This is a modern-English version of The Invention of the Sewing Machine, originally written by Cooper, Grace Rogers.
It has been thoroughly updated, including changes to sentence structure, words, spelling,
and grammar—to ensure clarity for contemporary readers, while preserving the original spirit and nuance. If
you click on a paragraph, you will see the original text that we modified, and you can toggle between the two versions.
Scroll to the bottom of this page and you will find a free ePUB download link for this book.
Transcriber’s Note: Corrections to typographical errors are underlined like this. Mouse over to view the original text.
Transcriber’s Note: Corrections to typographical errors are underlined like this. Hover over to see the original text.

SMITHSONIAN INSTITUTION
UNITED STATES NATIONAL MUSEUM

BULLETIN 254
BULLETIN 254
WASHINGTON, D.C.
D.C.
1968
1968

THE SMITHSONIAN INSTITUTION PRESS
SMITHSONIAN INSTITUTION PRESS
The Invention
Of the Sewing Machine

Grace Rogers Cooper
Grace Rogers Cooper
CURATOR OF TEXTILES
Textile Curator
Museum of History and Technology
History and Technology Museum
SMITHSONIAN INSTITUTION · WASHINGTON, · D.C. 1968
SMITHSONIAN INSTITUTION · WASHINGTON, D.C. 1968
Publications of the United States National Museum
The scholarly and scientific publications of the United States National Museum include two series, Proceedings of the United States National Museum and United States National Museum Bulletin.
The research and scientific publications of the United States National Museum include two series, Proceedings of the United States National Museum and United States National Museum Bulletin.
In these series, the Museum publishes original articles and monographs dealing with the collections and work of its constituent museums—The Museum of Natural History and the Museum of History and Technology—setting forth newly acquired facts in the fields of anthropology, biology, history, geology, and technology. Copies of each publication are distributed to libraries, to cultural and scientific organizations, and to specialists and others interested in the different subjects.
In these series, the Museum publishes original articles and monographs about the collections and activities of its constituent museums—The Museum of Natural History and the Museum of History and Technology—presenting newly acquired information in anthropology, biology, history, geology, and technology. Copies of each publication are sent to libraries, cultural and scientific organizations, as well as specialists and others interested in the various topics.
The Proceedings, begun in 1878, are intended for the publication, in separate form, of shorter papers from the Museum of Natural History. These are gathered in volumes, octavo in size, with the publication date of each paper recorded in the table of contents of the volume.
The Proceedings, which started in 1878, are meant for publishing shorter papers from the Museum of Natural History in a separate format. These papers are collected in volumes that are octavo in size, with the publication date of each paper listed in the table of contents of the volume.
In the Bulletin series, the first of which was issued in 1875, appear longer, separate publications consisting of monographs (occasionally in several parts) and volumes in which are collected works on related subjects. Bulletins are either octavo or quarto in size, depending on the needs of the presentation. Since 1902 papers relating to the botanical collections of the Museum of Natural History have been published in the Bulletin series under the heading Contributions from the United States National Herbarium and, since 1959, in Bulletins titled “Contributions from the Museum of History and Technology,” have been gathered shorter papers relating to the collections and research of that Museum.
In the Bulletin series, which started in 1875, you'll find longer, standalone publications made up of monographs (sometimes in multiple parts) and volumes that compile works on related topics. Bulletins come in either octavo or quarto sizes, depending on what’s needed for the presentation. Since 1902, papers about the botanical collections of the Museum of Natural History have been published in the Bulletin series under the title Contributions from the United States National Herbarium. Additionally, since 1959, shorter papers related to the collections and research of that Museum have been included in Bulletins titled “Contributions from the Museum of History and Technology.”
This work forms volume 254 of the Bulletin series.
This work is volume 254 of the Bulletin series.
Frank A. Taylor
Director, United States National Museum
Frank A. Taylor
Director, United States National Museum
For sale by Superintendent of Documents, U.S. Government Printing Office
Washington, D.C. 20402—Price $2.75
For sale by the Superintendent of Documents, U.S. Government Printing Office
Washington, D.C. 20402—Price $2.75
Contents
Preface | vii | ||
Acknowledgments | viii | ||
1. | Early Efforts | 1 | |
2. | Elements of a Successful Machine | 17 | |
3. | The “Sewing-Machine Combination” | 39 | |
4. | Less Expensive Machines | 43 | |
Appendixes | 55 | ||
I. | Notes on the Development and Commercial Use of the Sewing Machine | 57 | |
II. | American Sewing-Machine Companies of the 19th Century | 65 | |
III. | Chronological List of U.S. Sewing-Machine Patent Models in the Smithsonian Collections | 125 | |
IV. | 19th-Century Sewing Machine Leaflets in the Smithsonian Collections | 134 | |
V. | A Brief History of Cotton Thread | 135 | |
VI. | Biographical Sketches | 137 | |
Bibliography | 144 | ||
Indexes | 147 | ||
Geographical Index to Companies Listed in Appendix II | 149 | ||
Alphabetical Index to Patentees Listed in Appendix III | 151 | ||
General Index to Chapters 1-4 | 155 |
Preface
It had no instrument panel with push-button controls. It was not operated electronically or jet-propelled. But to many 19th-century people the sewing machine was probably as awe-inspiring as a space capsule is to their 20th-century descendants. It was expensive, but, considering the work it could do and the time it could save, the cost was more than justified. The sewing machine became the first widely advertised consumer appliance, pioneered installment buying and patent pooling, and revolutionized the ready-made clothing industry. It also weathered the protests of those who feared the new machine was a threat to their livelihood.
It didn't have a control panel with buttons. It wasn't operated electronically or jet-propelled. But to many people in the 19th century, the sewing machine was likely as amazing as a space capsule is to people in the 20th century. It was pricey, but considering the work it could do and the time it could save, the price was totally justified. The sewing machine became the first widely advertised consumer product, led the way for installment buying and patent pooling, and changed the ready-made clothing industry forever. It also faced opposition from those who worried the new machine would threaten their jobs.
The practical sewing machine is not the result of one man’s genius, but rather the culmination of a century of thought, work, trials, failures, and partial successes of a long list of inventors. History is too quick to credit one or two men for an important invention and to forget the work that preceded and prodded each man to contribute his share. It is no discredit to Howe to state that he did not invent the sewing machine. Howe’s work with the sewing machine was important, and he did patent certain improvements, but his work was one step along the way. It is for the reader to decide whether it was the turning point.
The practical sewing machine wasn't created by just one person's brilliance; instead, it represents a hundred years of ideas, effort, trials, failures, and partial successes from many inventors. History often too quickly attributes important inventions to one or two individuals and overlooks the contributions made by those who came before. It doesn't undermine Howe to say that he did not invent the sewing machine. Howe’s contributions to the sewing machine were significant, and he did patent certain improvements, but his work was just one part of a larger journey. It's up to the reader to determine if it was the pivotal moment.
Since the sewing machine has been considered by some as one of the most important inventions of 19th-century America, of equal importance to this story of the invention is the history of the sewing machine’s development into a practical, popular commodity. Since many new companies blossomed overnight to manufacture this very salable item, a catalog list of more than one hundred and fifty of these 19th-century companies is included in this study. Still, the list is probably incomplete. Many of the companies remained in business a very short time or kept their activities a secret to avoid payment of royalties to patent holders. Evidence of these companies is difficult to find. It is hoped that additional information will come to light[Pg viii] as a result of this initial attempt to list and date known companies. The dating of individual machines based on their serial numbers is also a difficult task. Individual company records of this type have not survived; however, using the commercial machines in the patent collection, for which we know one limiting date—the date the machine was deposited at the patent office—and using the records that have survived, an estimated date based on the serial number can be established for many of the better known machines.
Since the sewing machine is seen by some as one of the most significant inventions of 19th-century America, the story of its invention is just as important as its evolution into a practical and popular product. Many new companies sprang up overnight to produce this highly marketable item, and this study includes a catalog of over one hundred and fifty of these 19th-century companies. However, the list is likely incomplete. Many of the companies operated for only a short time or kept their activities under wraps to avoid paying royalties to patent owners. Finding evidence of these companies is challenging. It's hoped that more information will surface[Pg viii] from this initial effort to list and date known companies. Dating individual machines based on their serial numbers is also tricky. Records from individual companies of this nature have largely not survived; however, by using the commercial machines in the patent collection, which have one confirmed date—the date the machine was submitted to the patent office—and the existing records, it's possible to establish an estimated date based on the serial number for many of the more well-known machines.
Acknowledgments
Acknowledgments
I am greatly indebted to the late Dr. Frederick Lewton, whose interest in the history of the sewing machine initiated the collecting of information about it for the Smithsonian Institution’s Division of Textiles archives and whose out-of-print booklet “A Servant in the House” prompted the writing of this work. I would also like to thank Mr. Bogart Thompson of the Singer Manufacturing Company for his cooperation in arranging for the gift of an excellent collection of 19th-century sewing machines to the Smithsonian and for allowing me to use the Singer historical files. Acknowledgment is also made of the cooperation extended by The Henry Ford Museum and Greenfield Village for permitting me to study their collection of old sewing machines.
I am very grateful to the late Dr. Frederick Lewton, whose interest in the history of the sewing machine sparked the collection of information about it for the Smithsonian Institution’s Division of Textiles archives and whose out-of-print booklet “A Servant in the House” inspired the writing of this work. I would also like to thank Mr. Bogart Thompson from the Singer Manufacturing Company for his help in arranging the donation of an amazing collection of 19th-century sewing machines to the Smithsonian and for letting me use the Singer historical files. I also appreciate the support from The Henry Ford Museum and Greenfield Village for allowing me to research their collection of old sewing machines.
Grace Rogers Cooper
Grace Rogers Cooper
Chapter One

Figure 1.—After almost a century of attempts to invent a machine that would sew, the practical sewing machine evolved in the mid-19th century. This elegant, carpeted salesroom of the 1870s, with fashionable ladies and gentlemen scanning the latest model sewing machines, reflects the pinnacle reached by the new industry in just a few decades. This example, one of many of its type, is the Wheeler and Wilson sewing-machine offices and salesroom, No. 44 Fourteenth Street, Union Square, New York City. From The Daily Graphic, New York City, December 29, 1874. (Smithsonian photo 48091-A.)
Figure 1.—After almost a hundred years of efforts to invent a machine that could sew, the practical sewing machine emerged in the mid-19th century. This stylish, carpeted salesroom from the 1870s, with well-dressed ladies and gentlemen looking at the latest model sewing machines, showcases how far the new industry had come in just a few decades. This example, among many like it, is the Wheeler and Wilson sewing-machine offices and salesroom, No. 44 Fourteenth Street, Union Square, New York City. From The Daily Graphic, New York City, December 29, 1874. (Smithsonian photo 48091-A.)
Early Efforts
To 1800
For thousands of years, the only means of stitching two pieces of fabric together had been with a common needle and a length of thread. The thread might be of silk, flax, wool, sinew, or other fibrous material. The needle, whether of bone, silver, bronze, steel, or some other metal, was always the same in design—a thin shaft with a point at one end and a hole or eye for receiving the thread at the other end. Simple as it was, the common needle (fig. 2) with its thread-carrying eye had been an ingenious improvement over the sharp bone, stick, or other object used to pierce a hole through which a lacing then had to be passed.[1] In addition to utilitarian stitching for such things as the making of garments and household furnishings, the needle was also used for decorative stitching, commonly called embroidery. And it was for this purpose that the needle, the seemingly perfect tool that defied improvement, was first altered for ease of stitching and to increase production.
For thousands of years, the only way to stitch two pieces of fabric together was with a regular needle and a length of thread. The thread could be made from silk, flax, wool, sinew, or other fibrous materials. The needle, whether made of bone, silver, bronze, steel, or another metal, always had the same basic design—a thin shaft with a pointed end and a hole or eye for threading at the other end. As simple as it was, the common needle (fig. 2) with its thread-carrying eye was a clever improvement over the sharp bone, stick, or other objects used to poke a hole through which lacing had to be threaded. [1] Besides practical stitching for things like making clothes and home furnishings, the needle was also used for decorative stitching, often called embroidery. It was for this decorative purpose that the needle, which seemed like the perfect tool that couldn’t be improved, was first modified to make stitching easier and boost production.
One of the forms that the needle took in the process of adaptation was that of the fine steel hook. Called an aguja in Spain, the hook was used in making a type of lace known as punto de aguja. During the 17th century after the introduction of chainstitch embroideries from India, this hook was used to produce chainstitch designs on a net ground.[2] The stitch and the fine hook to make it were especially adaptable to this work. By the 18th century the hook had been reduced to needle size and inserted into a handle, and was used to chainstitch-embroider woven fabrics.[3] In France the hook was called a crochet and was sharpened to a point for easy entry into the fabric (fig. 3). For stitching, the fabric was held taut on a drum-shaped frame. The hooked needle pierced the fabric, caught the thread from below the surface and pulled a loop to the top. The needle reentered the fabric a stitch-length from the first entry and caught the thread again, pulling a second loop through the first to which it became enchained. This method of embroidery permitted for the first time the use of a continuous length of thread. At this time the chainstitch was used exclusively for decorative embroidery, and from the French name for drum—the shape of the frame that held the fabric—the worked fabric came to be called tambour embroidery. The crochet[4] [Pg 4]or small hooked needle soon became known as a tambour needle.
One of the forms that the needle adapted into was the fine steel hook. Known as an aguja in Spain, this hook was used to create a type of lace called punto de aguja. During the 17th century, after chainstitch embroidery techniques were brought over from India, this hook was used to create chainstitch designs on a net background.[2] The stitch and the fine hook used to make it were particularly suited for this kind of work. By the 18th century, the hook had been shaped down to needle size and inserted into a handle, which allowed it to be used for chainstitch-embroidering woven fabrics.[3] In France, the hook was called a crochet and was sharpened to a point for easier insertion into the fabric (fig. 3). While stitching, the fabric was held tight on a drum-shaped frame. The hooked needle pierced the fabric, caught the thread from underneath, and pulled a loop to the top. The needle then reentered the fabric a stitch-length away from the first entry, caught the thread again, and pulled a second loop through the first, creating a chain. This embroidery method allowed for the first time the use of a continuous length of thread. At this point, the chainstitch was used solely for decorative embroidery, and because of the French word for drum—the shape of the frame that held the fabric—the finished product came to be known as tambour embroidery. The crochet[4] [Pg 4]or small hooked needle soon became known as a tambour needle.

Figure 2.—Primitive needle. Bronze. Egyptian (Roman period, 30 B.C.-A.D. 642). (Smithsonian photo 1379-A.)
Figure 2.—Basic needle. Bronze. Egyptian (Roman period, 30 B.C.-A.D. 642). (Smithsonian photo 1379-A.)
In 1755 a new type of needle was invented for producing embroidery stitches. This needle had to pass completely through the fabric two times (a through-and-through motion) for every stitch. The inventor was Charles F. Weisenthal, a German mechanic living in London who was granted British patent 701 for a two-pointed needle (fig. 4). The invention was described in the patent as follows:
In 1755, a new kind of needle was created for making embroidery stitches. This needle needed to go all the way through the fabric twice (a through-and-through motion) for each stitch. The inventor was Charles F. Weisenthal, a German mechanic living in London who was awarded British patent 701 for a two-pointed needle (fig. 4). The invention was outlined in the patent as follows:
The muslin, being put into a frame, is to be worked with a needle that has two points, one at the head, and the other point as a common needle, which is to be worked by holding it with the fingers in the middle, so as not to require turning.
The muslin, placed in a frame, is to be worked with a needle that has two points: one at the head and the other point like a regular needle. It should be handled by gripping it in the middle with your fingers, so it doesn't need to be turned.
It might be argued that Weisenthal had invented the eye-pointed needle, since he was the first inventor to put a point at the end of the needle having the eye. But, since his specifically stated use required the needle to have two points and to be passed completely through the fabric, Weisenthal had no intention of utilizing the very important advantage that the eye-pointed needle provided, that of not requiring the passage of the needle through the fabric as in hand sewing.
It could be said that Weisenthal invented the eye-pointed needle, as he was the first to put a point at the end of a needle with an eye. However, because his specific use required the needle to have two points and be passed all the way through the fabric, Weisenthal didn’t intend to take advantage of the significant benefit that the eye-pointed needle offered, which was that it didn't need to go through the fabric like in hand sewing.
While no records can be found to establish that Weisenthal’s patent was put to any commercial use during the inventor’s lifetime, the two-pointed needle with eye at midpoint appeared in several 19th-century sewing-machine inventions.
While there are no records to show that Weisenthal's patent was commercially used during his lifetime, the two-pointed needle with an eye in the middle appeared in several sewing machine inventions from the 19th century.
The earliest of the known mechanical sewing devices produced a chain or tambour stitch, but by an entirely different principle than that used with either needle just described. Although the idea was incorporated into a patent, the machine was entirely overlooked for almost a century as the patent itself was classed under wearing apparel. It was entitled “An Entire New Method of Making and Completing Shoes, Boots, Splatterdashes, Clogs, and Other Articles, by Means of Tools and Machines also Invented by Me for that Purpose, and of Certain Compositions of the Nature of Japan or Varnish, which will be very advantageous in many useful Applications.” This portentously titled British patent 1,764 was issued to an English cabinetmaker, Thomas Saint, on July 17, 1790. Along with accounts of several processes for making various varnish compositions, the patent contains descriptions of three separate machines; the second of these was for “stitching, quilting, or sewing.” Though far from practical, the machine incorporated several features common to a modern sewing machine. It had a horizontal cloth plate or table, an overhanging arm carrying a straight needle, and a continuous supply of thread from a spool. The motion was derived from the rotation of a hand crank on a shaft, which activated cams that produced all the actions of the machine.
The earliest known mechanical sewing devices created a chain or tambour stitch, but they operated on a completely different principle than the needles just mentioned. Although the concept was patented, the machine went unnoticed for nearly a century because the patent was categorized under clothing. It was titled “An Entire New Method of Making and Completing Shoes, Boots, Splatterdashes, Clogs, and Other Articles, by Means of Tools and Machines also Invented by Me for that Purpose, and of Certain Compositions of the Nature of Japan or Varnish, which will be very advantageous in many useful Applications.” This grandly named British patent 1,764 was granted to English cabinetmaker Thomas Saint on July 17, 1790. In addition to descriptions of several processes for creating various varnish compositions, the patent includes details about three different machines; the second one was for “stitching, quilting, or sewing.” While it was far from practical, the machine featured several elements found in modern sewing machines. It had a horizontal cloth plate or table, an overhanging arm with a straight needle, and a continuous thread supply from a spool. The movement came from a hand crank that rotated a shaft, activating cams that performed all the machine's functions.
One cam operated the forked needle (fig. 5) that pushed the thread through a hole made by a preceding thrust of the awl. The thread was caught by a looper and detained so that it then became enchained in the next loop of thread. The patent described thread tighteners above and below the work and an adjustment to vary the stitches for different kinds of material. Other than the British patent records, no contemporary reference to Saint’s machine has ever been found. The stitching-machine contents of this patent was happened on by accident in 1873.[5] Using the patent description, a Newton Wilson of London attempted to build a model of Saint’s machine in 1874.[6] Wilson found, however, that it was necessary to modify the construction before the machine would stitch at all.
One cam operated the forked needle (fig. 5) that pushed the thread through a hole made by an earlier thrust of the awl. The thread was caught by a looper and held so that it became linked in the next loop of thread. The patent detailed thread tighteners both above and below the work and an adjustment to change the stitch length for different types of material. Aside from the British patent records, no current references to Saint’s machine have ever been found. The contents of this stitching machine patent were discovered by chance in 1873.[5] Using the patent description, a Newton Wilson from London tried to build a model of Saint’s machine in 1874.[6] However, Wilson found it necessary to modify the design before the machine would stitch at all.

Figure 3.—Tambour needle and frame, showing the method of forming the chainstitch, from the Diderot Encyclopedia of 1763, vol. II, Plates Brodeur, plate II. (Smithsonian photo 43995-C.)
Figure 3.—Embroidery hoop and needle, illustrating how the chainstitch is created, from the Diderot Encyclopedia of 1763, vol. II, Plates Brodeur, plate II. (Smithsonian photo 43995-C.)
[Pg 6]This raised the question whether Saint had built even one machine. Nevertheless, the germ of an idea was there, and had the inventor followed through the sewing machine might have been classed an 18th-century rather than a 19th-century contribution.
[Pg 6]This raised the question of whether Saint had built even a single machine. However, the core idea was present, and if the inventor had pursued it, the sewing machine could have been considered an 18th-century invention instead of a 19th-century one.

Figure 4.—Weisenthal’s two-pointed needle, 1755.
Figure 4.—Weisenthal’s dual-pointed needle, 1755.

Figure 5.—Saint’s sewing machine, 1790. (Smithsonian photo 42490-A.)
Figure 5.—Saint's sewing machine, 1790. (Smithsonian photo 42490-A.)
1800-1820
There is no doubt that the successful late-18th-century improvements in spinning and weaving methods, resulting in increased production of fabrics, had a great effect in spurring inventors to ideas of stitching by machinery. Several efforts were made during the first two decades of the 19th century to produce such machines.
There’s no doubt that the successful improvements in spinning and weaving techniques in the late 18th century, which led to a rise in fabric production, greatly inspired inventors to think about stitching with machines. Several attempts were made in the first two decades of the 19th century to create such machines.
On February 14, 1804, a French patent was issued to Thomas Stone and James Henderson for a “new mechanical principle designed to replace handwork in joining the edges of all kinds of flexible material, and particularly applicable to the manufacture of clothing.”[7] The machine used a common needle and made an overcast stitch in the same manner as hand sewing. A pair of jaws or pincers, imitating the action of the fingers, alternately seized and released the needle on each side of the fabric. The pincers were attached to a pair of arms arranged to be moved backward and forward by “any suitable mechanism.”[8] This machine was capable of making curved or angular as well as straight seams, but it was limited to carrying a short length of thread, necessitating frequent rethreading. The machine may have had some limited use, but it was not commercially successful.
On February 14, 1804, a French patent was granted to Thomas Stone and James Henderson for a “new mechanical principle designed to replace handwork in joining the edges of all kinds of flexible materials, particularly for making clothing.”[7] The machine used a standard needle and created an overcast stitch just like hand sewing. A pair of jaws or pincers mimicked the motion of fingers, alternately grabbing and releasing the needle on each side of the fabric. The pincers were attached to arms that could be moved back and forth by “any suitable mechanism.”[8] This machine could create curved, angular, and straight seams, but it was limited to using a short length of thread, which meant it needed frequent rethreading. It may have had some limited practical use, but it was not commercially successful.
On May 30 of the same year John Duncan, a Glasgow manufacturer, was granted British patent 2,769 for “a new and improved method of tambouring, or raising flowers, figures or other ornaments upon muslins, lawns and other cottons, cloths, or stuffs.” This machine made the chainstitch, using not one but many hooked needles that operated simultaneously. The needles, attached to a bar or carrier, were pushed through the vertically held fabric from the upper right side, which in this case was also the outer side. After passing through it, they were supplied with thread from spools by means of peculiarly formed hooks or thread carriers. The thread was twisted around the needle above the hook, so as to be caught by it, and drawn through to the outer surface. The shaft of the needle was grooved on the hook side and fitted with a slider. This slider closed upon the retraction of the needle from the fabric, holding the thread in place and preventing the hook from catching. The fabric was stretched between two rollers set in an upright frame capable of sliding vertically in a second frame arranged to have longitudinal motion. The combination of these two motions was sufficient to produce any required design. The principle developed by Duncan was used on embroidery machines, in a modified form, for many years. Of several early attempts, his was the first to realize any form of success.
On May 30 of that same year, John Duncan, a manufacturer from Glasgow, received British patent 2,769 for “a new and improved method of tambouring, or adding flowers, figures, or other designs onto muslins, lawns, and other cotton fabrics, cloths, or materials.” This machine created chainstitch using multiple hooked needles that worked at the same time. The needles, attached to a bar or carrier, were pushed through the fabric held vertically from the upper right side, which was also the outer side. Once they passed through, they were fed thread from spools using specially shaped hooks or thread carriers. The thread was twisted around the needle above the hook, allowing it to be caught by the hook and pulled through to the outer surface. The shaft of the needle was grooved on the hook side and fitted with a slider. This slider closed when the needle was retracted from the fabric, keeping the thread in place and preventing the hook from catching. The fabric was stretched between two rollers positioned in an upright frame that could slide vertically within another frame designed for longitudinal movement. The combination of these two movements was enough to create any desired design. The principle developed by Duncan was used in embroidery machines, in a modified form, for many years. Among several early attempts, his was the first to succeed in any significant way.

Figure 6.—Chapman’s sewing machine, first eye-pointed needle, 1807. (Smithsonian photo 33299-K.)
Figure 6.—Chapman's sewing machine, first eye-pointed needle, 1807. (Smithsonian photo 33299-K.)
A type of rope-stitching machine, which might be considered unimportant to this study, must be included because of its use of the eye-pointed needle, the needle that was to play a most important part in the later development of a practical sewing machine. The earliest reference to the use of a needle with an eye not being required to be passed completely through the fabric it was stitching is found in a machine invented by Edward Walter Chapman, for which he and William Chapman were granted British patent 3,078 on October 30, 1807. The machine (fig. 6) was designed to construct belting or flat banding by stitching together several strands of rope that had been laid side by side. Two needles were required and used alternately. One needle was threaded and then forced through the ropes. On the opposite side the thread was removed from the eye of the first needle before it was withdrawn. The second needle was threaded and the operation repeated. The needles could also be used to draw the thread, rather than push it, through the ropes with the same result. While being stitched, the ropes were held fast and the sewing frame and supporting carriage were moved manually as each stitch was made. Such a machine would be applicable only to the work described, since the necessity of rethreading at every stitch would make it impractical for any other type of sewing.
A type of rope-stitching machine, which may seem minor to this study, needs to be mentioned because of its use of the eye-pointed needle, a needle that would become crucial in the later development of a practical sewing machine. The earliest mention of a needle with an eye that didn't have to be fully passed through the fabric it was stitching is found in a machine invented by Edward Walter Chapman, for which he and William Chapman were granted British patent 3,078 on October 30, 1807. The machine (fig. 6) was designed to create belting or flat banding by stitching together several strands of rope laid side by side. It required two needles that were used alternately. One needle was threaded and then pushed through the ropes. On the other side, the thread was taken out of the eye of the first needle before it was pulled out. Then the second needle was threaded, and the process was repeated. The needles could also be used to draw the thread, instead of pushing it, through the ropes, achieving the same result. While stitching, the ropes were held in place, and the sewing frame and supporting carriage were moved manually with each stitch. This machine would be suitable only for the specified work since the need to rethread at every stitch would make it impractical for any other type of sewing.
Another early machine reported to have used the eye-pointed needle to form the chainstitch was invented about 1810 by Balthasar Krems,[9] a hosiery worker of Mayen, Germany. One knitted article produced there was a peaked cap, and Krems’ machine was devised to stitch the turned edges of the cap,[10] which was suspended from wire pins on a moving wheel. The needle of the machine was attached to a horizontal shaft and carried the thread through the fabric. The loop of thread was retained by a hook-shaped pin to become enchained with the next loop at the reentry of the needle. Local history reports that this device may have been used as early as 1800, but the inventor did not patent his machine and apparently made no attempt to commercialize it. No contemporary references to the machine could be found, and use of the machine may have died with the inventor in 1813.[Pg 8]
Another early machine that is said to have used the eye-pointed needle to create the chainstitch was invented around 1810 by Balthasar Krems,[9] a hosiery worker from Mayen, Germany. One knitted item produced there was a peaked cap, and Krems' machine was designed to stitch the turned edges of the cap,[10] which was held up by wire pins on a moving wheel. The machine's needle was connected to a horizontal shaft and threaded the yarn through the fabric. A hook-shaped pin held the thread loop to link it with the next loop as the needle reentered. Local history suggests that this device might have been in use as early as 1800, but the inventor didn't patent his machine and clearly made no effort to sell it. No current references to the machine have been found, and its use may have ended with the inventor's death in 1813.[Pg 8]

Figure 7.—Madersperger’s 1814 sewing machine. Illustration from a pamphlet by the inventor entitled Beschreibung einer Nähmaschine, Vienna, ca. 1816. (Smithsonian photo 49373.)
Figure 7.—Madersperger's 1814 sewing machine. Illustration from a brochure by the inventor called Description of a Sewing Machine, Vienna, around 1816. (Smithsonian photo 49373.)
About the same time, Josef Madersperger, a tailor in Vienna, Austria, invented a sewing machine, which was illustrated (fig. 7) and described in a 15-page pamphlet published about 1816.[11] On May 12, 1817, a Vienna newspaper wrote of the Madersperger machine: “The approbation which his machine received everywhere has induced his Royal Imperial Majesty, in the year 1814, to give to the inventor an exclusive privilege [patent] which has already been mentioned before in these papers.”[12] Madersperger’s 1814 machine stitched straight or curving lines. His second machine stitched small semicircles, as shown in the illustration, and also small circles, egg-shaped figures, and angles of various degrees. The machine, acclaimed by the art experts, must therefore have been intended for embroidery stitching. From the contemporary descriptions and the illustration, the machine is judged to have made a couched stitch—one thread was laid on the surface of the fabric and stitched in place with a short thread carried by a two-pointed needle of the type invented by Weisenthal. Two fabrics could have been stitched together, but not in the manner required for tailoring. The machine must have had many deficiencies in the tension adjustment, feed, and related mechanical operations, for despite the published wishes for success the inventor did not put the machine into practical[Pg 9] operation.[13] Years later Madersperger again attempted to invent a sewing machine using a different stitch (see p. 13).
Around the same time, Josef Madersperger, a tailor in Vienna, Austria, created a sewing machine, which was illustrated (fig. 7) and described in a 15-page pamphlet published around 1816.[11] On May 12, 1817, a Vienna newspaper commented on the Madersperger machine: “The praise his machine received everywhere led his Royal Imperial Majesty, in 1814, to grant the inventor an exclusive privilege [patent] that has already been mentioned in these papers.”[12] Madersperger’s 1814 machine could stitch straight or curved lines. His second machine could stitch small semicircles, as shown in the illustration, as well as small circles, egg-shaped shapes, and angles of various degrees. The machine, praised by art experts, was likely intended for embroidery stitching. From contemporary descriptions and the illustration, it's believed the machine used a couched stitch—one thread was laid on the fabric's surface and stitched in place with a short thread carried by a two-pointed needle designed by Weisenthal. Two pieces of fabric could be stitched together, but not in the way needed for tailoring. The machine probably had several issues with tension adjustment, feed, and other mechanical operations, because even with the hopes for success expressed, the inventor never put the machine into practical[Pg 9] operation.[13] Years later, Madersperger again tried to invent a sewing machine using a different stitch (see p. 13).

Figure 8.—An engraving of Thimonnier and his sewing machine of 1830, from Sewing Machine News, 1880. (Smithsonian photo 10569-C.)
Figure 8.—An engraving of Thimonnier and his sewing machine from 1830, from Sewing Machine News, 1880. (Smithsonian photo 10569-C.)
A story persists that about 1818-1819 a machine that formed a backstitch, identical to the one used in hand sewing, was invented in Monkton, Vermont. The earliest record of this machine that this author has found was in the second or 1867 edition of Eighty Years of Progress of the United States; the machine is not mentioned in the earlier edition. The writer of the article on sewing machines states that John Knowles invented and constructed a sewing machine, which used a single thread and a two-pointed needle with the eye in the middle to form the backstitch. This information must have come to light after the first edition was published, but from where and by whom is not known. Other sources state that two men, Adams and Dodge, produced this machine in Monkton.[14] While still others credit the Reverend John Adam Dodge, assisted by a mechanic by the name of John Knowles, with the same invention in the same location.[15] Vermont historical societies have been unable to identify the men named or to verify the story of the invention.[16] The importance of the credibility of this story, if proved, rests in the fact that it represents the first effort in the United States to produce a mechanical stitching device.
A story persists that around 1818-1819, a machine that created a backstitch, similar to what is used in hand sewing, was invented in Monkton, Vermont. The earliest record of this machine that I have found was in the second version, or 1867 edition, of Eighty Years of Progress of the United States; it isn’t mentioned in the earlier edition. The writer of the article on sewing machines claims that John Knowles invented and built a sewing machine that used a single thread and a two-pointed needle with the eye in the middle to create the backstitch. This information must have surfaced after the first edition was released, but the source and individual responsible for it are unknown. Other sources indicate that two men, Adams and Dodge, created this machine in Monkton.[14] Meanwhile, others credit Reverend John Adam Dodge, with help from a mechanic named John Knowles, with the same invention in the same place.[15] Vermont historical societies have been unable to identify the individuals mentioned or confirm the story of the invention.[16] The credibility of this story, if proven, is significant because it marks the first attempt in the United States to create a mechanical stitching device.
1820-1845
American records of this period are incomplete as a result of the Patent Office fire of 1836, in which most of the specific descriptions of patents issued to that date were destroyed. Patentees were asked to provide another description of their patents so that these might be copied, but comparatively few responded and only a small percentage was restored. Thus, although the printed index of patents[17] lists Henry Lye as patenting a machine for “sewing leather, and so forth” on March 10, 1826, no description of the machine has ever been located. Many patents whose original claim was for only a mechanical awl to pierce holes in leather or a clamp to hold leather for hand stitching were claimed as sewing devices once a practical machine had evolved. But no evidence has ever been found that any of these machines performed the actual stitching operation.
American records from this time are incomplete due to the Patent Office fire of 1836, which destroyed most of the detailed descriptions of patents issued up to that point. Patentees were asked to submit new descriptions of their patents for copying, but only a few responded, and just a small percentage were restored. So, even though the printed index of patents[17] lists Henry Lye as having patented a machine for “sewing leather, and so forth” on March 10, 1826, no description of the machine has ever been found. Many patents that initially claimed only a mechanical awl for making holes in leather or a clamp for holding leather for hand stitching were later classified as sewing devices once a functional machine was developed. However, no evidence has ever been discovered that any of these machines actually performed the stitching operation.

Figure 9.—An adapted drawing of Hunt’s sewing machine published by the Sewing Machine News, vol. 2, no. 8, 1881, to give some idea of its construction and operation. “The frame of the machine (A) rested on a base (B) that was supported by a table. The wheel (C) worked on a central shaft (E) and was set in motion by hand or foot power. On the front of the wheel (C) was a raised cam (D) into which the connecting rod (F) engaged to communicate motion to the vibrating arm (G) pivoted to the frame at (H) and carrying at the end (g) the curved needle (I). The take-up (J) served to tighten the thread after each stitch; it was connected to the vibrating arm by a rod (K). The cloth (L) was held in a vertical position between the fingers or nippers (M), which were attached to the frame. The bar (N) was toothed on one side (n) to mesh with the geared wheel (o). The lever (P) was operated by a cam (m) upon the periphery of the wheel (C), and carried the vertical pawl (S) which meshed with the ratchet (T) and moved the cloth as each stitch was made. The shuttle (U) worked in its race (V); it was operated by the vibrating lever (W), the upper end of which engaged into a groove on the face of the wheel (C).” (Smithsonian photo 42554.)
Figure 9.—A modified illustration of Hunt’s sewing machine published by the Sewing Machine News, vol. 2, no. 8, 1881, to give some idea of its construction and operation. “The frame of the machine (A) rested on a base (B) supported by a table. The wheel (C) operated on a central shaft (E) and was powered by hand or foot. On the front of the wheel (C) was a raised cam (D) where the connecting rod (F) engaged to transfer motion to the vibrating arm (G) pivoted to the frame at (H) and carrying at the end (g) the curved needle (I). The take-up (J) tightened the thread after each stitch; it was connected to the vibrating arm by a rod (K). The cloth (L) was held vertically between the fingers or nippers (M), which were attached to the frame. The bar (N) had teeth on one side (n) to mesh with the geared wheel (o). The lever (P) was operated by a cam (m) on the edge of the wheel (C), carrying the vertical pawl (S) that meshed with the ratchet (T) and moved the cloth with each stitch made. The shuttle (U) worked in its race (V); it was operated by the vibrating lever (W), the upper end of which fitted into a groove on the face of the wheel (C).” (Smithsonian photo 42554.)
[Pg 11]The first man known to have put a mechanical sewing device into commercial operation was Barthelemy Thimonnier,[18] a French tailor. After several years of fruitless effort he invented a machine for which he received a French patent in 1830.[19] The machine (fig. 8) made a chainstitch by means of a barbed or hooked needle. The vertically held needle worked from an overhanging arm. The needle thrust through the fabric laid on the horizontal table, caught a thread from the thread carrier and looper beneath the table, and brought a loop to the surface of the fabric. When the process was repeated the second loop became enchained in the first. The needle was moved downward by the depression of a cord-connected foot treadle and was raised by the action of a spring. The fabric was fed through the stitching mechanism manually, and a regular rate of speed had to be maintained by the operator in order to produce stitches of equal length. A type of retractable thimble or presser foot was used to hold the fabric down as required.
[Pg 11]The first person known to have successfully put a mechanical sewing machine into commercial use was Barthelemy Thimonnier,[18] a French tailor. After several years of trying without success, he invented a machine for which he received a French patent in 1830.[19] The machine (fig. 8) created a chainstitch using a barbed or hooked needle. The needle, held vertically, operated from an overhanging arm. It pierced the fabric placed on the horizontal table, caught a thread from the thread carrier and looper below the table, and brought a loop up to the surface of the fabric. When this process was repeated, the second loop got intertwined with the first. The needle was pushed down by a foot pedal connected by a cord and was raised by a spring. The fabric was manually fed through the stitching mechanism, and the operator had to maintain a consistent speed to produce stitches of equal length. A type of retractable thimble or presser foot was used to hold the fabric down as needed.
The needle, and the entire machine, was basically an attempt to mechanize tambour embroidery, with which the inventor was quite familiar. Although this work, which served as the machine’s inspiration, was always used for decorative embroidery, Thimonnier saw the possibilities of using the stitch for utilitarian purposes. By 1841 he had 80 machines stitching army clothing in a Paris shop. But a mob of tailors, fearing that the invention would rob them of a livelihood, broke into the shop and destroyed the machines. Thimonnier fled Paris, penniless. Four years later he had obtained new financial help, improved his machine to produce 200 stitches a minute, and organized the first French sewing-machine company.[20] The Revolution of 1848, however, brought this enterprise to an early end. Before new support could be found other inventors had appeared with better machines, and Thimonnier’s was passed by. In addition to the two French patents Thimonnier also received a British patent with his associate Jean Marie Magnin in 1848 and one in the United States in 1850. He achieved no financial gain from either of these and died a poor man.
The needle and the whole machine were pretty much an effort to automate tambour embroidery, which the inventor knew quite well. While this type of work was commonly used for decorative embroidery, Thimonnier recognized the potential of using the stitch for practical purposes. By 1841, he had 80 machines sewing army uniforms in a shop in Paris. However, a group of tailors, worried that the invention would take away their jobs, broke into the shop and wrecked the machines. Thimonnier escaped Paris with nothing. Four years later, he found new investors, improved his machine to sew 200 stitches per minute, and started the first French sewing-machine company. [20] Unfortunately, the Revolution of 1848 cut this venture short. Before he could secure more backing, other inventors came up with better machines, and Thimonnier's was left behind. In addition to the two French patents, Thimonnier also got a British patent with his partner Jean Marie Magnin in 1848 and one in the United States in 1850. He didn’t make any money from either and died poor.
While Thimonnier was developing his chainstitch machine in France, Walter Hunt,[21] perhaps best described as a Yankee mechanical genius, was working on a different kind of sewing machine in the United States. Sometime between 1832 and 1834 he produced at his shop in New York a machine that made a lockstitch.[22] This stitch was the direct result of the mechanical method devised to produce the stitching and represented the first occasion an inventor had not attempted to reproduce a hand stitch. The lockstitch required two threads, one passing through a loop in the and both interlocking in the heart of the seam. At the time Hunt did not consider the sewing machine any more promising than several other inventions that he had in mind, and, after demonstrating that the machine would sew, he sold his interest in it for a small sum and did not bother to patent it.
While Thimonnier was working on his chainstitch machine in France, Walter Hunt,[21] who could be called a Yankee mechanical genius, was developing a different type of sewing machine in the United States. Between 1832 and 1834, he created a machine in his New York shop that made a lockstitch.[22] This stitch was the direct result of the mechanical method he devised to create the stitching, marking the first time an inventor hadn't tried to imitate a hand stitch. The lockstitch used two threads, one passing through a loop in the and both interlocking at the center of the seam. At that time, Hunt didn't think the sewing machine was any more promising than several other inventions he was considering, and after demonstrating that the machine could sew, he sold his stake in it for a small amount and didn’t bother to patent it.
A description—one of few ever published—and sketch of a rebuilt Hunt machine (fig. 9) appeared in an article in the Sewing Machine News in 1881.[23] The important element in the Hunt invention was an eye-pointed needle working in combination with a shuttle carrying a second thread. Future inventors were thus no longer hampered by the erroneous idea that the sewing machine must imitate the human hands and fingers. Though Hunt’s machine stitched short, straight seams with speed and accuracy, it could not sew curved or angular work. Its stitching was not continuous, but had to be reset at the end of a short run. The validity of Hunt’s claim as the inventor of the lockstitch and the prescribed method of making it was argued many times, especially during the Elias Howe patent suits of the 1850s. The decision against Hunt was not a question of invention,[24] but one of right to ownership or control. Hunt did little to promote his sewing machine and sold it together with the right to patent to George A. Arrowsmith.
A description—one of the few ever published—and a sketch of a rebuilt Hunt machine (fig. 9) appeared in an article in the Sewing Machine News in 1881.[23] The key component of the Hunt invention was an eye-pointed needle that worked in conjunction with a shuttle carrying a second thread. This innovation freed future inventors from the mistaken belief that sewing machines had to replicate human hands and fingers. Although Hunt’s machine stitched short, straight seams quickly and accurately, it couldn't handle curved or angular designs. Its stitching was not continuous, requiring a reset at the end of each short run. The legitimacy of Hunt’s claim as the inventor of the lockstitch and the method of creating it was debated multiple times, especially during the Elias Howe patent cases of the 1850s. The verdict against Hunt wasn't about creativity,[24] but rather about the right to ownership or control. Hunt did little to promote his sewing machine and sold it along with the patent rights to George A. Arrowsmith.
Figure 10.—Madersperger’s 1839 sewing machine. Madersperger’s machine consisted of two major parts: the frame, which held the material, and the stitching mechanism, called the hand. The hand shown here is an original model. (Photo courtesy of Technisches Museum für Industrie und Gewerbe, Vienna.)
Figure 10.—Madersperger’s 1839 sewing machine. Madersperger’s machine had two main parts: the frame, which supported the fabric, and the stitching mechanism, known as the hand. The hand illustrated here is an original model. (Photo courtesy of Technisches Museum für Industrie und Gewerbe, Vienna.)

[Pg 13]For over fifteen years, from the mid-1830s to the early 1850s, the machine dropped out of sight. When the sewing-machine litigation developed in the 1850s, the I. M. Singer company searched out the Hunt machine, had the inventor rebuild one,[25] and attempted to use this to break the Howe patent. The plan did not work. The Honorable Charles Mason, Patent Commissioner, reported:
[Pg 13]For more than fifteen years, from the mid-1830s to the early 1850s, the machine disappeared from view. When the sewing machine lawsuits started in the 1850s, the I. M. Singer company sought out the Hunt machine, had the inventor recreate one,[25] and tried to use this to challenge the Howe patent. The strategy failed. Honorable Charles Mason, the Patent Commissioner, reported:
When the first inventor allows his discovery to slumber for eighteen years, with no probability of its ever being brought into useful activity, and when it is only resurrected to supplant and strangle an invention which has been given to the public, and which has been made practically useful, all reasonable presumption should be in favor of the inventor who has been the means of conferring the real benefit upon the world.[26]
When the original inventor lets their discovery sit unused for eighteen years, with little chance of it ever being put to practical use, and when it's only brought back to replace and stifle an invention that has already been made available to the public and is actually useful, all reasonable assumptions should favor the inventor who truly contributed a real benefit to the world.[26]
Hunt’s machine was an invention of the 1830s, but only because of the patent litigation was it ever heard of again.
Hunt’s machine was invented in the 1830s, but it only gained attention again because of the patent lawsuit.
During the time that a potentially successful sewing machine was being invented and forgotten in America, Josef Madersperger of Austria made a second attempt to solve the mechanical stitching problem. In 1839 he received a second patent on a machine entirely different from his 1814 effort. It was similar to Hunt’s in that it used an eye-pointed needle and passed a thread through the loop of the needle-thread—the thread carried by the needle—to lock the stitch. Madersperger’s machine was a multiple-needle quilting machine. The threaded needles penetrated the fabric from below and were retracted, leaving the loops on the surface. A thread was drawn through the loops to produce what the inventor termed a chain. The first two stitches were twisted before insertion into the next two, producing a type of twisted lockstitch. The mechanism for feeding the cloth was faulty, however, and the inventor himself stated in the specifications that much remained to perfect and simplify it before its general application. (This machine was illustrated [fig. 10] in the Sewing Machine Times, October 25, 1907, and mistakenly referred to as the 1814 model.) Madersperger realized no financial gain from either venture and died in a poorhouse in 1850.
During the time that a potentially successful sewing machine was being invented and forgotten in America, Josef Madersperger from Austria made a second attempt to tackle the mechanical stitching issue. In 1839, he got a second patent for a machine that was completely different from his 1814 attempt. It was similar to Hunt’s in that it used an eye-pointed needle and threaded a piece of thread through the loop of the needle-thread—the thread carried by the needle—to secure the stitch. Madersperger’s machine was a multiple-needle quilting machine. The threaded needles went through the fabric from below and were pulled back, leaving the loops on the surface. A thread was pulled through the loops to create what the inventor called a chain. The first two stitches were twisted before being inserted into the next two, forming a type of twisted lockstitch. However, the mechanism for feeding the fabric was flawed, and the inventor himself noted in the specifications that much work was still needed to perfect and simplify it before it could be widely used. (This machine was illustrated [fig. 10] in the Sewing Machine Times, October 25, 1907, and incorrectly referred to as the 1814 model.) Madersperger gained no financial benefit from either of his ventures and died in a poorhouse in 1850.
The first efforts of the 1840s reflected the work of the earlier years. In England, Edward Newton and Thomas Archbold invented and patented a machine on May 4, 1841, for tambouring or ornamenting the backs of gloves. Their machine used a hook on the upper surface to catch the loop of thread, but an eye-pointed needle from underneath was used to carry the thread up through the fabric. The machine was designed to use three needles for three rows of chainstitching, if required. Although the machine was capable of stitching two fabrics together, it was never contemplated as a sewing machine in the present use of the term. Their British patent 8,948 stated it was for “improvements in producing ornamental or tambour work in the manufacture of gloves.”
The first efforts of the 1840s reflected the work of earlier years. In England, Edward Newton and Thomas Archbold invented and patented a machine on May 4, 1841, for tambouring or decorating the backs of gloves. Their machine used a hook on the top to catch the loop of thread, while an eye-pointed needle from underneath brought the thread up through the fabric. It was designed to use three needles for three rows of chain stitching, if needed. Although the machine could stitch two fabrics together, it was never considered a sewing machine in the way we think of them today. Their British patent 8,948 stated it was for “improvements in producing ornamental or tambour work in the manufacture of gloves.”
The earliest American patent specifically recorded as a sewing machine was U.S. patent 2,466, issued to John J. Greenough on February 21, 1842. His machine was a short-thread model that made both the running stitch and the backstitch. It used the two-pointed needle, with eye at mid-length, which was passed back and forth through the material by means of a pair of pincers on each side of the seam. The pincers opened and closed automatically. The material to be sewn was held in clamps which moved it forward between the pincers to form a running stitch or moved it alternately backward and forward to produce a backstitch. The clamps were attached to a rack that automatically fed the material at a predetermined rate according to the length of stitch required. Since the machine was designed for leather or other hard material, the needle was preceded by an awl, which pierced a hole. The machine had a weight to draw out the thread and a stop-motion to stop the machinery when a thread broke or became too short. The needle was threaded with a short length of thread and required frequent refilling. Only straight seams could be stitched. The feed was continuous to the length of the rack bar; then it had to be reset. The motions were all obtained from the revolution of a crank. It is not believed that any machines, other than the patent model (fig. 11), were ever made. Little is known of Greenough other than his name.[Pg 14]
The first American patent specifically listed for a sewing machine was U.S. patent 2,466, granted to John J. Greenough on February 21, 1842. His machine was a short-thread model that performed both the running stitch and the backstitch. It used a two-pointed needle with an eye in the middle, which was moved back and forth through the fabric by a pair of pincers on either side of the seam. The pincers opened and closed automatically. The fabric to be sewn was held in clamps that advanced it forward between the pincers to create a running stitch or alternated it backward and forward to form a backstitch. The clamps were connected to a rack that automatically fed the fabric at a set rate based on the desired stitch length. Since the machine was intended for leather or other tough materials, the needle was preceded by an awl that made a hole. The machine had a weight to pull out the thread and a stop mechanism to halt the machinery if a thread broke or became too short. The needle was threaded with a short length of thread and needed frequent rethreading. It could only stitch straight seams. The feed was continuous up to the length of the rack bar; then it needed to be reset. All movements came from the rotation of a crank. It is believed that no machines, apart from the patent model (fig. 11), were ever produced. Little is known about Greenough beyond his name.[Pg 14]

Figure 11.—Greenough’s patent model, 1842. (Smithsonian photo 45525-G.)
Figure 11.—Greenough's patent prototype, 1842. (Smithsonian photo 45525-G.)
In the succeeding year, on March 4, 1843, Benjamin W. Bean received the second American sewing-machine patent, U.S. patent 2,982. Like Greenough’s, this machine made a running stitch, but by a different method. In Bean’s machine the fabric was fed between the teeth of a series of gears. Held in a groove in the gears was a peculiarly shaped needle bent in two places to permit it to be held in place by the gears and with a point at one end and the eye at the opposite end, as in a common hand needle. The action of the gears caused the fabric to be forced onto and through the threaded needle. Indefinite straight seams could be stitched as the fabric was continuously forced off the needle by the turning gears (fig. 12). A screw clamp held the machine to a table or other work surface. Machines of this and similar types reportedly had some limited usage in the dyeing and bleaching mills,[27] where lengths of fabric were stitched together before processing. Improved versions of Bean’s machine were to be patented in subsequent years in England and America. The same principle was also used in home machines two decades later.
In the following year, on March 4, 1843, Benjamin W. Bean received the second American sewing machine patent, U.S. patent 2,982. Like Greenough’s machine, this one created a running stitch, but it used a different method. Bean’s machine fed the fabric between the teeth of a series of gears. A uniquely shaped needle, bent in two places to stay in place with the gears, was held in a groove; it had a point at one end and an eye at the opposite end, similar to a standard hand needle. The movement of the gears forced the fabric onto and through the threaded needle. Continuous straight seams could be stitched as the turning gears constantly pushed the fabric off the needle (fig. 12). A screw clamp secured the machine to a table or other work surface. Machines like this one reportedly had some limited use in dyeing and bleaching mills,[27] where lengths of fabric were sewn together before processing. Improved versions of Bean’s machine were patented in the following years in England and America. The same principle was later used in home machines two decades later.
The third sewing-machine patent on record in the United States Patent Office is patent 3,389 issued on December 27, 1843, to George H. Corliss, better remembered as the inventor and manufacturer of the Corliss steam engine. It was his interest in the sewing machine, however, that eventually directed his attention to the steam engine.
The third sewing machine patent recorded in the United States Patent Office is patent 3,389, issued on December 27, 1843, to George H. Corliss, who is better known as the inventor and manufacturer of the Corliss steam engine. It was his interest in the sewing machine that ultimately led him to focus on the steam engine.
Corliss had a general store at Greenwich, New York. A customer’s complaint that the boots he had purchased split at the seams made Corliss wonder why someone had not invented a machine to sew stronger seams than hand-sewn ones. He considered the problem of sewing leather, analyzing the steps required to make the saddler’s stitch, one popularly used in boots and shoes. He concluded that a sewing machine to do this type of work must first perforate the leather, then draw the threads through the holes, and finally secure the stitches by pulling the threads tight. The machine Corliss invented (fig. 13) was of the same general type as Greenough’s, except that two two-pointed needles were required to make the saddler’s stitch. This stitch was composed of two running stitches made simultaneously, one from each side.[28] The machine used two awls to pierce the holes through which the needles passed; finger levers[Pg 15] approached from opposite sides, seized the needles, pulled the threads firmly, and passed the needles through to repeat the operation. The working model that Corliss completed could unite two pieces of heavy leather at the rate of 20 stitches per minute.
Corliss had a general store in Greenwich, New York. When a customer complained that the boots he bought split at the seams, Corliss wondered why no one had created a machine that could sew stronger seams than those made by hand. He thought about the process of sewing leather, breaking down the steps needed to create the saddler’s stitch, which is commonly used in boots and shoes. He figured that a sewing machine designed for this type of work would need to first punch holes in the leather, then draw the threads through those holes, and finally secure the stitches by tightening the threads. The machine Corliss invented (fig. 13) was similar to Greenough’s but required two pointed needles to create the saddler’s stitch. This stitch consisted of two running stitches made at the same time, one from each side.[28] The machine used two awls to pierce the holes for the needles; finger levers[Pg 15] came from opposite sides, grabbed the needles, pulled the threads tight, and pushed the needles through to repeat the process. The working model that Corliss completed could join two pieces of heavy leather at a speed of 20 stitches per minute.
Corliss, lacking capital, went to Providence, Rhode Island, in 1844 to secure backers. After months without success, he was forced to abandon the sewing machine and accept employment as a draftsman and designer. Though he considered himself a failure, this change of employment placed him on the threshold of his more rewarding life work, improvement of the steam engine.[29]
Corliss, short on funds, went to Providence, Rhode Island, in 1844 to find investors. After months of no luck, he had to give up on the sewing machine and take a job as a draftsman and designer. Although he saw this as a setback, this job set him up for his more fulfilling work ahead: improving the steam engine.[29]
On July 22, 1844, James Rodgers was granted U.S. patent 3,672, the fourth American sewing-machine patent. The patent model is not known to be in existence, but this machine was of minor importance for it offered only a negligible change in the Bean running-stitch machine. The same corrugated gears were used but were placed in different positions so that one bend in the needle was eliminated. When Bean secured a reissue of his patent in 1849, he had adapted it to use a straight needle. Rodgers’ machine is not known to have had any commercial success, although this type of machine experienced a brief period of popularity. By the early 1900s, however, the running-stitch machine was so little known that when one was illustrated in the Sewing Machine Times in 1907[30] it excited more curiosity than any of the other early types.
On July 22, 1844, James Rodgers was granted U.S. patent 3,672, the fourth American sewing machine patent. The patent model is not known to exist, but this machine was not significant because it offered only a minor modification to the Bean running-stitch machine. The same corrugated gears were used, but they were arranged differently, eliminating one bend in the needle. When Bean got a reissue of his patent in 1849, he had updated it to use a straight needle. Rodgers’ machine is not known to have achieved any commercial success, although this type of machine saw a short-lived surge in popularity. By the early 1900s, however, the running-stitch machine was so obscure that when one was featured in the Sewing Machine Times in 1907[30] it generated more curiosity than any of the other early models.
On December 7, 1844, the same year that Rodgers secured his American patent, John Fisher and James Gibbons were granted British patent 10,424 for “certain improvements in the manufacture of figured or ornamental lace, or net, or other fabrics.” From this superficial description of its work, the device might seem to be just another tambouring machine. It was not. Designed specifically for ornamental stitching, the machine made a two-thread stitch using an eye-pointed needle and a shuttle.[31] Several sets of needles and shuttles worked simultaneously. The needles were secured to a needlebar placed beneath the fabric. The shuttles were pointed at both ends to pass through each succeeding new loop formed by the needles. Each shuttle was activated by two vibrating arms worked by cams. Each needle was curved in the form of a bow, and in addition to the eye at the point each also had a second eye at the bottom of the curve. The shape of the needle[Pg 16] together with the position of the eyes permitted the pointed shuttle, carrying the second thread, to pass freely through the loop in the ascending needle thread. The fabric was carried by a pair of cloth rollers, capable of sliding in a horizontal plane in both a lateral and a lengthwise direction. These combined movements were sufficient to enable the operator to produce almost every embroidered design. The ornamenting, which might be a yarn, cord, or gimp, was carried by the shuttle thread. There was no tension on the shuttle thread, which was held in place by the thread from the needle. The stitch produced was a form of couching.[32] It was in no sense a lockstitch. Fisher, who was the inventor, readily admitted at a later date that he had not had the slightest idea of producing a sewing machine, in the utilitarian meaning of the term. Although it has not been established that this machine was ever put into practical operation, Fisher’s invention was to have a far-reaching effect on the development of the sewing machine in England.
On December 7, 1844, the same year Rodgers got his American patent, John Fisher and James Gibbons were given British patent 10,424 for “certain improvements in the manufacture of figured or ornamental lace, or net, or other fabrics.” From this basic description, the device might look like just another tambouring machine, but it wasn’t. Specifically designed for decorative stitching, the machine created a two-thread stitch using an eye-pointed needle and a shuttle. Several sets of needles and shuttles worked at the same time. The needles were attached to a needlebar positioned beneath the fabric. The shuttles were pointed at both ends to pass through each new loop formed by the needles. Each shuttle was powered by two vibrating arms operated by cams. Each needle was curved like a bow, and in addition to the eye at the tip, there was also a second eye at the bottom of the curve. The shape of the needle, along with the position of the eyes, allowed the pointed shuttle, carrying the second thread, to move freely through the loop created by the ascending needle thread. The fabric was held by a pair of cloth rollers that could slide both sideways and lengthwise. These combined movements allowed the operator to create almost any embroidered design. The ornamentation, whether yarn, cord, or gimp, was carried by the shuttle thread. There was no tension on the shuttle thread; it was kept in place by the thread from the needle. The resulting stitch was a type of couching. It was not a lockstitch at all. Fisher, the inventor, later admitted that he had no idea he was creating a sewing machine in the practical sense of the term. Although it’s not clear if this machine was ever actually used, Fisher’s invention would significantly influence the development of the sewing machine in England.
FOOTNOTES:
[8] Ibid.
Ibid.
[9] Erich Luth, Ein Mayener Strumpfwirker, Balthasar Krems, 1760-1813, Erfinder der Nähmaschine, p. 10, states that the machine used an eye-pointed needle. Wilhelm Renters, Praktisches Wissen von der Nähmaschine, p. 4, states that Krems used a hooked needle. Renters probably mistook the hooked retaining pin for the needle.
[9] Erich Luth, Ein Mayener Strumpfwirker, Balthasar Krems, 1760-1813, Erfinder der Nähmaschine, p. 10, mentions that the machine used a needle with an eye. Wilhelm Renters, Praktisches Wissen von der Nähmaschine, p. 4, claims that Krems used a hooked needle. Renters likely confused the hooked retaining pin with the needle.
[10] Dr. Dahmen, Burgermeister of Mayen, stated in a letter of October 8, 1963, that the original Krems machine was turned over to the officials of Mayen by Krems’ descendants about the turn of the century. He verified that the machine used an eye-pointed needle. About 1920 the machine was placed in the Eifelmuseum in Genovevaburg; some of the unessential parts were restored. The machine now at this museum is the one pictured in Luth’s book. A replica of the machine is in the Deutsches Museum, Munich, Germany.
[10] Dr. Dahmen, the mayor of Mayen, mentioned in a letter dated October 8, 1963, that the original Krems machine was handed over to the authorities in Mayen by the descendants of Krems around the turn of the century. He confirmed that the machine used a pointed needle. Around 1920, the machine was placed in the Eifelmuseum in Genovevaburg, where some non-essential parts were restored. The machine currently in this museum is the one shown in Luth’s book. A replica of the machine is located in the Deutsches Museum in Munich, Germany.
[11] Josef Madersperger, Beschreibung einer Nähmaschine (Vienna, ca. 1816). The exact date of this small booklet is not known. In the booklet Madersperger reports that he had received a patent in 1814 for his first machine adapted to straight sewing. However, the machine described and illustrated in this booklet was one that could stitch semicircles and small figures. In Kunst und Gewerbeblatt, a periodical (Munich, Germany, 1817, pp. 336-338), reference is made to the Madersperger machine and a statement to the effect that the inventor had published a leaflet describing his machine. The leaflet referred to is believed to be the one under discussion. For this reason it must have been published between 1814 and 1817, therefore ca. 1816. The only copy of this booklet known to this author is in the New York Public Library. It was probably not known to authors Luth and Renters. The author wishes to thank Miss Rita J. Adrosko of her staff for her important help in translating these German publications.
[11] Josef Madersperger, Description of a Sewing Machine (Vienna, around 1816). The exact date of this small booklet is not known. In the booklet, Madersperger mentions that he was granted a patent in 1814 for his first machine designed for straight sewing. However, the machine described and shown in this booklet could stitch semicircles and small shapes. In Kunst und Gewerbeblatt, a journal (Munich, Germany, 1817, pp. 336-338), there is a reference to the Madersperger machine and a statement indicating that the inventor had published a leaflet detailing his machine. The leaflet mentioned is believed to be the one currently under discussion. Therefore, it must have been published between 1814 and 1817, so around 1816. The only copy of this booklet known to this author is at the New York Public Library. It was probably not known to authors Luth and Renters. The author wishes to thank Miss Rita J. Adrosko of her staff for her significant help in translating these German publications.
[13] There are no known models of these early Madersperger machines in existence. Although the Sewing Machine Times reported in the 1907 issue that the 1814 sewing machine was then on exhibition in the Museum of the Vienna Polytechnic, the illustration shown was of Madersperger’s 1839 machine. In a letter from the director of the Technisches Museum für Industrie und Gewerbe in Vienna, received in 1962, it was stated that the original 1814 Madersperger machine was in their museum. The photographs that were sent, however, were of the 1839 machine. This machine is entirely different from the 1814-1817 machine, as can readily be seen by the reader (figs. 7 and 10).
[13] There are no known examples of these early Madersperger machines still existing. Although the Sewing Machine Times reported in the 1907 issue that the 1814 sewing machine was on display at the Museum of the Vienna Polytechnic, the illustration shown was actually of Madersperger’s 1839 machine. In a letter from the director of the Technisches Museum für Industrie und Gewerbe in Vienna, received in 1962, it was stated that the original 1814 Madersperger machine was in their museum. However, the photographs that were sent were of the 1839 machine. This machine is completely different from the 1814-1817 machine, as the reader can clearly see (figs. 7 and 10).
[15] “Sewing Machines,” Johnson’s Universal Cyclopaedia (New York, 1878), vol. 4, p. 205. The 1874 edition does not include this reference to Rev. John Adam Dodge.
[15] “Sewing Machines,” Johnson’s Universal Cyclopaedia (New York, 1878), vol. 4, p. 205. The 1874 edition doesn't mention this reference to Rev. John Adam Dodge.
[17] Edmund Burke. Commissioner of Patents, List of Patents for Inventions and Designs Issued by the United States from 1790 to 1847 (Washington, 1847).
[17] Edmund Burke. Commissioner of Patents, List of Patents for Inventions and Designs Issued by the United States from 1790 to 1847 (Washington, 1847).
[19] French patent issued to Barthelemy Thimonnier and M. Ferrand (who was a tutor at l’Ecole des Mines, Saint-Etienne, and helped finance the patent), July 17, 1830.
[19] French patent granted to Barthelemy Thimonnier and M. Ferrand (who was a teacher at l’École des Mines, Saint-Étienne, and helped fund the patent), July 17, 1830.
[22] The earliest known reference in print to Walter Hunt’s sewing machine is in Sewing by Machinery: An Exposition of the History of Patentees of Various Sewing Machines and of the Rights of the Public (I. M. Singer & Co., 1853). A more detailed story of Hunt’s invention is in Sewing Machine News (1880-81), vol. 2, no. 2, p. 4; no. 4, p. 5; and no. 8, pp. 3 and 8.
[22] The first known print reference to Walter Hunt’s sewing machine is in Sewing by Machinery: An Exposition of the History of Patentees of Various Sewing Machines and of the Rights of the Public (I. M. Singer & Co., 1853). A more detailed account of Hunt’s invention can be found in Sewing Machine News (1880-81), vol. 2, no. 2, p. 4; no. 4, p. 5; and no. 8, pp. 3 and 8.
[24] In the opinion and decision of C. Mason, Commissioner of the Patent Office, offered on May 24, 1854, for the Hunt vs. Howe interference suit, Mason stated: “He [Hunt] proves that in 1834 or 1835 he contrived a machine by which he actually effected his purpose of sewing cloth with considerable success.”
[24] In the opinion and decision of C. Mason, Commissioner of the Patent Office, given on May 24, 1854, for the Hunt vs. Howe interference case, Mason stated: “He [Hunt] shows that in 1834 or 1835 he designed a machine that successfully sewed cloth.”
[25] The rebuilt machine, according to a letter to the author from B. F. Thompson of the Singer company, is believed to have been one of the machines lost in a Singer factory fire at Elizabethport, N.J., in 1890.
[25] The reconstructed machine, based on a letter to the author from B. F. Thompson at the Singer company, is thought to have been one of the machines lost in a fire at the Singer factory in Elizabethport, N.J., in 1890.
[26] Op. cit. (footnote 24).
__A_TAG_PLACEHOLDER_0__ Same source (footnote 24).
[28] A seam using the saddler’s stitch appears as a neat line of touching stitches on both sides. Even when made by hand, it is sometimes misidentified by the casual observer as the lockstitch because of the uniformity of both sides. If the saddler’s stitch was formed of threads of two different colors, the even stitches on one side of the seam and the odd stitches on the reverse side would be of one color, and vice versa.
[28] A seam created with the saddler’s stitch looks like a clean line of stitches on both sides. Even when done by hand, someone not paying close attention might mistake it for the lockstitch because both sides look so uniform. If the saddler’s stitch used threads of two different colors, the evenly spaced stitches on one side of the seam would be a certain color, while the uneven stitches on the other side would be the other color, and vice versa.
[29] The Life and Works of George H. Corliss, privately printed for Mary Corliss by the American Historical Society, 1930. The Corliss family records were turned over to the Baker Library, Harvard University. In a letter addressed to this author by Robert W. Lovett of the Manuscripts Division on August 2, 1954, it was reported that there was a record on their Corliss card to the effect that a model of his sewing machine, received with the collection, was turned over to the Massachusetts Institute of Technology; however, Mr. Lovett also stated that from a manuscript memoir of Mr. Corliss that it would seem that he developed only the one machine—the patent model. In a letter dated November 15, 1954, Stanley Backer, assistant professor of mechanical engineering, stated that after extensive inquiries they were unable to locate the model at M.I.T. In 1964, Dr. Robert Woodbury, of M.I.T., turned over to the Smithsonian Institution the official copies of the Corliss drawings and the specifications which had been awarded to the inventor by the Patent Office. It is possible that this may have been the material noted on the Harvard University card as having been transferred to M.I.T.
[29] The Life and Works of George H. Corliss, privately printed for Mary Corliss by the American Historical Society, 1930. The Corliss family records were handed over to the Baker Library at Harvard University. In a letter addressed to this author by Robert W. Lovett from the Manuscripts Division on August 2, 1954, it was noted that there was an entry on their Corliss card indicating that a model of his sewing machine, included in the collection, was transferred to the Massachusetts Institute of Technology; however, Mr. Lovett also mentioned that from a manuscript memoir of Mr. Corliss it appeared that he only developed the one machine—the patent model. In a letter dated November 15, 1954, Stanley Backer, assistant professor of mechanical engineering, stated that after thorough inquiries they were unable to find the model at M.I.T. In 1964, Dr. Robert Woodbury from M.I.T. donated the official copies of the Corliss drawings and the specifications awarded to the inventor by the Patent Office to the Smithsonian Institution. It is possible that this may have been the material noted on the Harvard University card as having been transferred to M.I.T.
[32] In embroidery, couching is the technique of laying a decorative thread on the surface of the fabric and stitching it into place with a second less-conspicuous thread.
[32] In embroidery, couching is the technique of placing a decorative thread on top of the fabric and stitching it down with a second, less visible thread.
Chapter Two

Figure 14.—Howe’s prepatent model of 1845, and the box used by the inventor to carry the machine to England in 1847. (Smithsonian photo 45506-B.)
Figure 14.—Howe's pre-patent model of 1845, and the box used by the inventor to transport the machine to England in 1847. (Smithsonian photo 45506-B.)
Elements of a Successful Machine
The requirements for producing a successful, practical sewing machine were a support for the cloth, a needle to carry the thread through the fabric and a combining device to form the stitch, a feeding mechanism to permit one stitch to follow another, tension controls to provide an even delivery of thread, and the related mechanism to insure the precise performance of each operation in its proper sequence. Weisenthal had added a point to the eye-end of the needle, Saint supported the fabric by placing it in a horizontal position with a needle entering vertically, Duncan successfully completed a chainstitch for embroidery purposes, Chapman used a needle with an eye at its point and did not pass it completely through the fabric, Krems stitched circular caps with an eye-pointed needle used with a hook to form a chainstitch, Thimonnier used the hooked needle to form a chainstitch on a fabric laid horizontally, and Hunt created a new stitch that was more readily adapted to sewing by machine than the hand stitches had been, but, although each may have had the germ of an idea, a successful machine had not evolved. There were to be hundreds of patents issued in an attempt to solve these and the numerous minor problems that would ensue. But the problems were solved. And, in spite of its Old World inception, the successful sewing machine can be credited as an American invention.
The requirementsfor creating a successful, practical sewing machine included a support for the fabric, a needle to thread the fabric, a mechanism to form the stitch, a feeding system to allow one stitch to follow another, tension controls to ensure consistent thread delivery, and a related mechanism to guarantee the precise execution of each operation in the correct order. Weisenthal added a point to the eye-end of the needle, Saint supported the fabric by positioning it horizontally with a vertically entering needle, Duncan successfully created a chainstitch for embroidery, Chapman used a needle with an eye at its tip and didn’t pull it all the way through the fabric, Krems stitched circular caps using a pointed needle and a hook to make a chainstitch, Thimonnier used the hooked needle to make a chainstitch on a horizontally laid fabric, and Hunt developed a new stitch that was better suited for machine sewing than the hand stitches had been. However, even though each inventor had a piece of the puzzle, a successful machine hadn’t emerged yet. There would be hundreds of patents filed to tackle these and various smaller issues that would come up. But the challenges were eventually overcome. And, despite its Old World origins, the successful sewing machine can be credited as an American invention.
Although the invention of the practical sewing machine, like most important inventions, was a many-man project, historians generally give full credit to Elias Howe, Jr. Though such credit may be overly generous, Howe’s important role in this history cannot be denied.
Although the invention of the practical sewing machine, like most significant inventions, was a collaborative effort, historians typically attribute most of the credit to Elias Howe, Jr. While this credit might be a bit excessive, Howe’s crucial role in this story is undeniable.
Elias Howe, Jr., was born on a farm near Spencer, Massachusetts, but he left home at an early age to learn the machinist’s trade.[33] After serving an apprenticeship in Lowell, he moved to Boston. In the late 1830s, while employed in the instrument shop of Ari Davis, Howe is reported to have overheard a discussion concerning the need for a machine that would sew. In 1843, when illness kept him from his job for days at a time, he remembered the conversation and the promises of the rich reward that reputedly awaited the successful inventor. Determined to invent such a machine, he finally managed to produce sufficient results to interest George Fisher in buying a one-half interest in his proposed invention. By April 1845, Howe’s machine (fig. 14) was used to sew all the seams of two woolen suits for men’s clothing. He continued to demonstrate his machine but found that interest was, at best, indifferent.
Elias Howe, Jr., was born on a farm near Spencer, Massachusetts, but he left home at a young age to learn the machinist’s trade.[33] After completing an apprenticeship in Lowell, he moved to Boston. In the late 1830s, while working in the instrument shop of Ari Davis, Howe is said to have overheard a conversation about the need for a sewing machine. In 1843, when illness kept him from his job for several days, he remembered that conversation and the potential rewards that a successful inventor could receive. Determined to create such a machine, he eventually produced enough results to catch George Fisher's interest in buying a half-interest in his proposed invention. By April 1845, Howe’s machine (fig. 14) was used to sew all the seams of two woolen suits for men’s clothing. He continued to showcase his machine but found that interest was, at best, lukewarm.
Nevertheless, Howe completed a second machine (fig. 15), which he submitted with his application for a patent. The fifth United States patent (No. 4,750) for a sewing machine was issued to him on September 10, 1846. The machine used a grooved and curved eye-pointed needle carried by a vibrating arm, with the needle supplied with thread from a spool. Loops of thread from the needle were locked by a thread carried by a shuttle, which was moved[Pg 20] through the loop by means of reciprocating drivers. The cloth was suspended in a vertical position, impaled on pins projecting from a baster plate, which moved intermittently under the needle by means of a toothed wheel. The length of each stitching operation depended upon the length of the baster plate, and the seams were necessarily straight. When the end of the baster plate reached the position of the needle, the machine was stopped. The cloth was removed from the baster plate, which was moved back to its original position. The cloth was moved forward on the pins, and the seam continued.
Nevertheless, Howe completed a second machine (fig. 15), which he submitted with his patent application. The fifth United States patent (No. 4,750) for a sewing machine was issued to him on September 10, 1846. The machine used a grooved and curved eye-pointed needle mounted on a vibrating arm, with the needle receiving thread from a spool. Loops of thread from the needle were locked by a thread carried by a shuttle, which was moved[Pg 20] through the loop by reciprocating drivers. The fabric was held in a vertical position, secured on pins sticking out from a baster plate, which moved intermittently under the needle via a toothed wheel. The length of each stitching operation depended on the length of the baster plate, and the seams were always straight. When the end of the baster plate reached the needle position, the machine stopped. The fabric was taken off the baster plate, which was then moved back to its starting position. The fabric was advanced on the pins, and the seam continued.
In his patent specifications, Howe claimed the following:
In his patent documents, Howe stated the following:
1. The forming of the seam by carrying a thread through the cloth by means of a curved needle on the end of a vibrating arm, and the passing of a shuttle furnished with its bobbin, in the manner set forth, between the needle and the thread which it carried, under combination and arrangement of parts substantially the same with that described.
1. The seam is created by guiding a thread through the fabric using a curved needle attached to a vibrating arm, while a shuttle with its bobbin is passed between the needle and the thread it holds, all arranged and combined in a way that's fundamentally similar to what has been described.
2. The lifting of the thread that passes through the needle-eye by means of the lifting-rod, for the purpose of forming a loop of loose thread that is to be subsequently drawn in by the passage of the shuttle, as herein fully described, said lifting-rod being furnished with a lifting pin, and governed in its motion by the guide-pieces and other devices, arranged and operating substantially as described.
2. The raising of the thread that goes through the needle's eye using the lifting rod is intended to create a loop of loose thread that will later be pulled in by the shuttle, as fully described here. The lifting rod is equipped with a lifting pin and its movement is controlled by guide pieces and other components, arranged and functioning as described.
3. The holding of the thread that is given out by the shuttle, so as to prevent its unwinding from the shuttle-bobbin after the shuttle has passed through the loop, said thread being held by means of the lever or slipping-piece, as herein made known, or in any other manner that is substantially the same in its operation and result.
3. The thread released by the shuttle is held in place to stop it from unwinding from the shuttle-bobbin after the shuttle goes through the loop. This thread is secured using the lever or slipping piece described here, or in any other way that works similarly in function and outcome.
4. The manner of arranging and combining the small lever with the sliding box, in combination with the spring-piece, for the purpose of tightening the stitch as the needle is retracted.
4. The way of setting up and connecting the small lever with the sliding box, along with the spring piece, to tighten the stitch as the needle is pulled back.
5. The holding of the cloth to be sewed by the use of a baster-plate furnished with points for that purpose, and with holes enabling it to operate as a rack in the manner set forth, thereby carrying the cloth forward and dispensing altogether with the necessity of basting the parts together.
5. The cloth is held for sewing using a basting plate that has points designed for this purpose and holes that allow it to function like a rack, moving the cloth forward and completely eliminating the need to baste the parts together.
The five claims, which were allowed Howe in his patent, have been quoted to show that he did not claim the invention of the eye-pointed needle, for which he has so often been credited. The court judgment[34] that upheld Howe’s claim to his patented right to control the use of the eye-pointed needle in combination with a shuttle to form a lockstitch was mistakenly interpreted by some as verifying control of the eye-pointed needle itself.
The five claims granted to Howe in his patent have been cited to demonstrate that he did not claim the invention of the eye-pointed needle, which he has frequently been credited with. The court judgment[34] that supported Howe’s right to control the use of the eye-pointed needle in conjunction with a shuttle to create a lockstitch was wrongly interpreted by some as confirming control over the eye-pointed needle itself.

Figure 15.—Howe’s patent model, 1846. (Smithsonian photo 45525-B.)
Figure 15.—Howe's patent design, 1846. (Smithsonian photo 45525-B.)
After patenting his invention, Howe spent three discouraging years in both the United States and in England trying to interest manufacturers in building his sewing machine, under license. Finally, for £250 sterling, he sold the British patent rights to William Thomas and further agreed to adapt the machine to Thomas’ manufacture of umbrellas and corsets.[35] This did not prove to be a financial success for Howe and by 1849 he was back in the United States, once again without funds.[Pg 21]
After getting a patent for his invention, Howe spent three frustrating years in both the U.S. and England trying to get manufacturers interested in producing his sewing machine under license. Eventually, he sold the British patent rights to William Thomas for £250 and agreed to modify the machine for Thomas’ production of umbrellas and corsets.[35] This didn't turn out to be a financial success for Howe, and by 1849 he was back in the United States, once again short on cash.[Pg 21]

Figure 16.—An enlargement of the stitching area. (Smithsonian photo 45525-B.)
Figure 16.—A close-up shot of the stitching area. (Smithsonian photo 45525-B.)
On his return, Howe was surprised to find that other inventors were engaged in the sewing-machine problem and that sewing machines were being manufactured for sale. The sixth United States sewing-machine patent (No. 5,942) had been issued to John A. Bradshaw on November 28, 1848, for a machine specifically stated as correcting the defects in the E. Howe patent. Bradshaw did not purport that his machine was a new invention. His specifications read:
On his return, Howe was surprised to see that other inventors were working on the sewing-machine issue and that sewing machines were being made available for sale. The sixth United States sewing-machine patent (No. 5,942) was granted to John A. Bradshaw on November 28, 1848, for a machine specifically aimed at fixing the flaws in the E. Howe patent. Bradshaw didn't claim that his machine was a new invention. His specifications stated:
The curved needle used in Howe’s machine will not by itself form the loop in the thread, which is necessary for the flying bobbin, with its case, to pass through, and has, therefore, to be aided in that operation by a lifting-pin, with the necessary mechanism to operate it. This is a very bungling device, and is a great incumbrance to the action of the machine, being an impediment in the way of introducing the cloth to be sewed, difficult to keep properly adjusted, and very frequently gets entangled between the thread and the needle, by which the latter is frequently broken. This accident happens very often, not withstanding all the precaution which it is possible for the most careful operator to exercise; and inasmuch as the delay occasioned thereby is very considerable, and the needles costly and difficult to replace, it is therefore very important that their breaking in this manner be prevented, which in my machine is done in the most effectual manner by dispensing with the lifting-pin altogether, the loop for the flying bobbin to pass through being made with certainty and of the proper form by means of my angular needle moved in a particular manner just before the flying-bobbin case is thrown. The shuttle and its bobbin for giving off the thread in Howe’s machine are very defective ... my neat and simple bobbin-case ... gives off its thread with certainty and uniformity.... The baster-plate in the Howe machine is very inconvenient and troublesome ... in my machine ... the clamp ... is a very simple and efficient device.... The Howe machine is stationary, and the baster-plate or cloth-holder progressive. The Bradshaw machine is progressive and the cloth-holder stationary.
The curved needle used in Howe’s machine on its own cannot form the loop in the thread required for the flying bobbin, along with its casing, to pass through. Therefore, it needs assistance from a lifting pin and the necessary mechanism to operate it. This is a clumsy setup and significantly hinders the machine's function, making it difficult to feed the fabric to be sewn, hard to keep properly adjusted, and often causing tangles between the thread and the needle, resulting in frequent breakage. This issue occurs quite often, despite all the precautions a careful operator can take. Since the delays caused by this are substantial and the needles are expensive and hard to replace, it's essential to prevent breakage in this way. In my machine, this is effectively achieved by eliminating the lifting pin altogether; the loop for the flying bobbin to pass through is formed reliably and correctly with my angled needle, which moves in a specific way just before the flying bobbin case is engaged. The shuttle and its bobbin for delivering the thread in Howe's machine have significant flaws... my neat and simple bobbin case... dispenses the thread with reliability and consistency... The baster plate in the Howe machine is quite inconvenient and troublesome... in my machine... the clamp... is a very straightforward and effective solution... The Howe machine is stationary, while the baster plate or cloth holder moves. The Bradshaw machine is mobile and the cloth holder is stationary.
Bradshaw’s patent accurately described some of the defects of the Howe machine, but other inventors were later to offer better solutions to the problems.
Bradshaw's patent clearly outlined some of the flaws of the Howe machine, but other inventors would go on to provide better solutions to the issues.

Figure 17.—Morey and Johnson sewing machine, 1849. Below: The machine is marked with the name of its maker, Safford & Williams. The number 49 is a serial number. Missing parts have been replaced with plastic. (Smithsonian photo 48400; brass plate: 48400-H.)
Figure 17.—Morey & Johnson sewing machine, 1849. Below: The machine has the maker's name, Safford & Williams, marked on it. The number 49 is the serial number. Missing parts have been replaced with plastic. (Smithsonian photo 48400; brass plate: 48400-H.)

Although the Bradshaw machine was not in current manufacture, a machine based on it received the seventh United States sewing-machine patent. Patent 6,099 was issued to Charles Morey and Joseph B. Johnson on February 6, 1849. Their machine (fig. 17) was being offered for sale even before the patent was issued.
Although the Bradshaw machine was no longer being produced, a machine inspired by it was granted the seventh United States sewing-machine patent. Patent 6,099 was issued to Charles Morey and Joseph B. Johnson on February 6, 1849. They were already offering their machine (fig. 17) for sale even before the patent was granted.
This was the first American patent for a chainstitch machine. The stitch was made by an eye-pointed needle carrying the thread through the fabric; the thread was detained by a hook until the loop was enchained by the succeeding one. The fabric was held vertically by a baster plate in a manner similar to the Howe machine. Although not claimed in the patent description, the Morey and Johnson machine also had a bar device for stripping the cloth from the needle. This bar had a slight motion causing a yielding pressure to be exerted on the cloth. Although the patent was not granted until February 6, 1849, the application had been filed in April of the previous year. The machine was featured in the Scientific American on January 27, 1849 (fig. 18):
This was the first American patent for a chainstitch machine. The stitch was made by a pointed needle that threaded the fabric; the thread was held by a hook until the loop was secured by the next stitch. The fabric was held vertically by a backing plate, similar to the Howe machine. Although not mentioned in the patent description, the Morey and Johnson machine also included a bar device to strip the cloth from the needle. This bar had a slight motion that applied gentle pressure on the fabric. Although the patent wasn't granted until February 6, 1849, the application had been submitted in April of the previous year. The machine was highlighted in the Scientific American on January 27, 1849 (fig. 18):
Morey and Johnson Machine—These machines are very accurately adjusted in all their parts to work in harmony, without this they would be of no use. But they are now used in most of the Print Works and Bleach Works in New England, and especially by the East Boston Flour Company. It sews about one yard per minute, and we consider it superior to the London Sewing Machine the specification of which is in our possession. It [Morey and Johnson] is more simple—and this is a great deal.... The price of a machine and right to use $135.[36]
Morey and Johnson Machine—These machines are precisely adjusted in all their parts to work together; without this, they would be useless. However, they are now used in most Print Works and Bleach Works in New England, especially by the East Boston Flour Company. It sews about one yard per minute, and we consider it better than the London Sewing Machine, the specifications of which we have. The Morey and Johnson is simpler—and that’s a big deal.... The price of a machine and the right to use it is $135.[36]
An improvement in the Morey and Johnson machine was patented by Jotham S. Conant for which he was issued a patent on May 8, 1849. Conant’s machine offered a slight modification of the cloth bar and of the method of keeping the cloth taut during the stitching operation. No successful use of it is known.
An upgrade to the Morey and Johnson machine was patented by Jotham S. Conant, who received a patent on May 8, 1849. Conant's machine included a small change in the cloth bar and the technique for keeping the cloth tight during the stitching process. There’s no record of it being successfully used.
A second improvement of the Morey and Johnson patent was also issued on May 8, 1849; this United States patent (No. 6,439) was to John Bachelder for the first continuous, but intermittent, sewing mechanism. As shown in the patent model (fig. 19), his clothholder consisted of an endless belt supported by and running around three or any other suitable number of cylindrical rollers. A series of pointed wires projected from the surface of the belt near the edge immediately adjacent to the needle. The wires could be placed at regular or irregular distances as required. The shaft of one of the cylindrical[Pg 23] rollers, which supported the endless clothholder, carried a ratchet wheel advanced by the action of a pawl connected to the end of the crankshaft by a small crankpin, whose position or distance from the axis of rotation of the shaft could be adjusted.
A second improvement of the Morey and Johnson patent was also issued on May 8, 1849; this United States patent (No. 6,439) was awarded to John Bachelder for the first continuous, but intermittent, sewing mechanism. As shown in the patent model (fig. 19), his cloth holder consisted of an endless belt supported by and running around three or any other suitable number of cylindrical rollers. A series of pointed wires extended from the surface of the belt near the edge closest to the needle. The wires could be arranged at regular or irregular distances as needed. The shaft of one of the cylindrical[Pg 23] rollers, which supported the endless cloth holder, had a ratchet wheel that was advanced by the action of a pawl connected to the end of the crankshaft by a small crank pin, whose position or distance from the axis of rotation of the shaft could be adjusted.

Figure 18.—A Morey and Johnson sewing machine as illustrated in Scientific American, January 27, 1849. (Smithsonian photo 45771.)
Figure 18.—A Morey & Johnson sewing machine as shown in Scientific American, January 27, 1849. (Smithsonian photo 45771.)
By this adjustment the extent of the vertical travel of the impelling pawl was regulated to control the length of the stitch. A spring catch kept the ratchet wheel in place at the end of each forward rotation of the wheel by the pawl. A roller placed over the endless belt at its middle roller pressed the cloth onto the wire points. A curved piece of metal was bent over and down upon the top of the belt so that the cloth, as it was sewed, was carried toward and against the piece by the belt. The cloth rose upon and over the piece and was separated from the points. When the machine was in motion the cloth was carried forward, passed under the needle, was stitched, and finally, passed the separator and off the belt. A vertically reciprocating, straight, eye-pointed needle, a horizontal supporting surface, and a yielding cloth presser were all used, but none were claimed as part of the patent. These were later specifically claimed in reissues of this patent. Bachelder’s one specific claim, the endless feed belt, was not limited to belt feeding only. As he explained in the patent, a revolving table or a cylinder might be substituted.
By this adjustment, the vertical movement of the driving pawl was controlled to set the length of the stitch. A spring catch held the ratchet wheel in place at the end of each forward rotation by the pawl. A roller positioned over the middle of the endless belt pressed the fabric onto the wire points. A curved piece of metal was bent over and down onto the top of the belt so that as the fabric was sewn, it was pushed toward and against that piece by the belt. The fabric rose up and over the piece and was separated from the points. When the machine was running, the fabric moved forward, went under the needle, was stitched, and then passed the separator before coming off the belt. A vertically moving, straight, eye-pointed needle, a horizontal supporting surface, and a flexible fabric presser were all used, but none were claimed as part of the patent. These were later specifically claimed in reissues of this patent. Bachelder’s only specific claim, the endless feed belt, wasn't restricted to just belt feeding. As he stated in the patent, a rotating table or a cylinder could also be used.

Figure 19.—Bachelder’s patent model, 1849. (Smithsonian photo 45572).
Figure 19.—Bachelder's patent prototype, 1849. (Smithsonian photo 45572).
Bachelder did not manufacture machines, but his patent was sold in the mid-1850s to I. M. Singer.[37] It eventually became one of the most important patents to be contributed to the “Sewing-Machine Combination,” a patent pool, which is discussed in more detail on pages 41 and 42.
Bachelder didn't make machines, but he sold his patent in the mid-1850s to I. M. Singer.[37] It ended up being one of the key patents in the “Sewing-Machine Combination,” a patent pool that is explained in more detail on pages 41 and 42.
While new ideas and inventors continued to provide the answers to some of the sewing-machine problems, Elias Howe began a series of patent suits to sustain the rights that he felt were his. Since his interest had never been in constructing machines for sale, it was absolutely essential for Howe to protect his royalty rights in order to realize any return from his patent. He was reported[38] to have supervised the construction of 14 sewing machines at a shop[39] on Gold Street in New York toward the close of 1850. Sworn contemporary testimony indicates that the machines were of no practical use.[40] Elias stated, in his application for his patent extension,[41] that he made only one machine in 1850-51. In 1852 he advertised[42] territorial rights and machines, but apparently did not realize any financial success until he sold a half interest in his patent to George Bliss in November 1852.[43] Bliss later began manufacturing machines that he initially sold as “Howe’s Patent”; however, these machines were substantially different from the basic Howe machine.[Pg 24]
While new ideas and inventors kept coming up with solutions to some of the sewing machine issues, Elias Howe started a series of patent lawsuits to defend the rights he believed were his. Since he was never interested in building machines for sale, it was crucial for Howe to protect his royalty rights in order to earn anything from his patent. He was reported[38] to have supervised the construction of 14 sewing machines at a shop[39] on Gold Street in New York towards the end of 1850. Sworn testimony from that time indicates that the machines were not practically useful.[40] Elias stated in his patent extension application,[41] that he made only one machine in 1850-51. In 1852, he advertised[42] his territorial rights and machines, but it seems he didn’t achieve any financial success until he sold half of his patent to George Bliss in November 1852.[43] Bliss later started manufacturing machines that he initially marketed as “Howe’s Patent”; however, these machines were quite different from the original Howe machine.[Pg 24]

Figure 20.—Blodgett & Lerow sewing machine, 1850, as manufactured by A. Bartholf, New York; the serial number of the machine is 19. At right, an original brass plate from the same type of machine with needle arm and presser foot and arm, serial number 119; the plate, however, does not fit the machine correctly. (Smithsonian photo 48440-D; brass plate: 48440-K.)
Figure 20.—Blodgett & Lerow sewing machine, 1850, made by A. Bartholf, New York; the machine's serial number is 19. On the right, there’s an original brass plate from the same type of machine with the needle arm and presser foot and arm, serial number 119; however, the plate doesn’t fit the machine correctly. (Smithsonian photo 48440-D; brass plate: 48440-K.)
On May 18, 1853, Elias Howe granted his first royalty license to Wheeler, Wilson & Company. Within a few months licenses were also granted to Grover & Baker; A. Bartholf; Nichols & Bliss; J. A. Lerow; Woolridge, Keene, and Moore; and A. B. Howe, the brother of Elias. These licenses granted the manufacturer the right to use any part of the Howe patent,[44] but it did not mean that the machines were Elias Howe machines. When a royalty license was paid, the patent date and sometimes the name was stamped onto the machine. For this reason, these machines are sometimes mistakenly thought to be Elias Howe machines. They are not.
On May 18, 1853, Elias Howe issued his first royalty license to Wheeler, Wilson & Company. Within a few months, licenses were also granted to Grover & Baker; A. Bartholf; Nichols & Bliss; J. A. Lerow; Woolridge, Keene, and Moore; and A. B. Howe, Elias's brother. These licenses allowed the manufacturers to use any part of the Howe patent,[44] but it didn’t mean that the machines were made by Elias Howe. When a royalty license was paid, the patent date and sometimes the name were stamped onto the machine. Because of this, these machines are sometimes incorrectly assumed to be Elias Howe machines. They are not.
Howe was also prevented from manufacturing a practical machine unless he paid a royalty to other inventors. Three of the major manufacturers and Howe resolved their differences by forming the “Sewing Machine Combination.” Although Howe did not enter the manufacturing competition for many years, he profited substantially from the royalty terms of the combination. In 1860, he applied for and received a seven-year extension on his patent.
Howe was also stopped from making a practical machine unless he paid royalties to other inventors. Three of the major manufacturers and Howe worked out their differences by creating the “Sewing Machine Combination.” Although Howe didn’t compete in manufacturing for many years, he made a significant profit from the royalty agreement of the combination. In 1860, he applied for and received a seven-year extension on his patent.
Figure 21.—Blodgett & Lerow sewing machine, 1850, stamped with the legend “Goddard, Rice & Co., Makers, Worcester, Mass.” and the serial number 37. Below: An original brass plate marked “No. 38”; this plate fits the machine perfectly. (Smithsonian photo 48440-E; brass plate: 48440-J.)
Figure 21.—Blodgett & Lerow sewing machine, 1850, stamped with the label “Goddard, Rice & Co., Makers, Worcester, Mass.” and the serial number 37. Below: An original brass plate marked “No. 38”; this plate fits the machine perfectly. (Smithsonian photo 48440-E; brass plate: 48440-J.)


There were Howe family machines for sale during this period, but these were the ones that Amasa Howe had been manufacturing since 1853. The machine was an excellent one and received the highest medal for sewing machines, together with many flattering testimonials, at the London International Exhibition in 1862. After the publication of this award the demand for (Amasa) Howe sewing machines was greatly increased at home and abroad. Elias took this opportunity to gain entry into the manufacturing business by persuading Amasa to let him build a factory at Bridgeport, Connecticut, and manufacture the (Amasa) Howe machines. Two years passed before the factory was completed, and Amasa’s agents were discouraged. The loss could have been regained, but the machines produced at Bridgeport were not of the quality of the earlier machines. Amasa attempted to rebuild the Bridgeport machines, but finally abandoned them and resumed manufacturing machines in New York under his own immediate supervision.[45] Elias formed his own company and continued to manufacture sewing machines. In 1867 he requested a second extension of his patent, but the request was refused. Elias Howe died in October of the same year.
There were Howe family sewing machines for sale during this time, but these were the ones Amasa Howe had been making since 1853. The machine was excellent and won the top medal for sewing machines, along with many glowing reviews, at the London International Exhibition in 1862. After this award was announced, the demand for (Amasa) Howe sewing machines surged both domestically and internationally. Elias seized this chance to enter the manufacturing business by convincing Amasa to let him build a factory in Bridgeport, Connecticut, to produce (Amasa) Howe machines. It took two years for the factory to be finished, and Amasa’s agents were discouraged. The loss could have been recovered, but the machines made in Bridgeport didn’t match the quality of the earlier ones. Amasa tried to improve the Bridgeport machines but eventually gave up and went back to making machines in New York under his direct supervision.[45] Elias started his own company and continued to manufacture sewing machines. In 1867, he requested a second extension of his patent, but the request was denied. Elias Howe died in October of that same year.
Meanwhile, another important sewing machine of a different principle had also been patented in 1849. This was the machine of Sherburne C. Blodgett, a tailor by trade, who was supported financially by John A. Lerow. United States patent 6,766 was issued to both men on October 2, 1849. In the patent, the machine was termed as “our new ‘Rotary Sewing Machine’.” The shuttle movement was continuous, revolving in a circle, rather than reciprocating as in the earlier machines. Automatic tension was initiated, restraining the slack thread from interference with the point of the needle.[Pg 26]
Meanwhile, another significant sewing machine based on a different principle was patented in 1849. This was the invention of Sherburne C. Blodgett, a tailor by profession, who received financial backing from John A. Lerow. United States patent 6,766 was granted to both men on October 2, 1849. In the patent, the machine was referred to as “our new ‘Rotary Sewing Machine.’” The shuttle operated continuously, rotating in a circle, instead of moving back and forth like earlier machines. Automatic tension was introduced, preventing the slack thread from interfering with the needle’s point.[Pg 26]

Figure 22.—Wilson’s prepatent model for his reciprocating-shuttle machine, 1850. (Smithsonian photo 45525-A.)
Figure 22.—Wilson's prepatent model for his reciprocating-shuttle machine, 1850. (Smithsonian photo 45525-A.)
The Blodgett and Lerow machine was built by several shops. One of the earliest was the shop of Orson C. Phelps on Harvard Place in Boston. Phelps took the Blodgett and Lerow machine to the sixth exhibition of the Massachusetts Charitable Mechanics Association in September 1850 and won a silver medal and this praise, “This machine performed admirably; it is an exceedingly ingenious and compact machine, able to perform tailor’s sewing beautifully and thoroughly.”[46] Although Phelps had won the earliest known premium for a sewing machine, and although the machine was produced commercially to a considerable extent (figs. 20 and 21), one outstanding flaw in its operation could not be overlooked. As the shuttle passed around the six-inch circular shuttle race, it put a twist in the thread (or took one out if the direction was reversed) at each revolution. This caused a constant breaking of the thread, a condition that could not be rectified without changing the principle of operation. Such required changes were later to lead I. M. Singer, another well-known name, into the work of improving this machine.
The Blodgett and Lerow machine was created by several workshops. One of the first was Orson C. Phelps's shop on Harvard Place in Boston. Phelps showcased the Blodgett and Lerow machine at the sixth exhibition of the Massachusetts Charitable Mechanics Association in September 1850, where he won a silver medal and received this praise: “This machine performed admirably; it is an incredibly clever and compact machine, capable of executing tailor’s sewing beautifully and thoroughly.”[46] Even though Phelps had secured the earliest known award for a sewing machine and the machine was commercially produced to a significant extent (figs. 20 and 21), one major flaw in its operation couldn't be ignored. As the shuttle circled the six-inch shuttle race, it twisted the thread (or untwisted it if the direction was reversed) with each revolution. This caused constant thread breakage, a problem that couldn't be fixed without changing the fundamental operation of the machine. Such necessary modifications would later lead I. M. Singer, another well-known figure, to work on improving this machine.
Also exhibited at the same 1850 mechanics fair was the machine of Allen B. Wilson. Wilson’s machine received only a bronze medal, but his inventive genius was to have a far greater effect on the development of the practical sewing machine than the work of Blodgett and Lerow. A. B. Wilson[47] was one of the ablest of the early inventors in the field of mechanical stitching, and probably the most original.
Also showcased at the same 1850 mechanics fair was Allen B. Wilson's machine. Wilson’s machine earned only a bronze medal, but his inventive genius would have a much greater impact on the development of practical sewing machines than the work of Blodgett and Lerow. A. B. Wilson[47] was one of the most talented early inventors in the field of mechanical stitching, and likely the most innovative.
Wilson, a native of Willett, New York, was a young cabinetmaker at Adrian, Michigan, in 1847 when he first conceived of a machine that would sew. He was apparently unaware of parallel efforts by inventors in distant New England. After an illness, he moved to Pittsfield, Massachusetts, and pursued his idea in earnest. By November 1848 he had produced the basic drawings for a machine that would make a lockstitch. The needle, piercing the cloth, left a loop of thread below the seam. A shuttle carrying a second thread passed through the loop, and as the tension was adjusted a completed lockstitch was formed (fig. 22). Wilson’s shuttle was pointed on both ends to form a stitch on both its forward and backward motion, a decided improvement over the shuttles of Hunt and Howe, which formed stitches in only one direction. After each stitch the cloth was advanced for the next stitch by a sliding bar against which the cloth was held by a stationary presser. While the needle was still in the cloth and holding it, the sliding bar returned for a fresh grip on the cloth.
Wilson, originally from Willett, New York, was a young cabinetmaker in Adrian, Michigan, in 1847 when he first thought of a sewing machine. He seemed to be unaware of similar attempts by inventors in far-off New England. After getting sick, he moved to Pittsfield, Massachusetts, and focused on his idea seriously. By November 1848, he had created the basic designs for a machine that could produce a lockstitch. The needle would puncture the fabric, leaving a loop of thread below the seam. A shuttle carrying a second thread would pass through the loop, and as the tension was adjusted, a completed lockstitch would be formed (fig. 22). Wilson’s shuttle had pointed ends to create a stitch on both its forward and backward movements, which was a significant improvement over the shuttles of Hunt and Howe, which only stitched in one direction. After each stitch, a sliding bar would advance the fabric for the next stitch, with the cloth pressed against it by a stationary presser. While the needle was still in the fabric, holding it, the sliding bar would return for a new grip on the cloth.
Wilson made a second machine, on the same principle, and applied for a patent. He was approached by the owners of the Bradshaw 1848 patent, who[Pg 27] claimed control of the double-pointed shuttle. Although this claim was without justification, as can be seen by examining the Bradshaw patent specifications, Wilson did not have sufficient funds to fight the claim. In order to avoid a suit, he relinquished to A. P. Kline and Edward Lee, a one-half interest in his U.S. patent 7,776 which was issued on November 12, 1850 (fig. 23).
Wilson created a second machine based on the same principle and applied for a patent. He was contacted by the owners of the Bradshaw 1848 patent, who[Pg 27] claimed they had control over the double-pointed shuttle. Although this claim was unfounded, as can be seen by looking at the Bradshaw patent specifications, Wilson didn't have enough money to challenge the claim. To avoid a lawsuit, he agreed to give A. P. Kline and Edward Lee a half interest in his U.S. patent 7,776, which was issued on November 12, 1850 (fig. 23).

Figure 23.—Wilson’s patent model, 1850. (Smithsonian photo 45504-H.)
Figure 23.—Wilson's patent prototype, 1850. (Smithsonian photo 45504-H.)
Inventor Wilson had been associated with Kline and Lee (E. Lee & Co.) for only a few months, when, on November 25, 1850, he agreed to sell his remaining interest to his partners for $2,000. He retained only limited rights for New Jersey and for Massachusetts. The sale was fruitless for the inventor, as no payment was ever made. How much money E. E. Lee & Co. realized from the Wilson machine is difficult to determine, but they ran numerous ads in the 1851 and 1852 issues of Scientific American. A typical one reads:
Inventor Wilson had only been with Kline and Lee (E. Lee & Co.) for a few months when, on November 25, 1850, he agreed to sell his remaining stake to his partners for $2,000. He kept only limited rights for New Jersey and Massachusetts. The sale ended up being pointless for the inventor, as he was never paid. It's hard to say how much money E. E. Lee & Co. made from the Wilson machine, but they placed many ads in the 1851 and 1852 issues of Scientific American. A typical ad reads:
A. B. Wilson’s Sewing Machine, justly allowed to be the cheapest and best now in use, patented November 12, 1850; can be seen on exhibition at 195 and 197 Broadway (formerly the Franklin House, Room 23, third floor) or to E. E. Lee & Co., Earle’s Hotel. Rights for territory or machines can be had by applying to George R. Chittenden, Agent.[48]
A. B. Wilson's Sewing Machine, recognized as the most affordable and effective currently available, patented on November 12, 1850; can be viewed at 195 and 197 Broadway (previously the Franklin House, Room 23, third floor) or at E. E. Lee & Co., Earle's Hotel. You can obtain rights for territories or machines by contacting George R. Chittenden, Agent.[48]
Another reads:
Another says:

Figure 24.—Wilson’s prepatent model for his rotary hook, 1851. (Smithsonian photo 45506-E.)
Figure 24.—Wilson’s pre-patent model for his rotary hook, 1851. (Smithsonian photo 45506-E.)

Figure 25.—Wilson’s rotary-hook patent model, 1851. (Smithsonian photo 45505-B.)
Figure 25.—Wilson's rotary hook patent model, 1851. (Smithsonian photo 45505-B.)
Wilson severed relations with Lee and Kline in early 1851 shortly after meeting Nathaniel Wheeler, who was to become his partner in a happier, more profitable enterprise involving the sewing machine.[Pg 28]
Wilson cut ties with Lee and Kline in early 1851 soon after meeting Nathaniel Wheeler, who would become his partner in a more successful and profitable venture involving the sewing machine.[Pg 28]

Figure 26.—Wilson’s stationary-bobbin patent model, 1852; a commercial machine was used since Wheeler, Wilson, Co. had begun manufacturing machines the previous year. (Smithsonian photo 45504-B.)
Figure 26.—Wilson's stationary-bobbin patent model, 1852; a commercial machine was used since Wheeler, Wilson, Co. had begun manufacturing machines the previous year. (Smithsonian photo 45504-B.)
Wilson, with his two partners, was occupying a room in the old Sun Building at 128 Fulton Street, when Wheeler, on a business trip to New York City, learned of the Wilson sewing machine. Wheeler examined the machine, saw its possibilities, and at once contracted with E. Lee & Co. to make 500 of them. At the same time he engaged Wilson to go with him to Watertown, Connecticut, to perfect the machine and supervise its manufacture. Meanwhile, Wilson had been working on a substitute for the shuttle. He showed his model of the device, which became known as the rotary hook, to Wheeler who was so convinced of its superiority that he decided to develop this new machine and leave Wilson’s first machine to the others, who, by degrees, had become its owners.
Wilson, along with his two partners, was using a room in the old Sun Building at 128 Fulton Street when Wheeler, on a business trip to New York City, discovered the Wilson sewing machine. Wheeler checked out the machine, recognized its potential, and immediately made a deal with E. Lee & Co. to produce 500 of them. At the same time, he hired Wilson to come with him to Watertown, Connecticut, to improve the machine and oversee its production. In the meantime, Wilson had been working on an alternative to the shuttle. He presented his model of the device, later known as the rotary hook, to Wheeler, who was so convinced of its superiority that he decided to develop this new machine and leave Wilson’s original machine to those who had gradually become its owners.
Wilson now applied all his effort to improving the rotary hook, for which he received his second patent on August 12, 1851 (figs. 24 and 25). Wheeler, his two partners Warren and Woodruff, and Wilson now formed a new copartnership—Wheeler, Wilson, and Company. They began the manufacture of the machines under the patent, which combined the rotary hook and a reciprocating bobbin. The rotary hook extended or opened more widely the loop of the needle thread, while a reciprocating bobbin carried its thread through the extended loop. To avoid litigation which the reciprocating bobbin might have caused, Wilson contrived his third outstanding invention—the stationary bobbin. This was a feature of the first machine produced by the new company in 1851, though the patent for the stationary bobbin was not issued until June 15, 1852 (fig. 26).
Wilson now focused all his energy on improving the rotary hook, for which he received his second patent on August 12, 1851 (figs. 24 and 25). Wheeler, along with his two partners Warren and Woodruff, joined Wilson to create a new partnership—Wheeler, Wilson, and Company. They started manufacturing machines based on the patent that combined the rotary hook and a reciprocating bobbin. The rotary hook expanded the loop of the needle thread more widely, while a reciprocating bobbin threaded its thread through the wider loop. To prevent any legal issues that the reciprocating bobbin might cause, Wilson devised his third major invention—the stationary bobbin. This became a feature of the first machine produced by the new company in 1851, although the patent for the stationary bobbin wasn't granted until June 15, 1852 (fig. 26).
In all reciprocating-shuttle machines a certain loss of power is incurred in driving forward, stopping, and bringing back the shuttle at each stitch; also, the machines are rather noisy, owing to the striking of the driver against the shuttle at each stroke. These objections were removed by Wilson’s rotary hook and stationary bobbin. The locking of the needle thread with the bobbin thread was accomplished, not by driving a shuttle through the loop of the needle thread, but by passing that loop under the bobbin. The driving shaft carried the circular rotary hook, one of the sewing machine’s most beautiful contrivances. The success of the machine is indicated in an article that appeared in the June 1853 issue of Scientific American:
In all reciprocating-shuttle machines, there’s a certain loss of power when driving forward, stopping, and bringing back the shuttle for each stitch. Additionally, these machines are pretty noisy because the driver strikes the shuttle with each stroke. Wilson’s rotary hook and stationary bobbin solved these issues. Instead of driving a shuttle through the loop of the needle thread, the needle thread’s loop is passed under the bobbin to lock it with the bobbin thread. The driving shaft held the circular rotary hook, which is one of the sewing machine’s most elegant designs. The machine's success is highlighted in an article from the June 1853 issue of Scientific American:
There are 300 of these machines now in operation in various parts of the country, and the work which they can perform cannot be surpassed.... The time must soon come when every private family that has much sewing to do, will have one of these neat and perfect machines; indeed many private families have them now.... The price of one all complete is $125; every machine is made under the eye of the inventor at the company’s machine shop, Watertown, Connecticut, so that every one is warranted ... agreement between Mr. Howe and Messrs. Wheeler, Wilson & Co., so every customer will be perfectly protected....[50]
There are 300 of these machines currently in use across the country, and the work they can do is unmatched.... The time will soon come when every household that does a lot of sewing will have one of these efficient and high-quality machines; in fact, many families already own them.... The price for a complete machine is $125; each machine is manufactured under the supervision of the inventor at the company's workshop in Watertown, Connecticut, ensuring quality ... an agreement between Mr. Howe and Messrs. Wheeler, Wilson & Co., so every customer will be fully protected....[50]

Figure 27.—Wilson’s four-motion-feed patent model, 1854, is not known to be in existence; this is a commercial machine of the period. The plate is stamped “A. B. Wilson, Patented Aug. 12, 1851, Watertown, Conn., No. 1....” (Smithsonian photo 45504.)
Figure 27.—Wilson's four-motion-feed patent model from 1854 is not known to exist; this is a commercial machine from that time. The plate is stamped “A. B. Wilson, Patented Aug. 12, 1851, Watertown, Conn., No. 1....” (Smithsonian photo 45504.)
This agreement was important to sales, as Elias Howe was known to have sued purchasers of machines, as well as rival inventors and companies.
This agreement was crucial for sales because Elias Howe was known to have sued buyers of machines, along with competing inventors and companies.
The business was on a substantial basis by October 1853, and a stock company was formed under the name of Wheeler & Wilson Manufacturing Company.[51] A little more than a year later, on December 19, 1854, Wilson’s fourth important patent (U.S. patent 12,116)—for the four-motion cloth feed—was issued to him (fig. 27). In this development, the flat-toothed surface in contact with the cloth moved forward carrying the cloth with it; then it dropped a little, so as not to touch the cloth; next it moved backward; then in the fourth motion it pushed up against the cloth and was ready to repeat the forward movements. This simple and effective feed method is still used today, with only minor modifications, in almost every sewing machine. This feed with the rotary hook and the stationary circular-disk bobbin, completed the essential features of Wilson’s machine. It was original and fundamentally different from all other machines of that time.
The business was well-established by October 1853, and a stock company was formed under the name of Wheeler & Wilson Manufacturing Company.[51] A little over a year later, on December 19, 1854, Wilson received his fourth important patent (U.S. patent 12,116) for the four-motion cloth feed (fig. 27). In this innovation, the flat-toothed surface that contacted the cloth moved forward, carrying the cloth along; then it dropped slightly to avoid touching the cloth; next, it moved backward; and finally, it pushed up against the cloth, ready to repeat the forward movements. This simple and effective feeding method is still in use today, with only minor adjustments, in almost every sewing machine. This feed mechanism, along with the rotary hook and stationary circular-disk bobbin, completed the essential features of Wilson’s machine. It was original and fundamentally different from all other machines of that period.
The resulting Wheeler and Wilson machine made a lockstitch by means of a curved eye-pointed needle carried by a vibrating arm projecting from a rock shaft connected by link and eccentric strap with an eccentric on the rotating hook shaft. This shaft had at its outer end the rotary hook, provided with a point adapted to enter the loop of needle thread. As the hook rotated, it passed into and drew down the loop of needle-thread, which was held by means of a loop check, while the point of the hook entered a new loop. When the first loop was cast off—the face of the hook being beveled for that purpose—it was drawn upward by the action of the hook upon the loop through which it was then passing. During the rotation of the hook each loop was passed around a disk bobbin provided with the second thread and serving the part of the shuttle in other machines. The four-motion feed was actuated in this machine by means of a spring bar and a cam in conjunction with the mandrel.
The Wheeler and Wilson machine created a lockstitch using a curved, pointed needle attached to a vibrating arm that extended from a rock shaft. This shaft was linked via a strap to an eccentric on the rotating hook shaft. At the end of the shaft was a rotary hook with a point designed to catch the loop of needle thread. As the hook turned, it moved into the needle's thread loop, pulling it down, while a loop check held it in place and the hook engaged a new loop. When the first loop was released—thanks to the beveled edge of the hook—it was pulled upward as the hook continued to work through the loop it was passing through. As the hook rotated, each thread loop was wrapped around a disk bobbin that held the second thread, acting like the shuttle in other machines. The machine's four-motion feed was operated by a spring bar and a cam working together with the mandrel.
From the beginning, Wheeler and Wilson had looked beyond the use of the sewing machine solely by manufacturers and had seen the demand for a light-running, lightweight machine for sewing in the home. Wilson’s inventions lent themselves to this design, and Wheeler and Wilson led the way to the introduction of the machine as a home appliance. Other manufacturers followed.
From the start, Wheeler and Wilson had envisioned the sewing machine being used not just by manufacturers but also seeing the need for a lightweight, easy-to-use machine for home sewing. Wilson’s inventions were perfect for this design, and Wheeler and Wilson paved the way for the machine to be introduced as a household item. Other manufacturers soon followed suit.
When the stock company was formed, Mr. Wilson retired from active participation in the business at his own request. His health had not been good, and a nervous condition made it advisable for him to be freed from the responsibility of daily routine. During this period Wilson’s inventive contributions to the sewing machine continued as noted, and in addition he worked on inventions concerning cotton picking and illuminating gases.
When the stock company was formed, Mr. Wilson stepped back from being actively involved in the business at his own request. His health had not been great, and a nervous condition made it necessary for him to be relieved from the burden of daily responsibilities. During this time, Wilson continued to make inventive contributions to the sewing machine, as mentioned, and he also focused on inventions related to cotton picking and lighting gases.
Wheeler and Wilson’s foremost competitor in the[Pg 30] early years of sewing-machine manufacture was the Singer Company, which overtook them by 1870 and finally absorbed the entire Wheeler and Wilson Manufacturing Company in 1905.
Wheeler and Wilson’s main competitor in the[Pg 30] early days of sewing machine manufacturing was the Singer Company, which surpassed them by 1870 and ultimately merged with the entire Wheeler and Wilson Manufacturing Company in 1905.
The founder of this most successful 19th-century company was Isaac Singer, a native of Pittstown, New York.[52] Successively a mechanic, an actor, and an inventor, Singer came to Boston in 1850 to promote his invention of a machine for carving printers’ wooden type. He exhibited the carving machine in Orson Phelps’ shop, where the Blodgett and Lerow machines were being manufactured.
The founder of this highly successful 19th-century company was Isaac Singer, who was originally from Pittstown, New York.[52] He was a mechanic, an actor, and an inventor. In 1850, Singer moved to Boston to showcase his invention of a machine for carving wooden type for printers. He displayed the carving machine in Orson Phelps’ shop, where the Blodgett and Lerow machines were being made.
Because the carving machine evoked but little interest, Singer turned his attention to the sewing machine as a device offering considerable opportunity for both improvement and financial reward. Phelps liked Singer’s ideas and joined with George Zieber, the publisher who had been backing the carving-machine venture, to support Singer in the work of improving the sewing machine. His improvements in the Blodgett and Lerow machine included a table to hold the cloth horizontally rather than vertically (this had been used by Bachelder and Wilson also), a yielding vertical presser foot to hold the cloth down as the needle was drawn up, and a vertically reciprocating straight needle driven by a rotary, overhanging shaft.
Because the carving machine didn't generate much interest, Singer shifted his focus to the sewing machine, which offered great potential for both enhancements and financial gain. Phelps appreciated Singer’s ideas and teamed up with George Zieber, the publisher who had been supporting the carving machine project, to help Singer improve the sewing machine. His innovations on the Blodgett and Lerow machine included a table that held the fabric horizontally instead of vertically (which Bachelder and Wilson had also utilized), a flexible vertical presser foot to keep the fabric in place as the needle pulled up, and a vertically moving straight needle powered by a rotating, overhead shaft.
The story of the invention and first trial of the machine was told by Singer in the course of a patent suit sometime later:
The story of how the machine was invented and its first trial was recounted by Singer during a patent lawsuit a while later:
I explained to them how the work was to be fed over the table and under the presser-foot, by a wheel, having short pins on its periphery, projecting through a slot in the table, so that the work would be automatically caught, fed and freed from the pins, in place of attaching and detaching the work to and from the baster plate by hand, as was necessary in the Blodgett machine.
I explained to them how the work was supposed to be fed over the table and under the presser foot by a wheel with short pins around the edge, sticking through a slot in the table, so that the work would be automatically grabbed, fed, and released from the pins, instead of having to manually attach and detach the work from the baster plate as was required in the Blodgett machine.
Phelps and Zieber were satisfied that it would work. I had no money. Zieber offered forty dollars to build a model machine. Phelps offered his best endeavors to carry out my plan and make the model in his shop; if successful we were to share equally. I worked at it day and night, sleeping but three or four hours a day out of the twenty-four, and eating generally but once a day, as I knew I must make it for the forty dollars or not get it at all.
Phelps and Zieber were confident it would work. I didn't have any money. Zieber offered forty dollars to build a model machine. Phelps committed his best efforts to help me execute my plan and create the model in his shop; if we succeeded, we would split the profits equally. I worked on it day and night, sleeping only three or four hours a day out of the twenty-four, and usually eating just once a day, knowing I had to make it for the forty dollars or not get it at all.
The machine was completed in eleven days. About nine o’clock in the evening we got the parts together and tried it; it did not sew; the workmen exhausted with almost unremitting work, pronounced it a failure and left me one by one.
The machine was finished in eleven days. Around nine o’clock in the evening, we put the parts together and tried it out; it didn’t sew. The workers, worn out from almost nonstop labor, declared it a failure and left me one by one.
Zieber held the lamp, and I continued to try the machine, but anxiety and incessant work had made me nervous and I could not get tight stitches. Sick at heart, about midnight, we started for our hotel. On the way we sat down on a pile of boards, and Zieber mentioned that the loose loops of thread were on the upper side of the cloth. It flashed upon me that we had forgot to adjust the tension on the needle thread. We went back, adjusted the tension, tried the machine, sewed five stitches perfectly and the thread snapped, but that was enough. At three o’clock the next day the machine was finished. I took it to New York and employed Mr. Charles M. Keller to patent it. It was used as a model in the application for the patent.[53]
Zieber held the lamp while I kept trying the machine, but my anxiety and constant working made me tense, and I couldn't get the stitches right. Feeling defeated around midnight, we headed to our hotel. On the way, we sat on a pile of boards, and Zieber pointed out that the loose loops of thread were on the top side of the fabric. It suddenly hit me that we had forgotten to adjust the needle thread tension. We went back, made the adjustments, tried the machine again, sewed five perfect stitches, and then the thread snapped, but that was enough. By three in the afternoon the next day, the machine was complete. I took it to New York and hired Mr. Charles M. Keller to patent it. It was used as a model for the patent application.[53]
The first machine was completed about the last of September 1850. The partners considered naming the machine the “Jenny Lind,” after the Swedish soprano who was then the toast of America. It was reported[54] to have been advertised under that name when the machine was first placed on the market, but the name was soon changed to “Singer’s Perpendicular Action Sewing Machine” or simply the “Singer Sewing Machine”—a name correctly anticipated to achieve a popularity of its own.
The first machine was finished around the end of September 1850. The partners thought about naming the machine the “Jenny Lind,” after the Swedish soprano who was the sensation in America at the time. It was reported[54] that it was advertised under that name when the machine first hit the market, but the name was quickly changed to “Singer’s Perpendicular Action Sewing Machine” or just the “Singer Sewing Machine”—a name that was expected to become popular on its own.
According to the contract made by the partners, the hurriedly built first machine was to be sent to the Patent Office with an application in the name of Singer and Phelps. An application was made between the end of September 1850 and March 14, 1851, as Singer refers to it briefly in the application formally filed on April 16, 1851, stating, “My present invention is of improvements on a machine heretofore invented by me and for which an application is now pending.”[55]
According to the agreement made by the partners, the quickly assembled first machine was to be sent to the Patent Office along with an application under the names Singer and Phelps. The application was submitted sometime between the end of September 1850 and March 14, 1851, as Singer mentions briefly in the application that was officially filed on April 16, 1851, stating, “My current invention is an improvement on a machine that I previously invented and for which an application is currently pending.”[55]

Figure 28.—Singer’s patent model, 1851; a commercial machine was used, bearing the serial number 22. (Smithsonian photo 45572-D.)
Figure 28.—Singer's patent model, 1851; a commercial machine was used, showing the serial number 22. (Smithsonian photo 45572-D.)

Figure 29.—Singer’s Perpendicular Action sewing machine, an engraving from Illustrated News, June 25, 1853, which states: “The sewing machine has, within the last two years acquired a wide celebrity, and established its character as one of the most efficient labor saving instruments ever introduced to public notice.... We must not forget to call attention to the fact that this instrument is peculiarly calculated for female operatives. They should never allow its use to be monopolized by men.” (Smithsonian photo 48091-D.)
Figure 29.—Singer's Vertical Action sewing machine, an engraving from Illustrated News, June 25, 1853, which states: “The sewing machine has gained a lot of fame in the past two years and has proven to be one of the most effective labor-saving tools ever introduced to the public... We should also highlight that this machine is especially suited for female workers. They should never let men monopolize its use.” (Smithsonian photo 48091-D.)
In late December 1850 Singer had bought Phelps’ interest in the company. Whether the first application was later abandoned by Singer or whether it was rejected is not known,[56] but a patent on the first application was never issued. The final disposition of this first machine has remained a mystery.[57]
A few machines were manufactured in late 1850 and early 1851, and these attracted considerable attention; orders began to be received in advance of production. The pending patent application did not delay the manufacture, and a number of machines were sold before August 12, 1851, when the patent was granted. The patent model is shown in figure 28.[58] It made a lockstitch by means of a straight eye-pointed needle and a reciprocating shuttle. The patent claims, as quoted from the specifications, were as follows:
A few machines were made in late 1850 and early 1851, and they attracted a lot of attention; orders started coming in before production even began. The pending patent application didn't hold up the manufacturing process, and several machines were sold before August 12, 1851, when the patent was granted. The patent model is shown in figure 28.[58] It created a lockstitch using a straight, eye-pointed needle and a moving shuttle. The patent claims, as quoted from the specifications, were as follows:
1. Giving to the shuttle an additional forward motion after it has been stopped to close the loop, as described, for the purpose of drawing the stitch tight, when such additional motion is given at and in combination with the feed motion of the cloth in the reverse direction, and the final upward motion of the needle, as described, so that the two threads shall be drawn tight at the same time, as described.
1. Adding extra forward movement to the shuttle after it has stopped to close the loop, as outlined, in order to pull the stitch tight, when this additional movement is combined with the cloth's feed motion moving backward and the needle's final upward movement, as detailed, so that both threads are pulled tight simultaneously, as explained.
2. Controlling the thread during the downward motion of the needle by the combination of a friction-pad to prevent the slack above the cloth, with the eye on the needle-carrier for drawing back the thread, for the purposes and in the manner substantially as described.
2. Controlling the thread during the downward motion of the needle by using a friction pad to stop slack above the fabric, along with the eye on the needle carrier to pull back the thread, for the purposes and in the way described.
3. Placing the bobbin from which the needle is supplied with thread on an adjustable arm attached to the frame, substantially as described, when this is combined with the carrying of the said thread through an eye or guide attached to and moving with the needle-carrier, as described, whereby any desired length of thread can be given for the formation of the loop without varying the range of motion of the needle, as described.
3. Attaching the bobbin that supplies thread to the needle on an adjustable arm connected to the frame, similar to what was described, when this is used along with guiding the thread through an eye or guide that moves with the needle-holder, as mentioned, which allows for any desired length of thread to be used to form the loop without changing the needle's range of motion, as described.
The feeding described in the Singer patent was “by the friction surface of a wheel, whose periphery is formed with very fine grooves, the edges of which are slightly serrated, against which the cloth is pressed by a spring plate or pad.” Although claimed by the inventor in the handwritten specifications, it was not allowed as original.
The feeding described in the Singer patent was "by the friction surface of a wheel, whose edge is designed with very fine grooves, the edges of which are slightly serrated, against which the cloth is pressed by a spring plate or pad." Although claimed by the inventor in the handwritten specifications, it was not accepted as original.
The machines manufactured by the Singer company (fig. 29) were duplicates of the patent model. These machines were quite heavy and intended for manufacturing rather than for family use in the home.
The machines made by the Singer company (fig. 29) were copies of the patent model. These machines were fairly heavy and designed for manufacturing rather than for family use at home.

Figure 30.—I. M. Singer & Co. New York showroom of the mid-1850s, as illustrated in Frank Leslie’s Illustrated Newspaper, August 29, 1857; only manufacturing machines are shown in this illustration. (Smithsonian photo 48091-B.)
Figure 30.—I. M. Singer & Co. New York showroom from the mid-1850s, as shown in Frank Leslie’s Illustrated Newspaper, August 29, 1857; this illustration only displays manufacturing machines. (Smithsonian photo 48091-B.)
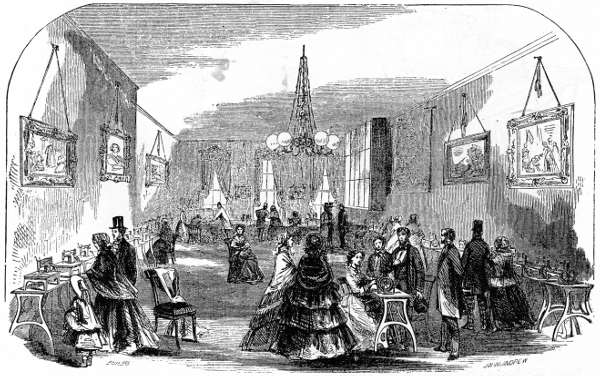
Figure 31.—Hunt and Webster’s sewing-machine manufactory exhibition and salesroom in Boston, as illustrated in Ballou’s Pictorial, July 5, 1856; only manufacturing machines are shown. (Smithsonian photo 45771-A.)
Figure 31.—Hunt and Webster's sewing machine factory showroom and salesroom in Boston, as shown in Ballou’s Pictorial, July 5, 1856; only manufacturing machines are displayed. (Smithsonian photo 45771-A.)
Singer enjoyed demonstrating the machine and showed it to church and social groups and even at circuses; this personal association then encouraged him to improve its reliability and convenience. He developed a wooden packing case which doubled as a stand for the machine and a treadle to allow it to be operated by foot. Because of the dimensions of the packing case, Singer put the pivot of the treadle toward its center, about where the instep of the foot would rest. This produced the heel-and-toe action treadle, a familiar part of the sewing machine until its replacement by the electric motor. Both hands were freed to guide and arrange the cloth that was being stitched. Singer also added a flywheel to smooth out the treadle action and later an iron stand with a treadle wide enough for both feet. The treadle had been in use for two years before a rival pointed out that it might have been patented. To Singer’s chagrin it was then too late for patent laws[Pg 34] did not permit patenting a device that had been in public use.
Singer enjoyed showing off the machine and presented it to church and social groups, even at circuses; this personal involvement motivated him to enhance its reliability and ease of use. He created a wooden packing case that served as both a stand for the machine and a treadle that allowed it to be operated by foot. Due to the size of the packing case, Singer positioned the pivot of the treadle toward its center, approximately where the arch of the foot would rest. This design resulted in the heel-and-toe action treadle, a familiar feature of sewing machines until they were replaced by electric motors. Both hands were freed to guide and arrange the fabric being stitched. Singer also added a flywheel to smooth out the treadle action and later introduced an iron stand with a treadle wide enough for both feet. The treadle had been in use for two years before a competitor pointed out that it might have been eligible for a patent. To Singer's dismay, it was then too late for patent laws[Pg 34] as they did not allow for patenting a device that had been publicly used.
A new obstacle appeared in the Singer company’s path when Howe demanded $25,000 for infringement of his patent. Singer and Zieber decided to fight, enlisting the legal aid of Edward Clark, a lawyer and financier. Howe’s action was opposed on the basis of Hunt’s machine of 1834, which they stated had anticipated Howe’s invention.
A new challenge emerged for the Singer company when Howe demanded $25,000 for violating his patent. Singer and Zieber chose to fight back, bringing in Edward Clark, a lawyer and financier, for legal support. They contested Howe's claim by referencing Hunt's machine from 1834, arguing that it had already anticipated Howe's invention.
While they were resisting, Howe sued three firms that were using and selling Singer machines. The court order required the selling firms and the purchasers to provide an account of the profits accrued from the sale and the use of the sewing machines and restrained the firms from selling the machines during the pendency of the suit.[59] As a result of this action, a number of Singer’s rivals purchased licenses from Howe and advertised that anyone could sell their machines without fear of a suit. This gave them a great competitive advantage, and Singer and Clark[60] decided it was best to seek a settlement with Howe. On July 1, 1854, they paid him $15,000 and took out a license.
While they were resisting, Howe sued three companies that were using and selling Singer machines. The court order required the selling companies and buyers to account for the profits made from the sale and use of the sewing machines, and it prohibited the companies from selling the machines while the lawsuit was ongoing.[59] As a result of this action, several of Singer’s competitors obtained licenses from Howe and promoted that anyone could sell their machines without the risk of a lawsuit. This gave them a significant competitive edge, leading Singer and Clark[60] to conclude that it would be best to reach a settlement with Howe. On July 1, 1854, they paid him $15,000 and secured a license.

Figure 32.—Singer’s new Family Sewing Machine, illustration from a brochure dating about 1858 or 1859 which states: “A few months since, we came to the conclusion that the public taste demanded a sewing machine for family purposes more exclusively; a machine of smaller size, and of a lighter and more elegant form; a machine decorated in the best style of art, so as to make a beautiful ornament in the parlor or boudoir; a machine very easily operated, and rapid in working.... To supply this public want, we have just produced, and are now prepared to receive orders for, ‘Singer’s new Family Sewing Machine.’” (Smithsonian photo 48091-H.)
Figure 32.—Singer's new family sewing machine, illustration from a brochure dated around 1858 or 1859 that says: “A few months ago, we realized that people wanted a sewing machine specifically for home use; a machine that was smaller, lighter, and more stylish; a machine designed beautifully to serve as a lovely decoration in the living room or bedroom; a machine that is very easy to use and works quickly.... To meet this demand, we have just created, and are now ready to take orders for, ‘Singer’s new Family Sewing Machine.’” (Smithsonian photo 48091-H.)
In spite of this defeat, the Singer company could claim several important improvements to the sewing machine and the acquisition of the patents rights to the Morey and Johnson machine of 1849, which gave them control of the spring or curved arm to hold the cloth by a yielding pressure. Although this point had not been claimed in the 1849 patent, the established principle of patent law allowed that a novel device introduced and used in a patented machine could be covered by a reissue at any time during the life of the patent. Upon becoming owners of the Morey and Johnson patent, Singer applied for a reissue which covered this type of yielding pressure. It was granted on June 27, 1854. The Singer company’s acquisition of the Bachelder patent had given them control of the yielding pressure bar also.
Despite this defeat, the Singer company could claim several important improvements to the sewing machine and the acquisition of the patent rights to the Morey and Johnson machine of 1849, which gave them control of the spring or curved arm to hold the fabric with a flexible pressure. Although this point wasn't included in the 1849 patent, established patent law allowed for a new device introduced and used in a patented machine to be covered by a reissue at any time during the patent's life. After becoming owners of the Morey and Johnson patent, Singer applied for a reissue that covered this type of flexible pressure. It was granted on June 27, 1854. The Singer company's acquisition of the Bachelder patent also gave them control of the flexible pressure bar.

Figure 33.—Singer Family Machine, 1858, head only. (Smithsonian photo 45524-F.)
Figure 33.—Singer Family Sewing Machine, 1858, head only. (Smithsonian photo 45524-F.)
Singer’s aggressive selling had begun to overcome the public’s suspicion of sewing machines. He pioneered in the use of lavishly decorated sewing-machine showrooms when the company offices were expanded in the mid-1850s (fig. 30). These were rich with carved walnut furniture, gilded ornaments, and carpeted floors, places in which Victorian women were not ashamed to be seen. The machines were demonstrated by pretty young women. The total effect was a new concept of selling, and Singer became the drum major of a new and coming industry that had many followers (see fig. 31).
Singer’s aggressive marketing started to win over the public's doubts about sewing machines. He was a trailblazer in creating beautifully decorated showrooms for sewing machines when the company's offices expanded in the mid-1850s (fig. 30). These showrooms featured elaborately carved walnut furniture, golden decorations, and carpeted floors—spaces where Victorian women felt comfortable being seen. The machines were showcased by attractive young women. The overall impact was a fresh approach to selling, and Singer became the leader of a new and emerging industry, inspiring many followers (see fig. 31).

Figure 34.—Grover and Baker’s patent model, 1851. (Smithsonian photo 32003-G.)
Figure 34.—Grover and Baker's patent model from 1851. (Smithsonian photo 32003-G.)
The first, light, family sewing machine by the Singer company was not manufactured until 1858 (figs. 32 and 33). Comparatively few of these machines were made as they proved to be too small and light. The men in the shop dubbed the machine “The Grasshopper,” but it was officially called the new Family Sewing Machine or the Family Machine.[61] Because of its shape, Singer company brochures of the 1920s referred to it as the Turtleback Machine.
The first lightweight family sewing machine from the Singer company wasn't made until 1858 (figs. 32 and 33). Not many of these machines were produced because they turned out to be too small and light. The guys in the shop nicknamed the machine “The Grasshopper,” but it was officially known as the new Family Sewing Machine or the Family Machine.[61] Due to its shape, Singer company brochures from the 1920s called it the Turtleback Machine.
Since the cost of sewing machines was quite high and the average family income was low, Clark suggested the adoption of the hire-purchase plan. Into the American economy thus came the now-familiar installment buying.
Since sewing machines were expensive and most families had low incomes, Clark proposed a hire-purchase plan. This led to the introduction of what we now know as installment buying in the American economy.
Singer and Clark continued to be partners until 1863 when a corporation was formed. At this time Singer decided to withdraw from active work. He received 40 percent of the stock and retired to Paris and later to England, where he died in 1875.[Pg 36]
Singer and Clark remained partners until 1863 when they formed a corporation. At that point, Singer chose to step back from active involvement. He received 40 percent of the shares and retired to Paris and later to England, where he passed away in 1875.[Pg 36]

Figure 35.—This Grover and Baker cabinet-style sewing machine of 1856 bears the serial number 5675 and the patent dates February 11, 1851, June 22, 1852, February 22, 1853, and May 27, 1856. (Smithsonian photo 45572-F.)
Figure 35.—This Grover and Baker cabinet-style sewing machine from 1856 has the serial number 5675 and the patent dates February 11, 1851, June 22, 1852, February 22, 1853, and May 27, 1856. (Smithsonian photo 45572-F.)
By the mid-1850s the basic elements of a successful, practical sewing machine were at hand, but the continuing court litigation over rival patent rights seemed destined to ruin the economics of the new industry. It was then that the lawyer of the Grover and Baker company, another sewing-machine manufacturer of the early 1850s, supplied the solution. Grover and Baker were manufacturing a machine that was mechanically good, for this early period. William O. Grover was another Boston tailor, who, unlike many others, was convinced that the sewing machine was going to revolutionize his chosen trade. Although the sewing machines that he had seen were not very practical, he began in 1849 to experiment with an idea based on a new kind of stitch. His design was for a machine that would take both its threads from spools and eliminate the need to wind one thread upon a bobbin. After much experimenting, he proved that it was possible to make a seam by interlocking two threads in a succession of slipknots, but he found that building a machine to do this was a much more difficult task. It is quite surprising that while he was working on this idea, he did not stumble upon a good method to produce the single-thread (as opposed to Grover and Baker’s two-thread) chainstitch, later worked out by another. Grover was working so intently on the use of two threads that apparently no thought of forming a stitch with one thread had a chance to develop.
By the mid-1850s, the essential components of a successful, practical sewing machine were in place, but ongoing court battles over competing patent rights threatened to undermine the industry's economics. It was then that the lawyer for Grover and Baker, another sewing machine maker from the early 1850s, provided a solution. Grover and Baker were producing a mechanically sound machine for that time. William O. Grover was another Boston tailor who, unlike many others, believed that the sewing machine would transform his trade. Although the machines he had seen were not very practical, he began experimenting in 1849 with an idea based on a new type of stitch. His design aimed to create a machine that would draw both threads from spools, eliminating the need to wind one thread onto a bobbin. After extensive experimentation, he demonstrated that it was possible to make a seam by interlocking two threads in a series of slipknots, but he discovered that building a machine to accomplish this was considerably more challenging. It's quite surprising that while he was focused on this idea, he didn't come across a viable method for producing the single-thread chain stitch (as opposed to Grover and Baker’s two-thread method), which was later developed by someone else. Grover was so absorbed in using two threads that it seems he never considered the possibility of forming a stitch with just one thread.
At this time Grover became a partner with another Boston tailor, William E. Baker, and on February 11, 1851, they were issued U.S. patent No. 7,931 for a machine that did exactly what Grover had set out to do; it made a double chainstitch with two threads both carried on ordinary thread spools. The machine (figs. 34 and 35) used a vertical eye-pointed needle for the top thread and a horizontal needle for the underthread. The cloth was placed on the horizontal platform or table, which had a hole for the entry of the vertical needle. When this needle passed through the cloth, it formed a loop on the underside. The horizontal needle passed through this loop forming another loop beyond, which was retained until the redescending vertical needle enchained it, and the process repeated. The slack in the needle thread was controlled by means of a spring guide. The cloth was fed by feeding rolls and a band.[Pg 37]
At this time, Grover partnered with another Boston tailor, William E. Baker, and on February 11, 1851, they received U.S. patent No. 7,931 for a machine that achieved exactly what Grover intended; it created a double chainstitch using two threads from standard thread spools. The machine (figs. 34 and 35) employed a vertical eye-pointed needle for the top thread and a horizontal needle for the underthread. The fabric was placed on a horizontal platform or table, which had an opening for the vertical needle. When this needle went through the fabric, it formed a loop on the underside. The horizontal needle passed through this loop, creating another loop beyond, which was held until the descending vertical needle locked it in place, repeating the process. The slack in the needle thread was regulated by a spring guide. The fabric was fed by feeding rolls and a band.[Pg 37]

Figure 36.—Grover’s patent model for the first portable case, 1856. The machine in the case is a commercial machine of 1854, bearing the serial number 3012 and the patent dates “Feby 11, 1851, June 22, 1852, Feby 22, 1853.” Powered by a single, foot-shaped treadle that was connected by a removable wooden pitman, it also could be turned by hand. (Smithsonian photo 45525-D.)
Figure 36.—Grover’s patent model for the first portable case, 1856. The machine inside the case is a commercial model from 1854, with the serial number 3012 and the patent dates “Feb 11, 1851, June 22, 1852, Feb 22, 1853.” It was powered by a single, foot-shaped treadle connected by a removable wooden pitman, but it could also be operated by hand. (Smithsonian photo 45525-D.)
A company was organized under the name of Grover and Baker Sewing Machine Company, and soon the partners took Jacob Weatherill, mechanic, and Orlando B. Potter, lawyer (who became the president), into the firm. Potter contributed his ability as a lawyer in lieu of a financial investment and handled the several succeeding patents of Grover and Baker. These patents were primarily for mechanical improvements such as U.S. patent No. 9,053 issued to Grover and Baker on June 22, 1852, for devising a curved upper needle and an under looper[62] to form the double-looped stitch which became known as the Grover and Baker stitch.[Pg 38] One of the more interesting of the patents, however, was for the box or sewing case for which Grover was issued U.S. patent No. 14,956 on May 27, 1856. The inventor stated “that when open the box shall constitute the bed for the machine to be operated upon, and hanging the machine thereto to facilitate oiling, cleansing, and repairs without removing it from the box.” It was the first portable sewing machine (fig. 36).
A company was established under the name Grover and Baker Sewing Machine Company, and soon the partners brought in Jacob Weatherill, a mechanic, and Orlando B. Potter, a lawyer (who became the president). Potter offered his legal expertise instead of a financial investment and managed the various patents of Grover and Baker. These patents were mainly for mechanical enhancements, including U.S. patent No. 9,053 issued to Grover and Baker on June 22, 1852, for creating a curved upper needle and an under looper[62] to produce the double-looped stitch known as the Grover and Baker stitch.[Pg 38] One of the more fascinating patents was for the box or sewing case for which Grover received U.S. patent No. 14,956 on May 27, 1856. The inventor noted “that when open the box shall serve as the bed for the machine to be operated upon, and attaching the machine to it to assist with oiling, cleaning, and repairs without taking it out of the box.” It was the first portable sewing machine (fig. 36).
Though the Grover and Baker company manufactured machines using a shuttle and producing the more common lockstitch, both under royalty in their own name and also for other smaller companies, Potter was convinced that the Grover and Baker stitch was the one that eventually would be used in both family and commercial machines. He, as president, directed the efforts of the company to that end. When the basic patents held by the “Sewing-Machine Combination” (discussed on pp. 41-42) began to run out in the mid-1870s, dissolving its purpose and lowering the selling price of sewing machines, the Grover and Baker company began a systematic curtailing of expenses and closing of branch offices. All the patents held by the company and the business itself were sold to another company.[63] But the members of the Grover and Baker company fared well financially by the strategic move.
Though the Grover and Baker company made machines that used a shuttle and produced the more common lockstitch, both under royalty in their own name and for other smaller companies, Potter was convinced that the Grover and Baker stitch would eventually be the one used in both household and commercial machines. As president, he directed the company's efforts toward that goal. When the basic patents held by the “Sewing-Machine Combination” (discussed on pp. 41-42) started to expire in the mid-1870s, reducing its significance and lowering the prices of sewing machines, the Grover and Baker company began systematically cutting expenses and closing branch offices. All the patents held by the company and the business itself were sold to another company.[63] However, the members of the Grover and Baker company benefited financially from this strategic move.
The Grover and Baker machine and its unique stitch did not have a great influence on the overall development of the mechanics of machine sewing. The merits of a double-looped stitch—its elasticity and the taking of both threads from commercial spools—were outweighed by the bulkiness of the seam and its consumption of three times as much thread as the lockstitch required. Machines making a similar type of stitch have continued in limited use in the manufacture of knit goods and other products requiring an elastic seam. But, more importantly, Grover and Baker’s astute Orlando B. Potter placed their names in the annals of sewing-machine history by his work in forming the “Combination,” believed to be the first “trust” of any prominence.
The Grover and Baker machine and its unique stitch didn’t significantly impact the overall progress of sewing machine mechanics. The advantages of a double-looped stitch—its flexibility and the ability to use threads from commercial spools—were outweighed by the bulky seam and the fact that it used three times more thread than the lockstitch. Machines that produce a similar type of stitch are still used in a limited way for making knit goods and other products that need an elastic seam. But more importantly, Grover and Baker’s sharp-minded Orlando B. Potter secured their place in sewing machine history by creating the “Combination,” which is considered the first major “trust.”
FOOTNOTES:
[34] In the Matter of the Application of Elias Howe, Jr. for an Extension of His Sewing Machine Patent Dated September 10, 1846, New York, 1860, with attachments A and B, U.S. Patent Office. [L.C. call no. TJ 1512.H6265]
[34] Regarding the Application of Elias Howe, Jr. for an Extension of His Sewing Machine Patent from September 10, 1846, New York, 1860, with attachments A and B, U.S. Patent Office. [L.C. call no. TJ 1512.H6265]
[35] It is interesting to note that when William Thomas applied for the British patent of the Howe machine (issued Dec. 1, 1846), the courts would not allow the claim for the combination of the eye-pointed needle and shuttle to form a stitch, due to the Fisher and Gibbons patent of 1844. For more details on Howe’s years in England see his biographical sketch, pp. 138-141.
[35] It's interesting to note that when William Thomas applied for the British patent for the Howe machine (issued on Dec. 1, 1846), the courts did not permit the claim for the combination of the eye-pointed needle and shuttle to create a stitch, because of the Fisher and Gibbons patent from 1844. For more details on Howe’s years in England, see his biographical sketch, pp. 138-141.
[36] The machine referred to as the London Sewing Machine is the British patent of the Thimonnier machine. This patent was applied for by Jean Marie Magnin and was published by Newton’s London Journal, vol. 39, p. 317, as Magnin’s invention.
[36] The device known as the London Sewing Machine is the British patent for the Thimonnier machine. This patent was submitted by Jean Marie Magnin and was published in Newton’s London Journal, vol. 39, p. 317, as Magnin’s invention.
[38] James Parton, History of the Sewing Machine, p. 12, (originally published in the Atlantic Monthly, May 1867), later reprinted by the Howe Machine Company as a separate.
[38] James Parton, History of the Sewing Machine, p. 12, (originally published in the Atlantic Monthly, May 1867), later reprinted by the Howe Machine Company as a separate.
[39] Sewing Machine Times (Feb. 25, 1907), vol. 17, no. 382, p. 1, “His [Bonata’s] shop was on Gold Street, New York, near the Bartholf shop, where Howe was building some of his early machines.”
[39] Sewing Machine Times (Feb. 25, 1907), vol. 17, no. 382, p. 1, “His [Bonata’s] shop was located on Gold Street in New York, close to the Bartholf shop, where Howe was creating some of his early machines.”
[41] Op. cit. (footnote 34).
[47] See biographical sketch, pp. 141-142.
[53] Chester McNeil, A History of the Sewing Machine in Union Sales Bulletin, vol. 3, Union Special Sewing Machine Co., Chicago, Illinois, pp. 83-85. 1903.
[53] Chester McNeil, A History of the Sewing Machine in Union Sales Bulletin, vol. 3, Union Special Sewing Machine Co., Chicago, Illinois, pp. 83-85. 1903.
[55] Singer gives this limited description of the first machine, with detailed improvements for which he was then applying for a patent: “In my previous machine, to which reference has been made, the bobbin was carried by the needle-carrier, and hence the motion of the needle had to be equal to the length of thread required to form the loop, which was objectionable, as in many instances this range of motion was unnecessarily long for all other purposes....” Quoted from U.S. patent 8,294 issued to Isaac M. Singer, Aug. 12, 1851. It should be noted that in some instances there was a considerable lapse of time from the date a patent application was made until the patent was issued. In this case the handwritten specifications were dated March 14, 1851, and the formal Patent Office receipt was dated April 16, 1851.
[55] Singer provides this brief description of the first machine, along with the detailed improvements he was then seeking a patent for: “In my earlier machine, which has been referenced, the bobbin was held by the needle carrier, and therefore the needle's movement had to match the length of thread needed to create the loop, which was problematic, as in many cases this range of motion was unnecessarily long for all other purposes....” Quoted from U.S. patent 8,294 issued to Isaac M. Singer, Aug. 12, 1851. It's important to note that in some cases, there was a significant delay from when a patent application was submitted to when the patent was granted. In this instance, the handwritten specifications were dated March 14, 1851, and the official Patent Office receipt was dated April 16, 1851.
[56] If a patent was not approved, for any reason, the records were placed in an “Abandoned File.” In 1930 Congress authorized the disposal of the old “Abandoned Files,” requiring them to be kept for twenty years only. There are no Singer Company records giving an account of the first patent application.
[56] If a patent wasn't approved for any reason, the records were put in an “Abandoned File.” In 1930, Congress allowed the disposal of old “Abandoned Files,” stating that they only needed to be kept for twenty years. There are no records from the Singer Company about the first patent application.
[57] Its whereabouts was unknown as early as 1908, as stated in the Sewing Machine Times (Aug. 25, 1908), vol. 18, no. 418. Models of abandoned patents frequently remained at the Patent Office. Approximately 76,000 models were ruined in a Patent Office fire in 1877. In 1908 over 3000 models of abandoned patents were sold at auction. Either incident could account for the machine’s disappearance.
[57] Its location was unknown as early as 1908, according to the Sewing Machine Times (Aug. 25, 1908), vol. 18, no. 418. Models of abandoned patents often stayed at the Patent Office. About 76,000 models were destroyed in a Patent Office fire in 1877. In 1908, more than 3,000 models of abandoned patents were sold at auction. Either event could explain the machine’s disappearance.
[58] The patent model of 8,294 is a machine that bears the serial number 22; it was manufactured before April 18, 1851, the date it was recorded as received by the Patent Office.
[58] The patent model of 8,294 is a machine with the serial number 22; it was made before April 18, 1851, the date it was officially recorded as received by the Patent Office.
[61] This first, family sewing machine should not be confused in name with a model brought out in the sixties. The name of this first, family machine was in the sense of a new “family” sewing machine. In 1859 a “Letter A” family machine was introduced. Thus in 1865 when the Singer Company brought out another family machine they called it the “New” Family Sewing Machine. Both the first-style Family machine and the Letter A machine are illustrated in Eighty Years of Progress of the United States (New York, 1861), vol. 2, p. 417, and discussed in an article, “The Place and Its Tenants,” in the Sewing Machine Times (Dec. 25, 1908), vol. 27, no. 893.
[61] This first family sewing machine should not be confused with a model released in the sixties. The name of this initial family machine referred to a new kind of “family” sewing machine. In 1859, a “Letter A” family machine was introduced. So, in 1865, when the Singer Company released another family machine, they called it the “New” Family Sewing Machine. Both the original Family machine and the Letter A machine are shown in Eighty Years of Progress of the United States (New York, 1861), vol. 2, p. 417, and discussed in an article, “The Place and Its Tenants,” in the Sewing Machine Times (Dec. 25, 1908), vol. 27, no. 893.
Chapter Three
A PARTIAL STATEMENT FROM RECORDS OF “THE SEWING-MACHINE COMBINATION,” SHOWING
NUMBER OF SEWING-MACHINES LICENSED ANNUALLY UNDER THE ELIAS HOWE PATENT. | ||||||||||||||
---|---|---|---|---|---|---|---|---|---|---|---|---|---|---|
Manufacturer's Name. | 1853. | 1854. | 1855. | 1856. | 1857. | 1858. | 1859. | 1860. | 1861. | 1862. | 1863. | 1864. | 1865. | 1866. |
Wheeler & Wilson Mfg. Co. | 799 | 756 | 1,171 | 2,210 | 4,591 | 7,978 | 21,306 | 25,102 | 18,556 | 28,202 | 29,778 | 40,062 | 39,157 | 50,132 |
I. M. Singer & Co. | 810 | 879 | 883 | 2,564 | 3,630 | 3,594 | 10,953 | 13,000(a) | 16,000(a) | 18,396 | .... | .... | .... | .... |
The Singer Manufacturing Co. | .... | .... | .... | .... | .... | .... | .... | .... | .... | .... | 20,030 | 23,632 | 26,340 | 30,960 |
Grover & Baker S. M. Co. | 657 | 2,034 | 1,144 | 1,952 | 3,680 | 5,070 | 10,280 | (b) | (b) | (b) | (b) | (b) | (b) | (b) |
A. B. Howe ” ” ” | .... | 60 | 53 | 47 | 133 | 179 | 921 | (b) | (b) | (b) | (b) | (b) | (b) | (b) |
Leavitt ” ” ” | 28 | 217 | 152 | 235 | 195 | 75 | 213 | (b) | (b) | (b) | (b) | (b) | (b) | (b) |
Ladd & Webster ” ” ” | 100 | 268 | 73 | 180 | 453 | 490 | 1,788 | (b) | (b) | (b) | (b) | (b) | (b) | (b) |
Bartholf ” ” ” | 135 | 55 | 31 | 35 | 31 | 203 | 747 | (b) | (b) | (b) | (b) | (b) | (b) | (b) |
A PARTIAL STATEMENT SHOWING NUMBER OF SEWING-MACHINES LICENSED ANNUALLY
FROM 1867 TO 1876 INCLUSIVE. | ||||||||||
---|---|---|---|---|---|---|---|---|---|---|
Manufacturer Name. | 1867. | 1868. | 1869. | 1870. | 1871. | 1872. | 1873. | 1874. | 1875. | 1876. |
The Singer Manufacturing Co. | 43,053 | 59,629 | 86,781 | 127,833 | 181,260 | 219,758 | 232,444 | 241,679 | 249,852 | 262,316 |
Wheeler & Wilson Mfg. Co. | 38,055 | (b) | 78,866 | 83,208 | 128,526 | 174,088 | 119,190 | 92,827 | 103,740 | 108,997 |
Grover & Baker S. M. Co. | 32,999 | 35,000(a) | 35,188 | 57,402 | 50,838 | 52,010 | 36,179 | 20,000(a) | 15,000(a) | .... |
Weed Sewing-Machine Co. | 3,638 | 12,000 | 19,687 | 35,002 | 39,655 | 42,444 | 21,769 | 20,495 | 21,993 | 14,425 |
Howe Sewing-Machine Co. | 11,053 | 35,000(a) | 45,000(a) | 75,156 | 134,010 | 145,000(a) | 90,000(a) | 35,000(a) | 25,000(a) | 109,294 |
A. B. Howe ” ” ” | .... | .... | .... | .... | 20,051 | .... | .... | .... | .... | .... |
B. P. Howe ” ” ” | .... | .... | .... | .... | .... | 14,907 | 13,919 | .... | .... | .... |
Willcox & Gibbs S. M. Co. | 14,152 | 15,000 | 17,201 | 28,890 | 30,127 | 33,639 | 15,881 | 13,710 | 14,522 | 12,758 |
Wilson (W. G.) ” ” ” | .... | .... | .... | .... | 21,153 | 22,666 | 21,247 | 17,525 | 9,508 | .... |
American B. H. & S. M. Co. | .... | .... | 7,792 | 14,573 | 20,121 | 18,930 | 14,182 | 13,529 | 14,406 | 17,937 |
Florence S. M. Co. | 10,534 | 12,000 | 13,661 | 17,660 | 15,947 | 15,793 | 8,960 | 5,517 | 4,892 | 2,978 |
Shaw & Clark S. M. Co. | 2,692 | 3,000 | .... | .... | .... | .... | .... | .... | .... | .... |
Gold Medal ” ” ” | .... | .... | .... | 8,912 | 13,562 | 18,897 | 16,431 | 15,214 | 14,262 | 7,185 |
Davis ” ” ” | .... | .... | .... | .... | 11,568 | 11,376 | 8,861 | .... | .... | .... |
Domestic ” ” ” | .... | .... | .... | .... | 10,397 | 49,554 | 40,114 | 22,700 | 21,452 | 23,587 |
Finkle & Lyon Mfg. Co. and Victor. | 2,488 | 2,000 | 1,339 | 2,420 | 7,639 | 11,901 | 7,446 | 6,292 | 6,103 | 5,750 |
Ætna Sewing-Machine Co. | 2,958 | 3,500 | 4,548 | 5,806 | 4,720 | 4,262 | 3,081 | 1,866 | 1,447 | 707 |
Blees ” ” ” | .... | .... | .... | .... | 4,557 | 6,053 | 3,458 | .... | .... | .... |
Elliptic ” ” ” | 3,185 | .... | .... | .... | 4,555 | .... | .... | .... | .... | .... |
Empire ” ” ” | 2,121 | 5,000 | 8,700 | .... | .... | .... | .... | .... | .... | .... |
Remington Sewing-Machine Co. | .... | .... | .... | 3,560 | 2,965 | 4,982 | 9,183 | 17,608 | 25,110 | 12,716 |
Parham ” ” ” | .... | .... | 1,141 | 1,766 | 2,056 | .... | .... | .... | .... | .... |
Bartram & Fanton Mfg. Co. | 2,958 | .... | .... | .... | 1,004 | 1,000 | 1,000 | 250 | .... | .... |
Bartlett Sewing-Machine Co. | .... | .... | .... | .... | 614 | 1,000 | .... | .... | .... | .... |
J. G. Folsom | .... | .... | .... | .... | 280 | .... | .... | .... | .... | .... |
McKay Sewing-Machine Asso. | .... | .... | .... | 129 | 218 | .... | .... | 128 | 161 | 102 |
C. F. Thompson | .... | .... | .... | .... | 147 | .... | .... | .... | .... | .... |
Union Buttonhole Machine Co. | .... | .... | .... | .... | 124 | .... | .... | .... | .... | .... |
Leavitt Sewing-Machine Co. | 1,051 | 1,000 | 771 | .... | .... | .... | .... | .... | .... | .... |
Goodspeed & Wyman S. M. Co. | 2,126 | .... | .... | .... | .... | .... | .... | .... | .... | .... |
Keystone Sewing-Machine Co. | .... | .... | .... | .... | .... | 2,665 | 217 | 37 | .... | .... |
Secor ” ” ” | .... | .... | .... | .... | .... | 311 | 3,430 | 4,541 | 1,307 | .... |
Centennial ” ” ” | .... | .... | .... | .... | .... | .... | 514 | .... | .... | .... |
(a) Number estimated.
(b) No data.
(a) Estimated number.
(b) No data.
Figure 37.—Table of sewing-machine statistics. From Frederick G. Bourne, “American Sewing Machines” in One Hundred Years of American Commerce, vol. 2. ed. Chauncey Mitchell Depew (New York: D. O. Haines, 1895), p. 530. (Smithsonian photo 42542-A.)
Figure 37.—Sewing machine stats table. From Frederick G. Bourne, “American Sewing Machines” in One Hundred Years of American Commerce, vol. 2. ed. Chauncey Mitchell Depew (New York: D. O. Haines, 1895), p. 530. (Smithsonian photo 42542-A.)
The “Sewing-Machine Combination”
With the basic elements of a successful sewing machine assembled, the various manufacturers should have been able to produce good machines unencumbered. The court order, however, which restrained several firms from selling Singer machines while the Howe suit was pending, started a landslide; soon Wheeler, Wilson and company, Grover and Baker company, and several others[64] purchased rights from Elias Howe. This gave Howe almost absolute control of the sewing-machine business as these companies agreed to his royalty terms of $25 for every machine sold. In an attempt to improve his own machine, Howe was almost immediately caught up in another series of legal battles in which he was the defendant; the companies he had defeated were able to accuse him of infringing on patents that they owned. To compound the confusion, individual companies also were suing each other on various grounds.
With the essential components of a successful sewing machine put together, the different manufacturers should have been able to produce quality machines without any issues. However, the court order that stopped several companies from selling Singer machines while the Howe lawsuit was ongoing triggered a chain reaction; soon Wheeler, Wilson and Company, Grover and Baker Company, and several others[64] bought rights from Elias Howe. This gave Howe almost complete control over the sewing machine market as these companies agreed to his royalty terms of $25 for each machine sold. In an effort to improve his own machine, Howe quickly found himself in another round of legal disputes where he was the defendant; the companies he had beaten were able to accuse him of violating patents they owned. To make matters worse, individual companies were also suing each other on various grounds.
Because of this situation Orlando B. Potter, president of the Grover and Baker company, advanced in 1856 the idea of a “Combination” of sewing-machine manufacturers. He pointed out how the various companies were harming themselves by continuing litigation and tried to convince Howe that all would benefit by an agreement of some kind. He proposed that Elias Howe; Wheeler, Wilson and company; I. M. Singer and company; and Grover and Baker company pool their patents covering the essential features of the machine. The three companies had started production about the same time and approved of Potter’s idea; Howe opposed it as he felt that he had the most to lose by joining the “Combination.” He finally consented to take part in Potter’s plan if the others would agree to certain stipulations. The first requirement was that at least twenty-four manufacturers were to be licensed. The second was that, in addition to sharing equally in the profits with the three companies, Howe would receive a royalty of $5 for each machine sold in the United States and $1 for each machine exported. It has been estimated that, as a result of this agreement, Howe received at least $2,000,000 as his share of the license fees between 1856 and 1867 when his patent expired.[65]
Due to this situation, Orlando B. Potter, president of the Grover and Baker company, proposed in 1856 the idea of a "Combination" of sewing machine manufacturers. He pointed out how the various companies were harming themselves by continuing legal battles and tried to convince Howe that everyone would benefit from some kind of agreement. He suggested that Elias Howe, Wheeler, Wilson and Company, I. M. Singer and Company, and Grover and Baker Company pool their patents covering the key features of the machine. The three companies had started production around the same time and supported Potter’s idea; Howe disagreed because he felt he had the most to lose by joining the "Combination." He eventually agreed to participate in Potter’s plan if the others would accept certain conditions. The first requirement was that at least twenty-four manufacturers needed to be licensed. The second was that, in addition to sharing profits equally with the three companies, Howe would receive a royalty of $5 for each machine sold in the United States and $1 for each machine exported. It’s estimated that, as a result of this agreement, Howe received at least $2,000,000 as his share of the license fees between 1856 and 1867 when his patent expired.[65]
The organization was called the Sewing-Machine Trust and/or the Sewing-Machine Combination. The important patents contributed to it were:
The organization was called the Sewing Machine Trust and/or the Sewing Machine Combination. The key patents that contributed to it were:
1. The grooved, eye-pointed needle used with a shuttle to form the lockstitch (E. Howe patent, held by E. Howe);
1. The grooved needle with a pointed eye, used with a shuttle to create the lockstitch (E. Howe patent, owned by E. Howe);
2. The four-motion feeding mechanism (A. B. Wilson patent, held by Wheeler and Wilson company);
2. The four-motion feeding mechanism (A. B. Wilson patent, owned by the Wheeler and Wilson Company);
3. The needle moving vertically above a horizontal work-plate (Bachelder patent), a continuous feeding device by belt or wheel (Bachelder patent), a[Pg 42] yielding presser resting on the cloth (Bachelder patent), the spring or curved arm to hold the cloth by a yielding pressure (Morey and Johnson patent), the heart-shaped cam as applied to moving the needle bar (Singer patent); all these patents, held by the Singer Company.[66]
3. The needle moving up and down above a flat work surface (Bachelder patent), a continuous feeding system using a belt or wheel (Bachelder patent), a[Pg 42] adjustable presser resting on the fabric (Bachelder patent), the spring or curved arm to hold the fabric in place with a gentle pressure (Morey and Johnson patent), the heart-shaped cam used to move the needle bar (Singer patent); all of these patents are owned by the Singer Company.[66]
The Grover and Baker company contributed several patents of relative importance, but its most important claim for admission was the fact that Potter had promoted the idea.
The Grover and Baker company contributed several important patents, but its most significant argument for recognition was the fact that Potter had championed the idea.
The consent of all four member-parties was required before any license could be granted, and all were required to have a license—even the member companies. The fee was $15 per machine. A portion of this money was set aside to pay the cost of prosecuting infringers, Howe received his initial fee, and the rest was divided between the four parties. The advantage to the licensee was that he was required to pay only one fee. Most license applications were granted; only those manufacturing a machine specifically imitating the product of a licensed manufacturer were refused.
The consent of all four member parties was necessary before any license could be issued, and everyone needed to have a license—even the member companies. The fee was $15 per machine. A part of this money was allocated to cover the costs of prosecuting violators, Howe received his initial payment, and the rest was split among the four parties. The benefit for the licensee was that they only needed to pay one fee. Most license applications were approved; only those making a machine that specifically copied a product from a licensed manufacturer were denied.
The three company members each continued to manufacture, improve, and perfect its own machine. Other than the joint control of the patents, there was no pooling of interests, and each company competed to attract purchasers to buy its particular type of machine, as did the companies who were licensed by them.
The three company members each kept making, improving, and perfecting their own machines. Aside from sharing control over the patents, there was no collaboration, and each company competed to draw buyers for its specific type of machine, just like the companies they licensed.
In 1860, the year Howe’s patent was renewed, the general license fee was reduced from $15 to $7, and Howe’s special royalty was reduced to $1 per machine. Howe remained a member until his patent ran out in 1867. The other members continued the “Combination” until 1877, when the Bachelder patent, which had been extended twice, finally expired. By that time the fundamental features of the sewing machine were no longer controlled by anyone. Open competition by the smaller manufacturers was possible, and a slight reduction in price followed. Many new companies came into being—some destined to be very short-lived.
In 1860, the year Howe’s patent was renewed, the general license fee was lowered from $15 to $7, and Howe’s special royalty was reduced to $1 per machine. Howe stayed a member until his patent expired in 1867. The other members continued the “Combination” until 1877, when the Bachelder patent, which had been extended twice, finally expired. By then, the basic features of the sewing machine were no longer controlled by anyone. Smaller manufacturers could enter the market, leading to a slight price drop. Many new companies were founded—some of which would be very short-lived.
From the beginning to the end of the “Combination” there was an army of
independents, including infringers and imitators, who kept up a constant
complaint against it, maintaining that its existence tended to retard
the improvement of the sewing machine and that the public suffered
thereby. In the period immediately following the termination of the
however, only a few improvements of any importance were
made, and most of these were by the member companies.[Pg 43]
From the start to the finish of the “Combination,” there was a group of independents, including violators and copycats, who constantly complained about it, arguing that its existence slowed down the advancement of the sewing machine and that the public was worse off because of it. In the time right after the end of the
however, only a few important improvements were
made, and most of these came from the member companies.[Pg 43]
FOOTNOTES:
[64] These included the American Magnetic Sewing Machine Co.; A. Bartholf; Nichols and Bliss; J. A. Lerow; Woolridge, Keene, and Moore; and A. B. Howe. New York Daily Tribune, Sept. 3, 1853.
[64] These included the American Magnetic Sewing Machine Company; A. Bartholf; Nichols and Bliss; J. A. Lerow; Woolridge, Keene, and Moore; and A. B. Howe. New York Daily Tribune, Sept. 3, 1853.
[66] Singer has sometimes been credited as the inventor of the various improvements covered by the patents that the Singer company purchased and later contributed to the efforts of the Combination.
[66] Singer has sometimes been recognized as the creator of the different enhancements associated with the patents that the Singer company acquired and later played a role in the efforts of the Combination.
Chapter Four

Figure 38.—Gibbs’ patent model, 1857. (Smithsonian photo 45504-E.)
Figure 38.—Gibbs' patent model, 1857. (Smithsonian photo 45504-E.)
Less Expensive Machines
While the “Combination” was attempting to solve the problems of patent litigation, another problem faced the would-be home users of this new invention. The budget limitations of the average family caused a demand for a less expensive machine, for this first consumer appliance was a most desirable commodity.[67]
While the "Combo" was trying to address the issues of patent lawsuits, another challenge confronted potential home users of this new invention. The financial constraints of typical families created a need for a more affordable machine, as this first consumer appliance was highly sought after.[67]
There were many attempts to satisfy this demand, but one of the best and most successful grew out of a young man’s curiosity. James E. A. Gibbs’ first exposure to the sewing machine was in 1855 when, at the age of 24, he saw a simple woodcut illustration of a Grover and Baker machine. The woodcut represented only the upper part of the machine. Nothing in the illustration indicated that more than one thread was used, and none of the stitch-forming mechanism was visible. Gibbs assumed that the stitch was formed with one thread; he then proceeded to imagine a mechanism that would make a stitch with one thread. His solution was described in his own statement:
There were many attempts to meet this demand, but one of the best and most successful came from a young man's curiosity. James E. A. Gibbs first encountered the sewing machine in 1855 when, at the age of 24, he saw a simple woodcut illustration of a Grover and Baker machine. The woodcut only showed the upper part of the machine. Nothing in the illustration indicated that more than one thread was used, and none of the stitch-forming mechanism was visible. Gibbs assumed that the stitch was made with just one thread; he then imagined a mechanism that would create a stitch using one thread. His solution was outlined in his own words:
As I was then living in a very out of the way place, far from railroads and public conveyances of all kinds, modern improvements seldom reached our locality, and not being likely to have my curiosity satisfied otherwise, I set to work to see what I could learn from the woodcut, which was not accompanied by any description. I first discovered that the needle was attached to a needle arm, and consequently could not pass entirely through the material, but must retreat through the same hole by which it entered. From this I saw that I could not make a stitch similar to handwork, but must have some other mode of fastening the thread on the underside, and among other possible methods of doing this, the chainstitch occurred to me as a likely means of accomplishing the end.
Since I was living in a really remote area, far from railroads and any kind of public transportation, modern advancements rarely reached our neighborhood. With my curiosity unlikely to be satisfied otherwise, I started to figure out what I could learn from the woodcut, which didn’t come with any description. I first realized that the needle was connected to a needle arm, so it couldn’t pass completely through the material and had to pull back through the same hole it had entered. This made me understand that I couldn’t create a stitch like hand sewing, so I needed another way to secure the thread on the underside. Among the various methods I considered, the chain stitch seemed like a promising option to achieve that.
I next endeavored to discover how this stitch was or could be made, and from the woodcut I saw that the driving shaft which had the driving wheel on the outer end, passed along under the cloth plate of the machine. I knew that the mechanism which made the stitch must be connected with and actuated by this driving shaft. After studying the position and relations of the needle and shaft with each other, I conceived the idea of the revolving hook on the end of the shaft, which might take hold of the thread and manipulate it into a chainstitch. My ideas were, of course, very crude and indefinite, but it will be seen that I then had the correct conception of the invention afterwards embodied in my machine.[68]
I then tried to figure out how this stitch was or could be made, and from the woodcut, I could see that the driving shaft with the driving wheel on the outer end ran underneath the cloth plate of the machine. I understood that the mechanism for making the stitch had to be connected to and powered by this driving shaft. After examining the positions and relationships of the needle and shaft, I came up with the idea of a revolving hook at the end of the shaft that could grab the thread and form it into a chainstitch. My ideas were, of course, pretty basic and unclear, but it’s clear that I had the right concept for the invention that later went into my machine.[68]

Figure 39.—One of the first commercial machines produced by the Willcox & Gibbs Sewing Machine Co. in 1857, this machine bears no serial number, although the name “James E. A. Gibbs” is inscribed in two places on the cloth plate. It was used as the patent model for Gibbs’ improvement on his 1857 patent issued the following year on August 10, 1858. (Smithsonian photo P. 6393.)
Figure 39.—One of the earliest commercial machines produced by the Willcox & Gibbs Sewing Machine Co. in 1857, this machine has no serial number, though the name “James E. A. Gibbs” is engraved in two spots on the cloth plate. It was used as the patent model for Gibbs’ improvement on his 1857 patent, which was granted the following year on August 10, 1858. (Smithsonian photo P. 6393.)
Gibbs had no immediate interest in the sewing machine other than to satisfy his curiosity. He did not think of it again until January 1856 when he was visiting his father in Rockbridge County, Virginia. While in a tailor’s shop there, he happened to see a Singer machine. Gibbs was very much impressed, but thought the machine entirely too heavy, complicated, and cumbersome, and the price exorbitant. It was then that he recalled the machine he had devised. Remembering how simple it was, he decided to work in earnest to produce a less-expensive type of sewing machine.
Gibbs didn’t have any real interest in the sewing machine beyond his curiosity. He didn’t think about it again until January 1856 when he was visiting his father in Rockbridge County, Virginia. While in a tailor’s shop, he happened to see a Singer machine. Gibbs was really impressed, but he thought the machine was way too heavy, complicated, and bulky, and the price was outrageous. That’s when he remembered the machine he had created. Remembering how simple it was, he decided to seriously work on making a more affordable type of sewing machine.
Gibbs had little time to spend on this invention since his family was dependent upon him for support, but he managed to find time at night and during inclement weather. In contemporary references, Gibbs is referred to as a farmer, but since he is also reported to have had employers, it may be surmised that he was a farmhand. In any event, his decision to try to produce a less-expensive sewing machine suffered from a lack of proper tools and adequate materials. Most of the machine had to be constructed of wood, and he was forced to make his own needles. By the end of April 1856, however, his model was sufficiently completed to arouse the interest of his employers, who agreed to furnish the money necessary to patent the machine.
Gibbs had limited time to work on his invention since his family relied on him for support, but he found time at night and during bad weather. In modern references, Gibbs is called a farmer, but since he also had employers, it seems likely he was a farmhand. Regardless, his attempt to create a more affordable sewing machine faced challenges due to a lack of proper tools and materials. Most of the machine had to be made of wood, and he had to make his own needles. By the end of April 1856, however, his model was advanced enough to catch the interest of his employers, who agreed to provide the funds needed to patent the machine.
Gibbs went to Washington, where he examined sewing-machine models in the Patent Office and other machines then on the market. Completing his investigations, Gibbs made a trip to Philadelphia and showed his invention to a builder of models of new inventions, James Willcox. Much impressed with the machine, Willcox arranged for Gibbs to work with his son, Charles Willcox, in a small room in the rear of his shop. After taking out two minor patents (on December 16, 1856, and January 20, 1857), Gibbs obtained his important one, U.S. patent No. 17,427 on June 2, 1857 (fig. 38). His association with Charles Willcox led to the formation of the Willcox & Gibbs Sewing Machine Company, and they began manufacturing chainstitch machines in 1857 (fig. 39). The machine used a straight needle to make a chainstitch. At the forward end of the main shaft was a hook which, as it rotated, carried the loop of needle-thread, elongated and held it expanded while the feed moved the cloth until the needle at the next stroke descended through the loop so held. When the needle descended through the first loop, the point of the hook was again in position to catch the second loop, at which time the first loop was cast off and the second loop drawn through it, the first loop having been drawn up against the lower edge of the cloth to form a chain.[Pg 47]
Gibbs went to Washington, where he checked out sewing machine models at the Patent Office and other machines available on the market. After finishing his research, Gibbs traveled to Philadelphia and presented his invention to a model builder of new inventions, James Willcox. Impressed by the machine, Willcox arranged for Gibbs to collaborate with his son, Charles Willcox, in a small room at the back of his shop. After securing two minor patents (on December 16, 1856, and January 20, 1857), Gibbs obtained his key patent, U.S. patent No. 17,427, on June 2, 1857 (fig. 38). His partnership with Charles Willcox led to the creation of the Willcox & Gibbs Sewing Machine Company, and they started manufacturing chainstitch machines in 1857 (fig. 39). The machine used a straight needle to create a chainstitch. At the front end of the main shaft was a hook that, as it rotated, carried the loop of needle-thread, stretching and holding it while the feed moved the fabric until the needle, on the next stroke, went down through the loop. When the needle went down through the first loop, the point of the hook was again ready to catch the second loop, at which point the first loop was released and the second loop pulled through it, with the first loop having been drawn tight against the bottom edge of the fabric to create a chain.[Pg 47]

Figure 40.—A dolphin sewing machine based on Clark’s patent of 1858. This design was first used by T. J. W. Robertson in 1855, but in his patent issued on May 22 of that year no claim was made for the machine design, only for the chainstitch mechanism. The same style was used by D. W. Clark in several of his chainstitch patents, but he also made no claim for the design, stating that the machine “may be made in any desired ornamental form.” The dolphin-style machines are all chainstitch models of solid brass, originally gilt. Although only about five inches long, they are full-size machines using a full-size needle. (Smithsonian photo 45505.)
Figure 40.—A dolphin sewing machine based on Clark’s patent from 1858. This design was first used by T. J. W. Robertson in 1855, but his patent issued on May 22 that year did not claim the machine design, only the chainstitch mechanism. D. W. Clark used the same style in several of his chainstitch patents, but he also didn’t claim the design, stating that the machine “can be made in any desired decorative form.” The dolphin-style machines are all chainstitch models made of solid brass, originally gilded. Though they are only about five inches long, they are full-size machines using a full-size needle. (Smithsonian photo 45505.)
A Gibbs sewing machine, on a simple iron-frame stand with treadle, sold for approximately $50 in the late 1850s,[69] while a Wheeler and Wilson[70] machine or a Grover and Baker[71] with the same type of stand sold for approximately $100. After the introduction of the Gibbs machine, the Singer company[72] brought out a light family machine in 1858 that was also first sold for $100. It was then reduced to $50, but it was not popular because it was too light (see discussion of Singer machines, pp. 34-35). In 1859, Singer brought out its second, more successful family machine, which sold for $75.
A Gibbs sewing machine, on a simple iron-frame stand with a foot pedal, sold for about $50 in the late 1850s,[69] while a Wheeler and Wilson[70] machine or a Grover and Baker[71] with the same type of stand sold for around $100. After the Gibbs machine was introduced, the Singer company[72] released a light family machine in 1858, which initially sold for $100. It was later marked down to $50, but it didn't catch on because it was too light (see discussion of Singer machines, pp. 34-35). In 1859, Singer introduced its second, more successful family machine, which sold for $75.
Like the other companies licensed by the “Combination,” Willcox and Gibbs company paid a royalty for the use of the patents it held. Although the Willcox and Gibbs machine was a single-thread chainstitch machine and the company held the Gibbs patents, the company was required to be licensed to use the basic feed, vertical needle, and other related[Pg 48] patents held by the “Sewing-Machine Combination.”
Like the other companies licensed by the “Combination,” the Willcox and Gibbs company paid a royalty for using the patents it owned. Although the Willcox and Gibbs machine was a single-thread chainstitch machine and the company owned the Gibbs patents, it still needed a license to use the basic feed, vertical needle, and other related[Pg 48] patents held by the “Sewing-Machine Combination.”
With the approach of the Civil War, Gibbs returned to Virginia. Poor health prevented him from taking an active part in the war, but he worked throughout the conflict in a factory processing saltpeter for gunpowder. Afterward, Gibbs returned to Philadelphia and found that Willcox had faithfully protected his sewing-machine interests during his long absence. The firm prospered, and Gibbs finally retired to Virginia a wealthy man. Interestingly, Gibbs named the Virginia village to which he returned in later life “Raphine”—derived, somewhat incorrectly, from the Greek word “to sew.”
With the approach of the Civil War, Gibbs went back to Virginia. His poor health stopped him from taking an active role in the war, but he worked throughout the conflict in a factory processing saltpeter for gunpowder. After the war, Gibbs returned to Philadelphia and saw that Willcox had effectively protected his sewing machine interests during his long absence. The business thrived, and Gibbs eventually retired to Virginia a wealthy man. Interestingly, he named the Virginia village he returned to later in life “Raphine”—a name derived, somewhat incorrectly, from the Greek word for “to sew.”
The Willcox & Gibbs Sewing Machine Company is one of the few old companies still in existence. It discontinued making and selling family-style machines many years ago and directed its energies toward specialized commercial sewing machines, many of which are based on the original chainstitch principle.
The Willcox & Gibbs Sewing Machine Company is one of the few old companies still around. It stopped making and selling home sewing machines many years ago and focused its efforts on specialized commercial sewing machines, a lot of which are based on the original chainstitch principle.
There was also an ever-increasing number of other patentees and manufacturers who, in the late 1850s and 1860s, attempted to produce a sewing machine that would circumvent both the “Combination” and the high cost of manufacturing a more complicated type of machine. Some of the more interesting of these are pictured and described in figures 40 through 54.
There was also a growing number of other patentees and manufacturers who, in the late 1850s and 1860s, tried to create a sewing machine that would avoid both the “Combination” and the high cost of making a more complex type of machine. Some of the more interesting ones are shown and described in figures 40 through 54.

Figure 41.—The cherub sewing machine was another Robertson first which was adopted by Clark. Robertson’s patent of October 20, 1857, once again makes no claim for the design; neither does Clark’s patent of January 5, 1858, illustrated here. The machine is approximately the same size as the dolphin and is made in the same manner and of the same materials. Two cherubs form the main support, one also supporting the spool and leashing a dragonfly which backs the needle mechanism. (Smithsonian photo 45504-D.)
Figure 41.—The angelic child sewing machine was another innovation by Robertson that was adopted by Clark. Robertson’s patent from October 20, 1857, once again does not claim the design; nor does Clark’s patent from January 5, 1858, shown here. The machine is about the same size as the dolphin and is made in a similar way and from the same materials. Two cherubs form the main support, with one also holding the spool and restraining a dragonfly that supports the needle mechanism. (Smithsonian photo 45504-D.)

Figure 42.—The foliage sewing machine originated with D. W. Clark. Once again he did not include the design in his June 8, 1858, patent, which was aimed at improving the feeding mechanism. Like most hand-turned models, these required a clamp to fasten them to the table when in operation. (Smithsonian photo 45504-C.)
Figure 42.—The leaf sewing machine was created by D. W. Clark. He again did not include the design in his patent from June 8, 1858, which focused on enhancing the feeding mechanism. Like most hand-turned models, these needed a clamp to secure them to the table while in use. (Smithsonian photo 45504-C.)

Figure 43.—The sewing shears was another popular machine of unusual style. Some models were designed to both cut and sew, but most derived their names from the method of motivating power. The earliest example of the sewing-shears machine was invented by Joseph Hendrick, who stated in his patent that he was attempting to produce “a simple, portable, cheap, and efficient machine.” His patent model of October 5, 1858, is illustrated. (Smithsonian photo 45504-F.)
Figure 43.—The tailor scissors was another popular machine with a unique design. Some versions were made to both cut and sew, but most got their names from how they were powered. The first example of the sewing-shears machine was created by Joseph Hendrick, who mentioned in his patent that he aimed to make “a simple, portable, cheap, and efficient machine.” His patent model from October 5, 1858, is shown here. (Smithsonian photo 45504-F.)

Figure 44.—The horse sewing machine is among the most unusual of the patents issued for mechanical improvements. Although James Perry, the patentee, made several claims for the looper, feeder, and tension, he made no mention of the unusual design of the machine, for which a patent was issued on November 23, 1858. Although it was probably one of a kind, the horse machine illustrates the extent to which the inventor’s mind struggled for original design. (Smithsonian photo 45505-C.)
Figure 44.—The horse-powered sewing machine is one of the most unique patents for mechanical improvements. While James Perry, the patent holder, claimed several features for the looper, feeder, and tension, he didn’t mention the machine’s unusual design, which received a patent on November 23, 1858. Even though it was likely one of a kind, the horse machine shows the lengths to which the inventor went in search of an original design. (Smithsonian photo 45505-C.)

Figure 45.—Many inventors attempted to cut the cost of manufacturing a complicated machine. One of these was Albert H. Hook, whose machine is only about four inches high and two inches wide. His patent, granted November 30, 1858, simplified the construction and arrangement of the various parts. Although Hook used a barbed needle reminiscent of the one used by Thimonnier, his method of forming the stitch was entirely different. The thread was passed through the necessary guides, and when the cloth was in place the needle was thrust up from below. Passing through the fabric, the needle descended, carrying with it a loop of thread. As the process was repeated, a chainstitch was formed with the enchained loop on the under side. In spite of its simple mechanism, Hook’s machine was not a commercial success. (Smithsonian photo 45505-D.)
Figure 45.—Many creators tried to reduce the cost of manufacturing a complex machine. One of them was Albert H. Hook, whose machine is only about four inches tall and two inches wide. His patent, granted on November 30, 1858, made the construction and arrangement of the various parts simpler. Although Hook used a barbed needle similar to the one used by Thimonnier, his method of forming the stitch was completely different. The thread was threaded through the necessary guides, and when the fabric was in place, the needle was pushed up from below. After going through the fabric, the needle descended, bringing with it a loop of thread. As this process repeated, a chain stitch was created with the loop connected underneath. Despite its simple mechanism, Hook’s machine did not achieve commercial success. (Smithsonian photo 45505-D.)

Figure 46.—In addition to mechanical patents, a number of design patents were also issued for sewing machines. These fall into a separate series in the Patent Office’s numerical records. This unusual example featured two semidraped female figures holding the spool of thread, a mermaid holding the needle, a serpent which served as the presser foot, and a heart-shaped baster plate. The design was patented by W. N. Brown, October 25, 1859, but no examples other than the patent model are known to have been made. (Smithsonian photo 45504-A.)
Figure 46.—With mechanical patents, several design patents were also granted for sewing machines. These are categorized separately in the Patent Office’s numerical records. This unique example showcased two partially draped female figures holding the spool of thread, a mermaid holding the needle, a serpent serving as the presser foot, and a heart-shaped baster plate. W. N. Brown patented the design on October 25, 1859, but no other examples besides the patent model are known to exist. (Smithsonian photo 45504-A.)

Figure 47.—The squirrel machine was another interesting design patent. S. B. Ellithorp had received a mechanical patent for a two-thread, stationary-bobbin machine on August 26, 1857. That same month he published a picture of his machine, shown here as republished in the Sewing Machine News, vol. 7, no. 11, November 1885. The machine was designed in the shape of “the ordinary gray squirrel so common throughout this country—an animal that is selected as a type of provident care and forethought, for its habits of frugality and for making provision for seasons of scarcity and want in times of plenty—and the different parts of the animal are each put to a useful purpose; the moving power being placed within its body, the needle stock through its head, one of its fore feet serving to guide the thread, and the other to hold down the cloth while being sewed, and the tip of its tail forming a support to the spool from which the thread is supplied.”
Figure 47.—The squirrel robot is another fascinating design patent. S. B. Ellithorp received a mechanical patent for a two-thread, stationary-bobbin machine on August 26, 1857. That same month, he published a picture of his machine, shown here as republished in the Sewing Machine News, vol. 7, no. 11, November 1885. The machine was designed in the shape of "the ordinary gray squirrel that is so common throughout this country—an animal chosen for its prudent behavior and foresight, due to its frugal habits and its ability to prepare for times of scarcity during periods of abundance—and the various parts of the animal are each assigned a practical purpose; the moving power is placed inside its body, the needle stock goes through its head, one of its forefeet helps guide the thread, the other holds down the fabric while it’s being sewn, and the tip of its tail serves as a support for the spool from which the thread is provided."
Although the design patent was not secured until June 7, 1859, the inventor was reported to have been perfecting his machine for manufacture in 1857. Ellithorp planned “to place them in market at a price that will permit families and individuals that have heretofore been deterred from purchasing a machine by the excessive and exorbitant price charged for those now in use, to possess one.” Patent rights were sold under the name of Ellithorp & Fox, but the machine was never manufactured on a large scale, if at all. No squirrel machines are known to have survived. (Smithsonian photo 53112.)
Although the design patent wasn't finalized until June 7, 1859, the inventor was said to have been refining his machine for production in 1857. Ellithorp intended “to market them at a price that would enable families and individuals, who have previously been discouraged from buying a machine due to the high and unreasonable prices of those currently available, to own one.” Patent rights were sold under the name of Ellithorp & Fox, but the machine was never produced on a large scale, if at all. No squirrel machines are known to have survived. (Smithsonian photo 53112.)

Figure 48.—Heyer’s pocket sewing machine patent model, November 17, 1863. This patent model is one piece, and measures about two inches in height and two inches in length. It will stitch—but only coarse, loosely woven fabrics. As can be expected, a great deal of manual dexterity is required to compensate for the omission of mechanical parts. Heyer advertised patent rights for sale, but evidence of manufactured machines of this type has yet to be discovered. (Smithsonian photo 18115-D[a].)
Figure 48.—Heyer’s portable sewing machine patent model, November 17, 1863. This patent model is a single unit, measuring about two inches tall and two inches long. It can stitch, but only coarse, loosely woven fabrics. As expected, a lot of manual skill is needed to make up for the lack of mechanical components. Heyer marketed the patent rights for sale, but there’s still no evidence of machines made from this design. (Smithsonian photo 18115-D[a].)

Figure 49.—Heyer’s machine as illustrated in Scientific American, July 30, 1864. The smallest and most original of all the attempts to simplify machine sewing, Heyer’s machine, which made a chainstitch, was constructed of a single strip of metal. The Scientific American stated: “It is simply a steel spring ingeniously bent and arranged and it is said to sew small articles very well. The whole affair can easily be carried in the coat pocket.”
Figure 49.—Heyer’s device as shown in Scientific American, July 30, 1864. The smallest and most innovative of all the efforts to make machine sewing easier, Heyer’s machine, which created a chainstitch, was made from a single strip of metal. The Scientific American reported: “It’s just a steel spring cleverly bent and arranged, and it’s said to sew small items very well. The whole thing can easily fit in a coat pocket.”
One method of operation, vibrating with the finger, was illustrated. The machine could be operated also by holding it in the hand and pressuring it between two fingers. Cloth was inserted at c, and the prongs of the spring feed f carried it along after each stitch. It was stated that the needle could be cut from the same strip of metal, but it was advised also that the needle could be made as a separate piece and attached. (Smithsonian photo 48221.)
One way to operate it, by vibrating with your finger, was shown. The machine could also be used by holding it in your hand and squeezing it between two fingers. Cloth was put in at c, and the prongs of the spring feed f moved it along after each stitch. It was mentioned that the needle could be made from the same strip of metal, but it was also recommended that the needle could be made as a separate piece and attached. (Smithsonian photo 48221.)

Figure 50.—Although Bean’s and Rodgers’ running-stitch machines, the second and fourth U.S. sewing-machine patents, experienced little commercial success, small manufactured machines based on Aaron Palmer’s patent of May 13, 1862, were popular in the 1860s. The patent model above is a small brass implement with crimping gears that forced the fabric onto an ordinary sewing needle. The full needle was then removed from its position, and the thread was pulled through the fabric by hand. (Smithsonian photo 45524.)
Figure 50.—Bean's and Rodgers' running-stitch machines, the second and fourth U.S. sewing-machine patents, didn’t achieve much commercial success, small machines based on Aaron Palmer’s patent from May 13, 1862, were quite popular in the 1860s. The patent model above is a small brass tool with crimping gears that pushed the fabric onto a regular sewing needle. The full needle was then taken out of its position, and the thread was pulled through the fabric by hand. (Smithsonian photo 45524.)

Figure 51.—One of the early commercial manufacturers of the Palmer patent was Madame Demorest, a New York dressmaker. She advertised her Fairy sewing machine in Godey’s Lady’s Book, vol. 66, 1863, and stated: “In the first place it will attract attention from its diminutive, fairy-like size, and with the same ease with which it can be carried, an important matter to a seamstress or dressmaker employed from house to house ... What no other sewing machine attempts to do, it runs, and does not stitch, it sews the more delicate materials an ordinary sewing machine cuts or draws....” (Smithsonian photo 43690.)
Figure 51.—One of the first commercial manufacturers of the Palmer patent was Madame Demorest, a dressmaker from New York. She promoted her Fairy sewing machine in Godey’s Lady’s Book, vol. 66, 1863, saying: “First of all, it will catch attention because of its small, fairy-like size, and it's easy to carry, which is important for a seamstress or dressmaker working from one house to another ... Unlike any other sewing machine, it runs without stitching; it sews delicate fabrics that regular machines would cut or pull....” (Smithsonian photo 43690.)

Figure 52.—The Fairy sewing machine sold for five dollars and was adequate for its advertised purpose, sewing or running very lightweight fabrics. The machine was marked with the Palmer patent, the date May 13, 1862, and the name “Mme. Demorest.”
Figure 52.—The Fairy sewing machine was sold for five dollars and was suitable for its intended use, sewing or handling very lightweight fabrics. The machine bore the Palmer patent, dated May 13, 1862, and the name “Mme. Demorest.”
A machine identical to the Fairy, but bearing both Palmer patent dates, May 13, 1862, and June 19, 1863, and the name “Gold Medal,” was manufactured by a less-scrupulous company. This machine was advertised as follows: “A first class sewing machine, handsomely ornamented, with all working parts silver plated. Put up in a highly polished mahogany case, packed ready for shipment. Price $10.00. This machine uses a common sewing needle, is very simple. A child can operate it. Cash with order.” Some buyers felt they were swindled, as they had expected a heavy-duty machine, but no recourse could be taken against the advertiser. Another similar machine was also manufactured under the name “Little Gem.” (Smithsonian photo 45525.)
A machine similar to the Fairy, but featuring both Palmer patent dates, May 13, 1862, and June 19, 1863, and the name “Gold Medal,” was produced by a less-reputable company. This machine was marketed with the following description: “A top-quality sewing machine, beautifully decorated, with all working parts silver-plated. Packaged in a highly polished mahogany case, ready for shipment. Price $10.00. This machine uses a standard sewing needle and is very simple. A child can use it. Payment required with order.” Some customers felt cheated, as they had anticipated a heavy-duty machine, but there was no action they could take against the advertiser. Another similar machine was also made under the name “Little Gem.” (Smithsonian photo 45525.)

Figure 53 and 54.—Running-stitch machines were also attempted by several other inventors. Shaw & Clark, manufacturers of chainstitch machines, patented this running-stitch machine on April 21, 1863. From the appearance of the patent model, it was already in commercial production. On May 26, 1863, John D. Dale also received a patent for an improvement related to the method of holding the needle and regulating the stitches in a running-stitch machine. Dale’s patent model was a commercial machine.
Figure 53 and 54.—Sewing machines with running stitch were also tried out by several other inventors. Shaw & Clark, known for chainstitch machines, patented this running-stitch machine on April 21, 1863. Based on the design of the patent model, it was already in commercial production. On May 26, 1863, John D. Dale also got a patent for an improvement related to how the needle was held and how the stitches were regulated in a running-stitch machine. Dale’s patent model was a commercial machine.
John Heberling patented several improvements in 1878 and 1880. His machine, which was a little larger and in appearance resembled a more conventional type of sewing machine, was a commercial success. (Shaw & Clark: Smithsonian photo P. 6395; Dale: Smithsonian photo P. 6394.)
John Heberling patented several enhancements in 1878 and 1880. His machine, which was slightly larger and looked similar to a more traditional sewing machine, was a commercial success. (Shaw & Clark: Smithsonian photo P. 6395; Dale: Smithsonian photo P. 6394.)

FOOTNOTES:
[67] Scientific American (Jan. 29, 1859), vol. 14, no. 21, p. 165. In a description of the new Willcox and Gibbs sewing machine the following observation is made: “It is astonishing how, in a few years, the sewing machine has made such strides in popular favor, and become, from being a mechanical wonder, a household necessity and extensive object of manufacture. While the higher priced varieties have such a large sale, it is no wonder that the cheaper ones sell in such tremendous quantities, and that our inventors are always trying to produce something new and cheap.”
[67] Scientific American (Jan. 29, 1859), vol. 14, no. 21, p. 165. In a description of the new Willcox and Gibbs sewing machine, it states: “It’s amazing how, in just a few years, the sewing machine has gained so much popularity, transforming from a mechanical marvel to an essential household item and a major product of manufacturing. While the higher-priced models sell really well, it’s no surprise that the more affordable ones are flying off the shelves and that our inventors are constantly looking to create something new and cheaper.”
[72] I. M. Singer & Co.’s Gazette, vol. 5, no. 4 (March 1, 1859), p. 4, and a brochure, Singer’s New Family Sewing Machine (in Singer Manufacturing Company, Historic Archives).
[72] I. M. Singer & Co.’s Gazette, vol. 5, no. 4 (March 1, 1859), p. 4, and a brochure, Singer’s New Family Sewing Machine (in Singer Manufacturing Company, Historic Archives).
Appendixes
I. Notes on the Development and Commercial Use of the Sewing Machine
INTRODUCTION
While researching the history of the invention and the development of the sewing machine, many items of related interest concerning the machine’s economic value came to light. The manufacture of the machines was in itself a boost to the economy of the emerging “industrial United States,” as was the production of attachments for specialized stitching and the need for new types of needles and thread. Moreover, the machine’s ability to speed up production permitted it to permeate the entire field of products manufactured by any type of stitching, from umbrellas to tents. Since this aspect of the story was not completed for this study, no attempt will be made to include any definitive statements on the economic importance of the sewing machine at home or abroad. This related information is of sufficient interest, however, to warrant inclusion in this first Appendix. Perhaps these notes will suggest areas of future research for students of American technology.
While researching the history of the invention and development of the sewing machine, I discovered many interesting details about its economic impact. The production of the machines itself helped boost the economy of the emerging industrial United States, as did the manufacturing of specialized sewing attachments and the demand for new types of needles and thread. Additionally, the machine's ability to increase production allowed it to penetrate the entire range of products made with any kind of stitching, from umbrellas to tents. Since this aspect of the story wasn’t completed for this study, I won't attempt to make any final statements about the economic significance of the sewing machine both domestically and internationally. However, this related information is interesting enough to be included in this first Appendix. Perhaps these notes will inspire future research for students of American technology.
READY-MADE CLOTHING
Whether of the expensive or the inexpensive type, the sewing machine was much more than a popular household appliance. Its introduction had far-reaching effects on many different types of manufacturing establishments as well as on the export trade. The newly developing ready-made clothing industry was not only in a state of development to welcome the new machine but also was, in all probability, responsible for its immediate practical application and success.
Whether expensive or inexpensive, the sewing machine was much more than just a popular household appliance. Its introduction had significant impacts on various manufacturing businesses and the export trade. The emerging ready-made clothing industry was not only ready to embrace the new machine but likely also played a key role in its quick adoption and success.
Until the early part of the second quarter of the 19th century, the ready-made clothing trade in the United States was confined almost entirely to furnishing the clothing required by sailors about to ship out to sea. The stores that kept these supplies were usually in the neighborhood of wharf areas. But other than the needs of these seamen, there was little market for ready-made goods. Out of necessity many of the families in the early years in this country had made their own clothing. As wealth was acquired and taste could be cultivated, professional seamstresses and tailors were in increasing demand, moved into the cities and towns, and even visited the smaller villages for as long as their services were needed. At the same time a related trade was also growing in the cities, especially in New York City, that of dealing in second-hand clothing. Industrious persons bought up old clothes, cleaned, repaired and refinished them, and sold the clothing to immigrants and transients who wished to avoid the high cost of new custom-made clothing.
Until the early part of the second quarter of the 19th century, the ready-made clothing trade in the United States was mainly focused on providing clothes for sailors preparing to leave for sea. The stores that stocked these supplies were typically located near wharf areas. However, aside from the needs of these sailors, there was little demand for ready-made clothing. Out of necessity, many families in the early years of this country made their own clothes. As people gained wealth and developed their tastes, professional seamstresses and tailors became increasingly sought after. They moved into cities and towns and even traveled to smaller villages for as long as their services were needed. At the same time, a related trade was growing in the cities, especially in New York City—dealing in second-hand clothing. Enterprising individuals bought up old clothes, cleaned, repaired, and refurbished them, and sold these garments to immigrants and transients who wanted to avoid the high cost of new custom-made clothing.
The repairing of this second-hand clothing led to the purchase of cheap cloth at auction— “half-burnt,” “wet-goods,” and other damaged yardage. When in excess of the repairing needs, this fabric was made into garments and sold with the second-hand items. Many visitors who passed through New York City were found to be potential buyers of this merchandise if a better class of ready-made clothes was made available. Manufacture began to increase. Tailors of the city began to keep an assortment of finished garments on hand. When visitors bought these, they were also very likely to buy additional garments for resale at home. The latter led to the establishment of the wholesale garment-manufacturing industry in New York about 1834-35.
The repair of second-hand clothing led to buying cheap fabric at auction— "half-burnt," "wet-goods," and other damaged materials. When there was more fabric than needed for repairs, it was turned into garments and sold alongside the second-hand items. Many visitors to New York City turned out to be potential buyers of this merchandise if better-quality ready-made clothes were available. Manufacturing started to ramp up. Tailors around the city began keeping a selection of finished garments in stock. When visitors bought these, they were also likely to purchase more items to sell back home. This eventually led to the creation of the wholesale garment-manufacturing industry in New York around 1834-35.
Most of the ready-made clothing establishments were small operations, not large factories. Large[Pg 58] quantities of cloth were purchased; cutting was done in multiple layers with tailor’s shears. Since many seamstresses were needed, the garments were farmed out to the girls in their homes. The manufacture of garments in quantity meant that the profit on each garment was larger than a tailor could make on a single custom-made item. The appeal of increased profits influenced many to enter the new industry and, due to the ensuing competition, the retail cost of each garment was lowered. Just as the new businesses were getting underway, the Panic of 1837 ruined most of them. But the lower cost and the convenience of ready-made clothing had left its mark. Not only was the garment-manufacturing business re-established soon after the Panic had subsided, but by 1841 the value of clothing sold at wholesale in New York was estimated at $2,500,000 and by 1850—a year before sewing machines were manufactured in any quantity—there were 4,278 clothing manufacturing establishments in the United States. Beside New York City, Cincinnati was also one of the important ready-made clothing centers. In 1850 the value of its products amounted to $4,427,500 and in 1860 to $6,381,190. Boston was another important center with a ready-made clothing production of $4,567,749 in 1860. Philadelphia, Baltimore, Louisville, and St. Louis all had a large wholesale clothing trade by 1860. Here was the ready market for a practical sewing machine.[73]
Most of the ready-made clothing businesses were small operations, not large factories. They bought large quantities of fabric, and cutting was done in multiple layers with tailor’s shears. Since many seamstresses were needed, the garments were assigned to the girls working from home. Producing clothes in bulk meant that the profit on each item was greater than what a tailor could earn on a single custom piece. The promise of higher profits attracted many to this new industry, and because of the resulting competition, the retail price of each garment went down. Just as these new businesses were starting to thrive, the Panic of 1837 devastated most of them. However, the lower prices and the convenience of ready-made clothing left a lasting impact. Not only was the clothing manufacturing business re-established soon after the Panic, but by 1841, the wholesale value of clothing sold in New York was estimated at $2,500,000, and by 1850—just a year before sewing machines were produced in significant numbers—there were 4,278 clothing manufacturing establishments in the United States. Alongside New York City, Cincinnati also emerged as a major center for ready-made clothing. In 1850, the value of its products was $4,427,500 and rose to $6,381,190 by 1860. Boston was another significant center, with ready-made clothing production valued at $4,567,749 in 1860. By 1860, Philadelphia, Baltimore, Louisville, and St. Louis all had a substantial wholesale clothing trade. This created a strong demand for a practical sewing machine.[73]
Clothing establishments grew and began to have agencies in small towns and the sewing work was distributed throughout the countryside. The new, competing sewing-machine companies were willing to deliver a machine for a small sum and to allow the buyer to pay a dollar or two a month until the full amount of the sale was paid. This was an extension of the hire-purchase plan (buying on credit) initiated by Clark of the Singer Company. The home seamstresses were eager to buy, for they were able to produce more piecework with a sewing machine and therefore earn more money. An example of the effect that the sewing machine had on the stitching time required was interestingly established through a series of experiments conducted by the Wheeler and Wilson company. Four hand sewers and four sewing-machine operators were used to provide the average figures in this comparative time study, the results of which were published in 1861;[74]
Clothing stores expanded and started opening branches in small towns, distributing sewing work throughout the countryside. The new, competitive sewing machine companies were willing to sell a machine for a low price and let buyers pay a dollar or two a month until the full price was settled. This was an extension of the hire-purchase plan (buying on credit) started by Clark of the Singer Company. Home seamstresses were eager to buy, as they could do more piecework with a sewing machine and earn more money. An interesting example of how the sewing machine impacted stitching time was shown through a series of experiments by the Wheeler and Wilson company. Four hand seamstresses and four sewing machine operators were used to gather average figures in this comparative time study, the results of which were published in 1861;[74]
NUMBER OF STITCHES PER MINUTE
STITCHES PER MINUTE
By Hand | By Machine | |
Patent leather, fine stitching | 7 | 175 |
Binding hats | 33 | 374 |
Stitching vamped shoes | 10 | 210 |
Stitching fine linen | 23 | 640 |
Stitching fine silk | 30 | 550 |
TIME FOR GARMENTS STITCHED
TIME FOR CLOTHES TO BE STITCHED
By Hand | By Machine | |
Frock coats | 16 hrs. 35 min. | 2 hrs. 38 min. |
Satin vests | 7 hrs. 19 min. | 1 hr. 14 min. |
Summer pants | 2 hrs. 50 min. | 0 hr. 38 min. |
Calico dress | 6 hrs. 37 min. | 0 hr. 57 min. |
Plain apron | 1 hr. 26 min. | 0 hr. 9 min. |
Gentlemen’s shirts | 14 hrs. 26 min. | 1 hr. 16 min. |
The factory manufacturer, with the sewing work done at the factory, was also developing. In 1860, Oliver F. Winchester, a shirt manufacturer of New Haven, Connecticut, stated that his factory turned out 800 dozen shirts per week, using 400 sewing machines and operators to do the work of 2,000 hand sewers. The price for hand sewing was then $3 per week, which made labor costs $6000 per week. The 400 machine operators received $4 per week, making the labor cost $1600 per week. Allowing $150 as the cost of each machine, the sewing machines more than paid for themselves in less than 14 weeks, increased the operators pay by $1 a week, and lowered the retail cost of the item.[75] The greatest savings of time, which was as much as fifty percent, was in the manufacture of light goods—such items as shirts, aprons, and calico dresses. The Commissioner of Patents weighed the monetary effect that this or any invention had on the economy against the monetary gain received by the patentee. When he found that the patentee had not been fairly compensated, he had the authority to grant a seven-year extension to the patent. [76] [Pg 59]
The factory manufacturer, with the sewing done in-house, was also growing. In 1860, Oliver F. Winchester, a shirt maker from New Haven, Connecticut, reported that his factory produced 800 dozen shirts each week, using 400 sewing machines and operators to do the work of 2,000 hand sewers. The cost for hand sewing at the time was $3 per week, which made labor costs $6,000 per week. The 400 machine operators earned $4 per week, bringing the labor cost to $1,600 per week. With each machine costing $150, the sewing machines paid for themselves in less than 14 weeks, increased the operators' pay by $1 a week, and lowered the retail price of the shirts. The biggest savings in time—up to fifty percent—was in producing lightweight items like shirts, aprons, and calico dresses. The Commissioner of Patents evaluated the economic impact of this or any invention against the financial benefits received by the patent holder. When he determined that the patent holder had not been adequately compensated, he had the authority to grant a seven-year extension to the patent. [Pg 59]
The sewing machine also contributed to the popularity of certain fashions. Ready-made cloaks for women were a business of a few years’ standing when the sewing machine was adopted for their manufacture in 1853. Machine sewing reduced the cost of constructing the garment by about eighty percent, thereby decreasing its price and increasing its popularity. In New York City alone, the value of the “cloak and mantilla” manufacture in 1860 was $618,400.[77] Crinolines and hoopskirts were easier to stitch by machine than by hand, and these items had a spirited period of popularity due to the introduction of the sewing machine. Braiding, pleating, and tucking adorned many costume items because they could be produced by machine with ease and rapidity.
The sewing machine also played a big role in the popularity of certain styles. Ready-made cloaks for women were a business that had been around for a few years when the sewing machine was used for their production in 1853. Machine sewing cut the cost of making the garment by about eighty percent, which lowered its price and boosted its popularity. In New York City alone, the value of "cloak and mantilla" production in 1860 was $618,400.[77] Crinolines and hoop skirts were much easier to sew by machine than by hand, and these garments enjoyed a vibrant period of popularity because of the sewing machine's introduction. Braiding, pleating, and tucking decorated many costume pieces since they could be done quickly and easily with machines.
In addition to using the sewing machine for the manufacture of shirts, collars, and related men’s furnishings, the machine was also used in the production of men’s and boy’s suits and reportedly gave “a vast impetus to the trade.”[78] The Army, however, was not quite convinced of the sewing machine’s practical adaptation to its needs. Although a sewing machine was purchased for the Philadelphia Quartermaster Depot as early as 1851, they had only six by 1860. On March 31, 1859, General Jesup of the Philadelphia Depot wrote to a Nechard & Company stating that the machine sewing had been tried but was not used for clothing, only for stitching caps and chevrons. In another letter, on the same day, to “Messers Hebrard & Co., Louisiana Steam Clothing Factory, N. Orleans,” Jesup states: “Machine sewing has been tried with us, and though it meets the requirements of a populous and civilized life, it has been found not to answer for the hard wear and tear and limited means of our frontier service. Particular attention has been paid to this subject, and we have abandoned the use of machines for coats, jackets and trousers, etc. and use them on caps and bands that are not exposed to much hard usage....”[79] At this period prior to the Civil War, the Army manufactured its own clothing. As the demands of war increased, more and more of the Army’s clothing supplies were furnished on open contract—with no specifications as to stitching.[80] Machine stitching, in fact, is found in most of the Civil War uniforms. One of the problems that most probably affected the durability of the machine stitching in the 1850s was the sewing thread, a problem that was not solved until the 1860s and which is discussed later under “thread for the machine.”
In addition to using the sewing machine for making shirts, collars, and other men's clothing, the machine was also used in producing men's and boys' suits and reportedly gave “a huge boost to the trade.”[78] The Army, however, wasn’t fully convinced of how suitable the sewing machine was for its needs. Even though a sewing machine was bought for the Philadelphia Quartermaster Depot as early as 1851, they only had six by 1860. On March 31, 1859, General Jesup of the Philadelphia Depot wrote to Nechard & Company saying that machine sewing had been tried but wasn’t used for clothing, only for stitching caps and chevrons. In another letter, on the same day, to “Messers Hebrard & Co., Louisiana Steam Clothing Factory, N. Orleans,” Jesup stated: “Machine sewing has been attempted here, and while it meets the needs of a populous and civilized life, it hasn’t proven effective for the heavy wear and limited resources of our frontier service. We’ve paid special attention to this issue and have stopped using machines for coats, jackets, trousers, etc., instead using them for caps and bands that aren't subjected to much rough use....”[79] At this time before the Civil War, the Army made its own clothing. As the demands of war increased, a growing amount of the Army’s clothing supplies were provided on open contract—with no specifications regarding stitching.[80] Machine stitching was indeed found in most Civil War uniforms. One of the issues that likely affected the durability of machine stitching in the 1850s was the sewing thread, a problem that wasn’t resolved until the 1860s and which is discussed later under “thread for the machine.”

Figure 55.—Blake’s leather-stitching machine patent model of July 6, 1858; the inventor claimed the arrangement of the mechanism used and an auxiliary arm capable of entering the shoe, which enabled the outer sole to be stitched both to the inner sole and to the upper part of the shoe. (Smithsonian photo 50361.)
Figure 55.—Blake's leather sewing machine patent model from July 6, 1858; the inventor claimed the setup of the mechanism and an additional arm that could reach inside the shoe, allowing the outer sole to be stitched to both the inner sole and the upper part of the shoe. (Smithsonian photo 50361.)
SHOE MANUFACTURE
Another industry that was aided by the new invention was that of shoe manufacture. Although the earliest sewing-machine patents in the United States reflect the inventors’ efforts to solve the difficult task of leather stitching, and, although machines were used to a limited extent in stitching some parts of[Pg 60] the shoe in the early and mid-1850s, it was not until 1858 that a machine was invented that could stitch the sole to the inner sole and to the upper part of the shoe. This was the invention of Lyman R. Blake and was patented by him on July 8, 1858; the patent model is shown in figure 55. Blake formed a chainstitch by using a hooked needle, which descended from above, to draw a thread through the supporting arm. Serving as the machine’s bedplate, the arm was shaped to accommodate the stitching of all the parts of the shoe.
Another industry that benefited from the new invention was shoe manufacturing. While the earliest sewing machine patents in the United States show the inventors' attempts to tackle the challenging task of stitching leather, and although machines were used to a limited extent for stitching some parts of[Pg 60] the shoe in the early and mid-1850s, it wasn't until 1858 that a machine was created that could stitch the sole to the inner sole and to the upper part of the shoe. This was the invention of Lyman R. Blake, patented by him on July 8, 1858; the patent model is shown in figure 55. Blake created a chainstitch using a hooked needle, which came down from above, to pull a thread through the supporting arm. The arm, acting as the machine’s bedplate, was designed to enable stitching of all parts of the shoe.

Figure 56.—Harris’ patent thread cutter, 1872. (Smithsonian photo P-6397.)
Figure 56.—Harris's patent thread cutter, 1872. (Smithsonian photo P-6397.)

Figure 57.—West’s patent thread cutter, 1874. (Smithsonian photo P-63100.)
Figure 57.—West's patent thread cutter, 1874. (Smithsonian photo P-63100.)
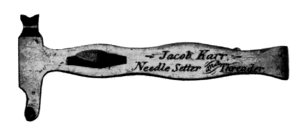
Figure 58.—Karr’s patent needle threader, 1871. (Smithsonian photo P-63101.)
Figure 58.—Karr's patent needle threader, 1871. (Smithsonian photo P-63101.)
The increased number of shoes required by the Army during the Civil War spurred the use of the sewing machine in their manufacture. The first “machine sewed bootees” were purchased by the Army in 1861. Inventors continued their efforts; the most prominent of these was Gordon McKay, who worked on an improvement of the Blake machine with Robert Mathies in 1862 and then with Blake in 1864. Reportedly, the Government at first preferred the machine-stitched shoes as they lasted eight times longer than those stitched by hand; during the war the Army purchased 473,000 pairs, but in 1871 the Quartermaster General wrote:
The growing demand for shoes by the Army during the Civil War led to the adoption of the sewing machine for their production. The first "machine-sewn bootees" were bought by the Army in 1861. Inventors kept working on enhancements; the most notable was Gordon McKay, who collaborated with Robert Mathies to improve the Blake machine in 1862 and then with Blake in 1864. Reports suggest that the Government initially preferred machine-stitched shoes because they lasted eight times longer than hand-stitched ones; during the war, the Army acquired 473,000 pairs, but in 1871, the Quartermaster General wrote:
No complaints regarding the quality of these shoes were received up to February 1867 when a Board of Survey, which convened at Hart’s Island, New York Harbor reported upon the inferior quality of certain machine sewed bootees of the McKay patent, issued to the enlisted men at that post. The acting Quartermaster General, Col. D. H. Rucker, April 10, 1867, addressed a letter to all the officers in charge of depots, with instructions not to issue any more of the shoes in question, but to report to this office the quantity remaining in store. From these reports it appears that there were in store at that time 362,012 pairs M. S. Bootees, all of which were ordered to be, and have since been sold at public auction.[81]
No complaints about the quality of these shoes were reported until February 1867, when a Board of Survey convened at Hart’s Island, New York Harbor, and reported on the poor quality of certain machine-sewn bootees of the McKay patent issued to the enlisted men at that post. The acting Quartermaster General, Col. D. H. Rucker, wrote a letter on April 10, 1867, to all officers in charge of depots, instructing them not to distribute any more of the problematic shoes and to report the quantity remaining in stock. According to these reports, there were 362,012 pairs of M. S. Bootees in storage at that time, all of which were ordered to be sold at public auction. [81]
The exact complaint against the shoes was not recorded. Possibly the entire shoe was stitched by machine. It was found that although machine-stitched shoes were more durable in some respects and the upper parts of most shoes continued to be machine stitched, pegged soles for the more durable varieties remained the fashion for a decade or more, as did custom hand-stitched shoes for those who could afford them.
The specific complaint about the shoes wasn't documented. It's likely that the whole shoe was made by machine. It turned out that while machine-stitched shoes were more durable in some ways and the tops of most shoes were still machine-stitched, pegged soles for the more durable styles stayed in fashion for over a decade, just like custom hand-stitched shoes for those who could pay for them.
OTHER USES
The use of sewing machines in all types of manufacturing that required stitching of any type continued to grow each year. While the principal purpose for which they were utilized continued to be the manufacture of clothing items, by the year 1900 they were also used for awnings, tents, and sails; cloth bags; bookbinding and related book manufacture; flags and banners; pocketbooks, trunks, and valises; saddlery and harnesses; mattresses; umbrellas; linen and rubber belting and hose; to the aggregate sum of nearly a billion dollars—$979,988,413.[82]
The use of sewing machines in all types of manufacturing that required stitching continued to grow each year. While their main purpose was still to make clothing, by 1900 they were also being used for awnings, tents, sails; cloth bags; bookbinding and related book production; flags and banners; wallets, trunks, and suitcases; saddles and harnesses; mattresses; umbrellas; linen and rubber belts and hoses; totaling nearly a billion dollars—$979,988,413.[82]
SEWING-MACHINE ATTACHMENTS
The growing popularity of the sewing machine offered still another boost to the economy—the development of many minor, related manufacturing[Pg 61] industries. The repetitive need for machine needles, the development of various types of attachments to simplify the many sewing tasks, and the ever-increasing need for more and better sewing thread—the sewing machine consumed from two to five times as much thread as stitching by hand—created new manufacturing establishments and new jobs.
The increasing popularity of the sewing machine provided an extra boost to the economy through the growth of several related manufacturing industries. The constant demand for machine needles, the creation of different attachments to make various sewing tasks easier, and the rising need for higher quality sewing thread—the sewing machine used two to five times more thread than hand sewing—led to the establishment of new manufacturing companies and the creation of new jobs.[Pg 61]

Figure 59.—Shank’s patent bobbin winder, 1870. (Smithsonian photo P-6398.)
Figure 59.—Shank's patented bobbin winder, 1870. (Smithsonian photo P-6398.)

Figure 60.—Sweet’s patent binder, 1853. (Smithsonian photo P-6396.)
Figure 60.—Sweet's patent binder, 1853. (Smithsonian photo P-6396.)

Figure 61.—Spoul’s patent braid guide, 1871. (Smithsonian photo P-63102.)
Figure 61.—Spoul's patent braid guide, 1871. (Smithsonian photo P-63102.)
The method of manufacturing machine needles did not differ appreciably from the method used in making the common sewing needle, but the latter had never become an important permanent industry in the United States. Since the manufacture of practical sewing machines was essentially an American development and the eye-pointed needle a vital component of the machine, it followed that the manufacture of needles would also develop here. Although such a manufacture was established in 1852,[83] foreign imports still supplied much of the[Pg 62] need in the 1870s. As more highly specialized stitching machines were developed, an ever-increasing variety of needles was required, and the industry grew.
The process of making machine needles was not very different from making regular sewing needles, but the latter had never turned into a significant permanent industry in the United States. Since the development of practical sewing machines was primarily an American innovation, and the eye-pointed needle was a crucial part of these machines, it made sense that needle manufacturing would grow here as well. Although needle production started in 1852,[83] foreign imports still met much of the[Pg 62] demand in the 1870s. As more specialized stitching machines were created, a wider variety of needles became necessary, and the industry expanded.

Figure 64.—The treadle of the machine was also used to help create music. George D. Garvie and George Wood received patent 267,874, Nov. 21, 1882, for “a cover for a sewing machine provided with a musical instrument and means for transmitting motion from the shaft of the sewing machine to the operating parts of the musical instrument.” Although no patent model was submitted by the inventors, the “Musical Sewing Machine Cover” was offered for sale as early as October 1882, as shown by this advertisement that appeared in The Sewing Machine News that month. (Smithsonian photo 57983.)
Figure 64.—The machine's pedal was also used to help make music. George D. Garvie and George Wood received patent 267,874 on Nov. 21, 1882, for “a cover for a sewing machine with a musical instrument and mechanisms to transmit motion from the sewing machine’s shaft to the musical instrument’s operating parts.” Although no patent model was provided by the inventors, the “Musical Sewing Machine Cover” was available for purchase as early as October 1882, as indicated by this advertisement that appeared in The Sewing Machine News that month. (Smithsonian photo 57983.)
Soon after the sewing machine was commercially successful, special attachments for it were invented and manufactured. These ranged from the simplest devices for cutting thread to complicated ones for making buttonholes (see figs. 56 through 66).
Soon after the sewing machine became a commercial success, special attachments for it were invented and produced. These included everything from simple tools for cutting thread to complex ones for making buttonholes (see figs. 56 through 66).

Figure 65.—This fanning attachment was commercially available from James Morrison & Co. in the early 1870s; it sold for one dollar as stated in the advertising brochure from which this engraving was copied. Other inventors also patented similar implements. (Smithsonian photo 45513.)
Figure 65.—This fan attachment was available for purchase from James Morrison & Co. in the early 1870s; it was priced at one dollar according to the advertising brochure that this engraving was based on. Other inventors also patented similar tools. (Smithsonian photo 45513.)
The first patent for an attachment was issued in 1853 to Harry Sweet for a binder, used to stitch a special binding edge to the fabric. Other related attachments followed; among these were the hemmer which was similar to the binder, but turned the edge of the same piece of fabric to itself as the stitching was performed. Guides for stitching braid in any pattern, as directed by the movement of the goods below, were also developed; this was followed by the embroiderer, an elaborate form of braider. The first machine to stitch buttonholes was patented in 1854 and the first buttonhole attachment in 1856, but the latter was not practical until improvements were made in the late 1860s. Special devices for refilling the bobbins were invented and patented as early as 1862, and the popularity of tucked and ruffled garments inspired inventors to provide sewing-machine attachments for these purposes also. To keep the seamstress cool, C. D. Stewart patented an attachment for fanning the operator by an action derived from the treadle (fig. 65). While electric[Pg 63] sewing machines did not become common until the 20th century, several 19th-century inventors considered the possibility of attaching a type of motor to the machine. One was the 1871 patent of Solomon Jones, who added an “electro motor” to an 1865 Bartlett machine (fig. 66). The attachments that were developed during the latter part of the 19th century numbered in the thousands; many of these were superfluous. Most of the basic ones in use today were developed by the 1880s and remain almost unchanged. Even the recently popular home zigzag machine, an outgrowth of the buttonhole machine, was in commercial use by the 1870s.
The first patent for an attachment was issued in 1853 to Harry Sweet for a binder, which was used to stitch a special binding edge onto the fabric. Other related attachments followed; among them was the hemmer, which was similar to the binder but folded the edge of the same piece of fabric back on itself as the stitching was done. Guides for stitching braid in any pattern, based on the movement of the fabric below, were also created; this was followed by the embroiderer, a more complex version of the braider. The first machine to stitch buttonholes was patented in 1854, and the first buttonhole attachment came in 1856, but the latter wasn’t practical until improvements were made in the late 1860s. Special devices for refilling the bobbins were invented and patented as early as 1862, and the popularity of tucked and ruffled garments led inventors to create sewing machine attachments for these purposes as well. To keep the seamstress cool, C. D. Stewart patented an attachment that fanned the operator using a motion derived from the treadle (fig. 65). While electric[Pg 63] sewing machines didn’t become common until the 20th century, several 19th-century inventors looked into attaching a type of motor to the machine. One was the 1871 patent of Solomon Jones, who added an “electro motor” to an 1865 Bartlett machine (fig. 66). The attachments developed during the latter part of the 19th century numbered in the thousands; many of these were unnecessary. Most of the basic ones still in use today were created by the 1880s and remain almost unchanged. Even the recently popular home zigzag machine, a result of the buttonhole machine, was commercially available by the 1870s.
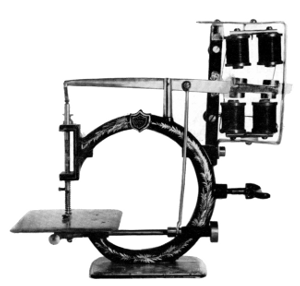
Figure 66.—Jones “electro motor” patent model of 1871 on a Bartlett sewing machine. (Smithsonian photo P-63104.)
Figure 66.—Jones "electric motor" patent model of 1871 on a Bartlett sewing machine. (Smithsonian photo P-63104.)
Sewing-machine improvements have been made from time to time. Like other mechanical items the machine has become increasingly automatic, but the basic principles remain the same. One of the more recent developments, patented[84] in 1933 by Valentine Naftali et al., is for a manufacturing machine that imitates hand stitching. This machine uses a two-pointed “floating needle” that is passed completely through the fabric—the very idea that was attempted over one hundred years ago. The machine is currently used by commercial manufacturers to produce decorative edge-stitching that very closely resembles hand stitching.
Sewing machine improvements have happened over time. Like other machines, these devices have become more automated, but the core principles are still the same. One of the latest innovations, patented[84] in 1933 by Valentine Naftali and others, is a manufacturing machine that mimics hand stitching. This machine features a two-pointed “floating needle” that completely goes through the fabric—the very concept that was tried over a hundred years ago. Today, this machine is used by commercial manufacturers to create decorative edge-stitching that closely resembles hand stitching.
THREAD FOR THE MACHINE
The need for a good thread durable enough to withstand the action of machine stitching first created a problem and ultimately another new industry in this country. When the sewing machine was first developed the inventors necessarily had to use the sewing thread that was available. But, although the contemporary thread was quite suitable for hand sewing, it did not lend itself to the requirements of the machine. Cotton thread, then more commonly a three-ply variety, had a glazed finish and was wiry. Silk thread frequently broke owing to abrasion at the needle eye. For the most part linen thread was too coarse, or the fine variety was too expensive. All of the thread had imperfections that went unnoticed in the hands of a seamstress, but caused havoc in a machine.[Pg 64] Quality silk thread that would withstand the rigors of machine stitching could be produced, but it was quite expensive also. A new type of inexpensive thread was needed; the obvious answer lay in improving the cotton thread.[85]
The demand for a durable thread that could handle machine stitching created both a challenge and eventually a new industry in this country. When the sewing machine was first invented, the creators had to use whatever sewing thread was available at the time. However, while the existing thread worked fine for hand sewing, it didn't meet the needs of the machine. Cotton thread, at that time typically a three-ply type, had a glazed finish that made it wiry. Silk thread often broke due to wear at the needle eye. For the most part, linen thread was either too thick, or the finer types were too pricey. All types of thread had flaws that a seamstress could overlook, but these flaws wreaked havoc in a machine.[Pg 64] Quality silk thread that could endure the demands of machine stitching could be made, but it was also quite costly. A new kind of affordable thread was necessary; the clear solution was to enhance the cotton thread.[85]
In addition to the popular three-ply variety, cotton thread was also made by twisting together either two single yarns or more than three yarns. Increasing the number of yarns produced a more cylindrical thread. The earliest record of a six-ply cotton thread was about 1840.[86] And in 1850 C. E. Bennett of Portsmouth, New Hampshire, received a gold medal for superior six-cord, or six-ply, spool cotton at the Fair of the American Institute. But the thread was still wiry and far from satisfactory. By the mid-1860s the demonstrated need for thread manufacturers in America brought George A. Clark and William Clark, third generation cotton-thread manufacturers of Paisley, Scotland, to Newark, New Jersey, where they built a large mill. George Clark decided that a thread having both a softer finish and a different construction was needed. He produced a six-cord cabled thread, made up of three two-ply yarns (see fig. 67). The thread was called “Clark’s ‘Our New Thread,’” which was later shortened to O.N.T. The basic machine-thread problem was solved. When other manufacturers used the six-cord cabled construction they referred to their thread as “Best Six-Cord”[87] or “Superior Six-Cord”[88] to distinguish it from the earlier variety made up of six single yarns in a simple twist. Another new side industry of the sewing machine was successfully established.
In addition to the popular three-ply type, cotton thread was also created by twisting together either two single yarns or more than three yarns. Increasing the number of yarns resulted in a thicker, more cylindrical thread. The earliest record of a six-ply cotton thread dates back to around 1840.[86] In 1850, C. E. Bennett from Portsmouth, New Hampshire, received a gold medal for outstanding six-cord, or six-ply, spool cotton at the Fair of the American Institute. However, the thread still had a wiry texture and was far from ideal. By the mid-1860s, the evident demand for thread manufacturers in America brought George A. Clark and William Clark, third-generation cotton-thread makers from Paisley, Scotland, to Newark, New Jersey, where they established a large mill. George Clark realized that a thread with both a softer feel and a different construction was necessary. He developed a six-cord cabled thread made from three two-ply yarns (see fig. 67). This thread was named "Clark's 'Our New Thread,'" which was later shortened to O.N.T. The fundamental machine-thread issue was resolved. When other manufacturers adopted the six-cord cabled design, they labeled their thread as "Best Six-Cord"[87] or "Superior Six-Cord"[88] to differentiate it from the earlier version made of six single yarns twisted together. A new side industry related to the sewing machine was successfully launched.
MANUFACTURE AND EXPORT, TO 1900
Sewing machines were a commodity in themselves, both at home and abroad. In 1850, there were no establishments exclusively devoted to the manufacture of sewing machines, the few constructed were made in small machine shops. The industry, however, experienced a very rapid growth during the next ten years. By 1860 there were 74 factories in 12 States,[89] mainly in the East and Midwest,[90] producing over 111,000 sewing machines a year. In addition, there were 14 factories that produced sewing-machine cases and attachments. The yearly value of these products was approximately four and a half million dollars, of which the amount exported in 1861 was $61,000. Although the number of sewing-machine factories dropped from 74 in 1860 to 69 by 1870, the value of the machines produced increased to almost sixteen million dollars.
Sewing machines became popular items, both at home and internationally. In 1850, there were no factories solely focused on making sewing machines; the few that existed were built in small machine shops. However, the industry saw rapid growth over the next ten years. By 1860, there were 74 factories in 12 states,[89] mostly in the East and Midwest,[90] producing over 111,000 sewing machines each year. Additionally, 14 factories made sewing machine cases and attachments. The total annual value of these products was around four and a half million dollars, with exports in 1861 reaching $61,000. Although the number of sewing machine factories dropped from 74 in 1860 to 69 by 1870, the value of the machines produced rose to almost sixteen million dollars.
The number of sewing-machine companies fluctuated greatly from year to year as many attempted to enter this new field of manufacture. Some were not able to make a commercial success of their products. The Civil War did not seem to be an important factor in the number of companies in business in the North. Although one manufacturer ceased operations in Richmond, Virginia, and a Vermont firm converted to arms manufacture, several companies began operations during the war years. Of the 69 firms in business in 1870, only part had been in business since 1860 or before; some were quite new as a result of the expiration of the Howe patent renewal in 1867.
The number of sewing machine companies varied a lot from year to year as many tried to get into this new manufacturing market. Some couldn’t turn their products into commercial successes. The Civil War didn’t seem to significantly impact the number of companies operating in the North. While one manufacturer shut down in Richmond, Virginia, and a firm from Vermont switched to making weapons, several companies started up during the war years. Of the 69 companies operating in 1870, only some had been around since 1860 or earlier; others were fairly new because the Howe patent renewal expired in 1867.
Probably due to the termination of many of the major patents, there were 124 factories in 1880, but the yearly product value remained at sixteen million dollars. The 1890 census reports only 66 factories with a yearly production of a little less than the earlier decade. But by 1900, the yearly production of a like number of factories had reached a value of over twenty-one million, of which four and a half million dollars worth were exported annually. The total value of American sewing machines exported from 1860 to 1900 was approximately ninety million dollars. The manufacture of sewing machines made a significant contribution to the economic development of 19th-century America.
Probably due to the expiration of many major patents, there were 124 factories in 1880, but the annual product value stayed at sixteen million dollars. The 1890 census shows only 66 factories producing slightly less than in the previous decade. However, by 1900, the annual production from a similar number of factories had increased to over twenty-one million dollars, with four and a half million dollars worth being exported each year. The total value of American sewing machines exported from 1860 to 1900 was around ninety million dollars. The manufacturing of sewing machines played a significant role in the economic growth of 19th-century America.
FOOTNOTES:
[75] George Gifford, “Argument of [George] Gifford in Favor of the Howe Application for Extension of Patent” (New York: United States Patent Office, 1860).
[75] George Gifford, “Argument of [George] Gifford in Support of the Howe Application for Patent Extension” (New York: United States Patent Office, 1860).
[76] Op. cit. (footnote 34).
[77] Eighth Census, 1860, Manufactures (United States Census Office, published Government Printing Office: Washington, D.C., 1865), “Women’s Ready-Made Clothing,” p. 83.
[77] Eighth Census, 1860, Manufactures (United States Census Office, published by Government Printing Office: Washington, D.C., 1865), “Women’s Ready-Made Clothing,” p. 83.
[78] Ibid., p. 64.
__A_TAG_PLACEHOLDER_0__ Same source, p. 64.
[80] The author wishes to acknowledge the valuable help of Mr. Donald Kloster of the Smithsonian Institution’s Division of Military History for the preceding four references and related information.
[80] The author wants to thank Mr. Donald Kloster from the Smithsonian Institution’s Division of Military History for his helpful contributions to the previous four references and related information.
[81] Letter of Nov. 4, 1871, to Col. Theo. A. Dodge, USA (Ret.), Boston, from Quartermaster General M. C. Meigs, in the National Archives, Record Group 92, Quartermaster General’s Office, Letters Sent, Clothing Supplies, 1871.
[81] Letter dated November 4, 1871, to Colonel Theodore A. Dodge, USA (Ret.), in Boston, from Quartermaster General M. C. Meigs, found in the National Archives, Record Group 92, Quartermaster General’s Office, Letters Sent, Clothing Supplies, 1871.
[82] Twelfth Census of the United States, 1900, vol. 10, Manufactures, Part 4, Special Reports on Selected Industries (United States Census Office, Washington, D.C., 1902).
[82] Twelfth Census of the United States, 1900, vol. 10, Manufactures, Part 4, Special Reports on Selected Industries (United States Census Office, Washington, D.C., 1902).
[83] Charles M. Karch, “Needles: Historical and Descriptive,” in Twelfth Census of the United States, 1900, vol. 10, Manufactures, Part 4, Special Reports on Selected Industries (United States Census Office: Washington, D.C., 1902), pp. 429-432.
[83] Charles M. Karch, “Needles: Historical and Descriptive,” in Twelfth Census of the United States, 1900, vol. 10, Manufactures, Part 4, Special Reports on Selected Industries (United States Census Office: Washington, D.C., 1902), pp. 429-432.
[84] U.S. patent 1,931,447, issued to Valentine Naftali, Henry Naftali, and Rudolph Naftali, Oct. 17, 1933. The Naftali machines are manufactured by the American Machine and Foundry Company and are called AMF Stitching Machines.
[84] U.S. patent 1,931,447, granted to Valentine Naftali, Henry Naftali, and Rudolph Naftali on October 17, 1933. The Naftali machines are produced by the American Machine and Foundry Company and are known as AMF Stitching Machines.
[88] Willimantic spool cotton.
Willimantic spool cotton.
[89] New Hampshire, Vermont, Massachusetts, Rhode Island, Connecticut, New York, Pennsylvania, Delaware, Ohio, Indiana, Illinois, Kentucky. Eighth Census, 1860, Manufactures (United States Census Office, published by Government Printing Office: Washington, D.C., 1865.)
[89] New Hampshire, Vermont, Massachusetts, Rhode Island, Connecticut, New York, Pennsylvania, Delaware, Ohio, Indiana, Illinois, Kentucky. Eighth Census, 1860, Manufactures (United States Census Office, published by Government Printing Office: Washington, D.C., 1865.)
[90] Sewing-machine manufacture in the South was just beginning to blossom when it was curtailed by the outbreak of the Civil War. See Lester sewing machine, figure 109 on page 102.
[90] The production of sewing machines in the South was just starting to thrive when it was interrupted by the start of the Civil War. See Lester sewing machine, figure 109 on page 102.
II. American Sewing-Machine Companies of the 19th Century
During the latter half of the 19th century, there was a total of two hundred or more sewing-machine companies in the United States. Although a great many manufacturing-type machines were sold, this business was carried on by relatively few companies and most were primarily concerned with the family-type machines. A representative number of these family machines together with information concerning both the company and serial-number dating are found in figures 68 through 132. A great many of the companies were licensed by the “Combination,” but, in addition, some companies were constructing machines that did not infringe the patents, other companies infringed the patents but managed to avoid legal action, and there were numerous companies that mushroomed into existence after the “Combination” was dissolved in 1877. Most of the latter were very short-lived. It is difficult to establish the exact dates of some of these companies as many of their records were incomplete or have since disappeared; even a great many of the “Combination” records were lost by fire. A summary of the existing records kept by the “Combination” is given in figure 37.
During the second half of the 19th century, there were over two hundred sewing machine companies in the United States. While many manufacturing-type machines were sold, this business was mainly handled by a relatively small number of companies, most of which focused on family-type machines. A representative selection of these family machines, along with information about the companies and serial number dating, can be found in figures 68 through 132. Many of these companies were licensed by the "Combination," but in addition, some created machines that didn’t infringe on patents, while others did infringe but managed to avoid legal action. Numerous companies also appeared after the "Combination" was dissolved in 1877, but most of them were very short-lived. It's hard to pinpoint the exact dates for some of these companies since many of their records were incomplete or have since been lost; even many records from the "Combination" were destroyed in a fire. A summary of the existing records maintained by the "Combination" is presented in figure 37.
As will be noted in the subsequent listing, only a small percentage of the companies were in business for a period longer than ten years; of those that continued longer, all but a few had disappeared by 1910. Today there are about sixty United States sewing-machine companies. Most of them manufacture highly specialized sewing machines used for specific types of commercial work; only a few produce family or home-style machines. Foreign competition has increased, and the high cost of skilled labor in this country has made competition in this consumer-product field increasingly difficult. The countless varieties of American family sewing machines, so evident in the 19th century, have passed away.
As you’ll see in the next listing, only a small percentage of companies were operational for more than ten years; of those that lasted longer, almost all had vanished by 1910. Nowadays, there are around sixty sewing machine companies in the United States. Most of them make highly specialized machines for specific types of commercial work; only a handful produce machines for home use. Foreign competition has increased, and the high cost of skilled labor in this country has made it tougher to compete in this consumer product market. The many varieties of American home sewing machines that were so common in the 19th century have disappeared.
Sewing Machine | Manufacturer or Company | First Made or Earliest Record | Discontinued or Last Record |
---|---|---|---|
Aetna | Aetna Sewing Machine Co., Lowell, Mass. | ca. 1867 | ca. 1877 |
Aiken and Felthousen | ——, Ithaca, N.Y. | ca. 1855 | before 1880 |
Alsop | —— | — | ca. 1880 |
American | American Sewing Machine Co. | 1854 | — |
American Buttonhole, Overseaming and Sewing Machine (fig. 68) | American Buttonhole, Overseaming and Sewing Machine Co., Philadelphia, Pa. | 1869 | ca. 1874 |
Later New American (fig. 69) | American Sewing Machine Co., Philadelphia, Pa. | ca. 1874 | ca. 1886 |
American Magnetic (fig. 70) | American Magnetic Sewing Machine Company, Ithaca, N.Y. | 1853 | 1854 |
[Pg 66] Atlantic (fig. 71) | —— | 1869 | ca. 1870 |
Atwater (fig. 87) | —— | 1857 | ca. 1860 |
Avery | Avery Sewing Machine Co., New York, N.Y. | 1852 | 185- |
Avery | Avery Manufacturing Co., New York, N.Y. | 1875 | 1886-1900 |
A. Bartholf Manfr. | A. Bartholf, manufacturer, New York, N.Y. | ca. 1850 | 185- |
Blodgett & Lerow patent 1849 (see also) | |||
A. Bartholf Manfr. | A. Bartholf, manufacturer, New York, N.Y. | 1853 | ca. 1856 |
Howe’s patent, 1846 (fig. 72) | |||
Bartholf | A. Bartholf, manufacturer | 1857 | 1859 |
Bartholf Sewing Machine Co. | 1859 | ca. 1865 | |
Bartlett (fig. 73) | Goodspeed & Wyman | 1866 | ca. 1870 |
Bartlett Sewing Machine Co., New York, N.Y. | ca. 1870 | 1872 | |
Baker | —— | — | before 1880 |
Bartram & Fanton (fig. 74) | Bartram & Fanton Mfg. Co., Danbury, Conn. | 1867 | 1874 |
Bay State | —— | — | before 1880 |
Beckwith (fig. 75) | Barlow & Son, New York, N.Y. | 1871 | 1872 |
Beckwith Sewing Machine Co., New York, N.Y. | 1872 | ca. 1876 | |
Blees | Blees Sewing Machine Co. | 1870 | 1873 |
Blodgett & Lerow | O. Phelps, Boston, Mass. | 1849 | 1849 |
(fig. 21) | Goddard, Rice & Co., Worcester, Mass. | 1849 | 1850 |
(fig. 20) | A. Bartholf, manufacturer, New York, N.Y. | 1849 | 185- |
Bond | —— | — | before 1880 |
Boston | J. F. Paul & Co., Boston, Mass. | 1880 | — |
Later New Boston | Boston Sewing Machine Co., Boston, Mass. | — | after 1886 |
Boudoir (fig. 76) | Daniel Harris, inventor and patentee Manufacturer—several | 1857 | ca. 1870 |
Bradford & Barber | Bradford & Barber, manufacturers, Boston, Mass. | 1860 | 1861 |
Brattleboro | Samuel Barker and Thomas White, Brattleboro, Vt. | ca. 1858 | 1861 |
Buckeye | Wilson [W.G.] Sewing Machine Company, Cleveland, Ohio | ca. 1867 | ca. 1876 |
Later New Buckeye (fig. 77) (see Wilson) | |||
[Pg 67]Buell, “E. T. Lathbury’s Patent” | A. B. Buell, Westmoreland, New York | ca. 1860 | — |
Burnet & Broderick | Burnet, Broderick and Co. | 1859 | ca. 1860 |
Centennial (fig. 78) | Centennial Sewing Machine Co. (see McLean and Hooper), Philadelphia, Pa. | 1873 | 1876 |
Chamberlain | Woolridge, Keene and Moore, Lynn, Mass. | 1853 | ca. 1854 |
Chicago Singer | Scates, Tryber & Sweetland Mfg. Co., Chicago, Ill. | 1879 | 1882 |
Later Chicago | Chicago Sewing Machine Co. | 1882 | ca. 1885 |
Chicopee | |||
(see Shaw & Clark) | |||
Clark (fig. 42) | D. W. Clark, Bridgeport, Conn. | ca. 1858 | after 1860 |
Clark’s Revolving Looper [double thread] (fig. 79) | Lamson, Goodnow & Yale, Windsor, Vt. | 1859 | 1861 |
(see Windsor) | |||
Clinton | Clinton Brothers, Ithaca, N.Y. | ca. 1861 | ca. 1865 |
Companion | Thurston Mfg. Co., Marlboro, N.H. | 1882 | — |
Crown | Florence Sewing Machine Co., Florence, Mass. | 1879 | after 1886 |
(see Florence) | |||
Dauntless (later New Dauntless) | Dauntless Mfg. Co., Norwalk, Ohio | 1877 | after 1882 |
Davis | J.A. Davis, New York, N.Y. | ca. 1860 | — |
Davis Vertical Feed | Davis Sewing Machine Co., Watertown, N.Y. | 1869 | after 1886 |
Davis Vertical Feed and Rotary Shuttle | Davis Sewing Machine Co., Dayton, Ohio | after 1886 | 1924 |
Decker (also The Princess) | Decker Mfg. Co., Detroit, Mich. | — | before 1881 |
Demorest | Demorest Mfg. Co (formerly N.Y. Sewing Machine Co.) | 1882 | 1908 |
Diamond (formerly Sigwalt) | Sigwalt Sewing Machine Co., Chicago, Ill. | 1880 | — |
Domestic | Wm. A. Mack & Co. and N. S. Perkins, Norwalk, Ohio | 1864 | 1869 |
[Pg 68]Domestic | Domestic Sewing Machine Co., Norwalk, Ohio, acquired by White Sewing Machine Co. in 1924 and maintained as a subsidiary at Cleveland, Ohio. | 1869 | [A] |
Dorcas | John P. Bowker, Boston, Mass. | 1853 | 185- |
Du Laney (fig. 80) | |||
Also called Little Monitor (see) | |||
Durgin | Charles A. Durgin, New York, N.Y. | 1853 | after 1855 |
Eldredge | Eldredge Sewing Machine Co., Chicago, Ill. | 1869 | 1890 |
Elliptic | |||
Sloat’s Elliptic | George B. Sloat and Co., Philadelphia, Pa. | ca. 1858 | ca. 1860 |
Sloat’s Elliptic | Union Sewing Machine Co., Richmond, Va. | 1860 | 1861 |
Elliptic | Wheeler & Wilson Mfg. Co. | 1861 | ca. 1867 |
Elliptic Sewing Machine Co., N.Y., N.Y. | 1867 | before 1880 | |
Empire (fig. 86) | Empire Sewing Machine Co., Boston, Mass. | ca. 1860 | 1869 |
Later Remington-Empire | |||
Empress | Manufactured on order through Jerome B. Secor, Bridgeport, Conn. | 1877 | — |
Estey | Estey Sewing Machine Co. | ca. 1880 | 1882 |
Estey, Fuller-Model | Brattleboro Sewing Machine Co., Brattleboro, Vt. | 1883 | after 1886 |
Eureka (fig. 81) | Eureka Shuttle Sewing New York, N.Y. | 1859 | — |
Excelsior | Excelsior Sewing Machine Co., New York, N.Y. | 1854 | 1854 |
Fairy (figs. 51, 52) | Madame Demorest, New York, N.Y. | 1863 | ca. 1865 |
Finkle, M. (fig. 82) | M. Finkle, Boston, Mass. | 1856 | ca. 1859 |
Finkle & Lyon | Finkle & Lyon Sewing Machine Co., Boston, Mass. | ca. 1859 | 1867 |
Later Victor | |||
First and Frost | First and Frost, New York, N.Y. | ca. 1859 | ca. 1861 |
Florence (fig. 83) | Florence Sewing Machine Co., Florence, Mass. | ca. 1860 | after 1878 |
Later Crown | |||
Folsom | Folsom, J. G., Winchendon, Mass. | 1865 | ca. 1871 |
(see Globe and New England) | |||
Fosket and Savage | Fosket and Savage, Meriden, Conn. | 1858 | 1859 |
Foxboro | Foxboro Rotary Shuttle Co., Foxboro, Mass. | ca. 1882 | — |
Franklin | Franklin Sewing Machine Co., Mason Village, N.H. | 1871 | 1871 |
[Pg 69]Free | Free Sewing Machine Co., Chicago and Rockford, Ill. | 1898 | [A] |
Gardner | C. R. Gardner, Detroit, Mich. | 1856 | — |
Globe (figs. 84, 85) | J. G. Folsom, Winchendon, Mass. | 1865 | 1869 |
Gold Medal (chainstitch) | Gold Medal Sewing Machine Co., Orange, Mass. | 1863 | 1876 |
Gold Medal (running stitch) | —— | 1863 | ca. 1865 |
Gold Hibbard | Hibbard, B. S., & Co. | 1875 | — |
Goodbody (sewing shears) | Goodbody Sewing Machine Co., Bridgeport, Conn. | 1880 | ca. 1890 |
Goodes | Rex & Bockius, Philadelphia, Pa. | ca. 1876 | before 1881 |
Goodrich | H. B. Goodrich, Chicago, Ill. | ca. 1880 | ca. 1895 |
Grant Brothers (fig. 90) | Grant Bros. & Co., Philadelphia, Pa. | 1867 | ca. 1870 |
Greenman and True (fig. 91) | Greenman and True Mfg. Co. Norwich, Conn. | 1859 | 1860 |
Morse and True | 1860 | 1861 | |
Green Mountain | —— | ca. 1860 | — |
Griswold Variety | L. Griswold, New York, N.Y. | ca. 1886 | ca. 1890 |
Grover and Baker (figs. 34-36, 92) | Grover and Baker Sewing Machine Co., Boston, Mass. | 1851 | 1875 |
Hancock (figs. 93, 94) | —— | 1868 | before 1881 |
Heberling Running Stitch | John Heberling | 1878 | ca. 1885 |
Herron’s Patent (fig. 95) | —— | 1857 | — |
Higby | Higby Sewing Machine Co., Brattleboro, Vt. | ca. 1882 | after 1886 |
Later Acme | |||
Home Home Shuttle | Johnson, Clark & Co., Orange, Mass. | 1869 | after 1876 |
Homestead | —— | ca. 1881 | — |
Household | Providence Tool Co., Providence, R.I. | 1880 | ca. 1884 |
Household Sewing Machine Co. | ca. 1885 | 1906 | |
Howe (figs. 96, 97) | Howe Sewing Machine Co., New York, N.Y. | 1853 | 1873 |
(company of A. B. Howe sold to Howe Machine Co.) | |||
Howe (fig. 98) | Howe Machine Co., Bridgeport, Conn. | 1867 | 1886 |
Howe’s Improved Patent (fig. 107) | Nichols and Bliss, Boston, Mass. | 1852 | 1853 |
J. B. Nichols & Co. | 1853 | 1854 | |
which became Leavitt | Nichols, Leavitt & Co., Boston, Mass. | 1854 | 1856 |
[Pg 70]N. Hunt, which became Hunt and Webster (figs. 99, 100) | N. Hunt & Co., Boston, Mass. | 1853 | 1854 |
Hunt and Webster, Boston, Mass. | 1854 | 1857 | |
Later Ladd and Webster (see) | |||
Improved Common Sense (fig. 102) | —— | ca. 1870 | — |
Independent Noiseless | Independent Sewing Machine Co., Binghamton, N.Y. | 1873 | — |
Jennie June | June Mfg. Co., Chicago, Ill. | 1881 | 1890 |
Later Belvidere, Ill. | |||
Jewel | Jewel Mfg. Co., Toledo, Ohio | 1884 | after 1886 |
Johnson (fig. 103) | Emery, Houghton & Co., Boston, Mass. | 1856 | after 1865 |
Keystone | Keystone Sewing Machine Co. | before 1872 | ca. 1874 |
Ladd & Webster (fig. 101) | Ladd, Webster & Co., Boston, Mass. | 1858 | ca. 1866 |
Ladies Companion (fig. 115) | —— | 1858 | ca. 1858 |
(see Pratt’s Patent) | |||
“Lady” (fig. 104) | —— | 1859 | — |
Landfear’s Patent (fig. 105) | Parkers, Snow, Brooks & Co., West Meriden, Conn. | 1857 | — |
Langdon | L.W. Langdon | 1856 | — |
Lathrop (fig. 106) | Lathrop Combination Sewing Machine Co. | 1873 | — |
Leader | Leader Sewing Machine Co., Springfield, Mass. | 1882 | — |
Leavitt (fig. 108) | Nichols, Leavitt & Co., Boston, Mass. | 1855 | 1857 |
Leavitt & Co. | 1857 | ca. 1865 | |
Leavitt Sewing Machine Co. | ca. 1865 | 1870 | |
Leslie Revolving Shuttle | Leslie Sewing Machine Co., Cleveland, Ohio | 1881 | — |
Lester (fig. 109) | J.H. Lester, Brooklyn, N.Y. | ca. 1858 | early 1860 |
Lester Mfg. Co., Richmond, Va. | early 1860 | late 1860 | |
Union Sewing Machine Co., Richmond, Va. | late 1860 | 1861 | |
Little Gem | —— | — | ca. 1870 |
Little Giant | Domestic Sewing Machine Co., Norwalk, Ohio | ca. 1882 | — |
Little Monitor (not associated with Monitor) | G.L. Du Laney, Brooklyn, N.Y. | ca. 1866 | after 1875 |
Love | Love Mfg. Co., Pittsburgh, Pa. | 1885 | after 1886 |
Lyon | Lyon Sewing Machine Co. | 1879 | ca. 1880 |
Macauley | Thos. A. Macauley Mfg., New York, N.Y. | before 1879 | — |
Manhattan | Manhattan Sewing Machine Co. | ca. 1868 | ca. 1880 |
[Pg 71]McKay | McKay Sewing Machine Assoc. | 1870 | 1876 |
McLean and Hooper | B. W. Lacy & Co., Philadelphia, Pa. | ca. 1869 | ca. 1873 |
(see Centennial) | |||
Meyers | J. M. Meyers | 1859 | — |
Miller’s Patent | —— | 1853 | — |
Monitor (fig. 88) | Shaw & Clark Sewing Machine Co., Biddeford, Me. | 1860 | 1864 |
Moore | Moore Sewing Machine Co. | ca. 1860 | — |
Morey & Johnson (fig. 18) | Safford & Williams Makers, Boston, Mass. | 1849 | ca. 1851 |
Morrison | Morrison, Wilkinson & Co., Hartford, Conn. | 1881 | — |
Mower | —— | ca. 1863 | — |
National | Johnson, Clark & Co., Orange, Mass. | 1874 | — |
National (also sold under distributor’s name) | National Sewing Machine Co. (consolidation of the June and Eldredge Companies), Belvidere, Ill. | 1890 | 1953 |
Ne Plus Ultra (fig. 110) | O. L. Reynolds Manufacturing Co., Dover, N.H. | 1857 | — |
Nettleton & Raymond (fig. 111) | Nettleton & Raymond, Brattleboro, Vt. | ca. 1857 | — |
New England (figs. 112, 113) | Charles Raymond (also by: | ca. 1859 | 1866 |
Grout & White, Orange, Mass.; | 1862 | 1863 | |
William Grout, Winchendon, Mass.; | 1863 | — | |
and J. G. Folsom, Winchendon, Mass.) | 1865 | 1865 | |
Newell | —— | 1881 | — |
New Fairbanks | J. H. Drew & Co. | 1878 | 1880 |
Thomas M. Cochrane Co., Belleville, Ill. | 1880 | — | |
New Home | New Home Sewing Machine Co., Orange, Mass. (in 1928 became affiliated with Free Sewing Machine Co.) | 1876 | [A] |
New York | ——, New York, N.Y. | ca. 1855 | ca. 1855 |
New York Shuttle | N.Y. Sewing Machine Co., New York, N.Y. (later Demorest Mfg. Co.) | before 1880 | 1882 |
[Pg 72]Noble | Noble Sewing Machine Co., Erie, Pa. | before 1881 | after 1886 |
Novelty | C. A. French, Boston, Mass. | 1869 | — |
Old Dominion | Old Dominion Sewing Machine Co., Richmond, Va. | ca. 1858 | 1860 |
Pardox | —— | ca. 1865 | — |
Parham | Parham Sewing Machine Co., Philadelphia, Pa. | ca. 1869 | ca. 1871 |
Parker | Charles Parker Co., Meriden, Conn. | before 1860 | after 1865 |
Later Parker Sewing Machine Co. | |||
Pearl | —— Bennett | ca. 1859 | — |
Philadelphia | Philadelphia Sewing Machine Co., Philadelphia, Pa. | ca. 1872 | ca. 1881 |
Post Combination | Post Combination Sewing Machine Co., Washington, D.C. | before 1885 | after 1886 |
Pratt’s Patent (fig. 114) | —— | 1857 | ca. 1858 |
Later Ladies Companion | |||
Queen | Dauntless Mfg Co., Norwalk, Ohio | ca. 1881 | — |
Quaker City (fig. 116) | Quaker City Sewing Machine Co., Philadelphia, Pa. | 1859 | ca. 1861 |
Remington Empire Later Remington | Remington Empire Sewing Machine Co. | 1870 | 1872 |
E. Remington & Sons, Philadelphia, Pa. | 1873 | ca. 1894 | |
Robertson (dolphin & cherub) (figs. 40, 41) | T. W. Robertson, New York, N.Y. | 1855 | after 1860 |
Robinson | F. R. Robinson, Boston, Mass. | 1853 | ca. 1855 |
Robinson’s patent sewing machine with Roper’s improvement (fig. 117) | Howard & Davis, Boston, Mass. | 1855 | — |
Later Robinson and Roper (fig. 118) | same | 1856 | before 1860 |
Royal St. John (formerly St. John) | Royal Sewing Machine Co., Springfield, Ohio (later Free Co.) | ca. 1883 | 1898 |
Ruddick | —— | ca. 1860 | — |
Secor | Secor Machine Co., Bridgeport, Conn. | 1870 | 1876 |
Sewing Shears (Hendrick’s patent) (fig. 43) | Nettleton & Raymond, Bristol, Conn. | ca. 1859 | — |
Sewing Shears | American Hand Sewing Machine Co., Bridgeport, Conn. | ca. 1884 | ca. 1900 |
[Pg 73]Shaw & Clark | Shaw & Clark Co., Biddeford, Me. | ca. 1857 | 1866 |
Running Stitch Machine (fig. 53) | |||
Chainstitch Machine (fig. 119) | |||
Chainstitch Machine (fig. 120) | Shaw & Clark Co., Chicopee Falls, Mass. | 1867 | 1868 |
Chicopee Sewing Machine Co., Chicopee Falls, Mass. | 1868 | ca. 1869 | |
Sigwalt | Sigwalt Sewing Machine Co., Chicago, Ill. | ca. 1879 | — |
Singer (figs. 28, 29, 30, 32, 33, 121, 122) | I. M. Singer & Co. (later Singer Mfg. Co.). Moved from Boston to New York to Elizabethport, N.J. (factory). | 1851 | [A] |
Springfield | Springfield Sewing Machine Co., Springfield, Mass. | 1880 | — |
Standard (chainstitch) (fig. 123) | —— | 1870 | — |
Standard (shuttle) | Standard Shuttle Sewing Machine Co., New York, N.Y. | 1874 | ca. 1881 |
Standard | Standard Sewing Machine Co., Cleveland, Ohio (acquired by Singer Co.) | 1884 | ca. 1930 |
Stewart | Henry Stewart & Co., N.Y., N.Y. | 1874 | 1880 |
Later New Stewart | Stewart Mfg Co. | 1880 | ca. 1883 |
St. John (later Royal St. John) | St. John Sewing Machine Co., Springfield, O. | 1870 | ca. 1883 |
Taggart & Farr (figs. 124, 125) | Taggart & Farr, Philadelphia, Pa. | 1858 | — |
Thompson | C. F. Thompson Co. | 1871 | 1871 |
T. C. Thompson, Ithaca, N.Y. | ca. 1854 | — | |
Union | Johnson, Clark & Co., Orange, Mass. | 1876 | — |
Victor | Finkle & Lyon Mfg. Co. | 1867 | ca. 1872 |
Victor Sewing Machine Co., Middletown, Conn. | ca. 1872 | ca. 1890 | |
Wardwell | Wardwell Mfg. Co., St. Louis, Mo. | ca. 1876 | 1890 |
Watson (fig. 126) | Jones & Lee | 1850 | ca. 1853 |
Watson & Wooster, Bristol, Conn. | ca. 1853 | ca. 1860 | |
Waterbury | Waterbury Co., Waterbury, Conn. | 1853 | ca. 1860 |
Weed | T. E. Weed & Co. (became Whitney & Lyons) | 1854 | — |
[Pg 74]Weed | Weed Sewing Machine Co. (reorganized from Whitney & Lyons), Hartford, Conn. | 1865 | — |
Family Favorite | 1867 | — | |
Manu. Favorite | 1868 | — | |
General Favorite | 1872 | — | |
Hartford | 1881 | ca. 1900 | |
Wesson | Farmer & Gardner Manufacturing Co. | 1879 | 1880 |
D. B. Wesson Sewing Machine Co., Springfield, Mass. | 1880 | — | |
West & Willson (fig. 127) | West & Willson Co., Elyria, Ohio | 1858 | — |
A. B. Wilson (fig. 23) | E. E. Lee & Co., New York, N.Y. | 1851 | 1852 |
A. B. Wilson’s patent seaming lathe | Wheeler, Wilson, Co., Watertown, N.Y. | late 1851 | 1856 |
Later Wheeler and Wilson (fig. 26, 27, 128, 129) | Wheeler & Wilson Mfg.Co., Bridgeport, Conn. | 1856 | 1905 |
Singer Co., Bridgeport, Conn. | 1905 | 1907 | |
White (fig. 130) | White Sewing Machine Co., Cleveland, Ohio | 1876 | [A] |
Whitehill | Whitehill Mfg. Co., Milwaukee, Wis. | ca. 1875 | after 1886 |
Whitney | Whitney Sewing Machine Co., Paterson, N.J. | ca. 1872 | ca. 1880 |
Whitney & Lyons | Whitney & Lyons (a machine based on the 1854 patent of T. E. Weed) | ca. 1859 | ca. 1865 |
Wickersham | Butterfield & Stevens Mfg. Co., Boston, Mass. | 1853 | — |
Willcox & Gibbs (figs. 39, 131) | Willcox & Gibbs Sewing Machine Co., New York, N.Y. | 1857 | [A] |
Williams & Orvis | Williams & Orvis Sewing Machine Co., Boston, Mass. | ca. 1859 | after 1860 |
Wilson (fig. 89) | Wilson (W.G.) Sewing Machine Co., Cleveland, Ohio | ca. 1867 | after 1885 |
(see Buckeye) | |||
Windsor (one thread) | Vermont Arms Co., Windsor, Vt. | 1856 | 1858 |
Windsor | Lamson, Goodnow & Yale, Windsor, Vt. | 1859 | 1861 |
(see Clark’s Revolving Looper) | |||
[Pg 75]Name Unknown | John W. Beane | 1853 | — |
“ | Henry Brind | 1860 | — |
“ | Garfield Sewing Machine Co. | 1881 | — |
“ | Geneva Sewing Machine Co. | 1880 | — |
“ | Gove & Howard | 1855 | — |
“ | Charles W. Howland, Wilmington, Del. | ca. 1860 | — |
“ | Miles Greenwood & Co., Cincinnati, Ohio | ca. 1861 | — |
“ | Hood, Batelle & Co. | 1854 | 1854 |
“ | Wells & Haynes | 1854 | 1854 |
“ | Wilson H. Smith, Birmingham, Conn. | ca. 1860 | — |
[A] Still in existence.
Still around.
Figure 68.—American Buttonhole, Overseaming & Sewing Machine of about 1870. Using serial numbers, these machines can be dated approximately as follows: 1-7792, 1869; 7793-22366, 1870; 22367-42488, 1871; 42489-61419, 1872; 61420-75602, 1873; 75603-89132, 1874; 89133-103539, 1875; and 103540-121477, 1876. Figures are not available for the years from 1877 to 1886. (Smithsonian photo 46953-E.)
Figure 68.—American Buttonhole, Overseaming & Sewing Machine from around 1870. By using serial numbers, these machines can be dated approximately as follows: 1-7792, 1869; 7793-22366, 1870; 22367-42488, 1871; 42489-61419, 1872; 61420-75602, 1873; 75603-89132, 1874; 89133-103539, 1875; and 103540-121477, 1876. There are no figures available for the years from 1877 to 1886. (Smithsonian photo 46953-E.)
Figure 69.—(New) American sewing machine of about 1874. Illustration is from a contemporary advertising brochure. (Smithsonian photo 33507.)
Figure 69.—American sewing machine from around 1874. Illustration is from a modern advertising brochure. (Smithsonian photo 33507.)
Figure 70.—American Magnetic sewing machine, 1854. Machines of this type were manufactured for only two years under the patent of Thomas C. Thompson, March 29, 1853, and later under the patents of Samuel J. Parker, April 11, 1854, and Simon Coon, May 9, 1854. On September 30, 1853, Elias Howe listed receipts of $1000 from the American Magnetic Sewing Machine Co. for patent infringement. The machines manufactured after that date carry the Howe name and 1846 patent date to show proper licensing. Judging by Howe’s usual license fee of $25 per machine, about 40 machines were manufactured prior to September 1853. The company was reported to have made about 600 machines in 1854 before it went out of business. The only American Magnetic machine known to be in existence is in the collection of the Northern Indiana Historical Society at South Bend, Indiana. (Photo courtesy of the Northern Indiana Historical Society.)
Figure 70.—Magnetic sewing machine by American, 1854. This type of machine was made for only two years under the patent of Thomas C. Thompson from March 29, 1853, and later under the patents of Samuel J. Parker from April 11, 1854, and Simon Coon from May 9, 1854. On September 30, 1853, Elias Howe reported receiving $1000 from the American Magnetic Sewing Machine Co. for patent infringement. The machines produced after that date display the Howe name and the 1846 patent date to indicate proper licensing. Based on Howe’s usual licensing fee of $25 per machine, about 40 machines were made before September 1853. The company was said to have produced around 600 machines in 1854 before going out of business. The only known American Magnetic machine still in existence is in the collection of the Northern Indiana Historical Society in South Bend, Indiana. (Photo courtesy of the Northern Indiana Historical Society.)
Figure 71.—Atlantic sewing machine, 1869. This machine is typical of the many varieties manufactured for a very short time in the 1860s and 1870s. It is about the size of the average hand-turned variety, 8 by 10 inches, but lighter in weight. The frame design was the patent of L. Porter, May 11, 1869, and the mechanism was patented by Alonzo Porter, February 8, 1870. The latter patent model bears the painted legend “Atlantic” and is stamped “Aprl 1, 69,” indicating that it was probably already in commercial production. This date possibly may refer also to L. Porter’s design patent, since actual date of issue was usually later than date of application. (Smithsonian photo 48329-A.)
Figure 71.—Atlantic sewing machine, 1869. This machine is representative of the many types produced for a brief period in the 1860s and 1870s. It's about the size of a typical hand-cranked machine, measuring 8 by 10 inches, but it's lighter. The frame design was patented by L. Porter on May 11, 1869, and the mechanism was patented by Alonzo Porter on February 8, 1870. The latter patent model features the painted name “Atlantic” and is stamped “Aprl 1, 69,” suggesting that it was likely already in commercial production. This date might also refer to L. Porter’s design patent, as the actual issue date was usually later than the application date. (Smithsonian photo 48329-A.)
Figure 72.—A. Bartholf sewing machine, 1853. Abraham Bartholf of New York began manufacturing Blodgett & Lerow machines (see fig. 20) about 1850; the style and mechanics of these machines, however, were primarily those of the Blodgett & Lerow patent as manufactured by O. C. Phelps and Goddard, Rice & Co. For this reason they are considered Blodgett & Lerow—not Bartholf—machines.
Figure 72.—A. Bartholf sewing machine, 1853. Abraham Bartholf from New York started making Blodgett & Lerow machines (see fig. 20) around 1850; however, the design and mechanics of these machines were mainly based on the Blodgett & Lerow patent as produced by O. C. Phelps and Goddard, Rice & Co. Because of this, they are regarded as Blodgett & Lerow machines, not Bartholf machines.
The true Bartholf machine evolved when the manufacturer substituted Howe’s reciprocating shuttle for the rotary shuttle of the Blodgett & Lerow machine, continuing to manufacture the machine in his own adapted style. Bartholf manufactured reciprocating-shuttle machines as early as 1853, and his was one of the first companies licensed by Howe.
The real Bartholf machine came about when the manufacturer replaced Howe’s reciprocating shuttle with the rotary shuttle from the Blodgett & Lerow machine, continuing to make the machine in his own modified style. Bartholf started producing reciprocating-shuttle machines as early as 1853, and his company was one of the first to be licensed by Howe.
All Bartholf machines licensed under Howe’s patent carry the Howe name and patent date. They are sometimes mistakenly referred to as Howe machines, but they are no more Howe machines than those manufactured by Wheeler & Wilson, Singer, or many others.
All Bartholf machines licensed under Howe’s patent have the Howe name and patent date on them. They are sometimes wrongly called Howe machines, but they aren't any more Howe machines than those made by Wheeler & Wilson, Singer, or many others.
On April 6, 1858, Bartholf was granted a patent for an improvement of the shuttle carrier. He continued to manufacture sewing machines under the name “Bartholf Sewing Machine Co.” until about 1865.
On April 6, 1858, Bartholf received a patent for an improved shuttle carrier. He kept producing sewing machines under the name “Bartholf Sewing Machine Co.” until around 1865.
Using serial numbers, Bartholf machines can be dated approximately as follows:
Using serial numbers, Bartholf machines can be dated roughly like this:
Serial Number | Year |
1-20 | 1850 |
21-50 | 1851 |
51-100 | 1852 |
101-235 | 1853 |
236-290 | 1854 |
291-321 | 1855 |
322-356 | 1856 |
357-387 | 1857 |
388-590 | 1858 |
591-1337 | 1859 |
No record of the number of machines produced by Bartholf after 1859 is available.
No records of the number of machines produced by Bartholf after 1859 are available.
The Bartholf machine illustrated bears the serial number 128 and the inscription “A. Bartholf Manfr., NY—Patented Sept. 1846 E. Howe, Jr.” This machine is in the collection of the Baltimore County Historical Society. Note the close similarity between it and the 1850 Blodgett & Lerow machine manufactured by Bartholf. (Photo courtesy of the Baltimore County Historical Society.)
The Bartholf machine shown has the serial number 128 and the label “A. Bartholf Manfr., NY—Patented Sept. 1846 E. Howe, Jr.” This machine is part of the Baltimore County Historical Society's collection. Notice the strong resemblance between it and the 1850 Blodgett & Lerow machine made by Bartholf. (Photo courtesy of the Baltimore County Historical Society.)
Figure 73.—Bartlett sewing machine, 1867. The Bartlett machine was first manufactured in 1866 under the January 31, 1865, and October 10, 1865, patents of Joseph W. Bartlett. The machines were made by Goodspeed & Wyman for the Bartlett Co. and were so marked. The inventor received another patent on April 7, 1868, and later machines carry this third date also. Although the first few hundred machines did not bear the dates of patents held by the “Combination,” before the end of the first year of production Bartlett was paying royalties. He continued to manufacture sewing machines until the early seventies when he converted to the manufacturing of street lamps.
Figure 73.—Bartlett sewing machine, 1867. The Bartlett machine was first made in 1866, based on the patents from January 31, 1865, and October 10, 1865, by Joseph W. Bartlett. Goodspeed & Wyman manufactured these machines for the Bartlett Co., and they were labeled accordingly. The inventor received another patent on April 7, 1868, and later machines included this third date as well. Although the initial few hundred machines didn’t have the patent dates associated with the “Combination,” by the end of the first year of production, Bartlett was paying royalties. He continued to produce sewing machines until the early seventies when he switched to making street lamps.
Using serial numbers, Bartlett’s machines can be dated approximately as follows: 1-1000, 1866; 1001-3126, 1867; 3127-?, 1868. There is no record of serial numbers for the succeeding years. (Smithsonian photo 45524-G.)
Using serial numbers, Bartlett’s machines can be dated approximately as follows: 1-1000, 1866; 1001-3126, 1867; 3127-?, 1868. There is no record of serial numbers for the following years. (Smithsonian photo 45524-G.)
Figure 74.—Bartram & Fanton sewing machine, 1867. These machines were first manufactured in 1867 under the patents of W. B. Bartram, notably his patent of January 1, 1867. Three machines were exhibited at The Eleventh Exhibition of the Massachusetts Charitable Mechanics Association in 1869 where they were awarded a bronze medal. They were compared favorably to the Willcox & Gibbs machine (see fig. 39), which they resembled. Bartram received additional patents in the early seventies and also manufactured lockstitch machines.
Figure 74.—Bartram & Fanton sewing machine, 1867. These machines were first made in 1867 under the patents of W. B. Bartram, especially his patent from January 1, 1867. Three machines were shown at The Eleventh Exhibition of the Massachusetts Charitable Mechanics Association in 1869, where they won a bronze medal. They were compared favorably to the Willcox & Gibbs machine (see fig. 39), which they looked similar to. Bartram received more patents in the early 1970s and also produced lockstitch machines.
Using serial numbers, machines may be approximately dated as follows: 1-2958, 1867; 2959-3958, 1868; 3959-4958, 1869; 4959-5958, 1870; 5959-6962, 1871; 6963-7961, 1872; 7962-8961, 1873; and 8962-9211, 1874. (Smithsonian photo P63198.)[Pg 80]
Using serial numbers, machines can be roughly dated as follows: 1-2958, 1867; 2959-3958, 1868; 3959-4958, 1869; 4959-5958, 1870; 5959-6962, 1871; 6963-7961, 1872; 7962-8961, 1873; and 8962-9211, 1874. (Smithsonian photo P63198.)[Pg 80]
Figure 75.—Beckwith sewing machine, 1871. Among the inventors whose patent claims were “to produce a cheap and effective sewing machine” was William G. Beckwith. His machine was first manufactured by Barlow & Son, and it realized considerable success in the few years of its production. The earliest model was operated like a pair of scissors or with a cord and ring as illustrated. Beckwith later added a hand crank. The machine was purchased in Crewe, Cheshire, England; it is stamped “Pat. April 18, 71 by Wm. G. Beckwith, Foreign Pats. Secured, Barlow & Son Manuf. N.Y., [serial number] 706.” By 1874 the machines were marked “Beckwith S.M. Co.” and two 1872 patent dates were added.
Figure 75.—Beckwith sewing machine, 1871. Among the inventors who aimed to "create a low-cost and efficient sewing machine" was William G. Beckwith. His machine was initially made by Barlow & Son and achieved significant success in the few years it was produced. The first model worked like a pair of scissors or with a cord and ring, as shown. Beckwith later included a hand crank. The machine was bought in Crewe, Cheshire, England; it is marked “Pat. April 18, 71 by Wm. G. Beckwith, Foreign Pats. Secured, Barlow & Son Manuf. N.Y., [serial number] 706.” By 1874, the machines were labeled “Beckwith S.M. Co.” and two 1872 patent dates were added.
Figure 76.—Boudoir sewing machine, 1858. This machine, a single-thread, chainstitch model was based on the patents of Daniel Harris, dated June 9, 1857, June 16, 1857, and October 5, 1858. Manufactured primarily by Bennett in Chicago in 1859, it also may have been produced in the East, although no manufacturer’s name can be found.
Figure 76.—Boudoir sewing machine, 1858. This machine, a single-thread, chainstitch model, was based on the patents of Daniel Harris, dated June 9, 1857, June 16, 1857, and October 5, 1858. It was primarily manufactured by Bennett in Chicago in 1859, but it may have also been produced in the East, although no manufacturer's name can be found.
In 1860, the Boudoir, also called Harris’s Patent sewing machine, was exhibited at the Massachusetts Charitable Mechanics Association Exhibition where it won a silver medal for “its combination of parts, its beauty and simplicity, together with its ease of operation.” At this time the machine was described as making a “double lock stitch” (another name for the double chainstitch). It was also described as having been before the public for some time and combining “the improvements of others for which the parties pay license.” The machine head was positioned on the stand similarly to that of the West & Willson (fig. 127) and stitched from left to right.
In 1860, the Boudoir, also known as Harris’s Patent sewing machine, was showcased at the Massachusetts Charitable Mechanics Association Exhibition, where it won a silver medal for “its combination of parts, its beauty and simplicity, along with its ease of use.” At that time, the machine was described as producing a “double lock stitch” (another term for the double chainstitch). It was also noted that the machine had been available to the public for some time and incorporated “the improvements of others for which the parties pay a license.” The machine head was mounted on the stand similarly to that of the West & Willson (fig. 127) and sewed from left to right.
It is not known exactly how many of these machines were made or how long they were in vogue. Manufacture, although probably ceasing in the 1860s, is known to have been discontinued before 1881, when a list of obsolete sewing machines was published in The Sewing Machine News. (Smithsonian photo P63199.)
It’s unclear how many of these machines were produced or how long they were popular. Production likely stopped in the 1860s, but it was definitely discontinued before 1881, when a list of outdated sewing machines was released in The Sewing Machine News. (Smithsonian photo P63199.)
Figure 77.—(New) Buckeye sewing machine of about 1875. The Buckeye machine was one of several manufactured by W. G. Wilson of Cleveland, Ohio. It was licensed under Johnson’s extended patent of April 18, 1867. Although it was small and hand turned, it used two threads and a shuttle to form a lockstitch. The machine was sufficiently popular for Wilson to introduce an improved model in the early 1870s, which he called the New Buckeye. W. G. Wilson continued to manufacture sewing machines until about the mid-eighties, although the Buckeye machines were discontinued in the seventies. (Smithsonian photo 45524-A.)
Figure 77.—(New) Buckeye sewing machine from around 1875. The Buckeye machine was one of several produced by W. G. Wilson of Cleveland, Ohio. It was made under Johnson’s extended patent from April 18, 1867. Even though it was small and operated by hand, it used two threads and a shuttle to create a lockstitch. The machine was popular enough for Wilson to launch an improved version in the early 1870s, which he named the New Buckeye. W. G. Wilson kept making sewing machines until about the mid-1880s, although Buckeye machines were phased out in the 1870s. (Smithsonian photo 45524-A.)
Figure 78.—Centennial sewing machine, 1876. The Centennial machine was basically a McLean and Hooper sewing machine which was renamed to take advantage of the coming Centennial celebration. It was based on the patents of J. N. McLean, March 30, 1869, and August 2, 1870, and made a two-thread chainstitch. Only about five hundred Centennial machines were manufactured in 1873, but by 1876 over three thousand had been constructed. The machines were advertised on white circulars which were printed in red and blue, and engraved with two women sewing, one by hand, labeled “Sewing in 1776,” and one at a Centennial sewing machine, labeled “Sewing in 1876.” There is no record that the machines were made after 1876. (Smithsonian photo 48216-T.)
Figure 78.—Centennial sewing machine, 1876. The Centennial machine was essentially a McLean and Hooper sewing machine that was renamed to capitalize on the upcoming Centennial celebration. It was based on the patents of J. N. McLean from March 30, 1869, and August 2, 1870, and produced a two-thread chainstitch. Only about five hundred Centennial machines were made in 1873, but by 1876, over three thousand had been built. The machines were advertised on white flyers printed in red and blue, featuring engravings of two women sewing: one labeled "Sewing in 1776," working by hand, and the other labeled "Sewing in 1876," using a Centennial sewing machine. There's no record of the machines being produced after 1876. (Smithsonian photo 48216-T.)
Figure 79.—Clark’s Revolving-Looper double-thread sewing machine, 1860. This machine was manufactured by Lamson, Goodnow, & Yale of Windsor, Vermont. It was an attempt to improve on the combined ideas of the Grover and Baker machine, the Nettleton & Raymond machine, and the earlier single-thread Windsor machine. The improvements were made and patented by Edwin Clark on December 6, 1859. Widely advertised, the machines sold for $35 with a foot-power table. They could also be operated by hand. Over three thousand were manufactured and sold, and preparations were being made to continue manufacture of the earlier single-thread Windsor, originally made by the company’s predecessor, Vermont Arms Co., when the Civil War broke out. A flood of arms orders arrived, and the sewing-machine manufacture was discontinued early in the summer of 1861. The sewing-machine equipment and business was sold to Grout & White of Massachusetts. (Smithsonian photo 48216.)
Figure 79.—Clark's Revolving-Looper double-thread sewing machine, 1860. This machine was made by Lamson, Goodnow, & Yale in Windsor, Vermont. It aimed to improve upon the combined concepts of the Grover and Baker machine, the Nettleton & Raymond machine, and the earlier single-thread Windsor machine. Edwin Clark made and patented these improvements on December 6, 1859. The machines were widely advertised and sold for $35 with a foot-powered table. They could also be operated by hand. Over three thousand units were manufactured and sold, and there were plans to continue making the earlier single-thread Windsor, originally produced by the company’s predecessor, Vermont Arms Co., when the Civil War started. A wave of arms orders came in, and sewing machine production was halted in early summer 1861. The sewing machine equipment and business were sold to Grout & White of Massachusetts. (Smithsonian photo 48216.)
Figure 80.—Du Laney sewing machine of about 1872. Most of the small, simple, chainstitch sewing machines of this period were constructed so that they could either be turned by hand or set into a treadle-powered table. Du Laney’s Little Monitor, manufactured for only a few years, was based on the patents of G.L. Du Laney, July 3, 1866, and May 2, 1871. It was a two-thread, chainstitch machine powered only by a foot treadle. By simple adjustment, the machine could also make the cablestitch and the lockstitch. (Smithsonian photo 48221-C.)
Figure 80.—Du Laney sewing machine from around 1872. Most of the small, straightforward, chainstitch sewing machines from this time were designed to be operated by hand or set up in a treadle-powered table. Du Laney’s Little Monitor, made for just a few years, was based on the patents of G.L. Du Laney, granted on July 3, 1866, and May 2, 1871. It was a two-thread, chainstitch machine powered solely by a foot treadle. With a simple adjustment, the machine could also create cablestitch and lockstitch. (Smithsonian photo 48221-C.)
Figure 81.—Eureka sewing machine, 1859. An example of the many short-lived types of which no written record can be found, this particular machine was used as a patent model for certain minor improvements in 1859. It has the name “Eureka” painted on the top and the following inscription incised on the baster plate: “Eureka Shuttle S. M. Co. 469 Broadway, N.Y.” Although it is a shuttle machine, it carries no patent dates and was not included in the Howe royalty records. Neither is it listed in the obsolescence list published in 1881. The company probably could not pay its royalty fees and was forced out of business almost immediately. If this machine had not been used as a patent model, no record of the company’s existence might remain. It should be noted that as in most shuttle machines the head was meant to be set into a treadle-powered table. Since most tables are very similar, they are not required for identification. (Smithsonian photo 48328-C.)
Figure 81.—Eureka sewing machine, 1859. This is an example of the many short-lived designs that have no written record. This specific machine was used as a patent model for some minor improvements in 1859. It has the name “Eureka” painted on the top, and the following inscription etched on the base plate: “Eureka Shuttle S. M. Co. 469 Broadway, N.Y.” Although it's a shuttle machine, it doesn’t have any patent dates and isn’t included in the Howe royalty records. It’s also not listed in the obsolescence list published in 1881. The company likely couldn’t afford its royalty fees and went out of business shortly after. If this machine hadn’t been used as a patent model, there might be no record of the company at all. It’s important to note that, like most shuttle machines, the head was designed to be fitted into a treadle-powered table. Since most tables are quite similar, they aren’t necessary for identification. (Smithsonian photo 48328-C.)
Figure 82.—M. Finkle sewing machine, 1857. The M. Finkle machines were manufactured in 1856 and 1857. Sometime before or about 1859, the inventor, Milton Finkle, formed a partnership and the machines were subsequently called M. Finkle & Lyon and later simply Finkle & Lyon. In 1859 the machine was awarded a silver medal by the American Institute for producing superior manufacturing and family lockstitch sewing machines. It also won a silver medal in Boston in 1860 at the Massachusetts Charitable Mechanics Association Exhibition. Although the name of the machine was changed to Victor in 1867, the company name remained Finkle & Lyon until about 1872 when it was changed to Victor also. Victor machines were manufactured until about 1890.
Figure 82.—M. Finkle sewing machine, 1857. The M. Finkle machines were made in 1856 and 1857. Somewhere around 1859, the inventor, Milton Finkle, partnered up, and the machines were then called M. Finkle & Lyon, and later just Finkle & Lyon. In 1859, the machine received a silver medal from the American Institute for its excellent manufacturing and family lockstitch sewing machines. It also won a silver medal in Boston in 1860 at the Massachusetts Charitable Mechanics Association Exhibition. Although the machine's name was changed to Victor in 1867, the company name stayed as Finkle & Lyon until about 1872, when it was also changed to Victor. Victor machines were produced until around 1890.
Machines can be dated by their serial number approximately as follows:
Machines can be dated by their serial number roughly like this:
Serial Number | Year |
1-200 | 1856 |
201-450 | 1857 |
451-700 | 1858 |
701-950 | 1859 |
951-1500 | 1860 |
1501-3000 | 1861 |
3001-5000 | 1862 |
5001-7000 | 1863 |
7001-9000 | 1864 |
9001-11000 | 1865 |
11001-13000 | 1866 |
13001-15490 | 1867 |
15491-17490 | 1868 |
17491-18830 | 1869 |
18831-21250 | 1870 |
21251-28890 | 1871 |
28891-40790 | 1872 |
40791-48240 | 1873 |
48241-53530 | 1874 |
53531-59635 | 1875 |
59636-65385 | 1876 |
No estimates are available for the years 1877 to 1890. (Smithsonian photo 48216-A.)
No estimates are available for the years 1877 to 1890. (Smithsonian photo 48216-A.)
[Pg 85]Figure 83.—Florence sewing machine. The Florence machine was based on the patents of Leander W. Langdon, whose first patent was obtained in 1855. Langdon sewing machines were manufactured by the inventor for a few years. It was his patent of March 20, 1860, that was the immediate forerunner of the Florence machine, whose name was derived from the city of manufacture, Florence, Massachusetts. The Howe royalty records of 1860 listed the Florence Sewing Machine Co. as one that took out a license that year. Langdon’s patent of July 14, 1863, was incorporated into the machines manufactured after that date; however, the date is always incorrectly stamped “July 18, 1863.” In 1865, the machine won a silver medal at the Tenth Exhibition of the Massachusetts Charitable Mechanics Association.
[Pg 85]Figure 83.—Florence sewing machine. The Florence machine was based on the patents of Leander W. Langdon, who secured his first patent in 1855. Langdon produced sewing machines for a few years. His patent from March 20, 1860, was the direct precursor to the Florence machine, named after its place of creation, Florence, Massachusetts. The Howe royalty records from 1860 identified the Florence Sewing Machine Co. as one that obtained a license that year. Langdon's patent dated July 14, 1863, was included in the machines produced after that point; however, the date is often incorrectly marked as “July 18, 1863.” In 1865, the machine earned a silver medal at the Tenth Exhibition of the Massachusetts Charitable Mechanics Association.
Over 100,000 Florence machines were manufactured by 1870. About 1880 the company changed the name of the machine to Crown. Improvements led to the name New Crown by 1885. About this time the right to use the name Florence for a sewing machine was purchased by a midwestern firm for an entirely different machine. In 1885 the Florence company began to manufacture lamp stoves and heating stoves and shortly thereafter they discontinued the manufacture of sewing machines.
Over 100,000 Florence machines were produced by 1870. Around 1880, the company renamed the machine to Crown. Upgrades resulted in the name New Crown by 1885. Around this time, a midwestern company bought the rights to use the name Florence for a completely different sewing machine. In 1885, the Florence company started making lamp stoves and heating stoves, and shortly after that, they stopped making sewing machines.
Using the serial numbers, Florence machines can be dated approximately as follows:
Using the serial numbers, Florence machines can be dated roughly as follows:
Serial Number | Year |
1-500 | 1860 |
501-2000 | 1861 |
2001-8000 | 1862 |
8001-20000 | 1863 |
20001-35000 | 1864 |
35001-50000 | 1865 |
50001-60000 | 1866 |
60001-70534 | 1867 |
70535-82534 | 1868 |
82535-96195 | 1869 |
96196-113855 | 1870 |
113856-129802 | 1871 |
129803-145592 | 1872 |
145593-154555 | 1873 |
154556-160072 | 1874 |
160073-164964 | 1875 |
164965-167942 | 1876 |
No record of the number of machines produced each year between 1877 and 1885 is available.
No records exist of the number of machines produced each year from 1877 to 1885.
The machine shown here, serial number 49131, was manufactured in 1865. It is stamped with the following patent dates: “Oct. 30, 1855, Mar. 20, 1860, Jan. 22, 1861, and July 18, 1863” and the Wilson patent date “Nov. 12, 1850.” The machines from 1860-1863 are marked with the early Langdon patents, excluding the 1863 one, and they have the additional patent dates of Howe and others: “Sept. 10, 1846, Nov. 12, 1850, Aug. 12, 1851, May 30, 1854, Dec. 19, 1854, Nov. 4, 1856.” (Smithsonian photo 45572-A.)
The machine shown here, serial number 49131, was made in 1865. It's stamped with the following patent dates: “Oct. 30, 1855, Mar. 20, 1860, Jan. 22, 1861, and July 18, 1863,” along with the Wilson patent date “Nov. 12, 1850.” The machines from 1860-1863 have the early Langdon patents, excluding the one from 1863, and they also include the additional patent dates from Howe and others: “Sept. 10, 1846, Nov. 12, 1850, Aug. 12, 1851, May 30, 1854, Dec. 19, 1854, Nov. 4, 1856.” (Smithsonian photo 45572-A.)
Figure 84.—Globe sewing machine. J. G. Folsom received two design patents in 1864, one on March 1 for a spool holder and one on May 17 for the basic style of the machine. Also in the same year, he was awarded a mechanical patent for an adjustment in the lower looper that would accommodate a change in needle size. Using these patents, he manufactured a single-thread, chainstitch machine, the Globe. Folsom also exhibited his machines at the Tenth Exhibition of the Massachusetts Charitable Mechanics Association in 1865. The Globe attracted particular attention and was awarded a silver medal.
Figure 84.—Globe sewing machine. J. G. Folsom received two design patents in 1864, one on March 1 for a spool holder and another on May 17 for the basic design of the machine. That same year, he was granted a mechanical patent for an adjustment in the lower looper that would allow for a change in needle size. Using these patents, he produced a single-thread, chainstitch machine called the Globe. Folsom also showcased his machines at the Tenth Exhibition of the Massachusetts Charitable Mechanics Association in 1865. The Globe drew special attention and was awarded a silver medal.
In 1866 Folsom devised a new treadle attachment for hand-operated machines; the invention was featured in Scientific American, volume 14, number 17, with a Globe machine. Folsom again exhibited at the Massachusetts Mechanics exhibition in 1869. In addition to an improved single-thread Globe, he also showed a double-thread, elastic-stitch (double chainstitch) machine for which he received a silver medal.
In 1866, Folsom created a new treadle attachment for hand-operated machines; the invention was highlighted in Scientific American, volume 14, number 17, featuring a Globe machine. Folsom showcased his work again at the Massachusetts Mechanics exhibition in 1869. Along with an upgraded single-thread Globe, he also presented a double-thread, elastic-stitch (double chainstitch) machine, for which he won a silver medal.
Folsom machines were manufactured until 1871; 280 machines were manufactured in that year.
Folsom machines were produced until 1871; 280 machines were made that year.
The Globe sewing machine illustrated is stamped “J. G. Folsom, Maker, Winchendon, Mass. Patented April 28, 1863 [Ketchum’s patent], Mar. 1, 1864. May 17, 1864.” The machine was manufactured before November 1864 or it would include the patent for the lower loop adjustment. (Smithsonian photo 48216-H.)
The Globe sewing machine shown is marked “J. G. Folsom, Maker, Winchendon, Mass. Patented April 28, 1863 [Ketchum’s patent], Mar. 1, 1864. May 17, 1864.” The machine was made before November 1864 or it would have the patent for the lower loop adjustment. (Smithsonian photo 48216-H.)
Note: At least five sewing machines, those in figures 84 through 89, are similar enough in appearance to cause some confusion, because their basic design stems from a short pillar.[Pg 86]
Note: At least five sewing machines, those in figures 84 through 89, look similar enough to confuse people, as their basic design comes from a short pillar.[Pg 86]
Figure 85.—Globe sewing machine with treadle attachment as illustrated in Scientific American, April 21, 1866. (Smithsonian photo 48221-A.)
Figure 85.—Globe sewing machine with treadle attachment as shown in Scientific American, April 21, 1866. (Smithsonian photo 48221-A.)
Figure 86.—Empire sewing machine, late 1860s. Although an Empire Sewing Machine Co. existed in New York in the 1860s (the predecessor of the Remington-Empire Co.), it is not known whether this machine was manufactured by that same company, which was primarily concerned with producing shuttle machines. This chainstitch machine is marked “Empire Co., Patented April 23, 1863,” the date referring again to Ketchum’s patent. It is very similar to Folsom’s Globe, except that it has claw feet rather than a closed base; the painted designs on the base of both are almost identical to those on the Monitor. Its spool holder, mounted in reverse, is a crude imitation of the Folsom patent. The Empire machines were probably manufactured about the same time as the Wilson machine. (Photo courtesy of The Henry Ford Museum and Greenfield Village, Dearborn, Michigan.)
Figure 86.—Empire sewing machine, late 1860s. Although an Empire Sewing Machine Co. was active in New York during the 1860s (the precursor to the Remington-Empire Co.), it’s unclear if this machine was made by that same company, which mainly focused on producing shuttle machines. This chainstitch machine is labeled “Empire Co., Patented April 23, 1863,” with the date referring to Ketchum’s patent. It closely resembles Folsom’s Globe, but instead of a closed base, it has claw feet; the painted patterns on the base of both machines are nearly identical to those on the Monitor. Its spool holder, which is mounted backward, is a rough imitation of the Folsom patent. The Empire machines were likely made around the same time as the Wilson machine. (Photo courtesy of The Henry Ford Museum and Greenfield Village, Dearborn, Michigan.)
Figure 87.—Atwater sewing machine, 1858. Atwater machines, based on the patent of B. Atwater, issued May 5, 1857, were manufactured from 1857 to about 1860. The machine illustrated, which is designed to be operated by a hand-turned wheel, has an upper forked dog feed, and its horizontally supported spool is directly over the stitching area. Like the others, it has a striated pillar and claw feet. The manufacturer is unknown. (Smithsonian photo P63200.)
Figure 87.—Atwater sewing machine, 1858. Atwater machines, based on the patent by B. Atwater, issued on May 5, 1857, were made from 1857 until around 1860. The machine shown here is designed to be operated by a hand-turned wheel, features an upper forked dog feed, and has its horizontally supported spool positioned directly above the stitching area. Like the others, it has a striated pillar and claw feet. The manufacturer is unknown. (Smithsonian photo P63200.)
Figure 88.—Monitor sewing machine, 1860-1866. The Monitor machines of this style were not marked by their manufacturers, Shaw & Clark of Biddeford, Maine. Later the company was forced by the “Combination” to pay a royalty, so it changed the style and began marking its machines with the company name and patent dates (see fig. 119 for copy of seal). The Monitor, which employed the conventional vertical spindle to hold the spool of thread, had a top feed in the form of a walking presser. Its striated pillar was similar to that of the Atwater machine, and both featured the same claw feet and urn-like top. Unlike the Atwater, however, the Monitor had a double drive from the hand-turned wheel, which was grooved for operation with belt and treadle. (Smithsonian photo 33458.)
Figure 88.—Check sewing machine, 1860-1866. The Monitor machines of this style were not labeled by their manufacturers, Shaw & Clark of Biddeford, Maine. Later, the company had to pay a royalty due to the “Combination,” so it changed the design and started labeling its machines with the company name and patent dates (see fig. 119 for a copy of the seal). The Monitor used a standard vertical spindle to hold the spool of thread and had a top feed designed like a walking presser. Its ridged pillar was similar to that of the Atwater machine, and both had the same claw feet and urn-like top. However, unlike the Atwater, the Monitor had a double drive from the hand-turned wheel, which was grooved for use with a belt and treadle. (Smithsonian photo 33458.)
Figure 89.—Wilson sewing machine, late 1860s to early 1870s. In addition to the Buckeye (see fig. 77), W. G. Wilson manufactured several other styles of sewing machines. This one, a combination of the varying styles of the earlier pillar machine has even duplicated the general style of the spool holder patented by Folsom. The pillar is not striated, but the machine does repeat the claw feet of the Atwater and Monitor machines. Wilson machines are usually marked “Wilson Sewing Mach. Manuf’g Co. Cleveland, Ohio, Ketchum’s Patent April 28, 1863.” The latter name and/or patent date are found on many of the machines of this general construction. The patent is that issued to Stephen C. Ketchum for his method of converting rotary motion into reciprocal motion. (Photo courtesy of The Henry Ford Museum and Greenfield Village, Dearborn, Michigan.)
Figure 89.—Wilson sewing machine, late 1860s to early 1870s. Besides the Buckeye (see fig. 77), W. G. Wilson produced several other types of sewing machines. This one combines various styles from earlier pillar machines and even mimics the general design of the spool holder patented by Folsom. The pillar isn't grooved, but the machine does feature the claw feet found on the Atwater and Monitor machines. Wilson machines are typically labeled “Wilson Sewing Mach. Manuf’g Co. Cleveland, Ohio, Ketchum’s Patent April 28, 1863.” The name and/or patent date appears on many machines with this design. The patent was granted to Stephen C. Ketchum for his method of converting rotary motion into reciprocating motion. (Photo courtesy of The Henry Ford Museum and Greenfield Village, Dearborn, Michigan.)
Figure 90.—Grant Brothers sewing machine, 1867. This machine was one of several styles that utilized Raymond’s 1861 patented chainstitch method. This machine, however, used an under feed rather than a top feed.
Figure 90.—Grant Brothers sewing machine, 1867. This machine was one of several types that used Raymond’s 1861 patented chainstitch method. However, this machine featured an under feed instead of a top feed.
Neither a name nor a date appears on the machine. In the June 25, 1907, issue of the Sewing Machine Times it was called the Common Sense machine, but detailed research has turned up no evidence to substantiate this name. However, a dated brochure advertising the Grant Brothers machine and showing a model identical to that illustrated in the Sewing Machine Times has been found. The brochure states that the machine made an elastic lockstitch; this was not a true lockstitch, however, but was in fact a simple chainstitch.
Neither a name nor a date is on the machine. In the June 25, 1907, issue of the Sewing Machine Times, it was referred to as the Common Sense machine, but thorough research has found no evidence to support this name. However, a dated brochure promoting the Grant Brothers machine, which features a model identical to the one shown in the Sewing Machine Times, has been discovered. The brochure claims that the machine produced an elastic lockstitch; however, this was not a true lockstitch but was actually a simple chainstitch.
Grant Brothers sold their machine, which had silver-plated mountings, for $18; the price included hemmer, Barnum’s self-sewer, oilcan, screwdriver, clamp, gauge, and four silver needles. An additional charge of $12 was made for a table and treadle. Compared to other chainstitch machines the price was high, and the company was short-lived. (Smithsonian photo 60794-E.)
Grant Brothers sold their machine with silver-plated parts for $18; the price included a hemmer, Barnum’s self-sewer, an oil can, a screwdriver, a clamp, a gauge, and four silver needles. An extra $12 was charged for a table and treadle. Compared to other chainstitch machines, the price was high, and the company didn’t last long. (Smithsonian photo 60794-E.)
Figure 91.—Greenman and True sewing machine. This lockstitch machine based on S. H. Roper’s patent of 1857 was manufactured at Norwich, Connecticut, from 1859 to 1861 by Cyrus B. True, the inventor, and Jared F. Greenman, True’s financial partner. Licensed by the “Combination” and carrying the Howe patent date, the machine had obvious merit: it was strong, well made—a good family machine. Exhibited at the Ninth Exhibition of the Massachusetts Charitable Mechanics Association in September 1860, it received a bronze medal. (At this time the company was listed as Morse and True—the inventor had obviously taken on a second financial backer.) Unfortunately, the best market for the machine lay in the South, and the outbreak of the Civil War made collections impossible. This greatly retarded business and finally drove the firm into bankruptcy. In all, it is doubtful that more than one thousand machines were produced in the three years of manufacture.
Figure 91.—Greenman and True sewing machine. This lockstitch machine, based on S. H. Roper’s 1857 patent, was made in Norwich, Connecticut, from 1859 to 1861 by Cyrus B. True, the inventor, and Jared F. Greenman, True’s financial partner. Licensed by the “Combination” and displaying the Howe patent date, the machine was clearly remarkable: it was sturdy, well-built—a great family machine. It was showcased at the Ninth Exhibition of the Massachusetts Charitable Mechanics Association in September 1860, where it won a bronze medal. (At this time, the company was listed as Morse and True—the inventor had evidently obtained a second financial backer.) Unfortunately, the best market for the machine was in the South, and the start of the Civil War made payments impossible. This significantly hurt business and ultimately led the firm to bankruptcy. Overall, it’s unlikely that more than a thousand machines were made during the three years of production.
The machine illustrated is marked “Greenman and True” and bears the serial number 402; it was probably manufactured early in 1860. (Smithsonian photo 48216-N.)
The machine shown is labeled “Greenman and True” and has the serial number 402; it was likely made in early 1860. (Smithsonian photo 48216-N.)
Figure 92.—Grover and Baker sewing machine. The Grover and Baker machine was one of the more popular machines from the 1850s until the early 1870s. The company produced iron-frame machines, fine cabinet models, and portables (figs. 35 and 36). Their machines may be dated by serial number approximately as follows:
Figure 92.—Grover & Baker sewing machine. The Grover and Baker machine was one of the more popular sewing machines from the 1850s until the early 1870s. The company made machines with iron frames, elegant cabinet designs, and portable options (figs. 35 and 36). You can estimate the manufacturing date of their machines by looking at the serial number roughly as follows:
Serial Number | Year |
1-500 | 1851 |
501-1000 | 1852 |
1001-1658 | 1853 |
1659-3893 | 1854 |
3894-5038 | 1855 |
5039-7000 | 1856 |
7001-10681 | 1857 |
10682-15752 | 1858 |
15753-26033 | 1859 |
26034-44869 | 1860 |
44870-63705 | 1861 |
63706-82641 | 1862 |
82642-101477 | 1863 |
101478-120313 | 1864 |
120314-139148 | 1865 |
139149-157886 | 1866 |
157887-190886 | 1867 |
190887-225886 | 1868 |
225887-261004 | 1869 |
261005-338407 | 1870 |
338408-389246 | 1871 |
389247-441257 | 1872 |
441258-477437 | 1873 |
477438-497438 | 1874 |
497439-512439 | 1875 |
(Smithsonian photo 45513-B, an engraving of a Grover and Baker sewing machine from an advertising brochure of about 1870.)
(Smithsonian photo 45513-B, an engraving of a Grover and Baker sewing machine from an advertising brochure from around 1870.)
Figure 93.—Hancock sewing machine, 1867. One of the many inventors who turned his talents to inventing and producing a mechanically simple and cheaper machine was Henry J. Hancock. His 1867 machine is only about six inches wide; it uses a tambour-type needle, pulling a loop of thread from below the stitching surface. (Smithsonian photo P63197.)
Figure 93.—Hancock sewing machine, 1867. One of the many inventors who applied his skills to create a simple and affordable machine was Henry J. Hancock. His 1867 machine is only about six inches wide; it uses a tambour needle that pulls a loop of thread from underneath the stitching surface. (Smithsonian photo P63197.)
Figure 94.—Hancock sewing machine, 1868. Hancock in 1868 received both a design patent and a mechanical patent now using the eye-pointed needle and a hook to form the chainstitch. The design was an open framework circle with a mirror mounted in front of the table clamp. The purpose of the designated “looking glass” was decorative only. The Hancock machines were only manufactured for a few years. They measure 10-1/2 inches in width, slightly larger than the earlier machine. (Smithsonian photo 48328-M.)
Figure 94.—Hancock sewing machine, 1868. In 1868, Hancock received both a design patent and a mechanical patent for its use of the eye-pointed needle and a hook to create the chain stitch. The design featured an open circular framework with a mirror placed in front of the table clamp. The purpose of the so-called “looking glass” was purely decorative. Hancock machines were produced for only a few years. They measure 10-1/2 inches in width, which is slightly larger than the earlier model. (Smithsonian photo 48328-M.)
Figure 95.—[A.C.] Herron’s patent sewing machine, 1858. The manufacturer of this machine is not known, but the machine was based on the patent of Abial C. Herron issued August 4, 1857. All the machines carry a small heart-shaped plate just above the needle descent bearing the patentee’s name and the patent date. The patent covered an improvement in the method of making the chainstitch. The machines were provided with a hand crank, but were also meant to be operated by a belt and treadle. No records of the extent of manufacture of this machine have been found. This machine head measures 14 inches in width, about standard size. (Smithsonian photo 48329-J.)
Figure 95.—Herron's patented sewing machine, 1858. The manufacturer of this machine is not known, but it was based on the patent granted to Abial C. Herron on August 4, 1857. All the machines have a small heart-shaped plate just above the needle that displays the inventor’s name and the patent date. The patent covered an improvement in how the chainstitch is made. The machines came with a hand crank but were also designed to be powered by a belt and treadle. There are no records showing how many of these machines were made. The machine head measures 14 inches wide, which is about the standard size. (Smithsonian photo 48329-J.)
Figure 96.—A. B. Howe sewing machine of about 1860. (Smithsonian photo 45525-C.)
Figure 96.—A. B. Howe sewing machine from around 1860. (Smithsonian photo 45525-C.)
Figures 96, 97, and 98.—The Howe machines. It is difficult for many to believe that the stamped legend “Elias Howe patent, Sept. 10, 1846” does not certify that a machine is an original Howe. Although Elias Howe was granted a patent for the lockstitch machine in 1846, he did not establish a sewing-machine factory for about twenty years. Early in the 1850s and later through the “Combination,” however, he licensed others to make machines using his patent. These machines bore that patent date for which a royalty was being paid.
Figures 96, 97, and 98.—The Howe sewing machines. Many people find it hard to believe that the stamped label “Elias Howe patent, Sept. 10, 1846” does not guarantee that a machine is an original Howe. While Elias Howe received a patent for the lockstitch machine in 1846, he didn’t set up a sewing machine factory until about twenty years later. However, in the early 1850s and later through the “Combination,” he allowed others to produce machines using his patent. These machines displayed that patent date, for which a royalty was paid.
Among his early licensees was his elder brother Amasa who organized the Howe Sewing Machine Co. in 1854. The Amasa Howe machines were very good ones, and in 1862 Amasa won the prize medal at the London International Exhibition. This immensely increased the popularity of the machine and Elias offered to join Amasa by building a large factory at Bridgeport, Connecticut, to fill the increasing demand for more machines. The machines produced at Bridgeport, however, although imitating the Amasa Howe machines, proved inferior in quality. Amasa found that, rather than helping his business reputation, his brother’s efforts were hurting him, and he severed business relations with Elias.
Among his early licensees was his older brother Amasa, who started the Howe Sewing Machine Co. in 1854. The Amasa Howe machines were high quality, and in 1862, Amasa won the prize medal at the London International Exhibition. This greatly boosted the popularity of the machine, and Elias offered to partner with Amasa by building a large factory in Bridgeport, Connecticut, to meet the growing demand for more machines. However, the machines made in Bridgeport, while trying to mimic the Amasa Howe machines, turned out to be of lower quality. Amasa realized that instead of enhancing his business reputation, his brother’s efforts were damaging it, so he cut ties with Elias.
Because of their brief association, the 1862 prize medal awarded to A. B. Howe was sometimes credited to Elias. The latter did receive awards for his patent, but never for his manufactured machines. When the two brothers dissolved their joint venture, Elias attempted to call his new company the Howe Sewing Machine Co., but Amasa’s claim that this name had been his exclusive property for many years was upheld by the courts. Elias then omitted the word “Sewing” and called his company simply the Howe Machine Co.
Because of their short partnership, the 1862 prize medal awarded to A. B. Howe was sometimes mistakenly attributed to Elias. While Elias did receive awards for his patent, he never earned any for the machines he manufactured. When the two brothers ended their joint venture, Elias tried to name his new company the Howe Sewing Machine Co., but Amasa's claim that this name had been his exclusive property for many years was upheld by the courts. Elias then dropped the word “Sewing” and named his company simply the Howe Machine Co.
After Elias died in 1867, the company was run by his sons-in-law, the Stockwell brothers. To distinguish their machines from those of A. B. Howe, they marked each machine with a brass medallion picturing the head and flowing locks of Elias Howe. They also continued to advertise their machine as the “original” Howe. In about 1873, B. P. Howe, Amasa’s son, sold the Howe Sewing Machine Co. to the Stockwell brothers, who continued to manufacture Howe machines until 1886.
After Elias died in 1867, his sons-in-law, the Stockwell brothers, took over the company. To set their machines apart from A. B. Howe's, they labeled each one with a brass medallion featuring the head and flowing hair of Elias Howe. They also kept promoting their machine as the “original” Howe. Around 1873, B. P. Howe, Amasa’s son, sold the Howe Sewing Machine Co. to the Stockwell brothers, who continued making Howe machines until 1886.
The machines of the A. B. Howe Sewing Machine Co. may be dated by serial number approximately as follows:
The sewing machines from A. B. Howe Sewing Machine Co. can be dated by their serial number roughly like this:
Serial Number | Year |
1-60 | 1854 |
61-113 | 1855 |
114-166 | 1856 |
167-299 | 1857 |
300-478 | 1858 |
479-1399 | 1859 |
No figures are available for 1860-1870, but 20,051 machines were manufactured in 1871.
No data is available for 1860-1870, but 20,051 machines were produced in 1871.
The machines of the [Elias] Howe Machine Co. are not believed to have begun with serial number 1, and no figures are available for 1865-1867. After that, the machines may be dated by serial number approximately as follows:
The machines from the [Elias] Howe Machine Co. likely didn’t start with serial number 1, and there are no records for 1865-1867. After that, you can estimate the manufacturing dates of the machines by their serial numbers, roughly as follows:
Serial Number | Year |
11,000-46,000 | 1868 |
46,001-91,843 | 1869 |
91,844-167,000 | 1870 |
167,001-301,010 | 1871 |
301,011-446,010 | 1872 |
446,011-536,010 | 1873 |
536,011-571,010 | 1874 |
571,011-596,010 | 1875 |
596,011-705,304 | 1876 |
No figures are available for 1877-1886.
No data is available for 1877-1886.
Figure 97.—Advertising brochure distributed by E. Howe during the brothers’ brief partnership; the machines are basically A. B. Howe machines, 1863. (Smithsonian photo 49373-A.)
Figure 97.—Promo brochure distributed by E. Howe during the brothers’ short partnership; the machines are essentially A. B. Howe machines, 1863. (Smithsonian photo 49373-A.)
Figure 98.—Howe (Stockwell brothers) machine, 1870. (Smithsonian photo 45572-E.)
Figure 98.—Howe machine (Stockwell brothers), 1870. (Smithsonian photo 45572-E.)
Figure 99.—Patent Model Of Christopher Hodgkins, November 2, 1852, assigned to Nehemiah Hunt. (Smithsonian photo 34551.)
Figure 99.—Patent Model by Christopher Hodgkins, November 2, 1852, assigned to Nehemiah Hunt. (Smithsonian photo 34551.)
Figures 99, 100, and 101.—The N. Hunt (later, in 1856, Hunt & Webster and finally in 1858 Ladd and Webster) sewing machine was based on the patents of Christopher Hodgkins, November 2, 1852, and May 9, 1854, both of which were assigned to Nehemiah Hunt. First manufactured in 1853, the machine, which closely resembled the Hodgkins’ patent, won a silver medal at the exhibition of the Massachusetts Charitable Mechanics Association that same year.
Figures 99, 100, and 101.—The N. Hunt (later, in 1856, Hunt & Webster and finally in 1858 Ladd and Webster) sewing machine was based on the patents of Christopher Hodgkins from November 2, 1852, and May 9, 1854, both of which were assigned to Nehemiah Hunt. First made in 1853, the machine, which looked a lot like Hodgkins’ patent, won a silver medal at the exhibition of the Massachusetts Charitable Mechanics Association that same year.
In 1856 Hunt took a partner, and the company became Hunt & Webster. An interesting account of this company appeared as a feature article in Ballou’s Pictorial, July 5, 1856, where it was reported that “the North American Shoe Company have over fifty of the latest improved machines, represented in these drawings [fig. 31], now running....” The article also estimated that a 55-million dollar increase in shoe manufacturing in Massachusetts in 1855 was due to the sewing machine. In 1856 the Hunt & Webster machine again won a silver medal at the exhibition. Very late in 1858 the company became Ladd, Webster, & Co. and continued to manufacture both family and manufacturing sewing machines until the mid-1860s.
In 1856, Hunt took on a partner, and the company was renamed Hunt & Webster. An interesting article about this company was featured in Ballou’s Pictorial on July 5, 1856, where it stated that "the North American Shoe Company has over fifty of the latest improved machines, shown in these drawings [fig. 31], currently in operation...." The article also estimated that a $55 million increase in shoe manufacturing in Massachusetts in 1855 was attributed to the sewing machine. In 1856, the Hunt & Webster machine won a silver medal at the exhibition once again. Late in 1858, the company became Ladd, Webster, & Co. and continued to produce both household and industrial sewing machines until the mid-1860s.
The approximate date of manufacture can be determined by serial number:
The manufacture date can be roughly identified by the serial number:
Serial Number | Year |
1-100 | 1853 |
101-368 | 1854 |
369-442 | 1855 |
443-622 | 1856 |
623-1075 | 1857 |
1076-1565 | 1858 |
1566-3353 | 1859 |
Figure 100.—Right: Hunt & Webster sewing machine of about 1855, serial number 414. (Smithsonian photo 48216-V.)
Figure 100.—Right: Hunt & Webster sewing machine from around 1855, serial number 414. (Smithsonian photo 48216-V.)
Figure 101.—Ladd, Webster & Co. sewing machine of about 1858, Boston, serial number 1497. (Smithsonian photo 46953.)
Figure 101.—Ladd, Webster & Co. sewing machine from around 1858, Boston, serial number 1497. (Smithsonian photo 46953.)
Figure 102.—Improved Common Sense sewing machine of about 1870. This machine is so very similar to the New England machines in its feed, threading, looping mechanism, and in its general design, that it is sometimes mistaken for the earlier New England machines (see figs. 112 and 113).
Figure 102.—Enhanced Common Sense sewing machine from around 1870. This machine is very similar to the New England machines in its feed, threading, looping mechanism, and overall design, to the point that it is occasionally confused with the earlier New England machines (see figs. 112 and 113).
Dating from the early 1870s, the Improved Common Sense machine is about 10 inches in width, two inches larger than the New England machine. The spool holder is similar to Folsom’s patented design, but is less refined. A page from an advertising brochure of the period verifies the name of the machine, but does not identify the manufacturer.
Dating from the early 1870s, the Improved Common Sense machine is about 10 inches wide, which is two inches wider than the New England machine. The spool holder is similar to Folsom’s patented design, but it's not as polished. A page from an advertising brochure from that time confirms the machine's name but doesn’t specify the manufacturer.
There are no patent dates or identifying names or numbers on the machine illustrated. Although the Empire Co. also produced a machine of this style, their models are marked with their name and with Ketchum’s patent date, April 23, 1863. Of the several styles of machine using the Raymond looper, this type seems to account for the largest volume manufactured, as evidenced by the proportionately higher number of examples still extant. (Smithsonian photo 48328-E.)
There are no patent dates or identifying names or numbers on the machine shown. While the Empire Co. also made a machine of this style, their models are labeled with their name and Ketchum’s patent date, April 23, 1863. Among the various styles of machines using the Raymond looper, this type appears to represent the largest volume produced, as indicated by the comparatively higher number of surviving examples. (Smithsonian photo 48328-E.)
Figure 103.—Johnson sewing machine, 1857. Another of the all-but-forgotten manufacturers of the 1850s was Emery, Houghton & Co., who constructed the A.F. Johnson machines. Examination of existing machines indicates that they were manufactured in 1856 and 1857, and possibly a little longer. This one from 1857 bears the serial number 624, so we know that several hundred were manufactured. The head is ornately attractive, slightly reminiscent of Wheeler & Wilson models, and of standard size. (Smithsonian photo 48329-B.)
Figure 103.—Johnson sewing machine, 1857. Another largely forgotten manufacturer from the 1850s was Emery, Houghton & Co., which produced the A.F. Johnson machines. A look at existing machines shows that they were made in 1856 and 1857, and possibly a little longer. This one from 1857 has the serial number 624, indicating that several hundred were produced. The head is beautifully designed, somewhat reminiscent of Wheeler & Wilson models, and is of standard size. (Smithsonian photo 48329-B.)
Figure 104.—“Lady” sewing machine of about 1859. The contemporary name of this machine is unknown. The unusual design of the head, or main support, is based in part on the design patent, number 216, of Isaac F. Baker, issued April 10, 1849, for a “new and useful design[,] for ornamenting furniture[,] called Cora Munro” who was a character in James Fenimore Cooper’s Last of the Mohicans. The design shows a female figure wearing a riding dress and hat that is ornamented with a plume and a bow. Her right hand holds a riding stick and the left, her skirt. Trunks of trees and foliage complete the Baker design, which is known to have been used for girandoles of the period. A companion design was also patented by Baker, number 215, which is in the form of a man in military costume and is named “Major Heyward,” for another character in Last of the Mohicans.
Figure 104.—"Lady" sewing machine from around 1859. The current name of this machine is unknown. The unique design of the head, or main support, is partly based on the design patent number 216 by Isaac F. Baker, issued on April 10, 1849, for a “new and useful design[,] for ornamenting furniture[,] called Cora Munro,” a character in James Fenimore Cooper’s Last of the Mohicans. The design features a female figure in a riding dress and hat adorned with a plume and bow. She holds a riding stick in her right hand and her skirt in her left. The design is completed with trunks of trees and foliage, and it is known to have been used for girandoles of that era. Baker also patented a companion design, number 215, which depicts a man in military costume named “Major Heyward,” after another character in Last of the Mohicans.
The sewing machines based on the “Cora Munro” design also use branch designs as the overhanging arms. A mother bird sits in the upper branch and descends to feed a young bird as the machine is in operation. The one illustrated was used as the machine submitted with a request for patent by George Hensel of New York City for which patent 24,737 was issued on July 12, 1859. Since Hensel’s patent application was for an improvement in the feed, there was no need for the highly decorative head unless such a machine was commercially available. The patent specifications merely state that the head is “ornamented.” Another sewing machine of this type was used as the patent model by Sidney Parker of Sing Sing, New York, number 24,780, issued on the same date as the Hensel patent. Parker’s patent also covered an improved feeding mechanism. In the patent description, however, the inventor states that “the general form of the machine is not unlike others now in use.” By this he might have meant in the design, or possibly in the basic structural form. Other than the two machines described, no other examples are known to have survived, but “Lady” or “Cora Munro” sewing machines were manufactured. (Smithsonian photo 45506-D.)
The sewing machines designed like the “Cora Munro” also feature branch designs for the overhanging arms. A mother bird is perched on the upper branch and flies down to feed her young as the machine operates. The one shown was submitted for a patent by George Hensel from New York City, for which patent 24,737 was granted on July 12, 1859. Since Hensel’s patent application was for an improved feed mechanism, there was no need for the highly decorative head unless such a machine was commercially available. The patent specifications simply say that the head is “ornamented.” Another sewing machine of this type was used as the patent model by Sidney Parker of Sing Sing, New York, number 24,780, which was issued on the same date as Hensel's patent. Parker’s patent also included an improved feeding mechanism. However, in the patent description, the inventor mentions that “the general form of the machine is not unlike others now in use.” By this, he may have been referring to the design or possibly the basic structure. Aside from the two machines described, no other examples are known to exist, but “Lady” or “Cora Munro” sewing machines were produced. (Smithsonian photo 45506-D.)
Figure 105.—Landfear’s Patent Sewing Machine of about 1857. Another of the many machines that, except for isolated examples, have almost completely disappeared from the records is Landfear’s machine. Fortunately, this manufacturer marked his machine—where many did not—stamping it: “Landfear’s patent-Decr 1856, No. 262, W. H. Johnson’s Patent Feb. 26th 1856, Manfrd by Parkers, Snow, Brooks & Co., West Meriden, Conn.” (There was a Parker sewing machine manufactured by the Charles Parker Co. of Meriden, but his machine was a double-thread chainstitch machine and was licensed by the “Combination.” The Landfear machine may have been an earlier attempt by a predecessor or closely related company.)
Figure 105.—Landfear's Sewing Machine Patent from around 1857. This is one of the many machines that, aside from a few exceptions, have mostly faded from history records—Landfear’s machine included. Thankfully, this manufacturer labeled his machine—unlike many others—stamping it: “Landfear’s patent-Decr 1856, No. 262, W. H. Johnson’s Patent Feb. 26th 1856, Manufactured by Parkers, Snow, Brooks & Co., West Meriden, Conn.” (There was a Parker sewing machine made by the Charles Parker Co. of Meriden, but that one was a double-thread chainstitch machine licensed by the “Combination.” The Landfear machine might have been an earlier version from a predecessor or a closely related company.)
The Landfear patent was for a shuttle machine, but it also included a mode for regulating stitch length. The name chosen for this machine may be incorrect, since the single-thread chainstitch mechanism is primarily that of W. H. Johnson, but since the Johnson patent also was used on other machines the name “Landfear” was assigned. The machine was probably another attempt to evade royalty payment to the “Combination.”
The Landfear patent was for a shuttle machine, but it also included a way to adjust stitch length. The name given to this machine might be inaccurate, since the single-thread chainstitch mechanism mainly belongs to W. H. Johnson. However, since the Johnson patent was used on other machines, the name “Landfear” was used instead. The machine was likely another attempt to avoid paying royalties to the “Combination.”
The serial number 262 indicates that at least that many machines were manufactured, although this model is the only one known to be in existence. The support arm of the machine head is iron, cast as a vase of flowers and painted in natural colors. The paint on the head is original, but the table has been refinished, and the iron legs, which had rusted, have been repainted. (Smithsonian photo 48440-G.)
The serial number 262 suggests that at least that many machines were made, although this model is the only one known to exist. The support arm of the machine head is made of iron, shaped like a vase of flowers and painted in natural colors. The paint on the head is original, but the table has been refinished, and the iron legs, which had rusted, have been repainted. (Smithsonian photo 48440-G.)
Figure 106.—Lathrop sewing machine of about 1873. These machines were manufactured by the Lathrop Combination Sewing Machine Co. under the patents of Lebbeus W. Lathrop of 1869, 1870, and 1873. The machine used two threads, both taken from spools; moreover, it produced not only the double chainstitch, but it was constructed to produce also a lockstitch and a combined “lock and chain stitch.” The machine illustrated bears the serial number 31 and the patent dates of Grover & Baker, and Bachelder among others, in addition to the first two Lathrop patent dates. The company lasted only a few years as it is included in the 1881 list of manufacturers that had ceased to exist. (Smithsonian photo 46953-F.)
Figure 106.—Lathrop sewing machine from around 1873. These machines were made by the Lathrop Combination Sewing Machine Co. under the patents of Lebbeus W. Lathrop from 1869, 1870, and 1873. The machine used two threads, both coming from spools; in addition, it produced not only a double chainstitch but was also designed to create a lockstitch and a combined “lock and chain stitch.” The machine shown has the serial number 31 and includes the patent dates of Grover & Baker, and Bachelder among others, along with the first two Lathrop patent dates. The company only operated for a few years, as it appears on the 1881 list of manufacturers that had gone out of business. (Smithsonian photo 46953-F.)

Figure 107.—Illustration from a brochure, marked in ink: “The National Portrait Gallery, 1855.” Singer Archives. (Smithsonian photo 48091-E.)
Figure 107.—Illustration from a pamphlet, marked in ink: “The National Portrait Gallery, 1855.” Singer Archives. (Smithsonian photo 48091-E.)
Figures 107 and 108.—The Nichols and Leavitt sewing machines. One of Elias Howe’s earliest licensees was J. B. Nichols. His machine, manufactured at first with George Bliss and later alone as J. B. Nichols & Co., was called Howe’s Improved Patent Sewing Machine. It was, however, no more a Howe machine than any of the others produced under the Howe patent.
Figures 107 and 108.—The Nichols and Leavitt sewing machines. One of Elias Howe’s earliest licensees was J. B. Nichols. His machine, initially produced with George Bliss and later on his own as J. B. Nichols & Co., was named Howe’s Improved Patent Sewing Machine. However, it was not any more a Howe machine than the other ones made under the Howe patent.
In July 1855 Nichols went into partnership with Rufus Leavitt, and the company name changed to Nichols, Leavitt & Co. In 1857 it was changed again to Leavitt & Co., and finally in the mid-1860s to Leavitt Sewing Machine Co. By the 1870s, it was defunct.
In July 1855, Nichols teamed up with Rufus Leavitt, and the company name was updated to Nichols, Leavitt & Co. By 1857, it was changed again to Leavitt & Co., and finally in the mid-1860s to Leavitt Sewing Machine Co. By the 1870s, it had shut down.
The Nichols-Leavitt machines can be dated by their serial numbers approximately as follows:
The Nichols-Leavitt machines can be dated by their serial numbers roughly as follows:
Serial Number | Year | Company |
1-28 | 1853 | Nichols & Bliss |
29-245 | 1854 | J. B. Nichols & Co. |
246-397 | 1855 | J. B. Nichols & Co.—Nichols, Leavitt & Co. |
398-632 | 1856 | Nichols, Leavitt & Co. |
633-827 | 1857 | Leavitt & Co. |
828-902 | 1858 | ” |
903-1115 | 1859 | ” |
1116-1436 | 1860 | ” |
1437-1757 | 1861 | ” |
1758-2077 | 1862 | ” |
2078-2400 | 1863 | ” |
2401-2900 | 1864 | ” |
2901-3900 | 1865 | Leavitt Sewing Machine Co. |
3901-4900 | 1866 | ” |
4901-5951 | 1867 | ” |
5952-6951 | 1868 | ” |
6952-7722 | 1869 | ” |
There is no record that the company was in existence after 1869.[Pg 101]
There’s no evidence that the company existed after 1869.[Pg 101]

Figure 108.—Leavitt sewing machine of about 1868, serial number 6907. (Smithsonian photo 48328.)
Figure 108.—Leavitt sewing machine from around 1868, serial number 6907. (Smithsonian photo 48328.)

Figure 109.—Lester sewing machine of about 1858. The Lester machine was first manufactured by J. H. Lester in Brooklyn, New York. His machine was based on the patents of William Johnson, John Bradshaw and others but not on the patents held by the “Combination,” although he had secured a license. When the Old Dominion Company applied for a license from the “Combination,” Lester learned of this, went to Richmond, and arranged to combine his business with theirs. Since the Lester machine was the better one, it was agreed to cease the manufacture of the Old Dominion machines early in 1860 and in March the company name was changed to the Lester Mfg. Co. Late in 1860, George Sloat entered the company with his Elliptic machine; the name was changed again, this time to Union Sewing Machine Co. The manufacture of both sewing machines continued until the outbreak of the Civil War the following year, which brought a conversion to arms production. The manufacture of Lester machines was never resumed.
Figure 109.—Lester sewing machine from around 1858. The Lester machine was first made by J. H. Lester in Brooklyn, New York. His machine was based on patents by William Johnson, John Bradshaw, and others but not on the patents owned by the “Combination,” even though he had obtained a license. When the Old Dominion Company sought a license from the “Combination,” Lester found out about it, traveled to Richmond, and arranged to merge his business with theirs. Since the Lester machine was superior, they agreed to stop making the Old Dominion machines in early 1860, and in March, the company name changed to Lester Mfg. Co. Later in 1860, George Sloat joined the company with his Elliptic machine; the name was changed again, this time to Union Sewing Machine Co. Production of both sewing machines continued until the Civil War broke out the following year, which led to a shift to arms manufacturing. The production of Lester machines was never resumed.
The machine illustrated was manufactured by J. H. Lester in Brooklyn; it bears the serial number 96. The number of Lester machines manufactured from 1858 through 1861 is not known, but it was probably less than 1,000. (Smithsonian photo P63359.)
The machine shown was made by J. H. Lester in Brooklyn; it has the serial number 96. The exact number of Lester machines made from 1858 to 1861 isn't known, but it was likely less than 1,000. (Smithsonian photo P63359.)

Figure 110.—Ne Plus Ultra of about 1867. Another of the interesting hand-turned chainstitch machines of the late 1850s and 1860s was patented by O.L. Reynolds. The baster plates and the handle on the wheel are missing on this machine, but an interesting shield and draped-flag pattern is painted on the base.
Figure 110.—The Ultimate from around 1867. Another intriguing hand-turned chainstitch machine from the late 1850s and 1860s was patented by O.L. Reynolds. The baster plates and the handle on the wheel are missing from this machine, but it features an interesting shield and draped-flag pattern painted on the base.
Another machine of this type has the following inscription stamped on the baster plate: “Ne Plus Ultra, Patent Applied For, 174, O.L. Reynolds, Patentee & Manufacturer, Dover N.H.” Reynold’s patent model, March 30, 1858, bears the serial number 110, indicating that the machine illustrated here—which bears the serial number 26—was manufactured before the patent was obtained. (Smithsonian photo 48216-F.)
Another machine of this type has the following inscription stamped on the baster plate: “Ne Plus Ultra, Patent Applied For, 174, O.L. Reynolds, Patentee & Manufacturer, Dover N.H.” Reynolds’ patent model, March 30, 1858, has the serial number 110, indicating that the machine shown here—which has the serial number 26—was made before the patent was granted. (Smithsonian photo 48216-F.)

Figure 111.—Nettleton & Raymond sewing machine. One of the most ornate of the early, small, hand-turned sewing machines was patented and manufactured by Willford H. Nettleton and Charles Raymond whose first patent was received on April 14, 1857. The patent model, believed to be a commercial machine, is beautifully silver-plated. Whether this was a special one-of-a-kind model, or whether the inventors tried to make a commercial success of a silver-plated machine is not known. The machine made a two-thread chainstitch, taking both threads from commercial spools. By October 1857, the inventors had received their second patent. This time the machine was brass and gilt—brighter, but less expensive. At the same time, Nettleton & Raymond began manufacturing sewing-shears machines under the patent of J. E. Hendricks.
Figure 111.—Nettleton & Raymond sewing machine. One of the most decorative early small hand-cranked sewing machines was patented and made by Willford H. Nettleton and Charles Raymond, who received their first patent on April 14, 1857. The patent model, thought to be a commercial machine, is beautifully silver-plated. It's unclear whether this was a unique model or if the inventors aimed to market a silver-plated machine successfully. The machine created a two-thread chainstitch, using both threads from commercial spools. By October 1857, the inventors had received their second patent. This time, the machine was made of brass and gilt—shinier but cheaper. At the same time, Nettleton & Raymond started manufacturing sewing-shears machines under the patent of J. E. Hendricks.
By the latter half of 1858, Nettleton & Raymond had moved from Bristol, Connecticut, to Brattleboro, Vermont. The patented improvement of the two-thread chainstitch machine received that year was in the name of “Raymond, assignor to Nettleton,” although the machines of this type bear neither name nor patent date. No record of the price for which they were sold has been found, but it would be fair to estimate that it was probably about $25. This style of machine was discontinued when the manufacture of the simpler, more profitable New England model began, a machine that Raymond had initiated just before the partners left Bristol. (Smithsonian photo 45505-E.)
By the second half of 1858, Nettleton & Raymond had relocated from Bristol, Connecticut, to Brattleboro, Vermont. The patented improvement for the two-thread chainstitch machine they received that year was under the name “Raymond, assignor to Nettleton,” although machines of this type don’t carry either name or patent date. There’s no record of how much they were sold for, but it’s reasonable to estimate it was around $25. This machine model was discontinued when production began on the simpler, more profitable New England model, which Raymond had started just before the partners moved from Bristol. (Smithsonian photo 45505-E.)

Figure 112.—Raymond patent model, March 9, 1858. (Smithsonian photo 32009-O.)
Figure 112.—Raymond patent prototype, March 9, 1858. (Smithsonian photo 32009-O.)

Figure 113.—New England sewing machine of about 1860, manufactured by Nettleton & Raymond; it bears the Raymond patent date of March 9, 1858. (Smithsonian photo 45505-G.)
Figure 113.—New England sewing machine from around 1860, made by Nettleton & Raymond; it has the Raymond patent date of March 9, 1858. (Smithsonian photo 45505-G.)
Figures 112 and 113.—New England sewing machines. The small, hand-turned, sewing machines some of which were called Common Sense, were manufactured by at least three companies and possibly more. The earliest ones were those made by Nettleton & Raymond based on Charles Raymond’s patent of March 9, 1858, which featured a hinged presser foot acting as the top feed. On July 30, 1861, Raymond received a patent for an improved looper; this date is found on all machines later manufactured by the inventor.
Figures 112 and 113.—New England sewing machines. The small, hand-cranked sewing machines, some of which were called Common Sense, were produced by at least three companies, and maybe more. The earliest models were made by Nettleton & Raymond, based on Charles Raymond’s patent from March 9, 1858, which had a hinged presser foot that served as the top feed. On July 30, 1861, Raymond received a patent for an improved looper; this date is marked on all machines made later by the inventor.
In 1858 Nettleton and Raymond had moved from Bristol, Connecticut, to Brattleboro, Vermont. Also in Brattleboro at this time were Thomas H. White and Samuel Barker, who were manufacturing a small machine called the Brattleboro. White left Vermont in 1862 and went to Massachusetts. There, in partnership with William Grout, he also began to manufacture New England machines; these were basically the same as the Raymond machines. After a short time, Grout left the partnership with White and moved to Winchendon, there continuing to make New England machines for approximately one more year. In 1865, J. G. Folsom of Winchendon exhibited a New England machine at the Tenth Exhibition of the Massachusetts Charitable Mechanics Association along with his Globe machine. Whether both machines were manufactured by him or whether he might have been exhibiting one of Grout’s machines is not known.
In 1858, Nettleton and Raymond relocated from Bristol, Connecticut, to Brattleboro, Vermont. At that time, Thomas H. White and Samuel Barker were also in Brattleboro, where they were producing a small machine called the Brattleboro. White left Vermont in 1862 and moved to Massachusetts. There, in partnership with William Grout, he started manufacturing New England machines, which were essentially the same as the Raymond machines. After a short period, Grout exited the partnership with White and moved to Winchendon, where he continued producing New England machines for about another year. In 1865, J. G. Folsom from Winchendon showcased a New England machine at the Tenth Exhibition of the Massachusetts Charitable Mechanics Association, alongside his Globe machine. It's unclear whether both machines were his or if he was exhibiting one of Grout's machines.
There is no record that New England machines were manufactured after 1865. There is a great similarity between these machines and the Improved Common Sense sewing machines of the 1870s. It is believed that the name “Common Sense” was given by frugal New Englanders to several of the cheaper chainstitch machines of the 1860s.
There’s no record of New England machines being made after 1865. These machines are very similar to the Improved Common Sense sewing machines from the 1870s. It’s thought that the name “Common Sense” was given by budget-conscious New Englanders to several of the more affordable chainstitch machines from the 1860s.

Figure 114.—Pratt’s second patent model, March 3, 1857, probably a commercial machine. (Smithsonian photo 48328-H.)
Figure 114.—Pratt's second patent prototype, March 3, 1857, probably a commercial machine. (Smithsonian photo 48328-H.)
Figures 114 and 115.—Pratt’s patent and the Ladies Companion sewing machine. The machines manufactured under the patents of Samuel F. Pratt were first sold in 1857 and 1858 as Pratt’s patent. These machines carry the Pratt name and the patent dates “Feb. 3, 1857 Mar. 3;” the latter is an 1857 patent date also. In 1859 the Pratt machine was called the Ladies Companion and was so marked. It was also marked with the 1857 patent dates, the date February 16, 1858, and a serial number, and was stamped “Boston, Mass.” Manufacture was discontinued after a few years.
Figures 114 and 115.—Pratt's patent and the Ladies Companion sewing machine. The machines made under Samuel F. Pratt's patents were first sold in 1857 and 1858 as Pratt’s patent. These machines bear the Pratt name along with the patent dates “Feb. 3, 1857 Mar. 3;” the latter is also from 1857. In 1859, the Pratt machine was renamed the Ladies Companion and was labeled as such. It was also marked with the 1857 patent dates, the date February 16, 1858, a serial number, and was stamped “Boston, Mass.” Production stopped after a few years.

Figure 115.—Ladies Companion, 1859. (Photo courtesy of The Henry Ford Museum and Greenfield Village, Dearborn, Michigan.)
Figure 115.—Women's Companion, 1859. (Photo courtesy of The Henry Ford Museum and Greenfield Village, Dearborn, Michigan.)

Figure 116.—Quaker City sewing machine. During the first decade of sewing-machine manufacture many types of handsome wooden cases were developed to house the mechanisms. Although such cases increased the total cost, they were greatly admired and were purchased whenever family funds permitted. The machine was based on the patents of William P. Uhlinger: a mechanical patent for a double chainstitch machine on August 17, 1858 (antedated May 8), and a patent for the casing on December 28, 1858. The machine head was lowered into the casing as the lid was brought forward and closed—an idea much ahead of its time.
Figure 116.—Quaker City sewing machine. In the early years of sewing-machine manufacturing, many stylish wooden cases were designed to enclose the mechanisms. While these cases added to the overall cost, they were highly valued and bought whenever families could afford them. The machine was built on the patents of William P. Uhlinger: a mechanical patent for a double chainstitch machine on August 17, 1858 (with an earlier date of May 8), and a patent for the casing on December 28, 1858. The machine head lowered into the casing as the lid was brought down and closed—an innovation that was well ahead of its time.
This Quaker City machine, serial number 18, was purchased by Benjamin F. Meadows of Lafayette, Alabama, for $150 just prior to the Civil War. Relatively few machines of this type were manufactured, and the Quaker City Sewing Machine Co. existed for only a few years. Its apparent hope for a southern market was short-lived, and it was unable to compete either with the companies licensed under the “Combination” or with those producing less expensive machines. (Smithsonian photo 46953-A.)
This Quaker City machine, serial number 18, was bought by Benjamin F. Meadows from Lafayette, Alabama, for $150 right before the Civil War. Only a limited number of machines like this were made, and the Quaker City Sewing Machine Co. operated for just a few years. Its apparent ambitions for a southern market didn't last long, and it couldn't compete with companies licensed under the “Combination” or those making cheaper machines. (Smithsonian photo 46953-A.)

Figure 117.—From an advertising brochure, marked in ink, “The National Portrait Gallery, 1855,” in the Singer Company’s archives. The brochure states “Howard & Davis, 34 Water Street, Boston, Massachusetts Sole Manufacturers of Robinson’s Patent Sewing Machine with Rope[r]’s Improvements.” (Smithsonian photo 48091-F.)
Figure 117.—From a marketing brochure, marked in ink, “The National Portrait Gallery, 1855,” in the Singer Company’s archives. The brochure states “Howard & Davis, 34 Water Street, Boston, Massachusetts Sole Manufacturers of Robinson’s Patent Sewing Machine with Rope[r]’s Improvements.” (Smithsonian photo 48091-F.)

Figure 118.—Sewing machine of about 1856 with inscription “Howard & Davis Makers, Boston, Mass. Robinson & Roper Pat. Dec. 10, 1850, Aug. 15, 1854”; the drive wheel and the circular stitching plate of this machine are missing. (Smithsonian photo 48440-C.)
Figure 118.—Sewing machine from circa 1856 with the inscription “Howard & Davis Makers, Boston, Mass. Robinson & Roper Pat. Dec. 10, 1850, Aug. 15, 1854”; the drive wheel and the circular stitching plate of this machine are missing. (Smithsonian photo 48440-C.)
Figures 117 and 118.—Robinson and Roper sewing machines, 1855-1856. This is one of the few machines producing a backstitch or half backstitch to realize any commercial success. Manufactured a very short time by Howard & Davis, it was a short-thread machine, based on the Frederick Robinson patent of December 10, 1850, and the Samuel Roper patent of August 15, 1854. Roper produced additional improvements for which he received a patent on November 4, 1856. In the Scientific American, November 1, 1856, the new machine was discussed: “Robinson & Roper exhibit their new improved sewing machines, which appear to operate with great success. Two needles are employed, the points of which are furnished with hooks that alternately catch the thread and form the stitch. The finest kind of cotton thread or silk can be used. The work appears well done. Price $100.”
Figures 117 and 118.—Robinson and Roper sewing machines, 1855-1856. This is one of the few machines that successfully created a backstitch or half backstitch for commercial use. Manufactured for a very short time by Howard & Davis, it was a short-thread machine based on the Frederick Robinson patent from December 10, 1850, and the Samuel Roper patent from August 15, 1854. Roper developed additional enhancements for which he obtained a patent on November 4, 1856. In the Scientific American, November 1, 1856, the new machine was mentioned: “Robinson & Roper showcase their newly improved sewing machines, which seem to function with great success. Two needles are used, each equipped with hooks that take turns catching the thread and forming the stitch. The finest cotton thread or silk can be utilized. The work looks very well done. Price $100.”

Figure 119.—Illustrated page in a Shaw & Clark advertising brochure, published in late 1864. (Smithsonian photo 61321.)
Figure 119.—Illustrated page in a Shaw & Clark advertising brochure, published in late 1864. (Smithsonian photo 61321.)

Figure 120.—Shaw & Clark sewing machine (Page patent) of 1867, Chicopee Falls, Massachusetts. (Smithsonian photo 48216-L.)
Figure 120.—Shaw & Clark sewing machine (Page patent) of 1867, Chicopee Falls, Massachusetts. (Smithsonian photo 48216-L.)
Figures 119 and 120.—Shaw & Clark sewing machines. In addition to the early style Monitor sewing machine sold by Shaw & Clark without a name or any identifying marks, the company continued to manufacture machines after a lawsuit with the “Combination” forced them to take out a license. They manufactured an adapted version of their Monitor and an entirely new design patented in 1861. Their machines were now marked with the company name and a list of patent dates including those of Howe, Wheeler and Wilson, Grover and Baker, and Singer and the Batchelder patent, together with their own design patents. In 1867 the company moved from Biddeford, Maine, to Chicopee Falls, Massachusetts. In the same year, they began manufacturing a machine of the design patented by T. C. Page. The company is believed to have become the Chicopee Sewing Machine Company which appeared the following year and remained in business only a very short time. One Chicopee sewing machine is in the Smithsonian collection.[Pg 112]
Figures 119 and 120.—Shaw & Clark sewing machines. Along with the early style Monitor sewing machine sold by Shaw & Clark without a brand name or any identifiable marks, the company continued to produce machines after a legal dispute with the “Combination” prompted them to obtain a license. They created a modified version of their Monitor and an entirely new design that was patented in 1861. Their machines were now branded with the company name and a list of patent dates, including those of Howe, Wheeler and Wilson, Grover and Baker, Singer, and the Batchelder patent, along with their own design patents. In 1867, the company relocated from Biddeford, Maine, to Chicopee Falls, Massachusetts. That same year, they started making a machine based on the design patented by T. C. Page. It's believed that the company transformed into the Chicopee Sewing Machine Company, which appeared the next year but only lasted a short time. One Chicopee sewing machine is part of the Smithsonian collection.[Pg 112]

Figure 121.—Singer “Traverse Shuttle Machine—Letter A.” (Smithsonian photo 58984.)
Figure 121.—Artist “Traverse Shuttle Machine—Letter A.” (Smithsonian photo 58984.)
Figures 121 and 122.—Singer sewing machines. From 1850 to 1858 the Singer company produced heavy manufacturing-type sewing machines similar to the patent model shown earlier (fig. 28). The first machine for family use, Singer’s new “Family” sewing machine (fig. 33) was manufactured from 1858-1861. Their second-style family machine was called the “Traverse Shuttle Machine—Letter A;” it was manufactured from 1859 to 1865, when they introduced their third family machine and called it the “New Family” sewing machine. This style machine continued until about 1883 when the “Improved Family” machine appeared. In addition to the lockstitch machines, Singer also manufactured chainstitch machines, and many highly specialized manufacturing machines.
Figures 121 and 122.—Singer sewing machines. From 1850 to 1858, the Singer company produced heavy-duty sewing machines similar to the patent model shown earlier (fig. 28). The first machine designed for home use, Singer’s new “Family” sewing machine (fig. 33), was manufactured from 1858 to 1861. Their second version for families was called the “Traverse Shuttle Machine—Letter A” and was produced from 1859 to 1865, when they introduced their third family machine known as the “New Family” sewing machine. This type of machine continued until around 1883 when the “Improved Family” machine was released. In addition to lockstitch machines, Singer also made chainstitch machines and many highly specialized manufacturing machines.
From 1857 through the 1880s, the Singer machines were marked with two serial numbers. It is possible that the numbers were related to the “Combination” royalties paid by the Singer company. Until about 1873 there was a difference of exactly 4,000 in the two numbers, thus one machine would be marked 12163 and directly below it would be marked 16163. From 1873 the last three digits of the two numbers continued to be the same but the lower number might be much lower in value than either number used in earlier years. The larger number is believed to have been a record of total production while the lower number may have referred to a machine of a particular style. The Singer company records can shed no light on the meaning of the top (or lower of the two) serial numbers. Generally, in the earlier machines, the difference in the two numbers will not affect the dating of a machine by more than one year. Since dating by serial number can only be estimated, the two numbers do not add an appreciable variable prior to 1873. Only the larger number, however, should be considered in dating machines after 1873.
From 1857 to the 1880s, Singer machines had two serial numbers. These numbers might have been linked to the “Combination” royalties paid by the Singer company. Until around 1873, there was a difference of exactly 4,000 between the two numbers, so one machine would be labeled 12163 and right underneath it would be 16163. After 1873, the last three digits of the two numbers remained the same, but the lower number could be significantly less than either number used in earlier years. It’s believed that the larger number tracked total production, while the lower number referred to a specific model. Unfortunately, the Singer company records do not clarify the meaning of the top (or lower of the two) serial numbers. Typically, in the earlier machines, the difference between the two numbers won't change the dating of a machine by more than one year. Since dating by serial number can only be an estimate, the two numbers don’t introduce a significant variable before 1873. After 1873, only the larger number should be used when dating the machines.
Serial Number Year | |
1-100 | 1850 |
101-900 | 1851 |
901-1711 | 1852 |
1712-2521 | 1853 |
2522-3400 | 1854 |
3401-4283 | 1855 |
4284-6847 | 1856 |
6848-10477 | 1857 |
10478-14071 | 1858 |
14072-25024 | 1859 |
25025-43000 | 1860 |
43001-61000 | 1861 |
61001-79396 | 1862 |
79397-99426 | 1863 |
99427-123058 | 1864 |
123059-149399 | 1865 |
149400-180360 | 1866 |
180361-223414 | 1867 |
223415-283044 | 1868 |
283045-369826 | 1869 |
369827-497660 | 1870 |
497661-678921 | 1871 |
678922-898680 | 1872 |
898681-1121125 | 1873 |
1121126-1362805 | 1874 |
1362806-1612658 | 1875 |
1612659-1874975 | 1876 |
Since records of annual production from 1877 to the turn of the century are not complete, it is difficult to establish yearly approximations. Using the machines submitted as patent models, and thus known to have been manufactured before the date of deposit, however, has provided us with the following date guides. By 1877 there had been 2 million machines manufactured, 3 million by 1880, 4 million by 1882, 5 million by 1884, 6 million by 1886, 7 million by 1888, 8 million by 1889, 9 million by 1890, and 10 million by 1891.[Pg 113]
Since records of annual production from 1877 to the turn of the century aren't complete, it’s hard to establish yearly estimates. However, using the machines that were submitted as patent models—so we know they were manufactured before the deposit date—has given us the following date indicators. By 1877, 2 million machines had been produced, 3 million by 1880, 4 million by 1882, 5 million by 1884, 6 million by 1886, 7 million by 1888, 8 million by 1889, 9 million by 1890, and 10 million by 1891.[Pg 113]

Figure 122.—Singer “New Family” sewing machine. (Smithsonian photo 58987.)
Figure 122.—Artist “New Family” sewing machine. (Smithsonian photo 58987.)

Figure 123.—Standard sewing machine of about 1870. This chainstitch machine is believed to have been made by the company that later became the Standard Shuttle Sewing Machine Company, when they began manufacturing lockstitch machines about 1874. This machine is marked with the name, “Standard,” and with the dates “Patented July 14, 1870, Patented Jan. 22, 1856, Dec. 9, 1856, Dec. 12, 1865.” The dates refer to the reissue and extended reissue of the Bachelder and the A. B. Wilson patents. The number of chainstitch machines of this type that were manufactured is not known. (Smithsonian photo 45506-C.)
Figure 123.—Sewing machine from around 1870. This chainstitch machine is thought to have been produced by the company that later became the Standard Shuttle Sewing Machine Company, when they started making lockstitch machines around 1874. This machine is labeled with the name “Standard” and the dates “Patented July 14, 1870, Patented Jan. 22, 1856, Dec. 9, 1856, Dec. 12, 1865.” The dates refer to the reissue and extended reissue of the Bachelder and A. B. Wilson patents. The exact number of chainstitch machines of this type that were made is unknown. (Smithsonian photo 45506-C.)

Figure 124.—Taggart & Farr sewing machine, front view. (Smithsonian photo 48216-P.)
Figure 124.—Taggart & Farr sewing machine, front view. (Smithsonian photo 48216-P.)
Figures 124 and 125.—Taggart & Farr sewing machine, 1860. The Taggart & Farr is an almost forgotten machine. It was based on Chester Farr’s patent of August 9, 1859. The machine, however, was in commercial production as early as 1858, the year the patent application was made. Using two threads—both taken directly from the spool—to form a chainstitch, the machine was operated basically by treadle but also by hand. The drive wheel is missing on this machine, but it would normally appear on the right.
Figures 124 and 125.—Taggart & Farr sewing machine, 1860. The Taggart & Farr is an almost forgotten machine. It was based on Chester Farr’s patent from August 9, 1859. However, the machine was already in commercial production in 1858, the same year the patent application was submitted. It used two threads—both coming directly from the spool—to create a chainstitch. The machine was primarily operated by a treadle but could also be used manually. The drive wheel is missing on this machine, but it would normally be located on the right.
The name and patent date were painted on the end of the machine. This was true of many other machines of this period, which is why so many go unidentified once the paint has become worn. Several thousand Taggart & Farr machines were manufactured, but the company is believed to have had a short life, for it was among those that had disappeared by 1881.
The name and patent date were painted on the end of the machine. This was true for many other machines from this time, which is why so many go unidentified once the paint has worn off. Several thousand Taggart & Farr machines were made, but the company is thought to have had a short lifespan, as it had disappeared by 1881.

Figure 125.—Taggart & Farr sewing machine, end view. (Smithsonian photo 48216-M.)
Figure 125.—Taggart & Farr sewing machine, end view. (Smithsonian photo 48216-M.)

Figure 126.—Watson sewing machine, 1856, illustrated in Scientific American, December 13, 1856. The earliest Watson machines were two-thread lockstitch machines, as described in the Scientific American, August 10, 1850. Although the magazine reported that the inventor had applied for a patent, the earliest lockstitch patent issued to William C. Watson was on March 11, 1856. A few of his machines were made in 1850, the article continued, “several of these machines are nearly finished ... persons desirous of seeing them can be gratified by calling upon Messrs. Jones & Lee.” A Watson machine was exhibited by Jones & Lee at the Sixth Exhibition of the Massachusetts Charitable Mechanics Association held in Boston in September 1850.
Figure 126.—Watson sewing machine, 1856, shown in Scientific American, December 13, 1856. The first Watson machines were two-thread lockstitch machines, as mentioned in Scientific American, August 10, 1850. Although the magazine noted that the inventor had applied for a patent, the first lockstitch patent issued to William C. Watson was on March 11, 1856. A few of his machines were made in 1850, the article went on, “several of these machines are nearly finished ... people interested in seeing them can stop by Messrs. Jones & Lee.” A Watson machine was displayed by Jones & Lee at the Sixth Exhibition of the Massachusetts Charitable Mechanics Association held in Boston in September 1850.
In 1853 a Watson machine was exhibited at the New York Industry of All Nations Exhibition, but this was a single-looping machine; Watson received a patent for this single-thread machine on November 25, 1856.
In 1853, a Watson machine was showcased at the New York Industry of All Nations Exhibition, but it was a single-loop machine; Watson was granted a patent for this single-thread machine on November 25, 1856.
In the December 13, 1856, issue of Scientific American a machine called Watson’s “Family” sewing machine was illustrated and described. It was a small machine (only 8 by 5 inches) manufactured by Watson & Wooster and selling for $10. References to the Watson single-thread machine occur as late as 1860, but no examples are known to have survived. (Smithsonian photo 48221-B.)
In the December 13, 1856, issue of Scientific American, there was an illustration and description of a machine called Watson’s “Family” sewing machine. It was a compact device (just 8 by 5 inches) made by Watson & Wooster, retailing for $10. Mentions of the Watson single-thread machine can still be found as late as 1860, but no examples are known to have survived. (Smithsonian photo 48221-B.)
Figure 127.—West & Willson sewing machine of about 1859. The West & Willson machine, manufactured under the patent of H. B. West and H. F. Willson, enjoyed a very brief span of popularity. The patent covered the peculiar method of operating a spring-looper in combination with an eye-pointed needle to form a single chainstitch, but whether machines of this single-thread variety were manufactured is unknown. The machine illustrated here is a two-thread machine of basically the same description. It stitches from left to right and bears serial number 1544 and the inscription “West & Willson Co. patented June 29, 1858.” (Smithsonian photo 49456-A.)
Figure 127.—West & Willson sewing machine from around 1859. The West & Willson machine, built under the patent of H. B. West and H. F. Willson, had a very short period of popularity. The patent covered a unique method of using a spring-looper along with an eye-pointed needle to create a single chainstitch, but it's unclear if machines of this single-thread type were ever made. The machine shown here is a two-thread version with a similar design. It sews from left to right and has the serial number 1544 and the marking “West & Willson Co. patented June 29, 1858.” (Smithsonian photo 49456-A.)

Figure 128.—Wheeler & Wilson sewing machine of about 1872. Serial number 670974. (Smithsonian photo P63149-A.)
Figure 128.—Wheeler & Wilson sewing machine from around 1872. Serial number 670974. (Smithsonian photo P63149-A.)

Figure 129.—Wheeler and Wilson No. 8 sewing machine of about 1876. (Smithsonian photo 17663-C.)
Figure 129.—Wheeler & Wilson No. 8 sewing machine from around 1876. (Smithsonian photo 17663-C.)
Figures 128 and 129.—Wheeler and Wilson sewing machines. The Wheeler and Wilson company was the largest manufacturer of sewing machines in the 1850s and the 1860s.
Figures 128 and 129.—Wheeler and Wilson sewing machines. The Wheeler and Wilson company was the biggest maker of sewing machines in the 1850s and 1860s.
It began in 1851 as A. B. Wilson; from 1852 to 1856 it was the Wheeler, Wilson & Co., Watertown, Connecticut; and from 1856 to 1876, it was Wheeler & Wilson Mfg. Co., Bridgeport, Connecticut.
It started in 1851 as A. B. Wilson; from 1852 to 1856, it was Wheeler, Wilson & Co., Watertown, Connecticut; and from 1856 to 1876, it was Wheeler & Wilson Mfg. Co., Bridgeport, Connecticut.
The style of the head changed very little during these years (see figs. 26 and 27). Both a table style with iron legs and a cabinet model were made: the head was usually mounted to stitch from left to right. In 1861, the company introduced the famous glass presser foot, patented on March 5 of that year by J. L. Hyde. The presser foot was made of metal but shaped like an open _ into which was slid a small glass plate, with a hole for the needle descent. The glass allowed the seamstress to observe the stitching and to produce very close-edge stitching. It remained a favorite of many women for years. In 1876, the new No. 8 machine was introduced and a new series of serial numbers was initiated. It is, therefore, imperative to know that the machine is one of the earlier style machines before using the following list of serial numbers to date the machines, approximately as follows:
The design of the head changed very little during these years (see figs. 26 and 27). There were both a table style with iron legs and a cabinet model available: the head was usually attached for stitching from left to right. In 1861, the company launched the famous glass presser foot, patented on March 5 of that year by J. L. Hyde. The presser foot was made of metal but shaped like an open _ into which a small glass plate was slid, featuring a hole for the needle. The glass allowed the seamstress to see the stitching and to achieve very close-edge stitching. It remained a favorite among many women for years. In 1876, the new No. 8 machine was introduced, and a new series of serial numbers was started. Therefore, it’s crucial to know that the machine is one of the earlier style machines before using the following list of serial numbers to date the machines approximately as follows:
Records of the second series of serial numbers dating from 1876 are not available.
Records of the second series of serial numbers from 1876 are not available.
Figure 130.—White Sewing Machine. Although the White sewing machines date from 1876, Thomas H. White had been busy in the manufacture of sewing machines for many years prior to this. White is known to have been associated with Barker in the manufacture of the Brattleboro machine and later with Grout in producing one of the several New England machines. In 1866 he moved to Cleveland, Ohio, and began manufacturing machines for sale under special trade names through selling organizations. In 1876, the White Sewing Machine Company was formed and machines were sold under the White name.
Figure 130.—White Sewing Machine. Although White sewing machines originated in 1876, Thomas H. White had been involved in making sewing machines for many years before that. White is known to have worked with Barker on the Brattleboro machine and later with Grout to produce one of the various machines from New England. In 1866, he moved to Cleveland, Ohio, and started making machines for sale under different trade names through sales organizations. In 1876, the White Sewing Machine Company was established, and machines were marketed under the White name.
The machine illustrated is a standard lockstitch machine, which would have been set into a sewing-machine table and operated by a treadle. The small handle was used to start the wheel, and thus the stitching operation, in the forward direction. This machine bears the serial number 28241 and the following patents: “Mar. 14, 1876, May 2, 1876, Oct. 24, 1876, Jan. 16, 1877, Mar. 20, 1877, Mar. 27, 1877,” which are primarily the patents of D’Arcy Porter and George W. Baker.
The machine shown is a typical lockstitch machine, which would have been fitted into a sewing machine table and operated with a foot pedal. The small handle was used to start the wheel, thereby beginning the stitching process in the forward direction. This machine has the serial number 28241 and the following patents: “Mar. 14, 1876, May 2, 1876, Oct. 24, 1876, Jan. 16, 1877, Mar. 20, 1877, Mar. 27, 1877,” which are mainly the patents of D’Arcy Porter and George W. Baker.
The machines of the 1870s may be dated approximately as follows:
The machines from the 1870s can be dated roughly like this:
Serial Number | Year |
1-9000 | 1876 |
9000-27000 | 1877 |
27001-45000 | 1878 |
45001-63000 | 1879 |
(Smithsonian photo 58986.)
(Smithsonian photo 58986.)
Figure 131.—Willcox And Gibbs sewing machine, serial number 296572, of about 1878. From 1857 to the turn of the century, the style of the Willcox and Gibbs sewing machine changed very little (fig. 39). It was the most popular and the most reliable of the many chainstitch machines. In addition to the basic mechanical patents, Gibbs also patented the design of the sewing-machine head in 1860. In the specifications, he described it as an open ring set on a base or pedestal. The lower part of the open section supported the cloth plate. The design of the head, intentionally or not, formed a perfect letter G, the initial of the inventor. Later the machine head as a letter G was incorporated into the company’s trademark. Additional patents were also granted to James Willcox for a leg and treadle design and to Charles Willcox for mechanical improvements.
Figure 131.—Willcox and Gibbs sewing machine, serial number 296572, from around 1878. From 1857 until the end of the century, the design of the Willcox and Gibbs sewing machine changed very little (fig. 39). It was the most popular and reliable of the many chainstitch machines. In addition to the basic mechanical patents, Gibbs patented the design of the sewing machine head in 1860. In the specifications, he described it as an open ring placed on a base or pedestal. The lower part of the open section supported the cloth plate. The design of the head, whether intentionally or not, formed a perfect letter G, the initial of the inventor. Later, the machine head shaped like a letter G was included in the company’s trademark. Additional patents were also granted to James Willcox for a leg and treadle design and to Charles Willcox for mechanical improvements.
It has not been possible to secure information on records of serial numbers from the late 1870s through the 1920s to aid in dating machines of that period. For the preceding years, however, the machines may be dated approximately as follows:
It has not been possible to find information on records of serial numbers from the late 1870s through the 1920s to help date machines from that time. For the years before that, though, the machines can be dated approximately as follows:
Serial Number | Year |
1-10000 | 1857 |
10001-20000 | 1858 |
20001-30000 | 1859 |
30001-40000 | 1860 |
40001-50000 | 1861 |
50001-60000 | 1862 |
60001-70000 | 1863 |
70001-80000 | 1864 |
80001-90000 | 1865 |
90001-100000 | 1866 |
100001-115000 | 1867 |
115001-130000 | 1868 |
130001-145000 | 1869 |
145001-160000 | 1870 |
160001-190127 | 1871 |
190128-223766 | 1872 |
223767-239647 | 1873 |
239648-253357 | 1874 |
253358-267879 | 1875 |
267880-279637 | 1876 |
Although the Willcox and Gibbs company is still in existence, for the past several decades the company has limited itself to the production of specialized manufacturing machines rather than family machines. (Smithsonian photo 58986.)
Although the Willcox and Gibbs company is still around, for the past several decades, it has focused on producing specialized manufacturing machines instead of family machines. (Smithsonian photo 58986.)
[Pg 123]Figure 132.—Illustration from Knights American Mechanical Dictionary, vol. 3, p. 2122. The 68 sewing-machine stitches in use by 1882 are as follows:
[Pg 123]Figure 132.—Illustration from Knights American Mechanical Dictionary, vol. 3, p. 2122. The 68 sewing machine stitches in use by 1882 are as follows:
Single Thread
Single Thread
1. Running stitch.
Running stitch.
2. Back stitch.
Backstitch.
3. Fast stitch.
3. Quick stitch.
4. Chainstitch.
Chain stitch.
5. Coiled-loop chainstitch.
Coiled loop chain stitch.
6. Knitted-loop chainstitch.
Knitted loop chain stitch.
7. Knotted-loop chainstitch.
Knotted loop chain stitch.
8. Loop enchained by second alternate stitch.
8. Loop connected by the second alternate stitch.
9. Each loop locks and enchains alternate loops.
9. Each loop locks and connects to alternate loops.
10. Staple stitch (for waxed threads only).
10. Staple stitch (for waxed threads only).
Two Threads
Two Threads
11. Double-needle chainstitch.
Double-needle chain stitch.
12. Double-thread chainstitch (one needle).
Double-thread chainstitch (single needle).
13. Double-looped chainstitch.
Double-loop chain stitch.
14. Chain with interlocking thread.
14. Interlocking thread chain.
15. Under-thread through its own loop.
15. Thread underneath through its own loop.
16. Two needles penetrate fabric from opposite sides.
16. Two needles go through the fabric from opposite sides.
17. Two needles working from the same side.
17. Two needles working from the same side.
18. Double interlocking loop.
Double interlocking loop.
19. Lockstitch.
Lockstitch sewing.
20. Twist in needle thread.
Twist the needle thread.
21. Double twist in needle thread.
21. Double twist in needle thread.
22. Twist in shuttle thread.
22. Twist in shuttle thread.
23. Double twist in shuttle thread.
23. Double twist in shuttle thread.
24. Knot stitch, shuttle thread knotted at every stitch.
24. Knot stitch, with the shuttle thread tied in a knot at each stitch.
25. Knot stitch, shuttle thread knotted at every other stitch.
25. Knot stitch, shuttle thread tied in a knot at every other stitch.
26. Knot stitch, shuttle thread through the needle thread loop and knotted around the loop.
26. Knot stitch, pull the shuttle thread through the needle thread loop and tie it around the loop.
27. Shuttle thread pulled to the surface and interlocked with succeeding stitch to form an embroidery stitch.
27. The shuttle thread was pulled to the surface and locked together with the next stitch to create an embroidery stitch.
28. Wire-lock stitch, thread locked in place with wire.
28. Wire-lock stitch, where the thread is secured in place with wire.
Three Threads
Three Threads
29. Two shuttles, each locking alternate loops.
29. Two shuttles, each securing alternate loops.
30. Double loop with interlocking third thread.
30. Double loop with interlocking third thread.
31. Two shuttle threads, both locking each loop.
31. Two shuttle threads, each locking every loop.
32. Two shuttle threads intertwining and locking each loop.
32. Two shuttle threads weaving together and securing each loop.
33. Single thread; loop of needle thread drawn up over the edge and locked by needle at its next descent.
33. A single thread; the loop of the needle thread pulled up over the edge and secured by the needle on its next downstroke.
34. Two threads; loops of needle thread, above and below, extend to the edge of the fabric, and are locked by shuttle thread.
34. Two threads; loops of needle thread, above and below, extend to the edge of the fabric and are locked in place by shuttle thread.
35. Two threads; needle penetrates back from edge, its loop passed to and interlocked by the needle at its next descent over the edge, and this second needle-loop locked by shuttle thread.
35. Two threads; the needle goes back from the edge, passing its loop to and interlocking it with the needle at its next descent over the edge, and this second needle loop is secured by the shuttle thread.
36. Two threads; shuttle thread drawn up over the edge of the fabric to the line of the needle thread.
36. Two threads; the shuttle thread is pulled up over the edge of the fabric to align with the needle thread.
37. Two threads; needle loop through the fabric locked by needle loop over the edge and second loop locked by second thread.
37. Two threads; the needle loops through the fabric and locks it by looping over the edge, while the second loop is secured by the second thread.
38. Two threads; edge of fabric covered by shuttle thread.
38. Two threads; the edge of the fabric is covered by the shuttle thread.
39. Three threads; third thread laid around the stitch at the edge of the fabric.
39. Three threads; the third thread wrapped around the stitch at the edge of the fabric.
Ornamental Stitches
Decorative Stitches
40. Zigzag; single thread chainstitch (4).
40. Zigzag; single thread chain stitch (4).
41. Zigzag; two-thread lockstitch (19).
Zigzag; two-thread lockstitch.
42. Zigzag; two-thread chainstitch (13).
42. Zigzag; two-thread chain stitch (13).
43. Zigzag; chain stitch with interlocking thread (14).
43. Zigzag; chain stitch with interlocking thread (14).
44. Zigzag; double loop with interlocking third thread (30).
44. Zigzag; double loop with an interlocking third thread (30).
45. Zigzag; running stitch (1).
45. Zigzag; running stitch (1).
46. Zigzag; two needles and shuttle.
46. Zigzag; two needles and a shuttle.
47. Zigzag; variation of 46.
Zigzag; variation of 46.
48-52. Zigzag stitches for sewing straw braid.
48-52. Zigzag stitches for sewing straw braid.
53-62. Straight straw-braid stitches.
Straight straw-braid stitches.
63-67. Special embroidery stitches.
Special embroidery stitches.
68. Saddler’s stitch.
Saddler's stitch.
In the Sewing Machine News, vol. 3, no. 5, p. 12 (1881), there were listed a number of then “defunct” machines and companies. Among these are many well-known names and little-known names for which at least one additional reference can be found. There are some, however, for which this is the only reference to date. These are: Blanchard, Babcock, Banner, Brown Rotary, Cottage, Cole, Duplex, Economist, Erie, Gutman, Hill, Hancock & Bennett, Jenks, Lockmar, La Favorite, Learned, Leggett, McCoy, McCardy, Medallion, McArthur & Co., Monopoly, Moreau, Mack, Niagra, New Cannaan, Orphean, Pride-of-the-West, Seamen & Guiness, Surprise, Stackpole, Shanks, Stanford, Troy, Utica, United States Family, Weaver, Wagner, and Williams. Some of these names may have been a “special” name given to machines manufactured by one of the known companies, but at least a few are names of machines manufactured for a very short time prior to 1881 about which we would like to know more.
In the Sewing Machine News, vol. 3, no. 5, p. 12 (1881), there was a list of several “defunct” machines and companies. Among these are many well-known names and some lesser-known ones for which at least one additional reference can be found. However, there are some that have this as the only reference so far. These include: Blanchard, Babcock, Banner, Brown Rotary, Cottage, Cole, Duplex, Economist, Erie, Gutman, Hill, Hancock & Bennett, Jenks, Lockmar, La Favorite, Learned, Leggett, McCoy, McCardy, Medallion, McArthur & Co., Monopoly, Moreau, Mack, Niagra, New Cannaan, Orphean, Pride-of-the-West, Seamen & Guiness, Surprise, Stackpole, Shanks, Stanford, Troy, Utica, United States Family, Weaver, Wagner, and Williams. Some of these names might have been special names given to machines made by one of the known companies, but at least a few are names of machines made for a very short time before 1881 that we would like to learn more about.
III. Chronological List of U.S. Sewing-Machine Patent Models in the Smithsonian Collections
There are more than seven hundred sewing-machine patent models and a similar number of attachment models in the Smithsonian collections. Most of these machines were received in 1926 when the Patent Office disposed of its collection of hundreds of thousands of models. Prior to 1880, models had been required with the patent application; although the requirement was discontinued that year, patentees continued to furnish models for another decade or so. All models prior to 1836 were lost in a Patent Office fire of that year, but since the sewing-machine patent history dates from the 1840s, most of the historically important ones of this subject have been preserved.
There are over seven hundred sewing machine patent models and a similar number of attachment models in the Smithsonian collections. Most of these machines were received in 1926 when the Patent Office got rid of its collection of hundreds of thousands of models. Before 1880, models were required with the patent application; even though this requirement was dropped that year, inventors continued to provide models for another decade or so. All models from before 1836 were lost in a fire at the Patent Office that year, but since the history of sewing machine patents starts in the 1840s, most of the historically significant ones have been preserved.
These models form a valuable part of the record of the invention, supplementing the drawings and the text of the written specifications. The early sewing-machine models were made to order, either by the inventor or a commissioned model maker. As soon as sewing machines were produced commercially, it was less expensive for the patentee to use a commercial machine of the period, to which he added his change or improvement, than to have a complete model constructed to order. Some of the commercial machines used in this way are the only examples known to be in existence, and as such, are of more interest in establishing the history of the manufactured machine than for the minor patented changes.
These models are an important part of the record of the invention, adding to the drawings and the written specifications. The early sewing machine models were custom-made, either by the inventor or by a model maker they hired. Once sewing machines started being produced commercially, it became cheaper for the patent holder to use a machine available at the time and add their modifications instead of having a whole model built from scratch. Some of the commercial machines used this way are the only known examples still in existence, and because of that, they are more significant for establishing the history of the manufactured machine than for the minor patented changes.
During the period of the “Sewing Machine Combination,” many patentees attempted to invent and patent “the different machine.” This was either a radical change in style or an attempt to produce a far less-expensive type of machine. These machines were not always put into commercial production, but the patent models give an indication of the extent to which some inventors went to simplify or vary the mechanics of machine sewing.
During the time of the “Sewing Machine Combination,” many inventors tried to create and patent “the different machine.” This involved either a complete redesign or an effort to create a much cheaper version. These machines weren't always mass-produced, but the patent models show how far some inventors went to simplify or change the mechanics of sewing machines.
The following is a list of those sewing-machine patent models in the Smithsonian Institution collections:
The following is a list of sewing machine patent models in the Smithsonian Institution collections:
Patentee | Date | Patent Number |
---|---|---|
Greenough, John J. | Feb. 21, 1842 | 2,466 |
Bean, Benjamin W. | March 4, 1843 | 2,982 |
Corliss, George H. | Dec. 27, 1843 | 3,389 |
Howe, Elias, Jr. | Sept. 10, 1846 | 4,750 |
Bachelder, John | May 8, 1849 | 6,439 |
Wilson, Allen B. | Nov. 12, 1850 | 7,776 |
Robinson, Frederick R. | Dec. 10, 1850 | 7,824 |
Grover & Baker | Feb. 11, 1851 | 7,931 |
Singer, Isaac M. | Aug. 12, 1851 | 8,294 |
Wilson, Allen B. | Aug. 12, 1851 | 8,296 |
Wilson, Allen B. | June 15, 1852 | 9,041 |
Miller, Charles | July 20, 1852 | 9,139 |
Avery, Otis | Oct. 19, 1852 | 9,338 |
Hodgkins, G. | Nov. 2, 1852 | 9,365 |
Bradeen, J. G. | Nov. 2, 1852 | 9,380 |
Bates, W. G. | Feb. 22, 1853 | 9,592 |
Thompson, T. C. | March 29, 1853 | 9,641 |
Wickersham, W. | April 19, 1853 | 9,679 |
Johnson, W. H. | March 7, 1854 | 10,597 |
Harrison, J., Jr. | April 11, 1854 | 10,763 |
Avery, Otis | May 9, 1854 | 10,880 |
Singer, Isaac | May 30, 1854 | 10,975 |
Hunt, Walter | June 27, 1854 | 11,161 |
Roper, S. H. | Aug. 15, 1854 | 11,531 |
Shaw, P. | Sept. 12, 1854 | 11,680 |
Ambler, D. C. | Nov. 1, 1854 | 11,884 |
Robertson, T. J. W. | Nov. 28, 1854 | 12,015 |
Lyon, W. | Dec. 12, 1854 | 12,066 |
Stedman, G. W. | Dec. 12, 1854 | 12,074 |
Ward, D. T. | Jan. 2, 1855 | 12,146 |
Conant, J. S. | Jan. 16, 1855 | 12,233 |
Smith, H. B. | Jan. 16, 1855 | 12,247 |
Singer, I. M. | Feb. 6, 1855 | 12,364 |
Stedman, G. W. | March 20, 1855 | 12,573 |
Stedman, G. W. | May 1, 1855 | 12,798[Pg 126] |
Chilcott, J., and Scrimgeour, J. | March 15, 1855 | 12,856 |
Durgin, Charles A. | May 22, 1855 | 12,902 |
Bond, J., Jr. | May 22, 1855 | 12,939 |
Singer, Isaac | June 12, 1855 | 13,065 |
Harrison, J., Jr. | Oct. 2, 1855 | 13,616 |
Singer, I. M. | Oct. 9, 1855 | 13,661 |
Singer, I. M. | Oct. 9, 1855 | 13,662 |
Langdon, L. W. | Oct. 30, 1855 | 13,727 |
Stedman, G. W. | Nov. 27, 1855 | 13,856 |
Swingle, A. | Feb. 5, 1856 | 14,207 |
Watson, Wm. C. | March 11, 1856 | 14,433 |
Singer, I. M. | March 18, 1856 | 14,475 |
Grover, W. O. | May 27, 1856 | 14,956 |
Blodgett, S. C. | Aug. 5, 1856 | 15,469 |
Roper, S. H. | Nov. 4, 1856 | 16,026 |
Singer, Isaac M. | Nov. 4, 1856 | 16,030 |
Gibbs, James E. A. | Dec. 16, 1856 | 16,234 |
Jennings, L. | Dec. 16, 1856 | 16,237 |
Johnson, A. F. | Jan. 13, 1857 | 16,387 |
Gibbs, J. E. A. | Jan. 20, 1857 | 16,434 |
Howe, Elias, Jr. | Jan. 20, 1857 | 16,436 |
Alexander, Elisa | Feb. 3, 1857 | 16,518 |
Gray, Joshua | Feb. 3, 1857 | 16,566 |
Belcher, C. D. | March 3, 1857 | 16,710 |
Pratt, S. F. | March 3, 1857 | 16,745 |
Nettleton & Raymond | April 14, 1857 | 17,049 |
Gibbs, J. E. A. | June 2, 1857 | 17,427 |
Harris, Daniel | June 9, 1857 | 17,508 |
Harris, Daniel | June 16, 1857 | 17,571 |
Sage, William | June 30, 1857 | 17,717 |
Lathbury, E. T. | July 7, 1857 | 17,744 |
Wickersham, W. | Aug. 25, 1857 | 18,068 |
Wickersham, W. | Aug. 25, 1857 | 18,069 |
Behn, Henry | Aug. 25, 1857 | 18,071 |
Nettleton, Wm. H., and Raymond, Charles | Oct. 6, 1857 | 18,350 |
Roper, S. H. | Oct. 27, 1857 | 18,522 |
Fetter, George | Dec. 1, 1857 | 18,793 |
Watson, W. C. | Dec. 8, 1857 | 18,834 |
Behn, H. | Dec. 15, 1857 | 18,880 |
Hubbard, George W. | Dec. 22, 1857 | 18,904 |
Lazelle, W. H. | Dec. 22, 1857 | 18,915 |
Clark, David W. | Jan. 5, 1858 | 19,015 |
Fetter, George | Jan. 5, 1858 | 19,059 |
Clark, David W. | Jan. 12, 1858 | 19,072 |
Clark, David W. | Jan. 19, 1858 | 19,129 |
Dimmock, Martial, and Rixford, Nathan | Jan. 19, 1858 | 19,135 |
Boyd, A. H. | Jan. 19, 1858 | 19,171 |
Angell, Benjamin J. | Feb. 9, 1858 | 19,285 |
Clark, David W. | Feb. 23, 1858 | 19,409 |
Raymond, Charles | March 9, 1858 | 19,612 |
Hendrick, Joseph E. | March 16, 1858 | 19,660 |
Parker, Sidney | March 16, 1858 | 19,662 |
Gray, Joshua | March 16, 1858 | 19,665 |
Coates, F. S. | March 23, 1858 | 19,684 |
Clark, David W. | March 23, 1858 | 19,732 |
Reynolds, O. S. | March 30, 1858 | 19,793 |
Bartholf, Abraham | April 6, 1858 | 19,823 |
Savage, E. | April 6, 1858 | 19,876 |
Atwood, J. E., J. C., and O. | April 13, 1858 | 19,903 |
Bosworth, Chas. F. | April 20, 1858 | 19,979 |
Clark, David W. | June 8, 1858 | 20,481 |
Herron, A. C. | June 15, 1858 | 20,557 |
Johnson, A. F. | June 22, 1858 | 20,686 |
Barnes, W. T. | June 29, 1858 | 20,688 |
Smith, E. H. | June 29, 1858 | 20,739 |
West, H. B., and Willson, H. F. | June 29, 1858 | 20,753 |
Miller, W. | June 29, 1858 | 20,763 |
Blake, Lyman R. | July 6, 1858 | 20,775 |
Carpenter, Lunan | July 27, 1858 | 20,990 |
Moore, Charles | July 27, 1858 | 21,015 |
Smith, E. H. | Aug. 3, 1858 | 21,089 |
Wheeler and Carpenter | Aug. 3, 1858 | 21,100 |
Gibbs, J. E. A. | Aug. 10, 1858 | 21,129 |
Uhlinger, W. P. | Aug. 17, 1858 | 21,224 |
Clark, David W. | Aug. 31, 1858 | 21,322 |
Blodgett, S. C. | Sept. 7, 1858 | 21,465 |
Hubbard, G. W. | Sept. 14, 1858 | 21,537 |
Hendrick, J. E. | Oct. 5, 1858 | 21,722 |
Gibbs, J. E. A. | Oct. 12, 1858 | 21,751 |
Sangster, Amos. W. | Oct. 26, 1858 | 21,929 |
Avery, O. and Z. W. | Nov. 9, 1858 | 22,007 |
Spencer and Lamb | Nov. 23, 1858 | 22,137 |
Perry, James | Nov. 23, 1858 | 22,148 |
Burnet and Broderick | Nov. 30, 1858 | 22,160 |
Hook, Albert H. | Nov. 30, 1858 | 22,179 |
Raymond, Charles | Nov. 30, 1858 | 22,220 |
Bishop, H. H. | Dec. 7, 1858 | 22,226 |
Pratt, S. F. | Dec. 7, 1858 | 22,240 |
Atwood, J. E. | Dec. 14, 1858 | 22,273 |
Fosket, W. A., and Savage, Elliot | Jan. 25, 1859 | 22,719 |
Snyder, W. | Feb. 15, 1859 | 22,987 |
Clark, D. W. | May 3, 1859 | 23,823 |
Boyd, A. H. | May 17, 1859 | 24,003 |
Gray, Joshua | May 17, 1859 | 24,022 |
Hook, Albert H. | May 17, 1859 | 24,027 |
Spencer, James C. | May 17, 1859 | 24,061 |
Carhart, Peter S. | May 24, 1859 | 24,098 |
McCurdy, J. S. | June 14, 1859 | 24,395[Pg 127] |
Goodwyn, H. H. | June 21, 1859 | 24,455 |
Grout, William | July 5, 1859 | 24,629 |
Hensel, George | July 12, 1859 | 24,737 |
Parker, Sidney | July 12, 1859 | 24,780 |
Hall, William | July 26, 1859 | 24,870 |
Hayden, H. W. | Aug. 2, 1859 | 24,937 |
Kelsey, D. | Aug. 2, 1859 | 24,939 |
Emswiler, J. B. | Aug. 9, 1859 | 25,002 |
Farr, C. N. | Aug. 9, 1859 | 25,004 |
Harrison, James, Jr. | Aug. 9, 1859 | 25,013 |
Tapley, G. S. | Aug. 9, 1859 | 25,059 |
Barnes, W. T. | Aug. 16, 1859 | 25,084 |
Booth, Ezekial | Aug. 16, 1859 | 25,087 |
Hinkley, J. | Aug. 23, 1859 | 25,231 |
Harrison, James, Jr. | Aug. 30, 1859 | 25,262 |
Buell, J. S. | Sept. 13, 1859 | 25,381 |
Vogel, Kasimir | Oct. 4, 1859 | 25,692 |
Woodward, F. G. | Oct. 11, 1859 | 25,782 |
Barrett, O. D. | Oct. 11, 1859 | 25,785 |
Barnes, William T. | Oct. 25, 1859 | 25,876 |
Sawyer, Irwin, and Alsop, T. | Oct. 25, 1859 | 25,918 |
Budlong, William G. | Nov. 1, 1859 | 25,946 |
Fosket, William A., and Savage, E. | Nov. 1, 1859 | 25,963 |
Hicks, W. C. | Nov. 8, 1859 | 26,035 |
Scofield, C. | Nov. 8, 1859 | 26,059 |
Pearson, William | Nov. 22, 1859 | 26,201 |
McCurdy, James S. | Nov. 22, 1859 | 26,234 |
Clark, Edwin | Dec. 6, 1859 | 26,336 |
Dickinson, C. W. | Dec. 6, 1859 | 26,346 |
Miller, Charles | Dec. 13, 1859 | 26,462 |
Rowe, Jas. | Dec. 27, 1859 | 26,638 |
Johnson, A. F. | Jan. 24, 1860 | 26,948 |
Thomson, J. | Feb. 7, 1860 | 27,082 |
Juengst, George | Feb. 14, 1860 | 27,132 |
Davis, Job A. | Feb. 21, 1860 | 27,208 |
Gibbs, James E. A. | Feb. 21, 1860 | 27,214 |
Rowe, James | Feb. 21, 1860 | 27,260 |
Dopp, H. W. | Feb. 28, 1860 | 27,279 |
Paine, A. R. | March 6, 1860 | 27,412 |
Smalley, J. | March 20, 1860 | 27,577 |
Newlove, T. | April 3, 1860 | 27,761 |
McCurdy, J. S. | May 1, 1860 | 28,097 |
Arnold, G. B. | May 8, 1860 | 28,139 |
Bean, E. E. | May 8, 1860 | 28,144 |
Holly, Birdsill | May 8, 1860 | 28,176 |
Chamberlain, J. N. | May 29, 1860 | 28,452 |
Ruddick, H. | May 29, 1860 | 28,538 |
Scofield, Chas., and Rice, Clarke | June 5, 1860 | 28,610 |
Smith, Wilson H. | June 19, 1860 | 28,785 |
Rose, I. M. | June 19, 1860 | 28,814 |
Gibbs, J. E. A. | June 26, 1860 | 28,851 |
McCurdy, J. S. | July 3, 1860 | 28,993 |
Mueller, H. | July 3, 1860 | 28,996 |
Sutton, Wm. A. | July 17, 1860 | 29,202 |
Hicks, W. C. | July 24, 1860 | 29,268 |
Tracy, D. | Sept. 11, 1860 | 30,012 |
Washburn, T. S. | Sept. 11, 1860 | 30,031 |
Arnold, G. B., and A. | Sept. 25, 1860 | 30,112 |
Leavitt, Rufus | Nov. 13, 1860 | 30,634 |
Payne, R. S. | Nov. 13, 1860 | 30,641 |
Heyer, Frederick | Nov. 27, 1860 | 30,731 |
Hardie, J. W. | Dec. 4, 1860 | 30,854 |
Earle, T. | Jan. 22, 1861 | 31,156 |
Bruen, J. T. | Jan. 22, 1861 | 31,208 |
Smith, J. M. | Feb. 5, 1861 | 31,334 |
Smith, L. H. | Feb. 12, 1861 | 31,411 |
Rice, Quartus | Feb. 12, 1861 | 31,429 |
Rose, I. M. | March 5, 1861 | 31,628 |
Ross, Noble G. | March 26, 1861 | 31,829 |
Boyd, A. H. | April 2, 1861 | 31,864 |
Mallary, G. H. | April 2, 1861 | 31,897 |
Shaw, H. L. | April 9, 1861 | 32,007 |
Burr, Theodore | April 9, 1861 | 32,023 |
Jones, William, and Haughian, P. | May 14, 1861 | 32,297 |
Wilder, M. G. | May 14, 1861 | 32,323 |
Smith, Lewis H. | May 21, 1861 | 32,385 |
Stoakes, J. W. | May 28, 1861 | 32,456 |
Fuller, William M. | June 4, 1861 | 32,496 |
Norton, B. F. | July 9, 1861 | 32,782 |
Raymond, C. | July 9, 1861 | 32,785 |
Raymond, Charles | July 30, 1861 | 32,925 |
Case, G. F. | Aug. 13, 1861 | 33,029 |
Hodgkins, C. | Aug. 20, 1861 | 33,085 |
Marble, F. E. | Oct. 8, 1861 | 33,439 |
Mann, Charles | Oct. 22, 1861 | 33,556 |
Grover, W. O. | Nov. 26, 1861 | 33,778 |
Hendrickson, E. M. | Feb. 4, 1862 | 34,330 |
Derocquigny, A. C. F., Gance, D., and Hanzo, L. | March 25, 1862 | 34,748 |
Thompson, R. | April 8, 1862 | 34,926 |
Smith, John C. | April 15, 1862 | 34,988 |
Palmer, Aaron | May 13, 1862 | 35,252 |
Hall, W. S. | Aug. 5, 1862 | 36,084 |
McCurdy, James S. | Aug. 19, 1862 | 36,256 |
Grover, W. O. | Sept. 9, 1862 | 36,405 |
Wilkins, J. N. | Sept. 30, 1862 | 36,591 |
Humphrey, D. W. G. | Oct. 7, 1862 | 36,617 |
House, H. A., and J. A. | Nov. 11, 1862 | 36,932 |
Crossby, C. O., and Kellogg, H. | Dec. 2, 1862 | 37,033 |
Shaw, A. B. | Dec. 16, 1862 | 37,202[Pg 128] |
Pipo, John A. | Jan. 27, 1863 | 37,550 |
Hollowell, J. G. | Feb. 10, 1863 | 37,624 |
Howe, A. B. | March 17, 1863 | 37,913 |
Weitling, W. | March 17, 1863 | 37,931 |
Shaw & Clark | April 21, 1863 | 38,246 |
Baldwin, Cyrus W. | April 28, 1863 | 38,276 |
Grote, F. W. | May 5, 1863 | 38,447 |
Palmer, C. H. | May 5, 1863 | 38,450 |
Mack, W. A. | May 19, 1863 | 38,592 |
Bosworth, C. F. | June 9, 1863 | 38,807 |
McCurdy, J. S. | June 16, 1863 | 38,931 |
Langdon, Leander W. | July 14, 1863 | 39,256 |
House, J. A., and H.A. (4 patents on 1 machine) | Aug. 4, 1863 | 39,442-39,445 |
Tracy and Hobbs | Sept. 15, 1863 | 40,000 |
Wagener, Jeptha A. | Oct. 13, 1863 | 40,296 |
Rehfuss, G. | Oct. 13, 1863 | 40,311 |
Lathrop, Lebbeus W., and de Sanno, Wm. P. | Oct. 27, 1863 | 40,446 |
Heyer, W. D. | Nov. 17, 1863 | 40,622 |
Simmons, A. G., and Scofield, C. | March 1, 1864 | 41,790 |
Guinness, W. S. | March 15, 1864 | 41,916 |
Willcox, Charles H. (4 patents on 1 machine) | March 22, 1864 | 42,036 |
Aug. 9, 1864 | 43,819 | |
Sept. 27, 1864 | 44,490 | |
Sept. 27, 1864 | 44,491 | |
Sibley, J. J. | March 29, 1864 | 42,117 |
Thompson, R. | April 19, 1864 | 42,449 |
McKay & Blake | May 24, 1864 | 42,916 |
Chittenden, H. H. | June 28, 1864 | 43,289 |
Hall, Luther | July 5, 1864 | 43,404 |
Planer, Louis | Aug. 23, 1864 | 43,927 |
Atwater, B. | Sept. 6, 1864 | 44,063 |
Dale, John D. | Oct. 11, 1864 | 44,686 |
Gritzner, M. C. | Oct. 18, 1864 | 44,720 |
Smith, DeWitt C. | Dec. 20, 1864 | 45,528 |
Weitling, W. | Jan. 3, 1865 | 45,777 |
Cadwell, C. | Jan. 24, 1865 | 45,972 |
Bartlett, J. W. | Jan. 31, 1865 | 46,064 |
McCurdy, James S. | Feb. 7, 1865 | 46,303 |
Lamb, Thomas, and Allen, John | Aug. 15, 1865 | 49,421 |
Humphrey, D. W. G. | Aug. 29, 1865 | 49,627 |
Tarbox, John N. | Sept. 5, 1865 | 49,803 |
Crosby, C. O. | Oct. 3, 1865 | 50,225 |
Cajar, E. | Oct. 3, 1865 | 50,299 |
Hart, William | Oct. 17, 1865 | 50,469 |
Hecht, A. | Oct. 17, 1865 | 50,473 |
Emerson, John | Nov. 14, 1865 | 50,989 |
Keats, John, and Clark, Wm. S. | Nov. 14, 1865 | 50,995 |
Rehfuss, George | Nov. 21, 1865 | 51,086 |
Eickemeyer, Rudolf | Feb. 20, 1866 | 52,698 |
Hanlon, John | Feb. 27, 1866 | 52,847 |
McCurdy, J. S. | April 3, 1866 | 53,743 |
Bartram, W. B. | May 15, 1866 | 54,670 |
Bartram, W. B. | May 15, 1866 | 54,671 |
Goodspeed, G. N. | May 15, 1866 | 54,816 |
Hayes, J. | May 22, 1866 | 55,029 |
McCloskey, John | June 19, 1866 | 55,688 |
House, J. A. and H. A. | June 26, 1866 | 55,865 |
Tucker, Joseph C. | July 24, 1866 | 56,641 |
Warth, Albin | July 24, 1866 | 56,646 |
Destouy, A. | July 31, 1866 | 56,729 |
Schwalback, M. | July 31, 1866 | 56,805 |
Cately, William H. | Aug. 7, 1866 | 56,902 |
Piper, D. B. | Aug. 7, 1866 | 56,990 |
Leyden, Austin | Aug. 14, 1866 | 57,157 |
Clements, James M. | Aug. 21, 1866 | 57,451 |
Davis, Job A. | Oct. 9, 1866 | 58,614 |
Rodier, Peter | Nov. 13, 1866 | 59,659 |
Duchemin, Wm. | Nov. 13, 1866 | 59,715 |
Kilbourn, E. E. | Nov. 20, 1866 | 59,746 |
Reed, T. K. | Dec. 4, 1866 | 60,241 |
Singer, I. M. | Dec. 11, 1866 | 60,433 |
Bartram, W. B. | Jan. 1, 1867 | 60,669 |
Rehfuss, G. | Jan. 8, 1867 | 61,102 |
Singer, Isaac | Jan. 15, 1867 | 61,270 |
Cajar, Emil | Feb. 5, 1867 | 61,711 |
Craige, E. H. | Feb. 19, 1867 | 62,186 |
Reed, T. K. | Feb. 19, 1867 | 62,287 |
Bartram, W. B. | March 5, 1867 | 62,520 |
Fuller, H. W. | March 19, 1867 | 63,033 |
Stannard, M. | April 23, 1867 | 64,184 |
Craige, E. H. | Aug. 13, 1867 | 67,635 |
Doll, Arnold | Sept. 3, 1867 | 68,420 |
Bruen, L. B. | Sept. 17, 1867 | 68,839 |
Hodgkins, C. | Oct. 8, 1867 | 69,666 |
Baker, G. W. | Oct. 29, 1867 | 70,152 |
Cadwell, Caleb | Nov. 19, 1867 | 71,131 |
Fanning, J. | Dec. 31, 1867 | 72,829 |
Warth, Albin | Jan. 7, 1868 | 73,064 |
Rehfuss, George | Jan. 7, 1868 | 73,119 |
Cornely, E. | Jan. 28, 1868 | 73,696 |
Blake, L. R. | Feb. 11, 1868 | 74,289 |
Fales, J. F. | Feb. 11, 1868 | 74,328 |
Jencks, G. L. | Feb. 18, 1868 | 74,694 |
Clark, Edwin E. | Feb. 25, 1868 | 74,751 |
Halbert, A. W. | March 31, 1868 | 76,076 |
Gritzner, M. C. | April 7, 1868 | 76,323 |
Bartlett, Joseph W. | April 7, 1868 | 76,385 |
Waterbury, Enos | June 16, 1868 | 79,037 |
Cole, W. H. | June 30, 1868 | 79,447[Pg 129] |
Lamson, Henry P. | July 7, 1868 | 79,579 |
French, S. | July 28, 1868 | 80,345 |
Stein, M. J. | Sept. 8, 1868 | 81,956 |
Hancock, H. J. | Oct. 27, 1868 | 83,492 |
Bartram, W. B. | Nov. 3, 1868 | 83,592 |
Benedict, C. P. | Nov. 3, 1868 | 83,596 |
Bonnaz, A. | Nov. 10, 1868 | 83,909 |
Bonnaz, A. | Nov. 10, 1868 | 83,910 |
Elliott, F. | Jan. 19, 1869 | 85,918 |
Canfield, F. P. | Jan. 19, 1869 | 86,057 |
Arnold B. | Jan. 26, 1869 | 86,121 |
Jones, John | Jan. 26, 1869 | 86,163 |
Russell, W. W. | Feb. 9, 1869 | 86,695 |
Eldridge, G. W. | March 2, 1869 | 87,331 |
House, J. A. and H. A. | March 2, 1869 | 87,338 |
Gird, E. D. | March 9, 1869 | 87,559 |
Carpenter, William | March 9, 1869 | 87,633 |
Dunbar, C. F. | March 30, 1869 | 88,282 |
McLean, J. N. | March 30, 1869 | 88,499 |
Billings, C. E. | April 6, 1869 | 88,603 |
Winter, Wm. | April 13, 1869 | 88,936 |
Tittman, A. | April 20, 1869 | 89,093 |
Swartwout, H. L. | April 27, 1869 | 89,357 |
Lyons, Lucius | April 27, 1869 | 89,489 |
Crosby, C. O. | May 25, 1869 | 90,507 |
Gutmann, J. | May 25, 1869 | 90,528 |
Duchemin, William | June 8, 1869 | 91,101 |
Adams, John Q. | July 6, 1869 | 92,138 |
Bond, Joseph, Jr. | Aug. 10, 1869 | 93,588 |
Hoffman, Geo. W. | Aug. 24, 1869 | 94,112 |
Brown, John H. | Aug. 31, 1869 | 94,389 |
Heery, Luke | Sept. 14, 1869 | 94,740 |
Gray, Joshua | Oct. 5, 1869 | 95,581 |
Smith, E. H. | Oct. 26, 1869 | 96,160 |
Page, Chas. | Nov. 2, 1869 | 96,343 |
Lyon, Lucius | Nov. 9, 1869 | 96,713 |
Clever, P. J. | Nov. 16, 1869 | 96,886 |
Mills, Daniel | Nov. 16, 1869 | 96,944 |
Woodruff, Geo. B., and Browning, Geo. | Nov. 16, 1869 | 97,014 |
Keith, Jeremiah | Dec. 7, 1869 | 97,518 |
Hurtu, Auguste J., and Hautin, Victor J. | Dec. 21, 1869 | 98,064 |
Lamb, Thomas | Dec. 28, 1869 | 98,390 |
Rudolph, B. | Feb. 1, 1870 | 99,481 |
Porter, Alonzo | Feb. 8, 1870 | 99,704 |
Smith, W. T. | Feb. 8, 1870 | 99,743 |
Meyers, N. | Feb. 15, 1870 | 99,783 |
Grover, W. O. | Feb. 22, 1870 | 100,139 |
Spoehr, F. | April 12, 1870 | 101,779 |
Kendall, George F. | April 12, 1870 | 101,887 |
Cooney, W. | April 26, 1870 | 102,226 |
Brown, F. H. | April 26, 1870 | 102,366 |
Howard E., and Jackson, W. H. | May 31, 1870 | 103,745 |
Bartram, W. B. | June 14, 1870 | 104,247 |
Henriksen, H. P. | June 21, 1870 | 104,590 |
Martine, Charles F. | June 21, 1870 | 104,612 |
Nasch, Isidor | June 21, 1870 | 104,630 |
Hall, L. | July 12, 1870 | 105,329 |
Lyon, Lucius | July 26, 1870 | 105,820 |
Bennor, Joseph | Aug. 9, 1870 | 106,249 |
Barnes, M. M. | Aug. 16, 1870 | 106,307 |
Leslie, Arthur M. | Oct. 18, 1870 | 108,492 |
Rayer, William A., and Lincoln, Wm. S. | Nov. 1, 1870 | 108,827 |
Landfear, Wm. R. | Nov. 22, 1870 | 109,427 |
Parham, Charles | Nov. 22, 1870 | 109,443 |
Lamb, I. W. | Nov. 29, 1870 | 109,632 |
Moreau, Eugene | Jan. 3, 1871 | 110,669 |
Robinson, Charles E. | Jan. 3, 1871 | 110,790 |
Goodyear, Charles, Jr. | Jan. 24, 1871 | 111,197 |
Stevens, G., and Hendy, J. | Jan. 31, 1871 | 111,488 |
Carpenter, Mary P. | Feb. 21, 1871 | 112,016 |
Hancock, Henry J. | Feb. 21, 1871 | 112,033 |
Sidenberg, W. | March 14, 1871 | 112,745 |
Chase, M. | April 11, 1871 | 113,498 |
Stein, M. J. | April 11, 1871 | 113,593 |
Tate, Wm. J. | April 11, 1871 | 113,704 |
House, J. A. and H. A. | May 2, 1871 | 114,294 |
Sidenberg, W. | May 23, 1871 | 115,117 |
Beuttels, Charles | May 23, 1871 | 115,155 |
Thompson, G. | May 23, 1871 | 115,255 |
Willcox and Carleton (3 patents on 1 machine) | June 27, 1871 | 116,521 |
116,522 | ||
116,523 | ||
Willcox and Carleton | July 4, 1871 | 116,783 |
Goodyear, Charles, Jr. | July 11, 1871 | 116,947 |
Necker, Carl | July 18, 1871 | 117,101 |
Pitt, James; Joseph; | July 18, 1871 | 117,203 |
Edward; and Wm. | ||
Jones, John T. | Aug. 1, 1871 | 117,640 |
West, E. P. | Aug. 1, 1871 | 117,708 |
Jones, Solomon (2 patents on 1 machine) | Aug. 29, 1871 | 118,537 |
118,538 | ||
Lamb, Thomas | Sept. 5, 1871 | 118,728 |
Bosworth, C. F. | Jan. 9, 1872 | 122,555 |
Smyth, D. M. | Jan. 9, 1872 | 122,673 |
Fish, Warren L. | Feb. 13, 1872 | 123,625 |
Palmer, C. H. | March 19, 1872 | 124,694 |
Baker, G. W. | April 9, 1872 | 125,374 |
Gordon and Kinert | April 16, 1872 | 125,807 |
Howard, C. W. | April 23, 1872 | 126,056 |
(second machine) | 126,057[Pg 130] | |
Smyth, D. M. | May 14, 1872 | 126,845 |
Beckwith, W. G. | May 21, 1872 | 126,921 |
Bouscay, Eloi, Jr. | May 28, 1872 | 127,145 |
Braundbeck, E. | June 11, 1872 | 127,675 |
Heidenthal, W. | June 11, 1872 | 127,765 |
Cleminshaw, S. | June 25, 1872 | 128,363 |
Wardwell, S. W., Jr. | July 2, 1872 | 128,684 |
Springer, W. A. | July 9, 1872 | 128,919 |
Fanning, John | July 16, 1872 | 129,013 |
Parks, Volney | July 30, 1872 | 129,981 |
Baker, G. W. | July 30, 1872 | 130,005 |
Smyth, D. M. | Aug. 6, 1872 | 130,324 |
McClure, A. T. | Aug. 13, 1872 | 130,385 |
Ashe, Robert | Aug. 20, 1872 | 130,555 |
Bartram, W. B. | Aug. 20, 1872 | 130,557 |
West, Elliot P. | Aug. 20, 1872 | 130,674 |
Happe, J., and Newman, W. | Aug. 20, 1872 | 130,715 |
Hinds, Jesse L. | Sept. 10, 1872 | 131,166 |
Brown, F. H. | Oct. 1, 1872 | 131,735 |
Beckwith, W. G. | Nov. 26, 1872 | 133,351 |
Turner, S. S. | Dec. 3, 1872 | 133,553 |
Chandler, R. | Dec. 10, 1872 | 133,757 |
Venner, O. | Dec. 10, 1872 | 133,814 |
Duchemin, W. | Jan. 21, 1873 | 135,032 |
Sheffield, G. V. | Jan. 21, 1873 | 135,047 |
Parham, Charles | Feb. 4, 1873 | 135,579 |
Goodes, E. A. | March 11, 1873 | 136,718 |
Tittman, A. | March 11, 1873 | 136,792 |
Happe, J., and Newman, W. | March 25, 1873 | 137,199 |
Ragan, Daniel | April 1, 1873 | 137,321 |
O’Neil, John | April 8, 1873 | 137,618 |
Kallmeyer, G. | April 8, 1873 | 137,689 |
Ross, J. G., and Miller, T. L. | May 13, 1873 | 138,764 |
West, Elliott P. | May 13, 1873 | 138,772 |
Koch and Brass | May 13, 1873 | 138,898 |
Arnold, B. | May 20, 1873 | 138,981 |
Arnold, B. | May 20, 1873 | 138,982 |
Lathrop, L. W. | May 20, 1873 | 139,067 |
Chandler, Rufus | May 27, 1873 | 139,368 |
Jones, S. H. | July 8, 1873 | 140,631 |
Smyth, D. M. | July 22, 1873 | 141,088 |
Wardwell, S. W., Jr. | July 29, 1873 | 141,245 |
Stewart, J., Jr. | July 29, 1873 | 141,397 |
Walker, William | July 29, 1873 | 141,407 |
Blanchard, Helen A. | Aug. 19, 1873 | 141,987 |
Springer, W. A. | Aug. 26, 1873 | 142,290 |
Cushman, C. S. | Sept. 2, 1873 | 142,442 |
Porter, D. A. | Nov. 25, 1873 | 144,864 |
Koch & Brass | Dec. 2, 1873 | 145,215 |
Richardson, E. F. | Dec. 16, 1873 | 145,687 |
Weber, Theo. A. | Dec. 23, 1873 | 145,823 |
Scribner, Benjamin, Jr. | Jan. 13, 1874 | 146,483 |
Black, Samuel S. | Jan. 20, 1874 | 146,642 |
Taylor, F. B. | Jan. 20, 1874 | 146,721 |
Richardson, Everett P. | Jan. 27, 1874 | 146,948 |
Muir, William | Feb. 3, 1874 | 147,152 |
Goodes, E. A. | Feb. 10, 1874 | 147,387 |
Springer, Wm. A. | Feb. 10, 1874 | 147,441 |
True, C. B. | March 10, 1874 | 148,336 |
Wardwell, S. W., Jr. | March 10, 1874 | 148,339 |
Shorey, Samuel W. | March 17, 1874 | 148,765 |
Smith, James H. | March 24, 1874 | 148,902 |
Horr, Addison D. | April 21, 1874 | 149,862 |
Page, Chas. | May 5, 1874 | 150,479 |
Crane, Thomas | May 5, 1874 | 150,532 |
Buhr, J. | May 26, 1874 | 151,272 |
Smyth, D. M. | June 9, 1874 | 151,801 |
Wensley, James | June 16, 1874 | 152,055 |
Dinsmore, A. S., and Carter, John T. | June 30, 1874 | 152,618 |
Speirs, J. | July 7, 1874 | 152,813 |
Brewer, A. G. | July 14, 1874 | 152,894 |
Baglin, Wm. | Aug. 18, 1874 | 154,113 |
Howard, E. L. | Aug. 25, 1874 | 154,485 |
Landfear, Wm. R. | Sept. 22, 1874 | 155,193 |
Drake, Ellis | Oct. 13, 1874 | 155,932 |
Barney, Samuel C. | Oct. 20, 1874 | 156,119 |
Moreau, Eugene | Oct. 20, 1874 | 156,171 |
Huntington, Thomas S. | Dec. 29, 1874 | 158,214 |
Bartlett and Plant | Jan. 26, 1875 | 159,065 |
Garland, H. P. | Feb. 16, 1875 | 159,812 |
Dinsmore, Alfred S. | March 9, 1875 | 160,512 |
McCloskey, John | March 30, 1875 | 161,534 |
Schmidt, Albert E. | April 27, 1875 | 162,697 |
Darling & Darling | May 25, 1875 | 163,639 |
Richardson, Everett P. | July 13, 1875 | 165,506 |
Whitehill, Robert | July 27, 1875 | 166,172 |
Weber, Theodore A. | Aug. 3, 1875 | 166,236 |
Pearson, Wm. | Aug. 17, 1875 | 166,805 |
Beckwith, William G. | Sept. 7, 1875 | 167,382 |
Hall, John S. | Oct. 11, 1875 | 168,637 |
Jones, J. T. | Oct. 26, 1875 | 169,106 |
Garland, H. P. | Oct. 26, 1875 | 169,163 |
Wormald & Dobson | Nov. 9, 1875 | 169,881 |
Rose, R. M. | Nov. 30, 1875 | 170,596 |
Keith, Jeremiah | Dec. 7, 1875 | 170,741 |
Keith, T. K. | Dec. 14, 1875 | 170,955 |
Leavitte, Albert | Dec. 14, 1875 | 171,147 |
Toll, Charles F. | Dec. 14, 1875 | 171,193 |
Keats, Greenwood, & Keats | Dec. 28, 1875 | 171,622[Pg 131] |
Thayer, Augustus | Jan. 11, 1876 | 172,205 |
Frese, B. | Jan. 18, 1876 | 172,308 |
Pearson, William | Jan. 18, 1876 | 172,478 |
Sawyer & Esty | Feb. 29, 1876 | 174,159 |
Porter & Baker | March 14, 1876 | 174,703 |
Walker, William | April 11, 1876 | 176,101 |
Upson, L. A. | April 18, 1876 | 176,153 |
Witherspoon, S. A. | April 18, 1876 | 176,211 |
Rice, T. M. | April 25, 1876 | 176,686 |
Murphy, E. | May 2, 1876 | 176,880 |
Bradford, E. F., and Pierce, V. R. | May 16, 1876 | 177,371 |
Applegate & Webb | May 25, 1876 | 177,784 |
Sullivan, John J. | June 27, 1876 | 179,232 |
Appleton, C. J., and Sibley, J. J. | July 4, 1876 | 179,440 |
Marin, Chas. | July 11, 1876 | 179,709 |
Gullransen, P. E., and Rettinger, J. C. | July 25, 1876 | 180,225 |
Butcher, Joseph | Aug. 1, 1876 | 180,542 |
Jackson, William | Sept. 5, 1876 | 181,941 |
Barton, Kate C. | Sept. 12, 1876 | 182,096 |
Eickemeyer, Rudolf | Sept. 12, 1876 | 182,182 |
Webster, W. | Sept. 12, 1876 | 182,249 |
Knoch, C. F. | Oct. 17, 1876 | 183,400 |
Cushman, C. S. | Nov. 21, 1876 | 184,594 |
Harris, David | Dec. 12, 1876 | 185,228 |
Wood, J. | Dec. 26, 1876 | 185,811 |
Oram, Henry | Jan. 2, 1877 | 185,952 |
Palmer, Frank L. | Jan. 2, 1877 | 185,954 |
Hall, John S. | Feb. 6, 1877 | 187,006 |
Palmateer, William A. | Feb. 20, 1877 | 187,479 |
Cummins, William G. | Feb. 27, 1877 | 187,822 |
Esty, William | Feb. 27, 1877 | 187,837 |
Leavitt & Drew | Feb. 27, 1877 | 187,874 |
Henriksen, H. P. | March 20, 1877 | 188,515 |
McKay, Gordon | March 27, 1877 | 188,809 |
Follett, J. L. | April 10, 1877 | 189,446 |
Bond, James, Jr. | April 17, 1877 | 189,599 |
Jacob, F. | April 24, 1877 | 190,047 |
Beck, A. | May 1, 1877 | 190,184 |
Hallett, H. H. | June 5, 1877 | 191,584 |
Randel, William | June 12, 1877 | 192,008 |
Corbett, E., and Harlow, C. F. | July 3, 1877 | 192,568 |
Brown, F. H. | July 24, 1877 | 193,477 |
Melhuish, R. M. | Aug. 28, 1877 | 194,610 |
Atwood, K. C. | Sept. 4, 1877 | 194,759 |
Macaulay, F. A. | Oct. 9, 1877 | 195,939 |
Dimond, George H. | Oct. 16, 1877 | 196,198 |
Sedmihradsky, A. J. | Oct. 23, 1877 | 196,486 |
Keith, J. | Nov. 6, 1877 | 196,809 |
Beck, August | Nov. 6, 1877 | 196,863 |
Keith, T. H. | Nov. 6, 1877 | 196,909 |
Keats, John | Dec. 11, 1877 | 198,120 |
Briggs, Thomas | Jan. 1, 1878 | 198,790 |
Corey, J. W. | Jan. 8, 1878 | 198,970 |
Howard, T. S. L. | Jan. 15, 1878 | 199,206 |
Bosworth, C. F. | Jan. 22, 1878 | 199,500 |
Dancel, C. | Jan. 29, 1878 | 199,802 |
Pearson, M. H. | Feb. 5, 1878 | 199,991 |
Morrell, Robert W.; Parkinson, Thomas; and Parkinson, Joseph | April 23, 1878 | 202,857 |
Barcellos, D. | April 30, 1878 | 203,102 |
Elderfield, F. D. | June 4, 1878 | 204,429 |
Heberling, J. | June 4, 1878 | 204,604 |
Beukler, William | June 11, 1878 | 204,704 |
Varicas, L. | June 11, 1878 | 204,864 |
Stewart, W. T. | July 2, 1878 | 205,698 |
House, Jas. A. | July 23, 1878 | 206,239 |
Martin, W., Jr.; Dawson, D. R.; and Orchar, R. | Aug. 6, 1878 | 206,743 |
Conklin, N. A. | Aug. 6, 1878 | 206,774 |
Wollenberg, H., and Priesner, J. | Aug. 6, 1878 | 206,848 |
Young, E. S., and Dimond, G. H. | Aug. 13, 1878 | 206,992 |
Hoffman, Clara P., and Meyers, Nicholas | Aug. 13, 1878 | 207,035 |
Wensley, Jas. | Aug. 20, 1878 | 207,230 |
Dimond, G. H. | Aug. 27, 1878 | 207,400 |
Steward, A. | Aug. 27, 1878 | 207,454 |
Wood, Richard G. | Sept. 10, 1878 | 207,928 |
McCombs, Geo. F. | Sept. 24, 1878 | 208,407 |
Keith, Jeremiah | Oct. 22, 1878 | 209,126 |
Wells, W. W. | Nov. 12, 1878 | 209,843 |
Bayley, C. H. | Feb. 11, 1879 | 212,122 |
Parmenter, Charles O. | Feb. 18, 1879 | 212,495 |
Ingalls, N., Jr. | Feb. 25, 1879 | 212,602 |
Cleminshaw, S. | March 18, 1879 | 213,391 |
Webb, T., and Heartfield, C. H. | March 25, 1879 | 213,537 |
Borton, Stockton | April 8, 1879 | 214,089 |
Henriksen, H. P. | May 20, 1879 | 215,615 |
Bland, Henry | June 3, 1879 | 216,016 |
Morrison, T. W. | June 10, 1879 | 216,289 |
Bosworth, Charles F. | June 17, 1879 | 216,504 |
Simmons, Frederick | June 24, 1879 | 216,902 |
Junker, Carl | July 1, 1879 | 217,112 |
Legat, Désiré Mathurin | Aug. 12, 1879 | 218,388 |
Willcox, C. H. | Aug. 12, 1879 | 218,413 |
Cornely, Emile | Sept. 2, 1879 | 219,225[Pg 132] |
Hamm, E. | Sept. 16, 1879 | 219,578 |
Tuttle, J. W., and Keith, T. K. | Sept. 16, 1879 | 219,782 |
Stackpole, G., and Applegate, J. H. | Oct. 7, 1879 | 220,314 |
Otis, S. L. | Oct. 28, 1879 | 221,093 |
Bland, H. | Nov. 11, 1879 | 221,505 |
Bracher, T. W. | Nov. 11,1879 | 221,508 |
Snediker, J. F. | Nov. 25, 1879 | 222,089 |
Mooney, J. H. | Dec. 2, 1879 | 222,298 |
Osborne, J. H. | Feb. 3, 1880 | 224,219 |
Smith, W. M. | March 2, 1880 | 225,199 |
Banks, C. M. | March 23, 1880 | 225,784 |
Haberling, J. | May 4, 1880 | 227,249 |
Haberling, J. | May 11, 1880 | 227,525 |
Wiseman, Edmund | June 8, 1880 | 228,711 |
Juengst, George | June 15, 1880 | 228,820 |
Morley, J. H. | June 15, 1880 | 228,918 |
Curtis, G. H. W. | June 22, 1880 | 228,985 |
Lipe, C. E. | June 29, 1880 | 229,322 |
Miller, L. B., and Diehl, P. | July 6, 1880 | 229,629 |
Willcox, C. H. | July 20, 1880 | 230,212 |
Shaw, E. | July 27, 1880 | 230,580 |
Dinsmore, A. S. | Aug. 17, 1880 | 231,155 |
Thurston, C. H. | Oct. 12, 1880 | 231,300 |
Butcher, J. | Oct. 26, 1880 | 233,657 |
Smyth, D. M. | Nov. 23, 1880 | 234,732 |
Hesse, J. | Dec. 7, 1880 | 235,085 |
Kjalman, H. N. | Dec. 21, 1880 | 235,783 |
Morley, J. H. | Jan. 4, 1881 | 236,350 |
Thomas, J. | Jan. 11, 1881 | 236,466 |
Benson, G. | March 8, 1881 | 238,556 |
Green, G. F. | March 8, 1881 | 238,678 |
Eickemeyer, Rudolf | March 29, 1881 | 239,319 |
Palmer, C. H. | April 26, 1881 | 240,758 |
Campbell, D. H. | May 17, 1881 | 241,612 |
Campbell, Duncan H. | May 17, 1881 | 241,613 |
Leslie, A. M. | May 24, 1881 | 241,808 |
Newell, George F. | June 7, 1881 | 242,470 |
Gritzner, Max C. | June 28, 1881 | 243,444 |
Keith, Jeremiah | July 5, 1881 | 243,710 |
Choquette, A. E. | July 12, 1881 | 244,033 |
Mooney, J. H. | July 19, 1881 | 244,470 |
Beardslee, W. F. | Aug. 16, 1881 | 245,781 |
Hine, Charlie M. | Aug. 23, 1881 | 246,136 |
Willcox, C. H. | Sept. 6, 1881 | 246,700 |
Hoefler, J. | Sept. 13, 1881 | 246,883 |
Woodward, E. | Sept. 20, 1881 | 247,285 |
Richards, Jean E. | Jan. 24, 1882 | 252,799 |
Abbott, W. W. | Jan. 31, 1882 | 252,984 |
Secor, J. B. | Feb. 14, 1882 | 253,772 |
Deschamps, O. L. | Feb. 21, 1882 | 253,915 |
Hull, E. H. | Feb. 28, 1882 | 254,217 |
Roberts, William | March 7, 1882 | 254,696 |
Willcox and Borton | March 28, 1882 | 255,576 |
Borton and Willcox | March 28, 1882 | 255,577 |
Borton and Willcox | March 28, 1882 | 255,580 |
Borton and Willcox | March 28, 1882 | 255,581 |
Veukler, W. | April 4, 1882 | 255,916 |
Hurtu, A. J. | May 30, 1882 | 258,761 |
Keats, Alphonso | July 11, 1882 | 260,990 |
Ramsden, John W. | Aug. 1, 1882 | 262,116 |
Koch, William | Aug. 8, 1882 | 262,298 |
Bigelow, J. | Aug. 29, 1882 | 263,467 |
Mills, Daniel | Oct. 10, 1882 | 265,850 |
Wilkinson, Charles E. | Dec. 19, 1882 | 269,251 |
Carlisle, W. S. | Jan. 9, 1883 | 270,540 |
Holden, O. J., and Griswold, L. | Feb. 13, 1883 | 272,050 |
Cameron, James W. | Feb. 20, 1883 | 272,527 |
Miller, L. B., and Diehl, P. | March 20, 1883 | 274,359 |
Ludeke, W. | April 10, 1883 | 275,506 |
Bolton, J., and Petnz, A. D. | May 8, 1883 | 277,106 |
Blodgett, John W. | June 12, 1883 | 279,320 |
Haberling, J. | Sept. 4, 1883 | 284,300 |
Thimonnier, E., and Vernaz, C. | Oct. 30, 1883 | 287,592 |
Duchemin, William | Nov. 20, 1883 | 288,929 |
Lawrence, G. H. | Dec. 25, 1883 | 290,895 |
Clever, Peter J. | April 8, 1884 | 296,529 |
Palmer, John H. | May 6, 1884 | 298,228 |
Dowling, James, and Connolly, John | May 27, 1884 | 299,118 |
Boecher, Adam | June 10, 1884 | 300,199 |
Luedeke, Waldemar | June 17, 1884 | 300,380 |
VanVechten, Orville R. | July 15, 1884 | 302,063 |
Carr, Wm. H., and Ostrom, F. W. | Aug. 12, 1884 | 303,361 |
Trip, J. | Dec. 2, 1884 | 308,711 |
Farrar, Arthur | Dec. 30, 1884 | 309,837 |
Turner, M. G. | Feb. 17, 1885 | 312,306 |
Mills, D. | March 3, 1885 | 313,359 |
Hurtu, August J. | April 7, 1885 | 315,037 |
Charmbury, Henry | April 28, 1885 | 316,745 |
Woodward & Keith | April 28, 1885 | 316,927 |
Walker, William | June 16, 1885 | 320,099 |
Tucker, R. D. | June 23, 1885 | 320,898 |
Wheeler and Dial | Oct. 13, 1885 | 328,165 |
Thomas, Joseph | Nov. 10, 1885 | 330,170 |
Muegge, C. A. | Dec. 8, 1885 | 332,207 |
Diehl, P. | April 13, 1886 | 339,623 |
Diehl, P. | Aug. 24, 1886 | 347,776[Pg 133] |
Helwig, Arthur | Oct. 5, 1886 | 350,364 |
Miehling, Charles | Nov. 2, 1886 | 351,992 |
Dieterle, H. E. | Nov. 30, 1886 | 353,542 |
Walker, William | Dec. 7, 1886 | 353,720 |
Rosenthal, S. A. | Dec. 7, 1886 | 353,970 |
Temple, John | Feb. 22, 1887 | 358,088 |
Gee, W. V. | April 19, 1887 | 361,406 |
Lingley, John W. | Aug. 16, 1887 | 368,538 |
Boppel, Jacob | Jan. 29, 1889 | 396,979 |
Webster, William | April 30, 1889 | 402,497 |
Osterhout and Hallenbeck | May 7, 1889 | 402,610 |
Bennett and Dowling | Aug. 27, 1889 | 409,728 |
Hine, Charles M. | Jan. 28, 1890 | 420,382 |
Wheeler, Nathaniel | Feb. 4, 1890 | 420,847 |
Hallenbeck, J. P. | April 8, 1890 | 425,422 |
Lisle, Myron C. | May 20, 1890 | 428,171 |
Walker and Bennet | May 20, 1890 | 428,548 |
Stewart, James, Jr. | July 15, 1890 | 432,449 |
Dewees, J. W. | July 22, 1890 | 432,746 |
Powell, Thomas | Dec. 16, 1890 | 442,695 |
Fletcher, James H. | Dec. 30, 1890 | 443,756 |
Rudolph, Ernst B., deceased, Boulter, W. E., administrator | April 7, 1891 | 449,927 |
Goodwin, Julius C. | April 21, 1891 | 450,793 |
Cook, Hugo | June 23, 1891 | 454,610 |
Bowyer, J. T. | June 23, 1891 | 454,708 |
Willcox, C. H., and Borton, S. | April 5, 1892 | 472,094 |
Legg and Weston | May 17, 1892 | 474,840 |
Kern, Ferdinand | July 19, 1892 | 479,369 |
Jackson, Francis | May 1, 1894 | 519,064 |
Charles Abercrombi | June 5, 1892 | 520,977 |
Taft, J. C. | Oct. 15, 1895 | 547,866 |
IV. 19th-Century Sewing-Machine Leaflets in the Smithsonian Collections
Machine or Manufacturer | Date | Type |
American B.H.O. and Sewing Machine | 1874 | Illustrated, advertising leaflet |
Buckeye sewing machine | ca. 1870 | Illustrated, directions for using the machine |
New Buckeye | ca. 1872 | Illustrated, directions for using the machine |
Centennial sewing machine | 1876 | Illustrated, advertising leaflet |
Domestic sewing machine | 1872 | Illustrated, advertising leaflet |
Florence sewing machine | 1873 | Illustrated, advertising leaflet |
Florence sewing machine | 1878 | Illustrated, directions for using the machine |
Goodes sewing machine | ca. 1876 | Advertising leaflet |
Grant Brothers sewing machine | 1867 | Illustrated, advertising leaflet (Xerox copy) |
Grover and Baker sewing machine | 1853 | Illustrated, advertising leaflet |
Grover and Baker sewing machine | ca. 1870 | Illustrated, advertising leaflet |
Home sewing machine | ca. 1870 | Illustrated, advertising leaflet |
Howe sewing machine, new “B” machine | 1868 | Illustrated, instruction booklet |
Howe sewing machine | 1876 | Illustrated, catalog of machines |
Independent Noiseless sewing machine | ca. 1874 | Illustrated, advertising leaflet |
Ladd, Webster sewing machine | 1861 | Illustrated, advertising leaflet |
Little Monitor sewing machine | ca. 1872 | Illustrated, advertising leaflet |
Remington Family sewing machine | ca. 1874 | Illustrated, advertising leaflet |
Shaw and Clark sewing machine | 1864 | Illustrated, advertising leaflet |
Singer sewing machine | 1871 | Illustrated, advertising leaflet |
Singer sewing machine | 1893 | Catalog of machines shown at the Columbian Exposition |
Standard Shuttle sewing machine | ca. 1875 | Illustrated, advertising leaflet |
Ten Dollar Novelty sewing machine | ca. 1870 | Illustrated, advertising leaflet |
Weed sewing machine | 1873 | Illustrated, advertising leaflet |
Wheeler and Wilson sewing machine | ca. 1869 | Illustrated, instruction booklet |
Wheeler and Wilson sewing machine | ca. 1870-1875 | Illustrated, advertising leaflet |
Wheeler and Wilson no. 8 machine | ca. 1878 | Illustrated, instruction booklet |
Wilson sewing machine | 1872 | Illustrated, advertising leaflet |
V. A Brief History of Cotton Thread
Although Samuel Slater’s wife is credited with making the first cotton sewing thread from yarns spun at the Pawtucket, Rhode Island, mill in about 1794, cotton thread did not become a manufactured item at that time. Slater turned all his interests to producing cotton-twist yarns needed for the warps of cotton fabrics. By 1809, however, the agents of Almy and Brown, partners and distributors for Slater, were advertising cotton thread as follows:
Although Samuel Slater’s wife is credited with making the first cotton sewing thread from yarns spun at the Pawtucket, Rhode Island, mill around 1794, cotton thread didn’t become a manufactured product at that time. Slater focused all his efforts on producing cotton-twist yarns needed for the warps of cotton fabrics. By 1809, however, the agents of Almy and Brown, partners and distributors for Slater, were advertising cotton thread as follows:
Factory Cotton and Thread Store, No. 26 Court Street opposite Concert Hall. George Connell, Agent for Almy and Brown of Providence and Pawtucket Manufactories, has now for sale from eight to ten thousand weight of yarn, for weaving ... five hundred pounds cotton thread, in hanks, from No. 12 to 60 of a superior quality and very white.[91]
Factory Cotton and Thread Store, No. 26 Court Street across from the Concert Hall. George Connell, Agent for Almy and Brown of the Providence and Pawtucket factories, currently has for sale between eight and ten thousand pounds of yarn for weaving ... five hundred pounds of cotton thread, in hanks, ranging from No. 12 to 60, of excellent quality and very white.[91]
Although it was a short hop from the spinning of cotton warps to the twisting of these cotton yarns to form a sewing thread, the general manufacture of cotton thread as an industry did not originate in the United States but rather in Scotland in the early 19th century. Napoleon’s blockade, which curtailed Great Britain’s importation of silk—needed not only for fabrics but also for making heddle strings for the looms—stimulated the production of cotton thread there. James and Patrick Clark, in desperation, attempted to substitute cotton for silk in their manufacture of these heddle strings. When they were successful, they considered that if cotton could be used successfully for this purpose it could also be made suitable for sewing thread. In 1812 they built a factory in Paisley, Scotland, which had long been noted for its textile industries. The thread was sold in hanks. About 1820 James’ sons, James and John, who were now running J. & J. Clark & Co., began to wind the thread on spools. For this service they charged an extra halfpenny, which was refunded when the empty spool was returned. The thread was usually a three-ply or so-called three-cord thread.
Although it was a quick transition from spinning cotton warps to twisting these cotton yarns into sewing thread, the overall cotton thread manufacturing industry began in Scotland in the early 19th century, not in the United States. Napoleon’s blockade, which limited Great Britain’s ability to import silk—essential not just for fabrics but also for making heddle strings for looms—boosted cotton thread production there. James and Patrick Clark, in a moment of desperation, tried to use cotton instead of silk for their heddle strings. Once they succeeded, they figured that if cotton worked for this purpose, it could also be adapted for sewing thread. In 1812, they established a factory in Paisley, Scotland, a region known for its textile industry. The thread was sold in hanks. Around 1820, James’ sons, James and John, who were now managing J. & J. Clark & Co., began winding the thread onto spools. They charged an extra halfpenny for this service, which was refunded when the empty spool was returned. The thread was typically a three-ply or three-cord thread.
About 1815 James Coats, also of Paisley, started manufacturing thread at Ferguslie, Scotland. His two sons took over the company in 1826 and formed the J. & P. Coats Company. Another brother, Andrew Coats, became the selling agent in the United States about 1840. But the cotton-thread industry was not fully launched.
About 1815, James Coats, who was also from Paisley, began making thread at Ferguslie, Scotland. His two sons took over the business in 1826 and established the J. & P. Coats Company. Another brother, Andrew Coats, became the sales agent in the United States around 1840. However, the cotton-thread industry was not fully developed.
As reported in an 1853 Scientific American, there was “more American thread made ten years ago than there is today.”[92] It was not until the six-cord cabled cotton thread, which was suitable for both machine and hand sewing, was perfected that the industry progressed into full operation.
As reported in a 1853 Scientific American, there was “more American thread made ten years ago than there is today.”[92] It wasn't until the six-cord cabled cotton thread, which was good for both machine and hand sewing, was perfected that the industry fully took off.
FOOTNOTES:
VI. Biographical Sketches
BARTHELEMY THIMONNIER
The first man known to have put a sewing machine into practical operation, Barthelemy Thimonnier, was a Frenchman of obscure parentage. His father, a textile dyer of Lyon, left that city in 1793 as a result of the Revolution and journeyed with his family to l’Arbresle where Barthelemy was born in August of that year.
The first person known to have put a sewing machine to practical use, Barthelemy Thimonnier, was a Frenchman from a modest background. His father, a textile dyer from Lyon, left the city in 1793 due to the Revolution and traveled with his family to l’Arbresle, where Barthelemy was born in August of that year.
The family resources were small, and, although the young Thimonnier was able to begin studies at the Seminaire de Saint-Jean at Lyons, he soon was forced to leave school for financial reasons and return to his home, then at Amplepuis. There he learned the tailoring trade and by 1813 was fairly well established in his own shop.
The family's resources were limited, and although young Thimonnier managed to start his studies at the Seminaire de Saint-Jean in Lyons, he quickly had to drop out due to financial issues and go back home, which was then in Amplepuis. There, he learned the tailoring trade and by 1813 had set up his own shop and was doing fairly well.
At that time many of the town’s inhabitants were weavers and almost every house possessed one or two looms. The noise of the shuttle echoed from these family workshops. Thimonnier noted the relatively small amount of time needed to weave a fabric compared with the slow painstaking task of sewing a garment by passing the needle in and out for each stitch of each seam. When his mind began to dwell on the idea of producing a machine to do this stitching, another of the town’s occupations supplied him with a clue and an additional incentive. This village industry produced a type of embroidery work called point de chainette, in which a needle with a small hook was used to form the chainstitch, a popular type of decorative stitch long used in countries all over the world. It was Thimonnier’s plan to use this type of hooked needle and produce the stitch by machine, employing it both as a decorative stitch and a seam-forming one.
At that time, many of the town’s residents were weavers, and almost every house had one or two looms. The sound of the shuttle echoed from these family workshops. Thimonnier noticed how much less time it took to weave a fabric compared to the slow, careful process of sewing a garment by pushing the needle in and out for each stitch of each seam. As he started to think about creating a machine to handle this stitching, another local industry gave him a clue and an extra motivation. This village industry specialized in a type of embroidery called point de chainette, which used a needle with a small hook to make the chainstitch, a popular decorative stitch that has been used in countries around the globe. Thimonnier planned to use this hooked needle to produce the stitch by machine, using it both as a decorative touch and for seams.
In 1825 Thimonnier moved to St. Etienne, where he became completely absorbed in the idea of inventing a sewing machine. Ignorant of any of the principles of mechanics, he worked alone and in secret for four years, neglecting his tailoring business to the extent that neighbors looked upon him as peculiar, if not crazy. By 1829 he had not only mastered the mechanical difficulties of bringing his dream to realization, but also had made the acquaintance of the man who helped him to success. Ferrand, of l’Ecole des Mines of Saint-Etienne, became interested in the machine and helped finance Thimonnier through his trials and disappointments. In 1830 Thimonnier received a patent on his machine, which produced the chainstitch by means of a needle shaped like a small crochet hook.
In 1825, Thimonnier moved to St. Etienne, where he became completely focused on inventing a sewing machine. Without any knowledge of mechanics, he worked alone and in secret for four years, ignoring his tailoring business to the point that his neighbors thought he was odd, if not insane. By 1829, he had not only figured out the mechanical challenges of making his vision a reality but had also met the person who helped him succeed. Ferrand, from l’Ecole des Mines of Saint-Etienne, became interested in the machine and supported Thimonnier financially through his struggles and setbacks. In 1830, Thimonnier received a patent for his machine, which created the chainstitch with a needle designed like a small crochet hook.

Figure 133.—Barthelemy Thimonnier, 1793-1857. From an engraving in the Sewing Machine Advance, November 15, 1880. (Smithsonian photo 10569-A.)
Figure 133.—Barthelemy Thimonnier, 1793-1857. From an engraving in the Sewing Machine Advance, November 15, 1880. (Smithsonian photo 10569-A.)
Thimonnier, together with Ferrand and a M. Beaunier, made attempts to introduce his machine in Paris. By 1841 they were successful in having eighty of Thimonnier’s machines in use sewing army clothing in a shop in Paris. But the fears of the tailors could not be quieted. The machines were destroyed by an ignorant and[Pg 138] infuriated mob, as had been earlier labor-saving devices such as the Jacquard attachment for the loom and Hargreaves’ spinning jenny. Thimonnier was forced to flee to his home in St. Etienne, once more penniless.
Thimonnier, along with Ferrand and Mr. Beaunier, tried to launch his machine in Paris. By 1841, they succeeded in getting eighty of Thimonnier’s machines operating to sew army clothing in a shop in Paris. However, the tailors' fears couldn't be calmed. The machines were destroyed by an angry and[Pg 138] uninformed mob, just like earlier labor-saving inventions such as the Jacquard attachment for the loom and Hargreaves’ spinning jenny. Thimonnier had to flee back to his home in St. Etienne, once again without any money.
Soon after this, Jean Marie Magnin, an engineer from Villefranche -sur-Saône became interested in Thimonnier’s machine and provided the inventor again with financial backing. In 1845 under the name of Thimonnier and Magnin the patent of 1830 was renewed, and under it they organized the first French sewing-machine company. The machines they manufactured could produce 200 stitches per minute.
Soon after this, Jean Marie Magnin, an engineer from Villefranche -sur-Saône became interested in Thimonnier’s machine and provided the inventor with financial support again. In 1845, under the name Thimonnier and Magnin, they renewed the patent from 1830 and established the first French sewing-machine company. The machines they produced could make 200 stitches per minute.
The Revolution of 1848 curtailed the manufacture and sale of the machines. Thimonnier, remembering his unpleasant experience in 1841, decided to go to England with Magnin, where, on February 8, 1848, they received the English patent for his chainstitch machine. He was also granted United States patent 7,622 on September 20, 1850. This later machine had some advantages over his French machine of 1830, but by this time other inventors had joined the field with machines that were more practical. Magnin entered a sewing machine (which from the description in the catalog must have been Thimonnier’s invention) in the Crystal Palace Exhibition in London in 1850, but because it was late in arriving it was overlooked by the judges and not even considered in the competition. Thimonnier died in poverty at Amplepuis on July 5, 1857.
The Revolution of 1848 limited the production and sale of the machines. Thimonnier, recalling his bad experience in 1841, decided to go to England with Magnin, where, on February 8, 1848, they obtained the English patent for his chainstitch machine. He also received United States patent 7,622 on September 20, 1850. This later machine had some benefits over his French machine from 1830, but by this time, other inventors had entered the market with machines that were more practical. Magnin submitted a sewing machine (which, based on the catalog's description, must have been Thimonnier’s creation) to the Crystal Palace Exhibition in London in 1850, but since it arrived late, the judges overlooked it and it wasn’t even considered in the competition. Thimonnier died in poverty at Amplepuis on July 5, 1857.
WALTER HUNT

Figure 134.—Walter Hunt, 1796-1860. From a daguerreotype owned by his great-grandson, C. N. Hunt. (Smithsonian photo 32066-A.)
Figure 134.—Walter Hunt, 1796-1860. From a daguerreotype owned by his great-grandson, C. N. Hunt. (Smithsonian photo 32066-A.)
Walter Hunt was born near Martinsburg, New York, on July 29, 1796. Although little is known of Hunt’s early childhood, we do learn from the author of his obituary, which appeared in Scientific American, July 9, 1860, that even as a child he was more interested in people and what he could do for them than in what he could do to insure his own welfare. He is said to have devoted his life to his friends, frequently giving away his last cent when he did not have enough to provide for himself.
Walter Hunt was born near Martinsburg, New York, on July 29, 1796. Although not much is known about his early childhood, we learn from the author of his obituary in Scientific American, July 9, 1860, that even as a child, he was more focused on helping others than on his own well-being. He reportedly dedicated his life to his friends, often giving away his last cent when he didn’t have enough to take care of himself.
There is no record that Hunt maintained a regular business other than the occupation of inventor. His interests were numerous and varied. He received his first patent on June 26, 1826, for a machine for spinning flax and hemp. During the next 33 years he patented 26 ideas. In addition he sold or dropped several more. His second patent was for a coach alarm, and through the years he also received patents for a variety of things including a knife sharpener, heating stove, ice boat, nail machine, inkwell, fountain pen, safety pin, bottle stopper, sewing machine (1854), paper collars, and a reversible metallic heel.
There’s no record that Hunt had a regular business besides being an inventor. He had many different interests. He got his first patent on June 26, 1826, for a machine that spun flax and hemp. Over the next 33 years, he patented 26 inventions. He also sold or abandoned several more. His second patent was for a coach alarm, and throughout the years, he received patents for various items including a knife sharpener, heating stove, ice boat, nail machine, inkwell, fountain pen, safety pin, bottle stopper, sewing machine (1854), paper collars, and a reversible metallic heel.
ELIAS HOWE, JR.
Elias Howe, Jr., was born on his father’s farm in Spencer, Massachusetts, on July 9, 1819. This was one of those barren New England farms with many rock-filled acres. All possible ingenuity was necessary to secure a living. The elder Howe supplemented his farming by having a small gristmill, a sawmill, and also by manufacturing cards for the fast-growing cotton industry of New England. Elias Jr.’s earliest recollections were of the latter. He worked with his brothers and sisters sticking wire teeth into strips of leather to make these cotton cards, but, not being very good at this, his family decided to let him “live out” with a neighboring farmer. (Children were leased in those days; they received their board and keep in exchange for chores they would perform.) After a few years, Elias returned home and worked in his father’s mill until he was sixteen. Then, against the wishes of his family, he went to Lowell, Massachusetts. Here, he obtained a[Pg 139] learner’s place in a machine shop where cotton-spinning machinery was made and repaired.
Elias Howe, Jr. was born on his father's farm in Spencer, Massachusetts, on July 9, 1819. This was one of those unproductive New England farms with lots of rocky land. It took a lot of creativity to make a living. His father supplemented the farming income by running a small gristmill, a sawmill, and also by making cards for the booming cotton industry in New England. Elias Jr.'s earliest memories were of this work. He helped his siblings insert wire teeth into strips of leather to create these cotton cards, but since he wasn't very good at it, his family decided to send him to "live out" with a nearby farmer. (Children were leased during that time; they received food and shelter in exchange for the chores they did.) After a few years, Elias returned home and worked in his father's mill until he turned sixteen. Then, against his family's wishes, he went to Lowell, Massachusetts. There, he got a[Pg 139] apprenticeship in a machine shop that made and repaired cotton-spinning machinery.
In 1837, when a financial panic hit the country, Howe lost his job. He then decided to go to Boston, and this marked a turning point in his career. In Boston he met Ari Davis, a maker of mariners’ instruments and scientific apparatus. Howe began to work in Davis’ shop, a place to which inventors often came to ask advice about their ideas. Davis sometimes helped them, but just as often he shouted at them in anger—he is said to have been one of the noisiest men in Boston. One day Howe overheard his employer bellowing at a man who had brought a knitting machine to the shop to seek Davis’ advice. “Why are you wasting your time over a knitting machine?” said Davis, “Take my advice, try something that will pay. Make a sewing machine.” “It can’t be done,” was the reply. “Can’t be done?” shouted Davis, “Don’t tell me that. Why—I can make a sewing machine myself.” “If you do,” interrupted the capitalist, “I can make an independent fortune for you.” Davis, like most men of many words, often talked of more than he planned to do. He never attempted to invent a sewing machine.
In 1837, when a financial crisis hit the country, Howe lost his job. He then decided to move to Boston, which marked a turning point in his career. In Boston, he met Ari Davis, a maker of marine instruments and scientific equipment. Howe began working in Davis' shop, a place where inventors frequently came to seek advice about their ideas. Davis sometimes helped them, but just as often he yelled at them in anger—he was said to be one of the loudest men in Boston. One day, Howe overheard his boss shouting at a man who had brought a knitting machine to the shop for Davis' advice. “Why are you wasting your time on a knitting machine?” Davis said, “Take my advice, try something that will actually make money. Make a sewing machine.” “It can't be done,” was the reply. “Can't be done?” shouted Davis, “Don't tell me that. I could make a sewing machine myself.” “If you do,” interrupted the capitalist, “I can help you make a fortune.” Davis, like many talkative people, often claimed he would do more than he actually intended. He never tried to invent a sewing machine.
But the loud voices interested Howe, who, it is said, determined then that he would produce a sewing machine and win the fortune that the prosperous-looking man had asserted was waiting for such a deed. A kind of lameness since birth had made physical tasks painful for Howe, and he perhaps felt that this would offer an opportunity to become independent of hard physical work.
But the loud voices caught Howe's attention, and reportedly, he decided right then that he would create a sewing machine and claim the fortune that the prosperous-looking man had claimed was waiting for such an invention. A kind of lameness he had had since birth made physical tasks painful for Howe, and he probably felt that this would give him a chance to be free from hard physical labor.
After marrying on a journeyman machinist’s pay of $9 a week, Howe’s health worsened and by 1843 was so bad that he had to stop work for days at a time. His wife was forced to take in sewing to maintain the family. It was the sight of his wife toiling at her stitches together with the pressure of poverty that recalled to Howe his earlier interest in a machine to sew. He decided to make an earnest attempt to invent one. Watching his wife for hours at a time, he tried to visualize a machine that would duplicate the motions of the arm. After many trials, he conceived the idea of using an eye-pointed needle in combination with a shuttle to form a stitch. It is possible that, as some authors state, the solution appeared to him in a dream, a manifestation of the subconscious at work. Others have suggested that he may have learned of Hunt’s machine. There is a general similarity in the two, not only in the combination of eye-pointed needle and shuttle but in the overhanging arm and vertical cloth suspension.
After marrying and earning $9 a week as a journeyman machinist, Howe's health got worse, and by 1843, it was so bad that he had to take days off work. His wife had to take in sewing to support the family. Seeing her struggling with her stitches, along with the stress of poverty, reminded Howe of his earlier interest in inventing a sewing machine. He decided to make a serious attempt to create one. By watching his wife for hours, he tried to imagine a machine that would mimic the movements of her arm. After numerous attempts, he came up with the idea of using an eye-pointed needle along with a shuttle to form a stitch. Some authors suggest that the solution came to him in a dream, a sign of his subconscious at work. Others think he might have been inspired by Hunt's machine. There is a general similarity between the two, not just in the combination of the eye-pointed needle and shuttle, but also in the overhanging arm and vertical cloth suspension.
After conceiving the idea, whatever his inspiration, Howe determined to devote all of his time to producing a working model of his machine. Elias’ father, who had then started a factory for splitting palm leaves in Cambridge, gave him permission to set up a lathe and a few tools in the garret of the factory. Elias moved his family to Cambridge. Soon after his arrival, unfortunately, the building burned down, and Howe despaired of finding a place to work. He had a friend, however, in George Fisher, who had just come into a small inheritance, and Howe persuaded him to enter into partnership with him for the development of the machine. Fisher agreed to board Howe and his family, which now included two children, while Howe completed the model. Fisher also agreed to supply $500 for material and tools in exchange for a half interest in a patent if one was obtained.
After coming up with the idea, whatever inspired him, Howe decided to dedicate all his time to building a working model of his machine. Elias’ father, who had started a factory for splitting palm leaves in Cambridge, allowed him to set up a lathe and a few tools in the attic of the factory. Elias moved his family to Cambridge. Unfortunately, shortly after they arrived, the building caught fire, and Howe struggled to find a place to work. However, he had a friend in George Fisher, who had just received a small inheritance, and Howe convinced him to partner up for the development of the machine. Fisher agreed to house Howe and his family, which now had two children, while Howe finished the model. Fisher also agreed to provide $500 for materials and tools in exchange for a half interest in a patent if one was secured.

Figure 135.—Elias Howe, Jr., 1819-1867. From an oil painting in the Smithsonian Institution presented by the inventor’s grandson, Elias Howe Stockwell. (Smithsonian photo 622.)
Figure 135.—Elias Howe Jr., 1819-1867. From an oil painting in the Smithsonian Institution presented by the inventor’s grandson, Elias Howe Stockwell. (Smithsonian photo 622.)
At long last Howe was able to spend his full time and concentration on building his machine. His family was being fed and had a roof over its head. Within a few months Howe had completed a model and by April 1845 had sewed his first seam (see fig. 14). In July of that year he sewed all the principal seams of two suits of wool clothes, one for George Fisher and one for himself.
At last, Howe was able to dedicate all his time and focus to building his machine. His family was well-fed and had a roof over their heads. Within a few months, Howe completed a model, and by April 1845, he had sewn his first seam (see fig. 14). In July of that year, he sewed all the main seams of two wool suits, one for George Fisher and one for himself.
Several efforts were made to solicit public interest in the new machine. One was installed in a public hall in Boston, and a tailor was employed to operate it at three times the regular wage. The reception was similar to that of Thimonnier’s: crowds came to see the “contraption,” but, when Howe tried to interest large clothing[Pg 140] establishments in using the machine, the protests of the tailors effectively blocked him. He took his sewing machine to the Quincy Hall Clothing Manufactory and offered to sew up any seams brought to him. Daily he sat in one of the rooms demonstrating his machine, and finally he challenged five of the swiftest seamstresses there to a race. Ten seams of equal length were prepared for stitching. One was given to each of the girls while the remaining five were given to Howe. Howe finished his five a little sooner than the girls each finished one, and his seams were declared the strongest and neatest. (Had any curved or angular work been brought, he could not have stitched it.) Still Howe did not receive a single order. The fear of throwing hand sewers out of work was again expressed, and, in addition, the cost of the machine was said to be too high. When it was estimated that a large shirtmaker would have to buy thirty or forty such machines, the necessary large investment was dismissed as ridiculous.
Several efforts were made to generate public interest in the new machine. One was set up in a public hall in Boston, and a tailor was hired to operate it at three times the normal wage. The response was similar to Thimonnier’s: crowds came to check out the “contraption,” but when Howe attempted to persuade large clothing establishments to use the machine, the protests from the tailors effectively blocked him. He took his sewing machine to the Quincy Hall Clothing Manufactory and offered to sew any seams brought to him. Every day, he sat in one of the rooms demonstrating his machine, and eventually, he challenged five of the fastest seamstresses there to a race. Ten seams of equal length were prepared for stitching. One was given to each of the girls while the remaining five were given to Howe. Howe finished his five a bit sooner than each of the girls completed one, and his seams were declared the strongest and neatest. (If any curved or angular work had been presented, he wouldn't have been able to stitch it.) Still, Howe did not receive a single order. Concerns about putting hand sewers out of work were again raised, and additionally, the cost of the machine was considered too high. When it was estimated that a large shirtmaker would need to buy thirty or forty of these machines, the required large investment was dismissed as ridiculous.
Howe was not too discouraged. In the meantime, he had finished a second machine for deposit with the patent specifications, as the patent laws then required. The second was a better made machine (fig. 15) and showed several minor changes. As soon as the patent was issued on September 10, 1846, Howe and his partner returned to Cambridge.
Howe wasn't too discouraged. In the meantime, he had completed a second machine for submission with the patent specifications, as the patent laws required at the time. The second machine was better constructed (fig. 15) and included several minor improvements. As soon as the patent was granted on September 10, 1846, Howe and his partner went back to Cambridge.
Without the inventor’s enthusiasm or love of his own invention, George Fisher became thoroughly discouraged. He had boarded Howe and his family for nearly two years, had furnished the money needed to purchase the tools and materials for making the two sewing machines, had met the expense of obtaining the patent and the trip of Howe and himself to Washington; representing in all an outlay of practically $2000. Since no orders for machines had been received from either garment makers or tailors, Fisher did not see the slightest probability of the machine’s becoming profitable and regarded his advances of cash as a dead loss.
Without the inventor's passion or pride in his own creation, George Fisher became completely discouraged. He had hosted Howe and his family for almost two years, funded the purchase of the tools and materials to make two sewing machines, and covered the costs of getting the patent and of the trip to Washington for both himself and Howe; this added up to nearly $2000. Since no orders for machines had come in from either garment makers or tailors, Fisher saw no chance of the machine becoming profitable and considered his financial contributions a total loss.
Howe moved back to his father’s house with a plan to look elsewhere for a chance to introduce the machine. Obtaining a loan from his father, he built another machine and sent it to England by his brother Amasa. After many discouraging attempts to interest the British, Amasa met William Thomas, a manufacturer of umbrellas, corsets, and leather goods. Thomas employed many workmen, all of whom stitched by hand, and he immediately saw the possibilities of a sewing machine. He proposed that Howe sell the machine to him for £250 sterling (about $1250). Thomas further proposed to engage the inventor to adapt this machine to the making of corsets, at a salary of £3 a week.
Howe moved back in with his father, planning to look for opportunities to introduce the machine elsewhere. After getting a loan from his dad, he built another machine and sent it to England with his brother Amasa. Despite many frustrating attempts to capture the interest of the British, Amasa met William Thomas, who manufactured umbrellas, corsets, and leather goods. Thomas employed many workers who all stitched by hand and immediately recognized the potential of a sewing machine. He proposed that Howe sell the machine to him for £250 sterling (about $1250). Thomas also suggested hiring the inventor to modify this machine for making corsets, offering a salary of £3 a week.
When Amasa Howe returned to Cambridge with the news, Elias was reluctant to accept Thomas’ offer but had nothing better in sight. So the brothers sailed for London in February 1847, taking with them Howe’s first machine and his patent papers. Thomas later advanced the passage money for Howe’s wife and three children so that they could join Howe in England.
When Amasa Howe got back to Cambridge with the news, Elias was hesitant to accept Thomas’ offer but didn’t have any better options. So the brothers set off for London in February 1847, bringing Howe’s first machine and his patent papers along. Later, Thomas paid for Howe’s wife and three kids to travel so they could be with Howe in England.
At this point, historians disagree on how long Howe was in Thomas’ employ and whether he succeeded in adapting the machine to meet Thomas’ needs. He was in England long enough, however, to find himself without employment in a strange country, his funds nearly exhausted, and his wife ill. He hoped to profit by the notice that his work had received and began to build another machine. He sent his family home to reduce expenses while he stayed on to finish the machine.
At this point, historians disagree on how long Howe worked for Thomas and whether he managed to adapt the machine to meet Thomas’ needs. He was in England long enough, though, to find himself jobless in a foreign country, his money running low, and his wife sick. He hoped to benefit from the attention his work had gotten and started building another machine. He sent his family back home to cut costs while he stayed behind to finish the machine.
After working on it for three or four months, he was forced to sell it for five pounds and to take a note for that. To collect enough for his passage home, he sold the note for four pounds cash and pawned his precious first machine and his patent papers. He landed in New York in April 1849 with but half a crown in his pocket to show for his labors. A short time after he arrived, he learned that his wife was desperately ill. Only with a loan from his father was he able to reach her side before she died. Friends were found to look after the children, and Elias returned to work as a journeyman machinist.
After working on it for three or four months, he had to sell it for five pounds and take a note for that. To raise enough for his ticket home, he sold the note for four pounds cash and pawned his beloved first machine and his patent papers. He arrived in New York in April 1849 with just half a crown in his pocket from all his hard work. Shortly after arriving, he found out that his wife was seriously ill. Only by borrowing money from his father was he able to reach her side before she passed away. Friends stepped in to take care of the children, and Elias went back to work as a journeyman machinist.
Howe discovered, much to his surprise, that during his absence in England the sewing machine had become recognized in the United States. Several machines made in Boston had been sold to manufacturers and were in daily operation. Upon investigating them, he felt that they utilized all or part of the invention that he had patented in 1846, and he prepared to secure just compensation for its use. The first thing he did was to regain his first machine and patent papers from the London pawnshop. It was no easy matter for Howe to raise the money, but by summer he had managed. It was sent to London with Anson Burlingame, who redeemed the loans, and by autumn of the same year the precious possessions were back in Howe’s hands. Though Howe gained nothing by his English experience, William Thomas by his modest expenditure obtained all rights to the machine for Great Britain. This later proved to be a valuable property.
Howe was surprised to find that while he was away in England, the sewing machine had become well-known in the United States. Several machines made in Boston had been sold to manufacturers and were in daily use. When he looked into them, he realized that they used all or part of the invention he had patented in 1846, so he set out to secure fair compensation for its use. The first thing he did was get back his original machine and patent papers from the London pawnshop. It was not easy for Howe to gather the money, but by summer he had succeeded. It was sent to London with Anson Burlingame, who paid off the loans, and by autumn of the same year, the valuable items were back in Howe’s possession. Although Howe gained nothing from his experience in England, William Thomas managed to obtain all rights to the machine for Great Britain with his modest investment. This later turned out to be a valuable asset.
Howe then began writing letters to those whom he considered patent infringers, requesting them to pay a fee or discontinue the manufacture of sewing machines which incorporated his patented inventions. Some at first were willing to pay the fee, but they were persuaded by the others to stand with them and resist Howe. This action forced Howe to the courts. With his father’s aid he began a suit, but soon found that considerably more money than either possessed was necessary for such actions. Howe turned once more to George Fisher, but years of investing money in Howe’s machine without any monetary return had cooled him to the[Pg 141] idea. Fisher, however, agreed to sell his half interest, and in February 1851 George S. Jackson, Daniel C. Johnson, and William E. Whiting became joint owners with Howe. These men helped Howe to procure witnesses in the furtherance of numerous suits, but more money was needed than they could raise. The following year a Massachusetts man by the name of George W. Bliss was persuaded to advance the money for the heavy legal expenses needed to protect the patent. Bliss did this as a speculation and demanded additional security. Once more Elias’ long-suffering parent came to the rescue and mortgaged his farm to get the necessary collateral.
Howe then started sending letters to those he considered to be infringing on his patent, asking them to either pay a fee or stop making sewing machines that used his patented inventions. Some agreed to pay at first, but they were convinced by others to join forces and resist Howe. This situation pushed Howe to go to court. With his father's help, he initiated a lawsuit but soon realized that much more money than they had was required for such legal action. Howe turned again to George Fisher, but years of investing in Howe's machine without any financial return had made Fisher hesitant about the idea. However, Fisher agreed to sell his half interest, and in February 1851, George S. Jackson, Daniel C. Johnson, and William E. Whiting became joint owners with Howe. These men assisted Howe in finding witnesses for several lawsuits, but they still needed more money than they could gather. The next year, a man from Massachusetts named George W. Bliss was persuaded to fund the substantial legal costs required to protect the patent. Bliss did this as a speculative investment and demanded extra security. Once again, Elias’ long-suffering father stepped in and mortgaged his farm to provide the necessary collateral.
Only one of these suits was prosecuted to a hearing, but this one, relatively unimportant in itself, set the precedent. In it the defense relied on the earlier invention of Walter Hunt to oppose Howe’s claims. The defendant succeeded in proving that Hunt invented, perfected, and sold two machines in 1834 and 1835 which contained all the essential devices in Howe’s machine of 1846. But Howe showed that the defendant’s machine (which was a Blodgett and Lerow) contained some features of Howe’s machine which were not in Hunt’s. The jury decided the case in favor of Howe. Howe later fought a vigorous battle with Isaac Singer, but after much legal controversy the ultimate decision in that case also was in Howe’s favor. The suits and payments to each patent holder for the right to use his idea were choking the sewing-machine industry. Even Howe could not manufacture a practical machine without an infringement. Finally an agreement was reached and a “Combination” was formed by the major patent holders (see pp. 41-42).
Only one of these lawsuits went to trial, but this one, relatively insignificant on its own, set a precedent. In this case, the defense relied on the earlier invention of Walter Hunt to counter Howe's claims. The defendant managed to prove that Hunt invented, improved, and sold two machines in 1834 and 1835 that included all the essential components of Howe's machine from 1846. However, Howe demonstrated that the defendant's machine (which was a Blodgett and Lerow) had some features of Howe's machine that weren't in Hunt's. The jury ruled in favor of Howe. Later, Howe engaged in a fierce legal battle with Isaac Singer, but after much controversy, the final ruling in that case also favored Howe. The lawsuits and the payments to each patent holder for the right to use their idea were overwhelming the sewing machine industry. Even Howe couldn't produce a functional machine without violating a patent. Eventually, an agreement was reached, and a "Combination" was formed by the main patent holders (see pp. 41-42).
In the meantime, eight years of the first term of Howe’s patent had expired without producing much revenue. This permitted Howe, upon the death of his partner, George Bliss, to buy Bliss’ half interest for a small sum. He became, then, the sole owner of his patent just as it was to bring him a fortune. He obtained a seven-year extension for his patent in 1860 without any difficulty, and in 1867, when he applied for another extension, he stated that he had received $1,185,000 from it. Though he endeavored to show that because of the machine’s great value to the public he was entitled to receive at least $150,000,000, the second application was denied.
In the meantime, eight years of the first term of Howe’s patent had passed without generating much income. This allowed Howe, after the death of his partner, George Bliss, to purchase Bliss's half-interest for a small amount. He then became the sole owner of his patent just as it was about to make him a fortune. He secured a seven-year extension for his patent in 1860 without any issues, and in 1867, when he applied for another extension, he claimed that he had earned $1,185,000 from it. Although he tried to argue that due to the machine's immense value to the public, he deserved at least $150,000,000, the second application was denied.
During the Civil War, Howe enlisted as a private soldier in the 17th Regiment Connecticut Volunteers. He went into the field and served as an enlisted man. On occasion when the Government was pressed for funds to pay its soldiers, he advanced the money necessary to pay his entire regiment.
During the Civil War, Howe signed up as a private in the 17th Regiment Connecticut Volunteers. He went to the front lines and served as a soldier. At times when the government was short on cash to pay its troops, he provided the funds needed to pay his entire regiment.
Howe did not establish a sewing-machine factory until just before his death in 1867. One of his early licensees had been his elder brother, Amasa, who had organized the Howe Sewing Machine Company about 1853. When Elias began manufacturing machines on his own, he sunk into the bedplate of each machine a brass medallion bearing his likeness. Elias gave his company the same name that his elder brother had used. As this had been Amasa’s exclusive property for many years, he took the matter to the courts where the decision went against Elias. He then organized the Howe Machine Company and began to manufacture sewing machines. On October 3, 1867, Elias died in Brooklyn, New York, at the home of one of his sons-in-law. The company was then carried on by his two sons-in-law, who were Stockwell brothers. In 1872 the Howe Sewing Machine Company was sold by Amasa’s son to the Stockwells’ Howe Machine Company, which in turn went out of business in the mid-1880s.
Howe didn’t start a sewing machine factory until just before he died in 1867. One of his early licensees was his older brother, Amasa, who set up the Howe Sewing Machine Company around 1853. When Elias began making machines on his own, he embedded a brass medallion with his likeness into the bedplate of each machine. Elias named his company after what his older brother had used. Since this name had been Amasa’s exclusive property for many years, he took the issue to court, where the ruling went against Elias. He then formed the Howe Machine Company and started producing sewing machines. On October 3, 1867, Elias died in Brooklyn, New York, at the home of one of his sons-in-law. The company was then run by his two sons-in-law, the Stockwell brothers. In 1872, Amasa’s son sold the Howe Sewing Machine Company to the Stockwells’ Howe Machine Company, which eventually went out of business in the mid-1880s.
ALLEN BENJAMIN WILSON

Figure 136.—Allen Benjamin Wilson, 1824-1888. From a drawing owned by the Singer Mfg. Co. Formerly, the drawing was owned by the Wheeler & Wilson Mfg. Co. (Smithsonian photo 32066.)
Figure 136.—Allen Benjamin Wilson, 1824-1888. From a drawing owned by the Singer Mfg. Co. Previously, the drawing belonged to the Wheeler & Wilson Mfg. Co. (Smithsonian photo 32066.)
Allen B. Wilson was born in the small town of Willett, Cortlandt County, New York, in 1824. At sixteen he was apprenticed to a distant relative, a cabinetmaker. Unfortunate circumstances caused him to leave this employ, and in 1847 Wilson was in Adrian, Michigan, working as a journeyman cabinetmaker. The place and year are important, for it was at this time that he conceived his idea of a sewing machine. Because of the distant location, it is believed that he was not aware of similar efforts being made in New England. Wilson became ill and for many months could not work at his trade. By August 1848 he was able to work again and found employment at Pittsfield, Massachusetts. Resolving to develop his idea of a sewing machine, he worked diligently and by November had made full drawings of all the parts, according to his previous conceptions.
Allen B. Wilson was born in the small town of Willett, Cortlandt County, New York, in 1824. At sixteen, he began an apprenticeship with a distant relative who was a cabinetmaker. Unfortunate circumstances led him to leave this job, and by 1847, Wilson was in Adrian, Michigan, working as a journeyman cabinetmaker. The time and place are significant because it was during this period that he came up with the idea for a sewing machine. Due to the distance, it's believed he was unaware of similar developments occurring in New England. Wilson fell ill and was unable to work in his trade for several months. By August 1848, he was back to work and found a job in Pittsfield, Massachusetts. Determined to bring his sewing machine idea to life, he worked hard and by November had completed detailed drawings of all the parts, based on his earlier concepts.
In comparison to the monetary returns received by the inventors Howe and Singer, Wilson himself did not receive as great a monetary reward for his outstanding sewing-machine inventions. Because of his health Wilson retired in 1853, when the stock company was formed, but he received a regular salary and additional money from the patent renewals. Wilson petitioned for a second extension of his patents on April 7, 1874, stating that, due to his early poverty, he had been compelled to sell a half interest in a patent (his first one) for the sum of $200. Also he stated that he had not received more than his expenses during the original fourteen-year term. Wilson also stated that he had received only $137,000 during the first seven-year extension period. These figures were verified by his partner. The petition was read before both Houses of Congress and referred to the Committee on Patents.[93] There was strong feeling against the extension of the Wilson patents. The New York Daily Graphic, December 30, 1874, reported:[Pg 142]
Compared to the financial benefits that inventors Howe and Singer received, Wilson didn’t earn as much from his remarkable sewing machine inventions. Due to health issues, Wilson retired in 1853 when the stock company was established, but he still got a regular salary and extra money from patent renewals. On April 7, 1874, Wilson requested a second extension of his patents, explaining that because of his early struggles with money, he had to sell half of his first patent for just $200. He also mentioned that he hadn’t made more than what covered his expenses during the original fourteen-year term. Wilson claimed that during the first seven-year extension period, he received only $137,000. His partner confirmed these figures. The petition was presented to both Houses of Congress and sent to the Committee on Patents.[93] There was significant opposition to extending the Wilson patents. The New York Daily Graphic, December 30, 1874, reported:[Pg 142]
So valuable has been this latter four-motion feed that few or no cloth-sewing machines are now made without it. The joint ownership of this feature of the Wilson patents has served to bind the combination of sewing-machine builders together, and enabled them to defy competition by force of the monopoly. It is this feature which the combination wishes to further monopolize for seven years by act of Congress. The inventor has probably realized millions for his invention. Singer admits that his patents, which are much less important, paid him two millions prior to 1870, since which time he has not been compelled to render an account. The Wilson patents with their extended terms were worth a much larger sum. They have been public property, so far as the feed is concerned, since June 15, 1873, and will remain so if too great a pressure is not brought to bear on Congress for their extension. A monopoly of this feed motion for seven years more would be worth from ten to thirty millions to the owner—and would cost the people four times as much.
So valuable has this four-motion feed been that very few cloth-sewing machines are now made without it. The joint ownership of this feature of the Wilson patents has helped unite sewing-machine manufacturers and allowed them to fend off competition through their monopoly. This is the feature that the group wants to further monopolize for seven more years through an act of Congress. The inventor has likely made millions from his invention. Singer admits that his patents, which are far less significant, earned him two million before 1870, after which he hasn’t had to account for any earnings. The Wilson patents, with their extended terms, were worth a much larger amount. They have been public property, at least concerning the feed, since June 15, 1873, and will remain so unless significant pressure is applied to Congress for an extension. A monopoly on this feed motion for another seven years would be worth between ten and thirty million to the owner—and would cost the public four times as much.
Wilson had not made the millions for he only received a small percentage of the renewals’ earnings plus his salary from the patents’ owner, the Wheeler and Wilson Manufacturing Company.
Wilson hadn't made millions because he only got a small percentage of the renewals' earnings along with his salary from the patents' owner, the Wheeler and Wilson Manufacturing Company.
The Congressional Committee on Patents made an adverse report in 1874 and again in 1875 and 1876, when applications for an extension were continued
The Congressional Committee on Patents submitted negative reports in 1874, and again in 1875 and 1876, when requests for an extension were ongoing.
Wilson died on April 29, 1888.
Wilson died on April 29, 1888.
ISAAC MERRITT SINGER

Figure 137.—- Isaac Merritt Singer, 1811-1875. From a charcoal drawing owned by the Singer Mfg. Co. (Smithsonian photo 32066-B)
Figure 137.—- Isaac Singer, 1811-1875. From a charcoal drawing owned by the Singer Mfg. Co. (Smithsonian photo 32066-B)
Isaac Singer, whose name is known around the world as a manufacturer of sewing machines, was the eighth child of poor German immigrants. Isaac was born on October 27, 1811, in Pittstown, New York, but most of[Pg 143] his early life was spent in Oswego. He worked as a mechanic and cabinetmaker, but acquired an interest in the theater. Under the name of Isaac Merritt, he went to Rochester and became an actor. In 1839, during an absence from the theater, he completed his first invention, a mechanical excavator, which he sold for $2000. With the money Singer organized a theatrical troupe of his own, which he called “The Merritt Players.” When the group failed in Fredericksburg, Ohio, Singer was stranded for lack of funds.
Isaac Singer, known worldwide as a sewing machine manufacturer, was the eighth child of poor German immigrants. He was born on October 27, 1811, in Pittstown, New York, but spent most of his early life in Oswego. Singer worked as a mechanic and cabinetmaker but developed an interest in theater. Using the name Isaac Merritt, he moved to Rochester and became an actor. In 1839, while away from the theater, he completed his first invention, a mechanical excavator, which he sold for $2,000. With that money, Singer started his own theater troupe, which he named “The Merritt Players.” When the group failed in Fredericksburg, Ohio, Singer found himself stranded due to lack of funds.
Forced to find some type of employment, Singer took a job in a Fredericksburg plant that manufactured wooden printers’ type. He quickly recognized the need for an improved type-carving machine. After inventing and patenting one, he found no financial support in Fredericksburg and decided to take the machine to New York City. Here, the firm of A. B. Taylor and Co. agreed to furnish the money and give Singer room in its Hague Street factory to build machines. A boiler explosion destroyed the first machine, and Taylor refused to advance more money.
Forced to find a job, Singer took a position at a Fredericksburg factory that made wooden printers' type. He quickly saw the need for a better type-carving machine. After he invented and patented one, he couldn't find any financial backing in Fredericksburg and chose to take the machine to New York City. There, the company A. B. Taylor and Co. agreed to provide funding and let Singer use space in its Hague Street factory to build machines. A boiler explosion destroyed the first machine, and Taylor refused to provide any more money.
While Singer was with Taylor, George B. Zieber, a bookseller who had seen the type-carving machine, considered its value to publishers. Zieber offered to help Singer and raised $1700 to build another model. In June 1850 the machine was completed. Singer and Zieber took the machine to Boston where they rented display space in the steam-powered workshop of Orson C. Phelps at 19 Harvard Place. Only a few publishers came to look at the machine, and none wanted to buy it.
While Singer was working with Taylor, George B. Zieber, a bookseller who had seen the type-carving machine, recognized its value for publishers. Zieber offered to assist Singer and raised $1,700 to build another model. In June 1850, the machine was finished. Singer and Zieber took the machine to Boston, where they rented display space in the steam-powered workshop of Orson C. Phelps at 19 Harvard Place. Only a few publishers stopped by to check out the machine, and none were interested in buying it.
Singer, contemplating his future, became interested in Phelps’ work, manufacturing sewing machines for J. A. Lerow and S. C. Blodgett. Phelps welcomed Singer’s interest as the design of the mechanism was faulty and purchasers kept returning the machines for repairs. Singer examined the sewing machine with the eyes of a practical machinist. He criticized the action of the shuttle, which passed around a circle, and the needle bar, which pushed a curved needle horizontally. Singer suggested that the shuttle move to and fro in a straight path and that a straight needle be used vertically. Phelps encouraged Singer to abandon the type-carving machine and turn his energies toward the improvement of the sewing machine. Convinced that he could make his ideas work, Singer sketched a rough draft of his proposed machine, and with the support of Zieber and Phelps the work began.
Singer, considering his future, became interested in Phelps’ work, making sewing machines for J. A. Lerow and S. C. Blodgett. Phelps was glad to have Singer’s interest since the machine's design had flaws, and customers kept sending them back for repairs. Singer looked at the sewing machine with the perspective of a practical machinist. He criticized the shuttle's action, which moved in a circle, and the needle bar, which pushed a curved needle sideways. Singer proposed that the shuttle should move back and forth in a straight line and that a straight needle should be used vertically. Phelps encouraged Singer to set aside the type-carving machine and focus his efforts on improving the sewing machine. Confident that he could make his ideas work, Singer created a rough sketch of his proposed machine, and with the help of Zieber and Phelps, the work began.
Singer continued to be active in the sewing-machine business until 1863. He made his home in Paris for a short time and then moved to England. While living at Torquay he conceived the idea of a fabulous Greco-Roman mansion, which he planned to have built at Paignton. Singer called it “The Wigwam.” Unfortunately, after all his plans, he did not live to see its completion. Singer died on July 23, 1875, of heart disease at the age of sixty-three.
Singer remained involved in the sewing machine business until 1863. He lived in Paris for a short period before moving to England. While he was in Torquay, he came up with the idea for an extravagant Greco-Roman mansion that he intended to have built in Paignton. Singer named it “The Wigwam.” Unfortunately, despite all his plans, he didn't live to see it finished. Singer passed away on July 23, 1875, from heart disease at the age of sixty-three.
FOOTNOTES:
[93] The Proceedings and Debates of the 43rd Congress, First Session, 1874 Congressional Record, vol. 2, part 3, petition read to the House by Mr. Creamer on April 7, 1874. In part 4 of the same, Mr. Buckingham read a similar petition to the Senate on May 19, 1874. Both were referred to the Committee on Patents; an extension was not granted.
[93] The Proceedings and Debates of the 43rd Congress, First Session, 1874 Congressional Record, vol. 2, part 3, petition presented to the House by Mr. Creamer on April 7, 1874. In part 4 of the same document, Mr. Buckingham presented a similar petition to the Senate on May 19, 1874. Both were sent to the Committee on Patents; an extension was not granted.
Bibliography
Adams, Charles K. Sewing machines. In vol. 7 of Johnson’s universal cyclopaedia, New York: D. Appleton and Company, 1895.
Charles K. Adams Sewing machines. In vol. 7 of Johnson’s universal cyclopaedia, New York: D. Appleton and Company, 1895.
Alexander, Edwin P. Sewing, plaiting, and felting machines. Pp. 341-353 in The Practical Mechanic’s Journal’s record of the great exhibition, 1862. 1862.
Alex, Edwin P. Sewing, braiding, and felting machines. Pp. 341-353 in The Practical Mechanic’s Journal’s record of the great exhibition, 1862. 1862.
——. On the sewing machine: Its history and progress. Journal of the Royal Society of Arts (April 10, 1863), vol. 2, no. 542, p. 358.
——. On the sewing machine: Its history and progress. Journal of the Royal Society of Arts (April 10, 1863), vol. 2, no. 542, p. 358.
American Historical Society. The life and works of George H. Corliss. (Privately printed for Mary Corliss by the Society.) 1930.
American History Association. The Life and Works of George H. Corliss. (Privately printed for Mary Corliss by the Society.) 1930.
Biography of Isaac M. Singer. The Atlas, New York, N.Y., March 20, 1853.
Biography of Isaac M. Singer. The Atlas, New York, NY, March 20, 1853.
Bishop, J. Leander. In vol. 2 of A history of American manufactures from 1608 to 1860, by Bishop; Philadelphia: Edward Young and Company, 1866.
Bishop J. Leander. In vol. 2 of A History of American Manufactures from 1608 to 1860, by Bishop; Philadelphia: Edward Young and Company, 1866.
Bolton, James. Sewing machines, special report on special subjects. In vol. 2 of Report of the Committee on Awards; Chicago: World’s Columbian Exposition, 1893.
Bolton, James. Sewing machines, special report on special topics. In vol. 2 of Report of the Committee on Awards; Chicago: World’s Columbian Exposition, 1893.
Brockett, Linus P. Sewing machines. In vol. 4 of Johnson’s universal cyclopaedia; New York: D. Appleton and Company, 1874.
Brockett, Linus P. Sewing machines. In vol. 4 of Johnson’s universal cyclopaedia; New York: D. Appleton and Company, 1874.
Burr, J. B. The great industries of the United States. Hartford: J. B. Burr and Hyde, n.d.
Burr, J.B. The Great Industries of the United States. Hartford: J. B. Burr and Hyde, n.d.
Cook, Rosamond C. Sewing machines. Peoria, Illinois: Manual Arts Press, 1922.
Cook, Rosamond C. Sewing Machines. Peoria, Illinois: Manual Arts Press, 1922.
Depew, C. M. 100 years of American commerce. In vol. 2, American sewing machines by F. G. Bourne. New York: D. O. Haines, 1895.
Depew, C. M. 100 years of American commerce. In vol. 2, American sewing machines by F. G. Bourne. New York: D. O. Haines, 1895.
District of Columbia Circuit Court. Case of Hunt vs. Howe. In Federal Cases, case 6891, book 12, 1855.
D.C. Circuit Court. Case of Hunt vs. Howe. In Federal Cases, case 6891, book 12, 1855.
Doolittle, William H. Inventions. Vol. in Library of modern progress. Philadelphia: Modern Progress Publishing Company, 1905.
William H. Doolittle Inventions. Vol. in Library of Modern Progress. Philadelphia: Modern Progress Publishing Company, 1905.
Durgin, Charles A. Digest of patents on sewing machines, Feb. 21, 1842-July 1, 1859. New York: Livesey Brothers, 1859.
Charles A. Durgin Digest of patents on sewing machines, Feb. 21, 1842-July 1, 1859. New York: Livesey Brothers, 1859.
Fairfield, George A. Report on sewing machines. In vol. 3 of Report of the commissioners of the United States to the international exhibition held at Vienna, 1873. 1874.
Fairfield, George A. Report on sewing machines. In vol. 3 of Report of the commissioners of the United States to the international exhibition held at Vienna, 1873. 1874.
Fiske, Bradley A. Invention, the master-key to progress. New York: E. P. Dutton and Company, 1921.
Fiske, Bradley A. Invention, the master key to progress. New York: E. P. Dutton and Company, 1921.
Gifford, George W. [Counsel for Elias Howe, Jr.] Argument of Gifford in favor of Howe’s application for extension of patent. Washington: U.S. Patent Office, 1860.
George W. Gifford [Lawyer for Elias Howe, Jr.] Gifford's Argument Supporting Howe’s Request for Patent Extension. Washington: U.S. Patent Office, 1860.
Granger, Jean. Thimonnier et la machine à coudre. In vol. 2 of Les publications techniques. Paris, 1943. [Source for biographical sketch on Barthelemy Thimonnier.]
Granger, Jean. Thimonnier and the sewing machine. In vol. 2 of Technical Publications. Paris, 1943. [Source for biographical sketch on Barthelemy Thimonnier.]
Gregory, George W. Machines, etc., used in sewing and making clothing. Vol. 7 of Reports and Awards. Philadelphia International Exhibition, 1876. U.S. Centennial Commission, Washington, D.C., 1880.[Pg 145]
Gregory, George W. Machines, etc., used in sewing and making clothing. Vol. 7 of Reports and Awards. Philadelphia International Exhibition, 1876. U.S. Centennial Commission, Washington, D.C., 1880.[Pg 145]
Hersberg, Rudolph. The sewing machine, its history, construction and application. Transl. Upfield Green. London: E. & F. N. Spon, 1864.
Hersberg, Rudy. The Sewing Machine, Its History, Construction, and Application. Translated by Upfield Green. London: E. & F. N. Spon, 1864.
Howe, Henry. Adventures and achievements of Americans. Published by the author, 1860.
Howe, Henry. Adventures and Achievements of Americans. Published by the author, 1860.
Howe Machine Company. The Howe exhibition catalog of sewing machines. Published by the company for the Philadelphia Centennial Exposition, 1876.
Howe Machine Co. The Howe exhibition catalog of sewing machines. Published by the company for the Philadelphia Centennial Exposition, 1876.
Hubert, Philip G., Jr. Men of achievement: inventors. New York: Charles Scribner’s Sons, 1894.
Hubert Philip G. Jr. Men of Achievement: Inventors. New York: Charles Scribner's Sons, 1894.
Hunt, Clinton N. Walter Hunt, American inventor. Published by the author, 1935. [Source for biographical sketch on Walter Hunt.]
Hunt, Clinton N. Walter Hunt, American inventor. Published by the author, 1935. [Source for biographical sketch on Walter Hunt.]
International Exhibition. Sewing and knitting machines. In Reports of the Juries, Class VII, Section A. London, 1862.
Global Expo. Sewing and knitting machines. In Reports of the Juries, Class VII, Section A. London, 1862.
Johnson Clark and Company. Sewing machines for domestic and export trade. Published by the company, 1883.
Johnson Clark & Co. Sewing machines for home and international markets. Published by the company, 1883.
Kaempffert, Waldemar. A popular history of American invention. Making clothes by machine, by John Walker Harrington, vol 2. New York: Charles Scribner’s Sons, 1924.
Kaempffert, Waldemar. A popular history of American invention. Making clothes by machine, by John Walker Harrington, vol 2. New York: Charles Scribner’s Sons, 1924.
Kilgare, C. B. Sewing-machines. Philadelphia: J. B. Lippincott Company, 1892.
Kilgare, C.B. Sewing Machines. Philadelphia: J. B. Lippincott Company, 1892.
Knight, Edward H. Vol. 3 of Knight’s American mechanical dictionary. Boston: Houghton, Mifflin and Company, 1882.
Edward H. Knight Vol. 3 of Knight’s American Mechanical Dictionary. Boston: Houghton, Mifflin and Company, 1882.
Lewton, Frederick L. The servant in the house: a brief history of the sewing machine. Pp. 559-583 in Annual Report of the Smithsonian Institution (1929); Washington: 1930.
Frederick L. Lewton The Servant in the House: A Brief History of the Sewing Machine. Pages 559-583 in Annual Report of the Smithsonian Institution (1929); Washington: 1930.
Luth, Erich. Ein Mayener Strumpfwirker, Balthasar Krems, 1760-1813, Erfinder der Nähmaschine. Hamburg, Germany: Verlag Herbert Luth, 1941.
Erich Luth. An Mayen Stocking Knitter, Balthasar Krems, 1760-1813, Inventor of the Sewing Machine. Hamburg, Germany: Herbert Luth Publishing, 1941.
——. Josef Madersperger oder der unscheinbore Genius. Hamburg, Germany: Reichsnerband des Deutschen Nähmaschinenhandels EV, 1933 [?].
——. Josef Madersperger or the Unnoticed Genius. Hamburg, Germany: Reichsnerband of the German Sewing Machine Trade EV, 1933 [?].
Obituary of Isaac M. Singer. New York Tribune, July 26, 1875.
Obituary of Isaac M. Singer. New York Tribune, July 26, 1875.
Madersperger, Joseph. Beschreibung einer Nähmaschine. Vienna, ca. 1816.
Joseph Madersperger. Description of a Sewing Machine. Vienna, around 1816.
O’Brien, Walter. Sewing machines. Textile American, reprinted March 1931. [A paper read at a meeting of the Leicester Textile Society.]
O'Brien, Walter. Sewing machines. Textile American, reprinted March 1931. [A paper presented at a meeting of the Leicester Textile Society.]
Orcutt, Rev. Samuel. A history of the old town of Stratford and the city of Bridgeport, Connecticut. 2 vols. Fairfield County Historical Society, 1886.
Rev. Samuel Orcutt. A History of the Old Town of Stratford and the City of Bridgeport, Connecticut. 2 vols. Fairfield County Historical Society, 1886.
Paris Universal Exposition. Reports of the U.S. Commissioners General Survey, vol. 1, pp. 293-297. 1867.
Paris World's Fair. Reports of the U.S. Commissioners General Survey, vol. 1, pp. 293-297. 1867.
Parton, James. History of the sewing machine. Atlantic Monthly, May 1867.
Parton, James. History of the sewing machine. Atlantic Monthly, May 1867.
Raymond, William Chandler. Curiosities of the Patent Office. Syracuse, N.Y.: published by the author, 1888.
Raymond William Chandler. Curiosities of the Patent Office. Syracuse, NY: self-published, 1888.
Reid, J. A. A monograph prepared for American industrial education conference and exposition. Elizabethport, N.J.: Singer Manufacturing Company, 1915.
Reid, J.A. A report created for the American industrial education conference and exhibition. Elizabethport, N.J.: Singer Manufacturing Company, 1915.
Scientific American. Issues of January 27, February 3, and November 24, 1849; July 17, 1852; July 9 and November 5, 1859; January 3 and May 16, 1863; October 19, 1867; and July 25, 1896.
Scientific American. Issues from January 27, February 3, and November 24, 1849; July 17, 1852; July 9 and November 5, 1859; January 3 and May 16, 1863; October 19, 1867; and July 25, 1896.
Scott, John. Genius rewarded, or the story of the sewing machine. New York: J. J. Caulon, 1880.
Scott, John. Genius Rewarded, or the Story of the Sewing Machine. New York: J. J. Caulon, 1880.
Sewing Machine Advance. Chicago. Vols. 1-35, no. 5, May 1879 to 1913.
Sewing Machine Advance. Chicago. Volumes 1-35, no. 5, May 1879 to 1913.
Sewing Machine Journal. September 1879 to December 1884.
Sewing Machine Journal. September 1879 to December 1884.
Sewing Machine News. New York. Vols. 1-6, 1877-1879; n.s. vols. 1-16, 1879-1893.[Pg 146]
Sewing Machine News. New York. Vols. 1-6, 1877-1879; n.s. vols. 1-16, 1879-1893.[Pg 146]
Sewing Machine Times. New York. Vols. 1-9, 1882-1890; n.s. vols. 1-38 (nos. 1-725), 1891-April 1924.
Sewing Machine Times. New York. Vols. 1-9, 1882-1890; n.s. vols. 1-38 (nos. 1-725), 1891-April 1924.
Stambaugh, John P. Sewing machines at the 22nd annual exhibition of the Maryland Institute, also a history of the sewing machine. Hartford, Conn.: Weed Sewing Machine Company, 1872.
John P. Stambaugh Sewing machines at the 22nd annual exhibition of the Maryland Institute, also a history of the sewing machine. Hartford, Conn.: Weed Sewing Machine Company, 1872.
Story of sewing machine patents. New York Tribune, May 23, 1862.
Story of sewing machine patents. New York Tribune, May 23, 1862.
Thompson, Holland. The age of invention. Vol. 37 of the Chronicles of America. New Haven: Yale University Press, 1921.
Thompson, Netherlands. The Age of Invention. Vol. 37 of the Chronicles of America. New Haven: Yale University Press, 1921.
Towers, Henry M. Historical sketches relating to Spencer, Massachusetts. Vol. 1. Spencer, Mass.: W. G. Heffernan, 1901.
Towers, Henry M. Historical Sketches Relating to Spencer, Massachusetts. Vol. 1. Spencer, Mass.: W. G. Heffernan, 1901.
Urquhart, J. W. Sewing machinery. Vol. 8 in Weale’s rudimentary scientific and educational series. London: Crosby Lockwood and Co., 1881.
Urquhart, J.W. Sewing machinery. Vol. 8 in Weale’s basic scientific and educational series. London: Crosby Lockwood and Co., 1881.
Van Slyck, J. D. New England manufacturers and manufactories. Vol. 2. Boston: Van Slyck and Company, 1879. [Source for biographical sketch on Allen Benjamin Wilson, Van Slyck, vol. 2, pp. 672-682.]
Van Slyck, J. D. New England Manufacturers and Manufactories. Vol. 2. Boston: Van Slyck and Company, 1879. [Source for biographical sketch on Allen Benjamin Wilson, Van Slyck, vol. 2, pp. 672-682.]
Walso, George C., Jr. History of Bridgeport and vicinity. Vol. 2. Bridgeport, Conn.: S. J. Clarke Publishing Company, 1917.
Walso, George C., Jr. History of Bridgeport and its surrounding areas. Vol. 2. Bridgeport, Conn.: S. J. Clarke Publishing Company, 1917.
Who invented the sewing machine? The Galaxy [article unsigned], vol. 4, August 1867.
Who invented the sewing machine? The Galaxy [article unsigned], vol. 4, August 1867.
Indexes
Geographical Index to Companies listed in Appendix II
CONNECTICUT
Bridgeport
D. W. Clark, 67
Jerome B. Secor, 68
Goodbody Sewing Machine Co., 69
Howe Machine Co., 69
Secor Machine Co., 72
American Hand Sewing Machine Co., 72
Wheeler & Wilson Mfg. Co., 74
Bristol
Nettleton & Raymond, 72
Watson & Wooster, 73
Danbury
Bartram & Fanton Mfg. Co., 66
Hartford
Morrison, Wilkinson & Co., 71
Weed Sewing Machine Co., 74
Meriden
Fosket and Savage, 68
Charles Parker Co., 72
Parker Sewing Machine Co., 72
Middletown
Victor Sewing Machine Co., 73
Norwich
Greenman and True Mfg. Co., 69
Waterbury
Waterbury Co., 73
West Meriden
Parkers, Snow, Brooks & Co., 70
DISTRICT OF COLUMBIA
Washington
Post Combination Sewing Machine Co., 72
ILLINOIS
Belleville
Thomas M. Cochrane Co., 71
J. H. Drew & Co., 71
Belvidere
June Mfg. Co., 70
National Sewing Machine Co., 71
Chicago
Chicago Sewing Machine Co., 67
Eldredge Sewing Machine Co., 68
Free Sewing Machine Co., 69
Scates, Tryber & Sweetland Mfg., 67
Sigwalt Sewing Machine Co., 67, 73
H. B. Goodrich, 69
June Mfg. Co., 70
Rockford
Free Sewing Machine Co., 69
MAINE
Biddeford
Shaw & Clark Sewing Machine Co., 71, 73
MASSACHUSETTS
Boston
O. Phelps, 66
J. F. Paul & Co., 66
Boston Sewing Machine Co., 66
Bradford & Barber, mfgs., 66
John P. Bowker, 68
Empire Sewing Machine Co., 68
Finkle & Lyon Sewing Machine Co., 68, 73
Grover and Baker Sewing Machine Co., 69
Nichols and Bliss, 69
J. B. Nichols & Co., 69
Nichols, Leavitt & Co., 69, 70
N. Hunt & Co., 70
Hunt and Webster, 70
Emery, Houghton & Co., 70
Ladd, Webster & Co., 70
Leavitt & Co., 70
Leavitt Sewing Machine Co., 70
Safford & Williams Makers, 71
C. A. French, 72
F. R. Robinson, 72
Howard & Davis, 72
I. M. Singer & Co., 73
Butterfield & Stevens Mfg. Co., 74
Williams & Orvis Sewing Machine Co., 74
Chicopee Falls
Shaw & Clark Co., 73
Chicopee Sewing Machine Co., 73
Florence
Florence Sewing Machine Co., 67, 68
Foxboro
Foxboro Rotary Shuttle Co., 68
Lowell
Aetna Sewing Machine Co., 65
Lynn
Woolridge, Keene and Moore, 67
Orange
Gold Medal Sewing Machine Co., 69
Johnson, Clark & Co., 69, 71, 73
Grout & White, 71
New Home Sewing Machine Co., 71
Springfield
Leader Sewing Machine Co., 70
Springfield Sewing Machine Co., 73
D. B. Wesson Sewing Machine Co.,74
Winchendon
J. G. Folsom, 68, 69, 71
William Grout, 71
Worcester
Goddard, Rice & Co., 66
MICHIGAN
Detroit
Decker Mfg. Co., 67
C. G. Gardner, 69
MISSOURI
St. Louis
Wardwell Mfg. Co., 73
NEW HAMPSHIRE
Dover
O. L. Reynolds Manufacturing Co., 71
Marlboro
Thurston Mfg. Co., 67
Mason Village
Franklin Sewing Machine Co., 68
NEW JERSEY
Elizabethport
Singer Mfg. Co. (manufactory, not office), 73
Paterson
Whitney Sewing Machine Co., 74
NEW YORK
Binghamton
Independent Sewing Machine Co., 70
Brooklyn
J. H. Lester, 70
G. L. Du Laney, 70
Ithaca
Aiken and Felthousen (patentees), 65
American Magnetic Sewing Machine Co., 65
Clinton Brothers, 67
T. C. Thompson, 73
New York
Avery Sewing Machine Co., 66
A. Bartholf, mfg., 66
Bartholf Sewing Machine Co., 66
Bartlett Sewing Machine Co., 66
Barlow & Son, 66
[Pg 150]Beckwith Sewing Machine Co., 66
J. A. Davis, 67
Demorest Mfg. Co., 67
Charles A. Durgin, 68
Elliptic Sewing Machine Co., 68
Eureka Shuttle Sewing Machine Co., 68
Excelsior Sewing Machine Co., 68
Madame Demorest, 68
First and Frost, 68
L. Griswold, 69
Howe Sewing Machine Co., 69
Thos. A. Macauley Mfg., 70
New York Sewing Machine Co., 71
T. W. Robertson, 72
I. M. Singer & Co., 73
Singer Mfg. Co., 73
Standard Shuttle Sewing Machine Co., 73
Henry Stewart & Co., 73
Stewart Mfg. Co., 73
E. E. Lee & Co., 74
Willcox & Gibbs Sewing Machine Co., 74
Watertown
Davis Sewing Machine Co., 67
Wheeler, Wilson & Co., 74
Westmoreland
A. B. Buell, 67
OHIO
Cleveland
Wilson (W. G.) Sewing Machine Co., 66, 74
Domestic Sewing Machine Co. (after 1924), 67
Leslie Sewing Machine Co., 70
Standard Sewing Machine Co., 73
White Sewing Machine Co., 74
Dayton
Davis Sewing Machine Co., 67
Elyria
West & Willson Co., 74
Norwalk
Dauntless Mfg. Co., 67, 72
Wm. A. Mack & Co., and N. S. Perkins, 67
Domestic Sewing Machine Co., 67, 70
Springfield
Royal Sewing Machine Co., 72
St. John Sewing Machine Co., 73
Toledo
Jewel Mfg. Co., 70
PENNSYLVANIA
Erie
Noble Sewing Machine Co., 72
Philadelphia
American Buttonhole, Overseaming and Sewing Machine Co., 65
Centennial Sewing Machine Co., 67
George B. Sloat and Co., 68
Rex & Bockius, 69
Grant Bros. & Co., 69
B. W. Lacey & Co., 71
Parham Sewing Machine Co., 72
Philadelphia Sewing Machine Co., 72
Quaker City Sewing Machine Co., 72
E. Remington & Sons, 72
Taggart & Farr, 73
Pittsburgh
Love Mfg. Co., 70
RHODE ISLAND
Providence
Household Sewing Machine Co., 69
Providence Tool Co., 69
VERMONT
Brattleboro
Samuel Barker and Thomas White, 66
Brattleboro Sewing Machine Co., 68
Estey Sewing Machine Co., 68
Higby Sewing Machine Co., 69
Nettleton & Raymond (Charles Raymond), 71
Windsor
Lamson, Goodnow & Yale, 67, 74
Vermont Arms Co., 74
VIRGINIA
Richmond
Lester Mfg. Co., 70
Union Sewing Machine Co., 68, 70
Old Dominion Sewing Machine Co., 72
WISCONSIN
Milwaukee
Whitehill Mfg. Co., 74
[Pg 151]
CONNECTICUT
Bridgeport
D. W. Clark, __A_TAG_PLACEHOLDER_0__
Jerome B. Secor, __A_TAG_PLACEHOLDER_0__
Goodbody Sewing Machine Co., __A_TAG_PLACEHOLDER_0__
Howe Machine Co., __A_TAG_PLACEHOLDER_0__
Secor Machine Co., __A_TAG_PLACEHOLDER_0__
American Hand Sewing Machine Co., __A_TAG_PLACEHOLDER_0__
Wheeler & Wilson Mfg. Co., __A_TAG_PLACEHOLDER_0__
Bristol
Nettleton & Raymond, __A_TAG_PLACEHOLDER_0__
Watson & Wooster, __A_TAG_PLACEHOLDER_0__
Danbury
Bartram & Fanton Mfg. Co., __A_TAG_PLACEHOLDER_0__
Hartford
Morrison, Wilkinson & Co., __A_TAG_PLACEHOLDER_0__
Weed Sewing Machine Co., __A_TAG_PLACEHOLDER_0__
Meriden
Fosket and Savage, __A_TAG_PLACEHOLDER_0__
Charles Parker Co., __A_TAG_PLACEHOLDER_0__
Parker Sewing Machine Company, __A_TAG_PLACEHOLDER_0__
Middletown
Victor Sewing Machine Co., __A_TAG_PLACEHOLDER_0__
Norwich
Greenman and True Mfg. Co., __A_TAG_PLACEHOLDER_0__
Waterbury
Waterbury Co., __A_TAG_PLACEHOLDER_0__
West Meriden
Parkers, Snow, Brooks & Co., __A_TAG_PLACEHOLDER_0__
DISTRICT OF COLUMBIA
Washington
Post Combination Sewing Machine Co., __A_TAG_PLACEHOLDER_0__
ILLINOIS
Belleville
Thomas M. Cochrane Co., __A_TAG_PLACEHOLDER_0__
J. H. Drew & Co., __A_TAG_PLACEHOLDER_0__
Belvidere
June Manufacturing Company, __A_TAG_PLACEHOLDER_0__
National Sewing Machine Co., __A_TAG_PLACEHOLDER_0__
Chicago
Chicago Sewing Machine Co., __A_TAG_PLACEHOLDER_0__
Eldredge Sewing Machine Company, __A_TAG_PLACEHOLDER_0__
Free Sewing Machine Company, __A_TAG_PLACEHOLDER_0__
Scates, Tryber & Sweetland Mfg., __A_TAG_PLACEHOLDER_0__
Sigwalt Sewing Machine Co., __A_TAG_PLACEHOLDER_0__, __A_TAG_PLACEHOLDER_1__
H.B. Goodrich, __A_TAG_PLACEHOLDER_0__
June Manufacturing Company, __A_TAG_PLACEHOLDER_0__
Rockford
Free Sewing Machine Co., __A_TAG_PLACEHOLDER_0__
MAINE
Biddeford
Shaw & Clark Sewing Machine Co., __A_TAG_PLACEHOLDER_0__, __A_TAG_PLACEHOLDER_1__
MASSACHUSETTS
Boston
O. Phelps, __A_TAG_PLACEHOLDER_0__
J. F. Paul & Co., __A_TAG_PLACEHOLDER_0__
Boston Sewing Machine Co., __A_TAG_PLACEHOLDER_0__
Bradford & Barber, manufacturers, __A_TAG_PLACEHOLDER_0__
John P. Bowker, __A_TAG_PLACEHOLDER_0__
Empire Sewing Machine Co., __A_TAG_PLACEHOLDER_0__
Finkle & Lyon Sewing Machine Co., __A_TAG_PLACEHOLDER_0__, __A_TAG_PLACEHOLDER_1__
Grover and Baker Sewing Machine Company, __A_TAG_PLACEHOLDER_0__
Nichols and Bliss, __A_TAG_PLACEHOLDER_0__
J. B. Nichols & Co., __A_TAG_PLACEHOLDER_0__
Nichols, Leavitt & Co., __A_TAG_PLACEHOLDER_0__, __A_TAG_PLACEHOLDER_1__
N. Hunt & Co., __A_TAG_PLACEHOLDER_0__
Hunt and Webster, __A_TAG_PLACEHOLDER_0__
Emery, Houghton & Co., __A_TAG_PLACEHOLDER_0__
Ladd, Webster & Co., __A_TAG_PLACEHOLDER_0__
Leavitt & Co., __A_TAG_PLACEHOLDER_0__
Leavitt Sewing Machine Co., __A_TAG_PLACEHOLDER_0__
Safford & Williams Makers, __A_TAG_PLACEHOLDER_0__
C. A. French, __A_TAG_PLACEHOLDER_0__
F. R. Robinson, __A_TAG_PLACEHOLDER_0__
Howard & Davis, __A_TAG_PLACEHOLDER_0__
I. M. Singer & Co., __A_TAG_PLACEHOLDER_0__
Butterfield & Stevens Mfg. Co., __A_TAG_PLACEHOLDER_0__
Williams & Orvis Sewing Machine Co., __A_TAG_PLACEHOLDER_0__
Chicopee Falls
Shaw & Clark Co., __A_TAG_PLACEHOLDER_0__
Chicopee Sewing Machine Co., __A_TAG_PLACEHOLDER_0__
Florence
Florence Sewing Machine Co., __A_TAG_PLACEHOLDER_0__, __A_TAG_PLACEHOLDER_1__
Foxboro
Foxboro Rotary Shuttle Co., __A_TAG_PLACEHOLDER_0__
Lowell
Aetna Sewing Machine Co., __A_TAG_PLACEHOLDER_0__
Lynn
Woolridge, Keene, and Moore, __A_TAG_PLACEHOLDER_0__
Orange
Gold Medal Sewing Machine Co., __A_TAG_PLACEHOLDER_0__
Johnson, Clark & Co., __A_TAG_PLACEHOLDER_0__, __A_TAG_PLACEHOLDER_1__, __A_TAG_PLACEHOLDER_2__
Grout & White, __A_TAG_PLACEHOLDER_0__
New Home Sewing Machine Co., __A_TAG_PLACEHOLDER_0__
Springfield
Leader Sewing Machine Co., __A_TAG_PLACEHOLDER_0__
Springfield Sewing Machine Co., __A_TAG_PLACEHOLDER_0__
D. B. Wesson Sewing Machine Co., __A_TAG_PLACEHOLDER_0__
Winchendon
J. G. Folsom, __A_TAG_PLACEHOLDER_0__, __A_TAG_PLACEHOLDER_1__, __A_TAG_PLACEHOLDER_2__
William Grout, __A_TAG_PLACEHOLDER_0__
Worcester
Goddard, Rice & Co., __A_TAG_PLACEHOLDER_0__
MICHIGAN
Detroit
Decker Mfg. Co., __A_TAG_PLACEHOLDER_0__
C. G. Gardner, __A_TAG_PLACEHOLDER_0__
MISSOURI
St. Louis
Wardwell Mfg. Co., __A_TAG_PLACEHOLDER_0__
NEW HAMPSHIRE
Dover
O. L. Reynolds Manufacturing Co., __A_TAG_PLACEHOLDER_0__
Marlboro
Thurston Mfg. Co., __A_TAG_PLACEHOLDER_0__
Mason Village
Franklin Sewing Machine Co., __A_TAG_PLACEHOLDER_0__
NEW JERSEY
Elizabethport
Singer Mfg. Co. (factory, not office), __A_TAG_PLACEHOLDER_0__
Paterson
Whitney Sewing Machine Company, __A_TAG_PLACEHOLDER_0__
NEW YORK
Binghamton
Independent Sewing Machine Co., __A_TAG_PLACEHOLDER_0__
Brooklyn
J. H. Lester, __A_TAG_PLACEHOLDER_0__
G. L. Du Laney, __A_TAG_PLACEHOLDER_0__
Ithaca
Aiken and Felthousen (patentees), __A_TAG_PLACEHOLDER_0__
American Magnetic Sewing Machine Co., __A_TAG_PLACEHOLDER_0__
Clinton Brothers, __A_TAG_PLACEHOLDER_0__
T.C. Thompson, __A_TAG_PLACEHOLDER_0__
New York
Avery Sewing Machine Company, __A_TAG_PLACEHOLDER_0__
A. Bartholf, manufacturer, __A_TAG_PLACEHOLDER_0__
Bartholf Sewing Machine Co., __A_TAG_PLACEHOLDER_0__
Bartlett Sewing Machine Co., __A_TAG_PLACEHOLDER_0__
Barlow & Son, __A_TAG_PLACEHOLDER_0__
[Pg 150]Beckwith Sewing Machine Co., __A_TAG_PLACEHOLDER_0__
J. A. Davis, __A_TAG_PLACEHOLDER_0__
Demorest Manufacturing Company, __A_TAG_PLACEHOLDER_0__
Charles A. Durgin, __A_TAG_PLACEHOLDER_0__
Elliptic Sewing Machine Company, __A_TAG_PLACEHOLDER_0__
Eureka Shuttle Sewing Machine Co., __A_TAG_PLACEHOLDER_0__
Excelsior Sewing Machine Company, __A_TAG_PLACEHOLDER_0__
Madam Demorest, __A_TAG_PLACEHOLDER_0__
First and Frost, __A_TAG_PLACEHOLDER_0__
L. Griswold, __A_TAG_PLACEHOLDER_0__
Howe Sewing Machine Company, __A_TAG_PLACEHOLDER_0__
Thos. A. Macauley Mfg., __A_TAG_PLACEHOLDER_0__
New York Sewing Machine Co., __A_TAG_PLACEHOLDER_0__
T. W. Robertson, __A_TAG_PLACEHOLDER_0__
I. M. Singer & Co., __A_TAG_PLACEHOLDER_0__
Singer Manufacturing Company, __A_TAG_PLACEHOLDER_0__
Standard Shuttle Sewing Machine Co., __A_TAG_PLACEHOLDER_0__
Henry Stewart & Co., __A_TAG_PLACEHOLDER_0__
Stewart Mfg. Co., __A_TAG_PLACEHOLDER_0__
E. E. Lee & Co., __A_TAG_PLACEHOLDER_0__
Willcox & Gibbs Sewing Machine Co., __A_TAG_PLACEHOLDER_0__
Watertown
Davis Sewing Machine Company, __A_TAG_PLACEHOLDER_0__
Wheeler, Wilson & Co., __A_TAG_PLACEHOLDER_0__
Westmoreland
A. B. Buell, __A_TAG_PLACEHOLDER_0__
OHIO
Cleveland
Wilson (W. G.) Sewing Machine Co., __A_TAG_PLACEHOLDER_0__, __A_TAG_PLACEHOLDER_1__
Domestic Sewing Machine Co. (after 1924), __A_TAG_PLACEHOLDER_0__
Leslie Sewing Machine Co., __A_TAG_PLACEHOLDER_0__
Standard Sewing Machine Co., __A_TAG_PLACEHOLDER_0__
White Sewing Machine Co., __A_TAG_PLACEHOLDER_0__
Dayton
Davis Sewing Machine Co., __A_TAG_PLACEHOLDER_0__
Elyria
West & Willson Co., __A_TAG_PLACEHOLDER_0__
Norwalk
Dauntless Mfg. Co., __A_TAG_PLACEHOLDER_0__, __A_TAG_PLACEHOLDER_1__
Wm. A. Mack & Co. and N. S. Perkins, __A_TAG_PLACEHOLDER_0__
Domestic Sewing Machine Co., __A_TAG_PLACEHOLDER_0__, __A_TAG_PLACEHOLDER_1__
Springfield
Royal Sewing Machine Co., __A_TAG_PLACEHOLDER_0__
St. John Sewing Machine Co., __A_TAG_PLACEHOLDER_0__
Toledo
Jewel Mfg. Co., __A_TAG_PLACEHOLDER_0__
PENNSYLVANIA
Erie
Noble Sewing Machine Co., __A_TAG_PLACEHOLDER_0__
Philadelphia
American Buttonhole, Overseaming and Sewing Machine Co., __A_TAG_PLACEHOLDER_0__
Centennial Sewing Machine Co., __A_TAG_PLACEHOLDER_0__
George B. Sloat & Co., __A_TAG_PLACEHOLDER_0__
Rex & Bockius, __A_TAG_PLACEHOLDER_0__
Grant Bros. & Co., __A_TAG_PLACEHOLDER_0__
B. W. Lacey & Co., __A_TAG_PLACEHOLDER_0__
Parham Sewing Machine Co., __A_TAG_PLACEHOLDER_0__
Philadelphia Sewing Machine Co., __A_TAG_PLACEHOLDER_0__
Quaker City Sewing Machine Co., __A_TAG_PLACEHOLDER_0__
E. Remington & Sons, __A_TAG_PLACEHOLDER_0__
Taggart & Farr, __A_TAG_PLACEHOLDER_0__
Pittsburgh
Love Mfg. Co., __A_TAG_PLACEHOLDER_0__
RHODE ISLAND
Providence
Household Sewing Machine Co., __A_TAG_PLACEHOLDER_0__
Providence Tool Company, __A_TAG_PLACEHOLDER_0__
VERMONT
Brattleboro
Samuel Barker and Thomas White, __A_TAG_PLACEHOLDER_0__
Brattleboro Sewing Machine Co., __A_TAG_PLACEHOLDER_0__
Estey Sewing Machine Co., __A_TAG_PLACEHOLDER_0__
Higby Sewing Machine Co., __A_TAG_PLACEHOLDER_0__
Nettleton & Raymond (Charles Raymond), __A_TAG_PLACEHOLDER_0__
Windsor
Lamson, Goodnow & Yale, __A_TAG_PLACEHOLDER_0__, __A_TAG_PLACEHOLDER_1__
Vermont Arms Co., __A_TAG_PLACEHOLDER_0__
VIRGINIA
Richmond
Lester Mfg. Co., __A_TAG_PLACEHOLDER_0__
Union Sewing Machine Co., __A_TAG_PLACEHOLDER_0__, __A_TAG_PLACEHOLDER_1__
Old Dominion Sewing Machine Co., __A_TAG_PLACEHOLDER_0__
WISCONSIN
Milwaukee
Whitehill Mfg. Co., __A_TAG_PLACEHOLDER_0__
[Pg 151]
Alphabetical Index to Patentees listed in Appendix III
Abercrombi, Charles, 520977
Abbott, W. W., 252984
Adams, John Q., 92138
Alexander, Elisa, 16518
Ambler, D. C., 11884
Angell, Benjamin J., 19285
Applegate, John H., and Webb, Charles B., 177784
Appleton, C. J., and Sibley, J. J., 179440
Arnold, B., 86121, 138981, 138982
Arnold, G. B. and A., 30112
Arnold, G. B., 28139
Atwater, B., 44063
Atwood, J. E., 22273
Atwood, K. C., 194759
Atwood, J. E., J. C., and O., 19903
Avery, Otis, 9338, 10880
Avery, O. and Z. W., 22007
Bachelder, J., 6439
Baglin, William, 154113
Baker, G. W., 70152, 125374, 130005
Baldwin, Cyrus W., 38276
Banks, C. M., 225784
Barcellos, D., 203102
Barnes, M. M., 106307
Barnes, William T., 20688, 25084, 25876
Barney, Samuel C., 156119
Barrett, O. D., 25785
Bartholf, Abraham, 19823
Bartlett, Joseph W., 46064, 76385
Bartlett, Joseph W., and Plant, Frederick, 159065
Barton, Kate C., 182096
Bartram, W. B., 54670, 54671, 60669, 62520, 83592, 104247, 130557
Bates, W. G., assignor to Johnson, William H., 9592
Bayley, C. H., 212122
Bean, Benjamin W., 2982
Bean, E. E., 28144
Beardslee, W. F., 245781
Beck, August, 190184, 196863
Beckwith, William G., 126921, 133351, 167382
Behn, Henry, 18071, 18880
Belcher, C. D., 16710
Benedict, C. P., 83596
Bennett, Frank Howard, and Dowling, James, 409728
Bennor, Joseph, 106249
Benson, George, 238556
Beukler, William, 204704
Beuttel, Charles, 115155
Bigelow, J., 263467
Billings, C. E., 88603
Bishop, H. H., 22226
Black, Samuel S., 146642
Blake, Lyman R., 20775, 74289
Blanchard, Helen A., 141987
Bland, Henry, 216016, 221505
Blodgett, S. C, 15469, 21465
Blodgett, John W., 279320
Boecher, Adam, 300199
Bond, Joseph Jr., 12939, 93588, 189599
Booth, Ezekiel, 25087
Boppel, Jacob, 396979
Borton, S., 214089
Borton, Stockton, and Willcox, Charles H., 255576, 255577, 255580, 255581
Bosworth, C. F., 19979, 38807, 122555, 199500, 216504
Bounaz, A., 83909, 83910
Bouscay, Eloi, Jr., 127145
Bowyer, J. T., 454708
Boyd, A. H., 19171, 24003, 31864
Bracher, T. W., 221508
Bradeen, J. G., 9380
Bradford, E. F. and Pierce, V. R., 177371
Braundbeck, E., 127675
Brewer, A. G., 152894
Briggs, Thomas, 198790
Brown, F. H., 94389, 102366, 131735, 193477
Bruen, J. T., 31208
Bruen, L. B., 68839
Budlong, William G., 25946
Buell, J. S., 25381
Buhr, Johannes, 151272
Burnet, S. S. and Broderick, W., 22160
Burr, Theodore, 32023
Butcher, Joseph, 180542, 233657
Cadwell, Caleb, 45972, 71131
Cajar, Emil, 50299, 61711
Cameron, James W., 272527
Campbell, Duncan H., 241612, 241613
Canfield, F. P., 86057
Carhart, Peter S., 24098
Carlisle, W. S., 270540
Carpenter, Lunan, 20990
Carpenter, Mary P., 112016
Carpenter, William, 87633
Carr, William H. and Ostrom, F. W., 303361
Case, George F., 33029
Cately, William H., 56902
Chamberlain, J. N., 28452
Chandler, Rufus, 133757, 139368
Charmbury, H., 316745
Chase, M., 113498
Chilcott, J. and Scrimgeour, J., 12856
Chittenden, H. H., 43289
Choquette, A. E., 244033
Clark, David W., 19015, 19072, 19129, 19409, 19732, 20481, 21322, 23823
Clark, Edwin, 26336
Clark, Edwin E., 74751
Clements, James M., 57451
Cleminshaw, S., 128363, 213391
Clever, P. J., 96886
Clever, Peter J., 296529
Coates, F. S., 19684
Cole, W. H., 79447
Conant, J. S., 12233
Conklin, N. A., 206774
Cook, Hugo, 454610
Cooney, W., 102226
Corbett, E. and Harlow, C. F., 192568
Corey, J. W., 198970
Corliss, George H., 3389
Cornely, E., 73696
Cornely, Emile, 219225
Craige, E. H., 62186, 67635
Crane, Thomas, 150532
Crosby, C. O., 50225, 90507
Crosby, C. O. and Kellogg, H., 37033
Cummins, William G., 187822
Curtis, G. H. W., 228985
Cushman, C. S., 142442, 184594
Dale, John D., 44686
Dancel, Christian, 199802
Darling and Darling, 163639
Davis, Job A., 27208, 58614
Derocquigny, A. C. F., Gance, D., and Hanzo, L., 34748
Deschamps, O. L., 253915
Destouy, Auguste, 56729
Dewees, John W., 432746
[Pg 152]
Dickinson, C. W., 26346
Diehl, Philipp, 339623, 347776, 347777, 348113
Dieterle, H. E., 353542
Dimmock, Martial and Rixford, Nathan, 19135
Dimond, George H., 196198, 207400
Dinsmore, Alfred S., 160512, 231155
Dinsmore, A. S., and Carter, John T., 152618
Doll, Arnold, 68420
Dopp, H. W., 27279
Dowling, James, and Connolly, John, 299118
Drake, Ellis, 155932
Duchemin, William, 59715, 91101, 135032, 288929
Dunbar, C. F., 88282
Durgin, Charles A., 12902
Earle, T., 31156
Eickemeyer, Rudolf, 52698, 182182, 239319
Elderfield, F. D., 204429
Eldridge, G. W., 87331
Elliott, F., 85918
Emerson, John, 50989
Emswiler, J. B., 25002
Esty, William, 187837
Fales, J. F., 74328
Fanning, John, 72829, 129013
Farr, Chester N., 25004
Farrar, Arthur, 309837
Fetter, George, 18793, 19059
Fish, Warren L., 123625
Fletcher, James N., 443756
Follett, Joseph L., 189446
Fosket, William A., and Savage, Elliot, 22719, 25963
French, Stephen, 80345
Frese, B., 172308
Fuller, H. W., 63033
Fuller, William M., 32496
Garland, H. P., 159812, 169163
Gee, W. V., 361406
Gibbs, James E. A., 16234, 16434, 17427, 21129, 21751, 27214, 28851
Gird, E. D., 87559
Goodes, E. A., 136718, 147387
Goodspeed, G. N., 54816
Goodwin, Julius C., 450793
Goodwyn, H. H., 24455
Goodyear, Charles Jr., 111197, 116947
Gordon, James, and Kinert, William, 125807
Gray, Joshua, 16566, 19665, 24022, 95581
Green, George F., 238678
Greenough, John J., 2466
Gritzner, M. C., 44720, 76323
Gritzner, Max C., 243444
Grote, F. W., 38447
Grout, William, 24629
Grover, William O., 14956, 33778, 36405, 100139
Grover, William O., and Baker, William E., 7931
Guinness, William S., 41916
Gullrandsen, P. E., and Rettinger, J. C., 180225
Gutmann, Julius, 90528
Halbert, A. W., 76076
Hall, William, 24870
Hale, William S., 36084
Hall, Luther, 43404
Hall, L., 105329
Hall, John S., 168637, 187006
Hallenbeck, J. P., 425422
Hallett, H. H., 191584
Hamm, E., 219578
Hancock, Henry J., 83492, 112033
Hanlon, John, 52847
Happe, J., and Newman, W., 130715, 137199
Hardie, J. W., 30854
Harris, Daniel, 17508, 17571
Harris, David, 185228
Harrison, J. Jr., 10763, 13616, 25013, 25262
Hart, William, 50469
Hayes, James, 55029
Hayden, H. W., 24937
Heberling, J., 204604, 227249, 227525, 284300
Hecht, A., 50473
Heery, Luke, 94740
Heidenthal, William, 127765
Helwig, Arthur, 350364
Hendrick, Joseph E., 19660, 21722
Hendrickson, E. M., 34330
Henriksen, H. P., 104590, 188515, 215615
Hensel, George, 24737
Herron, A. C., 20557
Hesse, Joseph, 235085
Heyer, W. D., 40622
Heyer, Frederick, 30731
Hicks, William C., 26035, 29268
Hinkley, Jonas, 25231
Hinds, Jesse L., 131166
Hine, Charles M., 420382
Hine, Charlie M., 246136
Hodgkins, Christopher, 9365, 33085, 69666
Hoefler, J., 246883
Hoffman, George W., 94112
Hoffman, Clara P., and Meyers, Nicholas, 207035
Holden, O. J., and Griswold, L., 272050
Hollowell, J. G., 27624
Holly, Birdsill, 28176
Hook, Albert H., 22179, 24027
Horr, Addison D., 149862
House, James A., 206239
House, James A., and House, Henry A., 36932, 39442, 39445, 55865, 87338, 114294
Howard, C. W., 126056, 126057
Howard, T. S. L., 199206
Howard, E. L., 154485
Howard, E., and Jackson, W. H., 103745
Howe, Amasa Bemis, 37913
Howe, Elias, 4750, 16436
Hubbard, George W., 18904, 21537
Hull, E. H., 254217
Humphrey, D. W. G., 36617, 49627
Hunt, Walter, 11161
Huntington, Thomas S., 158214
Hurtu, Auguste J., 258761, 315037
Hurtu, Auguste J., and Hautin, Victor J., 98064
Ingalls, N., Jr., 212602
Jackson, Francis, 519064
Jackson, William, 181941
Jacob, Frederick, 190047
Jencks, G. L., 74694
Jennings, L., 16237
Johnson, Albert F., 16387, 20686, 26948
Johnson, W. H., 10597
Jones, John T., 86163, 117640, 169106
Jones, Samuel H., 140631
Jones, Solomon, 118537, 118538
Jones, William, and Haughian, P., 32297
Juengst, George, 27132, 228820
Junker, Carl, 217112
Kallmeyer, G., 137689
Keats, Alphonso, 260990
Keats, John, 198120
Keats, John; Greenwood, Arthur; and Keats, Alphonso, 171622
[Pg 153]
Keats, John, and Clark. Wm. S., 50995
Keith, Jeremiah, 97518, 170741, 196809, 209126, 243710
Keith, T. H., 196909
Keith, T. K., 170955
Kelsey, D., 24939
Kendall, George F., 101887
Kern, Ferdinand, 479369
Kilbourn, E. E., 59746
Kjalman, H. N., 235783
Knoch, Charles F., 183400
Koch, William, 262298
Koch, Friederich, and Brass, Robert, 138898, 145215
Lamb, Isaac W., 109632
Lamb, Thomas, 98390, 118728
Lamb, Thomas, and Allen, John, 49421
Lamson, Henry P., 79579
Landfear, William R., 109427, 155193
Langdon, Leander W., 13727, 39256
Lathbury, E. T., 17744
Lathrop, Lebbeus W., 139067
Lathrop, Lebbeus W., and de Sanno, William P., 40446
Lawrence, G. H., 290895
Lazelle, W. H., 18915
Leavitte, Albert, 171147
Leavitt, Rufus, 30634
Leavitt, Albert, and Drew, Henry L., 187874
Legat, D. M., 218388
Legg, Albert, and Weston, Charles W., 474840
Leslie, A. M., 241808
Leyden, Austin, 57157
Lingley, John W., 368538
Lipe, C. E., 229322
Lisle, Myron C., 428171
Ludeke, Waldemar, 275506, 300380
Lyon, Lucius, 89489, 96713, 105820
Lyon, W., 12066
Macauley, F. A., 195939
Mack, William A., 38592
Mallary, G. H., 31897
Mann, Charles, 33556
Marble, F. E., 33439
Marin, Charles, 179709
Martin, W., Jr.; Dawson, D. R.; and Orchar, R., 206743
Martine, Charles F., 104612
Meyers, Nicholas, 99783
Melhuish, R. M., 194610
McCloskey, John, 55688, 161534
McClure, A. T., 130385
McKay, Gordon, and Blake, Lyman, 42916
McKay, Gordon, 188809
McLean, J. N., 88499
McCombs, George F., 208407
McCurdy, James S., 24395, 26234, 28097, 28993, 36256, 38931, 46303, 53743
Miehling, Charles, 351992
Miller, Charles, 9139, 26462
Miller, Westley, 20763
Miller, Lebbens B., and Diehl, Philipp, 229629, 274359
Mills, Daniel, 96944, 265850, 313359
Mooney, John H., 222298, 244470
Moore, Charles, 21015
Moreau, Eugene, 110669, 156171
Morley, J. H., 228918, 236350
Morrell, R. W.; Parkinson, T.; Parkinson, J., 202857
Morrison, T. W., 216289
Muegge, C. A., 332207
Mueller, H., 28996
Muir, William, 147152
Murphy, E., 176880
Nasch, Isidor, 104630
Necker, Carl, 117101
Nettleton, William H., and Raymond, Charles, 17049, 18350
Newell, George F., 242470
Newlove, Thomas, 27761
Norton, B. F., 32782
O’Neil, John, 137618
Oram, Henry, 185952
Osborne, J. H., 224219
Otis, S. L., 221093
Osterhout, James A., and Hallenbeck, Joseph P., 402610
Page, Charles, 96343, 150479
Paine, A. R., 27412
Palmateer, William A., 187479
Palmer, Aaron, 35252
Palmer, C. H., 38450, 124694, 240758
Palmer, Frank L., 185954
Palmer, John H., 298228
Parham, Charles, 109443, 135579
Parker, Sidney, 19662, 24780
Parks, Volney, 129981
Parmenter, Charles O., 212495
Payne, R. S., 30641
Pearson, M. H., 199991
Pearson, William, 26201
Pearson, William, 166805, 172478
Perry, James, 22148
Piper, D. B., 56990
Pipo, John A., 37550
Pitt, James; Joseph; Edward; and William, 117203
Planer, Louis, 43927
Porter, D. A., 144864
Porter, Alonzo, 99704
Porter, D’Arcy, and Baker, George W., 174703
Powell, Thomas, 442695
Pratt, Samuel F., 16745, 22240
Ragan, Daniel, 137321
Ramsden, John W., 262116
Randel, William, 192008
Rayer, William A., and Lincoln, William S., 108827
Raymond, Charles, 19612, 22220, 32785, 32925
Reed, T. K., 60241, 62287
Rehfuss, George, 40311, 51086, 61102, 73119
Reynolds, O. S., 19793
Rice, T. M., 176686
Rice, Quartus, 31429
Richards, Jean E., 252799
Richardson, E. F., 145687
Richardson, Everett P., 146948, 165506
Roberts, William, 254696
Robertson, T. J. W., 12015
Robinson, Charles E., 110790
Robinson, Frederick R., 7824
Rodier, Peter, 59659
Roper, S. H., 11531, 16026, 18522
Rose, Israel M., 28814, 31628
Rose, Reubin M., 170596
Rosenthal, Sally Adolph, 353970
Ross, Noble G., 31829
Ross, J. G., and Miller, T. L., 138764
Rowe, James, 26638, 27260
Ruddick, H., 28538
Rudolph, Bruno, 99481
Rudolph, Ernst B. (deceased), Boulter, W. E. (administrator), 449927
Russell, W. W., 86695
Sage, William, 17717
Sangster, Amos W., 21929
Savage, Elliott, 19876
Sawyer, Irvin P., and Alsop, T., 25918
Sawyer, Sylvanus, and Esty, William, 174159
Schmidt, Albert E., 162697
Schwalback, M., 56805
Scofield, Charles, 26059
[Pg 154]
Scofield, Charles, and Rice, Clarke, 28610
Scribner, Benjamin, Jr., 146483
Secor, J. B., 253772
Sedmihradsky, A. J., 196486
Shaw, E., 230580
Shaw, Philander, 11680
Shaw, A. B., 37202
Shaw, Henry L., 32007
Shaw and Clark, 38246
Sheffield, G. V., 135047
Shorey, Samuel W., 148765
Sibley, J. J., 42117
Sidenberg, William, 112745, 115117
Simmons, Frederick, 216902
Simmons, A. G., and Scofield, C., 41790
Singer, Isaac M., 8294, 10975, 12364, 13065, 13661, 13662, 14475, 60433, 61270
Smalley, J., 27577
Smith, DeWitt C., 45528
Smith, E. H., 20739, 21089, 96160
Smith, H. B., 12247
Smith, J. M., 31334
Smith, Lewis H., 31411, 32385
Smith, John C., 34988
Smith, James H., 148902
Smith, Wilson H., 28785
Smith, W. M., 225199
Smith, William T., 99743
Smyth, D. M., 126845, 234732
Snediker, J. F., 222089
Snyder, Watson, 22987
Spencer, James C., 24061
Spencer, James H., and Lamb, Thomas, 22137
Speirs, John, 152813
Spoehr, F., 101779
Springer, William A., 128919, 142290, 147441
Stackpole, G., and Applegate, J. H., 220314
Stannard, M., 64184
Stedman, G. W., 12074, 12573, 12798, 13856
Stein, M. J., 81956, 113593
Stevens, George, and Hendy, Joshua, 111488
Steward, A., 207454
Stewart, James, Jr., 141397, 432449
Stewart, W. T., 205698
Stoakes, J. W., 32456
Sullivan, John J., 179232
Sutton, William A., 29202
Swartwout, H. L., 89357
Swingle, A., 14207
Taft, J. C., 547866
Tapley, G. S., 25059
Tarbox, John N., 49803
Tate, William J., 113704
Taylor, F. B., 146721
Temple, John, 358088
Thayer, Augustus, 172205
Thimonnier, E., and Vernaz, C., 287592
Thomas, Joseph, 330170
Thomas, J., 236466
Thompson, J., 27082
Thompson, T. C., 9641
Thompson, Rosewell, 34926, 42449
Thurston, C. H., 233300
Tittman, Alexander, 89093, 136792
Toll, Charles F., 171193
Tracy, Dwight, 30012
Tracy, Dwight, and Hobbs, George, 40000
Trip, J., 308711
True, Cyrus B., 148336
Tucker, R. D., 320898
Tucker, Joseph C., 56641
Turner, M. G., 312306
Turner, S. S., 133553
Tuttle, J. W., and Keith, T. K., 219782
Thompson, George, 115255
Uhlinger, W. P., 21224
Upson, L. A., 176153
Van Vechten, O. R., 302063
Varicas, L., 204864
Venner, O., 133814
Veukler, W., 255916
Wagener, Jeptha A., 40296
Walker, William, 141407, 176101, 320099, 353720
Walker and Bennet, 428548
Ward, D. T., 12146
Wardwell, Simon W., Jr., 128684, 141245, 148339
Warth, Albin, 56646, 73064
Washburn, T. S., 30031
Waterbury, Enos, 79037
Watson, William C., 14433, 18834
Weber, Theodore A., 145823, 166236
Webb, T., and Heartfield, C. H., 213537
Webster, W., 182249, 402497
Weitling, W., 37931, 45777
Wells, W. W., 209843
Wensley, James, 152055, 207230
West, Elliott P., 117708, 130674, 138772
West, H. B., and Willson, H. F., 20753
Wheeler, Nathaniel, 420847
Wheeler, Nathaniel, and Dial, Wilbur F., 328165
Wheeler, Darius, and Carpenter, Lunan, 21100
Whitehill, Robert, 166172
Wickersham, William, 9679, 18068, 18069
Wilder, M. G., 32323
Wilkins, J. N., 36591
Wilkinson, Charles E., 269251
Willcox, Charles H., 42036, 43819, 44490, 44491, 218413, 230212, 246700
Willcox, C. H., and Borton, S., 472094
Willcox, C. H., and Carleton, C., 116521, 116523, 116783
Wilson, Allen B., 7776, 8296, 9041
Wiseman, Edmund, 228711
Witherspoon, S. A., 176211
Winter, William, 88936
Wollenberg, H., and Priesner, J., 206848
Wood, John, 185811
Wood, Richard G., 207928
Woodruff, George B., and Browning, George, 97014
Woodward, E., 247285
Woodward, F. G., 25782
Woodward, Erastus, and Keith, Thomas K., 316927
Wormald, William, and Dobson, Edmund, 169881
Young, E. S., and Dimond, G. H., 206992
Abercrombi, Charles, 520977
Abbott, W. W., 252984
Adams, John Q., 92138
Alexander, Elisa, 16518
Ambler, D. C., 11884
Angell, Benjamin J., 19285
Applegate, John H., and Webb, Charles B., 177784
Appleton, C. J., and Sibley, J. J., 179440
Arnold, B., 86121, 138981, 138982
Arnold, G. B. and A., 30112
Arnold, G. B., 28139
Atwater, B., 44063
Atwood, J. E., 22273
Atwood, K. C., 194759
Atwood, J. E., J. C., and O., 19903
Avery, Otis, 9338, 10880
Avery, O. and Z. W., 22007
Bachelder, J., 6439
Baglin, William, 154113
Baker, G. W., 70152, 125374, 130005
Baldwin, Cyrus W., 38276
Banks, C. M., 225784
Barcellos, D., 203102
Barnes, M. M., 106307
Barnes, William T., 20688, 25084, 25876
Barney, Samuel C., 156119
Barrett, O. D., 25785
Bartholf, Abraham, 19823
Bartlett, Joseph W., 46064, 76385
Bartlett, Joseph W., and Plant, Frederick, 159065
Barton, Kate C., 182096
Bartram, W. B., 54670, 54671, 60669, 62520, 83592, 104247, 130557
Bates, W. G., assignor to Johnson, William H., 9592
Bayley, C. H., 212122
Bean, Benjamin W., 2982
Bean, E. E., 28144
Beardslee, W. F., 245781
Beck, August, 190184, 196863
Beckwith, William G., 126921, 133351, 167382
Behn, Henry, 18071, 18880
Belcher, C. D., 16710
Benedict, C. P., 83596
Bennett, Frank Howard, and Dowling, James, 409728
Bennor, Joseph, 106249
Benson, George, 238556
Beukler, William, 204704
Beuttel, Charles, 115155
Bigelow, J., 263467
Billings, C. E., 88603
Bishop, H. H., 22226
Black, Samuel S., 146642
Blake, Lyman R., 20775, 74289
Blanchard, Helen A., 141987
Bland, Henry, 216016, 221505
Blodgett, S. C, 15469, 21465
Blodgett, John W., 279320
Boecher, Adam, 300199
Bond, Joseph Jr., 12939, 93588, 189599
Booth, Ezekiel, 25087
Boppel, Jacob, 396979
Borton, S., 214089
Borton, Stockton, and Willcox, Charles H., 255576, 255577, 255580, 255581
Bosworth, C. F., 19979, 38807, 122555, 199500, 216504
Bounaz, A., 83909, 83910
Bouscay, Eloi, Jr., 127145
Bowyer, J. T., 454708
Boyd, A. H., 19171, 24003, 31864
Bracher, T. W., 221508
Bradeen, J. G., 9380
Bradford, E. F. and Pierce, V. R., 177371
Braundbeck, E., 127675
Brewer, A. G., 152894
Briggs, Thomas, 198790
Brown, F. H., 94389, 102366, 131735, 193477
Bruen, J. T., 31208
Bruen, L. B., 68839
Budlong, William G., 25946
Buell, J. S., 25381
Buhr, Johannes, 151272
Burnet, S. S. and Broderick, W., 22160
Burr, Theodore, 32023
Butcher, Joseph, 180542, 233657
Cadwell, Caleb, 45972, 71131
Cajar, Emil, 50299, 61711
Cameron, James W., 272527
Campbell, Duncan H., 241612, 241613
Canfield, F. P., 86057
Carhart, Peter S., 24098
Carlisle, W. S., 270540
Carpenter, Lunan, 20990
Carpenter, Mary P., 112016
Carpenter, William, 87633
Carr, William H. and Ostrom, F. W., 303361
Case, George F., 33029
Cately, William H., 56902
Chamberlain, J. N., 28452
Chandler, Rufus, 133757, 139368
Charmbury, H., 316745
Chase, M., 113498
Chilcott, J. and Scrimgeour, J., 12856
Chittenden, H. H., 43289
Choquette, A. E., 244033
Clark, David W., 19015, 19072, 19129, 19409, 19732, 20481, 21322, 23823
Clark, Edwin, 26336
Clark, Edwin E., 74751
Clements, James M., 57451
Cleminshaw, S., 128363, 213391
Clever, P. J., 96886
Clever, Peter J., 296529
Coates, F. S., 19684
Cole, W. H., 79447
Conant, J. S., 12233
Conklin, N. A., 206774
Cook, Hugo, 454610
Cooney, W., 102226
Corbett, E. and Harlow, C. F., 192568
Corey, J. W., 198970
Corliss, George H., 3389
Cornely, E., 73696
Cornely, Emile, 219225
Craige, E. H., 62186, 67635
Crane, Thomas, 150532
Crosby, C. O., 50225, 90507
Crosby, C. O. and Kellogg, H., 37033
Cummins, William G., 187822
Curtis, G. H. W., 228985
Cushman, C. S., 142442, 184594
Dale, John D., 44686
Dancel, Christian, 199802
Darling and Darling, 163639
Davis, Job A., 27208, 58614
Derocquigny, A. C. F., Gance, D., and Hanzo, L., 34748
Deschamps, O. L., 253915
Destouy, Auguste, 56729
Dewees, John W., 432746
[Pg 152]
Dickinson, C. W., 26346
Diehl, Philipp, 339623, 347776, 347777, 348113
Dieterle, H. E., 353542
Dimmock, Martial and Rixford, Nathan, 19135
Dimond, George H., 196198, 207400
Dinsmore, Alfred S., 160512, 231155
Dinsmore, A. S., and Carter, John T., 152618
Doll, Arnold, 68420
Dopp, H. W., 27279
Dowling, James, and Connolly, John, 299118
Drake, Ellis, 155932
Duchemin, William, 59715, 91101, 135032, 288929
Dunbar, C. F., 88282
Durgin, Charles A., 12902
Earle, T., 31156
Eickemeyer, Rudolf, 52698, 182182, 239319
Elderfield, F. D., 204429
Eldridge, G. W., 87331
Elliott, F., 85918
Emerson, John, 50989
Emswiler, J. B., 25002
Esty, William, 187837
Fales, J. F., 74328
Fanning, John, 72829, 129013
Farr, Chester N., 25004
Farrar, Arthur, 309837
Fetter, George, 18793, 19059
Fish, Warren L., 123625
Fletcher, James N., 443756
Follett, Joseph L., 189446
Fosket, William A., and Savage, Elliot, 22719, 25963
French, Stephen, 80345
Frese, B., 172308
Fuller, H. W., 63033
Fuller, William M., 32496
Garland, H. P., 159812, 169163
Gee, W. V., 361406
Gibbs, James E. A., 16234, 16434, 17427, 21129, 21751, 27214, 28851
Gird, E. D., 87559
Goodes, E. A., 136718, 147387
Goodspeed, G. N., 54816
Goodwin, Julius C., 450793
Goodwyn, H. H., 24455
Goodyear, Charles Jr., 111197, 116947
Gordon, James, and Kinert, William, 125807
Gray, Joshua, 16566, 19665, 24022, 95581
Green, George F., 238678
Greenough, John J., 2466
Gritzner, M. C., 44720, 76323
Gritzner, Max C., 243444
Grote, F. W., 38447
Grout, William, 24629
Grover, William O., 14956, 33778, 36405, 100139
Grover, William O., and Baker, William E., 7931
Guinness, William S., 41916
Gullrandsen, P. E., and Rettinger, J. C., 180225
Gutmann, Julius, 90528
Halbert, A. W., 76076
Hall, William, 24870
Hale, William S., 36084
Hall, Luther, 43404
Hall, L., 105329
Hall, John S., 168637, 187006
Hallenbeck, J. P., 425422
Hallett, H. H., 191584
Hamm, E., 219578
Hancock, Henry J., 83492, 112033
Hanlon, John, 52847
Happe, J., and Newman, W., 130715, 137199
Hardie, J. W., 30854
Harris, Daniel, 17508, 17571
Harris, David, 185228
Harrison, J. Jr., 10763, 13616, 25013, 25262
Hart, William, 50469
Hayes, James, 55029
Hayden, H. W., 24937
Heberling, J., 204604, 227249, 227525, 284300
Hecht, A., 50473
Heery, Luke, 94740
Heidenthal, William, 127765
Helwig, Arthur, 350364
Hendrick, Joseph E., 19660, 21722
Hendrickson, E. M., 34330
Henriksen, H. P., 104590, 188515, 215615
Hensel, George, 24737
Herron, A. C., 20557
Hesse, Joseph, 235085
Heyer, W. D., 40622
Heyer, Frederick, 30731
Hicks, William C., 26035, 29268
Hinkley, Jonas, 25231
Hinds, Jesse L., 131166
Hine, Charles M., 420382
Hine, Charlie M., 246136
Hodgkins, Christopher, 9365, 33085, 69666
Hoefler, J., 246883
Hoffman, George W., 94112
Hoffman, Clara P., and Meyers, Nicholas, 207035
Holden, O. J., and Griswold, L., 272050
Hollowell, J. G., 27624
Holly, Birdsill, 28176
Hook, Albert H., 22179, 24027
Horr, Addison D., 149862
House, James A., 206239
House, James A., and House, Henry A., 36932, 39442, 39445, 55865, 87338, 114294
Howard, C. W., 126056, 126057
Howard, T. S. L., 199206
Howard, E. L., 154485
Howard, E., and Jackson, W. H., 103745
Howe, Amasa Bemis, 37913
Howe, Elias, 4750, 16436
Hubbard, George W., 18904, 21537
Hull, E. H., 254217
Humphrey, D. W. G., 36617, 49627
Hunt, Walter, 11161
Huntington, Thomas S., 158214
Hurtu, Auguste J., 258761, 315037
Hurtu, Auguste J., and Hautin, Victor J., 98064
Ingalls, N., Jr., 212602
Jackson, Francis, 519064
Jackson, William, 181941
Jacob, Frederick, 190047
Jencks, G. L., 74694
Jennings, L., 16237
Johnson, Albert F., 16387, 20686, 26948
Johnson, W. H., 10597
Jones, John T., 86163, 117640, 169106
Jones, Samuel H., 140631
Jones, Solomon, 118537, 118538
Jones, William, and Haughian, P., 32297
Juengst, George, 27132, 228820
Junker, Carl, 217112
Kallmeyer, G., 137689
Keats, Alphonso, 260990
Keats, John, 198120
Keats, John; Greenwood, Arthur; and Keats, Alphonso, 171622
[Pg 153]
Keats, John, and Clark. Wm. S., 50995
Keith, Jeremiah, 97518, 170741, 196809, 209126, 243710
Keith, T. H., 196909
Keith, T. K., 170955
Kelsey, D., 24939
Kendall, George F., 101887
Kern, Ferdinand, 479369
Kilbourn, E. E., 59746
Kjalman, H. N., 235783
Knoch, Charles F., 183400
Koch, William, 262298
Koch, Friederich, and Brass, Robert, 138898, 145215
Lamb, Isaac W., 109632
Lamb, Thomas, 98390, 118728
Lamb, Thomas, and Allen, John, 49421
Lamson, Henry P., 79579
Landfear, William R., 109427, 155193
Langdon, Leander W., 13727, 39256
Lathbury, E. T., 17744
Lathrop, Lebbeus W., 139067
Lathrop, Lebbeus W., and de Sanno, William P., 40446
Lawrence, G. H., 290895
Lazelle, W. H., 18915
Leavitte, Albert, 171147
Leavitt, Rufus, 30634
Leavitt, Albert, and Drew, Henry L., 187874
Legat, D. M., 218388
Legg, Albert, and Weston, Charles W., 474840
Leslie, A. M., 241808
Leyden, Austin, 57157
Lingley, John W., 368538
Lipe, C. E., 229322
Lisle, Myron C., 428171
Ludeke, Waldemar, 275506, 300380
Lyon, Lucius, 89489, 96713, 105820
Lyon, W., 12066
Macauley, F. A., 195939
Mack, William A., 38592
Mallary, G. H., 31897
Mann, Charles, 33556
Marble, F. E., 33439
Marin, Charles, 179709
Martin, W., Jr.; Dawson, D. R.; and Orchar, R., 206743
Martine, Charles F., 104612
Meyers, Nicholas, 99783
Melhuish, R. M., 194610
McCloskey, John, 55688, 161534
McClure, A. T., 130385
McKay, Gordon, and Blake, Lyman, 42916
McKay, Gordon, 188809
McLean, J. N., 88499
McCombs, George F., 208407
McCurdy, James S., 24395, 26234, 28097, 28993, 36256, 38931, 46303, 53743
Miehling, Charles, 351992
Miller, Charles, 9139, 26462
Miller, Westley, 20763
Miller, Lebbens B., and Diehl, Philipp, 229629, 274359
Mills, Daniel, 96944, 265850, 313359
Mooney, John H., 222298, 244470
Moore, Charles, 21015
Moreau, Eugene, 110669, 156171
Morley, J. H., 228918, 236350
Morrell, R. W.; Parkinson, T.; Parkinson, J., 202857
Morrison, T. W., 216289
Muegge, C. A., 332207
Mueller, H., 28996
Muir, William, 147152
Murphy, E., 176880
Nasch, Isidor, 104630
Necker, Carl, 117101
Nettleton, William H., and Raymond, Charles, 17049, 18350
Newell, George F., 242470
Newlove, Thomas, 27761
Norton, B. F., 32782
O’Neil, John, 137618
Oram, Henry, 185952
Osborne, J. H., 224219
Otis, S. L., 221093
Osterhout, James A., and Hallenbeck, Joseph P., 402610
Page, Charles, 96343, 150479
Paine, A. R., 27412
Palmateer, William A., 187479
Palmer, Aaron, 35252
Palmer, C. H., 38450, 124694, 240758
Palmer, Frank L., 185954
Palmer, John H., 298228
Parham, Charles, 109443, 135579
Parker, Sidney, 19662, 24780
Parks, Volney, 129981
Parmenter, Charles O., 212495
Payne, R. S., 30641
Pearson, M. H., 199991
Pearson, William, 26201
Pearson, William, 166805, 172478
Perry, James, 22148
Piper, D. B., 56990
Pipo, John A., 37550
Pitt, James; Joseph; Edward; and William, 117203
Planer, Louis, 43927
Porter, D. A., 144864
Porter, Alonzo, 99704
Porter, D’Arcy, and Baker, George W., 174703
Powell, Thomas, 442695
Pratt, Samuel F., 16745, 22240
Ragan, Daniel, 137321
Ramsden, John W., 262116
Randel, William, 192008
Rayer, William A., and Lincoln, William S., 108827
Raymond, Charles, 19612, 22220, 32785, 32925
Reed, T. K., 60241, 62287
Rehfuss, George, 40311, 51086, 61102, 73119
Reynolds, O. S., 19793
Rice, T. M., 176686
Rice, Quartus, 31429
Richards, Jean E., 252799
Richardson, E. F., 145687
Richardson, Everett P., 146948, 165506
Roberts, William, 254696
Robertson, T. J. W., 12015
Robinson, Charles E., 110790
Robinson, Frederick R., 7824
Rodier, Peter, 59659
Roper, S. H., 11531, 16026, 18522
Rose, Israel M., 28814, 31628
Rose, Reubin M., 170596
Rosenthal, Sally Adolph, 353970
Ross, Noble G., 31829
Ross, J. G., and Miller, T. L., 138764
Rowe, James, 26638, 27260
Ruddick, H., 28538
Rudolph, Bruno, 99481
Rudolph, Ernst B. (deceased), Boulter, W. E. (administrator), 449927
Russell, W. W., 86695
Sage, William, 17717
Sangster, Amos W., 21929
Savage, Elliott, 19876
Sawyer, Irvin P., and Alsop, T., 25918
Sawyer, Sylvanus, and Esty, William, 174159
Schmidt, Albert E., 162697
Schwalback, M., 56805
Scofield, Charles, 26059
[Pg 154]
Scofield, Charles, and Rice, Clarke, 28610
Scribner, Benjamin, Jr., 146483
Secor, J. B., 253772
Sedmihradsky, A. J., 196486
Shaw, E., 230580
Shaw, Philander, 11680
Shaw, A. B., 37202
Shaw, Henry L., 32007
Shaw and Clark, 38246
Sheffield, G. V., 135047
Shorey, Samuel W., 148765
Sibley, J. J., 42117
Sidenberg, William, 112745, 115117
Simmons, Frederick, 216902
Simmons, A. G., and Scofield, C., 41790
Singer, Isaac M., 8294, 10975, 12364, 13065, 13661, 13662, 14475, 60433, 61270
Smalley, J., 27577
Smith, DeWitt C., 45528
Smith, E. H., 20739, 21089, 96160
Smith, H. B., 12247
Smith, J. M., 31334
Smith, Lewis H., 31411, 32385
Smith, John C., 34988
Smith, James H., 148902
Smith, Wilson H., 28785
Smith, W. M., 225199
Smith, William T., 99743
Smyth, D. M., 126845, 234732
Snediker, J. F., 222089
Snyder, Watson, 22987
Spencer, James C., 24061
Spencer, James H., and Lamb, Thomas, 22137
Speirs, John, 152813
Spoehr, F., 101779
Springer, William A., 128919, 142290, 147441
Stackpole, G., and Applegate, J. H., 220314
Stannard, M., 64184
Stedman, G. W., 12074, 12573, 12798, 13856
Stein, M. J., 81956, 113593
Stevens, George, and Hendy, Joshua, 111488
Steward, A., 207454
Stewart, James, Jr., 141397, 432449
Stewart, W. T., 205698
Stoakes, J. W., 32456
Sullivan, John J., 179232
Sutton, William A., 29202
Swartwout, H. L., 89357
Swingle, A., 14207
Taft, J. C., 547866
Tapley, G. S., 25059
Tarbox, John N., 49803
Tate, William J., 113704
Taylor, F. B., 146721
Temple, John, 358088
Thayer, Augustus, 172205
Thimonnier, E., and Vernaz, C., 287592
Thomas, Joseph, 330170
Thomas, J., 236466
Thompson, J., 27082
Thompson, T. C., 9641
Thompson, Rosewell, 34926, 42449
Thurston, C. H., 233300
Tittman, Alexander, 89093, 136792
Toll, Charles F., 171193
Tracy, Dwight, 30012
Tracy, Dwight, and Hobbs, George, 40000
Trip, J., 308711
True, Cyrus B., 148336
Tucker, R. D., 320898
Tucker, Joseph C., 56641
Turner, M. G., 312306
Turner, S. S., 133553
Tuttle, J. W., and Keith, T. K., 219782
Thompson, George, 115255
Uhlinger, W. P., 21224
Upson, L. A., 176153
Van Vechten, O. R., 302063
Varicas, L., 204864
Venner, O., 133814
Veukler, W., 255916
Wagener, Jeptha A., 40296
Walker, William, 141407, 176101, 320099, 353720
Walker and Bennet, 428548
Ward, D. T., 12146
Wardwell, Simon W., Jr., 128684, 141245, 148339
Warth, Albin, 56646, 73064
Washburn, T. S., 30031
Waterbury, Enos, 79037
Watson, William C., 14433, 18834
Weber, Theodore A., 145823, 166236
Webb, T., and Heartfield, C. H., 213537
Webster, W., 182249, 402497
Weitling, W., 37931, 45777
Wells, W. W., 209843
Wensley, James, 152055, 207230
West, Elliott P., 117708, 130674, 138772
West, H. B., and Willson, H. F., 20753
Wheeler, Nathaniel, 420847
Wheeler, Nathaniel, and Dial, Wilbur F., 328165
Wheeler, Darius, and Carpenter, Lunan, 21100
Whitehill, Robert, 166172
Wickersham, William, 9679, 18068, 18069
Wilder, M. G., 32323
Wilkins, J. N., 36591
Wilkinson, Charles E., 269251
Willcox, Charles H., 42036, 43819, 44490, 44491, 218413, 230212, 246700
Willcox, C. H., and Borton, S., 472094
Willcox, C. H., and Carleton, C., 116521, 116523, 116783
Wilson, Allen B., 7776, 8296, 9041
Wiseman, Edmund, 228711
Witherspoon, S. A., 176211
Winter, William, 88936
Wollenberg, H., and Priesner, J., 206848
Wood, John, 185811
Wood, Richard G., 207928
Woodruff, George B., and Browning, George, 97014
Woodward, E., 247285
Woodward, F. G., 25782
Woodward, Erastus, and Keith, Thomas K., 316927
Wormald, William, and Dobson, Edmund, 169881
Young, E. S., and Dimond, G. H., 206992
General Index to Chapters 1-4
Adams and Dodge, 9
Aetna Sewing Machine Company, 40
American Buttonhole and Sewing Machine Company, 40
Archbold, Thomas, 13
Arrowsmith, George A., 11
Bachelder, John, 22, 30, 34, 41, 42
Baker, William E., 36 (see Grover & Baker)
Bartholf, A., 24, 40
Bartlett Sewing Machine Company, 40
Bartram & Fanton Manufacturing Company, 40
Bean, Benjamin W., 13, 14, 15
Blees Sewing Machine Company, 40
Bliss, George, 24
Blodgett and Lerow, 24, 26, 30
Blodgett, Sherbrune C., 25
Bradshaw, John A., 21, 22, 26, 27
Brown, W. N., 50
Centennial Sewing Machine Company, 40
Chapman, Edward Walter, 7, 19
Chapman, William, 7
Clark, D. W., 47, 49
Clark, Edward, 33, 34, 35
Combination, Sewing-Machine, 23, 24, 38, 41-42, 47, 48
Conant, Jotham S., 22
Corliss, George H., 14, 15, 16
Dale, John D., 54
Davis, Ari, 19
Davis Sewing Machine Company, 40
Demorest, Madame, 53
Dodge, Rev. John Adam, 9
Domestic Sewing Machine Company, 40
Duncan, John, 6, 19
Elliptic Sewing Machine Company, 40
Ellithorp, S. B., 51
Ellithorp & Fox, 51
Empire Sewing Machine Company, 40
Fairy Sewing Machine, 53
Family Sewing Machine (Singer), 35
Finkle & Lyon Manufacturing Company, 40
Fisher, George, 19
Fisher, John, 15, 16
Florence Sewing Machine Company, 40
Folsom, J. G., 40
Gibbons, James, 15
Gibbs, James E. A., 45, 48
Goddard, Rice & Co., 25
Gold Medal Sewing Machine Company, 40, 53
Goodspeed & Wyman Sewing Machine Company, 40
Grasshopper, The, 35
Greenough, John J., 13, 14
Grover & Baker Sewing Machine Company, 24, 35, 37, 38, 40, 41
Grover, William O., 35, 38
Heberling, John, 54
Henderson, James, 6
Hendrick, Joseph, 49
Heyer, W. D., 52
Hook, Albert H., 50
Howe, Amasa B., 24
Howe, Elias, Jr., 11, 18, 19, 20, 21, 22, 23, 24, 28, 29, 33, 34, 41, 42, 138 (biographical sketch)
Howe Machine Company (Elias), 25
Howe Sewing Machine Company (Amasa, then B. P.), 24, 25, 40
Hunt, Walter, 10, 11, 19, 33, 138 (biographical sketch)
Jenny Lind (sewing machine), 30
Johnson, Joseph B., 22
Keystone Sewing Machine Company, 40
Kline, A. P., 27
Knowles, John, 9
Krems, Balthasar, 7, 19
Ladd & Webster Sewing Machine Company, 40
Leavitt Sewing Machine Company, 40
Lee, Edward, 27
Lee, E. & Co., 27, 28
Lerow, John A., 24, 25
Little Gem, 53
London Sewing Machine, 22
Lye, Henry, 9
McKay Sewing Machine Association, 40
Madersperger, Josef, 8, 9, 12, 13
Magnin, Jean Marie, 11, 22
Mason, The Honorable Charles, 13
Morey, Charles, 22
Morey & Johnson, 23, 34, 42
Newton, Edward, 13
Nichols and Bliss, 24
Palmer, Aaron, 52
Parham Sewing Machine Company, 40
Perry, James, 49
Phelps, Orson C., 25, 30, 31
Potter, Orlando B., 37, 38, 41
Remington Sewing Machine Company, 40
Robertson, T. J. W., 47
Rodgers, James, 15
Safford & Williams Makers, 22
Saint, Thomas, 4, 5, 19
Secor Sewing Machine Company, 40
Shaw & Clark Sewing Machine Co., 40, 54
Singer, Isaac Merritt, 23, 25, 30, 31, 33, 34, 35, 41, 142 (biographical sketch)
Singer, I. M. Company, 13, 32, 34, 40
Singer Manufacturing Co., 30, 40, 42
Singer’s Perpendicular Action Sewing Machine, 30, 31
Stone, Thomas, 6
[Pg 156]
Thimonnier, Barthelemy, 11, 19, 137 (biographical sketch)
Thomas, William, 20
Thompson, C. F., 40
Turtleback Machine (Singer), 35
Union Buttonhole Machine Company, 40
Warren and Woodruff, 28
Weatherill, Jacob, 37
Weed Sewing Machine Company, 40
Weisenthal, Charles F., 4, 19
Wheeler & Wilson Manufacturing Company, 22, 29, 30, 40
Wheeler, Wilson and Company, 24, 28, 41
Wheeler, Nathaniel, 27, 28
Willcox and Gibbs Sewing Machine Company, 40, 46, 48
Willcox, Charles, 46, 48
Willcox, James, 46
Wilson, Allen Benjamin, 26, 27, 28, 29, 30, 141 (biographical sketch). (See Wheeler & Wilson.)
Wilson, Newton, 4
Wilson, (W. G.), Sewing Machine Company, 40
Woolridge, Keene, and Moore, 24
Zieber, George, 30, 33
Adams and Dodge, 9
Aetna Sewing Machine Company, 40
American Buttonhole and Sewing Machine Company, 40
Archbold, Thomas, 13
Arrowsmith, George A., 11
Bachelder, John, 22, 30, 34, 41, 42
Baker, William E., 36 (see Grover & Baker)
Bartholf, A., 24, 40
Bartlett Sewing Machine Company, 40
Bartram & Fanton Manufacturing Company, 40
Bean, Benjamin W., 13, 14, 15
Blees Sewing Machine Company, 40
Bliss, George, 24
Blodgett and Lerow, 24, 26, 30
Blodgett, Sherbrune C., 25
Bradshaw, John A., 21, 22, 26, 27
Brown, W. N., 50
Centennial Sewing Machine Company, 40
Chapman, Edward Walter, 7, 19
Chapman, William, 7
Clark, D. W., 47, 49
Clark, Edward, 33, 34, 35
Combination, Sewing-Machine, 23, 24, 38, 41-42, 47, 48
Conant, Jotham S., 22
Corliss, George H., 14, 15, 16
Dale, John D., 54
Davis, Ari, 19
Davis Sewing Machine Company, 40
Demorest, Madame, 53
Dodge, Rev. John Adam, 9
Domestic Sewing Machine Company, 40
Duncan, John, 6, 19
Elliptic Sewing Machine Company, 40
Ellithorp, S. B., 51
Ellithorp & Fox, 51
Empire Sewing Machine Company, 40
Fairy Sewing Machine, 53
Family Sewing Machine (Singer), 35
Finkle & Lyon Manufacturing Company, 40
Fisher, George, 19
Fisher, John, 15, 16
Florence Sewing Machine Company, 40
Folsom, J. G., 40
Gibbons, James, 15
Gibbs, James E. A., 45, 48
Goddard, Rice & Co., 25
Gold Medal Sewing Machine Company, 40, 53
Goodspeed & Wyman Sewing Machine Company, 40
Grasshopper, The, 35
Greenough, John J., 13, 14
Grover & Baker Sewing Machine Company, 24, 35, 37, 38, 40, 41
Grover, William O., 35, 38
Heberling, John, 54
Henderson, James, 6
Hendrick, Joseph, 49
Heyer, W. D., 52
Hook, Albert H., 50
Howe, Amasa B., 24
Howe, Elias, Jr., 11, 18, 19, 20, 21, 22, 23, 24, 28, 29, 33, 34, 41, 42, 138 (biographical sketch)
Howe Machine Company (Elias), 25
Howe Sewing Machine Company (Amasa, then B. P.), 24, 25, 40
Hunt, Walter, 10, 11, 19, 33, 138 (biographical sketch)
Jenny Lind (sewing machine), 30
Johnson, Joseph B., 22
Keystone Sewing Machine Company, 40
Kline, A. P., 27
Knowles, John, 9
Krems, Balthasar, 7, 19
Ladd & Webster Sewing Machine Company, 40
Leavitt Sewing Machine Company, 40
Lee, Edward, 27
Lee, E. & Co., 27, 28
Lerow, John A., 24, 25
Little Gem, 53
London Sewing Machine, 22
Lye, Henry, 9
McKay Sewing Machine Association, 40
Madersperger, Josef, 8, 9, 12, 13
Magnin, Jean Marie, 11, 22
Mason, The Honorable Charles, 13
Morey, Charles, 22
Morey & Johnson, 23, 34, 42
Newton, Edward, 13
Nichols and Bliss, 24
Palmer, Aaron, 52
Parham Sewing Machine Company, 40
Perry, James, 49
Phelps, Orson C., 25, 30, 31
Potter, Orlando B., 37, 38, 41
Remington Sewing Machine Company, 40
Robertson, T. J. W., 47
Rodgers, James, 15
Safford & Williams Makers, 22
Saint, Thomas, 4, 5, 19
Secor Sewing Machine Company, 40
Shaw & Clark Sewing Machine Co., 40, 54
Singer, Isaac Merritt, 23, 25, 30, 31, 33, 34, 35, 41, 142 (biographical sketch)
Singer, I. M. Company, 13, 32, 34, 40
Singer Manufacturing Co., 30, 40, 42
Singer’s Perpendicular Action Sewing Machine, 30, 31
Stone, Thomas, 6
[Pg 156]
Thimonnier, Barthelemy, 11, 19, 137 (biographical sketch)
Thomas, William, 20
Thompson, C. F., 40
Turtleback Machine (Singer), 35
Union Buttonhole Machine Company, 40
Warren and Woodruff, 28
Weatherill, Jacob, 37
Weed Sewing Machine Company, 40
Weisenthal, Charles F., 4, 19
Wheeler & Wilson Manufacturing Company, 22, 29, 30, 40
Wheeler, Wilson and Company, 24, 28, 41
Wheeler, Nathaniel, 27, 28
Willcox and Gibbs Sewing Machine Company, 40, 46, 48
Willcox, Charles, 46, 48
Willcox, James, 46
Wilson, Allen Benjamin, 26, 27, 28, 29, 30, 141 (biographical sketch). (See Wheeler & Wilson.)
Wilson, Newton, 4
Wilson, (W. G.), Sewing Machine Company, 40
Woolridge, Keene, and Moore, 24
Zieber, George, 30, 33

Transcriber’s Notes:
Minor punctuation errors have been corrected without note. Footnotes have been moved to Chapter ends. The following typographical errors have been corrected/noted:
Minor punctuation errors have been fixed without comment. Footnotes have been relocated to the ends of the chapters. The following typographical errors have been corrected/mentioned:
Footnote 9 “Praktisches Wissen von der Nähmaschine.”—was “Praktisches wissen von der Nähmaschine.”
Footnote 9 “Practical Knowledge of the Sewing Machine.”—was “Practical knowledge of the sewing machine.”
p. 11 “a loop in the other”—was “a loop in the the other”
p. 11 “a loop in the other”—was “a loop in the other”
p. 19 “chainstitch, Thimonnier used”—was “chainstitch, Thimmonier used”
p. 19 “chainstitch, Thimonnier used”—was “chainstitch, Thimmonier used”
p. 76 “known to be in existence is”—was “known to be in eixstence is”
p. 76 “known to be in existence is”—was “known to be in existence is”
p. 80 “7501-12500, 1873;”—was “7501-12500, 8173;”
p. __A_TAG_PLACEHOLDER_0__ “7501-12500, 1873;”—was “7501-12500, 8173;”
p. 119 “shaped like an open _ into which”— A letter or symbol appears to be missing in the original between open and into.
p. 119 “shaped like an open _ into which”— A letter or symbol appears to be missing in the original between open and into.
p. 119 “181161-220318”—overlaps range of previous entry.
p. __A_TAG_PLACEHOLDER_0__ “181161-220318”—overlaps previous entry range.
p. 130 “June 30, 1874 152,618”—was “Jan. 30, 1874 152,618”
p. 130 “June 30, 1874 152,618”—was “Jan. 30, 1874 152,618”
p. 138 “Villefranche-sur-Saône”—was “Ville-franche-sur-Saône”
p. __A_TAG_PLACEHOLDER_0__ “Villefranche-sur-Saône”—was “Villefranche-sur-Saône”
Download ePUB
If you like this ebook, consider a donation!