Transcriber’s Note
Transcription Note
This e-text uses a lot of uncommon Unicode characters, for example ℔ (U+2114 L B BAR SYMBOL), ꝥ (U+A765 LATIN SMALL LETTER THORN WITH STROKE), ♈ (U+2648 ARIES). If these (and others) don’t display for you, you may need to install additional fonts on your device. In particular, a Fraktur/‘black letter’ font (such as Old English Text MT) is recommended for the parts of the book dealing with German typography.
This e-text uses a lot of rare Unicode characters, for example ℔ (U+2114 L B BAR SYMBOL), ꝥ (U+A765 LATIN SMALL LETTER THORN WITH STROKE), ♈ (U+2648 ARIES). If these (and others) don’t show up for you, you might need to install extra fonts on your device. Specifically, a Fraktur/‘black letter’ font (like Old English Text MT) is recommended for the sections of the book that cover German typography.
Page numbering replicates that in the original: pp. i-xiv in Roman, followed by page 9 sqq. in Arabic numerals. No pages are missing or duplicated.
Page numbering matches the original: pp. i-xiv in Roman numerals, followed by page 9 and onwards in Arabic numerals. No pages are missing or duplicated.
Further notes appear at the end.
Further notes are available __A_TAG_PLACEHOLDER_0__.


THE
American Printer:
THE
American Printer:
A Manual of Typography,
A Typography Manual,
CONTAINING
CONTAINING
PRACTICAL DIRECTIONS FOR MANAGING ALL DEPARTMENTS
OF A PRINTING OFFICE,
PRACTICAL DIRECTIONS FOR MANAGING ALL DEPARTMENTS
OF A PRINTING OFFICE,
AS WELL AS
AND ALSO
Complete Instructions for Apprentices:
Apprenticeship Instructions:
WITH SEVERAL USEFUL TABLES,
NUMEROUS SCHEMES FOR IMPOSING FORMS IN EVERY VARIETY,
HINTS TO AUTHORS, ETC.
WITH SEVERAL USEFUL TABLES,
NUMEROUS SCHEMES FOR IMPRESSIVE DESIGNS IN EVERY VARIETY,
TIPS FOR AUTHORS, ETC.
By Thomas MacKellar, Ph. D.
By Thomas MacKellar, PhD.
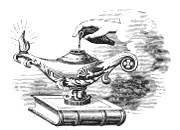
FIAT LUX.
Let there be light.
PHILADELPHIA:
MACKELLAR, SMITHS & JORDAN FOUNDRY.
1893.
PHILADELPHIA:
MACKELLAR, SMITHS & JORDAN FOUNDRY.
1893.

Entered, according to Act of Congress, in the year 1866, by
L. Johnson & Company,
In the Clerk’s Office of the District Court of the Eastern District of Pennsylvania.
Entered, according to the Act of Congress, in the year 1866, by
L. Johnson & Company,
In the Clerk’s Office of the District Court of the Eastern District of Pennsylvania.
Entered, according to Act of Congress, in the year 1878, by
MacKellar, Smiths & Jordan,
In the Office of the Librarian of Congress, at Washington, D. C.
Entered, according to the Act of Congress, in 1878, by
MacKellar, Smiths & Jordan,
In the Office of the Librarian of Congress, in Washington, D.C.
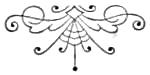
Eighteenth Edition—Revised and Enlarged.
18th Edition—Revised and Expanded.
ELECTROTYPED BY
MACKELLAR, SMITHS & JORDAN FOUNDRY,
PHILADELPHIA.
ELECTROTYPED BY
MACKELLAR, SMITHS & JORDAN FOUNDRY,
PHILADELPHIA.

EIGHTEENTH EDITION.
18th Edition.
This edition of the American Printer, while essentially the same as the previous one, contains some additional matter.
This edition of the American Printer, while basically the same as the last one, includes some extra content.
Philadelphia,
March, 1893.
Philadelphia, March 1893.


PREFACE TO FIRST EDITION.
Usefulness rather than originality has been aimed at in the preparation of the American Printer, which is offered as an improvement on the typographical work formerly published by us. In addition to the results of actual personal experience embodied in the volume, information has been gathered and extracts have been freely made from various publications, such as Ames and Dibdin’s Typographical Antiquities, Thomas’s History of Printing, Timperley’s Dictionary of Printers and Printing, Savage’s Dictionary of Printing, Johnson’s Typographia, Chambers’s Encyclopædia, Beadnell’s Guide to Typography, as well as other books referred to in the notes. The work has been prepared amid the manifold interruptions incident to business life; yet we think nothing has been overlooked that is essential for the instruction of the learner or for the assistance of the workman.
Utility instead of originality has been prioritized in creating the American Print, which is presented as an upgrade to the previous typographical work we published. Along with insights from personal experience included in the volume, information has been collected and quotes have been freely taken from various publications, such as Ames and Dibdin’s Typographical Antiquities, Thomas’s History of Printing, Timperley’s Dictionary of Printers and Printing, Savage’s Dictionary of Printing, Johnson’s Typographia, Chambers’s Encyclopædia, Beadnell’s Guide to Typography, and other books noted in the references. The work has been created amidst the many interruptions typical of business life; however, we believe nothing essential for teaching the learner or helping the worker has been missed.
Besides the matter relating to practical typography, the volume contains a sketch of the discovery of printing, and notices of type-founding, stereotyping, electrotyping, and lithography. The implements employed in typography are described and their uses explained; and complete schemes for imposition are laid down. The valuable tables and the plans of cases for various languages, and for music and labour-saving rule, will be found extremely useful; as well as the extensive lists of abbreviations and of foreign words and phrases, and orthographical hints.
Besides the practical typography aspects, this book includes an overview of the invention of printing, along with information on type-founding, stereotyping, electrotyping, and lithography. The tools used in typography are described, and their applications are explained; complete layouts for printing setups are provided. The useful tables and plans for cases in different languages, music, and time-saving rules will be very helpful, along with the extensive lists of abbreviations, foreign words and phrases, and spelling tips.
Special attention has been given in setting forth the functions and duties of the foreman and proof-reader, so that the operations of an office may be prosecuted with efficiency, comfort, and economy.
Special attention has been paid to outlining the roles and responsibilities of the foreman and proofreader, so that office operations can be carried out efficiently, comfortably, and cost-effectively.
Authors and publishers, as well as young printers, may consult the volume with profit; and, indeed, any intelligent person will find it serviceable.
Authors and publishers, along with new printers, will find this book helpful; in fact, anyone with a good sense will see its value.


CONTENTS.
PAGE. | |
The Rise and Progress of Printing | 13-48 |
Discovery of Printing—Laurentius Koster—Geinsfleisch—Gutenberg—Fust—Bible printed—Peter Schœffer—Caxton—Ulrich Zell—Lambert Palmaert—Abraham Colorito—Humphreys and De Vinne on the invention of printing—Lenox’s collection of rare Bibles—Ancient typographical peculiarities—Catchwords—Invention of Signatures—Printing introduced into America—Type-founding in Europe—Decree of the Star Chamber—Type-founding in America—Prices of Type—Stereotyping—Electrotyping—Lithography—Engraving—Walk over a type-foundry. | |
Tools or Equipment of the Craft | 49-120 |
Types—Roman letter—Italic—Black—Anglo-Saxon—Names and sizes of type—Gradations of type—Point System of Type bodies—A Bill of Pica—A Fount of type—Capitals—Small capitals—Points—Apostrophe—Hyphen—Parenthesis and Bracket—References—Accents—Numerals—Arabic figures—Old-style figures—Cancelled figures—Fractions—Signs—Metal rules or dashes—Braces—Spaces—Two-line letters—Quadrates—Quotations—Labour-saving quotation furniture—Hollow quadrates—Circular quadrates—Labour-saving curvatures—Leads—Flowers and borders—Brass rule—Brass labour-saving rule—Improved labour-saving rule case—Earliest written sounds—Hieroglyphic alphabet—Runic alphabets—Anglo-Saxon alphabet and plan of cases—German alphabet and plan of cases—Greek alphabet and plan of cases—Hebrew alphabet and plan of cases—Russian alphabet—Comparative table of bodies of Music type—Music composition—Music cases—Modern conveniences. | |
Composition | 121-140 |
General remarks—Requisites in an apprentice—American cases—Position of a compositor—Laying type—Distributing—Composing—Spacing—Justifying—Head-lines—Notes—Blanking—Paragraphs—Indexes—Titles—Dedications—Contents—Prefaces—Signaturing—Errata—Ironical rules—Advice to apprentices—Ironical rules for beginners in business. | |
[viii]Imposition | 141-199 |
General remarks—Tying up pages—Laying pages—Making up furniture—Making the margin—Locking up forms—Memoranda—Nomenclature of sheets—Schemes for imposing, from folio to 128mo. | |
Proofreading and Editing | 200-217 |
Qualifications of a reader—Should be a printer—Indebtedness of authors to proof-readers—Process of reading—Proof record—Errors made in correcting—Two readers desirable—Punctuation—Alterations in proof—Stower’s remarks—Revise—Correcting in the metal—Capricious alterations—Proper method of correcting—Over-running—Hints to authors—Table of proof-marks, with explanations—Table of signatures. | |
The Supervisor | 218-234 |
General duties—Treatment of compositors—Punctuality—Morning duties—Knowledge of all materials on hand—Order—Overseeing work—Regulating takes of copy—Prompt reading and correcting—Memorandum—Press-book—Press duties—Warehouse—Casting off copy—Managing hurried work—Companionships—Taking copy—Making up—Dividing the letter—Making up furniture—Imposing and distributing letter—Correcting—Transposition of pages—Rules to be observed in a printing-office. | |
The Press and Its Operations | 235-292 |
History of the printing-press—Blaeu, its first improver—Ramage press—Stanhope press—Clymer or Columbian press—Smith press—Washington press—Adams’s bed-and-platen power-press—Invention of the Cylinder press—Frederick König—William Nicholson—Dr. Kinsley—Applegath and Cowper—Account of the house of R. Hoe & Co.—Stop Cylinder press—Cottrell & Babcock presses—Campbell presses—Richard M. Hoe’s type-revolving printing machine—Bullock perfecting press—The Walter perfecting press—The Hoe perfecting press—Presses at the Centennial Exhibition, 1876—Railroad-ticket printing and numbering press—Job presses—Ruggles, Hoe, Gordon, Degener, Wells, and Gally—Franklin press—Nonpareil press—Fire-fly press—Liberty press—Globe press—Peerless press—Universal press—Amateur presses—Folding machines—Setting up a Washington press—Setting up the roller-stand—Composition rollers—Melting kettle—Covering tympans—Wetting paper—Blankets—Making ready a form on a hand-press—Pulling—Rules and remedies for pressmen—Ley-trough—Making ready on cylinder presses—Fine hand-presswork—Printing [ix]wood-cuts—Card printing—Gold printing—Bronze printing—Printing in colours—Ink stone and muller—How to use dry colours—How to multiply colours—Contrast of colours—Oiling a press—How to treat wood type. | |
Warehouse Team | 293-299 |
Warehouseman—Warehouse-Book—Receipt of paper and delivery of sheets—Giving out paper to wet—Over-sheets—Hanging up paper to dry—Taking down sheets when dry—Filling in and pressing sheets—Counting out and putting away sheets—Standard sizes of machine-made paper—Table for giving out paper for a thousand copies. | |
Freelance Services | 300-310 |
Selection of type and presses—How to make a paying business—Memorandum order—Estimate book—Ames’s paper and card scale—Le Blond’s chart—Cabinets and cases—Rules for the government of a job office—Job composing-sticks—Patent quoins—Corner quadrates—Shooting sticks—Mitering machine—Lead cutter—Perforating machines—Imposing stone—Copy-holder—Paper and card cutters—Megill’s patent gauge pin—Extension feed-guide—Automatic counters—Patent ink fountain—Iron furniture. | |
Helpful Receipts | 311-317 |
How to make printers’ rollers—German preservative for rollers—Directions for recasting rollers—Printers’ ley—Paste—Mucilage—Glue—Gum—Magenta surface paper—Coloured writing inks—Fire-proof ink—Printing ink varnish—Lithographic transfer ink—To give dark printing inks a bronze or changeable hue—An ink for marking tin or zinc—Drying preparations—Silvering solutions—To soften leather belting—How to open a ball of twine—To prevent adhesion of paper—To detect ground wood in paper—French gold printing—Transfer varnish—To make paper waterproof—To preserve books—To restore engravings. | |
Spelling | 318-332 |
Discrepancies—a or an before a vowel or silent h—o or oh—able and ible—im or in and em or en—in and un—ise and ize—or and our—sion and tion—Farther and further—Peas and pease—Omission of s in the possessive case—Formation of the plurals of words compounded of a noun and an adjective—Pointing of numbers, weights, measures, &c.—Derivation of English words—Rules for spelling—Plurals of nouns. | |
[x]How to Protect Copyrights | 333-335 |
Printed title required—Application to be made to Librarian of Congress—Style of printed title—Fees—Two complete copies required—Penalty—Notice of copyright to be given by imprint—Form of notice—Penalty for false notice—Authors may reserve the right to translate or dramatize—Form of notice—Original works only will be entered—Duration of copyright—Renewal—Form of application for renewal—Time of publication—Copyright may be secured for a projected as well as for a completed work—Assignments—Fees—Copies or duplicate certificates—Serials or separate publications—Copyright required for each volume or part of a book—Copyrights for works of art—Copyrights cannot be granted upon trade-marks or labels—Fee for registering at Patent Office—Citizens or residents of the United States only entitled to copyright—Full name and residence of claimant required. | |
The Metric System | 336, 337 |
Craft Technical Terms | 338-343 |
Abbreviations | 344-356 |
Foreign Terms and Expressions | 357-372 |
Table of Contents | 373-383 |
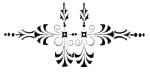

HORN-BOOK OF THE SEVENTEENTH CENTURY.
Seventeenth Century Horn-Book.
The Printer's Song.


Hereby, tongues are known, knowledge groweth, judgment increaseth, books are dispersed, the Scripture is read, stories be opened, times compared, truth discerned, falsehood detected and with finger pointed, and (all as I said) through the benefit of Printing.
With this, languages are understood, knowledge increases, judgment improves, books are spread, the Scripture is read, stories are revealed, times are compared, truth is recognized, falsehood is exposed and pointed out, and (as I mentioned) all thanks to the power of printing.
Fox’s Martyrs.
Fox's Martyrs.
At the very epoch when the greatness of Burgundy was most swiftly ripening, another weapon was secretly forging, more potent in the great struggle for freedom than any which the wit or hand of man has ever devised or wielded. When Philip the Good, in the full blaze of his power, and flushed with the triumphs of territorial aggrandizement, was instituting at Bruges the order of the Golden Fleece, “to the glory of God, of the blessed Virgin, and of the holy Andrew, patron saint of the Burgundian family,” and enrolling the names of the kings and princes who were to be honoured with its symbols, at that very moment, an obscure citizen of Haarlem, one Lorenz Coster, or Lawrence the Sexton, succeeded in printing a little grammar, by means of movable types. The invention of printing was accomplished, but it was not ushered in with such a blaze of glory as heralded the contemporaneous erection of the Golden Fleece. The humble setter of types did not deem emperors and princes alone worthy his companionship. His invention sent no thrill of admiration throughout Christendom; and yet, what was the good Philip of Burgundy, with his Knights of the Golden Fleece, and all their effulgent trumpery, in the eye of humanity and civilization, compared with the poor sexton and his wooden type?
At the very time when Burgundy was reaching its peak of greatness, another force was quietly being created, more powerful in the struggle for freedom than anything anyone has ever thought of or created. While Philip the Good, in all his glory and riding high on his successes of expanding his territory, was establishing the order of the Golden Fleece at Bruges “for the glory of God, the blessed Virgin, and Saint Andrew, the patron saint of the Burgundian family,” and listing the kings and princes who would be honored with its symbols, an unknown citizen of Haarlem, Lorenz Coster, or Lawrence the Sexton, managed to print a small grammar using movable types. The invention of printing was completed, but it didn't come with the same fanfare as the contemporary unveiling of the Golden Fleece. The humble type setter didn't believe that only emperors and princes deserved his company. His invention didn't inspire admiration across Christendom; yet, what was Philip of Burgundy, with his Knights of the Golden Fleece and all their flashy nonsense, when compared to the poor sexton and his wooden type?
Motley’s Rise of the Dutch Republic, Vol. i, 45.
Motley's Rise of the Dutch Republic, Vol. i, 45.


The American Printer.
RISE AND PROGRESS OF PRINTING.
DISCOVERY OF PRINTING.

The credit of inventing the art which perpetuates the history and achievements of all the arts and sciences has been obstinately contested, several cities having advanced rival claims to the honour of the discovery. This, however, should be no matter of surprise when we consider that the inventor of a new art, unprotected by law, would naturally endeavour to conceal its processes for his own use and advantage. After due consideration, we agree with Isaiah Thomas in the opinion that the probabilities point to Laurentius (sometimes called Coster, Koster, and Kustos) as the discoverer of the art of printing.[1]
The credit for inventing the art that preserves the history and achievements of all the arts and sciences has been fiercely debated, with several cities claiming the honor of the discovery. This shouldn't be surprising when we think about how the inventor of a new art, without legal protection, would likely try to keep its processes secret for personal benefit. After careful consideration, we agree with Isaiah Thomas that the evidence suggests Laurentius (also known as Coster, Koster, and Kustos) is the one who discovered the art of printing.[1]
Laurentius lived at Haarlem and was a man of property. He seems to have been engaged in printing books from wood blocks or plates, well known to antiquaries as the Block Books, in which the reading matter was illustrated by rude pictures. Fragments of works so printed by him are still in existence. Among others, the celebrated Biblia Pauperum, executed between 1410 and 1420, has been attributed to him. It was only natural that his thoughts should be led to the production of single types, as a means of cheapening and facilitating his work. These were first made of wood, and afterward of tin. The date of his invention of separate types is given as about the year 1429. Other dates have been stated, ranging from[11] 1422 to 1436. The first of his printed books, it is claimed, was the Speculum Humanæ Salvationis, of which about ten copies are now known to be in existence. A small primer, or Abecedarium, in our opinion, shows all the marks of the first attempt of an experimenter in a new art. Koster died in 1439.
Laurentius lived in Haarlem and was a wealthy man. He was involved in printing books using wooden blocks or plates, known to historians as the Block Books, where the text was accompanied by simple illustrations. Some fragments of his printed works still exist today. Among them, the famous Biblia Pauperum, created between 1410 and 1420, is attributed to him. It’s only natural that he would consider creating individual types to make his work easier and cheaper. These were initially made of wood and later of tin. His invention of separate types is dated to around 1429, though some sources suggest dates between [11] 1422 and 1436. It is said that his first printed book was the Speculum Humanæ Salvationis, of which about ten copies are known to exist today. A small primer, or Abecedarium, in our view, reflects all the signs of an early experimenter in a new craft. Koster died in 1439.
The necessity for employing workmen to assist in prosecuting the art led to the divulging of the secret. Among these men, it is supposed, was John Geinsfleisch, (or Gutenberg, Senior,) who, after learning the processes, returned to Mentz, his native place, and communicated the secret to his nephew, John Gutenberg, an ingenious artist of Strasburg. It is in evidence that the latter, in connection with two partners, spent a considerable amount of money in some private experiments. These appear to have occupied several years, from 1436 to 1439, when a legal contest arose as to the rights of one of the partners whose zealous activity had caused his death. Gutenberg continued at Strasburg till 1444, when, his means being exhausted, he rejoined his uncle at Mentz. Here he renewed his experiments, and, needing money, he procured an introduction to John Fust, a capitalist and money-lender, who seems to have been struck with the importance of the work, and who advanced a considerable amount (all the tools and presses being pledged as security) in furtherance of the enterprise. Two years were occupied in making the types and necessary machinery, when the great work of printing the Bible was begun. There can be little doubt that, during all his years of experiment, Gutenberg had executed smaller books, one of which is surmised to have been a reproduction of the Dutch Speculum of Koster. The Donatus of 1451, the Appeal against the Turks of 1454, and the Letters of Indulgence of 1454 and 1455, all appeared before the Bible,[2] which[12] was not published till 1455 or 1456. This great book marked an era in the art.[3]
The need to hire workers to help advance the art led to the revelation of the secret. Among these workers was John Geinsfleisch (or Gutenberg, Sr.), who, after learning the processes, returned to Mainz, his hometown, and shared the secret with his nephew, John Gutenberg, a talented artist from Strasbourg. It's noted that the latter, along with two partners, invested a significant amount of money into private experiments. These experiments seemed to take several years, from 1436 to 1439, when a legal dispute arose regarding the rights of one partner, whose enthusiastic efforts led to his death. Gutenberg stayed in Strasbourg until 1444, when, after running out of funds, he rejoined his uncle in Mainz. There, he resumed his experiments and, needing money, got an introduction to John Fust, a financier and moneylender, who seemed to recognize the importance of the work and lent a substantial amount (with all the tools and presses pledged as collateral) to support the project. Two years were spent creating the types and necessary equipment before the monumental task of printing the Bible began. There is little doubt that throughout his years of experimentation, Gutenberg produced smaller books, one of which is believed to be a copy of Koster's Dutch Speculum. The Donatus from 1451, the Appeal against the Turks from 1454, and the Letters of Indulgence from 1454 and 1455 all came out before the Bible,[2] which[12] was not published until 1455 or 1456. This great book marked a turning point in the art.[3]
It is painful to be told that about this time Fust foreclosed the mortgage, and the entire work with all the materials passed into his possession. It seems, however, that Gutenberg succeeded in re-establishing a press, and continued to practise the art, but produced no work at all comparable with the Bible. He died about 1468.
It’s hard to hear that around this time, Fust took over the mortgage, and all the work along with the materials became his. However, it seems that Gutenberg managed to set up a press again and kept practicing the craft, but he never created anything that matched the Bible. He passed away around 1468.
After securing possession of the establishment, Fust engaged the service of Peter Schœffer, who had been apprentice or assistant to Gutenberg, and who was distinguished for scholarship as well as mechanical skill. His skill and the improvements made by him in the art soon led Fust to take him into partnership, and the Bible, the Psalter, and other important works were produced. Schœffer was further rewarded by the hand of the grand-daughter of Fust.
After taking control of the business, Fust hired Peter Schœffer, who had been an apprentice or assistant to Gutenberg and was known for his intelligence as well as his mechanical talent. His expertise and the enhancements he made in the printing process quickly led Fust to partner with him, resulting in the production of the Bible, the Psalter, and other significant works. Schœffer was also further rewarded by marrying Fust's granddaughter.
From this rapid summary, we may conclude, 1. That the merit of the invention of printing, however rude it may have been, belongs to Koster of Haarlem; 2. That Gutenberg placed the art on a permanent foundation; and, 3. That its economical application was insured by Peter Schœffer’s invention of cast metal types.[4]
From this quick overview, we can conclude: 1. The credit for the invention of printing, no matter how primitive it might have been, goes to Koster from Haarlem; 2. Gutenberg established the art on a solid foundation; and 3. Its practical use was secured by Peter Schœffer’s creation of cast metal types.[4]
It was of course impossible to conceal the knowledge of an art so useful to man, and within ten years after the publication of the great Bible presses were established in several German cities, in Rome and other parts of Italy, and soon thereafter in France and England.
It was obviously impossible to hide the knowledge of an art so beneficial to humanity, and within ten years after the publication, major Bible printing presses were set up in several German cities, in Rome and other areas of Italy, and soon after in France and England.
William Caxton acquired a knowledge of the art in Germany, and carried it into practice at Westminster in England. The year 1477 is now accepted as the date of the introduction, the first book printed with a date in England being the Dictes and Sayinges of the Philosophers, emprynted by me, William Caxton, at Westmestre, the yere of our Lord m.cccc.l.xxvij. He had previously printed, without a date, The Recuyell of the Historyes of Troye, which was followed by The Game and Playe of the Chesse, fynysshid the last day of marche the yer of our lord god. a. thousand foure honderd and lxxiiii. These were, however, printed at Bruges; so, according to Mr. William Blades, “the first indisputable date we have to stand on is the printing of The Dictes in 1477.”
William Caxton learned the printing art in Germany and put it into practice in Westminster, England. The year 1477 is now recognized as the year it was introduced, with the first book printed with a date in England being the Dictes and Sayinges of the Philosophers, printed by me, William Caxton, at Westminster, in the year of our Lord 1477. He had previously printed, without a date, The Recuyell of the Historyes of Troye, followed by The Game and Playe of the Chesse, finished on the last day of March in the year 1474. However, these were printed in Bruges; so, according to Mr. William Blades, “the first indisputable date we can confirm is the printing of The Dictes in 1477.”
Though at that time over sixty years old, Caxton was notable for his industrious habit. He was possessed of good sense and sound judgment; steady, persevering, active, zealous, and liberal in his devices for that important art which he introduced into England, labouring not only as a printer, but as translator and author. The productions of his press amount to sixty-four. In the churchwardens’ books of St. Margaret’s Parish, Westminster, his death is thus recorded: “1491. Item, atte bureyng of William Caxton, for iiii. torches vjs. viijd. Item, for the belle atte same bureyng, vjd.”
Though he was over sixty years old at the time, Caxton was known for his hard work. He had good sense and sound judgment; he was steady, persistent, active, enthusiastic, and generous in his contributions to the important art he brought to England, working not only as a printer but also as a translator and author. The works produced by his press total sixty-four. In the churchwardens’ records of St. Margaret’s Parish, Westminster, his death is recorded as follows: “1491. Item, at the burial of William Caxton, for 4 torches 6s. 8d. Item, for the bell at the same burial, 6d.”
The Bible was printed in Spanish at Valencia in 1479 by Lambert Palmaert, a German; but so completely was it afterward suppressed by the Inquisition that only four leaves now remain in the archives of Valencia. The first Hebrew Bible ever printed came from the press of Abraham Colorito, at Soncino, in 1488—a very remarkable work. Iceland had its printing-office in 1530, at which a Bible was printed in 1584.
The Bible was printed in Spanish in Valencia in 1479 by Lambert Palmaert, a German. However, it was so thoroughly suppressed by the Inquisition that only four pages now exist in the archives of Valencia. The first Hebrew Bible ever printed was produced by Abraham Colorito's press in Soncino in 1488, which is a significant accomplishment. Iceland established its printing press in 1530, and a Bible was printed there in 1584.
ANCIENT PECULIARITIES.
The pages were either large or small folios, but sometimes quartos, and, the early books were therefore cumbrous and unhandy. Aldus Manuccio, of Venice, was the first to introduce the octavo form.
The pages were either large or small folios, but sometimes quartos, and the early books were therefore bulky and difficult to handle. Aldus Manuccio, from Venice, was the first to introduce the octavo format.
The leaves were without running titles, direction-words, paginal numbers, or divisions into paragraphs.
The leaves had no running titles, no direction words, no page numbers, or paragraphs.
The character itself was a rude old Gothic (similar to that now known as Old English or Black) mixed with Secretary, designed to imitate the handwriting of the times; the words were printed so close to one another that the matter was not easily read.
The font was a rough old Gothic (similar to what we now call Old English or Black) mixed with Secretary, meant to resemble the handwriting of that era; the letters were printed so close together that it was hard to read.
To avoid divisions, the early printers used vowels with a mark of abbreviation over them to denote that one or more letters were omitted in the word: e.g. co̅pose for compose, co̅pletio̅ for completion, &c. No punctuation-marks were used, except the colon and full point; but an oblique stroke (/) was after a while introduced, for which the comma was finally substituted. Logotypes were frequently employed.
To prevent breaks in words, early printers placed a mark over vowels to show that one or more letters were left out: e.g. co̅pose for compose, co̅pletio̅ for completion, etc. Only a colon and period were used as punctuation; eventually, a slash (/) was introduced, which was later replaced by the comma. Logotypes were commonly used.
Orthography was various and arbitrary. Proper names and sentences were often begun with small letters, as well as the first words in lines of poetry.
Orthography was varied and arbitrary. Proper names and sentences were often started with lowercase letters, as were the first words in lines of poetry.
Blanks were left for the places of titles, initial letters, and other ornaments, to be supplied afterward by illuminators, whose calling did not long survive the masterly improvements made by the printers in this branch of their art. These ornaments were exquisitely fine, and curiously variegated with the most beautiful colours, and even with gold and silver. The margins, likewise, were frequently charged with a variety of figures, of saints, birds, beasts, monsters, flowers, &c., which sometimes had relation to the contents of the page, though frequently none at all. These embellishments were often very costly.
Blanks were left for titles, initial letters, and other decorations, which would be filled in later by illuminators. Their craft didn’t last long after printers made significant advancements in this area of their art. These decorations were incredibly detailed and beautifully colored, often including gold and silver. The margins were also often filled with various images of saints, birds, animals, monsters, flowers, etc., which sometimes related to the content of the page, though often they didn’t. These embellishments were often very expensive.
The name of the printer, place of his residence, &c. were either omitted or put at the end of the book, with some pious ejaculation or doxology.
The printer's name, where he lived, etc., was either left out or listed at the end of the book, along with some religious remark or praise.
The date was also omitted, or involved in some cramped design, or printed either at full length or in numerical letters, and sometimes partly one and partly the other: thus, One[16] Thousand CCCC and lxxiiii; but always placed at the end of the book.
The date was either left out, cramped into a small design, or printed fully or in numbers, and sometimes a mix of both: for example, One[16] Thousand CCCC and lxxiiii; but it was always positioned at the end of the book.
There was no variety of character, nor intermixture of Roman and Italic, which were later inventions; but the pages were printed in a Gothic letter of the same size throughout. Catch-words at the end of the foot-line (now generally abolished) were first used at Venice, by Vindeline de Spire. The inventor of signatures is said to have been Antonio Zarotti of Milan, about 1470.
There was no mix of different typefaces or styles, like Roman and Italic, which came later; instead, the pages were printed in a uniform Gothic font of the same size. Catchwords at the end of the footline (which are mostly gone now) were first used in Venice by Vindeline de Spire. The person credited with creating signatures is thought to be Antonio Zarotti from Milan, around 1470.
Books were often encased in massive coverings, which were ornamented with florid and arabesque designs. Jewels and precious metals, the finest stuffs, and the most gorgeous colours were sometimes employed. Scaliger says, that his grandmother had a printed Psalter, the cover of which was two inches thick. On the inner side was a receptacle, containing a small silver crucifix, with the name of Berenica Codronia de la Scala behind it.
Books were often covered in thick bindings, decorated with elaborate and intricate designs. Sometimes, they used jewels, precious metals, luxurious fabrics, and vibrant colors. Scaliger mentions that his grandmother had a printed Psalter with a cover that was two inches thick. On the inside, there was a pocket containing a small silver crucifix, with the name Berenica Codronia de la Scala written behind it.
Two or three hundred copies of a work were considered to be a large edition.
Two or three hundred copies of a work were seen as a big edition.
PRINTING IN AMERICA.
Printing was introduced into America at Mexico by the Viceroy Mendoza in 1536. The first book printed was the Escala espiritual de San Juan Climaco, of which no copy is known to exist; but the oldest American book now extant is the Manual de Adultos, dated 1540, of which only the last four leaves are to be found in the library of the Cathedral of Toledo. The name of the earliest printer is a matter of question.
Printing was brought to America in Mexico by Viceroy Mendoza in 1536. The first book printed was the Escala espiritual de San Juan Climaco, but no copies are known to exist; however, the oldest American book that still exists is the Manual de Adultos, dated 1540, of which only the last four pages can be found in the library of the Cathedral of Toledo. The identity of the first printer is still a topic of debate.
Cambridge, Massachusetts, is entitled to the distinction of having the first printing-press in North America, which was under the charge of Stephen Daye. For this press the colony was mainly indebted to the Rev. Jesse Glover, a nonconformist minister possessed of a considerable estate, who had left England to settle among his friends in Massachusetts. Some gentlemen of Amsterdam also “gave towards furnishing of a printing-press with letters, forty-nine pounds and something more.” This was about 1638. The first book issued was the Bay Psalm-Book, in 1640.
Cambridge, Massachusetts, holds the title of having the first printing press in North America, managed by Stephen Daye. The colony largely owes this press to Rev. Jesse Glover, a nonconformist minister with a substantial estate, who moved from England to be with his friends in Massachusetts. A few gentlemen from Amsterdam also contributed to setting up the printing press with letters, donating forty-nine pounds and some additional funds. This occurred around 1638. The first book printed was the Bay Psalm-Book in 1640.
The first book issued in the Middle Colonies was an Almanac, printed by William Bradford in 1685, near Philadelphia.[17] Bradford was brought out from England in 1684 by William Penn. As the government of Pennsylvania became very restrictive in regard to the press, Bradford in 1693 removed to New York, and was appointed printer to that colony, where he established in 1725 the New York Gazette, the first newspaper published there. He died May 23, 1752, after an active and useful life of eighty-nine years.[5]
The first book published in the Middle Colonies was an Almanac, printed by William Bradford in 1685, near Philadelphia.[17] Bradford was brought over from England in 1684 by William Penn. As the government of Pennsylvania became quite strict about the press, Bradford moved to New York in 1693 and was appointed the printer for that colony, where he started the New York Gazette in 1725, the first newspaper published there. He passed away on May 23, 1752, after living an active and productive life of eighty-nine years.[5]
The first newspaper in America was the Boston News Letter, which was first issued by John Campbell on Monday, April 24, 1704: it was regularly published for nearly seventy-two years. The second was the Boston Gazette, begun December 21, 1719. The third was the American Weekly Mercury, issued in Philadelphia, by Andrew Bradford, on December 22, 1719. James Franklin, an elder brother of Benjamin, established the New England Courant, August 17, 1721.
The first newspaper in America was the Boston News Letter, which John Campbell started on Monday, April 24, 1704. It was published regularly for nearly seventy-two years. The second was the Boston Gazette, which began on December 21, 1719. The third was the American Weekly Mercury, released in Philadelphia by Andrew Bradford on December 22, 1719. James Franklin, an older brother of Benjamin, launched the New England Courant on August 17, 1721.
The oldest living paper of the United States is the New Hampshire Gazette, published at Portsmouth, now (Oct. 7, 1892) one hundred and thirty-six years old.
The oldest continuously published newspaper in the United States is the New Hampshire Gazette, based in Portsmouth, and as of October 7, 1892, it is one hundred thirty-six years old.
The North American and United States Gazette leads the existing daily press of this country in point of antiquity. It is the successor of the Pennsylvania Packet, (begun in 1771 and becoming a daily paper in 1784,) and is still the chief commercial journal of Philadelphia.
The North American and United States Gazette is the oldest daily newspaper in this country. It is the successor to the Pennsylvania Packet (which started in 1771 and became a daily paper in 1784) and remains the leading commercial journal in Philadelphia.
The first paper-mill in America was established near Germantown, Pa., in 1690, by William Rittenhouse.[6]
The first paper mill in America was set up near Germantown, PA, in 1690, by William Rittenhouse.[6]
TYPE-FOUNDING IN EUROPE.
For a long period after the discovery of printing, it seems that type-founding, printing, and binding went under the general term of printing, and that printers cast the types used by them, and printed and bound the works executed in their establishments. Type-founding became a distinct calling early in the seventeenth century. A decree of the Star Chamber, made July 11, 1637, ordained the following regulations concerning English founders:—
For a long time after the invention of printing, it appears that type-founding, printing, and binding were all referred to simply as printing, and that printers created the types they used, as well as printed and bound the works produced in their shops. Type-founding became a separate profession in the early seventeenth century. A decree from the Star Chamber, issued on July 11, 1637, established the following regulations regarding English founders:—
“That there shall be four founders of letters for printing, and no more.
“That there shall be four founders of letters for printing, and no more.
“That the Archbishop of Canterbury, or the Bishop of London, with six other high commissioners, shall supply the places of those four as they shall become void.
“That the Archbishop of Canterbury, or the Bishop of London, along with six other high commissioners, will fill the positions of those four as they become vacant.
“That no master-founder shall keep above two apprentices at one time.
“That no master-founder shall keep more than two apprentices at a time.
“That all journeyman-founders be employed by the masters of the trade, and that idle journeymen be compelled to work, upon pain of imprisonment and such other punishment as the court shall think fit.
“That all journeyman-founders must be employed by the masters of the trade, and that idle journeymen should be forced to work, under the threat of imprisonment and any other punishment the court deems appropriate.
“That no master-founder of letters shall employ any other person in any work belonging to the casting or founding of letters than freemen or apprentices to the trade, save only in pulling off the knots of metal hanging at the end of the letters when they are first cast; in which work every master-founder may employ one boy only, not bound to the trade.”
"That no master letter founder shall hire anyone else for any work related to casting or founding letters except for freemen or apprentices in the trade, except for removing the metal knots at the end of the letters when they are first cast; for this work, each master founder may employ only one boy who is not bound to the trade."
By the same decree, the number of master-printers in England was limited to twenty.
By the same order, the number of master printers in England was limited to twenty.
Regulations like the above were in force till 1693. The “polyglot founders,” as they have been called, were succeeded by Joseph Moxon and others. But the English were unable to compete with the superior productions of the Dutch founders, until the advent of William Caslon, who, by the beauty and excellence of his type, surpassed his Batavian competitors, when the importation of foreign type ceased, and his founts were, in turn, exported to the Continent.
Regulations like those lasted until 1693. The so-called “polyglot founders” were followed by Joseph Moxon and others. However, the English struggled to compete with the higher-quality work of the Dutch founders until William Caslon emerged. With the beauty and excellence of his type, he outshone his Dutch competitors, leading to the end of foreign type importation, and his fonts were eventually exported to the Continent.
By an act subsequently passed, no founder was to cast any letter for printing, no joiner to make any press, no smith to forge any iron-work for a press; no person to bring from parts[19] beyond the seas any letters founded or cast for printing; nor any person to buy any letters or any other materials belonging unto printing; without application to the master and wardens of the Company of Stationers.
By a later law, no founder was allowed to cast any letters for printing, no carpenter could make any press, no blacksmith was permitted to forge any ironwork for a press; no one could bring any letters that had been cast for printing from overseas; and no one could buy any letters or other printing materials without getting approval from the master and wardens of the Company of Stationers.
TYPE-FOUNDING IN AMERICA.
A foundry, principally for German type, was established at Germantown, Pennsylvania, about the year 1735, by Christopher Saur, (or Sower,) a printer, who executed in German the first quarto Bible printed in America, as well as other valuable works in the German language. Three editions of the Bible were printed—viz., in the years 1743, 1763, and 1776, the latter two by his son. In 1739, Saur published a newspaper in Germantown.
A metal shop, mainly for German type, was set up in Germantown, Pennsylvania, around 1735, by Christopher Saur (or Sower), a printer who produced the first quarto Bible printed in America in German, along with other important works in the German language. Three editions of the Bible were published—in the years 1743, 1763, and 1776, with the last two printed by his son. In 1739, Saur launched a newspaper in Germantown.
An abortive attempt was made about 1768 to set up a foundry at Boston by a Mr. Mitchelson from Scotland, and another in Connecticut in 1769 by Abel Buel. In 1775, Dr. Franklin brought from Europe to Philadelphia the materials for a foundry; but little use of them was made.
An unsuccessful attempt was made around 1768 to establish a foundry in Boston by a Mr. Mitchelson from Scotland, and another in Connecticut in 1769 by Abel Buel. In 1775, Dr. Franklin brought materials for a foundry from Europe to Philadelphia, but they weren't used much.
John Baine, a type-founder of Edinburgh, sent a relative to this country with tools for a foundry at the close of the Revolutionary War, and soon after came over himself. They carried on the business till 1790, when Mr. Baine died, and his kinsman returned to Scotland.
John Baine, a type founder from Edinburgh, sent a relative to this country with tools for a foundry at the end of the Revolutionary War, and shortly after, he came over himself. They operated the business until 1790, when Mr. Baine died, and his relative returned to Scotland.
A Dutch founder, Adam G. Mappa, settled at New York about 1787, and cast Dutch and German faces, as well as Roman styles and several Oriental alphabets. Want of capital prevented his success, and many of his matrices passed into the possession of Binny & Ronaldson.[7]
A Dutch founder, Adam G. Mappa, settled in New York around 1787 and created Dutch and German typefaces, as well as Roman styles and various Oriental alphabets. A lack of funding hindered his success, and many of his matrices ended up in the hands of Binny & Ronaldson.[7]
In 1796, type-founding was commenced in Philadelphia by Archibald Binny and James Ronaldson, natives of the city of Edinburgh, where Binny had carried on the same business. Their assortment was not extensive, but it embraced the essential founts,—Brevier, Bourgeois, Long Primer, Small Pica, Pica, and two-line letters. They were obliging and attentive, and in twenty years made a fortune. They improved their[20] foundry according to the increase of printing and the consequent demands of the trade, extending their assortment from Pearl, of 180 lines in a foot, to 12-line Pica, having 6 lines. Binny made an important improvement in the type-mould, by which a caster could cast 6000 letters in a day with as much ease as he before could cast 4000.[8]
In 1796, type-founding started in Philadelphia by Archibald Binny and James Ronaldson, both from Edinburgh, where Binny had previously run the same business. Their selection wasn't large, but it included the essential fonts: Brevier, Bourgeois, Long Primer, Small Pica, Pica, and two-line letters. They were friendly and attentive, and in twenty years, they built a fortune. They upgraded their foundry in response to the growth of printing and the resulting demands of the industry, expanding their selection from Pearl, which has 180 lines per foot, to 12-line Pica, which has 6 lines. Binny made a significant improvement to the type-mould, allowing a caster to produce 6,000 letters a day with the same ease as casting 4,000 before.
According to Holmes’s American Annals, about 200 newspapers were printed in the United States in the year 1801, of which 17 were issued daily, 7 three times a week, 30 twice a week, and 146 weekly. There must also have been at the same time as many as 60 offices engaged in miscellaneous printing. The whole business had increased threefold in eleven years. Another type-foundry was put in successful operation in Baltimore, about 1805, by Samuel Sower & Co. It had in it some moulds and matrices which had been used by Christopher Sower, who had printed in Germantown, near Philadelphia, and cast his own types. He printed with German characters; but now the foundry was revived with excellent Roman and Italic letters, and among other extraordinary things it had the size called Diamond, with a smaller face than had ever been cast before. It was the smallest type in the world.
According to Holmes’s American Annals, around 200 newspapers were published in the United States in 1801, with 17 released daily, 7 three times a week, 30 twice a week, and 146 weekly. There were also about 60 offices involved in various types of printing at that time. Overall, the industry had grown threefold in eleven years. Another type foundry began successful operations in Baltimore around 1805, run by Samuel Sower & Co. It had some molds and matrices that had been used by Christopher Sower, who printed in Germantown near Philadelphia and cast his own types. He printed with German characters, but now the foundry was back in action with excellent Roman and Italic letters, including a remarkable size known as Diamond, which was smaller than any type ever cast before. It was the smallest type in the world.
The demand for type was very brisk till the war of 1812 commenced, and the foundries were generally three or four months in arrears in their execution of orders.
The demand for type was very high until the War of 1812 started, and the foundries were usually three to four months behind in fulfilling orders.
The names of the newspapers published in the United States in April, 1810, are given in Thomas’s History of Printing, and amount to 359, of which 27 were daily papers, 38[21] were printed twice, 15 three times, and 279 once in a week. Add those required for general printing, and the whole number of offices could not be less than 500,—being an increase of 240 in nine years, and some of them using several thousand pounds of type for book-printing.
The names of the newspapers published in the United States in April 1810 are listed in Thomas’s History of Printing, totaling 359, which included 27 daily papers, 38[21] that were printed twice, 15 printed three times, and 279 published once a week. If you include those needed for general printing, the total number of offices would be at least 500, representing an increase of 240 in nine years, with some of them using several thousand pounds of type for book printing.
In 1811, Elihu White established a type-foundry in New York. He had been long engaged, in connection with Mr. Wing, in the manufacture of printing types at Hartford, Connecticut, upon a plan of their own invention, by which twenty or thirty letters were cast at once; but, abandoning that invention, he adopted the old plan of casting, and, having a good assortment of faces and bodies, his removal to New York was a great convenience to its printers, and they gave him a very satisfactory support. But the principal business in type-founding still continued, as formerly, to be carried on in Philadelphia.
In 1811, Elihu White set up a type foundry in New York. He had previously worked with Mr. Wing on making printing types in Hartford, Connecticut, using their own innovative method that could cast twenty or thirty letters at a time. However, he eventually moved away from that method and switched back to the traditional casting process. With a good variety of typefaces and sizes, his move to New York was a significant help to local printers, who supported him well. Despite this, the main type-founding business still continued to thrive in Philadelphia as it had before.
In 1813, another type-foundry was begun in the city of New York, by D. & G. Bruce, principally to cast types for their own use. They had carried on book-printing for seven years, and had now become acquainted with the stereotype art,—Mr. David Bruce having visited England in 1812 and acquired it by purchase and actual labour. For ordinary printing, it was customary to bevel off the body of the type at the face end, or shoulder, as it is usually called, which unfitted it for making a strong stereotype plate in the most approved way: hence the necessity for casting type expressly for stereotype. Their first fount was Bourgeois, with which they cast two sets of plates of the New Testament, (the Common School Testament,) and sold one of these to Mathew Carey, of Philadelphia, retaining the other for their own business. But these were not completed till 1814. In 1815, they cast the plates of the 12mo School Bible, on Nonpareil type, prepared, like the Bourgeois, at their own foundry expressly for stereotyping. They thus gave the first stereotype School Testament and School Bible to America; but not the first stereotype book. John Watts, of England, also commenced stereotyping in New York in 1813, and completed the Westminster Catechism that year, a volume of 120 pages 12mo. David Bruce invented the planing-machine for equalizing the thickness of stereotype plates, which is now used in every stereotype foundry in the United States. The process of stereotyping is, however, entirely[22] different from that of ordinary type-founding, and it is, therefore, generally carried on as a separate business, or connected with the composing department of a printing-office. Twenty compositors and two proof-readers will furnish full employment for one moulder, one caster, and three finishers, who will, among them, complete, on an average, 50 pages of octavo per day.
In 1813, a new type foundry was started in New York City by D. & G. Bruce, mainly to produce types for their own needs. They had been in book printing for seven years and were now familiar with the art of stereotyping—Mr. David Bruce had visited England in 1812 and learned it through purchase and hands-on work. For regular printing, it was common to bevel the body of the type at the face end, usually called the shoulder, which made it unsuitable for creating a strong stereotype plate in the best manner. This created a need to cast type specifically for stereotyping. Their first typeface was Bourgeois, with which they made two sets of plates for the New Testament (the Common School Testament) and sold one set to Mathew Carey in Philadelphia while keeping the other for their own use. However, these plates weren’t finished until 1814. In 1815, they produced the plates for the 12mo School Bible using Nonpareil type, prepared at their own foundry specifically for stereotyping, just like the Bourgeois. They thus provided America with its first stereotype School Testament and School Bible, though not the first stereotype book. John Watts from England also started stereotyping in New York in 1813 and completed the Westminster Catechism that year, which was a 120-page volume in 12mo. David Bruce invented the planing machine to standardize the thickness of stereotype plates, which is now used in every stereotype foundry in the United States. The process of stereotyping is, however, completely different from standard type founding, so it is usually operated as a separate business or linked to the composing department of a printing office. Twenty compositors and two proofreaders can fully employ one moulder, one caster, and three finishers, who together can produce an average of 50 pages of octavo each day.
In 1818, or soon after, a type and stereotype foundry was established in Boston, and another in Cincinnati, principally through the enterprise of the late Elihu White, who, having the means of multiplying matrices with facility, took this method for the extension of his business. Others followed his example, and type-foundries were established in Albany, Buffalo, Pittsburgh, Louisville, and St. Louis, with several additional in New York, Boston, Philadelphia, and Baltimore. The business, in fact, was overdone, and failures and suppressions took place, as competition reduced the prices of types.
In 1818, or shortly after, a type and stereotype foundry was opened in Boston, and another in Cincinnati, mainly thanks to the efforts of the late Elihu White, who, having the means to easily produce matrices, used this method to grow his business. Others followed his lead, and type foundries were set up in Albany, Buffalo, Pittsburgh, Louisville, and St. Louis, along with several more in New York, Boston, Philadelphia, and Baltimore. The industry became oversaturated, leading to failures and closures as competition drove down type prices.
The mode of type-founding has within forty years undergone important changes, which must no doubt be considered improvements. First among them is the introduction of machine-casting, in which a pump forces the fluid metal into the mould and matrix, and gives a sharper outline to the letter than was formerly given by the most violent throw of the caster. The old practice of casting a single type only at a time remains. The first idea of this machine originated with William M. Johnson, who obtained a patent for it in 1828. Elihu White put it into use in his type-foundry, and persevered in using and trying to improve it as long as he lived; but he did not succeed in removing the greatest fault, which was a hollowness in the body of the types cast by it, that inclined them to sink under the pressure of the printing-press. The first successful type-casting machine was invented by David Bruce, Jr., of New York, and was patented March 17, 1838. The patent was sold to George Bruce, and the machines were used by him until 1845. David Bruce meanwhile patented another machine in 1843, which, with new improvements, patented two years later, gave entire satisfaction, and is now in general use in American foundries. By Bruce’s machine, three times the quantity of type that was cast by Binny & Ronaldson’s improved mould is now cast in a given time, and nearly five times the quantity that was cast by the[23] common hand-mould eighty years ago. This improvement has passed into Europe, and been adopted by most of the German type-founders; but in Great Britain for some time it found little favour. A so-called “automatic machine,” for casting and finishing type, invented by Johnson & Atkinson, is in operation in London; but its rate of production seems to be less than that of the American machine, while, from its multiform operations, the proportion of imperfect type turned out must of necessity be considerably more.
The way type is made has changed a lot in the last forty years, and these changes can definitely be seen as improvements. The biggest change is the introduction of machine-casting, where a pump pushes molten metal into the mold and matrix, creating sharper letters than what was possible with the traditional method of casting. The old practice of casting one type at a time still exists. The idea for this machine came from William M. Johnson, who patented it in 1828. Elihu White implemented it in his type foundry and continued to refine it throughout his life; however, he couldn’t fix the main issue, which was that the type would be hollow, making them prone to sinking under the pressure of the printing press. The first successful type-casting machine was invented by David Bruce, Jr. from New York and was patented on March 17, 1838. The patent was sold to George Bruce, who used the machines until 1845. Meanwhile, David Bruce patented another machine in 1843, which, with new improvements patented two years later, provided full satisfaction and is now commonly used in American foundries. Bruce's machine produces three times the amount of type compared to Binny & Ronaldson’s improved mold in the same time frame, and nearly five times the amount produced by the common hand-mold from eighty years ago. This advancement has made its way to Europe and been adopted by many German type founders; however, it didn’t get much attention in Great Britain for a while. A so-called "automatic machine" for casting and finishing type, invented by Johnson & Atkinson, is currently in use in London; but its production rate seems to be lower than the American machine, and due to its multiple operations, the number of imperfect types produced is likely to be significantly higher.
The protection now afforded by the patent laws having checked the piratical production of matrices by electrotyping, (except in plain faces, a practice still pursued by unprincipled type-founders,) the leading founders in this country have been encouraged to produce types of new styles which in beauty and ingenuity surpass those of foreign origin.
The protection offered by patent laws has stopped the illegal production of matrices through electrotyping, (except for simple designs, which unprincipled type-founders still continue to do,) so the top type-founders in this country have been motivated to create new styles that are more beautiful and innovative than those from abroad.
There are now three type-foundries in Boston, seven in New York, one in Buffalo, four in Philadelphia, four in Baltimore, two in Cincinnati, four in Chicago, two in Milwaukee, two in St. Louis, one in Richmond, one in St. Paul, one in Cleveland, one in Kansas City, and three in California—in all, thirty-six. Some of these foundries not only supply the printers of the United States, but most of the printers in Canada, some in the British West India Islands, Mexico, South America, China, India and Australasia. American type, in quality, style, and finish, is equal, if not superior, to any made in Europe.
There are now three type foundries in Boston, seven in New York, one in Buffalo, four in Philadelphia, four in Baltimore, two in Cincinnati, four in Chicago, two in Milwaukee, two in St. Louis, one in Richmond, one in St. Paul, one in Cleveland, one in Kansas City, and three in California—making a total of thirty-six. Some of these foundries supply not only printers in the United States but also most printers in Canada, as well as some in the British West Indies, Mexico, South America, China, India, and Australasia. American type in quality, style, and finish is equal to, if not better than, any made in Europe.
The following are the prices at which plain types have been sold for the last seventy-five years, given at ten different dates, and naming only the principal and most useful sizes:—
The following are the prices at which standard types have been sold over the last seventy-five years, listed at ten different times, and mentioning only the main and most practical sizes:—
1806. | 1811. | 1819. | 1827. | 1831. | 1841. | 1860. | 1866. | 1876. | 1893. | |
---|---|---|---|---|---|---|---|---|---|---|
Pica | $0·44 | $0·55 | $0·44 | $0·42 | $0·36 | $0·38 | $0·32 | $0·56 | $0·46 | $0·32 |
Small Pica | ·48 | ·58 | ·48 | ·46 | ·38 | ·40 | ·34 | ·58 | ·48 | ·34 |
Lg. Primer | ·56 | ·66 | ·56 | ·50 | ·40 | ·42 | ·36 | ·62 | ·50 | ·36 |
Bourgeois | ·66 | ·76 | ·66 | ·58 | ·46 | ·46 | ·40 | ·66 | ·52 | ·38 |
Brevier | ·76 | ·86 | ·76 | ·70 | ·56 | ·54 | ·44 | ·70 | ·55 | ·42 |
Minion | 1·03 | 1·13 | 1·00 | ·88 | ·70 | ·66 | ·48 | ·76 | ·58 | ·46 |
Nonpareil | 1·40 | 1·75 | 1·40 | 1·20 | ·90 | ·84 | ·58 | ·84 | ·66 | ·52 |
Agate | 1·44 | 1·10 | 1·08 | ·72 | 1·00 | ·76 | ·60 | |||
Pearl | 1·75 | 1·40 | 1·40 | 1·08 | 1·40 | 1·20 | 1·20 | |||
Diamond | 1·60 | 1·80 | 1·62 | 1·60 |
STEREOTYPING.
Stereotyping is said to have been invented by J. Van der Mey, in Holland, about 1698. A quarto Bible and some other books were printed by him from plates, which were formed by soldering the bottoms of common type together. William Ged, of Edinburgh, discovered the present mode in 1725, and stereotyped parts of the Bible and Prayer-Book. He encountered malicious opposition, and the business was abandoned, the new method dying with the inventor. About 1745, Benjamin Mecom, a nephew of Dr. Franklin, cast plates for a number of the pages of the New Testament. Dr. Alexander Tilloch, of Glasgow, re-discovered the art in 1781. Stereotyping gradually spread, and soon effected a considerable reduction in the cost of books. The arguments that were advanced against its utility have a ridiculous look at the present day, when almost every important work is stereotyped or electrotyped.
Stereotyping is believed to have been created by J. Van der Mey in Holland around 1698. He printed a quarto Bible and several other books using plates made by soldering the bottoms of regular type together. William Ged from Edinburgh discovered the modern technique in 1725 and stereotyped sections of the Bible and Prayer Book. He faced harsh opposition, and his business was abandoned, causing the new method to die with him. Around 1745, Benjamin Mecom, a nephew of Dr. Franklin, cast plates for several pages of the New Testament. Dr. Alexander Tilloch from Glasgow re-discovered the technique in 1781. Stereotyping gradually became more common, significantly lowering the cost of books. The arguments against its usefulness seem absurd today, considering that almost every important work is now stereotyped or electrotyped.
Matter for stereotyping is set with high spaces and quadrates. The forms must be small, containing about two pages of common octavo. A slug type-high is put above the top line and another below the foot line of each page, to protect the ends of the plates from injury when they are passed through the shaving-machine. Beveled slugs, in height equal to the shoulder of the type, are placed on both sides and between the pages, to form the flange by which the plate is to be clasped by the hooks of the printing-block.
Matter for stereotyping is arranged in tall spaces and squares. The forms should be small, roughly two pages long in standard octavo size. A slug type-high is placed above the top line and another below the bottom line of each page to safeguard the edges of the plates from damage when they go through the shaving machine. Beveled slugs, equal in height to the shoulder of the type, are positioned on both sides and between the pages to create the flange that will be clamped by the hooks of the printing block.
Before the form is sent into the foundry, the type must be carefully compared with the proof, to detect any errors which may have been left uncorrected. Care must be taken to lock up the form perfectly square and quite tight, to prevent the types from being pulled out when the mould is raised from the pages. It must be evenly planed down, and no ink or dirt or incrustations from the ley be allowed to remain on the surface.
Before the form is sent to the foundry, the type must be carefully checked against the proof to catch any errors that might have been missed. It’s important to secure the form perfectly square and tightly to prevent the type from shifting when the mold is lifted off the pages. It should be evenly smoothed down, and no ink, dirt, or residue from the ley should be left on the surface.
The face of the type being clean and dry, and the bottoms free from particles of dirt, the form is laid on a clean moulding-stone, and brushed over with sweet-oil, which must be laid on as thinly as possible, care being taken that the entire surface of the types is covered. A moulding-frame, with a[25] screw at each corner, (called a flask,) and fitting neatly to the form, is next placed around it.
The type's face should be clean and dry, and the bottoms should be free of dirt. The form is put on a clean molding stone and brushed with sweet oil, applying it as thinly as possible while ensuring the entire surface of the type is covered. A molding frame, with a[25] screw at each corner (called a flask), is then placed around the form, fitting snugly.
The material for moulding is finely ground gypsum, nine parts of which are mixed with about seven parts of water, and well stirred up. A small quantity of the liquid mixture is poured over the pages, and gently pressed into the counter of the types with a small roller, for the purpose of expelling confined air; after which, the remainder of the gypsum is poured in, until the mould is somewhat higher than the upper edge of the flask. In a few minutes the mixture sets, and the upper side is smoothed over with a steel straight-edge. In about ten minutes the mould is gently raised by means of the screws at the corners of the flask; and, after being nicely trimmed at the sides, and nicked on the surface-edges to make openings for the metal to run in, it is placed on a shelf in an oven, and allowed to remain until the moisture has quite evaporated.
The material for molding is finely ground gypsum, nine parts of which are mixed with about seven parts of water and thoroughly stirred together. A small amount of the liquid mixture is poured over the pages and gently pressed into the typeface with a small roller to remove trapped air; then, the rest of the gypsum is poured in until the mold is slightly higher than the top edge of the flask. Within a few minutes, the mixture sets, and the top side is smoothed with a steel straightedge. After about ten minutes, the mold is carefully raised using the screws at the corners of the flask; and after being neatly trimmed on the sides and notched on the surface edges to create openings for the metal to flow in, it is placed on a shelf in an oven and left until all the moisture has completely evaporated.
The casting-pans may be large enough to hold three or four moulds. The dried moulds are placed in a pan face downward, upon a movable iron plate called a floater. The cover of the casting-pan, which has a hole at each corner for the passage of the metal, is then clamped to it, and lifted by a movable crane and gently lowered into the metal-pot,—containing, it may be, a thousand pounds of liquid metal,—till the metal begins to flow slowly in at the corners. When the pan is filled, it is sunk to the bottom of the pot. The metal should be hot enough to light a piece of brown paper held in it. After being immersed eight or ten minutes, the pan is steadily drawn out by means of the crane, and swung over to the cooling-trough, into which it is lowered and placed upon a stone so as just to touch the water, in order that the metal at the bottom of the pan may cool first. The metal contracts while cooling, and the caster occasionally pours in a small quantity at the corners from a ladle, till it will take no more. It may be here remarked that some stereotypers do not dry the moulds, but immerse them in a green condition into the metal.
The casting pans can be large enough to hold three or four molds. The dried molds are placed in the pan face down on a movable iron plate called a floater. The cover of the casting pan, which has a hole at each corner for the metal to flow through, is then clamped to it and lifted by a movable crane and gently lowered into the metal pot—which may contain up to a thousand pounds of liquid metal—until the metal starts to flow slowly in at the corners. When the pan is full, it's sunk to the bottom of the pot. The metal should be hot enough to ignite a piece of brown paper held in it. After being submerged for eight to ten minutes, the pan is carefully pulled out by the crane and swung over to the cooling trough, where it is lowered and placed on a stone just enough to touch the water so that the metal at the bottom of the pan cools first. The metal contracts while cooling, and the caster occasionally pours in a small amount from a ladle at the corners until it can’t take any more. It's worth noting that some stereotypers do not dry the molds but instead immerse them in a green state into the metal.
The plates are carefully removed from the solid mass which comes out of the pan, and the plaster is washed from the surface. If, after examination, the face is good and sharply set, the plates are passed over to a picker, who removes any slight defects arising from an imperfection of the[26] mould. They are then trimmed and passed through the shaving-machine, till all are brought to an equal thickness. The flanges are neatly side-planed, and the plates are then boxed, ready for the printing-press.
The plates are carefully taken off the solid mass that comes out of the pan, and the plaster is cleaned off the surface. If, after checking, the face looks good and sharp, the plates are given to a picker, who fixes any minor flaws from an imperfection of the[26] mold. They are then trimmed and run through the shaving machine until they all have the same thickness. The flanges are neatly side-planed, and the plates are then boxed up, ready for the printing press.
In England, the plates are merely turned on the back, and consequently vary in thickness. This must be a source of continual expense and annoyance to the pressman. The flanges, besides, are very imperfectly made,—so imperfectly that they cannot be used on American printing-blocks; and English plates, when imported into this country, are therefore sent to a foundry here, to be brought to an equal thickness and to be properly side-planed. An order given some years ago by an English printer for a set of American printing-blocks was afterward countermanded, on account of the prejudice against the introduction of new things.
In England, the plates are just flipped over, which leads to variations in thickness. This must cause ongoing costs and frustration for the press operator. Additionally, the flanges are poorly made—so poorly that they can't be used on American printing blocks. When English plates are brought into the U.S., they are sent to a local foundry to be adjusted to the correct thickness and properly side-planed. A request made a few years back by an English printer for a set of American printing blocks was later canceled due to hesitation about accepting new products.
Several methods of stereotyping are now practised. Many of the leading newspapers of England and America are printed from stereotype plates cast in moulds made of prepared paper: this mode, however, yields very inferior plates, quite unfit for fine books.
Several methods of stereotyping are currently used. Many of the major newspapers in England and America are printed from stereotype plates created using molds made of prepared paper; however, this method produces very low-quality plates that are not suitable for fine books.
Another method, styled the “mud-process,” is by spreading a thin coating of pulverized soapstone and gypsum over an iron plate, and a mould is then obtained by pressing the coated face against a page of type. Several of these mould-plates are then set on end in an iron box, separated from one another by a wire of the thickness of the stereotype desired, and hot metal is poured in. This is a very expeditious process, though not so good as the old method.
Another method, called the “mud-process,” involves spreading a thin layer of crushed soapstone and gypsum over an iron plate. A mold is created by pressing the coated surface against a page of type. Several of these mold plates are then placed upright in an iron box, separated by a wire of the thickness of the desired stereotype, and hot metal is poured in. This is a quick process, although it’s not as effective as the traditional method.
In 1804, before the introduction of stereotyping into this country, Mathew Carey, the well-known enterprising publisher in Philadelphia, had the Bible in quarto set up entire, and regularly imposed in chases, to print from at convenience, according to the demand for the volume. The type was cast by Binny & Ronaldson. Stereotyping would have saved much of the large outlay required to carry out the scheme, which, nevertheless, even under these circumstances, was doubtless highly remunerative. The weight of type must have amounted to 25,000 pounds, to say nothing of the number of chases and column-rules required.
In 1804, before stereotyping was introduced in this country, Mathew Carey, the well-known and enterprising publisher in Philadelphia, had the entire Bible typeset in quarto format and regularly placed in chases to print as needed, based on the demand for the volume. The type was cast by Binny & Ronaldson. Stereotyping could have significantly reduced the large costs required to execute the project, which, despite this, was certainly still very profitable. The total weight of the type must have been around 25,000 pounds, not to mention the number of chases and column rules needed.
ELECTROTYPING.
Stereotyping has been superseded by the process of electrotyping, as described below.
Stereotyping has been replaced by the process of electrotyping, as described below.
The pages, after being delicately polished with plumbago, are laid in a press; a pan of prepared wax, warmed, is placed over them and pressed down into the counter of the types. The wax mould is then dusted with plumbago, and suspended in the electric bath. On this, in a few hours, is deposited a thin shell of copper, which, after being coated with tin solder, is backed up with metal to the usual thickness of a stereotype plate.
The pages, after being carefully polished with graphite, are placed in a press; a pan of heated wax is put over them and pressed down onto the type. The wax mold is then dusted with graphite and put into an electric bath. After a few hours, a thin layer of copper forms on this, which is then coated with tin solder and backed with metal to the standard thickness of a stereotype plate.
The same care in preparing the pages for electrotyping must be observed as for stereotyping. For stereotyping, high slugs are placed only at the top and foot of the page; but, for electrotyping, they must be set around on all sides, and the bevelled flange must be afterward made by side-planing.
The same attention in preparing the pages for electrotyping needs to be taken as for stereotyping. For stereotyping, high slugs are placed only at the top and bottom of the page; however, for electrotyping, they must be placed around all sides, and the beveled flange must be created later by side-planing.
LITHOGRAPHY.
This is the art of printing, by a chemical process, from designs made with a greasy material upon stone. It was discovered about the beginning of the present century by Alois Senefelder, an actor of Munich, Bavaria, whose patience and perseverance under the most disadvantageous circumstances were truly remarkable and praiseworthy. Differing from all other methods of printing, the impressions are obtained from a level surface.
This is the art of printing using a chemical process, based on designs created with a greasy substance on stone. It was discovered around the beginning of this century by Alois Senefelder, an actor from Munich, Bavaria, whose patience and determination in challenging situations were genuinely impressive and commendable. Unlike all other printing methods, the prints are made from a flat surface.
The stone best calculated for lithographic purposes is a sort of calcareous slate found on the banks of the Danube, in Bavaria, the finest being found near Munich. A good stone is porous, yet brittle, of a pale yellowish drab, and sometimes of a gray neutral tint. The stones are formed into slabs from one and a-half to three inches in thickness. To prepare them for use, two stones are placed face to face with some fine sifted sand between them, and then are rubbed together with a circular motion, to produce the requisite granulation, which is made finer or coarser to suit the purpose of the artist.
The best stone for lithographic purposes is a type of calcareous slate found along the banks of the Danube in Bavaria, with the highest quality located near Munich. A good stone is porous but brittle, and has a pale yellowish drab color, sometimes with a gray neutral tint. The stones are shaped into slabs that are one and a half to three inches thick. To prepare them for use, two stones are placed face to face with fine sifted sand in between, and then rubbed together in a circular motion to create the necessary granulation, which can be adjusted to be finer or coarser depending on the artist's needs.
The principal agents used for making designs on stone are[28] called lithographic chalk and lithographic ink. They are composed of tallow, virgin wax, hard tallow soap, shellac, sometimes a little mastic or copal, and enough lampblack to impart a colour to the mass. These ingredients are put into an iron sauce-pan, and exposed to a strong fire till the mass is in a state of ignition. When the quantity is reduced one-half, the pan is carefully covered, or put into water to extinguish the flame and cool the mixture. After being well worked up, it is formed into small cakes or sticks. The ingredients are the same in the chalk and the ink, but the proportions are varied, and a little Venice turpentine is often added to the latter. The chalk is used in a dry state; but the ink is dissolved by rubbing in water, and is used in a pen or with a camel-hair pencil. The presence of soap renders it soluble in water.
The main materials used for creating designs on stone are[28] known as lithographic chalk and lithographic ink. They consist of tallow, virgin wax, hard tallow soap, shellac, and sometimes a bit of mastic or copal, along with enough lampblack to give color to the mixture. These ingredients are placed in an iron saucepan and heated over a strong fire until the mixture ignites. Once the amount is reduced by half, the saucepan is carefully covered or placed in water to put out the flame and cool the mixture. After being thoroughly mixed, it is shaped into small cakes or sticks. The ingredients are the same for both the chalk and the ink, but the proportions differ, and a little Venice turpentine is often added to the ink. The chalk is used in its dry form, while the ink is dissolved by mixing it with water and is applied with a pen or a camel-hair brush. The inclusion of soap makes it soluble in water.
The artist completes a drawing with the chalk upon a grained stone as he would make a drawing in pencil or chalk upon paper. If while in this state a wet sponge were passed over the face of the stone, the drawing would wash off. To prevent this, and to make it capable of yielding impressions, a weak solution of nitrous acid is poured over it, which unites with and neutralizes the alkali or soap contained in the chalk, and renders it insoluble in water. After this, the usual course is to float a solution of gum over the whole face of the stone; and, when this is taken off, the drawing is no longer removable by the application of a wet sponge, because the chalk is now insoluble. The stone is now ready for the printer, who obtains impressions by the following process.
The artist finishes a drawing with chalk on a textured stone just like he would with pencil or chalk on paper. If a wet sponge were to be applied to the surface of the stone while in this state, the drawing would wash away. To prevent this and to allow for impressions to be made, a weak solution of nitrous acid is poured over it, which combines with and neutralizes the alkali or soap in the chalk, making it insoluble in water. After that, the typical procedure is to spread a solution of gum over the entire surface of the stone; once this is removed, the drawing can no longer be wiped off with a wet sponge because the chalk is now insoluble. The stone is now ready for the printer, who makes impressions using the following process.
Having damped the surface of the stone equally with a sponge filled with water which has been slightly tinctured by acid, the printer finds that the water has been imbibed by only those parts of the stone which are not occupied by the drawing, which, being greasy, repels the water and remains dry. A roller covered with ink is now passed over the stone, which will not even be soiled where it is wet, from the antipathy of oil to water. But the parts occupied by the drawing, being dry and greasy, have an affinity for the printing-ink, which, therefore, leaves the roller and attaches itself to the drawing. In this state it is said to be charged or rolled in. A sheet of damped paper is then put over it, and, the[29] whole being passed through a press, the printing-ink is transferred from the stone to the paper, and the impression is obtained. Great nicety is requisite in the preparation of all the agents employed in this art, and in the process of printing as well as in making the drawing on the stone.
After dampening the surface of the stone with a sponge filled with water that's been slightly tinted with acid, the printer notices that the water has only soaked into the areas of the stone that aren't covered by the drawing. The drawing, being greasy, repels the water and stays dry. Next, a roller covered with ink is rolled over the stone, which won't even pick up ink where it's wet because oil and water don't mix. However, the areas with the drawing, being dry and greasy, attract the printing ink, which then leaves the roller and sticks to the drawing. At this point, it's said to be charged or inked up. A sheet of damp paper is placed over it, and once everything is passed through a press, the printing ink transfers from the stone to the paper, resulting in the impression. Careful attention is needed in preparing all the materials used in this art, as well as in the printing process and drawing on the stone.
The most important application of this process is in the production of copies of coloured drawings and paintings,—a process known as chromo-lithography. The object here being to produce as nearly as possible fac-similes in colour, touch, and texture, as well as in drawing and light and shadow, of pictures from the pencils of painters of the highest standing, it has been found necessary to employ a large number of stones, in order to produce the almost infinite varieties of tints which are found united in a single picture,—every stone giving a separate impression in its own particular colour or tint. The mode of procedure is somewhat as follows. First, an outline of the entire subject is made by means of transfer paper, or otherwise, on a stone which is called the outline or keystone of the work. This stone yields impressions which are transferred as guides to all the other stones. On a second and third stone which serve as the basis of the print the general effect of the drawing is washed in, and from these are printed what may be called the chiaroscuro, in a faint tint of sepia and of a neutral colour or gray,—corresponding, in fact, very nearly to the neutral or dead colouring of a water-colour drawing in the method adopted by the early water-colour painters. The stones which follow are each charged with a particular colour or tint, and each leaves its impression on only a particular portion of the print,—one stone printing only the parts which are intended to be yellow or a modification of yellow, another red, another blue, and so on. Other stones charged in parts with grays or secondary colours serve to blend and harmonize the crude colours; others follow which modify these; and, finally, one gives the sharp dark touches, and is usually followed by another which supplies a sort of glaze or finishing wash, and subdues and harmonizes the whole. Of course, we have merely indicated the general method. It will be understood that the sequence of the colours in the printing, the special quality and strength to be given to each particular tint, the effect to be produced[30] by their super-position, and many other particulars, have all to be taken into account in planning the arrangement of the colours on the stones;—since a sequence in some respects different, and an entirely different modification of colours, have to be employed for the works of most artists; and it happens that much of the colour on each of the earlier stones is covered by that of succeeding stones, and that thus only can the broken tints of the original be imitated. It is, in fact, only by watching the progress of a print through all its stages that any clear idea can be obtained of the beauty and accuracy of the whole process, of the prevision that must be exercised, and of the skill, care, and taste required at every step to carry it to a successful termination. For some of the more elaborate prints, from thirty to forty stones have been required to produce a finished print. And in order to produce this print, it must be borne in mind that each sheet of paper has to be passed as many times through the press as there are stones, since each stone imprints upon it only its own particular section of the work. Of course, in proportion to the increase in the number of the stones, does the difficulty increase of making the work upon each fall exactly upon its proper place in the general design; for, if any one were misplaced only the fiftieth of an inch, the drawing and colour of the whole would be disturbed. Hence it is found necessary to arrange the register, or adjustment of the stones, with the utmost care and precision, and to exercise the most careful supervision in the printing, since the sheet of paper expands considerably in passing through the press, and has to be dried and re-damped before it can be passed through again. But practically this is all accomplished with seeming ease, and a large and most complex subject will be found, when the last stage has been reached, to bear the most minute scrutiny; and the result, even when the copy is placed alongside the original, will surprise and delight equally those who have followed the work through its several steps and those who may only examine the completed work.
The most important use of this process is in creating copies of colored drawings and paintings, a process called chromo-lithography. The goal is to produce nearly identical replicas in color, texture, and shading, as well as in the drawing itself, from the works of highly esteemed artists. To achieve this, a large number of stones are required to create the almost endless variations of hues found in a single image—each stone produces a separate impression in its unique color or shade. The process works like this: First, an outline of the entire subject is made on a stone, known as the outline or keystone of the work, using transfer paper or another method. This stone creates impressions that serve as guides for all the other stones. On the second and third stones, which form the basis of the print, the overall effect of the drawing is filled in lightly, producing what can be called chiaroscuro, using a faint sepia tint and a neutral color or gray. This closely resembles the neutral wash used in water-color painting by early watercolor artists. Subsequent stones are each loaded with a specific color or hue, and each prints only a certain part of the artwork—one stone prints the areas meant to be yellow or a variation of yellow, another prints red, another blue, and so on. Additional stones with grays or secondary colors help to blend and balance the bold colors; others modify these; and finally, one stone adds the sharp dark details, often followed by another that provides a kind of glaze or final wash to soften and harmonize the entire piece. Of course, we’ve only outlined the general procedure. It should be clear that the order of colors in printing, the unique quality and intensity of each tint, the effect from their layers, and many other factors must all be considered when organizing the colors on the stones. Different sequences and color modifications are needed for different artists, and much of the color on the earlier stones gets covered by that of the later stones, which is essential for mimicking the original's subtleties. In fact, it's only by observing the progress of a print through all its phases that one can truly appreciate the beauty and precision of the entire process, along with the foresight, skill, care, and flair necessary at every step to achieve a successful outcome. Some intricate prints can require anywhere from thirty to forty stones to create a finished product. It’s also important to remember that each sheet of paper must go through the press as many times as there are stones, since each stone only impresses its designated section of the artwork. As the number of stones increases, so does the challenge of aligning each one perfectly within the overall design; if any stone is misaligned by even a tiny fraction of an inch, it disrupts the drawing and color of the entire piece. Therefore, precision in arranging the register of the stones is crucial, and careful oversight during printing is essential since the paper expands significantly when passing through the press and needs to be dried and re-damped before going through again. Despite this complexity, the process appears to be executed effortlessly, and when reaching the final stage, even a large and intricate subject withstands careful examination. The result, when placed next to the original, is sure to amaze and please both those who have witnessed the process firsthand and those who simply view the finished work.
Of late, many chromos have been beautifully printed from prepared blocks on an ordinary cylinder-press.
Recently, many chromos have been beautifully printed from prepared blocks using an ordinary cylinder press.
ENGRAVING.

The invention of wood engraving has been claimed for the Chinese, whose books have certainly been printed from engraved wood blocks for ages. It is not, however, until the beginning of the fifteenth century that we find any evidence of the existence of wood engraving as we now understand it.
The invention of wood engraving is attributed to the Chinese, who have definitely been printing books using engraved wood blocks for centuries. However, it isn't until the early fifteenth century that we see any evidence of wood engraving as we understand it today.
It is probable that Italy was the first European country to make engravings, but only for printing playing-cards. Holland and Germany soon applied the art to better ends.
It’s likely that Italy was the first European country to create engravings, but only for printing playing cards. Holland and Germany quickly used the technique for more significant purposes.
The earliest print of which any certain information can be obtained is in the collection of Earl Spencer. It was discovered in one of the most ancient convents of Germany,—the Chartreuse of Buxheim, near Memmingen in Bavaria,—pasted within the cover of a Latin MS.; it represents Saint Christopher carrying the infant Saviour across the sea, and is dated 1423. We give a reduced fac-simile of this curious engraving. The inscription at the bottom has been thus translated:—
The earliest print that we have reliable information about is in Earl Spencer's collection. It was found in one of the oldest monasteries in Germany—the Chartreuse of Buxheim, near Memmingen in Bavaria—taped inside the cover of a Latin manuscript. It shows Saint Christopher carrying the infant Savior across the sea and is dated 1423. We provide a resized facsimile of this interesting engraving. The inscription at the bottom has been translated as follows:—

Shortly afterward, a series of books printed entirely from wood engravings, called block-books, were issued. The most important of them were the Apocalypsis, seu Historia Sancti Johannis; the Historia Virginis ex Cantico Canticorum; and the Biblia Pauperum, the last containing representations of some of the principal passages of the Old and New Testaments, with explanatory texts. The illustrations seem to be drawn with a supreme contempt for perspective and proportion, but bear evidence of the draperies and hands and faces having been carefully studied. The above is a copy of one of the cuts in the Apocalypsis. It represents St. John preaching to three men and a woman, with the inscription: “Conversi ab idolis, per predicationem beati Johannis, Drusiana et ceteri,” (By the preaching of St. John, Drusiana and others are withdrawn from their idols.) The adjoining[33] cut, from the Biblia Pauperum, is curious as showing the general manner of representing the creation of Eve during the fifteenth century. Both have the appearance of careful drawings “spoiled in the engraving.” Previous to the invention of movable types, whole books of text were also engraved on wood, and the impressions were evidently taken by rubbing on the back of the paper, instead of a steady pressure, as in the printing-press, the ink used being some kind of distemper colour.
Shortly after, a series of books printed entirely from wood engravings, known as block-books, were released. The most significant among them were the Apocalypsis, seu Historia Sancti Johannis; the Historia Virginis ex Cantico Canticorum; and the Biblia Pauperum, the last of which includes illustrations of some key passages from the Old and New Testaments, along with explanatory texts. The illustrations appear to show a blatant disregard for perspective and proportion but demonstrate that the draperies, hands, and faces were carefully studied. The above is a copy of one of the cuts in the Apocalypsis. It depicts St. John preaching to three men and a woman, with the inscription: “Conversi ab idolis, per predicationem beati Johannis, Drusiana et ceteri” (By the preaching of St. John, Drusiana and others are turned away from their idols.) The adjacent [33] cut, from the Biblia Pauperum, is interesting as it shows the typical way of illustrating the creation of Eve during the fifteenth century. Both have the look of careful drawings “ruined in the engraving.” Before the invention of movable type, entire books of text were also engraved on wood, and the impressions were clearly made by rubbing the back of the paper, rather than using steady pressure like in a printing press, with the ink being some kind of distemper color.

The wood to be engraved on is carefully selected, and cut up into transverse slices seven-eighths of an inch thick. This is done by circular saws, which are necessarily very rigid, so as to insure good even cuts.
The wood chosen for engraving is carefully picked and cut into cross-sections that are seven-eighths of an inch thick. This is done using circular saws, which have to be very rigid to ensure clean, even cuts.
After being cut, the slices are placed in racks something like plate-racks, and thoroughly seasoned by slow degrees in gradually heated rooms. When sufficiently seasoned they are reduced to parallelograms of various sizes, the outer portion of the circular section near the bark being cut away, and all defective wood rejected; such, for instance, as knots, irregular grain, as that resulting from the position of branches, which are indicated by light-coloured markings in the wood, known in the trade as “comets,” from their resemblance in shape to those fiery bodies. They are softer than the surrounding wood, and consequently do not cut well with the graver; therefore much care and a practised eye are needed in selecting suitable wood. A section of boxwood almost always exhibits parts of widely different values; the more so as it deviates from the circle in form, for then the annual rings are compressed, and consequently closer on one side than on the other, the side with the wide open rings being usually far inferior in value to the denser and smaller side.
After being cut, the slices are placed in racks similar to plate racks and gradually seasoned in slowly heated rooms. Once they’re seasoned enough, they’re trimmed into parallelograms of various sizes, with the outer section near the bark being removed, and any defective wood discarded; this includes things like knots and irregular grain, which are indicated by lighter-colored markings in the wood, referred to in the industry as “comets” because they resemble those fiery bodies in shape. These softer areas don’t cut well with the chisel, so a keen eye and careful selection are essential when choosing suitable wood. A piece of boxwood typically shows parts of varying quality; this difference increases as it strays from a circular shape, causing the annual rings to be compressed, making them closer on one side than the other, with the side that has wider open rings usually being of much lower value than the denser and smaller side.
In former times, engravers’ blocks were cut parallel with the grain, the present system of cutting them across the grain being introduced about the middle of the last century. In the preparation of a block, say for a newspaper plate, the parallelograms before spoken of are assorted as to size and fitted together at the back by brass bolts and nuts. So accurately do the edges of the wood fit together, that after the artist has finished his drawing on the smooth face of this compound block, the screws and bolts are loosened, and the pieces separated and given to several men to engrave the design; all that is needed after they have finished their work[34] being to fit the pieces together and screw them up again, when they form one engraved block ready for the printing-press.
In the past, engravers’ blocks were cut along the grain, but the current method of cutting them across the grain started around the middle of the last century. When preparing a block, like for a newspaper plate, the parallelograms mentioned earlier are sorted by size and connected at the back with brass bolts and nuts. The edges of the wood fit together so precisely that once the artist completes their drawing on the smooth surface of this combined block, the screws and bolts are loosened, and the pieces are separated and given to several people to engrave the design. All that’s needed after they finish their work[34] is to put the pieces back together and tighten the screws, resulting in one engraved block ready for the printing press.
Turkey boxwood, from a region of country in the vicinity of the Black Sea, is used for fine engravings. The best is of a delicate yellow colour free from spots or “eyes,” and cuts smoothly without crumbling or tearing.
Turkey boxwood, sourced from an area near the Black Sea, is used for detailed engravings. The finest examples have a soft yellow color that is clear of blemishes or “eyes,” and they carve smoothly without breaking or tearing.
The tools or gravers necessary in wood-engraving are of three kinds,—viz., gravers proper (a); tint tools (b); and scoopers, or cutting-out tools, for clearing out the larger pieces (c). They are arranged in different sizes, to suit the various portions of the work.[9]
The tools or gravers needed for wood engraving come in three types: proper gravers (a), tint tools (b), and scoops or cutting-out tools for removing larger pieces (c). They are available in different sizes to fit various parts of the work.[9]

According to Vasari, the important discovery of chalcography or engraving on brass or copper was made by Tommaso Finiguerra, a Florentine goldsmith of the fifteenth century, who lived from 1400 to 1460. The manner in which he made this discovery is thus stated by the Rev. T. F. Dibdin:—
According to Vasari, the important discovery of chalcography, or engraving on brass or copper, was made by Tommaso Finiguerra, a Florentine goldsmith of the fifteenth century, who lived from 1400 to 1460. The way he made this discovery is described by the Rev. T. F. Dibdin:—
“Of engraving upon copper, the earliest known impression is that executed by one Tommaso Finiguerra, a goldsmith of Florence, with the date of 1460 upon it. One of the following circumstances is supposed to have given rise to the discovery. Finiguerra chanced to cast, or let fall, a piece of copper, engraved and filled with ink, into melted sulphur; and, observing that the exact impression of his work was left on the sulphur, he repeated the experiment on moistened paper, rolling it gently with a roller. This origin has been admitted by Lord Walpole and Mr. Landseer; but another has been also mentioned by Huber. ‘It is reported,’ says he, ‘that a washerwoman left some linen upon a plate or dish on which Finiguerra had just been engraving, and that an impression of the subject engraved, however imperfect, came off upon the linen, occasioned by its weight and moistness.’”
“Regarding engraving on copper, the earliest known print is by Tommaso Finiguerra, a goldsmith from Florence, dated 1460. It's believed that one of the following scenarios led to this discovery. Finiguerra accidentally dropped a piece of copper, which was engraved and filled with ink, into melted sulfur; and, noticing that an exact impression of his work was left on the sulfur, he tried the same technique with moistened paper, gently rolling it with a roller. This origin story has been accepted by Lord Walpole and Mr. Landseer, but Huber mentions another account. He states, ‘It is reported that a washerwoman left some linen on a plate or dish where Finiguerra had just been engraving, and that an impression of his engraving, though imperfect, transferred onto the linen due to its weight and moisture.’”
PHOTO-ENGRAVING.
Photo-engravings are produced by means of photography. It is a fact worthy of note that experiments in photographic engraving gave rise to photography itself. The aim of Nicéphore Niepce, when he began his researches in 1813, was not only to fix the image obtained by the camera obscura on a plate of metal, but to convert this plate into an engraving which could be used on a printing-press. His early death prevented his perfecting the process to which he had devoted much time and study.
Photo engravings are created using photography. It's important to note that experiments in photographic engraving led to the development of photography itself. When Nicéphore Niepce started his research in 1813, his goal was not just to capture the image from the camera obscura on a metal plate, but to turn that plate into an engraving that could be used on a printing press. His early death stopped him from perfecting the process to which he had dedicated so much time and effort.
Three distinct methods of photo-engraving are employed in the United States, viz.: swelled gelatine, photo-etching, and wash-out. The latter is known as photo-electrotyping.
Three different methods of photo-engraving are used in the United States: swollen gelatin, photo-etching, and wash-out. The last one is known as photo-electrotyping.
The first steps to produce a plate by any of these processes are exactly alike, i. e. a perfectly sharp negative, either in line or stipple, must be produced. If the copy furnished is a wood-cut, steel or lithographic print, in which the lines are absolutely black on white paper or card, the negative is made direct and no drawing is necessary, unless a very great reduction is required, when it becomes necessary to make a drawing, the lines of which are made open enough to stand the necessary reduction. Where the copy furnished is a photograph, or wash drawing, it is first photographed one half larger, or, where fine work is desired, twice the size the plate required. In cases where exceptionally fine work is required it is even made three times the size. The photograph thus obtained is technically termed a silver print, and is an untoned print on plain paper. On this silver print the artist makes his drawing, using the best India ink, which must be so black that the finest hair-line, when examined through a magnifying glass, appears absolutely jet black. After the drawing is made, an alcoholic solution of bichloride of mercury is poured over it, and quickly washed under the tap, leaving the drawing on perfectly white paper. The artist then does whatever retouching may be necessary, and the drawing is ready to be photographed. The advantages of this method of drawing are apparent. The artist, being able to work directly on the enlarged photograph of the object, obtains absolutely correct outlines and detail. The drawing, when finished, is sent to the gallery, where it is photographed to the required size of the plate. The[36] focus of the camera is carefully adjusted with the aid of a focusing glass, so that the negative resulting will be perfectly sharp. This must be carefully done, for unless the negative be sharp a perfect plate cannot be obtained by any process. The sensitized collodion plate is exposed in the camera from one to six minutes, after which it is taken again to the dark room, developed, and fixed. It is then intensified until the portions representing the whites of the picture are perfectly opaque. Up to this point all the processes are alike, and the differences from here will be noted.
The first steps to create a plate using any of these methods are exactly the same: a perfectly sharp negative, either in line or stipple, has to be produced. If the provided copy is a woodcut, steel, or lithographic print, where the lines are completely black on white paper or card, the negative is made directly and no drawing is needed, unless a significant reduction is required, in which case a drawing must be created with lines spaced wide enough to withstand the necessary reduction. When the supplied copy is a photograph or wash drawing, it is first photographed at one and a half times the size or, when fine work is desired, twice as large as the required plate. In cases where exceptionally fine work is needed, it is even produced three times the size. This resulting photograph is technically called a silver print, which is an untoned print on plain paper. The artist then makes their drawing on this silver print using the best India ink, which must be so black that the finest hairline looks completely jet black when viewed through a magnifying glass. After the drawing is completed, an alcoholic solution of bichloride of mercury is poured over it and quickly washed under running water, leaving the drawing on perfectly white paper. The artist then does any necessary retouching, and the drawing is ready to be photographed. The benefits of this drawing method are clear. The artist can work directly on the enlarged photograph of the object, achieving absolutely accurate outlines and details. Once finished, the drawing is sent to the gallery, where it's photographed to the required plate size. The[36] focus of the camera is carefully adjusted with a focusing glass to ensure that the resulting negative is perfectly sharp. This must be done carefully since a sharp negative is essential for obtaining a perfect plate through any process. The sensitized collodion plate is exposed in the camera for one to six minutes, after which it is taken back to the darkroom, developed, and fixed. It is then intensified until the areas representing the whites of the picture are completely opaque. Up to this point, all the processes are the same, and the differences will be noted from here.
If the plate is to be produced by the swelled gelatine process, the negative is varnished and sent to the gelatine room. Here the gelatine is dissolved and the sensitized solution of bichromate of potash is added, and it is flowed on plate glass, then placed in a drying box, where a current of air is continually passed over it. When the gelatine is dry it is placed in a printing frame, in close contact with the negative, and exposed to the light. On removing the negative the picture is plainly seen on the gelatine, the action of the light having changed the color of the exposed portions of the gelatine, besides rendering those parts insoluble, while the parts protected from the action of the light, by the opacity of the negative, remain soluble, and are swelled up by immersion in cold water. The gelatine is then an exact opposite of the plate, the whites being represented by the raised portions. From this mould, or relief, a cast is made in a preparation of wax or plaster, when it is ready for the stereotyper.
If the plate is going to be made using the swelled gelatine process, the negative is varnished and sent to the gelatine room. There, the gelatine is dissolved, and the sensitized bichromate of potash solution is added. This mixture is spread onto plate glass and then placed in a drying box, where a continuous current of air passes over it. Once the gelatine is dry, it is put into a printing frame in close contact with the negative and exposed to light. When the negative is removed, the image is clearly visible on the gelatine, as the light has changed the color of the exposed areas and made them insoluble, while the parts shielded from the light by the opacity of the negative stay soluble and swell up when immersed in cold water. The gelatine now has raised portions where the whites are represented, creating an exact opposite of the plate. From this mold, or relief, a cast is made in a wax or plaster preparation, making it ready for the stereotyper.
For the wash-out or photo-electrotype process, the negative, when dry, is not varnished, but is first coated with a rubber solution and then with plain collodion, after which it is immersed in a dish of acetic acid for about five minutes, when it is stripped from the glass and turned over. It is then what is termed a reversed negative. The method of preparing the gelatine is very much the same as for the swelled process, with the exception that it is cooked for about forty-eight hours, and with the addition of several preparations which are introduced at the time of sensitizing, to make it easily washed out. The negative is exposed in the same manner as described before, but the time of exposure is generally less. After being taken from the printing frame the gelatine is gently scrubbed with a line brush, and kept in tepid water[37] until a very slight relief is obtained. It is then immersed in alcohol for a few seconds, and dried with a cloth, when it is covered with a preparation of lamp black and glycerine, which is allowed to remain about five minutes, when the surface of the plate is carefully rubbed with clean muslin, exposing the surface of the lines,—all this being done in a dark room before an orange light, which is non-actinic. The gelatine is now placed in a frame and exposed to the light from five to twenty minutes, the lampblack protecting the spaces between the lines from the action of the light, so that those portions remain soluble. The gelatine is again scrubbed until the proper relief is obtained, after which it is allowed to dry for about twelve hours, when it becomes hard and is ready to be electrotyped.
For the wash-out or photo-electrotype process, the negative, once dry, is not varnished but is first coated with a rubber solution and then with plain collodion. After that, it’s immersed in a dish of acetic acid for about five minutes, at which point it is stripped from the glass and flipped over. It then becomes what is known as a reversed negative. The method for preparing the gelatin is quite similar to the swelled process, except it is cooked for about forty-eight hours and has several preparations added at the time of sensitizing to make it easier to wash out. The negative is exposed the same way as described earlier, but the exposure time is generally shorter. After being removed from the printing frame, the gelatin is gently scrubbed with a fine brush and kept in lukewarm water[37] until a very slight relief is achieved. It is then immersed in alcohol for a few seconds and dried with a cloth, after which it is covered with a mixture of lamp black and glycerin, which is left to sit for about five minutes. The surface of the plate is then carefully rubbed with clean muslin to expose the surface of the lines—all this is done in a dark room under orange light, which is non-actinic. The gelatin is now placed in a frame and exposed to light for five to twenty minutes, with the lamp black protecting the spaces between the lines from the light’s action, so those areas remain soluble. The gelatin is scrubbed again until the appropriate relief is achieved, and then it is allowed to dry for about twelve hours, at which point it becomes hard and is ready to be electrotyped.
The negatives for photo-etching are stripped and reversed in the same manner as for the wash-out process. The metal generally employed for this process is zinc, though copper is sometimes used for very fine work. The zinc is very highly polished, and a thin sensitizing solution is flowed over it and dried, after which it is exposed under the negative to the action of the light. It is then rolled up with lithographic ink, placed in a dish of cold water, and gently rubbed with absorbent cotton, the ink readily leaving the unexposed parts, but remaining on the exposed lines or dots. It is then quickly dried and dusted over with dragon’s-blood powder, which adheres only to the remaining inked portions. The plate is then heated and cooled, and is ready for the etching bath, which consists of a small portion of nitric acid and water. After the first bite the plate is again powdered, heated and cooled, and more acid added to the bath. This is repeated several times, after which the plate is ready for the press. The sides of the lines are protected by the manner in which the powder is applied after the first bite. The relief obtained in this way is greater than can be obtained by any other process.
The negatives for photo-etching are stripped and reversed just like in the wash-out process. Zinc is usually the metal used for this process, but copper can be used for very fine work. The zinc is polished to a high shine, and a thin sensitizing solution is spread over it and dried. After that, it’s exposed to light under the negative. Then, it’s inked with lithographic ink, placed in cold water, and gently rubbed with absorbent cotton. The ink easily washes off the unexposed areas but stays on the exposed lines or dots. Next, it’s quickly dried and dusted with dragon’s-blood powder, which only sticks to the remaining inked areas. The plate is then heated, cooled, and prepared for the etching bath, which contains a small amount of nitric acid and water. After the first bite, the plate is powdered again, heated and cooled, and more acid is added to the bath. This process is repeated several times, after which the plate is ready for the press. The sides of the lines are protected by how the powder is applied after the first bite. The relief achieved this way is greater than by any other method.
In reviewing the three processes above described, it is readily seen that the photo-etching process is the shorter method, no moulding or casting being necessary, and the sharpness of the finest lines is preserved in a manner impossible by the other methods. The plates are much deeper, and are equally suitable for the finest art work, down to the roughest newspaper work. This process, of which there are several modes of operating, has become very popular in the last few[38] years, owing to the many improvements introduced by the process inventors, who have turned their attention to it. It has many advantages, among which is the fact that a plate can be put on the press within two hours from the time the copy is ready; and the wearing capacity of the plates is greater. By this process more than 300,000 impressions have been taken from plates of fine work, while swelled gelatine plates of the same character of work would not stand over 5000, and electrotypes 50,000 impressions. The main advantage of photo-etchings to the printer is, that the plates do not require constant washing up, as is the case with plates made by the other processes.
In looking back at the three processes mentioned above, it's clear that the photo-etching process is the quickest method since it doesn't require any molding or casting. It also maintains the sharpness of the finest lines in a way that's not possible with the other methods. The plates are much deeper and are suitable for everything from high-quality art to basic newspaper work. This process, which has several different ways of operating, has gained a lot of popularity in the last few [38] years due to the numerous improvements made by the process inventors who have focused their efforts on it. It has many benefits, one of which is that a plate can go on the press within two hours after the copy is ready, and the durability of the plates is higher. With this process, more than 300,000 impressions have been made from plates of high-quality work, while swollen gelatin plates of the same quality could manage only about 5,000, and electrotypes could do about 50,000 impressions. The biggest advantage of photo-etchings for printers is that the plates don’t need constant cleaning, unlike those made using the other methods.
A photograph, brush drawing, or any copy that is not made up of line or stipple, can be produced without the necessity of a line drawing by the aid of the half-tone process. There are several of these processes in operation in this country; and, although originally introduced in Germany by Miesenbach, it has been so improved by American inventors that the European work is far below the standard of the United States. The principal methods of half-tone in this country are worked secretly by the inventors, each having modifications and improvements of his own. It is impossible to give a thorough description here, as none of the inventors are willing to risk patenting their processes, and a complete publication is not desirable. The copy is first photographed, giving a negative with all the details of the original. This negative is then exposed to the camera, and the result is a positive, or, as commonly called, a transparency. This positive is then placed in contact with a glass plate covered with ruled lines. This plate is termed a grating. Being placed in contact, they are then photographed together, giving a negative of the object made up of lines and dots, representing the lights and shades of the picture. Here the half-tone process ends, the resulting plate being produced by any of the photo-engraving methods; but the most satisfactory results are obtained by photo-etching. The main objection to the half-tone plates is their lack of relief. No great depth can be obtained without sacrificing the effect. In printing these plates the greatest care in making ready must be exercised, and a smooth surface paper must be used. It is also necessary that a fine grade of ink be used in small quantity, and that it should be properly distributed.
A photograph, brush drawing, or any copy that isn’t made just of lines or dots can be created using the half-tone process without needing a line drawing. There are several of these processes used in this country; although it was originally introduced in Germany by Miesenbach, it has been improved so much by American inventors that European work is far below the standards in the United States. The main methods of half-tone in this country are kept secret by the inventors, each having their own modifications and improvements. It's impossible to provide a detailed description here since none of the inventors want to risk patenting their processes, and a full publication wouldn't be ideal. The copy is first photographed, resulting in a negative that captures all the details of the original. This negative is then exposed to the camera, creating a positive, or what is commonly known as a transparency. This positive is then placed in contact with a glass plate that has ruled lines on it. This plate is called a grating. When they are in contact, they are photographed together, yielding a negative of the object made up of lines and dots that represent the lights and shades of the picture. This concludes the half-tone process; the resulting plate is created using various photo-engraving methods, but the most satisfying results come from photo-etching. The main issue with half-tone plates is their lack of relief. You can't achieve great depth without losing the effect. When printing these plates, great care in making ready is essential, and a smooth surface paper must be used. It's also important to use a fine grade of ink in small amounts and ensure it is properly distributed.

METAL HOUSE.
Metal House.
A WALK OVER OUR FOUNDRY.
Mr. Typograph, how are you, sir? Glad to see you. How is business with you? Plenty to do, and customers paying up? You are so prompt in paying us, that we have no doubt you have a noble set of customers. You wish to add to your stock our new things? All right, sir. You have a fine office already, but you want to keep up with the times, and give your patrons the best the type-founder can invent? That’s the way, sir. The man on the lookout sees[40] the sun the earliest. Mr. Faithful, show our new things to Mr. Typograph, and take his order.
Mr. Typeface, how are you, sir? It's great to see you. How's business? Got plenty to do, and are your customers paying up? You're so prompt in settling with us that we’re sure you’ve got a great group of customers. Interested in adding our new items to your stock? Sounds good, sir. Your office looks fantastic already, but you want to stay current and offer your patrons the best that the type-founder can come up with? That's the way to go, sir. The person who is attentive sees[40] the sun first. Mr. Faithful, please show our new items to Mr. Typograph and take his order.
You say, Mr. Typograph, that you have never gone over a type-foundry? We shall be happy to show you every thing. This way, sir. Here is the metal-house. These piles of dull lead, these casks of sparkling antimony, this copper, and this tin go to form the grand amalgam of which type is made. The worthy and kind-hearted man who is stirring at the kettle, unites, in bonds stronger than matrimony, immense masses of these metals every week. It may appear to you, Mr. Typograph, to be an exceedingly simple thing to throw into the kettle certain amounts of lead and antimony, and copper and tin, and produce type-metal. Not so, good friend. It is not an easy matter to compose a metal that shall be hard, yet not brittle; ductile, yet tough; flowing freely, yet hardening quickly. All these conditions must be met. Break a bar in two, and examine the grain of our metal: is it not beautiful?
You say, Mr. Typograph, that you've never visited a type foundry? We'd be happy to show you everything. This way, sir. Here’s the metal house. These piles of dull lead, these casks of shiny antimony, this copper, and this tin are all part of the mix that makes type. The dedicated and kind-hearted man stirring the kettle combines these metals in ways stronger than marriage every week. You might think, Mr. Typograph, that it’s pretty straightforward to throw certain amounts of lead, antimony, copper, and tin into the kettle and create type metal. Not so, my friend. It’s not easy to create a metal that is hard, yet not brittle; ductile, yet strong; flows easily, yet hardens quickly. All these factors must be considered. Break a bar in two and look at the grain of our metal: isn’t it beautiful?

PUNCH.
PUNCH.

MATRIX.
MATRIX.
Now, sir, let us up-stairs and see how these bars are fitted for printers’ use. This is a punch-cutter—a man of exquisite finger and unerring eye—sitting amid keen and delicate tools and accurate gauges. There are but few of this kind of men in the world. On the end of a piece of steel he is forming a letter. A touch here and a touch there, and frequent testing by gauges,—so he proceeds, till the letter is done; then another, and another, till the alphabet is complete; all the letters harmonizing entirely in height, breadth, appearance, length of stroke, &c. A smoke-proof of the dies is taken, and if approved the dies are one by one placed in a stamping-machine, so,—and an oblong piece of copper is set under it, so,—and then this lever is brought down, so,—and a perfect impression of the die is left, as you see, deep in the copper. This is the matrix. The matrices are passed over to other workmen in the adjoining room. Observe now the carefulness and skill exercised in fitting up these bits of copper, so that, when placed in the mould, the types cast in them shall range accurately and be of uniform height. The slightest variation would give the zigzag appearance which you may[41] have noticed in badly-made type. This we endeavour sedulously to avoid, and with how much success you can judge from our Specimen Book. Look at this drawer full of matrices. You say they are triumphs of art? True saying, evincive of good judgment.
Now, let’s head upstairs and check out how these bars are set up for printing. This is a punch-cutter—a skilled artisan with a precise touch and a sharp eye—surrounded by fine tools and accurate gauges. There are only a few people like him in the world. He’s shaping a letter on the end of a piece of steel. With a touch here and a touch there, and frequent checks with gauges, he works until the letter is finished; then he moves on to another, and another, until the entire alphabet is ready; all the letters matching perfectly in height, width, appearance, and length of stroke, etc. A smoke-proof impression of the dies is taken, and if it's approved, the dies are placed one by one into a stamping machine, set with an oblong piece of copper underneath, and then this lever is pressed down, leaving a perfect impression of the die deep in the copper. This is the matrix. The matrices are handed over to other workers in the next room. Now, notice the care and skill involved in preparing these bits of copper so that when they’re placed in the mold, the types cast in them will align perfectly and be of uniform height. Even the smallest variation could create the zigzag effect you may have noticed in poorly made type. We work hard to prevent that, and you can see how successful we are from our Specimen Book. Check out this drawer full of matrices. You say they are masterpieces of art? That's true, and it shows good judgment.

CASTING MACHINE.
Casting machine.
You wonder what these curious-looking instruments are which lie, in dusty repose, on the shelves around the room?[42] Those, Mr. Typograph, are hand-moulds, and at one time they provoked intense covetousness on the part of rival founders. One of our earliest predecessors, Mr. Archibald Binny (our foundry dates from 1796), added such valuable improvements to the ordinary mould, that no other foundry in the world could rival the expedition and accuracy with which types were cast in the establishment of which he was a co-proprietor. Their day has passed, however. They have been superseded by the machines which you will see in operation in another apartment. But they were capital things in their time, sir, and we regard them with somewhat of an antiquary’s reverence.
You’re curious about those interesting-looking tools sitting in dusty silence on the shelves around the room?[42] Those, Mr. Typograph, are hand-moulds, and at one point, they sparked intense jealousy among competing founders. One of our earliest predecessors, Mr. Archibald Binny (our foundry has been around since 1796), made such valuable improvements to the ordinary mould that no other foundry in the world could match the speed and precision with which types were cast at the establishment where he was a co-owner. However, their time has passed. They’ve been replaced by the machines you’ll see in operation in another room. But they were great tools in their day, sir, and we hold them in a sort of antique appreciation.
Now we enter the casting-rooms. These tiny machines, small as they are, can throw out more type in one day than you would be likely to count in a month, even if you could call off one hundred a minute, and occupy ten hours a day. Snug little fellows, are they not? They were invented by a New-Yorker, Mr. David Bruce, Jr. A very ingenious man, you say? That is true. Look at one carefully. The metal is kept fluid by a little furnace underneath, and is projected into the mould by a pump, the spout of which, you see, is in front of the metal-pot. The mould is movable, and at every revolution of the crank it comes up to the spout, receives a charge of metal, and flies back with a fully-formed type in its bosom; the upper half of the mould lifts, and out jumps a type as lively as a tadpole. You don’t see how the letter is formed on the end of the type? True, we had forgotten: well, this spring in front holds in loving proximity to the mould a copper matrix, such as you saw just now in the fitting-room. The letter a, for instance, stamped in the matrix, sits directly opposite the aperture in the mould which meets the spout of the pump; and when a due proportion of a’s is cast, another matrix with b stamped in it takes its place; and so on throughout the alphabet. Slow work, you say, one at a time? Well, the world is peopled after that fashion; and it fills up fast enough. But just time this machine: it is making small, thin type. Count the type made in a minute. One hundred and seventy-five, you say. One hundred per minute will probably be the average of the ordinary sizes of printing type.
Now we enter the casting rooms. These small machines, as tiny as they are, can produce more type in a single day than you could count in a month, even if you could call out one hundred per minute and work ten hours a day. They’re pretty neat, right? They were invented by a New Yorker, Mr. David Bruce, Jr. You think he's a very clever guy? That’s true. Take a close look at one. The metal is kept molten by a little furnace underneath and is pushed into the mold by a pump, the spout of which, as you can see, is in front of the metal pot. The mold is movable, and with every turn of the crank, it comes up to the spout, gets filled with metal, and then zooms back with a fully-formed type inside; the upper half of the mold lifts, and out jumps a type as lively as a tadpole. You don’t see how the letter is formed on the end of the type? Right, we had forgotten: this spring in front holds a copper matrix close to the mold, like the one you just saw in the fitting room. The letter "a," for example, stamped in the matrix, aligns directly opposite the opening in the mold that meets the pump’s spout; when a certain number of "a's" are cast, another matrix with "b" stamped in it takes its place, and so on throughout the alphabet. Slow work, you say, one at a time? Well, that’s how the world gets populated, and it fills up quickly enough. But just time this machine: it’s making small, thin type. Count the type made in a minute. One hundred and seventy-five, you say? One hundred per minute will probably be the average for regular sizes of printing type.
The types are not finished yet? Oh, no. These nimble-fingered boys are breaking off the jets, or waste ends of the[43] type. Quick, a’n’t they? Now let us go up stairs into the dressing-room. An immense beehive? Yes, indeed, it looks like one. The lads clustered around the large circular stones, with leather-protected fingers, rub off the rough edges of the type. But men as well as type require their rough edges taken off before they are good for much in the world. These boys at the tables set up the type in long lines. You think that if you could pick up dollars as fast as they pick up type, you would retire an independent man in a year or two? We wish you could, Mr. Typograph; we wish you could.
The types aren't finished yet? Oh no. These quick-fingered guys are breaking off the jets or leftover ends of the[43] type. Quick, right? Now let's head upstairs to the dressing room. An enormous beehive? Yes, it really looks like one. The guys are gathered around the large circular stones, using leather-protected fingers to smooth out the rough edges of the type. But just like type, people need their rough edges smoothed out before they can be really useful in the world. These guys at the tables are setting up the type in long lines. You think if you could grab dollars as quickly as they grab type, you'd be able to retire comfortably in a year or two? We wish you could, Mr. Typograph; we really do.
The lines of type now pass into the hands of the dresser. Observe how deftly he slips them into a long stick, shakes them down on their face, screws them up, fastens them into a planing-board, and with one or two pushes with a planing tool accurately grooves the bottom of the type, removing entirely the burr left when the jet is broken off, and giving each type a pair of legs to stand upon, till it is worn out and returned to the melting kettle. What is the eye-glass used for? Why, sir, as soon as the types are grooved, the dresser narrowly inspects the face of the type, and if an imperfect letter is discovered by the aid of the magnifying glass, it is incontinently turned out. Ah, sir, if we were all inspected as severely as he criticises type, some of us, perhaps, would hardly pass muster. The immaculate types are next put up in pages of convenient size, and are ready for the purchaser.
The lines of type now go to the dresser. Watch how skillfully he slips them into a long stick, shakes them down on their face, screws them up, secures them into a planing board, and with a few pushes using a planing tool, precisely grooves the bottom of the type, completely removing the burr left from breaking off the jet, and giving each type a pair of legs to stand on until it's worn out and sent back to the melting kettle. What’s the magnifying glass for? Well, as soon as the types are grooved, the dresser carefully checks the face of each type, and if he finds an imperfect letter with the help of the magnifying glass, it’s quickly tossed out. Ah, if we were all examined as strictly as he inspects type, some of us might not pass the test. The perfect types are then organized into convenient page sizes, ready for the buyer.
Let us drop into the large machine-room. Does not every thing hum here! Is it not a beautiful sight to see the shafts and belts and pulleys whirling around as if they were all alive? Here we fit up our machines, make our moulds, repair damages to machinery, &c. The multifarious uses of these lathes you must be familiar with: this ponderous machine is an iron planer: how it makes the iron chips fly! What is that curiously-arranged lathe? That is for cutting Labour-Saving Rule,—the rule which you have found so convenient and economical in your job-room. We make it of many different styles of faces: some single, some dotted or hyphen-lines, and others parallel or double, of varying thicknesses. They are all cut to Pica ems in length, and are furnished with mitred corner-pieces of different angles, so contrived, in most of the sizes, as to allow the rule to be used single or double, and with the fine lines inside or outside.
Let’s take a look inside the big machine room. Everything is humming away here! Isn’t it amazing to see the shafts, belts, and pulleys spinning around as if they were alive? This is where we set up our machines, create our molds, and fix any damage to the equipment, etc. You must be familiar with all the different uses of these lathes: this heavy machine is an iron planer—just watch those iron chips fly! What’s that oddly arranged lathe? That’s for cutting Labour-Saving Rules—the kind you find so handy and cost-effective in your workspace. We make it in various styles: some have single lines, some have dotted or hyphen lines, and others are parallel or double, with different thicknesses. They’re all cut to Pica ems in length and come with mitered corner pieces at different angles, designed in most sizes to allow the rule to be used single or double, and with fine lines either inside or outside.

SLOTTED BRASS CORNERS.
Brass corner brackets.
Here are specimens of our new slotted brass corners, so handsome and useful to the skilled printer. See how accurately the slotted pieces fit in one another, so that you cannot detect the joint. Are they not effective? Our brass is carefully rolled by the best manufacturers in the country, and is sent to us in strips or in sheets. That wicked-looking shears yonder cuts up the thinner brass with as much unction as Commissioner Yeh’s executioner slices off heads: the thick brass goes under a circular steam-saw.
Here are samples of our new slotted brass corners, which are both attractive and practical for skilled printers. Notice how perfectly the slotted pieces fit together, making the joint almost undetectable. Aren't they impressive? Our brass is meticulously rolled by the top manufacturers in the country and delivered to us in strips or sheets. That intimidating-looking shear over there cuts through the thinner brass effortlessly, just like Commissioner Yeh’s executioner takes off heads; the thick brass goes through a circular steam saw.

STEREOTYPE BLOCK.
STEREOTYPE BUSTING.
Now, sir, while we are up here, we will peep into the printers’ furnishing-room. Isn’t this a beautiful stereotype-block? Doesn’t it do your eyes good to look at such perfect workmanship? And these brass galleys, and mahogany galleys and composing sticks, are they not admirable? Our effort in this department, as in all others, is to do our work well. All our miscellaneous wood-work is done here,—stands, racks, drawers, stereotype and packing boxes, &c. Some curious work has been designed and executed for the Smithsonian Institution, as well as brass ciphering-frames for the blind.
Now, sir, while we're up here, let's take a look at the printers’ supply room. Isn’t this a beautiful stereotype block? Doesn’t it feel good to look at such perfect craftsmanship? And these brass galleys, mahogany galleys, and composing sticks—aren't they amazing? Our goal in this area, as in all others, is to do our job well. All our various woodwork is done here—stands, racks, drawers, stereotype and packing boxes, etc. Some interesting work has been designed and completed for the Smithsonian Institution, as well as brass counting frames for the blind.
Ah, we forgot to show you our large-type room. On our way to the electrotype department, we will glance in it. The types you see here cool too slowly to be cast in a machine, so we continue to pour them. Look over the drawers, and see the multitude of patterns. Some men fancy one style, and some another. So we try to meet all tastes. Feel how[45] solid the type is. You can’t squeeze the life out of that type on a power-press. No, indeed. It is made for wear.
Oh, we forgot to show you our large-type room. On our way to the electrotype department, we’ll take a quick look inside. The types you see here cool too slowly to be cast in a machine, so we keep pouring them. Check out the drawers and see all the different patterns. Some people prefer one style, while others like another. So we try to cater to all preferences. Feel how[45] solid the type is. You can’t wear that type down on a power press. No way. It’s built to last.
Now, Mr. Typograph, we enter the grimed and murky electrotype-room. Electrotyping, you are aware, is simply stereotyping in copper. Its advantages over stereotyping are, sharpness of outline in plates from wood-cuts, and great durability. Plates for books of large circulation are always electrotyped, as well as cuts, engravings, binders’ stamps, &c. The thing to be electrotyped, after being carefully and almost imperceptibly glazed with plumbago, is laid upon a press, and a prepared mould is placed over it, and an exact impression taken. This is well dusted with plumbago, and then deposited in the electric bath. Nature immediately takes up her part of the work, and a brilliant coating of copper is deposited upon the mould. When sufficiently thick, it is taken out of the battery, and, as you may notice, presents on the wrong side the appearance of a printed sheet of copper. This sheet is then filled up on the back to the requisite degree of thickness, and fastened to a block, ready to be used with type on a common printing-press. Plumbago, you remark, does not improve the countenances of the operatives? True; but a little soap and water, vigorously applied, proves the title of these intelligent workmen to rank among white folk.
Now, Mr. Typograph, we enter the dirty and dim electrotype room. Electrotyping, as you know, is just stereotyping but done with copper. Its benefits over stereotyping include sharper outlines in plates made from woodcuts and increased durability. Plates for books with a large circulation are always electrotyped, along with cuts, engravings, binders’ stamps, and so on. The item to be electrotyped is first carefully and almost invisibly coated with plumbago, then placed on a press with a prepared mold over it to take an exact impression. This is dusted with plumbago and then put in an electric bath. Nature quickly takes over, depositing a shiny coating of copper onto the mold. Once it’s thick enough, it’s taken out of the battery, and as you might notice, the backside looks like a printed sheet of copper. This sheet is then filled in on the back to the necessary thickness and attached to a block, ready to be used with type on a regular printing press. You may point out that plumbago doesn’t enhance the looks of the workers? True; but a bit of soap and water, applied vigorously, reveals that these skilled workers are just as worthy as anyone else.
To you, Mr. Typograph, our composing-rooms present nothing new, except, perhaps, in its vast number of job founts, due to the fact that we now mainly confine our work in this department to all kinds of jobbing; and yet in ten years we have set up in these rooms and stereotyped more than eight hundred considerable works,—most of them consisting of a single volume, but some of from two to twelve volumes each,—besides a multitude of smaller books, tracts, &c. Among the rest we may mention two Quarto Bibles, (one of them, now published by J. B. Lippincott & Co., the grandest ever got up in America,) Lippincott’s two great Gazetteers, Dr. Kane’s Explorations, The North American Sylva, Thiers’ Napoleon, and Macaulay’s England: Allibone’s magnificent Dictionary of Authors and Books among the number.
To you, Mr. Typograph, our composing rooms probably don’t show you anything new, except maybe the huge variety of job fonts we have, since we primarily focus on all kinds of job printing now. Yet, over the past ten years, we’ve set up in these rooms and created over eight hundred significant works—most being single volumes, but some ranging from two to twelve volumes each—along with a lot of smaller books, tracts, etc. Notable mentions include two Quarto Bibles (one of which is now published by J. B. Lippincott & Co., the finest ever produced in America), Lippincott’s two major Gazetteers, Dr. Kane’s Explorations, The North American Sylva, Thiers’ Napoleon, and Macaulay’s England: along with Allibone’s impressive Dictionary of Authors and Books.
After the pages have been set and carefully read, they are sent down to the casting-room. In the electrotype-room, every thing is as black as the brow of a coal-heaver: in the casting-room, all is as white as the neck of a belle. Take[46] care, sir, or your coat will commit a larceny of our plaster. The form of type is laid on this stone, and nicely oiled: and then a mixture of plaster and water—doesn’t it look like a good wife’s buckwheat batter?—is poured over it, and gently rolled in. In a short time the plaster sets, and the mould is removed by screws as tenderly as a nurse handles a baby. It is then dried in this hot-tempered oven, and, after the moisture is all evaporated, it is laid in a pan and fastened tightly, as you see, and plunged into this terrible bath of a thousand pounds of molten type-metal. Phew! you exclaim, what warm work! Yes, sir; but from that fiery sea of lead soon emerges the pan, and its hissing heat is gradually overcome by the water in the trough into which the pan is lowered. Now, caster, break it out. There, Mr. Typograph, is the plate, fixed,—immovable,—stereotyped. The mould is ruined; but the plate is comparatively immortalized. It is rough yet, and, like an uncouth boy, needs polishing.
After the pages have been set and carefully read, they are sent down to the casting room. In the electrotype room, everything is as dark as a coal miner's brow; in the casting room, everything is as bright as a socialite's neck. Watch out, or your coat might snag our plaster. The type is placed on this stone and nicely oiled, then a mixture of plaster and water—doesn’t it look like a good wife's buckwheat batter?—is poured over it and gently rolled in. In a short time, the plaster sets, and the mold is removed with screws as carefully as a nurse handles a baby. It is then dried in this hot oven, and once all the moisture has evaporated, it is placed in a pan and tightly secured, as you see, and plunged into this intense bath of a thousand pounds of molten type metal. Wow! you might say, what a hot job! Yes, but from that fiery sea of lead, the pan soon emerges, and its hissing heat is gradually cooled down by the water in the trough it’s lowered into. Now, caster, break it out. There, Mr. Typograph, is the plate, fixed, immovable, stereotyped. The mold is ruined, but the plate is fairly immortalized. It's still rough, and like an awkward boy, it needs some polishing.

STEREOTYPE CASTING-ROOM.
CASTING ROOM STEREOTYPES.
This next room is the finishing-room. Here the plates are carefully examined, picked, shaved, trimmed, and boxed, ready for the printer. Take a plate in your hand and examine it: it will bear inspection. You say it is far better than the untrimmed, uneven plates of English founders? We know that, sir; for we have often had to re-finish English plates imported by some publisher who imagined he could save a little by ordering a duplicate set of plates of a popular foreign[47] book. A mistake, sir. Both in type-founding and in stereotyping the Americans have driven the foreigner from the field,—and in the only legitimate way, too: simply by surpassing him.
This next room is the finishing room. Here, the plates are carefully checked, selected, shaved, trimmed, and boxed, making them ready for the printer. Take a plate in your hand and check it out: it will hold up under inspection. You say it’s much better than the untrimmed, uneven plates from English founders? We know that, because we've often had to re-finish English plates imported by some publisher who thought he could save a bit by ordering a duplicate set of plates for a popular foreign[47] book. A mistake, indeed. In both type-founding and stereotyping, Americans have pushed the foreigners out of the game—and in the only proper way, too: simply by doing it better.
In this nook below, our engraving is done. The drawing is made on the block by the designer, as you see: then patiently and skilfully the engraver cuts and digs out, till the lines and shapes and lights and shades are all revealed in the beautiful picture. Our work in this department gives so much satisfaction that we are seldom without orders.
In this corner down here, our engraving is complete. The designer creates the drawing on the block, just like you see: then the engraver carefully and skillfully cuts and carves until the lines, shapes, lights, and shadows are all brought to life in the beautiful picture. Our work in this area is so satisfying that we rarely run out of orders.
Now, Mr. Typograph, we shall admit you into our editorial parlour. Walk in, sir. It is not carpeted, and its principal furnishings comprise a desk or two, a few presses, stands and cases, with multitudinous type-surroundings. Here, sir, we edit and print our Specimen Books and our Typographic Advertiser. Don’t you see poetical flies buzzing around, and atoms of wit-dust floating in the air, and odours of sentiment stealing out at the key-holes, and grains of common sense sprinkled all over the floor. Will you have a few specimens as curiosities? You say you have already a good assortment in our Advertiser and our Book? Very well, sir: we hope you will treasure them up. You say truly when you remark, that the printing done in this room is seldom, if ever, surpassed in America. We know that; and we intend to stand on the topmost round of the typographical ladder, and to show our fellow-artists what can be done with type such as we manufacture.
Now, Mr. Typograph, we welcome you into our editorial space. Please come in, sir. It’s not carpeted, and the main furnishings include a couple of desks, some presses, stands, and cases, surrounded by lots of typesetting materials. Here, sir, we edit and print our Specimen Books and our Typographic Advertiser. Don’t you see poetic ideas buzzing around, bits of cleverness floating in the air, and hints of sentiment sneaking out through the keyholes, with bits of common sense scattered all over the floor? Would you like to take a few samples as keepsakes? You say you already have a good selection in our Advertiser and our Book? Well then, sir: we hope you’ll cherish them. You’re right when you say that the printing done in this room is rarely, if ever, matched in America. We know that, and we plan to reach the highest point of the typographic ladder and show our fellow artists what can be done with the type we produce.
We are afraid, Mr. Typograph, that your long excursion over the house has wearied you. Let us go down-stairs again. These, sir, are our warerooms. On these numerous shelves are ranged founts of all the various sorts of types made by us, carefully put up, labelled and classified, and all accessible at a minute’s notice. Our customers throughout the country keep actively employed all these porters, packers, clerks, salesmen, and bookkeepers. Many of our customers have never visited us; but we put up their orders with as conscientious fidelity and care as if they were standing before us and watching our every movement. We are happy to see them, and hope none will visit our city without calling in and taking us by the hand. We like to see them face to face, so that we can hang up their portraits in our mental gallery; and, when we[48] afterward receive a letter from them, we can imagine that we are hearing them talk to us rather than reading their writing.
We’re sorry, Mr. Typograph, if your long tour of the house has tired you out. Let’s head downstairs again. These are our storage rooms. On these many shelves are all the different types of fonts we’ve made, carefully organized, labeled, and ready for access at a moment’s notice. Our customers all over the country keep our porters, packers, clerks, salespeople, and bookkeepers busy. Many of our customers have never been here, but we fulfill their orders with the same dedication and care as if they were right in front of us, watching everything we do. We’re happy to see them, and we hope no one visits our city without stopping by to shake our hands. We love meeting them in person, so we can visualize their faces in our mental gallery; then, when we receive a letter from them later, it feels like they are speaking to us instead of just us reading their words.
The side-door on which your eye has just rested leads to one of our fire-proofs. Enter it. Here, sir, are safely stored many thousand matrices, as well as moulds, when not in use. As it would require the labour of many weary years to replace them if destroyed, we endeavour to keep them secure from the danger of ruin by fire. The upbuilding of a complete type-foundry is a work of generations.
The side door your eye just landed on leads to one of our fireproof areas. Go ahead and enter. Here, sir, we safely store thousands of matrices and molds when they're not in use. Since it would take many long years to replace them if they were destroyed, we make every effort to protect them from the risk of fire. Building a complete type foundry is a task that spans generations.
You will hardly care to look into the basement,—the storehouse of ink and other typographical appliances? Your time is exhausted? Then, sir, we bid you good-day. A safe return to your pleasant family, Mr. Typograph.
You probably don't want to check out the basement—the place for ink and other printing supplies? You're short on time? Then, sir, we wish you a good day. Have a safe trip back to your lovely family, Mr. Typograph.


IMPLEMENTS OR TOOLS OF THE ART.
TYPES.

The types or letters generally used for printing in Europe and America are termed Roman, Italic, and Old English, or Black Letter.
The categories or letters commonly used for printing in Europe and America are called Roman, Italic, and Old English, or Black Letter.
ROMAN LETTER.
Roman letters were employed in MSS. from the fifth to about the close of the twelfth century, when what are called Gothic letters (afterward Old English) came gradually into use; these continued for several centuries, when, in most countries, they were superseded by the Roman characters. All printing was in black letter down to 1465, when Sweinheim & Pannartz, in Subiaco near Rome, produced a volume entitled Lactantius, in a character approaching to the actual forms of our modern types. In 1467, they made an improved set of characters, and printed about forty volumes within the five years following. About 1469 John of Spires, in Venice, made a great advance in improving the form of the Roman character, and printed the Natural History of Pliny: the execution of this work is very remarkable. But Nicholas Jenson may fairly be considered the father of the style of Roman letter now in vogue. He printed in Venice four works[50] in the year 1470, the first of which was Eusebii Præparatio Novorum, &c., in types which were cut by him, more perfect in form than those of any earlier printer. The printers named above were all of them Germans.
Roman letters were used in manuscripts from the fifth century until around the end of the twelfth century, when what we now call Gothic letters (later known as Old English) gradually came into use. These letters were used for several centuries until, in many countries, they were replaced by Roman characters. All printing was done in black letter until 1465, when Sweinheim & Pannartz in Subiaco near Rome published a book called Lactantius, using a type that was close to the forms of our modern fonts. In 1467, they created an improved set of characters and printed about forty volumes within the next five years. Around 1469, John of Spires in Venice significantly advanced the Roman character's design and printed the Natural History of Pliny; the quality of this work is quite impressive. However, Nicholas Jenson is often regarded as the father of the Roman letter style we use today. He printed four works in Venice in 1470, the first of which was Eusebii Præparatio Novorum, featuring types he cut, which were more refined than those of any earlier printer. All the printers mentioned above were Germans.
The Roman letters consist of circles, arcs of circles, and straight lines; and, therefore, on the score of simplicity, precision, and elegance, they certainly deserve to be adopted as the standard for all nations.
The Roman letters are made up of circles, arcs, and straight lines; so, in terms of simplicity, precision, and elegance, they definitely deserve to be adopted as the standard for all nations.
A printer, in choosing type, should not only attend to the cut of the letter, but should also observe that its shank is perfectly true, and that it lines or ranges with accuracy, and is of equal height. The quality of the metal of which it is composed and the finish of the letter demand particular attention, as the competition among some of the smaller foundries (which have sprung into existence through the facilities afforded of multiplying matrices by the electrotype process) has led them to use an inferior metal, and produce types without due regard to nicety of finish and exactness of body and standing.
A printer, when selecting type, should not only pay attention to the style of the letter but also check that its shank is perfectly straight, aligns accurately, and is of the same height. The quality of the metal it’s made from and the finish of the letter are crucial, as the competition among some of the smaller foundries (which have emerged thanks to the ability to produce matrices through the electrotype process) has resulted in the use of lower-quality metal and types that lack precision in finish and consistency in body and height.
It is important that types should have a deep face, with strong, bevelled bases or foundations under the ceriphs or hairlines, and that the letters should have a deep nick, which should be different from other founts of like body in the same house.
It’s important for typefaces to have a deep face, with strong, beveled bases or foundations under the serifs or hairlines, and the letters should have a deep nick that is different from other fonts of the same size made by the same foundry.
ITALIC LETTER.
Aldo Manuccio, born at Bassano, succeeded Jenson at Venice and turned to good account the latter’s admirable founts of type. He also made many advances in the art of printing, the most notable of which is the invention of the style of type now known as Italic. It was first used in an octavo edition of Virgil issued by him in 1501, and Pope Leo X. gave him a letter of privilege, entitling him to the sole use of the type he had invented. It was said to be founded on the handwriting of Petrarch, which it closely resembles.
Aldo Manuccio, born in Bassano, took over from Jenson in Venice and made great use of Jenson's impressive typefaces. He also made several advancements in printing, the most significant of which was the creation of the type style now known as Italic. This was first used in an octavo edition of Virgil that he published in 1501, and Pope Leo X granted him a privilege letter, giving him exclusive rights to the type he invented. It was said to be based on Petrarch's handwriting, which it closely resembles.
Italic was largely employed to distinguish such parts of a book as might be considered appendages, as Prefaces, Introductions, Annotations, &c., all of which were formerly printed in this character; so that perhaps two-fifths of a fount was composed of Italic letter.
Italic was mostly used to highlight sections of a book that were seen as supplementary, like Prefaces, Introductions, Annotations, etc., which were all previously printed in this style. As a result, maybe two-fifths of a typeface was made up of italic letters.
At present it is used more sparingly, being superseded by[51] the more elegant mode of enclosing extracts within inverted commas, and by setting poetry and annotations in a smaller-sized type. It is very appropriately used to distinguish the head or subject-matter of a chapter, and is serviceable in grammars and other school-books as well as scientific works. The frequent use of Italic words among Roman in ordinary matter impairs the beauty of the page, and ought to be avoided; yet authors sometimes stubbornly insist on the gratification of their whimsies, even at the sacrifice of every principle of correct taste.
Right now, it's used less often, having been replaced by[51] the more stylish way of enclosing quotes in quotation marks, and by using a smaller font for poetry and annotations. It's very fitting for highlighting the title or topic of a chapter and is useful in grammar books and other educational materials as well as scientific texts. Using italicized words alongside regular text too frequently can ruin the page's appearance and should be avoided; however, authors sometimes stubbornly cling to their personal preferences, even at the cost of good taste.
BLACK LETTER.

This letter, which was used in the infancy of Printing, descended from the Gothic characters: it is called Gothic by some, and Old English by others; but printers term it Black Letter, on account of its heavy appearance.
This letter, which was used in the early days of printing, originated from Gothic characters. Some people call it Gothic, while others refer to it as Old English; however, printers call it Black Letter because of its bold look.
In Germany, the letters in common use are founded on the Gothic character; but even there scientific works are printed in the German language with Roman letters.
In Germany, the letters commonly used are based on the Gothic style; however, even there, scientific works are printed in German using Roman letters.
The Dutch adhere to the black letter in books of devotion and religious treatises; while they make use of the Roman in their curious and learned works.
The Dutch stick to the blackletter font in their books of devotion and religious writings, while they use the Roman font in their interesting and scholarly works.
SAXON CHARACTERS.
The Saxon characters originated probably from the Gothic, but were altered or modified after the Latin ones which the Saxons found in use in England in the fifth century. The first Saxon types were cut by John Daye, under the patronage of Archbishop Parker, about the year 1567. We give the Lord’s Prayer in modern Anglo-Saxon types:
The Saxon characters likely came from the Gothic, but they were changed or adapted after the Latin ones the Saxons encountered in England in the fifth century. The first Saxon typefaces were created by John Daye, with support from Archbishop Parker, around the year 1567. Here’s the Lord’s Prayer in modern Anglo-Saxon types:

Fæder ure þu þe eart on heofenum. Si þin nama gehalgod. Tobecume þin rice. Cepurðe þin pilla on eorþan, spa spa on heofenum. Urne dæghpamlican hlaf gyfe us to dæg. And forgyf us ure gyltas, spa ssa pe forgifað urum gyltendum. And ne gelædde þu ur on costnunge. ac alys us of yfele. So ðlice.
Father, you who are in heaven, holy is your name. Let your kingdom come. Your will be done on earth as it is in heaven. Give us this day our daily bread. And forgive us our debts, as we also forgive our debtors. And lead us not into temptation, but deliver us from evil. Amen.
NAMES AND SIZES OF TYPE.
The principal bodies to which printing letters are cast in England and America are the following:—
The main types of printing letters that are cast in England and America are the following:—
1. | Diamond. |
2. | Pearl. |
3. | Agate. |
4. | Nonpareil. |
5. | Minion. |
6. | Brevier. |
7. | Bourgeois. |
8. | Long Primer. |
9. | Small Pica. |
10. | Pica. |
11. | English. |
12. | Columbian. |
13. | Great Primer. |
14. | Paragon. |
15. | Double Small Pica. |
16. | Double Pica. |
17. | Double English. |
18. | Double Great Primer. |
19. | Double Paragon. |
20. | Canon. |
Besides the foregoing, a smaller size than Diamond, called Brilliant, is now cast in the foundry of MacKellar, Smiths & Jordan of Philadelphia, the body of which is just one-half of Minion. Even this is surpassed in smallness by a music type cast in the same foundry, named Excelsior, which is precisely one-half the size of Nonpareil. Another size omitted in the list is Minionette, (equivalent to six of the Didot points,) which is next above Nonpareil.
Besides the previous points, there's a smaller size than Diamond called Brilliant, which is now produced by the foundry of MacKellar, Smiths & Jordan in Philadelphia. Its body size is just half that of Minion. Even this is overshadowed by a music type made in the same foundry, named Excelsior, which is exactly half the size of Nonpareil. Another size not included in the list is Minionette (equivalent to six Didot points), which comes right above Nonpareil.
Canon is conceded to have been first produced by a French artisan, and was probably used in some work relating to the canons of the church; to which the German title, Missal, alludes.
Canon is acknowledged to have been first created by a French craftsman and was likely used in some work connected to the church's canons, which is referenced by the German title, Missal.
Two-line Great Primer, Two-line English, and Two-line Pica, owe their names to the respective bodies of which the depth of two em quadrates answers to one of the double sizes.
Two-line Great Primer, Two-line English, and Two-line Pica get their names from the specific point sizes where the height of two em quadrates corresponds to one of the double sizes.
Paragon was probably first cut in France. It is known as Text by the Germans.
Paragon was likely first created in France. The Germans refer to it as "Text."
Pica is universally considered as the standard type, and by it furniture, quotations and labour-saving rules are graduated. A line 83 Pica ems long is equivalent to 35 centimeters. The twelfth part of Pica is the unit, called a Point, by which type-bodies are measured. MacKellar, Smiths & Jordan cast their new borders, ornaments, and job type on Pica, and its subdivisions of Nonpareil, (½ Pica,) and Excelsior, (¼ Pica,) and their multiples.
Pica is widely recognized as the standard unit, and it is used to measure furniture, quotes, and efficiency guidelines. A line that is 83 Pica ems long is equal to 35 centimeters. The twelfth part of Pica is called a Point, which is used for measuring type size. MacKellar, Smiths & Jordan produce their new borders, ornaments, and job type using Pica, along with its subdivisions of Nonpareil (½ Pica) and Excelsior (¼ Pica), as well as their multiples.

Great Primer, called Tertia in Germany, is one of the major sizes of type which were early used for printing considerable works, and especially the Bible; on which account some persons term it Bible Text. The French name is Gros Romain.
Great Primer, known as Tertia in Germany, is one of the main type sizes that were used early on for printing significant works, especially the Bible; for this reason, some people refer to it as Bible Text. The French name is Gros Romain.
English is called Mittel by the Germans, and St. Augustin by the French and Dutch; the word Mittel (Middle) intimating that the former sizes of letter were seven in number, the centre of which was English, with Prima, Secunda, and Tertia on one side, and Pica, Long Primer, and Brevier on the other. The name St. Augustin was probably given because the writings of that Father were the first works done in that letter.
English is referred to as Mittel by the Germans, and St. Augustin by the French and Dutch. The term Mittel (Middle) suggests that the earlier type sizes included seven in total, with English in the center, surrounded by Prima, Secunda, and Tertia on one side, and Pica, Long Primer, and Brevier on the other. The name St. Augustin was likely assigned because the writings of that Father were the first works created using this type.
Pica is called Cicero by the French and Germans. As the preceding size was distinguished by the name of St. Augustin, so this has been honoured with that of Cicero, on account of the Epistles of that writer having been first done in letter of this size. It is doubtful whether the name was given by the French or the Germans.
Pica is known as Cicero by the French and Germans. Just like the previous size was named after St. Augustine, this one has been named after Cicero because his letters were the first to be printed in this size. It’s unclear whether the name was originally given by the French or the Germans.
Small Pica is a grade below Pica, and is now generally employed in octavo volumes, and is, indeed, almost the only size used for printing legal reports and other law books. The French call this letter Philosophie, which, however, is merely a Pica face on Small Pica body. The Germans call it Kleine Cicero.
Small Pica is a size smaller than Pica and is now mostly used in octavo volumes. It's practically the only size used for printing legal reports and other law books. The French refer to this font as Philosophie, which is essentially a Pica font in a Small Pica size. The Germans call it Kleine Cicero.
Long Primer. Upon the supposition that some bodies of letter took their names from works in which they were first employed, we are induced to believe that the Germans gave the name of Corpus to this character on account of their Corpus Juris being first done in this size. The French call this letter Petit Romain.
Long Primer. Assuming that some types of letters got their names from the works where they were first used, we believe that the Germans named this character Corpus because their Corpus Juris was first printed in this size. The French refer to this letter as Petit Romain.
Bourgeois is a very useful and convenient size of letter. It is frequently used in double-column octavo pages. The name indicates that it originated in France; although type of this body is now called Gaillarde by French printers. Two lines of this letter are equivalent to one line of Great Primer, or four lines of Diamond.
Bourgeois is a very useful and convenient font size. It's commonly used in double-column octavo pages. The name suggests that it came from France; although this type is now referred to as Gaillarde by French printers. Two lines of this font equal one line of Great Primer, or four lines of Diamond.
Brevier was first used for printing the Breviaries, or Roman Catholic Church books, and hence its name. The Germans call it Petit, and Jungfer (maiden letter). It is an admirable type, and cannot conveniently be dispensed with in any considerable printing-office.
Brevier was first used for printing the Breviaries, or Roman Catholic Church books, and that's how it got its name. The Germans call it Petit, and Jungfer (maiden letter). It’s a great type, and you can’t really do without it in any significant printing office.
Minion follows Brevier, and is commonly used for newspapers, and for notes and indexes in book-work. Its name is due probably to its being smaller than any type in use at the period of its invention. It fills a useful place in a printing-office.
Minion comes after Brevier and is commonly used for newspapers, as well as for notes and indexes in book work. Its name likely comes from being smaller than any type used when it was invented. It holds an important role in a printing office.
Nonpareil came next in order; and its originator, supposing that he had reached the extreme of diminutiveness, gave it this triumphant title. It is extensively used, though mostly on newspapers, and for notes and indexes for duodecimo books and smaller. It is certainly the smallest type that should be allowed in book-work.
Nonpareil came next in line; its creator, thinking he had reached the ultimate in small size, gave it this proud name. It's widely used, mostly in newspapers and for notes and indexes in duodecimo books and smaller. It’s definitely the smallest type that should be used in book printing.
Agate probably arose from the necessities of newspaper publishers. As patronage increased, it became desirable to have a type less in size than Nonpareil, for the advertisements, shipping news, markets, &c.; and Agate was made to meet the emergency. It is now extensively used for pocket editions of the Bible and Prayer Books.
Agate likely came about due to the needs of newspaper publishers. As patronage grew, there was a need for a type that was smaller than Nonpareil for advertisements, shipping news, markets, etc.; so Agate was created to address this need. It's now widely used for pocket editions of the Bible and Prayer Books.
Pearl may be said to have been born of ambition. As punch-cutters became more expert, some one possessed of a keen eye and a delicate mechanical finger determined to surpass in smallness the achievements of his predecessors. Hence the origin of this type. This type is also employed in printing miniature volumes.
Pearl can be described as being born from ambition. As punch-cutters grew more skilled, someone with a sharp eye and a delicate mechanical touch aimed to outdo the smallness of their predecessors' work. This is how this type came to be. This type is also used in printing miniature books.
Diamond followed, as a matter of course; for human ingenuity, when provoked, seems determined to go to the utmost verge of possibility. This type is so minute that a pound of it will contain more than 3300 of the letter i; yet, to produce each letter of an alphabet, a steel punch has to be cut and a matrix made, in which the types are cast one by one, and, being set up in lines, are rubbed and dressed by the founder for the use of the compositor.
Diamond followed, as usual; when pushed, human creativity seems intent on reaching the limits of what’s possible. This type is so tiny that a pound of it can hold over 3,300 of the letter i; however, to create each letter of the alphabet, a steel punch has to be made and a mold created, in which the types are cast individually, and, once arranged in lines, are polished and finished by the founder for the compositor’s use.
Brilliant. Expert penmen, it is said, have succeeded in writing the Lord’s Prayer upon the edge of a sheet of paper. A type-setter in Berlin, most surprisingly, has formed a type so minute as to be scarcely readable without a good magnifying glass. The type of this paragraph, though not so small as the microscopic letters produced in Prussia, is yet so diminutive that even Diamond is large by comparison. Of the letter i nearly 4600 go to a pound.
Brilliant. It's said that expert calligraphers have managed to write the Lord’s Prayer on the edge of a sheet of paper. Surprisingly, a typesetter in Berlin has created a type so tiny that it's barely readable without a good magnifying glass. The type in this paragraph, while not as small as the microscopic letters from Prussia, is still so small that even Diamond type looks big by comparison. There are nearly 4600 letter i's in a pound.
GRADATION OF TYPES.
The following specimen shows the proportion which one size of type bears to another in width; but it is necessary to observe that it must be taken with certain limitations, because each founder has letter of every size that will either drive out or get in with others of the same body, some faces being more extended and others being more condensed than the standard width of type. The scale contains thirteen sizes in order of gradation, viz., Great Primer, English, Pica, Small Pica, Long Primer, Bourgeois, Brevier, Minion, Nonpareil, Agate, Pearl, Diamond, and Brilliant.
The following example illustrates the relationship between different type sizes in width; however, it's important to note that this needs to be considered with certain limitations, as each type foundry offers letters in every size that may either fit in or clash with others of the same size, with some fonts being wider and others being narrower than the standard width of type. The scale includes thirteen sizes in order of gradation: Great Primer, English, Pica, Small Pica, Long Primer, Bourgeois, Brevier, Minion, Nonpareil, Agate, Pearl, Diamond, and Brilliant.

POINT SYSTEM OF TYPE-BODIES.
In 1882, MacKellar, Smiths & Jordan began to make type on the proportional system of bodies. The Pica em, being the eighty-third part of thirty five centimetres, was divided into twelve parts, or points. This system of exact proportional type-bodies was approved of and adopted by the American type-founders generally. It has been favourably received by printers in this country, and all printing offices will in due time be fully equipped with types of this description.
In 1882, MacKellar, Smiths & Jordan started producing type using the proportional system of sizes. The Pica em, which is one eighty-third of thirty-five centimeters, was divided into twelve parts, or points. This precise system of proportional type sizes was accepted and adopted by American type-founders overall. It has been well-received by printers in this country, and eventually, all printing offices will be fully equipped with this type of font.
The standard for the height of type was fixed at 2⅓ centimetres.
The standard height for type was set at 2⅓ centimeters.
In some European countries printing offices had their types cast to a height to suit the proprietor’s whim. Some of the foreign founders have sent young men to Philadelphia to be educated in the American system of heights and bodies, and at least two foundries in Germany have adopted the American plan.
In some European countries, printing shops had their type made to a height that fit the owner's preference. Some foreign type founders have sent young men to Philadelphia to learn the American system of type sizes and styles, and at least two foundries in Germany have adopted the American approach.
The following table shows the systematic gradation of bodies and position of nicks in the point system, one point being equivalent to 1/12 of a Pica em.
The following table shows the systematic grading of bodies and the placement of nicks in the point system, with one point equal to 1/12 of a Pica em.

3 Point. Excelsior.
3 Point. Awesome.
3½ Point. Brilliant.
3½ Points. Awesome.
4 Point. Semi-Brevier.
4 Point. Semi-Brevier.
4½ Point. Diamond.
4.5 Point. Diamond.
5 Point. Pearl.
5 Point. Pearl.
5½ Point. Agate.
5.5 Point. Agate.
6 Point. Nonpareil.
6 Point. Nonpareil.
7 Point. Minion.
7 Point. Minion.
8 Point. Brevier.
8 Point. Brevier.
9 Point. Bourgeois.
9 Point. Middle class.
10 Point. Long Primer.
10 Point Long Primer.
11 Point. Small Pica.
11 Point. Small Pica.
12 Point. Pica.
12 Point. Pica.
14 Point. English.
14 Point. English.
16 Point. Two-line Brevier.
16 Point. Two-line Brevier.
18 Point. Three-line Nonpareil.
18 Point. Three-line Nonpareil.
20 Point. Two-line Long Primer.
20 Point. Two-line Long Primer.
22 Point. Two-line Small Pica.
22 Point. Two-line Small Pica.
24 Point. Two-line Pica.
24 Point. Double-line Pica.
28 Point. Two-line English.
28 Point. Double-line English.
30 Point. Five-line Nonpareil.
30 Point. Five-line Nonpareil.
32 Point. Four-line Brevier.
32 Point. Four-line Brevier.
36 Point. Three-line Pica.
36 Point. Three-line Pica.
A BILL OF PICA.
The following is reckoned by the founders a regular fount, complete in all its sorts:—
The following is considered by the founders a reliable source, complete in all its forms:—
A BILL OF 800 LBS. OF PICA.
A BILL OF 800 LBS. OF PICA.
a | 8500 |
b | 1600 |
c | 3000 |
d | 4400 |
e | 12000 |
f | 2500 |
g | 1700 |
h | 6400 |
i | 8000 |
j | 400 |
k | 800 |
l | 4000 |
m | 3000 |
n | 8000 |
o | 8000 |
p | 1700 |
q | 500 |
r | 6200 |
s | 8000 |
t | 9000 |
u | 3400 |
v | 1200 |
w | 2000 |
x | 400 |
y | 2000 |
z | 200 |
& | 200 |
ff | 400 |
fi | 500 |
fl | 200 |
ffl | 100 |
ffi | 150 |
æ | 100 |
œ | 60 |
— | 150 |
⸺ | 90 |
⸻ | 60 |
, | 4500 |
; | 800 |
: | 600 |
. | 2000 |
- | 1000 |
? | 200 |
! | 150 |
’ | 700 |
( | 300 |
[ | 150 |
* | 100 |
† | 100 |
‡ | 100 |
§ | 100 |
∥ | 100 |
¶ | 60 |
1 | 1300 |
2 | 1200 |
3 | 1100 |
4 | 1000 |
5 | 1000 |
6 | 1000 |
7 | 1000 |
8 | 1000 |
9 | 1000 |
0 | 1300 |
é | 200 |
à | 200 |
â | 200 |
ê | 200 |
All other accents, each. | 100 |
A | 600 |
B | 400 |
C | 500 |
D | 500 |
E | 600 |
F | 400 |
G | 400 |
H | 400 |
I | 800 |
J | 300 |
K | 300 |
L | 500 |
M | 400 |
N | 400 |
O | 400 |
P | 400 |
Q | 180 |
R | 400 |
S | 500 |
T | 650 |
U | 300 |
V | 300 |
W | 400 |
X | 180 |
Y | 300 |
Z | 80 |
Æ | 40 |
Œ | 30 |
A | 300 |
B | 200 |
C | 250 |
D | 250 |
E | 300 |
F | 200 |
G | 200 |
H | 200 |
I | 400 |
J | 150 |
K | 150 |
L | 250 |
M | 200 |
N | 200 |
O | 200 |
P | 200 |
Q | 90 |
R | 200 |
S | 250 |
T | 326 |
U | 150 |
V | 150 |
W | 200 |
X | 90 |
Y | 150 |
Z | 40 |
Æ | 20 |
Œ | 15 |
Spaces. | |
Thick | 18000 |
Middle | 12000 |
Thin | 8000 |
Hair | 3000 |
Em Quads | 2500 |
En Quads | 5000 |
Large Quadrates, about 80 lbs. |
Italic, one-tenth of Roman.
Italic, 10% of Roman.
Owing to the varying styles of authors and the diverse subjects of books, some letters will now and then run short in a[58] fount, whatever the proportions may have been at first. A new fount of type may run evenly on a work in general literature written in the third person, while a novel filled with dialogues in the first person will rapidly exhaust certain letters, and require sorts to render the fount serviceable to its full general capacity. So with scientific and other books. Even in the case of two authors writing on the same subject, there is no certainty that the fount will run alike. The master-printer, therefore, to keep the entire letter in use, is compelled to order sorts, and his fount is thus constantly growing larger.
Due to the different writing styles of authors and the variety of topics in books, some letters will occasionally run short in a[58] font, no matter what the initial proportions were. A new font may work well for a general literature piece written in the third person, while a novel packed with first-person dialogues will quickly deplete certain letters and require additional sorts to make the font usable to its full potential. The same applies to scientific and other types of books. Even when two authors are writing about the same topic, there’s no guarantee that the font will wear evenly. Therefore, the master printer, to keep all the letters in circulation, has to order more sorts, and as a result, their font is always expanding.
A FOUNT OF TYPE.
A complete fount of type may be comprised under the following heads:—
A full set of type can be categorized under the following headings:—
CAPITALS.
capitals
A B C D E F G H I J K L M N O P Q R S T U V W X Y Z Æ Œ &
A B C D E F G H I J K L M N O P Q R S T U V W X Y Z Æ Œ &
SMALL CAPITALS.
SMALL CAPS.
A B C D E F G H I J K L M N O P Q R S T U V W X Y Z Æ Œ &
A B C D E F G H I J K L M N O P Q R S T U V W X Y Z Æ Œ &
LOWER CASE.
Lower case.
a b c d e f g h i j k l m n o p q r s t u v w x y z æ œ ff fi ffi fl ffl
a b c d e f g h i j k l m n o p q r s t u v w x y z æ œ ff fi ffi fl ffl
ITALIC CAPITALS.
ITALIC CAPITALS.
A B C D E F G H I J K L M N O P Q R S T U V W X Y Z Æ Œ &
A B C D E F G H I J K L M N O P Q R S T U V W X Y Z Æ Œ &
ITALIC LOWER CASE.
italic lower case.
a b c d e f g h i j k l m n o p q r s t u v w x y z æ œ ff fi ffi fl ffl
a b c d e f g h i j k l m n o p q r s t u v w x y z æ œ ff fi ffi fl ffl
FIGURES AND FRACTIONS.
Numbers and Fractions.
1 2 3 4 5 6 7 8 9 0 ¼ ½ ¾ ⅓ ⅔ ⅛ ⅜ ⅝ ⅞
1 2 3 4 5 6 7 8 9 0 ¼ ½ ¾ ⅓ ⅔ ⅛ ⅜ ⅝ ⅞
POINTS AND REFERENCES.
Points and References.
, ; : ? ! - ’ ( ) [ ] * † ‡ § ∥ ¶
, ; : ? ! - ’ ( ) [ ] * † ‡ § ∥ ¶
BRACES, DASHES AND COMMERCIAL SIGNS.
Braces, dashes, and commercial signs.
$ £ ° ` ´
- – — ⸺ ☞ ☜ @ ⅌ ℔
$ £ ° ` ´
- – — ⸺ ☞ ☜ @ ⅌ ℔
Four kinds of spaces; en, em, two and three em quadrates.
Four types of spaces: en, em, two-em, and three-em quadrates.
Accents.
Accents.
These are the ordinary sorts cast to a fount, and are classified by founders as long, short, ascending, descending, kerned, and double letters.
These are the standard types cast in a mold, and are categorized by foundry workers as long, short, ascending, descending, kerned, and double letters.
Long Letters fill the whole depth of the face of the body, and are both ascending and descending, such in the Roman as Q and j, and in the Italic f.
Long Messages take up the entire height of the body, and can be both tall and short, like the Roman letters Q and j, and the Italic f.
Short Letters have the face cast on the middle of the body, (by founders called shank,) as a, c, e, m, n, o, r, s, u, v, w, x, z, all of which will admit of being bearded above and below the face, both in Roman and Italic.
Short Messages have the design centered on the middle of the body, (referred to by founders as the shank,) such as a, c, e, m, n, o, r, s, u, v, w, x, z, all of which can feature beards above and below the face, in both Roman and Italic styles.
Ascending Letters are all the Roman and Italic capitals; in the lower case, b, d, f, h, i, k, l, t.
Ascending Letters are all the Roman and Italic capital letters; in lowercase, they are b, d, f, h, i, k, l, t.
Descending Letters are g, p, q, y, in Roman and Italic.
Descending Letters are g, p, q, y, in Roman and Italic.
Kerned Letters are types that have part of the face hanging over either one or both sides of the body. In Roman, f and j are the only kerned letters; but, in Italic, d, g, j, l, y are kerned on one side, and f on both sides of its face. Most Italic capitals are kerned on one side of the face.
Kerned Letters are characters that have part of the letter extending over one or both sides of the body. In Roman type, only f and j are kerned letters; however, in Italic type, d, g, j, l, and y are kerned on one side, while f is kerned on both sides. Most Italic capitals are kerned on one side of the letter.
The Double Letters in modern use are ff, fi, ffi, fl, ffl; and these are so cast to prevent the breaking of the beak of the f when used before a tall letter. The diphthongs æ and œ may be classed among double letters.
The Double Letters used today are ff, fi, ffi, fl, and ffl; and they are designed to prevent the beak of the f from breaking when it's placed before a tall letter. The diphthongs æ and œ can also be considered double letters.
Printers divide a fount of letter into two classes.
Printers split a set of type into two categories.
1. | The upper case | } | sorts. |
2. | The lower case |
The upper case sorts are capitals, small capital letters, references, dashes, braces, commercial signs and fractions.
The uppercase sorts include capital letters, small caps, references, dashes, braces, symbols, and fractions.
The lower case consists of small letters, double letters, figures, points, spaces and quadrates.
The lower case includes small letters, double letters, numbers, punctuation, spaces, and squares.
CAPITALS.
Lindley Murray gives the following judicious directions in regard to the use of capital letters:—
Lindley Murray provides the following sensible guidelines on the use of capital letters:—
It was formerly the custom to begin every noun with a capital; but as this practice was troublesome, and gave the writing or printing a crowded and confused appearance, it has been discontinued. It is, however, very proper to begin with a capital,—
It used to be customary to start every noun with a capital letter, but since this practice was cumbersome and made writing or printing look cluttered and confusing, it has been phased out. Nonetheless, it is still appropriate to start with a capital letter,—
1. The first word of every book, chapter, letter, note, or any other piece of writing; and,
1. The first word of every book, chapter, letter, note, or any other piece of writing; and,
2. The first word after a period; and, if the two sentences are totally independent, after a note of interrogation or exclamation. But if a number of interrogative or exclamatory sentences[60] are thrown into one general group, or if the construction of the latter sentences depends on the former, all of them, except the first, may begin with a small letter: as, How long, ye simple ones, will ye love simplicity? and the scorners delight in their scorning? and fools hate knowledge?—Alas! how different! yet how like the same!
2. The first word after a period; and, if the two sentences are totally independent, after a question mark or exclamation point. But if a bunch of question or exclamation sentences[60] are combined into one group, or if the construction of the latter sentences relies on the former, all of them, except the first, can start with a lowercase letter: like, How long, you simple ones, will you love simplicity? and the scorners enjoy their scorn? and fools hate knowledge?—Alas! how different! yet how similar!
3. The appellations of the Deity: as, God, Jehovah, the Almighty, the Supreme Being, the Lord, Providence, the Messiah, the Holy Spirit.
3. The names of God: such as God, Jehovah, the Almighty, the Supreme Being, the Lord, Providence, the Messiah, the Holy Spirit.
4. Proper names of persons, places, streets, mountains, rivers, ships: as, George, London, the Strand, the Alps, the Thames, the Seahorse.
4. Proper names of people, places, streets, mountains, rivers, ships: like, George, London, the Strand, the Alps, the Thames, the Seahorse.
5. Adjectives derived from the proper names of places: as, Grecian, Roman, English, French, Italian.
5. Adjectives derived from the proper names of places: like, Grecian, Roman, English, French, Italian.
6. The first word of a quotation, introduced after a colon, or when it is in a direct form: as, Always remember this ancient maxim: “Know thyself.”—Our great Lawgiver says, “Take up thy cross daily, and follow me.” But when a quotation is brought in obliquely after a comma, a capital letter is unnecessary: as, Solomon observes, “that pride goes before destruction.”
6. The first word of a quotation introduced after a colon, or when it's in a direct form: for example, Always remember this ancient saying: “Know yourself.”—Our great Lawgiver says, “Take up your cross daily, and follow me.” But when a quotation is included indirectly after a comma, a capital letter isn’t needed: for example, Solomon observes, “that pride goes before destruction.”
The first word of an example may also very properly begin with a capital: as, Temptation proves our virtue.
The first word of an example can also correctly start with a capital letter: for example, Temptation proves our virtue.
7. Every substantive and principal word in the titles of books: as, Johnson’s Dictionary of the English Language; Thomson’s Seasons; Rollin’s Ancient History.
7. Every important and main word in the titles of books: like, Johnson’s Dictionary of the English Language; Thomson’s Seasons; Rollin’s Ancient History.
8. The first word of every line in poetry.
8. The first word of each line in poetry.
9. The pronoun I and the interjection O are written in capitals: as, I write: Hear, O earth!
9. The pronoun I and the interjection O are written in capitals: as, I write: Hear, O earth!
Other words, besides the preceding, may begin with capitals when they are remarkably emphatical, or the principal subject of the composition.
Other words, in addition to the ones mentioned earlier, can start with capital letters when they are particularly emphasized or are the main subject of the piece.
The method of denoting capital letters in manuscript is by underscoring them with three distinct lines.
The way to highlight capital letters in a manuscript is by underlining them with three different lines.
SMALL CAPITALS.
Small Capitals are in general cast to Roman founts only, and are used for the purpose of giving a stronger emphasis to a word than that conveyed by Italic. They are likewise used for running heads, heads of chapters, &c. The first[61] word of every section or chapter is commonly put in small capitals; but when a two-line initial letter is used, the remainder of the word should be in capitals.
Small Caps are typically designed in Roman type only and are meant to provide more emphasis to a word than Italic does. They're also used for section headers, chapter titles, etc. The first[61] word of every section or chapter is usually set in small capitals; however, if a two-line initial letter is used, the rest of the word should be in capital letters.
The small capitals C, O, S, V, W, X, Z so closely resemble the same letters in the lower case, that care is required to prevent intermixing.
The small capitals C, O, S, V, W, X, Z look so much like their lowercase versions that you need to be careful to avoid mixing them up.
In manuscript, small capitals are denoted by two lines drawn under the words.
In manuscript, small capitals are shown by two lines drawn under the words.
Italic words are designated by a single stroke underneath.
Italic words are marked with a single line underneath.
POINTS.
Points consist of a comma, semicolon, colon, period or full-point, mark of interrogation, and mark of admiration. Shortly after the invention of printing, the necessity of stops or pauses in sentences for the guidance of the reader produced the colon and full-point. In process of time, the comma was added, which was then merely a perpendicular line, proportioned to the body of the letter. These three points were the only ones used till the close of the fifteenth century, when Aldo Manuccio gave a better shape to the comma, and added the semicolon; the comma denoting the shortest pause, the semicolon next, then the colon, and the full-point terminating the sentence. The marks of interrogation and admiration were introduced many years after.
Topics are made up of a comma, semicolon, colon, period, question mark, and exclamation mark. Soon after printing was invented, the need for stops or pauses in sentences to help readers led to the creation of the colon and period. Over time, the comma was added, originally as just a straight line proportional to the text. These three punctuation marks were the only ones in use until the end of the fifteenth century when Aldo Manuccio improved the design of the comma and introduced the semicolon; the comma indicates the shortest pause, followed by the semicolon, then the colon, and finally, the period ends the sentence. The question mark and exclamation mark came many years later.
Perhaps there never existed on any subject a greater difference of opinion among men of learning than on the true mode of punctuation. Some sprinkle the page with commas almost as promiscuously as if from a pepper-box, and make the pause of a semicolon where the sense will bear only a comma; while others are extremely careless, and omit points even when they are needed to give the true sense of a passage at the first reading.
Perhaps there has never been a greater difference of opinion among scholars about the right way to use punctuation. Some people scatter commas across the page almost as randomly as if they're using a pepper shaker, and they use semicolons in places where only a comma should go; while others are very careless and leave out punctuation even when it’s necessary to convey the meaning of a sentence on the first read.
The lack of an established practice is much to be regretted. The loss of time to a compositor occasioned by altering points arbitrarily is a great hardship. Manuscripts are often placed in the printer’s hands without being properly prepared: either the writing is illegible, the spelling incorrect, or the punctuation defective. Unless the author will take entirely on himself the responsibility of the pointing, it will be better to omit every point in the copy, except at the end of a sentence, rather[62] than confuse the mind of the compositor by commas and semicolons placed indiscriminately, in the hurry of writing, without any regard to propriety.[10]
The lack of a standard practice is really unfortunate. It’s a huge hassle for typesetters when they have to waste time changing punctuation randomly. Manuscripts are often handed to the printer without proper preparation: the writing can be hard to read, the spelling might be wrong, or the punctuation could be faulty. If the author doesn’t want to take full responsibility for the punctuation, it’s better to leave out all punctuation in the copy except at the end of sentences, rather than confuse the typesetter with commas and semicolons thrown in carelessly during the rushed writing, without any thought for what makes sense.[62][10]
The Comma [,] divides the clauses of a long or involved sentence, and commonly marks the shortest pause in reading.
The Comma [,] separates the clauses of a long or complicated sentence and usually indicates the briefest pause while reading.
Commas are used to denote extracts or quotations from other works, dialogue matter, or passages or expressions not original, by placing two of them inverted before the first word of the passage quoted, the ending being denoted by two apostrophes. A thin space is used to keep the inverted commas free from the matter. The method of running them down the sides to the end of the quotation has been found inconvenient, especially where a quotation occurs within a quotation, or a speech within a speech: the proper method of distinguishing these is by placing a single inverted comma before the extra quotation, and concluding with a single apostrophe. Where both quotations end together, put three apostrophes, observing after the first to place a thin space.
Commas are used to indicate extracts or quotations from other works, dialogue, or non-original passages or expressions by placing two inverted commas before the first word of the quoted passage, with the ending marked by two apostrophes. A thin space is used to separate the inverted commas from the text. Running the commas down the sides to the end of the quotation has been found inconvenient, especially when a quotation occurs within another quotation or a speech within a speech. The correct way to distinguish these is by placing a single inverted comma before the additional quotation and concluding with a single apostrophe. When both quotations end together, use three apostrophes, making sure to place a thin space after the first one.
Inverted commas were first used by Guillemet, a Frenchman, to supersede the use of Italic letter in emphasized words. As an acknowledgment, his countrymen call them after his name. French founders cast them double, thus [«»]. MacKellar, Smiths & Jordan, Philadelphia, furnish them in this way when desired.
Inverted commas were first used by Guillemet, a Frenchman, to replace Italic letters for emphasizing words. As a nod to him, his fellow countrymen named them after him. French printers created them as double quotes, like this [«»]. MacKellar, Smiths & Jordan in Philadelphia provide them like this upon request.
A single comma inverted is improperly used as an abbreviation of the word Mac, as in M’Gowen: c is preferable, as McGowen.
A single inverted comma is incorrectly used as a short form of the word Mac, like in M’Gowen: c is better, as in McGowen.
The Semicolon [;] denotes a pause greater than that of a comma, and is used between dependent clauses of compound sentences.
The Semicolon [;] indicates a longer pause than a comma and is used between dependent clauses in compound sentences.
The Colon [:] is employed in a sentence between clauses less connected than those which are divided by a semicolon, but not so independent as separate, distinct sentences.
The Colon [:] is used in a sentence between clauses that are less related than those separated by a semicolon, but not as independent as completely separate sentences.
The Period or Full-Point [.] serves to indicate the end of a complete sentence. When used in abbreviations, it has no effect as a full stop in the punctuation, unless at the end of a sentence. In some works this point is discarded as a mark of abbreviation, as in Mr Dr &c.
The . or Full Point [.] indicates the end of a complete sentence. When used in abbreviations, it doesn't act as a full stop in punctuation, except at the end of a sentence. In some works, this dot is omitted as a mark of abbreviation, like in Mr Dr &c.
Full-points are sometimes used as leaders in tables of contents, figure-work, &c.; but dotted rules or leaders are more economical for this purpose, as they save considerable time in the composition.
Full points are sometimes used as leaders in tables of contents, figure work, etc.; but dotted rules or leaders are more efficient for this purpose, as they save a significant amount of time in the layout.
The sign of Interrogation [?] is used to denote a question. Every interrogation or question should begin with a capital letter, (unless several questions follow one another in connected succession,) according to the method observed in the Bible, where questions and responses, and the beginning of sayings, &c. are denoted by a capital letter.
The sign of Questioning [?] is used to indicate a question. Every question should start with a capital letter, (unless multiple questions come one after another in a series,) following the method used in the Bible, where questions and answers, as well as the beginning of statements, etc., are marked by a capital letter.
The sign of Admiration or Exclamation [!] denotes surprise, astonishment, rapture, and other sudden emotions of the mind, whether of joy or sorrow. This sign is put after the interjections Ah! Alas! Oh! &c.; but there are exceptional cases, as, Ah me! Alas the day! &c.
The symbol of Respect or Exclamation! [!] represents surprise, shock, joy, and other sudden emotions of the mind, whether happy or sad. This symbol is placed after interjections like Ah! Alas! Oh! etc.; however, there are exceptions, such as Ah me! Alas the day! etc.
All the points, except the comma and the period, should be preceded by a hair-space; the comma and full-point do not require any space to bear them off.
All the punctuation marks, except for the comma and the period, should be preceded by a hair-space; the comma and period don’t need any space before them.
The em dash [—], though not ranked as a point, is often used by careless writers as a substitute for a comma or semicolon. It may be properly employed in parenthetical sentences, and in rhapsodical writing abounding in disconnected sentences.
The em dash [—], while not considered a punctuation mark on its own, is often used by careless writers as a replacement for a comma or semicolon. It can be properly used in parenthetical sentences and in expressive writing filled with disjointed sentences.
A dash stands for a sign of repetition in catalogues of goods, where it implies ditto; and in catalogues of books, where a dash signifies ejusdem, instead of repeating the author’s name with the title of every separate treatise of his writing. A sign of repetition should never appear at the top of a page, but the name of the author, or of the merchandise, should be set out again at length.
A dash represents a sign of repetition in product catalogs, meaning “ditto”; and in book catalogs, it indicates “ejusdem,” used instead of repeating the author's name with each separate title of their work. A sign of repetition should never be at the top of a page; instead, the author's name or the name of the product should be fully written out again.
A dash likewise stands for to; as, chap. xvi. 3-17; that is, from the third to the seventeenth verse inclusive. At other times it serves for an index, to give notice that what follows it is a corollary of what has preceded; thus:—
A dash also represents to; for example, chap. xvi. 3-17; meaning from the third to the seventeenth verse, inclusive. At other times, it acts as an index to indicate that what comes next is related to what came before it; thus:—
APOSTROPHE.
The apostrophe [’] is a comma cast on the upper edge of a type, and is used as a sign of contraction or abbreviation of words in poetry or familiar conversation, as We’re, o’er, don’t, &c. In poetry, it should not be employed where the[64] verb ends with e, as love, change, &c., but only in cases where the verb concludes with a consonant, as, reign, obtain, &c. It also marks the elision of a vowel at the beginning of words, as, ’scape, or of a syllable, as, ’prentice.
The apostrophe [’] is a comma placed at the top of a letter, and it’s used to show that letters are left out in contractions or abbreviations of words in poetry or casual conversation, like We’re, o’er, don’t, etc. In poetry, it shouldn’t be used when the[64] verb ends with an e, like love, change, etc., but only when the verb ends with a consonant, as in reign, obtain, etc. It also indicates the omission of a vowel at the start of words, as in ’scape, or of a syllable, as in ’prentice.
The monosyllables though and through are sometimes shortened to tho’ and thro’, but very improperly, as they retain the same sound, and the abbreviation cannot in the slightest degree assist the versification.
The monosyllables though and through are sometimes shortened to tho’ and thro’, but this is not correct, as they still have the same sound, and the abbreviation does not help with the rhythm at all.
Words in the possessive case are generally known by having ’s for their termination.
Words in the possessive case are usually recognized by ending in ’s.
All quotations which are denoted at the beginning by inverted commas are closed with apostrophes. There is no space required between the apostrophe and the matter.
All quotes that start with quotation marks are ended with apostrophes. No space is needed between the apostrophe and the text.
HYPHEN.
A hyphen is a sign of connection, and denotes that the part of a word at the end of a line belongs to the portion at the beginning of the next line.
A dash is a connection symbol and indicates that the part of a word at the end of a line is connected to the part at the beginning of the next line.
A compositor who studies propriety and neatness in his work will not allow an unnecessary division, even in a narrow measure, if he can avoid it by overrunning two or three lines of matter. In large type and narrow measures, the division of words cannot be avoided; but care should be taken that hyphens do not occur at the end of successive lines. In small type and wide measures, the hyphen may frequently be dispensed with, either by driving out or getting in the word, without interfering with the regularity of the spacing. The compositor who is careful on this point will find his advantage in the preference given to his work, and in the respect attached to his character as a master of his business. Numerous divisions down the side of a page and irregular spacing are the two greatest defects in composition.
A typesetter who values propriety and neatness in their work won’t allow unnecessary breaks, even in a tight space, if they can avoid it by stretching two or three lines of text. In large type with narrow columns, word breaks can’t be avoided, but care should be taken to ensure hyphens don’t appear at the end of consecutive lines. In small type with wide columns, hyphens can often be omitted, either by adjusting the placement of the word without disrupting the spacing. A typesetter who pays attention to this will benefit from the preference for their work and the respect earned as a skilled professional. Having multiple breaks running down a page and uneven spacing are the two biggest flaws in typesetting.
It is proper, if possible, to keep the derivative or radical word undivided: as, occur-rence, gentle-man, respect-ful, &c. In other cases, printers generally divide on the vowel, which is an excellent method.
It’s best, if possible, to keep derivative or radical words whole: like occur-rence, gentle-man, respect-ful, etc. In other situations, printers usually divide at the vowel, which is a great method.
The hyphen is also used to connect compound words, which are formed of two substantives, as, bird-cage, love-letter, &c.; also what are termed compound adjectives, as, well-built house, handsome-faced child, &c.
The hyphen is also used to connect compound words, which are made up of two nouns, like bird-cage, love-letter, etc.; it also connects what are called compound adjectives, like well-built house, handsome-faced child, etc.
The prepositions after, before, over, &c. are often connected with other words, but do not always make a proper compound: thus, before-mentioned is a compound when it precedes a substantive, as, in the before-mentioned place; but when it comes after a noun, as, in the place before mentioned, it should be two distinct words.[11]
The prepositions after, before, over, etc. are often combined with other words but don’t always form a proper compound: for example, before-mentioned is a compound when it comes before a noun, as in the before-mentioned place; however, when it follows a noun, as in the place before mentioned, it should be two separate words.[11]
PARENTHESIS AND BRACKET.
The use of the Parenthesis ( ) is to enclose interpolated words or sentences which serve to strengthen the argument, although the main sentence would be complete without the interpolated matter.
The use of the Parentheses ( ) is to enclose added words or sentences that reinforce the argument, even though the main sentence would still be complete without the added information.
Parentheses are not as much used as formerly: authors place their intercalations between commas,—frequently with a dash at the beginning and ending,—which make them quite as intelligible as though they were enclosed between parentheses.
Parentheses aren't used as much as they used to be: writers place their additions between commas—often with a dash at the start and end—which makes them just as clear as if they were inside parentheses.
Brackets [ ] are seldom made use of, except to indicate that the word enclosed within them had been carelessly omitted in the old MS. or copy, and was now inserted by the editor.
Brackets [ ] are rarely used, except to show that the word inside them was carelessly left out in the old manuscript or copy, and has now been added by the editor.
REFERENCES.
References are marks and signs employed to direct the attention of the reader to notes in the margin or at the bottom of a page.
References are marks and symbols used to guide the reader's attention to notes in the margin or at the bottom of a page.
The characters technically known by printers as references are the following, which are used in the order here given:—
The characters referred to by printers as references are the following, used in the order listed here:—
Asterisk | * |
Dagger | † |
Double Dagger | ‡ |
Section | § |
Parallel | ∥ |
Paragraph | ¶ |
In Roman church-books, the Asterisk divides each verse of a psalm into two parts, and marks the place where the responses begin: this in the Book of Common Prayer is denoted by a colon placed between the two parts of each verse. Asterisks also denote an omission, or an hiatus in the original copy; the number of asterisks being multiplied according to the extent of the omission.
In Roman church books, the Asterisk splits each verse of a psalm into two parts and indicates where the responses start: in the Book of Common Prayer, this is shown by a colon placed between the two parts of each verse. Asterisks also indicate an omission or a gap in the original text; the number of asterisks increases based on the length of the omission.
The Dagger, originally termed the Obelisk, or Long Cross, is frequently used in Roman Catholic church-books, prayers of exorcism, at the benediction of bread, water, and fruit, and upon other occasions, where the priest is to make the sign of the cross; but the square cross (✠) is the proper symbol for the purpose. The square cross is used, besides, in the pope’s briefs, and in mandates of archbishops and bishops, immediately before the signature of their names. It is not placed among references.
The Dagger, originally called the Obelisk or Long Cross, is often used in Roman Catholic church books, during prayers of exorcism, at the blessing of bread, water, and fruit, and on other occasions when the priest makes the sign of the cross; however, the square cross (✠) is the correct symbol for this purpose. The square cross is also used in the pope’s briefs and in the mandates of archbishops and bishops right before they sign their names. It is not included among references.
Besides its use as a reference mark, the Paragraph is now employed chiefly in Bibles, to show the parts into which a chapter is divided. In Common Prayer Books, paragraphs are put before the lines that direct the order of the service, and which are called the Rubrics because they were formerly printed in red.
Besides being used as a reference mark, the paragraph is now mainly found in Bibles to indicate the sections a chapter is divided into. In common prayer books, paragraphs are placed before the lines that guide the order of the service, known as the rubrics because they were previously printed in red.
The neatest references, when many are required in books, are either superior letters or superior figures,—thus, ¹, ², ³, or thus, ᵃ, ᵇ, ᶜ. Superior letters are used chiefly in Bibles and other books which have more than one sort of notes, and therefore require different references. When thus used, the letter ʲ should be omitted, as, from its similarity to the ⁱ, the reader might at times be led into error.
The best way to reference multiple items in books is to use superscript letters or superscript numbers—like this: ¹, ², ³, or like this: ᵃ, ᵇ, ᶜ. Superscript letters are mainly used in Bibles and other books that have various types of notes, so they need different referencing. When used this way, the letter ʲ should be avoided because its similarity to ⁱ could confuse the reader at times.
ACCENTED LETTERS.
Letters called accented by printers are the five vowels, marked thus:—
Messages that printers refer to as accented are the five vowels, marked like this:—
Acute | á é í ó ú |
Grave | à è ì ò ù |
Circumflex | â ê î ô û |
Diæresis | ä ë ï ö ü |
Long | ā ē ī ō ū |
Short | ă ĕ ĭ ŏ ŭ |
We may include the French ç, the Spanish ñ, the Portuguese ã and õ, the Swedish and Norwegian å and ö, and the Welsh ŵ and ŷ.
We may include the French ç, the Spanish ñ, the Portuguese ã and õ, the Swedish and Norwegian å and ö, and the Welsh ŵ and ŷ.
NUMERAL LETTERS.
The Greeks at first employed the letters of the entire alphabet to express the first twenty-four numbers; but the system was cumbrous, and they adopted the happy expedient of dividing their alphabet into three portions, using the first to symbolize the 9 digits, the second the 9 tens, and the third the 9 hundreds; and, as their alphabet contained only twenty-four letters, they invented three additional symbols. Their list of symbols then stood as follows:—
The Greeks initially used all the letters of the alphabet to represent the first twenty-four numbers; however, this method was unwieldy, so they cleverly divided their alphabet into three sections. They used the first part for the 9 digits, the second for the 9 tens, and the third for the 9 hundreds. Since their alphabet had only twenty-four letters, they created three extra symbols. Their list of symbols then looked like this:—
Units. | Tens. | Hundreds. | |||
---|---|---|---|---|---|
α represents | 1 | ι represents | 10 | ρ represents | 100 |
β | 2 | κ | 20 | σ | 200 |
γ | 3 | λ | 30 | τ | 300 |
δ | 4 | μ | 40 | υ | 400 |
ε | 5 | ν | 50 | φ | 500 |
ϝ (introduced) | 6 | ξ | 60 | χ | 600 |
ζ | 7 | ο | 70 | ψ | 700 |
η | 8 | π | 80 | ω | 800 |
θ or ϑ | 9 | Ϟ or ϟ (introduced) | 90 | ϡ, ![]() ![]() |
900 |
By these symbols, only numbers under 1000 could be expressed; but, by putting a mark called iota under any symbol, its value was increased a thousand-fold: thus, ᾳ = 1000, κͅ = 20,000; or, by subscribing the letter Μ, the value of a symbol was raised ten thousand-fold. For these two marks, single and double dots were afterward substituted. This improvement enabled them to express with facility all numbers as high as 9,990,000,—a range sufficient for all ordinary purposes.
By using these symbols, only numbers less than 1000 could be represented; however, by placing a mark called iota underneath any symbol, its value was increased a thousand times: for example, ᾳ = 1000, κͅ = 20,000; or, by adding the letter Μ, the value of a symbol was raised ten thousand times. Later, single and double dots were used as substitutes for these two marks. This improvement allowed them to easily express all numbers up to 9,990,000, which was enough for all common needs.
It has been supposed that the Romans used M to denote 1000 because it is the first letter of Mille, which is Latin for 1000; and C to denote 100, it being the first letter of Centum, the Latin term for 100. Some also suppose that D, being formed by dividing the old M in the middle, was therefore appointed to stand for 500,—that is, half as much as the M stood for when it was whole; and that L being half a C, was, for the same reason, used to denominate 50. But the most natural account of the matter appears to be this:—
It’s believed that the Romans used M to represent 1000 because it’s the first letter of Mille, which means 1000 in Latin; and C to represent 100, since it’s the first letter of Centum, the Latin word for 100. Some also think that D, which looks like the old M cut in half, was used to stand for 500—essentially half of what M represented when it was whole; and that L, being half of C, was used to represent 50 for the same reason. However, the most straightforward explanation seems to be this:—
The Romans probably put down a single stroke, Ⅰ, for one, as is still the practice of those who score on a slate, or with chalk; this stroke they doubled, trebled, and quadrupled, to express two, three, and four: thus, ⅠⅠ, ⅠⅠⅠ, ⅠⅠⅠⅠ. So far they could easily number the strokes with a glance of the eye; but they found that if more were added it would be necessary to count the strokes one by one: for this reason, when they came to five, it was expressed by joining two strokes together in an acute angle, thus, Ⅴ.
The Romans likely used a single stroke, I, to represent one, similar to how people today score on a slate or with chalk. They doubled, tripled, and quadrupled this stroke to express two, three, and four: so, II, III, IV. Up to this point, they could easily count the strokes at a glance. However, they realized that if they added more, it would be necessary to count each stroke individually. For this reason, when they reached five, they represented it by joining two strokes in an acute angle, like this: V.
After they had made this acute angle, Ⅴ, for five, they then added single strokes to the number of four, thus, ⅤⅠ, ⅤⅠⅠ, ⅤⅠⅠⅠ, ⅤⅠⅠⅠ, and then, as the strokes could not be further multiplied without confusion, they doubled their acute angle by prolonging the two lines beyond their intersection, thus, Ⅹ, to denote two fives, or ten. After they had doubled, trebled, and quadrupled this double acute angle, thus, ⅩⅩ, ⅩⅩⅩ, ⅩⅩⅩⅩ, they then, for the same reason which induced them to make a single angle first, and then to double it, joined two single strokes in another form, and, instead of an acute angle, made a right angle, Ⅼ, to denote fifty. When this was doubled, they then doubled the right angle, thus, ⊏, to denote one hundred, and, having numbered this double right angle four times, thus, ⊏⊏, ⊏⊏⊏, ⊏⊏⊏⊏, when they came to the fifth number, as before, they reverted it, and put a single stroke before it, thus,[69] Ⅰ⊐, to denote five hundred; and, when this five hundred was doubled, then they also doubled their double right angle, setting two double right angles opposite to each other, with a single stroke between them, thus, ⊏Ⅰ⊐, to denote one thousand: when this note for one thousand had been repeated four times, they then put down Ⅰ⊐⊐ for five thousand, ⊏⊏Ⅰ⊐⊐ for ten thousand, and Ⅰ⊐⊐⊐ for fifty thousand.
After they created this acute angle, V, for five, they added single strokes to the number four, forming VI, VII, VIII, and then, since the strokes couldn't be increased further without confusion, they doubled their acute angle by extending the two lines beyond their intersection, making X to represent two fives, or ten. After they doubled, tripled, and quadrupled this double acute angle, resulting in XX, XXX, and XXXX, they then, for the same reason that led them to create a single angle first and then double it, combined two single strokes in another way, and instead of an acute angle, formed a right angle, L, to represent fifty. When this was doubled, they also doubled the right angle, resulting in ⊏, to represent one hundred, and after numbering this double right angle four times, as ⊏⊏, ⊏⊏⊏, ⊏⊏⊏⊏, when they reached the fifth number, they reverted it, placing a single stroke before it, thus, [69] I⊐, to represent five hundred; when this five hundred was doubled, they also doubled their double right angle, placing two double right angles opposite each other, with a single stroke between them, thus, ⊏I⊐, to represent one thousand: when this notation for one thousand was repeated four times, they wrote I⊐⊐ for five thousand, ⊏⊏I⊐⊐ for ten thousand, and I⊐⊐⊐ for fifty thousand.
The corners of the angles being cut off by transcribers for despatch, these figures were gradually brought into what are now called numerical letters. When the corners of ⊏Ⅰ⊐ were made round, it stood thus, ⅭⅠↃ, which is so near the Gothic ന that it soon deviated into that character; so that Ⅰ⊐ having the corners made round stood thus, ⅠↃ, and then easily deviated into D. ⊏ also became a plain C by the same means: the single rectangle, which denoted fifty, was, without any alteration, a capital L; the double acute angle was an X; the single acute angle, a V; and a plain single stroke, the letter I. And thus these seven letters, M, D, C, L, X, V, I, became numerals. As a further proof of this assertion, let it be considered that ⅭⅠↃ is still used for one thousand, and ⅠↃ for five hundred, instead of M and D; and this mark, ന, is sometimes used to denote one thousand, which may easily be derived from this figure, ⊏Ⅰ⊐, but cannot be deviations from, or corruptions of, the Roman letter M. The Romans also expressed any number of thousands by a line drawn over any numeral less than one thousand: thus, V̅ denotes five thousand, L̅X̅ sixty thousand; so, likewise, M̅ is one million, M̅M̅ two millions, &c.
The corners of the angles being cut off by scribes for efficiency, these figures gradually transformed into what we now call numerical letters. When the corners of ⊏Ⅰ⊐ were rounded, it became ⅭⅠↃ, which is very similar to the Gothic ن, leading to its evolution into that character; so that Ⅰ⊐, with rounded corners, appeared as ⅠↃ, which easily changed into D. ⊏ also turned into a plain C through the same process: the single rectangle that represented fifty was, without any change, a capital L; the double acute angle was an X; the single acute angle was a V; and a plain single stroke represented the letter I. Thus, these seven letters, M, D, C, L, X, V, I, became numerals. As further proof of this claim, consider that ⅭⅠↃ is still used for one thousand, and ⅠↃ for five hundred, instead of M and D; and this mark, ن, is sometimes used to denote one thousand, which can easily be traced back to this figure, ⊏Ⅰ⊐, but cannot be seen as deviations from, or corruptions of, the Roman letter M. The Romans also represented any number of thousands by a line drawn over any numeral less than one thousand: for example, V̅ means five thousand, L̅X̅ means sixty thousand; similarly, M̅ is one million, M̅M̅ is two million, etc.
Upon the discovery of printing, and before capitals were invented, small letters served for numerals; not only when Gothic characters were in vogue, but when Roman had become the prevailing character. Thus, in early times, i b x l c d m were, and in Roman type are still, of the same signification as capitals when used as numerals. Though the capital J is not a numeral letter, yet the lower-case j is as often and as significantly used as the vowel i, especially where the former is employed as a closing letter, in ij iij bj bij biij dcij, &c. In Roman lower-case numerals, the j is not regarded, but the i stands for figure 1 wherever it is used numerically.
Upon the discovery of printing, and before capital letters were created, lowercase letters were used for numbers; not only when Gothic letters were popular, but also when Roman letters became the standard. In ancient times, i b x l c d m were, and in Roman type still are, understood the same way as capital letters when they represent numbers. Although the capital J is not a numeral, the lowercase j is just as frequently and meaningfully used as the vowel i, especially when it's the closing letter, as in ij iij bj bij biij dcij, etc. In Roman lowercase numerals, the j is not included, but the i represents the number 1 wherever it is used numerically.
During the existence of the French Republic, books were dated in France from the first year of the Republic: thus An. XII. (1803,) or twelve years from 1792.
During the time of the French Republic, books in France were dated starting from the first year of the Republic: so, for example, An. XII. (1803), means twelve years from 1792.
ARITHMETICAL FIGURES.
The arithmetical or Arabic numerals are 0, 1, 2, 3, 4, 5, 6, 7, 8, 9. Properly they should be styled Hindu or Indian numerals; for the Arabs borrowed them, along with the decimal system of notation, from the Hindus. They were probably first introduced from the East into Italy about 1202; yet they did not come into general use before the invention of printing. Accounts were kept in Roman numerals up to the sixteenth century. Figures are usually made one en thick; but of late a broader figure is cast for newspaper use, which is two-thirds or six-sevenths of an em in width.
The numerical system we use today, known as Arabic numerals, consists of 0, 1, 2, 3, 4, 5, 6, 7, 8, and 9. They are actually better referred to as Hindu or Indian numerals because the Arabs adapted them, along with the decimal system, from the Hindus. They were likely first brought from the East to Italy around 1202, but it wasn't until the invention of printing that they became widely used. Before that, financial records were kept in Roman numerals until the sixteenth century. Typically, the figures are made one en thick; however, recently a wider version has been created for newspapers, which is two-thirds or six-sevenths of an em in width.
OLD STYLE FIGURES.
Though uniform in height and appearance, we do not deem the modern figures an improvement on the variously-lining figures formerly in vogue, and now happily coming again into use. The latter can be caught by the eye with greater ease and certainty, just as lower-case letter can be read with more facility than continuous lines of capitals. In the new style the 3 and 8 may easily be mistaken for each other, and so with the 6, 9, and 0; but in the old style figures such errors are quite unlikely to happen, as some of them occupy the centre of the body only, and others are ascending or descending characters. The example here given will show the justice of our remarks:
Although uniform in height and appearance, we don’t consider the modern figures an improvement over the varied designs that were once popular and are now happily making a comeback. The latter can be recognized by the eye more easily and reliably, just like lower-case letters can be read more comfortably than continuous lines of capital letters. In the new style, the 3 and 8 can easily be confused with each other, as can the 6, 9, and 0; however, in the old style, these mistakes are much less likely to occur since some of them only take up the center of the body, while others are taller or shorter characters. The example provided will demonstrate the validity of our comments:

1 2 3 4 5 6 7 8 9 0
1 2 3 4 5 6 7 8 9 0
1 2 3 4 5 6 7 8 9 0
1 2 3 4 5 6 7 8 9 0
SCRATCHED OR CANCELLED FIGURES
1̷ 2̷ 3̷ 4̷ 5̷ 6̷ 7̷ 8̷ 9̷ 0̷
1̷ 2̷ 3̷ 4̷ 5̷ 6̷ 7̷ 8̷ 9̷ 0̷
Are used in arithmetical matter when certain figures require to be crossed over in an operation.
Are used in math when certain numbers need to be crossed over in a calculation.
FRACTIONS.
Common Fractions, or broken numbers in arithmetic, are cast solid to all sizes of type. A great improvement has been introduced by casting the numerator and denominator separately, on bodies of half size, with the line on the under figure, so that odd fractions of any amount may be readily formed, thus: ¹ ² ³ ⁄₂ ⁄₃ ⁄₄ ½ ⅔ ¾.
Fractions, or broken numbers in arithmetic, are available in all sizes of type. A significant improvement has been made by casting the numerator and denominator separately, in half-size bodies, with the line below the figures. This allows for the easy creation of various odd fractions, like this: ¹ ² ³ ⁄₂ ⁄₃ ⁄₄ ½ ⅔ ¾.
SIGNS.
COMMERCIAL SIGNS.
⅌ | Per, each. |
@ | At or to. |
% | Percentum. |
℀ | Account. |
¢ | Cent. |
$ | Dollar or dollars. |
£ | Libra, libræ, pound or pounds sterling. |
/ | Solidus, solidi, shilling or shillings. |
MATHEMATICAL, ALGEBRAICAL, AND GEOMETRICAL.
+ plus, or more, is the sign of real existence of the quantity it stands before, and is called an affirmative or positive sign. It is also the mark of addition: thus, a+b, or 6+9, implies that a is to be added to b, or 6 added to 9.
+ plus, or more, is the symbol that indicates the actual presence of the quantity it precedes, and it's known as an affirmative or positive sign. It's also the symbol for addition: so, a+b, or 6+9, means that a should be added to b, or 6 added to 9.
− minus, or less, before a single quantity, is the sign of negation, or negative existence, showing the quantity to which it is prefixed to be less than nothing. But between quantities it is the sign of subtraction: thus, a−b, or 8−4, implies b subtracted from a, or 8 after 4 has been subtracted.
− minus, or less, before a single quantity, indicates negation, or negative existence, showing that the quantity it’s attached to is less than nothing. However, between quantities, it represents subtraction: for example, a−b, or 8−4, means b is subtracted from a, or 8 after 4 has been taken away.
= equal. The sign of equality, though Des Cartes and some others use this mark, ∝: thus, a=b signifies that a is equal to b. Others use the mark = to denote identity of ratios.
= equal. The equality sign, although Des Cartes and some others use this symbol, ∝: thus, a=b means that a is equal to b. Others use the symbol = to indicate that ratios are identical.
× into or with. The sign of multiplication, showing that the quantities on each side the same are to be multiplied by one another: as, a×b is to be read, a multiplied into b; 4×8, the product of 4 multiplied into 8. Wolfius and others use a dot between the two factors: thus, 7·4 signifies the product of 7 and 4. In algebra the sign is commonly omitted, and the two quantities put together: thus, bd expresses the product of b and d. When one or both of the factors are compounded of several letters, they are distinguished by a line drawn over them: thus, the factum of a+b-c into d is written, d × a̅+̅b̅-̅c̅. Others distinguish the compound factors by including them in parentheses: thus, (a+b-c)d.
× into or with. The multiplication sign shows that the quantities on each side are to be multiplied by one another: for example, a×b is read as a multiplied by b; 4×8, the product of 4 multiplied by 8. Wolfius and others use a dot between the two factors: thus, 7·4 signifies the product of 7 and 4. In algebra, the sign is commonly omitted, and the two quantities are written together: thus, bd expresses the product of b and d. When one or both of the factors consist of several letters, they are distinguished by a line drawn over them: thus, the result of a+b-c multiplied by d is written as d × a̅+̅b̅-̅c̅. Others distinguish the compound factors by putting them in parentheses: thus, (a+b-c)d.
÷ by. The sign of division: thus, a÷b denotes the quantity a to be divided by b. Wolfius makes the sign of division two dots; 12:4 denotes the quotient of 12 divided by 4 = 3.
÷ by. The division sign: so, a÷b represents the amount a being divided by b. Wolfius uses two dots for the division sign; 12:4 represents the result of 12 divided by 4 = 3.
> or ⫍ are signs of majority: thus, a>b expresses that a is greater than b.
> or ⫍ are signs of majority: thus, a>b expresses that a is greater than b.
< or ⫎ are signs of minority,—when we would denote that a is less than b.
< or ⫎ are signs of minority,—when we want to show that a is less than b.
∞ is the character of similitude used by Wolfius, Leibnitz, and others. It is used in other authors for the difference between two quantities when it is unknown which is the greater of the two.
∞ is the symbol of similarity used by Wolfius, Leibnitz, and others. It is used by other writers to indicate the difference between two quantities when it’s unclear which one is larger.
∷ so is. The mark of geometrical proportion disjunct, and is usually placed between two pair of equal ratios: as, 3∶6∷4∶8 shows that 3 is to 6 as 4 is to 8.
∷ so is. The symbol of geometrical proportion is disjointed and is typically placed between two pairs of equal ratios: for example, 3∶6∷4∶8 indicates that 3 is to 6 as 4 is to 8.
∶ or ∴ is an arithmetical equal proportion: as, 7.3∶13.9; i. e. 7 is more than 3, as 13 is more than 9.
∶ or ∴ is a mathematical proportion: for example, 7.3∶13.9; i. e. 7 is greater than 3, just as 13 is greater than 9.
⬜ quadrate, or regular quadrangle,—viz. ⬜AB=⬜BC; i. e. the quadrangle upon the line AB is equal to the quadrangle upon the line BC.
⬜ quadrate, or regular quadrangle,—that is, ⬜AB=⬜BC; i. e. the quadrangle along line AB is equal to the quadrangle along line BC.
△ triangle: as, △ABC=△ADC.
△ triangle: as, △ABC=△ADC.
∠ an angle: as, ∠ABC=∠ADC.
∠ an angle: as, ∠ABC = ∠ADC.
⟂ perpendicular: as, AB⟂BC.
⟂ perpendicular: e.g., AB⟂BC.
▭ rectangled parallelogram, or the product of two lines.
▭ rectangular parallelogram, or the product of two lines.
∥ the character of parallelism.
∥ the nature of parallelism.
⧧ want of parallelism.
lack of parallelism.
≚ equiangular, or similar.
≚ equiangular or similar.
⫨ equilateral.
equilateral
▱ rhomboid.
▱ rhomboid.
◠ concentrix.
◠ Concentrix.
○ circle.
○ circle.
∟ right angle.
right angle.
∫ integration, (summa or sum).
∫ integration, (sum).
° denotes a degree: thus, 45° implies 45 degrees.
° indicates a degree: so, 45° means 45 degrees.
´ a minute: thus, 50´ is 50 minutes; ´´, ´´´, ´´´´, denote seconds, thirds, and fourths; and the same characters are used where the progressions are by tens, as it is here by sixties.
´ a minute: so, 50´ means 50 minutes; ´´, ´´´, ´´´´, represent seconds, thirds, and fourths; and the same symbols are used when the progressions are by tens, just as they are here by sixties.
∺ the mark of geometrical proportion continued, implies the ratio to be still carried on without interruption: as, 2, 4, 8, 16, 32, 64 ∺ are in the same uninterrupted proportion.
∺ the mark of geometrical proportion continued means the ratio is still maintained consistently: for example, 2, 4, 8, 16, 32, 64 ∺ are all in the same continuous proportion.
√ When used without a figure above it, indicates the square root, and is called the radical sign. Any other root is expressed by the index figure placed above the sign. √16 is the square root of 16, ∛27 the cube root of 27, &c.
√ When used without a number above it, it indicates the square root and is called the radical sign. Any other root is shown by placing the index number above the sign. √16 is the square root of 16, ∛27 is the cube root of 27, etc.
≅ difference equal.
≅ equal difference.
∹ the difference, or excess.
∹ the difference or excess.
Q or q, a square.
Q or q, a square.
C or c, a cube.
C or c, a cube.
QQ, the ratio of a square number to a square number.
QQ, the ratio of one square number to another square number.
In algebraical work, authors should be very exact in their copy, and compositors as careful in following it, so that no alterations may be necessary after it is composed, the over-running of this kind of matter being troublesome and costly.
In algebra work, writers should be very precise in their copy, and typesetters should be just as careful in following it, so that no changes are needed after it’s typeset, as correcting this kind of material can be annoying and expensive.
CELESTIAL AND ASTRONOMICAL SIGNS.
The Twelve Signs of the Zodiac.
♈ | Aries. |
♉ | Taurus. |
♊ | Gemini. |
♋ | Cancer. |
♌ | Leo. |
♍ | Virgo. |
♎ | Libra. |
♏ | Scorpio. |
♐ | Sagittarius. |
♑ | Capricornus. |
♒ | Aquarius. |
♓ | Pisces. |
The Sun and Major Planets.
☉ | Sun. |
☿ | Mercury. |
♀ | Venus. |
🜨 | Earth. |
♂ | Mars. |
♃ | Jupiter. |
♄ | Saturn. |
⛢ | Uranus. |
♇ | Neptune. |
⚳ Ceres, ⚴ Pallas, ⚵ Juno, ⚶ Vesta,
Astræa,
Hebe,
Iris,
and the other asteroids, or minor planets, are now commonly
designated by a circle enclosing a number which indicates
the order of their discovery: thus, ①, ②, ③, &c.
⚳ Ceres, ⚴ Pallas, ⚵ Juno, ⚶ Vesta,
Astræa,
Hebe,
Iris,
and the other asteroids, or minor planets, are now usually marked by a circle with a number inside that shows the order in which they were discovered: so, ①, ②, ③, etc.
Lunar Signs.
🌚 | New Moon. |
🌛 | First Quarter. |
🌝 | Full Moon. |
🌜 | Last Quarter. |
Aspects and Nodes.
☌ Conjunction; happens when two planets stand under each other in the same sign and degree.
☌ Conjunction; occurs when two planets are aligned in the same sign and degree.
☍ Opposition; happens when two planets stand diametrically opposite each other.
☍ Opposition; occurs when two planets are directly opposite each other.
△ Trine; happens when one planet stands from another four signs, or 120 degrees, which make one-third of the ecliptic.
△ Trine; occurs when one planet is positioned 120 degrees away from another, which is four signs apart, making one-third of the ecliptic.
□ Quartile; happens when two planets stand three signs from each other, which make 90 degrees, or the fourth part of the ecliptic.
□ Quartile; occurs when two planets are three signs apart from each other, forming a 90-degree angle, or a quarter of the ecliptic.
⚹ Sextile; is the sixth part of the ecliptic, which is two signs, and make 60 degrees.
⚹ Sextile is one-sixth of the ecliptic, which represents two signs and equals 60 degrees.
☊ The Dragon’s Head, or ascending node, and
☊ The Dragon’s Head, or ascending node, and
☋ The Dragon’s Tail, or descending node, are the two points in which the eclipses happen.
☋ The Dragon’s Tail, or descending node, are the two points where eclipses occur.
Planets that denote the Seven Days of the Week.
- Dies Solis—Sunday.
- Dies Lunæ—Monday.
- Dies Martis—Tuesday.
- Dies Mercurii—Wednesday.
- Dies Jovis—Thursday.
- Dies Veneris—Friday.
- Dies Saturni—Saturday.
Many signs and symbols have been invented by pseudo-astronomers to impose upon the credulity of the ignorant; among which are signs to give notice on what day it is proper to let blood, to bathe and to cup, to sow and to plant, to take physic, to have one’s hair cut, to cut one’s nails, to wean children, and many other absurdities; as well as symbols that serve to indicate hail, thunder, lightning, or any occult phenomena.
Many signs and symbols have been created by fake astronomers to take advantage of the gullibility of the uninformed; these include signs that indicate the best days to let blood, bathe, get cupped, sow and plant, take medicine, cut hair, trim nails, wean children, and many other ridiculous things; as well as symbols meant to signal hail, thunder, lightning, or any mysterious phenomena.
ECCLESIASTICAL SIGNS.
℟ Response, used in prayer-books.
℟ Response, used in worship books.
℣ Versicle, used in prayer-books to denote the part recited by the priest.
℣ Versicle, used in prayer books to indicate the part spoken by the priest.
✠ or ✝ A sign of the cross employed by Roman Catholic ecclesiastical dignitaries before their signatures. In Roman Catholic prayer-books, it also denotes the place where the priest is to make the sign of the cross.
✠ or ✝ A sign of the cross used by Roman Catholic church officials before their signatures. In Roman Catholic prayer books, it also indicates where the priest is supposed to make the sign of the cross.
* Used in Roman Catholic prayer-books to denote the place in a single verse where the response begins.
* Used in Roman Catholic prayer books to indicate the point in a single verse where the response starts.
MEDICAL SIGNS AND ABBREVIATIONS.
℞ stands for Recipe, or Take.
℞ stands for Recipe or Take.
ā, aa, of each a like quantity.
ā, aa, of each a like quantity.
℔ a pound.
℔ a lb.
℥ an ounce.
oz an ounce.
ʒ a drachm.
a dram.
℈ a scruple.
a scruple.
j stands for 1; ij for 2; iij for 3; and so on.
j stands for 1; ij stands for 2; iij stands for 3; and so on.
ss. signifies semi, or half.
ss. means semi, or half.
gr. denotes a grain.
gr. means a grain.
P. stands for particula, a little part, and means so much as can be taken between the ends of two fingers.
P. stands for particula, a small part, and means as much as can be held between the tips of two fingers.
P. æq. stands for partes æquales, or equal parts.
P. æq. means partes æquales, which refers to equal parts.
q. s. quantum sufficit, or as much as is sufficient.
q. s. quantum sufficit, or however much is enough.
q. p. quantum placit, or as much as you please.
q. p. quantum placit, or however much you want.
s. a. secundem artem, or according to art.
s. a. secundem artem, or according to art.
METAL RULES OR DASHES.
Metal Rules or dashes, [⸺] like quadrates, are commonly cast from one em to three ems in length. When cast to line and join accurately, they may be used instead of brass rule.
Metal Rules! or dashes, [⸺] like blocks, are usually made from one em to three ems long. When aligned correctly and joined properly, they can be used instead of brass rule.
BRACES.
Braces [⏞] are used chiefly in tables of accounts, botanical and geological tables, and similar matter. They are placed before or after a series of items of similar import; and are sometimes used horizontally in the margin, to cut off a chronological or other series from the proper notes or marginal references of the work. Braces, two, three, and four ems in length, are now cast for all sizes of common type.
Braces [⏞] are mainly used in financial tables, botanical and geological charts, and similar content. They are placed before or after a list of similar items; and they can also be used horizontally in the margin to separate a chronological series or other lists from the main notes or side references of the work. Braces, measuring two, three, and four ems in length, are now available for all sizes of standard type.
Middles and ends are also cast, [] which can be filled
out with dashes to any length required for the brace. Middles
and ends are convenient in genealogical tables, in which they
are used the flat way, and in which the directing point is not
always in the middle.
Middles and ends are also created, [] which can be filled in with dashes to any length needed for the brace. Middles and ends are useful in family trees, where they are used in a horizontal layout, and where the focal point isn't always centered.
Brass braces of any length, for music and jobbing purposes, are furnished by type-founders.
Brass braces of any length, for music and general use, are provided by type-founders.
SPACES.
Spaces are short blank types, and are used to separate
one word from another. To enable the compositor to space
even and to justify with nicety, they are cast to various thicknesses,—viz.
five to an em, [] or five thin spaces; four to an
em, [
] or four middle spaces; three to an em, [
] or three
thick spaces; and two to an em, [
] or two en quadrates,
which may with propriety be reckoned among the number of
spaces. Besides these, there is what is called the hair-space,
which is cast extremely thin, and is found useful in justifying
lines and assisting uniformity in spacing.
Spaces are short blank spaces that are used to separate one word from another. To help the typesetter space evenly and justify text precisely, they come in various thicknesses—specifically, five to an em, [] or five thin spaces; four to an em, [
] or four medium spaces; three to an em, [
] or three thick spaces; and two to an em, [
] or two en quadrates, which can also be considered as spaces. In addition to these, there is a hair-space, which is extremely thin and is useful for justifying lines and maintaining consistent spacing.
TWO-LINE LETTERS
Are equal in depth to two lines of the type in which they are to be used, and of proportionate width. They form the almost only proper type for principal lines in title-pages, and are used at the beginning of chapters and newspaper advertisements.
Are equal in depth to two lines of the type they will be used in and have a proportionate width. They are almost the only suitable type for main lines on title pages and are used at the start of chapters and newspaper ads.
QUADRATES.
An em quadrate [■] is a short blank type, in thickness equal to the square of the letter of the fount to which it belongs; an en quadrate [▮] is half that size.
An em quadrate [■] is a short blank type, with a thickness equal to the square of the font size it belongs to; an en quadrate [▮] is half that size.
The first line of a paragraph is usually indented an em quadrate; but when the matter is leaded or the measure is wide, an em and en, or two or even three ems may be used. An em quadrate is the proper space after a full-point when it terminates a sentence in a paragraph.
The first line of a paragraph is usually indented by an em quad; but when the text is spaced out or the width is wide, you might use an em and an en, or even two or three ems. An em quad is the correct space after a full stop when it ends a sentence in a paragraph.
En quadrates are generally used after the semicolon, colon, &c., and sometimes after an overhanging letter. They are useful in spacing.
En quadrates are usually used after a semicolon, colon, &c., and sometimes after a hanging letter. They are helpful for spacing.
Em and en quadrates, and figures as well, should be entirely exact and uniform in body, as even a trifling variation will be apparent when they are arranged in table or figure-work; and no ingenuity on the part of a compositor can rectify the zigzag appearance caused by irregular types.
Em and en squares, along with other figures, should be completely accurate and consistent in size, as even a slight difference will be noticeable when they are used in tables or graphical work; and no amount of skill from a typesetter can fix the uneven look caused by inconsistent type sizes.
The inconvenience arising from founts of the same body not agreeing in depth is great, where the quadrates, through necessity, are sometimes mixed. The founts cast by MacKellar, Smiths & Jordan are not liable to this charge, as their moulds for all regular type of a specific size harmonize perfectly, and the quadrates and spaces work together.
The trouble caused by fonts of the same style not matching in depth is significant, especially when the squares are sometimes mixed out of necessity. The fonts made by MacKellar, Smiths & Jordan don’t have this problem, as their molds for all standard types of a specific size fit together perfectly, and the squares and spaces work seamlessly.
QUOTATIONS.
Quotations are large blank type used for filling up considerable spaces at the beginning or end of a chapter, and also for job-work. They are cast to two sizes, and are called broad and narrow. They vary in size according to the standard of the foundry where they are cast. They are being superseded, however, by
Quotes are large blank letters used to fill significant spaces at the beginning or end of a chapter, as well as for job-work. They come in two sizes, known as broad and narrow. Their size varies based on the standard of the foundry where they are made. However, they are being replaced by
LABOUR-SAVING QUOTATION FURNITURE.

This is cast with great accuracy to Pica, of assorted widths and lengths; and, as its name imports, it serves not only for quotations in general job-work, but also for furniture.
This is made with high precision to Pica, in various widths and lengths; and, as its name suggests, it is used not only for general quotations in job work but also for furniture.
STANDARD METAL FURNITURE.
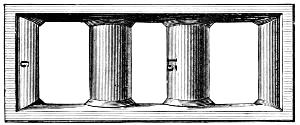
Owing to the large assortment of sizes contained in this furniture, it is useful for blanking out all varieties of work, from the card or circular to the large hand-bill or poster. As the above metal furnitures are not liable to warp or shrink, they form a highly economical substitute for wooden reglet.
Due to the wide range of sizes in this furniture, it is useful for various types of work, from cards or circulars to large handbills or posters. Since the metal furniture does not warp or shrink, it serves as a cost-effective alternative to wooden reglet.
HOLLOW QUADRATES

Answer many of the purposes of quotations, but are principally useful as frames or miniature chases for circular or oval jobs. The sizes are graduated from 5 × 8 to 12 × 18 Pica ems.
Answer serves many of the functions of quotations, but is mainly useful as a frame or small chase for circular or oval projects. The sizes range from 5 × 8 to 12 × 18 Pica ems.
CIRCULAR QUADRATES.

These are made of various sizes, so as to form circles or parts of circles from one to twenty-four inches in diameter. Each piece is exactly one-eighth of a full circle, and, when combined with similar pieces, will form quarter, half, three-quarter, and full circles. By reversing the combination of some of the pieces, serpentine and eccentric curves may be made of any length or depth.
These come in different sizes to create circles or sections of circles ranging from one to twenty-four inches in diameter. Each piece is precisely one-eighth of a full circle, and when paired with similar pieces, they can form quarter, half, three-quarter, and full circles. By rearranging some of the pieces, you can create serpentine and eccentric curves of any length or depth.
There are two kinds: inner quadrates, with convex surface, and outer quadrates, with concave surface. The curved line is produced by placing the convex and concave surfaces parallel to each other, so that when locked up firmly they hold the type inserted between them. The other sides of the quadrates are flat and right-angled, to allow a close introduction of type, and an easy justification with common quadrates.
There are two types: inner quadrates, which have a convex surface, and outer quadrates, which have a concave surface. The curved line is created by placing the convex and concave surfaces parallel to each other, so that when they are securely locked together, they hold the type inserted between them. The other sides of the quadrates are flat and have right angles, allowing for a tight fit of the type and easy adjustment with standard quadrates.
As these quadrates are perfect segments of a large circle, they cannot be increased or diminished without destroying the truth of the curve. If the thin ends are pieced out with common quadrates, good justification will be rendered impossible; if they are shortened by cutting off, they are ruined. Bits of[79] lead or short pieces of card between the curved surfaces are also wrong: they destroy that exact parallelism which is necessary for the security of the type. Very accurate justification of the outer extremities of the quadrates is also indispensable. If the curved surfaces are kept parallel, and the flat surfaces kept square, no difficulty will be found in using them, and they will prove a valuable aid in ornamental printing.
As these blocks are perfect segments of a large circle, they cannot be modified without compromising the integrity of the curve. If the thin edges are filled in with regular blocks, proper justification will be impossible; if they are trimmed, they are ruined. Pieces of[79] lead or short card sections between the curved surfaces are also inappropriate: they disrupt the precise parallelism needed for the stability of the type. Very precise justification of the outer edges of the blocks is also essential. If the curved surfaces stay parallel and the flat surfaces are kept square, there will be no trouble using them, and they will be a valuable asset in decorative printing.
LABOUR-SAVING CURVATURES, &c.

Morris’s Adjustable Line Formers, or Labour-Saving Curvatures, do away with bent leads, plaster, wax, and other methods of making curved lines. Their economical advantages, and the neatness and exactitude of curve secured by their use, will be appreciated at a glance by all practical job printers.
Morris’s Adjustable Line Formers, or Labour-Saving Curvatures, eliminate the need for bent leads, plaster, wax, and other techniques for creating curved lines. Their cost-saving benefits, along with the tidy and precise curves they produce, will be quickly recognized by all practical job printers.
LEADS.
Leads form an essential part of a printer’s outfit, since it is scarcely possible to set up a single page or job in which they may not be usefully employed; but their chief purpose is for spreading the lines apart so as to reduce the amount of matter in a page. Fine works are always thus leaded. They are usually cast by letter-founders in a long mould, and then cut to the required lengths. The bodies are regulated by Pica standard, and they are usually cast four, six, or eight to Pica, but are occasionally varied from one down to fourteen to Pica. Leads for jobbing purposes are now cut to graduated lengths, like labour-saving rule.
Leads are a crucial part of a printer's toolkit, as it's nearly impossible to set up a single page or job without them. Their main function is to space the lines apart to decrease the amount of text on a page. High-quality works are always leaded this way. They are typically cast by typefounders in a long mold and then cut to the desired lengths. The sizes follow the Pica standard, and they are usually cast in sizes of four, six, or eight to Pica, but can occasionally range from one to fourteen to Pica. Leads for job work are now cut to various lengths, similar to labor-saving rules.
FLOWERS AND BORDERS.
The flowers and borders designed and cast at the present time far surpass any made by founders of earlier days. Their richness and variety enable printers to execute delicate and elaborate work, rivalling plate engraving, and afford a wide scope for the display of taste and artistic skill. The combination borders are especially valuable from being cast on uniform bodies, thus rendering them susceptible of a vast number of changes.
The flowers and borders created today are far better than those made by earlier craftsmen. Their richness and variety allow printers to produce intricate and detailed work that competes with plate engraving, and they provide plenty of opportunities to showcase taste and artistic skill. The combination borders are particularly useful because they're cast on uniform bodies, making them capable of countless variations.
The ancient practice of ornamenting pages with head and tail pieces of flowers and odd designs seems to be coming in vogue again, particularly in works printed in the old-style type.
The old practice of decorating pages with floral head and tail designs and quirky patterns seems to be making a comeback, especially in books printed in a vintage style.
BRASS RULES.
Rules are required mainly for table-work, and for pages which contain two or more columns. They are also useful in titles and jobs. Brass rules should never be more than type height, unless for perforating purposes, to divide railroad checks, &c. A shade lower would be often better, as the pressman would be enabled to bring off their impression more clearly. In table-work, the rule and figures should be separated by a lead, and all the rules should fit closely and accurately.
Understood. Please provide the text to modernize. are mainly needed for table work and for pages that have two or more columns. They're also helpful in titles and tasks. Brass rules should never exceed the height of the type, except for perforating purposes, like dividing railroad checks, etc. A slightly lower height is often better, as it allows the pressman to achieve a clearer impression. In table work, the rule and figures should be separated by a lead, and all the rules should fit closely and accurately.
The lately-invented
The newly invented
BRASS LABOUR-SAVING RULE
Brass measuring tool
is of immense economical advantage to the printer. Being cut to a graduated scale, from one em to fifty ems Pica in length, advancing in the shorter pieces by ens and in the longer by ems, all waste in cutting is avoided by the printer, as rules of any length can be formed by employing two or more pieces. This rule is put up in regular founts, of various styles, with sufficient mitred pieces for outside bordering.
is of great economic benefit to the printer. It’s designed to a graduated scale, ranging from one em to fifty ems Pica in length, increasing by ens for shorter pieces and by ems for longer ones. This setup eliminates cutting waste for the printer since rules of any length can be created by using two or more pieces. This rule comes in standard fonts, in various styles, with enough mitered pieces for outside borders.

Metal space-rules, cast by type-founders, are commonly used for cross-rules in table-work; but the shorter pieces of labour-saving rule will answer as well.
Metal space rules, made by type founders, are often used for cross rules in table work; but the shorter pieces of labor-saving rule will work just as well.
On the next page we insert a plan of a case for labour-saving rules, with boxes suited for the various sizes, in which the rule should be kept when not in use.
On the next page, we include a plan for a case for labor-saving tools, with compartments designed for different sizes, where the tool should be stored when not in use.

IMPROVED LABOUR-SAVING RULE CASE.
Improved labor-saving rule case.
EARLIEST WRITTEN SOUNDS.
The hieroglyphic is the most ancient form of written sounds. The earliest known monuments containing phonetic hieroglyphics date about forty centuries ago, or six hundred years before the time of Moses, who is supposed to have been versed in the knowledge of the hieroglyphs. Yet nothing worthy of the name of an alphabet existed till a later period, when the Phœnicians invented a purely alphabetic system, but suppressing the vowels, and from this has originated all the modes of alphabetic writing now used.[12] The Greeks introduced the vowels into their graphic system, and so brought to perfection the invaluable invention of alphabetic writing.
The hieroglyph is the oldest form of written sounds. The earliest known monuments with phonetic hieroglyphics date back about four thousand years, or six hundred years before Moses, who is thought to have been knowledgeable about hieroglyphs. However, no true alphabet existed until later, when the Phoenicians created a purely alphabetic system that left out the vowels. From this, all the forms of alphabetic writing we use today have developed.[12] The Greeks added vowels to their writing system, which perfected the invaluable invention of alphabetic writing.
The discovery of the Rosetta stone furnished a clue to the method of deciphering the Egyptian hieroglyphics; and Dr. Young and Champollion were the first to make use of the suggestive opportunity. The words Ptolemy and Cleopatra were made out; and these served as a key or incentive to further investigations; and extensive and curious volumes have been devoted to the interpretation of Egypt’s mysterious inscriptions on monuments and writings on papyrus.
The discovery of the Rosetta Stone provided a clue to how to decipher Egyptian hieroglyphics, and Dr. Young and Champollion were the first to take advantage of this promising opportunity. The names Ptolemy and Cleopatra were identified, and these served as a key or motivation for further research. Many extensive and intriguing volumes have been dedicated to interpreting Egypt's mysterious inscriptions on monuments and writings on papyrus.
Among those who have investigated the Egyptian hieroglyphs, Mr. R. Lepsius is one of the most practical, for he has reduced the ancient characters to typographical uses for the behoof of the delvers into the earth’s earliest lore. He began the work soon after his return from a scientific expedition to Egypt during the years 1842-46, and his hieroglyphic types now completed number more than thirteen hundred. The Prussian government furnishing the needful pecuniary means, his first task was to ascertain the forms of hieroglyphic signs which would be most suitable for typographical purposes, and here the labour was immense. After laborious research, he reached the conclusion, that as European print had been formed, not from the monumental characters of the Greeks and Romans, but essentially from the current handwriting of documents on parchment and paper, so the hieroglyphic type should follow, not the chiseled or painted characters on the[84] monuments, but the style of those written on papyrus. The style and proportions having been established, the punch-cutting was mostly executed by Mr. Ferdinand Theinhardt, the excellent Prussian type-founder, who for a series of years has been skilfully engaged in producing the matrices. We are indebted to Mr. Theinhardt for the specimens here given; the first of which is the hieroglyphic alphabet, and the second is the beginning of an ancient text found in a leather roll of the Royal Museum of Berlin, referring to the foundation of the temple of the Sun at On or Heliopolis in Egypt.
Among those who have studied Egyptian hieroglyphs, Mr. R. Lepsius stands out as one of the most practical. He has transformed the ancient characters into typographical uses for the benefit of those exploring the earliest knowledge of the earth. He began this work shortly after returning from a scientific expedition to Egypt between 1842 and 1846, and he has now completed more than thirteen hundred hieroglyphic types. With financial support from the Prussian government, his first task was to determine which forms of hieroglyphic signs would be best suited for typography, which required immense effort. After extensive research, he concluded that just as European print was based not on the monumental characters of the Greeks and Romans but primarily on the everyday handwriting of documents on parchment and paper, hieroglyphic type should be derived from the styles written on papyrus rather than from chiseled or painted characters on the [84] monuments. Once the style and proportions were established, most of the punch cutting was done by Mr. Ferdinand Theinhardt, an excellent Prussian type-founder who had been skillfully creating the matrices for several years. We owe thanks to Mr. Theinhardt for the specimens provided here; the first is the hieroglyphic alphabet, and the second is the beginning of an ancient text found in a leather scroll at the Royal Museum of Berlin, concerning the foundation of the temple of the Sun at On or Heliopolis in Egypt.
HIEROGLYPHIC ALPHABET.


1 Renpt III ȧbeṭ III šat . . . xer ḥen n suten xet xeper-qu-rā sa-rā usertesen maā-xeru ānx tétta r neḥ:
1 Renpt III ȧbeṭ III šat . . . xer ḥen n suten xet xeper-qu-rā sa-rā usertesen maā-xeru ānx tétta r neḥ:
2 suten xāt m sexti, xeper ḥemes m tȧṭet, netńu re n ȧmu-xetef, semer nu
2 suten xāt m sexti, xeper ḥemes m tȧṭet, netńu re n ȧmu-xetef, semer nu
3 . . . ānx utȧ senb, seru r ȧst senentu, utu téṭet xeft setem set netńu re m
3 . . . ānx utȧ senb, seru r ȧst senentu, utu téṭet xeft setem set netńu re m
4 seun ḥer-sen. Mā-ten ḥen-a ḥer šau qat, sexa m sep m xut;
4 seun ḥer-sen. Mā-ten ḥen-a ḥer šau qat, sexa m sep m xut;
5 n-mxet ȧrí-ȧ mennu, semen-ȧ utu reṭu n ḥer xuti.
5 n-mxet ȧrí-ȧ mennu, semen-ȧ utu reṭu n ḥer xuti.
TRANSLATION.
Translation.
Done in the month of Hatoor of the third year of the King of Upper and Lower Egypt Kheperkara Usertesen I.—the blessed and eternally living.
Done in the month of Hatoor in the third year of King Kheperkara Usertesen I of Upper and Lower Egypt—the blessed and forever living.
The King, wearing the double crown, sat in the royal hall. There was held a council of his attendants, the counsellors of the apartments of the Pharao (may he live!) and the great (chiefs) for the site of the foundation. Speeches were made, while they listened; and they deliberated, stepping forward. “Well!” said the King, “let me order the work and fittingly commemorate deeds of glory. Henceforth I will erect buildings and lasting steles to the double Horus,” that is to the god of the rising and setting Sun, etc.
The King, wearing the double crown, sat in the royal hall. A council of his attendants, the advisors of the Pharaoh (may he live!) and the great chiefs for the foundation site was held. Speeches were made as they listened and deliberated, stepping forward. “Well!” said the King, “let me organize the work and properly commemorate glorious deeds. From now on, I will build structures and lasting steles to the double Horus,” referring to the god of the rising and setting Sun, etc.
RUNIC ALPHABETS.
Runes were the earliest alphabets in use among the Teutonic and Gothic nations of Northern Europe. The exact period of their origin is not known. The name is derived from the Teutonic rûn, a mystery; whence runa, a whisper, and helrûn, divination; and the original use of these characters seems to have been for purposes of secrecy and divination. Scandinavian and Anglo-Saxon tradition agree in ascribing the invention of runic writing to Odin or Wodin. The countries in which traces of the use of runes exist include Denmark, Norway, Sweden, Iceland, Germany, Britain, France, and Spain; and they are found engraved on rocks, crosses, monumental stones, coins, medals, rings, brooches, and the hilts and blades of swords. Runic letters were also often cut on smooth sticks called rûn-stafas, or mysterious staves, and used for purposes of divination. But there is no reason to believe that they were at any time in the familiar use in which we find the characters of a written language in modern times, nor have we any traces of their being used in books or on parchment. We have an explanation of the runic alphabet in various MSS. of the early middle ages, prior to the time when runes had altogether ceased to be understood.
Runes were the earliest alphabets used by the Teutonic and Gothic people of Northern Europe. The exact time of their creation isn't known. The name comes from the Teutonic rûn, meaning mystery; hence runa, a whisper, and helrûn, divination. These characters were originally used for purposes of secrecy and divination. Both Scandinavian and Anglo-Saxon traditions attribute the invention of runic writing to Odin or Wodin. Runes have been found in countries such as Denmark, Norway, Sweden, Iceland, Germany, Britain, France, and Spain, and they appear engraved on rocks, crosses, monuments, coins, medals, rings, brooches, and the hilts and blades of swords. Runic letters were also often carved on smooth sticks called rûn-stafas, or mysterious staves, which were used for divination. However, there’s no evidence that they were used in the same way we use written language today, nor do we have any records of them being found in books or on parchment. We do have explanations of the runic alphabet in various manuscripts from the early Middle Ages, before runes were no longer understood.
The systems of runes in use among the different branches of the Teutonic stock were not identical, though they have a strong general family likeness, showing their community of origin. The letters are arranged in an order altogether distinct from that of any other alphabetical system, and have a purely Teutonic nomenclature. Each letter is, as in the Hebrew-Phœnician, derived from the name of some well-known familiar object, with whose initial letter it corresponds. Runes, being associated in the popular belief with augury and divination, were to a considerable extent discouraged by the early Christian priests and missionaries, whose efforts were directed to the supplanting of them by Greek and Roman characters. But it was not easy suddenly to put a stop to their use, and we find runes continuing to be employed in early Christian inscriptions. This was to a remarkable extent the case in the Anglo-Saxon kingdoms of Northumbria, Mercia, and East Anglia, where we have traces of runic writing of dates varying from the middle[87] of the seventh to the middle of the tenth century. Runes are said to have been laid aside in Sweden by the year 1001, and in Spain they were officially condemned by the Council of Toledo in 1115.
The systems of runes used by different branches of the Teutonic people were not the same, but they share a strong resemblance that indicates a common origin. The letters are arranged in a way that is completely different from any other alphabetical system and have a uniquely Teutonic naming system. Each letter, like in Hebrew-Phœnician, comes from the name of a well-known object, corresponding with its initial letter. Runes were linked in popular belief to fortune-telling and divination, so early Christian priests and missionaries largely discouraged their use, aiming to replace them with Greek and Roman letters. However, it wasn't easy to suddenly stop using them, and we see runes still being used in early Christian inscriptions. This was particularly true in the Anglo-Saxon kingdoms of Northumbria, Mercia, and East Anglia, where we find examples of runic writing dating from the mid-seventh to the mid-tenth century. Runes are said to have been phased out in Sweden by the year 1001, and in Spain, they were officially condemned by the Council of Toledo in 1115.
The different systems of runes, all accordant up to a certain point, have been classed as the Anglo-Saxon, the German, and the Norse, each containing different subordinate varieties. The Norse alphabet is generally considered the oldest, and the parent of the rest. It has sixteen letters corresponding to our f, u, th, o, r, k, h, n, i, a, s, t, b, l, m, y, but has no equivalent for various sounds which exist in the language, in consequence of which the sound of k was used for g, d for t, b for p, and u and y for v: o was expressed by au, and e, by ai, i, or ia; and the same letter otherwise was made to serve for more than one sound. Other expedients came, in the course of time, to be employed to obviate the deficiency of the system,—as the addition of dots, and the adoption of new characters. But the runic system received a fuller development among the Germans and Anglo-Saxons, particularly the latter, whose alphabet was extended to no fewer than forty characters, in which seem to have been embraced, more nearly than in any modern alphabets, the actual sounds of a language. The table on the following page exhibits the best known forms of the Anglo-Saxon, German, and Norse runic alphabets, with the names and the power of the several letters.
The various systems of runes, which all align to some extent, are categorized as Anglo-Saxon, German, and Norse, each having different subordinate variations. The Norse alphabet is generally seen as the oldest and the origin of the others. It consists of sixteen letters that correspond to our f, u, th, o, r, k, h, n, i, a, s, t, b, l, m, y, but lacks equivalents for some sounds that exist in the language. As a result, the sound of k was used for g, d for t, b for p, and u and y for v; o was represented by au, and e by ai, i, or ia; and the same letter sometimes represented more than one sound. Over time, other methods were employed to address the shortcomings of the system, such as adding dots and creating new characters. However, the runic system became more developed among the Germans and Anglo-Saxons, especially the latter, whose alphabet was expanded to at least forty characters, which seemed to represent the actual sounds of the language closer than in any modern alphabets. The table on the following page shows the best known forms of the Anglo-Saxon, German, and Norse runic alphabets, along with the names and functions of the various letters.

The Anglo-Saxon runes, as here given, are derived from a variety of MS. authorities, the most complete containing forty characters, while some only extend as far as the twenty-fifth or twenty-eighth letter. Neither the name nor the power of some of the later letters is thoroughly known, and they are without any equivalents in the Norse runic system. The German runes are given from a MS. in the conventual library of St. Gall, in Switzerland. Though the various runic alphabets are not alike copious, the same order of succession among the letters is preserved, excepting that, in the Norse alphabet, laugr precedes madr, although we have placed them otherwise, with the view of exhibiting the correspondence of the three systems. The number of characters in the Anglo-Saxon alphabet is a multiple of the sacred number eight; and we have the evidence both of a Swedish bracteate containing twenty-four characters, and of the above mentioned St. Gall MS., that there was a [89]recognized division of the alphabet into classes of eight letters,—a classification which forms the basis of a system of secret runes, mentioned in that MS. Of these secret runes, there are several varieties specified: in particular, 1. Iis-runa and Lago-runa (of which specimens exist in Scandinavia), consisting of groups of repetitions of the character iis or lago, some shorter and some longer, the number of shorter characters in each group denoting the class to which the letter intended to be indicated belonged; the number of longer ones, its position in the class. 2. Hahal-runa, where the letters are indicated by characters with branching stems, the branches to the left denoting the class, and those to the right the position in that class. There is an inscription in secret runes of this description at Hackness, in Yorkshire. 3. Stof-runa, in which the class is indicated by points placed above, and the position in the class by points below, or the reverse.
The Anglo-Saxon runes provided here come from various manuscript sources, with the most complete version containing forty characters, while some versions only include up to the twenty-fifth or twenty-eighth letter. The names and functions of some later letters are not completely understood, and they don't have equivalents in the Norse runic system. The German runes come from a manuscript in the library of the St. Gall monastery in Switzerland. While the different runic alphabets aren't equally extensive, they maintain the same order of letters, except in the Norse alphabet where laugr comes before madr; we've arranged them differently to show the correspondence between the three systems. The number of characters in the Anglo-Saxon alphabet is a multiple of the sacred number eight; we also have proof from a Swedish bracteate containing twenty-four characters and the aforementioned St. Gall manuscript that there was a recognized division of the alphabet into groups of eight letters—this classification serves as the foundation for a system of secret runes mentioned in that manuscript. There are several types of these secret runes: specifically, 1. Iis-runa and Lago-runa (of which examples can be found in Scandinavia), made up of repeated groups of the character iis or lago, with some groups shorter and others longer; the number of shorter characters indicates the class of the letter, while the number of longer ones shows its position within that class. 2. Hahal-runa, where letters are represented by characters with branching stems, with branches to the left indicating the class and those to the right showing the position within that class. There is an inscription in this type of secret runes at Hackness, in Yorkshire. 3. Stof-runa, where the class is indicated by points above and the position in that class by points below, or vice versa.
The best-known inscriptions in the Anglo-Saxon character are those on two grave-stones at Hartlepool, in Northumberland, on a cross at Bewcastle, in Cumberland, and on another cross at Ruthwell, in Dumfriesshire. The inscription on the west side of Bewcastle cross, which we give as a specimen of Anglo-Saxon runes, is a memorial of Alcfrid, son of Oswiu, who was associated with his father in the government of the kingdom of Northumbria, in the seventh century.
The most famous inscriptions in the Anglo-Saxon style are found on two gravestones at Hartlepool, Northumberland, on a cross at Bewcastle, Cumberland, and on another cross at Ruthwell, Dumfriesshire. The inscription on the west side of the Bewcastle cross, which we present as an example of Anglo-Saxon runes, is a tribute to Alcfrid, son of Oswiu, who worked alongside his father in governing the kingdom of Northumbria in the seventh century.

RUNES.
RUNES.
It has been thus deciphered into the Anglo-Saxon dialect of the period:—
It has been translated into the Anglo-Saxon dialect of the time:—
Or, in Modern English:—
Or, in Modern English:—
The inscription on the Ruthwell cross, after being long a puzzle to antiquaries, was first deciphered in 1838 by Mr. John M. Kemble, an eminent Anglo-Saxon scholar. It is written alternately down one side of the stone and up another, and contains a portion of a poem on the subject of the Crucifixion. Mr. Kemble’s interpretation received a very satisfactory confirmation by the discovery of a more complete copy of the same poem in a MS. volume of Anglo-Saxon homilies at Vercelli.
The inscription on the Ruthwell cross, which had puzzled historians for a long time, was first decoded in 1838 by Mr. John M. Kemble, a well-known Anglo-Saxon scholar. It is written alternately down one side of the stone and up the other, and it includes part of a poem about the Crucifixion. Mr. Kemble’s interpretation was further confirmed when a more complete version of the same poem was found in a manuscript collection of Anglo-Saxon homilies in Vercelli.
Mr. D. M. Haigh, whose researches have added much to our knowledge of Anglo-Saxon runes, has endeavoured to set up for them a claim of priority over the Norse characters. Instead of considering the additional Anglo-Saxon letters as a development of the Norse system, he looks on the Norse alphabet of sixteen letters as an abridgment of an earlier system, and finds occasional traces of the existence of the discarded characters in the earliest Norse inscriptions, and in the Scandinavian Iis-runa and Hahal-runa, where the letters are classified in accordance with the Anglo-Saxon groups of eight.
Mr. D. M. Haigh, whose research has greatly expanded our understanding of Anglo-Saxon runes, has tried to establish their precedence over Norse characters. Rather than viewing the extra Anglo-Saxon letters as an evolution of the Norse system, he sees the Norse alphabet with its sixteen letters as a shortened version of an earlier system. He also finds occasional evidence of the omitted characters in the earliest Norse inscriptions and in the Scandinavian Iis-runa and Hahal-runa, where the letters are organized according to the Anglo-Saxon groups of eight.
The Scandinavian kingdoms contain numerous runic monuments, some of them written boustrophedon, or with the lines beginning alternately from the right and left; and there are many interesting inscriptions on Swedish gold bracteates. The Celtic races, from their connection with the Scandinavians, became acquainted with their alphabet, and made use of it in writing their own language; and hence we have, in the Western Islands of Scotland and in the Isle of Man, runic inscriptions, not in the Anglo-Saxon, but in the Norse character, with, however, a few peculiarities of their own. Some of the most perfect runic inscriptions are in Man; others of similar description exist at Holy Island, in Lamlash Bay, Arran; and there is an inscription in the same character on a remarkable brooch dug up at Hunterston, in Ayrshire. Dr. D. Wilson considers that the Celtic population of Scotland were as familiar with Norse as the Northumbrians with Saxon runes.
The Scandinavian kingdoms have many runic monuments, some of which are written boustrophedon, meaning the lines alternate starting from the right and left. There are also many fascinating inscriptions on Swedish gold bracteates. The Celtic peoples, through their connection with the Scandinavians, learned their alphabet and used it to write their own language. As a result, we find runic inscriptions in the Western Islands of Scotland and the Isle of Man, not in Anglo-Saxon but in Norse characters, with a few unique features of their own. Some of the best-preserved runic inscriptions are in the Isle of Man; others of similar type can be found on Holy Island, in Lamlash Bay, Arran, and there’s also an inscription in the same style on a notable brooch unearthed at Hunterston in Ayrshire. Dr. D. Wilson believes that the Celtic people of Scotland were as familiar with Norse as the Northumbrians were with Saxon runes.
We sometimes find the Norse runes used to denote numerals, in which case the sixteen characters stand for the numbers from 1 to 16; ar combined with laugr stands for 17, double madr for 18, and double tyr for 19. Two more letters are used to express higher numbers, as ur ur, 20; thurs thurs os, 34.[13]
We sometimes see Norse runes used to represent numbers, where the sixteen characters represent the values from 1 to 16; ar combined with laugr represents 17, double madr represents 18, and double tyr represents 19. Two additional letters are used for larger numbers, such as ur ur for 20 and thurs thurs os for 34.[13]
ANGLO-SAXON ALPHABET.
The Anglo-Saxon alphabet, and the forms and sounds of the letters, are shown in the following table:—
The Anglo-Saxon alphabet, along with the shapes and sounds of the letters, are displayed in the following table:—

Two useful Anglo-Saxon letters have disappeared from modern English,—namely, Þ or þ th (thin), and Ð or ð th (thine).
Two useful Anglo-Saxon letters have disappeared from modern English—specifically, Þ or þ (th in) and Ð or ð (th ine).
The Anglo-Saxon letters which vary from those now used were doubtless mere corruptions of the Roman forms,—viz. the capitals A, C, E, G, H, M, S, and W, and the small letters d, f, g, i, r, s, t, and w. Several marks of abbreviation were used by the Saxons, as ꝥ that, ⁊ and, &c. These were not original members of the alphabet, but were introduced probably for despatch.
The Anglo-Saxon letters that differ from the ones we use today were likely just corrupted versions of the Roman forms—specifically the capital letters A, C, E, G, H, M, S, and W, as well as the lowercase letters d, f, g, i, r, s, t, and w. The Saxons used several marks for abbreviations, such as ꝥ that, ⁊ and, and so on. These were not original parts of the alphabet, but they were probably introduced for efficiency.
About the year 1567, John Daye, who was patronized by Archbishop Parker, cut the first Saxon types which were used in England. In this year, Asserius Menevensis was published by the direction of the archbishop in these characters; in the same year, Archbishop Ælfric’s Paschal Homily; and in 1571, the Saxon Gospels.
About 1567, John Daye, who was supported by Archbishop Parker, created the first Saxon typefaces used in England. That year, Asserius Menevensis was published under the archbishop's direction in these typefaces; the same year also saw the release of Archbishop Ælfric’s Paschal Homily; and in 1571, the Saxon Gospels.
On the two following pages will be found a plan of cases for Saxon types.
On the next two pages, you'll find a layout for cases for Saxon types.

SAXON UPPER CASE.
SAXON UPPERCASE.

SAXON LOWER CASE.
saxon lowercase.
GERMAN ALPHABET.
Outside of Germany, there is perhaps no country in which German printing is so extensively carried on as in the United States. We present a table of German characters, with their names, and their corresponding forms in English.
Outdoors of Germany, there might not be any country where German printing is as widespread as in the United States. We provide a table of German characters, along with their names and their equivalent forms in English.
German Form. | English Form. | German Name. | ||
---|---|---|---|---|
A | a | A | a | ah |
B | b | B | b | bay |
C | c | C | c | tsay |
D | d | D | d | day |
E | e | E | e | a |
F | f ff | F | f ff | ef, ef-ef |
G | g | G | g | gay |
H | h ch | H | h ch | hah, tsay-hah |
I | i | I | i | e |
J | j | J | j | yot |
K | k ck | K | k ck | kah, tsay-kah |
L | l | L | l | el |
M | m | M | m | em |
N | n | N | n | en |
O | o | O | o | o |
P | p | P | p | pay |
Q | q | Q | q | koo |
R | r | R | r | er |
S | ſ s ſſ | S | s s ss | es, es-es |
ſz ſt | sz | es-tset, es-tay | ||
T | t | T | t | tay |
U | u | U | u | oo |
V | v | V | v | fōw |
W | w | W | w | vay |
X | x | X | x | iks |
Y | y | Y | y | ipsilon |
Z | z tz | Z | z tz | tset, tay-tset |
ä ë ü | ä ö ü or æ œ ue |
Several of the German letters, being somewhat similar in appearance, are liable to be mistaken one for another. To aid the learner, we give such letters together, and point out the difference.
Several of the German letters look quite similar, making it easy to confuse them. To help the learner, we group these letters together and highlight the differences.
B (B) and V (V).
The latter is open in the middle, the former joined across.
The latter is open in the center, while the former is connected across.
C (C) and E (E).
E (E) has a little stroke in the middle, projecting to the right, which C (C) has not.
E (E) has a small line in the middle that extends to the right, which C (C) does not have.
G (G) and S (S).
S (S) has an opening above, G (G) is closed, and has besides a perpendicular stroke within.
S (S) has an opening at the top, G (G) is closed and has an additional vertical line inside.
K (K), N (N), R (R).
K (K) is rounded at the top, N (N) is open in the middle, R (R) is united about the middle.
K (K) has a rounded top, N (N) has an opening in the middle, R (R) is connected around the middle.
M (M) and W (W).
M (M) is opened at the bottom, W (W) is closed.
M (M) is open at the bottom, W (W) is closed.
b (b) and h (h).
b (b) is entirely closed below, h (h) is somewhat open, and ends at the bottom, on one side, with a projecting hair-stroke.
b (b) is completely enclosed at the bottom, h (h) has a slight opening and finishes at the bottom on one side with a sticking-out hair-thin line.
f (f) and ſ (s).
f (f) has a horizontal line through it, ſ (s) on the left side only.
f (f) has a horizontal line through it, Unchanged. (s) on the left side only.
m (m) and w (w).
m (m) is entirely open at the bottom, w (w) is partly closed.
m (m) is completely open at the bottom, w (w) is partially closed.
r (r) and x (x).
x (x) has a little hair-stroke below, on the left.
x (x) has a small hairline mark underneath, on the left side.
v (v) and y (y).
v (v) is closed, y (y) is somewhat open below, and ends with a hair-stroke.
v (v) is closed, y (y) is slightly open at the bottom, and finishes with a thin line.

GERMAN UPPER CASE.
GERMAN UPPER CASE.

GERMAN LOWER CASE.
German lower case.
GREEK.
A small amount of Greek types is indispensable in every considerable book printing-office. The Greek alphabet contains twenty-four letters, which we give in the following table, with the name of each character expressed in Greek and English, and its sound and numerical value.
A tiny amount of Greek types is essential in every significant book printing office. The Greek alphabet consists of twenty-four letters, which we present in the following table, showing the name of each character in Greek and English, as well as its pronunciation and numerical value.
THE GREEK ALPHABET.
Forms. | Names in Greek and English. | Sounds. | Number. | ||
---|---|---|---|---|---|
Α | α | Άλφα | Alpha | a | 1 |
Β | β ϐ | Βῆτα | Beta | b | 2 |
Γ | γ | Γὰμμα | Gamma | g | 3 |
Δ | δ | Δέλτα | Delta | d | 4 |
Ε | ε | Ἒψῖλόν | Epsīlon | ĕ short | 5 |
Ζ | ζ | Ζῆτα | Zeta | z | 7 |
Η | η | Ἦτα | Eta | ē long | 8 |
Θ | ϑ θ | Θῆτα | Theta | th | 9 |
Ι | ι | Ἰῶτα | Iōta | i | 10 |
Κ | κ | Κάππα | Kappa | k c | 20 |
Λ | λ | Λάμβδα | Lambda | l | 30 |
Μ | µ | Μῦ | Mu | m | 40 |
Ν | ν | Νῦ | Nu | n | 50 |
Ξ | ξ | Ξῖ | Xi | x | 60 |
Ο | ο | Ὀμῖκρόν | Omĭcron | ŏ short | 70 |
Π | π | Πῖ | Pi | p | 80 |
Ρ | ρ | Ῥῶ | Rho | r | 100 |
Σ | σ ς | Σίγμα | Sigma | s | 200 |
Τ | τ | Ταῦ | Tau | t | 300 |
Υ | υ | Ύψῖλόν | Upsīlon | u | 400 |
Φ | φ | Φῖ | Phi | ph | 500 |
Χ | χ | Χῖ | Chi | ch | 600 |
Ψ | ψ | Ψῖ | Psi | ps | 700 |
Ω | ω | Ὠμεγα | Omĕga | ō long | 800 |
From a desire, probably, to imitate Greek manuscript, a multitude of ligatures, abbreviations, and contractions of letters, as well as duplicates, were cast by the early type-founders. These, however, with two or three exceptions, have been quite discarded; and a fount of modern Greek is readily accommodated in a single pair of cases. The only duplicated[99] characters in the preceding table are β and ϐ, ϑ and Θ, and σ and ς. β looks best when used as an initial letter, and ϐ as a medial. ϑ and Θ are used indiscriminately; but ς is employed as a final letter only.
From a desire, probably, to mimic Greek manuscripts, early type foundries created many ligatures, abbreviations, and letter contractions, along with some duplicates. However, with a couple of exceptions, these have largely been discarded; and modern Greek fonts can easily fit into a single pair of cases. The only duplicated[99] characters in the previous table are β and ϐ, ϑ and Θ, and σ and ς. β looks best as the initial letter, while ϐ works better in the middle. ϑ and Θ are used interchangeably, but ς is only used as a final letter.
There are twelve diphthongs or compound vowels in Greek, viz.:—
There are twelve diphthongs or compound vowels in Greek, namely:—
Six proper,—αι, αυ, ει, ευ, οι, ου; and
Six proper,—αι, αυ, ει, ευ, οι, ου; and
Six improper,—ᾳ, ῃ, ῳ, ηυ, υι, ωυ. The point under the first three letters denotes the iota, and is therefore called the subscript iota.
Six improper,—ᾳ, ῃ, ῳ, ηυ, υι, ωυ. The point under the first three letters indicates the iota and is therefore called the subscript iota.
ACCENTS AND ASPIRATES.
᾿ | Lenis. |
῾ | Asper. |
´ | Acute. |
` | Grave. |
῀ | Circumflex. |
῎ | Lenis acute. |
῍ | Lenis grave. |
῞ | Asper acute. |
῝ | Asper grave. |
῏ | Circumflex lenis. |
῟ | Circumflex asper. |
¨ | Diæresis. |
΅ | Diæresis acute. |
῭ | Diæresis grave. |
Accents are nothing more than small marks which have been introduced into the language to denote the pronunciation of words, and aid its acquisition by learners. The ancient Greeks never used them, as is demonstrated from Aristotle, old inscriptions, and ancient medals. It is not easy to tell the date when the practice of writing with accents first obtained, though it is probable not till after the Romans began to learn the Greek tongue and to send their children to study at Athens,—that is, about or a little before the time of Cicero.
Accents are just small marks added to the language to show how words are pronounced and to help learners pick it up. The ancient Greeks didn’t use them, as shown by Aristotle, old inscriptions, and ancient coins. It’s hard to pinpoint when the usage of accents started, but it likely began after the Romans began learning Greek and sending their kids to study in Athens—around the time of Cicero or just before.
Accents—by the Greeks called τόνοι, tones—show the rising or falling of the voice in pronouncing; either separately in distinct syllables, or conjunctively in the same syllable.
Accents—what the Greeks called τόνοι, tones—indicate the rising or falling of the voice when speaking; either separately in distinct syllables or together in the same syllable.
Wherefore there are two sorts of accents: two simple, viz.
the acute, ὀξύς, figured thus [´], which denotes the elevation
of the voice; and the grave, βαρὺς, shaped thus [`], to signify
the falling or depression of the voice: and the circumflex,
περισπώμενος which was formed first of these two lines or points
joined together thus [῍] and afterward was changed into a
round sort of a figure like an inverted upsilon, thus [], but at
length came to be figured like an s drawn crosswise [῀].[14]
There are two types of accents: two simple ones, namely the acute, ὀξύς, represented as [´], which indicates a rise in the voice; and the grave, βαρὺς, represented as [`], which signifies a drop in the voice. There’s also the circumflex, περισπώμενος, which was originally formed by combining these two marks into one, like this [῍], and was later changed into a rounded shape, resembling an upside-down upsilon, like this []. Eventually, it came to be depicted as an s drawn crosswise [῀].[14]
The acute accent raises the voice, and affects one or more of the last three syllables of a word, if it has so many.
The acute accent raises the pitch of the voice and affects one or more of the last three syllables of a word, if it has that many.
The grave depresses the voice, and affects the last syllable only.
The grave lowers the voice and influences just the last syllable.
The circumflex lengthens the sound, and affects either the last syllable of a word or the last but one.
The circumflex extends the sound and impacts either the last syllable of a word or the one just before it.
There are two spirits, or breathings: the asper [῾], which is equivalent to the modern letter h; and the lenis [᾿], which has no perceptible power, and indicates the bare opening of the mouth and simple emission of the voice.
There are two spirits, or breathings: the asper [῾], which is equivalent to the modern letter h; and the lenis [᾿], which has no noticeable sound and indicates just the opening of the mouth and the basic release of the voice.
All the words that begin with a vowel have one of these breathings over them; but the vowel upsilon admits of no other than the spiritus asper at the beginning of a word.
All the words that start with a vowel have one of these breathings over them; however, the vowel upsilon only allows the spiritus asper at the beginning of a word.
In diphthongs the spiritus is put over the second vowel: as αὐτὸς, not ἀυτὸς.
In diphthongs, the spiritus is placed over the second vowel: as αὐτὸς, not ἀυτὸς.
The letter ρ, at the beginning of a word, has an asper over it, as, ῥέω; and where two ρs meet in a word, the first has a lenis, and the other an asper.
The letter ρ, at the start of a word, has an asper over it, like in ῥέω; and when two ρs are together in a word, the first one has a lenis, and the second one has an asper.
The apostrophe [’] is used for cutting off the vowels α, ε, ι, ο, and the diphthongs αι and οι, when they stand at the end of a word and the next word begins with a vowel: as, παρ’ αὐτῷ for παρὰ αὐτῷ; πάντ’ ἔλεγον for πάντα ἔλεγον.
The apostrophe [’] is used to drop the vowels α, ε, ι, ο, and the diphthongs αι and οι when they appear at the end of a word and the following word starts with a vowel: for example, παρ’ αὐτῷ instead of παρὰ αὐτῷ; πάντ’ ἔλεγον instead of πάντα ἔλεγον.
Sometimes the apostrophe contracts two words into one: as, κᾳ’γὼ for καὶ ἐγὼ; ἐγῶ’μαι for ἐγῶ οἴμαι; κᾳ’κεῖνος for καὶ ἐκεῖνος.
Sometimes the apostrophe combines two words into one: as, κᾳ’γὼ for καὶ ἐγὼ; ἐγῶ’μαι for ἐγῶ οἴμαι; κᾳ’κεῖνος for καὶ ἐκεῖνος.
Sometimes an apostrophe supplies the place of the first vowel beginning a word: as ὦ ’γαθὲ for ὦ ἀγαθὲ; ποῦ ’ςι for ποῦ ἐςι. This is chiefly used in poetry.
Sometimes an apostrophe takes the place of the first vowel at the beginning of a word: for example, ὦ ’γαθὲ for ὦ ἀγαθὲ; ποῦ ’ςι for ποῦ ἐςι. This is mainly used in poetry.
But the prepositions περὶ and πρὸ suffer no apostrophe though the next word begin with a vowel; for we write περὶ υμῶν, πρὸ ἐμοῦ; περὶ αὐτον, πρὸ ἐτῶν, &c.
But the prepositions περὶ and πρὸ don’t take an apostrophe even if the next word starts with a vowel; so we write περὶ υμῶν, πρὸ ἐμοῦ; περὶ αὐτον, πρὸ ἐτῶν, etc.
The diæresis [¨] is put over the last one of two vowels that come together, to show that they must be pronounced separately, and not as a diphthong: thus, ἀϋτὴ with a diæresis makes three syllables; but without a diæresis αυ is a diphthong, and makes αὐτὴ two syllables.
The diaeresis [¨] is placed over the second of two vowels that are next to each other to indicate that they should be pronounced separately, not as a diphthong. For example, ἀϋτὴ with a diaeresis has three syllables, but without a diaeresis, αυ is a diphthong, making αὐτὴ have two syllables.
Diastole [,] is put between two particles that would bear a different sense without it: thus, ὄ,τε ὄ,τι signify whatever; whereas ὁτε stands for as, and ὁτι for that. Τό,τε with a diastole[101] implies and this; but when without, it answers to the adverb then.
Diastole is placed between two words that would have different meanings without it: so, ὄ,τε ὄ,τι means whatever; while ὁτε means as, and ὁτι means that. Τό,τε with a diastole[101] means and this; but when it’s without, it corresponds to the adverb then.
The sign of interrogation, in Greek, is made by a semicolon [;].
The question mark, in Greek, is represented by a semicolon [;].
The colon is made by an inverted full-point [·].
The colon is created by an upside-down full stop [·].
All other points are the same as in English.
All other points are the same as in English.
The compositor will find it advantageous to bear in mind the following rules:—
The typesetter will find it helpful to keep the following rules in mind:—
1. No accent can be placed over any other than one of the last three syllables of a word.
1. An accent can only be placed on one of the last three syllables of a word.
2. The grave accent never occurs but on the last syllable; and, this being the case, the asper grave ῝ and lenis grave ῍ can be wanted only for a few monosyllables.
2. The grave accent only appears on the last syllable; and since that’s the case, the sharp grave ῝ and soft grave ῍ can only be needed for a few one-syllable words.
3. No vowel can have a spirit, or breathing, except at the beginning of a word.
3. No vowel can have an accent mark or breathing symbol, except at the start of a word.
4. The letter ρ is the only consonant marked by a breathing.
4. The letter ρ is the only consonant that has a breathing mark.
5. Almost every word has an accent, but very seldom has more than one; and, when this happens, it is an acute thrown back upon the last syllable from one of those words called enclitics (leaning back), which in that case has none, unless it be followed by another enclitic. In no other case than this can a last syllable have an acute accent, except before a full-point, colon, or note of interrogation, when the grave accent of the last syllable is changed to an acute,—a circumstance which has often led printers, who were ignorant of the reasons for accenting the same word differently in different situations, to think that there was an error in their copy, and thus to make one in their proof. Most errors, however, proceed from those who do not think at all about the matter.
5. Almost every word has an accent, but very rarely has more than one; and when that happens, it's an acute accent on the last syllable from one of those words called enclitics (leaning back), which in that case doesn’t have one, unless it’s followed by another enclitic. In no other situation can a last syllable have an acute accent, except before a full stop, colon, or question mark, when the grave accent of the last syllable changes to an acute. This situation has often led printers, who were unaware of the reasons for accenting the same word differently in different contexts, to assume there was an error in their copy and thus to create one in their proof. Most errors, however, come from those who don’t think at all about the matter.
PLAN OF GREEK CASES.
The following plan of cases for Greek type is probably more convenient than any other. A Roman case may readily be altered to accommodate the lower-case sorts. Compositors who aspire to a full knowledge of their art should by all means make themselves familiar with Greek and Hebrew letters and cases.
The following plan for Greek type cases is likely more convenient than any other. A Roman case can easily be adjusted to fit the lowercase letters. Compositors who want to fully master their craft should definitely familiarize themselves with Greek and Hebrew letters and cases.

GREEK UPPER CASE.
GREEK UPPER CASE.

GREEK LOWER CASE.
greek lowercase.
HEBREW.
The Hebrew alphabet has twenty-two letters. Column No. 1 of the following table indicates the force of Hebrew letters when read without points. Column No. 2 gives their force when the language is printed with the Masoretic points or vowels, which are of later date than the letters. The names and numerical value of the characters are also shown.
The Hebrew alphabet has twenty-two letters. Column No. 1 of the following table shows the pronunciation of Hebrew letters when read without vowels. Column No. 2 shows their pronunciation when the language is printed with the Masoretic points or vowels, which were introduced later than the letters. The names and numerical values of the characters are also included.
THE HEBREW ALPHABET.
Names. | No. 1. | No. 2. | Num. Value. | |
---|---|---|---|---|
א | Aleph | Sounded a in war (vowel) | A gentle aspirate | 1 |
ב | Beth | ... | Bh | 2 |
ג | Gimel | g hard | Gh | 3 |
ד | Daleth | ... | Dh | 4 |
ח | He | a in hate (vow.) | A rough aspirate | 5 |
ו | Vau | u vowel, or before a vowel, w | ... | 6 |
ז | Zain | ... | Ds | 7 |
ה | Cheth | ... | Hh | 8 |
ט | Teth | Th | ... | 9 |
י | Jod | Like ee in English (vowel) | j consonant, or the softer y | 10 |
כ ך final | Caph | k or c hard | ... | 20 |
ל | Lamed | ... | ... | 30 |
מ ם final | Mem | ... | ... | 40 |
נ ן final | Nun | ... | ... | 50 |
ס | Samech | ... | Soft s | 60 |
ע | Ain | o long (vowel) | hg, or hgh, the roughest aspirate | 70 |
פ ף final | Phe | ... | ... | 80 |
צ ץ final | Tzaddi | j soft | ... | 90 |
ק | Koph | k or qu | ... | 100 |
ר | Resch | ... | ... | 200 |
ש | Shin or Sin | ... | s hard | 300 |
ת | Thau | ... | ... | 400 |
LETTERS THAT HAVE A LIKENESS TO OTHERS.
Beth | ב |
Caph | כ |
Daleth | ד |
Caph | ך |
Resch | ר |
Vau | ו |
Zain | ז |
Jod | י |
Nun | ן |
Mem | ם |
Samech | ס |
Gimel | ג |
Nun | נ |
He | ה |
Cheth | ח |
Thau | ת |
Teth | ט |
Mem | מ |
Ain | ע |
Tzaddi | צ |
The dividing of Hebrew words not being permitted, the five following letters are cast broad to enable the compositor to justify the lines without irregular spacing:—
The separation of Hebrew words is not allowed, so the following five letters are used widely to help the typesetter align the lines without uneven spacing:—
Aleph | ﬡ |
He | ﬣ |
Lamed | ﬥ |
Mem | ﬦ |
Thau | ﬨ |
Hebrew has no capitals, and therefore letters of the same shape, but of a larger body, are used at the beginning of chapters and other parts of Hebrew works.
Hebrew doesn't have capital letters, so larger versions of the same letter shape are used at the start of chapters and other sections of Hebrew texts.
Hebrew reads from the right to the left, which is the case with all other Oriental languages, except Ethiopic and Armenian. In composing it, the general method is to place the nick of the letter downward, and after putting the points to the top,[106] to turn the line and set the points that come under the letters. If the letter has but one leg, the point is placed immediately under it; but where the letter has two legs, it is put under the centre.
Hebrew is read from right to left, just like all other Eastern languages, except for Ethiopic and Armenian. When writing it, the general approach is to position the bottom part of the letter facing downwards. After placing the points on top, [106] the line is turned, and the points that go underneath the letters are set. If a letter has only one leg, the point is placed directly beneath it; however, if the letter has two legs, the point is placed under the center.
The Masoretic points or vowels are subjoined under the consonant בּ (beth).
The Masoretic points or vowels are added under the consonant בּ (beth).
1. The Long Vowels.
The Long Vowels.
Kametz | ׇ | aa | בָּ | baa |
Tzeri | ֵ | ee | בֵּ | bee |
Long Chirek | י | ii | בִּי | bii |
Cholem | וֹ | oo | בּבּוֹ | boo |
Shurek | וּ | uu | בּוּ | buu |
2. The Short Vowels.
2. The Short Vowels.
Patach | ַ | a | בַּ | ba |
Sœgol | ֶ | e | בֶּ | be |
Little Chirek | ִ | i | בִּ | bi |
Kametz-chataph | ָ | o | בָּ | bo |
Kibbutz | ֻ | u | בֻּ | bu |
3. Shevas, which imply a Vowel to be wanting.
3. Shevas, which imply a missing vowel.
Simple Sheva | חְ | |
Patach furtive | חַ | |
Chataph Patach | חֲ | a |
Chataph Sœgol | חֱ | e |
Chataph Kametz | חֳ | o |
The last three are called compound shevas; and, in fact, they are only the short vowels, to which the simple sheva [ְְ] is joined.
The last three are called compound shevas; and, in fact, they are just the short vowels combined with the simple sheva [ְְ].
ACCENTS.
Hebrew accents are either mere points, or lines, or circles.
Hebrew accents are either just points, lines, or circles.
Those which are mere points or dots consist of one or two or three such points, and are always placed above the middle of the accented letter, thus,
Those that are just points or dots consist of one, two, or three of these points and are always positioned above the middle of the accented letter, like this:
That consisting of | One, called rebia, ב֗ , i.e. sitting over. |
Two, called royal zakeph katon, ב֔, or, the little elevator, from its figure, which is composed of upright points. | |
Three, called royal segolta, ב֒, an inverted [ ֶ]. |
The lines are either upright, inclined, or transverse.
The lines are either vertical, slanted, or horizontal.
The upright is either solitary or with points or dots.
The upright can be either alone or have points or dots.
The solitary is either | between two words, ב׀ב, termed pesick, or musical pause, and terminating a song. | |
or under a word, | Metheg, בֽ or bridle, an euphonic accent at the beginning of a word. | |
Royal silluk, בֽ, end, which is placed before [׃], sophpasuk, i.e. toward the end. |
With points, namely, | two, above the letter, royal zakeph gadhol, ב֕, the great elevator, strains the sound. |
one, below the letter, royal tebhir, ב֛, broken sound, from its figure and tone. |
Inclined lines hang either above or below.
Inclined lines are positioned either above or below.
Above, toward | the right | Leader pashta, ב֙, extension, extends the voice or sound, and is placed above the last letter of the word. |
Subservient kadma, ב֨, antecedent, to the leader geresh; and is placed above the penult or antepenult letter. | ||
the left | Leader geresh, ב֜, expulsion, is sung with an impelled voice. | |
Gereshajim, ב֞, two expellers, from the figure being doubled. | ||
Below, toward | the right | Leader tiphcha, ב֖, fatigue, from the song or note. |
the left | Of subservient merca, ב֥, lengthening out, from its lengthening out the song or note. | |
Merca kephula, ב֦, a double lengthening out, from its music and figure. |
The transverse line is either right or curved: thus, ־ ֮ .
The transverse line can be either straight or curved: thus, ־ ֮ .
The right line is placed between two words, connecting them together, thus, ב־ב, and is called maccaph, i.e. connection.
The correct line is placed between two words, connecting them, thus, ב־ב, and is called maccaph, meaning connection.
The curved or waved line, ב֮, is called leader, zarka, or the disperser, from its modulation and figure.
The curved or wavy line, ב֮, is called a leader, zarka, or the disperser, based on its shape and form.
Circles are either entire or semi.
Circles can be whole or half.
The entire circle is placed always above, and has a small inclined line attached to it.
The whole circle is always positioned above and has a small angled line connected to it.
Either on the left, when it is placed at the head of the word, ב֠, and is called leader telisha the greater, or the great evulsion.
Either on the left, when it is placed at the beginning of the word, ב֠, and is called leader telisha the greater, or the great evulsion.
Or on the right, when it is placed at the end, ב֩, and is called subservient telisha the less.
Or on the right, when it is placed at the end, ב֩, and is called subservient telisha the less.
On both together, ב֟, called leader karne para, the horns of the heifer, from its modulation and figure.
On both together, ב֟, called leader karne para, the horns of the heifer, from its modulation and shape.
The semicircle is either solitary or pointed.
The semicircle is either solitary or pointed.
The solitary is either angular or reflected.
The solitary is either angular or mirrored.
The angular is | on the right | Subservient hillui, ב֬, elevated, from the elevation of the voice. |
Munach, ב֣, placed below, from its position. | ||
on the left | Leader jethith, ב֚, drawing back, from its figure. | |
Subservient mahpach, ב֤, inverted, also from its figure. | ||
The reflected is | either single subservient darga, ב֧, a degree. | |
or double, leader, shalsheleth, ב֓, a chain, from its figure and modulation. |
When joined with other points, it is either above or below the letter.
When combined with other points, it is either above or below the letter.
When above the letter, it has a small line attached to it on the left, ב֡, leader paser, the disperser from the diffusion of the note.
When above the letter, there’s a small line attached to it on the left, ב֡, leader paser, the disperser from the diffusion of the note.
When below the letter, it is pointed either downward, ב֑, called royal athnach, respiration, as the voice must rest upon it, and respire; or upward, ב֢, subservient, jerah-ben-jomo, the moon of its own day, from its figure.
When below the letter, it points either downward, ב֑, known as the royal athnach, breath, since the voice needs to pause on it and take a breath; or upward, ב֢, subordinate, jerah-ben-jomo, the moon of its own day, based on its shape.
PLANS OF HEBREW CASES.
The first plan shows a common case for Hebrew without points; the second exhibits a pair of cases with points.
The first plan shows a typical example of Hebrew without vowels; the second presents a couple of examples with vowels.

HEBREW LOWER CASE.
HEBREW lowercase.

HEBREW UPPER CASE.
HEBREW UPPERCASE.

HEBREW LOWER CASE.
HEBREW lowercase.
RUSSIAN ALPHABET.
Form. | Sound. | ||
---|---|---|---|
А | а | ah, a. | |
Б | б | b. | |
В | в | v. | |
Г | г | g, gh. | |
Д | д | d. | |
Е | е | yai or ai. | |
Ж | ж | zsh. | |
З | з | z. | |
И | и | ee. | |
І | і | ee. | |
К | к | k. | |
Л | л | l (guttural). | |
М | м | m. | |
Н | н | n. | |
О | о | o or ah. | |
П | п | p. | |
Р | р | r. | |
С | с | hard s or ss. | |
Т | т | t. | |
У | у | oo. | |
Ф | ф | f, ph. | |
Х | х | kh, ch. | |
Ц | ц | ts. | |
Ч | ч | ch, tch. | |
Ш | ш | ch. | |
Щ | щ | sh-tch. | |
Ъ | ъ | mute e. | |
Ы | ы | we, ee. | |
Ь | ь | half-mute e. | |
Ѣ | ѣ | yai or ai. | |
Э | э | ai. | |
Ю | ю | you, ew. | |
Я | я | yah. | |
Ѳ | ѳ | f, ph. | |
Ѵ | ѵ | e. | |
Й | й | short e. |
г, х, е, л, щ, ъ, ы, ь, ѣ, я, о, й, are the only letters whose pronunciation offers any difficulty.
г, х, е, л, щ, ъ, ы, ь, ѣ, я, о, й, are the only letters that can be challenging to pronounce.
Г has a sound nearly like g in the English word goose, as in гру́ша, a pear; read groòshah. But it has a guttural sound not found in English, and which nearly resembles that of the German ch. This sound is especially perceivable in the middle of a word when the г is followed by a consonant, also at the end of a word, as in но́гти, the nails; read nòchtee. In inflections аго, яго, ого, его, of adjectives and pronouns, the letter г is pronounced as v; as in кра́снаго, of beautiful; read kràsnavah.
Г has a sound similar to g in the English word goose, as in гру́ша, a pear; pronounced groòshah. However, it has a guttural sound that doesn't exist in English, and it closely resembles the German ch. This sound is particularly noticeable in the middle of a word when the г is followed by a consonant, as well as at the end of a word, like in но́гти, the nails; pronounced nòchtee. In inflections аго, яго, ого, его, of adjectives and pronouns, the letter г is pronounced as v; for example, кра́снаго, of beautiful; pronounced kràsnavah.
Е has three different sounds: 1. In Russian words, and in all syllables in which it is preceded by a vowel, е has a sound like that of yai, when the y is nearly sunk in the pronunciation, as in ему́, to him; read yaimoò. 2. At the beginning of words from foreign languages, and at the middle and end of a word when preceded by a consonant, it has the sound of e in met, as in берегу́, I guard; read bayregoò. 3. In the termination екъ of diminutives, in all the characteristic inflections of cases in the nouns, and of persons in the verbs, in fact, in almost all words, this letter when accented has a sound nearly like that of short yo or o; as in куле́къ, a little sack; веде́шь, thou leadest; медъ, the honey; read koolyòk, vaidyòsh, myod. This[113] sound yo or o of the letter е is commonly distinguished by a diæresis over the vowel, as кулёкъ, ведёшь, мёлъ.
Е has three different sounds: 1. In Russian words, and in all syllables where it’s preceded by a vowel, е sounds like yai, with the y nearly silent, as in ему́, to him; read yaimoò. 2. At the beginning of words from foreign languages, and in the middle and end of a word when it follows a consonant, it sounds like e in met, as in берегу́, I guard; read bayregoò. 3. In the ending екъ of diminutives, in all the typical inflections of cases in nouns, and persons in verbs, essentially in almost all words, this letter when stressed sounds almost like a short yo or o; as in куле́къ, a little sack; веде́шь, thou leadest; медъ, the honey; read koolyòk, vaidyòsh, myod. This[113] sound yo or o of the letter е is usually marked with a diaeresis over the vowel, as кулёкъ, ведёшь, мёлъ.
Л has a guttural sound nearly analogous to the English w. Писарлъ, he wrote, read pisaw or pisou.
Л has a deep sound almost like the English w. Писарлъ, he wrote, read pisaw or pisou.
Ль has a soft sound, as in the French word bouillon.
Ль has a soft sound, like in the French word bouillon.
Х corresponds to the German ch. It is a strong aspiration that nearly resembles the sound k when pronounced hastily from the throat; as in хвала́, the praise; read khvahlàh.
Х corresponds to the German ch. It's a strong breathy sound that almost sounds like k when said quickly from the throat; for example, in хвала́, the praise; pronounced khvahlàh.
Щ unites the sound of ш and ч, as in щитъ, the shield; read shtcheet.
Щ combines the sounds of ш and ч, as in щитъ, the shield; pronounced shtcheet.
Ъ. This letter has no sound; the preceding consonant, the last letter of the word, ought to be pronounced a little hollow, as in боо́ъ, a bean; read bop.
Ъ. This letter has no sound; the preceding consonant, the last letter of the word, should be pronounced a little hollow, as in боо́ъ, a bean; read bop.
Ы has a sound nearly like we when the w is pronounced rapidly; as in бу́квьшы, the letters, read boòkwe. It has this sound after the consonants б, в, м, п, ф; but after another consonant it is a thick e, as in сынъ, the son; read seen.
Ы sounds almost like we when the w is said quickly; as in бу́квьшы, the letters, pronounced boòkwe. It has this sound after the consonants б, в, м, п, ф; but after a different consonant, it becomes a heavy e, like in сынъ, the son; pronounced seen.
Ь. This letter at the end of a word has a sound nearly like that of the very short e. When followed by a consonant in the middle of a word it is mute, but is pronounced when followed by a vowel; as in знатъ, to know; read znaht.
Ь. This letter at the end of a word sounds almost like a very short e. When it comes before a consonant in the middle of a word, it is silent, but it is pronounced when followed by a vowel; for example, знатъ, to know; read znaht.
Ѣ at the beginning of a word has the sound of yai; as in Ѣсть, to eat; read yaist. In the middle of a word it is pronounced yai, the sound of y being almost sunk; as in нѣтъ, no; read nyaitt. At the end of a word it is sounded ay.
Ѣ at the beginning of a word sounds like yai; as in Ѣсть, to eat; read yaist. In the middle of a word, it is pronounced yai, with the sound of y being almost muted; as in нѣтъ, no; read nyaitt. At the end of a word, it is pronounced ay.
Я when accented has the sound of the diphthong yah; as in я́ма, a pit; read yàhmah. But if not accented it is pronounced yai, as in ядро́, a ball; read yaidrò. The pronoun ея́, of her, is pronounced yaiyò, and the syllable ся of pronominal verbs is pronounced sah, as in стара́ться, to exert one’s self; read stahràhtsah.
Я when accented sounds like the diphthong yah; as in я́ма, a pit; read yàhmah. But when it's not accented, it’s pronounced yai, as in ядро́, a ball; read yaidrò. The pronoun ея́, of her, is pronounced yaiyò, and the syllable ся in pronominal verbs is pronounced sah, as in стара́ться, to exert one’s self; read stahràhtsah.
О is pronounced as English o; but if unaccented it takes the sound of ah, as in ко́локолъ, a bell; колокола́, bells; read kòlahkall, kahlakahlà.
О is pronounced like the English o; but when it's unaccented, it sounds like ah, as in ко́локолъ, a bell; колокола́, bells; pronounced kòlahkall, kahlakahlà.
Й is a short e, pronounced very rapidly, as in дай, give; read dàï or die, giving utterance to a short e after the vowel.
Й is a short e, pronounced quickly, as in дай, give; read dàï or die, adding a short e after the vowel.
In general the pronunciation of Russian words depends especially upon the tonic accent, which is no longer printed in Russian books, except to distinguish some homonymous words, or some grammatical inflections of similar forms; as за́мокъ, a castle, and замо́къ, a lock; read zàhmok and zahmòk.
In general, the pronunciation of Russian words mainly relies on the stress accent, which is no longer indicated in Russian books, except to differentiate some homonymous words or certain grammatical forms; for example, за́мок, a castle, and замо́к, a lock; pronounced as zàhmok and zahmòk.
MUSIC TYPE.
In no department of letter-founding has the progress of improvement been more decided and satisfactory than in the production of music type. The finest work of the music-stamper cannot surpass the ingenious combinations of the type-founder and printer. The music of which specimens are here given is cast on the centre of the body, and any intelligent workman may learn to compose it with facility. Brass lines are now furnished with founts when desired.
In no area of type design has the advancement of improvement been more clear and satisfying than in the creation of music type. The best work of the music-stamper can't match the clever combinations of the type-founder and printer. The music shown in the examples here is cast in the center of the body, and any skilled worker can learn to compose it easily. Brass lines are now provided with fonts when needed.
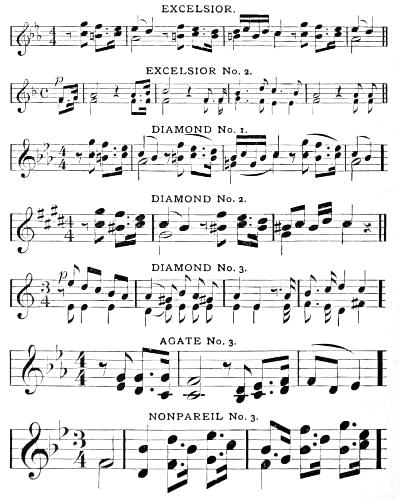

COMPARATIVE TABLE OF BODIES.
COMPARATIVE TABLE OF ORGANIZATIONS.
MUSIC COMPOSITION.
A knowledge of the rudiments of the art of music is essential to the correct composition of music type; for, unless the compositor is acquainted with the relative time-values of the notes and rests, he cannot space them properly.
Understanding the basics of music is essential for properly composing music type; because if the typesetter doesn't know the relative time values of the notes and rests, they can't space them correctly.
The manuscript copy is given to the compositor, with directions regarding the dimensions of the page required and the size of type to be employed. He counts the number of measures in the piece, and allots to each measure the amount of ems in length which the page will permit, so that there shall be a general equality of space throughout the piece.
The manuscript is handed over to the typesetter, along with instructions about the required page size and the font size to be used. He checks the number of measures in the piece and assigns the length in ems for each measure based on what the page can accommodate, ensuring a consistent spacing throughout the piece.
In instrumental music, and in pieces which are not interlined with poetry, the compositor will set two or more staves simultaneously, ranging the leading notes in the lower staves precisely under the corresponding ones in the upper staff; that is, a certain amount of space in each staff, in a brace, must contain the same amount of time-value. Where lines of poetry are interspersed, as in ballads and in church music, the staves are necessarily set singly; and in composing the second, third, and fourth staves the workman must therefore constantly refer to the first, in order to make the staves correspond.
In instrumental music, and in pieces that aren’t accompanied by lyrics, the typesetter will arrange two or more staves at the same time, placing the main notes in the lower staves directly beneath the corresponding notes in the upper staff. This means that a specific amount of space in each staff, within a brace, must represent the same time-value. When lines of poetry are included, like in ballads and church music, the staves have to be set up individually; therefore, when creating the second, third, and fourth staves, the composer must consistently refer back to the first to ensure the staves match.
A good compositor will be careful to make the lines overlap each other, brick-wise, and not allow a joint to fall directly under another. Masters who aim to do cheap rather than good work have the music lines cast double or triple, to expedite composition. Such work has a very slovenly look, as the joints of the lines, coming under one another, are apparent in the entire depth of the staff. We have seen books set in this manner, in which all the lines seem to be composed of dotted rule, instead of a continuous stroke.
A skilled compositor will make sure the lines overlap in a brick-like pattern and avoid placing a joint directly below another. Those who prioritize cost over quality often get the music lines printed double or triple to speed up the process. This approach looks very messy, as the joints of the lines become obvious throughout the entire staff. We've seen books produced this way, where all the lines appear to be made of dotted lines instead of a smooth, continuous stroke.
The compositor should be careful to make the stems of all the notes in a page of the same length, except those of grace-notes, which should be about half as long.
The compositor should be careful to make the stems of all the notes on a page the same length, except for grace notes, which should be about half as long.
PLAN OF CASES.

MUSIC UPPER CASE.
MUSIC

MUSIC LOWER CASE.
Music in lowercase.

MUSIC SIDE CASE.
Music case.
MODERN CONVENIENCES.
At no time since the invention of their art have printers been so fully supplied as at present with typographic implements for producing exact and beautiful work. In height of body, harmony and style of face, and excellence of material, modern type is doubtless superior to any heretofore made; but the most striking progression of type-founding is in the beauty and variety of ornamental letters and borders, and in these the American founders have taken the lead. A glance at their late Specimen Books proves the truth of this assertion. Among late novelties produced by The MacKellar, Smiths & Jordan Co. are several beautiful series of ingenious adjustable characters for the ornamentation of display lines, both straight and elliptical. A specimen is given below. Other appliances for job-printing are noted on pages 300-310.
At no time since the invention of their art have printers been so well equipped as they are now with tools for creating precise and beautiful work. In terms of body height, harmony, style, and quality of materials, modern type is definitely better than any made before; but the most impressive advancements in type-founding are in the beauty and variety of decorative letters and borders, where American founders have taken the lead. A quick look at their recent Specimen Books confirms this claim. Among the latest innovations from The MacKellar, Smiths & Jordan Co. are several stunning series of clever adjustable characters for embellishing display lines, both straight and curved. A specimen is shown below. Other tools for job printing are mentioned on pages 300-310.


THE ART OF COMPOSITION.
GENERAL REMARKS.

Experience proves that the apprentice foreshadows the workman, just as surely as the bend of the twig foretells the inclination of the tree. The upright, obedient, industrious lad will become a steady, skilful, and capable man, as unmistakably as the perverse, idling, careless boy will ripen into a lazy, dissolute, and worthless fellow. The fact is, a boy is measurably the maker of his own destiny; and if he fails to acquire a master-knowledge of the trade to which he is put, it will mainly be because he did not at his outset determine to be a master-workman. Good morals and steady industry are indispensable.
Experience shows that an apprentice reflects the workman, just like how the bend of a twig indicates which way the tree will grow. The upright, obedient, and hardworking kid will develop into a dependable, skilled, and competent man, just as definitely as the mischievous, lazy, and careless boy will turn into a slacker, irresponsible, and useless person. The truth is, a boy largely shapes his own future; and if he doesn’t master the skills of the trade he’s given, it’s mostly because he didn’t decide from the start to become a master craftsman. Good character and consistent hard work are essential.
When a lad who possesses these qualities proposes to learn the art and mystery of printing, it should be inquired of him, Has he had a fair common-school education? Is he a perfect speller? Has he a turn for reading? Is his eyesight good? Is he under fifteen years of age? A true affirmative answer to all these queries will entitle him to the position of reading and errand-boy. He is told the hours at which he is to come and go, and a strict punctuality is enjoined upon him. He sweeps the room,—he sorts out the pi,—he learns the position[122] of the various letters in the case. A year spent in this way is an excellent preparative for “going to case,” or learning the art of composing type.
When a young person with these qualities wants to learn the art and craft of printing, we should ask him, Has he had a good basic education? Is he a great speller? Does he enjoy reading? Is his eyesight good? Is he under fifteen years old? A positive answer to all these questions will qualify him for the role of reading and errand boy. He is informed of the hours he should arrive and leave, and he is expected to be punctual. He sweeps the room, sorts out the pi, and learns the arrangement of the various letters in the case. A year spent doing this is a fantastic preparation for “going to case,” or learning how to compose type.
When he is put to composition, he is told to set up one line and show it to the foreman or to the journeyman under whose care he may be placed. The errors in the line are pointed out to him, and he is required to correct them himself. When the words are perfectly correct, he justifies the line tight enough to prevent it from falling down when the composing-stick is slightly inclined, and yet sufficiently loose to enable him to lift it out with ease. In thus spacing out the line, the blanks between the words must be so graduated that, when the matter is printed, all the words will appear at equal distances apart. No matter how impatient he may be to get on, he must be drilled at this exercise till he becomes a thorough master of it. The grand doctrine to be instilled into him at first is, to do his work well and correctly; swiftness will follow as a natural consequence. He sets a second line; and after it has been made faultless he proceeds with the third, and so on till the stick is full. The utmost care must be taken to keep every letter and every line in an exact vertical position; and when he essays to empty the stick he must be taught to lift the entire mass in one square solid body, and to place it squarely and vertically on the galley. If the lines are allowed to slant either backward or sidewise, it is difficult afterward to make them stand accurately.
When he's tasked with composing, he's instructed to set up one line and show it to the foreman or the journeyman supervising him. The mistakes in the line are pointed out, and he has to correct them himself. Once the words are perfectly correct, he justifies the line tightly enough to keep it from falling when the composing stick is tilted slightly but loose enough to lift it out easily. While spacing out the line, the gaps between the words need to be even so that when printed, all the words appear at equal distances. No matter how eager he is to move on, he must practice this exercise until he masters it completely. The key lesson for him to learn early on is to do his work well and accurately; speed will come naturally afterward. He sets a second line, and after it’s flawless, he moves on to the third, and continues until the stick is full. He must be very careful to keep every letter and line perfectly vertical; and when he empties the stick, he should lift the whole mass in one solid piece and place it squarely and vertically on the galley. If the lines are allowed to tilt either backward or sideways, it will be hard to make them stand straight later.
After the apprentice has become thoroughly conversant with the shape of every type, and can distinguish “u” from “n,” “b” from “q,” and “d” from “p,” he is allowed to distribute type for his own use. He is taught to take up at one time no more matter than he can conveniently grasp in his left hand, which he holds so that the light falls on the face of the type, and his eye can readily read it. In distributing the various letters, he takes a word or two between the thumb and forefinger of his right hand, and the types are lightly dropped into their respective boxes.
After the apprentice has become completely familiar with the shape of every letter and can tell “u” from “n,” “b” from “q,” and “d” from “p,” he is allowed to sort type for his own use. He learns to grab only as much material as he can comfortably hold in his left hand, keeping it positioned so that the light shines on the face of the type, allowing his eye to read it easily. When sorting the different letters, he picks up a word or two between his thumb and index finger of his right hand, and the letters are gently placed into their respective boxes.
At the outset, and as he proceeds, the novitiate must be cautioned against the acquisition of bad habits; such as swinging the body as the types are picked up, nicking the type against the stick several times before placing it in line, standing on one leg, &c.
At the beginning, and as he continues, the beginner must be warned against picking up bad habits, like swinging the body while picking up the types, hitting the type against the stick multiple times before placing it in line, standing on one leg, etc.
While avoiding these ridiculous practices, a learner must acquire (if he does not possess them already) certain habitudes or principles which lie at the foundation of successful effort. The first is
While avoiding these silly practices, a learner must acquire (if they don’t already have them) certain habits or principles that are essential for achieving success. The first is
Punctuality. He must conscientiously observe the time-rules of the office in coming and leaving. The early hours are the best for work; and the mind being cheered by the consciousness of doing right, the body feels the influence, and is strengthened; and when the quitting hour arrives, the amount of work accomplished will satisfy himself and his master too. The most successful masters have been distinguished for punctuality. The apprentice’s time is not his own, but his master’s property; and wasting it by want of punctuality, or idling during his master’s absence, is simply equivalent to stealing. The second point is
Punctuality. He needs to consistently follow the office's schedule for arriving and leaving. The early hours are the best for productivity; when you're aware that you're doing the right thing, it boosts your mood and strengthens your body. By the time it's quitting time, the work you've completed will satisfy both yourself and your boss. The most successful leaders are known for their punctuality. An apprentice’s time doesn't belong to them; it belongs to their master. Wasting it by being late or goofing off while the master is away is essentially the same as stealing. The second point is
Obedience. The apprentice has no right to question orders given by the master or his deputy. His duty is promptly to do as he is told, without grumbling or dissatisfaction. Let him remember that he is under orders, and that, if he ever expects to learn how to command, he must learn in his youth how to obey. He will promote his own interests by seeking to anticipate his master’s wishes, and by endeavouring to make himself so useful that his services cannot well be dispensed with. Akin to this is
Obedience. The apprentice has no right to question the orders given by the master or their assistant. Their duty is to follow instructions promptly, without complaining or showing dissatisfaction. They should remember that they are under orders, and if they ever hope to learn how to lead, they must first learn how to follow in their youth. They will benefit their own interests by trying to anticipate their master's wishes and making themselves so valuable that their services cannot easily be replaced. Related to this is
Courtesy. Good manners in a youth are wonderfully pleasing, and effectively aid in his advancement. Courtesy toward his master is a matter of course, and deserving of little commendation; but he must be courteous to customers when sent out on an errand, and courteous to the workmen in the office. By this means he will secure good-will, and many a friendly hint will be given to him in acquiring a knowledge of the art. The habit when fixed will bless him and others as long as he lives.
Courtesy. Good manners in a young person are really impressive and help them get ahead. Being polite to their boss is expected and doesn’t require much praise; however, they should also be courteous to customers when out on an errand and respectful to the workers in the office. This way, they will gain goodwill, and many helpful tips will be offered to them as they learn the trade. Once this habit becomes second nature, it will benefit them and others for their entire life.
PLAN OF CASES.
The following schemes show the order in which the letters are kept in cases in this country. In some offices, however, slight deviations will be found,—such as the transposition of the comma and w, y, p, &c.
The following schemes show the order in which the letters are kept in cases in this country. In some offices, however, you might notice slight variations, like the switching of the comma with w, y, p, etc.

AMERICAN UPPER CASE.
American uppercase.

AMERICAN LOWER CASE.
american lowercase.

PROPOSED NEW PLAN FOR THE LOWER CASE.
PROPOSED NEW PLAN FOR THE LOWER CASE.
POSITION.
The standing position of a compositor should be perfectly upright, without stiffness or restraint; the shoulders thrown back, the feet firm on the floor, heels nearly closed, and toes turned out to form an angle of about forty-five degrees. The head and body should be kept perfectly steady, except when moving from the Roman to the Italic case, the operations of distributing and composing being performed by the various motions of the arm, from the shoulder-joint alone; and if, to reach a box placed in the further part of the cases, to put in or take out a letter, he should incline the body by a slight motion, he should immediately resume his erect position. The height of a compositor and his frame should be so adjusted that his right elbow may just clear the front of the lower case by the a and r boxes, without the smallest elevation of the shoulder-joint; his breast will then be opposite the space, h, and e boxes. Sitting at work should be rarely permitted, except for lameness, weakness, old age, or other infirmity; and then the stool should be a small piece of board fastened to a single leg. Habit will render a standing position familiar and easy; perseverance in conquering a little fatigue will be amply repaid by the prevention of knock knees, round shoulders, and obstructed circulation of the blood and respiration of the lungs.
The standing position of a compositor should be perfectly upright, without stiffness or discomfort; the shoulders should be back, feet solid on the ground, heels nearly together, and toes pointed out at about a forty-five-degree angle. The head and body should remain steady, except when transitioning from the Roman to the Italic case, with the tasks of distributing and composing carried out by moving the arm solely from the shoulder. If he needs to lean slightly to reach a box in the back of the cases to grab a letter, he should quickly return to the upright position. The height of a compositor and his build should be set so that his right elbow just clears the front of the lower case by the a and r boxes, without raising the shoulder. His chest will then align with the space, h, and e boxes. Sitting while working should only be allowed in cases of lameness, weakness, old age, or other disabilities; and in that case, the stool should be a small piece of board attached to a single leg. With time, a standing position will become comfortable and familiar; pushing through a bit of fatigue will be well worth it to avoid knock knees, hunched shoulders, and limited blood circulation and lung capacity.
LAYING TYPE.
Unwrap carefully the page received from the type-founder, and, laying it on a galley, soak it thoroughly with thin soap-water, to prevent the types from adhering to one another after they have been used a short time. Then, with a stout rule or reglet, lift as many lines as will make about an inch in thickness, and, placing the rule close up on one side of the bottom of the proper box, slide off the lines gently, taking care not to rub the face of the letter against the side of the box. Proceed thus with successive lines till the box is filled.
Open carefully the page you got from the type founder, and put it on a galley, soaking it completely with diluted soap water to stop the types from sticking together after they’ve been used for a bit. Then, using a sturdy rule or reglet, lift as many lines as you can to make about an inch thick, and rest the rule close up on one side of the bottom of the proper box. Gently slide off the lines, being careful not to rub the face of the letters against the box’s side. Keep doing this with the successive lines until the box is full.
Careless compositors are prone to huddle new types together, and, grasping them up by handfuls, plunge them pell-mell into the box, rudely jostling them about to crowd more in. This is an intolerable practice.
Careless typesetters tend to mix new typefaces together, grabbing them by the handful and tossing them haphazardly into the box, roughly shoving them around to fit more in. This is an unacceptable practice.
The type left over should be kept standing on galleys, in regular order, till the cases need replenishment. A fount of five hundred pounds of Pica may have, say, four cases allotted to it; the same amount of Nonpareil, from eight to ten cases.
The leftover type should be left standing on galleys, organized neatly, until the cases need to be refilled. A font of five hundred pounds of Pica might have about four cases assigned to it; the same weight of Nonpareil could have between eight and ten cases.
DISTRIBUTING.
When a learner can infallibly distinguish from each other the letters b and q, d and p, n and u, and l and I, he may be allowed to distribute type for himself.
When a learner can reliably tell apart the letters b and q, d and p, n and u, and l and I, they may be allowed to set type on their own.
The head of the page being turned toward him, the learner sets a composing-rule behind the portion to be lifted, and then, placing his thumbs against the rule and his forefingers against the top line, while his remaining fingers press together both sides, he raises the matter quickly. Then, inclining sidewise his right hand, he removes the left, and allows the matter to balance momentarily in his right, while he doubles in the third finger and stretches out the thumb of the left for the reception of the matter, which he at once places in it, the rule lying as a support on the third finger, while the thumb and other fingers embrace the sides. He should take up but a few lines at a time, until he acquires facility in lifting. Large handfuls should always be avoided, as the weight is fatiguing and weakening to the wrist.
The learner turns the page toward him, sets a composing stick behind the section to be lifted, and then, using his thumbs against the stick and his index fingers on the top line, while his other fingers press together both sides, he quickly raises the text. Next, tilting his right hand to the side, he removes his left hand and lets the text balance briefly in his right hand, while he bends his third finger and extends the thumb of his left hand to receive the text, which he then places into it, the stick resting on the third finger, with his thumb and other fingers holding the sides. He should only pick up a few lines at a time until he gets the hang of lifting. Large handfuls should always be avoided, as the weight can be tiring and weakens the wrist.
Keeping the handful in an inclined position, so that he may readily read the lines, he takes up as many letters as he can conveniently hold between his fingers,—an entire word, if practicable,—and drops the types slantingly, but with face upward, into the several boxes.
Keeping the handful in a tilted position, so he can easily read the lines, he picks up as many letters as he can comfortably hold between his fingers—an entire word, if possible—and drops the types at an angle, but facing up, into the different boxes.
The first aim of the learner must be accuracy, even though his progress be slow. Correct distribution aids in clean composition. In time he will be able to drop his types rapidly, with hardly a glance at the boxes; and, while his fingers are flying about correctly and expeditiously, his eyes will take in the next word to be distributed; thus proceeding till the case is filled.
The first goal of the learner should be accuracy, even if their progress is slow. Proper organization helps in creating clear compositions. Eventually, they will be able to quickly drop their types with barely a glance at the boxes; and while their fingers are moving correctly and efficiently, their eyes will spot the next word to be used, continuing this way until the case is filled.
In distributing, the utmost care should be taken in placing the various spaces in their appropriate boxes. A mixing of spaces characterizes the botch.
In distributing, great care should be taken in placing the different spaces in their correct boxes. Mixing up spaces is what creates a mess.
The letter-board should always be kept clean, and the bottom as well as the face of the form well washed before it is[129] laid on the board and unlocked; for, if any dirt remain in the type after the form is unlocked, it will sink into the matter. This precaution taken, the pages should be well opened, and the whole form washed till the water appears to run from it in a clean state. If the form is very dirty, it is best to lock it up again and rinse the bottom of it, and proceed as before.
The letter-board should always be kept clean, and both the bottom and the face of the form should be thoroughly washed before it is[129] placed on the board and unlocked; because if any dirt is left on the type after the form is unlocked, it will get pressed into the material. After taking this precaution, the pages should be thoroughly opened, and the whole form washed until the water runs off it clean. If the form is really dirty, it’s best to lock it up again, rinse the bottom, and repeat the process.
It is sometimes necessary to dry the letter at the fire after distributing. In this case, the type should not be used until it is perfectly cold, as very pernicious effects arise from the antimony in the composition of which the type is made. The noxious vapour which arises is sufficient warning of the effects. The compositor ought always to avoid it as a pestilence which will affect his respiration and his sinews, inducing lung-complaints, and causing paralysis of the hand or contraction of the fingers. Where it can be conveniently managed, it is better to distribute at night, or before meals, so that the letter may dry without artificial heat.
It’s sometimes necessary to dry the type by the fire after inking it. In this case, the type shouldn’t be used until it’s completely cool, as the antimony in the type can cause harmful effects. The toxic fumes that come off are a clear warning of the risks involved. Compositors should always avoid this like a disease, as it can impact their breathing and muscles, leading to respiratory issues and potentially causing paralysis in the hand or stiffness in the fingers. If possible, it’s better to distribute the type at night or before meals, so it can dry naturally without extra heat.
COMPOSING.
When copy is put into the hands of the compositor, he should receive directions respecting the width and length of the page; whether it is to be leaded, and with white lines between the breaks; and whether any particular method is to be followed in the punctuation and in the adoption of capitals. These instructions being given, the compositor will make his measure to the number of ems directed, which is done by laying them flatwise in the composing-stick, and then screwing it up sufficiently tight to prevent the slide from moving. He then fits a composing-rule to the measure, and, his case being supplied with letter, he commences his work.
When the text is handed over to the typesetter, he should receive instructions regarding the width and length of the page; whether it should be spaced with leading, and if there should be white lines between the breaks; and whether a specific style is to be followed for punctuation and capitalization. Once these guidelines are given, the typesetter will set the measure to the specified number of ems, which is done by placing them flat in the composing stick and then tightening it enough to keep the slide in place. He then adjusts a composing rule to the measure, and, with his type case filled with letters, he begins his task.
The left hand, which contains the composing-stick, should always follow the right, which takes up the letters. If the left be kept stationary, considerable time is lost in bringing each letter to the stick, because the right hand has, consequently, to traverse a much greater space than is necessary. The eye should always precede the hand, constantly seeking for the next letter while the fingers are picking up one just selected. Each letter should be taken up by the upper end. This method will effectually prevent any false motion, and preclude[130] the necessity of turning the letter when in the hand. If possible, a sentence of the copy should be taken at one time, and, while putting in the point and quadrate at the end of the sentence, the eye may revert to the copy for the next. It is to dexterity in these particulars that compositors are indebted for swiftness. The time thus gained is very considerable, while all appearance of bustle or fatigue is avoided. By taking a sentence into the memory at one time, the connection of the subject is preserved, and the punctuation rendered less difficult.
The left hand, which holds the composing stick, should always follow the right hand, which picks up the letters. If the left hand stays still, a lot of time is wasted in bringing each letter to the stick because the right hand has to move a much longer distance than necessary. The eyes should always lead the hands, constantly looking for the next letter while the fingers grab the one just chosen. Each letter should be picked up by the top end. This method will effectively prevent any unnecessary movements and eliminate the need to turn the letter while holding it. If possible, a whole sentence from the copy should be taken at once, and while placing the point and quadrate at the end of the sentence, the eyes can return to the copy for the next part. It’s this skill in these specifics that helps compositors work swiftly. The time saved is significant, while avoiding any signs of rush or fatigue. By memorizing a whole sentence at once, the connection of the subject is maintained, and punctuation becomes less challenging.
Those who are careful in distribution find the advantage of it in composition. Foul or slovenly workmanship is disgraceful. To avoid this, a compositor should accustom himself to glance over each line as he justifies it, and correct any error as he proceeds, which he may do with little impediment to his progress.
Those who are careful with how they distribute find benefits in how they compose. Poor or messy work is shameful. To avoid this, a typesetter should get into the habit of quickly checking each line as they set it, correcting any mistakes as they go, which they can do with minimal interruption to their work.
SPACING.
Uniformity in spacing is, unquestionably, a most important part of a compositor’s occupation; this requires both care and judgment, and, therefore, cannot be too strongly impressed upon the mind of the beginner. Close spacing is as unworkmanlike as wide spacing, and neither ought to be permitted except in very narrow measures; and, frequently, even then with care it might partly be prevented. What is commonly called the thick space is the proper separator between words; though this rule cannot always be adhered to in narrow measures when large type is used. It is not sufficient merely to have a line here and there uniformly spaced: a careful compositor will give every page that uniformity of appearance which is a chief excellency. The beginner should remember that it is better to do little, and do that little well, than to put together a great number of letters without any regard to accuracy and uniformity.
Uniform spacing is definitely a really important part of a compositor's job; it takes both care and good judgment, so beginners should really keep this in mind. Tight spacing is just as poor quality as wide spacing, and neither should be allowed except in very narrow settings; often, even then, it can be partly avoided with care. What people usually call a thick space is the right separator between words; however, this rule can't always be followed in narrow settings when using large type. It's not enough to have just a few lines spaced evenly: a careful compositor will make sure every page has that uniform appearance, which is a key quality. Beginners should remember that it's better to do a little and do it well than to throw together a lot of letters without paying attention to accuracy and uniformity.
Where a line is evenly spaced, and yet requires justification, the additional space should be put between those words in the line where it will be least observable: viz. a d and an h, being tall, perpendicular letters, will admit an increase of space between them, but not more than a middle and thin space to a thick-spaced line; and an additional space may be placed after a kerned letter, the beak of which may bear upon the top of an ascending letter,—as the f followed by h, &c.
Where a line is evenly spaced but needs justification, the extra space should be placed between the words in the line where it’s least noticeable: for example, a d and an h, which are tall, straight letters, can have a bit more space added between them, but not more than what would fit in a line with medium and thin spacing. You can also add extra space after a kerned letter if its top touches the top of a tall letter, like an f followed by an h, etc.
The same rule should be observed where it is necessary to reduce the spacing of a line, less space being required after a sloping letter than after a perpendicular one. The comma requires only a thick space, but the other points should have a hair space before and an en quadrate after them, except the full-point, which should have an em quadrate, as terminating a sentence. Should it be necessary to reduce the spacing generally, the spaces after the points must be altered in the same proportion. Spaces are cast to such regular gradations that the compositor can urge no reasonable excuse either for bad justification or improper spacing.
The same rule should be followed when it's necessary to reduce the spacing of a line; less space is needed after a slanted letter than after a straight one. A comma only requires a thick space, but the other punctuation marks should have a thin space before them and an en quad after, except for the full stop, which should have an em quad because it ends a sentence. If it's necessary to reduce the spacing overall, the spaces after the punctuation must be adjusted in the same way. Spaces are made in such regular measurements that the typesetter can't offer any reasonable excuse for poor justification or incorrect spacing.
In matter to be stereotyped, a hair space should be placed after the letter f and other kerned letters when they stand at the end of the line.
In terms of what needs to be standardized, there should be a space added after the letter f and other adjusted letters when they appear at the end of a line.
JUSTIFYING.
Accurate justification is absolutely essential, as the letters will be warped sidewise in a loose line, making it impossible to get a fair impression from the type. Besides, the letters are liable to be drawn out by the suction of the rollers, to the detriment of the form and the press. The instructor of an apprentice should occasionally pass his finger along the side of matter set by him; and if the lines should not prove evenly justified, they should be put into the composing-stick again and properly corrected.
Accurate justification is crucial, as the letters will be misaligned in a loose line, making it impossible to get a good impression from the type. Additionally, the letters may be pulled out by the suction of the rollers, which can harm the form and the press. The instructor of an apprentice should occasionally run their finger along the side of the text set by them; if the lines aren't evenly justified, they should be placed back into the composing stick and corrected properly.
HEAD-LINES.
Head-lines are generally set in small capitals of the same fount, or in Italic, and sometimes in capitals. Italic capitals of letter somewhat smaller than the body of the work, with folios of a proportionate size, have a neat appearance.
Headlines are usually formatted in small caps of the same font, or in italics, and sometimes in all caps. Italic capitals that are a bit smaller than the main text, along with proportionate folios, give a clean look.
NOTES.
The usual rule for note-type is two sizes less than the text of the work: thus, to Pica work, Long Primer; Small Pica, Bourgeois; Long Primer, Brevier. Side-notes are usually smaller in proportion. When side-notes or references drive down below the lines of the text to which they refer, the expedient of cut-in notes must be resorted to. This is a difficult[132] part of a compositor’s business, and requires skill and patience to adjust all parts, so that every line of note and text may have proper and equal bearing. The reglet or lead between the lines of matter and the side-note must be cut with as much nicety as possible to the length of the text, as far as where the note is to run under; and, having accurately adjusted, by means of the quotations and justifiers, the situation of the first line of the note, such lead or reglet is added to the text as will make it precisely correspond in depth with the lines of note that stand on the side before turning: the remainder of the note is then set in a long measure, to correspond in width with the text, reglet, and side-note; and the page is made up with note, or the text begun again after the note is finished. In Bibles with notes and annotations, in law-books, and other works, it frequently happens that a page exhibits several of these alternate frameworks of note and text, which, if done well, display a workman’s skill to great advantage.
The general guideline for the size of notes is to make them two sizes smaller than the main text of the work: so for Pica text, you use Long Primer; for Small Pica, you use Bourgeois; and for Long Primer, you use Brevier. Side notes are usually even smaller in relation to the main text. When side notes or references dip below the lines of the text they refer to, you have to use cut-in notes. This is a challenging part of a compositor’s job and requires skill and patience to align everything so that every line of notes and text looks balanced. The space or lead between the text and the side note needs to be cut as accurately as possible relative to the length of the main text where the note is to be placed. Once you’ve accurately positioned the first line of the note using quotes and justifiers, you add the exact amount of lead or reglet necessary to ensure that it aligns perfectly with the note lines beside it; the rest of the note is then set to a long measure to match the width of the text, reglet, and side note. Finally, the page is completed with the note, or you start the text again after finishing the note. In Bibles with notes and annotations, law books, and other types of work, it often occurs that a page features these alternating sections of notes and text, which, when done well, showcase the compositor’s craftsmanship to great effect.
BLANKING.
If the work is very open, consisting of heads, whites, &c., the compositor must be particularly attentive to their depth; so that though the white may be composed of different-sized quadrates, yet their ultimate depth must be equal to the regular body of the type the work is done in; otherwise the register of the work will be incomplete. The pressman cannot make the lines back if the compositor is not careful in making up his matter.
If the work is very open, consisting of heads, whites, etc., the typesetter needs to pay special attention to their depth. This way, even if the white spaces are made up of different-sized squares, their final depth must be the same as the standard size of the type the work is done in; otherwise, the alignment of the work will be off. The press operator can’t fix the lines later if the typesetter isn't careful in putting together the text.
PARAGRAPHS.
The first line of a new paragraph is indented an em quadrate, of whatever type the work may be; though, when the measure is very wide, two or even three ems are preferable. By this means the paragraph is more strongly marked, the indention of an em only being scarcely perceptible in a long line. Authors vary materially in the mode of making paragraphs. Some carry the argument of a position to a great length before they relieve the attention of the reader; while others break off at almost every place that will admit only of a full-point. But the author’s plan is to be followed, unless he direct otherwise. Authors should always make the beginning of a new paragraph conspicuous to the compositor, by[133] indenting the first line of it far enough to distinguish it from the preceding line in case it should be quite full.
The first line of a new paragraph is indented one em space, regardless of the type of work; however, if the line length is very wide, two or even three ems are better. This way, the paragraph stands out more, as a single em indentation can be hard to notice in a long line. Authors have different styles when it comes to creating paragraphs. Some explore their ideas extensively before giving the reader a break, while others tend to stop at almost every point that allows for a full stop. But the author's approach should be followed unless they specify otherwise. Authors should always make the start of a new paragraph clear to the typesetter by[133] indenting the first line enough to set it apart from the previous line in case it is completely full.
It is a practice too prevalent among compositors to drive out a word at the close of a paragraph, or even to divide it, in order to reap the advantage of a break-line. Part of a word, or a complete word, in a break-line, if it contain no more than three or four letters, is improper. It should be the business of the proof-reader to notice and check this irregularity.
It's a common practice among typesetters to end a paragraph with a word or even split a word to create a break in the line. Placing part of a word or a whole word in a break line when it has only three or four letters is inappropriate. It's the proofreader's job to catch and correct this issue.
The last line of a paragraph should not on any account begin a page, neither should the first line of a paragraph come at the bottom of a page if the work has white lines between the breaks: to prevent this, the compositor may make his page either long or short, as most convenient, always taking care that the odd and even pages back, so that the extra length or shortness of the page may escape observation.
The last line of a paragraph should never start a page, and the first line of a paragraph shouldn't be at the bottom of a page if there are white lines between the breaks. To avoid this, the typesetter can adjust the page length to make it longer or shorter as needed, always ensuring that odd and even pages align so that the extra length or shortness goes unnoticed.
INDEXES.
The index is generally placed at the end of the volume, and set in letter two sizes less than that of the work. It is always begun upon an uneven page. In setting an index, the subject-line should not be indented; but, if the article make more than one line, all but the first should be indented an em.
The index is usually located at the end of the book and is printed in a font size two sizes smaller than the main text. It's always started on an odd-numbered page. When creating an index, the subject line shouldn't be indented; however, if the entry is more than one line, all lines except the first should be indented by an em.
In preparing the copy of an index, care should be taken that the subject-words are arranged alphabetically, as the compositor will not transpose his matter afterward without remuneration.
In preparing the index, make sure that the subject words are arranged alphabetically, as the typesetter won't rearrange things later without being paid.
Where several index-figures are used in succession, a comma is put after each folio; but, to save figures and commas, the succession of the former is noted by putting a dash between the first and last figures: thus, 4-8. Again, if an article has been collected from two pages, the folio of the second is supplied by sq., or sequente, and by sqq., or sequientibus, when an article is touched upon in succeeding pages. A full-point is not put after the last figures, because it is thought that their standing at the end of the line is a sufficient stop. Neither is a comma or a full-point placed to the last word of an article in a wide measure and open matter with leaders; but it is proper to use a comma at the end of every article where the figures are put close to the matter, instead of running them to the end of the line.
Where several index figures are used in succession, a comma is placed after each folio; but to save figures and commas, the series is noted by placing a dash between the first and last figures: thus, 4-8. Furthermore, if an article is taken from two pages, the folio of the second is indicated by sq., or sequente, and by sqq., or sequientibus, when an article is mentioned in the following pages. A full stop is not placed after the last figures because it is believed that their position at the end of the line serves as enough of a pause. Likewise, no comma or full stop is used after the last word of an article in a wide measure and open matter with leaders; however, it is appropriate to use a comma at the end of every article where the figures are placed close to the text, instead of extending them to the end of the line.
TITLES.
Ornamental type may be used to good purpose in fancy jobs, and without violating any of the canons of a correct taste. The universal eye is pleased with ornament; and it is well to foster this fancy, just as we cultivate a poetical feeling, or a passion for music, or flowers, or any beautiful thing that God has made. But, as life should not be all music, or flowers, or poetry, so printing should not be all ornament. And as men whom nature puts in the fore-front of all other men are noted for a becoming simplicity of life and style, so the title-page that heralds all the inner pages of a book should be printed in a style of elegance severe and unadorned: no fancy type, except a line of Scribe Text, or Old English,—no italics, unless perchance a single-line motto in Pearl caps,—no bold-face type, nor Antique, nor Gothic,—but plain, clear, light-faced letters that seem the embodiment of the soul of thought. All experienced printers incline to this simple style; but publishers sometimes interfere with this province of art legitimate only to a typographer, and insist on the indulgence of a taste which certainly owes no allegiance to any of the laws of beauty; and the printer or stereotyper who executes the book receives credit for a title-page which he would fain utterly repudiate.
Ornamental type can be effectively used in decorative projects without compromising good taste. People generally enjoy ornamentation, and it’s beneficial to embrace this appreciation, just like we nurture a love for poetry, music, flowers, or any beautiful creation that God has made. However, just as life shouldn’t be solely about music, flowers, or poetry, printing shouldn’t be all about ornamentation. Those who stand out in life tend to be recognized for their simple and elegant style, and similarly, the title page that introduces the content of a book should be printed in a clean, serious, and unembellished style: no fancy type, except perhaps a line of Scribe Text or Old English—no italics, unless it’s a single motto in Pearl caps—no bold type, Antique, or Gothic—but rather plain, clear, light letters that capture the essence of thought. Most experienced printers lean towards this straightforward style; however, publishers sometimes meddle in this area of art, which rightfully belongs to the typographer, demanding styles that disregard any rules of beauty, resulting in a title page that the printer or stereotyper would prefer to entirely disown.
We add a few hints which may assist the learner. 1st. Having divided the title into lines, and decided upon the size of type suitable for the principal one, begin by composing those of the second and third class, both in ascending and descending order. 2d. Avoid having two lines of equal length to follow or come in contact with each other. 3d. Catch-words should be set on quite a reduced scale, and proportioned according to the strength of the preceding and succeeding lines; for bold catch-words detract from the general effect of the title. 4th. Close attention should be given to those title-pages which are acknowledged to be displayed with true taste and judgment.
We’ve included a few tips that might help the learner. 1st. After breaking the title into lines and choosing the right type size for the main title, start by working on the second and third class titles, both in ascending and descending order. 2nd. Make sure not to have two lines of equal length follow each other or touch. 3rd. Catch-words should be set in a much smaller size and should match the strength of the lines before and after them; bold catch-words can take away from the overall look of the title. 4th. Pay close attention to title pages that are recognized for being displayed with true style and judgment.
Authors should endeavour to make their title-pages as concise as possible; for a crowded title can never be displayed with elegance or taste.
Authors should strive to keep their title pages as concise as possible; a cluttered title can never be presented with elegance or style.
DEDICATIONS.
The dedication generally follows the title, and seldom exceeds one page. It should be set in capitals and small capitals, neatly displayed. The name of the person to whom the work is dedicated should always be in capitals, and the terms, Your very humble and very obedient, &c., should be in a smaller type, and the signature or name of the author in capitals of a smaller size than that in which the name of the personage is printed to whom the book is dedicated.
The dedication usually comes right after the title and rarely takes up more than a page. It should be formatted with capital and small capital letters, looking neat. The name of the person being honored should always be in capital letters, while phrases like "Your very humble and very obedient," etc., should be in a smaller font. The author's name or signature should be in capitals but in a smaller size than the name of the person to whom the book is dedicated.
CONTENTS.
The contents follow the preface or introduction, and may be set either in Roman or Italic, generally two sizes smaller than the body of the work; the first line of each summary full, and the rest indented an em quadrate, with the referring figures justified at the ends of the respective lines.
The contents come after the preface or introduction and can be set in either Roman or Italic font, typically two sizes smaller than the main text; the first line of each summary is flush left, and the rest is indented by an em quadrate, with the reference numbers aligned at the ends of their respective lines.
PREFACES.
Formerly, the preface was uniformly set in Italic; at present Roman is used, one size larger or smaller than the body of the work. The running title to the preface is commonly set in the same manner as that of the body of the work. If the work has been printed without a running title, and paged in the centre of the line only, then the preface should be treated in like manner.
Previously, the preface was always printed in Italic; now, Roman is used, either one size larger or smaller than the main text. The running title for the preface is usually styled the same way as the title of the main text. If the work has been printed without a running title and is paginated centered on the line, then the preface should follow the same format.
SIGNATURING.
The title, preface, &c. of a volume are commonly left till the body of the work is finished, as circumstances may arise in the course of its progress through the press which will induce the author to alter his original preface, date, &c., or the work may conclude in such a manner as to admit of their being brought in at the end, in order to fill out a sheet, and thus save both paper and press-work. For this reason, it is well to begin the first sheet of every work with signature B (or 2), leaving A (or 1) for the title-sheet.
The title, preface, etc. of a book are usually left until the main part of the work is complete, as things may come up during its progress through printing that will cause the author to change the original preface, date, etc., or the work may end in a way that allows them to be included at the end, helping to fill a sheet and save both paper and printing costs. For this reason, it’s a good idea to start the first sheet of every work with signature B (or 2), leaving A (or 1) for the title page.
It was formerly the custom to omit the letters J, V, and W in the list of signatures. But the greater convenience attending the use of twenty-five letters has recently induced several of our largest establishments to omit the letter J only.
It used to be common to leave out the letters J, V, and W in the list of signatures. However, the increased convenience of using twenty-five letters has recently led many of our biggest companies to only leave out the letter J.
ERRATA.
The errata are put immediately before the body of the work, or at the end of it. They should consist only of such corrections as are indispensably necessary, without noticing any defects in the punctuation, unless where the sense is perverted. It is strongly to be wished that works could be produced perfectly free from errors; but this is almost a vain hope while imperfection clings to humanity, and while every form is exposed to accident and every additional proof may be productive of fresh error.
The corrections are placed right before or at the end of the main content. They should only include corrections that are absolutely necessary, without addressing any punctuation issues unless it changes the meaning. It’s definitely desirable for works to be published completely free of errors; however, this is nearly an unrealistic expectation as long as imperfection is part of being human, and since every format is prone to accidents and each additional proof can introduce new mistakes.
HINTS HONOURED IN THE BREACH.
When you lay a fount of new type, don’t open the papers carefully, and place the lines evenly with a brass rule in the cases, nick up; but show your skill by tumbling over each package rapidly, and bringing it down with a rush on the imposing-stone; then, roughly throwing the a’s into a chaotic pile, grab them up by handfuls and work them well down in the appropriate box. The harder you jostle them down, the more you will get in. Proceed thus with each letter; and, if the operation has been vigorously performed, the value of the fount will have been reduced, say ten per cent.
When you set up a new typeface, don’t open the packages delicately. Instead, quickly toss the lines onto the cases with a brass rule, nicking them as you go. Show your expertise by rapidly flipping through each bundle and dropping it onto the imposing stone with a bang. Then, randomly toss the a’s into a messy pile, scoop them up by the handful, and pack them tightly into the right box. The more you shove them down, the more you'll fit in. Do this for every letter, and if you've done it with some energy, the value of the type will have dropped by about ten percent.
2. While you set out one case, let your galley lie on the overheaped type of another case.
2. While you prepare one box, let your workspace be cluttered with the piled-up supplies of another box.
3. If a line is rather too tight to permit the last letter to get in easily, push it down hard with your rule or a quadrate. The type may be injured; but why didn’t it fit in just right at first?
3. If a line is too tight for the last letter to fit in easily, push it down firmly with your ruler or a square. The type might get damaged, but why didn't it fit properly in the first place?
4. Empty your matter at a gentle inclination on the galley, and make it up at the same angle. You can bring it right afterward—perhaps—by the energetic application of mallet, shooting-stick, and planer.
4. Pour your material at a slight angle on the workbench, and shape it at the same angle. You can fix it up right afterward—maybe—by using a hammer, a chisel, and a planer.
5. When the case is half set out, shake up the type energetically, and do so very often. The exercise will strengthen your muscles.
5. When the case is halfway set up, shake the type vigorously, and do this quite often. This exercise will build your muscles.
6. Don’t brush off the stone before you lay the matter down. If any sand happens to get under, the type will show its impression beautifully deep and clear on the face of the planer,—perhaps a whole word or two.
6. Don’t dust off the stone before you finish the job. If any sand gets underneath, it will leave a clear and deep impression on the surface of the planer—maybe even a whole word or two.
7. Don’t plane till the form is locked up, as thus you save the trouble of the first planing. But, now that you do plane, hammer away, and show your musical ability in playing a tattoo on the form. Don’t lay the planer tenderly and lovingly on the types, as if you were afraid to hurt their feelings, and gently tap it; but hold it off about a quarter or three-eighths of an inch, and then bring down the mallet with a will. Phew! how the planer will descend obedient to the stroke, and rebound again, and perhaps again. If the form is not smooth on the surface now, it is not your fault. Repeat this each time when the form is locked up, till it goes to press; and you may depend on it the impression will gain in boldness, if not in looks.
7. Don’t plane until the form is locked up, as this saves you the hassle of the first planing. But now that you're planing, go ahead and really show your skills by playing a rhythm on the form. Don’t place the planer carefully and gently on the types, as if you’re worried about hurting their feelings, and lightly tap it. Instead, hold it about a quarter or three-eighths of an inch above, and then bring down the mallet with force. Wow! The planer will drop easily with the stroke, and bounce back, maybe even several times. If the surface of the form isn’t smooth now, that’s not your fault. Do this every time the form is locked up, until it goes to press; you can count on the impression getting bolder, if not better looking.
8. When correcting your numerous errors, don’t trouble yourself to lift the lines carefully at the ends, but dig right into the head of the erring letter, and, resting your bodkin on the type below it, pry up the sinner: it does not matter if you demolish two or three types in the under line.
8. When fixing your many mistakes, don’t bother trying to lift the lines carefully at the ends. Instead, go straight to the offending letter, and, placing your tool on the type below it, pry it up. It’s okay if you accidentally damage a couple of types in the line below.
9. Wash your form energetically, and apply the ley bountifully with a good stiff wiry brush. Never mind rinsing: clean type is an old-fogy notion.
9. Wash your body vigorously, and apply the treatment generously with a good, stiff brush. Don’t worry about rinsing: being clean is an outdated idea.
10. When the type is out of use, let it lie around promiscuously,—on a table, or board, or any place where it will be occasionally convenient to lay on it a mallet or tin basin. If one strip of matter is placed on another, room will be economized. Moreover, the under layers will be safe from dust.
10. When the type isn't in use, just leave it lying around anywhere—on a table, a board, or any spot where it will be easy to put a mallet or tin basin on top of it. If one piece is placed on another, space will be saved. Plus, the lower layers will be protected from dust.
11 (comprehensively). Do every thing in a loose way generally, letting matters go as they list, throwing your pi into spare boxes or secretly placing it on the letter-table or some out-of-the-way place, stealing sorts from your neighbour, overcharging time-work and extras, fishing for fat takes, &c.
11 (comprehensively). Generally, do everything in a casual manner, letting things happen as they will, tossing your items into spare boxes or discreetly setting them on the letter-table or some hidden spot, taking from your neighbor, charging extra for time and additional work, trying to get bigger profits, etc.
12. If you observe these things faithfully and constantly, and your employer does not kick you out of his office, why—you do not get your deserts.
12. If you pay close attention to these things and stick with them, and your boss doesn’t fire you, then you’re not getting what you deserve.
TO THE APPRENTICE.
Aspiring apprentice, a word or two in your ear. If you desire success in any matter pertaining to this life or the coming, you must have a purpose,—a determination that, God helping you, you will achieve success. You may be poor,[138] friendless, unknown,—your clothing scant, your stomach half filled,—your place may be at the foot of the ladder: no matter. Whatever your position may be, do your duty in it, stoutly and perseveringly, with your eye fixed far ahead and upward.
Aspiring apprentice, let me share a thought with you. If you want to succeed in anything in this life or the next, you need to have a goal—a strong determination that, with God's help, you will succeed. You might be poor,[138] without friends, or a stranger to many—your clothes might be worn, and your stomach might not be full—your position might be at the bottom of the ladder: it doesn’t matter. No matter where you are, do your job with courage and persistence, keeping your eyes fixed on the future and looking upward.
Keeping the purpose before you that you will rise, be obedient to your employer, attentive to your business, obliging to your shopmates, and courteous to strangers; and seize every opportunity to improve your heart, your mind, and your workmanship. Do every thing well,—no slighting, no hiding defects, aiming always at perfection. Watch those who are skilful, and strive to equal and excel them. Secure the friendship of all by deserving it. Allow no opportunity of rendering a service to pass without improving it, even if it cost you some labour and self-denial. Be of use to others, even if in a small way; for a time may come when they may be of service to you. A selfish man may get ahead faster than you; but selfishness is contemptible,—and you need not envy his success: when you achieve your object nobly, you will enjoy it, and be respected.
Keep your goal in mind that you will succeed. Be loyal to your boss, focused on your work, helpful to your colleagues, and polite to strangers. Take every chance to improve your heart, mind, and skills. Do everything well—don’t cut corners or hide mistakes, and always aim for perfection. Observe those who are skilled and try to match and surpass them. Build friendships by being worthy of them. Don’t let any chance to help others slip by, even if it requires extra effort and personal sacrifice. Be a resource for others, even in small ways; there may be a time when they can help you in return. A selfish person might get ahead faster than you, but selfishness is despicable—there's no need to envy their success. When you reach your goals with integrity, you will truly enjoy them and earn respect.
Always bear in mind that character is capital. To gain this, you must be so scrupulously honest that you would be as willing to put live coals in your pocket as a penny that is not yours. Never run in debt: do without what you cannot at once pay for, even though you should suffer somewhat. No matter what the amount of your earnings may be, save a portion every week, and invest it in a savings-bank of good standing: it will grow, and will stand you in good stead some day. Better temporary abstinence and constant plenty afterward, than unearned present comfort and future perpetual want. Never lie, openly or covertly, by word or action. A liar may deceive his fellows,—God and himself never. Conscious of falsity, a liar can have no self-respect; without self-respect, reputation cannot be achieved.
Always keep in mind that character is everything. To build this, you need to be so incredibly honest that you'd rather carry burning coals in your pocket than take a penny that doesn't belong to you. Never go into debt: live without what you can't pay for immediately, even if it means making sacrifices. No matter how much you earn, set aside a portion every week and invest it in a reputable savings account: it will grow and benefit you in the future. Better to go without for a while and have plenty later than to enjoy unearned comfort now and face constant scarcity later. Never lie, whether openly or subtly, by word or action. A liar may fool others—but never God or themselves. A liar, aware of their dishonesty, can't have any self-respect, and without self-respect, you can't build a good reputation.
With a noble purpose as the end of all your actions, and with actions becoming your purpose, your success is merely a question of time,—always provided you have some brain and abundant common sense.
With a noble purpose guiding all your actions, and your actions becoming your purpose, your success is just a matter of time—assuming you have some intelligence and plenty of common sense.
TO BEGINNERS.
Sanguine beginners sometimes fail in their attempts to establish themselves in business; and in many cases are disposed to lay the blame on every thing and on everybody except themselves. So we here give some rules—(in an ironical way, to make them stick in the memory)—
Hopeful newcomers often struggle to get a foothold in business; and in many instances, they're inclined to blame everything and everyone except themselves. So here are some rules—(in a sarcastic way, to help them stick in the memory)—
HOW NOT TO SUCCEED.
1. Get from your father, uncle, aunt, grandmother, or somebody, four or five thousand dollars. You need not give notes or any written obligations, as they may prove troublesome some day.
Get four or five thousand dollars from your dad, uncle, aunt, grandma, or someone else. You don’t need to sign any notes or written promises, as they might become a hassle later on.
2. Rent a comfortable room somewhere, no matter whether in a business centre or not, but let it be showy and pleasant.
2. Rent a comfy room somewhere, whether it's in a business center or not, but make sure it's stylish and nice.
3. Spend one-fourth of your capital in furnishing the room with matters of personal comfort. Provide an elegant desk, a luxurious lounge, and a pivot-chair: why shouldn’t the master of a printing office “take it easy”? Have a closet in your desk, it is so handy for your whisky-bottle and cigar-boxes.
3. Spend a quarter of your budget on making the room comfortable. Get a stylish desk, a cozy lounge, and a swivel chair: why shouldn’t the boss of a printing office “take it easy”? Include a closet in your desk; it’s perfect for your whiskey bottle and cigar boxes.
4. Get all you can from the type-founder, press-maker, and paper-manufacturers. If they will give you credit for one-half of what you buy, well and good: if they trust you for the whole amount, all the better for you, and the more money you will have on hand for jollifications.
4. Get everything you can from the type founder, press maker, and paper manufacturers. If they will give you credit for half of what you buy, that's great; if they trust you for the full amount, even better for you, and you'll have more money on hand for celebrations.
5. Put up your sign—a handsome one—
5. Put up your sign—a nice one—
B. Sipwell Lovepunch,
Printer.
B. Sipwell Lovepunch,
Printer.
and signalize its erection by keeping “open house” for all comers between 11 A.M. and midnight. The mothers and wives of all who become tight and go home loose will long remember your public spirit.
and mark its establishment by having “open house” for everyone between 11 A.M. and midnight. The mothers and wives of all who get drunk and return home inebriated will long remember your generosity.
6. Be at your office by nine in summer and ten in winter; and, following Charles Lamb’s witticism, that he who goes to work late should quit early, you need not return after dinner. Let your foreman attend to the business: isn’t he paid for it?
6. Be at your office by nine in the summer and ten in the winter; and, following Charles Lamb’s joke, that if you show up to work late, you should leave early, you don’t have to come back after dinner. Let your foreman handle the business: isn’t he getting paid for it?
7. When you do go into your office, curse and grumble[140] promiscuously, and be sure to swear at the apprentices, to show your spirit, and to let them know that you are master. Be careful never to praise them or any of the hands, or they may think they are worth higher wages.
7. When you enter your office, complain and grumble freely[140] and make sure to curse at the apprentices to assert your authority and remind them you are in charge. Be sure not to compliment them or any of the workers, or they might start to think they deserve higher pay.
8. Take work at any price that will keep it from a competitor, no matter whether it pays or not. Perhaps you can save something by giving short numbers, counting in imperfect copies, using very common ink, &c. The style is of no consequence: you want to make money if you can, let others improve the typographical art if they choose.
8. Take any job that keeps it away from a competitor, regardless of whether it pays or not. Maybe you can save some money by using smaller numbers, counting in rough copies, using very basic ink, etc. The style doesn’t matter: you want to make money if possible; let others focus on improving the print quality if they want.
9. Cultivate the acquaintance of fancy folk, politicians, and wit-livers. A fast horse or two wouldn’t be a bad thing to bind their friendship; and, besides, you will never be at a loss for a companion in your rides.
9. Get to know influential people, politicians, and witty individuals. Having a fast horse or two wouldn't hurt to strengthen those friendships; plus, you'll always have a companion for your rides.
10. If you want new type, and the founder who made your outfit won’t sell to you unless you pay off the old score, transfer your patronage to another foundry. How can you expect to get along if you pay your debts? Such a course would compel you to sell your horse and to taboo rum-shops and gay saloons, and to live economically; and this, you know, wouldn’t do at all.
10. If you want new type and the person who made your outfit won’t sell to you unless you pay off your old debt, switch your business to a different foundry. How can you expect to get by if you pay your debts? Doing that would force you to sell your horse, avoid bars and lively clubs, and live frugally; and you know, that just wouldn’t work at all.
11. Get out a newspaper, and advocate the principles of the strongest party, swearing thick and thin through every thing. You need not bother yourself about writing original matter; crib wherever you can. There are plenty of fellows who want office,—lawyers particularly,—and they will write slang enough to fill your columns. You might quietly levy a little black-mail or hush-money from neighbours guilty of indiscretions: dirty money will buy as much as clean.
11. Grab a newspaper and support the principles of the strongest party, passionately defending them no matter what. You don’t need to worry about writing original content; steal from wherever you can. There are plenty of people looking for jobs—especially lawyers—and they’ll write enough catchy stuff to fill your columns. You could also quietly extort a little hush money from neighbors who have made mistakes: dirty money can buy just as much as clean money.
12. You needn’t marry, unless some fond rich girl should happen to fancy a fool. You know, you need not trouble yourself much about her after you have secured her money: let her father look after her welfare. If she dies broken-hearted, why—she ought not to have been so sensitive.
12. You don’t have to marry unless some wealthy girl happens to like a fool. You know, you don’t need to worry too much about her once you’ve got her money: let her dad take care of her. If she dies heartbroken, well—she shouldn’t have been so sensitive.
13. You may be troubled occasionally by a qualm of conscience; but this can be settled by a dram or two. After a few doses, conscience will go to sleep, and trouble you no more, unless you should happen to see a Bible or hear a sermon, which as a matter of course you will try to avoid. It is true, wreck and ruin will be sure to overtake you, and the devil will catch you at last; but why worry yourself before the time?
13. You might feel some guilt now and then; but you can ease that with a drink or two. After a few sips, your conscience will quiet down and leave you alone, unless you accidentally come across a Bible or hear a sermon, which you’ll naturally try to dodge. It's true that disaster and destruction will eventually catch up to you, and the devil will get you in the end; but why stress about it now?
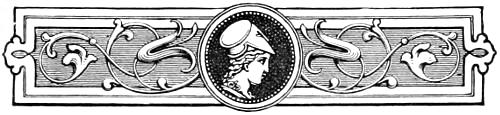
IMPOSING, OR PREPARING FOR PRESS.
IMPOSITION

Comprehends a knowledge of placing the pages so that they may regularly follow each other when printed and the sheet is folded up; and also the mode of dressing chases and the manner of making the proper margin. As many pages as are required for a whole or half sheet being made up, the compositor lays them upon the imposing-stone, placing the first page with the signature to the left hand facing him, and then proceeds according to one of the schemes on pp. 150-199. These will be found to contain every necessary imposition,—viz. folios, quartos, octavos, twelves, sixteens, eighteens, twenties, twenty-fours, thirty-twos, thirty-sixes, forties, forty-eights, sixty-fours, seventy-twos, ninety-sixes, and one hundred and twenty-eights. We also introduce schemes for imposing from the centre, by which means the blank or[142] open pages may be thrown in the centre of the form, leaving the solid pages on the outside to act as bearers for the rollers, as well as for the better regulation of the impression.
Understands how to arrange the pages so that they can consistently follow one another when printed and the sheet is folded; and also the process of preparing chases and how to create the correct margin. For as many pages as are needed for a whole or half sheet being set up, the compositor places them on the imposing stone, positioning the first page with the signature on the left side facing him, and then continues according to one of the layouts on pp. 150-199. These will include every necessary imposition,—like folios, quartos, octavos, twelves, sixteens, eighteens, twenties, twenty-fours, thirty-twos, thirty-sixes, forties, forty-eights, sixty-fours, seventy-twos, ninety-sixes, and one hundred and twenty-eights. We also provide layouts for imposing from the center, which allows the blank or [142] open pages to be placed in the center of the form, leaving the solid pages on the outside to serve as supports for the rollers, as well as for better control of the impression.
All odd matter, for any form, should be divided into fours, eights, twelves, and sixteens, which is the groundwork of all the impositions except the eighteens, which differ from all the others; for instance, sixteens, twenty-fours, and thirty-twos are only octavos and twelves doubled, or twice doubled, and imposed in half sheets: for example, the sixteens are two octavos imposed on one side of the short cross; the twenty-fours are two twelves imposed on each side of the long cross; and a thirty-two is four octavos imposed in each quarter of the chase. Thus, a sheet may be repeatedly doubled. By this division, any form or sheet may be imposed, always bearing in mind that the first page of each class must stand to the left hand, with the foot of the page toward you. Having set down the first page, then trace the remainder according to the scheme which applies to its number; in proof of which, the standard rule for all other impositions may be adopted,—namely, the folios of two pages, if placed properly beside each other, will when added together make one more than the number of pages in the sheet; that is, in a sheet of sixteens, pages 1 and 16 coming together will add up 17, and so 9 and 8 will make 17, &c.
All odd forms of matter should be divided into fours, eights, twelves, and sixteens, which forms the basis for all the setups except eighteens, which are different from the rest. For example, sixteens, twenty-fours, and thirty-twos are just octavos and twelves doubled, or doubled twice, and arranged in half sheets: for instance, sixteens are two octavos placed on one side of the short cross; twenty-fours are two twelves placed on each side of the long cross; and a thirty-two is made by placing four octavos in each quarter of the chase. This way, a sheet can be doubled multiple times. With this division, any form or sheet can be arranged, always remembering that the first page of each type must be on the left, with the bottom of the page facing you. After placing the first page, you then arrange the rest according to the system that relates to its number; to prove this, you can use the standard rule for all other setups—namely, the folios of two pages, if placed correctly next to each other, will add up to one more than the total number of pages in the sheet; so in a sheet of sixteens, pages 1 and 16 together equal 17, and likewise, 9 and 8 will also sum to 17, etc.
In half sheets, all the pages belonging to the white paper, and reiteration, are imposed in one chase. So that when a sheet of paper is printed on both sides with the same form, that sheet is cut in two in the short cross if quarto or octavo, and in the short and long cross of twelves, and folded as octavo or twelves.
In half sheets, all the pages of the white paper and repetition are arranged in one setup. This way, when a sheet of paper is printed on both sides with the same layout, that sheet is cut into two along the short side for quarto or octavo sizes, and cut along both the short and long sides for twelves, and then folded as octavo or twelves.
TYING UP PAGES.
In tying up a page, use fine twine, winding it four or five times round it, and fastening at the right-hand corner, by thrusting a noose of it between the several turnings and the matter with the rule, and drawing it perfectly tight, taking care always to keep the end of the cord on the face of the page. While tying it, keep the forefinger of the left hand tight on the corner, to prevent the page from being drawn aside.
To secure a page, use thin twine and wrap it around four or five times, fastening it at the top right corner by threading a loop between the different wraps and the paper with the ruler, and pulling it snugly while making sure the end of the twine stays on the front of the page. While tying it, press your left forefinger firmly on the corner to keep the page from shifting.
The twine being fastened, the compositor removes the page from the ledges of the galley, to see if the turns of cord lie[143] about the middle of the shank of the letter; if they lie too high,—as most commonly they do,—he thrusts them lower; and if the page be not too broad, he places the fore and middle finger of his right hand on the off side of the head of the page, and his thumb on the near; then, bending his other fingers under, he presses them firmly against the head of the page; he next places the fingers of his left hand in the same position at the foot of the page, and, raising it upright, lays it on a page-paper; then, with his right hand he grasps the sides of the page and the paper, which turns up against the sides of the page, and sets it in a convenient spot under his frame, placing it on the left hand, with the foot toward him, that the other pages that are in like manner set down afterward may stand by it in an orderly succession until he comes to impose them.
The twine tied, the typesetter takes the page off the galley to check if the cords are centered on the letter's shank; if they're too high—like they often are—he pushes them down. If the page isn't too wide, he puts his fore and middle fingers of his right hand on the outer side of the top of the page, and his thumb on the inner side; then, bending his other fingers underneath, he presses firmly against the top of the page. Next, he positions his left hand fingers in the same way at the bottom of the page, raises it upright, and lays it on a page-paper. With his right hand, he grips the sides of the page and the paper that folds against the sides of the page, and then sets it in a convenient spot under his frame, placing it on the left with the bottom facing him, so that other pages, set down in the same way later, can stand next to it in an orderly sequence until he’s ready to impose them.
If the page be a quarto, folio, or broadside, it is, of course, too wide for his grasp; and he therefore carries the galley and page to the imposing-stone, and turns the handle of the galley toward him, and, taking hold of the handle with his right hand, he places the ball of the thumb of his left hand against the inside of the head ledge of the galley, to hold it and keep it steady, and by the handle draws the slice with the page upon it out of the galley, letting the slice rest upon the imposing-stone; he then thrusts the head end of the slice so far upon it, that the foot of the page may stand an inch or two within the outer edge of the stone, and, placing his left hand against the foot of the page, he quickly draws the slice from under the bottom of the page.
If the page is a quarto, folio, or broadside, it’s obviously too wide for him to handle, so he carries the galley and page to the imposing stone. He turns the handle of the galley toward himself and, holding the handle with his right hand, places the ball of his left thumb against the inside of the head ledge of the galley to keep it steady. Then, using the handle, he pulls the slice with the page out of the galley and lets the slice rest on the imposing stone. He pushes the head end of the slice onto the stone far enough so that the foot of the page stands an inch or two inside the outer edge of the stone. Finally, he places his left hand against the foot of the page and quickly pulls the slice from under the bottom of the page.
LAYING PAGES.
In taking up his pages for imposition, the compositor tightly grasps the paper on both sides of the page, in order that it may be kept firm to the bottom of the page; for if it be left slack, the letters will be liable to slip out, unless it be particularly well tied up. Having conveyed it to the stone, he next places the last two fingers of his right hand under the head of the page, but not under the page-paper at the head of it, still grasping the sides with his forefingers and thumb; he then slips his left hand so that the palm of it may turn toward the bottom, and, lifting the page upright on his right hand,[144] with the left he removes the paper; he next grasps again the foot-end of the page with his left hand, in the same manner as the right holds the head of it, and, turning the face of the type toward him, lays it squarely and quickly down, so that the whole page may come in contact with the face of the stone at the same time.
When the compositor gets the pages ready for printing, he firmly holds the paper on both sides to keep it steady at the bottom; if he leaves it loose, the letters could slip out unless it's securely tied. Once he brings it to the stone, he places the last two fingers of his right hand under the top of the page, but not under the paper itself, still holding the sides with his forefingers and thumb. He then adjusts his left hand so that the palm faces down, lifts the page upright with his right hand,[144] and removes the paper with his left hand. He then grabs the bottom of the page with his left hand in the same way his right hand holds the top, turns the printed side towards him, and quickly lays it down straight so that the entire page touches the surface of the stone at the same time.
As this method, in inexperienced or careless hands, would frequently endanger a page containing intricate matter, it will be safer to place the pages at first on good, strong, but not coarse and rough papers, and, when they are brought to the stone, instead of lifting them up as just noticed, slide them off the papers in the same manner as before directed respecting a folio page on the slice galley, being careful that no particles of dirt remain under the page.
As this method, in inexperienced or careless hands, would frequently endanger a page containing intricate matter, it's safer to first place the pages on good, strong, but not coarse and rough paper. When you're ready to move them to the stone, instead of lifting them as previously mentioned, slide them off the paper in the same way as directed for a folio page on the slice galley, ensuring no dirt particles stay under the page.
MAKING UP FURNITURE.
Having ascertained that his pages are laid down right, the compositor proceeds to dress the chases, which we will suppose to be for a sheet of octavo. Accordingly he selects a good pair of chases that are fellows in all respects; and, having laid them over the pages for the two different forms, he puts such gutter-sticks between page and page, and such reglets along the sides of the two crosses, as will give the book proper margins after it is bound.
After confirming that his pages are organized correctly, the compositor goes on to prepare the chases, which we'll assume are for an octavo sheet. He chooses a matching pair of chases that are identical in every way; then, placing them over the pages for the two different forms, he inserts appropriate gutter sticks between each page and places reglets along the sides of the two crosses to ensure the book has proper margins once it’s bound.
To ascertain the proper distance, and to prevent wastage of furniture, he takes short pieces of furniture, or quotations, and quadrates or reglets, to fit the space between two pages; then, pushing the pages close to them, he finds the exact width of the furniture necessary, by trying the ends of various pieces, always measuring from the edge of the lines of type above the page-cords.
To determine the right distance and avoid wasting furniture, he uses short pieces of furniture, or quotations, and quadrates or reglets to fill the space between two pages. Then, by pushing the pages close to them, he finds the exact width of the furniture needed by testing the ends of different pieces, always measuring from the edge of the lines of type above the page-cords.
By observing a proper method in cutting up new furniture, the same will be serviceable for other works as well as the one for which it is intended, even though the size of the page may differ, provided it agrees with the margin of the paper. The gutters should be cut two or three lines longer than the page; the head-sticks wider; the back furniture may run nearly down to the rim of the chase, but must be level with the top of the page, which will admit of the inner head-stick running[145] in; the difference of the outer head-stick may go over the side-stick, and the gutter will then run up between them. The side-stick only need to be cut exact, and the furniture will completely justify.
By using the right technique to cut new furniture, it will also be useful for other projects, even if the size of the page varies, as long as it matches the paper's margin. The gutters should be cut two or three lines longer than the page; the head-sticks should be wider; the back furniture can extend almost to the edge of the chase but must be level with the top of the page, allowing the inner head-stick to fit in; the outer head-stick can extend over the side-stick, and the gutter will fit between them. The side-stick only needs to be cut precisely, and the furniture will align perfectly.
Wood and metal furniture, cut or cast to specific lengths and widths, may now be had from the type-founders, the use of which will save time, waste, and labour.
Wood and metal furniture, made or shaped to precise lengths and widths, can now be obtained from type-founders, which will save time, reduce waste, and minimize labor.
MAKING THE MARGIN.
The next business is to arrange the margin, so that each page may occupy one side of a leaf, and have the proper proportion of white paper left at the sides as well as at the head and foot. The page when printed should be a little higher than the middle of the leaf, and have a little more margin on the outside than in the back. This rule is often neglected by careless or ignorant printers, and the appearance of the book when bound is repulsive to the eye of taste.
The next step is to set the margins so that each page uses one side of a leaf and leaves the right amount of white space at the sides as well as at the top and bottom. The printed page should be slightly above the center of the leaf, and there should be a bit more margin on the outside than on the inside. This guideline is often overlooked by careless or uninformed printers, and the final look of the book when bound can be unappealing to those with good taste.
One mode of making margin is the following:—For octavos, measure and mark the width of four pages by compasses, on a sheet of paper designed for the work, beginning to measure at one extremity of the breadth of the sheet. The rest of the paper divide into four equal parts, allowing two-fourths for the width of two separate gutter-sticks; the remaining two-fourths divide again into four equal parts, and allow one-fourth for the margin along each side of the short cross, and one-fourth for the margin to each outside page. But as the thickness of the short cross adds considerably to the margin, reduce the furniture in the back accordingly, and thereby enlarge the outside margin, which requires the greatest share to allow for the unevenness of the paper itself, as well as for pressmen laying sheets unevenly when the fault is not in the paper. Having thus made the margin between the pages to the breadth of the paper, in the same manner proportion the margin at the head to the length, and accordingly measure and mark the length of two pages, dividing the rest into four parts, one-fourth of which is allowed for each side of the long cross, and one-fourth for the margin that runs along the foot of the two ranges of pages. The furniture on both sides of the long one must be lessened to enlarge the bottom margin, for the reason assigned for extending the side margin.
One way to create margins is as follows: For octavo pages, measure and mark the width of four pages using a compass on a sheet of paper meant for the task, starting at one end of the sheet's width. Divide the remaining paper into four equal parts, allowing two-fourths for the width of two separate gutter-sticks. Take the remaining two-fourths and divide it again into four equal parts, allowing one-fourth for the margin on each side of the short cross, and one-fourth for the margin on each outside page. However, since the thickness of the short cross significantly affects the margin, reduce the furniture in the back accordingly to increase the outside margin, which needs the most space to accommodate the paper's unevenness and the pressmen's potentially uneven sheet placement when the issue isn't with the paper itself. After making the margin between the pages according to the sheet's width, apply the same method to proportion the margin at the top according to the length. Measure and mark the length of two pages, dividing the rest into four parts, with one-fourth allowed for each side of the long cross and one-fourth for the margin at the bottom of the two rows of pages. The furniture on both sides of the long cross must be reduced to increase the bottom margin, for the same reason as extending the side margin.
Go the same way to work in twelves, where, for the outer margin along the foot of the pages, allow the amount of two-thirds of the breadth of the head-sticks, and the same for the inner margin, that reaches from the foot of the fifth page to the centre of the groove for the points; and from the centre of that groove to the pages of the quire, or the cut off, allow half of the breadth of the head-stick. The margin along the long cross is governed by the gutter-sticks; and it is common to put as much on each side of the long cross as amounts to half the breadth of the gutter-stick, without deducting almost any thing for the long cross, since that makes allowance for the inequality of the outer margin.
Go the same way to work in twelves, where, for the outer margin at the bottom of the pages, leave two-thirds of the width of the head-sticks, and do the same for the inner margin, which runs from the bottom of the fifth page to the center of the groove for the points; and from the center of that groove to the pages of the quire, or the cut-off, leave half the width of the head-stick. The margin along the long cross is determined by the gutter-sticks; and it’s common to put the same amount on each side of the long cross that equals half the width of the gutter-stick, without really reducing anything for the long cross, since that compensates for the unevenness of the outer margin.
Another plan, more simple, is the following:—Having laid the pages as nearly as possible in their proper places on the stone, with a suitable chase around them, fold a sheet of paper which has been wetted for the work, or one of the same size, into as many portions as there are pages in the form, and, holding the sheet thus folded on the first or left-hand page of the form, one edge even with the left-hand side of the type, place the adjoining page so that its left side may be even with the right-hand edge of the folded paper, which will leave a sufficient space between the two pages to admit the gutter-stick, which should then be selected of a proper width to suit the form in hand, as follows:—In octavos, about a Great Primer less in width than the space between the pages, as determined by the above rule; in duodecimos, about a Pica less; in sixteens, about a Long Primer; and proportionably less as the number of pages are increased. Having thus secured the proper width for the gutter-sticks, cut them somewhat longer than the page, and holding one of them between the two pages, above the page-cord, close the pages up to it; then open the folded sheet so as to cover the two pages, and, bringing the fold in the paper exactly in the middle of the gutter-stick, secure it there with the point of a pen-knife or bodkin; the right-hand edge of the paper thus opened must be brought to the centre of the cross-bar, which determines the furniture required between it and the pages. Having thus arranged the margins for the back and fore edge of the book, proceed in like manner to regulate the head and foot margins, by bringing the near edge of the folded paper even with the bottom of the first page, and so placing the adjoining off page[147] that its head may be barely covered by the off edge of the folded paper, which will give the required head margin. All other sections of the form must be regulated by the foregoing measurements, when the margins for the whole sheet will be found correct.
Another simpler plan is as follows:—Lay out the pages as closely as possible in their correct positions on the stone, with a proper chase around them. Then, fold a sheet of paper that’s been dampened for the task, or one of the same size, into as many sections as there are pages in the form. Hold the folded sheet against the first or left-hand page of the form, aligning one edge with the left side of the type. Position the next page so that its left side lines up with the right edge of the folded paper, leaving enough space between the two pages for the gutter-stick. Choose a gutter-stick of appropriate width for the form: for octavos, it should be slightly less than a Great Primer in width than the space between the pages as determined by the earlier rule; for duodecimos, about a Pica less; for sixteens, around a Long Primer; and proportionately less as the number of pages increases. Once the proper width for the gutter-sticks is secured, cut them slightly longer than the page, and hold one between the two pages above the page-cord, closing the pages up to it. Then, open the folded sheet to cover the two pages, bringing the fold in the paper to align with the middle of the gutter-stick, and secure it there with the point of a penknife or bodkin. The right edge of the opened paper must be adjusted to the center of the cross-bar, which determines the required furniture between it and the pages. After arranging the margins for the back and front edge of the book, proceed similarly to set the top and bottom margins, aligning the near edge of the folded paper with the bottom of the first page, and positioning the adjacent off page so that its top is just covered by the off edge of the folded paper, ensuring the necessary head margin is achieved. All other sections of the form should be adjusted based on these measurements, so the margins for the entire sheet will be correct.
The greater the number of pages in a sheet, the smaller in proportion should the margin be: the folded paper, therefore, should lie proportionally less over the edge of the adjoining page, both for gutter and back, in a form of small pages than in one of larger dimensions. A folio may require the page to be half an inch nearer the back than the fore-edge; while a duodecimo may not require more than a Pica em.
The more pages a sheet contains, the smaller the margin should be: therefore, the folded paper should extend less over the edge of the adjacent page for both the gutter and the back when you're using smaller pages compared to larger ones. A folio might need the page to be half an inch closer to the back than the front edge, while a duodecimo might only need a Pica em.
In imposing jobs where two or more of the same size, requiring equal margins, are to be worked together, fold the paper to the size appropriate for each, and so arrange the type that the distance from the left side of one page to the left side of the adjoining one shall be exactly equal to the width of the folded paper, as before described.
In setting up jobs where two or more of the same size, needing equal margins, are to be processed together, fold the paper to the appropriate size for each, and arrange the type so that the distance from the left side of one page to the left side of the next one is exactly equal to the width of the folded paper, as previously described.
Having dressed the inside of the pages, next place side- and foot-sticks to their outsides; being thus secured by the furniture, untie the pages, quarter after quarter, the inner page first, and then the outer, at the same time forcing the letter toward the crosses, and using every precaution to prevent the pages from hanging or leaning; and, in order to guard against accidents, when the quarter is untied, secure it with a couple of quoins.
Having dressed the inside of the pages, next place side and foot sticks on the outside; once secured with the furniture, untie the pages, quarter by quarter, starting with the inner page and then the outer. Be sure to push the letter toward the crosses and take care to prevent the pages from sagging or leaning. To avoid any mishaps, when you untie a quarter, secure it with a couple of quoins.
LOCKING UP FORMS.
First, carefully examine whether the pages of each quarter are of the same length; for even the difference of a lead will cause them to hang. Test their exactness: place the ball of each thumb against the centre of the foot-stick, raising it a little with the pressure, and, if the ends of both pages rise equally with the stick, it is a proof they will not bind; then fit quoins between the side and foot-stick of each quarter and the chase. After pushing the quoins as far as possible with the fingers, make use of the mallet and shooting-stick, and gently drive the quoins along the foot-sticks first, and then those along the side-sticks, taking care to use an equal force in the strokes, and to drive the quoins far enough up the shoulders[148] of the side- and foot-sticks, that the letter may neither belly out nor hang, and the lines be kept straight and even. Quoins should be slanted on one side only, but the edges should not be bevelled. The several quarters of a form should be partially tightened before either quarter is finally locked up; otherwise the cross-bar may be sprung.
First, check if the pages of each section are the same length; even a slight difference can cause them to misalign. Test their accuracy: press the ball of each thumb against the center of the foot stick, applying a little pressure. If both page ends rise evenly with the stick, it means they won't bind correctly. Next, fit quoins between the side and foot stick of each section and the chase. After pushing the quoins as far as possible with your fingers, use the mallet and shooting stick to gently drive the quoins along the foot sticks first, and then along the side sticks, making sure to apply an equal force with each strike. Drive the quoins up the shoulders[148] of the side- and foot sticks enough that the letters don't bow out or droop, and the lines stay straight and even. Quoins should be slanted on just one side, and the edges shouldn't be beveled. The different sections of a form should be tightened somewhat before locking any section completely; otherwise, the cross-bar might be warped.
Before locking up the form, plane the pages gently over all the face. If this be properly done, a second planing is hardly necessary, provided the justification is perfect and the pages are all of the same length. But, as this is seldom the case, the second planing can hardly be dispensed with.
Before locking up the form, lightly plane the pages across the entire surface. If done correctly, a second planing is usually unnecessary, as long as the justification is perfect and all the pages are the same length. However, since this is rarely the case, a second planing is almost always needed.
It often occurs that the quoins, when locked up wet, stick so tight to the furniture as to render it troublesome to unlock them: in such cases, drive the quoin up a little, and it afterward unlocks with ease.
It often happens that the quoins, when locked up wet, stick so tightly to the furniture that it makes them difficult to unlock: in these situations, lift the quoin a bit, and it will unlock easily afterward.
Before lifting a form after it is locked up, raise it gently a short distance, and look under it, to ascertain whether any types are disposed to drop out. If all is right, carry it to the proof-press, and pull a good proof. Then rub it over gently with a ley-brush, rinse it well, and place it in a rack, and deliver the proof, with the copy, to the proof-reader.
Before lifting a form after it's secured, gently raise it a short distance and check underneath to see if any types might fall out. If everything looks good, take it to the proof press and pull a solid proof. Then, gently rub it with a ley brush, rinse it thoroughly, and place it in a rack. Finally, deliver the proof along with the copy to the proofreader.
MEMORANDA.
Each part of the furniture should be in one piece where it is practicable,—as, for instance, the gutters, the backs, and the heads; but sometimes pieces will be wanted of a width that is not equal to any regular size, and then two must be used.
Every piece of furniture should ideally be made from one solid part whenever possible—like the gutters, backs, and heads; however, there are times when pieces may need to be wider than standard sizes, and in those cases, two must be used.
All the gutters of one sheet should be cut of a precise length; so also with the backs and the heads; but each sort should be of a different length from that of the others: thus they can be easily distinguished from each other, and mistakes be prevented.
All the gutters of one sheet should be cut to an exact length; the same goes for the backs and the heads; however, each type should be a different length than the others: this way, they can be easily distinguished from one another, and mistakes can be avoided.
The sheet being imposed, the stone should be cleared; the saw and saw-block put in their places, the shears, the mallet, planer, and shooting-stick, the surplus furniture, the leads, the quoins, and every other article. The compositor will tie up his page-cords, and, if he has any companions, will return to them their proportion.
The sheet is set, the stone should be cleared; the saw and saw-block stored away, along with the shears, mallet, planer, shooting-stick, extra furniture, leads, quoins, and everything else. The compositor will bundle up his page-cords and, if he has any colleagues, will give them back their share.
The chase and furniture of one form should always be used[149] for a similar form; that is, the chase and furniture of the outer form should be again used for an outer form, and the chase and furniture of the inner form should be again used for an inner form; they should also be put round the pages in the same order in which they were put about those of the preceding forms. For want of care or thought in these apparently trifling circumstances, trouble, inconvenience, and loss of time frequently occur; for the register will be almost sure to be wrong when this is neglected, and then the forms must be unlocked and the leads changed, to correct the fault.
The chase and furniture of one type should always be used[149] for a similar type; that is, the chase and furniture of the outer type should be used again for an outer type, and the chase and furniture of the inner type should be used again for an inner type; they should also be placed around the pages in the same order they were arranged for the previous types. A lack of care or attention to these seemingly minor details often leads to problems, inconvenience, and wasted time; the register is likely to be incorrect when this is overlooked, and then the types will need to be unlocked and the leads changed to fix the issue.
Before the form is printed, a proof should be taken and the sheet folded, to make sure of the correctness of the imposition.
Before the form is printed, a proof should be taken and the sheet folded to ensure the accuracy of the layout.
The preceding rules and directions were intended for type-forms, and were formerly of universal necessity. Now most books are printed from stereotyped or electrotyped plates. The same instructions, however, are generally as applicable to plate as to type pages.
The previous rules and guidelines were meant for type forms and were once essential for everyone. Now, most books are printed using stereotyped or electrotyped plates. However, the same instructions still generally apply to both plate and type pages.
NOMENCLATURE OF SHEETS.
When a sheet of paper of Medium or larger size is folded in two leaves, like most newspapers, it is called a folio; when folded in four leaves, it is named a quarto or 4to; when folded in eight leaves, an octavo or 8vo; in twelve leaves, a duodecimo or 12mo; in sixteen leaves, sextodecimo or 16mo; in eighteen leaves, octodecimo or 18mo; in twenty-four leaves, vigesimo-quarto, or 24mo, and so on. The Latin names beyond duodecimo are seldom used.
When a sheet of paper of medium or larger size is folded into two leaves, like most newspapers, it's called a folio; when folded into four leaves, it's known as a quarto or 4to; when folded into eight leaves, an octavo or 8vo; in twelve leaves, a duodecimo or 12mo; in sixteen leaves, sextodecimo or 16mo; in eighteen leaves, octodecimo or 18mo; in twenty-four leaves, vigesimo-quarto or 24mo, and so on. The Latin names beyond duodecimo are rarely used.

Abstract Title-Deeds of Estates.
Property Title Deeds.

Abstract Title-Deeds of Estates are printed with blanks at the back, with all the margin on the left side, and on single leaves, which are stitched together at the corner.
Abstract Title-Deeds of Estates are printed with blanks on the back, with all the margins on the left side, and on single sheets that are stitched together at the corner.
This method of imposing the form is to save presswork and the compositor’s charge.
This way of applying the format is to reduce printing costs and the compositor's fee.
A Single Sheet of Folio.
One sheet of paper.

Two Sheets of Folio, Quired, or lying one in another.
Two sheets of folio paper, either stacked or lying one inside the other.
Outer Form of the Outer Sheet.
Outer Shape of the Outer Layer.

Outer Form of the Inner Sheet.
Outer Form of the Inner Sheet.
Imposing in quires may be carried to any extent, by observing the following rule:—first ascertain the number of pages, then divide them into so many sheets of folio, and commence laying down the first two and last two, which form the first sheet, and so on to the centre one, always remembering that the odd pages stand on the left and the even on the right; the folios of each two forming one more than the number of pages in the work: for example, let us suppose the work to consist of thirty-six pages, which is nine sheets of folio, then they should be laid down according to the scheme at the foot of the opposite page.
Imposing in quires can be done to any extent by following this rule: first, determine the number of pages, then divide them into sheets of folio, and start by laying down the first two and the last two, which create the first sheet, and so on until you reach the center one. Always remember that the odd pages go on the left and the even pages on the right; the folios of each pair form one more than the total number of pages in the work. For example, if the work has thirty-six pages, which is nine sheets of folio, then they should be arranged according to the scheme at the bottom of the opposite page.
Two Sheets of Folio, Quired, or lying one in another.
Two sheets of folio, either gathered together or laid one inside the other.
Inner Form of the Outer Sheet.
Inner Form of the Outer Sheet.

Inner Form of the Inner Sheet.
Inner Form of the Inner Sheet.
Outer. | Inner. | Sheet. | ||
---|---|---|---|---|
1 | 36 | 35 | 2, | 1st |
3 | 34 | 33 | 4, | 2d |
5 | 32 | 31 | 6, | 3d |
7 | 30 | 29 | 8, | 4th |
9 | 28 | 27 | 10, | 5th |
11 | 26 | 25 | 12, | 6th |
13 | 24 | 23 | 14, | 7th |
15 | 22 | 21 | 16, | 8th |
17 | 20 | 19 | 18, | 9th |
The furniture must be reduced in the backs of the inner sheets, to allow for stitching.
The furniture needs to be cut back on the inner sheets to make room for stitching.
A Sheet of Common Quarto.
A Common Quarto Sheet.

Outer Form.
Outer Appearance.
A Sheet of Quarto, the Broad Way, commonly used in Works of Music.
A sheet of quarto, the broad format, commonly used in music works.

Outer Form.
Outer Style.
A Sheet of Common Quarto.
A Sheet of Standard Quarto.

Inner Form.
Inner Style.
A Sheet of Quarto, the Broad Way, commonly used in Works of Music.
A sheet of quarto, the wide format, commonly used in music works.

Inner Form.
Inner Shape.
Two Half-Sheets of Quarto, worked together.
Two quarto half-sheets, combined.

Outer Form.
Outer Appearance.
Half a Sheet of Common Quarto.
Half a Sheet of Common Quarto.

Two Half-Sheets of Quarto, worked together.
Two half-sheets of quarto, stitched together.

Inner Form.
Inner Shape.
Half a Sheet of Quarto, the Broad Way.
Half a Sheet of Quarto, the Broad Way.

Outer Form of a Sheet of Common Octavo.
Outer Form of a Sheet of Common Octavo.
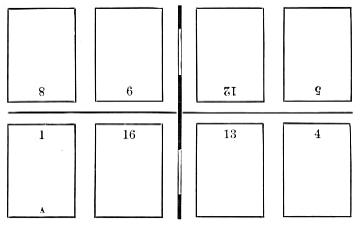
Outer Form of a Sheet of Octavo, the Broad Way.
Outer Form of an Octavo Sheet, the Wide Way.

Inner Form of a Sheet of Common Octavo.
Inner Form of a Sheet of Standard Octavo.

Inner Form of a Sheet of Octavo, the Broad Way.
Inner Form of a Sheet of Octavo, the Broad Way.
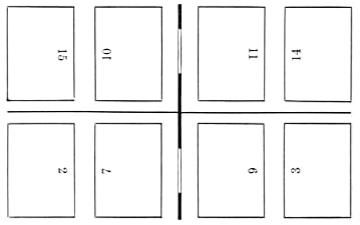
Outer Form of Two Half-Sheets of Common Octavo, worked together.
Outer form of two half-sheets of standard octavo, joined together.

Half a Sheet of Common Octavo.
Half a Sheet of Common Octavo.
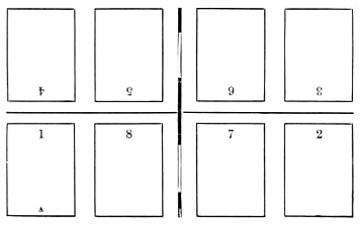
Inner Form of Two Half-Sheets of Common Octavo, worked together.
Inner Form of Two Half-Sheets of Common Octavo, stitched together.

Two Quarters of a Sheet of Octavo, worked together.
Two quarters of an octavo sheet, bound together.
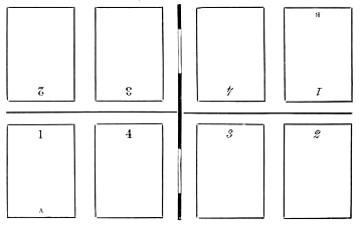
Outer Form of a Sheet of Octavo, 12 of the Work, and 4 of other Matter.
Outer Form of an Octavo Sheet, 12 of the Work, and 4 of Other Material.

Outer Form of a Sheet of Octavo, of Hebrew Work.
Outer Form of a Sheet of Octavo, of Hebrew Work.
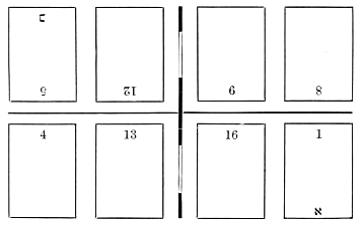
Inner Form of a Sheet of Octavo, 12 of the Work, and 4 of other Matter.
Inner Form of a Sheet of Octavo, 12 of the Work, and 4 of other Material.
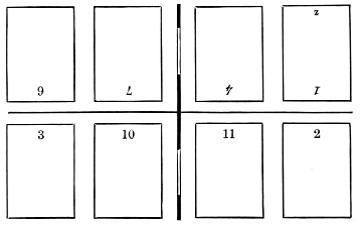
Inner Form of a Sheet of Octavo, of Hebrew Work.
Inner Form of a Sheet of Octavo, of Hebrew Work.

Outer Form of a Sheet of Octavo, Imposed from the Centre.
Outer Form of an Octavo Sheet, Laid Out from the Center.

A Half-Sheet of Octavo, Imposed from the Centre.
A half-sheet of octavo, printed from the center.

Inner Form of a Sheet of Octavo, Imposed from the Centre.
Inner Form of a Sheet of Octavo, Set Up from the Center.

Two Quarters of a Sheet of Octavo, Imposed from the Centre.
Two quarters of an octavo sheet, arranged from the center.

Outer Form of a Sheet of Twelves.
Outer Form of a Sheet of Twelves.

Inner Form of a Sheet of Twelves.
Inner Form of a Sheet of Twelves.
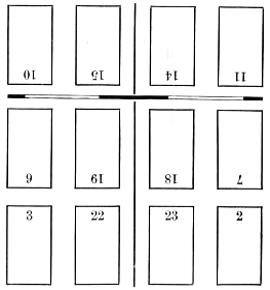
A Sheet of Twelves, without cutting.
A sheet of twelves, without cutting.

Outer Form. Inner Form.
Outer Form. Inner Form.
A Sheet of Twelves, with Two Signatures.
A Sheet of Twelves, with Two Signatures.

Outer Form. Inner Form.
Outer Shape. Inner Shape.
A Common Half-Sheet of Twelves.
A standard half-sheet of twelves.

Half-Sheet of Twelves, without cutting.
Half-Sheet of Twelves, uncut.

Different Methods of Imposing Half-Sheets of Twelves, from the Centre.
Different Ways to Apply Half-Sheets of Twelves from the Center.

A Sheet of Twelves, Imposed from the Centre.
A Sheet of Twelves, Arranged from the Center.
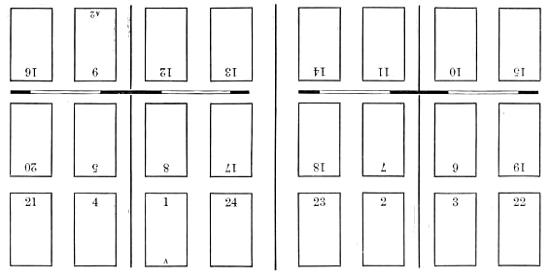
Outer Form of a Sheet of Long Twelves.
Outer Form of a Sheet of Long Twelves.

One-third, or 8 pages, of a Sheet of Twelves.
One-third, or 8 pages, of a Sheet of Twelves.
To be imposed as a slip, or in the off-cross.
To be enforced as a slip, or in the off-cross.

Outer Form.
Outer Shape.
Inner Form of a Sheet of Long Twelves.
Inner Form of a Sheet of Long Twelves.

One-third, or 8 pages, of a Sheet of Twelves.
One-third, or 8 pages, of a Sheet of Twelves.
To be imposed as a slip, or in the off-cross.
To be applied as a slip, or in the off-cross.
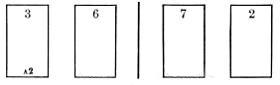
Inner Form.
Inner Shape.
Two Half-Sheets of Twelves, worked together.
Two half-sheets of twelve, combined.
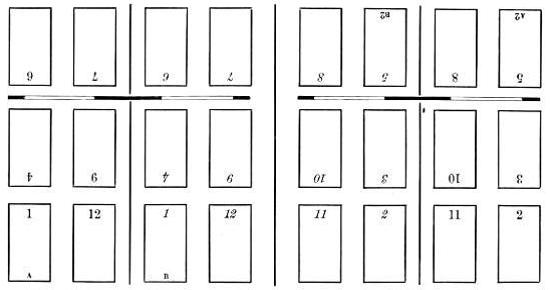
Outer Form. Inner Form.
Outer Shape. Inner Shape.
Half-Sheet of Twelves, with 2 Signatures. 4 pages of other matter.
Half-Sheet of Twelves, with 2 Signatures. 4 pages of additional content.

A Half-Sheet of Sixteens.
A Half-Sheet of Sixteens.

A Sheet of Sixteens, with One Signature.
A sheet of sixteens, featuring one signature.

Outer Form. Inner Form.
External Form. Internal Form.
A Half-Sheet of Eighteens.
An 18-Piece Half-Sheet.
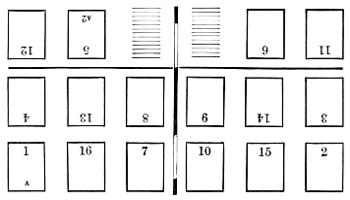
Containing 16 pages.
16 pages included.
The white paper of this half-sheet being worked off, the centre pages must be transposed,—viz. pages 7 and 10 in the room of 9 and 8, and pages 9 and 8 in the place of 7 and 10: when this is done, your imposition will be true.
The white paper of this half-sheet being used up, the center pages need to be rearranged—specifically, pages 7 and 10 should take the place of 9 and 8, and pages 9 and 8 should replace 7 and 10: once this is done, your layout will be correct.
A Half-Sheet of Eighteens.
An Eighteen Half-Sheet.
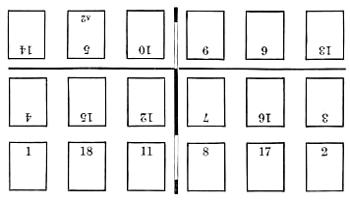
When the white paper is worked off, transpose the form,—viz. pages 11 and 8 in the room of 7 and 12, and pages 7 and 12 in the place of 11 and 8: this being done, the sheet will then fold up right.
When the white paper is used up, switch the form—specifically, pages 11 and 8 should replace 7 and 12, and pages 7 and 12 should take the place of 11 and 8: once this is done, the sheet will fold correctly.
Outer Form of a Sheet of Eighteens, to be folded together.
Outer Form of a Sheet of Eighteens, to be folded together.
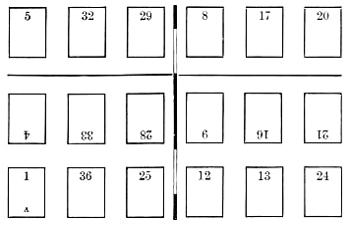
Outer Form of a Sheet of Eighteens, with One Signature.
Outer Form of a Sheet of Eighteens, with One Signature.

Inner Form of a Sheet of Eighteens, to be folded together.
Inner Form of a Sheet of Eighteens, to be folded together.

Inner Form of a Sheet of Eighteens, with One Signature.
Inner Form of a Sheet of Eighteens, with One Signature.

Outer Form of a Sheet of Eighteens, with Two Signatures.
Outer Form of a Sheet of Eighteens, with Two Signatures.

Outer Form of a Sheet of Eighteens, with Three Signatures.
Outer Form of a Sheet of Eighteens, with Three Signatures.

Inner Form of a Sheet of Eighteens, with Two Signatures.
Inner Form of a Sheet of Eighteens, with Two Signatures.

Inner Form of a Sheet of Eighteens, with Three Signatures.
Inner Form of a Sheet of Eighteens, with Three Signatures.

A Half-Sheet of Eighteens, without Transposition.
A half-sheet of eighteen pages, without rearrangement.

This mode of imposition is very objectionable, as there will be, when the paper is cut up, three single leaves.
This way of enforcing things is really problematic because, once the paper is cut, there will be three separate pages.
A Half-Sheet of Twenties, with Two Signatures.
A half-sheet of twenties, signed by two people.

Inner Form of a Sheet of Twenties.
Inner Form of a Sheet of Twenties.

Outer Form of a Sheet of Twenties.
Outer Form of a Sheet of Twenties.
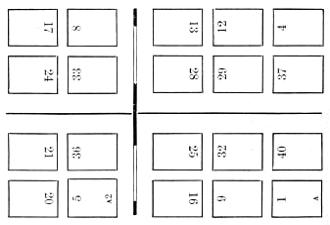
A Half-Sheet of Twenty-Fours.
A half-sheet of 24s.
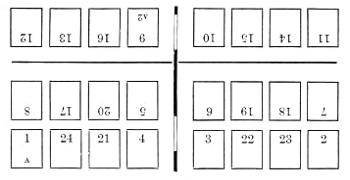
Outer Form of a Sheet of Twenty-Fours, with Two Signatures.
Outer Form of a Sheet of 24, with Two Signatures.

A Half-Sheet of Twenty-Fours, the Sixteen-way.
A Half-Sheet of Twenty-Fours, the Sixteen-way.

Inner Form of a Sheet of Twenty-Fours, with Two Signatures.
Inner Form of a Sheet of Twenty-Fours, with Two Signatures.

A Half-Sheet of Twenty-Fours, without Inset.
A half-sheet of twenty-four, without an inset.

A Half-Sheet of Twenty-Fours, without Inset.
A half-sheet of twenty-fours, without inset.

A Half-Sheet of Twenty-Fours, without Cutting.
A half-sheet of twenty-fours, without cutting.

A Half-Sheet of Thirty-Twos.
A half-sheet of 32s.

Outer Form of a Sheet of Thirty-Twos.
Outer Form of a Sheet of 32s.

Outer Form of a Sheet of Thirty-Twos, with Four Signatures.
Outer Form of a Sheet of 32, with Four Signatures.

Inner Form of a Sheet of Thirty-Twos.
Inner Form of a Sheet of Thirty-Twos.

Inner Form of a Sheet of Thirty-Twos, with Four Signatures.
Inner Form of a Sheet of 32s, with Four Signatures.

A Half-Sheet of Thirty-Twos, with Two Signatures.
A half-sheet of thirty-twos, signed in two places.

A Half-Sheet of Thirty-Twos, 20 pages of the Work, 4 pages of Title, &c., and 8 of other Matter.
A half-sheet of thirty-twos, 20 pages of work, 4 title pages, etc., and 8 pages of other material.

A Half-Sheet of Thirty-Sixes.
A half-sheet of 36s.

A Half-Sheet of Thirty-Sixes, without Cutting.
A half-sheet of thirty-sixes, no cutting.

A Half-Sheet of Thirty-Sixes, with Two Signatures.
A half-sheet of thirty-sixes, with two signatures.

A Half-Sheet of Forties.
A half-sheet of 40s.
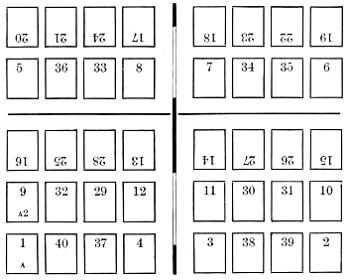
A Quarter-Sheet of Forty-Eights, with Two Signatures.
A quarter sheet of forty-eights with two signatures.

A Half-Sheet of Forty-Eights, with Two Signatures.
A half-sheet of forty-eights, featuring two signatures.

A Quarter-Sheet of Forty-Eights, without Cutting.
A quarter sheet of forty-eights, no cutting.
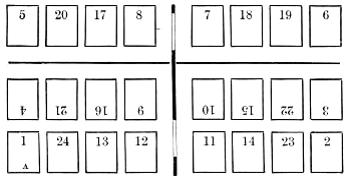
A Half-Sheet of Forty-Eights, with Three Signatures.
A half-sheet of forty-eights, with three signatures.

A Common Quarter-Sheet of Forty-Eights.
A Standard Quarter-Sheet of 48.

A Quarter-Sheet of Sixty-Fours, with Two Signatures.
A quarter sheet of sixty-fours, with two signatures.
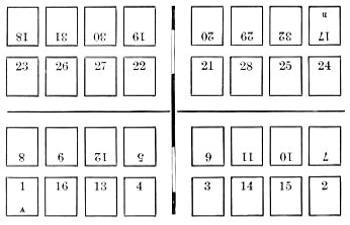
A Common Quarter-Sheet of Sixty-Fours.
A Standard 64-Sheet Notebook.

A Quarter-Sheet of Sixty-Fours, 20 pages of the Work, 8 of Title, and 4 of other Matter.
A Quarter-Sheet of Sixty-Fours, 20 pages of the Work, 8 of Title, and 4 of other Matter.
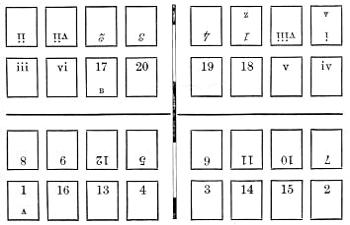
A Half-Sheet of Sixty-Fours.
A Half-Sheet of 64s.

A Half-Sheet of Seventy-Twos, with Three Signatures.
A half-sheet of seventy-twos, signed by three people.
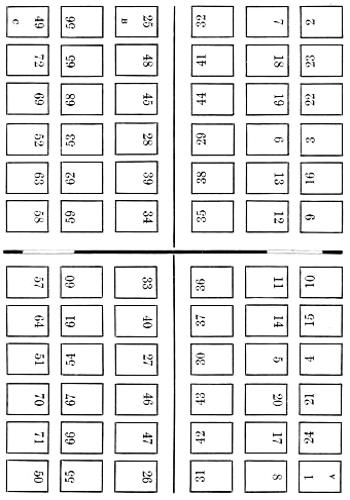
A Half-Sheet of Ninety-Sixes, with Six Signatures.
A half-sheet of ninety-sixes, with six signatures.
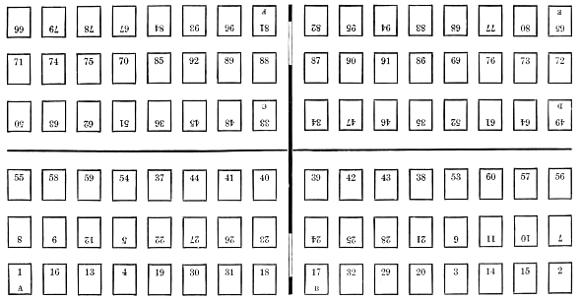
A Half-Sheet of One Hundred and Twenty-Eights, with Eight Signatures.
A half-sheet of 128, signed by eight people.
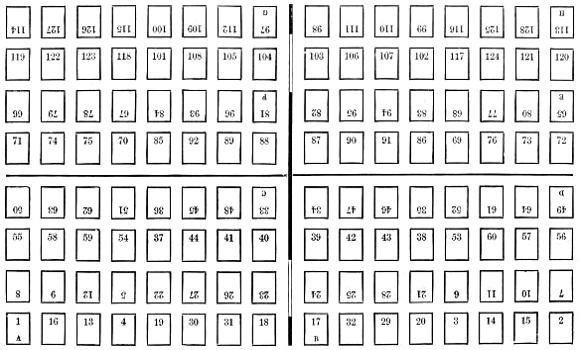
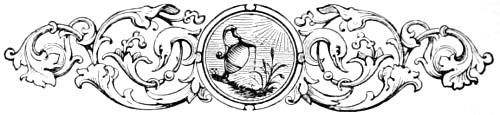
PROOF-READING AND CORRECTING.
PROOF-READING.

Undeniable as is the fact that a book marred by typographical errors and grammatical blemishes is a scandal to the profession, it must be admitted that a careful, steady, and competent reader is indispensable in every printing-office.
Unquestionable as it is that a book filled with typos and grammatical mistakes is a disgrace to the profession, it has to be acknowledged that a careful, attentive, and skilled reader is essential in every printing office.
It is eminently desirable that a reader should have been previously brought up a compositor. By a practical acquaintance with the mechanical departments of the business, he will be better able to detect those manifold errata which, unperceived by the man of mere learning and science, lie lurking, as it were, in a thousand different forms, in every sheet; and which, if overlooked, justly offend the taste and discernment of all appreciators of correct and beautiful typography.
It is highly desirable for a reader to have been trained as a typesetter. With practical knowledge of the mechanical aspects of the job, they will be better equipped to spot the many errors that, unnoticed by someone who just has academic knowledge, can hide in a thousand different forms on every page; and which, if missed, justifiably upset the preferences and judgment of everyone who values accurate and beautiful typography.
Some of the principal imperfections which are more easily observed by the man of practical knowledge in the art of printing are the following: viz. imperfect, wrong-founted, and inverted letters, particularly the lower-case n, o, s, and u, as well as p, d, b, and q; awkward and irregular spacing; uneven pages or columns; a false disposition of the reference[201] marks; crookedness in words and lines; bad making-up of matter; erroneous indention, &c. These minutiæ, which are rather imperfections of workmanship than literal errors, are apt to be overlooked and neglected by mere literary readers.
Some of the main flaws that someone with practical knowledge of printing is likely to notice are: incomplete, misprinted, and upside-down letters, especially the lowercase n, o, s, and u, as well as p, d, b, and q; awkward and inconsistent spacing; uneven pages or columns; incorrect placement of reference[201] marks; crooked words and lines; poorly arranged content; and wrong indentation, etc. These details, which are more about craftsmanship than textual errors, tend to be overlooked and ignored by casual readers.
A person of a thoroughly cultivated typographical taste, a quick eye, and a ready mind, though not a compositor, may doubtless be competent to detect those minor deviations from exact workmanship in a proof which the inexperienced and the careless are apt to overlook. But, without these qualifications, no person can be safely intrusted to read a sheet for press, and the labours of the printer are liable to go forth into the world in a manner that will reflect discredit on the employed and give offence to the employer. No form, therefore, ought to be put to press until it has been read and revised by an experienced reader.
A person with a well-developed sense of typography, a sharp eye, and a quick mind, even if not a typesetter, can certainly spot those minor errors in a proof that the inexperienced and careless often miss. However, without these skills, no one can be trusted to review a sheet for printing, and the printer's work might be released in a way that brings shame to the workers and displeasure to the employer. Therefore, no document should be sent to print until an experienced reader has reviewed and revised it.
A thorough proof-reader, in addition to a general and practical acquaintance with typography, should understand clearly the grammar and idiomatic structure of his mother-tongue, and have, as it were, an encyclopedic knowledge of the names, times, and productions of its writers, as well as an entire familiarity with the Bible especially, and with Shakspeare. He should be, in fact, a living orthographical, biographical, bibliographical, geographical, historical, and scientific dictionary, with some smattering of Hebrew, Greek, Latin, French, Spanish, Italian, and German. Yet all these accomplishments are valueless unless he also possess a keen and quick eye, that, like a hound, can detect an error almost by scent. There are eyes of this sort, that with a cursory glance will catch a solitary error in a page. The world is little aware how greatly many authors are indebted to a competent proof-reader for not only reforming their spelling and punctuation, but for valuable suggestions in regard to style, language, and grammar,—thus rectifying faults which would have rendered their works fair game for the critic.
A thorough proofreader, in addition to a solid understanding of typography, should clearly grasp the grammar and natural structure of their native language. They should also have an extensive knowledge of the names, timelines, and works of its authors, as well as complete familiarity with the Bible, especially, and Shakespeare. Essentially, they should be a living dictionary of spelling, biography, bibliographic details, geography, history, and science, with a bit of knowledge in Hebrew, Greek, Latin, French, Spanish, Italian, and German. However, all these skills are worthless unless they also have a sharp eye that can spot errors almost instinctively. There are some who, with just a quick glance, can catch a single mistake on a page. Most people don't realize how much many authors rely on a skilled proofreader not just to correct their spelling and punctuation, but to provide valuable suggestions about style, language, and grammar—thus fixing issues that could make their works easy targets for critics.
Although no corrector of the press can strictly be required to do otherwise than to follow his copy,—that is, faithfully to adhere to the original, with all its defects,—yet every one must perceive that he performs a friendly and perhaps a charitable service, by pointing out, in proper time, imperfections and mistakes which have escaped the observation of a quick or voluminous writer. With the spirit, the opinions, the whims[202] of an author, no corrector of the press has any business to interfere. In reprints of old and standard works, no license of alteration ought to be granted to either correctors or editors.
Although no proofreader can be strictly required to do anything other than follow their copy—that is, to stick closely to the original with all its flaws—everyone should recognize that they are doing a helpful and possibly kind service by pointing out, in a timely manner, any imperfections or mistakes that a fast or prolific writer might have missed. A proofreader should not interfere with the spirit, opinions, or quirks[202] of an author. In reprints of old and standard works, neither proofreaders nor editors should be allowed to make changes.
Strict uniformity should always be preserved in the use of capitals, in orthography, and punctuation. Nothing can be more vexatious to an author than to see the words honour, favour, &c. spelt with and without the u. This is a discrepancy which correctors ought sedulously to prevent. The above observations equally apply to the use of capitals to noun-substantives, &c. in one place, and the omission of them in another. However the opinions of authors may differ in these respects, still the system of spelling, &c. must not be varied in the same work.
Strict uniformity should always be maintained in the use of capital letters, spelling, and punctuation. Nothing is more frustrating for an author than to see words like honour, favour, etc., spelled with and without the u. This is a discrepancy that editors should diligently avoid. The same considerations apply to the use of capital letters with nouns in one instance and their absence in another. Regardless of authors' differing opinions on these matters, the system of spelling, etc., must not change within the same work.
When an author gives him the option, a proof-reader ought to spell ambiguous words and arrange compounds in a methodical and uniform way; and, to enable the compositors to become acquainted with and to observe his method, he should furnish for their guidance a list of such ambiguous words and compounds.[15]
When an author gives him the choice, a proofreader should resolve ambiguous words and organize compounds in a clear and consistent manner; and to help the typesetters understand and follow his approach, he should provide them with a list of those ambiguous words and compounds.[15]
Such being the qualifications of a reader, we exhibit the process which proof-sheets ought to undergo before the pages are put to press.
Such being the qualifications of a reader, we present the process that proof sheets should go through before the pages are printed.
When a first proof is pulled, the compositor who imposed the sheet ought to collect and arrange the copy, and deliver both to the reader, who, after folding the sheet to prove the accuracy of its imposition, carefully examines the signatures, head-lines, and paging. He then calls his reading-boy, to read the copy aloud to him. This boy should be able to read with ease and distinctness any copy put into his hands. The eye of the reader should not follow, but rather precede, the voice of the boy: accustomed to this mode, he will be able to anticipate every single word in the copy; and, should a word or sentence happen to be missing in the proof, his attention will the more sensibly be arrested by it when he hears it pronounced by his reading-boy. He ought to be careful lest his eyes advance too far before the words of the boy; because, in his attention to the author’s meaning, he will be apt to read words in the proof which do not actually appear there, and the accuracy of the reading-boy will but tend to confirm him in the mistake.
When a first proof is pulled, the compositor who set up the sheet should gather and organize the copy, then hand it over to the reader. After folding the sheet to check the accuracy of its setup, the reader carefully looks at the signatures, headings, and pagination. Then he calls in his reading boy to read the copy aloud to him. This boy should be able to read any copy handed to him clearly and confidently. The reader's eyes should lead rather than follow the boy's voice: by getting used to this method, he can anticipate every word in the copy, and if a word or sentence is missing from the proof, he will notice it more easily when he hears it read by his reading boy. He should be careful not to let his eyes jump too far ahead of the boy’s words because, in focusing on the author's meaning, he might mistakenly read words in the proof that aren’t actually there, and the reading boy's accuracy could just reinforce that misunderstanding.
When the reading of the sheet is concluded, the number (if more than one) of the volume, signature, and prima, or first word of the ensuing sheet, should be accurately marked on the margin of the copy, and a bracket made before the first word of the next sheet, in order that the compositor, should he not have composed beyond the sheet, may know where to begin, without having the trouble of referring either to the proof or the form, and the reader will be certain that the commencement is right when he gets the succeeding sheet. This prevents unnecessary trouble both to the reader and compositor.
When you've finished reading the sheet, you should clearly note the number (if there's more than one) of the volume, signature, and prima, or the first word of the next sheet, in the margin of the copy. Also, make a bracket before the first word of the next sheet. This way, the compositor, if they haven't gone beyond the sheet, will know where to start without having to check the proof or the form. The reader can then be sure that the beginning is correct when they receive the next sheet. This saves unnecessary trouble for both the reader and the compositor.
Before the proof is sent to the compositor to be corrected in the metal, an entry should be made in a book, according to the following plan:—
Before the proof is sent to the typesetter for correction in the metal, an entry should be made in a book, following this plan:—
DATE OF READING. | SIGNATURES. | NAMES OF WORKS. | SENT OUT. | RETURNED. | READ FOR PRESS. | ||||
---|---|---|---|---|---|---|---|---|---|
1878. | 1878. | 1878. | 1878. | ||||||
May | 2 | 11 | Decorative Printing | May | 2 | May | 4 | May | 5 |
” | 4 | 23 | American Printer, (Revised Edition) | ” | 4 | ” | 5 | ” | 6 |
” | 6 | 20 | Specific Heat Tables | ” | 8 | ” | 9 | ” | 9 |
” | 10 | 2 | The Great Exhibition | ” | 10 | ” | 12 | ” | 13 |
” | 27 | 13 | Masterpieces of European Art | ” | 29 | ” | 30 | ” | 30 |
This account being punctually kept, the reader can furnish the employer or overseer with an exact account of the state of each work without delay or inconvenience.
This record being consistently maintained, the reader can provide the employer or supervisor with an accurate update on the status of each project without any delay or hassle.
After the compositors have corrected the errors in the form, a clean proof is pulled, which, with the first proof, is handed to the reader, who then collates the corrected sheet with the one before read, in order to ascertain whether the corrections have been properly made, and whether new errors have not been caused by negligence in the process; and, if the work be a reprint, or if the author is not to examine the proof, he then proceeds to read it very carefully for press.
After the typesetters have fixed the errors in the document, a clean proof is printed out. This, along with the first proof, is given to the reader, who then checks the corrected sheet against the previous one to ensure that the corrections were made correctly and that no new mistakes were introduced due to carelessness during the process. If the work is a reprint or if the author is not reviewing the proof, the reader carefully reads it for publication.
Some proofs are so foul, that it is almost impossible for the compositor to correct all the marks at one time, and it is therefore necessary to have the neglected errors corrected and another sheet pulled before the proof is read finally. It not[204] unfrequently happens that compositors, in the course of correcting, transpose a letter or word, or alter a letter in a word that is not marked, thus not only leaving one error uncorrected, but also making another; sometimes also, in respacing a line, a space is transposed or a hyphen is left in. Consequently it is absolutely necessary, in revising a proof, that the reader should not only look at the word marked, but he ought also to glance his eye over every line in which an alteration has been made.
Some proofs are so messy that it's almost impossible for the typesetter to fix all the errors at once. So, it’s essential to get the overlooked mistakes corrected and print another sheet before the proof is reviewed again. It often happens that typesetters, while making corrections, switch around a letter or word, or change a letter in a word that wasn’t marked. This not only leaves one mistake uncorrected but also creates another one. Sometimes, when adjusting the spacing in a line, a space gets moved or a hyphen gets left in place. Therefore, when reviewing a proof, it's crucial for the reader to not only pay attention to the marked words but also to quickly scan every line where a change has been made.
In offices where two readers are employed, it is advisable that a proof-sheet should be read over by both; because the eye, in traversing the same ground, is liable to be drawn into mistake and oversight. The interest excited by the first reading having abated, a degree of listlessness imperceptibly steals upon the mind, which greatly endangers the correctness of a proof. Should outs or doubles occur in a proof, it ought to be again read by copy, to detect any improper correction in the overrunning or transposition of lines. Figure work should always be read twice by copy.
In offices with two readers, it’s a good idea for both to review a proof sheet. When we read the same text multiple times, it’s easy to make mistakes or overlook details. After the excitement of the first read wears off, a kind of dullness can set in, which can lead to errors in the proof. If there are any outs or doubles in a proof, it should be checked again against the original to catch any wrong corrections from moving things around or mixing up lines. Any work with figures should always be read twice against the original.
The duty of amending the punctuation should be generally confined to one reader. Where a compositor is liable, in this particular, to the whim or caprice of several readers, he certainly suffers injustice, because his time is unnecessarily frittered away; and not only is the work retarded, but the types are needlessly exposed to injury, to say nothing of the liability of creating fresh errors, &c.
The responsibility for fixing the punctuation should typically rest with one person. If a typesetter has to deal with the preferences or whims of multiple readers, it’s unfair to them because it wastes their time. This not only slows down the work but also puts the type at risk of being damaged, not to mention the chance of introducing new errors, etc.
Before a manuscript is brought to the printer, it ought to be as perfect as the author can make it. The compositor is bound to “follow the copy,” in word and sentiment, unless, indeed, he meets with instances of wrong punctuation or false grammar, (and such instances are not rare,) which his intelligence enables him to amend. After the matter has been read and corrected in the office, a proof is sent to the author; and, if it corresponds with the copy, the compositor’s responsibility is at an end. He has done all he is paid for; and, should the author desire any changes made in his matter, of course he must pay for them.
Before a manuscript is sent to the printer, it should be as flawless as the author can make it. The typesetter is required to "follow the copy" in both wording and meaning, unless he encounters mistakes in punctuation or grammar (and such mistakes aren't uncommon) that his judgment allows him to correct. Once the content has been read and corrected in the office, a proof is sent to the author; and if it matches the copy, the typesetter's responsibility ends there. He has done everything he's being paid for, and if the author wants any changes made to the content, he will need to pay for those.
Sentiments in print look marvellously different from the same ideas in manuscript; and we are not surprised that writers should wish to polish a little; nor do we object to their natural desire of amending or beautifying their mental[205] products. But let them not forget that pay-time will come,—when the item for alterations will loom out with a startling distinctness in the bill. They found it easy in the proof to erase a word or two here and insert a word or two there; without dreaming, perhaps, that in consequence of these little erasures and insertions the compositor would be compelled to alter and reconstruct much of his work. We know of a volume on which the alterations alone have consumed time equal to one man’s work for nearly two and a half years. How unreasonable—nay, how transparently unjust—the expectation that the printer should give gratuitously the time and trouble requisite for the radical changes in the type which an author’s whim or taste may demand!
Sentiments in print look remarkably different from the same ideas in manuscript, and it’s no surprise that writers want to polish things a bit; we don’t mind their natural desire to improve or enhance their thoughts[205]. But they shouldn’t forget that the bill for changes will eventually come—when the cost of alterations will stand out clearly. They may find it easy in the proof stage to delete a word or two here and add a word or two there; without realizing that these small changes can require the compositor to modify and redo much of his work. We know of one book where the alterations alone took as much time as one person working for nearly two and a half years. How unreasonable—and honestly, how obviously unfair—it is to expect that the printer should invest his time and effort for free to accommodate the radical changes that an author’s preferences may demand!
Stower says, “It may not be improper, in this place, just to take notice of the great danger to the correctness of a work which arises from the practice, too common with some authors, of keeping their proof-sheets too long in their hands before they are returned to the printer. As the pages in the metal get dry, the adhesion of the types to each other is weakened, and the swell or extension of the quoins and furniture, which the moisture had occasioned, is removed; so that there is great danger of letters falling out when a form is long kept from the press. Nor is the danger which is hereby occasioned to correctness the only inconvenience: the impatience of authors to see their works in a fit state for publication is almost proverbial. The pleasure arising from beholding, as it were, the ‘form and texture’ of one’s thoughts, is a sensation much easier felt than described. That authors, therefore, may partake of this pleasure in a speedy and regular succession, they should make a point of forwarding their proof-sheets to the printer as quick as possible, not only that they may the sooner be got ready for the press, but that the work may proceed in a regular manner, without being interrupted by the forwarding of other works in lieu of that the proof-sheets of which are detained beyond the proper time in the hands of the author.
Stower says, “It might not be inappropriate, in this context, to highlight the significant risk to the accuracy of a work that comes from the common habit among some authors of holding on to their proof-sheets for too long before sending them back to the printer. As the metal pages dry out, the bond between the types weakens, and any expansion caused by moisture is lost, leading to a high risk of letters falling out when a form is kept away from the press for an extended period. The resulting threat to accuracy isn’t the only issue; authors' impatience to see their works ready for publication is almost legendary. The joy of seeing the 'form and texture' of one's thoughts is a feeling that's much easier to experience than to describe. Therefore, to help authors enjoy this pleasure in a timely and consistent way, they should make it a priority to send their proof-sheets back to the printer as quickly as possible. This will not only speed up getting the work ready for press but also ensure that the process flows smoothly, without interruptions caused by other works that replace those proof-sheets which the author has held onto for too long.”
“Authors are very apt to make alterations, and to correct and amend the style or arguments of their works, when they first see them in print. This is certainly the worst time for this labour, as it is necessarily attended with an expense which, in large works, will imperceptibly swell to a serious[206] sum; when, however, this method of alteration is adopted by an author, the reader must always be careful to read the whole sheet over once more with very great attention before it is finally put to press.
“Authors often make changes and adjust the style or arguments of their works when they first see them in print. This is definitely the worst time for this kind of work, as it comes with costs that, in larger works, can quietly add up to a significant sum; however, when an author adopts this method of alteration, the reader must always be sure to read the entire sheet again with great attention before it’s finally printed. [206]”
“A proof-sheet, having duly undergone this routine of purgation, may be supposed to be as free from errata as the nature of the thing will admit, and the word ‘Press’ may be written at the top of the first page of it. This is an important word to every reader: if he have suffered his attention to be drawn aside from the nature of his proper business, and errors should be discovered when it is too late to have them corrected, this word ‘Press’ is as the signature of the death-warrant of his reputation. A reader, therefore, should be a man of one business,—always upon the alert,—all eye,—all attention. Possessing a becoming reliance on his own powers, he should never be too confident of success. Imperfection clings to him on every side. Errors and mistakes assail him from every quarter. His business is of a nature that may render him obnoxious to blame, but can hardly be said to bring him in any very large stock of praise. If errors escape him, he is justly to be censured; for perfection is his duty. If his labours are wholly free from mistake,—which is, alas! a very rare case,—he has done no more than he ought, and, consequently, can merit only a comparative degree of commendation, in that he had the good fortune to be more successful in his labours after perfection than some of his brethren in the same employment.”
“A proof-sheet, having properly gone through this process of cleaning up errors, can be considered as free from mistakes as possible, and the word ‘Press’ can be written at the top of the first page. This word is crucial for every reader: if they've allowed their attention to drift from their main task, and mistakes are found when it's too late to fix them, this word ‘Press’ becomes a signature on the death warrant of their reputation. A reader should, therefore, be someone focused—always alert, fully engaged, and attentive. With a healthy belief in their abilities, they should never be overly confident about succeeding. Imperfection surrounds them on all sides. Errors and mistakes can come at them from every direction. Their work is such that it may subject them to criticism, but it rarely earns them substantial praise. If mistakes slip by them, they rightly face criticism, as achieving perfection is part of their duty. Even if their work is completely error-free—which is, unfortunately, quite rare—they have only done what is expected, and therefore, can receive only a limited amount of praise, having simply been luckier in achieving perfection compared to others in the same field.”
The form being finally laid on the press, and a revise pulled by the pressman, he sends it to the overseer, who carefully examines whether all the marks have been attended to, and looks along the sides and heads of the respective pages, to observe whether any letter has fallen out, or there is any crookedness in the locking up of the form, any battered letters, or any bite from the frisket. Should the revise prove faultless, he returns it to the pressman, with the word “Revise” written on the margin; if otherwise, to the compositor to whom the form belongs, for immediate correction.
The form is finally placed on the press, and after the pressman pulls a proof, he sends it to the overseer, who carefully checks if all the marks have been addressed. He inspects the sides and tops of the pages to see if any letters have fallen out, if there’s any misalignment in the locking up of the form, any damaged letters, or any marks from the frisket. If the proof is flawless, he returns it to the pressman with the word “Revise” written in the margin; if not, he sends it back to the compositor responsible for the form for immediate correction.
CORRECTING IN THE METAL.
Correcting is the most disagreeable part of a compositor’s business, diminishing as it does his earnings, and causing great fatigue, and, by leaning over the stone, endangering his health. A foul proof, however, is a fault without extenuation, and seems to deserve some punishment. The noise and confusion which prevail in badly governed printing-offices, from light and frivolous conversation, not only retard business, but distract the attention of the compositor from the subject he has in hand, and cause him to make many mistakes. Some men, no doubt, can support a conversation and at the same time compose correctly; but their noise confuses those who are unable to preserve accuracy except by close attention to their copy in silence.
Editing is the least enjoyable part of a compositor’s job, as it reduces their pay, causes significant fatigue, and, while leaning over the typesetting, puts their health at risk. A foul proof, however, is an inexcusable mistake and seems to warrant some consequences. The noise and chaos that often occur in poorly managed printing shops, due to light and trivial chatter, not only slow down productivity but also distract the compositor from the task at hand, leading to many errors. Some people can handle a conversation while still composing correctly, but their noise can confuse those who need to focus silently on their work to maintain accuracy.
The first proof should contain merely the errors of the compositor; but it frequently happens that the corrector heightens them by his peculiarities. When this is unnecessarily done, it is an act of injustice to the compositor: it is sufficient for him to rectify such mistakes as arise either from inattention to his copy or want of judgment. The compositor ought not to suffer from the humour of a reader in capriciously altering commas and semicolons in the first proof, which he not unfrequently re-alters in the second, from a doubt as to the propriety of the points to be adopted.
The first proof should only show the compositor's mistakes; however, it often happens that the corrector makes things worse with their own idiosyncrasies. When this is done unnecessarily, it’s unfair to the compositor: it’s enough for them to fix errors that come from either not paying attention to the copy or a lack of judgment. The compositor shouldn't have to deal with a reader whimsically changing commas and semicolons in the first proof, which they often change again in the second because of uncertainty about which punctuation to use.
When a proof is handed to the compositor, he should immediately correct it; and the reader, correlatively, should be equally prompt in his department. Can it reasonably be expected that the compositor will feel inclined to forward his proof, when he knows that the reader will delay it for hours?
When a proof is given to the typesetter, he should correct it right away; and the reader should also be just as quick in his part. Can we really expect the typesetter to want to send his proof forward when he knows the reader will take hours to get to it?
Should a compositor have transposed two or more pages, either from an error in the folios or any other cause, he must unlock the quarter containing them, and, loosening the cross or crosses from the furniture, lift the chase and the remaining quarters off the stone. Should he have furniture sufficient round each page, he may move them into their proper stations by pressing the balls of his thumbs and fingers against the furniture at the head, foot, and sides of each page. If the letter be small, it will be advisable to wet the pages, because few imposing-stones are horizontal, or so steady that they[208] will not shake when touched, or by the motion of the floor occasioned by persons walking or dragging forms along.
If a typesetter has mixed up two or more pages, either due to an error in the folios or another reason, they need to unlock the quarter that holds them, and by loosening the cross or crosses from the furniture, lift the chase and the other quarters off the stone. If they have enough furniture around each page, they can move them into the correct positions by pressing their thumbs and fingers against the furniture at the top, bottom, and sides of each page. If the type is small, it's a good idea to wet the pages, because very few typesetting stones are perfectly horizontal or stable enough that they won’t shake when touched or when the floor vibrates from people walking or moving forms around.
Should a compositor find that his pages hang, he must unlock the quarter, and pat the face of the type with the balls of his fingers until he gets it into a square position.
Should a typesetter find that his pages hang, he must unlock the chase and gently tap the surface of the type with the tips of his fingers until it is aligned properly.
When a compositor unlocks a form, he should be careful not to leave the unlocked quoins too slack, as the force necessary to loosen the others may squabble the matter, or occasion it to hang.
When a compositor unlocks a form, he should be careful not to leave the unlocked quoins too loose, as the force needed to loosen the others may squabble the matter, or cause it to hang.
It has been aptly said, “What is required of a compositor when he goes about correcting a foul proof, is a sharp bodkin and patience; because, without them, the letter cannot escape suffering by the steel, and hurrying will not permit him to justify the lines true. No wonder, therefore, to see pigeon-holes in one place, and pi in another.”[16]
It has been accurately stated, “What a typesetter needs when correcting a rough draft is a sharp tool and some patience; because without those, the letters will get messed up, and rushing won’t allow him to align the lines correctly. So it’s no surprise to find jumble in one area and random letters in another.”[16]
When the compositor has as many corrections between the thumb and forefinger of his left hand as he can conveniently hold, or, what is better, in his composing-stick, (beginning at the bottom of the page, in order that they may follow regularly,) and an assortment of spaces on a piece of paper, or, what is more convenient, in a small square box with partitions in it,—let him take the bodkin in his right hand, and, instead of raising each letter he may have to alter, place the point of the bodkin at one end of the line, and, with the forefinger of his left hand against the other, raise the whole line sufficiently high to afford him a clear view of the spacing; he may then change the faulty letter and alter his spacing before he drops the line. By this method he will not injure the type, which he must do if he force the bodkin into their sides or heads; a greater degree of regularity is insured where there may be occasion to alter the spacing, and no more time is taken up than by the other method.
When the typesetter has as many corrections in the fingers of his left hand as he can comfortably hold, or better yet, in his composing stick (starting at the bottom of the page to keep everything in order), and a bunch of spaces on a piece of paper or, even better, in a small box with dividers, he should take the bodkin in his right hand. Instead of lifting each letter he needs to change, he can place the tip of the bodkin at one end of the line and use the finger of his left hand at the other end to lift the entire line high enough to see the spacing clearly. He can then fix the wrong letter and adjust the spacing before lowering the line. This way, he won’t damage the type, which would happen if he forced the bodkin into their sides or tops. Also, it maintains a better regularity when adjustments to spacing are needed, and it won't take longer than the other method.
In tables, and other matter, where rules prevent the lines from being raised, the letters must be drawn up by the bodkin. This is done by the compositor holding the instrument fast in his right hand, with the blade between his forefinger and thumb, within about three-quarters of an inch from the point: thus guiding it steadily to the faulty letter, he sticks the point of the bodkin into the neck of the letter between the beard and the face, and draws it up above the other types, so that he can take it out with the forefinger and thumb of his left hand. In performing this operation, the blade of the bodkin should be kept as flat as possible on the face of the type, but it should not touch any of the surrounding types, as the slightest graze imaginable will injure their face, and they will consequently appear imperfect in the next proof, when he will have the trouble of altering them, his employer suffering the loss of the type.
In tables and other materials where rules prevent the lines from being raised, the letters must be lifted with a bodkin. The compositor holds the tool firmly in their right hand, with the blade between their forefinger and thumb, about three-quarters of an inch from the point. This allows them to steady it towards the faulty letter; they stick the point of the bodkin into the neck of the letter, between the beard and the face, and lift it above the other types so that they can remove it with the forefinger and thumb of their left hand. While doing this, the blade of the bodkin should be kept as flat as possible on the face of the type, but it shouldn’t touch any of the surrounding types, as even the slightest contact can damage their face, resulting in an imperfect appearance in the next proof, leading to the need for corrections and causing their employer to lose the type.
The bodkin blade being held almost flat to the form, a small horizontal entrance of its point into the neck of the letter will raise it above the face of the form; but, if the bodkin be held nearly upright, it will not have sufficient purchase to draw the letter up, because the weight of the letter and the pressure of the surrounding types will have greater power than the sharp point of the steel. By pressing sidewise, the bodkin blade acts as a lever, even though it has no other purchase than the slight motion of the hand.
The bodkin blade held almost flat against the surface, with the tip making a small horizontal entry into the neck of the letter, will lift it above the surface. However, if the bodkin is held nearly upright, it won't have enough grip to pull the letter up because the letter's weight and the pressure from the surrounding types will overpower the sharp point of the steel. By applying sideways pressure, the bodkin blade functions like a lever, even with just the slight movement of the hand as its only support.

COMMON BODKIN.
COMMON BODKIN.

POCKET SPRING BODKIN.
Pocket Spring Bodkin.
In the olden times the printer made his own bodkin by inserting the blunt end of a large steel needle in a piece of wood or cork. At the present day, when every thing is prepared to the workman’s hand, bodkins are manufactured by printers’ furnishers, and he may take his choice of styles. The above cut shows a common form; but in some cases (as in table work) tweezers or a spring bodkin may be preferred. Knives may also be had with bodkin attached, which serve a double purpose. The objection to the knife-bodkin is that[210] the handle is too heavy and cumbersome, and it is sure to injure type should it happen to slip from the fingers and fall on the page.
In the past, printers made their own bodkins by sticking the blunt end of a large steel needle into a piece of wood or cork. Nowadays, with everything readily available for workers, bodkins are produced by printing suppliers, and they can choose from various styles. The image above shows a common design; however, in some situations (like table work), tweezers or a spring bodkin might be preferred. Knives with bodkins attached are also available, serving a dual purpose. The downside of the knife-bodkin is that[210] the handle is too heavy and awkward, and it can damage type if it slips from the fingers and falls onto the page.

TWEEZERS.
Tweezers.

SPRING BODKIN.
SPRING BODKIN.
The most careful compositor cannot at all times avoid leaving a word out, or composing the same word twice. When this happens, he should consider the best mode of rectifying the accident, by driving out or getting in, either above the error or below it. This ascertained, let the matter be taken upon a galley, and overrun in the composing-stick. Overrunning on the stone is an unsafe, unworkmanlike, and dilatory method, destroying the justification and rendering the spacing uneven.
The most careful typesetter can't always avoid leaving out a word or accidentally typing the same word twice. When this happens, they should figure out the best way to fix the mistake by either removing or adding something above or below the error. Once that's determined, the issue should be addressed on a galley and set in the composing stick. Going over it on the stone is an unreliable, unprofessional, and slow method that ruins the justification and makes the spacing uneven.

KNIFE AND BODKIN.
Knife and sewing needle.
In correcting, care should be taken to avoid hair-spacing a line, by overrunning either back or forward. In overrunning the matter, the division should be used as little as possible; for, though the compositor may carefully follow the instructions laid down in this work on the subject of spacing and dividing, yet the effect of his attention will be completely destroyed if not followed up at the stone.
In editing, be careful not to create gaps in a line by going over the text either backwards or forwards. When adjusting the text, use the division tool minimalistically; even if the typesetter closely follows the guidelines in this manual regarding spacing and dividing, the final result will be fully compromised if it's not consistently managed at the final stage.
We here emphatically remark that, if authors were careful to spell properly the names of persons and places, technical and scientific terms, &c., and to write legibly, marking the end of sentences clearly, the work of the compositor would be facilitated, many errors would be prevented, and time, temper, and expense greatly economized.
We strongly emphasize that if authors were careful to spell names of people and places, technical and scientific terms, etc., correctly and to write clearly, marking the end of sentences distinctly, the compositor’s job would be easier, many mistakes would be avoided, and time, patience, and costs would be significantly saved.
Further. Let us remind authors that every correction made on their proof that is a variation from the copy as furnished to the printer is charged for according to the time required to make it. The justice of the charge is obvious; yet, strange to say, there is probably no item so frequently disputed by publishers. A man employs a mechanic to build a house according to fixed specifications; but, in the course of its erection, he improves or changes the plan, and orders certain portions to be torn down and rebuilt: is the mechanic to bear the loss? Certainly not. So, when a compositor builds up his page of type according to the copy furnished, he is right in requiring compensation for alterations made in it. He is not to suffer for the author’s desire to improve his intellectual edifice.
Further. Let’s remind authors that any correction made on their proof that differs from the copy provided to the printer is charged based on the time it takes to make it. It’s clear why this charge is fair; however, surprisingly, it’s one of the most frequently disputed items by publishers. A person hires a builder to construct a house based on specific plans; but during the building process, they decide to improve or change the design and instruct certain parts to be demolished and rebuilt: should the builder take the loss? Of course not. Likewise, when a typesetter arranges a page of type based on the provided copy, they are justified in asking for compensation for changes made to it. They shouldn’t have to suffer because the author wants to enhance their intellectual creation.

PRINTER’S KNIFE.
Craft knife.
TYPOGRAPHICAL MARKS EXEMPLIFIED.
The following table will be appreciated by authors and by all who desire to become acquainted with the technical marks used by practical readers. Due attention to the explanations will insure an apt proficiency in the manual department of proof-reading.
The following table will be useful for authors and for anyone who wants to understand the technical symbols used by practical readers. Paying careful attention to the explanations will ensure you become skilled in the manual aspects of proof-reading.


Though several differing opinions exist as to the individual by whom the art of printing was first discovered; yet all authorities concur in admitting PETER SCHOEFFER to be the person who invented cast metal types, having learned the art of cutting the letters from the Gutenbergs: he is also supposed to have been the first who engraved on copper-plates. The following testimony is preserved in the family, by Jo. Fred. Faustus, of Ascheffenburg:
Although there are various opinions about who first discovered the art of printing, all experts agree that PETER SCHOEFFER is the one who invented cast metal types, having learned the technique of cutting the letters from the Gutenbergs. He is also believed to be the first person to engrave on copper plates. The following testimony is kept in the family by Jo. Fred. Faustus of Ascheffenburg:
‘Peter Schoeffer, of Gernsheim, perceiving his master Faust’s design, and being himself ardently desirous to improve the art, found out (by the good providence of God) the method of cutting (incidendi) the characters in a matrix, that the letters might easily be singly cast, instead of being cut. He privately cut matrices for the whole alphabet: and when he showed his master the letters cast from these matrices, Faust was so pleased with the contrivance, that he promised Peter to give him his only daughter Christina in marriage, a promise which he soon after performed. But there were as many difficulties at first with these letters, as there had been before with wooden ones, the metal being too soft to support the force of the impression: but this defect was soon remedied, by mixing the metal with a substance which sufficiently hardened it.’
Peter Schoeffer, from Gernsheim, noticing his master Faust’s plan, and being eager to enhance the craft, discovered (thanks to God's grace) a way to cut (incidendi) the characters in a matrix, so that the letters could easily be individually cast, instead of being cut. He secretly cut matrices for the entire alphabet: and when he showed his master the letters made from these matrices, Faust was so impressed with the invention that he promised Peter his only daughter Christina in marriage, a promise he soon fulfilled. However, there were just as many challenges at first with these letters as there had been with the wooden ones, since the metal was too soft to withstand the force of the impression: but this issue was quickly fixed by mixing the metal with a material that adequately hardened it.
EXPLANATION OF THE CORRECTIONS.
A wrong letter in a word is noted by drawing a short perpendicular line through it, and making another short line in the margin, behind which the right letter is placed. (See No. 1.) So with whole words also, a line being drawn across the wrong word and the right one written in the margin opposite.
A wrong letter in a word is marked by drawing a short vertical line through it and adding another short line in the margin, where the correct letter is placed. (See No. 1.) The same goes for whole words; draw a line through the incorrect word and write the right one in the margin next to it.
A turned letter is noted by drawing a line through it, and writing the mark No. 2 in the margin.
A turned letter is indicated by drawing a line through it and writing the mark No. 2 in the margin.
If letters or words require to be altered to make them more conspicuous, a parallel line or lines must be made underneath the word or letter,—viz. for capitals, three lines; small capitals, two lines; and Italic, one line; and, in the margin opposite the line where the alteration occurs, Caps, Small Caps, or Ital. must be written. (See No. 3.)
If letters or words need to be changed to make them stand out more, you should draw a line or lines underneath the word or letter—specifically, for capital letters, three lines; for small capitals, two lines; and for italics, one line. In the margin next to the line where the change happens, you should write Caps, Small Caps, or Ital.. (See No. 3.)
When letters or words are set double, or are required to be taken out, a line is drawn through the superfluous word or letter, and the mark No. 4 placed opposite in the margin.
When letters or words are duplicated or need to be removed, a line is drawn through the unnecessary word or letter, and the mark No. 4 is placed in the margin opposite.
Where the punctuation requires alteration, the correct point should be written in the margin. (See No. 5.)
Where the punctuation needs to be changed, the correct mark should be written in the margin. (See No. 5.)
When a space has been omitted between two words, a caret must be made where the separation ought to be, and the sign No. 6 placed opposite in the margin.
When there’s no space between two words, a caret should be placed where the separation should be, and the sign No. 6 should be marked in the margin.
When a word should form a compound with another, it is denoted as in No. 7.
When a word should combine with another, it is indicated as in No. 7.
When a letter has been omitted, a caret is put at the place of omission, and the letter marked as No. 8.
When a letter is missing, a caret is placed where it should be, and the letter is noted as No. 8.
Where a line is too widely spaced, the mark No. 9 must be placed between the words and also in the margin.
Where a line is too spaced out, mark No. 9 should be placed between the words and also in the margin.
Where a new paragraph is required, a quadrangle is drawn in the margin, and a caret placed at the beginning of the sentence. (See No. 10.)
Where a new paragraph is needed, a square is drawn in the margin, and a caret is placed at the start of the sentence. (See No. 10.)
No. 11 shows the way in which the apostrophe, inverted commas, the star and other references, and superior letters and figures, are marked.
No. 11 shows how to mark the apostrophe, quotation marks, stars, and other symbols, along with superscript letters and numbers.
Where two words are transposed, a line is drawn over one word and below the other, and the mark No. 12 placed in the margin; but where several words require to be transposed, their right order is signified by a figure placed over each word, and the mark No. 12 in the margin.
Where two words are switched, a line is drawn over one word and below the other, with the mark No. 12 placed in the margin; but when several words need to be switched, their correct order is indicated by a number placed over each word, along with the mark No. 12 in the margin.
Where words have been struck out that have afterward[215] been approved of, dots should be marked under them, and stet written in the margin. (See No. 13.)
Where words have been crossed out that have later[215] been approved, dots should be placed underneath them, and stet should be written in the margin. (See No. 13.)
Where a space sticks up between two words, a horizontal line is drawn under it, and the mark No. 14 placed opposite, in the margin.
Where there’s a gap between two words, a horizontal line is drawn underneath, and the mark No. 14 is placed next to it in the margin.
Where several words have been left out, they are transcribed at the bottom of the page, and a line drawn from the place of omission to the written words, (see No. 15;) but if the omitted matter is too extensive to be copied at the foot of the page, Out, see copy, is written in the margin, and the missing lines are enclosed between brackets, and the word Out is inserted in the margin of the copy.
Where several words have been left out, they are noted at the bottom of the page, and a line is drawn from the spot of omission to the written words (see No. 15); but if the omitted content is too long to be copied at the bottom of the page, Out, see copy is written in the margin, and the missing lines are enclosed in brackets, with the word Out inserted in the margin of the copy.
Where letters stand crooked, they are noted by a line, (see No. 16;) but, where a page hangs, lines are drawn across the entire part affected.
Where letters are misaligned, they are marked by a line, (see No. 16;) but, where a page is wrinkled, lines are drawn across the whole affected area.
When a smaller or larger letter, of a different fount, is improperly introduced into the page, it is noted by the mark No. 17, which signifies wrong fount.
When a smaller or larger letter, in a different font, is incorrectly added to the page, it is indicated by the mark No. 17, which means wrong font.
If a paragraph is improperly made, a line is drawn from the broken-off matter to the next paragraph, and No ¶ written in the margin. (See No. 18.)
If a paragraph is poorly constructed, a line is drawn from the incomplete part to the next paragraph, and No ¶ is written in the margin. (See No. 18.)
Where a word has been left out or is to be added, a caret must be made in the place where it should come in, and the word written in the margin. (See No. 19.)
Where a word is missing or needs to be added, place a caret where it should go and write the word in the margin. (See No. 19.)
Where a faulty letter appears, it is denoted by making a cross under it, and placing a similar mark in the margin, (see No. 20;) though some prefer to draw a perpendicular line through it, as in the case of a wrong letter.
Where a wrong letter shows up, it's marked with a cross underneath it and a similar mark in the margin (see No. 20); although some people prefer to draw a vertical line through it, like with an incorrect letter.
Where a word has been accidentally separated by a space, it is marked as in No. 21.
Where a word has been accidentally split by a space, it is indicated as in No. 21.
TABLE OF SIGNATURES.
On the two following pages will be found a complete list of signatures for books in octavo, twelves and eighteens, sixteens, and twenty-fours.
On the next two pages, you'll find a complete list of signatures for books in octavo, twelve, eighteen, sixteen, and twenty-four.
The 24mo signatures in this table are arranged to bring the second signature on either the 9th or 17th page of the form. If the sheet is to be folded as an 8vo and 16mo, the figure signatures may be used; but if as two 12mos, the letter signatures will be used.
The 24mo signatures in this table are arranged to place the second signature on either the 9th or 17th page of the form. If the sheet is folded as an 8vo and 16mo, the figure signatures can be used; but if it’s folded as two 12mos, the letter signatures will be used.
8vo. | 12mo and 18mo. | 16mo. | 24mo. | ||||||||||||||||||||
---|---|---|---|---|---|---|---|---|---|---|---|---|---|---|---|---|---|---|---|---|---|---|---|
1 | 1 | A | 481 | 61 | 3 L | 1 | 1 | A | 313 | 27 | 2 B | 625 | 53 | 3 C | 1 | 1 | A | 1 | 1 | A | 433 | 19 | T |
9 | 2 | B | 489 | 62 | 3 M | 5 | 1* | A two | 317 | 27* | 2 B 2 | 629 | 53* | 3 C 2 | 17 | 2 | B | 9 | 1* | 441 | 19* | ||
17 | 3 | C | 497 | 63 | 3 N | 13 | 2 | B | 325 | 28 | 2 C | 637 | 54 | 3 D | 33 | 3 | C | 17 | . . | A 2 | 449 | . . | T 2 |
25 | 4 | D | 505 | 64 | 3 O | 17 | 2* | B 2 | 329 | 28* | 2 C 2 | 641 | 54* | 3 D 2 | 49 | 4 | D | 25 | 2 | B | 457 | 20 | U |
33 | 5 | E | 513 | 65 | 3 P | 649 | 55 | 3 E | 65 | 5 | E | 33 | 2* | 465 | 20* | ||||||||
41 | 6 | F | 521 | 66 | 3 Q | 25 | 3 | C | 337 | 29 | 2 D | 653 | 55* | 3 E 2 | 81 | 6 | F | 41 | . . | B 2 | 473 | . . | You too |
49 | 7 | G | 529 | 67 | 3 R | 29 | 3* | C 2 | 341 | 29* | 2 D 2 | 97 | 7 | G | |||||||||
57 | 8 | H | 537 | 68 | 3 S | 37 | 4 | D | 349 | 30 | 2 E | 661 | 56 | 3 F | 113 | 8 | H | 49 | 3 | C | 481 | 21 | V |
65 | 9 | I | 545 | 69 | 3 T | 41 | 4* | D 2 | 353 | 30* | 2 E 2 | 665 | 56* | 3 F 2 | 129 | 9 | I | 57 | 3* | 489 | 21* | ||
73 | 10 | K | 553 | 70 | 3 U | 673 | 57 | 3 G | 145 | 10 | K | 65 | . . | C 2 | 497 | . . | V 2 | ||||||
81 | 11 | L | 561 | 71 | 3 V | 49 | 5 | E | 361 | 31 | 2 F | 677 | 57* | 3 G 2 | 161 | 11 | L | 73 | 4 | D | 505 | 22 | W |
89 | 12 | M | 569 | 72 | 3 W | 53 | 5* | E 2 | 365 | 31* | 2 F 2 | 177 | 12 | M | 81 | 4* | 513 | 22* | |||||
97 | 13 | N | 577 | 73 | 3 X | 61 | 6 | F | 373 | 32 | 2 G | 685 | 58 | 3 H | 193 | 13 | N | 89 | . . | D 2 | 521 | . . | W-2 |
105 | 14 | O | 585 | 74 | 3 Y | 65 | 6* | F 2 | 377 | 32* | 2 G 2 | 689 | 58* | 3 H 2 | 209 | 14 | O | 97 | 5 | E | 529 | 23 | X |
113 | 15 | P | 593 | 75 | 3 Z | 73 | 7 | G | 385 | 33 | 2 H | 697 | 59 | 3 I | 225 | 15 | P | 105 | 5* | 537 | 23* | ||
121 | 16 | Q | 601 | 76 | 4 A | 77 | 7* | G2 | 389 | 33* | 2 H 2 | 701 | 59* | 3 I 2 | 241 | 16 | Q | 113 | . . | E 2 | 545 | . . | X 2 |
129 | 17 | R | 609 | 77 | 4 B | 709 | 60 | 3 K | 257 | 17 | R | 121 | 6 | F | 553 | 24 | Y | ||||||
137 | 18 | S | 617 | 78 | 4 C | 85 | 8 | H | 397 | 34 | 2 I | 713 | 60* | 3 K 2 | 273 | 18 | S | 129 | 6* | 561 | 24* | ||
145 | 19 | T | 625 | 79 | 4 D | 89 | 8* | H2 | 401 | 34* | 2 I 2 | 289 | 19 | T | |||||||||
153 | 20 | U | 633 | 80 | 4 E | 97 | 9 | I | 409 | 35 | 2 K | 721 | 61 | 3 L | 305 | 20 | U | 137 | . . | F 2 | 569 | . . | Y 2 |
161 | 21 | V | 641 | 81 | 4 F | 101 | 9* | I too | 413 | 35* | 2 K 2 | 725 | 61* | 3 L 2 | 321 | 21 | V | 145 | 7 | G | 577 | 25 | Z |
169 | 22 | W | 649 | 82 | 4 G | 109 | 10 | K | 421 | 36 | 2 L | 733 | 62 | 3 M | 337 | 22 | W | 153 | 7* | 585 | 25* | ||
177 | 23 | X | 657 | 83 | 4 H | 113 | 10* | K 2 | 425 | 36* | 2 L 2 | 737 | 62* | 3 M 2 | 353 | 23 | X | 161 | . . | G 2 | 593 | . . | Z 2 |
185 | 24 | Y | 665 | 84 | 4 I | 121 | 11 | L | 433 | 37 | 2 M | 745 | 63 | 3 N | 369 | 24 | Y | 169 | 8 | H | 601 | 26 | 2 A |
193 | 25 | Z | 673 | 85 | 4 K | 125 | 11* | L 2 | 437 | 37* | 2 M 2 | 749 | 63* | 3 N 2 | 385 | 25 | Z | 177 | 8* | 609 | 26* | ||
201 | 26 | 2 A | 681 | 86 | 4 L | 757 | 64 | 3 O | 401 | 26 | 2 A | 185 | . . | H 2 | 617 | . . | 2 A 2 | ||||||
209 | 27 | 2 B | 689 | 87 | 4 M | 133 | 12 | M | 445 | 38 | 2 N | 761 | 64* | 3 O 2 | 417 | 27 | 2 B | 193 | 9 | I | 625 | 27 | 2 B |
217 | 28 | 2 C | 697 | 88 | 4 N | 137 | 12* | M 2 | 449 | 38* | 2 N 2 | 433 | 28 | 2 C | |||||||||
225 | 29 | 2 D | 705 | 89 | 4 O | 145 | 13 | N | 457 | 39 | 2 O | 769 | 65 | 3 P | 449 | 29 | 2 D | 201 | 9* | 633 | 27* | ||
233 | 30 | 2 E | 713 | 90 | 4 P | 149 | 13* | N 2 | 461 | 39* | 2 O 2 | 773 | 65* | 3 P 2 | 465 | 30 | 2 E | 209 | . . | I 2 | 641 | . . | 2 B 2 |
241 | 31 | 2 F | 721 | 91 | 4 Q | 157 | 14 | O | 469 | 40 | 2 P | 781 | 66 | 3 Q | 481 | 31 | 2 F | 217 | 10 | K | 649 | 28 | 2 C |
249 | 32 | 2 G | 729 | 92 | 4 R | 161 | 14* | O 2 | 473 | 40* | 2 P 2 | 785 | 66* | 3 Q 2 | 497 | 32 | 2 G | 225 | 10* | 657 | 28* | ||
257 | 33 | 2 H | 737 | 93 | 4 S | 793 | 67 | 3 R | 513 | 33 | 2 H | 233 | . . | K 2 | 665 | . . | 2 C 2 | ||||||
265 | 34 | 2 I | 745 | 94 | 4 T | 169 | 15 | P | 481 | 41 | 2 Q | 797 | 67* | 3 R 2 | 529 | 34 | 2 I | 241 | 11 | L | 673 | 29 | 2 D |
273 | 35 | 2 K | 753 | 95 | 4 U | 173 | 15* | P 2 | 485 | 41* | 2 Q 2 | 545 | 35 | 2 K | |||||||||
281 | 36 | 2 L | 761 | 96 | 4 V | 181 | 16 | Q | 493 | 42 | 2 R | 805 | 68 | 3 S | 561 | 36 | 2 L | 249 | 11* | 681 | 29* | ||
289 | 37 | 2 M | 769 | 97 | 4 W | 185 | 16* | Q 2 | 497 | 42* | 2 R 2 | 809 | 68* | 3 S 2 | 577 | 37 | 2 M | 257 | . . | L 2 | 689 | . . | 2 D 2 |
297 | 38 | 2 N | 777 | 98 | 4 X | 193 | 17 | R | 505 | 43 | 2 S | 817 | 69 | 3 T | 593 | 38 | 2 N | 265 | 12 | M | 697 | 30 | 2 E |
305 | 39 | 2 O | 785 | 99 | 4 Y | 197 | 17* | R 2 | 509 | 43* | 2 S 2 | 821 | 69* | 3 T 2 | 609 | 39 | 2 O | 273 | 12* | 705 | 30* | ||
313 | 40 | 2 P | 793 | 100 | 4 Z | 829 | 70 | 3 U | 625 | 40 | 2 P | 281 | . . | M 2 | 713 | . . | 2 E 2 | ||||||
321 | 41 | 2 Q | 801 | 101 | 5 A | 205 | 18 | S | 517 | 44 | 2 T | 833 | 70* | 3 U 2 | 641 | 41 | 2 Q | 289 | 13 | N | 721 | 31 | 2 F |
329 | 42 | 2 R | 809 | 102 | 5 B | 209 | 18* | S 2 | 521 | 44* | 2 T 2 | 657 | 42 | 2 R | 297 | 13* | 729 | 31* | |||||
337 | 43 | 2 S | 817 | 103 | 5 C | 217 | 19 | T | 529 | 45 | 2 U | 841 | 71 | 3 V | 673 | 43 | 2 S | 305 | . . | N 2 | 737 | . . | 2 F 2 |
345 | 44 | 2 T | 825 | 104 | 5 D | 221 | 19* | T 2 | 533 | 45* | 2 U 2 | 845 | 71* | 3 V 2 | 689 | 44 | 2 T | 313 | 14 | O | 745 | 32 | 2 G |
353 | 45 | 2 U | 833 | 105 | 5 E | 229 | 20 | U | 541 | 46 | 2 V | 853 | 72 | 3 W | 705 | 45 | 2 U | 321 | 14* | 753 | 32* | ||
361 | 46 | 2 V | 841 | 106 | 5 F | 857 | 72* | 3 W 2 | 721 | 46 | 2 V | 329 | . . | O 2 | 761 | . . | 2 G 2 | ||||||
369 | 47 | 2 W | 849 | 107 | 5 G | 233 | 20* | You too | 545 | 46* | 2 V 2 | 865 | 73 | 3 X | 737 | 47 | 2 W | 337 | 15 | P | 769 | 33 | 2 H |
377 | 48 | 2 X | 857 | 108 | 5 H | 241 | 21 | V | 553 | 47 | 2 W | 753 | 48 | 2 X | |||||||||
385 | 49 | 2 Y | 865 | 109 | 5 I | 245 | 21* | V 2 | 557 | 47* | 2 W 2 | 869 | 73* | 3 X 2 | 769 | 49 | 2 Y | 345 | 15* | 777 | 33* | ||
393 | 50 | 2 Z | 873 | 110 | 5 K | 253 | 22 | W | 565 | 48 | 2 X | 877 | 74 | 3 Y | 785 | 50 | 2 Z | 353 | . . | P 2 | 785 | . . | 2 H 2 |
401 | 51 | 3 A | 881 | 111 | 5 L | 257 | 22* | W 2 | 569 | 48* | 2 X 2 | 881 | 74* | 3 Y 2 | 801 | 51 | 3 A | 361 | 16 | Q | 793 | 34 | 2 I |
409 | 52 | 3 B | 889 | 112 | 5 M | 265 | 23 | X | 577 | 49 | 2 Y | 889 | 75 | 3 Z | 817 | 52 | 3 B | 369 | 16* | 801 | 34* | ||
417 | 53 | 3 C | 897 | 113 | 5 N | 269 | 23* | X 2 | 581 | 49* | 2 Y 2 | 893 | 75* | 3 Z 2 | 833 | 53 | 3 C | 377 | . . | Q 2 | 809 | . . | 2 I 2 |
425 | 54 | 3 D | 905 | 114 | 5 O | 277 | 24 | Y | 589 | 50 | 2 Z | 849 | 54 | 3 D | |||||||||
433 | 55 | 3 E | 913 | 115 | 5 P | 901 | 76 | 4 A | 865 | 55 | 3 E | 385 | 17 | R | 817 | 35 | 2 K | ||||||
441 | 56 | 3 F | 921 | 116 | 5 Q | 281 | 24* | Y 2 | 593 | 50* | 2 Z 2 | 905 | 76* | 4 A 2 | 881 | 56 | 3 F | 393 | 17* | 825 | 35* | ||
449 | 57 | 3 G | 929 | 117 | 5 R | 289 | 25 | Z | 601 | 51 | 3 A | 913 | 77 | 4 B | 897 | 57 | 3 G | 401 | . . | R 2 | 833 | . . | 2 K 2 |
457 | 58 | 3 H | 937 | 118 | 5 S | 293 | 25* | Z 2 | 605 | 51* | 3 A 2 | 917 | 77* | 4 B 2 | 913 | 58 | 3 H | 409 | 18 | S | 841 | 36 | 2 L |
465 | 59 | 3 I | 945 | 119 | 5 T | 301 | 26 | 2 A | 613 | 52 | 3 B | 925 | 78 | 4 C | 929 | 59 | 3 I | 417 | 18* | 849 | 36* | ||
473 | 60 | 3 K | 953 | 120 | 5 U | 305 | 26* | 2 A 2 | 617 | 52* | 3 B 2 | 929 | 78* | 4 C 2 | 945 | 60 | 3 K | 425 | . . | S 2 | 857 | . . | 2 L 2 |

THE FOREMAN OR OVERSEER.
GENERAL DUTIES.
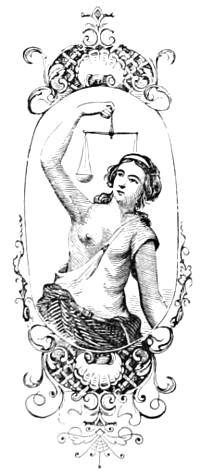
Vigilant and conscientious oversight is the price of profit and success. An overseer or foreman of a printing-office should be of more than ordinary capacity, and able to keep his temper in firm control. His conduct should be guided by justice and equity in regard to the interests of the employer and the employed. A strict impartiality should be observed in his treatment of the workmen, and no favouritism should be displayed. He should make himself acquainted with the capacity of the men, and apportion work among them accordingly. Some men are valueless except for plain, straightforward composition; others, distinguished for taste and skill, delight in intricate work or matter requiring ingenuity and delicacy, such as tables, music, and algebra. Put one of the first kind on this sort of composition, and he will botch it, and earn small wages; while a workman of the latter class will become restive and dissatisfied with plain, solid matter. While dealing justly with the men under his charge, the foreman should see to it that the employer suffers no detriment from negligent or dishonest practices of unconscientious workmen, whether from careless correcting, allowing dropped types to lie upon the[219] floor, or overcharging, or other methods well known in a printing-office. He should be the first and the last in attendance, in order to satisfy himself that every person does his duty in coming and leaving at the proper time.
Alert and attentive oversight is the cost of profit and success. A supervisor or manager at a printing office should be more than just capable and should manage their temper well. Their actions should be driven by fairness and consideration for both the employer's and employees' interests. They should treat the workers with strict impartiality and show no favoritism. It’s important for them to understand the skills of each worker and distribute tasks accordingly. Some workers are only good for basic, straightforward tasks; others, who excel in creativity and finesse, enjoy complex work that requires skill, like formatting tables, music, or algebra. If a basic worker is assigned intricate tasks, they will struggle and earn little, while a skilled worker will become frustrated with simple tasks. While treating the workers fairly, the supervisor must ensure that the employer doesn’t suffer due to the careless or dishonest actions of untrustworthy workers, like improper corrections, leaving dropped types on the[219] floor, or overcharging—methods commonly seen in a printing office. They should be the first to arrive and the last to leave, ensuring that everyone fulfills their responsibilities by arriving and departing on time.

LARGE SORT-CASE CABINET, FOR SORTS, QUADS, ETC.
LARGE SORT-CASE CABINET, FOR SORTS, QUADS, ETC.
The office having been thoroughly swept at an early hour, and the type found in any alley having been placed in the stick of the compositor occupying it, the foreman should pass around the room and see that it is immediately distributed, instead of being thrown on the window-frame or table. The type found in the body of the rooms should be sorted out and distributed at once, and not be allowed to accumulate. No pi should be permitted to remain over till the next day. This is an essential point to secure a tidy and well-regulated office.
The office was completely cleaned early in the morning, and any type found in the alley was put into the typesetting stick of the compositor using it. The foreman should walk around the room to make sure it’s distributed right away, instead of being tossed on the window ledge or table. The type found in the main areas of the office should be sorted and handed out immediately, not allowed to build up. No leftover type should be kept for the next day. This is a crucial step to ensure a tidy and well-organized office.
He should see to it that the proof-roller and press are in good condition, and that a sufficient supply of wetted proof-paper is on hand. A badly-printed proof should never be[220] allowed to go to the proof-reader or to the author, as neither can properly read a blurred or imperfect proof. An author will feel kindly toward an office that furnishes him with handsome impressions of his matter.
He should make sure that the proof roller and press are in good shape and that there’s enough damp proof paper available. A poorly printed proof should never be[220] sent to the proofreader or the author, since neither can properly read a blurry or flawed proof. An author will appreciate an office that provides him with nice copies of his work.

SORT-CASE CABINET.
Sort-case cabinet.
The foreman should keep himself fully informed as to the amount and the condition of the materials in the office, not only in gross, but in detail, including every style of type, every variety of accents and peculiar sorts, leads, chases, furniture, rules, borders, corner-pieces, &c. In this he will be greatly aided by insisting on the observance of the good old rule, A place for every thing, and every thing in its place when not in use, as well as by keeping a memorandum-book in which every thing should be entered under its proper head for facility of reference.
The foreman should stay fully updated on the quantity and condition of the materials in the office, not just overall but in detail, including every style of type, every kind of accents and unique pieces, leads, chases, furniture, rules, borders, corner pieces, etc. He will benefit significantly from enforcing the classic rule, A place for everything, and everything in its place when not in use, as well as by maintaining a notebook where everything should be recorded under its appropriate category for easy reference.

CABINET FOR SPACES, QUADS, ETC.
Cabinet for spaces, quads, etc.
If the office be well provided, it will contain one or more of the cabinets for sorts, such as are shown in these pages. Strict attention should be given to keeping them in perfect order, and in preventing them from becoming receptacles for pi.
If the office is well equipped, it will have one or more of the sorting cabinets shown on these pages. It's important to keep them organized and to make sure they don't turn into storage for junk.

COMBINATION CABINET, FOR SORTS AND QUADS.
COMBINATION CABINET FOR SORTS AND QUADS.

QUAD CABINET.
Quad Cabinet.
As a matter of course, he should watch the progress of every job and book, and make sure that they shall be completed within the time contracted for. He should never allow a compositor to have a large take of copy: small takes facilitate expedition, and really tend to the profit of the workmen by bringing an earlier return of letter. He should see to it that every man has his copy closed in proper time, so as not to detain the make-up, and that he passes the make-up without unnecessary delay. As soon as a form or sheet is made up, he should order it to be imposed and a proof pulled, which, with the copy properly arranged, is to be at once handed to the proof-reader. Nor[222] should he allow of any unnecessary delay on the part of the reader, nor on the part of the compositors in correcting the proof when read. When proofs are required by an author, the foreman must forward them promptly to him, and request him to return them at the earliest possible moment. If the proof is not to be sent out, he should have the second reading quickly performed, and the forms prepared for the foundry or the press.
As a matter of course, he should monitor the progress of every job and book, ensuring they are completed within the agreed timeframe. He should never let a compositor take on too much copy at once; smaller batches speed up the process and benefit the workers by generating quicker returns on their work. He must ensure that everyone finishes their copy on time to avoid holding up the make-up process, and that he moves through the make-up stage without unnecessary delays. As soon as a form or sheet is ready, he should order it to be imposed and a proof pulled, which, along with the properly arranged copy, should be handed over to the proofreader immediately. Nor[222] should he permit any unwarranted delays from the reader or from the compositors in making corrections to the proof. If an author requests proofs, the foreman must send them out promptly and ask for their return as soon as possible. If the proof isn’t going to be sent out, he should ensure the second reading is completed quickly, and the forms are prepared for the foundry or the press.
Systematic attention to the above points will tend to the comfort of the overseer, to the advantage of the workmen, and to the profit and satisfaction of the proprietor of the establishment.
Paying consistent attention to the above points will benefit the supervisor, help the workers, and increase the profit and satisfaction of the business owner.
The foreman will find a memorandum Press-Book very useful, in which to make entries of the amount of the paper given out by the warehouseman for the various works, the number printed, &c., as well as the names of the pressmen when the work is done on hand-presses.
The foreman will find a memo pad very useful for recording the amount of paper distributed by the warehouse worker for different jobs, the number printed, etc., as well as the names of the press operators when the work is completed on hand presses.
WHEN GIVEN OUT TO WET. | NAMES OF WORKS. | NO. | SIGNATURES. | DATE WHEN LAID ON. | NAMES OF PRESSMEN. | ||
---|---|---|---|---|---|---|---|
1878. | 1878. | ||||||
May | 8 | Specific Heat Tables | 1000 | 11 | May | 10 | Graham. |
” | 10 | The Great Exhibition | 5000 | 18 | ” | 12 | Landsdown. |
” | 12 | The American Printer | 1000 | 20 | ” | 13 | Windisch. |
” | 15 | Masterpieces of European Art | 3000 | 2 | ” | 17 | Smith. |
If not done by the proof-reader, the foreman should examine the press revise; in doing which, he will be careful not only to ascertain whether all the corrections marked in the proof are made, but also to look carefully over the sides, head, and bottom of each page. It frequently happens that the folios drop out of the form in lifting it off the imposing-stone; and in leaded matter, letters at the beginning and ends of lines sometimes fall out of place. Before the revise is given to the compositor, the name of the pressman who is to work off the form should be entered in the Press-Book. With foul compositors, he should require a second revise, in order to ascertain if all the corrections have been made which were marked in the first. He should (where there is not a pressman engaged expressly for the purpose, as is the case in houses employing[223] numerous machine-presses) go frequently to the different presses, and examine the work, point out defects, if any, and glance again over the heads, sides, and bottoms of the pages, to see if any thing has been drawn out by the rollers, which may occur from bad justification of the lines, and careless and improper locking up of the form.
If the proofreader hasn't done it, the foreman should check the press proofs. When doing this, he needs to make sure that all the corrections marked in the proof have been made, and also carefully look over the top, bottom, and sides of each page. It's common for pages to fall out of the form when it's being lifted off the imposing stone, and in typeset text, letters at the start and end of lines can sometimes get displaced. Before giving the proofs to the typesetter, the name of the pressman who will be working on the form should be written down in the Press Book. If the typesetters have a history of mistakes, he should request a second proof to confirm that all corrections from the first have been made. He should (unless there’s a pressman specifically assigned for this, which is typically the case in businesses with many machine presses) regularly visit the different presses to check the work, point out any errors, and review the tops, sides, and bottoms of the pages to make sure nothing has been accidentally removed by the rollers, which can happen due to poor line justification and careless locking of the form.
An active and conscientious foreman will not be content with merely managing the concerns of the composing room: he will also see that the business of the warehouse is attended to with regularity and accuracy, and that the warehouseman, errand-boys, and apprentices do their duty.
An active and responsible foreman won’t be satisfied with just managing the activities in the composing room; he will also ensure that the warehouse operations are handled consistently and accurately, and that the warehouse workers, errand boys, and apprentices fulfill their responsibilities.
CASTING OFF COPY.
To cast off manuscript with accuracy and precision is a task which requires great attention and mature deliberation. The trouble and difficulty are much increased when the copy is not only irregularly written, (which is generally the case,) but also abounds with interlineations, erasures, and variations in the size of paper. At times, so numerous are the alterations and additions as to baffle the skill and judgment of the most experienced calculators of copy. Such an imperfect and slovenly mode of sending works to the press cannot be too strongly censured.
To finalize a manuscript accurately and thoughtfully is a task that requires a lot of focus and careful consideration. The challenge becomes even greater when the writing is not only messy (which is usually the case) but also filled with changes, deletions, and different paper sizes. Sometimes, the number of changes and additions can overwhelm even the most skilled and experienced editors. This sloppy approach to sending works to the publisher deserves strong criticism.
The first step necessary is to take a comprehensive view of the copy, noticing whether it has been written even or has many interlineations, &c., and observing also the number of break-lines, and whether the work be divided into chapters and sub-heads, in order that allowance may be made for them in the calculation. These observations may be noted on a separate piece of paper, to assist the memory and save the trouble of re-examining the manuscript.
The first step is to take a thorough look at the copy, noticing if it’s consistent or has many corrections, etc., and also checking the number of breaks and whether the work is divided into chapters and sub-headings so that you can account for them in your calculations. You can jot down these observations on a separate piece of paper to help remember them and avoid having to re-examine the manuscript.
This preparation being made, we ascertain the number of words contained in the line by counting several separate lines in various parts of the copy, so that the one we adopt may be a fair average. We then take the number of lines in a page, and multiply by the number of words found in the average line: the result we then multiply by the quantity of folios the manuscript copy may contain, and thus we get the amount of words contained in the work with a tolerable degree of accuracy. The necessary allowances should be made for[224] break-lines, chapters, insertions, &c., according to the observations previously made on the memorandum.
Once we’ve made this preparation, we count the number of words in the line by checking several separate lines in different parts of the copy to ensure the one we choose is a fair average. Next, we take the number of lines on a page and multiply it by the number of words in the average line. We then multiply that result by the number of folios the manuscript has, giving us a reasonably accurate total word count for the work. We also need to account for [224] break-lines, chapters, insertions, and so on, based on the notes we made earlier.
If information has been furnished as to the size of letter the work is to be done in and the width of the page, we make our measure accordingly, and, by composing a few lines of the manuscript copy, we ascertain what number of words will come into each printed line: we then take the length of our page in lines, and multiply the one by the other, thus getting the number of words in the printed page. We divide the whole number of words in the manuscript by the number contained in the printed page: the quotient gives the number of pages the manuscript will make. If too many, the page must be enlarged; if too few, the page must be diminished in width and length. For example:—We take the number of words in a line of manuscript at 20, the lines in a page at 50; we multiply 50 by 20, which will produce 1000 words in a page; we then multiply 1000 by 422, the number of folios in the manuscript, and we find that it contains 422,000 words. The work being printed in Pica octavo, 20 ems measure, and each line containing 10 words, each page 40 lines, the case will stand thus:—
If we have details about the font size and page width for the work, we measure accordingly. By composing a few lines from the manuscript copy, we find out how many words fit in each printed line. We then multiply the length of the page in lines by the number of words per line to calculate the total number of words per printed page. We take the total number of words in the manuscript and divide it by the number of words that fit on a printed page; the result tells us how many pages the manuscript will be. If there are too many pages, we need to widen the page; if too few, we should reduce the width and length. For example: If there are 20 words in a line of manuscript and 50 lines in a page, we multiply 50 by 20 to get 1000 words per page. Then, we multiply 1000 by 422 (the number of folios in the manuscript) to find that it contains 422,000 words. The work is printed in Pica octavo, with a 20 ems measure, and each line has 10 words, with 40 lines per page, leading to the following situation:
MANUSCRIPT.
Draft.
50 | |
20 | |
1000 | |
422 | |
2000 | |
2000 | |
4000 | |
422000 | words in MS. |
PRINTED.
PRINTED.
40 | ||
10 | ||
400 | )422000 | words in MS. |
1055 | pages. | |
Divide | ||
16)1055 | (65 sheets, | |
15 pages. |
Another method for casting off copy is the following, as laid down by a predecessor:—
Another way to discard a copy is as follows, as stated by someone before:—
“After having made the measure for the work, we set a line of the letter that is designed for it, and take notice how much copy will come into the line in the stick,—whether less or more than a line of manuscript; and, as it is seldom that neither one nor the other happens, we make a mark in the copy where the line in the stick ends, and number the words that it contains. But, as this is not the safest way for casting off close, we count not only the syllables, but even the letters,[225] that are in a line in the stick, of which we make a memorandum, and proceed to set off a second, third, or fourth line, till a line of copy falls even with a line in the stick; and, as we did to the first line in the stick, so we do to the other, marking on the manuscript the end of each line in the stick, and telling the letters in each, to see how they balance against each other. This being carefully done, we begin counting off, each time, as many lines of copy as we know will make even lines in the stick. For example, if 2 lines of copy make 3 lines in print, then 4 make 6, 6 make 9, 8 make 12, and so on, calling every two lines of copy three in print. In like manner we say, if 4 lines make 5, then 8 make 10, and so on, comparing every four lines of copy to five lines in print. And in this manner we carry our calculation on as far as we have occasion, either for pages, forms, or sheets.
“After measuring for the job, we set a line for the letter designed for it and check how much text fits in the line in the stick—whether it's less or more than a line of manuscript. Since this rarely happens perfectly, we mark where the line in the stick ends in the copy and count the words it contains. However, since this isn't the most reliable method for precise layouts, we not only count the syllables but even the letters[225] in a line in the stick, which we make a note of, and then we start laying out a second, third, or fourth line until a line of copy aligns with a line in the stick. Just like we did with the first line in the stick, we do the same for the others, marking the end of each line in the stick on the manuscript and counting the letters in each to see how they balance against each other. Once this is done carefully, we start counting off as many lines of copy as we know will create even lines in the stick. For instance, if 2 lines of copy make 3 lines in print, then 4 make 6, 6 make 9, 8 make 12, and so on, categorizing every two lines of copy as three in print. Similarly, we say if 4 lines make 5, then 8 make 10, and so forth, comparing every four lines of copy to five lines in print. In this way, we continue our calculations as needed for pages, forms, or sheets."
The foregoing calculations are intended to serve where a line of print takes in less than a line of copy; and, therefore, where a line of print takes in more than a line of copy, the problem is reversed, and, instead of saying, if 2 lines make 3, we say, in this case, if 3 lines of copy make 2 lines in print, then 6 lines make 4, 9 make 6, 12 make 8, and so on, counting three lines of copy to make two lines in print. In this manner we may carry our calculation to what number of pages, forms, or sheets we will, remembering always to count off as many lines of copy at once as we have found they will make even lines in the stick. Thus, for example, if 5 lines make 7, the progression of 5 is 10, 15, 20, &c., and the progression of 7 will be 14, 21, 28, &c.
The calculations above are meant to apply when a line of print is shorter than a line of copy. Therefore, when a line of print is longer than a line of copy, the situation changes. Instead of saying that 2 lines equal 3, we now say that if 3 lines of copy equal 2 lines of print, then 6 lines make 4, 9 make 6, 12 make 8, and so on, counting three lines of copy to make two lines in print. This allows us to extend our calculations to as many pages, forms, or sheets as needed, always remembering to count as many lines of copy at once as we’ve established they will convert into even lines in the stick. For example, if 5 lines equal 7, the sequence for 5 will be 10, 15, 20, etc., and the sequence for 7 will be 14, 21, 28, etc.
In counting off copy, we take notice of the breaks; and where we judge that one will drive out, we intimate it by a mark of this shape [; and again, where we find that a break will get in, we invert it, thus, ]. And to render these marks conspicuous to the compositor, we write them in the margin, that he may take timely notice, and keep his matter accordingly. We also take care to make proper allowance for heads to chapters, sections, paragraphs, &c.
In counting off copies, we pay attention to the breaks; and when we think one will fit in, we indicate it with a mark like this [; and when we find that a break will be inserted, we flip it, like this, ]. To make these marks stand out for the typesetter, we write them in the margin so that they can notice them in time and adjust the content accordingly. We also ensure to allow for titles for chapters, sections, paragraphs, etc.
In examining the state of the copy, we must observe whether it has abbreviations, that we may guard against them in casting off, and allow for them according to the extent of the respective words when written out at length.”
In looking at the condition of the copy, we need to check if it has abbreviations so we can avoid them when finalizing it and account for them based on how long the respective words are when fully written out.
The foregoing will convey a sufficient idea as to the best[226] mode of casting off copy; still, these remarks more properly apply to regularly written and thoroughly revised copy. Upon this subject, Smith justly observes,—
The above will give a good understanding of the best[226]way to finalize written material; however, these comments are more relevant to well-written and carefully edited content. On this topic, Smith rightly points out,—
“But how often one or more of these requisites are wanting, compositors can best tell; though very few will imagine that among men of learning there should be some who write after such a manner that even those who live by transcribing rather shun than crave to be employed by them: no wonder, therefore, if compositors express not the best wishes to such promoters of printing. But it is not always the capacious genius that ought to be excused for writing in too great a hurry; for sometimes those of no exuberant brains affect uncouth writing, on purpose to strengthen the common notion that the more learned the man, the worse is his (hand) writing; which shows that writing well or bad is but a habit with those that can write.”
“But how often one or more of these necessary skills are missing, typesetters can best tell; though very few would think that among educated people there are some who write in such a way that even those who make a living by copying would rather avoid working for them: it's no surprise, then, if typesetters don’t have the best feelings toward such advocates of printing. However, it’s not always the highly talented individual who should be excused for writing too quickly; sometimes those with less impressive intellects purposely use awkward writing to reinforce the common belief that the more educated a person is, the worse their (hand) writing; which indicates that writing well or poorly is merely a habit for those who can write.”
HURRIED WORK.
It is sometimes necessary to print pamphlets and other works of a temporary nature in the course of a few hours. When a work of this kind is put in hand, the foreman selects the requisite number of swift and skilful compositors, whose first concern must be to appoint one from among them to make up the matter, and to do every thing which would interfere with the regular business of distributing, composing, and correcting. While they are distributing letter, the clicker, or person appointed to manage the work, procures the copy, with all necessary information respecting it, and provides leads, rules, and every other necessary sort. He then draws out the following table:—
It's sometimes necessary to print pamphlets and other temporary materials in just a few hours. When this type of work begins, the foreman selects the right number of quick and skilled typesetters, whose first task is to choose one among them to assemble the content and handle anything that might disrupt the normal process of distributing, typesetting, and proofreading. While they are sorting out the letters, the clicker, or the person in charge of managing the work, gathers the copy along with all the necessary information about it, and organizes leads, rules, and everything else needed. He then creates the following table:—
COMPOSITORS’ NAMES. | FOLIOS OF COPY. | LINES COMPOSED. | MEMORANDUMS. |
---|---|---|---|
Farroe | 1- 5 | 184 | |
Wilson | 6-10 | 168 | |
Stratz | 11-16 | 121 |
In the first column he writes the name of each compositor when he takes copy; and, in the second, the folio of the copy,[227] that he may be able to ascertain instantly in whose hands it lies. In the third column he sets down, opposite to the workman’s name, the number of lines composed, as fast as the galleys are brought to him. In the fourth, he inserts such remarks respecting the copy, &c. as may be necessary, and also any circumstances that may occur in the companionship.
In the first column, he writes the name of each typesetter when he takes the copy; in the second, he notes the folio of the copy,[227] so he can quickly check who has it. In the third column, he records the number of lines composed, as soon as the galleys are handed to him. In the fourth, he includes any comments about the copy, etc., as well as any relevant situations that arise during the process.
When the work is finished, each man’s share of lines is readily ascertained, and all disputes are avoided. The publisher may expedite the progress of the work by offering a copy of the book, or some other token, as a premium to the compositor who sets the largest number of ems. The maker-up or clicker usually receives for his compensation the head and foot lines, and two or three cents per thousand, which is deducted from the wages paid to the compositor. Sometimes the compositors work “in pocket,” as it is called, or share evenly in the proceeds. This, however, is not a satisfactory mode, and its tendency is to retard the work, as no man will be anxious to do more than his share.
When the job is done, it’s easy to figure out how many lines each person is responsible for, which prevents arguments. The publisher might speed things up by giving a copy of the book or some other reward to the typesetter who sets the most ems. The layout person or clicker typically gets paid with the first and last lines and a couple of cents per thousand, which is taken from what the typesetter earns. Sometimes, the typesetters work "in pocket," meaning they split the earnings evenly. However, this approach isn’t ideal, as it slows down the work because no one is motivated to do more than their part.
When the compositors are ready for their first taking of copy, it should be given to them in pieces as short as possible, the first two beginning with shorter takes than the others, to prevent delay in the making up. During the time the first take is in hand, the clicker sets the half-head, head-lines, white-lines, and signature-lines, together with notes and other extraneous matter.
When the compositors are ready for their first copy take, it should be given to them in the shortest pieces possible, with the first two being shorter than the others to avoid delays in assembly. While the first take is being worked on, the clicker sets the half-head, headlines, white-lines, and signature lines, along with notes and any other additional materials.
When the first person brings his matter, the clicker counts or measures off with a type-measure the number of lines, and inserts them in the table; he then gives him another take of copy, and proceeds with the making up. The same plan is observed with the rest of the compositors. When the first sheet is made up, the clicker lays the pages on the stone, and informs the foreman of it, who has previously had chases and furniture prepared and the clicker immediately imposes the form.
When the first person presents their work, the clicker counts or measures the number of lines using a measuring tape, and logs them into the table; then he gives them another copy and continues with the typesetting. The same process is followed with the other compositors. Once the first sheet is ready, the clicker arranges the pages on the stone and notifies the foreman, who has already prepared the chases and furniture, and the clicker immediately sets the form.

TYPE MEASURE.
TYPE MEASUREMENT.
The proofs should be read at once and given to the clicker to have them corrected. As soon as this is done, he lays up[228] the forms, and gives the proof to the compositor whose matter stands first, who should immediately correct it, then forward it to the next, and so on, till the sheet be corrected; the clicker then locks it up and pulls the second proof, which must be duly forwarded, and the type be locked up finally for press.
The proofs should be reviewed immediately and handed to the clicker for corrections. Once that's done, he files away[228] the forms and gives the proof to the compositor who has priority, who should correct it right away and then pass it on to the next person, continuing until the sheet is fully corrected. The clicker then secures it and pulls the second proof, which needs to be sent along properly, and the type should finally be locked up for printing.
The work will now proceed rapidly, provided the compositors stick close to their work and there be no hinderance with respect to letter, &c.: this depends on the good management of the foreman.
The work will now move quickly, as long as the typesetters stay focused on their tasks and there are no issues with the letters, etc.: this relies on the foreman's good management.
If the clicker find that he cannot make up the matter as fast as it is composed, he should call one of the compositors to his assistance, who must be the person last in copy.
If the clicker finds that he can't keep up with the material being produced, he should call one of the compositors for help, and that person must be the one who most recently handled the copy.
COMPANIONSHIPS.
Disputes sometimes arise in a printing-office upon trifling as well as important points, which should be settled by a reference to the general custom and usage of the trade. These annoying misunderstandings take place in companionships consisting of several compositors; it is therefore highly desirable that the generally received rules and regulations in this regard should be explicitly laid down for the comfort and government of the compositor.
Conflicts can sometimes happen in a print shop over both minor and major issues, which should be resolved by referring to the standard practices of the industry. These frustrating misunderstandings often occur in groups of multiple typesetters; therefore, it’s important that the commonly accepted rules and guidelines on this matter are clearly outlined for the benefit and management of the typesetter.
TAKING COPY.

STEEL COMPOSING RULE.
STEEL COMPOSING GUIDELINE.
When the work to be taken in hand is a reprint which is to be followed page for page, a fixed number of pages should be given to each compositor as he comes in turn for copy; or, if the work be in manuscript, an equal average amount should be allowed as a take for each compositor. None of the hands should have access to the copy, but the foreman should deal it out as wanted with perfect impartiality, fat or lean as it may happen to run. Otherwise, a compositor who has an acquaintance with the[229] copy may be tempted to loiter if the next take to be given out be lean, or, if it be fat, to apply for copy before his work in hand is finished. By this course, the foreman will prevent all such sorts of sharp practice, and secure harmony in the companionship. When the foreman gives out copy, he should plainly mark the name of the compositor at the head of the first page of the take if the work be a page-for-page reprint; if it be manuscript, or a reprint in a different measure from that of the copy, he should write the name at the beginning of the first paragraph of the take. Most compositors desire to have a large portion of copy, under the erroneous idea that it will be to their advantage to make up many pages at once. Small takes insure a more rapid execution of the work and bring a quicker return of letter, and so tend to the profit of the hands.
When the task at hand is a reprint that needs to follow the original page for page, each compositor should receive a fixed number of pages in turn; or, if the work is in manuscript, an equal average amount should be assigned to each compositor. None of the workers should have direct access to the copy, but the foreman should distribute it fairly as needed, whether it's a lot or a little. Otherwise, a compositor who is familiar with the copy might be tempted to slack off if the next batch is smaller or try to hog the copy if it’s larger before finishing their current work. This approach helps the foreman prevent such behavior and maintain harmony within the team. When the foreman distributes copy, they should clearly write the compositor's name at the top of the first page of the batch if it's a page-for-page reprint; if it's a manuscript or a reprint in a different format, the name should be placed at the beginning of the first paragraph of the batch. Most compositors mistakenly believe that having a large batch of copy will benefit them in producing many pages at once. However, smaller batches ensure faster work and quicker letter returns, ultimately benefiting the workers.
If one of the companionship absent himself, the man next in order should close his copy, whether it be good or bad, unless the larger portion of it be not set, in which case the person who has the last take must go on with it.
If one of the companions is absent, the next person in line should close his copy, whether it’s good or bad, unless the larger portion of it isn’t set, in which case the person who took the last should continue with it.
MAKING UP.
The compositor who has the first take on the work proceeds without delay to make it up as soon as he has completed it. Having completed as many pages as his matter will make, he passes the overplus, if less than half a page, with the correct head and folio, to the compositor whose matter follows his, at the same time taking an account of the number of lines loaned; if, on the contrary, the overplus makes more than half a page, he borrows a sufficient number of lines to complete his page; each compositor keeping an account of the number of lines borrowed and loaned. The second compositor, following the same course, passes the make-up to the next in succession; each man passing the make-up in like manner without unnecessary delay.
The compositor who first gets the job starts working on it right away as soon as he’s finished. Once he’s put together as many pages as his material allows, he passes on any extra, if it’s less than half a page, with the correct heading and page number, to the compositor whose material comes next. At the same time, he keeps track of how many lines he lent out. If the extra is more than half a page, he borrows enough lines to finish his page, with each compositor keeping a record of the lines borrowed and lent. The second compositor, following the same process, passes the work to the next person in line; each person passes their work along without unnecessary delay.

STEEL MAKE-UP RULE.
STEEL MAKEUP RULE.
MAKING UP OF LETTER.
The number of the companionship, if possible, should be determined on at the commencement of the work, to enable all to proceed upon an equal footing. The letter appropriated for the work should be adequate to keep the persons on it fully employed.
The number of people in the group should be decided at the start of the project to ensure everyone is on the same level. The resources allocated for the project should be enough to keep everyone fully engaged.
If any part of the matter for distribution, whether in chase or in paper, be desirable on account of the sorts it may contain, it should be divided equally, or the choice of it thrown for.
If any part of the items for distribution, whether it's in a collection or on paper, is valuable because of what it might contain, it should be divided equally, or the selection should be made by chance.
When a new companion is put on the work after the respective shares of letter are made up, and if there be not a sufficiency to carry on all the companionship without making up more, he must bring on an additional quantity before he can be allowed to partake of any part of that which comes from the press.
When a new partner starts working after the respective shares of letters are arranged, and if there isn't enough to continue the collaboration without creating more, they must provide an additional amount before they can be allowed to take part in anything that comes from the press.
MAKING UP FURNITURE.
The companions in rotation should make up the furniture in turn, the one who has the last matter in the first sheet leading off. Should an odd sheet be wanted, it will be better to throw for the chance of making it up.
The companions in rotation should take turns arranging the furniture, with the person who has the last piece on the first sheet starting off. If an extra sheet is needed, it's better to roll for the chance to decide who makes it up.
IMPOSING AND DISTRIBUTING LETTER.
The person to whose turn it falls to impose must lay up the form for distribution. To prevent disputes, it will be well to prepare a blank form, as follows, which may be filled up as the work proceeds:—
The person whose turn it is to impose must set up the form for distribution. To avoid disagreements, it's a good idea to prepare a blank form like this, which can be filled out as the work goes on:—
SIGNATURES. | THE GREAT INTERNATIONAL EXHIBITION. | BY WHOM IMPOSED. | ||||||
---|---|---|---|---|---|---|---|---|
BEATTY. | GOUDY. | FARROE. | WILSON. | CLARK. | MCGUIGAN. | MAYHEW. | ||
B | 3 | 2 | 2 | 2 | 2 | 3 | 2 | Clark. |
C | 2 | 2 | 3 | 2 | 3 | 2 | 2 | McGuigan. |
D | 3 | 2 | 2 | 3 | 2 | 2 | 2 | Farroe. |
E | 2 | 2 | 3 | 2 | 2 | 2 | 3 | Wilson. |
F |
When the form is laid up, the letter should be divided equally, and, if possible, each person should distribute the matter originally composed by him; by this means, the sorts which may have made his case uneven will return to him. If any man absent himself beyond a reasonable time, his undistributed matter should be divided equally among his companions, and when he returns he may have his share of the next division.
When the form is set aside, the letter should be divided evenly, and, if possible, each person should handle the parts they originally wrote; this way, any discrepancies in their contributions will come back to them. If anyone is absent for too long, their undistributed parts should be shared equally among their peers, and when they return, they can receive their portion in the next allocation.
CORRECTING, ETC.
The compositor whose matter is first in the proof should lay up the forms on the imposing-stone and correct it; he then hands the proof to the person who follows next. The compositor who corrects the last part of the sheet locks up the forms.
The compositor who has the first material in the proof should set up the forms on the imposing-stone and make corrections; then, they pass the proof to the next person. The compositor who corrects the last section of the sheet locks up the forms.
The compositor who has matter in the first and last part, but not the middle of the sheet, only lays up the forms and corrects his matter; the locking up is left to the person who corrects last in the sheet.
The typesetter who has text in the first and last parts but not in the middle of the page just sets up the forms and checks his text; the final locking is left to the person who does the last corrections on the page.
A compositor having the first page only of the sheet is required to lay up one form; also to lock up one form if he has but the last page.
A compositor who only has the first page of the sheet needs to set up one form; they also need to lock up one form if they only have the last page.
If, from carelessness in locking up the form,—viz. the furniture binding, the quoins badly fitted, &c.—any letters, or even a page, should fall out, the person who locked up the form should repair the damage. But, if the accident occur from bad justification, or from letters riding upon the ends of the leads, the loss should fall upon the person to whom the matter belongs.
If, due to careless locking of the type—like furniture binding, poorly fitted quoins, etc.—any letters, or even a page, come loose, the person who locked the type should fix the issue. However, if the problem arises from bad justification or from letters sitting on the ends of the leads, the loss should be taken by the person who owns the content.

CHASE CABINET.
CHASE CABINET.
It is the business of the locker-up to ascertain whether all the pages are of equal length; and, though a defect in this[232] respect is highly reprehensible in the maker-up, (whose duty it is to rectify it,) yet, if not previously discovered by the locker-up, and an accident happen, he must make good the defect.
It’s the locker-up’s job to check if all the pages are the same length; and while it’s pretty unacceptable for the maker-up to let this slip (since it’s their responsibility to fix it), if the locker-up doesn’t catch it beforehand and something goes wrong, they have to fix the problem.
The compositor who imposes a sheet must correct the alterations in that sheet. He must also rectify any defect in the register arising from want of accuracy in the furniture.
The compositor who arranges a sheet must fix the changes in that sheet. He must also fix any errors in the alignment caused by inaccuracies in the furniture.
Forms sometimes remain a considerable length of time before they are put to press. In this case, particularly in summer, the furniture is likely to shrink, and the pages may fall out. It is therefore the business of the locker-up to attend to it in this respect, or he will be subject to make good any accident which his neglect may occasion.
Forms sometimes sit for a long time before being printed. In this case, especially in summer, the materials are likely to shrink, and the pages might fall out. It’s the responsibility of the person in charge to take care of this, or they will have to fix any problems that their negligence might cause.
When forms which have been worked off are ordered to be kept standing, they are considered under the care of the foreman. When they are cleared away, it is to be done in equal proportions by the companionship. During the time any forms may have remained under the care of the foreman, should there have been any alteration as to form or substance which were not made by the original compositors, they are not subject to clear away those parts of the form thus altered. To prevent dust from settling in the face of the type, it is well to keep the forms in a chase cabinet.
When forms that have been finished are ordered to be kept aside, they are under the supervision of the foreman. When they are cleared away, it should be done evenly by the team. During the time any forms are with the foreman, if there are any changes in form or substance that were not made by the original compositors, they are not responsible for clearing away those altered parts of the form. To prevent dust from settling on the type, it's best to keep the forms in a chase cabinet.
If the pressman unlock a form on the press, and any part of it fall out from carelessness in the locking up, he is subject to the loss that may happen in consequence.
If the pressman unlocks a form on the press and any part of it falls out because of careless locking, he is responsible for any loss that may occur as a result.
The compositor who locks up a sheet takes it to the proof-press, and, after he has pulled a proof, hands it, together with the foul proof, to the reader, and deposits the form in a place appointed for that purpose.
The typesetter who locks up a sheet takes it to the proofing press, and after pulling a proof, gives it, along with the rough proof, to the reader, and places the form in a designated area for that purpose.
TRANSPOSITION OF PAGES.
Each person in the companionship must lay down his pages properly on the stone for imposition. The compositor whose turn it is to impose looks them over to see if they are rightly placed. Should they, after this examination, lie improperly, and be thus imposed, it will be his business to transpose them; but, should the folios be wrong, and the mistake arise from this cause, it must be rectified by the person to whom the matter belongs. Pages without folios or head-lines, laid down wrongly for imposition, must be rectified by the person who has been slovenly enough to adopt this plan.
Each person in the group must lay out their pages correctly on the stone for printing. The compositor, whose turn it is to set the type, checks them to ensure they're in the right order. If, after this check, they are placed incorrectly and printed that way, it will be his job to fix them; however, if the folios are wrong and the mistake comes from that, the person responsible for the matter must correct it. Pages without folios or headings, if laid down incorrectly for printing, must be fixed by the person who carelessly chose to do it this way.
RULES AND REGULATIONS TO BE OBSERVED IN A PRINTING-OFFICE.
Compositors are to receive their cases from the foreman or his assistant, free from all pi or improper sorts, with clean quadrate and space boxes, both Roman and Italic, which they are to return to him in equally good condition.
Typesetters will get their cases from the foreman or his assistant, without any incorrect or unwanted types, and with clean square and space boxes, both Roman and Italic, which they need to return to him in just as good condition.
2. When a compositor receives letter, furniture, &c. from the foreman, he is to return any portion not used, in as good state as he received it, the same day.
2. When a compositor gets letters, furniture, etc. from the foreman, he needs to return any unused parts in as good condition as he received them, on the same day.
3. When a case is taken out of the rack, the compositor is to return it into the proper place immediately after he has done with it.
3. When a case is removed from the rack, the typesetter must put it back in the correct spot right after he's finished using it.
4. No cases to be placed over others, or under the frames, or on the floor.
4. No cases should be stacked on top of each other, placed under the frames, or put on the floor.
5. Compositors are to impose their matter and pull a proof as soon as made up, unless directed otherwise, and to correct the proof without unnecessary delay.
5. Compositors should set up their material and pull a proof as soon as it's ready, unless told otherwise, and they need to correct the proof without unnecessary delay.
6. The proof, when pulled, to be given to the reader, the copy in regular order to accompany the first proof, and the foul proof the second.
6. The proof, when finalized, will be provided to the reader, the regular copy will accompany the first proof, and the draft proof will be the second.
7. Compositors are not to leave either type or furniture on the stone.
7. Compositors should not leave any type or furniture on the stone.
8. A compositor is not to detain an imposing-stone longer than the nature of the business may require.
8. A compositor shouldn't hold onto an imposing-stone any longer than necessary for the task at hand.
9. Head-lines, or other useful materials, on galleys, used during the course of a work, to be cleared away as soon as the work is finished.
9. Headlines or other helpful materials on galleys, used during the process of a project, should be removed as soon as the project is complete.
10. When a work is done, the compositor, before beginning another work, unless otherwise directed, is to clear away the forms, taking from them the head-lines, white-lines, and odd sorts, as well as the leads and reglets; which, with the furniture of each sheet, and the matter properly tied up for papering, are to be given to the foreman.
10. When a job is finished, the typesetter, before starting another project, unless instructed otherwise, should clear away the typesetting forms, removing the headlines, blank spaces, and any random types, along with the leads and reglets; these, along with the materials for each sheet and the content properly bundled for papering, should be given to the supervisor.
11. Types dropped on the floor to be picked up at once. Matter broken by accident to be cleared away on the same day.
11. Items dropped on the floor should be picked up immediately. Any accidental spills or breakages should be cleaned up the same day.
12. The saw, saw-block, bowl, sponge, letter-brush, shears, bellows, &c., to be returned to their respective places as soon as done with.
12. The saw, saw-block, bowl, sponge, letter brush, shears, bellows, etc., should be returned to their proper places as soon as you’re done using them.
13. Letter-boards, windows, frames, &c., to be kept free from pi.
13. Letter boards, windows, frames, etc., should be kept clear of pi.
14. No person to take sorts from the cases of another without leave, nor hoard useful sorts, not wanting or likely to want them.
14. No one should take kinds from someone else's collection without permission, nor should they hoard useful items they don't need or aren't likely to use.
15. Compositors employed by the week to work not less than ten hours per day.
15. Compositors were employed by the week to work at least ten hours a day.
16. Unnecessary conversation to be avoided.
16. Avoid small talk.

GALLEY CABINET.
Kitchen cabinet.

THE PRESS AND ITS WORKING.
HISTORY OF THE PRESS.

OLD COMMON PRESS.
OLD COMMON PRESS.
While poets and orators have expatiated on the glory and power of the press, rulers have exhausted their cunning in attempts to curb and regulate the art of which it is the symbol. Hedged in by arbitrary restrictions, it is not wonderful that printing was long carried on with clumsy implements. The earliest press resembled a screw-press, with a contrivance for running the form of types under the point of pressure. After the impression was taken, the screw was relaxed, and the form withdrawn and the sheet removed.
While poets and speakers have elaborated on the glory and power of the press, leaders have used their cleverness in efforts to control and regulate the very art it symbolizes. Limited by arbitrary restrictions, it’s not surprising that printing was long done with awkward tools. The earliest press looked like a screw press, with a mechanism to move the type under the pressure point. After the impression was made, the screw was loosened, the type was removed, and the sheet was taken out.
This rude press continued in general use till 1620, when Willem Jansen Blaeu, at first a joiner and afterward a mathematical instrument maker of Amsterdam, contrived a press in which the bed or carriage was brought under the point of pressure by moving a handle attached to a screw hanging in a beam with a spring, the spring causing the screw to fly back as soon as the impression was given. This movement was afterward effected by means of a double strap or belt, two ends of which were attached to an axle, and the others to opposite ends of the bed. The platen was so small that two pulls were necessary to print one side of a sheet, and each sheet, therefore, required four pulls to produce a complete impression.
This basic press remained commonly used until 1620, when Willem Jansen Blaeu, originally a carpenter and later a mathematical instrument maker from Amsterdam, invented a press that brought the bed or carriage under the point of pressure by moving a handle connected to a screw hanging from a beam with a spring. The spring would make the screw retract as soon as the impression was made. This operation was later accomplished using a double strap or belt, with one end attached to an axle and the other ends connected to opposite sides of the bed. The platen was so small that two pulls were needed to print one side of a sheet, meaning each sheet required four pulls to achieve a complete impression.
Adam Ramage, who came from Scotland to Philadelphia about 1790, and who for a long time was the chief press-builder in the United States, made some improvements in the old press, one of which was the substitution of an iron bed for the stone one before in use.
Adam Ramage, who moved from Scotland to Philadelphia around 1790, and who for many years was the leading press-builder in the United States, made several upgrades to the old press, one of which was replacing the stone bed with an iron one.
About the year 1800, Earl Stanhope contrived a press which obtained much notoriety. It was constructed of iron, and of a size sufficient to print the whole surface of a sheet, and such a combined action of levers was applied to the screw as to make the pull a great deal less laborious to the pressman.
About the year 1800, Earl Stanhope designed a press that gained a lot of attention. It was made of iron and was large enough to print an entire sheet at once, using a system of levers that made it much easier for the press operator to pull the screw.

COLUMBIAN PRESS.
COLUMBIAN PRESS.
The Stanhope press, however, was soon surpassed by the Columbian press, invented by George Clymer, of Philadelphia. Mr. Clymer, as early as 1797, endeavoured to improve the common wooden press. His next efforts were directed to the production of an iron press, till finally eminent success was the result of his labours. In beauty, durability, and power, as well as facility of pull, the Columbian press stands perhaps unsurpassed. The power in this press is procured by a long bar or handle acting upon a combination of exceedingly powerful levers above the platen; the return of the handle or levers being effected by means of counterpoises or weights.[237] The powerful command which the leverage enables the workman to exercise is favourable to delicacy and exactness of printing,—his arm feeling, as it were, through the series of levers to the very face of the types. The inventor removed to England in 1817, and introduced the press there, where it has long been held in high estimation.
The Stanhope press was quickly outdone by the Columbian press, invented by George Clymer from Philadelphia. Mr. Clymer started trying to improve the standard wooden press back in 1797. He then shifted his focus to creating an iron press, and ultimately achieved great success through his efforts. In terms of beauty, durability, power, and ease of use, the Columbian press is likely unmatched. The power for this press comes from a long bar or handle that operates a set of very strong levers above the platen; the handle or levers return with the help of counterweights. [237] The leverage this design provides allows the operator to work with precision and accuracy in printing, as if his arm is directly feeling the type through the levers. The inventor moved to England in 1817 and introduced the press there, where it has been highly regarded ever since.

WASHINGTON PRESS.
Washington Press.
In the United States, presses of simpler construction have displaced the imposing Columbian press,—the first of which was invented by Peter Smith, of New York, and the latest is Samuel Rust’s Washington press, which has secured general approbation and adoption, as being more simple and cheaper, if not more effective, than the Columbian press. Hand-presses are now restricted to country papers of small circulation, and to book-offices devoted to extra fine printing.
In the United States, simpler printing presses have replaced the impressive Columbian press—the first one of which was invented by Peter Smith from New York, and the latest is Samuel Rust's Washington press, which has gained widespread approval and use for being simpler and cheaper, if not more effective, than the Columbian press. Hand presses are now limited to small-town newspapers with low circulation and to publishing houses focused on high-quality printing.
The bed-and-platen power-press invented by Isaac Adams, of Boston, was for a considerable time the only machine-press capable of producing fine work and exact register. It will give from six to eight thousand impressions per day. As the platen rolls off and leaves the bed entirely exposed, forms can be made ready with great facility. The sheets are[238] taken from the feed-board by fingers, and, after being printed, are laid in a pile by a self-acting sheet-flyer.
The bed-and-platen power press invented by Isaac Adams in Boston was the only machine press for a long time that could deliver high-quality work and precise alignment. It can produce between six to eight thousand impressions a day. As the platen rolls off, it completely exposes the bed, making it easy to prepare forms. The sheets are [238] picked up from the feed board by hand, and after printing, they are stacked in a pile by a self-operating sheet flyer.
The Cylinder press, which may be run at a much higher rate of speed than the bed-and-platen machine, was of earlier invention. Frederick König, a Saxon, early in the present century turned his attention to cylinder printing, and was so successful that on November 28, 1814, the London Times announced the fact that the number issued on that day had been printed by machinery propelled by steam. The earliest suggestion of a cylinder press is due, however, to William Nicholson, of England, who, in 1790 took out a patent for such a machine, but it was never perfected. According to Mr. Isaiah Thomas, a Dr. Kinsley, of Connecticut, afterward produced a press varying somewhat from Nicholson’s.
The Cylinder press, which can operate at a much higher speed than the bed-and-platen machine, was invented earlier. Frederick König, a Saxon, focused on cylinder printing early in this century and was so successful that on November 28, 1814, the London Times announced that the issue released that day was printed by steam-powered machinery. However, the earliest idea for a cylinder press comes from William Nicholson of England, who patented such a machine in 1790, although it was never fully developed. According to Mr. Isaiah Thomas, a Dr. Kinsley from Connecticut later created a press that differed somewhat from Nicholson’s design.

STOP CYLINDER PRESS.
STOP CYLINDER PRESS.
In 1818, Applegath and Cowper made important improvements[239] in König’s press, which greatly enlarged its field of usefulness. This machine, with various modifications and improvements, is in general use in Europe and America, for newspapers of moderate circulation, and even for fine job and book work, as entirely accurate register can now be secured on the new cylinder presses of the best makers, such as Hoe & Co.,[17] Cottrell & Babcock, Campbell, and others. The stop cylinder press (the latest improvement) is particularly well adapted for fine printing.
In 1818, Applegath and Cowper made significant improvements[239] to König’s press, which greatly expanded its usefulness. This machine, with various modifications and enhancements, is commonly used in Europe and America for newspapers with moderate circulation, and even for high-quality job and book printing, as precise registration can now be achieved on the new cylinder presses from top manufacturers like Hoe & Co.,[17] Cottrell & Babcock, Campbell, and others. The stop cylinder press (the most recent improvement) is especially suited for fine printing.

HOE’S TYPE-REVOLVING MACHINE—SIDE VIEW.
HOE’S TYPE REVOLVING MACHINE—SIDE VIEW.
The invention of steam printing presses rendered books and periodicals so cheap that the progress of knowledge was amazingly accelerated; and soon the capacity of the cylinder press proved unequal to the work of printing the enormous editions of some of the leading newspapers of the world; and the first successful invention to meet the exigency was[241] made by Col. Richard M. Hoe, of New York, in the Type-Revolving Printing Machine, of which we give an engraving. It is, as its name indicates, on the rotary principle; that is, the form of type is placed on the surface of a horizontal revolving cylinder of about four and a half feet in diameter. The form occupies a segment of only about one-fourth of the surface of the cylinder, and the remainder is used as an ink-distributing surface. Around this main cylinder, and parallel with it, are placed smaller impression cylinders, varying in number from four to ten, according to the size of the machine. The large cylinder being put in motion, the form of types is carried successively to all the impression cylinders, at each of which a sheet receives the impression of the types as the form passes. Thus, as many sheets are printed at each revolution of the main cylinder as there are impression cylinders around it. One person is required at each impression cylinder to supply the sheets of paper, which are taken at the proper moment by fingers or grippers, and after being printed are carried out by tapes and laid in heaps by means of self-acting flyers, thereby dispensing with the hands required in ordinary machines to receive and pile the sheets. The grippers hold the sheet securely, so that the thinnest newspaper may be printed without waste.
The invention of steam printing presses made books and magazines so affordable that the spread of knowledge sped up dramatically. Soon, the capacity of the cylinder press couldn't keep up with the massive print runs of some of the world’s top newspapers. The first successful solution to this issue was created by Col. Richard M. Hoe from New York, with the Type-Revolving Printing Machine, which we illustrate here. As the name suggests, it operates on a rotary principle; specifically, the type is placed on the surface of a horizontal revolving cylinder about four and a half feet in diameter. The type form takes up only about a quarter of the cylinder's surface, while the rest serves as an ink distribution area. Smaller impression cylinders, typically four to ten, are arranged around this main cylinder. When the large cylinder is in motion, the type form moves successively to each impression cylinder, where a sheet receives an impression as it passes by. This way, as many sheets are printed with each turn of the main cylinder as there are impression cylinders surrounding it. Each impression cylinder needs one person to load the paper sheets, which are grabbed at the right moment by fingers or grippers. After printing, the sheets are transferred by tapes and stacked via self-acting flyers, eliminating the need for hands to handle and pile the sheets like in traditional machines. The grippers securely hold the sheets, ensuring that even the thinnest newspapers can be printed without wastage.
The ink is contained in a fountain placed beneath the main cylinder, and is conveyed by means of distributing rollers to the distributing surface on the main cylinder. This surface being lower, or less in diameter, than the form of types, passes by the impression cylinder without touching. For each impression there are two inking rollers, which receive their supply of ink from the distributing surface of the main cylinder: they rise and ink the form as it passes under them, after which they again fall to the distributing surface.
The ink is stored in a fountain located underneath the main cylinder, and it is delivered by distributing rollers to the surface of the main cylinder. This surface, being lower or smaller in diameter than the type, moves past the impression cylinder without making contact. For every impression, there are two inking rollers that take their ink supply from the distributing surface of the main cylinder: they lift up and ink the type as it moves beneath them, and then they drop back down to the distributing surface.
This press is capable of printing either from type or from stereotype plates bent to fit the curve of the cylinder. When type is used, each page of the paper is locked up on a detached segment of the large cylinder, which constitutes its bed and chase. The column-rules run parallel with the shaft of the cylinder, and are consequently straight; while the head, advertising, and dash rules are in the form of segments of a circle. The column-rules are in the form of a wedge, with the thin part directed toward the axis of the cylinder, so as to bind the[242] type securely. These wedge-shaped column-rules are held down to the bed by tongues projecting at intervals along their length, which slide in rebated grooves cut crosswise in the face of the bed. The spaces in the grooves between the column-rules are accurately fitted with sliding blocks of metal even with the surface of the bed, the ends of which blocks are cut away underneath to receive a projection on the sides of the tongues of the column-rules. The form of type is locked up in the bed by means of screws at the foot and sides, by which the type is held as securely as in the ordinary manner upon a flat bed,—if not even more so. The speed of these machines is limited only by the ability of the feeders to supply the sheet.
This press can print either from type or from stereotype plates shaped to fit the curve of the cylinder. When type is used, each page of the paper is secured on a separate segment of the large cylinder, which serves as its bed and chase. The column rules run parallel to the shaft of the cylinder, making them straight; meanwhile, the head, advertising, and dash rules are shaped like segments of a circle. The column rules are wedge-shaped, with the thin part facing the axis of the cylinder to hold the type securely. These wedge-shaped column rules are kept in place on the bed by tongues that extend at intervals along their length and slide into notched grooves cut across the bed's surface. The gaps in the grooves between the column rules are precisely filled with sliding metal blocks that are flush with the bed's surface, and the ends of these blocks are shaped to accommodate a projection on the sides of the column rules' tongues. The form of the type is locked in the bed using screws at the bottom and sides, which hold the type just as securely as it would be on a flat bed—if not even more securely. The speed of these machines is only limited by how quickly the feeders can supply the sheets.
This machine was first used by the Public Ledger of Philadelphia, and was afterward adopted by the leading newspapers of that city and New York, as well as of the chief cities of Great Britain and other countries.
This machine was first used by the Public Ledger of Philadelphia, and was later adopted by the major newspapers of that city and New York, as well as by the top newspapers in Great Britain and other countries.
To obtain the best results from the largest size of this press it was necessary to employ a dozen or more hands to feed and run it. This expensive feature was largely avoided in a new machine projected by Mr. William Bullock, whose press was the forerunner of several machines that may be classed under the general name of Self-feeding or Web Perfecting Presses.
To get the best results from the largest version of this press, it required a dozen or more people to operate and feed it. This costly requirement was mostly eliminated in a new machine designed by Mr. William Bullock, whose press was the precursor to several machines that can be categorized under the general term Self-feeding or Web Perfecting Presses.
THE BULLOCK WEB PERFECTING PRESS.
This machine is intended for printing on a continuous roll of dampened paper, which passes between a pair of cylinders (one of which is an impression cylinder, and the other a cylinder around which stereotyped plates are bent) and receives an impression on one side, and the sheet then goes forward and is printed on the other side while passing between a second pair of cylinders similar to the first, except that the impression cylinder is four times the diameter of the plate cylinder to prevent more effectually the ink from “setting off.” After being printed, and before delivery, the sheet is cut off by a fixed serrated cutting blade, the ingenious invention of Victor Beaumont of New York. A French device for making flexible papier-maché moulds rendered it possible to cast the type-plates to fit the printing cylinders.[243] Without this auxiliary, web perfecting presses would have been useless and impracticable.
This machine is designed for printing on a continuous roll of dampened paper, which moves between a pair of cylinders (one serving as the impression cylinder, and the other as the cylinder wrapped with stereotyped plates) and gets printed on one side. Then, the sheet advances and is printed on the other side while passing through a second pair of cylinders similar to the first. The difference is that the impression cylinder is four times the diameter of the plate cylinder to more effectively prevent the ink from "setting off." After printing, and before delivery, the sheet is cut off by a fixed serrated cutting blade, a clever invention by Victor Beaumont of New York. A French device for creating flexible papier-mâché molds made it possible to cast the type-plates to fit the printing cylinders.[243] Without this addition, web perfecting presses would have been useless and impractical.

THE BULLOCK SELF-FEEDING PERFECTING PRESS, WITH FOLDER,
WILL FLY THE SHEET FLAT, FOLD IT THREE OR FOUR TIMES AT WILL, OR CUT, FOLD, AND PASTE IT AS FAST AS PRINTED
THE BULLOCK SELF-FEEDING PERFECTING PRESS, WITH FOLDER,
WILL FLATLY FLY THE SHEET, FOLD IT THREE OR FOUR TIMES AS NEEDED, OR CUT, FOLD, AND PASTE IT AS QUICKLY AS IT'S PRINTED
Mr. Bullock, born in Greene County, New York, was a mechanical genius, and was the author of many inventions in[244] various departments of machinery.[18] About the year 1860, he began to work out the idea of a rotary self-feeding, or web perfecting press. After making a large working model, which is still in existence, he adopted a simpler plan, and in 1861 constructed a machine for the Cincinnati Times, which was successfully operated, but it was far from perfect. Three of these machines were used for a considerable time in the office of the Philadelphia Inquirer.
Mr. Bullock, who was born in Greene County, New York, was a mechanical genius and the inventor of many machines in[244] various fields of technology.[18] Around 1860, he started working on the concept of a rotary self-feeding, or web perfecting press. After creating a large working model, which still exists today, he opted for a simpler design and, in 1861, built a machine for the Cincinnati Times. It worked well, but it wasn't perfect. Three of these machines were used for quite some time at the office of the Philadelphia Inquirer.
He continued his efforts, and in 1865 he produced a press which met his original anticipation, and a company was formed to manufacture it. In 1867, while setting up a machine for the Public Ledger in Philadelphia, he suffered a serious injury which terminated his life. More than fifty of the presses are now in use in the United States. The New York Herald press, printing and cutting two copies at each delivery, is said to produce, with but three men to attend to it, 30,000 copies per hour. The New York Sun states: “When our seven Bullock Presses are working, we can turn off, without extravagant assertion, 210,000 copies an hour.” This assertion must be taken with some grains of allowance. The press is twelve feet long by five and a half feet wide.
He kept at it, and in 1865 he created a press that met his original expectations, leading to the formation of a company to manufacture it. In 1867, while setting up a machine for the Public Ledger in Philadelphia, he suffered a serious injury that ended his life. Over fifty of these presses are now in operation across the United States. The New York Herald press, which prints and cuts two copies at each run, is said to produce, with just three operators, 30,000 copies per hour. The New York Sun claims: “When our seven Bullock Presses are running, we can produce, without exaggeration, 210,000 copies an hour.” This claim should be taken with a grain of salt. The press measures twelve feet long by five and a half feet wide.
THE WALTER PERFECTING PRESS.
The Bullock press was not long allowed to be the only press for rapid printing from cylindrical stereotype plates fed by a so-called endless roll of paper. The principle was applied to a machine constructed in the London Times office, called, after the name of its celebrated proprietor, the Walter press. This appears to be an effective press, but it seems more complicated than either the Bullock or Hoe machine, and from its mode of delivering the sheets, it is excessively noisy. The New York Times was printed on it at the Centennial Exhibition in Philadelphia.
The Bullock press wasn't allowed to be the only press for fast printing using cylindrical stereotype plates fed by what's known as an endless roll of paper for long. The principle was used in a machine built in the London Times office, named after its famous owner, the Walter press. It seems to be an effective press, but it appears to be more complicated than either the Bullock or Hoe machine, and because of how it delivers the sheets, it’s really noisy. The New York Times was printed on it during the Centennial Exhibition in Philadelphia.
THE HOE PERFECTING PRESS.
The enterprise of R. Hoe & Co., of New York, soon gave birth to a web perfecting press combined with a folding machine that answers every requirement.
The business of R. Hoe & Co., based in New York, quickly led to the creation of a web perfecting press integrated with a folding machine that meets all needs.

THE HOE WEB PERFECTING PRESS.
THE HOE WEB PERFECTING PRESS.
The groundwork principle is the same as in other presses of this kind. The first pair of cylinders over which hangs the roll of paper consists of one type and one impression cylinder, and by it the first side of the paper is printed. The second pair, printing the second side, consists likewise of one type and one impression cylinder, but the latter is below the former and is of much greater size, so that the “set off” from the fresh ink shall not fall continuously on the same surface of blanket. There is a third pair of cylinders which cuts off the sheet, and a fourth (in which, however, one cylinder is replaced by a brace of rollers) gives the first fold and shoots the doubled sheet in the circular cutter, which slits it into two papers, sending them on to be folded again separately and delivered in their respective places in piles at the side of the press; or the papers are rolled up exactly on the top of each other, six in number, and flown perfectly on the fly-board.
The basic principle is the same as in other presses like this. The first pair of cylinders that holds the roll of paper includes one type cylinder and one impression cylinder, which prints the first side of the paper. The second pair, which prints the second side, also has one type cylinder and one impression cylinder, but the latter is positioned below the former and is much larger, so the “set off” from the fresh ink doesn’t continuously land on the same surface of the blanket. There’s a third pair of cylinders that cuts off the sheet, and a fourth set (where one cylinder is replaced by a pair of rollers) that creates the first fold and sends the doubled sheet into the circular cutter, which splits it into two sheets, moving them on to be folded again separately and delivered in their proper stacks at the side of the press; or the sheets are neatly rolled up on top of each other, six in total, and placed perfectly on the fly-board.
This machine printed and folded at the rate of more than 28,000 sheets an hour at the Centennial Exhibition, printing and folding at one time two copies of the Philadelphia Times.[246] It is already in use in a dozen newspaper establishments in various parts of the world.
This machine printed and folded at a speed of over 28,000 sheets per hour at the Centennial Exhibition, printing and folding two copies of the Philadelphia Times at once.[246] It's already being used in a dozen newspaper offices around the world.
All these machines were in operation at the great Centennial Exhibition in Philadelphia. A fourth press exhibited,—claimed by its inventor, Mr. A. Campbell of New York, to be capable of printing much faster than any other,—was set up too late to prove its capacity by actual test. No press however, can be made more simple and with fewer parts than this.
All these machines were in use at the big Centennial Exhibition in Philadelphia. A fourth press was displayed—claimed by its inventor, Mr. A. Campbell of New York, to be able to print much faster than any other—but it was set up too late to demonstrate its capabilities in an actual test. No press, however, can be made simpler and with fewer parts than this one.
RAILROAD-TICKET PRINTING AND NUMBERING PRESS.
These presses not only print, but at the same operation number consecutively, tickets and coupons of every size and pattern, which are also indented or cut apart by the machines as fast as printed. Ten local tickets twenty-six inches in length can be printed at one operation. The average rate of speed is about fourteen hundred impressions an hour,—equivalent to fourteen thousand tickets.
These presses not only print, but also produce tickets and coupons of every size and design in a single operation, cutting them apart as quickly as they are printed. Ten local tickets, each twenty-six inches long, can be printed at once. The average speed is about fourteen hundred impressions per hour, which is equivalent to fourteen thousand tickets.
JOB PRESSES.

GORDON’S FRANKLIN PRESS.
Gordon's Franklin Press.
The invention of machines for printing small work elegantly as well as swiftly is of vast advantage to the printer, and has greatly increased the jobbing department of typography. Here, as in other matters, American ingenuity has taken the lead of all nations; and the presses invented by Ruggles, Hoe, Gordon, Degener, Wells, and Gally,—not to mention numerous other inventors,—defy competition. The Ruggles presses[247] formerly commanded the trade; but the beautiful machines of Geo. P. Gordon, a man of decided genius, and the presses of other makers above named, have entirely displaced them. Hoe’s half medium cylinder job press will run 2500 impressions an hour.
The invention of machines that print small work both elegantly and quickly is a huge benefit to printers and has significantly boosted the jobbing department of typography. In this area, as in others, American ingenuity has outpaced all other nations. The presses created by Ruggles, Hoe, Gordon, Degener, Wells, and Gally—along with many other inventors—stand out in the market. The Ruggles presses[247] once dominated the industry, but the impressive machines from Geo. P. Gordon, a person of notable talent, along with those from the other mentioned makers, have completely taken their place. Hoe’s half medium cylinder job press can deliver 2500 impressions an hour.

NONPAREIL PRESS.
Nonpareil Press.
Gordon’s Firefly press is unique, and requires a so-called endless card-board, which it prints and cuts of the required shape as it goes, at the rate of about ten thousand per hour. This is not in general use; but his eighth medium, quarto medium, and half medium Franklin presses, have achieved a high reputation for expedition and excellent performance. Gordon’s Franklin press has been reproduced in Europe under a different name.
Gordon’s Firefly press is one-of-a-kind and needs a continuous cardboard, which it prints and cuts into the needed shape as it operates, at a speed of about ten thousand per hour. This isn't commonly used; however, his eighth medium, quarto medium, and half medium Franklin presses have gained a great reputation for speed and top-notch performance. Gordon’s Franklin press has been replicated in Europe under a different name.

LIBERTY PRESS.
LIBERTY PRESS.
We here present an engraving of another press which has achieved not a little reputation. It is called the Liberty press, and is manufactured by Degener & Weiler, of New York. In sizes as well as in prices, it corresponds with the Franklin. This press also is manufactured in Europe.
We now present an engraving of another press that has gained quite a reputation. It's called the Liberty press and is made by Degener & Weiler in New York. In terms of size and price, it matches the Franklin. This press is also made in Europe.
The Nonpareil, the Globe, the Peerless, and the Universal job presses all have special points which commend them to favour. Indeed, with so many good machines at the command of the printer, he is without excuse who does not produce handsome work.
The Nonpareil, the Globe, the Peerless, and the Universal job presses all have unique features that make them appealing. In fact, with so many excellent machines available to printers, there's no excuse for not producing quality work.

UNIVERSAL PRESS.
UNIVERSAL PRESS.
What are called amateur presses may do well enough to amuse the boys of a family and keep them out of mischief; but when they are employed by fledgelings in competition with properly trained printers, they become mere paper-smearers, the work produced on them being simply detestable to an educated eye.
What are known as amateur presses might be entertaining enough for the kids in a family and help keep them out of trouble; however, when they're used by novices competing with properly trained printers, they just become unskilled operators, and the work produced on them is simply awful to an educated eye.

PEERLESS PRESS.
Peerless Press.
FOLDING MACHINES.

BOOK-FOLDING MACHINE.
Book folding machine.
Book and Newspaper Folders are entitled to a high rank among modern labour-saving machines. For newspapers of large circulation and in book establishments they have become indispensable. The finest books may be folded by them with accuracy, speed, and economy; and periodicals can be folded, pasted, and covered at about one-fourth the cost of hand-folding alone; while the daily folio newspaper can be folded in two, three, or four folds as fast as the machine press can print; or an eight-page daily or weekly can be folded three or four times, and all the pages pasted together at the back fold, and the head margin trimmed. All these processes are successfully accomplished by the various machines made by Chambers, Brother & Co. of Philadelphia. The engraving given above represents a book-folding machine.
Book and Newspaper Folders deserve a top spot among today's time-saving machines. In large circulation newspapers and book publishers, they have become essential. They can fold even the finest books accurately, quickly, and cost-effectively; and periodicals can be folded, pasted, and covered for about a quarter of the cost of manual folding alone. Additionally, a daily folio newspaper can be folded into two, three, or four folds as fast as the printing press runs; or an eight-page daily or weekly can be folded three or four times, with all the pages pasted together at the back fold and the head margin trimmed. All these tasks are effectively done by the various machines produced by Chambers, Brother & Co. of Philadelphia. The engraving above shows a book-folding machine.
SETTING UP A WASHINGTON PRESS.
All the connecting parts being marked, or indented by points, if these be observed carefully, the press may be put together without difficulty.
All the connecting pieces are marked or indented by points; if you pay close attention to these, the press can be assembled easily.
After setting the frame upon its legs, and putting on the ribs and bed, lay the platen on the bed, placing under it two bearers about type high. Then put the springs in their places, and the nuts over them, and pass the suspending-rods through them, observing to place the rods so that the number of indentations on them correspond with those on the platen. Give the nuts two or three turns, then run in the bed so as to bring the platen under the rods, and screw them fast to the platen; after which, put in the bar-handle, standard, and lever, (or wedge and knees, if a Smith press.) Turn the nuts on the suspending-rods, so as to compress the springs just enough to give the platen a quick retrograde motion, observing at the same time to get the surface of the platen parallel with the surface of the bed.
After setting the frame on its legs and attaching the ribs and bed, lay the platen on the bed, placing two bearers underneath it that are about the height of the type. Next, position the springs in their spots, and place the nuts over them, threading the suspending rods through them while ensuring that the number of indentations on the rods matches those on the platen. Give the nuts two or three turns, then slide in the bed to position the platen under the rods, and secure them tightly to the platen; afterward, insert the bar handle, standard, and lever (or wedge and knees, if it's a Smith press). Adjust the nuts on the suspending rods to compress the springs just enough to allow the platen to move back quickly, making sure to keep the surface of the platen parallel to the surface of the bed.
After having put the press together and levelled it by means of a spirit-level, be particular not to raise the end of the ribs by the gallows, but let it go under rather loose, which will have a tendency to make the bed slide with more ease on the ribs.
After putting the press together and leveling it with a spirit level, make sure not to raise the ends of the ribs with the gallows. Instead, let it hang a bit loose, as this will help the bed slide more easily on the ribs.
SETTING UP THE ROLLER-STAND.
The roller-stand containing the distributing cylinder should be regulated to the height of the press, bringing the shelf or bridge even with the corner irons, and at sufficient distance from the bed to allow it to run clear; the stand should then be firmly braced, as the constant turning of the rounce is very apt to loosen it; meanwhile being cautious to observe that the rounce, in its revolutions, does not come in contact with the frame of the tympan when up. The position of the distributing cylinder should be sufficiently high to allow the two composition rollers, at least one inch apart, to rest on its top without danger of touching the shelf or bridge in front. It is advantageous to nail two narrow strips of sole leather on the face of the shelf, about eight or ten inches from each[251] end, which, acting as bearers, cause the rollers to pass very smoothly over them.
The roller stand with the distributing cylinder should be set to the height of the press, aligning the shelf or bridge with the corner irons, and leaving enough space from the bed for it to operate smoothly; the stand should then be securely braced, as the constant rotation of the rounce can easily loosen it. At the same time, care should be taken to ensure that the rounce, as it turns, does not touch the frame of the tympan when it's raised. The distributing cylinder should be high enough so that the two composition rollers, spaced at least one inch apart, can rest on its top without risking contact with the shelf or bridge in front. It's helpful to attach two narrow strips of sole leather to the face of the shelf, about eight or ten inches from each[251] end, which serve as supports, allowing the rollers to glide smoothly over them.

ROLLER STAND.
Roller stand.
The roller-handle while in use should lie in a horizontal position, the back end being supported by a bar of wood or iron running parallel with the distributing cylinder. There should be a notch, or hook, about two inches from the end of the handle, to catch on the wooden supporter, to prevent the rollers from jumping forward while distributing or changing. It is also necessary to have a back-board for the end of the roller to strike against in coming off the form, to prevent the rollers from falling backward.
The roller handle should be positioned horizontally while in use, with the back end supported by a wooden or metal bar that runs parallel to the distributing cylinder. There should be a notch or hook about two inches from the end of the handle to catch on the wooden support, preventing the rollers from moving forward while distributing or changing. It's also important to have a backboard for the end of the roller to hit against when coming off the form, to stop the rollers from falling backward.
The ink-block is placed about five or six inches to the right of the roller-handle, and about on a level with it. It is furnished with the ink-slice, and a brayer, or a small roller about four or five inches long, and of the same circumference with the larger rollers, being cast in the same mould.
The ink block is positioned around five or six inches to the right of the roller handle and is roughly at the same height. It comes with an ink slice and a brayer, which is a small roller about four or five inches long and has the same circumference as the larger rollers since it's made from the same mold.
COMPOSITION ROLLERS.
Put the glue in a bucket or pan, and cover it with water; let it stand until more than half penetrated with water, taking care that it shall not soak too long, and then pour it off and let it remain until it becomes soft, when it will be ready for the melting kettle. This is a double vessel, like a glue kettle. Put the soaked glue into the inner vessel, and as much water in the outer boiler as it will contain when the inner vessel is placed in it. When the glue is all melted, (if too thick, add a little water,) the molasses may be slowly poured into it, and well mixed with the glue by frequent stirring. When properly prepared, the composition does not require boiling more than an hour. Too much boiling candies the molasses, and the roller, consequently, will be found to lose its suction much sooner. In proportioning the material, much depends upon the weather and temperature of the place in which the rollers are to be used. Eight pounds of glue to one gallon of sugar-house molasses, or syrup, is a very good proportion for summer-time, and four pounds of glue to one gallon of molasses for winter use. Glue for rollers should be clear and bright in body, and even in texture, when held up to the light: it should break short, and with a clear, sharp edge like glass.
Put the glue in a bucket or pan, and cover it with water; let it sit until more than half is soaked with water, making sure it doesn't soak for too long. Then pour off the excess water and let it sit until it becomes soft, ready for the melting kettle. This uses a double vessel, like a glue kettle. Put the soaked glue in the inner vessel and fill the outer boiler with enough water to hold it when the inner vessel is placed inside. When the glue is fully melted (if it's too thick, add a little water), you can slowly pour in the molasses and mix it well with the glue by stirring frequently. When properly prepared, it shouldn’t be boiled for more than an hour. Boiling it too long will caramelize the molasses, causing the rollers to lose their suction much quicker. The amount of materials you use will vary depending on the weather and temperature where the rollers are being used. Eight pounds of glue to one gallon of sugar-house molasses or syrup is a good ratio for summer, while four pounds of glue to one gallon of molasses works well for winter. Glue for rollers should be clear and bright in appearance, and even in texture when held up to the light: it should break cleanly with a sharp edge like glass.

MELTING KETTLE.
Melting kettle.
For hand-press rollers more molasses should be used, as they are not subject to so much hard usage as cylinder-press rollers, and do not require to be as strong; for the more molasses that can be used the better will be the roller. Before pouring a roller, the mould should be perfectly clean, and well oiled with a swab, but not to excess, as too much oil makes the face of the roller seamy and ragged. The end pieces should then be oiled, and, together with the cylinder, placed in the mould, the upper-end piece being very open, to[253] allow the composition to pass down between the interior of the mould and the cylinder. The cylinder must be well secured from rising, before the composition is poured in, by placing a stick upon the end of it, sufficiently long to reach above the end of the mould, and be tied down with twine. The composition should be poured very slowly, and in such a manner as to cause it to run down only one side of the cylinder, allowing the air to escape freely up the other.
For hand-press rollers, you should use more molasses since they don’t go through as much wear and tear as cylinder-press rollers and don’t need to be as strong. The more molasses you can use, the better the roller will be. Before pouring a roller, make sure the mold is completely clean and well-oiled with a swab, but don’t overdo it, as too much oil can make the roller's surface uneven and rough. Next, oil the end pieces, and along with the cylinder, place them in the mold, ensuring the upper end piece is very open to [253] let the mixture flow down between the mold and the cylinder. You need to secure the cylinder well to prevent it from moving up before pouring in the mixture. Use a stick long enough to reach above the end of the mold and tie it down with twine. Pour the mixture very slowly and make sure it runs down only one side of the cylinder, allowing air to escape freely on the other side.
If the mould is filled at night, the roller may be drawn the next morning; but it should not be used for at least twenty-four hours after, except in very cold weather.
If the mold is filled at night, the roller can be taken out the next morning; however, it shouldn't be used for at least twenty-four hours afterward, unless it's really cold outside.
To determine when a roller is in order for working, press the hand gently on it: if the fingers pass smoothly over its surface, it may be said to be in order; but should it be so adhesive that the fingers cling to it, it is not sufficiently dry, and should be exposed to the air.
To check if a roller is ready to use, lightly press your hand on it: if your fingers glide smoothly over the surface, it's good to go; but if your fingers stick to it, it's not dry enough and needs to be left out in the air.
Rollers should not be washed immediately after use, but should be put away with the ink on them, as it protects the surface from the action of the air. When washed and exposed to the atmosphere for any length of time, they become dry and skinny. They should be washed about half an hour before using them. In cleaning a new roller, a little oil rubbed over it will loosen the ink: and it should be scraped clean with the back of a case-knife. It should be cleaned in this way for about one week, when ley may be used. New rollers are often spoiled by washing them too soon with ley. Benzine may be substituted for oil; but, owing to its combustible nature, it is objectionable, as disastrous accidents have ensued from its use.
Rollers shouldn’t be washed right after use; instead, they should be stored with the ink still on them because it protects the surface from air exposure. If they’re washed and left in the open air for too long, they’ll dry out and become brittle. You should wash them about half an hour before you need to use them. When cleaning a new roller, rubbing a bit of oil on it will help loosen the ink, and you should scrape it clean with the back of a case knife. Clean it this way for about a week, after which ley can be used. New rollers often get ruined when they’re washed too soon with ley. You can use benzine instead of oil, but it’s flammable, making it risky since there have been serious accidents from using it.
Mr. Hansard, an eminent English printer, says, “Take glue, made from the cuttings of parchment or vellum, fine green molasses, pure as from the sugar-refiners, and a small quantity of the substance called Paris-white, and you will have every ingredient requisite for good composition. The proportion as follows:—
Mr. Hansard, a well-known English printer, says, “Take glue made from the trimmings of parchment or vellum, fine green molasses, pure as it comes from the sugar refiners, and a small amount of the substance called Paris-white, and you will have everything you need for good composition. The proportions are as follows:—
- Glue, 2 lbs.
- Molasses, 6 lbs.
- Paris-white, ½ lb.
Put the glue in a little water for a few hours to soak; pour off the liquid; put the glue over the fire, and when it is dissolved add the molasses, and let them be well incorporated together for at least an hour; then, with a very fine sieve, mix the[254] Paris-white, frequently stirring the composition. In another hour, or less, it will be fit to pour into the mould.”
Put the glue in a little water for a few hours to soak; pour off the liquid; heat the glue over the fire, and when it’s dissolved, add the molasses, mixing them well for at least an hour; then, using a very fine sieve, combine the[254]Paris-white, stirring the mixture frequently. In another hour, or less, it will be ready to pour into the mold.
Various patented compositions for rollers may now be had from type-founders.
Various patented compositions for rollers are now available from type-founders.
COVERING TYMPANS.
Tympans are generally covered with parchment, which should be of an even thickness, and about two inches and a half wider and three inches longer than the tympans. Tympans have been sometimes covered with linen, which, on account of its evenness, would answer the purpose; but it is so apt to stretch, that the tympans become slack in a short time, and bag (as it is termed), and thus slur the impression. Silk is excellent for fine work.
Tympanums are typically covered with parchment that should be of uniform thickness and about two and a half inches wider and three inches longer than the tympans. Sometimes, tympans are covered with linen, which can work due to its smoothness; however, linen tends to stretch, making the tympans loose over time and causing them to bag, which leads to a poor impression. Silk is great for detailed work.
The pressman spreads as much good paste on the edges of the skin as will cover the frame of the tympan, which is also well pasted. He then lays the skin on the inner side of the frame, with the flesh side to face the type, and draws it regularly, as tight as possible, on all sides. The part of the skin that comes on the grooves of the tympan which receive the point-screws, is cut and wrapped round the inside edge of the grooves, which admits a free passage for the screws. After having fastened the skin on the sides of the tympan, he draws it toward the joints which receive the frisket, and with a knife cuts across these joints to let them through the skin; he then puts the frisket-pins through the parchment, and makes that end of the tympan fast. He next proceeds to the lower joints, and brings the skin as tight as he can round that part of the tympan. The point-screws and duck-bill are then put on, which prevent the skin from starting. The inner tympan, or drawer, is covered in the same manner. To prevent their warping when the skin begins to draw, pieces of furniture or wood of any kind should be placed across the centre till they are perfectly dry.
The pressman spreads enough good paste on the edges of the skin to cover the frame of the tympan, which is also well pasted. He then places the skin on the inner side of the frame, with the flesh side facing the type, and pulls it tight on all sides. The part of the skin that goes over the grooves of the tympan, which hold the point-screws, is cut and wrapped around the inside edge of the grooves, allowing free access for the screws. After securing the skin to the sides of the tympan, he pulls it toward the joints that hold the frisket and uses a knife to cut across these joints so they can fit through the skin; he then inserts the frisket-pins through the parchment and secures that end of the tympan. Next, he attends to the lower joints, pulling the skin as tight as possible around that section of the tympan. The point-screws and duck-bill are then added, which prevent the skin from shifting. The inner tympan, or drawer, is covered the same way. To avoid warping when the skin starts to tighten, pieces of furniture or any kind of wood should be placed across the center until they are completely dry.
The skins are put on either wet or dry: if dry, they should be afterward well wet, which will make them give somewhat; but when they dry they will contract, and by this means will be rendered much tighter than they would be if put on wet.
The skins can be applied either wet or dry: if they're dry, they should be thoroughly wet afterward, which will allow them to expand a bit; but as they dry, they'll shrink, making them much tighter than if they had been applied while wet.
WETTING PAPER.
The size of the wetting-trough should be about two inches longer and wider than the largest-sized paper, folded, that is to be wet in it, and about six inches deep. It should have a cover with hinges on the left side, that the cover may fall over on that side, and, resting horizontally, serve for a shelf to lay the paper upon previous to wetting it.
The wetting trough should be about two inches longer and wider than the largest piece of paper, when folded, that will be soaked in it, and about six inches deep. It should have a cover with hinges on the left side, allowing the cover to fall over that side and, when resting horizontally, serve as a shelf to place the paper on before wetting it.
Having received a certain amount of paper from the warehouseman, the pressman lays one heap on the shelf attached to the wetting-trough, laying the first token across the heap with the back of the quires toward his right hand, that he may know when to turn the token-sheet, and that he may more readily catch at the back of each quire with that hand, for the purpose of dipping it. He then places the paper-board with its breadth before him on his right, on a table, laying a wrapper or a waste sheet of paper on the board, to prevent soiling the first sheet of the heap.
After getting a certain amount of paper from the warehouse worker, the pressman puts a stack on the shelf next to the wetting trough. He lays the first token across the stack with the back of the quires facing his right hand, so he knows when to turn the token-sheet and can easily grab the back of each quire with that hand for dipping. Then, he places the paper-board with its width in front of him on his right, on a table, putting a wrapper or a scrap piece of paper on the board to avoid dirtying the first sheet of the stack.
He then takes a quire by the centre of the back with his right hand, and the edge of it in his left, and, closing his hands a little, that the quire may bend downward between his hands, he dips the back of the quire into the left-hand side of the trough, and, relinquishing his hold with the left hand, draws the quire briskly through the water with his right. As the quire comes out, he quickly catches the edge of it again in his left hand, and brings it to the heap, and, by lifting his left hand, bears the under side of the quire off the paper previously laid down, till he has placed the quire in an even position; if the paper be weak and spongy, he draws the quire through the water quickly; if strong and stubborn, slowly. To place the quire in an even position, he lays the back of it exactly upon the open crease of the former, and then lets the side of the quire in his left hand fall flat down upon the heap, and, discharging his right hand, brings it to the edge of the quire, and, with the assistance of his left thumb, still in its first position, opens or divides either a third or a half of the quire, according to the quality of the paper; then, spreading the fingers of his right hand as much as he can through the length of the quire, turns over his opened division of it upon his right-hand side of the heap.
He then grabs a stack of paper by the center of the back with his right hand and the edge with his left. By squeezing his hands a bit, he causes the stack to bend down between them. He dips the back of the stack into the left side of the trough and, releasing his grip with the left hand, quickly pulls the stack through the water with his right. As the stack emerges, he swiftly catches the edge with his left hand and brings it to the pile. By lifting his left hand, he removes the underside of the stack from the paper already laid down until he places it evenly. If the paper is weak and spongy, he pulls the stack through the water quickly; if it’s strong and stubborn, he does it slowly. To position the stack evenly, he sets the back directly on the open crease of the one before it, then lets the side in his left hand drop flat onto the pile. Releasing his right hand, he moves it to the edge of the stack, and with the help of his left thumb, still in place, he opens or divides either a third or a half of the stack, depending on the paper quality. Then, spreading the fingers of his right hand as much as he can along the length of the stack, he flips his opened section over to the right side of the pile.
A different process must be used in the wetting of drawing[256] and plate papers. These papers are usually sent in quite flat; that is, not folded into quires or half-quires. The best method of wetting these papers is to use a brush, such as is called a banister brush; and, instead of dipping the paper into the trough, he lays it on the paper-board by the side of the trough, and, dipping the brush into the water, he shakes it gently over the whole surface, to give an equal degree of moisture to all parts; and then proceeds as before described. The drawing-paper, being very hard-sized in the making, will require the brush, and much water, three, four, or even five times a quire; while the plate-paper should have as little water as it is possible to give it, so as to cover it all over; and twice a quire will often be too much. This same mode must also be adopted in wetting paper of extraordinary dimensions.
A different method should be used for wetting drawing[256] and plate papers. These papers usually come in flat packs, not folded into quires or half-quires. The best way to wet these papers is to use a brush known as a banister brush. Instead of dipping the paper into the trough, lay it on the paper-board next to the trough. Dip the brush into the water and shake it gently over the entire surface to ensure even moisture across all areas, then continue as previously described. The drawing paper, which is very hard-sized during production, will need the brush and a lot of water, three, four, or even five times per quire. In contrast, the plate paper should receive as little water as necessary to coat it entirely; often, even twice a quire is too much. This same approach should also be used for wetting paper of unusual sizes.
Having wet his first token, he doubles down a corner of the upper sheet of it on his right hand, so that the farther corner may be a little toward the left of the crease in the middle of the heap, and the other corner may hang out on the near side of the heap about an inch and a half. This sheet is called the token-sheet, being a mark for the pressman, when he is at work, to show how many tokens of that heap are worked off.
Having wet his first token, he folds down a corner of the upper sheet with his right hand, so that the far corner is slightly to the left of the crease in the middle of the stack, and the other corner sticks out on the near side of the stack by about an inch and a half. This sheet is called the token-sheet, serving as a guide for the pressman while he works, indicating how many tokens from that stack have been processed.
Having wet the whole heap, he lays a wrapper, or waste sheet of paper, upon it; then, three or four times, takes up as much water as he can in the hollow of his hand, and throws it over the waste sheet, to moisten and soak downward into the wet part of the last division of the quire; after which, he places in the heap the label which the warehouseman must always furnish for each heap, and upon which are written the title of the work and the date of wetting, one-half hanging out so as to be easily read.
Having soaked the entire pile, he lays a sheet of paper on top. Then, he fills his hand with water three or four times and splashes it over the paper to moisten and soak into the wet part of the last section of the stack. After that, he adds the label that the warehouseman must always provide for each stack, which includes the title of the work and the date it was wet, with half of it hanging out for easy reading.
The paper should be pressed for twelve hours, and then carefully turned by each three or four sheets, so that no lift be relaid in the same position with respect to the adjoining lift; at the same time, every fold and wrinkle must be carefully rubbed out by the action of the hand, so that nothing but a flat and even surface shall remain; the heap should then be pressed for about twenty-four hours in a screw-press, and it will be in good order for working.
The paper should be pressed for twelve hours, and then carefully turned every three or four sheets, making sure that no stack is laid back in the same position as the adjacent stack. At the same time, every fold and wrinkle must be gently smoothed out by hand, so that only a flat and even surface remains; the stack should then be pressed for about twenty-four hours in a screw press, and it will be ready for use.
The wetting of paper must, in all cases, depend entirely upon its fabric; and, since the printer has seldom the choice of the paper, it will require all his skill and patience to adapt[257] his labours to the materials upon which he is to work. The texture of the paper must be suited to the fineness and tenacity of the ink. To attempt doing fine work upon common paper is lost labour. A paper to take the best ink must be made entirely of linen rags, and not bleached by chemicals. A fine hand-made paper, fabricated a sufficient time to get properly hardened, and well and equally saturated with size, so as not to imbibe more water in one part of the dip than in another, nor resisting the water like a duck’s back, is most suitable for fine printing.
The way paper absorbs moisture completely depends on its material. Since printers often don’t have a choice in the paper they use, it takes all their skill and patience to adjust their work to fit the materials at hand. The paper's texture needs to match the quality and stickiness of the ink. Trying to do detailed work on low-quality paper is a waste of effort. The best ink requires paper to be made entirely of linen rags, and not bleached with chemicals. A high-quality handmade paper, made long enough to properly harden and evenly treated with size so it absorbs water consistently, is ideal for fine printing.
Machines for wetting paper are now used in most large printing-offices.
Machines for wetting paper are now used in most large print shops.
BLANKETS.
Woollen blankets are unnecessary when a book is printed from new type. Nothing more should be used than a sheet or two of paper, as in fine work only the face of the type should show in the impression. But when the types or plates are worn and rounded, fine cassimere or broadcloth should be used in the tympan. In this, as in all matters connected with artistic typography, the pressman must display good judgment and discretion.
Wool blankets aren't needed when a book is printed with fresh type. You only need a sheet or two of paper because in high-quality work, only the face of the type should be visible in the print. However, when the types or plates are worn and rounded, fine cashmere or broadcloth should be used in the tympan. In this, as in all areas of artistic typography, the pressman must show good judgment and discretion.
MAKING READY A FORM ON A HAND-PRESS.
Before a form is laid on the press, the pressman should carefully wipe the bottom of the type and the bed perfectly clean; for, if a particle of sand remain on it, it will cause a type or two to rise, and not only make a stronger impression, but probably injure the letters.
Before a form is placed on the press, the press operator should thoroughly clean the bottom of the type and the bed. If any grains of sand are left on it, they can cause one or two letters to shift, leading to a heavier impression and potentially damaging the letters.
An octavo form should be laid on the press with the signature-page to the left hand, or nearest the platen; a duodecimo, or its combinations, with the signature at the right hand, or nearest the tympan. The form should be laid under the centre of the platen, and properly quoined up. The tympan is then laid down, and wet if necessary, and paper or blanket put in. It was formerly customary to wet the tympans for all works, and even jobs of almost every description; but, since the introduction of fine printing, and particularly iron presses, the custom is well-nigh banished, excepting for very heavy forms,[258] composed with old letter, which, of course, require more softness to bring them off. After the inner tympan or drawer is put in, it is fastened with the hooks for that purpose, which serve to keep it from springing out. The tympan being lifted up, a sheet of the paper to be worked is folded in quarto, and the short crease is placed over the middle of the grooves of the short cross, if it lie in the centre of the form, as in octavo. In a form of twelves, the paper is folded in thirds, and the long crease placed in the middle of the long cross, and the short cross over the grooves. The sheet lying evenly on the form, the tympan is brought down, and a gentle pull will cause the paper to adhere, when it should be pasted to the tympan and fully stretched. The points are next screwed to the tympan, for large paper short-shanked points being used, and long-shanked for small paper. In twelves, the points must be placed at precisely equal distances from the edge of the paper. In octavo, the off-point may be a little larger than the near one, as it enables the pressman to detect a turned heap when working the reiteration or second side.
An octavo should be placed on the press with the signature page to the left, or closest to the platen; a duodecimo, or its combinations, should have the signature on the right, or nearest the tympan. The form needs to be positioned under the center of the platen and properly secured with quoins. Then, the tympan is lowered and moistened if necessary, and a sheet of paper or a blanket is inserted. It used to be standard practice to wet the tympans for all jobs, but since the advent of fine printing and especially iron presses, this practice has mostly faded, except for very heavy forms composed of old type, which obviously need more cushioning to transfer properly. After the inner tympan or drawer is inserted, it is secured with hooks to prevent it from popping out. With the tympan lifted, a sheet of the paper being used is folded in quarto, and the short crease is aligned over the middle of the grooves of the short cross, if it’s centered in the form, as in octavo. For a twelves form, the paper is folded into thirds, with the long crease in the center of the long cross and the short cross over the grooves. Once the sheet is evenly placed on the form, the tympan is lowered, and a gentle tug will make the paper stick; it should then be glued to the tympan and fully stretched. The points are then screwed to the tympan, using short-shanked points for larger paper and long-shanked ones for smaller sheets. In twelves, the points must be set at equal distances from the edge of the paper. In octavo, the off-point can be slightly larger than the near one, as this helps the pressman to identify a turned stack while working on the back side.
When a press is continued upon the same work, the quoins on the off-side of the bed may remain and serve as gauges for the succeeding forms; for, if the chases are equal in size, the register will be almost, if not quite, perfect.
When a press keeps working on the same job, the quoins on the opposite side of the bed can stay in place and act as guides for the next forms. If the chases are the same size, the registration will be nearly, if not completely, perfect.
The following operations are comprised in the term of making ready the form:—
The following actions are included in the term of preparing the form:—
1. The frisket should be covered with stout even paper, in the manner described for putting on parchment, the paper being carefully placed on the inside of the frame so as to lie close to the tympan, and to confine the sheet in its place when laid on for printing. When the paste is dry, the frisket is put on the tympan, and, after inking the form, an impression pulled upon it. The frisket is then taken off and laid on a board, or on the bank, and the impression of the pages cut out with a sharp knife about a Pica em larger than the page. After being replaced on the tympan, it is advisable to put a few cords across, to strengthen the bars of paper, and to keep the sheets close to the tympan. When the margin is too small to admit bars of paper, it is necessary to work with cords only.
1. The frisket should be covered with strong, even paper, following the same method used for applying it to parchment. The paper needs to be carefully placed on the inside of the frame to sit snugly against the tympan and hold the sheet in place when it's laid out for printing. Once the paste is dry, the frisket goes on the tympan, and after inking the form, an impression is made on it. The frisket is then removed and laid on a board or on the bank, and the impression of the pages is cut out with a sharp knife, about a Pica em larger than the page. After being put back on the tympan, it's a good idea to add a few cords across to reinforce the paper bars and keep the sheets close to the tympan. When the margin is too small to fit paper bars, you'll need to work with cords only.
2. The form should be examined, to see that it is properly locked up and planed down; that no letters or spaces lie in the white lines of the form, nor between the lines in leaded matter.
2. The form should be checked to ensure it's properly secured and evened out; that no letters or spaces are in the blank lines of the form, or between the lines in leaded text.
3. White pages which occur in a form must not be cut out; but, if the page be already cut out, a piece of paper must be pasted on the frisket, to cover the white page in the form, and a bearer put on to keep the adjoining pages from having too hard an impression. Some pressmen use reglets, others furniture cut to a proper height, and a third class adopt cork, which, from its elasticity, is very useful. Spring bearers, made of hard paper rolled up, are also employed to guard the sides and bottoms of light and open pages, when there is an inclination to slur.
3. White pages that appear in a form shouldn’t be cut out; however, if a page has already been cut out, you need to paste a piece of paper on the frisket to cover the white page in the form, and put a bearer on to prevent the adjacent pages from getting too hard of an impression. Some pressmen use reglets, others use furniture cut to the right height, and another group uses cork, which is quite useful because of its elasticity. Spring bearers made from rolled-up hard paper are also used to protect the sides and bottoms of light and open pages when there's a risk of blurring.
4. The pressman must examine whether the frisket bites; that is, whether it keeps off the impression from any part of the pages.
4. The pressman needs to check if the frisket is effective; that is, whether it prevents the impression from touching any part of the pages.
5. He must consider whether the catch of the frisket stands either too far forward or backward: if forward, he may be much delayed by its falling down, and, if backward, it will come down too slowly, and thus retard the progress of the work and not unfrequently cause the sheet to slip out of its proper place. He must, therefore, place the catch so that the frisket may stand a little more than perpendicularly backward, that, when lightly tossed up, it may just stand, and not come back.
5. He needs to think about whether the catch of the frisket is positioned too far forward or backward: if it's too far forward, it may fall and slow him down; if it's too far back, it will come down too slowly, which can disrupt the workflow and often cause the sheet to slip out of place. Therefore, he should adjust the catch so that the frisket leans slightly more than vertically backward, so that when it's tossed lightly up, it stays in place and doesn't fall back down.
6. He must fit the gallows so that the tympan may stand as much toward an upright as he can; because it is the sooner let down upon the form and lifted up again. But yet he must not place it so upright as to prevent the white sheets of the paper from lying secure on the tympan.
6. He has to adjust the gallows so that the tympan is as upright as possible; this way, it can be lowered onto the bed and lifted back up more quickly. However, he also shouldn't make it so upright that the white sheets of paper can’t sit securely on the tympan.
7. The range of the paper-bank should not stand at right angles with the bed of the press; but the farther end of the bank should be placed so that the near side may make an angle of about seventy-five degrees with the near side of the bed.
7. The paper bank shouldn't be positioned at a right angle to the press's bed; instead, the far end of the bank should be set up so that the near side creates an angle of about seventy-five degrees with the near side of the bed.
8. The heap of paper should be set on the horse on the near end of the paper-bank, near the tympan, yet not touching it. The uppermost or outside sheet should be laid on the bank; and the pressman then takes four or five quires off his heap, and shakes them at each end, to loosen the sheets, till he finds he has sufficiently loosened or hollowed the heap. Then, with the nail of his right-hand thumb, he draws or slides forward the upper sheet, and two or three more commonly follow gradually with it, over the hither edge of the heap, to prepare those sheets ready for laying on the tympan.
8. The stack of paper should be placed on the horse at the near end of the paper bank, close to the tympan, but not touching it. The top sheet should be laid on the bank; then the pressman takes four or five quires from the stack and shakes them at each end to loosen the sheets until he notices that the stack is sufficiently loosened. Next, using the nail of his right thumb, he pulls or slides forward the top sheet, and usually two or three more will gradually follow it over the edge of the stack to get those sheets ready to be laid on the tympan.
9. He must next pull a revise sheet, which must be sent up to the overseer for a final revision, and for examining whether any letters have dropped out of the form in putting it on the press, &c.
9. He must next pull a revise sheet, which needs to be sent up to the overseer for a final check and to see if any letters have been missed in the process of putting it on the press, &c.
10. While the sheet is undergoing a revision, the pressman should proceed to make register, if half-sheet-wise, which is done by pulling a waste sheet, and turning it, (without inking, as the sheets may afterward be used for slip sheets,) being particular not to stretch the point-holes in the least, or to draw the hand along the sheet in leaving it. In making register, the points must be knocked up or down in such a direction as will bring the first impression under the last, knocking the point only half the distance apparent on the sheet. If register cannot be made with the points, the difficulty must then be either in the furniture, the length of the pages, or in the springing of the cross-bars, from the forms being locked up by careless compositors, who commence at one quarter of the form, and lock it up tightly, and so go around, instead of gently tapping it at opposite sides till the whole is equally tightened. In locking up a form, the quoins at the feet should be gently struck first, to force up the pages and prevent their hanging; but, in unlocking, the side quoins must be first slackened.
10. While the sheet is being revised, the press operator should proceed to make register, if it’s half-sheet-wise, which is done by pulling a waste sheet and flipping it (without inking, since the sheets may later be used for slip sheets). Care should be taken not to stretch the point-holes at all or to drag your hand along the sheet when you leave it. To make the register, the points must be adjusted up or down in a way that brings the first impression under the last, moving the point only half the distance you see on the sheet. If you can’t make the register with the points, the issue must be either with the furniture, the length of the pages, or the springing of the cross-bars, often due to the forms being locked up by careless typesetters who start at one corner and lock it up tightly, working their way around instead of gently tapping it on opposite sides until everything is evenly tightened. When locking up a form, the quoins at the bottom should be gently struck first to lift the pages and prevent them from sagging, but when unlocking, the side quoins should be loosened first.
Altering the quoins will not make good register, when the compositor has not made the white exactly equal between all the sides of the crosses. The pressman, therefore, will ascertain which side has too much or too little white, and, unlocking the form, will take out or put in as many leads or reglets as will make good register.
Altering the corner pieces won’t fix the alignment if the typesetter hasn’t made the spacing perfectly equal on all sides of the crosses. So, the press operator will check which side has too much or too little space, and, unlocking the setup, will remove or add as many leads or strips as needed to achieve proper alignment.
PULLING.
In taking a sheet off the heap, the pressman places himself almost straight before the near side of the tympan, but nimbly twists the upper part of his body a little backward toward the heap, the better to see that he takes but one sheet off. This he loosens from the rest of the heap by drawing the back of the nail of his right thumb quickly over the bottom part of the heap, and, receiving the near end of the sheet with his left-hand fingers and thumb, catches it by the farther edge with his right hand, about four inches from the upper corner[261] of the sheet, and brings it swiftly to the tympan: having the sheet thus in both his hands, he lays the farther side and two extreme corners of the sheet down even upon the farther side and extreme farther corners of the tympan-sheet. In the reiteration, care should be taken to draw the thumb on the margin, or between the gutters, to avoid smearing the sheet. The sheet being properly laid on, he supports it in the centre by the fingers of the left hand, while his right hand, being disengaged, is removed to the back of the ear of the frisket, to bring it down upon the tympan, laying at the same moment the tympan on the form. He then, with his left hand, grasps the rounce, and quickly runs the form under the platen; and, after pulling, he gives a quick and strong pressure upon the rounce, to run the carriage out again. Letting go the rounce, he places the fingers of his left hand toward the bottom of the tympan, to assist the right hand in lifting it up, and also to be ready to catch the bottom of the sheet when the frisket rises, which he conveys quickly and gently to the catch: while it is going up, he slips the thumb of his left hand under the near lower corner of the sheet, which, with the aid of his two forefingers, he raises, the right hand at the same time grasping it at the top in the same manner. Lifting the sheet carefully and expeditiously off the points, and nimbly twisting about his body toward the paper-bank, he carries the sheet over the heap of white paper to the bank, and lays it down upon a waste sheet or wrapper; but, while it is coming over the white paper heap, though he has the sheet between both his forefingers and thumbs, yet he holds it so loosely that it may move between them as on two centres, as his body twists about from the side of the tympan toward the side of the paper-bank.
As he grabs a sheet from the pile, the pressman positions himself almost directly in front of the near side of the tympan but skillfully twists his upper body slightly back towards the pile to ensure he only takes one sheet. He separates it from the rest of the stack by quickly dragging the back of his right thumb across the bottom of the heap. He catches the near end of the sheet with his left fingers and thumb, then grabs the far edge with his right hand, about four inches from the upper corner[261] of the sheet, and swiftly brings it to the tympan. With the sheet held in both hands, he places the far side and the two extreme corners down evenly on the farther side and extreme corners of the tympan-sheet. During this process, he must take care to drag his thumb along the margin or between the gutters to avoid smudging the sheet. Once the sheet is correctly positioned, he supports it in the center with his left fingers while his right hand moves to the back of the frisket to bring it down onto the tympan, simultaneously laying the tympan on the form. He then grips the rounce with his left hand and swiftly runs the form under the platen; after pulling, he applies a quick, strong pressure on the rounce to return the carriage. Releasing the rounce, he positions his left fingers at the bottom of the tympan to help his right hand lift it, while also preparing to catch the bottom of the sheet as the frisket rises, which he quickly and gently directs to the catch. As it rises, he slides the thumb of his left hand under the near lower corner of the sheet, using his two forefingers to raise it while his right hand similarly grips the top. Carefully lifting the sheet off the points, he quickly twists his body towards the paper bank and carries the sheet over the stack of white paper to place it on a waste sheet or wrapper. However, while moving it over the white paper pile, even though he holds the sheet between his forefingers and thumbs, he keeps his grip loose enough so it can shift between them as his body turns from the tympan to the paper bank.
When the pressman comes to a token sheet, he undoubles it, and smooths out the crease with the back of the nails of his right hand, that the face of the letter may print upon smooth paper; and, being printed off, he folds it again, as before, for a token-sheet, when he works the reiteration.
When the pressman gets to a token sheet, he unfolds it and smooths out the crease with the back of his right hand's nails so that the letter prints on clean paper. After printing, he folds it again like before, preparing it for the next run.
Having worked off the white paper of a form of twelves, he places his right hand under the heap, and, his left hand supporting the end near him, turns it over on the horse, with the printed side downward. If the form be octavo, he places his left hand under the heap, supporting the outside near end with[262] his right hand, and turns it one end over the other. All turning of the paper for reiteration is treated in one of these modes. In performing this operation, he takes from the heap only as much at once as he can well handle without disordering the evenness of the sides of the paper.
Having worked through the white paper for a type of twelves, he places his right hand underneath the stack, using his left hand to support the end closest to him, and flips it over onto the horse, with the printed side facing down. If the format is octavo, he places his left hand under the stack, supporting the outside end with his right hand, and flips it end-over-end. All methods of flipping the paper for repetition are done in one of these ways. When performing this task, he only takes as much from the stack at once as he can handle without disrupting the neatness of the paper's sides.
Having turned the heap, he proceeds to work it off, as before described, except that with the left hand he guides the point-holes over the points, moving the sheet with the right hand, more or less, to assist him in so doing. The token-sheets, as he meets with them, he does not fold down again.
Having turned the pile, he goes on to work it off, as previously described, except that with his left hand he guides the point-holes over the points, using his right hand to move the sheet a bit to help him do this. He doesn’t fold the token-sheets down again as he comes across them.
RULES AND REMEDIES FOR PRESSMEN.
About every five or six sheets a small quantity of ink should be taken; yet this rule is subject to some variation from the nature of the work and quality of the ink. A form of large type or solid matter will require ink to be taken more frequently, and a light form of small type less frequently. During the intervals in which the roller-boy is not employed in brayering out or taking ink, he should be almost constantly engaged in distributing or changing his rollers. He should invariably take ink on the back roller, as it will the sooner be conveyed to the other roller, and, consequently, save time in distributing. When, through carelessness, too much ink has been taken, it should be removed by laying a piece of clean waste paper on one of the rollers, and working it off till the ink is reduced to the proper quantity.
About every five or six sheets, a small amount of ink should be used; however, this guideline can vary based on the type of work and the quality of the ink. A form with large type or solid areas will need ink more often, while a lighter form with smaller type will need it less frequently. When the roller boy isn’t busy applying or taking ink, he should be almost constantly engaged in distributing or changing his rollers. He should always take ink on the back roller, as this helps transfer it to the other roller more quickly, saving time in distribution. If, due to carelessness, too much ink is taken, it should be removed by placing a piece of clean waste paper on one of the rollers and working it off until the ink amount is reduced to the correct level.
If letters, quadrates, or furniture rise up and black the paper, they should be put down, and the quarter locked up tighter.
If letters, shapes, or objects appear and darken the paper, they should be set down, and the room locked up more securely.
If any letters are battered, the quarter they are in must be unlocked, and perfect ones put in by the compositor.
If any letters are damaged, the section they’re in must be unlocked, and flawless ones should be put in by the typesetter.
When bearers become too thin by long working, they should be replaced by thicker ones.
When carriers become too thin from prolonged work, they should be replaced with thicker ones.
When the form gets out of register,—which will often happen by the starting of the quoins which secure the chase,—it must be immediately put in again, as there can scarcely be a greater defect in a book than the want of uniformity in this particular.
When the form gets out of alignment—which often happens when the quoins that hold the chase in place shift—it needs to be fixed right away, because there's hardly a bigger flaw in a book than a lack of uniformity in this area.
If picks, produced by bits of paper, composition, or film of ink and grease or filth, get into the form, they must be removed with the point of a pin or needle; but if the form is[263] much clogged with them, it should be well rubbed over with clean ley, or taken off and washed: in either case, before the pressman goes on again, it should be made perfectly dry by pulling several waste sheets upon it, in order to suck up the water deposited in the cavities of the letter.
If bits of paper, ink, grease, or dirt end up in the type, they need to be removed with a pin or needle. However, if the type is really jammed with them, it should be thoroughly wiped down with clean lye, or taken off and washed. In either case, before the printer resumes, it should be completely dried by running several waste sheets over it to soak up the moisture trapped in the letter's cavities.
The pressman should accustom himself to look over every sheet as he takes it off the tympan: he will thus be enabled not only to observe any want of uniformity in the colour, but also to detect imperfections which might otherwise escape notice.
The press operator should get into the habit of checking every sheet as he removes it from the tympan. This way, he can not only spot any inconsistencies in the color but also catch any flaws that might otherwise go unnoticed.
In order to make perfect uniformity in the colour, the roller-boy should keep his ink well brayered out with the small roller, in proper quantities for the work in hand, and also should change his rollers well after taking ink, and at other times. The rollers are changed by moving the roller-handle slowly to the right and left, while the crank is being turned briskly with the left hand.
To achieve a perfect uniform color, the roller operator should ensure the ink is spread evenly with the small roller, using the right amount for the task at hand, and should also change the rollers appropriately after inking and at other times. The rollers are changed by slowly moving the roller handle to the right and left while quickly turning the crank with the left hand.
Torn or stained sheets met with in the course of work are thrown out and placed under the bank. Creases and wrinkles will frequently appear in the sheets when the paper has been carelessly wet: these should be carefully removed by smoothing them out with the back of the nails of the right hand.
Torn or stained sheets encountered during work are discarded and placed under the bank. Creases and wrinkles often appear in the sheets if the paper has been carelessly wet; these should be gently removed by smoothing them out with the back of the nails on your right hand.
If the frame of the tympan rub against the platen, it will inevitably cause a slur or mackle: this can easily be remedied by moving the tympan so as to clear the platen. The joints or hinges of the tympan should be kept well screwed up, or slurring will be the consequence. When the thumb-piece of the frisket is too long, it always produces a slur: this can be prevented by filing off a part of it. Loose tympans will at all times slur the work, and great care must therefore be observed in drawing them perfectly tight. The paper drying at the edges will also cause a slur: this may be remedied by wetting the edges frequently with a sponge.
If the frame of the tympan rubs against the platen, it will definitely cause a slur or mackle; this can easily be fixed by adjusting the tympan to clear the platen. The joints or hinges of the tympan should be kept tightly screwed, or slurring will happen. When the thumb-piece of the frisket is too long, it always creates a slur; this can be prevented by filing down part of it. Loose tympans will always cause slurring, so great care must be taken to pull them tight. If the paper dries at the edges, it will also cause a slur; this can be fixed by frequently wetting the edges with a sponge.
Slurring and mackling will sometimes happen from other causes: it will be well in such cases to paste corks on the frisket, or to tie as many cords as possible across it, to keep the sheet close to the tympan.
Slurring and mackling can sometimes occur for other reasons: in such cases, it’s a good idea to stick corks on the frisket, or to tie as many cords as possible across it to keep the sheet tight against the tympan.
The pressman should make the boy roll slowly, or the rollers will be apt to jump, and cause a friar. To prevent the rollers from jumping or bounding, bridges or springs made of thin steel, to reach across the gutters, may be used: these[264] springs should taper off at the ends, and having an oblong hole in each end, through which they may be tacked to the gutter-sticks. In very open forms, it may be necessary to put bearers or pieces of reglet where the blank pages occur at the end of the form, to prevent one end of the roller from falling down and leaving a friar at the opposite end. This difficulty may be obviated in a great measure by imposing the form in such a manner as to bring the blank pages in the centre. This mode should always be adopted for title-pages and other light matter.
The pressman should have the boy roll slowly, or the rollers might jump and create a friar. To stop the rollers from jumping or bouncing, thin steel bridges or springs can be used to span the gutters: these[264] springs should narrow at the ends, with an oblong hole in each end for tacking to the gutter sticks. In very open forms, you might need to add bearers or pieces of reglet where the blank pages appear at the end of the form to keep one end of the roller from dropping and leaving a friar at the opposite end. This issue can largely be avoided by positioning the form so that the blank pages are in the center. This approach should always be used for title pages and other light content.
Before the pressman leaves his work, he covers the heap of paper by first turning down a sheet like a token-sheet, to show where he left off, and then putting a quantity of the worked-off sheets on it, and a paper-board if convenient. Laying the blanket on the heap after leaving off work is a bad custom. If the paper be rather dry, it will be well to put wet wrappers on it, after damping the edges well. If the form be clean, he puts a sheet of waste paper between the tympan and frisket, and lays them down on the form; if it be dirty, it must be rubbed over with clean ley, and several waste sheets pulled on it, as before directed, to suck the dirty ley out of the cavities of the letter. On his return to work in the morning, he takes care to wet the tympan, provided the type be worn. If there should be any pages in the form particularly open, the parts of the tympan where they fall must not be wetted.
Before the pressman finishes his shift, he covers the stack of paper by first folding down a sheet like a placeholder to show where he stopped, then placing a number of the used sheets on top of it, and a board if it's convenient. Putting the blanket on the stack after finishing work is a bad habit. If the paper is a bit dry, it’s a good idea to put wet wrappers on it, making sure to dampen the edges well. If the printing plate is clean, he places a sheet of scrap paper between the tympan and frisket and lays them down on the plate; if it’s dirty, he needs to rub it with clean ley and stack several scrap sheets on top to absorb the dirty ley from the spaces in the letters. When he returns to work in the morning, he makes sure to wet the tympan, especially if the type is worn. If there are any open pages in the plate, the areas of the tympan where they fall should not be wet.
THE LEY-TROUGH.
The form being worked off, it is the pressman’s duty to wash it clean from every particle of ink, not only for the cleanly working and well standing of the letter in the subsequent composing, but to save his own time in making ready when the same letter gets to press again. Many an hour is lost from not bestowing a minute or two in thoroughly cleansing and rinsing the form.
The form being used, it's the pressman’s responsibility to clean it thoroughly from every bit of ink, not just for the neat operation and proper alignment of the letters in the next composing, but to save his own time when the same letters go to press again. Many hours are wasted by not taking a minute or two to properly clean and rinse the form.
For this purpose, printing-offices are provided with a ley-trough, suspended on a cross-frame, and swinging by iron ears fixed somewhat out of the precise centre, so that the gravity of the trough will cause it to fall in a slanting position forward. This trough is lined with lead, the top front edge being guarded from the pitching of the forms by a plate of[265] iron. The form having been placed in the trough, on its side, the pressman takes hold of the rim of the chase by the hook, or instrument for that purpose, and, laying it gently down, pours the ley upon it, and sluices it by swinging the trough on its pivots two or three times to and fro; then, taking the ley-brush, he applies it to the whole form, type, furniture, and chase; the ley is then let out into a receptacle, and the form well rinsed with clean water, by swinging the trough as before; the form is then lifted out, and consigned to the care of the compositor.
For this purpose, printing offices are equipped with a ley trough, hung on a cross-frame and swinging by iron ears fixed slightly off-center, so that the weight of the trough makes it tilt forward. This trough is lined with lead, and the front edge is protected from the movement of the forms by a plate of[265] iron. Once the form is placed in the trough on its side, the pressman grabs the rim of the chase with a hook or tool specifically for that, gently lays it down, pours the ley over it, and moves the trough back and forth on its pivots two or three times. Then, using a ley brush, he applies it to the entire form, including the type, furniture, and chase. The ley is then drained into a receptacle, and the form is thoroughly rinsed with clean water by swinging the trough as before. Finally, the form is lifted out and handed over to the compositor.
The ley is made of pot or pearl ash, or, what is better, of concentrated ley. A large earthen jar is usually chosen for the purpose; a sufficient quantity of ash or concentrated ley is added to the water to make it bite the tongue sharply in tasting.
The ley is made of potash or pearl ash, or, even better, of concentrated ley. A large earthen jar is typically used for this; a sufficient amount of ash or concentrated ley is added to the water until it tastes sharply on the tongue.
The ley-brush is made large, the hairs close, fine, and long, in order not to injure the type, while sufficient force is applied to search every interstice in the letter where the ink can have insinuated itself.
The ley-brush is large, with close, fine, and long bristles, so it won't damage the type, while enough pressure is used to reach every gap in the letter where the ink might have settled.
MAKING READY ON CYLINDER PRESSES.
Make clean the bed of the press and the impression segment of the cylinder. Adjust the bearers a trifle above ordinary type height. See that the impression screws have an even bearing on the journals, and that the cylinder fairly meets the bearers. Select a suitable tympan or impression surface.
Clean the bed of the press and the impression section of the cylinder. Adjust the bearers slightly higher than standard type height. Make sure the impression screws have an even grip on the journals, and that the cylinder properly aligns with the bearers. Choose an appropriate tympan or impression surface.
The tympan may be the India-rubber cloth which is furnished with the press, a thick woollen lapping cloth or blanket, several sheets of thick calendered printing paper, or one or more smooth and hard pasteboards. Each of these materials has merits not to be found in any other. Upon the proper selection of the tympan the presswork in great measure depends, and the pressman should be thus guided in making choice.
The tympan can be the rubber cloth that comes with the press, a thick wool blanket, several sheets of thick calendered printing paper, or one or more smooth, sturdy pasteboards. Each of these materials has unique advantages that the others don’t offer. The success of the presswork largely depends on the right choice of tympan, so the pressman should follow this guidance when making a selection.
A pasteboard tympan is most suitable for wood-cuts, for perfectly new type, and for the best kinds of presswork. It is not suitable for miscellaneous work, nor for heavy forms, nor mixed old and new type. If the overlaying is properly executed, a pasteboard tympan will enable the pressman to show a sharper edge and a more delicate impression of the type[266] than can be possible with any other, and it will wear the type less than any other. But it will require a very tedious and careful making ready, or it will prove very destructive to type.
A pasteboard tympan is best for woodcuts, brand new type, and high-quality presswork. It's not suited for mixed projects, heavy setups, or combinations of old and new type. If applied correctly, a pasteboard tympan allows the pressman to produce a sharper edge and a more delicate impression of the type[266] than any other option, and it will cause less wear on the type than any alternative. However, it requires a meticulous and time-consuming setup, or it can easily damage the type.
A woollen blanket is best adapted for old stereotype plates, for very old type which has been rounded on the edges, for posters with large wood type, and for all common work which requires a clear but dull impression. For such work a woollen blanket will enable the pressman to make ready a form more quickly than with any other material; but it is injurious to new type, and incapable of producing a fine and sharp impression.
A wool blanket is ideal for old stereotype plates, very old type that has rounded edges, posters with large wood type, and all standard jobs that need a clear but dull impression. For this kind of work, a wool blanket allows the pressman to prepare a form faster than with any other material; however, it can damage new type and doesn't produce a fine and sharp impression.
Thick paper is much used for book-work. It also answers well for script circulars and leaded forms. It will not answer so well for mixed old and new type, nor for table-work with unequal heights of brass rule, nor for mixed large and small type. It will prove most serviceable for the average of light and fine presswork.
Thick paper is commonly used for book projects. It also works well for written circulars and forms with leaded type. However, it’s not ideal for mixing old and new typefaces, nor for table work with uneven brass rule heights, or for combining large and small type. It will be most effective for standard light and fine press work.
The India-rubber cloth combines many good qualities not found in other tympans: it has something of the density of the pasteboard, the hardness and evenness of paper, and the flexibility of the blanket, combined with an elasticity peculiarly its own. It will compass a greater variety of work than any other: posters, script circulars, news and book forms, stereotype plates, and old or new type, can all be well printed with an India-rubber blanket. When it is intended to make one tympan answer for all kinds of work, the India-rubber blanket will be found decidedly superior to all others; but when very extra presswork is wanted, the tympan must be specially adapted to the form of type.
The India-rubber cloth combines many good qualities not found in other tympans: it has some of the density of pasteboard, the hardness and smoothness of paper, and the flexibility of a blanket, along with a unique elasticity. It can handle a wider variety of tasks than any other: posters, scripted circulars, news and book forms, stereotype plates, and both old and new type can all be printed effectively with an India-rubber blanket. If you're looking to use one tympan for all kinds of work, the India-rubber blanket is definitely superior to the rest; however, when very high-quality press work is needed, the tympan must be specifically tailored to the type's form.
There are forms for which none of these tympans are specially suitable. For such cases careful pressmen combine two or more together,—as Welsh flannel over rubber, or thin rubber over pasteboard or under paper. These, however, are exceptional cases, and are only thus combined when very good presswork is wanted from imperfect materials. Careful observation of the quality of the impression given by each style of tympan will teach a pressman how to combine to the best advantage. As it requires experience and discrimination, an arbitrary rule cannot be given.
There are situations where none of these tympans are particularly suitable. In such cases, skilled pressmen combine two or more materials together—like Welsh flannel over rubber, or thin rubber over pasteboard or under paper. However, these are exceptional cases, and this combination is only done when high-quality presswork is needed from less-than-ideal materials. Careful observation of the quality of the impressions produced by each type of tympan will teach a pressman how to combine them for the best results. Since this requires experience and discernment, there's no one-size-fits-all rule.
Whatever may be the material selected, the tympan must be stretched very tightly over the cylinder. All labour in overlaying[267] is but thrown away if this is not carefully attended to. A rubber or woollen blanket can be secured at one end of the cylinder by small hooks projecting inward, while it may be laced tightly with saddler’s thread at the other end; or, by sewing on that end of the blanket a piece of canvas, it may be wound tightly around the reel, and kept secure by the pawl and ratchet.
Whatever material you choose, the tympan needs to be stretched really tight over the cylinder. Any effort put into overlaying[267] is wasted if this isn't done carefully. You can attach a rubber or wool blanket at one end of the cylinder using small hooks that stick inward, and then lace it tightly with saddler's thread at the other end. Alternatively, by sewing a piece of canvas onto that end of the blanket, you can wind it tightly around the reel and hold it in place with the pawl and ratchet.
But paper and pasteboard require a different process,-viz.: Take a piece of Nonpareil cherry reglet of the full length of the cylinder. Trim down the paper or pasteboard to the width of the bed between the bearers, but leave it a little longer than the impression segment of the cylinder. Then crease the pasteboard at a uniform distance of half an inch from the narrower end, and lay this creased part on the flat edge of the impression segment of the cylinder, under the grippers. Put the reglet over this, and bring down the clamps hard on the reglet, so as to bind all securely. When this is done, a thin web of muslin may be stretched over the whole, in the same way in which a blanket is laid on, and rolled up tightly, which will prevent any slipping of the board or of the overlays pasted on it.
But paper and pasteboard need a different method: Take a piece of Nonpareil cherry reglet that's the full length of the cylinder. Trim the paper or pasteboard to the width of the bed between the bearers, but leave it a bit longer than the impression segment of the cylinder. Then crease the pasteboard at a uniform distance of half an inch from the narrower end, and place this creased part on the flat edge of the impression segment of the cylinder, under the grippers. Put the reglet over this, and tighten the clamps down on the reglet to secure everything. Once that's done, a thin layer of muslin can be stretched over the whole setup, just like you would lay on a blanket, and rolled up tightly, which will stop any movement of the board or the overlays pasted onto it.
A large poster, or newspaper form, or any large form with old type, will require a soft roller with much suction. Book-work, wood-cuts, or fine job-work, will require a harder roller, with very smooth, elastic, and clinging surface. Coloured inks are best printed with a still harder roller and with much less suction. All rollers should be perfectly clean, and free from cracks or holes. The suitableness of these rollers cannot well be explained by words: such a knowledge will be best acquired by observation and experience. It may, however, be necessary to state that one roller will not answer for all styles of presswork: the quality of the work, the size and wear of the type, and the speed of the press, must control the pressman in his choice.
A large poster, newspaper, or any big print using old-style type will need a soft roller with a lot of suction. For book work, woodcuts, or fine jobs, you'll need a harder roller with a very smooth, elastic, and gripping surface. Colored inks are best printed using an even harder roller with much less suction. All rollers should be perfectly clean and free of cracks or holes. The suitability of these rollers can't really be explained in words; the best way to understand is through observation and experience. However, it’s important to note that one roller won't work for all types of presswork: the quality of the work, the size and wear of the type, and the speed of the press will all influence the pressman's choice.
Posters, with large wood type, require a semi-fluid ink, but not surcharged with oil. Ordinary news-work requires a better grade, more tachy, and finely ground. Good book-work should have a stiffer-bodied ink, soft, smooth, and with little oil. Job ink, which is made expressly for presswork on dry paper, should be used only for such work. Book and job inks are not convertible: an ink for wet paper will not work well[268] on dry paper, and vice versâ. Very fine presswork—such as wood-cuts, or letter-press upon enamelled paper—calls for an ink impalpably fine, very stiff, of brilliant colour, and nearly or absolutely free from oil.
Posters, using large wooden letters, need a semi-fluid ink, but not overloaded with oil. Regular newsprint requires a higher quality, more fluid, and finely ground ink. Good book printing should use a thicker ink that's soft, smooth, and has minimal oil. Job ink, specifically made for printing on dry paper, should only be used for that purpose. Book and job inks are not interchangeable: ink designed for wet paper won't work well on dry paper, and vice versa. High-quality presswork—like woodcuts or letterpress on glossy paper—demands an extremely fine, very thick ink with bright color that is nearly or completely free of oil.[268]
Every job-office should keep four grades of ink,—news, book, job, and wood-cut. They can be compounded (if no ink-manufacturer is near) with each other, or reduced with varnish to suit any form. Good presswork is impossible without good inks.
Every job office should keep four types of ink—news, book, job, and wood-cut. They can be mixed together (if there's no ink manufacturer nearby) or thinned with varnish to fit any need. Good print work is impossible without good inks.
Charge the ink-fountain with the ink selected, and keep it well covered, to protect it from paper dust. Turn down the screws, and cut off all the ink evenly. When the form is ready, turn on the ink cautiously, and wait for ten or twelve impressions before again altering the screws. For small forms and short numbers of any piece of presswork in coloured ink or extra ink, a fountain is not necessary. The ink may be applied with a brayer or palette-knife.
Charge the ink fountain with the chosen ink and keep it covered to protect it from paper dust. Adjust the screws and cut off all the ink evenly. Once the form is ready, turn on the ink carefully and wait for ten to twelve prints before adjusting the screws again. For smaller forms and short runs of any presswork in colored ink or extra ink, a fountain isn’t necessary. You can apply the ink with a brayer or palette knife.
The adjustment of the margin is the next process. Although type can be printed from any quarter of the bed, it will be found most judicious to lay all forms close to the back part of the bed, and equidistant between the bearers. This will secure a good impression, give a fair average margin to every form, and allow the full use of the bed for a large form, without resetting the cylinder. The bed and cylinder travel together, and the grippers, which bring down the sheet to the form, should barely lap over the back part of the bed. So long as the toothed cylinder wheel, and the short toothed rack on the side of the bed, remain undisturbed, the grippers will always pass over the bed in exactly the same place. When the grippers are in this position, (slightly lapping over the back of the bed,) take measurement of the distance between the back edge of the bed and the point of one of the nearest grippers. With a piece of reglet cut a gauge exactly corresponding to this measurement. Let no form be laid upon the press until the distance between the type and the edge of the chase tallies with the gauge. This will prevent the grippers from closing on the form and crushing the type. If the chase will not admit of so wide a margin, or if an extra margin is wanted on the sheet, put a piece of furniture of the extra width behind the chase: the margin can thus be increased or diminished at pleasure.
The next step is adjusting the margin. Although type can be printed from any spot on the bed, it's usually best to position all forms close to the back of the bed and evenly spaced between the bearers. This ensures a good impression, provides a consistent margin for each form, and allows for the full use of the bed for a large form without needing to reset the cylinder. The bed and cylinder move together, and the grippers that pull down the sheet onto the form should slightly overlap the back of the bed. As long as the toothed cylinder wheel and the short toothed rack on the side of the bed stay undisturbed, the grippers will always pass over the bed in the same spot. Once the grippers are in this position (slightly overlapping the back of the bed), measure the distance from the back edge of the bed to one of the nearest grippers. Cut a reglet to make a gauge that matches this measurement exactly. Don't place any form on the press until the distance between the type and the edge of the chase matches the gauge. This will prevent the grippers from closing on the form and damaging the type. If the chase can't accommodate such a wide margin or if you need extra margin on the sheet, place a piece of furniture of the extra width behind the chase; you can then increase or decrease the margin as needed.
A book form may be locked up in a chase so large, with the type so far from the edge of the chase, that the grippers will bring down the sheet in such a position that it will be printed with the margin all on one side. To remedy this, the cylinder must be reset. Proceed thus. Remove the screw and washer, and draw the intermediate wheel out of gear, loosen screws in the gauge rack, then turn the cylinder to the point required, connect the intermediate wheel, adjust the gauge rack, and screw up tight.
A book form can be secured in a chase that's so large, with the type positioned so far from the edge, that the grippers might lower the sheet in a way that results in all the margin being on one side. To fix this, you need to reset the cylinder. Follow these steps: Remove the screw and washer, disengage the intermediate wheel, loosen the screws on the gauge rack, turn the cylinder to the desired position, reconnect the intermediate wheel, adjust the gauge rack, and tighten everything up.
The press having been adjusted, next examine the form to be printed. Not only see that it is gauged correctly, but also see that it is not locked up too tightly,—that chase, quoins, letter, and furniture are all level, and lie flat upon the bed. If the form springs, the quoins must be slackened; if this loosens the type too much, the justification should be amended. Make clean the type by rubbing it over with a dry brush. The rollers are often made foul and the colour of the ink changed by dust and particles of dirt clinging to the type.
The press has been set up, so now check the form to be printed. Make sure it's properly aligned, and that it isn’t locked down too tightly—everything, including the chase, quoins, letters, and furniture, should be level and flat on the bed. If the form is springy, you need to loosen the quoins; if that makes the type too loose, adjust the justification. Clean the type by brushing it gently with a dry brush. The rollers can get dirty and change the ink color due to dust and dirt sticking to the type.
Fasten the form so securely on the bed that it will not be moved by the action of the cylinder or the rollers. Take a proof on its own paper, using very little ink. Proceed to adjust the drop guides so as to bring the sheet exactly in the right position. Push out the iron tongues at the edge of the feed-board, and at equal distances from each other, so that they will equally sustain the paper. Slide the drop guides along the rod until they fall squarely over the tongues. Set the side guide so that it will give a true margin in length to the sheet to be printed. Adjust the grippers so that they will seize the sheet at proper intervals, making the margin exactly even by lengthening or shortening the drop guides. Then take a clean proof on its own paper, exactly in the right position, before making ready, when it may be shown to the reader. It frequently happens that an error in the margin, or an imperfection in the register, is thus noticed; and its timely discovery and correction before overlaying will save much time and trouble. A readable proof may be taken before overlaying, by running through a sheet or two of proof paper. Make register, if it is a book form, before underlaying.
Make sure the form is secured tightly on the bed so it won't be moved by the cylinder or rollers. Take a proof on its own paper using very little ink. Adjust the drop guides to position the sheet correctly. Extend the iron tongues at the edge of the feed-board, keeping them evenly spaced to support the paper equally. Slide the drop guides along the rod until they align perfectly over the tongues. Set the side guide to ensure a proper margin length for the sheet being printed. Adjust the grippers so they grab the sheet at the right intervals, making the margin perfect by lengthening or shortening the drop guides. Then take a clean proof on its own paper, ensuring it's correctly positioned, before getting ready, so it can be shown to the reader. It often happens that errors in the margin or issues with the registration are noticed this way; discovering and correcting them in time before overlaying will save a lot of time and hassle. A readable proof can be taken before overlaying by running through a sheet or two of proof paper. Make register, if it's a book form, before underlaying.
When every thing has been found correct, then proceed to regulate the impression. If the type is fair, the proof should show a decently uniform impression; but if the form is large,[270] or if it contains old and new or large and small type, then the proof will show an uneven impression. To rectify this inequality, pressmen use many expedients.
When everything has been checked and confirmed, then move on to adjust the impression. If the type is even, the proof should display a reasonably uniform impression; however, if the form is large,[270] or if it includes both old and new or large and small type, then the proof will show an uneven impression. To fix this inconsistency, printers employ various methods.
1. By lowering the bearers and putting on more impression. This, of itself, is a very poor way; for it wears down new type in order to show the face of the old, and invariably produces thick and coarse presswork.
1. By lowering the bearers and applying more pressure. This, in itself, is a very bad method; it damages new type to reveal the face of the old and consistently produces thick and粗糙的印刷品.
2. By raising the low type to a proper height with thicknesses of paper under them, which is called underlaying.
2. By elevating the low type to the right height using thicknesses of paper underneath, which is referred to as underlaying.
3. By giving additional thickness to the tympan over every part of the form which shows a weak impression, which is called overlaying.
3. By adding extra thickness to the tympan over any areas of the form that show a weak impression, which is called overlaying.
It is very rare that any one of these modes will prove sufficient: all should be used in conjunction. When the larger part of the proof-sheet shows a weak impression, almost approaching illegibility, then more impression should be added. When one side of the proof-sheet shows a weak impression, while that on the other side is full and clear, then more impression should be given to the paler side. The impression should be made decently uniform before any attempt at overlaying or underlaying. But the bearers should follow the impression screws, both being raised and lowered together, in order to secure the type from the unimpeded force of the impression cylinder. Not only should the bearers be of even height, but the cylinder shaft should always revolve on a true level. If the impression screws are carelessly used, and the bearers are rashly raised and lowered, this even bearing will soon be lost; the difficulty of obtaining a good impression will be much increased, and the press will receive a serious injury. For the same reason, the bearers should never be packed, (by the addition of cards, as is usual on a hand-press,) for it strains the cylinder and all its bearings with an irregular resistance. The bearers should be tampered with even less than the impression screws. When the impression screws are so set that the cylinder gives a fair uniform impression, they have done all that can be expected, and nothing more should be attempted by them. Sometimes the proof may show that a cut, or a line of type, or a set of brass rules, are higher than any other material in the form. But the impression should be set regardless of this: it will be found quicker and neater to reduce the impression on one or two such high lines, by cutting out the[271] tympan-sheet over them, than it would be to underlay and bring up all other types to such an irregular height. Pitch the impression so that it will face the larger portion of the type, and make the less conform to the greater. Those parts which are high must be cut out of the tympan, and those which are low should be raised by underlays, and all inequalities regulated by overlays.
It’s very rare that any one of these methods will be enough; all of them should be used together. When most of the proof sheet shows a weak impression that’s almost unreadable, more impression needs to be added. If one side of the proof sheet has a weak impression while the other side is clear and strong, then more impression should be added to the weaker side. The impression should be made fairly uniform before attempting any overlays or underlays. However, the bearers should move with the impression screws, both being raised and lowered together to protect the type from the direct force of the impression cylinder. Not only should the bearers be the same height, but the cylinder shaft should always turn on a true level. If the impression screws are used carelessly, and the bearers are haphazardly adjusted, this even bearing will quickly be lost; it will become much harder to get a good impression, and the press could be seriously damaged. For the same reason, bearers should never be packed (by adding cards, like on a hand press), because it places uneven stress on the cylinder and all its bearings. Bearers should be adjusted even less than the impression screws. When the impression screws are set to give a decent, uniform impression, that’s all that should be expected from them. Sometimes the proof might indicate that a cut, a line of type, or a set of brass rules are higher than any other material in the form. But the impression should be set without regard to this; it’s quicker and tidier to reduce the impression on one or two of those high lines by cutting out the tympan sheet over them than it is to underlay and bring up all the other types to that uneven height. Set the impression so that it faces the larger portion of the type and make the smaller conform to the larger. Parts that are high must be cut out of the tympan, while those that are low should be raised with underlays, and all inequalities should be adjusted with overlays.
When any part of the form is very low, it will not answer to attempt facing it with overlays: it must be brought up to meet the inking rollers as well as the impression cylinder. When the proof shows low type, cut out the impression of it, raise the form, and paste it over the feet of the letter. If some types are high and some are low, make proper distinction, and carefully avoid increasing the height of any type or rule which seems to have a full impression. Pursue the same course when a marked depression appears in the centre, or a dwindling impression at the edges. Cut out that section which is light, and affix it to the defective part. If the impression dwindles in any part, the underlays must be cut of irregular thickness to suit the tapering off of the impression. Cut out an underlay from the edge where the impression begins to fade; then cut another of smaller size where it is utterly illegible; paste one over the other, laying them carefully in their proper positions, and then paste them all on the bottom of the form, where it is needed, taking care to lay the smallest underlay nearest the bed. This will restore the type to a proper level, and the next proof should show a uniform impression. The same plan will answer for a low corner. Use as little paste as possible, thin and free from lumps. Be careful that the underlays are laid on smoothly, without fold or wrinkle. Cut all underlays from a proof; for the proof serves as a guide both in cutting and in affixing to the form.
When any part of the form is too low, trying to fix it with overlays won't work; it needs to be raised to align with the inking rollers and the impression cylinder. If the proof shows low type, cut out its impression, lift the form, and paste it over the feet of the letter. If some types are high and others are low, make a clear distinction and be careful not to increase the height of any type or rule that seems to have a full impression. Follow the same approach if there's a noticeable dip in the center or a fading impression at the edges. Cut out the light section and attach it to the flawed part. If the impression fades in any area, the underlays must be cut to varying thicknesses to match the diminishing impression. Cut an underlay from the edge where the impression starts to fade, then another smaller one where it’s completely illegible; paste them on top of each other in their correct spots and attach them all to the bottom of the form where needed, making sure the smallest underlay is placed closest to the bed. This will bring the type back to the right level, and the next proof should show a consistent impression. The same method works for a low corner. Use as little paste as possible, keeping it thin and lump-free. Ensure that the underlays are applied smoothly, without folds or wrinkles. Cut all underlays from a proof, as the proof acts as a guide for both cutting and attaching to the form.
Underlaying should not be done to any great extent upon a cylinder press. It is a valuable means of bringing up an old line of type, a hollow, or a low corner. The underlays of any type form should not constitute more than one-fourth of the surface; if more than this is attempted, they will rarely ever fail to work up the quadrates and furniture. The action of the quickly moving cylinder upon a form of type underlaid with yielding paper, must create a spring and a rocking of all the materials in the chase.
Underlaying shouldn't be done too much on a cylinder press. It's a useful way to raise an old line of type, a hollow, or a low corner. The underlays of any type form shouldn't take up more than a quarter of the surface; if you try to exceed this, they will usually end up causing the quadrates and furniture to shift. The fast-moving cylinder's action on a type form underlaid with soft paper will create a springy motion and a rocking effect of all the materials in the chase.
Of all materials, old stereotype plates need underlays most, as they are usually very irregular in height. Thin card or pasteboard will be found preferable to paper for the underlaying of plates secured on wood bodies. When the plates are on patent blocks, always underlay between the plate and the block. Always cut the underlay for a plate less in size than the faint impression would seem to require. This will allow for the spring of the plate. If it is cut of full size, the next impression will disappoint the pressman, by being much harder at the edges than he intended. Never attempt to build up a type form to a proper impression entirely or chiefly by underlaying.
Of all materials, old stereotype plates need underlays the most, as they are usually quite uneven in height. Thin cardboard or pasteboard is preferable to paper for underlaying plates attached to wood bodies. When the plates are mounted on patent blocks, always place an underlay between the plate and the block. Always cut the underlay for a plate slightly smaller than what the faint impression might seem to require. This will account for the flexibility of the plate. If it is cut to full size, the next impression will frustrate the press operator, as it will be much harder at the edges than expected. Never try to build up a type form to achieve the correct impression primarily or solely through underlaying.
Underlays should be put under all large and bold-faced types when used with much smaller types, so as to raise them above the level of the others. This is needed to give it closer rolling, extra supply of ink, and that extra force of impression to transfer the ink to paper which all large types require.
Underlays should be placed under all large and bold text when used with much smaller text, to raise them above the level of the others. This is necessary to provide closer rolling, extra ink supply, and the additional force of impression needed to transfer the ink to paper, which all large text requires.
When the type has been so levelled by underlays that all parts receive proper bearing from the inking rollers, and when the cylinder has a corresponding even impression, then overlaying may be commenced. For ordinary news, posters, or job-work, overlaying may be entirely unnecessary; the tapes and fly may be set, and the printing of the form may proceed without further delay. But fine press-work cannot be done without overlays. Underlays are chiefly valuable for securing an even impression; while overlays are indispensable for giving delicacy and finish to that impression.
When the type has been evenly leveled by underlays so that all parts properly contact the inking rollers, and when the cylinder has a smooth impression as well, then overlaying can begin. For regular news, posters, or general jobs, overlaying might not be needed at all; the tapes and fly can be adjusted, and printing can continue without any holdups. However, fine presswork requires overlays. Underlays are mainly useful for ensuring an even impression, while overlays are essential for adding delicacy and polish to that impression.
To overlay a form properly, the tympan should be covered with a sheet of thin, smooth, and hard paper, stretched tightly. Then take a pale impression on the tympan-sheet, and also run through the press two or three proofs on thin and hard paper. Examine the proofs carefully on both face and back. If any brass rules or letters appear too high, cut them out of the tympan-sheet in one or two thicknesses, as their varying height may require. Go over the whole proof, examining every line carefully, and, by cutting out, reduce the impression of all projecting letters to a uniform standard. For this, as for all other work on overlays, use a very sharp knife with a thin point, and cut on a smooth surface, so that there will be no dragged or torn edge to the cut.
To properly overlay a form, the tympan should be covered with a sheet of thin, smooth, and hard paper, stretched tightly. Then, take a light impression on the tympan-sheet and also run through the press two or three proofs on thin, hard paper. Carefully examine the proofs on both the front and back. If any brass rules or letters are too high, cut them out of the tympan-sheet in one or two layers, as needed based on their varying height. Go over the entire proof, checking every line closely, and by cutting out, reduce the impression of any projecting letters to a consistent height. For this, as with all other overlay tasks, use a very sharp knife with a thin point, and cut on a smooth surface to avoid any dragged or torn edges.
The next step should be to raise the impression of those[273] parts of the form when the type appears dull or weak. Cut out carefully, and paste the overlays over the tympan smoothly. Overlays are worse than useless if they are not laid on firmly and smoothly, as the slightest bagginess will cause slur or mackle. If, by accident, the tympan-sheets or overlays should bag or wrinkle, tear them off, and commence anew.
The next step should be to elevate the areas of the form where the type looks dull or weak. Carefully cut out and smoothly paste the overlays over the tympan. Overlays are counterproductive if they're not applied firmly and smoothly, as even the slightest bagginess can cause blurriness or blotchiness. If, by chance, the tympan sheets or overlays become baggy or wrinkled, remove them and start over.
Cut out and overlay the more prominent parts first; then try another impression, and from that cut new overlays for minor defects. Thus proceed until a perfectly smooth and even impression is obtained.
Cut out and layer the most noticeable parts first; then try another print, and from that, cut new layers for small flaws. Keep going until you achieve a perfectly smooth and even print.
With common work it will be sufficient to cut overlays in masses, as pages or parts of pages; but with fine work every line and letter needs examination, and letters and parts of single letters are often overlaid by careful pressmen. When the pressman is expert at making ready, it is not necessary that he should take a new impression with every successive set of overlays. Many pressmen take a dozen proofs of a form on different styles of paper, and proceed to cut out and overlay on one of the proofs, and finally paste this proof on the tympan. But this boldness and precision can be acquired only by long practice. It is better for the young pressman to feel his way step by step.
With regular work, it’s enough to cut overlays in bulk, like pages or parts of pages; but with detailed work, every line and letter needs to be checked, and letters and parts of letters are often overlaid by skilled press operators. When the press operator is skilled at preparation, it’s not necessary for them to take a new impression with every new set of overlays. Many press operators take a dozen proofs of a form on different types of paper, then cut out and overlay on one of the proofs, and finally paste this proof on the tympan. However, this level of confidence and accuracy can only be developed through extensive practice. It’s better for a young press operator to proceed cautiously, step by step.
The Impression.—A diversity of opinion exists among good printers as to the proper force of the impression: by some a heavy and solid indentation of the paper is considered necessary; while others insist that an impression which does not indent the paper is preferable. But the indentation of the paper is no test of the force of the impression. A light impression against a woollen blanket will show more forcibly than a strong impression against a paper or a pasteboard tympan.
The Impression.—There are differing opinions among skilled printers about the right force of the impression: some believe that a deep and solid indentation in the paper is essential, while others argue that a mark that doesn’t indent the paper is better. However, the indentation of the paper isn’t a reliable measure of the impression's force. A light impression on a wool blanket will appear more pronounced than a strong impression on paper or a pasteboard tympan.
Type is worn out not so much by the direct impression of the platen or cylinder on the flat face of a form, as by a grinding or rounding impression on the edges of the type, caused by the forcing of the tympan between the lines and around the corners of every letter. Every fount of worn-out type, whether from cylinder or platen press, has suffered less from a reduction in height than from a rounding of the edges. When the type is new and the tympan hard and smooth, the impression can be made so flat that the type will not round at the edges, and the impression will not show on the paper. But this cannot be done with old type or with a soft tympan: the impression[274] must be regulated to suit the tympan. On fine work, a rounding impression should be avoided, as it not only destroys type, but also thickens the hair-line and wears off the ceriphs.
Type wears out not so much from the direct impact of the platen or cylinder on the flat face of a form, but from a grinding or rounding effect on the edges of the type, caused by the tympan pressing between the lines and around the corners of each letter. Every set of worn-out type, whether from a cylinder or platen press, has been damaged more by edge rounding than by a loss of height. When the type is new and the tympan is hard and smooth, the impression can be made so flat that the edges of the type won't round, and the impression won't transfer to the paper. However, this isn't possible with old type or a soft tympan: the impression must be adjusted to match the tympan. For fine work, rounding impressions should be avoided, as they not only damage the type but also thicken the hair-line and wear down the serifs.
It is not sufficient that the paper should barely meet the type: there must be sufficient force in the impression to transfer the ink from type to paper. If there is not sufficient impression, it will be necessary to carry much ink on the rollers; and this produces two evils: the type is clogged with ink, and the form becomes foul; too much ink is transferred to the paper, which smears and sets off for want of force sufficient to impress it in the paper. Distinction must be made between a light and weak impression and a firm and even impression. The latter should be secured even if the paper is indented; though that is not always necessary. But a form of old type, a poster, or other solid form, must have a heavy impression, or else a very tedious and careful making-ready.
It’s not enough for the paper to just barely contact the type; there needs to be enough force in the impression to transfer the ink from the type to the paper. If the impression isn’t strong enough, you’ll have to carry more ink on the rollers, which leads to two problems: the type gets clogged with ink, and the form gets messy; too much ink transfers to the paper, causing smudging and failing to set properly due to insufficient pressure. It’s important to distinguish between a light and weak impression and a firm and even impression. The latter should be achieved even if the paper gets indented; although that’s not always necessary. However, a form with old type, a poster, or another solid form must have a heavy impression, otherwise, it requires a very meticulous and careful setup.
To set New Tapes.—Pass the tape around and close to the cylinder. Lap it over one of the tape pulleys, and then pass it around the small guide pulley on the shaft above. To increase its tightness, throw up the guide pulley from the shaft, and set the binding screw more tightly. All these pulleys are movable on their shafts, and distance between them may be altered at pleasure. Let the tapes rest upon the outer margin of the sheet, and see that the overlays on the tympan over which the tapes pass are of equal thickness; if not of equal thickness, the sheet will wrinkle.
To set New Tapes.—Wrap the tape around and close to the cylinder. Loop it over one of the tape pulleys, and then guide it around the small guide pulley on the shaft above. To make it tighter, lift the guide pulley from the shaft and snug the binding screw more securely. All these pulleys can move along their shafts, so you can adjust the distance between them as needed. Let the tapes rest on the outer edge of the sheet, and ensure that the overlaps on the tympan where the tapes go are the same thickness; if they’re not, the sheet will wrinkle.
To set the Fly.—Run through a sheet of the paper to be printed, and let it run down the fly so far that it is barely held by the fly pulleys. Then set the cam which works the fly, so that its point just clears the small friction roller on the shaft, and it will throw down the sheet correctly. Tighten the spring according to the size of the sheet, and set the spring crank so that it will prevent the fly from striking too hard on the table.
To set the Fly.—Run a sheet of paper to be printed through, allowing it to pass down the fly until it's nearly held by the fly pulleys. Next, adjust the cam that operates the fly so that its point just clears the small friction roller on the shaft, ensuring the sheet is thrown down correctly. Tighten the spring based on the size of the sheet, and set the spring crank to prevent the fly from hitting the table too hard.
It will be seen that good presswork does not depend entirely upon the press, nor yet upon the workman or the materials. Nor will a superiority in any one point compensate for a deficiency in another: the newest type will suffer from a poor roller, and the most careful making-ready will be of no avail if poor ink is used. It is necessary that all the materials should be of the best kind,—that they should be well adapted to each other, and fitly used. Although a good workman can[275] do much with insufficient materials, there are cases where a neglect to comply with one condition is equal to a neglect of all.[19]
It’s clear that good printing doesn’t depend solely on the press, the worker, or the materials. Being excellent in one area won’t make up for a lack in another: even the newest type will struggle with a poor roller, and careful setup won’t help if low-quality ink is used. It’s essential that all materials are of the highest quality—they need to complement each other well and be used correctly. While a skilled worker can do a lot with subpar materials, there are times when ignoring one requirement is just as bad as ignoring them all.[19]
FINE HAND-PRESSWORK.
Fine presswork is the art of printing perfect impressions from the surface of type or engravings in relief: that is, the subject transferred to paper should be an impression from the surface, and the surface only, of the types or engraved lines, of such a tone as to produce all the effect of which the subject is capable, without either superfluity or deficiency of colour.
Fine presswork is the art of creating perfect prints from the surface of type or relief engravings. In other words, the image printed on paper should be a direct impression from the surface of the types or engraved lines, capturing the full effect of the subject without excess or loss of color.
The press ought to be in the best condition; otherwise it will be impossible to get an equal impression without much trouble and loss of time. The joints of the tympan should not have any play, or the correctness of the register will be affected, and slurs and doubles be caused.
The press should be in top shape; otherwise, getting a consistent impression will be a hassle and a huge waste of time. The joints of the tympan shouldn’t have any movement, or it will mess up the accuracy of the register, causing slurs and doubles.
The parchments on the tympans should be thin, and of a uniform thickness, and stretched on the tympans so as not to be flaccid. On account of its thinness, smoothness, and uniformity, silk is probably preferable.
The sheets on the frames should be thin and of even thickness, stretched on the frames so they aren't loose. Because of its lightness, smoothness, and uniformity, silk is likely the better choice.
The face of the platen ought to be a true plane, and parallel to the press-stone, or table.
The surface of the platen should be perfectly flat and parallel to the press stone or table.
The advantage of having a good press is unavailing for the production of fine work if the types are much worn; for it is impossible to produce a sharp, clear impression when the type is worn and the fine lines are rounded by much use. In consequence of this roundness of the letter, it is necessary to use a thick blanket in the tympan to bring up the type; thus producing a gross and irregular impression of more than the surface.
The benefit of having a good printing press is useless for creating high-quality work if the type is very worn. It's impossible to achieve a sharp, clear impression when the type is worn and the fine lines have become rounded from extensive use. Because of this rounding, you need to use a thick blanket in the tympan to lift the type; this results in a rough and uneven impression that goes beyond just the surface.
Ink for fine work should be characterized by the following peculiarities:—
Ink for detailed work should have the following characteristics:—
Intenseness of colour.
Color intensity.
Impalpability.
Impalpability.
Covering the surface perfectly of the type or engraving.
Covering the surface perfectly of the type or engraving.
Quitting the surface of the type or engraving when the paper is pressed on it, and adhering to the paper.
Quitting the surface of the type or engraving when the paper is pressed against it, and sticking to the paper.
Not smearing after it is printed.
Preventing smudging after printing.
Complete retention of colour.
Total color retention.
Ink ought to be reduced to an impalpable smoothness, either in a mill or on a stone with a muller. This is essential, as the process gives it the next quality,—that of completely yet very thinly covering the surface of the type or the lines of the engraving, and insuring an even and perfect appearance to the impression on the paper. Another important requisite is, that the ink shall not only cover the surface of the lines on the paper printed, but that it shall also quit the face of the type or engraving and leave it quite clean when the paper is impressed on it, and attach itself to the paper, so as to give a perfect impression of the subject represented, without the colour of the paper appearing through the ink; and that this peculiarity of quitting the type or engraving and becoming attached to the paper shall continue the same through any number of impressions, without any accumulation of ink on the surface printed from. After having obtained these results, and when the printing is as perfect as it can be made by workmanship, something more is requisite,—viz.: that the ink shall not smear on being slightly rubbed, and that it shall retain its colour and appearance without spreading at the edges or tinging the paper.
Ink should be ground to a fine, smooth consistency, either in a mill or on a stone using a muller. This is crucial, as it helps achieve the next quality—completely yet very thinly covering the surface of the type or the lines of the engraving, ensuring an even and perfect appearance in the impression on the paper. Another important requirement is that the ink not only covers the surface of the lines printed on the paper but also leaves the face of the type or engraving completely clean when the paper is pressed against it. The ink should adhere to the paper, giving a perfect impression of the subject without the color of the paper showing through the ink. This characteristic of detaching from the type or engraving and sticking to the paper should remain consistent across any number of impressions, without any buildup of ink on the printed surface. Once these results are achieved, and the printing is as flawless as craftsmanship allows, something more is needed: the ink should not smudge when lightly rubbed, and it should maintain its color and appearance without spreading at the edges or staining the paper.
The rollers should be in good condition; otherwise the pressman may exert his skill in vain, with a great loss of time and waste of paper.
The rollers should be in good shape; otherwise, the pressman might use his skills for nothing, resulting in a lot of wasted time and paper.
The quality of the paper is of great consequence in fine printing; but it is frequently overlooked by the printer’s employers, who are apt to pay more attention to a showy appearance and a low price than to quality.
The quality of the paper is very important in fine printing, but it's often neglected by the printer’s employers, who tend to focus more on flashy looks and low prices than on quality.
The best paper for printing on is that which is made of fine linen rags and moderately sized, without the use of acids in bleaching, and without being adulterated with cotton rags: this paper takes water kindly, is easily got into good condition, receives a good impression, is durable, preserves its colour, and does not act upon the ink.
The best paper for printing is made from high-quality linen rags and is of a moderate size, without any acids used in the bleaching process, and not mixed with cotton rags: this paper absorbs water well, easily achieves a good finish, takes a clear impression, is long-lasting, maintains its color, and doesn’t react with the ink.
The use of cotton rags, the introduction of gypsum into the manufacture of fine and other papers, the application of acids and bleaching powders to improve the colour and produce apparently good paper from an inferior staple,—these form the grand hinderances to the American printer in his efforts to equal or excel foreign productions. Hence it is that[277] works printed in this country are less valued than those from the English press, which are printed on paper of fine fabric, made mostly of linen rags, and sufficiently strong to bear a fine ink.
The use of cotton rags, the addition of gypsum in the production of fine and other papers, and the use of acids and bleaching agents to enhance color and create decent paper from lower-quality materials—these are the main obstacles for American printers trying to match or surpass foreign products. That's why[277] works printed in the U.S. are less appreciated than those from English presses, which are printed on high-quality paper made mostly from linen rags and strong enough to hold fine ink.
A pressman should, as a matter of course, be well acquainted with the entire routine of presswork; in addition to which, to form his judgment, he should examine the most splendid productions of the press, and study them as patterns of workmanship.
A pressman should, as a matter of course, be well acquainted with the entire routine of presswork; in addition to which, to form his judgment, he should examine the most splendid productions of the press, and study them as patterns of workmanship.
In making ready, it must be evident that, when a clear, sharp impression is wanted, the pressure should be on the surface only. Of course the tympan ought not to be very soft, neither should a woollen blanket be used: the most perfect impression will be obtained when fine thick paper alone is placed in the tympans; and even of this article but few thicknesses should be employed.
In preparing, it should be clear that when a distinct, sharp impression is needed, the pressure should only be on the surface. Naturally, the tympan shouldn’t be too soft, and a wool blanket shouldn’t be used either: the best impression will be achieved when only fine thick paper is placed in the tympans; and even then, only a few layers of this material should be used.
After an impression is printed, the pressman examines if it be uniform throughout; if it be,—which is very rarely the case,—he goes on with the work; if not, he proceeds to overlay, in order to produce regularity of pressure and of colour over the whole form. Wherever the impression is weak he pastes a bit of thin, smooth paper, of the size and shape of the imperfect part, on the tympan-sheet; he then pulls another impression, to examine the effect of his overlays, and continues to add to them where wanted, till the pressure of the platen is the same in every part and the impression is of a uniform shade of colour.
After an impression is printed, the printer checks if it’s uniform throughout. If it is—which is very rarely the case—he continues with the work. If not, he starts to add layers to ensure consistent pressure and color across the entire form. Whenever the impression is weak, he pastes a piece of thin, smooth paper, matching the size and shape of the imperfect area, onto the tympan sheet. He then pulls another impression to see the results of his overlays and keeps adding more where needed until the pressure of the platen is consistent everywhere and the impression has a uniform shade of color.
If the impression come off too strong in parts, or at the edges or corners of the pages or on the head-lines, it will be necessary to cut away the tympan-sheet in those parts, and, if that does not ease the pressure sufficiently, to cut away the same parts from one or more of the sheets that are within the tympans.
If the impression comes off too strong in some areas, like the edges or corners of the pages or on the headlines, you'll need to trim the tympan sheet in those spots. If that doesn't reduce the pressure enough, you should also cut away those areas from one or more of the sheets inside the tympans.
It is generally preferable to overlay on a sheet of stout smooth paper inside the tympan, particularly where the same press does the whole or great part of the work: this sheet is cut to fit the interior of the tympan, so as not to slip about, and has overlays pasted on it where wanted, to bring up the impression till it is very nearly equal. In all succeeding sheets it saves the pressman a great deal of time, as he will be certain that when he pulls a sheet of another form of the same work[278] it will be nearly right, and he will only have to place thin overlays on occasional parts to make the impression perfect.
It’s usually better to put a thick, smooth sheet of paper inside the tympan, especially when the same press handles most of the work. This sheet is cut to fit the inside of the tympan snugly, so it doesn’t shift around, and has additional layers glued on where needed to make the impression nearly uniform. For all subsequent sheets, it saves the press operator a lot of time since he can be confident that when he pulls a sheet of a different form of the same job[278], it will be almost correct, and he will just need to add thin overlays to certain areas to achieve a perfect impression.
It is necessary, where short pages occur in a form, to have bearers to protect their bottom lines and the edges of the adjoining pages. These may be of double pica reglet, pasted on the frisket, so as to bear on some part of the furniture or chase; but bearers made to the height of the types are better, when they can be used.
It’s important to have bearers to protect the bottom lines and the edges of nearby pages when there are short pages in a form. These can be made from double pica reglet, glued onto the frisket, to support some part of the furniture or chase; however, bearers that match the height of the types are preferable when they can be used.
It happens occasionally that the tympan causes the paper to touch the form partially on being turned down, and occasions slurs. This may occur from the parchment being slack or the paper being thin and soft. To prevent this inconvenience, it is customary to roll up a piece of thick paper and paste it on the frisket adjoining the part. Many pressmen prefer pieces of cork cut to about the thickness of double pica, and pasted on the frisket.
It sometimes happens that the tympan causes the paper to partially touch the form when it is flipped down, leading to smudges. This can occur if the parchment is loose or if the paper is thin and soft. To avoid this issue, it's common to roll up a piece of thick paper and stick it to the frisket next to that area. Many press operators prefer using pieces of cork cut to about the thickness of double pica and glued to the frisket.
In working the white paper, instead of pins stuck into the tympan, to prevent the paper slipping, a duck’s bill (a tongue cut in a piece of stout paper) is frequently used: it is pasted to the tympan at the bottom of the tympan-sheet, and the tongue projects in front of it; indeed, the tympan-sheet appears to rest in it. The bottom of each sheet is placed behind this tongue, which supports it while the tympan is turned down.
In handling the white paper, instead of using pins stuck into the tympan to keep the paper from slipping, a duck’s bill (a tongue cut from a piece of thick paper) is often used: it is glued to the bottom of the tympan-sheet, and the tongue sticks out in front of it; in fact, the tympan-sheet seems to rest on it. The bottom of each sheet is placed behind this tongue, which holds it in place while the tympan is lowered.
The rollers should be kept clean, but should not be too moist, as this will prevent the ink from distributing equally over them, and from covering evenly the surface of the types or engraving; nor should they be too dry, as in that case they will not dispose of the ink smoothly enough to produce a fine impression, neither will they retain particles of dirt on their surface, but it will part with them to the form, thus causing picks.
The rollers should be kept clean, but not too wet, because that will stop the ink from spreading evenly on them and covering the surface of the types or engraving properly. They also shouldn't be too dry, as that will prevent them from applying the ink smoothly enough to create a good impression, and they won't hold onto dirt particles on their surface, which will then transfer to the plate and cause imperfections.
The ink ought to be rubbed out thinly and equally on the ink-block, so that when it is taken it may be diffused smoothly over the surface of the rollers. It is advisable to keep rubbing the ink out on the block with the brayer, and to distribute the roller almost constantly; the continual friction produces a small degree of warmth, which is of advantage, particularly in cold weather.
The ink should be spread thinly and evenly on the ink block so that when it's picked up, it smoothly covers the surface of the rollers. It's a good idea to keep spreading the ink on the block with the brayer and to constantly distribute the roller; the ongoing friction generates a bit of warmth, which is helpful, especially in cold weather.
As uniformity of colour is requisite for beauty in printing, where the form is large the pressman should take ink for every impression: this may be thought troublesome, but it is[279] advantageous in producing regularity of colour. It is unpleasant to see in a fine book two pages that face each other differing in colour,—the one a full black, surcharged with ink, the other deficient in quantity and of a gray colour; yet this must happen when, as is frequently the case, three or four sheets are printed with one taking of ink.
As having a consistent color is essential for beauty in printing, when the design is large, the printer should apply ink for each impression. This might seem annoying, but it’s beneficial for achieving color consistency. It’s unpleasant to see in a nice book two facing pages that are different colors—one a deep black, overloaded with ink, and the other lacking ink and appearing gray. However, this occurs often when, as is commonly the case, three or four sheets are printed with a single inking.
In fine books, particularly where the paper is large and heavy and the type large, set-off sheets are used to interleave the whole impression while working: these remain till the printed paper is taken down from the poles by the warehouseman. These set-off sheets are put in when the white paper is working, and moved from one heap to the other during the working of the reiteration. They prevent the ink from setting off from one sheet to another while they are newly printed, from the weight of the paper.
In high-quality books, especially those with large, heavy paper and big type, set-off sheets are used to separate the entire print run while it's being processed: these stay in place until the printed paper is taken down from the poles by the warehouse worker. These set-off sheets are added when the unprinted paper is in use and are shifted from one stack to another during the printing process. They stop the ink from transferring from one sheet to another while they are still fresh, due to the weight of the paper.
To secure uniformity of impression, the pull should be so adjusted in the first instance as to give a proper degree of pressure on the form when the bar is pulled home; then, checking the bar, it should be allowed to rest in that position during a short pause.
To ensure a consistent impression, the pull should initially be set to apply the right amount of pressure on the form when the bar is fully pulled back; then, by holding the bar in place, it should remain in that position for a brief pause.
It will be perceived that, to produce presswork of a highly superior character, great expense and much time are required; and that it is requisite to have a good press in good condition; to have new types, or types whose faces are not rounded by wear; to have good rollers in good condition; that the ink should be strong, of a full black colour, that it will not fade nor stain the paper, and ground so fine as to be impalpable; the paper should be of the best quality, made of linen rags, and not bleached by means of acids or bleaching powders, which have a tendency to decompose the ink; the rolling should be carefully and well done; the face of the type should be completely covered with ink, without any superfluity, so as to produce a full colour; and the pull should be so regulated as to have a slow and great pressure, and to pause at its maximum in order to fix the ink firmly upon the paper. These particulars observed, with nothing but paper in the tympans, perfect impressions of the face alone of the type will be obtained, and a splendid book will be produced in the best style of printing.[20]
It will be understood that to create high-quality print work, significant expense and a lot of time are necessary; it's essential to have a good press in working condition; to have new typefaces or typefaces that aren’t worn down; to have good rollers in proper condition; that the ink should be vibrant, rich black, not fade, not stain the paper, and be ground so finely that it's imperceptible; the paper should be top quality, made from linen rags, and not bleached with acids or bleaching powders, which can break down the ink; the rolling must be done carefully and well; the typeface should be fully covered with ink, without excess, to achieve a rich color; and the pull should be adjusted for slow and strong pressure, pausing at its peak to ensure the ink adheres firmly to the paper. If these details are followed, with only paper in the tympans, perfect impressions of just the typeface will be achieved, resulting in an outstanding book produced in the finest printing style.[20]
PRINTING WOOD-CUTS.
A single block, when imposed in a large chase, may spring out of the chase while being inked, from the quantity of furniture about it. A good plan is to impose it in a job-chase, and to impose this chase in a larger one: this will cause it to lie flatter on the press and firmer in the rolling, the large chase being secured firmly on the press by quoins and the corner irons.
One block, when placed in a large chase, can pop out while being inked due to the amount of furniture around it. A smart strategy is to set it up in a job-chase and then put that chase into a larger one: this will help it stay flatter on the press and more stable during the rolling, with the large chase being securely held on the press by quoins and corner irons.
Before pulling the first impression, the workman should see that the surface of the cut is perfectly clear from particles of dirt, and that no pin or lump of paste is on the tympan. He ought then to pull very gently, or he may injure some of the fine lines of the engraving.
Before making the first impression, the worker should ensure that the surface of the cut is completely clean of dirt particles and that there are no pins or lumps of paste on the tympan. They should then pull very gently, or they might damage some of the fine lines of the engraving.
Neither the pressure nor the impression of an engraving on wood should be uniformly equal: if it be, the effect intended to be produced by the artist will fail; and, instead of light, middle tint, and shade, an impression will be produced that possesses none of them in perfection: some parts will be too hard and black, while other parts will have neither pressure nor colour enough, nor any of the mildness of the middle tint, which ought to pervade a large portion of an engraving, and on which the eye reposes after viewing the strong lights and the deep shades.
Neither the pressure nor the impression of an engraving on wood should be consistently the same: if they are, the effect the artist intended to create will be lost; and, instead of highlights, mid-tones, and shadows, the impression will lack all of them in a balanced way: some areas will be too harsh and dark, while others won’t have enough pressure or color, and will miss the gentle touch of the mid-tone, which should fill a significant part of an engraving, allowing the eye to rest after looking at the bright highlights and deep shadows.
To produce the desired effect, great nicety and patience are required in the pressman: a single thickness of thin India paper, (the best for overlaying,) with the edges scraped down, is frequently required over very small parts. The overlay should never be cut at the edges; but, even where great delicacy of shape is not required, it should be torn into the form wanted: this reduces the thickness of the edges, and causes the additional pressure to blend with the surrounding parts As particular parts of the impression will frequently come up too strong, and other parts too weak, it will be necessary to take out from between the tympans a thickness of paper and add an additional tympan-sheet, cutting away the parts that come off too hard, and scraping down the edges. Scraping away half the thickness of a tympan-sheet in small parts that require to be a little lightened will improve the impression. The light parts require little pressure; but the depths should be brought up so as to produce a full and firm impression.
To achieve the desired effect, the press operator needs to be very precise and patient: a single layer of thin India paper (the best for overlaying), with the edges smoothed out, is often necessary for very small sections. The overlay should never be cut at the edges; instead, even when fine detail isn’t crucial, it should be torn into the desired shape: this reduces the thickness of the edges and helps the extra pressure blend with the surrounding areas. Since some parts of the impression will often come out too strong while others are too weak, it’s essential to remove some paper from between the tympans and add an extra tympan-sheet, trimming away the areas that come out too hard and smoothing down the edges. Reducing the thickness of a tympan-sheet in small areas that need a lighter touch will enhance the impression. The lighter areas require less pressure, while the deeper parts should be raised enough to create a full and solid impression.
If a block be hollow on the surface, underlaying the hollow part will bring up the impression better than overlaying it, at least so nearly that only a thickness or two of paper will be needed as overlays. If a block be too low, it is better to raise it to the proper height by underlays than to use overlays; as the latter act in some measure as blankets, and are pressed into the interstices, rendering the lines thicker than in the engraving.
If a block has a hollow surface, using underlays beneath the hollow area will produce a clearer impression than using overlays, at least to the point where only a couple of sheets of paper will be needed for overlays. If a block is too low, it's better to raise it to the correct height with underlays rather than using overlays; overlays can work like blankets, getting pressed into the gaps and making the lines appear thicker than they do in the engraving.
It will be necessary sometimes, when the surface of the block is very uneven, to tear away parts of the paper in the tympan, to equalize the impression where it is too hard.
It may be necessary at times, when the surface of the block is very uneven, to rip away parts of the paper in the tympan to balance the impression where it's too hard.
The pressman will find it convenient to pull a few impressions, while he is making ready, on soiled or damaged India paper. Out of these he can cut overlays to the precise shape and size wanted, which are always necessary when great accuracy is required in overlaying particular portions. He should be provided with a sharp penknife and a pair of good small scissors. A fine sharp bodkin and a needle or two, to take out picks, are also needful; but he should be particularly careful so to use them that he do no injury. The best way is, to draw the bodkin or needle point cautiously in the direction of the lines.
The pressman will find it helpful to pull a few test prints on used or damaged India paper while preparing. From these, he can cut overlays to the exact shape and size needed, which are always essential for achieving great accuracy when overlaying specific areas. He should have a sharp utility knife and a good pair of small scissors. A fine sharp awl and a couple of needles for removing any imperfections are also necessary, but he should be especially careful using them to avoid causing any damage. The best approach is to gently guide the awl or needle point along the lines.
Engravings in vignette form require great attention to keep the edges light and clear, and in general it is necessary to scrape away one or two thicknesses of paper in order to lighten the impression and keep it clean: the edges being irregular and straggling, they are likely to come off too hard. Bearers type-high placed beside the block will be found advantageous; if they cannot be used, pieces of reglet, pasted on the frisket in the usual way, and taking a bearing on the furniture, must be substituted; but the high bearer is to be preferred where it can be adopted. The bearers equalize the pressure on the surface of the engraving, and protect the edges from the severity of the pull, which is always injurious to the delicacy of the external lines. They also render the subject more manageable, by enabling the pressman to add to or diminish the pressure on particular parts, so as to produce the desired effect.
Engravings in vignette form require careful attention to keep the edges light and clear. Usually, it's necessary to scrape away one or two layers of paper to lighten the impression and keep it clean. Since the edges can be irregular and straggly, they might come off too harshly. Using type-high bearers next to the block is helpful; if they're not available, pieces of reglet, glued onto the frisket as usual and resting on the furniture, should be used instead. However, the high bearer is preferred when possible. The bearers help equalize the pressure on the engraving's surface and protect the edges from the harsh pull, which can damage the delicate outer lines. They also make the subject easier to manage by allowing the pressman to add or reduce pressure on specific areas to achieve the desired effect.
When great delicacy of impression is required in a vignette, it will be found beneficial, after the engraving is inked, to roll the extremities with a small roller without ink: this will not[282] only take away any superfluity of ink, but will prevent picks, and give lightness and softness to the edges, particularly where the effect of distance is required.
When you need a delicate impression in a vignette, it's helpful to roll the edges with a clean, small roller after inking the engraving. This will not only remove any excess ink but also prevent picks and add lightness and softness to the edges, especially where you want to create a sense of distance.
If the extremities are engraved much lighter than the central parts, underlays should be pasted on the middle of the block, which will give a firmer impression to the central parts of the subject. It would save trouble and aid in getting a good impression if the block were engraved a little rounded on the face.
If the edges are engraved much lighter than the center parts, backing should be applied to the middle of the block, which will create a stronger impression in the central areas of the design. It would be easier and help achieve a better impression if the block were slightly rounded on the face.
When highly finished engravings on wood are worked separately, woollen cloth, however fine, should never be used for blankets, as it causes too much impression; a sheet or two of hard smooth paper between the tympans is better; sometimes even a piece of glazed pasteboard is used inside the outer tympan. The parchments ought to be in good condition, stretched tight, of a smooth surface, thin, and of regular thickness, so as to enable the pressman to obtain an impression as nearly as possible from the surface only of the engraved lines.
When high-quality wood engravings are done separately, wool fabric, no matter how fine, should never be used for blankets, as it leaves too strong of an impression; one or two sheets of hard, smooth paper between the tympans work better; sometimes even a piece of glossy pasteboard is placed inside the outer tympan. The parchments should be in good condition, tightly stretched, with a smooth surface, thin, and uniformly thick, allowing the pressman to get an impression as close to the surface of the engraved lines as possible.
The rollers must be kept in perfect order; and the pressman should be very particular in taking ink and inking the block. He ought to use the best ink that can be procured.
The rollers must be kept in excellent condition; and the pressman should be very careful when taking ink and inking the block. He should use the best ink available.
When a wood-cut left on the press all night has become warped, lay it on its face upon the imposing-stone, with a few thicknesses of damp paper underneath it, and place over it the flat side of a planer, with sufficient weight upon it: in the course of a few hours the block will be restored to its original flatness. This method is preferable to steeping the block in water; as the steeping swells the lines of the engraving, and, consequently, affects the impression. To preserve the original effect of the cut as it came from the hands of the artist, the block should never be wet with water; and, when it has been worked in a form with types, it should be taken out before the form is washed.
When a woodcut left on the press all night has become warped, lay it face down on the imposing stone, placing a few layers of damp paper underneath, and put the flat side of a planer on top with enough weight. After a few hours, the block will return to its original flatness. This method is better than soaking the block in water since soaking causes the lines of the engraving to swell and affects the impression. To maintain the original effect of the cut as it was created by the artist, the block should never be wet with water; and if it has been used in a form with types, it should be removed before the form is washed.
To prevent warping during the dinner-hour or the night, turn the tympan down upon the form, run the carriage in, and, pulling the bar-handle home, fasten it so that it will remain in this position during the interim.
To avoid warping during dinner time or overnight, lower the tympan onto the form, push the carriage in, and pull the bar-handle back to secure it so it stays in that position for now.
However long boxwood may be kept in the log, it will always twist and warp when cut into slices for engraving, on account of fresh surfaces being exposed to the air. Large[283] blocks may be restored to their flatness in the course of a night by laying them on a plane surface, with the hollow side downward, without any weight on them.
However long you keep boxwood in the log, it will always twist and warp when it's sliced for engraving because fresh surfaces are exposed to the air. Large[283] blocks can be flattened overnight by laying them on a flat surface with the hollow side down, without any weight on top.
A fine engraving on wood should never be brushed over with ley: the best method is to wipe the ink off with a fine sponge damped with spirits of turpentine, and, if it get foul in working, clean it with a soft brush and spirits of turpentine; then wipe the surface dry and pull two or three impressions on dry waste paper. Spirits of turpentine take off the ink quicker, and affect the wood less, than any other article. The facility with which the block is again brought into a working state more than compensates for the trifling additional expense incurred.
A good wood engraving should never be cleaned with ley. The best way to remove the ink is to use a fine sponge dampened with turpentine. If it gets dirty while you’re working, clean it with a soft brush and turpentine. Then, dry the surface and make two or three prints on dry scrap paper. Turpentine removes the ink faster and is less damaging to the wood than anything else. The ease of getting the block back into working condition more than justifies the small extra cost.
When a few proofs only are wanted from a small engraving, good impressions may be obtained with little trouble on dry India paper, with about six thicknesses of the same sort of paper laid over it, and pulled without the tympan. If proofs are wanted from large ones, it will be found advantageous to put the India paper for a few minutes into a heap of damp paper.
When just a few proofs are needed from a small engraving, you can easily get good impressions on dry India paper by layering about six sheets of the same kind of paper over it and pulling it without the tympan. If proofs are needed from larger engravings, it's helpful to place the India paper in a stack of damp paper for a few minutes.
To do full justice to an engraving, the pressman should get a good impression from the engraver and place it before him as a pattern, and then arrange the overlays, &c. till he produce a fac-simile in effect. Better still is it for an unpractised hand to obtain the assistance of the artist at the press-side, to direct him in making ready the cut.[21]
To fully appreciate an engraving, the printer should get a solid impression from the engraver and keep it as a reference, then set up the overlays, etc., until he creates a perfect replica. It’s even better for someone inexperienced to get help from the artist at the printing press to guide them in preparing the cut.[21]
CARD PRINTING
Has, since the introduction of enamelled or polished cards, made rapid strides toward perfection; the fine absorbing quality of the enamel, under proper management, producing the most beautiful results,—in many cases scarcely discernible from copperplate. A card, to be well printed, requires as careful treatment as a wood engraving, (see p. 280,) so far as making ready is concerned, and in working without blankets and using the finest ink. Having made a light impression on the tympan-sheet, place the pins so as to bring the impression as nearly as possible in the centre of the card, one pin at the[284] lower side and two at the off side, taking care that the head of the pin does not come in contact with the types. The impression should be exceedingly light until properly regulated,—at no time more than is actually necessary to bring up the face of the type. Cards are now mostly printed on small card-machines, at the rate of one, two, and even ten thousand per hour. All cards should be printed dry.
Has, since the introduction of enamelled or polished cards, made quick progress towards perfection; the excellent absorbing quality of the enamel, when properly handled, creates stunning results—often barely distinguishable from copperplate. For a card to be printed well, it needs as careful treatment as a wood engraving (see p. 280), especially in terms of preparation and working without blankets while using the finest ink. After making a light impression on the tympan-sheet, position the pins to center the impression on the card as much as possible, placing one pin at the[284] lower side and two on the off side, ensuring that the pin head does not touch the types. The impression should be extremely light until properly adjusted—at no point should it be more than what's absolutely necessary to raise the face of the type. Most cards are now printed on small card machines at speeds of one, two, or even ten thousand per hour. All cards should be printed dry.
A small quantity of varnish put on the rollers and well distributed will prevent the enamel from peeling. The addition of a little ultramarine blue will beautifully intensify the black ink used in printing enamelled cards.
A small amount of varnish applied to the rollers and spread evenly will keep the enamel from peeling. Adding a little ultramarine blue will really enhance the black ink used for printing enamelled cards.
The patent extension feed guides, or tympan gauge pins, shown on page 310, will be found very convenient and useful.
The patent extension feed guides, or tympan gauge pins, shown on page 310, will be very handy and helpful.
GOLD PRINTING.
The types being made ready for press in the usual manner, the surface is covered in the ordinary way with gold size instead of ink, and the impression taken upon the paper. For a large job, remove only the back from a book of leaf-gold; for a small one, lay a straight edge across the book, and cut it through, of the size required, with the point of a sharp penknife. This must be done before using the size. Slightly wet the end of the forefinger of the right hand, and, placing the thumb of that hand on the pile of gold, raise the edge of the paper with the forefinger sufficiently to dampen it with the moisture of that finger; then press the moistened edge of the paper on the gold, and it will adhere sufficiently to enable the fingers to lift gold and paper together and place it on the impression. Proceed thus until the size is entirely covered; gently pat the gold with the balls of the fingers, or any soft, pliable substance, until it is set; then, with a very soft hat-brush, remove the superfluous gold, when a clear and beautiful impression will appear. Its sharpness will depend on the judgment of the printer in applying the size to the type.
The types are being prepared for printing in the usual way, with the surface covered with gold size instead of ink, and the impression taken on the paper. For a large job, take just the back from a book of leaf-gold; for a small one, place a straight edge across the book and cut through it with a sharp penknife to the required size. This should be done before applying the size. Slightly wet the tip of the forefinger of your right hand, and with the thumb of that hand on the pile of gold, lift the edge of the paper with your forefinger just enough to dampen it with the moisture from that finger; then press the moistened edge of the paper onto the gold, and it will stick well enough for you to lift both the gold and the paper together and place them on the impression. Continue doing this until the size is completely covered; gently pat the gold with your fingertips or any soft, flexible material until it sets; then, using a very soft hat brush, remove any excess gold, revealing a clear and beautiful impression. The sharpness will depend on the printer's skill in applying the size to the type.
BRONZE PRINTING
Is used more extensively than gold printing, being attended with far less expense in the cost of the material. The method of printing is the same, except that, instead of laying[285] on the gold-leaf, the impression is rubbed over with the bronze, by dipping a small block, covered with a short, fine fur, or a small wad of raw cotton, into the powder, and brushing off the superfluous bronze with a soft brush, as in gold printing. Bronze can be procured of various colours, and when laid on with judgment the effect is beautiful. The palest bronze is best. To produce a finished effect after bronzing, take finely-powdered soapstone, and apply in the same manner as bronze.
Is used more frequently than gold printing, as it costs much less for the materials. The printing method is the same, except that instead of applying[285] gold-leaf, the impression is covered with bronze. This is done by dipping a small block, wrapped in a short, soft fur or a small ball of raw cotton, into the powder and then brushing off the excess bronze with a soft brush, similar to gold printing. Bronze comes in various colors, and when applied with care, the result is stunning. The lightest bronze works best. To achieve a polished look after bronzing, use finely powdered soapstone and apply it in the same way as the bronze.
PRINTING IN COLOURS.
When red and black are to be printed on the same sheet,—the same process being applicable to all other colours,—the form is made ready in the usual way, and a chalk-line is traced around the outside of the chase on the press-bed, to show the exact situation in which the form must be replaced after having been lifted. The form is then laid with its face downward on a letter-board covered with the press-blankets. The words marked in the proof to be printed red are then forced down, and Nonpareil reglets nicely fitted into the vacancies, which raise the red lines and words an equal distance from the other matter. A sheet of paper is then pasted on the form, to keep the Nonpareil underlays in their proper places. The form is again laid on the press, observing the utmost care in placing it in its original position as indicated by the marks before made on the bed.
When red and black are printed on the same sheet—the same process applies to all other colors—the form is prepared in the usual way, and a chalk line is drawn around the outside of the chase on the press bed to indicate exactly where the form needs to be replaced after being lifted. The form is then positioned face down on a letter board covered with press blankets. The words marked in the proof to be printed in red are pressed down, and Nonpareil reglets are fitted neatly into the gaps, raising the red lines and words the same distance away from the other content. A sheet of paper is then pasted on the form to keep the Nonpareil underlays in place. The form is again placed on the press, taking great care to position it in its original spot as indicated by the marks previously made on the bed.
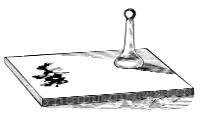
INK STONE AND MULLER.
Ink stone and muller.
It must then be made perfectly fast to the corner irons, as it is highly important that it remain firm and immovable during its stay on the press. The frisket (which is covered with strong paper) is then put on, the form rolled over with the red ink, and an impression made on it. The red words are then cut out with a sharp-pointed penknife, with so much nicety as not to admit the smallest soil on the paper from the other matter.
It must be securely attached to the corner brackets, as it’s really important that it stays stable and doesn’t move while on the press. The frisket (which is covered with sturdy paper) is then placed on, the form is rolled over with red ink, and an impression is made on it. The red words are then carefully cut out with a sharp penknife, with such precision that not a trace of the other ink touches the paper.
The red being finished and the form washed, the compositor unlocks it, (this should be done on the imposing-stone, as the pressman can easily lay it agreeably to the marks made on the press,) and draws out the red lines, filling up the space with quadrates. When this is done, the pressman cuts out the frisket for the black. An extra pair of points are used to prevent the black from falling on the red, or, as it is technically termed, riding. Generally, when a great number is to be printed, as many forms are used as there are colours to be printed. Another method of placing the underlays is adopted for broadsides, &c. with large letter and with but two or three lines of red. The red lines are taken out on the press, and underlays are put in, upon which the lines are placed, and the frisket is cut out as before mentioned.
The red is finished and the form is cleaned, the compositor unlocks it (this should be done on the imposing-stone, as the pressman can easily align it with the marks made on the press) and pulls out the red lines, filling the space with quadrates. Once this is done, the pressman cuts out the frisket for the black. An extra pair of points is used to prevent the black from overlapping the red, or as it’s technically called, riding. Generally, when a large number is to be printed, as many forms are used as there are colors to be printed. A different method for placing the underlays is used for broadsides, etc., with large letters and just two or three lines of red. The red lines are removed on the press, and underlays are inserted, on which the lines are placed, and the frisket is cut out as previously mentioned.
A more expeditious method can be employed for forms in which the lines of one colour are not too numerous to be easily lifted. After the form is ready, and the various colours are marked on the proof, a skeleton form is made up, with labour-saving quotation furniture or wood furniture fitted into the spaces of all the lines except those of the colour to be first printed. When the first colour is printed, its lines are lifted from the form, and the spaces filled with furniture, and the lines for the next colour are set in their proper places and printed; and so on till the job is completed.
A faster method can be used for forms where the lines of one color aren’t too many to lift easily. Once the form is ready and the different colors are marked on the proof, a skeleton form is created, with efficient quotation furniture or wood furniture placed in the spaces of all the lines except for the color to be printed first. After the first color is printed, its lines are removed from the form, the spaces are filled with furniture, and the lines for the next color are set in their correct positions and printed; this continues until the job is finished.
The custom of printing broadsides, &c. with several colours is so common that ink-makers generally now manufacture coloured inks; consequently the printer can be supplied without the delay and labour of making. We give the following particulars, however, for the benefit of those who wish to prepare their own colours.
The practice of printing broadsides, etc. in several colors is so popular now that ink manufacturers typically produce colored inks; as a result, printers can get supplies without the hassle and wait of making them. However, we provide the following details for those who want to make their own colors.
Varnish is the common menstruum adopted for all colours in printing. Red is the colour generally used with black. Trieste or English Vermilion, with a small portion of lake, produces a beautiful red, which should be ground with a muller on a marble slab till it be perfectly smooth. If it be in the smallest degree gritty, it clogs the form, and consequently produces a thick and imperfect impression; no pains should, therefore, be spared to render it perfectly smooth; it may then be made to work as clear and free from picks as black. A cheaper red, but not so brilliant, may be prepared with orange mineral, rose pink, and red lead.
Varnish is the standard medium used for all colors in printing. Red is usually paired with black. Trieste or English Vermilion, mixed with a small amount of lake, creates a beautiful red that should be ground with a muller on a marble slab until it's completely smooth. If there's even a slight grittiness, it will clog the printing plate and lead to a thick and imperfect impression; so, it's essential to make it perfectly smooth. Once smooth, it can work as clearly and cleanly as black. A more affordable red, though not as vibrant, can be made using orange mineral, rose pink, and red lead.
Prussian blue makes also an excellent colour, but will require much time and labour to make it perfectly smooth. It is also ground with the best varnish, but made considerably thicker, by allowing a greater portion of colour with the same quantity of varnish than the red; it will then work clear and free from picks. As this colour dries rather rapidly, the rollers should be frequently washed.
Prussian blue is also a great color, but it takes a lot of time and effort to get it perfectly smooth. It's mixed with the best varnish, but it's made considerably thicker by using more color with the same amount of varnish than the red. This way, it will apply smoothly and free from lumps. Since this color dries pretty quickly, the rollers should be washed often.
Other colours may be made,—viz., lake and Indian red, which produce a deep red; verditure and indigo, for blues; orpiment, pink, yellow ochre, for yellows; verdigris and green verditure, for green, &c. All these colours should be ground with soft varnish, being in themselves driers, or they will choke up the form. The consistency of the ink must be governed by the quality of the work to be executed. For a posting-bill or coarse job, the ink should be very thin, the proportion of varnish being much greater than required for fine work. Should the work be a wood-cut, or small type, the pigment should be made as thick as possible.
Other colors can be made, for example, lake and Indian red for a deep red; verditure and indigo for blue; orpiment, pink, and yellow ochre for yellow; verdigris and green verditure for green, etc. All these colors should be mixed with soft varnish, as they are naturally drying agents, or they will clog the form. The ink's consistency should match the type of work being done. For a posting bill or a coarse job, the ink should be very thin, with a much higher proportion of varnish than what’s needed for fine work. If the job involves woodcuts or small type, the pigment should be made as thick as possible.
The best colours for printing are those of the lightest body and brightest colour.
The best colors for printing are the lightest shades and the brightest hues.
HOW TO USE DRY COLOURS.
To produce fine qualities of coloured printing inks by mixing pure dry colours with varnish, the printer will do well to give heed to the following particulars:—
To create high-quality colored printing inks by blending pure dry colors with varnish, the printer should pay attention to the following details:—
1. No more should be mixed at a time than will be required for the job in hand.
1. Only mix what you'll need for the task at hand.
2. Coloured inks should be mixed upon a slate or marble slab, by means of the muller, and never upon an iron or other metallic table. The table, before mixing, should be thoroughly clean, and perfectly free from the slightest soil or trace of other inks.
2. Colored inks should be mixed on a slate or marble slab using a muller, and never on an iron or other metallic table. The table should be completely clean before mixing, and free from any dirt or traces of other inks.
3. For working coloured inks, the roller should not be too hard, and should possess a biting, elastic face. When change of colour is required, it should be cleaned with turpentine, and a moist sponge passed over the face, allowing a few minutes for the roller to dry before resuming its use.
3. For using colored inks, the roller shouldn’t be too hard and should have a soft, flexible surface. When you need to change colors, clean it with turpentine and wipe the surface with a damp sponge, letting the roller dry for a few minutes before using it again.
For bronze printing, the roller should have a firm face, or the tenacity of the preparation may destroy it; yet it must[288] have sufficient elasticity to deposit the preparation freely and cleanly on the type.
For bronze printing, the roller should have a solid surface, or the strength of the preparation might damage it; however, it needs[288] to have enough flexibility to apply the preparation smoothly and neatly onto the type.
4. Various shades may be produced by observing the following directions:—
4. You can create different shades by following these instructions:—
- Neon Pink Ink.—Use carmine or crimson lake.
- Deep Red.—To carmine add a little deep vermilion.
- Vibrant Red.—To pale vermilion add carmine.
- Deep Lilac.—To cobalt blue add a little carmine.
- Light Purple.—To carmine add a little cobalt blue.
- Bright Sky Blue.—Cobalt.
- Deep Bronze Blue.—Chinese.
- Green.—To pale chrome add Chinese blue; any shade can be obtained by increasing or diminishing either colour.
- Emerald Green.—Mix pale chrome with a little Chinese blue, then add the emerald until the tint is satisfactory.
- Amber.—To pale chrome add a little carmine.
- Dark Brown.—Burnt umber, with a little scarlet lake.
- Light Brown.—Burnt sienna; a rich shade is made by adding a little lake as above.
5. Gold Preparation. Print as with ordinary ink, then put on the bronze powder with a broad camel-hair brush; allow the impressions to remain a short time for the preparation to set, then clean off the superfluous bronze: the impressions will be much improved if passed through rollers.
5. Gold Processing. Print using regular ink, then apply the bronze powder with a wide camel-hair brush; let the prints sit for a bit to let the preparation set, then remove any excess bronze: the prints will look much better if they are passed through rollers.
HOW TO MULTIPLY COLOURS.
A printer who has on hand a stock of yellow, carmine, blue, and black inks, may produce other colours and shades by intermixing as follows:—
A printer who has a supply of yellow, red, blue, and black inks can create other colors and shades by mixing them together like this:—
Yellow and carmine, mixed, will give | Vermilion. |
Carmine and blue | Purple. |
Blue and black | Deep blue. |
Carmine, yellow, and black | Brown. |
Yellow and blue | Green. |
Yellow and black | Bronze green. |
Yellow, blue, and black | Deep green. |
Lighter shades may be obtained by adding proper proportions of white ink.
Lighter shades can be achieved by adding the right amounts of white ink.
CONTRAST OF COLOURS.
It is wrongly supposed that the art of arranging colours so as to produce the best effects in printing is entirely dependent on the taste of the operator; for harmony is determined by fixed natural laws. The increasing demand for decorative or ornamental work renders it of some importance to the letter-press printer to make himself acquainted with these laws; as, without some attention to them, the most elegant designs of the type founder, and the finest inks that can be made, may yield but an indifferent, if not a decidedly unpleasing, result.
It's a common misconception that the art of arranging colors to create the best effects in printing relies solely on the taste of the printer; in reality, harmony is guided by established natural laws. The growing demand for decorative or ornamental work makes it important for the letterpress printer to familiarize themselves with these laws; without paying attention to them, even the most elegant designs from the type founder and the finest inks can result in an unsatisfactory, if not downright unpleasant, outcome.
The following remarks will be of use to persons to whom the subject is new; but for a thorough explanation of it they should refer to Chevreul on Colours,—a valuable work in the French language, which has been translated into English.
The following comments will be helpful for those who are new to the topic; however, for a complete understanding, they should check out Chevreul on Colours,—a valuable book in French that has been translated into English.
I. We may, in the first place, consider WHITE LIGHT as composed of three primary colours—blue, red, and yellow—duly blended; these three, in an infinite variety of proportion, serving to produce all the hues in creation. If we take any two of these primaries and mix them, we have a secondary colour. Thus, blue and red form violet, blue and yellow give green, red and yellow make orange. Each of these secondary colours harmonizes perfectly with the primary which does not enter into its composition. Violet, for instance,—itself a mixture of red and blue,—harmonizes with yellow; green, having no red in its composition, agrees well with red; orange, in the same way, forms a perfect contrast with blue. Either of these contrasts has the effect of mutually brightening the colours employed; a red and a green, &c. being more beautiful when placed side by side than when viewed singly. This is termed the HARMONY OF CONTRAST OF COLOURS; and a good example of it is seen in the scarlet geranium, or the holly; the one showing a light green leaf opposed to a bright red flower, and the other a deep green leaf with a dark red berry.
I. First, we can look at White Light as being made up of three primary colors—blue, red, and yellow—properly blended together. These three, in countless different proportions, create all the colors we see. When we mix any two of these primary colors, we get a secondary color. For example, blue and red create violet, blue and yellow produce green, and red and yellow make orange. Each of these secondary colors pairs perfectly with the primary color not used in its mix. For instance, violet, which is a mix of red and blue, goes well with yellow; green, having no red, matches nicely with red; and orange contrasts perfectly with blue. These contrasts enhance the brightness of the colors involved, making combinations like red and green more attractive when seen together than when looked at separately. This is known as the Color Contrast Harmony; a good example can be found in the scarlet geranium or holly, where one displays a light green leaf against a bright red flower, and the other features a deep green leaf paired with a dark red berry.
The mixing of colours is a very different thing from contrasting them; for strange as it may seem, although one combination of the primary colours gives white, yet another proportion will produce black. While, then, red and green look beautiful side by side, it does not generally answer to[290] print red ink on green paper. The reason is, that as the ink is slightly transparent, some of the green shows through it, and appears somewhat black, and thus lowers the brilliance of the red in the same degree as so much black ink would, if mixed with it. This remark will apply to orange or yellow on a blue paper, &c. The darker and fuller the body of colour used, the less it is affected in this manner.
The mixing of colors is quite different from contrasting them; surprisingly, even though one combination of primary colors results in white, another mix can create black. While red and green look great together, it's usually not effective to[290] print red ink on green paper. This is because the ink is somewhat transparent, allowing some of the green to show through, which can make it look somewhat black, thereby dulling the brightness of the red, just like if you mixed it with black ink. This observation also applies to orange or yellow on blue paper, etc. The darker and richer the color used, the less it gets affected this way.
The most perfect contrasts are those above mentioned, which are formed by the complementary colours; yet the primaries blue, red, and yellow also agree well together. But if such colours as are not in harmony are placed near each other, the effect is very damaging to their brightness. While red is made more brilliant by the proximity of green, it is dimmed and spoiled by placing it next an orange. Neither blue nor red contrasts well with violet, because the latter contains each of these colours in its composition. In any case where they must come into juxtaposition, the unpleasant effect may be lessened by adding a little of the opposite colour: so, if a violet is to contrast with red, it will be well to give it a shade of blue, making it more purple; if, on the other hand, it is to contrast with blue or green, it should be made redder.
The best contrasts are those previously mentioned, created by complementary colors; however, the primary colors blue, red, and yellow also work well together. But when colors that don't harmonize are placed next to each other, it really hurts their brightness. While red looks more vibrant next to green, it loses its luster when placed next to orange. Neither blue nor red pairs well with violet, since violet contains both of these colors. In any situation where they have to be next to each other, the unpleasant effect can be reduced by adding a little of the opposite color: for instance, if violet is going to contrast with red, it’s a good idea to add a hint of blue, making it more purple; conversely, if it is to contrast with blue or green, it should be made redder.
II. Colours with Black. In all contrasts, the depth of the colour is an important element, but especially so in such as are to be affected by the presence of black. In but few instances will the latter bear the neighbourhood of a very deep colour to advantage, while it harmonizes with the lighter ones by contrast of tone. Yellow, from its near approach to white, should always be worked “full;” orange and green should also be full, and moderately deep in tone, to contrast with black. If a blue is employed, it should be light, or it will impoverish the black and be weakened itself. A very light blue border, with a broad margin of white between it and the body of matter enclosed, will give a clean, bright look to black ink, and whiteness to the paper. A light pink (such as carmine reduced with flake-white or with clear varnish) is also good; yet perhaps the preceding is preferable. Dark and heavy borders are frequently a positive injury to printing, where the working in a light shade would have secured a good effect; for the border should always be so far secondary to the matter enclosed as not to draw off the attention too much to itself.
II. Colors with Black. In all contrasts, the depth of color is a key factor, especially when it involves the presence of black. In most cases, black doesn’t work well with very deep colors, but it harmonizes better with lighter ones because of the tonal contrast. Yellow, being close to white, should always be used “full;” similarly, orange and green should also be full and moderately deep in tone to contrast with black. If using blue, it should be light; otherwise, it can diminish the effect of black and weaken itself. A very light blue border, with a wide margin of white between it and the main content, will create a clean, bright appearance with black ink, enhancing the whiteness of the paper. A light pink (like carmine diluted with flake-white or clear varnish) also works well, though the former might be preferable. Dark and heavy borders can often detract from the quality of printing, where using a lighter shade would have achieved a better effect; the border should always be secondary to the enclosed content and not draw too much attention to itself.
III. Colours on Tinted Papers and Tinted Grounds. Besides the kind of harmony already mentioned, there is another, which is produced by the contrast of light and dark shades of the same colour. This might be employed in letter-press more frequently than it is at present, with some advantage, as the effects it is capable of yielding are very chaste and pleasing. In a photograph or an engraving, all the effect is dependent on difference of tones of one colour; and the beauty of a wood in summer consists chiefly in the contrast displayed by a variety of shades of green only. A deep green ink on a paper of a light tone of the same colour is especially good, if a heavy letter is used; and indeed in most printing in colours, full, solid-faced letter should be preferred to outlines or shaded ones, which are difficult to work, and have at best but an inferior appearance unless the darkest tones are employed. A deep blue on a light blue ground, or against a light blue border, is also good; and without the latter accompaniment it is not unpleasant on a blue wove writing-paper. To secure the proper effect, however, the tints should be of the same hue; that is, if the groundwork is of a bluish green, the colour that is to be worked upon it should also be a green inclining to blue; if, on the other hand, the ground is of a yellower green, the body of ink should also be yellower; and so on. This may easily be managed by adding a small portion of ink of the colour required, until the hue is matched.
III. Colors on Tinted Papers and Tinted Backgrounds. In addition to the type of harmony mentioned earlier, there's another one created by contrasting light and dark shades of the same color. This could be used in letterpress more often than it currently is, with some benefits, as the results it can produce are very elegant and pleasing. In a photograph or engraving, all the impact relies on variations of tones of a single color; the beauty of a summer forest mainly comes from the contrast of different shades of green. A deep green ink on light-toned paper of the same color works particularly well when used with bold text; indeed, for most color printing, full, solid letters should be favored over outlines or shaded letters, which are tricky to work with and tend to look inferior unless darker tones are used. A deep blue on a light blue background, or against a light blue border, also works well; and even without the border, it doesn’t look bad on blue wove writing paper. To achieve the right effect, though, the shades need to be of the same hue; if the background is a bluish green, the color applied to it should also be a green with a blue tone; conversely, if the background is a yellower green, the ink should also be yellower, and so on. This can easily be adjusted by adding a small amount of ink of the desired color until the hue matches.
IV. Neutral Tints. In selecting borders for the more chaste description of printing, it is a pretty safe rule to avoid such as cover much surface, if they are to be worked in any strong colour or in black. When lighter tints are used, they will bear extension over a larger surface; and in this case a pale gray or neutral border will have a beneficial effect on any body with which it is contrasted, as well as on black itself, which is purified by its proximity. If the central printing is in black only, or in black and yellow, a lavender gray may be substituted for the border. And in any case in which the central matter is all in one colour, it will improve it to have a border of gray which is slightly tinged with the complementary of such colour. Thus, if the body be red, a very small portion of green may be added to the gray; and so forth.
IV. Neutral Shades. When choosing borders for more elegant printing, a good rule of thumb is to steer clear of those that cover a lot of surface, especially if they’re in strong colors or black. Lighter shades can work well over larger areas; in this case, a light gray or neutral border will enhance whatever it's paired with, as well as black itself, which looks better next to it. If the main text is in black only, or in black and yellow, you can use a lavender gray for the border instead. Moreover, whenever the main text is a single color, adding a gray border with a slight hint of the opposite color will improve it. For example, if the text is red, a touch of green can be mixed into the gray, and so on.
It must be remembered that in ornamental printing absolute[292] cleanliness is indispensable. The same roller should never be used for different colours, even after it has been washed. Instead of hanging exposed to dust and to the air, rollers should be kept in a tightly-closed box; and in this manner they will remain a long time in good order. The tins of ink should be similarly preserved, and the lids never left off except at the moment of using from them. These are small matters; but it is only by patient attention to minute details that excellence can be attained in printing.
It’s important to remember that in decorative printing, absolute[292] cleanliness is essential. The same roller should never be used for different colors, even after it’s been cleaned. Instead of being left out in the open where dust and air can affect them, rollers should be stored in a tightly sealed box; this way, they'll stay in good condition for a long time. Ink tins should be kept in the same way, with the lids only removed when you're using the ink. These may seem like small details, but it’s through careful attention to these specifics that you can achieve excellence in printing.
OILING A PRESS.
Excessive lubrication is wasteful, unclean, and hurtful to a press. A small quantity of oil should be used at a time, as a large amount will overrun on the press, and hold the dust and grit caused by sweeping the floor; these, working into the journals, will wear the press more than use. The best oil should be used, whether sperm, lard, or coal. Kerosene may be used to clean the ways of a press when they have become gummed by the use of improper oil. Presses should always be kept scrupulously clean.
Using too much lubrication is wasteful, messy, and damaging to a press. Only a small amount of oil should be applied at a time, since using too much will overflow on the press and trap the dust and dirt from sweeping the floor; these particles getting into the journals will wear down the press more than regular use will. You should use the best oil available, whether it’s sperm, lard, or coal. Kerosene can be used to clean the press’s ways when they have become sticky from the use of poor-quality oil. Presses should always be kept exceptionally clean.
HOW TO TREAT WOOD TYPE.
To prevent warping, all very large wood type should be set up on the edge when put away, so that both sides may be equally exposed to the air. In cleaning it, neither ley nor water should be employed under any circumstances. Turpentine, camphene, benzine, or kerosene oil may be used; but turpentine and camphene are the best. Procure a small, shallow pan; lay the form flat on a board; pour about six tablespoonfuls of turpentine into the pan; touch the face of the brush to the turpentine, and pass it quickly over the form before it evaporates. Six to eight spoonfuls of fluid will be found sufficient to clean a large form, if thus used.
To prevent warping, all large wood type should be stored on the edge to ensure both sides are evenly exposed to the air. When cleaning it, you should never use lye or water. Instead, you can use turpentine, camphene, benzine, or kerosene oil; however, turpentine and camphene are the best options. Get a small, shallow pan; lay the type flat on a board; pour about six tablespoons of turpentine into the pan; dip the brush into the turpentine and quickly brush it over the type before it evaporates. Using this method, six to eight tablespoons of fluid should be enough to clean a large type.

PALETTE KNIFE.
Palette knife.

WAREHOUSE DEPARTMENT.
THE WAREHOUSEMAN.

The warehouseman should be a man sober and upright, and thoroughly competent to the business, on whom entire reliance may be placed,—one who will act upon the principle of making his employer’s interest the end of all his action. The employer or foreman should frequently look to the concerns of the warehouse, and see that all the work is forwarded with despatch and accuracy.
The warehouse manager should be a sober and honest person who is fully competent for the job, someone who can be completely trusted—someone who will prioritize his employer’s interest in everything he does. The employer or supervisor should regularly check on the warehouse operations and ensure that all work is progressing quickly and accurately.
The warehouseman should be provided with a book, termed “The Warehouse Book,” with pages annexed, on the following plan, and about the size of foolscap quarto:—
The warehouse worker should be given a book called "The Warehouse Book," with attached pages, following this layout, and approximately the size of foolscap quarto:—
Butler's New American Arithmetic. (Number Printed: 5000.) | |||||
---|---|---|---|---|---|
DATE. | RECEIPT OF PAPER, AND OF WHOM. | NO. OF COPIES DELIVERED. | TO WHOM DELIVERED, AND RECEIPTED FOR. | FOR WHOM. | |
1878. | |||||
May | 3. | 43 reams of E. C. & P. H. Warren. | |||
June | 8. | 40 ditto. | |||
” | 24. | 2500 | Speel & Co. | J. H. Butler & Co. | |
” | 30. | 2000 | R. Eyelet, binder. | ||
Aug. | 4. | 300 | Paul Picot. | ” | |
” | 5. | With waste | 230 | Wm. Crouse. | ” |
5030 |
When the paper is brought, the warehouseman should at once compare it with the bill of delivery, and, if right, enter the quantity immediately into the warehouse book. The number of printed copies delivered to the binder or publisher should also be entered, and his signature be taken at the time of delivery. This plan will prevent disputes with the bookseller or author relative to the receipt of paper or the delivery of sheets.
When the paper arrives, the warehouse worker should immediately compare it with the delivery slip and, if everything checks out, record the quantity right away in the warehouse log. The number of printed copies given to the binder or publisher should also be noted, and their signature should be collected at the time of delivery. This method will help avoid disputes with the bookseller or author regarding the receipt of paper or the delivery of sheets.
Having entered the receipt of the paper, the warehouseman should then write on each bundle, with red chalk, the title of the book it is to be used for, and remove it into a convenient part of the warehouse, or into a store-room provided for that purpose.
Having received the paper, the warehouse worker should then write on each bundle, using red chalk, the title of the book it is intended for, and move it to a suitable spot in the warehouse, or into a storage room designated for that purpose.
GIVING OUT PAPER TO WET.
A bundle of paper consists of two reams, or forty quires, each quire containing twenty-four sheets. Formerly, the two outside quires were called cassie quires, as they were mostly made up of torn, stained, wrinkled, or otherwise imperfect sheets. At present, all the quires are considered good, although some outer sheets are injured by the twine used in tying up the bundles.
A package of paper is made up of two reams, or forty quires, with each quire containing twenty-four sheets. In the past, the two outer quires were referred to as cassie quires because they mostly consisted of torn, stained, wrinkled, or otherwise flawed sheets. Nowadays, all the quires are seen as good, although some outer sheets may be damaged by the twine used to tie up the bundles.
It is the general custom to print of every work what is termed an even number,—either 250, 500, 750, 1000, &c. These quantities are given out for the wetter in tokens,—viz.: for 250 sheets, one token, containing 10 quires 18 sheets; for 500, two tokens, one 11 quires, and the other 10 quires and a half; for 750, three tokens, two of them 11 quires each, and the other 10 quires 6 sheets; and for 1000, four tokens, three of them 11 quires each, and the other 10 quires. If a work is printed in half-sheets, it of course requires only half the above quantities.
It’s standard practice to print every work in what’s called an even number—typically 250, 500, 750, 1000, etc. These amounts are given out for the wetter in tokens: for 250 sheets, you get one token, which contains 10 quires and 18 sheets; for 500, you get two tokens, one for 11 quires and the other for 10 quires and a half; for 750, you receive three tokens—two of them are 11 quires each and the other is 10 quires and 6 sheets; and for 1000, you get four tokens, three of which are 11 quires each and the last one is 10 quires. If a work is printed in half-sheets, it only requires half of the amounts listed above.
It would be difficult to form any positive and invariable rule for the quantity to be given out for short numbers, as it must depend in some degree upon the quality of the paper. The more expensive papers, on which, generally, short numbers or line copies are printed, must be given out more sparingly than common paper, and the tympan and register sheets be supplied by a more common sort, cut to the size of the finer. For numbers up to 150, on ordinary paper, six[295] sheets over will be sufficient. Some publishers are very testy on this point of allowance for waste.
It would be tough to set any clear and consistent rule for how much should be used for short print runs, since it somewhat depends on the quality of the paper. The pricier papers, which are usually used for short runs or line copies, should be used more carefully than regular paper, and the tympan and register sheets should be made from a less expensive type, cut to match the size of the higher quality ones. For runs up to 150, on standard paper, six[295] sheets over will be enough. Some publishers are quite picky about the allowance for waste.
In giving out paper for what are termed jobs, the amount necessary can easily be found by a simple calculation in division.
In distributing paper for what are called jobs, the required amount can be easily determined by a simple division calculation.
For example, a job, (label or any thing else,) 750 in number, 32 on a sheet, will require 24 sheets, which will give an overplus of 18. Where a sheet has to be cut into many parts, allowance must be made for accidents. The overplus sheets are allowed for tympan-sheets, register-sheets, and other incidents, such as bad sheets, faults committed in rolling, pulling, bad register, &c.; in any of these casualties, the pressman doubles the sheet in the middle and lays it across the heap. In laying out the paper, the warehouseman reverses every other token, to enable the wetter to distinguish the different tokens. When this is done, he labels the heap, thus: American Printer, May 10, 1878,—that the pressman may know how long it has been wet, and the state it is in for working.
For example, if you have a job (label or anything else) totaling 750 items, with 32 items on a sheet, you'll need 24 sheets, which gives an excess of 18. When a sheet needs to be cut into multiple parts, you have to account for mistakes. The excess sheets are used for tympan sheets, register sheets, and other incidents like defective sheets, errors made during rolling, pulling, poor registration, etc.; in any of these cases, the pressman folds the sheet in half and lays it across the stack. When laying out the paper, the warehouse worker flips every other token to help the wetter identify the different tokens. Once that's done, he labels the pile like this: American Printer, May 10, 1878, so the pressman knows how long it's been wet and what condition it's in for printing.
32) | 750 | (23 |
64 | ||
110 | ||
96 | ||
14 |
HANGING UP PAPER TO DRY.
When the paper is worked off and counted, the warehouseman carries the heap to the drying-room, where the poles are fixed for the purpose of hanging the sheets upon to dry, and lays it down on a table of convenient height, with one end of the heap toward him. He then takes the handle of the peel in one hand, and lays the top part down upon the heap, so that the upper edge may reach near the middle of the sheet; then, with the other hand, he doubles over as much of the printed paper as he thinks sufficient to hang up at one lift, which should be about twelve sheets, according to the pole-room to hang them.
When the paper is finished and counted, the warehouse worker takes the stack to the drying room, where poles are set up for hanging the sheets to dry. He places it on a table at a comfortable height, with one end of the stack facing him. Then, he grabs the handle of the peel with one hand and lays the top part down on the stack, ensuring the upper edge reaches near the middle of the sheet. With his other hand, he folds over as much of the printed paper as he thinks is enough to hang at once, which should be about twelve sheets, depending on the setup of the pole room for hanging them.
In hanging up the lifts, he places them so that each lift will lap about an inch over the preceding one. It is necessary, where the end of the pole is exposed to a strong current of air from a window, to lock the last lift. This is done by folding a lift two or three times, so as to concentrate its weight in a small compass, and hanging this over the last lift near the window.
In hanging up the lifts, he positions them so that each lift overlaps the one before it by about an inch. When the end of the pole is exposed to a strong draft from a window, it’s essential to lock the last lift. This is done by folding a lift two or three times to concentrate its weight into a smaller area and hanging it over the last lift close to the window.
TAKING DOWN SHEETS WHEN DRY.
When the sheets are sufficiently dry, the warehouseman takes his peel and begins with the last lift hung up, on account of the wrapper being with that lift, and proceeds in the reverse order of hanging them up, successively taking them down, and brushing them, if dusty, till he has finished the whole.
When the sheets are dry enough, the warehouse worker grabs his peel and starts with the last one that was hung up, since the wrapper is with that lift, and takes them down in the reverse order they were hung. He brushes them off if they're dusty until he’s done with the entire batch.
Another way of taking the sheets down from the poles is, to lay the flat side of the peel against the edge of that lift which hangs over the other sheets, and push the peel forward, forcing them to slide, one lift over another. But by this method the dust which settles on the sheets while hanging is rubbed in.
Another way to take the sheets down from the poles is to lay the flat side of the peel against the edge of the lift that hangs over the other sheets and push the peel forward, making them slide, one lift over another. But with this method, the dust that settles on the sheets while they’re hanging gets rubbed in.
FILLING IN AND PRESSING SHEETS.
When the sheets are taken down, the warehouseman removes them to the warehouse, where they are filled in between smooth pasteboards made for the purpose. This operation is generally performed by boys, who, after a little practice, become exceedingly expert at it. We shall try to be somewhat minute in our description of this operation. We will suppose the pasteboards to have sheets between them, which will be the case after they have been once used. The warehouse being provided with long tables or benches, secured to the wall, and a sufficient number of movable tables about the size of the largest paper, the warehouseman places one of the small tables endwise against the long one, forming a right angle, upon which to lay the pressed sheets as they come out of the boards; the boy then takes his stand at the right side of the table, with the dry unpressed sheets at his right hand and the pasteboards at his left, somewhat elevated, leaving sufficient space before him to fill in the sheets. He then proceeds as follows. He first moistens the thumb of his right hand and reaches across to the pasteboards at his left, drawing one off with his thumb and placing it before him; he then catches a sheet of the dry paper also with his right hand and places it as near the centre of the pasteboard as possible; then, twisting his body nimbly round to the left, he slides the pressed sheet from the pile of pasteboards to the table at his[297] left side, and, in resuming his former position, again draws off a pasteboard with his thumb; and so on, till the gross or bundle is filled. It is then laid aside, and another bundle filled and laid across the former, taking care always to keep the bundles separated until they are put in press, when they are separated by smooth boards made of cherry or other hard wood. The bundles being all filled in, the warehouseman proceeds to fill up the standing-press, putting in one bundle at a time and placing a pressing-board between them; there should also be a stout plank introduced between the top board and the platen. In case the press should not hold quite as much as desired, more may be got in by unscrewing the press after it has been once screwed down. The press is finally screwed down as tight as possible. It should remain so for at least twelve hours, when it should be entirely emptied before the sheets are taken out of the boards. The sides of the piles or heaps must be kept perfectly even. In large offices, hydraulic presses are used.
When the sheets are taken down, the warehouse worker moves them to the warehouse, where they are placed between smooth pasteboards designed for this purpose. This task is usually done by boys who, after a bit of practice, become very skilled at it. We will provide a detailed description of this process. Let’s say the pasteboards have sheets between them, which is the case after they've been used. The warehouse has long tables or benches, secured to the wall, and enough movable tables approximately the size of the largest paper. The warehouse worker places one of the small tables end against the long one, creating a right angle, to lay the pressed sheets as they come out of the boards. The boy then stands to the right of the table, with the dry unpressed sheets on his right and the pasteboards on his left, slightly elevated, leaving enough space in front of him to fill the sheets. He then follows these steps. First, he moistens the thumb of his right hand and reaches over to the pasteboards on his left, pulling one off with his thumb and placing it before him. Next, he grabs a sheet of the dry paper with his right hand and places it as close to the center of the pasteboard as possible. Then, he quickly twists his body to the left, sliding the pressed sheet from the pile of pasteboards to the table on his [297] left, and, resuming his previous position, he again pulls off a pasteboard with his thumb; and he continues this process until the gross or bundle is filled. It is then set aside, and another bundle is filled and placed across the first one, always ensuring to keep the bundles separated until they are put in the press, where they are further separated by smooth boards made of cherry or other hardwood. Once all the bundles are filled, the warehouse worker continues to fill up the standing press, adding one bundle at a time and placing a pressing board between them; a sturdy plank should also be placed between the top board and the platen. If the press doesn’t hold as much as desired, more can be added by unscrewing the press after it has been once screwed down. Finally, the press is screwed down as tightly as possible. It should remain that way for at least twelve hours before it is completely emptied, ensuring the sheets are taken out of the boards. The sides of the stacks must be kept perfectly even. In large offices, hydraulic presses are used.

IMPROVED STANDING PRESS.
UPGRADED SHOULDER PRESS.
COUNTING OUT AND PUTTING AWAY SHEETS.
When the sheets are taken out, the warehouseman knocks them up, and, after counting them into quires, ties them up in wrappers, marking the name of the work and signature on each bundle. Two or three sheets of each signature should be laid aside, in case the author, bookseller, or employer should want a copy of the work or a specimen of as many sheets as are finished.
When the sheets are taken out, the warehouse worker stacks them, and, after counting them into groups, wraps them up, labeling each bundle with the name of the work and the signature. Two or three sheets of each signature should be set aside, in case the author, bookseller, or employer needs a copy of the work or a sample of the completed sheets.
STANDARD SIZES OF MACHINE-MADE PAPER.
(Furnished by A. G. Elliot & Co., Philadelphia.)
(Provided by A. G. Elliot & Co., Philadelphia.)
PRINTING PAPER.
Medium | inches, | 19 | × | 24 |
Royal | 20 | × | 25 | |
Super Royal | 21 | × | 27 | |
Imperial | 22 | × | 32 | |
Royal and Half, | 25 | × | 30 | |
Double Medium | 24 | × | 38 | |
Imperial and Half | 32 | × | 33 | |
Double Super Royal | 27 | × | 42 | |
Double Imperial, | 32 | × | 44. |
Other sizes kept on hand, but without technical names, are as follows:—22 × 28; 24 × 36; 25 × 39; 26 × 40; 28 × 42.
Other sizes available, but without technical names, are as follows:—22 × 28; 24 × 36; 25 × 39; 26 × 40; 28 × 42.
WRITING PAPER.
Note | inches, | 8 | × | 10 |
Packet Note | 9 | × | 11½ | |
Letter | 10 | × | 16 | |
Commercial Post | 11 | × | 17 | |
Packet Post | 11½ | × | 18½ | |
Foolscap | 13 | × | 16 | |
Flat Cap | 14 | × | 17 | |
Crown | 15 | × | 19 | |
Demy | 16 | × | 21 | |
Folio | 17 | × | 22 | |
Medium | 18 | × | 23 | |
Royal | 19 | × | 24 | |
Super Royal | 20 | × | 28 | |
Imperial | 23 | × | 31 | |
Elephant | 23 | × | 28 | |
Columbier | 23 | × | 34 | |
Atlas | 26 | × | 33 | |
Double Elephant | 27 | × | 40 | |
Antiquarian | 31 | × | 53 |

A TABLE
For ascertaining the Number of Forms for a Book of any Size, and the Quantity of Paper necessary to print a thousand copies in any form, from Octavo to 36mo, half-sheetwise.
To determine the number of forms needed for a book of any size, and the amount of paper required to print a thousand copies in any format, from Octavo to 36mo, half-sheetwise.
NO. OF FORMS. | 8vo. | 12mo. | 16mo. | 18mo. | 24mo. | 32mo. | 36mo. | PAPER FOR 1000 COPIES. | |
---|---|---|---|---|---|---|---|---|---|
PAGES. | PAGES. | PAGES. | PAGES. | PAGES. | PAGES. | PAGES. | REAMS. | QRS. | |
1 | 8 | 12 | 16 | 18 | 24 | 32 | 36 | 1 | 2 |
2 | 16 | 24 | 32 | 36 | 48 | 64 | 72 | 2 | 4 |
3 | 24 | 36 | 48 | 54 | 72 | 96 | 108 | 3 | 6 |
4 | 32 | 48 | 64 | 72 | 96 | 128 | 144 | 4 | 8 |
5 | 40 | 60 | 80 | 90 | 120 | 160 | 180 | 5 | 10 |
6 | 48 | 72 | 96 | 108 | 144 | 192 | 216 | 6 | 12 |
7 | 56 | 84 | 112 | 126 | 168 | 224 | 252 | 7 | 14 |
8 | 64 | 96 | 128 | 144 | 192 | 256 | 288 | 8 | 16 |
9 | 72 | 108 | 144 | 162 | 216 | 288 | 324 | 9 | 18 |
10 | 80 | 120 | 160 | 180 | 240 | 320 | 360 | 11 | |
11 | 88 | 132 | 176 | 198 | 264 | 352 | 396 | 12 | 2 |
12 | 96 | 144 | 192 | 216 | 288 | 384 | 432 | 13 | 4 |
13 | 104 | 156 | 208 | 234 | 312 | 416 | 468 | 14 | 6 |
14 | 112 | 168 | 224 | 252 | 336 | 448 | 504 | 15 | 8 |
15 | 120 | 180 | 240 | 270 | 360 | 480 | ... | 16 | 10 |
16 | 128 | 192 | 256 | 288 | 384 | 512 | ... | 17 | 12 |
17 | 136 | 204 | 272 | 306 | 408 | ... | ... | 18 | 14 |
18 | 144 | 216 | 288 | 324 | 432 | ... | ... | 19 | 16 |
19 | 152 | 228 | 304 | 342 | 456 | ... | ... | 20 | 18 |
20 | 160 | 240 | 320 | 360 | 480 | ... | ... | 22 | |
21 | 168 | 252 | 336 | 378 | 504 | ... | ... | 23 | 2 |
22 | 176 | 264 | 352 | 396 | ... | ... | ... | 24 | 4 |
23 | 184 | 276 | 368 | 414 | ... | ... | ... | 25 | 6 |
24 | 192 | 288 | 384 | 432 | ... | ... | ... | 26 | 8 |
25 | 200 | 300 | 400 | 450 | ... | ... | ... | 27 | 10 |
26 | 208 | 312 | 416 | 468 | ... | ... | ... | 28 | 12 |
27 | 216 | 324 | 432 | 486 | ... | ... | ... | 29 | 14 |
28 | 224 | 336 | 448 | 504 | ... | ... | ... | 30 | 16 |
29 | 232 | 348 | 464 | ... | ... | ... | ... | 31 | 18 |
30 | 240 | 360 | 480 | ... | ... | ... | ... | 33 | |
31 | 248 | 372 | 496 | ... | ... | ... | ... | 34 | 2 |
32 | 256 | 384 | 512 | ... | ... | ... | ... | 35 | 4 |
33 | 264 | 396 | 528 | ... | ... | ... | ... | 36 | 6 |
34 | 272 | 408 | 544 | ... | ... | ... | ... | 37 | 8 |
35 | 280 | 420 | 560 | ... | ... | ... | ... | 38 | 10 |
36 | 288 | 432 | 576 | ... | ... | ... | ... | 39 | 12 |
37 | 296 | 444 | 592 | ... | ... | ... | ... | 40 | 14 |
38 | 304 | 456 | 608 | ... | ... | ... | ... | 41 | 16 |
39 | 312 | 468 | ... | ... | ... | ... | ... | 42 | 18 |
40 | 320 | 480 | ... | ... | ... | ... | ... | 44 |
Example.—How many reams will be required for a 12mo book containing 408 pages? Find the number of pages (408) in the 12mo column: in the outer column on the left of the table the number of forms is seen, and in the outer column on the right the quantity of paper required is given.
Example.—How many reams are needed for a 12mo book with 408 pages? Look up the number of pages (408) in the 12mo column: the left outer column of the table shows the number of forms, and the right outer column lists the amount of paper needed.

JOBBING FACILITIES.

There is no department in the art that is better provided with means for its efficient prosecution than job printing. It is true that an establishment fully provided with all the old and new conveniences will involve a very considerable outlay; yet a beginner in a small way, who has to count the cost carefully, may avail himself of many facilities which were unknown a score of years ago. The smaller the capital, the more need for the exercise of a wise discretion in the selection of material. Regard should be had to the special line of work to be undertaken, and the type and presses adapted to that line should be selected. If the master himself shall work with head and hand, perseveringly and early and late, and shall do good work at fair prices—never cutting-under to secure a job at non-paying rates,—and shall be obliging in manner and punctual in delivery, and shall waste no dimes in drink or other useless expenses, the growth of his business will be only a matter of time; and he will gradually be able to order just what that growth necessitates, until he shall find himself the proprietor of a well-appointed office and a paying business. In his first outlay and in all his additions, the best of every kind should be gotten, if possible, as cheap things always prove dear.
There is no area in the printing industry that is better equipped for efficient operation than job printing. While it's true that having a full range of old and new tools requires a significant investment, a newcomer starting small can take advantage of many resources that didn't exist twenty years ago. The smaller the budget, the more important it is to choose materials wisely. It’s essential to consider the specific type of work you plan to do and select the appropriate types and presses for that work. If the owner is dedicated, working tirelessly both early and late, producing quality work at reasonable prices—never undercutting to secure jobs at unprofitable rates—while also being courteous and on time with deliveries, and avoiding unnecessary expenses on things like alcohol, the business will grow over time. Eventually, the owner will be able to acquire whatever is needed for that growth, leading to a well-run office and a profitable business. For initial investments and subsequent purchases, it’s crucial to get the best quality available, as cheap items often end up costing more in the long run.
It matters little how well appointed an office may be, there will be no gains in it unless the proprietor, counting the cost carefully, makes sure that every job shall pay a reasonable profit.
It doesn't matter how nicely decorated an office is; there won't be any benefits unless the owner, carefully calculating the expenses, ensures that every job brings in a reasonable profit.
When a job is taken in, it should be fully entered in a volume, giving all particulars in regard to the number of copies, style, and price. This may serve as a Day Book or Blotter. A memorandum-slip, like the following, may be filled out for each job, and kept on file after the work shall have been completed:—
When a job is received, it should be fully recorded in a volume, detailing all specifics regarding the number of copies, style, and price. This can act as a Day Book or Blotter. A memo slip, like the one below, can be filled out for each job and kept on file after the work is completed:—
It will be satisfactory to keep what may be called an Estimate Book, in which may be entered the particulars of estimates given for various kinds of work, whether the job be secured or not, these particulars will be time-saving when a similar piece of work comes in for estimate. Samples of paper, of all grades and colours, may be kept in a convenient receptacle, cut up into various sizes, and with memoranda written on each sample to denote the cost per ream, the weight, and the number of pieces in a sheet.
It would be helpful to maintain what's known as an Estimate Book, where you can record the details of estimates provided for different types of work, whether or not the job is secured. These details will save time when a similar job comes up for estimation. You can keep samples of paper, in all grades and colors, in a handy spot, cut into various sizes, with notes on each sample indicating the cost per ream, the weight, and the number of pieces in a sheet.
A useful thing to have in a job office is Ames’s Paper and Card Scale, for fractional sizes, showing the number of pieces of any required size that can be cut from a sheet without waste,[302] with a table giving the number of sheets required to cut 1000 pieces, and another showing the cost of paper by the quire, sheet, and hundred sheets, at any given price per ream. Besides the above, we may mention Le Blond’s Chart, a very compact affair, showing the number of any given size of card that can be cut out of a card sheet 22 × 28 inches.
A handy tool to have in an office is Ames’s Paper and Card Scale, designed for fractional sizes, which indicates how many pieces of any required size can be cut from a sheet without waste,[302] along with a table showing the number of sheets needed to cut 1000 pieces, and another listing the cost of paper by the quire, sheet, and hundred sheets, at any given price per ream. Additionally, we can mention Le Blond’s Chart, a very compact tool that shows the number of any specified size of card that can be cut from a card sheet measuring 22 × 28 inches.

JOB CASE.
Job case.

TRIPLE JOB CASE.
TRIPLE JOB SITUATION.
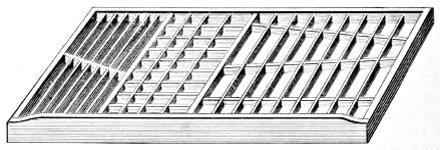
LABOUR-SAVING RULE CASE.
Labor-Saving Rule Case.
The modern printer has every convenience that can be desired in the way of cases, and his type and other material are amply provided with receptacles well adapted for each special use. There are not only large and small cabinets, filled with job cases of various styles and capacities, but there may be had cases for rules, leads, and furniture, as well as blank cases for indefinite uses. We give representations of these.
The modern printer has all the conveniences you could want, with cases and everything needed for type and other materials organized in ways that suit each specific purpose. There are large and small cabinets filled with job cases of different styles and sizes, along with cases for rules, leads, and furniture, as well as empty cases for various uses. We provide examples of these.
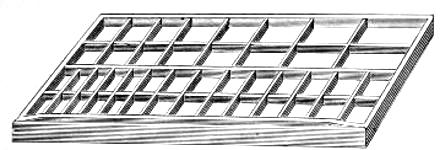
LABOUR-SAVING SLUG CASE.
LABOR-SAVING SLUG CASE.
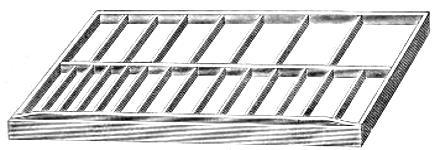
LABOUR-SAVING LEAD CASE.
LABOR-SAVING LEAD CASE.
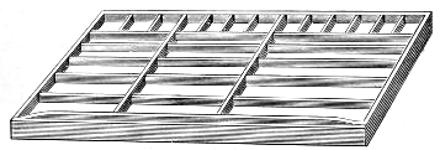
QUOTATION FURNITURE CASE.
Display cabinet.

BLANK CASE.
Empty case.
All cases should be labelled, and the label should be printed in the same type that is contained in the case.
All cases should be labeled, and the label should be printed in the same style that is contained in the case.
Capitals and lower-case job types should not be laid together in the same boxes. The saving of time in a year will pay for extra cases.
Capitals and lowercase job types shouldn't be placed together in the same boxes. The time saved over a year will cover the cost of additional cases.

CABINET OF CASES, WITH GALLEY TOP.
CABINET OF CASES, WITH GALLEY TOP.
Job type-cases should be kept in cabinets, and not in stand-racks, as the latter cannot be used without interfering with the hand whose stand may contain the case wanted. Various kinds of cabinets are shown on pages 219-221, 231 and 234, some of which are constructed to hold cases and quad and space boxes.
All matter should be cleared away as soon as done with. This work can be done by careful boys. Standing galleys, or cabinets with galley tops, for type to be kept awhile, will be found useful and convenient; but matter preserved for occasional future use were better papered up and labeled or stored away locked up in a chase cabinet. (See p. 231.) A rack with sloping boards to support the forms will prove to be a safe and convenient place for keeping the forms of type which need to be held standing.
All materials should be cleared away as soon as you're done. This task can be handled by careful boys. Standing galleys, or cabinets with galley tops for temporarily storing type, will be useful and convenient; however, material kept for occasional future use is better off wrapped up and labeled or stored away locked in a chase cabinet. (See p. 231.) A rack with sloping boards to support the forms will be a safe and convenient place for keeping the typeset forms that need to be held upright.
Labour-saving leads, and slugs, and reglets, cut to varying lengths, when not in use, should be kept in cases specially provided for them. And so with labour-saving brass rule, quotation furniture, rule, etc. It is economical as well as tidy to have appropriate places for every thing.
Labour-saving leads, slugs, and reglets, cut to different lengths, should be stored in cases designed for them when not in use. The same goes for labour-saving brass rules, quotation furniture, rules, etc. It's both economical and neat to have designated spots for everything.
For fixed measures, or measures not often changed, the standard screw composing-sticks are probably the best; but for jobbing and table-work, where the measure is frequently altered, it will be well to use the new styles, such as are shown above; no screw-key or screw-driver being required, the latter can be quickly and easily set to a new measure.
For fixed measurements, or measurements that don't change often, the standard screw composing sticks are probably the best choice. However, for jobs and tabletop work, where measurements need to be adjusted frequently, it's better to use the new styles shown above. These don't require a screw key or screwdriver, so they can be quickly and easily set to a new measurement.

WOODEN JOB STICK.
WOODEN JOB STICK.

FRANKLIN STICK.
Franklin Stick.

RAYMOND’S PATENT STICK.
RAYMOND'S PATENT PEN.

NEWBURY’S STICK.
Newbury's Stick.

HOE’S PATENT STICK.
HOE'S PATENT STICK.

GROVER’S STICK.
GROVER'S STICK.

ALBION STICK.
ALBION STICK.
The boxwood quoin will probably continue to hold its place, though not a few printers favour the use of the newly-invented iron articles offered by various manufacturers, such as Webb’s Mechanical Quoin, Ames’s, Hoe’s, Allen’s, and Hempel’s Patent Quoins. The latter quoin has, from its durability and easy application, crowded out all competitors.
The boxwood quoin will likely keep its position, even though a number of printers prefer the newly-invented iron options provided by various manufacturers, like Webb’s Mechanical Quoin, Ames’s, Hoe’s, Allen’s, and Hempel’s Patent Quoins. The latter quoin has, due to its durability and ease of use, outpaced all its competitors.

HEMPEL’S QUOINS IN POSITION.
HEMPEL'S QUOINS ARE IN PLACE.

HEMPEL’S QUOIN.
HEMPEL'S CORNERSTONE.

CORNER QUADRATES.
Corner squares.
Even so simple a thing as a shooting-stick, commonly made of hickory or ash, is now to be had in brass or iron. These latter are certainly more durable, but dangerous in careless hands.
Even something as simple as a shooting stick, usually made of hickory or ash, can now be found in brass or iron. These materials are definitely more durable, but they can be dangerous in careless hands.

WOODEN SHOOTING-STICK.
Wooden walking stick.

BRASS SHOOTING-STICK.
Brass shooting stick.

IRON SHOOTING-STICK.
Iron shooting stick.
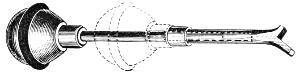
ARMSTRONG’S COMBINED MALLET AND SHOOTING-STICK.
ARMSTRONG’S MALLET AND SHOOTING STICK COMBO.
A novel invention is Armstrong’s Patent Combined Mallet and Shooting-Stick. This is desirable for general use, and for locking-up forms on the press, or of service where room for the use of the ordinary mallet and shooting-stick is limited to a confined space.
A new invention is Armstrong’s Patent Combined Mallet and Shooting Stick. This is useful for general use, for securing forms on the press, or in situations where space is limited for using a regular mallet and shooting stick.

MITERING MACHINE.
Miter saw.

LEAD CUTTER.
Lead cutter.
A mitering machine and lead-cutter are among the necessary adjuncts of a printing-office.
A mitering machine and lead cutter are essential tools in a printing office.
Perforating Rule is slightly higher than type, and is used in printing coupons and tickets which require to be partially severed while going through the press. It is made of brass or steel. A more convenient (as well as more expensive) article is Ames’s Patent Perforator: its knife, or perforator, lies below the surface of the type while the rollers pass over the form, and rises and makes a clean cut when the impression is on, without injuring the rollers.
Perforating Rule is a bit taller than type and is used for printing coupons and tickets that need to be partially cut while passing through the press. It's made of brass or steel. A more convenient (and also pricier) option is Ames’s Patent Perforator: its knife, or perforator, sits below the surface of the type while the rollers move over the form, and it rises to make a clean cut when the impression is on, without damaging the rollers.

PERFORATING RULE.
Perforating rule.
Machines for perforating round holes are manufactured of several sizes. The lowest-priced machine may be worked on a counter, and will perforate every kind of card-board or paper. We give a cut of this style.
Machines for punching round holes come in various sizes. The cheapest machine can be used on a countertop and will punch through any type of cardboard or paper. We provide an image of this style.

ROUND HOLE PERFORATING MACHINE.
Round hole punch machine.
Imposing Stones may be had with drawers and cases underneath; but these we do not deem advisable, unless the printer be cramped in room, as the cases may be wanted when the stone is in use while imposing or correcting forms. For common use, the plain stone with a single drawer, and without a rim, will be found the nicest. When made otherwise, the rim should be fitted snugly to the stone, or the interstices will become filled with types, dropped in while correcting.
Imposing stones can come with drawers and cases underneath, but we don’t think that’s a good idea unless the printer is tight on space, as the cases may be needed when the stone is being used for imposing or correcting forms. For regular use, a plain stone with a single drawer and no rim is usually the best choice. If it’s made differently, the rim should fit snugly against the stone; otherwise, gaps will get filled with types that get dropped in while making corrections.

IMPOSING STONE.
STRIKING STONE.
A very convenient device for the compositor is the Copy-Holder. This, however, is for the book compositor rather than for the jobber. Its utility consists in bringing the copy nearer to the eye of the workman, and in leaving all the boxes at command and uncovered by the manuscript or printed page. There is also a Lamp-Holder which will be found handy where gas is not accessible.
A very handy tool for the typesetter is the Copy Holder. However, this is more suitable for book typesetters than for job printers. Its usefulness lies in bringing the text closer to the worker's eyes and keeping all the trays easily accessible and not blocked by the manuscript or printed page. There's also a Lamp Holder that comes in handy when gas isn't available.

COPY-HOLDER.
COPY-HOLDER.

RUGGLES CARD CUTTER.
Ruggles Card Cutter.
Card Cutters are made of several styles, and at prices from fourteen dollars to forty-five; and Paper Cutters are yet more numerous, some of them simple and low-priced, and others massive and costing twelve hundred dollars. We give an engraving of one of moderate price. An extensive run of business only would require the employment of a large paper cutter.
Card cutters come in various styles, with prices ranging from fourteen dollars to forty-five dollars. Paper cutters are even more diverse; some are simple and inexpensive, while others are large and cost up to twelve hundred dollars. We include an illustration of one that's reasonably priced. A high volume of work would warrant the use of a large paper cutter.

MINERVA CUTTING MACHINE.
MINERVA CUTTING MACHINE.

MEGILL’S PATENT GAUGE PIN.
Megill's Patent Gauge Pin.

EXTENSION FEED-GUIDE.
Extension Feed Guide.
Several contrivances for facilitating press operations have been invented. We may mention Megill’s Patent Gauge Pin, of sizes suitable for various margins. Two small teeth, projecting from the lower side of the head of the pin, press into the tympan sheet and prevent the gauge from moving. There is also the Extension Feed-Guide, which furnishes a gauge below the edge of the platen, and is held firmly in place by the tympan-clamp.
Several devices have been created to make press operations easier. For example, there's Megill’s Patent Gauge Pin, available in sizes for different margins. Two small prongs on the underside of the pin’s head dig into the tympan sheet to keep the gauge in place. There’s also the Extension Feed-Guide, which provides a gauge below the edge of the platen and is securely held in position by the tympan clamp.

HART’S COUNTER.
HART'S COUNTER.
When long numbers are printed, the Automatic Counter may be attached to the press. It counts only when the form is being printed, and shows the exact number in plain figures up to 100,000. Several styles of counting machines are made.
When long numbers are printed, the Automatic Counter can be connected to the press. It only counts while the form is being printed and displays the exact number in regular digits up to 100,000. Several types of counting machines are available.

PATENT INK FOUNTAIN.
PATENT INK PEN.
An ink fountain has been contrived for attachment to the Gordon job press, or any other press with similar plate distribution. It is quite a cosey little thing, and is operated by the impression arm of the press.
An ink fountain has been designed to attach to the Gordon job press or any other press with a similar plate layout. It's a pretty neat little device, and it works with the impression arm of the press.
Iron furniture is made in sets containing twenty-one pieces, adapted for use on the eighth, quarter, and half medium job presses.
Iron furniture is made in sets that include twenty-one pieces, designed for use on eighth, quarter, and half medium job presses.

USEFUL RECEIPTS.[22]
Printers’ rollers.—10 lbs. French or Irish heavy glue, 12 lbs. sugar or good quality molasses, and 3 lbs. glycerine. This will be sufficient to make two rollers twenty-nine by three and one-half inches, and can be readily recast by following the directions given for recasting rollers.
Printer rollers.—10 lbs. of heavy French or Irish glue, 12 lbs. of sugar or quality molasses, and 3 lbs. of glycerin. This will be enough to make two rollers measuring twenty-nine by three and a half inches, and can be easily recast by following the instructions provided for recasting rollers.
Directions.—Soak the glue the necessary length of time that will enable it to melt with ease. After being melted, add the glycerine, and boil fifteen minutes or until thoroughly mixed, when the sugar or molasses may be added. Cook and stir continuously for fifteen minutes, the composition will then be ready for pouring. Strict attention should be given that the moulds be thoroughly cleansed and evenly oiled previous to pouring.
Instructions.—Soak the glue for the amount of time needed to make it melt easily. Once melted, add the glycerine and boil for fifteen minutes or until fully mixed, then you can add the sugar or molasses. Cook and stir continuously for fifteen minutes; then the mixture will be ready to pour. Make sure the molds are thoroughly cleaned and evenly oiled before pouring.
German Preservative for Rollers.—Corrosive sublimate 2 drachms, fine table salt 2 oz.; put together in half a gallon of soft water—let it stand twenty-four hours. When rollers are clean washed with ley, sponge them with the above mixture twice a week.
German Preservative for Rollers.—Corrosive sublimate 2 drachms, fine table salt 2 oz.; mix these in half a gallon of soft water and let it sit for twenty-four hours. After cleaning rollers with lye, sponge them with this mixture twice a week.
Directions for Recasting Rollers.—Sponge the face of the roller with hot water; scrape off the face thoroughly with a knife; take the composition off the stock and cut it up small. If the roller has been used only a short time, it may be melted about as readily as new composition; if it is older, put it in a sieve or basket and soak it in cold water for about fifteen or twenty minutes; take it out of the water, cover with a damp cloth, and leave over-night; then melt as usual. If composition[312] is too hard, wait till it is melted, and stir in a sufficient quantity of common molasses; avoid heavy, clarified syrups.
Instructions for Recasting Rollers.—Wet the roller's face with hot water; scrape the face thoroughly with a knife; remove the composition from the stock and chop it into small pieces. If the roller has been used for only a short time, it can be melted as easily as new composition; if it is older, place it in a sieve or basket and soak it in cold water for about fifteen or twenty minutes; take it out of the water, cover it with a damp cloth, and let it sit overnight; then melt it as usual. If the composition[312] is too hard, wait until it is melted, and mix in enough regular molasses; avoid heavy, clarified syrups.
Printers’ Ley.—No. 1.—Dissolve 28 lbs. of soda in 52 gallons of water, to which add 7 lbs. of soft-soap, boiled. Stir well together.
Printers’ Ley.—No. 1.—Dissolve 28 lbs. of soda in 52 gallons of water, then add 7 lbs. of boiled soft soap. Mix thoroughly.
Printers’ Ley.—No. 2.—Boil 3 gallons of water in a copper; throw in while boiling ½ lb. of unslacked lime and 2 lbs. of common soda; stir well for fifteen minutes. Let it settle till cold, when it must be taken out without disturbing the sediment, and the liquid is then fit for use.
Printers’ Ley.—No. 2.—Boil 3 gallons of water in a copper pot; add ½ lb. of unslaked lime and 2 lbs. of regular soda while it's boiling; stir well for fifteen minutes. Let it settle until it's cold, then carefully take it out without disturbing the sediment, and the liquid will be ready to use.
Printers’ Ley.—No. 3.—Table salt 2 oz., unslacked lime 2 lb., Scotch washing soda (bruised) 2 lb. Put together in 3 gallons of water, stir well; when settled, ready for use.
Printers’ Ley.—No. 3.—Table salt 2 oz., unslacked lime 2 lb., Scotch washing soda (crushed) 2 lb. Combine in 3 gallons of water, stir well; when settled, it’s ready to use.
Note.—This ley, if prepared carefully, is very strong, and will wash off almost any colour.
Note.—This formula, if made carefully, is very effective and can remove almost any color.
A Strong White Paste.—Dissolve 2½ oz. of gum-arabic in 2 quarts of water, and stir it into 1 pound of wheat flour until the whole becomes of a pasty consistency. It is then to be heated, and 1½ oz. each of sugar of lead and alum dissolved in a little water added thereto, and the composition well stirred until it shows signs of boiling, when it must be removed from the fire. Add while hot 6 drops of carbolic acid. This is a very tenacious and durable paste, and may be used on almost any substance.
A Strong White Paste.—Dissolve 2½ oz. of gum arabic in 2 quarts of water, then mix it with 1 pound of wheat flour until it reaches a pasty consistency. Heat the mixture, and add 1½ oz. each of lead sulfate and alum dissolved in a little water, stirring until it shows signs of boiling. Remove it from the heat. While it's still hot, add 6 drops of carbolic acid. This is a very strong and long-lasting paste that can be used on almost any material.
Pastes for Fixing Labels on Glass.—No. 1.—Take of gum-arabic 1 oz., boiling water and glycerine 2 fluid ounces each. Make a solution.
Pastes for Fixing Labels on Glass.—No. 1.—Take 1 oz. of gum arabic, and 2 fluid ounces each of boiling water and glycerin. Mix them to create a solution.
No. 2.—Take of gum-arabic and powdered gum tragacanth ½ oz. each, water 1½ oz., acetic acid 20 drops. Mix. The acid is used to prevent chemical change, although a stiff paste made of tragacanth alone is not inclined to spoil by fermentation.
No. 2.—Take ½ oz. of gum arabic and ½ oz. of powdered gum tragacanth, mix with 1½ oz. of water and 20 drops of acetic acid. Combine everything. The acid is used to stop chemical changes, though a thick paste made from just tragacanth doesn’t usually go bad through fermentation.
To Make a good Mucilage.—The best quality of mucilage is made by dissolving clear glue in equal volumes of water and strong vinegar, and adding one-fourth of an equal volume of alcohol, and a small quantity of a solution of alum in water.[313] The action of the vinegar is due to the acetic acid which it contains. This prevents the composition from gelatinizing by cooling; but the same result may be accomplished by adding a small quantity of nitric acid. Some of the preparations offered for sale are merely boiled starch, or flour, mixed with nitric acid to prevent the gelatinizing.
How to Make Good Mucilage.—The best mucilage is made by dissolving clear glue in equal parts of water and strong vinegar, then adding one-fourth of that total volume of alcohol, along with a small amount of an alum solution in water.[313] The vinegar works because of the acetic acid it contains. This keeps the mixture from turning into a gel when it cools; however, you can achieve the same effect by adding a little nitric acid. Some products sold are just boiled starch or flour mixed with nitric acid to stop them from gelatinizing.
Liquid Glue.—Take some good strong glue and mix it with full proof whisky. Let it digest for three or four days, and it will be ready for use.
Liquid Glue.—Take some strong glue and mix it with high-proof whiskey. Let it sit for three or four days, and it will be ready to use.
Strong Mucilage.—The Journal de Pharmacie states that if, to a strong solution of gum-arabic measuring 8⅓ fluid oz., a solution of 30 grains of sulphate of aluminium dissolved in ⅔ of an oz. of water be added, a very strong mucilage is formed, capable of fastening wood together, or mending porcelain or glass.
Strong Mucilage.—The Journal de Pharmacie reports that if you add a solution made by dissolving 30 grains of aluminum sulfate in ⅔ of an ounce of water to 8⅓ fluid ounces of a strong gum-arabic solution, you will create a very strong mucilage that's capable of bonding wood or repairing porcelain or glass.
Gum for Backing Labels.—Take any quantity of clear, pure dextrine and mix it with boiling water until it assumes the consistency of ordinary mucilage. Apply thinly with a full-bodied, evenly made, and wide camel’s-hair brush. The paper should not be too thin or unsized. The preparation will dry quickly, and adhere when slightly wet.
Glue for Backing Labels.—Take any amount of clear, pure dextrin and mix it with boiling water until it has the consistency of regular glue. Apply it thinly using a full-bodied, well-made, wide camel’s hair brush. The paper shouldn’t be too thin or unsized. The mixture will dry quickly and will stick when it’s slightly wet.
Note.—No more of the dextrine should be mixed at one time than can be used at once, as it cannot be remelted easily.
Note.—Only mix as much dextrin at a time as you can use right away, as it can't be easily melted down again.
Mucilage for Postage Stamps, Envelopes, etc., is composed of dextrine 2 parts, acetic acid 1 part, alcohol 1 part, water 5 parts.
Mucilage for Postage Stamps, Envelopes, etc. is made of 2 parts dextrin, 1 part acetic acid, 1 part alcohol, and 5 parts water.
Common Prepared Glue.—Dissolve 2 lbs. good common glue in 3 pints warm water, and add 1 quart of strong vinegar. Ready to use after twenty-four hours.
Common Prepared Glue.—Dissolve 2 lbs. of quality common glue in 3 pints of warm water, and add 1 quart of strong vinegar. It's ready to use after twenty-four hours.
For making Magenta Surface Paper.—1½ oz. of Magenta, (aniline,) ½ oz. Bismarck brown, (aniline,) 1 cake of glue; put these into 4 gallons of boiling water. Coat the paper with this, using an 8-inch double-filled camel’s-hair brush. Quantity given will coat two reams of double-crown. A hard-sized paper must be used.
For making Magenta Surface Paper.—1½ oz. of Magenta (aniline), ½ oz. of Bismarck brown (aniline), 1 cake of glue; mix these into 4 gallons of boiling water. Use an 8-inch double-filled camel’s-hair brush to coat the paper with this mixture. The amount provided will coat two reams of double-crown paper. Be sure to use a hard-sized paper.
Coloured Writing Inks.—The following receipts have been well tested, and are commended by good authorities as preferable to the solutions of aniline dyes, which are now so extensively used as coloured inks:—
Colored Writing Inks.—The following recipes have been well tested and are recommended by reputable sources as better alternatives to the solutions of aniline dyes, which are currently widely used as colored inks:—
Green.—Two parts acetate of copper, one part carbonate of potash, and eight parts of water. Boil until half evaporated, and filter.
Green.—Mix two parts copper acetate, one part potassium carbonate, and eight parts water. Boil until it's reduced by half, then filter.
Blue.—Three parts Prussian blue, one part oxalic acid, and thirty parts of water. When dissolved, add one part of gum-arabic.
Blue.—Three parts Prussian blue, one part oxalic acid, and thirty parts of water. Once dissolved, add one part of gum arabic.
Yellow.—One part fine orpiment, well rubbed up with four parts thick gum water.
Yellow.—Mix one part fine orpiment that’s thoroughly blended with four parts thick gum water.
Red.—With the aid of a gentle heat, dissolve four grains of carmine in 1 oz. of aqua ammoniæ, and add 6 grains of gum-arabic.
Red.—Using gentle heat, dissolve four grains of carmine in 1 oz. of ammonia water, and add 6 grains of gum arabic.
Gold.—Rub gold leaf, such as is used by bookbinders, with honey, till it forms a uniform mixture. When the honey has been washed out with water, the gold powder will settle at the bottom, and must be mixed with gum water in sufficient quantity.
Gold.—Rub gold leaf, like the kind used by bookbinders, with honey until it creates a smooth mixture. After washing out the honey with water, the gold powder will settle at the bottom and should be combined with enough gum water.
Silver.—Silver leaf treated in precisely the same manner gives a silver ink. Both these inks may be polished with ivory when dry.
Silver.—Silver leaf processed in exactly the same way produces silver ink. Both of these inks can be polished with ivory once they are dry.
Black.—Three ounces crushed gall-nuts, two ounces crystallized sulphate of iron, two ounces gum-arabic, and twenty-four ounces water.
Black.—Three ounces of crushed gall-nuts, two ounces of crystallized iron sulfate, two ounces of gum arabic, and twenty-four ounces of water.
White.—Fine French zinc-white, or white lead, rubbed up with gum water to the proper consistency.
White.—Quality French zinc-white, or white lead, mixed with gum water to the right consistency.
Fireproof Ink.—Fireproof ink, which can be used either for writing or printing:—Copal 12 grains, graphite 22 drachms, sulphate of iron 2 drachms, tincture of nut-galls 2 drachms, and sulphate of indigo 8 drachms; these are thoroughly mixed and boiled in water, and the ink so obtained is said to be both fireproof and insoluble in water. When any other colour than black is desired, the graphite is replaced by any other mineral pigment of the required colour.
Fireproof Ink.—Fireproof ink can be used for writing or printing. It consists of 12 grains of copal, 22 drachms of graphite, 2 drachms of iron sulfate, 2 drachms of nut-gall tincture, and 8 drachms of indigo sulfate. These ingredients are mixed thoroughly and boiled in water, resulting in ink that is both fireproof and water-insoluble. If a color other than black is needed, replace the graphite with any mineral pigment of the desired color.
Printing Ink Varnish.—Printing ink varnish is made by adding 4 oz. of boiled linseed or neat’s-foot oil to 6 oz. of yellow rosin.
Printing Ink Varnish.—Printing ink varnish is made by adding 4 oz. of boiled linseed oil or neat's-foot oil to 6 oz. of yellow rosin.
Lithographic Transfer Ink.—Three parts gum copal, 5 parts wax, 5 purified tallow, 4 soap, 5 shellac, 5 mastic, and one-half part sulphur. The copal is to be melted in a copper vessel, mixing in a little sweet oil, add the wax and tallow, and when these are well melted, light the mass and throw in the soap, well dried and cut in small pieces, then the shellac and mastic. The flame is to be increased by the addition of the flowers of sulphur, and so a perfect mixture of the copal with the other substances will be attained. The flame is to be alternately kindled and extinguished till the whole mass is reduced to one-fourth of its former bulk.
Lithographic Transfer Ink.—Combine three parts gum copal, five parts wax, five parts purified tallow, four parts soap, five parts shellac, five parts mastic, and half a part of sulfur. Melt the copal in a copper pot, mixing in a bit of sweet oil. Once melted, add the wax and tallow, and when they're fully melted, ignite the mixture and toss in the well-dried soap cut into small pieces, followed by the shellac and mastic. Increase the flame by adding sulfur flowers, which will help achieve a thorough blend of the copal with the other materials. Alternate between lighting and extinguishing the flame until the entire mixture reduces to a quarter of its original size.
To give dark Printing Inks a Bronze or Changeable Hue.—Take 1½ lb. gum shellac and dissolve it in 1 gallon 95 per cent. alcohol spirits of cologne for 24 hours; then add 14 oz. aniline red; let it stand a few hours longer, when it will be ready for use. Add this to good blue, black, or other dark inks, as needed, in quantities to suit, when, if carefully done, they will be found to have a rich bronze or changeable hue.
To give dark printing inks a bronze or shimmery color.—Take 1.5 lb. of gum shellac and dissolve it in 1 gallon of 95% alcohol (like cologne spirits) for 24 hours; then add 14 oz. of aniline red; let it sit for a few more hours, and it will be ready to use. Mix this with good blue, black, or other dark inks as needed, in amounts that work for you, and if done carefully, they will have a rich bronze or shimmery color.
An Ink for Marking Tin or Zinc.—An ink composed of copper one part, dissolved in ten parts nitric acid, ten parts water being afterward added, is useful for marking on tin or zinc.
An Ink for Marking Tin or Zinc.—An ink made from one part copper, dissolved in ten parts nitric acid, with ten parts water added afterward, is effective for marking on tin or zinc.
Quick-drying Preparations for Printers’ Inks to be used on Bookbinders’ Cases.—1 oz. beeswax, ¼ oz. gum-arabic dissolved in sufficient acetic acid to make a thin mucilage, ¼ oz. Brown’s Japan, ½ oz. asphaltum varnish. Incorporate with 1 lb. of wood-cut ink.
Quick-drying Preparations for Printers’ Inks to be used on Bookbinders’ Cases.—1 oz. beeswax, ¼ oz. gum-arabic dissolved in enough acetic acid to make a thin glue, ¼ oz. Brown’s Japan, ½ oz. asphaltum varnish. Mix with 1 lb. of wood-cut ink.
A Dryer.—No. 1, for fine job work. Damar varnish 6 oz., bergamot 2 drachms, balsam copaiba 2 drachms, balsam of fir 3 oz., creosote 1 drachm, copal varnish 1 drachm. To enough ink for 1000 ordinary business cards, add from 8 to 12 drops of the “Indispensable,” and to larger quantities in proportion. When used for bronze, dry colours, diamond printing, etc., take twice the quantity; and where an extra quick dryer is desired, add a few drops of dissolved gum-arabic to the ink, after it has been mixed with No. 1. In all cases, mix well with the ink before applying to the rollers.
A Dryer.—No. 1, for detailed job work. Damar varnish 6 oz., bergamot 2 drachms, balsam copaiba 2 drachms, balsam of fir 3 oz., creosote 1 drachm, copal varnish 1 drachm. For enough ink to print 1000 standard business cards, add 8 to 12 drops of the “Indispensable,” and adjust for larger amounts accordingly. When using for bronze, dry colors, diamond printing, etc., use double the amount; and if you need a faster drying time, mix a few drops of dissolved gum-arabic into the ink after blending it with No. 1. Always mix thoroughly with the ink before applying to the rollers.
Dryer.—No. 2.—For news and poster ink. Spirits of turpentine 1 qt., balsam copaiba 6 oz. Add a sufficient quantity to the ink to thin it to a proper consistency for working.
Dryer.—No. 2.—For news and poster ink. 1 qt. of turpentine, 6 oz. of balsam copaiba. Add enough to the ink to thin it to a suitable consistency for use.
Silvering Solution for Electrotype Plates.—Nitrate of silver 2 drachms, distilled water 37 drachms. Dissolve and add sal ammoniac 1 drachm, hypophosphate of soda 4 drachms, precipitated chalk 4 drachms. Agitate the preparation occasionally for twelve hours, when it will be ready for use. Apply with a piece of fine sponge.
Silvering Solution for Electrotype Plates.—2 grams of silver nitrate, 37 grams of distilled water. Dissolve and add 1 gram of ammonium chloride, 4 grams of sodium hypophosphate, and 4 grams of precipitated chalk. Shake the mixture occasionally for twelve hours, and it will be ready to use. Apply with a piece of fine sponge.
How to coat Electrotypes with Silver.—Electrotypes can be coated with silver (for working with red ink) in the following manner: One part copper, 5 parts pure tin; this alloy to be granulated, not too fine, and mixed with water and cream of tartar into a paste. To each 200 parts of the granulated alloy add 1 part oxide silver, the electro is then laid in it, and boiled for a short time, when it will be found to be beautifully plated. Fresh oxide must be added from time to time. This coating is quite equal in durability to silver or tin.
How to coat Electrotypes with Silver.—Electrotypes can be coated with silver (for use with red ink) in the following way: Combine 1 part copper with 5 parts pure tin; the alloy should be granulated, but not too finely, and mixed with water and cream of tartar to form a paste. For every 200 parts of the granulated alloy, add 1 part silver oxide. The electrotype is then placed in this mixture and boiled for a short time, resulting in a beautiful silver plate. Fresh silver oxide should be added periodically. This coating is just as durable as silver or tin.
To soften Leather Belting.—Castor oil is a good article for keeping leather belting soft and pliable.
To soften Leather Belting.—Castor oil is a great option for keeping leather belting soft and flexible.
How to open a Ball of Twine.—A ball of twine, if opened from the inside, will run off easily enough and give no trouble in the untwining; but if begun from the outside, it will speedily get tangled and knotted.
How to open a Ball of Twine.—A ball of twine, if unrolled from the inside, will come off easily and won't cause any problems while untangling; but if you start from the outside, it will quickly become tangled and knotted.
To prevent Adhesion.—M. Garde, in l’Imprimerie, tells paper-makers how to obviate the inconvenience of the adhesion together of sized papers, on damping, by the coagulation of the size. This is effected in the mills, by dipping the sheets in a solution of alum or tannin. A secondary advantage obtained is that the paper becomes tougher.
To prevent Adhesion.—M. Garde, in l’Imprimerie, informs paper makers on how to avoid the problem of sized papers sticking together when damp, due to the coagulation of the size. This is achieved in the mills by dipping the sheets in a solution of alum or tannin. A bonus benefit is that the paper becomes stronger.
To detect ground Wood in Paper.—Mix three parts of strong nitric acid with one part of sulphuric acid: a drop of this solution will immediately turn paper containing an admixture of ground wood a brown colour.
To detect ground wood in paper.—Mix three parts of strong nitric acid with one part of sulfuric acid: a drop of this solution will instantly turn paper that has ground wood in it a brown color.
French Gold Printing.—French copal varnish 1 oz., mastic varnish ¼ of an oz.; mix together and add twenty drops to the black ink table, and distribute; take an impression and apply, with wool, gold leaf, Dutch metal, or bronze. Apply the bronze with cotton wool and rub hard over the black ink. After each fifty printed, wipe off the superfluous gold from the type with a silk handkerchief.
French Gold Printing.—1 oz. of French copal varnish and ¼ oz. of mastic varnish; mix them together and add twenty drops to the black ink tray, then distribute it. Take an impression and apply it with wool, using gold leaf, Dutch metal, or bronze. Use cotton wool to apply the bronze and rub hard over the black ink. After every fifty prints, wipe off the excess gold from the type with a silk handkerchief.
Transfer Varnish.—Take equal quantities of fir balsam and spirits turpentine. Mix, shake well, and set in a warm place until clear. Used in decalcomania, and for maps, prints, drawings, and other articles of paper; and also to prepare tracing papers, and to transfer engravings.
Transfer Varnish.—Mix equal amounts of fir balsam and turpentine. Shake well and let it sit in a warm place until it becomes clear. It's used in decalcomania, as well as for maps, prints, drawings, and other paper items; it can also prepare tracing paper and transfer engravings.
To make Paper Waterproof.—Dissolve 8 oz. of alum and 3⅓ oz. of white soap in 4 pints of water. In another vessel dissolve 2 oz. of gum-arabic and 4 oz. of glue in 4 pints of water. Mix the two solutions and heat them over the fire. Then immerse the paper, sheet by sheet, in the hot liquid, then hang them up edgewise to dry, or pass them between heated cylinders.
To make Paper Waterproof.—Dissolve 8 oz. of alum and 3⅓ oz. of white soap in 4 pints of water. In another container, dissolve 2 oz. of gum arabic and 4 oz. of glue in 4 pints of water. Combine the two solutions and heat them over the fire. Then dip the paper, one sheet at a time, into the hot liquid, then hang them up on edge to dry, or pass them between heated rollers.
Books Preserved.—The bindings may be preserved from mildew by brushing them over with the spirits of wine. A few drops of any perfumed oil will secure libraries from the consuming effects of mould and damp. Russia leather, which is perfumed with the tar of the birch tree, never moulds or sustains injury from damp. The Romans used oil of cedar to preserve valuable manuscripts. Russia leather covered books placed in a stationer’s window will destroy flies and other insects.
Books Preserved.—You can protect the bindings from mildew by brushing them with some alcohol. A few drops of scented oil will keep libraries safe from mold and moisture damage. Russia leather, which is scented with birch tar, doesn’t mold or get damaged by dampness. The Romans used cedar oil to protect important manuscripts. Books covered in Russia leather that are displayed in a shop window will repel flies and other insects.
To restore Engravings, etc.—Old engravings, wood-cuts, or printed matter, that have turned yellow, may be rendered white by first washing carefully in water containing a little hyposulphite of soda, and then dipping for a minute in Javelle water. To prepare the latter, put 4 lbs. bicarbonate of soda in a kettle over a fire; add 1 gallon of boiling water, and let it boil for fifteen minutes. Then stir in 1 lb. of pulverized chloride of lime. When cold, the liquid can be kept in a jug ready for use.
To restore Engravings, etc.—Old engravings, woodcuts, or printed materials that have yellowed can be whitened by first washing them gently in water mixed with a bit of hyposulphite of soda, and then soaking them for a minute in Javelle water. To make Javelle water, put 4 lbs. of bicarbonate of soda in a pot over heat; add 1 gallon of boiling water and let it boil for fifteen minutes. Then stir in 1 lb. of powdered chloride of lime. Once it’s cold, the liquid can be stored in a jug for future use.

ORTHOGRAPHICAL.
A thorough reformation of the orthography of the English language, desirable as it is, can scarcely be hoped for in this century; though doubtless the time will come when an international convention will settle authoritatively the spelling of every word, as acceptably as has been done by the Academies of France and Spain in regard to the orthography of the languages of those countries.
Complete reformation of the spelling of the English language, as much as it is wanted, is unlikely to happen in this century; however, it’s certain that a time will come when an international convention will officially decide the spelling of every word, just as effectively as the Academies of France and Spain have done for the spelling of their languages.
A or AN before a Vowel or silent H.
In regard to the use of the indefinite article, Walker’s Dictionary very judiciously says,—
In terms of using the indefinite article, Walker’s Dictionary wisely states,—
“This indefinite, and, as it may be called, the euphonic article, is said by all our grammarians to be used before a vowel or h mute; but no notice is taken of using a instead of an before what is called a vowel, as, a useful book, a useful ceremony, a usurer, &c.; nor is any mention made of its constant usage before h when it is not mute, if the accent of the word be on the second syllable, as, an heroic action, an historical account, &c. This want of accuracy arises from a want of analyzing the vowels, and not attending sufficiently to the influence of accent on pronunciation. A proper investigation of the power of the vowels would have informed our grammarians that the letter u, when long, is not so properly a vowel as a semi-consonant, and perfectly equivalent to commencing y, and that a feeling of this has insensibly influenced the best speakers to prefix a to it in their conversation, while a confused idea of the general rule, arising from an ignorance of the nature of the letters, has generally induced them to prefix an to it in writing. The same observations are applicable[319] to the h. The ear alone tells us that, before heroic, historical, &c., the an ought invariably to be used; but, by not discovering that it is the absence of accent on the h that makes an admissible in these words, we are apt to prefix an to words where the h is sounded, as, an horse, an house, &c., and thus set our spoken and written language at variance. The article a must be used before all words beginning with a consonant, and before the vowel u when long; and the article an must be used before all words beginning with a vowel, except long u; before words beginning with h mute, as, an hour, an heir, &c.; or before words where the h is not mute, if the accent be on the second syllable, as, an heroic action, an historical account, &c.” The few words in our language in which the h is mute are heir, herb, honest, honour, hospital, hostler, hour, humble, humour, and their derivatives.
“This indefinite, and what could be called the euphonic article, is said by all grammarians to be used before a vowel or mute h; however, there is no mention of using a instead of an before what is considered a vowel, as in a useful book, a useful ceremony, a usurer, etc.; nor is there any mention of its constant use before h when it isn’t mute, if the accent is on the second syllable, as in an heroic action, an historical account, etc. This lack of accuracy comes from not analyzing the vowels and not paying enough attention to how accent influences pronunciation. A proper investigation of the vowels would have informed our grammarians that the letter u, when long, is more like a semi-consonant, and is equivalent to starting with y, and that this understanding has subconsciously influenced the best speakers to use a before it in conversation, while a confused perception of the general rule, stemming from a lack of understanding of the letters, has often led them to use an before it in writing. The same observations apply[319] to the h. The ear alone tells us that before heroic, historical, etc., an should always be used; but by failing to recognize that it’s the absence of accent on the h that makes an acceptable in these words, we might mistakenly use an with words where the h is pronounced, like an horse, an house, etc., which puts our spoken and written language at odds. The article a should be used before all words starting with a consonant, and before the long vowel u; and the article an should be used before all words starting with a vowel, except long u; before words starting with a mute h, like an hour, an heir, etc.; or before words where the h is not mute, if the accent is on the second syllable, like an heroic action, an historical account, etc.” The few words in our language where the h is mute are heir, herb, honest, honour, hospital, hostler, hour, humble, humour, and their derivatives.
O, or OH.
Oh should be used to express surprise, pain, sorrow, or anxiety. When the interjection is followed by a proper name, or as an exclamation of wishing the O should be employed singly, thus: O mother dear, Jerusalem! O Lord! O that I might find him.
Oh is used to show surprise, pain, sadness, or anxiety. When this interjection is followed by a proper name, or when it's an expression of longing, the O should be used alone, like this: O mother dear, Jerusalem! O Lord! O that I could find him.
ABLE and IBLE.
All English words, without regard to the source from which they have been derived, and those which come from Latin words ending in abilis or French ones in able, take the termination able in English, as, procurable, amendable, desirable, allowable, voidable, available, fordable, incontestable, &c.; but in words from Latin and French words terminating in ibilis or ible, then the ending will be ible in English. For instance: accessible, sensible, defensible, convertible, &c.
All English words, regardless of their source, and those that come from Latin words ending in abilis or French words ending in able, take the ending able in English, like procurable, amendable, desirable, allowable, voidable, available, fordable, incontestable, etc.; however, for words derived from Latin and French that end in ibilis or ible, the ending in English will be ible. For example: accessible, sensible, defensible, convertible, etc.
In words ending in ce or ge, the final e is preserved before the termination able, for the purpose of indicating the soft sound of the consonant, as in marriageable, chargeable, traceable, serviceable, &c.; but before the ending ible the final e of the primitive disappears, and there is no e before the termination. Examples: deducible, reducible, frangible, &c.
In words that end with ce or ge, the final e is kept before the suffix able to show that the consonant sounds soft, as in marriageable, chargeable, traceable, serviceable, etc.; however, before the ending ible, the final e from the original word is dropped, and there is no e before the suffix. Examples include deducible, reducible, frangible, etc.
The following list of words in ible is here added; all others end in able:—
The following list of words ending in ible is added; all others end in able:—
- accessible
- admissible
- adustible
- appetible
- apprehensible
- audible
- cessible
- coercible
- collectible
- comminuible
- compatible
- competible
- comprehensible
- compressible
- conceptible
- conclusible
- congestible
- contemptible
- contractible
- controvertible
- convertible
- convincible
- corrigible
- corrosible
- corruptible
- credible
- deceptible
- decerptible
- decoctible
- deducible
- defeasible
- defectible
- defensible
- depectible
- deprehensible
- descendible
- destructible
- digestible
- discernible
- discerptible
- dispraisible
- dissolvible
- distensible
- divisible
- docible
- edible
- effectible
- eligible
- eludible
- enforcible
- evincible
- expansible
- expressible
- extendible
- extensible
- fallible
- feasible
- fencible
- flexible
- forcible
- frangible
- fusible
- horrible
- ignoscible
- illegible
- immarcessible
- immiscible[23]
- impassible[24]
- intelligible
- irascible
- legible
- miscible
- partible
- passible[25]
- perceptible
- permiscible
- permissible
- persuasible
- pervertible
- plausible
- possible
- producible
- quadrible
- reducible
- referrible
- reflexible
- refrangible
- regible
- remissible
- reprehensible
- resistible
- responsible
- reversible
- revertible
- risible
- seducible
- sensible
- solvible
- tangible
- terrible
- transmissible
- visible
IM or IN, and EM or EN.
The prefix in is from the Latin, and that of en from the French and Greek. In generally signifies situation, and en mostly expresses action. Hence, perhaps, in strictness, inclose will signify “to close in,” and enclose, “to make close.” So, to inquire will be “to seek in, or to search in,” and enquire, to “make search.” Immigrate, “to pass into;” emigrate, “to go out of.” But this distinction is not attended to by writers, and is, indeed, too refined for general practice.
The prefix in comes from Latin, while en comes from French and Greek. In usually means situation, and en mostly conveys action. So, in a strict sense, inclose means “to close in,” and enclose means “to make close.” Likewise, to inquire means “to seek in, or to search in,” while enquire means “to make search.” Immigrate means “to pass into,” and emigrate means “to go out of.” However, most writers don’t pay attention to this distinction, and it’s actually too subtle for common use.
Before the letters b and p, en becomes em, as in embattle, empower; and in before some letters becomes ig, il, im, or ir, as in ignoble, illegal, improper, irresolute.
Before the letters b and p, en turns into em, as in embattle, empower; and in before some letters becomes ig, il, im, or ir, as in ignoble, illegal, improper, irresolute.
We give a list of those generally spelt with im or in; leaving it to be inferred that the rest are more usual with em or en.
We提供了一份通常用 im 或 in 拼写的单词列表;其余的则更常用 em 或 en 拼写。
- imbarn
- imbibe
- imboil
- imbound
- imbrue
- imbrute
- imbue
- imburse
- immanacle
- immense
- immerge
- immerse
- immigrate
- immingle
- immit
- immix
- immure
- impact
- impale
- imparadise
- impassioned
- impawn
- impeach
- impearl
- impel
- impen
- imperil
- impinge
- implant
- implead
- import
- impose
- impound
- impregnate
- impress
- imprint
- imprison
- inarch
- incase
- inclasp
- inclip
- incloud
- include
- incrassate
- increase
- incur
- indart
- indent
- indict
- indite
- indoctrinate
- indrench
- induce
- induct
- ineye
- infer
- infest
- inflix
- inflame
- inflate
- inflect
- inflict
- infringe
- infuscate
- infuse
- ingrane
- ingest
- inhabit
- inhale
- inhere
- inhold
- inhume
- initiate
- inject
- inlapidate
- inlay
- inlet
- inoculate
- inosculate
- inquire
- inrail
- inscribe
- insculp
- inseam
- insert
- inset
- inshell
- inship
- insinew
- insphere
- inspire
- inspirit
- install
- instate
- insteep
- instil
- instop
- insure
- inter
- intertwine
- intort
- intreasure
- intrench
- intrude
- intrust
- inumbrate
- inure
- inurn
- invade
- inveigh
- invert
- invest
- invigorate
- invite
- invocate
- invoice
- invoke
- inwall
- inweave
IN and United Nations.
In, as a prefix, also marks negation: it is probable that it came from the Romans. Un, as a prefix, is synonymous with in: it is of Saxon origin, and generally joined to words from a northern source; while in is oftener applied to those of Latin derivation.
In, when used as a prefix, also indicates negation: it likely originated from the Romans. Un, as a prefix, means the same as in: it comes from Saxon roots and is typically attached to words of northern origin; meanwhile, in is more frequently used with words derived from Latin.
ISE and IZE.
The variation in the terminations ise and ize is due to the different derivations of words,—ize characterizing words from the Greek and Latin, and ise from the French. The rule, however, is not inflexible. The following words are commonly spelled with the s.
The difference in the endings ise and ize comes from the different origins of words—ize is used for words derived from Greek and Latin, while ise comes from French. However, this isn't a strict rule. The following words are usually spelled with an s.
- advertise
- advise
- affranchise
- aggrandise
- amortise
- catechise
- chastise
- circumcise
- comprise
- compromise
- criticise
- demise
- despise
- devise
- disfranchise
- disguise
- divertise
- emprise
- enfranchise
- enterprise
- exercise
- exorcise
- galliardise
- manumise
- merchandise
- misprise (mistake)
- premise
- recognise
- reprise (take again)
- supervise
- surmise
- surprise
OR and OUR.
The ending our was in general use until the appearance of Webster’s Dictionary, in which the u was dropped in words terminating with our. This innovation has steadily gained ground. We do not approve of partial tinkerings with English orthography; and, until a general convention of British and American scholars settle the method of spelling English words, we shall adhere to the established usage. We append a list of words terminating in our.
The ending our was commonly used until Webster’s Dictionary was published, which removed the u from words ending with our. This change has gradually become more accepted. We don’t support making small changes to English spelling; and, until a general agreement is reached among British and American scholars about how to spell English words, we will stick to the traditional usage. We’ve included a list of words that end in our.
- arbour
- ardour
- armour
- behaviour
- candour
- clamour
- clangour
- colour
- contour
- demeanour
- dishonour
- dolour
- endeavour
- favour
- fervour
- flavour
- harbour
- honour
- humour
- labour
- neighbour
- odour
- parlour
- rancour
- rigour
- rumour
- savour
- saviour
- splendour
- succour
- tambour
- tumour
- valour
- vapour
- vigour
The u is dropped when the termination ous is added to any of these words; as, clamorous, dolorous, humorous, laborious, odorous, rancorous, rigorous, valorous, vigorous. And also in derivative words; such as armory, honorary, &c.
The u is dropped when the ending ous is added to any of these words, like clamorous, dolorous, humorous, laborious, odorous, rancorous, rigorous, valorous, vigorous. This also applies to derivative words, such as armory, honorary, etc.
SION and TION.
Primitive words which end in d, de, ge, mit, rt, se, or ss, take sion in their derivatives; but all other words have tion.
Primitive words that end in d, de, ge, mit, rt, se, or ss, take sion in their derivatives; but all other words use tion.
EXAMPLES.
- abscind, abscission
- condescend, condescension
- evade, evasion
- intrude, intrusion
- absterge, abstersion
- emerge, emersion
- admit, admission
- remit, remission
- revert, reversion
- convert, conversion
- confuse, confusion
- revise, revision
- impress, impression
- confess, confession
- admix, admixtion
- promote, promotion
IRREGULARS.
- adhesion
- cohesion
- compulsion
- declension
- decursion
- depulsion
- dissension
- divulsion
- evulsion
- exesion
- expulsion
- impulsion
- incursion
- propulsion
- recension
- recursion
- revulsion
- scansion
- tension
- transcursion
- version
- attention
- causation
- distention
- distortion
- coercion
- suspicion
- crucifixion
FURTHER and MORE.
Farther is nowadays only employed when speaking of distance; in all other acceptations of the word, further is generally adopted.
Farther is now only used when talking about distance; in all other meanings of the word, further is usually preferred.
PEAS and PEAS.
There are scarcely any words in which a mistake is more frequently made than in peas and pease. Yet the distinction between them is simple and well defined. Peas is the plural of pea, and, consequently, only follows numeral adjectives; as, “ten peas,” “a hundred peas,” “a few peas,” “many peas;” but pease is used when speaking of the legumen in the aggregate, or generally. Thus, we correctly say, “Pease are dear this year,” “Pease were plentifully supplied to the horses,” &c.
There are hardly any words where a mistake happens as often as with peas and pease. However, the difference between them is straightforward and clear. Peas is the plural of pea, and therefore, it only comes after numeral adjectives; for example, “ten peas,” “a hundred peas,” “a few peas,” “many peas;” but pease is used when referring to the legume as a whole or in general terms. So, we correctly say, “Pease are expensive this year,” “Pease were plentifully given to the horses,” etc.
Pease is also employed adjectively; as, “pease-pudding,” “pease-soup,” or “pea-soup,” &c.
Pease is also used as an adjective; for example, “pease-pudding,” “pease-soup,” or “pea-soup,” etc.
The Omission of S in the Possessive Case.
It is not uncommon with some persons to omit the s after the apostrophe in the possessive case of nouns, if the name itself ends in s; as, “James’ book,” “Barnes’ Notes.” But this is incorrect; for if we ask, Whose book? we should directly answer, James’s. The only case when the s can be judiciously omitted, and this solely to avoid the too hissing sound of so many s’s in succession, is when the first word ends with the sound of s in its last two syllables, and the next word begins with s; as in Misses’ spectacles, righteousness’ sake, conscience’ sake.
It's not uncommon for some people to drop the s after the apostrophe in the possessive form of nouns if the name itself ends in s; for example, “James’ book,” “Barnes’ Notes.” However, this is incorrect; if we ask, Whose book? the appropriate answer should be James’s. The only time the s can be justifiably omitted—primarily to avoid the awkward hissing sound of multiple s’s in a row—is when the first word ends with an s sound in its last two syllables and the next word starts with an s; as in Misses’ spectacles, righteousness’ sake, conscience’ sake.
Formation of the Plurals of Words compounded of a Noun and an Adjective.
Adjectives have no plural number. Therefore, in a word compounded of a noun and an adjective, the s denoting the plural number is attached to the end of the noun, as follows:—
Adjectives don’t have a plural form. So, in a compound word made up of a noun and an adjective, the s that indicates the plural is added to the end of the noun, like this:—
Governor-general | Governors-general. |
Attorney-general | Attorneys-general. |
Court-martial | Courts-martial. |
But where the adjective is taken substantively, the mark of the plural will properly follow it. For example: Brigadier-generals, major-generals, lieutenant-generals.
But when the adjective is used as a noun, the plural form should properly follow it. For example: Brigadier-generals, major-generals, lieutenant-generals.
Words compounded of a noun and the adjective full form their plurals thus: spoonfuls, cupfuls, bucketfuls, handfuls, mouthfuls.
Words made up of a noun and the adjective full form their plurals like this: spoonfuls, cupfuls, bucketfuls, handfuls, mouthfuls.
Pointing of Numbers, Weights, Measures, &c.
No comma should be placed between the constituent parts of the same number, however long it may be. Thus, we say, “One million one hundred thousand five hundred and twenty-one,” without any interpunction. The reason is, that there is no more than one numerical aggregate intended, or but one complex notion; and, consequently, no separation of parts or members can take place. The same reasoning holds good as respects values, weights, &c. For instance, when we say, “Six dollars and ten cents,” we merely mean that aggregate amount, but not necessarily any one of the coins indicated. If we did so intend, then two commas should be introduced,—one after “dollars,” and the other after “cents.” In like manner we should act with such sentences as, “Five tons three hundredweight two quarters and fifteen pounds;” or, “Ten acres four roods and twenty-seven perches;” and for the same reason: no division of parts is intended, but merely one aggregate amount.
No comma should be placed between the parts of the same number, no matter how long it is. So, we say, “One million one hundred thousand five hundred and twenty-one,” without any punctuation. The reason is that there’s only one numerical total intended, or just one complex idea; therefore, there’s no need to separate the parts. The same logic applies to values, weights, etc. For example, when we say, “Six dollars and ten cents,” we’re simply referring to that total amount, not necessarily to any individual coins mentioned. If we meant to indicate them separately, then we should use two commas—one after “dollars” and another after “cents.” Similarly, we should do the same with sentences like, “Five tons three hundredweight two quarters and fifteen pounds;” or, “Ten acres four roods and twenty-seven perches;” for the same reason: no separation of parts is intended, but just one total amount.
When figures are used to express amounts, a comma should not be inserted to cut off the tens unless the sum requires five figures: e.g. $10,600, 20,000 men, &c. In column matter this rule will not apply.
When numbers are used to show amounts, you shouldn't use a comma to separate the tens unless the total has five digits: e.g. $10,600, 20,000 people, etc. This rule doesn't apply to column data.
Derivation of English Words.
Of course the Saxon forms the basis of our language in its essential parts, and is the source whence we derive the greater part of our ordinary and most emphatic words. Nevertheless, various other languages have been put under contribution, especially the French, Latin, and Greek. This will be evident from the following statement of derivations, which will show the unlearned reader how important it is to him that he should acquire some knowledge of those languages, if he desires to attain to a thorough proficiency in his business as an educated printer.
Of course, the Saxon forms the foundation of our language in its key elements, and it's where we get most of our everyday and most impactful words. However, we’ve also drawn from various other languages, especially French, Latin, and Greek. This will be clear from the following list of derivations, which will illustrate to the average reader how crucial it is for them to learn a bit about those languages if they want to reach a high level of skill in their work as an educated printer.
I. From the Greek are derived—
I. From the Greek are derived—
1. Words ending in gram, graph, and graphy; as, telegram,[325] telegraph, geography, &c.; from the word γράφω, (grapho,) I write, and some other Greek word.
1. Words that end with gram, graph, and graphy, like telegram,[325] telegraph, geography, etc.; come from the word γράφω, (grapho,) meaning I write, along with some other Greek word.
2. Those in gon; from γωνια, (gonia,) an angle; as, octagon.
2. Those in gon; from γωνια, (gonia,) an angle; as, octagon.
3. All words in logue or logy; as, epilogue, astrology; from λόγος, (logos,) a discourse.
3. All words in logue or logy; such as, epilogue, astrology; from λόγος, (logos,) meaning a discourse.
4. Ic, ick, ics are also Greek terminations, generally of adjectives.
4. Ic, ick, ics are also Greek endings, typically used for adjectives.
5. Words in meter are all of Greek origin, coming from the verb μετρῶ, (metro,) I measure, in combination with some other word.
5. Words in meter all come from Greek, derived from the verb μετρῶ, (metro), meaning I measure, combined with another word.
6. Most words into which the terminations agogue, asis, esis, or ysis enter are also of Greek origin; such as demagogue, emphasis, parenthesis, analysis, &c.
6. Most words that include the endings agogue, asis, esis, or ysis are also of Greek origin, like demagogue, emphasis, parenthesis, analysis, etc.
II. But the main source whence we have derived words, with the exception of the Saxon, is the Latin, as will appear from an inspection of the following list:—
II. But the main source from which we've gotten words, except for the Saxon, is Latin, as will be evident from looking at the following list:—
1. Words ending in ance, ancy, or ant, and ence, ency, or ent, come from Latin words ending respectively in ans, antia, or ens, entia; as, abundance, from abundantia; infancy, from infantia; abundant, from abundans; absence, from absentia; excellency, from excellentia; and excellent, from excellens.
1. Words that end in ance, ancy, or ant, and ence, ency, or ent come from Latin words that end in ans, antia, or ens, entia; for example, abundance, from abundantia; infancy, from infantia; abundant, from abundans; absence, from absentia; excellency, from excellentia; and excellent, from excellens.
2. Words in al have their Latin representatives in alis; as, corporal, from corporalis.
2. Words in al have their Latin counterparts in alis; for example, corporal, from corporalis.
3. Verbs in ate mostly come from Latin verbs of the first conjugation; as, moderate, from modero.
3. Verbs in ate mostly come from Latin verbs of the first conjugation; for example, moderate, from modero.
4. Words in ator are generally the same in both languages; as, orator, senator, moderator.
4. Words in ator are generally the same in both languages; as, orator, senator, moderator.
5. The termination id comes mostly from Latin words ending in idus; as, acid, from acidus; but sometimes words of this ending are of Greek origin; as, oxide, (more correctly, oxyd,) from ὀξὺς, (oxys;) and, indeed, most scientific words of this ending; as, carotid, from καρώτιδες, &c.; rhomboid, from ῥομβοειδής.
5. The termination id mostly comes from Latin words ending in idus; for example, acid, from acidus; but sometimes words with this ending are of Greek origin; for instance, oxide (more correctly, oxyd), from ὀξὺς (oxys); and actually, most scientific words with this ending; such as carotid, from καρώτιδες, &c.; rhomboid, from ῥομβοειδής.
6. Il or ile is likewise from the Latin termination of adjectives in ilis; as, docile, from docilis; civil, from civilis.
6. Il or ile also comes from the Latin ending of adjectives in ilis; for example, docile comes from docilis; civil comes from civilis.
7. The Latin termination osus has its English representative in ious or ous; as, copious, from copiosus; numerous, from numerosus. But sometimes the English ending ous comes from a Latin word in ax; as, capacious, from capax.
7. The Latin ending osus corresponds to the English ious or ous; for example, copious, derived from copiosus; numerous, from numerosus. However, sometimes the English ending ous comes from a Latin word ending in ax; for instance, capacious, from capax.
8. The Latin ending io has its English corresponding word in ion; as, nation, from natio; oration, from oratio.
8. The Latin ending io corresponds to the English word ion; for example, nation, from natio; oration, from oratio.
9. The endings ne, re, and te after a vowel are also for the greater part of Latin origin; as, fortune, from fortuna; aquiline, from aquilinus; culture, from cultura; pure, from purus; complete, from completus, &c.
9. The endings ne, re, and te that follow a vowel mostly have Latin origins; for example, fortune, from fortuna; aquiline, from aquilinus; culture, from cultura; pure, from purus; complete, from completus, etc.
10. Words in ty come from Latin words in tas; as, equality, from æqualitas; bounty, from bonitas; rarity, from raritas, &c.
10. Words that end in ty come from Latin words that end in tas; for example, equality from æqualitas; bounty from bonitas; rarity from raritas, etc.
11. The termination ude is also of Latin origin, coming from words in udo; as, fortitude, from fortitudo; elude, from eludo.
11. The termination ude also comes from Latin, originating from words like udo; for example, fortitude, from fortitudo; elude, from eludo.
12. So also is uous, by inserting the letter o; as, ambiguous, from ambiguus; continuous, from continuus, &c.
12. The same goes for uous, by adding the letter o; for example, ambiguous, from ambiguus; continuous, from continuus, etc.
III. From the French have come—
III. From the French have come—
1. Most of our words in age; as, page, rage, usage.
1. Most of our words in age; like, page, rage, usage.
2. All those in eau; as, beau, flambeau, &c.
2. All those in water; like, handsome, torch, etc.
3. The French esse is represented by the English ess: as, princess, from princesse.
3. The French esse is shown by the English ess: for example, princess, from princesse.
4. Words in que mostly come to us from the French directly; some from the Latin directly or indirectly; as, antique, (L. antiquus, F. antique,) oblique, opaque.
4. Words in que mostly come to us directly from French; some come from Latin directly or indirectly, like antique (L. antiquus, F. antique), oblique, opaque.
5. Words ending in ment are nearly the same in both languages; as, commencement, advancement, (F. avancement,) &c.
5. Words ending in ment are almost the same in both languages; for example, commencement, advancement, (F. avancement,) &c.
We subjoin some rules for spelling, adapted from Laidlaw’s American Pronouncing Dictionary.[26]
RULE I.
Words ending in silent e after u or a consonant generally drop the e on taking an additional termination beginning with a vowel; as, sale, salable; plague, plaguy; sue, suing; eye, eying.
Words that end with a silent e after u or a consonant usually drop the e when adding a suffix that starts with a vowel; for example, sale becomes salable; plague becomes plaguy; sue becomes suing; eye becomes eying.
Exception I.—Words ending in ce and ge retain e before able and ous; as, service, serviceable; trace, traceable; courage, courageous; advantage, advantageous.
Exception I.—Words that end in ce and ge keep the e before able and ous; for example, service, serviceable; trace, traceable; courage, courageous; advantage, advantageous.
Exception II.—Compounds and prefixes retain e; as, firearms, foreordain, pole-axe, vice-admiral, fire-engine.
Exception II.—Compound words and prefixes keep the e; for example, firearms, foreordain, pole-axe, vice-admiral, fire-engine.
Remark.—From singe, springe, swinge, tinge, we write singeing, springeing, swingeing, tingeing, to distinguish from singing, springing, swinging, and tinging. Dyeing, from dye, retains e, to distinguish it from dying, the present participle of die. Mile retains e in mileage. Derivatives from proper names of persons retain e; as, daguerreotype, morseograph.
Remark.—From singe, springe, swinge, tinge, we write singeing, springeing, swingeing, tingeing, to distinguish from singing, springing, swinging, and tinging. Dyeing, from dye, keeps e, to set it apart from dying, the present participle of die. Mile keeps e in mileage. Words derived from proper names of people maintain e; for example, daguerreotype, morseograph.
RULE II.
Words ending in silent e generally retain the e on taking an additional termination beginning with a consonant; as, bereave, bereavement; issue, issueless.
Words that end with a silent e usually keep the e when adding a suffix that starts with a consonant; for example, bereave, bereavement; issue, issueless.
Remark.—Awful, awfully, awfulness, argument, argumentation, argumentative, woful, wofully, wofulness, duly, truly, and wholly, are undisputed exceptions; and abridgment, acknowledgment, judgment, misjudgment, prejudgment, lodgment, wobegone, and rhymster, are disputed exceptions. Some write abridgement, acknowledgement, judgement, misjudgement, prejudgement, lodgement, woebegone, and rhymester.
Remark.—Awful, awfully, awfulness, argument, argumentation, argumentative, woful, wofully, wofulness, duly, truly, and wholly are widely accepted exceptions; and abridgment, acknowledgment, judgment, misjudgment, prejudgment, lodgment, wobegone, and rhymster are debated exceptions. Some people write abridgement, acknowledgement, judgement, misjudgement, prejudgement, lodgement, woebegone, and rhymester.
RULE III.
Words ending in ie change them into y before ing; as, lie, lying. The following words conform to this rule:—
Words that end in ie change to y before ing; for example, lie, lying. The following words follow this rule:—
- lie
- belie
- outlie
- lie
- overlie
- underlie
- die
- hie
- tie
- untie
- vie
- outvie
RULE IV.
Words ending in y preceded by a consonant generally change y into i on taking an additional syllable; as, mercy, merciful, merciless; defy, defied, defies, defieth, defiant; busy, busier, busiest, business; ply, pliers; porphyry, porphyritic.
Words that end in y and are preceded by a consonant usually change y to i when adding another syllable; for example, mercy, merciful, merciless; defy, defied, defies, defieth, defiant; busy, busier, busiest, business; ply, pliers; porphyry, porphyritic.
Exception I.—Y after a consonant is not changed into i before ing or ish; as, dry, drying, dryish.
Exception I.—Y after a consonant does not change to i before ing or ish; for example, dry, drying, dryish.
Exception II.—Compounds usually retain y; as, mercy-seat, county-town, dairy-maid, skylight.
Exception II.—Compounds usually retain y; as, mercy-seat, county-town, dairy-maid, skylight.
Remark.—Dryer, dryest, dryly, dryness, shyer, shyest, shyly, shyness, are undisputed exceptions to the rule; and slyer, slyest, slyly, slyness, are disputed exceptions.
Remark.—Dryer, dryest, dryly, dryness, shyer, shyest, shyly, shyness, are clear exceptions to the rule; and slyer, slyest, slyly, slyness, are questionable exceptions.
RULE V.
Words ending in y preceded by a vowel retain the y; as, gay, gayly, gayness, gayety; pray, prayer, praying, prayed, prays.
Words that end with y and are preceded by a vowel keep the y; for example, gay, gayly, gayness, gayety; pray, prayer, praying, prayed, prays.
Remark.—From day, lay, pay, say, stay, are formed daily, laid, paid, said, saith, staid. The regular words dayly, layed, payed, sayeth, and stayed, are sometimes used.
Remark.—From day, lay, pay, say, stay, we get daily, laid, paid, said, saith, staid. The regular forms dayly, layed, payed, sayeth, and stayed are sometimes used.
RULE VI.
Monosyllables and words having the primary accent on the last syllable, when they end with a single consonant preceded by a single vowel, double their final consonant before an additional syllable that begins with a vowel; as, wet, wetter, wettest, wetting, wetted; drum, drumming, drummed; dispel, dispelling, dispelled.
Monosyllables and words with the main stress on the last syllable, when they end with a single consonant after a single vowel, double their final consonant before another syllable that starts with a vowel; for example, wet, wetter, wettest, wetting, wetted; drum, drumming, drummed; dispel, dispelling, dispelled.
Exception.—A final x, or the s in gas, should not be doubled; as, fix, fixes, fixed, fixing; annex, annexing; gases, gasefy.
Exception.—A final x, or the s in gas, should not be doubled; for example, fix, fixes, fixed, fixing; annex, annexing; gases, gasefy.
Remark I.—U after q is never reckoned a part of a diphthong or triphthong; so that from quit are formed quitting, quitted; and from quag, quaggy.
Remark I.—U after q is never considered part of a diphthong or triphthong; so that from quit we get quitting, quitted; and from quag, quaggy.
Remark II.—This rule applies only to derivatives which retain the accent of their primitives, and not to such as in´ferable, in´ference, pref´erable, pref´erence, ref´erable, and ref´erence, from infer, prefer, and refer. To the forms infer´rible, refer´rible, which are sometimes met with, the general rule applies. Transfer´able, from transfer, is an exception to the general rule; the regular form transfer´rible is not often used. Although parallel´ogram, from par´allel, and modal´ity from mo´dal, remove the primary accent to the point of duplication, they do not double the final l. See Remark II. under Rule VII.
Remark II.—This rule only applies to derivatives that keep the accent of their original words, not to ones like in´ferable, in´ference, pref´erable, pref´erence, ref´erable, and ref´erence, which come from infer, prefer, and refer. The forms infer´rible and refer´rible, which you sometimes see, follow the general rule. Transfer´able, derived from transfer, is an exception to the general rule; the regular form transfer´rible isn't used much. Although parallel´ogram, from par´allel, and modal´ity from mo´dal, shift the primary accent to the point of duplication, they do not double the final l. See Remark II. under Rule VII.
RULE VII.
A final consonant is not doubled when it is preceded by a diphthong, when the primary accent is either not on, or not retained upon, the last syllable, or when the additional syllable begins with a consonant; as, beat, beating, beaten; dif´fer, dif´fering, dif´fered, dif´ference, dif´ferent; prefer´, pref´erence; refer´, ref´erence; fit, fitful, fitly, fitness; ben´efit, ben´efited, ben´efiting.
A final consonant isn't doubled when it's preceded by a diphthong, when the main stress isn't on the last syllable, or when the extra syllable starts with a consonant; for example, beat, beating, beaten; dif´fer, dif´fering, dif´fered, dif´ference, dif´ferent; prefer´, pref´erence; refer´, ref´erence; fit, fitful, fitly, fitness; ben´efit, ben´efited, ben´efiting.
Exception I.—Compounds that remove the primary accent from the point of duplication retain the double letter; as, broad´-brimmed, heel´-tapping.
Exception I.—Words that take away the main stress from the duplicated part keep the double letter; for example, broad´-brimmed, heel´-tapping.
Remark I.—When ly is affixed to words ending in l, the l is not considered doubled; as in cool-ly, real-ly, gravel-ly, royal-ly.
Remark I.—When ly is added to words that end with l, the l is not regarded as doubled; like in cool-ly, real-ly, gravel-ly, royal-ly.
Remark II.—Nutmegged, kidnapping, kidnapped, kidnapper, zigzagging, zigzagged, excellence, and some others, are undisputed exceptions to the rule. There are nearly one hundred words, from which more than four hundred derivatives are formed, that are usually made exceptions to this rule. Webster is distinguished for making nearly all the derivatives conform to the rule. Webster and Smart accent the verb curv´et, on the first syllable, with which accentuation curveting and curveted are correct spellings; other orthoepists accent upon the last syllable, then curvet´ting and curvet´ted are correct.
Remark II.—Nutmegged, kidnapping, kidnapped, kidnapper, zigzagging, zigzagged, excellence, and a few others are widely accepted exceptions to the rule. There are around one hundred words, from which over four hundred derivatives are created, that are typically considered exceptions to this rule. Webster is known for ensuring that nearly all the derivatives follow the rule. Webster and Smart place the emphasis on the first syllable of the verb curv´et, which means curveting and curveted are the correct spellings; other experts place the emphasis on the last syllable, so curvet´ting and curvet´ted are correct.
RULE VIII.
Words ending in c accept of k before a termination beginning with e, i, or y; as, frolic, frolicked, frolicking; colic, colicky.
Words that end with c take a k before a suffix starting with e, i, or y; for example, frolic, frolicked, frolicking; colic, colicky.
ILLUSTRATIONS.
- colic
- colicky
- frolic
- frolicking
- frolicked
- havoc
- havocking
- havocked
- mimic
- mimicking
- mimicked
- mimicker
- physic
- physicking
- physicked
- rollic
- rollicking
- rollicked
- traffic
- trafficking
- trafficked
- trafficker
- talc
- talcky
- zinc
- zinckiferous
- (zinciferous)
- zincky
RULE IX.
Words ending in a double letter preserve it double after a prefix or before a termination beginning with a different letter; as, op-press, mis-spell, in-thrall, oversee; see-ing, op-pressive, stiff-ness, woo-ed, still-ness, assess-ment.
Words that end with a double letter keep the double letter when a prefix is added or when followed by a suffix starting with a different letter; for example, op-press, mis-spell, in-thrall, oversee; see-ing, op-pressive, stiff-ness, woo-ed, still-ness, assess-ment.
Remark I.—Annul, until, twibil, and the conservative fulfil, or the Websterian fulfill, are the only exceptions to the first part of this rule extensively recognized by present usage. The conservative distil and instil are at variance; but the Websterian distill and instill, and also twibill, as written by Reid, are in harmony with the rule.
Remark I.—Annul, until, twibil, and the traditional fulfil, or the Websterian fulfill, are the only exceptions to the first part of this rule that are widely accepted in current usage. The traditional distil and instil differ; however, the Websterian distill and instill, as well as twibill, as written by Reid, align with the rule.
Remark II.—Pontific, and all other derivatives of pontiff, are exceptions to the latter part of this rule, unless an f is discarded in the primitive word, as Webster suggests and the derivation warrants. The derivatives of dull, full, skill, and will, are disputed exceptions: if spelled as Webster writes them, dullness, fullness, skillful, willful, they conform to the rule.
Remark II.—Pontific and all other forms of pontiff are exceptions to the latter part of this rule, unless an f is dropped in the original word, as Webster suggests and the derivation supports. The derivatives of dull, full, skill, and will are debated exceptions: if spelled as Webster writes them, dullness, fullness, skillful, willful, they follow the rule.
RULE X.
The plural is usually formed from the singular by adding s; as, brave, braves; night, nights; hymn, hymns.
The plural is usually formed from the singular by adding s; for example, brave, braves; night, nights; hymn, hymns.
RULE XI.
Nouns ending in o preceded by a vowel accept of s in the plural; as, cameo, cameos; studio, studios.
Nouns that end in o and are preceded by a vowel take s in the plural; for example, cameo, cameos; studio, studios.
ILLUSTRATIONS.
- agios
- bagnios
- bamboos
- braggadocios
- cameos
- cuckoos
- curculios
- embryos
- folios
- imbroglios
- intaglios
- internuncios
- koodoos
- nuncios
- olios
- oratorios
- pistachios
- port-folios
- punctilios
- ratios
- seraglios
- solfeggios
- studios
- trios
RULE XII.
Nouns ending in y preceded by a vowel accept of s in the plural; as, money, moneys; attorney, attorneys; valley, valleys.
Nouns that end in y and are preceded by a vowel form the plural by adding s; for example, money, moneys; attorney, attorneys; valley, valleys.
RULE XIII.
Nouns ending in o preceded by a consonant usually accept of es in the plural; as, echo, echoes; embargo, embargoes.
Nouns that end in o and are preceded by a consonant typically take es in the plural; for example, echo, echoes; embargo, embargoes.
Remark.—There are more than fifty words that conform to this rule, and about thirty that accept of s only.
Remark.—There are over fifty words that follow this rule, and about thirty that only take s.
ILLUSTRATIONS.
- archipelagoes
- armadilloes
- bilboes
- bravadoes
- bravoes
- buffaloes
- buffoes
- calicoes
- cargoes
- desperadoes
- echoes
- embargoes
- farragoes
- frescoes
- grottoes
- gustoes
- heroes
- innuendoes
- juntoes
- lazarettoes
- lingoes
- lumbagoes
- mangoes
- manifestoes
- mottoes
- mulattoes
- negroes
- palmettoes
- passadoes
- peccadilloes
- potatoes
- prunelloes
- punchinelloes
- punctoes
- ranchoes
- recitativoes
- relievoes
- renegadoes
- ritornelloes
- rotundoes
- stilettoes
- supercargoes
- testudoes
- tomatoes
- tornadoes
- torpedoes
- umboes
- vetoes
- violoncelloes
- viragoes
- volcanoes
- zeroes
EXCEPTIONS.
- albinos
- cantos
- centos
- dominos
- duodecimos
- halos
- hidalgos
- inamoratos
- lassos
- limbos
- major-domos
- mementos
- merinos
- mosquitos
- octavos
- pianos
- porticos
- provisos
- quartos
- rancheros
- ridottos
- rondos
- salvos
- set-tos
- sirocos
- solos
- torsos
- tyros
It would be well if all words ending in o were made to conform to Rules XI. and XIII.
It would be great if all words ending in o followed Rules XI and XIII.
RULE XIV.
Nouns ending in ss, z, x, ch soft, and sh, accept of es in the plural; as, dress, dresses; buzz, buzzes; box, boxes; peach, peaches; dish, dishes.
Nouns that end in ss, z, x, soft ch, and sh add es in the plural; for example, dress, dresses; buzz, buzzes; box, boxes; peach, peaches; dish, dishes.
RULE XV.
Nouns ending in y after a consonant change y into ies in the plural; as, city, cities; daisy, daisies.
Nouns that end in y after a consonant change y to ies when they’re plural; for example, city becomes cities and daisy becomes daisies.
RULE XVI.
Compound nouns whose parts are connected by a hyphen accept of the sign of the plural after that part which essentially constitutes the noun; as, knight-errant, knights-errant; son-in-law, sons-in-law; man-of-war, men-of-war; step-child, step-children; ember-day, ember-days; man-singer, men-singers.
Compound nouns that have parts connected by a hyphen accept the sign of the plural after the part that essentially makes up the noun; for example, knight-errant, knights-errant; son-in-law, sons-in-law; man-of-war, men-of-war; step-child, step-children; ember-day, ember-days; man-singer, men-singers.
ILLUSTRATIONS.
- aides-de-camp
- beaus-ideal or
- beaux-ideal
- cartes-blanche
- charges-d’affaires
- chevaux-de-frise
- coups-de-main
- courts-martial
- cousins-german
- daughters-in-law
- fathers-in-law
- gendarmes or
- gens d’armes
- jets d’eau
- knights-errant
- mesdames
- men-of-war
- messieurs
- mothers-in-law
- poets-laureate
- porte-monnaies
- prices-current
- sergeants-at-arms
- sisters-in-law
- sons-in-law
- step-children
- step-fathers
- valets-de-chambre
Remark I.—If no hyphen is used, the sign of the plural is always placed at the end; as, spoonful, spoonfuls.
Remark I.—If no hyphen is used, the sign of the plural is always placed at the end; as, spoonful, spoonfuls.
Remark II.—The sign of the possessive case is always placed at the end of compound nouns; as, son-in-law’s house.
Remark II.—The sign of the possessive case is always placed at the end of compound nouns; for example, son-in-law's house.
RULE XVII.
The compounds of man form their plural in the same manner as the simple word; as, fisherman, fishermen; man-of-war, men-of-war.
The compounds of man form their plural in the same way as the simple word; for example, fisherman, fishermen; man-of-war, men-of-war.
Exceptions.—The only exceptions to this rule are dragoman, Mussulman, Ottoman, talisman, Turcoman, German, Norman, and landamman, which accept of s.
Exceptions.—The only exceptions to this rule are dragoman, Mussulman, Ottoman, talisman, Turcoman, German, Norman, and landamman, which accept s.
RULE XVIII.
Of the terminations eive and ieve, and of the derivatives of each, the former are found after c, and the latter after other letters; as, conceive, conceit, receive, receipt; relieve, relief, relieving, thieve, thievish.
Of the endings eive and ieve, and their related forms, the first tends to appear after c, while the second appears after other letters; for example, conceive, conceit, receive, receipt; relieve, relief, relieving, thieve, thievish.
ILLUSTRATIONS.
- achieve
- aggrieve
- bas-relief
- belief
- believe
- conceit
- conceivable
- conceive
- deceit
- deceitful
- deceive
- disbelief
- disbelieve
- grief
- grieve
- inconceivable
- lief
- lieve
- misbelief
- misconceive
- perceive
- preconceive
- receipt
- receive
- relief
- relieve
- relievo
- reprieve
- retrieve
- sieve
- thief
- thieve
- unbelief
- unbeliever
- undeceive
Plurals of Nouns which change F or FE into VES.
- beeves
- calves
- elves
- halves
- knives
- leaves
- lives
- loaves
- selves
- sheaves
- shelves
- thieves
- tipstaves
- wharves
- wives
- wolves
All other nouns ending in ff conform to Rule X. Wharfs prevails in Great Britain, wharves in America.
All other nouns ending in ff follow Rule X. "Wharfs" is common in Great Britain, while "wharves" is used in America.
Plurals of Nouns ending in F or FE which accept of S only in the Plural.
- briefs
- chiefs
- fiefs
- griefs
- mischiefs
- kerchiefs
- neckerchiefs
- handkerchiefs
- caliphs
- caufs
- clefs
- coifs
- delfs
- dwarfs
- turfs
- kerfs
- surfs
- fifes
- strifes
- safes
- scarfs
- waifs
- woofs
- hoofs
- roofs
- proofs
- reproofs
- disproofs
- waterproofs
- beliefs
- reliefs
- gulfs
Plurals of Nouns ending in WATER, IEU, and OU.
- beaux
- bureaux
- chapeaux
- chateaux
- flambeaux
- plateaux
- rondeaux
- jets d’eau
- portmanteaus
- purlieus
- adieux
- batteaux
- bijoux
- morceaux
- rouleaux
- tableaux
A number of these nouns admits of two forms in the plural.
A number of these nouns have two plural forms.
HOW TO SECURE COPYRIGHTS.
1. A printed copy of the title (besides the two copies to be deposited after publication) of the book, map, chart, dramatic or musical composition, engraving, cut, print, photograph, or a description of the painting, drawing, chromo, statue, statuary, or model or design for a work of the fine arts, for which copyright is desired, must be sent by mail or otherwise, prepaid, addressed:
1. A printed copy of the title (in addition to the two copies that need to be submitted after publication) of the book, map, chart, dramatic or musical work, engraving, cut, print, photograph, or a description of the painting, drawing, chromo, statue, sculpture, or design for a work of fine arts, for which copyright is sought, must be sent by mail or another method, prepaid, addressed:
Librarian of Congress,
Washington, D. C.
Library of Congress,
Washington, D.C.
This must be done before publication of the book or other article.
This needs to be done before the book or other article is published.
The printed title required may be a copy of the title page of such publications as have title pages. In other cases, the title must be printed expressly for copyright entry, with name of claimant of copyright. The style of type is immaterial, and the print of a type-writer will be accepted. But a separate title is required for each entry, and each title must be printed on paper as large as commercial note. The title of a periodical must include the date and number.
The printed title needed can be a copy of the title page from publications that have title pages. In other cases, the title must be specifically printed for copyright registration, including the name of the copyright claimant. The type style doesn't matter, and a typewriter print is acceptable. However, a separate title is required for each entry, and each title must be printed on paper that is at least the size of commercial note. The title of a periodical must include the date and number.
2. A fee of 50 cents, for recording the title of each book or other article, must be enclosed with the title as above, and 50 cents in addition (or one dollar in all) for each certificate of copyright under seal of the Librarian of Congress, which will be transmitted by early mail.
2. A fee of 50 cents for recording the title of each book or other item must be included with the title as mentioned above, along with an additional 50 cents (or a total of one dollar) for each copyright certificate with the seal of the Librarian of Congress, which will be sent by early mail.
3. Within ten days after publication of each book or other article, two complete copies of the best edition issued must be sent, to perfect the copyright, with the address:
3. Within ten days of the publication of each book or article, two complete copies of the best edition released must be sent to finalize the copyright, addressed to:
Librarian of Congress,
Washington, D. C.
Librarian of Congress,
Washington, DC
The postage must be prepaid, or else the publications inclosed in parcels covered by printed Penalty Labels, furnished by the Librarian, in which case they will come FREE by mail, according to rulings of the Post Office Department. Without the deposit of copies above required the copyright is void, and a penalty of $25 is incurred. No copy is required to be deposited elsewhere.
The postage needs to be prepaid, or the publications included in parcels with printed Penalty Labels provided by the Librarian will be sent Free by mail, following the rules of the Post Office Department. If the required copies aren't deposited, the copyright is invalid, and a penalty of $25 will apply. No copies need to be deposited anywhere else.
4. No copyright is valid unless notice is given by inserting in every copy published, on the title-page or the page following, if it be a book; or, if a map, chart, musical composition, print, cut, engraving, photograph, painting, drawing, chromo, statue, statuary, or model or design intended to be perfected as a work of the fine arts, by inscribing upon some portion thereof, or on the substance on which the same is mounted, the following words, viz.: “Entered according to act of Congress, in the year ⸺, by ⸺ ⸺, in the office of the Librarian of Congress, at Washington,” or, at the option of the person entering the copyright, the words: “Copyright, 18—, by ⸺.”
4. No copyright is valid unless notice is provided by including it in every published copy, either on the title page or the following page, if it's a book; or, if it's a map, chart, musical composition, print, cut, engraving, photograph, painting, drawing, chromo, statue, sculpture, or model or design meant to be finalized as fine art, by inscribing some portion of it, or on the material it’s mounted on, with the following words: “Entered according to act of Congress, in the year ⸺, by ⸺ ⸺, in the office of the Librarian of Congress, at Washington,” or, as an alternative for the person registering the copyright, the words: “Copyright, 18—, by ⸺.”
The law imposes a penalty of $100 upon any person who has not obtained copyright who shall insert the notice “Entered according to act of Congress,” or “Copyright,” etc., or words of the same import, in or upon any book or other article.
The law imposes a $100 fine on anyone who hasn't obtained copyright but still includes the notice "Entered according to act of Congress" or "Copyright" or similar phrases in any book or other item.
5. Any author may reserve the right to translate or to dramatize his own work. In this case, notice should be given by printing the words “Right of translation reserved,” or “All rights reserved,” below the notice of copyright entry, and notifying the Librarian of Congress of such reservation, to be entered upon the record.
5. Any author can keep the right to translate or dramatize their own work. In this case, notice should be given by printing the phrase “Right of translation reserved” or “All rights reserved” beneath the copyright notice, and informing the Librarian of Congress about this reservation to be recorded.
Since the phrase, all rights reserved, refers exclusively to the author’s right to dramatize or to translate, it has no bearing upon any publications except original works, and will not be entered upon the record in other cases.
Since the phrase, all rights reserved, specifically refers to the author’s right to dramatize or translate, it doesn’t apply to any publications other than original works, and it won’t be officially noted in other instances.
6. The original term of copyright runs for twenty-eight years. Within six months before the end of that time, the author or designer, or his widow or children, may secure a renewal for the further term of fourteen years, making forty-two years in all. Applications for renewal must be accompanied by explicit statement of ownership, in the case of the author, or of relationship, in the case of his heirs, and must state definitely the date and place of entry of the original copyright. Advertisement of renewal is to be made within two months of date of renewal certificate, in some newspaper, for four weeks.
6. The original copyright lasts for twenty-eight years. Six months before that time is up, the author or designer, or their spouse or children, can apply for a renewal for another fourteen years, totaling forty-two years. Applications for renewal must include a clear statement of ownership, if it’s the author, or proof of relationship, if it’s their heirs, and must specify the date and place of the original copyright registration. A renewal advertisement has to be published within two months of receiving the renewal certificate, in a newspaper, for four weeks.
7. The time within which any work entered for copyright may be issued from the press is not limited by any law or regulation, but depends upon the discretion of the proprietor. A copyright may be secured for a projected work as well as for a completed one.
7. The period during which any work submitted for copyright can be published is not restricted by any law or regulation; it is at the discretion of the owner. Copyright can be obtained for a planned work as well as for a finished one.
8. A copyright is assignable in law by any instrument of writing, but such assignment must be recorded in the office of the Librarian of Congress within sixty days from its date. The fee for this record and certificate is one dollar, and for a certified copy of any record of assignment one dollar.
8. A copyright can be transferred legally through any written document, but that transfer must be registered with the Librarian of Congress within sixty days from the date it was created. The fee for this registration and certificate is one dollar, and for a certified copy of any assignment record, it's also one dollar.
9. A copy of the record (or duplicate certificate) of any copyright entry will be furnished, under seal, at the rate of fifty cents each.
9. A copy of the record (or duplicate certificate) of any copyright entry will be provided, under seal, for fifty cents each.
10. In the case of books published in more than one volume, or of periodicals published in numbers, or of engravings, photographs, or other articles published with variations, a copyright is to be entered for each volume or part of a book, or number of a periodical, or variety, as to style, title, or inscription, of any other article. But a book published serially in a periodical, under the same general title, requires only one entry. To complete the copyright on such a work, two copies of each serial part, as well as of the complete work (if published separately), must be deposited.
10. For books released in multiple volumes, periodicals published in installments, or engravings, photographs, or other items that come in different versions, a copyright needs to be registered for each volume or part of a book, or each issue of a periodical, or each variation in style, title, or inscription of any other item. However, if a book is published serially in a periodical under the same main title, only one registration is required. To complete the copyright for such a work, two copies of each serial part, along with the full work (if it's published separately), must be submitted.
11. To secure a copyright for a painting, statue, or model or design intended to be perfected as a work of the fine arts, so as to prevent infringement by copying, engraving, or vending such design, a definite description must accompany the application for copyright, and a photograph of the same, at least as large as “cabinet size,” should be mailed to the Librarian of Congress within ten days from the completion of the work or design.
11. To obtain a copyright for a painting, sculpture, model, or design meant to be finalized as a work of fine art, and to protect it from being copied, engraved, or sold, a clear description must be included with the copyright application. Additionally, a photograph of the work, at least "cabinet size," should be sent to the Librarian of Congress within ten days of finishing the work or design.
12. Copyrights cannot be granted upon trade-marks, nor upon mere names of companies or articles, nor upon prints or labels intended to be used with any article of manufacture. If protection for such names or labels is desired, application must be made to the Patent Office, where they are registered, at a fee of $6 for labels and $25 for trade-marks.
12. Copyrights can't be granted for trademarks, company names, or product names, nor for prints or labels meant to be used with any manufactured item. If you want protection for these names or labels, you need to apply to the Patent Office, where they can be registered, with a fee of $6 for labels and $25 for trademarks.
13. Citizens or residents of the United States only are entitled to copyright.
13. Only citizens or residents of the United States are entitled to copyright.
14. Every applicant for a copyright should state distinctly the full name and residence of the claimant, and whether the right is claimed as author, designer, or proprietor. No affidavit or formal application is required.
14. Every applicant for a copyright must clearly state the full name and address of the claimant, as well as whether the right is claimed as an author, designer, or owner. No affidavit or formal application is needed.
Office of the Librarian of Congress,
Washington, 1885.
Office of the Librarian of Congress,
Washington, 1885.

THE METRIC SYSTEM.
The Metric System is a decimal system of measures and weights, based on the meter as its unit, which originated in France during the last decade of the eighteenth century, and has since been adopted by the greater number of States in Europe and America. In the United States its use was authorized in 1866 by Act of Congress. The length of the meter was intended to be one ten-millionth part of the distance from the equator to either pole, measured at the level of the sea, but it is in reality a trifle less. All other units for measuring and weighing are derived from it, and the higher or lower denominations of the same kind of measure are obtained by multiplying or dividing its unit by tens, and prefixing to its name the Greek numerals, deka 10, hekto 100, kilo 1000, or myria 10000, for the higher denominations, and the Latin numerals, deci 1/10, centi 1/100, or milli 1/1000, for the lower. The unit of weight, called the gram, is theoretically the weight in vacuo of a cubic centimeter of distilled water at the temperature of maximum density assumed to be 4° C. or 39° 1 Fe.
The Metric System is a decimal system of measurement and weight, based on the meter as its unit. It started in France during the last decade of the eighteenth century and has since been adopted by most countries in Europe and America. In the United States, its use was approved in 1866 by an Act of Congress. The length of the meter was meant to equal one ten-millionth of the distance from the equator to either pole, measured at sea level, but it is actually slightly less than that. All other units for measuring and weighing are based on it, and the larger or smaller denominations of the same type of measurement are obtained by multiplying or dividing its unit by tens, adding Greek prefixes like deka (10), hekto (100), kilo (1000), or myria (10000) for larger denominations, and Latin prefixes like deci (1/10), centi (1/100), or milli (1/1000) for smaller. The unit of weight, called the gram, is theoretically defined as the weight in a vacuum of a cubic centimeter of distilled water at its maximum density, assumed to be at 4° C or 39° 1 F.
Including the meter and gram, five units have been adopted in the metric system, viz.:—
Including the meter and gram, five units have been adopted in the metric system, namely:—
1. The Meter, the unit of length, = 3.280899 feet = 39.37079 inches.
1. The meter, which is the unit of length, equals 3.280899 feet or 39.37079 inches.
2. The Are, the unit of surface, = 1 square dekameter = 119.60332 square yards.
2. The are, a unit of area, equals 1 square dekameter, which is 119.60332 square yards.
3. The Liter, the unit of capacity, = 1 cubic decimeter = 0.26418635 gallon = 1.0567454 quarts.
3. The liter, the unit of capacity, = 1 cubic decimeter = 0.26418635 gallons = 1.0567454 quarts.
4. The Stere, the unit of solidity, = 1 cubic meter = 35.336636 cubic feet = 1.308764 cubic yards.
4. The stere, the unit of volume, = 1 cubic meter = 35.336636 cubic feet = 1.308764 cubic yards.
5. The Gram, the unit of weight, = 15.43234874 grains troy.
5. The gram, the unit of weight, equals 15.43234874 troy grains.
For practical purposes the following are commonly used as units, viz.:—
For practical purposes, the following are commonly used as units:—
For itinerary measure, the kilometer = 0.62138 mile. For land measure, the hektare = 2.47114 acres. For commercial weight, the kilogram = 2.20462125 pounds. The nickel five-cent piece, coined since 1866, weighs exactly 5 grams.
For itinerary measure, the kilometer = 0.62138 miles. For land measure, the hectare = 2.47114 acres. For commercial weight, the kilogram = 2.20462125 pounds. The nickel five-cent coin, minted since 1866, weighs exactly 5 grams.
Metric Equivalents of English Measurements and Weights.
LONG MEASURE.
1 inch | = | 2.540 centimeters. |
1 foot | = | 3.048 decimeters. |
1 yard | = | 9.144 decimeters. |
1 rod | = | 5.0291 meters. |
1 mile | = | 1.6093 kilometers. |
SQUARE MEASURE.
1 acre | = | 40.467 ares. |
LIQUID MEASURE.
1 gill | = | 1.1831 deciliters. |
1 pint | = | 4.7325 deciliters. |
1 quart | = | 9.4650 deciliters. |
1 gallon | = | 3.786 liters. |
DRY MEASURE.
1 pint | = | 5.5067 deciliters. |
1 quart | = | 1.1013 liters. |
1 peck | = | 8.8108 liters. |
1 bushel | = | 3.524 dekaliters. |
AVOIRDUPOIS WEIGHT.
1 ounce | = | 2.835 dekagrams. |
1 pound | = | 4.5359 hektograms. |
TROY WEIGHT.
1 grain | = | 6.480 centigrams. |
1 ounce | = | 3.1103 dekagrams. |
1 pound | = | 3.7324 hektograms. |
Table for Converting Pounds and Ounces to Kilograms.
Oz. | Kilo. | Lbs. | Kilo. | Lbs. | Kilo. | Lbs. | Kilo. | Lbs. | Kilo. |
---|---|---|---|---|---|---|---|---|---|
1 | 0.028 | 1 | 0.454 | 31 | 14.062 | 61 | 27.669 | 91 | 41.277 |
2 | 0.057 | 2 | 0.907 | 32 | 14.515 | 62 | 28.123 | 92 | 41.731 |
3 | 0.085 | 3 | 1.361 | 33 | 14.969 | 63 | 28.577 | 93 | 42.184 |
4 | 0.113 | 4 | 1.814 | 34 | 15.422 | 64 | 29.030 | 94 | 42.638 |
5 | 0.142 | 5 | 2.268 | 35 | 15.876 | 65 | 29.484 | 95 | 43.092 |
6 | 0.170 | 6 | 2.722 | 36 | 16.330 | 66 | 29.937 | 96 | 43.545 |
7 | 0.198 | 7 | 3.175 | 37 | 16.783 | 67 | 30.391 | 97 | 43.999 |
8 | 0.227 | 8 | 3.629 | 38 | 17.237 | 68 | 30.845 | 98 | 44.452 |
9 | 0.255 | 9 | 4.082 | 39 | 17.690 | 69 | 31.298 | 99 | 44.906 |
10 | 0.283 | 10 | 4.536 | 40 | 18.144 | 70 | 31.752 | 100 | 45.360 |
11 | 0.312 | 11 | 4.990 | 41 | 18.597 | 71 | 32.205 | 200 | 90.720 |
12 | 0.340 | 12 | 5.443 | 42 | 19.051 | 72 | 32.659 | 300 | 136.079 |
13 | 0.369 | 13 | 5.897 | 43 | 19.505 | 73 | 33.113 | 400 | 181.439 |
14 | 0.397 | 14 | 6.350 | 44 | 19.958 | 74 | 33.566 | 500 | 226.799 |
15 | 0.425 | 15 | 6.804 | 45 | 20.412 | 75 | 34.020 | 600 | 272.159 |
16 | 7.258 | 46 | 20.865 | 76 | 34.473 | 700 | 317.518 | ||
17 | 7.711 | 47 | 21.319 | 77 | 34.927 | 800 | 362.878 | ||
18 | 8.165 | 48 | 21.773 | 78 | 35.380 | 900 | 408.238 | ||
19 | 8.618 | 49 | 22.226 | 79 | 35.834 | 1000 | 453.598 | ||
20 | 9.072 | 50 | 22.680 | 80 | 36.288 | 2000 | 907.195 | ||
21 | 9.526 | 51 | 23.133 | 81 | 36.741 | 3000 | 1360.793 | ||
22 | 9.979 | 52 | 23.587 | 82 | 37.195 | 4000 | 1814.390 | ||
23 | 10.433 | 53 | 24.041 | 83 | 37.649 | 5000 | 2267.988 | ||
24 | 10.886 | 54 | 24.494 | 84 | 38.102 | 6000 | 2721.586 | ||
25 | 11.340 | 55 | 24.948 | 85 | 38.556 | 7000 | 3175.183 | ||
26 | 11.793 | 56 | 25.401 | 86 | 39.009 | 8000 | 3628.781 | ||
27 | 12.247 | 57 | 25.855 | 87 | 39.463 | 9000 | 4082.378 | ||
28 | 12.701 | 58 | 26.309 | 88 | 39.917 | 10000 | 4535.976 | ||
29 | 13.154 | 59 | 26.762 | 89 | 40.370 | ||||
30 | 13.608 | 60 | 27.216 | 90 | 40.824 |

TECHNICAL TERMS OF THE CRAFT.
Alley.—The space between two stands.
Alley.—The area between two stalls.
Ascending letters.—Letters that ascend into the upper shoulder; as, b, d, l, &c. and all the capitals.
Ascending letters.—Letters that rise into the upper part, such as b, d, l, etc., and all the capital letters.
Author’s proof.—The clean proof sent to an author after the compositors’ errors have been corrected.
Author’s proof.—The finalized proof sent to an author after the typesetters’ mistakes have been fixed.
Bank.—A table about four feet high, to lay sheets on at press.
Bank.—A table about four feet tall, used for laying sheets at the press.
Bastard title.—A short title preceding the general title of a work.
Bastard title.—A brief title that comes before the main title of a work.
Bastard type.—Type with a face larger or smaller than its regular body: as Nonpareil on Minion body, or Minion on Nonpareil body.
Bastard type.—Type with a face that is larger or smaller than its standard body: like Nonpareil on Minion body, or Minion on Nonpareil body.
Batter.—Types accidentally injured in a form.
Batter.—Types that were accidentally hurt in a form.
Beard of a letter.—The outer angles supporting the face of a type and extending to the shoulder.
Beard of a letter.—The outer angles that support the face of a type and extend to the shoulder.
Bearer.—A strip of reglet to bear off the impression from a blank page. A long piece of furniture, type-high, used in working jobs. A solid-faced type interspersed among the blank parts of a page composed for stereotyping, to resist the pressure of the knife when the plate is shaved.
Bearer.—A strip of reglet for holding the impression from a blank page. A long piece of furniture, type-high, used in job printing. A solid-faced type mixed in with the blank areas of a page made for stereotyping, to withstand the pressure of the knife when the plate is shaved.
Bearer-lines.—The top line and bottom line in a page prepared for stereotyping.
Bearer-lines.—The top and bottom lines on a page set up for stereotyping.
Bed.—The flat part of the press on which the form is laid.
Bed.—The flat surface of the press where the form is placed.
Bevels.—Slugs cast nearly type-high, with a beveled edge, used by stereotypers to form the flange on the side of the plates.
Bevels.—Slugs cast almost type-high, with a beveled edge, used by stereotypers to create the flange on the side of the plates.
Bite.—An irregular white spot on the edge or corner of a printed page, caused by the frisket not being sufficiently cut out.
Bite.—An uneven white spot on the edge or corner of a printed page, caused by the frisket not being cut out enough.
Blanket.—A woollen cloth used in the tympan.
Blanket.—A wool fabric used in the tympan.
Blank-line.—A line of quadrates.
Blank line.—A line of squares.
Blocks.—The mahogany forms on which stereotype plates are placed for printing.
Blocks.—The mahogany molds on which stereotype plates are set for printing.
Blocked up.—When the fount of type is all set, and none is available for present use.
Blocked up.—When the type is all set, and there’s none available for use right now.
Bodkin.—A delicate awl-like tool used for correcting errors in type.
Bodkin.—A fine, pointed tool used for fixing mistakes in typesetting.
Body.—The shank of the letter.
Body.—The main part of the letter.
Botch.—A bungling, incompetent workman.
Botch.—A clumsy, incompetent worker.
Bottled.—Type wider at the bottom than at the top.
Bottled.—Shape is broader at the base than at the opening.
Boxes.—The compartments of a case in which the types are placed.
Boxes.—The sections of a case where the types are stored.
Brayer.—A wooden or glass rubber, flat at the bottom, used to bray or spread out ink on the ink-block.
Brayer.—A wooden or glass tool, flat on the bottom, used to mix or spread out ink on the ink-block.
Break-line.—A short line.
Break line.—A short line.
Broad-side.—A form of one page, printed on one side of a whole sheet of paper.
Broadside.—A type of document that is printed on one side of a complete sheet of paper.
Broken matter.—Pages of type disrupted and somewhat intermingled.
Broken matter.—Pages of text disrupted and somewhat mixed up.
Bundle.—Two reams of paper.
Bundle.—Two packs of paper.
Bur.—Rough edge of a type which the founder neglected to take off in dressing.
Bur.—A rough edge on a typeface that the maker forgot to smooth out during finishing.
Cabinet.—A receptacle for cases, chases leads, &c.
Cabinet.—A container for cases, chases, leads, etc.
Cancelled figures.—Figures cast with a line across the face.
Cancelled figures.—Figures that have a line drawn across the face.
Caret.—A character [^] used in proofreading to denote the place where omitted words should be inserted.
Caret.—A symbol [^] used in proofreading to indicate where missing words should be added.
Case.—The receptacle for type, divided into numerous compartments.
Case.—The container for type, separated into various sections.
Cassie paper.—Formerly, the two outside quires of a ream, consisting of defective sheets.
Cassie paper.—Previously, the two outer packs of a ream contained flawed sheets.
Casting off.—Estimating how many pages a certain quantity of copy will make in type.
Casting off.—Figuring out how many pages a specific amount of text will fill when typeset.
Cattie.—Imperfect or smutty look of a printed sheet caused by an oily or unclean roller.
Cattie.—An imperfect or dirty appearance on a printed sheet caused by an oily or unclean roller.
Ceriphs.—The lines or cross-strokes at the ends of the stem of a letter.
Ceriphs.—The lines or cross-strokes at the ends of a letter's stem.
Chapel.—A printing-office.
Chapel.—A print shop.
Chapel laws.—Rules of a printing-office.
Chapel rules.—Printing office guidelines.
Chase.—A rectangular iron frame in which pages of type are imposed.
Chase.—A rectangular metal frame where typed pages are arranged.
Circular quadrates.—Blank types curved on one side.
Circular quadrates.—Blank types curved on one side.
Clean proof.—A proof containing few faults.
Clean proof.—A proof that has few mistakes.
Clearing away.—Properly disposing of materials after a work has been completed.
Clearing away.—Properly getting rid of materials after a job is finished.
Clicker.—The chief of a companionship.
Clicker.—The leader of a group.
Close matter.—Solid matter with few break-lines.
Close matter.—Solid material with few breaks.
Companionship.—All the hands employed on a work.
Companionship.—All the people involved in a task.
Composing.—Setting type.
Composing.—Typesetting.
Composing-rule.—A steel or brass rule, with a beak at one end, used in typesetting.
Composing-rule.—A steel or brass rule, with a pointed end, used in typesetting.
Composing-stick.—An instrument in which types are arranged in words and lines.
Composing stick.—A tool used to arrange types into words and lines.
Corner quadrates.—A quarter section of a hollow square or rectangle.
Corner quadrates.—A quarter section of a hollow square or rectangle.
Correct.—A compositor is said to correct when he amends the faults marked in a proof.
Correct.—A typesetter is considered to correct when they fix the errors noted in a proof.
Corrections.—The alterations or errors marked in a proof.
Corrections.—The changes or mistakes noted in a proof.
Cut-in letter.—A type of large size adjusted at the beginning of the first paragraph of a chapter.
Cut-in letter.—A type of large letter used at the beginning of the first paragraph of a chapter.
Cut-in note.—A note justified into the side of a page.
Cut-in note.—A note aligned to the side of a page.
Dead horse.—Matter charged and paid for before it is set.
Dead horse.—Money that has already been spent and is not recoverable before the task is done.
Dele, ₰.—A proof-reader’s mark, signifying to take out.
Dele, ₰.—A proofreader's mark indicating to remove.
Descending letters.—Letters that go down into the lower shoulder of the body; as, g, j, p, q, y.
Descending letters.—Letters that extend down into the lower part of the body; for example, g, j, p, q, y.
Devil.—The errand-boy of a printing-office.
Devil.—The intern at a printing office.
Dished.—A defect in electrotyped plates, the centre of a letter being lower than its edges.
Dished.—A flaw in electrotyped plates, where the center of a letter is lower than its edges.
Distributing.—Returning types to their various boxes after having been printed from. Spreading ink evenly over the surface of a roller.
Distributing.—Putting types back in their correct boxes after printing. Spreading ink evenly on the roller’s surface.
Double.—Among compositors, repetition of words; among pressmen, a sheet that is twice pulled and mackled.
Double.—For typesetters, it's when words are repeated; for pressmen, it's a sheet that has been printed twice and is smudged.
Dressing a chase or form.—Fitting the pages and chase with furniture and quoins.
Dressing a chase or form.—Arranging the pages and chase with furniture and quoins.
Drive out.—To space widely.
Spread out.—To space widely.
Duck’s-bill.—A tongue cut in a piece of stout paper and pasted on the tympan at the bottom of the tympan-sheet, to support the paper when laid on the tympan.
Duck’s-bill.—A piece of strong paper with a tongue cut out and glued to the bottom of the tympan-sheet to help support the paper when it's placed on the tympan.
Duodecimo, or 12mo.—Twelve pages to a form.
12mo—Twelve pages per sheet.
Em.—The square of the body of a type.
Em.—The square of the body of a type.
En.—Half the dimensions of the preceding.
En.—Half the size of the previous one.
Even page.—The 2d, 4th, 6th, or any even-numbered page of a book.
Even page.—The 2nd, 4th, 6th, or any even-numbered page of a book.
Fat.—Poetry and leaded matter.
Fat.—Poetry and heavy material.
Fat face, or Fat letter.—Broad stemmed letter.
Fat face, or Fat letter.—Letter with a broad stem.
Father of the chapel.—President or chairman of a composing-room or press-room chosen by the hands.
Father of the chapel.—President or chairperson of a composing room or press room elected by the members.
Feed guide.—An implement attached to a press to aid in correct feeding.
Feed guide.—A device attached to a press to help with proper feeding.
Feeding.—Supplying the press with sheets.
Feeding.—Supplying the printer with sheets.
First form.—The form first printed, which generally contains the first page of a sheet.
First form.—The initial version that was printed, which usually includes the first page of a sheet.
Fly.—The person or apparatus that takes off the sheets from the press.
Fly.—The individual or device that removes the sheets from the press.
Folio.—Two pages to a form.
Folio.—Two pages per form.
Foot-sticks.—Sloping pieces of furniture placed at the bottom of pages, between[340] which and the chase the quoins are driven to fasten the pages.
Foot-sticks.—Sloping pieces of furniture placed at the bottom of pages, between[340] which and the chase the quoins are driven to secure the pages.
Form.—The pages when imposed in a chase.
Form.—The pages when arranged in a chase.
Foul proof.—A proof with many faults marked in it.
Faulty proof.—A proof with many mistakes highlighted in it.
Fount.—A complete assortment of type, of the same nick, body, and face, put up by type-founders in accordance with an ascertained ratio.
Fount.—A full set of type, with the same style, size, and design, created by type founders based on a determined ratio.
Fountain.—Reservoir for ink, attached to printing-presses.
Fountain.—Ink reservoir connected to printing presses.
Friar.—A light patch in a printed sheet, caused by defective rolling.
Friar.—A light spot on a printed page, caused by uneven printing.
Frisket.—An iron frame fastened by a hinge to the upper part of the tympan, to hold the sheet of paper fast as it goes in and comes from the press.
Frisket.—An iron frame attached by a hinge to the top part of the tympan, used to secure the sheet of paper firmly as it enters and exits the press.
Fudge.—To contrive without proper materials.
Fudge.—To create without proper materials.
Full press.—When two men work at the press with hand rollers.
Full press.—When two guys operate the press using hand rollers.
Furniture.—Strips of wood or metal placed around and between pages to make the proper margin.
Furniture.—Wood or metal strips placed around and between pages to create the right margin.
Galley.—A wooden or brass flat oblong tray, with side and head ledges, for holding type when composed.
Galley.—A flat, rectangular tray made of wood or brass, with side and head ledges, used to hold type when set.
Galley-slaves.—An ancient term of derision applied by pressmen to compositors.
Galley-slaves.—An old insult used by printers to refer to typesetters.
Gauge.—A strip of reglet with a notch in it, passed with the make-up, to denote the length of the pages.
Gauge.—A strip of material with a notch in it, used alongside the setup to indicate the length of the pages.
Gauge-pin.—An instrument to aid in feeding job presses correctly.
Gauge-pin.—A tool used to help properly feed job presses.
Get in.—To set close.
Get in.—To set close.
Good colour.—Sheets printed neither too black nor too light.
Good color.—Sheets printed neither too dark nor too light.
Guide.—A strip of metal frequently used to denote the last line of copy set.
Guide.—A piece of metal often used to mark the final line of text that has been typeset.
Gutter-sticks.—Furniture used in imposition to separate the pages.
Gutter-sticks.—Tools used in layout to separate the pages.
Half press.—When but one person works at the press.
Half press.—When only one person works at the press.
Half-title.—The title of a book inserted in the upper portion of the first page of matter.
Half-title.—The title of a book placed at the top of the first page of content.
Hanging indention.—Where successive lines are set-in an em or more beyond the first line.
Hanging indentation.—Where subsequent lines are indented an em or more beyond the first line.
Head-sticks.—Furniture put at the head of pages in imposition, to make margin.
Head-sticks.—Furniture placed at the top of pages in imposition to create margin.
Hell.—The receptacle for broken or battered letters; the old-metal box; the shoe.
Hell.—The place for damaged or battered letters; the old metal box; the shoe.
High-line.—Term applied to a type that ranges above the rest in a line.
High-line.—A term used to describe something that stands out above the others in a line.
High (or low) to paper.—Applied to a type cast higher or lower than the rest of the fount.
High (or low) to paper.—Refers to a typeface that is cast higher or lower than the other characters in the font.
Hollow quadrates.—Metal quadrates mortised for the insertion of types, &c.
Hollow squares.—Metal squares carved to hold types, etc.
Horse.—The stage on the bank on which pressmen set the heap of paper.
Horse.—The platform by the riverbank where printers stack the pile of paper.
Horsing.—Charging for work before it is executed.
Horsing.—Collecting payment for work before it has been completed.
Imposing.—Arranging and locking up a form of type in a chase.
Imposing.—Setting up and securing a typeface in a chase.
Imposing-stone.—The stone on which compositors impose and correct forms.
Imposing-stone.—The stone that typesetters use to arrange and proofread printing forms.
Imprint.—The name of the printer or of the publisher appended to jobs or title-pages.
Imprint.—The name of the printer or publisher added to jobs or title pages.
Inferior letters.—Small letters cast near the bottom of the line.
Inferior letters.—Small letters placed near the bottom of the line.
Inset.—Same as offcut.
Inset.—Same as scrap.
Jeff.—To throw for the first choice with em quadrates instead of dice.
Jeff.—To roll for the first pick with squares instead of dice.
Justifying.—Spacing out lines accurately.
Justifying.—Proper line spacing.
Keep in.—To crowd in by thin spacing.
Keep in.—To pack together with limited spacing.
Keep out.—To drive out or expand matter by wide spacing.
Keep out.—To push away or stretch out matter by creating large gaps.
Kerned letter.—Type of which a part of the face hangs over the body.
Kerned letter.—A type of letter where part of the design extends beyond the main body.
Laying cases.—Filling cases with a fount of new type.
Laying cases.—Filling cases with a supply of new type.
Laying pages.—Placing pages of type on the stone in a proper order for imposition.
Laying pages.—Arranging pages of type on the stone in the correct order for printing.
Leaders.—Dots or hyphens placed at intervals of one or more ems in length, to guide the eye across the line to the folio in tables of contents, &c.
Leaders.—Dots or dashes placed at intervals of one or more ems in length, to guide the eye across the line to the page number in tables of contents, etc.
Leads.—Thin strips of metal cast of various thicknesses, quadrate-high, to separate lines of type.
Leads.—Narrow strips of metal made in different thicknesses, squared in height, used to separate lines of type.
Lean.—Close and solid matter.
Lean.—Compact and dense material.
Lean face.—Light, thin type.
Thin face.—Light, slim type.
Letter hangs.—When the page is out of square.
Letter hangs.—When the page is misaligned.
Letter-press printing.—Printing from types.
Letterpress printing.—Printing from type.
Ligatures.—Two or more letters cast on the same shank, as ff, fi, fl, ffi, ffl, æ, œ.
Ligatures.—Two or more letters combined on the same base, such as ff, fi, fl, ffi, ffl, æ, œ.
Line formers.—Brass rule bent in various shapes to aid in making curved lines of type.
Line formers.—Brass rules shaped into different designs to help create curved lines of type.
Locking up.—Tightening up a form by means of quoins.
Locking up.—Tightening a form using quoins.
Logotypes.—The same as ligatures.
Logotypes. —Same as ligatures.
Long cross.—The bar that divides a chase the longest way.
Long cross.—The bar that splits a chase the longest distance.
Long pull.—When the bar is brought close to the cheek of a press.
Long pull.—When the bar is brought close to the side of the face during a press.
Low case.—When the compositor has set almost all the letters out of his case.
Low case.—When the typesetter has placed nearly all the letters out of their case.
Lower case.—The case containing the small letters of the alphabet, figures, points, &c.
Lower case.—The box holding the small letters of the alphabet, numbers, punctuation, etc.
Low-line.—Applied to a type that ranges lower than the rest in a line.
Low-line.—Used to describe a type that is positioned lower than the others in a line.
Mackle.—When part of the impression appears double.
Mackle.—When part of the image looks duplicated.
Make-up.—To arrange the lines of matter into pages.
Make-up.—To organize the content into pages.
Make-up rule.—A steel rule with a projection on the top, for making up matter.
Make-up rule.—A steel ruler with an extension on the top, used for preparing material.
Making margin.—In imposition, arranging the space between the pages of a form so that the margin will be properly proportioned.
Making margin.—In imposition, arranging the space between the pages of a layout so that the margin is properly proportioned.
Making ready.—Preparing a form on the press for printing.
Getting ready.—Setting up a form on the press for printing.
Mallet.—A wooden hammer.
Mallet.—A wooden hammer.
Matter.—Composed type.
Type.—Set type.
Measure.—The width of a page.
Measure.—The page width.
Monk.—A black spot in a printed sheet, owing to the ink not being properly distributed.
Monk.—A black mark on a printed page, due to the ink not being spread evenly.
Naked form.—A form without furniture.
Naked form.—A form without furniture.
Nicks.—Hollows cast in the front of the lower part of the shank of a type, to show the compositor how to place it in his stick.
Nicks.—Notches created in the front of the lower part of a type's shank, used to guide the compositor on how to position it in their stick.
Octavo, or 8vo.—Eight pages to a form.
Octavo, or 8vo—Eight pages per sheet.
Octodecimo, or 18mo.—Eighteen pages to a form.
Octodecimo, or 18mo.—Eighteen pages in a single sheet.
Odd page or folio.—The 1st, 3d, and all uneven-numbered pages.
Odd page or folio.—The 1st, 3rd, and all uneven-numbered pages.
Off.—Signifies that the pressman has worked off the form.
Off.—Indicates that the press operator has finished working on the form.
Offcut.—A portion of a sheet that is cut off before folding.
Offcut.—A piece of a sheet that is cut off before being folded.
Off its feet.—When matter does not stand upright.
Off its feet.—When something isn't standing up properly.
Open matter.—Matter widely leaded or containing numerous break-lines.
Open matter.—Matter that is heavily spaced or has many breaks in the text.
Out.—An omission marked in a proof by the reader.
Out.—A missing part indicated in a proof by the reader.
Out of register.—When the pages do not back each other.
Out of register.—When the pages don't line up with each other.
Overlay.—A scrap of paper pasted on the tympan-sheet to bring up the impression.
Overlay.—A piece of paper glued onto the tympan sheet to enhance the impression.
Overrunning.—Carrying words backward or forward in correcting.
Overrunning.—Moving words back or forth to make corrections.
Page-cord.—Twine used for tying up pages.
Page-cord.—String used for binding pages together.
Passing the make-up.—Passing to the next hand in order the lines remaining (if any) after a compositor has made up his matter, together with the gauge and proper folio.
Passing the make-up.—Handing over the lines that are left (if any) after a typesetter has finalized his work, along with the gauge and the correct folio.
Peel.—A broad, thin board with a long handle.
Peel.—A wide, flat board with a long handle.
Perfecting.—Printing the second form of a sheet.
Perfecting.—Printing the second version of a sheet.
Perforating rule.—Brass or steel rule, somewhat higher than type.
Perforating rule.—Brass or steel rule, slightly taller than type.
Pi.—Type promiscuously intermingled.
Pi.—Types mixed randomly.
Pick.—A particle of ink or paper imbedded in the hollow of a letter, filling up its face and occasioning a spot.
Pick.—A small piece of ink or paper stuck inside the hollow part of a letter, filling its face and causing a mark.
Pigs.—An ancient nickname given in derision by compositors to pressmen. The press-room was called a pigsty.
Pigs.—An old nickname used mockingly by typesetters for printers. The print shop was referred to as a pigsty.
Planer.—A smooth block of wood used for levelling the surface of pages of type when imposed.
Planer.—A smooth piece of wood used for leveling the surface of typeset pages when arranged.
Planing down.—To bring down types evenly on their feet, by laying a planer on the page and striking it firmly with a mallet.
Planing down.—To level types evenly on their feet by placing a planer on the page and striking it firmly with a mallet.
Platen.—The part of a printing-press which, acted upon by the lever, gives the impression to a sheet.
Platen.—The component of a printing press that, when operated by the lever, impresses an image onto a sheet.
Point-holes.—Fine holes made by the points to register the second impression by
Point-holes.—Small holes created by the points to mark the second impression by
Points.—Two thin pieces of steel with a point at one end, adjusted to the tympan with screws, to make register.
Points.—Two slender pieces of steel with a point on one end, secured to the tympan with screws to ensure alignment.
Quadrate.—A low square blank type, used to indent the first line of a paragraph, and to fill up blank spaces.
Quadrate.—A low square blank type, used to indent the first line of a paragraph and to fill in empty spaces.
Quarters.—Octavos and twelves are said to be imposed in quarters, not from their equal divisions, but because they are imposed and locked up in four parts.
Quarters.—Octavos and twelves are said to be arranged in quarters, not due to their equal divisions, but because they are organized and secured in four sections.
Quarto, or 4to.—Four pages to a form.
Quarto, or 4to.—Four pages per sheet.
Quire.—Twenty-four sheets of paper.
Quire.—24 sheets of paper.
Quoins.—Small wedges for locking up a form.
Quoins.—Small wedges used to secure a form.
Quotation furniture.—Quotations cast of various sizes in length and width, used for blanking and as furniture.
Quotation furniture.—Quotations of different sizes in length and width, used for blanking and as furniture.
Quotations.—Large hollowed quadrates.
Quotes.—Large hollow squares.
Rack.—Receptacle for cases.
Rack.—Storage for cases.
Ratchet.—An instrument for turning the screws of stereotype blocks.
Ratchet.—A tool for turning the screws of stereotype blocks.
Ratting.—Working at less than the established prices.
Ratting.—Getting paid less than the standard rates.
Ream.—Twenty quires of paper.
Ream.—Twenty packets of paper.
Recto.—Right-hand page.
Recto.—Right page.
References.—Letters or characters serving to direct the reader’s attention to notes at the foot of a page.
References.—Letters or symbols that guide the reader’s attention to notes at the bottom of a page.
Register.—To cause the pages in a sheet to print precisely back to back.
Register.—To make sure the pages in a sheet print exactly back to back.
Register sheet.—The sheet used to make register.
Register sheet.—The sheet used for registering.
Reglet.—Thin furniture, of an equal thickness all its length. It is made to match the depth of type.
Reglet.—A narrow piece of furniture that is the same thickness along its entire length. It is designed to fit the depth of type.
Reiteration.—The form printed on the second side.
Reiteration.—The form printed on the back side.
Revise.—The last proof of a form before working it off.
Revise.—The final version of a form before finalizing it.
Riding.—One colour falling on another. Type at the end of a line catching against a lead.
Riding.—One color landing on top of another. Text at the end of a line getting caught on a lead.
Rise.—A form is said to rise when, in raising it from the correcting stone, no letters drop out.
Rise.—A form is said to rise when, in lifting it from the correcting stone, no letters fall out.
Roller.—A wooden cylinder covered with composition, which, set in an iron frame, revolves upon a rod, and is used for inking type.
Roller.—A wooden cylinder coated with a mixture that, placed in an iron frame, spins on a rod and is used for inking type.
Rounce.—The handle for running in and out the carriage of a hand-press.
Rounce.—The handle used for moving in and out of the carriage of a hand-press.
Round pick.—A dot in a letter in a stereotype plate caused by an air-bubble.
Round pick.—A dot in a letter in a printing plate caused by an air bubble.
Running title.—The title of the book or subject placed at the top of the pages.
Running title.—The title of the book or topic located at the top of the pages.
Runs on sorts.— Requiring an inordinate proportion of particular letters.
Runs on sorts.— Needing an excessive amount of specific letters.
Saw-block.—A box similar to a carpenter’s mitre-block, to guide in cutting furniture, &c.
Saw-block.—A box similar to a carpenter’s mitre-block, used to guide cutting furniture, etc.
Schedule.—A sheet of paper passed with the make-up, containing folios, on which the compositor marks his name opposite to the pages set by him.
Schedule.—A sheet of paper that comes with the layout, listing the folios, where the typesetter writes his name next to the pages he has worked on.
Set off.—When sheets that are newly worked off soil those that come in contact with them, they are said to set off.
Set off.—When freshly cleaned sheets soil those that touch them, they are said to set off.
Shank.—The metal body upon which the face of a letter stands.
Shank.—The metal part that supports the face of a letter.
Sheep’s-foot.—An iron hammer with a claw-end.
Sheep’s-foot.—A metal hammer with a claw end.
Sheetwise.—When the pages of a sheet are imposed in two forms, which are backed in printing.
Sheetwise.—When the pages of a sheet are arranged in two formats, which are printed on the back.
Shooting-stick.—A wedge-shaped instrument for locking up a form.
Shooting-stick.—A wedge-shaped tool for securing a form.
Short cross.—The short bar which, crossing the long bar, divides the chase into quarters.
Short cross.—The short bar that crosses the long bar, dividing the chase into four sections.
Shoulder.—The surface of the shank of a type not covered by the letter.
Shoulder.—The surface of the shank of a type not included in the letter.
Side sorts.—Types in the side and upper boxes of a case, consisting of letters not frequently used.
Side sorts.—Types in the side and top boxes of a case, made up of letters that aren't used very often.
Side-sticks.—Sloping furniture on the outside of the pages next to the chase, where the quoins are inserted.
Side-sticks.—Sloping furniture on the outside of the pages next to the chase, where the quoins are placed.
Signature.—A letter or a figure used at the bottom of the first page of a sheet, to direct the binder in placing the sheets in a volume.
Signature.—A letter or a symbol used at the bottom of the first page of a sheet to instruct the binder on how to arrange the sheets in a book.
Slice galley.—A galley with an upper movable bottom, called a slice, used for pages and jobs too large to be lifted by the fingers.
Slice galley.—A galley with an upper movable bottom, known as a slice, used for pages and jobs that are too large to be lifted by hand.
Slug.—A thick lead. Sometimes with a word or figure on top, used to denote the ownership of matter on galleys.
Slug.—A heavy piece of metal. Sometimes embossed with a word or symbol on top, used to indicate the ownership of material in printing typesetting.
Slur.—A blurred impression in a printed sheet.
Slur.—A smudged image on a printed page.
Solid pick.—A letter in a stereotype plate filled up with metal, resulting from an imperfect mould.
Good choice.—A letter in a stereotype plate filled with metal, created from an imperfect mold.
Sorts.—The letters in the several case-boxes are separately called sorts, in printers’ and founders’ language.
Sorts.—In the language of printers and founders, the letters in the various case boxes are referred to as sorts.
Space-rules.—Fine lines, cast type-high, and of even ems in length, for table and algebraical work.
Space-rules.—Thin lines, set at the same height as the type, and of consistent em lengths, for tables and math work.
Spaces.—Low blank types used to separate words.
Spaces.—Empty blank spaces used to separate words.
Squabble.—A page or form is squabbled when the letters are twisted out of a square position.
Squabble.—A page or form is in a squabble when the letters are twisted out of alignment.
Stand.—The frame on which the cases are placed.
Stand.—The structure on which the cases are set.
Stem.—The vertical strokes of a type.
Stem.—The upright parts of a typeface.
Stereotype printing.—Printing from stereotyped plates.
Stereotype printing.—Printing from stereotype plates.
Stet.—Written opposite to a word in a proof, to signify that the word erroneously struck out shall remain.
Stet.—Written next to a word in a proof to indicate that the word that was mistakenly deleted should stay.
Sub.—A compositor occasionally employed on a daily paper, to fill the place of an absentee.
Sub.—A freelance typesetter occasionally hired by a daily newspaper to take the place of someone who is absent.
Superior letters.—Letters of a small face, cast by the founder near the top of the line.
Superior letters.—Letters with a small design, created by the founder near the top of the line.
Table-work.—Matter consisting partly of rules and figures.
Table-work.—Material that includes some rules and figures.
Take, or Taking.—A given portion of copy.
Take, or Taking.—A specific section of text.
Token.—Two hundred and fifty sheets.
Token.—Two hundred fifty sheets.
Turn for a letter.—When a sort runs short, a letter of the same thickness is substituted, placed bottom upward.
Turn for a letter.—When one type runs low, a letter of the same thickness is used instead, positioned bottom side up.
Tympan.—A frame covered with parchment or muslin and attached to the press-bed to lay the sheet on before printing.
Tympan.—A frame covered with parchment or muslin that is attached to the press bed to place the sheet on before printing.
Underlay.—A piece of paper or card placed under types or cuts to improve the impression.
Underlay.—A piece of paper or card placed beneath types or images to enhance the impression.
Uppercase.—The case containing capital and small capital letters, fractions, &c.
Uppercase.—The box holding capital and small capital letters, fractions, etc.
Verso.—Left-hand page.
Verso.—Left page.
Wayz-goose.—A term given in England to the annual dinner customary among printers there during the summer months.
Wayz-goose.—A term used in England for the annual dinner that printers typically have during the summer months.
White line.—A line of quadrates.
White line.—A line of squares.
White page.—A blank page.
White page.—A blank page.
White paper.—Until the second side of a sheet is printed, pressmen call the heap white paper.
White paper.—Until the second side of a sheet is printed, printers refer to the stack as white paper.
Work and turn.—When a sheet is printed half-sheetwise, the paper must be turned and worked on the second side.
Work and turn.—When a sheet is printed on one side, the paper has to be flipped and printed on the other side.
Working in pocket.—When the hands share equally their earnings on a work.
Working in pocket.—When the hands equally share their earnings from a job.

PROOF PRESS.
Proof printing.

ABBREVIATIONS.
A.—Acting.
A.—Performing.
a.—are, (of the French metric system.)
a.—are, (of the French metric system.)
A. or Ans.—Answer.
A. or Ans.—Response.
A. A. G.—Assistant Adjutant-General.
A. A. G.—Assistant Adjutant General.
A. A. P. S.—American Association for the Promotion of Science.
A. A. P. S.—American Association for the Promotion of Science.
A. A. S.—Academiæ Americanæ Socius, Fellow of the American Academy (of Arts and Sciences).
A. A. S.—Academiæ Americanæ Socius, Fellow of the American Academy of Arts and Sciences.
A. A. S. S.—Americanæ Antiquarianæ Societatis Socius, Member of the American Antiquarian Society.
A. A. S. S.—Americanæ Antiquarianæ Societatis Socius, Member of the American Antiquarian Society.
A. B.—Artium Baccalaureus, Bachelor of Arts.
A. B.—Artium Baccalaureus, Bachelor of Arts.
A. B. C. F. M.—American Board of Commissioners for Foreign Missions.
A. B. C. F. M.—American Board of Commissioners for Foreign Missions.
Abp.—Archbishop.
Abp.—Archbishop.
Abr.—Abridgment.
Abr.—Abridgment.
A. C.—Ante Christum, before the birth of Christ.
A. C.—Ante Christum, before the birth of Christ.
A. C.—Archchancellor.
A. C.—Chancellor.
Acct.—Account.
Acct.—Account.
A. C. S.—American Colonization Society.
A. C. S.—American Colonization Society.
A. D.—Anno Domini, in the year of the Lord.
A. D.—Anno Domini, in the year of our Lord.
A. D. C.—Aide-de-camp.
A. D. C.—Assistant to the commander.
Adj.—Adjective.
Adj.—Adjective.
Adjt.—Adjutant.
Adjt.—Adjutant.
Adjt. Gen.—Adjutant-General.
Adjt. Gen.—Adjutant General.
Ad lib.—Ad libitum, at pleasure.
Ad lib.
Adm.—Admiral; Admiralty.
Adm.—Admiral; Naval Command.
Adm. Co.—Admiralty Court.
Adm. Co.—Admiralty Court.
Admr.—Administrator.
Admr.—Admin.
Admx.—Administratrix.
Admx.—Admin.
Ad v.—Ad valorem, at (or on) the value.
Ad v.—Ad valorem, based on the value.
Adv.—Adverb.
Adv.—Adverb.
Æt.—Ætatis, of age; aged.
Aged.
A. F. B. S.—American and Foreign Bible Society.
A. F. B. S.—American and Foreign Bible Society.
A. F. & A. M.—Ancient Free and Accepted Masons.
A.F. & A.A.M.—Ancient Free and Accepted Masons.
A. G.—Adjutant-General.
A. G.—Adjunct-General.
Ag.—Argentum, silver.
Ag.—Silver
Agr.—Agriculture.
Agriculture.
A. G. S. S.—American Geographical and Statistical Society.
A. G. S. S.—American Geographical and Statistical Society.
Agt.—Agent.
Agt.—Agent.
A. H.—Anno Hegiræ, in the year of the Hegira.
A. H.—Anno Hegiræ, in the year of the Hegira.
A. H. M. S.—American Home Missionary Society.
A. H. M. S.—American Home Missionary Society.
Ala.—Alabama.
Ala. — Alabama.
Ald.—Alderman.
Alderman
Alex.—Alexander.
Alex.—Alexander.
Alg.—Algebra.
Alg.—Algebra.
Alt.—Altitude.
Alt.—Altitude.
A. M.—Anno mundi, in the year of the world.
A. M.—Anno mundi, in the year of the world.
A. M.—Ante meridiem, before noon; morning.
A. M.—Ante meridiem, before noon; morning.
A. M.—Artium Magister, Master of Arts.
A. M.—Artium Magister, Master of Arts.
Amb.—Ambassador.
Ambassador
Amer.—American.
Amer. — American.
AMM.—Amalgama, amalgamation.
AMM.—Amalgam, amalgamation.
Amt.—Amount.
Amt.—Amount.
An.—Anno, in the year.
In the year.
An. A. C.—Anno ante Christum, in the year before Christ.
An. A. C.—Anno ante Christum, in the year before Christ.
Anat.—Anatomy.
Anat.—Anatomy.
Anc.—Ancient; anciently.
Anc.—Ancient; previously.
And.—Andrew.
And.—Andrew.
Ang.-Sax.—Anglo-Saxon.
Anglo-Saxon.
Anon.—Anonymous.
Anon.—Anonymous.
Anth.—Anthony.
Anth.—Tony.
Aor. or aor.—Aorist.
Aor. or aor.—Aorist.
A. O. S. S.—Americanæ Orientalis Societatis Socius, Member of the American Oriental Society.
A. O. S. S.—Americanæ Orientalis Societatis Socius, Member of the American Oriental Society.
Ap.—Apostle; Appius.
Ap.—Apostle; Appius.
Ap.—Apud, in the writings of; as quoted by.
Ap.—Apud, in the writings of; as quoted by.
A. P. G. or Ast. P. G.—Professor of Astronomy in Gresham College.
A. P. G. or Ast. P. G.—Professor of Astronomy at Gresham College.
Apo.—Apogee.
Apo — Apogee.
Apoc.—Apocalypse.
Apoc.—End times.
App.—Appendix.
App.—Appendix.
Apr.—April.
April
A. Q. M. G.—Assistant Quartermaster-General.
A.Q.M.G.—Assistant Quartermaster General.
A. R.—Anna Regina, Queen Anne.
A. R.—Anna Regina, Queen Anne.
A. R.—Anno regni, year of the reign.
A. R.—Anno regni, year of the reign.
A. R. A.—Associate of the Royal Academy.
A. R. A.—Associate of the Royal Academy.
Arch.—Archibald.
Arch.—Archie.
Arg.—Argumento, by an argument drawn from such a law.
Arg.—Argumento, based on an argument derived from that law.
Arith.—Arithmetic.
Math.
Ark.—Arkansas.
Ark.—Arkansas.
A. R. R.—Anno regni regis, in the year of the reign of the king.
A. R. R.—Anno regni regis, in the year of the king's reign.
A. R. S. S.—Antiquariorum Regiæ Societatis Socius, Fellow of the Royal Society of Antiquaries.
A. R. S. S.—Antiquariorum Regiæ Societatis Socius, Fellow of the Royal Society of Antiquaries.
Art.—Article.
Art. — Article.
A. S. or Assist. Sec.—Assistant Secretary.
A. S. or Assist. Sec.—Assistant Secretary.
A. S. A.—American Statistical Association.
A.S.A.—American Statistical Association.
A. S. S. U.—American Sunday-School Union.
A. S. S. U.—American Sunday-School Union.
Astrol.—Astrology.
Astrol.—Astrology.
Astron.—Astronomy.
Astron.—Astronomy.
A. T.—Archtreasurer.
A. T.—Arch Treasurer.
A. T. S.—American Tract Society.
A. T. S.—American Tract Society.
Ats.—At suit of.
Ats.—At the request of.
Atty.—Attorney.
Atty.—Lawyer.
Atty.-Gen.—Attorney-General.
Atty. Gen.—Attorney General.
A. U. A.—American Unitarian Association.
A. U. A.—American Unitarian Association.
Aub. Theol. Sem.—Auburn Theological Seminary.
Aub. Theol. Sem.—Auburn Theological Seminary.
A. U. C.—Anno urbis conditæ, or, ab urbe conditâ, in the year from the building of the city (Rome).
A. U. C.—Anno urbis conditæ, or, ab urbe conditâ, in the year since the founding of the city (Rome).
Aug.—August.
Aug.—August.
Aur.—Aurum, gold.
Gold.
Auth. Ver.—Authorized Version, (of the Bible.)
Auth. Ver.—Authorized Version, (of the Bible.)
Av.—Average; Avenue.
Av.—Avg.; Ave.
Avoir.—Avoirdupois.
Avoir.—Weight measurement.
A. Y. M.—Ancient York Masons.
A. Y. M.—Ancient York Masons.
b.—born; book.
b.—born; book.
B. A.—Bachelor of Arts.
B.A.—Bachelor of Arts.
Bal.—Balance.
Bal.—Balance.
Balt.—Baltimore.
Balto.—Baltimore.
Bar.—Baruch.
Bar.—Baruch.
Bart. or Bt.—Baronet.
Bart. or Bt.—Baronet.
bbl.—Barrel.
bbl.—Barrel.
B. C.—Before Christ.
B.C.—Before Christ.
B. C. L.—Bachelor of Civil Law.
B. C. L.—Bachelor of Civil Law.
B. D.—Baccalaureus Divinitatis, Bachelor of Divinity.
B. D.—Baccalaureus Divinitatis, Bachelor of Divinity.
Bds. or bds.—Boards (bound in).
Bds. or bds.—Bound volumes.
Benj.—Benjamin.
Benj. — Benjamin.
Bk.—Book.
Bk.—Book.
B. LL.—Baccalaureus Legum, Bachelor of Laws.
B. LL.—Baccalaureus Legum, Bachelor of Laws.
B. M.—Baccalaureus Medicinæ, Bachelor of Medicine.
B. M.—Baccalaureus Medicinæ, Bachelor of Medicine.
Bost.—Boston.
Boston.
Bot.—Botany.
Bot. — Botany.
Bp.—Bishop.
Bp.—Bishop.
B. R.—Banco Regis or Reginæ, the King’s or Queen’s Bench.
B. R.—Banco Regis or Reginæ, the King’s or Queen’s Bench.
Br.—Brig.
Brig.
Brig.—Brigade; Brigadier.
Brig.—Brigade; Brigadier.
Brig.-Gen.—Brigadier-General.
Brig. Gen. — Brigadier General.
Brit. Mus.—British Museum.
Brit. Mus.—British Museum.
Bro.—Brother.
Bro.
Br. Univ.—Brown University.
Br. Univ.—Brown University.
B. S.—Bachelor in the Sciences.
B.S.—Bachelor of Science.
bu.—bushel.
bu.—bushel.
B. V.—Beata Virgo, Blessed Virgin.
B. V.—Blessed Virgin.
B. V.—Bene vale, farewell.
B. V.—Bene vale, goodbye.
ca.—centiare, (metric system.)
ca.—centi, (metric system.)
C., ch. or chap.—Chapter.
C., ch. or chap.—Chapter.
C. or cent.—Centum, a hundred.
C. or cent.—Centum, one hundred.
Cæt. par.—Cæteris paribus, other things being equal.
Cæt. par.—Cæteris paribus, with everything else being equal.
Cal.—California; Calends.
Cal.—California; Calendar.
Can.—Canon.
Can. — Canon.
Cant.—Canticles.
Cant. — Songs.
Cap. or c.—Caput, capitulum, chapter.
Cap. or c.—Caput, capitulum, chapter.
Caps.—Capitals.
Caps.—Uppercase letters.
Capt.—Captain.
Capt.—Captain.
Capt.-Gen.—Captain-General.
Captain-General.
Cash.—Cashier.
Cash. — Cashier.
Ca. resp.—Capias ad respondendum, a legal writ.
Ca. resp.—Capias ad respondendum, a legal order.
Ca. sa.—Capias ad satisfaciendum, a legal writ.
Ca. sa.—Capias ad satisfaciendum, a legal order.
Cath.—Catherine.
Catherine.
C. B.—Communis Bancus, Common Bench.
C. B.—Communis Bancus, Common Bench.
C. B.—Companion of the Bath.
C. B.—Companion of the Bath.
C. C.—Caius College; Account Current.
C. C.—Caius College; Current Account.
C. C. C.—Corpus Christi College.
C.C.C.—Corpus Christi College.
C. C. P.—Court of Common Pleas.
C. C. P.—Court of Common Pleas.
C. E.—Canada East.
C. E.—Canada East.
C. E.—Civil Engineer.
C.E.—Civil Engineer.
Cel. or Celt.—Celtic.
Cel. or Celt.—Celtic.
Cf. or cf.—Confer, compare.
Cf. or cf.—Confer, compare.
cg.—centigram, (metric system.)
cg.—centigram (metric system)
C. G.—Commissary-General; Consul-General.
C. G.—Chief of Commissary; Consul-General.
C. H.—Court-House.
C.H.—Court House.
Ch.—Church; Chapter; Charles.
Ch.—Church; Chapter; Charles.
Chanc.—Chancellor.
Chancellor
Chap.—Chapter.
Chap.—Ch.
Chas.—Charles.
Chas.—Charles.
Chem.—Chemistry.
Chemistry
Chr.—Christopher.
Chr.—Chris.
Chron.—Chronicles.
Chronicles
Cin.—Cincinnati.
Cincy.
C. J.—Chief-Justice.
C. J.—Chief Justice.
cl.—centiliter, (metric system.)
cl.—centiliter, (metric system)
Clk.—Clerk.
Clk.—Clerk.
cm.—centimeter, (metric system.)
cm.—centimeter, (metric system).
C. M.—Common Metre.
C. M.—Common Meter.
C. M. G.—Companion of the Order of St. Michael and St. George.
C. M. G.—Companion of the Order of St. Michael and St. George.
Co.—Company; County.
Co.—Company; County.
C. O. D.—Cash (or collect) on delivery.
C. O. D.—Cash (or collect) on delivery.
Col.—Colorado; Colonel; Colossians.
Col.—CO; Colonel; Colossians.
Coll.—Collector; Colloquial; College; Collection.
Coll.—Collector; Colloquial; College; Collection.
Com.—Commerce; Committee; Commentary; Commissioner; Commodore.
Com.—Commerce; Committee; Commentary; Commissioner; Commodore.
Com. Arr.—Committee of Arrangements.
Com. Arr.—Event Planning Committee.
Comdg.—Commanding.
Comdg.—Commanding Officer.
Comm.—Commentary.
Comm.—Comment.
Comp.—Compare; Compound.
Comp.—Compare; Compound.
Com. Ver.—Common Version (of the Bible.)
Com. Ver.—Common Version (of the Bible.)
Con.—Contra, against; in opposition.
Con.—Contra, against; in opposition.
Con. Cr.—Contra credit.
Con. Cr.—Contra credit.
Conch.—Conchology.
Conch.—Shell collection.
Cong.—Congress; Congius, a gallon.
Cong.—Congress; Congius, a gallon.
Conj. or conj.—Conjunction.
Conj. or conj.—Conjunction.
Conn. or Ct.—Connecticut.
Conn. or Ct.—Connecticut.
Const.—Constable; Constitution.
Const.—Officer; Constitution.
Cont.—Contra.
Cont.—Against.
Cor.—Corinthians.
Cor.—Corinthians.
Corol.—Corollary.
Corol.—Corollary.
Cor. Sec.—Corresponding Secretary.
Cor. Sec.—Corresponding Secretary.
C. P.—Common Pleas.
C. P.—Court of Common Pleas.
C. P.—Court of Probate.
C. P.—Probate Court.
C. P. S.—Custos Privati Sigilli, Keeper of the Privy Seal.
C. P. S.—Custos Privati Sigilli, Keeper of the Privy Seal.
C. R.—Custos Rotulorum, Keeper of the Rolls.
C. R.—Custos Rotulorum, Keeper of the Rolls.
Cr.—Creditor; credit.
Cr.—Creditor; credit.
Crim. con.—Criminal conversation; adultery.
Crim. con.—Adultery.
C. S.—Court of Sessions.
C. S.—Sessions Court.
C. S.—Custos Sigilli, Keeper of the Seal.
C. S.—Custos Sigilli, Keeper of the Seal.
Ct., cts.—Cent; cents.
Ct., cts.—Cent; cents.
C. Theod.—Codice Theodosiano, in the Theodosian Code.
C. Theod.—Codex Theodosianus, in the Theodosian Code.
C. W.—Canada West.
C. W.—Western Canada.
Cwt.—Hundredweight.
Cwt.—Hundredweight.
Cyc.—Cyclopedia.
Cyc.—Encyclopedia.
d.—Denarius or denarii, penny or pence.
d.—Denarius or denarii, penny or pence.
d.—died.
d.—passed away.
D.—Five hundred.
D.—$500.
Dan.—Daniel; Danish.
Dan.—Daniel; Danish.
D. B. or Domesd. B.—Domesday-Book.
D. B. or Domesd. B.—Domesday Book.
D. C.—Da Capo, again.
D.C.—Da Capo, again.
D. C.—District of Columbia.
D.C.—Washington, D.C.
D. C. L.—Doctor of Civil Law.
D. C. L.—Doctor of Civil Law.
D. D.—Divinitatis Doctor, Doctor of Divinity.
D. D.—Divinitatis Doctor, Doctor of Divinity.
D. D. D.—Dat, dicat, dedicat, he gives, he devotes, he dedicates.
D. D. D.—Dat, dicat, dedicat, he gives, he devotes, he dedicates.
Dea.—Deacon.
Dea.—Deacon.
Dec.—December; Declination.
Dec.—December; Decline.
Deg.—Degree or degrees.
Deg.—Degree or degrees.
Del.—Delaware; Delegate.
Del.—Delaware; Rep.
Del. or del.—Delineavit, he drew it.
Del. or del.—Delineavit, he drew it.
Dem.—Democrat.
Dem.—Democrat.
Dep.—Deputy.
Dep.—Deputy.
Dept.—Department.
Dept. — Department.
Deut.—Deuteronomy.
Deut.—Deuteronomy.
D.F.—Dean of the Faculty.
D.F.—Dean of Faculty.
Dft. or deft.—Defendant.
Dft. or deft.—Defendant.
D.G.—Dei gratiâ, by the grace of God.
D.G.—Dei gratiâ, by the grace of God.
D.G.—Deo gratias, thanks to God.
D.G.—Thanks to God.
dg.—decigram, (metric system.)
dg — decigram (metric system)
Dg.—Dekagram, (metric system.)
Dg.—Dekagram (metric system)
D. H.—Dead-head.
D. H.—Free ticket.
Diam.—Diameter.
Diam.—Diameter.
Dict.—Dictator; Dictionary.
Dict.—Dictator; Dictionary.
Dim.—Diminutive.
Dim.—Small.
Disc.—Discount.
Disc.—Discount.
Diss.—Dissertation.
Diss.—Thesis.
Dist.—District.
Dist.—District.
Dist.-Atty.—District-Attorney.
Dist. Atty.—District Attorney.
dl.—deciliter, (metric system.)
dl.—deciliter, (metric system.)
Dl.—Dekaliter, (metric system.)
Dl.—Decaliter, (metric system.)
dm.—decimetre, (metric system.)
dm.—decimeter, (metric system.)
Dm.—Dekametre, (metric system.)
Dm.—Dekameter, (metric system.)
D. M.—Doctor of Music.
D.M. — Doctor of Music.
Do.—Ditto, the same.
Same.
Dols.—Dollars.
Dollars.
Dom. Ca.—Dominion of Canada.
Dom. Ca.—Dominion of Canada.
D.O.M.—Deo optimo maximo, to God, the best, the greatest.
D.O.M.—Deo optimo maximo, to God, the best, the greatest.
Doz.—Dozen.
Dozen.
D. P.—Doctor of Philosophy.
PhD—Doctor of Philosophy.
Dr.—Debtor; Doctor.
Dr. — Debtor; Dr.
D. S.—Dal segno, from the sign.
D. S.—Dal segno, from the sign.
ds.—Decistere, (metric system.)
ds.—Deci, (metric system.)
Ds.—Dekastere, (metric system.)
Ds.—Dekastere, (metric system.)
d. s. b.—Debit sans breve, charge without abatement.
d. s. b.—Debit sans breve, charge without reduction.
D. T.—Doctor Theologiæ, Doctor of Divinity.
D. T.—Doctor Theologiæ, Doctor of Divinity.
D. V.—Deo volente, God willing.
D.V.—God willing.
Dwt.—Pennyweight.
Dwt.—Pennyweight.
E.—East.
E.—East.
ea.—Each.
each
E. by S.—East by South.
E. by S.—Easterly by Southerly.
Eben.—Ebenezer.
Eben.—Ebenezer.
Eccl.—Ecclesiastes.
Ecclesiastes
Ecclus.—Ecclesiasticus.
Ecclesiasticus.
Ed.—Editor; Edition.
Ed.—Editor; Edition.
Edm.—Edmund.
Edm.—Edmund.
Edw.—Edward.
Edward.
E. E.—Errors excepted.
E. E.—All errors excepted.
e. g.—Exempli gratiâ, for example.
for example
e. g.—Ex grege, among the rest.
e. g.—Ex grege, among the others.
E. I.—East Indies or East India.
E. I.—East Indies or East India.
Eliz.—Elizabeth.
Eliz.—Liz.
E. lon.—East longitude.
E. lon.—East long.
Encyc.—Encyclopedia.
Encyc.—Encyclopedia.
E. N. E.—East-Northeast.
E. N. E.—East-Northeast.
Eng.—England; English.
Eng.—UK; English.
Ent.—Entomology.
Ent.—Entomology.
Env. Ext.—Envoy Extraordinary.
Envoy Extraordinary.
Ep.—Epistle.
Ep.—Message.
Eph.—Ephesians; Ephraim.
Eph. — Ephesians; Ephraim.
Esd.—Esdras.
Esdras
E. S. E.—East-Southeast.
E.S.E.—East-Southeast.
Esq.—Esquire.
Esq.—Attorney.
Esth.—Esther.
Esth.—Esther.
et al.—Et alii, and others.
et al.—and others.
et seq.—Et sequentia, and what follows.
et seq.—Et sequentia, and what comes next.
etc. or &c.—Et cæteri, et cæteræ, et cætera, and others; and so forth.
etc. or &c.—Et cæteri, et cæteræ, et cætera, and others; and so on.
Ex.—Example.
Ex.—Example.
Ex.—Exodus.
Ex.—Exodus.
Exc.—Excellency; exception.
Exc.—Excellency; exception.
Exch.—Exchequer.
Exch.—Treasury.
Exec. Com.—Executive Committee.
Exec. Com. – Exec Committee.
Execx.—Executrix.
Execx.—Executor.
Exr. or Exec.—Executor.
Exr. or Exec.—Executor.
Ez.—Ezra.
Ezra.
Ezek.—Ezekiel.
Ezekiel
E. & O. E.—Errors and omissions excepted.
E. & O. E.—Errors and omissions excluded.
Fahr.—Fahrenheit.
Fahr.—F°
F. A. M.—Free and Accepted Masons.
F. A. M.—Free and Accepted Masons.
Far.—Farthing.
Farthing.
F. A. S.—Fellow of the Antiquarian Society.
F. A. S.—Member of the Antiquarian Society.
fcap. or fcp.—Foolscap.
fcap. or fcp.—Foolscap.
F. D.—Fidei Defensor or Defensatrix, Defender of the Faith.
F. D.—Fidei Defensor or Defensatrix, Defender of the Faith.
Fe.—Ferrum, iron.
Fe.—Iron.
Feb.—February.
Feb.—February.
Fec.—Fecit, he did it.
Fec.—Fecit, he made it.
Fem.—Feminine.
Fem. — Female.
F. E. S.—Fellow of the Entomological Society; of the Ethnological Society.
F. E. S.—Fellow of the Entomological Society; of the Ethnological Society.
Ff.—The Pandects.
Ff.—The Digest.
F. G. S.—Fellow of the Geological Society.
F. G. S.—Fellow of the Geological Society.
F. H. S.—Fellow of the Horticultural Society.
F. H. S.—Fellow of the Horticultural Society.
Fi. fa.—Fieri facias, cause it to be done.
Fi. fa.—Fieri facias, make it happen.
Fid. Def.—Defender of the Faith.
Fid. Def.—Defender of Faith.
Fig.—Figure.
Fig. — Figure.
Fin. Sec.—Financial Secretary.
Fin. Sec.—Finance Secretary.
Fir.—Firkin.
Fir.—Firkin.
Fla.—Florida.
Fla. - Florida.
F. L. S.—Fellow of the Linnæan Society.
F. L. S.—Member of the Linnean Society.
f. o. b.—Free on board.
f. o. b.—Free on board.
Fol.—Folio.
Fol.—Folio.
For.—Foreign.
For. — International.
F. P. S.—Fellow of the Philological Society.
F. P. S.—Member of the Philological Society.
Fr.—Fragmentum, fragment.
Fr.—Fragment, fragment.
Fr.—Franc; Frau, (lady.)
Fr.—Franc; Frau, (woman.)
Fr.—Francis.
Fr. — Francis.
F. R. A. S.—Fellow of the Royal Astronomical Society.
F. R. A. S.—Fellow of the Royal Astronomical Society.
F. R. C. S. L.—Fellow of the Royal College of Surgeons, London.
F.R.C.S.L.—Fellow of the Royal College of Surgeons, London.
Fred.—Frederick.
Fred.—Freddie.
F. R. G. S.—Fellow of the Royal Geographical Society.
F. R. G. S.—Fellow of the Royal Geographical Society.
Fri.—Friday.
Fri. - Friday.
F. R. S.—Fellow of the Royal Society.
F. R. S.—Fellow of the Royal Society.
Frs.—Frisian.
Fris.
F. R. S. E.—Fellow of the Royal Society, Edinburgh.
F. R. S. E.—Fellow of the Royal Society, Edinburgh.
F. R. S. L.—Fellow of the Royal Society, London.
F. R. S. L.—Fellow of the Royal Society, London.
F. R. S. L.—Fellow of the Royal Society of Literature.
F.R.S.L.—Fellow of the Royal Society of Literature.
F. S. A.—Fellow of the Society of Arts.
F. S. A.—Fellow of the Society of Arts.
F. S. A. E.—Fellow of the Society of Antiquaries, Edinburgh.
F. S. A. E.—Fellow of the Society of Antiquaries, Edinburgh.
Ft.—Foot; feet; Fort.
Ft.—foot; feet; fort.
Fur.—Furlong.
Fur.—Furlong.
F. Z. S.—Fellow of the Zoological Society.
F. Z. S.—Fellow of the Zoological Society.
g.—gram, (metric system.)
g.—gram (metric system)
G. or g.—Guineas.
G. or g.—Guineas.
G. A.—General Assembly.
G. A.—General Assembly.
Ga.—Georgia.
Ga. — Georgia.
Gal.—Galatians; Gallon.
Gal.—Galatians; Gallon.
G. A. R.—Grand Army of the Republic.
G. A. R.—Grand Army of the Republic.
G. B.—Great Britain.
U.K.—United Kingdom.
G. C.—Grand Chapter.
G. C.—Grand Chapter.
G. C. B.—Grand Cross of the Bath.
G. C. B.—Grand Cross of the Bath.
G. C. H.—Grand Cross of Hanover.
G. C. H.—Grand Cross of Hanover.
G. C. L. H.—Grand Cross of the Legion of Honour.
G. C. L. H.—Grand Cross of the Legion of Honor.
G. E.—Grand Encampment.
G. E.—Grand Assembly.
Gen.—Genesis; General; Genitive case.
Gen.—Genesis; General; Genitive.
Gent.—Gentleman.
Gent. — Guy.
Geo.—George.
Geo.—George.
Geog.—Geography.
Geo.—Geography.
Geol.—Geology.
Geol.—Geology.
Geom.—Geometry.
Geom.—Geometry.
Ger.—Germany; German.
Ger.—Germany; German.
G. L.—Grand Lodge.
G. L.—Grand Lodge.
Gl.—Glossa, a gloss.
Gl.—Glossa, a note.
G. M.—Grand Master.
G. M.—Grandmaster.
G. O.—General Order.
G.O.—General Order.
Goth.—Gothic.
Goth. - Gothic.
Gov.—Governor.
Gov. — Governor.
Gov.-Gen.—Governor-General.
Governor-General.
G. R.—Georgius Rex, King George.
G. R.—King George.
Gr.—Greek; grain; gramme; groschen.
Gr.—Greek; grain; gram; groschen.
Gram.—Grammar.
Gram.—Grammar.
Gro.—Gross.
Gross.
Grot.—Grotius.
Grot.—Grotius.
Ha.—Hektare, (metric system.)
Ha.—Hectare, (metric system.)
h. a.—Hoc anno, this year.
this year
Hab.—Habakkuk.
Hab.—Habakkuk.
Hab. Corp.—Habeas corpus, you may have the body.
Hab. Corp.—Habeas corpus, you may have the person.
Hab. fa. poss.—Habere facias possessionem, a writ to put the plaintiff in possession.
Hab. fa. poss.—Habere facias possessionem, a legal order to place the plaintiff in possession.
Hab. fa. seis.—Habere facias seisinam, a writ now superseded by the preceding.
Hab. fa. seis.—Habere facias seisinam, a legal document that has now been replaced by the one before it.
Hag.—Haggai.
Hag.—Haggai.
Ham. Coll.—Hamilton College.
Ham. Coll.—Hamilton College.
H. B. C.—Hudson’s Bay Company.
HBC—Hudson's Bay Company.
H. B. M.—His or Her Britannic Majesty.
H. B. M.—His or Her Britannic Majesty.
H. C.—House of Commons.
H. C.—House of Commons.
hdkf.—Handkerchief.
hdkf.—Tissue.
h. e.—Hoc est, that is, or this is.
h. e.—Hoc est, which means, or this means.
Hectol.—Hectolitre, (metric system.)
Hectolitre (metric system).
Heb.—Hebrews.
Hebrews
Her.—Heraldry.
Heraldry.
Hf.-bd.—Half-bound.
Half-bound.
Hf.-cf.—Half-calf.
Half-calf
Hg.—Hektogram, (metric system.)
Hektogram (metric system)
Hg.—Hydrargyrum, mercury.
Hg.—Hydrargyrum, mercury.
hhd.—Hogshead.
Hogshead.
Hist.—History.
Hist.—History.
H. J. S.—Hic jacet sepultus, Here lies buried.
H. J. S.—Hic jacet sepultus, Here lies buried.
Hl.—Hectoliter, (metric system.)
Hectoliter (metric system)
H. L.—House of Lords.
H. L.—House of Lords.
Hm.—Hectometer, (metric system.)
Hm.—Hectometer (metric system).
H. M.—His Majesty.
H. M.—His Majesty.
H. M. P.—Hoc monumentum posuit, erected this monument.
H. M. P.—Hoc monumentum posuit, put up this monument.
Hon.—Honourable.
Hon. - Honorable.
Hort.—Horticulture.
Hort.—Gardening.
Hos.—Hosea.
Hosea
H. R.—House of Representatives.
H. R.—House of Representatives.
H. R. E.—Holy Roman Emperor.
H. R. E.—Holy Roman Emperor.
H. R. H.—His Royal Highness.
H.R.H. — His Royal Highness.
Hr. hrn.—Herr, Herrn—gentleman, gentlemen.
Mr., Ms.—mister, masters.
H. R. I. P.—Hic requiescit in pace, Here rests in peace.
H. R. I. P.—Hic requiescit in pace, Here rests in peace.
H. S.—Hic situs, Here lies.
H. S.—Here lies.
H. S. H.—His Serene Highness.
H. S. H.—His Serene Highness.
h. t.—Hoc titulum, this title; hoc tituli, in or under this title.
h. t.—Hoc titulum, this title; hoc tituli, in or under this title.
h. v.—Hoc verbum, this word; hic verbis, in these words.
h. v.—This word, this word; in these words.
hund.—Hundred.
hund.—Hundred.
I. II. III.—One, two, three, or first, second, third.
I. II. III.—One, two, three; or first, second, third.
Ia.—Iowa.
Ia.—Iowa.
Ib. or ibid.—Ibidem, in the same place.
Ib. or ibid.—Ibidem, in the same location.
Ich.—Ichthyology.
Ich.—Fish Science.
Ictus.—Jurisconsultus.
Ictus.—Legal expert.
Id.—Idem, the same.
Id.—The same.
Id. T.—Idaho Territory.
Idaho Territory
i.e.—Id est, that is.
i.e., that is.
I. H. S.—Jesus hominum Salvator, Jesus the Saviour of men.
I. H. S.—Jesus hominum Salvator, Jesus the Savior of humanity.
ij.—Two, (med.)
ij.—Two, (med.)
Ill.—Illinois.
Ill. — IL
In.—Inch; inches.
In.—Inches.
incog.—Incognito, unknown.
incog.—Incognito, anonymous.
Incor.—Incorporated.
Inc.—Incorporated.
Ind.—Indiana; Index.
Ind.—Indiana; Index.
I. N. D.—In nomine Dei, in the name of God.
I. N. D.—In nomine Dei, in the name of God.
Ind. Ter.—Indian Territory.
Ind. Ter.—Indian Territory.
Indef.—Indefinite.
Indef.—Indefinite.
In f.—In fine, at the end of the title, law, or paragraph quoted.
In f.—In fine, at the end of the title, law, or paragraph quoted.
Inf.—Infra, beneath or below.
Infra, beneath or below.
in lim.—In limine, at the outset.
in lim.—In limine, at the beginning.
in loc.—In loco, in the place; on the passage.
in loc.—In loco, in the place; on the passage.
in pr.—In principio, in the beginning and before the first paragraph of a law.
in pr.—In principio, in the beginning and before the first paragraph of a law.
I. N. R. I.—Jesus Nazarenus, Rex Judæorum, Jesus of Nazareth, King of the Jews.
I. N. R. I.—Jesus Nazarenus, Rex Judæorum, Jesus of Nazareth, King of the Jews.
Inst.—Instant, of this month; Institutes.
Inst.—Instant, of this month; Institutes.
In sum.—In summa, in the summary.
In summary.—In summa, in the summary.
Int.—Interest.
Int.—Interest.
Interj.—Interjection.
Interj.—Interjection.
in trans.—In transitu, on the passage.
in trans.—In transitu, on the journey.
Intro.—Introduction.
Intro.
I. O. O. F.—Independent Order of Odd-Fellows.
I. O. O. F.—Independent Order of Odd Fellows.
I. O. U.—I owe you.
I. O. U.—I owe you.
I. q.—Idem quod, the same as.
I. q.—Idem quod, the same as.
Isa.—Isaiah.
Isa.—Isaiah.
Isl.—Island.
Isl.—Island.
Ital.—Italic; Italian.
Ital.—Italic; Italian.
IV.—Four or fourth.
IV.—Four or 4th.
IX.—Nine or ninth.
Nine
J.—Justice or Judge. JJ.—Justices.
J.—Justice. JJ.—Justices.
j.—One (med.)
j.—One (med.)
J. A.—Judge-Advocate.
J. A.—Judge Advocate.
Jac.—Jacob.
Jac.—Jake.
Jan.—January.
Jan.—January.
Jas.—James.
Jas.—James.
J. C. D.—Juris Civilis Doctor, Doctor of Civil Law.
J. C. D.—Juris Civilis Doctor, Doctor of Civil Law.
J. D.—Jurum Doctor, Doctor of Laws.
J. D.—Jurum Doctor, Doctor of Laws.
Jer.—Jeremiah.
Jer.—Jeremiah.
Jno.—John.
John.
Jona.—Jonathan.
Jona.—Jon.
Jos.—Joseph.
Joe—Joseph.
Josh.—Joshua.
Josh. — Joshua.
J. P.—Justice of the Peace.
J. P.—Justice of the Peace.
J. Prob.—Judge of Probate.
J. Prob.—Probate Judge.
J. R.—Jacobus Rex, King James.
J. R.—King James.
Jr. or Jun.—Junior.
Jr. or Jun.—Junior.
J. U. D. or J. V. D.—Juris utriusque Doctor, Doctor of both Laws (of the Canon and the Civil Law).
J. U. D. or J. V. D.—Juris utriusque Doctor, Doctor of both Laws (Canon Law and Civil Law).
Jud.—Judith.
Jud.—Jude.
Judg.—Judges.
Judges
Judge-Adv.—Judge-Advocate.
Judge Advocate.
Jul. Per.—Julian Period.
Jul. Per.—Julian Period.
Jus. P.—Justice of the Peace.
Justice of the Peace.
Just.—Justinian.
Just.—Justinian.
J. W.—Junior Warden.
J. W.—Junior Warden.
K.—King.
K.—King.
K. A.—Knight of St. Andrew, in Russia.
K. A.—Knight of St. Andrew, in Russia.
K. A. N.—Knight of Alexander Nevskoi, in Russia.
K. A. N.—Knight of Alexander Nevsky, in Russia.
Kan.—Kansas.
Kan.—Kansas.
K. B.—King’s Bench.
K. B.—King’s Bench.
K. B.—Knight of the Bath.
K. B.—Knight of Bath.
K. B. A.—Knight of St. Bento d’Avis, in Portugal.
K. B. A.—Knight of St. Bento d'Avis, in Portugal.
K. B. E.—Knight of the Black Eagle, in Russia.
K. B. E.—Knight of the Black Eagle, in Russia.
K. C.—King’s Council.
K.C. — King’s Council.
K. C.—Knight of the Crescent, in Turkey.
K. C.—Knight of the Crescent, in Turkey.
K. C. B.—Knight Commander of the Bath.
K. C. B.—Knight Commander of the Bath.
K. C. H.—Knight Commander of Hanover.
K. C. H.—Knight Commander of Hanover.
K. C. S.—Knight of Charles III. of Spain.
K. C. S.—Knight of Charles III of Spain.
K. E.—Knight of the Elephant, in Denmark.
K. E.—Knight of the Elephant in Denmark.
K. F.—Knight of Ferdinand of Spain.
K. F.—Knight of Ferdinand of Spain.
K. F. M.—Knight of St. Ferdinand and Merit, in Sicily.
K. F. M.—Knight of St. Ferdinand and Merit, in Sicily.
Kg.—Kilogram, (metric system.)
Kg.—Kilogram, (metric system.)
K. G.—Knight of the Garter.
K.G.—Knight of the Garter.
K. G. C.—Knight of the Grand Cross.
K. G. C.—Knight of the Grand Cross.
K. G. C. B.—Knight of the Grand Cross of the Bath.
K. G. C. B.—Knight of the Grand Cross of the Bath.
K. G. F.—Knight of the Golden Fleece, in Spain.
K. G. F.—Knight of the Golden Fleece, in Spain.
K. G. H.—Knight of the Guelphs of Hanover.
K. G. H.—Knight of the Guelphs of Hanover.
K. G. V.—Knight of Gustavus Vasa of Sweden.
K. G. V.—Knight of Gustavus Vasa of Sweden.
K. H.—Knight of Hanover.
K. H.—Knight of Hanover.
Ki.—Kings.
Ki.—Kings.
Kingd.—Kingdom.
Kingdom.
K. J.—Knight of St. Joachim.
K. J.—Knight of St. Joachim.
Kl.—Kiloliter, (metric system.)
Kl.—Kiloliter (metric system).
K. L. or K. L. A.—Knight of Leopold of Austria.
K. L. or K. L. A.—Knight of Leopold of Austria.
K. L. H.—Knight of the Legion of Honour.
K. L. H.—Knight of the Legion of Honor.
Km.—Kilometer, (metric system.)
Km.—Kilometer (metric system).
K. M.—Knight of Malta.
K. M.—Knight of Malta.
K. Mess.—King’s Messenger.
K. Mess.—King's Messenger.
K. M. H.—Knight of Merit, in Holstein.
K. M. H.—Knight of Merit, in Holstein.
K. M. J.—Knight of Maximilian Joseph of Bavaria.
K. M. J.—Knight of Maximilian Joseph of Bavaria.
K. M. T.—Knight of Maria Theresa (of Austria.)
K. M. T.—Knight of Maria Theresa (of Austria).
Knick.—Knickerbocker.
Knick.—Knickers.
K. N. S.—Knight of the Royal North Star, (in Sweden.)
K. N. S.—Knight of the Royal North Star, (in Sweden.)
Knt. or Kt.—Knight.
Knt. or Kt.—Knight.
K. P.—Knight of St. Patrick; Knight of Pythias.
K. P.—Knight of St. Patrick; Knight of Pythias.
Kr.—Kreuzer, (German coin.)
Kr.—Kreuzer (German coin)
K. R. C.—Knight of the Red Cross.
K. R. C.—Knight of the Red Cross.
K. R. E.—Knight of the Red Eagle, (in Prussia.)
K. R. E.—Knight of the Red Eagle, (in Prussia.)
Ks.—Kansas.
KS – Kansas.
K. S. A.—Knight of St. Anne (of Russia.)
K. S. A.—Knight of St. Anne (of Russia.)
K. S. E.—Knight of St. Esprit, (in France.)
K. S. E.—Knight of the Holy Spirit, (in France.)
K. S. F.—Knight of St. Fernando (of Spain.)
K. S. F.—Knight of St. Fernando (of Spain.)
K. S. F. M.—Knight of St. Ferdinand and Merit, (in Naples.)
K. S. F. M.—Knight of St. Ferdinand and Merit, (in Naples.)
K. S. G.—Knight of St. George (of Russia.)
K. S. G.—Knight of St. George (of Russia).
K. S. H.—Knight of St. Hubert (of Bavaria.)
K. S. H.—Knight of St. Hubert (of Bavaria.)
K. S. I.—Knight of the Star of India.
K. S. I.—Knight of the Star of India.
K. S. J.—Knight of St. Januarius (of Naples.)
K. S. J.—Knight of St. Januarius (of Naples.)
K. S. L.—Knight of the Sun and Lion, (in Persia.)
K. S. L.—Knight of the Sun and Lion, (in Persia.)
K. S. M. & S. G.—Knight of St. Michael and St. George (of the Ionian Islands.)
K. S. M. & S. G.—Knight of St. Michael and St. George (of the Ionian Islands.)
K. S. P.—Knight of St. Stanislaus of Poland.
K. S. P.—Knight of St. Stanislaus of Poland.
K. S. S.—Knight of the Southern Star (of the Brazils.)
K. S. S.—Knight of the Southern Star (of Brazil.)
K. S. S.—Knight of the Sword, in Sweden.
K. S. S.—Knight of the Sword, in Sweden.
K. S. W.—Knight of St. Wladimir (of Russia.)
K. S. W.—Knight of St. Vladimir (of Russia.)
K. T.—Knight of the Thistle; Knight Templar.
K. T.—Knight of the Thistle; Knight Templar.
Kt.—Knight.
Kt. — Knight.
K. T. S.—Knight of the Tower and Sword (in Portugal.)
K. T. S.—Knight of the Tower and Sword (in Portugal.)
K. W.—Knight of William (of the Netherlands.)
K. W.—Knight of William (of the Netherlands.)
K. W. E.—Knight of the White Eagle, (in Poland.)
K. W. E.—Knight of the White Eagle, (in Poland.)
Ky.—Kentucky.
Ky. - Kentucky.
L.—Fifty or fiftieth; Liber, book.
L.—50 or 50th; Liber, book.
l.—liter, (metric system.)
l.—liter (metric system)
L., £ or l.—Libra, or libræ, pound or pounds sterling.
L., £ or l.—Libra, or libræ, pound or pounds sterling.
L. or £, s. d.—Pounds, shillings, pence.
L. or £, s. d.—Pounds, shillings, pence.
La.—Louisiana.
La. — Louisiana.
Lam.—Lamentations.
Lamentations.
Lat.—Latitude; Latin.
Lat.—Lat; Latin.
Lb. or ℔.—Libra or libræ, pound or pounds in weight.
Lb. or ℔.—Libra or libræ, pound or pounds in weight.
L. C.—Lord Chancellor; Lord Chamberlain.
L. C.—Lord Chancellor; Lord Chamberlain.
L. C.—Lower Canada.
L. C.—Quebec.
l. c.—Lower-case.
l. c.—lowercase.
L. C. J.—Lord Chief-Justice.
L. C. J.—Chief Justice.
L. D.—Lepide dictum, finely said; Lady-Day.
L. D.—Lepide dictum, well put; Lady-Day.
Ld.—Lord.
Ld.—Lord.
Ldp.—Lordship.
Ldp.—Lordship.
Leg.—Legate.
Leg. — Legate.
Legis.—Legislature.
Legislative Assembly.
Lev.—Leviticus.
Lev.—Lev.
Lex.—Lexicon.
Lex.—Dictionary.
L. I.—Long Island.
L. I.—Long Island.
Lib.—Liber, book.
Lib.—Book.
Lieut.—Lieutenant.
Lieut.—Lieutenant.
Lieut.-Col.—Lieutenant-Colonel.
Lieutenant Colonel
Lieut.-Gen.—Lieutenant-General.
Lieutenant General
Lieut.-Gov.—Lieutenant-Governor.
Lt. Gov.—Lieutenant Governor.
Linn.—Linnæan.
Linn.—Linnaean.
Lit.—Literally; Literature.
Lit.—Literally; Literature.
Liv.—Livre, book.
Liv.—Livre, book.
LL. B.—Legum Baccalaureus, Bachelor of Laws.
LL. B.—Legum Baccalaureus, Bachelor of Laws.
LL. D.—Legum Doctor, Doctor of Laws.
LL. D.—Legum Doctor, Doctor of Laws.
l. l.—Loco laudato, in the place quoted.
l. l.—Loco laudato, in the place quoted.
loc. cit.—Loco citato, in the place cited.
loc. cit.—Loco citato, in the place mentioned.
Lon.—Longitude.
Lon.—Longitude.
L. S.—Locus sigilli, place of the seal.
L. S.—Locus sigilli, the place for the seal.
Lt.—Lieutenant.
Lt.—Lieutenant.
LX.—Sixty or sixtieth.
60 or sixtieth.
LXX.—Seventy or seventieth.
Seventy.
LXX.—The Septuagint (Version of the Old Testament.)
LXX.—The Septuagint (Old Testament).
LXXX.—Eighty or eightieth.
80—Eighty or eightieth.
m.—Meter, (metric system.)
m.—Meter, (metric system).
M.—Mille, a thousand; Meridies, noon.
M.—Mille, a thousand; Meridies, noon.
M. or Mons.—Monsieur.
M. or Mons.—Mr.
M. A.—Master of Arts.
M.A.—Master of Arts.
Macc.—Maccabees.
Macc.—Maccabees.
Mad.—Madam.
Madam.
Mad. Univ.—Madison University.
Mad. Univ.—University of Madison.
Mag.—Magazine.
Mag.
Maj.—Major.
Maj.
Maj.-Gen.—Major-General.
Maj.-Gen.—Major General.
Mal.—Malachi.
Mal.—Malachi.
Man.—Manasses.
Man.—Manasseh.
Mar.—March; Maritime.
Mar.—March; Maritime.
M. A. N. S.—Member of the Academy of Natural Sciences.
M. A. N. S.—Member of the Academy of Natural Sciences.
March.—Marchioness.
March.—Marchioness.
Marg.—Margin.
Marg.—Margin.
Marg. Tran.—Marginal Translation.
Marg. Tran.—Marginal Translation.
Marq.—Marquis.
Marq.—Marquis.
Masc.—Masculine.
Masc. — Male.
Mass.—Massachusetts.
Mass.—MA.
Math.—Mathematics; Mathematician.
Math.—Math; Mathematician.
Matt.—Matthew.
Matt.—Matthew.
Max.—Maxim.
Max.—Max.
M. B.—Medicinæ Baccalaureus, Bachelor of Medicine.
M. B.—Medicinæ Baccalaureus, Bachelor of Medicine.
M. B.—Musicæ Baccalaureus, Bachelor of Music.
M. B.—Musicæ Baccalaureus, Bachelor of Music.
M. B. F. et H.—Great Britain, France, and Ireland.
M. B. F. et H.—Great Britain, France, and Ireland.
M. C.—Member of Congress.
M.C.—Member of Congress.
Mch.—March.
Mar.
Md.—Maryland.
Md.—MD.
M. D.—Medicinæ Doctor, Doctor of Medicine.
M. D.—Medicinæ Doctor, Doctor of Medicine.
M. E.—Methodist Episcopal; Military or Mechanical Engineer; Most excellent.
M. E.—Methodist Episcopal; Military or Mechanical Engineer; Most excellent.
Me.—Maine.
Me.—Maine.
Med.—Medicine.
Med.—Medicine.
Mem.—Memorandum.
Memorandum.
Mem.—Memento, remember.
Remember.
Merc.—Mercury.
Merc.—Mercury.
Messrs. or MM.—Messieurs, Gentlemen.
Messrs. or MM.—Gentlemen.
Met.—Metaphysics.
Metaphysics.
Metal.—Metallurgy.
Metal. — Metallurgy.
Meteor.—Meteorology.
Weather.—Meteorology.
Meth.—Methodist.
Meth.—Meth.
Mex.—Mexico or Mexican.
Mex.—Mexico or Mexican.
m. ft.—Mistura fiat, Let a mixture be made.
m. ft.—Mistura fiat, Make a mixture.
mg.—milligram, (metric system.)
mg—milligram (metric system).
Mg.—Myriagram, (metric system.)
Mg.—Myriagram (metric system).
M.-Goth.—Mœso-Gothic.
M.-Goth.—Moesian Gothic.
Mgr.—Monseigneur.
Mgr.—Monsignor.
M. H. S.—Member of the Historical Society; Massachusetts Historical Society.
M. H. S.—Member of the Historical Society; Massachusetts Historical Society.
Mic.—Micah.
Micah.
Mich.—Michigan.
Mich.—MI.
Mil.—Military.
Mil.—Military.
Min.—Mineralogy; Minute.
Min.—Mineralogy; Minute.
Minn.—Minnesota.
Minn. — Minnesota.
Min. Plen.—Minister Plenipotentiary.
Min. Plen.—Minister Extraordinary.
Miss.—Mississippi.
Miss. — Mississippi.
ml.—milliliter, (metric system.)
ml.—milliliters (metric system).
Ml.—Myrialiter, (metric system.)
Ml.—Myrialiter (metric system).
M. L. A.—Mercantile Library Association.
M. L. A.—Merchant Library Association.
Mlle.—Mademoiselle.
Mlle. — Miss.
mm.—millimeter, (metric system.)
mm - millimeter (metric system)
Mm.—Myriameter, (metric system.)
Mm.—Myriameter (metric system).
MM.—Their Majesties; Messieurs, Gentlemen; Two thousand.
MM.—Their Majesties; gentlemen; 2,000.
Mme.—Madame.
Madam.
M. M. S.—Moravian Missionary Society.
M. M. S.—Moravian Mission Society.
M. M. S. S.—Massachusettensis Medicinæ Societatis Socius, Fellow of the Massachusetts Medical Society.
M. M. S. S.—Massachusettensis Medicinæ Societatis Socius, Fellow of the Massachusetts Medical Society.
Mo.—Missouri; Month.
Mo.—Missouri; Month.
Mod.—Modern.
Mod.—Modern.
Mon.—Monday.
Mon. — Monday.
Mons.—Monsieur, Sir.
Mons.—Sir.
Mos.—Months.
Mos.—Months.
M. P.—Member of Parliament; Member of Police.
M. P.—Member of Parliament; Police Member.
M. P. P.—Member of Provincial Parliament.
M.P.P.—Member of Provincial Parliament.
M. R.—Master of the Rolls.
M. R.—Head of the Court.
Mr.—Mister.
Mr.
M. R. A. S.—Member of the Royal Asiatic Society; Member of the Royal Academy of Science.
M. R. A. S.—Member of the Royal Asiatic Society; Member of the Royal Academy of Science.
M. R. C. C.—Member of the Royal College of Chemistry.
M. R. C. C.—Member of the Royal College of Chemistry.
M. R. C. S.—Member of the Royal College of Surgeons.
M. R. C. S.—Member of the Royal College of Surgeons.
M. R. G. S.—Member of the Royal Geographical Society.
M. R. G. S.—Member of the Royal Geographical Society.
M. R. I.—Member of the Royal Institution.
M. R. I.—Member of the Royal Institution.
M. R. I. A.—Member of the Royal Irish Academy.
M. R. I. A.—Member of the Royal Irish Academy.
Mrs.—Mistress.
Mrs. — Missus.
M. R. S. L.—Member of the Royal Society of Literature.
M. R. S. L.—Member of the Royal Society of Literature.
M. S.—Memoriæ sacrum, Sacred to the memory; Master of the Sciences.
M. S.—Memoriæ sacrum, Sacred to the memory; Master of the Sciences.
MS.—Manuscriptum, manuscript.
MS.—Manuscript, manuscript.
MSS.—Manuscripta, manuscripts.
MSS.—Manuscripts.
Mt.—Mount or mountain.
Mt.—Mount or mountain.
Mus. B.—Bachelor of Music.
BMus.—Bachelor of Music.
Mus. D.—Doctor of Music.
Mus. D.—Doctor of Music.
M. W.—Most Worthy; Most Worshipful.
M. W.—Most Worthy; Most Worshipful.
Myth.—Mythology.
Mythology.
N.—North; Number; Noun; Neuter.
N.—North; No.; Noun; Neut.
n.—Note.
n.—Note.
N. A.—North America.
N.A.—North America.
Nah.—Nahum.
Nah.—Nahum.
Nat. Hist.—Natural History.
Nat. Hist.—Natural History.
Nath.—Nathanael or Nathaniel.
Nath.—Nathanael or Nathaniel.
N. B.—New Brunswick; North Britain; Nota bene, mark well; take notice.
N. B.—New Brunswick; North Britain; Nota bene, pay attention; take note.
N. C.—North Carolina.
N.C.—North Carolina.
n. d.—No date.
n.d.—No date.
N. E.—New England; Northeast.
N. E.—New England; Northeast.
Neb.—Nebraska.
Nebraska.
Neh.—Nehemiah.
Neh.—Nehemiah.
n. e. i.—Non est inventus, he is not found.
n. e. i.—Non est inventus, he is not found.
nem. con., or nem. diss.—Nemine contradicente, or nemine dissentiente, no one opposing; unanimously.
nem. con., or nem. diss.—Nemine contradicente, or nemine dissentiente, no one opposing; unanimously.
Neut.—Neuter (gender.)
Neut.—Neuter (gender)
Nev.—Nevada.
Nev. — Nevada.
New M.—New Mexico.
New Mexico.
New Test. or N. T.—New Testament.
New Test. or N. T.—New Testament.
N. F.—Newfoundland.
N.F.—Newfoundland.
N. G.—New Granada; Noble Grand.
N. G.—New Granada; Noble Grand.
N. H.—New Hampshire; New Haven.
N. H.—New Hampshire; New Haven.
N. H. H. S.—New Hampshire Historical Society.
N. H. H. S.—New Hampshire Historical Society.
Ni. pri.—Nisi prius.
Nisi prius.
N. J.—New Jersey.
N.J.—New Jersey.
n. l.—Non liquet, it does not appear.
n. l.—Non liquet, it doesn’t seem to be clear.
N. lat.—North latitude.
N. lat.—North lat.
N. M.—New Mexico.
N.M.—New Mexico.
N. N. E.—North-northeast.
N.N.E.—North-northeast.
N. N. W.—North-northwest.
N. N. W.—North-northwest.
N. O.—New Orleans.
N.O.—New Orleans.
No.—Numero, number.
No.—Number.
Nol pros.—Nolle prosequi, unwilling to proceed.
Nol pros.—Nolle prosequi, not willing to move forward.
Nom. or nom.—Nominative.
Nom. or nom.—Nominative.
Non con.—Not content; dissenting, (House of Lords.)
Non con.—Not satisfied; disagreeing, (House of Lords.)
Non. cul.—Non culpabilis, not guilty.
Not guilty.
Non obst.—Non obstante, notwithstanding.
Non obst.—Non obstante, nonetheless.
Non pros.—Non prosequitur, he does not prosecute.
Non pros.—Non prosequitur, he does not pursue.
Non seq.—Non sequitur, it does not follow.
Non seq.—Non sequitur, it doesn't follow.
Nos.—Numbers.
Nos.—Nums.
Nov.—November.
Nov.—November.
N. P.—Notary Public.
N. P.—Notary Public.
N. S.—New Style, (after 1752;) Nova Scotia.
N. S.—New Style (after 1752); Nova Scotia.
n. u.—Name or names unknown.
n. u.—Name(s) unknown.
Num.—Numbers; Numeral.
Num.—Numbers; Numerals.
N. V. M.—Nativity of the Virgin Mary.
N. V. M.—Birth of the Virgin Mary.
N. W.—Northwest.
N.W.—Northwest.
N. Y.—New York.
N.Y.—New York City.
N. Y. H. S.—New York Historical Society.
N. Y. H. S.—New York Historical Society.
O.—Ohio; Octarius, a pint.
O.—Ohio; Octarius, a beer.
Ob.—Obiit, he or she died.
Ob.—Obit, he or she died.
Obad.—Obadiah.
Obadiah.
Obs.—Obsolete; Observatory; Observation.
Obs.—Outdated; Observatory; Observation.
Obt. or obdt.—Obedient.
Obedient.
Oct.—October.
Oct.—October.
O. F.—Odd-Fellow or Odd-Fellows.
O. F.—Odd Fellow or Odd Fellows.
O. K.—All correct, (slang.)
Okay—All correct, (slang.)
Old Test. or O. T.—Old Testament.
Old Test. or O. T.—Old Testament.
Olym.—Olympiad.
Olym.—Olympics.
Opt.—Optics.
Opt. – Optics.
Or.—Oregon.
Or.—Oregon.
Orig.—Originally.
Orig.—Original.
Ornith.—Ornithology.
Bird study—Ornithology.
O. S.—Old Style, (before 1752.)
O. S.—Old Style, (before 1752).
O. U. A.—Order of United Americans.
O. U. A.—Order of United Americans.
Oxf.—Oxford.
Oxf. - Oxford.
Oxon.—Oxonia, Oxonii, Oxford.
Oxford.
oz.—Ounce.
oz.—Ounce.
P.—Particula, a little part, as much as can be taken between the ends of two fingers; pondere, by weight.
P.—Particula, a small piece, as much as can be held between the ends of two fingers; pondere, by weight.
P. or p.—Page; Part; Participle.
P. or p.—Page; Part; Part.
Pa. or Penna.—Pennsylvania.
Pa. or Penna.—Pennsylvania.
Pal.—Palæontology.
Pal.-Paleontology.
Par.—Paragraph.
Par.
Par. pas.—Parallel passage.
Par. pas.—Parallel passage.
Parl.—Parliament.
Parl.—Parliament.
Pathol.—Pathology.
Pathol.—Pathology.
Payt.—Payment.
Payt.—Payment.
Pb.—Plumbum, lead.
Pb.—Lead.
P. C.—Patres Conscripti, Conscript Fathers; Senators.
P. C.—Patres Conscripti, Conscript Fathers; Senators.
P. C.—Privy Council; Privy Councillor.
P. C.—Privy Council; Council member.
Pd.—Paid.
Pd.—Paid.
P. E.—Protestant Episcopal.
P.E.—Protestant Episcopal.
P. E. I.—Prince Edward Island.
P.E.I.—Prince Edward Island.
Pent.—Pentecost.
Pentecost.
Per, or pr.—By the, or per lb.
Per, or pr.—By the, or per lb.
Per an.—Per annum, by the year.
Per year, annually.
Per cent.—Per centum, by the hundred.
Per cent.—Per centum, meaning for every hundred.
Peri.—Perigee.
Peri.—Perigee.
Pet.—Peter.
Pet: Peter.
P. G.—Past Grand.
P.G.—Past Grand.
Phar.—Pharmacy.
Pharm.—Pharmacy.
Ph. B.—Philosophiæ Baccalaureus, Bachelor of Philosophy.
Ph. B.—Philosophiæ Baccalaureus, Bachelor of Philosophy.
Ph. D.—Philosophiæ Doctor, Doctor of Philosophy.
Ph.D.—Doctor of Philosophy.
Ph. G.—Pharmaciæ Graduatus, Graduate in Pharmacy.
Ph. G.—Pharmaciæ Graduatus, Graduate in Pharmacy.
Phil.—Philip; Philippians; Philosophy; Philemon.
Phil.—Philip; Philippians; Philosophy; Philemon.
Phila. or Phil.—Philadelphia.
Phila. or Phil.—Philadelphia.
Philem.—Philemon.
Philem.—Philemon.
Philom.—Philomathes, a lover of learning.
Philom.—Philomathes, a knowledge seeker.
Philomath.—Philomathematicus, a lover of the mathematics.
Philomath.—Philomathematicus, a math lover.
Phil. Trans.—Philosophical Transactions.
Phil. Trans.—Philosophical Transactions.
Phren.—Phrenology.
Phrenology.
P. H. S.—Pennsylvania Historical Society.
P.H.S.—Pennsylvania Historical Society.
Pinx. or pxt.—Pinxit, he painted it.
Pinx. or pxt.—Pinxit, he painted it.
P. J.—President Judge; Police Justice.
P. J.—Chief Judge; Police Justice.
Pl. or Plur.—Plural.
Pl. or Plur.—Plural.
Plff.—Plaintiff.
Plff. — Plaintiff.
P. M.—Post meridiem, afternoon; Post-master; Passed Midshipman.
P. M.—Post meridiem, afternoon; Postmaster; Passed Midshipman.
P. M. G.—Postmaster-General.
Postmaster General.
P. O.—Post-Office.
P.O.—Post Office.
Pop.—Population.
Pop. - Population.
Port.—Portugal or Portuguese.
Port.—Portugal or Portuguese wine.
P. P.—Pater patria, the father of his country; Propositum publice, public notification.
P. P.—Pater patria, the father of his country; Propositum publice, public announcement.
P. P. C.—Pour prendre congé, to take leave.
P. P. C.—Pour prendre congé, to say goodbye.
Pp. or pp.—Pages.
Pp. or pp.—Pages.
Pph.—Pamphlet.
Pph.—Pamphlet.
P. R.—Populus Romanus, the Roman people.
P. R.—Populus Romanus, the Roman people.
P. R. A.—President of Royal Academy.
P. R. A.—President of the Royal Academy.
P. R. C.—Post Romanum conditum, from the building of Rome.
P. R. C.—Post Romanum conditum, from the founding of Rome.
Pref.—Preface.
Preface.
Prep.—Preposition.
Prep.—Preposition.
Pres.—President.
Pres.—President.
Prin.—Principally.
Prin. — Mainly.
Prob.—Problem.
Prob.—Issue.
Prof.—Professor.
Prof. — Professor.
Pron.—Pronoun; Pronunciation.
Pron.—Pronoun; Pronunciation.
Prop.—Proposition.
Prop.—Proposal.
Prot.—Protestant.
Prot.—Protestant.
Pro tem.—Pro tempore, for the time being.
For now.
Prov.—Proverbs; Provost.
Prov.—Proverbs; Provost.
prox.—Proximo, next (month.)
next month
P. R. S.—President of the Royal Society.
P. R. S.—President of the Royal Society.
P. S.—Post scriptum, Postscript; Privy Seal.
P. S.—Post scriptum, Postscript; Private Seal.
Ps.—Psalm or Psalms.
Ps.—Psalm or Psalms.
Pt.—Part; Pint; Payment; Point; Port.
Pt.—Part; Pint; Payment; Point; Port.
p. t.—Post-town.
p. t.—Post-town.
P. T. O.—Please turn over.
P.T.O. — Please flip over.
Pub.—Publisher; Publication; Published; Public.
Pub.—Publisher; Publication; Published; Public.
Pub. Doc.—Public Documents.
Public Docs.
p. v.—Post-village.
p. v.—Post-village.
pwt.—Pennyweight; pennyweights.
pwt.—Pennyweight; pennyweights.
Q.—Queen; Question.
Q.—Queen; Inquiry.
q.—quintal; Quasi, as it were; almost.
q.—quintal; Quasi, so to speak; almost.
Q. B.—Queen’s Bench.
Q.B.—Queen’s Bench.
Q. C.—Queen’s College; Queen’s Counsel.
Q.C.—Queen’s College; Queen’s Counsel.
q. d.—Quasi dicat, as if he should say; quasi dictum, as if said; quasi dixisset, as if he had said.
q. d.—Quasi dicat, as if he were saying; quasi dictum, as if said; quasi dixisset, as if he had said.
q. e.—Quod est, which is.
q. e.—Quod est, meaning "which is."
q. e. d.—Quod erat demonstrandum, which was to be proved.
q. e. d.—Quod erat demonstrandum, which was to be proven.
q. e. f.—Quod erat faciendum, which was to be done.
q. e. f.—Quod erat faciendum, which was meant to be done.
q. e. i.—Quod erat inveniendum, which was to be found out.
q. e. i.—Quod erat inveniendum, which was to be discovered.
q. l.—Quantum libet, as much as you please.
q. l.—Quantum libet, as much as you want.
Q. M.—Quartermaster.
Q.M.—Quartermaster.
qm.—Quomodo, how; by what means.
qm.—Quomodo, how; by what means.
Q. M. G.—Quartermaster-General.
Q. M. G.—Quartermaster General.
q. p. or q. pl.—Quantum placet, as much as you please.
q. p. or q. pl.—Quantum placet, as much as you want.
Qr.—Quarter.
Qt.—Quarter.
Q. S.—Quarter Sessions.
Q.S. — Quarterly Sessions.
q. s.—Quantum sufficit, a sufficient quantity.
q. s.—Quantum sufficit, sufficient quantity.
qt.—Quart.
qt.—Quart.
qu. or qy. (?).—Quære, inquire; query.
qu. or qy. (?).—Quære, ask; question.
Quar.—Quarterly.
Qtr.—Quarterly.
Ques.—Question.
Ques. — Question.
q. v.—Quod vide, which see; Quantum vis, as much as you will.
q. v.—Quod vide, which see; Quantum vis, as much as you want.
℞.—Recipe, take; Response, in church books.
℞.—Recipe, take; Response, in church books.
R.—Regina, Queen; Rex, King; River; Rood; Rod.
R.—Regina, Queen; Rex, King; River; Rood; Rod.
R. A.—Royal Academy; Royal Academician; Royal Artillery.
R. A.—Royal Academy; Royal Academician; Royal Artillery.
R. A.—Royal Arch; Royal Association.
R. A.—Royal Arch; Royal Assoc.
R. E.—Royal Engineers.
R.E.—Royal Engineers.
Rec.—Recipe; Recorder.
Rec.—Recipe; Recorder.
Recd.—Received.
Recd.—Received.
Rec. Sec.—Recording Secretary.
Rec. Sec.—Recording Secretary.
Rect.—Rector; Receipt.
Rect.—Rector; Receipt.
Ref.—Reference.
Ref.
Ref. Ch.—Reformed Church.
Ref. Ch.—Reformed Church.
Reg.—Register; Regular.
Reg.—Register; Regular.
Reg. Prof.—Regius Professor.
Reg. Prof.—Regius Prof.
Regr.—Registrar.
Reg.—Registrar.
Regt.—Regiment.
Regt. — Regiment.
Rel.—Religion.
Rel.—Religion.
Rep.—Representative; Republican; Report.
Rep.—Rep; GOP; Report.
Rev.—Reverend; Revelation (Book of;) Review; Revenue; Revise.
Rev.—Reverend; Revelation (Book of); Review; Revenue; Revise.
Rhet.—Rhetoric.
Rhet—Rhetoric.
R. I.—Rhode Island.
R.I.—Rhode Island.
Richd.—Richard.
Richd.—Richard.
R. M.—Royal Marines; Royal Mail.
R. M.—Royal Marines; Royal Mail.
R. M. S.—Royal Mail Steamer.
R. M. S.—Royal Mail Ship.
R. N.—Royal Navy.
R. N.—Royal Navy.
Ro.—Recto, right—hand page.
Ro.—Recto, right page.
Robt.—Robert.
Robt. — Robert.
Rom.—Romans (Book of.)
Rom.—Romans (Book of.)
Rom. Cath.—Roman Catholic.
Rom. Cath.—Roman Catholic.
R. P.—Regius Professor, the King’s Professor.
R. P.—Regius Professor, the King’s Professor.
R. P. E.—Reformed Protestant Episcopal.
R. P. E.—Reformed Protestant Episcopal.
R. R.—Railroad.
R. R.—Train.
R. S.—Recording Secretary.
R. S.—Secretary of Records.
Rs.—Responsus, to answer.
Rs.—Response, to answer.
R. S. A.—Royal Society of Antiquaries; Royal Scottish Academy.
R. S. A.—Royal Society of Antiquaries; Royal Scottish Academy.
R. S. D.—Royal Society of Dublin.
R. S. D.—Royal Society of Dublin.
R. S. E.—Royal Society of Edinburgh.
R. S. E.—Royal Society of Edinburgh.
R. S. L.—Royal Society of London.
R. S. L.—Royal Society of London.
R. S. S.—Regiæ Societatis Socius, Fellow of the Royal Society.
R. S. S.—Regiæ Societatis Socius, Fellow of the Royal Society.
R. S. V. P.—Répondez, s’il vous plaît, answer, if you please.
R. S. V. P.—Répondez, s’il vous plaît, please respond.
Rt. Hon.—Right Honourable.
Rt. Hon.—Right Honorable.
Rt. Rev.—Right Reverend.
Right Rev.
Rt. Wpful.—Right Worshipful.
Rt. Worshipful—Right Worshipful.
R. W.—Right Worthy.
R. W.—Right Worthy.
S.—South; Saint; Scribe; Sulphur; Sunday; Sun; Series; Solidus, a shilling; Stere, (metric system.)
S.—South; Saint; Scribe; Sulfur; Sunday; Sun; Series; Solidus, a shilling; Stere, (metric system.)
S. A.—South America; South Africa; South Australia.
S. A.—South America; South Africa; South Australia.
s. a.—Secundum artem, according to art.
s. a.—Secundum artem, according to art.
Sam.—Samuel.
Sam.—Samuel.
S. A. S.—Societatis Antiquariorum Socius, Fellow of the Society of Antiquaries.
S. A. S.—Societatis Antiquariorum Socius, Fellow of the Society of Antiquaries.
Sat.—Saturday.
Sat.—Saturday.
Sax.—Saxon.
Sax—Saxon.
Sax. Chron.—Saxon Chronicle.
Sax. Chron.—Saxon Chronicle.
S. C.—Senatûs Consultum, a decree of the Senate; South Carolina.
S. C.—Senatûs Consultum, a Senate decree; South Carolina.
Sc.—Sculpsit, he engraved it.
Sc.—Sculpsit, he carved it.
sc. or scil.—Scilicet, namely.
sc. or scil.—Scilicet, namely.
Scan. Mag.—Scandalum magnatum, scandal of the great.
Scan. Mag.—Scandalum magnatum, scandal of the powerful.
Schol.—Scholium, a note.
Schol.—Note.
Schr.—Schooner.
Schooner.
Sci. fa.—Scire facias, to show cause.
Sci. fa.—Scire facias, to show cause.
Sclav.—Sclavonic.
Sclav.—Slavic.
Sculp. or sculp.—Sculpsit, he engraved it.
Sculp. or sculp.—Sculpsit, he engraved it.
S. D.—Salutem dicit, sends health.
S. D.—Hello, sends health.
S. E.—Southeast.
Southeast.
Sec.—Secretary; Second.
Sec.—Secretary; 2nd.
Sec. Leg.—Secretary of Legation.
Sec. Leg.—Secretary of State.
Sec. leg.—Secundum legem, according to law.
Sec. leg.—Secundum legem, according to law.
Sec. reg.—Secundum regulam, according to rule.
Sec. reg.—Secundum regulam, according to the rule.
Sect.—Section.
Sect. — Section.
Sem.—Semble, it seems.
Sem.—Seems, it seems.
Sen.—Senate; Senator; Senior.
Sen.
Sept.—September; Septuagint.
Sept.—September; LXX.
Seq.—Sequentia, following; sequitur, it follows.
Seq.—Sequentia, following; sequitur, it follows.
Ser.—Series.
Ser.—Series.
Serg.—Sergeant.
Sgt.—Sergeant.
Serg. Maj.—Sergeant-Major.
Sgt. Maj.—Sergeant-Major.
Servt.—Servant.
Servt.—Servant.
S. G.—South Georgia; Solicitor General.
S.G.—South Georgia; Solicitor General.
Shak.—Shakspeare.
Shakespeare.
S. H. S.—Societatis Historiæ Socius, Fellow of the Historical Society.
S. H. S.—Societatis Historiæ Socius, Fellow of the Historical Society.
Sing.—Singular.
Sing.—Single.
S. Isl.—Sandwich Islands.
S. Isl.—Hawaiian Islands.
S. J.—Society of Jesus.
S.J. — Society of Jesus.
S. J. C.—Supreme Judicial Court.
S.J.C.—Supreme Judicial Court.
Skr.—Sanskrit.
Skr.—Sanskrit.
S. L.—Solicitor at Law.
S. L.—Lawyer.
S. lat.—South latitude.
S. lat.—South latitude.
S. M.—State Militia; Short Metre; Sergeant-Major; Sons of Malta.
S. M.—State Militia; Short Meter; Sergeant Major; Sons of Malta.
sm. c.—Small capitals.
sm. c.—Small caps.
S. M. Lond. Soc. Cor.—Societatis Medicæ Londonensis Socius Cor., Corresponding Member of the London Medical Society.
S. M. Lond. Soc. Cor.—Societatis Medicæ Londonensis Socius Cor., Corresponding Member of the London Medical Society.
s. n.—Secundum naturam, according to nature.
s. n.—Secundum naturam, according to nature.
Soc. Isl.—Society Islands.
Soc. Isl.—Society Islands.
Sol.—Solomon; Solution.
Sol.—Solomon; Solution.
Sol.-Gen.—Solicitor-General.
Sol.-Gen.—Solicitor General.
S. of Sol.—Song of Solomon.
S. of Sol.—Song of Songs.
S. P.—Sine prole, without issue; salutem precatur, he prays for his prosperity.
S. P.—Sine prole, without children; salutem precatur, he prays for his well-being.
S. P. A. S.—Societatis Philosophicæ Americanæ Socius, Member of the American Philosophical Society.
S. P. A. S.—Societatis Philosophicæ Americanæ Socius, Member of the American Philosophical Society.
S. P. C. A.—Society for the Prevention of Cruelty to Animals.
S.P.C.A.—Society for the Prevention of Cruelty to Animals.
S. P. D.—Salutem plurimam dicit, he[355] wishes much health, or sends his best respects.
S. P. D.—Salutem plurimam dicit, he[355] wishes you all the best or sends his regards.
S. P. G.—Society for the Propagation of the Gospel.
S. P. G.—Society for the Propagation of the Gospel.
Sp. gr.—Specific gravity.
Sp. gr.—Specific gravity.
S. P. Q. R.—Senatus Populusque Romani, the Senate and people of Rome.
S. P. Q. R.—Senatus Populusque Romani, the Senate and the people of Rome.
S. P. R. S.—Sublime Prince of the Royal Secret.
S. P. R. S.—Sublime Prince of the Royal Secret.
Sq. ft.—Square foot or square feet.
Sq. ft.—Square foot or square feet.
Sq. in.—Square inch or inches.
Sq. in.—Square inch(es).
Sq. m.—Square mile or miles.
Sq. m.—Square meters.
Sq. r.—Square rood or roods.
Sq. r.—Square rod or rods.
Sq. yd.—Square yard.
Sq. yd.—Square yard.
Sr.—Sir; Senior.
Sr.—Sir; Senior.
S. R. I.—Sacrum Romanum Imperium, Holy Roman Empire.
S. R. I.—Sacrum Romanum Imperium, Holy Roman Empire.
S. R. S.—Societatis Regiæ Socius, Fellow of the Royal Society.
S. R. S.—Societatis Regiæ Socius, Fellow of the Royal Society.
S. S.—Sunday-school.
S.S.—Sunday school.
SS.—Saints.
Saints.
SS. or ss.—Scilicet, to wit.
SS. or ss.—Scilicet, to wit.
ss.—Semis, half.
ss.—Semis, half.
S. S. C.—Solicitor of the Supreme Court.
S. S. C.—Solicitor of the Supreme Court.
S. S. E.—South-southeast.
S. S. E.—Southeast by south.
S. S. W.—South-southwest.
S. S. W.—S-SW.
St.—Saint; Street; Strait.
St.—Saint; St.; Strait.
Stat.—Statute.
Stat.—Statute.
S. T. D.—Sacra Theologiæ Doctor, Doctor of Divinity.
S. T. D.—Sacra Theologiæ Doctor, Doctor of Divinity.
Ster. or Stg.—Sterling.
Ster. or Stg.—Sterling.
S. T. P.—Sacræ Theologiæ Professor, Professor of Divinity.
S. T. P.—Sacræ Theologiæ Professor, Professor of Theology.
Subj.—Subjunctive.
Subj.—Subjunctive.
Subst.—Substantive.
Subst.—Substantive.
Suff—Suffix.
Suff—Suffix.
Su.-Goth.—Suio-Gothic.
Suio-Gothic.
Su., Sun. or Sund.—Sunday.
Sun.—Sunday.
Sup.—Supplement; Superfine.
Sup.—Supp; Superfine.
Supt.—Superintendent.
Supt.—Superintendent.
Surg.—Surgeon; Surgery.
Surg.—Surgeon; Surgery.
Surg.-Gen.—Surgeon-General.
Surgeon General.
Surv.—Surveyor.
Surv.—Surveyor.
Surv.-Gen.—Surveyor-General.
Surveyor-General.
Sus.—Susannah.
Sus.—Susannah.
s. v.—Sub verbo, under the word or title.
s. v.—Sub verbo, under the word or title.
S. W.—Senior Warden; Southwest.
S.W.—Senior Warden; Southwest.
Syn.—Synonym; Synonymous.
Syn.—Synonym; Synonymous.
T.—Territory.
T.—Area.
t.—tonneau, (metric system.)
tonneau (metric system)
T.—Tutti, all together.
Everyone, all together.
T. or tom.—Tome, volume.
T. or tom.—Book, volume.
Ta.—Tantalum (Columbium.)
Ta.—Tantalum (Niobium.)
T. E.—Topographical Engineers.
T. E.—Topographical Engineers.
Tenn.—Tennessee.
Tenn. - Tennessee.
Ter.—Territory.
Ter. — Area.
Tex.—Texas.
Tex — Texas.
Text. Rec.—Textus Receptus, the Received Text.
Text. Rec.—Textus Receptus, the Received Text.
Thlr.—Thaler, (German coin.)
Thaler (German coin).
Th. or Thurs.—Thursday.
Thurs.—Thursday.
Theo.—Theodore.
Theo.—Theodore.
Theol.—Theology; Theological.
Theol.—Theology; Theological.
Theoph.—Theophilus.
Theoph.—Theophilus.
Thess.—Thessalonians.
Thess. — Thessalonians.
Tho’.—Though.
Though.
Thos.—Thomas.
Thos. - Thomas.
Thro’.—Through.
Through.
Tim.—Timothy.
Tim.—Timothy.
Tit.—Titus.
Tit.—Titus.
T. O.—Turn over.
T. O.—Flip over.
Tob.—Tobit.
Tob.—Tobit.
Tom.—Volume.
Tom.—Volume.
Topog.—Topography; Topographical.
Topog.—Topography; Topo.
Tr.—Transpose; Translator; Translation.
Tr.—Transpose; Translator; Translation.
Tr.—Trustee. Trs.—Trustees.
Tr.—Trustee. Trs.—Trustees.
tr.—Trillo, a shake.
tr.—Trillo, a shake.
Trans.—Translator; Translation; Transactions.
Trans.—Translator; Translation; Transactions.
Treas.—Treasurer.
Treas.—Treasurer.
Trin.—Trinity.
Trin. — Trinity.
Tues. or Tu.—Tuesday.
Tues. or Tu.—Tuesday.
Typ.—Typographer.
Typ.—Designer.
U. C.—Upper Canada.
U.C.—Ontario.
U. C.—Urbe conditâ, year of Rome.
U. C.—Urbe conditâ, year of Rome.
U. E. I. C.—United East India Company.
U. E. I. C.—United East India Company.
U. G. R. R.—Underground Railway.
U. G. R. R.—Underground Railroad.
U. J. D.—Utriusque Juris Doctor, Doctor of both Laws, (Civil and Canon.)
U. J. D.—Utriusque Juris Doctor, Doctor of both Laws, (Civil and Canon.)
U. K.—United Kingdom.
U.K.—United Kingdom.
ult.—Ultimo, last; of the last month.
ult.—Ultimo, last; referring to the last month.
Unit.—Unitarian.
Unit.—Unitarian.
Univ.—University.
Univ. — University.
U. P. C.—United Presbyterian Church.
United Presbyterian Church.
U. S.—United States.
U.S.—United States.
u. s.—Ut supra or uti supra, as above.
u. s.—Ut supra or uti supra, as mentioned above.
U. S. A.—United States of America; United States Army.
U.S.A.—United States of America; United States Army.
U. S. M.—United States Mail; United States Marines.
U. S. M.—United States Mail; United States Marines.
U. S. M. A.—United States Military Academy.
U.S.M.A.—United States Military Academy.
U. S. N.—United States Navy.
U.S. Navy
U. S. N. A.—United States Naval Academy.
U.S.N.A.—United States Naval Academy.
U. S. S.—United States Senate.
U.S. Senate.
U. S. V.—United States Volunteers.
U.S. Volunteers.
U. T.—Utah Territory.
U. T.—Utah Territory.
V.—Five or fifth.
V.—Five or 5.
V.—Violin; VV.—Violins.
V.—Violin; VV.—Violins.
v. or vid.—Vide, see.
v. or vid.—Vide, see.
v. or vs.—Versus, against; Versiculo, in such a verse.
v. or vs.—Versus, against; Versiculo, in such a verse.
Va.—Virginia.
VA — Virginia.
Vat.—Vatican.
Vat.—Vatican.
V. C.—Vice-Chancellor.
V. C.—Vice-Chancellor.
V. D. M.—Verbi Dei Minister, Minister of God’s Word.
V. D. M.—Verbi Dei Minister, Minister of God’s Word.
Ven.—Venerable.
Ven. - Venerable.
Ven. or Ven. Fa.—Venire facias, a writ to a sheriff to summon a jury.
Ven. or Ven. Fa.—Venire facias, a legal order to a sheriff to call a jury.
Ven. Ex.—Venditione exponas, a writ of execution directed to a sheriff to sell goods, etc.
Ven. Ex.—Venditione exponas, a court order for a sheriff to sell goods, etc.
Ver.—Verse.
Verse.
V. G.—Vicar-General.
V.G.—Vicar General.
v. g.—Verbi gratiâ, as for example.
e.g.—Verbi gratiâ, for example.
VI.—Six or sixth.
Sixth.
VII.—Seven or seventh.
VII.—Seven or 7.
VIII.—Eight or eighth.
VIII.—Eight.
Vice. Pres. or V. P.—Vice-President.
Vice President or VP.
Visc.—Viscount.
Viscount.
viz. or vl.—Videlicit, to wit; namely; that is to say.
viz. or vl.—Videlicit, namely; that is; in other words.
Vo.—Verso, left-hand page.
Vo.—Verso, left page.
Vol.—Volume.
Vol.—Vol.
V. R.—Victoria Regina, Queen Victoria.
V. R.—Victoria Regina, Queen Victoria.
Vt.—Vermont.
Vt. - Vermont.
Vul.—Vulgate (Version.)
Vul.—Vulgate (Version)
vv. ll.—Variæ lectiones, different readings.
Variæ lectiones, different readings.
v. y.—Various years.
v. y.—Different years.
W.—West.
W.—West.
Wash.—Washington.
Wash. — Washington.
Wed.—Wednesday.
Wed.—Wednesday.
w. f.—Wrong fount.
w. f.—Wrong font.
Whf.—Wharf.
Wharf.
W. I.—West India.
W.I.—West Indies.
Wisc.—Wisconsin.
Wisc. — Wisconsin.
Wisd.—Wisdom, (Book of.)
Wisd.—Wisdom (Book of)
Wk.—Week.
Wk. - Week.
W. lon.—West longitude.
W. lon.—West long.
W. M.—Worshipful Master.
W. M.—Master of the Lodge.
Wm.—William.
Wm.—Will.
W. N. W.—West-northwest.
W. N. W.—WNW.
Wpful.—Worshipful.
Wpful.—Worshipful.
W. S.—Writer to the Signet.
W. S.—Writer to the Signet.
W. S. W.—West-southwest.
W. S. W.—WSW.
W. T.—Washington Territory.
W. T. — Washington State.
Wt.—Weight.
Wt.—Weight.
W. Va.—West Virginia.
W. Va.—West Virginia.
X.—Ten or tenth.
10 or tenth.
XI.—Eleven.
11—Eleven.
XII.—Twelve.
12.—Twelve.
XIII.—Thirteen.
XIII.—13.
XIV.—Fourteen.
14.
XV.—Fifteen.
15.
XVI.—Sixteen.
16.
XVII.—Seventeen.
17—Seventeen.
XVIII.—Eighteen.
18—Eighteen.
XIX.—Nineteen.
19.
XX.—Twenty.
XX.—Twenty.
XXX.—Thirty.
XXX.—30.
XL.—Forty.
40.
XC.—Ninety.
90.
X. or Xt.—Christ.
X. or Xt.—Christ.
Xmas or Xm.—Christmas.
Xmas = Christmas.
Xn. or Xtian.—Christian.
Christian.
Xnty. or Xty.—Christianity.
Xtianity.
Xper. or Xr.—Christopher.
Xper. or Xr.—Chris.
Yd.—Yard.
Yard.
y. or yᵉ.—The.
y. or yᵉ.—The.
yᵐ.—Them.
yᵐ.—Them.
yⁿ.—Then.
Then.
yʳ.—Their; Your.
yʳ.—Their; Your.
yˢ.—This.
This.
yᵗ.—That.
That.
Y. M. C. A.—Young Men’s Christian Association.
Y. M. C. A.—Young Men's Christian Association.
Yrs.—Years; Yours.
Yrs.—Years; Yours.
Zach.—Zachary.
Zach. — Zachary.
Zech.—Zechariah.
Zech.—Zachary.
Zeph.—Zephaniah.
Zeph. — Zephaniah.
Zool.—Zoology.
Zool.—Zoology.
&.—And.
& and.
&c.—And so forth.
etc.

FOREIGN WORDS AND PHRASES, WITH TRANSLATIONS.
A bas.—Down with.
Down with.
A capite ad calcem.—From head to foot.
A capite ad calcem.—From head to toe.
A fin.—To the end.
A fin.—To the finish.
A fortiori.—With stronger reason.
With stronger reason.
A l’abandon.—At random.
A l’abandon.—By chance.
A la bonne heure.—Opportunely; in good time.
A la bonne heure.—Just in time; at the right moment.
A la dérobée.—By stealth.
A la dérobée.—Sneakily.
A la mode.—According to the fashion.
Fashionable.
A main armée.—With force of arms.
A main armée.—By the strength of arms.
A mensa et thoro.—From bed and board.
A mensa et thoro.—From bed and board.
A posteriori.—From effect to cause; from the latter.
A posteriori.—From effect to cause; from the latter.
A priori.—From cause to effect; from the former.
A priori.—From cause to effect; from the former.
A tempo giusto.—To sing or play in true time. (Music.)
A tempo giusto.—To sing or play in the correct timing. (Music.)
A tempo rimo.—To restore the original movement. (Music.)
A tempo rimo.—To return to the original pace. (Music.)
A vinculo matrimonii.—From the tie of marriage.
A vinculo matrimonii.—From the bond of marriage.
A votre santé.—To your health.
Cheers.
Ab extra.—From without.
From outside.
Ab initio.—From the beginning.
From the start.
Ab origine.—From the beginning.
From the beginning.
Ab ova.—From the beginning.
From the start.
Ab urbe conditâ.—From the building of the city (Rome); abridged A. U. C.
Ab urbe conditâ.—From the founding of the city (Rome); shortened A. U. C.
Abit invidia.—All offence apart; let there be no malice.
Abit invidia.—Setting aside all offense; let there be no hatred.
Absit omen.—May it not prove ominous.
Absit omen.—Hopefully, it won't turn out to be a bad sign.
Absque hoc.—Without this or that.
Without this or that.
Ac etiam.—And also.
And also.
Actum est de republica.—It is all over with the commonwealth.
Actum est de republica.—It's all over for the government.
Ad absurdum.—To show the absurdity.
To show the absurdity.
Ad arbitrium.—At pleasure.
At will.
Ad astra per aspera.—To the stars through difficulties.
Ad astra per aspera.—To the stars through challenges.
Ad captandum vulgus.—To catch the mob or the vulgar.
Ad captandum vulgus.—To grab the attention of the masses or the common people.
Ad eundem.—To the same point or degree.
Ad eundem.—To the same point or level.
Ad finem.—To the end.
To the end.
Ad Græcas Calendas.—An indefinite postponement. (The Greeks had no calends.)
Ad Græcas Calendas.—An indefinite postponement. (The Greeks didn't have calends.)
Ad hominem.—To the man (that is, to the interests or the passions of the man.)
Ad hominem.—To the person (that is, to the interests or the emotions of the person.)
Ad infinitum.—Without end.
Ad infinitum.—Forever.
Ad inquirendum.—For inquiry.
For inquiry.
Ad interim.—In the mean while.
In the meantime.
Ad libitum.—At pleasure.
Ad libitum.—As you like.
Ad litem.—For the action (at law.)
Ad litem.—For the legal action.
Ad nauseam.—To a disgusting degree.
Ad nauseam.—To an excessive degree.
Ad referendum.—For further consideration.
For further consideration.
Ad rem.—To the purpose.
To the point.
Ad unguem.—To the nail; exactly; nicely.
Ad unguem.—To the nail; perfectly; neatly.
Ad valorem.—According to the value.
According to the value.
Addendum.—An addition or appendix.
Addendum.—A supplement or appendix.
Adhuc sub judice lis est.—The affair is not yet decided.
Adhuc sub judice lis est.—The matter isn't resolved yet.
Ægrescit medendo.—The remedy is worse than the disease.
Ægrescit medendo.—The cure is worse than the illness.
Æquam servare mentem.—To preserve an equable mind.
Æquam servare mentem.—To maintain a balanced mind.
Æquo animo.—With an equable mind.
Æquo animo.—With a calm mind.
Ære perennius.—More lasting than brass; enduring ever.
Ære perennius.—More lasting than brass; enduring forever.
Affaire du cœur.—A love affair; an amour.
Affaire du cœur.—A love affair; a romance.
Afflatus.—Inspiration.
Inspiration.
Agenda.—Things to be done.
Agenda.—To-do list.
Agitato.—A broken style of performance, to awaken surprise. (Music.)
Agitato.—A fragmented style of performance, meant to evoke surprise. (Music.)
Agnus Dei.—Lamb of God.
Lamb of God.
Aide-de-camp.—Assistant to a general.
Aide-de-camp.—General's assistant.
Aide-toi, et le ciel t’aidera.—Help thyself, and Heaven will help thee.
Aide-toi, et le ciel t’aidera.—Help yourself, and the universe will help you.
Alere flammam.—To feed the flame.
Feed the flame.
Al fresco.—In the open air.
Al fresco.—Outdoors.
Alga.—A kind of sea-weed.
Seaweed.
Alguazil.—A Spanish constable.
Alguazil.—A Spanish police officer.
Alias.—Otherwise; elsewhere.
Otherwise; elsewhere.
Alibi.—Elsewhere; not present.
Alibi.—Somewhere else; not present.
Alis volat propriis.—She flies with her own wings.
Alis volat propriis.—She flies on her own.
Aliunde.—From some other quarter or person.
Aliunde.—From another source or person.
Allegretto.—A movement quicker than andante, but not so quick as allegro. (Music.)
Allegretto.—A movement faster than andante, but not as fast as allegro. (Music.)
Allemande.—A kind of German dance.
Allemande.—A type of German dance.
Alma mater.—Benign mother (applied to a university.)
Alma mater.—Kind mother (referring to a university.)
Alter ego.—A second self.
Alter ego.—A second self.
Alto octavo.—An octave higher.
Alto octavo.—An octave up.
Alto relievo.—High relief. (Sculpture.)
High relief. (Sculpture.)
Alto ripieno.—The tenor of a great chorus.
Alto ripieno.—The main part of a large choir.
Alto violino.—A small tenor violin.
Alto violino.—A small tenor violin.
Amende.—Compensation; apology.
Fine. — Compensation; apology.
Ami du peuple.—Friend of the people.
Ami du peuple.—Friend of the people.
Amicus curiæ.—A friend of the court.
Amicus curiæ.—A friend of the court.
Amor patriæ.—Love of country.
Love of country.
Amour propre.—Self-love; vanity.
Self-love; vanity.
Ancien régime.—Former administration; ancient order of things.
Ancien régime.—Old system; traditional way of doing things.
Andante.—Moderately slow movement, between largo and allegro. (Music.)
Andante.—Moderately slow movement, between largo and allegro. (Music.)
Anglicè.—In English.
In English.
Anguis in herbâ.—A snake in the grass.
Anguis in herbâ.—A snake in the grass.
Animis opibusque parati.—Ever ready with our lives and property.
Animis opibusque parati.—Always ready with our lives and resources.
Animo et fide.—By (or with) courage and faith.
Animo et fide.—With courage and faith.
Animo facto.—Really and truly.
Animo facto.—For real.
Animus furandi.—Felonious intent.
Animus furandi.—Theft intent.
Anno Domini.—In the year of our Lord.
Anno Domini.—In the year of our Lord.
Anno lucis.—In the year of light.
Anno lucis.—In the year of light.
Anno mundi.—In the year of the world.
Anno mundi.—In the year of the world.
Annus mirabilis.—Year of wonders.
Annus mirabilis.—Year of miracles.
Ante bellum.—Before the war.
Before the war.
Ante lucem.—Before light.
Ante lucem.—Before dawn.
Ante meridiem.—Before noon.
Before noon.
Aperçu.—A brief sketch of any subject.
Aperçu.—A quick overview of any topic.
Appogiatura.—A note in a smaller character than the regular notes of the piece. (Music.)
Appogiatura.—A note that is smaller in size compared to the regular notes in the piece. (Music.)
Apropos (Fr. à propos.)—To the purpose.
Apropos—To the point.
Aqua vitæ.—Water of life; brandy.
Aqua vitæ.—Water of life; liquor.
Arbiter elegantiarum.—Master of ceremonies; an umpire in matters of taste.
Arbiter elegantiarum.—Master of ceremonies; a judge in matters of style.
Arcana imperii.—State secrets.
Arcana imperii.—Government secrets.
Arcanum.—A secret.
Arcanum.—A secret.
Argumentum ad crumenam.—An argument to the purse.
Argumentum ad crumenam.—An argument based on financial gain.
Argumentum ad fidem.—An appeal to faith.
Argumentum ad fidem.—An appeal to belief.
Argumentum ad hominem.—An argument to the person.
Argumentum ad hominem.—An argument directed at the individual.
Argumentum ad ignorantiam.—An argument founded on an adversary’s ignorance of facts.
Argumentum ad ignorantiam.—An argument based on the opponent's lack of knowledge about the facts.
Argumentum ad judicium.—An appeal to the common sense of mankind.
Argumentum ad judicium.—A call to the common sense of humanity.
Argumentum ad populum.—An appeal to the people.
Argumentum ad populum.—A appeal to the public.
Argumentum ad verecundiam.—An argument to modesty.
Argumentum ad verecundiam.—A humility argument.
Argumentum baculinum.—Club law.
Argumentum baculinum.—Club rules.
Arioso.—Light, airy.
Arioso. —Light and airy.
Armiger.—One bearing arms; an esquire.
Armiger.—One who carries arms; an esquire.
Arpeggio.—The notes of a chord played in rapid succession, and not simultaneously. (Music.)
Arpeggio.—The notes of a chord played quickly one after another instead of all at once. (Music.)
Arrière-pensée.—Mental reservation.
Backdoor deal.
Ars est celare artem.—True art is to conceal art.
Ars est celare artem.—True art is to hide the art.
Assumpsit.—It is assumed or taken for granted.
Assumpsit.—It is assumed or taken for granted.
Astra castra, Numen lumen.—The stars my camp, the Deity my light.
Astra castra, Numen lumen.—The stars are my camp, the Deity is my light.
At spes non fracta.—But hope is not broken.
At spes non fracta.—But hope isn't broken.
Au fait.—Well instructed; master of it.
Au fait.—Well-informed; in control of it.
Au fond.—To the bottom, or main point.
Au fond.—At its core, or main point.
Au pied de la lettre.—Literally.
Au pied de la lettre.—Literally.
Au pis aller.—At the worst.
At worst.
Au revoir.—Farewell.
Goodbye.
Audi alteram partem.—Hear the other side.
Audi alteram partem.—Listen to the other side.
Aura popularis.—The gale of popular favour.
Aura popularis.—The wind of public favor.
Auri sacra fames.—The accursed thirst for gold.
Auri sacra fames.—The cursed desire for gold.
Auter droit.—Another’s right
Copyright.
Auter foit.—Another time.
Another time.
Auter vie.—Another’s life.
Another's life.
Aut vincere aut mori.—Victory or death.
Aut vincere aut mori.—Win or die.
Auto-da-fé, Auto-de-fe.—An act of faith; burning of heretics.
Auto-da-fé, Auto-de-fe.—A public declaration of faith; execution of heretics by fire.
Auxilium ab alto.—Help from on high.
Help from above.
Avant-coureur.—A forerunner.
Forerunner.
Ave, Maria.—Hail, Mary.
Hail, Mary.
Badinage.—Light or playful discourse.
Badinage.—Casual or playful chatter.
Bagatelle.—A trifle.
Bagatelle.—A trivial thing.
Bas bleu.—A blue-stocking; a literary woman.
Bas bleu.—A blue-stocking; a woman who is into literature.
Basso-continuo.—Thorough bass.
Thorough bass.
Basso-relievo.—Figures in low relief.
Basso-relievo.—Figures in low relief.
Bateau.—A long light boat.
Bateau.—A long lightweight boat.
Beau-idéal.—A model of ideal perfection.
Beau-idéal.—A standard of ideal perfection.
Beau monde.—The fashionable world.
Beau monde.—The trendy world.
Bel esprit.—A brilliant mind.
Bel esprit.—A sharp mind.
Bella-donna.—The deadly nightshade; fair lady.
Bella-donna.—The deadly nightshade; beautiful woman.
Belles-lettres.—Polite literature.
Belles-lettres.—Literary arts.
Bellum internecinum.—A war of extermination.
Bellum internecinum.—A total war.
Bellum lethale.—A deadly war.
Deadly war.
Bene placito.—At pleasure. (Music.)
At pleasure. (Music.)
Benigno numine.—-By the favour of Providence.
Benigno numine.—-By the grace of Providence.
Ben trovato.—Well found; an ingenious solution.
Ben trovato.—Nice find; a clever solution.
Billet-doux.—A love-letter.
Love letter.
Bis dat qui citò dat.—He gives twice who gives promptly.
Bis dat qui citò dat.—He gives twice who gives quickly.
Bis peccare in bello non licet.—To blunder twice is not allowed in war.
Bis peccare in bello non licet.—You can’t make the same mistake twice in war.
Bis vincit, qui se vincit in victoriâ.—He conquers a second time, who controls himself in victory.
Bis vincit, qui se vincit in victoriâ.—He conquers again who masters himself in victory.
Bizarre.—Odd; fantastic.
Bizarre.—Weird; amazing.
Blasé.—Surfeited.
Blasé.—Jaded.
Bon gré mal gré.—Willing or unwilling.
Bon gré mal gré.—Whether you like it or not.
Bon jour.—Good-day; good-morning.
Good day.
Bon mot.—A witty saying; a jest; a quibble.
Bon mot.—A clever remark; a joke; a playful comment.
Bon soir.—Good-evening.
Good evening.
Bon ton.—High fashion; first-class society.
Bon ton.—High fashion; elite society.
Bon vivant.—A high liver.
Bon vivant.—A socialite.
Bona fide.—In good faith.
In good faith.
Bon-bon.—A sweetmeat; confectionery.
Candy.
Bonhomie.—Good-natured simplicity.
Bonhomie.—Friendly simplicity.
Bonis nocet quisquis pepercerit malis.—He hurts the good who spares the bad.
Bonis nocet quisquis pepercerit malis.—He hurts the good who spares the bad.
Bonne bouche.—A delicious morsel.
Bonne bouche.—A tasty bite.
Bonus.—An extra payment for a service rendered or a thing received.
Bonus.—An additional payment for a service provided or a product received.
Boreas.—The north wind.
North wind.
Boudoir.—A small private apartment.
Boudoir.—A small private room.
Bourgeois.—A citizen of the trading class; a printing type.
Bourgeois.—A member of the merchant class; a typeface used in printing.
Bourgeoisie.—The body of citizens.
Bourgeoisie.—The class of citizens.
Bravura.—A song of difficult execution.
Bravura.—A technically challenging song.
Breveté.—Patented.
Patented.
Brutum fulmen.—A harmless thunderbolt; unreasoning bluster.
Brutum fulmen.—A harmless lightning bolt; unthinking noise.
Burletta.—A musical farce.
Burletta.—A musical comedy.
Cachet.—A seal.
Seal.
Cacoethes.—A bad habit or custom.
Cacoethes.—A bad habit.
Cacoethes carpendi.—A rage for finding fault.
Obsessive criticism.
Cacoethes loquendi.—An itch for speaking.
A desire to talk.
Cacoethes scribendi.—A passion for writing.
A passion for writing.
Cadenza.—The fall or modulation of the voice, in music.
Cadenza.—The rise and fall of the voice, in music.
Cæca est invidia.—Envy is blind.
Envy is blind.
Cætera desunt.—The remainder is wanting.
The rest is missing.
Cæteris paribus.—Other things being equal.
Cæteris paribus.—Other things being equal.
Calibre.—Capacity or compass; mental power; a term in gunnery.
Calibre.—Capacity or scope; mental ability; a term used in firearms.
Camera obscura.—A dark chamber used by artists.
Camera obscura.—A dark room used by artists.
Campus Martius.—The field of Mars; a place of military exercise.
Campus Martius.—The field of Mars; a place for military training.
Canaille.—The rabble.
Canaille.—The mob.
Candida Pax.—White-robed Peace.
Candida Pax.—Peace in white robes.
Cantata.—A poem set to music.
Song. — A poem set to music.
Cantate Domino.—Sing to the Lord.
Sing to the Lord.
Cap-à-pie.—From head to foot.
Head to toe.
Capias ad satisfaciendum.—You may take to satisfy.
Capias ad satisfaciendum.—You can take what's needed to settle.
Capriccio.—A fanciful irregular kind of musical composition.
Capriccio.—A whimsical, unconventional type of musical composition.
Capriole.—A leap without advancing; capers.
Capriole.—A jump without moving forward; capers.
Caput mortuum.—Dead head; the worthless remains.
Caput mortuum.—A dead head; the worthless leftovers.
Caret.—Is wanting or omitted.
Caret.—Is missing or left out.
Caret initio et fine.—It wants beginning and end.
Caret initio et fine.—It lacks a beginning and an end.
Carpe diem.—Enjoy the present day.
Seize the day.
Carte blanche.—Unconditional terms.
Carte blanche.—Blank check.
Casus belli.—An occasion for war.
Casus belli.—A reason for war.
Casus fæderis.—A case of conspiracy; the end of the league.
Casus fæderis.—A case of conspiracy; the end of the alliance.
Catalogue raisonné.—A catalogue of[360] books arranged according to their subjects.
Catalogue raisonné.—A catalog of[360] books organized by their topics.
Cause célèbre.—A remarkable trial in a court of justice.
Cause célèbre.—A high-profile trial in a court of law.
Caveat actor.—Let the doer beware.
Caveat actor.—Let the doer beware.
Caveat emptor.—Let the purchaser take heed or beware.
Caveat emptor.—Buyers should take heed or be cautious.
Cavendo tutus.—Safe through caution.
Cavendo tutus.—Stay safe through caution.
Ce n’est que le premier pas qui coûte.—It is only the first step which is difficult.
Ce n’est que le premier pas qui coûte.—It’s only the first step that’s tough.
Cedant arma togæ.—Let military power yield to the civil.
Cedant arma togæ.—Let military power give way to civil authority.
Cede Deo.—Submit to Providence.
Cede Deo.—Submit to Fate.
Certiorari.—To be made more certain.
Certiorari.—To be made clearer.
Cessio bonorum.—Yielding up of goods.
Goods surrender.
C’est une autre chose.—That is quite a different thing.
C’est une autre chose.—That’s a whole different story.
Chacun à son goût.—Every one to his taste.
Chacun à son goût.—Everyone has their own taste.
Chanson.—A song.
Song.
Chansonnette.—A little song.
Chansonnette.—A short song.
Chapeau.—A hat.
A hat.
Chapelle ardente.—The place where a dead person lies in state.
Chapelle ardente.—The location where a deceased individual is laid out for viewing.
Chaperon.—An attendant on a lady, as a guide and protector.
Chaperon.—A person who accompanies a woman to provide guidance and protection.
Chargé d’affaires.—An ambassador of second rank.
i Chargé d’affaires.—A second-in-command ambassador.
Château.—A castle; a country mansion.
Castle—A castle; a country house.
Chef-d’œuvre.—A masterpiece.
Masterpiece.
Chevalier d’industrie.—A knight of industry; one who lives by persevering fraud.
Chevalier d’industrie.—A con artist; someone who makes a living through persistent deception.
Chi tace confessa.—Silence is confession.
Silence is confession.
Chiaro-oscuro or Chiaroscuro.—Light and shadow in painting.
Chiaroscuro.—Light and shadow in painting.
Chose qui plaît est à demi vendue.—A thing which pleases is already half sold.
Chose qui plaît est à demi vendue.—A thing that appeals is already half sold.
Cicerone.—A guide or conductor.
Cicerone.—A guide.
Cicisbeo.—A dangler after a lady.
Cicisbeo.—A suitor for a lady.
Ci-devant.—Formerly; former.
Ci-devant.—Previously; previous.
Circa.—About.
About.
Citò maturum citò putridum.—Soon ripe, soon rotten.
Citò maturum citò putridum.—Soon ripe, soon rotten.
Clarior e tenebris.—More bright from obscurity.
Clarior e tenebris.—Brighter from the shadows.
Clique.—A party; a gang.
Clique.—A group; a crew.
Cognomen.—A surname.
Cognomen.—A last name.
Comme il faut.—As it should be.
Comme il faut.—The way it should be.
Commune bonum.—A common good.
Common good.
Communia propriè dicere.—To express common things with propriety.
Communia propriè dicere.—To properly express common things.
Communibus annis.—One year with another.
In the coming years.
Compos mentis.—Of sound mind.
Compos mentis.—Sane.
Con amore.—With love or hearty inclination.
Con amore.—With love or strong affection.
Concio ad clerum.—A discourse to the clergy.
Concio ad clerum.—A talk for the clergy.
Congé d’élire.—Permission to elect.
Congé d’élire.—Voting leave.
Connoisseur.—-A skilful judge.
Expert—A skilled judge.
Consensus facet legem.—Consent makes the law.
Consensus facet legem.—Agreement creates the law.
Contour.—The outline of a figure.
Outline. —The outline of a figure.
Contra.—Against.
Contra.—Against.
Contra bonos mores.—Against good manners.
Against good manners.
Contretemps.—A mischance; disappointment.
Contretemps.—An accident; setback.
Coram nobis.—Before us.
Coram nobis.—In our presence.
Coram non judice.—Before one who is not the proper judge.
Coram non judice.—In front of someone who is not the right judge.
Cornucopia.—The horn of plenty.
Cornucopia.—The abundance horn.
Corpus delicti.—The whole nature of the offence.
Corpus delicti.—The complete essence of the crime.
Corrigenda.—Corrections to be made.
Corrections to be made.
Coryphæus.—A leader, or chief.
Coryphæus.—A leader or chief.
Cotillon.—A lively dance.
Cotillon.—A fun dance.
Couleur de rose.—Rose-colour; an aspect of beauty and attractiveness.
Couleur de rose.—Rose color; a quality of beauty and appeal.
Coup de grâce.—The finishing stroke.
Final blow.
Coup de main.—A bold and rapid enterprise.
Coup de main.—A daring and quick action.
Coup de pied.—A kick.
Coup de pied.—A kick.
Coup de soleil.—A stroke of the sun.
Sunburn.
Coup d’état.—A master-stroke of state policy.
Coup d’état.—A brilliant move in government strategy.
Coup d’œil.—Rapid view or glance.
Quick look.
Coûte qu’il coûte.—Cost what it may.
Coûte qu’il coûte.—No matter what it costs.
Credat Judæus.—A Jew may believe it.
Credat Judæus.—A Jew may believe it.
Crescit amor nummi quantum ipsa pecunia crescit.—The love of money increases as rapidly as the money itself increases.
Crescit amor nummi quantum ipsa pecunia crescit.—The love of money grows just as quickly as money itself grows.
Crescit eundo.—It increases by going.
It grows by going.
Crescite et multiplicamini.—Increase and multiply.
Crescite et multiplicamini.—Grow and multiply.
Crimen falsi.—Falsehood; perjury.
Crimen falsi.—Lying; perjury.
Crux criticorum.—The cross or puzzle of critics.
Crux criticorum.—The challenge or dilemma of critics.
Cui bono?—To whose good?
Cui bono?—Who benefits?
Cui malo?—To whose harm?
To whose harm?
Cul de sac.—The bottom of the bag; a difficulty; a street or lane that has no outlet.
Cul de sac.—The end of the line; a challenge; a street or road that doesn’t lead anywhere.
Cum grano salis.—With a grain of salt; with some allowance.
Cum grano salis.—Take it with a grain of salt; be skeptical or cautious about it.
Cum multis aliis.—With many others.
With many others.
Cum privilegio.—With privilege.
With privilege.
Curia advisari vult.—The court wishes to be advised.
Curia advisari vult.—The court wants to be advised.
Curiosa felicitas.—A felicitous tact.
Curious happiness.—A lucky touch.
Currente calamo.—With a running pen; written off-hand.
Currente calamo.—With a quick pen; written spontaneously.
Custos rotulorum.—Keeper of the rolls.
Custos rotulorum.—Records keeper.
Da capo.—Over again.
Start over.
Damnant quod non intelligunt.—They condemn what they do not comprehend.
Damnant quod non intelligunt.—They condemn what they do not understand.
Data.—Things granted, (sing. datum.)
Data.—Things granted, (sing. datum.)
De bonis non.—Of the goods not yet administered on.
De bonis non.—Of the assets not yet handled.
De die in diem.—From day to day.
De die in diem.—From day to day.
De facto.—In fact; in reality.
In reality.
De gustibus non est disputandum.—There is no disputing about tastes.
De gustibus non est disputandum.—You can't argue about taste.
De jure.—By law or right.
De jure.—Legally.
De mortuis nil nisi bonum.—Say nothing but what is good of the dead.
De mortuis nil nisi bonum.—Say only good things about the dead.
De novo.—Anew.
Anew.
De profundis.—Out of the depths.
Out of the depths.
De trop.—Out of place; not wanted.
Unnecessary; unwelcome.
Debito justitiæ.—By debt of justice.
Debt of justice.
Début.—Beginning of an enterprise; first appearance.
Début.—Start of a project; first appearance.
Deceptio visûs.—An illusion of the sight.
Visual illusion.
Dedimus potestatem.—We have given power.
We have given power.
Deficit.—A want of deficiency.
Deficit.—A lack or shortfall.
Dei gratiâ.—By the grace of God.
Dei gratiâ.—By the grace of God.
Déjeûner à la fourchette.—A breakfast or luncheon with meats.
Déjeûner à la fourchette.—A breakfast or lunch with meats.
Dele.—Blot out or erase.
Delete. —Blot out or erase.
Delenda est Carthago.—Carthage must be blotted out.
Delenda est Carthago.—Carthage must be destroyed.
Delta (the Greek letter Δ,) a triangular tract of land toward the mouth of a river.
Delta (the Greek letter Δ,) a triangular piece of land at the mouth of a river.
Dénouement.—An unravelling or winding up.
Dénouement.—A resolution or conclusion.
Deo adjuvante, non timendum.—God helping, nothing need be feared.
Deo adjuvante, non timendum.—With God's help, there's nothing to fear.
Deo favente.—With God’s favour.
With God’s favor.
Deo gratias.—Thanks to God.
Thanks, God.
Deo juvante.—With God’s help.
With God’s help.
Deo non fortunâ.—From God, not fortune.
Deo non fortunâ.—From God, not luck.
Deo volente, or D. V.—God willing.
God willing.
Dépôt.—A store; the recruiting reserve of regiments.
Dépôt.—A storage place; the reserve pool for recruiting regiments.
Dernier ressort.—The last resort.
The last resort.
Desideratum.—Something desired or wanted.
Desideratum.—A desired item.
Desunt cætera.—The other things are wanting.
Desunt cætera.—The other things are missing.
Detinet.—He detains; he keeps.
Detinet.—He holds; he keeps.
Détour.—A circuitous march.
Detour.—A roundabout route.
Detur digniori.—Let it be given to the more worthy.
Detur digniori.—Let it be given to the more deserving.
Deus ex machinâ.—A god from the clouds; unexpected aid in an emergency.
Deus ex machinâ.—A god from the clouds; unexpected help in a crisis.
Devastavit.—He wasted.
Devastavit.—He wasted.
Devoir.—Duty.
Devoir.—Responsibility.
Dexter.—The right hand.
Dexter.—The right side.
Dictum.—A positive assertion (pl. dicta.)
Statement.—A positive assertion (pl. statements.)
Dictum de dicto.—Report upon hearsay.
Dictum de dicto.—Rumor report.
Dies faustus.—A lucky day.
Lucky day.
Dies iræ.—Day of wrath.
Dies iræ.—Day of judgment.
Dies non.—A day on which judges do not sit.
Dies non.—A day when judges don't work.
Dieu et mon droit.—God and my right.
Dieu et mon droit.—God and my right.
Dieu vous garde.—God protect you.
God bless you.
Dii majorum gentium.—The gods of the superior class; the twelve superior gods.
Dii majorum gentium.—The gods of the higher order; the twelve principal gods.
Dii penates.—Household gods.
Household gods.
Dilettanti.—Persons who devote themselves to science merely for amusement or relaxation. (Sing. Dilettante.)
Dilettanti.—People who engage in science just for fun or leisure. (Sing. Dilettante.)
Diluvium.—A deposit of superficial loam, sand, &c. caused by a deluge.
Diluvium.—A layer of topsoil, sand, etc., created by a flood.
Dirigo.—I direct or guide.
I direct.
Disjecta membra.—Scattered parts, limbs, or writings.
Disjecta membra.—Scattered pieces, limbs, or writings.
Distrait.—Absent in thought; absent-minded.
Distracted. —Absent in thought; absent-minded.
Distringas.—A writ for distraining.
Distringas.—A notice for seizing.
Divide et impera.—Divide and govern.
Divide and conquer.
Doce ut discas.—Teach, that you may learn.
Doce ut discas.—Teach so that you can learn.
Docendo dicimus.—We learn by teaching.
We learn by teaching.
Dolce.—Soft and agreeable. (Music.)
Dolce.—Sweet and pleasing. (Music.)
Dolce far niente.—Sweet idleness.
Sweet laziness.
Doli incapax.—Incapable of mischief.
Incapable of wrongdoing.
Doloroso.—Soft and pathetic. (Music.)
Doloroso.—Gentle and mournful. (Music.)
Domicile (L. domicilium.)—An abode.
Home.
Domine dirige nos.—O Lord, direct us.
Domine dirige nos.—O Lord, guide us.
Dominus vobiscum.—The Lord be with you.
Dominus vobiscum.—The Lord be with you.
Double entendre.—Double meaning (correctly written double entente.)
Double entendre.—A phrase or word with two meanings (properly written as double entente.)
Douceur.—A present or bribe; sweetness.
Sweetness.
Draco.—A dragon; a constellation.
Draco.—A dragon; a constellation.
Dramatis personæ.—The characters in a play.
Dramatis personæ.—The characters in a play.
Duet (Ital. duetto.)—A song for two performers.
Duet—A song for two singers.
Dulce est desipere in loco.—It is pleasant to jest, or revel, at the proper time.
Dulce est desipere in loco.—It's nice to joke around or have fun at the right time.
Dulce et decorum est pro patriâ mori.—It is sweet and pleasant to die for one’s country.
Dulce et decorum est pro patriâ mori.—It is sweet and honorable to die for your country.
Dulia.—An inferior kind of worship.
Dulia.—A lesser form of worship.
Dum spiro, spero.—Whilst I breathe, I hope.
Dum spiro, spero.—As long as I breathe, I hope.
Dum vivimus, vivamus.—While we live, let us live.
Dum vivimus, vivamus.—While we are alive, let's truly live.
Duo.—Two; a two-part song.
Duo.—Two; a two-part song.
Duodecimo.—A book having twelve leaves to a sheet.
Duodecimo.—A book with twelve leaves per sheet.
Durante placito, or durante beneplacito.—During pleasure.
During pleasure.
Durante vitâ.—During life.
During life.
Dux fœmina facti.—A woman was the leader to the deed.
Dux fœmina facti.—A woman was the leader of the action.
E pluribus unum.—One out of many; one composed of many: the motto of the United States.
E pluribus unum.—One from many; one made up of many: the motto of the United States.
Eau de vie.—Brandy; water of life.
Eau de vie.—Brandy; liquid of life.
Ecce homo.—Behold the man.
Ecce homo.—Check out the man.
Ecce signum.—Behold the sign.
Ecce signum.—Check out the sign.
Eclaircissement.—The clearing-up of an affair.
Clarification. — The clearing-up of an affair.
Eclat.—Splendour; applause.
Eclat.—Brilliance; applause.
Editio princeps.—The first edition.
First edition.
Eheu!—Ah, alas!
Oh no!
Elan.—Buoyancy; dash.
Elan.—Energy; spirit.
Elegit.—He hath elected; a writ of execution.
Elegit.—He has chosen; a writ of execution.
Elève.—A pupil.
Student.
Elite.—The best part.
Elite.—The top part.
Embonpoint.—Roundness; good condition.
Embonpoint.—Healthy plumpness.
Emeritus.—One retired from active official duties.
Emeritus.—Someone who has retired from active official duties.
Emeute.—Insurrection; uproar.
Emeute.—Riot; uproar.
Empressement.—Eagerness; ardour.
Eagerness; enthusiasm.
En ami.—As a friend.
En ami.—As a friend.
En avant!—Forward!
Forward!
En flûte.—Carrying guns on the upper deck only.
En flûte.—Only carrying guns on the upper deck.
En grande tenue.—In full dress.
In formal attire.
En masse.—In a mass; in a body.
En masse.—All together; as a group.
En passant.—By the way; in passing.
En passant.—By the way; just mentioning this.
En rapport.—In communication.
In touch.
En revanche.—In return.
On the other hand.
En route.—On the way.
On the way.
Enceinte.—Pregnant.
Enceinte.—Pregnant.
Enfans perdus.—Lost children; the forlorn hope.
Enfans perdus.—Lost kids; the hopeless dream.
Ennui.—Weariness; lassitude.
Ennui.—Boredom; fatigue.
Ense petit placidam sub libertate quietem.—By his sword he seeks the calm repose of liberty.
Ense petit placidam sub libertate quietem.—He uses his sword to pursue the peaceful rest of freedom.
Ensemble.—The whole taken together.
Together.
Entente cordiale.—The cordial understanding between two countries.
Entente cordiale.—The friendly agreement between two countries.
Entre nous.—Between ourselves.
Between us.
Entrée.—Entrance.
Entrée.—Entry.
Entremets.—Small and dainty dishes set between the principal ones at table.
Entremets.—Small and delicate dishes served between the main courses at the table.
Eo nomine.—By that name.
By that name.
Equilibrium.—Equality of weight; even balance.
Equilibrium.—Equal weight; balanced.
Ergo.—Therefore.
Therefore.
Eripuit cælo fulmen, sceptrumque tyrannis.—He snatched the thunderbolt from heaven, and the sceptre from tyrants.
Eripuit cælo fulmen, sceptrumque tyrannis.—He snatched the thunderbolt from the sky and the scepter from tyrants.
Erratum.—A mistake or error (pl. errata.)
Erratum.—A mistake or error (pl. errata.)
Escrow.—A deed or writing left with another, to be delivered on the performance of something specified.
Escrow.—A deed or document held by someone else that will be given to another party once certain conditions are met.
Espièglerie.—Waggish tricks.
Espièglerie.—Playful tricks.
Esprit de corps.—The animating spirit of a collective body.
Esprit de corps.—The motivating spirit of a group.
Est modus in rebus.—There is a medium in all things.
Est modus in rebus.—There is a balance in everything.
Estoppel.—A stop, a preventive plea.
Estoppel.—A stop, a preventive plea.
Esto perpetua.—May it last forever.
May it last forever.
Et cætera.—And the rest.
Et cætera.
Eureka.—I have found it.
Eureka.—I’ve found it.
Ex.—Out of; late (as, ex-consul.)
Out of; late (as, ex-consul.)
Ex animo.—Heartily.
Ex animo.—From the heart.
Ex cathedrâ.—From the chair; with high authority.
Ex cathedrâ.—From the chair; with great authority.
Ex concesso.—From what has been granted.
Ex concesso.—From what has been granted.
Ex curiâ.—Out of court.
Out of court.
Ex fumo dare lucem.—Out of smoke to bring light.
Ex fumo dare lucem.—From smoke to bring light.
Ex nihilo nihil fit.—Nothing can come of nothing.
Ex nihilo nihil fit.—Nothing comes from nothing.
Ex officio.—By virtue of his office.
Ex officio.—By the authority of his position.
Ex parte.—On one side only (before a noun, exparte.)
Ex parte.—From one side only (before a noun, ex parte.)
Ex pede Herculem.—We recognize a Hercules from the size of the foot:[363] that is, we judge of the whole from the specimen.
Ex pede Herculem.—We identify a Hercules by the size of his foot:[363] meaning, we assess the whole based on the example.
Ex post facto.—After the deed is done.
Ex post facto.—After the action is complete.
Ex tempore.—Without premeditation.
Spontaneously.
Ex uno disce omnes.—From one learn all; from one judge of the whole.
Ex uno disce omnes.—From one, learn about all; from one, judge the whole.
Excelsior.—More elevated; onward.
Excelsior.—Higher; onward.
Excerpta.—Extracts.
Extracts.
Exempli gratiâ.—As for example.
For example.
Exeunt omnes.—All retire.
Exeunt omnes.—Everyone leaves.
Experimentum crucis.—A decisive experiment.
Experimentum crucis.—A critical experiment.
Experto credo.—Believe one who has experience.
Experto credo.—Believe someone who has experience.
Exposé.—An exposition; recital.
Presentation. — An exposition; recital.
Faber suæ fortunæ.—The architect of his own fortune.
Faber suæ fortunæ.—The creator of his own destiny.
Facile primus, facile princeps.—By far the first or chiefest.
Facile primus, facile princeps.—Easily the first or the most important.
Facilis est descensus.—Descent is easy.
Descent is easy.
Fac simile.—Make it like; hence, an exact copy.
Fac simile.—Make it similar; therefore, an exact copy.
Fac totum.—Do all; a man of all work.
Fac totum.—Do everything; a person who can do any task.
Facta est lux.—There was light.
There was light.
Fas est ab hoste doceri.—It is allowable to learn even from an enemy.
Fas est ab hoste doceri.—It's okay to learn from an enemy.
Fata obstant.—The fates oppose it.
The fates oppose it.
Fauteuil.—An easy-chair.
Armchair.
Faux pas.—A false step.
Social blunder.
Felo de se.—A self-murderer.
Felo de se.—A suicide.
Feme couverte.—A married woman.
Feme couverte.—A wife.
Feme sole.—A woman unmarried.
Feme sole.—An unmarried woman.
Festina lente.—Hasten slowly; advance steadily rather than hurriedly.
Festina lente.—Make progress slowly; move forward steadily instead of rushing.
Fête.—A feast or celebration.
Fête.—A party.
Fête champêtre.—A rural feast.
Fête champêtre.—A countryside party.
Feu de joie.—A bonfire; a discharge of musketry on days of rejoicing.
Bonfire.—A bonfire; a firing of muskets on days of celebration.
Feuilleton.—A small leaf; a supplement to a newspaper; a pamphlet.
Feuilleton.—A small page; a supplement to a newspaper; a booklet.
Fiat.—Let it be done.
Fiat.—Let it happen.
Fiat justitia, ruat cœlum.—Let justice be done, though the heavens should fall.
Fiat justitia, ruat cœlum.—Let justice be served, even if it means the sky falls.
Fiat lux.—Let there be light.
Fiat lux.—Let there be light.
Fide, non armis.—By faith, not by arms.
Fide, non armis.—By faith, not by arms.
Fide, sed cui vide.—Trust, but see whom.
Fide, sed cui vide.—Trust, but see whom.
Fides et justitia.—-Fidelity and justice.
Fidelity and justice.
Fidus Achates.—Faithful Achates (that is, a true friend.)
Fidus Achates.—Loyal Achates (meaning, a genuine friend.)
Fieri facias.—Cause it to be done (a kind of writ.)
Fieri facias.—Make it happen (a type of writ.)
Filius nullius.—A son of nobody.
Son of nobody.
Fille-de-chambre.—A chambermaid.
Fille-de-chambre.—A maid.
Finale.—To close or end.
Finale.—To finish or conclude.
Finem respice.—Look to the end.
Look to the end.
Finis.—The end.
The end.
Finis coronat opus.—The end crowns the work.
Finis coronat opus.—The ending completes the work.
Flagrante bello.—While the war is raging.
Flagrante bello.—While the war is going on.
Flagrante delicto.—In the commission of the crime.
Flagrante delicto.—Caught in the act of committing a crime.
Flâneur.—A lounger.
Flâneur.—A chill person.
Flecti, non frangi.—To be bent, not to be broken.
Flecti, non frangi.—To be bent, not to be broken.
Fleur-de-lis.—The flower of the lily (pl. fleurs-de-lis.)
Fleur-de-lis.—The flower of the lily (pl. fleurs-de-lis.)
Forte.—In music, a direction to sing or play with force or spirit.
Forte.—In music, a term that means to sing or play with strength or energy.
Fortes fortuna juvat.—Fortune assists the brave.
Fortes fortuna juvat.—Luck helps those who are bold.
Fortissimo.—Very loud.
Fortissimo.—Very loud.
Fortiter in re.—Resolute in deed.
Fortiter in re.—Bold in action.
Fracas.—Bustle; a slight quarrel; more ado about the thing than it is worth.
Fracas.—Commotion; a minor argument; more fuss about the issue than it's really worth.
Fruges consumere nati.—Born merely to consume the fruits of the earth.
Fruges consumere nati.—Born just to consume the earth's bounty.
Fugam fecit.—He has taken to flight.
He has fled.
Fuit Ilium.—Troy has been.
Troy has been.
Functus officio.—Out of office.
Out of office.
Furore.—Excitement.
Furore.—Hype.
Gaieté de cœur.—Gayety of heart.
Joyful heart.
Gallicè.—In French.
Gallicè.—In French.
Gardez bien.—Take good care.
Take care.
Gardez la foi.—Keep the faith.
Keep the faith.
Gaucherie.—Awkwardness.
Awkwardness.
Gaudeamus igitur.—So let us be joyful.
Let's celebrate.
Gendarme.—A military policeman.
Gendarme.—A military police officer.
Gendarmerie.—The body of the gendarmes.
Gendarmerie.—The police force.
Genius loci.—The genius of the place.
Genius loci.—The spirit of the place.
Genus irritabile vatum.—Irritable tribe of poets.
Genus irritabile vatum.—Irritable group of poets.
Gloria in excelsis.—Glory to God in the highest.
Gloria in excelsis.—Glory to God in the highest.
Gratis.—Free of cost.
Free of charge.
Gratis dictum.—Mere assertion.
Free statement.—Just an assertion.
Gravamen.—The thing complained of.
Grievance.—The thing complained of.
Grisette.—Dressed in gray (a term applied to French shop-girls, &c.)
Grisette.—Wearing gray (a term used for French shop girls, etc.)
Gusto.—Great relish.
Taste. —Great relish.
Habeas corpus.—You are to have the body; a writ of right, by virtue of which every citizen can, when imprisoned, demand to be put on his trial.
Habeas corpus.—You must have the body; a legal order that allows any citizen, when imprisoned, to request a trial.
Habitué.—A frequenter.
Regular. — A frequenter.
Hæc olim meminisse juvabit.—It will be pleasant hereafter to remember these things.
Hæc olim meminisse juvabit.—It will be nice to look back on these things in the future.
Haricot.—A kind of ragout; a kidney-bean.
Haricot.—A type of stew; a kidney bean.
Haud passibus æquis.—Not with equal steps. [Wrongly quoted: see Non, &c.]
Haud passibus æquis.—Not with equal steps. [Wrongly quoted: see Non, &c.]
Haut gout.—High flavour.
Haut goût.—High flavor.
Hauteur.—Haughtiness.
Hauteur.—Arrogance.
Helluo librorum.—A book-worm.
Bookworm.
Hic et ubique.—Here, there, and everywhere.
Hic et ubique.—Here, there, and everywhere.
Hic jacet.—Here lies.
Here lies.
Hinc illæ lacrymæ.—Hence proceed these tears.
Hinc illæ lacrymæ.—That's where these tears come from.
Hoc age.—Do this; attend to what you are doing.
Hoc age.—Do this; focus on what you're doing.
Homme d’esprit.—A man of talent, or of wit.
Homme d’esprit.—A man with talent or wit.
Homo multarum literarum.—A man of much learning.
Homo multarum literarum.—A man of many subjects.
Honi soit qui mal y pense.—Evil be to him that evil thinks.
Honi soit qui mal y pense.—Shame on anyone who thinks evil.
Honores mutant mores.—Honours change men’s manners.
Honores mutant mores.—Honors change people's behavior.
Hora fugit.—The hour or time flies.
Time flies.
Horresco referens.—I shudder to relate.
I cringe to share.
Hors de combat.—Disabled for fighting; vanquished.
Hors de combat.—Out of action; defeated.
Hortus siccus.—A collection of dried plants.
Hortus siccus.—A collection of dried plants.
Hostis humani generis.—An enemy of the human race.
Hostis humani generis.—An enemy of the human race.
Hotel de ville.—A town-hall.
Hôtel de ville.—A city hall.
Hôtel-Dieu.—The chief hospital in French cities.
Hôtel-Dieu.—The main hospital in French cities.
Humanum est errare.—It is human to err.
Humanum est errare.—It's human to make mistakes.
Hunc tu caveto.—Beware of him.
Beware of him.
Ibidem, contracted ibid. or id.—In the same place.
Ibidem, contracted ibid. or id.—In the same place.
Ich dien.—I serve.
Ich dien.—I serve.
Id est.—That is; abridged i. e.
That is; abridged i.e.
Id genus omne.—All of that sort.
Id genus omne.—All of that type.
Idem, contracted id.—The same. (Id. ib., the same author; in the same place.)
Idem, contracted id.—The same. (Id. ib., the same author; in the same place.)
Idoneus homo.—A fit man.
A suitable man.
Ignoramus.—We are ignorant.
Ignoramus.—We're clueless.
Ignorantia legis neminem excusat.—Ignorance of the law excuses no one.
Ignorantia legis neminem excusat.—Ignorance of the law excuses no one.
Il a le diable au corps.—The devil is in him.
Il a le diable au corps.—He's got the devil in him.
Imitatores, servum pecus.—Imitators, a servile herd.
Imitatores, servum pecus.—Imitators, a mindless crowd.
Imperium in imperio.—One government existing within another.
Imperium in imperio.—One government existing inside another.
Impransus.—One who has not dined.
Not dined.
Imprimatur.—Let it be printed.
Imprimatur.—Go ahead and print it.
Imprimis.—In the first place.
First of all.
Impromptu.—A prompt remark without study.
Spontaneous.—A quick remark without preparation.
In articulo mortis.—At the point of death.
In articulo mortis.—At the moment of death.
In capite.—In the head.
In capite.—In the head.
In cœlo quies.—There is rest in heaven.
In cœlo quies.—There is peace in heaven.
In commendam.—In trust.
In trust.
In conspectu fori.—In the eye of the law; in the sight of the court.
In conspectu fori.—In the eyes of the law; in the view of the court.
In curiâ.—In the court.
In court.
In duplo.—Twice as much.
Twice as much.
In equilíbrio.—Equally balanced.
In balance.
In esse.—In being.
In existence.
In extenso.—At full length.
In full.
In extremis.—At the point of death.
In extremis.—At the brink of death.
In formâ pauperis.—As a pauper.
In forma pauperis.—As a low-income person.
In foro conscientiæ.—Before the tribunal of conscience.
In foro conscientiæ.—In the court of conscience.
In hoc signo vinces.—In this sign thou shalt conquer.
In hoc signo vinces.—In this sign you shall conquer.
In limine.—At the threshold.
At the threshold.
In loco.—In the place.
In loco.—On site.
In medias res.—Into the midst of things.
In medias res.—Right into the action.
In memoriam.—To the memory of.
In memory.
In perpetuum.—Forever.
Forever.
In petto.—In reserve; in one’s breast.
In reserve; kept inside.
In posse.—In possible existence.
In potential.
In posterum.—For the time to come.
For the future.
In propriâ personâ.—In his own person.
In propriâ personâ.—In his own person.
In puris naturalibus.—Quite naked.
In puris naturalibus.—Totally nude.
In re.—In the matter of.
In the matter of.
In situ.—In its original situation.
In situ.—In its original place.
In statu quo.—In the former state.
In statu quo.—In the previous state.
In te, Domine, speravi.—In thee, Lord, have I put my trust.
In te, Domine, speravi.—I have placed my trust in you, Lord.
In terrorem.—By way of warning.
In terrorem.—As a warning.
In totidem verbis.—In so many words.
In other words.
In toto.—Altogether.
Altogether.
In transitu.—On the passage.
In transitu.—In transit.
In utrumque paratus.—Prepared for either event.
In utrumque paratus.—Ready for either outcome.
In vacuo.—In empty space, or in a vacuum.
In vacuo.—In empty space, or in a vacuum.
In vino veritas.—There is truth in wine.
In vino veritas.—There’s truth in wine.
Incognito.—Disguised; unknown.
Incognito.—In disguise; anonymous.
Index expurgatorius.—A list of prohibited books.
Index expurgatorius.—A list of banned books.
Infra dignitatem.—Beneath one’s dignity.
Infra dignitatem.—Below one’s dignity.
Innuendo.—Covert meaning; indirect hint.
Innuendo.—Subtle meaning; indirect hint.
Inops consilii.—Without counsel.
Without advice.
Insouciance.—Carelessness; indifference.
Insouciance.—Apathy; indifference.
Instar omnium.—One will suffice for all; an example to others.
Instar omnium.—One is enough for everyone; an example for others.
Inter alia.—Among other things.
Among other things.
Inter arma leges silent.—In the midst of arms the laws are silent.
Inter arma leges silent.—In times of war, laws take a backseat.
Inter nos.—Between ourselves.
Between us.
Inter se.—Among themselves.
Among themselves.
Ipse dixit.—He himself said it; dogmatic assertion.
Ipse dixit.—He said it himself; a firm declaration.
Ipsissima verba.—The very words.
The exact words.
Ipso facto.—By the fact itself; actually.
Ipso facto.—By the fact itself; actually.
Ipso jure.—By the law itself.
By the law itself.
Ira furor brevis est.—Anger is brief madness.
Ira furor brevis est.—Anger is temporary madness.
Ita lex scripta est.—Thus the law is written.
Ita lex scripta est.—So the law is written.
Item.—Also.
Item.—Also.
Jacta est alea.—The die is cast.
Jacta est alea.—The die has been cast.
Jamais arrière.—Never behind.
Never behind.
Je ne sais quoi.—I know not what.
Je ne sais quoi.—I don't know what.
Jet d’eau.—A jet of water.
Water jet.
Jeu de mots.—Play upon words; a pun.
Jeu de mots.—A play on words; a pun.
Jeu d’esprit.—A witticism.
Jeu d’esprit.—A clever joke.
Judicium Dei.—The judgment of God.
Judicium Dei.—God's judgment.
Juniores ad labores.—Young men for labours.
Juniores ad labores.—Young men for work.
Jure divino.—By divine law.
By divine law.
Jure gentium.—By the law of nations.
Jure gentium.—Under international law.
Jure humano.—By human law.
By human law.
Jus civile.—Civil law.
Civil law.
Jus gladii.—Right of the sword.
Jus gladii.—Sword law.
Juste milieu.—The golden mean; a just medium.
Juste milieu.—The golden mean; a fair balance.
Justitiæ soror fides.—Faith is the sister of justice.
Justitiæ soror fides.—Faith is the sibling of justice.
La critique est aisée, et l’art est difficile.—Criticism is easy, but art is difficult.
La critique est aisée, et l’art est difficile.—Criticism is easy, but art is difficult.
Labor ipse voluptas.—Labour itself is pleasure.
Labor ipse voluptas.—Work itself is pleasure.
Labor omnia vincit.—Labour conquers all things.
Labor omnia vincit.—Hard work conquers all.
Laissez-nous faire.—Let us alone.
Let us be.
Lapsus calami.—A slip of the pen; an error in writing.
Lapsus calami.—A mistake made while writing; a writing error.
Lapsus linguæ.—A slip of the tongue.
Lapsus linguæ.—A slip of the tongue.
Lapsus memoriæ.—A slip of memory.
Slip of memory.
Lares et penâtes.—Household gods.
Household gods.
L’argent.—Money, or silver.
Money.
Laudator temporis acti.—A praiser of time past.
Laudator temporis acti.—Someone who appreciates the past.
Laus Deo.—Praise to God.
Praise God.
Laus propria sordet.—Praise of one’s own self defiles.
Self-praise is degrading.
Le beau monde.—The fashionable world.
The glamorous world.
Le bon temps viendra.—The good time will come.
Le bon temps viendra.—The good times will come.
Le grand œuvre.—The great work; the philosopher’s stone.
Le grand œuvre.—The great work; the philosopher's stone.
Le pas.—Precedence in place or rank.
Le pas.—Priority in position or status.
Le savoir-faire.—The knowledge how to act; address.
Le savoir-faire.—The know-how; the ability to tackle situations effectively.
Le tout ensemble.—All together.
All together.
Lege.—Read.
Read.
Leges legum.—The law of laws.
Leges legum.—The ultimate law.
Lèse majesté.—High treason.
Lèse majesté.—High treason.
L’étoile du nord.—The north star.
The North Star.
Lettre de cachet.—A sealed letter; a royal warrant.
Lettre de cachet.—A sealed letter; a royal order.
Levari facias.—That you cause to be levied; a writ of execution.
Levari facias.—That you have collected; a court order for enforcement.
Levée.—A morning visit or reception.
Morning visit.
Lex loci.—The law of the place.
Lex loci.—The law of the location.
Lex magna est, et prævalebit.—The law is great, and will prevail.
Lex magna est, et prævalebit.—The law is powerful, and it will prevail.
Lex non scripta.—The unwritten or common law.
Lex non scripta.—The unwritten or common law.
Lex scripta.—Statute law.
Statutory law.
Lex talionis.—The law of retaliation.
Lex talionis.—The law of revenge.
Lex terræ, lex patriæ.—The law of the land.
Lex terræ, lex patriæ.—The law of the land.
L’homme propose, et Dieu dispose.—Man proposes, and God disposes.
L’homme propose, et Dieu dispose.—Man proposes, and God disposes.
Libretto.—A little book or pamphlet.
Libretto.—A small book or pamphlet.
Licentia vatûm.—A poetical license.
A poetic license.
Lingua Franca.—The mixed language spoken by Europeans in the East.
Lingua Franca.—The hybrid language spoken by Europeans in the East.
Liqueur.—A cordial.
Liqueur—A cordial.
Lis litem generat.—Strife begets strife.
Lis litem generat.—Conflict leads to conflict.
Lis sub judice.—A case not yet decided.
Lis sub judice.—A case that hasn't been decided yet.
Lite pendente.—During the trial.
During the trial.
Litera scripta manet.—The written letter remains.
Litera scripta manet.—The written word endures.
Literati.—Men of letters or learning.
Literati.—Individuals of knowledge or learning.
Loco citato.—In the place cited.
In the cited location.
Loco parentis.—In the place of the parent.
Loco parentis.—In the role of a parent.
Locum tenens.—One who holds a place for another.
Locum tenens.—Someone who temporarily takes the position of another.
Locus sigilli (L. S.).—The place of the seal.
Locus sigilli (L. S.).—The location of the seal.
Longo intervallo.—At a great distance.
Longo intervallo.—At a long distance.
Ludere cum sacris.—To trifle with sacred things.
Ludere cum sacris.—To mess around with sacred things.
Lusus naturæ.—A sport or freak of nature.
Lusus naturæ.—A playful oddity or quirk of nature.
Macte virtute.—Proceed in virtue.
Keep up the good work.
Mademoiselle.—A young unmarried lady.
Miss.—A young unmarried lady.
Magna Charta.—The great charter of England.
Magna Charta.—The great charter of England.
Magna civitas, magna solitudo.—A great city is a great desert.
Magna civitas, magna solitudo.—A great city is a great desert.
Magna est veritas, et prævalebit.—The truth is great, and will prevail.
Magna est veritas, et prævalebit.—Truth is powerful, and it will prevail.
Magni nominis umbra.—The shadow of a great name.
Magni nominis umbra.—The shadow of a great name.
Magnum opus.—A great work.
Masterpiece.
Magnus Apollo.—Great Apollo; one of high authority.
Magnus Apollo.—Great Apollo; one of high authority.
Maison de ville.—The town-house.
Townhouse.
Maître d’hôtel.—An hotel-keeper; a house-steward.
Maître d’hôtel.—A hotel manager; a house steward.
Majordomo (Ital. maiordomo.)—One who has the management of a household.
Butler—Someone who manages a household.
Malâ fide.—In bad faith; treacherously.
In bad faith; treacherously.
Mal à propos.—Out of time; unbecoming.
Inappropriate; unsuitable.
Malaria.—Noxious exhalations.
Malaria.—Toxic fumes.
Malgré.—In spite of.
In spite of.
Malum in se.—Bad in itself.
Malum in se.—Evil in itself.
Mandamus.—We command: a peremptory writ to compel obedience.
Mandamus.—We order: a mandatory directive to ensure compliance.
Manège.—A riding-school.
Manège.—A riding school.
Mania a potu.—Madness caused by drunkenness.
Mania a potu.—Madness caused by drinking.
Manu forti.—With a strong hand.
With a strong hand.
Mardi gras.—Shrove-Tuesday.
Mardi Gras—Shrove Tuesday.
Mare clausum.—A closed sea; a bay.
Mare clausum.—A closed sea; a bay.
Materfamilias.—The mother of a family.
Materfamilias.—The matriarch.
Materia medica.—Substances used in the healing art.
Materia medica.—Substances used in medical practice.
Matinée.—A morning party.
Morning gathering.
Mauvais goût.—Bad taste.
Mauvais goût.—Bad taste.
Mauvais sujet.—A worthless fellow.
Bad topic.—A worthless person.
Mauvaise honte.—False modesty; bashfulness.
Mauvaise honte.—False humility; shyness.
Maximum.—The greatest.
Maximum.—The greatest.
Maximus in minimis.—Very great in trifling things.
Maximus in minimis.—Very great in small things.
Me judice.—I being judge; in my own opinion.
Me judice.—I, as the judge; in my own opinion.
Medio tutissimus ibis.—A medium course will be safest.
Medio tutissimus ibis.—A moderate approach will be the safest.
Meditatione fugæ.—In contemplation of flight.
In contemplation of flight.
Memento mori.—Remember death.
Memento mori.—Remember you will die.
Memorabilia.—Things to be remembered.
Memorabilia.—Things to remember.
Memoriter.—By rote.
By memory.
Ménage.—Household.
Household.
Mens sana in corpore sano.—A sound mind in a sound body.
Mens sana in corpore sano.—A healthy mind in a healthy body.
Metis sibi conscia recti.—A mind conscious of rectitude.
Metis sibi conscia recti.—A mind aware of what is right.
Mensa et thoro.—From bed and board.
Mensa et thoro.—From bed and board.
Merum sal.—Pure salt; genuine Attic wit.
Merum sal.—Pure salt; real Attic humor.
Meum et tuum.—Mine and thine.
Meum et tuum.—Mine and yours.
Minimum.—The least.
Minimum.—The minimum amount.
Minutiæ.—Minute concerns; trifles.
Minutiæ.—Minor issues; trifles.
Mirabile dictu.—Wonderful to be told.
Mirabile dictu.—Awesome to hear.
Mirabilia.—Wonders.
Wonders.
Mittimus.—We send: a warrant for the commitment of an offender.
Mittimus.—We send: a document authorizing the detention of a criminal.
Modus operandi.—Manner of operation.
M.O.
Montani semper liberi.—Mountaineers are always freemen.
Montani semper liberi.—Mountaineers are always free.
Morceau.—A morsel.
Morceau.—A bite.
More suo.—In his own way.
In his own way.
Mot du guet.—A watchword.
Mot du guet.—A password.
Multum in parvo.—Much in a small space.
Multum in parvo.—A lot in a small space.
Mutanda.—Things to be altered.
Mutanda.—Things to change.
Mutatis mutandis.—The necessary changes being made.
Mutatis mutandis.—The necessary changes have been made.
Mutato nomine.—The name being changed.
Mutato nomine.—Name changed.
Naïveté.—Ingenuousness; simplicity.
Naivety. — Innocence; simplicity.
Ne cede malis.—Yield not to misfortune.
Ne cede malis.—Don't give in to misfortune.
Ne exeat.—Let him not depart.
Ne exeat.—Don't let him leave.
Ne plus ultra.—Nothing further; the uttermost point.
Ne plus ultra.—Nothing beyond this; the absolute limit.
Ne quid nimis.—Not too much of any thing; do nothing to excess.
Ne quid nimis.—Don’t do anything in excess; everything in moderation.
Ne sutor ultra crepidam.—Let not the shoemaker go beyond his last.
Ne sutor ultra crepidam.—Let the shoemaker not venture beyond his expertise.
Ne tentes, aut perfice.—Attempt not, or accomplish thoroughly.
Ne tentes, aut perfice.—Don't try, or do it completely.
Nec pluribus impar.—Not an unequal match for numbers.
Nec pluribus impar.—Not an unequal match for numbers.
Nec scire fas est omnia.—It is not permitted to know all things.
Nec scire fas est omnia.—You can't know everything.
Necessitatis non habet legem.—Necessity has no law.
Necessitatis non habet legem.—Necessity has no law.
Née.—Born.
Born.
Nefasti dies.—Days upon which no public business was transacted; also, unlucky days.
Nefasti dies.—Days when no public business was conducted; also, days considered unlucky.
Nemine contradicente.—No one contradicting.
Nemine contradicente.—No one is disagreeing.
Nemine dissentiente.—Without opposition or dissent.
Without opposition or dissent.
Nemo me impune lacessit.—No one wounds me with impunity.
Nemo me impune lacessit.—No one can hurt me without facing the consequences.
Nemo mortalium omnibus horis sapit.—No one is wise at all times.
Nemo mortalium omnibus horis sapit.—No one is wise all the time.
Nemo repentè fuit turpissimus.—No man ever became a villain at once.
Nemo repentè fuit turpissimus.—No one ever turns into a villain overnight.
Nemo solus sapit.—No one is wise alone.
Nemo solus sapit.—No one is wise alone.
Niaiserie.—Silliness.
Silliness.
Nihil debet.—He owes nothing; a plea denying a debt.
Nihil debet.—He owes nothing; a claim that he has no debt.
Nihil quod tetigit, non ornavit.—Whatever he touched he embellished.
Nihil quod tetigit, non ornavit.—Everything he touched, he made beautiful.
Nil admirari.—To wonder at nothing.
Nil admirari.—Don’t be surprised by anything.
Nil desperandum.—Never despair.
Never lose hope.
Nimium ne crede colori.—Trust not too much to looks.
Nimium ne crede colori.—Don’t rely too much on appearances.
N’importe.—It matters not.
Whatever.
Nisi Dominus frustra.—Unless the Lord be with us, all efforts are in vain.
Nisi Dominus frustra.—Unless the Lord is with us, all efforts are pointless.
Noblesse oblige.—Rank imposes obligation.
Noblesse oblige.—Rank comes with responsibility.
Nolens volens.—Willing or unwilling.
Willing or unwilling.
Noli me tangere.—Don’t touch me.
Don’t touch me.
Nolle prosequi.—Unwilling to proceed.
Nolle prosequi.—Not willing to proceed.
Nolo episcopari.—I am not willing to be made a bishop (an old formal way of declining a bishopric.)
Nolo episcopari.—I don't want to be a bishop (an old formal way of declining a bishopric.)
Nom de guerre.—An assumed name.
Nom de guerre.—A pseudonym.
Nom de plume.—A literary title.
Pen name.
Nomen et omen.—Name and omen; a name that is ominous.
Nomen et omen.—Name and omen; a name that carries a bad sign.
Non compos mentis.—Not of sound mind.
Non compos mentis.—Not in a sound state of mind.
Non deficiente crumenâ.—If the money does not fail.
Non deficiente crumenâ.—If the money doesn't run out.
Non est disputandum.—It is not to be disputed.
Non est disputandum.—It shouldn't be argued.
Non est inventus.—Not found.
Non est inventus.—Not found.
Non libet.—It does not please me.
I don't like it.
Non mi ricordo.—I don’t remember.
I don’t remember.
Non nobis solum.—Not merely for ourselves.
Non nobis solum.—Not just for ourselves.
Non obstante.—Notwithstanding.
Notwithstanding.
Non omnis moriar.—I shall not wholly die.
Non omnis moriar.—I won't completely die.
Non passibus æquis.—Not with equal steps.
Non passibus æquis.—Not with equal steps.
Non sequitur.—It does not follow: an unwarranted conclusion.
Non sequitur.—It doesn't follow: an unwarranted conclusion.
Non sibi, sed omnibus.—Not for itself, but for all.
Non sibi, sed omnibus.—Not for itself, but for everyone.
Nonchalance.—Coolness; easy indifference.
Nonchalance.—Chill; effortless indifference.
Nonpareil.—Peerless; a small printing type.
Nonpareil.—Unmatched; a small font.
Nosce teipsum.—Know thyself.
Know yourself.
Noscitur ex sociis.—He is known by his companions.
Noscitur ex sociis.—You can tell someone by the company they keep.
Nota bene.—Mark well.
Nota bene.—Pay attention.
Nous verrons.—We shall see.
We’ll see.
Novus homo.—A new man.
Novus homo.—A new person.
Nudum pactum.—An invalid agreement.
Nudum pactum.—An invalid agreement.
Nulla crux, nulla corona.—No cross, no crown.
Nulla crux, nulla corona.—No cross, no crown.
Nulla nuova, bona nuova.—The best news is no news.
Nulla nuova, bona nuova.—No news is good news.
Nullius filius.—The son of nobody.
Nullius filius.—Son of no one.
Nunc aut nunquam.—Now or never.
Now or never.
O tempora! o mores!—Oh, the times! oh, the manners!
O tempora! o mores!—Oh, the times! oh, the manners!
Obiit.—He (or she) died.
Passed away.
Obiter dictum.—A thing said by the way, or in passing.
Obiter dictum.—A remark made casually, or in passing.
Obsta principiis.—Resist the first beginnings.
Obsta principiis.—Resist the early signs.
Odi profanum.—I loathe the profane.
I loathe the profane.
Odium theologicum.—The hatred of theologians.
Odium theologicum.—The hatred of theologians.
Ohe! jam satis.—Oh, there is now enough.
Ohe! jam satis.—Oh, that's enough now.
Olla podrida.—An incongruous mixture.
Olla podrida.—A mixed bag.
Omne ignotum pro magnifico.—Whatever is unknown is thought to be magnificent.
Omne ignotum pro magnifico.—Whatever is unknown is considered magnificent.
Omnes.—All.
All.
Omnia bona bonis.—All things are good with the good.
Omnia bona bonis.—All things are good for the good people.
Omnia vincit amor.—Love conquers all things.
Omnia vincit amor.—Love conquers all things.
On-dit.—A rumour; a flying report.
On-dit.—A rumor; a hearsay.
Onus.—Burden.
Burden.
Onus probandi.—The responsibility of producing proof.
Onus probandi.—The obligation to provide evidence.
Ope et consilio.—With assistance and counsel.
Ope et consilio.—With help and advice.
Ora et labora.—Pray and work.
Ora et labora.—Pray and work.
Orator fit, poeta nascitur.—The orator is made by education, but a poet must be born.
Orator fit, poeta nascitur.—An orator is shaped through education, but a poet is born.
Ore rotundo.—With full-sounding voice.
With a rich voice.
Otium cum dignitate.—Dignified leisure.
Dignified leisure.
Outré.—Preposterous; eccentric.
Outré.—Absurd; unconventional.
Oyer and Terminer.—A criminal court.
Oyer and Terminer.—A criminal court.
Pallida mors.—Pale death.
Pale death.
Par excellence.—By way of eminence.
Par excellence.—By definition.
Par nobile fratrum.—A noble pair of brothers; two just alike.
Par nobile fratrum.—A noble pair of brothers; two who are exactly the same.
Pari passu.—With equal step; in the same degree.
Pari passu.—At the same speed; to the same extent.
Parole d’honneur.—Word of honour.
Word of honor.
Pars pro toto.—Part for the whole.
Pars pro toto.—A part represents the whole.
Particeps criminis.—An accomplice.
Accomplice.
Parturiunt montes, nascetur ridiculus mus.—The mountains are in labour; a ridiculous mouse will be brought forth.
Parturiunt montes, nascetur ridiculus mus.—The mountains are in labor; a ridiculous mouse will be born.
Parva componere magnis.—To compare small things with great.
Parva componere magnis.—To compare small things with great.
Parvenu.—A new comer; an upstart.
Parvenu.—A newcomer; an upstart.
Pas.—A step; precedence.
No. —A step; precedence.
Passe-partout.—A master-key.
Passe-partout.—A universal key.
Passim.—In many places; everywhere.
Passim.—In many places; everywhere.
Paterfamilias.—The father of a family.
Head of the household.
Pater noster.—Our Father; the Lord’s prayer.
Pater noster.—Our Father; the Lord's prayer.
Pater patriæ.—Father of his country.
Father of the country.
Patois.—A provincial dialect.
Patois.—A regional dialect.
Pax in bello.—Peace in war.
Peace in war.
Peccavi.—I have sinned.
I have sinned.
Penchant.—An inclination; a leaning toward.
Penchant.—A tendency; an inclination.
Pendente lite.—While the suit is pending.
Pendente lite.—While the lawsuit is ongoing.
Penetralia.—Secret recesses.
Penetralia.—Hidden spaces.
Per aspera ad astra.—Through trials to glory.
Per aspera ad astra.—Through challenges to success.
Per capita.—By the head; equal division.
Per person; equal distribution.
Per cent. or per centum.—By the hundred.
Percent. — By the hundred.
Per contra.—Contrariwise.
Per contra.—On the contrary.
Per curiam.—By the court.
By the court.
Per diem.—By the day.
Daily rate.
Per fas et nefas.—Through right and wrong.
Per fas et nefas.—Through right and wrong.
Per saltum.—With a leap; at once.
Jump in. — With a jump; immediately.
Per se.—By itself; alone.
Per se.—On its own; alone.
Perdu.—Lost.
Lost.
Père de famille.—The father of a family.
Père de famille.—The dad of a family.
Petit.—Small; little.
Small.
Petitio principii.—A begging of the question.
Circular argument.
Petit-maître.—A fop.
Petit-maître.—A dandy.
Peu à peu.—Gradually; a little by little.
Peu à peu.—Gradually; little by little.
Pinxit.—Painted it: placed after the artist’s name on a picture.
Pinxit.—Painted it: this is placed after the artist's name on a painting.
Più.—More.
More.
Plateau.—A plain; a flat surface.
Plateau.—A flat area.
Plebs.—Common people.
Plebs.—Common folks.
Pluries.—Very often; a third writ, after two writs have issued.
Pluries.—Very often; a third writ, after two writs have been issued.
Poco.—A little.
A little.
Poeta nascitur, non fit.—A poet is born, not made.
Poeta nascitur, non fit.—A poet is born, not made.
Point d’appui.—Point of support; prop.
Support point; prop.
Poisson d’Avril.—April fool.
April Fool's Day.
Populus vult decipi.—People like to be deceived.
Populus vult decipi.—People enjoy being fooled.
Posse comitatûs.—The power of the county.
Posse comitatûs.—The authority of the county.
Postea.—Afterward; endorsement of the verdict upon the record.
Postea.—Afterward; confirmation of the verdict in the record.
Post mortem.—After death.
Post mortem.—Afterlife.
Postulata.—Things assumed.
Postulata.—Assumptions.
Præcognita.—Things previously known.
Præcognita.—Things already known.
Præmonitus, præmunitus.—Forewarned, forearmed.
Forewarned, forearmed.
Preux chevalier.—A brave knight.
Brave knight.
Primâ facie.—On the first view.
Primâ facie.—At first glance.
Primum mobile.—The primary motive, or moving power.
Primum mobile.—The main driving force or power.
Primus inter pares.—Chief among equals.
First among equals.
Principia, non homines.—Principles, not men.
Principles, not people.
Principiis obsta.—Resist the first innovations.
Principiis obsta.—Resist initial changes.
Pro aris et focis.—For our altars and our hearths.
Pro aris et focis.—For our altars and our homes.
Pro bono publico.—For the public good.
Pro bono publico.—For the public good.
Pro et con (for contra).—For and against.
For and against.
Pro formâ.—For form’s sake; according to form.
Pro formâ.—For the sake of form; in accordance with form.
Pro hâc vice.—For this turn or occasion.
Pro hâc vice.—For this time or occasion.
Pro loco et tempore.—For the place and time.
Pro loco et tempore.—For the place and time.
Pro patriâ.—For our country.
For our country.
Pro ratâ.—In proportion.
Pro ratâ.—In proportion.
Pro re natâ.—For a special emergency.
Pro re natâ.—For a specific emergency.
Pro tanto.—For so much.
For that much.
Pro tempore.—For the time-being.
For now.
Probatum est.—It has been tried and proved.
Probatum est.—It has been tested and confirmed.
Procès-verbal.—A written statement.
Procès-verbal.—A written report.
Prochein ami.—The next friend.
Next friend.
Procul, O procul este, profani!—Far, far hence, O ye profane!
Procul, O procul este, profani!—Get away, far away, you unclean ones!
Pronunciamento.—A public declaration.
Public statement.
Propagandâ fide.—For extending the faith.
Propagandâ fide.—To spread the faith.
Protégé.—A person taken charge of, or patronized; a ward, &c.
Protégé.—A person who is looked after or supported; a ward, etc.
Prudens futuri.—Thoughtful of the future.
Thoughtful of the future.
Pugnis et calcibus.—With fists and heels; with all the might.
Pugnis et calcibus.—With fists and heels; with all the strength.
Punica fides.—Punic faith; treachery.
Punic faith; treachery.
Quære.—Query; inquiry.
Query.
Quamdiu se bene gesserit.—So long as he shall conduct himself properly.
Quamdiu se bene gesserit.—As long as he behaves himself properly.
Quantum.—The due proportion.
Quantum. — The right balance.
Quantum libet.—As much as you please.
Quantum libet.—As much as you want.
Quantum meruit.—As much as he deserved.
Quantum meruit.—As much as he deserved.
Quantum sufficit.—A sufficient quantity; enough.
Quantum sufficit.—A sufficient amount; enough.
Quare clausum fregit.—An action for damages to real estate.
Quare clausum fregit.—A lawsuit for damages to real property.
Quare impedit.—Why he hinders.
Quare impedit.—Why he blocks.
Quasi dicas.—As if you should say.
Quasi dicas.—As if you should say.
Quelque chose.—A trifle.
Quelque chose.—A little something.
Qui capit, ille facit.—He who takes it makes it.
Qui capit, ille facit.—Whoever takes it, owns it.
Qui pense?—Who thinks?
Qui pense?—Who’s thinking?
Qui tam?—Who as well? the title given to a certain action at law.
Qui tam?—Who else? The title given to a specific legal action.
Qui transtulit sustinet.—He who brought us hither still preserves us.
Qui transtulit sustinet.—The one who brought us here still keeps us safe.
Qui va là?—Who goes there?
Who’s there?
Qui vive?—Who goes there? hence, on the qui-vive, on the alert.
Qui vive?—Who goes there? Hence, on the qui-vive, on high alert.
Quid-nunc?—What now? a newsmonger.
What’s next? a newsmonger.
Quid pro quo.—One thing for another; “tit for tat.”
Quid pro quo.—Something for something; “tit for tat.”
Quid rides?—Why do you laugh?
Why are you laughing?
Quis separabit?—Who shall separate us?
Who will separate us?
Quo animo?—With what intention.
With what intention?
Quo jure?—By what right?
By what right?
Quo warranto.—By what warrant or authority.
Quo warranto.—By what authority or power.
Quoad hoc.—To this extent.
Quoad hoc.—To this extent.
Quod avertat Deus?—Which may God avert!
Quod avertat Deus?—May God prevent it!
Quod vide.—Which see.
See that.
Quodlibet.—A nice point; a subtlety.
Quodlibet.—A good point; a nuance.
Quondam.—Former.
Quondam.—Once.
Quorum.—Of whom: a term signifying a sufficient number for a certain business.
Quorum.—Of whom: a term that means a sufficient number for a specific task.
Quos Deus vult perdere, prius dementat.—Those whom God wishes to destroy, he first deprives of understanding.
Quos Deus vult perdere, prius dementat.—Those whom God intends to ruin, he first takes away their understanding.
Ragout.—A highly-seasoned dish.
Ragout.—A flavorful dish.
Rara avis.—A rare bird; a prodigy.
Rara avis.—A rare find; a prodigy.
Re infectà.—The business being unfinished.
Incomplete business.
Recte et suaviter.—Justly and mildly.
Fairly and gently.
Rectus in curiâ.—Upright in the court; with clean hands.
Rectus in curiâ.—Upright in the court; with clean hands.
Redolet lucernâ.—It smells of the lamp; it is a laboured production.
Redolet lucernâ.—It smells like the lamp; it's a forced piece of work.
Reductio ad absurdum.—A reducing a position to an absurdity.
Reductio ad absurdum.—Reducing a position to an absurdity.
Regina.—Queen.
Regina.—Queen.
Regium donum.—A royal donation (a grant from the British crown to the Irish Presbyterian clergy.)
Regium donum.—A royal donation (a grant from the British crown to the Irish Presbyterian ministers.)
Regnant populi.—The people rule.
The people rule.
Rencontre.—An encounter.
Meeting.
Renaissance.—New birth: applied to the revival of the classic arts in the fifteenth and sixteenth centuries.
Renaissance.—New birth: refers to the revival of classical arts in the fifteenth and sixteenth centuries.
Requiescant in pace.—May they rest in peace.
Requiescant in pace.—May they rest in peace.
Requiescat in pace.—May he rest in peace.
Requiescat in pace.—May he rest in peace.
Rerum primordia.—The first elements of things.
Rerum primordia.—The basic elements of things.
Res angusta domi.—Narrow circumstances at home; poverty.
Res angusta domi.—Tight situation at home; poverty.
Res integra.—An entire matter.
Res integra.—A complete issue.
Respice finem.—Look to the end.
Look to the end.
Respublica.—The commonwealth.
Respublica.—The republic.
Restaurateur.—A tavern-keeper who provides dinners, &c.
Restaurateur.—A tavern owner who serves dinner, etc.
Résumé.—An abstract or summary.
Résumé.—A summary.
Resurgam.—I shall rise again.
I shall rise again.
Revenons à nos moutons.—Let us return to our subject.
Revenons à nos moutons.—Let's get back to our topic.
Rex.—King.
King.
Rouge.—Red colouring for the skin.
Red. —Red coloring for the skin.
Rouge et noir.—Red and black (a kind of game.)
Rouge et noir.—Red and black (a type of game.)
Rus in urbe.—The country in town.
Rus in urbe.—The countryside in the city.
Ruse contre ruse.—Diamond cut diamond: trick for trick.
Ruse contre ruse.—Diamond cut diamond: trick for trick.
Ruse de guerre.—A stratagem of war.
Military strategy.
Salle.—Hall.
Salle.—Room.
Salus populi suprema lex est.—The welfare of the people is in the supreme law.
Salus populi suprema lex est.—The well-being of the people is the highest law.
Salvo pudore.—Without offence to modesty.
Without offense to modesty.
Sanctum sanctorum.—Holy of Holies.
Sanctum sanctorum.—Holy of Holies.
Sang-froid.—Coolness; self-possession.
Sang-froid.—Composure; self-control.
Sans.—Without.
Without.
Sans cérémonie.—Without ceremony.
No formality.
Sans peur et sans reproche.—Without fear and without reproach.
Sans peur et sans reproche.—Without fear and without blame.
Sans souci.—Without care; free and easy.
Sans souci.—Without a care; relaxed and carefree.
Sans tâche.—Stainless.
Stainless.
Sans-culottes.—Without breeches: a term applied to the rabble of the French Revolution.
Sans-culottes.—Without pants: a term used for the common people of the French Revolution.
Sartor resartus.—The cobbler mended.
Sartor resartus.—The shoemaker fixed.
Satis, superque.—Enough, and more than enough.
Satis, superque.—Enough, and more than enough.
Satis verborum.—Enough of words; you need say no more.
Satis verborum.—Enough with the words; you don't need to say anything else.
Sauve qui peut.—Save himself who can.
Sauve qui peut.—Save yourself if you can.
Savant.—A learned man.
Savant.—A knowledgeable person.
Savoir-faire.—Ability; skill.
Savoir-faire.—Skill.
Scandalum magnatum.—Scandal of the great.
Scandalum magnatum.—Scandal of the elite.
Scienter.—Knowingly.
Scienter.—Knowingly.
Scilicet.—That is to say; to wit.
Sure thing!
Scire facias.—Cause it to be known.
Scire facias.—Know this.
Scripsit.—Wrote it.
Scripsit.—Wrote.
Sculpsit.—Engraved it: placed after the engraver’s name in prints.
Sculpsit.—Engraved it: placed after the engraver’s name in prints.
Secundum artem.—According to rule.
According to the rules.
Selon les règles.—According to rule.
According to the rules.
Semper fidelis.—Always faithful.
Always faithful.
Semper idem.—Always the same.
Always the same.
Semper paratus.—Always ready.
Always ready.
Senatûs consultum.—A decree of the senate.
Senate decree.
Seriatim.—In order; successively.
In order; successively.
Si quæris peninsulam amœnam, circumspice.—If thou seekest a beautiful peninsula, behold it here.
Si quæris peninsulam amœnam, circumspice.—If you’re looking for a beautiful peninsula, take a look around.
Sic in originali.—So it stands in the original.
Sic in originali.—That's how it is in the original.
Sic itur ad astra.—Such is the way to immortality.
Sic itur ad astra.—This is the path to immortality.
Sic passim.—So everywhere.
So everywhere.
Sic semper tyrannis.—So be it ever to tyrants.
Sic semper tyrannis.—So it shall always be for tyrants.
Sic transit gloria mundi.—Thus passes away the glory of the world.
Sic transit gloria mundi.—And that’s how the glory of the world fades away.
Sicut ante.—As before.
As before.
Similia similibus curantur.—Like things are cured by like.
Like treats like.
Simplex munditiis.—Of simple elegance.
Simple elegance.
Sine die.—Without naming a day.
Sine die.—Indefinitely.
Sine invidiâ.—Without envy.
Without envy.
Sine qua non.—An indispensable requisite.
Essential requirement.
Siste, viator.—Stop, traveller.
Stop, traveler.
Sobriquet.—A nickname.
Nickname.
Soi-disant.—Self-styled; pretended.
Self-proclaimed.
Soirée.—An evening party.
Soirée.—An evening gathering.
Souvenir.—Remembrance; a keepsake.
Souvenir.—Memory; a memento.
Spartam nactus es, hanc exorna.—You have got something good; make the most of it you can.
Spartam nactus es, hanc exorna.—You have something valuable; maximize its potential.
Spectas et spectaberis.—You will see and be seen.
Spectas et spectaberis.—You will see and be seen.
Spes mea Christus.—Christ is my hope.
Spes mea Christus.—Christ is my hope.
Spolia opima.—The richest booty.
Spolia opima.—The biggest prize.
Stans pede in uno.—Standing on one foot.
Stans pede in uno.—Standing on one foot.
Statu quo, or in statu quo.—In the same state.
Statu quo, or in statu quo.—In the same condition.
Stet.—Let it stand.
Stet.—Keep it as is.
Suaviter in modo, fortiter in re.—Gentle in manner, resolute in deed.
Suaviter in modo, fortiter in re.—Gentle in approach, strong in action.
Sub judice.—Under consideration.
Under consideration.
Sub rosâ.—Under the rose; privately.
Under the rose; privately.
Sub silentio.—In silence.
In silence.
Subpœna.—Under a penalty: a summons to attend a court as a witness.
Subpœna.—Under penalty: a request to appear in court as a witness.
Succedaneum.—A substitute.
Succedaneum.—A replacement.
Sui generis.—Of its own kind; peculiar.
Sui generis.—One of a kind; unique.
Summum bonum.—The chief good.
Summum bonum.—The ultimate good.
Supersedeas.—A writ to stay proceedings.
Stay order.
Super visum corporis.—Upon a view of the body.
Super visum corporis.—After seeing the body.
Suppressio veri, suggestio falsi.—A suppression of the truth is the suggestion of a falsehood.
Suppressio veri, suggestio falsi.—Hiding the truth is promoting a lie.
Supra.—Above.
Above.
Suum cuique.—Let every one have his own.
Suum cuique.—Let everyone have what belongs to them.
Table d’hôte.—An ordinary at which the master of the hotel presides.
Table d’hôte.—A fixed-price meal where the hotel owner is in charge.
Tabula rasa.—A smooth or blank tablet.
Tabula rasa.—An empty or clean slate.
Tædium vitæ.—Weariness of life.
Tædium vitæ.—Life fatigue.
Tale quale.—Such as it is.
Just as it is.
Tant mieux.—So much the better.
Glad to hear that.
Tant pis.—So much the worse.
Too bad.
Tapis.—The carpet.
Carpet.
Tartuffe.—A nickname for a hypocritical[371] devotee, derived from the principal character in Molière’s comedy so called.
Tartuffe.—A term for a hypocritical[371] devotee, taken from the main character in Molière’s play of the same name.
Te judice.—You may judge.
You may judge.
Tempora mutantur, et nos mutamur in illis.—The times are changed, and we are changed with them.
Tempora mutantur, et nos mutamur in illis.—Times have changed, and we have changed with them.
Tempus edax rerum.—Time the devourer of all things.
Tempus edax rerum.—Time, the great devourer of everything.
Tempus fugit.—Time flies.
Time flies.
Tempus omnia revelat.—Time reveals all things.
Tempus omnia revelat.—Time reveals all things.
Teres atque rotundus.—Smooth and round; polished and complete.
Teres atque rotundus.—Smooth and round; polished and whole.
Terra firma.—Solid earth; a safe footing.
Terra firma.—Solid ground; a stable foundation.
Terra incognita.—An unknown country.
Terra incognita.—An unexplored land.
Terre tenant.—A person in actual possession of the land.
Terre tenant.—A person who is currently in possession of the land.
Tertium quid.—A third something; a nondescript.
Tertium quid.—A third thing; something that doesn't fit into any particular category.
Tête-à-tête.—A conversation between two parties.
Face-to-face. —A conversation between two parties.
Tirade.—A tedious and bitter harangue.
Rant.—A tedious and bitter harangue.
Ton.—The fashion.
Ton.—The style.
Torso.—The fragmentary trunk of a statue.
Torso.—The incomplete body of a statue.
Tort.—A wrong; an injury.
Tort.—A wrong; an injury.
Tot homines, quot sententiæ.—So many men, so many minds.
Tot homines, quot sententiæ.—So many people, so many opinions.
Totidem verbis.—In just so many words.
In exactly those words.
Toties quoties.—As often as.
Toties quoties.—Whenever.
Toto cœlo.—By the whole heavens; diametrically opposite.
Toto cœlo.—Totally; totally the opposite.
Toto corde.—With the whole heart.
Wholeheartedly.
Toujours prêt.—Always ready.
Always ready.
Tour à tour.—By turns.
Tour à tour.—In turn.
Tout bien ou rien.—The whole or nothing.
Tout bien ou rien.—All or nothing.
Tout ensemble.—The whole.
The whole.
Tria juncta in uno.—Three united in one.
Tria juncta in uno.—Three combined into one.
Tu quoque, Brute!—And thou too, Brutus!
You too, Brutus!
Tuebor.—I will defend.
I will defend.
Tutto è buono che vien da Dio.—All is good which comes from God.
Tutto è buono che vien da Dio.—Everything that comes from God is good.
Tuum est.—It is your own.
It's yours.
Ubi jus incertum, ibi jus nullum.—Where the law is uncertain, there is no law.
Ubi jus incertum, ibi jus nullum.—Where the law is unclear, there is no law.
Ubi libertas, ibi patria.—Where liberty dwells, there is my country.
Ubi libertas, ibi patria.—Where freedom lives, that's my home.
Ubi supra.—Where above mentioned.
Ubi supra.—As mentioned above.
Ultima ratio regum.—The last argument of kings; military weapons; war.
Ultima ratio regum.—The final argument of kings; military force; war.
Ultima Thule.—The utmost boundary or limit.
Ultima Thule.—The farthest boundary or limit.
Ultimatum.—A final answer or decision.
Ultimatum.—A final answer or decision.
Un bel esprit.—A wit; a virtuoso.
Un bel esprit.—A clever person; a master of their craft.
Un sot à triple étage.—An egregious blockhead.
Un sot à triple étage.—A complete fool.
Unâ voce.—With one voice; unanimously.
With one voice; unanimously.
Unique.—Singular; the only one of its kind.
Unique.—One of a kind; the only one like it.
Usque ad nauseam.—To disgust.
To disgust.
Usus loquendi.—Usage in speaking.
Usus loquendi.—Speaking practice.
Ut infra.—As below.
As below.
Uti possidetis.—As you possess; state of present possession.
Uti possidetis.—As you own it; the condition of current ownership.
Utile dulci.—Utility with pleasure.
Utility with pleasure.
Vade-mecum.—Go with me; a constant companion.
Vade-mecum.—Come with me; a reliable companion.
Væ victis.—Woe to the vanquished!
Væ victis.—Woe to the defeated!
Vale.—Farewell.
Vale.—Goodbye.
Valet-de-chambre.—A servant who assists his master in dressing.
Valet-de-chambre.—A servant who helps his master get dressed.
Variæ lectiones.—Various readings.
Various readings.
Veluti in speculum.—As in a mirror.
Veluti in speculum.—Just like in a mirror.
Venditioni exponas.—That you expose to sale; writ of execution.
Venditioni exponas.—That you put up for sale; writ of execution.
Veni, vidi, vici.—I came, I saw, I conquered.
Veni, vidi, vici.—I came, I saw, I conquered.
Venire.—To come; a writ to a sheriff directing him to summon jurors.
Venire.—To come; a legal document issued to a sheriff instructing him to call for jurors.
Venue.—The place from which the jury are drawn.
Venue.—The location where the jury is selected.
Verbatim et literatim.—Word for word and letter for letter.
Verbatim et literatim.—Word for word and letter for letter.
Verbum sat sapienti.—A word is enough for a wise man.
Verbum sat sapienti.—A word is enough for a wise person.
Verdad es verde.—Truth is green.
Truth is green.
Veritas vincit.—Truth conquers.
Veritas vincit.—Truth wins.
Versus.—Against; toward.
Versus.—Against; toward.
Vertu, Virtù.—Virtue; taste; art; skill.
Virtue; taste; art; skill.
Veto.—I forbid.
Veto.—I forbid.
Vi et armis.—By force and arms.
Vi et armis.—By force and arms.
Viâ.—By the way of.
By the way.
Via media.—A middle course.
Middle way.
Vice.—In the room of.
Vice.—In the room.
Vice versâ.—The terms being exchanged; reversely.
Vice versâ.—The terms are being swapped; the opposite is true.
Vide.—See.
Vide.—Check it out.
Vide et crede.—See and believe.
See and believe.
Vide ut supra.—See as above.
See above.
Videlicet.—To wit, namely.
Videlicet.—In other words.
Videttes.—Sentinels on horseback.
Videttes.—Horseback sentinels.
Vignette.—A name given to slight engravings with which books, bank-notes, &c. are ornamented.
Vignette.—A term used for small engravings that decorate books, banknotes, and other items.
Vincit amor patriæ.—Love of country prevails.
Vincit amor patriæ.—Love of country prevails.
Vinculum matrimonii.—The bond of marriage.
Marriage bond.
Virtuoso.—One skilled in matters of taste or art.
Virtuoso.—A person who is highly skilled in matters of taste or art.
Virtute officii.—By virtue of office.
By virtue of office.
Vis inertiæ.—Inert power; the tendency of every body to remain at rest.
Vis inertiæ.—Inertia; the tendency of every object to stay at rest.
Vis medicatrix naturæ.—The healing tendency of nature.
Vis medicatrix naturæ.—The natural healing power.
Vis poetica.—Poetic genius.
Poetic genius.
Vis vitæ.—The vigour of life.
The vigor of life.
Vis-à-vis.—Face to face.
Face to face.
Vita brevis, ars longa.—Life is short, and art is long.
Vita brevis, ars longa.—Life is short, and art lasts forever.
Vivâ voce.—By word of mouth; by the living voice.
Vivâ voce.—By word of mouth; by a live voice.
Vivant rex et regina.—Long live the king and queen.
Vivant rex et regina.—Long live the king and queen.
Vivat regina.—Long live the queen.
Long live the queen.
Vivat respublica.—Live the republic.
Live the republic.
Vive la bagatelle.—Success to trifling.
Vive la bagatelle.—Long live the trivial.
Vive la reine.—Long live the queen.
Vive la reine.—Long live the queen.
Vive l’empereur.—Long live the emperor.
Long live the emperor.
Vive le roi.—Long live the king.
Vive le roi.—Long live the king.
Vive l’impératrice.—Long live the empress.
Long live the empress.
Vive, vale.—Farewell, and be happy.
Vive, vale.—Goodbye, and be happy.
Voilà tout.—That’s all.
That’s it.
Voilà une autre chose.—That’s quite a different matter.
Voilà une autre chose.—That’s a whole different issue.
Voir dire.—A preliminary examination to determine the competency of a witness.
Voir dire.—A preliminary examination to assess the qualifications of a witness.
Volens et potens.—Willing and able.
Willing and able.
Volgo gran bestia.—The mob is a great beast.
Volgo gran bestia.—The crowd is a powerful beast.
Volere è potere.—To will is to do.
Volere è potere.—Where there's a will, there's a way.
Volti subito.—Turn over quickly.
Turn over quickly.
Vox, et præterea nihil.—A voice, and nothing more.
Vox, et præterea nihil.—A voice, and nothing more.
Vox populi, vox Dei.—The people’s voice is God’s voice.
Vox populi, vox Dei.—The people's voice is God's voice.
Vox stellarum.—The voice of the stars: applied to almanacs.
Vox stellarum.—The voice of the stars: used for almanacs.
Vulgò.—Vulgarly; commonly.
Vulgò.—In common usage; colloquially.
Vuelta.—Over, to next page or (o.)
Vuelta.—Turn to the next page or (o.)
Vulnus immedicabile.—An irreparable injury.
Vulnus immedicabile.—An irreparable injury.
Vultus est index animi.—The countenance is the index of the mind.
Vultus est index animi.—The face is a reflection of the mind.
Zonam solvere.—To loose the virgin zone.
Zonam solvere.—To free the virgin zone.
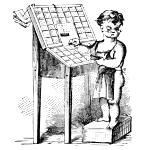

INDEX.
- Abbreviated syllables, 15.
- Abbreviations, list of, 344-356.
- Abecedarium, probably the earliest attempt at printing, 11.
- Accents and aspirates, Greek, 99-101.
- Hebrew, 106-108.
- Russian, 112, 113.
- Accented letters, 67.
- Acids used in making paper spoil the effect of ink, 276, 277.
- Adams, Isaac, inventor of the bed-and-platen power-press, 237, 238.
- Adhesion of paper, how to prevent, 316.
- Admiration, sign of, 63.
- Agate type, specimen of, 54.
- Alcfrid, Runic memorial of, 89.
- Alexandri Galli Doctrinale, one of the first printed books, 10.
- Almanac, first printed book in the Middle Colonies, 16, 17.
- Alphabet, Anglo-Saxon, 91.
- English, 58.
- German, 94.
- Greek, 98.
- Hebrew, 104.
- Hieroglyphic, 84.
- Runes, 86-90.
- Russian, 112, 113.
- Alterations in a proof justly chargeable, 204, 205, 211.
- not allowable in reprints of old and standard authors, 202.
- Amber ink, how to produce, 288.
- Ambiguous and compound words to be set uniformly, 202.
- American type, superior quality of, 23.
- American Weekly Mercury, third newspaper in America, 17.
- Ancient ornaments, exquisite and curious, 15, 16.
- press, clumsy, 235.
- typographical peculiarities, 15.
- Anglo-Saxon characters, how originated, 51.
- alphabetical table of, 91.
- cases for, 92, 93.
- Lord’s Prayer in, 51.
- runes, table of, 88.
- Apostrophe, how used, 63, 64.
- Appeal against the Turks, of 1454, 11.
- Applegath and Cowper, improvers of the cylinder press, 238, 239.
- Apprentice, how to instruct an, 122.
- must be punctual, obedient, and courteous, 123.
- qualifications required in an, 121.
- ridiculous practices to be avoided by, 122.
- Apprentices, advice to, 137, 138.
- Arithmetical figures, when introduced, 70.
- Article, the indefinite, rule for using, 318.
- Ascending letters, 59.
- Asterisk, use of, 66.
- Astronomical signs, 73, 74.
- Authors, detention of proofs by, 205.
- hints to, 211.
- impatience of, 205.
- whims of, 61.
- Automatic counter, illustrated, 310.
- machine, for casting and finishing type, 23.
- Support long or short pages, 133.
- Baine, John, sets up a type-foundry in Philadelphia, 19.
- Bay Psalm-Book, first book printed at Cambridge, 16.
- Bearers on hand-presses, how prepared, 259, 277, 278, 281.
- Beaumont, Victor, inventor of serrated cutting blade, 242.
- Beginners, ironical rules for, 139, 140.
- Bewcastle cross, Runic inscription on, 89.
- Bible, first, printed at Mentz, by Gutenberg, Fust and Schœffer, in 1455, of which there are four copies in Europe and two in the United States, 11.
- Brinley’s, 11.
- German, printed in Germantown, by Saur, 19.
- Lenox’s, 11.
- Mazarin, 11.
- printed in Iceland in 1584, 14.
- quarto, in standing type, in Philadelphia, 26.
- Biblia Pauperum, attributed to Koster, 10.
- Bill of type, 57.
- Binny, Archibald, first successful founder in Philadelphia, 19, 20.
- improver of the type-mould, 19, 42.
- [374]Black letter, when used, 51.
- Blades, William, 14.
- Blaeu, Willem Jansen, early inventor of a press, 235.
- Blankets for wood-cut printing, 282.
- India-rubber, 266.
- thick paper, 266.
- Welsh flannel, 266.
- when to be used, 257, 266.
- Blanking, remarks concerning, 259.
- Bleaching powders deleterious, 276.
- Block books, 10.
- Blue ink, how to make, 287, 288.
- Bodkin, how to use the, 208, 209.
- illustrated, 209, 210.
- Books, cheapening of, due to steam-presses, 240.
- early, printed in Gothic character, 16.
- first, printed on one side of the leaf only, 10.
- how to preserve, 317.
- Book-folding machine, illustrated, 249.
- Borders, 80, 120.
- Boston Gazette, second newspaper published in America, 17.
- News-Letter, first newspaper published in America, 17.
- Bourgeois, specimen of, 54.
- Boxwood, description of good, 36.
- liable to warp, 282, 283.
- quoin, 306.
- Braces, use of, 75.
- Bracket, how used, 65.
- Bradford, William, first printer in the Middle Colonies, 16, 17.
- Brass rules, remarks concerning, 80.
- slotted corners, description of, 44.
- Break-lines improperly driven over, 133.
- should never begin a page, 133.
- Brevier, specimen of, 54.
- Brilliant, smallest type in America, 52.
- specimen of, 54.
- Brinley’s collection of Bibles, 11.
- British founders reject American casting-machines, 23.
- Bronze printing, how executed, 284, 285.
- Brown ink, how to produce, 288.
- Bruce, David and George, type-founders in New York, 21, 22.
- David, Jr., type-casting machine invented by, 22.
- Bullock, William, inventor of the first perfecting press, 242-244.
- chain-running press, 244.
- self-feeding perfecting press, illustrated, 243.
- Bundle of paper described, 294.
- Cabinet for chases, illustrated, 231.
- with galley-top, illustrated, 304.
- Cabinets, job cases should be kept in, 304.
- of cases, for sorts, quads, etc., illustrated, 219-221.
- should be kept in perfect order, 221.
- Cambridge, first press in North America at, 16.
- Campbell’s cylinder presses, 239, 246.
- self-feeding perfecting press, 246.
- Cancelled figures, 70.
- Capital, good character is, 138.
- letters, 58-60.
- letters, how to use, 59, 60.
- Card-cutters, 309.
- printing, directions for, 283, 284.
- sheets, chart for cutting, (Le Blond,) 302.
- Carey, Mathew, 26.
- Cases, American plan of Roman, 124, 125.
- blank, 303.
- German, 96, 97.
- Greek, 102, 103.
- Hebrew, 109, 111.
- how to label job, 304.
- job, 302.
- labour-saving lead, 303.
- labour-saving rule, 82, 302.
- labour-saving slug, 303.
- music, 117-119.
- number of, to a fount, 128.
- proposed improvement in, 126.
- quotation furniture, 303.
- Saxon, 92, 93.
- triple job, 302.
- Caslon, William, 18.
- Cassie quires, why so called, 294.
- Casting off copy, methods of, 223-226.
- Catch-words, first used at Venice, 16.
- in titles, how to be set, 134.
- Caxton, William, introduces printing into England, 14.
- his first types not cast or founded, 13.
- Centennial Exhibition, 1876, presses exhibited at, 244-246.
- fast printing at, 245.
- Chalcography, inventor of, 34.
- Chromo-lithography, 29.
- Chromos, printed on cylinder presses, 31.
- Chronicle of Cologne, 9.
- Cicero, French and German name for Pica, 53.
- Circular quadrates, 78.
- Clicker, or maker-up, duties of, 226-228.
- Clymer, George, inventor of the Columbian press, 236, 237.
- Colon, use of, 62.
- Colorito, Abraham, printer at Soncino, 1488, 14.
- Colour, uniformity in, 263, 278, 279.
- Coloured inks, how to make, 286-288.
- printing, instructions for, 285-287.
- Colours, contrast of, 289-292.
- how to multiply, 288.
- how to use dry, 287, 288.
- Columbian press, illustrated, 236.
- introduced into England, 237.
- Combination borders, 80, 120.
- [375]Comma, use of, 62.
- Commercial post paper, size of, 298.
- signs, 71.
- Companionships, how managed, 228-232.
- misunderstandings in, 228.
- Composing, directions for, 129-136.
- how to avoid errors in, 130.
- position in, 127.
- rule, steel, illustrated, 228.
- sticks, illustrated, 305.
- screw, the best for fixed measures, 305.
- Composition rollers, how to make, 252-254, 311, 312.
- how to wash, 253.
- melting-kettle for, illustrated, 252.
- Compositors, differences in 218.
- rules to be observed by, 233, 234.
- Compound words, 64, 65, 331.
- Contents, rules for, 135.
- Continuous sheet, printing from a, 242.
- Contrast of colours, 289-292.
- Conversation in a printing office to be avoided, 234.
- Copy, casting off, 223-226.
- takes of, should be small, 221.
- to be carefully prepared, 204.
- Copyholder, illustrated, 309.
- Copyrights, how to secure, 333-335.
- application to be made to Librarian of Congress, 333.
- cannot be granted upon trade-marks or labels, 335.
- duration of, 334.
- form of notice, 334.
- penalty for false notice, 334.
- renewal of, 334.
- Cork bearers, 259.
- Corner quadrates, illustrated, 307.
- Corpus, German name for Long Primer, 54.
- Correcting in the metal, 207-211.
- directions for, 208-210.
- rules for, in a companionship, 231, 232.
- Coster, (see Koster,) 9-11.
- Cottrell & Babcock’s cylinder presses, 239.
- Counting out sheets, 297.
- Courtesy, importance of, 123.
- Creases and wrinkles in paper, how to remove, 263.
- Cross-bar, how to avoid springing, 148.
- Crown paper, size of, 298.
- Cut-in notes, how adjusted, 131, 132.
- Cuts, how to make ready, 280-283.
- Cylinder press, invention of the, 238.
- presses, making ready on, 265-275.
- Dagger or obelisk, use of, 66.
- Dash, use of, 63.
- Dates, method of, during the French Republic, 69.
- Daye, John, Anglo-Saxon types first cut by, 51.
- Daye, Stephen, first printer in North America, 16.
- Dedications, how displayed, 135.
- position of, 135.
- Degener & Weiler’s Liberty press, illustrated, 246, 247.
- Delicate impression, how to produce, 281, 282.
- Demy paper, size of, 298.
- Derivation of English words, 324-326.
- Descending letters, 59.
- De Vinne’s history of the invention of printing, 12.
- Diamond type, specimen of, 54.
- Diphthongs, Greek, 99.
- Distributing, directions for, 128, 129.
- how to wash matter for, 128, 129.
- pernicious effects from heating
- type for, 129.
- proper times for, 129.
- Dividing words, rules for, 64, 65.
- Donatus of 1451, 11.
- Double imperial paper, size of, 298.
- letters, 59.
- medium paper, size of, 298.
- super-royal paper, size of, 298.
- Drawing paper, how to be wet, 256.
- Dry colours, how to use, 287, 288.
- Duck’s bill, to prevent paper from slipping on the tympan, 278.
- Duodecimo, or twelves, scheme for imposing sheet of, 165.
- the same, without cutting, 166.
- the same, two signatures, 167.
- half-sheet, 168.
- the same, without cutting, 168.
- the same, from the centre, 169.
- sheet of, from the centre, 170.
- the same, long way, 171, 172.
- one-third of a sheet, 171, 172.
- two half-sheets, together, 173.
- half-sheet, two signatures, 174.
- Earl Stanhope’s printing-press, 236.
- Earliest printing-press, 235.
- written sounds, 83-85.
- Egyptian hieroglyphics, specimens of type for printing, 83-85.
- Eighteens, scheme for imposing half-sheet of, 176.
- the same, with two blanks, 176.
- sheet of, folded together, 177, 178.
- the same, with one signature, 177, 178.
- the same, with two signatures, 179, 180.
- the same, with three signatures, 179, 180.
- half-sheet of, without transposition, 181.
- Electro-stereotyping, 27, 43.
- Electrotyping, method of, 27.
- Emerald green, 288.
- [376]Enamelled cards, to be printed dry, 283, 284.
- English type, specimen of, 53.
- Engraver’s proof useful to pressmen, 283.
- Engravings, copper-plate, 34.
- how to print, 280-283.
- how to restore, 317.
- tools for, 34.
- wood, 31-34.
- Epitaph, printer’s, 208.
- Errata, list of, where placed, 136.
- Errors inevitable, 136.
- made in correcting a proof, 203, 204.
- Escala espiritual de San Juan Climaco, the first book printed in America, 16.
- Even impressions on a hand-press, how to obtain, 277-279.
- Exclamation, sign of, 63.
- Feed guides, Megill’s, illustrated, 310.
- Figgins’s, Vincent, opinion of Caxton’s type, 13.
- Figures, arithmetical, 70.
- old style, 70.
- scratched or cancelled, 70.
- Filling the standing press, 296, 297.
- Fine hand-presswork, remarks concerning, 275-279.
- printing, character of ink required for, 275, 276.
- paper suitable for, 257.
- why difficult in the United States, 276, 277.
- Finiguerra, Thomas, discoverer of chalcography, 34.
- Firefly press, Gordon’s, 247.
- Fireproof ink, 314.
- Flat cap paper, size of, 298.
- Flowers and borders, remarks on, 80.
- Fly on cylinder presses, how to be set, 274.
- Folding machines, 249.
- Folio, imposing single sheet of, 150.
- paper, size of, 298.
- two sheets quired, 151, 152.
- Follow copy, the compositor’s rule, 204.
- Foolscap paper, dimensions of, 298.
- Foreign words and phrases, translated, 357-372.
- Foreman, duties and qualifications of, 218-232.
- Form, how to make ready for hand-press, 257-260.
- of warehouse book, 293.
- Forms, directions for locking up, 147, 148.
- how to impose, 141, 142.
- how to wash, 264, 265.
- precautions in unlocking, 208.
- Forties, scheme for imposing half-sheet of, 191.
- Forty-eights, scheme for imposing quarter sheet of, with two signatures, 192.
- the same, without cutting, 193.
- half-sheet of, 192.
- the same, three signatures, 193.
- quarter sheet of, 194.
- Foul proof, a grievous fault, 207.
- Founders, English, ancient regulations concerning, 18.
- Fount of letter, complete, described, 58.
- Founts, irregularities of, 58.
- Fractions, 70.
- Franklin, Benjamin, attempts type-founding, 19.
- James, establishes the New England Courant, 17.
- Franklin presses, Gordon’s, 247.
- illustrated, 246.
- Friars, how to obviate, 263.
- Frisket, directions for preparing, 258.
- catch of, how to place, 259.
- Full point, use of, 62, 63.
- Furniture, how to make up, 144, 145.
- Fust, John, connection with Gutenberg and Schœffer, 11, 12.
- Gaillarde, French term for Bourgeois type, 54.
- Gallows, how to be placed, 259.
- Game of Chess, first book printed in England by Caxton, 14.
- Gauge pins, Megill’s, illustrated, 310.
- Ged, William, inventor of stereotyping, 24.
- Geometrical signs, 71, 72.
- German alphabet, 94.
- plan of cases for, 96, 97.
- similar letters elucidated, 94, 95.
- Germantown, first paper mill in America, near, 17.
- first quarto Bible in America, printed at, 19.
- type cast at, by Saur, 19.
- Giving out book paper to wet, 294.
- paper for jobs, 294, 295.
- Globe press, 248.
- Glover, Jesse, introduces printing into Cambridge, Mass., 16.
- Glue, common prepared, 313.
- liquid, how to make, 313.
- Gold preparation, how to use, 288.
- printing, how practised, 284, 317.
- size for gold printing, 284.
- Good habits inculcated, 121-123, 137, 138.
- presswork, conditions for securing, 279.
- Gordon’s Franklin press, illustrated, 246.
- job-presses, 246, 247.
- Gothic characters, early books printed in, 16.
- Gradation of type bodies, 56.
- Grant Thorburn, benevolence of, 239.
- Great Primer, specimen of, 53.
- Greek accents and aspirates, 98-101.
- alphabetical table of, 98.
- letters, numerical value of, 67, 98.
- ligatures now discarded, 98.
- numeral letters, table of, 67.
- plan of cases for, 102, 103.
- rules for composing, 101.
- [377]Green ink, how to make, 288.
- Gros Romain, French title for Great Primer, 53.
- Guillemet’s quotation marks, 62.
- Gutenberg, account of, 9-14.
- Gutter-sticks, directions for cutting, 148.
- Gypsum in paper, effects of, 276, 277.
- Haarlem, the birthplace of printing, 9.
- Hand-mould improved by Binny, 20.
- Hand-press, how to prepare impression on, 275-279.
- how to overlay on, 277.
- bearers used on, 277, 278.
- Hand-presswork, fine, how to produce, 275-279.
- Handwriting, erroneous notion concerning, 226.
- Hanging pages, how to rectify, 208.
- up paper to dry, 295.
- Hansard’s receipt for making rollers, 253, 254.
- Hard roller, best for fine work, 267.
- Head-lines, how displayed, 131.
- Heap of paper, how to treat, 259.
- Heated type, pernicious effects from distributing it, 129.
- Hebrew accents, 106-108.
- alphabet, identical with Phœnician, 83.
- alphabetical table of, 104.
- Bible, first printed, 14.
- letters, numeral value of, 104.
- letters of similar appearance, 105.
- lower case, without points, 109.
- Masoretic points or vowels, 106.
- method of composing, 105.
- plan of cases with points, 110, 111.
- scheme for imposing 8vo sheet of, 161, 162.
- spacing letters, 105.
- Height of type, standard for, 57, 58.
- Hieroglyphic alphabet, 84.
- Hinderances to fine printing in America, 276, 277.
- Hints honoured in the breach, 136, 137.
- Hoe & Co.’s cylinder presses, 239-242.
- Hoe, Richard M., inventor of type-revolving printing machine, 241.
- Robert, account of, 239, 240.
- Hoe’s web perfecting press, illustrated, 245.
- Hollow quadrates, use of, 77.
- Horn-book, illustration of, xi.
- Humphreys’s History of the Art of Printing, 12.
- Hurried work, how to expedite, 226-228.
- Hyphen, how employed, 64, 65.
- not used by the earliest printers, 15.
- Iceland, early printing office in, 14.
- Imperial and half paper, size of, 298.
- paper, dimensions of, 298.
- Imposing forms, directions for, 141, 142.
- in companionships, rules for, 230, 231.
- Imposing, memoranda concerning, 148, 149.
- abstract title-deeds, 150.
- Portfolio, single sheet, 150.
- two sheets, quired, 151, 152.
- Quarto, common sheet of, 153, 154.
- scheme for, music books, 153, 154.
- two half-sheets, together, 155, 156.
- half-sheet, broad way, 155, 156.
- Octavo, sheet of, 157, 158.
- the broad way, 157, 158.
- half-sheet, 159.
- two half-sheets, together, 159, 160.
- two quarters, together, 160.
- sheet, mixed, 161, 162.
- sheet of Hebrew, 161, 162.
- sheet, from the centre, 163, 164.
- half-sheet, from the centre, 163.
- two quarters, from the centre, 164.
- Twelvemo, or 12mo, sheet, 165.
- the same, without cutting, 166.
- the same, two signatures, 167.
- half-sheet, 168.
- the same, without cutting, 168.
- the same, from the centre, 169.
- sheet of, from the centre, 170.
- the same, long way, 171, 172.
- one-third of a sheet, 171, 172.
- two half-sheets, together, 173.
- half-sheet, two signatures, 174.
- Sixteen, half-sheet of, 174.
- sheet of, 175.
- Eighteen, half-sheet of, 176.
- the same, with two blanks, 176.
- sheet of, folded together, 177, 178.
- sheet of, one signature, 177, 178.
- the same, two signatures, 179, 180.
- sheet of, three signatures, 179, 180.
- half-sheet of, without transposition, 181.
- 20s, half-sheet of, with two signatures, 181.
- sheet of, 182.
- Twenty-Four Hours, half-sheet of, 183.
- sheet of, two signatures, 183, 184.
- half-sheet of, sixteen-way, 184.
- half-sheet of, long, 185.
- half-sheet, two signatures, 185.
- half-sheet, without cutting, 186.
- Thirty-Twos, half-sheet of, 186.
- sheet of, 187, 188.
- the same, four signatures, 187, 188.
- half-sheet, two signatures, 189.
- half-sheet of, mixed, 189.
- Thirty-Six, half-sheet of, 190.
- the same, without cutting, 190.
- the same, two signatures, 191.
- Forties, half-sheet of, 191.
- Forty-eights, quarter sheet of, with two signatures, 192.
- the same, without cutting, 193.
- common quarter-sheet of, 194.
- half-sheet of, two signatures, 192.
- the same, three signatures, 193.
- [378]64s, quarter sheet, 195.
- the same, two signatures, 194.
- sixty-fours, mixed, 195.
- half-sheet of, 196.
- Seventy-Two's, half-sheet of, 197.
- Nineties, half-sheet of, 198.
- One Hundred Twenty-Eights, half-sheet of, 199.
- Imposing stone, illustrated, 308.
- Impression on cylinder presses, how to regulate, 269-275.
- Indenting paragraphs, rule for, 132.
- Index, directions for preparing copy of, 133.
- rule for setting, 133.
- where placed, 133.
- India paper suitable for overlays, 280.
- India-rubber cloth, good qualities of, 266.
- Ink-block, how to be placed, 251.
- Ink, black, how to intensify, 284.
- coloured, 286, 287.
- requires a hard roller, 267.
- for cylinder presses, 267, 268.
- for fine work, indispensable qualities of, 275, 276.
- how to prevent setting off, 279.
- how to remove surplus from the roller, 262.
- how to produce amber, 288.
- blue, 287, 288.
- brown, 288.
- fire-proof, 314.
- green, 288.
- lilac, 288.
- pink, 288.
- purple, 288.
- red, 286-288.
- scarlet, 288.
- vermilion, 288.
- to mark tin or zinc, 315.
- driers, how to make, 315, 316.
- Ink-fountain, how to manage, 268.
- patent, illustrated, 310.
- Ink-stone and muller, illustrated, 285.
- Interleaving necessary in fine presswork, 279.
- Interrogation, sign of, 63.
- Iron furniture, how made, 310.
- Ironical rules for compositors, 136, 137.
- for beginners in business, 139, 140.
- Italic letter, invention of, 50.
- abuse of, 51.
- Job department, 300-310.
- capitals and lower-case should not be laid together, 304.
- cases should be labelled with the type which is in case, 304.
- how to conduct the business, 300.
- memorandum slip for record, 301.
- requisites for, 301-310.
- selection of material, 300.
- Job presses, American, unsurpassed, 246.
- varieties of, 246-248.
- Jobbing facilities, 300-310.
- Jobs, making margin for, 147.
- Johnson, Lawrence, type-founder in Philadelphia, 20.
- William M., invents a type-casting machine, 22.
- Journeymen, idle, 18.
- Junius, Hadrianus, 10.
- Justification, accurate, absolutely essential, 131.
- Adjusted letters, 59.
- Kinsley, Dr., invents a cylinder press, 238.
- Knowledge, progress of, accelerated by steam-presses, 240.
- König, Frederick, inventor of the cylinder press, 238.
- Koster, (or Coster,) Laurentius, inventor of printing, 9-14.
- printer of block books, 10.
- used wooden and tin type, 10.
- Labor-saving brass ruler, 81.
- plan of case for, 82.
- curvatures, 79.
- quotation furniture, 77.
- rule, 43, 81.
- Lamp-holder, 309.
- Laying a fount of type, directions for, 127.
- pages, 143, 144.
- Lead cutter, illustrated, 307.
- Leads, described, 80.
- Leather belting, how to soften, 316.
- Lenox, James, of New York, collection of Bibles, 11.
- Lepsius, R., hieroglyphic types of, 83.
- Letter paper, size of, 298.
- Letters of Indulgence, of 1454-5, 11.
- Letters, accented, 67.
- ascending, 59.
- descending, 59.
- double, 59.
- kerned, 59.
- long, 59.
- numeral, 67.
- short, 59.
- two-line, 76.
- Ley, directions for making, 312.
- not to be used on wood-cuts, 283.
- Ley-brush, how to be made, 265.
- Ley-trough, described, 264, 265.
- Liberty press, illustrated, 247.
- Lifting pages, 143.
- Lightning press, Hoe’s, 239-242.
- illustrated, 240.
- Lilac ink, how to make, 288.
- Lithographic chalk and ink, 28.
- stone, 27.
- transfer ink, how to make, 315.
- Lithography, discovery of, 27.
- practice of, 27-31.
- Locking up forms, 147, 148.
- [379]Long letters, 59.
- Long Primer, specimen of, 54.
- Lord’s Prayer in Anglo-Saxon, 51.
- Lower-case sorts, 59.
- Machine casting, 22.
- Machine-made paper, sizes of, 298.
- Machine-press of Isaac Adams, 237, 238.
- Frederick, König, 238.
- Applegath and Cowper, 238.
- Richard M. Hoe, 239-242.
- William Bullock, 242-244.
- Campbell, 239, 246.
- Cottrell & Babcock, 239.
- Walter, 244.
- Mackling, how to remedy, 263.
- Make-up rule, steel, illustrated, 229.
- Making margin, 145-147.
- for jobs, 147.
- ready a form, directions for, 257-260.
- on cylinder presses, 265-275.
- wood-cuts, directions for, 280-283.
- register, directions for, 260.
- Making up furniture, 144, 145.
- in companionship, 229.
- letter and furniture in companionships, 230.
- Manual de Adultos, one of the first books printed in America, 16.
- Manuccio, Aldo, 61.
- Mappa, Adam G., one of the early American type-founders, 19.
- Margin, how to make, 145-147.
- on cylinder presses, 268.
- Masoretic points, 106.
- Mathematical signs, 71, 72.
- Matrices, copper, 40.
- electrotyped, 23.
- Matrix, illustrated, 40.
- Mazarin Bibles, 11.
- Measure of stick, how to make by ems, 129.
- Mecom, Benjamin, 24.
- Medium paper, size of, 298.
- Melting-kettle, description of, 252.
- Metal rules, 75.
- Metric system, 336, 337.
- Minerva cutting machine, illustrated, 309.
- Minion type, specimen of, 54.
- Mitering machine, illustrated, 307.
- Mittel, German name for English type, 53.
- Modern conveniences, 120.
- Mucilage, directions for making, 312, 313.
- Mud process in stereotyping, 26.
- Music, comparative table of bodies, 115.
- directions for composing, 116.
- plan of cases for, 117-119.
- specimens of, 114.
- New Hampshire Gazette, oldest living paper of the United States, 17.
- Newspapers, number of, printed in the United States in 1801 and 1810, 20.
- New types, how to prevent them from adhering together, 127.
- New York Gazette, first newspaper published there, 17.
- Nicks, position of, 58.
- Nicholson, William, suggester of the cylinder press, 238.
- Ninety-sixes, to impose half-sheet, 198.
- Nonpareil press, illustrated, 247.
- type, specimen of, 54.
- Norse-Runic alphabet, 87, 88.
- North American and United States Gazette, of Philadelphia, oldest daily newspaper in the United States, 17.
- Note paper, size of, 298.
- Notes, proper size of type for, 131.
- cut in, how arranged, 132.
- Numeral letters, Gothic, 68, 69.
- Greek, 67.
- Roman, 68, 69.
- Numerical value of Greek letters, 67, 98.
- Hebrew letters, 104.
- Octavo, scheme for imposing sheet of, 157, 158.
- sheet of, the broad way, 157, 158.
- two half-sheets, together, 159, 160.
- sheet mixed, 161, 162.
- half-sheet, 159.
- two quarters, together, 160.
- sheet of Hebrew, 161, 162.
- sheet of, from the centre, 163, 164.
- half-sheet of, do., 163.
- two quarter-sheets, do., 164.
- Oiling a press, 292.
- Old English letter used by the early printers, 49.
- Old-style figures, advantages of, 70.
- Old works, no license of alteration allowable in reprinting, 202.
- One hundred and twenty-eights, scheme for imposing half-sheet of, 199.
- Ornaments, ancient, exquisite and curious, 15, 16.
- Orthography, hints on, 318-332.
- uniformity in, 202.
- Overlaying on cylinder presses, 272, 273.
- on hand-presses, 277.
- Overrunning, proper method of, 210.
- Overseer, duties of, 218-232.
- Over-sheets, rules for giving out, 294.
- Package note paper, size of, 298.
- post paper, size of, 298.
- Pages, how to tie up, 142, 143.
- how to lift, 143.
- how to lay, 143.
- Palmaert, Lambert, printed at Valencia, 1479, 14.
- Paper-bank, how to be placed, 259.
- Paper for jobs, rule for giving out, 294.
- cutters, 309.
- instructions for wetting, 255-257.
- qualities of good, 276.
- quantity required for a book, 299.
- sizes of, 298.
- suitable for fine printing, 257.
- [380]Papier-maché moulds, 242.
- Paragon type, so called by printers in all countries, 52.
- Paragraph mark, how used, 66.
- Paragraphs, authors’ irregularities in making, 132, 133.
- rule for indenting, 132.
- Parchment tympans, 254.
- Parenthesis, use of, 65, 66.
- Pasteboard tympan for a cylinder press, advantages of, 265.
- Paste, directions for making, 312.
- Pearl type, specimen of, 54.
- Peerless press, illustrated, 248.
- Penn, William, promotes printing in Pennsylvania, 17.
- Perforating machine for round holes, illustrated, 308.
- rule, illustrated, 308.
- Perforator, Ames’s Patent, 308.
- Period, use of, 62.
- Petit and Jungfer, German names of Brevier, 54.
- Petit Romain, French name of Long Primer, 54.
- Petri Hispani Tractatibus Logicis, one of the first printed books, 10.
- Phœnician alphabetic system, 83.
- Photo-engraving, 35-38.
- Phrases, foreign, translated, 357-372.
- Pica, specimen of, 53.
- the standard type, 52.
- Picks in types, how to remove, 262.
- in wood-cuts, how to take out, 281.
- Pietrison, Thomas, the inventor of printers’ ink, 10.
- Pink ink, how to produce, 288.
- Planetary signs, 73, 74.
- Plate paper, directions for wetting, 256.
- Plumbago, used in electrotyping, 27, 45.
- Point system of type bodies, 55, 56.
- Points, how to arrange, 258.
- Polyglot founders, 18.
- Position of nicks, 58.
- in composing, 127.
- Prefaces, rules concerning, 135.
- Press-book, form of, 222.
- Press arbitrarily restricted, 235.
- history of invention of, 235-248.
- old common, 235.
- to print and number railroad tickets and coupons, 246.
- Presses—see machine-presses.
- how to oil, 292.
- Pressing sheets, mode of, 296, 297.
- Pressmen should examine every sheet as printed, 263.
- rules and remedies for, 262-264.
- should study fine specimens of printing, 277.
- Presswork, requisites for producing fine, 275-279.
- Prima, 203.
- Printed sheets, how treated, 295-297.
- Printers, how not to succeed in business, 139, 140.
- ironical rules for, 136, 137.
- Printer’s knife, illustrated, 210, 211.
- Printing, discovery of, 9-14.
- extension of, 13.
- in bronzes, 284, 285.
- in colours, 285-288.
- in gold, directions for, 284.
- introduced into America, 16.
- manner of discovery, 9-12.
- Printing-machine, type-revolving, 240-242.
- Printing-offices, rules to be observed in, 233, 234.
- Printing-press, amateur, 248.
- Bullock, 242-244.
- Campbell, 239, 246.
- Cottrell & Babcock, 239.
- Degener, 246, 247.
- Earl Stanhope’s, 236.
- earliest, 235.
- first set up in North America, 16.
- Frederick König’s, 238.
- Gally, 246.
- George Clymer’s, 236.
- George P. Gordon’s, 246, 247.
- invention of the, 235-248.
- Isaac Adams’s, 237.
- Job, 246-248.
- Peter Smith’s, 237.
- Railroad-ticket, 246.
- Ramage’s, 236.
- Richard M. Hoe’s, 239-242.
- Ruggles, 246.
- Samuel Rust’s, 237.
- Walter, 244.
- Wells, 246.
- Willem Jansen Blaeu’s, 235.
- Proof-marks, explanation of, 214, 215.
- illustration of, 212, 213.
- Proof-press, illustrated, 343.
- Proof-reader, author’s obligations to, 201.
- duties of a, 202, 207.
- friendly offices of, 201.
- qualifications of, 200-206.
- should be a compositor, 200.
- Proof-readers, caprices of, 207.
- Proof-sheets, alterations in, justly chargeable, 204, 205, 211.
- detained by authors, 205.
- errors in correcting, 203, 204.
- method of reading, 202, 203.
- plan for keeping account of, 203.
- remarks concerning, 202.
- should be read by two readers, 204.
- Proofs of engravings, how to take, 283.
- Proper names should be plainly written, 211.
- Prussian blue ink, 287.
- Publishers’ interference with the printers’ province, 134.
- Pulling, directions for, 260-262, 279.
- [381]Punch, illustrated, 40.
- Punctuality indispensable in an apprentice, 123.
- Punctuation, amending of, should be confined to one reader, 204.
- and orthography to be uniform throughout a book, 202.
- points of later invention than printing, 61.
- variations in use of, 61.
- whims of authors, 61.
- Wilson’s Treatise on, 62, 65.
- Squares, circular, illustrated, and described, 78, 79.
- corner, illustrated, 306.
- directions for composing, 78, 79.
- hollow, illustrated, 77.
- Quantity of paper required to print a book of one thousand copies, 299.
- Quarto, scheme for imposing, 153, 154.
- the broad way for music, 153, 154.
- two half-sheets, together, 155, 156.
- half-sheet, the broad way, 155, 156.
- Quires, cassie, of what made up, 294.
- Quitting work, precautions to be used by the pressmen in, 264.
- Quoins, proper form of, 147, 148.
- how to unlock, 148.
- various patents, 306.
- Quotation furniture, illustrated, 77.
- marks, 62.
- Quotations, broad and narrow, 76.
- Train ticket printing-machine, 246.
- Ramage, Adam, 236.
- Reading-boy, 202.
- Receipts, various, 311-317.
- Red ink, how to make, 286, 288.
- References, use of, 66, 67.
- Register, how to make, 260.
- Regulations for a printing-office, 233, 234.
- Reprints from standard authors not to vary from the original, 202.
- Revise, 206.
- Revise sheet necessary, 260.
- Riding, how to prevent, 286.
- Rittenhouse, William, the first paper-maker in America, 17.
- Roller-boy, 262.
- Roller-handle, how to lie when used, 251.
- how to check, 251.
- Roller, hard, best for fine work, 267.
- soft, required for posters and old type, 267.
- Roller-mould, directions for using, 252.
- Roller-stand, how to set up, 250, 251.
- illustrated, 251.
- Rollers, composition, how made, 252-254, 311, 312.
- for hand-presses, how to keep, 278.
- hand-press, 252.
- precautions in using, 252.
- to be adapted to style of work, 267.
- when in working order, 253.
- Roman letter, invention of, 49.
- deserving general adoption, 50.
- Ronaldson, James, type-founder in Philadelphia, 19.
- Richard, type-founder in Philadelphia, 20.
- Rosetta stone, discovery of, 83.
- Royal and half paper, size of, 298.
- Royal paper, size of, 298.
- Ruggles’s job presses, 246.
- card cutter, illustrated, 309.
- Rule, brass, 80.
- labour-saving, illustrated, 81.
- plan of case for, 82.
- Rules and remedies for pressmen, 262-264.
- for beginners in business, ironical, 139, 140.
- for compositors, ironical, 136, 137.
- for perforating, illustrated, 308.
- Runes, earliest alphabets of the Teutons and Goths, 86.
- Runic alphabets, 86-90.
- inscription on Bewcastle cross, 89.
- Russian alphabet, 112, 113.
- Rust, Samuel, inventor of the Washington press, 237.
- Saur (or Sower), Christopher, first American type-founder, 19.
- issues the Germantown Chronicle in 1739, 19.
- prints the first quarto Bible, 19.
- Scarlet ink, how to make, 288.
- Schœffer, Peter, inventor of type-founding, 13, 14.
- Semicolon, invented by Aldo Manuccio, 61.
- use of, 62.
- Senefelder, Alois, discoverer of lithography, 27.
- Setting fly on a cylinder press, 274.
- off, how to prevent ink from, 279.
- tapes, process of, 274.
- up a Washington press, 250.
- up a roller-stand, 250, 251.
- Seventy-twos, scheme for imposing half-sheet of, 197.
- Shades of ink, how to produce, 288.
- Sheets, counting out and putting away, 294.
- filling in and pressing, 296.
- how to take down from the poles, 296.
- names of, 149.
- Shooting-sticks, illustrated, 307.
- Short letters, 59.
- numbers of sheets, allowance for, 294.
- pages, how to back, 133.
- Side notes, how arranged, 131, 132.
- Signatures, table of, 216, 217.
- inventor of, 16.
- Signaturing, remarks concerning, 135.
- [382]Signs, astronomical, 73, 74.
- Signs, commercial, 71.
- mathematical, 71, 73.
- medical, 74, 75.
- Silk tympan-covers, 254.
- Silvering solution, how to make, 316.
- Sitting at work improper, 127.
- Sixteens, scheme for imposing half-sheet of, 174.
- sheet of, 175.
- Sixty-fours, scheme for imposing quarter-sheet of, 195.
- scheme for imposing quarter-sheet of, with two signatures, 194.
- quarter sheet of, mixed, 195.
- half-sheet of, 196.
- Slotted brass corners, illustrated, 44.
- Slovenly copy, censurable, 223.
- Slurring, how to prevent, 263, 278.
- Small capital letters, 58, 60, 61.
- Pica, specimen of, 54.
- Smith, George Frederick, founder in Philadelphia, 20.
- Matthew, press-maker, 239.
- Peter, inventor of a hand-press, 237.
- Sorts, upper and lower case, 59.
- Sounds of German letters, 94.
- Greek letters, 98.
- Hebrew letters, 104.
- Sower—see Saur.
- Samuel & Co., early American type-founders, 20.
- Space-rules, metal, 81.
- Spaces, described, 75.
- various sizes of, should be kept separate, 128.
- Spacing, remarks on, 130, 131.
- Speculum Humanæ Salvationis, the first printed book, 11.
- Spelling, rules for, 318-332.
- Spiegal enser Behoudenisse, one of the first printed books, 10.
- Spring bearers, 259.
- Springing, to prevent wood-cuts from, 280.
- Square cross, where used, 66.
- Standard for height of type, 57, 58.
- metal furniture, 77.
- Standing press, how to fill, 296, 297.
- improved, illustrated, 297.
- Stanhope, Earl, press invented by, 236.
- Star chamber, regulations of, concerning English founders, 18.
- St. Augustin, French and Dutch name for English type, 53.
- Stereotype plates, English imperfections of, 18.
- how to underlay, 272.
- block, illustrated, 44.
- Stereotyping, invention of, 24.
- mode of, 24-26, 46.
- mud process, 26.
- Stop cylinder press, illustrated, 238.
- well adapted for fine printing, 239.
- Stower, extract from, 205, 206.
- Superiors, 67.
- Super-royal paper, size of, 298.
- Syllables, abbreviated, 15.
- how to divide, 64, 65.
- Symbols, absurd, 74.
- Table of paper required for a book, 299.
- proof-marks, 212.
- signatures, 216, 217.
- Takes of copy should be small, 221.
- Taking copy in companionships, 228, 229.
- Taking down sheets when dry, 296.
- Tapes, how to set, 274.
- Technical terms explained, 338-343.
- names should be legibly written, 211.
- Tertia, German name of Great Primer, 53.
- Theinhardt, Ferdinand, Prussian type-founder, 84.
- Thirty-sixes, scheme for imposing half-sheet of, 190.
- half-sheet of, without cutting, 190.
- the same, with two signatures, 191.
- Thirty-twos, scheme for imposing half-sheet of, 186.
- sheet of, 187, 188.
- sheet of, with four signatures, 187, 188.
- half-sheet, two signatures, 189.
- half-sheet of, mixed, 189.
- Thomas, Isaiah, 14.
- Tilloch, Dr. Alexander, 24.
- Tinted paper, coloured ink on, 291.
- Tints, neutral, 291.
- Title-deeds, scheme for imposing, 150.
- Title-pages, hints for setting, 134.
- remarks on, 134.
- Token-sheet, purpose of, 256.
- Tokens explained, 294.
- Tools for wood engraving, 34.
- Trade-marks, how to secure patents, 335.
- Transposing pages, directions for, 207.
- pages in companionships, 232.
- Turkey boxwood, best for engraving, 34.
- Turning a heap, directions for, 261, 262.
- Turpentine, spirits of, best for cleansing wood-cuts, 283.
- Tweezers, illustrated, 210.
- Twenties, scheme for imposing half-sheet of, with two signatures, 181.
- sheet of, 182.
- Twenty-fours, scheme for imposing half-sheet of, 183.
- sheet of, 183, 184.
- half-sheet, the sixteens way, 184.
- half-sheet of, long, 185.
- half-sheet of, without cutting, 186.
- Two-line letters, how used, 76.
- Tying up pages, 142, 143.
- Tympan suitable for cylinder press, 265.
- Tympans, how to cover, 254.
- Type bodies, point system of, 55, 56.
- Type-casting machine, description of, 42.
- illustrated, 41.
- origin of, 22.
- [383]Type-casting machine, perfected by David Bruce, Jr., 22, 23.
- Type-founding a distinct calling in the seventeenth century, 18.
- early, in New York, 19.
- early, in Philadelphia, 19.
- in America, 19.
- in Europe, 18.
- Type-foundries in the United States, 23.
- Type-foundry, first American, at Germantown, Pennsylvania, 19.
- walk over a, 39-48.
- Type, how to lay a fount of, 127.
- Type-measure, 227.
- Type-metal, 40.
- Type-revolving printing machine, Hoe’s, illustrated, 240.
- Types, bill of, 57.
- Black or Old English letter, 49, 51.
- directions for choosing, 50.
- fount of, 58.
- gradation of, 55.
- how to prevent them from adhering, 127.
- Italic, invention of, 50.
- names and sizes of, 52-54.
- prices of, since 1801, 25.
- process of manufacturing, 39-43.
- Roman, invention of, 49.
- specimens of, 53, 54.
- Typographic Advertiser, 20.
- Typographical errors, a blemish, 200.
- peculiarities, ancient, 17, 18.
- Underlay old stereotype plates, 282.
- Underlays, when proper on cylinder presses, 270-272.
- Uniformity in colors, how to secure, 263.
- in spacing essential, 130.
- Universal press, illustrated, 248.
- Unlocking forms, precautions in, 208.
- Upper-case sorts, 59.
- Van der Mey's method of stereotyping, 24.
- Variations from copy chargeable, 211.
- Varnish for printing ink, how to make, 314.
- the common menstruum for colours, 286.
- Varnish, prevents enamel from peeling, 284.
- Vignettes, how to prepare on the press, 281.
- Walter perfecting press, 244.
- Warehouse book, form of, 293.
- department, 293-298.
- Warehouseman, duties of, 293.
- Warping of a cut, how to cure, 282.
- how to prevent, 282.
- Washing forms, directions for, 264, 265.
- Washington press, how to set up, 250.
- invented by Samuel Rust, illustrated, 237.
- Waterproof paper, how to make, 317.
- Watts, John, 21.
- Web perfecting presses, 242-246.
- Wells’s job presses, 246.
- Wet paper, how to be protected overnight, 264.
- Wetting paper, directions for, 255-257.
- drawing and plate paper, 256.
- rules for giving out paper for, 294, 295.
- Wetting-trough, how to be made, 255.
- White, Elihu, type-founder in New York, 21, 22.
- White pages, how to be treated, 259.
- Wood-cuts, how to prepare on the press, 280-283.
- how to wash, 283.
- how to take proof of, 283.
- Wood engraving, tools for, 34.
- type, how to be cared for, 292.
- Woollen blankets, needless when new type is used, 257, 266.
- Words and phrases, foreign, 357-372.
- Working in pocket unsatisfactory, 227.
- Works, how to manage hurried, 226.
- Wrinkles in paper, how to remove, 263.
- Writing inks, coloured, how to make, 314.
- Yellow ink, how to produce, 287, 288.
- Zarotti, Antonio, the inventor of signatures, 16.
- Zell, Ulrich, printer of the Chronicle of Cologne, 9.
- Zodiacal signs, 73.

FOOTNOTES
[1] The earliest testimony in favour of Koster is contained in a German volume published at Cologne in 1499, known as the Chronicle of Cologne, which was printed by Ulrich Zell, originally of Mayence, and a well-known follower of Gutenberg and his system. Under the heading “Of the art of printing books, when and where, and by whom, was invented the inexpressibly useful art of printing books,” the author says, “Although the art, as now practised, was discovered at Mayence, nevertheless the first idea came from Holland, and the Donati, which had been previously printed there. Those books are therefore the origin of the art.”—See Humphreys, ch. iii. and iv.
[1] The earliest evidence supporting Koster is found in a German book published in Cologne in 1499, known as the Chronicle of Cologne, printed by Ulrich Zell, who was originally from Mayence and a well-known follower of Gutenberg and his methods. Under the section titled “On the invention of the printing of books: when, where, and by whom the incredibly useful art of printing was created,” the author states, “Although the art, as it is currently practiced, was discovered in Mayence, the initial concept originated in Holland, particularly with the Donati, which had been printed there previously. Those books are therefore the foundation of the art.”—See Humphreys, ch. iii. and iv.
We cite further the following well-known account:—
We further reference the following well-known account:—
“About one hundred and twenty-eight years ago, Laurens Zanssen Coster inhabited a decent and fashionable house in the city of Haarlem, situated on the market-place, opposite the royal palace. The name of Coster was assumed, and inherited from his ancestors, who had long enjoyed the honourable and lucrative office of coster or sexton to the church. This man deserves to be restored to the honour of being the first inventor of printing, of which he has been unjustly deprived by others, who have enjoyed the praises due to him alone. As he was walking in the wood contiguous to the city, which was the general custom of the richer citizens and men of leisure, in the afternoon and on holidays, he began to cut letters on the bark of the beech; with these letters he enstamped marks upon paper in a contrary direction, in the manner of a seal, until at length he formed a few lines for his own amusement and for the use of the children of his brother-in-law. This succeeding so well, he attempted greater things; and, being a man of genius and reflection, he invented, with the aid of his brother- or son-in-law, Thomas Pietrison, a thicker and more adhesive ink, as the common ink was too thin and made blotted marks. With this ink he was able to print blocks and figures, to which he added letters. I have seen specimens of his printing in this manner. In the beginning he printed on one side only. This was a Dutch book, entitled Spiegal enser Behoudenisse. That it was one of the first books printed after the invention of the art, appears from the leaves, which are pasted together, that the naked sides might not be offensive to the eyes; and none at first were printed in a more perfect manner. As this new species of traffic attracted numerous customers, thus did the profits arising from it increase his love for the art and his diligence in the exercise of it.
“About one hundred and twenty-eight years ago, Laurens Zanssen Coster lived in a nice and stylish house in the city of Haarlem, located in the marketplace, across from the royal palace. He inherited the name Coster from his ancestors, who had long held the honorable and profitable position of coster or sexton at the church. This man deserves to be recognized as the first inventor of printing, a title he has been unfairly denied by others who have received the credit that should belong to him alone. While walking in the woods near the city, which was a common pastime for wealthier citizens and those with leisure time on afternoons and holidays, he started carving letters into the bark of a beech tree; he used these letters to stamp marks onto paper in reverse, like a seal, until he eventually created a few lines for his own enjoyment and for the children of his brother-in-law. Once this worked out well, he aimed for greater achievements; being a clever and thoughtful person, he, along with his brother- or son-in-law, Thomas Pietrison, developed a thicker and stickier ink, as the regular ink was too watery and left messy marks. With this ink, he was able to print designs and figures, to which he added letters. I have seen examples of his printing done this way. At first, he printed on one side only. This was a Dutch book titled Spiegal enser Behoudenisse. That it was one of the first books printed after the invention of this art is evident from the leaves, which are glued together so that the blank sides wouldn’t be unsightly to readers; and no one at the beginning printed in a more perfect manner. As this new kind of business drew in many customers, the profits from it only fueled his passion for the art and his dedication to practicing it.”
“He engaged workmen, which was the source of the mischief. Among these workmen was one Jan ⸺: whether his surname be that of Faust, or any other, is of no great importance to me, as I will not disturb the dead, whose consciences must have smote them sufficiently while living. This Jan, who assisted at the printing press under oath, after he had learned the art of casting the types, setting them, and other articles belonging to the art, and thought himself sufficiently instructed, having watched the opportunity, as he could not find a better, he packed up the types and the other articles on Christmas eve, while the family was engaged in celebrating the festival, and stole away with them. He first fled to Amsterdam, thence to Cologne, until he could establish himself at Mentz, as a secure place, where he might open shop and reap the fruits of his knavery. It is a known fact that within the twelve months (that is, in the year 1440) he published the Alexandri Galli Doctrinale, (a grammar at that time in high repute,) with Petri Hispani Tractatibus Logicis, with the same letters which Laurens had used. These were undoubtedly the first products of his press. These are the principal circumstances that I have collected from creditable persons far advanced in years, which they have transmitted like a flaming torch from hand to hand: I have also met with others who have confirmed the same.”—Hadrianus Junius, 1568.
“He hired workers, which was the cause of the trouble. Among these workers was a man named Jan ⸺: whether his last name was Faust or something else isn't really important to me, since I won't disturb the dead, whose consciences must have haunted them enough while they were alive. This Jan, who worked at the printing press under oath, learned the skill of casting the types, setting them up, and other related tasks, and thought he was knowledgeable enough. Seizing an opportunity, as he couldn't find a better one, he packed up the types and other materials on Christmas Eve while the family was busy celebrating the holiday, and made off with them. He first ran to Amsterdam, then to Cologne, until he could settle in Mentz, a safe place where he could open a shop and benefit from his deceit. It's a well-known fact that within twelve months (that is, in the year 1440) he published the Alexandri Galli Doctrinale, a grammar that was quite popular at the time, along with Petri Hispani Tractatibus Logicis, using the same letters that Laurens had employed. These were definitely the first products of his press. These are the main details I've gathered from credible older individuals who have passed down this story like a flaming torch: I've also encountered others who have confirmed the same.” —Hadrianus Junius, 1568.
[2] The first copies of the Bible are not dated, and do not contain the printer’s name. Only a few impressions have been preserved to the present time; indeed, they were entirely lost to the world until the latter half of the last century, when a copy was discovered in the library of Cardinal Mazarin in Paris; hence, the few existing copies are generally spoken of as Mazarin Bibles. Some of these were printed on vellum, but the earliest copies were on paper. There are only six copies now extant; two of which are in the United States, one belonging to the collection of the late Mr. George Brinley of Connecticut, and the other owned by the late Mr. James Lenox of New York. These two copies are on paper. The Brinley copy is said to have a leaf or two in fac-simile, while the Lenox copy is perfect in every respect. This copy, together with his unequalled collection of rare Bibles, now enriches the magnificent Lenox Library, founded in New York, in 1870, by this excellent and wisely beneficent man. The four remaining copies are in Europe, two of which were sold in London at auction; one on vellum selling for $20,000, and the other, on paper, bringing $14,000.
[2] The first copies of the Bible don't have dates or the printer’s name. Only a few copies have survived to this day; in fact, they were completely lost to history until the second half of the last century, when one was found in the library of Cardinal Mazarin in Paris. As a result, the few existing copies are usually referred to as Mazarin Bibles. Some of these were printed on vellum, but the earliest ones were on paper. There are only six copies still around; two of them are in the United States, one from the late Mr. George Brinley's collection in Connecticut, and the other from the late Mr. James Lenox's collection in New York. Both of these copies are on paper. The Brinley copy is said to contain a leaf or two in facsimile, while the Lenox copy is flawless in every way. This copy, along with his unmatched collection of rare Bibles, now enhances the magnificent Lenox Library, which was established in New York in 1870 by this generous and thoughtful man. The other four copies are in Europe, two of which were sold at auction in London; one on vellum sold for $20,000, and the other, on paper, sold for $14,000.
[3] “The names of Koster and Gutenberg will ever remain associated with its positive invention; and to Koster, if we are to be guided by a vast mass of unanswerable evidence in his favour, must be assigned the glory of achieving the first actual steps in that art, of which Gutenberg was soon destined, not only to extend and solidify the basis, but to raise at once upon that basis a most noble superstructure.”—Humphreys, p. 50.
[3] “The names of Koster and Gutenberg will always be linked to this significant invention; and based on overwhelming evidence in his favor, Koster deserves the credit for taking the first real steps in this art, which Gutenberg would later not only expand and strengthen but also build a magnificent superstructure upon.”—Humphreys, p. 50.
[4] For detailed and conflicting accounts, see Humphreys’s History of the Art of Printing, (London,) and De Vinne’s Invention of Printing, (New York.)
[4] For detailed and differing accounts, see Humphreys’s History of the Art of Printing, (London), and De Vinne’s Invention of Printing, (New York).
Humphreys dispassionately goes over the ground, and while giving due credit to Gutenberg, awards to Koster the honour of the invention of the art of printing. A perusal of De Vinne, on the other hand, leaves the impression of an effort to prove a preconceived opinion, every probability in favour of Koster being curtly set aside, and every perchance on the side of Gutenberg being regarded as incontrovertible fact. De Vinne derides the idea that types were at first cut, and not cast or founded; and this in the face of the fact that in the earliest printed books, there are not two letters of one kind that are precisely alike in a page; that is, every letter a varies somewhat from all other a’s, and so with b and all other letters. This could not be the case if the types were cast or founded. To support his view, De Vinne copies from De la Borde a wood engraving representing letters cut and sawn apart; and from the imperfection of this experiment argues that the first types could not have been cut. This proves nothing except the incapacity of the experimenter. A dozen years ago an ingenious man in Philadelphia produced copper-headed types in a mass on type-metal bodies, which had to be cut apart singly. The specimen of these types here given proves conclusively that the thing can be done far better than was done by Koster on wood or metal, though his types were ten times larger than these:—
Humphreys calmly reviews the situation, and while he gives proper credit to Gutenberg, he attributes the honor of inventing the printing press to Koster. In contrast, reading De Vinne leaves the feeling that he's trying to defend a pre-existing belief, dismissing every possibility in favor of Koster and treating every chance in favor of Gutenberg as an undeniable fact. De Vinne mocks the idea that types were originally carved, rather than cast; yet the earliest printed books show that not two letters of the same kind are exactly alike on a page. That is, each "a" varies slightly from all other "a"s, and the same goes for "b" and all other letters. This variation wouldn't happen if the types were cast. To back up his opinion, De Vinne includes a wood engraving from De la Borde showing letters cut and sawn apart; he argues, based on this imperfect example, that the first types couldn't have been cut. This only demonstrates the failure of the experimenter. A dozen years ago, a clever person in Philadelphia created copper-headed types in bulk on type-metal bodies, which had to be cut apart individually. The example of these types proves conclusively that it can be done much better than Koster managed with wood or metal, even though his types were ten times larger than these:—

abcdefghijklmnopqrstuvwxyzABCDEFGHIJKLMNOPQRSTUVWXYZ
abcdefghijklmnopqrstuvwxyzABCDEFGHIJKLMNOPQRSTUVWXYZ
New York New Jersey Mississippi Georgia Virginia Louisiana Tennessee Arkansas
Kentucky New Hampshire Maine Massachusetts Kansas
New York, New Jersey, Mississippi, Georgia, Virginia, Louisiana, Tennessee, Arkansas
Kentucky, New Hampshire, Maine, Massachusetts, Kansas
We have repeated the experiment in our own foundry with Long Primer type, and with a similar result. These experiments are sufficient to show the ungroundedness of Mr. De Vinne’s argument. He further states that in some of the specimens given by him, the letters have been so worn that they have run into one another; but the fact is, such letters were logotypes, and cut on the same block. Any accurate type-founder can verify this fact almost at a glance. In a lecture by Mr. Josiah Marples, an accurate English printer, before the Liverpool Literary and Philosophical Society on Type-founders and Type-founding, the speaker alluded to Caxton and his types, and to Mr. Vincent Figgins’s reproduction of the “Game of Chesse,” whose nephew had enabled him to exhibit a copy of the same to the meeting. “Mr. Vincent Figgins, whose skill as a practical type-founder,” it was remarked, “entitled his opinion to great weight, believed that the book was not printed from types such as were cast by Schœffer, but from types which were cast with solid faces, upon which were cut with the graver each letter separately. To this Mr. Figgins attributed the fact that in the original book no pure style of letters was used, but a mixture between the old black and that called Secretary; that no two letters were exactly alike, and that frequent use was made of logotypes.”
We’ve repeated the experiment in our own foundry using Long Primer type, and we got similar results. These experiments clearly show that Mr. De Vinne’s argument doesn’t hold up. He also claims that in some of the samples he provided, the letters were so worn that they blended into each other; however, the truth is, those letters were logotypes and were cut on the same block. Any competent type-founder can confirm this fact almost instantly. In a lecture by Mr. Josiah Marples, a precise English printer, before the Liverpool Literary and Philosophical Society on Type-founders and Type-founding, the speaker referred to Caxton and his types, and to Mr. Vincent Figgins’s reproduction of the “Game of Chesse,” which his nephew helped him display to the meeting. “Mr. Vincent Figgins, known for his expertise as a practical type-founder,” it was noted, “believed that the book wasn’t printed from types like those cast by Schœffer, but from types that had solid faces on which each letter was individually engraved. Mr. Figgins believed this explained why the original book didn’t use a consistent style of letters, instead showing a mix between the old black and what’s called Secretary; that no two letters were exactly the same, and that logotypes were frequently used.”
Mr. De Vinne finds some difficulty in demolishing the Koster “legend” (as he and Van der Linde call it) in the fact that the existence of numerous volumes and fragments of ancient printing have to be somehow accounted for; and he thereupon adopts the hypothesis of an unknown printer, to whom he attributes these early productions. The admittedly ancient water-marks in the paper he rules out, simply because such water-marks were used long afterward. He gives fac-simile specimens of the types used in these books; but, in violation of all the laws of probability, he gives the inferior specimens last. The necessities of his theory compelled him to this course, the natural order being the reverse of the one adopted by him. The inferior specimens show clearly the first attempts of an inventor, an inventor too who had before been a block printer. The succeeding books show as clearly the successive stages of improvement, the last stage of which was equal or even superior to any thing executed by Gutenberg before the appearance of the great Bible. This “unknown printer” was doubtless Koster.
Mr. De Vinne struggles to debunk the Koster “legend” (as he and Van der Linde refer to it) because he needs to explain the many volumes and fragments of ancient printing. He then proposes the theory of an unknown printer, whom he credits with these early works. He dismisses the admittedly old watermarks in the paper, arguing that those watermarks were used long after. He includes facsimile samples of the types used in these books; however, contrary to probability, he places the inferior samples at the end. His theory forced him into this arrangement, as the natural order would have been the opposite. The inferior samples clearly illustrate the initial efforts of an inventor, someone who had previously been a block printer. The following books clearly display the progressive stages of improvement, with the final stage being equal to or even better than anything produced by Gutenberg before the great Bible was released. This “unknown printer” was likely Koster.
It is by no means a wild question whether the credit of even the first Bible belongs to Gutenberg or to Peter Schœffer; for, after the dissolution of the partnership between Gutenberg and Fust, the former produced nothing worthy of note, while Schœffer printed the Bible again, as well as other works, notably the Psalter, a most wonderful specimen of ancient typography. Schœffer appears to be as undoubtedly the inventor of type-founding as Koster was of printing,—Gutenberg was neither, though we must award him high credit for his skill in availing himself of the knowledge derived from Koster, and his perseverance through a series of years. But the almost impenetrable cloud of mystery that surrounds the discovery of printing should induce a spirit of hesitancy that is not at all characteristic of Van der Linde and others. Neither ifs, buts, nor perhapses, nor strained inferences, prove anything except the weakness of the argument that rests upon them.
There's definitely a debate about whether Gutenberg or Peter Schœffer deserves credit for the first Bible. After Gutenberg's partnership with Fust ended, he didn’t produce anything significant, while Schœffer reprinted the Bible and other works, especially the Psalter, which is an amazing example of early printing. Schœffer seems to be clearly the inventor of type-founding, just as Koster was the inventor of printing—Gutenberg wasn’t either, but we should give him credit for his skill in using what he learned from Koster and for his persistence over many years. However, the thick fog of mystery surrounding the invention of printing should make us cautious, which is not something we typically see in Van der Linde and others. Arguments filled with ifs, buts, and maybes, as well as forced conclusions, only show the weakness of the arguments that rely on them.
We are satisfied that the types used by the first printers were not cast or founded in a mode at all approximating to the modern method. The question is, not who was the first type-founder in the modern style, but who was the first printer with movable types, no matter whether of wood, pewter, or tin; and we agree with the judicious Isaiah Thomas in the opinion that Koster was that man.
We believe that the typefaces used by the first printers were not created in a way that resembles modern techniques at all. The real question isn't about who was the first type designer in a modern sense, but rather who was the first printer to use movable type, whether made of wood, pewter, or tin; and we align with the thoughtful Isaiah Thomas in thinking that Koster was that person.
See Haarlem the Birthplace of Printing, not Mentz, by J. H. Hessels, Cambridge, England, 1887: an emphatic confutation of the Gutenberg legend.
See Haarlem the Birthplace of Printing, not Mentz, by J. H. Hessels, Cambridge, England, 1887: a strong refutation of the Gutenberg legend.
[5] Two copies of Bradford’s Almanac are known to be in existence. We give the Address of
[5] Two copies of Bradford’s Almanac are known to exist. We provide the Address of
THE PRINTER TO THE READERS.
THE PRINTER TO THE READERS.
Hereby understand that after great charge & Trouble, I have brought that great Art & Mystery of Printing into this part of America; believing it may be of great service to you in several respects; hoping to find encouragement, not only in this Almanack, but what else I shall enter upon for the use & service of the Inhabitants of these Parts. Some irregularities there be in this Diary, which I desire you to pass by this year; for being lately come hither, my materials were misplaced & out of order, whereupon I was forced to use Figures & Letters of various Sizes: but understanding the want of something of this nature, & being importuned thereto, I ventured to make public this; desiring you to accept thereof; & by the next (as I find encouragement) shall endeavour to have things compleat. And for the ease of Clarks, Scriveniers, &c., I propose to print blank Bills, Bonds, Letters of Attorney, Indentures, Warrants, etc., & what else presents itself, wherein I shall be ready to serve you; and remain your friend.
I understand that after a lot of effort and trouble, I've brought the great Art & Mystery of Printing to this part of America. I believe it will be very useful to you in many ways, and I'm hoping for your support, not just for this Almanack but for anything else I plan to create for the benefit of the local community. There are some mistakes in this Diary that I hope you'll overlook this year. Since I just arrived, my materials were disorganized, which forced me to use figures and letters in different sizes. However, I recognized the need for something like this, and after being encouraged, I took the chance to publish it. I hope you'll accept it, and with your support, I'll strive to make everything complete in the next edition. Also, to help clerks, scribes, etc., I plan to print blank bills, bonds, letters of attorney, indentures, warrants, and anything else that comes to mind, so I'm ready to assist you and remain your friend.
W. BRADFORD.
W. Bradford.
Philadelphia, the
10th month, 1685.
Philadelphia, October 1685.
[6] Mr. Horatio Gates Jones, of Philadelphia, in his introduction to Frame’s Short Description of Pennsilvania, gives further interesting particulars. See, also, Munsell’s Chronology, &c. of Paper and Paper Making, Albany, N. Y., 1876.
[6] Mr. Horatio Gates Jones from Philadelphia shares more fascinating details in his introduction to Frame’s Short Description of Pennsylvania. Also, check out Munsell’s Chronology, &c. of Paper and Paper Making, Albany, NY, 1876.
[8] After the retirement of Binny & Ronaldson, Richard Ronaldson carried on the business of this foundry until 1833, when he in turn was succeeded by Lawrence Johnson and George F. Smith. Mr. Johnson, a man of great energy and enterprise, had (contemporaneously with Jedediah Howe) introduced stereotyping into Philadelphia, and now both callings were incorporated. Ten years afterward, Mr. Smith retired; and in the year 1845 Mr. Johnson associated with him Thomas MacKellar, John F. Smith and Richard Smith, who had, as it were, grown up with the business. The foundry now quickly grew in importance, and won a wide reputation. Mr. Johnson died April 26, 1860, and was succeeded by his three partners, who, with Peter A. Jordan, constituted the firm known as MacKellar, Smiths & Jordan, under whose management the establishment was brought to rank equal with and excel most of the type foundries in the world. Mr. Jordan died March 25, 1884. In 1885 Wm. B. MacKellar, G. Fredk Jordan and C. F. Huch were associated with the remaining partners, and a corporation was formed under the name of The MacKellar, Smiths & Jordan Company. Their “Typographic Advertiser” (begun in 1855) and Specimen Books are regarded as unique mechanical and literary productions. The height and body of the Pica of this Company have been universally adopted in the United States as the standard of size for the American Point System of type.
[8] After Binny & Ronaldson retired, Richard Ronaldson continued running the foundry until 1833, when he was succeeded by Lawrence Johnson and George F. Smith. Mr. Johnson, a highly energetic and enterprising individual, had introduced stereotyping to Philadelphia around the same time as Jedediah Howe, and now both trades were combined. Ten years later, Mr. Smith retired; in 1845, Mr. Johnson teamed up with Thomas MacKellar, John F. Smith, and Richard Smith, who had grown up with the business. The foundry quickly gained importance and developed a strong reputation. Mr. Johnson passed away on April 26, 1860, and his three partners, along with Peter A. Jordan, formed the firm MacKellar, Smiths & Jordan, which elevated the establishment to be on par with, and even surpass, most type foundries worldwide. Mr. Jordan died on March 25, 1884. In 1885, Wm. B. MacKellar, G. Fredk Jordan, and C. F. Huch joined the remaining partners, and a corporation was created under the name The MacKellar, Smiths & Jordan Company. Their "Typographic Advertiser" (started in 1855) and Specimen Books are considered unique mechanical and literary achievements. The height and body of the Pica from this company have been universally accepted in the United States as the standard size for the American Point System of type.
[9] Chambers’s Encyclopædia.
__A_TAG_PLACEHOLDER_0__ Chambers's Encyclopedia.
[10] Wilson’s Treatise on English Punctuation is a full and explicit work on this subject, and should be studied by every printer and author. It is worthy of adoption as the standard authority.
[10] Wilson’s Treatise on English Punctuation is a comprehensive and clear work on this topic, and it should be reviewed by every printer and writer. It deserves to be recognized as the standard reference.
[11] Wilson, in his Treatise on English Punctuation, says, very judiciously,—
[11] Wilson, in his Treatise on English Punctuation, wisely states,—
The hyphen is employed in words in such a manner as is best calculated to show their origin, composition, or import, and to exhibit the syllables in their neatest form. Agreeably to this rule,—
The hyphen is used in words in a way that best reveals their origin, composition, or meaning, and to present the syllables in their most organized form. According to this rule,—
1. Compound and derivative words are resolved into their primitives; as, school-master, hand-writing, pen-knife, snuff-box, looking-glass; arch-angel, geo-logy, theo-cracy, ortho-graphy.
1. Compound and derivative words are broken down into their original forms; for example, school-master, handwriting, penknife, snuffbox, looking glass; archangel, geology, theocracy, orthography.
2. Prefixes, affixes, and grammatical terminations are separated; as, dis-continue, en-able, trans-port; shear-er, load-ed, print-ing; king-dom, false-hood, differ-ence, command-ment.
2. Prefixes, suffixes, and grammatical endings are separated; for example, dis-continue, en-able, trans-port; shear-er, load-ed, print-ing; king-dom, false-hood, differ-ence, command-ment.
3. One consonant between two vowels is to be joined to the latter syllable; as, ta-lent, fa-tal; me-lon, le-ver; spi-rit, si-lence; cy-nic, ty-ro; le-ga-cy, mo-no-po-ly. Except x, and single consonants when they belong to the former portion of a derivative word; as, ex-ile, ex-ist, ex-amine; up-on, dis-ease, circum-ambient.
3. When there’s one consonant between two vowels, it should be attached to the second syllable, like in ta-lent, fa-tal; me-lon, le-ver; spi-rit, si-lence; cy-nic, ty-ro; le-ga-cy, mo-no-po-ly. The exception is x, and single consonants that are part of the first part of a derivative word, such as ex-ile, ex-ist, ex-amine; up-on, dis-ease, circum-ambient.
4. Two or more consonants belong to the latter syllable, when they are capable of beginning a word; as, ta-ble, sti-fle, lu-cre, o-gle, mau-gre, stro-phe, de-stroy.
4. Two or more consonants belong to the second syllable when they can start a word, like ta-ble, sti-fle, lu-cre, o-gle, mau-gre, stro-phe, de-stroy.
5. But when the consonants cannot begin a word, or when the vowel preceding them is short, the first should be separated; as, ab-bey, ac-cent, vel-lum, ab-ject, gar-den, laun-dry, pam-phlet; blas-pheme, dis-tress, min-strel.
5. But when consonants can't start a word, or when the vowel before them is short, the first should be separated; as, ab-bey, ac-cent, vel-lum, ab-ject, gar-den, laun-dry, pam-phlet; blas-pheme, dis-tress, min-strel.
It is desirable that compound and derivative words should, at the end of lines, be divided in such a manner as to indicate their principal parts. Thus, school-master is preferable to schoolmas-ter, dis-approve to disap-prove, resent-ment to re-sentment, ortho-doxy to or-thodoxy; though, as regards the analysis of words into syllables, the latter mode is unobjectionable. From the narrowness of the printed line, however, in some books, the principle recommended cannot always be adhered to.
It’s important that compound and derivative words be broken at the end of lines in a way that shows their main parts. So, school-master is better than schoolmas-ter, dis-approve is better than disap-prove, resent-ment is better than re-sentment, and ortho-doxy is better than or-thodoxy; although breaking words into syllables in the latter way is fine. However, due to the narrowness of printed lines in some books, this recommended practice can’t always be followed.
The terminations tion, sion, cial, tial, and many others, formerly pronounced as two syllables, but now only as one, must not be divided either in spelling or at the end of a line.
The endings tion, sion, cial, tial, and many others, which used to be pronounced with two syllables but are now pronounced as one, should not be divided either in spelling or at the end of a line.
A syllable consisting of only one letter, as the a in cre-ation, should not commence a line. This word would be better divided crea-tion; and so all others of a similar kind.
A syllable made up of just one letter, like the a in cre-ation, shouldn't start a line. This word would be better split as crea-tion; and the same goes for all similar words.
A line of print must not end with the first syllable of a word when it consists of a single letter; as, a-bide, e-normous; nor begin with the last syllable when it is formed of only two letters; as, nation-al, teach-er, similar-ly. For regard should be had to the principles of taste and beauty as well as to the laws of syllabication.
A line of text shouldn't end with the first syllable of a word that is just a single letter, like a-bide or e-normous; nor should it start with the last syllable if it only has two letters, like nation-al, teach-er, or similar-ly. It's important to consider taste and aesthetics, along with the rules of syllabication.
[14] Bell’s Greek Grammar.
__A_TAG_PLACEHOLDER_0__ Bell’s Greek Grammar.
[15] See pages 318-332.
[16] The following epitaph was no doubt written by a printer after performing the most disagreeable task attendant on his profession:—
[16] The following epitaph was certainly written by a printer after carrying out the most unpleasant task related to his job:—
[17] We are indebted to a friend for the following sketch of the origin, progress, and present condition of the world-famous house of R. Hoe & Co.
[17] We're grateful to a friend for the following overview of the origin, development, and current state of the world-renowned company R. Hoe & Co.
Robert Hoe, the founder of the present house of R. Hoe & Co. of New York, was born at Hose, in Leicestershire, England, in 1784. His father was a well-to-do farmer in that pleasant, sequestered district; but, as the family was large, Robert was apprenticed to a carpenter in a neighbouring town. His attention was early attracted and his mind impressed by the prosperity of the people of the United States; and, being a republican at heart, and conscious that the institutions of his own country presented almost insurmountable obstacles to the advancement of the working classes, he purchased his indentures from his employer, and in 1803 emigrated to New York.
Robert Hoe, the founder of the current R. Hoe & Co. in New York, was born in 1784 in Hose, Leicestershire, England. His father was a prosperous farmer in that nice, secluded area; however, because the family was large, Robert was apprenticed to a carpenter in a nearby town. He was early on drawn to and impressed by the success of people in the United States; being a republican at heart and aware that the institutions in his own country posed nearly insurmountable hurdles for the working class, he bought his indentures from his employer and emigrated to New York in 1803.
On his arrival he made the acquaintance of Grant Thorburn, who, becoming interested in him, received him into his family, and with great kindness nursed him with his own hands through an attack of the yellow fever, which was then raging in the city. He soon established himself in his trade, and, by his industry, integrity, and enterprise, became advantageously known to the public. At the age of twenty he married the daughter of Matthew Smith, of Westchester Co., New York, by whom he had three sons and six daughters. For a time he was in partnership with his brother-in-law, Matthew Smith, Jr., a carpenter and printers’ joiner, who, on their separation, associated with himself his brother, Peter Smith, who was educated at Yale College, and was the inventor of the well-known hand-press bearing his name.
Upon his arrival, he met Grant Thorburn, who took an interest in him and welcomed him into his family. With great kindness, he personally cared for him during a bout of yellow fever that was spreading throughout the city. He quickly established himself in his trade and, through hard work, honesty, and initiative, became well-known in the community. At the age of twenty, he married Matthew Smith's daughter from Westchester County, New York, and they had three sons and six daughters together. For a while, he partnered with his brother-in-law, Matthew Smith Jr., a carpenter and printers’ joiner, who, after their split, teamed up with his brother, Peter Smith. Peter was educated at Yale College and invented the famous hand-press that carries his name.
On the decease of these two brothers, Robert Hoe, in 1823, succeeded to the business, which was then in its infancy, giving employment to only a handful of men, and being conducted in the middle of the block bounded by Maiden Lane, Pine, William, and Pearl Streets, in some old buildings to which access was gained by an alley running from Maiden Lane to Pine Street. Here the business, under the style of Robert Hoe & Co., grew rapidly; but the extension of Cedar Street made necessary its removal to the present location in Gold Street. About this time, the flat-bed cylinder press, for newspaper printing, was introduced into England; and Mr. Hoe sent an intelligent mechanic there to examine it, and it was soon brought into use here, with valuable improvements. In 1832, Mr. Hoe’s failing health obliged him to relinquish the business to his eldest son, Richard M. Hoe, and Matthew Smith, son of his first partner. In the following year he died. Shortly after his decease, the firm erected extensive buildings in Broome Street, in the eastern part of the city, where the greater part of their manufacturing has since been carried on. They also commenced making cast-steel saws, which had previously been exclusively imported from England; and this branch has steadily increased in importance.
Upon the death of these two brothers, Robert Hoe took over the business in 1823, which was still in its early stages, employing only a small number of people and operating in some old buildings located in the middle of the block surrounded by Maiden Lane, Pine, William, and Pearl Streets, accessible via an alley from Maiden Lane to Pine Street. Under the name Robert Hoe & Co., the business grew quickly; however, the expansion of Cedar Street required a move to its current location on Gold Street. Around this time, the flat-bed cylinder press for newspaper printing was introduced in England; Mr. Hoe sent a skilled mechanic there to study it, and it was soon implemented here with valuable improvements. In 1832, Mr. Hoe’s declining health forced him to hand over the business to his eldest son, Richard M. Hoe, and Matthew Smith, the son of his first partner. The following year, he passed away. Shortly after his death, the company built large facilities on Broome Street in the eastern part of the city, where most of their manufacturing has been conducted since. They also began producing cast-steel saws, which had previously been imported exclusively from England, and this line of products has significantly grown in importance.
Matthew Smith, a man of uncommon ability and business talents, died in 1842. The business was then continued by Richard M. Hoe, with his two brothers, Robert Hoe and Peter Smith Hoe,—the eldest, as before, taking charge of the mechanical department, in which his industry and fertility of invention are attested by the number and value of his patents. In 1837, he patented here and in England his method of grinding circular saws, by which the thickness of any part of a saw can be regulated with accuracy. In 1846, he brought out the so-called “Lightning Press,” or Type-Revolving Printing Machine, described in the text,—the greatest innovation on the routine of the printing craft since the days of Gutenberg. This press entirely superseded all others for fast printing, and was introduced into the principal offices, not only in this country, but in England, Scotland, Ireland, and Australia.
Matthew Smith, a man with exceptional skills and business acumen, passed away in 1842. The business was then carried on by Richard M. Hoe and his two brothers, Robert Hoe and Peter Smith Hoe—the eldest continued to oversee the mechanical department, where his hard work and innovative ideas are proven by the many patents he holds. In 1837, he patented his method for grinding circular saws in both the U.S. and England, allowing for precise thickness adjustments on any part of a saw. In 1846, he launched the so-called “Lightning Press,” or Type-Revolving Printing Machine, mentioned in the text—this was the biggest breakthrough in the printing industry since Gutenberg. This press completely replaced all others for high-speed printing and was adopted by major printing offices, not just in the U.S., but also in England, Scotland, Ireland, and Australia.
In 1858, the firm purchased of Isaac Adams, of Boston, Massachusetts, his entire patent-rights, together with his establishment for the manufacture of his bed-and-platen book printing presses, and various machines for binders’ use, which they continue to conduct there, though with increased facilities and many improvements. Their works in different places now cover thirty-five city lots, or about two acres, and give employment to nearly six hundred hands. The office and warerooms of the house in England are at 13 Salisbury Square, Fleet Street, London, one of the partners, being a resident in that city, attending to the business there.
In 1858, the company bought the entire patent rights from Isaac Adams of Boston, Massachusetts, along with his manufacturing setup for bed-and-platen book printing presses and various machines for binders' use. They still operate the business there, but with more facilities and many enhancements. Their operations now span thirty-five city lots, or about two acres, and employ nearly six hundred people. The office and warehouse for the company in England are located at 13 Salisbury Square, Fleet Street, London, where one of the partners lives and manages the business.
[18] While publisher of a paper in Catskill, he produced within a week, aided by some village mechanics, a press for his own use. With the exception of a stone bed, the principal parts were made entirely of wood. It was a flat-bed press, having a series of impression cylinders connected by an endless chain, by means of which they passed over and around the bed continually. He called it the Chain-running Press. It was employed by Frank Leslie to print an edition of his Illustrated Newspaper.
[18] While he was the publisher of a newspaper in Catskill, he quickly built a press for himself within a week, with help from some local craftsmen. Aside from a stone bed, all the main parts were made completely of wood. It was a flat-bed press that had a series of impression cylinders linked by an endless chain, allowing them to continuously move over and around the bed. He named it the Chain-running Press. Frank Leslie used it to print an edition of his Illustrated Newspaper.
[19] R. Hoe & Co.’s Catalogue.
__A_TAG_PLACEHOLDER_0__ R. Hoe & Co.'s Catalog.
[20] Adapted from Savage.
__A_TAG_PLACEHOLDER_0__ Adapted from Savage.
[21] Adapted from Savage.
Adapted from Savage.
[24] Incapable of suffering.
Unable to feel pain.
[25] Capable of suffering.
Able to feel pain.


ET FACTA EST LUX.
And there was light.

ESTABLISHED, 1796.
Founded, 1796.
MacKellar, Smiths & Jordan Foundry,
Letter Founders,
Nos. 606-614 Sansom Street, Philadelphia.
MacKellar, Smiths & Jordan Foundry,
Letter Creators,
Nos. 606-614 Sansom Street, Philadelphia.
This establishment, the oldest in America, has kept even pace with all the improvements in type-founding; and its productions at the present day, in beauty of style, accuracy of standing, and durability of material, are all that skill, ingenuity, and long experience have been able to effect. Neither pains nor expense will be withheld to maintain its reputation.
This establishment, the oldest in America, has kept pace with all the advancements in type-founding; and its products today, in terms of style, accuracy, and material durability, reflect the best that skill, creativity, and extensive experience can achieve. No effort or expense will be spared to uphold its reputation.
Book and Newspaper Faces.
Book and Newspaper Covers.
Some are of light and dainty face, others of medium, and others again of broad and massive character. The Lightface Series; the French-Face Series; the celebrated Scotch-Face Series, introduced by us many years ago; the Book Series; the Large-Face Series; the Classic Series; the News Series; the Broadface Series; the Modern Series; the Original Old Style Series; the Bradford Series; the Binny Series; the Ronaldson Series; the MacKellar Series, and all others introduced by us, are kept constantly on hand, in large and small founts.
Some have a light and delicate appearance, others are medium, and some have a broad and strong character. The Lightface Series; the French Face Series; the well-known Scotch-Face Collection, which we introduced many years ago; the Book Series; the Big-Face Series; the Classic Series; the News Show; the Broadface Collection; the Modern Series; the Original Vintage Series; the Bradford Series; the Binny Series; the Ronaldson Series; the MacKellar Series, and all others introduced by us, are always available in both large and small sizes.
German Book and Newspaper Faces,
German Book and Newspaper Covers,
Of various styles, also kept on hand or furnished to order.
Of different styles, also available in stock or made to order.
Elegant Scripts and other Note and Circular Types,
Elegant Scripts and other types of Notes and Circulars,
In great variety of styles, for all kinds of Notes, Blanks, and Circular Printing.
In a wide range of styles, for all types of notes, forms, and bulk printing.
Greek, Hebrew and Music Type.
Greek, Hebrew, and Music Genre.
Music Type without an equal in America, or a superior in the world. The sizes are Excelsior, or half-Nonpareil, Diamond, Agate, and Nonpareil. Greek and Hebrew of all practical sizes.
Music Genre unmatched in America, and with no superior anywhere in the world. The sizes available are Excelsior, half-Nonpareil, Diamond, Agate, and Nonpareil. Greek and Hebrew in all practical sizes.
Fancy and Ornamental Type,
Fancy and Decorative Font,
Unrivalled for beauty, originality, extent, and variety. In this department, native and foreign genius and inventive skill are alike laid under contribution, and no other foundry in the world can furnish so complete and beautiful an assortment.
Unmatched in beauty, originality, scale, and variety. In this area, both local and international talent and creativity come together, and no other foundry in the world can provide such a complete and stunning collection.
Borders, Flourishes, Corners and Ornaments,
Borders, embellishments, corners, and accents
For finest artistic and ornamental printing, to meet every requirement of the printer.
For the best artistic and decorative printing, to fulfill every need of the printer.
Cuts and Ornaments,
Cuts and Accents,
For general use, from more than three thousand subjects, many of them very fine.
For general use, from over three thousand topics, many of which are very good.
Office Furnishings.
Office Furniture.
Cabinets of various kinds and prices. Stands, double or single, or made in different styles to order, of walnut or poplar. Cases of all kinds. Imposing Stones of regular sizes constantly on hand; special sizes and styles got up to order. Galleys of all kinds, either wood or brass. Stereotype Blocks, with or without rule borders. Chases of wrought or cast iron. Composing-Sticks of all kinds, large and small. Racks for cases. Ink Stones. Card, Paper, Lead and Rule Cutters. Labour-Saving Wood Rule. Labour-Saving Wood Furniture. Labour-Saving Curvatures. Furniture, Quoins, Mallets; Shooting-Sticks of brass, iron or dogwood; Planers, Bodkins, Ley and Washing Brushes, &c.
Cabinets of different types and prices. Stands, either double or single, or customized in various styles, made from walnut or poplar. Cases of all types. Impressive Rocks of standard sizes readily available; special sizes and styles can be made to order. Galleys of all types, whether wood or brass. Stereotype Barriers, with or without rule borders. Pursuits made of wrought or cast iron. Typing tools of all sizes, large and small. Racks for cases. Ink stones. Card, Paper, Lead, and Rule Cutters. Labor-Saving Wood Rule. Labor-Saving Wood Furniture. Labor-Saving Curvatures. Furniture, Quoins, Mallets; Shooting-Sticks made of brass, iron, or dogwood; Planers, Bodkins, Ley and Washing Brushes, etc.
Eureka Cabinets.
Eureka Cabinets.
Size to fit in space at left of double stand. Stained in imitation of cherry.
Size to fit in the space to the left of the double stand. Stained to look like cherry.
Sort-Case Cabinet.—Contains eight drawers, each divided into sixteen compartments. It will be found useful as a receptacle for quads, leaders or sorts.
Sort-Case Cabinet.—Has eight drawers, each divided into sixteen compartments. It’s useful for storing quads, leaders, or sorts.
Handy Cabinet.—Contains five drawers, arranged to hold twenty different sizes of spaces and quads, and eight blank drawers, for cuts or large type.
Convenient Cabinet.—Includes five drawers, designed to accommodate twenty different sizes of spaces and quads, plus eight empty drawers for cuts or large type.
Galley Cabinet.—No. 1, for twenty-four single and fourteen double column galleys. No. 2, for forty-eight single galleys. No. 3, for thirty-four double galleys.
Kitchen cabinet.—No. 1, for twenty-four single and fourteen double column galleys. No. 2, for forty-eight single galleys. No. 3, for thirty-four double galleys.
Ink Cabinet.—Contains four compartments for ink, &c., and marble slab 18 × 20 inches on top, for mixing inks.
Ink Drawer.—Has four compartments for ink, etc., and a marble slab measuring 18 × 20 inches on top for mixing inks.
Chase Cabinet.—Arranged to contain one-eighth, one-quarter, and one-half medium chases. With or without ink stone.
Chase Cabinet.—Designed to hold one-eighth, one-quarter, and one-half medium chases. Available with or without an ink stone.
Combination Cabinet.—No. 1, contains four blank drawers, three sort-case drawers, and four quad drawers. No. 2, contains four sort-case drawers and six quad drawers.
Combo Cabinet.—No. 1 has four blank drawers, three sorting drawers, and four quad drawers. No. 2 has four sorting drawers and six quad drawers.
Quad Cabinet.—Contains twelve drawers, each divided into two compartments, suitable for quads or leaders.
Quad Cabinet.—Holds twelve drawers, each split into two compartments, ideal for quads or leaders.
Labour-Saving Leads and Slugs.
Labor-Saving Leads and Slugs.
Two and three point (six and four-to-Pica) Leads, from 48 to 300 points (4 to 25 ems Pica) in length; put up in any useful quantity. Six and twelve point (Nonpareil and Pica) Slugs, cut to same lengths. Cases arranged specially for Labour-Saving Leads and Slugs.
Two and three point (six and four-to-Pica) Prospects, from 48 to 300 points (4 to 25 ems Pica) long; available in any useful quantity. Six and twelve point (Nonpareil and Pica) Slugs, cut to the same lengths. Cases set up specifically for Labour-Saving Leads and Slugs.
Labour-Saving Quotation Furniture.
Labor-Saving Quotation Furniture.
Accurately cast, and equally valuable either as furniture or as quotations. The pieces range from 48 to 240 points in length, and from 24 to 48 points in width, quadrate height, with suitable spaces.
Accurately cast and just as good for use as furniture or as quotes. The pieces vary in length from 48 to 240 points and in width from 24 to 48 points, with a square height and appropriate spacing.
Reversible Metal Furniture,
Reversible Metal Furniture,
For imposition of forms and general blank-work. Cast to our standard 12 point body.
For setting up forms and general blank work. Cast to our standard 12-point font.
Labour-Saving Rule,
Time-Saving Rule
(Matching our standard type bodies,) Single, Double, Parallel, Dotted, and Triple faces. Cut accurately of various lengths. It will be found of vast utility in tabular and job work, rendering the use of shears and file entirely unnecessary. Cases furnished specially adapted to it.
(Matching our standard type bodies,) Single, Double, Parallel, Dotted, and Triple faces. Cut accurately to various lengths. It will be extremely useful for tabular and job work, making the use of shears and files completely unnecessary. Cases provided are specially designed for it.
Brass Circles and Ovals,
Brass Circles and Ovals
Of various sizes and faces, for label and stamp borders.
Of different sizes and designs, for labels and stamp borders.
Slotted Brass Corners,
Brass Corner Brackets,
Of beautiful original patterns, matching our brass rules.
Of beautiful original designs that complement our brass rulers.
Hollow Quadrates,
Hollow Squares,
For the easy formation of Circles, Ellipses, &c., made in sizes to suit our Brass Circles and Ovals, from Nos. 1 to 13.
For the simple creation of Circles, Ellipses, etc., made in sizes that fit our Brass Circles and Ovals, from Nos. 1 to 13.
Corner Quadrates,
Corner Squares,
On 12 point and 6 point Metal and 2 point Brass bodies.
On 12-point and 6-point metal and 2-point brass bodies.
Printing Presses and Ink.
Printers and Ink.
Presses of the most celebrated makers in the United States, as well as all varieties and colours of American and Foreign Printing Inks, Sizes, Bronzes, Varnishes, &c. at manufacturers’ prices.
Presses from the most renowned manufacturers in the United States, along with all types and colors of American and foreign printing inks, sizes, bronze items, coatings, etc., at manufacturers’ prices.
Roller Composition.
Roller setup.
Glue for Rollers, and the various Patent Compositions, furnished to order at manufacturers’ prices.
Glue for rollers and various patented compositions available upon request at manufacturer prices.
Electrotyping
Electrotyping
Of Almanacs, Jobs, Wood-Cuts, Labels, Binders’ Stamps, &c.
Of Almanacs, Jobs, Wood-Cuts, Labels, Binders' Stamps, etc.
Wood Engraving.
Wood Engraving.
Cuts designed and engraved to order in the finest style of art.
Cuts made and engraved to order in the highest quality of art.
Outfits for Printing Offices.
Clothes for Printing Offices.
Estimates given in detail (with the cost) of all the materials required for either Newspaper or Job Offices.
Estimates provided in detail (including the cost) of all the materials needed for either Newspaper or Job Offices.
MacKellar, Smiths & Jordan Foundry,
Nos. 606-614 Sansom Street,
Philadelphia.
MacKellar, Smiths & Jordan Foundry,
Nos. 606-614 Sansom Street,
Philadelphia.
PRINTERS’ TEXT-BOOKS.
Printing Textbooks.
A Manual of Typography, containing Practical Directions for Managing all Departments of a Printing Office, as well as Complete Instructions for Apprentices. Eighteenth Edition. Revised and Enlarged. Price, $2.00. By mail, $2.10.
A Manual of Typography, featuring practical guidance for handling all areas of a printing office, as well as comprehensive instructions for apprentices. Eighteenth Edition. Revised and Expanded. Price: $2.00. By mail: $2.10.
“Most successful of the books of this class known to me.”—Correspondent of the Archiv für Buchdruckerkunst, Leipzig.
“Most successful of the books in this category that I know of.”—Correspondent of the Archiv für Buchdruckerkunst, Leipzig.
“Any intelligent person will find this work a serviceable companion.”—Journal of Commerce, Chicago.
“Any smart person will find this work a useful companion.”—Journal of Commerce, Chicago.
“A neat volume, beautifully printed.”—L’Imprimerie, Paris.
“A neat book, beautifully printed.”—L’Imprimerie, Paris.
“The most complete work on the subject.”—Daily Free Press, Atchison, Kansas.
“The most comprehensive work on the topic.”—Daily Free Press, Atchison, Kansas.
“A great amount of curious information, historical and illustrative.”—Evening Post, New York.
“A lot of interesting information, historical and illustrative.”—Evening Post, New York.
“The result of intelligent research and considerable personal experience.”—The Nation, New York.
“The result of smart research and significant personal experience.”—The Nation, New York.
“This is taken as the standard American treatise on practical printing, and is eminently worthy the high reputation it has attained.”—Springer’s History and Mystery of Printing.
“This is considered the standard American guide on practical printing, and it truly deserves the high reputation it has earned.” —Springer’s History and Mystery of Printing.
Wilson’s Punctuation.
Wilson's Punctuation.
A Treatise on Punctuation, designed for Printers, Letter-Writers, Authors, and Correctors of the Press. Price, $1.50. By mail, $1.60.
A Guide to Punctuation, made for printers, letter writers, authors, and proofreaders. Price: $1.50. By mail: $1.60.
“It is an excellent work for schools and academies, and for those who would become self-taught.”—Christian Freeman.
“It is a fantastic resource for schools and academies, and for anyone who wants to learn on their own.”—Christian Freeman.
“We have never before met with any work on Punctuation which gave us so great satisfaction as this.”—The Student.
“We have never come across any work on punctuation that has given us as much satisfaction as this one.”—The Student.
“This is a useful and valuable work on English Punctuation, and every one can read it with profit and pleasure.”—Boston Daily Atlas.
“This is a helpful and valuable book on English punctuation, and everyone can read it for both benefit and enjoyment.”—Boston Daily Atlas.
“It contains all the necessary directions for self-taught writers and editors.”—American Whig Review.
“It contains all the essential guidelines for self-taught writers and editors.”—American Whig Review.
American Encyclopædia of Printing.
American Encyclopedia of Printing.
Comprising (with plates) 550 imperial octavo pages, giving more than sixteen hundred definitions, descriptions, and articles relating to the History, Implements, Processes, Products, and auxiliary Arts of Printing; splendidly Illustrated by more than two hundred Chromo-Lithographs, Lithographs, Wood Engravings, Imitations of Water-Marks, Embossed and Ruled Pages, etc. Edited by J. Luther Ringwalt. Price, $6.00.
Comprising (with plates) 550 imperial octavo pages, providing over sixteen hundred definitions, descriptions, and articles related to the history, tools, processes, products, and supporting arts of printing; beautifully illustrated with more than two hundred chromo-lithographs, lithographs, wood engravings, imitations of watermarks, embossed and ruled pages, etc. Edited by J. Luther Ringwalt. Price, $6.00.
Typographic Advertiser.
Typography Advertiser.
Elegantly printed, and furnished free to all Printing Offices. Needful to those who desire to keep up with the improvements in Typography.
Elegantly printed and provided for free to all printing offices. Essential for those who want to stay updated with the latest in typography.
“This grand journal, the oldest in the country, maintains its place in the van against all comers. Its typographic appearance is unequalled in the world of printing, and a careful study of its peerless specimen pages will do more to advance the beautiful in job composition and presswork than all the tawdry imitations of lithography, and badly designed and worse executed rule work that has been thrust upon a suffering art from Caxton to to-day. Its editorial management is as good as its typography is handsome and artistic.”—Springer’s History and Mystery of Printing.
“This prestigious journal, the oldest in the country, holds its position at the forefront against all competitors. Its print design is unmatched in the world of publishing, and a detailed examination of its outstanding sample pages will do more to promote beauty in job composition and print quality than all the cheap knock-offs of lithography and poorly designed and executed layout work that have plagued this suffering art from Caxton to today. Its editorial management is as impressive as its typography is beautiful and artistic.” —Springer’s History and Mystery of Printing.
Money spent for good books is well invested; and in this day of typographical progress, no active-minded printer can really afford not to have the above works in his office library. Address all orders to
Money spent on good books is a smart investment; and in this era of printing advancements, no proactive printer can really afford to be without these works in their office library. Please send all orders to
MacKellar, Smiths & Jordan Foundry,
Nos. 606-614 Sansom Street,
Philadelphia.
MacKellar, Smiths & Jordan Foundry,
Nos. 606-614 Sansom Street,
Philadelphia.
Transcriber’s Note
Transcription Note
List of changes made to the text:
List of changes made to the text:
Page 273, “pressman” changed to “pressmen” (Many pressmen take a dozen proofs)
Page 273, “pressman” changed to “pressmen” (Many pressmen take around twelve proofs)
Page 358, “Felonius” changed to “Felonious” (Felonious intent.)
Page 358, “Felonius” changed to “Felonious” (Felonious intent.)
Letter sounds in the alphabet tables were usually but not always italicised—italic font has been added where it seemed needed to standardise.
Letter sounds in the alphabet tables were usually, but not always, italicized—italic font has been added where it seemed necessary to standardize.
Inconsistent use of hyphens and old-fashioned spelling are left unchanged.
Inconsistent use of hyphens and outdated spelling are left unchanged.
ന is used to represent a symbol described as “the Gothic M”. ⊏ and ⊐ are used to represent the primitive square-cornered forms of the Roman numeral Ⅽ and its reverse Ↄ.
ന is used to represent a symbol described as “the Gothic M”. ⊏ and ⊐ are used to represent the basic square-cornered shapes of the Roman numeral Ⅽ and its reverse Ↄ.
₰ is used for the proofreader’s “dele” mark, which inexplicably still doesn’t have its own Unicode codepoint.
₰ is used for the proofreader’s “dele” mark, which for some reason still doesn’t have its own Unicode codepoint.
Characters which have no sufficiently close Unicode equivalent are included as illustrations.
Characters that don't have a close Unicode equivalent are included as illustrations.