This is a modern-English version of An Unsinkable Titanic: Every Ship its own Lifeboat, originally written by Walker, John Bernard.
It has been thoroughly updated, including changes to sentence structure, words, spelling,
and grammar—to ensure clarity for contemporary readers, while preserving the original spirit and nuance. If
you click on a paragraph, you will see the original text that we modified, and you can toggle between the two versions.
Scroll to the bottom of this page and you will find a free ePUB download link for this book.

Photo by Brown Bros., New York
Photo by Brown Bros., New York
Stoke-hole of a Transatlantic Liner
Stokehole of a Transatlantic Liner
AN
UNSINKABLE
TITANIC
EVERY SHIP
ITS OWN LIFEBOAT
Every ship
is its own lifeboat
BY
J. BERNARD WALKER
Editor of the Scientific American
BY
J. Bernard Walker
Editor of SciAm

NEW YORK
DODD, MEAD AND COMPANY
1912
NEW YORK
DODD, MEAD AND COMPANY
1912
Published, July, 1912
Published July 1912
THE QUINN & BODEN CO. PRESS
RAHWAY, N. J.
THE QUINN & BODEN CO. PRESS
RAHWAY, NJ
PREFACE
It is the object of this work to show that, in our eagerness to make the ocean liner fast and luxurious, we have forgotten to make her safe.
It is the aim of this work to demonstrate that, in our desire to make the ocean liner quick and luxurious, we have neglected to ensure her safety.
The safest ocean liner was the Great Eastern; and she was built over fifty years ago. Her designer aimed to make the ship practically unsinkable—and he succeeded; for she passed through a more severe ordeal than the Titanic, survived it, and came into port under her own steam.
The safest ocean liner was the Great Eastern; and it was built over fifty years ago. Its designer aimed to make the ship nearly unsinkable—and he succeeded; because it went through a more intense ordeal than the Titanic, survived it, and arrived in port under its own power.
Since her day, the shipbuilder has eliminated all but one of the safety devices which made the Great Eastern a ship so difficult to sink. Nobody, not even the shipbuilders themselves, seemed to realise what was being done, until, suddenly, the world's finest vessel, in all the pride of her maiden voyage, struck an iceberg and went to the bottom in something over two and a half hours' time!
Since her day, the shipbuilder has removed all but one of the safety features that made the Great Eastern nearly unsinkable. Nobody, not even the shipbuilders themselves, seemed to realize what was happening, until suddenly, the world's best ship, in all the glory of her maiden voyage, hit an iceberg and sank in just over two and a half hours!
If we learn the lesson of this tragedy, we shall lose no time in getting back to first principles. We shall reintroduce in all future passenger ships those simple and effective elements of safety—the double skin, the longitudinal bulkhead, and the watertight deck—which were conspicuous in the Great Eastern, and which alone can render such a ship as the Titanic unsinkable.
If we take away the right lessons from this tragedy, we won’t waste any time returning to the basics. We will bring back the simple and effective safety features—like the double hull, the longitudinal bulkhead, and the watertight deck—in all future passenger ships. These were prominent in the Great Eastern, and they’re the only things that can make a ship like the Titanic unsinkable.
The author's acknowledgments are due to the "Scientific American" for many of the photographs and line drawings reproduced in this volume; to an article by Professor J. H. Biles, published in "Engineering," for material relating to the Board of Trade stipulations as to bulkheads; to Sir George C. V. Holmes and the Victoria and Albert Museum for data regarding the Great Eastern, published in "Ancient and Modern Ships"; to Naval Constructor R. H. M. Robinson, U.S.N., for permission to reproduce certain drawings from his work, "Naval Construction," and to Naval Constructor Henry Williams, U.S.N., who courteously read the proofs of this work and offered many valuable suggestions. The original wash and line drawings are by Mr. C. McKnight Smith.
The author would like to thank "Scientific American" for many of the photos and illustrations included in this book; Professor J. H. Biles for an article published in "Engineering" that provided material on the Board of Trade requirements for bulkheads; Sir George C. V. Holmes and the Victoria and Albert Museum for information about the Great Eastern, published in "Ancient and Modern Ships"; Naval Constructor R. H. M. Robinson, U.S.N., for allowing the use of specific drawings from his work, "Naval Construction"; and Naval Constructor Henry Williams, U.S.N., who kindly reviewed the proofs and offered many helpful suggestions. The original wash and line drawings are by Mr. C. McKnight Smith.
J. B. W.
J.B.W.
New York, June, 1912.
New York, June 1912.
CONTENTS
CHAPTER | PAGE | |
I. | Introductory | 1 |
II. | The Ever-Present Dangers of the Sea | 19 |
III. | Every Ship Its Own Lifeboat | 35 |
IV. | Safety Lies in Subdivision | 51 |
V. | The Unsinkable Great Eastern of 1858 | 69 |
VI. | The Sinkable Titanic | 91 |
VII. | How the Great Ship Went Down | 116 |
VIII. | Warship Protection Against Ram, Mine, and Torpedo | 136 |
IX. | Warship Protection as Applied to Some Ocean Liners | 161 |
X. | Conclusions | 179 |
ILLUSTRATIONS
Stoke-Hole of a Transatlantic Liner | Frontispiece |
PAGE | |
Riveting the Outer Skin on the Frames of a 65,000-Ton Ocean Liner | 3 |
Growth of the Transatlantic Steamer from 1840 to 1912 | 7 |
Receiving Submarine Signals on the Bridge | 13 |
Taking the Temperature of the Water | 17 |
Fire-Drill on a German Liner: Stewards are Closing Door in Fire-Protection Bulkhead | 21 |
Fire-Drill on a German Liner: Hose from Bellows Supplies Fresh Air to Man with Smoke Helmet | 25 |
Fire-Drill on a German Liner: Test of Fire-Mains is Made Every Time the Ship is in Port | 29 |
The 44,000-Ton, 25½-Knot Lusitania | 37 |
Provisioning the Boats During a Boat Drill | 43 |
Loading and Lowering Boats, Stowed Athwartships | 43 |
The Elaborate Installation of Telegraphs, Telephones, Voice-Tubes, etc., on the Bridge of an Ocean Liner | 47 |
Hydraulically-operated, Watertight Door in an Engine-Room Bulkhead | 53 |
Diagram Showing Protective Value of Transverse and Longitudinal Bulkheads, Watertight Decks, and Inner Skin | 57 |
Closing, from the Bridge, All Watertight Doors Throughout the Ship by Pulling a Lever | 63 |
Great Eastern, 1858; Most Completely Protected Passenger Ship Ever Built | 71 |
Longitudinal Section and Plan of the Great Eastern, 1858 | 77 |
Two Extremes in Protection, and a Compromise | 83 |
Great Eastern, Lying at Foot of Canal Street, North River, New York | 87 |
Fifty Years' Decline in Safety Construction | 93 |
Olympic, Sister to Titanic, reaching New York on Maiden Voyage | 97 |
The Framing and Some of the Deck Beams of the Imperator, as Seen from Inside the Bow, Before the Outside Plating is Riveted On | 103 |
How the Plating of the Inner Bottom of Such a Ship as the Titanic May Be Carried up the Side Frames to Form an Inner Skin | 107 |
Twenty of the Twenty-nine Boilers of the Titanic Assembled Ready for Placing in the Ship | 111 |
The Last Photograph of the Titanic, Taken as She was Leaving Southampton on Her Maiden Voyage | 117 |
Swimming Pool on the Titanic | 121 |
The Titanic Struck a Glancing Blow Against an Under-Water Shelf of the Iceberg, Opening up Five Compartments | 125 |
Comparison of Subdivision in Two Famous Ships | 129 |
The Vast Dining-Room of the Titanic | 133 |
The United States Battleship Kansas | 137 |
Plan and Longitudinal Section of the Battleship Connecticut | 143 |
Midship Section of a Battleship | 149 |
Safety Lies in Subdivision | 155 |
The 65,000-Ton, 23-Knot Imperator, Largest Ship Afloat | 159 |
Longitudinal Section and Plan of the Imperator | 163 |
The Rotor, or Rotating Element, of One of the Low-Pressure Turbines of the Imperator | 167 |
The 26,000-Ton, 23½-Knot Kronprinzessin Cecilie, a Thoroughly Protected Ship | 171 |
CHAPTER I
INTRODUCTION
Among the many questions which have arisen out of the loss of the Titanic there is one, which, in its importance as affecting the safety of ocean travel, stands out preëminent:
Among the many questions that have come up from the loss of the Titanic, there is one that, in terms of its importance for the safety of ocean travel, stands out as the most significant:
"Why did this ship, the latest, the largest, and supposedly the safest of ocean liners, go to the bottom so soon after collision with an iceberg?"
"Why did this ship, the newest, the biggest, and supposedly the safest of ocean liners, sink so quickly after hitting an iceberg?"
The question is one to which, as yet, no answer that is perfectly clear to the lay mind has been made. We know that the collision was the result of daring navigation; that the wholesale loss of life was due to the lack of lifeboats and the failure to fill completely the few that were available; and that, had it not been for the amazing indifference or stupidity of the captain of a nearby steamer, who failed to answer the distress signals of the sinking vessel, the whole of the ship's complement might have been saved.
The question is one that still doesn't have a clear answer for the average person. We know that the crash happened because of reckless navigation; that the massive loss of life was caused by not having enough lifeboats and not fully utilizing the few that were available; and that if it hadn't been for the shocking indifference or ignorance of the captain of a nearby ship, who ignored the distress signals from the sinking vessel, the entire crew and passengers might have been saved.
So far as the loss of the ship itself was concerned, it is certain that the stupefaction with which the news of her sinking was received was due to the belief that her vast size was a guarantee against disaster—that the ever-increasing dimensions of length, breadth, and tonnage had conferred upon the modern ocean liner a certain immunity against the dangers of travel by sea. The fetish of mere size seems, indeed, to have affected even the officers in command of these modern leviathans. Surely it must have thrown its spell over the captain of the ill-fated Titanic, who, in spite of an oft-repeated warning that there was a large field of ice ahead, followed the usual practice, if the night is clear, and ran his ship at full speed into the zone of danger, as though, forsooth, he expected the Titanic to brush the ice floes aside, and split asunder any iceberg that might stand in her way.
As far as the loss of the ship itself goes, it’s clear that the shock everyone felt when they heard about her sinking came from the belief that her enormous size would protect her from disaster—that the constantly growing length, width, and tonnage of modern ocean liners offered them some immunity against the risks of sea travel. The obsession with size seems to have influenced even the officers commanding these modern giants. It surely must have captivated the captain of the doomed Titanic, who, despite repeated warnings about a large field of ice ahead, followed the usual protocol for clear nights and drove his ship at full speed into the danger zone, as if he expected the Titanic to simply push the ice floes aside and break apart any iceberg that got in her way.

Courtesy of Scientific American
Thanks to Scientific American
Rivetting the Outer Skin on the Frames of a 65,000-Ton Ocean Liner
Riveting the Outer Skin onto the Frames of a 65,000-Ton Ocean Liner
Confidence in the indestructibility of the Titanic, moreover, was stimulated by the fact that she was supposed to be the "last word" in first-class steamship construction, the culmination of three-quarters of a century of experience in building safe and stanch vessels. In the official descriptions of the ship, widely distributed at the time of her launching, the safety elements of her construction were freely dwelt upon. This literature rang the changes on stout bulkheads, watertight compartments, automatic, self-closing bulkhead doors, etc.,—and honestly so. There is every reason to believe that the celebrated firm who built the ship, renowned the world over for the high character of their work; the powerful company whose flag she carried; aye, and even her talented designer, who was the first to pronounce the Titanic a doomed vessel and went down with the ship, were united in the belief that the size of the Titanic and her construction were such that she was unsinkable by any of the ordinary accidents to which the transatlantic liner is liable.
Confidence in the unsinkability of the Titanic was further boosted by the fact that she was meant to be the ultimate in first-class steamship design, the peak of 75 years of experience in building safe and sturdy ships. The official descriptions of the vessel, widely shared at the time of her launch, emphasized the safety features of her design. This material highlighted strong bulkheads, watertight compartments, automatic self-closing bulkhead doors, and more—accurately so. There is every reason to believe that the famous company that built the ship, known globally for the quality of their work; the powerful corporation whose flag she flew; and even her skilled designer, who was the first to declare the Titanic a doomed ship and went down with her, all shared the belief that the Titanic's size and construction made her unsinkable against any typical accidents that transatlantic liners might encounter.
How comes it, then, that this noble vessel lies to-day at the bottom of the Atlantic in two thousand fathoms of water?
How is it, then, that this noble ship lies today at the bottom of the Atlantic in two thousand fathoms of water?
A review of the progress of those constructive arts which affect the safety of human life seems to show that it needs the spur of great disasters, such as this, to concentrate the attention of the engineer and the architect upon the all-important question of safety. More important than considerations of convenience, economy, speed of construction, or even revenue-earning capacity, are those of the value and sanctity of human life. Too frequently these considerations are the last to receive attention. This is due less to indifference than to inadvertence—a failure to remember that an accident which may be insignificant in its effect on steel and stone, may be fatal to frail flesh and blood. Furthermore, the monumental disasters, and particularly those occurring in this age of great constructive works, are frequently traceable to hidden or unsuspected causes, the existence and potentialities of which are revealed only when the mischief has been done. A faulty method of construction, containing in itself huge possibilities of disaster, may be persisted in for years without revealing its lurking menace. Here and there, now and then, some minor mischance will direct the attention of the few to the peril; but the excitement will be local and passing. It takes a "horror"—a "holocaust" of human life, with all its attendant exploitation in the press and the monthly magazine, to awaken a busy and preoccupied world to the danger and beget those stringent laws and improved constructions which are the earmarks of progress towards an ideal civilisation.
A review of the progress of those constructive arts that impact human life safety seems to show that it takes major disasters, like this one, to grab the attention of engineers and architects for the essential question of safety. More important than concerns about convenience, cost, speed of construction, or even making money, are the value and sanctity of human life. Too often, these considerations are the last ones addressed. This happens not out of indifference but rather oversight—a failure to remember that an accident, which may seem minor for the structures made of steel and stone, can be devastating for fragile human beings. Moreover, the significant disasters, especially in this era of major construction projects, often stem from hidden or unexpected causes, whose existence and risks only become clear once damage has occurred. A flawed construction method, which carries significant disaster potential, can go on for years without showing its hidden danger. Every now and then, a minor mishap might bring the danger to the attention of a few, but the concern will be brief and local. It takes a "horror"—a "holocaust" of human lives, coupled with all its sensational coverage in the media and monthly magazines, to wake up a busy and distracted world to the risks and lead to the stricter laws and improved building practices that signify progress toward an ideal civilization.
![[click for larger image]](images/p007i.jpg)
Courtesy of Scientific American.
Thanks to Scientific American.
Note how far the Great Eastern was ahead of her time. She was not exceeded until the advent of the Oceanic in 1899.
Note how far the Great Eastern was ahead of her time. She wasn't surpassed until the arrival of the Oceanic in 1899.
Growth of the Transatlantic Steamer from 1840 to 1912
Growth of the Transatlantic Steamer from 1840 to 1912
Not many years ago, there was being erected across the St. Lawrence River a huge bridge, with the largest single span in the world, which it was believed would be not only the largest but the strongest and most enduring structure of its kind in existence. It was being built under the supervision of one of the leading bridge engineers of the world; its design was of an approved type, which had long been standard in the Western Hemisphere; and the steelwork was being fabricated in one of the best equipped bridge works in the country. Nevertheless, when one great cantilever was about completed, and before any live load had been placed on it, the structure collapsed under its own weight. One of the principal members—a massive steel column, five feet square and sixty feet long—crumpled up as though it had been a boy's tin whistle, and allowed the whole bridge to fall into the St. Lawrence, carrying eighty men to their death! The disaster was traced to a very insignificant cause—the failure of some small angle-bars, 3½ inches in width, by which the parts of the massive member were held in place. No engineer had suspected that danger lurked in these little angle-bars. Had the accident happened to a bridge of moderate size, the lessons of the failure would have been noted by the engineers and contractors; it would have formed the subject, possibly, of a paper before some engineering society, and the warning would have had results merely local and temporary. But the failure of this monumental structure, with a loss of life so appalling, gave to the disaster a world-wide notoriety. It became the subject of a searching enquiry by a highly expert board; the unsuspected danger which lurked in the existing and generally approved methods of building up massive steel columns was acknowledged; and safer rules of construction were adopted.
Not many years ago, a huge bridge was being built across the St. Lawrence River, featuring the largest single span in the world. It was thought to not only be the largest but also the strongest and most durable structure of its kind. The construction was overseen by one of the top bridge engineers globally, its design was an established type long recognized in the Western Hemisphere, and the steelwork was fabricated in one of the best-equipped bridge factories in the country. However, when one major cantilever was nearly finished, and before any load had been placed on it, the structure collapsed under its own weight. One of the main components—a massive steel column, five feet square and sixty feet long—crumbled as if it were a kid's tin whistle, causing the entire bridge to collapse into the St. Lawrence, claiming the lives of eighty men! The disaster was traced back to a very minor issue—the failure of some small angle-bars, 3½ inches wide, that held the massive member in place. No engineer had suspected that these small angle-bars posed a danger. If the accident had occurred on a smaller bridge, engineers and contractors would have noted the lessons from the failure; it might have even led to a presentation at some engineering society, resulting in warnings that would have had only local and temporary effects. But the collapse of this monumental structure, with such a horrific loss of life, gave the disaster worldwide attention. It became the focus of a thorough investigation by an expert board; the unexpected danger in the current and generally accepted methods of constructing massive steel columns was acknowledged, leading to the adoption of safer construction rules.
It took the Baltimore conflagration to teach us the strong and weak points of our much-vaunted systems of fireproof construction. Only when San Francisco, after repeated warnings, had seen the whole of its business section shaken down and ravaged by fire, did she set about the construction of a city that would be proof against fire and earthquake. It was the spectacle of maimed and dying passengers being slowly burned to death in the wreckage of colliding wooden cars, that led to the abolition of the heating stove and the oil lamp; and it was the risk of fire, coupled with the shocking injuries due to splintering of wooden cars, that brought in the era of the electrically lighted, strong, and incombustible steel car.
It took the Baltimore fire to show us the strengths and weaknesses of our so-called fireproof building methods. Only after San Francisco, despite numerous warnings, had its entire business district devastated by fire did it start building a city that could withstand fire and earthquakes. The sight of injured and dying passengers slowly burning in the wreckage of crashed wooden cars prompted the removal of heating stoves and oil lamps; and it was the threat of fire, combined with the severe injuries from breaking wooden cars, that ushered in the age of electrically lit, strong, and fire-resistant steel cars.
The conditions attending the loss of the Titanic were so heartrending, and its appeal has been so world-wide, as to lead us to expect that the tragedy will be preëminently fruitful in those reforms which, as we have shown, usually follow a disaster of this magnitude. Had the ship been less notable and the toll of human life less terrible, the disaster might have failed to awaken that sense of distrust in present methods which is at the root of all thorough-going reform. The measure of the one compensation which can be recovered from this awful loss of life and treasure, will depend upon the care with which its lessons are learned and the fidelity with which they are carried out.
The circumstances surrounding the loss of the Titanic were so heartbreaking, and its impact has been so widespread, that we expect this tragedy to lead to significant reforms, which, as we’ve shown, typically follow a disaster of this scale. If the ship had been less remarkable and the loss of life less horrific, the disaster might not have prompted the distrust in current methods that is essential for meaningful reform. The extent of the one compensation that can be gained from this tragic loss of life and resources will depend on the care taken to learn its lessons and the commitment to implementing them.
Unquestionably, public faith in the security of ocean travel has been rudely shaken. The defects, however, which are directly answerable for the sinking of this ship are fortunately of such a character that they can be easily corrected; and if certain necessary and really very simple changes in construction are made (and they can be made without any burdensome increase in the cost) we do not hesitate to say that future passenger travel on a first-class ocean-going steamship will be rendered absolutely safe.
Unquestionably, public trust in the safety of ocean travel has been badly shaken. However, the issues that directly led to the sinking of this ship can fortunately be easily fixed; and if certain essential and quite simple construction changes are made (and they can be done without significantly increasing costs), we confidently assert that future passenger travel on a first-class ocean-going steamship will be completely safe.

Small dial indicates whether signals come from port or starboard.
Small dial shows whether signals are coming from the left or right side.
Receiving Submarine Signals on the Bridge
Receiving Submarine Signals on the Bridge
The duty of a passenger steamer, such as the Titanic, may be regarded as threefold: She must stay afloat; she must provide a comfortable home for a small townful of people; and she must carry them to their destination with as much speed as is compatible with safety and comfort. Evidently the first condition, as to safety, should be paramount. When it has been determined to build a ship of a certain size and weight (in the case of the Titanic the weight was 60,000 tons, loaded) the designer should be permitted to appropriate to the safety elements of her construction every pound of steel that he may wish to employ. In a vessel like the Titanic, which is to be entrusted with the care of three or four thousand souls, he should be permitted to double-skin the ship, and divide and subdivide the hull with bulkheads, until he is satisfied that the vessel is unsinkable by any of the ordinary accidents of the sea. When these demands have been met, he may pile deck upon deck and crowd as big a boiler- and engine-plant into this unsinkable hull as the balance of the weights at his disposal will allow.
The duties of a passenger ship like the Titanic can be seen as threefold: it must stay afloat, it must provide a comfortable environment for a small town's worth of people, and it must transport them to their destination as quickly as possible while still ensuring safety and comfort. Clearly, the first priority, concerning safety, should be the most important. Once it's decided to build a ship of a certain size and weight (in the case of the Titanic, the weight was 60,000 tons when loaded), the designer should be allowed to allocate every pound of steel he chooses to the safety features of her construction. For a vessel like the Titanic, which will be responsible for the safety of three or four thousand people, he should be allowed to create a double-skinned hull and divide the interior with bulkheads until he feels confident that the ship is unsinkable against any typical maritime accidents. Once these requirements have been satisfied, he can stack deck upon deck and fit in as large a boiler and engine system as the remaining weight allows.
Unfortunately the Board of Trade requirements under which the Titanic was built—and very conscientiously built—proceed along no such common-sense lines. Instead, the Board many years ago framed a set of rules in which the safety requirements were cut down to such a low limit, that the question of a ship's surviving a serious collision was reduced to a mere gamble with Fate. The Board of Trade ship may fill two adjoining compartments, and then with the top of her bulkheads practically level with the sea, in the opinion of the Board, she will have a fighting chance to live in smooth water!
Unfortunately, the Board of Trade requirements under which the Titanic was built—and built very carefully—don’t follow any common-sense approach. Instead, many years ago, the Board created a set of rules that lowered safety standards so much that the chance of a ship surviving a serious collision became just a gamble with Fate. According to the Board, a ship might fill two adjoining compartments, and then with the top of her bulkheads nearly level with the sea, she would still have a fighting chance to survive in calm waters!
The Titanic filled at least five adjoining compartments, and hence,—thanks to these altogether inadequate and obsolete requirements, she is now at the bottom of the Atlantic; and, thanks again to the requirements of the Board as to lifeboat accommodations, over fifteen hundred of her passengers and crew went down with the ship!

Water is hauled up in the canvas bucket and its temperature taken by thermometer.
Water is lifted in the canvas bucket, and its temperature is measured with a thermometer.
Taking the Temperature of the Water
Taking the Temperature of the Water
CHAPTER II
THE CONSTANT DANGERS OF THE SEA
Boswell, that faithful, if over-appreciative chronicler, tells us that Dr. Johnson once described an ocean voyage as "going to jail with a chance of being drowned." Had some one quoted the grim witticism of the doctor in the spacious dining-room of the Titanic on the night of April the fourteenth, it would have provoked a smile of derisive incredulity. Going to sea in the cramped quarters of the frail sailing packet of Johnson's day was one thing; crossing the Atlantic at railroad speed in the spacious luxury of a 60,000-ton liner was quite another. Yet, five hours later, when the vast bulk of that noble ship was slanting to its final plunge, the pitiless truth was brought home to that awe-stricken crowd that, even to-day, travel by sea involves the "chance of being drowned."
Boswell, that loyal but overly admiring storyteller, tells us that Dr. Johnson once described an ocean voyage as "going to jail with a chance of being drowned." If someone had quoted the doctor's dark humor in the spacious dining room of the Titanic on the night of April 14th, it would have elicited a smile of sarcastic disbelief. Going to sea in the cramped quarters of Johnson's time was one thing; crossing the Atlantic at train speed in the luxurious comfort of a 60,000-ton liner was something else entirely. Yet, five hours later, as that magnificent ship tilted toward its final plunge, the harsh reality hit the awe-struck crowd that, even today, traveling by sea carries the "chance of being drowned."
The remarkable immunity of the high-speed Atlantic liners from such accidents as befell the Titanic has been due in part to careful seamanship and in part to an amazing run of good luck. Of this there can be no doubt whatever. On a recent occasion the subject was brought up for discussion in the officers' quarters of one of the fastest liners. In answer to the writer's question as to whether the dangers of running at high speed through fog or ice-infested regions were not enormous, one of the officers frankly admitted that, not only were the risks most serious, but the immunity from such disasters as that which befell the Titanic was to be explained on the ground of sheer good fortune. "I well remember," said he, "that the first time I found myself in charge of the bridge on a ship that was running through fog at a speed of over 20 knots, I fairly shivered with a sense of the possibilities of disaster that were involved. To-day—well—familiarity, you know——"
The impressive immunity of high-speed Atlantic liners from accidents like the one that happened to the Titanic is partly due to careful seamanship and partly thanks to an incredible streak of good luck. There's no doubt about that. Recently, this topic came up for discussion in the officers' quarters of one of the fastest liners. When I asked whether the dangers of running at high speed through fog or ice-infested areas weren’t enormous, one of the officers openly admitted that not only were the risks very serious, but that the safety from disasters like the one that happened to the Titanic could be attributed to sheer luck. "I clearly remember," he said, "the first time I was in charge of the bridge on a ship going through fog at over 20 knots; I was genuinely shaken by the potential for disaster involved. Today—well—familiarity, you know——"

Stewards are closing door in fire-protection bulkhead.
Stewards are closing the door in the fire-protection bulkhead.
Fire-drill on a German Liner
Fire drill on a German liner
Let it not be supposed, from the heading of this chapter, that it is the writer's purpose to draw any lurid picture of the dangers of ocean travel. These are no greater to-day than they were before the Titanic went down. Icebergs have swept down from the Arctic seas from time immemorial, and year by year they will continue to throw the shadow of their awful menace across the lines of steamship travel. Fog, with its ever-present dangers of collision, will continue to infest the ocean highways; and always, the half-submerged derelict, a peril scarcely less than that of the iceberg, will continue to sail its uncharted course over the high seas.
Let’s not assume, from the title of this chapter, that the author is trying to paint a dramatic picture of the dangers of ocean travel. These dangers today are no greater than they were before the Titanic sank. Icebergs have been coming down from the Arctic seas since forever, and every year they will keep casting their ominous shadow over the routes of steamship travel. Fog, with its constant risk of collisions, will continue to linger on ocean paths; and always, the partially submerged wreck, a danger almost on par with that of the iceberg, will keep drifting its uncharted path across the open seas.
The strength of the impulse to build unsinkable ships will be exactly in proportion to our realisation of the dangers which beset ocean travel. The toll of human life exacted in the recent disaster will lose its one possible compensation, if it fails to impress deeply the very serious lesson that since the sea is not man's natural element, he can hold his way safely across its surface only at the cost of most careful preparation and eternal vigilance.
The drive to create unsinkable ships will be directly related to our understanding of the dangers that come with ocean travel. The loss of human life in the recent disaster will lose its one possible justification if it doesn’t make us seriously consider the important lesson that since the sea isn't a natural environment for humans, we can only navigate it safely with thorough preparation and constant awareness.
Protracted and amazing immunity from disasters of portentous magnitude has bred in us something of that very contempt for the dangers of the sea above referred to. We have piled deck upon deck until the "floating palace" of the sea towers twice as far above the water-line as it extends below it. So rapidly have we added weight to weight and horsepower to horsepower, that both the mass and the power have been quadrupled. The giant steamship of to-day, as she rushes through the black night and the all-obscuring fog, represents a potential engine of destruction, for which no parallel can be found in the whole field of human activity.
Prolonged and incredible protection from disasters of significant scale has made us somewhat dismissive of the dangers of the sea mentioned earlier. We have stacked deck upon deck until the "floating palace" of the ocean rises twice as high above the waterline as it does below it. So quickly have we added weight upon weight and horsepower upon horsepower that both the size and the power have been increased fourfold. The massive steamship of today, as it speeds through the dark night and thick fog, embodies a potential force of destruction unmatched in any area of human activity.
Do you doubt it? Then learn that on that fatal night when the Titanic bore headlong into the icefield, she embodied in her onrushing mass an energy equal to that of the combined broadsides of our two most powerful battleships, the Florida and the Utah. Which is to say that, if the two dreadnoughts had discharged their twenty twelve-inch guns, at point-blank range, against the iceberg which sank this ship, they would have struck a combined blow of less energy than that delivered by the Titanic. And every one of these guns, be it remembered, delivers its shell with an energy of 50,000 foot-tons—sufficient to lift either of these battleships nearly two and a half feet into the air.
Do you doubt this? Then know that on that tragic night when the Titanic charged straight into the icefield, it carried with it a momentum equal to the combined firepower of our two strongest battleships, the Florida and the Utah. In other words, if those two dreadnoughts had fired their twenty twelve-inch guns at close range at the iceberg that sank the ship, their combined fire would have had less impact than the force produced by the Titanic. It's important to remember that each of these guns delivers its shell with an energy of 50,000 foot-tons—enough to lift either of these battleships nearly two and a half feet off the ground.

Hose from bellows supplies fresh air to man with smoke helmet.
Hose from the bellows provides fresh air to the person wearing the smoke helmet.
Fire-drill on a German Liner
Fire drill on a German liner
Of the serious risk to a ship of collision with an iceberg, it is superfluous to say anything here. The swift sinking of the world's greatest steamship has driven that lesson home, surely, for all time to come. But there are two other forms of accident on the high seas—collision with another ship and the running down of a derelict—whose possibilities of disaster are scarcely less. For if the huge steamships of our day, moving at high speed, are such potential engines of destruction, it follows that the damaging effects of collisions are proportionately increased.
Of the serious risk of a ship colliding with an iceberg, it's unnecessary to elaborate here. The rapid sinking of the world's largest steamship has made that lesson clear, without a doubt, for all time. But there are two other types of accidents at sea—collisions with other ships and hitting a derelict—whose potential for disaster is barely less significant. Since today’s massive steamships, traveling at high speeds, can be such serious threats, it stands to reason that the impact of collisions is proportionately greater.
If a 60,000-ton ship, such as the Titanic, while running at high speed, were struck on the beam by a vessel of large size, it is quite conceivable that the outside plating of three of her compartments (not merely the "two adjoining" of standard shipbuilding practice) might be broken in, or the seams and butts started, before the energy of the colliding ship was absorbed and the two vessels swung clear of each other. The average length of the compartments of the Titanic was about 53 feet. At 21 knots she would move forward about 35 feet in one second. Hence, in a few seconds' time (even allowing for her slowing down due to the drag of the other ship), her enormous energy of over 1,000,000 foot-tons would cause her to grind along past the broken bow, surely more than the 100 feet or so which would suffice to involve three compartments. If three compartments amidships were opened to the sea, it would mean the admission of some 12,000 to 15,000 tons of water.
If a 60,000-ton ship, like the Titanic, were to be hit on the side by a large vessel while traveling at high speed, it’s easy to imagine that the outer plating of three of her compartments (not just the "two adjoining" as is standard in shipbuilding) could get damaged, or the seams and joints could start to fail, before the force of the colliding ship was fully absorbed and the two vessels drifted apart. The average length of the Titanic's compartments was about 53 feet. At 21 knots, she would move forward about 35 feet in one second. So, in just a few seconds (even accounting for her slowing down due to the impact from the other ship), her massive energy of over 1,000,000 foot-tons would cause her to scrape past the damaged bow, definitely more than the 100 feet or so that would be needed to breach three compartments. If three compartments in the middle were opened to the sea, it would let in around 12,000 to 15,000 tons of water.
Even more insidious is the menace of the abandoned and water-logged ship—the justly dreaded derelict—which, floating low in the water, and without a light to reveal its position, may lie directly in the path of the high-speed ocean liner. So slightly does the derelict project above the surface, that it is almost impossible of detection by night from the lofty position of the lookout on a modern steamship.
Even more dangerous is the threat of the abandoned and waterlogged ship—the rightly feared derelict—which, floating low in the water and lacking any light to signal its location, could be directly in the path of a fast-moving ocean liner. The derelict sticks out so little above the surface that it's nearly impossible to spot at night from the high vantage point of the lookout on a modern steamship.

Test of fire mains is made every time the ship is in port.
Test of fire mains is done every time the ship is in port.
Fire-drill on a German Liner
Fire drill on a German liner
Another risk of the sea, which, because of long immunity from disaster, is in danger of being overlooked or underrated, is that of fire. The structural portions of a ship and its engine- and boiler-plant, being of metal, are proof against fire; but the stateroom partitions, the wooden floors and ceilings, the wainscoting, and the hundreds of tons of material used in decoration and general embellishment, to say nothing of the highly inflammable paint-work and varnish, constitute a mass of material, which, in the event of a serious fire, might turn the whole interior of a large passenger ship into one vast cauldron of flame. Fortunately, the bulkhead is as effective in confining a fire as it is in localising an inflow of water in the event of collision. Therefore, some of the bulkheads of the under-water portion of all passenger ships should be continued (of lighter construction) right through the decks reserved for passenger accommodations, to the topmost deck of the ship.
Another risk of the sea, which, due to a long time without disaster, is at risk of being overlooked or underestimated, is fire. The structural parts of a ship and its engine and boiler systems, being made of metal, are resistant to fire; however, the stateroom partitions, the wooden floors and ceilings, the paneling, and the hundreds of tons of materials used for decoration and general embellishment, not to mention the highly flammable paint and varnish, create a mass of materials that, in the event of a serious fire, could turn the entire interior of a large passenger ship into one massive inferno. Luckily, the bulkhead is just as effective at containing a fire as it is at limiting water inflow during a collision. Therefore, some of the bulkheads in the underwater sections of all passenger ships should be extended (but built lighter) all the way through the decks meant for passenger accommodations up to the top deck of the ship.
But, perhaps, after all said and done, the greatest perils of high-speed ocean travel are to be found in that spirit of nautical sangfroid, or indifference to danger, which, as this disaster has proved, may in time begin to characterise the attitude even of so experienced a navigator as the late captain of the Titanic.
But, maybe, after everything that's been said, the biggest risks of high-speed ocean travel come from that attitude of nautical sangfroid, or indifference to danger, which, as this disaster has shown, can eventually start to define the attitude of even the most experienced navigator, like the late captain of the Titanic.
Protection against the dangers of the sea may be sought in two directions: First, the enforcement of rules for more careful navigation; second, the embodiment of non-sinkable construction in the ship.
Protection against the dangers of the sea can be pursued in two ways: First, by enforcing stricter navigation rules; second, by incorporating unsinkable designs in the ship.
The protection afforded by the one is limited by the fallibility of human nature.
The protection offered by the one is limited by the shortcomings of human nature.
If we would make ocean travel safe we must make the ship, as far as possible, unsinkable. In other words, the naval architect must adopt that principle of construction, common in other lines of mechanical work, which has been aptly designated as "fool-proof." In the building of folly-proof ships, then (the term is here used in a modified sense and with not the least reflection upon that fine body of professional men whose duties lie on the bridge of our ocean liners), is to be found the one sure protection against the perils of the sea.
If we want to make ocean travel safe, we need to make ships as unsinkable as possible. In other words, naval architects should adopt that construction principle, which is common in other areas of engineering, known as "fool-proof." Therefore, in creating fool-proof ships (the term is used here in a specific sense and is not meant to reflect poorly on the skilled professionals who operate our ocean liners), we can find the best protection against the dangers of the sea.
We are well aware that the merchant ship, like the warship, is a compromise, and that the ingenuity of the naval architect is sorely taxed to meet the many demands for speed, coal capacity, freight capacity, and luxurious accommodations for passengers. All this is admitted. But the object of these chapters is to show that in designing the ship, the architect has given too little attention to the elements of safety—that, in the compromise, luxurious accommodations, let us say, have been favoured at the expense of certain protective structural arrangements, which might readily be introduced without any great addition to the cost of the ship, or any serious sacrifice of comfort or speed.
We know that the merchant ship, like the warship, is a compromise, and that the creativity of the naval architect is heavily challenged to meet the various demands for speed, fuel capacity, cargo space, and comfortable accommodations for passengers. Everyone agrees on this. However, the purpose of these chapters is to highlight that in designing the ship, the architect has paid too little attention to safety elements—that, in this compromise, luxurious accommodations, for example, have been prioritized over important protective structural arrangements, which could easily be added without significantly increasing the ship's cost or severely compromising comfort or speed.
Under the sobering effect of this calamity, caution and moderation are the watchwords of the hour. Steamships are leaving port crowded with lifeboats of every size and shape. Steamship routes have been moved far to the south of the accustomed lines of travel. The time occupied in passage is longer, distances are greater, and the coal bill runs into larger figures.
Under the serious impact of this disaster, caution and moderation are the keywords of the moment. Steamships are leaving the port packed with lifeboats of all sizes and shapes. Steamship routes have been shifted well south of the usual travel paths. The journey now takes longer, the distances are greater, and the coal costs are rising significantly.
But competition is keen, dividends must be earned, and amid all the fret and fever of our modern life, memories, even of stupendous happenings, have but a brief life. Steamship routes, under the strong pressure of competition, will tend to edge northward on to the older and shorter sailing lines. Immunity from disaster will beget the old sangfroid; and with the near approach of the age of motor-driven ships, we may look for an increase in speed such as the old Atlantic has never witnessed, even in the years of fiercest contest for the blue ribbon of the seas.
But competition is fierce, dividends need to be made, and with all the stress and hustle of our modern lives, even the most extraordinary events have a short lifespan in our memories. Steamship routes, fueled by intense competition, will likely shift northward toward the older, shorter sailing paths. Safety from disasters will bring back the old sangfroid; and with the impending arrival of motor-driven ships, we can expect speeds never before seen on the old Atlantic, even in the years of the toughest rivalry for the blue ribbon of the seas.
CHAPTER III
Every ship has its own lifeboat.
Say what we will, it cannot be denied that the lifeboat is a makeshift. The long white line of boats, conspicuous on each side of the upper deck of a large passenger ship, is, in a certain sense, a confession of failure—an admission on the part of the shipbuilder that, in spite of all that he has done in making travel by sea fast and comfortable, he has not yet succeeded in making it safe.
Say what we want, it can't be denied that the lifeboat is a temporary solution. The long white line of boats, noticeable on either side of the upper deck of a large passenger ship, is, in a way, a confession of failure—an acknowledgment from the shipbuilder that, despite all the efforts to make sea travel fast and comfortable, he still hasn't managed to make it safe.
Progress in shipbuilding and especially in the construction of fast and luxuriously appointed ships has been simply phenomenal, particularly during the past two decades. There is no art in the whole field of engineering that has made such rapid and astonishing strides; and it is not stretching the point too far to assert that man's mastery of the ocean is the greatest engineering triumph of all time.
Progress in shipbuilding, especially in creating fast and luxury ships, has been extraordinary, especially over the last twenty years. There's no area in engineering that has advanced so quickly and impressively; it's not an exaggeration to say that humanity's control over the oceans is the greatest engineering achievement of all time.
The fury of the elements, as shown in a heavy storm at sea, has always been regarded as one of the most majestic and terrifying exhibitions of the forces of nature. When the sailing packet was struck by the full fury of a gale, the skipper lay to, thankful if he could survive the racket, without carrying away boats, bulwarks, and deck gear. Frequently, with canvas blown out of the bolt ropes, he was obliged to run under bare poles, at the imminent risk of being swamped under the weight of some following sea. For many a decade, even in the era of the steamship, it was necessary, when heading into a heavy sea, to slow down the engines, maintaining only sufficient speed to give steerage way. To-day, so great are the weight and engine power that the giant steamship, if the captain is willing to risk some minor mishaps to her upper works, may be driven resistlessly along the appointed lines of travel regardless of wind and sea. So far as the loss of the ship from heavy weather is concerned, man has obtained complete mastery of the ocean.
The fury of the elements, as seen in a violent storm at sea, has always been considered one of the most impressive and frightening displays of the forces of nature. When the sailing ship was hit by the full force of a gale, the captain would hold steady, grateful just to survive the chaos without losing boats, railings, and deck equipment. Often, with the sails ripped from their seams, he was forced to sail with no sails up, at the serious risk of being swamped by overwhelming waves. For many decades, even during the steamship era, it was necessary, when facing a rough sea, to slow down the engines, maintaining just enough speed for steering. Today, the massive weight and engine power of a giant steamship allow it, if the captain is willing to take on some minor damage to the upper structure, to move forward effortlessly along its planned route, regardless of wind and waves. As far as losing a ship to severe weather is concerned, humans have gained complete control over the ocean.

This ship, with 34 compartments below a water-tight steel deck, would serve as its own lifeboat in the event of collision.
This ship, featuring 34 compartments beneath a watertight steel deck, would act as its own lifeboat in case of a collision.
The 44,000-Ton, 25½-Knot Lusitania
The 44,000-ton, 25½-knot Lusitania
The writer well remembers a trip to the westward on one of the subsidised mail steamers, built to naval requirements, which was made at a time when the ship was striving to accomplish the average speed of 24½ knots for the round trip from England to America, which was necessary before she could claim the government subsidy. In the run to the eastward, the ship had averaged for the whole passage 25 knots; therefore to win the coveted prize, it was necessary, on the return passage to New York, to maintain an average of 24 knots. As it happened, two hours out from Queenstown it began to blow hard from the southwest, and for the next four days the wind, veering from southwest to northwest, never fell below the strength of half a gale. On the fourth day out the wind rose to full cyclonic force, and against the most tempestuous weather that the North Atlantic can show, the ship was driven for twenty-four hours into what the captain's log-book designated as "enormous head seas." She averaged a speed of 23 knots for the whole four days of heavy weather, and came through the ordeal without starting a single rivet, or showing any signs of undue strain in her roughly-handled hull.
The writer clearly remembers a trip west on one of the subsidized mail steamers, built to naval standards, during a time when the ship was trying to reach an average speed of 24½ knots for the round trip from England to America, which was required before it could claim the government subsidy. On the eastward journey, the ship had averaged 25 knots for the entire passage; therefore, to achieve the desired subsidy, it needed to maintain an average of 24 knots on the return trip to New York. As it turned out, two hours after leaving Queenstown, the wind picked up from the southwest, and for the next four days, it shifted from southwest to northwest, never dropping below half a gale. On the fourth day, the wind intensified to full cyclonic strength, and against the North Atlantic's most brutal weather, the ship was pushed for twenty-four hours into what the captain's log called "enormous head seas." It averaged a speed of 23 knots over the four days of rough weather and made it through the ordeal without losing a single rivet or showing any signs of excessive strain on its rugged hull.
The large and powerful passenger steamer of to-day is proof against fatal damage due to wind and sea. True it is that these ships occasionally reach New York after a stormy passage, with porthole glasses broken, windows smashed, and rails and other light fittings carried away; but these are minor damages which in no way affect the integrity of the ship as a whole.
The big and powerful passenger ships of today can withstand serious damage from wind and waves. It's true that these vessels sometimes arrive in New York after a rough trip, with broken porthole glasses, smashed windows, and rails and other light fixtures lost; but these are minor damages that don’t impact the overall safety of the ship.
If, then, the shipbuilder has made such wonderful strides in the strength of his construction and in the development of engine power, is it not a strange anomaly that he should have so far failed in his attempt to provide against sinking through collision, as to be under the necessity of advertising the fact, by crowding the topmost deck with appliances for saving the lives of the passengers when the ship goes down?
If the shipbuilder has made such amazing progress in the strength of his construction and in engine power development, isn’t it quite strange that he has so far failed to prevent sinking from collisions? It’s as if he has to advertise this by overcrowding the top deck with life-saving equipment for passengers when the ship goes down.
But it will be objected that, even if the ship were made so far unsinkable that she might act as her own lifeboat, there would yet remain the risk of her destruction by fire, and that, if a fierce conflagration occurred, the passengers would have to abandon ship and take to the boats. The objection is well made, and if it be possible to introduce structural features which will render ships both fireproof and unsinkable, the thing should be done.
But some will argue that even if the ship is made so unsinkable that it could act as its own lifeboat, there would still be the risk of it being destroyed by fire. If a serious fire broke out, the passengers would have to evacuate the ship and get into the lifeboats. This is a valid concern, and if it's possible to add structural features that make ships both fireproof and unsinkable, then that should definitely be done.
It is sincerely to be hoped that one outcome of the present world-wide interest in the subject of safety at sea, will be a searching investigation of the whole question of fire protection. In some of the first-class passenger ships, notably those of the leading German companies, the subject has been given the attention which it merits; but there is no doubt that a large majority of the vessels engaged in the passenger-carrying trade contain no fire protection of a structural nature; that is to say, the spaces reserved for passenger accommodations are not laid out with any view to limiting the ravages of fire. On most of these ships a fire which once obtained strong headway might sweep through the decks devoted to passenger accommodations, without meeting with any fireproof wall to stay its progress.
It is genuinely hoped that one outcome of the current global interest in safety at sea will be a thorough investigation of the entire issue of fire protection. Some of the top passenger ships, especially those from leading German companies, have given this topic the attention it deserves; however, it's clear that a large majority of vessels in the passenger-carrying industry lack any structural fire protection. In other words, the areas designated for passenger accommodations are not designed to limit the spread of fire. On most of these ships, if a fire gains significant momentum, it could easily spread through the decks meant for passengers without encountering any fireproof barriers to stop it.
Now the most effective protection against a conflagration on board ship is to apply the same method of localisation which is used to such good effect in limiting the inflow of water resulting from collision. The steel bulkhead and the steel deck, acting as fire screens, may be made as effective in limiting the area of a fire as they are in limiting the area of flooding.
Now the best way to protect against a fire on a ship is to use the same method of containment that effectively limits water intake when there’s a collision. The steel bulkhead and the steel deck, functioning as fire barriers, can be just as effective in reducing the spread of a fire as they are in restricting flooding.
The passenger decks should be intersected at frequent intervals by steel bulkheads, extending from side to side of the ship and carried up to include the topmost tier of staterooms. Where the alleyways intersect the bulkheads, fireproof doors would afford all the necessary means of communication. The provision of many such bulkheads, coupled with the installation of an ample fire-main service and the faithful practice of fire-drills, would render the loss of a ship by fire practically impossible.
The passenger decks should be divided at regular intervals by steel bulkheads, running from one side of the ship to the other and extending up to the highest level of staterooms. Where the hallways meet the bulkheads, fireproof doors would provide all the necessary access. Having many of these bulkheads, combined with sufficient fire-main service and regular fire drills, would make it nearly impossible for a ship to be lost to fire.
The pathetic reluctance of her passengers to leave the Titanic for the lifeboats was justified, surely, by the seeming security of the one and frailty of the other. Perfectly natural was their belief that the mighty ship would survive, at least until the rescuing steamers should reach her vicinity and render the transfer of passengers a safe operation. Did not the Republic remain afloat for many hours after a collision scarcely less terrible than this, and was not the Titanic twice her size and, therefore, good as a lifeboat for many an hour to come?
The understandable hesitation of her passengers to leave the Titanic for the lifeboats made sense, given the appearance of safety onboard compared to the fragility of the lifeboats. It was completely natural for them to think that the massive ship would hold up, at least until the rescue boats arrived and made the evacuation safer. After all, didn’t the Republic stay afloat for hours after a collision that was nearly as severe as this one, and wasn’t the Titanic twice her size, making her a reliable refuge for a considerable time?

Courtesy of Scientific American
Thanks to Scientific American
Loading and Lowering Boats, Stowed Athwartships
Loading and Lowering Boats, Stored Sideways
In considering the excellent service rendered by the lifeboats of the Republic and the Titanic, it should be borne in mind that the weather conditions happened to be very favourable. The launching of lifeboats in rough weather is a difficult and perilous operation. Frequently the sinking ship will have a heavy list; if she lists to starboard, the boats on that side can be launched well clear of the ship, but the boats on the port or higher side cannot be so launched. As they are lowered, they will come in contact with the side of the ship and be damaged or capsized. Furthermore, should the ship be rolling, the boats are liable to be swung violently against the vessel and their sides may be crushed in or heavily strained, rendering them unseaworthy. Had a heavy sea, nay, even a moderate sea, been running at the time of the Titanic disaster, how long would her heavily loaded boats have survived in water that was infested with ice floes? Their helplessness will be more evident when we remember that they weighed between one and two tons, and that when they were loaded down with sixty-five people, the total weight must have been about six tons. Now a craft of six tons' displacement requires considerable handling, and the two or three sailors allotted to each boat, jammed in, as they were, among crowded passengers, would have been powerless in heavy weather to keep the boat from broaching broadside to the sea and capsizing.
In looking at the great service provided by the lifeboats of the Republic and the Titanic, we need to remember that the weather conditions were very favorable. Launching lifeboats in rough weather is challenging and risky. Often, the sinking ship will be tilted heavily; if it tilts to the right, the boats on that side can be launched clear of the ship, but the boats on the left side can't be launched the same way. As they are lowered, they might hit the side of the ship, causing damage or capsizing. Additionally, if the ship is rolling, the boats can swing violently against the vessel, which could crush their sides or heavily strain them, making them unseaworthy. If there had been a heavy wave, or even just moderate seas, during the Titanic disaster, how long would her heavily loaded boats have lasted in icy waters? Their vulnerability becomes clearer when we consider that they weighed between one and two tons, and that with sixty-five people onboard, the total weight would have been around six tons. A vessel with a six-ton displacement requires significant handling, and the two or three sailors assigned to each boat, cramped among packed passengers, would have been unable to keep the boat from tipping sideways to the waves and capsizing in rough weather.
The demand, then, for unsinkable ships is justified by the fact that the lifeboat is at best but a poor makeshift—that to put several thousand people adrift in mid-ocean is to expose them to the risk of ultimate death by starvation or drowning.
The need for unsinkable ships is justified because lifeboats are just a temporary solution. Putting several thousand people adrift in the open ocean puts them at risk of dying from starvation or drowning.

Courtesy of Scientific American
Thanks to Scientific American
Boat Deck of Titanic, Showing, in Black, Plan for Stowing Extra Boats, to Bring Total Accommodations Up to 3,100 Persons
Boat Deck of Titanic, Showing, in Black, Plan for Storing Extra Boats, to Bring Total Capacity Up to 3,100 People
However, in view of the fact that ninety-five passenger ships out of every hundred are built with the single skin, low bulkheads, and non-watertight decks, which characterised the Titanic, it is certain that the cry: "A lifeboat seat for every passenger" is fully justified. The problem of housing the large number that would be required presents no insuperable difficulties, and there are several alternative plans on which the boats might be disposed. On page 45 will be found a proposed arrangement, reproduced by the courtesy of the "Scientific American," which shows in white the twenty boats actually carried by the Titanic, and in black the additional boats which would be necessary to increase the total accommodation to about 3,100 people. This plan would necessitate the sacrifice of some of the deck-house structures. Between each pair of smoke-stacks two lines of four boats each are stowed athwartships. The boat chocks are provided with gunmetal wheels, which run in transverse tracks sunk in the deck. Along each side of the boat-deck there is a continuous line of boats.
However, considering that ninety-five out of every hundred passenger ships are built with a single skin, low bulkheads, and non-watertight decks, similar to the Titanic, it's clear that the demand for "A lifeboat seat for every passenger" is completely justified. The challenge of accommodating the large number needed isn’t insurmountable, and there are several alternative plans for how the boats could be arranged. On page 45 is a proposed layout, reproduced with the courtesy of the "Scientific American," which shows in white the twenty boats actually carried by the Titanic, and in black the extra boats that would be necessary to increase total capacity to about 3,100 people. This plan would require sacrificing some of the deck-house structures. Between each pair of smoke stacks, two lines of four boats each are stored across the ship. The boat chocks come with gunmetal wheels that run in transverse tracks set into the deck. Along each side of the boat deck, there’s a continuous line of boats.

Courtesy of Scientific American
Thanks to Scientific American
The Elaborate Installation of Telegraphs, Telephones, Voice-tubes, Etc., on the Bridge of an Ocean Liner
The Detailed Setup of Telegraphs, Telephones, Voice Tubes, and Other Equipment on the Bridge of an Ocean Liner
Another plan would be to take advantage of the full capacity of the Welin davit with which the Titanic was equipped, which is capable of handling two or even three boats stowed abreast. Three lines of boats carried on each side of the long boat-deck of a modern liner would provide ample accommodation for every person on board.
Another plan would be to make full use of the Welin davit that the Titanic was equipped with, which can handle two or even three boats stored side by side. Three rows of boats on each side of the long boat deck of a modern liner would have plenty of space for everyone on board.
But we repeat—and the point cannot be too strongly urged—that however complete the lifeboat accommodation may be, it is at the best a makeshift.
But we want to emphasize— and this cannot be overstated—that no matter how well-equipped the lifeboat accommodations are, they are at best a temporary solution.
The demand that every ship that is launched in the future shall be so far unsinkable as to serve as its own lifeboat in case of serious disaster is perfectly reasonable; for there are certain first-class transatlantic liners in service to-day—notably in certain leading English and German lines—which fulfil this condition. Considerations both of humanity and self-interest should lead to the adoption of similar principles of construction by every passenger steamship company. It is possible that the time will come, and it may indeed be very close at hand, when the most attractive page in the illustrated steamship pamphlet will be one containing plans of the ships, in which the safeguards against sinking—such as side bunkers, high bulkheads, and watertight decks—are clearly delineated.
The expectation that every ship launched in the future should be so resilient that it can act as its own lifeboat in case of a serious disaster is entirely reasonable; after all, there are currently some top-notch transatlantic liners in operation—particularly within leading English and German companies—that meet this standard. Both humanitarian concerns and self-interest should encourage all passenger steamship companies to adopt similar construction principles. It’s possible that the time will come, and it may be very soon, when the most appealing page in illustrated steamship brochures will be the one showcasing the ship designs, clearly outlining the safety features against sinking—like side bunkers, high bulkheads, and watertight decks.
CHAPTER IV
Safety is in the subdivision.
Other things being equal, the protection of a ship against sinking is exactly proportionate to the number of separate watertight compartments into which the interior of her hull is subdivided. If she contains no watertight partitions whatsoever, her sinking, due to damage below the water-line, is a mere matter of time. If the inflow exceeds the capacity of the pumps, water will flow into the ship until all buoyancy is lost. Protection against sinking is obtained by dividing the interior of the hull into a number of compartments by means of strong, watertight partitions, or bulkheads. Usually, these are placed transversely to the ship, extending from side to side and from the bottom to a height of one or two decks above the water-line. They are built of steel plates, stiffened by vertical I-beams, angle-bars, or other suitable members. The bulkheads are strongly riveted to the bottom, sides, and decks of the ship, and the joints are carefully caulked, so as to secure a perfectly tight connection. In the standard construction for merchant ships, as used in the Titanic, the bulkheads are placed transversely to the length of the ship, and the number of separate compartments is just one more than the number of bulkheads, ten such bulkheads giving eleven compartments, fifteen, as in the Titanic, giving sixteen compartments, and so on. In the case of a few high-class merchant steamers, built to meet special requirements as to safety, bulkheads are run lengthwise through the ship. These longitudinal bulkheads, intersecting the transverse bulkheads, greatly increase the factor of safety due to subdivision; for it is evident that one such, running the full length of the ship, would double, two would treble, and three would quadruple the number of separate compartments.
Other things being equal, protecting a ship from sinking is directly related to the number of separate watertight compartments that divide the interior of its hull. If there are no watertight partitions at all, it’s only a matter of time before the ship sinks if it takes damage below the waterline. If the water flowing in exceeds what the pumps can handle, the ship will fill with water until it loses all buoyancy. The way to protect against sinking is by dividing the interior of the hull into several compartments using strong, watertight partitions or bulkheads. These are usually placed across the width of the ship, extending from side to side and from the bottom up to one or two decks above the waterline. They’re made of steel plates, reinforced with vertical I-beams, angle bars, or other suitable materials. The bulkheads are firmly riveted to the bottom, sides, and decks of the ship, and the joints are carefully sealed to ensure a completely tight connection. In standard construction for merchant ships, such as the Titanic, the bulkheads are arranged across the ship's length, with the number of separate compartments being one more than the number of bulkheads; for example, ten bulkheads create eleven compartments, and fifteen, as in the Titanic, create sixteen compartments, and so on. In some high-end merchant steamers designed for enhanced safety, bulkheads run lengthwise through the ship. These longitudinal bulkheads, intersecting with the transverse ones, significantly boost safety by subdivision; clearly, one running the full length of the ship would double the number of separate compartments, two would triple it, and three would quadruple it.

Hydraulically-operated, Watertight Door in an Engine-room Bulkhead
Hydraulically-operated, watertight door in an engine room bulkhead
The bulkhead subdivision above described is all done in vertical planes. Its object is to restrict the water to such compartments as (through collision or grounding) may have been opened to the sea. As the water enters, the ship, because of the loss of buoyancy, will sink until the buoyancy of the undamaged compartments restores equilibrium and the ship assumes a new position, with the water in the damaged compartments at the same level as the sea outside. This position is shown in Fig. 2, page 57. It must be carefully noted, however, that this condition can exist only if the bulkheads are carried high enough to prevent the water in the damaged compartments from rising above them and flowing over the tops of the bulkheads into adjoining compartments.
The bulkhead subdivision described above is all set up in vertical planes. Its purpose is to contain water within compartments that may have been compromised due to a collision or grounding. As water enters, the ship will sink because of the loss of buoyancy until the buoyancy of the undamaged compartments brings it back to a balanced state, causing the ship to settle into a new position where the water in the damaged compartments is at the same level as the sea outside. This position is illustrated in Fig. 2, page 57. However, it's important to note that this situation can only happen if the bulkheads are high enough to stop the water in the damaged compartments from rising over them and spilling into adjacent compartments.
In addition to lateral and longitudinal subdivision by means of vertical bulkheads, the hull may be further subdivided by means of horizontal partitions in the form of watertight decks—a system which is universally adopted in the navies of the world. For it is evident that if the ship shown in Fig. 2, page 57, were provided with a watertight deck, say at the level of the water-line, as shown in Fig. 1, page 57, the water could rise only to the height of that deck, where it would be arrested. The amount of water entering the vessel would be, say, only one-half to two-thirds of that received in the case of the vessel shown in Fig. 2.
In addition to dividing the hull laterally and longitudinally with vertical bulkheads, the hull can also be further subdivided using horizontal partitions in the form of watertight decks—this system is widely used by navies around the world. It's clear that if the ship shown in Fig. 2, page 57, had a watertight deck at the waterline level, as illustrated in Fig. 1, page 57, the water could only rise to the height of that deck, where it would be stopped. The amount of water entering the vessel would be only about one-half to two-thirds of what would enter the vessel shown in Fig. 2.
If ships that are damaged below the water-line always settled in the water on an even keel, that is to say without any change of trim, the loss through collisions would be greatly reduced. But for obvious reasons, the damage usually occurs in the forward part of the ship, and the flooding of compartments leads to a change of trim, setting the ship down by the head, as shown in Figs. 3 and 4. If the transverse bulkheads are of limited height, and extend only to about 10 feet above the normal water-line, the settling of the bow may soon bring the bulkhead deck (the deck against which the bulkheads terminate) below the water. If, as is too often the case, this deck is not watertight—that is to say, if it is pierced by hatch openings, stair or ladder-ways, ventilator shafts, etc., which are not provided with watertight casings or hatch covers, the water will flow aft along the deck, and find its way through these openings into successive compartments, gradually destroying the reserve buoyancy of the ship until she goes down. The vessels shown in Figs. 3 and 4 are similar as to their subdivision, each containing thirteen compartments; but in Fig. 3 the bulkheads are shown carried only to the upper deck, say 10 feet above the water, whereas in Fig. 4 they extend to the saloon deck, one deck higher, or, say, 19 feet above the same point. Now, if both ships received the same injury, involving, say, the three forward compartments, a loss of buoyancy which would bring the tops of bulkheads in Fig. 3 below the surface, would leave the bulkheads in Fig. 4, which end at a watertight deck, with a safe margin, and any further settling of the ship would be arrested.
If ships that are damaged below the waterline always settled evenly in the water, without changing their trim, the loss from collisions would be significantly less. However, damage typically happens in the front part of the ship, causing flooding in compartments that alters the trim and makes the ship settle down by the bow, as seen in Figs. 3 and 4. If the transverse bulkheads are not very tall and only reach about 10 feet above the normal waterline, the bow settling may quickly lower the bulkhead deck (the deck where the bulkheads end) below the water. If, as often happens, this deck isn’t watertight—that is, if it has hatch openings, stairways, ventilator shafts, etc., without watertight seals or covers, water will flow aft along the deck and seep through these openings into other compartments, gradually eliminating the ship's reserve buoyancy until it sinks. The vessels in Figs. 3 and 4 have a similar layout, each with thirteen compartments; however, in Fig. 3, the bulkheads only go up to the upper deck, about 10 feet above the water, while in Fig. 4, they go up to the saloon deck, one deck higher, or about 19 feet above that same point. Now, if both ships were to sustain the same damage, say affecting the three front compartments, the loss of buoyancy could submerge the tops of the bulkheads in Fig. 3 but would leave the bulkheads in Fig. 4, which stop at a watertight deck, with a safe margin, and any further settling of the ship would be halted.
![[click for larger image]](images/p057i.jpg)
Fig. 1 WATERTIGHT DECK AT WATERLINE LIMITS INFLOW OF WATER
Fig. 1 WATERTIGHT DECK AT WATERLINE STOPS WATER FROM ENTERING
Fig. 2 HIGH BULKHEADS, WITHOUT WATERTIGHT DECK WOULD SAVE THE SHIP BUT PERMIT DEEP SUBMERSION
Fig. 2 HIGH BULKHEADS, WITHOUT A WATERTIGHT DECK, WOULD SAVE THE SHIP BUT ALLOW FOR DEEP SUBMERSION
Fig. 3 SINKING BY THE HEAD; WATER FLOWING ALONG LOW BULKHEAD DECK AND ENTERING COMPARTMENTS THROUGH DOORS OR HATCHWAYS
Fig. 3 HEAVY IN THE FRONT; WATER RUSHING OVER THE LOW BULKHEAD DECK AND ENTERING ROOMS THROUGH DOORS OR HATCHES
Fig. 4 DOWN BY THE HEAD, BUT SAVED BY HIGHER BULKHEADS AND WATERTIGHT BULKHEAD DECK
Fig. 4 UNDERWATER AT THE FRONT, BUT RESCUED BY ELEVATED BULKHEADS AND WATERTIGHT BULKHEAD DECK
Fig. 5 RELATIVE AREA OF FLOODING FROM SAME DAMAGE IN SHIPS,
"A" WITH DOUBLE SKIN; "B" WITH SIDE BUNKERS; "C" WITH A SINGLE SKIN.
TRANSVERSE BULKHEADS ON EACH SHIP
Fig. 5 RELATIVE AREA OF FLOODING FROM THE SAME DAMAGE IN SHIPS,
"A" WITH DOUBLE SKIN; "B" WITH SIDE BUNKERS; "C" WITH A SINGLE SKIN.
TRANSVERSE BULKHEADS ON EACH SHIP
Diagrams Showing Protective Value of Transverse and Longitudinal Bulkheads, Watertight Decks,and Inner Skin
Diagrams Showing Protective Value of Transverse and Longitudinal Bulkheads, Watertight Decks, and Inner Skin
Ordinarily, it would suffice to carry the first two bulkheads at the bow and the last two at the stern to the shelter deck, terminating the intermediate bulkheads one deck lower. But whatever the deck to which the bulkheads are carried, care should be taken to make it absolutely watertight. Otherwise, as already made clear, the so-called watertight subdivision of the ship may, in time of stress, prove to be a delusion and a snare.
Ordinarily, it would be enough to carry the first two bulkheads at the front and the last two at the back to the shelter deck, ending the middle bulkheads one deck lower. But no matter which deck the bulkheads are placed on, it’s important to ensure it’s completely watertight. Otherwise, as has already been pointed out, the so-called watertight separation of the ship may, during a crisis, turn out to be an illusion and a trap.
Although the longitudinal bulkhead, which is employed below the water-line, and chiefly in the holds and machinery spaces, is the least used, it is one of the most effective means of subdivision that can be employed. A certain amount of prejudice exists against it, on the ground that it confines the inflowing water to one side of the ship, causing it to list, if not ultimately to capsize. But this objection merely points the moral that all things must be used with discretion. A single longitudinal bulkhead, built through the exact centre of a ship, would invite a speedy capsize in the event of extensive injury below the water-line. The loss of the British battleship Victoria emphasised that truth many years ago. But longitudinal bulkheads, carried through the engine and boiler spaces, at the sides of the ship, are a most effective protection. Not only is each of the large compartments in the wider central body of the ship divided into three, but along each side is provided a row of comparatively small compartments, several of which could be flooded without causing a serious loss of buoyancy.
Although the longitudinal bulkhead, which is used below the waterline, mainly in the holds and machinery spaces, is the least common, it is one of the most effective ways to divide the ship. There is some bias against it, based on the idea that it traps incoming water on one side of the ship, making it list, and possibly even capsize. However, this objection simply highlights that everything must be used wisely. A single longitudinal bulkhead, running through the exact center of a ship, would lead to a quick capsize in case of significant damage below the waterline. The loss of the British battleship Victoria drove that point home many years ago. But longitudinal bulkheads, running through the engine and boiler spaces on the sides of the ship, provide excellent protection. Not only does each of the large compartments in the wider central section of the ship get divided into three, but there are also rows of relatively small compartments along each side, several of which could be flooded without causing a serious loss of buoyancy.
These bulkheads, built some 15 to 18 feet in from the side of the ship, not only form an inner skin for the ship, but they serve as the inner wall of the coal bunkers. They extend from the inner bottom to the under side of the lower deck, to both of which they are securely riveted, the joints being carefully caulked, to render them watertight. The space between the ship's side and the bulkhead is subdivided by transverse watertight partitions (see plan of Mauretania, Fig. 3, page 129), placed centrally between the main transverse bulkheads of the ship. A further and most effective means for protecting the buoyancy is to construct the ship with a double skin up to and preferably a few feet above the water-line. The inner skin should extend from the first bulkhead abaft the engine-room to the first or collision bulkhead, forward. This construction merely involves carrying the inner floor plating of the double bottom up the sides of the ship to the under side of the lower deck. As all merchant ships are built with a double bottom (see page 107), the cost of thus providing a double skin below the water-line is small in proportion to the security against flooding which it affords.
These bulkheads, built about 15 to 18 feet in from the side of the ship, not only provide an internal structure for the ship but also act as the inner walls of the coal bunkers. They stretch from the inner bottom to the underside of the lower deck, where they are securely riveted, with the joints carefully caulked to make them watertight. The space between the ship's side and the bulkhead is divided by transverse watertight partitions (see plan of Mauretania, Fig. 3, page 129), which are positioned centrally between the main transverse bulkheads of the ship. An additional and very effective way to enhance buoyancy is to design the ship with a double skin extending up to—and preferably a few feet above—the waterline. The inner skin should extend from the first bulkhead behind the engine room to the first or collision bulkhead at the front. This construction simply requires extending the inner floor plating of the double bottom up the sides of the ship to the underside of the lower deck. Since all merchant ships are constructed with a double bottom (see page 107), the cost of adding a double skin below the waterline is minimal compared to the protection it offers against flooding.
The description of the Titanic, published at the time of her launch, stated that any two of her adjoining compartments could be flooded without endangering the safety of the ship, and the question must frequently have occurred to the lay mind as to why the ability of the ship to sustain flooding of her interior was confined to two, and not extended to include three or even more compartments.
The description of the Titanic, published at the time of her launch, stated that any two of her adjoining compartments could be flooded without endangering the safety of the ship, and many people must have wondered why the ship's capacity to handle flooding was limited to two compartments, rather than extending to three or even more.
The ability to stand the flooding of two compartments only is not peculiar to the Titanic. It represents the standard practice which is followed in all passenger ships, the spacing and height of whose bulkheads is determined in accordance with certain stipulations of the British Board of Trade. These stipulations, as given by Prof. J. H. Biles of Glasgow University, in his book "Design and Construction of Ships," are as follows:
The ability to withstand flooding in just two compartments isn’t unique to the Titanic. It reflects the standard practice used on all passenger ships, where the spacing and height of the bulkheads are determined by specific regulations set by the British Board of Trade. These regulations, as outlined by Prof. J. H. Biles from Glasgow University in his book "Design and Construction of Ships," are as follows:
"A vessel is considered to be safe, even in the event of serious damage, if she is able to keep afloat with two adjoining compartments in free communication with the sea. The vessel must therefore have efficient transverse watertight bulkheads so spaced that when any two adjoining compartments are open to the sea, the uppermost deck to which all the bulkheads extend is not brought nearer to the surface of the water than a certain prescribed margin.
A ship is deemed safe, even if it suffers significant damage, as long as it can remain afloat with two adjacent compartments connected to the ocean. Therefore, the ship must have effective transverse watertight bulkheads positioned so that when any two adjacent compartments are open to the sea, the highest deck that all the bulkheads reach does not come closer to the water’s surface than a specified limit.
"The watertight deck referred to is called the bulkhead deck. The line past which the vessel may not sink is called the margin of safety line.
"The watertight deck referred to is called the bulkhead deck. The line beyond which the vessel cannot sink is known as the margin of safety line."
"The margin of safety line, as defined in the above report, is a line drawn round the side at a distance amidships of three-one-hundredths of the depth at side at that place below the bulkhead deck, and gradually approaching it toward the aft end, where it may be three-two-hundredths of the same depth below it."
"The margin of safety line, as defined in the report above, is a line drawn around the side at a distance, amidships, of three-one-hundredths of the depth at that location below the bulkhead deck, gradually moving closer to it toward the aft end, where it may be three-two-hundredths of the same depth below it."
By referring to the diagrams on page 66 showing the disposition of bulkheads on certain notable ships, it will be seen that, in the case of the Titanic, the application of the Board of Trade rule called for the extension of the bulkheads amidships only to the upper deck, which, at the loaded draft of 34 feet, was only 10 feet above the water-line! Compare this with the safe construction adopted by Brunel and Scott Russell over fifty-four years ago, who, in constructing the Great Eastern, extended all the bulkheads (see page 83) to the topmost deck, fully 30 feet above the water-line.
By looking at the diagrams on page 66 that show the arrangement of bulkheads on some notable ships, you can see that, in the case of the Titanic, the Board of Trade's rule required the bulkheads in the middle of the ship to extend only to the upper deck, which, at the loaded draft of 34 feet, was just 10 feet above the waterline! Compare this to the safe construction methods used by Brunel and Scott Russell over fifty-four years ago, who, when building the Great Eastern, extended all the bulkheads (see page 83) to the highest deck, a full 30 feet above the waterline.

Closing, from the Bridge, All Watertight Doors Throughout the Ship by Pulling a Lever
Closing, from the Bridge, All Watertight Doors Throughout the Ship by Pulling a Lever
Before leaving the question of bulkheads, the writer would enter a strong protest against the present practice of placing watertight doors in the main bulkheads below the water-line. They are put there generally for the convenience of the engine- and boiler-room forces, whose duties render it necessary for them to pass from compartment to compartment. As at present constructed, these doors are of the sliding type, and they can be closed simultaneously from the bridge, or separately, by hand. The safer plan is to permit no bulkhead doors below the water-line, and provide in their place elevators or ladders, enclosed in watertight trunks. Access from compartment to compartment must then be had by way of the bulkhead deck.
Before moving on from the topic of bulkheads, the author wants to strongly object to the current practice of installing watertight doors in the main bulkheads below the waterline. These doors are typically placed there for the convenience of the engine and boiler room teams, who need to move between compartments for their work. As they are currently designed, these doors slide open and can be closed at the same time from the bridge or individually by hand. A safer approach would be to eliminate any bulkhead doors below the waterline and replace them with elevators or ladders that are enclosed in watertight trunks. Access between compartments should then be through the bulkhead deck.
The advantage of lofty bulkheads was admirably illustrated in the case of the City of Paris and the City of New York, designed by Mr. Biles in 1888. Although these were small ships compared with the Titanic, their fourteen bulkheads were carried one deck higher. Biles laid down the rule that no doors were to be cut through the bulkheads, and in spite of strenuous objections on the grounds of passenger accommodation and general convenience in the operation of the ship, he carried his point.
The benefits of high bulkheads were clearly demonstrated in the case of the City of Paris and the City of New York, designed by Mr. Biles in 1888. Although these ships were smaller compared to the Titanic, they had their fourteen bulkheads extended one deck higher. Biles established a rule that no doors were to be cut through the bulkheads, and despite strong objections regarding passenger comfort and overall convenience in operating the ship, he stood his ground.

COURTESY OF ENGINEERING
COURTESY OF ENGINEERING
OLYMPIC AND TITANIC 1912
OLYMPIC AND TITANIC 1912
LUSITANIA 1906
Lusitania 1906
GREAT EASTERN 1858
GREAT EASTERN 1858
CAMPANIA 1893
CAMPANIA 1893
PARIS 1868
Paris 1868
A Comparison of Bulkhead Protection in Some Notable Ships
A Comparison of Bulkhead Protection in Some Notable Ships
The wisdom of this construction was demonstrated years later, when, as a result of an accident to her engines, the two largest adjoining compartments of the City of Paris were flooded, at a time when the ship was 150 miles off the coast of Ireland. There was no wireless in those days to send out its call for help, and for three days the ship drifted in a helpless condition. Thanks to her lofty bulkheads, the good ship stood the ordeal and was finally brought into port without the loss of a single passenger.
The wisdom of this construction was shown years later, when, due to an engine accident, the two largest connected compartments of the City of Paris were flooded, while the ship was 150 miles off the coast of Ireland. There was no wireless communication back then to send out a distress signal, and for three days the ship drifted in a helpless state. Thanks to her tall bulkheads, the sturdy ship withstood the ordeal and was eventually brought into port without losing a single passenger.
BULKHEAD SPACING ON NOTABLE SHIPS
BULKHEAD SPACING ON MAJOR SHIPS
NAME | Date of Building |
Registered Length, Feet[1] |
No. of Main W. T. Bulkheads |
Average Length of Compart- ments |
Per cent. of Length |
Titanic | 1911 | 852.5 | 15 | 53 | 6.2 |
Lusitania | 1907 | 762.0 | 16 | 45 | 5.9 |
George Washington | 1908 | 699.0 | 13 | 50 | 7.1 |
Great Eastern | 1854-59 | 680.0 | 9 | 68 | 10.0 |
Carmania | 1905 | 650.0 | 15 | 50 | 7.8 |
Campania | 1893 | 601.0 | 8 | 67 | 11.1 |
New York | 1888 | 517.0 | 14 | 37 | 6.7 |
Alma | 1894 | 270.7 | 11 | 23 | 8.3 |
An interesting study of bulkhead practice in some notable ships is afforded by the table and diagrams which are herewith reproduced by the courtesy of "Engineering." In the matter of height of bulkheads above the water-line, the Great Eastern stands first, followed by the Paris, the Lusitania, the Campania, and the Titanic.
An interesting study of bulkhead practices in some notable ships is provided by the table and diagrams reproduced here with permission from "Engineering." When it comes to the height of bulkheads above the waterline, the Great Eastern ranks first, followed by the Paris, the Lusitania, the Campania, and the Titanic.
CHAPTER V
THE UNSINKABLE GREAT EASTERN OF 1858
The term "unsinkable," as applied to ships, is used throughout the present work in an accommodated sense. There never was but one unsinkable craft, and for that we must go back to the age of primitive man, who doubtless paddled himself across the rivers and lakes upon a roughly fashioned log of wood.
The term "unsinkable," when referring to ships, is used throughout this text in a more flexible way. There has only ever been one truly unsinkable vessel, and for that, we need to look back to the time of early humans, who probably paddled across rivers and lakes on a roughly made wooden log.
In the modern sense, an unsinkable ship is one which cannot be sunk by any of the ordinary accidents of the open sea, such as those due to stress of weather, or to collision with icebergs, derelicts, or some other ship.
In today's terms, an unsinkable ship is one that can't be sunk by any of the typical risks of the open sea, like those caused by severe weather or collisions with icebergs, abandoned vessels, or other ships.
Can such a ship be built?
Can a ship like that be built?
Not only is it feasible to construct vessels of this type to-day; but, as far back as the year 1858, there was launched a magnificent ship, the Great Eastern, in which the provisions against foundering were so admirably worked out that probably she would have survived even the terrific collision which proved the undoing of the Titanic.
Not only is it possible to build ships like this today, but all the way back in 1858, a magnificent ship called the Great Eastern was launched. Its safety features against sinking were so well designed that it probably could have survived even the severe collision that led to the downfall of the Titanic.
The Great Eastern represented the joint labours of the two most distinguished engineers of the middle period of the nineteenth century, I. K. Brunel and John Scott Russell. The former was responsible for the original idea of the ship, and it was he who suggested that it should be built upon the principles adopted in the rectangular, tubular bridge that had recently been built across the Menai Straits. To Scott Russell, as naval architect, were due the lines and dimensions of the ship and the elaborate system of transverse and longitudinal bulkheads.
The Great Eastern was the result of the collaborative efforts of two of the most notable engineers of the mid-nineteenth century, I. K. Brunel and John Scott Russell. Brunel came up with the original concept for the ship and suggested that it be built based on the design principles used in the rectangular, tubular bridge recently constructed over the Menai Straits. Scott Russell, as the naval architect, was responsible for the ship's shape and size, as well as the complex system of transverse and longitudinal bulkheads.
Those were the days when the engineer was supreme. He worked with a free hand; and these two men set out to build a ship which should be not only the largest and strongest, but also the safest and most unsinkable vessel afloat. How they succeeded is shown by the fact, that on one of her voyages to New York, the Great Eastern ran over some submerged rocks off Montauk Point, Long Island, and tore two great rents in her outer skin, whose aggregate area was equivalent to a rupture 10 feet wide and 80 feet long. In spite of this damage, which was probably greater in total area than that suffered by the Titanic, the ship came safely to New York under her own steam.
Those were the days when engineers were in charge. They had the freedom to create, and these two men aimed to build a ship that would be not only the biggest and strongest but also the safest and most unsinkable vessel in the water. Their success is evident from the incident when the Great Eastern hit some hidden rocks near Montauk Point, Long Island, causing two huge gashes in her outer shell, with a total area equivalent to a tear 10 feet wide and 80 feet long. Despite this damage, which was likely more extensive in total area than what the Titanic sustained, the ship made it safely to New York on its own power.

Courtesy of Holmes' "Ancient and Modern Ships"
Courtesy of Holmes' "Ancient and Modern Ships"
Great Eastern, 1858; the Most Completely Protected Passenger Ship Ever Built
Great Eastern, 1858; the Most Fully Protected Passenger Ship Ever Made
There can be no doubt that in undertaking to build a ship of the then unprecedented length of 692 feet, the designers were as much concerned with the question of her strength as with that of her ability to keep afloat in case of under-water damage. But it so happens that the very forms of construction which conduce to strength are favourable also to flotation—a fact which renders all the more reasonable the demand that, in all future passenger-carrying steamships, a return shall be made to the non-sinkable construction of this remarkable ship of over fifty years ago.
There’s no doubt that when they set out to build a ship measuring an unprecedented 692 feet, the designers were just as focused on its strength as they were on its ability to stay afloat in case of underwater damage. However, it turns out that the very construction methods that enhance strength also support flotation—which makes it all the more reasonable to demand that future passenger-carrying steamships return to the unsinkable design of this remarkable ship from over fifty years ago.
Let it not be supposed, however, that Brunel and Russell were insensible to the risks of foundering through under-water damage, or that the fully protected buoyancy of this vessel was accidental rather than the result of careful planning. For in the technical descriptions of the ship, it is stated that the inner skin was carried forward right up to the bow, as a protection against "collision with an iceberg," and it is further stated that the combination of longitudinal and transverse bulkheads afforded such complete subdivision, that "several compartments might be opened to the sea without endangering the ship."
Let’s not assume, however, that Brunel and Russell were unaware of the risks of sinking due to underwater damage, or that the vessel’s fully protected buoyancy was just a coincidence rather than the product of careful planning. In the technical descriptions of the ship, it’s noted that the inner skin extended all the way to the bow to protect against "collisions with an iceberg," and it’s also mentioned that the combination of longitudinal and transverse bulkheads provided such complete subdivision that "several compartments could be opened to the sea without putting the ship in danger."
So remarkable in every respect was the Great Eastern, so admirable a model is she of safe construction, even for the naval architect of to-day, that a somewhat extended description of the construction of the vessel will doubtless be welcome.
So impressive in every way was the Great Eastern, and she serves as an excellent example of safe construction, even for today's shipbuilders, that a more detailed description of the vessel's construction will surely be appreciated.
It was at the close of the year 1851 that Brunel made a study of the problem of building a vessel of sufficient size to carry enough coal to make a round voyage to Australia and back, and at the same time afford comfortable accommodations for an unusually large number of passengers and carry a large amount of freight. With the thoroughness and frank open-mindedness which distinguished the man, he sought for information and advice from every promising quarter. Sir William White is of the opinion that all the leading features of the design, such as the structure, the arrangement of the propelling machinery, and the determination of dimensions, originated with Brunel, who said at the time: "I never embarked on any one thing to which I have so entirely devoted myself and to which I have devoted so much time, thought, and labour; on the success of which I have staked so much reputation, and to which I have so largely committed myself and those who were supposed to place faith in me." Sir William states that, after going carefully through Brunel's notes and reports, his admiration for the remarkable grasp and foresight therein displayed has been greatly increased. "In regard to the provision of ample structural strength with a minimum of weight, the increase of safety by watertight subdivision and cellular double-bottom, the design of propelling machinery and boilers, with a view to economy of coal and great endurance for long-distance steaming; the selection of forms and dimensions likely to minimise resistance and favour good behaviour at sea, Brunel displayed a knowledge of principles such as no other ship designer of that time seems to have possessed." The value of this tribute will be understood when it is borne in mind that Sir William White is the most widely known architect of the day.
It was at the end of 1851 that Brunel began studying how to build a ship large enough to carry enough coal for a round trip to Australia and back, while also providing comfortable accommodations for an unusually high number of passengers and carrying a significant amount of cargo. With the thoroughness and open-mindedness that defined him, he sought information and advice from every promising source. Sir William White believes that all the main features of the design, such as the structure, the arrangement of the propulsion system, and the determination of dimensions, originated with Brunel, who remarked at the time: "I have never thrown myself so completely into a single project, dedicating so much time, thought, and effort to it; I have staked so much of my reputation on its success, and I have so largely committed myself and those who were expected to trust me." Sir William notes that after carefully reviewing Brunel's notes and reports, his admiration for the impressive insight and foresight displayed has only grown. "Regarding the provision of sufficient structural strength with minimal weight, the enhancement of safety through watertight compartments and a cellular double-bottom, the design of propulsion systems and boilers aimed at coal efficiency and endurance for long-distance travel; and the selection of shapes and sizes to reduce resistance and promote good performance at sea, Brunel demonstrated a level of understanding of principles that no other ship designer of that time seems to have matched." The significance of this praise is highlighted by the fact that Sir William White is the most renowned architect of his era.
The principal dimensions of the Great Eastern were as follows:
The main dimensions of the Great Eastern were as follows:
Length between perpendiculars | 680 | feet |
Length on upper deck | 692 | " |
Extreme breadth of hull | 83 | " |
Width over paddle-boxes | 120 | " |
Depth from upper deck to keel | 58 | " |
Draught of water (laden) | 28 | " |
Weight of iron used in construction | 10,000 | tons |
The ship was propelled by two separate engines, driving respectively paddle-wheels and a single propeller. The engines for the paddle-wheels were of the oscillating type. The cylinders were four in number, 74 inches in diameter, by 14-feet stroke, and each one in the finished condition weighed 28 tons. The paddle-wheels were 56 feet in diameter. Steam for these engines was supplied by four, double-ended, tubular boilers, each 17 feet 9 inches long, 17 feet 6 inches wide, and 13 feet 9 inches high, and weighing, with water, 95 tons. Each boiler contained 10 furnaces. The screw engines, which were placed in the aftermost compartment of the machinery spaces, were of the horizontal, opposed type; there were four cylinders, 84 inches in diameter, by 4-feet stroke, and each one, in the finished condition, weighed 39 tons. The propeller shafting, 150 feet in length, weighed 60 tons. The four-bladed propeller was 24 feet in diameter. Steam was supplied to these engines by six tubular boilers of about the same dimensions as those for the paddle-wheel engines. The working pressure was 25 pounds per square inch.
The ship was powered by two separate engines that drove paddle wheels and a single propeller. The engines for the paddle wheels were of the oscillating type. There were four cylinders, each 74 inches in diameter and with a 14-foot stroke, and each finished unit weighed 28 tons. The paddle wheels were 56 feet in diameter. Steam for these engines was generated by four double-ended tubular boilers, each measuring 17 feet 9 inches long, 17 feet 6 inches wide, and 13 feet 9 inches high, with a total weight of 95 tons when filled with water. Each boiler had 10 furnaces. The screw engines, located in the back compartment of the machinery spaces, were of the horizontal opposed type; they had four cylinders, each 84 inches in diameter and with a 4-foot stroke, and each one weighed 39 tons when finished. The propeller shaft, measuring 150 feet in length, weighed 60 tons. The four-bladed propeller was 24 feet in diameter. Steam was provided to these engines by six tubular boilers roughly the same size as those for the paddle wheel engines. The working pressure was 25 pounds per square inch.
![[click for larger image]](images/p077i.jpg)
Length, 692 feet; beam, 83 feet; depth, 58 feet. Subdivision: Double hull; nine main bulkheads, 53 feet high, extending to upper deck, and six sub-bulkheads 35 feet high, extending to lower deck. Two longitudinal bulkheads through machinery spaces.
Length: 692 feet; beam: 83 feet; depth: 58 feet. Subdivision: Double hull; nine main bulkheads, 53 feet high, reaching up to the upper deck, and six sub-bulkheads 35 feet high, reaching down to the lower deck. Two longitudinal bulkheads in the machinery spaces.
Longitudinal Section and Plan of the Great Eastern, 1858
Longitudinal Section and Plan of the Great Eastern, 1858
The estimated speed of the Great Eastern was 15 knots; her best actual performance on an extended voyage was an average speed of 14 knots, which was realised on one of her trips to New York. She was designed to carry 4,000 passengers, namely 800 first, 2,000 second, and 1,200 third class, besides a crew of 400. She had a capacity of 5,000 tons of cargo, and 12,000 tons of coal. When fitted up for the accommodation of troops she could carry 10,000. Fully laden with passengers, cargo, and coal, she displaced, on a draft of 30 feet, about 27,000 tons;—her actual draft was from 26 to 28 feet. The accommodations for passengers would have done credit to one of our modern liners. There were five saloons on the upper, and another five on the lower deck. The uppermost deck afforded two unbroken and spacious promenades, one on each side of the ship, each of which was 20 feet wide and over 600 feet in length.
The estimated speed of the Great Eastern was 15 knots; her best actual performance on an extended journey was an average speed of 14 knots, achieved on one of her trips to New York. She was designed to carry 4,000 passengers: 800 first class, 2,000 second class, and 1,200 third class, along with a crew of 400. She had a cargo capacity of 5,000 tons and could hold 12,000 tons of coal. When set up to accommodate troops, she could carry 10,000. Completely loaded with passengers, cargo, and coal, she displaced about 27,000 tons with a draft of 30 feet; her actual draft ranged from 26 to 28 feet. The passenger accommodations would be impressive even by today’s standards. There were five lounges on the upper deck and another five on the lower deck. The top deck featured two continuous and spacious promenades, one on each side of the ship, each measuring 20 feet wide and over 600 feet long.
Because of the great length of the ship it was decided to launch her sideways,—a disastrous experiment which cost the company dear. The launching ways yielded under the great weight, the ship jammed on the ways, and she had to be laboriously forced into the River Thames, inch by inch, by the aid of powerful hydraulic jacks. The great cost of the launching, which occupied two and a half months' time, caused the failure of the original company, and the ship was sold for $900,000 to a new company, who completed her in 1859. She made several voyages to America; and although in this service she was unprofitable, the great ship proved that she was staunch, eminently seaworthy, and fast for a passenger ship of that period. Although the Great Eastern was never employed on the Australian service, for which she was designed, she was usefully employed in 1865 in laying two of the Atlantic telegraph cables, and, subsequently, in similar service in other parts of the world—a work for which her great strength and size rendered her peculiarly adapted. After serving an inglorious career in the hands of the showman, the Great Eastern was sold for the value of her metal and was broken up in the autumn of 1888.
Because the ship was so large, it was decided to launch her sideways, which turned out to be a costly mistake for the company. The launching ways buckled under her immense weight, causing the ship to get stuck. She had to be painstakingly pushed into the River Thames, little by little, using powerful hydraulic jacks. The high cost of the launching, which took two and a half months, led to the downfall of the original company, and the ship was sold for $900,000 to a new company, who finished her in 1859. She made several trips to America; while she wasn't profitable in this role, the massive ship proved to be sturdy, exceptionally seaworthy, and fast for a passenger ship of that time. Although the Great Eastern was never used in the Australian service for which she was designed, she was effectively employed in 1865 to lay two of the Atlantic telegraph cables and later in similar projects around the world—a job for which her size and strength were particularly suited. After a less-than-glamorous career under a showman, the Great Eastern was sold for her scrap metal value and was dismantled in the fall of 1888.
The financial failure of this ship was not due to any excessive first cost, resulting from the very thorough character of her construction, but rather to certain economic conditions of her time. Traffic across the Atlantic, both freight and passenger, was as yet in its infancy; and even if full cargoes had been available, the loading facilities of those days were so inadequate, that the ship would have been delayed in port for an unconscionable length of time. Furthermore, fuel consumption, in that early stage of development of the steam engine, was excessive, the coal consumed per horsepower per hour being about three and one-half to four pounds, as compared with a modern consumption of from one and a quarter to one and a half pounds per horsepower.
The financial failure of this ship wasn’t due to any excessive initial cost from her very thorough construction, but rather to the economic conditions of her time. Transatlantic traffic, both for freight and passengers, was still in its early stages; and even if there had been enough cargo, the loading facilities back then were so inadequate that the ship would have faced huge delays in port. Moreover, fuel consumption in the early days of the steam engine was high, with coal use at about three and a half to four pounds per horsepower per hour, compared to today’s consumption of about one and a quarter to one and a half pounds per horsepower.
A careful study of the construction of this remarkable vessel establishes the fact that over fifty years ago Brunel and Scott Russell produced in the Great Eastern a ship which stands as a model for all time. Realising, in the first place, how vulnerable is an iron vessel which carries only a single skin, they decided to provide a double skin and construct the ship with two separate hulls, placed one within the other and firmly tied together by a system of continuous longitudinal and lateral web-plates or frames. By reference to the cross-section, published on page 83, it will be seen that the double-skin construction extended entirely around the hull, and was carried up to a continuous plate-iron lower deck, which was from 8 to 10 feet above the water-line, the distance varying with the draft of the ship. The two skins were placed 2 feet 10 inches apart and they were tied together by 34 longitudinal web-members, which ran the entire length of the double hull, and divided the space between the two skins into separate watertight compartments. These were themselves further subdivided by a series of transverse webs which intersected the longitudinal webs. The cellular construction thus provided extended from the aftermost bulkhead right through to the bow, to which it was carried for the purpose of protecting the forward part of the ship against the effect of collision with icebergs, which at that early day were recognised as constituting a serious menace to navigation. The inner skin was not continued aft of the aftermost bulkhead, for the reason that at the stern it would have been unnecessary and somewhat inconvenient.
A close examination of the design of this remarkable ship shows that over fifty years ago, Brunel and Scott Russell created the Great Eastern, a vessel that serves as a timeless model. Understanding how vulnerable an iron ship can be with just a single skin, they opted for a double skin and built the ship with two separate hulls, one inside the other, securely connected by a continuous system of longitudinal and lateral web-plates or frames. Looking at the cross-section published on page 83, you'll see that the double-skin design went all the way around the hull and extended up to a continuous plate-iron lower deck, which was 8 to 10 feet above the water line, varying with the ship's draft. The two skins were 2 feet 10 inches apart and were linked by 34 longitudinal web-members that ran the entire length of the double hull, creating separate watertight compartments between the two skins. These compartments were further divided by a series of transverse webs that crossed the longitudinal webs. This cellular design extended from the rear bulkhead all the way to the bow, intended to protect the front part of the ship from collisions with icebergs, which were already recognized as a significant threat to navigation at that time. The inner skin did not continue behind the last bulkhead because it would have been unnecessary and somewhat impractical at the stern.

TITANIC BUILT 1912
MAURETANIA BUILT 1906
GREAT EASTERN BUILT 1858
TITANIC BUILT 1912
MAURETANIA BUILT 1906
GREAT EASTERN BUILT 1858
Two Extremes in Protection, and a Compromise
Two Extremes in Protection, and a Compromise
The double hull was closed in by a watertight iron deck (the lower deck), which served to entirely separate the boiler- and engine-rooms and the holds from the passenger quarters. Above the lower deck the hull was built with a single skin, which terminated at a flush, continuous, cellular steel deck, corresponding to the shelter deck of modern steamships, which extended unbroken from stem to stern. This deck was an unusually rigid structure. Its upper and lower surfaces were each one inch in thickness, and each consisted of two layers of half-inch plating riveted together. The double deck thus formed was two feet in depth, and the intervening space was intersected by longitudinal girders, the whole construction forming an unusually stiff and strong watertight deck, which was admirably suited to meet the heavy tensional and compressive stresses, to which a ship of the length of the Great Eastern is subjected when driving through head seas.
The double hull was sealed off by a watertight iron deck (the lower deck), which completely separated the boiler and engine rooms from the passenger areas. Above the lower deck, the hull was constructed with a single layer, ending at a smooth, continuous, cellular steel deck, similar to the shelter deck of modern steamships, which extended uninterrupted from front to back. This deck was an exceptionally sturdy structure. Its upper and lower surfaces were each one inch thick, made up of two layers of half-inch plating riveted together. The resulting double deck was two feet deep, with the space in between reinforced by longitudinal girders, creating an unusually stiff and strong watertight deck, perfectly designed to handle the heavy tensile and compressive stresses a ship like the Great Eastern experiences when cutting through head seas.
The watertight subdivision of the Great Eastern was more complete than that of any ship that was ever constructed for the merchant service, more thorough even than that of recent passenger ships which have been designed for use as auxiliary cruisers in time of war. In addition to the great protection afforded by her double hull, she was subdivided by nine transverse bulkheads, which extended from the bottom clear through to the upper deck, or to a height of 30 feet above the water-line. Compare this with the practice followed in the Titanic and in all but a very few of the merchant ships of the present day, whose bulkheads are carried up only from one-third to one-half of that height, and too often terminate at a deck which is not, in the proper sense of the term, watertight.
The watertight division of the Great Eastern was more thorough than any ship ever built for commercial service, even more so than recent passenger ships designed to be used as support cruisers during wartime. Besides the significant protection offered by her double hull, she was divided by nine transverse bulkheads, which extended from the bottom all the way to the upper deck, reaching a height of 30 feet above the waterline. Compare this to the standards used in the Titanic and in almost all present-day merchant ships, whose bulkheads extend only from one-third to one-half that height, often ending at a deck that isn’t truly watertight.
In addition to these main bulkheads, the Great Eastern contained six additional transverse bulkheads, which extended to the iron lower deck. Five of these were contained in the machinery spaces and one was placed aft of the aftermost main bulkhead. The submerged portion of the hull, or rather all that portion of it lying below the lower deck, was thus divided by 15 transverse bulkheads into 16 separate watertight compartments.
In addition to these main bulkheads, the Great Eastern had six extra transverse bulkheads that extended to the iron lower deck. Five of these were located in the machinery spaces, and one was positioned behind the last main bulkhead. The submerged part of the hull, or all of it that lies below the lower deck, was divided by 15 transverse bulkheads into 16 separate watertight compartments.

From an old photograph, taken in 1860
Great Eastern, Lying at Foot of Canal Street, North River, New York
From an old photo taken in 1860
Great Eastern, docked at the end of Canal Street, North River, New York
Not content with this, however, Brunel ran throughout the whole of the machinery and engine spaces two longitudinal bulkheads, which extended from the bottom of the ship to the top deck. A further subdivision consisted of a curved steel roof which separated the boiler-rooms from the coal-bunkers above them. Altogether the hull of the Great Eastern was divided up into between 40 and 50 separate watertight compartments. An excellent structural feature, from which later practice has made a wide departure, was the fact that no doors were cut through the bulkheads below the lower deck.
Not satisfied with this, Brunel installed two long bulkheads running through all the machinery and engine spaces, extending from the bottom of the ship to the top deck. There was also a curved steel roof that separated the boiler rooms from the coal bunkers above. In total, the hull of the Great Eastern was divided into about 40 to 50 separate watertight compartments. A notable structural feature, which later practices have largely ignored, was that no doors were cut through the bulkheads below the lower deck.
Such was the Great Eastern, a marvel in her time and an object lesson, even to-day, in safe and unsinkable construction. That her valuable qualities were not obtained at the cost of extravagance in the use of material is one of the most meritorious features of her design and construction. On this point we cannot do better than quote from the address of Sir William White, delivered when he was President of the Institution of Civil Engineers: "I have most thoroughly investigated the question of the weight absorbed in the structure of the Great Eastern, and my conclusion is that it is considerably less than that of steel-built ships of approximately the same dimensions and of the most recent construction. Of course these vessels are much faster, have more powerful engines, and have superstructures for passenger accommodation towering above the upper deck. These and other features involve additional weight; and the Great Eastern has the advantage of being deeper in relation to her length than the modern ships. After making full allowance for these differences, my conclusion is that the Great Eastern was a relatively lighter structure, although at the time she was built only iron plates of very moderate size were available."
Such was the Great Eastern, a marvel in its time and a lesson, even today, in safe and unsinkable construction. The fact that her valuable qualities were not achieved through excessive use of materials is one of the most commendable aspects of her design and construction. On this point, we can do no better than quote from the address of Sir William White, delivered when he was President of the Institution of Civil Engineers: "I have thoroughly investigated the question of the weight used in the structure of the Great Eastern, and my conclusion is that it is significantly less than that of steel-built ships of approximately the same size and of the most recent construction. Of course, these vessels are much faster, have more powerful engines, and have passenger accommodations that rise above the upper deck. These and other features add extra weight; and the Great Eastern benefits from being deeper in relation to her length than modern ships. After considering these differences, my conclusion is that the Great Eastern was a relatively lighter structure, even though at the time she was built, only iron plates of very moderate size were available."
CHAPTER VI
THE SINKABLE TITANIC
In all the long record of disasters involving the loss of human life there is none which appeals so strongly to the imagination as those which have occurred upon the high seas, and among these the loss of the Titanic stands out preëminent as the most stupendous and heartrending tragedy of them all. The ship itself was not only the latest and largest of those magnificent ocean liners which, because of their size and speed and luxurious appointments, have taken such a strong hold upon the public imagination, but it was popularly believed that because of her huge proportions, and the special precautions which had been taken to render her unsinkable, the Titanic was so far proof against the ordinary accidents of the sea as to survive the severest disaster and bring her passengers safely into port.
In the long history of disasters that have resulted in loss of human life, none captures the imagination quite like those that occurred on the high seas, and among them, the sinking of the Titanic stands out as the most remarkable and heartbreaking tragedy of all. The ship itself was not only the newest and largest of those impressive ocean liners that have captivated the public due to their size, speed, and luxurious features, but it was widely believed that because of its immense size and the specific measures taken to make it unsinkable, the Titanic was practically immune to the usual dangers of the sea, able to withstand even the worst disasters and safely bring its passengers to shore.
The belief that the Titanic stood for the "last word" in naval architecture certainly seemed to be justified by the facts. She was not a contract-built ship in the commonly accepted sense of that term. On the contrary, she was built under a system which conduces to high-class workmanship and eliminates the temptations to cheap work, which must always exist when a contract is secured in the face of keen competition.
The idea that the Titanic represented the pinnacle of naval design definitely seemed to be supported by the facts. She was not built under contract in the usual sense of the term. Instead, she was constructed using a system that promotes high-quality craftsmanship and removes the incentives for cutting corners, which are always present when a contract is won amid fierce competition.
The famous White Star Company have pointed with pride to the fact that the excellence of their ships was due largely to the fact that they had been built in the same shipbuilding yard and under an arrangement which encouraged the builders to embody in the ships the most careful design and workmanship. Under this arrangement, Messrs. Harland & Wolff, of Belfast, build the White Star vessels without entering into any hard and fast agreement as to the price: the only stipulation of this character being that, when the ship is accepted, they shall be paid for the cost of the ship, plus a certain profit, which is commonly believed to be ten per cent.
The well-known White Star Company proudly highlights that the quality of their ships is mainly because they were constructed in the same shipyard, which encouraged the builders to include the best design and craftsmanship. Under this setup, Harland & Wolff from Belfast build the White Star ships without a strict price agreement; the only condition being that, when the ship is accepted, they will be paid for the cost of the ship plus a profit, which is generally thought to be around ten percent.

GREAT EASTERN 1858
FOUR WATERTIGHT COMPARTMENTS
GREAT EASTERN 1858
FOUR WATERPROOF COMPARTMENTS
TITANIC 1912
ONE WATERTIGHT COMPARTMENT
TITANIC 1912
ONE WATERTIGHT SECTION
Titanic shows omission of inner skin, longitudinal bulkheads, and watertight decks. Transverse bulkheads are lower by 20 feet.
Titanic shows the absence of inner skin, longitudinal bulkheads, and watertight decks. Transverse bulkheads are situated 20 feet lower.
Fifty Years' Decline in Safety Construction
Fifty Years of Decreased Safety in Construction
Of the strength of the Titanic and the general high character of her construction there can be no doubt whatever. Not only was she built to the requirements of the Board of Trade and the insurance companies, but, as we have noted, she was constructed by the leading shipbuilding company of the world, under conditions which would inspire them to put into the world's greatest steamship the very best that the long experience and ample facilities of the yard could produce.
Of the strength of the Titanic and the overall quality of her construction, there’s no doubt at all. She wasn’t just built to meet the requirements of the Board of Trade and the insurance companies, but, as we’ve mentioned, she was constructed by the top shipbuilding company in the world, under conditions that would motivate them to incorporate the absolute best that their extensive experience and resources could offer into the world’s greatest steamship.
The principal dimensions of the Titanic, as furnished by her owners, were as follows:
The main measurements of the Titanic, provided by her owners, were as follows:
PARTICULARS OF THE TITANIC
DETAILS OF THE TITANIC
Ft. | Ins. | |
Length over all | 882 | 9 |
Length between perpendiculars | 850 | 0 |
Breadth extreme | 92 | 6 |
Depth moulded to shelter deck | 64 | 3 |
Depth moulded to bridge deck | 73 | 3 |
Total height from keel to navigating bridge | 104 | 0 |
Load draft | 34 | 6 |
Gross tonnage | 45,000 | |
Displacement in tons | 60,000 | |
Indicated horsepower of reciprocating engines | 38,000 | |
Shaft horsepower of turbine engine | 22,000 |
In this connection the following table, giving the dimensions of the most notable steamships, from the Great Eastern of 1858 to the Imperator of 1913, will be of interest. How rapidly the weight (displacement) increases with the length of these large ships, is shown by the fact that, although in length the Titanic is only about 27 per cent. greater than the Great Eastern, in displacement she exceeds her by considerably over 100 per cent.
In this context, the following table, showing the dimensions of the most notable steamships, from the Great Eastern of 1858 to the Imperator of 1913, will be of interest. The rapid increase in weight (displacement) with the length of these large ships is demonstrated by the fact that, although the Titanic is only about 27 percent longer than the Great Eastern, in terms of displacement, she exceeds it by over 100 percent.
PARTICULARS OF NOTED TRANSATLANTIC LINERS
DETAILS OF FAMOUS TRANSATLANTIC LINERS
NAME | Date | Length between Perpendi- culars |
Beam | Plated Depth |
Displace- ment |
Horse- power |
Speed |
Feet | Feet Ins. | Feet Ins. | Tons | Knots | |||
Great Eastern | 1858 | 680 | 83.0 | 58.0 | 27,000 | 7,650 | 14.0 |
City of Paris | 1888 | 528 | 63.0 | 41.9 | 13,000 | 20,700 | 21.8 |
Teutonic | 1890 | 565 | 57.6 | 42.2 | 12,000 | 19,500 | 21.0 |
Campania | 1893 | 600 | 65.0 | 41.6 | 18,000 | 30,000 | 22.01 |
St. Paul | 1895 | 536 | 63.0 | 42.0 | 16,000 | 18,000 | 21.08 |
K. Wilhelm der Grosse | 1897 | 625 | 66.0 | 43.0 | 20,890 | 30,000 | 22.5 |
Oceanic | 1899 | 685 | 68.5 | 49.0 | 28,500 | 27,000 | 20.7 |
Deutschland | 1900 | 663 | 67.0 | 44.0 | 23,600 | 36,000 | 23.5 |
Kaiser Wilhelm II | 1903 | 678 | 72.0 | 52.6 | 26,000 | 38,000 | 23.5 |
Adriatic | 1907 | 709 | 75.6 | 56.9 | 40,800 | 16,000 | 17.0 |
Mauretania | 1907 | 760 | 88.0 | 60.6 | 44,640 | 70,000 | 26.01 |
La France | 1912 | 685 | 75.5 | 52.10 | 27,000 | 45,000 | 23.5 |
Titanic | 1912 | 850 | 92.6 | 64.3 | 60,000 | 60,000 | 22.5 |
Imperator | 1913 | 880 | 96.0 | 62.0 | 65,000 | 70,000 | 23.0 |
The general structure of the Titanic is shown by the midship section, page 83, and the side elevation, page 129. For about 550 feet amidships she contained 8 steel decks, the boat deck, promenade deck, bridge deck, shelter deck, saloon deck, upper deck, middle deck, and lower deck. The highest steel deck that extended continuously throughout the full length of the ship was the shelter deck. For 550 feet amidships the sideplating of the ship was carried up one deck higher to the bridge deck. The moulded or plated depth of the ship to the shelter deck was 64 feet 3 inches and to the bridge deck 73 feet 3 inches. This great depth of over 73 feet, in conjunction with specially heavy steel decks on the bridge and shelter decks, and the doubling of the plating at the bilges, (where the bottom rounds up into the side,) conjoined with the deep and heavy double bottom, served to give the Titanic the necessary strength to resist the bending stresses to which her long hull was subjected, when steaming across the heavy seas of the Atlantic. The doubling of the plating on the bridge and shelter decks served the same purpose as the cellular steel construction which, as mentioned in the previous chapter, was adopted for the upper deck of the Great Eastern.
The general structure of the Titanic is illustrated by the midship section, page 83, and the side elevation, page 129. For about 550 feet in the middle, it had 8 steel decks: the boat deck, promenade deck, bridge deck, shelter deck, saloon deck, upper deck, middle deck, and lower deck. The highest steel deck that extended the full length of the ship was the shelter deck. For 550 feet in the middle, the side plating of the ship went up one deck higher to the bridge deck. The molded or plated depth of the ship to the shelter deck was 64 feet 3 inches, and to the bridge deck, it was 73 feet 3 inches. This significant depth of over 73 feet, along with the specially reinforced steel decks on the bridge and shelter decks and the double plating at the bilges (where the bottom curves into the side), combined with the deep and robust double bottom, provided the Titanic with the strength needed to withstand the bending stresses on her long hull when crossing the rough seas of the Atlantic. The double plating on the bridge and shelter decks served the same purpose as the cellular steel construction that, as mentioned in the previous chapter, was used for the upper deck of the Great Eastern.

Courtesy of the Scientific American
Thanks to Scientific American
Olympic, Sister to Titanic, Reaching New York on Maiden Voyage
Olympic, Sister Ship to Titanic, Arriving in New York on First Voyage
The dimensions of the frames and plating of the hull were determined by the builder's long experience in the construction of large vessels. The cellular double bottom, which extended the full width of the ship, was of unusual depth and strength. Throughout the ship, its depth was 5 feet 3 inches; but in the reciprocating engine-room, it was increased to 6 feet 3 inches. The keel consisted of a single thickness of plating, 1½ inches thick, and a heavy, flat bar, 3 inches in thickness and 19½ inches wide. Generally speaking, the shell plates were 6 feet wide, 30 feet long, and 2½ to 3 tons in weight. The largest of these plates was 36 feet long and weighed 4¼ tons.
The builder's extensive experience in constructing large vessels determined the dimensions of the frames and hull plating. The cellular double bottom, which stretched the full width of the ship, was notably deep and strong. Its depth measured 5 feet 3 inches throughout the ship, but it was increased to 6 feet 3 inches in the reciprocating engine room. The keel was made of a single layer of plating, 1½ inches thick, along with a heavy, flat bar that was 3 inches thick and 19½ inches wide. Generally, the shell plates measured 6 feet wide, 30 feet long, and weighed between 2½ to 3 tons. The largest plate was 36 feet long and weighed 4¼ tons.
Amidships, the framing, which consisted of channel sections 10 inches in depth, was spaced 3 feet apart. Throughout the boiler-room spaces, additional frames, 2½ feet deep, were fitted 9 feet apart, and in the engine- and turbine-rooms, similar deep frames were fitted on every second frame, 6 feet apart. These heavy web-frames extended up to the middle deck, a few feet above the water-line, and added greatly to the strength and stiffness of the hull.
Amidships, the framing, made of channel sections 10 inches deep, was spaced 3 feet apart. Throughout the boiler room areas, extra frames that were 2½ feet deep were placed 9 feet apart, and in the engine and turbine rooms, similar deep frames were installed on every second frame, 6 feet apart. These heavy web frames reached up to the middle deck, a few feet above the water line, and significantly enhanced the strength and rigidity of the hull.
Had the inside plating of the double bottom been carried up the sides and riveted on the inner flanges of these frames, as shown in the sketch on page 107, it would have served the purpose of an inner skin; and when the outer skin of her forward boiler-rooms was ruptured by the iceberg, it would have served to prevent the inflow of water to these two large compartments. Mr. Ismay, the President of the International Mercantile Marine Company, in his testimony at the Senate Investigation, stated that among the improvements, which would be made in the Gigantic, now under construction for the company, would be the addition of an inner skin. Doubtless he had in mind the construction above suggested.
Had the inner plating of the double bottom been extended up the sides and secured to the inner flanges of these frames, as depicted in the sketch on page 107, it would have acted as an inner skin; and when the outer skin of her forward boiler rooms was damaged by the iceberg, it would have helped prevent water from flooding those two large compartments. Mr. Ismay, the President of the International Mercantile Marine Company, during his testimony at the Senate Investigation, mentioned that among the upgrades planned for the Gigantic, which is currently being built for the company, would be the addition of an inner skin. He likely had the above construction in mind.
The 10-inch channel frames extended from the double bottom to the bridge deck, and some of these bars were 66 feet in length and weighed nearly 1 ton apiece. The frames were tied together along the full length of each deck by the deck beams of channel section, which, throughout the middle portion of the ship, were 10 inches deep and weighed as high as 1¼ tons apiece. The transverse stiffness of the framing was assured by stout bracket knees, riveted to the frames and deck beams at each point of connection, and by the 15 watertight bulkheads, which were riveted strongly to the bottom and sides of the ship, and also by 11 non-watertight bulkheads, which formed the inner walls of the coal bunkers on each side of the main bulkheads.
The 10-inch channel frames stretched from the double bottom to the bridge deck, with some of these bars measuring 66 feet long and weighing almost 1 ton each. The frames were connected along the entire length of each deck by the deck beams of channel section, which were 10 inches deep in the middle part of the ship and weighed as much as 1¼ tons each. The framing's transverse stiffness was ensured by sturdy bracket knees, which were riveted to the frames and deck beams at each connection point, along with the 15 watertight bulkheads that were strongly riveted to the bottom and sides of the ship, and the 11 non-watertight bulkheads that formed the inner walls of the coal bunkers on each side of the main bulkheads.
The bridge, shelter, saloon, and upper decks were supported and stiffened by four lines of heavy longitudinal girders, worked in between the beams, which were themselves carried by solid round pillars placed at every third deck beam. In the boiler-rooms, below the middle deck, the load of the superincumbent decks was carried down to the double bottom by means of heavy round pillars.
The bridge, shelter, saloon, and upper decks were supported and strengthened by four lines of heavy longitudinal girders placed between the beams, which were held up by solid round pillars positioned under every third deck beam. In the boiler rooms below the middle deck, the weight of the upper decks was transferred down to the double bottom through heavy round pillars.
Such was the construction of the Titanic; and it will be agreed that, so far as the strength and integrity of the hull were concerned, it was admirably adapted to meet the heavy stresses which are involved in driving so great and heavy a ship through the tempestuous weather of the North Atlantic.
Such was the design of the Titanic; and it’s clear that, in terms of the strength and integrity of the hull, it was perfectly built to handle the heavy stresses involved in navigating such a large and heavy ship through the rough weather of the North Atlantic.
The first sight of such a gigantic vessel as the Titanic produces an impression of solidity and invulnerability, which is not altogether justified by the facts. For, to tell the truth, the modern steamship is a curious compound of strength and fragility. Her strength, as must be evident from the foregoing description of the framing of the Titanic, is enormous, and ample for safety. Her fragility and vulnerability lie in the fact that her framework is overlaid with a relatively thin skin of plating, an inch or so in thickness, which, while amply strong to resist the inward pressure of the water, the impact of the seas, and the tensile and compressive stresses due to the motion of the ship in a seaway, etc., is readily fractured by the blow of a collision.
The first glimpse of such a massive ship as the Titanic gives a feeling of solidity and invincibility, which isn't entirely backed up by reality. Honestly, the modern steamship is a strange mix of strength and fragility. Its strength, as should be clear from the earlier description of the Titanic, is immense and sufficient for safety. However, its fragility and vulnerability come from the fact that its framework is covered with a relatively thin layer of plating, about an inch thick, which, while strong enough to withstand the pressure of the water, the force of the waves, and the stresses from the ship's movement in rough seas, can easily break upon impact during a collision.

The Framing and Some of the Deck Beams of the Imperator, as Seen from Inside the Bow, Before the Outside Plating Was Rivetted on
The framing and some of the deck beams of the Imperator, as seen from inside the bow, before the outer plating was riveted on.
In a previous chapter it was shown that when the Titanic is being driven at a speed of 21 knots, she represents an energy of over 1,000,000 foot-tons. If this enormous energy is arrested, or sought to be arrested, by some rigid obstruction, whether another ship, a rock, or an iceberg, the delicate outside skin will be torn like a sheet of paper.
In a previous chapter, it was shown that when the Titanic is traveling at a speed of 21 knots, she carries an energy of over 1,000,000 foot-tons. If this massive energy is halted, or attempted to be halted, by some solid obstacle, whether it’s another ship, a rock, or an iceberg, the fragile outer shell will tear like a sheet of paper.
It was shown in Chapter IV that protection against flooding of a ship through damage below the water-line is obtained by subdividing the hull into separate watertight compartments, and that, roughly speaking, the degree of protection is proportionate to the extent to which this subdivision is carried. Applying this to the Titanic, we find that she was divided by 15 transverse bulkheads into 16 separate compartments. But, in this connection it must be noted that these bulkheads did not extend through the whole height of the ship to the shelter deck, as they did in the case of the Great Eastern, and therefore it cannot be said that the whole of the interior space of the hull received the benefit of subdivision. As a matter of fact, only about two-thirds of the total cubical space contained below the shelter deck was protected by subdivision. Water, finding its way into the ship above the level of the decks to which the bulkheads were carried, was free to flow the whole length of her from stem to stern. Furthermore, the value of the subdivision below the bulkhead deck depends largely upon the degree to which this deck is made watertight. If the deck is pierced by hatchways, stairways, and other openings, which are not provided with watertight casings and hatch covers, the integrity of the deck is destroyed, and the bulkhead subdivision below loses its value.
It was shown in Chapter IV that protection against a ship flooding due to damage below the waterline is achieved by dividing the hull into separate watertight compartments, and generally speaking, the level of protection is proportional to how extensively this division is implemented. Applying this to the Titanic, we see that it was divided by 15 transverse bulkheads into 16 separate compartments. However, it should be noted that these bulkheads did not extend all the way to the shelter deck, as they did on the Great Eastern, so it can't be said that the entire interior space of the hull benefited from subdivision. In fact, only about two-thirds of the total volume below the shelter deck was protected by this subdivision. Water that entered the ship above the deck levels to which the bulkheads extended was free to flow throughout the ship from bow to stern. Additionally, the effectiveness of the subdivision below the bulkhead deck largely depends on how watertight this deck is made. If the deck has hatchways, stairways, and other openings that aren't fitted with watertight seals and covers, the integrity of the deck is compromised, and the value of the bulkhead subdivision below decreases.
It was largely this most serious defect—the existence of many unprotected openings in the bulkhead deck of the Titanic—that caused her to go down so soon after the collision.
It was mainly this significant flaw—the presence of numerous unprotected openings in the bulkhead deck of the Titanic—that led to her sinking so quickly after the collision.

This Drawing Shows How the Plating of the Inner Bottom of Such a Ship as the Titanic May Be Carried up the Side Frames to Form an Inner Skin
This drawing illustrates how the plating on the inner bottom of a ship like the Titanic can extend up the side frames to create an inner skin.
Referring now to the side elevation of the Titanic on page 129, it will be noted that the only bulkhead which was carried up to the shelter deck was the first, or collision bulkhead. The second bulkhead extended to the saloon deck, and on the after side of this and immediately against it was a spiral stairway for the accommodation of the crew, which led from their quarters down to the floor of the ship. Here the stairway terminated in a fireman's passage, which led aft through the third and fourth bulkheads, and gave access through a watertight door to the foremost boiler-room. The seven bulkheads, from No. 3 to No. 9, extended only to the upper deck, which, at load draft, was only about 10 feet above the water-line. Bulkhead No. 10 was carried up one deck higher to the saloon deck, as were also bulkheads 11, 12, 13, and 14. Bulkhead No. 15 terminated at the upper deck.
Referring now to the side elevation of the Titanic on page 129, you’ll notice that the only bulkhead that went up to the shelter deck was the first, or collision bulkhead. The second bulkhead reached up to the saloon deck, and right behind it was a spiral staircase for the crew, which led from their quarters down to the ship's floor. Here, the stairway ended in a firefighter's passage that led toward the back through the third and fourth bulkheads, providing access through a watertight door to the front boiler room. The seven bulkheads, from No. 3 to No. 9, only extended to the upper deck, which, at full load, was about 10 feet above the waterline. Bulkhead No. 10 was extended one deck higher to the saloon deck, along with bulkheads 11, 12, 13, and 14. Bulkhead No. 15 ended at the upper deck.
Now, it will be asked: what was the factor in the calculations which determined the height of these bulkheads? The answer is to be found in the Board of Trade stipulations, to which reference was made in Chapter IV, page 62. These stipulations establish an imaginary safety line, below which a ship may not sink without danger of foundering. The safety line represents the depth to which a ship will sink when any two adjoining compartments are opened to the sea and therefore flooded. If the two forward compartments are flooded, for instance, the bow may sink with safety, until the water is only three one-hundredths of the depth of the ship, at the side, from the bulkhead deck. If two central compartments are flooded, the ship is supposed to settle with safety until the bulkhead deck at that point is only three one-hundredths of the depth of the side, at that place, above the water.
Now, the question arises: what was the factor in the calculations that determined the height of these bulkheads? The answer lies in the Board of Trade regulations, which were mentioned in Chapter IV, page 62. These regulations set an imaginary safety line, below which a ship cannot sink without the risk of foundering. The safety line indicates the depth to which a ship will submerge when any two adjacent compartments are flooded. For example, if the two forward compartments are flooded, the bow can safely sink until the water level is only three hundredths of the ship's depth at the side, from the bulkhead deck. If two central compartments are flooded, the ship is expected to settle safely until the bulkhead deck at that point is just three hundredths of the side's depth above the water.
The raising of the height of the bulkheads, by one deck, at the engine-room, is due to the operation of this rule; for here the two adjoining compartments, those containing the reciprocating engines and the turbine, are the largest in the ship, and their flooding would sink the ship proportionately lower in the water.
The increase in the height of the bulkheads by one deck in the engine room is a result of this regulation. This is because the two adjacent compartments, which house the reciprocating engines and the turbine, are the largest in the ship, and if they were to flood, it would cause the ship to sit lower in the water.
Now it takes but a glance at the diagrams on page 66 to show that the application of the Board of Trade rule brought the bulkhead line of the Titanic down to a lower level than that of any of the other notable ships shown in comparison with her. It was the low bulkheads, acting in connection with the non-watertight construction of the bulkhead deck, that was largely answerable for the loss of this otherwise very fine ship.
Now, just a quick look at the diagrams on page 66 reveals that the Board of Trade rule applied lowered the bulkhead line of the Titanic to a level lower than that of any other notable ships compared to her. It was the low bulkheads, together with the non-watertight design of the bulkhead deck, that was mainly responsible for the loss of this otherwise impressive ship.

Courtesy of Scientific American
Thanks to Scientific American
Twenty of the Twenty-nine Boilers of the Titanic Assembled, Ready for Placing in the Ship
Twenty of the twenty-nine boilers of the Titanic assembled, ready to be placed in the ship.
Another grave defect in the Titanic was the great size of the individual compartments, coupled with the fact that the only protection against their being flooded was the one-inch plating of the outside skin. If this plating were ruptured or the rivets started along the seams, there was nothing to prevent the flooding of the whole compartment and the entry, at least throughout the middle portion of the ship, of from 4,000 to 6,000 tons of water—this last being the approximate capacity of the huge compartment which contained the two reciprocating engines. Now, if safety lies in minute subdivision, it is evident that in this ship safety was sacrificed to some other considerations. The motive for the plan adopted was the desire to place the coal-bunkers in the most convenient position with regard to the boilers. By reference to the hold plan of the Titanic, page 129, it will be seen that her 29 boilers were arranged transversely to the ship. With the exception of the five in the aftermost compartment, they were "double-ended," with the furnaces facing fore and aft. To facilitate shovelling the coal into the furnaces, the coal-bunkers were placed one on each side of each transverse watertight bulkhead. The coal supply was thus placed immediately back of the firemen, and the work of getting the coal from the bunkers to the furnaces was greatly facilitated. Now, while this was an admirable arrangement for convenience of firing, it was the worst possible plan as far as the safety of the Titanic was concerned; since any damage to the hull admitted water across the whole width of the ship. The alternative plan, which should be made compulsory on all large ocean-going passenger steamers, is the one adopted for the Mauretania, Kaiser Wilhelm II, Imperator, and a few other first-class ships, in which the coal-bunkers are placed at the sides of the ship, where they serve to prevent the flooding of the main boiler-room compartments. It is probable that any one of the ships named would have survived even the terrific collision which sank the Titanic.
Another serious flaw in the Titanic was the large size of the individual compartments, combined with the fact that the only protection against flooding was the one-inch plating of the outer skin. If this plating was damaged or the rivets began to come loose along the seams, there was nothing to stop the entire compartment from flooding and allowing, at least through the middle section of the ship, between 4,000 to 6,000 tons of water to enter—this amount being roughly the capacity of the massive compartment that housed the two reciprocating engines. If safety lies in smaller subdivisions, it’s clear that in this ship, safety was compromised for other reasons. The rationale behind the chosen design was the desire to position the coal bunkers in the most convenient place relative to the boilers. By looking at the hold plan of the Titanic, page 129, you can see that its 29 boilers were arranged across the ship. Except for the five in the last compartment, they were "double-ended," with the furnaces facing both ends. To make it easier to shovel coal into the furnaces, the coal bunkers were placed on either side of each transverse watertight bulkhead. This meant the coal supply was located directly behind the firemen, which greatly simplified the process of moving coal from the bunkers to the furnaces. While this setup was excellent for convenience in fueling, it was the worst possible plan concerning the safety of the Titanic, as any damage to the hull could allow water to flow across the whole width of the ship. The alternative plan, which should be mandatory for all large ocean-going passenger ships, is the one used in the Mauretania, Kaiser Wilhelm II, Imperator, and a few other top-tier vessels, where the coal bunkers are placed at the sides of the ship, helping to prevent flooding of the main boiler room compartments. It’s likely that any of the ships named would have survived even the catastrophic collision that sank the Titanic.
The objection has been raised against longitudinal coal-bunkers, that they are not so conveniently placed for the firemen. A large force of "coal passers" has to be employed in wheeling the coal from the bunkers to the front of the furnaces. This, of course, entails an increased expense of operation.
The issue has been pointed out about longitudinal coal bunkers that they're not very convenient for the firefighters. A large number of "coal passers" have to be hired to move the coal from the bunkers to the furnace front. This, of course, leads to higher operating costs.
The use of transverse coal-bunkers must be regarded as one among many instances, in which the safety of passenger ships is sacrificed to considerations of economy and convenience of operation.
The use of transverse coal-bunkers should be seen as one of many cases where the safety of passenger ships is compromised for the sake of cost-saving and operational convenience.
CHAPTER VII
HOW THE HUGE SHIP SANK
The Titanic, fresh from the builder's hands, sailed from Southampton, Wednesday, April 10, 1912. She reached Cherbourg on the afternoon of the same day, and Queenstown, Ireland, at noon on Thursday. After embarking the mails and passengers, she left for New York, having on board 1,324 passengers and a ship's complement of officers and crew of 899 persons. The passenger list showed that there were 329 first-class, 285 second-class, and 710 third-class passengers.
The Titanic, just out of the shipyard, set sail from Southampton on Wednesday, April 10, 1912. She arrived in Cherbourg later that afternoon and reached Queenstown, Ireland, at noon on Thursday. After taking on mail and passengers, she departed for New York with 1,324 passengers and a crew of 899. The passenger list indicated there were 329 first-class, 285 second-class, and 710 third-class passengers.
The weather throughout the voyage was clear and the sea calm. At noon on the third day out, a wireless message was received from the Baltic, dated Sunday, April 14, which read: "Greek steamship Athinai reports passing icebergs and large quantity of field ice to-day in latitude 41.51 north, longitude 49.52 west." At about 7 P.M. a second warning was received by the Titanic, this time from the Californian, which reported ice about 19 miles to the northward of the track on which the Titanic was steaming. The message read: "Latitude 42.3 north, longitude 49.9 west. Three large bergs five miles to southward of us." Later there was a third message: "Amerika passed two large icebergs in 41.27 north, 50.8 west on the 14th of April." A fourth message, sent by the Californian, reached the ship about an hour before the accident occurred, or about 10.40 o'clock, which said: "We are stopped and surrounded by ice."
The weather during the voyage was clear and the sea was calm. At noon on the third day out, a wireless message was received from the Baltic, dated Sunday, April 14, which said: "Greek steamship Athinai reports passing icebergs and a large amount of field ice today at latitude 41.51 north, longitude 49.52 west." At around 7 P.M., the Titanic got a second warning, this time from the Californian, which reported ice about 19 miles north of the track the Titanic was steaming on. The message read: "Latitude 42.3 north, longitude 49.9 west. Three large icebergs five miles south of us." Later, there was a third message: "Amerika passed two large icebergs at 41.27 north, 50.8 west on April 14." A fourth message, sent by the Californian, reached the ship about an hour before the accident happened, around 10:40, which said: "We are stopped and surrounded by ice."

Copyright by Underwood & Underwood, N. Y.
Copyright by Underwood & Underwood, N.Y.
The Last Photograph of the Titanic, Taken as She Was Leaving Southampton on Her Maiden Voyage
The Last Photo of the Titanic, Captured as She Departed Southampton on Her First Voyage
These wireless warnings prove that the captain of the Titanic knew there was ice to the north, to the south, and immediately ahead of the southerly steamship route on which he was steaming. The evidence shows that Captain Smith remarked to the officer doing duty on the bridge, "If it is in a slight degree hazy we shall have to go very slowly." The officer of the watch instructed the lookouts to "keep a sharp lookout for ice." The night was starlit and the weather exceptionally clear.
These wireless alerts show that the captain of the Titanic knew there was ice to the north, south, and straight ahead of the southern shipping route he was taking. Evidence indicates that Captain Smith told the officer on duty on the bridge, "If it's a bit foggy, we'll need to go really slowly." The officer of the watch instructed the lookouts to "stay on high alert for ice." The night was filled with stars and the weather was unusually clear.
After leaving Queenstown the speed of the Titanic had been gradually increased. The run for the first day was 464 miles, for the second 519 miles, and for the third day, ending at noon Sunday, it was 546 miles. Testimony given before the Court of Inquiry under Lord Mersey, showed that the Chief Engineer had arranged to drive the vessel at full speed for a few hours either on Monday or Tuesday. Twenty-one of the twenty-nine boilers were in use until Sunday night, when three more were "lighted." It is evident that the engines were being gradually speeded up to their maximum revolutions. Both on the bridge and in the engine-room there was a manifest reluctance to allow anything to interfere with the full-speed run of the following day. This is the only possible explanation of the amazing fact that, in spite of successive warnings that a large icefield with bergs of great size was drifting right across the course of the Titanic, fire was put under additional boilers and the speed of the ship increased.
After leaving Queenstown, the speed of the Titanic gradually increased. The distance covered on the first day was 464 miles, 519 miles on the second day, and 546 miles on the third day, ending at noon on Sunday. Testimony given before the Court of Inquiry under Lord Mersey indicated that the Chief Engineer had planned to run the ship at full speed for a few hours either on Monday or Tuesday. Twenty-one of the twenty-nine boilers were in use until Sunday night, when three more were "lit." It’s clear that the engines were being steadily pushed to their maximum revolutions. Both on the bridge and in the engine room, there was a noticeable reluctance to let anything disrupt the full-speed run for the next day. This is the only reasonable explanation for the astonishing fact that, despite repeated warnings about a large icefield with massive icebergs drifting directly across the Titanic's course, more boilers were ignited and the ship's speed was increased.
It was shown in a previous chapter on "The Dangers of the Sea," that one of the greatest risks of high-speed travel across the North Atlantic is a certain spirit of sangfroid which is liable to be begotten of constant familiarity with danger and a continual run of good luck. If familiarity ever bred contempt, surely it must have done so among the captain and officers of the Titanic on that fatal night. One looks in vain for evidence that the situation was regarded as highly critical and calling for the most careful navigation;—calling, surely, for something more than the mere keeping of a good lookout—an imperative duty at all times, whether by day or night. Yet the fate of that ship and her precious freight of human life hung upon the mere chance of sighting an obstruction in time to avoid collision by a quick turn of the helm. The question of hitting or missing was one not of minutes but of seconds. A ship like this, nigh upon a thousand feet in length, makes a wide sweep in turning, even with the helm hard over. At 21 knots the Titanic covered over a third of a mile in a minute's time. Even with her engines reversed she would have surged ahead for a half mile or so before coming to a stop. Should she strike an obstruction at full speed, the blow delivered would equal that of the combined broadsides of two modern dreadnoughts.
It was shown in a previous chapter on "The Dangers of the Sea" that one of the greatest risks of high-speed travel across the North Atlantic is a certain attitude of sangfroid that can come from being constantly surrounded by danger and having a streak of good luck. If familiarity ever bred contempt, it surely must have among the captain and officers of the Titanic on that tragic night. One looks in vain for signs that they saw the situation as highly critical and in need of the utmost careful navigation—requiring, without a doubt, much more than just keeping a good lookout—an essential duty at all times, whether during the day or at night. Yet the fate of that ship and her precious cargo of human lives depended on the mere chance of spotting an obstruction in time to dodge a collision with a quick turn of the wheel. The choice between hitting or missing was one not of minutes but of seconds. A ship like this, nearly a thousand feet long, makes a wide arc when turning, even with the wheel turned fully. At 21 knots, the Titanic covered more than a third of a mile in just one minute. Even with her engines in reverse, she would have continued moving forward for half a mile or so before coming to a stop. If she hit an obstruction at full speed, the impact would be equivalent to the combined firepower of two modern battleships.

Photograph by Underwood & Underwood, N. Y.
Photograph by Underwood & Underwood, New York.
The elimination of swimming pools, squash courts and summer gardens would cover the cost of additional bulkheads and inner skins.
Removing swimming pools, squash courts, and summer gardens would pay for the extra bulkheads and inner walls.
Swimming Pool on the Titanic
Swimming Pool on the Titanic
And so the majestic ship swept swiftly to her doom—a concrete expression of man's age-long struggle to subdue the resistless forces of nature—a pathetic picture both of his power and his impotence. As she sped on under the dim light of the stars, not a soul on board dreamed to what a death-grapple she was coming with the relentless powers of the sea. Latest product of the shipbuilder's art, she was about to brush elbows with another giant of the sea, launched by nature from the frozen shipyards of the north, and she was to reel from the contact stricken to the death like the fragile thing she was!
And so the magnificent ship raced toward her fate—a clear symbol of humanity's long struggle to control the unstoppable forces of nature—a sad reflection of both our strength and our helplessness. As she glided on beneath the faint light of the stars, no one on board had any idea of the deadly encounter she was about to face with the relentless powers of the ocean. The latest creation of shipbuilders, she was about to collide with another giant of the sea, forged by nature in the icy shipyards of the north, and she was destined to be devastated by the impact, struck down like the delicate entity she was!
At 11.46 P.M. the sharp warning came from the lookout: "Iceberg right ahead." Instantly the engines were reversed and the helm was put hard a-starboard. A few seconds earlier and she might have cleared. As it was, she struck an underwater, projecting shelf of the iceberg, and ripped open 200 feet of her plating, from forward of the collision bulkhead to a few feet aft of the bulkhead separating boiler-rooms numbers 5 and 6. It was a death wound! How deeply the iceberg cut into the fabric of the ship will never be known. Probably the first incision was deep and wide, the damage, as the shelf of ice was ground down by contact with the framing and plating of the ship becoming less in area as successive compartments were ruptured.
At 11:46 P.M., the lookout shouted a sharp warning: "Iceberg right ahead." Immediately, the engines were reversed, and the steering was turned hard to starboard. Just a few seconds earlier, and she might have avoided it. Instead, she hit an underwater ledge of the iceberg, tearing open 200 feet of her hull from just ahead of the collision bulkhead to a few feet behind the bulkhead that separated boiler rooms 5 and 6. It was a fatal blow! How severely the iceberg damaged the ship will never be fully known. Likely, the initial cut was deep and wide, and the damage lessened as the ice shelf was ground down by the ship's framing and plating as more compartments were breached.

Courtesy of Scientific American
Thanks to Scientific American
The Titanic Struck a Glancing Blow Against an Under-water Shelf of the Iceberg, Opening Up Five Compartments. Had She Been Provided With a Watertight Deck At or Near the Water Line, the Water Which Entered the Ship Would Have Been Confined Below That Deck, and the Buoyancy of That Portion of the Ship Above Water Would Have Kept Her Afloat. As It Was, the Water Rose Through Openings in the Decks and Destroyed the Reserve Buoyancy
The Titanic hit the iceberg at an angle, causing damage to five compartments. If she had a watertight deck near the water line, the water that entered the ship would have stayed below that deck, allowing the part of the ship above water to remain buoyant and keep her afloat. Instead, the water flowed through openings in the decks and compromised her buoyancy.
Whatever may have been the depth of the injury, it is certain from the evidence that the six forward compartments were opened to the sea. Immediately after the collision the whistling of air, as it issued from the escape pipe of the forepeak tank, indicated that the tank was being filled by an inrush of water. The three following compartments, in which were located the baggage-room and mail-room, were quickly flooded. Leading fireman Barrett, who was in the forward boiler-room, felt the shock of the collision. Immediately afterwards he saw the outer skin of the ship ripped open about two feet above the floor, and a large volume of water came rushing into the ship. He was quick enough to jump through the open door in the bulkhead separating boiler-rooms 6 and 5, before it was released from the bridge. The damage just abaft of this bulkhead admitted water to the forward coal-bunker of room No. 5, which held for a while, but being of non-watertight and rather light construction, must have soon given way; for the same witness testified to a sudden rush of water coming across the floor-plates between the boilers.
No matter how severe the damage was, the evidence clearly shows that the six front compartments were exposed to the ocean. Right after the collision, the sound of air escaping from the forepeak tank indicated that water was flooding in. The next three compartments, which included the baggage and mail rooms, quickly filled with water. Leading fireman Barrett, who was in the forward boiler room, felt the impact of the collision. Shortly after, he noticed the ship’s outer shell torn open about two feet above the floor, with a huge amount of water rushing in. He managed to leap through the open door between boiler-rooms 6 and 5 just before it was sealed off from the bridge. The damage just behind this bulkhead allowed water into the forward coal bunker of room No. 5, which held for a bit, but since it wasn’t watertight and was fairly flimsy, it likely collapsed soon; the same witness reported a sudden surge of water moving across the floor plates between the boilers.
In spite of the frightful extent of the damage, the Titanic, because of the great height to which her plated structure extended above the water-line, and the consequent large amount of reserve buoyancy which she possessed, would probably have remained afloat a great many hours longer than she did, had the deck to which her bulkheads extended been thoroughly watertight. As it was, this deck (upper deck E) was pierced by hatchways and stairways which, as the bow settled deeper and deeper, permitted the water to flow up over the deck and pass aft over the tops of the after bulkheads and so-called watertight compartments. See page 129.
Despite the terrible extent of the damage, the Titanic, due to her high plated structure above the waterline and the significant amount of buoyancy she had, probably would have stayed afloat much longer than she did, if the deck where her bulkheads reached had been completely watertight. However, this deck (upper deck E) was interrupted by hatchways and stairways that, as the bow sank deeper, allowed water to flow over the deck and move backwards over the tops of the aft bulkheads and so-called watertight compartments. See page 129.
Now, it so happened that for the full length of the boiler-rooms there had been constructed on upper deck E what was known as the "working-crew alleyway." On the inboard side of this passage six non-watertight doors opened on to as many iron ladders leading down to the boiler-rooms. Not only were these doors non-watertight, but they consisted of a mere open frame or grating, this construction having been adopted, doubtless, for purposes of ventilation. Unfortunately, although there was a watertight door at the after end of this alleyway, there was none at its forward end. The water which boiled up from the forward flooded compartments, as it flowed aft, poured successively through the open grating of the alleyway doors, flooding the compartments below, one after the other.
Now, it just so happened that along the entire length of the boiler rooms, what was known as the "working-crew alleyway" had been built on upper deck E. On the inboard side of this passage, six non-watertight doors opened onto six iron ladders leading down to the boiler rooms. Not only were these doors non-watertight, but they were simply open frames or gratings; this design was likely chosen for ventilation purposes. Unfortunately, while there was a watertight door at the back end of this alleyway, there was none at the front end. The water that boiled up from the flooded compartments at the front, as it flowed back, poured successively through the open grating of the alleyway doors, flooding the compartments below, one after the other.
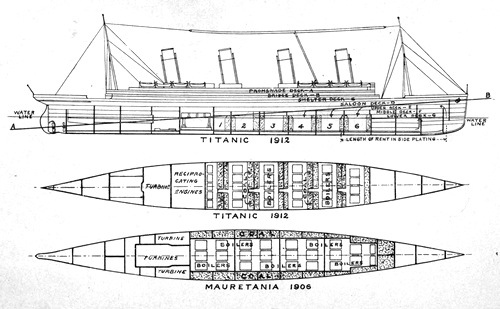
TITANIC 1912
MAURETANIA 1906
TITANIC 1912
MAURETANIA 1906
Titanic: Single skin, 16 compartments; Mauretania: double skin, 34 compartments.
Titanic: Single hull, 16 compartments; Mauretania: double hull, 34 compartments.
Comparison of Subdivision in Two Famous Ships
Comparison of Subdivision in Two Famous Ships
It does not take a technically instructed mind to understand from this that the safety elements of the construction of the Titanic were as faulty above the water-line as they were below it. The absence of an inner skin and the presence of these many openings in her bulkhead deck combined to sink this huge ship, whose reserve buoyancy must have amounted to at least 80,000 tons, in the brief space of two and one-half hours.
It doesn't take a technical expert to see that the safety features of the construction of the Titanic were just as flawed above the waterline as they were below it. The lack of an inner skin and the many openings in her bulkhead deck led to the sinking of this massive ship, which must have had a reserve buoyancy of at least 80,000 tons, in just two and a half hours.
Not until the designer, Mr. Andrews, had made known to the captain that the ship was doomed was the order given to man the lifeboats. The lifeboats, forsooth! Twenty of them in all with a maximum accommodation, if every one were loaded to its full capacity, of something over one thousand, for a ship's company that numbered 2,223 in all. Just here, in this very fatal discrepancy, is to be found proof of the widespread belief that a great ship like the Titanic was practically unsinkable, and therefore in times of dire stress such as this, was well able to act as its own lifeboat until rescuing ships, summoned by wireless, should come to her aid.
Not until the designer, Mr. Andrews, informed the captain that the ship was doomed did the order to man the lifeboats get issued. The lifeboats, indeed! There were twenty in total, with a maximum capacity, if every one was filled to the brim, of just over a thousand, for a crew that totaled 2,223. This glaring difference highlights the widespread belief that a massive ship like the Titanic was practically unsinkable, and therefore, in times of crisis like this, was perfectly capable of serving as its own lifeboat until rescue ships, called by wireless, arrived to help.
The manner of the stricken ship's final plunge to the bottom may be readily gathered from the stories told by the survivors. As compartment after compartment was filled by overflow from the decks above, her bow sank deeper and her stern lifted high in the air, until the ship, buoyed up by her after compartments, swung almost vertically in the water like a gigantic spar buoy. In this unaccustomed position, her engines and boilers, standing out from the floor like brackets from a wall, tore loose from their foundations and crashed down into the forward part of the ship. Probably it was the muffled roar of this falling machinery that caused some of the survivors to imagine that they witnessed the bursting of boilers and the breaking apart of the hull. As a matter of fact, the shell of the Titanic went to the bottom practically intact. One by one the after compartments gave way, until the ship, weighted at her forward end with the wreckage of engine- and boiler-rooms, sank, straight as an arrow, to bury herself deep in the ooze of the Atlantic bottom two miles below. There, for aught we know, with several hundred feet of her hull rising sheer above the ocean floor, she may now be standing, a sublime memorial shaft to the fifteen hundred souls who perished in this unspeakable tragedy!
The way the damaged ship sank to the bottom can be easily understood from the stories shared by the survivors. As water filled each compartment from the decks above, the bow sank lower while the stern lifted high into the air, until the ship, supported by its rear compartments, tilted almost vertically in the water like a giant buoy. In this unusual position, the engines and boilers, protruding from the floor like brackets on a wall, broke free from their mountings and crashed down into the front part of the ship. It’s likely that the loud noise of this falling machinery led some survivors to believe they saw the boilers explode and the hull break apart. In reality, the shell of the Titanic sank to the bottom mostly intact. One by one, the rear compartments gave way, until the ship, heavy at the front with the debris of the engine and boiler rooms, sank straight down like an arrow to bury itself deep in the mud of the Atlantic floor two miles below. There, for all we know, with several hundred feet of its hull looming above the ocean floor, it may now stand as a towering memorial to the fifteen hundred souls who lost their lives in this unimaginable tragedy!

Photograph by Underwood & Underwood, N. Y.
Photograph by Underwood & Underwood, New York.
Smaller rooms would admit of higher bulkheads and better fire-protection.
Smaller rooms would allow for taller bulkheads and improved fire safety.
The Vast Dining-room of the Titanic
The Huge Dining Room of the Titanic
CHAPTER VIII
WARSHIP PROTECTION AGAINST RAMMING, MINES, AND TORPEDOES
The most perfect example of protection by subdivision of the hull into separate compartments is to be found in the warship. It is safe to say that there is no feature of the design to which more careful thought is given by the naval constructor than this. Loss of stability in a naval engagement means the end of the fight so far as the damaged ship is concerned. Nay, even a partial loss of stability, causing the ship to take a heavy list, may throw a ship's batteries entirely out of action, the guns on the high side being so greatly elevated and those on the low side so much depressed, that neither can be effectively trained upon the enemy. Furthermore, deep submergence following the entrance of large quantities of water, will cut down the ship's speed; with the result, either that she must fall out of line or the speed of the whole fleet must be reduced.
The best example of protection through dividing the hull into separate sections is found in warships. It's safe to say there's no aspect of the design that naval engineers consider more carefully than this. Losing stability in a naval battle means the end of the fight for the damaged ship. In fact, even a partial loss of stability, causing the ship to tilt significantly, can render the ship's weapons completely useless, with the guns on the higher side being too elevated and those on the lower side being too depressed to aim effectively at the enemy. Additionally, if large amounts of water flood the ship, it will sink lower in the water, reducing its speed; as a result, either the ship has to fall out of formation or the entire fleet's speed has to slow down.
In the battle of the Sea of Japan it was the bursting of heavy 12-inch shells at or just below the water-line of the leading ship of the Russian line that sent her to the bottom before she had received any serious damage to her main batteries. Later in the fight, several other Russian battleships capsized from the same cause, assisted by the weight of extra supplies of coal which the Russians had stowed on the upper decks above the water-line.
In the battle of the Sea of Japan, it was the bursting of heavy 12-inch shells at or just below the waterline of the leading ship in the Russian line that sent her to the bottom before she sustained any serious damage to her main batteries. Later in the fight, several other Russian battleships capsized for the same reason, compounded by the extra weight of coal supplies that the Russians had stored on the upper decks above the waterline.

Courtesy of U. S. Navy Department
Thanks to U. S. Navy Department
Below the water line this ship is divided into 500 water-tight compartments.
Below the water line, this ship is divided into 500 watertight compartments.
The United States Battleship Kansas
USS Kansas
In the matter of subdivision as a protection against sinking, there is this important difference between the merchant ship and the warship, that, whereas the merchant ship is sunk through accident, the warship is sunk by deliberate intention. The amount of damage done to the former ship will be great or small according to the accidental conditions of the time; but the damage to the warship is the result of a deliberately planned attack, and is wrought by powerful agencies, designed to execute the maximum amount of destruction with every blow delivered.
In terms of subdivision as a safeguard against sinking, there's a significant difference between a merchant ship and a warship. The merchant ship sinks due to accidents, while the warship is sunk on purpose. The damage to the merchant ship can vary in severity depending on the circumstances at the time, but the damage to the warship comes from a carefully planned attack and is inflicted by powerful forces aimed at causing the most destruction with each strike.
A large proportion of the time and money which have been expended in the development of the instruments of naval warfare has been devoted to the design and construction of weapons, whose object is to sink the enemy by destroying the integrity of the submerged portion of the hull. Chief among these weapons are the ram, the torpedo, and the mine. There can be no question that the damage inflicted by the ram of a warship would be far greater, other things being equal, than that inflicted by the bow of a merchant ship. The ram is built especially for its purpose. Not only is it an exceedingly stiff and strong construction; but it is so framed and tied into the bow of the warship, that it will tear open a long, gaping wound in the hull of the enemy before it is broken off or twisted out of place. The bow of the merchant vessel is a relatively frail structure, and many a ship that has been rammed has owed its salvation to the fact that immediately upon contact, the bow of the ramming ship is crumpled up or bent aside, and the depth of penetration into the vessel that is rammed is greatly limited. Furthermore, because of its underwater projection, the ram develops the whole force of the blow beneath the water-line, where the injury will be most fatal. Even more potent than the ram is the torpedo, which of late years has been developed to a point of efficiency in range, speed, and destructive power which has rendered it perhaps the most dreaded of all the weapons of naval warfare. The modern torpedo carries in its head a charge of over 200 pounds of guncotton and has a range of 10,000 yards. Ordinarily, it is set to run at a depth of 10 to 12 feet below the water; and should it get home against the side of a ship, it will strike her well below the armour belt and upon the relatively thin plating of the hull.
A large amount of time and money spent on developing naval warfare instruments has gone into designing and constructing weapons, which aim to sink the enemy by damaging the submerged part of the hull. The main weapons include the ram, torpedo, and mine. There’s no doubt that the damage caused by a warship's ram would be significantly greater, all else being equal, compared to that of a merchant ship's bow. The ram is specifically designed for its function. It’s not only incredibly stiff and strong but is also integrated into the bow of the warship in a way that it creates a large, gaping wound in the enemy's hull before it breaks off or gets displaced. The bow of a merchant vessel is a relatively weak structure, and many ships that have been rammed have been saved because, right upon impact, the rammed ship's bow crumples or bends out of the way, limiting how deeply it penetrates. Additionally, due to its underwater positioning, the ram directs the full force of the impact below the waterline, where the damage is most catastrophic. Even more powerful than the ram is the torpedo, which in recent years has been developed to a remarkable level of efficiency in terms of range, speed, and destructive capability, making it possibly the most feared weapon in naval warfare. The modern torpedo carries over 200 pounds of guncotton in its warhead and has a range of 10,000 yards. Typically, it's set to run at a depth of 10 to 12 feet below the surface; if it hits a ship, it will strike well below the armor belt and on the relatively thin plating of the hull.
Most destructive of all weapons for underwater attack, however, is the mine, which sent to the bottom many a good ship during the Russo-Japanese war. The more deadly effects of the mine, as compared with the torpedo, are due to its heavy charge of high explosive, which sometimes reaches as high as 500 pounds. Contact, even with a mine, is not necessarily fatal; indeed the notable instances in which warships have gone to the bottom immediately upon striking a mine have been due to the fact that the mine exploded immediately under, or in close proximity to the ship's magazines, which, being set off by the shock, tore the ship apart and caused her to go down within a few minutes' time. This was what happened to our own battleship Maine in Havana harbour, and to the Russian battleship Petropavlovsk and the Japanese battleship Hatsuse at Port Arthur.
Most destructive of all underwater attack weapons, though, is the mine, which sank many good ships during the Russo-Japanese War. The mine's more deadly impact compared to the torpedo is due to its heavy charge of high explosive, which can be as much as 500 pounds. Contact with a mine doesn’t always result in destruction; in fact, the notable cases where warships sank right after hitting a mine were because the explosion occurred directly beneath or very close to the ship's magazines, which, triggered by the shock, ripped the ship apart and caused it to sink within a few minutes. This is what happened to our own battleship Maine in Havana harbor, and to the Russian battleship Petropavlovsk and the Japanese battleship Hatsuse at Port Arthur.
Enough has been said to prove that when the naval architect undertakes to build a hull that will be proof against the blow, not merely of one but of several of these terrific weapons, he has set himself a task that may well try his ingenuity to the utmost. Protection by heavy armour is out of the question. The weight would be prohibitive and, indeed, all the side armour that he can put upon the ship is needed at the water-line and above it, as a protection against the armour-piercing, high-explosive shells of the enemy.
Enough has been said to show that when the naval architect takes on the challenge of creating a hull that can withstand the impact of not just one but several of these powerful weapons, he is facing a task that will truly test his creativity. Heavy armor protection is not an option. The weight would be too much, and in fact, all the side armor he can add to the ship is required at the waterline and above it to protect against the enemy's armor-piercing, high-explosive shells.
Heavy armour, then, being out of the question, he has to fall back upon the one method of defense left at his disposal,—minute subdivision into watertight compartments. Associated with this is the placing at the water-line of a heavy steel deck, known as the protective deck, which extends over the whole length and breadth of the hull and is made thoroughly watertight.
Heavy armor, then, being out of the question, he has to rely on the only method of defense available to him—dividing the structure into watertight compartments. Along with this, a heavy steel deck, referred to as the protective deck, is positioned at the waterline. This deck runs the entire length and width of the hull and is designed to be completely watertight.

Courtesy of Robinson's "Naval Construction"
Thanks to Robinson's "Naval Construction"
Hold Plan.
Inboard Profile.
Hold Plan.
Inboard Profile.
These drawings show the minute subdivision of a battleship. Below the protective deck (shown by heavy line) the hull contains 500 water-tight compartments.
These drawings display the detailed breakdown of a battleship. Underneath the protective deck (indicated by the heavy line), the hull has 500 watertight compartments.
Plan and Longitudinal Section of the Battleship Connecticut
Plan and Longitudinal Section of the Battleship Connecticut
The double-skin construction, which was used to such good effect in the Great Eastern, is found in every large warship; and in a battleship of the first class, the two skins are spaced widely apart, a spacing of three or more feet being not unusual. The double-hull construction, with its exceedingly strong framing, is carried up to about water-line level, where it is covered in by the protective deck above referred to. Below the protective deck the interior is subdivided into a number of small compartments by transverse bulkheads, which extend from the inner bottom to the protective deck, and from side to side of the ship. The transverse compartments thus formed are made as small as possible, the largest being those which contain the boilers and engines. Forward and aft of the boiler- and engine-room compartments the transverse bulkheads are spaced much closer together, the uses to which these portions of the ship are put admitting of more minute subdivision.
The double-skin construction, which was used so effectively in the Great Eastern, is found in every large warship; and in a first-class battleship, the two skins are spaced widely apart, with a distance of three feet or more being quite common. The double-hull construction, with its very strong framing, extends up to about waterline level, where it is covered by the protective deck mentioned earlier. Below the protective deck, the interior is divided into several small compartments by transverse bulkheads, which reach from the inner bottom to the protective deck and span from side to side of the ship. The transverse compartments created this way are made as small as possible, with the largest being those that contain the boilers and engines. Forward and aft of the boiler and engine room compartments, the transverse bulkheads are spaced much closer together, as the uses of these sections of the ship allow for more detailed subdivision.
By the courtesy of Naval Constructor R. H. M. Robinson, U.S.N., we reproduce on page 143 from his work "Naval Construction" a hold plan and an inboard profile of a typical battleship,—the Connecticut,—which give a clear impression of the completeness with which the interior is bulkheaded. Although the ship shown is less than one-half as long as the Titanic, she has 27 transverse bulkheads as against the 15 on the larger ship; and all but nine of these are carried clear across the ship from side to side.
Thanks to Naval Constructor R. H. M. Robinson, U.S.N., we share on page 143 from his book "Naval Construction" a hold plan and an inboard profile of a typical battleship—the Connecticut—which clearly shows how thoroughly the interior is compartmentalized. Even though the ship is less than half the length of the Titanic, it features 27 transverse bulkheads compared to the 15 on the larger vessel; and almost all these are built straight across the ship from side to side.
Equally complete is the system of longitudinal bulkheads. Most important of these is a central bulkhead, placed on the line of the keel, and running from stem to stern. On each side of this and extending the full length of the machinery spaces, is another bulkhead, which forms the inner wall of the coal-bunkers. Forward and aft of the machinery spaces are other longitudinal bulkheads, which form the fore-and-aft walls of the handling-rooms and ammunition-rooms.
Equally comprehensive is the system of longitudinal bulkheads. The most important one is a central bulkhead, located along the centerline of the keel, running from the front to the back of the vessel. On each side of this bulkhead, extending the entire length of the engine spaces, is another bulkhead that forms the inner wall of the coal bunkers. In front of and behind the engine spaces are additional longitudinal bulkheads, which create the front and back walls of the handling rooms and ammunition rooms.
To appreciate the completeness of the subdivision, we must look at the inboard profile and note that the spaces forward and aft of the engine- and boiler-rooms are further subdivided, in horizontal planes, by several steel, watertight decks or "flats," as they are called. Including the compartments enclosed between the walls of the double hull, the whole interior of the battleship Connecticut, below the protective deck, is divided up into as many as 500 separate and perfectly watertight compartments.
To understand how well the subdivision is designed, we need to examine the interior layout and note that the areas in front of and behind the engine and boiler rooms are further divided, horizontally, by several steel, watertight decks or "flats," as they're called. Including the spaces created between the walls of the double hull, the entire interior of the battleship Connecticut, below the protective deck, is divided into as many as 500 separate and completely watertight compartments.
Moreover, in some of the latest battleships of the dreadnought type the practice has been followed of permitting no doors of any description to be cut through the bulkheads below the water-line. Access from one compartment to another can be had only by way of the decks above. Furthermore, all the openings through the protective deck are provided with strong watertight hatches or, as in the case of the openings for the smoke stacks, ammunition-hoists, and ventilators, they are enclosed by watertight steel casings, extending to the upper decks, far above the water-line.
Moreover, in some of the latest battleships of the dreadnought type, they have adopted the practice of not allowing any doors to be cut through the bulkheads below the waterline. Access from one compartment to another can only be made through the decks above. Additionally, all openings through the protective deck are fitted with strong watertight hatches or, in the case of the openings for the smokestacks, ammunition hoists, and ventilators, they are enclosed by watertight steel casings that extend to the upper decks, well above the waterline.
In the later warships, further protection is afforded by constructing the first deck above the protective deck of heavy steel plating and making it thoroughly watertight, every opening in this deck, such as those for stairways, being provided with watertight steel hatches. This deck, also, is thoroughly subdivided by bulkheads and provided with watertight doors.
In the later warships, additional protection is provided by building the first deck above the protective deck of heavy steel plating and making it fully watertight. Every opening in this deck, like those for stairways, is equipped with watertight steel hatches. This deck is also completely divided by bulkheads and equipped with watertight doors.
It sounds like a truism to say that a watertight bulkhead must be watertight; yet it is a fact that only in the navy are the proper precautions taken to test the bulkheads and make sure that they will not leak when they are subjected to heavy water pressure. Before a ship is accepted by the government, every compartment is tested by filling it with water and placing it under the maximum pressure to which it would be subjected if the ship were deeply submerged. If any leaks are observed in the bulkheads, decks, etc., they are carefully caulked up, and the test is repeated until the bulkhead is absolutely tight.
It may seem obvious to say that a watertight bulkhead has to be watertight; however, it's true that only in the navy are the right steps taken to test the bulkheads and ensure they won't leak under heavy water pressure. Before the government accepts a ship, every compartment is tested by filling it with water and putting it under the maximum pressure it would face if the ship were deeply submerged. If any leaks are found in the bulkheads, decks, etc., they are carefully sealed, and the test is done again until the bulkhead is completely tight.
Now, here is a practice which should be made compulsory in the construction of all passenger-carrying steamships. Only by filling a compartment with water is it possible to determine whether that compartment is watertight. To send an important ship to sea without testing her bulkheads is an invitation to disaster. The amount of water that may find its way through a newly-constructed bulkhead is something astonishing; for although the leakage along any particular joint or seam of the plating may be relatively small, the aggregate amount will be surprisingly large.
Now, this is a practice that should be mandatory in building all passenger-carrying ships. The only way to find out if a compartment is watertight is to fill it with water. Sending an important ship out to sea without testing its bulkheads is asking for trouble. The amount of water that can seep through a newly-built bulkhead is quite shocking; even though the leakage at any specific joint or seam might be relatively small, the total amount will be impressively large.

Between the boiler rooms and the sea are four, separate, watertight walls of steel. The whole is covered in by a 3-inch watertight steel deck.
Between the boiler rooms and the sea are four separate, watertight steel walls. The entire structure is topped with a 3-inch watertight steel deck.
Midship Section of a Battleship
Midship Section of a Ship
Let us now pass on to consider the actual efficiency of the watertight subdivision as thus so carefully worked out in the modern warship. Thanks to the Russo-Japanese war, which afforded a supreme test of the underwater protection of ships, the value of the present methods of construction has been proved to an absolute demonstration.
The following facts, which, were given to the writer by Captain (now Admiral) von Essen of the Russian Navy, at the close of the Russo-Japanese war, and were published in the "Scientific American," serve to show what great powers of resistance are conferred on a warship by the system of subdivision above described. The story of the repeated damage inflicted and the method of extemporised repairs adopted, is so full of interest that it is given in full:
The following facts, given to the writer by Captain (now Admiral) von Essen of the Russian Navy at the end of the Russo-Japanese war, were published in the "Scientific American." They demonstrate the significant ability of a warship to withstand damage due to the subdivision system mentioned earlier. The account of the repeated damage sustained and the improvised repairs made is so intriguing that it is presented in full:
"Immediately after the disaster of the night of February 8th," when the Japanese, in a surprise attack, torpedoed several of the Russian ships, "the cruiser Pallada was floated into drydock, and the battleships Czarevitch and Retvizan were taken into the inner harbour, and repairs executed by means of caissons of timber, built around the gaping holes which had been blown into their hulls by torpedoes. The repairs to the Pallada were completed early in April, and about the 20th of June the Czarevitch and Retvizan were also in condition to take the sea. On the 13th of April, during the sortie in which the Petropavlovsk was sunk with Admiral Makaroff on board, the battleship Pobieda, in returning to the harbour, struck a contact mine, and was heavily damaged. Similar repairs were executed, and this ship was able to take her station in the line in the great sortie of August 10.
"Right after the disaster on the night of February 8th," when the Japanese launched a surprise attack and torpedoed several Russian ships, "the cruiser Pallada was brought into dry dock, and the battleships Czarevitch and Retvizan were taken into the inner harbor, and repairs were carried out using timber caissons built around the large holes blown into their hulls by torpedoes. The repairs for the Pallada were finished by early April, and around June 20th, the Czarevitch and Retvizan were also ready to head back to sea. On April 13th, during the sortie that led to the sinking of the Petropavlovsk with Admiral Makaroff on board, the battleship Pobieda, while returning to the harbor, hit a contact mine and was severely damaged. Similar repairs were made, and this ship was able to take her place in line during the major sortie on August 10."
"On June 23 Captain von Essen's ship, the Sevastopol, was sent outside the harbour to drive off several Japanese cruisers that were shelling the line of fortifications to the east of Port Arthur. This she accomplished; but in returning she struck a Japanese mine, which blew in about 400 square feet on the starboard side, abaft the foremast, at a depth of about 7 feet below the water-line. The rent was from 7 to 10 feet in depth and 35 to 40 feet in length. The frames, ten in all, were bent inward, or torn entirely apart, and the plating was blown bodily into the ship. She was taken into the inner harbour, where the injured portion of the hull was enclosed by a timber caisson in the manner shown in the engravings on page 155. The caisson—a rectangular, three-sided chamber—was built of 9-in. by 9-in. timbers, tongued and grooved and carefully dovetailed. The floor of the caisson abutted against the bilge keel. The outer wall, which was at a distance of about 10 feet from the hull, had a total depth of about 34 feet, the total length of the caisson being about 75 feet. Knee-bracing of heavy timbers was worked in between the floor and the walls, and the construction was stiffened by heavy, diagonal bolts, which passed through from floor to outside wall, as shown in the drawing. Watertight contact between the edge of the caisson and the hull of the ship was secured by the use of hemp packing covered with canvas. The whole of the outside of the caisson was covered with canvas, and upon this was laid a heavy coating of hot tar. The caisson was then floated into position and drawn up snugly against the side of the ship by means of cables, some of which passed underneath the ship and were drawn tight on the port side, while others were attached to the top edge of the caisson and led across to steam winches on deck. After the water had been pumped out, the hydraulic pressure served to hold the caisson snugly against the hull. The damaged plating and broken frames were then cut away; new frames were built into the ship, the plating was riveted on, and the vessel was restored to first-class condition without entering drydock.
On June 23, Captain von Essen's ship, the Sevastopol, was sent out of the harbor to drive away several Japanese cruisers that were bombarding the fortifications east of Port Arthur. This was successful; however, on the return journey, the ship hit a Japanese mine, which blew out around 400 square feet on the starboard side, behind the foremast, about 7 feet below the waterline. The damage extended from 7 to 10 feet in depth and 35 to 40 feet in length. Ten frames were bent inward or torn apart, and the plating was completely blown into the ship. She was taken into the inner harbor, where the damaged part of the hull was enclosed by a timber caisson, as shown in the engravings on page 155. The caisson—a rectangular, three-sided chamber—was constructed from 9-inch by 9-inch timbers, carefully fitted together with tongue and groove joints and reinforced with dovetailing. The floor of the caisson extended to meet the bilge keel. The outer wall, about 10 feet away from the hull, was approximately 34 feet deep, with the total length of the caisson being about 75 feet. Heavy timber knee-bracing was added between the floor and the walls, and the structure was strengthened with large diagonal bolts that connected the floor to the outer wall, as shown in the drawing. A watertight seal between the edge of the caisson and the hull was achieved with hemp packing covered in canvas. The entire exterior of the caisson was wrapped in canvas, and then a thick layer of hot tar was applied. The caisson was floated into position and pulled tightly against the side of the ship using cables, some of which went under the ship and were tightened on the port side, while others were connected to the top edge of the caisson and led to steam winches on deck. Once the water was pumped out, the hydraulic pressure helped hold the caisson firmly against the hull. The damaged plating and broken frames were removed; new frames were installed in the ship, the plating was riveted back on, and the vessel was returned to first-class condition without needing to go into drydock.


The battleship Sevastopol was twice struck by a mine; but she remained afloat and was repaired by the use of caissons without entering dry dock.
The battleship Sevastopol was hit by a mine twice; however, it stayed afloat and was repaired using caissons instead of going into dry dock.
Safety Lies in Subdivision
Safety Is in Subdivision
"On September the 20th, during operations outside the harbour, the Sevastopol again struck a mine, and by a curious coincidence she was damaged in the exact spot where she received her first injury. This time, however, the mine was much larger and it was estimated to have contained fully 400 pounds of high explosive. The shock was terrific and the area of the injury was fully 700 square feet. The ship immediately took a heavy list to starboard, which was corrected by admitting water to compartments on the port side. She was brought back into the harbour, and a repair caisson was again applied. The repairing of this damage was, of course, a longer job. Moreover, it was done at a time when the Japanese 11-inch mortar batteries were getting the range and making frequent hits. One 11-inch shell struck the bridge just above the caisson and, when it burst, a shower of heavy fragments tore through the outer wall of the caisson, letting in the water and necessitating extensive repairs. Nevertheless, the Sevastopol was again put in seaworthy condition, this time the repairs taking about two and one-half months' time. During the eleven months of the siege of Port Arthur five big repair jobs of the magnitude above described were completed, and over one dozen perforations of the hull below water, due to heavy projectiles, were repaired, either in drydock or by the caisson method."
"On September 20th, during operations outside the harbor, the Sevastopol struck a mine again, and by a strange coincidence, it was damaged in the exact same spot as her first injury. This time, however, the mine was much larger, containing an estimated 400 pounds of high explosive. The impact was massive, affecting an area of about 700 square feet. The ship immediately listed heavily to starboard, which was corrected by letting in water to compartments on the port side. She was brought back into the harbor, and a repair caisson was used once more. Fixing this damage, of course, took longer. Furthermore, it occurred while the Japanese 11-inch mortar batteries were zeroing in and making frequent hits. One 11-inch shell hit the bridge just above the caisson, and when it exploded, it sent a shower of heavy fragments through the outer wall of the caisson, flooding it and requiring extensive repairs. Nevertheless, the Sevastopol was once again made seaworthy, with repairs taking about two and a half months. During the eleven months of the siege of Port Arthur, five major repair jobs of this nature were completed, along with over a dozen penetrations of the hull below the waterline, due to heavy projectiles, which were repaired either in dry dock or using the caisson method."
Now, when it is remembered that the Sevastopol was not a new ship, and that her internal subdivision was not nearly so complete as that which is found in the most modern battleships, it will be realised how effective are properly built bulkheads and thoroughly watertight compartments against even the most extensive injury to the outer shell of a ship. It is claimed for the latest battleships of the dreadnought type, built for the United States Navy, that they would remain afloat, even after having been struck by three or four torpedoes.
Now, considering that the Sevastopol wasn't a new ship and her internal design wasn't nearly as advanced as what's found in the latest battleships, it's clear how effective well-built bulkheads and completely watertight compartments can be against even severe damage to a ship's outer shell. The latest dreadnought-type battleships built for the United States Navy are said to stay afloat even after being hit by three or four torpedoes.
Now, it is inexpedient to build merchant ships with such an elaborate system of watertight compartments as that described in this chapter. Considerations of cost and convenience of operation render this impossible; but it is entirely possible to incorporate in the large passenger steamers a sufficient degree of protection of this character to render them proof against sinking by the accidents of collision, whether with another ship, a derelict, or even with the dreaded iceberg. The manner in which the problem has been worked out in several of the most noted passenger steamers of the present day is reserved for discussion in the following chapter.
Now, it's not practical to build merchant ships with such a complex system of watertight compartments as described in this chapter. Factors like cost and ease of operation make this unfeasible; however, it's definitely possible to include a sufficient level of protection in large passenger steamers to make them resistant to sinking from collisions, whether with another ship, a derelict, or even the feared iceberg. The way this issue has been addressed in several of today's most famous passenger steamers will be discussed in the next chapter.

This ship has twenty-four compartments below the water line. Fire-bulkheads protect passenger decks.
This ship has twenty-four compartments below the waterline. Fire bulkheads protect the passenger decks.
The 65,000-Ton, 23-Knot Imperator—Largest Ship Afloat
The 65,000-ton, 23-knot Imperator—Largest Ship on the Water
CHAPTER IX
WARSHIP PROTECTION APPLIED TO CERTAIN OCEAN LINERS
It was shown in the previous chapter that the most completely protected vessel, so far as its flotation is concerned, is the warship, and plans were given of a battleship whose hull below the water-line was subdivided into no less than five hundred separate watertight compartments. Facts were cited from the naval operations in and around the harbour of Port Arthur, which prove that the battleship is capable of sustaining an enormous amount of injury below the water-line without going to the bottom.
It was demonstrated in the previous chapter that the most secure vessel, in terms of staying afloat, is the warship. Plans were provided for a battleship whose hull below the waterline was divided into no less than five hundred separate watertight compartments. Examples were mentioned from naval operations in and around the harbor of Port Arthur, showing that the battleship can withstand significant damage below the waterline without sinking.
Now, if it were possible to apply subdivision to the large ocean liners on the liberal scale on which it is worked out in ships of war, it would not be going too far to say that they would be absolutely unsinkable by any of the usual accidents of collision. The 60,000-ton Titanic, were she subdivided as minutely as the warship shown on page 143, would contain at least 1,500 separate compartments below her lower deck, and under these conditions even the long rent which was torn in her plating would have done no more than set her down slightly by the head. Her pumps would have taken care of the leakage of water through the bulkheads, and the ship would have come into New York harbour under her own steam.
Now, if we could apply subdivision to large ocean liners on the same scale as it's done in warships, it wouldn't be an exaggeration to say they would be practically unsinkable from any typical collision incidents. The 60,000-ton Titanic, if subdivided as finely as the warship depicted on page 143, would have at least 1,500 separate compartments below her lower deck, and with that setup, even the significant damage caused by a long tear in her hull would have only made her slightly bow-heavy. Her pumps would have managed the water leakage through the bulkheads, and the ship would have arrived in New York harbor under her own power.
But a warship and a passenger ship are two very different propositions. The one, being designed to resist the attack of an implacable enemy, who is using every weapon that the ingenuity of man can devise to effect its destruction, is built with little if any regard to the cost. The other, built as a commercial proposition for the purpose of earning reasonable dividends for its owners, and exposed only to such risks of damage as are incidental to ocean transportation, is constructed as economically as reasonable considerations of strength and safety may permit.
But a warship and a passenger ship are two completely different things. A warship is designed to withstand attacks from a relentless enemy who will use every weapon imaginable to destroy it, so it's built without much concern for cost. On the other hand, a passenger ship is designed as a commercial venture to earn reasonable profits for its owners and only faces risks typically associated with ocean travel, so it's constructed as economically as practical considerations of strength and safety allow.
Another important limitation which renders it impossible to give a passenger ship the elaborate subdivision of a warship, is the necessity of providing large cargo spaces and wide hatchways for the convenient handling and stowage of the freight, upon which a large proportion of the passenger-carrying vessels chiefly depend for their revenue.
Another important limitation that makes it impossible to give a passenger ship the complex subdivision of a warship is the need to provide large cargo spaces and wide hatchways for the easy handling and storage of the freight, which a significant portion of the passenger-carrying vessels mainly rely on for their revenue.

Courtesy of Scientific American
Thanks to Scientific American
Longitudinal bulkheads form an inner skin through machinery spaces. Transverse bulkheads extend two decks (20 feet) above water line, the height increasing towards the ends.
Longitudinal bulkheads create an inner structure within the machinery areas. Transverse bulkheads rise two decks (20 feet) above the water line, with the height increasing towards the ends.
Longitudinal Section and Plan of the Imperator
Longitudinal Section and Plan of the Imperator
On the other hand, the main features of warship protection may be so applied to the large merchant ship as to render her as proof against collision with icebergs, derelicts, or with other vessels, as the warship is against the blow of the ram, the mine, or the torpedo. And the merchant ship of the size of our largest ocean liners has the great advantage over the warship (provided that the average size of her compartments be not too greatly increased) that her great size is in itself a safeguard against sinking.
On the other hand, the main features of warship protection can be adapted for large merchant ships, making them resistant to collisions with icebergs, derelicts, or other vessels, just like warships are protected against rams, mines, or torpedoes. Additionally, a merchant ship the size of our largest ocean liners has a significant advantage over a warship (as long as the average size of its compartments isn’t too dramatically increased) because its large size inherently provides greater safety against sinking.
By way of showing what can be done in applying warship principles of subdivision to merchant vessels, we shall consider in some detail three notable ships, the Mauretania, the Kronprinzessin Cecilie, and the recently launched Imperator.
By demonstrating how warship design principles can be applied to cargo ships, we will take a closer look at three significant vessels: the Mauretania, the Kronprinzessin Cecilie, and the newly launched Imperator.
The Mauretania and her sister, the Lusitania, were built under an agreement with the British Government, who stipulated that they would provide a sum sufficient to pay for the new vessels not to exceed $13,000,000, secured on debentures at 2¾ per cent. interest. The two ships were to be of large size and capable of maintaining a minimum average ocean speed of 24½ knots in moderate weather. The government also agreed that if the ships fulfilled these conditions, the Cunard Company was to be paid annually $750,000.00. In return for this extremely liberal assistance, the Cunard Company agreed to employ them in the British mail-carrying service; to so construct them that they would be available for use as auxiliary cruisers; and to hold them at the instant service of the government in case of war. In addition to holding the ships at the service of the government, it was agreed that all the officers and three-fourths of the crew should be British subjects, and that a large proportion should belong to the Royal Naval Reserve. The ships were thus to be utilised as a training school for officers and seamen, and with this point in view a record of the personnel was to be made each month.
The Mauretania and her sister ship, the Lusitania, were constructed under a deal with the British Government, which specified that they would provide enough funds to cover the cost of the new ships, not exceeding $13,000,000, secured by bonds at an interest rate of 2¾ percent. The two ships were designed to be large and capable of maintaining a minimum average ocean speed of 24½ knots in moderate weather. The government also committed to paying the Cunard Company $750,000 annually if the ships met these requirements. In exchange for this generous support, the Cunard Company agreed to operate them in the British mail-carrying service; to ensure they were built to be used as auxiliary cruisers; and to keep them on standby for the government in wartime. Additionally, it was agreed that all the officers and three-quarters of the crew would be British citizens, with a significant portion belonging to the Royal Naval Reserve. The ships were also to serve as a training ground for officers and sailors, and to facilitate this, a record of the personnel would be maintained each month.
The particulars of these two ships as finally constructed are as follows: Length over all 790 feet; beam, 88 feet; displacement, 46,000 tons; and horsepower, 70,000. Both vessels greatly exceeded the contract speed of 24½ knots, the Lusitania having maintained over 25½ knots and the Mauretania 26 knots for the whole run across the Atlantic.
The details of these two ships as they were ultimately built are as follows: Length overall 790 feet; beam, 88 feet; displacement, 46,000 tons; and horsepower, 70,000. Both vessels significantly surpassed the contract speed of 24½ knots, with the Lusitania maintaining over 25½ knots and the Mauretania averaging 26 knots for the entire journey across the Atlantic.

The Rotor, or Rotating Element, of One of the Low-pressure Turbines of the Imperator. Diameter Over Tips of Blades is 18 Feet
The rotor, or rotating part, of one of the low-pressure turbines of the Imperator. The diameter over the tips of the blades is 18 feet.
The purpose of the present chapter is to show how successfully the methods of underwater protection employed in naval ships may be applied to passenger ships of the first class; and the Mauretania is given first consideration, for the reason that she is the best example afloat to-day of a merchant ship fully protected against sinking by collision. The protective elements may be summed up as consisting of multiple subdivision, associated with a complete inner skin and a watertight steel deck, answering to the heavy protective deck at the water-line of the warship. By reference to the hold plan on page 129 it will be noticed that she is subdivided by 22 transverse bulkheads, 12 of which extend entirely across the ship and 10 from the side inboard to the longitudinal bulkheads. The space devoted to the turbine engines is subdivided by two lines of longitudinal bulkheading, and the compartment aft of the engine-room spaces is divided by a longitudinal bulkhead placed upon the axis of the ship. Altogether there are 34 separate watertight compartments below the water-line. The most important feature of the subdivision is the two lines of longitudinal bulkheads, which extend each side of the boiler-rooms and serve the double purpose of providing watertight bunker compartments and protecting the large boiler-room compartments from being flooded, in the event of damage to the outer skin of the ship. The main engine-room, containing the low-pressure turbines, is similarly protected against flooding.
The goal of this chapter is to demonstrate how the underwater protection methods used in naval ships can also be applied to first-class passenger ships. The Mauretania is highlighted first because it is currently the best example of a merchant ship that is fully protected against sinking from collisions. The protective features can be summarized as consisting of multiple subdivisions, along with a complete inner skin and a watertight steel deck, similar to the heavy protective deck at the waterline of a warship. According to the hold plan on page 129, you'll see that the ship is subdivided by 22 transverse bulkheads, with 12 extending completely across the ship and 10 running from the sides inward to the longitudinal bulkheads. The space for the turbine engines is divided by two lines of longitudinal bulkheads, and the compartment behind the engine room is split by a longitudinal bulkhead located along the ship's axis. In total, there are 34 separate watertight compartments below the waterline. The most critical feature of this subdivision is the two lines of longitudinal bulkheads that run on each side of the boiler rooms, serving both as watertight bunker compartments and protecting the large boiler-room compartments from flooding if the outer skin of the ship is damaged. The main engine room, which contains the low-pressure turbines, is similarly protected from flooding.
Now, all of these bulkheads are carried up to a watertight connection with the upper deck, which, amidships, is over two decks, or say about 20 feet above the water-line, the exception being the first or collision bulkhead, which extends to the shelter deck. A most important feature of the protection, borrowed from warship practice, is that the lower deck, which, amidships, is located at about the water-line, is built of extra heavy plating, and is furnished with strong watertight hatches. It thus serves the purpose of a protective deck, and water, which flooded any compartment lying below the water-line, would be restrained by this deck from finding its way through to the decks above. The Mauretania, therefore, could sustain an enormous amount of damage below the water-line without foundering. It is our belief that she would have survived the disaster which sank the Titanic. The first three compartments would have been flooded, it is true, but the water would have been restrained from her large forward boiler-compartment by the "inner skin" of the starboard bunkers. Furthermore, the watertight hatches of her lower, or protective, deck would have prevented that upward flow of water on to the decks above, which proved so fatal to the Titanic.
Now, all of these bulkheads are raised to form a watertight connection with the upper deck, which is located in the middle of the ship and is over two decks high, or about 20 feet above the waterline. The only exception is the first or collision bulkhead, which goes up to the shelter deck. A crucial feature of this protection, adapted from naval practices, is that the lower deck, situated in the middle of the ship at about the waterline, is made of extra heavy plating and equipped with strong watertight hatches. This deck acts as a protective barrier, so if water floods any compartment below the waterline, this deck will hold it back from flowing up to the decks above. The Mauretania could, therefore, withstand a significant amount of damage below the waterline without sinking. We believe she would have survived the disaster that sank the Titanic. It's true that the first three compartments would have been flooded, but the water would have been kept from reaching her large forward boiler compartment by the "inner skin" of the starboard bunkers. Additionally, the watertight hatches of her lower or protective deck would have stopped the upward flow of water to the decks above, which was so deadly for the Titanic.

In addition to transverse and longitudinal bulkheads, this ship has fire bulkheads in the passenger spaces.
In addition to cross and lengthwise bulkheads, this ship has fire-resistant bulkheads in the passenger areas.
The 26,000-Ton, 23½-Knot Kronprinzessin Cecilie, a Thoroughly Protected Ship
The 26,000-ton, 23½-knot Kronprinzessin Cecilie, a completely protected ship
In dealing with the question of safety, the German shipbuilders have shown that thorough study of the problem which characterises the German people in all their industrial work. Although German ships of the first class, such as the Kronprinzessin Cecilie and the Imperator are not built to naval requirements, they embody many of the same protective features as are to be found in the Mauretania and Lusitania, and, indeed, in some safety features, and particularly in those built in the ship as a protection against fire, they excel them.
In addressing safety concerns, German shipbuilders have demonstrated a thorough understanding of the issues that reflect the German dedication to their industrial work. Even though top-notch German ships like the Kronprinzessin Cecilie and the Imperator aren't designed to military standards, they include many of the same safety features found in the Mauretania and Lusitania. In fact, when it comes to certain safety elements, especially the onboard fire protection, they surpass those ships.
The existence of side bunkers, small compartments, and bulkheads carried well up above the water-line, is due to the close supervision and strict requirements of the German Lloyd and the immigration authorities, and it takes but a glance at the hold plan of the Kronprinzessin Cecilie to show how admirably this ship and her sister are protected against collision. There are 21 transverse bulkheads, 18 of which are shown in the hold plan, the other three being sub-bulkheads, worked in the after part of the ship abaft of the machinery spaces. The four engines are contained in four separate compartments, and the boiler-rooms are entirely surrounded by coal-bunkers. These, the largest compartments, are protected throughout their entire length by the inner skin of the coal-bunker bulkheads. The engine-rooms are further protected by extending the inner floor of the double bottom up the sides as shown on page 176. Altogether, the hold plan shows 33 separate, watertight compartments. The collision bulkhead is carried up to the shelter deck, and the other bulkheads terminate at the main deck, which is about 19 feet above the normal water-line.
The presence of side bunkers, small compartments, and bulkheads extending well above the waterline results from the strict oversight and requirements of German Lloyd and immigration authorities. Just a quick look at the hold plan of the Kronprinzessin Cecilie reveals how well this ship and her sister are safeguarded against collisions. There are 21 transverse bulkheads, 18 of which are shown in the hold plan; the other three are sub-bulkheads located in the aft section of the ship behind the machinery spaces. The four engines are housed in four separate compartments, and the boiler rooms are completely surrounded by coal bunkers. These, the largest compartments, are protected along their entire length by the inner walls of the coal-bunker bulkheads. The engine rooms have additional protection because the inner floor of the double bottom extends up the sides, as illustrated on page 176. In total, the hold plan displays 33 distinct watertight compartments. The collision bulkhead rises to the shelter deck, while the other bulkheads stop at the main deck, which is about 19 feet above the normal waterline.

This well-protected ship has side coal bunkers, and inner skin in engine-rooms. There are thirty-three compartments below the water-line.
This well-protected ship has side coal bunkers and an inner skin in the engine rooms. There are thirty-three compartments below the waterline.
Hold Plan of Kronprinzessin Cecilie
Hold Plan of Kronprinzessin Cecilie
It is greatly to the credit of the Germans that they have given such careful attention to the question of fire protection. We have shown in a previous chapter that the long stretch of staterooms, with alleyways several hundred feet in length running through them, offer dangerous facilities for the rapid spread of a fire, should it once obtain a strong hold on the inflammable material of which the stateroom partitions and furnishings are composed. On the Kaiser Wilhelm II and Cecilie the passenger accommodations on the main deck are protected against the spread of fire by four steel bulkheads, which extend from side to side of the ship. Where the alleyways intersect these bulkheads, fire-doors are provided which are closed by hand and secured by strong clamps.
It’s commendable that the Germans have paid such close attention to fire protection. In a previous chapter, we pointed out that the long corridor of staterooms, with passageways that extend several hundred feet, creates a risky situation for the quick spread of fire if it gains a strong hold on the flammable materials used in the stateroom partitions and furnishings. On the Kaiser Wilhelm II and Cecilie, the passenger areas on the main deck are shielded from fire spread by four steel bulkheads that stretch from one side of the ship to the other. Where the passageways cross these bulkheads, fire doors are installed that are closed manually and secured with strong clamps.

Courtesy of Engineering
Thanks to Engineering
Section Through Engine-Room of the Kaiser Wilhelm II, Showing Inner Bottom Carried Up Sides of Ship, to Form Double Skin
Section Through Engine-Room of the Kaiser Wilhelm II, Showing Inner Bottom Carried Up Sides of Ship, to Form Double Skin
The fire protection also includes both an outside and an inside line of fire-mains. Fire-drill, with full pressure on the mains, is carried on every time the ship is in port, the outside lines of fire-mains being used. Once every three months there is a fire-drill with the inside line of mains. Every time the ship reaches her home port, both fire-drills and lifeboat drills are carried out under the close inspection of German Government officials.
The fire protection system includes both an exterior and an interior line of fire mains. A fire drill, with full pressure on the mains, is conducted every time the ship is in port, using the outside lines of fire mains. Once every three months, a fire drill is held with the interior line of mains. Each time the ship arrives at her home port, both fire drills and lifeboat drills are performed under the close supervision of German government officials.
Now, the provision of fire bulkheads is such an excellent protection that it should be made compulsory upon every steamship of large carrying capacity. Moreover, they should be extended throughout the full tier of decks reserved for passenger accommodation. The bulkheads need not be of heavy construction, and they can be placed in the natural line of division of the staterooms, where they will cause no inconvenience.
Now, having fire bulkheads is such an effective form of protection that it should be mandatory for every large-capacity steamship. Additionally, they should be extended across all decks designated for passenger accommodations. The bulkheads don’t have to be heavily constructed, and they can be positioned along the natural divisions of the staterooms, where they won't cause any inconvenience.
Special interest attaches to the Imperator of the Hamburg-American Line, just now, because she is the latest and largest of those huge ocean liners, of which the Olympic and Titanic were the forerunners. This truly enormous vessel, 900 feet long and 96 feet broad, will displace, when fully loaded, 65,000 tons, or 5,000 tons more than the Titanic. A study of her hold plan and inboard profile, shown on page 163, proves that it is possible to provide for an even larger boiler and machinery plant than that of the Titanic, without making any of that sacrifice of safety, which is so evident in the arrangement of compartments and bulkheads on the Titanic. Not only are the bulkheads throughout the machinery and boiler compartments carried to the second deck above the water-line, but the same spaces, throughout their whole length, are protected by an inner skin in the form of the longitudinal bulkheads of the side bunkers. The large forward engine-room is also protected by two longitudinal bulkheads at the sides of the ship and the after engine-room is divided by a central longitudinal bulkhead. Protection against the spread of fire is assured by several bulkheads worked across the decks which are devoted to passenger accommodation.
Special interest surrounds the Imperator of the Hamburg-American Line right now because she is the newest and largest of the massive ocean liners, following in the footsteps of the Olympic and Titanic. This truly enormous vessel, 900 feet long and 96 feet wide, will displace 65,000 tons when fully loaded, which is 5,000 tons more than the Titanic. A look at her hold plan and inboard profile, shown on page 163, demonstrates that it's possible to fit an even larger boiler and machinery system than the Titanic has, without compromising safety, which is clearly lacking in the compartment and bulkhead layout of the Titanic. Not only are the bulkheads in the machinery and boiler compartments extended to the second deck above the waterline, but these spaces are also protected throughout their entire length by an inner skin made up of the longitudinal bulkheads of the side bunkers. The large forward engine room is safeguarded by two longitudinal bulkheads along the sides of the ship, while the aft engine room is divided by a central longitudinal bulkhead. Protection against fire spreading is ensured by several bulkheads running across the decks dedicated to passenger areas.
CHAPTER X
CONCLUSIONS
I. The fact that the Titanic sank in two hours and thirty minutes after a collision demonstrates that the margin of safety against foundering in this ship was dangerously narrow.
I. The fact that the Titanic sank in two hours and thirty minutes after it hit an iceberg shows that the safety margin against sinking in this ship was alarmingly slim.
II. It is not to the point to say that the collision was of an unusual character and may never occur again. Collision with an iceberg is one of the permanent risks of ocean travel, and this stupendous calamity has shown how disastrous its results may be. We cannot afford to gamble with chance in a hazard whose issue involves the life or death of a whole townful of people.
II. It's not relevant to say that the collision was unusual and might never happen again. Hitting an iceberg is one of the constant risks of ocean travel, and this massive disaster has demonstrated how severe the consequences can be. We can't take chances with a danger that could mean life or death for an entire town full of people.
III. If it be structurally possible, and the cost is not prohibitive, passenger ships should be so designed, that they cannot be sunk by any of the accidents of the sea,—not even by such a disaster as befell the Titanic.
III. If it's structurally feasible and not too expensive, passenger ships should be designed in a way that they can't be sunk by any maritime accidents—not even by a disaster like what happened to the Titanic.
IV. That such design and construction are possible is proved by the fact that the first of the large ocean liners, the Great Eastern, built over half a century ago, so far fulfilled these conditions, that, after receiving injuries to her hull more extensive than those which sank the Titanic, she came safely to port.
V. It is not to the point to attribute the financial failure of the Great Eastern to the costly character of her construction. She failed because, commercially, she was ahead of her time, passenger and freight traffic being yet in their infancy when the ship was launched. Cheap steel and modern shipyard facilities have made it possible to build a ship of the size and unsinkable characteristics of the Great Eastern, with a reduction in the cost of twenty to thirty per cent.
V. It's not relevant to blame the financial failure of the Great Eastern on the expensive nature of its construction. It failed because, in terms of commerce, it was ahead of its time; passenger and freight traffic were still in their early stages when the ship was launched. Affordable steel and modern shipyard technology have allowed for the construction of a ship like the Great Eastern, with its size and unsinkable features, at a cost reduction of twenty to thirty percent.
VI. The principles of unsinkable construction, as formulated by Brunel and worked out in this remarkable ship, have been adopted in their entirety by naval constructors, and are to be found embodied in every modern warship. These elements—the double skin, transverse and longitudinal bulkheads, and watertight decks—are the sine qua non of warship construction; and in the designing of warships, they receive the first consideration, all other questions of speed, armour-protection, and gun-power being made subordinate.
VI. The principles of unsinkable construction, as defined by Brunel and implemented in this remarkable ship, have been fully adopted by naval builders and are incorporated into every modern warship. These features—the double hull, transverse and longitudinal bulkheads, and watertight decks—are essential for warship construction; and in designing warships, they are given top priority, while other factors like speed, armor protection, and firepower are considered secondary.
VII. In the building of merchant ships, unsinkable construction has been sacrificed to considerations of speed, convenience of operation, and the provision of luxurious accommodations for the travelling public. The inner skin, the longitudinal bulkhead, and the watertight deck have been abandoned. Although the transverse bulkhead has been retained, its efficiency has been greatly impaired; for, whereas these bulkheads in the Great Eastern extended thirty feet above the water-line; in the Titanic, they were carried only ten feet above the same point.
VII. In the construction of merchant ships, the focus on being unsinkable has been sacrificed for speed, ease of operation, and the availability of luxurious accommodations for travelers. The inner skin, longitudinal bulkhead, and watertight deck have been removed. Although the transverse bulkhead is still in place, its effectiveness has significantly decreased; whereas these bulkheads in the Great Eastern reached thirty feet above the water line, in the Titanic, they only extended ten feet above the same point.
VIII. The portentous significance of this decline in the art of unsinkable construction will be realised, when it is borne in mind that the Titanic was built to the highest requirements of the Board of Trade and the insurance companies. She was the latest example of current and approved practice in the construction of high-class passenger ships of the first magnitude; and, judged on the score of safety against sinking, she was as safe a ship as ninety-five out of every hundred merchant vessels afloat to-day.
VIII. The important significance of this decline in the art of unsinkable construction will be understood when one considers that the Titanic was designed to meet the highest standards set by the Board of Trade and the insurance companies. She was the latest example of current and accepted practices in building top-tier passenger ships of the highest class; and, in terms of safety against sinking, she was as safe a ship as ninety-five out of every hundred merchant vessels in operation today.
IX. That the narrowing of the margin of safety in merchant ships during the past fifty years has not been due to urgent considerations of economy, is proved by the fact that shipowners have not hesitated to incur the enormous expense involved in providing the costly machinery to secure high speed, or the equally heavy outlay involved in providing the sumptuous accommodations which characterise the modern liner.
IX. The fact that the reduction in safety margins for merchant ships over the past fifty years hasn't been driven by urgent economic concerns is shown by how shipowners haven't hesitated to spend huge amounts of money on expensive machinery for high speeds or the substantial costs for the luxurious accommodations found on modern liners.
X. If, then, by making moderate concessions in the direction of speed and luxury, it would be possible, without adding to the cost, to reintroduce those structural features which are necessary to render a ship unsinkable, considerations of humanity demand that it should be done.
X. If, by making reasonable compromises in speed and luxury, we could bring back the necessary structural features to make a ship unsinkable without increasing the cost, then, out of consideration for humanity, we should do it.
XI. Should the stupendous disaster of April the 14th lead us back to the sane construction of fifty years ago, and teach us so to construct the future passenger ship that she shall be not merely fast and comfortable, but practically unsinkable, the hapless multitude who went down to their death in that unspeakable calamity will not have died in vain.
XI. If the incredible disaster of April 14th pushes us to return to the sensible designs of fifty years ago, and teaches us how to build future passenger ships that are not only fast and comfortable but practically unsinkable, the unfortunate people who tragically lost their lives in that awful disaster will not have died in vain.
XII. In conclusion, let us note what changes would render such a ship as the Titanic unsinkable:
XII. In conclusion, let's consider what changes would make a ship like the Titanic unsinkable:
(a) The inner floor of the double bottom should be extended up the sides to a watertight connection with the middle deck. This inner skin should extend from bulkhead No. 1 at the bow to bulkhead No. 14, the second bulkhead from the stern.
(a) The inner floor of the double bottom should be extended up the sides to create a watertight connection with the middle deck. This inner layer should reach from bulkhead No. 1 at the front to bulkhead No. 14, the second bulkhead from the back.
(b) The lower deck should be made absolutely watertight from stem to stern, so as to form practically a second inner bottom; and it should be strengthened to withstand a water pressure equal to that to which the outer bottom of the ship is subjected at normal draft.
(b) The lower deck needs to be completely watertight from front to back, essentially making it a second inner bottom; it should also be reinforced to handle a water pressure equivalent to what the ship's outer bottom experiences at its normal draft.
(c) All openings through this deck, such as those for hatches and ladders and for the boiler uptakes, should be enclosed by strong watertight casings, carried up to the shelter deck, and free from any doors or openings leading to the intervening decks,—the construction being such that the water, rising within these casings from the flooded spaces below the lower deck, could not find its way out to the decks above.
(c) All openings in this deck, like those for hatches, ladders, and boiler uptakes, should be surrounded by strong watertight casings that extend up to the shelter deck and have no doors or openings leading to the decks in between. The design should ensure that water rising within these casings from the flooded areas below the lower deck cannot escape to the decks above.
(d) The second bulkhead from the bow and the second from the stern should be carried up to the shelter deck. All the intermediate bulkheads should be extended one deck higher to the saloon deck, D.
(d) The second bulkhead from the front and the second from the back should be taken up to the shelter deck. All the intermediate bulkheads should be raised one deck higher to the saloon deck, D.
(e) The cargo spaces in compartments 3 and 4, lying below the middle deck, should be divided by a central longitudinal bulkhead, and the hatches, leading up from these holds, should be enclosed in watertight casings extending, without any openings, to the shelter deck, where they should be closed by watertight hatch covers. The huge reciprocating-engine-room should be divided by a similar, central, longitudinal bulkhead.
(e) The cargo areas in compartments 3 and 4, located below the middle deck, should be separated by a central longitudinal bulkhead. The hatches that lead up from these holds should be enclosed in watertight casings extending, with no openings, to the shelter deck, where they should be closed off with watertight hatch covers. The large engine room should also be divided by a similar central longitudinal bulkhead.
(f) Finally, the passenger spaces on decks A, B, C, and D, should be protected against fire by the construction, at suitable intervals, of transverse bulkheads of light construction, provided with fire-doors where they intersect the alleyways.
(f) Finally, the passenger areas on decks A, B, C, and D should be protected from fire by building lightweight transverse bulkheads at appropriate intervals, equipped with fire doors where they meet the corridors.
A Titanic, as thus modified, might reasonably be pronounced unsinkable. To such a ship we could confidently apply the verdict of Brunel, as recorded in his notes on the strength and safety of the Great Eastern: "No combination of circumstances, within the ordinary range of probability, can cause such damage as to sink her."
A Titanic, as modified here, could be considered unsinkable. To such a ship we could confidently apply the judgment of Brunel, as noted in his observations on the durability and safety of the Great Eastern: "No combination of events, within the normal range of possibility, can cause enough damage to sink her."
Transcriber's Note
Transcriber's Note
Some illustrations contain explanatory text; the keywords have been added to the captions.
Some illustrations include explanatory text; the keywords have been added to the captions.
The following modifications have been made,
The following changes have been made,
Page 10:
"3 1-2 inches" changed to "3½ inches"
(some small angle-bars, 3½ inches in width)
Page 10:
"3 1-2 inches" changed to "3½ inches"
(some small angle bars, 3½ inches wide)
Page 36:
"24 1-2 knots" changed to "24½ knots"
(to accomplish the average speed of 24½ knots)
Page 36:
"24 1-2 knots" changed to "24½ knots"
(to achieve the average speed of 24½ knots)
Page 96:
"TRANSLANTIC" changed to "TRANSATLANTIC"
(PARTICULARS OF NOTED TRANSATLANTIC LINERS)
Page 96:
"TRANSLANTIC" changed to "TRANSATLANTIC"
(PARTICULARS OF NOTED TRANSATLANTIC LINERS)
Page 145:
"U. S. N." changed to "U.S.N."
(courtesy of Naval Constructor R. H. M. Robinson, U.S.N.)
Page 145:
"U.S.N." changed to "U.S.N."
(courtesy of Naval Constructor R.H.M. Robinson, U.S.N.)
Not modified but retained as printed:
Not modified but retained as printed:
Inconsistent spelling of "underwater" / "under-water"
Inconsistent spelling of "underwater" / "under-water"
Inconsistent spelling of "watertight" / "water-tight"
Inconsistent spelling of "watertight" / "water tight"
Download ePUB
If you like this ebook, consider a donation!