the crank pin is the crank's throw, which is half the piston's stroke. An engine of this type is referred to as double-acting because the piston is pushed back and forth alternately by the steam. When the piston rod, connecting rod, and crank are in a straight line—that is, when the piston is fully extended or fully retracted—the crank is said to be at a "dead point;" if the crank is in this position, the steam admission would not create motion, as the thrust or pull would be completely absorbed by the bearings.

DOUBLE-CYLINDER ENGINES.
Double-cylinder engines.


Locomotive, marine, and all other engines which must be started in any position have at least two cylinders, and as many cranks set at an [Pg 48]angle to one another. Fig. 19 demonstrates that when one crank, C1, of a double-cylinder engine is at a "dead point," the other, C2, has reached a position at which the piston exerts the maximum of turning power. In Fig. 20 each crank is at 45° with the horizontal, and both pistons are able to do work. The power of one piston is constantly increasing while that of the other is decreasing. If single-action cylinders are used, at least three of these are needed to produce a perpetual turning movement, independently of a fly-wheel.
Locomotive, marine, and all other engines that need to start in any position have at least two cylinders, with cranks set at an angle of [Pg 48] to each other. Fig. 19 shows that when one crank, C1, of a double-cylinder engine is at a "dead point," the other crank, C2, is in a position where the piston provides maximum turning power. In Fig. 20, each crank is at a 45° angle to the horizontal, allowing both pistons to do work. The power of one piston keeps increasing while the other’s power decreases. If single-action cylinders are used, at least three are required to create a continuous turning motion, independent of a flywheel.
THE FUNCTION OF THE FLY-WHEEL.
The role of the flywheel.
A fly-wheel acts as a reservoir of energy, to carry the crank of a single-cylinder engine past the "dead points." It is useful in all reciprocating engines to produce steady running, as a heavy wheel acts as a drag on the effects of a sudden increase or decrease of steam pressure. In a pump, mangold-slicer, cake-crusher, or chaff-cutter, the fly-wheel helps the operator to pass his dead points—that is, those parts of the circle described by the handle in which he can do little work.
A flywheel serves as a reservoir of energy, helping the crank of a single-cylinder engine move past the "dead points." It's beneficial in all reciprocating engines for maintaining smooth operation, as a heavy wheel provides resistance against sudden changes in steam pressure. In tools like pumps, mangold slicers, cake crushers, or chaff cutters, the flywheel assists the operator in overcoming his dead points—that is, those parts of the handle's circular motion where little work can be done.
THE CYLINDER.
The Cylinder.

The cylinders of an engine take the place of the[Pg 49] muscular system of the human body. In Fig. 21 we have a cylinder and its slide-valve shown in section. First of all, look at P, the piston. Round it are white grooves, R R, in which rings are fitted to prevent the passage of steam past the piston. The rings are cut through at one point in their circumference, and slightly opened, so that when in position they press all round against the walls of the cylinder. After a little use they "settle down to their work"—that is, wear to a true fit in the cylinder. Each end of[Pg 50] the cylinder is closed by a cover, one of which has a boss cast on it, pierced by a hole for the piston rod to work through. To prevent the escape of steam the boss is hollowed out true to accommodate a gland, G1, which is threaded on the rod and screwed up against the boss; the internal space between them being filled with packing. Steam from the boiler enters the steam-chest, and would have access to both sides of the piston simultaneously through the steam-ways, W W, were it not for the
The cylinders of an engine take the place of the[Pg 49] muscular system of the human body. In Fig. 21, we have a cylinder and its slide valve shown in section. First, look at P, the piston. Around it are white grooves, R R, where rings are fitted to prevent steam from passing past the piston. The rings are cut through at one point in their circumference and slightly opened, so when they're in position, they press all around against the walls of the cylinder. After some use, they "settle down to their work"—meaning they wear to a true fit in the cylinder. Each end of[Pg 50] the cylinder is closed by a cover, one of which has a boss cast on it, pierced by a hole for the piston rod to pass through. To prevent steam from escaping, the boss is hollowed out to fit a gland, G1, which is threaded onto the rod and screwed up against the boss; the space between them is filled with packing. Steam from the boiler enters the steam chest and would have access to both sides of the piston simultaneously through the steam ways, W W, if it weren't for the
SLIDE-VALVE,
Slide valve,
a hollow box open at the bottom, and long enough for its edges to cover both steam-ways at once. Between W W is E, the passage for the exhaust steam to escape by. The edges of the slide-valve are perfectly flat, as is the face over which the valve moves, so that no steam may pass under the edges. In our illustration the piston has just begun to move towards the right. Steam enters by the left steam-way, which the valve is just commencing to uncover. As the piston moves, the valve moves in the same direction until the port is fully uncovered, when it begins to move back again; and just before the piston has finished its stroke the steam-way[Pg 51] on the right begins to open. The steam-way on the left is now in communication with the exhaust port E, so that the steam that has done its duty is released and pressed from the cylinder by the piston. Reciprocation is this backward and forward motion of the piston: hence the term "reciprocating" engines. The linear motion of the piston rod is converted into rotatory motion by the connecting rod and crank.
a hollow box open at the bottom, and long enough for its edges to cover both steam paths at the same time. Between W W is E, the passage for the exhaust steam to escape. The edges of the slide valve are perfectly flat, just like the face it moves over, to prevent any steam from leaking underneath. In our illustration, the piston has just started to move to the right. Steam enters through the left steam path, which the valve is just beginning to uncover. As the piston moves, the valve moves in the same direction until the port is fully uncovered, at which point it starts to move back again; and just before the piston completes its stroke, the steam path[Pg 51] on the right begins to open. The steam path on the left is now connected to the exhaust port E, allowing the steam that has done its work to be released and expelled from the cylinder by the piston. Reciprocation refers to this back-and-forth motion of the piston, which is why they are called "reciprocating" engines. The linear motion of the piston rod is converted into rotary motion by the connecting rod and crank.

The use of a crank appears to be so obvious a method of producing this conversion that it is interesting to learn that, when James Watt produced his "rotative engine" in 1780 he was unable to use the crank because it had already been patented by one Matthew Wasborough. Watt was not easily daunted, however, and within a twelvemonth had himself patented five other devices for obtaining rotatory motion from a piston rod. Before passing on, it may be mentioned that Watt was the father of the modern—that is, the high-pressure—steam-engine; and that, owing to the imperfection of the existing[Pg 52] machinery, the difficulties he had to overcome were enormous. On one occasion he congratulated himself because one of his steam-cylinders was only three-eighths of an inch out of truth in the bore. Nowadays a good firm would reject a cylinder 1⁄500 of an inch out of truth; and in small petrol-engines 1⁄5000 of an inch is sometimes the greatest "limit of error" allowed.
Using a crank seems like such an obvious way to create this conversion that it's interesting to note that when James Watt created his "rotative engine" in 1780, he couldn't use a crank because it was already patented by Matthew Wasborough. However, Watt wasn’t easily discouraged, and within a year, he had patented five other devices to get rotary motion from a piston rod. Before moving on, it's worth mentioning that Watt was the father of the modern high-pressure steam engine, and due to the limitations of the machinery at the time, he faced enormous challenges. At one point, he even congratulated himself because one of his steam cylinders was just three-eighths of an inch out of alignment in the bore. Today, a reputable company would reject a cylinder that is only 1/500 of an inch out of alignment; in small petrol engines, a tolerance of 1/5000 of an inch is sometimes the maximum "limit of error" accepted.

THE ECCENTRIC
THE WEIRD/UNUSUAL PERSON
is used to move the slide-valve to and fro over the steam ports (Fig. 23). It consists of three main parts—the sheave, or circular plate S, mounted on the crank shaft; and the two straps which encircle it, and in which it revolves. To one strap is bolted the "big end" of the eccentric rod, which engages at its other end with the valve rod. The straps are semicircular and held together by strong bolts, B B, passing through lugs, or thickenings at the ends of the semicircles. The sheave has a deep groove all round the edges,[Pg 53] in which the straps ride. The "eccentricity" or "throw" of an eccentric is the distance between C2, the centre of the shaft, and C1, the centre of the sheave. The throw must equal half of the distance which the slide-valve has to travel over the steam ports. A tapering steel wedge or key, K, sunk half in the eccentric and half in a slot in the shaft, holds the eccentric steady and prevents it slipping. Some eccentric sheaves are made in two parts, bolted together, so that they may be removed easily without dismounting the shaft.
is used to move the slide-valve back and forth over the steam ports (Fig. 23). It consists of three main parts—the sheave, or circular plate S, mounted on the crankshaft; and the two straps that encircle it and in which it revolves. One strap is bolted to the "big end" of the eccentric rod, which connects to the valve rod at its other end. The straps are semicircular and held together by strong bolts, B B, that pass through lugs, or thickened areas at the ends of the semicircles. The sheave has a deep groove all around the edges,[Pg 53] where the straps ride. The "eccentricity" or "throw" of an eccentric is the distance between C2, the center of the shaft, and C1, the center of the sheave. The throw must equal half the distance that the slide-valve has to travel over the steam ports. A tapering steel wedge or key, K, is sunk half into the eccentric and half into a slot in the shaft, which keeps the eccentric secure and prevents it from slipping. Some eccentric sheaves are made in two parts that are bolted together, so they can be easily removed without taking down the shaft.
The eccentric is in principle nothing more than a crank pin so exaggerated as to be larger than the shaft of the crank. Its convenience lies in the fact that it may be mounted at any point on a shaft, whereas a crank can be situated at an end only, if it is not actually a V-shaped bend in the shaft itself—in which case its position is of course permanent.
The eccentric is basically just a crank pin that's so exaggerated that it's bigger than the crank shaft. Its advantage is that it can be placed anywhere on a shaft, while a crank can only be at one end unless it's a V-shaped bend in the shaft itself, which would mean its position is fixed.
SETTING OF THE SLIDE-VALVE AND ECCENTRIC.
SETTING OF THE SLIDE-VALVE AND ECCENTRIC.
The subject of valve-setting is so extensive that a full exposition might weary the reader, even if space permitted its inclusion. But inasmuch as the effectiveness of a reciprocating engine depends largely on the nature and arrangement of the valves, we[Pg 54] will glance at some of the more elementary principles.
The topic of valve-setting is so broad that a complete explanation might bore the reader, even if there were enough space to include it. However, since the performance of a reciprocating engine relies heavily on the design and arrangement of the valves, we[Pg 54] will take a look at some of the basic principles.


In Fig. 24 we see in section the slide-valve, the ports of the cylinder, and part of the piston. To the right are two lines at right angles—the thicker, C, representing the position of the crank; the thinner, E, that of the eccentric. (The position of an eccentric is denoted diagrammatically by a line drawn from the centre of the crank shaft through the centre of the sheave.) The edges of the valve are in this case only broad enough to just cover the ports—that is, they have no lap. The piston is about to commence its stroke towards the left; and the eccentric,[Pg 55] which is set at an angle of 90° in advance of the crank, is about to begin opening the left-hand port. By the time that C has got to the position originally occupied by E, E will be horizontal (Fig. 25)—that is, the eccentric will have finished its stroke towards the left; and while C passes through the next right angle the valve will be closing the left port, which will cease to admit steam when the piston has come to the end of its travel. The operation is repeated on the right-hand side while the piston returns.
In Fig. 24, we see a cross-section of the slide-valve, the cylinder ports, and part of the piston. To the right, there are two lines at right angles—the thicker line, C, shows the crank's position; the thinner line, E, shows the eccentric's position. (The eccentric's position is diagrammatically represented by a line drawn from the center of the crankshaft through the center of the pulley.) The edges of the valve are only wide enough to just cover the ports—that is, they have no lap. The piston is about to start its stroke to the left, and the eccentric, [Pg 55], which is set at a 90° angle in advance of the crank, is about to start opening the left port. By the time C reaches the position that E originally occupied, E will be horizontal (Fig. 25)—meaning the eccentric will have completed its stroke to the left; and while C moves through the next right angle, the valve will be closing the left port, which will stop allowing steam in when the piston finishes its travel. This process is repeated on the right side as the piston returns.

It must be noticed here—(1) that steam is admitted at full pressure all through the stroke; (2) that admission begins and ends simultaneously with the stroke. Now, in actual practice it is necessary to admit steam before the piston has ended its travel, so as to cushion the violence of the sudden change of direction of the piston, its rod, and other moving parts. To effect this, the eccentric is set more[Pg 56] than 90° in advance—that is, more than what the engineers call square. Fig. 26 shows such an arrangement. The angle between E and E1 is called the angle of advance. Referring to the valve, you will see that it has opened an appreciable amount, though the piston has not yet started on its rightwards journey.
It should be noted here—(1) that steam is let in at full pressure throughout the stroke; (2) that the admission starts and ends at the same time as the stroke. In practical use, it’s necessary to let steam in before the piston finishes its travel to cushion the impact of the sudden change in direction of the piston, its rod, and other moving parts. To achieve this, the eccentric is set more [Pg 56] than 90° ahead—that is, more than what engineers refer to as square. Fig. 26 illustrates this setup. The angle between E and E1 is known as the angle of advance. Looking at the valve, you can see that it has opened a significant amount, even though the piston hasn’t started moving to the right yet.
"LAP" OF THE VALVE—EXPANSION OF STEAM.
"Valve Lap"—Steam Expansion.
In the simple form of valve that appears in Fig. 24, the valve faces are just wide enough to cover the steam ports. If the eccentric is not square with the crank, the admission of steam lasts until the very end of the stroke; if set a little in advance—that is, given lead—the steam is cut off before the piston has travelled quite along the cylinder, and readmitted before the back stroke is accomplished. Even with this lead the working is very uneconomical, as the steam goes to the exhaust at practically the same pressure as that at which it entered the cylinder. Its property of expansion has been neglected. But supposing that steam at 100 lbs. pressure were admitted till half-stroke, and then suddenly cut off, the expansive nature of the steam would then continue to push the piston out until[Pg 57] the pressure had decreased to 50 lbs. per square inch, at which pressure it would go to the exhaust. Now, observe that all the work done by the steam after the cut-off is so much power saved. The average pressure on the piston is not so high as in the first case; still, from a given volume of 100 lbs. pressure steam we get much more work.
In the simple valve design shown in Fig. 24, the valve faces are just wide enough to cover the steam ports. If the eccentric isn’t aligned with the crank, steam admission continues all the way to the end of the stroke; if it’s set slightly ahead—meaning it has some lead—steam is cut off before the piston travels the entire length of the cylinder and is readmitted before the return stroke is finished. Even with this lead, the operation is very inefficient, as the steam escapes to the exhaust at nearly the same pressure it entered the cylinder. Its ability to expand is overlooked. However, if steam at 100 lbs. pressure is let in until halfway through the stroke and then cut off suddenly, the steam's expansive nature will continue to push the piston until the pressure drops to 50 lbs. per square inch, at which point it will exhaust. Notice that all the work done by the steam after the cut-off is essentially power saved. The average pressure on the piston isn't as high as in the first scenario; still, from the same volume of 100 lbs. pressure steam, we achieve much more work.
HOW THE CUT-OFF IS MANAGED.
HOW THE CUT-OFF IS HANDLED.


Look at Fig. 27. Here we have a slide-valve, with faces much wider than the steam ports. The parts marked black, P P, are those corresponding to the faces of the valves shown in previous diagrams (p. 54). The shaded parts, L L, are called the lap. By increasing the length of the lap we increase the range of expansive working. Fig. 28 shows the piston full to the left; the valve is just on the point of opening to admit steam behind the piston.[Pg 58] The eccentric has a throw equal to the breadth of a port + the lap of the valve. That this must be so is obvious from a consideration of Fig. 27, where the valve is at its central position. Hence the very simple formula:—Travel of valve = 2 × (lap + breadth of port). The path of the eccentric's centre round the centre of the shaft is indicated by the usual dotted line (Fig. 28). You will notice that the "angle of advance," denoted by the arrow A, is now very considerable. By the time that the crank C has assumed the position of the line S, the eccentric has passed its dead point, and the valve begins to travel backwards, eventually returning to the position shown in Fig. 28, and cutting off the steam supply while the piston has still a considerable part of its stroke to make. The steam then begins to work expansively, and continues to do so until the valve assumes the position shown in Fig. 27.
Look at Fig. 27. Here we have a slide valve with faces that are much wider than the steam ports. The parts marked in black, P P, correspond to the faces of the valves shown in previous diagrams (p. 54). The shaded parts, L L, are known as the lap. By increasing the length of the lap, we expand the range of expansive working. Fig. 28 shows the piston all the way to the left; the valve is just about to open to let steam in behind the piston.[Pg 58] The eccentric has a throw equal to the width of a port plus the lap of the valve. This is clear from looking at Fig. 27, where the valve is in its central position. Hence the straightforward formula:—Travel of valve = 2 × (lap + width of port). The path of the center of the eccentric around the center of the shaft is shown by the usual dotted line (Fig. 28). You'll notice that the "angle of advance," indicated by the arrow A, is now quite significant. By the time the crank C reaches the position of the line S, the eccentric has passed its dead point, and the valve starts to move back, eventually returning to the position shown in Fig. 28, cutting off the steam supply while the piston still has a considerable portion of its stroke to complete. The steam then starts to work expansively and continues to do so until the valve reaches the position shown in Fig. 27.
If the valve has to have "lead" to admit steam before the end of the stroke to the other side of the piston, the angle of advance must be increased, and the eccentric centre line would lie on the line E2. Therefore—total angle of advance = angle for lap and angle for lead.
If the valve needs to have "lead" to let steam in before the piston reaches the end of its stroke, the angle of advance has to be increased, and the eccentric center line would be on the line E². So, the total angle of advance equals the angle for lap plus the angle for lead.
LIMIT OF EXPANSIVE WORKING.
LIMIT OF EXTENSIVE WORK.
Theoretically, by increasing the lap and cutting off the steam earlier and earlier in the stroke, we should economize our power more and more. But in practice a great difficulty is met with—namely, that as the steam expands its temperature falls. If the cut-off occurs early, say at one-third stroke, the great expansion will reduce the temperature of the metal walls of the cylinder to such an extent, that when the next spirt of steam enters from the other end a considerable proportion of the steam's energy will be lost by cooling. In such a case, the difference in temperature between admitted steam and exhausted steam is too great for economy. Yet we want to utilize as much energy as possible. How are we to do it?
Theoretically, by increasing the lap and cutting off the steam earlier and earlier in the stroke, we should be able to save more and more power. But in practice, we hit a big obstacle—specifically, that as the steam expands, its temperature decreases. If the cut-off happens early, like at one-third of the stroke, the significant expansion will drop the temperature of the metal walls of the cylinder so much that when the next burst of steam comes in from the other end, a substantial amount of the steam's energy will be wasted due to cooling. In this case, the temperature difference between the incoming steam and the exhausted steam is too large for it to be efficient. However, we want to make the best use of the energy possible. How can we achieve that?
COMPOUND ENGINES.
Compound Engines.
In the year 1853, John Elder, founder of the shipping firm of Elder and Co., Glasgow, introduced the compound engine for use on ships. The steam, when exhausted from the high-pressure cylinder, passed into another cylinder of equal stroke but larger diameter, where the expansion continued. In modern engines the expansion is extended to three and even four stages, according to the boiler pressure; for it is a rule that the higher the initial pressure is, the larger is the number of stages of expansion consistent with economical working.
In 1853, John Elder, the founder of the shipping company Elder and Co. in Glasgow, introduced the compound engine for ships. The steam, after it was released from the high-pressure cylinder, moved into another cylinder that had the same stroke but a larger diameter, where the expansion continued. In modern engines, the expansion is taken to three or even four stages, depending on the boiler pressure; generally, the rule is that the higher the initial pressure, the greater the number of expansion stages that can work efficiently.

In Fig. 29 we have a triple-expansion marine engine. Steam enters the high-pressure cylinder[4] at, say, 200 lbs. per square inch. It exhausts at 75 lbs. into the large pipe 2, and passes to the intermediate cylinder, whence it is exhausted at 25 lbs. or so through pipe 3 to the low-pressure cylinder. Finally, it is ejected at about 8 lbs. per square inch to the condenser, and is suddenly converted into water; an act which produces a vacuum, and diminishes the back-pressure of the exhaust from cylinder C. In fact, the condenser exerts a sucking power on the exhaust side of C's piston.
In Fig. 29, we have a triple-expansion marine engine. Steam enters the high-pressure cylinder[4] at around 200 psi. It exhausts at 75 psi into the large pipe 2 and flows to the intermediate cylinder, where it is exhausted at about 25 psi through pipe 3 to the low-pressure cylinder. Finally, it is released at roughly 8 psi to the condenser and is quickly turned into water; this process creates a vacuum and reduces the back-pressure of the exhaust from cylinder C. In fact, the condenser pulls on the exhaust side of C's piston.
ARRANGEMENT OF EXPANSION ENGINES.
Expansion engine layout.
In the illustration the cranks are set at angles of 120°, or a third of a circle, so that one or other is always at or near the position of maximum turning power. Where only two stages are used the[Pg 62] cylinders are often arranged tandem, both pistons having a common piston rod and crank. In order to get a constant turning movement they must be mounted separately, and work cranks set at right angles to one another.
In the illustration, the cranks are positioned at angles of 120°, which is a third of a circle, ensuring that one of them is always at or close to the point of maximum turning power. When only two stages are used, the[Pg 62] cylinders are often arranged in a tandem setup, with both pistons sharing a common piston rod and crank. To achieve a consistent turning motion, they need to be mounted separately, with the cranks positioned at right angles to each other.
COMPOUND LOCOMOTIVES.
Steam locomotives.
In 1876 Mr. A. Mallet introduced compounding in locomotives; and the practice has been largely adopted. The various types of "compounds" may be classified as follows:—(1) One low-pressure and one high-pressure cylinder; (2) one high-pressure and two low-pressure; (3) one low-pressure and two high-pressure; (4) two high-pressure and two low-pressure. The last class is very widely used in France, America, and Russia, and seems to give the best results. Where only two cylinders are used (and sometimes in the case of three and four), a valve arrangement permits the admission of high-pressure steam to both high and low-pressure cylinders for starting a train, or moving it up heavy grades.
In 1876, Mr. A. Mallet introduced compounding in locomotives, and this practice has been widely adopted. The different types of "compounds" can be categorized as follows: (1) one low-pressure and one high-pressure cylinder; (2) one high-pressure and two low-pressure; (3) one low-pressure and two high-pressure; (4) two high-pressure and two low-pressure. The last category is commonly used in France, America, and Russia, and tends to produce the best results. When only two cylinders are employed (and sometimes in the case of three and four), a valve setup allows for the entry of high-pressure steam into both high and low-pressure cylinders for starting a train or moving it up steep grades.
REVERSING GEARS.
Switching gears.

The engines of a locomotive or steamship must be reversible—that is, when steam is admitted to the[Pg 63] cylinders, the engineer must be able to so direct it through the steam-ways that the cranks may turn in the desired direction. The commonest form of reversing device (invented by George Stephenson) is known as Stephenson's Link Gear. In Fig. 30 we have a diagrammatic presentment of this gear. E1 and E2 are two eccentrics set square with the crank at opposite ends of a diameter. Their rods are connected to the ends of a link, L, which can be raised and lowered by means of levers (not shown). B is a block which can partly revolve on a pin projecting[Pg 64] from the valve rod, working through a guide, G. In Fig. 31 the link is half raised, or in "mid-gear," as drivers say. Eccentric E1 has pushed the lower end of the link fully back; E2 has pulled it fully forward; and since any movement of the one eccentric is counterbalanced by the opposite movement of the other, rotation of the eccentrics would not cause the valve to move at all, and no steam could be admitted to the cylinder.
The engines of a train or steamship need to be reversible. This means that when steam is let into the [Pg 63] cylinders, the engineer must be able to direct it through the steam pathways so that the cranks can turn in the intended direction. The most common type of reversing mechanism, created by George Stephenson, is called Stephenson's Link Gear. In Fig. 30, we see a diagram of this gear. E1 and E² are two eccentrics positioned perpendicular to the crank at opposite ends of a diameter. Their rods are linked to either end of a link, L, which can be raised and lowered using levers (not shown). B is a block that can partially rotate on a pin sticking out [Pg 64] from the valve rod, moving through a guide, G. In Fig. 31, the link is half raised, or in "mid-gear," as the drivers say. Eccentric E1 has pushed the lower end of the link all the way back, while E² has pulled it all the way forward. Since any movement of one eccentric is balanced by the opposite movement of the other, the rotation of the eccentrics does not cause the valve to move at all, preventing steam from entering the cylinder.
Let us suppose that Fig. 30 denotes one cylinder, crank, rods, etc., of a locomotive. The crank has come to rest at its half-stroke; the reversing lever is at the mid-gear notch. If the engineer desires to turn his cranks in an anti-clockwise direction, he raises the link, which brings the rod of E1 into line with the valve rod and presses the block backwards till the right-hand port is uncovered (Fig. 31). If steam be now admitted, the piston will be pushed towards the left, and the engine will continue to run in an anti-clockwise direction. If, on the other hand, he wants to run the engine the other way, he would drop the link, bringing the rod of E2 into line with the valve rod, and drawing V forward to uncover the rear port (Fig. 32). In either case the eccentric working the end of the link remote[Pg 65] from B has no effect, since it merely causes that end to describe arcs of circles of which B is the centre.
Let’s say Fig. 30 shows a cylinder, crank, rods, etc., of a locomotive. The crank has stopped at its halfway point; the reversing lever is at the mid-gear notch. If the engineer wants to spin the cranks in a counter-clockwise direction, he raises the link, which aligns the rod of E1 with the valve rod and pushes the block backwards until the right-hand port is uncovered (Fig. 31). If steam is now let in, the piston will be pushed to the left, and the engine will keep running counter-clockwise. Conversely, if he wants to run the engine the other way, he would drop the link, aligning the rod of E² with the valve rod, and pulling V forward to uncover the rear port (Fig. 32). In either scenario, the eccentric that activates the end of the link farthest from B has no effect, as it merely causes that end to trace arcs of circles with B as the center.
"LINKING UP."
"Connecting."
If the link is only partly lowered or raised from the central position it still causes the engine to run accordingly, but the movement of the valve is decreased. When running at high speed the engineer "links up" his reversing gear, causing his valves to cut off early in the stroke, and the steam to work more expansively than it could with the lever at full, or end, gear; so that this device not only renders an engine reversible, but also gives the engineer an absolute command over the expansion ratio of the steam admitted to the cylinder, and furnishes a method of cutting off the steam altogether. In Figs. 30, 31, 32, the valve has no lap and the eccentrics are set square. In actual practice the valve faces would have "lap" and the eccentric "lead" to correspond; but for the sake of simplicity neither is shown.
If the link is only partially lowered or raised from the central position, it still causes the engine to run accordingly, but the movement of the valve is reduced. When operating at high speed, the engineer "links up" the reversing gear, causing the valves to cut off early in the stroke, allowing the steam to work more efficiently than it would with the lever at full or end gear; this means that this device not only makes an engine reversible but also gives the engineer complete control over the expansion ratio of the steam entering the cylinder, and provides a way to completely cut off the steam. In Figs. 30, 31, 32, the valve has no lap and the eccentrics are set square. In actual practice, the valve faces would have "lap" and the eccentric "lead" to match; but for the sake of simplicity, neither is shown.
OTHER GEARS.
OTHER OPTIONS.
In the Gooch gear for reversing locomotives the link does not shift, but the valve rod and its block is raised or lowered. The Allan gear is so arranged[Pg 66] that when the link is raised the block is lowered, and vice versâ. These are really only modifications of Stephenson's principle—namely, the employment of two eccentrics set at equal angles to and on opposite sides of the crank. There are three other forms of link-reversing gear, and nearly a dozen types of radial reversing devices; but as we have already described the three most commonly used on locomotives and ships, there is no need to give particulars of these.
In Gooch gear for reversing locomotives, the link doesn't move, but the valve rod and its block are raised or lowered. The Allan gear is set up[Pg 66] so that when the link is raised, the block is lowered, and vice versa. These are really just tweaks of Stephenson's principle—specifically, using two eccentrics positioned at equal angles on opposite sides of the crank. There are three other types of link-reversing gear and almost a dozen kinds of radial reversing devices, but since we've already covered the three most commonly used on locomotives and ships, there's no need to go into detail about these.
Before the introduction of Stephenson's gear a single eccentric was used for each cylinder, and to reverse the engine this eccentric had to be loose on the axle. "A lever and gear worked by a treadle on the footplate controlled the position of the eccentrics. When starting the engine, the driver put the eccentrics out of gear by the treadle; then, by means of a lever he raised the small-ends[5] of the eccentric rods, and, noting the position of the cranks, or, if more convenient, the balance weight in the wheels, he, by means of another handle, moved the valves to open the necessary ports to steam and worked them by hand until the engine was moving; then, with the treadle, he threw the eccentrics over to engage the[Pg 67] studs, at the same time dropping the small-ends of the rods to engage pins upon the valve spindles, so that they continued to keep up the movement of the valve."[6] One would imagine that in modern shunting yards such a device would somewhat delay operations!
Before Stephenson's gear was introduced, each cylinder used a single eccentric, and to reverse the engine, this eccentric had to be loose on the axle. "A lever and gear operated by a foot treadle controlled the position of the eccentrics. When starting the engine, the driver disengaged the eccentrics using the treadle; then, with a lever, he raised the small ends[5] of the eccentric rods. He noted the position of the cranks, or, if it was easier, the balance weight in the wheels, and then, using another handle, adjusted the valves to open the necessary steam ports and manually operated them until the engine started moving. After that, he used the treadle to engage the eccentric studs while dropping the small ends of the rods to connect with pins on the valve spindles, ensuring the valve movement continued." [6] You might think that such a setup would slow down operations in modern shunting yards!
PISTON VALVES.
Piston valves.
In marine engines, and on many locomotives and some stationary engines, the D-valve (shown in Figs. 30–32) is replaced by a piston valve, or circular valve, working up and down in a tubular seating. It may best be described as a rod carrying two pistons which correspond to the faces of a D-valve. Instead of rectangular ports there are openings in the tube in which the piston valve moves, communicating with the steam-ways into the cylinder and with the exhaust pipe. In the case of the D-valve the pressure above it is much greater than that below, and considerable friction arises if the rubbing faces are not kept well lubricated. The piston valve gets over this difficulty, since such steam as may leak past it presses on its circumference at all points equally.
In marine engines, as well as many locomotives and some stationary engines, the D-valve (shown in Figs. 30–32) is replaced by a piston valve or circular valve that moves up and down in a tubular seating. It can be best described as a rod with two pistons that correspond to the faces of a D-valve. Instead of rectangular ports, there are openings in the tube where the piston valve moves, connecting with the steam ways into the cylinder and the exhaust pipe. With the D-valve, the pressure above it is much higher than that below, causing significant friction if the rubbing surfaces aren't well lubricated. The piston valve avoids this problem because any steam that might leak past it presses evenly around its circumference.
SPEED GOVERNORS.
Speed governors.

Practically all engines except locomotives and those[Pg 68] known as "donkey-engines"—used on cranes—are fitted with some device for keeping the rotatory speed of the crank constant within very narrow limits. Perhaps you have seen a pair of balls moving round on a seating over the boiler of a threshing-engine. They form part of the "governor," or speed-controller, shown in principle in Fig. 33. A belt driven by a pulley on the crank shaft turns a small pulley, P, at the foot of the governor. This transmits motion through two bevel-wheels, G, to a vertical shaft, from the top of which hang two heavy balls on links, K K.[Pg 69] Two more links, L L, connect the balls with a weight, W, which has a deep groove cut round it at the bottom. When the shaft revolves, the balls fly outwards by centrifugal force, and as their velocity increases the quadrilateral figure contained by the four links expands laterally and shortens vertically. The angles between K K and L L become less and less obtuse, and the weight W is drawn upwards, bringing with it the fork C of the rod A, which has ends engaging with the groove. As C rises, the other end of the rod is depressed, and the rod B depresses rod O, which is attached to the spindle operating a sort of shutter in the steam-pipe. Consequently the supply of steam is throttled more and more as the speed increases, until it has been so reduced that the engine slows, and the balls fall, opening the valve again. Fig. 34 shows the valve fully closed. This form of governor was invented by James Watt. A spring is often used instead of a weight, and the governor is arranged horizontally so that it may be driven direct from[Pg 70] the crank shaft without the intervention of bevel gearing.
Almost all engines, except for locomotives and those[Pg 68] called "donkey-engines"—used on cranes—have some mechanism to keep the crank's rotation speed consistent within very tight limits. You might have noticed a pair of balls spinning on a seat above the boiler of a threshing-engine. They are part of the "governor," or speed-controller, illustrated in principle in Fig. 33. A belt driven by a pulley on the crankshaft turns a small pulley, P, at the base of the governor. This passes motion through two bevel wheels, G, to a vertical shaft, where two heavy balls hang from links, K K.[Pg 69] Two more links, L L, connect the balls to a weight, W, which has a deep groove cut around its bottom. As the shaft rotates, the balls move outward due to centrifugal force, and as their speed increases, the four links create a shape that expands horizontally and contracts vertically. The angles between K K and L L become less and less obtuse, causing the weight W to rise, which in turn lifts the fork C of the rod A, with its ends fitting into the groove. As C rises, the other end of the rod lowers, pressing down on rod B, which depresses rod O, connected to a spindle that operates a sort of valve in the steam pipe. This means the steam supply is gradually restricted as the speed increases, until it's reduced enough for the engine to slow down, causing the balls to drop and reopen the valve. Fig. 34 shows the valve fully closed. This type of governor was invented by James Watt. Sometimes a spring is used instead of a weight, and the governor is configured horizontally so that it can be directly driven from[Pg 70] the crankshaft without bevel gearing.

The Hartwell governor employs a link motion. You must here picture the balls raising and lowering the free end of the valve rod, which carries a block moving in a link connected with the eccentric rod. The link is pivoted at the upper end, and the eccentric rod is attached to the lower. When the engine is at rest the end of the valve rod and its block are dropped till in a line with the eccentric rod; but when the machinery begins to work the block is gradually drawn up by the governor, diminishing the movement of the valve, and so shortening the period of steam admission to the cylinder.
The Hartwell governor uses a link motion. Imagine the balls raising and lowering the free end of the valve rod, which has a block moving in a link that connects to the eccentric rod. The link is pivoted at the top, and the eccentric rod is attached at the bottom. When the engine is at rest, the end of the valve rod and its block drop to align with the eccentric rod; however, when the machinery starts working, the governor gradually lifts the block, reducing the movement of the valve and, consequently, shortening the time steam is allowed into the cylinder.
Governors are of special importance where the load of an engine is constantly varying, as in the case of a sawmill. A good governor will limit variation of speed within two per cent.—that is, if the engine is set to run at 100 revolutions a minute, it will not allow it to exceed 101 or fall below 99. In very high-speed engines the governing will prevent variation of less than one per cent., even when the load is at one instant full on, and the next taken completely off.
Governors are especially important when the load on an engine constantly changes, like in a sawmill. A good governor will keep the speed variation within two percent. For example, if the engine is set to run at 100 revolutions per minute, it won’t let it go above 101 or drop below 99. In very high-speed engines, the governor will maintain a variation of less than one percent, even when the load is fully on one moment and completely off the next.
MARINE GOVERNORS.
MARINE GOVERNORS.
These must be more quick-acting than those used on engines provided with fly-wheels, which prevent very sudden variations of speed. The screw is light in proportion to the engine power, and when it is suddenly raised from the water by the pitching of the vessel, the engine would race till the screw took the water again, unless some regulating mechanism were provided. Many types of marine governors have been tried. The most successful seems to be one in which water is being constantly forced by a pump driven off the engine shaft into a cylinder controlling a throttle-valve in the main steam-pipe. The water escapes through a leak, which is adjustable. As long as the speed of the engine is normal, the water escapes from the cylinder as fast as it is pumped in, and no movement of the piston results; but when the screw begins to race, the pump overcomes the leak, and the piston is driven out, causing a throttling of the steam supply.
These need to act faster than those used on engines with flywheels, which help prevent sudden changes in speed. The screw is light compared to the engine's power, and if it's suddenly lifted out of the water because the vessel pitches, the engine would run away until the screw enters the water again, unless there's a regulating mechanism in place. Various types of marine governors have been tested. The most effective seems to be one where water is constantly pumped by an engine-driven pump into a cylinder that controls a throttle valve in the main steam pipe. The water leaks out through an adjustable outlet. As long as the engine speed is normal, the water escapes from the cylinder as quickly as it's pumped in, and the piston doesn't move; but when the screw starts to race, the pump surpasses the leak, pushing the piston out and reducing the steam supply.
CONDENSERS.
Capacitors.
The condenser serves two purposes:—(1) It makes it possible to use the same water over and over[Pg 72] again in the boilers. On the sea, where fresh water is not obtainable in large quantities, this is a matter of the greatest importance. (2) It adds to the power of a compound engine by exerting a back pull on the piston of the low-pressure cylinder while the steam is being exhausted.
The condenser has two main functions: (1) It allows for the same water to be reused multiple times[Pg 72] in the boilers. This is extremely important at sea, where fresh water isn't readily available in large amounts. (2) It increases the power of a compound engine by creating a pull on the piston of the low-pressure cylinder while the steam is being released.

Fig. 35 is a sectional illustration of a marine condenser. Steam enters the condenser through the large pipe E, and passes among a number of very thin copper tubes, through which sea-water is kept circulating by a pump. The path of the water is shown by the featherless arrows. It comes from the pump through pipe A into the lower part of a large cap covering one end of the condenser and divided[Pg 73] transversely by a diaphragm, D. Passing through the pipes, it reaches the cap attached to the other end, and flows back through the upper tubes to the outlet C. This arrangement ensures that, as the steam condenses, it shall meet colder and colder tubes, and finally be turned to water, which passes to the well through the outlet F. In some condensers the positions of steam and water are reversed, steam going through the tubes outside which cold water circulates.
Fig. 35 is a sectional illustration of a marine condenser. Steam enters the condenser through the large pipe E and passes through a series of very thin copper tubes, with seawater continuously circulated by a pump. The flow of water is indicated by the featherless arrows. It comes from the pump through pipe A into the bottom part of a large cap covering one end of the condenser, which is divided[Pg 73] across by a diaphragm, D. As the water moves through the pipes, it reaches the cap at the other end and returns through the upper tubes to the outlet C. This setup ensures that, as the steam condenses, it encounters progressively colder tubes, eventually turning into water that flows to the well through the outlet F. In some condensers, the positions of steam and water are reversed, with steam flowing through the tubes while cold water circulates outside.
[3] Also called ports.
Also called ports.
[6] "The Locomotive of To-day," p. 87.
__A_TAG_PLACEHOLDER_0__ "Today's Locomotive," p. 87.
Chapter III.
THE STEAM TURBINE.
How a turbine works—The De Laval turbine—The Parsons turbine—Description of the Parsons turbine—The expansive action of steam in a Parsons turbine—Balancing the thrust—Advantages of the marine turbine.
How a turbine works—The De Laval turbine—The Parsons turbine—Description of the Parsons turbine—The expansive action of steam in a Parsons turbine—Balancing the thrust—Advantages of the marine turbine.
More than two thousand years ago Hero of Alexandria produced the first apparatus to which the name of steam-engine could rightly be given. Its principle was practically the same as that of the revolving jet used to sprinkle lawns during dry weather, steam being used in the place of water. From the top of a closed cauldron rose two vertical pipes, which at their upper ends had short, right-angle bends. Between them was hung a hollow globe, pivoted on two short tubes projecting from its sides into the upright tubes. Two little L-shaped pipes projected from opposite sides of the globe, at the ends of a diameter, in a plane perpendicular to the axis. On fire being applied to the[Pg 75] cauldron, steam was generated. It passed up through the upright, through the pivots, and into the globe, from which it escaped by the two L-shaped nozzles, causing rapid revolution of the ball. In short, the first steam-engine was a turbine. Curiously enough, we have reverted to this primitive type (scientifically developed, of course) in the most modern engineering practice.
More than two thousand years ago, Hero of Alexandria created the first device that could truly be called a steam engine. Its design was essentially the same as the rotating jet used to water lawns during dry spells, with steam replacing water. From the top of a closed cauldron, two vertical pipes extended upward, each featuring short right-angle bends at the top. Between them, there was a hollow globe that pivoted on two short tubes sticking out from its sides into the upright pipes. Two small L-shaped pipes extended from opposite sides of the globe, at the ends of a diameter, positioned in a plane perpendicular to the axis. When fire was applied to the[Pg 75] cauldron, steam was produced. It rose through the upright pipes, passed through the pivots, and entered the globe, escaping through the two L-shaped nozzles, which caused the ball to spin rapidly. In summary, the first steam engine was a turbine. Interestingly, we have returned to this basic design (with scientific advancements, of course) in the latest engineering practices.
HOW A TURBINE WORKS.
HOW A TURBINE FUNCTIONS.
In reciprocating—that is, cylinder—engines steam is admitted into a chamber and the door shut behind it, as it were. As it struggles to expand, it forces out one of the confining walls—that is, the piston—and presently the door opens again, and allows it to escape when it has done its work. In Hero's toy the impact of the issuing molecules against other molecules that have already emerged from the pipes was used. One may compare the reaction to that exerted by a thrown stone on the thrower. If the thrower is standing on skates, the reaction of the stone will cause him to glide backwards, just as if he had pushed off from some fixed object. In the case of the reaction—namely, the Hero-type—turbine the nozzle from which the steam or water issues[Pg 76] moves, along with bodies to which it may be attached. In action turbines steam is led through fixed nozzles or steam-ways, and the momentum of the steam is brought to bear on the surfaces of movable bodies connected with the shaft.
In reciprocating—meaning cylinder—engines, steam is let into a chamber and the door is closed behind it. As it tries to expand, it pushes out one of the walls—specifically, the piston—and soon the door opens again, letting it escape once its job is done. In Hero's toy, the force of the escaping molecules hitting other molecules that have already come out of the pipes was utilized. You can think of the reaction like what happens when a stone is thrown by a person. If the thrower is on skates, the force of the stone will make them glide backward, just like if they had pushed off from a fixed object. In the case of the reaction—specifically, the Hero-type—turbine, the nozzle from which the steam or water flows[Pg 76] moves along with any bodies it may be attached to. In action turbines, steam is directed through fixed nozzles or steam channels, and the momentum of the steam impacts the surfaces of movable bodies connected to the shaft.
THE DE LAVAL TURBINE.
The De Laval turbine.
In its earliest form this turbine was a modification of Hero's. The wheel was merely a pipe bent in S form, attached at its centre to a hollow vertical shaft supplied with steam through a stuffing-box at one extremity. The steam blew out tangentially from the ends of the S, causing the shaft to revolve rapidly and work the machinery (usually a cream separator) mounted on it. This motor proved very suitable for dairy work, but was too wasteful of steam to be useful where high power was needed.
In its earliest form, this turbine was a modification of Hero's. The wheel was simply a pipe shaped like an S, connected at its center to a hollow vertical shaft that received steam through a stuffing box at one end. The steam blew out tangentially from the ends of the S, causing the shaft to spin quickly and operate the machinery (usually a cream separator) mounted on it. This motor was great for dairy work but wasted too much steam to be effective in high-power applications.

Fig. 36.—The wheel and nozzles of a De Laval turbine.
In the De Laval turbine as now constructed the steam is blown from stationary nozzles against vanes mounted on a revolving wheel. Fig. 36 shows the nozzles and a turbine wheel. The wheel is made as a solid disc, to the circumference of which the vanes are dovetailed separately in a single row. Each vane is of curved section, the concave side directed towards the nozzles, which, as will be[Pg 77] gathered from the "transparent" specimen on the right of our illustration, gradually expand towards the mouth. This is to allow the expansion of the steam, and a consequent gain of velocity. As it issues, each molecule strikes against the concave face of a vane, and, while changing its direction, is robbed[Pg 78] of its kinetic energy, which passes to the wheel. To turn once more to a stone-throwing comparison, it is as if a boy were pelting the wheel with an enormous number of tiny stones. Now, escaping high-pressure steam moves very fast indeed. To give figures, if it enters the small end of a De Laval nozzle at 200 lbs. per square inch, it will leave the big end at a velocity of 48 miles per minute—that is, at a speed which would take it right round the world in 8½ hours! The wheel itself would not move at more than about one-third of this speed as a maximum.[7] But even so, it may make as many as 30,000 revolutions per minute. A mechanical difficulty is now encountered—namely, that arising from vibration. No matter how carefully the turbine wheel may be balanced, it is practically impossible to make its centre of gravity coincide exactly with the central point of the shaft; in other words, the wheel will be a bit—perhaps only a tiny fraction of an ounce—heavier on one side than the other. This want of truth causes vibration, which, at the high speed mentioned, would cause the shaft to knock the bearings[Pg 79] in which it revolves to pieces, if—and this is the point—those bearings were close to the wheel M. de Laval mounted the wheel on a shaft long enough between the bearings to "whip," or bend a little, and the difficulty was surmounted.
In the De Laval turbine as it's currently built, steam is shot from stationary nozzles at vanes attached to a spinning wheel. Fig. 36 shows the nozzles and the turbine wheel. The wheel is made as a solid disc, to which the vanes are individually attached in a single row. Each vane has a curved shape, with the concave side facing the nozzles, which, as can be seen from the "transparent" sample on the right of our illustration, gradually widens toward the opening. This design allows the steam to expand, resulting in an increase in speed. As the steam exits, each particle hits the concave surface of a vane, changing its direction while losing its kinetic energy, which transfers to the wheel. To compare it to throwing stones, it's like a boy hurling a huge number of small stones at the wheel. The high-pressure steam moves very quickly. To give you an idea, if it enters the small end of a De Laval nozzle at 200 lbs. per square inch, it will exit the larger end at a speed of 48 miles per minute—that's fast enough to circle the globe in 8½ hours! The wheel itself won’t turn faster than about one-third of that speed at most. But even at this speed, it can make up to 30,000 rotations per minute. A mechanical issue arises—specifically, vibration. No matter how carefully the turbine wheel is balanced, it's nearly impossible to align its center of gravity perfectly with the central point of the shaft; in other words, one side of the wheel will be slightly heavier than the other. This imbalance leads to vibration, which, at the high speeds mentioned, could damage the bearings in which the shaft rotates, unless—this is crucial—those bearings are placed far enough from the wheel. M. de Laval mounted the wheel on a shaft long enough between the bearings so that it could "whip," or flex slightly, which solved the problem.
The normal speed of the turbine wheel is too high for direct driving of some machinery, so it is reduced by means of gearing. To dynamos, pumps, and air-fans it is often coupled direct.
The usual speed of the turbine wheel is too fast for directly powering some machinery, so it's lowered using gears. It’s often connected directly to dynamos, pumps, and air fans.
THE PARSONS TURBINE.
THE PARSONS TURBINE.
At the grand naval review held in 1897 in honour of Queen Victoria's diamond jubilee, one of the most noteworthy sights was the little Turbinia of 44½ tons burthen, which darted about among the floating forts at a speed much surpassing that of the fastest "destroyer." Inside the nimble little craft were engines developing 2,000 horse power, without any of the clank and vibration which usually reigns in the engine-room of a high-speed vessel. The Turbinia was the first turbine-driven boat, and as such, even apart from her extraordinary pace, she attracted great attention. Since 1897 the Parsons turbine has been installed on many ships, including several men-of-war, and it seems probable that the time is[Pg 80] not far distant when reciprocating engines will be abandoned on all high-speed craft.
At the grand naval review in 1897, celebrating Queen Victoria's diamond jubilee, one of the standout sights was the little Turbinia, weighing 44½ tons, as it zipped around the floating forts at a speed far exceeding that of the fastest destroyer. Inside this speedy little vessel were engines generating 2,000 horsepower, without the usual clanking and vibration found in the engine room of a high-speed ship. The Turbinia was the first turbine-driven boat, and even aside from its incredible speed, it drew a lot of attention. Since 1897, the Parsons turbine has been installed on many ships, including several warships, and it seems likely that it's not far off when reciprocating engines will be phased out on all high-speed vessels.
DESCRIPTION OF THE PARSONS TURBINE.
DESCRIPTION OF THE PARSONS TURBINE.

The essential parts of a Parsons turbine are:—(1) The shaft, on which is mounted (2) the drum; (3) the cylindrical casing inside which the drum revolves; (4) the vanes on the drum and casing; (5) the balance pistons. Fig. 37 shows a diagrammatic turbine in section. The drum, it will be noticed, increases its diameter in three stages, D1, D2, D3, towards the right. From end to end it is studded with little vanes, M M, set in parallel rings small distances apart. Each vane has a curved section (see Fig. 38), the hollow side facing towards the left. The vanes stick out from the drum like[Pg 81] short spokes, and their outer ends almost touch the casing. To the latter are attached equally-spaced rings of fixed vanes, F F, pointing inwards towards the drum, and occupying the intervals between the rings of moving vanes. Their concave sides also face towards the left, but, as seen in Fig. 38, their line of curve lies the reverse way to that of M M. Steam enters the casing at A, and at once rushes through the vanes towards the outlet at B. It meets the first row of fixed vanes, and has its path so deflected that it strikes the ring of moving (or drum) vanes at the most effective angle, and pushes them round. It then has its direction changed by the ring of F F, so that it may treat the next row of M M in a similar fashion.
The main components of a Parsons turbine are: (1) the shaft, which supports (2) the drum; (3) the cylindrical casing where the drum spins; (4) the vanes on both the drum and the casing; and (5) the balance pistons. Figure 37 shows a diagram of the turbine in section. You'll see that the drum increases in diameter in three stages, D1, D², D3, moving to the right. It is covered from end to end with small vanes, M M, arranged in parallel rings that are spaced slightly apart. Each vane has a curved shape (see Fig. 38), with the hollow side facing to the left. The vanes protrude from the drum like[Pg 81] short spokes, and their outer ends nearly touch the casing. The casing has equally spaced rings of fixed vanes, F F, that point inward towards the drum, filling the gaps between the rings of moving vanes. Their concave sides also face left, but, as shown in Figure 38, their curve is oriented opposite to that of M M. Steam enters the casing at A, instantly rushing through the vanes toward the outlet at B. Upon encountering the first row of fixed vanes, its path is redirected so that it strikes the ring of moving (or drum) vanes at the most effective angle, causing them to rotate. The steam's direction is then altered by the ring of F F, allowing it to engage the next row of M M in the same way.

THE EXPANSIVE ACTION OF STEAM IN A TURBINE.
THE WIDESPREAD ACTION OF STEAM IN A TURBINE.
On reaching the end of D1 it enters the second, or intermediate, set of vanes. The drum here is of a greater diameter, and the blades are longer and set somewhat farther apart, to give a freer passage to the now partly expanded steam, which has lost pressure but gained velocity. The process of movement is repeated through this stage; and again in D3, the low-pressure drum. The steam then escapes to the condenser through B, having by this time expanded very many times; and it is found advisable, for reasons explained in connection with compound steam-engines, to have a separate turbine in an independent casing for the extreme stages of expansion.
On reaching the end of D1, it enters the second, or intermediate, set of blades. The drum here is larger in diameter, and the blades are longer and spaced further apart to allow a smoother flow for the now partly expanded steam, which has lost pressure but gained speed. The movement process repeats in this stage, and again in D3, the low-pressure drum. The steam then escapes to the condenser through B, having expanded many times by this point; and for reasons explained in the context of compound steam engines, it is beneficial to have a separate turbine in an independent casing for the final stages of expansion.
The vanes are made of brass. In the turbines of the Carmania, the huge Cunard liner, 1,115,000 vanes are used. The largest diameter of the drums is 11 feet, and each low-pressure turbine weighs 350 tons.
The vanes are made of brass. In the turbines of the Carmania, the massive Cunard liner, 1,115,000 vanes are used. The largest diameter of the drums is 11 feet, and each low-pressure turbine weighs 350 tons.
BALANCING OF THRUST.
Thrust balancing.
The push exerted by the steam on the blades not only turns the drum, but presses it in the direction in which the steam flows. This end thrust is counterbalanced by means of the "dummy" pistons, P1, P2, P3. Each dummy consists of a number of discs revolving between rings projecting from the casing, the distance[Pg 84] between discs and rings being so small that but little steam can pass. In the high-pressure compartment the steam pushes P1 to the left with the same pressure as it pushes the blades of D1 to the right. After completing the first stage it fills the passage C, which communicates with the second piston, P2, and the pressure on that piston negatives the thrust on D2. Similarly, the passage E causes the steam to press equally on P3 and the vanes of D3. So that the bearings in which the shaft revolves have but little thrust to take. This form of compensation is necessary in marine as well as in stationary turbines. In the former the dummy pistons are so proportioned that the forward thrust given by them and the screw combined is almost equal to the thrust aft of the moving vanes.
The push from the steam on the blades not only turns the drum but also pushes it in the direction the steam flows. This forward thrust is balanced out by the "dummy" pistons, P1, P2, P3. Each dummy consists of several discs rotating between rings extending from the casing, with the distance[Pg 84] between the discs and rings being so small that only a little steam can pass through. In the high-pressure area, the steam pushes P1 to the left with the same force that it pushes the blades of D1 to the right. After completing the first stage, it fills the passage C, which connects to the second piston, P2, and the pressure on that piston counteracts the thrust on D². Similarly, the passage E makes the steam push equally on P3 and the vanes of D3. As a result, the bearings supporting the shaft have very little thrust to handle. This type of compensation is essential in both marine and stationary turbines. In marine turbines, the dummy pistons are sized so that the forward thrust from them and the screw combined is nearly equal to the thrust from the moving vanes.
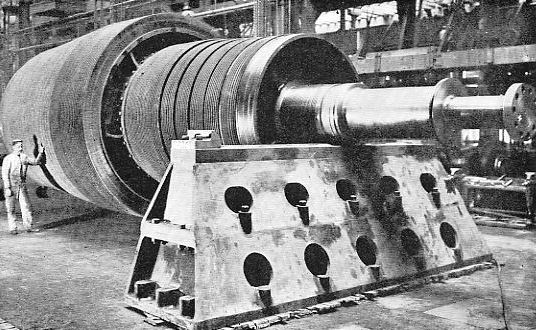
ADVANTAGES OF THE MARINE TURBINE.
BENEFITS OF THE MARINE TURBINE.
(1.) Absence of vibration. Reciprocating engines, however well balanced, cause a shaking of the whole ship which is very unpleasant to passengers. The turbine, on the other hand, being almost perfectly balanced, runs so smoothly at the highest speeds that, if the hand be laid on the covering, it is sometimes almost impossible to tell whether the machinery is in motion. As a consequence of this smooth running there is little noise in the engine-room—a pleasant contrast to the deafening roar of reciprocating engines. (2.) Turbines occupy less room. (3.) They are more easily tended. (4.) They require fewer repairs, since the rubbing surfaces are very small as compared to those of reciprocating engines. (5.) They are more economical at high speeds. It must be remembered that a turbine is essentially meant for high speeds. If run slowly, the steam will escape through the many passages without doing much work.
(1.) No vibration. Reciprocating engines, no matter how well balanced, cause the entire ship to shake, which is very uncomfortable for passengers. The turbine, on the other hand, is almost perfectly balanced and runs so smoothly at high speeds that if you place your hand on the cover, it can be nearly impossible to tell if the machinery is running. Because of this smooth operation, the engine room is much quieter—a nice change from the blaring noise of reciprocating engines. (2.) Turbines take up less space. (3.) They are easier to maintain. (4.) They need fewer repairs since the rubbing surfaces are much smaller compared to those of reciprocating engines. (5.) They are more efficient at high speeds. It's important to note that a turbine is primarily designed for high speeds. If operated slowly, the steam will escape through the many passages without generating much work.
Owing to its construction, a turbine cannot be reversed like a cylinder engine. It therefore becomes necessary to fit special astern turbines to one or more of the screw shafts, for use when the ship has to be stopped or moved astern. Under ordinary conditions these turbines revolve idly in their cases.
Due to its design, a turbine can't be reversed like a cylinder engine. So, it's essential to install special astern turbines on one or more of the screw shafts to be used when the ship needs to stop or move backward. Normally, these turbines turn freely in their housings.
The highest speed ever attained on the sea was the forty-two miles per hour of the unfortunate Viper, a turbine destroyer which developed 11,500 horse power, though displacing only 370 tons. This velocity would compare favourably with that of a good many expresses on certain railways that we could name. In the future thirty miles an hour will certainly be attained by turbine-driven liners.
The fastest speed ever reached at sea was the forty-two miles per hour of the ill-fated Viper, a turbine destroyer that generated 11,500 horsepower while only weighing 370 tons. This speed would stand up well against several express trains on certain railways we could mention. In the future, turbine-driven liners will definitely reach thirty miles an hour.
[7] Even at this speed the wheel has a circumferential velocity of two-thirds that of a bullet shot from a Lee-Metford rifle. A vane weighing only 250 grains (about ½ oz.) exerts under these conditions a centrifugal pull of 15 cwt. on the wheel!
[7] Even at this speed, the wheel moves at two-thirds the speed of a bullet fired from a Lee-Metford rifle. A vane weighing just 250 grains (about ½ oz.) produces a centrifugal force of 15 cwt. on the wheel under these conditions!
Chapter IV.
THE INTERNAL-COMBUSTION ENGINE.
The meaning of the term—Action of the internal-combustion engine—The motor car—The starting-handle—The engine—The carburetter—Ignition of the charge—Advancing the spark—Governing the engine—The clutch—The gear-box—The compensating gear—The silencer—The brakes—Speed of cars.
The meaning of the term—Action of the internal-combustion engine—The car—The starter handle—The engine—The carburetor—Ignition of the fuel—Advancing the spark—Controlling the engine—The clutch—The gearbox—The compensating gear—The muffler—The brakes—Speed of cars.
THE MEANING OF THE TERM "INTERNAL-COMBUSTION ENGINE."
THE MEANING OF THE TERM "INTERNAL-COMBUSTION ENGINE."
In the case of a steam-boiler the energy of combustion is transmitted to water inside an air-tight vessel. The fuel does not actually touch the "working fluid." In the gas or oil engine the fuel is brought into contact and mixed with the working fluid, which is air. It combines suddenly with it in the cylinder, and heat energy is developed so rapidly that the act is called an explosion. Coal gas, mineral oils, alcohol, petrol, etc., all contain hydrogen and carbon. If air, which contributes oxygen, be added to any of these in due proportion, the mixture becomes highly explosive. On a light being applied, oxygen and carbon unite, also hydrogen and oxygen, and violent heat is generated, causing a violent molecular bombardment of the sides of the vessel containing the mixture. Now, if the mixture be compressed it becomes hotter and hotter, until a point is reached at which it ignites spontaneously. Early gas-engines did not compress the charge before ignition. Alphonse Beau de Rochas, a Frenchman, first thought of making the piston of the engine squeeze the mixture before ignition; and from the year 1862, when he proposed this innovation, the success of the internal-combustion engine may be said to date.
In a steam boiler, the heat from combustion is transferred to water inside a sealed container. The fuel doesn't come into contact with the "working fluid." In a gas or oil engine, the fuel is mixed directly with the working fluid, which is air. This mixture ignites suddenly in the cylinder, producing heat energy so quickly that it’s referred to as an explosion. Fuels like coal gas, mineral oils, alcohol, and petrol all contain hydrogen and carbon. When air, which provides oxygen, is added in the right amounts, the mixture becomes highly explosive. When a flame is introduced, oxygen combines with carbon, and hydrogen combines with oxygen, creating intense heat that causes a violent molecular reaction against the walls of the container holding the mixture. If the mixture is compressed, it heats up progressively until it reaches a point where it ignites spontaneously. Early gas engines didn’t compress the mixture before ignition. Alphonse Beau de Rochas, a French engineer, was the first to suggest compressing the mixture with the piston before ignition; since he proposed this innovation in 1862, the development of the internal combustion engine has relied on this concept.


ACTION OF THE ENGINE.
ENGINE ACTION.
The gas-engine, the oil-engine, and the motor-car engine are similar in general principles. The cylinder has, instead of a slide-valve, two, or sometimes three, "mushroom" valves, which may be described as small and thick round plates, with bevelled edges, mounted on the ends of short rods, called stems. These valves open into the cylinder, upwards, downwards, or horizontally, as the case may be; being pushed in by cams projecting from a shaft rotated by the engine. For the present we will confine our attention to the[Pg 91] series of operations which causes the engine to work. This series is called the Beau de Rochas, or Otto, cycle, and includes four movements of the piston. Reference to Fig. 39 will show exactly what happens in a gas-engine—(1) The piston moves from left to right, and just as the movement commences valves G (gas) and A (air) open to admit the explosive mixture. By the time that P has reached the end of its travel these valves have closed again. (2) The piston returns to the left, compressing the mixture, which has no way of escape open to it. At the end of the stroke the charge is ignited by an incandescent tube I (in motor car and some stationary engines by an electric spark), and (3) the piston flies out again on the "explosion" stroke. Before it reaches the limit position, valve E (exhaust) opens, and (4) the piston flies back under the momentum of the fly-wheel, driving out the burnt gases through the still open E. The "cycle" is now complete. There has been suction, compression (including ignition), combustion, and exhaustion. It is evident that a heavy fly-wheel must be attached to the crank shaft, because the energy of one stroke (the explosion) has to serve for the whole cycle; in other words, for two complete revolutions of the crank. A single-cylinder steam-engine[Pg 92] develops an impulse every half-turn—that is, four times as often. In order to get a more constant turning effect, motor cars have two, three, four, six, and even eight cylinders. Four-cylinder engines are at present the most popular type for powerful cars.
The gas engine, oil engine, and car engine all share similar basic principles. Instead of using a slide valve, the cylinder has two, or sometimes three, "mushroom" valves, which are small, thick round plates with slanted edges, attached to the ends of short rods called stems. These valves open into the cylinder either upwards, downwards, or sideways, depending on the design; they are pushed open by cams that stick out from a shaft turned by the engine. For now, we will focus on the[Pg 91] series of actions that make the engine operate. This sequence is known as the Beau de Rochas or Otto cycle, which includes four piston movements. Referring to Fig. 39 will clearly show what happens in a gas engine—(1) The piston moves from left to right, and just as it begins to move, valves G (gas) and A (air) open to let in the explosive mixture. By the time P reaches the end of its travel, these valves have closed again. (2) The piston moves back to the left, compressing the mixture, which has no way to escape. At the end of the stroke, the charge is ignited by an incandescent tube I (or by an electric spark in car and some stationary engines), and (3) the piston shoots out again during the "explosion" stroke. Before it reaches the limit position, valve E (exhaust) opens, and (4) the piston flies back due to the momentum of the flywheel, pushing out the burnt gases through the still open E. The "cycle" is now complete. There has been suction, compression (including ignition), combustion, and exhaustion. It's clear that a heavy flywheel must be attached to the crankshaft because the energy from one stroke (the explosion) has to power the entire cycle; in other words, it needs to cover two complete revolutions of the crank. A single-cylinder steam engine[Pg 92] creates an impulse every half-turn—that is, four times more often. To achieve a more constant rotational effect, cars are designed with two, three, four, six, or even eight cylinders. Currently, four-cylinder engines are the most popular choice for powerful cars.
THE MOTOR CAR.
The car.

We will now proceed to an examination of the motor car, which, in addition to mechanical apparatus for the transmission of motion to the driving-wheels, includes all the fundamental adjuncts of the internal-combustion engine.[8] Fig. 40 is a bird's-eye view of the chassis (or "works" and wheels) of a car, from which the body has been removed. Starting at the[Pg 93] left, we have the handle for setting the engine in motion; the engine (a two-cylinder in this case); the fly-wheel, inside which is the clutch; the gear-box, containing the cogs for altering the speed of revolution of the driving-wheels relatively to that of the engine; the propeller shaft; the silencer, for deadening the noise of the exhaust; and the bevel-gear, for turning the driving-wheels. In the particular type of car here considered you will notice that a "direct," or shaft, drive is used. The shaft has at each end a flexible, or "universal," joint, which allows the shaft to turn freely, even though it may not be in a line with the shaft projecting from the gear-box. It must be remembered that the engine and gear-box are mounted on the frame, between which and the axles are springs, so that when the car bumps up and down, the shaft describes part of a circle, of which the gear-box end is the centre.
We will now look at the motor car, which, in addition to the mechanical parts that transfer motion to the driving wheels, includes all the essential components of the internal combustion engine.[8] Fig. 40 shows a bird's-eye view of the chassis (or "works" and wheels) of a car, with the body removed. Starting from the[Pg 93] left, we see the handle for starting the engine; the engine itself (a two-cylinder in this example); the flywheel, which has the clutch inside; the gearbox, which holds the gears for changing the speed of the driving wheels in relation to the engine; the propeller shaft; the silencer, which reduces the noise from the exhaust; and the bevel gear, which turns the driving wheels. In this specific type of car being discussed, you’ll notice that a "direct," or shaft, drive is used. The shaft has a flexible or "universal" joint at each end, allowing it to rotate freely, even if it’s not aligned with the shaft coming from the gearbox. It's important to remember that the engine and gearbox are mounted on the frame, and there are springs between them and the axles, so when the car goes up and down, the shaft moves in part of a circle, with the gearbox end as the center.
An alternative method of driving is by means of chains, which run round sprocket (cog) wheels on the ends of a shaft crossing the frame just behind the gear-box, and round larger sprockets attached to the hubs of the driving-wheels. In such a case the axles of the driving-wheel are fixed to the springs, and the wheels revolve round them. Where a Cardan (shaft)[Pg 94] drive is used the axles are attached rigidly to the wheels at one end, and extend, through tubes fixed to the springs, to bevel-wheels in a central compensating-gear box (of which more presently).
An alternative way to drive is by using chains, which go around sprocket (cog) wheels on the ends of a shaft that crosses the frame just behind the gearbox, and around larger sprockets attached to the hubs of the driving wheels. In this case, the axles of the driving wheels are fixed to the springs, and the wheels spin around them. When a Cardan (shaft)[Pg 94] drive is used, the axles are rigidly attached to the wheels at one end and extend through tubes fixed to the springs to bevel wheels in a central compensating gear box (which will be explained further).
Several parts—the carburetter, tanks, governor, and pump—are not shown in the general plan. These will be referred to in the more detailed account that follows.
Several parts—the carburetor, tanks, governor, and pump—aren't included in the general plan. These will be mentioned in the more detailed account that follows.
THE STARTING-HANDLE.
THE STARTING HANDLE.

Fig. 41 gives the starting-handle in part section. The handle H is attached to a tube which terminates in a clutch, C. A powerful spring keeps C normally apart from a second clutch, C1, keyed to the engine shaft. When the driver wishes to start the engine he presses the handle towards the right, brings the clutches together, and turns the handle in a clockwise[Pg 95] direction. As soon as the engine begins to fire, the faces of the clutches slip over one another.
Fig. 41 shows the starting handle in part section. The handle H is attached to a tube that ends in a clutch, C. A strong spring keeps C normally separated from a second clutch, C1, which is connected to the engine shaft. When the driver wants to start the engine, he pushes the handle to the right, brings the clutches together, and turns the handle in a clockwise[Pg 95] direction. As soon as the engine starts firing, the faces of the clutches slide over each other.
THE ENGINE.
THE ENGINE.

We next examine the two-cylinder engine (Fig. 42). Each cylinder is surrounded by a water-jacket, through which water is circulated by a pump[9] (Fig. 43). The heat generated by combustion is so great that the walls of the cylinder would soon become red-hot unless some of the heat were quickly[Pg 96] carried away. The pistons are of "trunk" form—that is, long enough to act as guides and absorb the oblique thrust of the piston rods. Three or more piston rings lying in slots (not shown) prevent the escape of gas past the piston. It is interesting to notice that the efficiency of an internal-combustion engine depends so largely on the good fit of these moving parts, that cylinders, pistons, and rings must be exceedingly true. A good firm will turn out standard parts which are well within 1⁄5000 of an inch of perfect truth. It is also a wonderful testimony to the quality of the materials used that, if properly looked after, an engine which has made many millions of revolutions, at the rate of 1,000 to 2,000 per minute, often shows no appreciable signs of wear. In one particular test an engine was run continuously for several months, and at the end of the trial was in absolutely perfect condition.
We now look at the two-cylinder engine (Fig. 42). Each cylinder is surrounded by a water jacket, where water circulates thanks to a pump[9] (Fig. 43). The heat produced by combustion is so intense that the cylinder walls would quickly become red-hot if some of that heat weren't swiftly[Pg 96] removed. The pistons have a "trunk" design—meaning they’re long enough to serve as guides and absorb the angled force from the piston rods. Three or more piston rings located in slots (not shown) stop gas from escaping past the piston. Interestingly, the efficiency of an internal-combustion engine relies heavily on how well these moving parts fit together, so the cylinders, pistons, and rings must be incredibly precise. A reputable manufacturer will produce standard parts that are accurate to within 1⁄5000 of an inch. It’s also remarkable that if properly maintained, an engine that has undergone millions of revolutions at speeds from 1,000 to 2,000 per minute often shows no significant signs of wear. In one specific test, an engine was run continuously for several months, and by the end of the test, it was in absolutely perfect condition.
The cranks revolve in an oil-tight case (generally made of aluminium), and dip in oil, which they splash up into the cylinder to keep the piston well lubricated. The plate, P P, through a slot in which the piston rod works, prevents an excess of oil being flung up. Channels are provided for leading oil[Pg 97] into the bearings. The cranks are 180° apart. While one piston is being driven out by an explosion, the other is compressing its charge prior to ignition, so that the one action deadens the other. Therefore two explosions occur in one revolution of the cranks, and none during the next revolution. If both cranks were in line, the pistons would move together, giving one explosion each revolution.
The cranks turn inside a sealed case (usually made of aluminum) and dip in oil, which they splash into the cylinder to keep the piston well-lubricated. The plate, P P, has a slot for the piston rod, preventing too much oil from being sprayed upward. There are channels to guide oil[Pg 97] into the bearings. The cranks are positioned 180° apart. While one piston is pushed out by an explosion, the other is compressing its charge before ignition, which means one action counters the other. As a result, two explosions happen in one crank revolution and none in the next. If both cranks were aligned, the pistons would move together, resulting in one explosion per revolution.

The valve seats, and the inlet and exhaust pipes, are seen in section. The inlet valve here works automatically, being pulled in by suction; but on many engines—on all powerful engines—the inlet, like the exhaust valve, is lifted by a cam, lest it should stick or work irregularly. Three dotted circles show A, a cog on the crank shaft; B, a "lay" cog, which transmits motion to C, on a short shaft rotating the cam that lifts the exhaust valve. C,[Pg 98] having twice as many teeth as A, revolves at half its rate. This ensures that the valve shall be lifted only once in two revolutions of the crank shaft to which it is geared. The cogs are timed, or arranged, so that the cam begins to lift the valve when the piston has made about seven-eighths of its explosion stroke, and closes the valve at the end of the exhaust stroke.
The valve seats, along with the inlet and exhaust pipes, are shown in section. The inlet valve operates automatically, being pulled in by suction; however, in many engines—especially powerful ones—the inlet, like the exhaust valve, is lifted by a cam to prevent it from sticking or operating irregularly. Three dotted circles indicate A, a cog on the crankshaft; B, a "lay" cog, which transmits motion to C, on a short shaft that rotates the cam lifting the exhaust valve. C,[Pg 98] has twice as many teeth as A, so it rotates at half the speed. This ensures that the valve is lifted only once every two revolutions of the crankshaft to which it is connected. The cogs are timed in such a way that the cam begins to lift the valve when the piston has completed about seven-eighths of its explosion stroke, and it closes the valve at the end of the exhaust stroke.
THE CARBURETTER.
THE CARBURETOR.
A motor car generally uses petrol as its fuel. Petrol is one of the more volatile products of petroleum, and has a specific gravity of about 680—that is, volume for volume, its weight is to that of water in the proportion of 680 to 1,000. It is extremely dangerous, as it gives off an inflammable gas at ordinary temperatures. Benzine, which we use to clean clothes, is practically the same as petrol, and should be treated with equal care. The function of a carburetter is to reduce petrol to a very fine spray and mix it with a due quantity of air. The device consists of two main parts (Fig. 44)—the float chamber and the jet chamber. In the former is a contrivance for regulating the petrol supply. A float—a cork, or air-tight metal box—is arranged to move freely up and down the stem of a needle-valve,[Pg 99] which closes the inlet from the tank. At the bottom of the chamber are two pivoted levers, W W, which, when the float rests on them, tip up and lift the valve. Petrol flows in and raises the float. This allows the valve to sink and cut off the supply. If the valve is a good fit and the float is of the correct weight, the petrol will never rise higher than the tip of the jet G.
A motor vehicle usually runs on gasoline. Gasoline is one of the more volatile products from petroleum and has a specific gravity of about 680—that means, weight for weight, it compares to water in a ratio of 680 to 1,000. It's really dangerous because it releases a flammable gas at normal temperatures. Benzene, which we use for cleaning clothes, is pretty much the same as gasoline and should be handled with the same care. The purpose of a carburetor is to break gasoline down into a fine mist and mix it with a specific amount of air. This device has two main parts (Fig. 44)—the float chamber and the jet chamber. The float chamber contains a mechanism that controls the gasoline supply. A float—either a cork or an airtight metal box—moves freely up and down the stem of a needle valve,[Pg 99] which closes off the inlet from the tank. At the bottom of the chamber are two pivoted levers, W W, which tip up and lift the valve when the float rests on them. Gasoline flows in and lifts the float. This allows the valve to lower and stop the supply. If the valve fits well and the float is the right weight, the gasoline will never rise higher than the tip of the jet G.

The suction of the engine makes petrol spirt through the jet (which has a very small hole in its end) and atomize itself against a spraying-cone, A.[Pg 100] It then passes to the engine inlet pipe through a number of openings, after mixing with air entering from below. An extra air inlet, controllable by the driver, is generally added, unless the carburetter be of a type which automatically maintains constant proportions of air and vapour. The jet chamber is often surrounded by a jacket, through which part of the hot exhaust gases circulate. In cold weather especially this is a valuable aid to vaporization.
The engine's suction pulls petrol through a jet with a tiny opening, causing it to atomize against a spraying cone, A.[Pg 100] It then moves to the engine inlet pipe through several openings, mixing with air that comes in from below. Usually, there's an additional air inlet that the driver can control, unless the carburetor is designed to automatically keep the right balance of air and vapor. The jet chamber is often surrounded by a jacket that allows some hot exhaust gases to flow through, which is especially helpful for vaporization in cold weather.

IGNITION OF THE CHARGE.
Firing the charge.
All petrol-cars now use electrical ignition. There are two main systems—(1) by an accumulator and induction coil; (2) magneto ignition, by means of a small dynamo driven by the engine. A general arrangement of the first is shown in Fig. 45. A disc, D, of some insulating material—fibre or vulcanite—is mounted on the cam, or half-speed, shaft. Into the circumference is let a piece of brass, called the contact-piece, through which a screw passes to the cam shaft. A movable plate, M P, which can be rotated concentrically with D through part of a circle, carries a "wipe" block at the end of a spring, which presses it against D. The spring itself is attached to an insulated plate. When the revolution[Pg 101] of D brings the wipe and contact together, current flows from the accumulator through switch S to the wipe; through the contact-piece to C; from C to M P and the induction coil; and back to the accumulator. This is the primary, or low-tension, circuit. A high-tension current is induced by the coil in the secondary circuit, indicated by dotted lines.[10] In this circuit is the sparking-plug (see Fig. 46), having a central insulated rod in connection with one terminal of the secondary coil. Between it[Pg 102] and a bent wire projecting from the iron casing of the plug (in contact with the other terminal of the secondary coil through the metal of the engine, to which one wire of the circuit is attached) is a small gap, across which the secondary current leaps when the primary current is broken by the wipe and contact parting company. The spark is intensely hot, and suffices to ignite the compressed charge in the cylinder.
All petrol cars now use electrical ignition. There are two main systems—(1) using an accumulator and induction coil; (2) magneto ignition, with a small dynamo powered by the engine. A general layout of the first system is shown in Fig. 45. A disc, D, made of insulating material—like fiber or vulcanite—is attached to the cam or half-speed shaft. A piece of brass, called the contact-piece, is set into the circumference, with a screw connecting it to the cam shaft. A movable plate, M P, can be rotated around D through part of a circle and carries a "wipe" block at the end of a spring, which presses it against D. The spring itself is attached to an insulated plate. When the rotation of D brings the wipe and contact together, current flows from the accumulator through switch S to the wipe; then through the contact-piece to C; from C to M P and the induction coil; and back to the accumulator. This is the primary, or low-tension, circuit. A high-tension current is generated by the coil in the secondary circuit, which is shown by dotted lines.[10] This circuit includes the sparking plug (see Fig. 46), which has a central insulated rod connected to one terminal of the secondary coil. There’s a small gap between it[Pg 101] and a bent wire that extends from the iron casing of the plug (making contact with the other terminal of the secondary coil via the engine metal, to which one wire of the circuit is linked). When the primary current is interrupted by the wipe and the contact moving apart, a spark leaps across this gap fueled by the secondary current. The spark is extremely hot, enough to ignite the compressed charge in the cylinder.
ADVANCING THE SPARK.
IGNITING THE SPARK.
We will assume that the position of W (in Fig. 45) is such that the contact touches W at the moment when the piston has just completed the compression[Pg 103] stroke. Now, the actual combustion of the charge occupies an appreciable time, and with the engine running at high speed the piston would have travelled some way down the cylinder before the full force of the explosion was developed. But by raising lever L, the position of W may be so altered that contact is made slightly before the compression stroke is complete, so that the charge is fairly alight by the time the piston has altered its direction. This is called advancing the spark.
We will assume that the position of W (in Fig. 45) is such that the contact touches W right when the piston has just finished the compression[Pg 103] stroke. Now, the actual combustion of the charge takes a noticeable amount of time, and when the engine runs at high speed, the piston would have moved some distance down the cylinder before the explosion's full force kicks in. However, by raising lever L, we can change the position of W so that contact is made slightly before the compression stroke ends, allowing the charge to be well ignited by the time the piston changes direction. This process is called advancing the spark.
GOVERNING THE ENGINE.
MANAGING THE ENGINE.
There are several methods of controlling the speed of internal-combustion engines. The operating mechanism in most cases is a centrifugal ball-governor. When the speed has reached the fixed limit it either (1) raises the exhaust valve, so that no fresh charges are drawn in; (2) prevents the opening of the inlet valve; or (3) throttles the gas supply. The last is now most commonly used on motor cars, in conjunction with some device for putting it out of action when the driver wishes to exceed the highest speed that it normally permits.
There are several ways to control the speed of internal combustion engines. Most of the time, the operating mechanism is a centrifugal ball governor. When the speed reaches the set limit, it either (1) raises the exhaust valve so that no fresh air or fuel is drawn in; (2) stops the inlet valve from opening; or (3) restricts the gas supply. The last option is now the most commonly used in cars, along with some device to disable it when the driver wants to exceed the maximum speed it normally allows.

A sketch of a neat governor, with regulating attachment, is given in Fig. 47. The governor shaft[Pg 104] is driven from the engine. As the balls, B B, increase their velocity, they fly away from the shaft and move the arms, A A, and a sliding tube, C, towards the right. This rocks the lever R, and allows the valves in the inlet pipe to close and reduce the supply of air and gas. A wedge, W, which can be raised or lowered by lever L, intervenes between the end of R and the valve stem. If this lever be lifted to its highest position, the governing commences at a lower speed, as the valve then has but a short distance to travel before closing completely. For high speeds[Pg 105] the driver depresses L, forces the wedge down, and so minimizes the effect of the governor.
A diagram of a neat governor with a regulating attachment is shown in Fig. 47. The governor shaft[Pg 104] is powered by the engine. As the balls, B B, spin faster, they move outward from the shaft and pivot the arms, A A, and a sliding tube, C, to the right. This tilts the lever R and allows the valves in the inlet pipe to close, reducing the flow of air and gas. A wedge, W, which can be raised or lowered by lever L, sits between the end of R and the valve stem. If this lever is lifted to its highest point, the governing begins at a lower speed since the valve has a shorter distance to close completely. For high speeds[Pg 105], the driver presses down on L, pushes the wedge down, and reduces the effect of the governor.
THE CLUTCH.
THE CLUTCH.
The engine shaft has on its rear end the fly-wheel, which has a broad and heavy rim, turned to a conical shape inside. Close to this, revolving loosely on the shaft, is the clutch plate, a heavy disc with a broad edge so shaped as to fit the inside of a fly-wheel. It is generally faced with leather. A very strong spring presses the plate into the fly-wheel, and the resulting friction is sufficient to prevent any slip. Projections on the rear of the clutch engage with the gear-box shaft. The driver throws out the clutch by depressing a lever with his foot. Some clutches dispense with the leather lining. These are termed metal to metal clutches.
The engine shaft has a flywheel at its back end, which has a wide and heavy rim shaped like a cone on the inside. Nearby, loosely rotating on the shaft, is the clutch plate, a heavy disc with a wide edge designed to fit the inside of the flywheel. It is usually covered with leather. A strong spring presses the plate against the flywheel, creating enough friction to stop any slipping. Projections on the back of the clutch connect with the gearbox shaft. The driver disengages the clutch by pressing a lever with their foot. Some clutches do not use leather lining; these are called metal to metal clutches.
THE GEAR-BOX.
THE GEARBOX.
We now come to a very interesting detail of the motor car, the gear-box. The steam-engine has its speed increased by admitting more steam to the cylinders. But an explosion engine must be run at a high speed to develop its full power, and when heavier work has to be done on a hill it becomes necessary to[Pg 106] alter the speed ratio of engine to driving-wheels. Our illustration (Fig. 48) gives a section of a gear-box, which will serve as a typical example. It provides three forward speeds and one reverse. To understand how it works, we must study the illustration carefully. Pinion 1 is mounted on a hollow shaft turned by the clutch. Into the hollow shaft projects the end of another shaft carrying pinions 6 and 4. Pinion 6 slides up and down this shaft, which is square at this point, but round inside the loose pinion 4. Pinions 2 and 3 are keyed to a square secondary shaft, and are respectively always in gear with 1 and 4; but 5 can be slid backwards[Pg 107] and forwards so as to engage or disengage with 6. In the illustration no gear is "in." If the engine is working, 1 revolves 2, 2 turns 3, and 3 revolves 4 idly on its shaft.
We now come to a really interesting detail of the car, the gearbox. The steam engine increases its speed by allowing more steam into the cylinders. However, a combustion engine needs to run at a high speed to generate its full power, and when heavier work needs to be done on a hill, it's necessary to[Pg 106] change the speed ratio between the engine and the driving wheels. Our illustration (Fig. 48) shows a section of a gearbox, which serves as a typical example. It offers three forward speeds and one reverse. To understand how it works, we should examine the illustration closely. Pinion 1 is mounted on a hollow shaft that’s turned by the clutch. The end of another shaft, which has pinions 6 and 4, extends into the hollow shaft. Pinion 6 slides up and down this shaft, which is square at this point, but round inside the loose pinion 4. Pinions 2 and 3 are attached to a square secondary shaft and are always engaged with 1 and 4, respectively; however, pinion 5 can slide back[Pg 107] and forth to engage or disengage with pinion 6. In the illustration, no gear is "engaged." If the engine is running, pinion 1 turns pinion 2, pinion 2 turns pinion 3, and pinion 3 turns pinion 4, which spins idle on its shaft.
To get the lowest, or "first," speed the driver moves his lever and slides 5 into gear with 6. The transmission then is: 1 turns 2, 2 turns 5, 5 turns 6, 6 turns the propeller shaft through the universal joint. For the second speed, 5 and 6 are disengaged, and 6 is moved up the page, as it were, till projections on it interlock with slots in 4; thus driving 1, 2, 3, 4, shaft. For the third, or "solid," speed, 6 is pulled down into connection with 1, and couples the engine shaft direct to the propeller shaft.
To reach the lowest, or "first," speed, the driver moves his lever and engages gear 5 with gear 6. The transmission setup then is: 1 turns 2, 2 turns 5, 5 turns 6, and 6 turns the propeller shaft through the universal joint. For the second speed, 5 and 6 are disengaged, and 6 is moved up the page, so to speak, until its projections fit into the slots in 4; this drives 1, 2, 3, and the shaft. For the third, or "solid," speed, 6 is pulled down to connect with 1, linking the engine shaft directly to the propeller shaft.
The "reverse" is accomplished by raising a long pinion, 7, which lies in the gear-box under 5 and 6. The drive then is 1, 2, 5, 7, 6. There being an odd number of pinions now engaged, the propeller shaft turns in the reverse direction to that of the engine shaft.
The "reverse" is achieved by lifting a long pinion, 7, which is located in the gear box beneath 5 and 6. The drive sequence is 1, 2, 5, 7, 6. Since there’s now an odd number of pinions engaged, the propeller shaft rotates in the opposite direction to that of the engine shaft.

THE COMPENSATING GEAR.
The compensation gear.
Every axle of a railway train carries a wheel at each end, rigidly attached to it. When rounding a corner the outside wheel has further to travel than the other, and consequently one or both wheels must[Pg 108] slip. The curves are made so gentle, however, that the amount of slip is very small. But with a traction-engine, motor car, or tricycle the case is different, for all have to describe circles of very small diameter in proportion to the length of the vehicle. Therefore in every case a compensating gear is fitted, to allow the wheels to turn at different speeds, while permitting them both to drive. Fig. 49 is an exaggerated sketch of the gear. The axles of the moving wheels turn inside tubes attached to the springs and a central casing (not shown), and terminate in large bevel-wheels, C and D. Between these are small bevels mounted on a shaft supported by the driving drum. If the latter be rotated, the bevels would turn C and D at equal speeds, assuming that[Pg 109] both axles revolve without friction in their bearings. We will suppose that the drum is turned 50 times a minute. Now, if one wheel be held, the other will revolve 100 times a minute; or, if one be slowed, the other will increase its speed by a corresponding amount. The average speed remains 50. It should be mentioned that drum A has incorporated with it on the outside a bevel-wheel (not shown) rotated by a smaller bevel on the end of the propeller shaft.
Every axle of a railway train has a wheel on each end, which are firmly attached. When turning a corner, the outside wheel has to cover more distance than the inside one, so one or both wheels must[Pg 108] slide. However, the curves are designed to be gentle, so the amount of sliding is very minor. In contrast, with a traction engine, motor car, or tricycle, the situation is different because they have to navigate much tighter circles relative to their length. Therefore, each of these vehicles is equipped with a compensating gear, which allows the wheels to turn at different speeds while still driving. Fig. 49 is an exaggerated sketch of this gear. The axles of the driving wheels rotate inside tubes connected to the springs and a central casing (not shown), ending in large bevel gears, C and D. Between these are smaller bevel gears mounted on a shaft supported by the driving drum. If the drum is rotated, the bevels would turn C and D at the same speed, assuming that[Pg 109] both axles rotate smoothly in their bearings. Let's say the drum is turned 50 times per minute. If one wheel is held, the other will turn 100 times a minute; or if one slows down, the other will speed up by a corresponding amount. The average speed stays at 50. It's worth noting that drum A has a bevel gear on its outside (not shown) that is turned by a smaller bevel on the end of the propeller shaft.
THE SILENCER.
THE SILENCER.
The petrol-engine, as now used, emits the products of combustion at a high pressure. If unchecked, they expand violently, and cause a partial vacuum in the exhaust pipe, into which the air rushes back with such violence as to cause a loud noise. Devices called silencers are therefore fitted, to render the escape more gradual, and split it up among a number of small apertures. The simplest form of silencer is a cylindrical box, with a number of finely perforated tubes passing from end to end of it. The exhaust gases pouring into the box maintain a constant pressure somewhat higher than that of the atmosphere, but as the gases are escaping from it in a fairly steady stream the noise becomes a gentle hiss rather than a[Pg 110] "pop." There are numerous types of silencers, but all employ this principle in one form or another.
The petrol engine, as it’s used today, releases combustion gases at high pressure. If left unchecked, they expand rapidly, creating a partial vacuum in the exhaust pipe, which causes air to rush back in violently, generating a loud noise. To handle this, devices called silencers are installed to make the exhaust flow more gradual and diffuse it through several small openings. The simplest type of silencer is a cylindrical box with a series of small perforated tubes running from one end to the other. The exhaust gases entering the box keep a constant pressure that's slightly higher than the atmosphere, but as they exit in a steady stream, the noise turns into a gentle hiss instead of a[Pg 110] "pop." There are many different kinds of silencers, but they all use this basic principle in one way or another.
THE BRAKES.
THE BRAKES.
Every car carries at least two brakes of band pattern—one, usually worked by a side hand-lever, acting on the axle or hubs of the driving-wheel; the other, operated by the foot, acting on the transmission gear (see Fig. 48). The latter brake is generally arranged to withdraw the clutch simultaneously. Tests have proved that even heavy cars can be pulled up in astonishingly short distances, considering their rate of travel. Trials made in the United States with a touring car and a four-in-hand coach gave 25⅓ and 70 feet respectively for the distance in which the speed could be reduced from sixteen miles per hour to zero.
Every car has at least two band-style brakes—one is usually controlled by a side hand-lever that acts on the axle or hubs of the driving wheel; the other is operated by the foot and affects the transmission gear (see Fig. 48). The foot brake is typically set up to disengage the clutch at the same time. Tests have shown that even heavy cars can stop in surprisingly short distances, given their speed. Trials conducted in the United States with a touring car and a four-in-hand coach recorded stopping distances of 25⅓ and 70 feet, respectively, when reducing speed from sixteen miles per hour to zero.
SPEED OF CARS.
CAR SPEED.
As regards speed, motor cars can rival the fastest express trains, even on long journeys. In fact, feats performed during the Gordon-Bennett and other races have equalled railway performances over equal distances. When we come to record speeds, we find a car, specially built for the purpose, covering a mile in less than half a minute. A speed of over 120 miles[Pg 111] an hour has actually been reached. Engines of 150 h.p. can now be packed into a vehicle scaling less than 1½ tons. Even on touring cars are often found engines developing 40 to 60 h.p., which force the car up steep hills at a pace nothing less than astonishing. In the future the motor car will revolutionize our modes of life to an extent comparable to the changes effected by the advent of the steam-engine. Even since 1896, when the "man-with-the-flag" law was abolished in the British Isles, the motor has reduced distances, opened up country districts, and generally quickened the pulses of the community in a manner which makes it hazardous to prophesy how the next generation will live.
When it comes to speed, cars can compete with the fastest express trains, even on long trips. In fact, achievements during the Gordon-Bennett and other races have matched railway performance over the same distances. Looking at recorded speeds, we see a car, specially designed for this purpose, covering a mile in under half a minute. A speed of over 120 miles[Pg 111] per hour has been reached. Engines with 150 horsepower can now fit into vehicles weighing less than 1½ tons. Even touring cars often have engines that produce between 40 to 60 horsepower, allowing them to climb steep hills at a truly impressive pace. In the future, the motor car will transform our lifestyles to a degree similar to the changes brought about by the steam engine. Since 1896, when the "man-with-the-flag" law was removed in the British Isles, cars have shortened distances, opened up rural areas, and generally energized the community in a way that makes it difficult to predict how the next generation will live.
Note.—The author is much indebted to Mr. Wilfrid J. Lineham, M. Inst. C.E., for several of the illustrations which appear in the above chapter.
Note.—The author is very grateful to Mr. Wilfrid J. Lineham, M. Inst. C.E., for many of the illustrations featured in the above chapter.
[9] On some cars natural circulation is used, the hot water flowing from the top of the cylinder to the tank, from which it returns, after being cooled, to the bottom of the cylinder.
[9] On some cars, natural circulation is used, with hot water flowing from the top of the cylinder to the tank, where it cools down before returning to the bottom of the cylinder.
[10] For explanation of the induction coil, see p. 122
[10] For an explanation of the induction coil, see p. 122
Chapter V.
ELECTRICAL APPARATUS.
What is electricity?—Forms of electricity—Magnetism—The permanent magnet—Lines of force—Electro-magnets—The electric bell—The induction coil—The condenser—Transformation of current—Uses of the induction coil.
What is electricity?—Types of electricity—Magnetism—The permanent magnet—Lines of force—Electromagnets—The electric bell—The induction coil—The capacitor—Current transformation—Uses of the induction coil.
WHAT IS ELECTRICITY?
WHAT IS ELECTRICITY?
Of the ultimate nature of electricity, as of that of heat and light, we are at present ignorant. But it has been clearly established that all three phenomena are but manifestations of the energy pervading the universe. By means of suitable apparatus one form can be converted into another form. The heat of fuel burnt in a boiler furnace develops mechanical energy in the engine which the boiler feeds with steam. The engine revolves a dynamo, and the electric current thereby generated can be passed through wires to produce mechanical motion, heat, or light. We must remain content, therefore, with assuming that electricity is energy or motion transmitted[Pg 113] through the ether from molecule to molecule, or from atom to atom, of matter. Scientific investigation has taught us how to produce it at will, how to harness it to our uses, and how to measure it; but not what it is. That question may, perhaps, remain unanswered till the end of human history. A great difficulty attending the explanation of electrical action is this—that, except in one or two cases, no comparison can be established between it and the operation of gases and fluids. When dealing with the steam-engine, any ordinary intelligence soon grasps the principles which govern the use of steam in cylinders or turbines. The diagrams show, it is hoped, quite plainly "how it works." But electricity is elusive, invisible; and the greatest authorities cannot say what goes on at the poles of a magnet or on the surface of an electrified body. Even the existence of "negative" and "positive" electricity is problematical. However, we see the effects, and we know that if one thing is done another thing happens; so that we are at least able to use terms which, while convenient, are not at present controverted by scientific progress.
Of the true nature of electricity, just like heat and light, we currently don’t know. However, it's clear that all three phenomena are just different expressions of the energy that fills the universe. With the right equipment, one form can be changed into another. The heat generated by fuel burned in a boiler produces mechanical energy in the engine that's powered by steam from the boiler. The engine turns a dynamo, and the electric current created can be sent through wires to generate mechanical motion, heat, or light. Therefore, we must accept that electricity is energy or motion transmitted[Pg 113] through the ether from one molecule to another, or from one atom to another, in matter. Scientific research has shown us how to create it on demand, how to use it for our needs, and how to measure it; but not what it actually is. That question might remain unanswered until the end of human history. A key challenge in explaining electrical action is that, except in a few cases, we can't compare it to the behavior of gases and liquids. When it comes to the steam engine, anyone with basic understanding can quickly grasp the principles governing the use of steam in cylinders or turbines. The diagrams hopefully clearly illustrate "how it works." But electricity is fleeting, invisible; and even the leading experts can't explain what happens at the poles of a magnet or on the surface of an electrified object. Even the existence of "negative" and "positive" electricity is questionable. Nevertheless, we observe the effects, and we know that if one action occurs, another follows; so we can use terms that, although convenient, aren't challenged by current scientific advancements.
FORMS OF ELECTRICITY.
Types of electricity.
Rub a vulcanite rod and hold one end near some[Pg 114] tiny pieces of paper. They fly to it, stick to it for a time, and then fall off. The rod was electrified—that is, its surface was affected in such a way as to be in a state of molecular strain which the contact of the paper fragments alleviated. By rubbing large surfaces and collecting the electricity in suitable receivers the strain can be made to relieve itself in the form of a violent discharge accompanied by a bright flash. This form of electricity is known as static.
Rub a vulcanite rod and hold one end near some[Pg 114] tiny pieces of paper. They will fly towards it, stick for a while, and then fall off. The rod became electrified—its surface was altered in a way that created molecular strain, which the contact with the paper pieces relieved. By rubbing large surfaces and collecting the electricity in suitable containers, the strain can be released in a powerful discharge accompanied by a bright flash. This type of electricity is known as static.
Next, place a copper plate and a zinc plate into a jar full of diluted sulphuric acid. If a wire be attached to them a current of electricity is said to flow along the wire. We must not, however, imagine that anything actually moves along inside the wire, as water, steam, or air, passes through a pipe. Professor Trowbridge says,[11] "No other agency for transmitting power can be stopped by such slight obstacles as electricity. A thin sheet of paper placed across a tube conveying compressed air would be instantly ruptured. It would take a wall of steel at least an inch thick to stand the pressure of steam which is driving a 10,000 horse-power engine. A thin layer of dirt beneath the wheels of an electric car can prevent the current which propels the car from passing to the[Pg 115] rail, and then back to the power-house." There would, indeed, be a puncture of the paper if the current had a sufficient voltage, or pressure; yet the fact remains that current electricity can be very easily confined to its conductor by means of some insulating or nonconducting envelope.
Next, place a copper plate and a zinc plate in a jar full of diluted sulfuric acid. If you connect a wire to them, an electric current is said to flow through the wire. However, we shouldn’t think that anything actually moves inside the wire like water, steam, or air flows through a pipe. Professor Trowbridge says,[11] "No other method of transmitting power can be interrupted by such minor obstacles as electricity. A thin sheet of paper placed across a tube carrying compressed air would be instantly torn apart. It would take a steel wall at least an inch thick to withstand the pressure of steam driving a 10,000 horsepower engine. A thin layer of dirt under the wheels of an electric car can stop the current that drives the car from reaching the[Pg 115] rail and then back to the power station." Indeed, there would be a rupture of the paper if the current had enough voltage or pressure; yet the fact remains that current electricity can be easily confined to its conductor with some insulating or nonconducting covering.
MAGNETISM.
MAGNETISM.
The most familiar form of electricity is that known as magnetism. When a bar of steel or iron is magnetized, it is supposed that the molecules in it turn and arrange themselves with all their north-seeking poles towards the one end of the bar, and their south-seeking poles towards the other. If the bar is balanced freely on a pivot, it comes to rest pointing north and south; for, the earth being a huge magnet, its north pole attracts all the north-seeking poles of the molecules, and its south poles the south-seeking poles. (The north-seeking pole of a magnet is marked N., though it is in reality the south pole; for unlike poles are mutually attractive, and like poles repellent.)
The most common form of electricity is what we call magnetism. When a bar made of steel or iron is magnetized, it's thought that the molecules inside it align so that all their north-seeking poles point toward one end of the bar and their south-seeking poles point toward the other. If the bar is balanced on a pivot, it will come to rest pointing north and south; this is because the Earth acts like a giant magnet, with its north pole attracting all the north-seeking poles of the molecules and its south pole attracting the south-seeking poles. (The north-seeking pole of a magnet is labeled N., but it’s actually the south pole; this is because opposite poles attract each other, while like poles repel.)
There are two forms of magnet—permanent and temporary. If steel is magnetized, it remains so; but soft iron loses practically all its magnetism as soon as the cause of magnetization is withdrawn. This is what we should expect; for steel is more[Pg 116] closely compacted than iron, and the molecules therefore would be able to turn about more easily.[12] It is fortunate for us that this is so, since on the rapid magnetization and demagnetization of soft iron depends the action of many of our electrical mechanisms.
There are two types of magnets—permanent and temporary. When steel is magnetized, it stays magnetized; however, soft iron loses almost all of its magnetism as soon as the magnetizing force is removed. This makes sense because steel is more[Pg 116] tightly packed than iron, allowing the molecules to move around more freely.[12] It's a good thing this happens, as the quick magnetization and demagnetization of soft iron is essential for many of our electrical devices to work.
THE PERMANENT MAGNET.
THE PERMANENT MAGNET.
Magnets are either (1) straight, in which case they are called bar magnets; or (2) of horseshoe form, as in Figs. 50 and 51. By bending the magnet the two poles are brought close together, and the attraction of both may be exercised simultaneously on a bar of steel or iron.
Magnets can be (1) straight, known as bar magnets, or (2) shaped like a horseshoe, as shown in Figs. 50 and 51. By bending the magnet, the two poles come close together, allowing both to attract a bar of steel or iron at the same time.
LINES OF FORCE.
FORCE LINES.
In Fig. 50 are seen a number of dotted lines. These are called lines of magnetic force. If you lay a sheet of paper on a horseshoe magnet and sprinkle it with iron dust, you will at once notice how the particles arrange themselves in curves similar in shape to those shown in the illustration. It is supposed (it cannot be proved) that magnetic force streams away from the N. pole and describes a[Pg 117] circular course through the air back to the S. pole. The same remark applies to the bar magnet.
In Fig. 50, you can see several dotted lines. These are called lines of magnetic force. If you place a sheet of paper over a horseshoe magnet and sprinkle iron dust on it, you'll instantly notice that the particles arrange themselves in curves similar to those shown in the illustration. It's believed (though it can't be proved) that magnetic force streams away from the N. pole and takes a[Pg 117] circular path through the air back to the S. pole. The same applies to the bar magnet.
ELECTRICAL MAGNETS.
ELECTROMAGNETS.

If an insulated wire is wound round and round a steel or iron bar from end to end, and has its ends connected to the terminals of an electric battery, current rotates round the bar, and the bar is magnetized. By increasing the strength and volume of the current, and multiplying the number of turns of wire, the attractive force of the magnet is increased. Now disconnect the wires from the battery. If of iron, the magnet at once loses its attractive force; but if of steel, it retains it in part. Instead of a simple horseshoe-shaped bar, two shorter bars riveted into a plate are generally used for electromagnets of this type. Coils of wire are wound round[Pg 118] each bar, and connected so as to form one continuous whole; but the wire of one coil is wound in the direction opposite to that of the other. The free end of each goes to a battery terminal.
If you wrap an insulated wire around a steel or iron bar from one end to the other, and connect the ends to a battery, current flows around the bar, magnetizing it. By boosting the strength and amount of the current, and increasing the number of wire turns, the magnet's pulling force is amplified. Now, disconnect the wires from the battery. If the bar is iron, it immediately loses its magnetic attraction; but if it’s steel, it retains some of that attraction. Instead of using a simple horseshoe-shaped bar, two shorter bars are usually riveted onto a plate for electromagnets like this. Coils of wire are wrapped around[Pg 118] each bar and connected to form a continuous circuit; however, the wire in one coil is wound in the opposite direction to that in the other. The free end of each connects to a battery terminal.
In Fig. 51 you will notice that some of the "lines of force" are deflected through the iron bar A. They pass more easily through iron than through air; and will choose iron by preference. The attraction exercised by a magnet on iron may be due to the effort of the lines of force to shorten their paths. It is evident that the closer A comes to the poles of the magnet the less will be the distance to be travelled from one pole to the bar, along it, and back to the other pole.
In Fig. 51, you'll see that some of the "lines of force" are curved towards the iron bar A. They move more easily through iron than through air and will prefer to go through iron. The attraction a magnet has on iron could be because the lines of force are trying to shorten their paths. It's clear that the closer A is to the magnet's poles, the shorter the distance will be for the lines of force to travel from one pole to the bar, along it, and back to the other pole.

Having now considered electricity in three of its forms—static, current, and rotatory—we will pass to some of its applications.
Having now looked at electricity in three forms—static, current, and rotational—we will move on to some of its applications.
THE ELECTRIC BELL.
THE ELECTRIC BELL.
A fit device to begin with is the Electric Bell, which has so largely replaced wire-pulled bells. These last cause a great deal of trouble sometimes, since if a wire snaps it may be necessary to take up carpets and floor-boards to put things right. Their installation is not simple, for at every corner must be put a crank to alter the direction of the pull, and the cranks mean increased friction. But when electric wires have once been properly installed, there should be no need for touching them for an indefinite period. They can be taken round as many corners as you wish without losing any of their conductivity, and be placed wherever is most convenient for examination. One bell may serve a large number of rooms if an indicator be used to show where the call was made from, by a card appearing in one of a number of small windows. Before answering a call, the attendant presses in a button to return the card to its normal position.
A great device to start with is the Electric Bell, which has mostly replaced wire-pulled bells. The latter can be quite troublesome sometimes, as if a wire breaks, you might need to pull up carpets and floorboards to fix it. Installing them isn't easy either, since you have to place a crank at every corner to change the direction of the pull, and these cranks create extra friction. However, once electric wires are properly installed, you shouldn't have to touch them for a long time. They can navigate as many corners as you want without losing any conductivity and can be positioned wherever it's most convenient for checking. One bell can serve many rooms if an indicator is used to show where the call came from, with a card appearing in one of several small windows. Before answering a call, the attendant presses a button to return the card to its normal position.
In Fig. 52 we have a diagrammatic view of an electric bell and current. When the bell-push is pressed in, current flows from the battery to [Pg 120]terminal T1, round the electro-magnet M, through the pillar P and flat steel springs S and B, through the platinum-pointed screw, and back to the battery through the push. The circulation of current magnetizes M, which attracts the iron armature A attached to the spring S, and draws the hammer H towards the gong. Just before the stroke occurs, the spring B leaves the tip of the screw, and the circuit is broken, so that the magnet no longer attracts. H is carried by its momentum against the gong, and is withdrawn by the spring, until B once more makes contact, and the magnet is re-excited. The hammer vibrations recur many times a second as long as the push is pressed in.
In Fig. 52, we see a diagram of an electric bell and current. When the button is pressed, current flows from the battery to the terminal T1, around the electromagnet M, through the pillar P and the flat steel springs S and B, through the platinum-tipped screw, and back to the battery through the button. This flow of current magnetizes M, which attracts the iron armature A connected to the spring S, pulling the hammer H towards the gong. Just before the hammer strikes, the spring B loses contact with the screw, breaking the circuit so the magnet no longer attracts. H continues moving towards the gong due to its momentum and is pulled back by the spring, until B makes contact again, reactivating the magnet. The hammer hits repeatedly several times a second as long as the button is pressed.

The electric bell is used for so many purposes that they cannot all be noted. It plays an especially important part in telephonic installations to draw the attention of the subscribers, forms an item in automatic fire and burglar alarms, and is a necessary adjunct of railway signalling cabins.
The electric bell is used for so many purposes that they can't all be listed. It plays a particularly important role in telephone systems to get the subscribers' attention, is a component in automatic fire and burglar alarms, and is essential for railway signaling cabins.
THE INDUCTION OR RUHMKORFF COIL.
The Induction or Ruhmkorff Coil.
Reference was made in connection with the electrical ignition of internal-combustion engines (p. 101) to the induction coil. This is a device for increasing the voltage, or pressure, of a current. The two-cell accumulator carried in a motor car gives a voltage (otherwise called electro-motive force = E.M.F.) of 4·4 volts. If you attach a wire to one terminal of the accumulator and brush the loose end rapidly across the other terminal, you will notice that a bright spark passes between the wire and the terminal. In reality there are two sparks, one when they touch, and another when they separate, but they occur so closely together that the eye cannot separate the two impressions. A spark of this kind would not be sufficiently hot to ignite a charge in a motor cylinder, and a spark from the induction coil is therefore used.
Reference was made in connection with the electrical ignition of internal-combustion engines (p. 101) to the induction coil. This is a device for increasing the voltage, or pressure, of a current. The two-cell battery found in a car provides a voltage (also known as electro-motive force = E.M.F.) of 4.4 volts. If you connect a wire to one terminal of the battery and quickly brush the loose end against the other terminal, you'll see a bright spark jump between the wire and the terminal. Actually, there are two sparks: one when they touch and another when they separate, but they happen so close together that the eye can't distinguish between the two. A spark like this wouldn't be hot enough to ignite a charge in a car's engine cylinder, so a spark from the induction coil is used instead.

We give a sketch of the induction coil in Fig. 53. It consists of a core of soft iron wires round which is wound a layer of coarse insulated wire, denoted by the thick line. One end of the winding of this primary coil is attached to the battery, the other to the base of a hammer, H, vibrating between the end of the core and a screw, S, passing through an upright, T, connected with the other terminal of the battery. The action of the hammer is precisely the same as that of the armature of an electric bell. Outside the primary coil are wound many turns of a much finer wire completely insulated from the[Pg 123] primary coil. The ends of this secondary coil are attached to the objects (in the case of a motor car, the insulated wire of the sparking-plug and a wire projecting from its outer iron casing) between which a spark has to pass. As soon as H touches S the circuit is completed. The core becomes a powerful magnet with external lines of force passing from one pole to the other over and among the turns of the secondary coil. H is almost instantaneously attracted by the core, and the break occurs. The lines of force now (at least so it is supposed) sink into the core, cutting through the turns of the "secondary," and causing a powerful current to flow through them. The greater the number of turns, the greater the number of times the lines of force are cut, and the stronger is the current. If sufficiently intense, it jumps any gap in the secondary circuit, heating the intermediate air to a state of incandescence.
Here’s a simplified version of the paragraph: We show a diagram of the induction coil in Fig. 53. It has a core made of soft iron wires wrapped with a layer of thick insulated wire, indicated by the thick line. One end of this primary coil is connected to the battery, and the other end connects to the base of a hammer, H, which moves between the end of the core and a screw, S, that goes through a vertical part, T, linked to the other terminal of the battery. The hammer works just like the armature of an electric bell. Surrounding the primary coil are many turns of a thinner, completely insulated wire, known as the secondary coil. The ends of this secondary coil connect to the devices (in the case of a motor car, the insulated wire of the spark plug and a wire sticking out from its outer iron casing) where a spark needs to jump. When H touches S, the circuit is closed. The core turns into a strong magnet, creating external lines of force that travel from one pole to the other through the turns of the secondary coil. H is quickly pulled toward the core, and the circuit breaks. The lines of force then (as it’s believed) sink into the core, cutting through the turns of the secondary coil, and generate a strong current. The more turns there are, the more times the lines of force are cut, which makes the current stronger. If the current is intense enough, it can jump across any gap in the secondary circuit, heating the air in between to the point of glowing.
THE CONDENSER.
THE CONDENSER.
The sudden parting of H and S would produce strong sparking across the gap between them if it were not for the condenser, which consists of a number of tinfoil sheets separated by layers of paraffined paper. All [Pg 124]the "odd" sheets are connected with T, all the "even" with T1. Now, the more rapid the extinction of magnetism in the core after "break" of the primary circuit, the more rapidly will the lines of force collapse, and the more intense will be the induced current in the secondary coil. The condenser diminishes the period of extinction very greatly, while lengthening the period of magnetization after the "make" of the primary current, and so decreasing the strength of the reverse current.
The sudden separation of H and S would create a strong spark across the gap between them if it weren't for the condenser, which is made up of several tinfoil sheets separated by layers of paraffined paper. All the "odd" sheets are connected to T, and all the "even" sheets are connected to T1. Now, the quicker the magnetism in the core fades after the "break" in the primary circuit, the faster the lines of force will collapse, and the stronger the induced current in the secondary coil will be. The condenser significantly reduces the period of extinction while extending the period of magnetization after the "make" of the primary current, thereby decreasing the strength of the reverse current.
TRANSFORMATION OF CURRENT.
CURRENT TRANSFORMATION.
The difference in the voltage of the primary and secondary currents depends on the length of the windings. If there are 100 turns of wire in the primary, and 100,000 turns in the secondary, the voltage will be increased 1,000 times; so that a 4-volt current is "stepped up" to 4,000 volts. In the largest induction coils the secondary winding absorbs 200–300 miles of wire, and the spark given may be anything up to four feet in length. Such a spark would pierce a glass plate two inches thick.
The difference in voltage between the primary and secondary currents depends on the length of the windings. If there are 100 turns of wire in the primary and 100,000 turns in the secondary, the voltage increases by 1,000 times; so a 4-volt current is "stepped up" to 4,000 volts. In the largest induction coils, the secondary winding can use 200–300 miles of wire, and the spark produced can be up to four feet long. Such a spark could pierce a glass plate two inches thick.
It must not be supposed that an induction coil increases the amount of current given off by a battery. It merely increases its pressure at the expense of its volume—stores up its energy, as it[Pg 125] were, until there is enough to do what a low-tension flow could not effect. A fair comparison would be to picture the energy of the low-tension current as the momentum of a number of small pebbles thrown in succession at a door, say 100 a minute. If you went on pelting the door for hours you might make no impression on it, but if you could knead every 100 pebbles into a single stone, and throw these stones one per minute, you would soon break the door in.
It shouldn't be assumed that an induction coil increases the amount of current produced by a battery. It just boosts its pressure at the cost of its volume—essentially storing its energy until there's enough to achieve what a low-tension flow couldn't do. A good comparison would be to envision the energy of the low-tension current as the momentum of a bunch of small pebbles being thrown at a door, say 100 per minute. If you kept throwing pebbles at the door for hours, you might not make any mark on it, but if you could combine every 100 pebbles into a single stone and throw those stones one per minute, you would quickly break the door down.
Any intermittent current can be transformed as regards its intensity. You may either increase its pressure while decreasing its rate of flow, or amperage; or decrease its pressure and increase its flow. In the case that we have considered, a continuous battery current is rendered intermittent by a mechanical contrivance. But if the current comes from an "alternating" dynamo—that is, is already intermittent—the contact-breaker is not needed. There will be more to say about transformation of current in later paragraphs.
Any intermittent current can be changed in terms of its intensity. You can either increase its voltage while reducing its flow rate, or amperage; or decrease its voltage and increase its flow. In the situation we've looked at, a continuous battery current is made intermittent by a mechanical device. But if the current comes from an "alternating" dynamo—that is, if it's already intermittent—the contact-breaker isn't necessary. There will be more to discuss about current transformation in later paragraphs.
USES OF THE INDUCTION COIL.
USES OF THE INDUCTION COIL.
The induction coil is used—(1.) For passing currents through glass tubes almost exhausted of air[Pg 126] or containing highly rarefied gases. The luminous effects of these "Geissler" tubes are very beautiful. (2.) For producing the now famous X or Röntgen rays. These rays accompany the light rays given off at the negative terminal (cathode) of a vacuum tube, and are invisible to the eye unless caught on a fluorescent screen, which reduces their rate of vibration sufficiently for the eye to be sensitive to them. The Röntgen rays have the peculiar property of penetrating many substances quite opaque to light, such as metals, stone, wood, etc., and as a consequence have proved of great use to the surgeon in localizing or determining the nature of an internal injury. They also have a deterrent effect upon cancerous growths. (3.) In wireless telegraphy, to cause powerful electric oscillations in the ether. (4.) On motor cars, for igniting the cylinder charges. (5.) For electrical massage of the body.
The induction coil is used—(1.) To pass currents through glass tubes that are almost empty of air[Pg 126] or contain highly rarefied gases. The glowing effects of these "Geissler" tubes are really beautiful. (2.) To produce the now famous X or Röntgen rays. These rays appear alongside the light rays emitted from the negative terminal (cathode) of a vacuum tube and are invisible to the eye unless they hit a fluorescent screen, which slows their rate of vibration enough for the eye to detect them. The Röntgen rays have the unique ability to penetrate many materials that are completely opaque to light, like metals, stone, wood, etc., making them extremely useful for surgeons to locate or assess the nature of internal injuries. They also have a certain effect on inhibiting cancerous growths. (3.) In wireless telegraphy, to create powerful electric oscillations in the ether. (4.) In motor cars, for igniting the cylinder charges. (5.) For electrical massage of the body.
[12] If a magnetized bar be heated to white heat and tapped with a hammer it loses its magnetism, because the distance between the molecules has increased, and the molecules can easily return to their original positions.
[12] If a magnetized bar is heated to white hot and struck with a hammer, it loses its magnetism because the distance between the molecules increases, allowing the molecules to easily return to their original positions.
Chapter VI.
THE ELECTRIC TELEGRAPH.
Needle instruments—Influence of current on the magnetic needle—Method of reversing the current—Sounding instruments—Telegraphic relays—Recording telegraphs—High-speed telegraphy.
Needle instruments—Effect of current on the magnetic needle—How to reverse the current—Sounding instruments—Telegraphic relays—Recording telegraphs—High-speed telegraphy.
Take a small pocket compass and wind several turns of fine insulated wire round the case, over the top and under the bottom. Now lay the compass on a table, and turn it about until the coil is on a line with the needle—in fact, covers it. Next touch the terminals of a battery with the ends of the wire. The needle at once shifts either to right or left, and remains in that position as long as the current flows. If you change the wires over, so reversing the direction of the current, the needle at once points in the other direction. It is to this conduct on the part of a magnetic needle when in a "magnetic field" that we owe the existence of the needle telegraph instrument.
Take a small pocket compass and wrap several turns of fine insulated wire around the casing, over the top and under the bottom. Now place the compass on a table and rotate it until the coil aligns with the needle—in fact, covers it. Next, connect the ends of the wire to the terminals of a battery. The needle will immediately shift to the right or left and stay in that position as long as the current is flowing. If you swap the wires, reversing the direction of the current, the needle will instantly point in the opposite direction. It's this behavior of a magnetic needle in a "magnetic field" that gives us the needle telegraph instrument.
NEEDLE INSTRUMENTS.
Needle tools.

Probably the best-known needle instrument is the Cooke-Wheatstone, largely used in signal-boxes and in some post-offices. A vertical section of it is shown in Fig. 54. It consists of a base, B, and an upright front, A, to the back of which are attached two hollow coils on either side of a magnetic needle mounted on the same shaft as a second dial needle, N, outside the front. The wires W W are connected to the telegraph line and to the commutator, a device which, when the operator moves the handle H to right and left, keeps reversing the direction of the current. The needles on both receiving and transmitting instruments wag in accordance with the movements of the handle. One or more movements form an alphabetical letter of the Morse code. Thus, if the needle points first to left, and then to right, and comes to rest in a normal position for a moment,[Pg 129] the letter A is signified; right-left-left-left in quick succession = B; right-left-right-left = C, and so on. Where a marking instrument is used, a dot signifies a "left," and a dash a right; and if a "sounder" is employed, the operator judges by the length of the intervals between the clicks.
Probably the most well-known needle instrument is the Cooke-Wheatstone, primarily used in signal boxes and some post offices. A vertical section of it is shown in Fig. 54. It consists of a base, B, and an upright front, A, to which two hollow coils are attached on either side of a magnetic needle mounted on the same shaft as a second dial needle, N, outside the front. The wires W W connect to the telegraph line and the commutator, a device that, when the operator moves the handle H to the left and right, keeps reversing the current's direction. The needles on both receiving and transmitting instruments move according to the handle's actions. One or more movements form a letter in Morse code. For example, if the needle points left first, then right, and then pauses in a normal position for a moment,[Pg 129] it signifies the letter A; right-left-left-left in quick succession = B; right-left-right-left = C, and so on. Where a marking instrument is used, a dot represents a "left," and a dash represents a right; if a "sounder" is employed, the operator assesses the length of the pauses between the clicks.
INFLUENCE OF CURRENT ON A MAGNETIC NEEDLE.
INFLUENCE OF CURRENT ON A MAGNETIC NEEDLE.

Figs. 55 and 56 are two views of the coils and magnetic needle of the Wheatstone instrument as they appear from behind. In Fig. 55 the current enters the left-hand coil from the left, and travels round and round it in a clockwise direction to the other end, whence it passes to the other coil and away to the battery. Now, a coil through which a current passes becomes a magnet. Its polarity[Pg 130] depends on the direction in which the current flows. Suppose that you are looking through the coil, and that the current enters it from your end. If the wire is wound in a clockwise direction, the S. pole will be nearest you; if in an anti-clockwise direction, the N. pole. In Fig. 55 the N. poles are at the right end of the coils, the S. poles at the left end; so the N. pole of the needle is attracted to the right, and the S. pole to the left. When the current is reversed, as in Fig. 56, the needle moves over. If no current passes, it remains vertical.
Figs. 55 and 56 show two views of the coils and magnetic needle of the Wheatstone instrument from behind. In Fig. 55, the current enters the left coil from the left side and flows around it in a clockwise direction to the other end, where it then goes to the other coil and continues to the battery. A coil that carries a current becomes a magnet. Its polarity[Pg 130] depends on the current's direction. Imagine you are looking through the coil and the current is entering from your side. If the wire is wound clockwise, the S. pole will be closest to you; if wound counterclockwise, the N. pole will be closest. In Fig. 55, the N. poles are at the right end of the coils, and the S. poles are at the left end; thus, the N. pole of the needle is attracted to the right, and the S. pole to the left. When the current is reversed, as shown in Fig. 56, the needle shifts position. If no current is flowing, it stays vertical.
METHOD OF REVERSING THE CURRENT.
METHOD FOR REVERSING THE CURRENT.

A simple method of changing the direction of the current in a two-instrument circuit is shown diagrammatically in Fig. 57. The principle is used in the[Pg 131] Wheatstone needle instrument. The battery terminals at each station are attached to two brass plates, A B, A1 B1. Crossing these at right angles (under A A1 and over B B1) are the flat brass springs, L R, L1 R1, having buttons at their lower ends, and fixed at their upper ends to baseboards. When at rest they all press upwards against the plates A and A1 respectively. R and L1 are connected with the line circuit, in which are the coils of dials 1 and 2, one at each station. L and R1 are connected with the earth-plates E E1. An operator at station 1 depresses R so as to touch B. Current now flows from the battery to B, thence through R to the line circuit, round the coils of both dials through L1 A1 and R to earth-plate E1, through the earth to E, and then back to the battery through L and A. The needles assume the position shown. To reverse the current the operator allows R to rise into contact with A, and depresses L to touch B. The course can be traced out easily.
A straightforward way to change the direction of the current in a two-instrument circuit is illustrated in Fig. 57. The principle is used in the[Pg 131] Wheatstone needle instrument. The battery terminals at each station are connected to two brass plates, A B, A1 B1. Crossing these at right angles (under A A1 and over B B1) are the flat brass springs, L R, L1 R1, which have buttons at their lower ends and are fixed at their upper ends to baseboards. When at rest, they all push upwards against the plates A and A. R and L1 are connected to the line circuit that includes the coils of dials 1 and 2, one at each station. L and R1 are connected to the earth-plates E E1. An operator at station 1 presses down R to touch B. Current now flows from the battery to B, then through R to the line circuit, around the coils of both dials through L1 A1 and R to earth-plate E1, through the earth to E, and then back to the battery through L and A. The needles take the shown position. To reverse the current, the operator lets R rise to contact A, and presses down L to touch B. The path can be easily traced out.
In the Wheatstone "drop-handle" instrument (Fig. 54) the commutator may be described as an insulated core on which are two short lengths of brass tubing. One of these has rubbing against it a spring connected with the + terminal of the battery; the other has[Pg 132] similar communication with the – terminal. Projecting from each tube is a spike, and rising from the baseboard are four upright brass strips not quite touching the commutator. Those on one side lead to the line circuit, those on the other to the earth-plate. When the handle is turned one way, the spikes touch the forward line strip and the rear earth strip, and vice versâ when moved in the opposite direction.
In the Wheatstone "drop-handle" instrument (Fig. 54), the commutator can be described as an insulated core with two short pieces of brass tubing attached. One of these has a spring pressing against it that connects to the + terminal of the battery; the other has[Pg 132] a similar connection to the – terminal. Each tube has a spike projecting from it, and there are four upright brass strips coming up from the baseboard that almost touch the commutator. The strips on one side connect to the line circuit, while those on the other side connect to the earth-plate. When the handle is turned in one direction, the spikes touch the forward line strip and the rear earth strip, and the opposite happens when the handle is turned in the other direction.
SOUNDING INSTRUMENTS.
Sonic Instruments.
Sometimes little brass strips are attached to the dial plate of a needle instrument for the needle to strike against. As these give different notes, the operator can comprehend the message by ear alone. But the most widely used sounding instrument is the Morse sounder, named after its inventor. For this a reversible current is not needed. The receiver is merely an electro-magnet (connected with the line circuit and an earth-plate) which, when a current passes, attracts a little iron bar attached to the middle of a pivoted lever. The free end of the lever works between two stops. Every time the circuit is closed by the transmitting key at the sending station the lever flies down against the lower stop, to rise again when the circuit is broken. The[Pg 133] duration of its stay decides whether a "long" or "short" is meant.
Sometimes small brass strips are attached to the dial plate of a needle instrument for the needle to hit against. Since these produce different notes, the operator can understand the message just by listening. However, the most commonly used sound instrument is the Morse sounder, named after its inventor. For this, a reversible current isn't required. The receiver is simply an electromagnet (connected to the line circuit and a ground plate) which, when current flows, pulls a small iron bar attached to the center of a pivoted lever. The free end of the lever moves between two stops. Every time the circuit is closed by the transmitting key at the sending station, the lever drops down against the lower stop, then rises again when the circuit is broken. The[Pg 133] length of time it stays there determines whether a "long" or "short" is signaled.
TELEGRAPHIC RELAYS.
Telegraph relays.

When an electric current has travelled for a long distance through a wire its strength is much reduced on account of the resistance of the wire, and may be insufficient to cause the electro-magnet of the sounder to move the heavy lever. Instead, therefore, of the current acting directly on the sounder magnet, it is used to energize a small magnet, or relay, which pulls down a light bar and closes a second "local" circuit—that is, one at the receiver end—worked by a separate battery, which has sufficient power to operate the sounder.
When an electric current travels a long distance through a wire, its strength decreases significantly due to the wire's resistance, and it may not be strong enough to move the sounder’s heavy lever. Instead of the current working directly on the sounder magnet, it powers a small magnet, or relay, which pulls down a light bar and closes a second "local" circuit—one at the receiving end—operated by a separate battery that has enough power to run the sounder.
RECORDING TELEGRAPHS.
Recording messages.
By attaching a small wheel to the end of a Morse-sounder lever, by arranging an ink-well for the wheel to dip into when the end falls, and by moving a paper[Pg 134] ribbon slowly along for the wheel to press against when it rises, a self-recording Morse inker is produced. The ribbon-feeding apparatus is set in motion automatically by the current, and continues to pull the ribbon along until the message is completed.
By adding a small wheel to the end of a Morse sounder lever, creating a space for an ink-well for the wheel to dip into when it drops, and slowly moving a paper[Pg 134] ribbon for the wheel to press against when it lifts, you get a self-recording Morse inker. The ribbon-feeding mechanism automatically operates with the current and keeps pulling the ribbon until the message is finished.
The Hughes type-printer covers a sheet of paper with printed characters in bold Roman type. The transmitter has a keyboard, on which are marked letters, signs, and numbers; also a type-wheel, with the characters on its circumference, rotated by electricity. The receiver contains mechanisms for rotating another type-wheel synchronously—that is, in time—with the first; for shifting the wheel across the paper; for pressing the paper against the wheel; and for moving the paper when a fresh line is needed. These are too complicated to be described here in detail. By means of relays one transmitter may be made to work five hundred receivers. In London a single operator, controlling a keyboard in the central dispatching office, causes typewritten messages to spell themselves out simultaneously in machines distributed all over the metropolis.
The Hughes type printer covers a sheet of paper with bold Roman type characters. The transmitter has a keyboard with letters, symbols, and numbers; it also features a type wheel with characters on its edge, which rotates using electricity. The receiver has mechanisms for rotating another type wheel in sync with the first, shifting the wheel across the paper, pressing the paper against the wheel, and moving the paper when a new line is needed. These details are too complex to explain here. Using relays, one transmitter can control up to five hundred receivers. In London, a single operator at the central dispatch office uses a keyboard to make typewritten messages appear simultaneously on machines spread throughout the city.
The tape machine resembles that just described in many details. The main difference is that it prints on a continuous ribbon instead of on sheets.
The tape machine is similar to the one just described in many ways. The key difference is that it prints on a continuous ribbon instead of on sheets.
Automatic electric printers of some kind or other are to be found in the vestibules of all the principal hotels and clubs of our large cities, and in the offices of bankers, stockbrokers, and newspaper editors. In London alone over 500 million words are printed by the receivers in a year.
Automatic electric printers can be found in the lobbies of all major hotels and clubs in our big cities, as well as in the offices of bankers, stockbrokers, and newspaper editors. In London alone, over 500 million words are printed by these machines each year.
HIGH-SPEED TELEGRAPHY.
High-Speed Messaging.
At certain seasons, or when important political events are taking place, the telegraph service would become congested with news were there not some means of transmitting messages at a much greater speed than is possible by hand signalling. Fifty words a minute is about the limit speed that a good operator can maintain. By means of Wheatstone's automatic transmitter the rate can be increased to 400 words per minute. Paper ribbons are punched in special machines by a number of clerks with a series of holes which by their position indicate a dot or a dash. The ribbons are passed through a special transmitter, over little electric brushes, which make contact through the holes with surfaces connected to the line circuit. At the receiver end the message is printed by a Morse inker.
At certain times or during important political events, the telegraph service would get overloaded with news if there wasn't a way to send messages much faster than manual signaling allows. A skilled operator can manage about fifty words per minute. However, using Wheatstone's automatic transmitter, that speed can ramp up to 400 words per minute. Special machines punch paper ribbons with holes that indicate dots or dashes, in a specific pattern, by several clerks. The ribbons are fed through a special transmitter with small electric brushes that make contact through the holes with connections to the line circuit. At the receiving end, the message gets printed by a Morse inker.
It has been found possible to send several messages[Pg 136] simultaneously over a single line. To effect this a distributer is used to put a number of transmitters at one end of the line in communication with an equal number of receivers at the other end, fed by a second distributer keeping perfect time with the first. Instead of a signal coming as a whole to any one instrument it arrives in little bits, but these follow one another so closely as to be practically continuous. By working a number of automatic transmitters through a distributer, a thousand words or more per minute are easily dispatched over a single wire.
It has been found possible to send several messages[Pg 136] at the same time over one line. To make this happen, a distributer is used to connect multiple transmitters at one end of the line with an equal number of receivers at the other end, powered by a second distributer that stays perfectly in sync with the first. Instead of one complete signal going to a single device, it arrives in small pieces, but these come in so quickly that they seem continuous. By operating several automatic transmitters through a distributer, it's easy to send a thousand words or more per minute over a single wire.
The Pollak Virag system employs a punched ribbon, and the receiver traces out the message in alphabetical characters on a moving strip of sensitized photographic paper. A mirror attached to a vibrating diaphragm reflects light from a lamp on to the strip, which is automatically developed and fixed in chemical baths. The method of moving the mirror so as to make the rays trace out words is extremely ingenious. Messages have been transmitted by this system at the rate of 180,000 words per hour.
The Pollak Virag system uses a punched ribbon, and the receiver spells out the message in letters on a moving strip of light-sensitive photographic paper. A mirror connected to a vibrating diaphragm reflects light from a lamp onto the strip, which is automatically developed and fixed in chemical baths. The way the mirror moves to make the light trace words is really clever. This system can transmit messages at a speed of 180,000 words per hour.
Chapter VII.
WIRELESS TELEGRAPHY.
The transmitting apparatus—The receiving apparatus—Syntonic transmission—The advance of wireless telegraphy.
The transmitting device—The receiving device—Syntonic transmission—The progress of wireless telegraphy.
In our last chapter we reviewed briefly some systems of sending telegraphic messages from one point of the earth's surface to another through a circuit consisting partly of an insulated wire and partly of the earth itself. The metallic portion of a long circuit, especially if it be a submarine cable, is costly to install, so that in quite the early days of telegraphy efforts were made to use the ether in the place of wire as one conductor.
In our last chapter, we briefly reviewed some methods of sending telegraphic messages from one point on the Earth's surface to another using a circuit that includes both insulated wire and the ground. The metal part of a long circuit, especially if it's a submarine cable, is expensive to set up, so in the early days of telegraphy, people tried to use the ether instead of wire as one of the conductors.
When a hammer strikes an anvil the air around is violently disturbed. This disturbance spreads through the molecules of the air in much the same way as ripples spread from the splash of a stone thrown into a pond. When the sound waves reach the ear they agitate the tympanum, or drum membrane, and we[Pg 138] "hear a noise." The hammer is here the transmitter, the air the conductor, the ear the receiver.
When a hammer hits an anvil, the air around it gets violently disturbed. This disturbance spreads through the air molecules just like ripples spread from a stone dropped into a pond. When the sound waves reach our ears, they shake the eardrum, and we[Pg 138] "hear a noise." In this case, the hammer is the transmitter, the air is the conductor, and the ear is the receiver.
In wireless telegraphy we use the ether as the conductor of electrical disturbances.[13] Marconi, Slaby, Branly, Lodge, De Forest, Popoff, and others have invented apparatus for causing disturbances of the requisite kind, and for detecting their presence.
In wireless telegraphy, we use the ether as the medium for electrical disturbances.[13] Marconi, Slaby, Branly, Lodge, De Forest, Popoff, and others have developed devices to create the necessary disturbances and to detect them.
The main features of a wireless telegraphy outfit are shown in Figs. 59 and 61.
The main features of a wireless telegraph system are shown in Figs. 59 and 61.
THE TRANSMITTER APPARATUS.
THE TRANSMITTER DEVICE.
We will first consider the transmitting outfit (Fig. 59). It includes a battery, dispatching key, and an induction coil having its secondary circuit terminals connected with two wires, the one leading to an earth-plate, the other carried aloft on poles or suspended from a kite. In the large station at Poldhu, Cornwall, for transatlantic signalling, there are special wooden towers 215 feet high, between which the aërial wires hang. At their upper and lower ends respectively the earth and aërial wires terminate in brass balls separated by a gap. When the operator depresses the key the induction coil[Pg 139] charges these balls and the wires attached thereto with high-tension electricity. As soon as the quantity collected exceeds the resistance of the air-gap, a discharge takes place between the balls, and the ether round the aërial wire is violently disturbed, and waves of electrical energy are propagated through it. The rapidity with which the discharges follow one another, and their travelling power, depends on the strength of the induction coil, the length of the air-gap, and the capacity of the wires.[14]
We will first look at the transmitting equipment (Fig. 59). It consists of a battery, a key for sending messages, and an induction coil with its secondary circuit terminals connected by two wires—one going to a ground plate and the other elevated on poles or suspended from a kite. At the large station in Poldhu, Cornwall, used for transatlantic signaling, there are special wooden towers 215 feet high, between which the aerial wires hang. At their top and bottom ends, the ground and aerial wires end in brass balls separated by a gap. When the operator presses the key, the induction coil[Pg 139] charges these balls and the wires connected to them with high-voltage electricity. As soon as the accumulated charge exceeds the resistance of the air gap, a discharge occurs between the balls, significantly disrupting the ether around the aerial wire, and waves of electrical energy are sent through it. The speed at which the discharges occur and their traveling capacity depends on the strength of the induction coil, the length of the air gap, and the capacity of the wires.[14]


RECEIVING APPARATUS.
Receiving device.
The human body is quite insensitive to these etheric waves. We cannot feel, hear, or see them. But at the receiving station there is what may be called an "electric eye." Technically it is named a coherer. A Marconi coherer is seen in Fig. 60. Inside a small glass tube exhausted of air are two silver plugs, P P, carrying terminals, T T, projecting through the glass at both ends. A small gap separates the plugs at the centre, and this gap is partly filled with nickel-silver powder. If the terminals of the coherer are attached to those of a battery, practically no current will pass under ordinary conditions, as the particles of nickel-silver touch each other very lightly and make a "bad contact." But if the coherer is also attached to wires leading into the earth and air, and ether waves strike those wires, at every impact the particles will cohere—that is, pack tightly together—and allow battery current to pass. The property of cohesion of small conductive bodies when influenced by Hertzian waves was first noticed in 1874 by Professor D.E. Hughes while experimenting with a telephone.
The human body is pretty unresponsive to these etheric waves. We can't feel, hear, or see them. But at the receiving end, there's something like an "electric eye." Technically, it's called a coherer. A Marconi coherer is shown in Fig. 60. Inside a small glass tube that's been evacuated of air are two silver plugs, P P, with terminals, T T, sticking out through the glass at each end. There's a small gap separating the plugs in the middle, and this gap is partly filled with nickel-silver powder. If the coherer's terminals are connected to a battery, practically no current will flow under normal conditions since the nickel-silver particles touch each other very lightly and create a "bad contact." However, if the coherer is also connected to wires that lead into the ground and air, and ether waves hit those wires, each impact will cause the particles to cohere—that is, pack tightly together—and let the battery current pass through. The ability of small conductive particles to stick together when influenced by Hertzian waves was first observed in 1874 by Professor D.E. Hughes while he was testing a telephone.

We are now in a position to examine the apparatus of which a coherer forms part (Fig. 61). First, we notice the aërial and earth wires, to which are attached other wires from battery A. This battery circuit passes round the relay magnet R and through two choking coils, whose function is to prevent the Hertzian waves entering the battery. The relay, when energized, brings contact D against E and closes the circuit of battery B, which is much more powerful than battery A, and operates the magnet M as well as the tapper, which is practically an electric bell minus the gong. (The tapper circuit is indicated by the dotted lines.)
We are now ready to look at the equipment that includes a coherer (Fig. 61). First, we see the aerial and ground wires, connected to additional wires from battery A. This battery circuit runs around the relay magnet R and through two choke coils, which prevent the Hertzian waves from entering the battery. When the relay is powered, it brings contact D against E and closes the circuit of battery B, which is significantly more powerful than battery A, and activates the magnet M as well as the tapper, which is essentially an electric bell without the gong. (The tapper circuit is shown by the dotted lines.)
We will suppose the transmitter of a distant station to be at work. The electric waves strike the aërial wire of the receiving station, and cause the coherer to cohere and pass current. The relay is closed, and both tapper and Morse inker begin to work. The tapper keeps striking the coherer and shakes the particles loose after every cohesion. If this were not done the current of A would pass continuously after cohesion had once taken place. When the key of the transmitter is pressed down, the waves follow one another very quickly, and the acquired conductivity of the coherer is only momentarily destroyed by the tap of the hammer. During the impression of a dot by the Morse inker, contact is made and broken repeatedly; but as the armature of the inker is heavy and slow to move it does not vibrate in time with the relay and tapper. Therefore the Morse instrument reproduces in dots and dashes the short and long depressions of the key at the transmitting station, while the tapper works rapidly in time with the relay. The Morse inker is shown diagrammatically. While current passes through M the armature is pulled towards it, the end P, carrying an inked wheel, rises, and a mark is made on the tape W, which is moved continuously[Pg 143] being drawn forward off reel R by the clockwork—or electrically-driven rollers R1 R2.
We’ll assume that the transmitter at a distant station is operational. The electric waves hit the aerial wire of the receiving station, causing the coherer to activate and allow current to pass through. This closes the relay, and both the tapper and Morse inker start functioning. The tapper continuously strikes the coherer and shakes the particles loose after each time they stick together. If this didn’t happen, the current from A would flow continuously after the initial cohesion. When the transmitter key is pressed down, the waves come in very quickly, and the coherer's increased conductivity is only briefly interrupted by the hammer tap. While the Morse inker is creating a dot, contact is made and broken repeatedly; however, since the inker's armature is heavy and slow to respond, it doesn’t move in sync with the relay and tapper. As a result, the Morse instrument translates the quick and long presses of the transmitter key into dots and dashes, while the tapper operates quickly in sync with the relay. The Morse inker is shown in a diagram. When the current flows through M, the armature is drawn towards it, lifting the end P with an inked wheel, which makes a mark on the continuously moving tape W, which is being pulled forward off reel R by the clockwork—or electrically driven rollers R1 R2.
SYNTONIC TRANSMISSION.
Syntonic transmission.
If a number of transmitting stations are sending out messages simultaneously, a jumble of signals would affect all the receivers round, unless some method were employed for rendering a receiver sensitive only to the waves intended to influence it. Also, if distinction were impossible, even with one transmitter in action its message might go to undesired stations.
If multiple broadcasting stations are sending out messages at the same time, there would be a mix of signals that would interfere with all the nearby receivers, unless some method is used to make a receiver only respond to the specific waves meant for it. Additionally, if there’s no way to differentiate, even with just one transmitter operating, its message could end up reaching the wrong stations.
There are various ways of "tuning" receivers and transmitters, but the principle underlying them all is analogous to that of mechanical vibration. If a weight is suspended from the end of a spiral spring, and given an upward blow, it bobs up and down a certain number of times per minute, every movement from start to finish having exactly the same duration as the rest. The resistance of the air and the internal friction of the spring gradually lessen the amplitude of the movements, and the weight finally comes to rest. Suppose that the weight scales 30 lbs., and that it naturally bobs twenty times a minute. If you now take a feather[Pg 144] and give it a push every three seconds you can coax it into vigorous motion, assuming that every push catches it exactly on the rebound. The same effect would be produced more slowly if 6 or 9 second intervals were substituted. But if you strike it at 4, 5, or 7 second intervals it will gradually cease to oscillate, as the effect of one blow neutralizes that of another. The same phenomenon is witnessed when two tuning-forks of equal pitch are mounted near one another, and one is struck. The other soon picks up the note. But a fork of unequal pitch would remain dumb.
There are different ways to "tune" receivers and transmitters, but the basic principle behind all of them is similar to mechanical vibration. If you hang a weight from a spiral spring and give it a quick upward push, it will bounce up and down a certain number of times per minute, with each bounce taking the same amount of time. The air resistance and the internal friction of the spring gradually reduce the height of the bounces, and eventually, the weight comes to a stop. Let's say the weight is 30 lbs and it naturally bounces twenty times a minute. If you take a feather[Pg 144] and give it a push every three seconds, you can get it to move vigorously, provided each push hits it right as it bounces back up. If you instead push it every 6 or 9 seconds, it will move, but more slowly. However, if you push it at 4, 5, or 7 second intervals, it will gradually stop bouncing, since one push cancels out the effect of another. This same effect occurs when two tuning forks of the same pitch are placed close together, and one is struck—the other will soon start to vibrate as well. But if one of the forks is a different pitch, it will stay silent.
Now, every electrical circuit has a "natural period of oscillation" in which its electric charge vibrates. It is found possible to "tune," or "syntonize," the aërial rod or wire of a receiving station with a transmitter. A vertical wire about 200 feet in length, says Professor J.A. Fleming,[15] has a natural time period of electrical oscillation of about one-millionth of a second. Therefore if waves strike this wire a million times a second they will reinforce one another and influence the coherer; whereas a less or greater frequency will leave it practically unaffected. By adjusting the receiving circuit to the[Pg 145] transmitter, or vice versâ, selective wireless telegraphy becomes possible.
Now, every electrical circuit has a "natural period of oscillation" where its electric charge vibrates. It's possible to "tune" or "synchronize" the aerial rod or wire of a receiving station with a transmitter. A vertical wire about 200 feet long, according to Professor J.A. Fleming,[15] has a natural electrical oscillation time period of about one-millionth of a second. So, if waves hit this wire a million times a second, they will reinforce each other and affect the coherer; however, a higher or lower frequency will leave it almost unaffected. By adjusting the receiving circuit to the[Pg 145] transmitter, or vice versa, selective wireless telegraphy becomes possible.
ADVANCE OF WIRELESS TELEGRAPHY.
Advancement of wireless telegraphy.
The history of wireless telegraphy may be summed up as follows:—
The history of wireless telegraphy can be summarized like this:—
1842.—Professor Morse sent aërial messages across the Susquehanna River. A line containing a battery and transmitter was carried on posts along one bank and "earthed" in the river at each end. On the other bank was a second wire attached to a receiver and similarly earthed. Whenever contact was made and broken on the battery side, the receiver on the other was affected. Distance about 1 mile.
1842.—Professor Morse sent wireless messages across the Susquehanna River. A line with a battery and transmitter was set up on posts along one bank and connected to the river at each end. On the opposite bank, there was a second wire attached to a receiver, also connected to the river. Whenever contact was made and interrupted on the battery side, the receiver on the other side responded. The distance was about 1 mile.
1859.—James Bowman Lindsay transmitted messages across the Tay at Glencarse in a somewhat similar way. Distance about ½ mile.
1859.—James Bowman Lindsay sent messages across the Tay at Glencarse in a similar way. The distance was about half a mile.
1885.—Sir William Preece signalled from Lavernock Point, near Cardiff, to Steep Holm, an island in the Bristol Channel. Distance about 5½ miles.
1885.—Sir William Preece sent a signal from Lavernock Point, near Cardiff, to Steep Holm, an island in the Bristol Channel. The distance was about 5½ miles.
In all these electrical induction of current was employed.
In all these cases, electrical induction of current was used.
1886.—Hertzian waves discovered.
1886.—Hertzian waves found.
1895.—Professor A. Popoff sent Hertzian wave messages over a distance of 3 miles.
1895.—Professor A. Popoff sent Hertzian wave messages over a distance of 3 miles.
1897.—Marconi signalled from the Needles Hotel, Isle of Wight, to Swanage; 17½ miles.
1897.—Marconi communicated from the Needles Hotel, Isle of Wight, to Swanage; 17½ miles.
1901.—Messages sent at sea for 380 miles.
1901.—Messages sent at sea for 380 miles.
1901, Dec. 17.—Messages transmitted from Poldhu, Cornwall, to Hospital Point, Newfoundland; 2,099 miles.
1901, Dec. 17.—Messages sent from Poldhu, Cornwall, to Hospital Point, Newfoundland; 2,099 miles.
Mr. Marconi has so perfected tuning devices that his transatlantic messages do not affect receivers placed on board ships crossing the ocean, unless they are purposely tuned. Atlantic liners now publish daily small newspapers containing the latest news, flashed through space from land stations. In the United States the De Forest and Fessenden systems are being rapidly extended to embrace the most out-of-the-way districts. Every navy of importance has adopted wireless telegraphy, which, as was proved during the Russo-Japanese War, can be of the greatest help in directing operations.
Mr. Marconi has perfected tuning devices so much that his transatlantic messages don't interfere with receivers on ships crossing the ocean unless they are specifically tuned to them. Atlantic liners now publish daily small newspapers featuring the latest news sent through space from land stations. In the United States, the De Forest and Fessenden systems are being quickly expanded to reach even the most remote areas. Every major navy has adopted wireless telegraphy, which, as demonstrated during the Russo-Japanese War, can be extremely useful for directing operations.
[15] "Technics," vol. ii. p. 566.
Chapter VIII.
THE TELEPHONE.
The Bell telephone—The Edison transmitter—The granular carbon transmitter—General arrangement of a telephone circuit—Double-line circuits—Telephone exchanges—Submarine telephony.
The Bell telephone—The Edison transmitter—The granular carbon transmitter—General setup of a telephone circuit—Dual-line circuits—Telephone exchanges—Underwater telephony.
For the purposes of everyday life the telephone is even more useful than the telegraph. Telephones now connect one room of a building with another, house with house, town with town, country with country. An infinitely greater number of words pass over the telephonic circuits of the world in a year than are transmitted by telegraph operators. The telephone has become an important adjunct to the transaction of business of all sorts. Its wires penetrate everywhere. Without moving from his desk, the London citizen may hold easy converse with a Parisian, a New Yorker with a dweller in Chicago.
For everyday life, the telephone is even more useful than the telegraph. Telephones now connect different rooms in a building, houses, towns, and even countries. An incredibly larger number of words travel through the world's telephone lines each year compared to those sent by telegraph operators. The telephone has become a vital tool for all kinds of business transactions. Its wires reach everywhere. Without leaving his desk, a person in London can easily chat with someone in Paris, and a New Yorker can talk to someone in Chicago.
Wonderful as the transmission of signals over great[Pg 148] distances is, the transmission of human speech so clearly that individual voices may be distinguished hundreds of miles away is even more so. Yet the instrument which works the miracle is essentially simple in its principles.
Wonderful as it is to transmit signals over great[Pg 148] distances, the ability to send human speech so clearly that individual voices can be distinguished from hundreds of miles away is even more impressive. Yet the device that makes this miracle happen is fundamentally simple in its principles.
THE BELL TELEPHONE.
THE BELL TELEPHONE COMPANY.

The first telephone that came into general use was that of Bell, shown in Fig. 62. In a central hole of an ebonite casing is fixed a permanent magnet, M. The casing expands at one end to accommodate a coil of insulated wire wound about one extremity of a magnet. The coil ends are attached to wires passing through small channels to terminals at the rear. A circular diaphragm, D, of very thin iron plate, clamped between the concave mouthpiece and the casing, almost touches the end of the magnet.
The first telephone that became widely used was Bell's, shown in Fig. 62. In the center of an ebonite casing is a fixed permanent magnet, M. The casing flares at one end to fit a coil of insulated wire wound around one end of the magnet. The ends of the coil are connected to wires that run through small channels to terminals at the back. A circular diaphragm, D, made of very thin iron, is clamped between the curved mouthpiece and the casing, nearly touching the end of the magnet.
We will suppose that two Bell telephones, A and B, are connected up by wires, so that the wires and the coils form a complete circuit. Words are spoken into A. The air vibrations, passing through the central hole in the cover, make the diaphragm vibrate towards and away from the magnet. The distances through which the diaphragm moves have been measured, and found not to exceed in some cases more than 1⁄10,000,000 of an inch! Its movements distort the shape of the "lines of force" (see p. 118) emanating from the magnet, and these, cutting through the turns of the coil, induce a current in the line circuit. As the diaphragm approaches the magnet a circuit is sent in one direction; as it leaves it, in the other. Consequently speech produces rapidly alternating currents in the circuit, their duration and intensity depending on the nature of the sound.
We’ll assume that two Bell phones, A and B, are connected by wires, forming a complete circuit with the wires and coils. Words are spoken into A. The air vibrations pass through the central hole in the cover, causing the diaphragm to vibrate towards and away from the magnet. The distances that the diaphragm moves have been measured and found in some cases to be no more than 1⁄10 million of an inch! Its movements alter the shape of the "lines of force" (see p. 118) coming from the magnet, which, when crossing through the coil turns, create a current in the circuit. When the diaphragm gets closer to the magnet, a circuit is sent in one direction; when it moves away, it sends it in the opposite direction. As a result, speech generates rapidly changing currents in the circuit, with their duration and intensity based on the sound quality.
Now consider telephone B. The currents passing through its coil increase or diminish the magnetism of the magnet, and cause it to attract its diaphragm with varying force. The vibration of the diaphragm disturbs the air in exact accordance with the vibrations of A's diaphragm, and speech is reproduced.
Now think about telephone B. The currents flowing through its coil increase or decrease the magnetism of the magnet, causing it to attract its diaphragm with varying strength. The diaphragm vibrates, disturbing the air in sync with the vibrations of A's diaphragm, and the speech is reproduced.
THE EDISON TRANSMITTER.
THE EDISON TRANSMITTER.
The Bell telephone may be used both as a transmitter and a receiver, and the permanent magnetism of the cores renders it independent of an electric battery. But currents generated by it are so minute that they cannot overcome the resistance of a long circuit; therefore a battery is now always used, and with it a special device as transmitter.
The Bell telephone can be used as both a transmitter and a receiver, and the permanent magnetism of the cores makes it independent of an electric battery. However, the currents it generates are so small that they can't overcome the resistance of a long circuit; therefore, a battery is always used along with a special device as a transmitter.
If in a circuit containing a telephone and a battery there be a loose contact, and this be shaken, the varying resistance of the contact will cause electrical currents of varying force to pass through the circuit. Edison introduced the first successful microphone transmitter, in which a small platinum disc connected to the diaphragm pressed with varying force against a disc of carbon, each disc forming part of the circuit. Vibrations of the diaphragm caused current to flow in a series of rapid pulsations.
If there's a loose connection in a circuit with a telephone and a battery, shaking it will change the resistance at the contact point, causing electrical currents of different strengths to flow through the circuit. Edison created the first successful microphone transmitter, which used a small platinum disc that pressed with varying pressure against a carbon disc, with both discs part of the circuit. The diaphragm's vibrations led to current flowing in quick pulses.

THE GRANULAR CARBON TRANSMITTER.
THE CARBON TRANSMITTER.
In Fig. 63 we have a section of a microphone transmitter now very widely used. It was invented, in its original form, by an English clergyman named Hunnings. Resting in a central cavity of an ebonite seating is a carbon block, C, with a face moulded into a number of pyramidal projections, P P. The space between C and a carbon diaphragm, D, is packed with carbon granules, G G. C has direct contact with line terminal T, which screws into it; D with T1 through the brass casing, screw S, and a small plate at the back of the transmitter. Voice vibrations compress G G, and allow current to pass[Pg 152] more freely from D to C. This form of microphone is very delicate, and unequalled for long-distance transmission.
In Fig. 63, we have a section of a microphone transmitter that is now very widely used. It was originally invented by an English clergyman named Hunnings. At the center of an ebonite casing is a carbon block, C, which has a surface shaped into several pyramid-like projections, P P. The space between C and a carbon diaphragm, D, is filled with carbon granules, G G. C is directly connected to line terminal T, which screws into it; D connects to T1 through the brass casing, screw S, and a small plate at the back of the transmitter. Voice vibrations compress G G and let current flow[Pg 152] more easily from D to C. This type of microphone is very sensitive and unmatched for long-distance transmission.

GENERAL ARRANGEMENT OF A TELEPHONE CIRCUIT.
GENERAL ARRANGEMENT OF A TELEPHONE CIRCUIT.
In many forms of subscriber's instruments both receiver and transmitter are mounted on a single handle in such a way as to be conveniently placed for ear and mouth. For the sake of clearness the diagrammatic[Pg 153] sketch of a complete installation (Fig. 64) shows them separated. The transmitters, it will be noticed, are located in battery circuits, including the primary windings P P2 of induction coils. The transmitters are in the line circuit, which includes the secondary windings S S2 of the coils.
In many types of subscriber instruments, both the receiver and transmitter are attached to a single handle, making them easy to access for the ear and mouth. For clarity, the diagrammatic[Pg 153] sketch of a complete setup (Fig. 64) shows them separated. It's important to note that the transmitters are positioned in battery circuits, which include the primary windings P P2 of induction coils. The transmitters are in the line circuit, which includes the secondary windings S S2 of the coils.
We will assume that the transmitters are, in the first instance, both hung on the hooks of the metallic switches, which their weight depresses to the position indicated by the dotted lines. The handle of the magneto-generator at the left-end station is turned, and current passes through the closed circuit:—Line A, E B2, contact 10, the switch 9; line B, 4, the other switch, contact 5, and E B. Both bells ring. Both parties now lift their receivers from the switch hooks. The switches rise against contacts 1, 2, 3 and 6, 7, 8 respectively. Both primary and both secondary circuits are now completed, while the bells are disconnected from the line wires. The pulsations set up by transmitter T in primary coil P are magnified by secondary coil S for transmission through the line circuit, and affect both receivers. The same thing happens when T2 is used. At the end of the conversation the receivers are hung on their hooks again, and the bell circuit is remade, ready for the next call.
We’ll start by assuming that both transmitters are hung on the hooks of the metal switches, which their weight presses down to the position indicated by the dotted lines. The handle of the magneto-generator at the left-end station is turned, allowing current to flow through the closed circuit:—Line A, E B2, contact 10, switch 9; line B, 4, the other switch, contact 5, and E B. Both bells ring. Now, both parties lift their receivers from the switch hooks. The switches rise and connect with contacts 1, 2, 3 and 6, 7, 8 respectively. Both primary and secondary circuits are now complete, while the bells are disconnected from the line wires. The pulses created by transmitter T in primary coil P are amplified by secondary coil S for transmission through the line circuit, affecting both receivers. The same occurs when T2 is used. At the end of the conversation, the receivers are hung back on their hooks, and the bell circuit is remade, ready for the next call.

DOUBLE-LINE CIRCUITS.
Double-line circuits.
The currents used in telephones pulsate very rapidly, but are very feeble. Electric disturbances caused by the proximity of telegraph or tram wires would much interfere with them if the earth were used for the return circuit. It has been found that a complete metallic circuit (two wires) is practically free from interference, though where a number of wires are hung on the same poles, speech-sounds may be faintly induced in one circuit from another. This defect is, however, minimized by crossing the wires about among themselves, so that any one line does not pass round the corresponding insulator on every pole.
The currents used in telephones pulse very quickly, but they're quite weak. Electric disturbances from nearby telegraph or tram wires could really disrupt them if the earth was used for the return circuit. It turns out that a complete metallic circuit (two wires) is almost free from interference, although when multiple wires are attached to the same poles, speech sounds can be faintly picked up from one circuit to another. However, this issue is reduced by mixing the wires around, so that any single line doesn't wrap around the same insulator on every pole.
TELEPHONE EXCHANGES.
PHONE SYSTEMS.
In a district where a number of telephones are used the subscribers are put into connection with one another through an "exchange," to which all the wires lead. One wire of each subscriber runs to a common "earth;" the other terminates at a switchboard presided over by an operator. In an exchange used by many subscribers the terminals are distributed over a number of switchboards, each containing 80 to 100 terminals, and attended to by an operator, usually a girl.
In an area where many telephones are used, subscribers connect with each other through an "exchange," which all the wires lead to. One wire from each subscriber connects to a common "ground," while the other ends at a switchboard managed by an operator. In an exchange with numerous subscribers, the terminals are spread across several switchboards, each with 80 to 100 terminals, and are typically handled by an operator, usually a woman.
When a subscriber wishes to be connected to another subscriber, he either turns the handle of a magneto generator, which causes a shutter to fall and expose his number at the exchange, or simply depresses a key which works a relay at the exchange and lights a tiny electric lamp. The operator, seeing the signal, connects her telephone with the subscriber's circuit and asks the number wanted. This given, she rings up the other subscriber, and connects the two circuits by means of an insulated wire cord having a spike at each end to fit the "jack" sockets of the switchboard terminals. The two subscribers are now in communication.
When a subscriber wants to connect with another subscriber, they either turn the handle of a magneto generator, which activates a shutter to display their number at the exchange, or simply press a key that triggers a relay at the exchange and lights up a small electric lamp. The operator, noticing the signal, connects her phone to the subscriber's line and asks for the desired number. Once provided, she dials the other subscriber and connects the two lines using an insulated wire cord with a spike on each end to fit the "jack" sockets of the switchboard terminals. The two subscribers are now in communication.

If a number on switchboard A calls for a number on switchboard C, the operator at A connects her subscriber by a jack cord to a trunk line running[Pg 157] to C, where the operator similarly connects the trunk line with the number asked for, after ringing up the subscriber. The central exchange of one town is connected with that of another by one or more trunk lines, so that a subscriber may speak through an indefinite number of exchanges. So perfect is the modern telephone that the writer remembers on one occasion hearing the door-bell ring in a house more than a hundred miles away, with which he was at the moment in telephonic connection, though three exchanges were in the circuit.
If someone on switchboard A calls a number on switchboard C, the operator at A connects her caller to a trunk line going[Pg 157] to C, where the operator connects the trunk line to the requested number after ringing the subscriber. The central exchange of one town is linked to another's with one or more trunk lines, allowing a subscriber to communicate through multiple exchanges. The modern telephone is so advanced that the writer recalls once hearing a doorbell ring in a house over a hundred miles away while he was on the phone, even though three exchanges were involved.
SUBMARINE TELEPHONY.
Submarine communication.
Though telegraphic messages are transmitted easily through thousands of miles of cable,[16] submarine telephony is at present restricted to comparatively short distances. When a current passes through a cable, electricity of opposite polarity induced on the outside of the cable damps the vibration in the conductor. In the Atlantic cable, strong currents of electricity are poured periodically into one end, and though much enfeebled when they reach the other they are sufficiently strong to work a very[Pg 158] delicate "mirror galvanometer" (invented by Lord Kelvin), which moves a reflected ray up and down a screen, the direction of the movements indicating a dot or a dash. Reversible currents are used in transmarine telegraphy. The galvanometer is affected like the coils and small magnet in Wheatstone's needle instrument (p. 128).
Though telegraphic messages are easily sent over thousands of miles of cable,[16] submarine telephony is currently limited to relatively short distances. When a current flows through a cable, electricity of the opposite polarity on the outside of the cable reduces the vibration in the conductor. In the Atlantic cable, strong electric currents are periodically sent into one end, and even though they are much weaker by the time they reach the other end, they are still strong enough to operate a very[Pg 158] delicate "mirror galvanometer" (invented by Lord Kelvin), which moves a reflected ray up and down a screen, with the direction of the movements indicating a dot or a dash. Reversible currents are used in transmarine telegraphy. The galvanometer behaves like the coils and small magnet in Wheatstone's needle instrument (p. 128).
Telephonic currents are too feeble to penetrate many miles of cable. There is telephonic communication between England and France, and England and Ireland. But transatlantic telephony is still a thing of the future. It is hoped, however, that by inserting induction coils at intervals along the cables the currents may be "stepped up" from point to point, and so get across. Turning to Fig. 64, we may suppose S to be on shore at the English end, and S2 to be the primary winding of an induction coil a hundred miles away in the sea, which magnifies the enfeebled vibrations for a journey to S3, where they are again revived; and so on, till the New World is reached. The difficulty is to devise induction coils of great power though of small size. Yet science advances nowadays so fast that we may live to hear words spoken at the Antipodes.
Telephonic currents are too weak to travel through many miles of cable. There is phone communication between England and France, as well as between England and Ireland. However, transatlantic phone calls are still a thing of the future. It is hoped that by adding induction coils at intervals along the cables, the currents can be "stepped up" from point to point, allowing them to cross. Looking at Fig. 64, we can imagine S onshore at the English end and S2 as the primary winding of an induction coil a hundred miles away in the sea, which amplifies the weakened vibrations for a trip to S3, where they are strengthened again; and this continues until reaching the New World. The challenge is to design induction coils that are powerful yet compact. Still, science is progressing so rapidly these days that we may soon hear words spoken from the other side of the world.
Chapter IX.
DYNAMOS AND ELECTRIC MOTORS.
A simple dynamo—Continuous-current dynamos—Multipolar dynamos—Exciting the field magnets—Alternating current dynamos—The transmission of power—The electric motor—Electric lighting—The incandescent lamp—Arc lamps—"Series" and "parallel" arrangement of lamps—Current for electric lamps—Electroplating.
A basic dynamo—Direct current dynamos—Multipolar dynamos—Energizing the field magnets—Alternating current dynamos—Power transmission—Electric motors—Electric lighting—Incandescent bulbs—Arc lamps—"Series" and "parallel" configurations of bulbs—Power for electric lamps—Electroplating.
In previous chapters we have incidentally referred to the conversion of mechanical work into electrical energy. In this we shall examine how it is done—how the silently spinning dynamo develops power, and why the motor spins when current is passed through it.
In previous chapters, we've casually mentioned how mechanical work gets turned into electrical energy. Now, we'll take a closer look at how this happens—how the quietly spinning dynamo generates power and why the motor spins when current flows through it.
We must begin by returning to our first electrical diagram (Fig. 50), and calling to mind the invisible "lines of force" which permeate the ether in the immediate neighbourhood of a magnet's poles, called the magnetic field of the magnet.
We need to go back to our first electrical diagram (Fig. 50) and remember the invisible "lines of force" that fill the space around a magnet's poles, known as the magnetic field of the magnet.
Many years ago (1831) the great Michael Faraday discovered that if a loop of wire were moved up[Pg 160] and down between the poles of an electro-magnet (Fig. 66) a current was induced in the loop, its direction depending upon that in which the loop was moved. The energy required to cut the lines of force passed in some mysterious way into the wire. Why this is so we cannot say, but, taking advantage of the fact, electricians have gradually developed the enormous machines which now send vehicles spinning over metal tracks, light our streets and houses, and supply energy to innumerable factories.
Many years ago (1831), the great Michael Faraday discovered that moving a loop of wire up[Pg 160] and down between the poles of an electromagnet (Fig. 66) generates a current in the loop, with its direction depending on how the loop is moved. The energy needed to cut through the lines of force somehow transfers into the wire. Though we can’t explain why this happens, electricians have taken advantage of this fact to gradually develop the massive machines that now propel vehicles over metal tracks, illuminate our streets and homes, and provide power to countless factories.

The strength of the current induced in a circuit[Pg 161] cutting the lines of force of a magnet is called its pressure, voltage, or electro-motive force (expressed shortly E.M.F.). It may be compared with the pounds-to-the-square-inch of steam. In order to produce an E.M.F. of one volt it is calculated that 100,000,000 lines of force must be cut every second.
The strength of the current generated in a circuit[Pg 161] that cuts through the magnetic field is called its pressure, voltage, or electromotive force (shortened to E.M.F.). This can be compared to the pressure of steam measured in pounds per square inch. To generate an E.M.F. of one volt, it's estimated that 100,000,000 magnetic field lines need to be cut every second.
The voltage depends on three things:—(1.) The strength of the magnet: the stronger it is, the greater the number of lines of force coming from it. (2.) The length of the conductor cutting the lines of force: the longer it is, the more lines it will cut. (3.) The speed at which the conductor moves: the faster it travels, the more lines it will cut in a given time. It follows that a powerful dynamo, or mechanical producer of current, must have strong magnets and a long conductor; and the latter must be moved at a high speed across the lines of force.
The voltage relies on three factors: (1) The strength of the magnet: the stronger it is, the more lines of force it generates. (2) The length of the conductor that cuts through the lines of force: the longer it is, the more lines it will intersect. (3) The speed at which the conductor moves: the faster it moves, the more lines it will cut within a certain time frame. This means that a powerful dynamo, or a mechanical generator of current, needs strong magnets and a long conductor; plus, the conductor needs to move quickly across the lines of force.
A SIMPLE DYNAMO.
A basic dynamo.
In Fig. 67 we have the simplest possible form of dynamo—a single turn of wire, w x y z, mounted on a spindle, and having one end attached to an insulated ring C, the other to an insulated ring C1. Two small brushes, B B1, of wire gauze or carbon, rubbing continuously against these collecting rings,[Pg 162] connect them with a wire which completes the circuit. The armature, as the revolving coil is called, is mounted between the poles of a magnet, where the lines of force are thickest. These lines are supposed to stream from the N. to the S. pole.
In Fig. 67, we see the simplest form of a dynamo—a single loop of wire, w x y z, placed on a spindle, with one end connected to an insulated ring C and the other to an insulated ring C1. Two small brushes, B B1, made of wire gauze or carbon, continuously touch these collecting rings,[Pg 162] linking them with a wire that completes the circuit. The armature, which is the rotating coil, is positioned between the poles of a magnet, where the lines of force are strongest. These lines are assumed to flow from the N. to the S. pole.
In Fig. 67 the armature has reached a position in which y z and w x are cutting no, or very few, lines of force, as they move practically parallel to the lines. This is called the zero position.
In Fig. 67, the armature is in a position where y z and w x are cutting almost no lines of force, as they are moving nearly parallel to those lines. This is known as the zero position.


In Fig. 68 the armature, moving at right angles to the lines of force, cuts a maximum number in a given time, and the current induced in the coil is therefore now most intense. Here we must stop a moment to consider how to decide in which direction the current flows. The armature is revolving in a clockwise direction, and y z, therefore, is moving downwards. Now, suppose that you rest your left hand on the N. pole of the magnet so that the arm lies in a line with the magnet. Point your forefinger towards the S. pole. It will indicate the direction of the lines of force. Bend your other three fingers downwards over the edge of the N. pole. They will indicate the direction in which the conductor is moving across the magnetic field. Stick[Pg 164] out the thumb at right angles to the forefinger. It points in the direction in which the induced current is moving through the nearer half of the coil. Therefore lines of force, conductor, and induced current travel in planes which, like the top and two adjacent sides of a box, are at right angles to one another.
In Fig. 68, the armature moves at right angles to the lines of force, cutting through a maximum number in a given time, which means the current induced in the coil is at its strongest. We need to pause for a moment to figure out the direction of the current flow. The armature is spinning clockwise, so y z is moving downward. Now, imagine resting your left hand on the N. pole of the magnet so that your arm aligns with the magnet. Point your forefinger toward the S. pole; it will show the direction of the lines of force. Curl your other three fingers down over the edge of the N. pole. They will indicate the direction in which the conductor is moving through the magnetic field. Extend your thumb at right angles to your forefinger; it points in the direction in which the induced current is flowing through the nearer half of the coil. Thus, the lines of force, the conductor, and the induced current exist in planes that are, like the top and two adjacent sides of a box, at right angles to each other.
While current travels from z to y—that is, from the ring C1 to y—it also travels from x to w, because w x rises while y z descends. So that a current circulates through the coil and the exterior part of the circuit, including the lamp. After z y has passed the lowest possible point of the circle it begins to ascend, w x to descend. The direction of the current is therefore reversed; and as the change is repeated every half-revolution this form of dynamo is called an alternator or creator of alternating currents. A well-known type of alternator is the magneto machine which sends shocks through any one who completes the external circuit by holding the brass handles connected by wires to the brushes. The faster the handle of the machine is turned the more frequent is the alternation, and the stronger the current.
While current flows from z to y—that is, from the ring C1 to y—it also flows from x to w, because w x rises while y z descends. This creates a current that circulates through the coil and the outer part of the circuit, including the lamp. After z y has passed the lowest point of the circle, it starts to rise, and w x begins to drop. The direction of the current is therefore reversed; and since this change happens every half-revolution, this type of dynamo is called an alternator or creator of alternating currents. A well-known example of an alternator is the magneto machine, which delivers shocks to anyone who completes the external circuit by holding the brass handles connected by wires to the brushes. The faster the handle of the machine is turned, the more frequent the alternation, and the stronger the current.

CONTINUOUS-CURRENT DYNAMOS.
Direct current dynamos.
An alternating current is not so convenient for some purposes as a continuous current. It is therefore sometimes desirable (even necessary) to convert the alternating into a uni-directional or continuous current. How this is done is shown in Figs. 69 and 70. In place of the two collecting rings C C1, we now have a single ring split longitudinally into two portions, one of which is connected to each end of the coil w x y z. In Fig. 69 brush B has just passed the gap on to segment C, brush B1 on to segment C1. For half a revolution these remain respectively in contact; then, just as y z begins to rise and w x to descend, the brushes cross the gaps again and exchange segments, so that the current is perpetually flowing one way[Pg 166] through the circuit. The effect of the commutator[17] is, in fact, equivalent to transposing the brushes of the collecting rings of the alternator every time the coil reaches a zero position.
An alternating current isn't as practical for some applications as a direct current. Therefore, it's sometimes necessary (or even essential) to convert the alternating current into a one-way or direct current. This process is illustrated in Figs. 69 and 70. Instead of two collecting rings C C1, we now have a single ring that is split lengthwise into two parts, with one part connected to each end of the coil w x y z. In Fig. 69, brush B has just moved past the gap onto segment C, while brush B1 moves onto segment C1. For half a revolution, these brushes stay in contact with their respective segments; then, just as y z starts to rise and w x starts to fall, the brushes cross the gaps again and switch segments, allowing the current to continuously flow in one direction[Pg 166] through the circuit. The action of the commutator[17] essentially replicates the effect of swapping the brushes of the collecting rings of the alternator every time the coil reaches a zero position.
Figs. 71 and 72 give end views in section of the coil and the commutator, with the coil in the position of minimum and maximum efficiency. The arrow denotes the direction of movement; the double dotted lines the commutator end of the revolving coil.
Figs. 71 and 72 show side views of the coil and the commutator, with the coil positioned for minimum and maximum efficiency. The arrow indicates the direction of movement, while the double dotted lines represent the commutator end of the rotating coil.

PRACTICAL CONTINUOUS-CURRENT DYNAMOS.
PRACTICAL CONTINUOUS-CURRENT GENERATORS.
The electrical output of our simple dynamo would[Pg 167] be increased if, instead of a single turn of wire, we used a coil of many turns. A further improvement would result from mounting on the shaft, inside the coil, a core or drum of iron, to entice the lines of force within reach of the revolving coil. It is evident that any lines which pass through the air outside the circle described by the coil cannot be cut, and are wasted.
The electrical output of our simple dynamo would[Pg 167] be stronger if we used a coil with multiple turns of wire instead of just one. An additional improvement would come from placing an iron core or drum on the shaft inside the coil to capture the magnetic lines of force as the coil spins. It's clear that any lines of force that pass through the air outside the circle made by the coil cannot be intercepted and are essentially wasted.
![]() |
![]() |
The core is not a solid mass of iron, but built up of a number of very thin iron discs threaded on the shaft and insulated from one another to prevent electric eddies, which would interfere with the induced current in the conductor.[18] Sometimes there are openings through the core from end to end to ventilate and cool it.
The core isn't a solid block of iron; it's made up of several very thin iron discs stacked on the shaft and insulated from each other to avoid electric eddies that could disrupt the induced current in the conductor.[18] Sometimes, there are openings from one end of the core to the other to allow for ventilation and cooling.

We have already noticed that in the case of a single coil the current rises and falls in a series of pulsations. Such a form of armature would be unsuitable for large dynamos, which accordingly have a number of coils wound over their drums, at equal distances round the circumference, and a commutator divided into an equal number of segments. The subject of drum winding is too complicated for brief treatment, and we must therefore be content with noticing that the coils are so connected to their respective commutator segments and to one another that they mutually assist one another. A glance at Fig. 73 will help to explain this. Here we have in section a number of conductors on the right of the drum (marked with a cross to show that current is moving, as it were, into the page), connected with[Pg 169] conductors on the left (marked with a dot to signify current coming out of the page). If the "crossed" and "dotted" conductors were respectively the "up" and "down" turns of a single coil terminating in a simple split commutator (Fig. 69), when the coil had been revolved through an angle of 90° some of the up turns would be ascending and some descending, so that conflicting currents would arise. Yet we want to utilize the whole surface of the drum; and by winding a number of coils in the manner hinted at, each coil, as it passes the zero point, top or bottom, at once generates a current in the desired direction and reinforces that in all the other turns of its own and of other coils on the same side of a line drawn vertically through the centre. There is thus practically no fluctuation in the pressure of the current generated.
We've already seen that in the case of a single coil, the current fluctuates in a series of bursts. This design wouldn’t work well for large generators, which have multiple coils wound around their drums, evenly spaced around the circumference, and a commutator divided into an equal number of segments. The topic of drum winding is too complex for a brief explanation, so we'll just point out that the coils are connected to their respective commutator segments and to each other in a way that they support one another. Looking at Fig. 73 helps clarify this. In the section, we see several conductors on the right side of the drum (marked with a cross to indicate current flowing into the page), connected with [Pg 169] conductors on the left (marked with a dot to represent current flowing out of the page). If the "crossed" and "dotted" conductors were the "up" and "down" turns of a single coil connected to a basic split commutator (Fig. 69), when the coil is turned 90°, some of the up turns would be moving up and some down, creating conflicting currents. However, we aim to make use of the entire surface of the drum; by winding several coils as described, each coil generates current in the desired direction as it passes the zero point, either at the top or bottom, reinforcing the current in all the other turns of its own and other coils on the same side of a vertical line drawn through the center. This effectively means there’s virtually no fluctuation in the generated current pressure.
The action of single and multiple coil windings may be compared to that of single and multiple pumps. Water is ejected by a single pump in gulps; whereas the flow from a pipe fed by several pumps arranged to deliver consecutively is much more constant.
The action of single and multiple coil windings can be compared to that of single and multiple pumps. A single pump ejects water in bursts; however, the flow from a pipe supplied by several pumps arranged to deliver consecutively is much more stable.
MULTIPOLAR DYNAMOS.
MULTIPOLAR DYNAMOS.
Hitherto we have considered the magnetic field produced by one bi-polar magnet only. Large dynamos[Pg 170] have four, six, eight, or more field magnets set inside a casing, from which their cores project towards the armature so as almost to touch it (Fig. 74). The magnet coils are wound to give N. and S. poles alternately at their armature ends round the field; and the lines of force from each N. pole stream each way to the two adjacent S. poles across the path of the armature coils. In dynamos of this kind several pairs of collecting brushes pick current off the commutator at equidistant points on its circumference.
So far, we've only looked at the magnetic field created by a single bi-polar magnet. Large dynamos[Pg 170] have four, six, eight, or more field magnets placed inside a casing, with their cores extending towards the armature until they're almost touching it (Fig. 74). The magnet coils are wrapped to create N. and S. poles alternately at the armature ends around the field, and the lines of force from each N. pole spread out toward the two nearby S. poles across the armature coils' path. In these types of dynamos, several pairs of collecting brushes extract current from the commutator at evenly spaced points around its circumference.

EXCITING THE FIELD MAGNETS.
POWERING THE FIELD MAGNETS.
Until current passes through the field magnet coils, no magnetic field can be created. How are the coils supplied with current? A dynamo, starting for the first time, is excited by a current from an outside source; but when it has once begun to generate current it feeds its magnets itself, and ever afterwards will be self-exciting,[19] owing to the residual magnetism left in the magnet cores.
Until current flows through the field magnet coils, no magnetic field can be created. How do the coils get their current? A dynamo, when it starts for the first time, is powered by a current from an external source; but once it begins generating current, it supplies its magnets on its own and will continue to be self-exciting,[19] thanks to the residual magnetism left in the magnet cores.

Look carefully at Figs. 77 and 78. In the first of these you will observe that part of the wire forming[Pg 172] the external circuit is wound round the arms of the field magnet. This is called a series winding. In this case all the current generated helps to excite the dynamo. At the start the residual magnetism of the magnet cores gives a weak field. The armature coils cut this and pass a current through the circuit. The magnets are further excited, and the field becomes stronger; and so on till the dynamo is developing full power. Series winding is used where the current in the external circuit is required to be very constant.
Take a close look at Figs. 77 and 78. In the first one, you’ll see that part of the wire making up[Pg 172] the external circuit is wrapped around the arms of the field magnet. This is known as a series winding. In this setup, all the current generated contributes to energizing the dynamo. Initially, the leftover magnetism in the magnet cores creates a weak magnetic field. The armature coils cut through this and generate a current in the circuit. The magnets get further energized, and the field gets stronger; this process continues until the dynamo reaches its full power. Series winding is utilized when a very steady current in the external circuit is needed.

Fig. 78 shows another method of winding—the shunt. Most of the current generated passes through the external circuit 2, 2; but a part is switched through a separate winding for the magnets, denoted by the fine wire 1, 1. Here the strength of the magnetism does not vary directly with the current, as only a small part of the current serves the magnets. The shunt winding is therefore used where the voltage (or pressure) must be constant.
Fig. 78 shows another method of winding—the shunt. Most of the current generated flows through the external circuit 2, 2; however, a portion is diverted through a separate winding for the magnets, indicated by the fine wire 1, 1. In this case, the strength of the magnetism doesn't change directly with the current, since only a small part of the current is used for the magnets. The shunt winding is therefore utilized when the voltage (or pressure) needs to be consistent.
![]() Fig. 77.—Illustration displaying a "series" winding. |
![]() |
A third method is a combination of the two already named. A winding of fine wire passes from brush to brush round the magnets; and there is also a series[Pg 174] winding as in Fig. 77. This compound method is adapted more especially for electric traction.
A third method combines the two previously mentioned. A winding of fine wire runs from brush to brush around the magnets, and there is also a series[Pg 174] winding as shown in Fig. 77. This combined method is particularly suited for electric traction.
ALTERNATING DYNAMOS.
ALTERNATING GENERATORS.
These have their field magnets excited by a separate continuous current dynamo of small size. The field magnets usually revolve inside a fixed armature (the reverse of the arrangement in a direct-current generator); or there may be a fixed central armature and field magnets revolving outside it. This latter arrangement is found in the great power stations at Niagara Falls, where the enormous field-rings are mounted on the top ends of vertical shafts, driven by water-turbines at the bottom of pits 178 feet deep, down which water is led to the turbines through great pipes, or penstocks. The weight of each shaft and the field-ring attached totals about thirty-five tons. This mass revolves 250 times a minute, and 5,000 horse power is constantly developed by the dynamo. Similar dynamos of 10,000 horse power each have been installed on the Canadian side of the Falls.
These use field magnets powered by a separate small continuous current generator. The field magnets usually spin inside a stationary armature (unlike a direct-current generator); or there might be a fixed central armature with field magnets rotating around it. This second setup is seen in the large power stations at Niagara Falls, where the massive field rings are placed on the top ends of vertical shafts, which are driven by water turbines at the bottom of pits 178 feet deep. Water is channeled to the turbines through large pipes, or penstocks. The total weight of each shaft and the attached field ring is about thirty-five tons. This mass spins at 250 times a minute, generating 5,000 horsepower continuously from the generator. Similar generators generating 10,000 horsepower each have been set up on the Canadian side of the Falls.

TRANSMISSION OF POWER.
Power Transfer.
Alternating current is used where power has to be transmitted for long distances, because such a current can be intensified, or stepped up, by a transformer somewhat similar in principle to a Ruhmkorff coil minus a contact-breaker (see p. 122). A typical example of transformation is seen in Fig. 79. Alternating current of 5,000 volts pressure is produced in the generating station and sent through conductors to a distant station, where a transformer, B, reduces the pressure to 500 volts to drive an alternating motor, C, which in turn operates a direct current dynamo, D. This dynamo has its + terminal connected with the insulated or "live" rail of an electric railway, and its – terminal with the wheel rails, which are metallically united at the joints to act as[Pg 176] a "return." On its way from the live rail to the return the current passes through the motors. In the case of trams the conductor is either a cable carried overhead on standards, from which it passes to the motor through a trolley arm, or a rail laid underground in a conduit between the rails. In the top of the conduit is a slit through which an arm carrying a contact shoe on the end projects from the car. The shoe rubs continuously on the live rail as the car moves.
Alternating current is used to transmit power over long distances because it can be boosted by a transformer similar to a Ruhmkorff coil without a contact-breaker (see p. 122). A typical transformation example is shown in Fig. 79. Alternating current of 5,000 volts is generated at the power station and sent through wires to a remote station, where a transformer, B, reduces the voltage to 500 volts to power an alternating motor, C, which then operates a direct current dynamo, D. This dynamo connects its + terminal to the insulated or "live" rail of an electric railway and its – terminal to the wheel rails, which are connected at the joints to act as a[Pg 176] "return." As the current flows from the live rail to the return, it passes through the motors. For trams, the power supply is either an overhead cable on poles, which goes to the motor through a trolley arm, or a rail placed underground in a conduit between the rails. The top of the conduit features a slit through which an arm with a contact shoe extends from the car. The shoe continuously rubs against the live rail as the car moves.
To return for a moment to the question of transformation of current. "Why," it may be asked, "should we not send low-pressure direct current to a distant station straight from the dynamo, instead of altering its nature and pressure? Or, at any rate, why not use high-pressure direct current, and transform that?" The answer is, that to transmit a large amount of electrical energy at low pressure (or voltage) would necessitate large volume (or amperage) and a big and expensive copper conductor to carry it. High-pressure direct current is not easily generated, since the sparking at the collecting brushes as they pass over the commutator segments gives trouble. So engineers prefer high-pressure alternating current, which is easily produced, and can be sent through[Pg 177] a small and inexpensive conductor with little loss. Also its voltage can be transformed by apparatus having no revolving parts.
To revisit the issue of converting current: "Why," one might ask, "can't we just send low-voltage direct current from the generator to a distant location without changing its type or voltage? Or, at the very least, why not use high-voltage direct current and convert that?" The answer is that transmitting a large amount of electrical energy at low voltage would require a high current and a large, costly copper conductor to handle it. High-voltage direct current is also tricky to generate because sparking at the brushes as they move over the commutator segments creates issues. Therefore, engineers prefer high-voltage alternating current, which is easier to generate and can be transmitted through a small, cost-effective conductor with minimal energy loss. Plus, its voltage can be adjusted using devices that don’t have any moving parts.
THE ELECTRIC MOTOR.
Electric motor.
Anybody who understands the dynamo will also be able to understand the electric motor, which is merely a reversed dynamo.
Anyone who understands the dynamo will also be able to understand the electric motor, which is just a reversed dynamo.
Imagine in Fig. 70 a dynamo taking the place of the lamp and passing current through the brushes and commutator into the coil w x y z. Now, any coil through which current passes becomes a magnet with N. and S. poles at either end. (In Fig. 70 we will assume that the N. pole is below and the S. pole above the coil.) The coil poles therefore try to seek the contrary poles of the permanent magnet, and the coil revolves until its S. pole faces the N. of the magnet, and vice versâ. The lines of force of the coil and the magnet are now parallel. But the momentum of revolution carries the coil on, and suddenly the commutator reverses its polarity, and a further half-revolution takes place. Then comes a further reversal, and so on ad infinitum. The rotation of the motor is therefore merely a question of repulsion and attraction of like and unlike poles. An ordinary[Pg 178] compass needle may be converted into a tiny motor by presenting the N. and S. poles of a magnet to its S. and N. poles alternately every half-revolution.
Imagine in Fig. 70 a dynamo replacing the lamp and passing current through the brushes and commutator into the coil w x y z. Now, any coil that has current flowing through it becomes a magnet with N. and S. poles at either end. (In Fig. 70, we will assume the N. pole is below and the S. pole is above the coil.) The coil poles therefore try to align with the opposite poles of the permanent magnet, and the coil spins until its S. pole faces the N. pole of the magnet, and vice versa. The lines of force from the coil and the magnet are now parallel. But the momentum from the rotation keeps the coil moving, and suddenly the commutator flips its polarity, resulting in another half-revolution. Then comes another flip, and so on ad infinitum. The rotation of the motor is simply a matter of repulsion and attraction between like and unlike poles. An ordinary[Pg 178] compass needle can be turned into a tiny motor by alternating the N. and S. poles of a magnet in front of its S. and N. poles every half-revolution.
In construction and winding a motor is practically the same as a dynamo. In fact, either machine can perform either function, though perhaps not equally well adapted for both. Motors may be run with direct or alternating current, according to their construction.
In construction and winding, a motor is basically the same as a dynamo. In fact, either machine can do either function, though they may not be equally suited for both. Motors can operate with either direct or alternating current, depending on how they're built.
On electric cars the motor is generally suspended from the wheel truck, and a small pinion on the armature shaft gears with a large pinion on a wheel axle. One great advantage of electric traction is that every vehicle of a train can carry its own motor, so that the whole weight of the train may be used to get a grip on the rails when starting. Where a single steam locomotive is used, the adhesion of its driving-wheels only is available for overcoming the inertia of the load; and the whole strain of starting is thrown on to the foremost couplings. Other advantages may be summed up as follows:—(1) Ease of starting and rapid acceleration; (2) absence of waste of energy (in the shape of burning fuel) when the vehicles are at rest; (3) absence of smoke and smell.
In electric cars, the motor is usually mounted on the wheel chassis, and a small pinion on the armature shaft meshes with a larger pinion on the wheel axle. One major benefit of electric traction is that each vehicle in a train can have its own motor, allowing the entire weight of the train to help grip the rails when starting. In contrast, a single steam locomotive only relies on the traction of its driving wheels to overcome the load's inertia, which puts all the strain of starting on the front couplings. Other advantages include: (1) Easy starting and quick acceleration; (2) no energy waste (like burning fuel) when the vehicles are stationary; (3) no smoke or odor.
ELECTRIC LIGHTING.
Electric Lighting.
Dynamos are used to generate current for two main purposes—(1) To supply power to motors of all kinds; (2) to light our houses, factories, and streets. In private houses and theatres incandescent lamps are generally used; in the open air, in shops, and in larger buildings, such as railway stations, the arc lamp is more often found.
Dynamos are used to generate electricity for two main reasons—(1) To provide power to all types of motors; (2) to illuminate our homes, factories, and streets. In private homes and theaters, incandescent lamps are typically used; outdoors, in shops, and in larger buildings like railway stations, the arc lamp is more commonly used.
INCANDESCENT LAMP.
Light bulb.
If you take a piece of very fine iron wire and lay it across the terminals of an accumulator, it becomes white hot and melts, owing to the heat generated by its resistance to the current. A piece of fine platinum wire would become white hot without melting, and would give out an intense light. Here we have the principle of the glow or incandescent lamp—namely, the interposition in an electric circuit of a conductor which at once offers a high resistance to the current, but is not destroyed by the resulting heat.
If you take a thin piece of iron wire and place it across the terminals of a battery, it will get extremely hot and melt because of the heat generated by its resistance to the current. A thin piece of platinum wire would get very hot without melting and would emit a bright light. This illustrates the principle behind the glow or incandescent lamp—specifically, the inclusion of a conductor in an electric circuit that provides high resistance to the current but doesn’t get destroyed by the heat it produces.
In Fig. 80 is shown a fan propelling liquid constantly through a pipe. Let us assume that the liquid is one which develops great friction on the inside of the pipe. At the contraction, where the[Pg 180] speed of travel is much greater than elsewhere in the circuit, most heat will be produced.
In Fig. 80, there is a fan pushing liquid continuously through a pipe. Let's assume that the liquid creates a lot of friction against the inside of the pipe. At the point of contraction, where the speed of flow is much higher than in other parts of the circuit, the most heat will be generated.

In quite the early days of the glow-lamp platinum wire was found to be unreliable as regards melting, and filaments of carbon are now used. To prevent the wasting away of the carbon by combination with oxygen the filament is enclosed in a glass bulb from which practically all air has been sucked by a mercury pump before sealing.
In the early days of the incandescent lamp, platinum wire was found to be unreliable when it came to melting, so carbon filaments are now used instead. To stop the carbon from deteriorating due to reactions with oxygen, the filament is enclosed in a glass bulb that has had almost all the air removed by a mercury pump before it’s sealed.
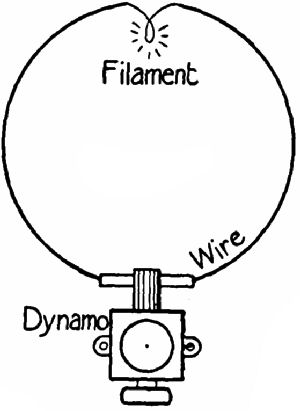
The manufacture of glow-lamps is now an important industry. One brand of lamp[20] is made as follows:—First, cotton-wool is dissolved in chloride of zinc, and forms a treacly solution, which is squirted through a fine nozzle into a settling solution which hardens it and makes it coil up like a very fine violin string. After being washed and dried, it is wound on a plumbago rod and baked in a furnace until only the carbon element remains. This is the filament in[Pg 181] the rough. It is next removed from the rod and tipped with two short pieces of fine platinum wire. To make the junction electrically perfect the filament is plunged in benzine and heated to whiteness by the passage of a strong current, which deposits the carbon of the benzine on the joints. The filament is now placed under the glass receiver of an air-pump, the air is exhausted, hydro-carbon vapour is introduced, and the filament has a current passed through it to make it white hot. Carbon from the vapour is deposited all over the filament until the required electrical resistance is attained. The filament is now ready for enclosure in the bulb. When the bulb has been exhausted and sealed, the lamp is tested, and, if passed, goes to the finishing department, where the two platinum wires (projecting through the glass) are soldered to a couple of brass plates, which make contact with two terminals in a lamp socket. Finally, brass caps are affixed with a special water-tight and hard cement.
The production of glow lamps is now a significant industry. One brand of lamp[20] is created like this: First, cotton wool is dissolved in zinc chloride, forming a sticky solution that is sprayed through a fine nozzle into a settling solution, which hardens it and causes it to coil like a very thin violin string. After washing and drying, it is wound onto a plumbago rod and baked in a furnace until only the carbon remains. This is the raw filament in[Pg 181]. Next, it is removed from the rod and tipped with two short pieces of fine platinum wire. To make the junction electrically perfect, the filament is dipped in benzene and heated to whiteness by passing a strong current, which deposits the carbon from the benzene onto the joints. The filament is then placed under the glass chamber of an air pump, the air is vacuumed out, hydrocarbon vapor is introduced, and a current is passed through the filament to make it glow white hot. Carbon from the vapor is deposited all over the filament until the desired electrical resistance is achieved. The filament is now ready to be enclosed in the bulb. Once the bulb has been vacuumed and sealed, the lamp is tested, and if it passes, it goes to the finishing department, where the two platinum wires (that stick out through the glass) are soldered to brass plates that connect with two terminals in a lamp socket. Finally, brass caps are attached using a special waterproof and hard cement.
ARC LAMPS.
Arc lamps.
In arc lighting, instead of a contraction at a point in the circuit, there is an actual break of very small extent. Suppose that to the ends of the wires leading from a dynamo's terminals we attach two carbon rods, and touch the end of the rods together. The tips become white hot, and if they are separated slightly, atoms of incandescent carbon leap from the positive to the negative rod in a continuous and intensely luminous stream, which is called an arc because the path of the particles is curved. No arc would be formed unless the carbons were first touched to start incandescence. If they are separated too far for the strength of the current to bridge the gap the light will flicker or go out. The arc lamp is therefore provided with a mechanism which, when the current is cut off, causes the carbons to fall together, gradually separates them when it is turned on, and keeps them apart. The principle employed is the effort of a coil through which a current passes to draw an iron rod into its centre. Some of the current feeding the lamp is shunted through a coil, into which projects one end of an iron bar connected with one carbon point. A spring normally presses the points together[Pg 183] when no current flows. As soon as current circulates through the coil the bar is drawn upwards against the spring.
In arc lighting, instead of a contraction at a point in the circuit, there is a small actual break. Imagine connecting two carbon rods to the ends of wires coming from a dynamo and touching their tips together. The tips get white hot, and if you pull them apart a little, incandescent carbon atoms jump from the positive rod to the negative rod in a steady, bright stream, called an arc because the particles travel in a curved path. An arc won't form unless the carbon tips are first touched to create incandescence. If they're separated too far for the current to bridge the gap, the light will flicker or go out. To address this, the arc lamp includes a mechanism that causes the carbon rods to press together when the current is off, gradually separates them when it's turned on, and keeps them apart. This works through a coil that pulls an iron rod into its center when a current runs through it. Some of the current powering the lamp is diverted through a coil, with one end of an iron bar connected to one carbon point. A spring usually keeps the points touching[Pg 183] when there’s no current. As soon as current flows through the coil, the bar is pulled upward against the spring.
SERIES AND PARALLEL ARRANGEMENT OF LAMPS.
SERIES AND PARALLEL ARRANGEMENT OF LAMPS.
When current passes from one lamp to another, as in Fig. 82, the lamps are said to be in series. Should one lamp fail, all in the circuit would go out. But where arc lamps are thus arranged a special mechanism on each lamp "short-circuits" it in case of failure, so that current may pass uninterruptedly to the next.
When electricity flows from one lamp to another, like in Fig. 82, the lamps are called series. If one lamp stops working, all the others in the circuit will turn off. However, when arc lamps are set up this way, each lamp has a special mechanism that "short-circuits" it if it fails, allowing the current to continue flowing to the next lamp.

Fig. 83 shows a number of lamps set in parallel. One terminal of each is attached to the positive conductor, the other to the negative conductor. Each[Pg 184] lamp therefore forms an independent bridge, and does not affect the efficiency of the rest. Parallel series signifies a combination of the two systems, and would be illustrated if, in Fig. 83, two or more lamps were connected in series groups from one conductor to the other. This arrangement is often used in arc lighting.
Fig. 83 shows several lamps connected in parallel. One terminal of each lamp is linked to the positive conductor, and the other terminal is linked to the negative conductor. Each[Pg 184] lamp operates independently, meaning it doesn’t affect the performance of the others. Parallel series refers to a combination of the two systems, which would be shown if, in Fig. 83, two or more lamps were connected in series groups between the two conductors. This setup is commonly used in arc lighting.

CURRENT FOR ELECTRIC LAMPS.
Current for electric lights.
This may be either direct or alternating. The former is commonly used for arc lamps, the latter for incandescent, as it is easily stepped-down from the high-pressure mains for use in a house. Glow-lamps usually take current of 110 or 250 volts pressure.
This can be either direct or alternating. Direct current is typically used for arc lamps, while alternating current is more commonly used for incandescent lamps, as it can be easily reduced from the high-pressure mains for home use. Glow lamps usually operate on currents of 110 or 250 volts.
In arc lamps fed with direct current the tip of the positive carbon has a bowl-shaped depression worn in it, while the negative tip is pointed. Most of the[Pg 185] illumination comes from the inner surface of the bowl, and the positive carbon is therefore placed uppermost to throw the light downwards. An alternating current, of course, affects both carbons in the same manner, and there is no bowl.
In arc lamps powered by direct current, the tip of the positive carbon forms a bowl-shaped depression, while the negative tip is pointed. Most of the[Pg 185] light comes from the inner surface of the bowl, so the positive carbon is positioned at the top to direct the light downwards. An alternating current, of course, impacts both carbons similarly, and there is no bowl.
The carbons need frequent renewal. A powerful lamp uses about 70 feet of rod in 1,000 hours if the arc is exposed to the air. Some lamps have partly enclosed arcs—that is, are surrounded by globes perforated by a single small hole, which renders combustion very slow, though preventing a vacuum.
The carbons need to be replaced often. A strong lamp uses about 70 feet of rod in 1,000 hours if the arc is exposed to air. Some lamps have partially enclosed arcs—that is, they are surrounded by globes with a single small hole, which slows down combustion while preventing a vacuum.
ELECTROPLATING.
Electroplating.
Electroplating is the art of coating metals with metals by means of electricity. Silver, copper, and nickel are the metals most generally deposited. The article to be coated is suspended in a chemical solution of the metal to be deposited. Fig. 84 shows a very simple plating outfit. A is a battery; B a vessel containing, say, an acidulated solution of sulphate of copper. A spoon, S, hanging in this from a glass rod, R, is connected with the zinc or negative element, Z, of the battery, and a plate of copper, P, with the positive element, C. Current flows in the direction shown by the arrows, from Z to C, C to P, P to S,[Pg 186] S to Z. The copper deposited from the solution on the spoon is replaced by gradual dissolution of the plate, so that the latter serves a double purpose.
Electroplating is the process of coating metals with other metals using electricity. Silver, copper, and nickel are the most commonly used metals for this. The item being coated is suspended in a chemical solution of the metal to be deposited. Fig. 84 shows a straightforward plating setup. A is a battery; B is a container with, for example, an acidified solution of copper sulfate. A spoon, S, hangs from a glass rod, R, and is connected to the zinc or negative terminal, Z, of the battery, while a copper plate, P, connects to the positive terminal, C. The current flows in the direction indicated by the arrows, from Z to C, C to P, P to S, [Pg 186] S back to Z. The copper that gets deposited onto the spoon comes from the gradual dissolution of the plate, which serves a dual purpose.

In silver plating, P is of silver, and the solution one of cyanide of potassium and silver salts. Where nickel or silver has to be deposited on iron, the article is often given a preliminary coating of copper, as iron does not make a good junction with either of the first two metals, but has an affinity for copper.
In silver plating, P is silver, and the solution contains potassium cyanide and silver salts. When nickel or silver needs to be applied to iron, the item is often first coated with copper because iron doesn't bond well with either of the first two metals but has a strong affinity for copper.
[17] From the Latin commuto, "I exchange."
__A_TAG_PLACEHOLDER_0__ From the Latin commuto, "I swap."
[20] The Robertson.
The Robertson.
Chapter X.
RAILWAY BRAKES.
The Vacuum Automatic brake—The Westinghouse air-brake.
The Vacuum Automatic brake—the Westinghouse air brake.
In the early days of the railway, the pulling up of a train necessitated the shutting off of steam while the stopping-place was still a great distance away. The train gradually lost its velocity, the process being hastened to a comparatively small degree by the screw-down brakes on the engine and guard's van. The goods train of to-day in many cases still observes this practice, long obsolete in passenger traffic.
In the early days of the railway, stopping a train meant shutting off the steam while the station was still quite far away. The train gradually slowed down, and this was sped up a bit by the brakes on the engine and the guard's van. Nowadays, many freight trains still follow this method, which is mostly outdated in passenger service.
An advance was made when a chain, running along the entire length of the train, was arranged so as to pull on subsidiary chains branching off under each carriage and operating levers connected with brake blocks pressing on every pair of wheels. The guard strained the main chain by means of a wheel gear in his van. This system was, however, radically[Pg 188] defective, since, if any one branch chain was shorter than the rest, it alone would get the strain. Furthermore, it is obvious that the snapping of the main chain would render the whole arrangement powerless. Accordingly, brakes operated by steam were tried. Under every carriage was placed a cylinder, in connection with a main steam-pipe running under the train. When the engineer wished to apply the brakes, he turned high-pressure steam into the train pipe, and the steam, passing into the brake cylinders, drove out in each a piston operating the brake gear. Unfortunately, the steam, during its passage along the pipe, was condensed, and in cold weather failed to reach the rear carriages. Water formed in the pipes, and this was liable to freeze. If the train parted accidentally, the apparatus of course broke down.
An improvement was made when a chain was set up along the entire length of the train to pull on smaller chains branching off under each carriage, which operated levers connected to brake blocks pressing on each pair of wheels. The guard tightened the main chain using a wheel mechanism in his van. However, this system was fundamentally flawed, because if any one branch chain was shorter than the others, it would bear the entire strain by itself. Additionally, it's clear that if the main chain snapped, the whole system would become useless. As a result, they tried using steam-operated brakes. A cylinder was placed under each carriage, connected to a main steam pipe running beneath the train. When the engineer wanted to apply the brakes, he would release high-pressure steam into the train pipe, and the steam would flow into the brake cylinders, pushing out a piston that operated the brake mechanism. Unfortunately, the steam condensed as it traveled along the pipe, and in cold weather, it didn't reach the rear carriages. Water accumulated in the pipes, which could freeze. If the train accidentally broke apart, the system would naturally fail.
Hydraulic brakes have been tried; but these are open to several objections; and railway engineers now make use of air-pressure as the most suitable form of power. Whatever air system be adopted, experience has shown that three features are essential:—(1.) The brakes must be kept "off" artificially. (2.) In case of the train parting accidentally, the brakes must be applied automatically, and quickly bring all[Pg 189] the vehicles of the train to a standstill. (3.) It must be possible to apply the brakes with greater or less force, according to the needs of the case.
Hydraulic brakes have been attempted, but they have several drawbacks, so railway engineers now use air-pressure as the most effective power source. Regardless of the air system chosen, experience has shown that three features are essential: (1) The brakes must be kept "off" manually. (2) If the train accidentally separates, the brakes must automatically engage and quickly stop all the train cars. (3) It must be possible to apply the brakes with varying levels of force as needed.
At the present day one or other of two systems is used on practically all automatically-braked cars and coaches. These are known as—(1) The vacuum automatic, using the pressure of the atmosphere on a piston from the other side of which air has been mechanically exhausted; and (2) the Westinghouse automatic, using compressed air. The action of these brakes will now be explained as simply as possible.
At present, almost all automatically-braked cars and coaches use one of two systems. These are known as: (1) the vacuum automatic, which uses atmospheric pressure on a piston while air has been mechanically removed from the other side; and (2) the Westinghouse automatic, which uses compressed air. Let's explain how these brakes work as simply as possible.
THE VACUUM AUTOMATIC BRAKE.
The automatic vacuum brake.
Under each carriage is a vacuum chamber (Fig. 85) riding on trunnions, E E, so that it may swing a little when the brakes are applied. Inside the chamber is a cylinder, the piston of which is rendered air-tight by a rubber ring rolling between it and the cylinder walls. The piston rod works through an air-tight stuffing-box in the bottom of the casing, and when it rises operates the brake rods. It is obvious that if air is exhausted from both sides of the piston at once, the piston will sink by reason of its own weight and that of its attachments. If air is now admitted below the piston, the latter will be pushed[Pg 190] upwards with a maximum pressure of 15 lbs. to the square inch. The ball-valve ensures that while air can be sucked from both sides of the piston, it can be admitted to the lower side only.
Under each car is a vacuum chamber (Fig. 85) mounted on trunnions, E E, allowing it to swing slightly when the brakes are applied. Inside the chamber is a cylinder, with the piston sealed tight by a rubber ring that rolls between it and the cylinder walls. The piston rod passes through an airtight stuffing box at the bottom of the casing, and when it rises, it activates the brake rods. It's clear that if air is removed from both sides of the piston at the same time, the piston will drop due to its own weight and that of its attachments. If air is then allowed in below the piston, it will be pushed[Pg 190] upwards with a maximum pressure of 15 lbs. per square inch. The ball valve ensures that while air can be drawn out from both sides of the piston, it can only be admitted to the lower side.


Let us imagine that a train has been standing in a siding, and that air has gradually filled the vacuum chamber by leakage. The engine is coupled on, and the driver at once turns on the steam ejector,[21] which[Pg 191] sucks all the air out of the pipes and chambers throughout the train. The air is sucked directly from the under side of the piston through pipe D; and from the space A A and the cylinder (open at the top) through the channel C, lifting the ball, which, as soon as exhaustion is complete, or when the pressure on both sides of the piston is equal, falls back on its seat. On air being admitted to the train pipe, it rushes through D and into the space B (Fig. 86) below the piston, but is unable to pass the ball, so that a strong upward pressure is exerted on the piston, and the brakes go on. To throw them off, the space below the piston must be exhausted. This[Pg 192] is to be noted: If there is a leak, as in the case of the train parting, the brakes go on at once, since the vacuum below the piston is automatically broken.
Let's imagine that a train has been parked on a siding, and air has gradually seeped into the vacuum chamber. The engine is connected, and the driver immediately turns on the steam ejector,[21] which[Pg 191] removes all the air from the pipes and chambers throughout the train. The air is drawn directly from beneath the piston through pipe D; and from the space A A and the cylinder (which is open at the top) through the channel C, raising the ball, which, once the vacuum is complete, or when the pressure on both sides of the piston is equal, falls back into place. When air is allowed into the train pipe, it rushes through D and into the space B (Fig. 86) below the piston, but it cannot pass the ball, so a strong upward pressure is applied to the piston, and the brakes engage. To release them, the space below the piston must be evacuated. This[Pg 192] is important to note: If there is a leak, like when the train separates, the brakes engage immediately, since the vacuum below the piston is automatically disrupted.

For ordinary stops the vacuum is only partially broken—that is, an air-pressure of but from 5 to 10 lbs. per square inch is admitted. For emergency stops full atmospheric pressure is used. In this case it is advisable that air should enter at both ends of the train; so in the guard's van there is installed an ingenious automatic valve, which can at any time be opened by the guard pressing down a lever, but which opens of itself when the train-pipe vacuum is rapidly destroyed. Fig. 87 shows this device in section. Seated on the top of an upright pipe is a valve, A, connected by a bolt, B, to an elastic diaphragm, C, sealing the bottom of the chamber D.[Pg 193] The bolt B has a very small hole bored through it from end to end. When the vacuum is broken slowly, the pressure falls in D as fast as in the pipe; but a sudden inrush of air causes the valve A to be pulled off its seat by the diaphragm C, as the vacuum in D has not been broken to any appreciable extent. Air then rushes into the train pipe through the valve. It is thus evident that the driver controls this valve as effectively as if it were on the engine. These "emergency" valves are sometimes fitted to every vehicle of a train.
For regular stops, the vacuum is only partially released—that is, an air pressure of just 5 to 10 lbs. per square inch is allowed in. For emergency stops, full atmospheric pressure is used. In this case, it's best for air to enter at both ends of the train; therefore, in the guard's van, there's a clever automatic valve installed. This valve can be opened anytime by the guard pressing a lever, but it also automatically opens when the train-pipe vacuum is quickly lost. Fig. 87 shows this device in section. A valve, A, is mounted on top of an upright pipe and is connected by a bolt, B, to an elastic diaphragm, C, which seals the bottom of the chamber D.[Pg 193] The bolt B has a very small hole drilled through it. When the vacuum is broken slowly, the pressure in D drops at the same rate as in the pipe; however, a sudden rush of air causes the valve A to be lifted off its seat by the diaphragm C, since the vacuum in D hasn't been significantly disturbed. Air then rushes into the train pipe through the valve. It’s clear that the driver can control this valve just as effectively as if it were on the engine. These "emergency" valves are sometimes installed on every vehicle of a train.
When a carriage is slipped, taps on each side of the coupling joint of the train pipe are turned off by the guard in the "slip;" and when he wishes to stop he merely depresses the lever E, gradually opening the valve. Under the van is an auxiliary vacuum chamber, from which the air is exhausted by the train pipe. If the guard, after the slip has parted from the train, finds that he has applied his brakes too hard, he can put this chamber into communication with the brake cylinder, and restore the vacuum sufficiently to pull the brakes off again.
When a carriage disengages, the guard turns off the taps on each side of the coupling joint of the train pipe while in the "slip." When he wants to stop, he just presses down on lever E, which gradually opens the valve. Under the van, there’s an auxiliary vacuum chamber that the train pipe exhausts air from. If the guard realizes he applied the brakes too strongly after the slip has separated from the train, he can connect this chamber to the brake cylinder and restore the vacuum enough to release the brakes again.
When a train has come to rest, the brakes must be sucked off by the ejector. Until this has been done the train cannot be moved, so that it is impossible for[Pg 194] it to leave the station unprepared to make a sudden stop if necessary.
When a train has come to a stop, the brakes must be released by the ejector. Until this is done, the train can't be moved, so it can’t leave the station without being ready to make a sudden stop if needed.
THE WESTINGHOUSE AIR-BRAKE.
The Westinghouse Air Brake.
This system is somewhat more complicated than the vacuum, though equally reliable and powerful. Owing to the complexity of certain parts, such as the steam air-pump and the triple-valve, it is impossible to explain the system in detail; we therefore have recourse to simple diagrammatic sketches, which will help to make clear the general principles employed.
This system is a bit more complex than the vacuum, but it's just as reliable and powerful. Because some parts, like the steam air-pump and the triple-valve, are complicated, it’s hard to explain the system in detail; instead, we'll use simple diagrams to illustrate the basic principles involved.
The air-brake, as first evolved by Mr. George Westinghouse, was a very simple affair—an air-pump and reservoir on the engine; a long pipe running along the train; and a cylinder under every vehicle to work the brakes. To stop the train, the high-pressure air collected in the reservoir was turned into the train pipe to force out the pistons in the coach cylinders, connected to it by short branch pipes. One defect of this "straight" system was that the brakes at the rear of a long train did not come into action until a considerable time after the driver turned on the air; and since, when danger is imminent, a very few seconds are of great importance, this slowness of operation was a serious fault. Also, it[Pg 195] was found that the brakes on coaches near the engine went on long before those more distant, so that during a quick stop there was a danger of the forward coaches being bumped by those behind. It goes without saying that any coaches which might break loose were uncontrollable. Mr. Westinghouse therefore patented his automatic brake, now so largely used all over the world. The brake ensures practically instantaneous and simultaneous action on all the vehicles of a train of any length.
The air brake, originally developed by Mr. George Westinghouse, was quite basic—an air pump and reservoir on the engine, a long pipe running along the train, and a cylinder under each vehicle to operate the brakes. To stop the train, the high-pressure air stored in the reservoir was released into the train pipe to push out the pistons in the coach cylinders connected by short branch pipes. One flaw of this “straight” system was that the brakes at the end of a long train didn’t engage until some time after the driver activated the air; and since a few seconds can be critical in emergencies, this delay was a significant issue. Additionally, it[Pg 195] was found that the brakes on coaches close to the engine engaged long before those further away, creating a risk that the forward coaches could be pushed into by those behind during a quick stop. Naturally, any coaches that might detach became uncontrollable. Mr. Westinghouse therefore patented his automatic brake, which is now widely used all over the world. The brake guarantees nearly instant and simultaneous activation on all the vehicles of a train of any length.

The principle of the brake will be gathered from Figs. 88 and 89. P is a steam-driven air-pump on the engine, which compresses air into a reservoir, A, situated below the engine or tender, and maintains a[Pg 196] pressure of from 80 to 90 lbs. per square inch. A three-way cock, C, puts the train pipe into communication with A or the open air at the wish of the driver. Under each coach is a triple-valve, T, an auxiliary reservoir, B, and a brake cylinder, D. The triple-valve is the most noteworthy feature of the whole system. The reader must remember that the valve shown in the section is only diagrammatic.
The brake's principle can be understood from Figs. 88 and 89. P is a steam-powered air pump on the engine that compresses air into a reservoir, A, located below the engine or tender, and maintains a[Pg 196] pressure of 80 to 90 psi. A three-way valve, C, connects the train pipe to A or lets it release into the open air at the driver's request. Each coach has a triple valve, T, an auxiliary reservoir, B, and a brake cylinder, D. The triple valve is the most important part of the entire system. Keep in mind that the valve depicted in the section is just a diagram.
Now for the operation of the brake. When the engine is coupled to the train, the compressed air in the main reservoir is turned into the train pipe, from which it passes through the triple-valve into the auxiliary reservoir, and fills it till it has a pressure of, say, 80 lbs. per square inch. Until the brakes are required, the pressure in the train pipe must be maintained. If accidentally, or purposely (by turning the cock C to the position shown in Fig. 89), the train-pipe pressure is reduced, the triple-valve at once shifts, putting B in connection with the brake cylinder D, and cutting off the connection between D and the air, and the brakes go on. To get them off, the pressure in the train pipe must be made equal to that in B, when the valve will assume its original position, allowing the air in D to escape.
Now let's discuss how the brake works. When the engine is connected to the train, the compressed air in the main reservoir flows into the train pipe, from where it goes through the triple-valve into the auxiliary reservoir, filling it up to about 80 lbs. per square inch. The pressure in the train pipe needs to be kept steady until the brakes are needed. If the train-pipe pressure is accidentally or intentionally reduced (by turning the cock C as shown in Fig. 89), the triple-valve immediately shifts, connecting B to the brake cylinder D, and disconnecting D from the air, which activates the brakes. To release the brakes, the pressure in the train pipe must be equalized with that in B, at which point the valve will go back to its original position, allowing the air in D to escape.
The force with which the brake is applied depends[Pg 197] upon the reduction of pressure in the train pipe. A slight reduction would admit air very slowly from B to D, whereas a full escape from the train pipe would open the valve to its utmost. We have not represented the means whereby the valve is rendered sensitive to these changes, for the reason given above.
The strength of the brake depends[Pg 197] on the decrease in pressure in the train pipe. A small decrease would let air in very slowly from B to D, while a complete release from the train pipe would fully open the valve. We haven't shown how the valve reacts to these changes for the reason mentioned earlier.

The latest form of triple-valve includes a device which, when air is rapidly discharged from the train pipe, as in an emergency application of the brake, opens a port through which compressed air is also admitted from the train pipe directly into D. It will easily be understood that a double advantage is hereby gained—first, in utilizing a considerable portion of the air in the train pipe to increase the[Pg 198] available brake force in cases of emergency; and, secondly, in producing a quick reduction of pressure in the whole length of the pipe, which accelerates the action of the brakes with extraordinary rapidity.
The latest version of the triple-valve includes a device that, when air is quickly released from the train pipe—like during an emergency brake application—opens a port that allows compressed air to flow in from the train pipe directly into D. It's easy to see that this provides two key benefits: first, it makes good use of a significant amount of air in the train pipe to boost the[Pg 198] available brake force in emergencies; and second, it creates a rapid drop in pressure throughout the entire pipe, which speeds up the brakes' response time dramatically.
It may be added that this secondary communication is kept open only until the pressure in D is equal to that in the train pipe. Then it is cut off, to prevent a return of air from B to the pipe.
It can be noted that this secondary communication stays open only until the pressure in D matches that in the train pipe. After that, it is closed off to stop air from B from flowing back into the pipe.
An interesting detail of the system is the automatic regulation of air-pressure in the main reservoir by the air-pump governor (Fig. 90). The governor is attached to the steam-pipe leading from the locomotive boiler to the air-pump. Steam from the boiler, entering at F, flows through valve 14 and passes by D into the pump, which is thus brought into operation, and continues to work until the pressure in the main reservoir, acting on the under side of the diaphragm 9, exceeds the tension to which the regulating spring 7 is set. Any excess of pressure forces the diaphragm upwards, lifting valve 11, and allowing compressed air from the main reservoir to flow into the chamber C. The air-pressure forces piston 12 downwards and closes steam-valve 14, thus cutting off the supply of steam to the pump. As soon as the pressure in the reservoir is reduced (by[Pg 199] leakage or use) below the normal, spring 7 returns diaphragm 9 to the position shown in Fig. 90, and pin-valve 11 closes. The compressed air previously admitted to the chamber C escapes through the small port a to the atmosphere. The steam, acting on the lower surface of valve 14, lifts it and its piston to the position shown, and again flows to the pump, which works until the required air-pressure is again obtained in the reservoir.
An interesting detail of the system is the automatic regulation of air pressure in the main reservoir by the air-pump governor (Fig. 90). The governor is connected to the steam pipe that runs from the locomotive boiler to the air pump. Steam from the boiler enters at F, flows through valve 14, and goes by D into the pump, activating it. The pump continues to operate until the pressure in the main reservoir, pushing on the underside of diaphragm 9, exceeds the tension set on the regulating spring 7. Any additional pressure pushes the diaphragm upward, lifting valve 11 and allowing compressed air from the main reservoir to flow into chamber C. The air pressure pushes piston 12 down, closing steam valve 14 and cutting off the steam supply to the pump. Once the pressure in the reservoir drops (due to[Pg 199] leakage or usage) below the normal level, spring 7 returns diaphragm 9 to the position shown in Fig. 90, and pin valve 11 closes. The compressed air that was previously let into chamber C escapes through the small port a into the atmosphere. The steam acting on the lower surface of valve 14 lifts it and its piston to the position shown, allowing steam to flow to the pump again, which operates until the required air pressure is reached in the reservoir.

[21] This resembles the upper part of the rudimentary water injector shown in Fig. 15. The reader need only imagine pipe B to be connected with the train pipe. A rush of steam through pipe A creates a partial vacuum in the cone E, causing air from the train pipe to rush into it and be expelled by the steam blast.
[21] This looks like the top part of the basic water injector shown in Fig. 15. You just need to picture pipe B connected to the train pipe. When steam rushes through pipe A, it creates a partial vacuum in cone E, pulling air from the train pipe into it and pushing it out with the steam blast.
Chapter XI.
RAILWAY SIGNALLING.
The block system—Position of signals—Interlocking the signals—Locking gear—Points—Points and signals in combination—Working the block system—Series of signalling operations—Single line signals—The train staff—Train staff and ticket—Electric train staff system—Interlocking—Signalling operations—Power signalling—Pneumatic signalling—Automatic signalling.
The block system—Signal positions—Interlocking the signals—Locking mechanisms—Switches—Switches and signals together—Operating the block system—A sequence of signaling actions—Single line signals—The train staff—Train staff and ticket—Electric train staff system—Interlocking—Signaling actions—Power signaling—Pneumatic signaling—Automatic signaling.
Under certain conditions—namely, at sharp curves or in darkness—the most powerful brakes might not avail to prevent a train running into the rear of another, if trains were allowed to follow each other closely over the line. It is therefore necessary to introduce an effective system of keeping trains running in the same direction a sufficient distance apart, and this is done by giving visible and easily understood orders to the driver while a train is in motion.
Under certain conditions—especially at sharp curves or in the dark—the strongest brakes might not be enough to stop a train from crashing into the back of another, if they were allowed to follow each other too closely on the tracks. Therefore, it's essential to have an effective system to keep trains moving in the same direction at a safe distance from each other, which is achieved by providing clear and easily understood signals to the driver while a train is in motion.
In the early days of the railway it was customary to allow a time interval between the passings of[Pg 201] trains, a train not being permitted to leave a station until at least five minutes after the start of a preceding train. This method did not, of course, prevent collisions, as the first train sometimes broke down soon after leaving the station; and in the absence of effective brakes, its successor ran into it. The advent of the electric telegraph, which put stations in rapid communication with one another, proved of the utmost value to the safe working of railways.
In the early days of the railway, it was common to have a waiting period between the departures of[Pg 201] trains, with a train not allowed to leave a station until at least five minutes after the previous one had started. This system didn’t completely stop collisions, as the first train sometimes broke down shortly after leaving the station; without effective brakes, the next train would crash into it. The arrival of the electric telegraph, which allowed stations to communicate quickly with each other, was extremely valuable for the safe operation of railways.
THE BLOCK SYSTEM.
THE BLOCK SYSTEM.
Time limits were abolished and distance limits substituted. A line was divided into blocks, or lengths, and two trains going in the same direction were never allowed on any one block at the same time.
Time limits were removed and distance limits were put in place. A line was divided into blocks, or segments, and two trains traveling in the same direction were never allowed on the same block at the same time.
The signal-posts carrying the movable arms, or semaphores, by means of which the signalman communicates with the engine-driver, are well known to us. They are usually placed on the left-hand side of the line of rails to which they apply, with their arms pointing away from the rails. The side of the arms which faces the direction from which a train approaches has a white stripe painted on a red background, the other side has a black stripe on a white background.
The signal posts with movable arms, or semaphores, that the signalman uses to communicate with the train driver are familiar to us. They are typically positioned on the left side of the railway line they correspond to, with their arms extending away from the tracks. The side of the arms that faces the incoming train has a white stripe on a red background, while the other side features a black stripe on a white background.
The distant and other signal arms vary slightly in shape (Fig. 91). A distant signal has a forked end and a V-shaped stripe; the home and starting signals are square-ended, with straight stripes. When the arm stands horizontally, the signal is "on," or at "danger"; when dropped, it is "off," and indicates "All right; proceed." At the end nearest the post it carries a spectacle frame glazed with panes of red and green glass. When the arm is at danger, the red pane is opposite a lamp attached to the signal post; when the arm drops, the green pane rises to that position—so that a driver is kept as fully informed at night as during the day, provided the lamp remains alight.
The distant and other signal arms have slightly different shapes (Fig. 91). A distant signal has a forked end and a V-shaped stripe; the home and starting signals have square ends with straight stripes. When the arm is horizontal, the signal is "on," or at "danger"; when it’s dropped, it is "off," indicating "All right; proceed." At the end closest to the post, it has a spectacle frame with panes of red and green glass. When the arm is at danger, the red pane is in front of a lamp on the signal post; when the arm drops, the green pane moves into that position—so that a driver stays fully informed at night just as they would during the day, as long as the lamp is lit.

POSITION OF SIGNALS.
SIGNAL POSITIONING.
On double lines each set of rails has its own separate signals, and drivers travelling on the "up" line[Pg 203] take no notice of signals meant for the "down" line. Each signal-box usually controls three signals on each set of rails—the distant, the home, and the starting. Their respective positions will be gathered from Fig. 92, which shows a station on a double line. Between the distant and the home an interval is allowed of 800 yards on the level, 1,000 yards on a falling gradient, and 600 yards on a rising gradient. The home stands near the approach end of the station, and the starting at the departure end of the platform. The last is sometimes reinforced by an "advance starting" signal some distance farther on.
On double tracks, each set of rails has its own distinct signals, and drivers on the "up" line[Pg 203] ignore signals meant for the "down" line. Each signal box typically manages three signals for each set of rails—the distant, the home, and the starting signal. Their specific locations can be understood from Fig. 92, which displays a station on a double line. There is a gap of 800 yards on flat ground, 1,000 yards on a downhill slope, and 600 yards on an uphill slope between the distant and the home signals. The home signal is located near the entrance to the station, and the starting signal is positioned at the exit end of the platform. The starting signal is sometimes accompanied by an "advance starting" signal placed some distance further down the track.
It should be noted that the distant is only a caution signal, whereas both home and starting are stop signals. This means that when the driver sees the distant "on," he does not stop his train, but slackens speed, and prepares to stop at the home signal. He must, however, on no account pass either home or starting if they are at danger. In short, the distant merely warns the driver of what he may expect at the home. To prevent damage if a driver should overrun the home, it has been laid down that no train shall be allowed to pass the starting signal of one box unless the line is clear to a point at least a quarter of a mile beyond the home of the next[Pg 204] box. That point is called the standard clearing point.
It should be noted that the distant signal is only a caution signal, while both the home and starting signals are stop signals. This means that when the driver sees the distant signal "on," he doesn’t stop his train, but slows down and prepares to stop at the home signal. He must, however, never pass either the home or starting signals if they are indicating danger. In short, the distant signal only warns the driver about what to expect at the home signal. To prevent accidents in case a driver overshoots the home signal, it has been established that no train is allowed to pass the starting signal of one box unless the track is clear for at least a quarter of a mile beyond the home of the next[Pg 204] box. That point is called the standard clearing point.
Technically described, a block is a length of line between the last stop signal worked from one signal-box and the first stop signal worked from the next signal-box in advance.
Technically described, a block is a stretch of track between the last stop signal operated from one signal box and the first stop signal operated from the next signal box ahead.

INTERLOCKING SIGNALS.
INTERLOCKING SIGNALS.
A signalman cannot lower or restore his signals to their normal positions in any order he likes. He is compelled to lower them as follows:—Starting and home; then distant. And restore them—distant; then starting and home. If a signalman were quite independent, he might, after the passage of a train, restore the home or starting, but forget all about the distant, so that the next train, which he wants to stop, would dash past the distant without warning and have to pull up suddenly when the home came in sight. But by a mechanical arrangement he is prevented[Pg 205] from restoring the home or starting until the distant is at danger; and, vice versâ, he cannot lower the last until the other two are off. This mechanism is called locking gear.
A signalman can't lower or return his signals to their normal positions in any order he wants. He has to lower them in this order: starting and home; then distant. And he has to restore them—distant; then starting and home. If a signalman were completely independent, he might, after a train passes, restore the home or starting signal but forget about the distant one, causing the next train he wants to stop to rush past the distant signal without warning and suddenly have to stop when it sees the home signal. But there's a mechanical system that prevents him[Pg 205] from restoring the home or starting signals until the distant signal is at danger; and, vice versa, he can't lower the last signal until the other two are clear. This system is called locking gear.
LOOKING GEAR.
Gear Up.
There are many different types of locking gear in use. It is impossible to describe them all, or even to give particulars of an elaborate locking-frame of any one type. But if we confine ourselves to the simplest combination of a stud-locking apparatus, such as is used in small boxes on the Great Western Railway, the reader will get an insight into the general principles of these safety devices, as the same principles underlie them all.
There are many different kinds of locking mechanisms being used today. It's impossible to describe them all or even to detail an elaborate locking frame of any specific type. However, if we focus on the simplest type of stud-locking system, like the ones used in small boxes on the Great Western Railway, the reader will gain an understanding of the basic principles behind these safety devices, as the same principles apply to all of them.

The levers in the particular type of locking gear which we are considering have each a tailpiece or "tappet arm" attached to it, which moves backwards and forwards with the lever (Fig. 93). Running at right angles to this tappet, and close to it, either under or above, are the lock bars, or stud bars. Refer now to Fig. 94, which shows the ends of the three tappet arms, D, H, and S, crossed by a bar, B, from which project these studs. The levers are all forward and the signals all "on." If the signalman[Pg 206] tried to pull the lever attached to D down the page, as it were, he would fail to move it on account of the stud a, which engages with a notch in D. Before this stud can be got free of the notch the tappets H and S must be pulled over, so as to bring their notches in line with studs b and c (Fig. 95). The signalman can now move D, since the notch easily pushes the stud a to the[Pg 207] left (Fig. 96). The signals must be restored to danger. As H and S are back-locked by D—that is, prevented by D from being put back into their normal positions—D must be moved first. The interlocking of the three signals described is merely repeated in the interlocking of a large number of signals.
The levers in the specific type of locking mechanism we’re looking at each have a tailpiece, or "tappet arm," attached to them, which moves back and forth with the lever (Fig. 93). Running at right angles to this tappet and close to it, either above or below, are the lock bars, or stud bars. Now refer to Fig. 94, which shows the ends of the three tappet arms, D, H, and S, intersected by a bar, B, from which these studs project. All the levers are in the forward position, and all the signals are "on." If the signalman[Pg 206] tried to pull down the lever connected to D, he wouldn’t be able to move it because of the stud a, which engages with a notch in D. Before this stud can be freed from the notch, the tappets H and S need to be moved over to align their notches with the studs b and c (Fig. 95). The signalman can now move D, as the notch easily pushes the stud a to the[Pg 207] left (Fig. 96). The signals must be returned to danger. Since H and S are back-locked by D—meaning they are prevented by D from returning to their normal positions—D must be moved first. The interlocking mechanism of these three signals is just a repetition of the interlocking found in a larger number of signals.


On entering a signal-box a visitor will notice that[Pg 208] the levers have different colours:—Green, signifying distant signals; red, signifying home and starting signals; blue, signifying facing points; black, signifying trailing points; white, signifying spare levers. These different colours help the signalman to pick out the right levers easily.
On entering a signal box, a visitor will notice that[Pg 208] the levers have different colors: Green, indicating distant signals; red, indicating home and starting signals; blue, indicating facing points; black, indicating trailing points; white, indicating spare levers. These different colors help the signalman quickly identify the right levers.
To the front of each lever is attached a small brass tablet bearing certain numbers; one in large figures on the top, then a line, and other numbers in small figures beneath. The large number is that of the lever itself; the others, called leads, refer to levers which must be pulled before that particular lever can be released.
At the front of each lever, there’s a small brass plaque with some numbers on it; one large number at the top, followed by a line, and then some smaller numbers underneath. The large number identifies the lever itself; the smaller numbers, called leads, indicate the levers that need to be pulled before this specific lever can be released.


POINTS.
Points.
Mention was made, in connection with the lever, of points. Before going further we will glance at the action of these devices for enabling a train to run from one set of rails to another. Figs. 98 and 99 show the points at a simple junction. It will be noticed that the rails of the line to the left of the points are continued as the outer rails of the main and branch lines. The inner rails come to a sharp V-point, and to the left of this are the two short rails which, by means of shifting portions, decide the direction of a train's travel. In Fig. 98 the main line is open; in Fig. 99, the branch. The shifting parts are kept properly spaced by cross bars (or tie-rods), A A.
Mention was made, in connection with the lever, of points. Before we go further, let's look at how these devices allow a train to switch from one set of rails to another. Figs. 98 and 99 show the points at a simple junction. You’ll notice that the rails of the line to the left of the points continue as the outer rails of the main and branch lines. The inner rails come to a sharp V point, and to the left of this are the two short rails that, by means of shifting sections, determine the direction in which a train travels. In Fig. 98, the main line is open; in Fig. 99, the branch line is. The shifting parts are kept properly spaced by cross bars (or tie-rods), A A.


It might be thought that the wheels would bump badly when they reach the point B, where there is a gap. This is prevented, however, by the bent ends E E (Fig. 98), on which the tread of the wheel rests until it has reached some distance along the point of V. The safety rails S R keep the outer wheel up against its rail until the V has been passed.
It might be thought that the wheels would bump badly when they reach the point B, where there's a gap. This is prevented, however, by the bent ends E E (Fig. 98), on which the tread of the wheel rests until it has moved some distance along the point of V. The safety rails S R keep the outer wheel pressed against its rail until the V has been passed.
POINTS AND SIGNALS IN COMBINATION.
Points and signals combined.
Let us suppose that a train is approaching the junction shown in Figs. 98 and 99 from the left. It is not enough that the driver should know that the tracks are clear. He must also be assured that the track, main or branch, as the case may be, along which he has to go, is open; and on the other hand, if he were approaching from the right, he would want to be certain that no train on the other line was converging on his. Danger is avoided and assurance given by interlocking the points and signals. To the left of the junction the home and distant signals are doubled, there being two semaphore arms on each post. These are interlocked with the points in such a manner that the signals referring to either line can be pulled off only when the points are set to open the way to that line. Moreover, before any shifting[Pg 212] of points can be made, the signals behind must be put to danger. The convergence of trains is prevented by interlocking, which renders it impossible to have both sets of distant and home signals at "All right" simultaneously.
Let’s assume a train is approaching the junction shown in Figs. 98 and 99 from the left. It’s not enough for the driver to just know that the tracks are clear; he also needs to be sure that the track, whether main or branch, that he’s supposed to take is open. On the other hand, if he were coming from the right, he would need to be certain that no train on the other line is heading toward him. Danger is avoided and certainty is provided by interlocking the points and signals. To the left of the junction, the home and distant signals are doubled, with two semaphore arms on each post. These are interlocked with the points in such a way that the signals for either line can only be cleared when the points are set to open the way for that line. Furthermore, before any shifting of points can take place, the signals behind must be set to danger. The convergence of trains is avoided by interlocking, which makes it impossible for both sets of distant and home signals to show "All right" at the same time.
WORKING OF BLOCK SYSTEM.
BLOCK SYSTEM OPERATION.
We may now pass to the working of the block system of signalling trains from station to station on one line of a double track. Each signal-box (except, of course, those at termini) has electric communication with the next box in both directions. The instruments used vary on different systems, but the principle is the same; so we will concentrate our attention on those most commonly employed on the Great Western Railway. They are:—(1.) Two tapper-bell instruments, connected with similar instruments in the adjacent boxes on both sides. Each of these rings one beat in the corresponding box every time its key is depressed. (2.) Two Spagnoletti disc instruments—one, having two keys, communicating with the box in the rear; and the other, in connection with the forward box, having no keys. Their respective functions are to give signals and receive them. In the centre of the face of each is a square[Pg 213] opening, behind which moves a disc carrying two "flags"—"Train on line" in white letters on red ground, and "Line clear" in black letters on a white ground. The keyed instrument has a red and a white key. When the red key is depressed, "Train on line" appears at the opening; also in that of a keyless disc at the adjacent signal-box. A depression of the white key similarly gives "Line clear." A piece of wire with the ends turned over and passed through two eyes slides over the keys, and can be made to hold either down. In addition to these, telephonic and telegraphic instruments are provided to enable the signalmen to converse.
We can now move on to how the block system for signaling trains works on one line of a double track. Each signal box (except, of course, those at the terminals) has electric communication with the next box in both directions. The instruments used vary across different systems, but the principle remains the same; so we'll focus on those most commonly used on the Great Western Railway. They are: (1) Two tapper-bell instruments, connected with similar instruments in the adjacent boxes on both sides. Each of these rings once in the corresponding box every time its key is pressed. (2) Two Spagnoletti disc instruments—one, with two keys, communicates with the box behind; and the other, connecting with the forward box, has no keys. Their respective functions are to give and receive signals. In the center of each face is a square[Pg 213] opening, behind which a disc carries two "flags"—"Train on line" in white letters on a red background, and "Line clear" in black letters on a white background. The keyed instrument has a red and a white key. When the red key is pressed, "Train on line" appears in the opening; this also shows in the keyless disc at the adjacent signal box. Pressing the white key similarly displays "Line clear." A wire with the ends turned over and passed through two eyes slides over the keys and can hold either down. Additionally, telephones and telegraphs are provided so the signalmen can communicate.
SERIES OF SIGNALLING OPERATIONS.
SIGNALING OPERATIONS SERIES.

We may now watch the doings[Pg 214] of signalmen in four successive boxes, A, B, C, and D, during the passage of an express train. Signalman A calls signalman B's attention by one beat on the tapper-bell. B answers by repeating it to show that he is attending. A asks, "Is line clear for passenger express?"—four beats on the bell. B, seeing that the line is clear to his clearing point, sends back four beats, and pins down the white key of his instrument. "Line clear" appears on the opening, and also at that of A's keyless disc. A lowers starting signal. Train moves off. A gives two beats on the tapper = "Train entering section." B pins indicator at "Train on line," which also appears on A's instrument. A places signals at danger. B asks C, "Is line clear?" C repeats the bell code, and pins indicator at "Line clear," shown on B's keyless disc also. B lowers all signals. Train passes. B signals to C, "Train entering section." B signals to A, "Train out of section," and releases indicator, which returns to normal position with half of each flag showing at the window. B signals to C, "Train on line," and sets all his signals to danger. C pins indicator to "Train on line." C asks, "Is line clear?" But there is a train at station D, and signalman D therefore gives no reply, which is equivalent to a negative.[Pg 215] The driver, on approaching C's distant, sees it at danger, and slows down, stopping at the home. C lowers home, and allows train to proceed to his starting signal. D, when the line is clear to his clearing point, signals "Line clear," and pins indicator at "Line clear." C lowers starting signals, and train proceeds. C signals to D, "Train entering section," and D pins indicator at "Train on line." C signals to B, "Train out of section," sets indicator at normal, and puts signals at danger. And so the process is repeated from station to station. Where, however, sections are short, the signalman is advised one section ahead of the approach of a train by an additional signal signifying, "Fast train approaching." The block indicator reminds the signalman of the whereabouts of the train. Unless his keyless indicator is at normal, he may not ask, "Is line clear?" And until he signals back "Line clear" to the box behind, a train is not allowed to enter his section. In this way a section of line with a full complement of signals is always interposed between any two trains.
We can now observe the actions[Pg 214] of signalmen in four consecutive boxes, A, B, C, and D, as an express train passes through. Signalman A gets signalman B's attention with one beat on the tapper bell. B replies with the same beat to confirm he is paying attention. A asks, "Is the line clear for the passenger express?" by tapping four times on the bell. B, noticing that the line is clear up to his clearing point, responds with four beats and presses the white key on his instrument. "Line clear" shows up on both his and A's keyless displays. A lowers the starting signal. The train starts moving. A taps twice on the tapper, signifying "Train entering section." B then sets his indicator to "Train on line," which also appears on A's instrument. A places signals at danger. B asks C, "Is the line clear?" C repeats the bell code and sets the indicator to "Line clear," which is also displayed on B's keyless disc. B lowers all signals. The train passes. B signals to C, "Train entering section." He signals to A, "Train out of section," and releases the indicator, which returns to its normal position, showing half of each flag at the window. B signals to C, "Train on line," and sets all his signals to danger. C sets the indicator to "Train on line." C asks, "Is the line clear?" However, because there is a train at station D, signalman D does not respond, which is understood as a negative.[Pg 215] As the driver approaches C's distant signal, he sees it is at danger, so he slows down and stops at the home signal. C lowers the home signal, allowing the train to proceed to his starting signal. When D sees the line is clear up to his clearing point, he signals "Line clear" and sets the indicator to "Line clear." C then lowers the starting signals, and the train moves on. C signals to D, "Train entering section," and D sets the indicator to "Train on line." C signals to B, "Train out of section," resets the indicator to normal, and puts the signals at danger. This process continues from station to station. However, in areas where sections are short, the signalman is alerted one section ahead of an approaching train by an additional signal that indicates, "Fast train approaching." The block indicator keeps the signalman informed about the train's location. If his keyless indicator is not in the normal position, he cannot ask, "Is the line clear?" And until he signals back "Line clear" to the box behind him, a train is not permitted to enter his section. This way, a fully signaled section of track is always placed between any two trains.
THE WORKING OF SINGLE LINES.
SINGLE LINE OPERATIONS.
We have dealt with the signalling arrangements pertaining to double lines of railway, showing that[Pg 216] a system of signals is necessary to prevent a train running into the back of its predecessor. Where trains in both directions pass over a single line, not only has this element of danger to be dealt with, but also the possibility of a train being allowed to enter a section of line from each end at the same time. This is effected in several ways, the essence of each being that the engine-driver shall have in his possession visible evidence of the permission accorded him by the signalman to enter a section of single line.
We have addressed the signaling systems related to double railway lines, demonstrating that[Pg 216] a signal system is essential to stop a train from colliding with the one ahead. When trains are traveling in both directions on a single line, we not only need to manage this risk, but also the chance of a train being allowed to enter a segment of track from both ends at the same time. This is managed in various ways, but the core principle is that the engineer must have visible proof of the authorization granted by the signalman to enter a section of single track.
A SINGLE TRAIN STAFF.
One train staff.
The simplest form of working is to allocate to the length of line a "train staff"—a piece of wood about 14 inches long, bearing the names of the stations at either end. This is adopted where only one engine is used for working a section, such as a short branch line. In a case like this there is obviously no danger of two trains meeting, and the train staff is merely the authority to the driver to start a journey. No telegraphic communication is necessary with such a system, and signals are placed only at the ends of the line.
The simplest way to operate is to assign a "train staff" to the length of the line—it's a piece of wood about 14 inches long, showing the names of the stations at either end. This method is used when only one engine operates on a section, like a short branch line. In this scenario, there's clearly no risk of two trains encountering each other, so the train staff simply acts as permission for the driver to begin a trip. There’s no need for telegraphic communication with this system, and signals are only positioned at the ends of the line.
TRAIN STAFF AND TICKET.
Staff training and ticketing.
On long lengths of single line where more than one[Pg 217] train has to be considered, the line is divided into blocks in the way already described for double lines, and a staff is assigned to each, the staffs for the various blocks differing from each other in shape and colour. The usual signals are provided at each station, and block telegraph instruments are employed, the only difference being that one disc, of the key pattern, is used for trains in both directions. On such a line it is, of course, possible that two or more trains may require to follow each other without any travelling intermediately in the opposite direction. This would be impossible if the staff passed uniformly to and fro in the block section; but it is arranged by the introduction of a train staff ticket used in conjunction with the staff.
On long stretches of single track where more than one[Pg 217] train needs to be managed, the line is divided into sections just like in double tracks, and a staff is assigned to each section, with the staffs for the different sections varying in shape and color. Standard signals are set up at each station, and block telegraph instruments are used, only differing in that one disc of the key pattern is employed for trains traveling in both directions. On such a line, it's certainly possible for two or more trains to need to follow each other without any trains traveling in the opposite direction in between. This would be impossible if the staff moved back and forth uniformly in the block section; however, it's handled by introducing a train staff ticket used alongside the staff.
No train is permitted to leave a staff station unless the staff for the section of line to be traversed is at the station; and the driver has the strictest possible instructions that he must see the staff. If a second train is required to follow, the staff is shown to the driver, and a train staff ticket handed him as his authority to proceed. If, however, the next train over the section will enter from the opposite end, the staff is handed to the driver.
No train is allowed to leave a staff station unless the necessary staff for the section of track to be traveled is at the station, and the driver has clear instructions that he must see the staff. If a second train needs to follow, the staff is shown to the driver, and a train staff ticket is given to him as his permission to proceed. However, if the next train on that section will come in from the other end, the staff is handed to the driver.
To render this system as safe as possible, train staff[Pg 218] tickets are of the same colour and shape as the staff for the section to which they apply, and are kept in a special box at the stations, the key being attached to the staff and the lock so arranged that the key cannot be withdrawn unless the box has been locked.
To make this system as safe as possible, train staff[Pg 218] tickets are the same color and shape as the staff for the section they belong to, and are stored in a special box at the stations. The key is attached to the staff, and the lock is designed so that the key cannot be removed unless the box is locked.
ELECTRIC TRAIN STAFF AND TABLET SYSTEMS.
ELECTRIC TRAIN STAFF AND TABLET SYSTEMS.
These systems of working are developments of the last mentioned, by which are secured greater safety and ease in working the line. On some sections of single line circumstances often necessitate the running of several trains in one direction without a return train. For such cases the train staff ticket was introduced; but even on the best regulated lines it is not always possible to secure that the staff shall be at the station where it is required at the right time, and cases have arisen where, no train being available at the station where the staff was, it had to be taken to the other station by a man on foot, causing much delay to traffic. The electric train staff and tablet systems overcome this difficulty. Both work on much the same principle, and we will therefore describe the former.
These working systems are advancements of the previously mentioned ones, providing greater safety and ease in operating the line. In certain areas with a single track, conditions often require several trains to run in one direction without a return train. To manage this, the train staff ticket was introduced; however, even on the best-managed lines, it's not always possible to ensure that the staff is at the required station at the right time. There have been situations where, with no train available at the station where the staff was located, it had to be carried to the other station by a person on foot, leading to significant delays in service. The electric train staff and tablet systems address this issue. Both operate on a similar principle, so we will describe the former.

At each end of a block section a train staff instrument (Fig. 101) is provided. In the base of these instruments are a number of train staffs, any one of which would be accepted by an engine-driver as permission to travel over the single line. The instruments are electrically connected, the mechanism securing that a staff can be withdrawn only by the co-operation of the signalman at each end of the section; that, when all the staffs are in the instruments, a staff may be withdrawn at either end; that, when a staff has been withdrawn, another cannot be obtained until the one out has been restored to one or other of the instruments. The safety of such a system is obvious, as also the assistance to the working by having a staff available for a train no matter from which end it is to enter the section.
At each end of a block section, there's a train staff instrument (Fig. 101). At the base of these instruments, there are several train staffs, each of which can be accepted by an engine driver as permission to travel on the single line. The instruments are electrically connected, ensuring that a staff can only be withdrawn with the cooperation of the signalman at both ends of the section. When all the staffs are in the instruments, a staff can be withdrawn from either end. Once a staff has been withdrawn, another one can't be obtained until the one out has been returned to one of the instruments. The safety of this system is clear, as is the convenience it provides by having a staff available for a train, regardless of which end it enters the section from.
The mechanism of the instruments is quite simple. A double-poled electro-magnet is energized by the depression of a key by the signalman at the further end of the block into which the train is to run, and by the turning of a handle by the signalman who requires to withdraw a staff. The magnet, being energized, is able to lift a mechanical lock, and permits the withdrawal of a staff. In its passage through the instrument the staff revolves a number of iron discs, which in turn raise or lower a switch controlling the electrical connections. This causes the electric currents[Pg 221] actuating the electro-magnet to oppose each other, the magnetism to cease, and the lock to fall back, preventing another staff being withdrawn. It will naturally be asked, "How is the electrical system restored?" We have said that there were a number of staffs in each instrument—in other words, a given number of staffs, usually twenty, is assigned to the section. Assume that there are ten in each instrument, and that the switch in each is in its lower position. Now withdraw a staff, and one instrument has an odd, the other an even, number of staffs, and similarly one switch is raised while the other remains lowered, therefore the electrical circuit is "out of phase"—that is, the currents in the magnets of each staff instrument are opposed to one another, and cannot release the lock. The staff travels through the section and is placed in the instrument at the other end, bringing the number of staffs to eleven—an odd number, and, what is more important, raising the switch. Both switches are now raised, consequently the electric currents will support each other, so that a staff may be withdrawn. Briefly, then, when there is an odd number of staffs in one instrument and an even number in the other, as when a staff is in use, the signalmen are unable to obtain a[Pg 222] staff, and consequently cannot give authority for a train to enter the section; but when there is either an odd or an even number of staffs in each instrument a staff may be withdrawn at either end on the co-operation of the signalmen.
The mechanism of the instruments is quite straightforward. A double-pole electromagnet is activated when the signalman at the far end of the block presses a key for the train to enter and when another signalman turns a handle to withdraw a staff. When powered, the magnet can lift a mechanical lock, allowing for the withdrawal of a staff. As the staff moves through the instrument, it turns a series of iron discs, which then raise or lower a switch that controls the electrical connections. This creates a situation where the electric currents[Pg 221] activating the electromagnet oppose each other, stopping the magnetism and causing the lock to reset, which prevents another staff from being withdrawn. Naturally, one might ask, "How is the electrical system reset?" We mentioned that there are several staffs associated with each instrument—in other words, a specific number of staffs, usually twenty, is allocated to the section. Let's assume there are ten staffs in each instrument and that the switch in each is in its lower position. Now, if a staff is withdrawn, one instrument will have an odd number of staffs while the other has an even number, resulting in one switch being raised and the other remaining lowered. This means the electrical circuit is "out of phase"—the currents in the magnets of each staff instrument are opposing, and thus cannot release the lock. The staff makes its way through the section and is placed in the instrument at the other end, increasing the number of staffs to eleven—an odd number, which importantly, raises the switch. Now, both switches are raised, allowing the electric currents to support one another, so a staff can be withdrawn. In summary, when there is an odd number of staffs in one instrument and an even number in the other, such as when a staff is in use, the signalmen cannot obtain a[Pg 222] staff, preventing them from authorizing a train to enter the section; however, when there is either an odd or an even number of staffs in each instrument, a staff can be withdrawn from either end with the cooperation of the signalmen.
We may add that, where two instruments are in the same signal-box, one for working to the box in advance, the other to the rear, it is arranged that the staffs pertaining to one section shall not fit the instrument for the other, and must be of different colours. This prevents the driver accidentally accepting a staff belonging to one section as authority to travel over the other.
We can also point out that when two instruments are in the same signal box—one for the track ahead and the other for the track behind—it’s set up so that the staffs for one section don't work with the instrument for the other, and they must be different colors. This stops the driver from mistakenly taking a staff from one section as permission to travel on the other.
INTERLOCKING.
INTERLOCKING.
The remarks made on the interlocking of points and signals on double lines apply also to the working of single lines, with the addition that not only are the distant, home, and starting signals interlocked with each other, but with the signals and points governing the approach of a train from the opposite direction—in other words, the signals for the approach of a train to a station from one direction cannot be lowered unless those for the approach to the station of a train from the opposite direction are at danger, and the points correctly set.
The comments about how points and signals are interconnected on double lines also apply to single lines. In addition, it's important to note that not only are the distant, home, and starting signals locked with each other, but they're also linked to the signals and points that control the arrival of a train coming from the opposite direction. In other words, the signals allowing a train to approach a station from one direction can't be switched to green unless the signals for a train approaching the station from the opposite direction are set to red, and the points are correctly aligned.
SIGNALLING OPERATIONS.
SIGNALING OPERATIONS.
In the working of single lines, as of double, the signalman at the station from which a train is to proceed has to obtain the consent of the signalman ahead, the series of questions to be signalled being very similar to those detailed for double lines. There is, however, one notable exception. On long lengths of single line it is necessary to make arrangements for trains to pass each other. This is done by providing loop lines at intervals, a second pair of rails being laid for the accommodation of one train while another in the opposite direction passes it. To secure that more than one train shall not be on a section of single line between two crossing-places it is laid down that, when a signalman at a non-crossing station is asked to allow a train to approach his station, he must not give permission until he has notified the signalman ahead of him, thus securing that he is not asking permission for trains to approach from both directions at the same time. Both for single and double line working a number of rules designed to deal with cases of emergency are laid down, the guiding principle being safety; but we have now dealt with all the conditions of everyday working, and must pass to the consideration of
In the operation of single lines, just like with double lines, the signalman at the station where a train is set to depart must get approval from the signalman ahead. The set of questions asked is quite similar to those used for double lines. However, there is one key difference. On long stretches of single line, trains need to be able to pass each other. This is arranged by creating loop lines at intervals, where an additional set of tracks is laid out for one train while another train traveling in the opposite direction passes it. To ensure that only one train is on a section of single line between two crossing points, it's required that when a signalman at a non-crossing station is asked to let a train approach, he can't give the go-ahead until he has informed the signalman ahead of him. This way, he makes sure he isn't allowing trains to approach from both directions at the same time. For both single and double line operations, there are numerous rules in place for emergencies, all emphasizing safety; but we have now addressed all the typical working conditions and must move on to the consideration of

"POWER" SIGNALLING.
"POWER" SIGNALING.
In a power system of signalling the signalman is provided with some auxiliary means—electricity, compressed air, etc.—of moving the signals or points under his control. It is still necessary to have a locking-frame in the signal-box, with levers interlocked with each other, and connections between the box and the various points and signals. But the frame is much smaller than an ordinary manual frame, and but little force is needed to move the little levers which make or break an electric circuit, or open an air-valve, according to the power-agent used.
In a signaling power system, the signalman has additional tools—like electricity and compressed air—to operate the signals or points under his control. However, it’s still essential to have a locking frame in the signal box, with levers that are interlocked and connect the box to the various points and signals. But this frame is significantly smaller than a traditional manual frame, and only a small amount of force is needed to move the small levers that either complete or interrupt an electric circuit, or open an air valve, depending on the power source being used.
ELECTRIC SIGNALLING.
ELECTRIC SIGNALLING.
Fig. 102 represents the locking-frame of a cabin at Didcot, England, where an all-electric system has been installed. Wires lead from the cabin to motors situated at the points and signals, which they operate through worm gearing. When a lever is moved it closes a circuit and sets the current flowing through a motor, the direction of the flow (and consequently of the motor's revolution) depending on whether the lever has been moved forward or backward. Indicators arranged under the levers tell the signalman when the desired movements at the points[Pg 226] and signals have been completed. If any motion is not carried through, owing to failure of the current or obstruction of the working parts, an electric lock prevents him continuing operations. Thus, suppose he has to open the main line to an express, he is obliged by the mechanical locking-frame to set all the points correctly before the signals can be lowered. He might move all the necessary levers in due order, yet one set of points might remain open, and, were the signals lowered, an accident would result. But this cannot happen, as the electric locks worked by the points in question block the signal levers, and until the failure has been set right, the signals must remain at "danger."
Fig. 102 shows the locking-frame of a cabin at Didcot, England, where an all-electric system has been set up. Wires connect the cabin to motors located at the points and signals, which they operate using worm gearing. When a lever is moved, it closes a circuit, allowing the current to flow through a motor. The direction of the flow (and thus the motor's rotation) depends on whether the lever is pushed forward or pulled back. Indicators placed under the levers inform the signalman when the necessary movements at the points[Pg 226] and signals have been completed. If any action is not executed, due to a current failure or obstruction of moving parts, an electric lock prevents him from continuing operations. For instance, if he needs to open the main line for an express train, the mechanical locking-frame requires him to set all the points correctly before he can lower the signals. He might move all the necessary levers in the correct order, but if one set of points remains open, lowering the signals could cause an accident. However, this situation can't arise, as the electric locks tied to the points in question block the signal levers, ensuring that the signals must stay at "danger" until the issue is resolved.
The point motors are connected direct to the points; but between a signal motor and its arm there is an "electric slot," consisting of a powerful electro-magnet which forms a link in the rod work. To lower a signal it is necessary that the motor shall revolve and a control current pass round the magnet to give it the requisite attractive force. If no control current flows, as would happen were any pair of points not in their proper position, the motor can have no effect on the signal arm to lower it, owing to the magnet letting go its grip. Furthermore, if the[Pg 227] signal had been already lowered when the control current failed, it would rise to "danger" automatically, as all signals are weighted to assume the danger position by gravity. The signal control currents can be broken by the signalman moving a switch, so that in case of emergency all signals may be thrown simultaneously to danger.
The point motors are directly connected to the points, but between a signal motor and its arm, there’s an "electric slot" made up of a strong electromagnet that acts as a link in the rod work. To lower a signal, the motor needs to turn and a control current must flow through the magnet to create the necessary attractive force. If no control current is flowing, which can occur if any pair of points is out of position, the motor can’t affect the signal arm to lower it because the magnet releases its grip. Additionally, if the[Pg 227] signal was already lowered when the control current stopped, it would automatically rise to "danger," since all signals are designed to fall back to the danger position by gravity. The signal control currents can be interrupted by the signalman flipping a switch, allowing all signals to be set to danger at once in an emergency.
PNEUMATIC SIGNALLING.
Pneumatic signaling.
In England and the United States compressed air is also used to do the hard labour of the signalman for him. Instead of closing a circuit, the signalman, by moving a lever half-way over, admits air to a pipe running along the track to an air reservoir placed beside the points or signal to which the lever relates. The air opens a valve and puts the reservoir in connection with a piston operating the points or signal-arm, as the case may be. This movement having been performed, another valve in the reservoir is opened, and air passes back through a second pipe to the signal-box, where it opens a third valve controlling a piston which completes the movement of the lever, so showing the signalman that the operation is complete. With compressed air, as with electricity, a mechanical locking-frame is of course used.
In England and the United States, compressed air is also used to take on the hard work of the signalman. Instead of closing a circuit, the signalman simply moves a lever halfway, allowing air to flow into a pipe running along the track to an air reservoir located next to the points or signal connected to that lever. The air opens a valve, linking the reservoir to a piston that operates the points or the signal arm, depending on the situation. Once this movement is completed, another valve in the reservoir opens, and air flows back through a second pipe to the signal box, where it opens a third valve that controls a piston, finishing the movement of the lever, thus indicating to the signalman that the operation is done. Just like with electricity, a mechanical locking frame is, of course, used with compressed air.
AUTOMATIC SIGNALLING.
AUTO SIGNALLING.
To reduce expense, and increase the running speed on lines where the sections are short, the train is sometimes made to act as its own signalman. The rails of each section are all bonded together so as to be in metallic contact, and each section is insulated from the two neighbouring sections. At the further end of a section is installed an electric battery, connected to the rails, which lead the current back to a magnet operating a signal stationed some distance back on the preceding section. As long as current flows the signal is held at "All right." When a train enters the section the wheels and axles short-circuit the current, so that it does not reach the signal magnet, and the signal rises to "danger," and stays there until the last pair of wheels has passed out of the section. Should the current fail or a vehicle break loose and remain on the section, the same thing would happen.
To cut costs and boost speed on short sections of track, the train sometimes operates as its own signalman. The tracks in each section are all connected to allow for electrical contact, and each section is isolated from the two neighboring sections. At the end of a section, there’s an electric battery linked to the rails, which sends current back to a magnet controlling a signal located a short distance along the previous section. As long as current flows, the signal stays at "All clear." When a train enters that section, the wheels and axles create a short circuit, stopping the current from reaching the signal magnet, which causes the signal to change to "danger," and it remains that way until the last set of wheels exits the section. If the current fails or a vehicle detaches and stays on the section, the same outcome will occur.
The human element can thus be practically eliminated from signalling. To make things absolutely safe, a train should have positive control over a train following, to prevent the driver overrunning the signals. On electric railways this has been effected[Pg 229] by means of contacts working in combination with the signals, which either cut the current off from the section preceding that on which a train may be, or raise a trigger to strike an arm on the train following and apply its brakes.
The human factor can basically be eliminated from signaling. To ensure complete safety, a train should have positive control over the train behind it, to stop the driver from passing signals. On electric railways, this has been achieved[Pg 229] through contacts that work in conjunction with the signals, which either cut off the power to the section before the train or trigger an arm on the following train to activate its brakes.
Chapter XII.
OPTICS.
Lenses—The image cast by a convex lens—Focus—Relative position of object and lens—Correction of lenses for colour—Spherical aberration—Distortion of image—The human eye—The use of spectacles—The blind spot.
Lenses—The image produced by a convex lens—Focus—The relative position of the object and lens—Correction of lenses for color—Spherical aberration—Distortion of image—The human eye—The use of glasses—The blind spot.
Light is a third form of that energy of which we have already treated two manifestations—heat and electricity. The distinguishing characteristic of ether light-waves is their extreme rapidity of vibration, which has been calculated to range from 700 billion movements per second for violet rays to 400 billion for red rays.
Light is a third type of energy, alongside the two we’ve already discussed—heat and electricity. The key feature of light waves in the ether is their incredibly fast vibration, which has been measured at about 700 billion movements per second for violet rays and 400 billion for red rays.
If a beam of white light be passed through a prism it is resolved into the seven visible colours of the spectrum—violet, indigo, blue, green, yellow, orange, and red—in this order. The human eye is most sensitive to the yellow-red rays, a photographic plate to the green-violet rays.
If you pass a beam of white light through a prism, it splits into the seven visible colors of the spectrum—violet, indigo, blue, green, yellow, orange, and red—in that order. The human eye is most sensitive to the yellow-red rays, while a photographic plate is more responsive to the green-violet rays.
All bodies fall into one of two classes—(1)[Pg 231] Luminous—that is, those which are a source of light, such as the sun, a candle flame, or a red-hot coal; and (2) non-luminous, which become visible only by virtue of light which they receive from other bodies and reflect to our eyes.
All bodies fall into one of two categories—(1)[Pg 231] Luminous—meaning those that produce their own light, like the sun, a candle flame, or a red-hot coal; and (2) non-luminous, which can be seen only because they reflect light that they get from other sources.
THE PROPAGATION OF LIGHT.
THE PROPAGATION OF LIGHT.
Light naturally travels in a straight line. It is deflected only when it passes from one transparent medium into another—for example, from air to water—and the mediums are of different densities. We may regard the surface of a visible object as made up of countless points, from each of which a diverging pencil of rays is sent off through the ether.
Light naturally moves in a straight line. It only bends when it moves from one clear substance to another—for instance, from air to water—if the substances have different densities. We can think of the surface of a visible object as being made up of countless points, each of which emits a diverging beam of light rays through the air.
LENSES.
Lenses.
If a beam of light encounters a transparent glass body with non-parallel sides, the rays are deflected. The direction they take depends on the shape of the body, but it may be laid down as a rule that they are bent toward the thicker part of the glass. The common burning-glass is well known to us. We hold it up facing the sun to concentrate all the heat rays that fall upon it into one intensely brilliant spot, which speedily ignites any inflammable substance[Pg 232] on which it may fall (Fig. 103). We may imagine that one ray passes from the centre of the sun through the centre of the glass. This is undeflected; but all the others are bent towards it, as they pass through the thinner parts of the lens.
If a beam of light hits a piece of transparent glass with non-parallel sides, the rays bend. The direction they take depends on the shape of the glass, but a general rule is that they bend toward the thicker part of the glass. The common magnifying glass is familiar to us. We hold it up to the sun to focus all the heat rays hitting it into one intensely bright spot, which quickly ignites any flammable material[Pg 232] that it falls on (Fig. 103). We can imagine that one ray travels from the center of the sun through the center of the glass. This ray remains straight, while all the others curve toward it as they pass through the thinner parts of the lens.

It should be noted here that sunlight, as we call it, is accompanied by heat. A burning-glass is used to concentrate the heat rays, not the light rays, which, though they are collected too, have no igniting effect.
It should be noted here that sunlight, as we call it, comes with heat. A magnifying glass is used to focus the heat rays, not the light rays, which, although they are gathered too, do not cause ignition.
In photography we use a lens to concentrate light rays only. Such heat rays as may pass through the lens with them are not wanted, and as they have no practical effect are not taken any notice of. To be of real value, a lens must be quite symmetrical—that is, the curve from the centre to the circumference must be the same in all directions.
In photography, we use a lens to focus light rays. Any heat rays that may pass through the lens with them aren't needed and aren't considered since they have no practical effect. For a lens to be truly valuable, it must be perfectly symmetrical—that is, the curve from the center to the edge must be the same in every direction.
There are six forms of simple lenses, as given in Fig. 104. Nos. 1 and 2 have one flat and one spherical surface. Nos. 3, 4, 5, 6 have two spherical surfaces. When a lens is thicker at the middle than at the sides it is called a convex lens; when thinner, a concave lens. The names of the various shapes are as follows:—No. 1, plano-convex; No. 2, plano-concave; No. 3, double convex; No. 4, double concave; No. 5, meniscus; No. 6, concavo-convex. The thick-centre lenses, as we may term them (Nos. 1, 3, 5), concentrate a pencil of rays passing through them; while the thin-centre lenses (Nos. 2, 4, 6) scatter the rays (see Fig. 105).
There are six types of simple lenses, as shown in Fig. 104. Numbers 1 and 2 have one flat and one curved surface. Numbers 3, 4, 5, and 6 have two curved surfaces. A lens that is thicker in the middle than at the edges is called a convex lens; if it's thinner, it's a concave lens. The different shapes are named as follows: No. 1 is plano-convex; No. 2 is plano-concave; No. 3 is double convex; No. 4 is double concave; No. 5 is meniscus; and No. 6 is concavo-convex. The thick-center lenses (Nos. 1, 3, and 5) concentrate a beam of light passing through them, while the thin-center lenses (Nos. 2, 4, and 6) scatter the light rays (see Fig. 105).

THE CAMERA.
The camera.

We said above that light is propagated in straight lines. To prove this is easy. Get a piece of cardboard and prick a hole in it. Set this up some[Pg 234] distance away from a candle flame, and hold behind it a piece of tissue paper. You will at once perceive a faint, upside-down image of the flame on the tissue. Why is this? Turn for a moment to Fig. 106, which shows a "pinhole" camera in section. At the rear is a ground-glass screen, B, to catch the image. Suppose that A is the lowest point of the flame. A pencil of rays diverging from it strikes the front of the camera, which stops them all except the one which passes through the hole and makes a tiny luminous spot on B, above the centre of the screen, though A is below the axis of the[Pg 235] camera. Similarly the tip of the flame (above the axis) would be represented by a dot on the screen below its centre. And so on for all the millions of points of the flame. If we were to enlarge the hole we should get a brighter image, but it would have less sharp outlines, because a number of rays from every point of the candle would reach the screen and be jumbled up with the rays of neighbouring pencils. Now, though a good, sharp photograph may be taken through a pinhole, the time required is so long that photography of this sort has little practical value. What we want is a large hole for the light to enter the camera by, and yet to secure a distinct image. If we place a lens in the hole we can fulfil our wish. Fig. 107 shows a lens in position, gathering up a number of rays from a point, A, and focussing them on a point, B. If the lens has 1,000 times the area of the pinhole, it will pass 1,000 times as many rays, and the image of A will be impressed on a[Pg 236] sensitized photographic plate 1,000 times more quickly.
We mentioned earlier that light travels in straight lines. It's easy to demonstrate this. Take a piece of cardboard and make a small hole in it. Position it a certain distance away from a candle flame, and hold a piece of tissue paper behind it. You'll immediately see a faint, upside-down image of the flame on the tissue. Why does this happen? Look at Fig. 106, which shows a "pinhole" camera in section. At the back is a ground-glass screen, B, to catch the image. Let’s say A is the lowest point of the flame. A bundle of rays radiating from it hits the front of the camera, which blocks all but the one that passes through the hole, creating a tiny bright spot on B, above the center of the screen, even though A is below the camera's axis. Similarly, the tip of the flame (above the axis) would show as a dot on the screen below its center. This holds true for all the millions of points of the flame. If we make the hole larger, we'll get a brighter image, but the outlines will be less sharp, since multiple rays from every point of the candle will reach the screen and mix with rays from neighboring points. Although a clear, sharp photograph can be taken with a pinhole, it takes so long that this type of photography is not very practical. What we want is a bigger opening for light to enter the camera and still get a clear image. If we place a lens in the hole, we can achieve this. Fig. 107 shows a lens in place, capturing a number of rays from a point, A, and focusing them on a point, B. If the lens has 1,000 times the area of the pinhole, it will allow 1,000 times as many rays to pass through, and the image of A will be captured on a[Pg 236] sensitized photographic plate 1,000 times faster.

THE IMAGE CAST BY A CONVEX LENS.
THE IMAGE PRODUCED BY A CONVEX LENS.
Fig. 108 shows diagrammatically how a convex lens forms an image. From A and B, the extremities of the object, a simple ray is considered to pass through the centre of the lens. This is not deflected at all. Two other rays from the same points strike the lens above and below the centre respectively. These are bent inwards and meet the central rays, or come to a focus with them at A1 and B1. In reality a countless number of rays would be transmitted from every point of the object and collected to form the image.
Fig. 108 shows how a convex lens creates an image. From A and B, the ends of the object, a single ray travels straight through the center of the lens without bending. Two other rays from the same points hit the lens above and below the center, respectively. These rays curve inward and meet the central rays at points A1 and B1. In reality, countless rays would come from every point of the object, gathering to form the image.

FOCUS.
Focus.
We must now take special notice of that word heard so often in photographic talk—"focus." What[Pg 237] is meant by the focus or focal length of a lens? Well, it merely signifies the distance between the optical centre of the lens and the plane in which the image is formed.
We need to pay attention to that word you hear all the time in photography—"focus." What[Pg 237] does the focus or focal length of a lens mean? It simply refers to the distance between the optical center of the lens and the plane where the image is created.

We must here digress a moment to draw attention to the three simple diagrams of Fig. 109. The object, O, in each case is assumed to be to the right of the lens. In the topmost diagram the object is so far away from the lens that all rays coming from a single point in it are practically parallel. These converge to a focus at F. If the distance between F and the centre of the lens is six inches, we say[Pg 238] that the lens has a six-inch focal length. The focal length of a lens is judged by the distance between lens and image when the object is far away. To avoid confusion, this focal length is known as the principal focus, and is denoted by the symbol f. In the middle diagram the object is quite near the lens, which has to deal with rays striking its nearer surface at an acuter angle than before (reckoning from the centre). As the lens can only deflect their path to a fixed degree, they will not, after passing the lens, come together until they have reached a point, F1, further from the lens than F. The nearer we approach O to the lens, the further away on the other side is the focal point, until a distance equal to that of F from the lens is reached, when the rays emerge from the glass in a parallel pencil. The rays now come to a focus no longer, and there can be no image. If O be brought nearer than the focal distance, the rays would diverge after passing through the lens.
We need to take a moment to look at the three simple diagrams in Fig. 109. The object, O, in each case is assumed to be to the right of the lens. In the top diagram, the object is so far from the lens that all rays coming from a single point in it are nearly parallel. These rays converge to a focus at F. If the distance between F and the center of the lens is six inches, we say[Pg 238] that the lens has a six-inch focal length. The focal length of a lens is determined by the distance between the lens and the image when the object is far away. To avoid confusion, this focal length is known as the principal focus, represented by the symbol f. In the middle diagram, the object is quite close to the lens, which must handle rays striking its front surface at a steeper angle than before (measured from the center). Since the lens can only change their paths to a certain extent, they won't converge until they reach a point, F1, which is farther from the lens than F. The closer we move O to the lens, the further the focal point shifts on the other side until we reach a distance equal to that of F from the lens, at which point the rays exit the glass in a parallel beam. The rays no longer converge, and no image can form. If O is brought closer than the focal distance, the rays will diverge after passing through the lens.
RELATIVE POSITIONS OF OBJECT AND IMAGE.
RELATIVE POSITIONS OF OBJECT AND IMAGE.

From what has been said above we deduce two main conclusions—(1.) The nearer an object is brought to the lens, the further away from the[Pg 239] lens will the image be. (2.) If the object approaches within the principal focal distance of the lens, no image will be cast by the lens. To make this plainer we append a diagram (Fig. 110), which shows five positions of an object and the relative positions of the image (in dotted lines). First, we note that the line A B, or A B1, denotes the principal focal length of the lens, and A C, or A C1, denotes twice the focal length. We will take the positions in order:—
From what we've discussed, we can draw two main conclusions—(1) The closer an object is to the lens, the farther away the image will be from the[Pg 239] lens. (2) If the object gets within the principal focal distance of the lens, no image will be formed by the lens. To clarify this, we include a diagram (Fig. 110), which shows five positions of an object and the corresponding image positions (in dotted lines). First, we note that the line A B, or A B1, represents the principal focal length of the lens, and A C, or A C1, represents twice the focal length. We'll examine the positions in order:—
Position I. Object further away than 2f. Inverted image smaller than object, at distance somewhat exceeding f.
Position I. Object situated more than 2f away. Inverted image is smaller than the object, at a distance slightly greater than f.
Position II. Object at distance = 2f. Inverted image at distance = 2f, and of size equal to that of object.
Position II. Object at distance = 2f. Inverted image at distance = 2f, and its size is equal to that of the object.
Position III Object nearer than 2f. Inverted image further away than 2f; larger than the object.
Position III Object closer than 2f. Inverted image farther away than 2f; bigger than the object.
Position IV. Object at distance = f. As rays are parallel after passing the lens no image is cast.
Position IV. Object at distance = f. Since rays are parallel after passing through the lens, no image is formed.
Position V. Object at distance less than f. No real image—that is, one that can be caught on a focussing screen—is now given by the lens, but a magnified, erect, virtual image exists on the same side of the lens as the object.
Position V. Object closer than f. No real image—that is, one that can be captured on a focusing screen—is produced by the lens, but a larger, upright, virtual image appears on the same side of the lens as the object.
We shall refer to virtual images at greater length presently. It is hoped that any reader who practises photography will now understand why it is necessary to rack his camera out beyond the ordinary focal distance when taking objects at close quarters. From Fig. 110 he may gather one practically useful hint—namely, that to copy a diagram, etc., full size, both it and the plate must be exactly 2f from the optical centre of the lens. And it follows from this that the further he can rack his camera out beyond 2f the greater will be the possible enlargement of the original.
We will discuss virtual images in more detail shortly. Any reader who practices photography should now understand why it's necessary to move the camera beyond the usual focal distance when photographing close-up objects. From Fig. 110, one practical tip can be gathered—specifically, that to copy a diagram or similar item at full size, both the object and the plate need to be exactly 2f from the optical center of the lens. Therefore, the farther you can extend your camera beyond 2f, the greater the potential enlargement of the original image.
CORRECTION OF LENSES FOR COLOUR.
Color lens correction.
We have referred to the separation of the spectrum colours of white light by a prism. Now, a lens is one form of prism, and therefore sorts out the colours. In Fig. 111 we assume that two parallel[Pg 241] red rays and two parallel violet rays from a distant object pass through a lens. A lens has most bending effect on violet rays and least on red, and the other colours of the spectrum are intermediately influenced. For the sake of simplicity we have taken the two extremes only. You observe that the point R, in which the red rays meet, is much further from the lens than is V, the meeting-point of the violet rays. A photographer very seldom has to take a subject in which there are not objects of several different colours, and it is obvious that if he used a simple lens like that in Fig. 111 and got his red objects in good focus, the blue and green portions of his picture would necessarily be more or less out of focus.
We’ve talked about how a prism separates the colors of white light. Now, a lens is a type of prism, so it also sorts out colors. In Fig. 111, we imagine that two parallel red rays and two parallel violet rays from a distant object pass through a lens. A lens bends violet rays more than red rays, while the other colors are affected in between. To keep it simple, we’ve only considered the two extremes. You can see that the point R, where the red rays converge, is much farther from the lens than V, the point where the violet rays meet. A photographer rarely has a subject with only one color, and it’s clear that if they used a basic lens like the one in Fig. 111 and focused on the red objects, the blue and green parts of the picture would end up being somewhat out of focus.


This defect can fortunately be corrected by the method shown in Fig. 112. A compound lens is needed, made up of a crown glass convex element, B, and a concave element, A, of flint glass. For the sake of illustration the two parts are shown separated; in practice they would be cemented together, forming one optical body, thicker in the centre than at the edges—a meniscus lens in fact, since A is not so concave as B is convex. Now, it was discovered by a Mr. Hall many years ago that if white light passed through two similar prisms, one of flint glass the other of crown glass, the former had the greater effect in separating the spectrum colours—that is, violet rays were bent aside more suddenly compared with the red rays than happened with the crown-glass prism. Look at Fig. 112. The red rays passing through the flint glass are but little deflected, while the violet rays turn suddenly outwards. This is just what is wanted, for it counteracts the unequal[Pg 243] inward refraction by B, and both sets of rays come to a focus in the same plane. Such a lens is called achromatic, or colourless. If you hold a common reading-glass some distance away from large print you will see that the letters are edged with coloured bands, proving that the lens is not achromatic. A properly corrected photographic lens would not show these pretty edgings. Colour correction is necessary also for lenses used in telescopes and microscopes.
This defect can luckily be fixed using the method shown in Fig. 112. A compound lens is required, made up of a crown glass convex element, B, and a concave element, A, made of flint glass. For illustration, the two parts are shown apart; in reality, they would be bonded together, forming a single optical unit that's thicker in the center than at the edges—a meniscus lens, since A is not as concave as B is convex. Years ago, a Mr. Hall discovered that when white light passes through two similar prisms, one made of flint glass and the other of crown glass, the flint glass prism has a greater effect on separating the spectrum colors—that is, violet rays are bent aside more sharply compared to the red rays than what happens with the crown glass prism. Look at Fig. 112. The red rays passing through the flint glass are barely deflected, while the violet rays rapidly curve outward. This is exactly what we need, as it counteracts the unequal inward refraction by B, allowing both sets of rays to focus in the same plane. Such a lens is called achromatic, or colorless. If you hold a typical reading glass a bit away from large print, you'll see that the letters have colored borders, indicating that the lens is not achromatic. A properly corrected photographic lens wouldn’t show these colorful edges. Color correction is also essential for lenses used in telescopes and microscopes.
SPHERICAL ABERRATION.
Spherical aberration.
A lens which has been corrected for colour is still imperfect. If rays pass through all parts of it, those which strike it near the edge will be refracted more than those near the centre, and a blurred focus results. This is termed spherical aberration. You will be able to understand the reason from Figs. 113 and 114. Two rays, A, are parallel to the axis and enter the lens near the centre (Fig. 113). These meet in one plane. Two other rays, B, strike the lens very obliquely near the edge, and on that account are both turned sharply upwards, coming to a focus in a plane nearer the lens than A. If this happened in a camera the results would be very bad. Either A or B would be out of focus.[Pg 244] The trouble is minimized by placing in front of the lens a plate with a central circular opening in it (denoted by the thick, dark line in Fig. 114). The rays B of Fig. 113 are stopped by this plate, which is therefore called a stop. But other rays from the same point pass through the hole. These, however, strike the lens much more squarely above the centre, and are not unduly refracted, so that they are brought to a focus in the same plane as rays A.
A lens that has been corrected for color is still not perfect. If light rays pass through all parts of it, those hitting the edge will bend more than those near the center, resulting in a blurry focus. This is called spherical aberration. You can understand why by looking at Figs. 113 and 114. Two rays, A, are parallel to the axis and enter the lens near the center (Fig. 113). These meet in one plane. Two other rays, B, hit the lens at a sharp angle near the edge, which causes them to bend sharply upwards, focusing in a plane closer to the lens than A. If this happened in a camera, the results would be very poor. Either A or B would be out of focus.[Pg 244] The issue is reduced by placing a plate with a central circular opening in front of the lens (shown by the thick, dark line in Fig. 114). The B rays from Fig. 113 are blocked by this plate, which is why it’s called a stop. However, other rays from the same point can pass through the hole. These rays hit the lens more directly above the center and are not overly refracted, so they come to focus in the same plane as rays A.


DISTORTION OF IMAGE.
IMAGE DISTORTION.

The lens we have been considering is a single meniscus, such as is used in landscape photography, mounted with the convex side turned towards the inside of the camera, and having the stop in front of it. If you possess a lens of this sort, try the following experiment with it. Draw a large square on a sheet of white paper and focus it on the screen. The sides instead of being straight bow outwards: this is called barrel distortion. Now turn the lens mount round so that the lens is outwards and the stop inwards. The sides of the square will appear to bow towards the centre: this is pin-cushion distortion. For a long time opticians were unable to find a remedy. Then Mr. George S. Cundell suggested that two meniscus lenses should be used in combination, one on either side of the stop, as in Fig 115.[Pg 246] Each produces distortion, but it is counteracted by the opposite distortion of the other, and a square is represented as a square. Lenses of this kind are called rectilinear, or straight-line producing.
The lens we've been discussing is a single meniscus, like those used in landscape photography, with the convex side facing inside the camera and the stop placed in front of it. If you have a lens like this, try the following experiment. Draw a large square on a sheet of white paper and project it onto the screen. Instead of having straight sides, they will curve outward; this is known as barrel distortion. Now rotate the lens mount so that the lens faces outward and the stop faces inward. The sides of the square will curve toward the center; this is pin-cushion distortion. For a long time, opticians struggled to find a solution. Then Mr. George S. Cundell suggested using two meniscus lenses in combination, one on each side of the stop, as shown in Fig 115.[Pg 246] Each lens creates distortion, but it's balanced out by the opposing distortion of the other, making a square appear as a square. Lenses like this are called rectilinear, or straight-line producing.
We have now reviewed the three chief defects of a lens—chromatic aberration, spherical aberration, and distortion—and have seen how they may be remedied. So we will now pass on to the most perfect of cameras,
We have now looked at the three main issues with a lens—chromatic aberration, spherical aberration, and distortion—and explored how to fix them. So, let’s move on to the most advanced cameras,
THE HUMAN EYE.
THE HUMAN EYE.
The eye (Fig. 116) is nearly spherical in form, and is surrounded outside, except in front, by a hard, horny coat called the sclerotica (S). In front is the cornea (A), which bulges outwards, and acts as a transparent window to admit light to the lens of the eye (C). Inside the sclerotica, and next to it, comes the choroid coat; and inside that again is the retina, or curved focussing screen of the eye, which may best be described as a network of fibres ramifying from the optic nerve, which carries sight sensations to the brain. The hollow of the ball is full of a jelly-like substance called the vitreous humour; and the cavity between the lens and the cornea is full of water.
The eye (Fig. 116) is almost spherical in shape and is surrounded on all sides, except the front, by a tough, hard layer called the sclera (S). At the front is the cornea (A), which bulges outward and serves as a clear window to let light into the lens of the eye (C). Inside the sclera, and next to it, is the choroid layer; and just inside that is the retina, the curved focusing surface of the eye, which can be best described as a network of fibers branching out from the optic nerve, responsible for transmitting visual signals to the brain. The hollow part of the eye is filled with a jelly-like substance called the vitreous humor, and the space between the lens and the cornea is filled with fluid.
We have already seen that, in focussing, the distance between lens and image depends on the distance between object and lens. Now, the retina cannot be pushed nearer to or pulled further away from its lens, like the focussing screen of a camera. How, then, is the eye able to focus sharply objects at distances varying from a foot to many miles?
We’ve already observed that when focusing, the distance between the lens and the image depends on how far the object is from the lens. However, the retina can’t be moved closer to or farther away from its lens like the focusing screen of a camera. So, how does the eye manage to focus clearly on objects that are anywhere from a foot away to several miles away?

As a preliminary to the answer we must observe that the more convex a lens is, the shorter is its focus. We will suppose that we have a box camera[Pg 248] with a lens of six-inch focus fixed rigidly in the position necessary for obtaining a sharp image of distant objects. It so happens that we want to take with it a portrait of a person only a few feet from the lens. If it were a bellows camera, we should rack out the back or front. But we cannot do this here. So we place in front of our lens a second convex lens which shortens its principal focus; so that in effect the box has been racked out sufficiently.
As a preliminary to the answer, we should note that the more curved a lens is, the shorter its focal length. Let's say we have a box camera[Pg 248] with a lens that has a six-inch focal length fixed in a position that allows us to get a sharp image of distant objects. Now, we want to take a portrait of someone just a few feet away from the lens. If we had a bellows camera, we would extend the back or front. But since we can’t do that here, we place a second convex lens in front of our lens to shorten its focal length; effectively, this means the box has been adjusted enough.
Nature, however, employs a much more perfect method than this. The eye lens is plastic, like a piece of india-rubber. Its edges are attached to ligaments (L L), which pull outwards and tend to flatten the curve of its surfaces. The normal focus is for distant objects. When we read a book the eye adapts itself to the work. The ligaments relax and the lens decreases in diameter while thickening at the centre, until its curvature is such as to focus all rays from the book sharply on the retina. If we suddenly look through the window at something outside, the ligaments pull on the lens envelope and flatten the curves.
Nature, however, uses a much better method than this. The eye lens is flexible, like a piece of rubber. Its edges are connected to ligaments (L L) that pull outward and tend to flatten its surfaces. The normal focus is set for faraway objects. When we read a book, our eyes adjust to the task. The ligaments relax, and the lens gets smaller in diameter while thickening in the center, until its curvature is just right to focus all rays from the book sharply on the retina. If we suddenly look out the window at something outside, the ligaments pull on the lens capsule and flatten the curves.
This wonderful lens is achromatic, and free from spherical aberration and distortion of image. Nor[Pg 249] must we forget that it is aided by an automatic "stop," the iris, the central hole of which is named the pupil. We say that a person has black, blue, or gray eyes according to the colour of the iris. Like the lens, the iris adapts itself to all conditions, contracting when the light is strong, and opening when the light is weak, so that as uniform an amount of light as conditions allow may be admitted to the eye. Most modern camera lenses are fitted with adjustable stops which can be made larger or smaller by twisting a ring on the mount, and are named "iris" stops. The image of anything seen is thrown on the retina upside down, and the brain reverses the position again, so that we get a correct impression of things.
This amazing lens is achromatic and free from spherical aberration and image distortion. We should also note that it has an automatic "stop," called the iris, with its central opening referred to as the pupil. We describe someone's eyes as black, blue, or gray based on the color of the iris. Similar to the lens, the iris adjusts to different lighting conditions, constricting when the light is bright and expanding when the light is dim, allowing as uniform an amount of light as possible to enter the eye. Most modern camera lenses come with adjustable stops that can be made larger or smaller by turning a ring on the mount, known as "iris" stops. The image of whatever we see is projected onto the retina upside down, and the brain flips it back, giving us an accurate perception of our surroundings.
THE USE OF SPECTACLES.
USING GLASSES.
![]() |
![]() |
![]() |
![]() |
The reader will now be able to understand without much trouble the function of a pair of spectacles. A great many people of all ages suffer from short-sight. For one reason or another the distance between lens and retina becomes too great for a person to distinguish distant objects clearly. The lens, as shown in Fig 117a, is too convex—has its minimum focus too short—and the rays meet and[Pg 250] cross before they reach the retina, causing general confusion of outline. This defect is simply remedied by placing in front of the eye (Fig. 117b) a concave lens, to disperse the rays somewhat before they enter the eye, so that they come to a focus on the retina. If a person's sight is thus corrected for distant objects, he can still see near objects quite plainly, as the lens will accommodate its convexity for them. The scientific term for short-sight is myopia. Long-sight, or hypermetropia, signifies that the eyeball is too short or the lens too flat. Fig. 118a represents the normal condition of a long-sighted eye. When[Pg 251] looking at a distant object the eye thickens slightly and brings the focus forward into the retina. But its thickening power in such an eye is very limited, and consequently the rays from a near object focus behind the retina. It is therefore necessary for a long-sighted person to use convex spectacles for reading the newspaper. As seen in Fig. 118b, the spectacle lens concentrates the rays before they enter the eye, and so does part of the eye's work for it.
The reader can now easily understand how a pair of glasses works. Many people of all ages experience short-sightedness. For various reasons, the distance between the lens and retina becomes too far, making it difficult for someone to see distant objects clearly. The lens, as shown in Fig 117a, is too convex—its minimum focus is too short—and the light rays meet and[Pg 250] cross before reaching the retina, resulting in a blurred outline. This problem can be easily fixed by placing a concave lens in front of the eye (Fig. 117b) to spread out the light rays a bit before they enter, so they focus on the retina. If someone’s vision is corrected for distant objects, they can still see nearby objects clearly since the lens can adjust its convexity for them. The scientific name for short-sightedness is myopia. Long-sightedness, or hypermetropia, means the eyeball is too short or the lens is too flat. Fig. 118a shows the normal condition of a long-sighted eye. When[Pg 251] looking at a distant object, the eye thickens slightly and shifts the focus forward onto the retina. However, its ability to thicken in such an eye is limited, so light rays from nearby objects focus behind the retina. Therefore, a long-sighted person needs to wear convex glasses to read the newspaper. As shown in Fig. 118b, the lens of the glasses concentrates the rays before they enter the eye, doing part of the eye's work.
Returning for a moment to the diagram of the eye (Fig. 116), we notice a black patch on the retina near the optic nerve. This is the "yellow spot." Vision is most distinct when the image of the object looked at is formed on this part of the retina. The "blind spot" is that point at which the optic nerve enters the retina, being so called from the fact that it is quite insensitive to light. The finding of the blind spot is an interesting little experiment. On a card make a large and a small spot three inches apart, the one an eighth, the other half an inch in diameter. Bring the card near the face so that an eye is exactly opposite to each spot, and close the eye opposite to the smaller. Now direct the other eye to this spot and you will find, if[Pg 252] the card be moved backwards and forwards, that at a certain distance the large spot, though many times larger than its fellow, has completely vanished, because the rays from it enter the open eye obliquely and fall on the "blind spot."
Returning for a moment to the diagram of the eye (Fig. 116), we notice a black patch on the retina near the optic nerve. This is the "yellow spot." Vision is clearest when the image of the object you're looking at is focused on this part of the retina. The "blind spot" is where the optic nerve enters the retina, and it’s called that because it doesn’t respond to light. Discovering the blind spot can be an interesting little experiment. On a card, create a large spot and a small spot three inches apart, the large one an eighth of an inch in diameter and the small one half an inch. Hold the card near your face so that one eye is directly opposite each spot, and close the eye that faces the smaller spot. Now direct the other eye towards this spot, and you’ll find that as you move the card back and forth, at a certain distance, the large spot—despite being many times bigger than the small one—will completely disappear because the light rays from it enter the open eye at an angle and hit the "blind spot."
Chapter XIII.
THE MICROSCOPE, THE TELESCOPE, AND THE MAGIC-LANTERN.
The simple microscope—Use of the simple microscope in the telescope—The terrestrial telescope—The Galilean telescope—The prismatic telescope—The reflecting telescope—The parabolic mirror—The compound microscope—The magic-lantern—The bioscope—The plane mirror.
The simple microscope—Using the simple microscope in the telescope—The terrestrial telescope—The Galilean telescope—The prismatic telescope—The reflecting telescope—The parabolic mirror—The compound microscope—The magic lantern—The bioscope—The plane mirror.
In Fig. 119 is represented an eye looking at a vase, three inches high, situated at A, a foot away. If we were to place another vase, B, six inches high, at a distance of two feet; or C, nine inches high, at three feet; or D, a foot high, at four feet, the image on the retina would in every case be of the same size as that cast by A. We can therefore lay down the[Pg 254] rule that the apparent size of an object depends on the angle that it subtends at the eye.
In Fig. 119, there is an eye looking at a vase that is three inches tall, located at A, one foot away. If we place another vase, B, which is six inches tall, two feet away; or C, nine inches tall, three feet away; or D, one foot tall, four feet away, the image on the retina will be the same size in each case as the image from A. We can therefore establish the[Pg 254] rule that the apparent size of an object depends on the angle it makes at the eye.

To see a thing more plainly, we go nearer to it; and if it be very small, we hold it close to the eye. There is, however, a limit to the nearness to which it can be brought with advantage. The normal eye is unable to adapt its focus to an object less than about ten inches away, termed the "least distance of distinct vision."
To see something more clearly, we move closer to it; and if it’s really small, we hold it up close to our eye. However, there’s a limit to how close we can get before it becomes unhelpful. A normal eye can’t focus on things that are less than about ten inches away, which is called the "least distance of distinct vision."
THE SIMPLE MICROSCOPE.
The Basic Microscope.
A magnifying glass comes in useful when we want to examine an object very closely. The glass is a lens of short focus, held at a distance somewhat less than its principal focal length, F (see Fig. 120), from[Pg 255] the object. The rays from the head and tip of the pin which enter the eye are denoted by continuous lines. As they are deflected by the glass the eye gets the impression that a much longer pin is situated a considerable distance behind the real object in the plane in which the refracted rays would meet if produced backwards (shown by the dotted lines). The effect of the glass, practically, is to remove it (the object) to beyond the least distance of distinct vision, and at the same time to retain undiminished the angle it subtends at the eye, or, what amounts to the same thing, the actual size of the image formed on the retina.[22] It follows, therefore, that if a lens be of such short focus that it allows us to see an object clearly at a distance of two inches—that is, one-fifth of the least distance of distinct vision—we shall get an image on the retina five times larger in diameter than would be possible without the lens.
A magnifying glass is really useful when we want to look at something up close. The glass is a lens with a short focal length, held at a distance slightly less than its main focal length, F (see Fig. 120), from[Pg 255] the object. The rays from the head and tip of the pin that enter the eye are shown by continuous lines. As they bend through the glass, the eye gets the impression that a much longer pin is positioned further back from the actual object, in a plane where the refracted rays would converge if extended backwards (indicated by the dotted lines). The practical effect of the glass is to move the object beyond the closest distance for clear vision, while still maintaining the same angle it forms at the eye, or, in other words, the actual size of the image created on the retina.[22] This means that if a lens has such a short focal length that it lets us see an object clearly from two inches away—that is one-fifth of the closest distance for clear vision—we will see an image on the retina that is five times larger in diameter than what we could see without the lens.
The two simple diagrams (Figs. 121 and 122) show why the image to be magnified should be nearer to the lens than the principal focus, F. We have already seen (Fig. 109) that rays coming from a point in the principal focal plane emerge as a[Pg 256] parallel pencil. These the eye can bring to a focus, because it normally has a curvature for focussing parallel rays. But, owing to the power of "accommodation," it can also focus diverging rays (Fig. 121), the eye lens thickening the necessary amount, and we therefore put our magnifying glass a bit nearer than F to get full advantage of proximity. If we had the object outside the principal focus, as in Fig. 122, the rays from it would converge, and these could not be gathered to a sharp point by the eye lens, as it cannot flatten more than is required for focussing parallel rays.
The two simple diagrams (Figs. 121 and 122) show why the image you want to magnify should be closer to the lens than the principal focus, F. As we saw earlier (Fig. 109), rays coming from a point in the principal focal plane come out as a[Pg 256] parallel beam. The eye can focus these rays because it usually has the right curvature for focusing parallel rays. However, thanks to the "accommodation" ability, the eye can also focus on diverging rays (Fig. 121), with the eye lens adjusting its thickness as needed. That's why we position our magnifying glass a little closer than F to make the most of the proximity. If the object is outside the principal focus, as shown in Fig. 122, the rays from it would converge, and the eye lens wouldn't be able to focus them sharply, since it can't flatten more than what is necessary for focusing parallel rays.


USE OF THE SIMPLE MICROSCOPE IN THE TELESCOPE.
USE OF THE SIMPLE MICROSCOPE IN THE TELESCOPE.

Let us now turn to Fig. 123. At A is a distant object, say, a hundred yards away. B is a double convex lens, which has a focal length of twenty inches. We may suppose that it is a lens in a camera. An inverted image of the object is cast by the lens at C. If the eye were placed at C, it would distinguish nothing. But if withdrawn to D, the least distance of distinct vision,[23] behind C, the image is seen clearly. That the image really is at C is proved by letting down the focussing screen, which at once catches it. Now, as the focus of the lens is twice d, the image will be twice as large as the object would appear if viewed directly without the lens. We may put this into a very simple formula:—
Let’s now look at Fig. 123. At A is a distant object, about a hundred yards away. B is a double convex lens with a focal length of twenty inches. We can assume that it’s a lens in a camera. An inverted image of the object is produced by the lens at C. If the eye is positioned at C, it won’t see anything. But if you pull back to D, the closest distance for clear vision,[23] behind C, the image becomes clear. The fact that the image is actually at C is confirmed by dropping the focussing screen, which immediately captures it. Now, since the focal length of the lens is twice d, the image will be twice as large as the object would appear when viewed directly without the lens. We can express this in a very simple formula:—
Magnification = | lens focal length d |

In Fig. 124 we have interposed between the eye and the object a small magnifying glass of 2½-inch focus, so that the eye can now clearly see the image when one-quarter d away from it. B already magnifies the image twice; the eye-piece again magnifies it four times; so that the total magnification is 2 × 4 = 8 times. This result is arrived at quickly by dividing the focus of B (which corresponds to the object-glass of a telescope) by the focus of the eye-piece, thus:—
In Fig. 124, we place a small magnifying glass with a 2½-inch focus between the eye and the object, allowing the eye to clearly see the image when it is one-quarter d away. B already magnifies the image twice; the eyepiece magnifies it again four times, resulting in a total magnification of 2 × 4 = 8 times. You can quickly find this result by dividing the focus of B (which acts like the object lens of a telescope) by the focus of the eyepiece, as follows:—
20 2½ |
= 8 |
The ordinary astronomical telescope has a very long focus object-glass at one end of the tube, and a very short focus eye-piece at the other. To see an object clearly one merely has to push in or pull out the eye-piece until its focus exactly corresponds with that of the object-glass.
The typical astronomical telescope has a long-focus objective lens at one end of the tube and a short-focus eyepiece at the other. To see an object clearly, you just need to adjust the eyepiece in or out until its focus matches that of the objective lens.
THE TERRESTRIAL TELESCOPE.
The Ground Telescope.
An astronomical telescope inverts images. This inversion is inconvenient for other purposes. So the terrestrial telescope (such as is commonly used by sailors) has an eye-piece compounded of four convex lenses which erect as well as magnify the image. Fig. 125 shows the simplest form of compound erecting eye-piece.
An astronomical telescope flips images upside down. This flip can be annoying for other uses. That's why the terrestrial telescope (like those often used by sailors) has an eyepiece made up of four convex lenses that not only magnify but also correct the image orientation. Fig. 125 shows the simplest version of a compound erecting eyepiece.

THE GALILEAN TELESCOPE.
THE GALILEO TELESCOPE.

A third form of telescope is that invented by the great Italian astronomer, Galileo,[24] in 1609. Its principle is shown in Fig. 126. The rays transmitted[Pg 260] by the object-glass are caught, before coming to a focus, on a concave lens which separates them so that they appear to meet in the paths of convergence denoted by the dotted lines. The image is erect. Opera-glasses are constructed on the Galilean principle.
A third type of telescope was invented by the famous Italian astronomer Galileo,[24] in 1609. Its principles are illustrated in Fig. 126. The rays captured[Pg 260] by the objective lens are intercepted, before they come to focus, by a concave lens that spreads them out so they seem to converge along the dotted lines. The image is upright. Opera glasses are designed based on the Galilean principle.
THE PRISMATIC TELESCOPE.
THE PRISMATIC TELESCOPE.
In order to be able to use a long-focus object-glass without a long focussing-tube, a system of glass reflecting prisms is sometimes employed, as in Fig. 127. A ray passing through the object-glass is reflected from one posterior surface of prism A on to the other posterior surface, and by it out through the front on to a second prism arranged at right angles to it, which passes the ray on to the compound eye-piece. The distance between object-glass and eye-piece is thus practically trebled. The best-known prismatic telescopes are the Zeiss field-glasses.
To use a long-focus lens without needing a long focusing tube, a system of glass reflecting prisms is sometimes used, as shown in Fig. 127. A ray that goes through the lens is reflected off one back surface of prism A onto the other back surface, and then it exits through the front to a second prism set at a right angle, which passes the ray to the compound eyepiece. This setup effectively triples the distance between the lens and the eyepiece. The most well-known prismatic telescopes are the Zeiss field glasses.

THE REFLECTING TELESCOPE.
The Reflecting Telescope.
We must not omit reference to the reflecting telescope,[Pg 261] so largely used by astronomers. The front end of the telescope is open, there being no object-glass. Rays from the object fall on a parabolic mirror situated in the rear end of the tube. This reflects them forwards to a focus. In the Newtonian reflector a plane mirror or prism is situated in the axis of the tube, at the focus, to reflect the rays through an eye-piece projecting through the side of the tube. Herschel's form of reflector has the mirror set at an angle to the axis, so that the rays are reflected direct into an eye-piece pointing through the side of the tube towards the mirror.
We shouldn't forget to mention the reflecting telescope,[Pg 261] which is widely used by astronomers. The front end of the telescope is open, with no object-glass. Rays from the object hit a parabolic mirror located at the back of the tube. This mirror reflects them forward to a focus. In the Newtonian reflector, a plane mirror or prism is positioned along the tube's axis, at the focus, to redirect the rays through an eyepiece that sticks out the side of the tube. Herschel's design has the mirror set at an angle to the axis, so the rays are reflected directly into an eyepiece that's pointing through the side of the tube towards the mirror.
THE PARABOLIC MIRROR.
The curved mirror.
This mirror (Fig. 128) is of such a shape that all rays parallel to the axis are reflected to a common point. In the marine searchlight a powerful arc lamp is arranged with the arc at the focus of a parabolic reflector, which sends all reflected light forward in a pencil of parallel rays. The most powerful searchlight in existence gives a light equal to that of 350 million candles.
This mirror (Fig. 128) is designed so that all rays parallel to the axis are reflected to a single point. In the marine searchlight, a strong arc lamp is positioned with the arc at the focus of a parabolic reflector, which directs all the reflected light forward in a beam of parallel rays. The most powerful searchlight in the world produces light equivalent to that of 350 million candles.

THE COMPOUND MICROSCOPE.
The compound microscope.
We have already observed (Fig. 110) that the[Pg 262] nearer an object approaches a lens the further off behind it is the real image formed, until the object has reached the focal distance, when no image at all is cast, as it is an infinite distance behind the lens. We will assume that a certain lens has a focus of six inches. We place a lighted candle four feet in front of it, and find that a sharp diminished image is cast on a ground-glass screen held seven inches behind it. If we now exchange the positions of the candle and the screen, we shall get an enlarged image of the candle. This is a simple demonstration of the law of conjugate foci—namely, that the distance between the lens and an object on one side and that between the lens and the corresponding image on the other bear a definite relation to each other; and an object placed at either focus will cast an image at the other. Whether the image is larger[Pg 263] or smaller than the object depends on which focus it occupies. In the case of the object-glass of a telescope the image was at what we may call the short focus.
We have already seen (Fig. 110) that the[Pg 262] closer an object gets to a lens, the farther away the real image forms behind it, until the object reaches the focal distance, at which point no image is formed at all, as it's at an infinite distance behind the lens. Let's assume that a certain lens has a focal length of six inches. We place a lit candle four feet in front of it and find that a sharp reduced image is projected onto a ground-glass screen held seven inches behind it. If we then switch the positions of the candle and the screen, we will get an enlarged image of the candle. This is a straightforward demonstration of the law of conjugate foci—specifically, that the distance between the lens and an object on one side and the distance between the lens and the corresponding image on the other have a specific relationship with each other; an object positioned at either focus will form an image at the other. Whether the image is larger[Pg 263] or smaller than the object depends on which focus it occupies. In the case of the objective lens of a telescope, the image was at what we can refer to as the short focus.
Now, a compound microscope is practically a telescope with the object at the long focus, very close to a short-focus lens. A greatly enlarged image is thrown (see Fig. 129) at the conjugate focus, and this is caught and still further magnified by the eye-piece. We may add that the object-glass, or objective, of a microscope is usually compounded of several lenses, as is also the eye-piece.
Now, a compound microscope is basically a telescope with the object at the long focus, positioned very close to a short-focus lens. A greatly enlarged image is projected (see Fig. 129) at the conjugate focus, and this is captured and further magnified by the eyepiece. Additionally, it's worth noting that the objective lens of a microscope is typically made up of several lenses, just like the eyepiece.
THE MAGIC-LANTERN.
THE PROJECTOR.
The most essential features of a magic-lantern are:—(1) The source of light; (2) the condenser for concentrating the light rays on to the slide;[Pg 264] (3) the lens for projecting a magnified image on to a screen.
The key components of a magic lantern are: (1) the light source; (2) the condenser to focus the light rays onto the slide; [Pg 264] (3) the lens to project a larger image onto a screen.
Fig. 130 shows these diagrammatically. The illuminant is most commonly an oil-lamp, or an acetylene gas jet, or a cylinder of lime heated to intense luminosity by an oxy-hydrogen flame. The natural combustion of hydrogen is attended by a great heat, and when the supply of oxygen is artificially increased the temperature of the flame rises enormously. The nozzle of an oxy-hydrogen jet has an interior pipe connected with the cylinder holding one gas, and an exterior, and somewhat larger, pipe leading from that containing the other, the two being arranged concentrically at the nozzle. By means of valves the proportions of the gases can be regulated to give the best results.
Fig. 130 shows this in a diagram. The light source is usually an oil lamp, an acetylene gas jet, or a cylinder of lime that gets intensely bright when heated by an oxy-hydrogen flame. The natural burning of hydrogen generates a lot of heat, and when the oxygen supply is artificially increased, the flame's temperature rises significantly. The nozzle of an oxy-hydrogen jet has an inner pipe connected to the cylinder with one gas and a larger outer pipe that connects to the cylinder with the other gas, with both pipes arranged concentrically at the nozzle. Valves allow for the regulation of gas proportions to achieve the best results.

The condenser is set somewhat further from the[Pg 265] illuminant than the principal focal length of the lenses, so that the rays falling on them are bent inwards, or to the slide.
The condenser is positioned a bit farther from the[Pg 265] light source than the main focal length of the lenses, so that the rays hitting them are directed inward, or toward the slide.
The objective, or object lens, stands in front of the slide. Its position is adjustable by means of a rack and a draw-tube. The nearer it is brought to the slide the further away is the conjugate focus (see p. 239), and consequently the image. The exhibitor first sets up his screen and lantern, and then finds the conjugate foci of slide and image by racking the lens in or out.
The objective, or object lens, is positioned in front of the slide. You can adjust its position using a rack and a draw-tube. The closer it is to the slide, the farther away the conjugate focus (see p. 239) and, as a result, the image will be. The presenter first sets up their screen and lantern, and then locates the conjugate foci of the slide and image by adjusting the lens in or out.
If a very short focus objective be used, subjects of microscopic proportions can be projected on the screen enormously magnified. During the siege of Paris in 1870–71 the Parisians established a balloon and pigeon post to carry letters which had been copied in a minute size by photography. These copies could be enclosed in a quill and attached to a pigeon's wing. On receipt, the copies were placed in a special lantern and thrown as large writing on the screen. Micro-photography has since then made great strides, and is now widely used for scientific purposes, one of the most important being the study of the crystalline formations of metals under different conditions.
If a very short focus lens is used, subjects that are tiny can be projected on the screen massively enlarged. During the siege of Paris in 1870–71, the Parisians set up a balloon and pigeon post to carry letters that had been photographed in tiny size. These copies could be rolled up in a quill and attached to a pigeon's wing. Upon arrival, the copies were placed in a special lantern and displayed as large writing on the screen. Since then, micro-photography has advanced significantly and is now widely used for scientific purposes, one of the most important being the study of how metals form crystals under different conditions.
THE BIOSCOPE.
THE MOVIE THEATER.
"Living pictures" are the most recent improvement in magic-lantern entertainments. The negatives from which the lantern films are printed are made by passing a ribbon of sensitized celluloid through a special form of camera, which feeds the ribbon past the lens in a series of jerks, an exposure being made automatically by a revolving shutter during each rest. The positive film is placed in a lantern, and the intermittent movement is repeated; but now the source of illumination is behind the film, and light passes outwards through the shutter to the screen. In the Urban bioscope the film travels at the rate of fifteen miles an hour, upwards of one hundred exposures being made every second.
"Living pictures" are the latest advancement in magic lantern entertainment. The negatives from which the lantern films are printed are created by feeding a strip of sensitized celluloid through a special type of camera, which moves the strip past the lens in a series of quick bursts, while a revolving shutter makes an exposure automatically during each pause. The positive film is placed in a lantern, and the intermittent movement is repeated; however, the light source is now behind the film, allowing light to pass out through the shutter to the screen. In the Urban bioscope, the film moves at a speed of fifteen miles per hour, making over one hundred exposures every second.
The impression of continuous movement arises from the fact that the eye cannot get rid of a visual impression in less than one-tenth of a second. So that if a series of impressions follow one another more rapidly than the eye can rid itself of them the impressions will overlap, and give one of motion, if the position of some of the objects, or parts of the objects, varies slightly in each succeeding picture.[25]
The feeling of constant movement comes from the eye's inability to process a visual impression in under one-tenth of a second. Therefore, if a series of impressions happen faster than the eye can clear them, they will overlap and create a sense of motion, especially if the position of some objects or parts of the objects changes slightly in each consecutive image.[25]
THE PLANE MIRROR.
The flat mirror.

This chapter may conclude with a glance at the common looking-glass. Why do we see a reflection in it? The answer is given graphically by Fig. 131. Two rays, A b, A c, from a point A strike the mirror M at the points b and c. Lines b N, c O, drawn from these points perpendicular to the mirror are called[Pg 268] their normals. The angles A b N, A c O are the angles of incidence of rays A b, A c. The paths which the rays take after reflection must make angles with b N and c O respectively equal to A b N, A c O. These are the angles of reflection. If the eye is so situated that the rays enter it as in our illustration, an image of the point A is seen at the point A1, in which the lines D b, E c meet when produced backwards.
This chapter might end with a look at the typical mirror. Why do we see a reflection in it? The answer is shown clearly in Fig. 131. Two rays, A b, A c, from a point A hit the mirror M at the points b and c. Lines b N, c O, drawn from these points perpendicular to the mirror are called[Pg 268] their normals. The angles A b N, A c O are the angles of incidence of rays A b, A c. The paths that the rays take after reflecting must form angles with b N and c O that are equal to A b N, A c O. These are the angles of reflection. If the eye is positioned in such a way that the rays enter it as shown in our illustration, an image of point A appears at point A, where the lines D b, E c meet when extended backward.

When the vertical mirror is replaced by a horizontal reflecting surface, such as a pond (Fig. 132), the same thing happens. The point at which the[Pg 269] ray from the reflection of the spire's tip to the eye appears to pass through the surface of the water must be so situated that if a line were drawn perpendicular to it from the surface the angles made by lines drawn from the real spire tip and from the observer's eye to the base of the perpendicular would be equal.
When the vertical mirror is replaced by a horizontal reflecting surface, like a pond (Fig. 132), the same thing occurs. The point where the[Pg 269] ray from the reflection of the spire's tip to the eye seems to pass through the water's surface must be positioned so that if a line were drawn straight up from the surface, the angles formed by lines drawn from the actual tip of the spire and from the observer's eye to the base of the vertical line would be equal.
[22] Glazebrook, "Light," p. 157.
__A_TAG_PLACEHOLDER_0__ Glazebrook, "Light," p. 157.
[23] Glazebrook, "Light," p. 157.
__A_TAG_PLACEHOLDER_0__ Glazebrook, "Light," p. 157.
Chapter XIV.
SOUND AND MUSICAL INSTRUMENTS.
Nature of sound—The ear—Musical instruments—The vibration of strings—The sounding-board and the frame of a piano—The strings—The striking mechanism—The quality of a note.
Nature of sound—The ear—Musical instruments—The vibration of strings—The sounding board and the frame of a piano—The strings—The striking mechanism—The quality of a note.
Sound differs from light, heat, and electricity in that it can be propagated through matter only. Sound-waves are matter-waves, not ether-waves. This can be proved by placing an electric bell under the bell-glass of an air-pump and exhausting all the air. Ether still remains inside the glass, but if the bell be set in motion no sound is audible. Admit air, and the clang of the gong is heard quite plainly.
Ssound is different from light, heat, and electricity because it can only travel through matter. Sound waves are waves of matter, not waves of ether. You can prove this by putting an electric bell under a bell jar of an air pump and removing all the air. Ether is still inside the jar, but if you try to ring the bell, you won't hear any sound. Once you allow air back in, the sound of the bell is clearly heard.
Sound resembles light and heat, however, thus far, that it can be concentrated by means of suitable lenses and curved surfaces. An echo is a proof of its reflection from a surface.
Sound is similar to light and heat, as it can be focused using appropriate lenses and curved surfaces. An echo is proof of its reflection from a surface.
Before dealing with the various appliances used[Pg 271] for producing sound-waves of a definite character, let us examine that wonderful natural apparatus
Before looking at the different devices used[Pg 271] for creating sound waves of a specific type, let’s take a look at that amazing natural system.
THE EAR,
THE EAR,
through which we receive those sensations which we call sound.
through which we experience the sensations we refer to as sound.

Fig. 133 is a purely diagrammatic section of the ear, showing the various parts distorted and out of proportion. Beginning at the left, we have the outer ear, the lobe, to gather in the sound-waves on to the membrane of the tympanum, or drum, to which is attached the first of a series of ossicles, or small bones. The last of these presses against an opening in the inner ear, a cavity surrounded by the bones of the head. Inside the inner ear is a watery fluid,[Pg 272] P, called perilymph ("surrounding water"), immersed in which is a membranic envelope, M, containing endolymph ("inside water"), also full of fluid. Into this fluid project E E E, the terminations of the auditory nerve, leading to the brain.
Fig. 133 is a simple diagram of the ear, showing the different parts in a distorted and disproportionate way. Starting on the left, we have the outer ear, the lobe, which collects sound waves to transmit to the tympanic membrane, or drum, where the first of a series of ossicles, or small bones, is connected. The last of these bones presses against an opening in the inner ear, a cavity surrounded by the bones of the skull. Inside the inner ear is a watery fluid,[Pg 272] P, called perilymph ("surrounding water"), in which a membranous envelope, M, containing endolymph ("inside water"), is immersed, also filled with fluid. Into this fluid extend E E E, the endings of the auditory nerve, which lead to the brain.
When sound-waves strike the tympanum, they cause it to move inwards and outwards in a series of rapid movements. The ossicles operated by the tympanum press on the little opening O, covered by a membrane, and every time they push it in they slightly squeeze the perilymph, which in turn compresses the endolymph, which affects the nerve-ends, and telegraphs a sensation of sound to the brain.
When sound waves hit the eardrum, they make it move in and out quickly. The small bones controlled by the eardrum press on a tiny opening O, which is covered by a membrane. Each time they push it in, they slightly compress the perilymph, which then squeezes the endolymph, affecting the nerve endings and sending a signal of sound to the brain.
In Fig. 134 we have a more developed sketch, giving in fuller detail, though still not in their actual proportions, the components of the ear. The ossicles M, I, and S are respectively the malleus (hammer), incus (anvil), and stapes (stirrup). Each is attached by ligaments to the walls of the middle ear. The tympanum moves the malleus, the malleus the incus, and the incus the stapes, the last pressing into the opening O of Fig. 133, which is scientifically known as the fenestra ovalis, or oval window. As liquids are practically incompressible, nature has made[Pg 273] allowance for the squeezing in of the oval window membrane, by providing a second opening, the round window, also covered with a membrane. When the stapes pushes the oval membrane in, the round membrane bulges out, its elasticity sufficing to put a certain pressure on the perilymph (indicated by the dotted portion of the inner ear).
In Fig. 134, we see a more detailed sketch that shows the parts of the ear in a larger scale, although not in their actual sizes. The ossicles M, I, and S are the malleus (hammer), incus (anvil), and stapes (stirrup), respectively. Each one is connected by ligaments to the walls of the middle ear. The tympanic membrane moves the malleus, the malleus moves the incus, and the incus moves the stapes, which in turn presses into the opening O from Fig. 133, scientifically known as the fenestra ovalis or oval window. Since liquids cannot be compressed, nature has allowed for the flexibility of the oval window membrane by providing a second opening, the round window, which is also covered by a membrane. When the stapes pushes the oval membrane inward, the round membrane bulges outward, and its elasticity creates pressure on the perilymph (shown by the dotted section of the inner ear).

The inner ear consists of two main parts, the cochlea—so called from its resemblance in shape to a snail's shell—and the semicircular canals. Each portion has its perilymph and endolymph, and contains a number of the nerve-ends, which are, however,[Pg 274] most numerous in the cochlea. We do not know for certain what the functions of the canals and the cochlea are; but it is probable that the former enables us to distinguish between the intensity or loudness of sounds and the direction from which they come, while the latter enables us to determine the pitch of a note. In the cochlea are about 2,800 tiny nerve-ends, called the rods of Corti. The normal ear has such a range as to give about 33 rods to the semitone. The great scientist Helmholtz has advanced the theory that these little rods are like tiny tuning-forks, each responding to a note of a certain pitch; so that when a string of a piano is sounded and the air vibrations are transmitted to the inner ear, they affect only one of these rods and the part of the brain which it serves, and we have the impression of one particular note. It has been proved by experiment that a very sensitive ear can distinguish between sounds varying in pitch by only 1⁄64th of a semitone, or but half the range of any one Corti fibre. This difficulty Helmholtz gets over by suggesting that in such an ear two adjacent fibres are affected, but one more than the other.
The inner ear has two main parts: the cochlea, named for its snail shell shape, and the semicircular canals. Each section contains perilymph and endolymph, and has a number of nerve endings, which are especially abundant in the cochlea.[Pg 274] We don’t know exactly what the canals and the cochlea do; however, it's likely that the canals help us tell the intensity or loudness of sounds and where they come from, while the cochlea helps us recognize the pitch of a note. Inside the cochlea, there are about 2,800 tiny nerve endings known as the rods of Corti. A typical ear can distinguish about 33 rods per semitone. The famous scientist Helmholtz proposed that these little rods act like tiny tuning forks, each responding to a specific pitch; so, when a piano string is struck and the resulting sound vibrations reach the inner ear, they stimulate just one of these rods and its related part of the brain, creating the perception of a particular note. Experiments have shown that a very sensitive ear can differentiate sounds with pitch differences as small as 1⁄64th of a semitone, which is half the range of any single Corti fiber. Helmholtz explains this by suggesting that in such an ear, two nearby fibers are activated, but one more than the other.
A person who has a "good ear" for music is presumably one whose Corti rods are very perfect.[Pg 275] Unlucky people like the gentleman who could only recognize one tune, and that because people took off their hats when it commenced, are physically deficient. Their Corti rods cannot be properly developed.
A person with a "good ear" for music likely has very well-developed Corti rods.[Pg 275] Unfortunately, individuals like the man who could only recognize one song, and only because people would take off their hats when it started, have a physical deficiency. His Corti rods aren't properly developed.
What applies to one single note applies also to the elements of a musical chord. A dozen notes may sound simultaneously, but the ear is able to assimilate each and blend it with its fellows; yet it requires a very sensitive and well-trained ear to pick out any one part of a harmony and concentrate the brain's attention on that part.
What applies to one single note applies also to the elements of a musical chord. A dozen notes may sound at the same time, but the ear can absorb each note and blend it with the others; however, it takes a very sensitive and well-trained ear to isolate any one part of a harmony and focus the brain's attention on that part.
The ear has a much larger range than the eye. "While the former ranges over eleven octaves, but little more than a single octave is possible to the latter. The quickest vibrations which strike the eye, as light, have only about twice the rapidity of the slowest; whereas the quickest vibrations which strike the ear, as a musical sound, have more than two thousand times the rapidity of the slowest."[26] To come to actual figures, the ordinary ear is sensitive to vibrations ranging from 16 to 38,000 per second. The bottom and top notes of a piano make respectively about 40 and 4,000 vibrations a second. Of course, some ears, like some eyes, cannot[Pg 276] comprehend the whole scale. The squeak of bats and the chirrup of crickets are inaudible to some people; and dogs are able to hear sounds far too shrill to affect the human auditory apparatus.
The ear can detect a much wider range of sounds than the eye can see. "While the ear can sense over eleven octaves, the eye manages only a bit more than one octave. The fastest vibrations that the eye perceives, as light, move at about twice the speed of the slowest; in contrast, the fastest vibrations that the ear picks up, like musical sounds, can move more than two thousand times faster than the slowest." [26] To put this into perspective, the typical ear can pick up vibrations from 16 to 38,000 per second. The lowest and highest notes on a piano create around 40 and 4,000 vibrations per second, respectively. Naturally, just like some people have difficulty seeing certain colors, some ears can't pick up the entire range of sounds. The high-pitched squeak of bats and the chirping of crickets might be unheard by some individuals, while dogs can hear sounds that are much too high-pitched for the human ear to detect.
Not the least interesting part of this wonderful organ is the tympanic membrane, which is provided with muscles for altering its tension automatically. If we are "straining our ears" to catch a shrill sound, we tighten the membrane; while if we are "getting ready" for a deep, loud report like that of a gun, we allow the drum to slacken.
Not the least interesting part of this amazing organ is the eardrum, which has muscles that automatically adjust its tension. When we are "straining our ears" to hear a high-pitched sound, we tighten the eardrum; whereas when we are "getting ready" for a deep, loud noise like that of a gun, we let the eardrum relax.
The Eustachian tube (Fig. 134) communicates with the mouth. Its function is probably to keep the air-pressure equal on both sides of the drum. When one catches cold the tube is apt to become blocked by mucus, causing unequal pressure and consequent partial deafness.
The Eustachian tube (Fig. 134) connects to the mouth. Its main role is likely to maintain equal air pressure on both sides of the eardrum. When someone catches a cold, the tube can get blocked by mucus, leading to uneven pressure and potential partial deafness.
Before leaving this subject, it will be well to remind our more youthful readers that the ear is delicately as well as wonderfully made, and must be treated with respect. Sudden shouting into the ear, or a playful blow, may have most serious effects, by bursting the tympanum or injuring the arrangement of the tiny bones putting it in communication with the inner ear.
Before we move on from this topic, it's important to remind our younger readers that the ear is both delicately and wonderfully constructed, and it should be treated with care. Yelling suddenly into someone's ear or giving it a playful hit can have serious consequences, like rupturing the eardrum or damaging the tiny bones that connect it to the inner ear.
MUSICAL INSTRUMENTS.
Music Instruments.
These are contrivances for producing sonorous shocks following each other rapidly at regular intervals. Musical sounds are distinguished from mere noises by their regularity. If we shake a number of nails in a tin box, we get only a series of superimposed and chaotic sensations. On the other hand, if we strike a tuning-fork, the air is agitated a certain number of times a second, with a pleasant result which we call a note.
These are devices designed to create loud sounds that follow each other quickly at consistent intervals. Musical sounds are different from simple noises because of their consistency. If we shake several nails in a tin box, we only get a mix of chaotic sensations. However, if we strike a tuning fork, the air vibrates a specific number of times per second, producing a pleasant sound we refer to as a note.
We will begin our excursion into the region of musical instruments with an examination of that very familiar piece of furniture,
We will start our journey into the world of musical instruments by looking at that well-known piece of furniture,
THE PIANOFORTE,
THE PIANO,
which means literally the "soft-strong." By many children the piano is regarded as a great nuisance, the swallower-up of time which could be much more agreeably occupied, and is accordingly shown much less respect than is given to a phonograph or a musical-box. Yet the modern piano is a very clever piece of work, admirably adapted for the production of sweet melody—if properly handled. The two forms of piano now generally used are the upright,[Pg 278] with vertical sound-board and wires, and the grand, with horizontal sound-board.[27]
which means literally "soft-strong." Many children see the piano as a big hassle, a time-waster that could be spent on more enjoyable activities, and it gets a lot less respect than a phonograph or a music box. However, the modern piano is a really smart piece of machinery, perfectly designed to create sweet melodies—if played correctly. The two common types of piano used today are the upright,[Pg 278] with a vertical soundboard and strings, and the grand, which has a horizontal soundboard.[27]
THE VIBRATION OF STRINGS.
STRING VIBRATION.
As the pianoforte is a stringed instrument, some attention should be given to the subject of the vibration of strings. A string in a state of tension emits a note when plucked and allowed to vibrate freely. The pitch of the note depends on several conditions:—(1) The diameter of the string; (2) the tension of the string; (3) the length of the string; (4) the substance of the string. Taking them in order:—(1.) The number of vibrations per second is inversely proportional to the diameter of the string: thus, a string one-quarter of an inch in diameter would vibrate only half as often in a given time as a string one-eighth of an inch in diameter. (2.) The length remaining the same, the number of vibrations is directly proportional to the square root of the tension: thus, a string strained by a 16-lb. weight would vibrate four times as fast as it would if strained by a 1-lb. weight. (3.) The number of vibrations is inversely proportional[Pg 279] to the length of the string: thus, a one-foot string would vibrate twice as fast as a two-foot string, strained to the same tension, and of equal diameter and weight. (4.) Other things being equal, the rate of vibration is inversely proportional to the square root of the density of the substance: so that a steel wire would vibrate more rapidly than a platinum wire of equal diameter, length, and tension. These facts are important to remember as the underlying principles of stringed instruments.
Since the pianoforte is a string instrument, it's important to understand how strings vibrate. A string under tension produces a note when plucked and allowed to vibrate freely. The pitch of the note depends on several factors: (1) the diameter of the string; (2) the tension of the string; (3) the length of the string; (4) the material of the string. Taking them one by one: (1) The number of vibrations per second is inversely related to the diameter of the string; for example, a string that is one-quarter of an inch thick would vibrate only half as much in the same amount of time as a string that is one-eighth of an inch thick. (2) If the length stays the same, the number of vibrations is directly related to the square root of the tension; so, a string under a 16-pound weight would vibrate four times faster than one under a 1-pound weight. (3) The number of vibrations is inversely related[Pg 279] to the length of the string; thus, a string that is one foot long would vibrate twice as fast as a two-foot string, provided they are under the same tension and have the same diameter and weight. (4) Other things being equal, the rate of vibration is inversely related to the square root of the density of the material; meaning that a steel wire would vibrate more quickly than a platinum wire of the same diameter, length, and tension. These concepts are important to keep in mind as the fundamental principles of stringed instruments.
Now, if you hang a wire from a cord, and hang a heavy weight from the wire, the wire will be in a state of high tension, and yield a distinct note if struck. But the volume of sound will be very small, much too small for a practical instrument. The surface of the string itself is so limited that it sets up but feeble motions in the surrounding air. Now hang the wire from a large board and strike it again. The volume of sound has greatly increased, because the string has transmitted its vibrations to the large surface of the board.
Now, if you suspend a wire from a cord and attach a heavy weight to the wire, it will be under high tension and produce a clear note if struck. However, the sound will be very quiet, far too quiet for a practical instrument. The surface area of the wire itself is so small that it creates only weak movements in the surrounding air. Now, suspend the wire from a large board and strike it again. The sound volume has significantly increased because the wire has transmitted its vibrations to the large surface of the board.
To get the full sound-value of the vibrations of a string, we evidently ought to so mount the string that it may influence a large sounding surface. In a violin this is effected by straining the strings over[Pg 280] a "bridge" resting on a hollow box made of perfectly elastic wood. Draw the bow across a string. The loud sound heard proceeds not from the string only, but also from the whole surface of the box.
To fully capture the sound produced by the vibrations of a string, we clearly need to set up the string in a way that allows it to affect a larger sound surface. In a violin, this is achieved by placing the strings over[Pg 280] a "bridge" that sits on a hollow box made of highly elastic wood. When you draw the bow across a string, the loud sound that you hear originates not just from the string itself but also from the entire surface of the box.
THE SOUNDING-BOARD AND FRAME OF A PIANO.
THE SOUNDING BOARD AND FRAME OF A PIANO.
A piano has its strings strained across a frame of wood or steel, from a row of hooks in the top of the frame to a row of tapering square-ended pins in the bottom, the wires passing over sharp edges near both ends. The tuner is able, on turning a pin, to tension its strings till it gives any desired note. Readers may be interested to learn that the average tension of a string is 275 lbs., so that the total strain on the frame of a grand piano is anything between 20 and 30 tons.
A piano has its strings stretched across a frame made of wood or steel, from a row of hooks at the top of the frame to a series of tapering square-ended pins at the bottom, with the wires passing over sharp edges near both ends. The tuner can adjust the tension of the strings by turning a pin until it produces the desired note. Readers might find it interesting that the average tension of a string is 275 lbs., meaning the total strain on the frame of a grand piano is between 20 and 30 tons.
To the back of the frame is attached the sounding-board, made of spruce fir (the familiar Christmas tree). This is obtained from Central and Eastern Europe, where it is carefully selected and prepared, as it is essential that the timber should be sawn in such a way that the grain of the wood runs in the proper direction.
To the back of the frame is attached the sounding-board, made of spruce fir (the kind of tree you see at Christmas). This comes from Central and Eastern Europe, where it is carefully chosen and processed, as it’s important that the wood is cut so the grain runs in the right direction.
THE STRINGS.
THE STRINGS.
These are made of extremely strong steel wire of[Pg 281] the best quality. If you examine the wires of your piano, you will see that they vary in thickness, the thinnest being at the treble end of the frame. It is found impracticable to use wires of the same gauge and the same tension throughout. The makers therefore use highly-tensioned thick wires for the bass, and finer, shorter wires for the treble, taking advantage of the three factors—weight, tension, and length—which we have noticed above. The wires for the deepest notes are wrapped round with fine copper wire to add to their weight without increasing their diameter at the tuning-pins. There are about 600 yards (roughly one-third of a mile) of wire in a grand piano.
These are made of extremely strong steel wire of[Pg 281] the highest quality. If you look at the wires of your piano, you'll notice they vary in thickness, with the thinnest ones at the treble end of the frame. It's not practical to use wires of the same gauge and tension throughout. Therefore, manufacturers use thick, highly-tensioned wires for the bass, and finer, shorter wires for the treble, taking advantage of the three factors—weight, tension, and length—that we've mentioned earlier. The wires for the lowest notes are wrapped with fine copper wire to increase their weight without increasing their diameter at the tuning pins. There are about 600 yards (roughly one-third of a mile) of wire in a grand piano.
THE STRIKING MECHANISM.
THE IMPRESSIVE MECHANISM.
We now pass to the apparatus for putting the strings in a state of vibration. The grand piano mechanism shown in Fig. 135 may be taken as typical of the latest improvements. The essentials of an effective mechanism are:—(1) That the blow delivered shall be sharp and certain; (2) that the string shall be immediately "damped," or have its vibration checked if required, so as not to interfere with the succeeding notes of other strings; (3) that the hammer shall be able to repeat the blows in quick[Pg 282] succession. The hammer has a head of mahogany covered with felt, the thickness of which tapers gradually and regularly from an inch and a quarter at the bass end to three-sixteenths of an inch at the extreme treble notes. The entire eighty-five hammers for the piano are covered all together in one piece, and[Pg 283] then they are cut apart from each other. The consistency of the covering is very important. If too hard, it yields a harsh note, and must be reduced to the right degree by pricking with a needle. In the diagram the felt is indicated by the dotted part.
We now move on to the system that puts the strings into motion. The grand piano mechanism shown in Fig. 135 represents the latest improvements. The key elements of an effective mechanism are: (1) the strike must be quick and reliable; (2) the string must be dampened immediately, or have its vibration stopped if necessary, to avoid interfering with the following notes from other strings; (3) the hammer must be able to strike repeatedly in quick succession. The hammer has a mahogany head covered with felt, with the thickness gradually tapering from one and a quarter inches at the bass end to three-sixteenths of an inch at the highest treble notes. All eighty-five hammers for the piano are covered together in one piece, and then they are separated. The quality of the covering is very important. If it's too hard, it produces a harsh sound and needs to be adjusted by pricking with a needle. In the diagram, the felt is indicated by the dotted part.

The action carriage which operates the hammer is somewhat complicated. When the key is depressed, the left end rises, and pushes up the whole carriage, which is pivoted at one end. The hammer shank is raised by the jack B pressing upon a knob, N, called the notch, attached to the under side of the shank. When the jack has risen to a certain point, its arm, B1, catches against the button C and jerks it from under the notch at the very moment when the hammer strikes, so that it may not be blocked against the string. As it rebounds, the hammer is caught on the repetition lever R, which lifts it to allow of perfect repetition.
The action carriage that operates the hammer is a bit complex. When you press the key down, the left end rises and lifts the entire carriage, which is pivoted at one end. The hammer shank is raised by the jack B pressing against a knob, N, known as the notch, attached to the underside of the shank. Once the jack has risen to a certain level, its arm, B1, catches against the button C and pulls it from under the notch right when the hammer strikes, ensuring it doesn’t get stuck against the string. As it bounces back, the hammer is caught by the repetition lever R, which lifts it to enable perfect repetition.
The check catches the tail of the hammer head during its descent when the key is raised, and prevents it coming back violently on the carriage and rest. The tail is curved so as to wedge against the check without jamming in any way. The moment the carriage begins to rise, the rear end of the key lifts a lever connected with the damper by a vertical wire,[Pg 284] and raises the damper of the string. If the key is held down, the vibrations continue for a long time after the blow; but if released at once, the damper stifles them as the hammer regains its seat. A bar, L, passing along under all the damper lifters, is raised by depressing the loud pedal. The soft pedal slides the whole keyboard along such a distance that the hammers strike two only out of the three strings allotted to all except the bass notes, which have only one string apiece, or two, according to their depth or length. In some pianos the soft pedal presses a special damper against the strings; and a third kind of device moves the hammers nearer the strings so that they deliver a lighter blow. These two methods of damping are confined to upright pianos.
The check catches the tail of the hammer head as it comes down when the key is raised, preventing it from slamming back forcefully on the carriage and rest. The tail is curved to fit against the check without getting stuck. As soon as the carriage starts to rise, the back end of the key lifts a lever that's connected to the damper by a vertical wire,[Pg 284] which raises the damper for the string. If the key is held down, the vibrations keep going for a long time after the strike; but if it's released quickly, the damper mutes them as the hammer returns to its resting position. A bar, L, runs along under all the damper lifters and is raised by pressing the loud pedal. The soft pedal shifts the entire keyboard so that the hammers hit only two out of the three strings assigned to all but the bass notes, which have either one or two strings depending on their depth or length. In some pianos, the soft pedal presses a special damper against the strings, and another kind of mechanism moves the hammers closer to the strings so they produce a softer sound. These two methods of damping are limited to upright pianos.
A high-class piano is the result of very careful workmanship. The mechanism of each note must be accurately regulated by its tiny screws to a minute fraction of an inch. It must be ensured that every hammer strikes its blow at exactly the right place on the string, since on this depends the musical value of the note. The adjustment of the dampers requires equal care, and the whole work calls for a sensitive ear combined with skilled mechanical knowledge, so that the instrument may have a light touch,[Pg 285] strength, and certainty of action throughout the whole keyboard.
A high-end piano is the outcome of meticulous craftsmanship. The mechanism for each note needs to be precisely adjusted by its tiny screws to an extremely small fraction of an inch. It’s essential that every hammer hits its mark on the string, as the musical quality of the note relies on this. The adjustment of the dampers requires equal precision, and the entire process demands a trained ear paired with expert mechanical knowledge, ensuring the instrument offers a light touch,[Pg 285] strength, and consistent action across the entire keyboard.
THE QUALITY OF A NOTE.
NOTE QUALITY.
If two strings, alike in all respects and equally tensioned, are plucked, both will give the same note, but both will not necessarily have the same quality of tone. The quality, or timbre, as musicians call it, is influenced by the presence of overtones, or harmonics, in combination with the fundamental, or deepest, tone of the string. The fact is, that while a vibrating string vibrates as a whole, it also vibrates in parts. There are, as it were, small waves superimposed on the big fundamental waves. Points of least motion, called nodes, form on the string, dividing it into two, three, four, five, etc., parts, which may be further divided by subsidiary nodes. The string, considered as halved by one node, gives the first overtone, or octave of the fundamental. It may also vibrate as three parts, and give the second overtone, or twelfth of the fundamental;[28] and as four parts, and give the third overtone, the double octave.
If two strings that are identical in every way and equally tight are plucked, both will produce the same note, but they won't necessarily have the same tone quality. The quality, or timbre, as musicians refer to it, is affected by the presence of overtones, or harmonics, along with the fundamental, or deepest, tone of the string. The truth is that while a vibrating string moves as a whole, it also vibrates in sections. There are, so to speak, small waves layered on top of the larger fundamental waves. Areas of least motion, called nodes, form on the string, dividing it into two, three, four, five, etc., parts, which can be further divided by additional nodes. When the string is viewed as being halved by one node, it produces the first overtone, or octave of the fundamental. It can also vibrate in three parts to create the second overtone, or twelfth of the fundamental;[28] and in four parts, it generates the third overtone, the double octave.
Now, if a string be struck at a point corresponding[Pg 286] to a node, the overtones which require that point for a node will be killed, on account of the excessive motion imparted to the string at that spot. Thus to hit it at the middle kills the octave, the double octave, etc.; while to hit it at a point one-third of the length from one end stifles the twelfth and all its sub-multiples.
Now, if a string is struck at a point corresponding[Pg 286] to a node, the overtones that require that point for a node will be eliminated because of the excessive motion caused at that spot. So, hitting it in the middle cancels the octave, the double octave, and so on; whereas hitting it one-third of the way from one end suppresses the twelfth and all its sub-multiples.
A fundamental note robbed of all its harmonics is hard to obtain, which is not a matter for regret, as it is a most uninteresting sound. To get a rich tone we must keep as many useful harmonics as possible, and therefore a piano hammer is so placed as to strike the string at a point which does not interfere with the best harmonics, but kills those which are objectionable. Pianoforte makers have discovered by experiment that the most pleasing tone is excited when the point against which the hammer strikes is one-seventh to one-ninth of the length of the wire from one end.
A fundamental note stripped of all its harmonics is hard to achieve, but that’s not something to feel sorry about because it's a really dull sound. To create a rich tone, we need to preserve as many useful harmonics as we can. That's why a piano hammer is positioned to hit the string at a spot that doesn’t disrupt the best harmonics but dampens the unwanted ones. Piano manufacturers have found through experimentation that the most pleasing tone occurs when the point where the hammer strikes is one-seventh to one-ninth of the length of the wire from one end.
The nature of the material which does the actual striking is also of importance. The harder the substance, and the sharper the blow, the more prominent do the harmonics become; so that the worker has to regulate carefully both the duration of the blow and the hardness of the hammer covering.
The type of material that makes the actual impact is also important. The harder the substance and the sharper the hit, the more noticeable the harmonics become; therefore, the worker has to carefully control both the length of the strike and the hardness of the hammer covering.
[26] Tyndall, "On Sound," p. 75.
Chapter XV.
WIND INSTRUMENTS.
Longitudinal vibration—Columns of air—Resonance of columns of air—Length and tone—The open pipe—The overtones of an open pipe—Where overtones are used—The arrangement of the pipes and pedals—Separate sound-boards—Varieties of stops—Tuning pipes and reeds—The bellows—Electric and pneumatic actions—The largest organ in the world—Human reeds.
Longitudinal vibration—Columns of air—Resonance of air columns—Length and pitch—The open pipe—The overtones of an open pipe—Where overtones are applied—The setup of the pipes and pedals—Separate soundboards—Types of stops—Tuning pipes and reeds—The bellows—Electric and pneumatic actions—The largest organ in the world—Human reeds.
LONGITUDINAL VIBRATION.
Longitudinal vibration.
In stringed instruments we are concerned only with the transverse vibrations of a string—that is, its movements in a direction at right angles to the axis of the string. A string can also vibrate longitudinally—that is, in the direction of its axis—as may be proved by drawing a piece of resined leather along a violin string. In this case the harmonics "step up" at the same rate as when the movements were transverse.
In string instruments, we focus only on the sideways vibrations of a string—that is, its movements at right angles to the string's length. A string can also vibrate lengthwise—that is, in the direction of its length— which can be demonstrated by rubbing a piece of resined leather along a violin string. In this case, the harmonics "step up" at the same rate as when the movements were sideways.
Let us substitute for a wire a stout bar of metal fixed at one end only. The longitudinal vibrations of this rod contain overtones of a different ratio.[Pg 288] The first harmonic is not an octave, but a twelfth. While a tensioned string is divided by nodes into two, three, four, five, six, etc., parts, a rod fixed at one end only is capable of producing only those harmonics which correspond to division into three, five, seven, nine, etc., parts. Therefore a free-end rod and a wire of the same fundamental note would not have the same timbre, or quality, owing to the difference in the harmonics.
Let’s replace a wire with a sturdy metal bar that’s fixed at one end. The long vibrations of this rod have overtones with different ratios. The first harmonic is not an octave but a twelfth. While a tensioned string is divided by nodes into two, three, four, five, six, etc., parts, a rod fixed at one end can only produce harmonics that correspond to divisions into three, five, seven, nine, etc., parts. As a result, a rod with a free end and a wire tuned to the same fundamental note would have different timbres or qualities because of the differences in their harmonics.[Pg 288]
COLUMNS OF AIR.
Air Columns.
In wind instruments we employ, instead of rods or wires, columns of air as the vibrating medium. The note of the column depends on its length. In the "penny whistle," flute, clarionet, and piccolo the length of the column is altered by closing or opening apertures in the substance encircling the column.
In wind instruments, we use columns of air as the vibrating medium instead of rods or wires. The pitch of the column depends on its length. In instruments like the penny whistle, flute, clarinet, and piccolo, the length of the column is changed by opening or closing holes in the material surrounding the column.
RESONANCE OF COLUMNS OF AIR.
Vibrations of columns of air.
Why does a tube closed at one end, such as the shank of a key, emit a note when we blow across the open end? The act of blowing drives a thin sheet of air against the edge of the tube and causes it to vibrate. The vibrations are confused, some "pulses" occurring more frequently than others. If[Pg 289] we blew against the edge of a knife or a piece of wood, we should hear nothing but a hiss. But when, as in the case which we are considering, there is a partly-enclosed column of air close to the pulses, this selects those pulses which correspond to its natural period of vibration, and augments them to a sustained and very audible musical sound.
Why does a tube closed at one end, like the shank of a key, make a sound when we blow across the open end? Blowing forces a thin sheet of air against the edge of the tube, causing it to vibrate. The vibrations are chaotic, with some "pulses" happening more often than others. If[Pg 289] we blew against the edge of a knife or a piece of wood, we would only hear a hiss. But in the situation we're discussing, where there's a partly-enclosed column of air near the pulses, it picks out those pulses that match its natural vibration frequency and amplifies them into a sustained and very loud musical sound.
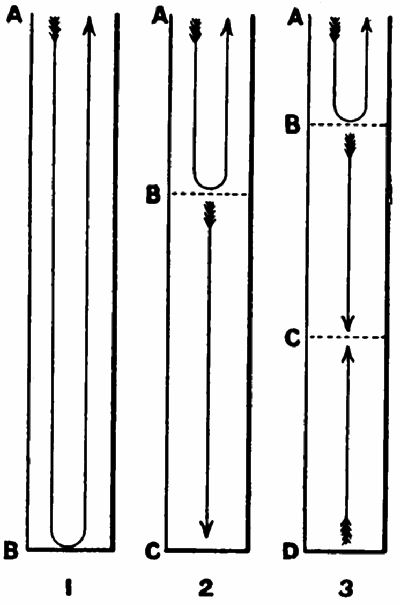
In Fig. 136, 1 is a pipe, closed at the bottom and open at the top. A tuning-fork of the same note as the pipe is struck and held over it so that the prongs vibrate upwards and downwards. At the commencement of an outward movement of the prongs the air in front of them is compressed. This impulse, imparted to the air in the pipe, runs down the column, strikes the bottom, and returns. Just as it reaches the top the prong is beginning to move inwards, causing a[Pg 290] rarefaction of the air behind it. This effect also travels down and back up the column of air in the pipe, reaching the prong just as it arrives at the furthest point of the inward motion. The process is repeated, and the column of air in the pipe, striking on the surrounding atmosphere at regular intervals, greatly increases the volume of sound. We must observe that if the tuning-fork were of too high or too low a note for the column of air to move in perfect sympathy with it, this increase of sound would not result. Now, when we blow across the end, we present, as it were, a number of vibrating tuning-forks to the pipe, which picks out those air-pulses with which it sympathizes.
In Fig. 136, 1 is a pipe that is sealed at the bottom and open at the top. A tuning fork that matches the note of the pipe is struck and held over it, causing the prongs to vibrate up and down. When the prongs move outward, the air in front of them gets compressed. This impulse travels down the air column in the pipe, hits the bottom, and bounces back. Just as it reaches the top, the prong is starting to move inward, creating a[Pg 290] rarefaction of the air behind it. This effect also travels down and back up the column of air in the pipe, reaching the prong just as it completes its inward motion. This cycle repeats, and the column of air in the pipe, striking the surrounding atmosphere at regular intervals, significantly amplifies the sound. It's important to note that if the tuning fork's note is too high or too low for the column of air to resonate perfectly with it, this sound amplification wouldn’t occur. Now, when we blow across the end, it’s like we’re presenting a bunch of vibrating tuning forks to the pipe, which selects the air pulses that it resonates with.
LENGTH AND TONE.
LENGTH AND TONE.
The rate of vibration is found to be inversely proportional to the length of the pipe. Thus, the vibrations of a two-foot pipe are twice as rapid as those of a four-foot pipe, and the note emitted by the former is an octave higher than that of the latter. A one-foot pipe gives a note an octave higher still. We are here speaking of the fundamental tones of the pipes. With them, as in the case of strings, are associated the overtones, or harmonics,[Pg 291] which can be brought into prominence by increasing the pressure of the blast at the top of the pipe. Blow very hard on your key, and the note suddenly changes to one much shriller. It is the twelfth of the fundamental, of which it has completely got the upper hand.
The vibration rate is inversely related to the length of the pipe. This means that the vibrations of a two-foot pipe are twice as fast as those of a four-foot pipe, and the sound produced by the two-foot pipe is an octave higher than that of the four-foot pipe. A one-foot pipe produces a sound that’s another octave higher. We are discussing the fundamental tones of the pipes. Similar to strings, these are accompanied by overtones, or harmonics,[Pg 291] which can be emphasized by increasing the air pressure at the top of the pipe. If you blow really hard on your key, the note changes to a much sharper one. This is the twelfth of the fundamental, completely dominating it.
We must now put on our thinking-caps and try to understand how this comes about. First, let us note that the vibration of a body (in this case a column of air) means a motion from a point of rest to a point of rest, or from node to node. In the air-column in Fig. 136, 1, there is only one point of rest for an impulse—namely, at the bottom of the pipe. So that to pass from node to node the impulse must pass up the pipe and down again. The distance from node to node in a vibrating body is called a ventral segment. Remember this term. Therefore the pipe represents a semi-ventral segment when the fundamental note is sounding.
We need to think carefully and try to understand how this happens. First, let's note that the vibration of a body (in this case, a column of air) means moving from one point of rest to another, or from node to node. In the air column in Fig. 136, 1, there’s only one point of rest for an impulse—at the bottom of the pipe. So, to go from node to node, the impulse must travel up the pipe and back down again. The distance from node to node in a vibrating body is called a ventral segment. Keep this term in mind. Therefore, the pipe represents a semi-ventral segment when the fundamental note is sounding.
When the first overtone is sounded the column divides itself into two vibrating parts. Where will the node between them be? We might naturally say, "Half-way up." But this cannot be so; for if the node were so situated, an impulse going down the pipe would only have to travel to the bottom[Pg 292] to find another node, while an impulse going up would have to travel to the top and back again—that is, go twice as far. So the node forms itself one-third of the distance down the pipe. From B to A (Fig. 136, 2) and back is now equal to from B to C. When the second overtone is blown (Fig. 136, 3) a third node forms. The pipe is now divided into five semi-ventral segments. And with each succeeding overtone another node and ventral segment are added.
When the first overtone is played, the column splits into two vibrating sections. Where will the node between them be? We might instinctively say, "Halfway up." But that can't be right; if the node were located there, an impulse traveling down the pipe would only have to reach the bottom[Pg 292] to find another node, while an impulse traveling up would need to go to the top and back—essentially traveling twice as far. So, the node actually forms one-third of the way down the pipe. From B to A (Fig. 136, 2) and back is now equal to the distance from B to C. When the second overtone is played (Fig. 136, 3), a third node appears. The pipe is now divided into five semi-ventral segments. And with each new overtone, another node and ventral segment are added.
The law of vibration of a column of air is that the number of vibrations is directly proportional to the number of semi-ventral segments into which the column of air inside the pipe is divided.[29] If the fundamental tone gives 100 vibrations per second, the first overtone in a closed pipe must give 300, and the second 500 vibrations.
The law of vibration of a column of air states that the number of vibrations is directly proportional to the number of semi-ventral segments that the column of air inside the pipe is divided into.[29] If the fundamental tone produces 100 vibrations per second, the first overtone in a closed pipe will produce 300, and the second will produce 500 vibrations.
THE OPEN PIPE.
The Open Pipe.
A pipe open at both ends is capable of emitting a note. But we shall find, if we experiment, that the note of a stopped pipe is an octave lower than that of an open pipe of equal length. This is[Pg 293] explained by Fig. 137, 1. The air-column in the pipe (of the same length as that in Fig. 136) divides itself, when an end is blown across, into two equal portions at the node B, the natural point to obtain equilibrium. A pulse will pass from A or A1 to B and back again in half the time required to pass from A to B and back in Fig. 136, 1; therefore the note is an octave higher.
A pipe open at both ends can produce a sound. However, if we experiment, we'll find that the sound from a closed pipe is an octave lower than that from an open pipe of the same length. This is[Pg 293] illustrated in Fig. 137, 1. When we blow across one end of the pipe (which has the same length as that in Fig. 136), the air column separates into two equal parts at the node B, which is the natural point for achieving equilibrium. A pulse will travel from A or A to B and back in half the time it takes to travel from A to B and back in Fig. 136, 1; this is why the sound is an octave higher.

THE OVERTONES OF AN OPEN PIPE.
THE OVERTONES OF AN OPEN PIPE.
The first overtone results when nodes form as in Fig. 137, 2, at points one-quarter of the length of the pipe from the ends, giving one complete ventral segment and two semi-ventral segments. The vibrations now are twice as rapid as before. The second overtone requires three nodes, as in Fig. 137, 3. The rate has now trebled. So that, while the[Pg 294] overtones of a closed pipe rise in the ratio 1, 3, 5, 7, etc., those of an open pipe rise in the proportion 1, 2, 3, 4, etc.
The first overtone occurs when nodes form as shown in Fig. 137, 2, at points one-quarter of the length of the pipe from each end, creating one complete ventral segment and two semi-ventral segments. The vibrations at this stage are now twice as fast as before. The second overtone needs three nodes, as illustrated in Fig. 137, 3. The frequency has now increased threefold. Thus, while the[Pg 294] overtones of a closed pipe increase in the ratio 1, 3, 5, 7, etc., those of an open pipe increase in the ratio 1, 2, 3, 4, etc.
WHERE OVERTONES ARE USED.
Where overtones are used.
In the flute, piccolo, and clarionet, as well as in the horn class of instrument, the overtones are as important as the fundamental notes. By artificially altering the length of the column of air, the fundamental notes are also altered, while the harmonics of each fundamental are produced at will by varying the blowing pressure; so that a continuous chromatic, or semitonal, scale is possible throughout the compass of the instrument.
In the flute, piccolo, and clarinet, as well as in the horn family of instruments, the overtones are just as important as the fundamental notes. By changing the length of the column of air, the fundamental notes are modified, while the harmonics of each fundamental can be produced by adjusting the blowing pressure; this allows for a continuous chromatic, or semitone, scale throughout the instrument's range.
THE ORGAN.
THE ORGAN.
From the theory of acoustics[30] we pass to the practical application, and concentrate our attention upon the grandest of all wind instruments, the pipe organ. This mechanism has a separate pipe for every note, properly proportioned. A section of an ordinary wooden pipe is given in Fig. 138. Wind rushes up through the foot of the pipe into a little chamber, closed by a block of wood or a plate except for a narrow slit, which directs it against the sharp[Pg 295] lip A, and causes a fluttering, the proper pulse of which is converted by the air-column above into a musical sound.
From the theory of acoustics[30] we move to practical application and focus on the most impressive of all wind instruments, the pipe organ. This instrument has a dedicated pipe for each note, accurately sized. A section of a standard wooden pipe is shown in Fig. 138. Air flows up through the base of the pipe into a small chamber, which is closed off by a block of wood or a plate, except for a narrow slit that directs the air against the sharp[Pg 295] lip A, creating a fluttering sound. This pulse is then transformed by the air column above into musical sound.

In even the smallest organs more than one pipe is actuated by one key on the keyboard, for not only do pipes of different shapes give different qualities of tone, but it is found desirable to have ranks of pipes with their bottom note of different pitches. The length of an open pipe is measured from the edge of the lip to the top of the pipe; of a stopped pipe, from the lip to the top and back again. When we speak of a 16 or 8 foot rank, or stop, we mean one of which the lowest note in the rank is that produced by a 16 or 8 foot open pipe, or their stopped equivalents (8 or 4 foot). In a big organ we find 32, 16, 8, 4, and 2 foot stops, and some of these repeated a number of times in pipes of different shape and construction.
In even the smallest organs, more than one pipe is activated by a single key on the keyboard. This is because pipes of different shapes produce different sound qualities, and it’s also useful to have ranks of pipes with their lowest note at different pitches. The length of an open pipe is measured from the edge of the lip to the top of the pipe; for a stopped pipe, it’s measured from the lip to the top and back again. When we refer to a 16 or 8 foot rank, or stop, we mean one where the lowest note produced is from a 16 or 8 foot open pipe, or their stopped equivalents (8 or 4 foot). In a large organ, you’ll find 32, 16, 8, 4, and 2 foot stops, and some of these can appear multiple times with pipes of different shapes and constructions.
THE ARRANGEMENT OF THE PIPES.
THE LAYOUT OF THE PIPES.
We will now study briefly the mechanism of a very simple single-keyboard organ, with five ranks of pipes, or stops.
We will now briefly examine how a basic single-keyboard organ works, which has five ranks of pipes, or stops.

It is necessary to arrange matters so that the pressing down of one key may make all five of the pipes belonging to it speak, or only four, three, two, or one, as we may desire. The pipes are mounted in rows on a sound-board, which is built up in several layers. At the top is the upper board; below it come the sliders, one for each stop; and underneath that the table. In Fig. 139 we see part of the table from below. Across the under side are fastened parallel bars with spaces (shown black) left between them. Two other bars are fastened across the ends, so that each groove is enclosed by wood at the top and on all sides. The under side of the table has sheets of leather glued or otherwise attached to it in such a manner that no air can leak from one groove to the next. Upper board, sliders, and table are pierced with rows of holes, to permit the passage of wind from the grooves to the pipes. The grooves under the big pipes are wider than those[Pg 297] under the small pipes, as they have to pass more air. The bars between the grooves also vary in width according to the weight of the pipes which they have to carry. The sliders can be moved in and out a short distance in the direction of the axis of the rows of pipes. There is one slider under each row. When a slider is in, the holes in it do not correspond with those in the table and upper board, so that no wind can get from the grooves to the rank over that particular slider. Fig. 140 shows the manner in which the sliders are operated by the little knobs (also called stops) projecting from the casing of the organ within convenient reach of the performer's hands. One stop is in, the other drawn out.
It’s essential to set things up so that pressing down one key can make all five pipes respond, or just four, three, two, or one, depending on what we want. The pipes are arranged in rows on a sound-board, which is built in multiple layers. At the top is the upper board; below that are the sliders, one for each stop; and underneath is the table. In Fig. 139, we see part of the table from below. Parallel bars are attached across the underside with spaces (shown in black) left between them. Two other bars are connected across the ends so that each groove is enclosed by wood on top and all sides. The underside of the table has sheets of leather glued or otherwise secured to it to prevent air from leaking between grooves. The upper board, sliders, and table have rows of holes to allow air to flow from the grooves to the pipes. The grooves beneath the larger pipes are wider than those [Pg 297] under the smaller pipes since they need to allow more air. The bars between the grooves also vary in width based on the weight of the pipes they support. The sliders can be moved in and out a short distance along the rows of pipes. There is one slider beneath each row. When a slider is in, the holes in it don’t line up with those in the table and upper board, so no air can move from the grooves to the row above that specific slider. Fig. 140 shows how the sliders are controlled by the small knobs (also known as stops) that stick out from the organ casing, making them easy for the performer to reach. One stop is in, while the other is pulled out.

In Fig. 141 we see the table, etc., in cross section, with a slider out, putting the pipes of its rank in communication with the grooves. The same diagram shows us in section the little triangular pallets which admit air from the wind-chest to the grooves; and Fig. 142 gives us an end section of table, sliders, and[Pg 298] wind-chest, together with the rods, etc., connecting the key to its pallet. When the key is depressed, the sticker (a slight wooden rod) is pushed up. This rocks a backfall, or pivoted lever, to which is attached the pulldown, a wire penetrating the bottom of the wind-chest to the pallet. As soon as the pallet opens, wind rushes into the groove above through the aperture in the leather bottom, and thence to any one of the pipes of which the slider has been drawn out. (The sliders in Fig. 142 are solid black.) It is evident that if the sound-board is sufficiently deep from back to front, any number of rows of pipes may be placed on it.
In Fig. 141, we see the table, etc., in cross-section, with a slider pulled out, connecting the pipes in its rank to the grooves. The same diagram also shows us in section the small triangular pallets that let air from the wind-chest into the grooves; and Fig. 142 provides an end section of the table, sliders, and[Pg 298] wind-chest, along with the rods, etc., linking the key to its pallet. When the key is pressed, the sticker (a small wooden rod) is pushed up. This tilts a backfall, or pivoted lever, to which the pulldown is attached, a wire that goes through the bottom of the wind-chest to the pallet. As soon as the pallet opens, air rushes into the groove above through the opening in the leather bottom, and then into any of the pipes from which the slider has been pulled out. (The sliders in Fig. 142 are solid black.) It is clear that if the soundboard is deep enough from back to front, any number of rows of pipes can be placed on it.

PEDALS.
Pedals.
The organ pedals are connected to the pallets by an action similar to that of the keys. The pedal stops are generally of deep tone, 32-foot and 16-foot, as they have to sustain the bass part of the musical harmonies. By means of[Pg 299] couplers one or more of the keyboard stops may be linked to the pedals.
The organ pedals connect to the pallets through a mechanism similar to the keys. The pedal stops usually have a deep tone, 32-foot and 16-foot, because they support the bass part of the musical harmonies. Using [Pg 299] couplers, one or more of the keyboard stops can be linked to the pedals.
SEPARATE SOUND-BOARDS.
Separate soundboards.
The keyboard of a very large organ has as many as five manuals, or rows of keys. Each manual operates what is practically a separate organ mounted on its own sound-board.
The keyboard of a very large organ can have up to five manuals, or rows of keys. Each manual controls what is essentially a separate organ set up on its own soundboard.

The manuals are arranged in steps, each slightly overhanging that below. Taken in order from the top, they are:—(1.) Echo organ, of stops of small scale and very soft tone, enclosed in a "swell-box." (2.) Solo organ, of stops imitating orchestral instruments. The wonderful "vox humana" stop also belongs to this manual. (3.) Swell organ, contained in a swell-box, the front and sides of which have shutters which can be opened and closed by the pressure of the foot on a lever, so as to regulate the amount of sound proceeding from the pipes inside. (4.) Great organ, including pipes of powerful tone. (5.) Choir organ, of soft, mellow stops, often enclosed in a swell-box. We may add to these the pedal organ, which can be coupled to any but the echo manual.
The manuals are organized in steps, each slightly overlapping the one below. Taken in order from the top, they are:—(1.) Echo organ, with stops that are small in scale and very soft in tone, enclosed in a "swell-box." (2.) Solo organ, featuring stops that mimic orchestral instruments. The amazing "vox humana" stop is also part of this manual. (3.) Swell organ, housed in a swell-box, the front and sides of which have shutters that can be opened and closed by pressing a lever with your foot, allowing you to control the sound coming from the pipes inside. (4.) Great organ, which includes pipes with a powerful tone. (5.) Choir organ, featuring soft, mellow stops, often enclosed in a swell-box. We can also include the pedal organ, which can be connected to any manual except the echo one.
VARIETIES OF STOPS.
TYPES OF STOPS.
We have already remarked that the quality of a stop depends on the shape and construction of the pipe. Some pipes are of wood, others of metal. Some are rectangular, others circular. Some have parallel sides, others taper or expand towards the top. Some are open, others stopped.
We’ve already noted that the quality of a stop relies on the shape and design of the pipe. Some pipes are made of wood, while others are made of metal. Some are rectangular, and others are circular. Some have parallel sides, while others narrow or widen toward the top. Some are open, and others are closed.
The two main classes into which organ pipes may be divided are:—(1.) Flue pipes, in which the wind is directed against a lip, as in Fig. 138. (2.) Reed pipes—that is, pipes used in combination with a simple[Pg 302] device for admitting air into the bottom of the pipe in a series of gusts. Fig. 144 shows a striking reed, such as is found in the ordinary motor horn. The elastic metal tongue when at rest stands a very short distance away from the orifice in the reed. When wind is blown through the reed the tongue is sucked against the reed, blocks the current, and springs away again. A free reed has a tongue which vibrates in a slot without actually touching the sides. Harmonium and concertina reeds are of this type. In the organ the reed admits air to a pipe of the correct length to sympathize with the rate of the puffs of air which the reed passes. Reed pipes expand towards the top.
The two main types of organ pipes are: (1.) Flue pipes, where the air is directed against a lip, as shown in Fig. 138. (2.) Reed pipes—these are pipes that work with a simple [Pg 302] mechanism to let air into the bottom of the pipe in bursts. Fig. 144 displays a striking reed, like the ones used in standard motor horns. The flexible metal tongue, when at rest, is only a tiny distance away from the opening in the reed. When air blows through the reed, the tongue gets pulled against it, stops the airflow, and then springs back out. A free reed has a tongue that vibrates in a slot without actually touching the sides. Harmonium and concertina reeds are examples of this type. In the organ, the reed allows air into a pipe of the right length to match the timing of the air bursts that the reed produces. Reed pipes widen toward the top.
TUNING PIPES AND REEDS.
Tuning pipes and reeds.
Pipes are tuned by adjusting their length. The plug at the top of a stopped pipe is pulled out or pushed in a trifle to flatten or sharpen the note respectively. An open pipe, if large, has a tongue cut in the side at the top, which can be pressed inwards or outwards for the purpose of correcting the tone. Small metal[Pg 303] pipes are flattened by contracting the tops inwards with a metal cone like a candle-extinguisher placed over the top and tapped; and sharpened by having the top splayed by a cone pushed in point downwards. Reeds of the striking variety (see Fig. 144) have a tuning-wire pressing on the tongue near the fixed end. The end of this wire projects through the casing. By moving it, the length of the vibrating part of the tongue is adjusted to correctness.
Pipes are tuned by changing their length. The plug at the top of a stopped pipe is pulled out or pushed in slightly to flatten or sharpen the note, respectively. An open pipe, if large, has a tongue cut into the side at the top, which can be pushed in or pulled out to correct the tone. Small metal[Pg 303] pipes are flattened by pressing the tops inward with a metal cone, like a candle snuffer, placed over the top and tapped; and sharpened by spreading the top with a cone pushed in point downwards. Reeds of the striking type (see Fig. 144) have a tuning wire pressing against the tongue near the fixed end. The end of this wire sticks out through the casing. By moving it, the length of the vibrating part of the tongue is adjusted for accuracy.
BELLOWS.
Bells.
Different stops require different wind-pressures, ranging from 1⁄10 lb. to 1 lb. to the square inch, the reeds taking the heaviest pressures. There must therefore be as many sets of bellows and wind-chests as there are different pressures wanted. A very large organ consumes immense quantities of air when all the stops are out, and the pumping has to be done by a powerful gas, water, or electric engine. Every bellows has a reservoir (see Fig. 143) above it. The top of this is weighted to give the pressure required. A valve in the top opens automatically as soon as the reservoir has expanded to a certain fixed limit, so that there is no possibility of bursting the leather sides.
Different stops need different wind pressures, ranging from 1⁄10 lb. to 1 lb. per square inch, with the reeds handling the highest pressures. Therefore, there must be as many sets of bellows and wind chests as there are different pressures required. A very large organ uses a huge amount of air when all the stops are activated, and pumping has to be done by a powerful gas, water, or electric engine. Every bellows has a reservoir (see Fig. 143) above it. The top is weighted to create the necessary pressure. A valve at the top opens automatically once the reservoir expands to a certain fixed limit, preventing the leather sides from bursting.

ELECTRIC AND PNEUMATIC ACTIONS.
Electric and pneumatic actions.
We have mentioned in connection with railway signalling that the signalman is sometimes relieved of the hard manual labour of moving signals and points by the employment of electric and pneumatic auxiliaries. The same is true of organs and organists. The touch of the keys has been greatly lightened by making the keys open air-valves or complete electric circuits which actuate the mechanism for pulling down the pallets. The stops, pedals, and couplers also employ "power." Not only are the performer's muscles spared a lot of heavy work when compressed air and electricity aid him, but he is able to have the console, or keyboard, far away from the pipes. "From the console, the player, sitting with the singers, or in any desirable part of the choir or chancel, would be able to command the working of the whole of the largest organ situated afar at the western end of the nave; would draw each stop in complete reliance on the sliders and the sound-board fulfilling their office; ... and—marvel of it all—the player, using the swell pedal in his ordinary manner, would obtain[Pg 306] crescendo and diminuendo with a more perfect effect than by the old way."[31]
We've mentioned in relation to railway signaling that signalmen are sometimes relieved from the heavy physical labor of moving signals and switches through the use of electric and pneumatic systems. The same goes for organs and organists. The pressure on the keys has been significantly eased by having the keys open air valves or complete electric circuits that activate the mechanisms for pulling down the pallets. The stops, pedals, and couplers also use "power." Not only do these advancements spare the performer's muscles from a lot of heavy lifting when assisted by compressed air and electricity, but they also allow the console, or keyboard, to be located far from the pipes. "From the console, the player, sitting with the singers or in any preferred spot in the choir or chancel, could control the operation of the entire largest organ located far at the western end of the nave; he would pull each stop knowing that the sliders and soundboard would do their job; ... and—miracle of miracles—the player, using the swell pedal as usual, would achieve crescendo and diminuendo with a more perfect effect than in the old way."
In cathedrals it is no uncommon thing for the different sound-boards to be placed in positions far apart, so that to the uninitiated there may appear to be several independent organs scattered about. Yet all are absolutely under the control of a man who is sitting away from them all, but connected with them by a number of tubes or wires.
In cathedrals, it's quite common for the various soundboards to be set up in far-apart locations, which might make it seem to an outsider that there are several separate organs scattered around. However, all of them are completely under the control of a person who is seated away from them, connected through a series of tubes or wires.
The largest organ in the world is that in the Town Hall, Sydney. It has a hundred and twenty-six speaking stops, five manuals, fourteen couplers, and forty-six combination studs. The pipes, about 8,000 in number, range from the enormous 64-foot contra-trombone to some only a fraction of an inch in length. The organ occupies a space 85 feet long and 26 feet deep.
The biggest organ in the world is in the Town Hall in Sydney. It has 126 speaking stops, five manuals, 14 couplers, and 46 combination studs. There are around 8,000 pipes, ranging from the massive 64-foot contra-trombone to some that are just a tiny fraction of an inch long. The organ takes up a space that is 85 feet long and 26 feet deep.
HUMAN REEDS.
HUMAN REEDS.
The most wonderful of all musical reeds is found in the human throat, in the anatomical part called the larynx, situated at the top of the trachea, or windpipe.
The most amazing musical instrument is found in the human throat, in the body part called the larynx, located at the top of the trachea, or windpipe.
Slip a piece of rubber tubing over the end of a pipe, allowing an inch or so to project. Take the[Pg 307] free part of the tube by two opposite points between the first fingers and thumbs and pull it until the edges are stretched tight. Now blow through it. The wind, forcing its way between the two rubber edges, causes them and the air inside the tube to vibrate, and a musical note results. The more you strain the rubber the higher is the note.
Slip a piece of rubber tubing over the end of a pipe, letting about an inch stick out. Hold the[Pg 307] free part of the tube at two opposite points with your first fingers and thumbs and pull it until the edges are stretched tight. Now blow through it. The air, pushing through the two rubber edges, makes them and the air inside the tube vibrate, producing a musical note. The more you stretch the rubber, the higher the note becomes.
The larynx works on this principle. The windpipe takes the place of the glass pipe; the two vocal cords represent the rubber edges; and the arytenoid muscles stand instead of the hands. When contracted, these muscles bring the edges of the cords nearer to one another, stretch the cords, and shorten the cords. A person gifted with a "very good ear" can, it has been calculated, adjust the length of the vocal cords to 1⁄17000th of an inch!
The larynx operates on this principle. The windpipe acts like the glass pipe; the two vocal cords represent the rubber edges; and the arytenoid muscles function like the hands. When these muscles contract, they pull the edges of the cords closer together, stretch the cords, and shorten them. It has been estimated that a person with a "very good ear" can adjust the length of the vocal cords to 1⁄17000th of an inch!
Simultaneously with the adjustment of the cords is effected the adjustment of the length of the windpipe, so that the column of air in it may be of the right length to vibrate in unison. Here again is seen a wonderful provision of nature.
At the same time the cords are adjusted, the length of the windpipe is also adjusted, so that the column of air inside it can be the right length to vibrate in harmony. Once again, we see a remarkable feature of nature.
The resonance of the mouth cavity is also of great importance. By altering the shape of the mouth the various harmonics of any fundamental note produced by the larynx are rendered prominent,[Pg 308] and so we get the different vocal sounds. Helmholtz has shown that the fundamental tone of any note is represented by the sound oo. If the mouth is adjusted to bring out the octave of the fundamental, o results. a is produced by accentuating the second harmonic, the twelfth; ee by developing the second and fourth harmonics; while for ah the fifth and seventh must be prominent.
The shape of the mouth cavity is really important. By changing how the mouth is shaped, the different harmonics of any main note produced by the larynx become more noticeable,[Pg 308] which gives us various vocal sounds. Helmholtz has shown that the basic tone of any note corresponds to the sound oo. If the mouth is adjusted to emphasize the octave of the fundamental, it results in o. a is created by highlighting the second harmonic, the twelfth; ee is achieved by focusing on the second and fourth harmonics; and for ah, the fifth and seventh must be emphasized.
When we whistle we transform the lips into a reed and the mouth into a pipe. The tension of the lips and the shape of the mouth cavity decide the note. The lips are also used as a reed for blowing the flute, piccolo, and all the brass band instruments of the cornet order. In blowing a coach-horn the various harmonics of the fundamental note are brought out by altering the lip tension and the wind pressure. A cornet is practically a coach-horn rolled up into a convenient shape and furnished with three keys, the depression of which puts extra lengths of tubing in connection with the main tube—in fact, makes it longer. One key lowers the fundamental note of the horn half a tone; the second, a full tone; the third, a tone and a half. If the first and third are pressed down together, the note sinks two tones; if the[Pg 309] second and third, two and a half tones; and simultaneous depression of all three gives a drop of three tones. The performer thus has seven possible fundamental notes, and several harmonics of each of these at his command; so that by a proper manipulation of the keys he can run up the chromatic scale.
When we whistle, we turn our lips into a reed and our mouth into a pipe. The tension of the lips and the shape of the mouth determine the note. The lips also function as a reed for playing the flute, piccolo, and all the brass instruments like the cornet. When blowing a coach horn, the different harmonics of the main note are created by changing the lip tension and airflow. A cornet is basically a coach horn shaped into a more compact form and equipped with three valves, pressing which connects extra lengths of tubing to the main tube—essentially making it longer. One valve drops the main note of the horn by a half step; the second drops it by a whole step; and the third drops it by a step and a half. If the first and third valves are pressed together, the note goes down two steps; if the second and third are pressed together, it drops by two and a half steps; and if all three are pressed at once, it lowers by three steps. This way, the performer has seven possible main notes, along with several harmonics for each of them, allowing for a full range of chromatic scales through skillful use of the valves.
We should add that the cornet tube is an "open" pipe. So is that of the flute. The clarionet is a "stopped" pipe.
We should mention that the cornet tube is an "open" pipe. The same is true for the flute. The clarinet is a "stopped" pipe.
[29] It is obvious that in Fig. 136, 2, a pulse will pass from A to B and back in one-third the time required for it to pass from A to B and back in Fig. 136, 1.
[29] It's clear that in Fig. 136, 2, a pulse will travel from A to B and back in one-third the time it takes to travel from A to B and back in Fig. 136, 1.
[31] "Organs and Tuning," p. 245.
Chapter XVI.
TALKING-MACHINES.
The phonograph—The recorder—The reproducer—The gramophone—The making of records—Cylinder records—Gramophone records.
The phonograph—The recorder—The reproducer—The gramophone—Making records—Cylinder records—Gramophone records.
In the Patent Office Museum at South Kensington is a curious little piece of machinery—a metal cylinder mounted on a long axle, which has at one end a screw thread chased along it. The screw end rotates in a socket with a thread of equal pitch cut in it. To the other end is attached a handle. On an upright near the cylinder is mounted a sort of drum. The membrane of the drum carries a needle, which, when the membrane is agitated by the air-waves set up by human speech, digs into a sheet of tinfoil wrapped round the cylinder, pressing it into a helical groove turned on the cylinder from end to end. This construction is the first phonograph ever made. Thomas Edison, the "wizard of the West," devised it in 1876; and from this rude parent have descended[Pg 311] the beautiful machines which record and reproduce human speech and musical sounds with startling accuracy.
In the Patent Office Museum at South Kensington, there’s a fascinating little piece of machinery—a metal cylinder mounted on a long axle, with a screw thread at one end. The screw end spins in a socket that has a matching thread. A handle is attached to the other end. Next to the cylinder, there’s a kind of drum mounted on an upright. The drum’s membrane has a needle that, when moved by the sound waves from human speech, presses into a sheet of tinfoil wrapped around the cylinder, creating a helical groove from end to end. This setup is the first phonograph ever created. Thomas Edison, the "wizard of the West," invented it in 1876. From this rudimentary device have evolved[Pg 311] the impressive machines that record and reproduce human speech and music with astonishing accuracy.

We do not propose to trace here the development of the talking-machine; nor will it be necessary to describe in detail its mechanism, which is probably well known to most readers, or could be mastered in a very short time on personal examination. We will content ourselves with saying that the wax cylinder of the phonograph, or the ebonite disc of the gramophone, is generally rotated by clockwork concealed in the body of the machine. The speed of rotation has to be very carefully governed, in order that the record may revolve under the reproducing point at a uniform speed. The principle of the governor commonly[Pg 312] used appears in Fig. 146. The last pinion of the clockwork train is mounted on a shaft carrying two triangular plates, A and C, to which are attached three short lengths of flat steel spring with a heavy ball attached to the centre of each. A is fixed; C moves up the shaft as the balls fly out, and pulls with it the disc D, which rubs against the pad P (on the end of a spring) and sets up sufficient friction to slow the clockwork. The limit rate is regulated by screw S.
We’re not going to cover the development of the talking machine here; it’s also not necessary to go into detail about its mechanism since most readers probably already know a lot about it, or could easily figure it out by examining it briefly. Instead, we'll just mention that the wax cylinder of the phonograph or the ebonite disc of the gramophone is usually rotated by clockwork hidden inside the machine. The rotation speed must be carefully controlled so that the record turns under the reproducing point at a consistent speed. The principle of the governor commonly used is shown in Fig. 146. The last gear of the clockwork system is mounted on a shaft that carries two triangular plates, A and C, to which three short pieces of flat steel spring with a heavy ball attached to the center of each are connected. A is fixed, while C moves up the shaft as the balls fly out, pulling the disc D with it, which rubs against the pad P (at the end of a spring) and creates enough friction to slow down the clockwork. The maximum speed is adjusted using screw S.
THE PHONOGRAPH.
The record player.
Though the recording and reproducing apparatus of a phonograph gives very wonderful results, its construction is quite simple. At the same time, it must be borne in mind that an immense amount of experimenting has been devoted to finding out the most suitable materials and forms for the parts.
Though the recording and reproducing setup of a phonograph delivers amazing results, its design is actually pretty straightforward. However, it’s important to remember that a huge amount of experimentation has gone into discovering the best materials and shapes for its components.

The recorder (Fig. 147) is a little circular box about one and a half inches in diameter.[32] From the top a tube leads to the horn. The bottom is a circular plate, C C, hinged at one side. This plate supports a glass disc, D, about 1⁄150th of an inch thick, to which is attached the cutting stylus—a tiny sapphire rod with a cup-shaped end having very[Pg 313] sharp edges. Sound-waves enter the box through the horn tube; but instead of being allowed to fill the whole box, they are concentrated by the shifting nozzle N on to the centre of the glass disc through the hole in C C. You will notice that N has a ball end, and C C a socket to fit N exactly, so that, though C C and N move up and down very rapidly, they still make perfect contact. The disc is vibrated by the[Pg 314] sound-impulses, and drives the cutting point down into the surface of the wax cylinder, turning below it in a clockwork direction. The only dead weight pressing on S is that of N, C C, and the glass diaphragm.
The recorder (Fig. 147) is a small circular box about one and a half inches wide.[32] From the top, a tube connects to the horn. The bottom has a circular plate, C C, hinged on one side. This plate holds a glass disc, D, about 1⁄150th of an inch thick, to which a cutting stylus is attached—a tiny sapphire rod with a cup-shaped end that has very[Pg 313] sharp edges. Sound waves enter the box through the horn tube, but instead of filling the entire box, they are focused by the adjustable nozzle N onto the center of the glass disc through the hole in C C. You’ll notice that N has a ball end and C C has a socket to fit N perfectly, so even though C C and N move up and down very quickly, they still maintain perfect contact. The disc vibrates from the[Pg 314] sound impulses and pushes the cutting point into the surface of the wax cylinder, which rotates beneath it in a clockwork direction. The only dead weight pressing on S is that of N, C C, and the glass diaphragm.

As the cylinder revolves, the recorder is shifted continuously along by a leading screw having one hundred or more threads to the inch cut on it, so that it traces a continuous helical groove from one end of the wax cylinder to the other. This groove is really a series of very minute indentations, not exceeding 1⁄1000th of an inch in depth.[33] Seen under a microscope, the surface of the record is a succession of hills and valleys, some much larger than others (Fig. 151, a). A loud sound causes the stylus to give a vigorous dig, while low sounds scarcely move it at all. The wonderful thing about this sound-recording is, that not only are the fundamental tones of musical notes impressed, but also the harmonics, which enable us to decide at once whether the record is one of a cornet, violin, or banjo performance. Furthermore, if several instruments are playing simultaneously near the recorder's horn, the stylus catches all the different shades of tone of every note of a chord. There are, so to speak, minor hills and valleys cut in the slopes of the main hills and valleys.
As the cylinder spins, the recorder is continuously moved along by a leading screw with over a hundred threads per inch, allowing it to trace a continuous helical groove from one end of the wax cylinder to the other. This groove consists of a series of tiny indentations, not more than 1⁄1000th of an inch deep.[33] When viewed under a microscope, the record's surface reveals a series of hills and valleys, some much larger than others (Fig. 151, a). A loud sound makes the stylus dig deep, while soft sounds barely affect it. The amazing thing about this sound recording is that it captures not only the basic tones of musical notes but also the harmonics, which help us instantly determine whether the recording is from a cornet, violin, or banjo performance. Additionally, if multiple instruments are playing near the recorder’s horn, the stylus picks up all the different tonal nuances of every note in a chord. There are, so to speak, smaller hills and valleys carved into the slopes of the main hills and valleys.


Fig. 150.—3D view of a phonograph reproducer.
The reproducer (Fig. 149) is somewhat more complicated than the recorder. As before, we have a circular box communicating with the horn of the instrument. A thin glass disc forms a bottom to the box. It is held in position between rubber rings, R R, by a screw collar, C. To the centre is attached a little eye, from which hangs a link, L. Pivoted at P from one edge of the box is a floating weight, having a circular opening immediately under the eye. The link passes through this to the left end of a tiny lever, which rocks on a pivot projecting from the weight. To the right end of the lever is affixed a sapphire bar, or stylus, with a ball end of a diameter equal to that of the cutting point of the recorder. The floating weight presses the stylus against the record, and also keeps the link between the rocking lever of the glass diaphragm in a state of tension. Every blow given to the stylus is therefore[Pg 317] transmitted by the link to the diaphragm, which vibrates and sends an air-impulse into the horn. As the impulses are given at the same rate as those which agitated the diaphragm of the recorder, the sounds which they represent are accurately reproduced, even to the harmonics of a musical note.
The reproducer (Fig. 149) is a bit more complex than the recorder. As before, there's a circular box that connects to the horn of the instrument. A thin glass disc acts as the bottom of the box. It's held in place between rubber rings, R R, by a screw collar, C. In the center, there's a small eye with a link, L, hanging from it. A floating weight is pivoted at P at one edge of the box, featuring a circular opening directly beneath the eye. The link passes through this opening to the left end of a tiny lever that pivots on a point extending from the weight. At the right end of the lever, there’s a sapphire bar, or stylus, with a ball end that matches the diameter of the cutting point of the recorder. The floating weight applies pressure to the stylus against the record while also keeping the link between the rocking lever and the glass diaphragm taut. Every time the stylus strikes the record, [Pg 317] the link transmits this movement to the diaphragm, which vibrates and generates an air impulse into the horn. Since these impulses occur at the same rate as those that agitated the diaphragm of the recorder, the sounds they represent are reproduced accurately, including the harmonics of a musical note.
THE GRAMOPHONE.
THE RECORD PLAYER.
This effects the same purpose as the phonograph, but in a somewhat different manner. The phonograph recorder digs vertically downwards into the surface of the record, whereas the stylus of the gramophone wags from side to side and describes a snaky course (Fig. 151b). It makes no difference in talking-machines whether the reproducing stylus be moved sideways or vertically by the record, provided that motion is imparted by it to the diaphragm.
This serves the same purpose as the phonograph, but in a slightly different way. The phonograph recorder carves straight down into the surface of the record, while the stylus of the gramophone moves side to side in a wavy pattern (Fig. 151b). It doesn’t matter in talking machines whether the reproducing stylus moves sideways or vertically as long as it transfers that motion to the diaphragm.
![]() |
![]() |

In Fig. 151c the construction of the gramophone reproducer is shown in section. A is the cover which screws on to the bottom B, and confines the diaphragm[Pg 318] D between itself and a rubber ring. The portion B is elongated into a tubular shape for connection with the horn, an arm of which slides over the tube and presses against the rubber ring C to make an air-tight joint. The needle-carrier N is attached at its upper end to the centre of the diaphragm. At a point indicated by the white dot a pin passes through it and the cover. The lower end is tubular to accommodate the steel points, which have to be replaced after passing once over a record. A screw, S, working in a socket projecting from the[Pg 319] carrier, holds the point fast. The record moves horizontally under the point in a plane perpendicular to the page. The groove being zigzag, the needle vibrates right and left, and rotating the carrier a minute fraction of an inch on the pivot, shakes the glass diaphragm and sends waves of air into the horn.
In Fig. 151c, the design of the gramophone reproducer is shown in cross-section. A is the cover that screws onto the bottom B, enclosing the diaphragm[Pg 318] D between itself and a rubber ring. The part B is extended into a tubular shape for connecting to the horn, with an arm that slides over the tube and presses against the rubber ring C to create an air-tight seal. The needle carrier N is attached at its top end to the center of the diaphragm. A pin passes through the diaphragm and the cover at the point marked by the white dot. The lower end is tubular to hold the steel points, which need to be replaced after one use on a record. A screw, S, fits into a socket that juts out from the[Pg 319] carrier to keep the point secure. The record moves horizontally under the point in a plane that is perpendicular to the page. Since the groove is zigzag, the needle vibrates from side to side, and by rotating the carrier just a tiny bit on the pivot, it shakes the glass diaphragm and sends sound waves into the horn.
The gramophone is a reproducing instrument only. The records are made on a special machine, fitted with a device for causing the recorder point to describe a spiral course from the circumference to the centre of the record disc. Some gramophone records have as many as 250 turns to the inch. The total length of the tracing on a ten-inch "concert" record is about 1,000 feet.
The gramophone is just a playback device. The records are produced on a special machine equipped with a mechanism that allows the recorder to move in a spiral from the edge to the center of the record. Some gramophone records have as many as 250 grooves per inch. The total length of the grooves on a ten-inch “concert” record is about 1,000 feet.
THE MAKING OF RECORDS.
Making Records.
For commercial purposes it would not pay to make every record separately in a recording machine. The expense of employing good singers and instrumentalists renders such a method impracticable. All the records we buy are made from moulds, the preparation of which we will now briefly describe.
For commercial purposes, it wouldn't be cost-effective to make each record individually using a recording machine. The cost of hiring talented singers and musicians makes this approach impractical. All the records we purchase are made from molds, and we will now briefly describe how these are prepared.
CYLINDER, OR PHONOGRAPH RECORDS.
Cylinder or vinyl records.
First of all, a wax record is made in the ordinary way on a recording machine. After being tested and[Pg 320] approved, it is hung vertically and centrally from a rotating table pivoted on a vertical metal spike passing up through the record. On one side of the table is a piece of iron. On each side of the record, and a small distance away, rises a brass rod enclosed in a glass tube. The top of the rods are hooked, so that pieces of gold leaf may be suspended from them. A bell-glass is now placed over the record, table, and rods, and the air is sucked out by a pump. As soon as a good vacuum has been obtained, the current from the secondary circuit of an induction coil is sent into the rods supporting the gold leaves, which are volatilized by the current jumping from one to the other. A magnet, whirled outside the bell-glass, draws round the iron armature on the pivoted table, and consequently revolves the record, on the surface of which a very thin coating of gold is deposited. The record is next placed in an electroplating bath until a copper shell one-sixteenth of an inch thick has formed all over the outside. This is trued up on a lathe and encased in a brass tube. The "master," or original wax record, is removed by cooling it till it contracts sufficiently to fall out of the copper mould, on the inside surface of which are reproduced, in relief, the indentations of the wax "master."
First, a wax record is created in the usual way on a recording machine. After testing and[Pg 320] approval, it’s hung vertically and centrally from a rotating table balanced on a vertical metal spike that goes up through the record. On one side of the table, there’s a piece of iron. On each side of the record, a short distance away, stands a brass rod enclosed in a glass tube. The tops of the rods are hooked so that pieces of gold leaf can hang from them. A bell-jar is then placed over the record, table, and rods, and the air is pumped out to create a vacuum. Once a good vacuum is achieved, the current from the secondary circuit of an induction coil is sent into the rods holding the gold leaves, causing the gold to evaporate as the current jumps from one rod to the other. A magnet, spinning outside the bell-jar, pulls the iron armature on the pivoted table, which causes the record to spin, allowing a very thin layer of gold to be deposited on its surface. The record is then placed in an electroplating bath until a copper shell one-sixteenth of an inch thick forms all over the outside. This is smoothed on a lathe and encased in a brass tube. The "master," or original wax record, is removed by cooling it until it shrinks enough to fall out of the copper mold, which has the impressions of the wax "master" in relief on its inside surface.
Copies are made from the mould by immersing it in a tank of melted wax. The cold metal chills the wax that touches it, so that the mould soon has a thick waxen lining. The mould and copy are removed from the tank and mounted on a lathe, which shapes and smooths the inside of the record. The record is loosened from the mould by cooling. After inspection for flaws, it is, if found satisfactory, packed in cotton-wool and added to the saleable stock.
Copies are created from the mold by dipping it into a tank of melted wax. The cold metal cools the wax that comes in contact with it, causing the mold to develop a thick layer of wax. The mold and the copy are taken out of the tank and placed on a lathe, which shapes and smooths the inside of the record. The record is released from the mold by cooling. After checking for defects, if it passes inspection, it is packed in cotton wool and added to the inventory for sale.
Gramophone master records are made on a circular disc of zinc, coated over with a very thin film of acid-proof fat. When the disc is revolved in the recording machine, the sharp stylus cuts through the fat and exposes the zinc beneath. On immersion in a bath of chromic acid the bared surfaces are bitten into, while the unexposed parts remain unaffected. When the etching is considered complete, the plate is carefully cleaned and tested. A negative copper copy is made from it by electrotyping. This constitutes the mould. From it as many as 1,000 copies may be made on ebonite plates by combined pressure and heating.
Gramophone master records are created on a circular zinc disc, covered with a very thin layer of acid-resistant fat. When the disc spins in the recording machine, the sharp stylus cuts through the fat and reveals the zinc underneath. When placed in a chromic acid bath, the exposed areas are etched, while the unexposed parts remain unaffected. Once the etching is finished, the plate is carefully cleaned and tested. A negative copper copy is then produced using electrotyping, which serves as the mold. From this mold, up to 1,000 copies can be made on ebonite plates through a combination of pressure and heat.
[33] Some of the sibilant or hissing sounds of the voice are computed to be represented by depressions less than a millionth of an inch in depth. Yet these are reproduced very clearly!
[33] Some of the hissing sounds in the voice are estimated to be represented by dips smaller than a millionth of an inch deep. Still, these are reproduced very clearly!
Chapter XVII.
WHY THE WIND BLOWS.
Why the wind blows—Land and sea breezes—Light air and moisture—The barometer—The column barometer—The wheel barometer—A very simple barometer—The aneroid barometer—Barometers and weather—The diving-bell—The diving-dress—Air-pumps—Pneumatic tyres—The air-gun—The self-closing door-stop—The action of wind on oblique surfaces—The balloon—The flying-machine.
Why the wind blows—Land and sea breezes—Light air and moisture—The barometer—The column barometer—The wheel barometer—A very simple barometer—The aneroid barometer—Barometers and weather—The diving bell—The diving suit—Air pumps—Pneumatic tires—The air gun—The self-closing doorstop—The action of wind on slanted surfaces—The balloon—The aircraft.
When a child's rubber ball gets slack through a slight leakage of air, and loses some of its bounce, it is a common practice to hold it for a few minutes in front of the fire till it becomes temporarily taut again. Why does the heat have this effect on the ball? No more air has been forced into the ball. After perusing the chapter on the steam-engine the reader will be able to supply the answer. "Because the molecules of air dash about more vigorously among one another when the air is heated, and by striking the inside of the ball with greater force put it in a state of greater tension."
Wthen a child's rubber ball gets soft from a little air leakage and loses some of its bounce, it's common to hold it in front of a fire for a few minutes until it becomes firm again. Why does heat do this to the ball? No extra air has been pumped into it. After reading the chapter on the steam engine, the reader will be able to answer. "Because the air molecules move around more energetically when heated, and by colliding with the inside of the ball with greater force, they put it in a state of greater tension."
If we heat an open jar there is no pressure developed, since the air simply expands and flows out of the neck. But the air that remains in the jar, being less in quantity than when it was not yet heated, weighs less, though occupying the same space as before. If we took a very thin bladder and filled it with hot air it would therefore float in colder air, proving that heated air, as we should expect, tends to rise. The fire-balloon employs this principle, the air inside the bag being kept artificially warm by a fire burning in some vessel attached below the open neck of the bag.
If we heat an open jar, no pressure builds up because the air just expands and flows out of the neck. However, the air that’s left in the jar is less in quantity than it was before heating, so it weighs less, even though it takes up the same space as before. If we took a very thin balloon and filled it with hot air, it would float in colder air, showing that hot air, as we would expect, tends to rise. The fire balloon uses this principle, with the air inside the bag kept warm by a fire burning in a container attached below the open neck of the bag.
Now, the sun shines with different degrees of heating power at different parts of the world. Where its effect is greatest the air there is hottest. We will suppose, for the sake of argument, that, at a certain moment, the air envelope all round the globe is of equal temperature. Suddenly the sun shines out and heats the air at a point, A, till it is many degrees warmer than the surrounding air. The heated air expands, rises, and spreads out above the cold air. But, as a given depth of warm air has less weight than an equal depth of cold air, the cold air at once begins to rush towards B and squeeze the rest of the warm air out. We may[Pg 324] therefore picture the atmosphere as made up of a number of colder currents passing along the surface of the earth to replace warm currents rising and spreading over the upper surface of the cold air. A similar circulation takes place in a vessel of heated water (see p. 17).
Now, the sun shines with varying levels of heat in different parts of the world. Where its impact is the strongest, the air there is the hottest. Let's imagine, for the sake of discussion, that at a specific moment, the air surrounding the globe has the same temperature. Suddenly, the sun shines and heats the air at a point, A, until it’s much warmer than the surrounding air. The heated air expands, rises, and spreads out above the cooler air. However, since a certain depth of warm air weighs less than the same depth of cold air, the cold air immediately starts to rush toward B and pushes the warm air out. So we can picture the atmosphere as consisting of several colder currents moving along the surface of the earth to replace the warm currents that are rising and spreading over the top of the cold air. A similar circulation occurs in a container of heated water (see p. 17).
LAND AND SEA BREEZES.
Land and sea breezes.
A breeze which blows from the sea on to the land during the day often reverses its direction during the evening. Why is this? The earth grows hot or cold more rapidly than the sea. When the sun shines hotly, the land warms quickly and heats the air over it, which becomes light, and is displaced by the cooler air over the sea. When the sun sets, the earth and the air over it lose their warmth quickly, while the sea remains at practically the same temperature as before. So the balance is changed, the heavier air now lying over the land. It therefore flows seawards, and drives out the warmer air there.
A breeze that blows from the sea onto the land during the day often switches direction in the evening. Why does this happen? The land heats up or cools down faster than the sea. When the sun shines intensely, the land warms up quickly and heats the air above it, making it lighter, which causes it to be pushed away by the cooler air over the sea. When the sun sets, the land and the air above it lose heat quickly, while the sea stays at nearly the same temperature as before. This changes the balance, with the heavier air now sitting over the land. As a result, it flows toward the sea, pushing out the warmer air there.
LIGHT AIR AND MOISTURE.
Air and moisture.
Light, warm air absorbs moisture. As it cools, the moisture in it condenses. Breathe on a plate, and[Pg 325] you notice that a watery film forms on it at once. The cold surface condenses the water suspended in the warm breath. If you wish to dry a damp room you heat it. Moisture then passes from the walls and objects in the room to the atmosphere.
Light, warm air takes in moisture. As it cools, the moisture condenses. If you breathe on a plate, you’ll see a watery film form on it immediately. The cold surface causes the water in your warm breath to condense. If you want to dry a damp room, you heat it up. The moisture will then move from the walls and objects in the room into the air.
THE BAROMETER.
THE BAROMETER.
This property of air is responsible for the changes in weather. Light, moisture-laden air meets cold, dry air, and the sudden cooling forces it to release its moisture, which falls as rain, or floats about as clouds. If only we are able to detect the presence of warm air-strata above us, we ought to be in a position to foretell the weather.
This property of air is what causes changes in the weather. Light, moisture-filled air encounters cold, dry air, and the sudden drop in temperature causes it to release its moisture, which falls as rain or forms clouds. If we could just detect warm air layers above us, we would be able to predict the weather.
We can judge of the specific gravity of the air in our neighbourhood by means of the barometer, which means "weight-measurer." The normal air-pressure at sea-level on our bodies or any other objects is about 15 lbs. to the square inch—that is to say, if you could imprison and weigh a column of air one inch square in section and of the height of the world's atmospheric envelope, the scale would register 15 lbs. Many years ago (1643) Torricelli, a pupil of Galileo, first calculated the pressure by a very simple experiment. He took a long glass tube[Pg 326] sealed at one end, filled it with mercury, and, closing the open end with the thumb, inverted the tube and plunged the open end below the surface of a tank of mercury. On removing his thumb he found that the mercury sank in the tube till the surface of the mercury in the tube was about 30 inches in a vertical direction above the surface of the mercury in the tank. Now, as the upper end was sealed, there must be a vacuum above the mercury. What supported the column? The atmosphere. So it was evident that the downward pressure of the mercury exactly counterbalanced the upward pressure of the air. As a mercury column 30 inches high and 1 inch square weighs 15 lbs., the air-pressure on a square inch obviously is the same.
We can determine the specific gravity of the air in our area using a barometer, which means "weight-measurer." The normal air pressure at sea level on our bodies or any other objects is about 15 lbs. per square inch. This means that if you could trap and weigh a column of air that is one inch square and has the height of the Earth's atmosphere, the scale would show 15 lbs. Many years ago, in 1643, Torricelli, a student of Galileo, first calculated this pressure through a simple experiment. He took a long glass tube[Pg 326] sealed at one end, filled it with mercury, and closed the open end with his thumb. He then inverted the tube and immersed the open end in a tank of mercury. When he removed his thumb, he found that the mercury inside the tube sank until the surface of the mercury in the tube was about 30 inches above the surface of the mercury in the tank. Since the top was sealed, there must have been a vacuum above the mercury. What was supporting the column? The atmosphere. It turned out that the downward pressure of the mercury exactly balanced the upward pressure of the air. Since a mercury column that is 30 inches high and 1 inch square weighs 15 lbs., the air pressure on a square inch must obviously be the same.

FORTIN'S COLUMN BAROMETER
Fortin's column barometer
is a simple Torricellian tube, T, with the lower end submerged in a little glass tank of mercury (Fig. 152). The bottom of this tank is made of washleather. To obtain a "reading" the screw S, pressing on the washleather, is adjusted until the mercury in[Pg 327] the tank rises to the tip of the little ivory point P. The reading is the figure of the scale on the face of the case opposite which the surface of the column stands.
is a simple Torricellian tube, T, with the lower end submerged in a small glass tank of mercury (Fig. 152). The bottom of this tank is made of wash leather. To get a "reading," the screw S, pressing on the wash leather, is adjusted until the mercury in [Pg 327] the tank rises to the tip of the small ivory point P. The reading is the number on the scale on the front of the case where the surface of the column stands.

THE WHEEL BAROMETER
The Wheel Barometer
also employs the mercury column (Fig. 153). The lower end of the tube is turned up and expanded to form a tank, C. The pointer P, which travels round a graduated dial, is mounted on a spindle carrying a pulley, over which passes a string with a weight at each end. The heavier of the weights rests on the top of the mercury. When the atmospheric pressure falls, the mercury in C rises, lifting this weight, and the pointer moves. This form of barometer is not so delicate or reliable as Fortin's, or as the siphon barometer, which has a tube of the same shape as the wheel instrument, but of the same diameter from end[Pg 328] to end except for a contraction at the bend. The reading of a siphon is the distance between the two surfaces of the mercury.
also uses the mercury column (Fig. 153). The lower end of the tube is bent upward and widened to create a tank, C. The pointer P, which moves around a graduated dial, is fixed on a spindle that holds a pulley. A string with a weight on each end goes over the pulley. The heavier weight rests on top of the mercury. When the atmospheric pressure decreases, the mercury in C rises, lifting this weight, and the pointer moves. This type of barometer isn't as sensitive or reliable as Fortin's or the siphon barometer, which has a tube similar in shape to the wheel instrument but is the same diameter from one end[Pg 328] to the other, except for a narrowing at the bend. The reading of a siphon is the distance between the two surfaces of the mercury.
A VERY SIMPLE BAROMETER
A super simple barometer
is made by knocking off the neck of a small bottle, filling the body with water, and hanging it up by a string in the position shown (Fig. 154). When the atmospheric pressure falls, the water at the orifice bulges outwards; when it rises, the water retreats till its surface is slightly concave.
is made by breaking the neck off a small bottle, filling the body with water, and hanging it up by a string in the position shown (Fig. 154). When the atmospheric pressure drops, the water at the opening bulges outwards; when it rises, the water pulls back until its surface is slightly concave.

THE ANEROID BAROMETER.
The Aneroid Barometer.
On account of their size and weight, and the comparative difficulty of transporting them without derangement of the mercury column, column barometers are not so generally used as the aneroid variety. Aneroid means "without moisture," and in this particular connection signifies that no liquid is used in the construction of the barometer.
Because of their size and weight, and the relative challenge of moving them without disturbing the mercury column, column barometers aren't as commonly used as aneroid barometers. Aneroid means "without moisture," and in this case, it means that no liquid is used in building the barometer.
Fig. 155 shows an aneroid in detail. The most[Pg 329] noticeable feature is the vacuum chamber, V C, a circular box which has a top and bottom of corrugated but thin and elastic metal. Sections of the box are shown in Figs. 156, 157. It is attached at the bottom to the base board of the instrument by a screw (Fig. 156). From the top rises a pin, P, with a transverse hole through it to accommodate the pin K E, which has a triangular section, and stands on one edge.
Fig. 155 shows a detailed view of an aneroid. The most[Pg 329] noticeable feature is the vacuum chamber, V C, a circular box with a top and bottom made of thin, elastic, corrugated metal. Sections of the box are displayed in Figs. 156 and 157. It's attached at the bottom to the base board of the instrument by a screw (Fig. 156). From the top, a pin, P, rises with a transverse hole through it to fit the pin K E, which has a triangular shape and stands on one edge.

Returning to Fig. 155, we see that P projects[Pg 330] through S, a powerful spring of sheet-steel. To this is attached a long arm, C, the free end of which moves a link rotating, through the pin E, a spindle mounted in a frame, D. The spindle moves arm F. This pulls on a very minute chain wound round the pointer spindle B, in opposition to a hairspring, H S. B is mounted on arm H, which is quite independent of the rest of the aneroid.
Returning to Fig. 155, we see that P projects[Pg 330] through S, a strong spring made of sheet steel. Attached to this is a long arm, C, the free end of which moves a link that rotates, through the pin E, a spindle mounted in a frame, D. The spindle moves arm F. This pulls on a very tiny chain wound around the pointer spindle B, against a hairspring, H S. B is mounted on arm H, which is completely independent of the rest of the aneroid.
![]() |
![]() |
The vacuum chamber of an aneroid barometer expanded and contracted. |
The vacuum chamber is exhausted during manufacture and sealed. It would naturally assume the shape of Fig. 157, but the spring S, acting against the atmospheric pressure, pulls it out. As the pressure varies, so does the spring rise or sink; and the slightest movement is transmitted through the multiplying arms C, E, F, to the pointer.
The vacuum chamber is evacuated during production and sealed. It would normally take the shape shown in Fig. 157, but the spring S, which works against the air pressure, pulls it out. As the pressure changes, the spring moves up or down; even the smallest movement is passed through the multiplying arms C, E, F, to the pointer.
A good aneroid is so delicate that it will register the difference in pressure caused by raising it from the floor to the table, where it has a couple of feet less of air-column resting upon it. An aneroid is[Pg 331] therefore a valuable help to mountaineers for determining their altitude above sea-level.
A good aneroid is so sensitive that it will detect the difference in pressure when you lift it from the floor to the table, where there’s a couple of feet less of air pressure above it. An aneroid is[Pg 331] therefore a useful tool for mountaineers to figure out their altitude above sea level.
BAROMETERS AND WEATHER.
Barometers and Weather.
We may now return to the consideration of forecasting the weather by movements of the barometer. The first thing to keep in mind is, that the instrument is essentially a weight recorder. How is weather connected with atmospheric weight?
We can now go back to discussing how to forecast the weather using the movements of the barometer. The first thing to remember is that the instrument is basically a weight recorder. How is weather related to atmospheric weight?
In England the warm south-west wind generally brings wet weather, the north and east winds fine weather; the reason for this being that the first reaches us after passing over the Atlantic and picking up a quantity of moisture, while the second and third have come overland and deposited their moisture before reaching us.
In England, the warm south-west wind usually brings rainy weather, while the north and east winds bring clear skies. This happens because the south-west wind comes from across the Atlantic, picking up a lot of moisture, whereas the north and east winds come from overland and have already released their moisture before arriving.
A sinking of the barometer heralds the approach of heated air—that is, moist air—which on meeting colder air sheds its moisture. So when the mercury falls we expect rain. On the other hand, when the "glass" rises, we know that colder air is coming, and as colder air comes from a dry quarter we anticipate fine weather. It does not follow that the same conditions are found in all parts of the world. In regions which have the ocean to the east[Pg 332] or the north, the winds blowing thence would be the rainy winds, while south-westerly winds might bring hot and dry weather.
A drop in the barometer signals the arrival of warm, moist air, which releases its moisture when it meets cooler air. So, when the mercury goes down, we expect rain. Conversely, when the barometer rises, it indicates that cooler air is coming in, and since this cooler air often comes from a dry area, we can look forward to nice weather. However, the same patterns don’t apply everywhere in the world. In areas where the ocean is to the east[Pg 332] or north, the winds coming from those directions tend to be rainy, while south-west winds can bring hot and dry conditions.
THE DIVING-BELL.
The Diving Bell.
Water is nearly 773 times as heavy as air. If we submerge a barometer a very little way below the surface of a water tank, we shall at once observe a rise of the mercury column. At a depth of 34 feet the pressure on any submerged object is 15 lbs. to the square inch, in addition to the atmospheric pressure of 15 lbs. per square inch—that is, there would be a 30-lb. absolute pressure. As a rule, when speaking of hydraulic pressures, we start with the normal atmospheric pressure as zero, and we will here observe the practice.
Water is almost 773 times heavier than air. If we dip a barometer just a little below the surface of a water tank, we will immediately notice the mercury column rising. At a depth of 34 feet, the pressure on any submerged object is 15 lbs. per square inch, plus the atmospheric pressure of 15 lbs. per square inch—so, there would be a total of 30 lbs. absolute pressure. Generally, when discussing hydraulic pressures, we treat the normal atmospheric pressure as zero, and we will follow that convention here.

The diving-bell is used to enable people to work under water without having recourse to the diving-dress.[Pg 333] A sketch of an ordinary diving-bell is given in Fig. 158. It may be described as a square iron box without a bottom. At the top are links by which it is attached to a lowering chain, and windows, protected by grids; also a nozzle for the air-tube.
The diving bell is used to allow people to work underwater without needing a diving suit.[Pg 333] A sketch of a standard diving bell is shown in Fig. 158. It can be described as a square iron box with no bottom. At the top, there are links to connect it to a lowering chain, along with windows that are protected by grids, and a nozzle for the air tube.

A simple model bell (Fig. 159) is easily made out of a glass tumbler which has had a tap fitted in a hole drilled through the bottom. We turn off the tap and plunge the glass into a vessel of water. The water rises a certain way up the interior, until the air within has been compressed to a pressure equal to that of the water at the level of the surface inside. The further the tumbler is lowered, the higher does the water rise inside it.
A basic model bell (Fig. 159) can be easily created using a glass tumbler that has a tap attached to a hole drilled through the bottom. We close the tap and submerge the glass in a container of water. The water rises to a certain level inside, until the air inside is compressed to a pressure that matches the water level at the surface inside. The deeper the tumbler is submerged, the higher the water rises inside it.
Evidently men could not work in a diving-bell which is invaded thus by water. It is imperative to keep the water at bay. This we can do by attaching a tube to the tap (Fig. 160) and blowing into the tumbler till the air-pressure exceeds that of the water, which is shown by bubbles rising to[Pg 334] the surface. The diving-bell therefore has attached to it a hose through which air is forced by pumps from the atmosphere above, at a pressure sufficient to keep the water out of the bell. This pumping of air also maintains a fresh supply of oxygen for the workers.
Clearly, men can't work in a diving bell that's flooded with water. It's crucial to keep the water out. We can do this by connecting a tube to the tap (Fig. 160) and blowing into the tumbler until the air pressure is higher than that of the water, which is indicated by bubbles rising to[Pg 334] the surface. So, the diving bell has a hose attached to it through which pumps push air from the atmosphere above, at a pressure strong enough to prevent water from entering the bell. This air pumping also ensures a fresh supply of oxygen for the workers.

Inside the bell is tackle for grappling any object that has to be moved, such as a heavy stone block. The diving-bell is used mostly for laying submarine masonry. "The bell, slung either from a crane on the masonry already built above sea-level, or from a specially fitted barge, comes into action. The block is lowered by its own crane on to the bottom. The bell descends upon it, and the crew seize it with[Pg 335] tackle suspended inside the bell. Instructions are sent up as to the direction in which the bell should be moved with its burden, and as soon as the exact spot has been reached the signal for lowering is given, and the stone settles on to the cement laid ready for it."[34]
Inside the bell is equipment for grabbing any object that needs to be moved, like a heavy stone block. The diving bell is mainly used for underwater construction. "The bell, which is either hung from a crane on the masonry already built above sea level or from a specially equipped barge, gets put to work. The block is lowered by its own crane to the seabed. The bell descends onto it, and the crew grabs it with[Pg 335] the equipment inside the bell. Instructions are sent up about which way to move the bell with its load, and once the exact spot is reached, a signal is given to lower it, allowing the stone to settle onto the prepared cement."[34]
For many purposes it is necessary that the worker should have more freedom of action than is possible when he is cooped up inside an iron box. Hence the invention of the
For many reasons, it's important that the worker has more freedom to act than what is possible when they are trapped inside a metal box. That's why the invention of the
DIVING-DRESS,
Diving suit,
which consists of two main parts, the helmet and the dress proper. The helmet (Fig. 161) is made of copper. A breastplate, B, shaped to fit the shoulders, has at the neck a segmental screw bayonet-joint. The headpiece is fitted with a corresponding screw, which can be attached or removed by one-eighth of a turn. The neck edge of the dress, which is made in one piece, legs, arms, body and all, is attached to the breastplate by means of the plate P1, screwed down tightly on it by the wing-nuts N N, the bolts of which pass through the breastplate. Air enters the helmet[Pg 336] through a valve situated at the back, and is led through tubes along the inside to the front. This valve closes automatically if any accident cuts off the air supply, and encloses sufficient air in the dress to allow the diver to regain the surface. The outlet valve O V can be adjusted by the diver to maintain any pressure. At the sides of the headpiece are two hooks, H, over which pass the cords connecting the heavy lead weights of 40 lbs. each hanging on the diver's breast and back. These weights are also attached to the knobs K K. A pair of boots, having 17 lbs. of lead each in the soles, complete the dress. Three glazed windows are placed in the headpiece, that in the front, R W, being removable, so that the diver may gain free access to the air when he is above water without being obliged to take off the helmet.
which consists of two main parts: the helmet and the suit. The helmet (Fig. 161) is made of copper. A breastplate, B, is shaped to fit the shoulders and has a screw bayonet joint at the neck. The headpiece is equipped with a matching screw that can be attached or removed with a quarter turn. The neck edge of the suit, which is made in one piece for the legs, arms, and body, is connected to the breastplate using plate P1, which is tightened down with wing nuts N N; the bolts pass through the breastplate. Air enters the helmet[Pg 336] through a valve at the back and is directed through tubes to the front. This valve automatically closes if an accident interrupts the air supply, trapping enough air in the suit for the diver to return to the surface. The outlet valve O V can be adjusted by the diver to maintain any pressure. On the sides of the headpiece are two hooks, H, for cords that connect heavy lead weights of 40 lbs. each, which hang on the diver's chest and back. These weights are also connected to knobs K K. A pair of boots, each containing 17 lbs. of lead in the soles, complete the suit. Three glazed windows are fitted in the headpiece, with the front one, R.W., being removable, allowing the diver to access air when above water without needing to take off the helmet.

By means of telephone wires built into the life-line (which passes under the diver's arms and is used for lowering and hoisting) easy communication is established between the diver and his attendants above. The transmitter of the telephone is placed inside the helmet between the front and a side window, the receiver and the button of an electric bell in the crown. This last he can press by raising his head. The life-line sometimes also includes the wires for an electric lamp (Fig. 162) used by the diver at depths to which daylight cannot penetrate.
Using telephone wires integrated into the lifeline (which goes under the diver's arms and is used for lowering and lifting), clear communication is set up between the diver and the crew above. The phone's transmitter is located inside the helmet, positioned between the front and a side window, while the receiver and the button for an electric bell are in the crown. The diver can press this button by tilting his head back. The lifeline may also include wires for an electric lamp (Fig. 162) that the diver uses at depths where sunlight can't reach.
The pressure on a diver's body increases in the[Pg 338] ratio of 4⅓ lbs. per square inch for every 10 feet that he descends. The ordinary working limit is about 150 feet, though "old hands" are able to stand greater pressures. The record is held by one James Hooper, who, when removing the cargo of the Cape Horn sunk off the South American coast, made seven descents of 201 feet, one of which lasted for forty-two minutes.
The pressure on a diver's body increases at a rate of 4⅓ lbs. per square inch for every 10 feet he goes down. The normal working limit is around 150 feet, although experienced divers can handle greater pressures. The record is held by a man named James Hooper, who, while clearing the cargo of the Cape Horn that sank off the coast of South America, made seven dives of 201 feet, with one of those dives lasting forty-two minutes.

A sketch is given (Fig. 163) of divers working below water with pneumatic tools, fed from above with high-pressure air. Owing to his buoyancy a diver has little depressing or pushing power, and he cannot bore a hole in a post with an auger unless he is able to rest his back against some firm object, or is[Pg 339] roped to the post. Pneumatic chipping tools merely require holding to their work, their weight offering sufficient resistance to the very rapid blows which they make.
A sketch is provided (Fig. 163) of divers working underwater with pneumatic tools that receive high-pressure air from above. Due to buoyancy, a diver has limited downward or upward force, and he can't bore a hole in a post with an auger unless he's able to lean his back against something solid or is [Pg 339] tied to the post. Pneumatic chipping tools only need to be held against the work, as their weight provides enough resistance to the very quick blows they deliver.

AIR-PUMPS.
Air pumps.
![]() |
![]() |
Mention having been made of the air-pump, we append diagrams (Figs. 164, 165) of the simplest form of air-pump, the cycle tyre inflator. The piston is composed of two circular plates of smaller diameter than the barrel, holding between them a cup leather. During the upstroke the cup collapses inwards and allows air to pass by it. On the downstroke (Fig. 165) the edges of the cup expand against the barrel, preventing the passage of air round the piston. A double-action air-pump requires a long, well-fitting piston with a cup on each side of it, and the addition of extra valves[Pg 341] to the barrel, as the cups under these circumstances cannot act as valves.
Mentioning the air pump, we include diagrams (Figs. 164, 165) of the simplest type of air pump, the cycle tire inflator. The piston consists of two circular plates that are smaller in diameter than the barrel, with a cup leather held between them. During the upstroke, the cup collapses inward, allowing air to pass by it. On the downstroke (Fig. 165), the edges of the cup expand against the barrel, blocking the airflow around the piston. A double-action air pump requires a long, well-fitting piston with a cup on each side, plus additional valves[Pg 341] in the barrel, since the cups can't function as valves in this setup.
PNEUMATIC TYRES.
Air-filled tires.
![]() |
![]() |
The action of the pneumatic tyre in reducing vibration and increasing the speed of a vehicle is explained by Figs. 166, 167. When the tyre encounters an obstacle, such as a large stone, it laps over it (Fig. 166), and while supporting the weight on the wheel, reduces the deflection of the direction of movement. When an iron-tyred wheel meets a similar obstacle it has to rise right over it, often jumping a considerable distance into the air. The resultant motions of the wheel are indicated in each case by an arrow. Every change of direction[Pg 342] means a loss of forward velocity, the loss increasing with the violence and extent of the change. The pneumatic tyre also scores because, on account of its elasticity, it gives a "kick off" against the obstacle, which compensates for the resistance during compression.
The way a pneumatic tire reduces vibration and boosts a vehicle's speed is shown in Figs. 166 and 167. When the tire hits an obstacle like a big rock, it rolls over it (Fig. 166) while supporting the weight on the wheel, minimizing the change in direction. In contrast, when a wheel with iron tires encounters a similar obstacle, it needs to lift completely over it, often launching high into the air. The resulting motions of the wheel are illustrated by an arrow in each case. Every change in direction[Pg 342] leads to a decrease in forward speed, and this loss increases with the intensity and extent of the change. The pneumatic tire also has an advantage because its elasticity provides a "kick off" against the obstacle, which helps counteract the resistance during compression.

THE AIR-GUN.
The air gun.
This may be described as a valveless air-pump. Fig. 168 is a section of a "Gem" air-gun, with the mechanism set ready for[Pg 343] firing. In the stock of the gun is the cylinder, in which an accurately fitting and hollow piston moves. A powerful helical spring, turned out of a solid bar of steel, is compressed between the inside end of the piston and the upper end of the butt. To set the gun, the catch is pressed down so that its hooked end disengages from the stock, and the barrel is bent downwards on pivot P. This slides the lower end of the compressing lever towards the butt, and a projection on the guide B, working in a groove, takes the piston with it. When the spring has been fully compressed, the triangular tip of the rocking cam R engages with a groove in the piston's head, and prevents recoil when the barrel is returned to its original position. On pulling the trigger, the piston is released and flies up the cylinder with great force, and the air in the cylinder is compressed and driven through the bore of the barrel, blocked by the leaden slug, to which the whole energy of the expanding spring is transmitted through the elastic medium of the air.
This can be described as a valveless air pump. Fig. 168 shows a section of a "Gem" air gun, with the mechanism set and ready for[Pg 343] firing. In the stock of the gun is the cylinder, where a precisely fitting and hollow piston moves. A strong helical spring, made from a solid steel bar, is compressed between the inner end of the piston and the upper end of the butt. To prepare the gun, the catch is pressed down so its hooked end disengages from the stock, and the barrel is bent downwards on pivot P. This slides the lower end of the compressing lever towards the butt, and a projection on the guide B, moving in a groove, pulls the piston along with it. When the spring is fully compressed, the triangular tip of the rocking cam R fits into a groove in the piston’s head, preventing recoil when the barrel is returned to its original position. When the trigger is pulled, the piston is released and shoots up the cylinder with great force, compressing and forcing the air in the cylinder through the bore of the barrel, which is blocked by the lead slug, to which the entire energy of the expanding spring is transferred through the elastic medium of the air.
There are several other good types of air-gun, all of which employ the principles described above.
There are several other good types of air guns, all of which use the principles mentioned above.
THE SELF-CLOSING DOOR-STOP
The automatic doorstop
is another interesting pneumatic device. It consists of a cylinder with an air-tight piston, and a piston rod working through a cover at one end. The other end of the cylinder is pivoted to the door frame. When the door is opened the piston compresses a spring in the cylinder, and air is admitted past a cup leather on the piston to the upper part of the cylinder. This air is confined by the cup leather when the door is released, and escapes slowly through a leak, allowing the spring to regain its shape slowly, and by the agency of the piston rod to close the door.
is another interesting pneumatic device. It consists of a cylinder with an airtight piston and a piston rod that extends through a cover at one end. The other end of the cylinder is connected to the door frame. When the door is opened, the piston compresses a spring inside the cylinder, and air flows past a leather cup on the piston to the upper part of the cylinder. This air is held in place by the leather cup when the door is released, and it escapes slowly through a small opening, allowing the spring to gradually return to its original shape and, via the piston rod, to close the door.
THE ACTION OF WIND ON OBLIQUE SURFACES.
THE ACTION OF WIND ON SLOPED SURFACES.
Why does a kite rise? Why does a boat sail across the wind? We can supply an answer almost instinctively in both cases, "Because the wind pushes the kite or sail aside." It will, however, be worth while to look for a more scientific answer. The kite cannot travel in the direction of the wind because it is confined by a string. But the face is so attached to the string that it inclines at an angle to the direction of the wind. Now, when a[Pg 345] force meets an inclined surface which it cannot carry along with it, but which is free to travel in another direction, the force may be regarded as resolving itself into two forces, coming from each side of the original line. These are called the component forces.
Why does a kite fly? Why does a boat sail against the wind? We can almost instinctively answer both questions with, "Because the wind pushes the kite or sail away." However, it’s worth searching for a more scientific explanation. The kite can't move in the direction of the wind because it's attached to a string. But the kite’s surface is angled relative to the wind direction. Now, when a[Pg 345] force encounters an angled surface that it can’t move along but which can shift in another direction, the force can be seen as breaking down into two forces, emerging from either side of the original line. These are known as component forces.
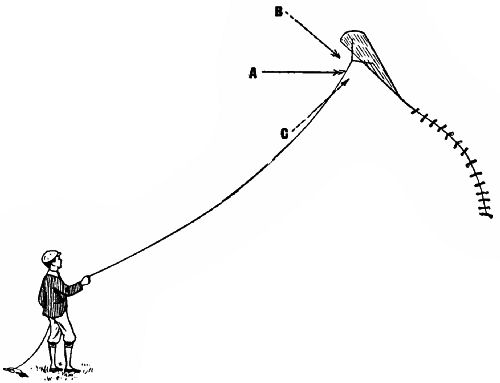
To explain this we give a simple sketch of a kite in the act of flying (Fig. 169). The wind is blowing in the direction of the solid arrow A. The oblique surface of the kite resolves its force into the two components indicated by the dotted arrows B and C. Of these C only has lifting power to overcome the[Pg 346] force of gravity. The kite assumes a position in which force C and gravity counterbalance one another.
To explain this, we provide a simple sketch of a kite in flight (Fig. 169). The wind is blowing in the direction of the solid arrow A. The angled surface of the kite breaks its force into two components shown by the dotted arrows B and C. Of these, only C has the lifting power to overcome the[Pg 346] force of gravity. The kite positions itself so that force C and gravity balance each other out.

A boat sailing across the wind is acted on in a similar manner (Fig. 170). The wind strikes the sail obliquely, and would thrust it to leeward were it not for the opposition of the water. The force A is resolved into forces B and C, of which C propels the boat on the line of its axis. The boat can be made to sail even "up" the wind, her head being brought round until a point is reached at which the force B on the boat, masts, etc., overcomes the[Pg 347] force C. The capability of a boat for sailing up wind depends on her "lines" and the amount of surface she offers to the wind.
A boat sailing against the wind is affected in a similar way (Fig. 170). The wind hits the sail at an angle and would push it sideways if it weren't for the resistance of the water. The force A is broken down into forces B and C, with C driving the boat along its axis. The boat can even sail "up" against the wind by turning its head until it gets to a point where the force B on the boat, masts, etc., is stronger than the[Pg 347] force C. A boat’s ability to sail into the wind depends on its shape and the amount of surface it presents to the wind.
THE BALLOON
THE BALLOON
is a pear-shaped bag—usually made of silk—filled with some gas lighter than air. The tendency of a heavier medium to displace a lighter drives the gas upwards, and with it the bag and the wicker-work car attached to a network encasing the bag. The tapering neck at the lower end is open, to permit the free escape of gas as the atmospheric pressure outside diminishes with increasing elevation. At the top of the bag is a wooden valve opening inwards, which can be drawn down by a rope passing up to it through the neck whenever the aeronaut wishes to let gas escape for a descent. He is able to cause a very rapid escape by pulling another cord depending from a "ripping piece" near the top of the bag. In case of emergency this is torn away bodily, leaving a large hole. The ballast (usually sand) carried enables him to maintain a state of equilibrium between the upward pull of the gas and the downward pull of gravity. To sink he lets out gas, to rise he throws out ballast;[Pg 348] and this process can be repeated until the ballast is exhausted. The greatest height ever attained by aeronauts is the 7¼ miles, or 37,000 feet, of Messrs. Glaisher and Coxwell on September 5, 1862. The ascent nearly cost them their lives, for at an elevation of about 30,000 feet they were partly paralyzed by the rarefaction of the air, and had not Mr. Coxwell been able to pull the valve rope with his teeth and cause a descent, both would have died from want of air.
is a pear-shaped bag—usually made of silk—filled with gas that’s lighter than air. The fact that heavier materials push lighter ones out of the way makes the gas rise, along with the bag and the wicker basket connected by a network around it. The narrow opening at the bottom allows gas to escape freely as the atmospheric pressure outside decreases with height. At the top of the bag, there’s a wooden valve that opens inward, which can be pulled down by a rope running through the neck whenever the pilot wants to release gas for a descent. The pilot can make gas escape quickly by pulling another cord attached to a "ripping piece" near the top of the bag. In emergencies, this can be torn away completely, creating a large opening. The ballast (usually sand) helps maintain balance between the upward force of the gas and the downward force of gravity. To descend, he releases gas; to ascend, he drops ballast;[Pg 348] and this can be repeated until the ballast runs out. The highest altitude ever reached by balloonists is 7¼ miles, or 37,000 feet, achieved by Messrs. Glaisher and Coxwell on September 5, 1862. The ascent nearly cost them their lives because, at around 30,000 feet, they became partly paralyzed from the thin air, and had Mr. Coxwell not been able to pull the valve rope with his teeth to descend, both would have died from lack of air.

The flying-machine, which scientific engineers have so long been trying to produce, will probably be quite independent of balloons, and will depend for its ascensive powers on the action of air on oblique surfaces. Sir Hiram Maxim's experimental air-ship embodied the principles shown by Fig. 171. On a deck was mounted an engine, E, extremely[Pg 349] powerful for its weight. This drove large propellers, S S. Large aeroplanes, of canvas stretched over light frameworks, were set up overhead, the forward end somewhat higher than the rear. The machine was run on rails so arranged as to prevent it rising. Unfortunately an accident happened at the first trial and destroyed the machine.
The flying machine, which engineers have been working to create for so long, will likely be completely separate from balloons and will rely on the movement of air against angled surfaces for lift. Sir Hiram Maxim's experimental airship demonstrated the principles shown in Fig. 171. An engine, E, which was very[Pg 349] powerful for its size, was mounted on a deck. This engine powered large propellers, S S. Large wings made of canvas stretched over lightweight frames were positioned above, with the front end slightly higher than the back. The machine was placed on rails set up to keep it from lifting off. Unfortunately, during the first test, an accident occurred that destroyed the machine.
In actual flight it would be necessary to have a vertical rudder for altering the horizontal direction, and a horizontal "tail" for steering up or down. The principle of an aeroplane is that of the kite, with this difference, that, instead of moving air striking a captive body, a moving body is propelled against more or less stationary air. The resolution of forces is shown by the arrows as before.
In real flight, it would be essential to have a vertical rudder for changing the horizontal direction and a horizontal "tail" for adjusting altitude. The concept of an airplane is similar to that of a kite, with the key difference being that instead of moving air hitting a stationary object, a moving object is pushed through relatively still air. The breakdown of forces is illustrated by the arrows as mentioned earlier.
Up to the present time no practical flying-machine has appeared. But experimenters are hard at work examining the conditions which must be fulfilled to enable man to claim the "dominion of the air."
Up to now, no practical flying machine has been developed. However, researchers are actively investigating the requirements that need to be met for humans to achieve the "dominion of the air."
Chapter XVIII.
HYDRAULIC MACHINERY.
The siphon—The bucket pump—The force-pump—The most marvellous pump—The blood channels—The course of the blood—The hydraulic press—Household water-supply fittings—The ball-cock—The water-meter—Water-supply systems—The household filter—Gas traps—Water engines—The cream separator—The "hydro."
The siphon—the bucket pump—the force pump—the most amazing pump—the blood vessels—the flow of blood—the hydraulic press—home water supply fittings—the ball cock—the water meter—water supply systems—the household filter—gas traps—water engines—the cream separator—the "hydro."
In the last chapter we saw that the pressure of the atmosphere is 15 lbs. to the square inch. Suppose that to a very long tube having a sectional area of one square inch we fit an air-tight piston (Fig. 172), and place the lower end of the tube in a vessel of water. On raising the piston a vacuum would be created in the tube, did not the pressure of the atmosphere force water up into the tube behind the piston. The water would continue to rise until it reached a point 34 feet perpendicularly above the level of the water in the vessel. The column would then weigh 15 lbs., and exactly counterbalance the atmospheric pressure; so that[Pg 351] a further raising of the piston would not raise the water any farther. At sea-level, therefore, the lifting power of a pump by suction is limited to 34 feet. On the top of a lofty mountain, where the air-pressure is less, the height of the column would be diminished—in fact, be proportional to the pressure.
In the last chapter, we learned that the atmospheric pressure is 15 lbs. per square inch. Imagine a long tube with a cross-sectional area of one square inch and a sealed piston fitted into it (Fig. 172). If we place the lower end of the tube in a container of water and lift the piston, a vacuum will form in the tube unless the atmospheric pressure pushes water up behind the piston. The water will rise until it reaches a height of 34 feet above the water level in the container. At that point, the weight of the water column would equal 15 lbs., perfectly balancing the atmospheric pressure. Therefore, [Pg 351] further lifting of the piston wouldn’t raise the water any higher. At sea level, the maximum suction lift of a pump is limited to 34 feet. However, on top of a high mountain, where atmospheric pressure is lower, the height of the water column would be reduced—in fact, it would be proportional to the pressure.
![]() |
![]() |
THE SIPHON
THE SYphon
is an interesting application of the principle of[Pg 352] suction. By its own weight water may be made to lift water through a height not exceeding 34 feet. This is explained by Fig. 173. The siphon pipe, A B C D, is in the first instance filled by suction. The weight of the water between A and B counter-balances that between B and C. But the column C D hangs, as it were, to the heels of B C, and draws it down. Or, to put it otherwise, the column B D, being heavier than the column B A, draws it over the topmost point of the siphon. Any parting between the columns, provided that B A does not exceed 34 feet, is impossible, as the pressure of the atmosphere on the mouth of B A is sufficient to prevent the formation of a vacuum.
is an interesting application of the principle of[Pg 352] suction. Water can lift water due to its own weight, but only up to a height of 34 feet. This is illustrated in Fig. 173. The siphon pipe, A B C D, is initially filled by suction. The weight of the water between A and B balances out the weight of the water between B and C. However, the column C D effectively pulls down on B C. In other words, the column B D, being heavier than the column B A, pulls it over the highest point of the siphon. Any separation between the columns is impossible as long as the height of B A doesn’t exceed 34 feet, since the atmospheric pressure at the mouth of B A is strong enough to stop a vacuum from forming.
THE BUCKET PUMP.
The bucket pump.
We may now pass to the commonest form of pump used in houses, stables, gardens, etc. (Fig. 174). The piston has a large hole through it, over the top of which a valve is hinged. At the bottom of the barrel is a second valve, also opening upwards, seated on the top of the supply pipe. In sketch (a) the first upstroke is in progress. A vacuum forms under the piston, or plunger, and water rises up the barrel to fill it. The next diagram (b) shows the first[Pg 353] downstroke. The plunger valve now opens and allows water to rise above the piston, while the lower closes under the pressure of the water above and the pull of that below. During the second upstroke (c) the water above the piston is raised until it overflows through the spout, while a fresh supply is being sucked in below.
We can now move on to the most common type of pump used in homes, stables, gardens, etc. (Fig. 174). The piston has a large hole in it, with a valve hinged over the top. At the bottom of the barrel is a second valve, also opening upward, which sits on top of the supply pipe. In sketch (a), the first upstroke is happening. A vacuum forms under the piston, or plunger, and water rises up the barrel to fill it. The next diagram (b) shows the first[Pg 353] downstroke. The plunger valve now opens, allowing water to rise above the piston, while the lower valve closes due to the pressure of the water above and the pull of the water below. During the second upstroke (c), the water above the piston rises until it overflows through the spout, while fresh water is drawn in from below.

THE FORCE-PUMP.
The power pump.
![]() Fig. 175. Force pump; suction stroke. |
![]() Fig. 176. Force pump; delivery stroke. |
For driving water to levels above that of the pump a somewhat different arrangement is required. One type of force-pump is shown in Figs. 175, 176. The piston now is solid, and the upper valve is situated in the delivery pipe. During an upstroke this closes, and the other opens; the reverse happening during a downstroke. An air-chamber is[Pg 355] generally fitted to the delivery pipe when water is to be lifted to great heights or under high pressure. At each delivery stroke the air in the chamber is compressed, absorbing some of the shock given to the water in the pipe by the water coming from the pump; and its expansion during the next suction stroke forces the water gradually up the pipe. The air-chamber is a very prominent feature of the fire-engine.
To pump water to levels higher than the pump itself, a slightly different setup is needed. One type of force pump is shown in Figs. 175, 176. The piston is now solid, and the upper valve is located in the delivery pipe. During the upstroke, this valve closes, and the other one opens; the opposite occurs during the downstroke. An air chamber is[Pg 355] typically added to the delivery pipe when water needs to be lifted to significant heights or under high pressure. With each delivery stroke, the air in the chamber gets compressed, which helps absorb some of the shock experienced by the water in the pipe as it comes from the pump; during the next suction stroke, the air expands and gradually pushes the water up the pipe. The air chamber is a key feature of a fire engine.
A double-action force-pump is seen in Fig. 177, making an upward stroke. Both sides of the piston are here utilized, and the piston rod works through a water-tight stuffing-box. The action of the pump will be easily understood from the diagram.
A double-action force-pump is shown in Fig. 177, making an upward stroke. Both sides of the piston are used here, and the piston rod passes through a water-tight packing. The pump's operation will be easily understood from the diagram.

THE MOST MARVELLOUS PUMP
THE MOST AMAZING PUMP
known is the heart. We give in Fig. 178 a diagrammatic[Pg 356] sketch of the system of blood circulation in the human body, showing the heart, the arteries, and the veins, big and little. The body is supposed to be facing the reader, so that the left lung, etc., is to his right.
known is the heart. We provide a diagrammatic[Pg 356] sketch of the blood circulation system in the human body, illustrating the heart, the arteries, and the veins, both large and small. The body is shown facing the reader, so the left lung, etc., is on the reader's right side.
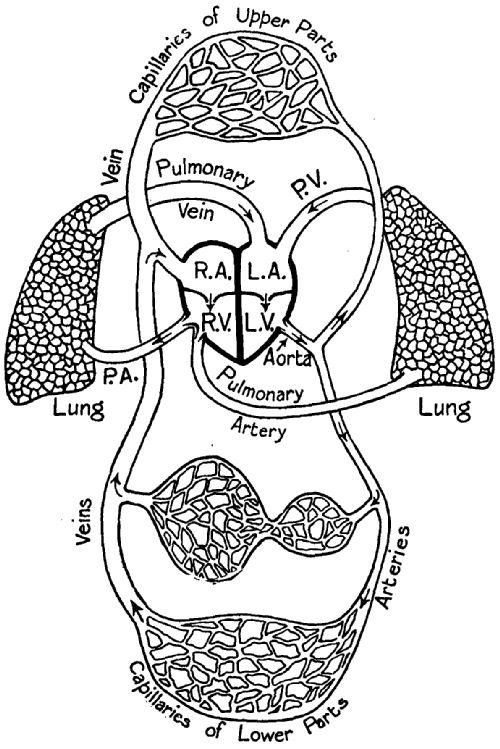
The heart, which forces the blood through the body, is a large muscle (of about the size of the clenched fist) with four cavities. These are respectively known as the right and left auricles, and the right and left ventricles. They are arranged in two pairs, the auricle uppermost, separated by a fleshy partition. Between each auricle and its ventricle is a valve, which consists of strong membranous flaps, with loose edges turned downwards. The left-side valve is the mitral valve, that between the right auricle and ventricle the tricuspid valve. The edges of the valves fall together when the heart contracts, and prevent the passage of blood. Each ventricle has a second valve through which it ejects the blood. (That of the right ventricle has been shown double for the sake of convenience.)
The heart, which pumps blood throughout the body, is a large muscle (about the size of a clenched fist) with four chambers. These are known as the right and left auricles, and the right and left ventricles. They are arranged in two pairs, with the auricles on top, separated by a fleshy wall. Each auricle has a valve leading to its ventricle, which consists of strong membrane flaps with loose edges that hang downward. The valve on the left side is called the mitral valve, and the one between the right auricle and ventricle is the tricuspid valve. The edges of the valves close together when the heart contracts to stop blood from flowing backward. Each ventricle has a second valve that allows it to push blood out. (The valve of the right ventricle is shown as double for clarity.)
The action of the heart is this:—The auricles and ventricles expand; blood rushes into the auricles from the channels supplying them, and distends them and the ventricles; the auricles contract and fill the ventricles below quite full (there are no valves above the auricles, but the force of contraction[Pg 358] is not sufficient to return the blood to the veins); the ventricles contract; the mitral and tricuspid valves close; the valves leading to the arteries open; blood is forced out of the ventricles.
The heart works like this: The upper chambers (auricles) and lower chambers (ventricles) expand; blood flows into the auricles from the veins, filling them and the ventricles below. Then, the auricles contract, pushing blood into the ventricles completely (there are no valves above the auricles, but the contraction force[Pg 358] isn't strong enough to push blood back into the veins); the ventricles then contract; the mitral and tricuspid valves close; the valves to the arteries open; blood gets pumped out of the ventricles.
THE BLOOD CHANNELS
THE BLOOD VESSELS
are of two kinds—(1) The arteries, which lead the blood into the circulatory system; (2) the veins, which lead the blood back to the heart. The arteries divide up into branches, and these again divide into smaller and smaller arteries. The smallest, termed capillaries (Latin, capillus, a hair), are minute tubes having an average diameter of 1⁄3000th of an inch. These permeate every part of the body. The capillary arteries lead into the smallest veins, which unite to form larger and larger veins, until what we may call the main streams are reached. Through these the blood flows to the heart.
are of two kinds—(1) The arteries, which carry blood into the circulatory system; (2) the veins, which return blood to the heart. The arteries branch out, and these further divide into smaller arteries. The tiniest ones, called capillaries (from the Latin, capillus, meaning hair), are tiny tubes with an average diameter of 1⁄3000th of an inch. They penetrate every part of the body. The capillary arteries connect to the smallest veins, which come together to form larger veins until we reach what we can call the main streams. Blood flows through these to the heart.
There are three main points of difference between arteries and veins. In the first place, the larger arteries have thick elastic walls, and maintain their shape even when empty. This elasticity performs the function of the air-chamber of the force-pump. When the ventricles contract, driving blood into the arteries, the walls of the latter expand, and their[Pg 359] contraction pushes the blood steadily forward without shock. The capillaries have very thin walls, so that fluids pass through them to and from the body, feeding it and taking out waste matter. The veins are all thin-walled, and collapse when empty. Secondly, most veins are furnished with valves, which prevent blood flowing the wrong way. These are similar in principle to those of the heart. Arteries have no valves. Thirdly, arteries are generally deeply set, while many of the veins run near the surface of the body. Those on the front of the arm are specially visible. Place your thumb on them and run it along towards the wrist, and you will notice that the veins distend owing to the closing of the valves just mentioned.
There are three main differences between arteries and veins. First, larger arteries have thick elastic walls that keep their shape even when they're empty. This elasticity works like the air chamber of a force-pump. When the ventricles contract and push blood into the arteries, the walls of the arteries expand, and their contraction pushes the blood forward steadily without any jolt. The capillaries have very thin walls, allowing fluids to move in and out, feeding the body and removing waste. Veins have thin walls and collapse when empty. Second, most veins have valves that prevent blood from flowing backward. These work similarly to the valves in the heart. Arteries do not have valves. Third, arteries are generally located deeper in the body, while many veins are closer to the skin's surface. The veins on the front of the arm are particularly noticeable. If you place your thumb on them and slide it toward the wrist, you'll see the veins swell because of the closing of those valves.
Arterial blood is red, and comes out from a cut in gulps, on account of the contraction of the elastic walls. If you cut a vein, blue blood issues in a steady stream. The change of colour is caused by the loss of oxygen during the passage of the blood through the capillaries, and the absorption of carbon dioxide from the tissues.
Arterial blood is red and flows in bursts from a cut because of the contraction of the elastic walls. If you cut a vein, blue blood flows out in a steady stream. The color change happens because the blood loses oxygen as it moves through the capillaries and absorbs carbon dioxide from the tissues.
The lungs are two of the great purifiers of the blood. As it circulates through them, it gives up the carbon dioxide which it has absorbed, and[Pg 360] receives pure oxygen in exchange. If the air of a room is "foul," the blood does not get the proper amount of oxygen. For this reason it is advisable for us to keep the windows of our rooms open as much as possible both day and night. Fatigue is caused by the accumulation of carbon dioxide and other impurities in the blood. When we run, the heart pumps blood through the lungs faster than they can purify it, and eventually our muscles become poisoned to such an extent that we have to stop from sheer exhaustion.
The lungs are two of the main purifiers of the blood. As blood flows through them, it releases the carbon dioxide it has picked up and[Pg 360] takes in fresh oxygen in return. If the air in a room is "stale," the blood doesn't get enough oxygen. That's why it's a good idea to keep our windows open as much as possible, day and night. Fatigue happens when carbon dioxide and other impurities build up in the blood. When we run, the heart sends blood through the lungs faster than they can clean it, and eventually our muscles become so depleted that we have to stop from sheer tiredness.
THE COURSE OF THE BLOOD.
BLOOD FLOW PATH.
It takes rather less than a minute for a drop of blood to circulate from the heart through the whole system and back to the heart.
It takes just under a minute for a drop of blood to travel from the heart, through the entire body, and back to the heart.
We may briefly summarize the course of the circulation of the blood thus:—It is expelled from the left ventricle into the aorta and the main arteries, whence it passes into the smaller arteries, and thence into the capillaries of the brain, stomach, kidneys, etc. It here imparts oxygen to the body, and takes in impurities. It then enters the veins, and through them flows back to the right auricle; is driven into the right ventricle; is expelled into the[Pg 361] pulmonary (lung) arteries; enters the lungs, and is purified. It returns to the left auricle through the pulmonary veins; enters the left auricle, passes to left ventricle, and so on.
We can briefly summarize how blood circulates like this: It’s pumped from the left ventricle into the aorta and the main arteries, then moves into smaller arteries and into the capillaries of the brain, stomach, kidneys, and other organs. Here, it releases oxygen to the body and picks up waste. It then enters the veins and flows back to the right atrium, gets pushed into the right ventricle, and is expelled into the [Pg 361] pulmonary (lung) arteries; goes into the lungs, where it gets purified. Finally, it returns to the left atrium through the pulmonary veins, moves to the left ventricle, and the cycle continues.
A healthy heart beats from 120 times per minute in a one-year-old infant to 60 per minute in a very aged person. The normal rate for a middle-aged adult is from 80 to 70 beats.
A healthy heart beats about 120 times per minute in a one-year-old baby and around 60 times per minute in an elderly person. The normal rate for a middle-aged adult ranges from 70 to 80 beats per minute.
Heart disease signifies the failure of the heart valves to close properly. Blood passes back when the heart contracts, and the circulation is much enfeebled. By listening through a stethoscope the doctor is able to tell whether the valves are in good order. A hissing sound during the beat indicates a leakage past the valves; a thump, or "clack," that they shut completely.
Heart disease means the heart valves aren't closing properly. When the heart pumps, blood flows back, weakening circulation. By using a stethoscope, the doctor can determine if the valves are functioning well. A hissing sound during the heartbeat suggests a leak past the valves; a thump, or "clack," indicates they are closing completely.
THE HYDRAULIC PRESS.
The Hydraulic Press.
It is a characteristic of fluids and gases that if pressure be brought to bear on any part of a mass of either class of bodies it is transmitted equally and undiminished in all directions, and acts with the same force on all equal surfaces, at right angles to those surfaces. The great natural philosopher Pascal first formulated this remarkable fact, of which[Pg 362] a simple illustration is given in Fig. 179. Two cylinders, A and B, having a bore of one and two inches respectively, are connected by a pipe. Water is poured in, and pistons fitting the cylinders accurately and of equal weight are inserted. On piston B is placed a load of 10 lbs. To prevent A rising above the level of B, it must be loaded proportionately. The area of piston A is four times that of B, so that if we lay on it a 40-lb. weight, neither piston will move. The walls of the cylinders and connecting pipe are also pressed outwards in the ratio of 10 lbs. for every part of their interior surface which has an area equal to that of piston B.
Fluids and gases have a unique characteristic: when pressure is applied to any part of a body in either state, it gets transmitted uniformly and without reduction in all directions, acting with the same force on all equal surfaces that are perpendicular to those surfaces. The renowned natural philosopher Pascal was the first to describe this remarkable principle, which is simply illustrated in Fig. 179. Two cylinders, A and B, with bores of one and two inches respectively, are connected by a pipe. Water is poured in, and pistons that fit the cylinders perfectly and weigh the same are inserted. A weight of 10 lbs. is placed on piston B. To keep A from rising above the level of B, it must be loaded proportionately. The area of piston A is four times that of B, so if we place a 40-lb. weight on it, neither piston will move. The walls of the cylinders and the connecting pipe are also pushed outward in the ratio of 10 lbs. for every part of their interior surface that has an area equal to that of piston B.


The hydraulic press is an application of this law. Cylinder B is represented by a force pump of small bore, capable of delivering water at very high pressures (up to 10 tons per square inch). In the place of A we have a stout cylinder with a solid plunger, P (Fig. 180), carrying the table on which the object to be pressed is placed. Bramah, the inventor of the hydraulic press, experienced great difficulty in preventing the escape of water between the top of the cylinder and the plunger. If a "gland" packing of the type found in steam-cylinders were used, it failed to hold back the water unless it were screwed down so tightly as to jam the plunger. He tried all kinds of expedients without success; and his invention, excellent though it was in principle, seemed doomed to failure, when his foreman, Henry Maudslay,[35][Pg 364] solved the problem in a simple but most masterly manner. He had a recess turned in the neck of the cylinder at the point formerly occupied by the stuffing-box, and into this a leather collar of U-section (marked solid black in Fig. 180) was placed with its open side downwards. When water reached it, it forced the edges apart, one against the plunger, the other against the walls of the recess, with a degree of tightness proportionate to the pressure. On water being released from the cylinder the collar collapsed, allowing the plunger to sink without friction.
The hydraulic press is an example of this law. Cylinder B is a force pump with a small diameter, capable of delivering water at very high pressures (up to 10 tons per square inch). Instead of A, we have a sturdy cylinder with a solid plunger, P (Fig. 180), holding the table where the object to be pressed is placed. Bramah, the inventor of the hydraulic press, faced significant challenges in preventing water from leaking between the top of the cylinder and the plunger. When he used a "gland" packing like that found in steam cylinders, it couldn't hold back the water unless it was tightened so much that it jammed the plunger. He tried many different solutions without success, and although his invention was excellent in principle, it seemed doomed to fail until his foreman, Henry Maudslay,[35][Pg 364] found a simple yet brilliant solution. He had a recess turned in the neck of the cylinder where the stuffing-box used to be, and into this, he placed a leather collar shaped like a U (marked solid black in Fig. 180) with the open side facing down. When water filled it, it pushed the edges apart—one against the plunger and the other against the walls of the recess—creating a seal that got tighter with more pressure. When the water was released from the cylinder, the collar collapsed, allowing the plunger to lower smoothly.
The principle of the hydraulic press is employed in lifts; in machines for bending, drilling, and riveting steel plates, or forcing wheels on or off their axles; for advancing the "boring shield" of a tunnel; and for other purposes too numerous to mention.
The hydraulic press is used in elevators, machines for bending, drilling, and riveting steel plates, as well as for putting wheels on or taking them off their axles, moving the "boring shield" for tunnels, and many other applications that are too many to list.
HOUSEHOLD WATER-SUPPLY FITTINGS.
Home Water Supply Fixtures.
Among these, the most used is the tap, or cock. When a house is served by the town or district water supply, the fitting of proper taps on all pipes connected with the supply is stipulated for by the water-works authorities. The old-fashioned "plug" tap is unsuitable for controlling high-pressure water on[Pg 365] account of the suddenness with which it checks the flow. Lest the reader should have doubts as to the nature of a plug tap, we may add that it has a tapering cone of metal working in a tapering socket. On the cone being turned till a hole through it is brought into line with the channel of the tap, water passes. A quarter turn closes the tap.
Among these, the most commonly used is the tap, or faucet. When a house gets its water from the local supply, the authorities require that proper faucets be installed on all pipes connected to it. The old-fashioned "plug" faucet isn't suitable for managing high-pressure water because it abruptly stops the flow. In case the reader is unsure about what a plug faucet is, it features a tapered metal cone that fits into a tapered socket. When the cone is turned to align a hole in it with the tap's channel, water flows through. A quarter turn closes the faucet.

Its place has been taken by the screw-down cock. A very common and effective pattern is shown in Fig. 181. The valve V, with a facing of rubber, leather, or some other sufficiently elastic substance,[Pg 366] is attached to a pin, C, which projects upwards into the spindle A of the tap. This spindle has a screw thread on it engaging with a collar, B. When the spindle is turned it rises or falls, allowing the valve to leave its seating, V S, or forcing it down on to it. A packing P in the neck of B prevents the passage of water round the spindle. To open or close the tap completely is a matter of several turns, which cannot be made fast enough to produce a "water-hammer" in the pipes by suddenly arresting the flow. The reader will easily understand that if water flowing at the rate of several miles an hour is abruptly checked, the shock to the pipes carrying it must be very severe.
Its place has been replaced by the screw-down valve. A very common and effective design is shown in Fig. 181. The valve V, with a surface made of rubber, leather, or another suitably flexible material,[Pg 366] is attached to a pin, C, which sticks up into the spindle A of the tap. This spindle has a screw thread that connects with a collar, B. When the spindle is turned, it moves up or down, allowing the valve to lift off its seat, V S, or pressing it down onto it. A packing P in the neck of B stops water from leaking around the spindle. To fully open or close the tap requires several turns, which are slow enough to prevent creating a "water-hammer" effect in the pipes by suddenly stopping the flow. The reader can easily understand that if water flowing at several miles an hour is suddenly stopped, the impact on the pipes carrying it must be quite intense.
THE BALL-COCK
The ballcock
is used to feed a cistern automatically with water, and prevent the water rising too far in the cistern (Fig. 182). Water enters the cistern through a valve, which is opened and closed by a plug faced with rubber. The lower extremity of the plug is flattened, and has a rectangular hole cut in it. Through this passes a lever, L, attached at one end to a hollow copper sphere, and pivoted at the other on the valve casing. This casing is not quite circular in section, for two slots are cast in the circumference to allow water[Pg 367] to pass round the plug freely when the valve is open. The buoyancy of the copper sphere is sufficient to force the plug's face up towards its seating as the valve rises, and to cut off the supply entirely when a certain level has been attained. If water is drawn off, the sphere sinks, the valve opens, and the loss is made good.
is used to automatically fill a cistern with water and prevent the water from rising too high in the cistern (Fig. 182). Water enters the cistern through a valve that is opened and closed by a rubber-faced plug. The bottom of the plug is flattened and has a rectangular hole cut into it. A lever, L, passes through this hole, attached at one end to a hollow copper sphere and pivoted at the other end on the valve casing. This casing isn't completely circular; it has two slots cast into the circumference to let water[Pg 367] flow around the plug easily when the valve is open. The buoyancy of the copper sphere is enough to push the plug's face up against its seating as the valve rises, completely shutting off the supply when a certain level is reached. If water is drawn off, the sphere sinks, the valve opens, and the loss is compensated.

THE WATER-METER.
THE WATER METER.

Some consumers pay a sum quarterly for the privilege of a water supply, and the water company allows them to use as much as they require. Others, however, prefer to pay a fixed amount for every thousand gallons used. In such cases, a water-meter is required to record the consumption. We append[Pg 368] a sectional diagram of Kennedy's patent water-meter (Fig. 183), very widely used. At the bottom is the measuring cylinder, fitted with a piston, (6), which is made to move perfectly water-tight and free from friction by means of a cylindrical ring of india-rubber, rolling between the body of the piston and the internal surface of the cylinder. The piston rod (25), after passing through a stuffing-box in the cylinder cover, is attached to a rack, (15), which gears[Pg 369] with a cog, (13), fixed on a shaft. As the piston moves up and down, this cog is turned first in one direction, then in the other. To this shaft is connected the index mechanism (to the right). The cock-key (24) is so constructed that it can put either end of the measuring cylinder in communication with the supply or delivery pipes, if given a quarter turn (see Fig. 184). The weighted lever (14) moves loosely on the pinion shaft through part of a circle. From the pinion project two arms, one on each side of the lever. When the lever has been lifted by one of these past the vertical position, it falls by its own weight on to a buffer-box rest, (18). In doing so, it strikes a projection on the duplex lever (19), which is joined to the cock-key, and gives the latter a quarter turn.
Some consumers pay a fee every three months for access to water, and the water company lets them use as much as they need. Others, however, choose to pay a set amount for every thousand gallons they use. In these situations, a water meter is needed to track the usage. We include[Pg 368] a sectional diagram of Kennedy's patented water meter (Fig. 183), which is very commonly used. At the bottom is the measuring cylinder, equipped with a piston, (6), which moves in a completely watertight and frictionless manner thanks to a cylindrical rubber ring that rolls between the piston body and the inside surface of the cylinder. The piston rod (25), after passing through a stuffing box in the cylinder cover, is connected to a rack, (15), which meshes[Pg 369] with a cog, (13), fixed on a shaft. As the piston moves up and down, this cog rotates first in one direction and then in the other. The index mechanism (to the right) is linked to this shaft. The cock key (24) is designed so that it can connect either end of the measuring cylinder to the supply or delivery pipes with a quarter turn (see Fig. 184). The weighted lever (14) moves freely on the pinion shaft along part of a circle. Two arms extend from the pinion, one on each side of the lever. When one of these arms lifts the lever past the vertical position, it falls under its own weight onto a buffer-box rest, (18). In doing so, it hits a projection on the duplex lever (19), which is connected to the cock key, causing it to make a quarter turn.
In order to follow the working of the meter, we must keep an eye on Figs. 183 and 184 simultaneously. Water is entering from A, the supply pipe. It flows through the cock downwards through channel D into the lower half of the cylinder. The piston rises, driving out the water above it through C to the delivery pipe B. Just as the piston completes its stroke the weight, raised by the rack and pinion, topples over, and strikes the key-arm, which it sends[Pg 370] down till stopped by the buffer-box. The tap is then at right angles to the position shown in Fig. 184, and water is directed from A down C into the top of the cylinder, forcing the piston down, while the water admitted below during the last stroke is forced up the passage D, and out by the outlet B. Before the piston has arrived at the bottom of the cylinder, the lifter will have lifted the weighted lever from the buffer-box, and raised it to a vertical position; from there it will have fallen on the right-hand key-arm, and have brought the cock-key to[Pg 371] its former position, ready to begin another upward stroke.
To keep track of how the meter works, we need to look at Figs. 183 and 184 at the same time. Water is entering from A, the supply pipe. It flows through the valve downward through channel D into the lower half of the cylinder. The piston rises, pushing the water above it out through C to the delivery pipe B. Just as the piston finishes its stroke, the weight, lifted by the rack and pinion, tips over and hits the key-arm, which moves[Pg 370] down until it's stopped by the buffer-box. The tap then turns to a right angle compared to the position shown in Fig. 184, directing water from A down C into the top of the cylinder, forcing the piston down, while the water that was let in below during the last stroke is pushed up the passage D and out through the outlet B. Before the piston reaches the bottom of the cylinder, the lifter will have raised the weighted lever from the buffer-box and lifted it to a vertical position; from there, it will have fallen onto the right-hand key-arm, returning the cock-key to[Pg 371] its original position, ready to start another upward stroke.
The index mechanism makes allowance for the fact that the bevel-wheel on the pinion shaft has its direction reversed at the beginning of every stroke of the piston. This bevel engages with two others mounted loosely on the little shaft, on which is turned a screw thread to revolve the index counter wheels. Each of these latter bevels actuates the shaft through a ratchet; but while one turns the shaft when rotating in a clockwise direction only, the other engages it when making an anti-clockwise revolution. The result is that the shaft is always turned in the same direction.
The index mechanism takes into account that the bevel wheel on the pinion shaft reverses direction at the start of each piston stroke. This bevel connects with two others that are loosely mounted on a small shaft, which has a screw thread for rotating the index counter wheels. Each of these bevels operates the shaft via a ratchet; however, one turns the shaft only when it rotates clockwise, while the other engages it during an anti-clockwise rotation. As a result, the shaft always turns in the same direction.
WATER-SUPPLY SYSTEMS.
Water supply systems.
The water for a town or a district supply is got either from wells or from a river. In the former case it may be assumed to be free from impurities. In the latter, there is need for removing all the objectionable and dangerous matter which river water always contains in a greater or less degree. This purification is accomplished by first leading the water into large settling tanks, where the suspended matter sinks to the bottom. The water is then drawn off[Pg 372] into filtration beds, made in the following manner. The bottom is covered with a thick layer of concrete. On this are laid parallel rows of bricks, the rows a small distance apart. Then come a layer of bricks or tiles placed close together; a layer of coarse gravel; a layer of finer gravel; and a thick layer of sand at the top. The sand arrests any solid matter in the water as it percolates to the gravel and drains below. Even the microbes,[36] of microscopic size, are arrested as soon as the film of mud has formed on the top of the sand. Until this film is formed the filter is not in its most efficient condition. Every now and then the bed is drained, the surface mud and sand carefully drained off, and fresh sand put in their place. A good filter bed should not pass more than from two to three gallons per hour for every square foot of surface, and it must therefore have a large area.
The water for a town or district supply comes either from wells or from a river. In the first case, it can be considered free from impurities. In the second case, it's necessary to remove all the unwanted and harmful substances that river water often contains to some extent. This purification process starts by directing the water into large settling tanks, where the suspended particles settle to the bottom. The water is then drawn off[Pg 372] into filtration beds, which are constructed in the following way: the bottom is covered with a thick concrete layer. On this, parallel rows of bricks are laid, with a small space between each row. Next comes a layer of bricks or tiles placed closely together, followed by a layer of coarse gravel, a layer of finer gravel, and finally a thick layer of sand on top. The sand captures any solid particles in the water as it flows through to the gravel and drains below. Even tiny microbes[36] are filtered out as soon as a film of mud forms on the top of the sand. Until this film develops, the filter is not operating at its most efficient level. Periodically, the bed is drained, the surface mud and sand are carefully removed, and fresh sand is added. A good filter bed should not allow more than two to three gallons per hour for every square foot of surface, meaning it needs to be quite large.
It is sometimes necessary to send the water through a succession of beds, arranged in terraces, before it is sufficiently pure for drinking purposes.
It is sometimes necessary to pass the water through a series of beds, set up in terraces, before it is clean enough for drinking.
THE HOUSEHOLD FILTER.
The Home Filter.
When there is any doubt as to the wholesomeness[Pg 373] of the water supply, a small filter is often used. The microbe-stopper is usually either charcoal, sand, asbestos, or baked clay of some kind. In Fig. 185 we give a section of a Maignen filter. R is the reservoir for the filtered water; A the filter case proper; D a conical perforated frame; B a jacket of asbestos cloth secured top and bottom by asbestos cords to D; C powdered carbon, between which and the asbestos is a layer of special chemical filtering medium. A perforated cap, E, covers in the carbon and prevents it being disturbed when water is poured in. The carbon arrests the coarser forms of matter; the asbestos the finer. The asbestos jacket is easily removed and cleansed by heating over a fire.
When there's any doubt about the safety[Pg 373] of the water supply, a small filter is often used. The microbe-stopper is usually made of charcoal, sand, asbestos, or some type of baked clay. In Fig. 185, we show a section of a Maignen filter. R is the reservoir for the filtered water; A is the filter case itself; D is a conical perforated frame; B is a jacket of asbestos cloth held in place at the top and bottom by asbestos cords to D; C is powdered carbon, with a layer of special chemical filtering medium between it and the asbestos. A perforated cap, E, covers the carbon to keep it stable when water is poured in. The carbon captures the larger particles, while the asbestos filters out the finer ones. The asbestos jacket can be easily removed and cleaned by heating it over a fire.

The most useful form of household filter is one which can be attached to a tap connected with[Pg 374] the main. Such a filter is usually made of porcelain or biscuit china. The Berkefeld filter has an outer case of iron, and an interior hollow "candle" of porcelain from which a tube passes through the lid of the filter to a storage tank for the filtered water. The water from the main enters the outer case, and percolates through the porcelain walls to the internal cavity and thence flows away through the delivery pipe.
The most effective type of household filter is one that can be attached to a tap connected with[Pg 374] the main supply. This filter is usually made of porcelain or fine china. The Berkefeld filter has an iron outer case and a hollow "candle" made of porcelain inside, with a tube that runs through the lid of the filter to a storage tank for the filtered water. Water from the main supply enters the outer case, seeps through the porcelain walls into the internal chamber, and then flows out through the delivery pipe.
Whatever be the type of filter used it must be cleansed at proper intervals. A foul filter is very dangerous to those who drink the water from it. It has been proved by tests that, so far from purifying the water, an inefficient and contaminated filter passes out water much more highly charged with microbes than it was before it entered. We must not therefore think that, because water has been filtered, it is necessarily safe. The reverse is only too often the case.
No matter what type of filter is used, it needs to be cleaned regularly. A dirty filter is very dangerous for anyone drinking the water from it. Tests have shown that rather than purifying the water, an ineffective and contaminated filter can actually release water that has a much higher concentration of microbes than it had before filtering. Therefore, we shouldn't assume that just because water has been filtered, it is automatically safe. Unfortunately, that is often not the case.
GAS TRAPS.
Gas traps.
Dangerous microbes can be breathed as well as drunk into the human system. Every communication between house and drains should be most carefully "trapped." The principle of a gas trap between, say, a kitchen sink and the drain to carry[Pg 375] off the water is given in Fig. 186. Enough water always remains in the bend to rise above the level of the elbow, effectually keeping back any gas that there may be in the pipe beyond the bend.
Dangerous germs can enter the human body through both air and drinking water. Every connection between a house and its drainage system needs to be meticulously sealed off. The idea of a trap, like the one between a kitchen sink and the drain that carries[Pg 375] away water, is illustrated in Fig. 186. A sufficient amount of water stays in the bend to create a barrier above the elbow, effectively preventing any gas from the pipe beyond the bend from entering the home.

WATER-ENGINES.
Water engines.
Before the invention of the steam-engine human industries were largely dependent on the motive power of the wind and running water. But when the infant nursed by Watt and Stephenson had grown into a giant, both of these natural agents were deposed from the important position they once held. Windmills in a state of decay crown many of our hilltops, and the water-wheel which formerly brought wealth to the miller now rots in its mountings at the end of the dam. Except for pumping and moving boats and ships, wind-power finds its occupation gone. It is too uncertain in quantity and quality to find a place in modern economics. Water-power, on the other hand, has received a[Pg 376] fresh lease of life through the invention of machinery so scientifically designed as to use much more of the water's energy than was possible with the old-fashioned wheel.
Before the steam engine was invented, human industries mostly relied on the power of wind and running water. But as the technology developed thanks to Watt and Stephenson, these natural sources lost their once crucial roles. Decaying windmills can still be seen on many hilltops, and the water wheel that used to bring wealth to millers now rots in place at the edge of the dam. Except for pumping and moving boats and ships, wind power has lost its purpose. It’s too inconsistent in both quantity and quality to fit into modern economics. On the other hand, water power has experienced a[Pg 376] revival due to new machinery that is designed to utilize much more of the water's energy than the old-fashioned wheel could.

The turbine, of which we have already spoken in our third chapter, is now the favourite hydraulic engine. Some water-turbines work on much the same principle as the Parsons steam-turbine; others resemble the De Laval. Among the latter the Pelton[Pg 377] wheel takes the first place. By the courtesy of the manufacturers we are able to give some interesting details and illustrations of this device.
The turbine, which we discussed in our third chapter, is now the most popular hydraulic engine. Some water turbines operate on principles similar to the Parsons steam turbine, while others are like the De Laval. Among these, the Pelton[Pg 377] wheel is the top choice. Thanks to the manufacturers, we can share some interesting details and illustrations of this device.
The wheel, which may be of any diameter from six inches to ten feet, has buckets set at regular intervals round the circumference, sticking outwards. Each bucket, as will be gathered from our illustration of an enormous 5,000 h.p. wheel (Fig. 187), is composed of two cups. A nozzle is so arranged as to direct water on the buckets just as they reach the lowest point of a revolution (see Fig. 188). The water strikes the bucket on the partition between[Pg 378] the two cups, which turns it right and left round the inside of the cups. The change of direction transfers the energy of the water to the wheel.
The wheel, which can range from six inches to ten feet in diameter, has buckets positioned at regular intervals around its edge, sticking outwards. Each bucket, as shown in our illustration of a massive 5,000 h.p. wheel (Fig. 187), consists of two cups. A nozzle is designed to direct water onto the buckets right as they reach the lowest point of a revolution (see Fig. 188). The water hits the bucket on the barrier between[Pg 378] the two cups, which causes it to rotate around the inside of the cups. This change in direction transfers the water's energy to the wheel.

The speed of the wheel may be automatically regulated by a deflecting nozzle (Fig. 189), which has a ball and socket joint to permit of its being raised or lowered by a centrifugal governor, thus throwing the stream on or off the buckets. The power of the wheel is consequently increased or diminished to meet the change of load, and a constant speed is maintained. When it is necessary to waste as little water as possible, a concentric tapered needle may be fitted inside the nozzle. When the nozzle is[Pg 379] in its highest position the needle tip is withdrawn; as the nozzle sinks the needle protrudes, gradually decreasing the discharge area of the nozzle.
The speed of the wheel can be automatically adjusted by a deflecting nozzle (Fig. 189), which features a ball and socket joint that allows it to be raised or lowered by a centrifugal governor, thereby controlling the flow of water to the buckets. This means the power of the wheel can be increased or decreased to match the load, ensuring a consistent speed. When it's important to use as little water as possible, a concentric tapered needle can be placed inside the nozzle. When the nozzle is[Pg 379] at its highest position, the tip of the needle is withdrawn; as the nozzle lowers, the needle extends, gradually reducing the opening of the nozzle.
Pelton wheels are designed to run at all speeds and to use water of any pressure. At Manitou, Colorado, is an installation of three wheels operated by water which leaves the nozzle at the enormous pressure of 935 lbs. per square inch. It is interesting to note that jets of very high-pressure water offer astonishing resistance to any attempt to deflect their course. A three-inch jet of 500-lb. water cannot be cut through by a blow from a crowbar.
Pelton wheels are built to operate at any speed and utilize water with any pressure. In Manitou, Colorado, there's a setup of three wheels powered by water that exits the nozzle at a staggering pressure of 935 lbs. per square inch. It's fascinating to observe that streams of extremely high-pressure water are incredibly resistant to any attempts to change their direction. A three-inch stream of 500-lb. water can't be pierced by a strike from a crowbar.
In order to get sufficient pressure for working hydraulic machinery in mines, factories, etc., water is often led for many miles in flumes, or artificial channels, along the sides of valleys from the source of supply to the point at which it is to be used. By the time that point is reached the difference between the gradients of the flume and of the valley bottom has produced a difference in height of some hundreds of feet.
To get enough pressure for operating hydraulic machines in mines, factories, and so on, water is often channeled for miles in flumes or artificial waterways along the sides of valleys from the supply source to where it will be used. By the time it arrives at that point, the difference in elevation between the flume and the valley floor has created a height difference of several hundred feet.

Fig. 190.—The Laxey water-wheel, Isle of Man. In the top right-hand corner is a Pelton wheel that is sized appropriately to perform the same amount of work using the same amount of water at the same pressure.
The full-page illustration on p. 380 affords a striking testimony to the wonderful progress made in engineering practice during the last fifty years. The huge water-wheel which forms the bulk of the picture is that at Laxey, in the Isle of Man. It is 72½ feet in diameter, and is supposed to develop 150 horse-power, which is transmitted several hundreds of feet by means of wooden rods supported at regular intervals. The power thus transmitted operates a system of pumps in a lead mine, raising 250 gallons of water per minute, to an elevation of 1,200 feet. The driving water is brought some distance to the wheel in an underground conduit, and is carried up the masonry tower by pressure, flowing over the top into the buckets on the circumference of the wheel.
The full-page illustration on p. 380 provides a stunning example of the incredible advancements in engineering over the past fifty years. The large water wheel in the picture is the one at Laxey, in the Isle of Man. It has a diameter of 72½ feet and is believed to generate 150 horsepower, which is transmitted several hundred feet through wooden rods that are supported at regular intervals. The power generated operates a system of pumps in a lead mine, raising 250 gallons of water per minute to a height of 1,200 feet. The driving water is funneled from a distance to the wheel through an underground conduit and is propelled up the masonry tower by pressure, spilling over the top into the buckets around the wheel's edge.
The little cut in the upper corner represents a Pelton wheel drawn on the same scale, which, given an equal supply of water at the same pressure, would develop the same power as the Laxey monster. By the side of the giant the other appears a mere toy.
The small cut in the upper corner shows a Pelton wheel drawn to the same scale, which, with an equal water supply at the same pressure, would generate the same power as the Laxey monster. Next to the giant, the other one looks like just a toy.
THE CREAM SEPARATOR.
The cream separator.
In 1864 Denmark went to war with Germany, and emerged from the short struggle shorn of the provinces of Lauenburg, Holstein, and Schleswig. The loss of the two last, the fairest and most fertile districts of the kingdom, was indeed grievous. The Danish king now ruled only over a land consisting largely[Pg 382] of moor, marsh, and dunes, apparently worthless for any purpose. But the Danes, with admirable courage, entered upon a second struggle, this time with nature. They made roads and railways, dug irrigation ditches, and planted forest trees; and so gradually turned large tracts of what had been useless country into valuable possessions. Agriculture being much depressed, owing to the low price of corn, they next gave their attention to the improvement of dairy farming. Labour-saving machinery of all kinds was introduced, none more important than the device for separating the fatty from the watery constituents of milk. It would not be too much to say that the separator is largely responsible for the present prosperity of Denmark.
In 1864, Denmark went to war with Germany and came out of the brief conflict stripped of the provinces of Lauenburg, Holstein, and Schleswig. Losing the latter two, which were the most beautiful and fertile areas of the kingdom, was indeed painful. The Danish king was left ruling over a territory mainly made up of moorland, marshes, and dunes, seemingly worthless for any use. But the Danes, with impressive determination, took on a new challenge, this time against nature. They built roads and railways, dug irrigation ditches, and planted forests, gradually transforming large areas of land that had been useless into valuable assets. With agriculture struggling due to low corn prices, they shifted their focus to improving dairy farming. They introduced all kinds of labor-saving machinery, the most significant being the device that separates the cream from the milk. It wouldn’t be an exaggeration to say that the separator is a key reason for Denmark's current prosperity.

How does it work? asks the reader. Centrifugal force[37] is the governing principle. To explain its application we append a sectional illustration (Fig. 191) of Messrs. Burmeister and Wain's hand-power separator, which may be taken as generally representative of this class of machines. Inside a circular casing is a cylindrical bowl, D, mounted on a shaft which can be revolved 5,000 times a minute by means of the cog-wheels and the screw thread chased on it near the bottom extremity. Milk flows from the reservoir R (supported on a stout arm) through tap A into a little distributer on the top of the separator, and from it drops into the central tube C of the bowl. Falling to the bottom, it is flung outwards by centrifugal force, finds an escape upwards through the holes a a, and climbs up the perforated grid e, the surface of which is a series of pyramidical excrescences, and finally reaches the inner surface of the drum proper. The velocity of rotation is so tremendous that the heavier portions of the milk—that is, the watery—crowd towards the point furthest from the centre, and keep the lighter fatty elements away from contact with the sides of the drum. In the diagram the water is represented by small circles, the cream by small crosses.
How does it work? the reader asks. Centrifugal force[37] is the main principle behind it. To illustrate this, we include a sectional diagram (Fig. 191) of Messrs. Burmeister and Wain's hand-powered separator, which is generally representative of this type of machine. Inside a circular casing is a cylindrical bowl, D, mounted on a shaft that can spin 5,000 times per minute using cog-wheels and a screw thread located near the bottom. Milk flows from the reservoir R (held up by a sturdy arm) through tap A into a small distributor at the top of the separator, from where it drops into the central tube C of the bowl. As it falls to the bottom, it's thrown outward by centrifugal force, escapes upwards through the holes a a, and rises through the perforated grid e, which has a series of pyramid-like bumps on its surface, eventually reaching the inner surface of the drum. The speed of rotation is so high that the heavier parts of the milk—specifically, the watery components—move towards the outer edge, keeping the lighter fatty elements away from the drum sides. In the diagram, water is shown as small circles, and cream as small crosses.
As more milk enters the drum it forces upwards what is already there. The cap of the drum has an inner jacket, F, which at the bottom all but touches the side of the drum. The distance between them is the merest slit; but the cream is deflected up outside F into space E, and escapes through a hole one-sixteenth of an inch in diameter perforating the plate G. The cream is flung into space K and[Pg 385] trickles out of spout B, while the water flies into space H and trickles away through spout A.
As more milk fills the drum, it pushes up what’s already there. The cap of the drum has an inner layer, F, which almost touches the side of the drum at the bottom. There’s just a tiny gap between them; however, the cream is pushed up and flows outside F into space E, escaping through a hole that’s one-sixteenth of an inch wide in plate G. The cream shoots into space K and [Pg 385] trickles out of spout B, while the water rushes into space H and trickles away through spout A.
THE "HYDRO.,"
THE "HYDRO,"
used in laundries for wringing clothes by centrifugal force, has a solid outer casing and an inner perforated cylindrical cage, revolved at high speed by a vertical shaft. The wet clothes are placed in the cage, and the machine is started. The water escapes through the perforations and runs down the side of the casing to a drain. After a few minutes the clothes are dry enough for ironing. So great is the centrifugal force that they are consolidated against the sides of the cage, and care is needed in their removal.
used in laundries for wringing clothes by centrifugal force, has a sturdy outer casing and an inner perforated cylindrical cage that spins at high speed on a vertical shaft. The wet clothes are placed in the cage, and the machine is started. The water drains out through the holes and runs down the side of the casing to a drain. After a few minutes, the clothes are dry enough for ironing. The centrifugal force is so strong that the clothes are pressed against the sides of the cage, so caution is required when removing them.
[35] Inventor of the lathe slide-rest.
__A_TAG_PLACEHOLDER_0__ Inventor of the lathe slide-rest.
[37] That is, centre-fleeing force. Water dropped on a spinning top rushes towards the circumference and is shot off at right angles to a line drawn from the point of parting to the centre of the top.
[37] That means a force moving away from the center. Water that lands on a spinning top moves toward the edge and is propelled off at an angle perpendicular to a line drawn from the point where it leaves to the center of the top.
Chapter XIX.
HEATING AND LIGHTING.
The hot-water supply—The tank system—The cylinder system—How a lamp works—Gas and gasworks—Automatic stoking—A gas governor—The gas meter—Incandescent gas lighting.
The hot water supply—The tank system—The cylinder system—How a lamp works—Gas and gasworks—Automatic stoking—A gas governor—The gas meter—Incandescent gas lighting.
HOT-WATER SUPPLY.
Hot water supply.
A well-equipped house is nowadays expected to contain efficient apparatus for supplying plenty of hot water at all hours of the day. There is little romance about the kitchen boiler and the pipes which the plumber and his satellites have sometimes to inspect and put right, but the methods of securing a proper circulation of hot water through the house are sufficiently important and interesting to be noticed in these pages.
A well-prepared house today is expected to have effective systems for providing ample hot water at any time of the day. There isn’t much charm in the kitchen boiler and the pipes that the plumber and his crew occasionally need to check and fix, but the techniques for ensuring proper hot water circulation throughout the house are important and interesting enough to be mentioned here.
In houses of moderate size the kitchen range does the heating. The two systems of storing and distributing the heated water most commonly used are—(1) The tank system; (2) the cylinder system.
In average-sized homes, the kitchen stove provides the heating. The two main systems for storing and distributing heated water are—(1) the tank system; (2) the cylinder system.
THE TANK SYSTEM
THE TANK SYSTEM
is shown diagrammatically in Fig. 192. The boiler is situated at the back of the range, and when a "damper" is drawn the fire and hot gases pass under it to a flue leading to the chimney. The almost boiling water rises to the top of the boiler and thence finds its way up the flow pipe into the hot-water tank A, displacing the somewhat colder water there, which descends through the return pipe to the bottom of the boiler.
is shown diagrammatically in Fig. 192. The boiler is located at the back of the range, and when a "damper" is opened, the fire and hot gases flow underneath it into a flue that leads to the chimney. The nearly boiling water rises to the top of the boiler and then moves up the flow pipe into the hot-water tank A, pushing the somewhat cooler water down, which then descends through the return pipe to the bottom of the boiler.
Water is drawn off from the flow pipe. This pipe projects some distance through the bottom of A, so that the hottest portion of the contents may be drawn off first. A tank situated in the roof, and fed from the main by a ball-cock valve, communicates with A through the siphon pipe S. The bend in this pipe prevents the ascent of hot water, which cannot sink through water colder than itself. From the top of A an expansion pipe is led up and turned over the cold-water tank to discharge any steam which may be generated in the boiler.
Water is drawn from the flow pipe. This pipe extends some distance through the bottom of A, allowing the hottest part of the contents to be extracted first. A tank located on the roof, filled by a ball-cock valve from the main supply, connects to A through the siphon pipe S. The bend in this pipe stops hot water from rising, as it can't sink through water that’s colder than it. An expansion pipe runs from the top of A and is turned over the cold-water tank to release any steam that might be produced in the boiler.
A hot-water radiator for warming the house may be connected to the flow and return pipes as shown. Since it opens a "short circuit" for the circulation, the water in the tank above will not be so well heated while it is in action. If cocks are fitted to the radiator pipes, the amount of heat thus deflected can be governed.
A hot-water radiator for heating the house can be connected to the flow and return pipes as shown. Since it creates a "short circuit" for the circulation, the water in the tank above won't get heated as well while it's running. If valves are installed on the radiator pipes, the amount of heat redirected can be controlled.

A disadvantage of the tank system is that the tank, if placed high enough to supply all flows, is sometimes so far from the boiler that the water loses much of its heat in the course of circulation. Also, if for any reason the cold water fails, tank A may be entirely emptied, circulation cease, and the water in the boiler and pipes boil away rapidly.
A downside of the tank system is that if the tank is positioned high enough to provide all the water flow, it can be so far from the boiler that the water loses a lot of its heat as it circulates. Additionally, if the cold water supply fails for any reason, tank A could be completely drained, circulation would stop, and the water in the boiler and pipes could boil away quickly.
THE CYLINDER SYSTEM
The Cylinder System
(Fig. 193) is open to neither of these objections. Instead of a rectangular tank up aloft, we now have a large copper cylinder situated in the kitchen near the range. The flow and return pipes are continuous, and the cold supply enters the bottom of the cylinder through a pipe with a siphon bend in it. As before, water is drawn off from the flow pipe, and a radiator may be put in the circuit. Since there is no draw-off point below the top of the cylinder, even if the cold supply fails the cylinder will remain full, and the failure will be discovered long before there is any danger of the water in it boiling away.
(Fig. 193) is not subject to either of these issues. Instead of a rectangular tank up high, we now have a large copper cylinder located in the kitchen near the stove. The flow and return pipes are continuous, and the cold supply enters the bottom of the cylinder through a pipe with a siphon bend. As before, water is taken from the flow pipe, and a radiator can be added to the circuit. Since there is no draw-off point below the top of the cylinder, even if the cold supply stops, the cylinder will stay full, and the issue will be noticed long before there's any risk of the water boiling away.

Boiler explosions are due to obstructions in the pipes. If the expansion pipe and the cold-water supply pipe freeze, there is danger of a slight accumulation of steam; and if one of the circulation pipes is also blocked, steam must generate until "something has to go,"[38] which is naturally the boiler. Assuming that the pipes are quite full to the points of obstruction, the fracture would result from the expansion of the water. Steam cannot generate unless there be a space above the water. But the expanding water has stored up the heat which would have raised steam, and the moment expansion begins after fracture this energy is suddenly let loose. Steam forms instantaneously, augmenting the effects of the explosion. From this it will be gathered that all pipes should be properly protected against frost; especially near the roof.
Boiler explosions happen because of blockages in the pipes. If the expansion pipe and the cold-water supply pipe freeze, there’s a risk of a small buildup of steam; and if one of the circulation pipes is also blocked, steam will keep building up until "something has to go,"[38] which is usually the boiler. Assuming the pipes are completely filled to the points of blockage, the break would occur due to the expansion of the water. Steam can’t form without a space above the water. However, the expanding water has stored the heat that would have created steam, and as soon as expansion starts after the break, this energy is released suddenly. Steam forms instantly, increasing the impact of the explosion. From this, it’s clear that all pipes should be properly insulated against freezing, especially near the roof.
Another cause of disaster is the furring up of the pipes with the lime deposited by hard water when heated. When hard water is used, the pipes will sooner or later be blocked near the boiler; and as the deposit is too hard to be scraped away, periodical renewals are unavoidable.
Another cause of disaster is the furring up of the pipes due to lime deposits from hard water when it's heated. When hard water is used, the pipes will eventually get blocked near the boiler; and since the deposits are too hard to scrape away, regular replacements will be necessary.
HOW A LAMP WORKS.
HOW A LIGHTBULB WORKS.
From heating we turn to lighting, and first to the ordinary paraffin lamp. The two chief things to notice about this are the wick and the chimney. The wick, being made of closely-woven cotton, draws up the oil by what is known as capillary attraction. If you dip the ends of two glass tubes, one half an inch, the other one-eighth of an inch in diameter, into a vessel of water, you will notice that the water rises higher in the smaller tube. Or get two clean glass plates and lay them face to face, touching at one end, but kept slightly apart at the other by some small object. If they are partly submerged perpendicularly, the water will rise between the plates—furthest on the side at which the two plates touch, and less and less as the other edge is approached. The tendency of liquids to rise through porous bodies is a phenomenon for which we cannot account.
From heating, we move on to lighting, specifically to the typical paraffin lamp. The two main things to notice about this are the wick and the chimney. The wick, made of tightly woven cotton, draws up the oil through what is known as capillary attraction. If you dip the ends of two glass tubes—one half an inch in diameter and the other one-eighth of an inch in diameter—into a container of water, you will see that the water rises higher in the smaller tube. Alternatively, take two clean glass plates and place them face to face, touching at one end but slightly apart at the other end, held by a small object. If they are partially submerged vertically, the water will rise between the plates—highest on the side where the two plates touch and decreasing as you move toward the other edge. The tendency of liquids to rise through porous materials is a phenomenon we can't explain.
Mineral oil contains a large proportion of carbon and hydrogen; it is therefore termed hydro-carbon. When oil reaches the top of a lighted wick, the liquid is heated until it turns into gas. The carbon and hydrogen unite with the oxygen of[Pg 393] the air. Some particles of the carbon apparently do not combine at once, and as they pass through the fiery zone of the flame are heated to such a temperature as to become highly luminous. It is to produce these light-rays that we use a lamp, and to burn our oil efficiently we must supply the flame with plenty of oxygen, with more than it could naturally obtain. So we surround it with a transparent chimney of special glass. The air inside the chimney is heated, and rises; fresh air rushes in at the bottom, and is also heated and replaced. As the air passes through, the flame seizes on the oxygen. If the wick is turned up until the flame becomes smoky and flares, the point has been passed at which the induced chimney draught can supply sufficient oxygen to combine with the carbon of the vapour, and the "free" carbon escapes as smoke.
Mineral oil has a high amount of carbon and hydrogen, so it's called a hydro-carbon. When the oil reaches the top of a lit wick, it gets heated until it turns into gas. The carbon and hydrogen mix with the oxygen in[Pg 393] the air. Some carbon particles don’t combine right away, and as they move through the hot part of the flame, they get heated to a point where they shine brightly. This is why we use a lamp, and to burn oil efficiently, we need to provide the flame with plenty of oxygen, more than it can naturally get. So we enclose it with a transparent chimney made of special glass. The air inside the chimney heats up and rises; fresh air comes in from the bottom, gets heated, and replaces the old air. As the air moves through, the flame grabs the oxygen. If the wick is turned up too much and the flame gets smoky and flares, it means we’ve gone past the point where the chimney can supply enough oxygen to react with the carbon in the vapor, causing "free" carbon to escape as smoke.
The blower-plate used to draw up a fire (Fig. 194) performs exactly the same function as the lamp chimney, but on a larger scale. The plate prevents air passing straight up the chimney over the coals, and compels it to find a way through the fire itself to replace the heated air rising up the chimney.
The blower-plate used to start a fire (Fig. 194) works just like a lamp chimney, but on a bigger scale. The plate stops air from going directly up the chimney over the coals and forces it to move through the fire itself to replace the hot air that’s rising up the chimney.

GAS AND GASWORKS.
Gas and gas services.
A lamp is an apparatus for converting hydro-carbon mineral oil into gas and burning it efficiently. The gas-jet burns gases produced by driving off hydro-carbon vapours from coal in apparatus specially designed for the purpose. Gas-making is now, in spite of the competition of electric lighting, so important an industry that we shall do well to glance at the processes which it includes. Coal gas may be produced on a very small scale as follows:—Fill a tin canister (the joints of which have been made by folding the metal, not by soldering) with coal, clap on the lid, and place it, lid downwards, in a bright fire, after punching a hole in the bottom. Vapour soon begins to issue from the hole. This is probably at first only steam, due to the coal[Pg 395] being more or less damp. But if a lighted match be presently applied the vapour takes fire, showing that coal gas proper is coming off. The flame lasts for a long time. When it dies the canister may be removed and the contents examined. Most of the carbon remains in the form of coke. It is bulk for bulk much lighter than coal, for the hydrogen, oxygen, and other gases, and some of the carbon have been driven off by the heat. The coke itself burns if placed in a fire, but without any smoke, such as issues from coal.
A lamp is a device that turns hydrocarbon mineral oil into gas and burns it efficiently. The gas jet burns the gases that come from releasing hydrocarbon vapors from coal using specially designed equipment. Despite the competition from electric lighting, gas-making is still an important industry, so it's worth looking at the processes involved. Coal gas can be produced on a small scale like this: Fill a tin canister (with joints made by folding the metal, not by soldering) with coal, put on the lid, and place it lid-down in a bright fire after punching a hole in the bottom. Soon, vapor starts to come out of the hole. At first, this is probably just steam from the coal being somewhat damp. But if you apply a lit match, the vapor will ignite, indicating that coal gas is being released. The flame can last a long time. When it goes out, you can remove the canister and check the contents. Most of the carbon remains as coke. Per unit of weight, it's much lighter than coal because hydrogen, oxygen, other gases, and some carbon have been removed by the heat. The coke itself will burn if placed in a fire but does so without any smoke, unlike burning coal.

Our home-made gas yields a smoky and unsatisfactory flame, owing to the presence of certain impurities—ammonia, tar, sulphuretted hydrogen, and carbon bisulphide. A gas factory must be equipped with means of getting rid of these objectionable constituents. Turning to Fig. 195, which displays very diagrammatically the main features of a gas plant, we observe at the extreme right the retorts, which correspond to our canister. These are usually long fire-brick tubes of D-section, the flat side at the bottom. Under each is a furnace, the flames of which play on the bottom, sides, and inner end of the retort. The outer end projecting beyond the brickwork seating has an iron air-tight[Pg 396] door for filling the retort through, immediately behind which rises an iron exit pipe, A, for the gases. Tar, which vaporizes at high temperatures, but liquefies at ordinary atmospheric heat, must first be got rid of. This is effected by passing the gas through the hydraulic main, a tubular vessel half full of water running the whole[Pg 397] length of the retorts. The end of pipe A dips below the surface of the water, which condenses most of the tar and steam. The partly-purified gas now passes through pipe B to the condensers, a series of inverted U-pipes standing on an iron chest with vertical cross divisions between the mouths of each U. These divisions dip into water, so that the gas has to pass up one leg of a U, down the other, up the first leg of the second pipe, and so on, till all traces of the tar and other liquid constituents have condensed on the inside of the pipe, from which they drop into the tank below.
Our homemade gas produces a smoky and unsatisfactory flame due to certain impurities—ammonia, tar, hydrogen sulfide, and carbon disulfide. A gas factory needs to have ways to eliminate these unwanted components. Looking at Fig. 195, which shows the main features of a gas plant, we notice on the far right the retorts, which are similar to our canister. These are typically long fire-brick tubes with a D-shaped cross-section, flat on the bottom. Under each retort is a furnace, where flames heat the bottom, sides, and inner end of the retort. The outer end extends beyond the brick framework and has an iron airtight [Pg 396] door for filling the retort, just behind which is an iron exit pipe, A, for the gases. Tar, which vaporizes at high temperatures but turns to liquid at normal atmospheric temperatures, must be removed first. This is done by routing the gas through the hydraulic main, a tubular vessel filled halfway with water that runs the entire[Pg 397] length of the retorts. The end of pipe A dips below the water's surface, which condenses most of the tar and steam. The partially purified gas then flows through pipe B to the condensers, a series of inverted U-shaped pipes mounted on an iron chest with vertical dividers between the openings of each U. These dividers dip into water, so the gas must travel up one leg of a U, down the other, up the first leg of the next pipe, and continue this way until all traces of tar and other liquid components have condensed inside the pipe, where they drop into the tank below.
The next stage is the passage of the scrubber, filled with coke over which water perpetually flows. The ammonia gas is here absorbed. There still remain the sulphuretted hydrogen and the carbon bisulphide, both of which are extremely offensive to the nostrils. Slaked lime, laid on trays in an air-tight compartment called the lime purifier, absorbs most of the sulphurous elements of these; and the coal gas is then fit for use. On leaving the purifiers it flows into the gasometer, or gasholder, the huge cake-like form of which is a very familiar object in the environs of towns. The gasometer is a cylindrical box with a domed top, but no bottom,[Pg 398] built of riveted steel plates. It stands in a circular tank of water, so that it may rise and fall without any escape of gas. The levity of the gas, in conjunction with weights attached to the ends of chains working over pulleys on the framework surrounding the holder, suffices to raise the holder.
The next step is the passage of the scrubber, which is filled with coke that has water flowing over it continuously. This is where the ammonia gas gets absorbed. However, there are still sulphuretted hydrogen and carbon bisulphide left, both of which smell really bad. Slaked lime, placed on trays in a sealed compartment called the lime purifier, absorbs most of the sulphurous elements. After this process, the coal gas is ready to use. Once it leaves the purifiers, it goes into the gasometer, or gasholder, which has a huge cake-like shape that is very recognizable in town areas. The gasometer is a cylindrical container with a domed top but no bottom,[Pg 398] made of riveted steel plates. It sits in a circular tank of water, allowing it to rise and fall without any gas escaping. The lighter gas, combined with weights attached to the ends of chains that run over pulleys on the frame around the holder, is enough to lift it.

Some gasometers have an enormous capacity. The record is at present held by that built for the South Metropolitan Gas Co., London, by Messrs. Clayton & Son of Leeds. This monster (of which we append an illustration, Fig. 196) is 300 feet in diameter and 180 feet high. When fully extended it holds 12,158,600 cubic feet of gas. Owing to its immense size, it is built on the telescopic principle in six "lifts," of 30 feet deep each. The sides of each lift, or ring, except the topmost, have a section shaped somewhat like the letter N. Two of the members form a deep, narrow cup to hold water, in which the "dip" member of the ring above it rises and falls.
Some gasometers have a huge capacity. The current record is held by the one built for the South Metropolitan Gas Co. in London by Clayton & Son from Leeds. This giant (for which we include an illustration, Fig. 196) is 300 feet in diameter and 180 feet tall. When fully extended, it holds 12,158,600 cubic feet of gas. Because of its massive size, it is constructed on a telescopic principle with six "lifts," each 30 feet deep. The sides of each lift, or ring, except for the topmost one, have a shape somewhat like the letter N. Two of the sections form a deep, narrow cup to hold water, in which the "dip" section of the ring above it moves up and down.

AUTOMATIC STOKING.
Auto Stoking.
The labour of feeding the retorts with coal and removing the coke is exceedingly severe. In the illustration on p. 400 (made from a very fine photograph taken by Mr. F. Marsh of Clifton) we see a man engaged in "drawing" the retorts through the iron doors at their outer ends. Automatic machinery is now used in large gasworks for both operations. One of the most ingenious stokers is the De Brouwer, shown at work in Fig. 198. The machine is suspended from an overhead trolley running on rails along the face of the retorts. Coal falls into a funnel at the top of the telescopic pipe P from hoppers in the story above, which have openings, H H, controlled by shutters. The coal as it falls is caught by a rubber belt working round part of the[Pg 402] circumference of the large wheel W and a number of pulleys, and is shot into the mouth of the retort. The operator is seen pulling the handle which opens the shutter of the hopper above the feed-tube, and switching on the 4 h.p. electric motor which drives the belt and moves the machine about. One of these feeders will charge a retort 20 feet long in twenty-two seconds.
Feeding the retorts with coal and removing the coke is extremely hard work. In the illustration on p. 400 (taken from a high-quality photograph by Mr. F. Marsh of Clifton), we see a man "drawing" the retorts through the iron doors at their outer ends. Nowadays, large gasworks use automatic machinery for both tasks. One of the most clever stokers is the De Brouwer, shown in Fig. 198. The machine hangs from an overhead trolley that runs on rails along the face of the retorts. Coal drops into a funnel at the top of the telescopic pipe P from hoppers above, which have openings H H controlled by shutters. As the coal falls, it's caught by a rubber belt working around part of the[Pg 402] circumference of the large wheel W and a series of pulleys, and is shot into the retort's mouth. The operator can be seen pulling the handle to open the hopper shutter above the feed tube and starting the 4 h.p. electric motor that drives the belt and moves the machine. One of these feeders can fill a 20-foot-long retort in just twenty-two seconds.

A GAS GOVERNOR.
A gas regulator.
Some readers may have noticed that late at night a gas-jet, which a few hours before burned with a somewhat feeble flame when the tap was turned fully on, now becomes more and more vigorous, and finally may flare up with a hissing sound. This is because many of the burners fed by the main supplying the house have been turned off, and consequently there is a greater amount of gas available for the jets still burning, which therefore feel an increased pressure. As a matter of fact, the pressure of gas in the main is constantly varying, owing partly to the irregularity of the delivery from the gasometer, and partly to the fact that the number of burners in action is not the same for many minutes together. It must also be remembered that houses near the gasometer end of the main will receive their gas[Pg 403] at a higher pressure than those at the other end. The gas stored in the holders may be wanted for use in the street lamps a few yards away, or for other lamps several miles distant. It is therefore evident that if there be just enough pressure to give a good supply to the nearest lamp, there will be too little a short distance beyond it, and none at all at the extreme point; so that it is necessary to put on enough pressure to overcome the friction on all these miles of pipe, and give just enough gas at the extreme end. It follows that at all intermediate points the pressure is excessive. Gas of the average quality is burned to the greatest advantage, as regards its light-giving properties, when its pressure is equal to that of a column of water half an inch high, or about 1⁄50 lb. to the square inch. With less it gives a smoky, flickering light, and with more the combustion is also imperfect.
Some readers might have noticed that late at night a gas jet, which a few hours earlier burned with a weak flame when the tap was fully open, now becomes stronger and may even flare up with a hissing sound. This happens because many of the burners connected to the main supply in the house have been turned off, resulting in more gas available for the jets that are still on, which means they experience increased pressure. In fact, the pressure of gas in the main fluctuates constantly, partly due to the uneven delivery from the gasometer, and partly because the number of active burners changes frequently. It's also important to remember that houses near the gasometer end of the main receive their gas[Pg 403] at a higher pressure than those at the far end. The gas stored in the holders may be needed for street lamps just a few yards away, or for other lamps several miles away. So, if there's just enough pressure to adequately supply the nearest lamp, there will be insufficient pressure a short distance beyond it, and none at all at the farthest point; thus, it's necessary to apply enough pressure to counteract the friction along all those miles of pipe and provide just enough gas at the farthest end. As a result, the pressure at all intermediate points is excessive. Gas of average quality burns most efficiently in terms of its light-producing properties when its pressure equals that of a column of water half an inch high, or about 1⁄50 lb. per square inch. With less pressure, it produces a smoky, flickering light, and with more, the combustion is also incomplete.

Every house supply should therefore be fitted with a gas governor, to keep the pressure constant. A governor frequently used, the Stott, is shown in section in Fig. 199. Gas enters from the main on the right, and passes into a circular elbow, D, which has top and bottom apertures closed by the valves V V. Attached to the valve shaft is a large inverted[Pg 404] cup of metal, the tip of which is immersed in mercury. The pressure at which the governor is to act is determined by the weights W, with which the valve spindle is loaded at the top. As soon as this pressure is exceeded, the gas in C C lifts the metal cup, and V V are pressed against their seats, so cutting off the supply. Gas cannot escape from C C, as it has not sufficient pressure to force its way through the mercury under the lip of the cup. [Pg 405]Immediately the pressure in C C falls, owing to some of the gas being used up, the valves open and admit more gas. When the fluctuations of pressure are slight, the valves never close completely, but merely throttle the supply until the pressure beyond them falls to its proper level—that is, they pass just as much gas as the burners in use can consume at the pressure arranged for.
Every household gas system should be equipped with a gas governor to maintain constant pressure. A commonly used governor, the Stott, is illustrated in section in Fig. 199. Gas enters from the main on the right and flows into a circular elbow, D, which has top and bottom openings sealed by the valves V V. Attached to the valve shaft is a large inverted [Pg 404] metal cup, the tip of which is submerged in mercury. The pressure at which the governor operates is set by the weights W that load the valve spindle from above. As soon as this pressure is exceeded, the gas in C C raises the metal cup, and the V V valves are pressed against their seats, cutting off the gas supply. Gas cannot escape from C C since it lacks sufficient pressure to push through the mercury under the cup's edge. [Pg 405] When the pressure in C C drops because some gas is consumed, the valves reopen to allow more gas in. When the pressure fluctuations are minor, the valves do not close entirely; instead, they simply throttle the supply until the pressure drops to the correct level—that is, they allow just enough gas for the burners in use to consume at the designated pressure.
Governors of much larger size, but working on much the same principle, are fitted to the mains at the point where they leave the gasometers. They are not, however, sensitive to local fluctuations in the pipes, hence the necessity for separate governors in the house between the meter and the burners.
Governors that are much larger in size, but operate on a similar principle, are connected to the mains where they exit the gas holders. However, they aren't responsive to local changes in the pipes, which is why separate governors are needed inside the house between the meter and the burners.
THE GAS-METER
THE GAS METER
commonly used in houses acts on the principle shown in Fig. 200. The air-tight casing is divided by horizontal and vertical divisions into three gas-chambers, B, C, and D. Gas enters at A, and passes to the valve chamber B. The slide-valves of this allow it to pass into C and D, and also into the two circular leather bellows E, F, which are attached to the central division G, but are quite independent of one another.
commonly used in houses operates on the principle shown in Fig. 200. The air-tight casing is divided by horizontal and vertical sections into three gas chambers, B, C, and D. Gas enters at A and goes into the valve chamber B. The slide valves here let it move into C and D, as well as into the two circular leather bellows E, F, which are connected to the central division G but operate independently of each other.

We will suppose that in the illustration the valves are admitting gas to chamber C and bellows F. The pressure in C presses the circular head of E towards the division G, expelling the contents of the bellows through an outlet pipe (not shown) to the burners in operation within the house. Simultaneously the inflation of F forces the gas in chamber D also through the outlet. The head-plates of the bellows are attached to rods and levers (not shown) working the slide-valves in B. As soon as E is fully in, and F fully expanded, the valves begin to open and put the inlet pipe in communication with D and E, and allow the contents of F and C to escape to the outlet. The movements of the valve mechanism operate a train of counting wheels, visible through a glass window in the side of the case. As the bellows have a definite capacity, every stroke that they give means that a certain volume of gas has been ejected either from them or from the chambers in which they move: this is registered by the counter.[Pg 407] The apparatus practically has two double-action cylinders (of which the bellows ends are the pistons) working on the same principle as the steam-cylinder (Fig. 21). The valves have three ports—the central, or exhaust, leading to the outlet, the outer ones from the inlet. The bellows are fed through channels in the division G.
We can assume that in the illustration, the valves are letting gas into chamber C and bellows F. The pressure in C pushes the circular head of E towards the divider G, forcing the contents of the bellows through an outlet pipe (not shown) to the burners that are currently running in the house. At the same time, the inflation of F pushes the gas in chamber D out through the outlet. The head plates of the bellows are connected to rods and levers (not shown) that operate the slide valves in B. Once E is fully in and F is fully expanded, the valves start to open, connecting the inlet pipe to D and E, allowing the contents of F and C to flow out to the outlet. The movements of the valve mechanism drive a series of counting wheels, visible through a glass window on the side of the case. Since the bellows have a specific capacity, every stroke they make indicates that a certain volume of gas has been released either from them or from the chambers in which they operate: this is recorded by the counter.[Pg 407] The device essentially has two double-action cylinders (with the ends of the bellows acting as the pistons) working on the same principle as a steam cylinder (Fig. 21). The valves have three ports—the center one is for exhaust, leading to the outlet, while the outer ones are for the inlet. The bellows receive gas through channels in the divider G.
INCANDESCENT GAS LIGHTING.
Gas lighting.
The introduction of the electric arc lamp and the incandescent glow-lamp seemed at one time to spell the doom of gas as an illuminating agent. But the appearance in 1886 of the Welsbach incandescent mantle for gas-burners opened a prosperous era in the history of gas lighting.
The introduction of the electric arc lamp and the incandescent light bulb once seemed to signal the end of gas as a source of light. However, the arrival of the Welsbach incandescent mantle for gas burners in 1886 marked the beginning of a successful period in the history of gas lighting.
The luminosity of a gas flame depends on the number of carbon particles liberated within it, and the temperature to which these particles can be heated as they pass through the intensely hot outside zone of the flame. By enriching the gas in carbon more light is yielded, up to a certain point, with a flame of a given temperature. To increase the heat of the flame various devices were tried before the introduction of the incandescent mantle, but they were found to be too short-lived to have any commercial[Pg 408] value. Inventors therefore sought for methods by which the emission of light could be obtained from coal gas independently of the incandescence of the carbon particles in the flame itself; and step by step it was discovered that gas could be better employed merely as a heating agent, to raise to incandescence substances having a higher emissivity of light than carbon.
The brightness of a gas flame relies on the amount of carbon particles released within it and how hot these particles can get as they move through the extremely hot outer layer of the flame. Increasing the carbon in the gas produces more light, but only up to a certain limit for a flame at a specific temperature. Various methods were tested to boost the flame's heat before the incandescent mantle was introduced, but they were too short-lived to be commercially viable[Pg 408]. As a result, inventors looked for ways to generate light from coal gas without depending on the glow of carbon particles in the flame itself; gradually, they discovered that gas could be more effectively used just as a heating source to raise other materials that emit light more efficiently than carbon to incandescence.
Dr. Auer von Welsbach found that the substances most suitable for incandescent mantles were the oxides of certain rare metals, thorium, and cerium. The mantle is made by dipping a cylinder of cotton net into a solution of nitrate of thorium and cerium, containing 99 per cent. of the former and 1 per cent. of the latter metal. When the fibres are sufficiently soaked, the mantle is withdrawn, squeezed, and placed on a mould to dry. It is next held over a Bunsen gas flame and the cotton is burned away, while the nitrates are converted into oxides. The mantle is now ready for use, but very brittle. So it has to undergo a further dipping, in a solution of gun-cotton and alcohol, to render it tough enough for packing. When it is required for use, it is suspended over the burner by an asbestos thread woven across the top, a light is[Pg 409] applied to the bottom, and the collodion burned off, leaving nothing but the heat-resisting oxides.
Dr. Auer von Welsbach discovered that the best materials for incandescent mantles were the oxides of certain rare metals, thorium and cerium. The mantle is created by soaking a cylinder of cotton net in a solution of thorium and cerium nitrates, which contains 99% thorium and 1% cerium. Once the fibers are fully soaked, the mantle is removed, squeezed, and placed on a mold to dry. It is then held over a Bunsen gas flame, which burns away the cotton while converting the nitrates into oxides. The mantle is now ready for use but is quite fragile. To make it tough enough for packaging, it undergoes an additional soaking in a solution of gun-cotton and alcohol. When it's needed, it's suspended over the burner by an asbestos thread woven across the top, a flame is[Pg 409] applied to the bottom, and the collodion is burned off, leaving only the heat-resistant oxides.
The burner used with a mantle is constructed on the Bunsen principle. The gas is mixed, as it emerges from the jet, with sufficient air to render its combustion perfect. All the carbon is burned, and the flame, though almost invisible, is intensely hot. The mantle oxides convert the heat energy of the flame into light energy. This is proved not only by the intense whiteness of the mantle, but by the fact that the heat issuing from the chimney of the burner is not nearly so great when the mantle is in position as when it is absent.
The burner that works with a mantle is based on the Bunsen principle. The gas mixes with enough air as it comes out of the jet to ensure complete combustion. All the carbon burns away, and the flame, while nearly invisible, is extremely hot. The mantle oxides convert the heat energy from the flame into light energy. This is evident not only from the bright whiteness of the mantle but also from the fact that the heat coming from the burner's chimney is significantly less when the mantle is in place compared to when it isn’t.
The incandescent mantle is more extensively used every year. In Germany 90 per cent. of gas lighting is on the incandescent system, and in England about 40 per cent. We may notice, as an interesting example of the fluctuating fortunes of invention, that the once doomed gas-burner has, thanks to Welsbach's mantle, in many instances replaced the incandescent electric lamps that were to doom it.
The incandescent mantle is used more and more each year. In Germany, 90% of gas lighting relies on the incandescent system, while in England, it's about 40%. It's interesting to see how the fate of inventions can change; the gas burner, which once seemed on its way out, has, thanks to Welsbach's mantle, taken the place of the incandescent electric lamps that were meant to replace it.
Chapter XX.
VARIOUS MECHANISMS.
Clocks and Watches:—A short history of timepieces—The construction of timepieces—The driving power—The escapement—Compensating pendulums—The spring balance—The cylinder escapement—The lever escapement—Compensated balance-wheels—Keyless winding mechanism for watches—The hour hand train. Locks:—The Chubb lock—The Yale lock. The Cycle:—The gearing of a cycle—The free wheel—The change-speed gear. Agricultural Machines:—The threshing-machine—Mowing-machines. Some Natural Phenomena:—Why sun-heat varies in intensity—The tides—Why high tide varies daily.
Clocks & Watches:—A brief history of timepieces—The design of timepieces—The source of power—The escapement—Compensating pendulums—The spring balance—The cylinder escapement—The lever escapement—Compensated balance wheels—Keyless winding mechanisms for watches—The hour hand train. Locks:—The Chubb lock—The Yale lock. The Cycle:—The gearing of a cycle—The freewheel—The change-speed gear. Farm Equipment:—The threshing machine—Mowing machines. Natural Phenomena:—Why sun-heat varies in intensity—The tides—Why high tide varies daily.
CLOCKS AND WATCHES.
Clocks and Watches.
A SHORT HISTORY OF TIMEPIECES.
A Brief History of Watches.
The oldest device for measuring time is the sun-dial. That of Ahaz mentioned in the Second Book of Kings is the earliest dial of which we have record. The obelisks of the Egyptians and the curious stone pillars of the Druidic age also probably served as shadow-casters.
The oldest device for measuring time is the sundial. The one from Ahaz mentioned in the Second Book of Kings is the earliest sundial we have on record. The obelisks of the Egyptians and the interesting stone pillars from the Druidic age likely also functioned as shadow-casters.
The clepsydra, or water-clock, also of great antiquity,[Pg 411] was the first contrivance for gauging the passage of the hours independently of the motion of the earth. In its simplest form it was a measure into which water fell drop by drop, hour levels being marked on the inside. Subsequently a very simple mechanism was added to drive a pointer—a float carrying a vertical rack, engaging with a cog on the pointer spindle; or a string from the float passed over a pulley attached to the pointer and rotated it as the float rose, after the manner of the wheel barometer (Fig. 153). In 807 A.D. Charlemagne received from the King of Persia a water-clock which struck the hours. It is thus described in Gifford's "History of France":—"The dial was composed of twelve small doors, which represented the division of the hours. Each door opened at the hour it was intended to represent, and out of it came a small number of little balls, which fell one by one, at equal distances of time, on a brass drum. It might be told by the eye what hour it was by the number of doors that were open, and by the ear by the number of balls that fell. When it was twelve o'clock twelve horsemen in miniature issued forth at the same time and shut all the doors."
The clepsydra, or water-clock, which is also very old,[Pg 411] was the first device to measure the passage of time without relying on the Earth's movement. Its simplest version involved a container where water flowed in drop by drop, with hour markers on the inside. Later, a basic mechanism was added to move a pointer—a float attached to a vertical rack, which engaged with a gear on the pointer spindle; or a string from the float that ran over a pulley connected to the pointer, turning it as the float rose, similar to a wheel barometer (Fig. 153). In 807 A.D., Charlemagne received a water-clock from the King of Persia that struck the hours. Gifford's "History of France" describes it like this: "The dial had twelve small doors representing the hours. Each door opened at the hour it was supposed to indicate, releasing a small number of balls that dropped one by one, at equal intervals, onto a brass drum. You could tell what hour it was by looking at the number of open doors and by listening to the number of balls that dropped. At twelve o'clock, twelve miniature horsemen would come out simultaneously and shut all the doors."
Sand-glasses were introduced about 330 A.D.[Pg 412] Except for special purposes, such as timing sermons and boiling eggs, they have not been of any practical value.
Sand-glasses were introduced around 330 A.D.. Aside from specific uses, like timing sermons and boiling eggs, they haven't really been useful.
The clepsydra naturally suggested to the mechanical mind the idea of driving a mechanism for registering time by the force of gravity acting on some body other than water. The invention of the weight-driven clock is attributed, like a good many other things, to Archimedes, the famous Sicilian mathematician of the third century B.C.; but no record exists of any actual clock composed of wheels operated by a weight prior to 1120 A.D. So we may take that year as opening the era of the clock as we know it.
The clepsydra naturally led to the idea of creating a timekeeping mechanism using gravity acting on something other than water. The invention of the weight-driven clock is often credited to Archimedes, the famous Sicilian mathematician from the third century BCE; however, there are no existing records of any actual clock made with wheels driven by a weight before 1120 A.D. Therefore, we can consider that year as the beginning of the clock era as we know it.
About 1500 Peter Hele of Nuremberg invented the mainspring as a substitute for the weight, and the watch appeared soon afterwards (1525 A.D.). The pendulum was first adopted for controlling the motion of the wheels by Christian Huygens, a distinguished Dutch mechanician, in 1659.
About 1500, Peter Hele from Nuremberg created the mainspring as a replacement for the weight, and the watch came out shortly after (1525 AD). The pendulum was first used to control the movement of the wheels by Christian Huygens, a notable Dutch mechanic, in 1659.
To Thomas Tompion, "the father of English watchmaking," is ascribed the honour of first fitting a hairspring to the escapement of a watch, in or about the year 1660. He also introduced the cylinder escapement now so commonly used in[Pg 413] cheap watches. Though many improvements have been made since his time, Tompion manufactured clocks and watches which were excellent timekeepers, and as a reward for the benefits conferred on his fellows during his lifetime, he was, after death, granted the exceptional honour of a resting-place in Westminster Abbey.
To Thomas Tompion, "the father of English watchmaking," is credited with the honor of being the first to fit a hairspring to the escapement of a watch around the year 1660. He also introduced the cylinder escapement, which is now commonly used in[Pg 413] inexpensive watches. Although many improvements have been made since his time, Tompion produced clocks and watches that were excellent timekeepers. As recognition for the benefits he brought to his peers during his lifetime, he was granted the exceptional honor of a burial place in Westminster Abbey after his death.
THE CONSTRUCTION OF TIMEPIECES.
WATCHMAKING.
A clock or watch contains three main elements:—(1) The source of power, which may be a weight or a spring; (2) the train of wheels operated by the driving force; (3) the agent for controlling the movements of the train—this in large clocks is usually a pendulum, in small clocks and watches a hairspring balance. To these may be added, in the case of clocks, the apparatus for striking the hour.
A clock or watch has three main parts: (1) the power source, which can be a weight or a spring; (2) the set of gears that the power moves; (3) the mechanism that controls the movement of the gears—typically, a pendulum for larger clocks and a hairspring balance for smaller clocks and watches. Additionally, clocks may include a mechanism for chiming the hour.
THE DRIVING POWER.
THE MAIN DRIVER.
Weights are used only in large clocks, such as one finds in halls, towers, and observatories. The great advantage of employing weights is that a constant driving power is exerted. Springs occupy much less room than weights, and are indispensable for portable timepieces. The employment of them[Pg 414] caused trouble to early experimenters on account of the decrease in power which necessarily accompanies the uncoiling of a wound-up spring. Jacob Zech of Prague overcame the difficulty in 1525 by the invention of the fusee, a kind of conical pulley interposed between the barrel, or circular drum containing the mainspring, and the train of wheels which the spring has to drive. The principle of the "drum and fusee" action will be understood from Fig. 201. The mainspring is a long steel ribbon fixed at one end to an arbor (the watchmaker's name for a spindle or axle), round which it is tightly wound. The arbor and spring are inserted in the barrel. The arbor is prevented from turning by a ratchet, B, and click, and therefore the spring in its effort to uncoil causes the barrel to rotate.
Weights are used only in large clocks, like those found in halls, towers, and observatories. The main benefit of using weights is that they provide a steady driving force. Springs take up much less space than weights and are essential for portable timepieces. However, their use[Pg 414] created issues for early experimenters because of the loss of power that happens when a wound-up spring unwinds. Jacob Zech of Prague solved this problem in 1525 with the invention of the fusee, a type of conical pulley placed between the barrel, which is the circular drum holding the mainspring, and the gear train that the spring drives. The principle of the "drum and fusee" mechanism can be understood from Fig. 201. The mainspring is a long steel strip fixed at one end to an arbor (the watchmaker's term for a spindle or axle), around which it is tightly coiled. The arbor and spring are housed in the barrel. The arbor is kept from turning by a ratchet, B, and click, so as the spring expands, it causes the barrel to rotate.

A string of catgut (or a very fine chain) is[Pg 415] connected at one end to the circumference of the drum, and wound round it, the other end being fixed to the larger end of the fusee, which is attached to the driving-wheel of the watch or clock by the intervention of a ratchet and click (not shown). To wind the spring the fusee is turned backward by means of a key applied to the square end A of the fusee arbor, and this draws the string from off the drum on to the fusee. The force of the spring causes the fusee to rotate by pulling the string off it, coil by coil, and so drives the train of wheels. But while the mainspring, when fully wound, turns the fusee by uncoiling the string from the smallest part of the fusee, it gets the advantage of the larger radius as its energy becomes lessened.
A string made of catgut (or a very fine chain) is[Pg 415] attached at one end to the edge of the drum, and wrapped around it, with the other end connected to the larger end of the fusee. This is linked to the driving wheel of the watch or clock through a ratchet and click (not shown). To wind the spring, the fusee is turned backward using a key inserted into the square end A of the fusee arbor, which pulls the string off the drum and onto the fusee. The force of the mainspring makes the fusee rotate by pulling the string off it, coil by coil, powering the train of wheels. When the mainspring is fully wound, it turns the fusee by uncoiling the string from the smallest part of the fusee, taking advantage of the larger radius as its energy decreases.
The fusee is still used for marine chronometers, for some clocks that have a mainspring and pendulum, and occasionally for watches. In the latter it has been rendered unnecessary by the introduction of the going-barrel by Swiss watchmakers, who formed teeth on the edge of the mainspring barrel to drive the train of wheels. This kind of drum is called "going" because it drives the watch during the operation of winding, which is performed by rotating[Pg 416] the drum arbor to which the inner end of the spring is attached. A ratchet prevents the arbor from being turned backwards by the spring. The adoption of the going-barrel has been made satisfactory by the improvements in the various escapement actions.
The fusee is still used in marine chronometers, some clocks with a mainspring and pendulum, and occasionally in watches. In the latter, it has become unnecessary due to the introduction of the going-barrel by Swiss watchmakers, who created teeth on the edge of the mainspring barrel to drive the gear train. This type of drum is called "going" because it powers the watch while it's being wound, which is done by rotating[Pg 416] the drum arbor that the inner end of the spring is attached to. A ratchet stops the arbor from turning backward because of the spring. The adoption of the going-barrel has been successful thanks to improvements in various escapement mechanisms.
THE ESCAPEMENT.
THE ESCAPEMENT.

The spring or weight transmits its power through a train of cogs to the escapement, or device for regulating the rate at which the wheels are to revolve. In clocks a pendulum is generally used as the controlling agent. Galileo, when a student at Pisa, noticed that certain hanging lamps in the cathedral there swung on their cords at an equal rate; and on investigation he discovered the principle that the shorter a pendulum is the more quickly will it swing to and fro. As has already been observed, Huygens first applied the principle to the governing of clocks. In Fig. 202 we have a simple representation of the "dead-beat" escapement commonly used in clocks. The escape-wheel is mounted on the shaft of the last cog of the driving train, the pallet on a spindle from[Pg 417] which depends a split arm embracing the rod and the pendulum. We must be careful to note that the pendulum controls motion only; it does not cause movement.
The spring or weight delivers its energy through a series of gears to the escapement, which regulates the speed at which the wheels turn. In clocks, a pendulum is typically used as the controlling element. Galileo, while studying at Pisa, noticed that certain hanging lamps in the cathedral there swung on their cords at the same rate; upon further investigation, he found out that the shorter a pendulum is, the faster it swings back and forth. As mentioned earlier, Huygens was the first to use this principle to control clocks. In Fig. 202, we have a basic illustration of the "dead-beat" escapement commonly found in clocks. The escape wheel is attached to the shaft of the last gear in the driving train, and the pallet is on a spindle from[Pg 417], which has a split arm that supports the rod and the pendulum. It's important to note that the pendulum controls the motion only; it does not generate movement.
The escape-wheel revolves in a clockwise direction. The two pallets a and b are so designed that only one can rest on the teeth at one time. In the sketch the sloping end of b has just been forced upwards by the pressure of a tooth. This swings the pallet and the pendulum. The momentum of the latter causes a to descend, and at the instant when b clears its tooth a catches and holds another. The left-hand side of a, called the locking-face, is part of a circle, so that the escape-wheel is held motionless as long as it touches a: hence the term, "dead beat"—that is, brought to a dead stop. As the pendulum swings back, to the left, under the influence of gravity, a is raised and frees the tooth. The wheel jerks round, and another tooth is caught by the locking-face of b. Again the pendulum swings to the right, and the sloping end of b is pushed up once more, giving the pendulum fresh impetus. This process repeats itself as long as the driving power lasts—for weeks, months, or years, as the case may be, and the mechanism continues to be in good working order.
The escape wheel turns in a clockwise direction. The two pallets a and b are designed so that only one can rest on the teeth at a time. In the drawing, the sloping end of b has just been pushed up by the pressure of a tooth. This moves the pallet and the pendulum. The momentum from the pendulum causes a to drop, and at the moment when b clears its tooth, a catches and holds onto another one. The left side of a, known as the locking face, is part of a circle, which keeps the escape wheel still as long as it touches a: hence the term "dead beat"—meaning it comes to a complete stop. As the pendulum swings back to the left under the force of gravity, a rises and releases the tooth. The wheel jumps forward, and another tooth is caught by the locking face of b. Once again, the pendulum swings to the right, and the sloping end of b gets pushed up again, giving the pendulum new energy. This process continues as long as the driving power lasts—for weeks, months, or even years, as long as the mechanism is well-maintained.
COMPENSATING PENDULUMS.
Balancing pendulums.
Metal expands when heated; therefore a steel pendulum which is of the exact length to govern a clock correctly at a temperature of 60° would become too long at 80°, and slow the clock, and too short at 40°, and cause it to gain. In common clocks the pendulum rod is often made of wood, which maintains an almost constant length at all ordinary temperatures. But for very accurate clocks something more efficient is required. Graham, the partner of Thomas Tompion, took advantage of the fact that different kinds of metal have different ratios of expansion to produce a self-compensating pendulum on the principle illustrated by Fig. 203. He used steel for the rod, and formed the bob, or weighted end, of a glass jar containing mercury held in a stirrup; the mercury being of such a height that, as the pendulum rod lengthened with a rise of temperature, the mercury expanded upwards sufficiently to keep the distance between the point of suspension and the centre of gravity of the bob always the same. With a fall of temperature the rod shortened, while the mercury sank in the jar. This device has not been improved upon, and is[Pg 419] still used in observatories and other places where timekeepers of extreme precision are required. The milled nut S in Fig. 203 is fitted at the end of the pendulum rod to permit the exact adjustment of the pendulum's length.
Metal expands when heated; so a steel pendulum that is the exact length needed to keep a clock accurate at 60° would become too long at 80°, causing the clock to run slow, and too short at 40°, making it run fast. In typical clocks, the pendulum rod is often made of wood, which keeps a nearly constant length at all normal temperatures. However, for very precise clocks, something better is needed. Graham, who partnered with Thomas Tompion, took advantage of the fact that different types of metal expand at different rates to create a self-compensating pendulum, as shown in Fig. 203. He used steel for the rod and made the bob, or weighted end, from a glass jar filled with mercury, held in a stirrup; the mercury was at a height that allowed it to expand upwards enough to keep the distance between the point of suspension and the center of gravity of the bob constant as the pendulum rod lengthened with rising temperature. When the temperature dropped, the rod shortened, and the mercury fell in the jar. This design has not been improved upon and is[Pg 419] still used in observatories and other settings where high-precision timekeeping is needed. The milled nut S in Fig. 203 is attached at the end of the pendulum rod to allow for precise adjustments to its length.
For watches, chronometers, and small clocks
For watches, chronometers, and small clocks
THE SPRING BALANCE
THE SPRING SCALE
takes the place of the pendulum. We still have an escape-wheel with teeth of a suitable shape to give impulses to the controlling agent. There are two forms of spring escapement, but as both employ a hairspring and balance-wheel we will glance at these before going further.
takes the place of the pendulum. We still have an escape wheel with teeth shaped to provide impulses to the controlling agent. There are two types of spring escapement, but since both use a hairspring and balance wheel, we will take a look at these before moving on.

The hairspring is made of very fine steel ribbon, tempered to extreme elasticity, and shaped to a spiral. The inner end is attached to the arbor of the balance-wheel, the outer end to a stud projecting from the plate of the watch. When the balance-wheel, impelled by the escapement, rotates, it winds up the spring. The energy thus stored helps the wheel to revolve the other way during the locking of a tooth of the escape-wheel. The time occupied[Pg 420] by the winding and the unwinding depends upon the length of the spring. The strength of the impulse makes no difference. A strong impulse causes the spring to coil itself up more than a weak impulse would; but inasmuch as more energy is stored the process of unwinding is hastened. To put the matter very simply—a strong impulse moves the balance-wheel further, but rotates it quickly; a weak impulse moves it a shorter distance, but rotates it slowly. In fact, the principle of the pendulum is also that of the hairspring; and the duration of a vibration depends on the length of the rod in the one case, and of the spring in the other.
The hairspring is made of a very fine steel ribbon that's tempered for maximum elasticity and shaped into a spiral. The inner end is attached to the arbor of the balance-wheel, while the outer end connects to a stud that sticks out from the watch's plate. When the balance-wheel rotates, pushed by the escapement, it winds up the spring. The energy stored in the spring helps the wheel move in the opposite direction when a tooth of the escape-wheel locks. The time taken[Pg 420] for winding and unwinding depends on the length of the spring. The strength of the impulse doesn’t matter. A strong impulse makes the spring coil up more than a weak one would, but since more energy is stored, the unwinding happens faster. Simply put—a strong impulse moves the balance-wheel further, but does so quickly; a weak impulse moves it a shorter distance, but does so slowly. In fact, the principle of the pendulum is the same as that of the hairspring; the length of the rod in one case and the length of the spring in the other determines how long a vibration lasts.
Motion is transmitted to the balance by one of two methods. Either (1) directly, by a cylinder escapement; or (2) indirectly, through a lever.
Motion is transferred to the balance in one of two ways. Either (1) directly, using a cylinder escapement; or (2) indirectly, through a lever.

THE CYLINDER ESCAPEMENT
The cylinder escapement
is seen in Fig. 204. The escape-wheel has sharp teeth set on stalks. (One tooth is removed to show the stalk.) The balance-wheel is mounted on a small steel cylinder, with part of the circumference cut away at the level of the teeth, so that if seen from above it[Pg 421] would appear like a in our illustration. A tooth is just beginning to shove its point under the nearer edge of the opening. As it is forced forwards, b is revolved in a clockwise direction, winding up the hairspring. When the tooth has passed the nearer edge it flies forward, striking the inside of the further wall of the cylinder, which holds it while the spring uncoils. The tooth now pushes its way past the other edge, accelerating the unwinding, and, as it escapes, the next tooth jumps forward and is arrested by the outside of the cylinder. The balance now reverses its motion, is helped by the tooth, is wound up, locks the tooth, and so on.
is seen in Fig. 204. The escape wheel has sharp teeth set on stalks. (One tooth is removed to show the stalk.) The balance wheel is mounted on a small steel cylinder, with part of the circumference cut away at the level of the teeth, so that if seen from above it[Pg 421] would look like a in our illustration. A tooth is just starting to push its point under the nearer edge of the opening. As it moves forward, b turns in a clockwise direction, winding up the hairspring. When the tooth has passed the nearer edge, it flies forward, hitting the inside of the farther wall of the cylinder, which holds it while the spring unwinds. The tooth then pushes its way past the other edge, speeding up the unwinding, and, as it escapes, the next tooth jumps forward and is stopped by the outside of the cylinder. The balance then reverses its motion, is assisted by the tooth, winds up, locks the tooth, and so on.
THE LEVER ESCAPEMENT
The lever escapement
is somewhat more complicated. The escape-wheel teeth are locked and unlocked by the pallets P P1 projecting from a lever which moves on a pivot (Fig. 205). The end of the lever is forked, and has a square notch in it. On the arbor of the balance-wheel is a roller, or plate, R, which carries a small pin, I. Two pins, B B, projecting from the plate of the watch prevent the lever moving too far. We must further notice the little pin C on the lever, and a notch in the edge of the roller.
is somewhat more complicated. The escape-wheel teeth are locked and unlocked by the pallets P P1 that extend from a lever which pivots (Fig. 205). The end of the lever is forked and has a square notch in it. On the arbor of the balance-wheel is a roller, or plate, R, which has a small pin, I. Two pins, B B, extending from the plate of the watch prevent the lever from moving too far. We also need to note the little pin C on the lever and a notch on the edge of the roller.

In the illustration a tooth has just passed under the "impulse face" b of P1. The lever has been moved upwards at the right end; and its forked end has given an impulse to R, and through it to the balance-wheel. The spring winds up. The pin C prevents the lever dropping, because it no longer has the notch opposite to it, but presses on the circumference of R. As the spring unwinds it strikes the lever at the moment when the notch and C are opposite. The lever is knocked downwards, and the tooth, which had been arrested by the locking-face a of[Pg 423] pallet P, now presses on the impulse face b, forcing the left end of the lever up. The impulse pin I receives a blow, assisting the unwinding of the spring, and C again locks the lever. The same thing is repeated in alternate directions over and over again.
In the illustration, a tooth has just passed under the "impulse face" b of P1. The lever has been pushed up on the right end, and its forked end has given an impulse to R, which then transfers the force to the balance wheel. The spring winds up. The pin C stops the lever from dropping because it no longer has the notch opposite it but instead presses against the edge of R. As the spring unwinds, it hits the lever at the moment when the notch and C are aligned. The lever is pushed downward, and the tooth, which was held back by the locking face a of[Pg 423] pallet P, now pushes on the impulse face b, forcing the left end of the lever up. The impulse pin I takes a hit, helping the spring unwind, and C once again locks the lever. This process repeats back and forth continuously.
COMPENSATING BALANCE-WHEELS.
Compensating balance wheels.
The watchmaker has had to overcome the same difficulty as the clockmaker with regard to the expansion of the metal in the controlling agent. When a metal wheel is heated its spokes lengthen, and the rim recedes from the centre. Now, let us suppose that we have two rods of equal weight, one three feet long, the other six feet long. To an end of each we fasten a 2-lb. weight. We shall find it much easier to wave the shorter rod backwards and forwards quickly than the other. Why? Because the weight of the longer rod has more leverage over the hand than has that of the shorter rod. Similarly, if, while the mass of the rim of a wheel remains constant, the length of the spokes varies, the effort needed to rotate the wheel to and fro at a constant rate must vary also. Graham got over the difficulty with a rod by means of the compensating pendulum. Thomas Earnshaw mastered it in wheels by means[Pg 424] of the compensating balance, using the same principle—namely, the unequal expansion of different metals. Any one who owns a compensated watch will see, on stopping the tiny fly-wheel, that it has two spokes (Fig. 206), each carrying an almost complete semicircle of rim attached to it. A close examination shows that the rim is compounded of an outer strip of brass welded to an inner lining of steel. The brass element expands more with heat and contracts more with cold than steel; so that when the spokes become elongated by a rise of temperature, the pieces bend inwards at their free ends (Fig. 207); if the temperature falls, the spokes are shortened, and the rim pieces bend outwards (Fig. 208).[39] This ingenious contrivance keeps the leverage of the rim constant[Pg 425] within very fine limits. The screws S S are inserted in the rim to balance it correctly, and very fine adjustment is made by means of the four tiny weights W W. In ships' chronometers,[40] the rim pieces are sub-compensated towards their free ends to counteract slight errors in the primary compensation. So delicate is the compensation that a daily loss or gain of only half a second is often the limit of error.
The watchmaker has faced the same challenge as the clockmaker regarding how metal expands in the controlling mechanism. When a metal wheel heats up, its spokes get longer, and the rim moves away from the center. Now, let’s say we have two rods of equal weight, one three feet long and the other six feet long. If we attach a 2-lb. weight to each end, we’ll find it much easier to quickly wave the shorter rod back and forth compared to the longer one. Why? Because the weight of the longer rod has more leverage on the hand than the shorter one does. Similarly, if the mass of a wheel’s rim stays the same and the length of the spokes changes, the effort required to rotate the wheel back and forth at a constant speed will also change. Graham solved this issue with a rod using the compensating pendulum. Thomas Earnshaw tackled it in wheels with the compensating balance, applying the same principle—specifically, the unequal expansion of different metals. Anyone who owns a compensated watch will notice, when stopping the tiny flywheel, that it has two spokes (Fig. 206), each supporting almost a complete semicircle of rim. A closer look reveals that the rim consists of an outer strip of brass welded to an inner lining of steel. The brass expands more with heat and contracts more with cold than steel does; so when the spokes extend due to rising temperatures, the ends bend inwards (Fig. 207); if the temperature drops, the spokes shorten, and the rim pieces bend outwards (Fig. 208).[39] This clever design keeps the leverage of the rim constant[Pg 425] within very narrow limits. The screws S S are placed in the rim for proper balancing, and fine adjustments are made using the four tiny weights W W. In ship chronometers,[40] the rim pieces are sub-compensated at their free ends to correct minor errors in the primary compensation. The compensation is so delicate that a daily error of only half a second is often the maximum limit.
![]() |
![]() |
![]() |
A "compensating" watch balance at normal, high, and low temperatures. |
KEYLESS WINDING MECHANISM FOR WATCHES.
Keyless winding mechanism for watches.
The inconvenience attaching to a key-wound watch caused the Swiss manufacturers to put on the market, in 1851, watches which dispensed with a separate key. Those of our readers who carry keyless watches will be interested to learn how the winding and setting of the hands is effected by the little serrated knob enclosed inside the pendant ring.
The hassle of using a key to wind a watch led Swiss manufacturers to release keyless watches in 1851. Those of you who own keyless watches might be interested to know how winding and setting the hands works with the small, serrated knob inside the pendant ring.
There are two forms of "going-barrel" keyless mechanism—(1) The rocking bar; (2) the shifting sleeve. The rocking bar device is shown in Figs. 209, 210. The milled head M turns a cog, G, which is always in gear with a cog, F. This cog gears[Pg 426] with two others, A and B, mounted at each end of the rocker R, which moves on pivot S. A spring, S P, attached to the watch plate presses against a small stud on the rocking bar, and keeps A normally in gear with C, mounted on the arbor of the mainspring.
There are two types of "going-barrel" keyless mechanisms: (1) the rocking bar; (2) the shifting sleeve. The rocking bar device is illustrated in Figs. 209, 210. The milled head M turns a cog, G, which is always engaged with another cog, F. This cog connects[Pg 426] with two other cogs, A and B, that are mounted at each end of the rocker R, which pivots on S. A spring, S P, attached to the watch plate presses against a small stud on the rocking bar, keeping A normally engaged with C, which is mounted on the mainspring arbor.

To wind the watch, M is turned so as to give F an anti-clockwise motion. The teeth of F now press[Pg 427] A downwards and keep it in gear with C while the winding is done. A spring click (marked solid black) prevents the spring uncoiling (Fig. 209). If F is turned in a clockwise direction it lifts A and prevents it biting the teeth of C, and no strain is thrown on C.
To wind the watch, M is turned to make F move counter-clockwise. The teeth of F now push [Pg 427] A downwards and keep it engaged with C while the winding happens. A spring click (shown in solid black) stops the spring from uncoiling (Fig. 209). If F is turned clockwise, it lifts A and keeps it from engaging with the teeth of C, meaning there’s no strain on C.
To set the hands, the little push-piece P is pressed inwards by the thumb (Fig. 210) so as to depress the right-hand end of R and bring B into gear with D, which in turn moves E, mounted on the end of the minute-hand shaft. The hands can now be moved in either direction by turning M. On releasing the push-piece the winding-wheels engage again.
To set the hands, press the small button P inward with your thumb (Fig. 210) to push down the right end of R and connect B with D, which then moves E, located at the end of the minute-hand shaft. You can now turn M to move the hands in either direction. When you release the button, the winding gears engage again.
The shifting sleeve mechanism has a bevel pinion in the place of G (Fig. 209) gearing with the mainspring cog. The shaft of the knob M is round where it passes through the bevel and can turn freely inside it, but is square below. On the square part is mounted a little sliding clutch with teeth on the top corresponding with the other teeth on the under side of the bevel-wheel, and teeth similar to those of G (Fig. 209) at the end. The clutch has a groove cut in the circumference, and in this lies the end of a spring lever which can be depressed by the push-piece. The mechanism much resembles on a small scale the motor car changing gear (Fig. 49). Normally,[Pg 428] the clutch is pushed up the square part of the knob shaft by the spring so as to engage with the bevel and the winding-wheels. On depressing the clutch by means of the push-piece it gears with the minute-hand pinion, and lets go of the bevel.
The shifting sleeve mechanism includes a bevel pinion instead of the G (Fig. 209) gearing with the mainspring cog. The shaft of the knob M is round where it goes through the bevel and can turn freely inside it, but it's square below. On the square part, there's a small sliding clutch with teeth on the top that match the teeth on the underside of the bevel-wheel, and similar teeth to those of G (Fig. 209) at the end. The clutch has a groove cut around it, where the end of a spring lever rests, which can be pressed down by the push-piece. The mechanism is quite similar on a smaller scale to the gear changing in a motor car (Fig. 49). Normally, [Pg 428] the clutch is pushed up the square part of the knob shaft by the spring, allowing it to engage with the bevel and the winding-wheels. When the clutch is pressed down using the push-piece, it connects with the minute-hand pinion and releases the bevel.

In one form of this mechanism the push-piece is[Pg 429] dispensed with, and the minute-wheel pinion is engaged by pulling the knob upwards.
In one version of this mechanism, the push-piece is[Pg 429] removed, and the minute-wheel pinion is engaged by pulling the knob up.
THE HOUR-HAND TRAIN.
THE CLOCK HAND TRAIN.

The teeth of the mainspring drum gear with a cog on the minute-hand shaft, which also carries one of the cogs of the escapement train. The shaft is permitted by the escapement to revolve once an hour. Fig. 211 shows diagrammatically how this is managed. The hour-hand shaft A (solid black) can be moved round inside the cog B, driven by the mainspring drum. It carries a cog, C. This gears with a cog, D, having three times as many teeth. The cog E, united to D, drives cog F, having four times as many teeth as E. To F is attached the collar G of the[Pg 430] hour-hand. F and G revolve outside the minute-hand shaft. On turning A, C turns D and E, E turns F and the hour-hand, which revolves ⅓ of ¼ = 1⁄12 as fast as A.[41]
The teeth of the mainspring drum gear connect to a cog on the minute hand shaft, which also holds one of the cogs of the escapement train. The escapement allows the shaft to rotate once every hour. Fig. 211 visually explains how this works. The hour-hand shaft A (solid black) can rotate inside the cog B, which is driven by the mainspring drum. It has a cog, C, that meshes with a cog, D, which has three times as many teeth. The cog E, connected to D, drives cog F, which has four times as many teeth as E. Attached to F is the collar G of the[Pg 430] hour-hand. Both F and G rotate outside the minute-hand shaft. When A turns, C rotates D and E, and E turns F and the hour-hand, which turns ⅓ of ¼ = 1⁄12 as quickly as A.[41]
LOCKS.
LOCKS.
On these unfortunately necessary mechanisms a great deal of ingenuity has been expended. With the advance of luxury and the increased worship of wealth, it becomes more and more necessary to guard one's belongings against the less scrupulous members of society.
On these sadly essential mechanisms, a lot of creativity has been put to work. As luxury grows and the admiration of wealth escalates, it becomes more and more important to protect one's possessions from the less principled members of society.

The simplest form of lock, such as is found in[Pg 431] desks and very cheap articles, works on the principle shown in Fig. 212. The bolt is split at the rear, and the upper part bent upwards to form a spring. The under edge has two notches cut in it, separated by a curved excrescence. The key merely presses the bolt upwards against the spring, until the notch, engaging with the frame, moves it backwards or forwards until the spring drives the tail down into the other notch. This primitive device affords, of course, very little security. An advance is seen in the
The simplest type of lock, like those found in[Pg 431] desks and very inexpensive items, operates based on the principle shown in Fig. 212. The bolt is cut at the back, and the upper part is bent upward to create a spring. The bottom edge has two notches cut into it, separated by a curved bump. The key simply pushes the bolt upward against the spring until the notch, which connects with the frame, moves it back and forth until the spring pushes the tail down into the other notch. This basic mechanism provides very little security, but there is an improvement seen in the
TUMBLER LOCK.
Tumbler lock.

The bolt now can move only in a horizontal direction. It has an opening cut in it with two[Pg 432] notches (Figs. 213, 214). Behind the bolt lies the tumbler T (indicated by the dotted line), pivoted at the angle on a pin. From the face of the tumbler a stud, S, projects through the hole in the bolt. This stud is forced into one or other of the notches by the spring, S1, which presses on the tail of the tumbler.
The bolt can now only move horizontally. It has a slot cut into it with two[Pg 432] notches (Figs. 213, 214). Behind the bolt is the tumbler T (shown by the dotted line), which pivots at an angle on a pin. A stud, S, sticks out from the face of the tumbler through the hole in the bolt. This stud is pushed into one of the notches by the spring, S1, that presses on the tail of the tumbler.

In Fig. 213 the key is about to actuate the locking mechanism. The next diagram (Fig. 214) shows how the key, as it enters the notch on the lower side of the bolt to move it along, also raises the tumbler stud clear of the projection between the two notches. By the time that the bolt has been fully "shot," the key leaves the under notch and allows the tumbler stud to fall into the rear locking-notch.
In Fig. 213, the key is about to activate the locking mechanism. The next diagram (Fig. 214) illustrates how the key, as it fits into the notch on the bottom side of the bolt to slide it over, also lifts the tumbler stud out of the way of the projection between the two notches. By the time the bolt has been completely "fired," the key exits the lower notch, letting the tumbler stud drop into the back locking notch.
A lock of this type also can be picked very easily, as the picker has merely to lift the tumbler and move the bolt along. Barron's lock, patented in 1778, had two tumblers and two studs; and the opening in the bolt had notches at the top as well as at the bottom (Fig. 215). This made it necessary for both tumblers to be raised simultaneously to exactly the right height. If either was not lifted sufficiently, a stud could not clear its bottom notch; if either rose too far, it engaged an upper notch. The chances therefore were greatly against a wrong key turning the lock.
A lock like this can also be easily picked, as the person picking it just needs to lift the tumbler and slide the bolt. Barron's lock, patented in 1778, had two tumblers and two studs, and the bolt had notches both at the top and bottom (Fig. 215). This meant that both tumblers had to be raised at the same time to the exact height. If either one wasn't lifted high enough, a stud couldn't pass its bottom notch; if either was raised too high, it would catch on an upper notch. So, the odds were heavily against a wrong key being able to turn the lock.

THE CHUBB LOCK
THE CHUBB LOCK
is an amplification of this principle. It usually has several tumblers of the shape shown in Fig. 216. The lock stud in these locks projects from the bolt itself, and the openings, or "gates," through which the stud must pass as the lock moves, are cut in the[Pg 434] tumblers. It will be noticed that the forward notch of the tumbler has square serrations in the edges. These engage with similar serrations in the bolt stud and make it impossible to raise the tumbler if the bolt begins to move too soon when a wrong key is inserted.
is an expansion of this principle. It usually has several tumblers shaped like those shown in Fig. 216. The lock stud in these locks sticks out from the bolt itself, and the openings, or "gates," through which the stud must pass as the lock operates, are cut in the[Pg 434] tumblers. You’ll notice that the forward notch of the tumbler has square notches along the edges. These interlock with similar notches in the bolt stud, making it impossible to lift the tumbler if the bolt starts to move too soon when a wrong key is inserted.

Fig. 217 is a Chubb key with eight steps. That nearest the head (8) operates a circular revolving curtain, which prevents the introduction of picking tools when a key is inserted and partly turned, as the key slot in the curtain is no longer opposite that in the lock. Step 1 moves the bolt.
Fig. 217 is a Chubb key with eight steps. The one closest to the head (8) operates a circular revolving curtain that stops picking tools from getting in when a key is inserted and partially turned, since the key slot in the curtain is no longer aligned with the one in the lock. Step 1 moves the bolt.

In order to shoot the bolt the height of the key steps must be so proportioned to the depth of their tumblers that all the gates in the tumblers are simultaneously raised to the right level for the stud to pass through them, as in Fig. 218. Here you will observe that the tumbler D on the extreme right (lifted by step 2 of the key) has a stud, D S, projecting from it over the other tumblers. This is called the detector tumbler. If a false key or picking tool is inserted it is certain to raise one of the tumblers too far. The detector is then over-lifted by the stud D S, and a spring catch falls into a notch at the rear. It is now impossible to pick the lock, as the detector can be released only by the right key shooting the bolt a little further in the locking direction, when a projection on the rear of the bolt lifts the catch and allows the tumbler to fall. The detector also shows that the lock has been tampered with, since even the right key cannot move the bolt until the overlocking has been performed.
To shoot the bolt, the height of the key steps must be proportional to the depth of their tumblers so that all the gates in the tumblers are raised to the correct level for the stud to pass through, as shown in Fig. 218. You’ll see that the tumbler D on the far right (lifted by step 2 of the key) has a stud, D S, sticking out over the other tumblers. This is known as the detector tumbler. If a fake key or picking tool is used, it will definitely lift one of the tumblers too much. The detector will then be over-lifted by the stud D S, causing a spring catch to fall into a notch at the back. At this point, it’s impossible to pick the lock, as the detector can only be released by the correct key pushing the bolt a little further in the locking direction, which lifts the catch and allows the tumbler to drop. The detector also indicates that the lock has been tampered with, since even the correct key cannot move the bolt until the overlocking has occurred.

Each tumbler step of a large Chubb key can be[Pg 436] given one of thirty different heights; the bolt step one of twenty. By merely transposing the order of the steps in a six-step key it is possible to get 720 different combinations. By diminishing or increasing the heights the possible combinations may be raised to the enormous total of 7,776,000!
Each tumbler step of a large Chubb key can be[Pg 436] set to one of thirty different heights; the bolt step can be set to one of twenty. Simply changing the order of the steps in a six-step key allows for 720 different combinations. By adjusting the heights, the total possible combinations can be increased to a staggering 7,776,000!

THE YALE LOCK,
The Yale lock,
which comes from America, works on a quite different system. Its most noticeable feature is that it permits the use of a very small key, though the number of combinations possible is still enormous (several millions). In our illustrations (Figs. 219, 220, 221) we show the mechanism controlling the turning of[Pg 437] the key. The keyhole is a narrow twisted slot in the face of a cylinder, G (Fig. 219), which revolves inside a larger fixed cylinder, F. As the key is pushed in, the notches in its upper edge raise up the pins A1, B1, C1, D1, E1, until their tops exactly reach the surface of G, which can now be revolved by the key in Fig. 220, and work the bolt through the medium of the arm H. (The bolt itself is not shown.) If a wrong key is inserted, either some of the lower pins will project upwards into the fixed cylinder F (see Fig. 221), or some of the pins in F will sink into G. It is then impossible to turn the key.
which comes from America, operates on a different system. Its most noticeable feature is that it allows the use of a very small key, although the number of possible combinations is still huge (several million). In our illustrations (Figs. 219, 220, 221), we show the mechanism that controls the key's turning.[Pg 437] The keyhole is a narrow twisted slot in the face of a cylinder, G (Fig. 219), which rotates inside a larger fixed cylinder, F. As the key is inserted, the notches on its upper edge lift the pins A1, B1, C1, D1, E1 until their tops reach the surface of G, allowing the key to turn as shown in Fig. 220 and engage the bolt through the arm H. (The bolt itself isn't shown.) If an incorrect key is used, either some of the lower pins will stick up into the fixed cylinder F (see Fig. 221), or some of the pins in F will drop into G. In that case, it’s impossible to turn the key.

There are other well-known locks, such as those invented by Bramah and Hobbs. But as these do not lend themselves readily to illustration no detailed[Pg 438] account can be given. We might, however, notice the time lock, which is set to a certain hour, and can be opened by the right key or a number of keys in combination only when that hour is reached. Another very interesting device is the automatic combination lock. This may have twenty or more keys, any one of which can lock it; but the same one must be used to unlock it, as the key automatically sets the mechanism in favour of itself. With such a lock it would be possible to have a different key for every day in the month; and if any one key got into wrong hands it would be useless unless it happened to be the one which last locked the lock.
There are other famous locks, like those created by Bramah and Hobbs. However, since they aren't easy to illustrate, we can't provide a detailed[Pg 438] account. We can mention the time lock, which is set to a specific hour and can only be opened with the correct key or a combination of keys when that hour arrives. Another intriguing device is the automatic combination lock. This type can have twenty or more keys, any one of which can lock it; however, the same key must be used to unlock it, as the key automatically adjusts the mechanism in its favor. With this kind of lock, you could have a different key for each day of the month, and if one key fell into the wrong hands, it would be useless unless it happened to be the key that last locked the lock.
THE CYCLE.
THE CYCLE.
There are a few features of this useful and in some ways wonderful contrivance which should be noticed. First,
There are a few features of this useful and in some ways wonderful contraption that should be pointed out. First,
THE GEARING OF A CYCLE.
CYCLE GEARS.
To a good many people the expression "geared to 70 inches," or 65, or 80, as the case may be, conveys nothing except the fact that the higher the gear the faster one ought to be able to travel. Let us therefore examine the meaning of such a phrase before going farther.
To many people, the phrase "geared to 70 inches," or 65, or 80, depending on the situation, means little more than the idea that the higher the gear, the faster you should be able to go. So, let's take a closer look at what that phrase actually means before we continue.
The safety cycle is always "geared up"—that is, one turn of the pedals will turn the rear wheel more than once. To get the exact ratio of turning speed we count the teeth on the big chain-wheel, and the teeth on the small chain-wheel attached to the hub of the rear wheel, and divide the former by the latter. To take an example:—The teeth are 75 and 30 in number respectively; the ratio of speed therefore = 75⁄30 = 5⁄2 = 2½. One turn of the pedal turns the rear wheel 2½ times. The gear of the cycle is calculated by multiplying this result by the diameter of the rear wheel in inches. Thus a 28-inch wheel would in this case give a gear of 2½ × 28 = 70 inches.
The safety cycle is always "geared up"—meaning one turn of the pedals turns the rear wheel more than once. To find the exact turning speed ratio, we count the teeth on the large chain wheel and the teeth on the small chain wheel connected to the hub of the rear wheel, then divide the number of teeth on the large wheel by the number on the small wheel. For example, if there are 75 teeth on the large wheel and 30 on the small wheel, the speed ratio would be 75⁄30 = 5⁄2 = 2½. This means one turn of the pedal makes the rear wheel turn 2½ times. The gear of the cycle is calculated by multiplying this result by the diameter of the rear wheel in inches. So, for a 28-inch wheel, the gear would be 2½ × 28 = 70 inches.
One turn of the pedals on a machine of this gear would propel the rider as far as if he were on a high "ordinary" with the pedals attached directly to a wheel 70 inches in diameter. The gearing is raised or lowered by altering the number ratio of the teeth on the two chain-wheels. If for the 30-tooth wheel we substituted one of 25 teeth the gearing would be—
One turn of the pedals on a machine with this gear would move the rider as far as if he were on a tall "ordinary" bike with the pedals connected directly to a wheel that’s 70 inches in diameter. The gearing is adjusted by changing the number ratio of the teeth on the two chain wheels. If we replaced the 30-tooth wheel with one that has 25 teeth, the gearing would be—
75⁄25 × 28 inches = 84 inches.
75⁄25 × 28 inches = 84 inches.
A handy formula to remember is, gearing = T/t × D, where T = teeth on large chain-wheel; t = teeth on small chain-wheel; and D = diameter of driving-wheel in inches.
A simple formula to remember is gearing = T/t × D, where T = teeth on the large chain-wheel; t = teeth on the small chain-wheel; and D = diameter of the driving wheel in inches.
Two of the most important improvements recently added to the cycle are—(1) The free wheel; (2) the change-speed gear.
Two of the most important improvements recently added to the bike are—(1) the freewheel; (2) the gear shift.
THE FREE WHEEL
THE FREE WHEEL
is a device for enabling the driving-wheel to overrun the pedals when the rider ceases pedalling; it renders the driving-wheel "free" of the driving gear. It is a ratchet specially suited for this kind of work. From among the many patterns now marketed we select the Micrometer free-wheel hub[Pg 441] (Fig. 222), which is extremely simple. The ratchet-wheel R is attached to the hub of the driving-wheel. The small chain-wheel (or "chain-ring," as it is often called) turns outside this, on a number of balls running in a groove chased in the neck of the ratchet. Between these two parts are the pawls, of half-moon shape. The driving-wheel is assumed to be on the further side of the ratchet. To propel the cycle the chain-ring is turned in a clockwise direction. Three out of the six pawls at once engage with notches in the ratchet, and are held tightly in place by the pressure of the chain-ring on their rear ends. The other three are in a midway position.
is a device that allows the driving wheel to spin freely when the rider stops pedaling; it disengages the driving wheel from the driving gear. It's a ratchet specifically designed for this purpose. Among the various models currently available, we highlight the Micrometer free-wheel hub[Pg 441] (Fig. 222), which is very straightforward. The ratchet-wheel R is fixed to the hub of the driving wheel. The small chain-wheel (or "chain-ring," as it is often called) rotates around this, on several balls that roll in a groove cut into the neck of the ratchet. Between these two components are the pawls, shaped like half-moons. We assume the driving wheel is on the far side of the ratchet. To move the cycle, the chain-ring is turned in a clockwise direction. Three of the six pawls engage with notches in the ratchet at the same time and are held firmly in place by the pressure of the chain-ring against their rear ends. The other three are positioned midway.

When the rider ceases to pedal, the chain-ring becomes stationary, but the ratchet continues to revolve. The pawls offer no resistance to the ratchet teeth, which push them up into the semicircular recesses in the chain-ring. Each one rises as it[Pg 442] passes over a tooth. It is obvious that driving power cannot be transmitted again to the road wheel until the chain-wheel is turned fast enough to overtake the ratchet.
When the rider stops pedaling, the chain-ring stops moving, but the ratchet keeps turning. The pawls don’t resist the ratchet teeth, which push them up into the semicircular notches in the chain-ring. Each one lifts as it[Pg 442] moves past a tooth. It's clear that power cannot be transferred back to the road wheel until the chain-wheel turns fast enough to catch up with the ratchet.
THE CHANGE-SPEED GEAR.
The gear shifter.
A gain in speed means a loss in power, and vice versâ. By gearing-up a cycle we are able to make the driving-wheel revolve faster than the pedals, but at the expense of control over the driving-wheel. A high-geared cycle is fast on the level, but a bad hill-climber. The low-geared machine shows to disadvantage on the flat, but is a good hill-climber. Similarly, the express engine must have large driving-wheels, the goods engine small driving-wheels, to perform their special functions properly.
A gain in speed means a loss in power, and vice versa. By gearing up a bike, we can make the driving wheel turn faster than the pedals, but this comes at the cost of control over the driving wheel. A high-geared bike is great on flat ground, but struggles on hills. The low-geared bike doesn’t perform as well on flat surfaces, but is excellent for climbing hills. Likewise, an express train needs large driving wheels, while a freight train needs smaller driving wheels to do their specific jobs effectively.
In order to travel fast over level country, and yet be able to mount hills without undue exertion, we must be able to do what the motorist does—change gear. Two-speed and three-speed gears are now very commonly fitted to cycles. They all work on the same principle, that of the epicyclic train of cog-wheels, the mechanisms being so devised that the hub turns more slowly than, at the same[Pg 443] speed as, or faster than the small chain-wheel,[42] according to the wish of the rider.
To travel quickly across flat terrain while still being able to climb hills without too much effort, we need to do what drivers do—shift gears. Two-speed and three-speed gears are now commonly found on bikes. They all operate on the same principle, which is the epicyclic system of cogs. The mechanisms are designed so that the hub turns slower than, at the same speed as, or faster than the small chain-wheel, depending on what the rider wants.
We do not propose to do more here than explain the principle of the epicyclic train, which means "a wheel on (or running round) a wheel." Lay a footrule on the table and roll a cylinder along it by the aid of a second rule, parallel to the first, but resting on the cylinder. It will be found that, while the cylinder advances six inches, the upper rule advances twice that distance. In the absence of friction the work done by the agent moving the upper rule is equal to that done in overcoming the force which opposes the forward motion of the cylinder; and as the distance through which the cylinder advances is only half that through which the upper rule advances, it follows that the force which must act on the upper rule is only half as great as that overcome in moving the cylinder. The carter makes use of this principle when he puts his hand to the top of a wheel to help his cart over an obstacle.
We don't plan to do more here than explain the concept of the epicyclic train, which means "a wheel on (or running around) a wheel." Place a measuring stick on the table and roll a cylinder along it using a second stick, parallel to the first, but resting on the cylinder. You'll notice that while the cylinder moves forward six inches, the top stick moves forward twice that distance. If there’s no friction, the work done by the force moving the top stick is equal to the work done in overcoming the force that resists the forward movement of the cylinder. Since the distance the cylinder moves forward is only half of what the top stick moves, it means that the force acting on the top stick is only half as much as the force needed to move the cylinder. A cart driver uses this principle when he places his hand on top of a wheel to help his cart over an obstacle.
![]() |
![]() |
![]() |
Now see how this principle is applied to the change-speed gear. The lower rule is replaced by a cog-wheel, C (Fig. 223); the cylinder by a cog, B, running round it; and the upper rule by a ring, A, with internal teeth. We may suppose that A is the chain-ring, B a cog mounted on a pin projecting from the hub, and C a cog attached to the fixed axle. It is evident that B will not move so fast round C as A does. The amount by which A will get ahead of B can be calculated easily. We begin with the wheels in the position shown in Fig. 223. A point, I, on A is exactly over the topmost point of C. For the sake of convenience we will first assume that instead of B running round C, B is revolved on its axis for one complete revolution in a clockwise direction, and that A and C move as in Fig. 224. If B has 10 teeth, C 30, and A 40, A will have been moved 10⁄40 = ¼ of a revolution[Pg 445] in a clockwise direction, and C 10⁄30 = ⅓ of a revolution in an anti-clockwise direction.
Now, see how this principle is applied to the change-speed gear. The lower part is replaced by a cog-wheel, C (Fig. 223); the cylinder by a cog, B, rotating around it; and the upper part by a ring, A, with internal teeth. We can assume that A is the chain-ring, B is a cog mounted on a pin sticking out from the hub, and C is a cog attached to the fixed axle. It's clear that B won’t move as quickly around C as A does. The difference in how much A will get ahead of B can be easily calculated. We start with the wheels in the position shown in Fig. 223. A point, I, on A is directly above the topmost point of C. For convenience, let's first assume that instead of B rotating around C, B rotates on its axis for one full turn in a clockwise direction, and that A and C move as shown in Fig. 224. If B has 10 teeth, C has 30, and A has 40, then A will have moved 10⁄40 = ¼ of a turn[Pg 445] in a clockwise direction, while C will have moved 10⁄30 = ⅓ of a turn in an anti-clockwise direction.
Now, coming back to what actually does happen, we shall be able to understand how far A rotates round C relatively to the motion of B, when C is fixed and B rolls (Fig. 225). B advances ⅓ of distance round C; A advances ⅓ + ¼ = 7⁄12 of distance round B. The fractions, if reduced to a common denominator, are as 4:7, and this is equivalent to 40 (number of teeth on A): 40 + 30 (teeth on A + teeth on C.)
Now, getting back to what actually happens, we can understand how much A rotates around C in relation to the motion of B, when C is fixed and B rolls (Fig. 225). B moves forward ⅓ of the distance around C; A moves forward ⅓ + ¼ = 7⁄12 of the distance around B. When the fractions are reduced to a common denominator, they are in the ratio of 4:7, which is equivalent to 40 (the number of teeth on A): 40 + 30 (teeth on A plus teeth on C).
To leave the reader with a very clear idea we will summarize the matter thus:—If T = number of teeth on A, t = number of teeth on C, then movement of A: movement of B:: T + t: T.
To give the reader a clear understanding, we'll summarize it like this: If T = number of teeth on A, t = number of teeth on C, then the movement of A is to the movement of B as T + t is to T.
Here is a two-speed hub. Let us count the teeth. The chain-ring (= A) has 64 internal teeth, and the central cog (= C) on the axle has 16 teeth. There are four cogs (= B) equally spaced, running on pins projecting from the hub-shell between A and C. How much faster than B does A run round C? Apply the formula:—Motion of A: motion of B:: 64 + 16: 64. That is, while A revolves once, B and the hub and the driving-wheel will revolve only 64⁄80 = ⅘ of a turn. To use scientific language, B revolves 20 per cent. slower than A.
Here’s a two-speed hub. Let’s count the teeth. The chainring (= A) has 64 internal teeth, and the central cog (= C) on the axle has 16 teeth. There are four cogs (= B), evenly spaced and running on pins that extend from the hub shell between A and C. How much faster does A spin compared to B? Use this formula:—Motion of A: motion of B:: 64 + 16: 64. This means that while A makes one full turn, B, along with the hub and the driving wheel, will only complete 64⁄80 = ⅘ of a turn. In scientific terms, B turns 20 percent slower than A.
This is the gearing we use for hill-climbing. On the level we want the driving-wheel to turn as fast as, or faster than, the chain-ring. To make it turn at the same rate, both A and C must revolve together. In one well-known gear this is effected by sliding C along the spindle of the wheel till it disengages itself from the spindle, and one end locks with the plate which carries A. Since B is now being pulled round at the bottom as well as the top, it cannot rotate on its own axis any longer, and the whole train revolves solidly—that is, while A turns through a circle B does the same.
This is the gearing we use for climbing hills. On flat surfaces, we want the driving wheel to turn as fast as, or faster than, the chain ring. To make it turn at the same speed, both A and C have to rotate together. In one well-known setup, this is achieved by sliding C along the spindle of the wheel until it disconnects from the spindle, and one end locks with the plate that holds A. Since B is now being pulled around at both the top and the bottom, it can no longer spin on its own axis, and the entire mechanism moves solidly—that is, while A makes a full circle, B does the same.
To get an increase of gearing, matters must be so arranged that the drive is transmitted from the chain-wheel to B, and from A to the hub. While B describes a circle, A and the driving-wheel turn through a circle and a part of a circle—that is, the driving-wheel revolves faster than the hub. Given the same number of teeth as before, the proportional rates will be A = 80, B = 64, so that the gear rises 25 per cent.
To increase the gearing, everything needs to be set up so that the drive is transferred from the chain-wheel to B, and from A to the hub. While B moves in a circle, A and the driving-wheel also move in a circle and part of a circle—meaning the driving-wheel turns faster than the hub. With the same number of teeth as before, the proportional rates will be A = 80, B = 64, resulting in a gear increase of 25 percent.
By means of proper mechanism the power is transmitted in a three-speed gear either (1) from chain-wheel to A, A to B, B to wheel = low gear; or (2) from chain-wheel to A and C simultaneously = solid,[Pg 447] normal, or middle gear; or (3) from chain-wheel to B, B to A, A to wheel = high gear. In two-speed gears either 1 or 3 is omitted.
Using the right mechanism, power is transmitted in a three-speed gear either (1) from the chain-wheel to A, then from A to B, and from B to the wheel = low gear; or (2) from the chain-wheel to both A and C at the same time = solid, [Pg 447] normal, or middle gear; or (3) from the chain-wheel to B, then from B to A, and from A to the wheel = high gear. In two-speed gears, either 1 or 3 is left out.
AGRICULTURAL MACHINES.
Farming Equipment.
THE THRESHING-MACHINE.
The Threshing Machine.
Bread would not be so cheap as it is were the flail still the only means of separating the grain from the straw. What the cream separator has done for the dairy industry (p. 384), the threshing-machine has done for agriculture. A page or two ought therefore to be spared for this useful invention.
Bread wouldn't be as cheap as it is if the flail were still the only way to separate the grain from the straw. Just like the cream separator revolutionized the dairy industry (p. 384), the threshing machine has transformed agriculture. So, a page or two should definitely be dedicated to this valuable invention.

In Fig. 226 a very complete fore-and-aft section of the machine is given. After the bands of the sheaves have been cut, the latter are fed into the mouth of the drum A by the feeder, who stands in the feeding-box on the top of the machine. The drum revolves at a very high velocity, and is fitted with fluted beaters which act against a steel concave, or breastwork, B, the grain being threshed out of the straw in passing between the two. The breastwork is provided with open wires, through which most of the threshed grain, cavings (short straws), and chaff passes on to a sloping board. The straw is flung forward on to the shakers C, which gradually move the straw towards the open end and throw it off. Any grain, etc., that has escaped the drum falls through the shakers on to D, and works backwards to the caving riddles, or moving sieves, E. The main blower, by means of a revolving fan, N, sends air along the channel X upwards through these riddles, blowing the short straws away to the left. The grain, husks, and dust fall through E on to G, over the end of which they fall on to the chaff riddle, H. A second column of air from the blower drives the chaff away. The heavy grain, seeds, dust, etc., fall on to I, J, and K in turn, and are shaken until only the grain remains to pass along L to the elevator bottom, M. An endless band with cups attached to it scoops up the grain, carries it aloft, and shoots it into hopper P. It then goes through the shakers Q, R, is dusted by the back end blower, S, and slides down T into the open end of the rotary screen-drum U, which is mounted on the slope, so that as it turns the grain travels gradually along it. The first half of the screen has wires set closely together. All the small grain that falls through this, called "thirds," passes into a hopper, and is collected in a sack attached to the hopper mouth. The "seconds" fall through the second half of the drum, more widely spaced, into their sack; and the "firsts" fall out of the end and through a third spout.
In Fig. 226, there's a detailed front-and-back section of the machine. After the bands of the pulleys are cut, they are fed into the mouth of the drum A by the feeder, who stands in the feeding-box at the top of the machine. The drum spins at a very high speed and has fluted beaters that strike against a steel concave, or breastwork, B, which threshes the grain out of the straw as it passes between them. The breastwork has open wires, allowing most of the threshed grain, short straws (cavings), and chaff to drop onto a sloping board. The straw is thrown forward onto the shakers C, which gradually move it toward the open end and toss it out. Any grain that escaped the drum falls through the shakers onto D and works its way back to the caving riddles, or moving sieves, E. The main blower, using a rotating fan, N, pushes air through the channel X upwards through these riddles, blowing the short straws away to the left. The grain, husks, and dust fall through E onto G, and from there they drop onto the chaff riddle, H. A second stream of air from the blower blows the chaff away. The heavier grain, seeds, dust, and so on fall onto I, J, and K sequentially and are shaken until only the grain remains to move along L to the elevator bottom, M. An endless belt with attached cups scoops up the grain, lifts it up, and throws it into hopper P. It then goes through the shakers Q, R, gets dusted by the back end blower, S, and slides down T into the open end of the rotary screen-drum U, which is angled so that as it rotates, the grain gradually moves along it. The first half of the screen has closely spaced wires. All the small grain that falls through this part, called "thirds," goes into a hopper and is collected in a sack attached to the bottom of the hopper. The "seconds" fall through the second half of the drum, which has wires spaced further apart, into their own sack; and the "firsts" exit out of the end and through a third spout.
MOWING-MACHINES.
Lawn mowers.
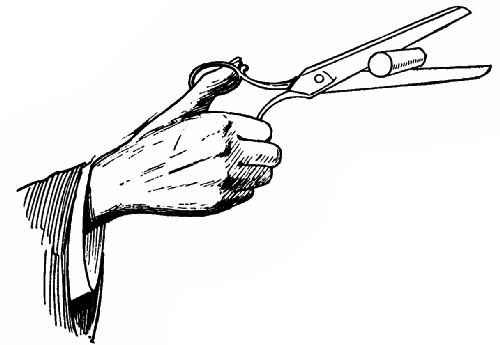
The ordinary lawn—mower employs a revolving reel, built up of spirally-arranged knives, the edges of which pass very close to a sharp plate projecting from the frame of the mower. Each blade, as it turns, works along the plate, giving a shearing cut to any grass that may be caught between the two cutting edges. The action is that of a pair of scissors (Fig. 227), one blade representing the fixed, the other the moving knife. If you place a cylinder of wood in the scissors it will be driven forward by the closing of the blades, and be marked by[Pg 451] them as it passes along the edges. The same thing happens with grass, which is so soft that it is cut right through.
The typical lawn mower uses a spinning reel made up of spirally arranged blades, whose edges come very close to a sharp plate sticking out from the mower's frame. As each blade spins, it moves along the plate, giving a clean cut to any grass caught between the two cutting edges. The action is like a pair of scissors (Fig. 227), where one blade acts as the fixed part and the other as the moving knife. If you place a piece of wood in the scissors, it will get pushed forward as the blades close together, and it will be marked by[Pg 451] them as it moves along the edges. The same thing happens with grass, which is soft enough to be cut clean through.
HAY-CUTTER.
Hay cutter.
The hay-cutter is another adaptation of the same principle. A cutter-bar is pulled rapidly backwards and forwards in a frame which runs a few inches above the ground by a crank driven by the wheels through gearing. To the front edge of the bar are attached by one side a number of triangular knives. The frame carries an equal number of spikes pointing forward horizontally. Through slots in these the cutter-bar works, and its knives give a drawing cut to grass caught between them and the sides of the spikes.
The hay-cutter is another version of the same principle. A cutter bar moves quickly back and forth in a frame that sits a few inches above the ground, powered by a crank connected to the wheels through gears. Triangular blades are attached to the front edge of the bar on one side. The frame has an equal number of spikes that point forward horizontally. The cutter bar operates through slots in these spikes, and its knives make a slicing cut to the grass caught between them and the sides of the spikes.
SOME NATURAL PHENOMENA.
SOME NATURAL PHENOMENA.
WHY SUN-HEAT VARIES IN INTENSITY.
WHY SUNLIGHT INTENSITY VARIES.
The more squarely parallel heat-rays strike a surface the greater will be the number that can affect that surface. This is evident from Figs. 228, 229, where A B is an equal distance in both cases. The nearer the sun is to the horizon, the more obliquely do its rays strike the earth. Hence[Pg 452] midday is necessarily warmer than the evening, and the tropics, where the sun stands overhead, are hotter than the temperate zones, where, even in summer at midday, the rays fall more or less on the slant.
The more directly the heat rays hit a surface, the more of them can impact that surface. This is clear from Figs. 228, 229, where A B is the same distance in both cases. The closer the sun is to the horizon, the more angled its rays hit the earth. Therefore, [Pg 452] midday is always warmer than the evening, and the tropics, where the sun is directly overhead, are hotter than the temperate zones, where even in summer at noon, the rays hit at more of an angle.
![]() |
![]() |
The atmospheric envelope which encompasses the earth tends to increase the effect of obliquity, since a slanting ray has to travel further through it and is robbed of more heat than a vertical ray.
The layer of atmosphere surrounding the earth tends to enhance the impact of obliquity because a slanted ray has to pass through more of it and loses more heat than a vertical ray.
THE TIDES.
THE TIDES.
All bodies have an attraction for one another. The earth attracts the moon, and the moon attracts the earth. Now, though the effect of this attraction is not visible as regards the solid part of the globe, it is strongly manifested by the water which covers a large portion of the earth's surface. The moon attracts the water most powerfully at two points, that nearest to it and that furthest away from it;[Pg 453] as shown on an exaggerated scale in Fig. 230. Since the earth and the water revolve as one mass daily on their axis, every point on the circumference would be daily nearest to and furthest from the moon at regular intervals, and wherever there is ocean there would be two tides in that period, were the moon stationary as regards the earth. (It should be clearly understood that the tides are not great currents, but mere thickenings of the watery envelope. The inrush of the tide is due to the temporary rise of level.)
All bodies attract each other. The earth pulls on the moon, and the moon pulls on the earth. While this attraction isn’t obvious when it comes to the solid part of the planet, it shows up clearly in the water that covers a large part of the earth's surface. The moon exerts the strongest pull on the water at two points: the point closest to it and the point farthest away from it; [Pg 453] as illustrated on an exaggerated scale in Fig. 230. Since the earth and the water rotate together around their axis each day, every point on the edge will be closest to and farthest from the moon at regular intervals, meaning that wherever there is ocean, there will be two tides during that time, if the moon were stationary relative to the earth. (It’s important to note that tides aren't strong currents, but rather slight increases in the water level. The rise of the tide is caused by the temporary increase in surface level.)
![]() |
![]() |
WHY HIGH TIDE VARIES DAILY.
WHY HIGH TIDE CHANGES DAILY.
The moon travels round the earth once in twenty-eight days. In Fig. 231 the point a is nearest the moon at, say, twelve noon. At the end of twenty-four[Pg 454] hours it will have arrived at the same position by the compass, but yet not be nearest to the moon, which has in that period moved on 1⁄28th of a revolution round the earth.[43] Consequently high tide will not occur till a has reached position b and overtaken the moon, as it were, which takes about an hour on the average. This explains why high tide occurs at intervals of more than twelve hours.
The moon orbits the earth every twenty-eight days. In Fig. 231, point a is closest to the moon at, say, twelve noon. After twenty-four[Pg 454] hours, it will return to the same position on the compass, but it won't be closest to the moon because the moon will have moved about 1⁄28th of a revolution around the earth.[43] As a result, high tide won't happen until a reaches position b and passes the moon, which takes about an hour on average. This is why high tide occurs more than twelve hours apart.
![]() Fig. 232.—Positions of the sun, moon, and earth during "spring" tides. |
![]() Fig. 233.—Positions of the sun, moon, and earth during "neap" tides. |
NEAP TIDES AND SPRING TIDES.
Neap tides and spring tides.
The sun, as well as the moon, attracts the ocean,[Pg 455] but with less power, owing to its being so much further away. At certain periods of the month, sun, earth, and moon are all in line. Sun and moon then pull together, and we get the highest, or spring tides (Fig. 232). When sun and moon pull at right angles to one another—namely, at the first and third quarters—the excrescence caused by the moon is flattened (Fig. 233), and we get the lowest, or neap tides.
The sun, along with the moon, influences the ocean,[Pg 455] but it has a weaker effect since it’s so much farther away. At certain times of the month, the sun, earth, and moon are all aligned. When the sun and moon work together, we experience the highest tides, known as spring tides (Fig. 232). When the sun and moon pull at right angles to each other—specifically during the first and third quarters—the effect of the moon is diminished (Fig. 233), resulting in the lowest tides, called neap tides.
[40] As the sun passes the meridian (twelve o'clock, noon) the chronometer's reading is taken, and the longitude, or distance east or west of Greenwich, is reckoned by the difference in time between local noon and that of the chronometer.
[40] When the sun hits its highest point (twelve o'clock noon), the chronometer's reading is noted, and the longitude, or distance east or west of Greenwich, is calculated by comparing the local noon to the chronometer's time.
INDEX.
Note.—Figures in italics signify that an illustration of
the thing
referred to appears on the page.
Note.—Italics indicate that there is an illustration of
the item mentioned on the page.
Aberration, spherical, of lens, 243.
Acoustics, 294.
Achromatic lens, 243.
Action carriage of piano, 283.
Advancing the spark, 102.
Air-gun, 342.
Air-pump for cycle tyres, 340;
for Westinghouse brake, 199.
Alternating currents, 164;
dynamo, 164.
Amperage, 125.
Angle of advance, 57, 58;
incidence, 268;
reflection, 268.
Aorta, 360.
Arc lamp, 182.
Archimedes, 412.
Armature, 162.
Arteries, 358.
Arterial blood, 359.
Atmospheric pressure, 350.
Auditory nerve, 272.
Automatic brakes, 188;
signalling, 228;
stoker, 399.
Backfall, 298.
Balance-wheel, 419.
Ball cock, 366, 367.
Balloon, fire, 323;
gas, 347.
Barometer, aneroid, 328, 329;
and weather, 331;
Fortin's, 326;
meaning of, 325;
simple, 328;
wheel, 327.
Beau de Rochas, 89.
Bell, diving, 332;
electric, 119, 120.
Bellows of organ, 303.
Bioscope, 266.
Blades, turbine, 81, 83.
Block system, 201, 212.
Blood, arterial, 359;
circulation of, 356, 357, 360;
venous, 359.
Blower-plate, 393, 394.
Boat, sails of, 346.
Boiler, Babcock and Wilcox, 21, 22;
explosions, 34, 391;
fire-tube, 21;
fittings, 31;
Lancashire, 25, 26;
locomotive, 20, 23;
multitubular, 21;
principle of, 15;
stored energy in, 32;
vertical, 25;
water supply to, 39;
water-tube, 21.
Brakes, hydraulic, 188;
motor car, 110;
railway, 187;
vacuum, 189, 190, 191;
Westinghouse, 194, 195, 197.
Bramah, 363, 437.
Breezes, land and sea, 324.
Brushes of dynamo, 161, 172.
Bunsen burner, 409.
Burning-glass, 232.
Camera, the, 233;
pinhole, 234, 235.
Canals, semicircular, 273.
Capillary attraction, 392;
veins, 358.
Carbon dioxide, 27, 359;
monoxide, 27.
Carburetter, 98, 99.
Cardan shaft, 93.
Carmania, the, 83.
Centrifugal force, 382.
Change-speed gear, 105, 442.
Chassis of motor car, 92.
Circulation of water in a boiler, 17, 18, 19;
of water in a motor car, 95, 97.
Clarionet, 308.
Clock, first weight-driven, 412;
water, 410.
Clutch of motor car, 105.
Coal, as fuel, 15;
gas, 394;
gas making, 394;
gas plant, 396;
gas, purification of, 397.
Cochlea, 273.
Coherer, 140.
Coil, Ruhmkorff, 121.
Coke, 395.
Combinations in Chubb lock, 436;
Yale lock, 436.
Combustion, 26, 393;
perfect, 28.
Compensating gear, 107, 108.
Compound engines, 59;
arrangement of, 61;
invention of, 59.
Compound locomotives, 62.
Compound microscope, 261.
Condenser, marine, 71, 72;
of Ruhmkorff coil, 123.
Conduit, 176.
Convex lens, image cast by, 236.
Conjugate foci, 262.
Cornet, 308.
Corti, rods of, 274.
Coxwell, 348.
Cream separator, 381, 383.
Current, reversal of electric, 130, 131;
transformation of, 124.
Cushioning of steam, 55.
Cycle, gearing of, 439.
Cylinder, hydraulic press, 363;
steam, 49.
Danes, 382.
Dead point, 47.
De Brouwer stoker, 401.
Detector in Chubb lock, 435.
Diving-bell, 332;
simple, 333, 334.
Diving-dress, 335.
Direction of current in dynamo circuit, 163.
Diver's feats, 338;
helmet, 336;
lamp, 338.
Donkey-engines, 68.
Doorstop, self-closing, 344.
Double-cylinder engines, 47.
Draught, forced, 28, 29;
induced, 29.
Drum and fusee, 414.
Durability of motor-car engine, 96.
D-valve, 67.
Dynamo, alternating, 164, 174;
brushes, 172;
compound, 174;
continuous-current, 165;
multipolar, 169;
series wound, 173;
shunt wound, 173;
simple, 161, 162.
Ear, the, 271, 273;
a good, 274, 307;
sensitiveness of, 275.
Eccentric, 52, 53;
setting of, 53.
Edison, Thomas, 310.
Edison-Bell phonograph, 310.
Electricity, current, 115;
forms of, 113;
nature of, 112;
static, 114.
Electric bell, 119, 120;
signalling, 225;
slot, 226.
Electroplating, 185, 186.
Electro-magnets, 117.
Endolymph, 272.
Engines, compound, 59;
donkey, 68;
double-cylinder, 47;
internal-combustion, 87, 95;
reciprocating, 44.
Escapement of timepieces, 416;
cylinder, 420;
lever, 421, 422.
Ether, 270.
Eustachian tube, 276.
Eye, human, 246, 247;
self-accommodation of, 248.
Expansive working of steam, 56.
Faraday, Michael, 159.
Field, magnetic, 159;
magnets, 171;
ring, 174.
Filters, 374;
Maignen, 373;
Berkefeld, 374.
Filtration beds, 372.
Flute, 308.
Flying-machines, 348.
Fly-wheel, use of, 48.
Focus, meaning of, 237;
principal, 238.
Foci, conjugate, 262.
Force, lines of, 116.
Forces, component, 345.
Free wheel, 440.
Furring-up of pipes, 391.
Fusee, drum and, 414.
Galileo, 259, 325, 416.
Galilean telescope, 259.
Gas, coal, 394;
governor, 402;
meter, 405;
traps, 374;
works, 394.
Gasometer, 397;
largest, 398, 399.
Gauge, steam, 36, 38;
water, 35, 36.
Gear, compensating, 107, 108.
Gear-box of motor car, 105.
Gearing of cycle, 439.
Glaisher, 348.
Gland, 50, 363.
Glass, flint and crown, 242.
Going-barrel for watches, 415.
Gooch reversing gear, 65.
Governors, speed, 67;
of motor car, 103, 104.
Graham, 418.
Gramophone, 317;
records, 319, 321;
reproducer, 318.
Hairspring, 412.
Hay-cutter, 451.
Heart, the, 355;
disease, 361;
rate of pulsation of, 361;
size of, 357.
Heat of sun, 451.
Hele, Peter, 412.
Helmet, diver's, 336.
Helmholtz, 274, 308.
Hero of Alexandria, 74.
Herschel, 261.
Hertz, Dr., 138.
Hertzian waves, 138.
Hot-water supply, 386.
Hour-hand train in timepieces, 429.
Household water supply, 364.
Hughes type-printer, 134.
Hydraulic press, 361, 362.
Hydro, 385.
Ignition of charge in motor-car cylinder, 100, 101.
Image and object, relative positions of, 239;
distortion of, 245.
Incandescent gas mantle, 407;
electric lamp, 179.
Incus, 272.
Index mechanism of water-meter, 37.
Indicator of electric bell, 119.
Induction coil, 121;
uses of, 125.
Injector, 39;
Giffard's, 41;
principle of, 40;
self-starting, 42.
Interlocking of signals, 204, 222.
Internal-combustion engine, 87.
Iris of eye, 249;
stop, 249.
Kelvin, Lord, 158.
Keyless winding mechanism, 425, 426, 428.
Kite, 345.
Lamp, arc, 182;
how it works, 392;
incandescent, 179;
manufacture of incandescent lamps, 180.
Lap of slide-valve, 57, 59.
Larynx, 306.
Laxey wheel, 380, 381.
Leads, 208.
Lenses, 231;
correction of for colour, 240, 241;
focus of, 236;
rectilinear, 245;
spherical aberration in, 243.
Levers, signal, colours of, 208.
Limit of error in cylinder, 52.
Light, electric, 179;
nature of, 230;
propagation of, 231.
Li Hung Chang, 157.
Lindsay, James Bowman, 145.
Lines of force, 116, 162.
"Linking up," 65.
Locks, 430;
Barron, 433;
Bramah, 437;
Chubb, 433, 434;
Hobbs, 437;
simplest, 431;
tumbler, 432;
Yale, 436.
Locking gear for signals, 205.
Locomotive, electric, 178;
advantages of, 179.
Lungs, 359.
Magic-lantern, 263, 264.
Magnet, 115;
permanent, 115, 116;
temporary, 115.
Magnetism, 115.
Magnetic needle, influence of current on, 129.
Mainspring, invention of, 412.
Malleus, 272.
Marconi, 140, 146.
Marine chronometers, 415;
delicacy of, 425.
Marine speed governor, 71.
Marine turbine, advantages of, 84.
Maudslay, Henry, 363.
Maxim, Sir Hiram, 348.
Micrometer free wheel, 441.
Micro-photography, 265.
Microscope, 254;
compound, 261, 263;
in telescope, 257;
simple, 254.
Mineral oil, 392.
Mirror, parabolic, 261, 262;
plane, 267.
Morse, 132, 145;
code, 128;
inker, 142;
sounder, 132.
Motor car, the, 92;
electric, 177.
Mouth, 307.
Mowing-machines, 450.
Musical sounds, 277.
Nerve, auditory, 272;
optic, 246.
Nodes on a string, 285;
column of air, 291.
Note, fundamental, 285;
quality of, 285.
Niagara Falls, power station at, 174.
Organ, the, 294, 300;
bellows, 303;
console, 305;
echo, solo, swell, great, and choir, 301;
electric and pneumatic, 305;
largest in the world, 306;
pedals, 298;
pipes, 295;
pipes, arrangement of, 295;
sound-board, 296;
wind-chest, 297.
Otto cycle, 91.
Overtones, 285.
Pallets of organ, 297.
Parallel arrangement of electric lamps, 184.
Paris, siege of, 265.
Pedals of organ, 298.
Pelton wheel, 377.
Pendulum, 412;
compensating, 418, 419.
Perilymph, 272.
Perry, Professor, 16.
Petrol, 98.
Phonograph, 310;
governor, 311;
recorder, 312, 313;
records, making of, 319;
reproducer, 315;
tracings on record of, 317.
Pianoforte, 277;
sounding-board, 280;
striking mechanism, 281;
strings, 281.
Piccolo, 308.
Pipes, closed, 289;
flue, 301;
open, 292;
organ, 295;
reed, 301, 302;
tuning, 302.
Piston valve, 67.
Pneumatic tyres, 341.
Poldhu, signalling station at, 138.
Points, railway, 208, 210;
and signals in combination, 211.
Poles of a magnet, 115.
Popoff, Professor A., 138, 145.
Power, transmission of, 175.
Preece, Sir William, 145.
Primary winding of induction coil, 122.
Pump, air, 340;
bucket, 352, 353;
force, 354;
most marvellous, 355;
Westinghouse air, 199.
Railway brakes, 187;
signalling, 200.
Rays, converging and diverging, 256;
heat, concentrated by lens, 232;
light, 232, 235, 236, 237.
Records, master, 319, 320.
Reciprocation, 51.
Reed, human, 306;
pipes, 301, 302.
Reflecting telescope, 260.
Relays, telegraphic, 133, 141.
Retina, 247.
Retorts, 395.
Reversing gear, 62;
Allan, 65;
Gooch, 65;
radial, 66.
Rocking bar mechanism for watches, 425.
Rods of Corti, 274.
Ruhmkorff coil, 121, 122.
Safety-valve, 32, 33, 391.
Sand-glasses, 411.
Scissors, action of, 450.
Secondary winding of induction coil, 122.
Series arrangement of electric lamps, 183.
Series winding of dynamo, 173.
Shunt wound dynamo, 173.
Sight, long and short, 250.
Signalling, automatic, 228;
electric, 225;
pneumatic, 225;
power, 225.
Signal levers, 206.
Signals, interlocking of, 204;
position of, 202;
railway, 200;
single line, 215.
Silencer on motor cars, 109.
Siphon, 351.
Slide-valve, 49, 50, 51;
setting of, 53.
Sliders, 297.
Sound, nature of, 270;
board of organ, 296;
board of piano, 280.
Spagnoletti disc instrument, 212.
Sparking-plug, 102.
Spectacles, use of, 249.
Spectrum, colours of, 230.
Speed governors, 67, 68, 69;
Hartwell, 70;
marine, 71.
Speed of motor cars, 110.
Spot, blind, in eye, 251;
yellow, in eye, 251.
Spring balance for watches, 419;
compensating, 423, 424.
Stapes, 272.
Steam, what it is, 13;
energy of, 14;
engines, 44;
engines, reciprocating, 45;
expansive working of, 59, 81;
gauge, 36;
gauge, principle of, 37;
turbine, 74;
turbine, De Laval, 76, 77;
turbine, Hero's, 74;
turbine, Parsons, 79, 80;
volume of, as compared with water, 15.
Stephenson, George, 63, 375.
Stop, in lens, 244;
iris, 249;
use of, 244.
Sun-dial of Ahaz, 410.
Syntonic transmission of wireless messages, 143.
Talking-machines, 310.
Tapper in wireless telegraphy receiver, 141.
Tappet arm, 205.
Telegraph, electric, 127;
insulator, 133;
needle, 128;
recording, 133;
sounder, 132.
Telegraphy, high-speed, 135;
wireless, 137.
Telephone, 147;
Bell, 148;
circuit, double-line, 155;
circuit, general arrangement, 152, 153;
exchange, 154, 155.
Telephony, submarine, 157.
Telescope, 257;
Galilean, 259;
prismatic, 260;
reflecting, 260;
terrestrial, 259.
Threshing-machine, 447, 448.
Thurston, Professor, 31.
Tides, 452;
high, 453;
neap and spring, 455.
Timbre, 285.
Tompion, Thomas, 412.
Torricelli, 325.
Trachea, 306.
Train staff signalling, 216;
single, 216;
and ticket, 217;
electric, 218.
Transformation of current, 124, 176.
Transmission of power, 174, 175.
Transmitter, Edison telephone, 150;
granular carbon, 150, 151.
Triple-valve, 196.
Trolley arm, 176.
Turbines, steam, 74.
Turbinia, the, 79.
Tympanum, 137, 271, 272.
Universal joint, 93.
Vacuum brake, 189, 190, 191.
Vacuum chamber of aneroid barometer, 330.
Valve, piston, 67;
safety, 32;
of internal-combustion engine, 89.
Valves of the heart, 357.
Veins, 358;
capillary, 358;
pulmonary, 361.
Ventral segments, 291.
Ventricles, 357.
Vibration of columns of air, 288, 289;
of rods, 287;
of strings, 278;
of strings, conditions regulating, 278.
Viper, the, 86.
Virag, Pollak—high-speed telegraphy, 136.
Vitreous humour, 246.
Voltage, 121, 161.
Vowel sounds, 308.
Wasborough, Matthew, 51.
Watches, first, 412.
Water cock, 365;
engines, 375;
gauge, 35, 36;
jacket, 19, 95;
meter, 368;
supply, 371;
turbines, 174, 376;
wheels, 375.
Watt, James, 51, 69, 375.
Welsbach incandescent mantle, 407.
Westinghouse air-brake, 194, 195, 197;
George, 194.
Wheatstone needle instrument, 128, 131;
automatic transmitter, 135.
Wind, why it blows, 323;
action of on kites, 345;
on sails, 346.
Windmills, 375.
Window, oval, in ear, 272;
round, in ear, 272.
Wireless telegraphy, 137;
advance of, 145;
receiver, 140, 141;
syntonic, 143;
transmitter, 138, 139.
Yale lock, 436, 437.
Yellow spot, in eye, 251.
Zech, Jacob, 414.
Zeiss field-glasses, 260.
Aberration, spherical, of lens, 243.
Acoustics, 294.
Achromatic lens, 243.
Action carriage of piano, 283.
Advancing the spark, 102.
Air-gun, 342.
Air-pump for cycle tyres, 340;
for Westinghouse brake, __A_TAG_PLACEHOLDER_0__.
Alternating currents, 164;
dynamo, __A_TAG_PLACEHOLDER_0__.
Amperage, 125.
Angle of advance, 57, 58;
incidence, __A_TAG_PLACEHOLDER_0__;
reflection, __A_TAG_PLACEHOLDER_0__.
Aorta, 360.
Arc lamp, 182.
Archimedes, 412.
Armature, 162.
Arteries, 358.
Arterial blood, 359.
Atmospheric pressure, 350.
Auditory nerve, 272.
Automatic brakes, 188;
signaling, __A_TAG_PLACEHOLDER_0__;
stoker, __A_TAG_PLACEHOLDER_0__.
Backfall, 298.
Balance-wheel, 419.
Ball cock, 366, 367.
Balloon, fire, 323;
gas, __A_TAG_PLACEHOLDER_0__.
Barometer, aneroid, 328, 329;
and weather, __A_TAG_PLACEHOLDER_0__;
Fortin's, 326;
meaning of, __A_TAG_PLACEHOLDER_0__;
easy, 328;
wheel, 327.
Beau de Rochas, 89.
Bell, diving, 332;
electric, __A_TAG_PLACEHOLDER_0__, 120.
Bellows of organ, 303.
Bioscope, 266.
Blades, turbine, 81, 83.
Block system, 201, 212.
Blood, arterial, 359;
circulation of, 356, 357, __A_TAG_PLACEHOLDER_2__;
venous, __A_TAG_PLACEHOLDER_0__.
Blower-plate, 393, 394.
Boat, sails of, 346.
Boiler, Babcock and Wilcox, 21, 22;
explosions, __A_TAG_PLACEHOLDER_0__, __A_TAG_PLACEHOLDER_1__;
fire tube, __A_TAG_PLACEHOLDER_0__;
fittings, __A_TAG_PLACEHOLDER_0__;
Lancashire, __A_TAG_PLACEHOLDER_0__, 26;
locomotive, 20, __A_TAG_PLACEHOLDER_1__;
multitubular, __A_TAG_PLACEHOLDER_0__;
principle of __A_TAG_PLACEHOLDER_0__;
stored energy in, __A_TAG_PLACEHOLDER_0__;
vertical, 25;
water supply to, __A_TAG_PLACEHOLDER_0__;
water tube, __A_TAG_PLACEHOLDER_0__.
Brakes, hydraulic, 188;
car, __A_TAG_PLACEHOLDER_0__;
train, __A_TAG_PLACEHOLDER_0__;
vacuum, __A_TAG_PLACEHOLDER_0__, 190, 191;
Westinghouse, __A_TAG_PLACEHOLDER_0__, 195, 197.
Bramah, 363, 437.
Breezes, land and sea, 324.
Brushes of dynamo, 161, 172.
Bunsen burner, 409.
Burning-glass, 232.
Camera, the, 233;
pinhole, 234, 235.
Canals, semicircular, 273.
Capillary attraction, 392;
veins, __A_TAG_PLACEHOLDER_0__.
Carbon dioxide, 27, 359;
monoxide, __A_TAG_PLACEHOLDER_0__.
Carburetter, 98, 99.
Cardan shaft, 93.
Carmania, the, 83.
Centrifugal force, 382.
Change-speed gear, 105, 442.
Chassis of motor car, 92.
Circulation of water in a boiler, 17, 18, 19;
of water in a car, __A_TAG_PLACEHOLDER_0__, 97.
Clarionet, 308.
Clock, first weight-driven, 412;
water, __A_TAG_PLACEHOLDER_0__.
Clutch of motor car, 105.
Coal, as fuel, 15;
gas, __A_TAG_PLACEHOLDER_0__;
gas production, __A_TAG_PLACEHOLDER_0__;
gas plant, 396;
gas purification, __A_TAG_PLACEHOLDER_0__.
Cochlea, 273.
Coherer, 140.
Coil, Ruhmkorff, 121.
Coke, 395.
Combinations in Chubb lock, 436;
Yale lock, __A_TAG_PLACEHOLDER_0__.
Combustion, 26, 393;
perfect, __A_TAG_PLACEHOLDER_0__.
Compensating gear, 107, 108.
Compound engines, 59;
arrangement of, __A_TAG_PLACEHOLDER_0__;
invention of, __A_TAG_PLACEHOLDER_0__.
Compound locomotives, 62.
Compound microscope, 261.
Condenser, marine, 71, 72;
of Ruhmkorff coil, __A_TAG_PLACEHOLDER_0__.
Conduit, 176.
Convex lens, image cast by, 236.
Conjugate foci, 262.
Cornet, 308.
Corti, rods of, 274.
Coxwell, 348.
Cream separator, 381, 383.
Current, reversal of electric, 130, 131;
transformation of __A_TAG_PLACEHOLDER_0__.
Cushioning of steam, 55.
Cycle, gearing of, 439.
Cylinder, hydraulic press, 363;
steam, 49.
Danes, 382.
Dead point, 47.
De Brouwer stoker, 401.
Detector in Chubb lock, 435.
Diving-bell, 332;
simple, 333, 334.
Diving-dress, 335.
Direction of current in dynamo circuit, 163.
Diver's feats, 338;
helmet, 336;
lamp, 338.
Donkey-engines, 68.
Doorstop, self-closing, 344.
Double-cylinder engines, 47.
Draught, forced, 28, 29;
induced, __A_TAG_PLACEHOLDER_0__.
Drum and fusee, 414.
Durability of motor-car engine, 96.
D-valve, 67.
Dynamo, alternating, 164, 174;
brushes, 172;
compound, __A_TAG_PLACEHOLDER_0__;
continuous current, __A_TAG_PLACEHOLDER_0__;
multipolar, __A_TAG_PLACEHOLDER_0__;
series wound, 173;
shunt-wound, 173;
simple, __A_TAG_PLACEHOLDER_0__, 162.
Ear, the, 271, 273;
a good, __A_TAG_PLACEHOLDER_0__, __A_TAG_PLACEHOLDER_1__;
sensitivity of, __A_TAG_PLACEHOLDER_0__.
Eccentric, 52, 53;
setting of, __A_TAG_PLACEHOLDER_0__.
Edison, Thomas, 310.
Edison-Bell phonograph, 310.
Electricity, current, 115;
forms of, __A_TAG_PLACEHOLDER_0__;
nature of, __A_TAG_PLACEHOLDER_0__;
static, __A_TAG_PLACEHOLDER_0__.
Electric bell, 119, 120;
signaling, __A_TAG_PLACEHOLDER_0__;
slot, __A_TAG_PLACEHOLDER_0__.
Electroplating, 185, 186.
Electro-magnets, 117.
Endolymph, 272.
Engines, compound, 59;
donkey, __A_TAG_PLACEHOLDER_0__;
double-cylinder, __A_TAG_PLACEHOLDER_0__;
internal combustion, __A_TAG_PLACEHOLDER_0__, __A_TAG_PLACEHOLDER_1__;
reciprocating, __A_TAG_PLACEHOLDER_0__.
Escapement of timepieces, 416;
cylinder, 420;
lever, __A_TAG_PLACEHOLDER_0__, 422.
Ether, 270.
Eustachian tube, 276.
Eye, human, 246, 247;
self-accommodation of, __A_TAG_PLACEHOLDER_0__.
Expansive working of steam, 56.
Faraday, Michael, 159.
Field, magnetic, 159;
magnets, __A_TAG_PLACEHOLDER_0__;
ring, __A_TAG_PLACEHOLDER_0__.
Filters, 374;
Maignen, 373;
Berkefeld, __A_TAG_PLACEHOLDER_0__.
Filtration beds, 372.
Flute, 308.
Flying-machines, 348.
Fly-wheel, use of, 48.
Focus, meaning of, 237;
principal, __A_TAG_PLACEHOLDER_0__.
Foci, conjugate, 262.
Force, lines of, 116.
Forces, component, 345.
Free wheel, 440.
Furring-up of pipes, 391.
Fusee, drum and, 414.
Galileo, 259, 325, 416.
Galilean telescope, 259.
Gas, coal, 394;
governor, __A_TAG_PLACEHOLDER_0__;
meter, __A_TAG_PLACEHOLDER_0__;
traps, __A_TAG_PLACEHOLDER_0__;
works, __A_TAG_PLACEHOLDER_0__.
Gasometer, 397;
largest, 398, __A_TAG_PLACEHOLDER_1__.
Gauge, steam, 36, 38;
water, __A_TAG_PLACEHOLDER_0__, 36.
Gear, compensating, 107, 108.
Gear-box of motor car, 105.
Gearing of cycle, 439.
Glaisher, 348.
Gland, 50, 363.
Glass, flint and crown, 242.
Going-barrel for watches, 415.
Gooch reversing gear, 65.
Governors, speed, 67;
of car, __A_TAG_PLACEHOLDER_0__, 104.
Graham, 418.
Gramophone, 317;
records, __A_TAG_PLACEHOLDER_0__, __A_TAG_PLACEHOLDER_1__;
reproducer, 318.
Hairspring, 412.
Hay-cutter, 451.
Heart, the, 355;
disease, __A_TAG_PLACEHOLDER_0__;
pulsation rate of __A_TAG_PLACEHOLDER_0__;
size of, __A_TAG_PLACEHOLDER_0__.
Heat of sun, 451.
Hele, Peter, 412.
Helmet, diver's, 336.
Helmholtz, 274, 308.
Hero of Alexandria, 74.
Herschel, 261.
Hertz, Dr., 138.
Hertzian waves, 138.
Hot-water supply, 386.
Hour-hand train in timepieces, 429.
Household water supply, 364.
Hughes type-printer, 134.
Hydraulic press, 361, 362.
Hydro, 385.
Ignition of charge in motor-car cylinder, 100, 101.
Image and object, relative positions of, 239;
distortion of __A_TAG_PLACEHOLDER_0__.
Incandescent gas mantle, 407;
electric lamp, __A_TAG_PLACEHOLDER_0__.
Incus, 272.
Index mechanism of water-meter, 37.
Indicator of electric bell, 119.
Induction coil, 121;
uses of __A_TAG_PLACEHOLDER_0__.
Injector, 39;
Giffard's, 41;
principle of, __A_TAG_PLACEHOLDER_0__;
self-motivated, __A_TAG_PLACEHOLDER_0__.
Interlocking of signals, 204, 222.
Internal-combustion engine, 87.
Iris of eye, 249;
stop, __A_TAG_PLACEHOLDER_0__.
Kelvin, Lord, 158.
Keyless winding mechanism, 425, 426, 428.
Kite, 345.
Lamp, arc, 182;
how it works, __A_TAG_PLACEHOLDER_0__;
incandescent, __A_TAG_PLACEHOLDER_0__;
making incandescent bulbs, __A_TAG_PLACEHOLDER_0__.
Lap of slide-valve, 57, 59.
Larynx, 306.
Laxey wheel, 380, 381.
Leads, 208.
Lenses, 231;
correction of for color, __A_TAG_PLACEHOLDER_0__, 241;
focus on, __A_TAG_PLACEHOLDER_0__;
straight, 245;
spherical aberration in __A_TAG_PLACEHOLDER_0__.
Levers, signal, colours of, 208.
Limit of error in cylinder, 52.
Light, electric, 179;
nature of, __A_TAG_PLACEHOLDER_0__;
spreading of, __A_TAG_PLACEHOLDER_0__.
Li Hung Chang, 157.
Lindsay, James Bowman, 145.
Lines of force, 116, 162.
"Linking up," 65.
Locks, 430;
Barron, __A_TAG_PLACEHOLDER_0__;
Bramah, __A_TAG_PLACEHOLDER_0__;
Chubb, __A_TAG_PLACEHOLDER_0__, __A_TAG_PLACEHOLDER_1__;
Hobbs, __A_TAG_PLACEHOLDER_0__;
simplest, 431;
tumbler, 432;
Yale, 436.
Locking gear for signals, 205.
Locomotive, electric, 178;
advantages of, __A_TAG_PLACEHOLDER_0__.
Lungs, 359.
Magic-lantern, 263, 264.
Magnet, 115;
permanent, __A_TAG_PLACEHOLDER_0__, __A_TAG_PLACEHOLDER_1__;
temporary, __A_TAG_PLACEHOLDER_0__.
Magnetism, 115.
Magnetic needle, influence of current on, 129.
Mainspring, invention of, 412.
Malleus, 272.
Marconi, 140, 146.
Marine chronometers, 415;
delicacy of __A_TAG_PLACEHOLDER_0__.
Marine speed governor, 71.
Marine turbine, advantages of, 84.
Maudslay, Henry, 363.
Maxim, Sir Hiram, 348.
Micrometer free wheel, 441.
Micro-photography, 265.
Microscope, 254;
compound, __A_TAG_PLACEHOLDER_0__, 263;
in telescope, __A_TAG_PLACEHOLDER_0__;
simple, 254.
Mineral oil, 392.
Mirror, parabolic, 261, 262;
plane, 267.
Morse, 132, 145;
code, __A_TAG_PLACEHOLDER_0__;
inker, __A_TAG_PLACEHOLDER_0__;
sounder, __A_TAG_PLACEHOLDER_0__.
Motor car, the, 92;
electric, __A_TAG_PLACEHOLDER_0__.
Mouth, 307.
Mowing-machines, 450.
Musical sounds, 277.
Nerve, auditory, 272;
optic, __A_TAG_PLACEHOLDER_0__.
Nodes on a string, 285;
air column, __A_TAG_PLACEHOLDER_0__.
Note, fundamental, 285;
quality of, __A_TAG_PLACEHOLDER_0__.
Niagara Falls, power station at, 174.
Organ, the, 294, 300;
bellows, __A_TAG_PLACEHOLDER_0__;
console, __A_TAG_PLACEHOLDER_0__;
echo, alone, awesome, great, and choir, __A_TAG_PLACEHOLDER_0__;
electric and pneumatic, __A_TAG_PLACEHOLDER_0__;
largest in the world, __A_TAG_PLACEHOLDER_0__;
pedals, __A_TAG_PLACEHOLDER_0__;
pipes, __A_TAG_PLACEHOLDER_0__;
pipe arrangement, __A_TAG_PLACEHOLDER_0__;
soundboard, 296;
wind chest, __A_TAG_PLACEHOLDER_0__.
Otto cycle, 91.
Overtones, 285.
Pallets of organ, 297.
Parallel arrangement of electric lamps, 184.
Paris, siege of, 265.
Pedals of organ, 298.
Pelton wheel, 377.
Pendulum, 412;
compensating, __A_TAG_PLACEHOLDER_0__, 419.
Perilymph, 272.
Perry, Professor, 16.
Petrol, 98.
Phonograph, 310;
governor, 311;
recorder, __A_TAG_PLACEHOLDER_0__, 313;
recording, creation of, __A_TAG_PLACEHOLDER_0__;
reproducer, __A_TAG_PLACEHOLDER_0__;
tracings on record of, 317.
Pianoforte, 277;
sounding board, __A_TAG_PLACEHOLDER_0__;
striking mechanism, __A_TAG_PLACEHOLDER_0__;
strings, __A_TAG_PLACEHOLDER_0__.
Piccolo, 308.
Pipes, closed, 289;
flue, __A_TAG_PLACEHOLDER_0__;
open, __A_TAG_PLACEHOLDER_0__;
organ, __A_TAG_PLACEHOLDER_0__;
reed, __A_TAG_PLACEHOLDER_0__, 302;
tuning, __A_TAG_PLACEHOLDER_0__.
Piston valve, 67.
Pneumatic tyres, 341.
Poldhu, signalling station at, 138.
Points, railway, 208, 210;
and signals together, __A_TAG_PLACEHOLDER_0__.
Poles of a magnet, 115.
Popoff, Professor A., 138, 145.
Power, transmission of, 175.
Preece, Sir William, 145.
Primary winding of induction coil, 122.
Pump, air, 340;
bucket, __A_TAG_PLACEHOLDER_0__, 353;
force, __A_TAG_PLACEHOLDER_0__;
most amazing, __A_TAG_PLACEHOLDER_0__;
Westinghouse air, __A_TAG_PLACEHOLDER_0__.
Railway brakes, 187;
signaling, __A_TAG_PLACEHOLDER_0__.
Rays, converging and diverging, 256;
heat, focused by lens, 232;
light, __A_TAG_PLACEHOLDER_0__, __A_TAG_PLACEHOLDER_1__, __A_TAG_PLACEHOLDER_2__, __A_TAG_PLACEHOLDER_3__.
Records, master, 319, 320.
Reciprocation, 51.
Reed, human, 306;
pipes, __A_TAG_PLACEHOLDER_0__, 302.
Reflecting telescope, 260.
Relays, telegraphic, 133, 141.
Retina, 247.
Retorts, 395.
Reversing gear, 62;
Allan, __A_TAG_PLACEHOLDER_0__;
Gooch, __A_TAG_PLACEHOLDER_0__;
radial, __A_TAG_PLACEHOLDER_0__.
Rocking bar mechanism for watches, 425.
Rods of Corti, 274.
Ruhmkorff coil, 121, 122.
Safety-valve, 32, 33, 391.
Sand-glasses, 411.
Scissors, action of, 450.
Secondary winding of induction coil, 122.
Series arrangement of electric lamps, 183.
Series winding of dynamo, 173.
Shunt wound dynamo, 173.
Sight, long and short, 250.
Signalling, automatic, 228;
electric, __A_TAG_PLACEHOLDER_0__;
air-powered, __A_TAG_PLACEHOLDER_0__;
power, __A_TAG_PLACEHOLDER_0__.
Signal levers, 206.
Signals, interlocking of, 204;
position of, __A_TAG_PLACEHOLDER_0__;
train, __A_TAG_PLACEHOLDER_0__;
single line, __A_TAG_PLACEHOLDER_0__.
Silencer on motor cars, 109.
Siphon, 351.
Slide-valve, 49, 50, 51;
setting of, __A_TAG_PLACEHOLDER_0__.
Sliders, 297.
Sound, nature of, 270;
organ board, __A_TAG_PLACEHOLDER_0__;
piano keyboard, __A_TAG_PLACEHOLDER_0__.
Spagnoletti disc instrument, 212.
Sparking-plug, 102.
Spectacles, use of, 249.
Spectrum, colours of, 230.
Speed governors, 67, 68, 69;
Hartwell, __A_TAG_PLACEHOLDER_0__;
marine, __A_TAG_PLACEHOLDER_0__.
Speed of motor cars, 110.
Spot, blind, in eye, 251;
yellow in eye, __A_TAG_PLACEHOLDER_0__.
Spring balance for watches, 419;
compensating, __A_TAG_PLACEHOLDER_0__, 424.
Stapes, 272.
Steam, what it is, 13;
energy of, __A_TAG_PLACEHOLDER_0__;
engines, __A_TAG_PLACEHOLDER_0__;
reciprocating engines, 45;
expansive workings of, __A_TAG_PLACEHOLDER_0__, __A_TAG_PLACEHOLDER_1__;
gauge, __A_TAG_PLACEHOLDER_0__;
gauge principle, __A_TAG_PLACEHOLDER_0__;
turbine, __A_TAG_PLACEHOLDER_0__;
turbine, De Laval, __A_TAG_PLACEHOLDER_0__, 77;
turbine, Hero, __A_TAG_PLACEHOLDER_0__;
turbine, Parsons, __A_TAG_PLACEHOLDER_0__, 80;
volume of, compared to water, __A_TAG_PLACEHOLDER_0__.
Stephenson, George, 63, 375.
Stop, in lens, 244;
iris, __A_TAG_PLACEHOLDER_0__;
use of, __A_TAG_PLACEHOLDER_0__.
Sun-dial of Ahaz, 410.
Syntonic transmission of wireless messages, 143.
Talking-machines, 310.
Tapper in wireless telegraphy receiver, 141.
Tappet arm, 205.
Telegraph, electric, 127;
insulator, 133;
needle, 128;
recording, __A_TAG_PLACEHOLDER_0__;
sounder, __A_TAG_PLACEHOLDER_0__.
Telegraphy, high-speed, 135;
wireless, __A_TAG_PLACEHOLDER_0__.
Telephone, 147;
Bell, 148;
circuit, double line, __A_TAG_PLACEHOLDER_0__;
circuit, overall layout, 152, __A_TAG_PLACEHOLDER_1__;
exchange, 154, __A_TAG_PLACEHOLDER_1__.
Telephony, submarine, 157.
Telescope, 257;
Galilean, 259;
prismatic, 260;
reflecting, __A_TAG_PLACEHOLDER_0__;
terrestrial, 259.
Threshing-machine, 447, 448.
Thurston, Professor, 31.
Tides, 452;
high, __A_TAG_PLACEHOLDER_0__;
neap and spring, __A_TAG_PLACEHOLDER_0__.
Timbre, 285.
Tompion, Thomas, 412.
Torricelli, 325.
Trachea, 306.
Train staff signalling, 216;
single, __A_TAG_PLACEHOLDER_0__;
and ticket, __A_TAG_PLACEHOLDER_0__;
electric, __A_TAG_PLACEHOLDER_0__.
Transformation of current, 124, 176.
Transmission of power, 174, 175.
Transmitter, Edison telephone, 150;
granular carbon, __A_TAG_PLACEHOLDER_0__, 151.
Triple-valve, 196.
Trolley arm, 176.
Turbines, steam, 74.
Turbinia, the, 79.
Tympanum, 137, 271, 272.
Universal joint, 93.
Vacuum brake, 189, 190, 191.
Vacuum chamber of aneroid barometer, 330.
Valve, piston, 67;
safety, __A_TAG_PLACEHOLDER_0__;
of internal combustion engine, __A_TAG_PLACEHOLDER_0__.
Valves of the heart, 357.
Veins, 358;
capillary, __A_TAG_PLACEHOLDER_0__;
pulmonary, __A_TAG_PLACEHOLDER_0__.
Ventral segments, 291.
Ventricles, 357.
Vibration of columns of air, 288, 289;
of rods, __A_TAG_PLACEHOLDER_0__;
of strings, __A_TAG_PLACEHOLDER_0__;
of strings, regulating conditions, __A_TAG_PLACEHOLDER_0__.
Viper, the, 86.
Virag, Pollak—high-speed telegraphy, 136.
Vitreous humour, 246.
Voltage, 121, 161.
Vowel sounds, 308.
Wasborough, Matthew, 51.
Watches, first, 412.
Water cock, 365;
engines, __A_TAG_PLACEHOLDER_0__;
gauge, __A_TAG_PLACEHOLDER_0__, 36;
jacket, __A_TAG_PLACEHOLDER_0__, __A_TAG_PLACEHOLDER_1__;
meter, 368;
supply, __A_TAG_PLACEHOLDER_0__;
turbines, __A_TAG_PLACEHOLDER_0__, __A_TAG_PLACEHOLDER_1__;
wheels, __A_TAG_PLACEHOLDER_0__.
Watt, James, 51, 69, 375.
Welsbach incandescent mantle, 407.
Westinghouse air-brake, 194, 195, 197;
George, __A_TAG_PLACEHOLDER_0__.
Wheatstone needle instrument, 128, 131;
automatic transmitter, __A_TAG_PLACEHOLDER_0__.
Wind, why it blows, 323;
action of flying kites, __A_TAG_PLACEHOLDER_0__;
on sails, __A_TAG_PLACEHOLDER_0__.
Windmills, 375.
Window, oval, in ear, 272;
round, in-ear, __A_TAG_PLACEHOLDER_0__.
Wireless telegraphy, 137;
advance of, __A_TAG_PLACEHOLDER_0__;
receiver, __A_TAG_PLACEHOLDER_0__, __A_TAG_PLACEHOLDER_1__;
syntonic, __A_TAG_PLACEHOLDER_0__;
transmitter, __A_TAG_PLACEHOLDER_0__, 139.
Yale lock, 436, 437.
Yellow spot, in eye, 251.
Zech, Jacob, 414.
Zeiss field-glasses, 260.
THE END.
THE END.
Download ePUB
If you like this ebook, consider a donation!