This is a modern-English version of Rustic Carpentry, originally written by unknown author(s).
It has been thoroughly updated, including changes to sentence structure, words, spelling,
and grammar—to ensure clarity for contemporary readers, while preserving the original spirit and nuance. If
you click on a paragraph, you will see the original text that we modified, and you can toggle between the two versions.
Scroll to the bottom of this page and you will find a free ePUB download link for this book.
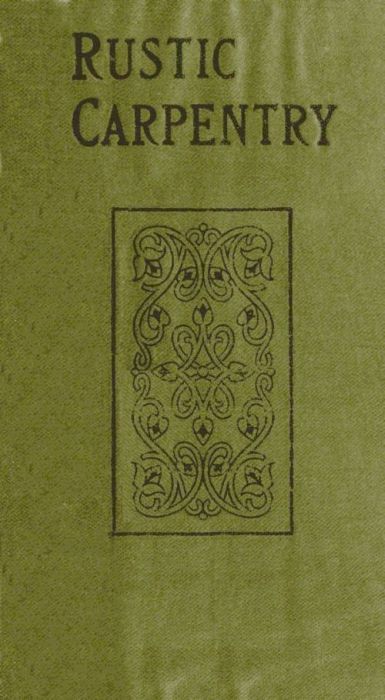
AUTHOR OF "HANDYBOOKS FOR HANDICRAFTS," AND OTHERS.

PREFACE.
This Handbook contains, in a form convenient for everyday use, a number of articles on Rustic Carpentry contributed by various authors to Work—one of the journals it is my fortune to edit.
This Handbook includes, in an easy-to-use format, several articles on Rustic Carpentry contributed by different authors to Job—one of the journals I have the pleasure of editing.
Readers who may desire additional information respecting special details of the matters dealt with in this Handbook, or instructions on kindred subjects, should address a question to the Editor of Work, La Belle Sauvage, London, EC., so that it may be answered in the columns of that journal.
Readers who want more information about specific details in this Handbook or guidance on related topics should send their questions to the Editor of Job, La Belle Sauvage, London, EC., so they can be addressed in that journal.
April 1907.
CONTENTS.
CHAPTER | PAGE | ||
I. | — | Light Rustic Work | 9 |
II. | — | Flower Stands, Vases, etc. | 22 |
III. | — | Tables | 36 |
IV. | — | Chairs and Seats | 40 |
V. | — | Gates and Fences | 52 |
VI. | — | Rosery Walk | 66 |
VII. | — | Porches | 71 |
VIII. | — | Canopy for Swing | 77 |
IX. | — | Aviary | 83 |
X. | — | Foot-bridges | 92 |
XI. | — | Verandahs | 98 |
XII. | — | Tool Houses, Garden Shelters, etc. | 106 |
XIII. | — | Summer Houses | 126 |
Index | 159 |
LIST OF ILLUSTRATIONS.
Fig. | PAGE | ||
1. | Understood. Please provide the text you would like me to modernize. | Combined Photograph Frame and Wall Bracket | 10 |
2. | Please provide the short phrases you would like me to modernize. | Bracket Section | 11 |
3. | Understood. Please provide the text you would like me to modernize. | Mini Easel | 12 |
4. | Got it! Please provide the text you'd like me to modernize. | Attaching Support to Easel | 13 |
5. | Sure, please provide the text you'd like me to modernize. | Mitered Joint | 13 |
6. | Understood! Please provide the text you would like me to modernize. | Mortise and Tenon Joint | 14 |
7, 8. | Understood. Please provide the text you would like me to modernize. | Vase | __A_TAG_PLACEHOLDER_0__, __A_TAG_PLACEHOLDER_1__ |
9/11 | Understood. Please provide the text for modernization. | Rustic Hall Tree | 17 |
12, 13. | Understood! Please provide the short piece of text you would like me to modernize. | Plant Stand | 18 |
14-16. | Understood. Please provide the text you want modernized. | Window Planter | __A_TAG_PLACEHOLDER_0__, __A_TAG_PLACEHOLDER_1__ |
17. | Understood. Please provide the text for me to modernize. | Plant Stand | 23 |
18. | Understood. Please provide the text you'd like me to modernize. | Bending Young Trees | 24 |
19. | Understood! Please provide the text you would like me to modernize. | Fixing Rails, etc., to Poles | 24 |
20. | Understood! Please provide the text you would like me to modernize. | Vase on Tripod Holder | 25 |
21. | Understood. Please provide the text for modernization. | Joint of Hexagon Sides of Vase | 25 |
22. | Understood! Please provide the text you'd like me to modernize. | Attaching the Sides and Legs of the Vase to the Base | 25 |
23. | I'm ready for your text. Please provide it. | Section of Twigs at Angles of Vase | 25 |
24, 25. | Understood! Please provide the text you'd like me to modernize. | Potted plant Stan | 26 |
26. | Understood! Please provide the text you would like me to modernize. | Connecting Rails to Uprights | 27 |
27. | Understood! Please provide the text you would like me to modernize. | Supporting End Shelves of Flower Pot Stand | 27 |
28. | Understood! Please provide the text you'd like me to modernize. | Fixing shelves of the stand | 27 |
29. | Understood. Please provide the text for modernization. | Large Square Planter | 28 |
30. | Understood! Please provide the text you'd like me to modernize. | Large Hex Vase | 28 |
31. | Understood. Please provide the text you'd like modernized. | Claw Foot Vase | 29 |
32. | Understood! Please provide the text you'd like me to modernize. | Foot of Rustic Table | 30 |
33. | Understood. Please provide the text you'd like me to modernize. | Planter Box | 31 |
34, 35. | Understood! Please provide the text you'd like me to modernize. | Moldings | 32 |
36. | Understood. Please provide the text for modernization. | Plant Pot | 32 |
37. | Understood! Please provide the text you'd like me to modernize. | Rectangular Garden Planter Stand | 33 |
38-40. | Understood. Please provide the text you would like me to modernize. | Rustic Stand | 34 |
41. | Understood. Please provide the text for modernization. | Plant Stand | 35 |
42. | Understood. Please provide the short phrases you would like me to modernize. | Square Table | 36 |
43. | Understood! Please provide the text you would like me to modernize. | Hexagonal Table | 37 |
44, 45. | Understood! Please provide the text you'd like me to modernize. | Hexagon Table Surface | __A_TAG_PLACEHOLDER_0__, __A_TAG_PLACEHOLDER_1__ |
46. | Understood! Please provide the text you'd like me to modernize. | Chair | 40 |
47. | Understood. Please provide the text you would like modernized. | Attaching Seat Rails to the Leg of the Armchair | 41 |
48. | Understood. Please provide the text you would like me to modernize. | Armchair Seat Frame Plan | 41 |
49, 50. | Understood! Please provide the text for modernization. | Garden Bench | __A_TAG_PLACEHOLDER_0__, __A_TAG_PLACEHOLDER_1__ |
51. | Understood. Please provide the text. | Rail and Post Joints | 43 |
52. | No text provided to modernize. | Armrest for Garden Seat | 44 |
53. | Got it! Please provide the text you'd like me to modernize. | Seat Layout Plan | 44 |
54, 55. | Understood. Please provide the text for modernization. | Garden Bench | __A_TAG_PLACEHOLDER_0__, __A_TAG_PLACEHOLDER_1__ |
56. | Please provide the text you'd like me to modernize. | Front Rail, Cross Rail, and Battens | 45 |
57. | Understood. Please provide the text you'd like me to modernize. | Seat Layout | 46 |
58-60. | Sure! Please provide the text you would like me to modernize. | Canopy Garden Bench | __A_TAG_PLACEHOLDER_0__-__A_TAG_PLACEHOLDER_1__ |
61. | Unchanged. | Canopy Plan | 50 |
62, 63. | Understood! Please provide the phrases you would like me to modernize. | Canopy Covers | 50 |
64. | Understood! Please provide the text you want me to modernize. | Seating Plan | 50 |
65-67. | Understood. Please provide the text you'd like me to modernize. | Garden Gate | __A_TAG_PLACEHOLDER_0__, __A_TAG_PLACEHOLDER_1__ |
68-70. | Understood! Please provide the short text you would like me to modernize. | Joints in Gate Frame | 54 |
71, 72. | Understood. Please provide the text you'd like me to modernize. | Fixing Twig Ends | 54 |
73. | Understood. Please provide the text you would like me to modernize. | Closing Style | 54 |
74-77. | Understood! Please provide the text you want me to modernize. | Joints in Gate Frame | __A_TAG_PLACEHOLDER_0__, __A_TAG_PLACEHOLDER_1__ |
78-80. | Understood. Please provide the text you would like me to modernize. | Fences | __A_TAG_PLACEHOLDER_0__, __A_TAG_PLACEHOLDER_1__ |
81, 82. | Understood. Please provide the text you'd like me to modernize. | Rustic Trellis with Seating and Gate | 59 |
83. | Understood! Please provide the text you'd like me to modernize. | Vertical Trellis Section | 60 |
84. | Understood. Please provide the text you would like me to modernize. | End Post and Trellis | 60 |
85. | Understood. Please provide the text you would like me to modernize. | Trellis Seatback | 60 |
86. | Understood! Please provide the text you'd like modernized. | Alternative Gate Design | 61 |
87. | Understood. Please provide the text you'd like me to modernize. | Hanging and Latching Gate | 62 |
88. | Understood! Please provide the text you'd like me to modernize. | Gate Catch | 63 |
89, 90. | Understood! Please provide the text you would like me to modernize. | Rustic Cart Entrance | __A_TAG_PLACEHOLDER_0__, __A_TAG_PLACEHOLDER_1__ |
91. | Understood. Please provide the text for modernization. | Rose Walk | 67 |
92. | Understood. Please provide the text you would like me to modernize. | Roof of Rosery Walk | 68 |
93. | Understood. Please provide the text you'd like me to modernize. | Entrance to Rose Garden Walk | 69 |
94, 95. | Sure! Please provide the text you would like me to modernize. | Veranda | __A_TAG_PLACEHOLDER_0__, __A_TAG_PLACEHOLDER_1__ |
96. | Understood! Please provide the text you'd like me to modernize. | Seat and Floor of the Cottage Porch | 74 |
97. | Understood! Please provide the text you would like me to modernize. | Gable Porch | 74 |
98. | Understood. Please provide the text you would like me to modernize. | Eaves Porch | 75 |
99. | Understood. Please provide the text to modernize. | Porch Roof | 75 |
100. | Understood. Please provide the text you'd like me to modernize. | Porch Gable | 76 |
101, 102. | Understood! Please provide the text you'd like me to modernize. | Rustic Swing Canopy | __A_TAG_PLACEHOLDER_0__, __A_TAG_PLACEHOLDER_1__ |
103. | Sure! Please provide the text you'd like me to modernize. | Attaching the Middle Post of the Canopy to the Sill | 79 |
104. | Understood! Please provide the text you'd like me to modernize. | Joints of Rails, Struts, and Posts for Canopy | 79 |
105. | Understood! Please provide the text you would like me to modernize. | Attaching Cross Rails to Plates and Posts of Canopy | 80 |
106, 107. | Understood. Please provide the text for modernization. | Hook and Thimble for Tent | 80 |
FIG. | PAGE | ||
108, 109. | Understood. Please provide the text for modernization. | Enclosed Seat for Canopy | 81 |
110. | Understood. Please provide the text you would like me to modernize. | Attaching Rope to Eyelet | 81 |
111, 112. | Understood. Please provide the text you would like me to modernize. | Birdhouse | __A_TAG_PLACEHOLDER_0__, __A_TAG_PLACEHOLDER_1__ |
113, 114. | Understood! Please provide the text you would like me to modernize. | Joint of Rails and Uprights for Aviary | 85 |
115. | Understood! Please provide the text you would like me to modernize. | Aviary Layout Plan | 86 |
116. | Understood. Please provide the short piece of text for modernization. | Aviary Cross Section | 87 |
117. | Understood. Please provide the text you'd like modernized. | Half Under View of the Bottom of the Aviary | 88 |
118. | Understood. Please provide the text you want me to modernize. | Aviary Door Wires | 88 |
119. | Got it! Please provide the text you would like me to modernize. | Part Longitudinal Section of Aviary | 89 |
120. | Understood. Please provide the text you'd like me to modernize. | Half Plan of Birdhouse Roof | 90 |
121, 122. | Sure, please provide the text you'd like me to modernize. | Rustic Footbridge | __A_TAG_PLACEHOLDER_0__, __A_TAG_PLACEHOLDER_1__ |
123. | Understood. Please provide the text you'd like me to modernize. | Beams for Footbridge | 93 |
124, 125. | Understood! Please provide the text you'd like me to modernize. | Post and Beam Joint | 93 |
126. | Understood. Please provide the text you would like me to modernize. | Middle rail and post of footbridge | 94 |
127, 128. | Understood. Please provide the text you would like me to modernize. | Connection of Strut to Post of Footbridge | 94 |
129. | Understood. Please provide the text you'd like me to modernize. | Twig Shaped to Fit Rail | 94 |
130. | Understood! Please provide the text that you'd like me to modernize. | Skyway Bridge | 95 |
131. | Understood. Please provide the text you would like modernized. | Girder and post bolted to sleeper | 96 |
132. | Got it! Please provide the text for modernization. | Elevated Footbridge at Lower Step (__A_TAG_PLACEHOLDER_0__) | 96 |
133, 134. | Understood! Please provide the text you'd like me to modernize. | Veranda | __A_TAG_PLACEHOLDER_0__, __A_TAG_PLACEHOLDER_1__ |
135. | Understood! Please provide the text you would like me to modernize. | Bottom of Post for Glazed Verandah | 103 |
136. | Sure! Please provide the text you'd like me to modernize. | Top of Post for Glazed Veranda | 103 |
137, 138. | Ready for your input! | Tool Shed | __A_TAG_PLACEHOLDER_0__, __A_TAG_PLACEHOLDER_1__ |
139. | Understood! Please provide the text you'd like modernized. | Common Way to Use Slabs | 108 |
140. | Understood. Please provide the text you would like me to modernize. | Ground Plan of Rustic Tool House | 109 |
141. | Understood. Please provide the short text for me to modernize. | Cap of Tool House Post | 111 |
142. | Understood. Please provide the text for modernization. | Garden Retreat | 112 |
143. | Understood! Please provide the short text you would like me to modernize. | Ground Framework of Garden Lounge | 113 |
144. | Got it! Please provide the short text you'd like me to modernize. | Back Framework for Garden Lounge | 113 |
145. | Understood! Please provide the text you would like modernized. | Cozy Porch | 114 |
146. | Understood! Please provide the text you'd like me to modernize. | Window sill | 115 |
147, 148. | Understood. Please provide the text for modernization. | Parts of Cozy Walls | 117 |
149-151. | Understood. Please provide the text you would like me to modernize. | Garden Getaway | __A_TAG_PLACEHOLDER_0__-__A_TAG_PLACEHOLDER_1__ |
152. | Understood! Please provide the text you'd like me to modernize. | Garden Retreat Seating | 122 |
153. | Understood. Please provide the text for modernization. | Joint of Garden Retreat at C (__A_TAG_PLACEHOLDER_0__) | 123 |
154. | Sure! Please provide the text you want me to modernize. | Detail of Front Joints (see C, __A_TAG_PLACEHOLDER_0__) | 124 |
155. | Understood! Please provide the text you'd like me to modernize. | Alternative Way to Attach Rails to Posts | 124 |
156. | Sure! Please provide the text you'd like me to modernize. | Section of Middle Rail at A (__A_TAG_PLACEHOLDER_0__) | 125 |
157. | Understood. Please provide the text you'd like me to modernize. | Detail of Middle Rail at B (__A_TAG_PLACEHOLDER_0__) | 125 |
158-161. | Understood. Please provide the text you would like me to modernize. | Lean-to Cabin | __A_TAG_PLACEHOLDER_0__-__A_TAG_PLACEHOLDER_1__ |
162-164. | Understood. Please provide the text you would like me to modernize. | Tennis court shelter | __A_TAG_PLACEHOLDER_0__, __A_TAG_PLACEHOLDER_1__ |
165. | Understood! Please provide the text you'd like me to modernize. | Connecting Plates to Corner Post | 135 |
166. | Understood! Please provide the text you would like me to modernize. | Attaching Sleeper to Posts | 135 |
167. | I'm ready to assist! Please provide the text you would like me to modernize. | Flooring Section | 135 |
168. | Understood. Please provide the text you would like me to modernize. | Finial | 135 |
169. | Got it! Please provide the text you want me to modernize. | Front Eaves Garden Shelter | 135 |
170. | Understood. Please provide the text you would like me to modernize. | Seat Section | 135 |
171. | Understood. Please provide the text for modernizing. | Securing Cushion to Seat | 137 |
172-174. | Understood. Please provide the text you want me to modernize. | Octagonal Summerhouse | __A_TAG_PLACEHOLDER_0__, __A_TAG_PLACEHOLDER_1__ |
175. | Understood! Please provide the text you would like me to modernize. | Collar Posts and Ends of Wall Plates | 141 |
176. | Understood! Please provide the text you would like me to modernize. | Beams above the entrance of the octagonal summer house | 141 |
177. | Understood. Please provide the text you would like modernized. | Window Side of Octagonal Gazebo | 143 |
178, 179. | Understood. Please provide the text for me to modernize. | Octagonal Summer House Table | 145 |
180. | Understood! Please provide the text you would like me to modernize. | Side Seating of the Octagonal Summer House | 147 |
181. | Understood! Please provide the text you'd like me to modernize. | Mosaic Chairs | 149 |
182-184. | Understood! Please provide the short piece of text you'd like me to modernize. | Octagonal Summer House with Three Roof Gables | __A_TAG_PLACEHOLDER_0__-__A_TAG_PLACEHOLDER_1__ |
185, 186. | I'm ready to assist! Please provide the text you'd like me to modernize. | Roof for Octagonal Garden House | 153 |
187. | Understood! Please provide the text you would like me to modernize. | Securing Glass to Rustic Window | 154 |
188, 189. | Understood. Please provide the short text you would like me to modernize. | Door for Octagonal Garden Shed | 155 |
190. | Understood. Please provide the text you would like me to modernize. | Part Plan of Octagonal Summer House | 156 |
191. | Understood! Please provide the text you'd like me to modernize. | Horizontal Section through Door Frames | 156 |
192. | Understood! Please provide the text you would like me to modernize. | Side Panel Part Section | 157 |
193. | Understood. Please provide the text you'd like me to modernize. | Attaching Plate to Posts | 157 |
194. | Understood. Please provide the short piece of text for modernization. | Finial | 157 |
RUSTIC CARPENTRY.
CHAPTER I.
LIGHT RUSTIC WORK.
Rustic carpentry does not demand great skill in woodworking, but it does require a large amount of artistic perception. The tools needed are but few, and the materials employed are comparatively cheap, although in many districts they are becoming dearer every year.
Rustic carpentry doesn't require advanced woodworking skills, but it does call for a good amount of artistic vision. The tools needed are minimal, and the materials used are relatively inexpensive, although in many areas they are getting more expensive each year.
It may be said that any articles made from the now popular bamboo may be made quite as effectively in light rustic work.
It can be said that any items made from the currently trendy bamboo can be made just as effectively in light rustic style.
For light rustic work, sticks of hazel, cherry, yew, blackthorn, birch, larch, fir, and the prunings of many varieties of shrubs may be used; but it is necessary that the material should be cut at the proper season, and thoroughly dried before being worked up. The sticks should be cut in mid-winter, as at that time the sap is at rest; if cut in the summer time the bark will peel off. If peeled sticks are required, they should be cut in the spring, when the sap is rising, as at that time the rind will come off easily. In some districts the copses are cleared of undergrowth periodically, and the sticks (generally hazel) sold to hurdle and spar makers. A selection of these sticks would be very suitable for the purpose here described.
For light rustic work, you can use sticks from hazel, cherry, yew, blackthorn, birch, larch, fir, and the trimmings from various shrubs; however, it's important that the material is cut at the right time and thoroughly dried before being used. The sticks should be cut in mid-winter when the sap is dormant; cutting them in the summer will cause the bark to peel off. If you need peeled sticks, they should be cut in spring when the sap is rising, as the bark will come off easily then. In some areas, they periodically clear the undergrowth in coppices, and sell the sticks (usually hazel) to makers of hurdles and spars. A selection of these sticks would work well for the purpose described here.
The sticks should be stacked in an open shed in an upright position if possible, and in such a manner that the air can freely circulate around them. When they are required for fishing rods or walking sticks they are hung up to season—this keeps them straighter; but the hanging of them up is not necessary for the work about to be dealt with. When the sticks have been put away for from six to twelve months, according to size, they will be ready for use, after being rubbed with a cloth or brushed to clean off the dust and bring up the colour of the bark. Fir cones may often be worked into a design, and bits of rough bark and the warts and burrs found on old elm trees may be collected by the rustic worker and put by for future use.
The sticks should be stacked in an open shed in an upright position if possible, allowing air to circulate around them freely. When they're needed for fishing rods or walking sticks, they are hung up to dry—this helps them stay straighter; however, hanging them up isn’t necessary for the task at hand. After being stored for six to twelve months, depending on their size, they will be ready for use, simply needing to be wiped down with a cloth or brushed to remove dust and enhance the bark's color. Fir cones can often be incorporated into designs, and pieces of rough bark and the warts and burrs found on old elm trees can be collected by the rustic worker for future projects.
One method of treatment for designs in light rustic work is to split the sticks and use them to overlay the work with a Swiss pattern, as [Pg 11] shown by Fig. 1; another method is to work the sticks up after the manner that canes are used in bamboo furniture (see Figs. 3 and Fig. 42, pp. 12 and 36).
Fig. 1 represents a wall bracket with a photograph or mirror in the frame. To make this, the piece forming the back is first cut out of 3/8-in. deal. The shelf, of ¾-in. deal, is then nailed to the bottom edge. Some straight hazel, fir, or other sticks are next selected and split; these are nailed round the edges of the back, and round the opening at the centre. The pieces round the opening overlap the edges about ¼ in., to form a rebate for the glass. The bare spaces at the sides and top may be covered in the following manner: Take a piece of brown elm bark and run a saw into it. Catch the sawdust, and, after warming the wood, cover it with thin glue.
Fig. 1 is a wall bracket designed to hold a photograph or mirror in a frame. To create this, start by cutting out the back piece from 3/8-inch wood. Next, nail a ¾-inch piece of wood to the bottom edge to serve as a shelf. Select some straight hazel, fir, or other sticks, then split them; these should be nailed around the edges of the back and around the opening in the center. The pieces surrounding the opening should overlap the edges by about ¼ inch to create a groove for the glass. The exposed areas on the sides and top can be covered like this: Take a piece of brown elm bark and saw into it. Collect the sawdust, and after warming the wood, apply thin glue to it.
Sprinkle the brown sawdust on the glued surface, and sufficient will adhere to cover the deal and give the frame a rustic appearance. Cork-dust or filings may be used instead of sawdust. Bunches of fir or larch cones are nailed to the corners, as illustrated; these should be pared at the back with knife or chisel to a flat surface. The outer edge of the shelf is finished with an edging of short [Pg 13] lengths of split stick nailed on. The general construction of the bracket, and the method of fixing the glass, will be clear from Fig. 2, which is a section through the centre.
Sprinkle the brown sawdust on the glued surface, and enough will stick to cover it and give the frame a rustic look. You can use cork dust or shavings instead of sawdust. Bunches of fir or larch cones are nailed to the corners, as shown; these should be trimmed at the back with a knife or chisel to make them flat. The outer edge of the shelf is finished with a border of short lengths of split stick nailed on. The overall design of the bracket and how to fix the glass will be clear from Fig. 2, which is a section through the center.
A small easel for photographs, or, if constructed larger, for a fire-screen, is shown by Fig. 3. It is made entirely of round sticks. Fig. 4 illustrates the method of attaching the back support—namely, by means of a couple of staples, which may be made out of a hairpin. In jointing round sticks together, the joints may be mitred by notching a V-shaped piece out of one stick and cutting the other to fit (Fig. 5); or a mortise and tenon, as represented by Fig. 6, may be used.
A small easel for photos, or, if made larger, for a fire screen, is shown by Fig. 3. It's made entirely of round sticks. Fig. 4 shows how to attach the back support—using a couple of staples that can be fashioned from a hairpin. When joining round sticks together, the joints can be mitered by notching a V-shaped piece out of one stick and cutting the other to fit (Fig. 5); or a mortise and tenon, as shown by Fig. 6, can be used.
In making the easel (Fig. 3), the top and bottom bars are mitred to the sides, and the central upright to the top and bottom bars. The joints are secured by either brads or panel pins. Care must be taken to bore for the nails with a bradawl, as nothing looks worse than splits in the work. The upright piece in the centre of the top bar may be secured by driving a long panel pin into the lower upright through the top bar, filing the head to a point to form a dowel, and driving the top piece on with a hammer.
In making the easel (Fig. 3), the top and bottom bars are cut at an angle to fit the sides, and the vertical piece is connected to the top and bottom bars. The joints are held together with either brads or panel pins. You need to be careful to drill the holes for the nails with a bradawl, as nothing looks worse than splits in the wood. The vertical piece in the center of the top bar can be secured by driving a long panel pin into the lower upright through the top bar, shaping the head into a point to make a dowel, and then tapping the top piece on with a hammer.
Where a small stick is joined to a larger one, as in the case of the filling-in pieces, a flat may be made with a knife or chisel on the larger stick, and the smaller one cut to fit and nailed on. In making a small easel, only a single stick attached to the [Pg 15] centre upright will be required to form a back support, but for a larger one it will be preferable to frame it as shown by Fig. 3.
Where a small stick connects to a larger one, like in the case of the filling pieces, you can create a flat surface with a knife or chisel on the larger stick, then cut the smaller one to fit and nail it on. When making a small easel, you only need one stick attached to the center upright to serve as a back support, but for a larger easel, it’s better to frame it as shown by Fig. 3.
The finished articles may be either stained and varnished or left plain. Cherry sticks look well if the bark is left the natural colour, and the ends, where exposed, cleaned off and varnished without being stained. Some sticks improve in colour if rubbed over with a rag moistened with linseed oil.
The completed pieces can be either stained and varnished or kept plain. Cherry sticks look nice when the bark is left its natural color, and the ends, where they are exposed, should be cleaned and varnished without staining. Some sticks also get better in color when you rub them with a rag that’s been dampened with linseed oil.
If a stain is required, one that is sold in bottles would be suitable, but a little vandyke brown, ground in water, and applied with a sponge, answers the purpose. Sometimes, as in the case of the table top (see Fig. 42, p. 36), it is [Pg 16] a good plan to stain the wood before nailing on the pattern work, or there will be danger, if the sticks are dark in colour, of the lighter wood showing through.
If you need a stain, one that comes in bottles would work well, but a bit of vandyke brown mixed with water and applied with a sponge does the job too. Sometimes, like with the tabletop (see Fig. 42, p. 36), it’s a smart idea to stain the wood before nailing on the pattern work, or you risk the lighter wood showing through if the sticks are dark-colored.
If the rustic work is intended to be placed out of doors, it should be given two or three coats of hard outside varnish.
If the rustic piece is meant to be outdoors, it should be covered with two or three coats of durable outdoor varnish.
The rustic flower-holder for table decoration, shown by Fig. 7, consists simply of a gipsy tripod formed with six rustic sticks, put together in the form shown, and tied with a length of bass. There is no attempt made at finish, but the sticks must be firmly tied together at the joints, and the ends of the bass can be left, either hanging loose or tied in a bow. The holder for the flowers is a cocoanut shell, which has been sawn in two, so as to leave one part a sort of cup or egg shape; three holes are bored with a bradawl at equal distances round the edge, and it is suspended from the tripod with three more pieces of the bass, which completes the arrangement. Of course, any small receptacle can be used in place of the cocoanut shell, but that, perhaps, carries out the rustic appearance the best, and is very easily obtained. Fig. 8 is an attempt to show the tripod when decorated.
The rustic flower holder for table decoration, shown by Fig. 7, is simply a gypsy tripod made of six rustic sticks arranged in the displayed shape and tied together with a length of bass. There’s no attempt at a polished finish, but the sticks need to be securely tied at the joints, and the ends of the bass can be left loose or tied in a bow. The holder for the flowers is a coconut shell that has been cut in half to create a cup or egg shape; three holes are drilled evenly spaced around the edge, and it’s suspended from the tripod with three additional pieces of bass, completing the setup. Of course, any small container can be used instead of the coconut shell, but that option emphasizes the rustic look best and is easy to find. Fig. 8 is an attempt to show the tripod when decorated.
The rustic hall-stand shown by Figs. 9 to 11 was made actually from branches and twigs of an old apple tree. The uprights and principal cross-pieces are 7/8 in. thick, and the criss-cross pieces are ½ in. thick. The bottom is made of four pieces 1½ in. thick. The longer ones measure 1 ft. 8 in., and the shorter ones 1 ft. 2 in.; they are nailed together in such a manner that the ends at the two front corners each cross and project 2½ in. The front uprights are 2 ft. high, the back ones 2 ft. 2 in.; the longer cross-pieces are 1 ft. 8 in., the shorter 11 in. The ends intersect and project 3 in. at each of the front corners; only the longest piece projects 3 in. at the back corners, the shorter pieces being cut off flush with the frame to allow of the stand fitting close to a wall.
The rustic hall stand shown in Figs. 9 to 11 was made from branches and twigs of an old apple tree. The vertical supports and main crosspieces are 7/8 inches thick, and the crisscross pieces are ½ inch thick. The bottom is made of four pieces that are 1½ inches thick. The longer pieces measure 1 foot 8 inches, and the shorter ones are 1 foot 2 inches; they are nailed together so that the ends at the two front corners cross and project 2½ inches. The front uprights are 2 feet high, while the back ones are 2 feet 2 inches; the longer crosspieces are 1 foot 8 inches, and the shorter ones are 11 inches. The ends intersect and project 3 inches at each of the front corners; only the longest piece projects 3 inches at the back corners, while the shorter pieces are cut flush with the frame so the stand can fit close to a wall.
Figs. 9 and 10.—Front and Side Views of Rustic Hall Stand. |
Fig. 11.—Design of Rustic Hall Stand, featuring Umbrella Pan. |
These cross-pieces are nailed to the uprights to allow the top ends of the latter to project 2 in. above them, this bringing the measurement of the oblong inner framework to 1 ft. 10 in. by 1 ft. 2 in. [Pg 18] The thin pieces are nailed on as shown in Fig. 9, being interlaced as much as possible. The back of the stand is treated in a similar manner. The whole of the wood is used as rough as possible, the bark being retained, with the knots, etc.; the ends are, however, pared off smooth with a chisel. Two coats of varnish finish the stand, save for the addition of a receptacle to catch the drainings from umbrellas, and for this the stand illustrated has a painted baking-tin A (Fig. 11).
These crosspieces are nailed to the vertical posts, allowing the top ends of the latter to stick out 2 inches above them, making the inner frame measure 1 foot 10 inches by 1 foot 2 inches. [Pg 18] The thin pieces are nailed on as shown in Fig. 9, being woven together as much as possible. The back of the stand is done in the same way. The wood is kept as rough as possible, leaving the bark and knots intact; however, the ends are smoothed out with a chisel. Two coats of varnish complete the stand, except for adding a container to catch the drips from umbrellas, for which the stand shown has a painted baking tin A (Fig. 11).
The rustic stool (Figs. 12 and 13) is intended to be made in pairs, and placed one on each side of the umbrella-stand above described, each supporting a plant, such as a fern or palm. The top of each stool is cut from 9 in. square 1-in. wood (wood from an old box answers well), and is sawn into an octagonal shape. A double row of pieces of apple, maple, or some other wood with good bark, is nailed around the edges, thicker pieces being used at the bottom than at [Pg 19] the top to give a graduated appearance. The entire top is then covered with straight pieces of stick, selected for the beauty of their bark. All pieces are nailed on with cut brads. The four legs are formed of 1-in. apple-wood 9 in. long. They are bevelled at the top to fit a square block of wood, 2 in. thick and 3 in. long, which is firmly secured to the top by two screws. This piece of wood should be fastened to the top before the rustic rods are placed in position. Two 2½-in. wire nails through each of the legs hold them quite securely to the central block. Portions of rustic wood, from ¼ in. to 3/8 in. in diameter, are then nailed across the legs, as shown in Fig. 12, the ends being allowed to cross each other and project about 1 in. all ways. The whole stool, when finished, stands 10½ in. high, and is so strong that it will support a heavy man with safety. The block of wood to which the legs are attached should be stained to match the rustic wood; permanganate of potash solution will effect this. Finally, two coats of clear varnish give a good finish to the work.
The rustic stool (Figs. 12 and 13) is meant to be made in pairs, positioned on either side of the previously mentioned umbrella stand, each holding a plant like a fern or palm. The top of each stool is cut from a 9-inch square of 1-inch wood (wood from an old box works well) and shaped into an octagon. A double row of pieces of apple, maple, or another type of wood with nice bark is nailed around the edges, using thicker pieces at the bottom than at the top for a graduated look. The entire top is then covered with straight pieces of stick chosen for the beauty of their bark. All pieces are secured with cut brads. The four legs are made from 1-inch apple wood and measure 9 inches long. They are beveled at the top to fit a square block of wood, 2 inches thick and 3 inches long, which is firmly attached to the top with two screws. This wood block should be secured to the top before the rustic rods are put in place. Two 2½-inch wire nails through each leg hold them securely to the central block. Pieces of rustic wood, ranging from ¼ inch to 3/8 inch in diameter, are then nailed across the legs, as shown in Fig. 12, with the ends crossing each other and extending about 1 inch on every side. The completed stool, when finished, stands 10½ inches tall and is sturdy enough to support a heavy person safely. The block of wood that the legs are attached to should be stained to match the rustic wood; a permanganate of potash solution will achieve this. Lastly, two coats of clear varnish provide a nice finish to the project.
Take care that the boards are stout enough to hold the brads firmly. The box measures about 21 in. by 7 in. by 7 in., and is wholly covered with mosaic of dark and light strips in panels. Strips are also nailed on the upper edges.
Make sure the boards are sturdy enough to hold the brads securely. The box is approximately 21 inches by 7 inches by 7 inches and is completely covered with a mosaic of dark and light strips in panels. Strips are also nailed along the upper edges.
The more elaborate window box (Figs. 15 and 16) can be made of a size to fit the window for which it is intended. A few holes should be bored in the bottom for drainage, and the front board is cut to the shape shown and the rustic ornament is nailed to the box and forms no part of the construction. In Fig. 16 wedge pieces are shown fitted to the stone sill to bring the box level; it is kept in position by two metal angle-pieces screwed both to the wood sill and to the back of the box.
The more detailed window box (Figs. 15 and 16) can be made to fit the size of the window it's meant for. A few holes should be drilled in the bottom for drainage, and the front board is cut into the shape shown, with the rustic decoration nailed to the box, which is not part of the main construction. In Fig. 16, wedge pieces are shown fitted to the stone sill to level the box; it is secured in place by two metal angle brackets that are screwed into both the wood sill and the back of the box.
CHAPTER II.
FLOWER STANDS, VASES, ETC.
The rustic-work flower stand (Fig. 17) may be 3 ft. high by 3 ft. 6 in. long by 9 in. wide. For the legs, select four curved saplings 3 ft. 3 in. long by 2½ in. in diameter; and as some difficulty may be experienced in obtaining them with the natural curves sufficiently alike, artificial methods of bending must be resorted to. Therefore get the saplings from 2 ft. to 3 ft. longer than the finished length, and bend them to shape by means of the Spanish windlass as shown in Fig. 18. Flexible six-strand fixing wire or stout hemp cord can be used; or a straining screw and link, as employed for tightening fencing wire, will answer equally well; keep the tension on till the wood is curved permanently, the time varying with the nature and condition of the wood, and the strain being applied gradually at intervals. The rails are tenoned to fit mortises in the legs, and battens are nailed to the lower long rails, to support the flower pots (see Fig. 19). The rustic work is then fixed diagonally to the rails. The ends that abut against the legs and centre-piece are pared away so as to make a neat joint, and angle boards are fitted to the under side of the lower rails to support the rustic work where it curves downwards.
The rustic-style flower stand (Fig. 17) can be 3 ft. high, 3 ft. 6 in. long, and 9 in. wide. For the legs, choose four curved saplings that are 3 ft. 3 in. long and 2½ in. in diameter. Since it might be hard to find saplings with natural curves that match, you'll need to use artificial methods to bend them. So, get the saplings that are 2 ft. to 3 ft. longer than the final length and bend them into shape using a Spanish windlass as shown in Fig. 18. You can use flexible six-strand fixing wire or strong hemp cord; a straining screw and link, like the ones used for tightening fencing wire, will work just as well. Keep the tension on until the wood is permanently curved, which will take different amounts of time depending on the type and condition of the wood, applying the strain gradually at intervals. The rails are tenoned to fit into mortises in the legs, and battens are nailed to the lower long rails to support the flower pots (see Fig. 19). The rustic work is then attached diagonally to the rails. The ends that touch the legs and center piece are trimmed for a clean joint, and angle boards are added to the underside of the lower rails to support the rustic work where it curves downwards.
The vase shown by Fig. 20 is hexagonal in shape, with vandyked sides fixed to a base supported upon tripod legs, and stands about 3 ft. 3 in. high. Elm boards are suitable for the sides and bottom; they are 1 ft. 3 in. high by 9 in. wide at the top end, and 6½ in. wide at the bottom by 1 in. thick. Shoot the edges of the boards to a bevel of 60°, and fix them with nails driven as shown at Fig. 21. When the six sides are completed, prepare the hexagon baseboard to suit. Bore holes in it for drainage, and also bore three equidistant holes, 1¼ in. in diameter, at an angle of about 60°, for the tenons of the legs to enter (see Fig. 22). Next screw the base to the sides, and fix on the barked rustic work. The twigs for this should be seasoned at least one year before using. They are sawn in halves, straight twigs being selected for the purpose. If necessary, shoot the edges slightly, so as to obtain a closer fit when fixing them in parallel. Begin by attaching the lower border to the hexagonal base, then the upright pieces over the angles, hollowed as shown at Fig. 23; next fix the top sloping pieces, and finally the horizontal twigs. The legs are nailed at the base of the vase (see Fig. 22); and at the centre, where they cross, they are further secured with twigs, which do the duty of rungs, as shown in Fig. 20.
The vase shown by Fig. 20 has a hexagonal shape, with angled sides attached to a base supported on tripod legs, and it stands about 3 ft. 3 in. tall. Elm boards work well for the sides and bottom; they are 1 ft. 3 in. high, 9 in. wide at the top, and 6½ in. wide at the bottom, with a thickness of 1 in. Bevel the edges of the boards to 60° and secure them with nails as shown at Fig. 21. Once the six sides are done, prepare the hexagon baseboard accordingly. Drill holes for drainage and also drill three evenly spaced holes, 1¼ in. in diameter, angled at about 60° for the legs’ tenons to fit into (see Fig. 22). Then screw the base to the sides and attach the rustic bark work. The twigs for this should be seasoned for at least a year before use. Cut them in half, choosing straight twigs for the job. If needed, slightly bevel the edges for a tighter fit when securing them in parallel. Start by attaching the lower border to the hexagonal base, then add the upright pieces at the corners, hollowed as shown at Fig. 23; next, attach the top sloped pieces, and finally, the horizontal twigs. The legs are nailed at the base of the vase (see Fig. 22); at the center where they cross, they are further secured with twigs, which serve as rungs, as illustrated in Fig. 20.
Figs. 24 and 25.—Side and End Views of Flower Pot Stand. |
The flower stand shown in front and end view by Figs. 24 and 25 has accommodation for sixteen pots. The two uprights are 2 ft. 8 in. high by about 2½ in. in diameter. The three rails are 2 ft. 9 in. long, and are tenoned to the posts as shown by Fig. 26; the posts are also tenoned and nailed to the sills (bottom rails), and strutted, as shown in Fig. 25. The method of fixing the shelves A and B (Fig. 24) is shown in Fig. 27, which is an under-side view; struts are also fitted, as shown in Fig. 25. The method of fixing the centre shelves is indicated at Fig. 28. The shelf, and also the struts C, D, E, and E1 (Figs. 24 and 25), are fixed to the centre rail; then the top diagonal braces are nailed to both the shelf and [Pg 28] the top rail, thus keeping the whole secure. The remainder of the work calls for no special instructions. Split twigs are used for the fencing around the shelves.
The flower stand shown in the front and side views by Figs. 24 and 25 can hold sixteen pots. The two vertical supports are 2 ft. 8 in. tall and about 2½ in. wide. The three horizontal rails are 2 ft. 9 in. long, and they are tenoned to the posts as indicated by Fig. 26; the posts are also tenoned and nailed to the bottom rails, and supported with struts, as shown in Fig. 25. The way of fixing the shelves A and B (Fig. 24) is illustrated in Fig. 27, which is a view from underneath; struts are also added, as shown in Fig. 25. The method of attaching the center shelves is detailed at Fig. 28. The shelf and the struts C, D, E, and E1 (Figs. 24 and 25) are attached to the center rail; then the top diagonal braces are nailed to both the shelf and the top rail, which keeps everything secure. The rest of the work does not require any special instructions. Split twigs are used for the fencing around the shelves.
Fig. 29 shows a square vase constructed from elm boards 1¼ in. thick. A fair size for the sides [Pg 29] will be 1 ft. 8 in. at the top and 1 ft. 5 in. at the base by 2 ft. high, including the 2½-in. plinth. The split twigs forming the decoration are 1½ in. wide, and spaced about 2 in. apart edge to edge.
Fig. 29 shows a square vase made from 1¼-inch thick elm boards. A good size for the sides will be 1 ft. 8 in. at the top and 1 ft. 5 in. at the bottom, standing 2 ft. tall, including the 2½-inch base. The split twigs used for decoration are 1½ inches wide and spaced about 2 inches apart from edge to edge. [Pg 29]
The vase shown by Fig. 30 is hexagonal in shape, the sides being 1 ft. 8 in. high by 1 ft. 2 in. wide at the top edge, and 1 ft. 0-½ in. at the base. The sides and bottom of both vases are connected as in Figs. 21 and 22. Five 1-in. holes are bored for drainage. The short feet having been secured [Pg 30] with screws driven from the inside, the split rustic work is bradded on in the same order as that described for Fig. 20.
The vase shown by Fig. 30 has a hexagonal shape, with sides measuring 1 ft. 8 in. high by 1 ft. 2 in. wide at the top edge, and 1 ft. 0-½ in. at the base. The sides and bottom of both vases are joined as in Figs. 21 and 22. Five 1-in. holes are drilled for drainage. The short feet are secured with screws driven in from the inside, and the split rustic work is attached in the same order as described for Fig. 20. [Pg 30]
The stands and vases should be given two coats of oil varnish, allowing the first coat to dry before applying the second.
The stands and vases should be given two coats of oil varnish, letting the first coat dry before putting on the second.
A big plant vase made from half a paraffin cask is illustrated by Fig. 31. An ordinary 40-gal. cask stands, roughly, some 3 ft. high, has a diameter of some 2 ft., and is made of good stout oak. Sawn through the middle, the paraffin barrel makes two admirable tubs. One such half is shown in Fig. 31. This it is proposed to render suitable for some large bushy plant, so it will have to be mounted on legs. The legs shown are simply so many pieces cut from rough branches. From a heap of stuff one can generally choose pieces sufficiently adapted to the purpose, though their exact contours will, of course, vary. Oak branches, technically known as "bangles," from which the bark has been taken to make tan, will do well; or if the bark is liked, apple-tree or elm boughs will be suitable. That these sticks should be rough and gnarled and knotted adds [Pg 31] to their effect. As the tub will be only partly covered with rustic mosaic work, it will be well before nailing anything upon it to paint it. A good dark brown or chocolate will go well with the natural bark. The rustic pieces will have to be cut through with the saw, the lengths being too great to be safely split with the hatchet—that is, with the exception of those round the lip, which are of thicker rod than the zig-zags; say, 1½ in. as compared with 1 in. In the zig-zags the light central strip is supposed to be of peeled withy, the darker ones on each side having the bark on, and being probably of hazel. Generally speaking, wrought brads are to be recommended for fixing rustic mosaic, but where, as in the present case, the strips have to be bent over a curved surface, small wire nails will be found more secure. Groups of fir cones, as shown, will prettily ornament the triangular spaces.
A large plant vase made from half a paraffin cask is shown in Fig. 31. An ordinary 40-gallon cask is about 3 feet tall, has a diameter of about 2 feet, and is made of sturdy oak. When cut in half, the paraffin barrel creates two excellent tubs. One of these halves is displayed in Fig. 31. This one is intended for a large bushy plant, so it will need to be set on legs. The legs shown are just several pieces cut from rough branches. From a pile of materials, you can typically find pieces suitable for the purpose, although their exact shapes will vary. Oak branches, technically referred to as "bangles," which have had their bark removed for tanning, will work well; or if you prefer the bark, apple-tree or elm branches will be appropriate. Having these sticks be rough, gnarled, and knotted adds to their charm. Since the tub will only be partly covered with rustic mosaic work, it's a good idea to paint it before nailing anything on. A nice dark brown or chocolate color will complement the natural bark. The rustic pieces will need to be cut with a saw, as their lengths are too long to be safely split with an axe—except for those around the rim, which are thicker than the zig-zag pieces; about 1.5 inches compared to 1 inch. In the zig-zags, the light center strip is meant to be made from peeled willow, while the darker strips on either side retain their bark, likely coming from hazel. Generally, wrought brads are recommended for attaching rustic mosaic, but since the strips need to bend around a curved surface in this case, small wire nails will be more secure. Groups of fir cones, as shown, will add a nice decorative touch to the triangular spaces.
A style of foot suitable for a one-leg flower stand or table is illustrated in plan and part section by Fig. 32.
A foot design that's ideal for a one-legged flower stand or table is shown in the plan and partial section by Fig. 32.
Fig. 33 shows the other half of the cask arranged for, say, a dwarf shrub, an orange-tree, [Pg 32] or the like. In small town or suburban premises, such tubs are specially useful where there is a back court into which anything green cannot otherwise be introduced. In this, it will be seen that by way of variety the tops of the staves have been sawn to a zig-zag line, which is followed a little below by a moulding of split rods. Alternative styles of moulding are shown by Figs. 34 and 35. Half-way between this and the bottom a band of mosaic is arranged in light and dark strips of withy and hazel. The bits filling the diamond-shaped centres of this pattern are cut from thicker stuff than the rest, so that they may project as bosses beyond the general level. Over the unavoidable iron hoop at bottom, from which place short strips would, if nailed, be often detached, a rough "dry-cask" wooden hoop has been fixed. At the sides two pieces of rough branch stuff have been placed to serve as handles, and to resist strain these should be secured from within by strong screws.
Fig. 33 shows the other half of the cask set up for, say, a dwarf shrub, an orange tree, [Pg 32] or something similar. In small towns or suburban areas, these tubs are especially handy where there’s a back yard that needs greenery but can’t accommodate regular planting. Here, you’ll notice that for variety, the tops of the staves have been cut into a zig-zag shape, which is followed slightly below by a molding of split rods. Different styles of molding are shown by Figs. 34 and 35. Halfway down to the bottom, there's a band of mosaic arranged in light and dark strips of willow and hazel. The pieces filling the diamond-shaped centers of this pattern are cut from thicker material than the rest, so they can stick out as raised details beyond the overall level. Over the unavoidable iron hoop at the bottom, from which short strips might often come loose if nailed, a rough "dry-cask" wooden hoop has been attached. On the sides, two pieces of rough branches have been added to serve as handles, and to withstand strain, these should be secured from the inside with strong screws.
The vase shown by Fig. 36 is intended for a somewhat low-growing flowering plant—say, a large bushy geranium. In its original character [Pg 33] it is an American lard pail. As in the last tub, the staves have been sawn to a more ornamental outline, and they have also been perforated. The ornamental strips of split rod have been arranged in straight vertical lines, to avoid the difficulty of bending and keeping them in place if bent round so small a vessel. The bottom of the pail is screwed down to an octagonal slab of wood, to the under side of which four short bits of rough bough are nailed as feet. As neither this nor the last tub is wholly covered with mosaic, they should, of course, first be painted. The slab at bottom will look very well rough, as shown, but if painted it will be improved by strips of split rod nailed round its edges.
The vase shown by Fig. 36 is designed for a low-growing flowering plant—like a large bushy geranium. Originally, it's an American lard pail. As in the last tub, the staves have been shaped into a more decorative outline and have also been perforated. The decorative strips of split rod are arranged in straight vertical lines to avoid the challenge of bending them and keeping them in place if they were curved around such a small vessel. The bottom of the pail is attached to an octagonal wooden slab, with four short pieces of rough branch nailed underneath as feet. Since neither this nor the last tub is completely covered with mosaic, they should definitely be painted first. The slab on the bottom will look nice rough, as shown, but it can be enhanced with strips of split rod nailed around its edges.
A garden plant stand, made from a soap box and mounted on legs is shown by Fig. 37. The easiest way to fix one of these legs on is to saw the piece of stuff in half to a distance from the top equal to the depth of the box, and then to cross-cut and remove one half. The corner of the box will be [Pg 34] brought to the middle of the cross-cut, and the leg nailed on to the side of the box. The piece which has been sawn off will then be cut through (quartered), and the proper quarter replaced and nailed to the end of the box. Frets, such as those shown in these two examples, are patterns of a kind well adapted to be worked out in rustic mosaic.
A garden plant stand, made from a soap box and set on legs, is shown by Fig. 37. The easiest way to attach one of these legs is to cut the piece in half at a distance from the top equal to the depth of the box, then cross-cut and remove one half. The corner of the box will be aligned with the middle of the cross-cut, and the leg will be nailed onto the side of the box. The piece that was cut off will then be quartered, and the right quarter will be put back and nailed to the end of the box. Frets, like those shown in these two examples, are patterns that work well for rustic mosaic projects.
Figures 38 to 40—Elevation, Section, and Horizontal Section of Rustic Pedestal. |
A design for a rustic flower-pot stand in imitation of bamboo is represented by Fig. 41. The height should be about 2 ft. 6 in. to the top, and the length from 3 ft. to 3 ft. 6 in. The box at the top may be about 9 in. wide and 8 in. deep. Care must be taken when putting the work together to get the frames true and square. Slovenliness in construction will completely spoil the appearance of the finished article. The box at the top is made to fit inside, and should be lined with a zinc tray. The outside may be covered with glue and brown sawdust.
A design for a rustic flower pot stand modeled after bamboo is shown by Fig. 41. The height should be about 2 feet 6 inches to the top, and the length should be between 3 feet and 3 feet 6 inches. The box at the top can be about 9 inches wide and 8 inches deep. Care must be taken when assembling the piece to ensure the frames are level and square. Sloppiness in construction will completely ruin the appearance of the finished piece. The box on top is designed to fit inside and should be lined with a zinc tray. The outside can be covered with glue and brown sawdust.
CHAPTER III.
TABLES.
A small rustic table which may, if desired, be used as a flower-pot stand, is illustrated by Fig. 42. The top may be made of ¾-in. stuff, and should have two ledges nailed underneath to prevent twisting. The table may be 1 ft. 10 in. high, with the top 15 in. square, or, if a larger size is required, 2 ft. 1 in. high, with the top [Pg 37] 18 in. square. The design is not suitable for tables of a larger size.
A small rustic table that can also be used as a flower-pot stand is shown in Fig. 42. The top should be made from ¾-in. material and have two ledges nailed underneath to prevent it from twisting. The table can be 1 ft. 10 in. high, with a top that is 15 in. square, or if you need a larger size, it can be 2 ft. 1 in. high, with a top that is 18 in. square. This design isn't suitable for larger tables.
The legs may be secured to the top by boring holes in the ledges and driving them in. The cross bars must be firmly secured to the legs, and, for the joints, the mortise and tenon shown at Fig. 6 (see p. 14) would be suitable. If the sticks used to form the legs are rather small, it will be better if the cross bars are kept a little higher on two of the sides, so that the mortises do not meet each other.
The legs can be attached to the top by drilling holes in the sides and driving them in. The cross bars need to be firmly attached to the legs, and for the joints, the mortise and tenon shown at Fig. 6 (see p. 14) would work well. If the sticks used for the legs are fairly small, it's better to place the cross bars a bit higher on two sides, so the mortises don't intersect.
The top is covered with a Swiss overlay pattern, made of split sticks. The design may be set out by drawing lines from corner to corner on the top, and across the top in the centre of each side. A smaller square is then drawn in the centre of the top, with diagonals at right angles to the sides of the top. Lines drawn from the corners of the small square to the corners of the top will form a four-pointed star. The pattern should be clearly outlined with a pencil. In nailing on the sticks, those round the outer edge of the top should be put on first and mitred at the corners. Next the outside sticks of the small square should be nailed on, then the eight pieces from the corners of the small square to the corners of the top.
The top is covered with a Swiss overlay pattern, made of split sticks. The design can be laid out by drawing lines from corner to corner on the top, and across the top in the center of each side. A smaller square is then drawn in the center of the top, with diagonals at right angles to the sides of the top. Lines drawn from the corners of the small square to the corners of the top will create a four-pointed star. The pattern should be clearly outlined with a pencil. When nailing on the sticks, those around the outer edge of the top should be attached first and cut at an angle at the corners. Then, the outside sticks of the small square should be nailed on, followed by the eight pieces from the corners of the small square to the corners of the top.
In working up patterns of the above description, always nail on the sticks that follow the outline of the design first. The filling-in pieces may be put on afterwards. Variety may be given to the patterns by using sticks of different colours; for instance, the design may be outlined in hazel or blackthorn, and filled in with hawthorn or peeled willow. The edges of the table top are concealed by nailing on an edging of short sticks or cones.
In creating patterns like the ones described above, always attach the sticks that outline the design first. The pieces that fill in can be added later. You can add variety to the patterns by using sticks in different colors; for example, you might outline the design with hazel or blackthorn and fill it in with hawthorn or stripped willow. The edges of the tabletop are covered by nailing on a trim of short sticks or cones.
Fig. 43 shows a small hexagon-top table for use in a summer-house or on the lawn. The following dimensions are suitable: Height 2 ft. 6 in., and diameter of circle for the hexagon top 2 ft. 9 in. The top is made from two or three 7/8-in. boards cramped together to the required width and fixed underneath with two battens 3½ in. wide by 1 in. thick. The four legs are dowelled and nailed to these battens and further stiffened by the rungs and the diagonal braces which are nailed to the legs. A corona is fixed around the edges of the table top, and the method of securing the board is shown in Fig. 44. In Fig. 45 the half plans show two ways of ornamenting the top. The twigs should be sawn so that in section they are less than a semicircle, and it will be an advantage to shoot their edges slightly, as then they will fit closer and cover the rough boards that form the table top.
Fig. 43 shows a small hexagon-shaped table meant for use in a summer house or on the lawn. The following dimensions are suitable: Height 2 ft. 6 in., and a diameter of 2 ft. 9 in. for the hexagon top. The top is made from two or three 7/8-inch boards pressed together to the required width and secured underneath with two battens that are 3½ inches wide by 1 inch thick. The four legs are doweled and nailed to these battens, further braced by rungs and diagonal supports that are nailed to the legs. A border is attached around the edges of the table top, and the method of securing the board is shown in Fig. 44. In Fig. 45, the half plans display two ways to decorate the top. The twigs should be cut so that in cross-section they are less than a semicircle, and it will help to angle their edges slightly, as this will allow them to fit tighter and cover the rough boards that make up the table top.
CHAPTER IV.
CHAIRS AND SEATS.
For the armchair (Fig. 46) select four slightly curved legs about 3 in. in diameter; the front pair are 2 ft. high and the back pair are 2 ft. 9 in. high. The front seat rail is 1 ft. 2 in. long by 2½ in. in diameter, the back rail is 1 ft. long, and the side rails are 1 ft. 3 in. long, their ends being trimmed to fit the legs, and fixed with inserted ash or elm dowels 7/8 in. in diameter; see Fig. 47. The height from the ground line to the [Pg 41] seat top is 1 ft. 4½ in. The battens forming the seat rest on the side rails, and cleats are fixed to the inner sides of the four legs (see Fig. 48) to support the extreme back and front battens. The arms and back are made in three parts, the scarfed joints coming immediately over the back legs. The trellis work is then added, and finally the struts and dentils are fixed around the seat. The chair can be made from unbarked wood without any dressing, or the bark may be removed and the wood, when dry, can be finished in stain and outside varnish.
For the armchair (Fig. 46), choose four slightly curved legs about 3 inches in diameter; the front pair should be 2 feet high, and the back pair should be 2 feet 9 inches high. The front seat rail is 1 foot 2 inches long and 2½ inches in diameter, the back rail is 1 foot long, and the side rails are 1 foot 3 inches long, with their ends trimmed to fit the legs and secured with inserted ash or elm dowels 7/8 inches in diameter; see Fig. 47. The height from the ground line to the seat top is 1 foot 4½ inches. The battens forming the seat rest on the side rails, and cleats are attached to the inner sides of the four legs (see Fig. 48) to support the extreme back and front battens. The arms and back are made in three parts, with the scarfed joints positioned directly over the back legs. The trellis work is then added, and finally, the struts and dentils are attached around the seat. The chair can be made from unbarked wood without any finishing, or the bark can be removed, and the wood, once dry, can be treated with stain and exterior varnish.
The garden-seats about to be described will look very effective if made of oak that has had the bark removed and the small twigs trimmed off clean; they should be finished in stain and varnish. In construction they are fairly simple.
The garden seats that will be described soon will look great if they're made of oak with the bark removed and the small twigs cut off neatly; they should be finished with stain and varnish. They're pretty simple to make.
For making the seat shown by Fig. 49, first select the three back posts, with their natural curves as much alike as possible. In diameter they should be from 2½ in. to 3 in. Select also two arm-posts and one centre leg for the front. Next cut two seat rails for the back and one rail for the front, 5 ft. or 6 ft. long as desired, and cut two side rails (see Fig. 50) and one centre rail, each 1 ft. 7 in. long. Work the ends of the rails to the shape of the posts as shown by Figs. 51 and 52, so that they make a fairly good joint, and bore the posts and rails with a 7/8-in. bit 1¼ in. deep, to receive dowels made of ash or elm. These are preferable to tenons formed on the rails themselves. Now try the whole together temporarily, and make good any defects.
To make the seat shown by Fig. 49, first select three back posts that have similar natural curves. They should be between 2½ inches and 3 inches in diameter. Also, choose two arm posts and one center leg for the front. Next, cut two back seat rails and one front rail, each 5 to 6 feet long, depending on your preference, and cut two side rails (see Fig. 50) and one center rail, each 1 foot 7 inches long. Shape the ends of the rails to fit the posts as shown by Figs. 51 and 52, so they create a decent joint, and drill the posts and rails with a 7/8-inch bit, 1¼ inches deep, to fit dowels made from ash or elm. These are better than tenons made on the rails themselves. Now, temporarily assemble everything together and fix any issues.
Then take the pieces apart, and coat the joints with a thick priming consisting of two parts of white-lead (ground in oil) and one part of red-lead thinned with boiled linseed oil. Drive the joints home and fix them with nails or screws and wipe off the surplus paint.
Then take the pieces apart and cover the joints with a thick primer made of two parts white lead (ground in oil) and one part red lead thinned with boiled linseed oil. Fit the joints tightly together and secure them with nails or screws, then wipe off any excess paint.
The top back rail and the arm-rest can next be fitted. The ends of the back rail are worked bird's mouth, to fit the posts. The arm-rests are treated in the same way at the back; they fit in vees cut in the front posts, and are fixed with nails.
The top back rail and the armrest can be attached next. The ends of the back rail are cut in a bird's mouth shape to fit the posts. The armrests are handled the same way at the back; they fit into V-shaped cuts in the front posts and are secured with nails.
Measure off and mark equal spaces for the struts, the ends of which are trimmed to fit the rails and posts. Secure them with two nails at each end. The seat (Fig. 53) is made up of split saplings laid as shown, with the ends pared to fit the rails and bradded on. Finally, fit the struts between the seat rails and the lower part of the posts.
Measure and mark equal spaces for the struts, which should be trimmed to fit the rails and posts. Secure them with two nails at each end. The seat (Fig. 53) consists of split saplings arranged as shown, with the ends shaped to fit the rails and fastened on. Finally, fit the struts between the seat rails and the lower part of the posts.
The framework for the chair shown by Figs. 54 and 55 is on the same principle as that already described. The segmental battens forming the seat run longitudinally, and their ends are shaped to fit the outer rails. The battens rest on a flat worked on the centre cross rail (see Figs. 55, Fig. 56, and Fig. 57). Fig. 56 also gives a part cross section near the centre leg, and shows the front rail placed out of centre and the cross rail resting on the leg, to which it is firmly nailed. When the seat is more than 5 ft. in length the battens require intermediate supports, which can be cut from split saplings. The panelling on the back is fixed to the top and bottom rails and supported in the centre by a wide longitudinal rail and two vertical rails at the mitres of the diamond centres. These are fitted in and secured, and then the vertical split twigs are fixed partly on them and also on the rails. Finally, struts are fixed to the seat rails and legs and covered with short twigs, with their lower ends running in a regular curve.
The design for the chair shown by Figs. 54 and 55 is based on the same principle as previously described. The segmental slats that make up the seat run lengthwise, and their ends are shaped to fit the outer rails. The slats rest on a flat surface crafted on the center cross rail (see Figs. 55, Fig. 56, and Fig. 57). Fig. 56 also provides a partial cross-section near the center leg, indicating that the front rail is positioned off-center, and the cross rail rests on the leg, to which it is securely nailed. If the seat is longer than 5 ft., the slats need additional supports, which can be made from split saplings. The paneling on the back is attached to the top and bottom rails and supported in the center by a wide lengthwise rail and two vertical rails at the corners of the diamond shapes. These are fitted in and secured, and then the vertical split twigs are attached partly to them and also to the rails. Finally, struts are attached to the seat rails and legs and covered with short twigs, with their lower ends curving regularly.
The upright posts and all the more important pieces will best be formed of somewhat small larch stuff; the smaller straight sticks may be hazel, birch, or withy. The last named, stripped of its bark, and used in some parts only, will form a pretty contrast with the darker rods. In filling spaces in back and canopy, a few pieces of crooked stuff are used; these will probably be of apple-tree.
The vertical posts and the more significant components should ideally be made from smaller larch wood; the thinner straight branches can be hazel, birch, or willow. The willow, which should be stripped of its bark and used only in certain sections, will create a nice contrast with the darker branches. When filling gaps in the back and canopy, a few curved pieces are used; these will likely be from apple trees.
The two posts A, on which almost the entire weight is sustained, should be let into the ground not less than 2 ft. They rise 5 ft. above the ground-line. They are set at a distance, measuring from centre to centre, of 4 ft. apart. The smaller posts (marked B), which support the seat, stand 17 in. in advance of those last named, and should be let into the earth 1 ft. The broad seat thus given is essential to comfort when the back of the chair is upright, as it must be in this instance.
The two posts A, which need to support almost all the weight, should be set into the ground at least 2 ft deep. They extend 5 ft above the ground line. They are spaced 4 ft apart from center to center. The smaller posts (marked B), which hold up the seat, should be placed 17 in. in front of the larger ones and should be set into the ground 1 ft deep. This wide seat is crucial for comfort when the chair's back is upright, as it needs to be in this case.
Two principal cross-pieces are nailed against the main posts. The lower one, of halved stuff, is 15 in. from the ground, and carries the back of the seat. The other is close to the top of the posts, and carries the back of the canopy. The canopy is chiefly supported on the three wall-plates, C (Fig. 59), which rest at one end on the heads of the posts, and towards the other on the struts, D (Fig. 60). Fig. 61 shows in plan the arrangement of the principal pieces forming the canopy: E E are the rafters of the gables, the lower ends of which rest on the wall-plates, and the upper against the pinnacle, F (Fig. 61). The back rafters are marked G G, and these rest their lower ends on the cross-piece and their upper against the pinnacle. Fig. 62 shows the filling-in of the two back panels of canopy; Fig. Fig. 63 that of the four side panels.
Two main cross-pieces are nailed to the main posts. The lower one, made of halved wood, is 15 inches from the ground and supports the back of the seat. The other is near the top of the posts and supports the back of the canopy. The canopy is mainly held up by the three wall-plates, C (Fig. 59), which rest on the tops of the posts at one end and on the struts at the other end, D (Fig. 60). Fig. 61 shows the layout of the main components that make up the canopy: E E are the rafters of the gables, with their lower ends resting on the wall-plates and their upper ends against the pinnacle, F (Fig. 61). The back rafters are marked G G, and their lower ends rest on the cross-piece while their upper ends are against the pinnacle. Fig. 62 shows the filling of the two back panels of the canopy; Fig. Fig. 63 shows that of the four side panels.
The filling-in of the back of the seat is clearly shown in Fig. 59.
The padding in the back of the seat is clearly shown in Fig. 59.
In Fig. 64 the seat proper appears in plan. Its front and ends are of halved stuff, nailed to the posts. The spars forming the seat are placed with spaces between them, that they may not hold moisture; for the same reason, it is advised that they should be of peeled withy.
In Fig. 64 the seat itself is shown in the diagram. Its front and ends are made from split materials, secured to the posts. The supports making up the seat are spaced apart to prevent moisture buildup; for the same reason, it’s recommended that they be made from stripped willow.
CHAPTER V.
GATES AND FENCES.
In many gardens there is a space devoted to the tool-house, potting shed, refuse head, etc. Shrubberies of course hide the unsightly appearance of this particular spot to a certain extent, but it may be found desirable to close the entrance to this part of the garden from the remainder, and the gate illustrated in front elevation by Fig. 65 [Pg 53] is, from its semi-rustic nature, particularly suitable. Fig. 66 shows a plan and Fig. 67 is a part back view. The gate is quite simple in construction, and should be of sufficient height to obstruct the view from each side.
In many gardens, there's an area dedicated to the tool shed, potting shed, waste area, etc. Shrubs tend to hide the unattractive look of this spot to some extent, but it might be a good idea to block off the entrance to this part of the garden from the rest. The gate shown in the front elevation by Fig. 65 [Pg 53] is quite fitting due to its semi-rustic design. Fig. 66 presents a plan, and Fig. 67 provides a partial back view. The gate is fairly simple to build and should be high enough to prevent visibility from either side.
Cut the closing and hingeing stiles 6 ft. long out of stuff 6 in. wide by 2½ in. thick. The three rails are of the same dimensions, and can be halved and dovetailed to the stiles or, better, mortised, tenoned, and wedged and braced, as shown in Figs. 68, 69, and 70. Separate pieces of stuff are fixed up the centre to form a muntin for supporting the rustic work; the necessity is obvious [Pg 55] from Fig. 66, where it will be noticed the twigs are outlined on the frame. Each twig has a bearing on the frame, and can thus be nailed individually.
Cut the closing and hingeing stiles to 6 ft. long from material that is 6 in. wide by 2½ in. thick. The three rails should be the same size and can be halved and dovetailed to the stiles or, preferably, mortised, tenoned, and wedged and braced, as shown in Figs. 68, 69, and 70. Separate pieces of material are attached in the center to create a muntin for supporting the rustic work; the need for this is clear [Pg 55] from Fig. 66, where it can be seen that the twigs are outlined on the frame. Each twig is supported by the frame and can be nailed in place individually.
**Figs. 74 and 75.—Designs for Rustic Gates.** |
Two stout gate hinges and hooks are required, and they can be bolted on with 7/16-in. Whitworth bolts and nuts, or secured from the back with square-headed coach screws. Now commence fixing on the unbarked twigs; they should be as straight as possible and used in their natural shape, without being split in halves.
Two sturdy gate hinges and hooks are needed, and they can be attached using 7/16-inch Whitworth bolts and nuts, or secured from the back with square-headed coach screws. Now start attaching the unbarked twigs; they should be as straight as possible and used in their natural shape, without being split in half.
The posts are 9 in. or 10 in. in diameter by 9 ft. long, 3 ft. being underground. Cut three mortises in the posts to receive the rails for the side fencing. These rails are nailed flush to the secondary posts, nails also being driven through [Pg 56] each mortise in the gate posts. Next dig the holes for the posts, these being kept at correct distances apart by nailing battens to the top and at the ground line while ramming in the posts. Two parts of old brickwork and one part of Portland cement will make a good concrete for the posts.
The posts are 9 in. or 10 in. in diameter and 9 ft. long, with 3 ft. buried underground. Cut three notches in the posts to hold the rails for the side fencing. These rails are attached flush to the secondary posts, with nails also being driven through [Pg 56] each notch in the gate posts. Next, dig the holes for the posts, keeping them properly spaced apart by nailing battens to the top and at ground level while securing the posts. Combine two parts of old brickwork with one part of Portland cement to create a strong concrete for the posts.
A week or more should elapse before the gate is hung to the posts. This may then be propped up fair between the two posts, and the positions should be marked for the staple of the latch, and hooks for the hinges. A rebate is formed for the gate on the posts by nailing on split sapling; see Figs. 67 and 73. Finally, a short post can be driven in the ground and fitted with a hook for retaining the gate when open wide.
A week or more should pass before the gate is attached to the posts. It can then be propped up nicely between the two posts, and the spots for the latch staple and hinge hooks should be marked. A groove is created for the gate on the posts by nailing on split sapling; see Figs. 67 and 73. Finally, a short post can be driven into the ground and fitted with a hook to hold the gate open wide.
**Figs. 76 and 77.—Designs for Rustic Gates.** |
Suitable designs for small rustic gates are given by Figs. 74 to 77. The wood for making gates to the two designs (Figs. 76 and 77) should have the bark removed. The chief rails and posts are about 2 in. thick, filled in with 1½-in. or 1-in. pieces, halved and nailed together where they cross. The joints may be hidden by bosses of planed wood (see Fig. 77). If the gate is to be removable, fix a hook on the hanging stile to engage [Pg 57] with a staple in the joint, and a pin in the bottom to turn round in a socket. The gate is then easily taken out of its hangings. Varnish the wood on completion.
Suitable designs for small rustic gates are provided by Figs. 74 to 77. The wood used for making gates in the two designs (Figs. 76 and 77) should have the bark removed. The main rails and posts should be about 2 inches thick, filled in with 1½-inch or 1-inch pieces, halved, and nailed together where they cross. The joints can be covered with decorative wooden bosses (see Fig. 77). If the gate is meant to be removable, attach a hook on the hanging stile to connect with a staple in the joint, and use a pin at the bottom that can rotate in a socket. This way, the gate can be easily taken out of its hangings. Varnish the wood once it’s completed.
The garden trellis illustrated at Fig. 81 will [Pg 58] form an attractive addition to the grounds of a suburban or country villa residence. In the case of new houses, the existence of such a trellis, with creepers ready planted, will often prove a deciding factor in effecting a quick sale or letting. The structure extends to a length of about 20 ft., but the dimensions may readily be altered to suit requirements. The material may be fir or other straight unbarked saplings and twigs. The posts are 12 ft. long; the four for the arch being 4 in. in diameter, and the others 3 in. or 3½ in. The rails are 2½ in. in diameter, and the twigs for the trellis, etc., 1¾ in. or 2 in. The bay seat with canopy is 6 ft. long by 1 ft. 4 in. wide.
The garden trellis shown at Fig. 81 will [Pg 58] be a beautiful addition to the grounds of a suburban or country villa. For new homes, having a trellis with climbing plants already in place can be a key factor in making a quick sale or rental. The structure is about 20 ft. long, but the dimensions can easily be adjusted to fit your needs. It can be made from fir or other straight, unbarked saplings and twigs. The posts are 12 ft. long; the four for the arch are 4 in. in diameter, while the others are 3 in. or 3½ in. The rails are 2½ in. in diameter, and the twigs for the trellis, etc., are 1¾ in. or 2 in. The bay seat with canopy measures 6 ft. long by 1 ft. 4 in. wide.
The position of the seats and posts and of the shores A, B, and C is clearly shown in the plan ( Fig. 82). The arrangement of the double posts adds materially to the stiffness of the framework, making long shores unnecessary. The shores are placed 3 ft. 6 in. above the ground line, and are inclined at an angle of 50°. The posts are sunk into the ground a distance of 3 ft., and well rammed in; rubble stones being mixed with the earth, as shown in the vertical section (Fig. 83).
The positions of the seats, posts, and shores A, B, and C are clearly indicated in the plan (Fig. 82). The setup of the double posts significantly adds to the stiffness of the structure, making long shores unnecessary. The shores are set 3 ft. 6 in. above the ground level and are angled at 50°. The posts are embedded in the ground to a depth of 3 ft. and are well packed; rubble stones are mixed with the soil, as shown in the vertical section (Fig. 83).
The arch may with advantage be entirely fitted together before being put in position, as a better job can thus be made of the joints of the short rails and struts. The joints in the remainder of the work, with the exception of the gate, are of the simplest description. The rail ends are bevelled and notched to the posts, and secured with nails as shown in the sectional view of the trellis at Fig. 84.
The arch can be fully assembled before installation, which allows for better fitting of the joints in the short rails and struts. The joints in the rest of the structure, except for the gate, are very straightforward. The ends of the rails are beveled and notched to fit the posts, and are secured with nails as illustrated in the sectional view of the trellis at Fig. 84.
Having erected the framework in position, next sink and well ram the shores deep into the ground, and splay and nail the top ends to the [Pg 62] uprights. Also fix the shorter posts for the seats, letting them into the ground about 1 ft. 6 in. The end seat bearers are fixed to the end posts, and the centre bearers to the front and back central posts. The seat battens are saplings split in two, the flat portion being laid downwards and nailed to the bearers (see Fig. 83). Fig. 85 is an enlarged section through the seat back, showing the method of securing the smaller twigs to the rails. The fixing of the vertical pieces in the lower part, and the inclined lengths above, will complete this portion of the screen.
Having set the framework in place, now drive the supports deep into the ground and spread and nail the top ends to the uprights. Also, attach the shorter posts for the seats, embedding them into the ground about 1 ft. 6 in. The end seat bearers are secured to the end posts, and the center bearers are attached to the front and back central posts. The seat battens are saplings split in two, with the flat side facing down and nailed to the bearers (see Fig. 83). Fig. 85 is an enlarged section through the seat back, showing how to secure the smaller twigs to the rails. Securing the vertical pieces at the bottom and the angled pieces above will finish this part of the screen.
The gate, shown enlarged at Fig. 86, which gives an alternative design, is 3 ft. 9 in. wide by 4 ft. 6 in. high. The stiles are 4 ft. 9 in. long and about 2½ in. in diameter, and should be as straight as possible, with the twigs neatly trimmed on; the rails should be at least 2¼ in. in diameter, trimmed to fit the stiles, and secured with inserted hardwood dowels 1 in. in diameter, as shown at Fig. 26, p. 27.
The gate, shown enlarged at Fig. 86, offers an alternative design and measures 3 ft. 9 in. wide by 4 ft. 6 in. high. The vertical posts are 4 ft. 9 in. long and about 2½ in. in diameter, and they should be as straight as possible, with the twigs neatly trimmed. The horizontal rails should be at least 2¼ in. in diameter, cut to fit the vertical posts, and secured with inserted hardwood dowels that are 1 in. in diameter, as shown at Fig. 26, p. 27.
The diagonal struts in the top panel should be fitted and in place before the rails and stiles are finally secured; the vertical twigs in the lower panel should be similarly fitted and nailed before the rails are secured to the stiles. Ordinary forged hooks and eyes are used for hanging the gate; these are secured to the stile and post with nuts and washers, as shown in the enlarged horizontal section (Fig. 87).
The diagonal support beams in the top panel should be properly installed before the rails and vertical pieces are finally secured. The vertical supports in the lower panel should also be fitted and nailed down before the rails are attached to the vertical pieces. Standard forged hooks and eyes are used to hang the gate; these are attached to the vertical piece and post with nuts and washers, as illustrated in the enlarged horizontal section (Fig. 87).
A mortice is cut in the closing stile to receive the latch, the catch for the latter being a simple forging (see Fig. 88) with a pointed tang for driving into the post.
A mortice is cut in the closing stile to hold the latch, with the catch for it being a simple forged piece (see Fig. 88) that has a pointed tang for driving into the post.
A rustic carriage entrance is shown by Fig. 89. The intention is, of course, that the rustic archway above the gates shall be more or less clothed with climbing plants. It is for roses that the structure will be best adapted, though clematis or honeysuckle will look well upon it. Ivy would look too heavy, and, if neglected, might even prove too heavy in other respects. Light as the arch may appear, the four posts grouped to form the turret on either side are so tied and braced together as to be, to all intents and purposes, a solid pillar, 30 in. square, and fully equal to resisting any outward thrust of the rafters. In the elevation (Fig. 89), to avoid confusion, no indication is given of the work forming the farther side of the arch, though something of it would necessarily be seen from the front; the two sides will be alike. Figs. 89 and 90 are drawn to a scale of ½ in. to the foot.
A rustic carriage entrance is shown by Fig. 89. The idea is that the rustic archway above the gates will be covered with climbing plants. Roses are the best fit for this structure, but clematis or honeysuckle will also look nice on it. Ivy would be too heavy, and if neglected, could become problematic in other ways. Although the arch may seem light, the four posts on either side that create the turret are securely tied and braced together to act as a solid pillar, measuring 30 inches square, and capable of withstanding any outward pressure from the rafters. In the elevation (Fig. 89), to avoid confusion, there’s no indication of the work making up the far side of the arch, although some of it would still be visible from the front; both sides will be the same. Figs. 89 and 90 are drawn to a scale of ½ inch to the foot.
The posts, and at least all the more important straight pieces, should be of larch. The wood chosen for filling-in should have picturesque forks and contortions. Small oak bangles will, perhaps, be most appropriate.
The posts, especially the more important straight ones, should be made of larch. The wood selected for infill should have interesting forks and twists. Small oak rings will probably be the most suitable.
In the ground plan of the left-hand turret (Fig. 90) it will be seen that the posts used—four at each end—are some 5 in. or 6 in. in diameter, and that the largest is selected as hanging-post for the gate. From centre to centre they are set 2 ft. 3 in. apart. They are 13 ft. long—that is, 10 ft. 4 in. above ground and 2 ft. 8 in. below. The rafters of the arch spring from them 7 ft. from the ground, and at this point each post is surrounded by a cap, formed of four pieces of [Pg 64] quartered stuff nailed upon it. The rafters are not mortised into the post, but if, instead of being merely nailed, they are attached by a bolt and nut, a stronger joint will be made.
In the layout of the left-hand turret (Fig. 90), you can see that the posts used—four at each end—are about 5 to 6 inches in diameter, and the largest one is chosen as the hanging post for the gate. They are spaced 2 feet 3 inches apart from center to center. Each post is 13 feet long, which means 10 feet 4 inches is above ground and 2 feet 8 inches is below. The rafters of the arch rise from them at 7 feet above the ground, and at this point, each post is surrounded by a cap made of four pieces of [Pg 64] quartered material nailed on. The rafters are not mortised into the post, but if they are attached by a bolt and nut instead of just being nailed, a stronger joint will be created.
The upper rafters, back and front, are connected by five straight cross-pieces, whose ends show in Fig. 89. The spaces between these are filled up very much at random with crooked stuff.
The upper rafters, both back and front, are connected by five straight cross-pieces, whose ends are visible in Fig. 89. The spaces between these are filled quite haphazardly with twisted materials.
The four posts of each turret are bound together close beneath their tops by cross-pieces [Pg 65] nailed outside them, whilst from their tops, and nailed down to them, slant four short rafters, which meet pyramid-wise in the centre. The filling up of the upper parts of the turrets, as well as of the front and back of the arch, is with a mixture of straight and crooked stuff, the arrangement of which is clearly shown in the elevation (Fig. 89).
The four posts of each turret are connected just below their tops by cross-pieces nailed to the outside. From their tops, four short rafters slant down and meet in a pyramid shape in the center. The upper parts of the turrets, as well as the front and back of the arch, are filled with a mix of straight and crooked materials, which is clearly illustrated in the elevation (Fig. 89). [Pg 65]
The lower parts of the turrets and the gates must be constructed in such a way as to exclude animals; the palings are so arranged as not to leave a space between them wider than 3 in. The rails of the gates should, of course, be mortised into the heads and hinge-trees.
The lower sections of the turrets and gates should be built to keep out animals; the fence is designed so that there is no gap wider than 3 inches between the slats. The rails of the gates should clearly be fitted into the tops and hinge posts.
CHAPTER VI.
ROSERY WALK.
The rustic construction here illustrated is intended primarily as a trellis over which to train roses, and to form a shady and fragrant walk, and generally to contribute to the adornment of the flower garden. It can readily be adapted so as to form a roofed-in track from a door to the public roadway; and the means of so adapting it will be explained later.
The rustic structure shown here is mainly designed as a trellis for growing roses, creating a shaded and fragrant pathway, and adding to the beauty of the flower garden. It can easily be modified to become a covered path from a door to the public road, and instructions for making these adjustments will be provided later.
The materials will be entirely rough wood in its natural bark. For the posts fir poles of some kind should be chosen, and larch is especially to be preferred both as regards durability and appearance. All the smaller pieces which show as straight stuff may well be of the same kind of wood as the posts, though hazel is best for the finer rods. It will be seen that in the mere filling-in much crooked stuff is used, and for this apple branches, or indeed almost anything that comes to hand, will answer.
The materials will be all rough wood with its natural bark. For the posts, you should choose fir poles, and larch is especially preferred for both durability and looks. All the smaller pieces that are straight can be made of the same type of wood as the posts, although hazel is better for the finer rods. You'll notice that in just filling in, a lot of crooked pieces are used, and for this, apple branches, or really anything you have on hand, will work.
The rosery walk (Fig. 91) is 4 ft. wide, and the rustic erection is carried on two rows of pillars or collar-posts ranged at intervals of 3 ft. These posts should be let into the ground 2 ft., and well rammed in. They should have an average diameter of 3 in. or 3½ in., except in the case of each third one, as that which in Fig. 91 is seen standing in the middle of the portion with the lower roof; such pillars may be smaller as having little weight to bear, and will look better than they would do if equal in size to the others. Resting on the line of posts lies the wall-plate (A A, Fig. 92), the top of which is 5 ft. 6 in. from the ground line.
The rosary walk (Fig. 91) is 4 ft wide, and the rustic structure is supported by two rows of pillars or collar-posts spaced 3 ft apart. These posts should be set into the ground by 2 ft and packed in well. They should have an average diameter of 3 in. or 3½ in., except for every third post, like the one seen in Fig. 91 that stands in the middle of the section with the lower roof; those pillars can be smaller since they carry less weight and will look better than if they were the same size as the others. The wall-plate (A A, Fig. 92) rests on the line of posts, with the top at a height of 5 ft 6 in. from the ground line.
From each group of four large collar-posts rise four rafters (B, B, Fig. 92), meeting at top pyramid-wise. They rise to a height from the ground of 7 ft. 6 in., and have, therefore, to be 3 ft. 4 in. long. Half-way up them—that is, 6 ft. 6 in. from the ground line—the purlins (C, C, Fig. 92) are nailed upon them. Figs. 91 [Pg 69] and 92 alike show how the space between wall-plate and purlin is filled in, and Fig. 92 shows how the space, 7 ft. 3 in. long, stretching from one pyramidal portion to the next, is covered with a flat roof of open rustic work lying upon the purlins. This space, it will be observed, is chiefly filled in with crooked stuff.
From each group of four large collar posts, four rafters (B, B, Fig. 92) rise toward each other in a pyramid shape. They reach a height of 7 ft. 6 in. from the ground and need to be 3 ft. 4 in. long. Halfway up—meaning 6 ft. 6 in. off the ground—the purlins (C, C, Fig. 92) are attached to them. Figs. 91 [Pg 69] and 92 show how the area between the wall plate and purlin is filled in, and Fig. 92 illustrates how the space, which is 7 ft. 3 in. long, stretching from one pyramidal section to the next, is covered with a flat roof made of open rustic work sitting on the purlins. It's worth noting that this space is mainly filled with twisted materials.
Fig. 93 shows how the upper part of the rosery would appear at one of its ends, and explains how the roof would be in section—the shaded parts give the form of the roof in its lower portions; whilst if the cross-piece, D (which is on a level with the purlins), is supposed to be removed, there is presented with the dotted lines, B, B, a section through the middle of one of the higher pyramidal portions.
Fig. 93 shows how the top part of the rosery would look at one of its ends, and explains how the roof would appear in section—the shaded areas indicate the shape of the roof in its lower sections; while if the cross-piece, D (which is level with the purlins), is assumed to be taken out, the dotted lines, B, B, illustrate a section through the center of one of the taller pyramid-shaped sections.
Over the middle of the entrance is a rough knot or a piece of root.
Over the middle of the entrance is a rough knot or a piece of root.
The filling-in of the sides of the rosery is plainly shown in the elevation, Fig. 91. For its better preservation from damp, this work is kept 4 in. from the ground.
The filling of the sides of the rosery is clearly shown in the elevation, Fig. 91. To protect it better from moisture, this work is kept 4 inches off the ground.
Supposing that, as was suggested above, the design is to be utilised for a dry path with a covering of metal or other light material, it will be well to keep the whole roof to the level of the pyramidal portions—a ridge-piece will have to [Pg 70] be used—and the rafters, instead of following the present arrangement, will meet in pairs opposite to the pillars. Instead of round stuff, also, use halved stuff for the rafters and purlins, the sawn side being uppermost. The space between ridge-piece and purlin can then be filled in the same manner as that between purlin and wall-plate.
Supposing that, as mentioned earlier, the design is meant for a dry path covered with metal or another lightweight material, it's a good idea to keep the entire roof level with the pyramidal sections—a ridge piece will need to be used—and the rafters, instead of following the current setup, will meet in pairs opposite the pillars. Also, instead of using round materials, use split materials for the rafters and purlins, with the sawn side facing up. The space between the ridge piece and purlin can then be filled in the same way as that between the purlin and wall plate.
CHAPTER VII.
PORCHES.
The rustic porch shown in front elevation by Fig. 94 and in vertical section by Fig. 95 is constructed from straight, well-seasoned saplings and twigs, from which, in each case, the bark has been removed. The design is eminently suitable for a farmhouse or a country cottage. The porch is of large dimensions, and is provided with seating accommodation on each side. The seats do not appear in the elevations, but one side is shown in the part plan (Fig. 96).
The rustic porch depicted in the front view by Fig. 94 and in the vertical section by Fig. 95 is made from straight, well-seasoned saplings and twigs, with the bark removed from each. The design is perfect for a farmhouse or country cottage. The porch is spacious and features seating on both sides. While the seats aren't shown in the elevations, one side is depicted in the partial plan (Fig. 96).
The seats are 1 ft. 6 in. high by 1 ft. 2 in. wide. The battens are 1¾ in. wide by 1½ in. thick, and are supported on cross-pieces fixed to the front posts and wall; a centre batten being fixed to the centre panel, and supported by a diagonal bracket running from the front down to the sill-piece. The floor space is 7 ft. wide, and stands out 5 ft. from the walls.
The seats are 1 ft. 6 in. high and 1 ft. 2 in. wide. The battens are 1¾ in. wide and 1½ in. thick, supported on cross-pieces attached to the front posts and the wall; a center batten is fixed to the center panel and is supported by a diagonal bracket running from the front down to the sill piece. The floor space is 7 ft. wide and extends 5 ft. from the walls.
The posts are 7 ft. 6 in. long by 4 in. in diameter. The front posts are preferably dropped over metal dowels leaded into the stone floor, at 1 ft. 2 in. centres, while the side posts are at 10½ in. centres, and of smaller section—say about 3 in. in diameter. One post, 5 in. in diameter, sawn longitudinally through the centre, does duty for the two wall-posts, the flat portion being, of course, scribed to the wall, the latter having been previously plugged for the reception of the fixing nails.
The posts are 7 ft. 6 in. long and 4 in. in diameter. The front posts are preferably placed over metal dowels set into the stone floor, spaced 1 ft. 2 in. apart, while the side posts are spaced 10½ in. apart and are smaller in size—around 3 in. in diameter. One post, 5 in. in diameter, cut lengthwise through the center, serves as the two wall posts, with the flat part fitting against the wall, which has been previously drilled for the nails to secure it.
The rails are tenoned to the posts, and 1¼ in. diameter holes are bored in the posts, and also in the ends of the rails, for the reception of the inserted tenons. The ends of the rails are also [Pg 72] hollowed to fit roughly the posts (see Fig. 97). The lower rail is 10 in. up from the floor, while the centre rail is 3 ft. 4 in. up. The rail immediately below (Fig. 95) is 10 in. below the centre rail.
The rails are fitted into the posts with tenons, and 1¼ inch diameter holes are drilled into the posts, as well as the ends of the rails, to accommodate the inserted tenons. The ends of the rails are also hollowed out to roughly fit the posts (see Fig. 97). The lower rail is positioned 10 inches above the floor, while the center rail is 3 feet 4 inches above the floor. The rail directly below (Fig. 95) is 10 inches below the center rail.
The top ends of the front posts are hollowed, and fitted with inserted dowels for the reception of the front rail. The six side-posts are finished off square, and have tenons which fit into the plates. The front ends of the plates are notched to the front top rail. The rafters are 5 ft. 7 in. long by 3 in. deep and 2 in. wide, wrought and [Pg 74] chamfered and birdsmouthed to the plates as shown at Fig. 98. The ridge piece, 4 in. deep by 1½ in. thick, projects 5 ft. 2 in. from the wall. On the front end of the ridge is fixed the finial, which is 2 in. square. The rafters are covered with 1-in. V-jointed, wrought, grooved and tongued boarding, cut in 5-ft. 4-in. lengths, and laid horizontally or at right angles to the rafters.
The top ends of the front posts are hollowed out and fitted with inserted dowels to hold the front rail. The six side posts are squared off and have tenons that fit into the plates. The front ends of the plates are notched to align with the front top rail. The rafters are 5 ft. 7 in. long, 3 in. deep, and 2 in. wide, shaped and chamfered with birdsmouth cuts to fit onto the plates as shown at Fig. 98. The ridge piece measures 4 in. deep by 1½ in. thick and extends 5 ft. 2 in. from the wall. The finial, which is 2 in. square, is fixed to the front end of the ridge. The rafters are covered with 1-in. V-jointed, shaped, grooved, and tongued boards cut to 5-ft. 4-in. lengths, laid out horizontally or at right angles to the rafters. [Pg 74]
The roof may be covered with slates, with Broseley tiles, with wood shingles, or with thatch. A part plan of the roof is shown in Fig. 99. An enlarged section of the front angle of the gable is given in Fig. 100. Two boards, each 1 ft. 1 in. wide by 1¼ in. thick, are fixed to the outer rafters and run parallel with them; the heels of the two [Pg 75] boards abutting on the front top rail, to which they are nailed. The split-twig herringbone ornament is also nailed to these boards. On the inner edges of the boards are secured twigs of about 1¾-in. in diameter, which are rebated to fit to the edges as shown in Fig. 100. The front projecting ends of the roofing boards are concealed by split twigs of about 2½-in. or 3-in. diameter, which do duty as bargeboards. The method is shown at A (Fig. 100).
The roof can be covered with slates, Broseley tiles, wood shingles, or thatch. A partial plan of the roof is shown in Fig. 99. An enlarged section of the front angle of the gable is provided in Fig. 100. Two boards, each 1 ft. 1 in. wide by 1¼ in. thick, are attached to the outer rafters and run parallel to them; the ends of the two boards meet the front top rail, to which they are nailed. The split-twig herringbone ornament is also nailed to these boards. On the inner edges of the boards, twigs about 1¾ in. in diameter are secured, which are shaped to fit the edges as shown in Fig. 100. The projecting front ends of the roofing boards are hidden by split twigs about 2½ in. or 3 in. in diameter, which serve as bargeboards. The method is illustrated at A (Fig. 100).
The panels have now to be filled with stuff ranging from 1½ in. to 2¼ in. in diameter. The [Pg 76] vertically placed twigs between the posts and rails should be fitted in place before the rails are finally jointed up to the posts. The ends are roughly hollowed, and are secured with cut nails. Alternatively, the vertical members could be fitted so that their inner edges coincided with the centre of the rails. The major portion of the twigs being on the outer side, the smaller diameter of the twigs will thus bring their front edges flush with the larger diameter edges of the rails. The herringbone and the diagonally placed twigs are quite easy to fit, the ends being simply pared off till they are sufficiently shortened to assume their correct position in the panels.
The panels need to be filled with materials ranging from 1½ inches to 2¼ inches in diameter. The [Pg 76] vertically placed twigs between the posts and rails should be secured before the rails are finally attached to the posts. The ends are roughly hollowed out and secured with cut nails. Alternatively, the vertical members can be adjusted so their inner edges align with the center of the rails. With most of the twigs on the outer side, the smaller diameter of the twigs will cause their front edges to be flush with the larger edges of the rails. The herringbone pattern and the diagonally placed twigs are easy to fit; just trim the ends until they are short enough to fit properly in the panels.
The decorative effect of the porch will be greatly improved by the addition of a suitable door, as shown in the front elevation (Fig. 94). The cost of manufacture of such a door is but slightly more than that of an ordinary six-panel door. The bottle ends in the top glazed panel form a quaint and pleasing feature of the general scheme.
The decorative look of the porch will be greatly enhanced by adding a suitable door, as shown in the front elevation (Fig. 94). The cost to make this type of door is only a little more than a regular six-panel door. The bottle ends in the top glass panel create a charming and attractive aspect of the overall design.
CHAPTER VIII.
CANOPY FOR A SWING.
The middle posts are slightly larger in section, as they have to carry the cross rail supporting the swing; a good size for these is 6-in. diameter at the base by 10 ft. or 12 ft. high. The outer posts may be 4¾-in. to 5-in. diameter at the base. The posts are sub-tenoned (see Fig. 103) to elm sills 10 ft. 6 in. long by 8 in. diameter. Tenons are formed on both ends of the posts, and seatings and mortices at 4-ft. centres are made in both the sills (bottom rails) and plates (top rails) to receive them.
The middle posts are a bit larger in size since they need to support the cross rail for the swing; a good size for these is 6 inches in diameter at the base and 10 to 12 feet high. The outer posts can be 4¾ to 5 inches in diameter at the base. The posts are sub-tenoned (see Fig. 103) to elm sills that are 10 feet 6 inches long and 8 inches in diameter. Tenons are made on both ends of the posts, and slots and mortices at 4-foot intervals are created in both the sills (bottom rails) and plates (top rails) to fit them.
The short rails are 4 in. in diameter by 3 ft. 6 in. long, and are stub-tenoned and pinned to the posts at a height of 3 ft. 9 in. from the ground line. The struts also are tenoned and pinned to the middle posts and sills, as shown in Fig. 104, where, it will be noticed, the struts are in one piece and the braces in two, the latter being hollowed to fit in the angles and over the struts.
The short rails are 4 inches in diameter and 3 feet 6 inches long. They are stub-tenoned and pinned to the posts at a height of 3 feet 9 inches from the ground. The struts are also tenoned and pinned to the middle posts and sills, as shown in Fig. 104, where it's noted that the struts are in one piece and the braces are in two pieces, with the latter hollowed out to fit into the angles and over the struts.
Figs. 106 and 107.—Hook and Thimble for Canopy. |
When all the members are ready for the final [Pg 81] drive home, the tenons of the rails should be just entered to the posts; the struts and braces are next placed in position and driven up, then the sill and plate are entered and driven home, and finally the several joints are secured with oak pins. This operation will be carried out better with the work in a horizontal position. When the two sides are so far completed, they may be erected in position and fixed with temporary battens, at a distance apart of 7 ft. 9 in. centres, while the top cross rails are being fitted.
When everyone is ready for the final [Pg 81] drive home, the tenons of the rails should be just inserted into the posts; then the struts and braces are positioned and secured. After that, the sill and plate are inserted and fastened, and finally, all the joints are secured with oak pins. This task will be done more efficiently with the work laid flat. Once the two sides are mostly finished, they can be put up in place and secured with temporary battens, spaced 7 ft. 9 in. apart, while the top cross rails are being installed.
The middle cross rail which carries the swing is 6 in. in diameter and 8 ft. 6 in. long. A seating is formed on the plates, and a shallow one upon the rails, which are secured with long 3/4-in. [Pg 82] diameter bolts and nuts; the latter are let into the posts at a distance of 8 in. from the top, as shown in Fig. 105, which is a cross section through the plate near the middle rail. Short struts may also be fixed between the posts and cross rail, as in Fig. 105; they are not shown in Fig. 101. A floor is formed of saplings, connected to the sills, thus preventing them from spreading. The trellis-work, both on the roof and sides, is now fixed. This is composed of 1¾-in. and 2-in. twigs.
The middle cross rail that supports the swing is 6 inches in diameter and 8 feet 6 inches long. A seating area is created on the plates, and a shallow one on the rails, which are fastened with long 3/4-inch diameter bolts and nuts; the nuts are embedded in the posts 8 inches from the top, as shown in Fig. 105, which is a cross-section through the plate near the middle rail. Short struts can also be installed between the posts and cross rail, as seen in Fig. 105; these are not included in Fig. 101. A floor is made from saplings, attached to the sills, preventing them from spreading. The trellis work, both on the roof and sides, is now in place. This consists of 1¾-inch and 2-inch twigs.
The swing hooks (Fig. 106) pass right through the rails, and are secured with nuts and washers. Collars should be forged on the shanks to prevent the hooks being drawn too far into the wood when screwing up the nuts. The shank is screwed ¾-in. Whitworth pitch thread, and the hook is 1¼ in. in diameter at the thickest part. The hemp rope is spliced around galvanised iron thimbles (see Fig. 107), which take the wear on the hooks. The rope is usually secured to the seat by simply knotting the ends.
The swing hooks (Fig. 106) go right through the rails and are secured with nuts and washers. Collars should be forged onto the shanks to prevent the hooks from being pulled too far into the wood when tightening the nuts. The shank is screwed with a ¾-inch Whitworth pitch thread, and the hook has a diameter of 1¼ inches at its thickest point. The hemp rope is spliced around galvanized iron thimbles (see Fig. 107), which bear the wear from the hooks. The rope is usually secured to the seat by simply knotting the ends.
Should the swing be used for very young children, a seat provided with a fence will be necessary, as shown at Figs. 108 and 109, which are front and end views respectively. The back rail and the two side rails are fixed to the seat with the balusters; but the front rail is tenoned to open-ended mortices in the side rails, and thus made to hinge, to facilitate the lifting of the children on and off the seat, the rail being secured in its closed position with a brass pin and retaining chain. The suspending rope in this case is passed through the end rails and knotted to the seat. Fig. 110 shows the rope passed around and whipped to an eyelet.
If the swing is intended for very young children, a seat with a protective fence will be necessary, as shown at Figs. 108 and 109, which are the front and end views respectively. The back rail and the two side rails are attached to the seat with the balusters; however, the front rail is tenoned into open-ended mortices in the side rails, allowing it to pivot for easier lifting of the children on and off the seat. The rail is secured in its closed position with a brass pin and a retaining chain. The suspending rope in this design goes through the end rails and is knotted to the seat. Fig. 110 shows the rope wrapped around and secured to an eyelet.
CHAPTER IX.
AVIARY.
Hazel sticks, with the bark on, should be used, the straightest obtainable being best for the frame; if at all crooked or bent, the sticks can be straightened by steaming, or, if not too dry, by the heat of a spirit lamp.
Hazel sticks with the bark still on should be used, with the straightest ones being the best for the frame; if they are at all crooked or bent, the sticks can be straightened by steaming them or, if they aren't too dry, by using the heat from a spirit lamp.
Four uprights, 1 ft. 5½ in. by 5/8 in., are first cut; then six rails, ½ in. thick, are made, with the ends shaped as shown in Fig. 113, to fit the uprights, measuring 2 ft. 10 in. inside the hollow ends when finished. Four of these should be laid on the bench side by side, and marked with a pair of compasses for the wires, which are 5/8 in. apart. They are then drilled, the holes being bored right through the two sticks for the top rails, but only half through the bottom rails. If the stuff is not too hard, the holes may be pierced with a well-sharpened brad awl.
Four vertical pieces, measuring 1 ft. 5½ in. by 5/8 in., are cut first; then, six horizontal rails, each ½ in. thick, are created with the ends shaped as shown in Fig. 113, to fit the vertical pieces, measuring 2 ft. 10 in. inside the hollow ends when complete. Four of these should be placed on the bench side by side and marked with a pair of compasses for the wires, which are 5/8 in. apart. They are then drilled, with holes bored all the way through the two sticks for the top rails, but only halfway through the bottom rails. If the material isn't too hard, the holes can be pierced with a well-sharpened brad awl.
The uprights are now secured to the rails with 2-in. wire nails, driven so as to avoid the holes (see Fig. 114), and glue is applied at the joints. The bottom rail is flush with the lower ends, the next one being placed ½ in. above it; the third is ¼ in. from the top ends. These form the front and back frames, and should be quite square and out of winding. The rails for the ends, also six in number, measure 1 ft. 3 in., and are bored and fixed to the uprights to correspond with the others in exactly the same way.
The uprights are now attached to the rails with 2-inch wire nails, driven in a manner that avoids the holes (see Fig. 114), and glue is applied at the joints. The bottom rail is level with the lower ends, the next one is placed ½ inch above it; the third is ¼ inch from the top ends. These make up the front and back frames and should be perfectly square and not twisted. The end rails, which are also six in number, measure 1 foot 3 inches, and are drilled and secured to the uprights in the same way as the others.
The two rails supporting the tree perches are placed about 7 in. from the ends. Before they are fixed, however, the tree perches must be arranged. These should be cut from the limb of a leafless tree, in winter, in order to retain the bark. Suitable pieces may be prepared by cutting off badly placed twigs and fixing them where required. They are then put on the perch rails, employing the same joint as the rails and upright, but securing with a strong screw.
The two rails that hold the tree perches are set about 7 inches from the ends. Before they are secured, the tree perches need to be arranged. These should be cut from a branch of a leafless tree in winter to keep the bark intact. You can prepare suitable pieces by trimming off poorly placed twigs and attaching them where needed. They are then placed on the perch rails, using the same joint as the rails and uprights, and secured with a strong screw.
**Figs. 113 and 114.—Details of Joint for Rails and Uprights in an Aviary.** |
When all is ready, the perches are fixed in the framework (see Figs. 115 and 116), and narrow [Pg 86] strips of ¼-in. board are fitted between the lower rails of the back and ends, to be faced with split stuff, put on diagonally as shown in Figs. 111 and 112. The best plan would be to take a sufficient quantity of material to the nearest sawmill to be divided by a circular or band saw; the material must be free from grit, or objections will be raised against cutting it.
When everything is ready, the perches are secured in the framework (see Figs. 115 and 116), and narrow strips of ¼-inch board are installed between the lower rails of the back and ends, which will be covered with split material, applied diagonally as shown in Figs. 111 and 112. The best approach would be to take enough material to the nearest sawmill to be cut with a circular or band saw; the material must be clean, free from grit, or there will be issues with cutting it.
A stain, made by thinning down brunswick black with turps, should be at hand to stain the wood before fixing on the split stuff, which is secured with fine panel pins.
A stain, created by mixing brunswick black with turpentine, should be ready to color the wood before attaching the split pieces, which are secured with small panel pins.
The wood bottom is 3 ft. 1½ in. by 1 ft. 5½ in. by 3/8 in.; it is planed both sides, and secured in place with screws. The top side is treated round the margin, as shown in Fig. 115, and the under side as shown in Fig. 117. The centre of the design of the under side, covering a space of 2 ft. 3 in. by 8 in., is worked first; it is worked from the centre outwards, each strip being mitred [Pg 87] as shown. The marginal strips are pieces of split cut slanting at the ends where they fit other pieces, and flush with the edge of the wood bottom, which is surrounded with the same stuff.
The wooden base measures 3 ft. 1½ in. by 1 ft. 5½ in. by 3/8 in.; it's planed on both sides and secured in place with screws. The top side has a decorative edge, as shown in Fig. 115, and the underside is detailed as shown in Fig. 117. The center design on the underside, covering an area of 2 ft. 3 in. by 8 in., is worked on first; it's done from the center outward, with each strip being mitred as shown. The edge strips are pieces of split wood, cut at an angle at the ends where they join other pieces, and are flush with the edge of the wooden base, which is surrounded by the same material. [Pg 87]
The wiring is all straightforward work. The wires are passed through the top rails to those below and clipped off level at the top. Six feeding-holes are required, one in the centre at each end, and two at the back and front close to the perches. The top ends of these wires are pushed up through the rails; the circular ends are slightly sunk and fixed with small staples. Six wires are omitted from the middle of the front to allow for the door. The cross-wires, which should be of a stronger gauge, are then put in. In the back and ends it is immaterial whether they are put inside or out, but at the front they must be inside. The six wires above the door are inserted in twos, being returned in the same manner as the lower ends of the door wires (see Fig. 118), and soldered to the cross-wire, which is afterwards bound to the others with thin pliable coil wire. In making the sliding door, the returned ends of the wires are soldered to the base wire inside, so that the ends may fit round the wires of the doorway; the top ends fit round those above the cross-wire, and when the door is in place a scroll-piece is soldered on outside (see Fig. 111).
The wiring is all pretty simple. The wires are routed through the top rails to the ones below and cut off level at the top. You need six feeding holes: one in the center at each end and two at the back and front near the perches. The top ends of these wires are pushed up through the rails; the circular ends are slightly recessed and secured with small staples. Six wires are removed from the middle of the front to make space for the door. The cross-wires, which should be a stronger gauge, are then added. For the back and ends, it doesn't matter if they are on the inside or outside, but at the front, they must be inside. The six wires above the door are inserted in pairs, returned in the same way as the lower ends of the door wires (see Fig. 118), and soldered to the cross-wire, which is then tied to the others with thin, flexible coil wire. When making the sliding door, the returned ends of the wires are soldered to the base wire inside, so they fit around the doorway wires; the top ends fit around those above the cross-wire, and when the door is in place, a scroll piece is soldered on the outside (see Fig. 111).
Eight corner-pieces of the split stuff are put on close against the wires, being secured to the uprights and rails with pins. Two pieces of ¼ in. [Pg 90] board are next got out for the top, measuring 2 ft. 10 in. long, 4 in. across the centre, and slanting at the upper edge to ¼ in. at the ends. The design is worked on these in split, the boards being kept in place with pins driven through the top rails, and the back and front connected at the top point by a length of wood of 2-in. by 1-in. section (see Fig. 119). The roof-pieces, 1 ft. 5½ in. by 1 ft. 7¼ in. by ¼ in., are nailed on and covered with split stuff, as shown by Fig. 120.
Eight corner pieces of the split material are placed tightly against the wires and secured to the uprights and rails with pins. Two pieces of ¼ in. [Pg 90] board are cut for the top, measuring 2 ft. 10 in. long and 4 in. wide at the center, slanting to ¼ in. at the ends. The design is applied to these in split, with the boards held in place by pins driven through the top rails, and the back and front joined at the top by a piece of wood measuring 2 in. by 1 in. (see Fig. 119). The roof pieces, measuring 1 ft. 5½ in. by 1 ft. 7¼ in. by ¼ in., are nailed on and covered with split material, as shown by Fig. 120.
A sliding bottom or tray is required for cleaning purposes; this is of ¼ in. board, and is nailed to the strip that fits between the rails in front; other strips about 1 in. wide are nailed on the upper side at the extreme ends and back edge to form a tray for the sand, runners being put in against the lower end rails. The front strip is treated with the split, and to draw out the tray, the door may be slightly raised to admit the fingers to push it forward from the inside. Two [Pg 91] additional perches put across from the wires, and fixed with staples, give strength to the front and back.
A sliding bottom or tray is needed for cleaning. This is made from a ¼ inch board and is nailed to the strip that fits between the rails in front. Additional strips, about 1 inch wide, are nailed on the upper side at the extreme ends and back edge to create a tray for the sand, with runners placed against the lower end rails. The front strip is treated with a split, and to pull out the tray, the door can be slightly raised to let fingers push it forward from the inside. Two [Pg 91] extra perches are added across from the wires and secured with staples to strengthen the front and back.
The aviary is now gone over with fine glass-paper, all white places being touched up with the stain and nicely varnished, with the exception of the perches. The aviary will stand on a table, but may be hung from the ceiling if desired. For hanging purposes, four screw-eyes are put in the top, two on the ridge, about 3 in. from the front and back, and one towards each end, placed midway to catch the rails. The four ceiling hooks should screw into the joists, the aviary being suspended with chains.
The aviary is now finished with fine sandpaper, with all the white areas touched up with stain and nicely varnished, except for the perches. The aviary will sit on a table but can also be hung from the ceiling if preferred. For hanging, four screw eyes are installed at the top, two on the ridge, about 3 inches from the front and back, and one toward each end, positioned midway to secure the rails. The four ceiling hooks should be screwed into the joists, and the aviary will be suspended with chains.
CHAPTER X.
FOOT-BRIDGES.
Very pleasing effects may be produced in public or private recreation grounds by the constructional use of rustic work of good design.
Very pleasing results can be achieved in public or private parks by using well-designed rustic structures.
Fig. 122.—Cross Section of Footbridge.
Fig. 123.—Detailed Section of Girders for Footbridge. Figs. 124 and 125.—Components of the Joint Between Post and Girder. |
Fig. 126.—Close-up of the middle rail and post of the footbridge. Figs. 127 and 128.—Connection of the strut to the post of the footbridge. |
Fig. 121 is a perspective view of a rustic foot-bridge suitable for a span of 8 ft. or 12 ft. The banks of the stream to be bridged are excavated to allow of the building of a low rubble wall, on which the sleepers rest, as shown in Fig. 122. The girders are formed of spruce or larch spars. In the present instance, four are used; and they may be 8 in. or 10 in. in diameter, according to the length of the span. They are roughly adzed down to sit on the sleepers, and each girder is also worked down tolerably flat on the inner sides. The girders are then bolted together in [Pg 95] pairs with six ¾ in. diameter coach bolts, as shown by Fig. 123. The posts are tenoned and wedged to fit mortices in the girders. Figs. 124 and 125 show the mortice and tenon joint.
Fig. 121 is a side view of a rustic footbridge suitable for spans of 8 ft. or 12 ft. The banks of the stream being bridged are excavated to allow for the construction of a low rubble wall, on which the sleepers rest, as shown in Fig. 122. The girders are made of spruce or larch beams. In this case, four are used, and they can be 8 in. or 10 in. in diameter, depending on the length of the span. They are roughly shaped to rest on the sleepers, and each girder is also flattened on the inner sides. The girders are then bolted together in [Pg 95] pairs using six ¾ in. diameter coach bolts, as shown by Fig. 123. The posts are mortised and wedged to fit into the girders. Figs. 124 and 125 show the mortise and tenon joint.
The posts and top rails are 4½ in. or 5½ in. in diameter, and the intermediate rails 3 in. in diameter. Fig. 126 indicates the method of jointing the rails to the posts. The girder spars, with posts and rails fitted, having been placed in position on the sleepers, and plumbed up and stayed, the floor battens, 11 in. by 2½ in., [Pg 96] are fixed and the struts are fitted and pinned or spiked to the posts and sleepers. The joint for the struts is shown by Figs. 127 and 128.
The posts and top rails are 4½ inches or 5½ inches in diameter, and the intermediate rails are 3 inches in diameter. Fig. 126 indicates how to join the rails to the posts. Once the girder spars are in place with the posts and rails attached, positioned on the sleepers, plumbed up, and secured, the floor battens, which are 11 inches by 2½ inches, [Pg 96] are attached, and the struts are fitted and pinned or spiked to the posts and sleepers. The connection for the struts is shown by Figs. 127 and 128.
If the bridge happens to be in a locality that is subject to periodical flooding, it should be anchored to prevent its being unseated by flood water. The anchoring can be best effected by driving four short piles into the soil on the inside of both girders and near their ends. The girders can be fastened to the piles with coach bolts. The tops of the piles will be concealed by the end floor battens. The smaller twigs forming the [Pg 97] ornamentation are now fixed, and Fig. 129 shows the vertical piece hollowed to fit the rails.
If the bridge is located in an area that experiences periodic flooding, it should be secured to prevent it from being dislodged by floodwaters. The best way to anchor it is by driving four short piles into the ground on the inside of both girders, close to their ends. The girders can be attached to the piles using coach bolts. The tops of the piles will be hidden by the end floor battens. The smaller twigs that make up the decoration are now in place, and Fig. 129 shows the vertical piece shaped to fit the rails.
Fig. 130 gives a part view, in longitudinal section, of an elevated bridge, suitable for a span of 12 ft. to 18 ft., and raised on piles to enable small boats and canoes to pass under. Elm logs are suitable for the pile foundation. An iron ring must be fitted over the tops of the logs while they are being driven, and it will be necessary to use a pile-driver. The logs, having been sufficiently driven, are cut off to the required height from the ground line. Three piles on each side are required to carry the sleepers. The bridge is 5 ft. 6 in. wide, and the spars for girders are 12 in. in diameter. The sleepers are bolted to the piles, and the girders are also bolted to the sleepers as shown by Fig. 131. A row of smaller piles is now driven, and a plank, 11 in. by 3 in., is housed to the top ends of these piles, and also connected to the projecting ends of the girders. The treads of the steps rest upon the tops of the smaller piles, and the outer side of the piles and planks is covered with split saplings (see Fig. 130, and the cross-section, Fig. 132). The handrails and balustrades are fixed in similar manner to those in Fig. 121.
Fig. 130 shows a side view, in a longitudinal section, of an elevated bridge designed for a span of 12 ft. to 18 ft., elevated on piles so that small boats and canoes can pass underneath. Elm logs are ideal for the pile foundation. An iron ring should be placed over the tops of the logs while they are being driven, and using a pile driver is necessary. After the logs have been driven in sufficiently, they are cut to the required height from the ground line. Three piles on each side are needed to support the sleepers. The bridge is 5 ft. 6 in. wide, and the girders are made from spars that are 12 in. in diameter. The sleepers are bolted to the piles, and the girders are also bolted to the sleepers as illustrated by Fig. 131. A row of smaller piles is then driven in, and a plank measuring 11 in. by 3 in. is attached to the top ends of these piles, and also connected to the extending ends of the girders. The treads of the steps rest on the tops of the smaller piles, and the outer sides of the piles and planks are covered with split saplings (see Fig. 130, and the cross-section, Fig. 132). The handrails and balustrades are installed in a similar way to those in Fig. 121.
CHAPTER XI.
VERANDAHS.
The front elevation of a rustic verandah is presented by Fig. 133, which shows a part only, which may be extended to any required length at either end. As to the width, that indicated is 3½ ft. from the wall to the middle of the collar-posts, the eaves having a further projection of 6 in. For a cottage verandah the width given is a satisfactory one. It gives sufficient room for seats on a hot day, or for a promenade on a wet one. The width, as also the height, can easily be increased to suit a larger house. The verandah is supposed to be built on a raised platform of brick or stone.
The front view of a rustic verandah is shown by Fig. 133, which displays only a portion that can be extended to any desired length at either end. The width indicated is 3½ feet from the wall to the center of the collar posts, with the eaves extending an additional 6 inches. For a cottage verandah, this width is appropriate. It provides enough space for seating on a hot day or for walking around on a rainy one. Both the width and height can easily be adjusted to fit a larger house. The verandah is expected to be built on a raised platform of brick or stone.
All parts of the actual framework are of straight natural wood, preferably larch; whilst the mere filling-in of rustic open-work is of small crooked stuff—probably oak or apple tree. The roof, as illustrated, is of tiles.
All parts of the actual framework are made of straight natural wood, preferably larch, while the filling of the rustic open-work is made of small, crooked pieces—probably oak or apple wood. The roof, as shown, is tiled.
It will be seen that the posts which support the verandah are arranged in pairs, so that 3 in. or 3½ in. poles will suffice for them. Their bases are supposed to be dowelled to the masonry of the platform on which they stand; they are 6 ft. 6 in. high. Except at the entrances, a sill of half-stuff runs from post to post on the platform. At a height of 3 ft. 3 in. they are connected by a round bar of smaller material, and, again, by a second cross-bar of similar size to the last, at 6 in. from their upper ends. On the tops of the posts rests a lintel of half-stuff of larger diameter—say 5 in. The upper and lower cross-bars come opposite to the middles of the posts, but need not be mortised into them, for if their ends are cut V-shaped, so as to clip the posts, they can be nailed quite firmly.
It can be seen that the posts supporting the verandah are arranged in pairs, so 3 in. or 3½ in. poles will be sufficient for them. Their bases are expected to be dowelled to the masonry of the platform they sit on; they are 6 ft. 6 in. tall. Except at the entrances, a sill of half-stuff runs from post to post on the platform. At a height of 3 ft. 3 in., they are connected by a round bar made of smaller material, and again by a second cross-bar of similar size to the last, positioned 6 in. from their upper ends. Atop the posts sits a lintel of half-stuff with a larger diameter—around 5 in. The upper and lower cross-bars align with the centers of the posts but don’t need to be mortised into them; if their ends are cut into a V-shape to fit around the posts, they can be nailed down securely.
The lower cross-rail is placed at a convenient height for leaning upon. At a height of 5 ft. 6 in. caps are formed by simply nailing four pieces of quartered stuff round each post. The diagonal braces which start from above the capitals pass in front of the upper cross-bars, to which and to the [Pg 100] lintel they are nailed. Fig. 133 sufficiently shows how the panels between the pairs of posts and the frieze between the upper cross-bar and lintel are filled with open-work of small crooked branches, which contrasts in a pleasing manner with the straight pieces of the framework. This open-work may be made available for, and will be found useful as, a support for climbing plants.
The lower cross-rail is set at a comfortable height for leaning on. At a height of 5 ft. 6 in., caps are created by simply nailing four pieces of quartered material around each post. The diagonal braces that extend from above the caps come in front of the upper cross-bars, to which they are nailed, along with the lintel. [Pg 100] Fig. 133 clearly illustrates how the panels between the pairs of posts and the frieze between the upper cross-bar and the lintel are filled with open-work made of small crooked branches, creating a nice contrast with the straight pieces of the structure. This open-work can be utilized as support for climbing plants.
In so narrow a structure the rafters alone will suffice to keep all in place, without anything of the nature of a tie-beam being called for. These rafters will be of half-stuff, and for the given width a length of 5 ft. will be enough; this will allow of such a projection beyond the lintel as will give the eaves a width of 6 in.; the pitch will be rather less than a true pitch, but amply steep for the purpose. A piece of half-stuff nailed to the wall will support the upper ends of the rafters.
In such a narrow structure, the rafters alone will be enough to hold everything in place, without needing any tie-beams. These rafters will be made from half-stuff, and for the specified width, a length of 5 ft. will be sufficient; this will allow for a projection beyond the lintel that gives the eaves a width of 6 in. The pitch will be slightly less than a true pitch, but it will be sufficiently steep for the purpose. A piece of half-stuff nailed to the wall will support the upper ends of the rafters.
In forming the roof it is proposed to board over the whole space upon the rafters, and to nail the tiles or other covering upon the boards. The inside may be lined beneath the boarding with rush matting. This is an inexpensive material; its brownish-green hue is pleasing to the eye, and it is so inartificial in appearance as to harmonise well with the natural wood. After fixing the rafters, the matting is to be stretched tightly across them before the boards are nailed down. It is probable that the rafters will be arranged with intervals of about a foot between them, and to hold the matting more closely to the boards a strip of split rod may be nailed up the middle of each space, or strips may be nailed so as to form a simple ornamental pattern; an intricate one will not be desirable, as fixing it will be overhead work.
To build the roof, we plan to cover the entire area with boards on the rafters and nail tiles or another covering onto the boards. The underside can be lined with rush matting, which is an affordable material. Its brownish-green color is nice to look at and blends well with the natural wood. After the rafters are in place, the matting should be stretched tightly across them before the boards are nailed down. The rafters will likely be spaced about a foot apart, and to keep the matting snug against the boards, we can nail a strip of split rod in the middle of each section, or we can create a simple decorative pattern with strips. A complicated design isn't practical since it requires working overhead.
A neat, but less characteristic, ceiling may be formed by painting the boards a suitable colour and slightly ornamenting them with split strips of rod. In this case the boards should be planed. None will be better for this purpose than ¾ in. flooring boards, and these are commonly sold planed on one side. Other ways of lining the roofs of rustic buildings are discussed in Chapter XIII. For summer-houses thatch makes a good-looking roof, but a thatched verandah would scarcely be desirable unless attached to a thatched cottage. Practically the choice lies between shingles, metal, and tile or slate. A metal roof is, undoubtedly, that most easily fixed by the beginner; black sheet iron looks better than galvanised, and must be kept painted. As a matter of taste, metal looks thin and poor, but it becomes less objectionable when painted; a deep, dull red would be the colour to be preferred. Perhaps, of all available coverings, nothing will look better than tiles, as drawn. Red or buff tiles will in themselves look best, but the choice must, to an extent, be influenced by the general covering of the house. It may be, if that is of slate, that small slates will come in most appropriately; but whichever of these coverings is used, the best finish against the wall will be with a "flashing" of metal, as shown.
A clean, but less distinctive, ceiling can be created by painting the boards a suitable color and adding a bit of decoration with split strips of wood. In this case, the boards should be planed. The best option for this purpose is ¾ inch flooring boards, which are usually sold planed on one side. Other methods for lining the roofs of rustic buildings are discussed in Chapter XIII. For summer houses, thatch makes an attractive roof, but a thatched verandah wouldn’t look great unless it’s attached to a thatched cottage. Essentially, the options are shingles, metal, and tile or slate. A metal roof is definitely the easiest for beginners to install; black sheet iron looks better than galvanized metal, but it needs to be kept painted. Although metal can look thin and cheap, it becomes less objectionable when painted; a deep, dull red would be the preferred color. Of all the available roof coverings, nothing looks better than tiles, as illustrated. Red or buff tiles will look best on their own, but the choice should also consider the general style of the house. If the house is covered in slate, then small slates may be the most suitable option; however, no matter which covering is used, the best finish against the wall will be with a "flashing" of metal, as shown.
It has been asserted by some who consider themselves authorities in matters of taste that nothing of the nature of a greenhouse ever harmonises with natural surroundings, or is otherwise than an eyesore in a garden in other respects beautiful. The hard, straight lines of wood or metal, and wide surfaces of shining glass, are not pleasing, and are too suggestive of the shop and factory to accord well with natural objects. It has been suggested that the difficulty might be overcome by combining rustic work with glass. This, at the first glance, looks fairly easy; but, on consideration, it will be seen to be otherwise. Rustic carpentry is in its nature irregular, and cannot be brought to those level planes and straight [Pg 103] lines essential to glass-work; whilst for interiors, and especially those of houses intended for vines, rough bark-coloured surfaces afford too much shelter to insect pests—so that, in reality, rustic-work can only be made applicable to a very limited extent. In the grape-growing verandah shown by Fig. 134, therefore, only a limited amount of rustic-work has been introduced, and that on the outside.
Some people who see themselves as experts on taste claim that nothing resembling a greenhouse truly fits in with natural surroundings and is often just an eyesore in an otherwise beautiful garden. The hard, straight lines of wood or metal and the wide surfaces of shiny glass are not visually appealing and remind us too much of shops and factories to blend well with natural elements. It has been proposed that this issue could be solved by combining rustic design with glass. At first, this seems fairly simple, but upon further reflection, it becomes clear that it’s not. Rustic carpentry is inherently uneven and can't be shaped into the level surfaces and straight lines that glasswork demands. Additionally, for interiors—especially in homes designed for vines—rough, bark-colored surfaces provide too much hiding space for insect pests, making rustic work only suitable to a very limited extent. In the grape-growing verandah shown by Fig. 134, only a small amount of rustic work has been included, and that is on the exterior. [Pg 103]
Such of the materials as are of a rustic kind [Pg 104] are, for the parapet and uprights, some rather small larch poles or other tolerably straight, round stuff, and for the panels, some of those "slabs," or rough outside planks. As to the posts, and such parts as are not rustic, they are supposed to be of good deal. The sash-bars, which carry the glass both in roof and walls, are to be bought struck by steam at a lower price than they can be worked by hand, or sashes may be bought ready glazed. For glazing work of this kind, 16-oz., or sometimes 20-oz., glass is used.
The materials that are a bit rustic include some smaller larch poles or other reasonably straight, round pieces for the parapet and upright supports, and for the panels, some of those "slabs," or rough outer planks. As for the posts and parts that aren't rustic, they are expected to be made of a better quality. The sash-bars, which hold the glass in both the roof and walls, should be purchased made by steam at a lower price than hand-worked options, or sashes can be bought pre-glazed. For this type of glazing work, 16-oz. or sometimes 20-oz. glass is used.
As in the design for an open rustic verandah (see Fig. 133) it is intended that the collar-posts should be set upon and dowelled into a raised platform of masonry. The present structure is, of course, intended for the warmer sides of a house, south or west. The width, to meet particular cases, can be varied, but is, according to the drawings, 4½ ft. The posts are 6 ft. high and 3½ in. square. They are set with spaces between them alternately of 3 ft. and 4½ ft. On their tops rests a wall-plate of the same width as themselves, and 2½ in. deep. The rafters, which are sash-bars rebated to carry the glass, rest on this wall-plate, and against a second vertical one fixed to the house wall.
As in the design for an open rustic verandah (see Fig. 133), the collar-posts should be mounted and doweled into a raised masonry platform. This structure is meant for the warmer sides of a house, either south or west. The width can be adjusted for specific cases but is, according to the drawings, 4½ ft. The posts are 6 ft. high and 3½ in. square. They are spaced alternately at 3 ft. and 4½ ft. apart. A wall-plate of the same width as the posts and 2½ in. deep rests on top of them. The rafters, which are sash-bars notched to hold the glass, rest on this wall-plate and against a second vertical one attached to the house wall.
Fig. 134 is a front elevation of a portion of the verandah, whilst Fig. 135 gives a side view of the lower half of one of the collar-posts. At a, in Fig. 135, is seen the section of the upper cross-rail, which has its top 2½ ft. from the ground; at b is the lower cross-rail, or sill. Both are of quartered rough stuff, and are mortised to the post ¾ in. from its inner edge, so that when the ¾ in. boarding, c, is nailed against them, it will come flush with the inner side of the post. At d is indicated the sash-frame, with its rebate for glass, which occupies the upper part of the opening; and at e is a metal flashing between rail and sash to throw off rain. It is proposed [Pg 105] that the sashes in the narrower openings only should be made to push outwards at bottom for ventilation. At f is a piece of halved rough stuff nailed to the front of the post.
Fig. 134 shows the front view of part of the verandah, while Fig. 135 presents a side view of the lower half of one of the collar-posts. At a, in Fig. 135, you can see the section of the upper cross-rail, which is 2½ ft. above the ground; at b is the lower cross-rail, or sill. Both are made of quartered rough lumber and are mortised into the post ¾ in. from the inner edge, so that when the ¾ in. boarding, c, is nailed on, it will be flush with the inner side of the post. At d is the sash-frame with its rebate for glass, which is in the upper part of the opening; and at e is a metal flashing between the rail and sash to divert rain. It is suggested that the sashes in the narrower openings should only push outwards at the bottom for ventilation. At f is a piece of halved rough lumber nailed to the front of the post.
The panels, which occupy the lower part of the space between the collar-posts, are filled with pieces of rough plank or "slab," as shown in Fig. 134. These pieces should wear their natural bark as far as possible; they are nailed to the inner boarding.
The panels, which fill the lower part of the space between the collar-posts, are made up of rough planks or "slabs," as shown in Fig. 134. These pieces should retain their natural bark as much as possible; they are nailed to the inner boarding.
In Fig. 136 the upper part of a post is in like manner shown in profile: g is the wall-plate in section, and h is the lower end of a rafter. At i will be observed a strip of quartered stuff nailed across the post (with a fir-cone bradded beneath it), which gives a starting-point to the upright k, by which the openwork rustic parapet is supported. These uprights are of small round stuff, slightly flattened on the side towards the post. The openwork parapet is too plainly figured to need description; it is intended to break to a certain extent the straight lines, and partially to conceal the glass-work of the roof, without seriously interfering with sunshine.
In Fig. 136, the top part of a post is similarly shown in profile: g is the wall-plate in cross-section, and h is the bottom end of a rafter. At i, you can see a strip of quartered material nailed across the post (with a fir cone nailed underneath it), which serves as a starting point for the vertical k, which supports the openwork rustic parapet. These verticals are made from small round material, slightly flattened on the side facing the post. The openwork parapet has a design that is clear enough to not need further description; it’s meant to soften the straight lines and partially hide the glasswork of the roof, without significantly blocking sunlight.
So much of the planed wood-work as shows outside should be painted of a good brown, to assimilate with the rustic-work.
So much of the wooden work that shows on the outside should be painted a nice brown to match the rustic style.
CHAPTER XII.
TOOL HOUSES, GARDEN SHELTERS, ETC.
For the small rustic tool house shown by Figs. 137 and 138 the materials used are what are known as "slabs" or "rough planks." These are cheap, and have, when judiciously handled, a good picturesque effect. These slabs are the outside slices cut from logs of rough timber. These slabs generally retain their bark (except in the case of oak), and in most districts they will commonly be of elm. Their thickness and outlines are necessarily irregular: one end will frequently be narrower than the other; and this will account for the arrangement seen in the walls and door of the tool house. They are to be bought at saw-mills, and often sold at a fire-wood price. Where their cost is not sensibly increased by carriage, no other material comes so cheaply for building rough sheds. The ordinary country way of using them is as in the horizontal section, Fig. 139. This plan, however, is not suitable for the present ,[Pg 108] purpose. In so small a structure, rough planks on the inner side would take up too much space It is, therefore, proposed to straighten the edges, either by sawing or by chopping with the axe, according to circumstances, and lining their inner sides with thin board. If the cost be not objected to, ½ in. match-boarding will be neatest for this purpose; if economy is an object, the boards of packing-boxes, bought from the grocer, might suffice. There are, it will be seen, three sides only to be lined.
For the small rustic tool house shown by Figs. 137 and 138, the materials used are what we call "slabs" or "rough planks." These are inexpensive and, when used wisely, can have a nice visual appeal. These slabs are the outer slices cut from logs of rough timber. They usually keep their bark (except for oak), and in many areas, they are typically made of elm. Their thickness and shapes are often irregular: one end is usually narrower than the other, which explains the arrangement seen in the walls and door of the tool house. You can buy them at sawmills, and they are often sold at firewood prices. Where transportation costs aren't too high, there are no other materials that are as affordable for building rough sheds. The common country method of using them is shown in the horizontal section, Fig. 139. However, this plan isn't suitable for the current purpose. In such a small structure, rough planks on the inside would take up too much space. Therefore, it's suggested to straighten the edges, either by sawing or chopping with an axe, depending on the situation, and to line the inner sides with thin boards. If cost isn't an issue, ½ inch match-boarding would look the best for this purpose; if saving money is a priority, the boards from packing boxes, bought from the grocery store, might work. It's worth noting that only three sides need to be lined.
Among a lot of rough planks, it is likely that stuff may be found sufficient for the posts and other scantling. As to the six pilasters, which are added for appearance merely, it is possible that stuff might be found which would, when sawn to width, do for them; in the illustration they are supposed to be fir poles or elm saplings; four sticks only are needed to supply the six halves and four quarters used.
Among many rough planks, it's likely that there’s enough material for the posts and other framework. Regarding the six pilasters, which are just for looks, it’s possible to find material that could work once it's cut to width; in the illustration, they are assumed to be fir poles or elm saplings. You only need four sticks to provide for the six halves and four quarters required.
At the corners are four main posts, 4 in. square (see a, Fig. 140). These enclose a space of 7 ft. by 5 ft. (outside measurement). They are let into the ground 2 ft., and rise 5 ft. 3 in. above the ground line.
At the corners, there are four main posts, 4 inches square (see a, Fig. 140). These form a space of 7 feet by 5 feet (external measurement). They are set into the ground 2 feet and stand 5 feet 3 inches above the ground line.
On their tops, and coming flush with their outer edges, rest the wall-plates, which are 3 in. deep; these are needed at the back and sides only, and not at the front. On the same three sides will also be cross-rails, 2 in. to 3 in. thick, the ends of which will be let flush into the posts about a foot from the ground. To the wall-plates and these rails the slabs are nailed. In the side elevation, Fig. 138, the nails driven into the cross-rails appear, but not those driven into the wallplate, [Pg 109] a piece of rough stuff being there shown as fixed over the latter to support the eaves of the thatch.
On top of the posts, flush with their outer edges, rest the wall-plates, which are 3 inches deep; these are needed only on the back and sides, but not at the front. On the same three sides, there will also be cross-rails, 2 to 3 inches thick, the ends of which will be set flush into the posts about a foot from the ground. The slabs are nailed to the wall-plates and these rails. In the side elevation, Fig. 138, the nails driven into the cross-rails are visible, but not those driven into the wall-plate, as a rough piece is shown fixed over it to support the eaves of the thatch. [Pg 109]
To the front are to be seen the two door-posts, b, b, Fig. 140, which are 2 ft. 8 in. apart, and should be about 3 in. square. As their tops are nailed to the front pair of rafters, they rise to a height of 6 ft. 6 in. The space between door-post and corner-post is filled up by a single slab nailed to the two—5 ft. 6 in. long by 10 in. broad. [Pg 110] Above these, instead of a wall-plate, comes the piece of strong slab, shown in Fig. 137 as having an opening cut in it for the head of the door. This is nailed against the door-posts, rafters, etc.
To the front are the two door posts, b, b, Fig. 140, which are 2 ft. 8 in. apart and should be about 3 in. square. Since their tops are nailed to the front pair of rafters, they rise to a height of 6 ft. 6 in. The space between the door post and corner post is filled by a single slab nailed to both, measuring 5 ft. 6 in. long by 10 in. wide. [Pg 110] Above these, instead of a wall plate, there is a strong slab, shown in Fig. 137 with an opening cut out for the door's head. This is nailed against the door posts, rafters, etc.
The pilasters are only a matter of ornament. As drawn, they are of halved stuff; the corner ones are so placed that their middles come opposite to the corners of the posts, on the other faces of which pieces of quartered stuff are nailed to meet them. The simple arrangement of the caps of these pilasters, with their decorations of fir cones, is shown on a larger scale in Fig. 141. The horizontal piece beneath the eaves, nailed over the slabs, has the effect of resting on the caps. Beneath the thatch at front and back corresponding pieces are fixed, those at the front being ornamented with fir cones nailed upon them.
The pilasters are just for decoration. They're made from halved materials, and the corner ones are positioned so their centers line up with the corners of the posts, which have quartered materials attached to meet them. The straightforward design of the tops of these pilasters, decorated with fir cones, is shown on a larger scale in Fig. 141. The horizontal piece under the eaves, nailed over the slabs, looks like it’s resting on the tops. Under the thatch at both the front and back, corresponding pieces are installed, with the ones at the front featuring fir cones attached to them.
The roof is shown in the elevations as thatched. No other covering will look so well, or be so thoroughly in keeping with other parts. The non-professional builder finds it easy to prepare for thatch, any rough stuff serving as rafters and laths, and inequalities being of no account. The rafters for thatch should be arranged about 1 ft., the laths about 6 in. apart.
The roof is depicted in the elevations as thatched. No other covering will look as good or match so well with the other parts. A non-professional builder can easily prepare for thatch; any rough materials can be used as rafters and laths, and imperfections don’t matter. The rafters for thatch should be spaced about 1 foot apart, while the laths should be about 6 inches apart.
Should there, however, be reasons for not employing thatch, the building may be more quickly and easily, if not more cheaply, roofed with galvanised iron; only the gables will then best be made sharp instead of blunt, as at present.
Should there be reasons not to use thatch, the building can be roofed more quickly and easily, if not more cheaply, with galvanized iron; however, the gables should then ideally be made sharp instead of blunt, as they are now.
Regarding the door, its outer slabs, which appear in Fig. 137, are simply nailed to three ledgers of the same. Being of such rough materials, it will open better if hung on hooks and thimbles than on butt hinges.
Regarding the door, its outer panels, which appear in Fig. 137, are simply nailed to three ledgers of the same. Being made of such rough materials, it will open better if hung on hooks and thimbles than on butt hinges.
The dotted line at c, Fig. 140, marks the projection of a set of shelves, about five in number, which fill the whole of the left-hand side. Of these, the lower will be for flower-pots, the upper for lines, setting-pins, trowels, etc. At d is [Pg 111] shown a strip of wood fixed across the floor to hold the wheel of the barrow from running back when that useful vehicle is tilted up against the end wall, which will be the place assigned for it. In the gable and upper part of this end will be hooks or pegs on which to hang the riddle, watering-cans, and such matters. At e is an upright let into the ground, which, at the height of 2 ft., supports rails running to side and back; these form a kind of stand for spades, forks, and tools of that description. Above, against the wall-plate, may be more hooks or pegs.
The dotted line at c, Fig. 140, indicates the outline of a set of shelves, around five in total, that occupy the entire left side. The lower shelf will hold flower pots, while the upper one is for strings, setting pins, trowels, and similar items. At d is [Pg 111] a strip of wood secured across the floor to prevent the wheel of the wheelbarrow from rolling back when the useful vehicle is leaned up against the end wall, which is where it will be stored. In the gable and upper section of this end, there will be hooks or pegs to hang items like the riddle, watering cans, and similar tools. At e, there is a vertical post set into the ground, which, at a height of 2 ft., supports rails extending to the side and back; these will serve as a kind of stand for spades, forks, and tools of that nature. Above, along the wall plate, there may be additional hooks or pegs.
It is suggested that at f a seat might be fixed to fold down like the leaf of a table when not [Pg 112] wanted. As this building would form a snug shelter in a shower, such a seat would be a convenience; but the more important use of this space is that slightly below the level of the eaves it will be fitted with a rack for hoes, rakes, and similar implements. Such a rack is best made by boring ½ in. holes in a strip of wood at intervals of 3 in., and driving pegs into them 5 in. or 6 in. long. This has to be nailed so that the pegs will slope upwards, at an angle of about 45°. Rakes, etc., hung in a rack so made cannot fall.
It is recommended that at f, a seat be designed to fold down like a table leaf when it's not in use. Since this building would provide a cozy shelter during rain, such a seat would be useful; however, the more significant function of this space is that just below the eaves, it will have a rack for hoes, rakes, and similar tools. The best way to create this rack is by drilling ½ inch holes in a strip of wood, spaced 3 inches apart, and inserting 5 or 6 inch pegs into them. This should be attached so that the pegs slope upwards at about a 45° angle. Rakes and other tools hung on this type of rack won't fall.
The garden snuggery, of which a general view is shown at Fig. 142, and a ground plan at Fig. 143, is built chiefly of wood, and measures 10 ft. by 7 ft. 8 in. inside, not including the porch, which is 3 ft. wide; it may serve as a summer-house. A building as small as this needs but little foundation. If the ground is level, it is only necessary to lay four large flat stones on the surface, A A (Fig. 144), to carry the timbers, the floor being thus raised enough to keep it dry.
The garden snug, with a general view shown at Fig. 142 and a floor plan at Fig. 143, is primarily made of wood and measures 10 ft by 7 ft 8 in inside, not counting the porch, which is 3 ft wide; it can be used as a summer house. A structure this small requires very little foundation. If the ground is level, you just need to place four large flat stones on the surface, A A (Fig. 144), to support the timbers, raising the floor enough to keep it dry.
The two side sills B (Fig. 143) are each 10 ft. 8 in. long, 6 in. wide, and 4 in. thick, and rest on the stones; on them lie the end sills C C, which are 8 ft. 2 in. long. These sills are halved together at the ends, and a hole is bored through them where the middle of the collar-post will rest. This hole should be bored a couple of inches into the stone, and an iron pin or dowel 8 in. long driven in; the pin will thus stand a couple of inches above the face of the sill, and will fit into a hole in the collar post.
The two side sills B (Fig. 143) are each 10 feet 8 inches long, 6 inches wide, and 4 inches thick, resting on the stones; on them are the end sills C C, which are 8 feet 2 inches long. These sills are halved together at the ends, and a hole is drilled through them where the middle of the collar post will sit. This hole should be drilled a couple of inches into the stone, and an 8-inch long iron pin or dowel should be driven in; the pin will then stick up a couple of inches above the face of the sill and will fit into a hole in the collar post.
The joists D (Fig. 143) for supporting the floor are five in number, each being 8 ft. long, 2½ in. wide, and 3 in. deep. They are halved for a distance of 2 in. at each end to fit into slots, 1½ in. deep, made for them in the sills, and are nailed in place. When fixed their upper surfaces are level with the sills.
The joists D (Fig. 143) that support the floor are five in total, each measuring 8 ft. long, 2½ in. wide, and 3 in. deep. They are notched for 2 in. at each end to fit into 1½ in. deep slots created for them in the sills, and they are nailed in place. Once installed, their upper surfaces are flush with the sills.
The four collar-posts E (Figs. 143 and 144) are [Pg 115] each 6 ft. 9 in. long and 4 in. square, and, when set up, their outer sides come flush with the sills. The uprights F (Figs. 143 and 144) are 3 in. square, and need to be 2 in. longer than the collar-posts, as their lower ends are halved for this distance to fit slots in the outer sides of the sills. There are four of such uprights at each side, three at the back and two at the front, the latter serving also as door cheeks. They are nailed in place with their outer sides flush with those of the collar-posts and sills.
The four collar posts E (Figs. 143 and 144) are [Pg 115] each 6 feet 9 inches long and 4 inches square, and when set up, their outer sides are flush with the sills. The uprights F (Figs. 143 and 144) are 3 inches square and need to be 2 inches longer than the collar posts since their lower ends are halved for this distance to fit into slots on the outer sides of the sills. There are four of these uprights on each side, three at the back, and two at the front, with the latter also acting as door cheeks. They are nailed in place so their outer sides are flush with those of the collar posts and sills.
For the rustic pillars of the portico G (Fig. 145) nothing will be more suitable than larch poles about 4½ in. in diameter at the base; failing larch, fairly straight pieces of any rough, round wood could be used. The pillars are shown in Figs. 142 and 145 standing upon and dowelled to pieces of stone. When in position, their tops will be level with the collar-posts and uprights, their centres being 2 ft. 4 in. in advance of the front sill.
For the rustic pillars of the portico G (Fig. 145) nothing will be more appropriate than larch poles about 4½ inches in diameter at the base; if larch isn't available, fairly straight pieces of any rough, round wood can be used. The pillars are depicted in Figs. 142 and 145, standing on and secured to pieces of stone. Once in place, their tops will be level with the collar-posts and uprights, with their centers positioned 2 feet 4 inches in front of the front sill.
On the collar-posts, uprights, and pillars are placed the wall plates H (Fig. 144), of which there are four belonging to the snuggery proper, each 5 in. wide and 3 in. thick. The side plates are [Pg 116] 13 ft. 4 in. long, and are halved where they rest on the collar-posts and pillars, to receive the ends of the cross-plates, which are 8 ft. 2 in. long and halved to a distance of 5 in. from their ends. The wall-plates come flush with the collar-posts and uprights on which they rest, and to which they are nailed. There is also a fifth wall-plate which lies along the tops of the pillars in the front. The best material to use for this would be half of a pole like those used for the pillars, the flat side resting on the pillar tops. It will be observed that the front ends of the side wall-plates project about 4 in. beyond this piece.
On the collar posts, upright supports, and pillars, the wall plates H (Fig. 144) are installed, totaling four for the main snug area, each measuring 5 in. wide and 3 in. thick. The side plates measure 13 ft. 4 in. long and are halved where they sit on the collar posts and pillars to accommodate the ends of the cross plates, which are 8 ft. 2 in. long and halved to 5 in. from their ends. The wall plates align flush with the collar posts and uprights they rest on and are nailed to them. Additionally, there’s a fifth wall plate that runs along the tops of the front pillars. The best material for this would be half of a pole, similar to those used for the pillars, with the flat side resting on the tops of the pillars. The front ends of the side wall plates extend about 4 in. beyond this piece.
Ten rafters, K (Fig. 144), will be required for the roof, each 5 ft. long and 3 in. square. The two outer pairs come flush with the outer sides of the sills and wall-plates. A sixth pair of rafters to stand over the pillars and their wall-plates are made from a round pole cut in half, with the sawn side laid uppermost. The tops of the rafters butt against a ridge-piece L (Fig. 144), made of 1-in. board 4 in. deep and 13 ft. 4 in. long. As shown in Fig. 144, continuations of the uprights are in the back carried from the wall-plate to the roof, the front being treated in a similar manner.
Ten rafters, K (Fig. 144), will be needed for the roof, each measuring 5 ft. long and 3 in. square. The two outer pairs align with the outer edges of the sills and wall plates. A sixth pair of rafters, positioned above the pillars and their wall plates, will be made from a round pole sliced in half, with the flat side facing up. The tops of the rafters will meet a ridge piece L (Fig. 144), which is made of a 1-inch thick board that is 4 inches deep and 13 ft. 4 in. long. As shown in Fig. 144, extensions of the uprights at the back extend from the wall plate to the roof, and the front will be constructed in a similar way.
The lintel of the doorway is 6 ft. above the sill, the door opening being 5 ft. 11¼ in. by 2 ft. 6 in. after the floor has been laid. The window shown in Fig. 142 is 3 ft. above the sill, and is 3 ft. high; including the two mullions, it is 5 ft. 10 in. wide. The board shown nailed in front of the window sill is sloped a little downwards to throw off the rain, whilst above there is a board 9 in. wide, nailed at a steeper slope upon brackets, as seen in Fig. 146, to shelter the window. The ¾ in. flooring boards which are used for the floor should be bought ready planed on one side, and must be well seasoned, and cramped tightly together in laying, or there will be chinks [Pg 117] between them. Similar boards may be used for the outside of the snuggery, being nailed to the uprights at the back and sides, as shown in Fig. 147. At the sides this weather-boarding will extend as far forward as the rustic pillars, thus enclosing the sides of the porch. For the inside of the snuggery use ½ in. matchboarding, as shown in Fig. 147. This may be carried up beneath the rafters to the ridge-piece. The porch may be also matchboarded throughout if desired, although this is not essential.
The doorway lintel is 6 ft. above the sill, with the door opening measuring 5 ft. 11¼ in. by 2 ft. 6 in. after the floor is laid. The window shown in Fig. 142 is 3 ft. above the sill and is 3 ft. high; including the two mullions, it's 5 ft. 10 in. wide. The board nailed in front of the window sill is sloped slightly downwards to shed rain, while above it, there is a 9 in. wide board nailed at a steeper angle on brackets, as seen in Fig. 146, to protect the window. The ¾ in. flooring boards for the floor should be purchased already planed on one side, and they must be well-seasoned and tightly cramped together during installation, or there will be gaps between them. Similar boards can be used for the outside of the snuggery, nailed to the uprights at the back and sides, as shown in Fig. 147. The weatherboarding at the sides will extend forward to the rustic pillars, thus enclosing the porch sides. For the inside of the snuggery, use ½ in. matchboarding, as shown in Fig. 147. This may be extended up beneath the rafters to the ridge piece. The porch can also be matchboarded throughout if desired, although it's not necessary.
Figs. 147 and 148.—Cross-sections of Snuggery Walls. |
There are several methods of making the wooden walls non-conductors of heat, the most thorough being to pack the space between the inner and outer casings with sawdust. Shavings or similar materials could also be used, but less effectually. Another plan is to tack felt over the inner side of the weather-boarding before nailing up the interior casing. But even without any packing, two thicknesses of board with an air space between make a reasonably good non-conductor. Felt is fastened over the matchboard lining of the roof before the iron is put on.
There are several ways to make wooden walls good insulators against heat, with the most effective method being to fill the space between the inner and outer layers with sawdust. Shavings or similar materials can also be used, but they're not as effective. Another option is to staple felt on the inside of the outer layer before putting up the interior layer. However, even without any insulation, having two layers of board with an air gap in between provides decent insulation. Felt is attached over the matchboard lining of the roof before the metal is installed.
To reduce the cost, the snuggery can be cased with wood obtained from packing cases. Boards thus obtained will, of course, be in short lengths, and will involve more labour; but the design is so arranged that it will be quite practicable to carry it out with them.
To cut costs, the cozy room can be covered with wood sourced from packing crates. The boards will likely be shorter in length and require more work; however, the design is set up in a way that makes it completely doable with this material.
The short lengths can be made to fit between the uprights instead of lying upon them, and the house will thus look as shown in Fig. 142, the section of the wall being as shown in Fig. 148, instead of as in Fig. 147. A strip of lath—that sold for tiling—1 in. wide and 5/8 in. thick, is nailed to the sides of the uprights, as shown, and to this the weather-boarding [Pg 120] and internal casing are fastened; the effect being that the walls both inside and out appear to be divided into long panels. The effect may be heightened by painting the framework a darker colour than the boarding. In boarding the roof with this material, the easiest plan will be to nail the pieces on the upper sides of the rafters, to cover them with felt, and upon that to screw the iron. The space between the two casings of the walls, although much narrower than before, can be packed with sawdust, etc.
The short pieces can be fitted between the vertical supports instead of resting on them, making the house look like what's shown in Fig. 142, with the wall section depicted in Fig. 148, rather than as in Fig. 147. A strip of lath—1 inch wide and 5/8 inch thick, is nailed to the sides of the supports, as shown, and the weatherboarding and internal casing are attached to this; the result is that the walls inside and outside appear to be divided into long panels. This effect can be enhanced by painting the framework a darker color than the boarding. When covering the roof with this material, the easiest method is to fasten the pieces to the upper sides of the rafters, cover them with felt, and then screw the iron onto that. The space between the two wall casings, while much narrower than before, can still be filled with sawdust or similar materials. [Pg 120]
On reference to Fig. 145 it will be seen that the caps to the rustic pillars of the porch are formed by nailing round each pillar four short pieces of rough wood quartered, the two sawn sides being placed upwards and inwards. Four rough sticks crossing each other fill the space between wall-plate and the rafters. The bargeboards M M are sawn from ¾-in. board, 9 in. wide, and are nailed to the ends of the side wall-plates and ridge-piece. They thus project some inches beyond the line of the pillars. They are shown ornamented with fir cones bradded on them; virgin cork might be used instead. The porch may also have its interior decorated with virgin cork or with rustic mosaic work. At each side of the doorway there is a seat 16 in. high and 14 in. wide. The door is made by merely nailing the boards to four cross-ledgers.
On reference to Fig. 145, it can be seen that the tops of the rustic porch pillars are created by nailing four short pieces of rough wood around each pillar, with the two sawn sides facing up and inwards. Four rough sticks cross each other to fill the space between the wall plate and the rafters. The bargeboards M M are cut from ¾-inch boards, 9 inches wide, and are nailed to the ends of the side wall plates and the ridge piece. They extend a few inches past the line of the pillars. They are illustrated with fir cones added as decoration; virgin cork could be used instead. The porch interior may also be decorated with virgin cork or rustic mosaic work. On each side of the doorway, there is a seat that is 16 inches high and 14 inches wide. The door is simply made by nailing the boards to four cross ledgers.
The window lights in Fig. 142 are shown filled with fancy lead work, which is the most suitable way of treating them for a building of this kind. A strip of lath is nailed around the window opening, as in Fig. 148, and the leaded light fastened in the rebate thus formed with small wire nails, a little putty being used to make the joints waterproof. It will, of course, be much cheaper to glaze each light with a single sheet of glass puttied in the rebate, but the effect will not be so good. For the roof, fourteen 6-ft. sheets of corrugated galvanised iron and a 14-ft. run of ridge capping will be needed.
The window lights in Fig. 142 are filled with decorative lead work, which is the best way to handle them for a building like this. A strip of lath is nailed around the window opening, as in Fig. 148, and the leaded light is secured in the groove created with small wire nails. Some putty is used to make the joints waterproof. It would definitely be cheaper to glaze each light with a single sheet of glass puttied into the groove, but the result won't look as good. For the roof, you'll need fourteen 6-ft. sheets of corrugated galvanized iron and a 14-ft. piece of ridge capping.
The iron should be screwed, not nailed, to the rafters, and should not cost more than 40s., including 1½ gross of galvanised screws and washers. The dotted lines at N N (Fig. 143) indicate the area covered. Its low cost, the ease with which it is fixed, and the few timbers required to carry it, make an iron roof very suitable for a building erected by an amateur workman. It, however, has drawbacks, [Pg 122] the chief of which are that it conducts heat too freely, and has not a very artistic appearance. Some precautions against the first defect have already been suggested, and if the snuggery is erected where it will be shaded by trees during the hotter part of the day, this disadvantage will be somewhat overcome. Its inartistic appearance is greatly due to its colour, and some improvement may be made by painting. If surrounded by trees, an iron roof looks very well when painted a reddish-brown colour, while in other situations a buff, or a dull sage green, might be suitable. The paint needs renewing often. Another method is to cover the roof with trellis work raised a few inches above the iron, and upon this to train ivy or other climbing plants.
The iron should be screwed, not nailed, to the rafters, and should cost no more than 40s., which includes 1½ gross of galvanized screws and washers. The dotted lines at N N (Fig. 143) indicate the area covered. Its low cost, ease of installation, and minimal timber requirements make an iron roof a great choice for a building put up by an amateur. However, it does have some downsides, [Pg 122] the main ones being that it conducts heat too well and isn’t very visually appealing. Some measures to address the heat issue have already been mentioned, and if the small room is built in a spot that gets shade from trees during the hotter parts of the day, this drawback will be somewhat mitigated. Its unattractive look largely comes from its color, and painting it can help improve this. When surrounded by trees, an iron roof looks quite nice when painted a reddish-brown, while in other locations, a buff or a muted sage green might work better. The paint needs to be touched up frequently. Another option is to cover the roof with trellis work elevated a few inches above the iron and grow ivy or other climbing plants on it.
It will be better to paint the inside of the snuggery than to paper it, as paper would crack on the boards. Should the second and cheaper plan of boarding be adopted, the rafters, which are left exposed, might be coloured dark brown, and the intermediate spaces of the ceiling painted a buff colour, whilst on the walls a dark sage green might be used for the framework and a lighter [Pg 123] sage green for the panels. If the whole interior is lined with matchboarding, according to the first method, the simplest and perhaps best finish would be to use a varnish that had raw or burnt umber ground into it. No fireplace has been provided, but in ordinary winter weather an oil stove would suffice to warm so small a room; if more warmth is wanted, a coal stove might easily be provided, a hole for its pipe being cut through the roof. In either case a ventilator, which can be opened or closed at pleasure, should be arranged near the ridge at each end of the building.
It would be better to paint the inside of the snug room rather than wallpaper it, as the paper would crack on the boards. If the second, cheaper option of boarding is chosen, the exposed rafters could be painted dark brown, and the spaces in the ceiling could be painted a buff color, while the walls could feature a dark sage green for the framework and a lighter sage green for the panels. If the entire interior is lined with matchboarding, as in the first method, the simplest and probably best finish would be to use a varnish that has raw or burnt umber mixed in. There is no fireplace, but an oil stove would be enough to warm such a small room in regular winter weather; if more heat is needed, a coal stove could easily be installed with a hole for its pipe cut through the roof. In either case, a ventilator that can be opened or closed as needed should be placed near the ridge at both ends of the building.
The garden retreat shown in front view by Fig. 149, and in plan and side elevation by Figs. 150 and 151, is constructed from straight unbarked fir saplings, the small twigs of which should be carefully trimmed off. As the bark is to be left on, it should not be cut or bruised; then no artificial finish will be necessary, the bark in itself being sufficient protection against climatic conditions, and presenting the desired rustic appearance. A new feature in the design is the introduction of a roof or canopy, which may be covered with a sun blind as shown in Fig. 151; or a creeping plant may be trained over it.
The garden retreat shown from the front by Fig. 149, and in plan and side elevation by Figs. 150 and 151, is built from straight, unbarked fir saplings, with the small twigs carefully trimmed off. Since the bark is to remain on, it shouldn't be cut or damaged; this way, no artificial finish will be needed, as the bark itself provides enough protection against weather conditions and gives the desired rustic look. A new feature of the design is the addition of a roof or canopy, which can be covered with a sun blind as shown in Fig. 151, or a climbing plant can be trained to grow over it.
The two front posts are 3 in. in diameter at [Pg 124] the base by 6 ft. high, and the back posts 3 in. in diameter by 5 ft. 6 in. high; the middle back post is 3 ft. 2 in. high, and the front leg 1 ft. 4 in. The seat rails are 2½ in. in diameter. The front rail is 6 ft. long; the back is in two parts, dowelled to the middle post, which comes between. The side rails are 1 ft. 9 in. long; it is advisable to allow a fair margin for hollowing the ends to fit the posts—3 in. on the length would probably be sufficient. After the ends of the rails have been shaped roughly to fit the posts, they are bored for the reception of 11/8-in. oak or elm dowels; these are driven into the rails, and should also be a good fit in the posts. The dowel joint is shown in the top corner of Fig. 152.
The two front posts are 3 inches in diameter at the base and 6 feet tall, while the back posts are also 3 inches in diameter and 5 feet 6 inches high; the middle back post is 3 feet 2 inches tall, and the front leg is 1 foot 4 inches. The seat rails have a diameter of 2½ inches. The front rail measures 6 feet long; the back rail is in two parts, dowelled to the middle post that is situated in between. The side rails are 1 foot 9 inches long; it's a good idea to leave a bit of extra length for hollowing the ends to fit the posts—about 3 inches should work well. Once the ends of the rails have been roughly shaped to fit the posts, they are drilled to receive 11/8-inch oak or elm dowels; these dowels are inserted into the rails and should also fit snugly in the posts. The dowel joint is illustrated in the top corner of Fig. 152.
The lower rungs, arm-rests, and back rails are jointed to the posts by tapering their ends slightly, and then tapering the dowel holes to suit with a gouge, so that the rails will just drive up nicely; this joint is shown in the bottom corner of Fig. 1522. The rails, etc., are finally driven home, and secured with nails or screws inserted at suitable angles. The back and the side panels are filled with twigs about 1¼ in. in diameter, the ends of the twigs being trimmed to fit the rails, and afterwards nailed in position.
The lower rungs, armrests, and back rails are joined to the posts by slightly tapering their ends, and then tapering the dowel holes with a gouge so that the rails fit together nicely. This joint is shown in the bottom corner of Fig. 1522. The rails, etc., are finally pushed into place and secured with nails or screws inserted at appropriate angles. The back and side panels are filled with twigs about 1¼ inches in diameter, with the ends of the twigs trimmed to fit the rails and then nailed into position.
The canopy must now be put together. The tops of the posts are first hollowed to form a seating for 2¼-in. saplings, 4 ft. 6 in. long; these act as principal rafters. Before nailing or screwing them to the posts, it is advisable to sight across them to see if they are in the same plane; any alteration that may be required to bring them to lie in the same angle can be effected at the seating on the top of the posts. The halved joint at each end of the principals should also be cut (before fixing up) for receiving the purlins; the principals are further steadied with struts, screwed or nailed to the posts. The purlins are about 2 in. in diameter by 8 ft. 6 in. long, and are fixed to the halved joint previously made on the principal rafters. Smaller twigs, which act as common rafters, are in turn fixed to the purlins. Fig. 153 shows the method of jointing at the back of the canopy at C (Fig. 151), and Fig. 154 is the detail of the front joints. Fig. 129 (p. 94) is the top of the post hollowed to receive the principal rafter, Fig. 155 is an alternative method of joining the rails to the posts, Fig. 156 is a section near the middle rail at A (Fig. 152), while Fig. 157 is a detail of middle rail at B (Fig. 152).
The canopy needs to be assembled now. The tops of the posts should first be hollowed out to create a spot for 2¼-inch saplings that are 4 feet 6 inches long; these will serve as the main rafters. Before attaching them to the posts with nails or screws, it's a good idea to check if they’re level with each other; any adjustments needed to align them at the same angle can be made at the top of the posts where they fit. The halved joint at each end of the main rafters should also be cut beforehand to accommodate the purlins; the main rafters are further secured with struts that are screwed or nailed to the posts. The purlins are approximately 2 inches in diameter and 8 feet 6 inches long, fixed to the halved joints made on the main rafters. Smaller twigs, which function as common rafters, are then attached to the purlins. Fig. 153 shows the jointing method at the back of the canopy at C (Fig. 151), and Fig. 154 provides details of the front joints. Fig. 129 (p. 94) illustrates the top of the post hollowed out to receive the main rafter, Fig. 155 shows an alternative method of joining the rails to the posts, Fig. 156 is a section near the middle rail at A (Fig. 152), while Fig. 157 details the middle rail at B (Fig. 152).
CHAPTER XIII.
SUMMER-HOUSES.
The lean-to summer-house shown by Fig. 158 is intended for a small garden. Perhaps in no better way can a dead wall or the back of some unsightly outhouse be better utilised than as the background for such a building. The dimensions of the structure are: length, 8 ft.; breadth, 3 ft. 3 in.; height, 8 ft.
The lean-to summer house shown by Fig. 158 is meant for a small garden. There's no better way to use a blank wall or the back of an unattractive shed than as the backdrop for a building like this. The dimensions of the structure are: length, 8 ft.; width, 3 ft. 3 in.; height, 8 ft.
Its general arrangement is seen in the ground plan (Fig. 159). Four pillars, A, B, B, A, occupy the front. These are poles 3½ in. or 4 in. in diameter. Any rough and tolerably straight wood will do, but larch is to be preferred. These rise 5 ft. above ground, and should not have less than 2 ft. below the surface. The dwarf pillars C supporting the seat are of similar stuff, but rather smaller. They show 14 in. above, and [Pg 128] should be buried about 9 in. below ground. The pilasters D are of rather larger stuff sawn in half. These are only 5 ft. long, as they need not enter into the ground, being fixed only by strong nails to the wall.
Its general layout is shown in the ground plan (Fig. 159). Four pillars, A, B, B, A, are positioned at the front. These are poles with a diameter of 3½ inches or 4 inches. Any rough, reasonably straight wood will work, but larch is preferred. They should extend 5 feet above ground and have at least 2 feet buried below the surface. The shorter pillars C that support the seat are made from similar material, but are slightly smaller. They stand 14 inches above, and should be buried about 9 inches below ground. The pilasters D are made from somewhat larger material, cut in half. They are only 5 feet long, as they don’t need to be buried in the ground, being secured only with strong nails to the wall.
The ends of the summer-house (the space from A to D) are of smaller half-stuff, ranged side by side (as seen at E, E), and nailed to the [Pg 129] cross-pieces, F and G, which appear in Fig. 160. In this last-named figure also appears one of the wall-plates, resting on and nailed to the tops of the pillars (H, at Fig. 160), and at I is seen where one of the front wall-plates meets it. There are two of these front wall-plates, each resting on the two pillars to right and left of the entrance, and their inner ends appear in Fig. 158, where the ends of the purlins which form the small gable rest upon them. The wall-plates are of large half-stuff, with the flat side above. In Fig. 160 will be seen how the short cross-piece which carries the sloping end of the roof is supported; and Fig. 161, which is a section through the centre of the building, explains how the ridge-piece of the small gable, E, rests at its inner end on a crosspiece M from rafter to rafter, seen in section only, whilst N shows the point at which the purlins meet and support the ridge-piece towards its outer end. The intersection of the diagonal braces in the gable is indicated at O, and P shows the course of one of the rafters, and how its upper end rests against the wall, and upon a ridge-piece of half-stuff, Q, strongly nailed to the masonry.
The ends of the summer house (the space from A to D) are made of smaller half-stuff, placed side by side (as shown at E, E), and nailed to the cross-pieces, F and G, which appear in Fig. 160. In this last figure, one of the wall-plates is also shown, resting on and nailed to the tops of the pillars (H, at Fig. 160), and at I you can see where one of the front wall-plates meets it. There are two of these front wall-plates, each resting on the two pillars on either side of the entrance, and their inner ends appear in Fig. 158, where the ends of the purlins that form the small gable rest on them. The wall-plates are made of large half-stuff, with the flat side on top. In Fig. 160, you can see how the short cross-piece that supports the sloping end of the roof is held up; and Fig. 161, which is a section through the center of the building, explains how the ridge-piece of the small gable, E, rests at its inner end on a cross-piece M from rafter to rafter, seen in section only, while N shows the point where the purlins meet and support the ridge-piece towards its outer end. The intersection of the diagonal braces in the gable is indicated at O, and P shows the path of one of the rafters and how its upper end rests against the wall and on a ridge-piece of half-stuff, Q, which is strongly nailed to the masonry.
The elevation (Fig. 158) explains pretty clearly the ornamental details of the front. They are not elaborate. It will be seen that the top of each pillar has a small cap, formed of four pieces of quartered stuff, mitred at the corners, and that across the opening on each side of the entrance, near the top, is a "transom" of straight wood, with a little arrangement of crooked bangles round it. Over the entrance are diagonal braces crossing, and also a little filling-in with bangles. The entrance is 5 ft. 10 in. high.
The elevation (Fig. 158) clearly outlines the decorative details of the front. They aren't overly intricate. You’ll notice that the top of each pillar has a small cap made of four pieces of quartered material, joined at the corners. Across the opening on each side of the entrance, near the top, is a straight wooden "transom," adorned with a little arrangement of curved ornaments around it. Over the entrance are diagonal braces that cross each other, along with some additional decorative pieces. The entrance stands 5 ft. 10 in. high.
In order that an ornamental and appropriate lining may be given to the back of our summer-house, it is recommended to plug the wall, and nail over it a level covering of thin boards—say, [Pg 130] ½-in. matchboarding. Upon this the decorative work can be bradded. The back of the seat is shown in Fig. 158 to be of rustic mosaic. Above this, as well as under the seats, a covering of bark has been introduced. British-grown bark, such as elm, can be made to lie flat, but as in any but rural districts this may be difficult to get, virgin cork may be made to take its place.
To give an ornamental and suitable lining to the back of our summer house, it’s suggested to fill the wall and attach a flat covering of thin boards—about ½-inch matchboarding. On this, the decorative work can be added. The back of the seat is shown in Fig. 158 to be made of rustic mosaic. Above this and under the seats, a layer of bark has been added. British-grown bark, like elm, can be flattened out, but since this might be hard to find in non-rural areas, virgin cork can be used as a substitute.
Fig. 160 gives an inside view of one of the ends, and from this it will be seen that the ornamentation of those parts varies little from that of the back. The lower band, however, answering to the strip under the seats, is not bark, which, in this place, would be liable to be kicked and destroyed by the feet, but of smaller half-stuff, so arranged as to break joint with the outside pieces. This will be seen by referring to the ground plan. Any chinks in the ends should be neatly tucked with moss, so as to make them wind-proof.
Fig. 160 provides a closer look at one of the ends, showing that the decoration in those areas is quite similar to that on the back. However, the lower band, corresponding to the strip underneath the seats, isn’t made of bark, which would easily get kicked and damaged. Instead, it consists of smaller half-stuff, arranged to fit together seamlessly with the outer pieces. You can see this by looking at the ground plan. Any gaps in the ends should be neatly filled with moss to make them windproof.
The roof is of wooden shingles—things which any rough hand at carpentry can prepare and put on for himself. As will be seen from Fig. 158, it is easy to give an ornamental character to these. They will have a rustic look, which will go well with other parts of the structure, and, if clumsily made, the effect will be none the worse. For the present purpose, suppose the shingles to be 12 in. by 4 in. The lower ends may be sawn to a variety of ornamental shapes.
The roof is made of wooden shingles—something that anyone with basic carpentry skills can prepare and install themselves. As will be seen from Fig. 158, it's easy to add decorative touches to these. They will have a rustic appearance that will complement the rest of the structure, and even if they're made a bit clumsily, it won't really affect the overall look. For now, let's assume the shingles are 12 inches by 4 inches. The lower ends can be cut into various decorative shapes.
If this covering is used, instead of nailing laths across the rafters, it is proposed to cover the whole roof with similar boarding to the back, and upon this it is a simple thing to nail the shingles, placing them just as tiles might be placed. Whilst nailing them on, it will be necessary to have some person within to hold a heavy hammer against the place, otherwise the vibration will jar off the shingles as fast as they are fixed. A ¾-in. board, rather wider than half the length of the shingles, should first be nailed along the eaves to make up the required thickness.
If this covering is used, instead of nailing laths across the rafters, the plan is to cover the entire roof with similar boarding to the back, and then it's easy to nail the shingles on, just like you would lay tiles. While nailing them on, someone will need to hold a heavy hammer inside against the spot, otherwise the vibration will knock the shingles off as fast as they’re put on. A ¾-inch board, slightly wider than half the length of the shingles, should first be nailed along the eaves to create the necessary thickness.
It will be noticed that the ends of the rafters are made to project so as to give a good breadth of eaves—a desirable feature in so narrow a building, alike for shade, shelter, and the appearance of cosiness. If, however, the roof should be thatched, the projecting [Pg 132] rafters will be unnecessary, as the thatch alone will form sufficient eaves.
It will be noticed that the ends of the rafters stick out to provide a nice wide eave—a great feature for such a narrow building, providing shade, shelter, and a cozy appearance. However, if the roof is thatched, the extended [Pg 132] rafters won’t be needed, as the thatch will create enough eaves on its own.
Down the "valleys" at the juncture of the main roof and the entrance gable a strip of zinc will, of course, be nailed before the shingles are put on, whilst along the ridges a strip of zinc will be nailed upon the shingles; and this latter will need painting to match the colour of the wood.
Down in the "valleys" where the main roof meets the entrance gable, a strip of zinc will be nailed down before the shingles are installed. Additionally, a strip of zinc will be nailed on top of the shingles along the ridges, and this will need to be painted to match the color of the wood.
Various suggestions may be given for finishing the inside of the roof. Supposing that round or half-round larch stuff has been used for the rafters (the latter is to be preferred for shingles, as giving a level surface to board upon), the space between the rafters may be covered with bark—virgin cork or otherwise—the chinks being stuffed with moss. But if this is done it will be well to fix the bark with screws, as the vibration caused by driving nails would displace or loosen the shingles.
Various suggestions can be made for finishing the inside of the roof. Assuming that round or half-round larch wood has been used for the rafters (the latter is preferred for shingles, as it provides a flat surface to board onto), the space between the rafters can be covered with bark—virgin cork or something similar—with the gaps filled with moss. However, if this is done, it's a good idea to secure the bark with screws, as the vibration from driving nails could shift or loosen the shingles.
A second plan under the like circumstances would be before nailing the boards upon the rafters to stretch matting across the latter—either ordinary garden bast matting or, better, the more substantial rush matting, both of which are very inexpensive. These have a pleasant natural colour (the last-named especially, of a greenish hue), and are so unartificial in their structure as to appear in no way out of place among rustic work.
A second option in similar situations would be to lay down matting across the rafters before nailing the boards on. You can use regular garden matting or, even better, the sturdier rush matting, both of which are very affordable. These materials have a nice natural color (especially the rush matting, which has a greenish tint) and their unrefined texture makes them blend perfectly with rustic surroundings.
Or it may so happen that suitable larch stuff is not to hand, and that ordinary sawn scantling has to be used for the rafters. If so, the whole roof may be hung with ling; or the rush matting may be stretched across the lower side of the rafters and tacked there, being afterwards more completely secured and finished by nailing a split hazel or other rod down the middle of each rafter. This last plan makes a neat and pleasing roof.
Or it might happen that suitable larch material isn't available, and regular cut lumber has to be used for the rafters. In that case, the entire roof can be covered with heather; or rush matting can be stretched across the underside of the rafters and tacked in place, then further secured and finished by nailing a split hazel or another rod down the center of each rafter. This last method creates a tidy and attractive roof.
Figs. 162 and 163.—Front and Side Views of the Shelter for the Tennis Court. |
It scarcely needs to be said that to make such a summer-house look its best the wall on each side ought to be covered with ivy or other creepers; and it will also be obvious that, if the height of the wall permits the floor of the summer-house to be raised a step or two above the surrounding [Pg 135] level, the structure will gain thereby both in effectiveness of appearance and in pleasantness as a place in which to sit.
It hardly needs mentioning that to make a summer house look its best, the walls on each side should be covered with ivy or other climbing plants. It’s also clear that if the wall is tall enough to allow the floor of the summer house to be raised a step or two above the surrounding level, the structure will look more appealing and be a nicer place to sit. [Pg 135]
Fig. 165.—Connecting Plates to Corner Post.
Fig. 166.—Attaching Sleeper to Posts.
Fig. 167.—Flooring Section.
Fig. 168.—Finial.
Fig. 169.—Detail of Garden Shelter at Front Eaves.
Fig. 170.—Seat Section.
|
The rustic summer-house or tennis lawn shelter illustrated in front and side elevations by Figs. 162 [Pg 136] and 163 is constructed from straight saplings and twigs that have had their bark removed, and have been subjected to a reasonable period of seasoning. A new feature in the design is the accommodation under the seats for the reception of the croquet or tennis gear, and also the extended eaves and floor (see Fig. 164) and the open front, giving at once an uninterrupted view of the game and shelter from the direct rays of the sun.
The rustic summer house or tennis lawn shelter shown in the front and side elevations by Figs. 162 [Pg 136] and 163 is made from straight saplings and twigs that have had their bark stripped and have dried out for a reasonable amount of time. A new feature in the design is the space under the seats for storing croquet or tennis equipment, along with the extended eaves and floor (see Fig. 164) and the open front, which provides an unobstructed view of the game while offering protection from the sun.
The shelter is 10 ft. long by 5 ft. 6 in. wide, the height from the floor to the eaves being 6 ft. 3 in., and from the floor to the ridge 9 ft. The four posts are 6 ft. 9 in. long by 6 in. in diameter. The middle and lower end and the back rails are tenoned to the posts, a flat being formed on the post by the mortise and a corresponding shoulder on the rails. The remaining portion is worked to fit roughly the contour of the post.
The shelter is 10 feet long and 5 feet 6 inches wide, with a height from the floor to the eaves of 6 feet 3 inches, and from the floor to the ridge of 9 feet. The four posts are 6 feet 9 inches long and 6 inches in diameter. The middle and lower end and the back rails are fitted into the posts with a tenon, creating a flat on the post with a matching shoulder on the rails. The remaining part is shaped to roughly match the contour of the post.
The plates are 5 in. by 5 in. in section, and are secured to the posts with long galvanised bolts and nuts and a 3½-in. square washer under the heads of the bolts. When halving the front plate, allow it to house into the side plates 1½ in.; by this method it will have a bearing on both posts. In Fig. 165 the left-hand plate represents the front. The front posts are connected at the floor line by a scantling, 4 in. by 3 in., which also forms a sleeper for the floor joists; see Figs. 166 and 167.
The plates are 5 inches by 5 inches in size and are attached to the posts with long galvanized bolts and nuts, along with a 3½-inch square washer under the heads of the bolts. When cutting the front plate in half, make sure to inset it into the side plates by 1½ inches; this way, it will rest on both posts. In Fig. 165, the left-hand plate represents the front. The front posts are linked at the floor level by a beam that is 4 inches by 3 inches, which also serves as a support for the floor joists; see Figs. 166 and 167.
The structure rests on a low plinth of bricks, spaces being left for the circulation of air under the floor.
The structure sits on a low brick base, leaving gaps for air to circulate beneath the floor.
The sides are filled with 5/8-in. vee-grooved and tongued boarding, to which is attached the rustic work.
The sides are filled with 5/8-in. vee-grooved and tongued boarding, to which the rustic work is attached.
The stained glass windows are fixed, and on the outer side of the back are diagonal braces made from split saplings, while in the centre a vertical post runs from sill to plate.
The stained glass windows are securely in place, and on the outside of the back, there are diagonal braces made from split branches, while in the center, a vertical post runs from the sill to the plate.
The braces and post are shown in the plan (Fig. 164).
The braces and post are shown in the plan (Fig. 164).
The cushions are retained in place by straps passing through slots and fastening over suitable studs on the under side; see Fig. 171. This method provides a means of easily removing and quickly replacing the cushions when required for use. A space of 3 in., or a distance equal to the thickness of the cushions, must be left at the sloping back, to allow the seat to open properly.
The cushions are held in place by straps that go through slots and attach to appropriate studs underneath; see Fig. 171. This system allows for easy removal and quick replacement of the cushions whenever needed. A gap of 3 inches, or a distance equal to the thickness of the cushions, must be left at the sloping back to ensure the seat opens correctly.
The nature of the locker is partly concealed by the rustic work of split twigs that is nailed to the front.
The locker is partially hidden by the rustic arrangement of split twigs that’s nailed to the front.
Next fix the lattice work between the finials and under the front plate. The short struts on the front posts are more for effect than for any real support.
Next, repair the lattice work between the finials and under the front plate. The short struts on the front posts are more for show than for any actual support.
The roof is boarded on the inside, the work being carried on the rafters as far as the collar ties, and continued flat on these. Moulding is fixed in the angles formed between the rafters and ties, and a cornice is fixed at the plates. The heels of the rafters and plates are also boarded around, as shown in Fig. 169.
The roof is finished on the inside, with work being done on the rafters up to the collar ties, and then continuing flat on these. Molding is installed in the corners where the rafters meet the ties, and a cornice is attached at the plates. The ends of the rafters and plates are also covered, as shown in Fig. 169.
The roof may be covered with thatch of wheat, straw, reeds, broom, or heather, and the whole of the woodwork visible should be varnished.
The roof can be covered with wheat thatch, straw, reeds, broom, or heather, and all visible woodwork should be varnished.
The summer-house illustrated by Fig. 172 is suited to a garden of moderate size, one in which space is not so restricted as to necessitate crowding the building close against a wall. This octagonal summer-house has a continuous seat some 15 ft. long. From side to side each way it measures 10 ft. Fig. 172 is an elevation of the front of the house.
The summer house shown in Fig. 172 is ideal for a moderately sized garden, where there's enough space to avoid pushing the building up against a wall. This octagonal summer house features a continuous seat that's about 15 ft. long. It measures 10 ft. from side to side in both directions. Fig. 172 is a front view of the house.

Fig. 173.—Ground Plan of an Octagonal Summer House.
Fig. 174.—Section of the Octagonal Summer House at Y Z (__A_TAG_PLACEHOLDER_0__), displaying the Framework.
Its framework and the main part of it are of larch poles; other woods are, however, used for minor purposes. The roof is of thatch. In the arrangement of this building there is a certain resemblance to a tent. It has a central pillar, A, not unlike a tent pole, which sustains much of the weight of the roof. Being of first importance, this pillar is somewhat larger than any of the other timbers—say 6 in. in diameter near its bottom, and tapering as little as may be. A rod of iron or wood rises from its top to form the centre of the straw pinnacle seen crowning the roof in Fig. 172. This pillar shows a height of 11 ft. 2 in. above ground, and it should be let 3 ft. or more into the soil; for it will need to be firmly fixed, or it may be forced out of the perpendicular during the erection of the roof; when the roof timbers are once fixed in place, it will have little further chance of moving. The diagram Fig. 173 is a ground plan, and Fig. 174 is a section showing the timbers from the interior; both are drawn on a scale of ¼ in. to the foot.
Its structure and main components are made of larch poles; however, other types of wood are used for smaller elements. The roof is thatched. The design of this building resembles a tent to some extent. It features a central pillar, A, which is similar to a tent pole and supports much of the roof's weight. Being crucial, this pillar is slightly larger than the other timbers—about 6 inches in diameter near the bottom, tapering minimally. An iron or wooden rod extends from its top, forming the center of the straw pinnacle that crowns the roof in Fig. 172. This pillar reaches a height of 11 feet 2 inches above ground and should be set 3 feet or deeper into the soil; it needs to be securely anchored, or it may lean during the roof assembly. Once the roof timbers are secured, there will be little chance of shifting. The diagram Fig. 173 is a ground plan, and Fig. 174 is a section that shows the internal timbers; both are drawn to a scale of ¼ inch to the foot.
The ground plan of a building in this shape is readily laid out. The space being levelled, a string is taken which has a loop at each end, and is 5 ft. 2 in. long. With a stake driven through the loop at one end as a centre, and with a stick passed through the loop at the other to serve as the travelling leg of the compasses, a circle is struck 10 ft. 4 in. in diameter, and into this pegs are driven at equal intervals (4 ft. apart) to mark the centres of the eight collar-posts. Whilst digging the holes for the posts, these points are kept by drawing two straight lines on the ground which intersect at the peg.
The layout for a building in this shape is easy to establish. Once the area is leveled, take a string that's 5 ft. 2 in. long, with a loop at each end. Drive a stake through one loop to act as a center point, and use a stick through the other loop as the compass's arm. This way, you can draw a circle with a diameter of 10 ft. 4 in., and then place pegs at equal intervals (4 ft. apart) to mark the centers of the eight collar-posts. While digging the holes for the posts, keep track of these points by drawing two straight lines on the ground that cross at the peg.
The cross-pieces which rest on the collar-posts, [Pg 141] and which serve as wall-plates, are a trifle smaller stuff than the posts—say 3 in. Fig. 175 shows how they are cut to fit the tops of the posts, and nailed there. In this building there are no mortise and tenon joints. On these ends above the posts rest the lower ends of the eight main rafters, D, the upper ends of which rest against and are nailed to the central pillar. The eight intermediate rafters, E, rest at the bottom on the middles of the side plates, and at top are cut to fit upon and between the tops of the main rafters.
The cross pieces that sit on the collar posts, [Pg 141] and act as wall plates, are slightly smaller than the posts—about 3 in. Fig. 175 illustrates how they are trimmed to fit the tops of the posts and nailed in place. In this building, there are no mortise and tenon joints. The lower ends of the eight main rafters, D, rest on these ends above the posts, while the upper ends are attached and nailed to the central pillar. The eight intermediate rafters, E, rest at the bottom on the middle of the side plates and are cut at the top to fit onto and between the tops of the main rafters.
The laths used are in this case in no way particular—any sticks will do; they will not be seen, and under thatch there is no necessity that a level surface should be formed by them, as for slates or tiles. They are nailed 6 in. or 8 in. apart.
The laths used here are not specific—any sticks will work; they won't be visible, and under thatch, there's no need for them to create a level surface like with slates or tiles. They are nailed 6 inches or 8 inches apart.
The gable over the entrance is arranged as in Fig. 176. The laths, when nailed on, will have to run over the little ridge formed by F, instead of keeping the level, as on the other sides. This will cause no special difficulties in the thatching.
The gable above the entrance is set up like in Fig. 176. When the laths are nailed on, they will need to go over the small ridge made by F, instead of staying level like on the other sides. This won’t create any particular issues with the thatching.
The walls are of larch poles sawn in half. To split a number of heavy poles with the handsaw [Pg 142] is tedious work, and it is better to get them run through by the nearest steam saw. The quantity of half-stuff required may be easily calculated; one of these sides will take about five and a half 6-ft. lengths of 4-in. stuff. The tops of these wall-pieces are sawn obliquely to fit against the round wall-plates to which they are nailed. In their lower parts they are nailed to the lower cross-pieces, G, G, G, Fig. 174.
The walls are made of larch poles cut in half. Cutting a bunch of heavy poles with a handsaw is slow work, so it’s better to take them to the nearest steam saw. You can easily figure out how much half-stuff you need; one of these sides will use about five and a half 6-ft. lengths of 4-in. lumber. The tops of these wall pieces are cut at an angle to fit against the round wall plates they’re nailed to. At the bottom, they’re nailed to the lower crosspieces, G, G, G, Fig. 174.
These latter will best be made of rather large stuff quartered, since their upper sides on which the seat-boards rest should be level, as well as their backs, which go against the wall-pieces. The middle cross-pieces are of smaller half-stuff, and should be nailed to the wall-pieces rather than that the wall-pieces should be nailed to them; for they are in a conspicuous place, and nails driven through them and clenched would be unsightly.
These should be made from reasonably large, quartered material, as the tops where the seat boards rest need to be level, along with the backs that touch the wall pieces. The middle crosspieces can be made from smaller material and should be nailed to the wall pieces instead of the other way around; this is because they're in a visible area, and nails driven through them and bent over would look unattractive.
The front supports of the seats are let into the ground some 6 in., and rise 14½ in. above the ground line. The seats should be cut from 1-in. board, and should be about 16½ in. wide.
The front supports of the seats are set into the ground about 6 in. and rise 14½ in. above the ground line. The seats should be made from 1-in. board and should be approximately 16½ in. wide.
In the two window sides of the octagon (see Figs. 177 and 172), the space below the windows is filled with whole poles, their bottoms resting on a sill let in level with the ground, and their tops nailed into through a cross-piece of half-stuff (K, Fig. 177). The mullions and transoms of the windows—mere sticks—are of small straight larch stuff, but the ornamental filling in above is of crooked branches—oak bangles by preference, though apple-wood would do very well. It often happens that an old apple-tree is cut down, and at once condemned as firewood; yet its stem may have grotesque knots, and its branches picturesque contortions which would make it valuable for rustic work. Whenever rustic building is contemplated, it is well that such wood should be laid by; a single tree would supply all the small [Pg 143] quantity of crooked stuff that is required in the present instance. Even the interlaced stems of ivy, when an old growth has covered a wall, have sometimes been utilised to excellent effect.
In the two window sections of the octagon (see Figs. 177 and 172), the space below the windows is filled with whole poles, their bottoms resting on a sill even with the ground, and their tops nailed into a cross-piece of half-timber (K, Fig. 177). The window frames—just simple sticks—are made of small straight larch wood, but the decorative filling above is made from twisted branches—preferably oak, although apple wood would work just as well. It often happens that an old apple tree is cut down and immediately classified as firewood; however, its trunk might have unique knots, and its branches could have interesting shapes that would make it valuable for rustic projects. Whenever rustic building is considered, it’s good to save such wood; a single tree would provide all the small amount of twisted wood needed in this case. Even the intertwined stems of ivy, when an old growth has covered a wall, have sometimes been used to great effect.
It may be observed that any chinks between the pieces beneath the windows, as well as in the walls generally, are most readily and appropriately rendered wind-proof by neatly stuffing with moss. Fig. 177 gives a full front elevation of one of the window sides (they being only seen obliquely in Fig. 172), and it is on the ½-in. scale.
It can be noticed that any gaps between the pieces under the windows, as well as in the walls overall, are easily and effectively sealed against the wind by carefully stuffing them with moss. Fig. 177 shows a full front view of one side of the window (as they can only be seen from an angle in Fig. 172), and it is on a ½-inch scale.
Four stout crooked pieces are used as struts to support the table (drawn to 1 in. scale in Figs. 178 [Pg 144] and 179); 3/4-in. board will suffice for the top of this table, and it will probably be cut from two widths. To give proper strength to the ornamental border (seen in Fig. 179), a second thickness of the board is attached below each corner, extending 3 or 4 in. to each side, so as to allow each of the longer bits of split rod to be fixed, as shown, with two brads.
Four sturdy, bent pieces are used as supports for the table (drawn to 1 in. scale in Figs. 178 [Pg 144] and 179); a 3/4-in. board will be sufficient for the table top, which will likely be cut from two widths. To add proper strength to the decorative border (seen in Fig. 179), a second layer of the board is attached below each corner, extending 3 or 4 in. on each side, allowing the longer pieces of split rod to be secured, as shown, with two brads.
A really satisfactory material in which to finish the top of a rustic table is not easily found; it must give a level surface, and at the same time be in harmony with its surroundings. Board, planed or painted, oilcloth, or any manufactured material, is felt to be out of place; marble or slate looks cold and hard. Nothing that is absolutely level satisfies the requirements; the best alternative is rustic mosaic. By this is meant split rods of wood so bradded down as to form patterns. For the present purpose, however, the mosaic must be kept more neat and smooth than usual. Fig. 178 shows the top of the table thus treated.
A truly satisfying material to finish the top of a rustic table isn't easy to find; it needs to provide a flat surface while also blending well with its surroundings. Board, whether planed or painted, oilcloth, or any manufactured material just feels out of place; marble or slate appears cold and hard. Nothing that’s perfectly flat meets the needs; the best alternative is a rustic mosaic. This involves splitting wooden rods and bradding them down to create patterns. For this particular purpose, though, the mosaic should be kept neater and smoother than usual. Fig. 178 shows the top of the table done this way.
The rods most in favour for rustic mosaic are those of the hazel. They are to be bought cheaply and abundantly when the undergrowth of woods is cut. They have a smooth and pretty bark, and the useful size is from ¾ in. to 1½ in. Sticks of other kinds of the same size can also be used: birch and wild cherry may be named among those with smooth bark, and wych elm and maple among those with rough; willow or withy, again, is of most common growth, and exceedingly useful. In river-side neighbourhoods it is often the cheapest and most plentiful of all woods. For mosaic work, it is always peeled, for its bark is unattractive, and its light colour when stripped makes it tell well in contrast to the dark bark of other woods. If used, as it often is, for outdoor purposes in garden carpentry, it should always be peeled. Country carpenters have a saying that withy lasts twice as long without its bark as with it; and in this there is much truth, for the loose bark holds the wet to the wood and causes it to rot. To make it peel freely, it should be cut just as the young leaves make their appearance. The like holds good with other woods; but if it is desired that the bark should hold firmly, the wood should be cut down in dead of winter, when all the sap is down.
The best rods for rustic mosaic are hazel. They can be bought cheaply and are readily available when the underbrush in woods is cleared. They have a smooth, attractive bark, and the ideal size ranges from ¾ inch to 1½ inches. Other types of sticks of the same size can also be used: birch and wild cherry have smooth bark, while wych elm and maple have rough bark. Willow, or withy, grows abundantly and is very useful. In areas near rivers, it's often the most affordable and readily available wood. For mosaic work, it's always stripped of its bark since it looks dull, and the light color of the stripped wood contrasts nicely with the dark bark of other woods. If it's used, as it often is, for outdoor projects in the garden, it should always be peeled. Country carpenters say that withy lasts twice as long without its bark than with it, and there's a lot of truth to that because loose bark retains moisture against the wood, causing it to rot. To make it strip easily, it should be cut just as the young leaves begin to appear. This also applies to other types of wood, but if you want the bark to stay firmly attached, the wood should be cut down in the dead of winter when all the sap has gone down.
The top of the table is supposed to be mainly composed of peeled withy. The pattern contains only the double dark line bounding the star and the single strip round the edge in hazel. So much white will not look amiss in this place, and withy is easily worked. Hazel and most woods twist so much in the grain that it is rarely safe to split them except with the saw, but withy—in short lengths like these, at least—can be split with a hatchet.
The top of the table should mainly be made of peeled willow. The design only features the double dark line outlining the star and the single strip around the edge in hazel. A lot of white will fit in well here, and willow is easy to work with. Hazel and most kinds of wood are so twisted in the grain that it’s usually not safe to split them except with a saw, but willow—in these short lengths, at least—can be split with a hatchet.
In rough carpentry there is no more pretty or interesting work than these mosaics. The backs of the seats (Fig. 180), and the seats themselves (Fig. 181), are decorated in this way. On the seats themselves, as on the table top, hazel and withy are contrasted, and form a design in alternate triangles; the separating bands, it may be noticed, have a light strip against the dark, and a dark strip against the light, triangle. Along the edge of the seats one or two strips merely are nailed lengthwise. In such a situation an ornamental edging like that round the table would be too liable to be broken. It is recommended that the back of the seats should be in dark bark-covered woods only, for the mosaic in that position will look better without any mixture of the light-coloured withy.
In rough carpentry, there's no work more beautiful or interesting than these mosaics. The backs of the seats (Fig. 180) and the seats themselves (Fig. 181) are decorated this way. On the seats, just like on the tabletop, hazel and withy are contrasted to create a design of alternating triangles; the separating bands have a light strip against the dark and a dark strip against the light triangle. Along the edge of the seats, one or two strips are just nailed lengthwise. In this case, an ornamental edging like the one around the table would be too prone to breaking. It’s suggested that the backs of the seats should only be made of dark bark-covered woods, as the mosaic in that position will look better without any light-colored withy mixed in.
The upper compartments of the sides with which the backs of those sitting down will not come in contact may be more quickly and yet pleasingly covered with sheets of bark. Elm bark [Pg 147] is good for the purpose. It may be peeled in large sheets from the trunks of trees felled in spring, when the sap is rising; and whilst it is drying should have bricks or stones laid on it to press it flat. When dried, it is nailed to the walls, and any cracks which appear can be neatly filled with moss. The space beneath the seats is also shown as roughly covered with bark.
The upper sections of the sides that won't touch the backs of people sitting can be covered more quickly and nicely with sheets of bark. Elm bark is great for this. It can be peeled in large sheets from the trunks of trees cut down in the spring, when the sap is rising; and while it's drying, it should have bricks or stones placed on top to keep it flat. Once dried, it's nailed to the walls, and any cracks that show up can be neatly filled with moss. The area under the seats is also depicted as being roughly covered with bark.
The almost conical roof is thatched. No other covering is so pleasing as thatch for a rustic building. Its colour and rough texture harmonise well with the natural wood, and all its associations are of a rustic character; no other covering so effectually excludes the summer heat, and nowhere [Pg 148] can one find a retreat so suggestive of coolness, quiet, and repose, as under the low eaves of a thatched building. Thatch has, it must be admitted, certain practical disadvantages—birds and winds are apt to scatter fragments from it, and it needs renewing at comparatively short intervals. The common saying is that a thatched roof needs re-coating every ten years. Often, no doubt, this is near the truth, yet really good work will frequently stand for almost twenty years. The materials in use in this country are reeds, straw, and stubble. Reeds make a strong thatch, but are not easily to be procured, except in fenny districts. Stubble, which is the lower and stronger part of the wheat stem, stands better than straw, which is its upper and weaker portion; to last properly, however, stubble should be cut immediately after harvest, and should not be left standing, as it frequently is, till the spring, for then the winter rains, collecting in its hollow stems, cause it to rot before it is cut. On small buildings like summer-houses especially, stubble makes a much more compact and sightly roof than straw.
The almost cone-shaped roof is thatched. No other covering is as appealing as thatch for a rustic building. Its color and rough texture blend nicely with the natural wood, and all its associations have a rustic feel; no other covering keeps out the summer heat as effectively, and there's nowhere you can find a place that feels as cool, quiet, and peaceful as under the low eaves of a thatched building. Thatch does have some practical drawbacks—birds and wind tend to scatter bits of it, and it needs to be replaced at relatively short intervals. The common saying is that a thatched roof should be re-coated every ten years. Often, this is pretty close to the truth, though really good work can sometimes last almost twenty years. In this country, the materials used are reeds, straw, and stubble. Reeds make a strong thatch, but they’re not easy to find, except in marshy areas. Stubble, which is the lower and tougher part of the wheat stem, lasts longer than straw, which is the upper and weaker part; however, for it to hold up well, stubble should be cut right after harvest and shouldn’t be left standing until spring; otherwise, the winter rains can collect in its hollow stems and cause it to rot before it’s cut. For smaller buildings like summer houses, stubble makes a much denser and more attractive roof than straw.
Thatching is not costly or difficult work. In agricultural districts a load of stubble—sufficient to thatch three such buildings as the one illustrated—costs 30s., and a thatcher expects the wages of a first-class labourer only, not those of a mechanic. He needs an assistant, whose business it is to straighten the material into convenient bundles (called "yelvens"), and to supply him as he requires them. If he is re-thatching an old building, he merely thrusts the ends of his new material into the old thatch with a wooden spud; but if he is covering a new roof he sews down his "yelvens" to the laths and rafters with a huge needle and stout tarred string. He begins at the eaves, laying as wide a breadth as he can conveniently reach on one side of his ladder, this [Pg 149] breadth being called a "stelch." He works upwards, each new layer covering the tar-cord which secures that beneath it; and thus he goes on till he has reached the ridge.
Thatching isn't expensive or difficult work. In agricultural areas, a load of stubble—enough to thatch three buildings like the one shown—costs £1.50, and a thatcher only expects to earn the wages of a top-level laborer, not those of a mechanic. He needs an assistant whose job is to organize the material into manageable bundles (called "yelvens") and hand them to him as needed. If he’s re-thatching an old building, he simply pushes the ends of the new material into the old thatch with a wooden spud; but if he's covering a new roof, he stitches down his "yelvens" to the laths and rafters using a large needle and strong tarred string. He starts at the eaves, laying as wide a strip as he can comfortably reach on one side of his ladder, which is called a "stelch." He works his way up, with each new layer covering the tar cord that secures the layer below it, continuing until he reaches the ridge.
In his second "stelch" he is careful to blend together its edge and the edge of that already laid, so that no rain may find its way between them; and in doing this completely lies much of the superiority of good over bad thatching. When laid, the thatch is smoothed down and straightened with a gigantic comb, like the head of a large rake, one end being without teeth, and serving as a handle. In the present instance, the tops of all the stelches meeting in a point are finished and capped by the little bundle of thatching material forming the pinnacle, which is tightly bound round the rod of wood or iron in its centre.
In his second "stelch," he carefully blends its edge with the edge of the one already laid down, ensuring that no rain can seep between them. Achieving this properly is a big part of what makes good thatching better than bad thatching. Once laid, the thatch is smoothed and straightened with a large comb, resembling the head of a big rake, one end being toothless and serving as a handle. In this case, the tops of all the stelches meeting at a point are finished and capped with a small bundle of thatching material forming the peak, which is tightly bound around a rod made of wood or iron in the center.
It is usual to bind thatching down with at least two belts of buckles and runners. In the summer-house (Fig. 172) two double belts are shown. The buckles have some resemblance to ladies' hair-pins on a colossal scale. They are made of slips of withy, twisted and doubled in their middles and pointed at their ends; the runners are long straight slips of the same. These latter are laid across the thatch, and the buckles, being placed over them, are pushed tightly into it—their points being driven upwards, that wet may not be let [Pg 150] into the roof by them. The short diagonal runners seen in the illustration crossing each other between the horizontal lines are used in ornamental thatching only, and are rather for appearance than for use. Lastly, the eaves are cut to shape, and trimmed with paring-knife and shears.
It’s common to secure thatching with at least two belts of buckles and straps. In the summer house (Fig. 172), two double belts are shown. The buckles are somewhat like oversized hairpins. They’re made of strips of willow, twisted and doubled in the middle, with pointed ends. The straps are long, straight strips made of the same material. These are laid across the thatch, and the buckles, placed over them, are pushed tightly into the thatch—their points driven upwards to prevent water from getting into the roof. The short diagonal straps shown in the illustration crossing each other between the horizontal lines are used for decorative thatching only and are more about looks than function. Finally, the eaves are shaped and finished with a paring knife and shears.
The roof looks most pretty and cosy within if lined with ling. The ling is fixed in a way somewhat akin to thatching. A layer is placed along the bottom opposite to the eaves, and secured by a strip of wood nailed from rafter to rafter; the layer next above hides this strip, and so the work is carried on to the apex, where a knot cut from an apple-tree trunk, a bunch of fir-cones fastened together, or some such matter, finishes the whole. In districts where ling is not to be had, gorse or furze in short pieces may serve instead, but stout gloves are required to handle it; or the ends of fir branches may do, if nothing better offers.
The roof looks really nice and cozy inside if it’s lined with heather. The heather is attached in a way similar to thatching. A layer is placed along the bottom opposite the eaves and secured with a wood strip nailed from rafter to rafter; the layer above hides this strip, and this process continues up to the peak, where a knot cut from an apple tree trunk, a bunch of fir cones tied together, or something similar finishes the whole look. In areas where heather isn’t available, short pieces of gorse or furze can be used instead, but you’ll need tough gloves to handle it; or the ends of fir branches might work if there’s nothing better available.
It is not always easy to decide on the best way of forming a floor. Boards may look out of place. A pitching of pebbles is more in character: it is dry and cleanly, and especially if some variety of colour is obtainable, and the stones are arranged in some geometrical design, it may add to the ornamental effect. Pebbles are not, however, pleasing to the feet of those who wear thin shoes. Gravel, where it is always dry, is apt to become dusty, and to disagree with ladies' dresses. If, however, gravel should be used, perhaps the best plan to prevent the rising of damp, and to obviate dust as far as possible, is to asphalt it: on the foundation of broken stones and a layer of coarse gravel to put a course of asphalt or of ordinary gas tar, and on this to sift enough fine washed gravel to hide it. Yet a wood pavement of small larch poles, cut into 5-or 6-in. billets, and pitched with some attention to geometrical arrangement, will make the most dry and comfortable of floors, and one which will not harmonise [Pg 151] badly with any of the decorative work of our summer-house.
It’s not always easy to figure out the best way to create a floor. Boards can sometimes look out of place. A layout of pebbles fits the style better: it’s dry and clean, and especially if you can find some variety in color and arrange the stones in a geometric design, it can enhance the overall look. However, pebbles aren’t comfortable for people wearing thin shoes. Gravel, when dry, can get dusty and can clash with women’s dresses. If you do decide to use gravel, the best way to minimize dampness and dust is to asphalt it: lay down a foundation of broken stones and a layer of coarse gravel, then put down a layer of asphalt or regular gas tar, and finally, add enough fine washed gravel to cover it. Still, a wood floor made of small larch poles cut into 5- or 6-inch pieces, arranged with some attention to design, will create the driest and most comfortable floor, and it will blend well with the decorative elements of our summer house. [Pg 151]
The octagonal house illustrated by Fig. 182 is made up of varnished rustic work. The saplings and twigs should be as straight and as regular as possible, and divested of their bark.
The octagonal house shown in Fig. 182 is built from polished rustic materials. The saplings and branches should be as straight and uniform as possible and stripped of their bark.
The eight posts are 4 in. in diameter by 6 ft. 8 in. long. The short sill pieces are also 4 in. in diameter, while the middle rails are 3½ in. in diameter, and the plate is 3 in. by 4½ in. The [Pg 154] floor and roof are constructed from ordinary scantlings.
The eight posts are 4 inches in diameter and 6 feet 8 inches long. The short sill pieces are also 4 inches in diameter, while the middle rails are 3.5 inches in diameter, and the plate is 3 inches by 4.5 inches. The [Pg 154] floor and roof are made from standard lumber.
The posts form a circle 6 ft. 6 in. in diameter. They are spaced about 2 ft. 3 in. apart, except the door-posts, which are 2 ft. 7 in. centres. Flats may be worked on the posts for the better fitting of the door, panels, and casements, and the top edge of the sill is also planed flat to receive the floorboards, and a rebate is formed for the 5/8-in. matchboard (see Fig. 183).
The posts create a circle with a diameter of 6 ft. 6 in. They are spaced about 2 ft. 3 in. apart, except for the door posts, which are 2 ft. 7 in. apart. The posts can be flattened for a better fit of the door, panels, and casements, and the top edge of the sill is also smoothed out to hold the floorboards, with a groove made for the 5/8-in. matchboard (see Fig. 183).
The sill and middle rails are scribed and stub-tenoned to the posts. The plate is halved, dowelled, and nailed to the posts. The joists are 2 in. by 4 in., and are notched to the sills (Fig. 184) and covered with 1-in. floorboards.
The sill and middle rails are marked and stub-tenoned to the posts. The plate is cut in half, dowelled, and nailed to the posts. The joists are 2 inches by 4 inches, notched to the sills (Fig. 184) and topped with 1-inch floorboards.
The roof is formed with three gables, four being deemed unnecessary, as a summer-house is generally fixed with its back to a shrubbery. Eight hip rafters are required, and by fixing the heels of each pair of rafters on the sides of the plate marked 1, 2, 3, and 4 (see Fig. 185) more space is acquired for the gables. The ridges and valley-pieces of the gables are attached to a wide batten screwed to the under side of the hip rafters (see Figs. 185 and 186). Some of the small battens are omitted from Fig. 185 to give a better view of the gables, etc.
The roof has three gables, as four would be seen as too much, since a summer house usually faces away from the shrubbery. Eight hip rafters are needed, and by attaching the heels of each pair of rafters to the sides of the plates marked 1, 2, 3, and 4 (see Fig. 185), we create more space for the gables. The ridges and valley pieces of the gables are connected to a wide batten that is screwed to the underside of the hip rafters (see Figs. 185 and 186). Some of the smaller battens are left out from Fig. 185 to provide a clearer view of the gables, etc.
Fig. 188.—Half Front and Half Back View of Door for Octagonal Summerhouse. Fig. 189.—Section of Door for Octagonal Summerhouse. |
The roof-covering is generally wheat straw, with a top dressing of either broom or heather. The dark colour of the two latter materials harmonises [Pg 156] much better with a varnished house than does a covering wholly of straw. The four lower panels are filled in with matchboarding, which is carried right up to the plate in the three back divisions. The rustic work, excepting the back panels, is then fitted and nailed.
The roof is typically covered with wheat straw, topped with either broom or heather. The dark color of the latter two materials blends much better with a varnished house than a roof made entirely of straw. The four lower panels are fitted with matchboarding, extending all the way to the plate in the three back sections. The rustic work, except for the back panels, is then assembled and nailed.
There are four casement windows, which open outward. A section of casement and frame enlarged is shown in Fig. 187. A shallow rebate is formed to receive the leaded lights, which are retained in position with split bamboo fixed with round-headed brass screws.
There are four casement windows that open outward. A section of the casement and frame, enlarged, is shown in Fig. 187. A shallow groove is made to hold the leaded lights, which are kept in place with split bamboo secured by round-headed brass screws.
The door (Figs. 188 and 189) is 6 ft. 1 in. by 2 ft. 3 in. The rustic work is overlaid on the frame of the door. The centre of the diamond-shaped panel is filled with cork. The top panel [Pg 157] is glazed with stained glass. Three butts and a rim lock are fitted on the inside of the door, and the lower panel is filled with matchboarding.
The door (Figs. 188 and 189) measures 6 ft. 1 in. by 2 ft. 3 in. The rustic design is applied to the door frame. The center of the diamond-shaped panel is filled with cork. The top panel [Pg 157] is covered with stained glass. There are three hinges and a rim lock installed on the inside of the door, and the lower panel is made of matchboarding.
A seat 13 in. wide, supported on wide battens, which in turn rest on shaped brackets, is fixed at each angle. A sloping back (see Fig. 183) is [Pg 158] fitted, which adds to the general comfort. The decoration of the inside should now receive attention. The floor may be covered with linoleum, the seats carpeted or cushioned. The sloping backs of the seats and the walls will look well if covered with Indian matting or Japanese leather paper. Split cane or bamboo may be used with good effect at the joints or angles. The under side of the roof or ceiling should be first covered by stretching canvas across the rafters, and to this is attached the decorative material.
A seat that's 13 inches wide, supported by wide battens that rest on shaped brackets, is fixed at each corner. A sloping back (see Fig. 183) is fitted, which adds to overall comfort. Now, the decoration of the interior should be addressed. The floor can be covered with linoleum, and the seats can be carpeted or cushioned. The sloping backs of the seats and the walls will look nice if covered with Indian matting or Japanese leather paper. Split cane or bamboo can be used effectively at the joints or angles. The underside of the roof or ceiling should first be covered by stretching canvas across the rafters, to which the decorative material is attached.
The summer-house stands on stone slabs raised about 1 in. above the ground. The lower ends of the posts are dressed with pitch, or are stood on sheet lead. The triangular spaces in the gables can be made to open inwards if desired, and used for ventilation.
The summer house rests on stone slabs raised about 1 inch above the ground. The lower ends of the posts are treated with pitch or are placed on sheet lead. The triangular spaces in the gables can be opened inwards if needed, and used for ventilation.
INDEX.
[A] [B] [C] [D] [E] [F] [G] [H] [J]
[L] [M] [O] [P] [R] [S] [T] [V] [W]
[Y]
A
Footbridges with Anchors, __A_TAG_PLACEHOLDER_0__
Armchair, __A_TAG_PLACEHOLDER_1__, __A_TAG_PLACEHOLDER_2__
Aviary, __A_TAG_PLACEHOLDER_3__-__A_TAG_PLACEHOLDER_4__
——, Bottom, __A_TAG_PLACEHOLDER_5__
——, Perches for, __A_TAG_PLACEHOLDER_6__, __A_TAG_PLACEHOLDER_7__
——, Sliding Tray for, __A_TAG_PLACEHOLDER_8__
——, Wiring for, __A_TAG_PLACEHOLDER_9__, __A_TAG_PLACEHOLDER_10__
——, Wood for, __A_TAG_PLACEHOLDER_11__
B
"Bangles," __A_TAG_PLACEHOLDER_12__
Bending Wood Using Spanish Windlass, __A_TAG_PLACEHOLDER_13__
Window Boxes, __A_TAG_PLACEHOLDER_14__-__A_TAG_PLACEHOLDER_15__
Wall Bracket, __A_TAG_PLACEHOLDER_16__, __A_TAG_PLACEHOLDER_17__
C
Canopied Garden Seat, __A_TAG_PLACEHOLDER_18__-__A_TAG_PLACEHOLDER_19__
Canopy for Garden Retreat, __A_TAG_PLACEHOLDER_20__, __A_TAG_PLACEHOLDER_21__
—— for Swing, __A_TAG_PLACEHOLDER_22__-__A_TAG_PLACEHOLDER_23__
Carriage Entrance, __A_TAG_PLACEHOLDER_24__-__A_TAG_PLACEHOLDER_25__
Armchair, __A_TAG_PLACEHOLDER_26__, __A_TAG_PLACEHOLDER_27__
Chairs and Seats, __A_TAG_PLACEHOLDER_28__-__A_TAG_PLACEHOLDER_29__
Collar-posts, __A_TAG_PLACEHOLDER_30__, __A_TAG_PLACEHOLDER_31__, __A_TAG_PLACEHOLDER_32__
Cottage Porch, __A_TAG_PLACEHOLDER_33__
D
Tool House Door, __A_TAG_PLACEHOLDER_34__
E
Easel with Mitred Joint, __A_TAG_PLACEHOLDER_35__
——, for Photographs, __A_TAG_PLACEHOLDER_36__-__A_TAG_PLACEHOLDER_37__
——, Stain for, __A_TAG_PLACEHOLDER_38__, __A_TAG_PLACEHOLDER_39__
Elevated Footbridges, __A_TAG_PLACEHOLDER_40__
Carriage Entrance, __A_TAG_PLACEHOLDER_41__-__A_TAG_PLACEHOLDER_42__
F
Fenced Seat for Swing, __A_TAG_PLACEHOLDER_43__
Fences, __A_TAG_PLACEHOLDER_44__
Fire Screen, __A_TAG_PLACEHOLDER_45__
Tripod Flower Holder, __A_TAG_PLACEHOLDER_46__
Flower Pot Stand, __A_TAG_PLACEHOLDER_47__, __A_TAG_PLACEHOLDER_48__, __A_TAG_PLACEHOLDER_49__
Footbridges, __A_TAG_PLACEHOLDER_50__
——, Anchored, __A_TAG_PLACEHOLDER_51__
——, Elevated, __A_TAG_PLACEHOLDER_52__
——, Girders for, __A_TAG_PLACEHOLDER_53__, __A_TAG_PLACEHOLDER_54__
G
Gables for Octagonal Summer-house, __A_TAG_PLACEHOLDER_55__, __A_TAG_PLACEHOLDER_56__-__A_TAG_PLACEHOLDER_57__
Garden Gate, __A_TAG_PLACEHOLDER_58__-__A_TAG_PLACEHOLDER_59__, __A_TAG_PLACEHOLDER_60__
—— Plant Tub, __A_TAG_PLACEHOLDER_61__, __A_TAG_PLACEHOLDER_62__
—— Retreat, __A_TAG_PLACEHOLDER_63__-__A_TAG_PLACEHOLDER_64__
—— Seat with Canopy, __A_TAG_PLACEHOLDER_65__-__A_TAG_PLACEHOLDER_66__
—— Seats, __A_TAG_PLACEHOLDER_67__-__A_TAG_PLACEHOLDER_68__
—— Snuggery, __A_TAG_PLACEHOLDER_69__-__A_TAG_PLACEHOLDER_70__
—— ——, Collar-posts for, __A_TAG_PLACEHOLDER_71__
—— ——, Door for, __A_TAG_PLACEHOLDER_72__, __A_TAG_PLACEHOLDER_73__
—— ——, Joists for, __A_TAG_PLACEHOLDER_74__
—— ——, Caps for Pillars, __A_TAG_PLACEHOLDER_75__
—— ——, Rafters for, __A_TAG_PLACEHOLDER_76__
—— ——, Roof Boarding, __A_TAG_PLACEHOLDER_77__
—— —— ——, Coverings for, __A_TAG_PLACEHOLDER_78__, __A_TAG_PLACEHOLDER_79__
—— ——, Rustic Pillars of, __A_TAG_PLACEHOLDER_80__, __A_TAG_PLACEHOLDER_81__
—— ——, Non-conducting Walls, __A_TAG_PLACEHOLDER_82__
Garden, Tool House for (see Tool House)
—— Trellis with Seats and Gate, __A_TAG_PLACEHOLDER_83__-__A_TAG_PLACEHOLDER_84__
Gates and Fences, __A_TAG_PLACEHOLDER_85__-__A_TAG_PLACEHOLDER_86__
Girders for Rustic Footbridges, __A_TAG_PLACEHOLDER_87__, __A_TAG_PLACEHOLDER_88__
Glazed Veranda for Grape Culture, __A_TAG_PLACEHOLDER_89__
H
Hall Stand, __A_TAG_PLACEHOLDER_90__-__A_TAG_PLACEHOLDER_91__
Hazel Rods for Rustic Mosaic Work, __A_TAG_PLACEHOLDER_92__
Hexagonal Table, __A_TAG_PLACEHOLDER_93__, __A_TAG_PLACEHOLDER_94__
—— Vase, __A_TAG_PLACEHOLDER_95__, __A_TAG_PLACEHOLDER_96__
Tool House Door, __A_TAG_PLACEHOLDER_97__
——, Doorposts for, __A_TAG_PLACEHOLDER_98__
——, Folding Seat for, __A_TAG_PLACEHOLDER_99__, __A_TAG_PLACEHOLDER_100__
——, Pilaster for, __A_TAG_PLACEHOLDER_101__
——, Plan of, __A_TAG_PLACEHOLDER_102__, __A_TAG_PLACEHOLDER_103__
——, "Rough Planks" for, __A_TAG_PLACEHOLDER_104__
J
Mitred Joint, __A_TAG_PLACEHOLDER_105__
Joists for Garden Snuggery, __A_TAG_PLACEHOLDER_106__
L
Lean-to Summer House, __A_TAG_PLACEHOLDER_107__-__A_TAG_PLACEHOLDER_108__
—— —— ——, Walls Lining for, __A_TAG_PLACEHOLDER_109__
—— —— ——, Mosaic Work for Walls, __A_TAG_PLACEHOLDER_110__
—— —— ——, Roof of, __A_TAG_PLACEHOLDER_111__
Lining Roof with Ling, __A_TAG_PLACEHOLDER_112__
—— Summer House Walls, __A_TAG_PLACEHOLDER_113__
M
Mitred Joint, __A_TAG_PLACEHOLDER_114__
Mosaic Work, __A_TAG_PLACEHOLDER_115__-__A_TAG_PLACEHOLDER_116__
—— ——, Hazel Rods for, __A_TAG_PLACEHOLDER_117__
—— ——, Withy for, __A_TAG_PLACEHOLDER_118__
—— ——, for Summer House Walls, __A_TAG_PLACEHOLDER_119__
O
Octagonal Summer House, __A_TAG_PLACEHOLDER_120__-__A_TAG_PLACEHOLDER_121__
—— —— ——, Collar-posts for, __A_TAG_PLACEHOLDER_122__
—— —— ——, Gable for, __A_TAG_PLACEHOLDER_123__
—— —— ——, Ground Plan of, __A_TAG_PLACEHOLDER_124__
—— —— ——, Roof for, __A_TAG_PLACEHOLDER_125__
—— —— ——, Table for, __A_TAG_PLACEHOLDER_126__
—— —— ——, Thatched, __A_TAG_PLACEHOLDER_127__-__A_TAG_PLACEHOLDER_128__
—— —— ——, Three-gabled, __A_TAG_PLACEHOLDER_129__-__A_TAG_PLACEHOLDER_130__
—— —— ——, Walls for, __A_TAG_PLACEHOLDER_131__
P
Pedestal for Sundial, __A_TAG_PLACEHOLDER_132__
Pilaster for Tool House, __A_TAG_PLACEHOLDER_133__
Pillars for Garden Snuggery, __A_TAG_PLACEHOLDER_134__, __A_TAG_PLACEHOLDER_135__
Plant Stand, Rectangular, __A_TAG_PLACEHOLDER_0__
—— Tub for Garden, __A_TAG_PLACEHOLDER_1__, __A_TAG_PLACEHOLDER_2__
—— Vase, Large, __A_TAG_PLACEHOLDER_3__, __A_TAG_PLACEHOLDER_4__
—— ——, Ornamental, __A_TAG_PLACEHOLDER_5__, __A_TAG_PLACEHOLDER_6__
Porches, __A_TAG_PLACEHOLDER_7__-__A_TAG_PLACEHOLDER_8__
R
Rectangular Garden Plant Stand, __A_TAG_PLACEHOLDER_9__
Retreat, Garden, __A_TAG_PLACEHOLDER_10__-__A_TAG_PLACEHOLDER_11__
Roof for Garden Snuggery, __A_TAG_PLACEHOLDER_12__-__A_TAG_PLACEHOLDER_13__
—— for Lean-to Summerhouse, __A_TAG_PLACEHOLDER_14__
——, Materials for, __A_TAG_PLACEHOLDER_15__
—— for Tennis Lawn Shelter, __A_TAG_PLACEHOLDER_16__
—— of Tool House, __A_TAG_PLACEHOLDER_17__
—— for Verandah, __A_TAG_PLACEHOLDER_18__
Rosery Walk, __A_TAG_PLACEHOLDER_19__-__A_TAG_PLACEHOLDER_20__
"Rough Planks" for Tool House, __A_TAG_PLACEHOLDER_21__
S
Seats and Chairs, __A_TAG_PLACEHOLDER_22__-__A_TAG_PLACEHOLDER_23__
Shelter for Tennis Lawn, __A_TAG_PLACEHOLDER_24__
"Slabs," Fixing, __A_TAG_PLACEHOLDER_25__, __A_TAG_PLACEHOLDER_26__
Snuggery, Garden, __A_TAG_PLACEHOLDER_27__-__A_TAG_PLACEHOLDER_28__
——, ——, Collar-posts for __A_TAG_PLACEHOLDER_29__, __A_TAG_PLACEHOLDER_30__
——, ——, Door for, __A_TAG_PLACEHOLDER_31__, __A_TAG_PLACEHOLDER_32__
——, ——, Joists for, __A_TAG_PLACEHOLDER_33__
——, ——, Pillars for, __A_TAG_PLACEHOLDER_34__
——, ——, Rafters for, __A_TAG_PLACEHOLDER_35__
——, ——, Roof for, __A_TAG_PLACEHOLDER_36__-__A_TAG_PLACEHOLDER_37__
——, ——, —— Coverings for, __A_TAG_PLACEHOLDER_38__, __A_TAG_PLACEHOLDER_39__
——, ——, Rustic Pillars of, __A_TAG_PLACEHOLDER_40__
——, ——, Walls of, __A_TAG_PLACEHOLDER_41__
Spanish Windlass for Bending Wood, __A_TAG_PLACEHOLDER_42__
Stain for Easel, __A_TAG_PLACEHOLDER_43__, __A_TAG_PLACEHOLDER_44__
Stand, Flower, __A_TAG_PLACEHOLDER_45__, __A_TAG_PLACEHOLDER_46__
——, Flower-pot, in imitation of Bamboo, __A_TAG_PLACEHOLDER_47__
——, Hall, __A_TAG_PLACEHOLDER_48__-__A_TAG_PLACEHOLDER_49__
——, Rectangular Plant, __A_TAG_PLACEHOLDER_50__
"Stelch" for Thatching, __A_TAG_PLACEHOLDER_51__
Stool, __A_TAG_PLACEHOLDER_52__, __A_TAG_PLACEHOLDER_53__
Summer-house, Lean-to, __A_TAG_PLACEHOLDER_54__-__A_TAG_PLACEHOLDER_55__
—— ——, ——, Lining for Walls, __A_TAG_PLACEHOLDER_56__
—— ——, ——, Mosaic Work for Walls of, __A_TAG_PLACEHOLDER_57__
—— ——, ——, Roof of, __A_TAG_PLACEHOLDER_58__
—— ——, Octagonal, __A_TAG_PLACEHOLDER_59__-__A_TAG_PLACEHOLDER_60__
—— ——, ——, Collar-posts for, __A_TAG_PLACEHOLDER_61__
—— ——, ——, Floor for, __A_TAG_PLACEHOLDER_62__
—— ——, ——, Gable for, __A_TAG_PLACEHOLDER_63__
—— ——, ——, Ground Plan of, __A_TAG_PLACEHOLDER_64__
—— ——, ——, Roof for, __A_TAG_PLACEHOLDER_65__
Summer-house, Octagonal, Table for, __A_TAG_PLACEHOLDER_66__, __A_TAG_PLACEHOLDER_67__-__A_TAG_PLACEHOLDER_68__
—— ——, ——, Thatched Roof of, __A_TAG_PLACEHOLDER_69__
—— ——, ——, with Three Gables, __A_TAG_PLACEHOLDER_70__-__A_TAG_PLACEHOLDER_71__
—— ——, ——, Walls for, __A_TAG_PLACEHOLDER_72__
—— ——, ——, Windows for, __A_TAG_PLACEHOLDER_73__
—— ——, Thatched Octagonal, __A_TAG_PLACEHOLDER_74__-__A_TAG_PLACEHOLDER_75__
Swing, Canopy for, __A_TAG_PLACEHOLDER_76__-__A_TAG_PLACEHOLDER_77__
——, Fenced Seat for, __A_TAG_PLACEHOLDER_78__
T
Table for Octagonal Summer-house, __A_TAG_PLACEHOLDER_79__-__A_TAG_PLACEHOLDER_80__
——, Hexagon, __A_TAG_PLACEHOLDER_81__, __A_TAG_PLACEHOLDER_82__
——, Square, __A_TAG_PLACEHOLDER_83__-__A_TAG_PLACEHOLDER_84__
Tables, __A_TAG_PLACEHOLDER_85__-__A_TAG_PLACEHOLDER_86__
Tennis Lawn Shelter, __A_TAG_PLACEHOLDER_87__-__A_TAG_PLACEHOLDER_88__
—— —— ——, Roof for, __A_TAG_PLACEHOLDER_89__
Thatched Octagonal Summer-house, __A_TAG_PLACEHOLDER_90__-__A_TAG_PLACEHOLDER_91__
Thatching, Cost of, __A_TAG_PLACEHOLDER_92__
——, "Stelch," __A_TAG_PLACEHOLDER_93__
——, Roof of Octagonal Summer-house, __A_TAG_PLACEHOLDER_94__-__A_TAG_PLACEHOLDER_95__
——, "Yelvens," __A_TAG_PLACEHOLDER_96__
Tool House, __A_TAG_PLACEHOLDER_97__-__A_TAG_PLACEHOLDER_98__
—— ——, Door, __A_TAG_PLACEHOLDER_99__
—— ——, Doorposts, __A_TAG_PLACEHOLDER_100__, __A_TAG_PLACEHOLDER_101__
—— ——, Folding Seat for, __A_TAG_PLACEHOLDER_102__, __A_TAG_PLACEHOLDER_103__
—— ——, Pilaster, __A_TAG_PLACEHOLDER_104__
—— ——, Roof, __A_TAG_PLACEHOLDER_105__
—— ——, "Rough Planks" for, __A_TAG_PLACEHOLDER_106__
Trellis, Garden, with Seats and Gate, __A_TAG_PLACEHOLDER_107__-__A_TAG_PLACEHOLDER_108__
V
Vase, Hexagonal, __A_TAG_PLACEHOLDER_109__, __A_TAG_PLACEHOLDER_110__
——, Plant, __A_TAG_PLACEHOLDER_111__, __A_TAG_PLACEHOLDER_112__, __A_TAG_PLACEHOLDER_113__, __A_TAG_PLACEHOLDER_114__
——, Square, __A_TAG_PLACEHOLDER_115__, __A_TAG_PLACEHOLDER_116__
——, on Tripod Stand, __A_TAG_PLACEHOLDER_117__-__A_TAG_PLACEHOLDER_118__
Verandahs, 98-105
——, for Grape Culture, __A_TAG_PLACEHOLDER_119__
——, Open, __A_TAG_PLACEHOLDER_120__
——, Posts Supporting, __A_TAG_PLACEHOLDER_121__, __A_TAG_PLACEHOLDER_122__
——, Rafters for, __A_TAG_PLACEHOLDER_123__
——, Roof for, __A_TAG_PLACEHOLDER_124__
——, —— Materials for, __A_TAG_PLACEHOLDER_125__
W
Walk, Rosery, __A_TAG_PLACEHOLDER_126__-__A_TAG_PLACEHOLDER_127__
Wall Bracket, __A_TAG_PLACEHOLDER_128__, __A_TAG_PLACEHOLDER_129__
Windlass, Spanish, __A_TAG_PLACEHOLDER_130__
Window Boxes, __A_TAG_PLACEHOLDER_131__-__A_TAG_PLACEHOLDER_132__
Wiring Aviary, __A_TAG_PLACEHOLDER_133__, __A_TAG_PLACEHOLDER_134__
Withy for Rustic Mosaic Work, __A_TAG_PLACEHOLDER_135__
Wood Bending with Spanish Windlass, __A_TAG_PLACEHOLDER_136__
—— for Rustic Work, __A_TAG_PLACEHOLDER_137__
Download ePUB
If you like this ebook, consider a donation!