This is a modern-English version of Staffordshire pottery and its history, originally written by Wedgwood, Josiah C. (Josiah Clement).
It has been thoroughly updated, including changes to sentence structure, words, spelling,
and grammar—to ensure clarity for contemporary readers, while preserving the original spirit and nuance. If
you click on a paragraph, you will see the original text that we modified, and you can toggle between the two versions.
Scroll to the bottom of this page and you will find a free ePUB download link for this book.
STAFFORDSHIRE
POTTERY AND
ITS HISTORY
STAFFORDSHIRE
POTTERY AND
ITS HISTORY
STAFFORDSHIRE
POTTERY AND
ITS HISTORY
By
JOSIAH C. WEDGWOOD, M.P., C.C.
Hon. Sec. of the William Salt Archæological Society.
By
JOSIAH C. WEDGWOOD, M.P., C.C.
Honorary Secretary of the William Salt Archaeological Society.
LONDON
SAMPSON LOW, MARSTON & CO. LTD.
LONDON
SAMPSON LOW, MARSTON & CO. LTD.
DEDICATED
TO MY CONSTITUENTS,
WHO DO THE WORK
DEDICATED
TO MY COMMUNITY,
WHO PUT IN THE EFFORT
Chapter | I. | The Creation of the Potteries. |
” | II. | A Peasant Industry. |
” | III. | Elers and Art. |
” | IV. | The Salt Glaze Potters. |
” | V. | The Beginning of the Factory. |
” | VI. | Wedgwood and Cream Colour. |
” | VII. | The End of the Eighteenth Century. |
” | VIII. | Spode and Blue Printing. |
” | IX. | Methodism and the Capitalists. |
” | X. | Steam Power and Strikes. |
” | XI. | Minton Tiles and China. |
” | XII. | Modern Men and Methods. |
This account of the potting industry in North Staffordshire will be of interest chiefly to the people of North Staffordshire. They and their fathers before them have grown up with, lived with, made and developed the English pottery trade. The pot-bank and the shard ruck are, to them, as familiar, and as full of old associations, as the cowshed to the countryman or the nets along the links to the fishing population. To them any history of the development of their industry will be welcome.
This account of the pottery industry in North Staffordshire will mainly interest the people of North Staffordshire. They and their parents before them have grown up with, lived with, created, and shaped the English pottery trade. The pot-bank and the shard ruck are as familiar to them and filled with memories as the cowshed is to a farmer or the nets along the shore are to fishermen. For them, any history about the growth of their industry will be appreciated.
But potting is such a specialized industry, so confined to and associated with North Staffordshire, that it is possible to study very clearly in the case of this industry the cause of its localization, and its gradual change from a home to a factory business. The rise of capitalism, the attempts at revolt on the part of the workers, the increase of machinery and steam power, all these can be studied very closely in the potting industry, just[x] because the history of the district is the history of potting and of the inhabitants’ whole lives. So that I venture to hope that many students of history and of sociology will find such a trade history as this of some value in their researches.
But the pottery industry is so specialized, so tied to North Staffordshire, that it's easy to clearly see why it developed there and how it gradually shifted from a home-based craft to a factory system. The rise of capitalism, the workers' attempts to revolt, and the growth of machinery and steam power can all be closely examined within the pottery industry, just[x] because the history of the area reflects the history of pottery and the lives of the people living there. Therefore, I hope that many history and sociology students will find this trade history valuable for their research.
The collector, too, may I hope find his special studies assisted by the identification and linking together of the relationships of the old master-potters, of their inventions, and factory sites and dates.
The collector may also find that their specific studies are enhanced by identifying and connecting the relationships of the old master potters, along with their inventions, factory locations, and dates.
A hundred years ago Simeon Shaw wrote a book of this nature. It had its merits, but since then research among ancient documents, systematic collection and excavation, the publications of the William Salt Archæological Society, and, above all, the modern work of such men as William Burton and Professor Church, have made it possible to restate far more exactly what happened, and when, to potting in North Staffordshire. Mr Burton’s “History and Description of English Earthenware” and his various works on porcelain have been drawn upon very largely in the following pages.
A hundred years ago, Simeon Shaw wrote a book like this. It had its strengths, but since then, research on ancient documents, systematic collection and excavation, the publications of the William Salt Archaeological Society, and especially the modern work of people like William Burton and Professor Church have made it possible to clarify in much greater detail what happened and when in potting in North Staffordshire. Mr. Burton’s “History and Description of English Earthenware” and his various works on porcelain have been heavily referenced in the following pages.
Both to him and to Professor Church, M. Solon[xi] and to many others, who have given me so much personal assistance in this work, I desire to express my gratitude. I can only regret that my own contribution to original research on the subject has been confined to the Tunstall Court Rolls, kindly lent me by Mr Sneyd, and to the MSS of my great-great-grandfather, Josiah Wedgwood, now in the museum of the Wedgwood firm at Etruria. Lastly I would express my indebtedness to my brother Frank Wedgwood, who has read through the proofs and made many corrections, such as would occur to one whose whole life has been devoted to the practice of the art of potting.
Both to him and to Professor Church, M. Solon[xi] and to many others who have provided me with so much personal help in this work, I want to express my gratitude. I can only wish that my own contribution to original research on the subject has been limited to the Tunstall Court Rolls, which were kindly lent to me by Mr. Sneyd, and to the manuscripts of my great-great-grandfather, Josiah Wedgwood, now housed in the museum of the Wedgwood firm at Etruria. Lastly, I want to acknowledge my brother Frank Wedgwood, who has read through the proofs and made many corrections, which would come naturally to someone whose whole life has been dedicated to the craft of pottery.
Slip decorated Staffordshire ware. c. 1660 | Page 14 |
Earliest known piece of Staffordshire salt glaze ware, 1701 | 32 |
Red china teapot, probably by Elers. c. 1760 | 36 |
Sample of later date, with moulded spout | 36 |
Samples of solid agate ware, made by Wedgwood or Weildon. c. 1760 | 36 |
Salt glaze teapot, drab body, supposed to be by Thomas Wedgwood, died 1737 | 54 |
Burslem in 1750 (map) | 60 |
Scratched blue salt glaze cup, dated 1750 | 68 |
Enamelled salt glaze jug, probably by Baddeley of Shelton, dated 1760 | 70 |
Staffordshire figures decorated with Weildon glaze, probably by Wedgwood, c. 1760 | 79 |
Etruria Works | 83 |
J. Wedgwood | 87 |
William Turner, Master Potter | 100 |
Hackwood, the Modeller | 103 |
Hanley in 1800 (map) | 107[xiv] |
Vase by John Turner of Lane End, died 1786 | 109 |
Thomas Minton | 111 |
William Adams | 122 |
John Wood, of Brownhills | 125 |
Burslem in 1800 (map) | 131 |
Josiah Spode | 134 |
Herbert Minton | 137 |
Job Ridgway | 141 |
Josiah Wedgwood II | 149 |
William Adams | 162 |
Ald. W. T. Copeland, M.P. | 178 |
In no country is there a district so utterly associated with one trade as is the North Staffordshire Potteries. One even speaks of the Potteries in the singular as of a pure place-name. If you spoke in Timbuctoo or California of the Potteries, none could doubt that you were thinking of North Staffordshire.
In no country is there a region so completely linked to a single industry as the North Staffordshire Potteries. People even refer to the Potteries in the singular, as if it's a specific place name. If you mentioned the Potteries in Timbuktu or California, no one would question that you were talking about North Staffordshire.
The reason is not that the district is or ever was given over entirely to pot-banks. Potting was incidental, a pastime in the middle of agriculture; as potting grew, so coal and iron mining grew too. The district is less confined to potting than Walsall to saddlery or Sheffield to knives. Even a thirteenth century reference to Walsall will expose harness; it is difficult to trace pots in the Potteries before 1650; you find only bloom-smithies and sea-coal mines. Potting is neither so ancient here, nor so exclusive as to have made the name. The real reason of the place-name, the Potteries, is that[2] no man who valued time could say Tunstall, Burslem, Hanley, Stoke and Longton, whenever he wanted to refer to one place—the place where men made pots—and few people outside the five towns ever wanted to speak of them separately, or could even distinguish one from others.
The reason isn’t that the area has ever been fully dedicated to pottery. Pottery was just a side activity among farming; as pottery production increased, so did coal and iron mining. The area is less focused on pottery than Walsall is on saddlery or Sheffield is on cutlery. Even a reference from the thirteenth century will show harness making in Walsall; it’s hard to find evidence of pottery in the Potteries before 1650; what you typically see are bloom smithies and coal mines. Pottery isn’t as ancient here nor is it unique enough to define the name. The real reason behind the name, the Potteries, is that[2] no one who valued their time would say Tunstall, Burslem, Hanley, Stoke, and Longton every time they wanted to refer to one place—the place where pots were made—and few people outside these five towns wanted to talk about them separately or could even tell them apart.
The first reference to “the Potteries” will be found in the latter half of the eighteenth century; before that time it was hardly necessary to refer to them at all.
The first mention of “the Potteries” can be found in the second half of the eighteenth century; before that time, it was hardly necessary to talk about them at all.
The area where pots were made in North Staffordshire has always been peculiarly local and circumscribed. It extends, and extended, in a line from Golden Hill to Meir Lane End. Occasionally, at times, we hear of Pot-works at Red—or Ridge—Street, at Bagnal or at Bucknall, outside this narrow area. They only receded finally from Chesterton during the last century. But, generally speaking, Staffordshire potters have persisted always in making pots just where their fathers made them before, in the hilly land between the Foulhay Brook and the sources of the Trent.
The area where pots were made in North Staffordshire has always been quite local and limited. It stretches, and has stretched, in a line from Golden Hill to Meir Lane End. Occasionally, we hear about potteries at Red—or Ridge—Street, at Bagnal, or at Bucknall, outside this small area. They finally disappeared from Chesterton only in the last century. But overall, Staffordshire potters have consistently continued making pots exactly where their fathers did before, in the hilly land between the Foulhay Brook and the sources of the Trent.
There was no need in old times for the people[3] who made pots to specialize in one district. The art of potting is as old and as universal as the art of cooking. In old times it was as simple. Like most modern trades it was practised at first, and anywhere, as a branch of housekeeping. Every family made what pots they required for their kitchen, and one can see such rude earthenware utensils among the miscellanea of any excavation. And like most modern trades the development from the housekeeping to the manufacturing stage meant specialization in particular districts.
In the past, there was no need for potters to focus on one area. The craft of making pots is as ancient and widespread as cooking itself. Back then, it was just as straightforward. Like many contemporary trades, it started out as a part of everyday home life. Every household created the pots they needed for their kitchens, and you can find rough earthenware items in the remains of any archaeological dig. As with most modern industries, the shift from domestic production to manufacturing led to specialization in specific regions.
But why should potting have settled in the Potteries?
But why should pottery have become established in the Potteries?
So long as all that was wanted was clay and firewood, almost any place would do. In England, it was about the year 1600 that the time arrived when brushwood became rare and costly; clay and coal were then found to be the necessaries of a “potteries.” North Staffordshire had both. Burslem, and it is Burslem alone which one need consider in this problem of the first cause, had something more than clay and coal. The land was split up into a great number of small copyhold owners, and immediately after 1600 the copyholds were[4] enfranchised. There were no demesne lands. The people were independent, both of big farmers and of great landlords. There was security of tenure, and every opportunity for initiative—initiative which could not then take the shape of intensive cultivation.
As long as all that was needed was clay and firewood, almost any location would work. In England, around the year 1600, the time came when brushwood became scarce and expensive; clay and coal were recognized as essential for “potteries.” North Staffordshire had both. Burslem, and it’s Burslem alone that we should focus on regarding the original cause, had something more than just clay and coal. The land was divided among many small copyhold owners, and right after 1600, the copyholds were[4] enfranchised. There were no estate lands. The people were independent from large farmers and wealthy landlords. There was security of tenure, providing ample opportunity for initiative—an initiative that couldn’t take the form of intensive farming at that time.
So we find in Burslem and Tunstall at the beginning of the seventeenth century clay, coal and the opportunity. By the end of that century the next requisite was to hand—skilled workmen. By the end of the next century the last requisite of trade was in place—the cheap water transport of the Trent and Mersey Canal.
So in Burslem and Tunstall at the start of the seventeenth century, there were clay, coal, and the chance to thrive. By the end of that century, the next essential was available—skilled workers. By the end of the next century, the final requirement for trade was met—the affordable water transport provided by the Trent and Mersey Canal.
It is well known that the safest way to test the presence in early days of particular trades or forms of employment is to study any local lists of the surnames of common people of the thirteenth and fourteenth centuries. We find our first such list for the Manor of Tunstall (which included Burslem) in 1299.[1] Not a single name that one can associate with potting is to be found. A similar list for Audley of the same date shows a Robert le Pottere, Thomas Potinger and Richard le Throware.[5] Probably most similar lists for that date would provide some such solitary reference to so common a trade, and I do not jump from this to the conclusion that Audley was the real mother of the Potteries. There are Subsidy Rolls giving Tunstall taxpayers in 1327 and 1333; still no Potter is to be found. We have also now available a varied selection of the Tunstall Court Rolls. The earliest, 1326, has nothing that one can twist into a reference to potting; but then we can collect in subsequent years the following:—
It's well known that the safest way to check for the presence of specific trades or types of jobs in early days is to look at local lists of common people's surnames from the thirteenth and fourteenth centuries. Our first such list for the Manor of Tunstall (which included Burslem) is from 1299. Not a single name associated with pottery appears. A similar list for Audley from the same time includes Robert le Pottere, Thomas Potinger, and Richard le Throware. It's likely that most similar lists from that period would show at least one reference to such a widespread trade, but I won’t jump to the conclusion that Audley was the true origin of the Potteries. There are Subsidy Rolls listing Tunstall taxpayers from 1327 and 1333, and still no Potter can be found. We also now have a variety of Tunstall Court Rolls. The earliest, from 1326, contains nothing that can be related to pottery; however, we can gather in later years the following:—
1348. William the Pottere gives 6d. for licence to make earthern pots (facere ollas terreas).
1348. William the Pottere pays 6d. for permission to make earthen pots (facere ollas terreas).
1353. Thomas the Throgher is amerced for a default at Chatterley.
1353. Thomas the Throgher is fined for a default at Chatterley.
1363. John Pottere is presented for an affray in Borewaslym (Burslem).
1363. John Pottere is charged with a fight in Borewaslym (Burslem).
1369. Robert le Potter gives 12d. for licence to get earth for making pots until the following Michaelmas.
1369. Robert le Potter pays 12d. for permission to collect clay for making pots until the next Michaelmas.
1372. Thomas le Thrower takes up land in Thursfield.
1372. Thomas le Thrower takes on land in Thursfield.
1405. Robert Potter is recently dead in Burslem.
1405. Robert Potter has recently died in Burslem.
In several of the leases of land by copy of Court Roll of the fifteenth and sixteenth century the right to dig marl or clay (argillium or luteum) is conceded, but I suspect it was usual even then to use such marl as manure. The filling in of pits or lakes (laca) in the roads is also a constant cause of trouble in these Rolls, but they may have been due to honest wear and tear and not to the temptations of a cheap raw material.
In several land leases recorded in the Court Roll from the fifteenth and sixteenth centuries, the right to dig marl or clay (argillium or luteum) is granted, but I think it was common even back then to use this marl as fertilizer. Filling in pits or lakes (laca) along the roads frequently causes issues in these Rolls, but these problems might have resulted from normal wear and tear rather than the lure of an inexpensive raw material.
It should be mentioned however that we have hardly one quarter of these early Tunstall Court Rolls, and must not assume that these few casual notices of clay or pots is exhaustive. We now skip a century and pass to:—
It should be noted, however, that we have barely one quarter of these early Tunstall Court Rolls, and we shouldn’t assume that these few random mentions of clay or pots are complete. We now skip a century and move on to:—
1549. The jurors present Richard Denyell for that he dug mud called clay (fodit luteum vocatum cley) in the King’s way at Bronehillslane (Brownhills), and in Burselem.
1549. The jurors present Richard Denyell for digging up mud known as clay (fodit luteum vocatum cley) in the King’s road at Bronehillslane (Brownhills), and in Burselem.
1604. Penalty laid (i.e. sub pœna). It is ordained by the jury that any person who digs “argillum vocatum clay” in a certain way called Wall Lane, which shall be prejudicial to[7] the passage by that way, or if he do not fill up the same well and sufficiently, shall forfeit to the lord 6s. 8d.
1604. Penalty imposed (i.e. sub pœna). The jury has determined that anyone who digs “argillum vocatum clay” in a specific manner along Wall Lane, which harms the passage through that area, or fails to properly fill it in afterward, will be fined 6s. 8d.
So far still no mention of potting. Various leisured people began now to describe England, relating what they saw and heard. Many of them dealt with Staffordshire, but they notice no special and curious feature about the North Staffordshire moorlands. Leyland in 1537, Camden in 1586, Erdeswick in 1590, say nothing of a “Potteries.” Speed’s list of the Shire products in 1625 omits pottery.
So far, there's still no mention of pottery. Various leisure-seekers began to describe England, sharing what they saw and heard. Many focused on Staffordshire, but they didn’t highlight any unique or interesting features about the North Staffordshire moorlands. Leyland in 1537, Camden in 1586, and Erdeswick in 1590 all fail to mention a “Potteries.” Speed’s list of county products in 1625 leaves out pottery.
It is just possible that some of the impetus for the local manufacture may have come from the dissolution of the monasteries. There is reason to believe, judging from the remains at the Cistercian Abbey of Hulton, that the monks there made such encaustic tiles as are to this day called Cistercian. Now Hulton Abbey and the Abbey’s grange of Rushton both lie in Burslem parish. Some rudimentary practice in the art and mystery of potting may well have come from the seven[2] scattering[8] brethren of this dissolved monastery, and may account in part for the development which was to come.
It’s possible that some of the drive for local production came from the closing of the monasteries. Evidence from the remains at the Cistercian Abbey of Hulton suggests that the monks there created the encaustic tiles that are still referred to as Cistercian today. Hulton Abbey and the Abbey’s grange of Rushton are both located in Burslem parish. Some basic skills in pottery may have originated from the seven scattered monks of this dissolved monastery, which could partly explain the development that followed.
For now we begin to find potters thick on the ground in Burslem.
For now, we start to see a lot of potters in Burslem.
In legal documents the practice grew of adding after any man’s name, his trade; leases, depositions, wills, all show this. After 1600 one would certainly expect to find some trade description, and at last, in 1616, we find our first “potters.”
In legal documents, it became common to add a person's occupation after their name; leases, depositions, and wills all reflect this. After 1600, one would definitely expect to see some description of a person's trade, and finally, in 1616, we see the first instances of "potters."
1616. Richard Middleton demises to Thomas Danyell of Burselem senior, potter, a pasture called Brownehills and another pasture called The Hill in Burslem containing 3 acres, with right to dig claye, “ffillinge upe the pitts after him,” for 21 years at a rent of 4s. He demises also to John Leigh 3 acres in Withiemore, with liberty to dig clay in the Withiemore when need be. (Tunstall Court Rolls.)
1616. Richard Middleton leases to Thomas Danyell of Burslem senior, potter, a pasture called Brownehills and another pasture called The Hill in Burslem, totaling 3 acres, with the right to dig clay, “filling up the pits after him,” for 21 years at a rent of 4s. He also leases to John Leigh 3 acres in Withiemore, with permission to dig clay in Withiemore when needed. (Tunstall Court Rolls.)
Next year, 1617, William Adams of Burslem describes himself in his Will as “potter”; and among the depositions of witnesses in the Chancery suit of “Mainwaring v. Shaw” of 1640, one of the witnesses, Ralph Simpson of Burslem, aged 80,[9] is described as “potter.” Thereafter every reference to Burslem or Tunstall is replete with “potters” or “earth-potters,” and men trained to the trade were acquiring the skill necessary for the localization of the coming industry.
Next year, 1617, William Adams from Burslem refers to himself in his Will as a “potter”; and in the witness statements for the Chancery case of “Mainwaring v. Shaw” from 1640, one of the witnesses, Ralph Simpson from Burslem, who is 80 years old,[9] is also referred to as a “potter.” After that, every mention of Burslem or Tunstall is filled with references to “potters” or “earth-potters,” and men trained in the trade were gaining the skills needed for the upcoming industry.
The men were ready. The clay and coal are found together cropping out in the country of the Staffordshire Potteries. The clay, though not now used for earthenware, is, and always has been, suitable for the saggars in which the ware is packed while being fired, and for the fire-bricks of the kiln in which the ware is baked. The coals were so cheap that, in 1680, they cost apparently only 16d. a ton at the pit’s mouth, and although such coal had to be carried usually on horseback, yet it never had to be carried more than two miles to reach the pot ovens.
The men were ready. The clay and coal are found together in the Staffordshire Potteries. The clay, although not currently used for earthenware, has always been suitable for the saggars used to pack the ware while it's fired, and for the fire-bricks in the kiln where the ware is baked. The coal was so cheap that, in 1680, it apparently cost only 16d. a ton at the pit’s mouth, and even though this coal usually had to be transported on horseback, it never had to be carried more than two miles to reach the pot ovens.
One other raw material was wanted—lead. It was the most expensive, almost the only part of the master potter’s equipment that required capital. The ore was got at Lawton Park, six miles to the north. The capital stock-in-trade of the early potter is shown by the Will of John Colclough alias Rowley, of Burslem, who died in[10] 1656, leaving “to Thomas Wedgwood of the Churchyard of Burslem ... all my pottinge boards and all other necessary implements and materialls belonginge to the trade of pottinge (lead and lead orre onely excepted).” This same Thomas Wedgwood was great-grandfather of Josiah Wedgwood, and he, as well as two of his brothers, Aaron and Moses, also describe themselves in their Wills as “Potters.”
One more raw material was needed—lead. It was the most expensive, nearly the only part of the master potter’s equipment that required investment. The ore was sourced from Lawton Park, six miles to the north. The capital stock-in-trade of the early potter is illustrated by the Will of John Colclough also known as Rowley, of Burslem, who passed away in[10] 1656, leaving “to Thomas Wedgwood of the Churchyard of Burslem ... all my potting boards and all other necessary tools and materials related to the pottery trade (lead and lead ore only excluded).” This same Thomas Wedgwood was the great-grandfather of Josiah Wedgwood, and he, along with two of his brothers, Aaron and Moses, also referred to themselves in their Wills as “Potters.”
Burslem was by 1670 full of potters; making no doubt butter-pots or the commonest of ware.[3][11] A little further off, in the valley of Tinkersclough, Thomas Toft was actually attempting decoration. The Toft dishes are well known. They are signed with the name, Thomas Toft or Ralph Toft, written in liquid slip clay upon the plate. They are made of red, buff or yellow clay, and other coloured slip-clays are dribbled over them through a quill, so as to make pictures of Charles II, or Queen Anne, or a pelican picking its breast to feed its young. Then the whole is dusted over with powdered lead ore, and fired till the lead fuses into the plate and forms a rich yellowish glaze.
Burslem was full of potters by 1670, undoubtedly producing butter pots and the most basic types of pottery.[3][11] A little farther down in the Tinkersclough valley, Thomas Toft was actually trying his hand at decoration. The Toft dishes are quite famous. They are marked with the names Thomas Toft or Ralph Toft, written in liquid slip clay on the plate. They're made from red, buff, or yellow clay, and other colored slip clays are drizzled over them with a quill to create images of Charles II, Queen Anne, or a pelican feeding its young by pecking at its breast. After that, everything is sprinkled with powdered lead ore and fired until the lead melts into the plate, creating a rich yellowish glaze.
Some of these productions, of what has come to be called the Toft school, are dated. There is a candlestick, very elaborate, dated 1649, and[12] claimed for Staffordshire. Shaw mentions two dishes marked, one “Thos. Sans,” and the other “Thos. Toft,” each dated 1650.[4] M. Solon had seen a slip dish, in a cottage in Hanley, bearing this inscription scratched on its back, “Thomas Toft, Tinkers Clough, I made it 166-.”[5] A dish with the picture of a soldier bearing a sword in each hand, and inscribed in slip “Ralph Toft, 1677” is also mentioned by M. Solon.[6] Another, marked Ralph Toft, and bearing the image of a very wasp-waisted lady is in the Salford Museum, dated “1676.”[7]
Some of these works, known as the Toft school, are dated. There's an elaborate candlestick from 1649, claimed to be from Staffordshire. Shaw mentions two marked dishes, one labeled “Thos. Sans” and the other “Thos. Toft,” both dated 1650. M. Solon saw a slip dish in a Hanley cottage, which had the inscription scratched on its back: “Thomas Toft, Tinkers Clough, I made it 166-.” Another dish, featuring a soldier holding swords in both hands and inscribed in slip “Ralph Toft, 1677,” is also mentioned by M. Solon. There's yet another dish, marked Ralph Toft, showing a very wasp-waisted lady, located in the Salford Museum and dated “1676.”
Other makers of this school were Thomas and William Sans, Ralph Simson and William Taylor. They made two-handled drinking mugs called “tygs” with similar decoration; and small model cradles made in clay and slip—presents for young married couples, according to their local custom. Puzzle Jugs were another “freak” production, speaking the humour of the time. The jug was so contrived with multiple spouts and hidden passages[13] as to spill however one tried to drink from it. A sample of these puzzle jugs in stoneware bears the inscription “John Wedgwood 1691.”[8] This man was the eldest son of the Thomas Wedgwood previously mentioned, and did not pot himself. I think this jug was made for him by his nephew, Richard Wedgwood, to whom he both leased the Overhouse Works and married his daughter and heiress. Several pieces are marked with the name “Joseph Glass,” who is known to have been a potter in Hanley in 1710-15.
Other makers from this group were Thomas and William Sans, Ralph Simson, and William Taylor. They created two-handled drinking mugs called "tygs" with similar designs, as well as small model cradles made from clay and slip—gift items for young married couples, following local tradition. Puzzle Jugs were another quirky creation that reflected the humor of the time. The jug was designed with multiple spouts and hidden passages[13] so that it would spill no matter how someone tried to drink from it. A sample of these puzzle jugs in stoneware has the inscription "John Wedgwood 1691." This man was the eldest son of the previously mentioned Thomas Wedgwood and did not pot himself. I believe this jug was made for him by his nephew, Richard Wedgwood, to whom he both leased the Overhouse Works and married his daughter and heiress. Several pieces are marked with the name "Joseph Glass," who is known to have been a potter in Hanley around 1710-15.
All these early master potters were handy men of many trades. They made their pots in sheds at the “backsides” of their dwelling houses, alongside the cow-shed. They dug their own clay, often in front of their own front doors. The Wedgwoods at least owned and dug their own coal, wherewith to fire the oven. It was a peasant industry, carried on by the family, among the pigs and fowls; and when they were not making show pieces for presentation they made butter-pots, in which farmers might market their butter at Uttoxeter—at least so says Dr Plot.
All these early master potters were skilled in many trades. They crafted their pots in sheds at the back of their houses, next to the cow barn. They dug their own clay, often right in front of their own doors. The Wedgwoods at least owned and mined their own coal to fire the kiln. It was a rural industry run by the family, amid the pigs and chickens; and when they weren’t creating decorative pieces for display, they made butter pots for farmers to sell their butter at Uttoxeter—at least that's what Dr. Plot says.
Dr Plot seems to have visited the Potteries in 1677. In 1686 he published his “Natural History of Staffordshire.” Although he obviously takes the most lively interest in the dances of witches, and that strange chemical process called “striking with galls,” yet he was also a keen observer, and found time to set down the earliest account—and at the same time an intelligent account—of the North Staffordshire potting industry. A contemporary account of this early date must obviously be of the greatest importance, and it is here given in full.
Dr. Plot appears to have visited the Potteries in 1677. In 1686, he published his “Natural History of Staffordshire.” While he clearly had a lively interest in witch dances and the unusual chemical process known as “striking with galls,” he was also a keen observer who made time to document the earliest and most insightful account of the North Staffordshire potting industry. An account from this early period is undoubtedly of great importance, and it is provided here in full.
“As for tobacco-pipe clays, they are found all over the County ... whereof they make pipes at Armitage and Lichfield ... also at Darlaston, but of late disused, because of better and cheaper found in Monway field betwixt Wednesbury and Willingsworth, which make excellent pipes. And Charles Rigg, of Newcastle, makes very good[15] pipes of three sorts of clay; a white, and a blew, which he has from between Shelton and Handley Green.”
“Tobacco-pipe clays can be found all over the county, where they make pipes in Armitage and Lichfield. They used to make them in Darlaston too, but that's not done much anymore because better and cheaper options are available in Monway field between Wednesbury and Willingsworth, which produce excellent pipes. Charles Rigg from Newcastle makes really good[15] pipes from three types of clay: a white one and a blue one, which he sources from between Shelton and Handley Green.”

Slip decorated Staffordshire ware. c. 1660. In the Stoke-on-Trent Museums.
Slip-decorated Staffordshire ware. c. 1660. In the Stoke-on-Trent Museums.
“The most preferable clay of any is that of Amblecot, of a dark blewish color, whereoff they make the best pots for the glass-houses of any in England; ... Other potters clays for the more common wares, there are ... at Horseley Heath, Tipton and in Monway field ... of these they make diverse sorts of vessells at Wednesbury, which they paint with slip made of a reddish sort of earth gotten at Tipton.
The best clay of all is from Amblecot, which has a dark bluish color, and it's used to make the finest pots for glasshouses in England; ... Other potters' clays for more common wares are found ... at Horseley Heath, Tipton, and in Monway field ... From these, they create various types of vessels in Wednesbury, which they decorate with slip made from a reddish type of earth sourced from Tipton.
“But the greatest pottery they have in this County is carried on at Burslem, near Newcastle-under-Lyme, where for making their severall sorts of pots they have as many different sorts of clays, which they dig round about the towne, all within half a miles distance, the best being found nearest the coale; and are distinguished by their colours and uses as followeth:—
“But the best pottery in this county is made in Burslem, near Newcastle-under-Lyme, where they use many different types of clay to create various kinds of pots. They dig the clay from around the town, all within half a mile, with the best clay found closest to the coal. The clays are categorized by their colors and uses as follows:—
1. Bottle clay, of a bright whitish streaked yellow colour.
1. Bottle clay, with a bright whitish streaked yellow color.
3. Red blending clay, which is of a dirty red colour.
3. Red blending clay, which is a dull red color.
4. White-clay, so called, it seems though of a blewish colour, and used for making a yellow-coloured ware, because yellow is the lightest colour they make any ware of.[9]
4. White clay, as it's called, actually has a bluish tint and is used to create yellow pottery, since yellow is the lightest color they use for any pottery.[9]
all which they call throwing clays, because they are of a closer texture, and will work on the wheel;
all of which they call throwing clays, because they have a finer texture and can be worked on the wheel;
“Which none of the three other clays, they call slips, will any of them doe, being of looser and more friable natures; these mixed with water they make into a consistence thinner than a syrup, so that being put into a bucket it will run out through a quill; this they call Slip, and is the substance wherewith they paint their wares; whereof the
“None of the three other clays, which they call slips, can do what this one does, as they are looser and more fragile. When mixed with water, they create a consistency thinner than syrup, so that when placed in a bucket, it will flow out through a quill. This is what they call Slip, and it is the substance they use to paint their wares; of which the
1-sort is called the Orange slip, which before it is worked, is of a greyish colour mixt with orange balls, and gives the ware when annealed an orange colour.
1-sort is known as the Orange slip, which, before it's processed, has a greyish color mixed with orange particles, and gives the piece an orange color when it's been annealed.
3. The Red slip, made of a dirty reddish clay, which gives wares a black colour.
3. The red slip, made of a gritty reddish clay, gives the pottery a black color.
neither of which clays or slips must have any gravel or sand in them; upon this account before it be brought to the wheel they prepare the clay by steeping it in water in a square pit, till it be of a due consistence; then they bring it to their beating board, where with a long spatula they beat it till it be well mixed; then being first made into great squarish rolls, it is brought to the wageing board, where it is slit into flat thin pieces with a wire, and the least stones or gravel pickt out of it; This being done, they wage it, i.e. knead or mould it like bread, and make it into round balls proportionable to their work, and then tis brought to the wheel, and formed as the workman sees good.
neither of which clays or slips should contain any gravel or sand; for this reason, before it goes to the wheel, they prepare the clay by soaking it in water in a square pit until it reaches the right consistency; then they take it to their beating board, where they mix it thoroughly with a long spatula; next, it's shaped into large, square rolls and brought to the wedging board, where it's cut into flat, thin pieces with a wire, and any small stones or gravel are removed; Once that’s done, they wedge it, meaning they knead or shape it like bread, forming it into round balls suitable for their work, and then it’s taken to the wheel, where the craftsman shapes it as desired.
“When the potter has wrought the clay either into hollow or flat ware, they are set abroad to dry in fair weather, but by the fire in foule, turning them as they see occasion, which they call whaving: when they are dry they stouk them,[18] i.e. put ears and handles to such vessels as require them: These also, being dry, they then slip or paint them with their several sorts of slip, according as they design their work,—when the first slip is dry, laying on the others at their leasure, the orange slip making the ground, and the white and red the paint; which two colours they break with a wire brush, much after the manner they do when they marble paper, and then cloud them with a pensil when they are pretty dry. After the vessels are painted they lead them, with that sort of lead ore they call smithum, which is the smallest ore of all, beaten into dust, finely sifted and strewed upon them; which gives them the gloss, but not the colour;[10] all the colours being chiefly given by the variety of slips, except the motley colour, which is procured by blending the lead with manganese, by the workmen called ‘magnus.’[11] But when they have a mind to show the utmost of their skill in giving their wares a fairer gloss than ordinary,[19] they lead them then with lead calcined into powder, which they also sift fine and strew upon them as before, which not only gives them a higher gloss, but goes much further too in their work, than lead ore would have done.
“When the potter has shaped the clay into either hollow or flat wares, they are left outside to dry in good weather or put by the fire in bad weather, turning them as necessary, which they call whaving. Once they are dry, they stouk them,[18] meaning they attach handles and ears to vessels that need them. After these are dry, they slip or paint them with different types of slip, depending on their design. When the first slip is dry, they apply the others at their convenience, with the orange slip serving as the base and the white and red as the paint. They break up these two colors with a wire brush, similar to how they marble paper, and then add clouds with a brush when they are mostly dry. After painting, they lead them with a type of lead ore called smithum, which is the finest ore, ground into dust, sifted, and sprinkled on them. This gives a gloss but not the color; all colors primarily come from the various slips, except for the mottled color, which is achieved by mixing lead with manganese, known to workers as ‘magnus.’ But when they want to showcase their skill by giving their wares a better-than-usual gloss,[19] they lead them with lead that has been calcined into powder, which is also finely sifted and spread on like before, resulting in a much higher gloss that lasts longer than the lead ore would allow."
“After this is done they are carried to the oven, which is ordinarily above 8 foot high, and about 6 foot wide, of a round copped forme, where they are placed one upon another from the bottom to the top: if they be ordinary wares such as cylindrical butter pots &c. that are not leaded, they are exposed to the naked fire, and so is all their flatware though it be leaded, haveing only parting-shards, i.e. thin bits of old pots put between them, to keep them from sticking together. But if they be leaded hollow-wares, they do not expose them to the naked fire, but put them in shragers, that is, in coarse metall’d pots, made of marle (not clay) of divers formes, according as their wares require, in which they put commonly three pieces of clay called Bobbs for the ware to stand on, to keep it from sticking to the shragers; as they put them in the shragers to keep them from sticking to one another (which they would certainly otherwise[20] doe by reason of the leading) and to preserve them from the vehemence of the fire, which else would melt them downe, or at least warp them. In 24 hours an oven of pots will be burnt, then they let the fire goe out by degrees which in 10 hours more will be perfectly done, and then they draw them for sale, which is chiefly to the poor cratemen, who carry them at their backs all over the whole Countrey, to whome they reckon them by the piece, i.e. Quart, in hollow ware, so that 6 pottle, or 3 gallon bottles make a dozen, and so more or less to a dozen, as they are of greater or lesser content; The flat wares are also reckon’d by pieces and dozens, but not (as the hollow) according to their content, but their different bredths.”[12]
“After this is done, they are taken to the oven, which is usually over 8 feet high and about 6 feet wide, with a rounded top shape. They are stacked one on top of the other from bottom to top. If they are regular items like cylindrical butter pots that aren’t leaded, they are exposed directly to the fire, as well as all their flatware, even if it is leaded, using only parting shards—thin pieces of old pots placed between them to prevent sticking. However, if they are leaded hollow ware, they are not placed directly in the fire but are put into shragers, which are coarse metal pots made of marl (not clay) in various shapes according to the items being fired. In these, they usually add three pieces of clay called Bobbs to lift the ware off the bottom and keep it from sticking to the shragers, as well as preventing the pieces from sticking to each other (which they definitely would due to the lead). This method also protects them from the intense heat, which could otherwise melt or warp them. In 24 hours, a kiln full of pots will be fired, after which the fire is gradually allowed to go out, taking about another 10 hours to be completely extinguished. Then the pots are taken out for sale, mostly to the poor potters who carry them on their backs all over the country. They are sold by the piece, meaning by quart for hollow ware, so that 6 pottle or 3-gallon bottles make a dozen, and likewise more or less to complete a dozen, depending on their size. The flat wares are also counted by pieces and dozens, but unlike the hollow ware, they are not calculated by their volume but by their various widths.”[12]
Again, in discussing the great dairy produce market at Uttoxeter, at which the Cheesemongers of London had thought it worth while to set up a “factorage,” Plot says:—“the factors many mercat days (in the season) lay out no less than £500 a day, in these two commodities [butter and cheese] only. The butter they buy by the pot, of a long cylindrical form, made at Burslem in this County of a certain size, so as not to weigh above 6 lbs. at most, and yet to contain at least 14 lbs. of butter, according to an Act of Parliament made about 14-16 years agoe, for regulating the abuses of this trade in the make of the pots and false packing of the butter.”[13]
Once again, when talking about the large dairy produce market in Uttoxeter, where the Cheesemongers of London found it worthwhile to establish a "factorage," Plot states:—“the factors invest no less than £500 a day on many market days (during the season) in these two products [butter and cheese] alone. They purchase the butter in pots, which are long and cylindrical in shape, made in Burslem in this county, weighing no more than 6 lbs. at most, but designed to hold at least 14 lbs. of butter, according to a law passed about 14-16 years ago to regulate the abuses in this trade regarding the construction of the pots and the deceptive packaging of the butter.”[13]
Later on, too, he describes how the lead ores are “dug in a yellowish stone, with cawk and spar, on the side of Lawton Park;[14] where the workmen distinguisht it into three sorts, viz. round ore, small ore, and smithum.” He describes how the ores are cleaned; “which done, it is sold to the potters at Burslem for 6 or 7 pounds per tun, who have[22] occasion for most that is found here for glaseing their pots.”
Later on, he describes how the lead ores are “dug from a yellowish stone, with cawk and spar, on the side of Lawton Park;[14] where the workers sort it into three types: round ore, small ore, and smithum.” He explains how the ores are cleaned; “once that’s done, it is sold to the potters in Burslem for 6 or 7 pounds per tun, who need most of what is found here for glazing their pots.”
For a contemporary inventory of a nascent industry Plot’s account is extraordinarily full and accurate. It is so important and so unique, that no apology need be made for quoting it at length.
For a current overview of a new industry, Plot's account is remarkably detailed and precise. It is so significant and distinct that there's no need to apologize for quoting it extensively.
The pot-oven described by Plot would be surrounded by a wall of clods of turf to keep in the heat, or by a “hovel” with walls of broken saggars, roofed with boughs and clods of earth. Each pot-works consisted of a hovel such as this, some thatched open sheds for drying the ware, and an open tank or sun-pan in which the clay mixed with water was evaporated. These sun-pans or sun-kilns were 12 to 20 feet long and wide and about 18 inches deep. One portion partitioned off, and deeper and lined with flag-stones, was used for mixing. Here the clay was “blunged” by a man with a long pole or paddle, and thoroughly mixed with the water. The mixture was then poured through a sieve from the blunging vat into the sun-pan.
The pot-oven described by Plot would be surrounded by a wall of turf clumps to keep in the heat, or by a "hovel" made of broken saggars, with a roof of branches and clods of earth. Each potworks included a hovel like this, some thatched open sheds for drying the pottery, and an open tank or sun-pan where the clay mixed with water would evaporate. These sun-pans or sun-kilns were 12 to 20 feet long and wide and about 18 inches deep. One section was partitioned off, deeper, and lined with flagstones, used for mixing. Here the clay was “blunged” by a person with a long pole or paddle, thoroughly mixing it with the water. The mixture was then poured through a sieve from the blunging vat into the sun-pan.
It was a very raw industry in 1677. What led to the artistic development of pottery in England as a whole was the trading contact with the advancing civilization of Holland and Germany. The English were learning all through the reigns of Elizabeth and the Stuarts to adapt pottery to drinking and eating purposes; and the London and Bristol potters were learning to copy the tin-enamelled dishes from Delft, and the stoneware drinking mugs from the Rhine. The ideas which Holland and Germany had passed on to London, found their way at last to North Staffordshire. In that narrow area were to be found the requisites needed for a manufacture;—the clays to make, the coals to fire, the men with experience. All that was still needed was the artist and experimental chemist. It might even be said that the artists were already there and in a sense they were.
It was a very rough industry in 1677. The artistic development of pottery in England overall was driven by trading relationships with the advancing civilizations of Holland and Germany. Throughout the reigns of Elizabeth and the Stuarts, the English were learning to adapt pottery for drinking and eating; London and Bristol potters were copying the tin-enamelled dishes from Delft and the stoneware drinking mugs from the Rhine. The ideas that Holland and Germany had shared with London eventually made their way to North Staffordshire. In that small region, everything needed for manufacturing was available—the clays for making, the coals for firing, and skilled workers. All that was left was the artist and experimental chemist. One could even say that the artists were already present, and in a way, they were.
Probably the commonest production of the North Staffordshire Potteries in 1677, after the redoubtable butter-pots, was the marbled ware that Plot mentions. This method of decoration[24] consists of laying on lines or splashes of the different coloured slips, and then combing or sponging them together. This marbled ware remained popular for a hundred years, and was the legitimate precursor of the solid agate wares of Whieldon and Wedgwood.
Probably the most common product from the North Staffordshire Potteries in 1677, after the impressive butter pots, was the marbled ware that Plot mentions. This decoration method consists of applying lines or splashes of various colored slips and then blending them together with a comb or sponge. This marbled ware remained popular for a hundred years and was the true precursor to the solid agate wares of Whieldon and Wedgwood.
A later historian, Simeon Shaw, writing in 1828, tells us on the authority of tradition that, besides makers of the butter-pots, and the mottled and marbled ware, and the slip-decorated ware, there was in 1685 a potter, Thomas Miles of Shelton, who was even then making from a local clay, mixed with white sand from Baddeley Edge, something which he calls “stone-ware.”[15] Certain it is, as will be shown later, that Aaron Wedgwood and his sons Thomas and Richard and also Matthew Garner were making brown stoneware and red teapots in Burslem in 1693. Stoneware, as we understand it, is so hard and dense that it requires no glaze to make it impervious to water, because it can be fired at such a high temperature as to partially fuse the body of the ware. This stoneware, afterwards glazed with salt, was to be the[25] most distinctive product of North Staffordshire.
A later historian, Simeon Shaw, writing in 1828, tells us based on tradition that, in addition to makers of butter pots, mottled and marbled ware, and slip-decorated ware, there was a potter named Thomas Miles from Shelton in 1685 who was making something he called “stoneware” from local clay mixed with white sand from Baddeley Edge. It’s clear, as will be shown later, that Aaron Wedgwood and his sons Thomas and Richard, along with Matthew Garner, were producing brown stoneware and red teapots in Burslem in 1693. Stoneware, as we know it, is so hard and dense that it doesn’t need a glaze to make it waterproof, because it can be fired at such a high temperature that it partially fuses the body of the ware. This stoneware, later glazed with salt, would become the most distinctive product of North Staffordshire.
These peasant potters “fired” and “drew out” one oven a week. They drew the cold oven on Monday; refilled it with new ware about Thursday, and fired it on Friday, giving it a last stoking up on Saturday morning, after which it cooled till Monday again. The ordinary ware was at this time only fired once, and only fired to a moderate temperature, just sufficient to melt the dusted lead ore and fuse it into a glaze on the surface of the ware, thus making it impervious to water. Though the native potters were even then trying to improve their craft from the German or Dutch potters employed in London, yet, as M. Solon has shown, they owed very little to the science or knowledge of the world, even the limited knowledge of that period. The colouring properties of Copper Oxide were known and employed throughout England at this period, yet there is no trace on the wares of the North Staffordshire potters till the eighteenth century is well advanced of the distinctive blue given by this invaluable colouring material.
These peasant potters “fired” and “emptied” one oven a week. They pulled out the cold oven on Monday, refilled it with new items around Thursday, and fired it on Friday, giving it a final stoking on Saturday morning, after which it cooled down until Monday again. At that time, ordinary pottery was only fired once and at a moderate temperature, just enough to melt the powdered lead ore and fuse it into a glaze on the pottery’s surface, making it waterproof. Although the local potters were already trying to improve their craft by learning from the German and Dutch potters working in London, as M. Solon has shown, they relied very little on the science or knowledge of the world, even the limited knowledge of that era. The coloring properties of Copper Oxide were known and used throughout England at that time, but there is no sign on the wares of the North Staffordshire potters until well into the eighteenth century of the distinctive blue created by this valuable coloring material.
The ware produced was sold to the travelling packmen, and, at great cost, distributed on horseback throughout the country. Everything was coarse and elementary. There were no turning lathes to give neatness to the thrown article; there was no white body or ground upon which to enamel colours; there were no moulds for any but the smallest ornamental “spriggs”; no enamel paints; and there was practically no means of getting to a market.
The goods made were sold to traveling packmen and, at a high cost, distributed by horseback across the country. Everything was rough and basic. There were no lathes to create neatness in the thrown items; there wasn't any white clay or surface to apply enamel colors; there were no molds for anything other than the smallest decorative "spriggs"; no enamel paints; and there was basically no way to reach a market.
Such was the state of the Staffordshire potting trade in the year 1693, when those mysterious foreigners, John Philip Elers and David Elers, appeared upon the scene, like Cortez among the Mexicans, and broke up for ever the placid uneventful course of the old peasant industry.
Such was the state of the Staffordshire pottery trade in 1693, when those mysterious foreigners, John Philip Elers and David Elers, appeared on the scene, like Cortez among the Mexicans, and forever disrupted the calm, uneventful flow of the old peasant industry.
The brothers Elers are supposed to have come from Amsterdam in the train of the Prince of Orange. Jewitt has studied their pedigree and says they were originally of a noble family of Saxony—their father an ambassador, their grandfather an admiral! However that may be, the first notice we have of them is in a note in the Philosophical Transactions of 1693 by Dr Martin Lister. He says: “I have this to add, that this clay Haematites, is as good, if not better, than that which is brought from the East Indies. Witness the teapots now to be sold at the potters in the Poultry in Cheapside, which not only for art, but for beautiful colour too, are far beyond any we have from China; these are made from the English Haematites in Staffordshire, as I take it, by two Dutchmen incomparable artists.”[16] We too may call them incomparable artists if we compare[28] this evidence with Plot’s account of fifteen years before, or their teapots sold at a guinea a time,[17] with the almost barbaric puzzle-jars of the native potter.
The Elers brothers are believed to have come from Amsterdam accompanying the Prince of Orange. Jewitt has researched their background and claims they were originally from a noble family in Saxony— their father was an ambassador, and their grandfather was an admiral! Regardless, the first mention of them appears in a note in the Philosophical Transactions of 1693 by Dr. Martin Lister. He says: “I have this to add, that this clay Haematites is as good, if not better, than that which is brought from the East Indies. Look at the teapots currently available at the potters in the Poultry in Cheapside, which not only excel in craftsmanship but also in beautiful color, surpassing anything we get from China; these are made from the English Haematites in Staffordshire, as I understand, by two Dutchmen who are exceptional artists.” [16] We might also call them exceptional artists when we contrast[28] this evidence with Plot’s account from fifteen years earlier, or their teapots sold at a guinea each,[17] with the almost primitive puzzle-jars from the local potter.
It has hitherto been assumed from this statement of Dr Lister’s that the Elers were in Staffordshire in 1693. It does not follow from the extract that the teapots were made in Staffordshire, only that the clay came from thence. In the same year, 1693, they were sued by Dwight of Fulham for copying his red teapots, and in the suit they are described as “of Fulham.” Moreover Dr Martin Lister, writing again in 1698 in his “Account of a Journey to Paris in the Year 1698,” says, after speaking of the porcelain made at St Cloud, “As for the red ware of China, that has been and is done in England.... But we are in this particular beholden to two Dutchmen who wrought in Staffordshire, as I have been told, and were not long since in Hammersmith.”[18] This, it will be seen, confirms the supposition that they first made their teapots and stoneware in Fulham or Hammersmith.
It has previously been assumed based on Dr. Lister's statement that the Elers were in Staffordshire in 1693. However, the excerpt does not indicate that the teapots were made there, only that the clay came from that area. In the same year, 1693, they were sued by Dwight of Fulham for copying his red teapots, and in the lawsuit, they are referred to as “of Fulham.” Furthermore, Dr. Martin Lister, writing again in 1698 in his “Account of a Journey to Paris in the Year 1698,” mentions, after discussing the porcelain made at St. Cloud, “As for the red ware of China, that has been and is being produced in England.... But we owe this particularity to two Dutchmen who worked in Staffordshire, as I have been told, and were not long ago in Hammersmith.”[18] This, as can be seen, supports the idea that they originally made their teapots and stoneware in Fulham or Hammersmith.
The important Chancery Suit, discovered by Prof. Church, in which Dwight sued his copyists at Fulham, Nottingham and Burslem is as follows:
The significant Chancery Suit, found by Prof. Church, where Dwight took legal action against his copyists in Fulham, Nottingham, and Burslem is as follows:
June 20, 1693. The complaint of John Dwight of Fulham in the County of Middlesex, gentleman, showing that the complainant having ... invented and set up at Fulham several new manufactures of earthenwares called White Gorges, marbled porcelaine vessells, statues and figures and fine stone gorges and vessells never before made in England or elsewhere, and alsoe discovered the mystery of opacous red and dark coloured porcelaine and china ... obtained lettres patent dated June 12, 1684 ... he and his servants have for several years past used ... said invention ... and sold them.... But having formerly hired one John Chandler of Fulham ... and employed him in the making ... thereupon John Elers and David Elers, both of Fulham (who are forreigners and by trade silversmiths) together with James Morley of Nottingham and also Aaron Wedgwood Thomas Wedgwood and Richard Wedgwood of Berslem in the County of Stafford and Matthew Garner ... did insinuate themselves into the acquaintance of the[30] said John Chandler and ... inticed him to instruct them ... and to desert the complainant’s service to enter into partnership together with them to make and sell the said wares ... but far inferior to them.... And the said confederates, “the better to colour their said unjust and injurious practises,” pretend that the earthenwares made and sold by them are in no way like those invented by the complainant but differ from them in form and figure and have several additions and improvements ... whereas the truth is they are made in imitation of the complainants wares ... prays that writs of subpena be directed to John Chandler, John Elers, David Elers, Aaron Wedgwood, Thomas Wedgwood, Richard Wedgwood and Matthew Garner and James Morley.
June 20, 1693. The complaint of John Dwight of Fulham in the County of Middlesex, gentleman, states that the complainant has invented and set up several new types of earthenware in Fulham, known as White Gorges, marbled porcelain vessels, statues and figures, and fine stone gorges and vessels that have never been made in England or elsewhere. He has also discovered the process for creating opaque red and dark-colored porcelain and china. He obtained letters patent dated June 12, 1684. He and his employees have been using and selling this invention for several years. However, he previously hired one John Chandler of Fulham and employed him in the manufacturing process. Following this, John Elers and David Elers, both from Fulham (who are foreigners and work as silversmiths), along with James Morley of Nottingham and Aaron Wedgwood, Thomas Wedgwood, Richard Wedgwood of Burslem in the County of Stafford, and Matthew Garner, insinuated themselves into John Chandler's circle. They persuaded him to teach them his skills and to leave the complainant's services to partner with them in the making and selling of these goods, but their products are of much lower quality. The said confederates, “to better disguise their unjust and harmful practices,” claim that the earthenware they make and sell is not similar to the complainant’s inventions, but rather they differ in shape and have several additions and improvements. However, the truth is they are imitating the complainant’s wares. The complainant requests that writs of subpoena be directed to John Chandler, John Elers, David Elers, Aaron Wedgwood, Thomas Wedgwood, Richard Wedgwood, Matthew Garner, and James Morley.
The answer, dated June 8, 1694, of the man with the Staffordshire name of Garner to this Bill of Complaint, shows that he was apprenticed about 1680 for eight years to one Thomas Harper of Southwark, potmaker, and he says that, afterwards, he invented a way of making earthen brown pans and mugs, which art he still practises. The answer of David Elers to the same Bill, dated[31] July 28, 1693, states that he learnt at Cologne the manufacture of “earthenware commonly called Cologne or Stone wares,” and that about three years ago he and his brother began to make brown mugs and red teapots “within this kingdom of England,” and employed John Chandler. He says that neither he nor his brother nor Morley nor any of the other defendants knew John Chandler while he was in the employ of Dwight. He denies that James Morley was ever a partner with him or his brother, or that Chandler was more than a hired labourer. He complains that he and his brother ought not to be deprived of their living.
The response, dated June 8, 1694, from the man named Garner from Staffordshire regarding this Bill of Complaint, indicates that he was apprenticed for eight years around 1680 to one Thomas Harper, a potmaker from Southwark. He mentions that afterwards he developed a method for making earthen brown pans and mugs, which he still practices. The response from David Elers to the same Bill, dated [31] July 28, 1693, states that he learned in Cologne how to manufacture “earthenware commonly known as Cologne or Stone wares,” and that about three years ago he and his brother started making brown mugs and red teapots “within this kingdom of England,” while employing John Chandler. He asserts that neither he nor his brother nor Morley nor any of the other defendants knew John Chandler while he was working for Dwight. He denies that James Morley was ever a business partner with him or his brother, or that Chandler was anything more than a hired laborer. He argues that he and his brother should not be deprived of their livelihood.
An order was made on August 10, 1693, for a trial of the action against Morley and the Elers for the making of a brown mug and two red teapots in imitation of china. Before the trial came on in November the Elers came to terms with Dwight, and Morley put off his case by claiming that he only made brown mugs and not the red teapots. On December 15, 1693, the three Wedgwoods were ordered to be added to the Bill as defendants, and on May 5, 1694, Matthew Garner was added also. On May 19, 1694, the Wedgwoods[32] “for delay have craved a dedimus to answer in the country,” and yet in the meantime proceed to make and vend the several wares, against which continuance the plaintiff Dwight obtained an injunction “until they shall directly answer to the complaint and the Court shall make other order to the contrary against them their workmen servants and agents.” On June 21, 1694, a similar injunction was obtained against Matthew Garner; and on July 26, 1695, against Morley. Garner in his turn wanted his witnesses examined in the country, and the cases against him and Morley and one Luke Talbott dragged on till July, 1696, though nothing more is to be found of the suit against the Wedgwoods. Probably they too compromised on the basis of each paying their own costs, for the last notice there is of these suits is one dated July 1, 1696, which shows Dwight suing his solicitor for excessive costs.
An order was issued on August 10, 1693, for a trial against Morley and the Elers for creating a brown mug and two red teapots that copied china. Before the trial took place in November, the Elers reached an agreement with Dwight, while Morley postponed his case by claiming he only made brown mugs, not the red teapots. On December 15, 1693, the three Wedgwoods were ordered to be added as defendants to the Bill, and on May 5, 1694, Matthew Garner was included as well. On May 19, 1694, the Wedgwoods[32] "requested a dedimus to respond in the country" due to delays, but in the meantime, they continued to produce and sell the various items. Dwight, the plaintiff, obtained an injunction "until they directly respond to the complaint and the Court gives a different order regarding them, their workers, servants, and agents." On June 21, 1694, a similar injunction was issued against Matthew Garner, and on July 26, 1695, against Morley. Garner, in turn, wanted his witnesses to be examined in the country, and the cases against him, Morley, and one Luke Talbott dragged on until July 1696, although no further information is available regarding the suit against the Wedgwoods. They likely also reached a compromise based on each paying their own costs, as the last notice concerning these suits is dated July 1, 1696, indicating Dwight was suing his solicitor for excessive fees.
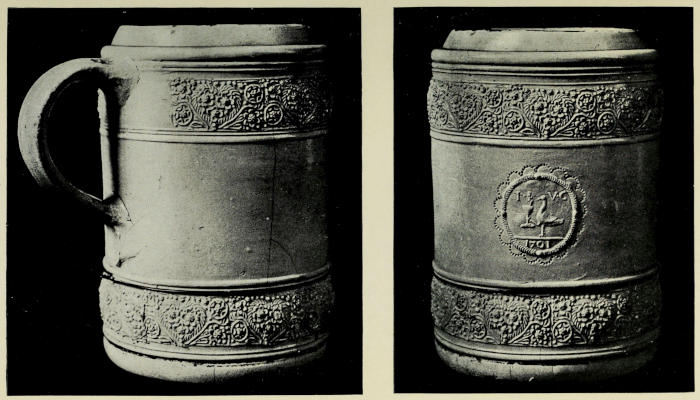
Earliest known piece of Staffordshire salt glaze ware, 1701. From the Stoke-on-Trent Museums.
Earliest known piece of Staffordshire salt glaze ware, 1701. From the Stoke-on-Trent Museums.
This suit, given by Professor Church in the “Burlington Magazine” (February, 1908) upsets a good many preconceptions, and throws considerable light on the stage at which the development of the potting craft had arrived in 1693. In the[33] first place Garner, a Staffordshire lad to judge from his name, is apprenticed to a London potter. This shows communication between London and Staffordshire, and a clear desire to improve a potting trade in Staffordshire by contact with more civilized methods. Then the injunction obtained against Aaron Wedgwood and his sons, “Doctor” Thomas and Richard “of the Overhouse,” shows that they were making in 1693 the red teapots, known to collectors as Elers and Dwight, and the brown stoneware which, glazed with salt, was later the characteristic work of Dr Thomas Wedgwood. We must, therefore, call these Wedgwoods and Matthew Garner the first known Staffordshire makers of stoneware, and as Garner was out of his apprenticeship in 1688, and Elers started in Fulham in 1690, we can give the date 1690 as the starting point of the stoneware glazed with salt in Staffordshire.
This article, written by Professor Church in the "Burlington Magazine" (February 1908), challenges several assumptions and provides significant insight into the level of development in the pottery craft by 1693. First, Garner, a kid from Staffordshire based on his name, is apprenticed to a potter in London. This indicates communication between London and Staffordshire and a clear intention to enhance the pottery trade in Staffordshire by learning from more advanced techniques. Then, the legal action taken against Aaron Wedgwood and his sons, “Doctor” Thomas and Richard “of the Overhouse,” shows that by 1693, they were producing red teapots, which collectors refer to as Elers and Dwight, as well as the brown stoneware that later became the signature style of Dr. Thomas Wedgwood, known for its salt glaze. Therefore, we should consider these Wedgwoods and Matthew Garner as the first known Staffordshire producers of stoneware. Since Garner finished his apprenticeship in 1688 and Elers began working in Fulham in 1690, we can pinpoint 1690 as the beginning of salt-glazed stoneware production in Staffordshire.
If there was a definite partnership between the Elers and the Wedgwoods I expect it was confined to the supply of red Staffordshire clay to the factory at Fulham. It may well be that, as a result of this very action, the Elers determined to shift their[34] workshops and put them up in the place whence hitherto they had got their clay, and where the unfortunate leakage that had perhaps betrayed Dwight’s secrets could, in their case, be more easily prevented. Be the cause what it may, between 1693 and 1698 John Philip Elers, the elder brother, was established in a secluded farm in Bradwell Wood under Red Street. It should be noticed that at this time, and for half a century afterwards, Red Street was important as a potting village. Messrs Mayer & Moss of Red Street were, about 1740, among the most considerable potters of their day.
If there was a specific partnership between the Elers and the Wedgwoods, it likely only involved supplying red Staffordshire clay to the factory in Fulham. It's possible that, as a result of this arrangement, the Elers decided to relocate their workshops closer to where they sourced their clay, making it easier to prevent any leaks that might reveal Dwight’s secrets. Whatever the reason, between 1693 and 1698, John Philip Elers, the older brother, settled in a remote farm in Bradwell Wood under Red Street. It's worth noting that at this time, and for the next fifty years, Red Street was a significant pottery village. Messrs Mayer & Moss of Red Street were, around 1740, among the most prominent potters of their time.
Here, at Bradwell, the Elers put up their workshops and small kiln, while they lived at another old house, Dimsdale Hall, which is still standing about a mile to the south. Shaw[19] had a legend about an elaborate underground speaking-tube, fixed from Bradwell to Dimsdale, through which notice might be given to the works of the approach of strangers. And it is a curious tribute to the value of such legends that, within the last few years, white earthenware voice-pipes have actually been[35] dug up on the site of the Bradwell factory. They did not, of course, really extend from Bradwell to Dimsdale, but they went from one part of the factory to another, and were probably devised to secure secrecy rather than modern economy. These pipes are now to be seen in the Hanley Museum, and the curious thing is that one of them is glazed with salt. This, besides confirming the legend of the voice-pipes, is the only certain living witness that the Elers used salt glaze.
Here at Bradwell, the Elers set up their workshops and a small kiln while living in another old house called Dimsdale Hall, which still stands about a mile to the south. Shaw[19] had a legend about an intricate underground speaking tube that connected Bradwell to Dimsdale, allowing for alerts to be sent to the workers about the approach of strangers. It’s interesting to note that in recent years, white earthenware voice pipes have actually been[35] excavated at the site of the Bradwell factory. They didn’t truly extend from Bradwell to Dimsdale, but rather linked different parts of the factory and were likely designed to maintain secrecy rather than for modern efficiency. These pipes are now displayed in the Hanley Museum, and the fascinating detail is that one of them is coated with salt glaze. This not only supports the legend of the voice pipes but also serves as the only undeniable proof that the Elers used salt glaze.
We have spoken of the two brothers going to Staffordshire, but the recently accepted view is that John Philip Elers alone worked at Bradwell, while David remained in London at the shop in the Poultry, where he sold his brother’s teapots at from 12s. to 24s. apiece.[20]
We talked about the two brothers going to Staffordshire, but the current understanding is that John Philip Elers was the only one who worked at Bradwell, while David stayed in London at the shop on Poultry, where he sold his brother’s teapots for between 12s. and 24s. each.[20]
The first pottery ware made at Bradwell was the same as Dwight’s “red porcelaine.” On the land at Bradwell Farm was the seam of red clay which formed the foundation of the ware, giving when fired a dense hard red stoneware of fine texture.[21] There are in the South Kensington Museum two[36] pieces of “red porcelain” credited by Burton to Elers and illustrated in his book. They are in marked contrast to the slip decorated and marbled Staffordshire ware of the same time. They have been turned in the lathe after throwing, and thus made thin and light. The clay body is homogeneous and smooth, showing greater care in the preparation of the body. The ornamentation is delicate and artistic, and has been made by sealing a soft piece of the clay on to the ware with a metal seal pressed over the soft clay. There is no glaze, but a high fire has produced a ware so hard as to be almost forged solid. These things show the hand of the ex-silversmith in size and shape and finish. The Burslem imitators—Garner and the Wedgwoods—never made things like these. Elers, though he may have stolen Dwight’s secrets, went ahead and showed the possibilities of potting. He is said also to have produced black ware of a similar character by mixing oxide of manganese—the “magnus” of Dr Plot—with the clay body, and, though no known pieces of black Elers ware can now be certainly identified,[37] it is this black ware that his copyists chiefly developed.[22]
The first pottery made at Bradwell was similar to Dwight’s “red porcelain.” At Bradwell Farm, there was a seam of red clay that formed the base of the pottery, which, when fired, created a dense, hard red stoneware with a fine texture.[21] In the South Kensington Museum, there are two[36] pieces of “red porcelain” attributed to Elers and shown in his book. They contrast sharply with the slip-decorated and marbled Staffordshire pottery of the same period. These pieces were turned on a lathe after being thrown, making them thin and light. The clay body is uniform and smooth, indicating greater care in its preparation. The decoration is delicate and artistic, created by attaching a soft piece of clay onto the pottery with a metal seal pressed onto the soft clay. There is no glaze, but a high fire has made the pottery so hard that it is nearly solid. These features reflect the craftsmanship of a former silversmith in size, shape, and finish. The imitators from Burslem—Garner and the Wedgwoods—never produced anything like these. Elers, despite possibly taking Dwight's secrets, moved forward and demonstrated the potential of pottery. He is also said to have created black ware of a similar nature by mixing manganese oxide—the “magnus” of Dr Plot—with the clay body. Although no specific pieces of black Elers ware can currently be definitively identified,[37] it is this black ware that his imitators primarily developed.[22]

1. Red china teapot, probably by Elers. c. 1700.
1. Red china teapot, likely made by Elers. c. 1700.
2. Sample of later date, with moulded spout. Stoke-on-Trent Museums.
2. Sample from a later date, featuring a molded spout. Stoke-on-Trent Museums.
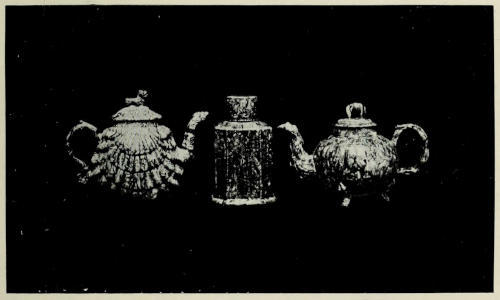
Samples of solid agate ware made by Wedgwood or Whieldon. c. 1760.
Samples of solid agate pottery made by Wedgwood or Whieldon. c. 1760.
From the Stoke-on-Trent Museums (see p. 74).
From the Stoke-on-Trent Museums.
For Nemesis overtook John Philip Elers, and in spite of all his secrecy, perhaps because of it, he was copied. Two potters, Twyford and Astbury,[23] one of whom at least had already made pots after local methods in Shelton, set themselves independently to acquire the arts of the Dutchman. To lull the suspicions of Elers, Twyford shammed stupidity, and Astbury, who was younger, passed himself off as an idiot. Recommended by these strange qualifications, they asked and obtained employment and, in time, the knowledge they desired. They went back to Shelton with their acquired arts, and, in a few years, the most intelligent potters of North Staffordshire knew how to make civilized pottery. But by 1710 John Philip Elers was tired of his exile and of the[38] treatment he had received. The true porcelain which should detect poison was still unattained, and his “red porcelain” and his black ware were become by somewhat sharp practice a staple product of the district. So he shook off the clay of Staffordshire from his feet and rejoined his brother in London.
For Nemesis caught up with John Philip Elers, and despite all his secrecy, or maybe because of it, he was copied. Two potters, Twyford and Astbury, one of whom at least had already made pots using local techniques in Shelton, independently decided to learn the skills of the Dutchman. To throw off Elers’ suspicions, Twyford pretended to be clueless, and the younger Astbury acted like a fool. Endorsed by these odd disguises, they asked for and got jobs, and eventually, the knowledge they sought. They returned to Shelton with their newfound skills, and within a few years, the most skilled potters in North Staffordshire knew how to make fine pottery. But by 1710, John Philip Elers was fed up with his exile and the treatment he endured. The true porcelain capable of revealing poison was still out of reach, and his “red porcelain” and black ware had become, through somewhat dubious means, a staple product of the area. So he shook the Staffordshire clay off his feet and reunited with his brother in London.
Years later Josiah Wedgwood, who had every reason to know the history of the potteries from hearsay, legend and family tradition, gave an account to his partner Bentley of what John Philip Elers had done. The son, Paul Elers, had asked Wedgwood to make a medallion of his father’s head, surrounded by the motto: “Plasticis Britannicae Inventor.” Josiah Wedgwood—looking back on the long array of his ancestors, all potters born and bred in Burslem before ever Elers put his hand to the thrower’s wheel—says the motto “conveys a falsehood,” and that John Philip Elers merely improved the Art. “The reason,” he writes in 1777, “for Mr Elers fixing upon Staffordshire to try his experiments, seems to be that the Pottery was carried on there in a much larger way, and in a more improved state, than in any other[39] part of Great Britain.” “The improvements Mr Elers made in our manufactory were precisely these. Glazing our common clays with salt, which produced Pot d’Grey or Stone Ware.... I make no doubt but glazing with salt, by casting it among the ware while it is red hot, came to us from Germany, but whether Mr Elers was the person to whom we are indebted for the improvement I do not know.... The next improvement introduced by Mr Elers was the refining our common red clay by sifting, and make it into Tea and Coffee ware in imitation of the Chinese red Porcelain, by casting it in plaster moulds, and turning it upon the outside upon lathes, and ornamenting it with the tea-branch in relief.”[24]
Years later, Josiah Wedgwood, who had every reason to know the potteries' history through hearsay, legends, and family tradition, shared his account with his partner Bentley about what John Philip Elers had accomplished. Elers' son, Paul Elers, had asked Wedgwood to create a medallion of his father's head, framed by the motto: “Plasticis Britannicae Inventor.” Reflecting on the long line of his ancestors, all potters raised in Burslem long before Elers ever touched the potter's wheel, Wedgwood claimed that the motto “conveys a falsehood,” stating that John Philip Elers merely improved the Art. “The reason,” he wrote in 1777, “that Mr. Elers chose Staffordshire to experiment seems to be because pottery was conducted there on a much larger scale and in a more advanced state than anywhere else in Great Britain.” “The improvements Mr. Elers made in our manufacturing were specifically these: glazing our common clays with salt, which produced Pot d’Grey or Stone Ware.... I have no doubt that glazing with salt by casting it among the ware while it is red hot came to us from Germany, but whether Mr. Elers is the one we owe this improvement to, I do not know.... The next improvement introduced by Mr. Elers was refining our common red clay by sifting and making it into Tea and Coffee ware to mimic the Chinese red Porcelain, by casting it in plaster molds, turning it on lathes, and decorating it with the tea branch in relief.”[24]
It is impossible to say why Wedgwood attributed “casting in plaster moulds” to Elers, for all the evidence goes to show that the process known technically as “casting” only came in with the introduction of alabaster “blocks” and pitcher moulds after 1730. As to the far more important and debatable point—the introduction of the process of glazing with salt—this evidence of[40] Wedgwood’s is perhaps the most reliable that we can get.
It's unclear why Wedgwood credited Elers with "casting in plaster molds," since all evidence suggests that the process, technically called “casting,” only started with the use of alabaster "blocks" and pitcher molds after 1730. As for the much more significant and controversial issue—the introduction of the glazing process using salt—this evidence from Wedgwood is likely the most dependable we have.[40]
As the invention of salt glazing not only made, at one stroke, a new manufacture possible, but one that was peculiar to North Staffordshire, it may be as well to examine more closely the evidence as to its discoverer and its discovery.
Since the invention of salt glazing not only made a new type of manufacturing possible all at once but also one that was unique to North Staffordshire, it might be a good idea to take a closer look at the evidence regarding who discovered it and how it came about.
The idea that salt glazing was accidentally discovered at Bagnal by some strong brine solution boiling away in an earthen pot which became automatically glazed[25] may be dismissed at once for the simple reason that it could not happen as described. It may be urged too in Elers’ favour that, long before this, salt glazing was practised in Germany. Again, Aikin in his “History of Manchester,” written in 1794, gives an elaborate account of the novelty as practised by Elers. He writes: “It was in the memory of some old persons with whom a friend of ours was well acquainted that the inhabitants of Burslem flocked with astonishment to see the immense volumes of smoke which arose from the Dutchmen’s ovens on casting in the salt; a circumstance which sufficiently shows[41] the novelty of this practice in Staffordshire Potteries.”[26] Probably this part of Dr Aikin’s work was written by Alex. Chisholm, secretary to Josiah Wedgwood.
The idea that salt glazing was accidentally discovered at Bagnal by some strong brine solution boiling away in an earthen pot that became automatically glazed[25] can be dismissed right away because it couldn’t happen as described. It can also be argued in Elers’ favor that, long before this, salt glazing was used in Germany. Moreover, Aikin in his “History of Manchester,” written in 1794, provides a detailed account of the process as practiced by Elers. He writes: “It was within the memory of some older people whom a friend of ours knew well that the residents of Burslem gathered in amazement to see the huge clouds of smoke that rose from the Dutchmen’s ovens when they added the salt; a situation that clearly demonstrates[41] the novelty of this practice in Staffordshire Potteries.”[26] Likely, this part of Dr. Aikin’s work was written by Alex. Chisholm, secretary to Josiah Wedgwood.
At least the same story was told to Josiah Wedgwood in 1765 by an old workman named Steel, aged 84, who could remember the Dutchmen at work at Bradwell, and who joined those who ran to the place amazed at this unusual mode of firing. No doubt this is what was in Wedgwood’s mind when he wrote to Bentley in 1777, as quoted above.
At least the same story was recounted to Josiah Wedgwood in 1765 by an elderly worker named Steel, who was 84 years old and could remember the Dutch workers at Bradwell. He joined those who rushed to see this unusual method of firing. This was likely on Wedgwood's mind when he wrote to Bentley in 1777, as mentioned earlier.
On the other hand we have the evidence of Simeon Shaw,[27] first that William Adams and Thomas Miles produced salt glaze in 1680 (a very doubtful supposition in view of the Chancery suit recently discovered), and then that “Mr. John Mountford, 27 years since (i.e. in 1801), took down the remains of the (Elers’) oven, and he states that the height was about 7 feet, but not like the salt-glaze ovens.” And again: “E. Wood and J. Riley both separately measured the inside diameter of the remains, at about 5 feet; while other[42] ovens, of the same date, in Burslem, were 10 or 12 feet. The oven itself had 5 mouths, but neither holes over the inside flues nor bags, to receive the salt, had any been used by them.” “The foundations,” he adds, “were very distinctly to be seen in 1808, though now covered by an enlargement of the barn.”
On the other hand, we have the evidence from Simeon Shaw, first noting that William Adams and Thomas Miles produced salt glaze in 1680 (which is quite questionable considering the recently discovered Chancery suit), and then that “Mr. John Mountford, 27 years ago (in 1801), dismantled the remains of the (Elers’) oven, and he states that the height was about 7 feet, but it didn’t resemble the salt-glaze ovens.” Additionally: “E. Wood and J. Riley both separately measured the inside diameter of the remains to be about 5 feet; while other ovens from the same time period in Burslem measured 10 or 12 feet. The oven itself had 5 openings, but they hadn’t used any holes over the inside flues or bags to hold the salt.” “The foundations,” he adds, “were clearly visible in 1808, although now they’re covered by an expansion of the barn.”
Also there is the fact that no salt glaze ware that could be conclusively shown to be Elers’ has ever been excavated on the site of his factory, except the white voice-pipes previously mentioned.
Also, there’s the fact that no salt glaze ware that can be definitively proven to be Elers' has ever been excavated at his factory site, except for the white voice-pipes mentioned earlier.
Taking everything into consideration—the impossibility of saying definitely who the makers of early pieces of salt glaze were; the possibility of Elers having made his salt-glaze in a different oven and on a different site to that seen and excavated; the fact that in 1710-1715 Staffordshire potters were making stoneware, and that Plot does not mention it in 1677—none but Garner and the Wedgwoods were sued for making even stoneware in 1693—we may assume that the Elers did, in actual fact, introduce the salt glaze into North Staffordshire.
Taking everything into account—the uncertainty of definitively identifying the creators of early salt glaze pieces; the possibility that Elers produced his salt glaze in a different kiln and location than the one that was uncovered; the fact that between 1710 and 1715, Staffordshire potters were creating stoneware, and that Plot didn't mention it in 1677—only Garner and the Wedgwoods were sued for making even stoneware in 1693—we can assume that the Elers actually introduced salt glaze to North Staffordshire.
The red and black bodies made by Elers are[43] still in fashion, but even more valuable than the doubtful invention of the particular ware was his careful method of refining and mixing the clay body, and the exact turning of the pieces to extreme thinness and precision of outline. On the excellence of his work, rather than on inventions which were not really new, his fame deserves to rest. He may not, for example, have been the first to introduce the method of sealing on the clay ornaments, but the ornaments themselves were for the first time in really good taste. It was this refined taste and precision of execution—and the proof that it paid financially—which taught the Staffordshire potters the most valuable lesson.
The red and black pottery made by Elers is[43] still stylish, but what's even more impressive than the uncertain invention of this specific type of pottery was his meticulous approach to refining and mixing the clay. His ability to shape the pieces to extreme thinness and precise outlines was remarkable. His reputation should be built on the quality of his work, rather than on inventions that weren't truly original. For instance, he might not have been the first to use the method of sealing on clay decorations, but those decorations were, for the first time, genuinely tasteful. It was this refined taste and precision in execution—and the evidence that it was financially successful—that taught the Staffordshire potters the most important lesson.
Thus it was that, when Queen Anne and tea drinking came in, North Staffordshire had not only the clay and the coal, but also the tradesmen to make the ware required.
Thus it was that, when Queen Anne and tea drinking became popular, North Staffordshire had not only the clay and coal but also the craftsmen to produce the necessary wares.
The successors of Elers—Robert Astbury, Joshua Twyford, and especially Dr Thomas Wedgwood—built up the reputation of the salt-glazed stoneware, which for fifty years was the glory of North Staffordshire; and, in the improvements they effected, the first two atoned for anything that to the modern mind was irregular in the manner by which they got their start.
The successors of Elers—Robert Astbury, Joshua Twyford, and especially Dr. Thomas Wedgwood—enhanced the reputation of salt-glazed stoneware, which was the pride of North Staffordshire for fifty years. In the improvements they made, the first two made up for any irregularities in the way they got their start, as seen from a modern perspective.
It was to Dr Thomas Wedgwood (1655-1717), and his son Thomas (1695-1737), who made stoneware at “Ruffleys” in Burslem, that local tradition ascribes most of the improvements in salt-glazed wares. Mr Burton writes of the younger Dr Thomas: “It has never been suggested that Dr Thomas Wedgwood, like Twyford or Astbury, learned anything directly from Elers, but as he was a man of intelligence and commercial aptitude, as well as one of the best practical potters of the day,[45] he would naturally adopt such new ideas as were brought in his way. Judging by the fragments of drab salt-glazed stonewares that have been found on the site of his old works in the centre of the town of Burslem, collectors are in the habit of attributing to him, with some show of justice, the finest pieces of this type.”[28][29]
It was Dr. Thomas Wedgwood (1655-1717) and his son Thomas (1695-1737), who produced stoneware at “Ruffleys” in Burslem, that local tradition credits with most of the advancements in salt-glazed wares. Mr. Burton mentions the younger Dr. Thomas: “It has never been suggested that Dr. Thomas Wedgwood, like Twyford or Astbury, learned anything directly from Elers, but since he was an intelligent man with business skills, as well as one of the best practical potters of his time,[45] he would naturally adopt any new ideas that came his way. Based on the fragments of drab salt-glazed stonewares discovered on the site of his former works in the center of Burslem, collectors often credit him, quite justifiably, with the finest pieces of this kind.”[28][29]
The secret of the salt-glaze process consists in firing the ware, specially composed of clay mixed with some siliceous sand or flint, to a temperature higher than ordinary earthenware will stand, and then, when red hot, shovelling common salt on to it through the top of the furnace. The salt fumes, passing through large holes in the saggars, cover the ware with a fine coat of colourless soda glaze. This glaze can always be distinguished from lead glazes by its peculiar pock-marked roughness, which indeed makes it somewhat unsuitable for plates or dishes for ordinary use; and, although for fifty years salt glaze did more than hold its own in public estimation, improvements in the old earthenware finally drove it out. By the end of the[46] eighteenth century salt glazing had ceased to be practised.
The secret of the salt-glaze process involves firing the pottery, which is made from clay mixed with some siliceous sand or flint, at a temperature higher than what regular earthenware can handle. Then, when it's red hot, common salt is shoveled onto it through the top of the furnace. The salt fumes, passing through large holes in the saggars, coat the pottery with a fine layer of colorless soda glaze. This glaze can always be recognized from lead glazes by its unique pock-marked roughness, which makes it somewhat impractical for regular plates or dishes. Although salt glaze was highly regarded for fifty years, improvements in traditional earthenware eventually led to its decline. By the end of the[46] eighteenth century, salt glazing had stopped being practiced.
Without Astbury,[30] who is said to have died in 1743, aged 65,[31] it is doubtful whether even salt glazing could have been a really great success. He it was that obtained a body white enough to show off the transparent salt glaze to the best advantage. Dr Thomas Wedgwood had only the drab body to work on—a far less effective medium.
Without Astbury,[30] who is believed to have died in 1743 at the age of 65,[31] it's questionable whether salt glazing could have achieved true success. He was the one who created a white body that showcased the transparent salt glaze perfectly. Dr. Thomas Wedgwood only had the dull body to work with—a much less effective medium.
With the object of whitening the clay body, Astbury began to import the white clays of Devonshire.[32] At first he used them only as a wash or dip to whiten the surface of the ware, just as the tin-enamel had been used to conceal and coat the coarse body of the Delft ware. Then he developed the use of the white sands of Baddeley Edge and Mow Cop to harden the body; and, in 1720, according to tradition, he made the really vital discovery of the value of calcined flint stones for both these purposes—to whiten and to harden the clay body from which the stone ware was[47] made. Josiah Wedgwood, writing in 1777, attributed this discovery to a potter of Shelton called Heath instead of to Astbury,[33] but whoever it was that first noticed the whiteness of burnt flints, it was Astbury who first determined the value of the new material and the manner of using it. This discovery marks the first stage in the production of cream-coloured earthenware as well as in the production of the perfect salt glaze.[34]
To whiten the clay body, Astbury started importing the white clays from Devonshire.[32] Initially, he only used them as a wash or dip to whiten the surface of the pottery, similar to how tin-enamel was used to cover and coat the rough body of Delft ware. He then began using the white sands from Baddeley Edge and Mow Cop to strengthen the body; and, in 1720, according to tradition, he made the crucial discovery of the importance of calcined flint stones for both whitening and hardening the clay body used for making stoneware.[47] Josiah Wedgwood, in 1777, credited this discovery to a potter from Shelton named Heath instead of Astbury,[33] but whether it was Astbury or someone else who first noticed the whiteness of burnt flints, it was Astbury who recognized the value of this new material and figured out how to use it. This discovery marks the initial phase in the production of cream-colored earthenware as well as the perfect salt glaze.[34]
Astbury and his son Thomas made red and black ware also, after the pattern of Elers, but with this difference, the ornamentation of Astbury’s red or black ware is generally done in white clay,[35] instead of in the same colour as the body; and this[48] is one sign by which collectors distinguish these two makers. Robert (or John) Astbury was succeeded by his son Thomas, who had started potting at Lane Delf in 1725. Their name does not occur among the potters of the latter half of the eighteenth century, but Margaret, Thomas Astbury’s daughter, married Robert Garner, a master potter of Longton, who attained a considerable position.
Astbury and his son Thomas also created red and black pottery in the style of Elers, but with one key difference: the decoration on Astbury’s red or black pottery is usually done in white clay instead of being the same color as the piece itself. This is one way that collectors can tell the two makers apart. Robert (or John) Astbury was followed by his son Thomas, who began potting at Lane Delf in 1725. Their names don’t appear among the potters in the latter half of the eighteenth century, but Margaret, Thomas Astbury’s daughter, married Robert Garner, a master potter from Longton, who became quite prominent.
Joshua Twyford (1640-1729), like Astbury, had his factory in Shelton; one stood on either side of the mound where the church now is. Twyford is best known for his stoneware, chiefly red and black in the style of Elers, but he is also supposed to have made salt-glazed ware.
Joshua Twyford (1640-1729), similar to Astbury, had his factory in Shelton; one was on either side of the hill where the church is now. Twyford is most famous for his stoneware, mainly red and black in the style of Elers, but he's also believed to have produced salt-glazed ware.
A particularly full account of the potters of 1710-15, especially of those in Burslem, is preserved in a document drawn up by Josiah Wedgwood in 1765. He gives both the weekly cost-account of a typical pot factory of this period; and also a list of the potters’ names and the kind of ware they produced. The document is in his own handwriting, and it appears from a letter of Wedgwood’s to Lord Auckland in 1792 that he obtained the information given in this document by “having[49] examined some of the oldest men in the pottery here, near thirty years ago, who knew personally the masters in the pottery, and very nearly the value of the goods they got up, fifty years before that.” ... “From these data,” he goes on to say, “I can pretty nearly ascertain the annual value of the goods made here at that time; which was something under £10,000 a year.”[36] He then proceeds to guess at the annual value of the trade in 1792, which he says may be between £200,000 and £300,000. I cannot help thinking that his estimate was purposely on the low side, for the manufacturers of this date always lived in fear of special taxation. In 1821 the export trade alone was worth £423,399 a year,[37] and in 1822 £489,732.
A detailed account of the potters from 1710-15, especially those in Burslem, is kept in a document created by Josiah Wedgwood in 1765. He provides both the weekly cost breakdown of a typical pottery factory from that time and a list of the potters’ names along with the types of ware they produced. The document is handwritten by him, and a letter from Wedgwood to Lord Auckland in 1792 shows that he gathered the information in this document by “having examined some of the oldest men in the pottery here, nearly thirty years ago, who personally knew the masters in the pottery and were very familiar with the value of the goods they produced, fifty years prior.” ... “From these details,” he continues, “I can pretty accurately estimate the annual value of the goods made here at that time, which was just under £10,000 a year.”[36] He then goes on to estimate the annual value of the trade in 1792, which he says could be between £200,000 and £300,000. I can’t help but think that his estimate was intentionally low, as manufacturers at that time always worried about special taxes. In 1821, the export trade alone was worth £423,399 a year,[37] and in 1822 it was £489,732.
The document runs as follows:
The document is structured as follows:
“Men necessary to make an oven of Black and Mottled, per week, and other expences—
“Men necessary to make an oven of Black and Mottled, per week, and other expenses—
“N.B.—The wear and tear, master’s profits, and some other things are rated too high. £4 per oven-full is thought to be sufficient, or more than sufficient, for the black and mottled works of the largest kind, upon an average, as the above work was a large one for those times.”
“N.B.—The wear and tear, the master’s profits, and a few other factors are valued too high. £4 per oven-full is considered adequate, or even more than adequate, for the black and mottled works of the largest kind, on average, as the aforementioned work was quite large for that period.”
“POT-WORKS IN BURSLEM ABOUT THE YEAR 1710 TO 1715.”
“Pottery Production in Burslem Around 1710 to 1715.”
Potters’ Names | Kinds of Ware | Supposed amount | Residence | ||
---|---|---|---|---|---|
£ | s. | d. | |||
Thos. Wedgwood | Black & Motled | 4 | 0 | 0 | Churchyard. |
John Cartlich | Moulded | 3 | 0 | 0 | Flash. |
(“Small”) Robt. Daniel | Black & Motled | 2 | 0 | 0 | Holehouse. |
(“Small”) Thos. Malkin | Black & Motled | 3 | 0 | 0 | Hamel. |
Richd. Malkin | Black & Motled | 2 | 10 | 0 | Knole. |
Dr Thos. Wedgwood | Brown Stone | 6 | 0 | 0 | Ruffleys. |
Wm. Simpson | ? | 3 | 0 | 0 | Stocks. |
Isa Wood | ? | 4 | 0 | 0 | Back of the “George.” |
Thos. Taylor | Moulded | 3 | 0 | 0 | Now Mrs Wedgwoods. |
Wm. Harrison | Motled | 3 | 0 | 0 | Bournes Bank.[51] |
Isaac Wood | Cloudy | 3 | 0 | 0 | Top of Robins Croft. |
John Adams[38] | Black & Motled | 2 | 10 | 0 | Brick House. |
Marsh’s | Not worked | — | Top of Daniels Croft. | ||
Moses Marsh | Stone Ware | 6 | 0 | 0 | Middle of the Town. |
Robt. Adams | Motled & Black | 2 | 10 | 0 | Next on the east side. |
Aaron Shaw | Stone & dippt white | 6 | 0 | 0 | Next on the east side. |
(“Conick”) Saml. Cartlich | Motled | 3 | 0 | 0 | Next to the South. |
Aaron Wedgwood | Motled & Black | 4 | 0 | 0 | Next to the “Red Lyon.” |
Thomas Taylor | Stone ware and Freckled | ? | Next to the North. | ||
Moses Shaw | Stone ware and Freckled | 6 | 0 | 0 | Middle of the Town. |
Thos. Wedgwood | Moulded | 2 | 10 | 0 | Middle of the Town, now Grahams. |
Isaac Ball | ? | 4 | 0 | 0 | S.W. end of the Town. |
Saml. Edge | Stone Ware | 6 | 0 | 0 | Next to the West. |
Thos. Lockett | Motled | 3 | 0 | 0 | Late Cartlichs. |
Tunstals | Not worked | 3 | 0 | 0 | Opposite. |
(“Double Rabbit”) John Simpson | ? | 3 | 0 | 0 | West end of the Town. |
Rd. Simpson | Red Dishes, &c. | 3 | 0 | 0 | The Pump, West End. |
Thos. Cartwright | Butter Pots | 2 | 0 | 0 | West end of the Town. |
Thos. Mitchel | Not worked | ? | Rotten Row (now High Street). | ||
Moses Steel | Cloudy | 3 | 0 | 0 | Rotten Row (now High Street). |
John Simpson, Chell | Motled & Black | 4 | 0 | 0 | Rotten Row (now High Street). |
J. Simpson, Castle | Red dishes & pans | 3 | 10 | 0 | Rotten Row (now High Street). |
Isaac Malkin | Motled & Black | 3 | 0 | 0 | Green Head. |
Rd. Wedgwood | Stone ware | 6 | 0 | 0 | Middle of the Town. |
John Wedgwood | Not worked | ? | Upper House.[52] | ||
Jno. or Joseph Warburton | ? | 6 | 0 | 0 | Hot lane or Cobridge. |
Hugh Mare | Motled | 3 | 0 | 0 | Hot lane or Cobridge. |
Robt. Bucknal | Motled | 4 | 0 | 0 | Hot lane or Cobridge. |
Ra. Daniel | ? | 3 | 0 | 0 | Hot lane or Cobridge. |
Bagnal | Butter Pots | 2 | 0 | 0 | Grange (i.e. Rushton Grange). |
Jno. Stevenson | Cloweded (sic.) | 3 | 0 | 0 | Sneyd Green. |
? | Clouded | 3 | 0 | 0 | Sneyd Green. |
H. Beech | Butter Pots | 2 | 0 | 0 | Holdin. |
£139 | 10 | 0 | at 46 weeks to the year, is £6,417. |
“(£6417) annual produce of the pottery in the beginning of the eighteenth century in Burslem parish. Burslem was at this time so much the principle part of the pottery that there were very few pot works anywhere else.
“(£6417) annual output of the pottery at the start of the eighteenth century in Burslem parish. At this time, Burslem was such a key area for pottery that there were very few potteries located anywhere else."
“Potters at Hanley, the beginning of the 18th centy.
“Potters at Hanley, the beginning of the 18th century.
Joseph Glass | Clowdy a sort of dishes painted with difft’ color’d slips, and sold at 3s. and 3s. 6d. a doz. |
Wm. Simpson | Clowdy and Motled. |
Hugh Mare [Mayer] | Black and Motled. |
John Mare | I'm sorry, but there doesn't appear to be any text to modernize. Please provide a short phrase of 5 words or fewer. I'm sorry, but there's no text provided for me to modernize. Please provide a specific short phrase for me to work with. |
Rd. Marsh | Motled and Black. Lamprey Pots and Venison Pots. |
John Ellis | Butter Pots &c. |
Moses Sandford | Milk Pans and Small Ware. |
“Only one horse and one mule kept at Hanley. No carts scarcely in the country. Coals carried upon men’s backs. Hanley Green like Wolstanton marsh. Only two houses (meaning potteries) at Stoke; Wards, and Poulsonson’s.”[39]
“Only one horse and one mule are kept at Hanley. There are hardly any carts in the area. Coal is carried on men’s backs. Hanley Green is like Wolstanton marsh. There are only two houses (meaning potteries) at Stoke: Wards and Poulsonson’s.”[39]
If this list is to be regarded as satisfactory evidence, and it must be remembered that it only professes to be a report of the fifty-year-old recollections of old men, then it would appear that Burslem was still the narrow home of the Potteries. It shows us the master potter of that day, employing 11 hands at wages not exceeding 6s. a week, working himself, and out of his single oven-full a week making a profit of 10s. As represented it is still a peasant industry. But the scope and range of the pottery produced has increased since Dr Plot described “the greatest pottery they have in this County.” The butter-pots; the cloudy, mottled, speckled and black; probably the red dishes and pans; these all existed in Plot’s time; but what is the “moulded” ware made by Cartlich and Thomas Taylor and by Dr Thomas Wedgwood, jun., in the middle of Burslem? The stone[54] ware too is new since Plot’s time. The five biggest factories all make this stoneware, Dr Thomas Wedgwood, sen., Moses Marsh, Aaron Shaw, Moses Shaw, Sam. Edge and Richard Wedgwood, the brother of Dr Thomas.
If we consider this list as solid evidence, we have to remember that it’s just the fifty-year-old memories of older men. It seems that Burslem was still a small part of the Potteries. It shows us the leading potter of that time, hiring 11 workers at wages no more than 6 shillings a week, working himself, and making a profit of 10 shillings from just one oven full a week. It still looks like a peasant industry. However, the variety and scope of pottery produced have expanded since Dr. Plot described “the greatest pottery in this County.” The butter pots, the cloudy, mottled, speckled, and black pieces, and probably the red dishes and pans all existed in Plot’s time. But what about the “moulded” ware created by Cartlich and Thomas Taylor and by Dr. Thomas Wedgwood, Jr., in the middle of Burslem? The stoneware is also new since Plot's time. The five largest factories all produce this stoneware: Dr. Thomas Wedgwood, Sr., Moses Marsh, Aaron Shaw, Moses Shaw, Sam Edge, and Richard Wedgwood, the brother of Dr. Thomas.
Undoubtedly this was the new salt-glazed stoneware. The brown stoneware ascribed in the list to Dr Thomas Wedgwood coincides exactly with the drab salt-glazed teapot by him now in the South Kensington Museum. It is supposed to have been made by mixing the lightest burning local clay with the fine white sand from Baddeley Edge or Mow Cop.[40]
Undoubtedly, this was the new salt-glazed stoneware. The brown stoneware listed under Dr. Thomas Wedgwood matches perfectly with the drab salt-glazed teapot he made, which is now in the South Kensington Museum. It is believed to have been created by mixing the lightest burning local clay with fine white sand from Baddeley Edge or Mow Cop.[40]
The list gives no potworks at all at the Longton end of the district, yet then or shortly afterwards Delft ware was probably made at the place called Lane Delf, now part of Fenton. Shaw says that in 1710 Thomas Heath of Lane Delf was making a strange kind of pottery, and he proceeds to describe a particular dish in such a way as to show that it was really Delft ware.[41] There is no trace of Delft ware having been made anywhere[55] else in the Potteries, or indeed at any subsequent time at Lane Delf itself, so that we may fairly ascribe to this solitary experiment of Thomas Heath’s the name of the locality.[42]
The list shows no pottery works at all at the Longton end of the district, but around that time or shortly after, Delftware was likely produced at a place called Lane Delf, now part of Fenton. Shaw notes that in 1710, Thomas Heath of Lane Delf was making a unique type of pottery, and he describes a specific dish in a way that clearly indicates it was actually Delftware. There’s no evidence of Delftware being made anywhere else in the Potteries, or even later at Lane Delf itself, so we can reasonably attribute this one experiment of Thomas Heath to the name of the locality.
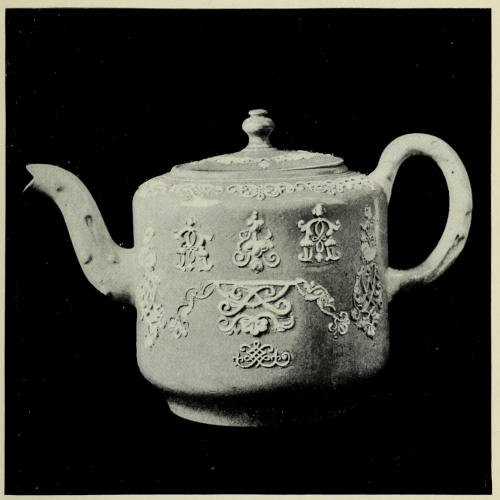
Salt glaze teapot, drab body, supposed to be by Thomas Wedgwood, died 1737. From the Stoke-on-Trent Museums.
Salt glaze teapot, dull body, believed to be by Thomas Wedgwood, died 1737. From the Stoke-on-Trent Museums.
At this Longton end, soon after 1710, there was also made white ware of a greenish type, called Crouch Ware. It was made from clay found in Derbyshire that bore this name, and survived as a fairly white ware till Astbury drove it out with his whiter body. In 1725 Thomas Astbury, the younger, set up his new factory in Fenton, and from this date we may say that the whole of the present Pottery area was engaged in the production of Earthenware.[43]
At this Longton end, shortly after 1710, they also began making a greenish type of white ware known as Crouch Ware. This was made from clay sourced from Derbyshire, which had this name, and it remained a relatively white ware until Astbury replaced it with his whiter body. In 1725, Thomas Astbury the younger established his new factory in Fenton, and from this point on, we can say that the entire current Pottery area was involved in producing Earthenware.[43]
In fact all that was wanted to convert the peasant pottery of North Staffordshire into a great business was the stimulus given by the refined hand of Elers, and the new demand in the new clubs and coffee houses. When once improvements in manufacture began, invention followed invention; and though the records during the second quarter of[56] the eighteenth century are full of entries of patents, registered for the performance of every possible and impossible pottery process, yet most of the improvements—especially the vital changes in body and glaze made by Astbury and Booth—became public property unchecked by patent law.
Actually, all that was needed to turn the peasant pottery of North Staffordshire into a thriving business was the inspiration from Elers’s skilled craftsmanship and the new demand from clubs and coffee houses. Once improvements in manufacturing started, one invention led to another; and although the records from the second quarter of[56] the eighteenth century are filled with patent registrations for every conceivable pottery process, most of the advancements—especially the crucial changes in body and glaze introduced by Astbury and Booth—became public knowledge without any restrictions from patent law.
First there was Astbury’s new white body, made with a fixed mixture of powdered flint and Devon clay, imported on horseback from the sea-port of Chester. Twenty years earlier the idea of bringing clay from Devon would have been regarded as madness, and, even in 1720, carts could not get to Burslem, and the clay must have been brought inland on pack saddles. But the invention of the calcined flint body meant also the invention of that terrible disease known as “potter’s asthma” or “potter’s rot,” which used to cause an even greater mortality than lead poisoning. When white flints were first used they were ground and powdered in the dry state, in an atmosphere of flint dust, in underground cellars, so that the secret of this valuable new preparation should not leak out.[44] This state of things was soon partially remedied,[57] for between 1726 and 1732 several patents were taken out—by Gallimore, Bourne, and finally by Benson—for grinding the flint stones in water.[45] Benson’s final process has survived to this day as the universal form of flint mill. A vertical shaft with four radiating arms revolves in a circular horizontal pan. The pan, with a hard stone bottom of chert, is filled with water, and similar chert blocks, pushed round by the arms, grind the flints down to a cream. Flint grinding became an industry, and in the well-watered valleys of North Staffordshire, wherever there was both water-power and flint, these flint mills sprung up and flourished. Though most of them are now closed down through the progress of railways and steam, there are some still to be seen working in the Moddershall valley, whence the creamy slip is sent in by water-cart to Longton.
First, there was Astbury’s new white body, made with a fixed mix of powdered flint and Devon clay, brought in on horseback from the sea port of Chester. Twenty years earlier, the idea of importing clay from Devon would have seemed crazy, and even in 1720, carts couldn’t reach Burslem, so the clay had to be brought inland on pack saddles. However, the invention of the calcined flint body also meant the emergence of that awful condition known as “potter’s asthma” or “potter’s rot,” which used to cause even more deaths than lead poisoning. When white flints were first used, they were ground and powdered in a dry state, surrounded by flint dust, in underground cellars, to keep the secret of this valuable new preparation from leaking out.[44] This situation was soon partially improved, [57] as between 1726 and 1732, several patents were issued—by Gallimore, Bourne, and finally by Benson—for grinding the flint stones in water.[45] Benson’s final process has lasted to this day as the standard design for flint mills. A vertical shaft with four extending arms rotates in a circular horizontal pan. The pan, with a hard stone bottom of chert, is filled with water, and similar chert blocks pushed around by the arms grind the flints down to a creamy consistency. Flint grinding became an industry, and in the well-watered valleys of North Staffordshire, wherever there was both water power and flint, these flint mills appeared and thrived. Although most of them have now shut down due to the advancement of railways and steam, some can still be seen operating in the Moddershall valley, from where the creamy slip is sent by water cart to Longton.
About this same time a workman named Alsager perfected the potter’s throwing wheel as we know it at this day.[46] And now that potters were using these mixed ingredients, Devon clay, ground flint syrup, and native clay in special and patented[58] proportions, the old method of evaporating the slip under the sun in an open pan had to go. It is said to have been Ralph Shaw, a most litigious personage, who began specially to mix clays in a liquid form in a fire-heated trough—locked, of course, that no neighbour might discover the “mystery.”[47] This same Ralph Shaw, of Burslem, took out a patent in 1732, professing—as was almost common form in those days—to make earthenware like Chinese Porcelain. It was to be white within, and white when required without. It was made in reality by dipping the ordinary ware in a white clay dip—just the process Astbury had invented some twenty years before. But there was this that was new to North Staffordshire; Shaw scratched away the white dip on the outside of the jug so that the blue ground became visible. He produced indeed what the mediæval Italians called “graffiato” ware, and very beautiful much of it is.[48]
Around this time, a worker named Alsager improved the potter's throwing wheel as we know it today. And now that potters were using these mixed ingredients—Devon clay, ground flint syrup, and local clay in special patented proportions—the old method of drying the slip out in the sun in an open pan had to go. It's said that Ralph Shaw, a very litigious figure, was the one who started specially mixing clays in a liquid form in a fire-heated trough—locked up, of course, so no neighbor could discover the "mystery." This same Ralph Shaw from Burslem got a patent in 1732, claiming, as was almost typical back then, that he could make earthenware like Chinese porcelain. It was supposed to be white on the inside and white on the outside when needed. In reality, it was made by dipping regular ware in a white clay dip—just like the process Astbury had invented about twenty years earlier. But what was new for North Staffordshire was that Shaw scraped away the white dip on the outside of the jug, revealing the blue base. He actually produced what the medieval Italians referred to as "graffiato" ware, and much of it is very beautiful.
Shaw, however, tried to prevent anybody using the white slip at all, and became such a nuisance to his neighbours that they united in 1736 to take[59] up the case of John Mitchell, of Burslem Hill Top, who was prosecuted by Shaw for infringing his patent.[49] Great was the rejoicing in the Potteries when the Judge at Stafford declared, or is reported to have declared:—“Gooa whomm, potters, an’ mak what soourts o’ pots yoa leykin.” “An,” says our narrator, “when they coom ’nto’ Boslum, aw th’ bells i’ Hoositon (Wolstanton), and Stoke, and th’ tahin, wurn ringin’ loike hey go’ mad, aw th’ dey.” Ralph Shaw is said to have been so disgusted at the result that he emigrated to Paris, where he made pots for many years.[50]
Shaw, however, tried to stop anyone from using the white slip altogether and became such a nuisance to his neighbors that they banded together in 1736 to take up the case of John Mitchell, from Burslem Hill Top, who was prosecuted by Shaw for infringing on his patent.[59] There was great celebration in the Potteries when the Judge at Stafford declared, or is reported to have declared:—“Go on, potters, and make whatever kind of pots you like.” “And,” says our narrator, “when they came into Burslem, all the bells in Hoositon (Wolstanton) and Stoke, and the town, were ringing like crazy all day.” Ralph Shaw is said to have been so disgusted by the outcome that he moved to Paris, where he made pots for many years.<[50]>
Ralph Shaw’s ware was known as “bit-stone ware.” The “bit-stones” were put between two pieces of ware when they were fired in the saggars in order to keep them from sticking to each other. They were the more necessary in that Shaw’s ware was dipped in a light slip. The “bit-stones” have long since been replaced by “spurs” and “stilts” and other small earthenware objects, the special manufacture of which is now a great industry by itself. The single stilt and spur factory of Thos.[60] Arrowsmith in Burslem employs now 230 hands on this manufacture alone.
Ralph Shaw’s pottery was called “bit-stone ware.” The “bit-stones” were placed between two pieces of pottery when they were fired in the saggars to prevent them from sticking together. They were especially important because Shaw’s pottery was dipped in a light slip. The “bit-stones” have long been replaced by “spurs,” “stilts,” and other small earthenware items, which have become a significant industry on their own. The single stilt and spur factory of Thos.[60] Arrowsmith in Burslem now employs 230 workers just for this production.

Burslem in 1750
Burslem in 1750
Scale 100 yards to the inch
Scale 100 yards to the inch
Based on a plan by Enoch Wood
Based on a plan by Enoch Wood
If the old potters had had to rely only on the thrower’s wheel for their shapes, no improvement in whiteness of ware, or in the salt glaze, would have availed much to increase the demand for earthenware. The development of the various use of moulds became of the greatest importance. The six workmen required at such a potworks, as is shown on the 1710 list, would be—slipmaker, thrower, turner, “stouker,” to put on handles and spouts, fireman and warehouseman. A good workman, such as the master, could throw, turn and stouk. But the fresh developments of the salt-glazed stoneware arising from the use of moulds converted potting into a specialized industry.
If the old potters had only relied on the potter's wheel for their shapes, improvements in the whiteness of the clay or in the salt glaze wouldn't have done much to boost the demand for earthenware. The development of various uses of molds became extremely important. The six workers needed at such a pottery, as shown on the 1710 list, would include a slip maker, thrower, turner, "stouker" (who adds handles and spouts), fireman, and warehouseman. A skilled worker, like the master, could throw, turn, and stouk. However, the new developments in salt-glazed stoneware that came from using molds turned pottery into a specialized industry.
We have seen that Elers used metal seals to press his ornamental “spriggs” on to his teapots. Such metal moulds could only be used for small articles or ornaments, for the mould stuck to the clay, and had to be carefully oiled. Both for the “sprigging on” of ornaments, and for the shaping of ware, a new form of mould was wanted. At first the alabaster of Derbyshire supplied the want. It was[61] carved into shaped blocks, and from the blocks were made “pitcher,” or porous clay moulds, which could be replaced when worn out from the blocks, and could be used in various ways for the manufacture of ware: for sprigging, pressing, or “casting.” Then—a last step—about 1745, Ralph Daniel, of Cobridge, brought from France the secret of plaster of Paris moulds which replaced both pitcher and alabaster.[51]
We’ve seen that Elers used metal seals to imprint his decorative “spriggs” onto his teapots. These metal molds could only be used for small items or decorations, as the mold would stick to the clay and needed to be carefully oiled. For both applying ornaments and shaping the pottery, a new type of mold was necessary. Initially, Derbyshire alabaster fulfilled this need. It was carved into shaped blocks, from which “pitcher” or porous clay molds were made. These molds could be replaced when worn out and could be used in various ways for producing pottery: for sprigging, pressing, or “casting.” Then—a final development—around 1745, Ralph Daniel from Cobridge brought back the secret of plaster of Paris molds from France, which replaced both pitcher and alabaster.
Under competition, the Staffordshire potters were getting critical. The white salt-glazed ware was competing with Chinese porcelain, and had to be made as thin and light and transparent as possible. The ware made by pressing the clay into the moulds sufficed for plates, basins and any lead-glazed ware, but it came out much too heavy for complicated shapes such as sauce-boats, teapots and vases, etc. To get these shapes Elers would have had them thrown and turned down in the lathe: they would all have been round. The process known as “casting” in a mould produced a finer result, and gave infinite scope for variation. In casting, the clay is run in a liquid form into[62] a porous mould. After standing a few minutes, the slip is run out again, leaving behind a clay shell. This “cast” shell, taken out when dry, may be as fine and as varied in shape as the skill of the potter and the heat of his furnace will permit.
Under competition, the Staffordshire potters were becoming critical. The white salt-glazed ware was competing with Chinese porcelain and needed to be made as thin, light, and transparent as possible. The ware created by pressing clay into molds was fine for plates, basins, and any lead-glazed items, but it turned out too heavy for intricate shapes like sauce boats, teapots, and vases. To create these shapes, Elers would have had them thrown and turned on the lathe: they would all have been round. The process known as “casting” in a mold produced a finer result and allowed for endless variations. In casting, the clay is poured in liquid form into[62] a porous mold. After standing for a few minutes, the slip is poured out again, leaving behind a clay shell. This “cast” shell, removed once dry, can be as fine and varied in shape as the potter’s skill and his furnace’s heat allow.
The process of casting came into use about 1730, and the carving of these moulds (in alabaster first, from which the “pitcher” mould could be made), became the most critical operation of all the potter’s work. This work required all the skill and artistic instinct of the carver and of the designer. Block-cutters, as they were called, became famous. The best known were the two brothers, Aaron and Ralph Wood of Burslem. Aaron Wood (1717-85) was bound apprentice in 1731 to Dr Thomas Wedgwood, some of whose best models he is supposed to have made.[52] He afterwards worked for J. Mitchell, of Burslem,[53] and for Wheildon of Fenton, acquiring such a reputation that he was allowed to work in a locked room, that his art might thereby be kept secret.
The process of casting started around 1730, and carving these molds (first in alabaster, from which the “pitcher” mold could be created) became the most important part of the potter’s work. This task required all the skill and artistic talent of the carver and the designer. The block-cutters, as they were known, became quite famous. The most well-known were the two brothers, Aaron and Ralph Wood from Burslem. Aaron Wood (1717-85) became an apprentice in 1731 to Dr. Thomas Wedgwood, and he is believed to have created some of his best models.[52] He later worked for J. Mitchell of Burslem,[53] and for Wheildon of Fenton, gaining such a reputation that he was allowed to work in a locked room to keep his art a secret.
The industry was entering on a new phase. The introduction of moulds had required specialized block-cutters, flat and hollow-ware pressers and casters. And the specializing in the mixtures of the clay body lead to further changes. Till 1740 the same clay body served for both salt glaze and lead glaze, but about this time manufacturers began to specialize in either salt or lead glaze, and to use different bodies and mixtures to suit the varied glazes.
The industry was entering a new phase. The introduction of molds required specialized block cutters, flat and hollow-ware pressers, and casters. Specializing in the mixtures of the clay body led to further changes. Until 1740, the same clay body was used for both salt glaze and lead glaze, but around this time, manufacturers began to specialize in either salt or lead glaze, using different bodies and mixtures to match the various glazes.
And, just as they had to arrange to import clays, so they had also to arrange to export their wares. A London agent, a Liverpool agent, perhaps a Birmingham agent became necessary. This sort of business could no longer be carried on by a master potter on sixteen shillings a week. The master potter became a capitalist. No business could be successfully carried on with a turnover of one ovenful a week. The first attempt to increase the[64] output was made by either one Shrigley, of Burslem Hadderidge,[54] or by John Mitchell of the Hill Top.[55] As no potter, so goes the story, had ever had more than one oven, their inventive faculty went no farther than to construct a larger oven than usual. The pioneer, whoever he was, built a new one so large that it collapsed, to the great joy of his conservative rivals. Soon afterwards, however, the Baddeleys, said to have been the sons of a Moddershall flint-grinder, put up behind their factory at Shelton a row of no fewer than four ovens; and about 1743, Thomas and John Wedgwood, known as “of the Big House,” built a tiled factory with five ovens.[56]
And just as they had to figure out how to import clays, they also needed to arrange for exporting their products. They needed an agent in London, Liverpool, or maybe Birmingham. This kind of business couldn’t be run by a master potter earning sixteen shillings a week anymore. The master potter turned into a capitalist. No business could thrive with only one oven's worth of output each week. The first attempt to boost production was made by either Shrigley from Burslem Hadderidge or John Mitchell from the Hill Top. The story goes that no potter had ever operated more than one oven, so their innovative ideas only led them to build a larger oven than usual. The first innovator, whoever he was, built one so big that it collapsed, much to the delight of his traditional competitors. Soon after, however, the Baddeleys, believed to be the sons of a flint-grinder from Moddershall, constructed a row of at least four ovens behind their factory in Shelton; and around 1743, Thomas and John Wedgwood, known as “of the Big House,” built a tiled factory with five ovens.
The family of Baddeley continued as master potters in Shelton into the nineteenth century. They were, with the exception of Wedgwood and possibly Warburton, the largest exporters of earthenware of their day.[57] Their cream colour was good, but their renown with later generations is due to their basket-pattern salt glaze, often perforated. John Baddeley died in 1772, but the[65] family carried on the making of enamelled and plain salt glaze to a later date than other manufacturers, certainly after 1780, and good salt glaze of late date is usually ascribed to the Baddeleys of Shelton.[58] The Wedgwoods of the Big House made the white salt glaze of a somewhat earlier description—the cast hexagonal cups and teapots in plain white—and with such financial success, that they built for themselves in 1750 a “Big House” in Burslem, which stands to this day at the corner of the Market Place looking south down the new Waterloo Road.[59] It is now the Conservative Club. Thomas was an expert thrower to begin with, and John the best oven fireman in the town.[60] They retired from business in 1765 with a large fortune.
The Baddeley family continued as master potters in Shelton into the 1800s. Aside from Wedgwood and possibly Warburton, they were the biggest exporters of earthenware in their time.[57] Their cream color was good, but their lasting fame comes from their basket-pattern salt glaze, often with holes. John Baddeley passed away in 1772, but the[65] family continued producing both enamelled and plain salt glaze longer than other manufacturers, definitely after 1780, and quality late salt glaze is typically associated with the Baddeleys of Shelton.[58] The Wedgwoods of the Big House created white salt glaze of an earlier type—the cast hexagonal cups and teapots in plain white—and achieved such financial success that they built a “Big House” in Burslem in 1750, which still stands today at the corner of the Market Place, looking south down the new Waterloo Road.[59] It is now the Conservative Club. Thomas was a skilled thrower from the start, and John was the best oven fireman in town.[60] They retired from business in 1765 with a significant fortune.
It is said that in 1750 no fewer than sixty factories were making salt glaze in the Potteries, and every Saturday, for five hours at the time of firing up, the whole country was black with the smoke of the burning salt—so black, it is said, that people groped their way through the streets of[66] Burslem. But meanwhile Enoch Booth at Tunstall had invented the fluid lead-glaze destined in time to turn plain earthenware into “cream-colour”; Josiah Wedgwood at Burslem was already devising new mixtures which should convert “cream-colour” into “Queen’s Ware”; and in Hot Lane, near by, John Warburton was starting that enamelling work which, applied to the Queen’s Ware, was to make it the standard earthenware of the whole world. These three potters were to alter entirely the course of the industry, and make salt glaze a thing of the past, for museums and collections. Unfortunately they did not abolish the smoke.
It's said that in 1750, at least sixty factories were producing salt glaze in the Potteries. Every Saturday, during the five hours of firing up, the entire country was shrouded in smoke from the burning salt—so thick that people had to feel their way through the streets of[a id="Page_66">Burslem. Meanwhile, Enoch Booth in Tunstall had invented the fluid lead-glaze that would eventually transform plain earthenware into “cream-color”; Josiah Wedgwood in Burslem was already creating new mixtures to turn “cream-color” into “Queen’s Ware”; and nearby in Hot Lane, John Warburton was launching an enameling process that, applied to the Queen’s Ware, would establish it as the standard earthenware throughout the world. These three potters were set to completely change the trajectory of the industry and render salt glaze a thing of the past, relegated to museums and collections. Sadly, they didn’t eliminate the smoke.
Enoch Booth had married Ann, daughter of Thomas Child of Tunstall. It was on his father-in-law’s land that, about 1745, he started the first considerable earthenware factory in Tunstall. Booth was the legitimate successor of Astbury. He took the earthenware body, white as Astbury had left it, and, instead of using it for salt glaze, he worked out the most suitable lead glaze, and the best way of applying it to the piece. Instead of dusting it over the ware in the dangerous dry[67] condition, he ground the lead ore up with flint and clay and water. Into this fluid glaze the ware was dipped. Not only did this give a uniform glossy coat on each piece of ware, but different pieces were all glazed alike. Booth had the ware dipped after it had been fired, while it was in the porous or “biscuit” condition but sufficiently firm to be handled. A second firing to fuse on the glaze was given to the ware after dipping. These two firings, in the biscuit oven and in the “glost” oven, are the ordinary processes of manufacture to this day. Shaw gives 1750 as the date of this important improvement;[61] it is possible that fluid glazes were used before this and by others, but it was the combination of fluid glaze and double firing that is important, and this with some certainty we may put down to Enoch Booth and the year 1750.
Enoch Booth married Ann, the daughter of Thomas Child from Tunstall. Around 1745, he started the first significant earthenware factory on his father-in-law’s land in Tunstall. Booth was the rightful successor of Astbury. He took the earthenware body, which was white as Astbury had left it, and instead of using it for salt glaze, he developed the most effective lead glaze and the best method of applying it to the pieces. Rather than dusting it onto the ware in the hazardous dry form, he mixed lead ore with flint, clay, and water. The ware was dipped into this liquid glaze. This method not only provided a uniform glossy coating on each piece but also ensured all pieces were glazed the same. Booth dipped the ware after it had been fired, while it was still in the porous or “biscuit” state but firm enough to handle. A second firing was done to fuse the glaze onto the ware after dipping. These two firings, in the biscuit oven and in the “glost” oven, are standard manufacturing processes even today. Shaw notes 1750 as the date of this crucial improvement; while it's possible that fluid glazes were used earlier by others, it was the combination of fluid glaze and double firing that matters, and we can confidently attribute this to Enoch Booth in the year 1750.
Booth’s original factory at Tunstall was probably the “Old Bank” at the corner of Cross Street and Well Street, but he extended his works at an early date over the whole of the area now bounded by Well Street, Market Square, High Street and Calver Street, where he built the Phœnix Works.[68] Sometime before 1781[62] he had been succeeded by Anthony Keeling who had married his daughter Ann. Anthony Keeling built Calver House in 1793, but his trade suffered in the French wars, and in 1810 he retired from business and went to Liverpool where he died in 1816.[63] The Phœnix Works were carried on by Thomas Goodfellow till they were pulled down about 1860.
Booth’s original factory in Tunstall was likely the “Old Bank” located at the corner of Cross Street and Well Street, but he expanded his operations early on across the entire area now defined by Well Street, Market Square, High Street, and Calver Street, where he constructed the Phœnix Works.[68] Before 1781[62], he was succeeded by Anthony Keeling, who had married his daughter Ann. Anthony Keeling built Calver House in 1793, but his business struggled during the French wars, and in 1810 he retired from business and moved to Liverpool, where he passed away in 1816.[63] The Phœnix Works were operated by Thomas Goodfellow until they were demolished around 1860.
Ware, besides being thrown, moulded or cast, and coated with the transparent glaze of salt or lead, requires decoration. This decoration could be given by coloured clay slips, after the manner of the old Toft dishes, or after the manner of Ralph Shaw’s “graffiato” ware, or as what is called “scratched blue.” But decoration could also be given by means of enamelling paints. Paints that is which are mixed with glass, and, on being heated, fuse into the glaze and become fast. This enamelling was in the early days a special trade and no part of the potter’s business. The shopkeeper might, if he liked, employ somebody called an enameller to enamel his particular cups and saucers. The enameller used a small “muffle”[69] stove where the ware could be heated sufficiently to fuse the glaze and paint together, while at the same time it was kept away from direct contact with flames or smoke.
Ware, besides being thrown, molded, or cast, and coated with a clear glaze of salt or lead, also needs decoration. This decoration could come from colored clay slips, similar to the old Toft dishes, or like Ralph Shaw’s “graffiato” ware, or what’s known as “scratched blue.” Decoration could also be added using enameling paints, which are mixed with glass and, when heated, fuse into the glaze and become permanent. In the early days, enameling was a separate trade and not part of the potter’s work. A shopkeeper could hire someone called an enameler to decorate their specific cups and saucers. The enameler used a small “muffle” stove where the ware could be heated enough to fuse the glaze and paint together while keeping it away from direct flames or smoke.

Scratched blue salt glaze cup, dated 1750. From the Stoke-on-Trent Museums.
Scratched blue salt glaze cup, dated 1750. From the Stoke-on-Trent Museums.
The best enamellers were to be found in London, engaged in enamelling the porcelain of Bow and Chelsea; but it soon became obvious that enamellers were wanted in the Staffordshire potteries also. It was again two Dutchmen who initiated into this art the native potters of Staffordshire. They probably knew the Warburtons and set up their enamelling ovens near them in Hot Lane.[64] Here they worked and attempted to keep their art secret, with the usual result of attracting special attention. Their stoves, their mixtures and their temperatures soon became public property, and a regular enamelling industry was soon established round Hot Lane. It is said to have been Ralph Daniel, the man who had brought the secret of plaster of Paris moulds from Paris, who did most to develop enamelling.[65] He imported workmen from London, Bristol and Liverpool, and soon after 1750 the enamelling of earthenware and[70] salt glaze became a Staffordshire industry. Among enamellers too should be mentioned a Shelton potter, Walter Edwards, who was chemist and enameller as well as potter. He had as partner the Rev. John Middleton, curate of Hanley from 1737-1802, but Edwards, unlike the curate, died young in 1753, leaving a book full of receipts for glazes and enamels. The difficulty always was to get metallic oxides which would stand heat.
The best enamellers were found in London, working on the porcelain from Bow and Chelsea. However, it quickly became clear that the Staffordshire potteries also needed enamellers. It was once again two Dutchmen who introduced this craft to the local potters in Staffordshire. They likely knew the Warburtons and set up their enamelling ovens nearby on Hot Lane. Here, they worked and tried to keep their techniques secret, but as typically happens, this attracted a lot of attention. Their stoves, mixtures, and temperature methods soon became common knowledge, and a thriving enamelling industry quickly developed around Hot Lane. Ralph Daniel, the person who had brought the secret of plaster of Paris molds from Paris, is said to have played a major role in advancing enamelling. He brought in workers from London, Bristol, and Liverpool, and shortly after 1750, the enamelling of earthenware and salt glaze became a Staffordshire industry. It's also important to mention a potter from Shelton, Walter Edwards, who was both a chemist and enameller as well as a potter. He had a partner in the Rev. John Middleton, who was the curate of Hanley from 1737-1802, but Edwards, unlike the curate, died young in 1753, leaving behind a book full of recipes for glazes and enamels. The ongoing challenge was always obtaining metallic oxides that could withstand heat.
From an artistic point of view they had much better have left their salt glaze plain white, or drab, or uniformly tinted by a slip dip. The salt-glaze body compared with Chinese porcelain; their painting did not compare with Chinese painting, or only compared in an unfortunate sense for Staffordshire. Earthenware, being made for use, had less decoration, and what it got was less gaudy and more suited for serviceable articles.
From an artistic perspective, it would have been better for them to keep their salt glaze plain white, drab, or consistently colored with a slip dip. The salt-glaze body was nothing like Chinese porcelain; their painting didn’t measure up to Chinese painting, and in comparison, it reflected poorly on Staffordshire. Earthenware, made for practical use, featured less decoration, and what it did have was less flashy and more appropriate for functional items.
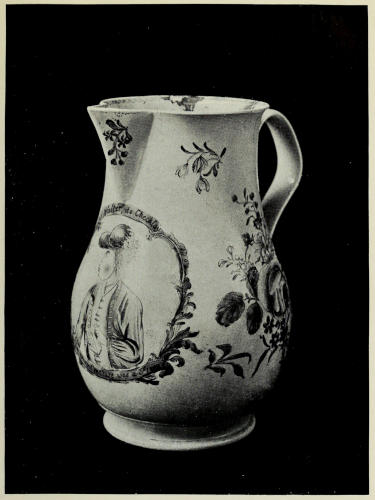
Enamelled salt glaze jug, probably by Baddeley of Shelton, dated 1760. From the Stoke-on-Trent Museums. The jug was a presentation piece from the Rev. J. Middleton, who was a partner with the above Baddeley.
Enamelled salt glaze jug, likely by Baddeley of Shelton, dated 1760. From the Stoke-on-Trent Museums. The jug was a gift from Rev. J. Middleton, who was a partner with Baddeley.
There was however one very successful, or at least artistically successful, manner of colouring the salt glaze. It was practised by William Littler and Aaron Wedgwood (1717-1763), two brothers-in-law who about 1740 were making salt-glaze pottery at Brownhills. Taking a hint from Astbury,[71] they dipped their ware in a bath of carefully lawned slip, so as to gave it a smooth surface before firing. In this slip they proceeded to put cobalt, which gave a beautiful uniform blue to the whole piece, and this smooth blue body, under the salt glaze, acquired a tint of great brilliance. On the strength of Shaw’s account of this process,[66] many writers have mistakenly attributed to William Littler and Aaron Wedgwood the first introduction of liquid glazes, but it is quite clear, as Mr Burton has pointed out, that this was no leaded blue glaze, but a blue slip subsequently glazed with salt.[67]
There was, however, one very successful, or at least artistically successful, way of coloring the salt glaze. It was used by William Littler and Aaron Wedgwood (1717-1763), two brothers-in-law who, around 1740, were making salt-glaze pottery at Brownhills. Taking a cue from Astbury,[71] they dipped their pieces in a bath of carefully prepared slip to give it a smooth surface before firing. In this slip, they added cobalt, which gave a beautiful uniform blue to the entire piece, and this smooth blue body, under the salt glaze, acquired a vivid brilliance. Based on Shaw’s account of this process, many writers have mistakenly credited William Littler and Aaron Wedgwood with the first introduction of liquid glazes, but it is clear, as Mr. Burton has pointed out, that this was not a leaded blue glaze, but a blue slip that was later glazed with salt.[66] [67]
Their success with the salt glaze induced Littler and Wedgwood to make the first attempt to produce real porcelain in Staffordshire. The proper distinction between earthenware and porcelain is the complete vitrification of the body in the case of porcelain, as opposed to the vitrifying and glazing of the surface only in the case of earthenware.
Their success with the salt glaze encouraged Littler and Wedgwood to make the first attempt to produce real porcelain in Staffordshire. The key difference between earthenware and porcelain is that porcelain is fully vitrified throughout, while earthenware is only vitrified and glazed on the surface.
The Bow porcelain factory had started in 1744, Chelsea in 1745, Worcester in 1751. In 1752[72] Littler and Wedgwood left their Brownhills factory and removed to Longton Hall. Here they began to make the well-known Longton Hall porcelain. Perhaps Wedgwood or Littler had worked at Chelsea. However that may be, the porcelain manufactured was of the Chelsea type. The body was largely made of ground glass, while china clay, the basis of true porcelain, was not used at all. The characteristic feature of this Longton Hall porcelain is the bright under-glaze blue that previously adorned Littler’s salt-glaze ware. This Longton Hall factory only continued till 1758.[68] Owing to the lack of demand for this kind of ware, they lost all their money in the venture and finally discontinued it. The stock-in-trade is said to have been bought up by Duesbury, who transferred it to the Derby porcelain factory, started in 1756.[69] It was not till the discovery of China Clay and China Stone and of their fusing properties in 1768 that porcelain was again attempted in Staffordshire. Through his daughter[73] Ann this Aaron Wedgwood was the grandfather of William Clowes, known as the “founder” of Primitive Methodism.
The Bow porcelain factory started in 1744, Chelsea in 1745, and Worcester in 1751. In 1752[72] Littler and Wedgwood left their Brownhills factory and moved to Longton Hall. There, they began producing the well-known Longton Hall porcelain. It's possible that either Wedgwood or Littler had experience at Chelsea. Regardless, the porcelain they created was similar to the Chelsea style. The body was mainly made of ground glass, and they didn’t use china clay, which is essential for true porcelain. The standout feature of this Longton Hall porcelain is the bright under-glaze blue that previously decorated Littler’s salt-glaze ware. The Longton Hall factory only operated until 1758.[68] Due to low demand for this type of ware, they lost all their investment in the business and eventually shut it down. The inventory is said to have been purchased by Duesbury, who moved it to the Derby porcelain factory, which was started in 1756.[69] It wasn't until the discovery of China Clay and China Stone and their fusing properties in 1768 that porcelain was attempted again in Staffordshire. Through his daughter[73] Ann, Aaron Wedgwood became the grandfather of William Clowes, known as the “founder” of Primitive Methodism.
While the manufacture of salt glaze was flourishing, more especially at the northern end of the district, the old soft-fired earthenware, mottled, black and cloudy, was still being made, and the old slip decorated ware had not entirely vanished. But the only famous potter in what might be called the old Staffordshire style was Thomas Whieldon.
While the production of salt glaze was thriving, especially in the northern part of the area, the traditional soft-fired earthenware, which was mottled, black, and cloudy, was still being produced, and the old slip-decorated pottery hadn't completely disappeared. However, the only well-known potter in what could be described as the classic Staffordshire style was Thomas Whieldon.
Thomas Whieldon began making pots at Little Fenton about 1740. He was a better educated class of man than the ordinary potter. He potted well; enjoyed trials and experiments for their own sake; and, through his connection with both Wedgwood and Spode, he may be said to have had the same influence on the taste and education of the Staffordshire potters that Elers had unintentionally half a century before. If we are to believe Shaw, writing in 1828, he began in a very humble way. He says: “In 1740 Mr Thomas Whieldon’s manufactory at Little Fenton consisted of a small range of low buildings, all thatched. His early productions[74] were knife hafts for the Sheffield cuttlers; and snuffboxes for the Birmingham hardwaremen, to finish with hoops, hinges and springs; which he himself usually carried in a basket to the tradesmen; and being much like agate they were greatly in request.”[70]
Thomas Whieldon started making pottery at Little Fenton around 1740. He was more educated than the average potter. He crafted well, enjoyed experimenting just for the fun of it, and through his connections with both Wedgwood and Spode, he influenced the style and training of Staffordshire potters in a way similar to what Elers did unintentionally fifty years earlier. According to Shaw, writing in 1828, Whieldon began very modestly. He notes: “In 1740, Mr. Thomas Whieldon’s workshop at Little Fenton consisted of a small group of low buildings, all thatched. His early products[74] included knife handles for the Sheffield cutlers and snuffboxes for the Birmingham hardware dealers, which he finished with hoops, hinges, and springs. He usually carried these to the tradesmen in a basket, and since they resembled agate, they were in high demand.”[70]
Plot mentions how the old potters used to marble their ware by combing together the different coloured slips, just as the paper on the inside of book-bindings is now marbled. Whieldon carried on this imitation work, and made it artistic and important. Instead, however, of marbling the slip or the glaze, he marbled his clay body in the solid. Flat “bats” of clay of different colours—coloured either naturally or else artificially with manganese, cobalt or copper—were laid on each other, and pressed and sliced again and again; care being taken to preserve the same run of the grain. In this way a streaked body was produced, which, when pressed into moulds, retained the curious markings of agate or marble. This was Whieldon’s “solid agate,” with which the new trade in snuff boxes and knife handles was supplied.[71]
Plot mentions how old potters used to marble their pieces by mixing different colored slips, similar to how bookbinding paper is marbled today. Whieldon continued this practice, making it both artistic and significant. Rather than marbling the slip or glaze, he marbled the clay body itself. Flat “bats” of clay in various colors—either naturally or artificially colored with manganese, cobalt, or copper—were stacked on top of each other, pressed, and sliced repeatedly; care was taken to keep the grain consistent. This created a streaked body that, when pressed into molds, showcased unique markings resembling agate or marble. This was Whieldon’s “solid agate,” which supplied the emerging market for snuff boxes and knife handles. [71]
He made toys, too, and chimney ornaments of this same new material, or else glazed with brilliant coloured glazes in splashes of irregular colour. He made larger goods also—teapots, dishes and vases in solid agate. All these were pressed in moulds; and for moulder or block-cutter he had, from about 1746 onwards, the celebrated Aaron Wood. The cream-coloured body, with Enoch Booth’s transparent lead glaze, afforded Whieldon another material on which to work. He took the colourless fluid glaze and turned it madder brown with manganese, or yellow with iron oxide, or green with copper, or blue with cobalt. Then he mixed them to give every shade of coloured glaze, and laid these glazes on the ware to give infinite variety. In this way he produced those beautiful tortoiseshell wares for which he is most renowned. His agate ware is solid; his tortoiseshell ware is a glaze.[72]
He also made toys and chimney decorations out of this same new material, or else coated them with vibrant glazes in random splashes of color. He created larger items too—teapots, dishes, and vases in solid agate. All these were pressed in molds; and from around 1746 onwards, he employed the famous Aaron Wood as his molder or block-cutter. The cream-colored body, with Enoch Booth’s clear lead glaze, offered Whieldon another material to work with. He took the clear fluid glaze and turned it madder brown with manganese, or yellow with iron oxide, or green with copper, or blue with cobalt. Then he mixed them to create every shade of colored glaze and applied these glazes to the wares to achieve endless variety. This is how he produced those stunning tortoiseshell wares for which he is most famous. His agate ware is solid; his tortoiseshell ware is glazed.[72]
He had acquired fame as a skilful potter before Josiah Wedgwood joined him in 1754, and probably produced already both the solid agate and the tortoiseshell. In his last popular production—the[76] melon, cauliflower, and pineapple wares, with their brilliant green glaze—it is probable that Wedgwood’s incessant experiments played a decisive part.
He had gained fame as a skilled potter before Josiah Wedgwood joined him in 1754, and he likely already produced both the solid agate and the tortoiseshell. In his last popular creation—the[76] melon, cauliflower, and pineapple wares, with their bright green glaze—it’s likely that Wedgwood’s constant experimentation had a significant impact.
Besides having Wedgwood as a partner, he had in his employ such examples of the new race of potters as Josiah Spode, Robert Garner, J. Barker, and Wm. Greatbach. Jewitt[73] has preserved for us some of the hiring books and accounts of Thomas Whieldon, in which the names and pay of three of these four apprentices occur, and which, as they are unique evidence of wages, are here given:
Besides having Wedgwood as a partner, he employed some of the new generation of potters like Josiah Spode, Robert Garner, J. Barker, and Wm. Greatbach. Jewitt[73] has preserved some of the hiring books and accounts of Thomas Whieldon, which include the names and pay of three of these four apprentices. These records are unique evidence of wages and are presented here:
1749 | |||||
---|---|---|---|---|---|
Jany | 27 | Hired Jno Austin for placeing white &c. per week | 5 | 6 | |
Pd his whole earnest[74] | 3 | 0 | |||
Feby | 14 | Then hired Thos. Dutton | 6 | 6 | |
Pd 1 pr Stockings | 3 | 6 | |||
Earnest for vineing (? veining) | 15 | 0 | |||
Feby | 20 | Hired Wm. Cope for handleing and vineing cast ware | 7 | 0 | |
Pd his whole earnest | 10 | 6 | |||
28 | Hird Robt. Garner per week | 6 | 6[77] | ||
Earnest | 10 | 6 | |||
Pd him towards it | 1 | 0 | |||
I am to make his earnest about 5s. more in something.[75] | |||||
Mar | 8 | Then hired Jno Barker for ye huvels (ovens) @ | 5 | 6 | |
Pd earnest in part | 1 | 0 | |||
Pd it to pay more | 1 | 0 | |||
Ap. | 9 | Hired Siah Spoade, to give him from this time to Martelmas next 2s. 3d., or 2s. 6d. if he deserves it | |||
2nd year | 2 | 9 | |||
3rd year | 3 | 3 | |||
Pd full earnest | 1 | 0 | |||
June | 2 | Hired a boy of Ann Blowers for treading ye lathe, @ | 2 | 0 | |
Pd earnest | 6 | ||||
1751 | |||||
Jany | 11 | Then hired Saml. Jackson for Throwing Sagers and fireing, per week | 8 | 0 | |
Whole earnest | 2 | 2 | 0 | ||
Pd in part | 1 | 2 | 0 | ||
Pd more [sic] | 1 | 1 | 0 | ||
1752 | |||||
Febry | 22 | Hired Josiah Spoad for next Martlemas, per week | 7 | 0 | |
I am to give him earn’ | 5 | 0 | |||
Pd in part | 1 | 0 | |||
Pd do. | 4 | 0 | |||
1753 | |||||
June | 21 | Hired Wm. Marsh for 3 years. He is to have 10s. 6d. earnest each year, and 7s. per week. I am to give an old coat or something abt 5s. value. | [78] | ||
Aug. | 29 | Hired Westaby’s 3 children, per week | 4 | 0 | |
Pd earnest | 6 | ||||
1754 | |||||
Feby | 25 | Hired Siah Spode per week | 7 | 6 | |
Earnest | 1 | 11 | 6 | ||
Pd in part | 16 | 0 |
Apparently workmen were hired by the year,[76] and the highest wages paid were 8s. a week. It will be seen that there has been practically no increase in wages since the early days of the century. One wonders where Wedgwood and Spode obtained the capital wherewith to start their businesses.
Apparently, workers were hired on an annual basis, [76] and the highest wages paid were 8 shillings a week. It's clear that there has been almost no increase in wages since the early days of the century. One wonders where Wedgwood and Spode found the capital to start their businesses.
Josiah Wedgwood was Whieldon’s partner from 1754 to 1759. One of the stipulations of the partnership is said to have been that Wedgwood might keep his experiments to himself. It is certain that he did experiment extensively, and we may attribute to him the green glaze and successful patterns of the “cauliflower” and “pineapple” wares.[77] It would be a mistake to depreciate these patterns as[79] being unsuitable and vulgar imitations of nature. The natural shapes were adapted and conventionalized in a thoroughly artistic way, as anyone who looks at Whieldon’s or Wedgwood’s samples of this ware preserved in the South Kensington Museum can see at a glance. Slavish imitations there were later, but that was not Whieldon’s way.
Josiah Wedgwood was Whieldon’s partner from 1754 to 1759. One of the conditions of the partnership was that Wedgwood could keep his experiments private. It’s clear that he did experiment a lot, and we can credit him with the green glaze and successful designs of the “cauliflower” and “pineapple” wares.[77] It would be a mistake to dismiss these designs as unsuitable and cheap copies of nature. The natural shapes were adapted and stylized in a genuinely artistic manner, as anyone who looks at Whieldon’s or Wedgwood’s pieces of this ware preserved in the South Kensington Museum can easily see. There were indeed later slavish imitations, but that wasn’t Whieldon’s style.

Staffordshire figures decorated with Whieldon glaze, probably by Wedgwood. c. 1760. Stoke-on-Trent Museums.
Staffordshire figures decorated with Whieldon glaze, probably by Wedgwood. c. 1760. Stoke-on-Trent Museums.
Taste changed, however, and Whieldon’s wares became unfashionable. It is only of quite recent years that the agate and marble, perfected later by Wedgwood, or the quaint cottage chimney ornaments and tortoiseshell ware of Whieldon, Wedgwood and Ralph Wood, have come to be valued as a native and genuine Staffordshire art. When Whieldon found that his market had left him he made no attempt to follow in the wake of his pupils, and about 1780 retired from business. His factory was just south of the present railway station at Stoke, and he built and lived in the house which still looks down upon the Trent and the railway. In 1786 he served as High Sheriff for the county. He died in 1798, and is buried at Stoke. His widow died in 1828, and one of his sons, Edward, was for many years Rector of Burslem, and lived[80] at Hales Hall, near Cheadle. But his descendants are now no longer to be found in the potteries.
Taste changed, and Whieldon’s products fell out of style. It’s only in recent years that the agate and marble work, perfected later by Wedgwood, along with the charming cottage chimney ornaments and tortoiseshell pieces from Whieldon, Wedgwood, and Ralph Wood, have been appreciated as authentic Staffordshire art. When Whieldon realized he had lost his market, he didn’t try to keep up with his students and retired from business around 1780. His factory was located just south of the current railway station at Stoke, and he built and lived in a house that still overlooks the Trent and the railway. In 1786, he served as High Sheriff for the county. He passed away in 1798 and is buried in Stoke. His wife died in 1828, and one of his sons, Edward, was the Rector of Burslem for many years and lived[80] at Hales Hall, near Cheadle. However, his descendants are no longer found in the potteries.
We know of two other manufacturers who made agate and tortoiseshell ware—Daniel Bird, called “the flint potter” because of his experiments with different proportions of flint in the clay body,[78] and John and Thomas Alders of Cliff Bank. There were probably many others. These two made buttons and knife handles very largely. Both worked at the Stoke end of the Potteries.
We know of two other manufacturers who made agate and tortoiseshell items—Daniel Bird, nicknamed “the flint potter” due to his experiments with different amounts of flint in the clay body,[78] and John and Thomas Alders from Cliff Bank. There were likely many more. These two primarily produced buttons and knife handles. Both worked at the Stoke end of the Potteries.
Before entering on the fresh epoch in the History of Potting which opens with the work of Wedgwood, it will be as well to recount the end of the salt-glaze industry. It was a risky manufacture. The ware was thin, and many accidents happened in firing. Therefore the ware was costly; and only small pieces could be so glazed. The fluid lead glazes used by the skilful potters of the latter half of the century gave a surface smoother and more suitable for food. The demand for ornamental salt glaze was small, and the enormous demand for useful ware sent all the best potters into the useful trade; while in the ornamental lines Wedgwood’s[81] Greek and Etruscan shapes entirely ruled the market. All these causes conspired to ruin the salt glaze, and by 1770 it had fallen into general disuse. The last considerable makers of salt glaze were the Baddeleys and Christopher and Charles Whitehead of the Old Hall, Hanley.[79] No single maker of salt glaze occurs on the 1787 lists. It was a fine ware, characteristic of and peculiar to Staffordshire, and when one considers the difficulties under which its production was carried on, a tribute of praise is due to those potters who so quickly developed it to its highest state of perfection.
Before we dive into the new era in the history of pottery that starts with Wedgwood’s work, it's important to talk about the decline of the salt-glaze industry. It was a risky production process. The pottery was thin, which led to many accidents during firing. As a result, the ware was expensive, and only small pieces could be glazed that way. The liquid lead glazes used by skilled potters in the later part of the century created a surface that was smoother and more suitable for food. There was little demand for decorative salt glaze pieces, while the huge demand for functional ware drove the best potters into making useful items. In the realm of decorative pottery, Wedgwood’s[81] Greek and Etruscan designs completely dominated the market. All these factors combined led to the decline of salt glaze, and by 1770, it was largely abandoned. The last notable producers of salt glaze were the Baddeleys and Christopher and Charles Whitehead of the Old Hall, Hanley.[79] No salt glaze makers appeared on the 1787 lists. It was a fine type of ware, unique to Staffordshire, and considering the challenges involved in its production, we owe a tribute of praise to those potters who quickly brought it to its peak of perfection.
Shaw had an account, from the lips of an old man of eighty-three, born in 1720, showing the conditions under which this old-world industry was carried on.[80] And before we come to the modern life with its canals and steam and complete “factory system,” it is worth while to give this recollection of potting in 1750.
Shaw had a story from an eighty-three-year-old man, born in 1720, detailing how this old-school industry operated.[80] And before we dive into modern life with its canals, steam power, and fully developed “factory system,” it’s important to share this memory of pottery in 1750.
“Ralph Leigh was employed by John Taylor of the Hill Top, to look after his horses, and was the first man whose wages were raised from 10d. to 12d. a day. With four or six horses he went[82] twice to Whitfield, or thrice to Norton, in a day for coals; of which each horse brought 2½ cwt. on its back; along lanes extremely dirty. At the pit, coals then cost 7d. the draught, whether 2, 2½, or 3 cwt., for the colliers guessed at the quantity. The charge for carrying each load from Norton to Burslem was 3d., a penny a mile.[81] During a long time he carried crates of pottery to Winsford, and brought back ball clay. Each horse carried a crate on a pack saddle, and a small panier on each side was used to hold two or three balls of clay, weighing 60 or 70 lbs. Each horse was muzzled to prevent it biting the hedges, and the roads were narrow and bad and without toll gates. Afterwards with a cart and four horses he went to Winsford and delivered his crates the same day; and on the second day brought back a ton of Chester clay to Burslem. He was allowed four days to take crates to Bridgenorth, and bring back shop goods for Newcastle. He went with crates to Willington Ferry, and returned with flint, plaister stone and shop goods. He has gone to Liverpool and also as far as Exeter, before there were regular carriers.”
Ralph Leigh worked for John Taylor of Hill Top, taking care of his horses, and he was the first person whose pay was raised from 10d. to 12d. a day. With four or six horses, he made two trips to Whitfield or three trips to Norton in a day for coal; each horse carried 2½ cwt. on its back, navigating extremely dirty lanes. At the pit, coal cost 7d. per load, regardless of whether it was 2, 2½, or 3 cwt., since the colliers estimated the amount. The fee for hauling each load from Norton to Burslem was 3d., which is a penny a mile.[81] For a long time, he transported crates of pottery to Winsford and brought back ball clay. Each horse carried a crate on a pack saddle, and a small panier on each side held two or three balls of clay weighing 60 or 70 lbs. Each horse was muzzled to stop it from biting the hedges, and the roads were narrow, rough, and free from toll gates. Later, he used a cart and four horses to deliver his crates to Winsford on the same day and brought back a ton of Chester clay to Burslem the next day. He was allowed four days to take crates to Bridgenorth and return with shop goods for Newcastle. He also transported crates to Willington Ferry and came back with flint, plaster stone, and shop goods. He traveled to Liverpool and even as far as Exeter, before there were regular carriers.

ETRURIA WORKS
ETRURIA FACTORY
Such were the conditions under which the salt glaze of Staffordshire and the agate of Staffordshire were produced and perfected; and having traced these manufactures to their climax, it now remains to describe the rise of cream-coloured earthenware—the cream colour, which under Wedgwood became universal and perfected as we know it to-day. But it would be a mistake to attribute all good cream colour to Wedgwood. Just as all red teapots get put down to Elers; or as salt glaze is divided between Dr Thomas Wedgwood and Astbury according to character; and just as all another class of ware with irregular splashes of coloured glaze is called “Whieldon,” so much that Wedgwood never put his hand to has got dubbed with his name, to the exclusion of contemporaries as enterprising, such as Warburton and Turner, and to the neglect of predecessors who,[84] like Astbury and Booth, had already done very much to make Wedgwood’s development of the cream colour possible.
These were the conditions under which the salt glaze and agate ceramics of Staffordshire were created and refined. After tracing these crafts to their peak, we now need to discuss the emergence of cream-colored earthenware—the cream color that became ubiquitous and was perfected under Wedgwood as we know it today. However, it would be misleading to credit all quality cream color solely to Wedgwood. Just as all red teapots are attributed to Elers, or salt glaze is split between Dr. Thomas Wedgwood and Astbury based on style, and another type of ware with random splashes of colored glaze is labeled “Whieldon,” much that Wedgwood didn’t create has unfortunately been associated with his name. This overshadows other contemporary innovators like Warburton and Turner and overlooks earlier artisans such as Astbury and Booth, who played significant roles in making Wedgwood’s advancement in cream color possible.
The ordinary earthenware cream-colour body was composed of ball clay from Dorsetshire, calcined flint, and the lighter burning local clays. After the discovery of china clay and china stone in Cornwall about 1770, these two bodies both came to be added to the standard mixture, and the local clays were gradually dropped.[82] The glaze invented[85] by John Greatbach while at Etruria, and called “Greatbach’s China Glaze,” finally completed the development of the cream colour.[83] In practice the results depended so largely upon the exact composition of body and glaze, the exact temperature of firing in biscuit and glost ovens, and the subsequent decoration, that different potters achieved different results from their cream ware, and very different reputations. Josiah Wedgwood, with whom we must now deal, with his so-called Queen’s Ware, achieved undisputed pre-eminence, and became the greatest agent in the world-wide distribution of the cream-coloured earthenware of North Staffordshire.[84]
The typical cream-colored earthenware body consisted of ball clay from Dorsetshire, calcined flint, and lighter burning local clays. After china clay and china stone were discovered in Cornwall around 1770, these two materials were added to the standard mixture, and the local clays were gradually phased out.[82] The glaze created[85] by John Greatbach while at Etruria, known as “Greatbach’s China Glaze,” ultimately completed the development of the cream color.[83] In practice, the outcomes varied significantly based on the precise composition of the body and glaze, the exact firing temperatures in biscuit and glost ovens, and the decoration applied afterwards, leading to different potters achieving varying results with their cream ware, along with quite different reputations. Josiah Wedgwood, who we will now discuss, with his so-called Queen’s Ware, attained undeniable prominence and became the leading figure in the global distribution of the cream-colored earthenware from North Staffordshire.[84]
Josiah Wedgwood, thirteenth child of Thomas Wedgwood, master potter of the Churchyard works in Burslem, was baptized in Burslem church on July 12, 1730. He was a son, grandson and great-grandson of potters. His brothers, his cousins and his uncles made pots, and many had left an enduring reputation behind them. Josiah too was apprenticed to the trade in 1744 in his eldest brother’s works by the Churchyard side at Burslem.
Josiah Wedgwood, the thirteenth child of Thomas Wedgwood, a master potter working in Burslem, was baptized at Burslem church on July 12, 1730. He was the son, grandson, and great-grandson of potters. His brothers, cousins, and uncles all made pottery, leaving behind a lasting legacy. In 1744, Josiah was also apprenticed to the trade at his oldest brother’s workshop by the Churchyard in Burslem.
In 1752 he went into partnership with John Harrison, a tradesman of Newcastle, and they took the factory of the Alders’ at Cliff Bank, Stoke. Here they turned out the agate knife-blades and buttons that Alders had produced before. In two years Wedgwood was able to leave this partnership and join with Whieldon, the best potter of the day. For five years at least these two men were in partnership. Whieldon supplied the skill and traditional knowledge, and Wedgwood the extraordinary energy which was his chief characteristic. His experiments were incessant, and the fine green glaze seen on his cauliflower ware, his first real success, was his reward.
In 1752, he partnered with John Harrison, a tradesman from Newcastle, and they took over the Alders’ factory at Cliff Bank, Stoke. There, they produced the agate knife blades and buttons that Alders had made before. After two years, Wedgwood was able to leave this partnership and team up with Whieldon, the top potter of the time. For at least five years, these two worked together. Whieldon brought the skill and traditional expertise, while Wedgwood contributed his remarkable energy, which was his defining trait. His experiments were constant, and the fine green glaze seen on his cauliflower ware, his first real success, was the result of his efforts.

Truly and affectionately yours,
Sincerely and affectionately yours,
J. WEDGWOOD
J. Wedgwood
Etruria, 14th Feb. 1774
Etruria, Feb 14, 1774
The Relationships between the various members of this family that have been mentioned in the course of this history are shown on the following outline pedigree:—
The relationships among the different members of this family mentioned throughout this story are displayed in the following outline pedigree:—

As soon as he was able to afford a factory of his own, he went back to Burslem, and in 1759 he hired, from his uncles John and Thomas Wedgwood of the Big House, a factory known as the Ivy House Works. Here, or at the “Brick House” Works which he hired in 1762,[85] he made cauliflower, cream colour, and, later, black basalt ware. There worked for him at the Ivy House Works a first cousin, Thomas Wedgwood, who afterwards became his partner in the production of “useful” ware.
As soon as he could afford his own factory, he returned to Burslem, and in 1759 he rented a factory called the Ivy House Works from his uncles John and Thomas Wedgwood of the Big House. Here, or at the “Brick House” Works that he rented in 1762,[85] he produced cauliflower, cream-colored, and later, black basalt ware. Working with him at the Ivy House Works was his first cousin, Thomas Wedgwood, who later became his partner in making “useful” ware.
A great number of the letters of Josiah Wedgwood have survived, and they show the chief cause of his success to have been his restless passion for experiment and novelty, coupled with an almost American love for the extension of business—particularly profitable business. He was first a skilful potter, secondly a pushing man of business,[89] and only thirdly, perhaps, a great artist. When he broke with his stick some imperfect vase, saying, “That won’t do for Josiah Wedgwood,” it was not because the delinquent vase offended his taste, but because it might damage his reputation and the sale of his wares. He wanted perfection, and he got perfection; but he wanted it to sell, as a business proposition. And when we find him wondering whether he can keep up the price of his common cream plates to four shillings a dozen, while the other potters have brought their price for the same plates down to two shillings a dozen,[86] then we catch a glimpse of how well it paid.
A large number of Josiah Wedgwood's letters have survived, and they reveal that his main success came from his relentless passion for experimentation and new ideas, along with an almost American enthusiasm for expanding his business—especially if it was profitable. He was primarily a skilled potter, then a driven businessman,[89] and perhaps only thirdly a great artist. When he would break an imperfect vase with his stick, saying, “That won’t do for Josiah Wedgwood,” it wasn't just because the flawed vase bothered him aesthetically, but because it could harm his reputation and the sales of his products. He wanted perfection, and he achieved it; but his goal was to sell it as a business venture. And when we see him questioning whether he can keep the price of his regular cream plates at four shillings a dozen, while other potters have lowered their price for the same plates to two shillings a dozen,[86] we get a hint of how profitable this was.
The cream-coloured Queen’s Ware was the chief product of Wedgwood’s early times in Burslem. It was at first decorated, when required, by the widow Warburton, of Hot Lane. But the invention of the cheap method of printing designs on to the glazed ware, made in 1755 by Saddler and Green of Liverpool, provided an excellent substitute for enamelling on the more useful ware. Wedgwood used to send his ware to Liverpool to be printed, and was often there himself, importing clay, or[90] looking after the export trade to America, then, as now, the most important branch of the export trade. It was on one of these visits to Liverpool that he first met his life-long friend, Thomas Bentley, a dissenting radical merchant of the Clapham school, who became his partner in 1768.[87]
The cream-colored Queen’s Ware was the main product of Wedgwood’s early days in Burslem. Initially, it was decorated by the widow Warburton from Hot Lane when needed. However, the invention of a cost-effective method for printing designs on glazed ware by Saddler and Green in Liverpool in 1755 offered a great alternative to enameling on the more practical ware. Wedgwood would send his products to Liverpool to be printed and was often there himself, importing clay or[90] managing the export trade to America, which was, and still is, the most crucial part of the export business. It was during one of these trips to Liverpool that he met his lifelong friend, Thomas Bentley, a dissenting radical merchant from the Clapham school, who became his partner in 1768.[87]
Wedgwood had moved entirely into the Brick House Works, afterwards called the Bell Works, early in 1763, but in 1766 he bought the Ridge House estate of about 150 acres in Shelton, where he proceeded to build his new “Etruria”—factory, dwelling house and village. The Etruria works were opened for the production of the black basalt and other ornamental ware in 1769, and here ever since his descendants have carried on the same work. The factory at Burslem continued to produce the useful cream colour, and in this branch of the business, his cousin Thomas Wedgwood was his partner from 1766 till his death in 1788. In 1773, however, Wedgwood, finally closed down the Burslem works, and transferred the last of the “useful” work to join the rest at Etruria.[88]
Wedgwood completely moved into the Brick House Works, later known as the Bell Works, in early 1763. By 1766, he purchased the Ridge House estate, which was about 150 acres in Shelton, where he began building his new "Etruria"—a factory, a home, and a village. The Etruria works started producing black basalt and other decorative items in 1769, and ever since, his descendants have continued this work. The factory in Burslem kept making the practical cream color, with his cousin Thomas Wedgwood as his partner from 1766 until his death in 1788. However, in 1773, Wedgwood finally shut down the Burslem works and moved the last of the "useful" production to Etruria.[88]
Wedgwood was now becoming famous. In 1765 he opened his first London warehouse under the charge of his brother John. After John Wedgwood’s death in 1766,[89] he finally induced Bentley to take permanent charge of the London office and showrooms, which became a sort of fashionable lounge.
Wedgwood was becoming well-known. In 1765, he opened his first London warehouse, managed by his brother John. After John Wedgwood's death in 1766,[89] he convinced Bentley to take permanent control of the London office and showrooms, which turned into a stylish gathering spot.
But that which chiefly brought Wedgwood before the public was his determination to secure better transport facilities to and from the Potteries. In 1762 he and others were busy pressing for a new turnpike road[90] from Cliff Bank, on the Newcastle and Uttoxeter turnpike, through Burslem to the “Red Bull” at Lawton, on the London, Newcastle and Liverpool road.[91] The petition sent up on this occasion gives a description of the state of the industry which is worth quoting. The petition says:—
But what really brought Wedgwood into the public eye was his commitment to improving transportation options to and from the Potteries. In 1762, he and others were actively advocating for a new turnpike road[90] from Cliff Bank, connecting the Newcastle and Uttoxeter turnpike, through Burslem to the “Red Bull” at Lawton, on the London, Newcastle, and Liverpool road.[91] The petition submitted at this time provides a description of the state of the industry that is worth quoting. The petition states:—
“In Burslem and its neighbourhood are near[92] 500 separate potteries for making various kinds of stone and earthenware, which find constant employment and support for near 7000 people. The ware of these potteries is exported in vast quantities from London, Bristol, Liverpool, Hull etc., to our several colonies in America and the West Indies, as well as to almost every port in Europe. Great quantities of flint stones are used in making some of the ware, which are brought by sea from various parts of the coast to Liverpool and Hull; and the clay for making the white ware is brought from Devonshire and Cornwall chiefly to Liverpool, the materials from whence are brought by water up the rivers Mersey and Weaver to Winsford in Cheshire; those from Hull up the Trent to Willington; and from Winsford and Willington the whole are brought by land carriage to Burslem. The ware, when made, is conveyed to Liverpool and Hull in the same manner.
“In Burslem and its surroundings, there are about[92] 500 separate potteries that produce various types of stone and earthenware, providing jobs and livelihoods for nearly 7,000 people. The products from these potteries are shipped in large quantities from London, Bristol, Liverpool, Hull, and other places to our various colonies in America and the West Indies, as well as to nearly every port in Europe. A significant amount of flint stones is used to make some of the items, which are transported by sea from different parts of the coast to Liverpool and Hull; the clay for producing white ware mainly comes from Devonshire and Cornwall to Liverpool. The materials are then transported by water up the rivers Mersey and Weaver to Winsford in Cheshire; those from Hull travel up the Trent to Willington; and from Winsford and Willington, everything is transported by land to Burslem. Once made, the ware is sent to Liverpool and Hull using the same transportation methods.”
“Many thousand tons of shipping ... are employed in carrying materials for the Burslem ware; and as much salt is consumed in glazing one species of it as pays annually near £5000 duty to Government.[93] Add to these considerations the prodigeous quantity of coal used in the Potteries ... and it will appear that ... those who are supported by the pot trade, amount to a great many thousand people; ... and the trade flourishes so much as to have increased two-thirds within the last 14 years.”[92]
“Many thousands of tons of shipping are used to transport materials for Burslem ware, and just as much salt is used in glazing one type of it as pays nearly £5000 in annual duty to the Government.[93] Considering the enormous amount of coal consumed in the Potteries, it becomes clear that those who rely on the pottery trade number in the many thousands; the trade has thrived so much that it has increased by two-thirds in the last 14 years.”[92]
The determined opposition of the Newcastle tradesmen and inn-keepers, afraid of loss of traffic, prevented the full scheme being carried out. The Bill, as passed in 1763, provided for the turnpike from Lawton as far as Burslem only.
The strong resistance from the Newcastle tradespeople and innkeepers, worried about losing business, stopped the complete plan from being implemented. The Bill, as approved in 1763, only allowed for the turnpike from Lawton to Burslem.
A Newcastle and Leek turnpike through the future Etruria and Cobridge followed. On February 1, 1765, we find Josiah Wedgwood writing to his brother John in London, “we have another turnpike broke out amongst us here betwixt Leek and Newcastle, and they have, vi et armis, mounted me upon my hobby-horse again.... He carried me yesterday to Leek, from whence I am just returned much satisfied with our reception there. Tomorrow I wait upon Sir Nigel (Gresley) to beg his concurrence, and on Monday must attend[94] a meeting to settle the petition etc. at Mony Ash at yr frd Isaac Whieldons. We pray to have the Utoxeter and Burslem turnpike joined [i.e. Cliff Bank, Shelton, Cobridge and Burslem], and to have the road made turnpike from Buxton and Bakewell to Leek, and from Leek to Newcastle. Whether or not our good friends at Newcastle will give us battle on this occasion we do not know, if they do there will be some probability of my having a commⁿ and seeing the great City again. £2000 is wanting for this road. My uncles Thos. and John (of the Big House) have, I am quite serious, at the first asking subscribed ... five hundred pounds. I have done the like intending 2 or 300 of it for you, and if you choose any more you must let me know in time.”[93]
A Newcastle and Leek toll road went through what will become Etruria and Cobridge. On February 1, 1765, Josiah Wedgwood wrote to his brother John in London, “we have another toll road issue popping up here between Leek and Newcastle, and they have, vi et armis, put me back on my hobby-horse again.... He took me to Leek yesterday, and I just returned feeling quite pleased with our welcome there. Tomorrow, I’ll meet with Sir Nigel (Gresley) to ask for his support, and on Monday I have to go to a meeting to finalize the petition, etc. at Mony Ash at your friend Isaac Whieldon's place. We hope to merge the Utoxeter and Burslem toll roads [i.e. Cliff Bank, Shelton, Cobridge, and Burslem], and to make the road a toll road from Buxton and Bakewell to Leek, and from Leek to Newcastle. We’re not sure if our friends in Newcastle will oppose us this time; if they do, there's a chance I might have a commission and see the great City again. We need £2000 for this road. My uncles Thos. and John (of the Big House) have, I’m serious, subscribed at the first request ... five hundred pounds. I’ve done the same, planning to allocate 2 or 300 of it for you, and if you want any more, you need to let me know in time.”[93]
What these roads were like one can gather from Arthur Young’s travels. He describes the road from Knutsford to Newcastle as “in general a paved causeway, as narrow as can be conceived, and cut into perpetual holes, some of them two feet deep; a more dreadful road cannot be imagined....[95] Let me persuade all travellers to avoid this terrible country....”[94]
What these roads were like can be understood from Arthur Young’s travels. He describes the road from Knutsford to Newcastle as “generally a paved causeway, as narrow as you can imagine, and full of constant holes, some of them two feet deep; a worse road is hard to picture....[95] Let me urge all travelers to steer clear of this awful area....”[94]
Yet even these roads and lanes seem to have been moving with the times, for we hear, in 1763, of one Daniel Morris introducing wagons and carts for the first time, and acting as carrier.[95] “Pot-wagons” now took crates of ware to Bewdley on the Severn and to Willington Ferry on the Trent. The general rate of transport was 9s. per ton for 10 miles. To the port of Liverpool the rate was 28s. per ton, but flint and clay up from Liverpool cost only 15s. a ton.[96] To Willington the charge was 35s. a ton; and the transit down the river to Hull was almost as expensive.
Yet even these roads and lanes seem to have been keeping up with the times, because in 1763, we hear about one Daniel Morris introducing wagons and carts for the first time and serving as a carrier. “Pot-wagons” now transported crates of goods to Bewdley on the Severn and to Willington Ferry on the Trent. The standard transport rate was 9s. per ton for 10 miles. To the port of Liverpool, the rate was 28s. per ton, but flint and clay coming from Liverpool only cost 15s. a ton. To Willington, the charge was 35s. a ton; and the journey down the river to Hull was almost as costly.
The Duke of Bridgewater was at this time developing his estates in Cheshire by means of the great Bridgewater Canal. In 1761 it was open from Manchester to Worsley, and James Brindley, “the schemer,” was engaged in extending it to tide-water below Warrington. Brindley was already well known in the Potteries. He was born[96] in the High Peak in 1716, and after serving his apprenticeship as a mill-wright at Macclesfield, and designing many improvements in spinning factories and mine drainage, he settled more or less in the Potteries. In or about 1758 he put up a windmill for grinding calcined flint on an estate called the Jenkins, near Burslem, belonging to John Wedgwood of the Big House; and many other pieces of engineering for the convenience of potters were invented by him. But in 1759 he commenced, under the Duke of Bridgewater, those 365 miles of canal which made his name famous.[97]
The Duke of Bridgewater was at this time developing his lands in Cheshire with the great Bridgewater Canal. In 1761, it was open from Manchester to Worsley, and James Brindley, known as “the schemer,” was working on extending it to the tidewater below Warrington. Brindley was already well-known in the Potteries. He was born in the High Peak in 1716, and after serving his apprenticeship as a millwright in Macclesfield and designing many improvements in spinning factories and mine drainage, he settled mostly in the Potteries. Around 1758, he built a windmill for grinding calcined flint on an estate called the Jenkins, near Burslem, owned by John Wedgwood of the Big House; and he invented many other engineering solutions for the benefit of potters. But in 1759, he started, under the Duke of Bridgewater, the 365 miles of canal that made his name famous.[97]
Acting under the orders of Lord Gower and Lord Anson, Brindley had, in 1758, made a preliminary survey for a canal to connect the Trent and Mersey. The success of the Bridgewater canal caused this project to be revived in 1764, and an association was formed to obtain Parliamentary powers. In December of that year a meeting was held at Lichfield between Lord Gower and others, at which they discussed the conflicting interests of the proprietors, the landlords, the manufacturers[97] and the public.[98] The scheme was dropped for that session, but all through 1765 Wedgwood, who saw the prime importance of this new method of transport, was engaging support, combating the opposition of rival interests, and getting Bentley to issue pamphlet after pamphlet showing all its advantages.
Acting on the instructions of Lord Gower and Lord Anson, Brindley conducted a preliminary survey in 1758 for a canal to link the Trent and Mersey. After the success of the Bridgewater canal, this project was revived in 1764, and a group was formed to secure Parliamentary approval. In December of that year, a meeting took place in Lichfield where Lord Gower and others discussed the competing interests of the owners, landlords, manufacturers[a id="Page_97"> and the public.[98] The plan was put on hold for that session, but throughout 1765, Wedgwood, who recognized the crucial importance of this new transport method, was rallying support, fighting against the opposition from rival interests, and getting Bentley to publish pamphlet after pamphlet outlining all its benefits.
At last, on May 14, 1766, the Bill received the Royal Assent. On June 3, a meeting of the proprietors was held, presided over by Lord Gower. There were present Lord Grey, Mr Bagot, Mr Anson, Mr Gilbert, Mr Smith of Fenton, Mr Sam. Robinson and others. A committee was formed and the following officers appointed:
At last, on May 14, 1766, the Bill got the Royal Assent. On June 3, a meeting of the proprietors took place, led by Lord Gower. Present were Lord Grey, Mr. Bagot, Mr. Anson, Mr. Gilbert, Mr. Smith of Fenton, Mr. Sam Robinson, and others. A committee was formed, and the following officers were appointed:
“James Brindley, Surveyor General, | £200 | per ann. |
Hugh Henshall, Clerk of the works, | £150 | ” |
T. Sparrow, Clerk to the proprietors, | £100 | No text provided to modernize. |
Jos. Wedgwood, Treasurer, | £000 | "” |
out of which he bears his own expenses, and it was ordered that the work be begun on immediately, both sides of Harecastle and at Wilden.”[99]
out of which he covers his own expenses, and it was ordered that the work be started immediately, on both sides of Harecastle and at Wilden.”[99]
The first sod was cut by Wedgwood on July 26 at Brownhills, between Burslem and Tunstall,[98] before a great concourse of people, and we are told that an ox was roasted whole for the populace.[100]
The first sod was cut by Wedgwood on July 26 at Brownhills, between Burslem and Tunstall,[98] in front of a huge crowd, and we hear that an entire ox was roasted for the people.[100]
The Trent and Mersey canal is 93 miles long, with 75 locks, and rises at the Harecastle tunnel to a height of 326 feet above the Mersey. It is 20 feet broad at the top, 16 feet at the bottom, and 4 feet 6 inches deep, and it cost £300,000.[101] It is carried on aqueducts over the Dove, Trent and Dane, and there are five tunnels. It was pushed on by Brindley with great energy till his death, and completed at last in 1777 by Hugh Henshall, his son-in-law, together with a branch to the Severn from Great Haywood. Brindley died at Turnhurst in Wolstanton on Sept. 27, 1772. In 1786 we read that freight for general goods on the canal was 1¼d. per ton per mile, or less than one-seventh what freight cost before the canal[99] was cut.[102] At the same time the £200 shares in the canal were standing at £600-£700 apiece.[103] It was carrying over 1,350,000 tons of goods and minerals a year in 1849, when it was bought out by the railway company for £1,170,000.
The Trent and Mersey Canal is 93 miles long, with 75 locks, and rises at the Harecastle Tunnel to a height of 326 feet above the Mersey. It is 20 feet wide at the top, 16 feet at the bottom, and 4 feet 6 inches deep, costing £300,000.[101] It is supported by aqueducts over the Dove, Trent, and Dane rivers, and there are five tunnels. Brindley pushed for its construction with great energy until his death, and it was finally completed in 1777 by Hugh Henshall, his son-in-law, along with a branch to the Severn from Great Haywood. Brindley died at Turnhurst in Wolstanton on Sept. 27, 1772. In 1786, we see that freight for general goods on the canal was 1¼d. per ton per mile, which is less than one-seventh of the freight costs before the canal[99] was built.[102] At that time, shares in the canal that were worth £200 were trading at £600-£700 each.[103] In 1849, it was transporting over 1,350,000 tons of goods and minerals a year when it was purchased by the railway company for £1,170,000.
A fresh development of the potting industry took place even while this canal was building. China clay and china stone were discovered by Cookworthy in Cornwall. This was in 1768, and Cookworthy took out a patent for the use of these materials. He never succeeded in producing porcelain on a commercial scale, and in 1773 sold his patent rights to Richard Champion.[104] Mr Champion was one of the chief supporters in Bristol of Edmund Burke, member for that city, and conceived in 1775 the idea of getting with his aid a Bill passed through Parliament to extend the patent which he had bought from Cookworthy for a further seven years. But china clay and china stone had during these last few years been proved of value not only for making china, but also as a constituent of the clay body used for making the[100] cream-coloured earthenware of Staffordshire. It had been imported and used by Wedgwood, Turner of Lane End, the Warburtons and others, and an extension of Cookworthy’s patent, giving to Champion of Bristol the monopoly for seven more years of the right to use this material, whether for making china or earthenware, was naturally resisted by the earth potters of Staffordshire. In this opposition Wedgwood and Turner took a leading part; and their action has been criticized by many who thought they saw in Champion the struggling inventor penalized by pushing capitalists. From another and as reasonable a point of view Champion was a speculator who tried to use political influence to increase the value of a monopoly that he had bought on a different basis. As Mr Burton says, “It certainly seems that the fullest justice was done when Champion was allowed an extension of the patent for the use of china clay and china stone in porcelain, the only substance ever produced by Cookworthy or Champion, and the other potters were allowed to use the same materials in earthenware bodies.”[105]
A new development in the pottery industry happened while this canal was being built. Cookworthy discovered china clay and china stone in Cornwall back in 1768 and patented their use. He never managed to produce porcelain commercially, and in 1773, he sold his patent rights to Richard Champion. Mr. Champion was one of the main backers of Edmund Burke, the city’s representative in Bristol, and in 1775, he came up with the idea of passing a bill in Parliament to extend the patent he had bought from Cookworthy for another seven years. However, china clay and china stone had recently proven valuable not just for making china, but also as a key ingredient in the clay used to create the cream-colored earthenware of Staffordshire. It had been imported and used by Wedgwood, Turner of Lane End, the Warburtons, and others. Naturally, the earth potters of Staffordshire opposed an extension of Cookworthy’s patent, which would give Champion in Bristol the monopoly on using this material for both china and earthenware for seven more years. Wedgwood and Turner played a leading role in this opposition; their actions have been criticized by many who believed they were punishing the struggling inventor, Champion, in favor of wealthy capitalists. From another reasonable perspective, Champion was a speculator trying to leverage political influence to boost the value of the monopoly he had acquired on a different basis. As Mr. Burton states, “It certainly seems that the fullest justice was done when Champion was allowed an extension of the patent for the use of china clay and china stone in porcelain, the only material ever produced by Cookworthy or Champion, while the other potters were allowed to use the same materials in earthenware.”

WILLIAM TURNER, MASTER POTTER
WILLIAM TURNER, MASTER CERAMIST
Fl.: 1780
Fl.: 1780
Yet for the part he played in this business John Turner was afterwards made to suffer and in this manner. On Lord Gower’s estates he discovered a clay which made a singularly hard white body, but the agent for the Earl, remembering, it is said, the action Turner had taken against Champion, told him he might look for his clays elsewhere, and refused to let him work the clay.
Yet for the role he played in this situation, John Turner later faced consequences. On Lord Gower's estates, he found a type of clay that produced an unusually hard white material, but the Earl's agent, remembering the action Turner had taken against Champion, allegedly told him to look for his clays elsewhere and refused to allow him to work with that clay.
The use of china clay and china stone, and the new glaze called “Greatbach’s china glaze,” completed the perfection of the cream-coloured earthenware, and Wedgwood drifted more and more away from the agate and cauliflower ware of his youth to the new body—the Queen’s Ware.[106] Cream colour for the table—printed, enamelled or plain—became ever more important. In 1770 he received an order for an enormous dinner service from the Empress of Russia. Each piece was to have enamelled on it a different view of some English gentleman’s seat. To complete this extraordinary order artists and enamellers were collected from the whole country, and set to work at Chelsea under Bentley’s guidance. The results do not seem[102] very attractive. A picture of a gentleman’s seat, generally in black or drab on a cream-coloured plate, is only interesting. A good border pattern is the most suitable decoration for a dinner plate.
The use of china clay and china stone, along with the new glaze known as “Greatbach’s china glaze,” perfected the cream-colored earthenware. Wedgwood increasingly moved away from the agate and cauliflower ware of his youth towards the new body—the Queen’s Ware. Cream color for the table—printed, enameled, or plain—became increasingly important. In 1770, he received a huge order for a dinner service from the Empress of Russia. Each piece was to feature a different view of an English gentleman’s estate. To fulfill this remarkable order, artists and enamellers were gathered from across the country and put to work in Chelsea under Bentley’s guidance. The results don’t appear very appealing. A depiction of a gentleman’s estate, usually in black or drab on a cream-colored plate, is merely interesting. A good border pattern is the most fitting decoration for a dinner plate.
Having got his staff of enamellers together, Wedgwood decided to do his own enamelling in future instead of sending his ware to the Warburtons to be enamelled.[107] The sober border decorations of his tea and dinner ware, which is to some tastes the very best part of his work, were done at Chelsea by these artists. His most successful patterns are mere enamelled borders, perfectly enamelled on perfectly potted plates.
Having gathered his team of enamellers, Wedgwood decided to handle the enamelling himself from now on instead of sending his products to the Warburtons to be enamelled. The simple border designs on his tea and dinner ware, which some people consider the best part of his work, were created at Chelsea by these artists. His most successful patterns consist of beautifully enamelled borders on flawlessly shaped plates.
But this was “useful” ware, and all the time he was aiming at the development of his ornamental ware along classical lines. The black basalt—plain; the black basalt—decorated with encaustic red paintings unglazed, after the manner of the Etruscans; the jasper vases and plaques; all are attempts to reproduce the survivals of Greece and Rome. This neo-classic style, if not original, was at least a change from the endless rococo of Dresden, and the shepherdesses of Chelsea and[103] Sèvres; and, compared with the “art china” productions of the first half of the nineteenth century, the copies of even decadent Rome seem to be the acme of good taste. One is also tempted to regret that in them the whole art of the potter is devoted to the most exact reproduction of bronze, of Parian marble, of natural cameos, or even of the glassy Barberini Vase. The reproduction is splendid, and probably nothing would have shocked Wedgwood more than to think that posterity could prefer his lavender tea service, or the vine pattern on his Queen’s Ware.
But this was "useful" ware, and all the while he was focused on developing his decorative pieces in a classical style. The plain black basalt; the black basalt adorned with unglazed encaustic red paintings in the style of the Etruscans; the jasper vases and plaques—these were all efforts to replicate the remnants of Greece and Rome. This neo-classic style, while not original, was at least a departure from the endless rococo styles of Dresden and the shepherdesses of Chelsea and Sèvres; and compared to the "art china" of the first half of the nineteenth century, even copies of decadent Rome seem to embody good taste. It's also hard not to feel regret that in these works, the entire craft of pottery is dedicated to mimicking bronze, Parian marble, natural cameos, or even the glossy Barberini Vase. The reproduction is stunning, and likely nothing would have shocked Wedgwood more than the thought that future generations might prefer his lavender tea service or the vine pattern on his Queen’s Ware.

HACKWOOD, THE MODELLER
HACKWOOD, THE MODEL MAKER
It is however undoubtedly on his jasper that his fame with succeeding generations has been based:—the white classical figures, designed by Flaxman or by Hackwood, embossed on a blue or black ground. The discovery of the jasper body, with its admixture of barium sulphate, gave him a perfectly white hard stoneware body, which would take a high fire, and become semi-vitrified without glazing. The body could be stained light or dark blue, pink, green or black, by the addition of suitable oxides, and then formed the ground of his jasper ware; while the white body, pressed into[104] small plaster moulds, taken out and then “sprigged on,” formed the ornamental embossments. This jasper ware could be used, and is still found, as panels in Adam fireplaces, with Flaxman’s “Dancing Hours” or “Medusa Head” clean cut on the blue plaque; as cameo medallions, bearing the heads of personages of state, for show cabinets; or as vases under a glass case, such as the Portland Vase, completed in 1790. And it is this jasper ware that is called to mind when “Old Wedgwood” is spoken of by amateurs. A proper description is impossible here of these Jasper or Black Basalt vases, statues or plaques, in which he received the invaluable assistance of Flaxman as a modeller, and the advice of every gentleman of the period who prided himself upon his taste. Description of manufacture and details of patterns must alike be left to special monographs, such as that of Prof. Church.
However, it is undoubtedly his jasper that has established his fame with future generations: the white classical figures, designed by Flaxman or Hackwood, embossed on a blue or black background. The discovery of the jasper body, with its mix of barium sulfate, gave him a perfectly white, hard stoneware body that could endure high temperatures and become semi-vitrified without glazing. The body could be stained light or dark blue, pink, green, or black with the right oxides, forming the base of his jasper ware; while the white body, pressed into[104] small plaster molds, taken out and then “sprigged on,” created the decorative embossments. This jasper ware could be used, and is still found, as panels in Adam fireplaces, with Flaxman’s “Dancing Hours” or “Medusa Head” neatly etched on the blue plaque; as cameo medallions featuring the heads of state figures, for display cabinets; or as vases under glass, like the Portland Vase, finished in 1790. It is this jasper ware that comes to mind when enthusiasts mention “Old Wedgwood.” A complete description of these Jasper or Black Basalt vases, statues, or plaques, which he created with invaluable assistance from Flaxman as a model maker, along with advice from every gentleman of the time who took pride in their taste, is impossible here. Detailed descriptions of manufacturing processes and patterns must be referred to specialized monographs, such as that by Prof. Church.
To complete a bald account of Wedgwood’s career as a potter we must add the following notes. Between the years 1759 and 1769 he perfected the cream colour, between 1766 and 1769 the black Etruscan ware was brought to its highest perfection;[105] the jasper body and glaze was undergoing development from 1773 to 1777, and the jasper dip from 1780 to 1786. His mechanical bent showed itself in a persistent and successful effort to develop the turning lathe so as to give a ribbed surface to the ware. This he called “engine turning,” and it is a device which has been largely employed ever since on decorative pieces. In 1783 he invented a neat pyrometre for registering the heat of ovens, and was elected in consequence a Fellow of the Royal Society. His great partner Bentley died in 1780, and for a few years Wedgwood carried on his works alone; but in 1790 he took into partnership his three sons John, Josiah and Thomas, and his sister’s son Thomas Byerley. The style and title of the Firm which had been “Wedgwood and Bentley” from 1768-80, “Wedgwood” from 1780-90, now became for a short time “Wedgwood, Sons and Byerley.” In 1793 his sons John and Thomas, having no aptitude for the systematic work of a master-potter, and being rich enough to be idle, retired from the firm, and conveyed their shares to the younger Josiah. Till[106] Thomas Byerley’s death in 1810, the firm was known as “Wedgwood, Son and Byerley.”[108]
To summarize Wedgwood’s career as a potter, we need to add the following details. Between 1759 and 1769, he perfected the cream color; from 1766 to 1769, he achieved peak quality in black Etruscan ware; the jasper body and glaze were in development from 1773 to 1777, and the jasper dip from 1780 to 1786. His mechanical inclination was evident in his ongoing and successful efforts to develop the turning lathe to create a ribbed surface on the ware, which he called “engine turning.” This technique has been widely used since for decorative pieces. In 1783, he invented a compact pyrometer to measure oven heat, earning him a Fellowship in the Royal Society. His significant partner Bentley passed away in 1780, and for a few years, Wedgwood ran the business alone. However, in 1790, he brought in his three sons, John, Josiah, and Thomas, as well as his sister’s son, Thomas Byerley, as partners. The firm was known as “Wedgwood and Bentley” from 1768 to 1780, then just “Wedgwood” from 1780 to 1790, and for a short time became “Wedgwood, Sons and Byerley.” In 1793, his sons John and Thomas, lacking the skills for the detailed work of a master potter and feeling wealthy enough to take it easy, left the firm and transferred their shares to the younger Josiah. Until Thomas Byerley’s death in 1810, the business was called “Wedgwood, Son and Byerley.”[105][106]
Josiah Wedgwood himself died on January 3, 1795. He bequeathed to his second son Josiah his share in the factory and an estate of 363 acres in Stoke and Hanley, and to his other children a fortune of about £160,000.[109] Mr Burton sums up the result of his work as follows: “His influence was so powerful, and his personality so dominant, that all other English potters worked on the principles he had laid down, and thus a fresh impulse and a new direction was given to the pottery of England and of the civilized world. He is the only potter of whom it may truly be said that the whole subsequent course of pottery manufacture has been influenced by his individuality, skill and taste.”[110]
Josiah Wedgwood passed away on January 3, 1795. He left his second son Josiah his share of the factory and a 363-acre estate in Stoke and Hanley, while his other children benefited from a fortune of about £160,000.[109] Mr. Burton summarizes the impact of his work as follows: “His influence was so strong, and his personality so commanding, that all other English potters operated based on the principles he established, giving a new energy and direction to the pottery of England and the civilized world. He is the only potter for whom it can honestly be said that the entire future of pottery manufacturing has been shaped by his unique character, skill, and taste.”[110]

MAP OF HANLEY IN 1800
MAP OF HANLEY IN 1800
Wedgwood’s financial success with his Jasper and Black Etruscan ware, a success hitherto quite unique in the experience of the Potteries, led every potter of any capacity to attempt the same lines. They cannot be blamed for trying to imitate what was demanded by the fashionable market. The whole progress of the industry had been based upon the copying of successful processes, and Wedgwood did not patent his patterns or methods, even could he have done so.
Wedgwood’s financial success with his Jasper and Black Etruscan ware, a success that was previously unparalleled in the history of the Potteries, inspired every potter with any ability to try and create similar products. They can’t be blamed for wanting to replicate what was popular in the market. The entire advancement of the industry had relied on copying successful techniques, and Wedgwood did not patent his designs or methods, even if he could have.
All over the Potteries they followed in his steps, content to reap with little trouble the advantages of his past labours—reproducing his patterns and avoiding all dangerous novelty. Invention died and the wares, tamely and ignorantly copied by inartistic workmen, sank artistically throughout the next half century. The copyist, imitator or[108] rival, who annoyed Wedgwood most in his lifetime was Humphrey Palmer of Hanley. Most of the Palmer and Neale ware we now know of seems original enough—and good enough—but from 1769-1776 Wedgwood regards him as a copyist of the most objectionable description.[111] It must be said however that he always stamped his imitations with his own name and not Wedgwood’s; a precaution which is not always observed at this present day, even with a patent law to enforce a man’s right to his own trade-mark. It is noticeable too that when Wedgwood did, in 1771, patent the method of painting with an encaustic red on the Black Etruscan ware, Palmer produced the same results and forced him to share the patent rights.[112] Palmer however got into financial difficulties, in 1776, and his business was taken over by his brother-in-law Henry Neale. Neale, in conjunction later on with David Wilson, continued the same style of ornamental ware, and so excellent are some of his granitic ornamental pieces now in museums that he must take rank as a rival[109] rather than as an imitator of Wedgwood. Both Neale and Palmer had married daughters of that Thomas Heath who tried to make Delft ware at Lane End early in the century. Another daughter is said to have married Mr Pratt, a potter of Lane Delf, whose descendants have ever since continued to make pottery on what may be the very spot where Thomas Heath made his original Delft ware.[113]
All over the Potteries, people followed his lead, happy to benefit from the advantages of his past work without much effort—copying his designs and steering clear of risky innovations. Creativity faded away, and the products, meekly and cluelessly duplicated by uninspired workers, declined artistically over the next fifty years. The person who bothered Wedgwood the most during his lifetime was Humphrey Palmer from Hanley. Most of the Palmer and Neale pottery we know today seems original enough—and pretty good—but from 1769 to 1776, Wedgwood saw him as a highly objectionable copyist. However, it should be noted that he always marked his copies with his own name, not Wedgwood’s; a caution that isn't always followed today, even with patent laws to protect a person's trademark. It's also worth mentioning that when Wedgwood patented the method of painting with an encaustic red on the Black Etruscan ware in 1771, Palmer produced the same results and forced him to share the patent rights. However, Palmer ran into financial trouble in 1776, and his business was taken over by his brother-in-law, Henry Neale. Neale later teamed up with David Wilson to continue the same style of decorative ware, and some of his granitic ornamental pieces found in museums today are so excellent that he should be considered a competitor rather than a mere imitator of Wedgwood. Both Neale and Palmer married daughters of Thomas Heath, who attempted to create Delft ware at Lane End early in the century. Another daughter is said to have married Mr. Pratt, a potter from Lane Delf, whose descendants have carried on making pottery on what might be the very spot where Thomas Heath produced his original Delft ware.
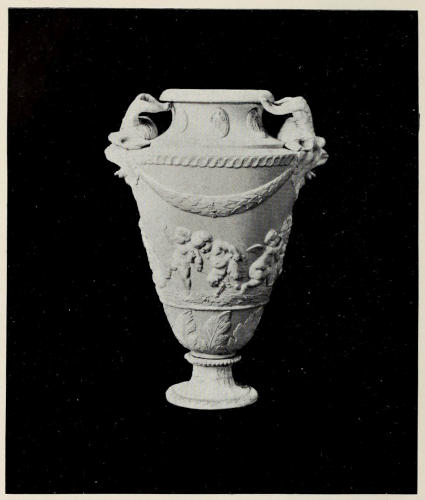
Vase by John Turner of Lane End. d. 1786. From the Stoke-on-Trent Museums.
Vase by John Turner of Lane End. d. 1786. From the Stoke-on-Trent Museums.
John Turner, of Lane End, was another competitor of Wedgwood. He was almost as confirmed an experimenter, and produced a jasper ware very close on Wedgwood’s heels. He was born in 1738,[114] and started his own works at Lane End in 1762, and his chief productions were the fashionable cream colour and a cane-coloured stoneware. He was one of the first to appreciate the value of the newly discovered china stone for the cream-coloured body, and he therefore took an active part in opposing the extension of Cookworthy’s patent. Afterwards, in 1775, he joined Wedgwood[110] in leasing some of the Cornish clay mines. A discovery of a good local clay at Green Dock, close by Longton Cemetery, led to his most characteristic production—the cane-coloured stoneware, ornamented with embossed decoration in the same colour. The material was also found very suitable for busts and statuettes. It is recorded that he could, in this material, make a most life-like representation of pie-crust, and that once, as a tour de force, he reproduced exactly an entire banquet with everything, from the roast beef to the custards, realistically translated into stoneware. It will be understood from this that there was room for a revival of taste in pottery. Turner’s jasper is quite different to that of Wedgwood, or of those who made it when the secret of the mixture had become known. Its ground is an unfortunate slaty blue, which does not improve the appearance of the ware, and the designs of the bas-reliefs are rococo, which is worse than neo-classical.
John Turner, from Lane End, was another rival of Wedgwood. He was nearly as dedicated to experimentation and produced jasper ware that closely followed Wedgwood’s innovations. Born in 1738, he established his own workshop at Lane End in 1762, focusing primarily on the trendy cream color and a cane-colored stoneware. He was one of the first to recognize the importance of the newly discovered china stone for creating the cream-colored body, which led him to actively oppose the extension of Cookworthy’s patent. Later, in 1775, he partnered with Wedgwood in leasing some of the Cornish clay mines. A discovery of quality local clay at Green Dock, near Longton Cemetery, resulted in his signature product—the cane-colored stoneware, decorated with embossed designs in the same color. This material also proved to be ideal for busts and statuettes. It’s noted that he was able to create a remarkably life-like representation of pie crust with this material, and once, as a tour de force, he exactly recreated an entire banquet, with everything from roast beef to custards, realistically rendered in stoneware. This illustrates that there was a demand for a revival of taste in pottery. Turner’s jasper is quite different from Wedgwood’s or that of others who made it once the mixture’s secret was revealed. Its base color is an unfortunate slaty blue, which detracts from the overall look of the ware, and the designs of the bas-reliefs are rococo, which is even less appealing than neo-classical styles.

THOMAS MINTON
THOMAS MINTON
c. 1765-1836
c. 1765-1836
John Turner died in 1786, and was succeeded by his two sons, John and William, who continued to produce black basalt as well as this strange[111] jasper. Their business was ruined by the French wars, and in 1803 they were compelled to close down. John Turner, jun., became manager to Thomas Minton, then starting his historic factory in Stoke.
John Turner died in 1786 and was succeeded by his two sons, John and William, who kept producing black basalt as well as this unusual[111] jasper. Their business was destroyed by the French wars, and in 1803 they were forced to shut down. John Turner Jr. became the manager for Thomas Minton, who was just starting his historic factory in Stoke.
We have seen that Turner went to Lane End in 1762. “About 1750,” says Shaw, but probably some years later, “Mr John Barker, with his brother and Mr Robert Garner, commenced the manufacture of shining black and white stoneware salt glaze at the Row Houses, near the Foley, Fenton, where afterwards they made tolerable cream colour. They realized a good property here; and Mr R. Garner erected a separate manufactory and the best house of the time in Lane End, near the old Turnpike Gate.”[115] This was after 1762, for among the Wedgwood MSS. is an account of that date from Messrs Robert Garner and J. Barker jointly for brown china tea-pots and pineapple jars supplied to Wedgwood at Burslem,[116] doubtless to complete an order. Roger Woods too is said to have built in 1756 a factory, afterwards known as Sampson Bridgwoods, by the brook at[112] the Lower Market Place in Longton. And about the same time Thomas and Joseph Johnson started making good salt glaze just opposite Lane End church.[117]
We know that Turner went to Lane End in 1762. "Around 1750," according to Shaw, but likely a few years later, "Mr. John Barker, along with his brother and Mr. Robert Garner, began making shiny black and white stoneware salt glaze at the Row Houses near the Foley in Fenton, where they later produced decent cream-colored pieces. They did well here; Mr. R. Garner built a separate factory and the best house of the time in Lane End, close to the old Turnpike Gate."[115] This was after 1762, as there's a record from that time among the Wedgwood MSS. indicating that Messrs. Robert Garner and J. Barker jointly supplied brown china teapots and pineapple jars to Wedgwood in Burslem,[116] probably to fulfill an order. Roger Woods is also said to have constructed a factory in 1756, later known as Sampson Bridgwoods, by the brook at[112] the Lower Market Place in Longton. Around the same time, Thomas and Joseph Johnson began producing quality salt glaze right across from Lane End church.[117]
In this manner potting spread to the Longton end of the Potteries. In 1756 there are said to have only been 100 houses in Longton and Lane End, and even by 1773 an old estate map of the Heathcotes’ shows but 180 houses, or a population of less than 1,000.
In this way, pottery making expanded to the Longton area of the Potteries. In 1756, it’s reported that there were only 100 houses in Longton and Lane End, and even by 1773, an old estate map of the Heathcotes shows just 180 houses, which means a population of less than 1,000.
As early as 1770 we obtain a familiar glimpse of the working of the factory system. Some of the master-potters in that year tried, for the first time on record, to form a ring to keep up prices. The bond runs as follows: “We whose hands are hereunto subscribed do bind ourselves ... in £50 ... not to sell ... under the within specified prices, as witness our hands: John Platt, John Lowe, John Taylor, John Cobb, Robt. Bucknall, John Daniel, Thos. Daniel jun., Richd. Adams, Saml. Chatterley, Thos. Lowe, John Allen, Wm. Parrott, Jacob Warburton, Warburton and Stone, Jos. Smith, Joshua Heath, John Bourn, Jos. Stephens, Wm.[113] Smith, Jos. Simpson, John Weatherby, J. and Rd. Mare, Nic. Pool, John Yates, Chas. Hassells, Ann Warburton and son, Thos. Warburton, Wm. Meir.” A list of prices for dishes, tureens, saucers, etc., is given; and manufacturers of the present day will be interested to see the first attempt at checking those “rebates” which have successfully broken down this and all subsequent attempts to keep prices artificially high. “To allow no more than 5 per cent for breakage, and 5 per cent for ready money.” Then follows a sentence which misled Shaw and made him think that these potters made salt-glaze stoneware: “To sell to the manufacturers of earthenware at the above prices, and to allow no more than 7½ per cent, beside discount for breakage and prompt payment.”[118] It was the custom of many, particularly the larger manufacturers, to buy ware from other makers, either to decorate, or, more usually, to complete orders in lines which they did not happen to have in hand; (orders were far more all-embracing in those days). Thus we find William Greatbach starting a works at Lower Lane in 1762 under an agreement with[114] Wedgwood to be paid by him fixed prices for his ware.[119] In any case Shaw is obviously wrong in calling these men salt-glaze potters, for makers of salt glaze did not usually apply it to the baking dishes and chamber pots whose prices were under discussion; and it is only in common and standard lines that prices can ever be regulated by a ring. Makers of ornamental salt glaze would have been the last people to combine, and the only ones known to have been making salt glaze at this time, Christopher Whitehead and the Baddeleys, do not appear on this list of Shaw’s at all.
As early as 1770, we get a clear look at how the factory system worked. Some master potters that year tried, for the first time, to form a group to keep prices up. The agreement states: “We whose names are signed here do bind ourselves ... in £50 ... not to sell ... below the prices specified below, as witnessed by our signatures: John Platt, John Lowe, John Taylor, John Cobb, Robt. Bucknall, John Daniel, Thos. Daniel jun., Richd. Adams, Saml. Chatterley, Thos. Lowe, John Allen, Wm. Parrott, Jacob Warburton, Warburton and Stone, Jos. Smith, Joshua Heath, John Bourn, Jos. Stephens, Wm.[113] Smith, Jos. Simpson, John Weatherby, J. and Rd. Mare, Nic. Pool, John Yates, Chas. Hassells, Ann Warburton and son, Thos. Warburton, Wm. Meir.” A list of prices for dishes, tureens, saucers, etc., is included, and manufacturers today will find it interesting to see the first attempt at controlling those “rebates” which have effectively undermined this and all later efforts to keep prices artificially high. “To allow no more than 5 percent for breakage, and 5 percent for cash payments.” Then there’s a sentence that misled Shaw and made him think these potters produced salt-glaze stoneware: “To sell to the manufacturers of earthenware at the above prices, and to allow no more than 7.5 percent, in addition to discounts for breakage and prompt payment.”[118] It was common for many, particularly larger manufacturers, to buy ware from other makers, either for decoration or, more often, to fulfill orders for lines they didn't currently have in stock; (orders were much broader back then). So, we see William Greatbach starting a workshop at Lower Lane in 1762 under an agreement with[114] Wedgwood to be paid fixed prices for his ware.[119] In any case, Shaw is clearly mistaken in calling these men salt-glaze potters, as those who made salt glaze typically didn’t apply it to the baking dishes and chamber pots that were being priced; and it’s only with common and standard lines that prices can ever be regulated by a group. Makers of ornamental salt glaze would have been the last ones to band together, and the only known producers of salt glaze at that time, Christopher Whitehead and the Baddeleys, don’t appear on Shaw’s list at all.
The most notable potters on this list of 1770 were the Warburtons and the Daniels of Cobridge. When the art of enamelling became localized at Hot Lane about 1750, John and Ann Warburton were among the most successful. They were potters of old standing, for a Warburton appears as a master-potter in the Burslem district in 1710-15. They did most of the enamelling for Wedgwood in his early days, and their son, Jacob Warburton (1740-1826), became a potter of great repute, above all on the Continent where his business[115] was very extensive.[120] He spent many years travelling abroad and was a strange man among the rough potters of that day—a Roman Catholic, a great linguist, a famous skater; and for some reason he was always known as Captain Warburton. He was an intimate friend of Wedgwood, and in 1771 acted as his arbitrator in his case against Palmer.[121] When Enoch Booth invented the fluid glaze, the Warburtons were among the first to take it up, and their cream-coloured ware, enamelled with all their exceptional artistic skill, is often confounded with Wedgwood’s best productions.
The most notable potters on this list from 1770 were the Warburtons and the Daniels of Cobridge. When enamelling became established at Hot Lane around 1750, John and Ann Warburton were among the most successful potters. They had a long-standing reputation, as a Warburton was recorded as a master potter in the Burslem area between 1710 and 1715. They did most of the enamelling for Wedgwood during his early years, and their son, Jacob Warburton (1740-1826), became a well-known potter, especially on the Continent where his business[115] was quite extensive.[120] He spent many years traveling abroad and was quite unique among the rough potters of his time—a Roman Catholic, a skilled linguist, a famous skater; and for some reason, he was always referred to as Captain Warburton. He was a close friend of Wedgwood and served as his arbitrator in a case against Palmer in 1771.[121] When Enoch Booth invented the fluid glaze, the Warburtons were among the first to adopt it, and their cream-colored ware, decorated with their exceptional artistic skill, is often mistaken for Wedgwood’s finest products.
But to Jacob Warburton the Potteries are chiefly indebted for the revival of Littler’s attempt to introduce the manufacture of hard paste porcelain into Staffordshire. It will be remembered that Richard Champion of Bristol had in 1775 obtained an extension of his monopoly of the use of china clay and china stone in the manufacture of porcelain. In spite of this monopoly he met with but little success in Bristol, and in 1781 he sold his patent to a company in Staffordshire—the first[116] instance recorded of a potting company. Of this company Jacob Warburton was the moving spirit. After John Turner, of Lane End, and Anthony Keeling, of the Phœnix Works in Tunstall, had withdrawn from the scheme, the company—consisting then of Warburton, Sam. Hollins (the red china potter of Shelton) and two financiers—settled their manufactory at Shelton New Hall.[122] Their porcelain is always spoken of as “New Hall China,” but it was of little importance or artistic merit. John Daniel, son of that Richard Daniel who had introduced plaster of Paris moulds from France, was appointed manager and became a partner some years before his death in 1821.[123] Jacob Warburton himself died at Rushton in the old Abbey Grange in 1826, but even before that time the manufacture of hard paste porcelain at the New Hall had ceased.[124]
But Jacob Warburton is mainly responsible for reviving Littler’s attempt to start making hard paste porcelain in Staffordshire. It’s worth noting that Richard Champion from Bristol had secured an extension of his monopoly on the use of china clay and china stone in porcelain production back in 1775. Despite this monopoly, he had minimal success in Bristol, and in 1781, he sold his patent to a company in Staffordshire—the first recorded potting company. Jacob Warburton was the key figure in this company. After John Turner from Lane End and Anthony Keeling from the Phœnix Works in Tunstall pulled out of the venture, the company—now made up of Warburton, Sam. Hollins (the red china potter from Shelton), and two investors—set up their factory at Shelton New Hall. Their porcelain is always referred to as “New Hall China,” but it lacked significance or artistic value. John Daniel, the son of Richard Daniel who had brought plaster of Paris molds from France, was appointed manager and became a partner several years before he passed away in 1821. Jacob Warburton himself died at Rushton in the old Abbey Grange in 1826, but by then, the production of hard paste porcelain at New Hall had already stopped.
Another enameller who attained success by perfecting the cream-coloured ware was Elijah Mayer. He is said to have been originally foreign agent for the Chatterleys, and as late as 1787 he appears[117] as an enameller pure and simple, though already in business on his own account. Soon after this date his factory at Hanley began turning out not only cream colour, admirably enamelled in the sober artistic style of Wedgwood’s best Queen’s Ware, but also black basalt, which is every bit as good and has as good a reputation as the best that was turned out at Etruria.[125]
Another enameller who found success by perfecting the cream-colored pottery was Elijah Mayer. He is said to have originally worked as a foreign agent for the Chatterleys, and as late as 1787 he appears[117] as simply an enameller, even though he was already running his own business. Shortly after this, his factory in Hanley started producing not only cream color, beautifully enamelled in the refined artistic style of Wedgwood’s best Queen’s Ware, but also black basalt, which is just as good and has a reputation equal to the best produced at Etruria.[125]
Other very early makers of porcelain were Messrs Baddeley and Fletcher. For some time after 1763 they attempted, with William Littler as manager, to make glassy porcelain similar to that of Longton Hall. Mr Fletcher was the father of Sir Thomas Fletcher, M.P. for Newcastle, and ancestor of the Fletcher-Bougheys, Baronets of Aqualate. Mr John Baddeley the elder was the father of Ralph and John Baddeley, who carried on the works and made an early success with blue printed earthenware.[126]
Other early porcelain makers were Baddeley and Fletcher. For a while after 1763, they tried, with William Littler as manager, to create glassy porcelain similar to that of Longton Hall. Mr. Fletcher was the father of Sir Thomas Fletcher, M.P. for Newcastle, and an ancestor of the Fletcher-Bougheys, Baronets of Aqualate. Mr. John Baddeley the elder was the father of Ralph and John Baddeley, who continued the business and achieved early success with blue printed earthenware.[126]
The Chatterleys of Shelton were another very successful potting family of this date. Dr Samuel Chatterley made the ordinary black Egyptian teapots,[118] but Charles Chatterley went in for the newer cream colour and secured a large foreign connexion. His brother Ephraim became his partner, and ultimately carried on the business alone till 1793, when he handed it over to his nephews, James and Charles Whitehead, sons of Christopher Whitehead of the Old Hall Factory.[127] Ephraim Chatterley lived at what is now Chatterley House, and had the singular distinction of being, in 1784, the first of a long and honourable series of “mock mayors” of Hanley.[128] Though Hanley and Shelton were united in 1812, yet it was not till 1856 that they became incorporated as a borough, and obtained their first genuine Mayor, John Ridgway of Cauldon Place.
The Chatterleys of Shelton were another very successful pottery family at this time. Dr. Samuel Chatterley made the regular black Egyptian teapots,[118] but Charles Chatterley focused on the newer cream color and established a large foreign connection. His brother Ephraim became his partner and eventually ran the business on his own until 1793, when he passed it on to his nephews, James and Charles Whitehead, sons of Christopher Whitehead of the Old Hall Factory.[127] Ephraim Chatterley lived at what is now Chatterley House and had the unique distinction of being, in 1784, the first in a long and honorable line of “mock mayors” of Hanley.[128] Although Hanley and Shelton were united in 1812, it wasn’t until 1856 that they became officially incorporated as a borough and got their first real Mayor, John Ridgway of Cauldon Place.
The list of potters of 1787, which has already been quoted from, occurs in a rare “Survey of Staffordshire” made by Wm. Tunnicliffe. The Survey consists of little but an itinerary of the main roads, and lists of the manufacturers in each town. As we have to rely so much on the fallible recollections of Shaw, this piece of contemporary evidence is worth quoting in full.
The list of potters from 1787, which we've referenced before, can be found in a rare “Survey of Staffordshire” created by Wm. Tunnicliffe. The Survey mainly consists of a guide to the main roads and includes lists of manufacturers in each town. Since we heavily depend on the unreliable memories of Shaw, this piece of contemporary evidence is worth quoting in full.
“Survey of the Counties of Stafford, Chester and Lancaster, compiled and published at Namptwich in 1787 by Wm. Tunnicliffe, land surveyor, of Yarlet near Stone; and a Directory of the principal merchants and manufacturers.”
“Survey of the Counties of Stafford, Chester and Lancaster, compiled and published at Nantwich in 1787 by Wm. Tunnicliffe, land surveyor, of Yarlet near Stone; and a Directory of the main merchants and manufacturers.”
In the Potteries they give:—
In the Potteries, they provide:—
- Burslem.
- (a) Wm. Adams & Co. Cream-coloured ware and China glaze ware painted.
- Wm. Bagley, potter.
- John Bourne, China glaze, blue painted, enamelled and cream coloured earthenware.
- Bourne & Malkin, China glaze, blue painted, enamelled and cream coloured earthenware.
- S. & J. Cartlidge, potters.
- Thos. Daniel, potter.
- John Daniel, cream colour and red earthenware.
- Timothy Daniel, Do. do.
- (b) Walter Daniel, Do. do.
- John Graham jun., white stone, and enamelled white and cream earthenware.
- John Green.
- (c) Thos. Holland, black and red china ware, and gilder.
- (d) Anthony Keeling, Queens ware in general, blue painted, and enamelled, and Egyptian black.
- Timothy & John Lockett, white stone potters.
- Burnham Malkin.
- (e) John Robinson, enameller and printer of cream colour and china glazed ware.
- (f) John & George Rogers, china glazed, blue painted, and cream coloured ware.
- Ambrose Smith & Co., cream coloured ware, china glazed, blue painted.
- John & Joseph Smith.
- Chas. Stevenson & sons, cream coloured ware, blue painted.[120]
- Thos. Wedgwood, (Big House), cream coloured ware, china glazed, painted with blue etc.
- Thos. Wedgwood, (Overhouse), cream coloured ware, china glazed, painted with blue etc.
- James Wilson, enameller.
- (g) John Wood, potter.
- (h) Enoch & Ralph Wood, all kinds of useful and ornamental earthenware, Egyptian black, cane, and various other colours, also black figures, seals and cyphers.
- Josiah Wood [sic, but should be Wedgwood], fine black, glazed, variegated and cream coloured ware, and blue.
- Cobridge.
- Joseph Blackwell, blue and white stone ware, cream and painted ware.
- John Blackwell, Do. do.
- Robert Blackwell, Queens ware, blue painted, enamelled, printed etc.
- Thos. & Benj. Goodwin, Queens ware and china glazed blue.
- Hales & Adams, potters.
- Robinson & Smith, potters.
- Jacob Warburton, potter.
- Handley.
- Sampson Bagnall, potter.
- Joseph Boon, potter.
- C. & E. Chatterley, potters.
- (i) John Glass, potter.
- (j) Heath [sic], Warburton & Co., china manufacturers.
- Edw. Keeling, potter.
- John & Ric. Mare, potters.
- Elijah Mayer, enameller.
- Wm. Miller, potter.
- (k) Neale & Wilson, potters.
- Samuel Perry, potter.
- Geo. Taylor, potter.
- Thos. Wright, potter.
- John Yates, potter.[121]
- Shelton.
- J. & E. Baddeley.
- John Hassells.
- Heath & Bagnall.
- (l) Samuel Hollins.
- Anthony Keeling.
- Taylor & Pope.
- G. Twemlow.
- (m) Christopher & Charles Whitehead.
- (n) John Yates.
- Stoke.
- Sarah Bell, potter.
- (o) Hugh Booth, china, china glazed, and Queens ware in all its branches.
- James Brindley, potter.
- (p) Josiah Spode, potter.
- Joseph Straphan, merchant and factor in all kinds of earthenware.
- (q) Thos. Woolfe, Queens ware in general, blue printed and Egypt black, cane, etc.
- Fenton.
- Wm. Bacchus, Queens ware in all its various branches.
- Edw. Boon, Queens ware and blue painted.
- Taylor Brindley, potter.
- Clowes & Williamson, potters.
- John Turner, potter.
- Josiah & Thos. Wedgwood, potters.
- Lane End.
- John Barker, cream colour, china glaze and blue wares.
- Wm. Barker, potter.
- Ric. Barker, potter.
- (r) Joseph Cyples, Egyptian black and pottery in general.
- Wm. Edwards, potter.
- Forrester & Meredith, Queensware, Egypt black, red china, etc.
- Joseph Garner, potter.[122]
- (s) Robert Garner, Queens ware and various other wares.
- Michael Shelley, potter.
- Thos. Shelley, potter.
- Turner & Abbott, potters.
- (t) Mark Walklate, potter.
(a) Of Greengates Tunstall; (b) afterwards of Newport; (c) of Hill Top; (d) of the Phœnix Works, Tunstall; (e) of Hill Top; (f) of Longport; (g) of Brownhills; (h) of Fountain Place; (i) of Market St.; (j) of Shelton New Hall; (k) of High St.; (l) of Vale Pleasant; (m) of Shelton Old Hall; (n) of Broad St. Works; (o) of Cliffgate Bank; (p) afterwards Copelands; (q) afterwards Adams’; (r) of Market St., Longton; (s) of the Foley Works; (t) of High St., Longton.
(a) Of Greengates Tunstall; (b) afterwards of Newport; (c) of Hill Top; (d) of the Phoenix Works, Tunstall; (e) of Hill Top; (f) of Longport; (g) of Brownhills; (h) of Fountain Place; (i) of Market St.; (j) of Shelton New Hall; (k) of High St.; (l) of Vale Pleasant; (m) of Shelton Old Hall; (n) of Broad St. Works; (o) of Cliffgate Bank; (p) afterwards Copelands; (q) afterwards Adams’; (r) of Market St., Longton; (s) of the Foley Works; (t) of High St., Longton.
Of course this list is fallible. Josiah and Thomas Wedgwood potted at Etruria, not Fenton; John Turner, shown at Fenton, should probably be the Turner of Lane End; the Josiah “Wood” of Burslem is almost certainly Josiah Wedgwood, who owned at that time the old Churchyard Works, in which he had been born. (They were sold in 1795 to Thomas Green, and on his bankruptcy in 1811 passed to John Moseley). Again, both S. and J. Cartlich, and Wm. Adams, who certainly potted at Golden Hill and Greengates respectively, are included with other Tunstall potters in the Burslem list.
Of course, this list has its errors. Josiah and Thomas Wedgwood worked at Etruria, not Fenton; John Turner, who is listed at Fenton, should likely refer to the Turner from Lane End; the Josiah "Wood" from Burslem is almost certainly Josiah Wedgwood, who at that time owned the old Churchyard Works, where he was born. (These were sold in 1795 to Thomas Green, and after his bankruptcy in 1811, they were passed on to John Moseley). Additionally, both S. and J. Cartlich, along with Wm. Adams, who definitely worked at Golden Hill and Greengates respectively, are mistakenly included with other Tunstall potters in the Burslem list.

WILLIAM ADAMS
WILLIAM ADAMS
1777-1805
1777-1805
This William Adams of Greengates (1745-1805)[129] achieved a great reputation for his Jasper[123] and Black Basalt ware. He was a cadet of the Adams family, a family which is almost as much identified with the potting industry as is the family of Wedgwood. Four generations had potted at Burslem “Brickhouse” in succession to Thomas Adams who died a “potter” in 1629, and at the end of the eighteenth century the representative of this branch of the family, another William Adams, was a master-potter at Cobridge, and could lay some claim to the introduction of under-glaze blue printing into Staffordshire. The life of Adams of Greengates is given in “William Adams—an old English Potter,” Ed. by Wm. Turner, F.S.S. Born in 1745, he was apprenticed to Josiah Wedgwood, and became his most adept pupil. He commenced manufacturing on his own account at Greengates about 1787, and the jasper he turned out is difficult to distinguish from that of Wedgwood. No doubt he had full particulars of body and firing, but other potters had that information and yet failed to produce the same class of ware.[130] This William Adams died in 1805, and his son wasted his property and sold the Greengates[124] works about 1820 to John Meir.[131] Of recent years, however, the Greengates works have been repurchased by the senior branch of the Adams family, and it is now managed in conjunction with their old Greenfield works adjoining.
This William Adams of Greengates (1745-1805)[129] achieved a significant reputation for his Jasper[123] and Black Basalt ware. He was a member of the Adams family, which is nearly as closely associated with the pottery industry as the Wedgwood family. Four generations of potters worked at Burslem “Brickhouse” following Thomas Adams, who passed away as a “potter” in 1629. By the end of the eighteenth century, a different William Adams, representing this branch of the family, was a master potter at Cobridge and had some claim to introducing under-glaze blue printing into Staffordshire. The life of Adams of Greengates is detailed in “William Adams—an old English Potter,” edited by Wm. Turner, F.S.S. Born in 1745, he apprenticed under Josiah Wedgwood and became his most talented student. He started his own manufacturing at Greengates around 1787, and the jasper he produced is hard to tell apart from Wedgwood's. He likely had complete knowledge of body and firing techniques, but other potters had that information too and still couldn’t create the same quality of ware.[130] This William Adams passed away in 1805, and his son squandered his inheritance and sold the Greengates[124] works around 1820 to John Meir.[131] In recent years, however, the Greengates works have been reacquired by the senior branch of the Adams family, and it is now managed alongside their old Greenfield works next door.
For the first time in 1787 the mail coaches to London began to run daily. The best days of coach travel were yet to come, but even these early coaches kept up a steady seven miles an hour. Their time table is given as follows: London (“Swan with Two Necks”) 9 p.m., St Albans 11 p.m., Coventry 9 a.m., Lichfield 1 p.m., Stone 5 p.m., Newcastle (149 miles) 7 p.m., Warrington 2 a.m., Carlisle 2 p.m.[132]
For the first time in 1787, mail coaches to London started running daily. The best days of coach travel were still ahead, but even these early coaches maintained a steady speed of seven miles an hour. Their timetable is as follows: London (“Swan with Two Necks”) 9 p.m., St Albans 11 p.m., Coventry 9 a.m., Lichfield 1 p.m., Stone 5 p.m., Newcastle (149 miles) 7 p.m., Warrington 2 a.m., Carlisle 2 p.m.[132]

JOHN WOOD OF BROWNHILLS
John Wood of Brownhills
1746-1797
1746-1797
Three other potters on the 1787 list deserve special mention: John, Ralph and Enoch Wood. They all came of one still celebrated potting family. Ralph Wood, miller, of Burslem, was their common ancestor. His eldest son, Ralph, was a modeller of distinction, and about 1754 started a works at Burslem, where he, and his son Ralph after him, made those quaint Staffordshire figures now in such demand. They are usually decorated[125] with coloured tortoiseshell glaze, applied with a brush, and have a singularly decorative effect. Ralph Wood, the first figure maker of the name, married the sister of that Aaron Wedgwood who had once made china at Longton Hall. He died in 1772, and was succeeded in his work by his sons John and Ralph.[133] John Wood soon left his brother, and began, in 1782,[134] to pot at Brownhills. Ralph kept to figures, and adopted the enamel process of decoration for some of his busts and figures. Other makers who were prolific in this style of figure decoration were John Walton of Burslem (1800-40), Robert Garner of Lane End, c. 1786, son of that Robert Garner of the Foley Works who married Margaret Astbury, Ralph Salt of Hanley (1812-46), Lakin and Poole of Hanley (1770-94).[135]
Three other potters on the 1787 list are worth mentioning: John, Ralph, and Enoch Wood. They all came from a well-known pottery family. Ralph Wood, a miller from Burslem, was their common ancestor. His eldest son, Ralph, was a distinguished modeller who started a workshop in Burslem around 1754, where he and his son Ralph after him created the charming Staffordshire figures that are now very sought after. These figures are typically decorated with colorful tortoiseshell glaze applied with a brush, resulting in a uniquely decorative look. Ralph Wood, the first figure maker of that name, married the sister of Aaron Wedgwood, who had once produced china at Longton Hall. He passed away in 1772, and his sons John and Ralph took over his work. John Wood soon parted ways with his brother and began potting at Brownhills in 1782. Ralph focused on figures and used enamel decoration for some of his busts and figures. Other potters who were also known for this style of figure decoration included John Walton from Burslem (1800-40), Robert Garner from Lane End, circa 1786, the son of Robert Garner of the Foley Works who married Margaret Astbury, and Ralph Salt from Hanley (1812-46), along with Lakin and Poole from Hanley (1770-94).
Meanwhile the eldest son, John Wood, was making ordinary earthenware at Brownhills. This John Wood was murdered in 1797 by Dr Oliver[126] of Burslem, a rejected suitor of his daughter.[136] His son married the heiress of John Wedgwood of Bignal End, with whom he acquired a large fortune.[137] He removed the factory from Brownhills to Tunstall, where he erected the Woodlands Works in 1831-5.[138] A third John Wedg Wood of Brownhills carried on these pot works in Tunstall in partnership with Mr Edward Challenor. He died in 1857, and was succeeded at the Woodlands Works by his brother Edmund Thomas Wedg Wood. This factory was in 1887 sold to Mr W. H. Grindley.[139]
Meanwhile, the eldest son, John Wood, was making regular earthenware at Brownhills. This John Wood was murdered in 1797 by Dr. Oliver[126] of Burslem, who had been rejected as a suitor for his daughter.[136] His son married the heiress of John Wedgwood of Bignal End, and with her, he gained a substantial fortune.[137] He moved the factory from Brownhills to Tunstall, where he built the Woodlands Works between 1831 and 1835.[138] A third John Wedg Wood from Brownhills continued these pottery works in Tunstall in partnership with Mr. Edward Challenor. He passed away in 1857 and was succeeded at the Woodlands Works by his brother Edmund Thomas Wedg Wood. This factory was sold in 1887 to Mr. W. H. Grindley.[139]
Ralph Wood, the miller, had another son—that Aaron Wood who made for himself so great a reputation as a block cutter when block moulds were first introduced and the salt glaze was at the height of its glory. Aaron Wood worked for Dr Thomas Wedgwood, Thomas Mitchell of the Hill Top Works, Burslem, and for Whieldon of Fenton. His eldest son, William, was apprenticed to Josiah Wedgwood in 1762, and worked with[127] him, first at the Burslem “useful” works, and afterwards at Etruria, all his life long. Most of the Queen’s Ware articles made by Wedgwood are said to be from block moulds of his carving.[140]
Ralph Wood, the miller, had another son—Aaron Wood, who built a great reputation as a block cutter when block molds were first introduced and salt glaze was at its peak. Aaron Wood worked for Dr. Thomas Wedgwood, Thomas Mitchell of the Hill Top Works, Burslem, and Whieldon of Fenton. His eldest son, William, was apprenticed to Josiah Wedgwood in 1762 and worked with[127] him, first at the Burslem "useful" works and later at Etruria, his entire life. Most of the Queen’s Ware pieces made by Wedgwood are said to be from block molds of his carving.[140]
But it was the youngest son of Aaron Wood, Enoch by name, to whom potters of all time are most indebted, for he was the first collector of pottery. And he collected it to illustrate specially what his family and district had done, and how the industry had progressed. His splendid collection was never catalogued, and as it was divided into four parts at his death and scattered,[141] it is of less value than it ought to have been; but, without it, this or any account of the North Staffordshire Potters’ work must have been a shadow indeed.
But it was the youngest son of Aaron Wood, Enoch, who potters everywhere owe the most to, since he was the first person to collect pottery. He gathered it to showcase what his family and region had accomplished and how the industry had evolved. His amazing collection was never cataloged, and when he passed away, it was split into four parts and scattered, which diminishes its value more than it should have had; however, without it, any account of the work done by the North Staffordshire Potters would have been insignificant.
Enoch Wood (1759-1840) was apprenticed to Palmer of Hanley and remained there some time as a modeller. In 1783 he commenced business at[128] Fountain Place, Burslem, so called from the fountain or pump which he erected there for his factory and work people.[142] He was at first in partnership with his cousin Ralph Wood, who made the Staffordshire figures. About 1790 he was joined by James Caldwell of Lindley Wood, and the firm became “Wood and Caldwell.” He bought Mr Caldwell out in 1819, and thenceforth conducted business as “Enoch Wood and Sons.” He had 12 children and died in 1840 at Fountain Place, the patriarch of the Potteries. His most famous work probably was the well-known bust of John Wesley, made in 1781 when Wesley was stopping at his house during one of his preaching tours in the Potteries. His factory turned out the usual cream colour, black basalt and jasper,[143] but soon after his death the firm got into financial difficulties and closed down. His third son, Edward, was fortunate in being associated with a clever Italian, Count Kuntz, in the development of Italian borax, introduced into the Potteries first in 1828 as a flux for the glaze. In this new business[129] they realized a fortune, and Edward Wood’s descendants are now settled at Browhead in Cumberland. But the borax works in Newcastle are carried on as “H. Coghill and Son” by Douglas and Archibald Coghill.
Enoch Wood (1759-1840) was apprenticed to Palmer of Hanley and worked there for some time as a model maker. In 1783, he started his own business at[128] Fountain Place, Burslem, named after the fountain or pump he built for his factory and employees.[142] He initially partnered with his cousin Ralph Wood, who created Staffordshire figures. Around 1790, he teamed up with James Caldwell from Lindley Wood, and the business became “Wood and Caldwell.” He bought Caldwell out in 1819, and from then on operated as “Enoch Wood and Sons.” He had 12 children and passed away in 1840 at Fountain Place, hailed as the patriarch of the Potteries. His most famous work is likely the well-known bust of John Wesley, created in 1781 while Wesley was staying at his home during one of his preaching tours in the Potteries. His factory produced typical cream color, black basalt, and jasper,[143] but shortly after his death, the firm faced financial issues and shut down. His third son, Edward, was fortunate to partner with a talented Italian, Count Kuntz, to develop Italian borax, introduced into the Potteries for the first time in 1828 as a flux for the glaze. This new venture[129] made them a fortune, and Edward Wood’s descendants now live in Browhead, Cumberland. However, the borax works in Newcastle are operated as “H. Coghill and Son” by Douglas and Archibald Coghill.

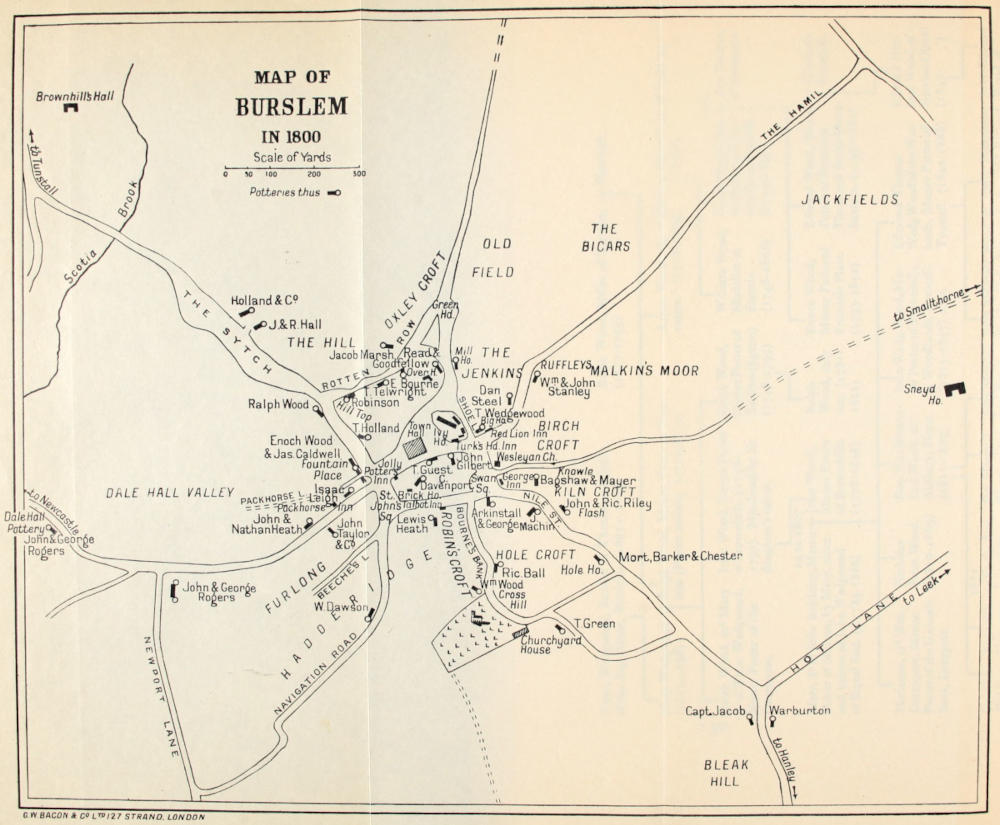
MAP OF BURSLEM IN 1800
Burslem Map, 1800
When earthenware or salt glaze was enamelled at Hot Lane it required artists to do the work. But the eighteenth century was the age of mechanical invention, and the hand artists were continually being superseded by mechanical processes. Saddler and Green, for instance, invented the method of printing designs on top of the glaze, so that the artist had only to fill in the outline with colours. But there was something hard and crude about the effect of the on-glaze printing, which prevented it ever really competing with the best hand-painted ware. The under-glaze printing, particularly the under-glaze blue printing, was a more difficult competitor for the artist to meet; for the glaze gave a rich soft tone to the colouring matter underneath it which was partly absorbed in the biscuit ware. And if this blue printing, with which the willow pattern will be always associated, drove out the girl artists from[132] their pleasant work on the pot-banks, yet the new decoration caused an enormous expansion in the demand for cream-coloured earthenware. From 1790 onwards “blue printed” seems to have superseded every other sort of earthenware. It was the first opportunity common folk had had of getting a decorative plate to eat off; and it made the fortunes of the Spodes, the Adamses, the Bournes, the Mintons, the Ridgways, and many another master of the good old days. As a mechanical process under-glaze printing was an unqualified success, and in course of time the artists too rediscovered their work in decorating that porcelain which, on the tables of the rich, replaced the now vulgarized earthenware. The last ten years of the eighteenth century were devoted to blue printed, but with the new century came that development of Staffordshire porcelain with which run the names of Spode, Minton and Davenport.
When earthenware or salt glaze was enamelled at Hot Lane, it needed artists to do the work. But the eighteenth century was a time of mechanical invention, and hand artists were continually replaced by mechanical processes. For example, Saddler and Green came up with a method of printing designs on top of the glaze, allowing the artist to simply fill in the outlines with colors. However, the on-glaze printing looked harsh and rough, which kept it from truly competing with the best hand-painted ware. The under-glaze printing, especially the under-glaze blue printing, was more challenging for artists to contend with since the glaze gave a rich, soft tone to the color beneath it, which was partially absorbed into the biscuit ware. Although this blue printing, which will always be linked to the willow pattern, pushed female artists out of their enjoyable work at the pot-banks, it also led to a huge increase in the demand for cream-colored earthenware. From 1790 onward, “blue printed” seemed to take over every other type of earthenware. It was the first time everyday people could afford a decorative plate for dining, and it created fortunes for the Spodes, Adamses, Bournes, Mintons, Ridgways, and many other masters of that time. As a mechanical process, under-glaze printing was a complete success, and eventually, artists rediscovered their craft in decorating the porcelain that replaced the now-common earthenware on the tables of the wealthy. The last decade of the eighteenth century focused on blue printing, but with the start of the new century came the rise of Staffordshire porcelain, linked with the names Spode, Minton, and Davenport.
The first Josiah Spode made no porcelain. He set the fashion in “blue printed,” and his blue printed is probably the best of its kind ever made. Born in 1733, Spode was apprenticed to Whieldon, and after leaving him about 1759 he worked for[133] Banks of Stoke.[144] It is said of him that he dearly loved to play the fiddle, and he would go out any evening to play at public-houses for his friends. So that “ready and willing as Spode’s fiddle” became a proverb in the Potteries.
The first Josiah Spode didn't make porcelain. He set the trend for “blue printed” pottery, and his blue printed pieces are probably the best ever made. Born in 1733, Spode was apprenticed to Whieldon, and after leaving him around 1759, he worked for[133] Banks of Stoke.[144] It's said that he really enjoyed playing the fiddle and would go out any evening to play at pubs for his friends. Because of this, the saying “ready and willing as Spode’s fiddle” became a proverb in the Potteries.
In 1770 he leased Banks’ works in the centre of Stoke, and began making printed cream colour. This was the old “on-glaze,” or “black” printed ware, used to guide the enameller rather than as a decoration by itself. Cobalt was a cheap paint, and the designs were filled in with blue. This was becoming the common ware, and invention was busy to simplify the process. Attempts were made by William Adams of Cobridge and, about 1777, by John Baddeley of Shelton to print in blue upon the biscuit ware before the ware was glazed, but without any commercial success.[145] It was Turner of Worcester who first found a satisfactory way of transferring an oily-coloured pattern from a copper plate to a sheet of transfer paper, and then from the paper to the biscuit ware. He too designed the willow pattern which seems likely to characterize[134] “blue printed” for all time. This was in 1780, and in 1783 Spode got two men from the Caughley china works, near Worcester, and they taught him to print in blue under the glaze on earthenware, as they did on china at Worcester. The invention spread with enormous rapidity and Spode made his fortune. He died in 1797,[146] leaving his son Josiah Spode II to carry on his business.
In 1770, he leased Banks' works in the center of Stoke and started making printed cream color. This was the old “on-glaze” or “black” printed ware, used to guide the enameller rather than as a decoration on its own. Cobalt was an inexpensive paint, and the designs were filled in with blue. This was becoming the common ware, and innovation was focused on simplifying the process. William Adams of Cobridge and, around 1777, John Baddeley of Shelton attempted to print in blue on the biscuit ware before it was glazed, but they had no commercial success.[145] It was Turner of Worcester who first found a reliable way to transfer an oily-colored pattern from a copper plate to a sheet of transfer paper, and then from the paper to the biscuit ware. He also designed the willow pattern, which seems likely to define “blue printed” for all time. This was in 1780, and in 1783, Spode brought in two men from the Caughley china works near Worcester, and they taught him to print in blue under the glaze on earthenware, as they did on china at Worcester. The invention spread rapidly, and Spode made his fortune. He died in 1797,[146] leaving his son, Josiah Spode II, to carry on his business.
The second Spode married in 1779 the eldest daughter of John Barker, master potter of the Row Houses, Fenton. He had been a dealer in earthenware, glass and china in London. William Copeland, a native of Stoke, had been his traveller and assistant in London. On his father’s death young Spode made Copeland his partner and put him in charge of the London office. Even in his father’s lifetime Spode had begun decorating their ware with the Japan reds and blues and heavy gilding that was afterwards the distinguishing mark of Spode and Copeland porcelain; and in 1800 they began to make their bone-paste porcelain.[147]
The second Spode got married in 1779 to the eldest daughter of John Barker, a master potter from the Row Houses in Fenton. Barker had been a seller of earthenware, glass, and china in London. William Copeland, who was from Stoke, had worked as Barker’s salesman and assistant in London. After his father passed away, young Spode made Copeland his partner and assigned him to manage the London office. Even during his father's lifetime, Spode had started decorating their ware with Japan reds and blues, along with heavy gilding, which later became the signature style of Spode and Copeland porcelain. In 1800, they began producing their bone-paste porcelain.[147]

JOSIAH SPODE
JOSIAH SPODE
1754-1827
1754-1827
Porcelain is a transparent vitreous body which fuses on being fired, and does not require any glaze. The early porcelain had been made largely of glass; Cookworthy’s porcelain, and that made at Shelton New Hall, relied solely on china clay and china stone from Cornwall. None of these bodies were certain, and they failed to become commercial successes. But when the New Hall Company ceased, the manufacture of their hard-paste porcelain in England ceased too, and an entirely new porcelain body was destined to take its place. It was not until Spode introduced bone into the body that the cheap china we know to-day could be produced.[148]
Porcelain is a transparent, glass-like material that melts when fired and doesn’t need any glaze. Early porcelain was mainly made from glass; Cookworthy’s porcelain and that made at Shelton New Hall used only china clay and china stone from Cornwall. None of these materials were reliable, and they didn’t become commercial successes. However, when the New Hall Company went out of business, the production of their hard-paste porcelain in England stopped as well, leading to the creation of a completely new type of porcelain. It wasn’t until Spode added bone to the mixture that the affordable china we know today could be made.[148]
The modern soft-paste bone porcelain consists of nearly equal portions of china clay, china stone and bone ash, fired to a temperature of about 1250 C. and then glazed with a feldspar and china-clay glaze and refired.[149] The chief porcelain factories at this time were at Worcester and Derby, but they were soon outdistanced and beaten by the[136] better conducted factories of Spode, Minton and Davenport, who managed to centre the china trade in North Staffordshire, just as the earthenware trade had been localized there in the previous century.
The modern soft-paste bone china is made up of nearly equal parts of china clay, china stone, and bone ash, fired at about 1250°C, and then glazed with a feldspar and china clay glaze before being refired.[149] At this time, the main porcelain factories were in Worcester and Derby, but they were quickly surpassed by the better-managed factories of Spode, Minton, and Davenport, which managed to establish the china trade in North Staffordshire, just as the earthenware trade had been centralized there in the previous century.
To modern taste all the china of the first half of the nineteenth century, with its florid colouring and lavish gilding, seems to warrant little success or praise. In their own day however the success of the Spodes was very great. The second Spode died in 1827; William Copeland had died in the previous year, and in 1833 a third Josiah Spode died also. From the executors of the last Spode the whole factory was bought by William Taylor Copeland, M.P., the second of the name, Alderman of the City of London.
To today's taste, all the china from the first half of the nineteenth century, with its bright colors and heavy gold trim, doesn’t seem to deserve much success or praise. However, during its time, the Spodes were extremely popular. The second Spode passed away in 1827; William Copeland had died the year before, and in 1833, the third Josiah Spode also died. William Taylor Copeland, M.P., the second of his name and an Alderman of the City of London, bought the entire factory from the executors of the last Spode.

HERBERT MINTON
Herbert Minton
1793-1858
1793-1858
Mintons have long been the historic rivals of Copeland, late Spode. Their factories are almost side by side in Stoke, lying along the Newcastle canal, which was cut in 1795. Just across the Trent, too, lay Whieldon’s old works at Little Fenton. Wedgwood, in his list of the potters of 1715, says that there were then only two factories in Stoke—Ward’s and Poulson’s. He meant probably[137] that the factories carried on when he wrote in 1785 by Ward and Poulson were in existence in 1715. However that may be, in 1793 Thomas Minton, financed by a Mr Pownall, joined Joseph Poulson, a practical potter already at work, and began to make “blue-printed” ware at Stoke.[150] A few years later they began to make porcelain. In 1802 the firm was “Minton, Poulson & Co.,” and by 1817 it had become “Thomas Minton & Sons.” This first Minton died in 1836, and it was his son, Herbert Minton (1793-1858), that brought the Minton china to its highest perfection, and started the manufacture of encaustic and dust tiles.
Mintons have long been the historical rivals of Copeland, formerly known as Spode. Their factories are almost next to each other in Stoke, situated along the Newcastle canal, which was constructed in 1795. Just across the Trent, you can also find Whieldon’s old works at Little Fenton. Wedgwood, in his list of potters from 1715, notes that there were only two factories in Stoke at that time—Ward’s and Poulson’s. He likely meant that the factories operated by Ward and Poulson when he wrote in 1785 were already in existence in 1715. Regardless, in 1793, Thomas Minton, backed by Mr. Pownall, teamed up with Joseph Poulson, a skilled potter already in operation, and began producing “blue-printed” ware in Stoke.[150] A few years later, they expanded to making porcelain. By 1802, the firm was known as “Minton, Poulson & Co.,” and by 1817, it had changed to “Thomas Minton & Sons.” This original Minton passed away in 1836, and it was his son, Herbert Minton (1793-1858), who brought Minton china to its highest level of excellence and began the production of encaustic and dust tiles.
A word should be said here on the methods of gilding—so marked a feature of both Spode and Minton china. Originally, when gilding was put on the ware, it was laid on in the form of gold-leaf, and attached with printers’ size. This sort of gilding does not usually wear well, and it was only in his very late years that Wedgwood began to burn gold into the ware.[151] About 1790, the[138] method of painting on the gold with mercury, and burnishing it afterwards, was introduced from the Continent, and a new decoration was super-imposed upon the already overladen ware. It is only within the last decade that a form of liquid gold has been discovered which requires no burnishing, and yet is fairly durable.
A note should be made about the methods of gilding—such a distinctive aspect of both Spode and Minton china. Initially, when gilding was applied to the items, it was done using gold leaf and secured with printers’ size. This style of gilding typically doesn't last long, and it was only in his later years that Wedgwood started to fuse gold into the pieces. About 1790, the technique of painting gold with mercury and then burnishing it afterward was brought in from the Continent, adding yet another layer of decoration to the already intricate pieces. Only in the last ten years has a type of liquid gold been developed that doesn’t need burnishing and is fairly durable.
Another form of decoration in which gold was employed was lustre ware. Mr Burton thinks the application of a gold lustre to Staffordshire pottery was introduced first about 1792 at Etruria, and was used on Wedgwood’s “Pearl” dessert ware, made in the form of shells. If this lustre, or silver lustre, is laid on thickly, it converts the earthenware in appearance into gold or silver plate—an inartistic transformation. When, however, the lustre is thinly applied, the glaze of the ware is stained to a purplish-pink colour, on which the metallic lustre sparkles like shot silk. The newly discovered metal platinum was used to produce the similar silver lustre, and during the period 1792-1810 many fine pieces were produced by the Wedgwoods (and by, among others,[139] John Aynsley of Longton), covered with either the gold or silver plating or lustre.[152]
Another way gold was used for decoration was in lustre ware. Mr. Burton believes that the application of gold lustre to Staffordshire pottery was first introduced around 1792 at Etruria, and it was used on Wedgwood’s “Pearl” dessert ware, shaped like shells. When this lustre, or silver lustre, is applied thickly, it makes the earthenware look like gold or silver plating, which isn't very artistic. However, when the lustre is applied thinly, the glaze of the ware is stained to a purplish-pink color, and the metallic lustre sparkles like shot silk. The newly discovered metal platinum was used to create a similar silver lustre, and from 1792 to 1810, many fine pieces were made by the Wedgwoods (and others, including [139] John Aynsley of Longton), covered with either gold or silver plating or lustre.[152]
Other Stoke potters at the end of the eighteenth century were the Booths of Cliff Bank, and Thomas Woolfe. Their factories are both shown on the map of the Potteries in 1802 which is here inserted. Hugh Booth (1732-89)[153] made a considerable fortune, and was succeeded by his brother and nephews, Ephraim, Hugh and Joseph Booth. Thomas Woolfe (died 1818)[154] contests with the elder Spode[155] the credit of being the first to employ steam power in their factories, to drive the flint and glaze mills. Both Aikin and Shaw agree in dating this innovation about 1793. Woolfe’s son-in-law, Robert Hamilton, joined the firm for a time, but before 1817 the factories of both Woolfe and the Booths had passed into the hands of William Adams (1772-1829), the successful progenitor of the present potting family of Adams.
Other Stoke potters at the end of the eighteenth century were the Booths of Cliff Bank and Thomas Woolfe. Their factories are both shown on the map of the Potteries in 1802, which is included here. Hugh Booth (1732-89)[153] made a significant fortune and was succeeded by his brother and nephews, Ephraim, Hugh, and Joseph Booth. Thomas Woolfe (died 1818)[154] competes with the elder Spode[155] for credit as the first to use steam power in their factories to operate the flint and glaze mills. Both Aikin and Shaw agree that this innovation occurred around 1793. Woolfe’s son-in-law, Robert Hamilton, joined the firm for a time, but before 1817, the factories of both Woolfe and the Booths had come under the control of William Adams (1772-1829), the successful ancestor of the current potting family of Adams.
Yet another Staffordshire family founded on “blue-printed” ware is that of Ridgway. Ralph Ridgway was a master-potter at Chell, who failed in business in 1766, and departed with his family to Swansea, where the manufacture of porcelain was just commencing.[156] His younger son, Job (1759-1813), returned to the Potteries in 1781, and divided his time between acting as a Wesleyan missionary and work as a journeyman potter in Hanley.[157] There for some time he also manufactured lawn for the sieves used in sifting the clay slip, but this he gave up, on the strange ground that it led to bribery and drunkenness, and returned to his potter’s bench. At last, in 1792, he and his brother George started a factory of their own in Shelton, at the bottom of Albion Street, said to have been formerly[141] that of Warner Edwards.[158] It has been the “Bell Works,” from the Blue Bell Inn which stood opposite. Of course they made “blue printed,” and prospered. In 1802 Job left his brother, and built the well-known house and works at Cauldon Place on the Cauldon canal, now occupied by the porcelain works of Brown, Westhead, Moore & Co.[159] At Cauldon Place the firm, “Job Ridgway & Sons,” began in 1808 to make china. Here, too, Job died in 1813, and was succeeded by his son John Ridgway, under whom the Cauldon Place china achieved so great renown. His other son William went back to the Bell Works, and, adding factory to factory, soon became by far the most important potter in Hanley.
Another Staffordshire family known for “blue-printed” ware is the Ridgways. Ralph Ridgway was a master potter in Chell who went out of business in 1766 and relocated with his family to Swansea, where porcelain manufacturing was just starting. His younger son, Job (1759-1813), returned to the Potteries in 1781 and split his time between being a Wesleyan missionary and working as a journeyman potter in Hanley. For a while, he also produced lawn for the sieves used in sifting the clay slip, but he stopped, claiming it led to bribery and drunkenness, and returned to his potter’s bench. Finally, in 1792, he and his brother George opened their own factory in Shelton, at the bottom of Albion Street, which was reportedly once that of Warner Edwards. It became known as the “Bell Works,” named after the Blue Bell Inn that was across the street. Naturally, they produced “blue printed” ware and thrived. In 1802, Job parted ways with his brother and built the well-known house and factory at Cauldon Place on the Cauldon canal, now home to the porcelain works of Brown, Westhead, Moore & Co. At Cauldon Place, the firm “Job Ridgway & Sons” began making china in 1808. Job passed away there in 1813 and was succeeded by his son John Ridgway, under whom the Cauldon Place china gained great fame. His other son William returned to the Bell Works and, by adding factory after factory, quickly became the most significant potter in Hanley.

JOB RIDGWAY
JOB RIDGWAY
1759-1813
1759-1813
Photo by H. J. Gover & Co., Hanley
Photo by H. J. Gover & Co., Hanley
Job Ridgway married the sister of Elijah Meyer, and made the fortune of his family. But his potting was not so interesting as his religious zeal, so typical of the sentiments of the Potteries at this time; and as the Methodist revival of the last quarter of the eighteenth century had a profound effect upon the habits of the pottery people, and permanently changed their affections from cock-fighting[142] to psalm singing, it is worth while, even in a history of potting, to mention this side also of the work of Job Ridgway. He was “converted” while working at Leeds in 1781. When he came to his brother’s house in Hanley, there were only twenty-five Methodists in Hanley. He formed a congregation and opened their first chapel in 1784. No sooner was Methodism firmly established than he quarrelled with these confining bonds also, and, in 1797, he did more than any other layman to establish the Methodist New Connexion.[160] Bethesda Chapel was built in the following year, and by 1802 Burslem and Lane End also had chapels of this new itinerant society. By 1843 there were five chapels of this denomination in Hanley alone. If you worked for Job Ridgway, you had to attend his chapel also.
Job Ridgway married Elijah Meyer's sister and made his family wealthy. However, his pottery work wasn't as captivating as his strong religious passion, which reflected the sentiments of the Potteries at that time. The Methodist revival in the late eighteenth century significantly impacted the pottery community's habits, shifting their interests from cock-fighting to singing psalms. Therefore, it's important to mention this aspect of Job Ridgway's work, even in a history of pottery. He had his "conversion" while working in Leeds in 1781. When he came to his brother’s house in Hanley, there were only twenty-five Methodists there. He started a congregation and opened their first chapel in 1784. Once Methodism was firmly established, he quickly grew tired of those limits, and by 1797, he contributed more than any other layman to create the Methodist New Connexion. Bethesda Chapel was built the following year, and by 1802, Burslem and Lane End also had chapels from this new itinerant society. By 1843, there were five chapels belonging to this denomination in Hanley alone. If you worked for Job Ridgway, you also had to attend his chapel.

There are some names of manufacturers on the 1802 map of the Potteries which have not received so far, and yet deserve, special mention. The brothers John and George Rogers, for instance, built their factory at Dale Hall near Burslem about 1780. John Rogers built too, about 1800, the house called “Watlands” in Wolstanton, the home of many potters, and lived there till his death in 1816. His son Spencer Rogers succeeded to the firm, which continued to flourish for over half a century as “John Rogers and Sons.”[161] Mr Samuel Ford now owns these works.
There are some manufacturer names on the 1802 map of the Potteries that haven't been mentioned yet but deserve special attention. The brothers John and George Rogers, for example, established their factory at Dale Hall near Burslem around 1780. John Rogers also built a house called “Watlands” in Wolstanton around 1800, which became home to many potters, and he lived there until his death in 1816. His son Spencer Rogers took over the business, which thrived for more than fifty years as “John Rogers and Sons.” [161] Mr. Samuel Ford currently owns these works.
Joseph Machin of Burslem was the progenitor of the Machins of the Hole House Works, afterwards, in 1843, “Machin and Potts” of the[144] Waterloo Works. This firm were the first successful manufacturers of porcelain in Burslem and they invented too the present method of printing the transfer papers from revolving steel cylinders, thereby greatly accelerating the work of producing these transfers and printing the ware.
Joseph Machin from Burslem was the founder of the Machins of the Hole House Works, which later became “Machin and Potts” at the[144] Waterloo Works in 1843. This company was the first to successfully manufacture porcelain in Burslem and they also developed the current method of printing transfer papers using rotating steel cylinders, significantly speeding up the process of creating these transfers and printing the ceramics.
The Goodwins of Cobridge had no fewer than four factories in the neighbourhood as late as 1843;[162] and the firm of John Glass & Sons appears to have existed in Hanley ever since the beginning of the 18th century and the days of slip dishes and “tygs.” William Baddeley, with his works at Eastwood on the banks of the Cauldon canal, was chiefly noted for his large flint-grinding mills. Miles Mason, of Lane Delf, and his son Charles J. Mason had their factory where the Stoke and Hanley tram-lines now branch. In 1813 the elder Mason introduced the patent “ironstone” china, which became very popular and was the precursor of the “granite” trade of later days.[163] The senior partner in the firm of Bourne and Baker of Fenton made a fortune, built the[145] church at Fenton, and bought the Hilderstone Hall estate, where his descendants now live.
The Goodwins of Cobridge had at least four factories in the area as recently as 1843; [162] and the company of John Glass & Sons seems to have been operating in Hanley since the early 18th century during the time of slip dishes and “tygs.” William Baddeley, with his factories at Eastwood along the Cauldon Canal, was mainly known for his large flint-grinding mills. Miles Mason from Lane Delf and his son Charles J. Mason had their factory where the Stoke and Hanley tram lines now split. In 1813, the elder Mason introduced the patented “ironstone” china, which became very popular and was the forerunner of the later “granite” trade.[163] The senior partner in the firm of Bourne and Baker of Fenton made a fortune, built the[145] church at Fenton, and purchased the Hilderstone Hall estate, where his descendants still live.
In Longton the firm of Charles Harvey is notable, since the proprietor became, about 1820, the first banker at the Longton end. Mrs Mary Cyples represents a family of potteresses whose factory is perpetuated in Cyples Lane. Messrs Cheetham and Wooley invented a hard white stone body resembling porcelain, very useful for relief decoration,[164] and flourished in Commerce Street for more than half a century. The Locketts are one of the few firms which have lasted over a hundred years.
In Longton, the company Charles Harvey stands out, as the owner became the first banker at the Longton end around 1820. Mrs. Mary Cyples represents a family of female potters whose factory lives on in Cyples Lane. Messrs Cheetham and Wooley created a hard white stone body that looks like porcelain, which is very useful for relief decoration, [164], and thrived in Commerce Street for over fifty years. The Locketts are one of the few businesses that have lasted more than a hundred years.
The potting industry, like all others, suffered stagnation during the French wars. Till 1810 however the growing American trade compensated to a certain extent for the loss of the continental market. But in 1810 the Orders in Council stopped both the continental and American trade. These Orders were rescinded in 1812, but the continental trade languished till 1814, and had to be rediscovered and re-established as an entirely new business when peace came.
The potting industry, like all others, faced stagnation during the French wars. Until 1810, the rising American trade somewhat made up for the loss of the continental market. However, in 1810, the Orders in Council halted both the continental and American trade. Although these Orders were lifted in 1812, the continental trade struggled until 1814 and had to be reinvented and set up as a completely new business once peace was established.
When at last the Continent was reopened to English china and earthenware one particular firm came to the front and took the greater part of the ornamental trade. This was the firm of John Davenport & Sons. John Davenport came of a small yeoman family settled near Leek, and he started in 1785, first as a workman and later as a partner, with Thomas Woolfe of Stoke. In 1794 he commenced making china on his own account at Longport.[165]
When the Continent finally reopened to English china and pottery, one company stood out and took most of the decorative trade. This was John Davenport & Sons. John Davenport came from a small farming family near Leek, and he began his career in 1785, first as a worker and later as a partner with Thomas Woolfe in Stoke. In 1794, he started making china on his own at Longport.[165]
The first factory built on the canal at Longport was, appropriately enough, put up in 1773 by John Brindley, the younger brother of the engineer. Edward Bourne and Robert Williamson followed, and in 1795 Walter Daniel put up a fine house and factory at Newport near by. All these factories became, early in the nineteenth century, the property of the great firm of Davenport, attached to the “Unicorn Bank.” John Davenport had built the “Unicorn Bank” in 1794 for the manufacture of china. In 1797 they started the chemical preparation of litharge and white lead; and in 1801 was added the manufacture of flint glass.[166]
The first factory built on the canal at Longport was, fittingly, established in 1773 by John Brindley, the younger brother of the engineer. Edward Bourne and Robert Williamson followed, and in 1795, Walter Daniel built a fine house and factory nearby in Newport. All these factories became, early in the nineteenth century, part of the prominent firm of Davenport, associated with the “Unicorn Bank.” John Davenport had constructed the “Unicorn Bank” in 1794 for making china. In 1797, they began the chemical preparation of litharge and white lead, and in 1801, they added the production of flint glass.[166]
Davenport china and stained glass attained a very high reputation, and for many years the Davenports represented the type of the most successful potters of the age. They are said in 1836 to have produced earthenware and china alone to the value of nearly £100,000 and to have employed 1400 workpeople.[167] They had branch establishments at London, Liverpool, Hamburg and Lübeck. They enjoyed Royal favour and acquired princely fortunes. The first John Davenport bought Westwood near Cheddleton in 1813. He was a major of volunteers at the time of the French scare in 1803, and Conservative M.P. for Stoke-on-Trent from 1832 to 1841. His sons, John, Henry and William carried on the business and established themselves, John at Foxley, Co. Hereford, and William at Maer. William Davenport was Master of the North Staffordshire Foxhounds. The third generation also went into politics, and Henry T. Davenport, after failing to secure a seat at Newcastle and at Stoke in 1874, became, from 1880-6, member for the northern division of the county. As they lost touch with[148] their works, however, the affairs of the Davenport firm gradually suffered. In 1868 they sold Westwood; in 1885 Maer; and in 1887 the “Unicorn Bank” was closed down and sold to Mr Thomas Hughes, who died in 1901.
Davenport china and stained glass gained a stellar reputation, and for many years, the Davenports were seen as the top potters of their time. In 1836, they reportedly produced earthenware and china worth nearly £100,000 and employed 1,400 workers. They had branch locations in London, Liverpool, Hamburg, and Lübeck. They enjoyed royal favor and built significant fortunes. The first John Davenport purchased Westwood near Cheddleton in 1813. He was a major of volunteers during the French scare in 1803 and served as Conservative M.P. for Stoke-on-Trent from 1832 to 1841. His sons, John, Henry, and William, continued the business and established themselves, with John at Foxley, Herefordshire, and William at Maer. William Davenport was the Master of the North Staffordshire Foxhounds. The third generation also entered politics; Henry T. Davenport, after unsuccessful bids for a seat in Newcastle and Stoke in 1874, became a member for the northern division of the county from 1880 to 1886. However, as they became less involved with their operations, the Davenport firm gradually declined. In 1868, they sold Westwood; in 1885, Maer; and in 1887, the “Unicorn Bank” was shut down and sold to Mr. Thomas Hughes, who passed away in 1901.
The Davenports were the only manufacturers of glass of any importance in North Staffordshire, and no attempt is now made to rival the productions in this line of the southern part of the county.
The Davenports were the only significant glass manufacturers in North Staffordshire, and no efforts are currently being made to compete with the products from the southern part of the county.
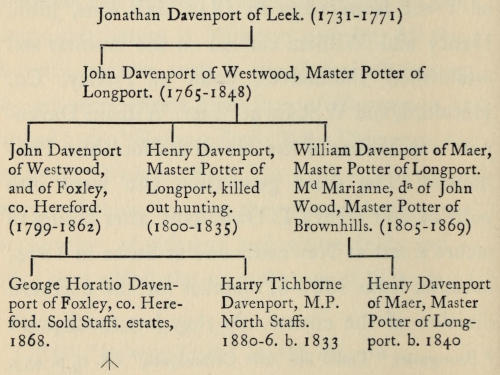
The success of the Davenports with their china in the continental trade, which began to be marked during the short peace of 1803-4, affected, no doubt seriously, the trade of the Wedgwood firm,[149] which since the first Josiah’s death had been carried on nominally by the second Josiah, but actually by Thomas Byerley. It is not surprising, therefore, to find that in 1805 Wedgwoods also commenced the manufacture of porcelain, and to find them repeating on china dinner and tea services the patterns which had been so successful on the Queen’s Ware. Josiah Wedgwood II bought Maer in 1803 (where he was succeeded by Davenport), and began again to attend to business. Though the new china and the jasper and black basalt with reliefs in Egyptian red turned out under his regime fully maintained the reputation of the firm—as witness the medallions of the admirals and the Egyptian basalt so typical of the second period[168]—yet they never recovered the undisputed position they had held in the ornamental trade of the Continent.
The success of the Davenports with their china in the continental trade, which started to become notable during the short peace of 1803-4, seriously impacted the trade of the Wedgwood firm,[149] which had been run nominally by the second Josiah since the death of the first, but actually by Thomas Byerley. So, it’s not surprising that in 1805, Wedgwoods also began producing porcelain, and they recycled the patterns that had been so successful on the Queen’s Ware for their china dinner and tea sets. Josiah Wedgwood II bought Maer in 1803 (where he was succeeded by Davenport) and got back to business. Although the new china and the jasper and black basalt with reliefs in Egyptian red produced under his leadership fully upheld the firm’s reputation—as seen in the medallions of the admirals and the Egyptian basalt typical of the second period[168]—they never regained the undisputed status they had held in the ornamental trade of the Continent.

JOSIAH WEDGWOOD II
Josiah Wedgwood II
1769-1843
1769-1843
By 1819 or 1820[169] indeed they ceased to try and compete in the china trade, and it was not till 1872 that Wedgwoods again produced the porcelain for which they are now so famous. In 1828 even their London showrooms were closed down, and Josiah[150] Wedgwood II committed the unpardonable vandalism of selling off the stock, patterns, and moulds there stored. The collections in the Mayer Museum at Liverpool and the collection now in the possession of Sir W. H. Lever were formed out of purchases made at this sale. After contesting Newcastle vainly in the interests of “reform” in 1831, Wedgwood was returned as first radical member for Stoke-on-Trent in the reformed Parliament of 1832, and died at Maer in 1843. From 1823 he had had the assistance of his eldest son Josiah, but from 1827 onwards the works were managed almost entirely by his third son, Francis Wedgwood. The firm, which had been called “Josiah Wedgwood” after Byerley’s death in 1810 and “Josiah Wedgwood & Son” until 1827, was thenceforth known as “Josiah Wedgwood & Sons,” which title it retains at the present day.
By 1819 or 1820, they stopped trying to compete in the china trade, and it wasn't until 1872 that Wedgwoods began producing the porcelain they are now famous for. By 1828, even their London showrooms were shut down, and Josiah[150] Wedgwood II committed the unforgivable act of selling off the stock, patterns, and molds stored there. The collections in the Mayer Museum in Liverpool and the collection now owned by Sir W. H. Lever were created from purchases made during this sale. After unsuccessfully contesting Newcastle in the name of “reform” in 1831, Wedgwood was elected as the first radical member for Stoke-on-Trent in the reformed Parliament of 1832, and he died in Maer in 1843. Since 1823, he had the help of his eldest son Josiah, but from 1827 onward, the works were mostly managed by his third son, Francis Wedgwood. The company, which was called “Josiah Wedgwood” after Byerley's death in 1810 and “Josiah Wedgwood & Son” until 1827, has been known as “Josiah Wedgwood & Sons” since then, and it retains that name today.
Pedigree of the Later Wedgwoods:
Later Wedgwood Family Tree:

The progress of invention and specialization had brought into existence quite a number of manufactures subsidiary to potting, and we will take advantage of a little-known Directory of 1818 to show both the names of potters then in business, and also the number and nature of these dependent trades.
The advancements in invention and specialization had led to the creation of several industries related to pottery, and we’ll use a little-known Directory from 1818 to highlight both the names of potters operating at the time and the variety and scope of these related trades.
The Directory for 1818 was compiled by W. Parson and T. Bradshaw, and printed by Leigh of Manchester. The manufactories of earthenware on the list are as follows:
The Directory for 1818 was put together by W. Parson and T. Bradshaw, and printed by Leigh of Manchester. The potteries included in the list are as follows:
- Newcastle.
- Sam. Bagshaw, Basford.
- Golden-Hill, Tunstall, Red Street.
- Ben. Adams, Tunstall (Greengates).
- John Boden, Tunstall.
- Jesse Breeze, Greenfield.
- Ric. Cartledge, Golden Hill.
- Jas. Cartledge, Golden Hill.
- Child & Clive, Newfield.
- Jas. Collinson, Golden Hill.
- J. & R. Hall, Tunstall and Burslem.[170]
- T. & J. Knight, Clayhill.
- Marsh & Haywood, Brownhills.
- John Meir, Tunstall.
- T. & H. Moss, Red Street.
- Ben. Myatt, Red Street.
- Nixon & Whalley, Tunstall.
- H. Powis & Co., Sandiford.
- W. S. & I. Rathbone, Tunstall.
- Daniel Vawdrey, Golden Hill.
- Wood & Brittell, Brownhills.
- Burslem, Longport, Cobridge.
- T. & E. Bathwell, Chapel Bank.
- J. & R. Blackwell, Cobridge.
- W. Bourne, Bell Works.[153]
- Jos. Bradshaw, Booden Brook (Cobridge).
- Philip Brooks & Co., Sitch.
- Cartledge & Beech, Knowle.
- Ralph & J. Clews, Cobridge.
- J. & J. Davenport, Newport.
- Frank & N. Dillon, Cobridge.
- B. & S. Godwin, Cobridge.
- T. & B. Godwin, New Basin.
- Goodfellow & Bathwell, Upper House Works.
- John & Ralph Hall, Sitch & Tunstall.
- John Heath, Sitch.
- Henshall & Williamson, Longport.
- Thos. Heath, Hadderage
- Ephraim Hobson, Cobridge.
- Holdcroft & Box, Cobridge.
- Anne Holland, Hill Top, Burslem.
- Ric. Jarvis, Nile Street, Burslem.
- Ralph Johnson, Church St., Burslem.
- Jonathan Leak, The Row.
- Machin & Baggaley, Low St.
- Joseph Machin, Waterloo Road.
- Sam. Marsh, Brownhills.
- Ric. Massey, Castle St.
- S. & T. Massey, Nile St.
- John Mellor, near the Market Place.
- John Moseley, Cobridge.
- John Moseley, Churchyard Works.
- Wm. Moseley, Queen St., Black Works.
- Oliver & Bourne, Cobridge.
- J. & R. Riley, Hill Works.
- J. & C. Robinson, Hill Top Works.
- John Rogers & Sons, Longport.
- Spencer Rogers, Dale Hall.
- Wm. Stanley, Knowle Works.
- Dan. Steel, St. Johns St.
- Ralph Stevenson, Cobridge.
- Andrew Stevenson, Cobridge.
- Ben. Stubbs, Longport.[154]
- Sam. Tompkinson, Church Street.
- Wm. Walsh, Furlong.
- John Walton, Hadderage.
- James Warburton, Hot Lane.
- John Warburton, Hot Lane.
- Wedgwood & Johnson, High Street.
- Wood & Caldwell, Fountain Place.
- Ephraim Wood, Hole House.
- Hanley and Shelton.
- Wm. Baddely, Eastwood.
- Joseph Bradshaw, Booden Brook.
- W. & G. Brownfield, Keelings Lane.
- John Glass & Sons, Market St.
- Hackwood, Dimmock & Co., Hanley.
- Hicks & Meigh, Shelton.
- J. J. & R. Hollins, Upper Hanley.
- Hollings & Co., Brook St., Shelton.
- Reuben Johnson, Miles Bank.
- Jas. Keeling, New Street, Hanley.
- Mansfield, Pawley & Co., Market Place.
- Mare, Matthew & Co., Vale Pleasant.
- Elijah Mayer & Son, High St.
- Job Meigh & Son, Hill St., Hanley.
- Thos. Morris, Marsh St.
- Fred. Peover, High St.
- John & Wm. Ridgway, Shelton (Bell Bank).
- Rivers & Clews, Shelton.
- John Shorthouse, Tontine St.
- T. & J. Taylor, High St.
- Exors of Chas. Whitehead, Shelton.
- D. Wilson & Sons (assignees of), High St.
- John Yates, Broad St., Shelton.
- Stoke and Etruria.
- Wm. Adams, Stoke.
- Robt. Hamilton, Stoke.
- T. Minton & Sons, Stoke.[155]
- Poulson & Dale, Stoke.
- Josiah Spode, Stoke.
- Ward & Co., Stoke.
- Josiah Wedgwood, Etruria.
- Thos. Wolf, Stoke.
- Lane End, etc.
- Thos. Baggaley, Lane Delf.
- R. J. & J. Barker, Flint St.
- Batkin & Deakin, Waterloo, Flint St.
- Beardmore & Carr, Lane End.
- J. & T. Booth, Lane End.
- Bourne, Baker & Bourne, Fenton.
- Chas. Bourne, Foley.
- Joseph Burrow, Foley Works.
- Maria Bridgwood, Market St.
- Kitty Bridgwood & Son, Market St.
- Thos. Brough, Green Dock.
- Carey & Son, Lane End.
- M. Cheetham & Son, Commerce St.
- Lydia Cyples, Market St.
- T. Drury & Son, Daisy Bank.
- Hugh Ford, Green Dock.
- Geo. Forrester, Market Place.
- Robt. Garner, Lane End.
- S. Ginder & Co., Lane Delf.
- Harley & Seckerson, Lane End.
- Chas. Harvey & Sons, Gt. Chas. St.
- John Hewitt & Son, Green Dock.
- Hilditch & Martin, Lane End.
- Thos. Hughes, Lane Delf.
- John Lockett & Co., King St.
- W. & J. Lowe, Church St.
- Jacob Marsh, Lane Delf.
- Wm. Mason, Lane Delf.
- Geo. & Chas. Mason, Lane Delf.
- Mathers & Ball, Lane End.
- Mayor and Newbold, Market Place.[156]
- Ben. & Jos. Myatt, Lane End.
- Wm. Nutt, Flint St.
- Jas. Pattison, High St.
- Wm. Poulson, Chancery Lane.
- F. & R. Pratt, Fenton.
- John Pratt, Lane Delf.
- John Robinson, High St.
- John Robinson, George St.
- Shelley, Booth & Co., Lane End.
- J. H. Sheridan, Union Market Place.
- Simkin & Waller, Lane End.
- Thos. Stirrup, Flint St.
- John Unett, High St.
- H. & R. Walklate, High St.
- Geo. Weston, High St.
The trades of that day dependent on potting were: Makers of the crates wherein to pack the ware; gilders; cobalt-refiners and colour-makers, of whom Machin and Bagguley of the new “Waterloo” Road were perhaps the most important; enamellers; engravers of designs on copper, from which the transfer prints for the under-glaze blue printing were made; flint-grinders; lead and litharge makers for the glaze; saggar makers; lathe makers and lawn manufacturers.
The trades of that time that depended on pottery included: makers of crates for packing the goods; gilders; cobalt refiners and color makers, with Machin and Bagguley of the new “Waterloo” Road being some of the most significant; enamelers; engravers of designs on copper, which were used for the transfer prints for under-glaze blue printing; flint grinders; lead and litharge manufacturers for the glaze; saggar makers; lathe makers; and lawn manufacturers.
The lawn manufacturers made the lawn sieve through which the clay body in the slip state was passed in order to remove all coarse particles. Indeed the preparation of the clay body was now[157] carried out so carefully that magnets were used to attract any particle of iron that might be ground up with the flint; and the old process of evaporation which converted the slip into the solid clay body gave way about 1860 to the clay press now used to squeeze out the water from the clay. Samuel Allen, lathe maker of Dale Hall, is the sole representative to be found in 1818 of the makers of potters’ machinery, now so important a branch of manufacture. But the “jiggers,” which exactly reproduce plates by the thousand, and the “jollies,” for the mechanical moulding and pressing of hollow ware, were the creation of a much later age. Even now these machine tools may be said to be in their infancy though they are developing under the hands of skilled engineers such as Messrs Boulton of Burslem.
The lawn manufacturers created the lawn sieve that filtered the clay body while in its slip state to remove all coarse particles. The preparation of the clay body was done so meticulously that magnets were used to attract any iron particles that might have been mixed in with the flint. The old evaporation process that turned the slip into solid clay gave way around 1860 to the clay press, which is now used to squeeze out the water from the clay. Samuel Allen, a lathe maker from Dale Hall, was the only representative of the potters’ machinery makers in 1818, a now significant sector of manufacturing. However, the “jiggers,” which perfectly reproduce plates by the thousands, and the “jollies,” used for mechanically molding and pressing hollow ware, were developed in a much later period. Even now, these machine tools are still in their infancy, though they are progressing thanks to skilled engineers like Messrs Boulton from Burslem.
A subsidiary manufacture which does not appear on the 1818 list at all is that of borax. Borax, or as it was originally called “tincal,” had been first introduced about 1796 when it was brought from Thibet. In that year Ralph Wedgwood (see p. 87), who spent his life inventing things, and was then a master-potter at Ferrybridge in[158] Yorkshire,[171] took out a patent for “making glass upon new principles” by using this tincal. By Hickling’s patent of 1799 it was also applied to the enamelling of metal vessels, and it appears again in the leadless glaze of Mr. Rose of Coalport in 1820.[172] All this time, however, the price was almost prohibitive of the commercial use of borax. In 1815 it cost 3s. to 4s. a lb., and it was only on the development of the Etruscan borax deposits in 1828 that it came into general use as a flux for the glazes, partially displacing the lead oxides. As the borax—as well as the soda used in the glaze—is soluble in water, glazes containing these have to be “fritted” or vitrified before being ground with the other components into a slip for dipping the ware. This melting or fritting, besides making the glaze insoluble in water and suitable for dipping, will, if the lead be fritted with the other components and not just ground in afterwards, make the lead more or less innocuous. Unfortunately, however, the fritted lead requires more exact firing to produce a good glaze, and can hardly compete[159] commercially at present. Glazes can be made without any lead at all by using borax alone as a flux, but the surface is always full of imperfections and less glossy than that given by a leaded glaze.
A manufacturing process that doesn’t show up on the 1818 list at all is that of borax. Borax, which was originally known as “tincal,” was first introduced around 1796 when it was brought from Tibet. That year, Ralph Wedgwood (see p. 87), an inventor and master potter at Ferrybridge in[158] Yorkshire, patented a method for “making glass using new principles” that involved this tincal. According to Hickling’s patent from 1799, it was also used for enameling metal vessels, and it appeared again in Mr. Rose’s leadless glaze from Coalport in 1820.[172] Throughout this period, however, the cost of borax was almost too high for commercial use. In 1815, it was priced at 3s. to 4s. per pound, and it wasn't until the Etruscan borax deposits were developed in 1828 that it became widely used as a flux for glazes, partly replacing lead oxides. Because borax—and the soda used in glazes—are soluble in water, glazes with these ingredients need to be “fritted” or vitrified before being mixed with the other components to create a slip for dipping the ware. This melting or fritting not only makes the glaze insoluble in water and suitable for dipping but also renders lead less harmful if it’s fritted with the other components rather than just ground in later. Unfortunately, fritted lead requires more precise firing to achieve a good glaze and struggles to compete commercially at this time. Glazes can be made without any lead at all by using only borax as a flux, but the surface will be full of imperfections and not as glossy as one made with lead.
The first important manufactory of borax in the Potteries was that of Wood, Kuntz & Co.,[173] a firm in which the sons of Enoch Wood were interested. Because the risk of lead poisoning is always present in the preparation and uses of the lead glazes, attempts have been made for 100 years to produce a good glaze free from lead—or rather free from unfritted lead—soluble in hydrochloric acid. Josiah Wedgwood produced such a glaze, but it gave a rough surface wherewith it was useless in those days to try to compete. The Society of Arts awarded its gold medal in 1823 to Job Meigh of Hanley for his invention of a leadless glaze. But Meigh’s leadless glaze was only to be applied to coarse red pottery.[174] Of recent years Mr. Furnival and Mr. William Burton have done most to make safe glazes commercially practicable. There is no doubt but that by the use of borax a[160] safe glaze, free from lead, can be made; it will not be mechanically perfect perhaps, but artistically it need not be considered inferior to the heavy smooth lead glaze.
The first major borax factory in the Potteries was Wood, Kuntz & Co., a company where the sons of Enoch Wood were involved. Due to the constant risk of lead poisoning during the creation and use of lead glazes, there have been attempts for the past 100 years to develop a good glaze that is free from lead—or, more accurately, free from unfritted lead that dissolves in hydrochloric acid. Josiah Wedgwood created such a glaze, but it resulted in a rough surface, making it impractical to compete at that time. In 1823, the Society of Arts awarded its gold medal to Job Meigh of Hanley for his invention of a lead-free glaze. However, Meigh’s lead-free glaze could only be applied to coarse red pottery. In recent years, Mr. Furnival and Mr. William Burton have contributed significantly to making safe glazes commercially viable. There’s no doubt that with the use of borax, a safe, lead-free glaze can be produced; it may not be mechanically perfect, but it shouldn’t be seen as artistically inferior to the heavy, smooth lead glaze.
About 1826 an even more dangerous lead process was introduced by Henry Daniel, who began in that year to make stoneware “china” in Shelton. This was the process of “ground laying” and “colour dusting,” in which the enamel paints are dusted in a dry state over a sticky oily surface to which they adhere. The leaded particles of paint dust are easily breathed into the lungs and caused a heavy mortality. The ærograph, invented in 1890, which lays the ground mechanically, reduced the risks of this process, and more recently the Home Office regulations regarding ventilation, mufflers, etc., have helped in the same direction.
Around 1826, a more hazardous lead process was introduced by Henry Daniel, who started making stoneware “china” in Shelton that year. This process, known as “ground laying” and “colour dusting,” involved applying dry enamel paints over a sticky, oily surface where they would stick. The lead particles from the paint dust could easily be inhaled, leading to high mortality rates. The ærograph, invented in 1890, which applies the ground mechanically, reduced the risks associated with this process. More recently, the Home Office regulations concerning ventilation and mufflers have also contributed to safety improvements.
Among the Tunstall potters on the list of 1818 occur the names of Benjamin Adams and Jesse Breeze. Benjamin Adams was the son and successor of that William Adams who made jasper at Greengates and died in 1805. Within a year or two of 1818 he had to sell his factory, which was bought[161] by John Meir, another Tunstall potter.[175] John Breeze had bought the house and factory built by Theophilus Smith in 1793 and called Smithfield. Smith had, in 1800, committed suicide in prison after failing three times to murder his wife’s lover.[176] His tragic end caused the name of his house to be changed to Greenfield; and in 1827 Jesse, son of this John Breeze of Greenfield, having no sons, married one of his daughters to William Adams, son of the successful potter of Stoke, and bequeathed his factory to him. In this way another branch of the Adams family returned to Tunstall. From 1827 to the present day the Adams family from father to son have continued to make earthenware at Greenfield. They have recently bought up Greengates also, and joined the two old Adams’ factories together. The firm has had a somewhat chequered career, but under the management of the present brothers and partners, William and Percy W. L. Adams, it has resumed its high reputation as one of the largest exporters of useful and ornamental ware.
Among the Tunstall potters listed in 1818 are Benjamin Adams and Jesse Breeze. Benjamin Adams was the son and successor of William Adams, who made jasper at Greengates and passed away in 1805. Within a year or two of 1818, he had to sell his factory, which was purchased by John Meir, another Tunstall potter.[161] John Breeze had bought the house and factory built by Theophilus Smith in 1793, known as Smithfield. Smith had, in 1800, committed suicide in prison after failing three times to kill his wife’s lover.[162] His tragic end led to the renaming of his house to Greenfield; and in 1827, Jesse, son of this John Breeze of Greenfield, having no sons, married one of his daughters to William Adams, son of the successful potter from Stoke, and left his factory to him. This way, another branch of the Adams family returned to Tunstall. From 1827 to today, the Adams family has continued to produce earthenware at Greenfield from father to son. They have recently acquired Greengates as well and merged the two old Adams factories. The firm has had a somewhat mixed history, but under the management of the current brothers and partners, William and Percy W. L. Adams, it has regained its distinguished reputation as one of the largest exporters of practical and decorative ware.


WILLIAM ADAMS
WILLIAM ADAMS
1772-1829
1772-1829
As the nineteenth century advanced, steam power gradually replaced hand and water power on the pot-banks. Before 1800, steam had been introduced to drive the flint mills; the glaze-grinding mills, the pumps and lawn sifters came next. But lathes and throwers’ wheels were still driven by hand, and so were the “jiggers”—revolving moulds on which flat bats of clay were “flat-pressed” to make plates and saucers. A tramway was laid about 1815 from Longton and Fenton to the canal wharf at Stoke; but transport along both tramway and canal was still drawn by horses. With the opening of the Manchester and Liverpool Railway, however, in 1830, a new era began in transport, as important as the first canal for the potting industry.
As the 19th century progressed, steam power slowly took over from manual and water power in the pottery factories. Before 1800, steam had been used to operate the flint mills; next came the glaze-grinding mills, pumps, and lawn sifters. However, lathes and throwers’ wheels were still operated by hand, as were the “jiggers”—revolving molds where flat pieces of clay were pressed to create plates and saucers. A tramway was established around 1815 connecting Longton and Fenton to the canal wharf at Stoke, but transportation on both the tramway and canal was still pulled by horses. The opening of the Manchester and Liverpool Railway in 1830 marked the beginning of a new transportation era, as significant for the pottery industry as the first canal.
Land transport had, of course, become thoroughly organized and cheapened, and coaches, carrier carts and wagon transport had kept[164] increasing in speed and numbers. In the 1818 Directory, for instance, we find that no less than eleven coaches passed through the district each way every day. Every afternoon the “Light Post Coach,” from Liverpool to Burton and London, ran through the Potteries from the “Red Bull” at Lawton to Lane End; and two hours later the “Prince Coburg” from Liverpool passed through, branching off from the other route at Stoke, and going through Trent Vale, Stone and Lichfield to London. The “Regulator” too, on three days of the week, ran through the Potteries by the same route on its journey from Liverpool to Birmingham. In addition to these coaches three others ran from Liverpool to London, and one from Manchester to London, passing through Newcastle, as did also one from Liverpool and two from Manchester on their way to Birmingham. You could travel from Newcastle at 6 a.m. to the “Swan with Two Necks,” in Fetter Lane, in fifteen hours.
Land transport had become well-organized and affordable, with coaches, carrier carts, and wagons increasing in speed and number. In the 1818 Directory, for example, we see that at least eleven coaches traveled through the district in each direction every day. Every afternoon, the “Light Post Coach” would run from Liverpool to Burton and London, passing through the Potteries from the “Red Bull” at Lawton to Lane End; two hours later, the “Prince Coburg” from Liverpool would come through, taking a different route at Stoke and continuing through Trent Vale, Stone, and Lichfield to London. The “Regulator” also traveled through the Potteries on its journey from Liverpool to Birmingham three days a week along the same route. In addition to these coaches, three other routes ran from Liverpool to London, and one from Manchester to London, going through Newcastle, as well as one from Liverpool and two from Manchester on their way to Birmingham. You could travel from Newcastle at 6 a.m. to the “Swan with Two Necks” in Fetter Lane in fifteen hours.
In 1833, however, the Bill for the Grand Junction Railway, from Birmingham to Manchester, was passed, and by the completion of[165] this railway in 1837, Whitmore, the nearest station, five miles from the Potteries, was brought within seven hours of London by four trains a day.
In 1833, the Bill for the Grand Junction Railway, connecting Birmingham to Manchester, was approved. By the time this railway was finished in 1837, Whitmore, the closest station located five miles from the Potteries, became accessible from London in just seven hours with four trains running daily.
Coal gas had been introduced in 1826 into Burslem, and by 1840 the beginnings of a water supply were visible. At this period, just before modern sanitation, locomotion, economies and “civilization” took root, John Ward, in his “Stoke-on-Trent,” gives us a table showing the dimensions of the trade. It runs as follows:[177]
Coal gas was introduced in 1826 to Burslem, and by 1840, the first signs of a water supply were evident. During this time, just before modern sanitation, transportation, economies, and “civilization” began to take hold, John Ward, in his “Stoke-on-Trent,” provides a table that outlines the dimensions of the trade. It is as follows:[177]
A Table, showing the amount of conveyance of Goods and Merchandise to and from the Boro’ of Stoke-upon-Trent, by the navigation from the Trent to the Mersey, for one year ending 30th June 1836.
A Table showing the amount of transport of Goods and Merchandise to and from the Borough of Stoke-upon-Trent, by the navigation from the Trent to the Mersey, for the year ending June 30, 1836.
It will be noticed that the Stourbridge bricks were already in request for the pot-ovens, and that the total weight of ware exported out of the district amounted to 72,500 tons, of which nearly three-quarters went abroad. Through the courtesy of Mr Philips, Manager of the N. S. Ry. Co., I am able to give some corresponding figures for later dates, as follows:
It’s evident that the Stourbridge bricks were already in demand for the pot-ovens, and the total weight of goods exported from the area reached 72,500 tons, with nearly three-quarters going overseas. Thanks to Mr. Philips, Manager of the N. S. Ry. Co., I can provide some corresponding figures for later dates, as follows:
This shows an export trade from the North Staffordshire Potteries of 184,000 tons of ware in 1906 against 72,500 tons exported in 1836, but it must be remembered that ware is now much finer and lighter than it was seventy years ago, so that the real increase in value is more marked than the increase in weight seems to indicate.
This demonstrates an export trade from the North Staffordshire Potteries of 184,000 tons of goods in 1906 compared to 72,500 tons exported in 1836. However, it's important to note that the products are now much finer and lighter than they were seventy years ago, so the actual increase in value is more significant than the increase in weight suggests.
As trade and population increased within the narrow limits of the Potteries the conditions of life became harder and poverty more severe. Already in 1792 we read of troops being sent, to Wolverhampton of all places, to keep order during a strike in the Potteries of Staffordshire.[178] While in 1813 a Chamber of Commerce was formed and attempted to fix a uniform increased price for[169] earthenware. A price list was in fact drawn up for the commoner sorts of ware, and remained in force for twenty years or more, though it was regularly evaded by special rebates and discounts.[179]
As trade and population grew in the limited area of the Potteries, life became tougher and poverty worsened. By 1792, we hear about troops being sent to Wolverhampton, of all places, to maintain order during a strike in the Potteries of Staffordshire.[178] In 1813, a Chamber of Commerce was established and tried to set a standard price increase for[169] earthenware. A price list was actually created for the more common types of ware, and it lasted for over twenty years, although it was frequently undermined by special discounts and rebates.[179]
The first Trade Union is heard of in 1824. It was formed immediately on the passage of the combination laws, and the men struck for a rise at Martinmas 1825. The men were utterly beaten and their union destroyed. Little capital was required to start a pot-factory in those days, and the strikers tried to employ themselves in an early example of a co-operative factory. They were however before their time and the experiment only hastened their defeat.[180]
The first Trade Union appeared in 1824. It was created right after the combination laws were passed, and the workers went on strike for a pay raise at Martinmas 1825. They were completely defeated, and their union was dismantled. Back then, starting a pot factory didn’t require much capital, so the strikers attempted to set up a co-operative factory. However, they were ahead of their time, and this experiment only sped up their defeat.[180]
The best days for the Trade Unions came in 1833, when Robert Owen, the socialist, visited the Potteries and brought them all the enthusiasm of a great cause. A new union was founded, and was welcomed by many of the best employers as a lever to raise prices as well as wages. Chas. J. Mason, who was then supplying the world with his “ironstone” china, formed a Masters’ Association to[170] work with the men’s union; and wages were raised. The dissentient masters refused to grant the rise, and a four months’ strike began at Martinmas 1834, and ended in a victory for the men.[181]
The best days for the Trade Unions came in 1833, when Robert Owen, the socialist, visited the Potteries and brought them all the enthusiasm of a significant cause. A new union was established, and it was welcomed by many of the leading employers as a way to increase both prices and wages. Chas. J. Mason, who was then supplying the world with his “ironstone” china, formed a Masters’ Association to[170] collaborate with the men’s union; and wages were raised. The dissenting employers refused to grant the increase, leading to a four-month strike that began at Martinmas 1834 and ended in victory for the workers.[181]
During the years 1833-5 wages are said to have increased by 25 per cent.[182] But in March 1836 the masters united in a Pottery Chamber of Commerce and preparations were made for war. Before however an account is given of what is still known as “the great strike,” the two customs of the trade must be described, against which, then and for years thereafter, the men struggled in vain.
During the years 1833-1835, wages reportedly increased by 25 percent. [182] But in March 1836, the employers came together to form a Pottery Chamber of Commerce, and plans were made for conflict. However, before detailing what is still referred to as “the great strike,” it's necessary to describe the two customs of the trade that the workers fought against in vain, both then and for many years after.
By the “Annual Hiring” Agreement men were engaged only at Martinmas (Nov. 11). They were bound to serve all the following year to make ware at fixed prices, and if they broke their agreement they could be, and were, imprisoned. It was entirely a one-sided bargain. An employer could keep a man tied to a situation which gave him but one day’s work a week, yet if the man left he might be prosecuted. Even if not prosecuted, nobody could engage him without a written discharge. The[171] system was similar to the Native Pass Laws of South Africa.
By the “Annual Hiring” Agreement, men were only hired at Martinmas (Nov. 11). They were required to work for the entire following year to make goods at set prices, and if they broke their agreement, they could be—and often were—imprisoned. It was a completely one-sided deal. An employer could keep a man in a position that provided him with just one day of work a week, but if the man decided to leave, he could face legal consequences. Even if he wasn't prosecuted, no one could hire him without a written release. The[171] system was similar to the Native Pass Laws of South Africa.
The greatest number of male workers were flat or hollow-ware pressers and throwers. These men were paid by piece, and only for those pieces which were good. By a strange trade custom, however, they were not paid for those pieces which left their hands in good condition, but only for those that ultimately came good from the oven. In other words, they suffered for other people’s breakages and carelessness. The men could get no proof that the ware was bad at all. They had no appeal. Some masters were even said to refuse to pay for what they themselves afterwards sold as “seconds.”
The largest group of male workers were pressers and throwers of flat or hollow ware. These guys were paid per item, but only for the ones that turned out okay. Oddly enough, due to a trade custom, they weren’t paid for the pieces that left their hands in good shape, but only for those that came out well from the oven. In other words, they took the hit for other people’s mistakes and carelessness. The workers had no way to prove that the ware was defective at all. They had no recourse. Some employers even reportedly refused to pay for items they later sold as “seconds.”
Against these customs the men decided to strike. They demanded the right to give a month’s notice to leave and to be paid for all ware which came “good-from-hand.” The masters replied that they “could not allow the old usages of the trade to be broken up,” and they drew up a new clause to be added to the annual agreements in future. By this new clause the agreement was to be suspended if work at a factory ceased, but only till work was[172] resumed again. In fact the men were to be suspended from work and wages but not from servitude. If they found work during the “suspension” they were to throw it up as soon as their old master wanted them back.[183]
Against these customs, the men decided to go on strike. They demanded the right to give a month's notice before leaving and to be paid for all goods that arrived "good-from-hand." The masters responded that they "could not allow the old practices of the trade to be disrupted," and they drafted a new clause to be added to future annual agreements. This new clause stated that the agreement would be suspended if work at a factory stopped, but only until work resumed again. In reality, the men would be suspended from work and wages but not from servitude. If they found work during the "suspension," they were expected to abandon it as soon as their old master wanted them back.[172]
As soon as notice of the new agreement was given to the men, the workmen at fourteen factories came out. This was on Sept. 1, 1836. When Martinmas came round sixty-four more of the biggest factories were laid idle, and seven-ninths of the trade stopped. It is doubtful whether the whole history of Trade Unionism records a more desperate fight than the one that followed. Strike pay never exceeded 6s. for married men and 4s. for single men, but the funds became exhausted. Help came—£7,000 of it—from Sheffield and Manchester, and that too vanished. Twenty thousand potters were out of work, and so were the retail tradesmen and all allied trades. The men began to dribble back at Christmas, for it was a very hard winter and the savings were all gone. Then several hundred devoted men, taking the remains of their clothes and household furniture,[173] marched in procession to the pawn-shops and paid over all the money they could raise into the common fund. This example inspired the last 10,000 to hold out three weeks longer, and at least got terms for the men. A conference was presided over by Mr Twemlow of Betley on January 20, 1837, and the masters agreed to guarantee four days’ work a week, and to break in the presence of the man all ware for which they refused to pay him, on the ground that it came “bad from oven.”[184]
As soon as the new agreement was announced to the workers, the laborers at fourteen factories went on strike. This happened on September 1, 1836. By Martinmas, sixty-four more of the largest factories were shut down, and seven-ninths of the industry came to a halt. It’s unclear if there’s a more intense struggle documented in the history of Trade Unionism than the one that followed. Strike pay never went beyond 6 shillings for married men and 4 shillings for single men, but the funds were depleted quickly. Support of £7,000 arrived from Sheffield and Manchester, and that too disappeared. Twenty thousand potters were out of work, along with retail tradesmen and all related industries. The workers started to trickle back by Christmas because it was a harsh winter and their savings were wiped out. Then several hundred dedicated individuals, carrying whatever was left of their clothes and household items,[173] marched in a procession to the pawn shops and contributed all the money they could gather to the communal fund. This act motivated the last 10,000 to hold out for three more weeks, ultimately securing terms for the workers. A conference led by Mr. Twemlow of Betley took place on January 20, 1837, and the employers agreed to guarantee four days of work each week and to break, in the presence of the worker, any goods for which they refused to pay, claiming they came "bad from the oven."
But even these concessions were futile for the union was broken. The men took what they could get. Gradually all the old wrongs crept back again into the trade customs, and even the wage-prices of 1833-6 were whittled away by a system of “allowances.” A potter of 1843 gives an account of his engagement. He applied for work as a journeyman, and was asked what kind of a journeyman he wanted to be, as there were several kinds. “There were,” said the manufacturer, “some, like those of so-and-so, who took pay in provisions; others, like those of such a one, who took their[174] pay in haberdashery and jewellery; but the class to which he wished to direct particular attention was the one which allowed 2d. in the shilling, which class was divided into two parties; those who consented to the twopences being stopped out of their wages on Saturday evening, and those who preferred to compound with their dignity, get their money in full on Saturday and pay back the twopences on Monday morning.”[185]
But even these concessions were useless because the union had fallen apart. The workers took whatever they could get. Slowly, all the old injustices returned to the trade practices, and even the wage rates from 1833-6 were diminished by a system of "allowances." A potter from 1843 shares his experience. He applied for work as a journeyman and was asked what type of journeyman he wanted to be, since there were different kinds. “There were,” said the manufacturer, “some, like those from so-and-so, who were paid in food; others, like those from a certain person, who were paid in clothing and jewelry; but the particular group I want to highlight is the one that allowed 2d. in the shilling, which was split into two factions: those who agreed to have their two pence deducted from their wages on Saturday evening, and those who preferred to maintain their dignity, receive their full payment on Saturday, and pay back the two pence on Monday morning.”[174]
Wages in fact sank to subsistence level, and the smaller the master the more he beat down his men by allowances and undercut his selling prices. Some of them kept shops as well as factories, and broke the Truck Act every day. The Chamber of Commerce in 1836 stated the average wages as follows: In 1833-4, men 17s. to 21s., women 6s. to 11s., child of 14, 3s. to 3s. 6d.; in 1836, men 21s. to 28s., women 10s. to 15s., child 3s. 6d. to 4s. 6d. These figures probably exaggerate slightly the rise in wages, and under the allowance system they soon sank again to the pre-union level.
Wages actually dropped to the bare minimum, and the smaller the employer, the more he exploited his workers by cutting their allowances and underpricing his products. Some of them ran shops in addition to factories and violated the Truck Act daily. In 1836, the Chamber of Commerce reported average wages as follows: In 1833-4, men earned 17s. to 21s., women 6s. to 11s., and a child of 14 earned 3s. to 3s. 6d.; in 1836, men earned 21s. to 28s., women 10s. to 15s., and children earned 3s. 6d. to 4s. 6d. These figures likely slightly overstate the wage increase, and under the allowance system, wages soon fell back to pre-union levels.
The general election took place in the middle of the black year 1837, and the return of the two[175] Conservative masters, Davenport and Copeland, for Stoke-on-Trent, resulted in rioting on the part of the wage-earners who were then non-voters. These riots were repeated in a more serious form at the election of 1841, but it was the houses rather than the factories of the unpopular side that were demolished.
The general election happened in the midst of the tough year 1837, and the election of the two Conservative leaders, Davenport and Copeland, for Stoke-on-Trent led to protests from the wage-earners who couldn't vote. These protests escalated in a more serious way during the election of 1841, but it was the homes, not the factories, of the unpopular side that were destroyed.
During those busy years of the railway boom, the Trade Unions again raised their head in North Staffordshire. The third union was started in September 1843. It began with a small success—a partial strike lasting nine months—but as a rule it avoided conflicts and tried to work by moral suasion and public opinion. With this end in view they published a paper, “The Potters’ Examiner,” in which the more flagrant cases of “truck” and “allowance” were exposed. They succeeded in gradually levelling up the bad masters. A few prosecutions stopped the truck system, and allowances vanished in 1844 under gentle pressure from a strong union and doubts as to their legality. It is only fair to say that the best firms had never countenanced the “allowances,” and were glad to see the worse makers forced to drop them.
During the busy years of the railway boom, Trade Unions re-emerged in North Staffordshire. The third union was established in September 1843. It had a small success with a partial strike that lasted nine months, but typically, it avoided conflicts and focused on influencing through moral persuasion and public opinion. To achieve this, they published a paper called “The Potters’ Examiner,” which highlighted the most egregious cases of "truck" and "allowance." They were successful in gradually improving conditions with the bad employers. A few prosecutions put an end to the truck system, and allowances disappeared in 1844 due to the pressure from a strong union and questions about their legality. It's important to note that the best companies had never supported the "allowances" and were pleased to see the worst producers forced to stop using them.
A development, however, that helped the union at first more than anything else, was the invention of pot-making machines. The potting industry had survived so long without machinery, that the workmen had begun to think themselves safe. These flat and hollow ware-pressers had skill, and they were paid by the piece. At one fell swoop, and in the middle of their settled lives, they saw themselves suddenly deprived of all the value of their skill and training, and likely to be replaced by women and lads. During 1845-6 Mr Ridgway tried a “paste-box” machine, and Chas. J. Mason bought some sort of a plate “jolly.”[186] The men promptly struck and prevented their adoption, but the panic was intensified when Messrs Copeland introduced a similar dread machine, which the potters in their terror called the “Scourge.” This machine too was withdrawn, but not because of the union. The general election of 1847 was approaching and Alderman Copeland stood for Stoke-on-Trent. It is curious to think that the panic fear of the workers postponed the introduction of these machines for twenty years. And indeed the[177] pottery workers themselves have lost something through the introduction of machinery. The proportion of women and young persons employed in the industry is double what it was in 1850, and the work of married women is not good for the rest of the people.
A development that initially helped the union more than anything else was the invention of pot-making machines. The potting industry had managed to survive without machinery for so long that the workers began to feel secure. These flat and hollow ware-pressers had skills and were paid per piece. Then, all at once, in the middle of their stable lives, they found themselves suddenly stripped of the value of their skills and training, and at risk of being replaced by women and boys. During 1845-6, Mr. Ridgway tried out a “paste-box” machine, and Chas. J. Mason purchased some form of plate “jolly.” The men immediately went on strike to stop their adoption, but the panic increased when Messrs. Copeland introduced a similar frightening machine, which the potters in their fear called the “Scourge.” This machine was also withdrawn, but not because of the union. The general election of 1847 was coming up, and Alderman Copeland was running for Stoke-on-Trent. It’s interesting to consider that the workers' panic held off the introduction of these machines for twenty years. In fact, the pottery workers themselves have lost something with the introduction of machinery. The number of women and young people working in the industry is now double what it was in 1850, and the work of married women isn’t beneficial for the rest of the workforce.
Incidentally this machinery panic broke down the union. Encouraged by William Evans, their leader and the editor of the “Examiner,” the union attempted to emigrate the unemployed—almost to emigrate en masse and fly from the wrath to come. They bought a great estate in Wisconsin, called it Pottersville, and to it in 1846 they sent out settlers as to a new Utopia. The scheme failed, and with it, in 1849, collapsed the third potters’ union. Drained of money for America, it had been growing weaker ever since 1847—they could only humbly petition against Copeland’s “Scourge,” and as the union weakened “allowances” crept back into use, while “good-from-oven” and the annual hiring flourished as before.[187]
Incidentally, this machinery panic caused the union to fall apart. Encouraged by their leader William Evans, who was also the editor of the “Examiner,” the union tried to help the unemployed emigrate—almost to leave in bulk and escape the coming disaster. They bought a large estate in Wisconsin, named it Pottersville, and in 1846, they sent settlers there as if it were a new Utopia. The plan failed, and with it, the third potters’ union collapsed in 1849. Stripped of funds for America, it had been weakening since 1847—they could only humbly petition against Copeland’s “Scourge,” and as the union grew weaker, “allowances” returned while “good-from-oven” and the annual hiring thrived as before.[187]
It is said that but for the opposition of the Newcastle innkeepers the main line of the London and[178] Manchester Railway would have run up the Trent valley, and Newcastle would now occupy the position of Crewe as a universal junction. However that may be, in 1846 a company was formed for giving the potteries direct railway communication with the main trunk lines. The moving spirit in this enterprise was Alderman Copeland, M.P. for Stoke, and senior partner in Messrs Copeland and Garrett—the pottery firm that had once been Spode’s.
It is said that if it weren't for the resistance of the Newcastle innkeepers, the main line of the London and[178] Manchester Railway would have gone up the Trent valley, and Newcastle would now be in the same boat as Crewe as a major junction. In any case, in 1846, a company was formed to provide the potteries with direct railway access to the main trunk lines. The driving force behind this venture was Alderman Copeland, M.P. for Stoke, and the senior partner at Messrs Copeland and Garrett—the pottery firm that used to be Spode’s.

ALD. W. T. COPELAND, M.P.
ALD. W. T. COPELAND, M.P.
1797-1868
1797-1868
William Taylor Copeland (1797-1868),[188] son of William Copeland, the partner of the second Spode, had become sole owner of the old Spode china factory at Stoke in 1833. He had been Lord Mayor of London in 1835, and from 1837 till 1865 was generally Conservative member for Stoke-on-Trent. With the help of his partner, Thomas Garrett, Lord Ingestre, Richard Cobden, and some London financiers, the North Staffordshire Railway was formed. Bills were passed through Parliament in 1846, and by the end of 1849 Stoke was connected up with Stafford, Derby, Crewe, and Manchester. They were forced by Parliament to[179] buy out the Canal Company’s monopoly at a very high figure—£1,700,000—which large addition to the capital of the company has always been urged as an excuse for any exceptionally high transport rates on this railway.
William Taylor Copeland (1797-1868), [188] son of William Copeland, who was a partner at the second Spode, became the sole owner of the old Spode china factory in Stoke in 1833. He served as the Lord Mayor of London in 1835 and was a Conservative member for Stoke-on-Trent from 1837 until 1865. With the support of his partner, Thomas Garrett, Lord Ingestre, Richard Cobden, and some investors from London, the North Staffordshire Railway was established. Legislation was passed in Parliament in 1846, and by the end of 1849, Stoke was connected to Stafford, Derby, Crewe, and Manchester. They were compelled by Parliament to buy out the Canal Company’s monopoly for a very high sum—£1,700,000—which has often been used as a justification for the unusually high transport rates on this railway.
We may add here that the loop line through Tunstall was finished in 1875; while the tramways with horse draft were commenced in 1861, turned into steam traction in 1895, and into the present electric system by the British Electric Traction Company in 1902.
We can mention that the loop line through Tunstall was completed in 1875; the horse-drawn tramways began in 1861, switched to steam traction in 1895, and transitioned to the current electric system by the British Electric Traction Company in 1902.
The railway at first affected principally the passenger traffic, and it was only gradually that it came into use for the carrying trade of the district, as the following figures show:
The railway initially impacted mainly passenger travel, and it gradually began to be used for freight in the area, as the following figures illustrate:
Total weight of goods and minerals carried by N.S.R. in 1,000 tons
Total weight of goods and minerals transported by N.S.R. in 1,000 tons
Canal | Rail | Year | |
---|---|---|---|
1370 | — | 1819 | |
1286 | — | 1840 | |
1356 | — | 1849 | |
1259 | 273 | 1850 | |
1595 | 1245 | 1860 | |
1563 | 2324 | 1870 | |
1244 | 3369 | 1880 | |
1076 | 4309 | 1890 | |
1168 | 5587 | 1900 | |
1130 | 6515 | 1906 | [189] |
The partnership between Copeland and Garrett was dissolved in 1847, and the firm took the title of “W. T. Copeland, late Spode.” This was again changed in 1867 when Alderman Copeland’s four sons were admitted into the business, and the name became “W. T. Copeland & Sons.” It was about 1846 that Messrs Copeland developed the “Parian” body, a hard white stoneware second only to marble as a material for statuettes and bas-reliefs. It is composed largely of feldspar, and figures in this material, modelled by some of the best artists of the last half century, still form a large part of Messrs Copeland’s productions.
The partnership between Copeland and Garrett was ended in 1847, and the business adopted the name “W. T. Copeland, late Spode.” This changed again in 1867 when Alderman Copeland’s four sons joined the company, and the name became “W. T. Copeland & Sons.” Around 1846, the Copeland team developed the “Parian” body, a hard white stoneware that is second only to marble for making statuettes and bas-reliefs. It is mainly made of feldspar, and pieces created in this material, crafted by some of the best artists of the last fifty years, still make up a significant portion of Copeland’s offerings.
Alderman Copeland, who was also a great patron of the Turf, died in 1868 and his son, Richard Pirie Copeland, then became sole owner of the works. Mr R. P. Copeland bought Kibblestone Hall, and served as High Sheriff for the county in 1902. His sons have now joined him in the management of the historic works at Stoke.
Alderman Copeland, a major supporter of horse racing, passed away in 1868, and his son, Richard Pirie Copeland, became the sole owner of the business. Mr. R. P. Copeland purchased Kibblestone Hall and served as High Sheriff for the county in 1902. His sons are now involved in managing the historic works in Stoke.
While the Copelands have continued to perfect the old Spode china, their rivals, Mintons, have tried several new fields—tiles, majolica, pâte-sur-pâte. Herbert Minton (1793-1858)[190] and an elder brother joined their father’s firm in 1817, and, after his father and brother retired, he took Robert Boyle as a partner in these works at Stoke. Here in 1828 Herbert Minton first turned his attention towards producing tiles.[191] In 1830 Samuel Wright of Shelton patented a process for making encaustic tiles in the manner of the old Cistercian monks. The patterns were pressed in hollows into the tiles, the hollows were filled up with different coloured slip clays, and then the face was all cut level and flush. This patent was bought up by Minton and Boyle, and after great difficulties the first successful encaustic tiles were made in 1836.[192]
While the Copelands have continued to refine the classic Spode china, their competitors, Mintons, have explored several new areas—tiles, majolica, pâte-sur-pâte. Herbert Minton (1793-1858)[190] and his older brother joined their father's company in 1817, and after their father and brother retired, he partnered with Robert Boyle in their Stoke operations. It was here, in 1828, that Herbert Minton first focused on producing tiles.[191] In 1830, Samuel Wright of Shelton patented a method for making encaustic tiles inspired by the old Cistercian monks. The designs were pressed into the tiles, the impressions were filled with different colored slip clays, and then the surface was smoothed out to be level and flush. Minton and Boyle purchased this patent, and after facing numerous challenges, they successfully produced the first encaustic tiles in 1836.[192]
But it was the patent of Richard Prosser of Birmingham in 1840 which gave us the tile industry of the present day. He compressed clay dust between metal dies, and made the dry dust solid under the pressure of a differential screw. The process was intended at first for making buttons, door-knobs, etc., and it was for these purposes that Minton immediately bought the patent. J. M. Blashfield, who had already had experience in making mosaic pavements, saw the value of the machine for making tiles, and developed this line so effectively that by 1842 no less than sixty-two presses were at work making white glazed dust tiles.[193] Herbert Minton took his wife’s nephew, Michael Daintry Hollins, into partnership in 1841 to look after the tile branch.[194]
But it was Richard Prosser's patent from Birmingham in 1840 that gave us today’s tile industry. He compressed clay dust between metal molds and solidified the dry dust under the pressure of a differential screw. The process was initially meant for making buttons, door knobs, and similar items, and it was for these uses that Minton quickly bought the patent. J. M. Blashfield, who had already gained experience in creating mosaic pavements, recognized the machine's potential for making tiles and effectively developed this line so much that by 1842, no fewer than sixty-two presses were in operation producing white glazed dust tiles.[193] Herbert Minton brought his wife’s nephew, Michael Daintry Hollins, into the partnership in 1841 to oversee the tile division.[194]
Tiles—dust and encaustic—were the first of Minton’s improvements. The next change, due in some degree at least to Minton, was a general improvement in taste. The financial success of common blue printed ware had done away with[183] any inducement to improve ornamental ware. The brilliant natural art of Whieldon had been forgotten; the classic style of Wedgwood fell out of favour under the Regency; and instead we find the gaudy decoration of old shapes by artists ever more mechanical and less artistic. As M. Solon has said: “Worse and worse became the shapes and models; lower and lower sank the work of the decorators; nor could this deplorable state of things be altered by the inspiring study of fine works of art. The Potteries were situated very far from the artistic centre; good examples and good advice were equally wanting. It is not to be denied that all that remains of the most pretentious examples of the pottery of that period (1800-1850) bears the stamp of an unmitigated bad taste.”[195] Some second-rate china painter from Worcester or Derby came over to the Potteries to direct workmen and was called an artist. The modest cream colour was embossed and gilded; the white earthenware was entirely covered with badly engraved blue printing; and the porcelain pieces of importance were decorated in the manner which[184] one now associates with the mantelpiece of the cheap lodging house.
Tiles—dust and encaustic—were the first of Minton’s improvements. The next change, at least partly due to Minton, was a general improvement in taste. The financial success of common blue printed ware eliminated any reason to enhance ornamental ware. The vibrant natural art of Whieldon was forgotten; the classic style of Wedgwood fell out of favor during the Regency; and instead, we see the gaudy decoration of old shapes by artists who became increasingly mechanical and less artistic. As M. Solon said: “Worse and worse became the shapes and models; lower and lower sank the work of the decorators; nor could this deplorable state of affairs be changed by the inspiring study of fine works of art. The Potteries were located far from the artistic center; quality examples and good advice were both lacking. It cannot be denied that all that remains of the most pretentious examples of the pottery from that period (1800-1850) bears the mark of unmitigated bad taste.”[195] Some second-rate china painter from Worcester or Derby came to the Potteries to oversee workmen and was called an artist. The modest cream color was embossed and gilded; the white earthenware was completely covered with poorly engraved blue printing; and the important porcelain pieces were decorated in a style that one now associates with the mantelpiece of a cheap lodging house.
Gradually this has been changed. The exhibitions of 1849 in Birmingham, of 1851, 1862, and 1871 in London, and of 1867 in Paris, induced healthy competition in excellence as an alternative to competition in cheapness and wage cutting. The public museums of Hanley, Stoke and Tunstall came later, but the Museum of Practical Geology, opened in 1851, and the South Kensington Museum, opened in 1857, helped to raise taste. Above all the Wedgwood Institute at Burslem, opened in 1865 under the fostering care of Thos. Hulme and William Woodall, M.P., with its admirable classes for students in applied art, has given a certain artistic training to the designer, decorator and moulder. But much credit also must be given to Herbert Minton for bringing over to Staffordshire the first of a series of French artists who have added extraordinarily to the ornamental value of Staffordshire ware.
Gradually, this has changed. The exhibitions of 1849 in Birmingham, and those in 1851, 1862, and 1871 in London, along with the one in 1867 in Paris, inspired healthy competition based on quality instead of just focusing on low prices and cutting wages. The public museums in Hanley, Stoke, and Tunstall came later, but the Museum of Practical Geology, which opened in 1851, along with the South Kensington Museum, which opened in 1857, played a role in improving taste. Most notably, the Wedgwood Institute in Burslem, established in 1865 under the support of Thos. Hulme and William Woodall, M.P., with its excellent classes for students in applied art, has provided valuable artistic training for designers, decorators, and molders. Much credit must also go to Herbert Minton for bringing the first in a series of French artists to Staffordshire, who significantly enhanced the ornamental value of Staffordshire pottery.
M. Leon Arnoux (1816-1902) was engaged in 1849 by Messrs Minton, and became thenceforth the art manager of the works. He improved the[185] decoration of their porcelain and the whiteness of its body, but his chief claim to notice rests on his “majolica” and his imitation of the old Pallissy, or Henri II, ware. For 30 years nothing was more popular than Minton’s majolica, whether for ornamental ware, tiles or façades. Arnoux was followed by such artists as Jeanest, Lessore, Protat,[196] and in 1870 by Mons. M. L. Solon, whose special work—pâte-sur-pâte decoration—still holds the public taste and deserves to become classical. In this process white slip clay-paste is painted on to a dark clay body, and the varying thickness and transparency of the layers of paint produce an effect which differs completely from either plain enamelling or the high relief of jasper. At the same time it lends itself to the individual taste of the artist and can never become merely mechanical.
M. Leon Arnoux (1816-1902) was hired in 1849 by Messrs Minton and became the art manager of the works from then on. He enhanced the decoration of their porcelain and improved its whiteness, but his main contribution was in his “majolica” and his imitation of the old Pallissy, or Henri II, ware. For 30 years, Minton’s majolica was incredibly popular, whether for decorative items, tiles, or facades. Arnoux was succeeded by artists like Jeanest, Lessore, Protat, [196] and in 1870 by Mons. M. L. Solon, whose specialty—pâte-sur-pâte decoration—still appeals to the public and deserves to be recognized as classic. In this technique, white slip clay-paste is applied to a dark clay body, and the varying thickness and transparency of the paint layers create an effect that is completely different from plain enameling or the high relief of jasper. At the same time, it allows for the individual artist's touch and can never become just mechanical.
When Herbert Minton died in 1858 his firm employed 1500 workpeople,[197] a number which has never been exceeded by any ornamental factory before or since. His two nephews, M. D. Hollins and Colin Minton Campbell (1827-1885)—the[186] latter had become a partner in 1849—carried on the business jointly under the title of Herbert Minton & Co. for china and earthenware, and Minton, Hollins & Co. for tiles. In 1863 they were joined for a few years by another partner, Robert Minton Taylor, and on his leaving in 1868 Hollins and Campbell divided the business between them. Hollins took the tiles, and Campbell the main factory. One of the conditions of the division was that Campbell had to take over the stock of moulds at a valuation. It is said that they were valued at the unexpected and extraordinary figure of £30,000, the compulsory payment of which dissolved the friendship as well as the partnership of the two cousins. It may have been the recollection of this heavy grievance that induced Campbell in 1871 to start the Campbell Tile Co., a serious competitor for Minton, Hollins & Co., and the progenitor of many lawsuits.
When Herbert Minton died in 1858, his company had 1,500 employees, a number that has never been surpassed by any decorative factory before or since. His two nephews, M. D. Hollins and Colin Minton Campbell (1827-1885)—the latter became a partner in 1849—continued the business together under the name Herbert Minton & Co. for china and earthenware, and Minton, Hollins & Co. for tiles. In 1863, they were joined for a few years by another partner, Robert Minton Taylor, and after he left in 1868, Hollins and Campbell split the business between them. Hollins took the tile division, while Campbell took over the main factory. One of the conditions of the split was that Campbell had to take on the stock of molds at a valuation. It’s said that they were valued at the surprising and outrageous amount of £30,000, and the mandatory payment of this amount ended both the friendship and partnership between the two cousins. It may have been this significant grievance that led Campbell to establish the Campbell Tile Co. in 1871, a serious competitor to Minton, Hollins & Co., which resulted in many lawsuits.
Colin Minton Campbell was High Sheriff of Staffordshire in 1869, Chairman of the North Stafford Railway, and Conservative Member of Parliament for North Staffs 1874-80. He died in 1885, and his statue stands in the High Street of[187] Stoke. The Minton Works are now the property of his son John Campbell of Woodseat, but he takes no share in the business, which is managed by Mr J. Robinson. Another John Campbell owns and manages the Campbell Tile Co. in Stoke.
Colin Minton Campbell was the High Sheriff of Staffordshire in 1869, the Chairman of the North Stafford Railway, and a Conservative Member of Parliament for North Staffs from 1874 to 1880. He passed away in 1885, and his statue is located on the High Street of[187] Stoke. The Minton Works are now owned by his son John Campbell of Woodseat, but he doesn’t participate in the business, which is run by Mr. J. Robinson. Another John Campbell owns and manages the Campbell Tile Co. in Stoke.
As for the rival nephew and potter, Michael Hollins, he built in 1870 the modern factory of Minton, Hollins & Co. in Shelton Old Road, Stoke, and continued till his death in 1898 to make the best encaustic and glazed dust tiles. The factory, employing some 400 workers, is now carried on, but under far keener competition, by his grandson, Michael Daintry Hollins.
As for the rival nephew and potter, Michael Hollins, he established the modern factory of Minton, Hollins & Co. in 1870 on Shelton Old Road, Stoke, and continued until his death in 1898 to produce the finest encaustic and glazed dust tiles. The factory, which employed about 400 workers, is still in operation today, but now faces much tougher competition from his grandson, Michael Daintry Hollins.
Another important tile factory is that of T. & R. Boote in Burslem. This firm was founded in 1842 by Thomas Latham Boote and Richard Boote at the “Central Pottery” in Burslem. About 1850 they bought several old pot-banks, put up their present “Waterloo Potteries” in Waterloo Road, and started to make tiles. Mr T. L. Boote retired in 1879, Mr. R. Boote died in 1891, and the works are now carried on by the sons of the former, Richard L. and Charles E. Boote.[198]
Another important tile factory is T. & R. Boote in Burslem. This company was started in 1842 by Thomas Latham Boote and Richard Boote at the “Central Pottery” in Burslem. Around 1850, they purchased several old pot-banks, built their current “Waterloo Potteries” on Waterloo Road, and began producing tiles. Mr. T. L. Boote retired in 1879, Mr. R. Boote passed away in 1891, and the business is now run by the sons of the former, Richard L. and Charles E. Boote.[198]
The British manufacture of tiles is not so entirely localized in North Staffordshire as is that of china and earthenware, but 6 out of the 17 largest English firms have their works here. Such are, beside those already mentioned, G. Woolliscroft and Sons and the Porcelain Tile Co., both of Hanley, Henry Richards Tile Co., of Tunstall, and the Malkin Tile Co. of Burslem.[199]
The production of tiles in Britain isn't as concentrated in North Staffordshire as that of china and pottery, but 6 out of the 17 largest English companies are located here. These include G. Woolliscroft and Sons and the Porcelain Tile Co., both from Hanley, the Henry Richards Tile Co. from Tunstall, and the Malkin Tile Co. from Burslem.[199]
But the manufacture of tiles, though economically the most important part of Minton’s work, ought not to distract attention from that great artistic development of his school, which gave us from 1855-1885 the halcyon days of the English china trade. With this period the names of Minton, Ridgway, Brown Westhead and Brownfield are chiefly associated, while such old firms as Copelands and Wedgwoods acquired fresh lustre.
But the production of tiles, although the most economically significant aspect of Minton’s work, shouldn't overshadow the great artistic advancements of his school, which brought us the golden years of the English china trade from 1855 to 1885. During this time, the names Minton, Ridgway, Brown Westhead, and Brownfield are mainly linked, while older companies like Copelands and Wedgwoods gained renewed prominence.
John Ridgway of Cauldon Place is reputed to have produced the best china at the 1851 exhibition, and when he died in 1860 the Cauldon Place Works were bought by Messrs T. C. Brown Westhead, Moore and Co., who have continued to this day to produce the china for which Cauldon Place has always been renowned. William Ridgway, the brother of John, had half a dozen factories in Hanley—George Taylor’s, Elijah[190] Mayer’s, Toft and May’s, D. Wilson’s, Hicks’, Meigh and Johnson’s, besides the old Bell Works, and made both earthenware and china.[200] His son Edward John Ridgway built their present Bedford Works in Hanley, where this family still produce china, as well as “Granite” and printed ware for the American trade.
John Ridgway of Cauldon Place is known for having produced the best china at the 1851 exhibition, and when he passed away in 1860, the Cauldon Place Works were purchased by Messrs T. C. Brown Westhead, Moore and Co., who have continued to make the china that Cauldon Place has always been famous for. William Ridgway, John's brother, owned several factories in Hanley—George Taylor’s, Elijah[190] Mayer’s, Toft and May’s, D. Wilson’s, Hicks’, Meigh and Johnson’s, along with the old Bell Works—and produced both earthenware and china.[200] His son Edward John Ridgway built their current Bedford Works in Hanley, where this family still produces china, as well as “Granite” and printed ware for the American market.
Nor must the name of William Brownfield of Cobridge be omitted from any account of the prosperous days of the china trade. This firm, which has now closed down, made trial recently of a profit-sharing scheme, which deserved well of the community. Unfortunately it fell upon the bad times near the end of the last century and was discontinued.
Nor should the name of William Brownfield of Cobridge be left out of any account of the successful days of the china trade. This company, which has now shut down, recently tested a profit-sharing plan that greatly benefited the community. Unfortunately, it faced tough times toward the end of the last century and was discontinued.
The success of Minton in majolica, tiles and porcelain led the Wedgwoods at Etruria to depart so far from their special black basalt and jasper as to take up similar lines of manufacture. Their brown majolica glaze, known as “rockingham,” perhaps the most permanently successful form of majolica, was introduced about 1860.[201] (This[191] “rockingham” glaze had been first employed about 1796 near Rotherham on the Marquis of Rockingham’s estate in Yorkshire.)[202] Then, in 1872, they began again to make porcelain, and this time with great success. A Wedgwood china dinner service of 1296 pieces was selected by President Roosevelt for the White House in open competition with the whole world. From 1880 till 1902 Wedgwoods also made encaustic and white-glazed tiles, though without any financial success. This firm now employs about 700 people, and is carried on by Messrs Lawrence, Cecil and Francis Hamilton Wedgwood, the great-grandson and great-great-grandsons of Josiah Wedgwood, making altogether eight generations of master-potters from father to son, probably a unique example in any industry.
The success of Minton in majolica, tiles, and porcelain prompted the Wedgwoods at Etruria to move away from their signature black basalt and jasper to pursue similar manufacturing lines. Their brown majolica glaze, known as “rockingham,” which is perhaps the most enduring form of majolica, was introduced around 1860.[201] (This[191] “rockingham” glaze was first used around 1796 near Rotherham on the Marquis of Rockingham’s estate in Yorkshire.)[202] Then, in 1872, they started making porcelain again, and this time with great success. A Wedgwood china dinner service of 1,296 pieces was selected by President Roosevelt for the White House in an open competition with entries from all over the world. From 1880 to 1902, Wedgwoods also produced encaustic and white-glazed tiles, although without any financial success. Today, the company employs about 700 people and is run by Messrs Lawrence, Cecil, and Francis Hamilton Wedgwood, the great-grandson and great-great-grandsons of Josiah Wedgwood, representing a total of eight generations of master potters from father to son, probably a unique occurrence in any industry.
While Mintons, Copelands and Wedgwoods were producing the most costly porcelain, the trade in the commoner china had centred more and more at the Longton end of the Potteries. Charles J. Mason with his “ironstone china” at Fenton between 1820 and 1850 was the precursor of this[192] trade, and it was on this export trade that Longton grew so rapidly throughout the 19th century. The manufacture of cheap “jet” and “rockingham” has become of recent years an important branch of manufacture at this Longton end, and very opportunely, for the cheap china trade has suffered more than any other from the German and Dutch competition. Messrs Wileman’s factory at the Foley, now owned by Mr Percy Shelley, is the most important, but the Longton china trade generally is in the hands of small men. A great part of this china trade was formerly with America, and, apart from ornamental potting, it has always been the solid American trade which has made the fortunes of the Staffordshire potters. In the forties the chief exporters of earthenware to America were Enoch Wood of Fountain Place, and Samuel Alcock of the Hill Top Works, both in Burslem. Samuel Alcock had several factories in Burslem, and deserves mention for his “Parian” figures, but his great trade was in plain white and cream colour with the United States.[203] Alcock’s old Hill Top Works, where John Mitchell once[193] used to entertain Wesley, belong now to Samuel Johnson, noted for his tea-pots.
While Mintons, Copelands, and Wedgwoods were making the most expensive porcelain, the market for everyday china increasingly focused on the Longton area of the Potteries. Between 1820 and 1850, Charles J. Mason in Fenton introduced “ironstone china,” paving the way for this trade, and it was this export business that fueled Longton's rapid growth throughout the 19th century. The production of inexpensive “jet” and “Rockingham” china has recently become an important segment of manufacturing in Longton, and this is quite timely, as the budget china market has been hit harder than any other by competition from Germany and the Netherlands. Wileman’s factory at the Foley, now owned by Mr. Percy Shelley, is the most significant, but the Longton china trade is mainly controlled by small businesses. A large part of this china trade used to be with America, and aside from decorative pottery, the solid American market has consistently built the fortunes of Staffordshire potters. In the 1840s, the main exporters of earthenware to America were Enoch Wood of Fountain Place and Samuel Alcock of the Hill Top Works, both in Burslem. Samuel Alcock operated several factories in Burslem and deserves recognition for his “Parian” figures, but his major trade was in plain white and cream-colored ware with the United States. Alcock’s old Hill Top Works, where John Mitchell once entertained Wesley, now belongs to Samuel Johnson, known for his teapots.
The close of the American war, 1865, saw the rise of another potting firm destined to grow to importance in the American trade. This was the firm of James and George Meakin. They were the sons of James Meakin, who had been a small master-potter in Hanley, and they produced an uniform hard white earthenware called “granite”—serviceable, plain and cheap. James Meakin, a man of great business capacity, financed and gradually came to control a large proportion of the American buyers, and all through the seventies this firm almost monopolized the trade of the United States in cheap earthenware. James Meakin bought Darlaston Hall, and died in 1885. His “Eagle Works” at Hanley are now carried on by his sons Kenneth and Bernard and by his nephew George Meakin of Cresswell Hall. Alfred Meakin started a similar manufacture at the Victoria and Albert Works in Tunstall in 1874, now taken over by Johnson Bros. These Johnsons, too, nephews of James Meakin, began soon after 1880 to rival the Eagle Works in the production of “granite” and[194] plain printed ware. They have now no less than five factories in Hanley, Tunstall and Burslem specially equipped for this trade. The fourth of the firms known as “The Big American Four” (now reduced to three) is that of W. H. Grindley, who began in 1887 to make “granite” at Wood and Challenor’s old Woodland Works in Tunstall. His new factory at Brownhills is said to afford the best example of up-to-date economical[195] manufacture, and stands out in striking contrast to most of the older “artistic” works. Another factory which owes its reputation to strict specialization and the latest economical machinery is that of Samuel Gibson, in the Moorland Road, at Burslem. Here five hundred men and girls make tea-pots for the world—only tea-pots—in jet and brown and rockingham.
The end of the American Civil War in 1865 marked the emergence of another pottery company that would become significant in the American market. This was the company founded by James and George Meakin. They were the sons of James Meakin, who had been a small-scale potter in Hanley, and they created a consistent hard white earthenware known as “granite”—practical, simple, and affordable. James Meakin, a man with exceptional business skills, financed the venture and gradually gained control over a large part of the American market, and throughout the 1870s, this company almost monopolized the trade of inexpensive earthenware in the United States. James Meakin purchased Darlaston Hall and passed away in 1885. His “Eagle Works” in Hanley are now run by his sons Kenneth and Bernard, along with his nephew George Meakin of Cresswell Hall. Alfred Meakin initiated a similar operation at the Victoria and Albert Works in Tunstall in 1874, which has since been taken over by Johnson Bros. These Johnsons, also nephews of James Meakin, began competing with the Eagle Works around 1880 in producing “granite” and plain printed wares. They now operate five factories in Hanley, Tunstall, and Burslem specifically designed for this industry. The fourth of the companies known as “The Big American Four” (now reduced to three) is W. H. Grindley, who started manufacturing “granite” in 1887 at the old Woodland Works of Wood and Challenor in Tunstall. His new factory in Brownhills is regarded as the best example of modern, cost-effective production and stands in stark contrast to many of the older “artistic” facilities. Another factory renowned for its strict specialization and state-of-the-art machinery is Samuel Gibson's, located on Moorland Road in Burslem. Here, five hundred men and women manufacture tea pots exclusively—only tea pots—in jet, brown, and Rockingham finishes.

The china trade and the American “granite” trade had their best days from 1870 to 1876. No doubt the general expansion of trade and the temporary absence of foreign competition were the chief factors in producing this prosperity. But a great deal was due to the increased use of steam power and the introduction of automatic machinery, and also to the institution of the Potteries Board of Conciliation and Arbitration.
The china trade and the American “granite” trade experienced their peak from 1870 to 1876. The overall growth of trade and the temporary lack of foreign competition were undoubtedly the main reasons for this prosperity. However, much of it also came from the increased use of steam power, the introduction of automatic machinery, and the establishment of the Potteries Board of Conciliation and Arbitration.
The clay filter press, with its steam slip-pumps—patented by Needham and Kite in 1856—had replaced the old method of evaporating the moisture out of the clay slip; and during the seventies a mechanical steam-driven “blunger” and a similar “pug-mill” did away with the old laborious “blunging” and “wedging” in the preparation[196] of the clay body. Then that form of the thrower’s wheel, known as the plate “jigger”—which revolved the flat plate moulds—came to be driven by steam instead of by a boy at the wheel handle; and instead of the skilled hand of the flat-presser, a mechanical “form” or “jolly” was used to press the “bat” on to the mould, and give the plate the right contour and thickness.[204]
The clay filter press, featuring its steam slip-pumps—patented by Needham and Kite in 1856—had taken over the old method of evaporating moisture from the clay slip. During the 1870s, a mechanical steam-driven "blunger" and a similar "pug-mill" eliminated the old, tedious “blunging” and “wedging” processes involved in preparing the clay body. Then, a type of potter's wheel known as the plate "jigger" began to be powered by steam instead of requiring a boy to operate the wheel handle. Instead of relying on the skilled hand of the flat-presser, a mechanical "form" or "jolly" was used to press the “bat” onto the mold, providing the plate with the correct shape and thickness.[196]
Such machines for making plates had been invented as long ago as 1845, but for twenty years the objections of the workmen and practical imperfections had postponed their introduction. The “form” used to be applied by hand, and the plates consequently varied in thickness, and it required great skill on the part of the presser to make them properly. The machine, on the other hand, made every plate exactly alike, and made them ten times as quickly as the old hand process. This machine did away with the work of the old skilled “flat-pressers,” and was in general use by 1870. A similar machine, with a somewhat more complicated “jolly,” or “form,” made hollow-ware,[197] such as basins and cups, or even bellied ware, such as ewers or chamber-pots. These came into use gradually from 1870 onwards, and replaced much of the work of hollow-ware pressers and throwers. Then in the eighties came a machine for flattening out those bats of clay which were to be pressed on to the “jigger” moulds and “jollied” into flat or hollow ware.[205] About the same time, too, the steam drive came to be used for turning the thrower’s wheel and for the turner’s lathe—fitted with various devices for controlling the speed of revolution. The manufacture of potters’ machinery is now a considerable industry, and, thanks to the energy and inventive readiness of Messrs Boulton of Burslem, this industry also is centred in the Staffordshire Potteries, and has as wide a range of markets as the Staffordshire pots themselves.
Machines for making plates were invented as far back as 1845, but for twenty years, the concerns of workers and practical issues delayed their introduction. The “form” was applied by hand, which led to variations in thickness, and it required a lot of skill from the presser to make them correctly. On the other hand, the machine produced every plate exactly the same and did so ten times faster than the old hand process. This machine eliminated the need for the old skilled “flat-pressers,” and it was commonly used by 1870. A similar machine, which had a slightly more complex “jolly” or “form,” made hollow ware, such as basins and cups, or even shaped ware, like ewers or chamber pots. These were gradually introduced from 1870 onward, replacing much of the work done by hollow-ware pressers and throwers. Then in the 1880s, a machine was developed for flattening the bats of clay that were to be pressed onto the “jigger” molds and “jollied” into flat or hollow ware. Around the same time, steam power was used to operate the thrower’s wheel and the turner’s lathe, which were equipped with various devices to control the speed of rotation. The production of potters’ machinery is now a significant industry, and due to the energy and inventive spirit of Messrs Boulton of Burslem, this industry is also centered in the Staffordshire Potteries, with as broad a range of markets as the Staffordshire pots themselves.
The introduction of all these labour-saving appliances was facilitated by the co-operation of masters and men on an arbitration board. A Trades Union—the fourth—had been reconstituted in 1863 from a few surviving branches of the old[198] Union. They started a fresh newspaper, “The Potteries Examiner,” under the able management of the new Leader, William Owen, the nephew of Robert Owen, the Socialist. By 1865 they were strong enough to strike against that good old trade custom—the annual hiring. The oven-men’s Union, always the most determined branch of the Potters Trades Unions, refused to give up the fight when the other trades were prepared to go in, and by holding out alone they at last succeeded in abolishing the annual hiring, and secured for the potter the right to give a month’s notice. This was in 1866, and the whole trade shared the benefits of the change.[206]
The introduction of all these labor-saving devices was made possible by the cooperation of employers and workers on an arbitration board. A Trades Union—the fourth—was reestablished in 1863 from a few remaining branches of the old Union. They launched a new newspaper, “The Potteries Examiner,” under the skilled management of the new Leader, William Owen, who was the nephew of Robert Owen, the Socialist. By 1865, they had become strong enough to strike against the old trade custom—the annual hiring. The oven-men's Union, always the most determined group within the Potters Trades Unions, refused to back down when the other trades were ready to join in, and by holding out alone, they ultimately succeeded in abolishing the annual hiring and secured for potters the right to give a month's notice. This was in 1866, and the entire trade benefited from the change.[198]
The Staffordshire Potters Unions seem at each burst of activity to have evolved some special enthusiasm or eccentricity. There was the attempt at co-operative manufacture in 1825; the enthusiastic idealism of Robert Owen in 1833; the attempt to put the unemployed on the land in Wisconsin, and so relieve the labour market, which absorbed the enthusiasm and funds of 1845-6; and now the new Union of 1863, under the guidance[199] of William Owen, originated a far more important and practical movement—arbitration in industrial disputes.
The Staffordshire Potters Unions seem to develop some unique enthusiasm or quirk each time they become active. There was the effort for cooperative manufacturing in 1825; the passionate idealism of Robert Owen in 1833; the initiative to provide land for the unemployed in Wisconsin to help ease the labor market, which captured the enthusiasm and resources of 1845-6; and now the new Union of 1863, led by William Owen, has started a much more significant and practical movement—arbitration in industrial disputes.[199]
At Nottingham, Mr Mundella had in 1867 established a Board of Arbitration in the stocking trade. Its success made it attractive to both masters and men. William Owen approached Mr Mundella, who brought his influence to bear successfully on the pottery masters also, and in July, 1868, a similar Board of Conciliation and Arbitration was established in the potting industry.[207] On it there were ten representatives of each side, who were wherever possible to decide questions that arose. When they could not agree an umpire was to be appointed, whose decision was to be binding. Such men as H. T. Davenport, M.P., Mr Mundella, Sir Thomas Brassey, “Tom” Hughes, have at different times been umpires.
At Nottingham, Mr. Mundella established a Board of Arbitration in the stocking trade in 1867. Its success attracted both employers and workers. William Owen approached Mr. Mundella, who successfully used his influence with the pottery employers as well. In July 1868, a similar Board of Conciliation and Arbitration was set up in the pottery industry.[207] It included ten representatives from each side, who were tasked with resolving issues that came up whenever possible. If they couldn't agree, an umpire would be appointed, and their decision would be binding. Individuals like H. T. Davenport, M.P., Mr. Mundella, Sir Thomas Brassey, and “Tom” Hughes have served as umpires at different times.
At first the Board worked well. The introduction of each machine was made the occasion for a readjustment of prices; and, although the struggle over “good-from-oven” goes on to this day, the first step was taken before the Board in 1869 on[200] the motion of one of the masters’ delegates, Mr Francis Wedgwood, to abolish this old trade custom and substitute “good-from-hand.”[208] An arbitration award in 1871 raised wages generally.[209]
At first, the Board functioned smoothly. Each new machine brought about a price adjustment; and while the debate over “good-from-oven” continues to this day, the initial move was made before the Board in 1869 on[200] the suggestion of one of the masters’ delegates, Mr. Francis Wedgwood, to eliminate this old trade practice and replace it with “good-from-hand.”[208] An arbitration decision in 1871 generally increased wages.[209]
But the strain came when the masters tried by arbitration to reduce wages. The award in 1877 went against them; in 1879, however, they were more fortunate, for Lord Hatherton awarded a reduction of 1d. in the shilling.[210] A journeyman potter’s wages may be said to have averaged 30s. a week when in full employ, and what are still remembered as “Lord Hatherton’s pennies” were a great grievance in the Potteries. Probably the Board would have broken down at once had it not been for Owen, and for the hope that arbitration next year would put it all right again. But Sir Thomas Brassey’s award on next year’s arbitration made no change,[211] and the Board broke down. At Martinmas 1881 a strike began. It was an immediate failure, for thirteen years of arbitration had sapped the strength of the Union.
But the pressure intensified when the employers attempted to reduce wages through arbitration. The decision in 1877 went against them; however, in 1879, they had better luck, as Lord Hatherton granted a reduction of 1d. in the shilling.[210] A journeyman potter's wages generally averaged around 30s. a week when fully employed, and what are still referred to as “Lord Hatherton’s pennies” were a significant source of frustration in the Potteries. The Board likely would have collapsed immediately if it weren't for Owen and the hope that arbitration would resolve everything the following year. But Sir Thomas Brassey’s ruling in the next year's arbitration changed nothing,[211] and the Board ultimately fell apart. At Martinmas 1881, a strike began. It was an instant failure since thirteen years of arbitration had drained the strength of the Union.
For a short time—1885-91—an Arbitration Board was re-established, but it was tolerated rather than supported by either masters or men. In 1891 another award was given against the men, and the Board was painlessly extinguished by a strike of the fighting oven-men. Since then the Union has gradually gained strength, but even now, after a successful strike in 1900 which raised wages by 5 per cent. all round, the potters in all the Unions do not much exceed 20 per cent. of the adult male workers alone. Trades Unions have special difficulties in the Potteries owing to the large number of small masters employing only two or three people in each trade; owing to the prevailing piecework prices which makes the levelling up process difficult; and owing to the number of small Unions into which the working potters are divided. John Lovatt is at present the secretary of the General Union, while Alderman Thomas Edwards for long looked after the special interests of the oven-men.
For a brief period—from 1885 to 1891—an Arbitration Board was set up again, but it was more tolerated than supported by either the employers or the workers. In 1891, another ruling was made against the workers, and the Board was quietly dissolved by a strike from the oven-men. Since then, the Union has steadily gained strength, but even now, after a successful strike in 1900 that increased wages by 5 percent across the board, potters in all the Unions still make up only about 20 percent of the adult male workforce. Trade Unions face unique challenges in the Potteries due to the many small employers who hire just two or three people in each trade; the common piecework pay rates that complicate the standardization process; and the numerous small Unions into which the working potters are scattered. John Lovatt is currently the secretary of the General Union, while Alderman Thomas Edwards has long been involved in advocating for the oven-men's specific interests.
Invention of recent years has busied itself mostly with the firing of the ovens. Mr J. P. Holdcroft, of Hanley, patented in 1898 a new thermoscope[202] which directs with far greater certainty the exact heating of the ovens.[212] New methods of firing these ovens are also on trial. Both “Producer” and “Mond” gas have been tried and offer some hope not only of more regular firing, but also of abolishing the columns of smoke which have blackened the Potteries for 200 years. The “Climax Kiln” is another device of quite recent date for regulating the firing, and saving the piling up and unpiling of saggars of ware. The ware is packed in an iron cage on wheels and pulled in and out of the furnace mechanically, without drawing the fire.
Recent inventions have mainly focused on optimizing oven firing. Mr. J. P. Holdcroft from Hanley patented a new thermoscope in 1898[202] that allows for much more accurate heating of the ovens. [212] New firing methods are also being tested. Both “Producer” and “Mond” gas have been experimented with, showing promise not only for more consistent firing but also for eliminating the smoke clouds that have polluted the Potteries for 200 years. The “Climax Kiln” is another recent innovation aimed at managing the firing process while reducing the need for stacking and unstacking saggars of ware. The ware is loaded into a wheeled iron cage, which is then mechanically pulled in and out of the furnace without interrupting the fire.
Both the “Climax Kiln” and a new method of polychrome printing—whereby one transfer only is used to impart many colours to the piece of ware to be printed—have been introduced within the last six years by Mr Leonard Grimwade, perhaps the most enterprising potter of recent times. Mr Grimwade has specialized for the Colonial markets, and holds in them much the position held by Meakins in the American trade. His factories are in Hanley and Stoke, adjoining the Stoke Railway Station.
Both the “Climax Kiln” and a new method of polychrome printing—where a single transfer is used to apply multiple colors to a piece of ware—have been introduced in the last six years by Mr. Leonard Grimwade, arguably the most innovative potter in recent times. Mr. Grimwade has focused on the Colonial markets, holding a similar position to Meakins in the American trade. His factories are located in Hanley and Stoke, next to the Stoke Railway Station.
An off-shoot of the potting trade which almost amounts to an invention by itself is the manufacture of stilts, spurs and thimbles. These are the small “bits” put between the wares to prevent them sticking together when fired in the saggars, and they used to be made when and as wanted in each separate pot-works. It was Charles Ford of Hanley who, about 1840, first made a special factory for these spurs and stilts. He used metal die-stamps driven by a steam hammer which stamped out stilts by the score at a time. James Gimson followed with the invention of the “thimble.” These conical thimbles fit into and one above each other and have a lug on the rim, so that three pillar-supports are built up on which a whole “nest” of plates can rest while in the oven without touching each other. Stacked in this way, the “bits” make no marks on the face of the plate. Somewhat later Wentworth Buller, a member of the well-known Devon family, started a stilt and spur factory at Bovey Tracy in Devonshire, and, finding the cost of carriage to his market prohibitive, he moved his works about 1865 to Hanley. Here he began[204] in 1866-7 to make telegraph insulators—a new pottery industry. He was joined shortly after by his cousin, Captain Ernest Wentworth Buller, the brother of Sir Redvers and an engineer, who became sole owner in 1869. In 1872 J. T. Harris joined the firm, which is now controlled and carried on by his son, John Harris. Having obtained a foothold in the electrical trade, this firm was naturally called on to do all the early electrical work. Just as they had stamped stilts and spurs so they stamped switches, cut-outs, “roses,” and all manner of electric fittings. In 1896 Captain Buller sold out and retired. The elaborate insulators now used are thrown by hand and then turned and screwed, and nearly half the world’s supply comes from Bullers Limited.
An offshoot of the pottery industry, which is almost an invention in its own right, is the production of stilts, spurs, and thimbles. These are the small "bits" placed between the items to stop them from sticking together when fired in the saggars, and they used to be made as needed at each individual pottery. It was Charles Ford of Hanley who, around 1840, first created a dedicated factory for these spurs and stilts. He used metal die-stamps powered by a steam hammer that could produce dozens of stilts at a time. James Gimson then invented the "thimble." These conical thimbles fit into each other and have a lug on the rim, allowing three pillar supports to be stacked up so a complete "nest" of plates can rest in the oven without touching each other. Stacked this way, the "bits" leave no marks on the surface of the plate. A bit later, Wentworth Buller, a member of the prominent Devon family, started a stilt and spur factory in Bovey Tracy, Devonshire. Finding the shipping costs to his market too high, he relocated his factory to Hanley around 1865. There, he began in 1866-67 to produce telegraph insulators—a new pottery industry. He was soon joined by his cousin, Captain Ernest Wentworth Buller, the brother of Sir Redvers and an engineer, who became the sole owner in 1869. In 1872, J. T. Harris joined the business, which is now managed and operated by his son, John Harris. After establishing themselves in the electrical trade, this company was naturally called upon to handle all the early electrical work. Just as they had stamped stilts and spurs, they also stamped switches, cut-outs, "roses," and various electrical fittings. In 1896, Captain Buller sold his shares and retired. The complex insulators used today are hand-thrown, then turned and screwed, with nearly half of the world’s supply coming from Bullers Limited.
A somewhat similar trade was carried on by James Mackintyre and William Woodall, M.P., at Burslem, in the manufacture of furniture fittings. Door plates, door knobs, knobs and buttons of all sorts for the furniture trade are stamped in dies by the score, as are the stilts and spurs. Messrs. Mackintyre are still the chief makers of furniture pottery, though they have by no means a monopoly.
A similar business was run by James Mackintyre and William Woodall, M.P., in Burslem, where they made furniture fittings. They stamp door plates, door knobs, and all kinds of knobs and buttons for the furniture industry using numerous dies, as well as stilts and spurs. Mackintyre and Woodall are still the leading producers of furniture pottery, although they certainly don’t have a monopoly.
Saggars in which ware is packed for firing are also made by the direct pressure of a large die or press upon the plastic marl.
Saggars used to pack pottery for firing are also made by applying direct pressure from a large die or press onto the wet marl.
Messrs Bullers’ most formidable rival in the making of insulators is the firm of Doulton’s Limited; and this last firm carry on also several other variations of the staple trade. Sir Henry Doulton (1820-97)[213] began by making sewage pipes at Lambeth. His trade increased, and he started branch works for making these things at St Helens and at Rowley Regis and Smethwick in South Staffordshire. Between 1867 and 1873, however, he diverted his attention to the more ambitious “Electric” and “Sanitary” ware, and also to the characteristic stoneware known as “Doulton’s.” This new stoneware caught the public fancy, and to it he devoted his Lambeth works. He continued to make the drain pipes at Rowley Regis, and at Burslem he bought in 1877 Pinder & Bourne’s works in Nile Street for his other manufactures. Here Doulton’s produce high-class china and earthenware as well as sanitary and electric pottery and employ nearly 1,300 hands.[206] Sir Henry Doulton was knighted in 1887, the only potter ever so honoured, and died in 1897. In 1899 his son, Henry Lewis Doulton, converted the business into a limited company.[214]
Messrs Bullers' biggest rival in making insulators is the company Doulton's Limited, which also produces several other variations of the main trade. Sir Henry Doulton (1820-97)[213] started by manufacturing sewage pipes in Lambeth. His business grew, and he opened branch factories for making these products in St Helens, Rowley Regis, and Smethwick in South Staffordshire. However, between 1867 and 1873, he shifted his focus to the more ambitious “Electric” and “Sanitary” ware, as well as the distinctive stoneware known as “Doulton’s.” This new stoneware captivated the public, and he dedicated his Lambeth factory to it. He continued producing drain pipes in Rowley Regis, and in 1877, he acquired Pinder & Bourne’s works on Nile Street in Burslem for his other products. At this location, Doulton's produces high-quality china and earthenware, as well as sanitary and electric pottery, employing nearly 1,300 workers.[206] Sir Henry Doulton was knighted in 1887, the only potter to receive this honor, and he passed away in 1897. In 1899, his son, Henry Lewis Doulton, turned the business into a limited company.[214]
But the branch of the trade known as sanitary pottery owes most of its development in Staffordshire to Mr Thomas William Twyford. His father Thomas Twyford started making plumbers’ ware about 1860, and when he died in 1872 both the Abbey Works and the Bath Street Works in Hanley were making basins and closet-pans of an elementary kind. But no real advance took place till the eighties. In 1885 the wash-out Pedestal closets were introduced, made entirely of earthenware, and in 1889 the latest “deluge” type followed. Those who can remember the old dirty enamelled iron pans will recognize the debt that sanitary science owes to the enterprise of Twyford.
But the part of the industry known as sanitary pottery owes most of its growth in Staffordshire to Mr. Thomas William Twyford. His father, Thomas Twyford, began producing plumbing fixtures around 1860, and when he passed away in 1872, both the Abbey Works and the Bath Street Works in Hanley were making basic basins and toilet pans. However, no significant progress occurred until the 1880s. In 1885, the wash-out pedestal toilets were introduced, made entirely of earthenware, and in 1889, the latest "deluge" type followed. Those who remember the old, dirty enameled iron pans will recognize how much sanitary science owes to Twyford's innovation.
All Twyford’s sanitary pottery was in 1887 concentrated at the present Cliff Vale Works, and experiments were at once set on foot for yet another branch of manufacture. This was the production of very large clay pieces coated with a[207] smooth white surface and suitable for baths and lavatories. The common or fire clay is coated while in the plastic state with a porcelain enamel, which on firing gives a surface enamel polished as marble and more adhesive than any enamel on metal. Very large pieces are coated in this way, and the earthenware article has since 1890 been replacing alike the enamelled metal of Wolverhampton and the marble of Italy. Messrs Twyford’s chief rivals in Staffordshire are the firm of John Taylor Howson of Hanley.
All of Twyford’s sanitary pottery was concentrated at the current Cliff Vale Works in 1887, and experiments quickly began for a new manufacturing line. This involved creating very large clay pieces that were covered with a[207] smooth white surface, making them suitable for baths and toilets. The common or fire clay is coated while still moldable with a porcelain enamel, which, when fired, results in a surface enamel that is polished like marble and sticks better than any enamel on metal. This method allows very large pieces to be coated, and since 1890, this earthenware has been replacing both the enamelled metal from Wolverhampton and the marble from Italy. The main competitors of Messrs Twyford in Staffordshire are the John Taylor Howson firm based in Hanley.
From an artistic point of view the only improvements of recent times are—beside M. Solon’s pâte-sur-pâte and Doulton’s stoneware—the lustre ware of Mr William Burton and the “flambé” ware of Mr Bernard Moore. Mr Burton’s factory unfortunately lies outside Staffordshire, but much of his work, both public and private, is still done in North Staffordshire. He and Mr Moore are the most enterprising chemists and experimenters of the present race of master-potters, and their efforts have also been accompanied by a marked improvement of taste in enamelled earthenware and porcelain.
From an artistic perspective, the only notable advancements in recent times are—besides M. Solon’s pâte-sur-pâte and Doulton’s stoneware—the lusterware by Mr. William Burton and the “flambé” ware by Mr. Bernard Moore. Unfortunately, Mr. Burton’s factory is located outside Staffordshire, but much of his work, both public and private, is still produced in North Staffordshire. He and Mr. Moore are the most innovative chemists and experimenters among today’s master potters, and their work has also led to a significant improvement in the taste for enameled earthenware and porcelain.
There remains one modern improvement to point out. It is in the health of the potters. For generations potter’s asthma and lead poisoning have taken their toll of the workers on the pot-banks, but within the last ten years changes have been made, unfortunately only as a result of State interference, which are very sensibly affecting the rate of mortality in the industry.
There’s one modern improvement worth mentioning. It’s about the health of the potters. For generations, potter’s asthma and lead poisoning have harmed the workers in the potteries, but in the last decade, changes have been made, unfortunately only because of government intervention, which are noticeably impacting the mortality rate in the industry.
It was not till 1864 that the Factory Acts interfered in the potting industry. In that year women, young persons and children in the pottery trade first came under the protection of the State. Their hours were limited to ten a day, and Saturday became a statutory half-holiday. This meant a half-holiday for all workers on the pot-banks. Half-time employment has never been considerable in the Potteries, and since the passing of the Education Acts it has gradually and entirely died out. Later Factory Acts have applied to Potteries as well as to other factories, but it was when the Bill of 1891 got into committee that the potting trade became specially and vitally interested in these Acts.
It wasn't until 1864 that the Factory Acts stepped in to regulate the pottery industry. That year, women, young people, and children in the pottery trade were first protected by the State. Their working hours were capped at ten a day, and Saturday was established as a mandatory half-holiday. This meant that all workers in the pot-banks also enjoyed this half-holiday. Half-time employment has never been significant in the Potteries, and since the Education Acts were enacted, it has gradually faded away entirely. Later Factory Acts have applied to the Potteries as well as to other factories, but it was when the 1891 Bill went to committee that the pottery trade became particularly and crucially engaged with these Acts.
During the passage of the 1891 Factory and Workshop Bill the working potters managed to[209] get added to it a provision empowering the Home Office to make, after due investigation, special rules for the conduct of “dusty processes” in dangerous trades, including potting. As soon as the Act passed, a committee was appointed, and on their recommendation special rules were drawn up, making for greater cleanliness in the dusty and dangerous processes. The employers objected, and a conference followed in 1894 under the presidency of Mr G. W. E. Russell. Nevertheless the rules, slightly modified, were approved and became law.
During the discussion of the 1891 Factory and Workshop Bill, the working potters successfully added a provision that allowed the Home Office to establish, after careful investigation, specific rules for managing “dusty processes” in hazardous industries, including pottery. Once the Act was passed, a committee was formed, and based on their recommendations, special rules were created to improve cleanliness in these dusty and dangerous processes. The employers objected, leading to a conference in 1894 chaired by Mr. G. W. E. Russell. However, the rules, with minor adjustments, were approved and became law.
These special rules, however, were concerned more with general dusty evils and affected potter’s asthma rather than the lead poisoning question. But in 1898 Prof. Thorpe and Dr Oliver drew up their celebrated report on lead poisoning for the Home Office—a report which for a time threw the whole trade into the most furious excitement. The doctors averred that glaze could be made without lead, or without lead in any but the innocuous “fritted” state. What the employers said was emphatic and contradictory. They threatened to close down the whole trade, and no doubt[210] the report was hasty and ill-considered. For four years the controversy raged, and at last in 1902 an arbitration court was held before Lord James of Hereford. Under his award a new set of special rules were drawn up. These rules, besides enforcing sanitary provisions such as those for monthly medical inspection of workers “in the lead,” compelled those manufacturers who continued to use lead in a dangerous state to compensate those of their workers who suffered from lead poisoning, a liability now generally embodied in the 1907 Workmen’s Compensation Act.
These special rules, however, focused more on general dusty issues and potter’s asthma rather than the lead poisoning problem. But in 1898, Prof. Thorpe and Dr. Oliver put together their famous report on lead poisoning for the Home Office—a report that caused a huge stir in the entire industry for a while. The doctors claimed that glaze could be made without lead, or only using a harmless “fritted” form. What the employers said was clear but contradictory. They threatened to shut down the entire industry, and undoubtedly[210] the report was rushed and poorly thought out. The controversy went on for four years, and finally, in 1902, an arbitration court was held before Lord James of Hereford. Based on his ruling, a new set of special rules was established. These rules, in addition to enforcing health measures like monthly medical check-ups for workers “in the lead,” required manufacturers who still used lead in a dangerous way to compensate workers who suffered from lead poisoning, a responsibility that is now generally included in the 1907 Workmen’s Compensation Act.
When one remembers the intense hostility to this Home Office interference, it is curious to see how satisfactory and easily the rules have worked in practice. Potter’s asthma is nearly extinct, and lead-poisoning cases in the Potteries have fallen from an average of 362 a year in the period 1896-8 to 93 a year over the years 1905-7.[215] About 5 per cent of the cases result in death. The chief credit for this new departure should be attributed to William Owen of the Potters’ Union, and to the Duchess of Sutherland and Sir Charles Dilke.
When we think about the strong resistance to this Home Office intervention, it's interesting to see how well the rules have worked in practice. Potter's asthma is almost gone, and lead poisoning cases in the Potteries have dropped from an average of 362 a year from 1896 to 1898 to just 93 a year from 1905 to 1907. About 5 percent of the cases result in death. The main credit for this new approach should go to William Owen from the Potters’ Union, along with the Duchess of Sutherland and Sir Charles Dilke.
The latest statistics of the industry show that in 1901 there were about 400 factories employing some 21,000 adult males, 16,000 adult females, and 13,000 young persons under 18 years of age.[216] The employment of great numbers of married women (some 8,000) and the consequent high rate of infantile mortality are now the most serious features of the industry from the sociological point of view.
The latest industry statistics reveal that in 1901, there were around 400 factories employing about 21,000 adult men, 16,000 adult women, and 13,000 young people under 18 years old.[216] The employment of a large number of married women (around 8,000) and the resulting high rates of infant mortality are now the most significant social concerns in the industry.
In conclusion the official figures are given for the export of china and earthenware, so as to show the prosperity at different times of the staple trade of North Staffordshire.
In conclusion, the official figures for the export of china and ceramics are provided to illustrate the prosperity of the main industry in North Staffordshire at various times.
The Foreign Trade, since 1840. Exports and Imports.
The Foreign Trade, since 1840. Exports and Imports.
Year. | 1840 | 1841 | 1842 | 1843 | 1844 | 1845 | 1846 | 1847 | 1848 | 1849 | |
---|---|---|---|---|---|---|---|---|---|---|---|
Value of Exports China, Earthenware and Stoneware £’000 | 573, | 601, | 555, | 629, | 767, | 828, | 793, | 834, | 722, | 807, | |
Value of Imports | |||||||||||
Year. | 1850 | 1851 | 1852 | 1853 | 1854 | 1855 | 1856 | 1857 | 1858 | 1859 | |
Exports £’000 | 999, | 1,121, | 1,152, | 1,338, | 1,306, | 1,001, | 1,334, | 1,492, | 1,154, | 1,314, | |
Imports £’000 | |||||||||||
Year. | 1860 | 1861 | 1862 | 1863 | 1864 | 1865 | 1866 | 1867 | 1868 | 1869 | |
Exports £’000 | 1,451, | 1,071, | 1,220, | 1,341, | 1,439, | 1,469, | 1,686, | 1,666, | 1,683, | 1,828, | |
Imports £’000 | |||||||||||
Year. | 1870 | 1871 | 1872 | 1873 | 1874 | 1875 | 1876 | 1877 | 1878 | 1879 | |
Exports £’000 | 1,746, | 1,865, | 2,142, | 2,206, | 1,862, | 1,859, | 1,771, | 1,853, | 1,794, | 1,800, | |
Imports £’000 | 165, | 202, | 263, | 383, | 370, | 382, | 399, | 365, | 441, | 433, | |
Year. | 1880 | 1881 | 1882 | 1883 | 1884 | 1885 | 1886 | 1887 | 1888 | 1889 | |
Exports £’000 | 2,066, | 2,204, | 2,309, | 2,333, | 1,956, | 1,838, | 1,901, | 1,984, | 2,098, | 2,287, | |
Imports £’000 | 469, | 555, | 596,[217] | 533[217] / 603[218] | 482,[218] | 465,[218] | 451,[218] | 472,[218] | 549,[218] | 590,[218] | |
Year. | 1890 | 1891 | 1892 | 1893 | 1894 | 1895 | 1896 | 1897 | 1898 | 1899 | 1900 |
Exports £’000 | 2,251, | 2,165, | 2,057, | 1,985, | 1,759, | 1,992, | 1,967, | 1,900, | 1,820, | 2,042, | 2,038, |
Imports £’000 less Re-exports | 586, | 620, | 623, | 594, | 594, | 627, | 743, | 724, | 782, | 779, | 777, |
Year. | 1901 | 1902 | 1903 | 1904 | 1905 | 1906 | 1907 | 1908 | 1909 | 1910 | 1911 |
Exports £’000 | 1,993, | 1,900, | 2,176, | 2,106, | 2,098, | 2,382, | 2,649, | 2,344, | 2,315, | 2,780, | 3,030, |
Imports £’000 less Re-exports | 758, | 742, | 788, | 765, | 789, | 845, | 880, | 792, | 735, | 746, | 858, |
The direction of the Foreign Trade in 1911.
The direction of Foreign Trade in 1911.
£ | |
---|---|
Exports to the United States | 428,000 |
” Canada | 395,000 |
” Australia | 309,000 |
” the Argentine | 279,000 |
"” India | 232,000 |
” Brazil | 210,000 |
” South Africa | 133,000 |
“ New Zealand | 125,000 |
"" France | 87,000 |
” Germany | 81,000 |
” all other countries | 751,000 |
Total Foreign Exports. | 3,030,000 |
The nature of the Foreign Trade in 1911.
The nature of Foreign Trade in 1911.
£ | |
---|---|
Earthenware, Semi-porcelain and Majolica | 1,828,000 |
Sanitary Ware | 461,000 |
Red Pottery, Stoneware, Brown Ware | 307,000 |
Porcelain, China and Parian | 175,000 |
Tiles (ex floor, roofing and street paving) | 116,000 |
Floor Tiles | 86,000 |
Electric and Chemical Ware, and Furniture Fittings | 51,000 |
Jet, Rockingham and Glazed Terra Cotta Ware | 6,000 |
3,030,000 |
Nature of Total Pottery Production for Home and Foreign Trade of the United Kingdom in 1907. Of this production less than 5 per cent. comes from Scotland and Ireland, and about two-thirds of the whole is produced in North Staffordshire.
Nature of Total Pottery Production for Home and Foreign Trade of the United Kingdom in 1907. Of this production, less than 5 percent comes from Scotland and Ireland, and around two-thirds of the total is made in North Staffordshire.
Home. | Foreign. | Total. | |
---|---|---|---|
Earthenware, Semi-Porcelain and Majolica | 1,683,000[219] | 1,545,000[219] | 3,228,000 |
Sanitary Ware | 472,000[219] | 300,000[219] | 772,000 |
Red Pottery, Stoneware, Brown Ware | 331,000 | 291,000 | 622,000 |
Porcelain, China and Parian | 830K | 195,000 | 1,025,000 |
Tiles—White, Cream, Glazed or Decorated | 362,000[219] | 80,000[219] | 442,000 |
Tiles—For Floors, Pavements and Mosaics | 55,000[219] | 78,000[219] | 133,000 |
Jet, Rockingham and Glazed Terra Cotta Ware | 250K | 3,000 | 253,000 |
Electric and Chemical Ware, Crucibles and Furniture Fittings | 365,000[219] | 181K | 546,000 |
Tobacco Pipes[220] | ? | ? | 90,000 |
Bricks and Fireclay Goods[220] | ? | ? | 64,000 |
Potters’ Materials | 213,000 | ? | 213,000 |
Other processes of partial manufacture | 146K | Nil. | 146,000 |
Total | 4.88 million | £2.65 million | £7,534,000 |
Average number of persons employed in China and Earthenware Factories and Workshops in England, Wales and Ireland, 1907.
Average number of people employed in China and Earthenware Factories and Workshops in England, Wales, and Ireland, 1907.
Males over 18. |
Females over 18. |
Males under 18. |
Females under 18. |
Total. | |
---|---|---|---|---|---|
Wage earners | 29,000 | 19,364 | 5,790 | 7,509 | 61,663 |
Salaried persons | 3,015 | 286 | 299 | 84 | 3,684 |
Of these over two-thirds work in the North Staffordshire Potteries.
Of these, more than two-thirds work in the North Staffordshire Potteries.
[3] 1671. List of inhabitants of Burslem from the Head-borough’s presentments in the Tunstall Court Rolls.
[3] 1671. List of residents of Burslem from the Head-borough’s presentations in the Tunstall Court Rolls.
- John Muchell
- Thos. Flecher
- John Royle
- Raphe Bech
- Ric. Edge
- John Hord
- Wm. Hord
- Moses Wedgwood
- Moses Wedgwood
- Thos. Lounes
- Samuel Leigh
- Fras. Foster
- Wm. Marsh
- John Barlow
- Wm. Hord
- Wm. Simson
- Joseph Simson
- Raphe Simson
- Thos. Cartlech
- Arthur Monsfield
- John Roden
- Wm. Monsfield
- Thos. Denyell
- Wm. Denyell
- John Clowes
- Sam. Clowes
- John Denyell
- Joseph Malken
- Wm. Wedgwood
- John Jones
- Sam. Cartlech
- Thos. Marsh
- John Marsh
- Thos. Copland
- Thos. Armstrong
- Ric. Stonner
- Rob. Wood
- Rob. Wood
- Wm. Twomlow
- Rob. Simson
- Ric. Hand
- Thos. Cartlech
- Thos. Addames
- Raphe Borne
- Jas. Rushen
- Jossua Leigh
- Izac Ball
- Izac Monsfield
- Raphe Flecher
- John Flecher
- Ric. Flecher
- Wm. Steele
- Wm. Steele
- Raphe Steele
- John Simson
- John Ward
- John Cartlech
- John Lockett
- Jas. Standley
- John Rowley
- Raph Shaw
- Hen. Bourne
- Wm. Harrison
- Rob. Denell
- Wm. Marsh
- John Shaw
- John Sickes
- John Tonstall
- Thos. Gratbache
- Ric. Twomlow
- Wm. Browne
- Wm. Edge
- Fras. Rogers
- Ric. Borne
- John Denyell
[4] Shaw, “Staffordshire Potteries,” p. 103.
__A_TAG_PLACEHOLDER_0__ Shaw, “Staffordshire Potteries,” p. 103.
[6] ibid., p. 35.
__A_TAG_PLACEHOLDER_0__ same source, p. 35.
[8] Brit. Museum.
__A_TAG_PLACEHOLDER_0__ British Museum.
[12] M. Solon explains this method of reckoning as follows: “Art of the Old English Potter,” p. 32. “The unit was represented by a dozen small pieces, and that unit served as the basis of reckoning for all the rest. For instance, a dish might have been worth a ‘dozen’; a very large dish ‘counted 2 dozen’; of bowls, jugs, cups, and other articles of middle sizes it required 2, 3 or 4 to make a dozen. The potter knew at once the value of the contents of his oven by the number or ‘dozens’ put in; while the workman could easily calculate his wages by the number of ‘dozen’ he made in the week.... So convenient was this method of reckoning that it is kept up to this day in many manufactories both in England and on the Continent.”
[12] M. Solon explains this method of counting as follows: “Art of the Old English Potter,” p. 32. “The unit was represented by a dozen small pieces, and that unit served as the basis for all calculations. For example, a dish might be worth a ‘dozen’; a very large dish ‘counted as 2 dozen’; for bowls, jugs, cups, and other items of medium size, it took 2, 3, or 4 to make a dozen. The potter could quickly determine the value of his oven's contents by the number of ‘dozens’ he put in; meanwhile, the worker could easily calculate his wages based on the number of ‘dozens’ he made in the week.... This method of counting was so convenient that it is still used today in many factories both in England and on the Continent.”
[17] Burton’s “English Earthenware,” p. 77.
__A_TAG_PLACEHOLDER_0__ Burton’s "English Earthenware," p. 77.
[18] Burton, op. cit. 76.
__A_TAG_PLACEHOLDER_0__ Burton, same source 76.
[20] S. Shaw, op. cit., 118.
__A_TAG_PLACEHOLDER_0__ S. Shaw, op. cit., 118.
[21] Burton, “English Earthenware,” p. 74.
__A_TAG_PLACEHOLDER_0__ Burton, “English Earthenware,” p. 74.
[22] Burton, “English Earthenware,” p. 74.
__A_TAG_PLACEHOLDER_0__ Burton, “English Earthenware,” p. 74.
[23] A list of those who joined the “Association to defend and avenge King William” in 1696 is preserved at the Record Office. Among 100 names given in Stoke-on-Trent, which included Hanley, Shelton, Longton, &c., occur side by side the names of Joshua Twiford and Robert Astbry. Is it possible that even then they had their pot-banks side by side, as tradition says, on the knoll where Shelton Church now stands?
[23] A list of people who joined the “Association to defend and avenge King William” in 1696 is kept at the Record Office. Among the 100 names from Stoke-on-Trent, which included Hanley, Shelton, Longton, etc., are the names of Joshua Twiford and Robert Astbry. Could it be true that even back then they had their potteries next to each other, as tradition suggests, on the hill where Shelton Church now stands?
[24] Wedgwood’s Letters II, 367-70.
__A_TAG_PLACEHOLDER_0__ Wedgwood’s Letters Vol. II, 367-70.
[25] Shaw, op. cit., pp. 108-9.
__A_TAG_PLACEHOLDER_0__ Shaw, op. cit., pp. 108-9.
[26] Aikin, “Manchester,” 526.
__A_TAG_PLACEHOLDER_0__ Aikin, “Manchester,” 526.
[27] Shaw, op. cit., p. 121.
__A_TAG_PLACEHOLDER_0__ Shaw, same source, p. 121.
[28] Burton, op. cit., p. 86.
__A_TAG_PLACEHOLDER_0__ Burton, op. cit., p. 86.
[31] Shaw, op. cit., p. 130.
__A_TAG_PLACEHOLDER_0__ Shaw, op. cit., p. 130.
[32] Shaw, op. cit., p. 126.
__A_TAG_PLACEHOLDER_0__ Shaw, op. cit., p. 126.
[33] “Wedgwood’s Letters, II,” p. 368.
__A_TAG_PLACEHOLDER_0__ “Wedgwood’s Letters, Vol. II,” p. 368.
[34] The incident referred to, which Shaw says occurred to Astbury, and Wedgwood to Heath, was as follows:—One of them was on a business journey to London, then naturally taken on horseback; before reaching Dunstable or Banbury, his horse’s eyes became inflamed. The ostler of the Inn put a piece of flint into the fire; when it was red-hot he quenched it with water and pounded it to a fine powder, a little of which was blown into the horse’s eye, relieving the inflammation. The potter, noticing the extreme whiteness of the calcined flint, and also the ease with which it was powdered, was led to try this material to improve the whiteness of his ware, and with the most successful results.
[34] The incident mentioned, which Shaw claims happened to Astbury and Wedgwood to Heath, was as follows: One of them was on a business trip to London, naturally traveling by horseback; before reaching Dunstable or Banbury, his horse’s eyes became swollen. The stable worker at the Inn put a piece of flint into the fire; when it was red-hot, he cooled it with water and ground it into a fine powder, some of which was blown into the horse’s eye, easing the swelling. The potter, noticing the bright whiteness of the burned flint and how easily it could be ground, decided to use this material to enhance the whiteness of his pottery, achieving very successful results.
[35] Shaw, op. cit., p. 141.
__A_TAG_PLACEHOLDER_0__ Shaw, same source, p. 141.
[36] “Wedgwood Letters,” III, p. 190.
__A_TAG_PLACEHOLDER_0__ “Wedgwood Letters,” III, p. 190.
[37] “Monthly Magazine,” November 1823.
__A_TAG_PLACEHOLDER_0__ “Monthly Magazine,” Nov 1823.
[38] A family of Adams lived and potted at the Brick House in Burslem for over 200 years. In 1762 Josiah Wedgwood rented the Brick House works for seven years during the minority of the then Adams of Brick House. The family became extinct early in the nineteenth century.
[38] A family named Adams lived and worked at the Brick House in Burslem for more than 200 years. In 1762, Josiah Wedgwood rented the Brick House facilities for seven years during the youth of the then Adams of Brick House. The family died out early in the nineteenth century.
[39] Wedgwood MSS.
__A_TAG_PLACEHOLDER_0__ Wedgwood Papers.
[40] Burton, op. cit., p. 86.
__A_TAG_PLACEHOLDER_0__ Burton, op. cit., p. 86.
[41] Shaw, op. cit., p. 126.
__A_TAG_PLACEHOLDER_0__ Shaw, op. cit., p. 126.
[43] Burton, op. cit., p. 83.
__A_TAG_PLACEHOLDER_0__ Burton, op. cit., p. 83.
[44] Aikin, “Manchester,” p. 527.
__A_TAG_PLACEHOLDER_0__ Aikin, “Manchester,” p. 527.
[45] Shaw, op. cit., p. 145.
__A_TAG_PLACEHOLDER_0__ Shaw, same source, p. 145.
[46] Aikin, op. cit., p. 528.
__A_TAG_PLACEHOLDER_0__ Aikin, op. cit., p. 528.
[47] Burton, op. cit., p. 89.
__A_TAG_PLACEHOLDER_0__ Burton, op. cit., p. 89.
[48] Burton, op. cit., p. 88.
__A_TAG_PLACEHOLDER_0__ Burton, op. cit., p. 88.
[49] Shaw, op. cit., p. 147.
__A_TAG_PLACEHOLDER_0__ Shaw, op. cit., p. 147.
[50] Ward, “Stoke-on-Trent,” p. 227.
__A_TAG_PLACEHOLDER_0__ Ward, “Stoke-on-Trent,” p. 227.
[51] Shaw, op. cit., p. 163.
__A_TAG_PLACEHOLDER_0__ Shaw, ibid., p. 163.
[52] Shaw, op. cit., p. 150, 151.
__A_TAG_PLACEHOLDER_0__ Shaw, same source, p. 150, 151.
[53] Shaw, op. cit., p. 153.
__A_TAG_PLACEHOLDER_0__ Shaw, op. cit., p. 153.
[54] Ward, op. cit., p. 230.
__A_TAG_PLACEHOLDER_0__ Ward, op. cit., p. 230.
[55] Shaw, op. cit., pp. 152, 153.
__A_TAG_PLACEHOLDER_0__ Shaw, op. cit., pp. 152, 153.
[56] Shaw, op. cit., p. 161.
__A_TAG_PLACEHOLDER_0__ Shaw, same source, p. 161.
[57] Wedgwood’s Letters, II, 24.
__A_TAG_PLACEHOLDER_0__ Wedgwood's Letters, Vol. II, 24.
[58] Burton, op. cit., p. 102.
__A_TAG_PLACEHOLDER_0__ Burton, op. cit., p. 102.
[59] Shaw, op. cit., p. 161.
__A_TAG_PLACEHOLDER_0__ Shaw, op. cit., p. 161.
[60] Shaw, op. cit., p. 157.
__A_TAG_PLACEHOLDER_0__ Shaw, same source, p. 157.
[62] Shaw, op. cit., p. 201.
__A_TAG_PLACEHOLDER_0__ Shaw, same source, p. 201.
[63] Shaw, op. cit., p. 93.
__A_TAG_PLACEHOLDER_0__ Shaw, op. cit., p. 93.
[64] Ward, op. cit., p. 283.
__A_TAG_PLACEHOLDER_0__ Ward, ibid., p. 283.
[65] Shaw, op. cit., p. 179.
__A_TAG_PLACEHOLDER_0__ Shaw, same source., p. 179.
[66] Shaw, op. cit., p. 168.
__A_TAG_PLACEHOLDER_0__ Shaw, same source, p. 168.
[67] Burton, op. cit., p. 104.
__A_TAG_PLACEHOLDER_0__ Burton, ibid., p. 104.
[70] Shaw, op. cit., 155.
__A_TAG_PLACEHOLDER_0__ Shaw, same source, 155.
[71] Burton, “English Earthenware,” p. 111.
__A_TAG_PLACEHOLDER_0__ Burton, “English Earthenware,” p. 111.
[72] Burton, op. cit., p. 114-5.
__A_TAG_PLACEHOLDER_0__ Burton, previously cited, p. 114-5.
[76] It is recorded of the Rev. J. Middleton, Master Potter and Curate of Hanley, c. 1750, that he refused to hire men by the year, deeming it slavery. It was not till 1866 that the Trade Unions put an end to the annual hiring of grown men by a year’s binding agreement.
[76] It’s documented that Rev. J. Middleton, Master Potter and Curate of Hanley, c. 1750, refused to hire men for the year, considering it a form of slavery. It wasn't until 1866 that Trade Unions put a stop to the yearly hiring of adult men under binding contracts.
[77] Burton, “English Earthenware,” p. 119.
__A_TAG_PLACEHOLDER_0__ Burton, “English Earthenware,” p. 119.
[78] Shaw, op. cit., p. 157.
__A_TAG_PLACEHOLDER_0__ Shaw, op. cit., p. 157.
[79] Ward, “Stoke-on-Trent,” p. 372.
__A_TAG_PLACEHOLDER_0__ Ward, “Stoke-on-Trent,” p. 372.
[80] Shaw, op. cit., pp. 148-9.
__A_TAG_PLACEHOLDER_0__ Shaw, op. cit., pp. 148-9.
[82] Professor Church quotes the following memorandum, done in red enamel on the back of a large dish of Wedgwood’s Queen’s Ware in the possession of Mr Sidney Locock:—“This dish was made at Etruria by Messrs Wedgwood & Bentley, the first year after Messrs Wedgwood & Bentley removed from Burslem to Etruria. Ric. Lawton served his apprenticeship at turning with them, and has had it in his house more than fifty years. It is my brother William’s modelling. It was turned on a hand lathe, as plates were at that date. I preserve this to show the quality of common cream ware before the introduction of growan or Cornwall stone. This body is formed of flint and clay only, the same as used for salt-glazed ware at that time, and flint and lead only instead of salt glaze, and it is fired in the usual and accustomed way and manner, as usual for glazed tea-pots, tortoiseshell, mottled, and agate, and cauliflower, &c. Also sand from the Mole Cop and Baddley Edge was used either in the body or glaze. N.B. Before flint was used they used a certain proportion of slip for the body in the glaze to prevent crazing, and to make it bear a stronger fire in the glaze oven. I was the first person that made use of bone in earthenware when in my apprenticeship at Mr Palmers at Hanley Green.
[82] Professor Church quotes the following memorandum, written in red enamel on the back of a large dish from Wedgwood’s Queen’s Ware owned by Mr. Sidney Locock:—“This dish was made at Etruria by Messrs. Wedgwood & Bentley, the first year after they moved from Burslem to Etruria. Ric. Lawton did his apprenticeship in turning with them and has kept it in his home for over fifty years. It was modeled by my brother William. It was turned on a hand lathe, as plates were made at that time. I keep this to show the quality of regular cream ware before the introduction of growan or Cornwall stone. This body is made of flint and clay only, the same as used for salt-glazed ware back then, with flint and lead instead of salt glaze, and it is fired in the usual way for glazed teapots, tortoiseshell, mottled, agate, cauliflower, etc. Also, sand from Mole Cop and Baddley Edge was used either in the body or glaze. N.B. Before flint was used, they employed a certain proportion of slip for the body in the glaze to prevent crazing and to make it withstand higher temperatures in the glaze oven. I was the first person to use bone in earthenware during my apprenticeship at Mr. Palmers in Hanley Green.”
Burslem, Sept. 26th, 1826.
Burslem, Sept. 26, 1826.
Enoch Wood.”
Enoch Wood.
Church, “English Earthenware,” pp. 81-82.
Church, “English Earthenware,” pp. 81-82.
[83] Shaw, op. cit., p. 184.
__A_TAG_PLACEHOLDER_0__ Shaw, op. cit., p. 184.
[84] Many “lives” of Wedgwood have been written, and this is not the place to repeat them. Miss Meteyard has two large volumes on him; Jewitt has one; Smiles holds him up in a recent work as a model of self-help; Professor Church has written a monograph on him and his Jasper Ware; and lastly, Mr Elbert Hubbard, of New York, has made his courtship and marriage the subject of an exhaustive and wholly imaginary study. But many of these works, and some of the Histories of Potting too, are marred by indiscriminating eulogy and a fertile imagination. Simeon Shaw, for instance, within 120 pages, manages to distinguish no fewer than 47 favoured manufacturers by name with praise of this stereotyped character:—“of whom we may observe that great professional ability is in him joined with philanthropy, and a readiness to accelerate every meritorious enterprise.” This, however, is perhaps preferable to the style:—“Wedgwood, poor dear, old soul, got terribly worried,” which distinguishes another of these Histories.
[84] Many biographies of Wedgwood have been written, and this isn’t the place to go over them again. Miss Meteyard has published two large volumes about him; Jewitt has one; Smiles features him as a model of self-help in a recent work; Professor Church has penned a detailed study on him and his Jasper Ware; and lastly, Mr. Elbert Hubbard from New York has turned his courtship and marriage into a thorough and completely fictional analysis. However, many of these works, along with some histories of pottery, suffer from excessive praise and vivid imagination. For example, Simeon Shaw, in just 120 pages, manages to name 47 favored manufacturers with praise like this:—“of whom we may observe that great professional ability is in him joined with philanthropy, and a readiness to accelerate every meritorious enterprise.” This, however, might be better than the style:—“Wedgwood, poor dear, old soul, got terribly worried,” which characterizes another one of these histories.
[86] Wedgwood’s Letters, II, 24.
__A_TAG_PLACEHOLDER_0__ Wedgwood's Letters, Vol. II, 24.
[87] Meteyard’s “Wedgwood,” I, 486.
__A_TAG_PLACEHOLDER_0__ Meteyard’s “Wedgwood,” I, 486.
[88] Meteyard’s “Wedgwood,” II, 235.
__A_TAG_PLACEHOLDER_0__ Meteyard's "Wedgwood," II, 235.
[89] Wedgwood’s Letters, I.
__A_TAG_PLACEHOLDER_0__ Wedgwood’s Letters, I.
[90] The converting of a road into a turnpike road was the only way in which it could be kept in really good repair. Tolls were charged and used partly to repair the road and to attract more traffic.
[90] Turning a road into a toll road was the only way to keep it in really good condition. Tolls were collected and used partly for road repairs and to draw in more traffic.
[91] Wedgwood’s Letters, I.
__A_TAG_PLACEHOLDER_0__ Wedgwood's Letters, Vol. I.
[92] Jewitt, op. cit., pp. 162-3.
__A_TAG_PLACEHOLDER_0__ Jewitt, op. cit., pp. 162-3.
[93] Wedgwood’s Letters, I.
__A_TAG_PLACEHOLDER_0__ Wedgwood's Letters, Vol. I.
[95] Meteyard, op. cit., I, 273.
__A_TAG_PLACEHOLDER_0__ Meteyard, op. cit., I, 273.
[96] Wedgwood’s Letters, III, 249.
__A_TAG_PLACEHOLDER_0__ Wedgwood’s Letters, Vol. III, 249.
[97] “Dict. Nat. Biog.”: “Jas. Brindley.”
__A_TAG_PLACEHOLDER_0__ “Dict. Nat. Biog.”: “James Brindley.”
[98] Wedgwood’s Letters, I.
__A_TAG_PLACEHOLDER_0__ Wedgwood's Letters, Volume I.
[99] Wedgwood’s Letters, I, pp. 85-7.
__A_TAG_PLACEHOLDER_0__ Wedgwood’s Letters, Vol. I, pp. 85-7.
[100] Ward, op. cit., p. 154.
__A_TAG_PLACEHOLDER_0__ Ward, op. cit., p. 154.
[101] Wedgwood’s Letters, III, p. 31.
__A_TAG_PLACEHOLDER_0__ Wedgwood’s Letters, III, p. 31.
The original proposition was for a canal 3 feet deep in general, but at the fords only 30 inches; and the original estimate of cost, excluding the tunnel, was £700 a mile south of Harecastle and £1,000 north of that place. The tunnel, a single one, was to cost £10,000.—Wedgwood’s Letters, III, p. 290.
The initial plan was for a canal that was 3 feet deep overall, but only 30 inches deep at the fords. The initial cost estimate, not including the tunnel, was £700 per mile south of Harecastle and £1,000 per mile north of it. The tunnel, which was a single one, was expected to cost £10,000.—Wedgwood’s Letters, III, p. 290.
[102] Wedgwood’s Letters, III, p. 30.
__A_TAG_PLACEHOLDER_0__ Wedgwood’s Letters, vol. III, p. 30.
[103] Wedgwood’s Letters, III, p. 206.
__A_TAG_PLACEHOLDER_0__ Wedgwood’s Letters, Vol. III, p. 206.
[105] Burton, “Hist. Porcelain,” p. 135.
__A_TAG_PLACEHOLDER_0__ Burton, “History of Porcelain,” p. 135.
[106] Burton, “English Earthenware,” p. 128.
__A_TAG_PLACEHOLDER_0__ Burton, “English Earthenware,” p. 128.
[107] Meteyard, op. cit., II, 118.
__A_TAG_PLACEHOLDER_0__ Meteyard, op. cit., II, 118.
[108] Jewitt, op. cit., p. 319, etc.
__A_TAG_PLACEHOLDER_0__ Jewitt, op. cit., p. 319, etc.
[110] Burton, “English Earthenware,” p. 151.
__A_TAG_PLACEHOLDER_0__ Burton, “English Earthenware,” p. 151.
[111] See Wedgwood’s Letters, passim.
__A_TAG_PLACEHOLDER_0__ See Wedgwood’s Letters, various places.
[112] See Wedgwood’s Letters, II, 30-2.
__A_TAG_PLACEHOLDER_0__ See Wedgwood’s Letters, II, 30-2.
[113] Shaw, op. cit., p. 127.
__A_TAG_PLACEHOLDER_0__ Shaw, ibid., p. 127.
[115] Shaw, op. cit., p. 170.
__A_TAG_PLACEHOLDER_0__ Shaw, op. cit., p. 170.
[116] Wedgwood MSS.
__A_TAG_PLACEHOLDER_0__ Wedgwood Archives.
[117] Shaw, op. cit., p. 171-2.
__A_TAG_PLACEHOLDER_0__ Shaw, ibid., p. 171-2.
[118] Shaw, op. cit., p. 206-8.
__A_TAG_PLACEHOLDER_0__ Shaw, op. cit., p. 206-8.
[119] Wedgwood MSS.
__A_TAG_PLACEHOLDER_0__ Wedgwood Papers.
[120] Burton, “English Earthenware,” 152-3.
__A_TAG_PLACEHOLDER_0__ Burton, “English Earthenware,” 152-3.
[121] Meteyard, “Wedgwood,” II, 198.
__A_TAG_PLACEHOLDER_0__ Meteyard, “Wedgwood,” Volume II, 198.
[122] Shaw, op. cit., p. 201.
__A_TAG_PLACEHOLDER_0__ Shaw, same source, p. 201.
[123] Ward, op. cit., p. 373.
__A_TAG_PLACEHOLDER_0__ Ward, ibid., p. 373.
[124] Shaw, op. cit., p. 205.
__A_TAG_PLACEHOLDER_0__ Shaw, op. cit., p. 205.
[125] Burton, “English Earthenware,” p. 162.
__A_TAG_PLACEHOLDER_0__ Burton, “English Earthenware,” p. 162.
[126] Shaw, op. cit., 199, 204.
__A_TAG_PLACEHOLDER_0__ Shaw, op. cit., 199, 204.
[127] Shaw, op. cit., 209-10.
__A_TAG_PLACEHOLDER_0__ Shaw, op. cit., 209-10.
[128] Ward, “Stoke-on-Trent,” p. 367.
__A_TAG_PLACEHOLDER_0__ Ward, “Stoke-on-Trent,” p. 367.
[129] “Dict. Nat. Biog.”: “William Adams.”
__A_TAG_PLACEHOLDER_0__ “Dict. Nat. Biog.”: “William Adams.”
[130] Burton, “English Earthenware,” p. 163.
__A_TAG_PLACEHOLDER_0__ Burton, “English Earthenware,” p. 163.
[131] Ward, “Stoke-on-Trent,” p. 103.
__A_TAG_PLACEHOLDER_0__ Ward, “Stoke-on-Trent,” p. 103.
[132] “Carey’s Atlas,” 1787.
__A_TAG_PLACEHOLDER_0__ “Carey’s Atlas,” 1787.
[133] “Wedgwood’s Letters,” II, 140.
__A_TAG_PLACEHOLDER_0__ “Wedgwood’s Letters,” II, 140.
[134] Ward, “Stoke-on-Trent,” p. 152.
__A_TAG_PLACEHOLDER_0__ Ward, “Stoke-on-Trent,” p. 152.
[137] Ward, “Stoke-on-Trent,” p. 152.
__A_TAG_PLACEHOLDER_0__ Ward, “Stoke-on-Trent,” p. 152.
[138] H. Wedgwood, op. cit., III, p. 53.
__A_TAG_PLACEHOLDER_0__ H. Wedgwood, op. cit., III, p. 53.
[140] Shaw, op. cit., p. 170.
__A_TAG_PLACEHOLDER_0__ Shaw, op. cit., p. 170.
[141] One part is at present in the Royal Museum at Dresden, uncatalogued, and much of the rest has found its way into the Victoria and Albert Museum at South Kensington, though Mr Wood’s catalogue, if it ever existed, is not there to illustrate and explain the pieces.
[141] One part is currently in the Royal Museum in Dresden, uncatalogued, and much of the rest has been moved to the Victoria and Albert Museum in South Kensington, although Mr. Wood's catalogue, if it ever existed, isn't there to describe and explain the pieces.
[142] Shaw, op. cit., p. 223.
__A_TAG_PLACEHOLDER_0__ Shaw, same reference, p. 223.
[145] Shaw, op. cit., p. 212.
__A_TAG_PLACEHOLDER_0__ Shaw, op. cit., p. 212.
[146] “Gent.’s Magazine,” 1797, p. 802.
__A_TAG_PLACEHOLDER_0__ “Gentlemen's Magazine,” 1797, p. 802.
[149] Burton, “Porcelain,” p. 19-20.
__A_TAG_PLACEHOLDER_0__ Burton, “Porcelain,” p. 19-20.
[151] Church, op. cit., p. 85.
__A_TAG_PLACEHOLDER_0__ Church, same source, p. 85.
[152] Burton, “English Earthenware,” p. 150.
__A_TAG_PLACEHOLDER_0__ Burton, “English Earthenware,” p. 150.
[153] Ward, “Stoke-on-Trent,” 476.
__A_TAG_PLACEHOLDER_0__ Ward, “Stoke-on-Trent,” 476.
[154] Shaw, op. cit., p. 63.
__A_TAG_PLACEHOLDER_0__ Shaw, same source, p. 63.
[155] Aikin, “Manchester,” p. 522.
__A_TAG_PLACEHOLDER_0__ Aikin, “Manchester,” p. 522.
[157] Wedgwood, op. cit., p. 7.
__A_TAG_PLACEHOLDER_0__ Wedgwood, same source, p. 7.
[158] Wedgwood, op. cit., p. 14.
__A_TAG_PLACEHOLDER_0__ Wedgwood, op. cit., p. 14.
[159] Wedgwood, op. cit., p. 24.
__A_TAG_PLACEHOLDER_0__ Wedgwood, same source, p. 24.
[160] H. Wedgwood, op. cit., p. 15.
__A_TAG_PLACEHOLDER_0__ H. Wedgwood, op. cit., p. 15.
[161] Ward, op. cit., p. 159.
__A_TAG_PLACEHOLDER_0__ Ward, same source, p. 159.
[162] Ward, op. cit., p. 286.
__A_TAG_PLACEHOLDER_0__ Ward, op. cit., p. 286.
[164] Shaw, op. cit., p. 225.
__A_TAG_PLACEHOLDER_0__ Shaw, ibid., p. 225.
[165] Sleigh, “Leek,” p. 46, 47.
__A_TAG_PLACEHOLDER_0__ Sleigh, “Leek,” p. 46, 47.
[166] Ward, “Stoke-on-Trent,” pp. 156, 157.
__A_TAG_PLACEHOLDER_0__ Ward, “Stoke-on-Trent,” pp. 156, 157.
[168] Church, “English Earthenware,” p. 84.
__A_TAG_PLACEHOLDER_0__ Church, “English Earthenware,” p. 84.
[169] Wedgwood MS.
__A_TAG_PLACEHOLDER_0__ Wedgwood Manuscript.
[170] Figure-makers.
__A_TAG_PLACEHOLDER_0__ Sculptors.
[171] Burton, “English Earthenware,” p. 176.
__A_TAG_PLACEHOLDER_0__ Burton, “English Earthenware,” p. 176.
[173] Ward, “Stoke-on-Trent,” p. 266.
__A_TAG_PLACEHOLDER_0__ Ward, “Stoke-on-Trent,” p. 266.
[174] Shaw, op. cit., p. 235-6.
__A_TAG_PLACEHOLDER_0__ Shaw, op. cit., p. 235-6.
[175] Ward, “Stoke-on-Trent,” p. 103.
__A_TAG_PLACEHOLDER_0__ Ward, “Stoke-on-Trent,” p. 103.
[177] Ward, “Stoke-on-Trent,” p. 389.
__A_TAG_PLACEHOLDER_0__ Ward, “Stoke-on-Trent,” p. 389.
[178] London “Star” Nov. 26, 1792.
__A_TAG_PLACEHOLDER_0__ London "Star" Nov 26, 1792.
[179] Ward, “Stoke-on-Trent,” pp. 66-67.
__A_TAG_PLACEHOLDER_0__ Ward, “Stoke-on-Trent,” pp. 66-67.
[182] Harold Owen, op. cit., p. 26.
__A_TAG_PLACEHOLDER_0__ Harold Owen, ibid., p. 26.
[183] Harold Owen, op. cit., p. 34.
__A_TAG_PLACEHOLDER_0__ Harold Owen, same source, p. 34.
[184] Harold Owen, op. cit., p. 43.
__A_TAG_PLACEHOLDER_0__ Harold Owen, ibid., p. 43.
[185] Owen, op. cit., p. 57.
__A_TAG_PLACEHOLDER_0__ Owen, same source, p. 57.
[187] Owen, op. cit., p. 98.
__A_TAG_PLACEHOLDER_0__ Owen, ibid., p. 98.
[190] “Dict. Nat. Biog.”: “Herbert Minton.”
__A_TAG_PLACEHOLDER_0__ "Dict. Nat. Biog.": "Herbert Minton."
[191] L. Jewitt, “Ceramics,” II, 195.
__A_TAG_PLACEHOLDER_0__ L. Jewitt, “Ceramics,” II, 195.
[192] Jewitt, op. cit., II, 195-8.
__A_TAG_PLACEHOLDER_0__ Jewitt, op. cit., II, 195-8.
[193] Jewitt, “Ceramics,” II, 202.
__A_TAG_PLACEHOLDER_0__ Jewitt, “Ceramics,” Vol. II, 202.
[194] Report of Trial, “Hollins v. Campbell,” 1871.
__A_TAG_PLACEHOLDER_0__ Trial Report, “Hollins v. Campbell,” 1871.
[197] “Dict. Nat. Biog.”: “H. Minton”
__A_TAG_PLACEHOLDER_0__ “Dict. Nat. Biog.”: “H. Minton”
[200] Ward, “Stoke-on-Trent,” p. 374.
__A_TAG_PLACEHOLDER_0__ Ward, “Stoke-on-Trent,” p. 374.
[201] Furnival, op. cit., p. 189.
__A_TAG_PLACEHOLDER_0__ Furnival, op. cit., p. 189.
[202] Burton, “English Earthenware,” 174.
__A_TAG_PLACEHOLDER_0__ Burton, “English Earthenware,” 174.
[203] Ward, “Stoke-on-Trent,” p. 264-5.
__A_TAG_PLACEHOLDER_0__ Ward, “Stoke-on-Trent,” pp. 264-265.
[207] Harold Owen, op. cit., p. 115.
__A_TAG_PLACEHOLDER_0__ Harold Owen, same source, p. 115.
[208] Harold Owen, op. cit., p. 124.
__A_TAG_PLACEHOLDER_0__ Harold Owen, op. cit., p. 124.
[209] Harold Owen, op. cit., p. 144.
__A_TAG_PLACEHOLDER_0__ Harold Owen, same source, p. 144.
[210] Harold Owen, op. cit., p. 160.
__A_TAG_PLACEHOLDER_0__ Harold Owen, ibid., p. 160.
[213] “Dict. Nat. Biog.”: “Henry Doulton.”
__A_TAG_PLACEHOLDER_0__ “Dict. Nat. Biog.”: “Henry Doulton.”
[215] Official Returns.
__A_TAG_PLACEHOLDER_0__ Official Reports.
[220] Estimated figures.
__A_TAG_PLACEHOLDER_0__ Estimated numbers.
- Adams, Benjamin, 152, 160
- John, 51
- Percy, W. L., 161
- Richard, 5, 112
- Robert, 51
- Thomas, 10, 123
- William, 5, 8, 41, 119, 122, 132, 133, 139, 154, 161
- Adams Pedigree, 162
- Alcock, Samuel, 192
- Alders, John, 80, 86
- Thomas, 80, 86
- Allen, John, 112
- Samuel, 157
- Alsager, —, 57
- Anson, Lord, 96
- Mr, 97
- Armstrong, Thomas, 10
- Arnoux, Leon, 184, 185
- Arrowsmith, Thomas, 60
- Astbury, Margaret, 48
- Robert, 37, 44, 46, 48, 83
- Thomas, 47, 48, 58, 66, 71
- Thomas, Jun., 55, 56
- Aynsley, John, 139
- Bacchus, William, 121
- Baddeley, E., 121
- John, 64, 81, 114, 121, 133
- William, 144, 153
- Baddeley & Fletcher, 117
- Bagguley, William, 119, 155, 156
- Bagnal, —, 52, 121
- Sampson, 120
- Bagot, Mr, 97
- Bagshaw, Samuel, 152
- Ball, Isaac, 11, 51
- Barker, John, 76, 111, 121, 134, 155
- Richard, 121
- William, 121
- Barlow, John, 10
- Beech, H., 52, 153
- Ralph, 10
- Bell, Sarah, 121
- Benson, —, 57
- Bentley, Thomas, 38, 41, 90, 105
- Bird, Daniel, 80
- Blashfield, J. M., 182
- Blackwell, John, 120, 152
- Joseph, 120
- Robert, 120, 152
- Boden, John, 152
- Boon, Edward, 121
- Joseph, 120
- Boote, Charles E., 187
- Richard, 187
- Richard L., 187
- Thomas Latham, 187
- T. & R., 187
- Booth, Enoch, 56, 66, 67, 75, 84, 115
- Hugh, 121, 139
- J. & T., 155
- Boulton, Mr, 157, 197
- Bourne, Charles, 155
- Edward, 146
- Henry, 11
- John, 112, 119
- Mr, 57, 132, 144, 155
- Ralph, 10
- Richard, 11
- William, 152
- Boyle, Robert, 181
- [224]Bradshaw, Joseph, 152, 154
- Brassey, Sir Thomas, 199, 200
- Breeze, Jesse, 152, 160
- John, 161
- Bridgewater, Duke of, 95, 96
- Bridgwood, Maria, 155
- Sampson, 111
- Brindley, James, 95, 96, 97, 98, 121
- John, 146
- Taylor, 121
- Brown, William, 11
- Brownfield, William, 154, 190
- Brough, Thomas, 155
- Bucknal, Robert, 52, 112
- Buller, E. W., 203
- Wentworth, 203
- Burke, Edmund, 99
- Burrows, Joseph, 155
- Burton, William, 159, 207
- Byerley, Thomas, 105, 106, 149
- Caldwell, James, 128, 154
- Campbell, Colin Minton, 185, 186
- John, 187
- Cartlich, James, 152
- John, 11, 50, 53, 119, 153
- Richard, 152
- Samuel, 10, 57, 119, 122
- Thomas, 10
- Cartwright, Thomas, 51
- Challenor, Edward, 126
- Champion, Richard, 99, 100, 101, 115
- Chandler, John, 29, 30, 31
- Chatterley, Charles, 118, 120
- Ephraim, 118, 120
- Samuel, 112, 117
- Cheetham, M., 155
- Child, Thomas, 66
- —, 152
- Chisholm, Alex., 41
- Clive, —, 152
- Clowes, John, 10, 153
- Samuel, 10
- Clowes, William, 73, 121
- Cobb, John, 112
- Cobden, Richard, 178
- Coghill, Archibald, 129
- Douglas, 129
- Colclough, John, 9
- Collinson, James, 152
- Cookworthy, —, 99, 109
- Cope, William, 76
- Copeland, Alderman, 180
- Richard Pirie, 180
- Thomas, 10
- William, 134, 136
- William Taylor, 136, 178
- W. T. & Sons, 180
- & Garrett, 180
- Cyples, Joseph, 121
- Lydia, 155
- Mary, 145
- Dale, —, 155
- Daniel, Henry, 160
- John, 10, 11, 112, 114, 116, 119
- Ralph, 61, 69
- Richard, 6
- Robert, 11, 50, 52
- Thomas, 8, 10, 112, 114, 119
- Timothy, 119
- Walter, 119, 146
- William, 10
- Davenport, Henry, 147
- Henry T., 147, 199
- John, 132, 146, 147, 153
- William, 147
- Davenport Pedigree, 148
- Dilke, Sir Charles, 210
- Dillon, Frank, 153
- Doulton, Henry Lewis, 206
- Sir Henry, 205, 206
- [225]Duesbury, —, 72
- Dwight, John, 28, 29, 31, 32, 36
- Edge, Richard, 10
- Samuel, 51, 54
- William, 11
- Edwards, W., 70, 121
- Elers, David, 42, 44, 55, 60, 61, 73, 83
- John Philip, 26-39
- Paul, 38
- Ellis, John, 52
- Evans, William, 177
- Flaxman, —, 103, 104
- Fletcher, John, 11
- Mr, 117
- Ralph, 11
- Richard, 11
- Thomas, 10
- Ford, Charles, 203
- Hugh, 155
- Samuel, 143
- Forrester, George, 155
- Foster, Francis, 10
- Furnival, Mr, 159
- Gallimore, —, 57
- Garner, Joseph, 121
- Matthew, 24, 29-33, 36, 42
- Robert, 48, 76, 111, 122, 125, 155
- Garrett, Thomas, 178
- Gibson, Samuel, 195
- Gimson, James, 203
- Ginder, S., 155
- Glass, John, 120, 144, 154
- Joseph, 13, 52
- Goodfellow, Thomas, 68, 153
- Goodwin’s, 144, 153
- Gower, Lord, 96, 101
- Graham, John, 119
- Greatbach, John, 85
- Thomas, 11
- William, 76, 113
- Green, John, 119
- Thomas, 122
- Grey, Lord, 97
- Grimwade, Leonard, 202
- Grindley, W. H., 126, 194
- Hackwood, —, 103, 154
- Hales, —, 120
- Hall, J. & R., 153
- Hamilton, Robert, 139, 154
- Hand, Richard, 10
- Harper, Thomas, 30
- Harris, John, 204
- J. T., 204
- Harrison, John, 86
- William, 11, 50
- Harvey, Charles, 145, 155
- Hassells, John, 121
- Hatherton, Lord, 200
- Heath, John, 153
- Joshua, 112
- —, 47, 120
- Thomas, 54, 55, 109, 153
- Henshall, Hugh, 97, 98, 153
- Hobson, Ephraim, 153
- Holdcroft, J. P., 153, 201
- Holland, Thomas, 119, 153
- Hollins, Michael Daintry, 182, 185, 186, 187
- Sam, 116, 121, 154
- Hord, John, 10
- William, 10
- Howson, John Taylor, 207
- Hughes, “Tom”, 199
- Thomas, 148, 155
- Hulme, Thomas, 184
- Ingestre, Lord, 178
- Jackson, Samuel, 77
- James of Hereford, Lord, 210
- [226]Jarvis, Richard, 153
- Jeanest, 185
- Johnson, Fred, 193
- Henry, 193
- Joseph, 112
- Ralph, 153
- Reuben, 154
- Robert, 193
- Samuel, 193
- Thomas, 112
- Jones, John, 10
- Keeling, Anthony, 68, 116, 119, 121
- Edward, 120
- James, 154
- Lakin, —, 125
- Lawton, Richard, 84
- Leigh, John, 8
- Josiah, 11
- Ralph, 81
- Samuel, 10
- Lessore, 185
- Littler, William, 70, 71, 72
- Lockett, John, 11, 119, 155
- Thomas, 51
- Timothy, 119
- Lounes, Thomas, 10
- Lovatt, John, 201
- Lowe, John, 112
- Thomas, 112
- William, 155
- Machin, Joseph, 143, 153
- —, 153
- Machin & Bagguley, 156
- Mackintyre, James, 204
- Malkin, Burnham, 119
- Isaac, 51
- Joseph, 10
- Richard, 50
- Thomas, 50, 51, 126
- Malkin Tile Co., 188
- Mansfield, Arthur, 10, 154
- Isaac, 11
- William, 10
- Marsh, Jacob, 155
- John, 10
- Moses, 51
- Richard, 52
- Samuel, 153
- Thomas, 10
- William, 10, 11, 77, 152
- Mason, Charles J., 144, 155, 169, 176, 191
- Miles, 144
- William, 155
- Massey, Richard, 153
- Mayer, Elijah, 116, 120, 141, 154
- Hugh, 52
- John, 52, 113, 120
- Richard, 120
- Mayer & Moss, 34
- Meigh, Job, 154, 159
- Meir, John, 124, 152, 161
- William, 113
- Meakin, Alfred, 193
- Bernard, 193
- George, 193
- James, 193
- Kenneth, 193
- Meakin Pedigree, 194
- Middleton, Richard, 8
- Rev John, 70, 78
- Miles, Thomas, 24, 41
- Miller, William, 120
- Minton, Herbert, 137, 181, 182, 184, 185
- Herbert, & Co., 186
- Hollins & Co., 186, 187
- Thomas, 111, 132, 137, 154
- Messrs, 184
- Mitchell, John, 10, 57, 62, 64, 192
- Thomas, 51, 126
- [227]Moore, Bernard, 207
- Morley, James, 29, 30, 31, 32
- Morris, Daniel, 95, 154
- Moss, Thomas, 152
- Moseley, John, 122, 153
- William, 153
- Mountford, John, 41
- Mundella, Mr, 199
- Myatt, Benjamin, 152, 156
- Joseph, 156
- Neale, Henry, 108, 109, 120
- Nixon, —, 152
- Nutt, William, 156
- Oliver, Dr, 125, 209
- —, 153
- Owen, Robert, 169, 198
- William, 198, 199, 200, 210
- Palmer, Humphrey, 108, 109, 127
- Parrott, William, 112
- Perry, Samuel, 120
- Phillips, W. D., 179
- Platt, John, 122
- Pool, Nicholas, 113
- Poole, —, 125
- Pottere, John, 5
- Robert Le, 4, 5
- William the, 5
- Potinger, Thomas, 4
- Powis, H., 152
- Pratt, F. & R., 109, 156
- John, 156
- Poulson, Joseph, 137
- William, 156
- Poulson’s, 53, 155
- Pownall, Mr, 137
- Prosser, Richard, 182
- Protat, 185
- Rathbone, W. S. & I., 152
- Richards (Henry) Tile Co., 188
- Ridgway, Edward John, 109
- Ridgway, George, 140
- Job, 140, 141, 142, 143
- John, 118, 132, 141, 154, 176, 189
- Ralph, 140
- William, 141, 154, 189
- Ridgway Pedigree, 142
- Rigg, Charles, 14
- Riley, J., 41, 153
- Robinson, John, 119, 153, 155
- J., 187
- Sam, 97
- Roden, John, 10
- Rogers, Francis, 11
- George, 119, 143
- John, 119, 143, 153
- Spencer, 143, 153
- Roosevelt, President, 191
- Rowley, John, 11
- Royle, John, 10
- Rushton, James, 10
- Russell, G. W. E., 209
- Saddler & Green, 89, 131
- Salt, Ralph, 125
- Sandford, Moses, 52
- Sans, Thomas, 12
- William, 12
- Shaw, Aaron, 51, 54
- John, 11
- Moses, 51, 54
- Ralph, 11, 58
- Simeon, 41
- Shelley, Percy, 192
- Thomas, 122, 156
- Sheridan, J. H., 156
- Shrigley, —, 64
- Sickes, John, 11
- Simpson, John, 11, 17
- Joseph, 10, 113
- Ralph, 8, 10, 12
- Richard, 51
- [228]Robert, 10
- Simpson, William, 10, 50, 52
- Smith, —, 97
- Ambrose, 119
- John, 119
- Joseph, 112, 119
- Theophilus, 161
- William, 113
- Solon, M., 183, 185, 207
- Sparrow, T., 97
- Spode, Josiah I, 73, 76, 77, 78, 121, 132, 134, 155
- Josiah II, 134, 136
- —, 180, 181
- Standley, James, 11
- Stanley, William, 153
- Steel, —, 41, 51, 153
- William, 11
- Ralph, 11
- Stephens, Joseph, 112
- Stevenson, Andrew, 153
- Charles, 119
- John, 52
- Ralph, 153
- Stirrup, Thomas, 156
- Stonier, Richard, 10
- Straphan, Joseph, 121
- Sutherland, Duchess of, 210
- Talbot, Luke, 32
- Taylor, George, 120
- John, 81, 112, 154
- Robert Minton, 186
- Thomas, 50, 51, 53, 154
- William, 12
- Thorpe, Prof., 209
- Throgher, Thomas the, 5
- Throware, Richard le, 4
- Thrower, Thomas le, 5
- Toft, Ralph, 11
- Thomas, 11, 12
- Tunnicliffe, William, 118
- Tunstall, John, 11
- Tunstals, 51
- Turner, John, 83, 100, 101, 109, 110, 116, 121, 122
- John, 110, 111
- William, 110
- (Worcester), 133
- Twemlow, Mr, 121, 173
- William, 10
- Richard, 11
- Twyford, Joshua, 37, 44, 48
- Thomas William, 206
- Thomas, 206
- Unett, John, 156
- Walklate, Mark, 122
- Walton, John, 125, 154
- Warburton, Ann, 113, 114
- Jacob, 112, 114, 115, 116, 120, 154
- John, 52, 64, 66, 69, 83, 100, 102, 114, 154
- Thomas, 113, 114
- Warburton & Stone, 112
- Ward, —, 53, 136, 137, 155
- John, 11
- Weatherby, John, 113
- Wedgwood, Aaron, 29, 33, 70-73
- Cecil, 191
- Francis, 150, 200
- Francis Hamilton, 191
- John, 13, 51, 64, 65, 88, 91, 96, 125
- John, 105, 126, 130
- Josiah I, 38, 41, 47, 48, 66, 75, 78, 79, 80, 85, 86, 88, 93, 97, 100, 102, 104, 105, 106, 114, 115, 120, 121, 123, 126, 137, 159
- [229]Josiah II, 105, 106, 149, 150, 155
- Lawrence, 191
- Moses, 10
- Ralph, 157
- Richard, 13, 24, 29, 30, 31, 32, 33, 36, 42, 51, 54
- Dr Thomas, 10, 13, 24, 29, 30, 31, 32, 33, 36, 42, 44, 46, 50, 54, 83, 86
- Dr Thomas, Jun., 44, 50, 51, 53, 62, 64, 65, 88, 90
- Thomas, 105, 120, 121
- William, 10
- Wedgwood Pedigree, 87, 151
- Wesley, John, 128
- Weston, George, 155
- Wheildon, Edward, 79
- Thomas, 24, 62, 73, 74, 75, 76, 78, 79, 86, 126, 132
- (?), 183
- Whitehead, Charles, 81, 118, 121, 154
- Christopher, 87, 114, 121
- Whitehead, James, 118
- Williamson, Robert, 146, 153
- Wilson, David, 108, 120, 154
- James, 120
- Woodall, William, 204
- Wood, Aaron, 62, 75, 126
- Edward, 128, 129
- Enoch, 41, 85, 120, 124, 127, 154, 192
- Ephraim, 154
- Isaac, 50, 51
- John, 120, 124, 125, 152
- John Wedg, 126
- Ralph, 62, 79, 120, 124, 126, 128
- Robert, 10
- William, 126
- Kuntz & Co., 159
- Wood Pedigree, 130
- Woodall, William, 184
- Woods, Roger, 111
- Woolfe, Thomas, 121, 139, 146, 155
- Woolliscroft & Son, G., 188
- Wright, Samuel, 181
- Thomas, 120
- Yates, John, 120, 121, 154
Letchworth: At the Arden Press.
Letchworth: At Arden Press.
Plain text pedigrees
+-Thomas Wedgwood, Master Potter of the Churchyard and of Burslem | | Overhouse, (c. 1617-1679) | | | +-John Wedgwood, Master Potter of Burslem Overhouse. (1654-1705) | | O.S.P.M. | | | +-Thomas Wedgwood, Master Potter of the Churchyard Works. (1660-1716) | | | +-Thomas Wedgwood, Master Potter of Churchy'd. (1685-1739) | | | | | +-Thomas Wedgwood, Master Potter of the Churchy'd & Overhouse. | | | (1717-1773) | | | | | +-Josiah Wedgwood, Master Potter of Etruria. (1734-1788) | | | +-Aaron Wedgwood, of Burslem Hamil. (1697-c. 1750) | | | +-Thomas Wedgwood, Master Potter of Etruria. (1730-1795) | | | +-Ralph Wedgwood, Inventor and Master Potter of Burslem | and of Ferrybridge (Yorks). (1766-1837) | +-Aaron Wedgwood, Master Potter of Burslem. (c. 1624-1700) | | | +-Dr. Thos. Wedgwood, senr., Master Potter of Burslem. (1655-1717) | | | | | +-Dr. Thos. Wedgwood, jun., Master Potter of Rowleys’ in Burslem. | | | (1695-1737) | | | | | +-Eve = 1721 Ralph Shaw, Master Potter of Burslem. | | | +-Aaron Wedgwood, Master Potter of Burslem. (1666-1743) | | | | | +-Aaron Wedgwood. (1695-1722) | | | | | | | +-Aaron Wedgwood, Master Potter of Longton Hall. (1717-1763) | | | | | +-Richard Wedgwood, of Spen Green, co. Chester. (1701-1780) | | | | | | | +-Sarah, m'd Josiah Wedgwood, Master Potter (1734-1815) | | | | | +-Thomas Wedgwood, Master Potters (1703-1776) O.S.P. | | | | | +-John Wedgwood, of the Big H'o. (1705-1780) | | | | | +-John Wedgwood, of Bignal End. (1758-1838) O.S.P. | | | | | +-Thomas Wedgwood, Master Potter of the Big House, Burslem. | | | (1762-1826) O.S.P. | | | | | +-Mary, m'd John Baddeley, Master Potter of Shelton. | | | (1764-c. 1810) | | | | | +-Mary, d'a and h., m'd John Wood, Master Potter of Brownhills. | | | +-Richard Wedgwood, Master Potter of Burslem Overhouse, m'd Katherine | d'a and h. of John Wedgwood of the Overhouse. | +-Moses Wedgwood, Potter of Burslem. (c. 1626-1677)
Aaron Wedgwood, brother of Thomas and John of the Big House, Burslem. | (1695- around 1725) | +-Mary Wedgwood (1715-1756) = -----------------------------------------+ | Ralph Wood, miller of Burslem, (1677-1753) = Elizabeth. | | | +-Ralph Wood, master potter of Burslem (figure maker). (1716-1772) = --+ | | | +-Josiah Wood, married Mary daughter of Thomas Wedgwood, master potter of the | | Overhouse. | | | +-John Wood, master potter of Brownhills. (1746-1797). Murdered by | | | his daughter’s suitor. | | | | | +-John Wood, master potter of Brownhills. (1778-1848) = 24 XI. | | | 1807 Mary, daughter of John Baddeley, master potter of Shelton, by | | | Mary, sister and heiress of John Wedgwood of Bignal End. | | | (around 1785-1866) | | | | | +-Marianne, married William Davenport, master potter of the Unicorn | | | Bank, Longport. | | | | | +-Nicholas Price Wood. (1810-1869) | | | | | +-Rev. Richard Mountford Wood, of Aldbury, Herts. (1811-1889) | | | | | | | +-Colonel George Wilding Wood. born 1840. | | | | | | | | | +-[symbol indicating ‘had issue’] | | | | | | | +-Reginald Newcome Wood, of Bignal End. born 1841. = Emily | | | | | Ann, daughter of William Davenport, master potter. | | | | | | | | | +-[symbol indicating ‘had issue’] | | | | | | | +-Rev. Henry T. Wood, of Aldbury, Herts. born 1850. | | | | | | | | | +-[symbol indicating ‘had issue’] | | | | | | | +-John Mountford Wood, of Holkham, co. Norfolk. born 1861. | | | Collector of Staffs. Pottery. | | | | | +-John Wedgwood, master potter of Brownhills, & Woodlands, | | | Tunstall. (1813-1857) O.S.P. | | | | | +-Edmund Thomas Wedgwood of the Watlands, master potter of | | | Tunstall. (1822-1886) | | | | | +-John Baddeley Wood of Henley Hall, Salop, married Elizabeth daughter & | | | | heiress of Nicholas Price Wood. Collector of Staffs. | | | | Pottery. | | | | | | | +-[symbol indicating ‘had issue’] | | | | | +-Emily Henrietta, married 1868 Richard Pirie Copeland, master | | potter of Stoke. | | | +-Ralph Wood, master potter of Burslem (figures) (1748-1795) | | | +-Ralph Wood, only son. (1781-1801) | +-Aaron Wood, the “Block cutter.” (1718-1785) = Mary Meir, of | Stoke-on-Trent. | +-William Wood, modeller at Etruria. (1746-1808) | +-Enoch Wood, master potter of Fountain Place, Burslem. | (1759-1840) = 1780 Ann Bourne, of Newcastle. | +-Enoch Wood, master potter of Fountain Place. (1793-1852) | +-Edward Wood, master potter of Fountain Place, and borax | manufacturer. (1796-1882) = Elizabeth Schofield. | +-Edward Herbert Wood of Newbold Revel (1847- ) | +-A. H. Edward Wood of Browhead, co. Cumb. born 1870.
Ralph Ridgway, Master Potter of Chell. | +-George Ridgway, Master Potter of the Bell Works, Shelton. | (c. 1758-1823) | +-Job Ridgway, Master Potter of the Bell Works, and of Cauldon Place, | Shelton. (1759-1813) = 1785 Elizabeth, sister of Elijah Meyer, | Master Potter of Hanley. (1755-1810) | +-John Ridgway, Master Potter of Cauldon Place. 1st Mayor of Hanley | 1856. (1786-1860) | +-William Ridgway, Master Potter of Shelton and Hanley. | (1787-c. 1865) | +-Edward John Ridgway, Master Potter of the Bedford Works, | Hanley. (1814-1896) | +-John Ridgway, Master Potter of the Bedford Works, b. 1843 | +-Edward Akroyd Ridgway, Master Potter of the Bedford Works, | | b. 1846 = Susan, daughter of Wm Meakin, of the Eagle Works. | | | +-Henry Akroyd Ridgway, Master Potter of the Bedford Works, | b. 1883. | +-Emily, married James Meakin, Master Potter of the Eagle Works, Hanley.
Jonathan Davenport of Leek. (1731-1771) | +-John Davenport of Westwood, Master Potter of Longport. (1765-1848) | +-John Davenport of Westwood, and of Foxley, Hereford County. | | (1799-1862) | | | +-George Horatio Davenport of Foxley, Hereford County. Sold Staffordshire | | | estates, 1868. | | | | | +-[symbol indicating ‘had issue’] | | | +-Harry Tichborne Davenport, M.P. North Staffordshire. 1880-6. b. 1833 | +-Henry Davenport, Master Potter of Longport, killed while hunting. | (1800-1835) | +-William Davenport of Maer, Master Potter of Longport. Married Marianne, | daughter of John Wood, Master Potter of Brownhills. (1805-1869) | +-Henry Davenport of Maer, Master Potter of Longport. b. 1840
Josiah Wedgwood, Master Potter of Etruria. (1730-1795) | +- John Wedgwood, Partner at Etruria 1790-2. (1766-1844) | +- Josiah Wedgwood of Maer, Master Potter of Etruria. (1769-1843) | | | +- Josiah Wedgwood of Leith Hill Place, Partner at Etruria 1823-42. | | (1795-1880) | | | +- Francis Wedgwood of Barlaston, Master Potter of Etruria. | | | (1800-1888) | | | | | +- Godfrey Wedgwood, Master Potter of Etruria. (1833-1905) | | | | | | | +- Cecil Wedgwood, D.S.O. b. 1863. Master Potter of Etruria. | | | 1st Mayor of Stoke-on-Trent 1910. | | | | | +- Clement Francis Wedgwood of Barlaston, Master Potter of Etruria. | | | | (1840-1889) | | | | | | | +- Francis Hamilton Wedgwood, Master Potter of Etruria. | | | | | | | +- Josiah Clement Wedgwood, M.P. b. 1872. The writer of this | | | book. | | | | | +- Lawrence Wedgwood, Master Potter of Etruria, b. 1844 | | | | | +-[symbol indicating ‘had issue’] | | | +- Emma (1808-1896) = -----------------------------+ | | +- Thomas Wedgwood, Partner at Etruria 1790-2. | | Chemist and Photographer. (1771-1805) | [symbol indicating | | ‘had issue’] +- Susannah, married R. W. Darwin. (1765-1817) | | | +- Charles Robert Darwin, F.R.S. (1809-1882) = ----+
William Adams (brother of Thomas Adams, Master Potter of the Brickhouse, Burslem), Master Potter of Burslem. d. 1617. | +-John Adams of Sneyd Green. Will proved 1641. | +-William Adams of Sneyd Green. Will proved 1677. | +-William Adams of Bank Hᵒ, Bagnal. Said to have been a salt-glaze potter. Will proved 1712. | +-Edward Adams of Sneyd Green and Bagnal. Will proved 1728. | +-William Adams of Bank Hᵒ, Bagnal. (1702-1775) | | | +-Richard Adams, Master Potter. (1739-1811) | | | +-William Adams, Master Potter of Stoke-on-Trent. | | (1772-1829) = 1793 Sarah, daughter of Lewis Heath, Master Potter of the Hadderage. | | | +-William Adams, Master Potter of Greenfield. | | (1798-1865) = 1827 Jane (1804-1864) -----------+ | | | | +-William Adams, Master Potter of Greenfield and | | | Greengates, (1833-1905) | | | | | +-William Adams. } Master Potters of | | | } Greenfields and | | +-Percy W. L. Adams. } Greengates, Tunstall. | | | +-Edward Adams (1709-1745) | | | +-William Adams, Master Potter of Greengates, Tunstall. | | (1745-1805) | | | +-Benjamin Adams, Master Potter of Greengates. | | John Breeze, Master Potter of Greenfield. | | | +-Jesse Breeze, Master Potter of Greenfield. | | | +-------------------------------------------------------------------------+
James Meakin, Master Potter of Hanley, died 1855. | +-Sarah. = Robert Johnson died around 1910 | | | +-Henry Johnson. } | | } | +-Robert Johnson. } Master Potters of Hanley—“Johnson Bros.” | | } | +-Fred. Johnson. } | +-James Meakin of Darlaston, Master Potter of the Eagle Works. | | (1833-1885) = Emily, daughter of Ed. J. Ridgway, Master Potter of the | | Bedford Works, Hanley. | | | +-Kenneth Meakin, Master Potter. | | | +-Bernard Meakin of the Eagle Works. | +-George Meakin, Master Potter of the Eagle Works, died 1891 | | | +-George Elliot Meakin, Master Potter of the Eagle Works, born around | 1865 | +-William Meakin, Master Potter of the Eagle Works, Hanley, died 1889 | | | +-Susan = Edward Akroyd Ridgway, Master Potter of Bedford Works, | Hanley. | +-Charles Meakin, Master Potter of Joiners Square. | +-Alfred Meakin, Master Potter of the Victoria and Albert Works, | Tunstall, died 1904 | +-[symbol indicating ‘had issue’]
Download ePUB
If you like this ebook, consider a donation!