This is a modern-English version of The story of the invention of steel pens : with a description of the manufacturing process by which they are produced, originally written by Bore, Henry.
It has been thoroughly updated, including changes to sentence structure, words, spelling,
and grammar—to ensure clarity for contemporary readers, while preserving the original spirit and nuance. If
you click on a paragraph, you will see the original text that we modified, and you can toggle between the two versions.
Scroll to the bottom of this page and you will find a free ePUB download link for this book.
THE STORY
OF THE INVENTION
OF STEEL PENS
WITH A DESCRIPTION OF
THE MANUFACTURING PROCESS BY
WHICH THEY ARE PRODUCED
BY HENRY BORE
LONDON
NEW YORK
1890
In these days of Public Schools and extended facilities for popular education it would be difficult to find many people unaccustomed to the use of steel pens, but although the manufacture of this article by presses and tools must have been introduced during the first quarter of the present century, the inquirer after knowledge would scarcely find a dozen persons who could give any definite information as to when, where, and by whom this invention was made. Less than two decades ago there were three men living who could have answered this question, but two of them passed away without making any sign, and the third—Sir Josiah Mason—has left on record that his friend and patron—Mr. Samuel Harrison—about the year 1780, made a steel pen for Dr. Priestley.
In today's world of public schools and widespread access to education, it would be hard to find many people unfamiliar with steel pens. However, even though the production of this item by presses and tools likely started in the early 1800s, a knowledge-seeker would be hard-pressed to find a dozen individuals who could provide clear details on when, where, and by whom this invention was created. Less than twenty years ago, three men could have answered this question, but two of them passed away without sharing any insights. The third—Sir Josiah Mason—has recorded that his friend and supporter, Mr. Samuel Harrison, made a steel pen for Dr. Priestley around the year 1780.
This interesting fact does not contribute anything toward solving the question, Who was the first manufacturer of steel pens by mechanical appliances? In the absence of any definite information, the balance of testimony tends to prove that steel pens were first made by tools, worked by a screw press, about the beginning of the third decade of the present century, and the names associated with their manufacture were John Mitchell, Joseph Gillott, and Josiah Mason, each, in his own way, doing something toward perfecting the manufacture by mechanical means.
This interesting fact doesn't help answer the question: Who was the first to make steel pens using machines? Without any solid information, the evidence suggests that steel pens were first made with tools operated by a screw press around the start of the 1820s. The names linked to their production include John Mitchell, Joseph Gillott, and Josiah Mason, each contributing in their own way to improving the manufacturing process through mechanical methods.
The earliest references to pens are probably those in the Bible, and are to be found in Judges v. 14, 1st Kings xxi. 8, Job xix. 24, Psalm xlv. 1., Isaiah viii. 1, Jeremiah viii. 8 and xvii. 1. But these chiefly refer to the iron stylus, though the first in Jeremiah—taken in reference to the mention of a penknife, xxxvi. 23—would seem to imply that a reed was in use at that period
The first mentions of pens are likely found in the Bible, specifically in Judges 5:14, 1 Kings 21:8, Job 19:24, Psalm 45:1, Isaiah 8:1, Jeremiah 8:8, and Jeremiah 17:1. However, these mostly refer to the iron stylus. Jeremiah's first mention, related to the mention of a penknife in 36:23, suggests that a reed was also being used at that time.
There is a reference to “pen and ink” in the 3d Epistle of John xiii. 5, which was written about A.D. 85, and as pens made in brass and silver were used in the Greek and Roman Empires at that time, it is probable that a metallic pen or reed was alluded to.
There is a reference to “pen and ink” in the 3rd Epistle of John xiii. 5, which was written around A.D. 85. Since pens made of brass and silver were used in the Greek and Roman Empires during that time, it’s likely that a metallic pen or reed was being referred to.
Pens and reeds made in the precious metals and bronze appear to have been in use at the commencement of the present era. The following are a few notable instances:
Pens and reeds made from precious metals and bronze seem to have been used at the beginning of the current era. Here are a few notable examples:
“The Queen of Hungary, in the year 1540, had a silver pen bestowed upon her, which had this inscription upon it: 'Publii Ovidii Calamus,' found under the ruins of some monument in that country, as Mr. Sands, in the Life of Ovid (prefixed to his Metamorphosis) relates. —“Humane Industry; or, a History of Mechanical Arts”, by Thos. Powell, D.D.: London, 1661, page 61.
“In 1540, the Queen of Hungary received a silver pen, which had the inscription: 'Publii Ovidii Calamus,' discovered beneath the ruins of a monument in that region, as Mr. Sands recounts in the Life of Ovid (included in his Metamorphosis). —“Humane Industry; or, a History of Mechanical Arts”, by Thos. Powell, D.D.: London, 1661, page 61.
This was probably a silver reed, and, from the locality in which it was found, was once the property of the poet Ovid. Publius Ovidius Naso was born in the year 43 B.C., and died 18 A.D. He was exiled at the age of 30 to Tomi, a town south of the delta of the Danube. This at present is in modern Bulgaria, but at the period mentioned was in the ancient kingdom of Hungary.
This was likely a silver reed, and, based on where it was found, it once belonged to the poet Ovid. Publius Ovidius Naso was born in 43 B.C. and died in 18 A.D. He was exiled at age 30 to Tomi, a town south of the Danube delta. Today, this is in modern Bulgaria, but back then it was part of the ancient kingdom of Hungary.
From “Notes and Queries,” in Birmingham Weekly Post, we take the following:
From “Notes and Queries,” in Birmingham Weekly Post, we take the following:
“EARLY METALLIC PENS.—-Metallic pens are generally supposed to have been unknown before the early part of the last century, when gold and silver pens are occasionally referred to as novel luxuries. I have, however, recently found a description and an engraving of one found in excavating Pompeii, and which is now preserved in the Museum at Naples. It is described in the quarto volume 'Les Monuments du Musée National de Naples, gravés sur cuivre par les meillures artistes Italienes. Texte par Domenico Monaco, Conservateur du même Musée, Naples, 1882,' and is in the Catalogue:
“' Plate I26 (v) Plume en bronze, taillée parfaitement a la facon de nos plumes 0.13 cent.
“' Plate I26 (y) Plume en roseau [reed] trouvée près d'un papyrus à Herculaneum.'
“The former (v) is engraved to look like an ordinary reed pen, as now used universally in the East; and the other (y) has a spear shape, or almond shape (like many modern metallic pens), but with a sort of fillet or ring on the stem, which indicates that the 'y' example is not a reed, but a metallic stylus, or pen, while the 'v' example is shown clearly as a 'reed.' The two are, however, certainly older than A.D. 79, when Pompeii and Herculaneum were buried by the eruption of Vesuvius.”
“EARLY METALLIC PENS.—Metal pens are generally believed to have been unknown before the early years of the last century, when gold and silver pens began to be seen as new luxuries. However, I recently discovered a description and an engraving of one that was found during the excavation of Pompeii, which is now on display at the Museum in Naples. It is detailed in the quarto volume 'Les Monuments du Musée National de Naples, gravés sur cuivre par les meilleures artistes Italiennes. Texte par Domenico Monaco, Conservateur du même Musée, Naples, 1882,' and listed in the Catalogue:
“' Plate I26 (v) Bronze pen, perfectly shaped like our pens 0.13 cent.
“' Plate I26 (y) Reed pen found near a papyrus in Herculaneum.'
“The first (v) is engraved to resemble a regular reed pen, which is still commonly used in the East; while the second (y) has a spear or almond shape (similar to many modern metallic pens), but features a kind of band or ring on the stem, indicating that the 'y' example is not a reed but a metallic stylus or pen, while the 'v' example is clearly identified as a 'reed.' However, both were certainly made before A.D. 79, when Pompeii and Herculaneum were buried by the eruption of Vesuvius.”
According to Father Montfaucon, the patriarchs of Constantinople, under the Greek Empire, were accustomed to sign their allocutions with tubular pens of silver, similar in shape to the reed pens which are still used by Oriental nations.
According to Father Montfaucon, the patriarchs of Constantinople during the Greek Empire used to sign their speeches with silver tubular pens, shaped like the reed pens that are still used by Eastern nations.
The following are translated from the French “Notes and Queries “— L'Intermémediare:
The following are translated from the French “Notes and Queries “— L'Intermédiaire:
“A METALLIC PEN IN THE FOURTEENTH CENTURY.—M. Reni de Bellwal, in a very learned volume which he has published recently, on the first campaign of Edward III. in France, says (p. 95) with respect to the fictitious pieces (documents) fabricated by Robert d'Artois, that a clerk of Jeanne wrote the deeds, and made use of a bronze pen to enable him the better to disguise his writing. This plainly refers to a pen, and not to a stylus. Is there any record of the use of metallic pens at any period anterior to the fourteenth century? It is very satisfactory, however, to establish (as the French used to say) 'les preuves de 1300.'”—L'Intermémediare.
In the Vieux-Neuf of M. Ed. Fournier (vol. ii., p. 22, note) there is mentioned—according to the documents used in the prosecution of Robert d'Artois, which are in the Archives—'the bronze pen' with which the forgers in the pay of the count wrote the false papers which he required. M. Fournier also quotes from 'Montfaucon' 'the silver reeds' with which the Constantinople patriarchs used to write their letters.”—CUTHBERT, L'Intermémediare, 1st June, 1864.
“METALLIC PENS (XV., 68).-Writing was done in the Middle Ages sometimes with a metal stylus, or perhaps with a metal pen; with the former on wax, and with the pen on parchment or vellum. 'At Trinity College, Cambridge, is a manuscript illustration of Eadwine, a monk of Canterbury, and at the end the writer is represented with a metal pen in his hand.' (See Bibliomania in the Middle Ages, p. 103). I have in my possession a metal pen of Dutch manufacture, dating certainly from the year 1717, mounted on the same pencilholder, with a piece of solid plumbago, in a memorandum book of the same year.”—SAM: TIMMINS.
“Mr. Le Chauviné Gal, Prior of the collegiate of St. Peter and St. Bars at Aosta, had in his collection of Roman antiquities a bronze pen, slit, found in a tomb, among a number of lamps and lachrymatory vases. M. Aubert has given a drawing and description of it in a work on Aosta. It was subsequently stolen from him by a collector.”—CHAMBERY, Un Savoyard, L'Intermémediare, 25th May, 1868.
“METALLIC PENS,—In a precious volume (an account of the books of the Decretalia) preserved in the library of Saint Antoine, of Padua, the following notice is to be found at the bottom of the last page: 'This work is fashioned and by diligence finished for the service of God, not with ink of quill nor with brazen reed, but with a certain invention of printing or reproducing by John Fust, citizen of Mayence, and Peter Schoeiffer, of Gernsheim, Dec. 17th, 1465, A.D.' Here, then, we have a document proving the existence of metallic pens in the Middle Ages. But has any such pen come down to us? If so, could a detailed description of it be obtained? On the other hand, I am curious to know if it is possible that platinum was used in the eighteenth century in the manufacture of pens, or whether it is necessary to attribute a peculiar meaning to the 'platinum pen' in the following passage of the system of shorthand by Bertin (edit. of the year iv., p. 93) (1793). 'Those of steel and platinum are most convenient; these latter have the advantage of all others, in that they hold the ink a long time, and run over the paper easily, and are not liable to corrosion by any simple acid.' I am ignorant of what the same author means when he mentions the endless pen, which would certainly be the best. “'—J. CAMUS, L'Intermémediare.
“Metallic pens were used before the fifteenth century; they were in use at the court of Augustus.” See L'Intermémed. (I. 69, 94, 141; II. 319.) Consult also Le Vieux-Neuf Ed. Fournier.—A.D.
“A METAL PEN IN THE FOURTEENTH CENTURY.—M. Reni de Bellwal, in a very scholarly book he recently published about Edward III.'s first campaign in France, mentions (p. 95) that regarding the fake documents created by Robert d'Artois, a clerk of Jeanne wrote the deeds using a bronze pen to better disguise his handwriting. This clearly refers to a pen, not a stylus. Is there any record of the use of metal pens before the fourteenth century? Nonetheless, it is quite satisfying to establish (as the French used to say) 'les preuves de 1300.'”—L'Intermémediare.
In the Vieux-Neuf by M. Ed. Fournier (vol. ii., p. 22, note), it is mentioned—based on documents used in the prosecution of Robert d'Artois, which are in the Archives—'the bronze pen' used by the forgers working for the count to write the false papers he needed. M. Fournier also quotes 'Montfaucon' regarding 'the silver reeds' used by the patriarchs of Constantinople to write their letters.”—CUTHBERT, L'Intermémediare, June 1, 1864.
“METAL PENS (XV., 68).—Writing during the Middle Ages was sometimes done with a metal stylus or possibly a metal pen; the former was used on wax and the latter on parchment or vellum. 'At Trinity College, Cambridge, there is a manuscript illustration of Eadwine, a monk of Canterbury, in which the writer is depicted holding a metal pen.' (See Bibliomania in the Middle Ages, p. 103). I own a metal pen of Dutch origin, definitely made in 1717, attached to the same pencil holder along with a solid piece of plumbago, found in a memorandum book from that same year.”—SAM: TIMMINS.
“Mr. Le Chauviné Gal, Prior of the collegiate church of St. Peter and St. Bars in Aosta, had in his collection of Roman antiquities a bronze pen with a slit, found in a tomb alongside several lamps and lachrymatory vases. M. Aubert has provided a drawing and description of it in a work on Aosta. It was later stolen from him by a collector.”—CHAMBERY, Un Savoyard, L'Intermémediare, May 25, 1868.
“METAL PENS,—In a valuable volume (an account of the books of the Decretalia) kept in the library of Saint Antoine in Padua, the following note appears at the bottom of the last page: 'This work is crafted and completed with care for the service of God, not with ink from a quill nor with a brass reed, but with a certain invention of printing or reproducing by John Fust, citizen of Mainz, and Peter Schoeiffer of Gernsheim, Dec. 17, 1465, A.D.' Here, we have a document confirming the existence of metal pens in the Middle Ages. But has any such pen survived to this day? If so, could a detailed description be provided? Additionally, I am curious if platinum was used in pen manufacture during the eighteenth century, or if the 'platinum pen' mentioned in Bertin's shorthand system (4th edition, p. 93) (1793) has some special meaning. 'Those made of steel and platinum are the most convenient; the latter have the advantage over all others, as they hold ink for a long time, glide smoothly over paper, and are not easily corroded by simple acids.' I am unsure what the same author means when he refers to the endless pen, which would certainly be the best.” —J. CAMUS, L'Intermémediare.
“Metal pens were used before the fifteenth century; they were utilized at the court of Augustus.” See L'Intermémed. (I. 69, 94, 141; II. 319.) Please also consult Le Vieux-Neuf by Ed. Fournier.—A.D.
The following extracts show there have been several claimants, on the Continent, who profess to have invented metallic pens, made from steel, in the early part of the eighteenth century; but the reader had better suspend his judgment until he has read the notes that follow them:
The following extracts show that there have been several claimants on the Continent who claim to have invented steel pens in the early eighteenth century; however, the reader should hold off on making a judgment until they have read the notes that follow:
“A manuscript, entitled 'Historical Chronicle of Aix-la-Chapelle, second book, 1748,' places on record the claims of Johann Janssen, a magistrate of that place, as the inventor of steel pens. 'Just at the meeting of the congress [after the Austrian war] I may without boasting, claim the honour of having invented a new pen. It is, perhaps, not an accident that God should have inspired me at the present time with the idea of making steel pens, for all the envoys here assembled have bought the first that have been made; therewith, as may be hoped, to sign a treaty of peace, which, with God's blessing, shall be as permanent as the hard steel with which it is written. Of these pens, as I have invented them, no man hath before seen or heard. If kept clean and free from rust and ink, they will continue fit for use for many years. Indeed, a man may write twenty reams of paper with one, and the last line would be written as well as the first. They are now sent into every corner of the world as a rare thing—to Spain, France, England and Holland. Others will no doubt make imitations of my pens, but I am the man who first invented and made them. I have sold a great number of them at home and abroad at 1s. each, and I dispose of them as quickly as I can make them.”'
“A manuscript titled 'Historical Chronicle of Aix-la-Chapelle, second book, 1748' documents the claims of Johann Janssen, a magistrate from that area, as the inventor of steel pens. 'Right at the congress meeting [after the Austrian war], I can humbly claim the honor of having invented a new pen. It might not be a coincidence that God inspired me at this moment to create steel pens, as all the envoys gathered here have purchased the first ones made; hopefully, they will use these to sign a peace treaty that, with God's blessing, will be as lasting as the hard steel it's written with. Of these pens, as I have crafted them, no one has seen or heard of before. If kept clean and free from rust and ink, they will remain usable for many years. In fact, one can write twenty reams of paper with just one, and the last line will be as good as the first. They are now being sent to every corner of the world as a rare item—to Spain, France, England, and Holland. Others will surely try to imitate my pens, but I am the original inventor and creator. I have sold a large number of them both at home and abroad for 1s. each, and I sell them as fast as I can make them.”
In an article on Writing Instruments, which appeared in the Berlin Paper Zeitung, on the 19th of May, 1887, the author says:
In an article about Writing Instruments, published in the Berlin Paper Zeitung on May 19, 1887, the author states:
“A school teacher of Koningberg, named Burger, in the year 1808, made pens from metal, but he got poor by his trials. After this time, and probably imitating the pens of Burger, the English began to take in hand the manufacture of pens; especially Perry, he having perfected the pens, as he did not restrict himself to the simple straight slit, but he made cuts in the sides of different kinds.”
“A school teacher from Koningberg named Burger, in the year 1808, made metal pens, but he went bankrupt due to his experiments. After that, likely inspired by Burger's work, the English began to produce pens as well; especially Perry, who improved the design by not just sticking to the basic straight slit but instead adding various cuts on the sides.”
In a pamphlet upon the manufacture of steel pens, published in Paris, in 1884, the writer says:
In a pamphlet about making steel pens, published in Paris in 1884, the author states:
“The invention of the metallic pen is due to a French mechanic— Arnoux—who lived in the eighteenth century, who made as far back as 1750 a number of metallic pens as a curiosity. This invention did not have any immediate result in France but spread to England, and became in Birmingham, about 1830, a very prosperous industry. A very curious fact about this trade is that, in England, it does not exist out of Birmingham, where there are about ten manufactories. In France it has become localized in Boulogne.”
"The metallic pen was invented by a French mechanic named Arnoux, who lived in the eighteenth century and created several metallic pens as curiosities back in 1750. This invention didn't have an immediate impact in France but spread to England, where it became a thriving industry in Birmingham around 1830. It's interesting to note that this trade only exists in Birmingham, which has about ten manufacturers. In France, it has become concentrated in Boulogne."
There is also the “nameless Sheffield Artisan,” who so frequently figures in newspaper paragraphs as the inventor of steel pens; and William Gadsby, a mathematical instrument maker, who for his own use constructed a clumsy article from the mainspring of a watch; but it is not till the beginning of the eighteenth century that we get anything authentic respecting the making of metallic pens. “Este,” writing in “Local Notes and Queries” (Birmingham Weekly Post) mentions a remarkable little volume supplied to the members of the States General of Holland, in the possession of Mr. W. Bragge, of Sheffield, dated 1717. It contained a silver pencil case, in two parts, one holding a piece of plumbago, mounted like a crayon, and the other a metallic pen. We have seen this unique book (now the property of Mr. Sam: Timmins). The pen is of the barrel shape, apparently silver, and it must be regarded as the earliest authentic metallic pen. Of the date there can be no doubt, as the pen is made to pass through loops in the cover of the volume to keep it closed, after the manner of pocket books, and the book bears the date, printed on the title page, 1717.
There is also the “nameless Sheffield Artisan,” who often appears in newspaper articles as the inventor of steel pens; and William Gadsby, a maker of mathematical instruments, who created a clunky tool for himself from a watch's mainspring. However, it isn't until the early eighteenth century that we find anything credible about the production of metallic pens. “Este,” writing in “Local Notes and Queries” (Birmingham Weekly Post), mentions a remarkable little book given to the members of the States General of Holland, owned by Mr. W. Bragge of Sheffield, dated 1717. It contained a silver pencil case with two parts: one held a piece of plumbago mounted like a crayon, and the other held a metallic pen. We have seen this unique book (now owned by Mr. Sam Timmins). The pen is barrel-shaped, appears to be silver, and should be considered the earliest genuine metallic pen. There is no doubt about the date, as the pen is designed to slide through loops in the book's cover to keep it closed, similar to pocketbooks, and the book is printed with the date 1717 on the title page.
Pope, about the same time, received from Lady Frances Shirley a present of a standish, containing a STEEL and a gold pen. In acknowledging the receipt of this present, the poet wrote an ode, in which the following lines occur:
Pope, around the same time, received a gift from Lady Frances Shirley: a desk set with a steel nib and a gold pen. In response to this gift, the poet wrote an ode that includes the following lines:
“Take at this hand celestial arms;
Secure the radiant weapons wield;
This golden lance shall guard desert,
And, if a vice dares keep the field,
This steel shall stab it to the heart.
Awed, on my bended knees I fell,
Received the weapons of the sky,
And dipped them in the sable well—
The fount of fame or infamy.
What well? What weapon? Flavia cries,
A standish, steel and golden pen!
It came from Bertrand's,* not the skies,
I gave it you to write again.”
“Look at this hand with heavenly weapons;
Take hold of the bright weapons I wield;
This golden lance will protect the land,
And if a vice dares to take a stand,
This steel will pierce it to the heart.
Awed, I fell to my knees,
Accepted the arms of the heavens,
And dipped them in the dark well—
The source of either glory or shame.
What well? What weapon? Flavia asks,
An inkwell, steel and golden pen!
It came from Bertrand's,* not from the heavens,
I gave it to you so you could write again.”
*Bertrand kept a fancy shop in Bath. He died in 1755. His wife is mentioned by Horace Walpole, in his letter to George Montague, May 18th, 1749, which letter is printed in his Correspondence.
*i>Bertrand ran an upscale shop in Bath. He passed away in 1755. His wife is mentioned by Horace Walpole in his letter to George Montague dated May 18th, 1749, which can be found in his Correspondence.
In No. 503 of the Spectator, bearing the date of October 7, 1712, Steele, mentioning the conspicuous manner in which a certain lady conducted herself in church, says:
In No. 503 of the Spectator, dated October 7, 1712, Steele points out the noticeable way a certain lady behaves in church, saying:
“For she fixed her eyes upon the preacher, and as he said anything she approved, with one of Charles Mather's fine tablets, she set down the sentence, at once showing her fine hand, the gold pen, her readiness in writing, and her judgments in choosing what to write.”
“For she focused her gaze on the preacher, and whenever he said something she agreed with, she noted down the sentence using one of Charles Mather's elegant notebooks, showcasing her beautiful handwriting, the gold pen, her quickness in writing, and her ability to choose what to write.”
Edmund Waller, about the middle of the seventeenth century, acknowledged the receipt of a silver pen from a lady, in the following verses:
Edmund Waller, around the middle of the seventeenth century, acknowledged receiving a silver pen from a lady in the following verses:
Madam! intending to have try'd,
The silver favour which you gave,
In ink the shining point I dy'd,
And drench'd it in the sable wave
When, grieved to be so foully stained,
On you it thus to me complained.
Madam! I planned to try,
The silver token you gave me,
I dipped the shiny tip in ink,
And soaked it in the dark liquid.
When, upset to be so badly stained,
It complained to you about me.
So I, the wronged pen to please,
Made it my humble thanks express
Unto your Ladyship, in these,
And now 'tis forced to confess
That your great self did ne'er indite
Nor that to me more noble write.”
So I, the wronged pen hoping to please,
Made it my humble thanks express
To your Ladyship, with these,
And now I’m forced to admit
That your great self never wrote
Nor wrote anything more noble to me.”
Mr. G. A. Lomas, writing to the Scientific American, November 23, 1878, says:
Mr. G. A. Lomas, writing to the Scientific American, November 23, 1878, says:
“I write to inquire if you can give me information concerning the manufacture of metal pens in this country. I may be vain in the supposition, but I am persuaded that my people—the Shakers—were the originators of metal pens. I write this to you with a silver pen, one slit, that was made in the vear 1819, at this village, by the Shakers. Two or three years previously to the use of silver pens, our people used brass plates for their manufacture, but soon found silver preferable. Some people sold these pens in the year 1819, at this village, for twenty-five cents, and disposed of all that could be made.”
“I’m reaching out to ask if you can provide me with information about the production of metal pens in this country. I might be a bit vain in thinking this, but I genuinely believe that my community—the Shakers—were the pioneers of metal pens. I'm writing this with a silver pen, one with a slit, that was made in 1819, right here in this village, by the Shakers. A few years before silver pens became common, our community used brass plates for their production, but soon realized silver was a better option. Some people sold these pens in 1819 in this village for twenty-five cents, and managed to sell all they could produce.”
The writer further says the metal was made from silver coins.
The writer also mentions that the metal was created from silver coins.
This communication called forth the following from another correspondent:
This message prompted the following response from another correspondent:
“The letter in the Scientific American, November 23, 1878, with regard to the early manufacture of steel pens, reminds me of the following note which appeared in the Boston Mechanic, for August, 1835. 'The inventor of steel pens,' says the Journal of Commerce, was an American and a well-known resident of our city (New York), Mr. Peregrine Williamson. In the year 1800, Mr.W., then a working jeweler, at Baltimore, while attending an evening school, finding some difficulty in making a quill pen to suit him, made one of steel. It would not write well, however, for want of flexibility. After a while he made an additional slit on each side of the main one, and the pens were so much improved that Mr. W. was called to make them in such numbers as to eventually occupy his whole time, and that of a journeyman. At first the business was very profitable and enabled Mr. W. to realize for the labor of himself and journeyman a clear profit of six hundred dollars per month. The English soon borrowed the invention, and some who first engaged in the business realized immense fortunes.”'
“The letter in the Scientific American, November 23, 1878, about the early production of steel pens, reminds me of the following note that appeared in the Boston Mechanic in August 1835. 'The inventor of steel pens,' stated the Journal of Commerce, was an American and a well-known resident of our city (New York), Mr. Peregrine Williamson. In 1800, Mr. W., then a working jeweler in Baltimore, while attending evening classes, experienced some difficulty in making a quill pen that suited him, so he created one out of steel. However, it didn’t write well due to a lack of flexibility. Eventually, he added an extra slit on each side of the main one, which significantly improved the pens, leading Mr. W. to make them in such quantities that it eventually consumed all of his time and that of an apprentice. Initially, the business was very profitable, allowing Mr. W. to earn a clear profit of six hundred dollars a month for his and his apprentice’s labor. The English soon adopted the invention, and some of those who first entered the business made enormous fortunes.”'
We do not know how much reliance may be placed upon this statement, but, if the last assertion “that those who first engaged in the business realized immense fortunes” may be taken as a test, the whole must be received with a grain of salt. The letter appeared in the Boston Mechanic, in 1835, and at that date there were penmakers who had made a modest competence, but in no case were they possessed of immense fortunes.
We can't be sure how much trust we can put in this statement, but if we take the last claim—that those who started this business made huge fortunes—as a measure, we should be skeptical. The letter was published in the Boston Mechanic in 1835, and at that time, there were pen makers who had earned a comfortable living, but none of them were actually wealthy.
In London Notes and Queries, the following appears respecting early steel pens:
In London Notes and Queries, the following is found regarding early steel pens:
“THE FIRST STEEL PEN.—(5th S., iii., 395.) Ten years before Dr. Priestley was born steel pens were in use. There are references to them in the Diary of John Byrom, who required them when writing shorthand. In a letter to his sister Phoebe, dated August, 1723, he mentions them as follows: 'Alas! alas! I cannot meet with a steel pen, no manner of where I believe I have asked at 375 places, but that which I have is at your service, as the owner himself always is.”' (Remains, Vol. i., 39.)
“THE FIRST STEEL PEN.—(5th S., iii., 395.) Ten years before Dr. Priestley was born, steel pens were already in use. There are mentions of them in the Diary of John Byrom, who needed them for writing shorthand. In a letter to his sister Phoebe, dated August 1723, he stated: 'Alas! alas! I can't find a steel pen anywhere; I believe I've asked at 375 places, but the one I have is yours, as the owner himself always is.'” (Remains, Vol. i., 39.)
Mr. Ralph N. James, writing to Notes and Queries, gives the following extract from the very amusing “journey to Paris,” by Dr. Martin Lister, 1698:
Mr. Ralph N. James, writing to Notes and Queries, provides the following excerpt from the entertaining “journey to Paris,” by Dr. Martin Lister, 1698:
“There was one thing very curious, and that was a Writing lnstrument of thick and strong silver wire, bound up like a hollow button or screw, with both ends pointing one way, and at a distance, so that a man might easily put his forefinger betwixt the two points, and the point divided in two, just like our steel pens.”—London Notes and Queries, vol. iii., page 346.
“There was one very interesting thing, and that was a Writing Instrument made of thick and strong silver wire, shaped like a hollow button or screw, with both ends pointing the same way and spaced apart so that a person could easily fit their forefinger between the two points, with the point split in two, just like our steel pens.”—London Notes and Queries, vol. iii., page 346.
This note caused another writer, Mr. C.A. Ward, to send the following:
This note prompted another writer, Mr. C.A. Ward, to send this:
“STEEL PENS.—The extract given from Dr. M. Lister's, by Mr. Ralph N. James, is very interesting. The doctor there speaks of 'our steel pens,' as if they were not at all uncommon. When the poet Churchill's effects were sold up, after his death, Nov. 10, 1764, they fetched extravagant prices; 'a common steel pen' brought L.5.”—London Notes and Queries, vol iii., page 474.
“STEEL PENS.—The excerpt from Dr. M. Lister's work, shared by Mr. Ralph N. James, is quite intriguing. The doctor refers to 'our steel pens,' as if they were quite ordinary. When the belongings of the poet Churchill were auctioned after his death on November 10, 1764, they sold for outrageous prices; 'a common steel pen' went for £5.” —London Notes and Queries, vol iii., page 474.
The following extract from London Notes and Queries gives very plausible reasons against placing confidence in the preceding and other notices of ancient steel pens:
The following extract from London Notes and Queries provides valid reasons for being skeptical about trusting the earlier and other mentions of ancient steel pens:
“STEEL PENS. (5th S., vol. iii., pp. 346, 474.) May I ask whether, in giving the interesting references to the use of steel pens before the time of Priestley (one reference even going so far back as the seventeenth century) your correspondents have carefully considered what is meant by the terms. For my own part (of course I maybe quite wrong) I should naturally have anticipated steel pens in these references to mean not the modern steel nib for ordinary penmanship, but the ancient steel pen for drawing lines or ruling circles, such as is contained in every box of mathematical instruments. This would explain (to some extent) the great price fetched for a good one of Churchill's; a mere old steel nib would scarcely enter into a sale at all. It would explain, too, why a special process of hardening should be applied to a quill, in order to make it do duty for the steel instrument. One would scarcely think of hardening a quill in order to enable it to compete with a steel nib in some of the least desirable qualities, though one often wishes one could accomplish the reverse process, and soften or supple a steel 'stick frog,' so as to give it the elasticity of the grey goose quill. “—V. H. I. L. L. C. IV. (iv., 37, 5th S., London Notes and Queries.)
“STEEL PENS. (5th S., vol. iii., pp. 346, 474.) May I inquire whether, in providing the fascinating references to the use of steel pens before Priestley's time (with one reference dating back to the seventeenth century), your correspondents have carefully thought about the definitions of the terms? Personally, I (of course, I might be completely wrong) would naturally assume that steel pens in these references refer not to the modern steel nib used for regular writing, but to the old steel pen used for drawing lines or ruling circles, similar to those found in every box of mathematical tools. This would help clarify (to some degree) the high price that a good one of Churchill's could fetch; a simple old steel nib would hardly be valued in a sale at all. It would also explain why a special hardening process is applied to a quill to enable it to function similarly to the steel instrument. One would hardly consider hardening a quill to allow it to compete with a steel nib in some of its least desirable qualities, although one often wishes to turn that process around and soften or make a steel 'stick frog' more flexible, like a grey goose quill.” —V. H. I. L. L. C. IV. (iv., 37, 5th S., London Notes and Queries.)
Mr. R. Prosser, author of “Birmingham Inventors and Inventions,” in writing to the compiler of this work, says:
Mr. R. Prosser, author of “Birmingham Inventors and Inventions,” in writing to the compiler of this work, says:
“It has often occurred to me that some of the very early references to metallic pens may perhaps mean the draughtsman's 'ruling pen,' and not an instrument made after the fashion of a quill pen with a slit in it. That it is possible to write with such an instrument this paragraph will show, but I must admit that it is not equal to one of Perry's J's.”
“I've often thought that some of the earliest mentions of metallic pens might actually refer to the draughtsman's 'ruling pen,' rather than a tool designed like a quill pen with a slit. This paragraph will demonstrate that it's possible to write with such a tool, but I have to admit it's not as good as one of Perry's J's.”
From an entry in “Pepys' Diary,” October 24, 1660, drawing pens appear to have been in use in London, at the time of the Restoration:
From an entry in “Pepys' Diary,” October 24, 1660, drawing pens seem to have been used in London during the Restoration:
“To Mr. Lilly's, where, not finding Mr. Spong, I went to Mr. Greatorex, where I met him, and where I bought a drawing pen.”
“I went to Mr. Lilly's, but since I couldn't find Mr. Spong, I went to see Mr. Greatorex, where I met him and bought a drawing pen.”
In London Notes and Queries (4th S., xi., 440), the Rev. E. Smedley, editor of the Encyclopoedia Metropolitana, writing to his friend, Mr. H. Hawkins, April 10, 1833, says:
In London Notes and Queries (4th S., xi., 440), Rev. E. Smedley, editor of the Encyclopaedia Metropolitana, wrote to his friend, Mr. H. Hawkins, on April 10, 1833, saying:
“The process of nibbing and shaving is one which I always abominated, and for years past I have taken refuge under the Perryian pens. The one with which I now write has been in use daily, and all day long, for more than a fortnight, and I consider that it still owes me quite as much worth as it has already furnished. Every packet contains nine pens, and on an average two out of that number fail to suit my hand, but the remaining seven are faithful servants, and their price is 2s.”
“I've always hated the process of nibbing and shaving, and for years, I've relied on the Perryian pens. The one I'm using to write this has been in daily use for over two weeks, and I think it still owes me as much value as I've gotten from it so far. Each pack contains nine pens, and on average, two of them don't suit me, but the other seven are reliable, and they cost 2s.”
In London Notes and Queries (4th S., xii., 57) a writer says:
In London Notes and Queries (4th S., xii., 57) a writer states:
“I bought my first steel pen from Bramah, Piccadilly, in 1825. The price was 1s. 6d. It was very thick and hard, with very little elasticity. In 1829 I read advertised in the Times, steel pens, with holder, 3s. per dozen, at Kendal's, in Holborn. They were hand made, and much easier to write with than Bramah's. Soon after the price fell, and steel pens became common.”
“I bought my first steel pen from Bramah in Piccadilly in 1825. It cost 1 shilling and 6 pence. It was very thick and hard, with hardly any flexibility. In 1829, I saw an ad in the Times for steel pens with a holder for 3 shillings per dozen, available at Kendal's in Holborn. They were handmade and much easier to write with than Bramah's. Shortly after, the price dropped, and steel pens became widely available.”
In London Notes and Queries (4th S., x., 309), October 19, 1872, Mr. William Bates, speaking of a visit he paid to an old lady, at Studley (Worcestershire) about 1825, says that he saw an exquisitely-finished inkstand of pure gold, the gift of one of the Earls of Plymouth to her father, 100 years before. The inkstand was provided with a jointed gold penholder, terminating in a barrel (one slit) pen, resembling the metallic pen of the present day, except that he found that it would not write.
In London Notes and Queries (4th S., x., 309), October 19, 1872, Mr. William Bates mentions a visit he made to an elderly woman in Studley (Worcestershire) around 1825. He describes seeing a beautifully crafted inkstand made of pure gold, which was a gift from one of the Earls of Plymouth to her father, 100 years earlier. The inkstand came with a jointed gold penholder that ended in a barrel (one slit) pen, similar to today’s metallic pens, but he found that it wouldn’t write.
In “Local Notes and Queries,” published in the Birmingham Journal and Weekly Post, there have appeared a number of contributions relating to the early manufacture of steel pens. We reproduce them here. A correspondent writing on June 22, 1869, says: “Daniel Fellows, of Sedgley, made steel pens about 1800.”
In “Local Notes and Queries,” published in the Birmingham Journal and Weekly Post, several contributions have been made about the early production of steel pens. We’ve included them here. A correspondent wrote on June 22, 1869, stating: “Daniel Fellows, from Sedgley, made steel pens around 1800.”
Another writer, on the same date, says, “The first makers of steel pens were John Edwards, Hill Street, and Francis Heeley, Mount Street, Birmingham.”
Another writer, on the same date, says, “The first makers of steel pens were John Edwards, Hill Street, and Francis Heeley, Mount Street, Birmingham.”
Respecting, the former of these, in Wrightson's Birmingham Directory, 1823, the following advertisement appears: “John Edwards, manufacturer of improved gold, silver, and elastic sleel pens, mounted in all kinds of cases, and desk handles, No. 40 Hill Street. N.B.—The pens are warranted to write exceedingly fine and free.”
Respecting the former, in Wrightson's Birmingham Directory, 1823, the following ad appears: “John Edwards, maker of improved gold, silver, and elastic steel pens, available in all types of cases and desk handles, No. 40 Hill Street. Note: The pens are guaranteed to write very fine and smooth.”
This advertisement contained engravings of a barrel and “nibbed” or “slip” pen.
This advertisement featured images of a barrel and a "nibbed" or "slip" pen.
J. Sargent, writing from Tettenhall, June 28, 1869, says:
J. Sargent, writing from Tettenhall, June 28, 1869, says:
“A journeyman blacksmith, named Fellows, of Sedgley, was the first originator of steel pens. I resided at Sedgley in 1822, when Sheldon, Fellows's apprentice, made some of these pens. He made two for me. I wrote very well with them. Sheldon himself told me that Mr. Gillott commenced making the pen from seeing some of his (Sheldon's) make.”
"A journeyman blacksmith named Fellows, from Sedgley, was the first creator of steel pens. I lived in Sedgley in 1822, when Sheldon, Fellows's apprentice, made some of these pens. He made two for me. I wrote very well with them. Sheldon himself told me that Mr. Gillott started making the pen after seeing some of his (Sheldon's) work."
Some one writing under the nom de plume of “Un Qui Sait,” says:
Somebody writing under the pen name of “Un Qui Sait,” says:
“I distinctly recollect, about the year 1806, being at Fellows's home in Sedgley, and there seeing Thomas Sheldon, his apprentice, making steel pens. He knew of an entry in his books of pens bought from Fellows in 1807. He paid Sheldon L.100 in 1822. He believed Fellows made pens in 1793. Beilby and Knott (Birmingham stationers) sold these pens in considerable quantities from 1818 to 1828. Sheldon continued the trade until it was destroyed through inability to compete with the machine-made pens of Mitchell and Gillott.”
“I clearly remember being at Fellows's home in Sedgley around 1806 and seeing Thomas Sheldon, his apprentice, making steel pens. He mentioned an entry in his books about pens purchased from Fellows in 1807. He paid Sheldon £100 in 1822. He believed Fellows started making pens in 1793. Beilby and Knott, stationers from Birmingham, sold these pens in large quantities from 1818 to 1828. Sheldon continued the business until it was wiped out because he couldn't compete with the machine-made pens from Mitchell and Gillott.”
Another writer, “T. S.,” says:
Another writer, “T. S.,” states:
“In 1815, an uncle of mine used to purchase these pens from Sheldon, of Sedgley. The price was eighteen shillings per dozen, ten per cent. for cash. They were barrel shape. B. Smith and Co. had in their pattern book of engravings of steel toys a drawing of one of these pens, which were sold at thirty shillings per dozen; also one in a bone handle, the top of which screwed off, for carrying in the pocket, at thirty-six shillings per dozen.”
“In 1815, my uncle used to buy these pens from Sheldon in Sedgley. The price was eighteen shillings for a dozen, with a ten percent discount for cash. They were barrel-shaped. B. Smith and Co. had a drawing of one of these pens in their steel toy engraving catalog, which was sold for thirty shillings per dozen; they also had one with a bone handle that screwed off for pocket carrying, priced at thirty-six shillings per dozen.”
Another correspondent, writing on July 24, 1869, mentions (on authority of the late Mr. Alderman Yates) that an old man named Spittle made steel pens before any of the present makers.
Another correspondent, writing on July 24, 1869, mentions (on the authority of the late Mr. Alderman Yates) that an old man named Spittle made steel pens before any of the current manufacturers.
In note 319 this man Spittle is mentioned by another writer, who says:
In note 319, another writer mentions this man Spittle, stating:
“A man named Spittle, one of the earliest makers of steel pens, lived in Chequers' Walk, Bath Row, Birmingham. He made steel pens for sale, and charged one shilling each for them. They were made with a tube to fit on a quill. I bought one from him forty-five years ago (1824).”
“A man named Spittle, one of the first producers of steel pens, lived on Chequers' Walk, Bath Row, Birmingham. He sold steel pens for one shilling each. They were designed with a tube that fit onto a quill. I bought one from him forty-five years ago (1824).”
“E.W.,” writing in 1869, says:
"E.W.," writing in 1869, states:
“In 1821 there was a B. Smith, steel toy maker, St. Paul's [Mary's] Square, Birmingham. He had a book of engravings of steel toys, among which were steel pens, made to screw on and off. This pattern book might have been one hundred years old. I sold his pens in 1823.”
“In 1821, there was a B. Smith, a steel toy maker in St. Paul's [Mary's] Square, Birmingham. He had a book of engravings of steel toys, including steel pens that were designed to screw on and off. This pattern book could have been a hundred years old. I sold his pens in 1823.”
The Editor of “Notes and Queries” says “Smith's pattern book was probably fifty years old,” and further remarks that steel pens must have been a regular article of manufacture before they appeared in a steel toy maker's pattern book.
The editor of “Notes and Queries” says, “Smith's pattern book was probably fifty years old,” and also notes that steel pens must have been regularly produced before they showed up in a steel toy maker's pattern book.
“C.J.,” in note 372, says:
“C.J.,” in note 372, says:
“The pattern book of John Barnes, Eagle Works, Wolverhampton, contains engravings of early steel pens.”
“The pattern book of John Barnes, Eagle Works, Wolverhampton, has engravings of early steel pens.”
Mr. Robert Griffin says:
Mr. Robert Griffin says:
“In 1824 I wrote very much with a steel pen made under the direction of James Perry—a pen that lasted about eight or nine weeks, writing eight hours a day.”
"In 1824, I wrote a lot with a steel pen designed by James Perry—a pen that lasted about eight or nine weeks, writing eight hours a day."
In note 344, “Anon” says he remembered his father (who had premises in Water Street, Birmingham), in the summer of 1823, bringing a tall, quiet, respectable man to the manufactory. He had a piece of iron, or steel, which he required to be cut up into strips of about two inches wide. The man said he was going to get the strips rolled to make into steel pens. He gave the writer of the note sixpence and a barrel pen for his trouble. In answer to inquiries the writer put to his father, the latter stated he did not know the man's name nor where he lived, but “that he met with him in a smoke room, where he (the father) sometimes spent his evenings.” The writer further remarks: “Where the man had got his ideas from which induced him to try his hand at making steel pens I do not know, but I have an impression that there were several experimenters in existence at that time; and very soon afterward Mr. William (Joseph) Gillott, with whom my father was on terms of intimacy, came into notice as a maker of steel pens.” This is a very important statement, as it fixes a date respecting pens being made from sheet steel.
In note 344, “Anon” recalls that his father (who had a shop on Water Street, Birmingham) brought a tall, quiet, respectable man to the factory in the summer of 1823. The man had a piece of iron or steel that he needed cut into strips about two inches wide. He mentioned that he planned to roll the strips to create steel pens. He gave the note writer sixpence and a barrel pen as a thank you. When the writer asked his father about the man, his father said he didn't know the man's name or where he lived, but “he met him in a smoke room where he (the father) sometimes spent his evenings.” The writer also notes, “I don't know where the man got the idea to try making steel pens, but I have a feeling there were several people experimenting at that time; and shortly after, Mr. William (Joseph) Gillott, who was friends with my father, gained recognition as a steel pen maker.” This is a significant statement because it establishes a timeline for when pens began to be made from sheet steel.
One of the oldest toolmakers in the trade has informed us that, about the year 1823 or 1824, he was frequently taken by his father to visit an uncle named Clulee, who rented power at the Water Street mill. On these occasions his father and uncle would talk about the visits of Gillott to the latter, and the hopeful manner in which he spoke of the experiments he was then making. Gillott rented power at the Water Street mill, and was engaged in grinding and finishing penknife blades, which were inserted in one end of a silver pencil case, which his relative—Mitchell—was then making.
One of the oldest toolmakers in the business told us that around 1823 or 1824, he often went with his father to visit an uncle named Clulee, who rented power at the Water Street mill. During these visits, his father and uncle would discuss Gillott’s visits to Clulee and the optimistic way Gillott talked about the experiments he was working on at the time. Gillott rented power at the Water Street mill and was focused on grinding and finishing penknife blades, which were placed in one end of a silver pencil case that his relative—Mitchell—was making at that time.
Now, who was this “tall, quiet, respectable man?” It could not have been Gillott, as he was not tall and the father of “Anon” knew him; and Mitchell was also a short man. We have failed to trace him, and his identity is lost among the “sowers” who failed to reap the harvest of their inventions.
Now, who was this “tall, quiet, respectable man?” It couldn’t have been Gillott, since he wasn't tall and the father of “Anon” knew him; and Mitchell was also a short guy. We haven’t been able to identify him, and his identity is lost among the “sowers” who didn’t benefit from their inventions.
Mr. George Wallis, speaking of steel pens, remarks:
Mr. George Wallis, talking about steel pens, says:
“I wrote with one when a boy (1822 to 1826), having found several in a stock of old steel waste in the warehouse of a relative, a retired ornamental steel worker, at Wolverhampton. These pens were made (so I was told) for the London market, late in the last or early in the present century. Certainly they were made fifteen or, perhaps, twenty years, when I found them, as the manufactory in which they had been produced had been closed the former number of years. They consisted of a holder of steel, with flutings and facets. One was solid and tapered to lighten it; the other had a barrel with an internal screw. The pen had two screws; one was used to screw the pen into the barrel for use, and the other to secure it when turned inwards as a protection when not in use, or to carry in the pocket.”
"I used one when I was a boy (1822 to 1826), having discovered several in a stock of old steel scraps in the warehouse of a relative, a retired ornamental steel worker in Wolverhampton. These pens were supposedly made for the London market, either late last century or early this one. They were definitely made fifteen or maybe twenty years before I found them, as the factory where they were produced had been closed for that many years. They featured a steel holder with flutings and facets. One was solid and tapered to make it lighter; the other had a barrel with an internal screw. The pen had two screws: one to screw the pen into the barrel for use, and the other to secure it when turned inwards for protection when not in use or when carrying it in my pocket."
The following letter from Mr. Alderman Manton to Mr. Sam: Timmins makes us acquainted with another manufacturer of steel pens:
The following letter from Mr. Alderman Manton to Mr. Sam Timmins introduces us to another steel pen manufacturer:
“THE METAL PENS OF 1823.—In a badly-constructed and unsanitary manufactory (Mr. James Collins's), at the back of 119 Suffolk Street, (Birm.), I witnessed the process of making silver and steel pens. As both metals were manufactured in the same manner, one description will serve. It will be remembered by a few that at that time there was a patent silver pencil case somewhat extensively manufactured, which in addition to the pencil, had a penknife, pen and toothpick provided. The penknife was supplied by two brothers—Joseph and William Gillott—who at that time rented a small shop in a corner of the yard belonging to the rolling mill of George and P.F. Muntz, Water Street, and from whose engine they obtained the small amount of steam power needed. The process of making the pens was as follows: Two narrow strips were cut from a sheet of silver or steel; they were then, by the help of the hammer and a lead cake, or piece of hard wood, curved. Afterwards the two strips were placed opposite to each other on a well-polished steel wire, and drawn through a draw-plate, the wire and plate being supplied by Wm. Billings, a celebrated tool manufacturer, occupying premises near the top of Snow Hill (Birm.). By the aid of a press, a small hole was made at a distance of half an inch or five-eighths from the end, the slit was then made by a fine saw made of watch springs. A bent pair of shears was used for cutting the end of strip into the shape of a pen; and a half-round file or smooth was used for finishing the pen. The pen was then sawn off the strip by the same saw which was used for slitting the pen. The only hardening process was the friction of the draw-plate and steel wire. I not only witnessed the process, but was a manipulator. The cost of making at that time, by a journeyman, was 2d. each; by an apprentice, about one-third of that amount. Within less than thirty years of that time, in a manufactory adjoining my own, pens were made and sold (wholesale) at 2d. per gross, and a box containing them into the bargain.” (Signed) Henry Manton, September 15, 1886.
“THE METAL PENS OF 1823.—In a poorly built and unsanitary factory (Mr. James Collins's), located behind 119 Suffolk Street, (Birm.), I observed how silver and steel pens were made. Since both metals were produced in the same way, one description will suffice. A few may remember that at that time there was a patented silver pencil case that was quite popular, which included not only a pencil but also a penknife, pen, and toothpick. The penknife was provided by two brothers—Joseph and William Gillott—who at that time rented a small shop in a corner of the yard belonging to the rolling mill of George and P.F. Muntz on Water Street. They obtained the small amount of steam power necessary from their engine. The pen-making process was as follows: Two narrow strips were cut from a sheet of silver or steel; then, using a hammer and a lead cake or a piece of hard wood, they were curved. After that, the two strips were positioned opposite each other on a well-polished steel wire and pulled through a draw-plate, the wire and plate supplied by Wm. Billings, a renowned tool manufacturer located near the top of Snow Hill (Birm.). A press was used to make a small hole about half an inch or five-eighths from the end, and a fine saw made from watch springs was used for making the slit. Bent shears were used to cut the end of the strip into the shape of a pen, and a half-round file or smooth file was used for finishing. The pen was then cut off the strip with the same saw used for slitting. The only hardening process was the friction from the draw-plate and steel wire. I not only watched the process but also participated in it. At that time, the cost of making a pen by a journeyman was 2d. each; for an apprentice, it was about one-third of that amount. Less than thirty years later, in a factory next to mine, pens were made and sold (wholesale) for 2d. per gross, with a box of them included in the deal.” (Signed) Henry Manton, September 15, 1886.
Mr. T. Vary writes that James Perry began making steel pens in Manchester, and quotes the Saturday Magazine to show that metallic pens were given by him as rewards of merit in schools as far back as 1819.
Mr. T. Vary writes that James Perry started producing steel pens in Manchester and cites the Saturday Magazine to demonstrate that he had been giving metallic pens as rewards for achievement in schools since 1819.
Mr. James Cocker, writing in the Sheffield Daily Telegraph, in 1869, says: “That he rolled steel wire for James Perry for penmaking in 1829.”
Mr. James Cocker, writing in the Sheffield Daily Telegraph, in 1869, says: “He rolled steel wire for James Perry for making pens in 1829.”
The death of Mr. Gillott seems to have revived the discussion of the origin of steel pens, and a correspondent in the Sheffield Daily Telegraph, in the issue of January 11, 1872, in the following letter, puts forth a claim on behalf of a Sheffield man:
The death of Mr. Gillott seems to have sparked a renewed debate about the creation of steel pens, and a writer in the Sheffield Daily Telegraph, in the edition from January 11, 1872, presents a claim on behalf of a Sheffield resident:
“The well-written and well-merited memoir of the late Mr. Gillott, the Birmingham steel pen maker, which has just appeared in the newspapers, affords a curious and instructive illustration of the success which not seldom attends the combined action of ingenuity, industry, shrewdness, and integrity among our labouring classes. Born in the humblest rank of our local workmen, a steady scholar in our Boys' Lancasterian School, and apprenticed to a scissors grinder, the deceased worked his way upwards into a position of influence and opulence as a manufacturer, which entitled him to take social rank with the merchant princes of the land. And if his name has long since ceased to be familiar among his once contemporary workmen in Sheffield, and is not even mentioned in the Directory, it has for several years past been recognized and respected by the visitors at the annual exhibitions of our School of Art, in connection with the many rare and valuable pictures lent by him on those occasions. The printed fac-simile of the autograph appeared in the 'advertising columns' of almost every newspaper in the world, and perhaps, as an expert might have said, was characteristic. In the admirable account of his life above referred to stress is laid upon one prominent and praiseworthy feature of his character, viz., his readiness to acknowledge the obscurity of his origin and the steps of his industrial success. In those details no mention is made of his Sheffield master and predecessor in the ingenious art of steel pen making. And as the notice alluded to is without dates, it is difficult to furnish information on the material point of priority, though the fact of supremacy in the trade is clear enough. In one of the columns of Lardner's Cyclopedia, published in 1833, the names of Perry, Heeley, and Skinner are mentioned as steel pen makers. With the latter, who if he did not make wealth, certainly earned a wide reputation for the low price and excellent temper of his 'steel nibs,' Mr. Gillett was a workman, in Nursery Street, Sheffield, having gone with his master from the scissors grinding stone to the making of polished steel ornaments for ladies' work, then fashionable. How much, in what way, or whether at all, he was indebted to his experience in Mr. Skinner's establishment may be questionable, but that he learnt and first saw practised in Sheffield the art that ultimately enriched him in Birmingham, he would probably be the last to deny. It is well remembered by a worthy dealer in almost every useful article, from a mouse-trap to a railroad wagon, that Gillott, soon after his establishment in Birmingham, came into our townsman's shop, and seeing on the counter a model steam engine of half-horse power, at once purchased and carried it off to give motion to some part of his pen machinery. Brass pens were made in Sheffield before the close of the last century. They mostly accompanied an 'inkpot,' called from its users an 'exciseman.' The writer of this paragraph himself made hundreds of dozens of them, which, however, be never used, nor steel ones either, as long as he could get a 'goose quill,' good, bad or indifferent. The matter of slitting the nib was kept secret by Skinner, and the double slit of Gillott more than doubled the value of his old master's invention; but a 'four-slit' pen, i.e., with five points, if possible to make, would be useless. The earliest experimenter in form and material was Perry, flexibility being the great desideratum; but it is curious to see how world-wide a currency Gillott's name and trade have given to the simplest shape; and still more curious to note how the makers of writing ink and paper have conformed these articles to the requirements of the uses of the steel pen. It is always gratifying, and not unprofitable, to contrast the small and feeble beginnings of any manufacturing enterprise with a large and well-merited success.”
“The recently published memoir of the late Mr. Gillott, the steel pen maker from Birmingham, offers an interesting and educational example of how a mix of creativity, hard work, cleverness, and honesty can lead to success among our working-class individuals. Starting from the most modest background, he was a diligent student at our Boys' Lancasterian School and trained as a scissors grinder. Over time, he rose to a position of influence and wealth as a manufacturer, earning him social status comparable to the merchant princes of the country. Although his name may not be widely recognized by the workmen in Sheffield anymore and isn’t listed in the Directory, it has been acknowledged and respected by visitors at our School of Art’s annual exhibitions for years, primarily due to the many rare and valuable artworks he lent during those events. The printed fac-simile of his autograph has appeared in the ‘advertising columns’ of nearly every newspaper globally, and perhaps, as an expert might have noted, it was quite distinctive. The remarkable account of his life emphasizes a significant and commendable aspect of his character: his willingness to acknowledge his humble beginnings and the path of his industrial success. However, the details provided do not mention his Sheffield master or predecessor in the innovative field of steel pen making. Because the notice lacks dates, it is hard to provide information about the crucial issue of priority, though his dominance in the industry is clear. In a column of Lardner's Cyclopedia published in 1833, the names Perry, Heeley, and Skinner are noted as steel pen makers. Mr. Gillott worked with Mr. Skinner, who, even if he didn’t amass wealth, certainly gained widespread recognition for his affordable and well-tempered 'steel nibs.' They collaborated in Nursery Street, Sheffield, having transitioned from scissors grinding to crafting polished steel ornaments, which were fashionable at the time. Whether or not he benefited from his time in Mr. Skinner's shop is uncertain, but it’s likely he would acknowledge that he learned the essential skills that later made him prosperous in Birmingham during his time in Sheffield. A respected merchant who sold everything from mouse traps to railroad cars recalls that shortly after establishing his business in Birmingham, Gillott visited his shop, saw a half-horsepower model steam engine on the counter, and immediately bought it to power some part of his pen machinery. Brass pens were manufactured in Sheffield before the end of the last century, typically sold with an ‘inkpot’ known as an ‘exciseman’ due to its users. The author of this paragraph personally made hundreds of dozens of them, but he never used them or steel pens as long as he could find a 'goose quill', regardless of its quality. The method for slitting the nib was a secret held by Skinner, and Gillott’s double slit design significantly increased the value of his former master's invention, although a ‘four-slit’ pen, meaning one with five points, would be impractical if it could be made. Perry was the earliest experimenter in form and material, with flexibility being the primary goal; however, it’s interesting to see how widely Gillott’s name and trade have popularized the simplest pen design. It’s even more fascinating to observe how ink and paper manufacturers have adapted their products to meet the needs of the steel pen. It’s always satisfying and beneficial to compare the small and humble beginnings of any manufacturing venture with its substantial and well-deserved success.”
This communication appears to have caused a Mr. William Levesley to call upon the writer of the preceding epistle, and the following which appeared in the Sheffield Daily Telegraph, January 30, 1872, was written:
This message seems to have prompted Mr. William Levesley to reach out to the author of the previous letter, and the next one, which was published in the Sheffield Daily Telegraph, on January 30, 1872, was written:
“I have to thank you for the insertion of my queries as to the early connection of Sheffield with steel pen making. In consequence of the appearance of my letter in the Telegraph, a cutlery manufacturer of the name of William Levesley, called upon me, and informed me that he was not only an early associate with the late Mr. Gillott, of Birmingham, but the first person who made a steel pen out of London. Stress has been laid upon Gillott's ability 'to forge and grind a knifeblade.' It is not likely he ever used the hammer on hot steel, but he was when young, and working with father, accounted an excellent penknife grinder; Skinner being a scissors grinder, and Levesley a workboard hand for the same master. A man of the name of Mitchell having married Gillott's mother, went to Birmingham, and began the cutlery business, the latter removing thither to grind for his father- in-law. His brother had also gone thither, and commenced making an article that had some run, and may be said to have united the ingenious handicrafts of Birmingham, viz., the insertion of a penknife blade at the end of a silver pencil case. Meanwhile, about the year 1825, Levesley saw a steel pen, made by Perry, of London, in Ridge's shop window, in High Street. He bought it for one shilling, and immediately set about making tools to imitate and improve upon it. He spent, he said, L.30 in not unsuccessful, though unremunerative, experiments. The flypress was at least as well known in Sheffield as in Birmingham, and its power was at once brought into requisition to work the tools for shaping, bending, and slitting the pens which were made out of sheet steel, Perry's being made out of thick wire, rolled flat, by Cocker, in Nursery Street. In 1829, Levesley was making pens for sale, and that year is said to be the earliest date of actual sales in Skinner's ledger. In 1831 he was doing a considerable business in Sheffield, and making experiments upon the article, as appears from specimens before me bearing his name. Stress has been laid upon the improvement of the double slit, introduced by Gillott, but if Levesley's statement is to be taken literally, he was the inventor of a specialty upon which, even more than on excellence of material, the merit of a steel pen is found to depend, viz., the grinding of a small hollow at the back of the nib, and about the eighth of an inch from the point. My informant described not only the beneficial action of this thinning of the metal, as well in yielding the gradual flow of the ink as in flexibility of writing, but the pleasure with which he took a specimen to Birmingham to show Gillott, and the surprise of the latter at so great and so beneficial an effect, provided by so small a cause. He at once adopted an improvement of which every pen made by him bears evidence; and when his friend visited him he told him he had fifty women employed in grinding pen points. It is pleasant to add that Gillott never visited Sheffield without calling to see his old friend Levesley, while the latter spoke of his early and later life with respect and commendation, especially in his domestic relations. It is pleasing to review a life of such humble beginnings, culminating in opulence and usefulness like that of the late Joseph Gillott, of Birmingham; nor is it less to name in connection therewith, as an early experimenter in steel pen making, our worthy townsman, William Levesley, to whose ingenious improvement every writer is so much indebted, and of whose verbal communication to me the foregoing is an imperfect sketch.”
“I want to thank you for including my questions about the early connection of Sheffield with steel pen making. After my letter was published in the Telegraph, a cutlery manufacturer named William Levesley came to see me. He informed me that he was not only an early associate of the late Mr. Gillott from Birmingham but also the first person to make a steel pen outside of London. People have emphasized Gillott's ability 'to forge and grind a knifeblade.' It’s unlikely he ever used a hammer on hot steel, but when he was young and working with his father, he was considered an excellent penknife grinder; Skinner was a scissor grinder, and Levesley worked on the workboard for the same employer. A man named Mitchell, who married Gillott's mother, moved to Birmingham and started the cutlery business, with Gillott moving there to grind for his father-in-law. His brother had also gone there and started making a product that gained some popularity, effectively combining the ingenious crafts of Birmingham, specifically the addition of a penknife blade at the end of a silver pencil case. Around 1825, Levesley saw a steel pen made by Perry from London displayed in Ridge's shop window on High Street. He bought it for a shilling and immediately started making tools to replicate and improve it. He claimed to have spent £30 on somewhat successful, though unprofitable, experiments. The fly press was as well-known in Sheffield as in Birmingham, and its power was quickly used to shape, bend, and slit the pens made from sheet steel, while Perry’s pens were made from thick wire that was rolled flat by Cocker in Nursery Street. By 1829, Levesley was making pens for sale, and that year is considered the earliest date of actual sales recorded in Skinner's ledger. In 1831, he was running a significant business in Sheffield and experimenting with his product, as shown by specimens in front of me that bear his name. People have focused on the improvement of the double slit, which Gillott introduced, but if Levesley’s statement is taken literally, he was the inventor of a particular feature upon which the effectiveness of a steel pen relies, namely, the grinding of a small hollow at the back of the nib, about an eighth of an inch from the point. My informant described not just the beneficial effect of this thinning of the metal in allowing for gradual ink flow and improved writing flexibility, but also the pleasure he felt when he took a sample to Birmingham to show Gillott, who was surprised by such a significant and beneficial effect resulting from such a small change. Gillott quickly adopted this improvement, which can be seen in every pen he made, and when his friend visited him, he mentioned having fifty women employed in grinding pen points. It's nice to add that Gillott never visited Sheffield without stopping by to see his old friend Levesley, who spoke highly of both his early and later life, particularly in his family life. It’s gratifying to look back on a life that started from such humble beginnings and ended in wealth and usefulness, like that of the late Joseph Gillott from Birmingham; it’s also worth mentioning our worthy townsman William Levesley as an early pioneer in steel pen making, to whose clever improvements every writer owes a great deal, and what I’ve shared here is an incomplete account of our conversation.”
Now, in this statement, there are some dales given, but others are omitted, and that is a very unfortunate circumstance. Levesley told the writer of the article in the Sheffield Daily Telegraph that he made use of the fly press for working tools for shaping, bending, and slitting pens. If the writer had only given the date of this it would have been a valuable contribution toward a history of the invention. The claim of Levesley to having invented the process of grinding pens and teaching Gillott seems, to say the least, curious, because the latter was a Sheffield grinder, and the idea would certainly be quite as likely to occur to Gillott as Levesley. Besides, why did Levesley communicate the idea to Gillott in preference to Skinner, with whom he had business relations? The statement that Gillott had fifty girls employed when Levesley* called upon him on his next visit to Birmingham looks like a mistake. Fifty girls would grind on an average seven thousand gross of pens in a week, and as this correspondence appears to refer to the early part of Gillott's career, it is scarcely possible that such a number of pens were produced weekly at that period. Besides, as a matter of fact, boys were, in the first instance, employed to grind pens.
Now, in this statement, some details are included, but others are left out, which is a real shame. Levesley told the writer for the Sheffield Daily Telegraph that he used the fly press to work on tools for shaping, bending, and slitting pens. If the writer had provided the date for this, it would have been a valuable addition to the history of the invention. Levesley's claim to have invented the grinding process for pens and to have taught Gillott is, at best, questionable, since Gillott was a Sheffield grinder, and the idea could easily have occurred to him as well. Plus, why did Levesley share the idea with Gillott instead of Skinner, who he had business ties with? The claim that Gillott had fifty girls working for him when Levesley visited on his next trip to Birmingham seems incorrect. Fifty girls would grind around seven thousand gross of pens in a week, and since this corresponds to the early days of Gillott's career, it's highly unlikely that such a volume of pens was produced weekly back then. Additionally, boys were initially employed to grind pens.
* Mr. Sam: Timmins says, “that Levesley told him that Gillott started in Birmingham as a jobbing cutler; that Mitchell had the secret of pen making; that Mitchell sent for Gillott to come to Birmingham, and that he (J.G.) first lived at the top of Water Street; that Gillott began to make pens in Bread Street; that Perry made pens from flattened steel wire, the breadth of the pen (the steel was 3s. 6d. per lb., and drawn at Old Ford); that he had seen cross grinding (at Gillott's) in Newhall Street, and fifty women at work; and that pens had double slits and cut holes. Levesley certainly knew all the Gillott family, personally, in Sheffield, and he (S. T.) had a long interview with him shortly before his death, when he mentioned all the facts given here.”
* Mr. Sam: Timmins states, “that Levesley told him that Gillott started in Birmingham as a jobbing cutler; that Mitchell had the secret to making pens; that Mitchell called for Gillott to come to Birmingham, and that he (J.G.) initially lived at the top of Water Street; that Gillott began making pens on Bread Street; that Perry made pens from flattened steel wire, the width of the pen (the steel cost 3s. 6d. per lb. and was drawn at Old Ford); that he had seen cross grinding (at Gillott's) in Newhall Street, with fifty women working; and that pens had double slits and cut holes. Levesley certainly knew all the Gillott family personally in Sheffield, and he (S. T.) had a long conversation with him shortly before his death, when he mentioned all the facts given here.”
Herr Ignaz Nagel, in his “Report on Writing, Drawing, and Painters' Requisites,” at the Vienna Exhibition, 1873, says:
Herr Ignaz Nagel, in his “Report on Writing, Drawing, and Painters' Requisites,” at the Vienna Exhibition, 1873, says:
“From careful inquiries that we made in Birmingham, we learned that a knife cutler, of Sheffield, was the first man who had the idea of making pens of steel, and that a tinman of the name of Skipper [Skinner], of Sheffield, afterwards manufactured the pens in great quantities. His son developed the idea still further. This, according to our informant, was fifty years ago. A steel pen artisan, working in Birmingham, remembers perfectly well reading the announcement in a window of the High Street, in Sheffield, 1816: 'Steel pens are repaired here at sixpence apiece.' There was a man named Spittle, in Birmingham, who used to make steel pens by hand. He was succeeded by the brothers John and William Mitchell, who were manufacturers of steel pens, wholesale and by machinery, about forty- five years ago. Perry came afterwards, and took out a patent for the first steel pens, and after him Gillott, who had learnt the business with the Mitchells.”
“From our careful inquiries in Birmingham, we found out that a knife maker from Sheffield was the first person to come up with the idea of making steel pens. Later, a tinman named Skipper [Skinner] from Sheffield started producing these pens in large quantities. His son further developed the concept. According to our source, this was about fifty years ago. A steel pen craftsman working in Birmingham clearly remembers seeing an announcement in a window on High Street in Sheffield in 1816 that said: 'Steel pens are repaired here for sixpence each.' There was a man named Spittle in Birmingham who made steel pens by hand. He was followed by the brothers John and William Mitchell, who were steel pen manufacturers using wholesale and machinery methods about forty-five years ago. Perry came next and secured a patent for the first steel pens, followed by Gillott, who learned the trade with the Mitchells.”
A writer in Herbert's Encyclopoedia published in 1837, says
A writer in Herbert's Encyclopedia published in 1837, says
“The first decided attempt to introduce metallic pens to general use was made by Mr. Wise, whose perpetual pens will doubtless be remembered by many of our readers. The name of Wise was rendered conspicuous in most of our stationers' shops some twenty-five or thirty years since, as the original inventor and general manufacturer of the steel pens.”
“The first determined effort to introduce metal pens for widespread use was made by Mr. Wise, whose everlasting pens will surely be remembered by many of our readers. Wise's name became well-known in most stationery stores about twenty-five or thirty years ago, as he was the original inventor and main manufacturer of steel pens.”
We stated at the beginning of this article that of three men— Mitchell, Gillott, and Mason—who might have done something toward fixing the date of the invention of manufacturing pens by the adaptation of tools worked by the screw press, only one—Mason—made a statement:
We mentioned at the start of this article that of the three men—Mitchell, Gillott, and Mason—who could have contributed to determining the date of the invention of making pens by adapting tools operated by the screw press, only one—Mason—made a statement:
“The first making of steel pens that I know of was about the year 1780, by my late friend Mr. Harrison, for Dr. Priestley. He took sheet steel, made a tube of it, and the part joined formed the slit of the pen. He then filed away the barrel and formed the pen. I found some of the identical pens amongst other articles and used them for a long time.
“The second mode of making pens was by punching a rough blank out of thin sheet steel. This blank formed the well-known barrel pen. It was brought into the barrel shape by rounding, but before rounding it had to be filed into a better form about the nib, and when rounded in the soft state, a sharp chisel was used to mark the inside of the pen which became the slit, after hardening. Before tempering, this mark was 'tabbered' with a small hammer, and it would crack where the inside mark was made. Then it was tempered and underwent grinding, and shaping the nib until a point suitable for fine or broad, as required.
“I made barrel pens in 1828, and 'slip' pens for Perry in 1829, and the first lot of 100 at one time was sent November 20, 1830. Frequently, lots of 20 or 30 gross were sent between 1829 and 1830, and in 1831 I sent pens to Perry amounting to L.1421, 1s. 3d.
“Perry certainly never made a pen as they are now made, viz., the slit cut with press tools; all he made were cracked slit.
“I made steel barrel pens some time before I made 'slip' pens for Perry.
“It is doubtful when metal pens were made. The first I know of were made by Mr. Harrison, for Dr. Priestley. Perry was certainly not the first maker of steel pens, but I have no doubt that he was the first steel slip pen maker, and no doubt the first to use a goose quill for a pen holder, hence the slip pen.
“The first stick pen holders I made for Perry in 1832, and for Gillott in 1835, and sold sticks to Gillott in 1840—L.293 18s. 7d.”
“The first known creation of steel pens was around 1780, by my late friend Mr. Harrison, for Dr. Priestley. He took a sheet of steel and made a tube out of it, and the part that connected formed the slit of the pen. He then filed down the barrel and shaped the pen. I found some of those original pens among other items and used them for a long time.
“The second way of making pens involved punching a rough blank out of a thin sheet of steel. This blank became the classic barrel pen. It was shaped into a barrel by rounding, but before rounding, it had to be filed into a better shape around the nib. Once rounded in its soft state, a sharp chisel was used to mark the inside of the pen, creating the slit after hardening. Before tempering, this mark was 'tabbered' with a small hammer, which caused it to crack at the point of the inside mark. Then it was tempered and went through grinding and shaping the nib until it reached a point suitable for fine or broad writing, as needed.
“I made barrel pens in 1828 and 'slip' pens for Perry in 1829, with the first batch of 100 sent out all at once on November 20, 1830. Often, batches of 20 or 30 gross were sent between 1829 and 1830, and in 1831, I sent pens to Perry totaling L.1421, 1s. 3d.
“Perry definitely never made a pen as they are made today, meaning the slit cut with press tools; all he made were cracked slits.
“I produced steel barrel pens long before I made 'slip' pens for Perry.
“It’s unclear when metal pens first appeared. The first ones I’m aware of were made by Mr. Harrison for Dr. Priestley. Perry was certainly not the first maker of steel pens, but I have no doubt he was the first maker of steel slip pens, and probably the first to use a goose quill for a pen holder, hence the slip pen.
“The first stick pen holders I made for Perry in 1832, and for Gillott in 1835, and I sold sticks to Gillott in 1840 for L.293 18s. 7d.”
Mason claimed to have made barrel pens for Perry, of London, in 1828, and “slip or nibbed” pens in 1829; but he does not appear to have made any claim to priority of invention over Mitchell and Gillott.
Mason said he made barrel pens for Perry, from London, in 1828, and “slip or nibbed” pens in 1829; however, he doesn't seem to have claimed to have invented them before Mitchell and Gillott.
Now, although Mitchell made no claim himself, on the death of Mr. Gillott the following letter appeared in the Daily Post:
Now, even though Mitchell didn’t make any claims himself, the following letter showed up in the Daily Post:
“The remarks which have appeared in a local paper upon the death of Mr. J. Gillott, that the steel pen owes its existence to him, and that the adaptation of machinery to the manufacture of metallic pens was his invention, lead the public to wrong conclusions. It is due to the memory of my late father—John Mitchell—that I should state that he not only made steel pens, but used machinery in their production, for some time before Mr. Gillott commenced in that branch of business.”— HENRY MITCHELL, January 12, 1872.
"The comments that appeared in a local newspaper about the death of Mr. J. Gillott, claiming that he was the one who invented the steel pen and that he adapted machinery for making metallic pens, are misleading the public. I feel it's important to clarify, in memory of my late father—John Mitchell—that he not only produced steel pens, but also utilized machinery in their manufacturing long before Mr. Gillott started in that field." — HENRY MITCHELL, January 12, 1872.
In October, 1876, Mr. Henry Mitchell writes to Aris's Gazette, and says:
In October 1876, Mr. Henry Mitchell writes to Aris's Gazette and says:
“You review, in your impression of the 23d inst., a work entitled 'British Manufacturing Industries—the Birmingham Trades,' in which the history of steel pens forms a prominent chapter. I beg to point out that my late father's name—John Mitchell—is certainly mentioned in a list of the manufacturers of the article, and, to my great surprise, simply so. In a part of the work the author states that 'The early history of steel pens is involved in obscurity.' My object in writing to you is to remove that obscurity, as I am satisfied you will be equally desirous of giving honor to whom honor is due. I claim that honor for my late father—John Mitchell—who was the first to introduce the making of steel pens by means of tools, which were purely his own invention, and I will leave it to an enlightened public to judge if it is not one of the greatest benefits conferred on any civilized community. Whatever others may have done does not remove the fact that the inventor I have named was my father; and it is only due to him that posterity should know who originated the means whereby millions of human beings of the present time, and generations yet unborn are, and will be, enabled to communicate their thoughts to each other with a facility they otherwise would not have had. For, unless the steel pen had been manufactured by tools and machinery, that useful article would virtually be at a prohibitory price. The date of the invention I believe to be 1822 or thereabouts.”
"In your review from the 23rd of this month, you discuss a work titled 'British Manufacturing Industries—the Birmingham Trades,' which features a significant chapter on the history of steel pens. I would like to point out that my late father's name—John Mitchell—is listed among the manufacturers of this product, and I was quite surprised to see it mentioned only in passing. The author notes that 'The early history of steel pens is shrouded in obscurity.' I am reaching out to you to clarify that obscurity because I believe you share the desire to give credit where it is due. I assert that credit goes to my late father—John Mitchell—who was the first to develop the process of making steel pens with tools entirely of his own invention. I leave it to an informed public to decide whether this invention is not one of the greatest contributions to any civilized society. Regardless of what others may have achieved, the fact remains that the inventor I named was my father; it is only right that future generations know who created the means for millions of people today, and for those yet to come, to express their thoughts to one another with a convenience they otherwise wouldn’t have. Without the development of steel pens through tools and machinery, this useful item would essentially have a price beyond reach. I believe the date of this invention was around 1822.”
This is very emphatic; but how far may it be taken as an unprejudiced statement of facts? Well, it has never been contradicted; and Gillott never made a claim on his own behalf, as having made pens before Mitchell. Mason gave the year 1828 as the date when he commenced making pens, so that the evidence is in favor of Mitchell.
This is quite strong; but how much can it be considered an unbiased account of the facts? Well, it has never been challenged; and Gillott never claimed he made pens before Mitchell. Mason stated that he started making pens in 1828, which means the evidence supports Mitchell.
We have heard this statement of Henry Mitchell confirmed by a man who worked for Mitchell, as a boy, and who remembered pens being made for Sheldon by Mitchell. It is probable at this early period the pens were made for a few dealers, and the general public was unacquainted with the names of the manufacturers. This circumstance has no doubt contributed to involve in obscurity the early operations of Mitchell and Gillott. In a notice in Lardner's Cyclopoedia (written by Mr. John Holland, of Sheffield), published in 1833, the names of three penmakers only are given—Perry, Heeley, and Skinner. From this it might be supposed that there were no other penmakers at this date; but Gillott had taken out a patent in 1831, and the names of both Mitchell and Gillott appeared as penmakers in Wrightson's Birmingham Directory for 1830. It cannot be supposed that Mr. Holland wilfully omitted to mention the names of Mitchell and Gillott, for this writer was an impartial and painstaking collector of facts, but it is probable the notice was written some time before it was published; and, like many little masters, Mitchell and Gillot were only known as penmakers to the wholesale dealers in Birmingham, upon whom they depended for orders, consequently Mr. Holland would be ignorant of their existence.
We have heard this statement from Henry Mitchell confirmed by a man who worked for Mitchell as a boy and who remembered Mitchell making pens for Sheldon. It's likely that at this early stage, the pens were made for just a few dealers, and the public didn't know the names of the manufacturers. This situation has probably contributed to the obscurity surrounding the early activities of Mitchell and Gillott. In a notice in Lardner's Cyclopoedia (written by Mr. John Holland of Sheffield), published in 1833, only three penmakers are mentioned—Perry, Heeley, and Skinner. From this, it might seem that there were no other penmakers at that time; however, Gillott had secured a patent in 1831, and both Mitchell and Gillott were listed as penmakers in Wrightson's Birmingham Directory for 1830. It can't be assumed that Mr. Holland intentionally left out Mitchell and Gillott’s names, as he was an unbiased and diligent collector of facts, but it's possible the notice was written some time before it was published; and like many small manufacturers, Mitchell and Gillott were only known as penmakers to the wholesale dealers in Birmingham, who they relied on for orders, which is why Mr. Holland might not have been aware of them.
In speaking of the demand for steel pens, the writer in Lardner's says: “The rage originated chiefly, if not altogether, in the successful speculations of Mr. James Perry, of London, whose pens, however short their merits may fall of the praise of the inventor, are certainly superior to most others composed of a like material. Perry began to make steel pens, in Manchester, in 1819, and in London in 1824.” The press and tools with which these pens were made are still in the possession of Perry and Co., at their warehouse in the Holburn Viaduct. This fact tends to confirm the statement that Mr. James Perry was one of the earliest experimenters in the manufacture of the article. Levesley says he bought one of Perry's pens, which he saw in a shop window in Sheffield, in 1825, and he took it to his workshop and improved upon it. This is somewhat similar to the account given by Mason of his first experiment in pen making. Mason saw a pen of Perry's in the window of a bookseller named Peart, in Bull Street, Birmingham, in 1828, which he purchased and took home. Finding he could produce a better article, which could be sold at a cheaper rate, he made some and sent them to Mr. James Perry, in, London, and that gentleman shortly after waited upon Josiah Mason, at his place of business in Lancaster Street, and the interview resulted in Mason beginning to make pens for Perry. It will be remembered that the writer in the Sheffield Daily Telegraph stated that the earliest experimenter in form and material was Perry.
In discussing the demand for steel pens, the writer in Lardner's says: “The craze started mainly, if not entirely, because of the successful business of Mr. James Perry in London. His pens, regardless of how they compare to the inventor's praise, are definitely better than most others made with similar materials. Perry began making steel pens in Manchester in 1819 and in London in 1824.” The press and tools used to make these pens are still owned by Perry and Co. at their warehouse in Holburn Viaduct. This supports the claim that Mr. James Perry was one of the first to experiment with manufacturing this product. Levesley mentions that he bought one of Perry's pens, which he spotted in a shop window in Sheffield in 1825, and took it to his workshop to improve it. This is quite similar to the account Mason gives about his first pen-making experiment. Mason saw one of Perry's pens in the window of a bookseller named Peart on Bull Street, Birmingham, in 1828, which he bought and took home. Realizing he could make a better pen for a lower price, he produced some and sent them to Mr. James Perry in London, who soon visited Josiah Mason at his business location on Lancaster Street, leading to Mason starting to manufacture pens for Perry. It should be noted that the writer in the Sheffield Daily Telegraph stated that Perry was the earliest experimenter in form and material.
Leaving the honor of having originated the application of labor-saving machinery for the manufacture of steel pens to Mitchell, it would appear that the merit of having popularized the article is due to Perry. In 1830, Mr. James Perry issued a circular containing a series of engravings of metallic pens, showing the improvements he had patented in their manufacture. In this circular it is stated: “Till about six months ago the public had heard little of metallic pens. At present, it would seem that comparatively few of any other kind are in the hands of any class of the community. This sudden transition may clearly be traced to the announcement of the Patent Perryian Pens in various periodicals, about six months ago, and to the general demand which ensued for that pen in every part of the empire,”
Leaving the credit for creating labor-saving machinery for making steel pens to Mitchell, it seems that the credit for popularizing the product goes to Perry. In 1830, Mr. James Perry sent out a circular featuring several engravings of metal pens, highlighting the improvements he had patented in their production. The circular states: “Until about six months ago, the public had heard little about metal pens. Now, it seems that relatively few pens of any other kind are being used by any segment of the community. This sudden shift can be clearly traced back to the announcement of the Patent Perryian Pens in various publications about six months ago, along with the widespread demand that followed for that pen throughout the empire,”
Although this might be regarded as an ex-parte statement, it is confirmed by independent testimony that Perry popularized the article. The Saturday Magazine, 1838, says:
Although this might be seen as a one-sided statement, it's backed by unbiased testimony that Perry made the article popular. The Saturday Magazine, 1838, says:
“About twelve years ago (1825), the celebrated Perryian pens first appeared. Mr. Perry may be regarded in the light of a great improver; many of his pens are ingenious and original in construction. He arranges his pens into genera and species. Mr. Perry first overcame the rigidity complained of in steel pens by introducing apertures between the shoulder and point of the pen, thus transferring the elasticity of the pen to a position below instead of above the shoulder. This was the subject of his patent in 1830.”
“About twelve years ago (1825), the famous Perryian pens were introduced. Mr. Perry can be seen as a significant innovator; many of his pens are clever and uniquely designed. He categorizes his pens into genera and species. Mr. Perry was the first to address the stiffness that people complained about in steel pens by creating openings between the shoulder and the tip of the pen, which shifted the pen's flexibility to a position below the shoulder rather than above it. This was the focus of his patent in 1830.”
Mr. Sam: Timmins, in 1866, writes:
Mr. Sam: Timmins, in 1866, writes:
“No skill in manufacture, however, could conquer the prejudice against any metallic pen, and to Mr. James Perry the world is much indebted for persevering advocacy of the steel pen, and for one of the most important improvements in its form. Mr. Perry, with his characteristic energy, almost forced the steel pen into use, and was supplied with pens of a first-class quality by Mr. Josiah Mason, of this town.”
"No manufacturing skill could overcome the bias against any metal pen, and we owe a great deal to Mr. James Perry for his persistent support of the steel pen, as well as for one of the key improvements in its design. Mr. Perry, with his typical drive, practically pushed the steel pen into use, and he was provided with top-quality pens by Mr. Josiah Mason, of this town."
Furthermore, it is certain that about this time, steel pens began rapidly to supersede the use of quills,* and the trade was recognized as a rising industry. It is true that it still retained the secretive character with which its operations were conducted in its earlier days, which indeed in some respects distinguish it at the present time. Its activity or dullness seldom troubles the writers of the “Trade Reports” in the local press, although they sometimes inform their readers about good orders having been placed for mousetraps, stove screws, snuffer trays, candle extinguishers, and sad irons.
Furthermore, it's clear that around this time, steel pens quickly started to replace quills,* and the industry was recognized as emerging. It's true that it still kept the secretive nature with which it operated in its early days, which in some ways still sets it apart today. Its levels of activity or inactivity rarely catch the attention of the "Trade Reports" in the local press, although they sometimes tell readers about significant orders for mousetraps, stove screws, snuffer trays, candle extinguishers, and sad irons.
*In a humorous article, “The Web-footed Interests,” which appeared in Tait's Edinburgh Magazine, vol. iii., page 280 (1833), there is a petition to the House of Commons, from Ganders, Geese & Goslings, setting forth the evils likely to ensue from the use of metallic pens. It prognosticates depression in agriculture and manufactures consequent upon a diminution in the amount of grain consumed, and a falling off in the demand for penknives; and draws an alarming picture of the possible failure of the supply of iron ware, and the total extinction of literature, likely to ensue through a stoppage in the supply of steel pens,—the web-footed interest being supposed to have ceased to exist. The petition concludes with a prayer that the manufacture of metallic pens be prohibited.
*In a humorous article titled “The Web-footed Interests,” published in Tait's Edinburgh Magazine, vol. iii., page 280 (1833), there is a petition to the House of Commons from Ganders, Geese & Goslings, outlining the potential problems that could arise from using metal pens. It warns of a downturn in agriculture and manufacturing due to a decrease in grain consumption and a drop in penknife demand. The article paints a dire picture of the possible shortage of iron goods and the complete demise of literature that could occur from a halt in the supply of steel pens—assuming that the web-footed interests no longer exist. The petition ends with a request for the ban on the production of metal pens.
To the writers of the present generation, who can purchase fairly-good pens at one shilling or one shilling and sixpence per gross, it seems hard to realize that people once gave one shilling each for substitutes for quills. It is true that quills could then be bought for a halfpenny and penny each, but how difficult it was to acquire the art of successfully manipulating the same into a pen the following anecdote from “Edwards' Life of Rowland Hill” will testify:
To today's writers, who can buy decent pens for just one shilling or one shilling and sixpence per gross, it’s hard to believe that people used to pay one shilling each for alternatives to quills. It's true that quills could be purchased for half a penny or a penny each, but mastering the skill of turning them into pens was quite a challenge, as the following anecdote from “Edwards' Life of Rowland Hill” will show:
“Mrs. Sinkinson, of Jamaica Row, Birmingham, tells me she went to a school in Hurst Street, and that she remembered that old Mr. Hill came one day a week to teach arithmetic, and Rowland [Sir Rowland Hill] on another to teach writing. In those days there were no steel pens, and Rowland couldn't mend a pen, so that whenever he came he was accompanied by his brother, Matthew Davenport, whose office it was to mend the pens used by the pupils the preceding week.”
“Mrs. Sinkinson, from Jamaica Row, Birmingham, told me she attended a school on Hurst Street and remembers that old Mr. Hill came once a week to teach arithmetic, while Rowland [Sir Rowland Hill] came on another day to teach writing. Back then, there were no steel pens, and Rowland couldn't fix a pen, so every time he visited, he was joined by his brother, Matthew Davenport, whose job was to repair the pens that the students used the week before.”
Sir Josiah Mason used to relate a similar circumstance in his own life, when at Kidderminster, that he accompanied his brother Richard, who was a Sunday-school teacher, to mend the pens.
Sir Josiah Mason used to share a similar story from his life when he was in Kidderminster, where he helped his brother Richard, who was a Sunday-school teacher, fix the pens.
Comparing the crude specimens of early steel pens with the finished productions of the present day, we may be inclined to think that some praise was due to the people who persevered in the use of them; but that the purchasers of these early productions did appreciate them we have the testimony of Mr. Robert Griffin, who says that he wrote for eight weeks, eight hours a day, with a pen made by Perry, in 1824. Now, the old ”scribes,” as the law stationers' writers were called, were generally allowed one quill a day, and as the work of the day usually wore out the longest quill, a considerable amount of time must have been occupied in the renovation of the article.* This would be a serious inconvenience to those who could manufacture a quill into a pen, but as this was by no means an universal accomplishment, we can form an idea how even these clumsy substitutes found purchasers at such high prices.
Comparing the rough early steel pens to the polished versions we have today, we might feel that some credit is due to those who stuck with them; however, we know that buyers of these early pens did value them thanks to Mr. Robert Griffin's account. He stated that he wrote for eight weeks, eight hours a day, using a pen made by Perry in 1824. Back then, the old ”scribes,” the writers for law stationers, were typically given one quill a day. Since a day’s work would usually wear out the longest quill, a significant amount of time must have been spent replacing it. This would have been a major hassle for anyone able to convert a quill into a pen, but since this wasn’t a skill everyone had, it gives us an idea of how even these awkward substitutes were sold for such high prices.
*The writer recollects the tedious waiting for the patient usher, who from desk to desk with his penknife, mending pens, and paying very little attention to anything else; also the wonder felt and expressed at the first sight of steel nibs, and how they dug into the paper.
*The writer remembers the boring wait for the slow usher, who moved from desk to desk with his penknife, fixing pens and hardly paying attention to anything else. There was also the amazement felt and shared upon first seeing steel nibs and how they scratched into the paper.
Tom Hood, in his “Whims and Oddities,” gives some idea of the pre- steel-pen era:
Tom Hood, in his “Whims and Oddities,” gives some idea of the pre-steel-pen era:
In times begone, when each man cut his quill,
With little Perryian skill;
What horrid, awkward, bungling tools of trade
Appeared the writing instruments, home made!
What pens were sliced, hewed, hacked, and haggled out,
Slit or unslit, with many a various snout,
Aquiline, Roman, crooked, square, and snubby,
Humpy and stubby;
Some capable of ladye-billets neat,
Some only fit for ledger-keeping clerk,
And some to grub down, Peter Stubbs, his mark,
Or smudge through some illegible receipt,
Others in florid caligraphic plans,
Equal to ships, and wiggy heads, and swans!
To try in any common inkstands then,
With all their miscellaneous stocks,
To find a decent pen,
Was like a dip into a lucky-box;
You drew, and got one very curly,
And split like endive in some hurly-burly;
The next unslit, a square at end, a spade;
The third, incipient pop-gun, not yet made;
The fourth a broom; the fifth of no avail,
Turned upwards, like a rabbit's tail;
And last, not least, by way of a relief,
A stump that Master Richard, James, or John
Had tried his candle cookery upon,
Making 'roast beef!'”
In days gone by, when everyone made their own quills,
With little skill to speak of;
What terrible, clumsy, makeshift tools of trade
The writing instruments were, all homemade!
What pens were cut, shaped, hacked, and messed with,
Split or not, with all kinds of tips,
Curved, straight, crooked, square, and stubby,
Chunky and chubby;
Some good for love letters neat,
Some just right for the office clerk,
And some to mark down Peter Stubbs’ stamp,
Or scribble over some unreadable receipt,
Others with fancy calligraphy,
Like ships, and fancy wigs, and swans!
To try any of the common inkstands back then,
With all their random selections,
To find a decent pen,
Was like reaching into a lucky box;
You’d pull one out that was all curly,
And broke like a leaf in a chaotic swirl;
The next one, unsplit, had a square tip, a spade;
The third, just the beginnings of a pop-gun, not quite made;
The fourth a broom; the fifth, no use at all,
Pointed upwards, like a rabbit's tail;
And last, but not least, as a bit of relief,
A stub that Master Richard, James, or John
Had tried their candle cooking on,
Making 'roast beef!'”
These early pens were at first made from a piece of steel formed into a tube, and filed into the shape of a pen by hand, the joint of the two edges forming the slit. Afterward a blank was roughly punched out, filed into shape, and the slit marked out with a chisel while the blank was in a soft state. It was then shaped, hardened, tempered, ground, and the slit cracked through by means of a hammer and tool at the place where the mark had been made. The engravings of the pens by Edwards, which appeared in Wrightson's Directory, 1823, seem to indicate that the piercing, side cutting and slitting were executed by mechanical appliances. Possibly, Edwards was not a manufacturer himself, but had his pens made for him by Mitchell.
These early pens were initially made from a piece of steel shaped into a tube and manually filed into the form of a pen, with the edges creating the slit. Later, a blank was roughly punched out, shaped by filing, and the slit was marked with a chisel while the blank was still soft. It was then shaped, hardened, tempered, ground, and the slit was cracked open using a hammer and tool at the marked spot. The engravings of the pens by Edwards that appeared in Wrightson's Directory, 1823, suggest that the piercing, side cutting, and slitting were done using mechanical equipment. It's possible that Edwards wasn't a manufacturer himself but had his pens made by Mitchell.
In the pre-steel-pen era there were many attempts made to supersede quills. In “Peveril of the Peak,” Mistress Chiffinch speaks of her diamond pen. There was a pen the nibs of which were of ruby, set in gold, made by Doughty. Dr. Wollaston made gold pens tipped with, rhodium.
In the time before steel pens, there were many attempts to replace quills. In “Peveril of the Peak,” Mistress Chiffinch talks about her diamond pen. There was a pen with ruby nibs set in gold, made by Doughty. Dr. Wollaston created gold pens with rhodium tips.
During the time the early makers of steel pens were perfecting the article, several experimenters were offering to the public writing instruments made from various materials. Bramah patented ”quill nibs,” made by splitting quills and cutting the semi-cylinders into sections, which were shaped into pens, and adapted to be placed in a holder. Hawkins and Mordan, in 1823, made use of horn and tortoise- shell, which was cut into “nibs,” softened in water, and small pieces of ruby and other precious stones were then embedded in by pressure. In this way they insured durability and great elasticity. In order to give stability to the nib thin pieces of gold or other metal were affixed to the tortoise-shell.
During the time the early makers of steel pens were refining their product, several inventors were introducing writing tools made from different materials. Bramah patented “quill nibs,” created by splitting quills and cutting the semi-cylinders into sections, which were shaped into pens and designed to fit into a holder. In 1823, Hawkins and Mordan used horn and tortoise-shell, which were cut into “nibs,” softened in water, and small pieces of ruby and other precious stones were pressed in for added durability and elasticity. To ensure the nib's stability, thin pieces of gold or other metals were attached to the tortoise-shell.
Looking back at the early operations of the trade, and considering that steel pens were made by hand at the beginning of the present century, we can scarcely understand why the idea of cheapening the production by the application of labor-saving contrivances did not occur to those inventive geniuses, the proprietors of Soho. Boulton had expended some time in perfecting the manufacture of steel buttons. That local Admirable Crichton, Humphrey Jefferies, does not appear to have ever directed his attention to the manufacture of this article, which has now become a prime necessity of civilization. Yet we hear of his success in the improvement of buttons, and button-makers must have used the screw press and tools for cutting out the blank and shaping it into form; and the process of slitting had been anticipated, for printers had a brass rule-cutting machine in use, the cutters of which bore a strong resemblance to those now used for slitting steel pens. Like most of the pioneers in the path of invention, the majority of the early makers of pens were men whose business pursuits gave them no special facilities for entering upon the manufacture of steel pens. The progress of the trade from 1829 (with the exception of the period when Perry and Gillott first commenced advertising) had been gradual, but satisfactory. In one of Gillott's early advertisements, he stated that he made 490,361 gross in 1842, and 730,031 in 1843. This was an advance by leaps and bounds which has not since been maintained. Although Mason commenced making pens for Perry in the year 1828, yet it was not till 1861 that his name became known in England as a steel-pen maker. Many merchants in Birmingham and Wolverhampton, who purchased steel rings from him, had no idea that he was a maker of pens; yet on the Continent of Europe pens bearing his name were eagerly sought after. Subsequent to 1861 he was associated with Perry, until, in 1876, the trade-marks, patents, etc., were purchased by a limited liability company, who now, under the name of “Perry & Co.,” have become the largest manufacturers of pens in the world.
Looking back at the early days of the trade, and considering that steel pens were handmade at the start of this century, it's hard to understand why the idea of reducing production costs with labor-saving devices didn’t occur to the inventive minds at Soho. Boulton spent some time perfecting the manufacturing of steel buttons. That local genius, Humphrey Jefferies, doesn’t seem to have ever focused on making this item, which has now become essential to civilization. Yet we know of his success in improving buttons, and button-makers must have used the screw press and tools to cut out and shape the blanks; the slitting process had already been anticipated, as printers used a brass rule-cutting machine that resembled those used for slitting steel pens today. Like most pioneers in invention, most of the early pen makers were individuals whose business background didn’t give them special advantages in producing steel pens. The trade progressed gradually but satisfactorily from 1829 (except for the time when Perry and Gillott first started advertising). In one of Gillott's early ads, he mentioned that he produced 490,361 gross in 1842, and 730,031 in 1843. This was a significant leap that hasn’t been sustained since. Although Mason began making pens for Perry in 1828, it wasn't until 1861 that he became known in England as a steel pen maker. Many merchants in Birmingham and Wolverhampton who bought steel rings from him had no idea he was also a pen maker; however, on the European continent, pens with his name were highly sought after. After 1861, he partnered with Perry until 1876, when the trademarks, patents, etc., were bought by a limited liability company, which now operates under the name “Perry & Co.” and has become the largest pen manufacturer in the world.
At the present time (1889) there are thirteen firms engaged in the trade in Birmingham, and they make up about twenty-four tons of steel per week into pens and penholder tips. Making due allowance for the material used in the latter article, this consumption would probably represent a weekly average production of 200,000 grosses of pens. The Birmingham penmakers employ about 3,500 women and girls, and 650 men and boys; and besides these the number of women and girls working at making paper boxes, in which the pens are packed, would probably exceed 300. In addition to this there are several mills where steel is rolled for those firms who have not sufficient power on their own premises, but there is a difficulty in stating the number of hands employed. The wages of the females range from four shillings to fifteen shillings; those of the boys from five shillings to ten shillings. The unskilled workmen earn from twelve shillings to twenty-four shillings; and skilled men, or toolmakers, command wages varying from twenty-five shillings to three pounds. Most of the females work upon the piece-work system, but the men are paid weekly wages.
At present (1889), there are thirteen companies in Birmingham involved in the pen trade, producing about twenty-four tons of steel each week for pens and penholder tips. After accounting for the materials used in the latter, this consumption likely translates to an average weekly production of 200,000 gross of pens. The Birmingham penmakers employ around 3,500 women and girls and 650 men and boys. Additionally, the number of women and girls making paper boxes for packaging the pens probably exceeds 300. There are also several mills that roll steel for those companies that lack sufficient power on their own premises, but it’s hard to determine the exact number of employees there. Women’s wages range from four to fifteen shillings, while boys earn between five and ten shillings. Unskilled workers make from twelve to twenty-four shillings, and skilled workers, like toolmakers, earn between twenty-five shillings and three pounds. Most women work on a piece-work basis, while men receive weekly wages.
In 1835, upon the authority of a writer in the Mechanics' Magazine, two tons two hundred weight of steel were used weekly in the manufacture of pens. Mr. Sam: Timmins made an approximate estimate that six and a half tons of steel were used per week for steel pens in 1849, and again, in 1886, he gives the amount of steel as having increased to ten tons. It is at all times difficult to form an accurate estimate of the quantity of material used, but we believe we are within the mark in putting down the present consumption of steel at twenty-two tons weekly. From this it would appear that the trade has doubled its production during the last twenty years. Besides these Birmingham houses there are some four or five manufactories on the Continent, and two in the United States, but their productions have not increased in the same ratio as that of their English rivals.
In 1835, a writer from the Mechanics' Magazine stated that two tons and two hundred weight of steel were used each week to make pens. Mr. Sam Timmins estimated that in 1849, six and a half tons of steel were used weekly for steel pens, and in 1886, he reported that the amount had risen to ten tons. It's always challenging to accurately gauge how much material is used, but we believe we're being conservative in estimating the current steel consumption at twenty-two tons each week. This suggests that the industry has doubled its production over the past twenty years. In addition to these Birmingham companies, there are four or five manufacturers on the Continent and two in the United States, but their output hasn't increased at the same rate as their English competitors.
During the last twenty years a great improvement has taken place in the style of boxes and labels in which the pens are packed. Formerly (with the exception of the goods issued by Gillott and Sommerville) most of the pens were sold in boxes of the plainest description; now the covers or labels are printed in a number of colors from elaborate designs, by first-class artists, and in some cases the boxes are ornamented with well-executed portraits of royal, political, literary, or artistic celebrities. There are many peculiarities connected with the public taste as manifested in the demand for pens. The Germans use a greater variety of patterns than any other nation. The English taste is more restricted, and is generally confined to articles of the plainer shapes. Autocratic Russia and democratic America make use of the fewest patterns. By a regulation of the Imperial Government, pens in boxes, bearing portraits of the Russian royal family are prevented from entering the country, and in America public taste does not favor a demand for portrait boxes. By a law which came into operation the 1st of January, 1886, no pens can be imported into Russia bearing the name of a Russian firm. The probable purpose of this law was to encourage the establishment of a Russian manufactory. At present there are no pen works in Russia. An attempt was made in Moscow, in 1876-8, to manufacture steel pens, but the experiment proved a failure. The Germans and French are the largest buyers of first-class pens, but the Italians are content with articles of the commonest character. The chief demand for three-pointed pens comes from Spain. At present the demand for steel pens is chiefly confined to European nations and their descendants. The great Asiatic nations still write with pens made from reeds, or camel-hair pencils. A few of the natives of India and Japan, and some of the subjects of the Sultan and Khe'dive are beginning to make use of steel pens adapted to the peculiarities of their writing. From this it would appear that the possibilities of the progress of the trade in the future are very favorable; but in the meantime its productions are scattered over the globe, and even in some of the darkest corners of the earth pioneers of civilization are to be found transcribing the results of their experience with the aid of that great factor of nineteenth-century progress—an English Steel Pen.
Over the last twenty years, there has been a significant improvement in the design of boxes and labels used for packing pens. Previously, most pens (except for those made by Gillott and Sommerville) were sold in very plain boxes. Now, the covers or labels are printed in various colors with intricate designs by top artists, and some boxes feature well-executed portraits of famous royal, political, literary, or artistic figures. There are several unique trends in public taste regarding the demand for pens. Germans use a wider variety of patterns than any other nation, while English preferences tend to lean towards simpler designs. Autocratic Russia and democratic America stick to the fewest patterns. Due to a regulation from the Imperial Government, pens in boxes with portraits of the Russian royal family are banned from entering the country, and in America, public taste does not support a demand for portrait boxes. According to a law that took effect on January 1, 1886, no pens bearing the name of a Russian firm can be imported into Russia, likely intended to encourage local manufacturing. Currently, there are no pen factories in Russia. An attempt was made in Moscow between 1876 and 1878 to manufacture steel pens, but it was unsuccessful. The Germans and French are the largest buyers of high-quality pens, while Italians prefer more basic items. The main demand for three-pointed pens comes from Spain. Right now, the demand for steel pens is primarily among European nations and their descendants. The major Asian countries still rely on pens made from reeds or camel-hair pencils. A few people in India and Japan, as well as some from the Sultan's and Khe'dive's territories, are starting to use steel pens tailored to their writing styles. This suggests that the future prospects for the pen trade are quite promising; however, at present, its products are distributed worldwide, and even in some of the most remote parts of the world, pioneers of civilization are documenting their experiences with the help of that crucial element of 19th-century progress—an English steel pen.
THE MANUFACTURING PROCESSES
OF STEEL PENS.
The steel from which the greater part of the metallic pens are manufactured comes from Sheffield. Notwithstanding the many names given by the venders of steel pens to the material from which they are manufactured there are but two sorts—good and bad—and therefore Peruvian, Damascus, Amalgam, and Silver Steel are but fancy names. As a matter of fact, where a number of prefixes are used to describe the quality of an article it is generally found to have no claim to any of them.
The steel used to make most metallic pens comes from Sheffield. Despite the many names that sellers of steel pens use to describe the material, there are really only two types—good and bad. So, names like Peruvian, Damascus, Amalgam, and Silver Steel are just fancy terms. In reality, when a product has lots of prefixes to describe its quality, it usually doesn't deserve any of them.
The raw material is received from Sheffield in sheets six feet in length, one foot five inches in width, and 23 or 26 Birmingham wire- gauge in thickness. The first operation is the cutting of these sheets into strips of convenient width. They are then packed in an oblong iron box, placed with the open top downward in another box of the same material, and the interstices are filled up with a composition to exclude the air. The boxes are placed in a muffle, where they remain until they have gradually attained a dull red heat, and the muffle is allowed to gradually cool, or else the boxes are placed in a cooling chamber. When the boxes have been reduced to a temperature which will admit of their being handled, the contents (technically called a charge) are emptied out. Now, it will be found that the strips of steel are covered with bits of small scale, sticking to them like a loose skin, and if this were not removed before the next process— rolling—the steel, instead of being perfectly smooth, would be marked with a number of indentations, rendering it very unsightly. In order to get rid of this excrescence, the strips are immersed in a bath of diluted sulphuric acid, which loosens the scale, and are then placed in wood barrels to which broken pebbles and water are added. The barrels are kept revolving until the whole of the scaly substance has been removed and the strips have assumed a silver-gray appearance. The steel is now ready for manipulation in the rolling mill, where it is passed between successive pairs of rolls until it has been reduced to the required gauge, and this operation has to be performed with such nicety that a variation of one thousand part of an inch in the thickness of the strip would make such an alteration in the flexibility of the pens made from it as to cause considerable dissatisfaction to the purchasers of the article.
The raw material comes from Sheffield in sheets that are six feet long, one foot five inches wide, and either 23 or 26 Birmingham wire-gauge thick. The first step is to cut these sheets into strips of a convenient width. They are then packed into a rectangular iron box, which is placed upside down in another box of the same material, and the spaces in between are filled with a composition to keep out the air. The boxes go into a muffle, where they stay until they gradually reach a dull red heat, and then the muffle is allowed to cool down slowly, or the boxes are put in a cooling chamber. Once the boxes have cooled down to a safe temperature for handling, the contents (technically called a charge) are emptied out. At this stage, you'll find that the steel strips are covered with small scale pieces that cling to them like a loose skin, and if this isn’t removed before the next process—rolling—the steel will end up with indentations, making it look unattractive. To get rid of this unwanted material, the strips are soaked in a bath of diluted sulfuric acid, which loosens the scale. They are then placed in wooden barrels filled with broken pebbles and water. The barrels are kept spinning until all the scaly stuff is removed and the strips take on a silver-gray appearance. The steel is now ready to be processed in the rolling mill, where it is passed through successive pairs of rolls until it reaches the desired gauge. This step must be done with such precision that a variation of just one thousandth of an inch in the thickness of the strip would significantly affect the flexibility of the pens made from it, leading to dissatisfaction among buyers.
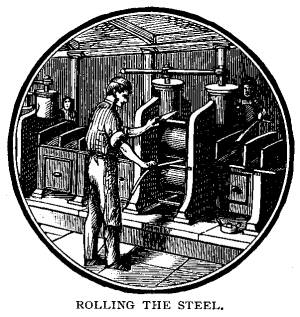
The steel on leaving the mill is conveyed to the gauging room, and it will be found to have increased to three times its original length, and now appears with a bright surface. Hitherto the operations have been conducted by men and boys; but now, in the course of manufacture, the pens will enter on a series of processes in which the quick and delicate fingers of women and girls play an important part. The strips of steel are now given out to the cutters. The Toolmaker, who, as a rule, both makes and sets the tools, has placed in what is known as a bolster a die, having a hole perforated through it of the exact shape of the blank to be cut; and attached to the bottom of the screwed bolt of the press is a punch, also bearing the exact shape of the blank. The girl with her left hand introduces one of the strips of steel at the back of the press, and, pulling the handle toward her with the right hand, the screw descends, driving the punch into the bed, and in so doing has perforated the strip of steel with a scissors-like cut, making a blank which falls through the opening in the die into a drawer below. Now, with her left hand she pulls the strip toward her until it is stopped by a little projection called a guide; and again the right hand moves the handle, the screw descends, and another blank is cut. The operation is continued until the whole of one side of the strip is perforated; it is then reversed and the other side treated in a similar way. If you were to hold up the strip thus manipulated—now called scrap—you would find that in some particular part the perforations approach so nearly to each other as to form a slight bar, which breaks easily between the thumb and finger. This is rendered necessary from the fact that steel scrap is worth only one-fifth of the value of the raw material, and, as under the most favorable conditions, the scrap averages one-third the original weight given out for cutting, it behooves the manufacturer to reduce the scrap as much as practicable. If these blanks are examined, a small V-shaped indentation, looking like a defect, will be found upon the upper edge of that part inserted in the holder. This small mark plays an important part in the succeeding processes. To a casual observer there does not appear much difference between the two sides of the blank; but, however well the tools are made, that side of the blank which is uppermost in cutting out will be rougher than the under side. This mark enables the operator to distinguish at a glance the smooth side, and by always keeping the rough side upward the burr is polished off in a later process.
The steel, once it leaves the mill, is taken to the gauging room and is now three times its original length, appearing with a shiny surface. Up to this point, the work has been done by men and boys, but now women and girls play a crucial role in the next steps of the manufacturing process. The strips of steel are assigned to the cutters. The Toolmaker, who usually both creates and adjusts the tools, has placed a die in a bolster, featuring a hole in the exact shape of the blank to be cut. Attached to the bottom of the press’s screwed bolt is a punch that also matches the shape of the blank. The girl uses her left hand to insert one of the steel strips at the back of the press, and with her right hand, she pulls the handle towards her. As the screw descends, it drives the punch into the bed, cutting through the strip of steel with a scissors-like action, creating a blank that falls through the die's opening into a drawer below. Next, with her left hand, she pulls the strip toward her until it stops at a little projection known as a guide. Again, her right hand moves the handle, the screw descends, and another blank is cut. This process continues until one side of the strip is fully perforated; then it is flipped over to treat the other side similarly. If you hold up the manipulated strip—now referred to as scrap—you’ll notice that in certain areas, the perforations are close enough together to create a small bar that can be easily broken between your thumb and finger. This is necessary because steel scrap is worth only one-fifth of the value of the raw material, and, under the best conditions, the scrap averages one-third of the original weight allocated for cutting, so it’s important for the manufacturer to minimize scrap as much as possible. When examining these blanks, you’ll find a small V-shaped indentation on the upper edge of the part that was inserted in the holder. While it may look like a defect, this small mark is significant for the next steps. To the casual observer, there doesn’t seem to be much difference between the two sides of the blank, but no matter how well the tools are made, the upper side will always be rougher than the underside. This mark helps the operator quickly identify the smooth side, and by consistently keeping the rough side facing up, any burr is polished off in a later process.
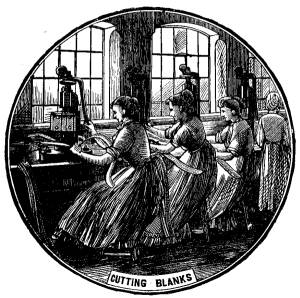
The blanks are now ready to be passed to the next process—marking. This operation is performed by a female, with the aid of a stamp. The precise mark required is cut upon a piece of steel, and, being placed in the hammer of the stamp, the girl puts her right foot into a stirrup attached to a rope, which is passed round a pulley, and, pressing downward, causes the hammer to ascend. Taking a handful of blanks with her left hand, by a dexterous motion she makes a little train of them between the thumb and finger in parallel order, presenting the first in the most ready position to be passed to the other hand. The right hand is brought toward the left, and, taking a blank, places it with the point toward the worker in a guide upon the bed of the stamp, then by suddenly letting the hammer descend a blow is struck upon the blank, which gives an impression of the name cut upon the punch. The quick fingers of the operator pass backward and forward with such rapidity that a skillful girl will mark from two hundred to two hundred and fifty gross per day. If the mark required is unusually large, the marking process is deferred until after the pen has been pierced, in order that the blank may be annealed (or softened), which takes the impression more readily than the hard steel.
The blanks are now ready to move on to the next step—marking. This task is carried out by a woman, using a stamp. The exact mark needed is carved onto a piece of steel. When the steel is placed in the stamp's hammer, the woman steps into a stirrup attached to a rope that goes around a pulley. By pressing down, she makes the hammer rise. With her left hand, she gathers a handful of blanks and quickly arranges them between her thumb and finger in a neat line, positioning the first one to easily transfer to her other hand. She brings her right hand over to her left, grabs a blank, and places it point-up in a guide on the stamp's bed. Then, by quickly releasing the hammer, it strikes the blank, leaving an impression of the name carved on the punch. The operator's nimble fingers move back and forth so quickly that a skilled woman can mark two hundred to two hundred and fifty gross in a single day. If the needed mark is particularly large, the marking is postponed until after the pen has been pierced so that the blank can be annealed (or softened), which allows it to take the impression more easily than the hard steel.
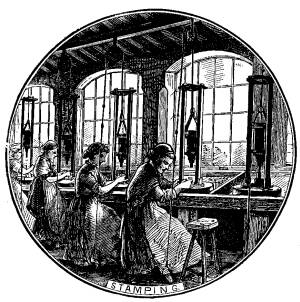
Now, in order to make a metallic pen suitable for writing it is necessary to consider some means of producing elasticity, and also to devise some method by which the smooth steel shall cause the ink to attach itself to the pen. This is brought about by the next process— piercing. In this operation the tools are of a very delicate character, and as the center pierce (the aperture in which the slit terminates) is frequently of an ornamental design the tools, being small, have to be made with great precision. The piercing punch and bed having been fixed in a screw press, and an ingenious arrangement of guides fastened thereto, the girl selects a blank from a tray on her left hand, and, placing it in its proper position by the aid of the guides, pushes the fly of the press from her, the screw descends, driving the punch into the bed, and the operation of piercing is completed.
Now, to create a metal pen that's good for writing, we need to come up with a way to make it flexible and figure out how to get the smooth steel to hold the ink. This is achieved through the next process—piercing. In this step, the tools are very delicate, and since the center pierce (the opening where the slit ends) often has an ornamental design, the tools must be made with great precision. Once the piercing punch and bed are set in a screw press, along with a clever arrangement of guides, the worker picks a blank from a tray on her left side, positions it correctly using the guides, and then pushes the press handle away from her. The screw goes down, pushing the punch into the bed, and the piercing process is completed.
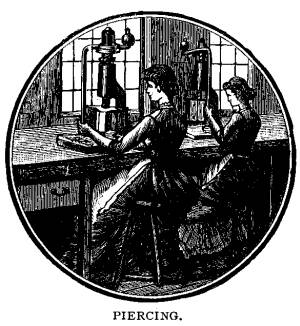
The blanks are still moderately hard, and before they can be made to take the shape of a pen it is necessary that they should be softened, which is effected by the process called annealing. The blanks having been freed from the dust and garbase that has become attached to them are carefully placed in round iron pots, which are again inclosed in larger ones and covered over with charcoal dust to prevent the entrance of gases, and put into the muffle, heated to a dull red, and then allowed to cool.
The blanks are still somewhat hard, and before they can be shaped into a pen, they need to be softened, which is done through a process called annealing. Once the blanks have been cleaned of the dust and debris that has stuck to them, they are carefully placed in round iron pots. These pots are then put inside larger ones and covered with charcoal dust to keep gases out, and then placed into the muffle, heated to a dull red, and allowed to cool.
The blanks are now soft and pliable, readily taking the various shapes into which pens are made by the next process, called raising. This operation is performed by the aid of a punch and die fitted into a screw-press. The punch is fitted into a contrivance called a false nose, fixed in the bottom of the screw of the press; and the die or bed is placed in a cylindrical piece of steel (called a bolster) with a groove cut for the reception of the die, the bolster being fastened to the bottom of the press by a screw underneath. The punch and die being fixed so as to exactly fit each other, the toolmaker places a small piece of tissue paper between them, takes an impression, examines it, and proceeds to rectify any inequality in the pressure, so as to insure perfection in the shape. This being accomplished, the toolmaker fixes four pieces of steel (called guides) to the bolster in such positions that the operator is enabled to slide the blank into the bed, where it is held by the guides till the punch descends, forces the blank into the bed, and gives the pen its shape. The article is now narrower than it was in its blank form, and the girl pushes it through the tools with a small stick held in the hand with which she works the press handle, while with the other hand she places another blank in its position in the bed.
The blanks are now soft and flexible, easily taking the shapes into which pens are formed in the next step, called raising. This process uses a punch and die set up in a screw-press. The punch fits into a device called a false nose, which is attached to the bottom of the press screw; the die or bed is located in a cylindrical piece of steel (called a bolster) that has a groove for the die, and the bolster is secured to the bottom of the press with a screw. With the punch and die positioned to match perfectly, the toolmaker places a small piece of tissue paper between them, takes an impression, examines it, and adjusts any uneven pressure to ensure the shape is perfect. Once that's done, the toolmaker attaches four pieces of steel (called guides) to the bolster so that the operator can slide the blank into the bed, where it is held by the guides until the punch comes down, pushes the blank into the bed, and forms the pen. The item is now narrower than it was in blank form, and the girl pushes it through the tools with a small stick held in the hand that operates the press handle, while with the other hand she positions another blank in the bed.
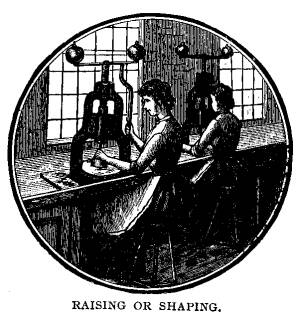
The pen is now shaped or raised, but it is still soft, and consequently another process is necessitated—hardening. This is effected by placing the pens in thin layers in round pans with lids. They are placed in the muffle for a period varying from twenty to thirty minutes, during which time they have acquired a bright red heat. The workman then withdraws them and empties the contents into a large bucket immersed in a tank of oil. The bucket is perforated at the bottom, and being elevated, the oil drains off. The pens are next placed in a perforated cylinder, which, being set in motion, revolves and drains off the remainder of the oil. The pens are still greasy, and as brittle as glass; and in order to free them from the grease they are again placed in perforated buckets and immersed in a tank of boiling soda water. After they are freed from the grease the pens are put into an iron cylinder, which is kept revolving over a charcoal fire until they are softened or tempered down to the special degree required. In this process the workman is guided by the color, which indicates the varying temperature of the metal of which the articles are made. Brittleness has given place to pliability, but the pens are black in color and scratch at the point, and to remedy this defect they are subjected to the next process—scouring. In order to do this the pens are dipped in a bath of diluted sulphuric acid—called pickle—which frees the articles from any extraneous substances they may have acquired in the hardening and tempering processes. This requires to be done with great care, or the acid would injure the steel. The pens are then placed in iron barrels with a quantity of water and small pebbly-looking material. This latter material is composed of annealing pots broken and ground fine enough to pass readily through a fine riddle. The barrel being set in motion, the pens are scoured for periods varying from five to eight hours, and are placed again in barrels with dry pot for about the same period, after which they are put into other barrels together with a quantity of dry sawdust. On being taken out of these barrels the body of the pen has acquired a bright silver color, and the point has been rounded.
The pen is now shaped, but it's still soft, which means it needs to go through another process—hardening. This is done by laying the pens in thin layers in round pans with lids. They're put in the muffle for about twenty to thirty minutes, during which they reach a bright red heat. The worker then takes them out and pours the contents into a large bucket that's submerged in a tank of oil. The bucket has holes in the bottom, and since it's elevated, the oil drains out. Next, the pens are placed in a perforated cylinder, which spins to drain off the remaining oil. They are still greasy and as brittle as glass, so to remove the grease, they're placed again in perforated buckets and immersed in boiling soda water. Once freed from the grease, the pens are put into an iron cylinder that keeps rolling over a charcoal fire until they are softened or tempered to the required degree. The worker uses the color to guide him, which indicates the varying temperature of the metal. Brittleness is replaced by pliability, but the pens are now black and scratchy at the tip, so they undergo the next process—scouring. To do this, the pens are dipped in a bath of diluted sulfuric acid—known as pickle—which removes any foreign substances they picked up during hardening and tempering. This step requires great care, or the acid could damage the steel. The pens are then placed in iron barrels with water and small pebble-like material. This material is made from broken annealing pots ground fine enough to pass through a fine sieve. As the barrel spins, the pens are scoured for five to eight hours, after which they go into barrels with dry pot for about the same amount of time, and then into other barrels filled with dry sawdust. When taken out of these barrels, the pen's body has gained a bright silver color, and the tip has been rounded.
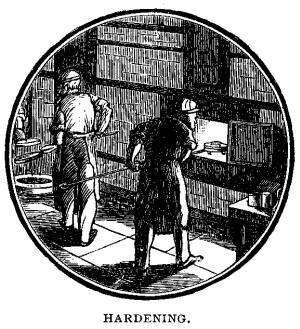

The article has now the shape and appearance of a finished pen, and yet it possesses none of its characteristics, and, if tried, will be found to have no more action than a lead pencil, as it is deficient in that important part of a writing instrument—the slit. Before being slit the pen is ground between the centre pierce and the point. This process is performed by girls, with the aid of what is called a “bob” or “glazer.” The “bob” is a circular piece of alder wood about ten and a half inches in diameter and half an inch in width. Round this a piece of leather is stretched and dressed with emery. A spindle is driven through the centre, and the two ends placed in sockets. The “bob” is set in motion by means of a leather band, and the girl holding a pen firmly, with a light touch grinds off a portion of the surface.
The article now looks like a finished pen, but it doesn't have any of its features, and if you try to use it, you'll find it performs just like a pencil, since it lacks the essential part of a writing instrument—the slit. Before being slitted, the pen is ground between the center pierce and the tip. This process is done by girls using a tool called a “bob” or “glazer.” The “bob” is a circular piece of alder wood about ten and a half inches in diameter and half an inch thick. A piece of leather is wrapped around it and treated with emery. A spindle is placed through the center, with both ends fitted into sockets. The “bob” is set in motion with a leather band, and the girl holds the pen steadily, lightly grinding off a portion of the surface.
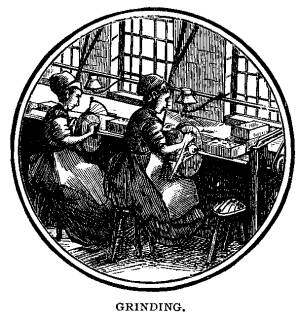
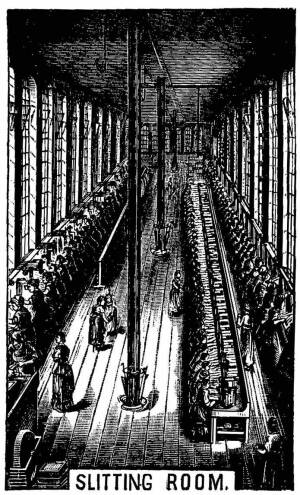
This operation being completed, the last and most important mechanical operation has to be performed—slitting. The tools with which this process is effected are two oblong pieces of steel about an inch and a half long, three-eighths of an inch thick, and an inch and a quarter wide. These are called the cutters, and upon the preparation and setting of these the successful issue of the process depends. The edges of these cutters are equal in delicacy to the cutting edge of a razor, but the shape is more suggestive of a portion cut from the thickest part of a large pair of shears. The cutter being fixed in the press, a pair of guides are screwed on either side, and a small tool called a table, or rest, being attached to the contrivance called a bolster, which holds the bottom cutter, the operator takes a pen, places it on the table, pushes the point up toward the guide, pulls the handle, the upper cutter descends, meets the lower one, and the process of slitting is completed.
Once this operation is finished, the final and most crucial mechanical task must be carried out—slitting. The tools used for this process are two rectangular pieces of steel about an inch and a half long, three-eighths of an inch thick, and an inch and a quarter wide. These are known as the cutters, and the success of the process relies on how well they are prepared and set. The edges of these cutters are as sharp as a razor, but their shape resembles a section taken from the thickest part of a large pair of shears. With the cutter secured in the press, a pair of guides are attached on either side, and a small tool called a table, or rest, is connected to the device known as a bolster, which holds the bottom cutter. The operator takes a pen, places it on the table, pushes the point up toward the guide, pulls the handle, the upper cutter descends, meets the lower one, and the slitting process is complete.
Now, although this operation completes the mechanical processes of pen making, the article is by no means finished. If you examine the pen now you will find that the outer edge of each point is smooth, while the inside edges which have just been made by the slit are sharp and scratch. To remove this defect the operation of “barreling” has to be again resorted to. The pens are again placed in the iron barrels with pounded pot, kept revolving from five to six hours, and finally polished in sawdust.
Now, even though this process wraps up the mechanical steps of making a pen, the product isn’t finished yet. If you look at the pen now, you’ll notice that the outer edge of each point is smooth, while the inner edges created by the slit are sharp and can scratch. To fix this issue, we need to go through the “barreling” process again. The pens are placed back in the iron barrels with ground pot, rotating for five to six hours, and finally polished with sawdust.
The pens are now of a bright silver-steel color and perfectly smooth, but as they are required in various tints, they are colored and afterward varnished to prevent rust. To accomplish the first of these results the articles are placed in a copper or iron cylinder and kept revolving over a coke fire until the requisite tint is obtained, the color depending upon the temperature of the cylinder. If the pens are intended to be lacquered they are placed in a solution of shellac dissolved in methylated spirits. The spirit is drained off, and the pens are placed in wire cylinders and kept revolving until the action of the air dries the lacquer. They are then scattered upon iron trays, inserted in an oven, and the heat diffuses the lacquer equally over the surface of the pens, so that when they have cooled down they have a glossy appearance, which gives to them an air of finish and prevents rust.
The pens are now a bright silver-steel color and perfectly smooth, but since they come in various colors, they're dyed and then varnished to prevent rust. To achieve the dyeing, the pens are placed in a copper or iron cylinder and kept rotating over a coke fire until the desired color is reached, which depends on the temperature inside the cylinder. If the pens are meant to be lacquered, they are soaked in a solution of shellac dissolved in methylated spirits. The spirits are drained off, and the pens are placed in wire cylinders, where they keep rotating until the air dries the lacquer. Then, they are spread out on iron trays, put in an oven, and the heat evenly distributes the lacquer over the surface of the pens, so that when they cool down, they have a glossy finish that gives them a polished look and prevents rust.
The pen is now finished as far as manufacturing processes are concerned, yet before it can be offered to the public it has to undergo a rigid examination called ”looking over.” This is performed by trained girls, and when the defective ones have been sorted out the good pens are sent to the finished warehouse to be put up into boxes. These boxes are of various descriptions, adapted to suit the markets for which they are intended. In many instances the labels which form the covers of the boxes are elaborately printed from first-class designs, and some of them have highly-finished steel engravings of royal personages and celebrities in the scientific, literary, musical, and political world. The quantities contained in these boxes vary with the countries for which they are intended; for the manufacturers study the wants of their customers, and do not offer articles counted in dozens to people who reckon by tens.
The pen is now complete in terms of manufacturing, but before it can be released to the public, it has to go through a strict examination called ”looking over.” This is done by trained women, and once the defective ones are sorted out, the good pens are sent to the finished goods warehouse to be packed into boxes. These boxes come in various types, tailored to fit the markets they’re intended for. In many cases, the labels that make up the covers of the boxes are beautifully printed from high-quality designs, and some feature finely done steel engravings of royalty and notable figures from the scientific, literary, musical, and political fields. The quantities in these boxes differ according to the countries they're meant for; manufacturers study their customers' needs and don’t offer items in dozens to people who count by tens.
We have now traced the manufacture of this little article from its beginning as a plain piece of steel through all its stages until it has developed into that indispensable requisite of daily life—a pen.
We have now followed the process of making this small item from its start as a simple piece of steel through all its stages until it has evolved into that essential part of daily life—a pen.
HISTORY OF THE PERRYIAN
PEN WORKS.
The firm of Messrs. Perry & Co., London, was founded in the year 1824 by Mr. James Perry, who carried on business originally in Manchester, then in London. Mr. James Perry died in the year 1843. Mr. Stephen Perry, who conducted the business afterward in partnership with Mr. Hayes and others, died in the year 1873, and was succeeded by his sons, Messrs. Joseph John and Lewis Henry Perry. The firm of Perry & Co. was known all over Europe as the house which first introduced to the commercial world steel pens of a superior quality, and in many countries steel pens are now known under the general denomination of ”Perry pens.” The first pens were manufactured by Perry & Co. in London, principally from flattened or ribbon steel wire, and in the year 1828 Mr. Josiah, afterward Sir Josiah, Mason, then a manufacturer of steel split rings, produced steel pens so much superior to the pens made up to that period that Messrs. Perry & Co. entered into contracts with him for the sole supply of all the pens they might require; this connection continued up to the time of the formation of this company. In the meantime, Messrs. Perry & Co. had also introduced the sale of elastic bands and pencil cases; the production of the latter was confided to Mr. W.E. Wiley, who, in the year 1850, began the manufacture first of gold pens, afterward of pencil cases. Messrs. Perry & Co. also contracted with Mr. Wiley for the purchase of all the pencil cases they might dispose of, and thus Mr. Wiley's works assumed gigantic proportions. Mr. Alfred Sommerville, who had been connected with the steel-pen trade since its infancy, established the firm of A. Sommerville & Co. in the year 1851. Although he, in the year 1857, began manufacturing steel pens in connection with a partner, he likewise contracted with Mr. Josiah Mason for a superior class of steel pens, principally intended for the Continental markets, and many of which were either his own invention or suggested by him. Mr. Sommerville desiring to retire from business, Sir Josiah Mason purchased his trade in the year 1870, but continued to carry it on under the old style of A. Sommerville & Co. These four businesses being so intimately connected and dependent upon each other, some gentlemen of eminence in the manufacturing town of Birmingham decided, in conjunction with some of the leading proprietors, to establish a limited company, for the purpose of uniting and amalgamating inseparably the various establishments, and thus the company of ”Perry & Co., Limited,” was formed.
The firm of Messrs. Perry & Co., London, was established in 1824 by Mr. James Perry, who initially ran the business in Manchester before moving it to London. Mr. James Perry passed away in 1843. Mr. Stephen Perry, who took over the business afterward in partnership with Mr. Hayes and others, died in 1873 and was succeeded by his sons, Messrs. Joseph John and Lewis Henry Perry. The firm of Perry & Co. became well-known throughout Europe as the company that first introduced high-quality steel pens to the market, and in many countries, steel pens are now commonly referred to as "Perry pens." The first pens manufactured by Perry & Co. in London were primarily made from flattened or ribbon steel wire. In 1828, Mr. Josiah, later Sir Josiah, Mason, then a manufacturer of steel split rings, created steel pens that were far superior to those made previously, leading Messrs. Perry & Co. to enter into contracts for the exclusive supply of all the pens they needed. This partnership lasted until the formation of this company. Meanwhile, Messrs. Perry & Co. also started selling elastic bands and pencil cases; the production of the latter was entrusted to Mr. W.E. Wiley, who began making gold pens in 1850 and later pencil cases. Messrs. Perry & Co. also contracted with Mr. Wiley to buy all the pencil cases they could sell, allowing Mr. Wiley's business to grow significantly. Mr. Alfred Sommerville, who had been involved in the steel pen trade since its early days, founded the firm of A. Sommerville & Co. in 1851. Although he began manufacturing steel pens with a partner in 1857, he also contracted with Mr. Josiah Mason for a higher quality of steel pens mainly aimed at the Continental markets, many of which were either his inventions or inspired by him. When Mr. Sommerville wished to retire from business, Sir Josiah Mason bought his trade in 1870 but continued to operate under the original name of A. Sommerville & Co. Since these four businesses were closely linked and depended on one another, a group of prominent individuals from the manufacturing town of Birmingham, along with some leading owners, decided to establish a limited company to unite and merge the various establishments into one. Thus, the company "Perry & Co., Limited," was formed.

On the spot forming the principal entrance to the works, Mr. Samuel Harrison, in the year 1778, founded a manufactory in which he carried on his invention of steel split rings; but Mr. Harrison, who was an ingenious mechanic, also manufactured mathematical instruments, some of which were used by Dr. Priestley in his researches, and on one occasion he made a steel pen for Dr. Priestley, probably the first steel pen ever produced. Mr. Josiah Mason succeeded to the business of Mr. Harrison in 1823, and in 1828 began the manufacture of steel pens. For several years he gave his whole attention to improvements in the manufacture of steel pens, and Mr. Perry took out several most important patents for the improvement of steel pens, many of which have not been surpassed in ingenuity or in utility, and the principal among them, the so-called “double patent,” is universally applied by the pen trade to a great number of pens to this very day. In 1842 Mr. Mason's attention was absorbed by the process of electroplating and gilding, at that time invented and carried on by Mr. Elkington, in partnership with whom he founded the great firm of Elkington, Mason & Co. For some years the production of pens flagged, but in 1852 a nephew of Sir Josiah Mason, Mr. Isaac Smith (deceased in 1868), gave a new stimulus to the manufacture of pens, and from that time the production gradually increased until it assumed its present proportions. The manufactory now covers nearly two acres; it occupies a whole square and fronts four streets. In the building fronting Lancaster Street (five stories high) the offices, warehouses and storerooms of finished goods are distributed. The underground floor forms a huge machine shop, in which all the presses, rolls, and general iron and machine work employed throughout the manufactory are produced by skillful mechanics. Behind the front building there are several courtyards and quadrangles, in the largest of which are placed in a row five double-flue boilers, each 20 feet long by 7 feet diameter, working at a pressure of more than 55 lb. to the square inch, supplying the steam power both for propelling the steam engines and for heating the manufactory. In the rolling mill, measuing 64 by 38 feet, three double-cylinder engines, working up to 293 indicated horsepower, give motion to 18 pairs of rolls, rolling four to six tons of steel per week. The largest workshops are the slitting and grinding rooms, 64 by 38 feet, the latter 24 feet high. In the slitting room 90 girls apply the last mechanical process to the manufacture of steel pens, in slitting them by presses of ingenious construction. In the grinding room more than 160 girls are busily employed cross and straight grinding steel pens on wood cylinders covered with emery. The room in which the finished pens are placed in boxes measures 54 by 30 feet, and in it alone are employed 50 girls boxing and labeling steel pens, or fitting penholder tips on handles of various materials, principally of cedar. In that part of the building having a frontage on Corporation Street there is a dining room 86 feet 6 inches long by 68 feet wide, fitted up with tables to accommodate 600 people. Here the employees are served with a warm dinner at prices varying from 2d. to 6d. At one end of the room there is a stage, where dramatic entertainments and concerts are given in the winter season by the workpeople. At the other end there is a library, in a glazed partition, containing about 2,000 volumes of standard works. These books are issued to the hands employed by the firm free. One of the important features of this manufactory is the employment of muffles heated by gas produced from Siemens's gas generators. These muffles allow the heat to be regulated to a nicety, and enable the company to carry on the process of annealing and hardening to very great perfection.
On the site that serves as the main entrance to the factory, Mr. Samuel Harrison established a manufacturing business in 1778 where he developed his invention of steel split rings. Mr. Harrison, who was a clever mechanic, also produced mathematical instruments, some of which were used by Dr. Priestley in his research. On one occasion, he made a steel pen for Dr. Priestley, likely the first steel pen ever created. Mr. Josiah Mason took over Mr. Harrison’s business in 1823 and started making steel pens in 1828. For several years, he focused entirely on improving steel pen production, and Mr. Perry obtained several important patents that enhanced the design of steel pens, many of which are still considered innovative and useful today. The most notable among these is the “double patent,” which is widely used in the pen industry even now. In 1842, Mr. Mason became focused on the electroplating and gilding processes, which had just been developed by Mr. Elkington. He partnered with him to establish the major firm of Elkington, Mason & Co. Production of pens declined for a few years, but in 1852, a nephew of Sir Josiah Mason, Mr. Isaac Smith (who passed away in 1868), revitalized the pen manufacturing business, and from then on, production gradually increased until it reached its current scale. The factory now spans nearly two acres, occupying an entire block and facing four streets. The building on Lancaster Street, which is five stories tall, houses the offices, warehouses, and storerooms for finished goods. The basement serves as a large machine shop where skilled mechanics produce all the presses, rolls, and general iron and machine work used throughout the factory. There are several courtyards and quadrangles behind the main building, with five double-flue boilers in the largest courtyard, each measuring 20 feet long and 7 feet in diameter, operating at over 55 pounds per square inch of pressure, supplying steam power for the steam engines and heating the factory. The rolling mill, measuring 64 by 38 feet, has three double-cylinder engines producing up to 293 horsepower, powering 18 pairs of rolls that process four to six tons of steel each week. The largest workshops are the slitting and grinding rooms, each 64 by 38 feet, with the grinding room reaching a height of 24 feet. In the slitting room, 90 women perform the final mechanical step to manufacture steel pens, using presses of clever design to slit them. In the grinding room, over 160 women work on cross and straight grinding steel pens on wooden cylinders covered with emery. The area where the finished pens are packed into boxes measures 54 by 30 feet, employing 50 women who box and label the pens or attach penholder tips to handles made from various materials, primarily cedar. In the section of the building facing Corporation Street, there is a dining room that is 86 feet 6 inches long and 68 feet wide, furnished with tables for 600 people. Here, employees are served warm meals at prices ranging from 2d. to 6d. One end of the room features a stage for dramatic performances and concerts held during the winter months by the staff. At the other end, there is a library in a glass-enclosed area that contains about 2,000 volumes of classic literature, available to employees for free. A significant aspect of this factory is the use of muffles heated by gas from Siemens's gas generators, which provide controlled heat and enable the company to carry out refining and hardening processes with great precision.
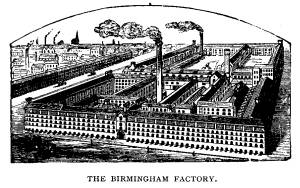
The manufacture of steel pens employs in all about 900 workpeople, the weekly production is 45,000 gross, which quantity will shortly be increased to 50,000 gross, per week. Six smaller steam engines are employed independently of those already mentioned in various parts of the works. The manufacture of penholder sticks is carried on in two separate buildings. Penholder sticks were produced by Mr. Mason as far back as 1835, but their manufacture had lapsed; it was only resumed eight years ago, since which time, by new and ingenious machinery, principally the inventions of Mr. W. E. Wiley, the managing director, it has assumed proportions of great magnitude.
The production of steel pens involves around 900 workers, with a weekly output of 45,000 gross, which will soon increase to 50,000 gross each week. Six smaller steam engines are used separately from those already mentioned in different areas of the factory. The production of penholder sticks takes place in two separate buildings. Mr. Mason produced penholder sticks way back in 1835, but that production stopped; it only restarted eight years ago. Since then, thanks to new and innovative machinery, mainly the creations of Mr. W. E. Wiley, the managing director, the manufacturing has grown significantly.
The pencil case and solitaire works carried on by Mr. Wiley, first alone, and then in co-partnership with his son in Graham Street, have now been transferred to Lancaster Street.
The pencil case and solitaire operations run by Mr. Wiley, initially on his own and later in partnership with his son on Graham Street, have now been moved to Lancaster Street.
Pencil cases, first introduced by Messrs. Mordan & Lund, in London, have undergone various changes and improvements, the principal of which was a lead holder passing through the point of the pencil case, which was slit for that purpose. This invention was patented by Mr. Wiley in the year 1857, and created a complete revolution in the pencil-case trade, as it enabled the manufacturers to use a thicker and longer lead, which could be propelled and withdrawn at will and would last in daily use more than six months. This patented mechanism was introduced into cases made from hard wood, bone and ivory, but since the year 1868 a composition called aluminium gold, so resembling gold that it cannot be distinguished from it, and resisting the effects of oxidation, consequently free from tarnish, made a further revolution in the pencil-case trade, enabling the million to possess an elegant and highly-wrought pencil case at a very moderate price. Messrs. Perry & Co., of London, gave to this manufacture publicity in every part of Europe, and the quantities produced and sold are incredible.
Pencil cases, first introduced by Mordan & Lund in London, have gone through various changes and improvements. The main innovation was a lead holder that runs through the tip of the pencil case, which was designed with a slit for that purpose. This invention was patented by Mr. Wiley in 1857 and completely transformed the pencil-case market, as it allowed manufacturers to use thicker and longer lead that could be pushed out and retracted as needed, lasting more than six months with daily use. This patented mechanism was included in cases made from hardwood, bone, and ivory, but since 1868, a material called aluminum gold—a composition so similar to gold that it’s virtually indistinguishable and resistant to oxidation, thus free from tarnish—initiated another revolution in the pencil-case market. This allowed many people to buy an elegant and intricately designed pencil case at a very affordable price. Perry & Co. of London helped to promote this production throughout Europe, and the quantities produced and sold are remarkable.
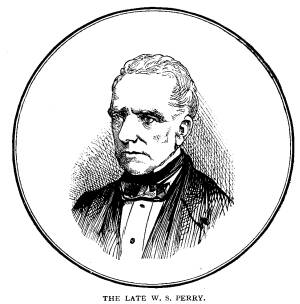
In 1874 a new patent was added to the many inventions for which this establishment was famous. Its purpose was to produce a solitaire stud made in two parts, so as to enable its ready application without the trouble of passing a button of large diameter through a small buttonhole. A self-acting steel spring is fixed in the upper part of the stud, and snaps as soon as inserted into the lower part, where a slight pressure on two projections releases the springs and permits the separation of the two parts. These solitaires are manufactured of gold, silver, and a variety of other metals, the principal of which is gold plate. There are now more than five hundred patterns in existence, and this useful manufacture grows daily in extension. Perry & Co.'s paper binders, an article now universally used for fastening together loose papers, cloth patterns, etc., are produced in infinite styles and sizes, principally by self-acting machinery.
In 1874, a new patent was added to the many inventions that made this company famous. Its purpose was to create a two-part solitaire stud, allowing for easy application without the hassle of pushing a large button through a small buttonhole. A self-acting steel spring is fixed in the upper part of the stud and snaps in place as soon as it’s inserted into the lower part. A slight pressure on two projections releases the springs, allowing the two parts to separate. These solitaires are made from gold, silver, and various other metals, with gold plate being the main one. There are now over five hundred different patterns available, and this useful product continues to expand daily. Perry & Co.'s paper binders, an item that is now universally used to fasten together loose papers, cloth patterns, etc., are produced in countless styles and sizes, mainly using self-acting machinery.
The total number of workpeople employed in the company's manufactories exceeds 1,300.
The total number of employees working in the company's factories exceeds 1,300.
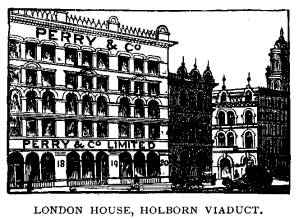
The business of Perry & Co. was carried on for more than forty years at 37 Red Lion Square, London, but the increase of business and the reconstruction of London required that a more central position should be found for the development of the commercial department of the company. Large and handsome warehouses having been constructed on the Holborn Viaduct, the company transferred their London depot to a building five stories high on the side fronting the Holborn Viaduct and eight stories high at the back. In this immense warehouse are stored not only the produce of the manufactories of this company, but also special articles for which this firm has been famous for the last thirty years, principally the elastic or endless bands, patented by Mr. Daft and Mr. Stephen Perry, and originally introduced by Perry & Co. in conjunction with McIntosh & Co., afterward in conjunction with Warne & Co. Perry's Royal Aromatic Bands are now an indispensable article, and may be procured in every city of the world. Every fancy article required by stationers can be found in these vast stores. An illustrated price current which appears monthly, and which numbers more than 120 pages, gives fair idea of the variety of articles of which samples and stock can be found ready for daily delivery. The increase of business has been so rapid that the company found it necessary to lease the adjoining premises, which is stored with some of the two thousand articles forming the staple trade of the London depot, and the principal of which are the following: American Letter Files, Clips (now manufactured in Lancaster Street), Marking and other Inks, Aromatic Bands, Audascript Pens, Bostonite Goods, Cigar Lighters, Copying Ink and Copying Ink Powder, Copying Ink Pencils, Copying Presses, Corrugated Imperial Bands, Essence of Ink, Grease Extractors, India Rubber for Erasing, Ink and Pencil Erasers, Ink Extractors, Patent and other Inkstands in every variety, Key Rings, Letter Clips, Letter Files, Metallic Books, Paper Binders, Pencil Point Protectors, Pencils and Pencil Cases, Penholders, Pen Knives, Pen Racks, Gold Pens, Portfolios, Presses, Scotch Tartan Fancy Goods, Solitaires or Sleeve Links, etc., etc., etc.
The business of Perry & Co. operated for over forty years at 37 Red Lion Square, London, but the growth of business and the redevelopment of London required a more central location for the company’s commercial department. After large and impressive warehouses were built on Holborn Viaduct, the company moved their London depot to a five-story building facing the Holborn Viaduct and eight stories high at the rear. In this massive warehouse, they store not only the products made by this company but also the special items for which they have been known for the past thirty years, mainly the elastic or endless bands patented by Mr. Daft and Mr. Stephen Perry, first introduced by Perry & Co. in partnership with McIntosh & Co., and later with Warne & Co. Perry's Royal Aromatic Bands are now essential items available in every city around the globe. Every specialty product that stationers might need can be found in these vast inventories. A monthly illustrated price list, consisting of more than 120 pages, provides a good overview of the variety of items available for immediate delivery. The surge in business has been so rapid that the company had to lease the neighboring premises, which is stocked with some of the two thousand items that make up the core inventory of the London depot, the main ones including: American Letter Files, Clips (now produced in Lancaster Street), Marking and other Inks, Aromatic Bands, Audascript Pens, Bostonite Goods, Cigar Lighters, Copying Ink and Copying Ink Powder, Copying Ink Pencils, Copying Presses, Corrugated Imperial Bands, Essence of Ink, Grease Extractors, India Rubber for Erasing, Ink and Pencil Erasers, Ink Extractors, various Patent and other Inkstands, Key Rings, Letter Clips, Letter Files, Metallic Books, Paper Binders, Pencil Point Protectors, Pencils and Pencil Cases, Penholders, Pen Knives, Pen Racks, Gold Pens, Portfolios, Presses, Scotch Tartan Fancy Goods, Solitaires or Sleeve Links, and so on.
This establishment is under the exclusive management of Mr. Joseph J. Perry, managing director.
This establishment is managed exclusively by Mr. Joseph J. Perry, the managing director.
[The illustrations in this work are engraved from pen-and-ink sketches executed by Walter Langley with a Perry's No. 25 pen.]
[The illustrations in this work are engraved from pen-and-ink sketches created by Walter Langley using a Perry's No. 25 pen.]
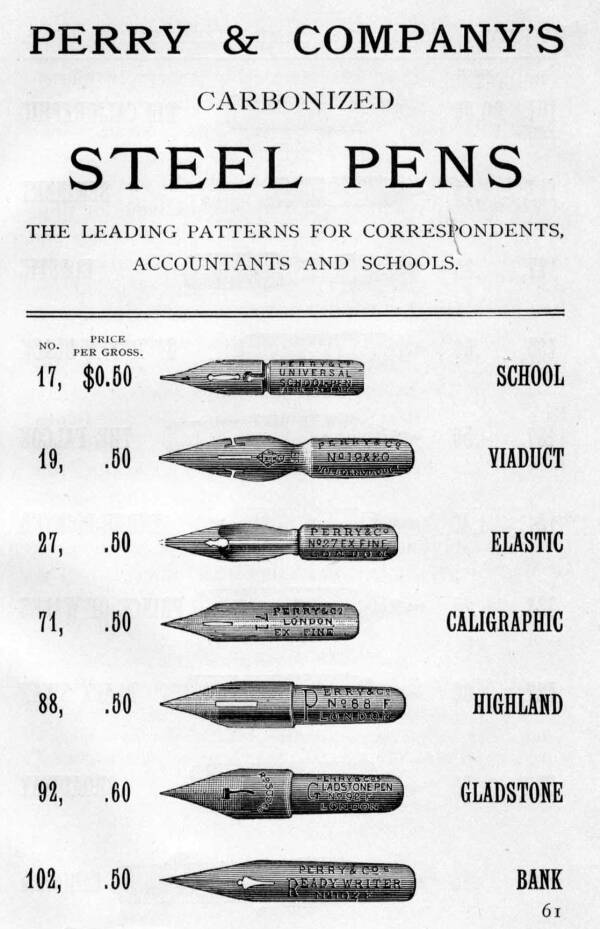

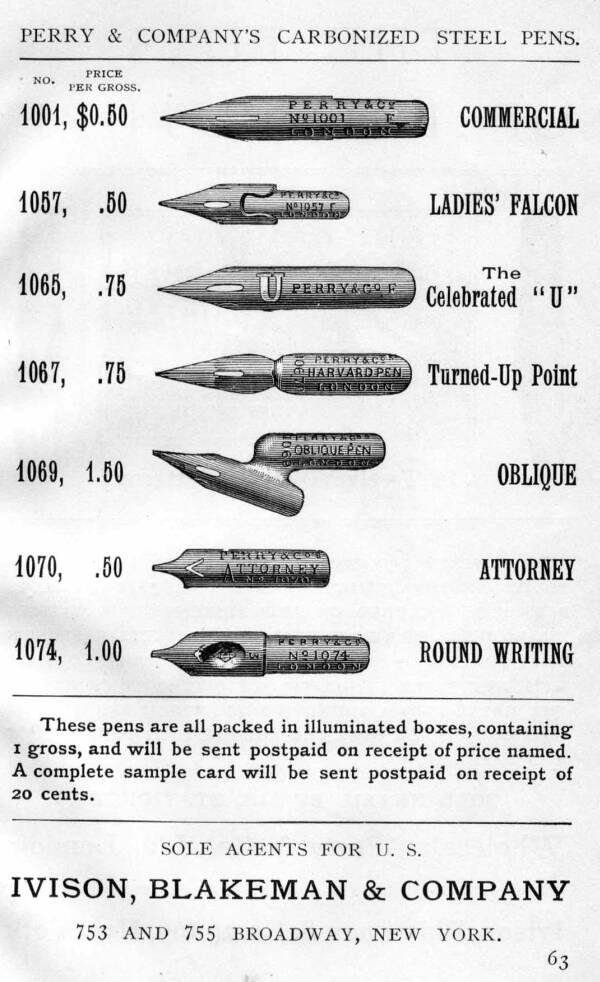
THE PENS
OF THE FUTURE
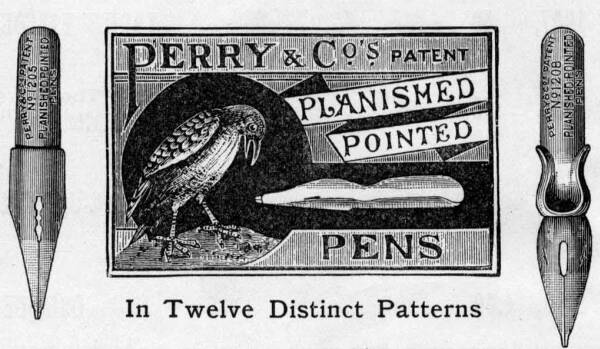
THIS NOVELTY (PROTECTED BY LETTERS PATTENT)EMBODIES AN IMPROVEMENT WHICH BIDS FAIR TO MAKE PENS MANUFACTURED ON THIS PRINCIPLE THE WRITING INSTRUMENTS OF THE FUTURE. BY A PECULIAR PROCESS THAT PORTION OF THE POINT WHICH COMES IN CONTACT WITH THE PAPER IS SHAPED OUT OF THE THICKNESS OF THE METAL INTO A ROUNDED FORM, WHICH ENABLES THE WRITER TO GLIDE OVER THE ROUGHEST PAPER WITH EASE AND RAPIDITY.
THIS INNOVATION (PROTECTED BY PATENT) REPRESENTS AN ADVANCE THAT IS LIKELY TO MAKE PENS PRODUCED USING THIS METHOD THE WRITING TOOLS OF THE FUTURE. THROUGH A UNIQUE PROCESS, THE PART OF THE TIP THAT TOUCHES THE PAPER IS SHAPED FROM THE METAL'S THICKNESS INTO A ROUNDED FORM, ALLOWING THE WRITER TO MOVE SMOOTHLY OVER EVEN THE ROUGHEST PAPER WITH EASE AND SPEED.
SOLD RETAIL BY ALL STATIONERS
Wholesale—Perry & Co., L'd, London
SOLE AGENTS FOR THE UNITED STATES
Ivison, Blakeman & Company, New York
Download ePUB
If you like this ebook, consider a donation!